"Regional market reports Germany Part 4 REGIONAL MARKET REPORTS 14 PETplanet insider Vol. 11 No. 04/10 www.petpla.net Part 4 Germany identity by enlisting the help of two well-known and popular Swabian TV characters, “Äffle“ (Little monkey) and “Pferdle“ (Little pony) under the strapline “We are Swabians“. For the EiszeitQuell brand, Sander envisages an ambitious market penetration programme with its focus on Baden-Württemberg. In addition, they are looking at new markets, with an on-line shop, currently in the pipeline, showing the way forward. Sander sums his strategy up as follows: “What we are looking for is steady organic growth”. To help the company achieve this, the MD will be investing exclusively in PET plant. It is well-known that within Germany Baden-Württemberg is regarded as a stronghold of traditional glass bottles (for mineral water, that is). The company’s dual brand name strategy also takes this into account. It was in 2001 that Romina commissioned its first PET plant with an output at the time of 14,000bph. In order to cope with the increasing demand for EiszeitQuell products in PET, they carried out some fine-tuning on the plant in 2005. At the time the Krones-SBM/filler plant had a capacity of 22,000bph. The brands produced at the PET plant at Romina are EiszeitQuell (sparkling,medium and natural), SilberBrunnen (classic and medium) as well as SilberBrunnen Apfelschorle (apple spritzer), Cola Mix and different kinds of lemonades in1 l and 1.5l single serve and returnable packaging. According to Ralph Sander, with EiszeitQuell the company is marketing “the best water there is in Germany”. After all, consider the USP of his leading brand: In the prehistoric Ice Age spring there are no traces of modern civilisation to be found. And because the water is so good as it is, Romina has no plans to introduce near water products, which are increasingly gaining ground in the market place at the moment. Own brands and trade brands Ralph Möller, engineer at Hansa Heemann AG Hansa Heemann Hansa Heemann supply not only their own brands but also trade brands to the big supermarkets. Their range In our last part of our Regional Market Report Germany we report on the filling companies Hansa Heemann and Romina. by Alexander Büchler Regional brand, supra-regional ambition Romina Mineralbrunnen Formed more than 10,000 years ago and lying hidden 400m deep underground, protected by formidable stone formations, is the Ice Age spring from which Romina draws its mineral water. We visited Romina, a regional mineral water bottling company in Baden-Württemberg where attention is increasingly focused on mighty brand names, packaged in PET. With around 100 members of staff and an annual turnover of €25m in 2009, Romina is one of the leading mineral water bottling companies in Baden-Württemberg. Reflecting the proud local traditions of Swabia, the mineral water goes under the regional brand name of Silber Brunnen “ (Silver Spring) whilst its supra-regional aspirations are captured under the ‘EiszeitQuell’ (Ice Age Spring) brand. Ralph Sander, Managing Director of Romina Mineralbrunnen, is in no doubt about the glowing health of Romina, and its healthy interest in growing its brands. For the company, growth means investing in the Marketing / Sales sector and, with this in mind, Sander has one or two strategies up his sleeve. The SilberBrunnen brand emphasises its local Ralph Sander, Managing Director of Romina Mineralbrunnen","@ID":16} "REGIONAL MARKET REPORTS 15 PETplanet insider Vol. 11 No. 04/10 www.petpla.net includes reusable glass bottles and disposable PET bottles, both system-orientated (PET cycle) and without any system orientation. With a capacity of 7.9 millionhl, the company, which has five plants in Germany, ranks as one of the largest bottling enterprises. In 2005 the company decided to set up its own preform production. “Being a beverage filler nowadays, you cannot earn your money on the contents of a bottle. Beyond this you have to consider every possibility to generate potential savings.” Due to short cycle times and low energy consumption, HansaHeemann quickly decided to place the order with Husky and Motan. “The efficiency factor for our entire production was planned to be 95%. Now we achieve more than 97%.” “We use far less energy with these new installations. Our investment costs provide a rapid return on investment in a very short period of time,” says engineer Ralph Möller. At the beginning of the 1990s, Hansa-Heemann – emerged from the Nordgetränke GmbH in Hamburg – decided to move their headquarters to Kloster Lehnin. “We wanted to secure the bustling Berlin market and Kloster Lehnin had a good transport connection,” explains the engineer. The first installation for soft packaging, glass and cans had already started production at the new site in Brandenburg at the end of 1995. At the time PET bottles had a rather slow start in Germany, but three years later the Lehnin staff thought about using plastic bottles. In the meantime, German consumers began purchasing at discount supermarkets where more and more PET bottles were displayed. “In 1998 we brought into service our first blow moulding machine which was actually only the third machine of its kind ever built by a well-known manufacturer,” says the branch director. From that point on, production increased steadily in Kloster Lehnin. By 2002 four more blow moulding machines were brought into service. As the demand for glass bottles abated completely, Kloster Lehnin converted entirely to PET within the Hansa-Heemann-Group. The Lehnin staff increased its production from 28,000bph in the very beginning to more than 40,000bph. “We even adapted the existing filling installations to the 0.5l plastic bottles with a minimum of effort,” remembers Mr Möller. “Right from the beginning, preform production was taken into account.” Several calculations were made, right down to the last penny. Due to the bargain-hunting mentality prevalent at that time, there was little chance of making profit on the actual contents of the bottles. “We had to squeeze out savings wherever we could generate more savings potentials,” Möller tells us. To this end, in 2005/2006, Lehnin staff reviewed potential solutions and extended the dialogue with the Luxemburg site of Husky as well as with Motan. “Our objectives were: to save energy, optimise personnel, improve quality assurance, explore the possibility of inline measurements during preform production and fine tune the traceability of records on production data. All these were extremely important factors to us. “ It is exactly this high efficiency factor of the nine new injection moulding installations and ancillary equipment that makes Ralph Möller from Hansa-Heemann AG happy. “As I mentioned before, the production is unobstructed, and energywise we are far more efficient. It has all worked out very well.” Enjoy completeness Sacmi Imola S.C. Via Selice Prov.le, 17/a 40026 Imola (BO) Italy Tel. +39 0542 607111 - Fax +39 0542 642354 E-mail: sacmi@sacmi.it www.sacmi.com Sacmi offers turnkey solutions for the beverage and packaging industry: complete bottling lines for product preparation, container manufacture, filling and closing, labelling and final packaging operations. The extensive experience acquired since the company was established in 1919, in addition to its reputation for supplying advanced technology, financial solidity and a network of 70 companies throughout the world, enables Sacmi to meet all your requirements wherever you are.","@ID":17} "PATENTS 43 PETplanet insider Vol. 11 No. 04/10 www.petpla.net PETpatents www.verpackungspatente.de Multilayer bottle International patent No. WO 2009 / 133783 A1 Applicant: Yoshino Kogyosho Co. Ltd., Tokyo (JP) Date of application: 20.4.2009 The concept, design and manufacturing process for a plastic bottle with an impermeable gas-proof layer. Shaped container International patent No. WO 2008 / 088824 A1 Applicant: The Coca-Cola Company, Atlanta (US) Date of application: 17.1.2008 A plastic container designed to hold a carbonated beverage. The container is so shaped that after opening it supports the pressure applied by the user’s fingers and does not suddenly collapse. This type of container is also easy to stack and does not roll away on its own. Tamper evidence International patent No. WO 2009 / 128640 A2 Applicant: Chul Park, Gyeonggi-Do (KR) Date of application: 14.4.2009 A ring with two inter-reactive substances is fitted around the neck of a bottle. When the bottle is first opened this ring is broken, the two substances react with each other and the colour of the ring changes. Thus a bottle that has previously been opened is easy to recognise. Container with separate handle European patent No. EP 2110335 A1 Applicant: Toyo Seikan Kaisha Ltd., Tokyo (JP) Date of application: 26.5.2006 A hot-fill container has an adequate surface to compensate for the changes in pressure and a feature to allow the secure fixing of a handle. RFID in the cap European patent No. EP 2123570 A1 Applicant: Toyo Seikan Kaisha Ltd, Japan Crown Cork Co. Ltd., Tokyo (JP) Date of application: 17.3.2008 A cap is described which allows the fitting of an RFID label and sure reading of the data even under difficult conditions. It also includes a degree of moisture proofing. Insulate preform International patent No. WO 2009 / 158397 A1 Applicant: Plastic Technologies Inc., Holland (US) Date of application: 24.6.2009 Improvement and procedure for the manufacturer of a container made from a preform which is given an additional outer layer of foamed material. The international application describes the advantages of this container with an insulating layer.","@ID":45} "imprint EDITORIAL PUBLISHER Alexander Büchler, Managing Director HEAD OFFICE heidelberg business media GmbH Landhausstr. 4 69115 Heidelberg, Germany phone: +49(0)6221-65108-0 fax: +49(0)6221-65108-28 info@hbmedia.net EDITORIAL Doris Fischer fischer@hbmedia.net Ruari McCallion Tony O´Neill Ilona Trotter Wolfgang von Schroeter MEDIA CONSULTANTS Ute Andrä andrae@hbmedia.net Miriam Kiesler kiesler@hbmedia.net phone: +49(0)6221-65108-0 fax: +49(0)6221-65108-28 France, Italy, Spain, UK Elisabeth Maria Köpke phone: +49(0)6201-878925 fax: +49(0)6201-878926 koepke@hbmedia.net LAYOUT AND PREPRESS EXPRIM Kommunikationsdesign www.exprim.de PRINT WDW Druck GmbH Gustav-Throm-Straße 1 69181 Leimen-St.Ilgen Germany WWW www.petpla.net | www.pet-point.net PETplanet insider ISSN 1438-9459 is published 10 times a year. This publication is sent to qualified subscribers (1-year subscription 149 EUR, 2-year subscription 289 EUR, Young professionals’ subscription 99 EUR. Magazines will be dispatched to you by airmail). Not to be reproduced in any form without permission from the publisher. Note: The fact that product names may not be identified as trade marks is not an indication that such names are not registered trademarks. 3 PETplanet insider Vol. 11 No. 04/10 www.petpla.net How much theory do we actually need? When theory comes up against practice the outcome may well be a measure of clarity. This was the case at the 25th International Plastics Technology Colloquium hosted by the nstitute for Plastics Processing, Aachen, Germany (IKV). This was the year when, for the first time, stretch blow moulding of bottles featured in the Great Hall of the Eurogress in Aachen, a venue where the scientific developments and practical experiences of the automotive manufacturers normally take centre stage. Two interesting presentations from the IKV line-up caught our attention. The first, delivered by Dipl.-Ing Thorsten Leopold, was on the subject of a promising approach to simulating oxygen permeation in PET bottles. The second, from Dipl.