"TRADE SHOW PREVIEW 53 BKG Bruckmann & Kreyenborg Granuliertechnik GmbH Hall 9 Booth A44 A48 / 55 / A57 Prewashing technology Recently Sorema, a division of Previero N. srl, commissioned a new design RPET wash line with 4t/h output capacity. The plant is successfully in operation in an Eastern European country. The system is said to allow the processing of the most contaminated bales of PET bottles and convert them into high quality rPET flakes. The process is claimed to combine the advantages of the bottle prewashing (wet-process) system with dry and clean environment after the patented wet prewashing system. The machine cleans the surface and removes the labels of the bottles, including shrink labels. The labels are said to be perfectly separated from the bottles immediately after the pre-washing phase. The possibility of running clean bottles without labels and eliminating the ingress of water into the bottles improves the efficiency of the recycling operation. Advantages include a reduced consumption of energy, chemicals, and water as well as reduced space requirements. The advantages of the system are to enable the dry phase approach to be reconsidered before the wet grinder. In line with the latest technical development, the rPET fines wash lines are attracting growing interest. The system is already in operation and others will follow in the coming months. The system allows the recovery of a growing quantity of fines which are mostly generated by the increasing percentage of thermoforms into the bottles stream. The fines are hot or cold washed, dried and if necessary sorted by colour and / or by polymers. The material, converted into pellets, have applications in thermoforming and fibres (fines are mostly used in fibres). www.sorema.it A COLOUR IDENT I TY K 2016 19-26 October - Düsseldorf, Germany Hall 6 Stand B24 Sorema Hall 9 Booth D41 & D55 PETplanet insider Vol. 17","@ID":57}, "TRADE SHOW REVIEW 66 PETplanet insider Vol. 17 No. 09/16 petpla.net Review of ProPak Asia 2016: June 15-18, Bangkok, Thailand ProPak Asia grows further The 24th edition of ProPak Asia was another record-breaking event. It hosted 1,976 exhibitors from 48 countries and welcomed more than 40,000 visitors from 68 countries, who were able to see over 5,000 machines on display. The exhibition showcased the latest developments in the field of food and packaging, many of them in PET. One reason for the high number of exhibitors and visitors was the anticipation of the new Asean Economic Community (AEC). Chinese machinery manufacturers’ backyard If judgement is to be solely based on the number of exhibiting companies present at ProPak Asia, Chinese machinery manufacturers are now the leading force for moulds and equipment for injection and stretch-blow moulding in the region. Tech-Long can be considered one of the most advanced Chinese suppliers of turnkey systems for PET manufacturing systems, including injection moulding, stretch-blow moulding, filling and conveying. Previously nestled and almost hidden between other small stands, the company this year had a prime location alongside PET machine heavyweights Krones, Sidel and KHS. In common with the established Western machinery manufacturers, Tech-Long put its focus on communication and discussion with customers, rather than running machines. The neighbouring KHS stand was presenting a very interesting development. The company debuted FreshSafePET, a special coating technology that combines the advantages of glass and PET in a single bottle. A very thin glass inner layer keeps sensitive beverages fresh for longer periods, while the PET outer layer keeps the bottle light and provides the properties PET is well-known for. The market for preform systems and blow moulds gets more crowded. Leading Chinese mould supplier GDXL faces more intense competition from “Unique” (Guangzhou Unique Injection Molding Systems), who presented 72 cavity moulds at its stand. In contrast with GDXL, it offers complete PET preform moulding systems, including injection moulding machines, hot runners and take-off robots. This puts Unique in direct competition with Demars (Zhejiang Demark Machinery) which also offers complete 72 cavity moulds and stretch blow moulding systems, for outputs of up to 24,000bph. Another competitor in this market segment, Guangdong Friend Machinery, showcased a 10-cavity stretch blow moulding machine with a capacity of 18,000bph for 0.5l water bottles. Continuing cap & closures light weighting trend Lightweight design still dominates the mass market. At the Asia Drink Conference, held concurrently with ProPak Asia, Mr Vivek Chabra, President of Sermsuk PLC, delivered a presentation on the emerging beverage markets in Southeast Asia. One of his suggestions for bottle producers was to go into neck bottle set-ups of 33mm in diameter. Closure specialist Bericap introduced HexaLite UL 29/11 SFB, which fits with 29/25mm neck size. It claims weight savings of up to 37%, compared to a 30/25 neck and closure combination. The company also introduced its new flip top press-on closures (CTC IP 29/19 and CTC IP 29/20). The tamper evidence band is designed for left and right-hand opening. Once the flip top is opened with just the thumb, a second tamper evidence function, in the form of a tearoff membrane, safeguards product integrity. Easy pouring is facilitated by an integrated marguerite flow control. Functionality and customisation, rather than light weight, are the main focus of Mikasa from Japan. It produced its first plastic closure back in 1953 and is now one of the leadby Michael Maruschke","@ID":70}, "PACKING / PALLETISING 50 PETplanet insider Vol. 17 No. 09/16 petpla.net SPONSORS The China Road Show Packaging specialist global May 30, 2016 - Engel China We met: Gero Willmeroth, Sales and Service President of Engel Machinery Shanghai Engel is present in Asia with three plants: Korea with a facility for machines from 28 to 400t, Changzhou where they manufacture the new brand Wintec, and Shanghai producing the large machine duo line at 350 to 4000t. While the two Engel plants manufacture 100% Engel machines as per the Austrian model, the new Wintec brand is a slimmeddown-product range of its own and will serve the upper range of the growing mid-market segment. We visited the large machine plant. Austrian technology requires trained staff and so Engel, in conjunction with Alpla, initiated a 4-year apprenticeship programme training course in China that allows young school graduates in China to acquire an Austrian qualification. The programme is running very well; the first year group is close to completion and almost all apprentices from day one are still there. In the Chinese market, the Engel brand is especially well-represented within the automobile sector. The large machine plant thus also obtains 70% of its turnover in this sector. While in the past in China western automobile technology only came to market after years of delays, model changeovers now happen in China within a few months of being released in Germany or USA. Thus Engel manufactures large machines in China complete with all current technology, just as it does in Austria. Back injection, multi-components and glazing are just a few notable processes. Engel does not manufacture the large all-electric packaging machines in China. These are imported as required.Nevertheless, Willmeroth is sticking with the packaging market. For him, the entire logistics sector is still in its infancy. Parcel services unload their packages at street junctions to re-sort them and then deliver them to the addressees. For him, China is an Eldorado for plastic box manufacturers to professionalise the logistics sector. The packaging sector is where he envisions a large potential for growth also for his Chinese-produced Engel machines. www.engelglobal.com Gero Willmeroth, Sales and Service President of Engel Machinery Shanghai (left) and Alexander Büchler","@ID":54}, "PREFORM PRODUCTION 18 PETplanet insider Vol. 17 No. 09/16 petpla.net Interview with SGT - Société Générale Des Techniques The French preform giant upgrades its machinery By Kay Barton June 14, 2016 We met: Mr Frédéric Mignot, General Manager Mrs Lilia Jolly, Manager Marketing and Communications US$15.7 million investment at SGT France promises a billion additional preforms per year Family-run preform manufacturer SGT (Société Générale Des Techniques), which is based in Rezé, France, serves Europe and parts of the African continent. In 2015, 35% of the 2.8 billion preforms that left the factory in France were exported to Africa. Two other production sites in Setif and Rouiba, Algeria, serve local markets exclusively (see interview in PETplanet Insider, issue 5/15). We visited the headquarters and talked with General Manager Frédéric Mignot, nephew and son of the company founders, and with Marketing and Communications Manager Lilia Jolly about the technology and future strategic alignment of SGT. SGT currently has a total of 44 injection moulding machines – all of them Husky brand, which it uses exclusively. Its roll of about 400 customers includes multinational CSD bottlers and national water bottlers. The total turnover of all of the factories was €212 million in 2015. Of that total, €110 million was generated at the Rezé site, which underwent a programme of expansion from February to December 2015. All the production machinery is now in operation; the company’s intention is to increase its output in France by around one billion preforms. “Our investment of US$15.7 million in the new buildings enabled us to expand our site by about 1,100m2. We now have five of the latest Husky HPP5 machines in full production, mainly using 72-cavity tools, which keep us flexible. The whole design is based on full automation, as in the other production areas,” Mignot explains. “One of the new Husky lines is even designed for multilayer preforms.” SGT will increasingly be using this line for customers from the soft drink industry. The first projects are already underway, Jolly divulges, and this market will now be fully tapped and expanded. With its new lines, SGT Rezé now has a total of 21 preform machines. “Depending on requirements, we can deliver more than 200 different models in the drinks and non-food segment, from 9.5g to 650g, with any additives necessary. This includes 19 different neck types – some of which are our own design, such as the 27/31 Frédéric Mignot in front of a new Husky HPP5 Lilia Jolly showing a water gallon preform in front of some product samples.","@ID":22}, "PETpatents www.verpackungspatente.de 76 PETplanet insider Vol. 17 No. 09/16 petpla.net Folded bottle Intern. patent no. WO 2014 / 101956 A1 Applicant: S.A. des Eaux Minerales D’Evian, Evian-les-Bains (FR) Date of application: 28.12.2012 Large volume bottle made of PET for holding water. The bottle that is set upside down into a dispenser, is formed in such a way that it “folds together” on its own when emptied in a prescribed way. Plastic bottle US - patent no. US 2014 / 0183202 A1 Applicant: Niagara Bottling LLC., Ontario (CA) Date of application: 3.7.2014 A lightweight PET bottled that features specials grooves in all areas – neck, grip area, body, and base – in order to achieve optimal load bearing and stability. Aerosol container made of plastic Europ. patent no. EP 2763908 B1 Applicant: Procter & Gamble Comp., Cincinnati (US) Date of application: 16.4.2013 Container for holding and dispensing an aerosol. The container is made out of a mix of PET and PEF to increase stability and resistance to cracks. Form of base Intern. patent no. WO 2014 / 113371 A1 Applicant: Graham Packaging Comp., York (US) Date of application: 14.1.2014 The international application describes several forms for the base of a plastic bottle filled with hot products. The base deforms