"MATERIAL / RECYCLING 10 PETplanet insider Vol. 17 No. 03/16 petpla.net Polymetrix EcoSphere technology Energy and yield optimised Polymetrix’ EcoSphere technology brings to the market the very latest technological developments in bottle grade virgin PET production. EcoSphere technology answers the rising demand for energy-saving along with process reliability and increased yield, while maintaining polymer quality. Among the key features of EcoSphere is the link between melt phase and solid phase polymerisation, which allows the recovery of energy from the melt phase for reduced energy consumption but still leaves the option for independent operation. The low transition viscosity from the melt phase to the solid phase is said to assure maximum quality of the final PET. Polymetrix asserts that the technology enables improved economies of scale, with a capacity of circa 1mio./t in one installation. At first glance, the EcoSphere Technology appears to be simply the link from the continuous melt phase polymerisation (CP) to solid state polymerisation (SSP) but without intermediate storage of amorphous PET pellets. This allows heat to be recovered from the PET melt for the crystallisation step. (Fig.1) Polymetrix says that closer examination will show that the technology offers users opportunities for improvements in process reliability, energy efficiency, plant layout and capacity, as well as product quality. The EcoSphere system comprises one or multiple underwater pelletising lines feeding an actively heated crystalliser. The main equipment for solid state polymerisation (SSP) is similar to conventional nitrogen SSP but with the difference that crystallisation is smaller, a deduster is added and, for preference, with gas cleaning by an EG scrubber column. Nitrogen crystallisation is also an option. (Fig.2) Conventional SSP in traditional, or established systems, typically uses PET with a relatively low starting IV and is more or less independent from the CP plant, which means that energy recovery from the melt is impossible. While energy recovery technology was developed in the 1960s for a wide range of starting IVs, it was commercialised in large scale only for direct melt processes, which make the transition from the melt to the solid phase treatment at a relatively high starting IV. This left customers with a dilemma: they could opt for energy savings or elect for the quality advantages of the lower starting IV – but not both. Fig.3: Energy costs and quality comparison Fig.1: Process flow conventional CP/SSP and EcoSphere technology Fig.2: Process flow detail EcoSphere technology","@ID":12}, "INSPECTION 24 PETplanet insider Vol. 17 No. 03/16 petpla.net Tour Sponsors: Detecting and eliminating faults MHI instead of HMI by Waldemar Schmitke I NSPECT I ON S P E C I A L February 26, 2015 We met: Carl J. Bonnan, General Manager, Heuft USA We are visiting Heuft USA, Inc., in Downers Grove, Illinois, a subsidiary of Heuft Systemtechnik Germany, where we meet General Manager Carl J. Bonnan. Heuft Systemtechnik GmbH is a private company with headquarters in Burgbrohl, Germany, which develops and builds inspection systems for use in Quality Assurance in beverages, food and pharma-oriented production applications. Here quality control and inspection activities relate to the product and its packaging. Alongside the automated solutions for the quality inspection of empty as well as filled containers, the company’s product portfolio also comprises high performance labelling machines, transport, sorting and discharge systems offering gentle container handling, together with modifications aimed at increasing line efficiency. Also used are image processing methods for empty bottle inspection, x-ray systems for inspecting filled products, labelling technology and tools for transport optimisation and line analysis. The company, established in 1979, employs approximately 700 people in Germany (figures for 2014), 20% of whom work in the R&D sector. Production and R&D activities are handled exclusively in Germany. Sales and Service are distributed worldwide on a decentralised basis, encompassing 14 companies abroad as well as agencies. Altogether Heuft employs more than 1,000 people worldwide. Heuft USA The USA branch here in Downers Grove is responsible for Sales and Service in the USA. According to Carl J. Bonnan, who has been here since the branch was established in 1988, a number of employees work here in Downers Grove permanently whilst others are spread across the State. “Our market was initially made up chiefly of high speed inspection lines for soft drinks and beer. Today we are able to look back on having achieved a significant expansion of our field of business to incorporate inline inspection systems for beverages, food, household, personal care and pharmaceuticals products.” Future plans include a considerable expansion of the markets in North America for non-beverage applications. As regards the packaging mix (glass, cans and other plastics), PET has a share of approximately 50%, primarily in the beverages sector. However, according to Carl J., there is a trend among the craft brewers to drop glass bottles in favour of cans as they grow. The proportion in Canada is already 50%. In the PET sector, Heuft inline inspection systems are predominantly used in conjunction with the blow moulding and filling lines. Based on performance and inspection criteria, the modules are selected and assembled from the plethora of inspection machines featured in the range. The biggest line in the USA has a capacity of 150,000 cans per hour. Quality assurance and inspection in the PET sector Empty bottles or containers Base and outlet inspection Container dimensions Thread inspection Identification of pollution or damage Identification of inclusions (e.g. black spot) Colour tinting Carl J. Bonnan, General Manager, against the background of a PET bottle inspection machine in the showroom at Downers Grove, Illinois.","@ID":26}, "MARKET SURVEY 35 PETplanet insider Vol. 17 No. 03/16 petpla.net Sipa Via Caduti del Lavoro n. 3 31029 Vittorio Veneto (TV) Italy +39 0438 911511 www.sipa.it Mr Matteo Tagliaferri Marketing and Communication +39 0521 548111 matteo.tagliaferri@zoppas.com Highly Hygienic Filler (H2F) Rotary Weigh Filler (R) Isofill P StillFill S StillFill R\\HR Flextronic C Flextronic SE Flextronic S Flextronic W BigFill 6-90 4- 90 20-160 20-120 20-120 50-160 20-160 20-160 20-80 60ml - 2l 50ml - 20l 0,125ml-3l 0,125ml-3l 0,125ml-3l 0,125ml-3l 0,125ml-3l 0,125ml-3l 0,125ml - 3l 3l - 12l Up to 48,000 Up to 48,000 60,000 62,000 60,000 62,000 63,000 25,000 16,000 (3l) 51,000 55,000 (CMW) Up to 48,000 Up to 48,000 (+1l pasteurised milk) 62,000 62,000 25,000 Up to 48,000 Up to 48,000 (+1l fresh fruit juice) 53,000 62,000 55,000 59,000 62,000 62,000 25,000 Electronic net weigh filling Electronic net weigh filling Yes Yes Yes Yes Yes Yes Yes Yes Yes Yes Electronic net weigh filling Electronic net weigh filling Yes Yes Yes Electronic net weigh filling Electronic net weigh filling Electronic net weigh filling Electronic net weigh filling Yes Yes Yes Electronic net weigh filling, Multiflow (patented) magnetic valves with flow monitoring Electronic net weigh filling, pneumatic valves isobaric mechanical level filling mechanical gravity filling mechanical gravity filling walve with recirculation isobaric volumetric filling valve gravity volumetric filling valve gravity volumetric filling valve electronic weight filler gravity volumetric filling valve Krones AG KHS GmbH Böhmerwaldstr. 5 93073 Neutraubling, Germany +49 9401 70 0 www.krones.com Mr Stefan Kraus Product Manager Filling Division +49 9401 3144 +49 9401 3056 stefan.kraus@krones.com Juchostr. 20 44143 Dortmund, Germany +49 231 569 0 www.khs.com Modulfill InnoPET Blofill 16 - 216 50 - 216 0,2ml - 5l 12,000 - 81,000 Up to 72,000 81,000 Up to 65,000 80,000 Up to 60,000 Up to 60,000 60,000 Volumetric filling system; net weight filling system; height filling system Contactless filling; contactless filling; short tube or long tube NV filling system, free-flow, contact free Volumetric filling system; net weight filling system; height filling system Contactless filling; contactless filling; short tube or long tube filling system DRV filling system, short tube volumetric Volumetric filling system; net weight filling system; height filling system Contactless filling; contactless filling; short tube or long tube NV filling system, free-flow, contact free PETAsept L / PETAsept D / ContiformAseptBloc Contactless filling systems; dry preform sterilisation only Ultra-Clean-filling Height filling system; pre-dosing system Long tube; full bore filling / contactless / for pulp, fibres or fruit pieces NV-HF filling system, free-flow, contact free Volumetric filling system; net weight filling system; height filling system Magnetic flow meter; weighing cell; electronic fill height measuring Inductive Flow Meter (IDM), mechanical flow meter","@ID":37}, "MARKET SURVEY 34 PETplanet insider Vol. 17 No. 03/16 petpla.net 03/2016 MARKETsurvey Company name Fogg Filler SMI S.p.A. Serac group Postal address Telephone number Web site address Contact name Function Direct telephone number Fax E-Mail 3455 John F. Donelly Drive Holland, MI 49424, USA +1 616 786 9644 www.foggfiller.com Ms Susan Lamar Media Relations Manager +1 616 786 3644 +1 616 786 0350 Via Carlo Ceresa, 10 24015 San Giovanni Bianco, Italy +39 0345 40111 www.smigroup.it Mr Pietro Volpi Marketing Dept. Manager +39 0345 40316 +39 0345 40209 pietro.volpi@smigroup.net 12, route de Mamers, BP 46 72402 La Ferté Bernard Cedex, France +33 2 4360 28 28 www.serac-group.com Mr Roland Nicolas Dairy & Aseptic Business Development Director +33 2 43 60 28 32 +33 2 43 60 28 37 ronicolas@serac.fr 1. Machine designation / model number F Series Ecobloc and Ecobloc Ergon compact systems of blowing, filling & capping Serac Aseptic System 4 (SAS 4) Serac Aseptic System (SAS PL) 2. Number of filling heads (range: from/to) Up to 100 Electronic volumetric fillers (18 - 126) 8 - 90 1 - 2 3. Min to max bottle contents (in liters) 50ml - 5l 0.25 - 10l 50ml - 2l 50ml - 2l 4. Filling speed: output (bph) (min to max): 4,800 - 36,000 6,000 - 48,000 Up to 1,200 specifiy: 1l bottle / still water (bph) Up 60,000bph 4,800 - 36,000 1l bottle / CSD (bph) Up 60,000bph 4,800 - 36,000 1l bottle / Milk (bph) Up 60,000bph 4,800 - 36,000 6,000 - 48,000 Up to 1,200 1l bottle / Juice (bph) Up 60,000bph 4,800 - 36,000 6,000 - 48,000 Up to 1,200 5. Filling process Pressureless (still drinks) Gravity fill Yes Electronic net weigh filling Mass flow meter fill Pressure filling (carbonated drinks) Yes Hot filling Gravity fill No Electronic net weigh filling Cold aseptic filling Cold fill - gravity fill No Electronic net weigh filling Mass flow meter fill Juices with high pulp content Gravity fill No Electronic net weigh filling Mass flow meter fill 6. Type of filling valve and metering system No metering system - gravity filling vales (fill to a level) Electronic volumetric filling valves, Flowmeters (metering system) Electronic net weigh filling, Multiflow (patented) magnetic valves with flow monitoring, pressure filler tank sterilisable Magnetic valves and flow meter Company name Sidel International AG Sacmi Filling S.p.A Postal address Telephone number Web site address Contact name Function Direct telephone number Fax E-Mail Bösch 67, PO Box 6331 Hünenberg, Switzerland +41 41 785 23 60 www.sidel.com Mr Stefano Baini Filling Product Manager stefano.baini@sidel.com info@sacmifilling.it +39 0521 695411 www.sacmifilling.it Mr Iacopo Bianconcini Area & Marketing Manager +39 0542 607 111 +39 0542 64 2354 sacmi@sacmi.it 1. Machine designation / model number Sidel Matrix SF 300 FM Sidel Matrix SF 100 FM Sidel Matrix SF 700 FM Sensofill FMa AWS, AWF, AWE, AWG, AHF, AHG, VSF, VSG, EWS, EWF, EWE, EHF, EHC, ESF, ELF, ELG, ELT, ECF 2. Number of filling heads (range: from/to) 32-216 24-120 32-108 27-100 8 - 216 filling valves 3. Min to max bottle contents (in liters) 0,2-3,0 0,2-3,0 0,2-2,0 0,2-2,0 0,15ml-12l 4. Filling speed: output (bph) (min to max): 4,000-81,000 (18°C) 5,000-81,000 6,000-60,000 6,000-60,000 250ml - 750ml: speed 36,000 specifiy: 1l bottle / still water (bph) 80,000 70,000 5,000 - 75,000 1l bottle / CSD (bph) 68,000 (18°C) 5,000 - 75,000 1l bottle / Milk (bph) 48,000 4,000 - 60,000 1l bottle / Juice (bph) 48,000 48,000 4,000 - 60,000 5. Filling process Pressureless (still drinks) Yes Yes Yes Yes Pressure filling (carbonated drinks) Yes Yes Hot filling Yes Yes Cold aseptic filling Yes Juices with high pulp content Yes Yes Yes Yes Yes 6. Type of filling valve and metering system Electropneumatic volumetric filler with flowmeter volume control Electropneumatic volumetric filler with flowmeter volume control, with no bottle/valve contact Electronic volumetric filler, with electropneumatic system with magnetic flowmeter volume control, with no bottle/valve contact Electronic volumetric filler Isobarometric with vent tube, magnetic flow meters, mass flowmeters, volumetric long tube, strain gauges, level probes, magnetic flowmeters & time","@ID":36}, "TRADE SHOW PREVIEW 44 PETplanet insider Vol. 17 No. 03/16 petpla.net Chinaplas 2016 Chinaplas 2016, the 30th international exhibition dedicated to the plastics and rubber industries, will be held on April 25-28 at the Shanghai New International Expo Center, PR China. It is expected that some 140,000 professional buyers from 150 countries and regions will visit this year’s show. In response to the high demand for plastic waste management, this year’s trade show will unveil a new “Recycling Technology Zone”, gathering over 20 leading exhibitors offering solutions for the recycling chain. In total, the show will see over 150 exhibitors featuring recycling technologies, covering the entire recycling process from sorting, shredding and cleaning, to dewatering, drying and pelletising. In addition, the trade show will amongst others focus on green, functional and intelligent packaging solutions. Contamination prevention, conforming to the shelf life and preservation of the quality of the goods as basic requirements will be spotlighted. The choice of materials and manufacturing technology of packaging is crucial to its safety requirements in an ever-changing world of markets and needs. Questions to be examined are: What technology or equipment boosts productivity and reduces energy consumption? How can packaging become diversified and multifunctional? With the latest plastic packaging solutions available out there, Chinaplas will focus on industry safety, environmental protection, efficiency, lightweightness, multi-functionalities and intelligentisation to promote the continuous and innovative development of the packaging industry. The show also intends to emphasise new developments in in-mould labelling with its potentials to improve the appearance of product packaging, anti-forgery functions and degree of automation. www.ChinaplasOnline.com PiovanHall E2 - Booth G51 Customised granulators Piovan has introduced a new range of small, medium and large granulators which are all fitted with a tangential cutting system. The rotary blades are inclined with respect to the fixed blades and are positioned as close as possible to the geometric tangent of the cutting circle, therefore optimising and improving cutting precision. In this way, high production capacities are achieved using smaller motors, with the additional benefit of minimising dust production and heat generation. These features are said to ensure a more regular cut and more dimensionally consistent regrind. The cutting chamber is made from machined pieces, which are assembled rather than being cast or welded. According to the company, this design has enabled the construction of high-precision components that improve the efficiency of the cut and the quality of the ground product, while improving the life of the granulator, as worn pieces can be replaced. Another distinctive feature is that even the most basic versions can be modified to suit the specific needs of the process (e.g. blow moulding, extrusion, injection) and to comply with specific customer requests in terms of space, granulator loading and unloading requirements and protection of the operating environment. Complementing the range of granulators is the single-shaft shredder line, intended for recovering purgings from start-ups or material replacements during all transformation processes. The Piovan range of single-shaft shredders includes four different models, each with a hopper that can vary in size from 600x600mm to 1,500x1,500mm. www.piovan.com Granulator featuring a 90° adjustable hopper for four loading positions","@ID":46}, "TRADE SHOW PREVIEW 47 PETplanet insider Vol. 17 No. 03/16 petpla.net Otto Hofstetter Hall E5 - Booth T51 Injection moulds and services Otto Hofstetter AG will be presenting their complete company portfolio and services. Beginning with an initial concept, followed by design consultancy, Otto Hofstetter aims to provide a complete customer service right up to the final product. Once an injection mould is built, the company’s after sales service completes the package with their expertise. In addition to this presentation, the company will also be displaying PET preform moulds (2 up to 192 cavities) as well as solutions for thin-walled packaging and inmould labelling (IML) systems. www.otto-hofstetter.ch 128cav injection mould","@ID":49}, "NEWS 9 PETplanet insider Vol. 17 No. 03/16 petpla.net First birthday for Krones’ Training and Customer Center South America In March 2015, Krones unveiled to its clients in South America its new Training and Customer Center at the company’s LCS Center in São Paulo/Brazil. This year, this facility is celebrating one year in operation. “In the new premises, we are able to simulate process sequences, and hold training events plus product presentations matched to our clients’ own machines and lines”, says Jens Hoyer, who heads the LCS Center in Brazil. Whereas previously only a few courses could be held in São Paulo, the new centre now regularly hosts courses for electricians and training events on many different Krones machines, like fillers, inspectors and labellers. Besides conference rooms and lounges, the centre also provides some smaller training rooms, for courses in subjects like automation, for example, and on blow-moulding stations and filling simulators, which constitute extremely important training instruments. With the aid of simulators, the instructors can teach the participants how to recognise problems at an early stage, and thus avoid possible downtimes in operation, by assuring a trouble-free production run. The clients as well as service technicians and staff of Krones’ subsidiaries in South America shall benefit from the facility. Firstly, they have an opportunity to upgrade their skills and capabilities, and secondly, they can also prepare themselves to handle the specific lines and machines up and running in this region. www.krones.com Engel: Dr Stefan Engleder new chairman of executive board Effective November 30th 2016, Peter Neumann, long-term chairman of the executive board of the Engel Group of Companies, withdraws from operational business after 35 years. “This step has been long planned on the occasion of my 60th birthday and is the result of a clear mutual agreement between myself and the owning families of the Engel Group of Companies”, explains Neumann the background for this change. Indeed, the generation change within the family-run business had been initiated several years ago by introducing the fourth generation of members of the owning family step by step into the executive board. Dr Stefan Engleder has been responsible for R&D, engineering and production for more than three years and Dr Christoph Steger for Sales and Marketing for more than two years. Now, the final step will be set by Dr Stefan Engleder, great-grand-son of Engel’s founder Ludwig Engel, taking over the position as chairman of the executive board effective December 1st, 2016. The executive board will continue to consist of four persons: besides Dr Stefan Engleder as new Chairman also responsible for R&D, the board will be constituted of Dr Christoph Steger (also a family member and responsible for Sales, Marketing und in future CSD), Dipl.