NGR
NGR Next Generation Recyclingmaschinen GmbH | |
---|---|
Headquarters | Feldkirchen, Austria |
Website | www.ngr.att |
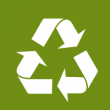
NGR has been building plastics recycling machines in Austria for more than twenty years. These machines turn plastics waste into high-quality pellets in more than 70 countries worldwide. The company is continuously developing and improving plastics processing and machine components. The NEXT GENERATION GROUP consists of NGR, Britas and Collin, and with 225 employees, the Group has an annual sales of EUR 55 million. Next Generation Recyclingmaschinen GmbH provides recycling solutions for industrial plastics processors with the aim of implementing zero-scrap production. The main driver here is clearly the desire to reduce costs in plastics recycling. With machine models for preparing end-of-life plastics, we round out the plastics cycle. Britas filtration systems are specially engineered for filtering of heavily contaminated PE melts. Dr. Collin GmbH was acquired in March 2014 by the NEXT GENERATION GROUP. With extensive know-how in the fields of polymer testing and process optimization, Collin will continue to drive forward the area of product design for all plastics and ensure that pellets also meet the high standards of quality applied to virgin material. The NEXT GENERATION GROUP serves the global market. Alongside the corporate headquarters in Feldkirchen an der Donau, two further production sites are located in Germany – one in Hanau near Frankfurt for Britas and one in Ebersberg near Munich for Collin. All assembly and tests to ensure the high quality of the system are conducted in Europe. With customer care centers in the US and China, customer-specific tests are also performed on site; technical service and spare parts are also provided. This proximity to the client allows us to provide prompt and accurate support.
Products / Technology
The market introduction of P:REACT was world premiere at the NPE2015. The P:REACT follows the design principles of LSP (Liquid State Polycondensation) and considerably improves the properties of PET – ideal for PET-Converters or PET-Recyclers. The LSP-Process utilizes the inherent capability of PET to post condensate in the molten phase under vacuum. This post condensation leads to an increase of IV. The high performance vacuum effectively decontaminates the material from harmful chemicals - securing further use of the material for 100% food contact. As molten PET enters the vertical part of P:REACT, strands are formed to create a suitable surface to volume ratio. The material is then collected in a horizontal drum and slowly pushed forward. Post condensation starts immediately as the strands are formed and is set forth until PET exits P:REACT. IV increase is controlled by the residue time of the molten PET inside P:REACT and therefore can be adjusted to a desired level. The settings of parameters allow the control unit to maintain the desired IV-level within a small tolerance-band. The decontamination performance is extremely effective, as carried out in the liquid phase of PET. The cleaning of the material exceeds limits set by recognized food safety standards, but also effectively removes spin oil from fibers. The IV increase can be measured in approx. 0,01 dl/g per minute. Continuous Operation, Rapid IV-Increase and High Decontamination Performance The continuous operation of P:REACT provides rPellets within a narrow IV-range, suitable for usage in valuable high end applications (i.e. fiber-spinning or sheet extrusion). Batch related IV-fluctuations are simply designed out. The favorable conditions inside P:REACT (temperature/surface:volume ratio of the melt/high performance vacuum), easily initiates the post-condensation-process of PET. This results in IV increase rates of some 0,01 dl/g per minute. Faster reaction leads to faster results and a more profitable oper ation. The separation of harmful contaminants, as spin-oils or those components not desired for food contact, are removed by high performance vacuum. This high decontamination performance allows the use of P:REACT for many applications for highest flexibility. Scientific, third party tests show, that harmful components in the PET-melt are easily and securely removed within P:REACT, ensuring highest safety standards for 100% food-contact. Automatic Control of IV-Level and High Energy Efficiency P:REACT actively controls the residue-time of the PET-melt inside the reactor and automatically adjusts the machine parameters to receive the desired IV at a consistent level. The recycling of PET requires the material to be melted. P:REACT uses the melt-energy for post-condensing PET. The reactor itself only maintains the heat-level. P:REACT is therefore highly energy-efficient, which results in low operating costs.
History
References
PETplanet Insider Articles
Issue 09 / 2015: Rethinking the next generation of PET recycling