-Ing.Karim Bahroun on the brightly illuminated plasma coating of PET, PLA and PP, revealed that there is still a gulf between theory and practice. For example, in the case of oxygen permeation, the interim results as regards theory and practice differed by a factor of 2. Further research will surely enable the men of Aachen to succeed in aligning theory and practice, just as they have so often done before where a number of other plastics issues are concerned. I just wonder whether we in the PET industry are purely and simply tradesmen without any scientific background whatsoever? Have our successes come about solely as a result of performing endless tests? If it is true that the gulf between theory and practice is indeed wide, how much further forward we would be now, I wonder, if we, as the PET industry, had made a start years ago on supporting basic research? How many trials and service life tests could we have saved ourselves? One wonders how much more weight could have been trimmed off the PET bottles by now had the wish expressed by the moderator, Dr. Ing. Klaus Hartwig of Nestle Waters, Vitell, France, to simulate the permeability of a broad diversity of gases with a very wide range of barrier layers and stretch ratios been met. Without doubt there are still many other PET topics that require a structured scientific study in order to further accelerate the rapid growth in PET bottles. After many decades of practical experience with PET we should at least give theory the chance to catch up. Yours, Alexander Büchler EDITORIAL dear readers, Dr. Ing. Klaus Hartwig of Nestlé Waters, Vitell, France, moderator at the IKV Colloquium","@ID":5} "REGIONAL MARKET REPORTS 13 PETplanet insider Vol. 11 No. 04/10 www.petpla.net The use of PET does not have to be restricted to the beverage business - today there are an increasing number of applications in the pharmaceutical industry and for domestic and industrial cleaners. The Taba Group in Cairo has established a very good reputation in these newer applications. However since 1988 the history of the company has been in the cap business, and today Taba produces caps for pharmaceutical and medical products on injection moulding machines. These include three-piece caps with a safety band and a suitable liner, complex 4-piece child-proof caps with liner, inner cap, outer cap and safety band, caps with an integrated pipette, as well as measuring cups from 2.5 to 36ml. The work carried out includes assembly and printing of the caps. The Taba Group supplies all of the big names in the pharmaceutical and cleaning chemicals industries. A fairly good percentage of the products remain in Egypt, and Taba exports to clients in the Middle East and North Africa region and some countries in Europe”. We asked general manager Ahmed Shalaby why these international groups are ordering from him. “There are three reasons,” he said. “Firstly the price. In comparison with European manufacturers we can produce for about 10 % less. But also international groups in the Arab states have to pay high import tariffs which we, within the Arab world, do not have to pay, or we pay only a very small percentage. This ultimately means a price advantage over European production. Secondly, and perhaps more important, is the quality. Our injection moulding machines up to 50t in size come from Dr. Boy, and from 50t to 200t they are from Krauss-Maffei. The cap tools also come from European toolmakers such as KTW in Austria.This means that the clients get the same quality as they find in Europe. Thirdly, we have a high degree of flexibility here. Whilst in Europe production schedules and capacities are planned well in advance, we are in a position to respond quickly to different volume requirements”. Taba was in fact almost forced into the PET business by its clients. “Can you make bottles for us as well?” was a frequent question from them. No sooner said than done! Taba first started producing PET bottles for the pharmaceutical industry using single-stage machines, but the demand soon grew and for big quantities they had to start using the twostage system. Based on their good experience with the Krauss-Maffei injection moulding machines used for caps, in 2007 the company decided to invest in a KM preform system from Munich. Ahmed Shalaby looked at all of the big five manufacturers of stretch blow moulding machines and finally decided that the Sipa SFL 4/4 was the optimum machine for his needs. So today the Krauss-Maffei preform system stands alongside the linear stretch blow moulder producing the bottles. “Because the changeover from one preform to another takes a lot of time we let the machine run for up to a month with one preform type and build up some stock. After all, a preform is very compact. For bottles, on the other hand, we make frequent changeovers on the SBM because bottles take up a lot of space,” explained Ahmed Shalaby. Business is growing and a further production hall is currently being built, in which another Krauss-Maffei and another SBMmachine will be installed.","@ID":15} "PREFORM PRODUCTION 18 PETplanet insider Vol. 11 No. 04/10 www.petpla.net Energy: first things first … Energy saving was and always has been an important topic for the company. The first step was to assess the potential for energy saving in terms of screw geometry, the screw drive, the clamping unit and the robotics. Savings of up to 30% were achieved in these areas. Compared to the situation ten years ago, the energy required to produce a kilo of PET has been more than halved! As a result of this movement towards reducing energy consumption on the PET-Line systems featuring significant energy values amounting to less than 200Wh/kg PET have been achieved. Moreover, the potential for determining product energy consumption with an accuracy of +/- 5% as early as the offer phase has also been explored. Next: … the other suppliers The next stage was to look at energy consumption of the whole auxiliary equipment. Particular attention was paid to the material dryers, where the amount of energy required to plasticate the material is significant. Studies undertaken with the manufacturers of materials dryers have shown that the drying of the raw material is another key element that merits attention. Just as significant is the energy input into the raw material, because there is nowhere that the PET material can absorb energy in a gentler way than in the dryer hopper. In a best case scenario, it is even possible to achieve a slight reduction in the proportion of acetaldehyde (AA) proportion as early as the heating up phase. As a result, the machine requires correspondingly less energy to bring about fusion in the material. This means that, due to the (now) lower proportion of energy that is still to be transferred into the material via the plastication unit, the material will plasticate considerably more gently resulting in a further reduction in the occurrences of AA. These findings have helped to make it possible to formulate, together with the dryer manufacturers, a precise definition not only of the state of dryness of the raw material but also its energy content as it is transferred from the dryer for plastication. Establishing the energy input in the dryer hopper is extremely costly, and difficult to achieve, which is why Netstal has developed its own monitoring facilities. In addition to the dryer, there is potential for more savings in the cooler unit used for cooling the mould. This could only be achieved by close cooperation with both manufacturers. The primary stage involved mould Energy savings and improving cost efficiency Over the past two years, the Swiss company Netstal-Maschinen AG has launched a number of new developments aimed at saving energy and improving cost efficiency in the manufacture of PET preforms. We look at how they got on. * Netstal moves towards reducing energy consumption on their PETline systems C O S TEFFICIENCY ENERGYEFFICIENCY","@ID":20} "PREFORM PRODUCTION 17 PETplanet insider Vol. 11 No. 04/10 www.petpla.net 4. Check that transition position is set to about 13% of shotsize + cushion. Lower values may result in overfilling. 5. Ensure clamp tonnage is adequate for the preform size, cavitation, and process. Typical values are about 0.28 - 0.56t/cm2 (2 - 4t/in2) of projected preform area. 6. Check that there is no debris on the mould mating surfaces. These surfaces should be kept clean at all times. 7. Check to ensure that the mould neck inserts are properly aligned and seated. 8. Check all temperature readings and correct if necessary. PET resin should be melted at about 280ºC (536ºF) +/- 10ºC (18ºF). 9. Check that all thermocouples are properly inserted and contacting the bottom of the wells. 10. Check extruder back pressure and minimize if possible. Back pressure should be sufficient to provide good melt mixing, but not too little to cause bubbles to appear. Typical range is 15 – 20 bar (200 – 300 psi). 11. Check screw rpm and minimize if possible. Screw speed should be reduced as much as possible to minimize shear heating, yet still recover within the cycle time of the machine. The stopped time at the end of recovery should be about 2sec to offset any fluctuations during screw recovery. 12. Check hardware for worn, damaged or failed components, specifically the mould neck inserts, cavity tapers, and lock ring tapers. name ................................................................................................................ company ........................................................................................................... function ............................................................................................................. street................................................................................................................. city ................................................................................................................... country .............................................................................................................. phone ............................................................................................................... fax.................................................................................................................... e-mail................................................................................................................ credit card ......................................................................................................... expiration date.................................................................................................... name on card ..................................................................................................... PETplanet print Vol. 6: The Rapid Guide to Perfect Preforms by Rick Unterlander and Ottmar Brandau prices in EUR + VAT. fax: +49 (0) 6221-65108-28 info@hbmedia.net www.petpla.net Order your copy now! 1- 3 exemplar each 129,- € 4 - 10 exemplar each 99,- € 10 exemplar each 69,- € Table of Contents i..................................... About the Authors ii............................................. Introduction chapter 1.......................................... AA Level High 2..................................... Accordion Preform 3....................................Air hooks / Streaks 4............................................ Black Specks 5................................................... Bubbles 6.............................................. Burn Marks 7..........................Colour Streaking / Peeling 8.............................................. Crystallinity 9............................................. Drool Marks 10.......................................................Flash 11......................................Gate Depressions 12............................................ Gate Peeling 13.............................. Gate Voids / Pin Holes 14......................................Internal Gate Sink 15............................................ Internal Sinks 16.....................................................IV Loss 17........................................ Long Gate Nub 18........................................... Milky Preform 19.........................................Moisture Marks 20............................ Neck Finish out of Round 21....................................Parting Line Crease 22............................. Parting Line Deformation 23......................................Preform Yellowing 24...............................................Short Shots 25.......................................................Sinks 26......................................................Splay 27........................................Stretched Necks 28..................................................Stringing 29......................................Surface Blemishes 30......................................Thread Flow Lines 31.....................TSS (Top Sealing Surface) Sink 32................................................... Unmelts 33............................. Wall Thickness Variation 34..............................................Wavy Body 35...............................................Weld Lines","@ID":19} "NEWS 8 PETplanet insider Vol. 11 No. 04/10 www.petpla.net P E T C O R E C O L U M N Uses for recycled PET Since 2001 Petcore has commissioned an annual review of the European PET bottle collection figures from PCI. We duly report to the press each year how many tonnes were collected and the percentage of recycled PET used to produce fibre, sheet, and containers etc. In this column we give more details about these end uses. Fibre was the original outlet for recycled PET and it still consumes a very large tonnage. In 2001 144,000t of RPET (62% of all European supply) were used in fibre applications whereas in 2008 363,000t of RPET (45% of European supply) was used in fibre. Early uses of RPET were for fibres in the higher dTex range such as staple fibre for fillings for duvets, ski jackets etc using the insulation properties of PET fibre. Continuous development and improvement in RPET quality led to the production of polar fleece fabric and outdoor wear made from finer fibres spun from 100% RPET. Premium quality back packs, travel goods and computer cases are now made utilising recycled PET. RPET is also a major feedstock for non-wovens such as geotextiles, filters and wipes. RPET has often been the “unsung hero” in these fibre outlets but this year it has been given full recognition. At the Winter Olympics in Vancouver, Coca Cola supplied their representatives with outdoor wear made from 100% RPET and Nike has announced that it is supplying 9 World Cup football teams in South Africa with official strips made entirely from RPET. These teams’ replica strips will also be made from the same RPET-derived fabrics. Nike estimates it will use 275,000t of RPET in this application. 177,000t of RPET were used to produce clear sheet in 2008. The majority of this sheet was thermoformed to produce blisters, collation trays, clam shells and punnets to protect soft fruits and other contents. The sheet industry has long had the ability to extrude multi-layer sheet and this enabled them to sandwich an RPET layer between two outer layers of virgin PET particularly for food outlets. In 2001 just 16,000t of RPET were used to produce containers, almost all for non food. The passing of EU Regulation 282/2008 on recycled plastic materials and articles intended to come into contact with foods has meant that all EU member countries will allow RPET from approved plants to be used in food contact containers. Large and small brands used 163,000t of RPET in containers in 2008. Strapping tape, the green bands that keep bricks and boxes firmly held on their transport pallets, has been a steady outlet for RPET. 88,000t were used in Europe in 2008. The final category in PCI’s review of end markets is in injection moulding/ other outlets. These applications account for less than 20,000t /a of RPET at present and are very varied. The RPET can be filled with e.g. glass fibre and injection moulded to form complex engineering components. It is also injection moulded to form the barrel of the Pilot B2P (bottle to pen). This clear cylinder is designed to look like a PET water bottle, complete with a label panel, a quality pen with the body made from 100% RPET. A new application from Dymon Pallets Pty in Australia is a transport pallet moulded from a 25kg preform (big enough to contain a 10 year old child). The company estimates that in 2005 over 1 million timber pallets were made in the USA alone and RPET pallets could absorb the world’s production of RPET! It can be seen that RPET has outlets for every quality. The clear, higher grade pellets and flakes are used by the food packaging industry and flakes that haven’t been through the final purification process for food contact, or coloured flakes find a market in “hidden” and coloured applications. Moreover, there is continual research into RPET applications and RPET recovery techniques. Novel processes drive new applications for RPET. Some of the methods involve dissolving post consumer PET, treating post consumer and post industrial waste at high pressures and hot and cold temperatures to produce novel end products with novel properties. Although still in the early stages of development these innovations have the potential to improve our collection and recovery of Europe’s most recycled packaging polymer. Petcore is keen to support these developments and will help facilitate their growth. Details of many of these end uses for RPET can be found in the Document Library by those who register with the Petcore website. www.petcore.org Global crisis puts Krones in the red Krones AG, the beverage filling and packaging technology company, says that the global economic crisis made the 2009 business year the most difficult in the company’s 59 years of existence. Demand in the packaging machinery market fell worldwide by more than 25%. With the exception of China, all regions were affected by a significant decline, particularly North and South America, and Eastern Europe and Russia. Order bookings at the Group fell 18% in 2009 compared with 2008, to €1,916 million. There was no discernible turnaround in clients’ ordering until Q4, which showed an increase of 10% compared with the weak fourth quarter of 2008. Order backlog on 31 December 2009 totalled €888 million (preceding year: €837 million). Consolidated sales in 2009 were 22% lower than the record year of 2008, totalling €1,865 million. The consolidated result was a loss of €34.5 million. Krones does not anticipate any reversal of the sales trend until the first half of 2010. Despite the 2009 loss, the company increased free cash flow by five per cent, to €83 million. As at December 31, 2009, Krones Group had no debts with banks and possessed liquid funds (net cash) amounting to more than €135 million (2008: €107 million). Krones says that its long-term growth prospects continue to be good, as the mega-trends are positive for its chosen sector. The company is cautiously optimistic for 2010, anticipating a turnaround in the overall trend for the first half of 2010, with an increase in sales during the 2010 business year of five to 15% and a return to positive results. www.krones.com DAK Americas responds to patent infringement DAK Americas LLC has announced that it is reviewing the Eastman Chemical Company Patent Infringement complaint filed against it on March 1, 2010. The complaint alleges infringement of three Eastman patents that represent a portion of Eastman’s IntegRex PET Technology. Hector Camberos, President and CEO of DAK Americas, said that the company respects intellectual property rights and intends a vigorous defence against the claims. www.dakamericas.com","@ID":10} "BOTTLING / FILLING 28 PETplanet insider Vol. 11 No. 04/10 www.petpla.net “A bottle of Bisleri, please” Whenever anyone in India orders bottled water there is very strong chance that he or she will say exactly that - “A bottle of Bisleri, please”. With a 60% market share across its brands Bisleri has no serious competitors. But that isn’t enough. For the future the company is targeting an 80 % share, and to do it they have 8 bottling plants of their own and over 50 co-packers and franchisees in India. Service is the key to their business. Bisleri is growing by 40% year on year. Reducing the bottle weight doesn’t seem to be a good idea in the eyes of Mr Kadeer Khan, Director Corporate Affairs. A lighter bottle would be too soft and flexible. In particular the roads over which the water is transported demand a sturdy bottle. Then there is the fact that most bottles of water are sold out on the street, which means that they are exposed to direct sunlight for long periods. The refillable 5 ,10 and 20l containers start to take on a yellowish colour after just a couple of cycles. This has been solved by introducing a light green tint to the preforms. The company would very much like to add the green tint to their single trip bottles but unfortunately Indian law, for some incomprehensible reason, forbids the colouring of single trip bottles. Generally for Bisleri colour goes right to the heart of the matter. Until 2006 all labels were blue - and “all” means all water bottles from all suppliers! This of course made product differentiation on the store shelf almost impossible. Bisleri took a course of action which, from a marketing point of view, was double edged. In 2006 they changed their main colour from blue to green, despite the fact that for decades their corporate branding had been blue. Not only were the labels changed to green, but so were all of the buildings, delivery trucks and employee uniforms. Even the furniture is now in the new house colour. Today they can say that the new market Bisleri has concentrated on still water, which is bottled exclusively in PET. from 250ml to 2l the bottles are single trip, and refillables are used for the 5, 10 and 20l sizes. Most fillings are of the 1l size. In the North Pearl Drinks supply the required 22g preforms, made from virgin PET and using the weight-saving Alaska neck. For Mr. R. K. Garg, Director Northern India, the quality and availability is crucial, if the price is right too, then he is satisfied. Ten to fifteen years ago the company tried moulding their own preforms but finally decided to stick to their core capability - i.e. manufacturing and selling pure and safe water. Alexander Büchler (left) had the opportunity to visit two of the Indian Bisleri plants, together with Vijay Walia (right), Deputy General Manager of Pearl Drinks. R.K. Garg (centre). Director Northern India, Bisleri, is proud of the 40% annual growth of Bisleri.","@ID":30} "PRODUCTS 33 PETplanet insider Vol. 11 No. 04/10 www.petpla.net New Electric Reheaters for 5-Gal PET Water Containers Canadian company W. Amsler Equipment Inc has unveiled a three-model line of electric reheat stretch-blow molding machines for production of PET water containers up to 18.9L (5 gal). They are designed to produce BPA-free replacements for polycarbonate. The fully automatic L120 convertible can be used in one, two, or three-cavity modes for production of 4l to 22l bottles. Production rates are: 18.9l at 300/h; 15l at 1000/h, and 3.8l at 3000/h. Neck sizes range from 28mm to 70mm. With neck sizes from 33mm to 63 mm the LM 120 is a semiautomatic, monoblock reheat machine with manual preform loading, producing 18.9l bottles at 170/h. The manual M120 has separate preheat and blowing units. It makes 120 3.8l bph and 80 18.9l bph. Neck sizes are from 33mm to 80mm. Amsler supplies 18.9l preforms for its machines