{"pages":{"page":[{"@ID":8, "PETnews 6 NEWS PETplanet Insider Vol. 24 No. 01+02/23 www.petpla.net Chinaplas 2023 Green, Smart, Advance are the 3 keywords the organisers chose for the 2023 edition of Chinaplas. The trade show will take place from April 17-20, 2023 in Shenzhen World Exhibition and Convention Center (SWECC), Shenzhen, PR China. Visitors are invited to immerse themselves in these 3 hot technologies under one roof, helping inspire new ideas and explore new opportunities. Innovations towards a Circular Economy: Under the theme “A Brighter and Shared Future, Powered by Innovation”, Chinaplas intends to provide visitors with a whole spectrum of sustainable solutions in 3 theme zones, including Recycled Plastics Zone, Bioplastics Zone, and Recycling Technology Zone. With over 14,000 m2, 200+ machine makers and materials providers are to showcase latest environmentally-friendly plastic materials and processing technologies. Plastics and rubber industries go smart: The adoption of a smart manufacturing process in all aspects of production – from product design, actual production, supply chain, distribution and sales, and delivery – has made it possible for plastic companies to withstand current and future challenges. Digitalisation has been increasingly applied particularly in plastics production processes. There is a growing need for advanced machinery and auxiliary equipment, sensors, process control software and other products to transform a plastics production facility into a smart manufacturing plant. In the rising trend of digitalisation among plastics and rubber industries, the trade show will bring together almost 330 solution providers around the world in Injection Moulding and Smart Manufacturing Solutions Zone with over 60,000m2. Advance - Automation + 3D Printing: The 3D printing, or additive manufacturing, market has seen a tremendous growth in recent years. The global 3D printing plastics market reached USD 786.9 million in 2021 and is expected to grow at a CAGR of 23.9% from 2022 to 2030. In addition to the advanced automation and robotics technologies in the Injection Moulding Solutions Zone, a 3D Tech Zone will also be set up. At the theme zone, visitors will be able to discover new 3D printing materials, technologies and hardware. China relaxes travel restriction Three years after border controls were imposed, China relaxed travel restriction from January 8, 2023. Overseas travellers will only have to show a negative nucleic acid test result obtained within 48 hours of travel and will no longer need to undergo health code and quarantine upon arrival, and will be able to enter society directly. China will improve visa arrangements for foreigners and resume international flights gradually. www.chinaplasonline.com Remo Heusi appointed new Vice President Global Service at Netstal Remo Heusi has been appointed as the new Vice President Global Service to lead and further develop the strategically important global service business of the Netstal Group. As a member of the Executive Board of Netstal Maschinen AG, he will report directly to Renzo Davatz, CEO of Netstal and member of the Executive Committee of KraussMaffei. Predecessor Frank Arnold is leaving Netstal at his own request effective March 31, 2023. He has successfully led the Service Division since January 2018 and actively promoted the reconstruction of the independent service organisation of the Netstal Group last year. Remo Heusi comes from Bühler Group, a globally operating Swiss technology group, where he has held various service and sales functions since 2007, including Head of Business Development Customer Service and Head of Single Machine Business. www.netstal.com UK: Deposit Return Scheme for drinks containers moves a step closer A new cash incentive system, placing deposits on drinks bottles and cans, is intended to boost recycling in the UK from 2025. New plans set out in a consultation response detail that, through small cash deposits placed on single-use drinks containers, people will likely be incentivised to recycle their drinks bottles and cans, reducing litter and plastic pollution. The scheme would include reverse vending machines and designated sites where people can return their bottles and receive their cash back. In most cases it would be the retailers who sell drinks covered by the scheme who would host a return point. The new scheme, covering England, Wales and Northern Ireland, is set to be introduced in 2025, following extensive work with industry to prepare for the necessary changes – including setting up infrastructure and amending labelling. A target is in place to collect over 85% of returnable drinks containers once the scheme is up and running. www.gov.uk"},{"@ID":19, "MATERIALS / RECYCLING PETplanet Insider Vol. 24 No. 01+02/23 www.petpla.net 17 South Africa’s plastics production & recycling both growing This sum included locally produced and imported virgin material, as well as locally recycled material, which increased its market share from 20.6% to 21.7%. Anton Hanekom, Plastics SA Executive Director, welcomed the growth as indicating that the market and industry are recovering from the effects of the Covid-19 pandemic. Packaging accounted for half of South Africa’s overall plastic consumption. Rigid packaging made up 29%; flexible packaging totalled 21%. Building and construction is the third-largest sector. South Africa is not noted as a ‘packaging powerhouse’, Mr Hanekom observed, while noting that the non-packaging sector is a weakness for the country. Recycling is developing strongly. South Africa recycled 344,527 t of plastics in 2021, which was 10% more than the previous year, but Plastics SA stressed that more needs to be done to support local recyclers and develop the industry. Mr Hanekom called for more products to be designed for recycling; for the systems and infrastructure to be put in place to collect recyclable material early in the solid waste stream; for standards to be developed and adhered to for recycling processes and their product; and for environmental claims to be substantiated. South Africa’s recycling sector is showing strong growth over a sustained period; production has increased by 36% since 2012. The average proportion of recycled content in new products has risen from 14.8% to 16.7% over the same period. However, “New endmarkets for recycled plastics are critical to ensure the industry’s longterm viability,” Mr Hanekom said. Plastics converters were severely strained as the overall economic climate deteriorated in 2021. Recyclers have had to work harder than ever before to find sustainable markets for their materials; only 7.7% of S Africa’s recyclate was exported as raw material to Asian and Southern African Development Community (SADC) plastics converters. “While plastics collection and recycling have improved slightly, we are still not back to pre-Covid year levels recorded in 2019,” he declared. “Although still considerably less than virgin polymers, recycling still consumes a lot of energy. To ensure economic quantities, recyclables must also be transported to reprocessing plants.” Strategic partnerships boost recycling and generate income opportunities Communities across South Africa are responding. More than 40 local, district and provincial municipalities countrywide benefitted from strategic sustainability partnerships in 2021/2, according to PET Plastic Recycling South Africa (Petco), which has been engaging with municipalities on sustainability, waste management and recycling projects for over 17 years. These initiatives also create income opportunities, which are of great value in a country whose unemployment rate exceeded 35% in Q4 2021. They are also helping to develop the circular economy. The Zonda Insila Programme (ZIP), for example, was launched in Breyton, Mpumalanga, about 200 km East of Johannesburg, in 2019. It had only four projects initially but now has 14, supporting 240 community members in another three district municipalities in Mpumalanga. Informal waste picking is a valuable source of income in the area. Petco provides equipment and infrastructure support, buy-back centres and training and skills development for municipal employees involved in waste management. The structure aims to help informal wastepickers into the formal recycling sector, which will bring benefits of steady employment and income. There are significant opportunities. “Currently, there are very few municipal separation-at-source collection systems, so we work with interested municipalities to establish collection projects and expand PET collection into new areas,” said Petco CEO Cheri Scholtz. “This year so far, we have conducted 28 training workshops for 1,357 waste pickers in eight provinces, and a further three accredited business training workshops.” Municipalities across South Africa are required by law to develop Integrated Waste Management Plans (IWMP) in line with the implementation of the National Waste Management Strategy. Drakenstein Municipality, in Western Cape Province, is one of the first municipalities to successfully integrate waste pickers into the formal waste industry at municipal level. “As our Material Recovery Facility [MRF] and Refuse Transfer Station become fully functional in 2022/23, these wastepreneurs will be accommodated. They will be able to increase their production and it will also mean that approximately 50 t less material will reach the landfill site,” said Thys Serfontein, Senior Manager, Solid Waste and Landfill Management at Drakenstein Municipality. In the past year, Petco and its partners diverted 90,402 t of post-consumer PET, equivalent to 2.1 bn bottles, was collected for recycling. This saved 560,495m3 of municipal landfill space. In addition, R1.2 bn (US$ 70 million) was injected into the national economy from the sale of recycled materials. www.petco.co.za www.plasticsinfo.co.za The latest report on South Africa’s plastics manufacturing and recycling industries, published by Plastics South Africa (Plastics SA) at the end of 2022, recorded total growth of 4.7% in 2021. A total of 1,904,924 t of polymer were converted into new plastics products during the year. MATERIALS / RECYCLING"},{"@ID":7, "BOTTLE MAKING 39 PETplanet Insider Vol. 24 No. 01+02/23 www.petpla.net Polyoak goes big in bottles with Sipa Moving into new territory The large South African packaging company Polyoak Packaging has its headquarters in Cape Town and produces bottles for juices, mineral water and edible oils. Now, with the help of Sipa, the company is breaking new ground: at its Johannesburg plant, Polyoak has commissioned an SFL Performance 4H linear stretch blow-moulding machine for the production of bottles with a volume of up to 10 litres. At other sites in southern Africa, Polyoak Packaging already has seven SFL linear stretch blow moulders producing smaller bottles and eight Sipa injection moulders producing PET preforms. The new SFL Performance with four blowing cavities is already in operation and produces 5 l bottles in various shapes for water, juices and oils, alternating with 10 l bottles for different products. It can produce up to 1,600 bph in 10 l, increasing to 4,800 bph for the 5 l bottle. Gary Bloom, Regional Executive at Polypet division says the SFL Performance was chosen primarily for its flexibility, blowing 5 l bottles in four cavities and 10 l bottles in two cavities. “We can maximise output on our 5 l bottles, which are already bestsellers, and use the same machine to test the market for water and other products in 10 l bottles without having to make a major investment,” he says. The blower is equipped with a quick-change configuration that makes changing the preform neck a breeze. “In addition, we have green ovens that reduce power consumption and make bottle production costs extremely competitive.” Polyoak is one of the largest packaging manufacturers in southern Africa, with production facilities across the country and in neighbouring countries. The company has been working with Sipa for about 15 years. Recently, Sipa has expanded and diversified its range of premium linear blow moulding machines. Today, it includes models like the SFL Flex with 1 or 2 cavities for small batch production, the SFL Dynamic for large bottles, but also for oval and custom shapes, SFL Performance for higher cavity counts and production (up to 8 cavities and an output of up to 16,000 bph), the SFL Big for medium/ high productivity of containers up to 12 l. For the really big containers, up to 30 l, Sipa offers the SFL Maxi, while in the case of wide-mouth jars, the intuitive brand name SFL WM gets the job done. www.sipa-solutions.com Polyoak Packaging chose the Sipa SFL Performance 4H for its flexibility. 2023 Training Schedule Technology&Application of PET Plastic Packaging for Hot-Fill &Aseptic Beverages Join our expert team for small group training on a variety of subjects - frommaterials to recycling. Scan to learn more & register for classes! ©2023 Plastic Technologies | 1440 Timberwolf Drive, Holland, Ohio USA 43528 www.pti-usa.com info@pti-usa.com info@pti-europe.com"},{"@ID":16, "MATERIALS / RECYCLING PETplanet Insider Vol. 24 No. 01+02/23 www.petpla.net 14 A conversation with India’s largest private company PET raw material and recyclate from India by Kay Barton December 9, 2022 Reliance Industries Ltd. We met: Mr Bharat B Mehta, Vice President – PET Marketing Mr Rakesh Bali, Senior Vice President, Head Marketing (Petchem) Mr Raghunath Datar, Regional Manager Mr Rajiv Kumar, AVP – PET Marketing Mr Aditya Pahurkar, Manager Sales & Marketing (PET) Mr Shubhang Shanbag, Manager Sales & Marketing (PET) Reliance Industries Ltd (RIL) is the largest private sector company in India. Founded in 1966, the corporate giant today houses Petchem (petrochemicals), Jio (telecom), Retail (around 15,000 retail outlets), Hydrocarbon Exploration and Production and Refining (petroleum). As of year-end 2022, Reliance became the first Indian company ever to achieve a turnover of more than US$ 100 billion. Petchem business, which includes the plastics division, accounts for about 35% of total sales. In addition to its PET brand “Relpet”, Reliance also produces PP, PE and PVC. The PET material production division, the company points out, is fully integrated thanks to its refining division, as everything from crude oil to finished PET production is carried out under one corporate umbrella. In Mumbai, PETplanet met the Reliance team to discuss the company’s current and future developments in PET. PET material production The meeting point for our discussion was a meeting room at the Reliance Jio Infocomm site in Mumbai’s financial and business district BKC. There, the team led by Senior Vice President & Head of Marketing at Petchem, Mr Rakesh Bali and Vice President for PET Marketing, Bharat B Mehta welcomed us. Mr Mehta began by explaining where the company is headed in the future in terms of PET manufacturing and postconsumer PET bottle recycling: “We currently have a total capacity of manufacturing 1.15 million t/a of virgin food grade PET. The capacity is spread in India and Malaysia, with Indian manufacturing plants in Hazira, Surat which has 350 kt capacity and Dahej, Bharuch with 650 kt. The remaining 150 kt is produced at our plant in Malaysia.” RIL also produces 6 kt/a of food grade rPET under its brand “Relpet green” at Nagothane facility. This puts the company in first place in India for PET production, followed by IVL Dhunseri with 720 kt and JBF with just over 180 kt. A unique pilot project of rPET resin, which is to be commercialised in the later part of 2023, is currently in the test phase: it involves traceability of PET material via integrated markers in finished blown bottles for the purpose of tracking material flows. Bottle and material demand Currently, about 1.2 million tonnes of PET bottles are consumed in a year across India and are expected to grow by 20% by the end of 2022, according to Reliance. Commenting on this, Bharat Mehta said, “Glass prices have gone up by 60% due to which many bottlers have switched to PET bottles, especially in CSD, milk and liquor.” The increasing demand for material is due to the continuing trend towards smaller bottle sizes due to “shrinkflation”, which refers to shrinking the size of the pack to keep the product affordable in times of inflation. He added: “A 2 l bottle uses 54 g of material whereas eight 0.25 l bottles each use 10 g of material, a total of 80 g which results in 26 g more usage.” Post-consumer waste, PET recycling and EPR Things are also happening in the recycling sector. “For PET recycling, we maintain three sites in the states of Punjab, Uttar Pradesh and MATERIALS / RECYCLING F.l.t.r.: Rakesh Bali, Raghunat Datar, Kay Barton, Bharat B Mehta and Rajiv Kumar Bharat B Metha displays a PET promotional bottle showing the various stages from PET bottle flakes to the company’s “R-Elan” textile yarn"},{"@ID":14, "MATERIALS / RECYCLING PETplanet Insider Vol. 24 No. 01+02/23 www.petpla.net 12 Investment in state-of-the-art equipment pays off rPET and preform production under one roof by Heike Fischer From Spain, we passed the Pyrenees and were warmly welcomed in France in Chalonsur-Saône, 135 km north of Lyon, at the SGT & SGR factory site. Our last visit was already six years ago, and a lot has happened since then. The SGR/SGT team looked somewhat surprised and incredulous when we parked the Editour-mobile in the car park and assured them that we were indeed living in it during our road trip. MATERIALS / RECYCLING We met: Jean Marc Wiencek, Factory Manager SGT & SGR, Anthony Dio, SGR Team Leader Fabien Tabart, SGT Production Workshop Manager The SGT and SGR factory is located in Chalon-sur-Saône on 5ha of land in the Saône Or business park. “The location of the site was chosen because of its strategic position since it benefits from a good connection with the road and motorway networks. The 10,000m2 factory for the SGR part has been operational since 2019. In June 2022, the SGT/ SGR has been expanded,“ explained Jean-Marc Wiencek. We asked for some updates since our last meeting in 2016. “In 2016, we put a lot of effort in SGT Algeria Spa. We equipped it with new cap injection presses. In 2017, SGT Algeria was FSSC 22000 certified for its two manufacturing plants in Rouïba and Setif. One year later SGT Algeria inaugurates its third plant dedicated to HDPE caps localised in Setif. In 2018/19, we started the extension of the Rezé site, close to Nantes and commencement of works on the new preforms manufacturing plant and a recycling production unit SGR in Chalon-Sur-Saône, in Saône-et-Loire,” Fabien Tabart, SGT production workshop manager told us. While starting a tour through the new SGR plant, Anthony Dio, SGR Team Leader reported about the PET recycling plant: “For four years, SGT has obtained the European label “MORE” Mobilised to REcycle. Created by the Federation of Plastics and Composites Polyvia, this label awarded manufacturers who incorporate recycled plastic materials in their production. It is saluted our commitment to a circular economy. In addition, in 2022 SGR obtains a favourable opinion from Efsa for its PET bottles recycling process.” He continued: “With SGR we assist our customers with their voluntary commitments to move towards a circular and responsible economy. With the plant we supply superior quality rPET suitable for food contact. From old plastic bottles we manufacture new preforms and therefore new bottles. Thus, SGR offers a second life to used bottles, so they are no longer perceived as waste but as reusable resources. 