- Oec. Klaus Siegmund (responsible for Finance, Personnel and IT) as well as DI Joachim Metzmacher (so far division manager production large-tonnage machines) for Global Production. www.engelglobal.com Future-oriented packaging systems Shorter changeover times, lower energy costs and use of fewer resources: at the in-house KHS exhibition at the production site in Kleve, Germany, the company’s product innovations and further developments met with great interest. Under the motto of “Less is more” the systems provider presented its approach to greater economy and sustainability in the packaging process. One of the concepts to attract considerable attention was Nature MultiPack powered by KHS, a PET or can pack which needs almost no packaging materials. Business on the Lower Rhine has developed positively over the past few years that KHS plans to invest in the Kleve site in 2016. “The great response to our plant engineering shows that we are able to recognise market demands early on and develop systems accordingly,” says Norbert Pastoors, Head of Packaging Products Division. “We not only offer bottlers innovative and sustainable secondary packaging systems; the retail trade also benefits from the customer-friendly presentation of goods enabled by our developments.” The interest in KHS’ new or further developed machinery at the in-house exhibition staged at the KHS production site in Kleve was therefore considerable. Customers from various branches of industry, such as the food and beverage sectors, expressed great curiosity in the diverse ways of saving packaging materials. www.khs.com","@ID":11}, "BOTTLES 59 PETplanet insider Vol. 17 No. 03/16 petpla.net Refill for scented oil The Parisian firm Lampe Berger works in the area of room air improvement and has, in its “Ambiances Berger” range, been selling several dispensers which continually release scents via scent sticks which are placed in a container with scented oil. A transparent PET bottle containing 180ml is used for refilling. The slightly flammable product is protected against unauthorised and accidental opening by a safety cap. The self-adhesive labels contain information on the product and safety advice. www.lampeberger.ch Hand soap from method The Ecover-owned brand “method”, which is characterised in particular for recycling materials, natural ingredients and sustainable management, distributes its plant-based “waterfall” hand soap in a teardrop-shaped transparent PET dispenser. The stable bottle contains 354ml of the greenish-blue shimmering gel-type soap, which comes out via the screw-on pump dispenser. The product and trade information are printed direct onto the container and an embossed brand logo on the front rounds off the product image. www.methodhome.de info@hasplastik.com Tel: +90 212 695 50 00 Fax: +90 212 694 97 24 100815dmyR .com","@ID":61}, "TRADE SHOW PREVIEW 51 PETplanet insider Vol. 17 No. 03/16 petpla.net Starlinger Hall W1 Booth B41 High-tenacity polyester fibre recycling Meeting a growing demand Based on an article by Elfriede Hell, General Manager Starlinger recycling technology rPET produced both from fibre/fabric scrap and post-consumer PET bottle collection is currently being used at a rate of 14,4% in polyester fibre production, mostly for polyester staple fibre. China is by far the greatest user of rPET in fibres, processing almost 80% of the 7 million tons produced worldwide in 2015. This is why Starlinger will be spotlighting polyester fibre recycling as one of its highlights at Chinaplas. High-tenacity polyester fibres feature low water absorption and minimal shrinkage in comparison to other industrial fibres. They are used for threads and ropes, safety belts, etc. Tenacity is the general measure of the specific strength of a fibre or yarn, also called strength-to-weight ratio. The challenges in recycling include different levels of humidity and that the material comes in bales, lumps or fabric. Due to the high strength of the material it is very tough and requires shredding in a single-shaft cutter. In addition, requirements for colour values allow no oxidative or thermal degradation. The reuse rate lies usually around up to 30%, in the same application it can reach up to 100%. Selecting the correct recycling equipment The input material and intended use of the regranulate are important factors for choosing the right recycling equipment. High-tenacity PES fibre recycling applications demand special machine features such as pre-shredding, drying before extrusion, high-vacuum degassing and fine melt filtration. Also, solid stating for IV increase in the produced pellets may be necessary to achieve the characteristics required for reuse. Starlinger’s recycling lines for PES fibre recycling – the recoStar dynamic and recoStar universal recycling lines – have been installed for a number of high-tenacity fibre recycling applications worldwide. In the Smart feeder, a rotating disc at the bottom cuts the input material and creates friction. This frictional process heats and dries the mixed material, densifies it and brings it close to the melting point before it is fed into the extruder. Six extruder sizes from 150 – 2,600kg/h (output with degassing) are available. The recoStar universal recycling line is suited for processing hard-to-grind materials such as bales, fibres, fabrics and start-up lumps. In the Active shredder arranged parallel to the extruder a hydraulic pusher presses the material against a water-cooled rotating shaft and thus provides efficient crushing. In combination with the software and the dosing screw, this kind of material preparation allows the processing of materials with different bulk densities without having to change process parameters. Five extruder sizes from 150-1,300kg/h (output with degassing) are available. It is claimed that both lines feature high-vacuum degassing for PES recycling to ensure the effective removal of volatile contaminants such as additives and finishing agents. Concerning filtration, reuse and the required filtration fineness at the production line are determining factors; standard filter fineness is 50μm, fine filtration (25μm) with cascade filter system is also possible. The type of pelletiser is mostly a question of which pellets shape of the rPET is preferred – both (automatic) strand pelletising or underwater pelletising are possible. Special features are inline viscosity and colour measurement. Optionally, crystallisation and solidstating of PET pellets and flakes can be included. www.recycling.starlinger.com PES yarn bobbins Starlinger’s recoStar dynamic recycling line for fibre and fabric scrap with increased humidity","@ID":53}, "ON SITE 55 PETplanet insider Vol. 17 No. 03/16 petpla.net ONsite Iranian Khosh Form invests in Sipa IM systems Iran’s largest producers of PET preforms Khosh Form invested in Sipa’s XForm 500 injection moulding systems. Khosh Form, which has operations in the cities of Mashhad (Khosh Form Toos) and Qazvin (Khosh Form Caspian), has, in addition to ten different Husky machines, seven XForm 500 preform injection moulding systems at both locations, all of them running with 96-cavity moulds. The XForm 500 systems produce preforms for carbonated soft drinks, 38mm-neck dairy products and for mineral water bottles; the XForm 500 also has the capability to run legacy tooling. Khosh Form has enjoyed a steep growth path since it started making PET preforms in 2003. Both of its sites have benefitted from surging demand for drinks bottled in PET, both at home and in neighbouring countries. It has connections to numerous major international brand owners. The company makes preforms weighing as little as 10.4g and as much as 54.75g, for bottles ranging in size from 300 to 2,500ml. Khosh Form has only recently turned to Sipa after carrying out a technical survey, and appreciates the XForm 500 injection moulding system as a solid tool with a robust design and construction. According to Sipa, the efficiency appears especially for the sorts of preforms used for CSD bottles, which have thicker walls than some other types, thanks in part to their multi-stage cooling robots. Sipa has also the advantage of being able to provide local service from technicians close by - another important selection criterion for Khosh Form. www.sipa.it Want the secret to bottle light weighting? Process Pilot® automated blowmolder control system takes the guesswork out of material distribution management and can help ensure the success of even the most aggressive light weighting program. Featuring 24/7 blowmolder control, the Process Pilot system continuously maintains proper material distribution, on every bottle, to an unmatched level of accuracy. With the Process Pilot system, you have the means to push light weighting to the limit without sacrificing bottle quality or performance. Not convinced? Talk to one of our specialists today to schedule a free seminar and evaluation of the Process Pilot system on one of your blowmolding lines. Web: agrintl.com Tel: +1.724.482.2163 E-mail: sales@agrintl.com F.l.t.r.: Dr Hajrezapour, owner of Kosh Form and Stefano Baldassar, Sales Manager at Sipa","@ID":57}, "BOTTLE MAKING 14 PETplanet insider Vol. 17 No. 03/16 petpla.net From an Andalusian garage to a global player by Kay Barton We met: Mr Antonio Ortega Ruiz, General Director Mrs Caridad Ortega Suárez, Sales Engineer Mr Antonio Ortega Suárez, Sales Director Mr Juan Pablo Ortega Suárez, Production Manager Spanish family business And & Or has, from its foundation 30 years ago, been totally focused on the development and manufacture of blow moulding and bottling machinery for the packaging industry. It has grown from a “one-man band” operating out of a garage in Andalusia, in southern Spain, to become a worldwide operation, with a number of global brands among its customers. The company’s 30th anniversary provided an excellent reason for us to take a look behind the scenes and learn more about the story of its success. And & Or is headquartered in the El Limón industrial park in Palomares del Rio, about 15km southwest of the centre of Seville. The company’s modern building with its large silver logo attracts attention, not least because of the many empty lots and half-finished warehouses in the immediate vicinity – a legacy of the 2009 recession, we were told. At the head of the family company are founder and general director Antonio Ortega Ruiz; his daughter, Caridad Ortega Suárez, who works as a sales engineer; and sons Antonio Ortega Suárez, a sales director; and Juan Pablo Ortega Suárez, a production manager. Antonio Ortega Ruiz is an electronic engineer. He worked in the 1970s for a plastic converter in the area who, among other things, manufactured bottles for Coca-Cola. In that position, he was mainly involved in the development of technical aids for optimising extrusion blow-moulded plastic bottles. These aids included leak testers, devices for controlling the wall thickness of PVC bottles, and technologies for the automation of packaging machinery. It closed down in the 1990s, unable to cope with the competition presented by the widespread introduction of PET bottles. Antonio Sr had already left that company by then; his entrepreneurial inclination drove him to establish his own business, which would capitalise on his experience in the plastics sector. And & Or was founded in 1986 in the 60m² garage of his current residence in Coria del Río, barely 5km southwest of the company’s current location. “At that time, the garage was both headquarters and workshop. I built the first leak tester here, completely on my own,” Antonio Sr recalls. The garage is still there but Antonio has, in the intervening years, built a stately Andalusianstyle home around it. “Our company name symbolises a logic gate as well as the first letters of my first name and first surname,” he continues. Within a short time, he received the first orders from the surrounding area. When it became clear that the small garage no longer provided enough room, Antonio Sr acquired premises in town with about 300m2 of working space. Along with the workplace expansion and the growing customer base, Antonio Sr developed the first handle applicator machine for 5l edible oil bottles, in 1994. Attendance at trade fairs and word of mouth led to the first exports, to France and Portugal, in the following year. In 2000, for the Heineken brewery in Russia, the company launched a rotary handle applicator for a production speed of 24,000bph, followed in 2004 by a fully automatic bagging machine for the packing of empty bottles. In 2007, the company developed the first side-handle applicator. Sales director Antonio Ortega Suárez says this product is particularly popular in China. Where the story began, f.l.t.r.: Antonio Jr and Antonio Sr","@ID":16}, "INSPECTION 37 PETplanet insider Vol. 17 No. 03/16 petpla.net Enhanced rejection rates on filling lines during the manufacture of beverage closures Perfect position The chuck penetration depth simulator determines the position of the manufactured closures in a simulated chuck of a capping machine. During the process of applying beverage closures to PET bottles, minor gradations can determine whether the closure will be grasped and placed on the bottle correctly in the filling line. At filling speeds of up to 100,000bph, even slight variations at the closure can result in unacceptably high rejection rates. In any economically sensible manufacturing process, the production process for beverage closures relies on manufacturing tolerances, and therefore the challenge lies in differentiating between variations within the tolerance limits and those outside. For this purpose, Corvaglia Mould AG has developed and launched what is known as a chuck penetration depth simulator. Corvaglia analysed the causes of high rejection rates in filling systems and determined that different combinations of a wide variety of critical characteristics (various dimensions, deformations, irregularities in the raw materials, colours, etc.) can result in an unacceptable application. As the core element of the newly developed validation method, the chuck penetration depth simulator determines the position of the manufactured closures in a simulated chuck of a capping machine. If closures are positioned too deep in the simulated chuck, this could break the bridges of the tamper-evidence band. Closures that protrude too far out of the chuck can result in insufficient centring, which in turn results in cocked closures or prevents closures from being applied. Using the chuck penetration depth simulator, manufacturers can quickly differentiate between closures that can be correctly applied and closures that cannot – and they can now do so during production of the closures, and not, as previously, when the closures are being applied. Thanks to this pre-application testing, potential rejects amount to only a few individual closures, whereas previously, finished, filled bottles had to be disposed of. The new tool from Corvaglia is intended to reduce costs and conserve resources. Minimising rejection rates In addition, the