and says that the products offer output, energy, precision and changeover advantages compared to hydraulics. www.amslerequipment.com Panelless hotfill PET bottles and lightweight PET wine bottles. E-proplast GmbH’s panelless, hot-fillable, disposable PET bottle has been developed from a combination of the special heatset blow moulding process and a modified glass filling line. The panelless Hotfill bottles can be filled with popular fruit juices such as orange, fruit punch and apple. A shelflife between 9 and 12 months is possible, depending on the product. The technology allows reduced weight and, therefore, savings in materials. A 1l hotfill weighs 40g; a 330ml panelless version just 21.5g. E-proplast says that existing glass filling lines can be converted with relatively simple instruments. The company has also extended its EproWine range, with the introduction of a lighter PET bottle for wine. It has the same appearance as traditional glass wine bottles but weighs just 49g. www.e-proplast.eu Cost-effective PET bottle handling Sismatico UK Ltd, of Doncaster, UK, has introduced two machines for conveying PET bottles – the APF 3002 and APF 6004. The former is designed to handle up to 3000 1.5l bphur and the latter is capable of 6000 bottles/hour. Sismatico manufactures air conveying systems for food and beverage producers. The aim of its PET AirConveyor System is to provide a low maintenance accumulation link between system infeed machines such as blow moulders, de-palletisers and unscramblers, to the end of the line machines such as fillers, rinsers, labellers and palletisers. The Sismatico Clipmatic neck guide material incorporates a special low friction plastic profile, which allows for a 150m joint-free running surface. Its dry lubrication system allows increased neck rail life and reduced air conveyor power consumption. www.sismatico-uk.com C O S TEFFICIENCY ENERGYEFFICIENCY C O S TEFFICIENCY ENERGYEFFICIENCY","@ID":35} "BOTTLING / FILLING 29 PETplanet insider Vol. 11 No. 04/10 www.petpla.net positioning has been a success. A recent addition to the product range is carbonated water in a 0.5l, 25g bottle with a 28 PCO cap. The carbonation level is 4%. For the coming year the first filling line for flavoured water will be installed in Sahibabad. Here, because of the law prohibiting coloured bottles, Bisleri has a problem of shelf life but they are working hard to solve the problem as they expect to open up new markets with this product. In India we had the opportunity to visit two of the Bisleri plants. These were the plant in Sahibabad, well developed industrial area of Uttar Pradesh and only a few kilometres north-east of Delhi, which was inaugurated only in 2006, and the plant in Delhi itself, which is currently undergoing renovation. Both plants are very similar in their basic layout. The water goes through a 7-stage purification process; two SBM machines feed the containers to a single filling line where the water is bottled. The filling speed is about 120bpm. Both plants have plenty of space available for expansion and at the moment are filling between 30 and 50 lakh* cases per annum, which equates to between 42 and 70 million litres. * 1 lakh = 100,000 Sahab Singh (centre) DGM -Technical at Bisleri Kadeer Khan (centre), Director Corporate Affairs at Bisleri","@ID":31} "BOTTLE MAKING 26 PETplanet insider Vol. 11 No. 04/10 www.petpla.net Four new lightweight neck designs PMCI, the PET moulds and containers division of Italian company Sipa SpA, has developed a new range of lightweight neck designs that are suitable for water, carbonated soft drinks (CSD) and hot-fill containers. Materials for mineral water packaging represent 70-75% of total packaging costs. PMCI says that its new design for the Alcoa 26mm thread finish, which is already very light, takes weight down from 2.4g to 1.8g – a 25% saving. The thread design has been developed and patented in partnership with a US mineral water producer and is already deployed in the customer’s manufacturing plant. Material savings on the 26mm Novembal shaped neck amount to 1g – weight is claimed to be cut to 2.6g. While hot fill technology is popular for its advantages in reducing the use of preservatives in food and avoiding the need for aseptic processes, its value has had to be balanced against the need for robust packaging design. PMCI claims that its new neck designs enable significant resin savings for 28mm necks. The company’s Hotlight 28 weighs just 3.8g, which is less than half the standard 7.8g. It is an evolution of a neck design usually found in CSD applications and allows the production of hot fill and CSD products on the same line, without any compromise to sealing. www.sipa.it The company’s new design for PCO 1810 standard CSD closures uses the same height of the thread finish (21mm) but offers 27% material savings, bringing individual weight down from 5.1g to 3.7g – 1.4g per neck. The company says that this can add up to savings of many kilograms of PET a year. No change is required for the neck shape and the solution is fully compatible with existing bottle lines. Medium and large users will be able to convert from their existing thread to the PMCI design. PCO 1810 5.1g New PMCI PCO 1810 3.7g C O S TEFFICIENCY ENERGYEFFICIENCY","@ID":28} "MARKET SURVEY 22 MARKETsurvey 03/10 Company name GEA Procomac S.p.A. Zecchetti Srl Accs Europe Intec Solutions Postal address Telephone number Web site address Contact name Function Direct telephone number Fax E-Mail Via A. Moro, 1/A - 43044 Collecchio (Parma) Italy +39 0521 333711 www.procomacpackaging.com/ Fabio Borrini Product and Export Sales Manager +39 0521 333752 +39 0521 333823 Fabio.Borrini@geagroup.com Via Galileo Galilei, 1-1/A 42027 Montecchio Emilia (RE) Italy 0039 0522 867411 www.zecchetti.it Francesco Parma Sales Manager 0039 0522 867411 0039 0522 866034 f.parma@zecchetti.it 33 rue Victor Tilmant 59000 Lille, France 00.33.(0)9.81.68.94.43 www.accseurope.com Francis Antson Sales Director 00.33.(0)6.66.01.88.00 00.33.(0)3.20.52.94.43 contact@accseurope.com 2382 Bolton rd Nw, Atlanta,Ga 30138 404 815 9983 www.intecsolutionsusa.com A. Manier President 404 815 9983 404 601 9778 amanier@intecsolutionsusa.com Preform: From Injection Moulding Machine into the Box: Box-filling system (Yes/No) No No Yes Yes Maximum drop from conveyor belt to base of carton (in cm) 45 cm / 18 '' In-line Control (Yes/No) No No Yes Yes Special features Preform: From Box into Stretch Blowmoulding Machine up to 60 000 preforms/hr Dumper (Yes/No) Yes Yes Yes Conversion to different neck diameters (No/mechanical/ electrical) No Yes , by mechanical adjustment - In-line Control (Yes/No) No Yes Yes Special features Box automatic storage/retrieval preform unscrambler Bottle: From SBM to Filler, Air Conveyor Air Conveyor (incl. vertical) (Yes/No) Yes Yes Yes Yes Purity levels (Which?) 99.99 DOP – photometric test method. 3 levels: (a) 1-stage filtering : G4 – EN779:2002 - min 90% galvanometric (b) 2-stage filtering : F9 – EN779:2002 - min 95% opacimetric on 0,4 micron (c) 3-stage Absolute Filtering: H14 – EN1822 Hepa Filter - 99,995 MPPS 0,12-0,17 micron – min 99,999 NaCI – 0,65 micron; Filtered air class: 100 (according to the Federal Standard 209) - 5 (according to the ISO Standard 14644) H14 c100 or ISO5 Bottle format conversion Yes, automatic available (a) Fully automatic by means of pneumatic cylinders (b) Fully automatic by means of unlimited position drives Yes Yes Conversion to different neck diameters Yes, manual available (a) Fully automatic by means of pneumatic cylinders (b) Fully automatic by means of unlimited position drives under request Yes Special features Special air jets design, with air cushion effects on the bottles, thus reducing the electric power consumption (up to 40% less) smooth, low-friction, special plastic clip-on neck guides / highspeed driven splitters / EST (Energy Saving Target) facility / automatic control of the air flow delivery / *line sinoptic on PC / fully flexible recipes Quick change under neck guide, cleaning service Quick change neck guide; Universal guiding system; Blower speed management Bottle Storage Systems Bottle Up-ender (Yes/No) No Yes Yes Yes Buffer Systems Capacity (Number of Bottles from to ) (Number of Bottles from 1,000 to 50,000 ) silo or tote systems from 0 to 55, 000 Storage Systems Capacity (Number of Bottles from to) No Silo from 0 to 350, 000 Palleter and De-Palleter for empty PET bottles (Yes/No) Yes, depalletisers Yes Yes No Special features buffer systems for light and fragile bottles palletizer/depalletizer combi to provide: top-up to filling line / continuous SBM running around the clock / back-up in case of filler downtime / infinite accumulation We propose a tote system,which optimize the space to 90% of the volume of the truck. It is stackable without racks inside the warehouse and ultimately eliminates packaging material (plastic and wood)","@ID":24} "BOTTLING / FILLING 31 PETplanet insider Vol. 11 No. 04/10 www.petpla.net emphasis of the bottles is different to most manufacturers’. Rather than light weight The need is for strength for the long journey from Tibet to the markets. The bottles also need the ability to withstand the changes in air pressure as they travel from the factory’s 4,600 metres elevation to sea level. Once they reach consumers’ hands, they have to feel comfortable and substantial. The preforms, weighing 18g; 23.5g; 36.8g and 47.6g respectively, are produced in-house. From idea to inception The first Krones 24,000 bph blowmoulder/filler bloc, plus a Contiroll labeller, was delivered in 2006. The testing ground for 5100 was Tibet itself; having been proved in its local market, 5100 was launched into China. In 2007 and the second Krones filler bloc and an Autocol pressure-sensitive label applier followed in 2008. Also rated at 24,000bph, its installation allowed production to be doubled. A third line, made up of a complete 36,000bph Krones PET line, arrived in early 2009. The company is already looking to the future – the new Tibet Glacier production hall has room for a further three lines. Challenges of height The bottling plant’s elevation required a series of special measures in order to assure reliable bottle production, filling and labelling. The ratings of all the drives had to be at least 20% higher than standard. Since Tibet Glacier also sells the water down to sea level, the bottles have to withstand a pressure differential of about 0.4 bar. The PET containers are filled as closely as possible to the brim in order to prevent bottle deformation; liquid is less susceptible to compression and expansion than headspace air. Air consumption of Tibet Glacier’s stretch blow-moulding machine at high altitude is considerably more than normal. At sea level and standard barometric pressure, consumption is 581m³/h; in Lhasa, at 4,600m elevation, it almost doubles, to 999m³/h. The high-performance compressors, supplied by Krones, were specified with 70% more capacity, while the Contiform coolers are 25% more powerful than the norm. Other machine configurations largely conformed to Krones’ normal standards. However, an unforeseen issue arose with the touch-screen computer control panels. They are normally rated up to 3,500m elevation; the equipment for Tibet Glacier had to be specially tested and certified as suitable for the thin air of the Tibetan Plateau. Installation work high up in the mountains was an entirely new experience for the Krones staff involved and a few were affected by altitude sickness. Additional service personnel ensured the installation schedule was achieved. Tibet Glacier now has production capacity of two million b/day, or 300,000t/a. Within the next five years, the company is aiming to be listed on the stock exchange and to increase production capacity to 400,000t/a. The