100% of SGR’s rPET ends up in our preform production. SGR is not selling its rPET externally, only including in customers preform production. We collect or buy crystal and blue-coloured flakes. SGR produces the highest quality of rPET suitable for food contact. By the end of the year 2022 we approximately will have an output of 12,000 t of rPET.” As we walked past the preform machines into the recycling hall, we can see the material flow of the rPET in pipes that are guided along the ceiling. Finally, we arrive at the reycling hall and are greeted by the finest recycling equipment: Bühler-Sortex, Unisensor, Erema Basic extruder (Efsa-Q201900488) and Polymetrix SSP (EfsaQ2020-00129). “When SGR takes delivery of PET flakes, it performs four additional grading processes: optical, metal, colour and material. Everything is meticulously inspected. Our recycling line is at the cutting edge of the latest technologies currently available on the market, enabling us to produce rPET of the highest quality. The site uses a vacuum-assisted Solid State"},{"@ID":28, "MATERIALS / RECYCLING PETplanet Insider Vol. 24 No. 01+02/23 www.petpla.net 26 Building the circular economy Demand more from PET, less from the planet According to the United Nations’ “Baseline Report on Plastic Waste”, published in 2020, PET is currently the most recycled plastic in the world. Its share of the recycled market is likely to increase, as the world adopts a shared responsibility approach to waste management. Mismanagement of post-consumer materials and contamination are challenging the supply of feedstocks but more investment in recycling infrastructure is already underway. Investment in advanced and monomer/chemically recycled volumes over the coming decade will see collection of post-consumer beverage bottles reach up to 90%, in regions with proper collection systems. Indorama Ventures’ (IVL) new purpose statement – Reimagining chemistry together to create a better world – reflects the key elements of its Vision 2030 plan. It maps out the route by which both bio-basedrenewable and recycled feedstocks are intended to deliver reduced emissions, divert waste from the environment and build circular manufacturing. Vision 2030 will see IVL invest up to US$8bn to increase biomass to 2.4mn tons and recycled to 1.5mn. Indorama Ventures Investments & Holdings (IVIH) has been created to identify, invest and deliver those objectives. IVL has set a goal to recycle 50bn PET beverage bottles annually by 2025. These objectives are very much in line with consumer demands for sustainable and recyclable materials and global brands’ targets for increased recycled content. Many governments already have plans to collect 90% of post-consumer PET bottles. Recycling of PET bottles is already at scale, across many countries. Even through the Covid-19 pandemic, IVL added to its portfolio of recycling facilities in Europe, the Americas and Asia, with the acquisition of assets in Brazil, Poland, Texas and the Czech Republic, where recycling capacity is planned to be increased to over 1 bn bottles/a by 2025. In the USA, IVL is increasing bottle washing capacity to 43,000 t/a. In partnership with Coca-Cola Beverages Philippines, it opened a new PET Value bottle-to-bottle recycling plant. These investments have cemented IVL’s position as the world’s largest producer of recycled resin for beverage bottles. The company is also operating beyond bottles: IVL and partners are collaborating to develop technologies to recycle PET trays. Today, 500 t of PET trays are being processed monthly. MATERIALS / RECYCLING"},{"@ID":23, "MATERIALS / RECYCLING PETplanet Insider Vol. 24 No. 01+02/23 www.petpla.net 21 Supporting the chemical dissolution of PET with glycol Nordson’s recycling history started way back in the 70ies when hardly anybody else was talking about it. Their film silo was one of the first technologies in the market for in-house recycling. The silo was designed to store and melt shredded pieces of film, which were then fed to the extruder for further processing. the extruder. The next step is a pre-filter which catches the larger dirt particles. Nordson provides several filtration options, but the BKG HiCon K-SWE4K has proven to be the most efficient. It provides a large filtration area and manages throughputs up to 8,000kg/h. In addition, it protects the following / booster pump, which provides the needed pressure for the fine filtration process, where the BKG HiCon V-Type 3G comes into play. In combination with the BKG FlexDisc, the BKG HiCon V-Type 3G can reach a filtration area of up to 12,800cm² resulting in high tonnages of recycled material per hour and is therefore capable of matching the need for high capacities. A melt pump builds the necessary pressure and pumps the material to the mixing point, where the virgin material is added to the process. The melt enters the reactor, where the process of repolyermerisation begins by rebuilding the polymer chains. After the discharge from the reactor and additional filtration step, the material is pelletised and ready for further processing. Nordson has mainly provided BKG CrystallCut systems, which have proven to be an efficient and elegant solution for PET pelletising. The pre-and fine filtration is of utmost importance for this process. The cleaner the material is before it enters the reactor, the more efficient the repolymerisation process. Clean material reduces residence time in the reactor while being easy to mix to reach maximum homogeneity. The tandem filtration ensures that the recycled material is extremely clean and can be further processed without any trouble. The PET-Glycol mix has a very low viscosity, and Nordson’s BKG filtration systems have effective sealing methods and tolerances to prevent leakages. The low viscosity level has an advantage: The The story continued with the development of the first backflush screen changer in 1989. Already almost entirely automated, the BKG HiCon K-SWE/ RS was able to process material with higher contamination grades and was a significant first step down the road for more sustainability – at a time when this was not such a buzzword yet. It went on with further developments improving the classic mechanical recycling process. The overall goals were more filtration area, more pressure consistency, and producing less scrap or waste. With the launch of the BKG HiCon V-Type 3G, designed explicitly for PET, Nordson provides a system that is a filter capable of processing high throughputs at maximum pressure consistency. It is obvious that the recycling goals can’t be met with just mechanical recycling, and material quantity and quality requirements have increased substantially. Besides the milestones currently made in different chemical recycling applications, glycosylation has become an efficient method to process higher throughputs with high recycled material contents. With the price decline for virgin PET, larger-scale plants are more economically efficient than smaller production lines, which spurred the need for higher tonnages. The consistent call for more sustainability in the plastic industry has also led to new laws and regulations which force producers to increase their use of recycled material significantly, and the industry needs to react. Chemical dissolution of PET Nordson has been providing equipment for the chemical dissolution of PET with glycol for major industry partners, steadily increasing capabilities, performance, and end-product quality. After pre-treatment, the PET flakes are blended with glycol to break up the polymer chains. The mix is then fed to lower the viscosity, the finer the filtration can be used. With Nordson’s BKG filtration system, fine filtration down to 40μm is possible, so even microscopic contaminants are removed from the melt efficiently. After being combined with virgin material, capacities of up to 30 t of rPET pellets with 20% recycled material content are achievable, depending on process parameters, feedstock, and filtration fineness. The newest developments include intelligent sensor locations for the most efficient pressure monitoring to improve pressure consistency and protect downstream components from overpressure. With several small process adaptions, Nordson reduced the amount of material loss during backflushing to below 1.5%, resulting in significant savings, especially in this large-scale environment. The BKG HiCon V-Type 3G with the FlexDisc combines the advantages of piston filtration technology with the capabilities of large-area filtration. The process-independent backflushing procedure and the large filtration area are claimed to ensure maximum product quality, minor operator intervention, and reduced operating costs. www.nordson.com The BKG HiCon V-Type 3G and BKG FlexDisc MATERIALS / RECYCLING"},{"@ID":25, "MATERIALS / RECYCLING PETplanet Insider Vol. 24 No. 01+02/23 www.petpla.net 23 Varying quality rPET The quality of mechanically recycled rPET can vary greatly. The quality is influenced and impacted by several different factors like the effectiveness of sorting and contamination. This means that there is a high demand and poor availability of high quality, clear rPET, the cost of rPET is sky-rocketing. Costs: conclusion These factors all contribute to a massive demand for high quality rPET. The industry is putting a lot of efforts on making more high quality rPET available through better collection, separation, sorting, washing and reprocessing. Holland Colours witnesses a shift in terms of food contact rPET purchase strategy. Brand owners have actively sought out ways to secure a steady supply of rPET that meets their standards by investing in and widening the Deposit Return Schemes and reprocessing facilities. This ensures a steady flow of rPET which can be collected and processed according to their standards. More recently integration, consolidation and expansion of recycling capacity in the value chain has become the standard. But high quality rPET is still scarce. In order to hit the 25% rPET mark for PET bottles, concessions in quality of mechanically recycled rPET most likely have to be made. Now obviously there can be no concession in food contact safety, but there are other alternatives to ensure a steady supply of high quality rPET. But what factors diminish the quality of rPET in the first place? The major hurdles of high quality rPET One of the biggest hurdles when it comes to the visual quality of rPET has to do with its consistency. But what factors play a role in the lack of visual consistency of rPET? One of the biggest hurdles is the discolouration: after recycling, most of the time rPET experiences yellowing or other slight discolourations. Undesirable discolouration of rPET during reprocessing is predominantly caused by remaining trace amounts of components like functional additives, colourants, adhesives, inks and other plastics from caps, labels and sleeves. Multiple heat cycles combined with residual component traces result in a higher level of discolouration. Hence it is key to ensure adequate washing and decontamination of the input material before reprocessing. These are by themselves in many cases harmless and do not affect food contact safety but are undesirable due to their negative effect on colour. This aesthetic deviation has proven to be unattractive for end-consumers. This is quite understandable: drinking milk from a somewhat ‘yellowish’ transparent bottle feels strange for consumers who equate this colour with a lack of hygiene and find it unattractive."},{"@ID":4, "MATERIALS / RECYCLING PETplanet Insider Vol. 24 No. 01+02/23 www.petpla.net 34 From pre-sorting to material analysis Istanbul-based Engin Group has built up a number of group companies over the past decades that are active in the marketing and distribution of cosmetic and household products for Turkey and the Caucasus region. The establishment of Futurapet in 2020 was a logical step towards sustainability and environmental protection, values which the Engin Group have committed to. The recycling of plastic products is another building block for sustainable production, closing the recycling loop. In a plant equipped with state-of-the-art sorting technology, Futurapet recycles plastic waste. The secondary raw materials obtained are returned to the plastics processing industry. When Futurapet was founded, General Manager Oğuz Engin and his team were looking for solutions that would deliver high-quality end products. Only single-variety rPET can be used for a wide range of new products, thus conserving resources and the environment. Solutions for the entire production line were a decisive factor in the selection of components. Somplast, Sesotec‘s sales partner in Turkey, was able to convince Futurapet of the function and quality of the Sesotec sorting systems in combination with the new material analysis system. Futurapet now relies on Sesotec’s new generation Varisort+ units, equipped with the Flash technology and a working width of 2,816mm, which are used in the multi-stage preparation process for bottle sorting; the final sorting of the PET flakes is carried out by the Flake Purifier+ sorting systems. They are claimed to deliver PET material of high purity and quality. The new Flake Scan analysis system from Sesotec ensures the final inspection of each BigBag leaving the plant. Pre-sorting of bottles Futurapet receives plastic bottles pressed into bales. The recycling process starts when the bales are broken up: first, light materials are separated by ballistic sifter and then non-ferrous and ferrous metals are separated. After the washing and drying processes, the pressed bottles are sent over the Sesotec Varisort+ sorting systems. These latest-generation units feature an impressive working width of 3m and can thus handle high throughputs in the respective sorting step. On a Varisort+ N, positive sorting separates PET bottles from all other types of plastic, such as non-PET bottles, labels, or films. This fraction then passes through a Varisort+ Flash CN unit, which is equipped with the Flash technology for the best possible colour detection. This technology, equipped with reflected and transmitted light units, is claimed to make free-fall colour detection possible for distinguishing fine colour nuances in transparent, non-transparent and semi-transparent materials. In the process, the Varisort+ Flash CN uses two valve bars to sort into three different chutes. The good material PET clear and light blue falls through the natural fall curve into the middle chute. Non-PET and PET coloured fractions are selectively separated in the other chutes. This process is also known as negative sorting. All other components are specifically sorted out, whilst the good material remains in the material stream. The next sorting step is performed by another Varisort+ Flash CN sorting system. The special feature of this device is that by dividing the 3m-wide conveyor belt and subdividing it into three chutes, sorting of six different fractions can be realised. On the left-hand conveyor track, the second sorting step is repeated in order to achieve a very high degree of purity in bottle sorting for the PET clear and light blue fraction. On the right lane, the material rejected from three sorting stages is returned via a re-sorting step to the first Varisort+ N sorter. MATERIALS / RECYCLING Varisort+ for pre-sorting plastic bottles Material analysis system Flake Scan for quality analysis within minutes"},{"@ID":21, "MATERIALS / RECYCLING PETplanet Insider Vol. 24 No. 01+02/23 www.petpla.net 19 bottle back’ but – I’ve lost count – over 50 different articles saying plastics can’t be recycled into new bottles. That’s a lie,” he declared. “I heard about some great innovations today but how much of it will matter if the consumer doesn’t believe you? I have no problem with support and investment in recycling. I think that it’s good idea for us to volunteer and help clean up the oceans and streamline refined plastics usage. viscoZERO – processing PP, PE, PET & PS! ZERO contamination. ZERO odour. ZERO limits. foodgrade without compromise viscoZERO Upgrade your existing recycling plant with viscoZERO technology. North American rates on rPET usage and PET bottle collection (source: Napcor) “But we have to find a way to show the world our efforts in these areas and to do it, we need a marketing campaign, which needs funding, it needs direction, it has to talk about the facts. But you can’t do one of these things and not the others; they have to be done in unison. If we don’t do this, the anti-plastic messaging is going to continue,” Schiavone declared. “I’ve heard today about new plastics or new processes and it’s going to change the world – but if you don’t include the consumer, will any of that matter? If we can at least improve consumer perception it will affect our bottom lines. If you’re doing anything that’s helping improve the process, think about how you involve the consumer. Share the facts, on your company website, on social media – there’s a lot of good information out there, that we should be