chuck penetration depth simulator can also be used for in-process control in order not only to minimise rejection rates, but rather to ensure that rejection is prevented in advance. In production line trials in filling systems that had unacceptably high rejection rates, Corvaglia has been able to prove that the use of the chuck penetration depth simulator resulted in a reduction of these rates to below 50ppm (= 0.005%). The tool is already in use today at Corvaglia’s manufacturing locations in Switzerland and Mexico, as well as at selected partner companies. www.corvaglia.ch During production of the closures, their correct application can be checked with the chuck penetration depth simulator I NSPECT I ON S P E C I A L","@ID":39}, "INSPECTION 23 PETplanet insider Vol. 17 No. 03/16 petpla.net Three steps for higher preform quality Multiple cameras for extensive tests Top cameras for a precise neck & support ring inspection Side cameras for a full 360° outside inspection Specific side camera with polarisation filter Camera for bottom inspection A new added side camera for cavity recognition IMDvista offers with its Peco Lux a preform monitoring system that can be added to every existing or new preform production line. Combined with the established IMDvista offline preform testing system with a M. Tanner AG sorter and tipper, accruing problems can be sorted to make sure, that most of the production can be sold with a high quality. Preform production is one of the most automated and optimised production processes in the plastic industry. Factory layouts are optimised to the limits and no square meter stays “unused”. Driven by the need to use recycled material, using UV Blocker etc., defects can no more be excluded. Problems like black spots, colour deviations, crystallisations etc. happen during production, appear and go away again. Out of this IMD Ltd got more and more the request for an inline preform monitoring system for each production line. The IMDvista Portal links all the systems together offering the production people a fast and easy overview of the monitored production. Problems are displayed and alerted immediately when they happen and corrective actions can be immediately initiated. Peco Lux: Inline prefom monitoring system, step no 1 Installed after the existing conveyor, the preforms are sliding over the Peco Lux slide with integrated “light plate”. No adjustments are necessary, no parts to change for different preform designs and sizes. It requires no additional floor space.The vision system automatically detects the preforms and is taking pictures to analyse every shot of the production. Typical defects like burn marks, haze, too long injection gates etc. can be detected. Colour variations are monitored to a high accuracy and defects like milky preform, crystallinity and yellowing are also detected. Alarms will be displayed on the vision system and transferred to the IMDvista Portal. The software V5, based on self-learn functions, is said to be easy to use for all operator levels. The Peco Lux is a customer driven innovation and opens a perspective to smart and economic inspection routines for all preform production lines. Peco offline sorting with M. Tanner AG feeding system and tipper, step no 2 The IMDvista Peco offline preform testing system is sorting out the bad preforms because usually not all I NSPECT I ON S P E C I A L cavaties were affected by any inaccuracy. Faulty productions detected by Peco Lux can be re-sorted. Tanner preform tipper & feeding system For more than 25 years, M. Tanner AG has been developing, designing and manufacturing preform feeding systems worldwide. Tippers with features like the electrical container cover the falling height of preforms can be reduced for a smoother and adjustable tipping procedure. With the Tanner roller sorter preforms of almost any design are handled in a gentle way, compared to rotary sorters. With a wide range of configuration possibilities the layout of the feeding system is flexible and can be designed according to customer needs. IMDvista Peco preform testing system The Peco preform testing system takes carefully the preforms from the sorter to keep the flow of the product in one line with a gentle handling. The flexible system can handle preforms from 7,9g to 150g without changing any size parts. Peco inline inspection system, step no 3 The system is available with a special setup to be connected inline directly after the preform production machine. The testing of all parameters, including cavity number reading is recommended for critical products or main projects. Although it uses floor space, the setup is flexible and easy to use. www.imdvista.ch www.mtannerag.ch","@ID":25}, "PETbottles 58 PETplanet insider Vol. 17 No. 03/16 petpla.net Home + Personal Care Bubble bath from duschdas Unilever has extended the palette of its “duschdas” brand, with a series of bubble baths. The four varieties have lots of words on them but one word which stands out; the words are happy, relaxed, powerful and stress-free varieties. The “... powerful...“ version, with the scent of blackberries and ginger, should appeal in particular to men when they take a bath. The word “men” can be clearly seen on the label. Each slim clear PET bottle with a rectangular base contains 500ml. Two transparent selfadhesive labels on the front and back provide the necessary user information. Coloured screw caps which match the contents complete the product’s appearance. www.duschdas.de Guhl with something extra In connection with a promotional or discount activity, the German company Guhl-Ikebana GmbH was selling 275ml of its shampoos at an attractive price in a double pack – consisting of the known 200ml bottles and smaller version of the bottle containing 75ml. Both bottles were joined together at the POS into one unit with the help of a sleeve label. The small bottle is easier to pack into a travel or sports bag. Both bottles are made from PET, have a conical shape, are easy to hold and are decorated with non-label-look labels. Where they differ is in the closing devices, the large bottle having a screw-on hinged cap with a dose aperture and the small one just has a screw top. www.guhl.com Keratin oil for hair The cosmetics manufacturer OGX puts 118ml of his Keratin Oil hairspray, consisting of proteins and argan oil, into an easy-to-hold plastic bottle. The product is designed to stop hair splitting and improve combing and hair management. It is applied to still-damp hair via a screw-on multi-coloured pump dispenser with a protective cap. Two self-adhesive labels provide the necessary user information and give a view of the product. www.ogxbeauty.com Pampering oil from Balea The German discount chemist dm is expanding its own brand Balea Luxury even further with new product ideas. The most recent example comes with the name Golden Glamour, a pampering body oil with a shimmering effect. The product has the scent of patchouli and vanilla. A clear PET bottle is filled with 100ml and has an all-round label which still allows the product to be seen. Under the pull-off top there is a black pump dispenser with a locking function. www.dm.de","@ID":60}, "TRADE SHOW PREVIEW 50 PETplanet insider Vol. 17 No. 03/16 petpla.net VISIT US AT: CHINAPLAS 2016 Booth Nr. W1 T03 V Motan colortronic Hall E1 - Booth L41 Modular building block principle The focus of Motan-Colortronic Plastics Machinery (Taicang) will be the Metro G material loaders, which can now be fully integrated into existing Colortronic systems. At the same time, to offer flexibility and to save costs, existing Colortronic material loaders can now be integrated into new Motan systems. Metro G’s modular building block system is said to allow users to configure and create the optimal material loader for any application. Different sizes of material inlets which can be matched exactly to material throughputs and conveying distances, are offered in addition to the various different material loader volumes. Modules with a tangential material inlet that operate with a cyclone effect are still available for materials with difficult separation behaviour. Customers can also choose between different vacuum valves. Thus, a standard unit can be upgraded to a clean room version with a special membrane vacuum valve. In addition, the company will showcase the new synchronous dosing unit Miniblend V for free and normal flowing materials, suitable for translucent and opaque parts. www.motan-colortronic.com The blowing-fillingcapping Combiblock Newamstar Hall W4 - Booth A41 A smart Newamstar Newamstar, a global packaging machinery supplier, will share its complete set of smart equipment and comprehensive solutions in five areas: beverage, dairy, alcohol, condiments and personal care products. Water treatment system, pre-treatment system and blowing machines as well as filling machines, secondary packaging system, transportation robot and stereoscopic intelligent warehouse will be exhibited at the booth. Newamstar will show their latest generation of a high speed rotary blowing machine with one single capacity of 2,250-2,400bph. www.newamstar.com","@ID":52}, "Hong Kong Chongqing Xi'an Taiyuan Shenyang Qingdao Nanjing Guangzhou Shanghai Beijing Jinan Sponsors The China Road Show The worldwide round trip with www.china.petpla.net 2016 is both the Year of the Monkey in Chinese astrology and the occasion of our first Editourmobil quest to sample the far-eastern culture of China. Following our successful Editours in the past few years, our voyage into the Middle Kingdom begins in Shanghai in April. We are scheduled to cover a distance of approximately 7,000 kilometres between then and October, which will be covered is a series of stages in the eastern part of the People‘s Republic - and, as always, the whole distance will be travelled by road! During our trip, we will take in the entire PET process chain and discuss facts and trends with a great variety of users from the bottling, processing and recycling industries, as well as with suppliers, toolmakers and mechanical engineers. As always, reports and reviews of all of our visits and interviews with local and global players will be published in PETplanet Insider. We will keep you right up to date on our travel experiences through near-live event coverage on our Editourblog at www.china.petpla.net. Come and join us on an incredible exploration of the Chinese PET market, right from the start. As the saying goes: ॹ䠂ҁ㺂θခ᯲䏩сȾ (A journey of a thousand miles begins with a single step). April – October 2016","@ID":38}, "CAPPING / CLOSURES 40 PETplanet insider Vol. 17 No. 03/16 petpla.net enger is used. These are often made from cobalt salts, a material that is predisposed to bond with oxygen it finds in its environment. It is triggered by the high humidity during filling so that these closures can be stored for a reasonable amount of time (up to 12 months at moderate temperature/ humidity levels) without the scavenger being exhausted before it comes into play in the bottle. Oxygen may also be dissolved in the product as a result of the product coming in contact with it during transfer and filling, and even the PET bottle wall itself gives off oxygen (“matrix oxygen”) that may dissolve in the product. Properly working scavengers almost immediately absorb oxygen from all these sources and so contribute significantly to maintain the product’s sensory properties. They continue absorbing oxygen for several months and therefore extend the shelf life of the product considerably. Material O 2 permeability coefficient (x10^6) [cm3 cm/cm3 dy bar] EVA 1,990 - 2,780 EVOH (100% RH) 2.16 - 4.33 EVOH (dry) 0.0276 - 0.187 HDPE 238 - 1110 LDPE 1030 - 1910 Nylon 6 7.87 - 11.8 Nylon MXD6 0.59 PET 22 PP 596 - 1030 Note: Units are (amount of permeant * wall thickness) /area * time * pressure difference Figure 4.19 Permeability factor for various materials. Note the dependence of EVOH on humidity. This is one reason why Nylon MXD6 has become so popular. A combination of pulp/polysan/ wax has proven successful in limiting oxygen ingress and is used for jars containing mayonnaise, salad dressing or horse radish. 4.4 Tamper-evident bands A tamper-evident band (also called pilfer-proof ring) is a short skirt of plastic underneath the thread that will disengage from the main body of the closure once the consumer unthreads the cap for use. The loose band is a sign that the bottle has been opened. There are many reasons why companies have increasingly resorted to using these bands. It discourages consumers from sampling the product; prevents criminals to insert nonproduct content into the bottle (and later suing the product company for damages); and makes it harder, though not impossible, to replace the brandname product with a generic one without the consumer noticing. The last practice had been such a problem in the alcoholics business that brand owners went to great lengths to get dispensing closures manufactured that were impossible to take off the bottle without destroying them. In the beverage business, caps have to be taken off, but at least there is some safeguarding against malicious action. All bands consist of a series of nubs oriented on a ring that itself has an interrupted connection to the cap above. When the cap is unthreaded, these nubs hold the band motionless against protuberances moulded into the bottle neck finish. At this point the band may either stay on the bottle neck or on the cap as a “pigtail”. Both solutions have their merits. Consumers usually prefer the band to stay on the bottle neck as it may interfere with the resealing of the bottle. Previously, the band was considered a challenge to recycling, but because relatively simple flotation devices that are able to remove them are part of every recycling operation, this no longer seems to be a problem. However, bands do have to stay on caps when it comes to refillable bottles as it is virtually impossible to get them off in an economical way. The unruly pigtail may also be a more obvious sign of tampering than the band on the neck. Pigtails differ in how easy they come off the cap. If it is easy enough for consumers to pull them off, they may end up littering up cities or, worse, being pushed into refillable bottles and very difficult to remove from there. There are two ways how a tamperevident band may be accomplished. It can be either moulded right into the cap at the time of manufacture or slit afterward in a secondary operation. In the former case, the mould parts that form the ring interruptions are undercuts in the direction of cap ejection and must be retracted inside the tool before ejection can take place. This adds costs to injection tooling. However, these may outweigh the costs and operational headaches associated with unscrambling, orienting, and slitting the finished caps in a specialpurpose machine. 4.4.1 Construction methods There are two basic construction methods for pilfer-proof rings. The most common for the one-way PET bottle is the drop away system. For the returnable PET and glass bottles a detachable pilfer-proof ring is needed. In some countries law requires even one-way bottles to have detachable bands. This is because some people are under the misconception that it is necessary to separate the HDPE or PP closure from the PET bottle before recycling. However, this is not the case because today’s recycling systems are perfectly capable of separating all elements during the recycling process (Figs 4.20–4.29). Fig. 4.20: 1. closed position Fig. 4.21: 2. after 90° turning Fig. 4.22: 3. completely detached","@ID":42}, "SERVICES 43 PETplanet insider Vol. 17 No. 03/16 petpla.net Events and innovations In the events area there are platforms where events in the PET industry are listed. Sites for individual trade fairs provide general information about the events, but more importantly about exhibitors relevant to the PET industry (with halls and stand numbers) and their technologies and areas of application. From there, companies organising their own in-house exhibitions can provide links to their WikiPETia profiles, and exhibit technologies and areas of applications specific to each trade fair. This is what makes individually adjusted searches possible: For the first time, for K 2016, all relevant PET companies exhibiting at K are set to have their websites linked on the WikiPETia K 2016 site, with content to describe their technologies. Detec t ing defec t s even on s t ruc tured sur f aces . The SpotWatcher. Live at Chinaplas . W W W . I N T R A V I S . C O M V I S I T U S A T B O O T H E 1 F 0 5 How to use the software Based on MediaWiki software the system is easy to use, both for page creators and readers. By entering your search word WikiPETia will guide you to relevant page matches. If no matches are found, you will be asked to create an article. If you do not wish to do so, just give us a hint that this might be an interesting topic for WikiPETia users and we will encourage suitably qualified authors to contribute an article. To create content, you first have to create an account. Once done, start writing! Formatting is easy to handle; for standard sites such as events or company presentations, templates will be available on request. Don´t have an account? Join WikiPETia.info Quality of content We anticipate that the system will encourage a large number of contributors to participate. To ensure consistently high content quality, the experienced PETplanet insider editorial team will also be moderating all WikiPETia content. This means that pages will be edited and moderated before going public. Be part of the PETnetwork by joining WikiPETia, searching, creating and contributing. We are looking forward to