elastically in a predetermined way for volume reduction. Internal coating Intern. patent no. WO 2015 / 182383 A1 Applicant: Toyo Seikan Group Holdings Ltd., Tokio (JP) Date of application: 13.5.2015 A plastic bottle is coated on the inside in order to positively affect the pouring properties from the container for highly viscous liquids over its working life, and to reduce the amount of what remains. Plastic bottle Intern patent no. WO 2015 / 188515 A1 Applicant: Sidel Participations, Octeville-sur-Mer (FR) Date of application: 9.6.2015 To give stability to a lightweight PET plastic bottle against bursting or other stresses, forming and stiffening the base is especially important. The application describes a particular design for the base.","@ID":80}, "PETcontents 09/16 4 PETplanet insider Vol. 17 No. 09/16 petpla.net INSIDE TRACK 3 Editorial 4 Contents 6 News 68 Products 72 PET bottles for Beverage + Liquid Food 74 PET bottles for Home + Personal Care 76 Patents MATERIAL / RECYCLING 12 Far Eastern Industries in China, part 1 16 A new generation of Holcomer 38 Reaching bursting point PREFORM PRODUCTION 18 The French preform giant upgrades its machinery MOULD MAKING 20 MHT opens Service Centre in Taicang BOTTLE MAKING 21 Suntory’s technology now follows market demand “heavier weight” 22 Greater economy from lower weight 26 Clear containers for coloured concentrates 28 View the elements 30 Second 4l PET bottling line running for Nongfu Spring 32 PET kegs enjoy rapid growth BOTTLING / FILLING 34 Sino Belgium Beer Far Eastern Industries, part 2 BEVERAGE INGREDIENTS 36 A trendy contemporary blend of fruits and vegetables MARKET SURVEY 41 Suppliers of bottle-to-bottle recycling plants CAPPING/CLOSURES 14 Local closure manufacturer making inroads in beverage market 44 Bottles, Preforms and Closures, part 8 AUTOMATION 49 Safe, sound and efficient PACKING / PALLETISING 50 Packaging specialist global TRADE SHOW PREVIEW 52 K Show preview 60 Premiere at the K trade fair: PET Crystal Batch 61 New serie of fully electronic strech-blow moulders EBS Ergon 62 Measuring layer thickness of bottles and preforms with terahertz-technology 64 FachPack 2016 preview TRADE SHOW REVIEW 66 Propak Asia grows further BUYER’S GUIDE 77 Get listed! The China Road Show Page 60 Page 18 Page 30 bottle making","@ID":8}, "BEVERAGE INGREDIENTS 37 PETplanet insider Vol. 17 No. 09/16 petpla.net for decades, and creates new trends and standards on a regular basis. Its “Fruit&Veggie” product portfolio combines the very best that vegetables and fruits have to offer: healthy ingredients and beautifully balanced flavours. WFSI has now composed several new “Fruit&Veggie” concepts for still drinks as well as beverages with high juice content. All of these innovations have a great flavour, combine the classic and the new, and are compelling in their distinctiveness. This gives manufacturers a way to distinguish themselves from their competitors and appeal to a large target group. Still drinks: juicy, fruity, refreshing For those who want an exciting non-carbonated drink with an assortment of additional flavour notes, the current portfolio of WFSI’s Fruit&Veggie concepts has plenty to offer. These beverages are delicious, full of fruit and have a subtle hint of vegetable that will stir up people’s curiosity. They have a fruit content of 27% and 3% vegetable, and the options available include for example orange, pumpkin and ginger, as well as beet with strawberry. The fruits are harmoniously complemented by the right kind of vegetable, creating a fruity non-carbonated beverage with a touch of vegetable. The concept also provides other appealing choices, such as integrating the ever-popular flavour of ginger or a refreshing hint of mint. The product range is also available as a low-calorie option with steviol glycosides derived from the stevia plant. This satisfies consumers’ desire for lower-calorie products and a focus on naturalness with a sweetener from a plant source. The phrases “natural” and “no artificial flavours and colours added” can be stated on the product label. These drinks can also be enriched with vitamins. Juice: endless opportunities to customise products WFSI’s product palette has new brilliantly-coloured concepts for everyone who enjoys juice often and wants to try innovative new flavours. The company’s selection of beverages with a high juice content is diverse and combines several different kinds of fruits and vegetables in green, red, purple, yellow and orange. Consumers can select blends made of concentrates or not-from-concentrate juices with options such as cucumber, kiwi and spinach, or apple, beet and black currant. The vegetable content ranges from 10-38%. If the drink profile is supposed to be more “vegetable-y,” WFSI also has juice concepts with 50% fruit and 50% vegetables. The product range includes delicious choices such as apple, pear, parsnip and yellow carrot or beet, black currant and chili. Certain product options can highlight a special added touch, such as a hint of chili or a peppery note. The bonus feature for the product label: each portion can be counted towards the “five a day” recommendation about fruits and vegetables, thus irrefutably making it part of a balanced diet. www.wildflavors.com","@ID":41}, "MATERIAL / RECYCLING 12 PETplanet insider Vol. 17 No. 09/16 petpla.net SPONSORS The China Road Show Far Eastern Industries in China, part 1 May 30, 2016 We met: Mr S.Y. Lai, Executive President Mr C.J. Lee, PH.D., Sino Belgium Beer and Mr Shih-Fong Lee, bottleplant Manager Far Eastern Industries was founded in 1949 in Taiwan, and is active in many industries. One area is the production of PET, and its precursor and end products. With its 1.3 million tonnes worldwide (total 26mt), it occupies 5th place among bottle grade manufactures. By 2018, production is expected to rise to 1.6mt. The portfolio is partly made up of faster reheat resin, which saves up to 20% of energy when heating up the preforms, or stretch blow machines, which have an oven that is slightly too short for 2 or 2.5l bottles, which allow it to reach full capacity. In China, they are selling PET material and preforms for multinational companies such as Coca Cola. For this purpose, they have set up a preform plant in Suzhou with five Husky-HyPETmachines. On asking S.Y. Lai, Executive President, about whether customers start asking questions if the raw material producer also manufactures his customers’ products, I received the answer: “When we started operating in China, it was mainly to serve our international brands better in this area, such as Coca Cola and Pocari, so in 2011 we decided to install the first two preform machines. That this was the right path to take is evidenced by the fact that we have five lines running today, three of which boast 96-cavity tools, and two with 144cavity tools.” The injection moulding hall is hermetically sealed; we could only enter the production site through a complex disinfection area. The injection moulding machines are separated by a wall for packing the preforms; here they fall into the octabins. The preforms are not shaken, as customers do not want this. Altogether, 73,000t of the PET production go into their own preform plants in China, Taiwan, and Malaysia. By 2018, it will be 106,000t. In terms of growth markets, Lai specifically has Japan in his sights: “We have been delivering preforms for various applications to Japan for many years. I think we will set ourselves up even better there in the future.” He is expecting another disproportionate growth area in the production of APET for sheets. “Today we produce 115,000t of PET sheets for packaging; I believe in 2018 it will be 200,000t. Many companies are moving away from PVC foil and towards PET. In addition, the demand is growing, especially for food packaging.” For the future, Lai is looking at an inexpensive mono-material that better meets all requirements for barrier coatings than the previous material, in particular regarding UV protection, oxygen barrier and CO 2 impermeability. Vertical integration at Far Eastern is by no means complete yet. From the production of MEG and PTA to the production of PET and preforms, an internal brewery has been added with its own PET bottle production. More on this in part 2, page 34. www.feg.cn Outside of China, the Taiwanese also produce rPET on a Bühler machine (bottle grade). At the moment they produce 90,000t/a, in 2018 it is expected to be 125,000t.","@ID":16}, "ON SITE 71 PETplanet insider Vol. 17 No. 07+08/16 petpla.net ONsite An ErgoBloc L twice over Gaseosas Posada Tobón (Postobón), Colombia’s market leader in the CSD segment, is stepping up operations at its plants in Yumboand Bogotá. In the summer of 2016, Postobón is commissioning two complete lines from Krones. One of these is tasked with filling CSDs in the Yumbo facility at a speed of 54,000bph, while the second one in Bogotá, rated at 40,000bph, will be handling water. It is on the latter line, too, that the Cristal brand will be bottled, for which Krones has developed new lightweight PET containers: The 0.33l bottle, for example, weighs a mere 8.4g. For the first time, ErgoBloc L technology will be used in both plants. The ErgoBloc L system consists of a stretch blow moulder, a labeller and a filler, and will be complemented in each line by a conventional dry end. Krones can look back on a long-standing business relationship with Postobón. The Colombian beverage producer has already installed 14 Krones PET lines in its facilities, and together with Krones has achieved purposefully planned growth. www.krones.com","@ID":75}, "PRODUCTS 69 PETplanet insider Vol. 17 No. 09/16 petpla.net Bericap’s new closure developments for 5-gallon container The closures used for 5-gallon water containers are known as HOD-Home and Office Delivery-closures. The necks of these containers are standard across the world. Due to the blow moulding process, however, the necks usually exhibit poor quality and a variation in diameter which often results in leakage from 5-gallon containers, except where an adequate HOD closure is used. In response to the poor quality of the bottle necks of up to 5-gallon containers, several years ago Bericap developed a 2K HOD closure (shell plus liner) which ensured absolute tightness even on poor bottle necks and under extreme supply chain circumstances. In line with the global trend towards improving the quality of packaging and cutting costs, Bericap has developed a lightweight 2K HOD closure, saving about 30% of resin. Over the last few years some HOD bottlers in North America, Europe and Asia have started to improve the packaging quality of the HOD containers by moving from a blow-moulded container to an injection-moulded PET container. The necks of such containers are of good quality with only small neck diameter tolerances. Bericap has successfully developed a liner-less one-piece closure fitted with a specific seal “Valvelock Trumpet”. It was tested successfully on new PET necks and the 5-gallon containers have proven to be leaktight. Both new closure types are available with a centre shutter and also with a low-cost pierced centre membrane. In addition, Bericap has developed an ultra-light neck/closure solution, Valvelock SuperShort, for one-way PET containers in cooperation with Sipa. Weight savings in excess of 18% on the neck and 40% on the closure are achievable. www.bericap.com","@ID":73}, "petpla.net D 51178; ISSN: 1438-9452 No. 9 2016 MAGAZ I NE FOR BOT T L E R S AND BOT T L E - MAK E R S IN THE AMERICAS, ASIA, EUROPE AND ALL AROUND THE PLANET 07 . 09 . 