sharing.” www.napcor.com www.rdleverage.com"},{"@ID":30, "MARKET SURVEY 28 PETplanet Insider Vol. 24 No. 01+02/23 www.petpla.net 01+02/2023 MARKETsurvey Additives Suppliers of resins & additives There is rapidly increasing demand for packaging materials that give even greater protection to their contents. Functional additives and resins are an important technology in meeting this demand for greater product protection in the plastic packaging market. A functional additive modifies the properties of packaging to impart desirable or beneficial functions. That is why we won’t stop a well-established tradition in opening our market surveys overview in 2023 with suppliers of resins and additives. Please find here the news of the companies: Repi S.r.l, Sukano AG, Avient Corp., Köksan, Neo Group, Reliance Industries and Novapet, S.A. Although the publishers have made every eff ort to ensure that the information in this survey is up to date, no claims are made regarding completeness or accuracy. Resins & additives Preform machinery Preform production & inspection systems Preform & SBM mould manufacturer SBM 2-stage Compressors All about caps Filling equipment & inspection systems Palletising & shrink film machinery Recycling machinery Company name Sukano AG Repi Avient Corporation Postal address Telephone number Web site address Contact name Function Direct telephone number E-Mail Chaltenbodenstrasse 23, 8834 Schindellegi, Switzerland +41 44 787 57 77 www.sukano.com +41 44 787 57 77 media@sukano.com Via B. Franklin 2, 21050 Lonate Ceppiono, Italy +39 0331819511 www.repi.com Ms Lucia Buffoni Group Marketing Manager +41 79 9093 735 l.buffoni@repi.com 33587 Walker Road Avon Lake, 44012 OH, USA +1 440 930 1000 www.avient.com Mr Marco Schäfer Marketing EMEA +49 4102 487 158 marco.schaefer@avient.com Additives and Colours for PET Liquid colours Yes Yes Microgranule colours Yes Yes Masterbatch colours Yes Yes UV protection additive (solid) Yes Yes UV protection additive (liquid) Yes Yes AA reduction (solid) Yes AA reduction (liquid) Yes Yes Oxygen scavenger (solid) Yes Oxygen scavenger (liquid) No IV Enhancer Yes Yes Yes Reheating Yes Yes Blowing additive Yes Yes Yes Slipping agent Yes Yes Yes Other PET additives: Antifog, antimicrobial, antistatic, melt enhancer, voiding agent, optical brightener, nucleating agent, mobility aid, mould release, matting agent, slip/antiblock, light diffusor, impact modifi er, fl ame retardant, plasticiser, foaming agent, NIR-detectable colours and blacks Anti yellow, optical brightener, heat stabiliser for PET Recycling friendly toners, special effects, matting agent, slip additives, NIR black, light blocking additive for UHT milk bottles"},{"@ID":46, "44 TRADE SHOW REVIEW PETplanet Insider Vol. 24 No. 01+02/23 www.petpla.net ICIS PET Value Chain Conference Join Europe’s largest gathering of PET professionals Don’t miss out! events.icis.com/website/9095 PETPLANET10 for 10% off Ritz-CarltonHotel, Vienna 7-8 March 2023 ICIS PET Conferences For market intelligence and unrivalled business networking on a global scale, there’s only one place to be Empty bottle inspection The US inspection equipment manufacturer Filtec from California demonstrated its “Omnivision 4” inline empty bottle inspection system. The machine operates on Filtec’s “Intellect” platform and is equally suitable for (refillable) PET and glass bottles. The platform provides an intuitive user interface, which has a 19-inch touch screen and RFID receiver for operator registration, and can be operated in a similar way to a conventional smartphone. The Starwheel has been improved and can now reduce the time required for format changes to a few minutes, as well as enhancing bottle positioning. Any internal or external damage, foreign bodies or impurities can be detected and a dark field inspection undertaken as alternative option if required. The Omnivision 4 can be controlled and adjusted remotely and, according to the company, can process up to 1,400 containers per minute. The manufacturer also demonstrated its “Vision Pressure” system which is also based on Intellect. The machine provides consistent pressure, vacuum and leak detection, as well as three-dimensional, high resolution 360° views of the container in the cap area. Measuring accuracy is within a 2 μm range and capable of processing many types of caps and beverages. Furthermore, self-correcting algorithms ensure that inspections are accurate despite variances. Several adaptive algorithms evaluate 3D image data in real time at a rate of over 1,200bpm, with the system easy to integrate within existing production lines. www.fi ltec.com"},{"@ID":56, "OUTER PLANET 54 PETplanet Insider Vol. 24 No. 01+02/23 www.petpla.net OUTER PLANET Best (eco-) mate, ocean safe by Ruari McCallion Experiences of marine pollution while scuba diving led Scott Nicholas to establish Supa Products and to develop eco-mate, a totally plant-based, paper bottle that he says is ‘ocean friendly’; it will biodegrade completely, without leaving any long-lasting contaminants or pollutants in the environment. “After I sold my previous business I spent a lot of time diving in the sea and I saw the damage being done to the marine environment by plastic bottles,” said Scott Nicholas, CEO of Supa Products. Supa stands for Single Use Plastic Alternative. “These things are sitting at the bottom of the ocean and it is getting worse and worse. I am a design engineer; I like making things and I thought that if there is a way that I can do something to try and help, to have some impact with a bottle that doesn’t rely on fake recycling, that could break down without causing long term damage, that I should do so.” Scott’s previous business was architectural components, which is very different from packaging. He took the time to learn about the needs of the industry and set about realising his objective. The result is the Supa ecomate bottle, which is made of paper constructed from byproduct waste fibre from the refining of sugar cane. The biggest challenge for packaging made of porous material, like paper or board, is making it proof against fluid leaks and loss of material integrity if it is soaked. The liquid-proof membrane is where a lot of good intentions fall down. Using plastic, such as LDPE, makes the pack a composite that can be difficult to recycle; if left unprocessed then the board or paper will biodegrade but the plastic membrane will persist in the environment. “Our membrane is a natural latex, made from plant sap. We have gone out of our way to make sure that our bottle will not leave anything nasty in the environment; it will completely break down,” Scott explains. He won’t say exactly how the material is made, for commercial and intellectual property reasons, but is adamant that it has been independently verified to be plantbased and fully compostable. “There is nothing in the bottle that isn’t bio-based. You can bury it in your garden compost heap, where it will get nice and warm and break down into dissolvable pieces. How much time it will take depends on the circumstances but however long it takes, it will not leave any microplastics behind.” The company was formed in 2019 and the eco-mate bottle has been in use commercially since mid-2022. Currently, it is targeted at household cleaning and non-food markets; testing for barrier effectiveness and food contact certification is ongoing. It is produced with two distinct appearances: either straw-coloured ‘natural’ or an opaque white. The latter has the advantage of being identifiable as a cleaning product package; the natural, unbleached version appears to be the more popular. “That rustic, natural look and feel slots into that eco trend. The trouble with fine surface finishes, which you can get with paper, is that it then looks like everything else on the shelf,” Scott says. “The mottled, papery look stands out and identifies itself as a different sort of material.” The closure is made of cork waste and bamboo fibres. The current range is 500ml capacity, with a 350ml version under development and Supa has received enquiries for a 650ml version from a Swiss cosmetics company. In terms of weight, while paper is lighter than glass or PET, dies and tooling for the bottle are supplied to customers, who make them themselves for on-site filling and thus reduce transportation costs. The Supa bottle is, currently, more expensive than the established alternatives but Scott Nicholas says that costs are coming down as production scales up. “We have a lot of testing and development ongoing, especially on compostability. There are some tough standards that have to be met and a minimum of eight months before any kind of certification can be achieved but I think that we will see some exciting developments about March or April 2023,” he concluded. “We are quite excited about it.” www.supa-water.co.uk"},{"@ID":27, "MATERIALS / RECYCLING PETplanet Insider Vol. 24 No. 01+02/23 www.petpla.net 25 Prevention of ageing and discolouration of rPET based on an article by Lucia Buffoni, Repi Group Marketing Manager Over the past two and a half years the packaging industry has had the opportunity to demonstrate its crucial role in offering safety and hygiene in health emergencies such as the one still ongoing. On the other hand, there is no doubt that the packaging world has been increasingly under intense pressure brought about by the tremendous push towards sustainability and recycling. MATERIALS / RECYCLING Repi, a manufacturer of liquid colours and additives for plastic packaging has been focusing for decades on advanced additive and colour solutions for PET and rPET. The ranges of the anti-yellow, optical brighteners and IV enhancers have been considered over the years a valid aid to rPET recyclers and packaging converters, offering an answer for anyone facing the challenge of including increasing rates of recycled material in their plastic packaging. Such additives can be used at different stages of the rPET value chain, for example, from recycling up to preform or tray manufacturing with no impact on processes, thus offering high flexibility. The increasing demand for recycled percentages and the scarcity of food grade rPET flakes present challenges in respect of quality and colour consistency between one batch and another. A particular problem which both recyclers and converters struggle to manage is the drop of L* of CieLab numbers while respectively recycling and moulding or extruding the final packaging. Whilst it is in fact possible to correct off-shade rPET pellets with custom-made formulations that act both on the a* and on the b*, the darkening of material (precisely the drop of L*) is very difficult to avoid. This is where StabiPlus additive comes in, the latest development by Repi: a liquid formulation acting specifically as proactive stabiliser that prevents rPET from ageing and discolouration, cycle after cycle. The additive can be used both at the recycling stage, added to a mechanical recycling process with SSP, and directly by converters at their packaging production stage, where the stabiliser can be added in quantities appropriate to the process. StabiPlus offers a new protection technology that does not affect Intrinsic Viscosity and therefore the mechanical properties of the recycled PET whilst at the same time widening the window for sustainable use of recycled PET. StabiPlus is claimed to boost the use of different incoming material quality since it improves aesthetics cycle after cycle. StabiPlus Repi shows how the technology of chemical additives makes a crucial contribution to polymer recycling. It further emphasises the need for close cooperation in amongst the whole value chain of plastic packaging to share the challenges, so that all parties move towards the well-defined key objectives of “reduce” (weight without losing performance), “reuse” (packaging whenever sustainable), “recycle” (thanks to the most advanced technologies developed so far). www.repi.com rPET brightness and shade improve cycle after cycle. Each of the three cycles has been designed to put maximum stress on the material in order to show the additive’s performance: one lab cycle delivering double the stress of an industrial process. StabiPlus has been added to the first recycling loop only. Bottles of 100% rPET from mechanical recycling containing StabiPlus. Being a liquid formulation, concentration is very high and related dosages minimal."},{"@ID":47, "PETplanet Insider Vol. 24 No. 01+02/23 www.petpla.net 45 TRADE SHOW REVIEW Focus on the circular economy brings Herbold Meckesheim many orders at K 2022 Round and round The fact that K2022 focused on the circular economy naturally played into the order books of the manufacturer of recycling systems and machines Herbold Meckesheim. In addition, the company has formed together with the Stuttgart-based machine manufacturer Coperion a new Recycling Business Unit in October 2022, which is claimed to offer complete solutions for plastics processing, as it continues to develop. The Herbold Meckesheim sales team at the booth. (Photos: Herbold Meckesheim) Herbold Meckesheim’s résumé reflects the international orientation of the plastics trade fair: The majority of the relevant discussions related to projects abroad, with Spain, France, Turkey, India, Sweden, Poland or Brazil, for example, being strongly represented in addition to the USA. “You can see how seriously recycling is being treated in many countries,” comments the special machine manufacturer on the inquiries from six of the seven continents, “which show that there is an increasing demand worldwide for the reprocessing of post-consumer waste, especially PET.” Fittingly, the core area of the customer inquiries was even more clearly on washing lines and the interest in the projects was of a more sustainable nature, Herbold Meckesheim states. In the field of recycling plants, most of the orders discussed were for PET washing lines, while those for films were in demand on a similar scale. The plant manufacturer’s solutions for the recycling of rigid plastics and big bags also met with an unbroken response. Among the machine solutions, the classic granulators continue to be a top seller, in addition to shredders, pulverisers and drying systems, says Herbold Meckesheim, Accordingly, the company had brought a further developed version of its SML 60/100 SB 2 granulator to the fair which – whether dry or wet – is suited for grinding PET bottles, for example, and is equipped with a horizontal forced feeding device. A mechanical dryer T 2016 PA, which is claimed to achieve an equally high drying performance with different types of plastic materials, was also exhibited at the Herbold booth. As well as a HV 70 plastcompactor with silo, which produces agglomerates of high bulk density with high throughput and minimal thermal stress. Merger with Coperion The merger of Coperion and Herbold Meckesheim and the resulting opportunities were positively received, according to Herbold’s impression. The newly founded Recycling Business Unit is able to offer modular system and plant solutions on an industrial scale and combines the complementary technologies of both companies for the benefit of the customers. Visitors to K 2022 were able to get a first impression of this at the Coperion booth and in the Recycling Pavilion on the open-air fairground, where a virtual complete PET plant made the future vivid. From mechanical processing – shredding, washing, separating, drying, and agglomerating of plastics – to bulk material handling, feeding and extrusion, as well as compounding and pelletising, the business unit’s jointly developed and highly automated plants encompass the entire process and thus value chain. www.herbold.com Living recycling technology: a granulator, a dryer and a plastcompactor (from right) Detailed insights for customers: disks equipped with kneading bars of the HV 70"},{"@ID":10, "8 NEWS PETplanet Insider Vol. 24 No. 01+02/23 www.petpla.net Biorecycling of PET: Carbios and Novozymes strengthen collaboration with long-term exclusive strategic partnership Carbios and Novozymes, leaders in biological solutions, announced an exclusive long-term global strategic partnership. This agreement ensures the long-term production and supply of Carbios’ proprietary PET-degrading enzymes at an industrial scale for the world’s first biological PET-recycling plant due to start production in 2025 in Longlaville, France, as well as Carbios’ future licensee customers. Carbios and Novozymes have had a partnership since 2019 to develop enzyme-based solutions and address the sustainability challenge of plastic pollution, both within PETrecycling and PLA-biodegradation. Building on the current Joint Development Agreement (JDA), under the new agreement, Carbios and Novozymes will extend their collaboration to develop, optimise and produce enzymes that will subsequently be supplied by Novozymes to all licensees of Carbios’ technology. The new agreement grants both parties exclusivity in the field of the partnership. The strategic partnership supports the large-scale industrial deployment of Carbios’ patented PET-recycling technology starting with Carbios’ future industrial reference unit in Longlaville, which will be the world’s first biological PET-recycling plant. Construction will begin later this year, and both building and operating permits having been filed with local authorities. Production at the plant is set to start in 2025 and the processing capacity will be 50,000 t/a of waste. www.carbios.com Petcore Executive Director Christian Crépet to assume an Ambassador role and becomes a honorary member of the board Petcore Europe announced that Christian Crépet, who has served as Executive Director of the association since 2017, moved into an Ambassador role as of January 1, 2023. Christian Crepét has spent his career within the industry and has a deep knowledge of PET collection and recycling. During his tenure, Petcore has grown to comprise 140 members which has enabled the association to adapt its working groups to the EU regulatory priorities. Petcore’s public and regulatory objectives are to drive towards more collection, safety, recycling and circularity, and to position PET as the packaging that is made to be remade and designed to be reused. During his time as Executive Director Christian also held a series of