meeting you on WikiPETia.info. Join us at www.wikipetia.info","@ID":45}, "PETbottles 56 PETplanet insider Vol. 17 No. 03/16 petpla.net Beverage + Liquid Food Aldi’s coffee syrup Three different varieties of the “Expressi” brand coffee syrup are being sold by the German discount store Aldi Süd in elegant 250ml bottles. The varieties – caramel, vanilla and hazelnut – are fitted with differently coloured hinged caps with a self-closing silicone valve. Before first use, the cap must be screwed off and a sealing membrane removed. There are strengthening grooves under the labels, designed to achieve a better pressure point when pressing the bottle and to make dosing easier. www.aldi-sued.de Pin-ups help Müllermilch In a promotion, Müllermilch had an offer of various mixed milk drinks which had scantily-clad ladies on the label, to catch the eye. The images were a reminder of the pin-ups in the Fifties and caused quite a stir on social media. Which meant the design was a successful marketing coup. In the picture, the banana and chiba varieties were filled each into the familiar, easy-to grasp tapered white 400ml PET bottles. The sleeve label went right up to and over the cap and in this area there was a sticker with the words “Happy Love Fest”. www.muellermilch.de Slim bottle for syrup Holderhof Produkte AG from the Swiss town of Nierderwil distributes its 500ml pasteurised elderflower syrup without preservatives to German retailers via its German sister company in a slim plastic bottle. In the paper label area, there are horizontal strengthening grooves for stabilising the bottle when it is being held. The bottle is closed by a screw cap with a tamper-proof band. www.holderhof.ch Jaunty outer shape “Bruno’s Best”, the Swiss specialist in high-value foods, which taste homemade and are made only from the best ingredients, has several salad sauces on offer. Each 500ml of the gluten- and lactose-free sauces, which also has no binders, are filled into jauntily-designed PET bottles. Wave-shaped grooves have been worked into the label area, which jointly with the wave-shaped label make them eye-catching on the shelves. The bottle is closed by a screw cap with a tamper-proof band. www.brunosbest.ch","@ID":58}, "PRODUCTS 53 PETplanet insider Vol. 17 No. 03/16 petpla.net Reduction of waste BTB PET-Recycling, established in 2006, and headquartered in Bad Salzuflen, Germany, processes approximately 20,000t of PET bottles per year. The owner-managed company with some 30 employees primarily produces PET granulate both for bottle-to-bottle and for foil manufacturers. The PET bottles to be processed undergo a preparation process of several stages before they pass as PET flakes through installed Sesotec flake sorting system. This system comprises a chute machine of type Flake Purifier CM 1536 and an already existing belt machine dating from 2011, which after modification could be integrated in the new installation. In accordance with the idea of BTB PET-Recycling, Sesotec, in addition to the optical sorters also supplied the steel construction, the pneumatic conveying technology, and the control technology. The objective of this was to better coordinate the work that had to be performed, and to shorten the down-time of the complete plant in the construction phase. “Because of continuously falling prices for low-grade PET material on the Asian market we had to develop new economic solutions for PET waste, and our strategy was to reduce the waste volume”, says plant manager Mr Zajontz. “With the new installation of the Sesotec sorting system we have reached this objective. There is no question regarding the profitability of the system.” He went on to add: “The integration of remote access makes it possible to monitor the sorting system through the network. Sesotec service engineers also can use remote diagnostics for short-term error remedying or for software updates, which makes processes in everyday operations much easier.” www.sesotec.com Consumer friendly capping Danone Waters has chosen Global Closure Systems (GCS) to cap the latest 1l bottle of its Volvic brand of natural mineral water. GCS has developed a screw cap with a TPE strip to provide a perfect grip, making it easier for consumers of all ages to open the bottle. The bi-injected cap is coloured in white and green and offers an on-shelf appeal. The closure is said to offer both increased convenience for consumers and on-shelf differentiation. “This cap is very well perceived by consumers, solving the micro-stresses we identified in the day-to-day usage” says Eric Maffert, International Marketing Manager for Volvic. The custom-made cap was designed and developed by Zeller Plastik in France, one of GCS’ 21 production plants. “Our experienced and dedicated field engineers were able to satisfy Danone’s brief by utilising their expertise in personal care packaging and thereby devising a closure that ensures both convenience and brand differentiation,” states Franck Doucet, Key Account Manager, GCS. www.gcs.com www.danone-waters.de","@ID":55}, "INSPECTION 29 PETplanet insider Vol. 17 No. 03/16 petpla.net Six cameras, taking multiple pictures during rotation for the sideview: More raw data enable better decisions floor space of a PreWatcher III, the periphery equipment like bunker, feed and diverter requires a lot more floor space. To be able to deliver entire downstream lines like those, the production space of Intravis has to grow accordingly to the size of the company. But these challenges have always been taken, as Gerd Fuhrmann states: “We are happy to expand and we keep developing our company structure to meet all requirements – just as we have always done.” www.intravis.de MARKET BENCHMARK DOUBLE ACTING DIRECT COUPLED MOTOR HEAT RECOVERY SYSTEM HORIZONTAL OPPOSED www.abc-compressors.com BRAU BEVIALE - Nuremberg 8-10 November Stand: 7A – 318 EMBALLAGE - Paris 14-17 November DJAZAGRO - Algiers 18-21 April Stand: 1 H 005 PROPAK ASIA - Bangkok 15-18 June Stand: 1B22 CBB - Shanghai 11-14 October Stand: 2Y 141","@ID":31}, "INSPECTION 28 PETplanet insider Vol. 17 No. 03/16 petpla.net by monitoring more parameters Detecting defects before they occur Preforms, closures and labels have to be top quality. In theory, this sounds so simple but in practice, this is difficult to ensure. In production, the defect rate can be from around 0.1% up to 10% when using recyclates. This is why inspection systems are so important to help sort good parts from bad parts. But inspection systems can also help to prevent the bad from ever being produced in the first place. I NSPECT I ON S P E C I A L Separating bad parts from good is a classic aspect of quality control. But quality control can also do more: Correctly applied it can stop defective parts from ever existing in the first place. Dr Gerd Fuhrmann, founder and CEO of Intravis in Aachen, Germany, pursues this extremely costeffective approach with his inspection devices for closures, preforms, bottles, layers and decorations. Normally, a defect is discovered in production. At first only very small changes occur in the measured values, which still lie within the tolerance range. It is only when they fall outside the tolerance limits that reject parts are detected. In order to be able to detect these extremely small initial deviations, however, it is necessary to have inspection systems with very high resolution. The data volumes must be analysed and presented at an appropriate speed. “The more data we have, the more we are able to detect the beginnings of defects,” says Fuhrmann. For the inspection of preforms, the PreWatcher III of Intravis is equipped with up to eight highresolution cameras, making it possible to monitor up to 72,000 preforms per hour. It detects even smallest material defects, geometrical deviations, defects in the mouth ring and other features. Furthermore, it is able to read cavity numbers. But it is not just the early detection of defects that promises an early return on investment. The accuracy of the defect detection ensures that if defective objects are in the production flow the smallest possible amount is rejected. Due to their lower resolution, conventional inspection systems have to have a wider defect tolerance range in order to be really accurate, whereas Intravis can keep the rejection window very small. Depending on the defect, this can mean an advantage of up to 1% of the total production. In order to monitor even more parameters, the company offers the Sample-PreWatcher, a system to inspect individual batches extremely detailed. Additionally to cavity number reading and material defects, it also inspects for contaminations, colour, weight, geometrical deviations and more. The remaining preforms can be sold on, because they have not been touched by human hand. In the cap segment it is also the case that the high-resolution cameras of the CapWatcher III produce a high volume of data which allows an accurate and, above all, early defect analysis. The performance here is up to 240,000 closures per hour, inspecting for ovality, sealing surface, contaminations, reading cavity numbers and more. During the past few years, Intravis has grown by about 20% a year to 190 employees. Adapting the internal structures to growth time after time is the same great challenge for Fuhrmann on the technological side. Last year, he brought Gabriele Fellerhoff on board as Quality Manager, who is – as is the norm now for the company – not seeking out mistakes. Instead she adapts their processes in such a way that problems are detected before they occur, according to the company’s vision. An important tool in this is the ISO 9001 certification, which has existed since the year 1999. A recurrent theme in company growth is laboratory and production space. It is not just the number of inspection systems being processed that is increasing but also their size. Despite the compact 8m² The Sample-PreWatcher: Detailed inspection of individual shots – also inline Intravis CEO Dr. Gerd Fuhrmann and quality manager Gabriele Fellerhoff: Together identifying problems before they occur","@ID":30}, "PETcontents 03/16 4 PETplanet insider Vol. 17 No. 03/16 petpla.net INSIDE TRACK 3 Editorial 4 Contents 6 News 52 Products 55 On site 56 PET bottles for Beverage + Liquid Food 58 PET bottles for Home + Personal Care 60 Patents Page 18 MATERIAL / RECYCLING 10 Energy and yield optimised Polymetrix EcoSphere technology BOTTLE MAKING 14 From an Andalusian garage to a global player 16 Aseptic filling at higher speed 20% increase for Sidel’s aseptic dry preform decontamination technology BOTTLING / FILLING 18 Flexible filling function Stepless volume-flow adjustment at the filling valve COMPRESSORS 20 Compressors for high air demanding processes Energy-efficient technology for stretch blow moulding machines INSPECTION 22 Better checking - KHS InnoPET Blomax machines with in-house developed preform inspector 23 Three steps for higher preform quality 24 MHI instead of HMI - Detecting and eliminating faults 26 Bottle control - Optimising material distribution and material orientation 28 Detecting defects before they occur by monitoring more parameters 30 Interacting inspections - From quality control to overall equipment effectiveness 37 Perfect position - Enhanced rejection rates on filling lines during the manufacture of beverage closures Page 28 MARKET SURVEY 33 Suppliers of filling equipment CAPPING / CLOSURES 38 Bottles, Preforms and Closures Closure for PET bottles - Different applications, neck finishes for various, part 6 SERVICES 42 Search, create and contribute! WikiPETia: the new PETplanet online service TRADE SHOW PREVIEW 44 Chinaplas 2016 April 25-28 at the Shanghai New International Expo Center BUYER’S GUIDE 61 Get listed! INSPECTION S P E C I A L Page 59","@ID":6}, "BOTTLE MAKING 15 PETplanet insider Vol. 17 No. 03/16 petpla.net “Our customers like having the option of, for example, making a brand-specific colour selection for the attached handle, which might match the cap,” he explains. And & Or has occupied its current premises since 2011, the year that it first built high-speed palletising machines for empty bottles, followed a year later by display palletisers for filled units. The production hall covers 6,200m², where 70 employees currently work in parallel on between 20 and 25 projects. Twelve members of staff work in development and machine design. The current product line includes around 100 different types of machines, almost all of which are custom designed. Between 2012 and 2015 the company delivered products to 243 different customers in 56 countries. Its main market is Europe, which takes about 50% of sales; 10% to Spain itself. North and South America account for nearly 30% and Asia 10%. The remaining business is in the Middle East and Africa. The range of customers includes plastic converters (about half), 23% in the bottling industry and 20% machinery manufacturers and OEMs, which supply their machines mainly to the bottling industry. Dealers account for the remainder. Customers include Alpla, Graham Packaging and RPC in bottle manufacturing; Coca-Cola, Danone, Heineken, Johnson & Johnson and Nestlé in bottling; and KHS, Krones, Sidel and Sipa on the OEM side. Turnover amounted to nearly US$ 13,1 million in 2015. All development and manufacturing is carried out internally. A few external service providers can also be found in the halls, working in the area of electronics or for welding for example. And & Or remains very much a family business – but how did so many family members end up working for the father’s company? “For me, it wasn’t clear from the start that I would join my father’s company,” Caridad explains. “I have realised over time, though, the development possibilities are of course considerably greater in your own company than elsewhere. I think it’s certainly the same way with my brothers. We are grateful to be part of this.” “For customers, our strengths are certainly our family business philosophy and our customer-oriented mentality, which is practiced by all employees here. We also emphasise steady, but not hurried, growth, step by step,” Antonio Sr adds. The family inside this company does indeed impart a kind of motivational energy, which is noticeably reflected in the workforce. What can we expect from And & Or in the future? “New developments are not necessarily our current focus. In the breadth of our product line and in the different areas that we service, I already see a great deal of growth potential. We will focus rather on the further development of our existing products,” Antonio Jr says. “In recent years, it has been possible to significantly increase the speed of our machines. Many further developments also arise through our close collaboration with customers. We see future growth particularly in Asia and North America. At the moment around 25% of our sales go to Latin America and only around 5% to North America. We want to expand that and plan to open a local sales office soon.” www.andyor.com F.l.t.r.: Juan Pablo Ortega Suárez, Caridad Ortega Suárez, Antonio Ortega Suárez and father Antonio Ortega Ruiz Family business with (f.l.t.r.) Antonio Jr, Antonio Sr, Juan Pablo and Caridad Machine assembly area","@ID":17}, "INSPECTION 26 PETplanet insider Vol. 17 No. 03/16 petpla.net Optimising material distribution and material orientation Bottle control One of the biggest challenges for a process engineer in the production of PET bottles is to control the blowing process by managing the stretching process in such a way that material orientation (strain induced crystallinity) is optimised without negatively affecting bottle material distribution. The degree of orientation and its optimisation directly affect performance in the areas of burst pressure, volume expansion, top load, impact strength, dimensional stability, permeability and environmental stress crack resistance, and is therefore critical to producing consistently high performance bottles. Producing bottles that have accurate material distribution on a consistent basis is a challenge. The Process Pilot blowmoulder management system from Agr International, Butler, PA, USA conquers this dilemma. Installed within the blow moulder, the Process Pilot system utilises infrared technology to precisely measure material distribution, and any changes thereof, on every bottle produced. Continuous data on material distribution, trends and changes are captured and work as feedback for blowmoulder management. Using this information, the Process Pilot system automatically adjusts the blowmoulder oven and mould control parameters based on the location of material to minimise overall process variation. Unlike operator adjustments, the Process Pilot system can adjust one or all of the blowmoulder controls simultaneously to achieve the best possible material distribution. of pearlescence by detecting the very edge of where the process gets too cold and pearlescence begins to form. How it works The CrystalView measurement system is an optical device that works in conjunction with the Process Pilot blowmoulder management system. It incorporates a set of discrete vision components that are mounted inside a reheat stretch blowmoulder. As bottles exit the mould, the CrystalView system scans every bottle for the onset of pearlescence. When viewed by the CrystalView system, the onset of pearlescence can be detected well before the human eye. Sophisticated control algorithms incorporated into the system actively monitor the levels of pearlescence. When evaluating possible solutions for material optimisation, Agr engineers determined early on that managing orientation while maintaining thickness would be quite a balancing act. More often than