strategy is to build up the company’s image within China and then to look to other markets. Tibet Glacier is meanwhile operating three lines from Krones. The air consumption for the stretch blow-moulding machine is almost twice as high as at sea level. SurShot™ | Monosorb™ | Mono-Layer Active & Passive","@ID":33} "REGIONAL MARKET REPORTS 10 PETplanet insider Vol. 11 No. 04/10 www.petpla.net Part 2 Egypt The second part of ‘Egypt’ shows us that it is not only beverages that are bottled in PET. Our report on Taba shows very neatly that PET is also de rigueur in the medical sector in Egypt. We give the two other major converters in the Land of the Pharaohs – namely, Marina Plast and Aquah Group – the chance to make their voice heard. After all, where would local reporting be if we didn’t let at least one of the big Colas have their say? by Alexander Büchler Aquah Group Salah Al Aquah, President Karim Al Aquah, Vice President Fayek Shoukry, Group Technical Director The company founder, Salah Al Aquah (right), allows the Aquah Group to keep on growing. The expansion can’t be stopped - the photo shows the second Husky HyPET, which will be followed in a few days by the third. In front of the machine are (from left to right) Group Technical Director Fayek Shoukry, Vice President Karim Al Aquah and Alexander Büchler Regional market reports Egypt Part 2","@ID":12} "PETbottles 34 PETplanet insider Vol. 11 No. 04/10 www.petpla.net The PET dab of mustard The Krallmann Group develops and produces caps for PET bottles that operate by means of a valve system. On Messrs. Carl Kühne’s ‘K-squeezes’, this is how the cap is produced using the 2-component procedure. The TPE valve, which is injection moulded directly into the cap, has been individually coordinated with the product requirements and, in conjunction with the shapely PET bottle made by cooperation partner Gizeh PET, enables clean, fault-free dispensing and metering of precisely the amount of mustard required. The bottle is designed to stand on its cap. This ensures that there is always sufficient mustard at the valve opening so you don’t have to shake the bottle. www.krallmann.de Single-serve PET bottle for health drink Amcor PET Packaging is supplying organic beverage manufacturer Sambazon, Inc., with a new range of specially designed 11 fl oz (33cl) single-serve PET bottles for its new, premium Antioxidant Elixir acai drink. The easy grip, clear packages are covered with a full-body PET shrink label and aimed at the ‘on-the-go’ market. Clarity was the deciding factor over HDPE. www.amcor.com Unusual sauce bottle The French subsidiary of Bakkavor, based in Mâcon, is selling various salad dressings and sauces in an unusual long-necked 150 ml PET bottle. The bottles have a self-adhesive label and are sealed by a silvercoloured PE screw cap with tear-off tamper evidence. Sweetener in PET Krüger of Bergisch-Gladbach has a 300 ml pack of “Cologrin“ sweetener, based on sodium cyclamate and sodium saccharine, in a clear PET bottle. The screw-on, colour-coordinated dispenser cap, which tapers to a point, and the conical fold-back overcap, have a snapoff tamper-evident feature. A wraparound paper label carries the required product and commercial data and nicely finishes off this modern pack. “Karamalz” in PET By changing the packaging of their “Karamalz” malt beverage to a modern, lightweight 0.75 litre PET bottle, with a unique design and shape, the Eichbaum brewery of Mannheim, Germany, hope to increase their market share. The dark coloured bottle has an embossed logo in the upper area and the word “Karamalz” further down. A colour coordinated, tamper evident screw cap and a wrap-around paper label give this package an attractive look on the shelves. Lidl chooses PET The European discount supermarket chain Lidl, headquartered in Neckarsulm, Germany, is selling a 1l pack of “Hatherwood” brand blackcurrant syrup in a PET bottle. The bottle has embossing in the upper and lower parts that significantly improve its stability. A wrap-around paper and a colour coordinated screw cap with tear-off tamper evidence complete this attractive, high quality pack. Chilli sauce from a clear bottle The 300 ml pack of chilli sauce with mango and pineapple is sold by the Dutch company Go-Tan of Vesteren in PET bottles. The bottle has neck and base areas with good stability and is dressed with a wrap-around plastic label that carries all of the important product information. The screw cap is fitted with a hinged lid for easy dispensing and the bottle is tamper-proofed and sealed by an aluminium composite foil over the neck.","@ID":36} "PETnews 6 PETplanet insider Vol. 11 No. 04/10 www.petpla.net Sacmi reorganisation and executive appointments Vezio Bernardi made Managing Director of Sacmi Filling Sacmi Imola, the Italian packaging and labelling equipment company, has announced a reorganisation of its business and the appointment of a new executive team. A new division – Sacmi Beverage – has been created and will combine the activities of Sacmi Filling, Sacmi Labelling, Sacmi Packaging and Sacmi Imola. What the company describes as a strategic development began in early 2009, with the acquisition by Sacmi Imola of a minority holding in Sacmi Filling and Labelling. The purchase was followed by investment in new storage facilities and production plant facilities amounting to more than €50 million. Sacmi Beverage integrates plant engineering and budgeting part and also coordinates the management administration of the four companies. Ireneo Orlandi is the senior director of Sacmi Beverage. Vezio Bernardi has been appointed to guide the transition stage. He previously held a senior position with Sacmi Imola Closure Division. Plant engineering manager Giovanni Nervo will have responsibility for operations management and co-ordination of the plant engineering product range that integrates the Division’s component companies companies’ products. www.sacmi.com 25th international IKV Colloquium The 25th International Plastics Technology Colloquium was held on 3 and 4 March 2010 in the Eurogress Aachen, Germany. With some 500 experts attending, the number of participants remained constant compared with 2008, despite the economic downturn. Participants represented the entire spectrum of the plastics industry and included raw materials manufacturers, machine and mould manufacturers and plastics processors plus their customers. Those taking part in Aachen came from 15 countries, with more than 250 companies and institutions represented. At its Jubilee Colloquium, the IKV once again presented the latest research results, covering all the various different facets of plastics processing. The IKV highlighted the future prospects for plastics processing, under the strapline motto “Plastics technology – looking ahead”. In the Part Design and Materials Technology Department, the latest development in the field of plasma-based refinement processes met with particular interest on the part of the attendees. In addition to the barrier coating of alternative materials such as polypropylene (PP) or polylactide (PLA), a new process variant was presented for the combined inner and outer coating of beverage bottles by the low-pressure process. The demonstration equipment developed specifically at the IKV allows a barrier layer system to be applied in a single process, where previously two separate processes were required. The result is greater cost efficiency. www.ikv-aachen.de Amcor PET Packaging renamed Following the US$1.9 billion acquisition of parts of Alcan Packaging by Amcor Ltd and subsequent company reorganisation, Amcor PET Packaging has been renamed Amcor Rigid Plastics. Based in Ann Arbor, Michigan, USA, the renamed business group is one of seven operating units within its parent group. Amcor Rigid Plastics consists of Amcor PET Packaging; Bericap North America, a plastic closures joint venture between Amcor and the Bericap Group; and the plastics container unit of Alcan’s global pharmaceutical business. Bill Long, who had been president of Amcor PET Packaging, will head up the new business. The company says that the new name and identity reflects an expansion of its product range. Included in the acquisition were Alcan’s pharmaceutical rigid container business, which is a producer of containers made of PP, PE, and PET for over-the-counter drugs, vitamins, and other pharmaceutical needs. Amcor now owns Alcan’s extensive processing capabilities in stretch-blow, extrusion-blow, and injection blow moulding, along with expertise in multi-material processing. These resources will enable Amcor to move into new applications, materials and processes, the company said. The acquisition adds approximately US$160 million in sales and 800 employees across six plants, located in Millville, NJ, DesPlaines, IL, Bethlehem, PA, Youngsville, NC in the US and Cayey, Puerto Rico, and Diadema, Brazil. Amcor is headquartered in Melbourne, Australia and is listed on the Australian Securities Exchange. www.amcor.com New hotrunner factory in India Hotrunner technology company Mold-Masters announced on March 17, 2010 that it has opened a new production facility in Coimbatore, India. The company already has a global design centre in India, which was opened in December 2006. Mold-Masters has had a presence in India since 1994, when it began selling and servicing its products in the country. It reported a significant increase in sales after establishing a presence in the sub-continent. The new facility will enable the company to manufacture for the growing Indian market and to enhance its support for new and existing customers, with technical service, application engineering and rapid spare parts delivery. www.moldmasters.com Sale of Equipolymers manufacturing facility in Italy Equipolymers, the 50-50 joint venture between The Dow Chemical Company and Petroleum Industries Company (PIC) of Kuwait, announced in March that it is to sell its pure terephthalic acid (PTA) and polyethylene terephthalate resins (PET) production facilities at its manufacturing site in Ottana, Sicily, Italy to a joint venture between Ottana Energia and Indorama. The company said it will continue to run its manufacturing, R&D and new technologies activities at Schkopau, Germany. Ottana Energia, owned by Paolo Clivati, currently operates a 140 megawatt power and utilities plant on the Ottana manufacturing site. Indorama is a global chemical producer of PTA, PET and polyester fibres and operates facilities in Thailand, the Netherlands, Lithuania, and the USA. The Ottana facility currently employs around 120 people. The sale is expected to complete on June 1, 2010. www.equipolymers.com","@ID":8} "PETbottles 36 PETplanet insider Vol. 11 No. 04/10 www.petpla.net Personal Care “Creme 21” shower cream The current owner of the relaunched “Creme 21“ brand is now trying to position the shower gels at the point of sale. Creme 21 GmbH of Bad Homburg has launched, for example, 250ml packs of “Milk & Honey” and “Waterfall”. The shower gels are packaged in white PET with an attractive shrink sleeve. An embossed white hinged cap completes this pack. Sagrotan in PET During the outbreak of “swine flu” there was an increased interest in products that clean the hands particularly intensively and that kill, bacteria. ReckittBenckiser of Mannheim, Germany, now have two Sagrotan brand 250ml packs of liquid soap on the shelves that are claimed to remove 99.9% of bacteria. The PET bottles have a “no-label look” label on the front and an informative self-adhesive paper label on the back, shaped to match the pack shape. A dispenser pump, with a lock position, is used to dispense the products. 