high-profile annual conferences gathering stakeholders from across the industry and the EU institutions. As of January 1, 2023, Ermis Panagiotopoulos took on the role of interim Executive Director for the next few months, while the association has begun an executive search to appoint a permanent replacement. Ermis comes with more than 15 years of experience in European public affairs, having worked for industry associations, NGOs and the European Commission. He joined Indorama Ventures PCL as Head of Sustainability Advocacy EMEA in September 2022 after 6 years as Sustainability Director of Natural Mineral Waters Europe (NMWE). www.petcore-europe.org Icis PET Value Chain Conference 2023 This year‘s Icis PET Value Chain conference will be taking place in the city of Vienna, Austria, at the Ritz Carlton Hotel from March 7-8, 2023. The conference will bring together the leading experts in the PET industry to discuss the latest trends and developments. The agenda for the two-day event will cover an array of topics to help keep PET professionals up-to-date with the most current industry insights. From reviewing the supply and demand outlook and feedstock dynamics to exploring regulation updates and uncertainty surrounding energy costs, attendees will have the opportunity to gain valuable knowledge from the experts. Additionally, the conference will feature panel discussions examining the transition towards a circular economy while defending the region’s competitive position as well as assessing the impact of consumer purchase behaviour changes on the PET industry. At the Icis PET Value Chain conference, PET professionals will also have the chance to network with their peers and share their own experiences and best practices. PETplanet readers can register here and benefit from a 10% discount: bit.ly/3wmQpJk Christian Crépet Ermis Panagiotopoulos"},{"@ID":29, "MATERIALS / RECYCLING 27 PETplanet Insider Vol. 24 Science based targets initiative The Science Based Targets initiative (SBTi), a collaboration between CDP, the United Nations Global Compact, the World Resources Institute and the World-Wide Fund for Nature, helps businesses set emissions reduction targets based on the most recent climate science. IVL’s sustainability strategy, to reduce greenhouse gas intensity by 30%, increase its use of renewable energy and implement new decarbonisation technologies including carbon capture, is in alignment with SBTi. Brand platform Deja is IVL’s new brand platform for global, low carbon, high performance PET, rPET and polymer. The brand covers carbon neutral virgin and recycled PET resins and a range of rPET products, including flakes, resins, fibers, and yarns. Applications include packaging, lifestyle, apparel, automotive and medical equipment. It is claimed to give converters credibility, accreditation to retailers and assurances of sustainability to end consumers. Deja “demands more from PET and less from the planet”, by recycling and transforming PET into innovative ingredient products, across multiple applications. In 2022, IVL was presented with Chemical Week Sustainability Awards’ Best Sustainable Product Award for Deja Carbon Neutral pellets, virgin PET resins achieve a carbon-neutral final carbon footprint through the use of recycled water, low-impact water transport and recycled feedstocks. IVL partnered with South Pole, a leading provider of global climate solutions, to offset unavoidable emissions with carbon credits. www.indoramaventures.com"},{"@ID":2, "MATERIALS / RECYCLING 11 PETplanet Insider Vol. 24 & Power Generation. The engineering projects focuss on realising plastic circular economy, water treatment e.g. urban water treatment plants or any project that has to do with general waste recycling. The group has its own office and staff for African EPC operations in Angola. In the power generation area, Mikel leads us into a somewhat deserted-looking part of the factory premises. “True to our environmental responsibility, our combined heat and power plant covers all the electricity and heat needs of our production facilities. In this way, we avoid supply from less environmentally friendly sources and feed our excess electricity into the general grid. The cogeneration plant consists of a cycle combined by two Rolls Royce natural gas engines, developing a power of 5,100KWe plus a 269 kWe condensation Dresser Rand steam turbine. The thermal utilisation of the cogeneration plant is used for the production of: factory steam used in the production of polyester fibre, PET film, PET recycling and operates as district heating for neighboring industries; the hot water for the absorption refrigeration group and the steam for use in the condensing steam turbine.” Impressed by this holistic view of the circular economy, we have to say goodbye to Mikel, to whom we must decline an invitation for lunch with a guilty conscience, as our schedule is pressing. We thank him for his willingness to provide information and his hospitality and wish him every success with EkoRec! www.ekorec.net Two Rolls-Royce natural gas engines developing 5,100 KWe of power and a 269 kWe condensing steam turbine from Dresser Rand."},{"@ID":45, "43 TRADE SHOW REVIEW PETplanet Insider Vol. 24 No. 01+02/23 www.petpla.net Non-destructive quality control Quality inspection equipment manufacturer Antares Vision Group showed the Robo-QCS developed by FT System which is part of the group since 2019. With Robo-QCS, usually installed after capping in beverage lines, a robot arm samples automatically the bottles and carries out a wide range of non-destructive quality controls using one single analysis platform. It checks net weight and correct cap application by measuring the opening torque and the closing angle. It can also measure gas concentration in the headspace (e.g. CO2, N2 etc.) and micro leaks between the cap and the preform. Compliant samples are automatically returned to the production line by the robot. “It’s not necessary to change the line speed for sampling and no operator interventions are required,” explained Emanuele Melloni, the group business development manager for beverage. This means the system can carry out inspections and quality controls completely autonomously in real time in the automated analysis station beside the production line, replacing the manual checks. The data gathered are then compared automatically with the expected product quality settings, giving the chance to evaluate the packaging production, the line efficiency and the correct operation of the filling and capping system. “It will make it possible to react quickly and to recalibrate the process promptly when there is a deviation from specifications,” continued Mr Melloni. “Furthermore, trends can be recognised, and timely, predictive maintenance measures can be taken”. According to the company, the device compiles automatically date and time reports, which can be shared digitally and used later during an audit to optimise internal processes or to recover data from a specific batch. It can also carry out destructive quality checks such as TPO,°Brix, %DIET, CO2 and O2 to integrate also quality controls on the beverage. www.antaresvision.com Visual inspection of container features Miho, a machine manufacturer based in Ahnatal, Germany, specialising in beverage filling inspection technology, demonstrated its modularbased, extendable, visual test head “TopCam”. According to marketing officer Martina Wagner, the machine inspects filled and sealed drink bottles inline prior to the secondary packaging stage for the features on the closure, shoulder and base area of the containers. This is achieved by means of a colour camera and an application-specific LED lighting system. Containers can be checked for the presence and completeness of the coding such as BBD and LOT number, as well as colour recognition of the closure. The height of the machine can be adjusted, enabling a number of different container sizes and packaging materials such as plastic, glass and cardboard or aluminium containers to be inspected. For PET bottle applications, the company recommends the Top-Cam extension module for UV illumination. For example, laser engraving codes on PET bottle necks can be checked by means of UV fluorescence. No special alignment of the container is necessary. The maximum speed is 72.000 bph. Using a touch panel on the Multi-PC inspection unit, control and evaluation of the recorded data can be carried out using Windows 10 with Miho’s Vidios SC image processing system. Multi-PC can also be used as a central inspection unit for other Miho test heads such as the Newton series for fill level monitoring, the Vacu for vacuum detection, the Feeler 2 for checking the sealing of PET bottles and the EC-Cam for label inspection. www.miho.de 450+ Molds Proven Globally Acme Drinktec Solutions LLP Ph +91-9810418975, +91-9819020785, +91-9810631426 Email: sales@acmedrinktec.com Website: www.acmedrinktec.com #MOLD@70DPW MOLDS FOR ASB [50MB / 12M 70DPH / 70DPW], AOKI, SIPA, ETC Balanced HR System Creating Molds with a Difference YOU CAN HAVE FROM THE SAME RESOURCE Enhanced Cavitation Superior Tool Steel"},{"@ID":20, "MATERIALS / RECYCLING PETplanet Insider Vol. 24 No. 01+02/23 www.petpla.net 18 US PET recycling reaches record levels but more to be done Bob Schiavone from R&D/Leverage, an Adler Co. says that the industry has to raise its game to educate the public and to ensure sufficient and genuine recycling capacity and infrastructure. Bob Schiavone, Global Marketing Communications Director of R&D/Leverage, addressed the issues of public perception of the plastics industry and recycling at the Blow Moulding Conference and Exhibition in Brussels, Belgium, at the end of 2022. At the same time, the USA’s National Association for PET Container Resources (Napcor) published its 2021 PET Recycling Report. It documented the largest amount of postconsumer PET ever collected in the USA and noted a new record for thermoform collection in the USA and Canada. Recycling rates in the USA alone were recorded to have increased to 28.6%; across the whole of North America (USA, Canada and Mexico), the rate rose to 36.8%. Bottle collection in the US exceeded 1.9 bn lbs (862 million kg), with total thermoformed plastic collections in the US and Canada reported to have reached 142 million lbs (64.4 million kg). Schiavone has firm views on recycling, on what he describes as the ‘anti-plastics agenda’ of some lobby groups, and on the industry’s failure to proclaim and spread positive messages about its products and its achievements in collection, reuse and recycling. PET reclaimers in the U.S. and Canada collected and processed 73% of PET thermoforms. For the second year in succession, market consumption of rPET in both food & beverage and non-food & beverage bottles exceeded demand in the fibre market in the USA and Canada. PET collected via deposit redemption schemes increased 46%, compared with 2020, indicating a rebound from the Covid19 downturn and that pandemic-driven disruptions to recycling services are being resolved. The wider North American recycling rate is over the Ellen McArthur Foundation’s 30% threshold, regarded as the postconsumer benchmark for proving that recycling works in practice and at scale. However, in the face of campaigns that deliver more in the way of headlines than solid endeavour and real environmental benefits, the message about the gains the industry has made over the past several decades is not getting across, Schiavone maintains. He ascribes this to the industry’s failure to spend on B2C (business to consumer) communications. While a lot of money is spent on marketing it is primarily B2B (business to business). The environmental message is reaching only the converted, within the plastics industry, which allows misinformation to gain traction in the wider world. The most important audience – the consumers – are not being involved in the debates. “We all understand the industry, we understand the polymers, the science and the processes, so why aren’t people believing us?” he asked. He ran through a brief history of plastics since the 1950s and into the 1960s, when the term ‘reusable plastic’ was abandoned; single use was presented as the hygienic approach. Mixed messages and inconsistency, mountains of trash in landfills and a general failure to ‘walk the talk’ lead to the messenger being viewed with suspicion. A significant part of any message is delivery “I know there are about 20,000 local governments within the US – communities and townships – who used to make money from their recycling; they got income from it. Now, it costs them,” Schiavone said. “What some of these townships have to pay out now is enormous. They are trying to balance their budgets, to pay for schools, policing and so on – the recycling system is really broken.” He says that this failure to practice what is preached makes the job of the anti-plastics lobby very much easier. Some of the opposition bodies are very well funded and have highly skilled marketing strategists and technicians. “Polling has shown that consumers want to know what the industry is doing about the problem. Polling showed that, back in the 1990s and 2000s, when we spent money talking to consumers, they had a much more favourable opinion of plastics,” he said. “Now, Hollywood doesn’t want to show any more single-use plastics on any of their movies or television shows. If you’re in packaging design you’ll get a special award if you can show how you’ve eliminated plastics in your design. In national parks throughout the US all single-use plastics have been banned from being sold. I see anti-plastics groups making headway in creating laws and taxes here in Belgium.” Belgium used to be known for some of the best recycling rates in the world and it still has but that message is being lost. The plastics industry has to stand up for itself. “The American Beverage council is doing a really good job of ‘bring every MATERIALS / RECYCLING Robert Schiavone, Global Marketing Director, R&D/Leverage during his presentation on ‘Plastics – The Battle of Perception’"},{"@ID":43, "MARKET SURVEY 29 PETplanet Insider Vol. 24 No. 01+02/23 www.petpla.net Resins Company name Novapet, S.A. Köksan PET Packaging Industry NEO Group Reliance Industries Ltd Postal address Telephone number Web site address Contact name Function Direct telephone number E-Mail P° Independencia, 21, 3°, PC 50001, Zaragoza, Spain + 34 976 216129 www.novapet.es Mr Ricardo Monfi l Head of Polymers Division +34 976 216129 rmonfi l@samca.com 4.Organize Sanayi Böglesi 83422 Nolu Cadde No: 10 Şehitkamil, Gaziantep, Turkey +90 342 357 03 30 www.koksan.com Mr Serhat Tümer Board Member +90 532 696 55 86 serhat.tumer@koksan.com Industrijos St. 2, Rimkai, Dovilai eld., LT-95346 Klaipėda district, Lithuania +37 0464 66 710 www.neogroup.eu Mr Gediminas Paulauskas Sales Manager +37 046466 710 Building 8B, Reliance Corporate Park, Ghansoli, Navi Mumbai 400701, India +91 22 79670000 www.ril.com Mr Bharat B Mehta VP Marketing +917710022861 bharat.b.mehta@ril.com RESINS 1. Brand name of the resins NovaPET K084 - K080 - K076 NEOPET Virgin PET \"Relpet\", rPET \"Relpet Green\" 2. IV Range 0.76 - 0.80, 0.84 0.56 - 0.82 0.59 - 1.00dl/gm a. of Homo-Polymers 0.58 - 0.96dl/g Homo polymers 0.76 - 0.84 0.76dl/gm b. of Co-Polymers 0.60 - 1.30dl/g 0.59 - 1.00dl/gm 3. Speciality resins No NEOPET Cycle Opaque grade for milk, Relpet OP5821 CSD LBS Soft, CR Available NEOPET 80, NEOPET 82 Relpet QH5821, Relpet G5841, Relpet Green B84 Water MW Soft, CR Available NEOPET 76, NEOPET 78 Relpet G5761, Relpet Green B76 Beer Glasstar + Sprit No NEOPET 80, NEOPET 82, NEOPET 84 Relpet B9845 (Barrier resin) Edible oil CR, Glasstar Available Relpet G5761, Relpet G5801 Wine / Liquors Glasstar, , LBS Soft No NEOPET 80, NEOPET 82 Relpet G5801, Relpet B9845, Relpet Green B80 Personal care / Pharmaceuticals Glasstar, Sprit Available NEOPET 80 Relpet G5801 Slow crystallisation Glasstar, Sprit No Relpet GL5000 Hotfi ll HF No NEOPET 82 HF Relpet H7761 Pre-coloured DCU, Luz, Polygloss No Fast reheat LB Soft Availabe NEOPET 82 FR, NEOPET 84 FR Relpet QH5821 Other CPET, HT, REX (for EBM), Sol (aerosol bodies), PET grades for other non-packaging applications Ultra NEOPET Relpet IM5590 for blood collection tubes 4. Increased barrier properties Light barrier: Dairy, Luz , DCU, Polygloss Gas barrier: Glasstar, Sprit No Relpet B9845 5. PEN mixes available No 6. Recycled blends available Yes, under customer requirements Yes NEOPET Cycle PET resins (2530% PCR content) 100% rPET under Relpet Green brand 7. Special comments Focused on innovation at the service of packaging; specialised in light barrier protection; committed to create new markets for PET. MTS ( Melt-to-Resin) NEOPET Cycle - Innovation dedicated to sustainable future Customised grades can be developed"},{"@ID":18, "MATERIALS / RECYCLING PETplanet Insider Vol. 24 No. 01+02/23 www.petpla.net 16 New site and technology centre for colour and additive development in Singapore Just in mid-January, US colours and functional additives manufacturer Penn Color from Hatfield, Pennsylvania, inaugurated its brand new Technology Center in Singapore to serve customers throughout the Asia-Pacific region. In an interview, company president and CEO Mr Kevin Putman Jr explained what the location is all about and what benefits will be offered to customers from now on. January 16, 2023 Penn Color, Inc. We met: Kevin Putman Jr, President and CEO PETplanet: Penn Color has announced the opening of its new Technology Center in Singapore. What is the purpose of this institution? Kevin Putman Jr: The Technology Center complements the existing technology centres that we have established in the United States and in Europe, bringing together our process and colour technology services with specialist personnel. It is meant to inspire designers, engineers, brand managers, business leaders, converters, equipment OEM manufacturers, suppliers, and other partners and harness their collective creative power and expertise. Here, our customers will be able to condense weeks of development time to days, bringing production-ready products forward faster than ever before. PETplanet: How do you think this Technology Center can make a difference for your customers? Kevin Putman Jr: The facility allows us to bring our products and the Penn Color experience directly to the doorstep of our customers and partners in Asia Pacific to ensure their needs are met. This design studio, like the other two in the US and Europe, is designed to be agile, transparent and dynamic. This means that our teams can develop specific products in the presence of and together with our customers, in a collaborative and engaging setting. PETplanet: Why did you choose Singapore? Kevin Putman Jr: Over the years, as we expanded our company’s capabilities around the world, establishing an innovation presence in Asia became a top priority. When this project was launched, a number of countries were considered as innovation locations for Penn Color in Asia Pacific, but when it came down to it, no country offered the economic stability, access to a talented workforce, proximity to customers, and overall focus on innovation and creativity to the extent that Singapore does. It’s no surprise that many well-known international companies are choosing Singapore as their Asia-Pacific base. PETplanet: What went into the design of the facility itself? Kevin Putman Jr: When it came to designing the Technology Center, I knew we needed a space that not only served a very specific functional purpose, but also exuded comfort, style, and creativity, seamlessly blending people, innovation, architecture, and the elegant aesthetic of Asian hospitality. To design this space, we selected DP Design, a Singapore-based design firm involved in the design of some of the Singapore’s most iconic buildings. To lead the project, we were fortunate to work with Mike Lim, Principal Designer of DP Design, and winner of the Design Excellence and Designer of the Year awards in 2018 and 2019. He and his team did an incredible job, incorporating natural light, tropical elements, and industrial equipment to create a welcoming, comfortable, and inspiring environment. PETplanet: What role do you think the Singapore location will play in Penn Color’s strategy in the near future? Kevin Putman Jr: The new site is dedicated to implementing capabilities that go beyond today’s standards, as well as reinventing colour and additive development. At the same time, it is designed to further solidify Penn Color’s position as a global leader in thermoplastic products, particularly in the packaging and consumer goods markets. PETplanet: Thank you! www.penncolor.com MATERIALS / RECYCLING President & CEO Kevin Putman Jr Clear and inviting architecture awaits customers."