not, changes made to optimise one would adversely affect the other. The CrystalView technology is said to have the capability of monitoring pearlescence with high precision. The Process Pilot system on the other hand can manage multiple blowmoulder controls simultaneously while maintaining material distribution at a specified thickness to within ~0.0025mm. Processing temperature and lightweighting In the cold mould process, typically higher than necessary processing temperatures are used in order to safely manage process and blowmoulder variability. As a rule, colder is better when optimising orientation. However, without proper feedback it is difficult to determine appropriate temperature limits. With the CrystalView system, the point in which orientation is optimal, just at the “edge” of the transition state where pearlescence becomes visible, is defined precisely. The CrystalView technology makes it Optimising material orientation Maintaining appropriate material distribution, and at the same time optimising material orientation, requires great skills. In a continuation of its work to fine tune and simplify the management of the blowmoulding process, Agr has announced the pending introduction of its CrystalView system to address the needs of bottle manufacturers using the chilled mould process. The CrystalView system is designed to optimise material orientation. In the cold-mould process, pearlescence results from overstretching or running the process too cold. Under these conditions, the material is stretched beyond the point for optimal orientation and molecules are broken, creating reduction in performance and clarity. The CrystalView measurement system offers a simple, reliable and hands-free means to optimise material orientation while avoiding the creation Material optimisation using a colder process can result in improved PET bottle performance. The CrystalView technology facilitates blowmoulder operation at the coldest possible temperature in which orientation is optimal for maximising bottle performance. I NSPECT I ON S P E C I A L","@ID":28}, "BOTTLING / FILLING 19 PETplanet insider Vol. 17 No. 03/16 petpla.net been solved,” says Martin van den Booren, plant manager at the Heerhugowaard facility. Another aspect of crucial importance was that by using the new technology, the group was able to increase filler output by 15-20%. Martin van den Booren detects some more advantages: “All of the control kit need no longer be accommodated in the filler turret, but has been grouped together directly in the valve, thus eliminating the possibility of malfunctions between turret and valve. And that has beneficial effects on maintenance as well,” he explains. It is claimed that maintenance outlay in the event of a fault is minimal. Since the electronic and mechanical equipment is accommodated together in a single housing, a defective PFR is replaced in its entirety, eliminating time-consuming fault-finding. With conventional filling technology, by contrast, trouble-shooting is definitely more complicated, because the electronics are in the control cabinet and the mechanical parts are on the valve. Thanks to the The Burg Groep makes vinegar, fruit syrups and fruit-juice concentrates, household cleaning agents, plus cleaning and care products for the car, marketed as private labels. It operates seven state-of-the-art production facilities in the Netherlands, Belgium, Germany, France and the Czech Republic. The group’s registered headquarters is in the Dutch town of Heerhugowaard, 50km to the north of Amsterdam. In the Netherlands, the company has a total of four plants; in Belgium natural vinegar is filled on one line, while in France special types of vinegar are made, like balsamic, for instance. In the south of Germany, Burg processes vinegar in canisters for the preserved-food industry. Another vinegar plant is located in the Czech Republic. In one of its four Dutch plants, the Burg Groep produces fruit syrups in a widely varied range of flavours, sugar-free syrups, concentrated juices, and vitamin-C-fortified fruit syrups. All these products are available in PET containers, glass bottles and cans. plug-and-play principle, the flow regulator is quickly ready for operation: during maintenance, the times for replacing a complete valve are short – all that is needed is to move three cable plugs and two flanges. Energy-economy As Europe’s second-biggest vinegar producer, the Burg Groep likewise wishes to play a pioneering role in terms of sustainability, which is why it is continually optimising its production processes. Teams comprising technicians and researchers examine the options provided by new raw materials and production methods. As far as PFR is concerned, energy will only be consumed when something actually moves, since pneumatics have been dispensed with. A valve self-locking function is provided using a trapezoidal spindle solution. For the first machine in actual operation, this resulted in the energy consumed at the filling valves being reduced by up to 90%. In 2015, the Burg Groep intends, in the next stage of its investment programme, to also replace the now-too-small PET blow-moulder in this line with a higher-output model, thus increasing overall line output to 16,000 containers an hour. www.krones.com www.kosme.com","@ID":21}, "TRADE SHOW PREVIEW 49 PETplanet insider Vol. 17 No. 03/16 petpla.net Sipa Hall E3 - Booth K01 Mould making, refurbishing and conversion services Sipa’s mould refurbishing and conversion services in China are one element of its complete PET preform and bottle mould offering. To improve the preform quality Sipa is offering its customers a service to replace old by new components, refurbishment, or to convert the mould to produce a complete new preform design. Customers can choose a mould audit with Sipa experts to discuss their development potentialities. The mould refurbishing and conversion services complement Sipa’s in-house capability to develop and produce high performance moulds and hot runners. The company’s range of solutions benefits from Sipa’s special focus on reducing energy consumption. With better distribution flow and a higher water temperature, 14-15°C instead of 8°C, water consumption is minimised and performance in terms of condensation reduction is improved. Sipa hot runners are said to reduce stress on material, resulting in better preform quality and reduced acetaldehyde (AA) level. Sipa’s service centre in Hangzhou, China, operating since 2004, complements two other centres in Vittorio Veneto, Italy, the company’s headquarters, and in Atlanta, USA. The production capacity in Hangzhou is 300 cavities a month in blow moulding and 800 cavities in injection moulding. The mould plate manufacturing has a 144-cavity cold half and can, it is claimed, be constructed in six weeks. Sipa experts in Hangzhou are able to design moulds, preforms and bottles, and doing perform lab tests, for example pressure testing, heat sinking, tensile strength, top load, and mould quality. www.sipa.it Sipa’s toolshop","@ID":51}, "INSPECTION 25 PETplanet insider Vol. 17 No. 03/16 petpla.net INSPECTION 25 Full inspected! PROPAK AFRICA, 15/18.03.2016 - Johannesburg SOUTH AFRICA SEMINAR ON PACKAGING INNOVATION, 15/16.03.16, Kolkata INDIA ENOLITECH, 10/13.04.2016 - F VIC N7 , Verona ITALY IRAN PET CONFERENCE, 11/12.04.2016, Teheran IRAN DJAZAGRO, 18/21.04.2016 - 1M022/26, Algiers ALGERIA CHINAPLAS, 25/28.04.2016 - E2B51, Shanghai CHINA CRAFT BREWERS&BREW, 3/6.05.16 - 4059, Philadelphia USA Filled bottles or containers Fill level measurement Leakage detection (in pharmaceuticals sector also including microleakage and cracks) Internal pressure measurement Vacuum measurement (e.g. in the case of juices) Inspection of closure (damage to retaining ring and position of closure) Inspection of foil closures (seal in outlet area) Identification of foreign objects and any contamination Monitoring of filler valves and capping heads Rejection of faulty containers Correct position for identification Series fault identification and statistical analysis with graphic representation Process monitoring of entire filling line and downstream Service The inspection machines are equipped with remote diagnosis facilities. The service stations in Germany, North America and China have access to direct intervention when faults are identified and need to be eliminated. Furthermore, the high degree of automation of the Heuft Spectrum device platform reduces the need for intervention by the operator. However if something has to be done the selfexplanatory user guidance Heuft NaVi makes his work simply easy: “Instead of Human Machine Interface (HMI)”, Carl J. Bonnan explains us, “we are now working with Machine Human Interface (MHI). It focuses on the human being, takes him by the hand and provides him with targeted audiovisual support. So he can find the appropriate remedy even without previous knowledge. That way the operator turns into a user.” We wish our hosts every success in the future with this additional facility aimed at detecting and eliminating faults. www.heuft.com","@ID":27}, "PRODUCTS 54 PETplanet insider Vol. 17 No. 03/16 petpla.net P.E. Labellers and KHS cut plastic and boost flexibility P.E. Labellers states that it prides itself on its responsiveness to customer needs in the competitive packaging market. A recent example is its collaboration with KHS on a project to reduce the use of plastic in the production of PET bottles and, at the same time, to improve packaging format flexibility and cut production costs. The project, which began in the second quarter of 2014, reached a successful conclusion in Q2 2015, with the presentation of a new triblock blowing-labelling-filling and capping machine for PET bottles. The flexibility of the triblock approach means that bottles can be packaged in various shapes and sizes, including traditional cylindrical bottles formats and both regular and irregular designs. They can be finished with ultra-thin labels. The new PE/KHS solution can be used for carbonated beverages with up to 7.9g CO 2 /l in 10g/500ml preforms, finished with 19 micron adhesive labels. The companies claim total material saving of up to 35%, compared with other solutions currently available on the market. PE and KHS claim further savings, up to double, when thermal shrink labelling is used with carbonated beverages. The reduced amount of plastic used in the bottle construction also means that bottlers can save on the cost of buying a sleever machine; a P.E. Adhesleeve is already suitable for this sort of application. Additional savings of up to 50% can be achieved through the use of ROSO labels, compared with PET-PVC sleeves. The blowing-labelling-filling-capping triblock solution is also claimed to offer opportunities for lightweighting in the case of still beverages, through the use of P.E. Adhesleeve technology applied to thinner plastic labels. The cost of managing the entire triblock, the P.E. labelling machine in particular, is reduced by the use of patented technologies in the Adhesleeve unit. It avoids the risk of glue contamination of the packaged product by dispensing with glue altogether; Adhesleeve has only a cutting cylinder and label application, it does not use hot glue inside the triblock. P.E. says that this helps to minimise running and maintenance costs. www.pelabellers.com Yake Food entering the mineral water market with Changbai Springs In Zhengzhou, a strategic city for the food and beverage sector, located in the central plains of the People’s Republic of China, a conference was held to launch the first brand dedicated to mineral water by Yake Food, well known in the Chinese confectionery industry. Moreno Barel, CEO of PET Engineering, was invited to present the packaging chosen by Yake Food for its Changbai Springs premium brand. “In a market like China,” said Moreno Barel, “the association of a quality product and a container with strong shelf-appeal is the key to a secure and lasting success. Yake Food, after a careful analysis of the competitors, decided to be aside the economic waters on the market, with a current market price of 2 yuan per a half liter bottle, and propose higher quality water at 3 yuan per half liter, in a packaging that materialises and transmits this premium quality. Therefore, from the very first meeting Mr. Chen Hua Sheng, General Manager of Yake food, chose 1851, a registered model which has already won many awards.” 1851, presented at Drinktec 2013, was born from the idea of enhancing the PET through a distinctive design and a glass-like finish, thereby highlighting the concepts of elegance, character and refined simplicity while keeping it as affordable, unbreakable and lightweight. PET Engineering normally uses this material in the HO.RE.CA. sector and for all premium products. Yake Food chose 1851 for the natural correspondence between the message that it communicates and the brand strategy choice for Changbai Springs water. The three-dimensional decoration recalls the regular shapes and geometrically perfect ice crystals, associated with the idea of purity, which is the key message Yake Food wishes to communicate. Changbai Spring aims to be “the water that starts the day”. The registered design of 1851 has won a number of awards, including the prestigious Oscar dell’Imballaggio 2015 for Quality Design and the World Star Award. www.petengineering.com","@ID":56}, "PETpatents www.verpackungspatente.de 60 PETplanet insider Vol. 17 No. 03/16 petpla.net Base shape Intern. Patent No. WO 2015 / 084324A1 Applicant: Amcor Ltd., Victoria (AU) Date of application: 3.12.2014 The shape of the base of a bottle with carbonated contents must be especially shaped to withstand the increased inner pressure, whilst at the same time offering a sufficiently break-proof footprint. Improved look Intern. Patent No. WO 2015 / 084369 A1 Applicant: Nestec S.A., Vevey (CH) Date of application: 5.12.2013 The international application describes a PET bottle, which has high stability in relation to the negative pressure in the bottle and with strengthening grooves which are visually appropriate. Base shape Intern. Patent No. WO 2015 / 092172 A1 Applicant: Sidel Participations, Octeville sur Mer (FR) Date of application: 27.10.2014 The base of a PET bottle is designed in such a way that when several bottles are stacked on top of one another, the stacking crush pressure can be optimally withstood. Closing cap Registered design DE 202012007857 U1 Applicant: Incap International Ltd., Hong Kong (CN) Date of application: 9.8.2012 A closing cap for a container, simple to produce and cost-effective. The easy-touse cap contains an additional product which is only mixed in shortly before being used with the main product. The additional product is protected against environmental influences. Light bottle Intern. Patent No. WO 2015 / 099813 A1 Applicant: Niagara Bottling LLC, Ontario (US) Date of application: 16.1.2014 The application describes the various possibilities for groove design, groove positioning and the base shape, in order to make a weight-reduced plastic bottle sufficiently stable. Stable plastic bottle Intern. Patent No. WO 2015 / 098961 A1 Applicant: Suntory Holdings Ltd., Osaka (JP) Date of application: 24.12.2014 The application describes a plastic bottle with circumferential grooves for stabilisation and for taking up the pressure and/or volume variables. Several shapes of the bottle neck are shown.","@ID":62}, "INSPECTION 27 PETplanet insider Vol. 17 No. 03/16 petpla.net possible to operate the blowmoulder at the coldest possible temperature without moving beyond that point. Processing temperature can be reduced with confidence, making it possible to achieve temperature reductions from 2-6°C. Having the ability to ensure maximum performance on a given design and the confidence that it will perform as expected offers additional opportunities to fully realise lightweighting opportunities. With ultralight bottles, performance characteristics can vary dramatically due to process variability. The ability to produce lightweight CSD and water bottles where the material is fully optimised provides the ability to realise the maximum bottle performance with minimal weight from a given design. Bottles are stronger with better performance and as a result provide greater stability and an increased ability to confidently process without incidence in filling, labelling and capping operations. The CrystalView product is currently undergoing beta tests at several sites. A full commercial launch of this product is planned for early third quarter of 2016. Agr’s Process Pilot automated blowmoulder control system has been on the market for several years and has proven to be a vital tool in the production of light weight bottles. www.agrintl.com Agr’s Process Pilot system measures distribution on every bottle and proactively adjusts the blowmoulder to produce bottles with like consistency and performance INSPECTION 27 BERICAP Technology The plastic closure company committed to your success www.bericap.com Research and Development Mould Technology | Global Presence Capping Technology and Know-How Innovation and Flexibility","@ID":29}, "MARKET SURVEY 33 PETplanet insider Vol. 17 No. 03/16 petpla.net 03/2016 MARKETsurvey Preforms Filling equipment Resins /additives Preform / stretch blow moulds Caps and closures Preform and single stage machinery Bottle-to-bottle recycling plants Compressors Closure systems Two stage SBM machinery Suppliers of filling equipment: This year’s second market survey presenting an overview of filling equipment suppliers. Nine companies from different countries taking part. They are shown in order in which their details were