16 MARKETsurvey Bottle-to-bottle recycling plants Page 41 The China Road Show Page 20 bottle making Page 21 Page 52 k-online.com Messe Düsseldorf GmbH P.O. Box 101006 40001 Düsseldorf _ Germany Tel. +49(0)211/4560-01 Fax +49(0)211/4560-668 www.messe-duesseldorf.de After 3 years, we’re ready to go again. K 2016 presents you the best that engineers, chemists and researchers currently have on offer: machinery, technology, materials, tools, applications, and forwardlooking products, processes and solutions. The best basis for global business, the perfect decision-making platform for investment. With some 3,200 exhibitors in 19 exhibition halls on more than 171,000 sqm of exhibition space, the world’s premier trade fair for the plastics and rubber industry will once again be presenting the entire range of products and services that the industry has to offer. Everything that will move the world in the future. Plan your visit now. I t ’ s K T i m e T i m e f o r D e c i s i o n s","@ID":3}, "TRADE SHOW PREVIEW 58 PETplanet insider Vol. 17 No. 09/16 petpla.net Agr Int. to display the CrystalView system for managing PET bottle crystallinity Agr International offers a number of products that are designed to aid bottle manufacturers achieve their most aggressive light weighting goals while maintaining the highest quality. Agr products are designed to assist container producers, converters and fillers stay competitive while meeting the increased quality demands of today’s changing world. Agr will display their latest developments in this line of products as well as an array of quality management and process control equipment for plastic containers. The Process Pilot system interfaces with the blowmoulder to provide precise material thickness distribution on a per bottle basis while managing the blowmoulder to eliminate the effect of process and environmental variables that impact bottle material distribution throughout the production cycle. With the trend towards ever lighter bottles, the Process Pilot system is the light-weighting tool. This system offers bottle producers the ability to aggressively light weight bottles to the absolute minimum, while providing the confidence that material is distributed appropriately. The Process Pilot system makes it possible to produce consistent high-quality bottles on a 24/7 basis regardless of operator skills, environmental changes and preform variations. The latest enhancement to the Process Pilot product line is the CrystalView material optimisation system. The CrystalView system provides PET bottle manufacturers with the means for automatic management of material orientation/crystallinity. The CrystalView system works in conjunction with the Agr Process Pilot blowmoulder management system to simultaneously manage material distribution and optimise material orientation. By doing so, material orientation is optimised over the entire bottle, making it possible to produce the best possible bottles at the coldest practical processing temperature. www.agrintl.com Agr International Hall 11 Booth B40 Jomar launches next-generation injection blow moulding machine Jomar Corp., a global manufacturer of injection blow moulding (IBM) machinery for the pharmaceutical, healthcare, personal care, beauty, food and beverage, and household products industries, has announced the launch of a next-generation injection blow moulding (IBM) machine series that incorporates a customdesigned servo-driven hydraulic system. The new Jomar IntelliDrive series delivers major improvements in energy consumption, output, and performance while also maintaining the machine’s footprint. The Jomar IntelliDrive series features precise servo-driven hydraulics that reduces energy consumption by 40-50% and boasts a dry cycle time of 1.8s which is significantly faster than standard hydraulic machines. Jomar engineers worked in partnership with Bosch Rexroth, Charlotte, N.C., USA to develop a proprietary use of servo-driven hydraulic technology to power the machine and plastifier. The machine also features a closed-loop system for the machine’s clamping system, which delivers exact control over the clamp’s speed and position. This creates faster speeds for opening and closing while simultaneously reducing impact upon tooling, thus prolonging the lifespan of the moulds. The new featureenhanced IntelliDrive IBM machine has exactly the same footprint as its standard hydraulic counterpart. www.jomarcorp.com Jomar Corp Hall 14 Booth A32 competence inside ® Crystallisation without detours Efficient processing with PET-CrystalBatch Direct path to crystalline PET masterbatch: cpc unites the pelletizing and crystallisation process with an innovative method. This results in homogeneous, dust-free pellets that feature a superior structure thanks to the gentle production. PET CrystalBatch: reliable premium quality, readily available and highly efficient for processing. www.colorplasticchemie.de New Hall 6, Stand D 76 Colour and additiv masterbatch","@ID":62}, "TRADE SHOW PREVIEW 57 CHOOSE THE NUMBER ONE. DISCOVER EREMA's SECRETS at K2016 Hall 9 / StandC05 What's the secret of success? careformance! Negri Bossi presents “The show goes on” On the stand will be the first showing of its new generation of all electric “Project ELE”. With both improved physical specification and performance this completely new product is designed to have a wider appeal in areas such as packaging and medical. The machine has the all new Tactum multi-touch controller with features such as remote access, in built camera and of course gesture navigation thanks to the introduction of the multi-touch. The machine also features its new “smart flex 2” locking unit with a different toggle geometry designed to be coupled specifically with electric closing and to have characteristics optimised to its target market. The range has 11 models from 50 to 650. Available to see at the show will be two new X concept clamp units, an 850 unit with hydraulic actuation and 720 with electric actuation. The new clamp units are designed to have all the positive characteristics of a toggle whilst competing with two platen units in such aspects as footprint and cleanliness. The 850 unit will be shown as a complete machine which will highlight certain concepts and technologies that the brand will look to release on future series models. Negri Bossi already at the forefront in controller technology with both the Tactus (single touch) and Tactum (Multi touch) controllers, will also give visitors a glimpse into the future of how new technology can be applied to make the interface more intuitive and easy informative. www.negribossi.com Negri Bossi Hall 15 Booth B22 Coordinate operation All of the components within a compressed air system should operate as efficiently as possible: compressors, compressed air treatment and distribution systems. True efficiency is measured at the system level. In other words, components do not work in isolation, they work together in perfect coordination. In modern compressed air stations from Kaeser, this aspect is performed by the advanced Sigma Air Manager 4.0 (SAM 4.0) compressed air management system. This system automatically monitors operating conditions, together with current air demand, in order to coordinate operation of the connected system components. The result: a dependable supply of quality compressed air with cost-effectiveness, reliability and availability. This concept minimises service costs and improves value retention of the entire system. Also on display is the technology of the CSD/CSDX series of rotary screw compressors and Secotec TF and TE series refrigeration dryers providing efficient compressed air treatment. www.kaeser.com Kaeser Hall 11 Booth C65","@ID":61}, "BOTTLE MAKING 29 PETplanet insider Vol. 17 No. 09/16 petpla.net would meet the targeted launch date; a process that included simultaneous development of four custom tools including a new 16oz. PET production mould developed in only eight weeks. The development process involved TricorBraun engineers, Prestone stakeholders and a contract manufacturer that could efficiently and costeffectively fill the complex package. Prestone was able to get to market in record time. The final package consists of four components: a 16oz. PET primary bottle, a 3oz. fitment bottle made of injection moulded clarified PP, a 3oz. clarified PP canister with a 51mm custom squeeze and turn closure, and a PP lid that snaps on top of the primary bottle. The fitment bottle features a “wagon wheel” openwork neck ring that mates with the primary bottle, allowing both liquids to pour simultaneously during application. All of the bottle’s elements were moulded by Currier Plastics, Inc. using moulds designed by TricorBraun and built by its manufacturing partners. The filled bottles are shrink labelled with labels that carry both branding and use instructions for each product. The label includes two perforations: one down the side of the top canister and one around its base, allowing users to remove the canister. With a pinch and a turn, the cap of the top canister is removed for dispensing. The complexity of the package and Prestone’s tight deadlines required TricorBraun and Prestone to collaborate closely to ensure that everything would work together, including running test bottles down a filling line to confirm its stability and functionality. “We have been extremely pleased with TricorBraun’s ability to work closely with us in timely fashion to complete this very complex project,” Kalagher says. “Designs were approved in January and by April we had our products on shelves.” www.dupont.com www.tricorbraun.com S.M.A.R.T.* * Self-Monitoring, Analysis andReportingTechnology The truly S.M.A.R.T. REVOLUTION at the K2016 Time is your money – improve and decontaminate your PET within minutes Add value to your rPET – adjust the IV-level and keep it in a narrow band – automatically Make sure everything is running well – monitor the machine performance and pellet quality on your mobile device Experience the Next Generation of S.M.A.R.T. plastic recycling innovations! Düsseldorf, 19-26th October 2016, Hall 09 Booth 9C30 Take advantage from the new PET-Improvement Process LSP (Liquid State Polycondensation) and be one step ahead. MEMBER OF for PETUp/Recycling","@ID":33}, "BOTTLE MAKING 31 PETplanet insider Vol. 17 BIG CONTAINERS, ONE STOP SOLUTIONS 7 INJECT BLOW FILL PALLETIZE SIPA S.p.A. - Via Caduti del Lavoro, 3 - 31029 Vittorio Veneto (TV) - Italy Tel. +39 0438 911511 - Fax +39 0438 912273 - e-mail: sipa@zoppas.com ^^^ ZPWH P[ Nongfu Spring, which was established in 1996, is best known for its natural spring water drawn from the ‘Lake of a Thousand Islands’. Designated as one of China’s most important tourist destinations, the lake spans an area of 573km2 and includes 1,079 islands. Although Nongfu Spring has developed several other natural springs subsequently, its site at the ‘Lake of a Thousand Islands’ remains the largest and is the best-known. For each of its production sites, the company has built large-scale facilities dedicated to bottling water from na-tural springs. The water reaches the production line in its natural state, retaining the original taste and purity of the spring water. A second Combi PET line Nongfu Spring’s first PET 4l bottles were launched commercially in the Chinese market in 2014 and immediately received a positive response from Chinese consumers. They met the growing market demand for such family-oriented packaging in China – which registered a growth in sales in 2013 of 53% in the 4l bottled water format. Since the launch of its PET bottles, Nongfu has seen its sales increase significantly in this market segment. Based on the success of this first line running in the main Nongfu Spring production site at the ‘Lake of a Thousand Islands’ (known as Qiandaohu in Chinese), located just 350km Southwest of Shanghai, the company emphasised its confidence in Sidel by acquiring a second line, based on the same Combi 14 technology. It is now running