2 phases in PET Brown PET for shampoo The French cosmetics manufacturer Laboratoires Vendome of Quentigny is marketing 250ml packs of shampoo under the “ Petit Marseillais“ brand and packaged in a brown PET bottle. The front of the pack has a “no-label” look label whilst on the back there is an informative self-adhesive paper composition label. The glossy metallic-coloured hinged cap gives the product a high quality look and is an eye-catcher on the store shelf. Wooden collar for PET bottle The German discount chain Lidl of Neckarsulm have decorated their 250ml PET bottle of “Suhada” body lotion with an attractive wooden collar The collar gives the pack a natural and high quality look and is very eyecatching on the store shelf. Front and rear labels in a light, woody colour reinforce the brand image and carry the required product and commercial data. A screw-on pump dispenser with a locking mechanism finishes off this unusual cosmetics pack Under the “Ombia“ brand Luhn of Wuppertal, Germany, is supplying the Aldi discount chain with 500 ml packs of 2-phase bath gel containing milk and aloe vera, and packaged in a compact clear PET bottle dressed with two self-adhesive paper labels. The aluminium screw cap is particularly eye-catching and attractive.","@ID":38} "PREFORM PRODUCTION 25 PETplanet insider Vol. 11 No. 04/10 www.petpla.net Manufacturing Advisory Services – PET case study The Husky Manufacturing Advisory Services team provides operational consulting, design and project management services to help customers increase the operating efficiency of their plastic injection moulding facilities. A case study explains how Husky worked with a PET customer to improve the overall operating efficiency of their operation. The customer is a PET preform manufacturer in Europe with eleven injection moulding machines for water, CSD and edible oil preforms. The situation The Husky Manufacturing Advisory Services team has worked with this manufacturer since 2003, performing yearly plant audits of the entire operation, identifying, quantifying, prioritising and following up on the implementation of improvement opportunities. Flexible maintenance and asset management software solutions Husky Injection Molding Systems has launched two software packages as part of its services offerings. Pro-Act is described as a flexible maintenance program; Shotscope NX is an integrated process and production monitoring system. The company says that the Pro-Act maintenance program is based on a proactive maintenance model. It is intended to maintain high performance and to avoid system degradation by using monitoring and measurable results to pre-plan and customise maintenance schedules, and to identify and respond to issues before they become problems. The program offers three levels of service, from entry-level to advanced. Shotscope NX is presented by Husky as an integrated process and production monitoring system that provides expedited information to help manufacturers control processes and improve productivity while minimizing scrap and downtime. The software is designed to help manufacturers characterise and report on production and process statistics at both the discrete systems and plant-wide levels. The company says that Shotscope’s real-time monitoring and analysis helps manufacturers simplify reporting, improve data flow and coordinate more efficient plant scheduling. Additions over the previous Shotscope system include an enhanced user interface. The software is web-based, which allows access from anywhere and at any time. It is compatible with any brand of equipment and able to connect with both PDA and webcam. www.husky.ca 15% reduction in energy consumption (in kwh) since 2003, through: Migrating to the latest drying and chilled water technology Improvements to plant HVAC sys- tems Increase in machine efficiency. 8.3% conversion cost reduction between 2008 and 2009 (excluding materials), as a result of: 10% reduction in maintenance and repair costs 7% reduction in labour costs. Average payback for projects implemented approximately 1.2 years. SPHERO® underwater pelletizers ... … refreshingly different Automatik – Your system supplier for all pellet shapes. If you want more than the usual, contact us. www.automatikgroup.com Please visit our Open House June 11, 2010 Key results OEE (Overall Equipment Effectiveness) has improved from 81.9% in 2003 to 91.2% in 2009. Key areas of improvement include: Implementation of a Total Pro- ductive Maintenance program 7% - 10% cycle time improve- ments through the implementation of a process optimisation program and process monitoring software Process standardisation resulting in reduction of scrap material. C O S TEFFICIENCY ENERGYEFFICIENCY","@ID":27} "PETproducts 32 PETplanet insider Vol. 11 No. 04/10 www.petpla.net Auto-adaptive drying system claims major energy savings The drying of PET is a crucial stage in its transformation from resin to finished product. Failure to ensure proper drying and conditioning can lead to a rapid drop-off in inherent viscosity (IV), with negative effects on the blow-moulding process. Drying consumes a large volume of energy, requiring the resin to be exposed to hot, dry air for up to as much as 6 hours. Italian company Piovan, headquartered near Venice, Italy, has introduced Genesys, a drying system that it says improves this process and makes it more energy efficient. Genesys is claimed to achieve the industry’s lowest-ever energy consumption. The system uses state-of-the-art technology, such as loss in weight control, airflow management and stabilisation, an intelligent regeneration process and advanced industrial PC-based control. The company says it is the only auto-adaptive system available today. The system has integrated an automatic airflow control and adjustment to reduce energy consumption by 35 – 55% below conventional resin drying systems. It also has the capability to further optimise energy use by stabilising the airflow in the drying hopper. It is further designed to recover almost all the energy used in regeneration of the desiccant material and, in so doing, to achieve savings of 50 – 80%, compared with traditional or current regeneration technology. With claimed overall system savings of 30% and more, Piovan says that a Genesys system producing PET performs running resin at a rate of 1,000kg/h can achieve savings in excess of 220,000kWh/yr. www.piovan.com/genesys Fully automatic mobile plant for disaster areas and production flexibility Plast Engineering Knauff e.K. has recently demonstrated and sold a number of fully automatic stretch blow-mould bottling, filling and labelling plants that are installed into a standard 40ft (12m) container. Designated as the Compact A 4C, the company says that the mobile plant is suitable for disaster emergency relief operations and for periods of heavy commercial demand. The Compact A 4C manufactures up to 2,800 PET 500 to 1,500cl bph from preforms; other volumes can also be specified. The PET bottles are automatically disinfected by UV radiation and transferred directly to the filling station, which fills them with UV disinfected drinking water. They are then closed with UV radiated caps, labelled, and covered with tamper-evident sleeves. The ready-for-sale bottles are discharged through a window in the container wall. Operation of the blow moulder requires clean air at 15 bar. The filling/capping, labelling, and sleeving units are supplied by a screw compressor, which is installed in an insulated compartment at one end of the container. Ventilation flaps enable proper airflow for each component. The complete system requires an 80 kW power supply; a potable water supply has to be provided on site. EC electrical power and two-inch water supply connections are installed on the outside of the container. www.pet-equipments.de www.plastics-equipments.de 22g ultra-light 1500ml water bottle Sipa says that it has used its TriBloc technology, presented at Drinktec 2009, to produce the world’s lightest 1,500ml bottle for still or carbonated water. The 22g bottle is blown in Sipa rotary blow-moulders at 2,000bph per cavity and filled and labelled in the Sipa TriBloc. Sipa is now offering complete turnkey lines, including TriBloc and a Sipa packaging and palletising line, which is designed to handle very light containers throughout the process. This eliminates the need for conveyor switches or setting and management at each changeover. PE roll-adhesive technology eliminates hot melt glue and traditional label cutting knives and makes the packing line simpler as bottles are delivered from the TriBloc, onto table-top conveyors straight to the shrink-packer. Space required is 40% less than conventional lines and the bottle itself can hold 60kg of top load. One operator can monitor the complete line, assisted by forklift drivers for raw materials supply. www.sipa.it Volumetric filling system AMS Ferrari, of Modena, Italy, celebrated the presentation of its Infinity volumetric filler/capper system with a sale to an Iranian company at drinktec 2009. The 52-valve Infinity system uses a Windows-based PC control for entering required capacity into the machine and shows three fills at once, to aid in monitoring and fault-finding. It is supplied from a pressurised tank, with electronic monitor, along a single pipe to the volumetric fillers. A second pipe controls the pneumatic valve opening and shutting. It is capable of handling a range of hot or cold fill beverages and liquids, from low-density water to high-density products such as tomato sauce, ketchup and fruit preserves, as well as detergents and delicate fluids like milk. It is designed to respond automatically to changes in temperature and viscosity. www.amsferrari.it C O S TEFFICIENCY ENERGYEFFICIENCY C O S TEFFICIENCY ENERGYEFFICIENCY","@ID":34} "MARKET SURVEY 23 Krones AG KHS AG Sidel Posimat, S.A. Böhmerwaldstraße 5 93073 Neutraubling 49 9401 70-0 www.Krones.com Reiner Kahl Vice President of Division Conveyor Technology 49 9401 70-3065 49 9401 709-1-3065 Reiner.Kahl@krones.com Juchostr. 20 D-44143 Dortmund 49 231 569 0 www.khs.com Thorsten Kahe Manager Container Conveyors +49 231 569 1583 +49 231 569 1657 thorsten.kahe@khs.com Sidel Blowing & Services SAS, Avenue de la Patrouille de France, Octeville-sur-Mer, BP 204, 76053 Le Havre cedex 33 2 32 85 83 00 www.sidel.com Sylvie Rak Business Communication Manager 33 2 32 85 82 46 33 2 32 85 81 34 sylvie.rak@sidel.com Avda Arraona 23,P.O.Box 306 08210 Barberà del Vallès, Barcelona, Spain 00 34 93 729 76 16 www.posimat.com Maribel Rodríguez Area Sales Manager 00 34 93 729 76 16 00 34 93 718 88 56 maribel.rodriguez@posimat.com Preform conveyor in mass flow available not availabale Yes not availabale not availabale Yes not availabale Preform feeder Yes Yes Yes mechanical Mechanical Electrical Yes Yes Yes automatic change over at feed rail system via pneumatic cylinders, automatic elimination of the malfunction Failure detection cells Yes Yes (HW) Yes Yes F5, F8, H13(HEPA) Standard Gravi F5, OPA F8, DOP H12 Hepa filters, DOP efficiency at 0,3 microns: 99,9% automatic adjustable body guide rail via multi position cylinder (up to 12 positions) or stepless adjustment via linear motor Manually Yes, different automatic side guiding + adapted regulation Yes, even automatically automatic adjustable neck-ring guide rail via pneumatic cylinders, also in curves No Yes (automatic change over) Yes, even automatically Triangle chute, standard and enhanced hygienic design, easy replaceable neck-ring and body guide rail, high efficiency blowing unit, automatic pressure control, ultrasonic sensors x Range of mergers, dry lubrication on neck guide Double guide system to convey safely even very short neck bottles. Vertijet is the only conveyor able to go up or down from 0 to 90° with or without accumulation. No No Yes Buffer Table (1400x8000mm) Tailor made, upon customer demands and available room x Tailor made, upon customer demands and available room Exit system designed to handle lightweight delicate PET bottles. Great flexibility for different formats and frequent production changes. Yes Yes Yes Yes, depalletiser x up to 30,000bph Sweep-off depalletiser into a hopper, simple and more economical than conventional systems.","@ID":25} "PREFORM PRODUCTION 20 PETplanet insider Vol. 11 No. 04/10 www.petpla.net optimisation to ensure close-contour mounting of the cooling sections wherever possible. Although manufacturing moulds of this kind involves considerably greater expense, this is compensated for by a significant reduction in cycle time. A further effect was that the temperature required for the cooling water was increased by approx. 