received by the editors. Fogg Filler (USA), GEA Procomac (Italy), Sacmi (Italy), Serac (France), Sidel (Switzerland), Sipa (Italy), SMI (Italy), KHS (Germany) and Krones (Germany). Although the publishers have made every effort to ensure that the information in this survey is up to date, no claims are made regarding completeness or accuracy. Company name GEA Procomac Postal address Telephone number Web site address Contact name Function Direct telephone number Fax E-Mail Via Fedolfi 29 43038 Sala Baganza (PR), Italy +39 0521 839 411 www.gea.com Mr Alessandro Bellò Sales Director +39 0521 839411 +39 0521 833879 alessandro.bello@gea.com 1. Machine designation / model number Aseptic filling ESL filling Traditional filling Hot Fill 2. Number of filling heads (range: from/to) 15 - 140 filling heads 18 - 140 filling heads 30 - 140 filling heads 50 - 140 filling heads 3. Min to max bottle contents (in liters) 0,06l - 3l 0,06l- 3l 0,06l - 3,0l 0,1l - 3,0l 4. Filling speed: output (bph) (min to max): 6,000 - 60,000 6,000 - 60,000 6,000 - 60,000 6,000 - 40,000 specifiy: 1l bottle / still water (bph) Up to 60,000 1l bottle / CSD (bph) Up to 40,000 Up to 60,000 1l bottle / Milk (bph) Up to 60,000 Up to 60,000 Up to 48,000 1l bottle / Juice (bph) Up to 60,000 Up to 60,000 Up to 40,000 5. Filling process Pressureless (still drinks) Yes Yes Yes Pressure filling (carbonated drinks) Yes Yes Hot filling Yes Cold aseptic filling Yes Juices with high pulp content Yes Yes Yes 6. Type of filling valve and metering system Electronic filler; Volumetric piston doser for drinks with fibres, pulps and fruit pieces Electronic filler Electronic filler Mechanical filler Electronic filler Mechanical filler","@ID":35}, "SERVICES 42 PETplanet insider Vol. 17 No. 03/16 petpla.net WikiPETia: the new PETplanet online service Search, create and contribute! With WikiPETia, PETplanet is providing a new online service for the PET industry. WikiPETia is a moderated knowledge management system that will bring together in a single tool people and companies, technologies and events throughout the PET value chain. Launched on the occasion of the Petcore Europe Conference on 23rd February, the project began with the topic of PET recycling. WikiPETia is integrated on the PETplanet website, so it is easily accessible. WikiPETia provides an interactive component for network building and knowledge sharing within the PET value chain. This has not been available until now, and will keep you abreast of the latest developments. In addition to our push-services PETplanet insider and PETplanet Pulse where we pre-select relevant topics for you, pull-medium WikiPETia enables a search and selection process that is individually adjusted to your needs. The basic idea of WikiPETia is that different PET sources can keep their knowledge up to date and network with one another, creating a networked knowledge structure. We prepare the different subject areas along the PET value chain in a structured manner and then invite different participants to add their factual know-ledge regarding the topics concerned. We began with PET recycling, as one of the current key topics in the PET industry. The next area to be addressed will be resins and additives for the manufacturing of PET preforms and bottles. All manufacturers are now invited to showcase themselves and their products. allow technologies and their manufacturers to be consulted. Central to this cluster of topics are our market surveys that are now available in WikiPETia. For example, for PET bottle recycling, a market overview will display relevant companies (such as Starlinger and Erema). Links to the companies will take the user to their company profile and display links to technologies that introduce certain processes. Companies, people, technologies and applications This structured approach along the value chain means that both companies and technologies can be searched for and found in a targeted manner. Individual company entries enable detailed information to be given about companies and players in the PET industry. Inputs into higher-level topics","@ID":44}, "RECORD BREAKING SPEED IN CLOSURE PRODUCTION The world’s fastest plastic closure folding and slitting machine capable of more than 60 parts/second, designed and built using Swiss precision technology. Slitting tamper evident bands is more efficient and accurate than molding bridges in the mold Multiple injection molds processed on one folding/slitting machine possible Higher efficiency and faster cycle times Lower energy consumption on a small footprint PackSys Global – a cut above the rest, easily meeting the performance demands of the beverage industry. PackSys Global AG T +41 55 253 3700 info@packsysglobal.com @packsysglobal PackSys Global designs and builds full lines for manufacturing: Laminate, extruded and aluminum tubes Plastic beverage caps Monobloc aerosol cans PackSys Global also provides solutions for decorating aluminum screw caps. PackSys Global now comprises three other Swiss companies: Combitool Solutions, Madag Printing Systems and Texa Packaging. A Member of Brückner Group www.packsysglobal.com","@ID":23}, "BOTTLE MAKING 17 PETplanet insider Vol. 17 No. 03/16 The Sidel Predis technology is used by many beverage and dairy companies, with more than 90 production lines equipped around the world. Now that it is compatible with the latest generation of Matrix equipment, the company expects a further boost to its popularity. equipped with more powerful UV lamps for external preform decontamination, adapted to higher output production. The air management in the oven has also been improved. Improved energy consumption Compared to traditional aseptic filling systems, the new Sidel Matrix Combi Predis FMa is said to give producers both the benefits of cost-efficiency and an improved environmental footprint. This ensures preform sterilisation with no water and using a small amount of chemicals. According to the company, the Matrix Ecoven requires fewer heating modules and lamps, yet reduces preformheating time and cuts electrical consumption by up to 45% compared to Sidel’s previous generation of equipment. In addition, the Combi Predis FMa optimises production simplicity by requiring only one operator, which can also reduce operating costs by up to 30% compared with standalone equipment. The system is designed to offer a continuous production run of 165 hours between two cleaning and sterilising cycles. www.sidel.com","@ID":19}, "BOTTLE MAKING 16 PETplanet insider Vol. 17 No. 03/16 petpla.net 20% increase for Sidel’s aseptic dry preform decontamination technology Aseptic filling at higher speed Sidel has announced that its dry preform decontamination technology Predis is now available for the company’s latest generation of modular Matrix blowing and Combi equipment. Thus, preform decontamination, blowing, filling and capping of aseptic products are now possible in a single, safe environment. Sidel’s proven Predis dry preform decontamination technology is now available in a configuration compatible with the latest generation of modular Matrix blowing and Combi equipment. No specific adaptation is required to connect it to the aseptic filling function because the mechanical interface remains unchanged. The Combi configuration for Predis includes preform decontamination, blowing, filling and capping in a single, safe environment. Sidel Matrix Predis will be available for production of up to 60,000bph, representing an increase in output of 20% compared to when Predis is integrated with the previous generation of Sidel blowers. This provides a Combi for high speed production, as the proven aseptic filling range also offers a capacity of up to 60,000bph for on-the-go 0,5l bottles. The Sidel Matrix Combi Predis FMa is more competitive for the same number of blow moulding stations as the output is higher per mould - up to 2,300 bottles per mould per hour. The electrical stretching included in the Sidel Matrix blowing station is said to allow simple, fast and safe changeover with limited manual intervention. This expands the flexibility for beverages producers to handle a wide variety of sensitive beverages aseptically, whatever the recipe or bottle format, ranging from 0,2 to 2l at high running outputs of up to 2,300 bottles per mould per hour. The Matrix equipment is based on a hygienic concept, fully compliant with hygienic design standards (European Hygienic Engineering & Design Group: EHEDG) and beverage industry regulations. The simplified Sidel Matrix Predis design, with fewer transfer wheels, is said to be compact and easily accessible for easier production and maintenance operations. The decontamination of the surfaces of the transfer wheel is now automatic, further reducing manual interventions in the machine. Only the relevant parts have been retained in the blowing area to improve production environment safety. The oven is Sales of sensitive beverages are expected to grow by 6% by 2016.","@ID":18}, "TRADE SHOW PREVIEW 48 PETplanet insider Vol. 17 No. 03/16 petpla.net Gneuß Booth E1C21 Direct reuse of fibre and fibre waste Gneuss will be showing the latest generation of its Multi Rotation System extrusion technology. The MRS extrusion technology is said to be established as one of the key technologies for processing PET reclaim without pre-drying. Even fibre coated with spin finish oils and other contaminants and with a high residual moisture level can be fed directly without any pre-treatment into the extruder where the material is plasticised, devolatilised and decontaminated. The material’s intrinsic viscosity is said to be consistent even when different moistures are employed. Thanks to the patented combination of single screw extruder with a multiple screw section, it is claimed that the extruder is sturdy and well suited for recycling applications. Depending on the feed product and the requirements profile, the shredding, compacting and extruding segments are brought together to form an industrial waste recycling system in modular design. The process for feeding into the extruder is selected individually for every type of waste produced. The MRS removes moisture, spinning oils or other adhering volatile components and solid contaminants are removed in the subsequent filtration, with the result that the melt produced comes close to having the properties of new product. A self-cleaning, process-constant and pressure-constant Rotary Filtration System RSFgenius 75 will be on display at the show. www.gneuss.com MRS extrusion system with Multi Rotation Extruder MRS, Rotary Filtration System RSFgenius, Online Viscometer VIS","@ID":50}, "MATERIAL / RECYCLING 12 PETplanet insider Vol. 17 No. 03/16 petpla.net MATERIAL / RECYCLING 12 Fig.6: Plant lay-out of large scale EcoSphere plant EG generated from the PET polycondensation reaction is recycled in the melt phase, while it is usually incinerated in a conventional SSP using a catalytic combustion system in the nitrogen purification unit. As an alternative, a scrubber system can be used in the nitrogen purification unit to recover the EG from the polycondensation reaction and recycle it to the melt phase. This technique has been demonstrated in several SSP plants already; it is employed as part of the EcoSphere technology. Two features of the EcoSphere technology help to avoid off-spec material. One is the actively- heated delta Q crystalliser, which supplies a temperature and crystallinity adjustment independently of the granulation conditions. The other is the opportunity to re-feed material from off-line storage through the delta Q crystalliser into the SSP. All of this helps to maximise yield from the PET production plant. Yield advantages also result from the lower IV melt in the underwater granulation process. Less dust is generated leading to extended life for the knives and die plates, leading to consequently fewer changeovers and, consequently therefore, reduced start-up waste. EcoSphere technology offers potential for higher single line capacity. Conventional SSP covers a wide range of starting IVs and is already in operation in plants exceeding 900t/d capacity. Direct melt processes – which, by definition, focus on a higher starting IV – have not reached these capacities. EcoSphere offers more. A first installation has already exceeded its nameplate capacity of 600t/d. Polymetrix is currently building two SSP plants with over 1,500t/d capacity each, following two IPT/Chemtex CP plants with the same capacity. (Fig.6) EcoSphere technology is not limited to new installations. Many older conventional CP/SSP plants can accommodate change to granulation systems and accept a delta Q crystalliser. Capacity increases are usually achieved at the same time. Similarities in the granulation step allow EcoSphere technology to be retrofitted to direct melt processes. www.polymetrix.com","@ID":14}, "COMPRESSORS 20 PETplanet insider Vol. 17 No. 03/16 petpla.net Energy-efficient technology for stretch blow moulding machines Compressors for high air demanding processes At the Brau Beviale 2015 in Nuremberg we met the Spanish manufacturer ABC Compressors. The company was showcasing its latest improvement on site, namely, its range of compressors known as “Horizon”. In a discussion with Sales Director Mikel Urain, we found out more about the technical details and new features. “The development of Horizon started in 2011. The first unit was installed at Coca Cola Barcelona; more machinery was built-in at key customers in Europe, Africa, Asia and America - with good results. Based on this success we decided that it is now the perfect point in time to launch a new range in the market“, explains Mikel Urain. “The main technical developments are the combination of the optimised design of the horizontal-boxer type with double acting compressors and the directly coupled transmission”. The two platforms, Horizon and Horizon Plus offer a range from 400 to 6,000m³/h. Horizon, with a production from 400m³/h – 75kW to 3,000 m³/h – 450kW, is designed to cover most of the PET blowing capacities; it is suited for water and CSDs high volume lines in the bottling industry and for smaller pharma- and cosmetic lines with a wide variety of requirements. The range of Horizon Plus, from 3,200m³/h – 450kW to 6,000m³/h – 900kW, is focused on mega plants and lines with high air demanding processes, such as hot filling. “The efficiency of the machine was the key factor for further developments. This is a very important point because the energy consumption is a cost factor customers are very aware of. With Horizon compressors we can achieve double digit savings, thanks to the compressor design itself, cylinders with improved volumetric design and optimally balanced compression ratios. We offer the regulation of capacity by using VSD-frequency converters, up to 55%”, says Mikel Urain, referring to extensive energy requirements at packaging plants. One big energy loser is always the transmission between the electrical motor and the compressor shaft. Making use of their experience in the oil & gas market, ABC constructed the direct coupled configuration proposed for Horizon. “Five percent less energy consumption and more reliable operation, no stopping for belt exchange or typical tensioning matters are the result”, Mikel Urain claimed. From an operational point of view Horizon maintains ABC’s traditional robustness and reliability, for example the absence of vibrations. “You can put a coin edgeways in our cylinders and it will stay this way during the operation of the compressor at full capacity of 40bar,” is Mr Urain’s challenge. Following the total cost of ownership (TCO) topic, the maintenance cost of Horizon had been positively affected by the new cylinder configuration, reducing the moving parts by 33%. This part reduction plus longer lifetime components allows an average saving of 50% maintenance cost compared to previous ABC units. www.abc-compressors.com","@ID":22}, "TRADE SHOW PREVIEW 46 PETplanet insider Vol. 17 No. 03/16 petpla.net Netstal Booth A10 High output rates The PET-Line 5000, designed for moulds with 96 to 144 cavities, will be presented by Netstal to meet the high output rates demanded by the Asian PET market. As with their smaller models, the PET-Line 5000 is said to offer good parameters in the areas of energy consumption, control technology and machine control. The lock-to-lock time, from unlocking the mould to preform removal and locking, has been reduced by up to half a second, according to the company. For standard applications with cycle times of less than 10s, this equates to an increased output performance of tens of thousands of preforms per day. In addition, Netstal will be highlighting the Elion series and the numerous versions for the caps and closures sector as well as inmould labelling (IML) systems technology for the Asian packaging market. www.netstal.com An Elion 800-270 will be on display, demonstrating the production of petri dishes for the medical sector. ALPS machines leak test more than 25 billion PET bottles annually. DID YOU KNOW? www.alpsleak.com/PET info@alpsleak.com www.alpsleak.com FIND OUT WHY gwk Hall E1 - Booth F07 Compact chiller As part of the joint German stand, the presentation given by gwk Gesellschaft Wärme Kältetechnik mbH of Meinerzhagen, Germany include, among other things, a compact chiller of the weco 09A type. This compact chiller, with a rated cooling capacity of 9.1 kW had been upgraded, as had the complete range, by the installation of a user-friendly touchscreen with new integrated features. As part of the modernisation of the product range, the main eye-catching feature of the developments lay in the further increase in energy efficiency as well