at 14,000bph, which increases Nongfu Spring’s production capabilities while achieving a great level of performance. www.sidel.com www.nongfuspring.com","@ID":35}, "PETnews 6 PETplanet insider Vol. 17 No. 09/16 petpla.net 50 companies already and counting! In www.wikipetia.info we have now posted details of 50 companies in the PET sector together with their products and services. https://petpla.net/wiki?title=Companies Would you like to be part of our century of companies? Open an account at doris.fischer@hbmedia.net and submit your company profile - free of charge. We look forward to welcoming you to the Wikipetia community. www.wikipetia.info The LiquiForm Group announces Krones AG as new development partner The LiquiForm Group has announced that Krones AG, a global manufacturer of filling and packaging equipment, has entered into a technology licensing agreement to further develop and commercialise LiquiForm’s forming and filling manufacturing technology. “With the LiquiForm technology, Krones has an opportunity to build on existing bottling technology, intellectual property and know-how to develop unique industrial solutions for improving the total cost of ownership for our customers even further,” said Dr Christian Compera, head of bottling technology at Krones AG. LiquiForm technology combines container forming and filling processes into a single step. The technology uses liquid product instead of compressed air to form a rigid plastic container, a process which is said to offer an opportunity for more sustainable and efficient operations as compared to traditional blow and fill technology. “We are pleased to have Krones as a licensee, given its history of technology and innovation leadership in processing, filling and packaging,” said Ashish Saxena, vice president and general manager of The LiquiForm Group. “Adding to the existing efforts of Sidel, Amcor, and Yoshino, Krones will aid the technology commercialisation and enable LiquiForm to reach its full potential.” www.krones.com www.liquiformgroup.com Greiner Packaging establishes joint venture with Indian packaging manufacturer Greiner Packaging is continuing to broaden its international market position by expanding in India. This move will make Greiner Packaging India Pvt. Ltd., a joint venture with the New Delhi-based Century Ultrapack, one of the leading providers of plastic packaging in the Indian dairy industry. Greiner Packaging is establishing a joint venture with the successful Indian company, Century Ultrapack. The new venture is doing business under the name Greiner Packaging India Pvt. Ltd., Greiner Packaging has acquired majority ownership. On the heels of its expansion in Turkey last year, Greiner packaging is thus taking another step toward the growing Asian markets. The goal of the joint venture is to be able to offer Greiner Packaging’s high standards in India as well. This will make it possible to supply large multinational customers in the country for the first time, greatly improving product quality and safety, and focusing on hygiene and production by modernising the available infrastructure. In the first year alone, investments will also be made in a significant expansion of production capacities using Western technology. Headquartered in New Delhi, Century Ultrapack was established in 1980 and is owned by the Bajaj family. Altogether, a total of 135 employees, 62 of them temporary workers, are working for the company, which is among the leading suppliers of plastic packaging in the Indian dairy industry. To date, it has most notably been supplying customers such as Mother Dairy, Amul or Pepsico in the northern part of the country. Its portfolio includes over 250 different packaging products, mainly for milk products and ice cream. www.greiner-gpi.com Indorama Ventures enters long-term agreement with Cepsa Indorama Ventures Public Company Limited (IVL), a leading producer of intermediate petrochemicals, and Compañía Española de Petróleos S.A.U. (“Cepsa”), an energy group, announced the expansion of their strategic partnership with the signing of an exclusive supply agreement for metaxylene, a key feedstock for the production of Isopthalic Acid (“IPA”), a high value-added chemical additive used in the manufacture of PET, coatings and other resins. Following the supply agreement, Cepsa will construct its second metaxylene unit for exclusive supply to IVL. The new Sorbex unit, a near replication of the existing unit, will have a capacity up to 70,000 metric tonnes per annum. Together with the existing metaxylene unit, Cepsa will be able to supply the entire production to Indorama Ventures’ co-located site, which is integrated with Cepsa’s refinery in San Roque, Cádiz, Spain. The additional new supply is expected to come onstream in 2018. Indorama Ventures acquired the vertically-integrated business of IPA, PTA and PET from Cepsa in Spain in April 2016 and expects to make further investments at this location to improve the capacity, reliability of supply and service of goods to customers in a competitive environment, maintaining the site’s excellent track record driven by its employees. Mr Aloke Lohia, Group CEO of IVL said, “This agreement will allow us to cater to our customers’ growing IPA needs globally, from a reliable production platform with proven technology and a competitive supply chain infrastructure. The global IPAmarket is growing at 5%/a and it is our responsibility as a leader to support the growth effectively.” www.indoramaventures.com","@ID":10}, "CAPPING / CLOSURES 15 PETplanet insider Vol. 17 No. 09/16 petpla.net CAPPING / CLOSURES 15 info@hasplastik.com Tel: +90 212 695 50 00 Fax: +90 212 694 97 24 100815dmyR .com Bericap has also improved the opening and closing of the upper lid (now made out of PP material which improves the functionality of the hinge and provides a more premium look). With a slight push of the opened lid, it will almost completely closed the opening in the closure and a slight press on the lid, this now has an audible click. The whole operation of opening and closing the lid can be easily accomplished with one hand. The developmental centre in Spain developed the closure for the Chinese market. It is, of course, also intended to be available for the other Asian markets. Depending on design, the closure has now become lighter thanks to the flex band, and in the neck area the bottler can also achieve some savings in PET resin (switching from double neck ring to single neck ring), while at the same time, achieve even better functionality and appearance of the closure. For Michael, this project is typical for his customer relationships. He values togetherness in this constant struggle for the best solution. In this project, the customer now has a distinctly higher security standard, an improved sealing procedure, and can save on material at the same time. For the beverage industry, as the overall market stagnated last year, Uni-President of Taiwan was the star performer with their RTD Tea with Michael Chen talking about the major neck finishing 30/25 in the Chinese water market Bericap’s latest development’s 38mm closure with overcap last year. Specifically for the water market in China, the major neck finish is still the 30/25 neck finish, while there is also a trend to go into the 29/13 neck finish as well. It looks like these may be the two major neck finishes in the future. Michael estimates the inhouse production of beverage closures to be at more than 50%. In his opinion, the typical mind-set in China is to make everything yourself, and this won’t change in the next few years. Apart from foreign closure manufacturers, he is increasingly seeing local closure manufacturers making inroads into the beverage market, with a marked downward effect on prices. Within the next five year, two more plants are planned to be set up in South-western and Northern China. Strategically, this will allow Bericap to have a more complete market coverage of the whole China market and strategically important as well for key customers or potential key customers whose sales coverage is nation-wide China. www.bericap.com","@ID":19}, "PRODUCTS 70 PETplanet insider Vol. 17 No. 09/16 petpla.net PET Engineering designs the bottle for ‘everyday climbers’ Levissima, belonging to the Sanpellegrino Group, presents its new ‘#LA75’, whose packaging is the result of the collaboration with PET Engineering based in Treviso, Italy, which already handled the development of Levissima 0.5l, launched in 2009, and Levissima LaLitro, winner of the 2011 Packaging Oscar, both of which are still in the market. The brief given to PET Engineering stated two ‘must-haves’ for the packaging: create a bottle that could easily be carried around every day and which also could visibly express the unspoilt purity of the Levissima water that gushes from the Valtellina glacier. PET Engineering’s team came up with a slender and clean shape with an ergonomic and functional grip. The decorations around the grip actually work together with the push & pull top, allowing the bottle to return to its initial shape after every use. The cone-shaped neck has a raised feature showing the Valtellina Mountains, keeping the theme of the other Levissima-branded bottles, such as the prestigious 750ml glass container for the Ho.re.ca. channel. The new ‘#LA75’ is transparent and intended to represent the purity of Levissima water. It is very light, making it easy to slide inside your handbag, gym bag or computer backpack; it is easy to handle and ergonomic, perfect for both indoor and outdoor activities. www.petengineering.com www.levissima.it Prototype tooling for stretch-blown PET beverage bottles Clariant announced availability of new blow-moulding tools that can help customers evaluate how Clariant colour and additive masterbatches perform in real-world applications. The tooling is available for use on full-size production blow-moulding machines located in the Company’s West Chicago, IL, USA technical centre. The new single-cavity tool, which is intended for reheat stretch blow moulding of clear or coloured PET polyester resins, produces a 12-oz (355ml) round bottle with a long neck and curved sides. The design is intended to reflect current design trends for liquor bottles, but can also be used to evaluate wine, soft-drinks and other food and beverage containers too. “This new mould includes the details that customers told us they wanted in prototype tooling,” explains Peter Prusak, Head of Marketing, Clariant Masterbatches North America. “The tooling we’ve had in the past produced flask-shaped bottles and the broad, flat panels where not as representative of the shapes that producers of liquor bottles and other beverage containers are looking for today.” The tooling can be used to evaluate not only colour, but also performanceenhancing additives and barrier properties as well. Prusak says that the way plastic materials stretch to create a bottle’s shape can vary depending on the colour and other ingredients in the compound. A resin/masterbatch combination that works well in one shape can develop cosmetic flaws or unacceptable physical properties in another. This is why it is so important to produce shapes that more accurately mimic the actual end-product containers. www.clariant.com","@ID":74}, "NEWS 10 PETplanet insider Vol. 17 No. 09/16 petpla.net www.bericap.com Unique range of light weight screw and sports closures for light weight PET neck standards for water • Closures for all common neck sizes 26/22, 28mm (PCO 1810, PCO 1881), 29/25, 30/25 • Light weight Hexalite range allowing light weight neck • Still water closures suitable for N 2 dosing • Sports closures fulfill BSDA requirements • Boreseal systems for excellent tightness • Consumer friendly opening forces BERICAP Technology for still water Husky