2°C with a simultaneous reduction in the amount of cooling water, whilst at the same time it proved possible to increase the difference in temperature between cooling water inlet and discharge. These steps led to energy savings in excess of 17% in the cooler unit. Cost effectiveness: reducing the cycle time In addition to the energy savings in relation to the PET system, achieving shorter cycle times is the key objective since investment-hungry preform systems need to be used in the most efficient way possible. Netstal has taken this requirement into account and presented the newly-developed Calitec aimed at an intelligent reduction of cycle time. Due to the fact that it is possible to seal the preform, still hot from the injection moulding process, in the neck area without damaging it and to support it with compressed air, significant savings and improvements have been made: the cycle time has been reduced by up to 20% whilst the quality of the preform has been enhanced. The Calitec system has already been installed on a number of occasions in Netstal systems with up to 192 cavities. Further systems have been installed in several European countries, and additional retrofitting packages or new machines with Calitec will shortly be ready for delivery. The efficiency of the Calitec System has been further increased by making use of more intensive cooling of the moulds as described above; as a result of the cooling, the outer skin of the preform becomes highly robust so that, even where cycle times are very short, Calitec sustains the cooling chain and thus prevents any reheating. This means that, with the new developments OH X-Cool (Otto Hofstetter) and HPStack (MHT), Calitec is able to demonstrate particular efficiency in operation, especially where preforms with smaller wall thicknesses are concerned. Overmoulding to the fore The Swiss company are also able to manufacture 2-layer preforms where the first layer can have a wall thickness of less than 1mm. This is made possible by means of a core support.The possibilities offered by this process could be considerable; worthy of mention are, for example, Prelactia (recently launched on the market) or various barrier applications based on different raw materials (PS, PP) together with a wide range of colour applications. Since the launch of Prelactia this product has undergone consistent development.The composition of the two raw materials used, to which the necessary additives are added as early as the polymerisation phase, has been further optimised in order to elevate the light barrier. As a result of these endeavours success has been achieved in reducing the preform weight selected in the first stage from 28g for a 1l bottle to just 24g. At the same time the bottle did not suffer any restrictions either in terms of the barrier characteristics or in terms of the strength characteristics required. In the meantime, new Prelactia products developed for yoghurt or creamer pots have come on to the market. The product Prelactia received an award at the Emballage packaging exhibition in Paris in the autumn of 2008. Further applications of overmouldings that may be of interest also include the use of recyclates on the outer layer of cap manufacture: by way of example, we would mention here 2-colour caps or the use of two different components. *Based on an article by Stefan Bock, Netstal Maschinen AG www.netstal.com Although Netstal may have not invented overmoulding, they apply the process for manufacturing 2-layer preforms with high level reproducibility using this process. Prelactia received an award at Emballage 2008.","@ID":22} "BOTTLING / FILLING 30 PETplanet insider Vol. 11 No. 04/10 www.petpla.net On top of the world Tibet Glacier produces water from the Roof of the World – bottled by three Krones lines Tibet Glacier Mineral Water Co. Ltd. is the first company to have succeeded in bottling mineral water from Tibet, in south-west China, and launching it on the Chinese market. Three Krones lines have been installed at the company’s bottling plant near the Tibetan capital of Lhasa, located a mere 14,300ft (4,600m) above sea level. The water source itself is even higher still, rising from the Nianqing Tanggula mountains at 5,100m. The plant’s elevation and distance from its main markets presented some significant challenges that had to be overcome, including transport, air pressure differences, the thin air in the factory and even for computer equipment specifications. Hong-Kong-based Mineral Water Resources Ltd., the parent company of Tibet Zhongji Jiahua and Tibet Glacier, opened the plant in 2006. It did so after a ten-year planning period, during which time it investigated water sources all over the Tibetan plateau. While it is one of the least-polluted areas left on earth, Tibet is also very remote. It is surrounded on all sides by mountains, including the Himalayas in the south. Communications have never been good – but they are improving, quite significantly, in some respects. A key catalyst for the launch of the Lhasa plant was the opening of the Qinghai-Tibet Railway on July 1, that year. Up until that time, the only route to market was a tortuous journey by truck via the ‘Friendship Highway’ to Nepal, to the south-west. It took two to three weeks, or even more. The rail line enabled delivery from Lhasa to Beijing in two or three days and provided Tibet Glacier with a viable option for accessing the growing cities of China, 2,000km to the east. A distinctive taste The new mineral water, 5100, is named for the spring’s altitude. At RMB8 (€0.80) for a 500ml bottle in supermarkets, it is priced for the premium market. However, the retail segment is the minority; 80% of sales are to restaurants, hotels, golf clubs, night clubs and the restaurant cars of China’s high-speed trains – the places where the rowing middle classes are to be found. The Qinghai-Tibet plateau is also home to one of Buddhism’s three sacred lakes, the ‘Heavenly Lake’ of Namtso. Tibet Glacier water’s micro-element and mineral constituents appeal to the Chinese market’s attachment to traditional, herbal and natural medicines and health products. The main sales are in 330ml bottles. In order to set itself apart and to create a distinct visual identity for its upmarket clientele, Mineral Water Resources Ltd worked with Krones’ PET design team in creating a distinctive square-shaped bottle, carried through 330, 500, 1,000 and 1,500ml sizes. For Tibet Glacier, the 5001. A very special kind of water","@ID":32} "BOTTLE MAKING 27 PETplanet insider Vol. 11 No. 04/10 www.petpla.net Lightweight bottles for hot filling Sidel claims that its new Skyward and Curvy models are the lightest PET bottles available for hot filling. The two 500cl bottles weigh just 18.9g each but have distinctive appearance and functional features. The lightweight bottles have been made possible by the development of new technical solutions that extend possibilities of lightweighting for heat-set packaging. You will feel better having made the right decision. Reduce your energy consumption. Gesellschaft Wärme Kältetechnik mbH Friedrich-Ebert-Str. 306 · D-58566 Kierspe Tel. +49 2359 665-0 · www.gwk.com Mould inserts Temperature control technology Water treatment Cooling technology Temperature controllers Chillers Energy saving cooling systems Skyward has a long silhouette, a belt and four panels, rather than the more common six or eight. As its name suggests, Curvy features curves, spirals and a twisted back, which acts as a support beam. Sidel Packaging & Tooling Centre achieved the lightweighting of the new bottles by completely redesigning the neck, body and base. The 28mm amorphous (non-crystallized) neck has been made lighter, and it accepts a standard cap for carbonated soft drinks. Revisions to the base have made it stiffer, while using fewer raw materials. The geometric structure of the bottle bodies are designed to compensate for deformations due to vacuum absorption after cooling. Sidel says that the new bottles’ blow-moulds can achieve 1,800bph per mould with a standard HR process, which is obtained by heating optimisation with the SBO Universal range. The company’s bell nozzle is claimed to enable the blowing of lighter, amorphous necks without deformation. www.sidel.com C O S TEFFICIENCY ENERGYEFFICIENCY","@ID":29} "21 Conveyors for preforms and empty bottles Whoever would have thought that so many suppliers would be involved in this sector? When we put this topic alongside the others on the list of market surveys for the first time, we were thinking primarily of the usual suspects. “If we’re lucky, we’ll find ten suppliers”, we said to ourselves. Subsequent research quickly proved us wrong: the number of companies involved rapidly reached double figures. Our address department worked late into the night and over the weekend to make sure they got hold of every address and every contact – so a huge thank you to the team for their efforts. In the end nine companies responded to our questionnaire. We know from other market surveys that we have carried out that companies tend to be cautious in their responses, but our experience shows that, once a survey is repeated, at least twice as many companies as expected take the trouble to fill out the questionnaires. Whilst PETplanet insider has have made every effort to ensure that the information in this new survey is up to date no claims are made regarding completeness or accuracy. All data is as supplied by the manufacturers. 