as the user-friendly maintenance and use. With new fans, the noise level was also reduced. The modular machine concept can be adjusted for varying areas of use via a number of useful options, such as redundant operating pumps, stainless steel pumps and various evaporator designs. Because of their compact construction, both air- and water-cooled compact chillers are ideal for display even where space is limited. www.gwk.com","@ID":48}, "CAPPING / CLOSURES 38 PETplanet insider Vol. 17 No. 03/16 petpla.net Different applications, neck finishes for various, part 6 Closure for PET bottles PETplanet insider is publishing extracts from successive chapters of Ottmar Brandau’s “Bottles, Preforms and Closures”, which was published by hbmedia. A newly revised version is reissued under the Elsevier imprint. The flow through the open closure must be large enough to accommodate the drinking behavior of users. Obviously, it can never match a fully open 28- or 30mm neck with the closure unthreaded. However, today’s sports closures go through flow measurements, and a flow of around 2l/ min with a 20kg load seems to be a standard. For flip-tops, the distance between the opened hinged-top and the user’s lips is also important. If the hinge is too close to the cap it gets in the way. Around 30mm centre-to-centre cap and open top seem to be a minimum, with higher values of course being even better. Fillers and brand owners are also looking for caps that can be sterilised with a liquid agent to avoid costly irradiation sterilisation, and push–pull designs typically do not lend themselves easily to this because rinsing liquid gets trapped in the crevices of the cap. 4.3.4 Closures and shelf life There are many products now filled in plastic bottles that are sensitive to oxygen ingress. The effects are different depending on the product. Juices may oxidise, lose vitamin C, and change colour. Horseradish may turn brown and become unsightly. Beer is also a very sensitive product that loses organoleptic properties when exposed to very small quantities (5ppm) of oxygen. Although most of the work to improve the barrier properties of PET packaging is done on the bottles with multilayer and coating systems as well as improved materials, the closure plays an important role in the overall barrier performance of the package. Figure 4.17 This innovative flip-top design combines ease of opening and reclosure with child safety. The relatively long distance of 37.5mm between the center of the cap body and the center of the opened hingedtop together with a 180° opening angle contributes to a comfortable drinking experience for the consumer. (Pictures courtesy of Bericap). Another popular sports closure is a flip-top cap. Here the spout is moulded into the base and a hingedtop covers it. The top can then be flipped open with a thumb, thus allowing the one-hand operation. Over the years, several design criteria, many of them not obvious at first, have been developed. The dust cover has several disadvantages. For once, it has to be thrown away and so leads to a pollution issue similar to the rip-loop on metal cans. The cover may also pose a choking hazard for young children and therefore has to be large and long enough so that it does not block a child’s throat. The opening torque for both the dust cover and the push or flip feature must be small enough to allow weaker hands easy access but strong enough to hold the pieces in place during transport and use or when very small children try to pry them off. Easy reclosing of dust cover and spout or flip-top is of course also important for the overall functionality. Opening and closing forces between 20 and 30N allow children to handle the closure on their own and are target values.","@ID":40}, "PETnews 6 PETplanet insider Vol. 17 No. 03/16 petpla.net Athena – Sipa relationship ends The agreement entered by Athena Automation Ltd., Ontario, Canada, and Sipa S.p.A., Italy, in December 2012 has expired. Athena will support Sipa in shipping and servicing the remaining “Athena for Sipa” machine inventory. Athena’s next-generation PET preform moulding machines will be sold and serviced directly by Athena, alongside its non-PET machines. According to Robert Schad, President of Athena, there are no plans to form an alliance with a specific mould maker. Instead Athena customers will be able to choose the mould maker they want to use with the post-mould cooling and quick mould-change technologies from Athena. Athena currently builds 150, 300 and 450 metric ton injection moulding machines. A new 14,400m2 plant for just-in-time manufacturing of machines only is in the early start-up phase. The existing 3,700m2 building will remain as head office and will include Sales and Customer Services. www.athenaautomation.com Drinktec 2017: Focus on water and energy management Water is the most important basic ingredient for the brewing and beverages industry. But that’s just part of the story - in the production processes water fulfills many other functions, either as process water, an energy carrier or in cleaning operations. Water demand and water consumption is therefore correspondingly high. For this reason in the production of beverages and liquid food the emphasis is more and more on a holistic consideration of the way resources are consumed. Economic factors, but also image concerns, in relation to sustainable production, play an important role. Next year, Drinktec, the “World´s Leading Trade Fair for the Beverage and Liquid Food Industry” will be highlighting the whole theme of water and energy management. The approximately 1,600 exhibitors from all over the world will be presenting sustainable solutions in this field. Solutions for efficient water and energy management will be presented by the exhibitors at Drinktec 2017 right across all sections of the exhibition. In the Drinktec Forum, too, this theme will play an important role. In the opinion of Richard Clemens, Managing Director of the VDMA Food Processing and Packaging Machinery Association (Fachverband Nahrungsmittelmaschinen und Verpackungsmaschinen), efficient resource and energy management has not yet penetrated all corners of the beverages and food industry, neither in Germany, nor in the markets worldwide. “We would therefore like to turn the spotlight on the themes of water processing, recycling and disposal, and on the contribution of hygienic design towards reducing water consumption – and we will be doing this not least at our own booth at Drinktec 2017. We are going to put on a program specifically for the target group of energy managers in the beverage and food industry, in which they can gather information, learn about best-practice examples and engage in discussion with experts and colleagues from across the sector. Both for the exhibitors from this segment, and also for the trade-fair visitors, we are therefore delivering real added value.” www.drinktec.com Development and commercialisation of bio-based PET Anellotech, a company focused on producing renewable chemicals from non-food biomass, has announced the opening of a fully-integrated development and testing facility (TCat-8). Construction of a building and related facilities to house the pre-built unit began in Silsbee, Hardin Country, TX, USA on the site of Anellotech’s operating partner, South Hampton Resources, a wholly owned subsidiary of Trecora Resources. As an integral component in the bio-based value chain, Anellotech’s proprietary thermal catalytic biomass conversion technology (Bio-TCat) produces “drop-in” green aromatic chemicals (benzene, toluene and xylenes, “BTX”) from nonfood biomass. Scheduled to be fully installed and operational during 2016, TCat-8 is intended to confirm the viability and suitability of the Bio-TCat process for scale-up, and generate the data needed to design commercial plants using Bio-TCat technology. The TCat-8 unit was jointly designed by Anellotech and its R&D partner IFPEN, and will use a novel catalyst under joint development by Anellotech and Johnson Matthey. Anellotech recently made several key announcements supporting the development and commercialisation of its BioTCat technology, including a multi-year partnership with global beverage company Suntory to advance the development and commercialisation of cost-competitive 100% bio-based PET beverage bottles. The partnership began in 2012 under a collaboration agreement that has provided more than $15 million in funding to date. Following verification of the continuous operation of TCat-8, Suntory plans to move ahead with studies to consider the development of the first commercial-scale Bio-TCat plant. www.anellotech.com","@ID":8}, "MATERIAL / RECYCLING 11 PETplanet insider Vol. 17 No. 03/16 petpla.net The EcoSphere technology resolves this dilemma by providing cost savings and quality at the same time. (Fig.3) Polymetrix says that the energy savings available by using EcoSphere are significant; the extent is revealed when examining the way that temperature develops in each process step. A conventional SSP heats PET pellets from room temperature to about 210°C, some time after the PET melt has been cooled down from about 290°C. The EcoSphere technology restricts cooling to the crystallisation temperature, around 150°C. This enables an SSP plant to cut energy consumption by more than half, compared to conventional processes. (Fig.4) A range of quality advantages result from the lower starting IV. Higher IV build-up in the solid state leads to lower oligomer contents, lower acetaldehyde (AA) values and much lower 2-Methyl-1,3-dioxolane (MDO) values. MDO is formed from AA and ethylene glycol (EG), when PET is treated under air especially. In contact with water it decomposes to EG and AA. This means that MDO is, essentially, a hidden form of AA; this is often missed in PET resin quality control. The reduced shear in the melt phase eliminates the formation of gels and black spots. Residence time in a solid state reactor is not a main cost driver. It facilitates reduced catalyst concentrations, which is important in markets where antimony concentrations are restricted. Together with the reduced shear, this leads to higher L (brightness) values and lower yellowness. The quality advantages become more obvious when the PET is recycled. While intermediate storage prevents energy savings it does provide the flexibility to run the CP and the solid phase process independently of each other. At the same time, the wider operation window resulting from transition at a lower starting IV increases overall plant reliability. EcoSphere is said to provide the best of both worlds: greater flexibility and the established robustness of a conventional SSP plant. (Fig.5) An important process advantage with EcoSphere technology is the uninterrupted operation of the CP plant at moderate viscosity targets; typically below 0.6dl/g. It also offers an option to run the CP and solid phase plants independently of each other. EcoSphere retains the usual flexibility in plant layout that allows the use of either candle filters or screen changers and leaves room to position cutters in a way that facilitates access to the equipment for operation, maintenance and upgrade work. Fig 5: Operation flexibility and reliability An aspect crucial to the long term success of a PET manufacturing plant is the yield of grade A quality material. Fig.4: Temperature profile: conventional CP/SSP compared with EcoSphere technology","@ID":13}, "PETproducts 52 PETplanet insider Vol. 17 No. 03/16 petpla.net Reduced yellowing in recycled PET bottles Clariant has announced the introduction of a liquid additive masterbatch that is said to minimise yellowing and greying of PET polymers caused by the introduction of post-consumerrecycled resin (PCR). The optical brightening products, which are part of the HiFormer family of liquid masterbatch solutions and application technology, can be used in a wide variety of PET resin grades and processes, including injection blow moulding, injection moulding and extrusion. The additive has received approval for food-contact applications from the U.S. Food & Drug Administration. It is claimed that the Clariant liquid masterbatches are resistant to sedimentation and segmentation so they offer extended storage-shelf life. They are also said to be easy to use in gravimetric metering systems that ensure accurate dosing and clean operation. Let-down ratios as low as 0.025% have been used successfully. The liquid additives were tested on a production scale blow moulding machine in Clariant’s facility in East Chicago, IL, USA. Bottles made using 25% recycled PET and 75% virgin PET and no brightening additive were compared against bottles made with the same PCR resin and the additive in concentrations of 0.025, 0.035 and 0.05%. While the unmodified bottles showed significant yellowing, all the bottles made with the HiFormer additive were visibly brighter (less yellow and more blue), according to the company. www.clariant.com Tumble’s big brother PET Power has redesigned its standard 250ml Tumble bottle into a larger 300ml size. While maintaining the teardrop design of the original, the larger bottle’s sleeker lines into its neck have allowed for a more streamlined shape which helps maximise on-shelf appeal. For added versatility, the new variant features the standard and frequently-used 28SP410 neck finish, and it can be combined with a wide range of standard closures and pumps, making the bottle suitable for many different products. The distinctive shape can be further enhanced by highimpact decoration for effective branding. The bottle can be produced in a variety of colours and complemented by attractive screen printing. Its shape is particularly suited to shrink sleeves, which help to accentuate its stylish contours. The new 300ml Tumble bottle is the latest addition to the range of standard PET bottles and containers from PET Power. www.petpower.eu The uncoloured PET bottle on the left was made using 25% PCR while the one on the right has the same PCR content but with 0.05% of the PET enhancer added.","@ID":54}, "TRADE SHOW PREVIEW 45 Sacmi Hall E2 - Booth B51 Caps, labels and more A plant engineering solution for the manufacture of plastic caps - made up of a CCM 48 SC compression machine directly linked to the cutting machine via a timing system – will make its debut appearance in China. The application on display manufactures S30Wstandard caps in HDPE, produced by the new CCM 48 SC with a cycle time of 1,8s. This results in output rates of 1,600 caps per minute. Such production and energy performance has been made possible by compression technology that, compared to alternative technologies, is said to ensure total process repeatability and, therefore, the manufacture of caps with improved weight and size consistency. Among the exhibits is also the Arena RF labeller, produced at Sacmi Nanhai. The solution was developed to meet local producer’s demands for a machine that combines flexibility of use with an ability to handle labels and containers in various materials and formats at output rates of up to 36,000 pieces per hour with minimal label and/or size changeover times. Also of special interest for visitors related to the PET industry are China’s integrated in-line and test facility inspection and quality control solutions: these include the preform vision system (PVS) for preform quality control. Visitors to the fair will have the opportunity to see the new PVS002 Plus, an evolution of the PVS 2 series, capable of testing up to 1,100 preforms per hour with cycle times of just 3s. This solution is said to allow execution of all routine lab tests and – thanks to modularity – can also provide additional functions such as weight and body checks via a patented Sacmi system. Incorporated on the displayed CCM compression machine will be the cap inspection system CVS052. This forms part of a range of solutions developed by Sacmi’s Automation & Service Division for comprehensive control of caps (plastic caps plus decorated aluminium caps and crown caps), labels (LVS) and the entire cap-bottle system. www.sacmi.it The CCM 48 SC compression machine will debut in China with the production of HDPE caps.","@ID":47}, "INSPECTION 22 PETplanet insider Vol. 17 No. 03/16 petpla.net The Innocheck PPI (PET preform inspection) KHS InnoPET Blomax machines with in-house developed preform inspector Better checking I NSPECT I ON S P E C I A L The German supplier of filling and packaging systems has been equipping its KHS InnoPET Blomax stretch blow moulders in series III and IV with inspection devices for many years. This equipment detects errors and damage to preforms and containers. Around 40% of all stretch blow moulders are now fitted with an inspection system. With immediate effect KHS is now integrating its own Innocheck PPI preform inspection unit developed inhouse into its plant engineering. This supplements the Innocheck portfolio which also includes the Innocheck PCI PET container inspector. Typical faults detected by a preform inspector can be foreign objects in the preform or the slightest damage to the preform’s sealing surface which could cause leaks and products to spoil at a later date. If the preform which enters the stretch blow moulder is faulty, this can thus be clearly detected. The Innocheck PPI preform inspector is directly integrated into the stretch blow moulder’s preform separator where it first assesses the quality of the sealing surface. A second end cap imaging camera then reliably detects any distortion or contamination of transparent and practically opaque PET preforms. Even the smallest deviations in colour are detected and the preform length determined with an accuracy of ±1mm. Special