continues investment to better serve Hot Runner customers Husky Injection Molding Systems announced that a state-of-the-art, automated manufacturing line is now in operation at its Luxembourg facility. This is the third straight year that Husky has made a significant investment in new manufacturing equipment to support its growing base of hot runner and controller customers. In January 2016, Husky began producing hot runner manifolds on one of the advanced automated manufacturing lines. “As our global customer base for Hot Runner and Controller solutions continues to grow so does the complexity of the moulded parts that we help solution. I’m very excited about where we are taking our business and how this significant technology investment will enable us to support our customers and help them to grow their businesses,” said Stefano Mirti, Husky’s President of Hot Runners and Controllers. “Our new manufacturing line will enable shorter lead times and provide even more capability to produce highly repeatable manifolds of the best quality.” Husky currently produces hot runners and controllers on three continents in more than 54,000m2 of manufacturing space. Additional investments are planned for hot runner manufacturing in its United States and China facilities. Husky’s goal is to be the industry’s first choice for melt delivery systems, as seen by its innovative approach to reducing sources of waste and variability in the injection moulding process. The continued investments in Husky’s Hot Runners and Controllers business is intended to ensure Husky is best able to meet the need of its hot runner customers on a global scale. www.husky.co Graham Packaging will close New Jersey plant According to a WARN notice filed with the New Jersey Department of Labor and Workforce Development, Graham Packaging is going to close its plant in Belvidere, New Jersey, USA. The effective date is September 26, 2016. The closing of the plastic container manufacturers’ facility will affect 71 employees. www.grahampackaging.com 12th China International Recycled Polyester and PET Packaging Conference & Exhibition At the 12th China International Recycled Polyester and PET Packaging Conference & Exhibition, organised by China Chemical & Fiber Economic Information Network (CCFEI) and Dr. Thiele Polyester Technology, PETplanet will be amongst the conference speakers. In 2015, this annual event has been attended by more than 400 participants. Date: September 21-23, 2016 Venue: Holiday Inn Shanghai Pudong Kangqiao, China Alexander Büchler will speak about the PET beverage market in China. Having visited around 30 companies involved in the PET beverage market during the PETplanet insider China Road Show, Alexander will share the insights he gained concerning trends in Chinese mould making, machinery manufacturing, preforming, bottling and capping.Other conference topics will include in-depth analysis of the current economic environment and China’s beverage and polyester market today and in the H2 perspective. In addition, there will be a focus on idled PTA units, beer in PET and bio-BGPET as well as a session on r-PET and virgin polyester as each other’s substitute. Supported by Recycled Fiber Commission of China Chemical Fiber Association and China National Chemical Fiber Corp., CCFEI and Dr. Thiele Polyester Technology are also to hold the 2nd China International PET Packaging Conference. Relevant government officials, industry associations, raw material suppliers, polyester producers, beverage companies and traders, from home and abroad, will gather again to discuss economic background, industry performance and highlight issues for the year of 2016, and look into market future. www.ccfei.net","@ID":14}, "CAPPING / CLOSURES 14 PETplanet insider Vol. 17 No. 09/16 petpla.net SPONSORS The China Road Show Local closure manufacturers making inroads into beverage market May 31, 2016 - Bericap Shanghai We met: Michael Chen, Managing Director F.l.t.r.: Michael Chen, Managing Director of Bericap China and Alexander Büchler, PETplanet Insider in front of the Editourmobil In 1997, the plant in Kunshan near Shanghai was Bericap’s first plant in Asia. Since then, a second plant has been added in the south, and the new plant in Malaysia that replaced the facility in Singapore is only one year young. We are meeting Michael Chen, who has been Bericap China’s Managing Director for ten years. In the Kunshan plant, Bericap produces for almost all target markets, such as beverages, foods and non-foods. As the peak seasons of the different sectors in general follow one another with some overlap, this provides a good overall workload for the plant, with its 66 injection moulding machines and a production of 4.2 billion closures. Beverages do well in the summer, from April to September. The festival season, which reaches its peak with the Chinese New Year in February, is hot on summer’s heels, foods and non-food applications ensure fully-occupied machines in between these times. One focus is the closure for edible oil and sauce. In China there have been a few scandals around oil, where used oil was collected, cleaned, and sold again in original bottles. For this reason, Chinese consumers are very wary today, making sure they’re only getting originally sealed containers. So far, Bericap has been supplying a closure for this with a safety tear-off band that fits onto a double clips neck finish. Refilling while not destroying the original closure was difficult, but feasible. In discussions with his customers, Bericap China has been undeterred in offering something that can no longer be resealed without leaving traces. This became a closure that looks the same from the outside with a safety tear-off band, but attaches itself at the single ring neck using a flex band in such a way that it cannot be taken off anymore without showing signs of tampering.","@ID":18}, "BOTTLE MAKING 21 PETplanet insider Vol. 17 No. 09/16 petpla.net SPONSORS Suntory’s technology now follows market demand “heavier weight” bottle making The China Road Show June 1, 2016, Huiyuan Suntory (Shanghai) Beverage, Shanghai We met: Hioki Munetaka, Beverage Technology & Quality Assurance Department Director and Atsuhiko Iida Brand Division, Director The Japanese beverage company Suntory, with its total turnover of almost US$23bn, is one of the ten largest food manufacturers in the world. Some of its most famous brands are Yemon (green tea), Orangina and Jim Beam. In China, Suntory has been running its own production since 1984. Initially, the company started brewing beer. In 1995, a joint venture for hot-filled beverages such as tea was set up. In 1996, a second brewery followed in Shanghai. In 2003, the company bought itself out of the joint venture, then again formed strategic alliances with new partners in 2015. In recent years, China has moved in a completely new direction. Together with its local partner Huiyuan, the Japanese re-set the market. Suntory made a decision that they would not have their own plants, all production go to contracted factories (OEM). Since then Santory has been focusing on product development and brand management. The beer activities were sold to Tsingtao. At the intersection between production at Huiyuan and Suntory sits Hioki Munetaka, Beverage Technology & Quality Assurance Department Director. He ensures that the 250 million PET bottles are all of the best quality. Suntory is committed to Japanese principles, such as safety and quality. This cannot be achieved with discount brands, and so all products by Suntory are pitched at a reasonable mid-price point. Clocking in at over 20 years, hot-filled tea has been running the longest. The product is now entering its second generation on the Chinese market. This is unusual, as the Chinese market moves very fast and is prone to change, Atsuhiko Iida, Director of the Brand Division, explains. A new line of flavoured water market is primarily a market where packaged beverages are consumed on the go. Sports caps are still not on Alex’s radar. With a final price of about CNY 5 (EUR 0.67), it is difficult to turn the added value of sports caps into turnover. In China, Alex is seeing another trend in e-commerce. They order whole cases (24 bottles) on the internet for delivery direct to their homes for their convenience. The price per bottle then goes below the retail price. Neither Hioki nor Alex is keen to forecast trends in China over the coming five years. The market there is too fast-paced. The only thing that is certain is that that they will continue to research, develop, and bring new flavours to market there, always under the watchful Japanese premise of safety and quality. www.suntoryfoods-china.com brand that was launched three years ago took off in a big way which has become a new category in the market. 30% of the products are running on hot-fill machines, 60% on aseptic and 10% in cans. In respect of the weight of hot-fill bottles, Hioki has been working on weight reduction. In 2012, he was able to go from 26.5g to 23.5g by design optimisation. In the last year, with a new neck finish, he was able to reduce it to 21.3g. He has also been devoting considerable effort over the years to aseptic bottles. In 2014, he got the weight down to 16.8g, in 2015 to 14.8g, and then Marketing issued a cautionary note: Chinese consumers associate soft bottles with cheapness, so the weight was increased again. For Hioki, this was the first time in his career that he was able to properly put on weight. Currently in China, the Suntory aseptic bottle is being produced at 22.04g, and even that is slightly heavier than the hot-fill bottle. Despite the high weight, savings are made at the base of the bottles via Husky’s Ecobase design. In Japan and everywhere else, Suntory is continuing to fill lightweight bottles. At Toyo Seikan in Shanghai, the aseptic products are bottled profitably by machines developed by Toyo Seikan in collaboration with Lehui, a Chinese filler manufacturer. The preforms and closures are also produced at Toyo Seikan. Apart from 0.5l, small packaging sizes of about 350ml are also important, because the Chinese F.l.t.r.: Atsuhiko lida, Alexander Büchler and Hioki Munetaka","@ID":25}, "TRADE SHOW PREVIEW 65 PETplanet insider Vol. 17 No. 09/16 petpla.net PETnology/tecPET GmbH | Regensburg, Germany Phone: +49 941 870 23 74 | Fax: +49 941 870 23 73 info@petnology.com PET Passion Week2016 NUREMBERG, GERMANY 07-10 NOVEMBER 2016 CONFERENCE 07-08 NOVEMBER www.petnology.com Free entry or VIP tickets End-User Special: PET AT BRAUBEVIALE 08-10 NOVEMBER www.petpassionweek.com INFORMATION PARTNER SUPPORTED BY GernepHall 3 Stand 3-105 Due to flexibility of the Gernep-rotary labelling machines to be equipped with different glueing systems and the possibility to design the labelling machine in accordance with different equipment requirements - Gernep labellers are in duty in breweries, wine, spirits, water and soft drink bottling plants as well as in the chemical, pharmaceutical and cosmetics industries worldwide. Features of Gernep-rotary labelling machines are on the one hand, the modular design of the basic machine with the opportunity, to vary different container orientation processes, label control units and bottle plate drives. On the other hand Gernep rotary labelling machines provide the flexibility to use different glueing processes like: cold glue labelling from the magazine, hot melt wrap-around labelling from the magazine, hot melt labelling from the roll and self-adhesive labelling with all its individual advantages in combination on one flexible platform. To meet all decoration demands in different industries, the rotary labelling machine Gernep Labetta is specialised in universal cold glue labelling, Gernep Rollina in affordable hot melt wraparound labelling out