},{"@ID":39, "37 PRODUCTS PETplanet Insider Vol. 24 No. 01+02/23 www.petpla.net Novapet rPET production plant features Erema’s Vacunite system Novapet is closing the loop into the PET value chain, with its REnovaPET division, with a sustainable project based on a rPET production plant based in Barbastro (Huesca), where Novapet has its resins and preforms production facilities. This project, which started its construction in the summer 2022, is reaching its final stretch on the next incoming weeks. Thanks to Erema’s recycling systems, which are intended to make PET recycling efficient and profitable, Novapet will complete the rPET production process by incorporating it into its injection processes itself. The Erema model that REnovaPET has installed in Barbastro is the Vacunite 2318 T, 1500 bottle-to-bottle system. The hourly production will be 1,500 kg/h of 100% recycled pellets from bottle flakes. The destination will initially be for Novapet’s self-consumption, in the adjacent preform injection plant, which is marketed by Noven, not ruling out the sale to third parties, in tanks or in big-bags, if so decided. Regarding the process, the key components of the system include a vacuum reactor with integrated nitrogen flushing which is connected directly to a single-screw extruder. Thanks to the ingenious function of the mixers in the vacuum reactor they feature three ultra-efficient function zones which interact with each other to decontaminate and predry the PET material before extrusion. As a result, no additional degassing ports are required on the extruder itself. This means that the technology drastically reduces the length of the extruder, reduces its energy consumption, improves the colour values of the processed material and keeps AA values at a low level. In addition to decontamination and drying, the bulk density increase inside the reactor is up to 100% and the flakes are crystallised. This allows the extruder to be fed in a constant flow – an essential prerequisite for consistent throughput rates. www.novapet.com New PET bottle-to-bottle recycling line reduces production costs To design the recycling process as efficient and energy-saving as possible has been one of the focal points in the technical development at Starlinger recycling technology for many years. The latest result in this respect is the newly conceived PET bottle-tobottle recycling system RecoStar PET art scores with 25% less energy consumption compared to the previous model, and it also requires 46% less maintenance time, has a 21% smaller machine footprint, and a production output increase of 15%, as Starlinger states. In total, according to the company, bottleto-bottle recyclers can save about 21% in production cost with the new system. Streamlined production process Instead of the former two drying units the new RecoStar PET art now features one large drying unit. Together with changes at the extrusion unit and SSP, this reduces energy consumption, the machine footprint, and maintenance requirements. The expanded SSP capacity helps to achieve the production output increase stated above. “For the new machine concept, we analysed the PET recycling process and our technical solutions for it from top to bottom, searching for ways to make them better”, explained Paul Niedl, Commercial Head of Starlinger recycling technology. “We especially improved energy consumption, but also succeeded in shortening some of the process steps – such as material preparation and extrusion – and in making machine maintenance a lot easier and shorter. At the same time we increased the output capacity. All this with the goal not to compromise the high regranulate quality Starlinger is known for. To achieve this, we analysed, combined and implemented know-how from various areas, creating a synthesis of arts, so to say. Hence the name of the new system: recoStar PET art.” www.recycling.starlinger.com The right tools and expertise to help with your rPET goals! Agr is uniquely positioned to support your venture into rPET bottle manufacturing with a powerful combination of Process Control tools, Process Consultants, and decades of industry experience. AGRINTL.COM • +1.724.482.2163"},{"@ID":12, "MATERIALS / RECYCLING PETplanet Insider Vol. 24 No. 01+02/23 www.petpla.net 10 Recycling plastic packaging “Our activities are circular and local” Our last visit in Spain is already close to the French border. In the north-east, 20 km from the Atlantic coast, a good acquaintance, Mikel Urain, an expert in the PET industry, welcomes us to his company EkoRec. We are curious about his new company and torture the Editourmobile the last kilometres through the Spanish heat. MATERIALS / RECYCLING Mikel Urain has been in the PET industry for about 15 years. At ABC Compressors as Global Sales & Technical Service Director CCO, then as General Manager at BeandBe Beverages. Now he welcomes us in the mid of pressed and tied PET bales. In his office he tells us about his company EkoRec. “Ekorec Group was created in 2012 as a key player on Spanish circular economy. Part of our industrial equipment and background comes from the extinguished textile activity that was performed in our facilities. Ekorec industrial know-how on recycling and PET transformation was powered in 2021 through the merge operation with its mother company Bascotecnia (EPC Engineering Group created in 1976). The resulting industrial group is a unique example of integrated circular economy adding recycling activities with PET transformation and engineering consultancy. Three factories are located on 75,000m2 of industrial space and house four business units. Not to forget the company’s own combined heat and power plant;” Mikel explained. EkoRec integrates in the same industrial area PET recycling plant and rPET sheet, reducing CO2 footprint of the whole process. “Our activities are circular and local. Taking care and controlling the whole flow from each individual bottle recycling act to the processed rPET sheets and flakes that will close the loop and become again a sustainable packaging solution,” Mikel mentioned. He continues, “Our facilities and production machinery allow us to be flexible with our customers and offer highest food grade products under BRC certification. We recycle post consumer and post industrial bottles, preforms and PET sheet into new raw materials for bottle-to-bottle granule production and rPET sheet. Our sheet production business unit manufactures 100% rPET sheet, multilayer and medium - high barrier sheets. We manage full logistics to final destinations, with regular deliveries to main industrial areas in Spain and Europe.”EkoRec works in high demanding sectors such as food & beverage, automotive and pharmamedical industry. “Therefore, quality is a strong value that rules all we do. 100% of our rPET flakes and any raw material used for our plastic processing goes through our quality department and laboratory. Our general processes and procedures are certified under ISO9001 and our products do have BRC Packaging Materials certification.” In the PET recycling area, we see a state-of-the-art sorting and recycling equipment from STF Germany with sorting technology of Sesotec. “We have a warehousing capacity for bales and flakes of about 3,000 t and a production capacity of 15,000 t a year. Our own quality flakes are called Eko PET. We also process random samples and laboratory analyses for control before delivery, as well as specific checks for raw density, colours, adhesive residues, foreign plastics, impurities, grain size distribution and residual moisture.” Mikel told us that the Packaging Division has been providing sustainable solutions for the food, pharmaceutical and industrial sectors since 1996. “We work closely with the fruit and vegetable sector on the Mediterranean coast, the Atlantic fishing industry, the Spanish jam and meat industry, the bakery industry through out Europe and a wide range of pharmaceutical and industrial applications. To produce packaging material for these industries EkoRec use Bandera and Reifenhauser machinery. The multilayer sheet lines produce 2,000 kg/h with up to five layers. A third PET sheet line is planned for 2024,” he summarised. There are two more business units under the roof of EkoRec, the Engineering Projects F.l.t.r.: Mikel Urain and Heike Fischer in front of stacked PET bales STF and Sesotec recycling and sorting technology with a production capcity of 15,000 t/a PET sheet production at the EkoRec plant"},{"@ID":32, "MATERIALS / RECYCLING PETplanet Insider Vol. 24 No. 01+02/23 www.petpla.net 30 Sustainablility - enabling additives for food and beverage packaging by Marco Schaefer, Sr. Marketing Manager Food & Beverages Packaging EMEA, Avient Corporation Functional additives are crucial to making PET a versatile packaging material. Additives can extend the performance of PET by protecting against food spoilage caused by oxygen ingress, UV radiation, visible light, and/or by-product migration. They can also help with retaining packaging material’s mechanical properties. The circular use of PET will significantly reduce reliance on fossil fuels and reduce carbon emissions. The use of mechanically recycled PET yields 79% less CO2 emissions than virgin PET. This circular use of PET will significantly reduce reliance on fossil fuels in the manufacturing process as recycled PET use yields 79% less CO2 emissions than virgin PET. However, the recycled material has different qualities than virgin PET, often darker or yellow in colour with lower intrinsic viscosity (IV), and is also more challenging to process. To address the increased use of rPET and the multiple processing loops it will undergo, manufacturers will require additives that meet these additional challenges. As rPET content increases, additives need to adapt so that: 1) they do not negatively impact rPET aesthetically or during processing; 2) they function as intended when used in conjunction with rPET; 3) they have no negative impact on non-intentionally added substances (NIAS) through the recycling process. A shift from functional additives to sustainability-enabling functional additives will be required in this rapidly changing market. Additives that provide the necessary functionality have no negative impact on rPET, and show improvements in rPET quality, processability, or performance, are currently available. If adopted globally, additives like these would enable improved quality and availability of bottle-grade rPET in the future, enabling the continued circularity of PET through multiple recycle loops. Colour When PET is recycled, degradation reactions can lead to yellowing. In addition, degradation reactions of PET additives can also occur, potentially leading to additional yellowing and colour variation. As the levels of rPET used in PET packaging are set to increase, the number of heat exposures of rPET will increase; hence, the yellowing and colour variation of rPET resin will increase. To overcome these issues, Avient developed a range of solutions that will have a minimal impact on the additional discolouration of rPET even after repetitive recycling steps. And to mimic more realistic conditions, Avient has set up an internal recycling protocol that is evaluating colour stability as MATERIALS / RECYCLING"},{"@ID":35, "MATERIALS / RECYCLING PETplanet Insider Vol. 24 No. 01+02/23 www.petpla.net 33 Higher performance without loss of quality Plasticising in a gentle way As the demand for recycled plastics grows, so does the size of the machines. This applies to the processing of polyolefins as well as to PET recycling. The new models of Erema’s Vacurema Basic technology have a throughput of up to 6t/h and consume 10% less energy than comparable systems without the new EcoGentle plasticising technology. In the PET recycling segment, Erema proved its expertise as a partner for large-scale recycling projects several times last year. At the end of 2021, the recycling machine manufacturer delivered a large-scale Vacurema Basic 2628 T plant for the first time with a production capacity of up to 40,000 t/a of rPET granulate. Since then, throughput capacity has again been significantly increased. “Up to 6 t/h are possible with our new plasticising technology,” Michael Heitzinger, Managing Director at Erema, pointed out. The recycling machine manufacturer calls this plasticising unit EcoGentle because it significantly reduces energy consumption. Measurements on a Vacurema Basic 2628 T system resulted in up to 12% total energy saving (specific total energy consumption, kWh/kg) and 30-47% energy saving for the extruder drive on Vacurema Basic plants from size 2021 upwards. In addition, EcoGentle handles the melt in a gentle way. At the same time as achieving unprecedented high throughputs. “All in all, this is a package that enables our customers to increase productivity and noticeably reduce costs,” stated Heitzinger. The decisive factor is the further precise interaction of the intake section and extruder screw as a result of the combination of the EcoGentle plasticising unit with the proven counter current technology. The optimisation of compression ratios is claimed to ensure better feeding performance, and the selective exploitation of elongation flows, together with a number of other rheological optimisations, results in a particularly homogeneous melt and a wider process window. This makes it easier to compensate for fluctuations in the input material without negatively impacting process stability. Due to the lower temperature, the melt is processed more gently overall. The result is even lower acetaldehyde (AA) values, which translate into producing higher quality rPET pellets, said Erema. This development is based on the know-how bundled in the Erema Group. Essential core components MATERIALS / RECYCLING for EcoGentle are manufactured in Austria by 3S, one of Erema GmbH’s sister companies. Currently, Erema’s large-scale plant focus is on PET recycling. But it will not stop there - the recycling machine manufacturer is already working intensively on upscaling the technologies for polyolefin recycling to achieve high throughput volumes. “The push for a circular economy demands it, and we will deliver with our usual quality and reliability,” confirmed Heitzinger. www.erema-group.com The new EcoGentle plasticising unit from Erema Faster and cooler than ever optiSTACK saves your time and money! German Technology"},{"@ID":34, "MATERIALS / RECYCLING PETplanet Insider Vol. 24 No. 01+02/23 www.petpla.net 32 nology will reduce AA levels in PET bottles by up to 80%. Furthermore, it allows for further optimisation in the bottle-blowing process, producing a better quality bottle with improved mechanical strength while reducing carbon emissions. This can help to increase rPET content by reducing processing issues such as bottle blowouts, which can often lead to a loss of productivity. ColorMatrix AAzure has a light blue tint, useful for offsetting any yellowing from using rPET. Use of sustainability-enabling additives that can address these challenges and help grow the percentage of rPET employed in the future stand to play a fundamental role in the packaging market. Conclusions In the coming years, the industry will see several significant changes within the packaging market. Sustainability initiatives need to be front and centre in order to achieve a truly circular economy by the middle of the century. The use of rPET is already mandated with specific targets in certain regions. Its composition and the number of recycling loops the material goes through will drastically change the makeup of PET bottles that enter the market. Additive manufacturers will need to adapt their offerings to help converters and brand owners operate in such a changing environment. Bottle manufacturers will have to choose products to help move the industry towards a real circular