04/10 MARKETsurvey PET bottle-to-bottle recycling plants Caps and closures Conveyers for preforms and empty bottles Preforms Preform moulds and SBM moulds 2-stage SBM machinery Preform and single stage machinery Resins and additives Filling equipment Compressors Company name SMI S.p.A. Postal address Telephone number Web site address Contact name Function Direct telephone number Fax E-Mail Via Piazzalunga, 30 24015 S.Giovanni Bianco BG - Italy 0039 0345 40111 www.smigroup.it Pietro Volpi Marketing Manager 0039 0345 40316 0039 0345 40209 info@smigroup.it Preform: from injection moulding machine into the box: Box-filling system (Yes/No) Yes Maximum drop from conveyor belt to base of carton (in cm) 120 cm In-line control (Yes/No) Yes Special features Main specifications: Easily accessible modular frame, which can be integrated into any production line. Frame and supports made of stainless steel AISI 304. Supporting feet and flat link chain made of plastic. Chain slip tracks, driving and idle wheels made of printed plastic. Covering system to protect products from external agents. Preform: from box into stretch blowmoulding machine up to 60, 000 preforms/h Dumper (Yes/No) Yes Conversion to different neck diameters (No/ mechanical/electrical) (mechanical/ectrical) - In-line Control (Yes/No) Yes Special features See above mentioned point Bottle: from SBM to filler, air conveyor Air conveyor (incl. vertical) (Yes/No) Yes Purity levels (Which?) G3/F9/H14 Bottle format conversion Yes Conversion to different neck diameters Yes Special features Frame and supports made of stainless steel AISI 304. Possibility to regulate the air distributing system according to the bottle handled (by means of manual valves or by electronic control of the motors speed) Bottle body guides made of stainless steel and UHMW antifriction plastic.Bottle body guides to align the products in the conveyor trajectories. Supporting frames on the floor, on the wall, or on the ceiling e ejecting automatic system at the blowmoulder outlet. -Bottle inserting manual system at the blowmoulder outlet.. Automatic or manual change-over of the bottle body guides, according to the line requirements. Bottle storage systems Bottle up-ender (Yes/No) Yes Buffer systems capacity (number of bottles from to ) Depending on the bottle diameter Storage systems capacity (number of bottles from to ) Depending on the bottle diameter Palleter and de-palleter for empty PET bottles (Yes/No) No Special features See above mentioned point","@ID":23} "REGIONAL MARKET REPORTS 12 PETplanet insider Vol. 11 No. 04/10 www.petpla.net In the hot fill sector New Marina Plast is the only company in Africa producing hot fill preforms and hopes to open up whole new market sectors with the help of the preform user Juhayna. As far as caps are concerned the company has so far produced 30/25 and PCO 28 caps for still drinks. Amr Fathi is in talks with Rexam with regard to producing hot fill caps and 1881 cap for CSDs. Alongside organic growth, Savola is also looking to grow through acquisitions. If everything goes smoothly Amr Fathi wants to produce enough preforms in 2011 to require more than 40,000t of PET in Egypt for Africa. Taba Group The first of two Krauss-Maffei lines is currently producing small and large preforms on alternate months. In front of the machine are Alexander Büchler (left), Ahmed Shalaby, General Manger of the Taba Group, and Basant El Debaiky, the daughter of the proprietor who has recently joined the company. The Sipa blower produces bottles from the preforms moulded on the Krauss-Maffei (currently an oval bottle for cleaning chemicals) From left to right: Basant El Debaiky, Ahmed Shalaby and Alexander Büchler New Marina Plast Amr Fathi, General Manger Amr Fathi, General Manager of Marina Plast (right) explains to Alexander Büchler the gradual take-over of New Marina Plast in Alexandria by Savola of Saudi Arabia. It seems that we have New Marina Plast to “blame” for this Regional Report on Egypt. When we reported on Saudi Arabia 5 years ago we also met Shihab Izzat at Savola. He told us all about the emerging Egyptian market and the expansion plans that Savola had, including preform production. So now that we are looking at Africa we naturally wanted to know how far these plans, and the market, had evolved, which is how our Egyptian report started. Savola took over a majority interest (70%) in New Marina Plast in 2006, and in 2008 a further 25% was acquired. The remaining 5% was acquired by Savola in 2009. Standard injection mouldings, such as garden chairs and household items, were not taken over. Savola concentrated on the production of caps for still beverages, preforms and plastic pots, plus in-mould labelling (IML). There are now 25 machines dedicated to IML work. Savola, as one of the biggest edible oil producers, not only in Saudi Arabia but also in Egypt, is therefore ensuring that the oil industry can supply its own preforms. Preforms for water, CSDs and also oil are sold on the open market. The company uses BMB moulding and Husky machines Husky. With a throughput of PET resin in 2009 of 20,000t New Marina Plast is the biggest preform manufacturer in Egypt. Together with the parent company in Jeddah the group buys 80,000t of PET per annum. Amr Fathi, General Manager of New Marina Plast, took over the management of the company just a few months ago. Previously he was 15 years at Savola in Saudi Arabia, where he held various senior positions. His main objectives are firstly to bring the software systems at New Marina Plast up to the standards of those at Savola, to ensure best practice in the production system, and to drive organic growth along with exports to the region. This is targeted at a minimum of 20% per annum. To support this aim there will be a new 96-cavity Husky line this year to enable them to cover the 1881 neck finish requirements of the whole CSD market","@ID":14} "Vol.6 PETplanet print PREFORM PRODUCTION 16 PETplanet insider Vol. 11 No. 04/10 www.petpla.net The Rapid Guide to Perfect Preforms by Rick Unterlander and Ottmar Brandau Symptom: A thin layer of plastic protrudes out of the preform at one of the parting lines. Cause: Plastic material that has seeped through intersecting mould components either from too low a melt viscosity or insufficient clamping tonnage. Solutions: 1. Check injection time isn’t too low (injection rate too fast) and adjust if necessary. Injection rate should be about 10 – 12g/sec/cavity. 2. Check to ensure injection pressure isn’t too high, especially when peaking at the transition point. 3. Check to ensure hold (packing) pressure isn’t too high, especially near the beginning of hold time. Troubleshooting guides have suffered in the past from being locked away in offices and not being available to the people that actually need them. Considering the high cost of machine and tools high scrap rates can be a costly proposition eating away at already tight margins. PETplanet’s “Rapid Guide to Perfect Preforms” takes a different approach. Bound in laminated paper that is easy to clean off, the small format of the book of 108 mm by 151 mm (4.25” by 6”) allows easy storage in back pockets or tool boxes. It has been written for the people on the floor of injection moulding companies to support their daily work in making the best preforms possible. The product of two industry experts, Rick Unterlander and Ottmar Brandau, it gives concrete advice on 35 of the most common problems in preform manufacture, most illustrated by pictures. From high AA levels to wavy bodies processors can find help when they need it. PETplanet print vol.6 The Rapid Guide to Perfect Preforms machine no./name 10. Flash","@ID":18} "REGIONAL MARKET REPORTS 11 PETplanet insider Vol. 11 No. 04/10 www.petpla.net As early as 1974 the company founder, Salah Al Aquah, was selling, for his own account, single-stage Nissei ASB machines. In 1982 they were used to produce the first PET jars and thus Salah Al Aquah produced the first PET containers in Egypt. Even today he still supplies jars and bottles from 0.125l up to 20l for a very wide range of applications. In 1992 he established his El Aquah Group of Companies, where a key element of the business was the supply of preforms and bottles for the edible oil market. Today his empire includes eight companies making preforms, bottles resins and other plastic products. He produces preforms and bottles for non-beverage applications and 450 million preforms for the beverage sector, of which 50% is for the CSD market. His business with the CSD market is growing by an above-average 30% per annum. Every year he has bought a preform system - each with 72 cavities. In 2007 it was an Engel, in 2008 and 2009 it was Husky, and for 2010 another Husky is on the way in order to be able to respond to the growing demand. For the relatively near future he sees the adoption of the lightweight PCO 1881, especially for 1l and 2l bottles. For three years his son Karim Al Aquah has worked with him in the business. As a trained electronics and telecommunications engineer his main task was to ensure that all aspects of the steadily growing business were operating in line with the latest technological standards. If he meets his old college friends they tend to talk about telecommunication. He, on the other hand, is now more concerned with things like PCO and IV. His father now devotes more time to customer contacts. Hence father and son make a really well-rounded team. Coca-Cola North and West Africa Ehab Afifi, Technical Operations Manager Alexander Büchler (left) and Ehab Afifi, Technical Operations Manager Coca-Cola North and West Africa, talking about the new 0.4l Coca-Cola bottle. The meeting was organised by Sherif El Bakary, Manager of Sidel S.A.S. Coca-Cola in Egypt The Coca-Cola bottler in Egypt has recently introduced the 0.4l PET bottle. We spoke with Ehab Afifi, Technical Operations Manager Coca-Cola North and West Africa, about the background to this project. PETplanet: Mr Ehab Afifi, you are the person responsible for the technical aspects of bottling Coca-Cola in North and West Africa where the introduction of the PET bottle is concerned, are you not? Mr Ehab Afifi: That’s not exactly true. I have to look after all of the technical aspects, including glass and can filling. PETplanet: So what is the main focus of your work? Mr Ehab Afifi: We support the bottlers mainly in environmental matters - how they can save water and reduce energy consumption, not only in the filling operation but also in the management offices or down the beverage distribution chain. PETplanet: Were environmental concerns the reasons that Coca-Cola introduced the 0.4l bottle? Mr Ehab Afifi: The reason has more to do with changes in consumer demand. There have been lifestyle changes and single-trip is the main driver now. And by single-trip I mean PETand cans. PETplanet: You offer CSDs in 0.4, 1.0, 1.5 and 2l PET containers. Which size is the most popular? Mr Ehab Afifi: Good question! PETplanet: With the newly-introduced 0.4l bottle the product has a shelf-life of 3 months. Which barrier technology do you use to achieve this shelf life? Mr Ehab Afifi: We are using our technology that has been tried and tested in South Africa. The monolayer PET package comes at a solid 28.7g with a properly stretched side wall providing an acceptable level of barrier for such a size container – quality control and consistent processes being the basis. At the moment we are importing preforms from there. PETplanet: And what about the introduction of the lightweight PCO 1881 at Coca-Cola? Mr Ehab Afifi: That is ultimately a decision for the bottlers. We, for our part, do back the new cap. It saves material and energy. PETplanet: Does that mean that you also provide financial backing to support the necessary investment in new tooling? Mr Ehab Afifi: No, not that. Each company has to make its own investment. The converter in new tooling, and the bottler in the required changes to his filling line. At the end of the day they will all win. We want to be Number 1 in terms of environmental factors and energy savings. PETplanet: What is the situation with regard to bottleto-bottle recycling? From an environmental point of view this is a major factor. Mr Ehab Afifi: Certainly. Our parent company in Atlanta has made great strides in this area, but we mustn’t forget the Egyptian viewpoint. I don’t believe that Egyptians would accept beverage packaging made from “trash”. We can argue as long as we want from a theoretical point of view, but ultimately the people won’t accept it. PETplanet: Many thanks for your time Mr. Afifi.","@ID":13} "PETcontents 04/10 4 PETplanet insider Vol. 11 No. 04/10 www.petpla.net INSIDE TRACK 3 Editorial 4 Contents 6 News 32 Products 34 PET bottles for food and beverages 36 PET bottles for personal care 43 Patents BUYER’S GUIDE 37 Get listed! BOTTLE MAKING 26 Four new lightweight neck designs 27 Lightweight bottles for hot filling BOTTLING /FILLING 28 “A bottle of Bisleri, please” 30 On top of the world REGIONAL MARKET REPORT 10 Egypt - Part 2 14 Germany - Part 4 PREFORM PRODUCTION 16 The Rapid Guide to Perfect Preforms - Part 10 18 Energy savings and improving cost efficiency 25 Manufacturing Advisory services - PET case study MARKET SURVEY 21 Conveyors for preforms and empty bottles Page 26 Page 32 Page 16 C O S TEFFICIENCY ENERGYEFFICIENCY S P E C I A L","@ID":6}]}}
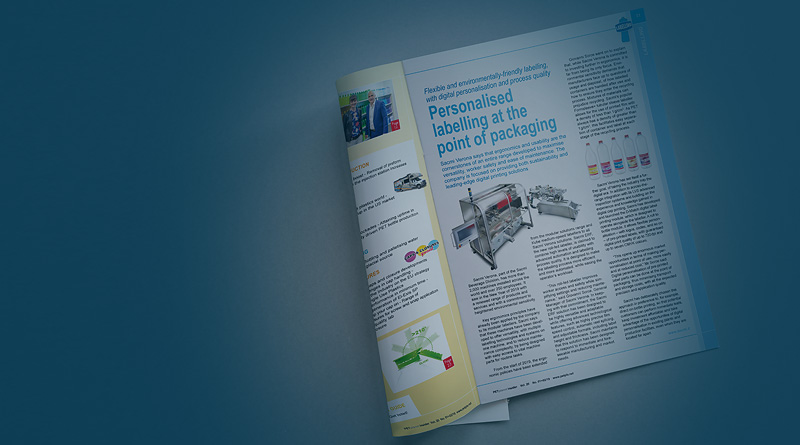