of the magazine and the Gernep Rollfed in efficient wrap-around labelling with hot melt from the roll. The newly developed Gernep Soluta - in the optimised control and security design – is the answer to match the constantly increasing demand for flexible and diverse container decoration in self adhesive labelling. The objective of developing the Gernep Labetta “2/3/4 480” is to offer a system with proven technology for small breweries and craft beer scene with an unbeatable priceperformance ratio. Continuous improvements of the proven cold glue aggregate from the Gernep Labetta with its stainless steel glue roller, individually, three-dimensionally adjustable rubber pallets, a divided glue knife and a superposition gearbox ensure an accurate label positioning for perfect configuration. Especially in the area of functional safety, stability and especially the aggregate sealing has been extensively reworked. Various equipment features Thanks to the possible combination there are hardly no boundaries in any kind of compilation. The benefit of combining different labelling processes on only one machine platform is based in the minimised time for changeover and the simplicity to switch on/off the labelling aggregates on the machine table just as they are needed by activation switches in the HMI. For flexible use of different container formats, or for maximum flexibility for the future Gernep provides for all labelling machines alternatively servo driven bottle plates. All Gernep labellers can be equipped with mechanical, electronic and camera-based container orientation systems on bottom notch, side notch, tactility marks, relief or bottle seam and various label check devices, coding systems and seal labelling in L- and U-Shape. www.gernep.de","@ID":69}, "MARKET SURVEY 41 PETplanet insider Vol. 17 No. 09/16 petpla.net 09/2016 MARKETsurvey Preforms Filling equipment Resins / additives Preform / stretch blow moulds Caps and closures Preform and single stage machinery Bottle-to-bottle recycling plants Compressors Closure systems Two stage SBM machinery Suppliers of bottle-to-bottle recycling plants This year ten companies took part in the poll for bottle-to-bottle recycling plants market survey. The companies are shown in the order in which their details were received by the editors. The following are presented: Amut S.p.A., Tecnofer Recycling Equipment & Machinery, Erema Group GmbH, Zhejiang Boretech Co, Ltd., Starlinger & Co. Gesellschaft m.b.H., STF Maschinen & Anlagenbau GmbH, Polymetrix AG, Gneuss Kunststofftechnik GmbH , Krones AG and Herbold Meckesheim GmbH. Although the publisher have made every effort to ensure that the information in this survey is up to date, no claims are made regarding completeness or accuracy. Company name Amut SpA Tecnofer Ecoimpianti srl Postal address Telephone number Web site address Contact name Function Direct telephone number Fax E-Mail Via Cameri, 16 28100 Novara, Italy +39 0321 6641 www.amut.it Mr Piergianni Milani President +39 0321 664941 +39 0321 474200 p.milani@amut.it Via Calto, 409 - Ceneselli (RO) Italy +39 0425 849090 www.tecnofer.biz Mr Mauro Garbellini Sales Manager info@tecnofer.biz Bottle to granulate Input variable: collected pressed bottles, various colours Yes Output: Granulate with approval Questions: Capacity [t/a] 3,600-45,000 Floor space [m²] In function of size and stream quality Which approvals Fresh water consumption per tonne output [m³/t] 1m³/t Consumption kWh per tonne output [kWh/t] 250-300 Flakes to granulate Yes Input variable: Flakes, coloured proportion max 5%, not much chlorine Output: Granulate with approval Flakes to granulate Capacity [t/a] 3,600-45,000 Floor space [m²] In function of size and stream quality Which approvals Fresh water consumption per tonne output [m³/t] 1m³/t Consumption kWh per tonne output [kWh/t] 100-400 Bottles to flakes Yes Yes Input variable: collected pressed bottles, various colours Output: Flakes with/without approval Bottles to flakes Capacity [t/a] 3,600-45,000 800-4,000 Floor space [m²] In function of size and stream quality Min. floor space from 700-800m² (depending on customer needs) Which approvals Food grate parameters / food contact Fresh water consumption per tonne output [m³/t] 1m³/t 2,5-3m³/t Consumption kWh per tonne output [kWh/t] 250-300 580-620 kWh/t Miscellaneous Pre-sorting system for mixed plastics, delabeller machine for sleeves, complete removal Company also offers systems for Bottle-to-film Yes Lines can be applied and customised to each of the listed applications Bottle-to-fibre Yes Bottle-to-strapping Yes","@ID":45}, "MATERIAL / RECYCLING 39 PETplanet insider Vol. 17 No. 09/16 petpla.net Where F is the force applied and A is the cross sectional area of the body. Strain (ϵ) is the amount of extension of the body in the direction of the applied force and is defined by: Where l is the original length of the body and Δl is the extension of the body in the direction of the force. Looking at the definitions of stress and strain it can be seen that there is a link between these and the values measured during a burst test. Stress is defined as a force divided by an area, which also defines a pressure so this can be substituted for the pressure applied during the test. The strain is defined as a change in length divided by the original length which can be substituted by volume expansion over original volume, or a percentage volume expansion. Plotting applied pressure (bar) against volume expansion (%) produces an indicative stress-strain curve, see figure 3. Figure 3 Indicative Stress-Strain curve for a burst bottle The resulting stress-strain curve provides the necessary information to determine key material properties. A generic stress-strain curve is shown in figure 4. Figure 4 Typical stress-strain curve for a ductile material Fracture point The point at which a sample catastrophically fails, typically resulting in a break in the material. It is also where the measurements cease at the endpoint of the curve in figure 4. Any damage to a sample, or irregularities in the composition of the material may lead to a premature fracture. When applied to finished bottles, the fracture point directly corresponds to the burst point. Any defects during manufacture may cause a premature split in the body or base causing an early burst. Low burst pressures can signify a process problem or an issue with preform design. Inspecting and comparing a number of bottles after bursting is an easy way to identify a defected part. If the burst pressure is higher than required this may allow the product to be lightweighted, reducing material costs. Elastic & plastic regions Ductile materials, such as plastics/ polymers, have two distinct regions on their respective stress-strain curves. The elastic region is the initial linear gradient of the curve and represents the area where the material would return to its original size and shape if the stress is removed. The gradient of this elastic region is defined as the Young’s modulus (E) of the material and is calculated by: The latter section of the curve is where permanent deformation takes place and is known as the plastic region. Once plastic deformation occurs, the sample will not return to its original size and shape when the stress is removed. Yield point Defined as the stress at which the deformation of a material becomes irreversible. Beyond this point the material begins to rapidly stretch with continuous addition of stress. For finished bottles, this can be identified on a volume expansion graph as the point at which the gradient of the slope begins to rapidly increase, as shown in figure 2. An indicative yield point can be found by analysing the recorded volume data. This is done by locating the change in gradient of the volume expansion curve and performing a least squares linear regression on both regions of the curve to find the intersection point. This process is shown graphically in figure 5. Figure 5 Finding the intersection points on a volume time graph The yield point indicates a bottle’s resilience and its ability to absorb impact energy if dropped or damaged during transportation. Additionally, two supposedly identical bottles could have the same burst point, but one may yield earlier and have a larger expansion volume. This signifies a potential problem during injection moulding which could have affected the molecular weight. Intrinsic viscosity (IV) IV defines the average molecular chain length of a polymer and is therefore a measure of its molecular weight. This reflects properties such as tensile strength and crystallinity. It is important to realise however that many other aspects influence the mechanical properties; the amount of any copolymer added is one of these factors. The expansion volume between the yield point and burst point is related to the IV of the polymer. A higher IV corresponds to a smaller post-yield expansion, and conversely a lower IV corresponds to a larger post-yield expansion. This is due to higher molecular weight polymers reaching the strain hardening point sooner, therefore the yield point is reached later. Figure 6 (page 40) shows how the IV value can be interpreted from a graph of volume expansion versus time. However, a change in IV value should not be assumed by a change in the yield point, as material composition and process parameters will also affect this property.","@ID":43}, "BOTTLE MAKING 23 PETplanet insider Vol. 17 the jaycap. KHS made the definitive weight savings in the bottle body. Using the finite element method (FEM), KHS engineers used their company’s extensive bottle shape database to analyse the existing design and optimised it, maintaining bottle stability despite the reduction in weight. “We have at our disposal a database of absolute quality which allows us to effectively simulate reductions in bottle weight, on the computer,” says Christian Rommel, Bottles&Shapes project engineer at KHS. A further advantage of this digital method is that a bottle is simulated much faster on a computer than it would be if physically developed in a laboratory, enabling bottlers to save costs for complex bottle designs. As well as saving development time, the company was able to achieve a weight that was actually well below the given target corridor. The 0.9 and 1.0l bottles now only clock up 26g on the scales; the weight of the 1.5l bottle has been reduced to 36.5g. “KHS has managed to make structural changes to our bottles that our customers can’t see, but which have a positive impact on the overall bottle stability,” says Lauría, enthusiastic about the savings in material. The optimised style of bottle weighs less, has a better distribution of materials, features a grip that is both ergonomic and convenient, and is modern and aesthetically pleasing. The new design alone creates cost advantages for AGD in the production process; on the one hand the producer of edible oil ascribes this saving to the lower use of resources per bottle. Processing less material during production also means lower overheads for energy. In addition, the reduction in weight You make a great product – why hide it? We’ve seen the future of canning and it’s Klear. Milacron’s Klear Can technology gives manufacturers a cutting-edge, cost-competitive alternative to metal cans for fruits, vegetables, soups, meats and other products – and it’s transparent, so you can show off your goods. Using the same machinery as metal cans, going Klear requires minimal investment. With the option to use colored plastic cans, in-mold labels, or standard labels, the possibilities are endless. Ready to see what you can do? Contact us or visit www.Milacron.com to learn more. cuts shipping costs – while bottle stability remains the same. New line technology for a higher output There was a gap of just 14 months between