economy. Selecting the proper additives for PET will enable the ease of use of rPET and help maintain PET as the material of choice for the future. www.avient.com Blow molds | Blow molding machines | PET bottle design | Packaging equipment APF-Max series All-electric FRQɍJXUDWLRQ 4XLFN FKDQJHRYHU IRU RWKHU SUHIRUP W\\SH %ORZ PROGV TXLFN FKDQJH NIR KHDWLQJ V\\VWHP Hot Fill RSWLRQ 6SDFH VDYLQJ RYHUDOO GLPHQVLRQV HEAD OFFICE PET Technologies GmbH Grünlandgasse 5/1/12 2620 Neunkirchen, Austria w .pet-eu.com tel.: +43 720 775 196 RIɍFH#SHW HX FRP"},{"@ID":33, "MATERIALS / RECYCLING PETplanet Insider Vol. 24 No. 01+02/23 www.petpla.net 31 ∆E* (Delta E) through five melt heat histories which is the equivalent of two full recycle loops, focusing on the total colour shift of the L*, a*, b* values. This approach can be used to screen the heat stability of additives, such as PET toners. The below chart is an example of how ∆E* can be used to compare two toner products. ColorMatrix Optica toner was formulated with specific colourants that show improved stability through these multiple cycles and therefore contribute less to yellowing and colour variation in the rPET stream than a standard toner. Processability As the number of heat exposures to rPET increases due to rising use levels, the processability of rPET will decrease. Mechanical recycling of PET produces a PET product with a lower mechanical strength compared to virgin PET with an equivalent intrinsic viscosity. These materials process differently, particularly during the bottle-blowing process. They heat up differently, stretch differently, and, when used in combinations or blends, can lead to a number of bottle-blowing process issues. This significantly narrows the bottle-blowing parameters for achieving a good quality PET bottle, resulting in poor quality bottles, reduced line speeds, increased blowouts, increased downtime, and increased scrap rates. Bottle-blowing process aides, such as ColorMatrix Smartheat RHC, improve the preform heat up rate and heating uniformity, allowing for a wider bottle-blowing window. This enables optimisation of the bottle-blowing process and polymer weight distribution within the bottle sections. The resultant will deliver improved quality and mechanical strength, helping to reduce processing issues such as blowouts, downtime, and scrap rates even at higher usage of rPET. In contrast to other reheat agents, SmartHeat RHC has minimal impact on final product colour or aesthetics and is accredited by the American Plastic Recyclers (APR). Performance Maintaining the desired processability is one of many challenges that additives will have to face within a market contemplating the increased use of rPET. Additive performance with rPET will also have to be addressed. This is true for oxygen or acetaldehyde scavengers as well as toners or process aids. For example, oxygen scavenger technology is essential to the food packaging industry because it prevents or delays oxygen ingress into plastic packaging to extend shelf life and reduce food waste. Many commercial technologies are based on metal catalysis to function. This catalysis has been proven successful and offers full compatibility and performance when used with virgin resins. As the amount of rPET is set to increase, oxygen scavengers will face the challenge of maintaining performance regardless of the quantity or quality of rPET utilised. Impurities from different rPET grades can cause the deactivation of the metal catalysts currently used. Suppliers of oxygen scavenger technologies must help the market implement and achieve their sustainability targets by developing new technologies that can perform equally well with increasing amounts of rPET and with the prospect of utilising up to 100% recycled content in the future. For this purpose, Avient has developed ColorMatrix Amosorb 4020R, an oxygen scavenger designed to maintain consistent oxygen scavenging with the most commonly employed rPET grades, regardless of the quantity of rPET utilised in the bottle. Amosorb 4020R thus gives performance, raw material choice flexibility, and supports achieving multiple recyclability targets at once. The amount and quality of rPET that will be used could also affect specific market segments more than others. Acetaldehyde is intrinsically present in variable quantities in materials such as rPET. Its presence can profoundly affect the water bottle market because even a small migration of such substance from packaging can change the organoleptic properties of water. The use of ColorMatrix AAzure acetaldehyde control tech-"},{"@ID":48, "TRADE SHOW REVIEW PETplanet Insider Vol. 24 No. 01+02/23 www.petpla.net 46 Energy-saving Pac-E packaging machine debuts at K 2022 In Düsseldorf, the company initially demonstrated the new machine’s capabilities and sustainability credentials on a 350 t clamp force Pac-E model. Three additional clamp force variants - 420, 250 and 300 t – will subsequently follow in this order. “Pac-E is a global development project that combines all our company know-how from Germany and Japan,” Arnaud Nomblot, Director Business Development Packaging reveals. The toggle levers, plates, tie bars and plasticising elements, including the screws and cylinders, were developed in Germany, while the electric drives and the newly developed injection unit stem from the Group’s Japanese parent company. Sumitomo Demag states that two critical innovations differentiate Pac-E from the existing hybrid packaging series, notably, the solely electric-driven axes deliver up to 50 per cent in energy savings. Converting a 30 cents (€) per kW/h saving in electricity consumption, this can save manufacturers approximately € 70,000 (US$ 71,285) per annum when measured against a high-speed hybrid packaging machine. Additionally, the lubrication of the toggle lever no longer causes cleanliness issues; being a completely closed-circuit design it is leak free. Oil is instead extracted, filtered and recycled. This eliminates the need to clean the toggle lever, which has the added benefit of reducing oil consumption for customers. Not only is the reduced energy consumption of Pac-E less resource intensive, the machine’s dimensions are more compact, thus meeting calls from customers for space-saving machines. With its injection capacity of 550mm/s, Pac-E can also be used for thin-wall and food packaging with IML, confirms Nomblot. “This machine will enable processors to produce even thinner and lighter packaging items, resulting in a significant reduction in raw materials, waste and shipping costs.” Market launch of Pac-E commences in mid-2023 starting with the 350 t. The company plans to roll out the remaining clamp force sizes in succession. www.sumitomo-shi-demag.eu You can watch an exclusive presentation of the Pac-E by Arnaud Nomblot, Director Business Development Packaging, in our PETinar recording: https://petpla.net/2022/09/06/ review-technical-highlights-drinktec-2022/ With the Pac-E, Sumitomo (SHI) Demag Plastics Machinery GmbH, Schwaig, was presenting its all-electric high-speed injection moulding machine for the first time live on stage that is tailored to the packaging market and here specifically to the needs of beverage closure manufacturers. The new machine builds upon the success of the El-Exis SP packaging machine."},{"@ID":55, "9 NEWS PETplanet Insider Vol. 24 No. 01+02/23 www.petpla.net An endless range of production possibilities with single-stage SIPA S.p.A. - Via Caduti del Lavoro, 3 - 31029 Vittorio Veneto (TV) - Italy - Tel. +39 0438 911511 - sipa@zoppas.com - www.sipa.it ECS SP models stand for a guarantee of quality based on 35 years of experience in Injection Stretch-Blow Molding technologies (ISBM) technology. Their robust system, produced in Italy, allows for the production of high quality containers in a wide variety of different sizes, threads and shapes. Tooling investment can often be optimized by using one single (i.e. shared) hot runner withmultiple cold halves. ECS SPmachines have features that enable quick change-overs, accept legacy molds and are also characterized by their compact layouts and high HQHUJ\\ HIĆFLHQF\\. Injection Stretch BlowMolding System"},{"@ID":42, "TRADE SHOW REVIEW PETplanet Insider Vol. 24 No. 01+02/23 www.petpla.net 40 Market developments in the plastics industry and the NPE 2024 Mr Seaholm opened the press conference and referred, among other things, to the Association’s future strategy in which sustainability and the circular economy, promoting the importance and indispensability of plastics and the involvement of political decision-makers in reinforcing a positive image of plastics would have a prominent role. “Overall, the opportunities for the industry and the Association could outweigh present-day challenges. Plastics is the sixth largest industry in America and we as an Association, with our sound strategy and thought leadership, can be the voice of this industry, as well as continuing to improve our services to the sector,” said Mr Seaholm. Dr Pineda presented the highlights of his Global Trends 2022 report. For the first time since 1997, the US plastics industry recorded a trade deficit of US$10.1 billion in 2021, with US$81.5 billion in imports and US$71.3 billion in exports. Half of all imports came from China (30%) and Canada (20%), followed by Mexico in third place with 8.8%. In terms of exports, Mexico was in first place with 25.2%, just ahead of Canada with 21% and China with 8.7%. Referring to the figures, Pineda drew attention to the top five external balance countries, with Mexico in first place in terms of surplus and China for deficit. He explained: “The industry recorded a trade surplus of nearly US$11 billion with Mexico in 2021 whilst having a deficit of US$18.2 billion with China. However, this was partially offset by a trade surplus in resin of US$2.6 billion”. Trading in US plastics machinery also showed a deficit of US$1.2 billion in the first half of 2022 (US$600 million in exports versus US$1.8 billion in imports) while trade in moulds totalled US$1.5 billion (US$533.8 million in exports versus US$ 2.04 billion in imports). In the global top 10 rankings for trade in plastic goods, China came first with US$229.6 billion in 2021, followed by the USA with US$164.6 billion and Germany with US$141.2 billion. “Inflation has been a major contributory factor to the increase in the dollar value of exports”, Pineda added. “Although this year’s outlook for commodity trading may fall short of expectations given the slowdown in world economic growth, demand in the global plastics market is continuing unabated”. The first half of 2022 saw US plastics exports grow by 16.9% compared to the first half of last year, while imports rose by 17%, with a 17.4% increase in the balance of trade. Plastics foresees potential risks for trade in plastics in 2023, although international trade remains part of the overall growth strategy for 2022 and beyond. Mr Seaholm highlighted the USA’s second place in the top 10 rankings and commenting on the figures said: “The fact that our Global Trends report expects positive results for our industry despite an increased trade deficit speaks to the importance of plastics to the world we live in”. Finally, Mr Anderson spoke about what to expect at the upcoming NPE in 2024. He explained that the trade fair would have two dedicated fora for trending topics and innovations for training and professional development purposes, as well as specialist workshops, two outdoor recycling and sustainability demonstrations and guided sustainability tours. In addition to the regular exhibitor stands, there will also be seven specialist areas known as “Technology Zones”. These are the Bottle Zone, Advanced Manufacturing, Business Solutions, Materials Science, Packaging, Mould-making and Recycling and Sustainability. “As of October 19, 2022 we have received 564 registrations for the trade fair”, said Mr Anderson. A total of 39,500m2 of space has been requested so far. 52% of all applications have come from 295 Association members and 26% (144) from international exhibitors. 33% of exhibitors have asked for stand space in one of the Technology Zones. www.plasticsindustry.org On October 20, 2022, the Plastics Industry Association (Plastics) held a press conference at the K’ trade fair. As well as the latest news from the Association, there were discussions on the global development of the plastics industry during a pandemic, supply chains and changing import/ export behaviour, together with a look ahead to the North American plastics trade fair NPE taking place in 2024. Matt Seaholm, President and CEO, Dr Perc Pineda, Chief Economist and Glenn Anderson, COO, gave presentations on various topics and answered questions from those present. Dr Perc Pineda presents the PIA’s Plastics 2022 Global Trends report."},{"@ID":54, "42 TRADE SHOW REVIEW PETplanet Insider Vol. 24 No. 01+02/23 www.petpla.net Drinktec review, part 3 Introducing HyPET Complete Husky introduced via video presentation the new HyPET Complete, a complete end-to-end, connected production solution. Developed to address ongoing top-of-mind challenges of global producers, HyPET Complete is modelled to transform variabi l ity into stabi l ity throughout every stage of PET preform production. “To truly succeed in today’s global climate, it has become clear that to be competitive, producers need to think beyond just hardware to a more holistic approach to manufacturing,” said Robert Domodossola, Husky’s President of Rigid Packaging. “HyPET Complete goes one step further enabling producers to build more resilient, stable manufacturing models that are less affected by shifting external factors. This is particularly relevant today as we see producers who are increasingly looking for more energy efficient manufacturing processes and packaging materials, such as PET, to offset fluctuating costs.” HyPET Complete was founded on a holistic approach that incorporates factory planning and tooling lifecycle optimisation, workforce training and development, a fully digitised delivery model and OEM parts solution, as well as the company’s recently introduced Advantage+Elite proactive, predictive and transparent monitoring solution. All components are designed to work together to enable producers to successfully navigate through today’s most prevalent challenges, including achieving circularity and sustainability, mitigating supply chain risks, preparing for skilled labour shortages, optimising material and operational efficiency, as well as offsetting rising material costs and inflation. HyPET Complete is supported by Husky’s latest generation platform of proven HyPET systems tailored for the production of rPET that include a purposebuilt drying solution, optimised energy management, enhanced melt control, automated mould cleaning, integrated part quality inspection etc. www.husky.co Stackable PET bottles US-based PET bot t l e techno l - ogy manufacturer Saniton Plastic has showcased an exciting PET packaging concept, the Interlocking Bottle. The company is making use of a bottle design they developed in-house, which, according to their information, should save on logistics costs and emissions by up to 35%. The PET bottles have been designed in such a way that they can be linked together, therefore saving space compared to regular bottles, as well as increasing their transport stability. “We call it ‘interlocking bottle technology’”, explained CEO Alaa Hattab at the trade fair stand, showing his promotional PET bottle with a two-part Drinktec label. With the space savings achieved by the design, it should be possible to minimise any wasted space in the traditional transport from the bottler to the point of sale and even further to the retail shelf and the consumer’s fridge. Additionally, the design could help in space-sensitive areas like passenger transport, for example airline catering on flights. Side by side comparison of 500 ml traditional bottles and the Saniton Plastic Interlocking Bottle demonstrated notable space savings. “In this test, Saniton Bottles delivered up to 364 bottles per pallet level. The standard bottle only came to 270 bottles per pallet level,” said Hattab. Furthermore, due to the improved stability of the stacked bottles, one or more additional pallet levels could be added. Additional benefits include reduced packaging. Saniton Plastic offers a turnkey, fully automated production line from blow moulding machine to palletising. The current production capacity is 7,000 bph at 500ml and soon a 9,000 bph line will also be offered. www.sanitonplastic.com CEO Alaa Hattab shows his stackable PET bottles."},{"@ID":5, "imprint EDITORIAL PUBLISHER Alexander Büchler, Managing Director HEAD OFFICE heidelberg business media GmbH Hubweg 15 74939 Zuzenhausen, Germany phone: +49 6221-65108-0 fax: +49 6221-65108-28 info@petpla.net EDITORIAL Kay Barton Heike Fischer Gabriele Kosmehl Michael Maruschke Ruari McCallion Anthony Withers WikiPETia. info petplanet@petpla.net MEDIA CONSULTANTS Martina Hirschmann hirschmann@petpla.net Johann Lange-Brock lange-brock@petpla.net phone: +49 6221-65108-0 fax: +49 6221-65108-28 LAYOUT AND PREPRESS EXPRIM Werbeagentur | exprim.de Matthias Gaumann READER SERVICES reader@petpla.net PRINT Chroma Druck Eine Unternehmung der Limberg-Druck GmbH Danziger Platz 6 67059 Ludwigshafen, Germany WWW www.hbmedia.net | www.petpla.net PETplanet Insider ISSN 1438-9459 is published 10 times a year. This publication is sent to qualified subscribers (1-year subscription 149 EUR, 2-year subscription 289 EUR, Young professionals’ subscription 99 EUR. Magazines will be dispatched to you by airmail). Not to be reproduced in any form without permission from the publisher. Note: The fact that product names may not be identified as trademarks is not an indication that such names are not registered trademarks. 