image processing software evaluates any possible errors in real time, enabling up to 81,000 preforms to be inspected per hour. Faulty preforms are reliably rejected prior to stretch blow moulding. This saves on compressed air and increases both line availability and consumer safety as only preforms of perfect quality are blown to form bottles. The number of rejected blown bottles is reduced. Thanks to their modular design, all KHS inspection systems integrated into Blomax models or retrofitted into existing Series IV machines are also centrally and conveniently operated through just one control unit. www.khs.com Under the name of Innocheck PPI (PET Preform Inspection) KHS is offering a multistage preform inspection program which it has developed in-house. This is intended to recognise faulty preforms, to find foreign objects in preforms and to detect even minor damage. The Innocheck PPI is therefore said to assist operators with their quality assurance and to help to ensure a troublefree, efficient stretch blow moulding process with a detection rate of almost 100%. Preform sealing surface","@ID":24}, "BOTTLING / FILLING 18 PETplanet insider Vol. 17 No. 03/16 petpla.net Stepless volume-flow adjustment at the filling valve Flexible filling function Based on an article by Florian Angerer, Krones AG With its Proportional Flow Regulator (PFR), Krones introduces a filling-valve component that is said to create the preconditions for a flexible filling function. Instead of the two previously customary fixed flow rates (slow/fast), the flow regulator can create any flow velocity desired up to and including the level- and pressure-related maximum filling speed. Krones put the PFR to the test at the Burg Groep in the Netherlands: for filling vinegar, an extremely acidic liquid with a pH-value of 2.2, and prone to vigorous foaming as well. Vinegar is one of the most demanding liquids around when it comes to its commercial filling. With its pH-value of 2.2 to 2.5, it aggressively attacks all parts coming into contact with it, such as stainless steel, but also, and especially, the seals. What doesn’t make things any easier is its marked susceptibility to foaming, which is why vinegar is a tough challenge for any filling operation. Krones was eager to take on this challenge, and test for its practical utility the PFR filling-valve component, developed specifically for handling vigorously foaming products. The Burg Groep is one of the leading companies on the global vinegar-production market. The firm manufactures natural vinegar with an outstandingly high acidity of up to (or even exceeding) 20%. The vinegars are available as ready-to-use articles for the consumer and also as a semifinished product. In its plant at Heerhugowaard, the Netherlands, a total of three filling lines are up and running, two of which are rated at 7,000 and 8,000 containers an hour respectively. The third line was installed by the group in 2010. From the filler to the packer, it consists entirely of machines from Kosme and Krones, and permits a maximum output of 16,000 containers per hour. At present, however, the line’s speed is limited to 11,000bph, due to the existing blow-moulder. The line comprises an AirCo conveyor, a pressureless Modulfill VFJ filler with 48 valves and an integrated Checkmat F-G, an existing Kosme Star 12T labeller, a Kosme Divipack container spacer and a Kosme Flypack packer. It is used to fill a variety of vinegar-based products, both household vinegar and domestic vinegar-based cleaning agents. Proportional Flow Regulator In developing the Proportional Flow Regulator (PFR), Krones’ intention was to create a component which marries top performance to a maximum of functional dependability for the future, irrespective of the boundary conditions involved. It can be combined with all commonly used metering systems, like a flow meter, a weighing cell or a short-circuit sensor. The electronic control components are installed in every filling valve for a decentralised configuration. The PFR has already undergone tests with milk, juice, vinegar, ice tea, wine, soy sauce and CSDs. As it runs off electricity, there is no need for any pneumatics in this system. Another option is what is called a hybrid structure, in which conventional pneumatic valves are combined with the stepless regulators. One of the advantages in practical operation is that the flow velocity is user-selectable; so the machine can always be run at its maximum possible speed, thus permitting it to be optimally matched to all product-bottle combinations. The PFR makes rigorous use of field-proven materials: stainless steel, PTFE and EPDM, so as to comply with hygiene standards. Intelligent monitoring systems are said to ensure a maximum of functional dependability and machine availability while continual adjustment of the valve function makes for a consistently high level of filling quality. Practical test The technology was installed and tested at the Burg Groep step by step, mostly at weekends, so as not to hamper ongoing production operations. The filler, meanwhile, has been running with the PFR for more than 3,000 operating hours. “Given that filling is performed at continuously changeable speeds, foaming is severely reduced, or even entirely prevented. The foaming problem has","@ID":20}, "CAPPING / CLOSURES 39 PETplanet insider Vol. 17 No. 03/16 petpla.net Figure 4.18 Sports drinks cap in crosssection In glass bottles, for example, practically all the oxygen ingress into the package can be attributed to the closure as glass does not allow oxygen inside the package. Oxygen may enter the package through the wall of PP or HDPE and the liner, the space between the bottle neck and the closure wall, and the interface between the closure seal and the bottle. There are several factors that contribute to the performance of a closure with respect to barrier performance: Headspace: This is the space between the top of the liquid and the bottom of the cap. The larger the headspace, the more oxygen is trapped, and it can interact with the product. Most juice bottles are now filled brimful to avoid any oxygen. Other products are topped off with a shot of nitrogen replacing headspace air. Closure size:The larger the closure, the more the oxygen trapped inside the headspace. Additionally, the larger surface area allows for more opportunities for oxygen to migrate into the bottle. Type of seal: Whenever an end user is concerned about oxygen ingress, the best seal for the type of neck should be chosen regardless of other considerations, e.g., price! Type of liner: Besides the mechanical seal, liners have been developed that incorporate several functions in a multilayer package. 4.3.5 Multilayer liners A lot of development work has been done to make multilayer liner materials that not only seal the bottle but also use passive and active components against oxygen ingress whether it resides in the headspace or migrates from the outside. Experiments have shown that around 80% of the oxygen ingress can be attributed to the bottle sidewall and 20% to the closure. Closure design plays, therefore, a crucial role in protecting the product. There are commercial closures with eight layers of various materials. Usually EVA is present for the mechanical seal. A passive barrier may be provided with EVOH or Nylon. This is necessary as the PP or HDPE wall is permeable to oxygen over time. For carbonated beverages such as beer, the passive layer increases carbonation retention up to five times. As an active component an oxygen scavIn cooperation with In cooperation with IMDvista CLDP Closure Digital Print Full flexibility in formats & design with integrated vision system. IMDvista / PackSys Global SDL Inspection, Slitting and Folding Complete downstream equipment for closure production. IMDvista PECO LUX Inline Preform Process Monitoring In perfect combination with IMDvista Offline Offline Preform Sorting. www.imdvista.ch CLOSURE, PREFORM, BOTTLE and BARRIER Testing New SMART Line | Swiss Made","@ID":41}, "CAPPING / CLOSURES 41 PETplanet insider Vol. 17 No. 03/16 petpla.net Please order your copy at the PETplanet insider book shop: https://petpla.net/books Bottles, Preforms and Closures - A Design Guide for PET Packaging Second Edition by Ottmar Brandau € 115,00 180 pages © Copyright Elsevier 2012 * This article was published in Bottles, Preforms and Closures, Ottmar Brandau, Chapter 4.4 Copyright Elsevier 2012 MHT MOLD & HOTRUNNER TECHNOLOGY AG Your Machine - Our Solution Booth E1E59 1996-2016 20YEARS Fig. 4.23: 4. back to the bottle visible cap Fig. 4.24: 1. closed position Fig. 4.25: 2. after 90° turning Fig. 4.26: 3. after 180° turning Fig. 4.27: 4. after vertical pulling Fig. 4.27: 5. detached pilfer proof ring Fig. 4.28: 6. bock the bottle","@ID":43}, "BOTTLES 57 PETplanet insider Vol. 17 No. 03/16 petpla.net Volvic gets Star Wars fever Right at the start of or just before the premiere of the latest Star Wars film “The Force Awakens”, commercial businesses were getting busy with items connected to the film. Many manufacturers used this opportunity to develop promotional products and offer them to consumers. One example is the Volvic 0.33l PET bottle in the shape of a character. The bottle, which is filled with natural non-carbonated mineral water, is tapered twice, sits easily in the hand and is decorated with a sleeve label. Altogether there are five different designs to collect. The bottle is closed using the well-known green screwcap with writing and a tamper-proof band. www.volvic.de Neckless bottles for orange juice The Swiss Co-op is selling two different sizes of bottle for orange juice with 100% fruit. The clear bottles contain 250 or 750ml and have a large drink opening, their shape making them stand out on the shelves. There is some tapering near the bottom and the closing device fits almost seamlessly with the bottle shape. Under the screw cap with ridges for easier opening, there is a fresh membrane, which must be removed before consumption. www.coop.ch Bulbous bottle for juice Andros, the French producer of juices, fruit desserts, fruit preparations (compote) has been keen since the company was founded to use organic cultivation and careful recycling. The juices are free of sugar additives, colourants and preservatives. The only conservation process used is pasteurisation. Each litre of the 100% directly pressed juice is filled into bulbous clear PET bottles – a reminder of traditional glass bottles – which make the product highly visible. Several paper labels and a green screw cap with a tamper-proof band round off the natural look. www.andros.ch product development caps & closures design high cavitation moulds multi-component moulds closure production systems after sales service competent – professional – inspiring Hoechster Strasse 8 | 6850 Dornbirn | Austria | www.z-moulds.com CHINAPLAS 2016 April 25th-28th meet us at booth W1-T05","@ID":59}, "imprint EDITORIAL PUBLISHER Alexander Büchler, Managing Director HEAD OFFICE heidelberg business media GmbH Bunsenstr. 14 69115 Heidelberg, Germany phone: +49 6221-65108-0 fax: +49 6221-65108-28 info@hbmedia.net EDITORIAL Kay Barton Heike Fischer Gabriele Kosmehl Michael Maruschke Ruari McCallion Waldemar Schmitke Wolfgang von Schröter Anthony Withers WikiPETia.info Doris Fischer doris.fischer@hbmedia.net MEDIA CONSULTANTS Martina Hirschmann hirschmann@hbmedia.net Johann Lange-Brock lange-brock@hbmedia.net phone: +49 6221-65108-0 fax: +49 6221-65108-28 FRANCE, ITALY, UK Elisabeth Maria Köpke phone: +49 6201-878925 fax: +49 6201-878926 koepke@hbmedia.net LAYOUT AND PREPRESS EXPRIM Werbeagentur Matthias Gaumann | www.exprim.de READER SERVICES Till Kretner reader@hbmedia.net PRINT Chroma Druck & Verlag GmbH Werkstr. 25 67354 Römerberg Germany WWW www.hbmedia.net | petpla.net PETplanet insider ISSN 1438-9459 is published 10 times a year. This publication is sent to qualified subscribers (1-year subscription 149 EUR, 2-year subscription 289 EUR, Young professionals’ subscription 99 EUR. Magazines will be dispatched to you by airmail). Not to be reproduced in any form without permission from the publisher. Note: The fact that product names may not be identified as trademarks is not an indication that such names are not registered trademarks. 3 PETplanet insider Vol. 17 No. 03/16 petpla.net WikiPETia.info is here! Dear friends of PETplanet insider, Have you ever tried searching Wikipedia for PET-related subjects? It can be pretty frustrating for the most part. The information is there, it’s just that it is dotted about all over the place. At PETplanet insider we got to thinking about this, and came up with the idea of systematically bringing together all relevant PET related topics and then building them all into our new www.WikiPETia.info site. PET recycling was our starting point and with the help of companies such as Starlinger and Erema we have produced a first rate presentation of this important topic. As with Wikipedia, you’ll find not just items on technologies but also on companies, people and events, and of course, links to external sources. Again, like Wikipedia, everything is easily to hand, allowing you to access, browse, and hopefully find what you’re looking for. For you, our readers, WikiPETia will, we hope, become a vital information resource, and for you, as a supplier, a powerful marketing tool. This is an open system, which means that you have a vital role to play in its success. You can enter, free of charge, a brief profile of your company and its technology, browse the articles already included and thus keep yourself constantly updated on what is happening in this fastmoving sector. Further items on PET will be added on a regular basis. To ensure everything runs smoothly, Doris Fischer will be on hand to help you input your data, and answer any queries you may have relating to content. I look forward to co-operating with you on this exciting initiative. Yours Alexander Büchler","@ID":5}, "INSPECTION 30 PETplanet insider Vol. 17 No. 03/16 petpla.net From quality control to overall equipment effectiveness Interacting inspections The PVS024 offer inspection rates of up to 72,000 preforms/h. Sacmi presents a series of incremental developments intended to facilitate faster, more effective inspection systems. Its solutions can interact with each other and provide essential information on the efficiency of the entire production process. Sacmi’s Automation & Inspection Systems Division is launching technology that is intended to enhance its product range and respond to the most advanced manufacturing needs. First up is an enhancement to Sacmi’s CHS (cap handling system) for quality control of plastic or aluminium caps, which performs inspections directly at the press outfeed or offline. The new CHS4000 model, coupled to the new high speed cap positioning device, can inspect up to 4,000 caps/minute and uses up to seven high resolution cameras to provide a comprehensive range of checks. The CHS4000 can be equipped with optional modules for spark-test identification of micro-holes on the caps and monitoring of the visible, decorated section. The CVS360-3D module inspects the cap perimeter; the company says that this module can detect, directly on the line, every type of defect. It minimises the risk of false rejects by the use of an acquisition method that allows perfect 2D reconstruction of the 3D object. After over two years of extending and refining its PET preform injection press range with the IPS 220 and the IPS 400 with 96 and 128 cavities, Sacmi has developed its PVS (preform vision system) range to enable it to deliver faster, higher-performance inspection of preforms exiting the press. The PVS002, PVS003 and up to the PVS024 offer inspection rates of up to 72,000 preforms/hr. The company’s patented, grid-type control module detects defects normally visible only with polarised light. Another module reads the number of the cavity stamped on the preform itself; this enables real-time sorting by cavity number and thus correlates any defects with the specific cavity where they originated. Sacmi says that the use of up-to-date Artificial Intelligence technology means that number reading is fully reliable, accurate and independent of the font used to stamp the number itself. Upgrades to the BVS (bottle vision system) include the availability of more powerful capture devices. Up to seven high-resolution cameras can inspect all bottle parts, from opening to neck, body and bottom. The BVS has also been equipped with the module that reads the number of the production cavity, which allows manufacturers to trace any defects with faster and more accurately than ever. The infrared illuminator enables integration of the BVS system on any container type, whether IBM (injection blow moulding) or EBM (extrusion blow moulding) technology. The LVS (label vision system) family extends from the electronic positioning system integrated in Sacmi Opera labellers to the LVS360, which can check labelling quality on containers and bottles of any shape. Its CVS360-3D is the first equivalent machine in the world to use 5 megapixel ultra-high resolution colour cameras. It can inspect up to 72,000 bph. Sacmi says that the CVS3000 software used in all of the inspection systems developed by its Automation & Inspection Systems Division provides high levels of interoperability and user-friendliness. Its latest features include the CVSWEB module, which makes machine operation and line efficiency (OEE, overall equipment efficiency) parameters and data available on the Web, which allows them to be seen via any authorised account. www.sacmi.it I NSPECT I ON S P E C I A L","@ID":32},
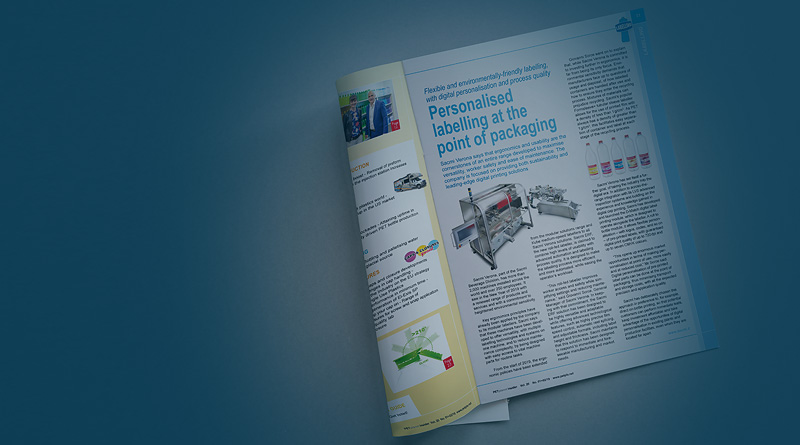