the initial query being submitted to KHS and the first bottle being filled at AGD, which is, according to Lauría, a very short time indeed for the integration of such a complex bottle design. The development period saw the new bottle shape designed, the new stretch blow moulder built, the line technology inspected at the KHS site in Hamburg, Germany, and the new machinery commissioned in General Deheza in the Córdoba region. It was clear even before the project was implemented: if KHS could design a bottle prototype according to the required specifications, the company would also be awarded the contract for the new stretch blow moulder. Two InnoPET Blomax 10 Series II systems","@ID":27}, "TRADE SHOW PREVIEW 54 Vol. 17 No. 09/16 petpla.net IDEA AN AHEAD Innovative solutions for: • polymer processing • polymer recycling • thermoforming sheet lines • decontamination of polyester waste Visit our website for further information, animations and videos: www.gneuss.com Leading Technologies Extrusion. Filtration. Measurement. Stand 9/A38 Husky launches next generation HyCap 4 system – global debut at K 2016 Husky Injection Molding Systems has announced the launch of its next generation system for high output beverage closure moulding, HyCap 4. Husky launched its HyCap platform in 2009. “Husky is committed to reducing our customers’ total cost to produce,” said Gerardo Chiaia, Husky’s President of Global Beverage Packaging. “We do this by focusing our development effort on meaningful innovations that deliver on what the processor needs most. More productivity, increased ease-of-use, reduced energy consumption – these are all achieved by specifically designing the mould, machine, hot runner, auxiliary equipment and software to work in harmony – while adding more automation to make the system fully integrated and intelligent.” Exclusive adjustments have been made to strike the perfect balance between maximising productivity and achieving industry-leading energy savings. These adjustments include electrification of the clamp motion, servo-variable pumping technology and a regenerative clamp stroke. Combined, these enhancements deliver up to a 40% improvement in energy consumption over the previous generation system, without sacrificing performance. www.husky.co Husky Hall 13 Booth A61 Dry ice cleaning solutions The Cold Jet Plastics Edition is a comprehensive line of accessories that will come packaged with Cold Jet’s Aero Series dry ice cleaning systems to provide cleaning solution for the plastics industry. It is available in either pellet blasting systems (Performance or Industrial line) or in the patented shaved ice technology (i³ Microclean and SDI Select 60). The shaved ice technology features Cold Jet’s patented MicroParticle technology. MicroParticles is said to allow cleaning and surface preparation with more precision, more fineness, less air and noise as traditional dry ice pellet systems. With dry ice MicroParticles the surface gets cleaned faster and more evenly, because it gets hit by more MicroParticles at the same time. Less noise compared to pellets or fragmented pellets is going to lead into a better working environment and an increased safety, according to the company. MicroParticles eliminate the risk of damages to surfaces, vents/ ducts, bridges, high gloss polished forms or ejectors. Also they reduce the consumption of dry ice and compressed air because less power and pressure (kinetic energy) are needed in the acceleration process. During the tradeshow one can witness live manual cleaning with an i³ Microclean and customised automated cleaning with a mini robot. www.coldjet.com Cold Jet Hall 10 Booth B48","@ID":58}, "CAPPING / CLOSURES 46 PETplanet insider Vol. 17 No. 09/16 petpla.net 4.5.2.1 Properties HDPE is flexible, shows good weather resistance, is tough at low tem-peratures up to -60 °C, and is highly resistant to many acids, alkalis, and solvents. It is quite easy to process and at the lower end when it comes to cost (fig. 4.35). Disadvantages of HDPE are its lower heat resistance and higher propensity for stress cracking. Closures with high molded-in stress may fail the drop test many applications require. Closed-loop control of injection parameters is recommended to avoid this situation. Physical Properties Tensile Strengh 0.20 - 0.40 N/mm² Notched Impact Strengh no break Kj/m² Thermal Coefficient of expansion 100 - 220 x 10-6 Max Cont Use Temp 65 °C Density 0.944 - 0.965 g/cm³ Resistance to Chemicals Dilute Acid **** Dilute Alkalis **** Oil and Greases **variable Aliphatic Hydrocarbons * Aromatic Hydrocarbons * Halogenated Hydrocarbons * Alcohols **** Key * poor ** moderate *** good **** very good Figure 4.35 HDPE properties at a glance 4.6 Manufacturing Methods may get damaged or worn over time and should be checked on a regular basis. They often fail intermittently causing inconsistencies in the molded closures, which may lead to hours of fruitless troubleshooting. A cold or hot runner divides the single stream of molten plastic into the appropriate number of cavities. All modern tools use hot runners that heat the material continuously on its way to the mould and produce no scrap in the process. In contrast, plastic in cold runner channels solidifies during each cycle and this must be ejected. This is neither practical nor economical in beverage closure production. As the plastic in the water-cooled mould cools and shrinks, the screw keeps the so-called hold or packing pressure on the material and supplies enough molten resin to replace the material that shrank away. The screw then starts turning and keeps plasticising material while the tool opens and ejects the parts. During the ejection, the caps are mostly “bumped” off, i.e., the undercuts created by the thread beads are pushed forward and this forces the caps to bulge out by the amount of the thread depth. To accomplish this, caps have to be fairly warm, around 70 °C. The tooling is made to such a dimension that the caps will shrink back to their desired dimension when they cool down. Caps may also be unthreaded by hydraulic or mechanical devices instead of being bumped, but the high cost and cycle time penalties these devices demand have led tool manufacturers to come up with nifty solutions that make them unnecessary. The point where plastic is injected into the cavity (the “sprue point”) through a suitable injection nozzle is slightly raised as the plastic is cut off there. In order not to have a protrusion on the cap surface that may scratch a consumer’s finger, modern caps slightly indent the area around it so that the protrusion stays shy of the surface. IM is the most flexible process, and closures of any kind including Caps are either injection or compression moulded. There are distinct advantages and disadvantages for either system. This chapter gives an overview of both methods with the goal of helping users to make the right decision on which system can be used when there is a choice. 4.6.1 Injection Moulding IM of closures is using one male core and one female cavity for each cap produced per cycle. These are mounted in configurations of multicavity tools up to 192 cavities with most moulds in the 24- to 64-cavity range. Most machines cycle horizontally open and close, and caps usually fall onto a conveyor after each cycle. Plastic pellets are fed into the machine via a hopper. If coloured caps are to be produced, the resin may be precoloired or, more likely, colour is fed just underneath the hopper into the resin stream in ratios of 0.5–4%. Colour comes as masterbatch pellets or micro-pellets or in liquid form. Liquid colour is somewhat messy to deal with but allows very precise dosing and is especially suitable for very small colour percentages. Masterbatch and micropellets use LDPE as a carrier often at a ratio of about 50%. The resin is then taken by a rotating extrusion screw and melts under the combined effects of friction and heat. Usually the screw both melts the resin and injects it into the tool. During the melt phase or recovery phase, the screw turns and moves backward. Once enough material is in front of the screw, the screw stops and injects the melt into the closed tool after the caps made in the previous shot have been ejected. Screw size must be chosen so that screw recovery time is shorter than cooling time plus tool moving time. This is to ensure that the machine does not have to wait for screw recovery to finish before starting the next cycle. A suitable check valve sits at the end of the screw closest to the mould. It allows material to pass to the front of the screw during recovery but prevents material from moving back during injection. Check valves Figure 4.34 The HDPE molecule","@ID":50}, "BEVERAGE INGREDIENTS 36 PETplanet insider Vol. 17 No. 09/16 petpla.net WFSI concepts are stimulating the beverage sector A trendy contemporary blend of fruits and vegetables Many consumers want unique and premium quality products which complement their modern lifestyle and mindful approach to eating. They prefer foods and beverages that are rich in fruit, delicious, and offer variety. Wild Flavors & Specialty Ingredients (WFSI), a business unit of Archer Daniels Midland (ADM), has developed new attention-generating concepts for still drinks and juices. They feature different juice contents and distinctive blends of fruits and vegetables, customised to specific target groups and consumption situations. Many people are paying more and more attention to what they eat and what enhances their well-being. They spend more time reading about both positive and negative product characteristics, and their goal is a conscientious and healthy diet. On the one hand, they want foods that are delicious and feel familiar, and on the other hand, they are increasingly open to new taste experiences beyond the tried and true classics. Great Britain, Germany, and Poland are leading the way. In addition to beverages with carrot, which has been popular for years, more and more modern kinds of vegetables have established them and given fruit juices new flavour profiles: examples include beet, cucumber and pumpkin. In a sense, they are the next generation of multivitamin ACE drinks. In these days of street-food festivals, homemade smoothies, to-go products in the supermarket, and craft beverages, it has never been as trendy and popular to consume vegetables in other forms. This is an excellent opportunity for juices with an extra touch of vegetable. WFSI has been focusing on fruitand-vegetable combinations for many years now: this ADM business unit developed the first multivitamin ACE drink nearly 20 years ago, has been intimately familiar with the juice segment Vegetables are growing in popularity – both at home and on the go According to the Mintel marketresearch institute, over the past five years new product launches with fruits and vegetables have nearly quintupled in the European juice sector. Whereas there were 62 new products in 2011, in 2015 the number had grown to 296 fruit and vegetable blends on the shelves.","@ID":40}, "MATERIAL / RECYCLING 40 PETplanet insider Vol. 17 No. 09/16 petpla.net Figure 6 How inherent viscosity affects yield point and volume expanson (a) low IV (b) higher IV (c) highest IV The solution A considerably more detailed overview of a bottle’s mechanical performance can be achieved by analysing each of the properties previously mentioned; taking bottle testing beyond single burst point measurement. Torus’ B303 Burst Gauge, see Figure 7. offers this functionality in a robust and user-friendly design. Bottles are loaded individually into custom location discs. Once secured the burst routine can start behind a locked, waterproof safety door, providing a controlled test environment. A user-definable test procedure is performed and live graphs