3 PETplanet Insider Vol. 24 No. 01+02/23 www.petpla.net Dear readers, PETplanet is finally back in India! The pandemic interfered with our visits to India for a long time. We have continued to report from afar, but in such a market with its 1.4 billion people, where consumer behaviour is changing more rapidly than almost anywhere else, it is almost sacrilegious not to be able to be there in person for so long. Last December, after a forced break of two years, I was finally back on the ground, both at the local beverage trade fair Drink Technology India (DTI) in Mumbai and at some processors and bottlers, including the Pepsi bottler of the Jaipuria Group in the city of Jammu, where Alexander Buechler had last been in 2009. This time, DTI was co-organised with Pack Mach Asia Expo and World Tea & Coffee. The organiser Messe München India counted a total of 13,104 visitors from 33 countries - an increase of around 8% compared to the last DTI in Mumbai in 2018. The mood of optimism and enthusiasm was palpable. One of the most moving topics in the industry is sustainability, recycling and the future use of rPET in beverage and food packaging. This topic, which has been discussed in India since the possibility of producing food-grade recyclate was first mooted and is now expected to be implemented this year, is set to shake up the PET packaging market. Enjoy reading our first issue of 2023! Yours, Kay Barton"},{"@ID":57, "1 The worldwide round trip with The Middle East Roadshow EDITOURS PET world in the Middle East New year, new tour! After our successful Drinktec tour, the PETplanet team is going to the Middle East in the last quarter of 2023! In a spectacular project taking us well into 2024, we will be travelling in a wide variety of ways to various countries and regions of the Middle East with different mobile editors. There we will interview machine manufacturers, the supply industry, bottle and beverage producers, as well as PET recyclers and everyone involved in the process chain. What market-specific trends are there now or will arise in the future? What developments and technologies are in vogue on the consumer and plant construction site in some of the hottest regions of the world? What special requirements are there? What role do topics such as food safety, shelf life and sustainability play in PET packaging and how are companies preparing themselves for the coming years? This, and much more we will be discussing face-to-face with all the key players and then our results will be presented to you in a series of must-read reports in PETplanet Insider. Please join on this enchanting voyage to the world of PET in the Middle East. We look forward to welcoming you on board! Our previous Road Shows at a glance 2010-2011-2012-2013-2014-2015- 2016-2017-2018-2019-2020-2022 Interested in being visited? barton@petpla.net Autumn 2023 - 2024 EDITOUR - THE MIDDLE EAST ROADSHOW 6 countries numerous interviews with PET companies"},{"@ID":26, "MATERIALS / RECYCLING PETplanet Insider Vol. 24 No. 01+02/23 www.petpla.net 24 During Holland Colours interviews both the converters and brand owners seem to agree that a yellowish off-colour is not accepted by the average consumer because it is associated with spoilt product. Other aspects related to rPET quality are Intrinsic Viscosity (IV), absence of black spots and haze. Different solutions to retain rPET value It is a given that high quality, transparent rPET is scarce and prohibitively expensive to come by. There are several options being worked on to address the problem of limited availability of high quality rPET. Most of these are clearly described in the Design for Recycling Guidelines by the various recycling platforms and associations. A solution that has already been implemented on a wide scale is to use completely clear packaging. Eliminating colour in packaging will ensure that the value is retained. Reason being that packaging materials are predominantly separated in two recycling streams, i.e. clear and coloured. Mixing and reprocessing various colours, even transparent versions, results in a lower quality output. As stated before the discolouration of clear rPET is due to multiple heat cycles in combination with residual component traces. Another solution has been to use closed loops in the recycling process. For example, large brand owners own a stake in deposit return systems for PET bottles. This helps to ensure the quality of the PET bottles being collected and it allows them to standardise a significant portion of the PET collected for the recycling. This can help in some ways, but inevitably, after multiple heat cycles the same undesirable discolouration issues might arise. A technical solution to the undesirable yellowish discolouration is colour neutralisation. Using opposite colourants allows for a wider colour range of rPET to be used, which of course means that while the total amount of rPET stays the same, more of the available rPET can now be utilised. How does colour neutralisation work? What are the different product forms and what are their pros and cons? An undesirable colour cast can be neutralised by means of adding an opposite colourant in the melt processing step, among others the extrusion and injection moulding process. The melt processing step could take place at a recycling facility but also at a (packaging) converter. By addition of the right amount of opposite colourant the rPET will be as close to virgin PET as possible from a colouristic point of view. However, depending on the starting value of the input material, the L-value will always be affected. Monochromatic colour wheel The different forms These concentrates are available in various product forms, depending on the type of carrier used, liquid or solid. A liquid concentrate allows for a low dosing rate also called let down rate (LDR). It’s easy to control and dispersed effectively in the target plastic. However it might have some stability issues with functional colourants or additives settling out. Furthermore some housekeeping challenges might occur when spilled. A solid concentrate or masterbatch might be based on a wax or polymer and allows for cleaner and easier handling and depending on the type of carrier material either disperses very easily or requires somewhat more melt mixing shear. The colourant, carrier material and LDR of a formulation can be tailored to specific needs. Seeing as there is a trend towards 100% rPET, a wax based solid masterbatch might be preferred. From a sustainability perspective, a nonpetroleum, non-food source based wax based solid masterbatch is an option which helps in the goal towards 100% rPET. Also regulatory requirements in relation to the end-use have to be considered in the composition of the concentrate or masterbatch. The optimal specific product form depends on several factors like the needs and production setup. www.hollandcolours.com “Opposite colourants used for optimising rPET colour are preferably pre-dispersed and encapsulated in a carrier material resulting in a concentrate or masterbatch allowing for economical and effi cient dosing and dispersion in the fi nal product. This solution off ers enormous fl exibility and can help create a reliable and consistent stream of high quality rPET that matches customer needs. These solutions are paramount in order to meet global sustainability needs.” Raymond Jongman, EMEIA Sales Manager, Holland Colours"},{"@ID":1, "No.1+2 2023 www.petpla.net D 51178; ISSN: 1438-9452 06 . 02 . 23 PETplanet is read in more than 140 countries MAGAZ I NE FOR BOT T L E R S AND BOT T L E - MAK E R S IN THE AMER ICAS, AS IA, EUROPE AND AL L AROUND THE PLANET MARKETsurvey Suppliers of resins & additives Page 28 Page 10 MATERIALS / RECYCLING Page 14"},{"@ID":38, "36 PETplanet Insider Vol. 24 No. 01+02/23 www.petpla.net PETproducts Energy-saving solution for pelletising of rPET/PET When it comes to the pelletising of PET, an energy-saving process as well as a certain degree of crystallisation is very important. Econ launched an underwater pelletiser especially adapted to these requirements. The result is the Econ PET-edition, which has been optimised for PET and rPET. With the help of the Econ patented Thermal Insulation Technology, a safe start-up process is obtained. By preventing heat transfer from the die plate unit into the process water, not only is the freezing of die holes prevented, but a considerable amount of energy is saved. In addition, special attention has been paid to an appropriate insulation of the water tank and the piping in order to achieve an end temperature of the pellets of at least 140 °C. Depending on a customer’s requirements, Econ provides a tailormade solution to ensure the required pellet end temperature. Not only is the pelletiser engineered to operate with minimum energy consumption, but the downstream equipment ECS (Econ Crystallisation System for PET) is as well. This uses the intrinsic heat of the pellets for crystallisation and is therefore one of the most efficient methods of crystallising PET, says Econ. The system is designed to keep the PET pellets at a constant temperature and to achieve a degree of crystallisation of 30-40 %. In the crystallisation channel, the pellets are conveyed further by gentle vibration and mixed to prevent sticking during crystallisation. The high degree of crystallisation enables a faster pre-drying of the pellets before further processing (e.g. injection moulding), which saves a considerable amount of time. In the food sector, a low acetaldehyde (AA) content of recycled PET is required in order to meet the legal guidelines. “Our goal in the development of the Econ PET-Edition was to achieve a significantly improved value in comparison to conventional pelletising systems,” explains Dominik Neumann, team leader of the R&D department. By reducing the pressure build-up at the die plate by 40%, a lower AA content of 30-40 % was achieved directly after pelletising. Previous tests have shown that a lower energy input can be expected during dehydration, since the reduced AA content represents a different starting position. www.econ.eu NIR detectable black bottle Ho.Bag Corporate, an Italian company specialised in the production and distribution of packaging for the cosmetic, herbal and pharmaceutic sector, introduces a new black bottle that can be fully recycled thanks to the carbon free pigments. The packaging is designed as a communication tool: graphics and colours are to attract consumers’ eyes and capture their attention through targeted messages. However, today, the needs of brands in terms of design and image have also to satisfy various sustainability requirements. In the case of cosmetics packaging, where the lifecycle is typically short, it is important to consider how the product will be disposed of after use. An example are black bottles. Eyecatching but difficult to recycle. Why? The carbon black pigments used to give the bottle the dark and full colour, absorb the ultraviolet and infrared spectrum used by near-infrared optical sensors installed in the plastic wastes sorting plants. As a result, the bottle cannot be disposed of in the correct stream. Ho.Bag Corporate, introduced a new black bottle with all the necessary green characteristics thanks to state-of-the-art NIR detectable pigments. www.hobagsrl.com Pigments for NIR detection and automatic sorting Automatic plastic sorting systems in recycling plants work with NIR sensors that do not always correctly identify certain colourants such as conventional silver shades. With NIR Silver, Eckart has developed a pigment solution that is tailored to the needs of automatic sorting. NIR spectroscopy uses the wavelength signature of specific polymers to distinguish between them. NIR Silver optimally reflects these specific wavelengths and thus supports the sorting of plastics. The pigments are claimed to be easy to process in all conventional plastics and provide impressive silver metallic effects. Particularly in combination with post-consumer resins, NIR Silver is intended to offer the packaging industry an opportunity to further strengthen its efforts with regard to sustainability. www.eckart.net MATERIALS / RECYCLING"},{"@ID":53, "47 TRADE SHOW REVIEW PETplanet Insider Vol. 24 No. 01+02/23 www.petpla.net PET recycling system Next Generation Recycling Machines (NGR) company from Feldkirchen in Austria demonstrated its popular “P-React” recycling solution. This PET recycling waste system, which has been operational since 2011 and relies on NGR’s liquid rather than solid state polycondensation, is used by over 50 converters worldwide for various applications such as fibre sheet or bottle-to-bottle applications and has recently been technically upgraded, particularly in terms of energy consumption and footprint. In an original way and with the wink of an eye, the company invited visitors to a press conference held on October 19 to suggest how far P-React’s potential could reach. The management team around CEO Gerhard Ohler, COO and Managing Director Erich Fürst and CTO Günther Klammer showed in a short film presentation how even a distant planet called PETtras-h completely littered with plastic becomes clean again thanks to the company’s own LSP technology. The partly animated film also offered real insights into construction areas and the company’s development, as well as discussing LSP recycling, the various process stages and system technology. “A major advantage of using LSP over conventional SSP in the processing of PET waste is the amount of time saved and resultant savings in costs. SSP processes usually take several hours, while LSP can perform decontamination in minutes”, said Tobias Huber, Head of Marketing, Communications and Public Relations. “By processing the material at the liquid stage, we also ensure that the plastic is upgraded and decontaminated to the highest standards demanded by the brand owners which are proven to exceed regulatory requirements in terms of food safety”. The process removes practically all impurities and hazardous substances contained in PET such as benzenes and bisphenol A. According to the company, the chemically-induced degradation of a material’s properties during PET processing is completely counterbalanced, providing PET converters with pristine quality recyclate. A number of tests conducted by the brand owner confirmed that material properties following completion of the LSP process are even better than those of the input material as required. www.ngr-world.com F.l.t.r.: CEO Gerhard Ohler, CTO Günther Klammer and Head of Marketing Tobias Huber at the press conference Clever use of the melting phase During the K’ show, Gneuss used the opportunity to demonstrate their Omniboost recycling system in their Technical Centre in Westphalia, Germany. On two days, more than 150 guests from all over the world witnessed demonstrations of the new Gneuss Omniboost Recycling System for processing PET industrial fibre waste (POY). This fibre waste had a residual moisture level of 6 % and an intrinsic viscosity of 0.64dl/g. The material was fed into the Omniboost system with at throughput rate of 150kg/h and thanks to the Gneuss liquid melt phase IV booster, the viscosity was increased. The visitors were impressed by the speed of the IV boost: with a residence time within minutes, the IV was increased to 0.66dl/g. For an IV boost to 0.84dl/g a residence time less than half an hour was required. The Omniboost recycling system is designed for recycling both postindustrial and post-consumer PET waste with a low bulk density, such as waste fibres, or thin film. Without the need for any thermal pre-treatment, the material is fed into the Gneuss 3C rotary feeder, which cuts and compacts the material as well as feeding it directly into the MRS extruder screw. The Gneuss MRS extruder is based on the simple and rugged single screw extruder, however it is equipped with a multiple screw section for optimised degassing. The patented multiple screw design from Gneuss has a section of extruder screw (Multi Rotation Section MRS) with a number of satellite screws, which rotate in the opposite direction to the main screw, creating a huge surface area and ensuring an extremely rapid surface area exchange rate. This ensures unparalleled degassing performance in the melt phase, with minimal stress on the material and can decontaminate post-consumer PET to food contact requirements without the need for thermal pre-treatment of the material prior to extrusion. After passing through the extruder, the polymer melt is filtered with the highly efficient Gneuss RSFgenius melt filtration system. This system ensures that even with high contamination loads, fine filtration is possible without pressure or flow disturbances and with minimised polymer loss, said Gneuss. Still in the melt phase, the polymer flows into the Gneuss Jump liquid phase IV booster reactor. The viscosity of the melt is measured both on the inlet and outlet of the reactor. The viscosity is boosted to the required level by regulating the vacuum level, residence time and surface area exchange rate in the reactor vessel. With an assured, constant output viscosity the material can be fed to the production process (for example: fibre spinning, strapping tape) whilst still in the melt phase. By ensuring that the polymer remains in the melt phase from the extruder to the final processing stage, the Omniboost recycling process represents a fast and efficient way to reprocess PET where a viscosity boost is required. www.gneuss.com Omniboost recycling system in operation at Gneuss technical centre in Bad Oeynhausen"},{"@ID":22, "MATERIALS / RECYCLING PETplanet Insider Vol. 24 No. 01+02/23 www.petpla.net 20 Recycling of 4 billion plastic bottles per year Bariq for Techno and Advanced Industries, a subsidiary of Intro Resource Recovery Holding, was the first PET bottle-to-bottle manufacturer in the Middle East and Africa. Founded in 2011, Bariq is an independent Egyptian PET recycler who started production in 2012. Bariq benefitted from Egypt’s FTA (Free Trade Agreement) with EU, US and the COMESA - The Common Market for Eastern and Southern Africa. The company has already recycled 15 billion of 100% locally-sourced plastic bottles which is equivalent to the production of 122,000 t of food grade pellets and 260,000 t of CO2 emissions mitigation. The material is 100% traced and using AI technology the origin of the bottles and the bales can be detected. By 2023, Bariq production output capacity is expected to reach 50,000 t/a of food grade quality PET, which will position the company as one of the largest producers in Africa and the Middle East. With a stellar team of industry veterans and environmental enthusiasts working with state-of-the-art technology, Bariq is currently building the largest recycling factory in Africa with the capacity to recycle 4 billion bottles/a. To herald this expansion, Bariq is hosting new Autosort models from Tomra equipped with flying beam and sharp eye technology, gain, and deep laiser providing the highest safety standards. In addition, Bariq will increase production capacity and efficiency by adapting the robotic arm from Max-AI technology. Moreover, to enhance the quality of the PET flakes, the company is installing a magnetic separation solution from Steinert. This superior fine-polesystem is the Type 6119. Additionally, flakes sorters by Tomra will be installed. They are equipped with a hopper including level sensors combining simultaneous detection of colour, enhanced material and metal using high resolution Near Infrared (NIR). The Bariq leadership team aim to meet the needs of the global players in the packaging industry including major brand owners names such as: Coca-Cola, Nestlé, L’Oréal, Unilever, Henkel, Ikea as well as other significant bottlers. Bariq states to comply 100% with 15 Global Certifications including: USFDA, Efsa, Health Canada, EU CertPlast and EU Reach and registered under Registered under Ecoembes Spain as the only non-European PET recycler. Currently, Bariq is currently studying various growth opportunities in the Middle East and implementation is expected to commence during 2023. Bariq is also expanding its PET recycling to areas in the Middle East, Africa & USA. The company aims to be a significant global player in the waste management industry taking advantage of MRFs, up & down stream integration, waste digitisation, HDPE Recycling as well as chemical recycling. The company is targeting to recycle 50 billion bottles saving 1 million tons of CO2 emissions by 2030. The range was shown to exhibitors at the K’ show. Bariqs products were launched in three new markets and at the Cop27 conference, held recently in Egypt and at the Fifa World Cup. www.bariq-eg.com MATERIALS / RECYCLING"},{"@ID":52, "PETcontents 4 PETplanet Insider Vol. 24 No. 01+02/23 www.petpla.net 1+2/2023 Page 46 MATERIALS / RECYCLING 10 “Our activities are circular and local” - Recycling plastic packaging 12 rPET and preform production under one roof - Investment in state-of-the-art equipment pays off 14 PET raw material and recyclate from India - A conversation with India’s largest private company 16 New site and technology centre for colour and additive development in Singapore 17 South Africa’s plastics production & recycling both growing 18 US PET recycling reaches record levels but more to be done 20 Recycling of 4 billion plastic bottles per year 21 Supporting the chemical dissolution of PET with glycol 22 Mechanically recycled clear rPET - Issues facing the rPET market 25 Prevention of ageing and discolouration of rPET 26 Demand more from PET, less from the planet - Building the circular economy 30 Sustainablility-enabling additives for food and beverage packaging 33 Plasticising in a gentle way - Higher performance without loss of quality 34 From pre-sorting to material analysis MARKET SURVEY 28 Suppliers of resins & additives BOTTLE MAKING 39 Moving into new territory - Polyoak goes big in bottles with Sipa TRADE SHOW REVIEW 40 Market developments in the plastics industry and the NPE 2024 42 Drinktec 2022, review part 3 45 K 2022, review part 2 BUYER’S GUIDE 48 Get listed! INSIDE TRACK 3 Editorial 4 Contents 6 News 36 Products: Materials / Recycling 54 Outer Planet Page 10 Page 43 MATERIALS / RECYCLING"},{"@ID":24, "MATERIALS / RECYCLING PETplanet Insider Vol. 24 No. 01+02/23 www.petpla.net 22 Issues facing the rPET market Mechanically recycled clear rPET Everyone in the industry knows there are complex issues with regards to the availability, affordability and consistency of high quality clear rPET. There are so many factors that play into this that Holland Colours wanted to showcase the different aspects to better understand this problem. Holland Colours interviewed several brand owners, recyclers and other players in the market to get their perspective. While virgin PET is clear, recycled PET comes in a variety of colour shades and corresponding prices. These colour differences are caused by remainders from their previous life influencing the value of the recycled material. The clearer the recycled plastic is, the higher the value and the higher the price – to the point where high quality rPET is often more expensive than virgin PET. The result is that it can make more sense for processors and brand owners to use higher levels of virgin PET simply to remain cost competitive. Costs The reality is that high quality clear rPET is expensive. To fully understand why this is, it’s important to understand some of the underlying mechanics driving up the price. New regulations There are new European regulatory requirements that mandate that as of 2025, PET bottles must contain on average 25% rPET. This means that in the European Union, these new requirements are creating a massive demand for high quality rPET in order for brands to be able to continue to sell in this region. In the Americas similar drivers are arising. Below is an overview of some of the regulations: The EU has mandated the industry to include 25% recycled content in PET bottles by 2025 and 30% in all plastics bottles by 2030 under the Single-Use Plastics (SUP) Directive. Likewise, in the US state of California, manufacturers are required to include an annual average of 15% PCR in beverage containers starting in 2022. By 2025, the mandate is set to increase to 25% and by 2030 to 50%. Washington state has also recently announced a schedule for postconsumer recycled (PCR) requirements for different product categories, starting with beverage containers and trash bags in 2023, adding certain household cleaning and personal care products in 2025, and expanding to dairy milk containers in 2028. (PackForwardLaws and regulations https://packforward.eu/theme/policy-and-strategy/laws-and-regulations) Commitments of global brand owners Holland Colours sees a large push from brand owners who are moving in the direction of rPET independently and setting even higher targets for themselves than the 25% rPET content. So beyond the initial demand, these goals for even higher percentages of rPET are driving up demand even further. It is up to the market to develop suitable solutions the address this increasing demand and avoid transitions to alternative, less desirable packaging materials. “In our interviews with converters, they’ve often stated they they see the colour cast of incoming rPET changing more and more. Moreover, consumer as well as market perception of a changing colour cast of beverage bottles is inevitable. The expectation from brand owners is that in time the colour-cast will be associated with sustainability. However, we’re not there yet.” Mark, Kalisvaart, Global Product Market Manager Additives, Holland Colours MATERIALS / RECYCLING"},{"@ID":9, "7 NEWS PETplanet Insider Vol. 24 No. 01+02/23 www.petpla.net ClipAside, drink, love! Tethered ClipAside closure wins high acceptance Contact us and arrange your line trials now! www.bericap.com PET 38 PET 29/25 PCO 1881 PET 33 PET 26 PET 26 GME 30.40 A recent consumer real-life “diary study” conducted in France found a high level of acceptance among consumers for the innovative new closure. After just one or two experiences, even the youngest and oldest users could handle the smart closure without difficulty – often with one hand. What’s more, many praised the eco-friendly nature of the cap, which remains on the bottle neck and avoids creating additional plastic waste. Best of all for you, this premium product can be integrated into most lines and any popular bottle neck format without major modification of your production equipment. Get to knowour complete ClipAside range at Interpack 2023!"},{"@ID":40, "38 PRODUCTS PETplanet Insider Vol. 24 No. 01+02/23 www.petpla.net Stadler designs and installs light packaging sorting plant for TBM in Yokosuka, Japan TBM is a Japanese company specialised in the development of environmentally friendly materials and resource recycling models. Its flagship product is the material Limex, a limestonebased material claimed to be an alternative to plastic and paper that can be used in the production of a wide variety of products. Once used, it can be recycled to produce new plastic alternative materials. These characteristics have earned Limex the Asia-Pacific Stevie Award 2017 in the category of Innovation in Energy & Sustainability. As part of its strategy to accelerate the use of Limex products and reduce consumption of natural resources, TBM commissioned Stadler to design and install a new state-of-theart sorting plant. The facility uses the latest technologies to separate Limex and plastic light packaging, which is recycled into pellets for use in the production of packaging. The plant is part of a collaboration between TBM and the city of Yokosuka to promote the collection and recycling of plastic waste and Limex for the entire city and surrounding areas. The sorting plant receives bales of light packaging made of plastic materials and Limex, and sorts them into metals, PET, PP, PE, PS, and mixed plastics for RDF, a 2D fraction and fines. The sorted output materials are stored in bunkers, and the 3D PET, PP, PE, PS, and mixed plastics for RDF are subsequently fed to a baling press. The plant uses the latest technologies to achieve the high quality required to recycle the output products. These include Stadler’s double-deck ballistic separator, 2.9m wide high-speed conveyors and bunker system, as well as five Near-Infrared (NIR) automated optical sorters. Due to the particular characteristics of the sorted materials and the space limitations in the building housing the plant, the project required some innovative thinking. “The plastic material we are processing at the plant is extremely light,” explains Ursina Mutzner, International Sales at Stadler. “When we ran trials with similar materials at our Test Centre in Germany, we saw that the paddles in the double deck ballistic separator needed to be inclined more than the maximum 25 degrees the machine is designed for. So, when we designed the plant, we decided to place the ballistic separator on a slightly sloping steel structure in order to achieve the inclination of the paddles required to ensure the best sorting quality.” Takuya Sugiyama, Division Head, Recycling Plant Business, TBM, adds: “The plant roof is quite low, so there wasn’t much space between the ballistic separator and the ceiling. At first, we thought we might have to remove part of the roof to place the machine, but Stadler’s commissioning team made the installation without any additional work.” www.w-stadler.de - Efficient and Smart - Small Area Requirement Highly Modularized Super Washing Performances High-Quality rPET Flakes \t \n \r MATERIALS / RECYCLING"},{"@ID":37, "MATERIALS / RECYCLING PETplanet Insider Vol. 24 No. 01+02/23 www.petpla.net 35 Futurapet thus achieves minimum material loss at high throughput rates. Fine sorting of PET flakes After pre-sorting, the clear PET bottles are shredded. Washing, drying, and air separation processes follow. Finally, fine sorting of the flakes is carried out by the Sesotec Flake Purifier+ sorting systems, which are equipped with three sensors. False colours, false polymer types, and metal contaminants are reliably and precisely separated from the PET flakes. An additional sorting track enables further purification of the rejected material, allowing the maximum amount of high-quality PET to be recovered. Material analysis system Futurapet is committed to ensuring that only high quality rPET leaves the plant. Each BigBag content is checked in the in-house laboratory by random sample analysis. For this purpose, Futurapet uses the Flake Scan material analysis system from Sesotec. It enables efficient and precise quality analysis of the plastic flakes and quickly delivers reliable and reproducible results of the material sample, says Sesotec. This means that a decision on the usability of the material can be made within a very short time. The integrated sensors analyse material samples according to plastic types, colours and metal contaminants. www.sesotec.com Efficient fine sorting of PET flakes by Flake Purifier+ www.prseventeurope.com Platinum Sponsor Silver Sponsors Organised by PRSE 2023 will feature: TWO halls | TWO conference theatres NEW Chemical Recycling feature Plastics Recycling Awards Europe 2023 Over 275 exhibitors Register for your FREE visitor entry badge at www.prseventeurope.com"},{"@ID":17, "MATERIALS / RECYCLING PETplanet Insider Vol. 24 No. 01+02/23 www.petpla.net 15 MATERIALS / RECYCLING 15 Maharashtra,” says Mr Mehta. “With bottle recycling start-ups in Hoshiapur in Punjab and Barabanki in Uttar Pradesh in early 2000s, we began to produce synthetic fibres from postconsumer PET bottles. In each of these two locations, bottle bales are recycled into flakes and then into polyester staple fibre (PSF). The capacity is 50 kt and we plan to expand to 80 kt. The plant in Nagothane, Maharashtra, has been producing rPET resin since 2010.” Currently, it is producing 6 kt/a there, but expansion plans in rPET envisage an increase to 35 kt by 2025. This is a logical step, especially against the background of the draft “Food Safety and Standards Packaging (Amendment) Regulations” issued by the Food Safety and Standards Authority of India (FSSAI) in June 2022. After years of discussion, the draft provides for approval of recycled PET in food contact and is currently being reviewed by The Bureau of Indian Standards. Industry experts expect the finalisation of rPET standards in 2023. India is one of the countries with the highest PET recycling rate. Around 90% collection rate of the aforementioned 1.2 million tonnes of bottles can be recorded in the market. A large part of the bottles is collected by an unorganised sector of waste collectors and taken to collection points and then to recyclers, for which they receive 15-20 rupees per kg of material and often earn their living with it. By means of manual sorting, the bottles are then separated according to colour and foreign materials are removed. Industry is transforming in India as more and more companies and small businesses are coming forward in PET bottle collection business, resulting in reduced share of unorganised sector. “This is also an important part of the much-discussed EPR,” says Mr Rakesh Bali. “Brand owners could hire or at least pay the waste pickers in the long run. EPR also plays a pivotal role for us as a producer. The industry provides direct and indirect employment to over 400,000 people. We are providing technological know-how and guidance to encourage more entrepreneurs to come forward to become part of the industry. www.ril.com (MKMXEP VEXMSREP TVSƤXEFPI ;LEX IPWI# SACMI.COM 300 4VIJSVQ MRWTIGXMSR ERH TVSGIWW IRLERGIQIRX MRGPYHIH DIGITAL (MKMXEP TVSGIWW GSRXVSP VIEGLIW TVIZMSYWP] YRXLMROEFPI PIZIPW STIRMRK YT XLI MRHYWXV] XS -S8 WGIREVMSW RATIONAL 7%'1- 4VIJSVQ :MWMSR 7]WXIQ MRGPYHIH JSV EHZERGIH GSQTVILIRWMZI TVSGIWW GSRXVSP PROFITABLE '330 TSWX GSSPMRK MRWMHI GSSPMRK W]WXIQ\r WLSVXIRW G]GPI XMQIW ERH PIEHW XS QSVI TVSƤXEFPI TVSHYGXMSR momic"},{"@ID":50, "MATERIALS / RECYCLING PETplanet Insider Vol. 24 No. 01+02/23 www.petpla.net 13 MATERIALS / RECYCLING 13 Polycondensation (SSP) technology that guarantees industrial security at all stages of the thermal process and eliminates all remaining impurities on a molecular scale. SGR also has an extruding machine with underwater cutting and an ultra-efficient decontamination system that produces rPET pellets whose visible qualities (transparency and colour), mechanical qualities (viscosity) and organoleptic qualities match those of virgin PET. The whole process requires little consumption of energy. During extrusion, the decontamination reactor makes the PET suitable for food contact. It allows the flakes to melt, to filter them (at 36μm) before leaving them in the form of granules. Our extruder is equipped with an underwater cutting allowing direct crystallisation of the granule. The flow rate of our equipment is 1,500kg/h. The decontamination process takes part on a molecular scale. At this stage, the viscosity index (IV) of the granules obtained is similar to virgin PET. Nitrogen vacuum depression is at 200mbar, the temperature is 200 °C. The residence time of PET granules is about 10 hours. SGR has invested 8 million euros in its decontamination line,” Anthony proudly announced. While walking back we passed the preform production area again. Fabien Tabart, SGT Production Workshop Manager explained us some hard facts on SGT and SGR: “With a workforce of 170 employees in Rezé and 50 employees in Chalon-SurSaône and finally SGT Algeria with 330 employees, we have an overall turnover of €152.7 million for SGT France, €136 million for SGT Algeria and €12 million for SGR. With growth of 5% in each plant, we export about 25% of our production. SGT offers a broad range of more than 270 customisable preforms (from 100ml to 20 l) and seven types of caps and handle in high-density polyethylene (HDPE). The SGT group’s annual production capacity totals 7 billion preforms and 2.8 billion caps. The bestselling preform is the one for the 1.5 l water bottle. 80% of our preform production is sold to the food and beverage (50% water, 25% CSD, dairy drinks 8%, juices 5%) and 20% to the non-food market. We expect the African continent, with its growing population, to achieve significant growth rates in the coming years.” After the factory tour and some interesting conversation, we ask Jean Marc Wiencek for a final statement on the current situation: “Between logistical difficulties, geopolitical instability (Ukraine), the health crisis, plastic bashing and now the energy crisis, we have to face every adversity. The yesterday’s certainties are now replaced by caution. Despite everything, if we had to stay positive, I would say that we are learning to live in an uncertain and increasingly risky environment. That is what we call resilience.” We thank our hosts and climb into the cab of our Editour truck - our journey continues, because communication and information exchange are an important means to overcome any crisis! www.sgt-pet.com"}]}}
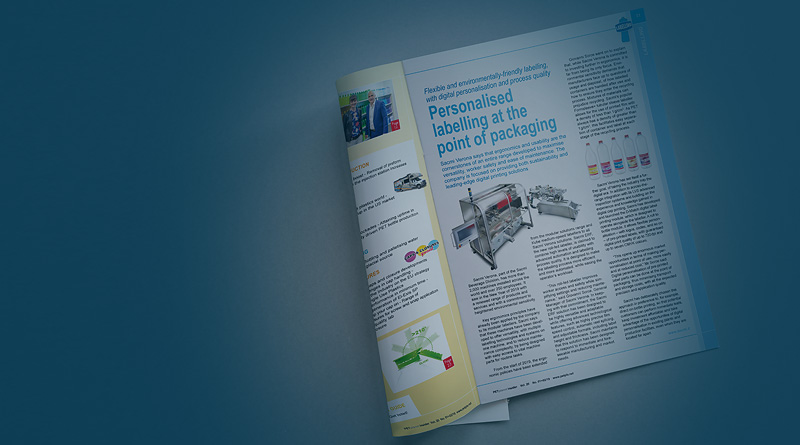