are updated on screen. Additional numerical and graphical results are displayed when the test is complete. Figure 7 Torus’ B303 Bottle Burst Gauge Examples of the user-definable test modes include Burst Mode & Hold Mode. Burst mode is the simplest of the modes available within the gauge software. A pressure ramp rate can be set by the user along with a maximum pressure, or it can be selected to ramp until burst. This can be used to find all of the mechanical properties described in this article, highlighting the pressure and volume at both yield and burst points along with data describing the volume expansion. Hold mode allows holds to be added into the tests in order to replicate states the bottle will endure during its lifecycle. Up to three holds and their relative durations can be set at user defined pressures, see Figure 8. Figure 8 Pressure hold graph New PET aerosol testing Furthermore, Torus Measurement Systems have a newly developed high pressure burst gauge designed for testing more robust PET aerosol bottles. The gauge holds all the capabilities of the current B303 gauge with the added benefit of testing up to pressures of 40 bar, doubling the current gauge limit. www.torus-group.com","@ID":44}, "MATERIAL / RECYCLING 16 PETplanet insider Vol. 17 No. 09/16 petpla.net SPONSORS The China Road Show A new generation of Holcomer June 1, 2016, Holland Colours China, Shanghai We met: Florian Balogh, General Manager With committed employee shareholders and operations in the Americas, Europe and Asia, Holland Colours provides personal local service on a global scale. Asia is controlled from the site in Indonesia. In China, Holland Colours first appeared with a sales office in 2002. From 2003 onwards, local laboratory can serve the customers with custom made colourants. Production in Shanghai began in 2006. Today, mainly colourants for the silicone and construction industry are being manufactured. China imports the colourants for PET from other Holland Colours’ sites. Holland Colours China started out as a small company, but over the years, with enthusiasm and professional calling, managed to build up a solid customer basis by supplying brand owners. “As an employee-owned company teamwork, pro-activeness, competence and accountability dominate our company culture. We are passionate about colour and passionate about our customers,” says Florian Balogh, General Manager Holland Colours China. PET packaging market in China is very colourful. The colour variations are high for water, from light blue to violet. The CSD is also more colourful than in other parts of the world. Pink, black and green are used. The variety of colour shades presents the suppliers with a specific challenge, but exactly this is where Holland Colours has knowledge and experience. With its result-oriented approach, Holland Colours is focused on finding solutions to the market needs and keeping thousands of shades on the product palette. To be able to meet the technical requirements, multiple product formats can be offered, which afford the possibility of a tailor-made solutions perfectly suited to any manufacturing environment and end use. In China, for the CSD segment, mainly liquid colourants are sold from the product range of Holland Colours. Keeping in mind the customers’ needs for consistent, cost-effective, problemtion of knowledge and co-creation is claimed to guarantee unparalleled product performance and a continuous flow of new products and customised solutions. The colourants correspond to Chinese, European and American regulations for food contact. Good entrepreneurship is more than gaining the maximum profit, therefore since the establishment of the Chinese factory, Holland Colours has sought to treat its personnel in a socially responsible and ethical manner. Safety, good labour conditions, care for the environment are key factors in this. www.hollandcolours.com free production, the colourant was developed with the characteristics of good colour distribution, high pigment/ additive loading and stability. Holland Colours has also developed a technology of its own, with the recent introduction of the advanced light barrier technology for dairy packaging, named Holcomer III. Customers are said to get the same industry-leading benefits of the existing Holcomer II solution, 100% UV blocking and up to 99.9% visiblelight blocking in a monolayer PET bottle, but at lower cost. Light penetration is a significant issue with UHT milk. Consumers are sensitive to even slight changes in odour and taste, and light penetration of UHT milk packaging causes the photo-oxidation of riboflavins, like vitamin B2 and B12, and the secondary auto-oxidation of liquids. The development of Holland’s Holcomer range is a result of its dedication to research and development, which is helping it keep up with requirements. Holland Colours’ knowhow, often in open partnership with suppliers and customers, is focused on dispersion technology, pigments, colour pallet development, colouring systems, carrier materials and customer processing technology. This combinaF.l.t.r.: Florian Balogh, General Manager of Holland Colours Shanghai and Alexander Büchler, PETplanet Insider","@ID":20}, "74 PETplanet insider Vol. 17 No. 09/16 petpla.net PETbottles Home + Personal Care 2in1 beard shampoo by Brisk The almost forgotten classic brand Brisk, famous since 1951 for its hair styling cream, has seen a window of opportunity – the trend towards groomed beards – in order to bring to market special beard grooming products. One example is the “2in1” beard shampoo, which gently cleans the beard hair and softens it. The shampoo additionally gently cleans the facial skin without drying it out. 150ml of the shampoo with tea tree and cedar wood oil are filled into a shapely, brown coloured plastic bottle with a screwed on, black hinged lid closure. The self-adhesive label is designed in red and white, typical of the brand. www.brisk-bartpflege.de Decorative soap dispenser by Palmolive Colgate-Palmolive extended its liquid soap range by one variety with a special scent in decorative packaging. Both scents – Lemongrass and Mulberry – are colour matching and filled into visually appealing bottles made of clear PET. 250ml each are filled into the easy-to-grip bottles with a screwed-on pump dispenser with lock function. The multi-part dispenser is fixed to the bottle edge with a shiny metallic ring. Transparent self-adhesive labels make the soap dispenser a decorative eye-catcher in kitchen and bathroom. www.colgate.de Babassu oil for hair In its moisture build-up series, the German Guhl Ikebana GmbH has a two-phase, non-rinse, intensive spray cure on offer. The product uses babassu oil derived from the seeds of a type of palm tree, in order to spend moisture to the hair, to lend it a silky feeling, and to improve combability. The clear bottle used as packaging contains 180ml and makes the two phases easy to see. Before spraying onto the damp or dry hair, the two phases must be mixed by shaking. The screwedon pump dispenser is protected from damage and incorrect operation by a protective cap. www.guhl.com","@ID":78}, "TRADE SHOW REVIEW 67 PETplanet insider Vol. 17 No. 09/16 petpla.net ing Asian closure manufacturers, for both food and non-food. The company used ProPak to showcase its recently-developed flip closure with a PET squeezing bottle for seasoning sauces. Testing and inspection on the rise The high number of companies providing systems for testing and inspection was particularly notable. Filtec demonstrated OMNIvision 3 empty bottle inspection system, which is claimed to be the fastest in the world. The newly redesigned system is able to operate at speeds of up to 1,400 CPM. The system is designed to detect foreign objects and flaws in the base, sidewall, finish, and threads of empty transparent glass and REFPET containers. Hawkeye Inspection System Machine Tech’s Leak Inspector L-5110 is positioned between the filler and the labelling machine. The inspection module checks for leakage, cap and liquid level with a maximum detection capability of 36,000bph. Canneed Instrument is a relatively new player in the world of testing and inspection. Founded in Hongkong, the company started with inspection instruments for aluminium cans. It now offers a wide range of inspection systems, including wall thickness gauges, secure seal testers, and burst pressure systems for PET preforms and bottles. Filling the niche The high-output filling segment is dominated by companies such as Krones, Sidel and KHS. However, filling machines for the low to medium output range have also found their place, in the context of burgeoning segmentation and the emergence of many niche markets, in Thailand especially. Filling machines for this area come almost entirely from local Thai or Asian machinery manufacturers. Thai company Anake Machinery, established in 1996, presented a gravity filling Super Bloc machine (rinser, filler & capper) for 120-130bpm. The company also offers automatic rotary filling machines, monobloc filler & capper units and labelling machines. The company says that its machines are exported worldwide, including to USA and Canada. Machconfill, another Thai manufacturer that was established in 1991, showcased an automatic rotary filling and capping system that includes rinser, filler, capper, conveyor system and cap sorter. Other exhibitors for filling machines included Taiwanese Autofill Enterprise (up to 300bpm) of Taiwan, Better Pack (China), and Malaysian MH Multipack, who showcased a fully automatic twin liquid filler and capper (dual capping heads) machine with a speed of up to 120bpm. It is suitable to fill syrup, suspension and medicated oil. The AEC effect The good mood at the exhibition could be linked to the newly founded ASEAN Economic Community (AEC), which aims to establish a single market, reduce tariffs and allow a freer flow of labour and capital. ASEAN’s ten economies include Thailand, Indonesia, Malaysia, Philippines, Singapore, Cambodia, Laos, Myanmar, Vietnam and Brunei. With a gross domestic product of US$2.6 trillion, the AEC is the seventh-largest economy in the world. With a population of more than 620 million, it is the third largest in Asia after China and India. The 25th edition, ProPak Asia 2017, will take place from 14th to 17th June at Bangkok International Trade Exhibition Centre (BITEC), Thailand. www.propakasia.com ALPS machines leak test more than 25 billion PET bottles annually. DID YOU KNOW? Visit us at the K-Show inHall 10, Booth B65 or visit www.alpsleak.com/PET info@alpsleak.com www.alpsleak.com FIND OUT WHY","@ID":71}, "BOTTLING / FILLING 34 PETplanet insider Vol. 17 No. 09/16 petpla.net SPONSORS The China Road Show Far Eastern Industries part 2 Sino Belgium Beer On the site of Far Eastern Industries, there is also a brewery with an annual capacity of about 3m hectolitres of beer (at 4.5% alcohol). It was founded in 2007 in cooperation with the Belgian Martens brewery. Unlike the usual procedure in China, the beer does not flow into cans or glass bottles, but rather into PET bottles. A Sidel machine does the blowing, internal coating and filling. The concept of the brewery and bottling plant came from Belgium. Two stretch-blow SBO 20s each feed two Sidel Actis 48 plasma coating machines, which maximally produce 60,000bph. From there, the bottles travel to an installed filler with a capacity of 40,000bph, optionally also into intermediate storage. Mr C.J. Lee, who is responsible for the brewery, has the beer filled at 500ml and 660ml there – depending on the target market, into green bottles with green screw caps, or into transparletiser. The main product is the 500ml bottle, for which the weight of Coca Cola bottles was the inspiration. With its weight-saving Ecobase design it weighs in at 22.28g. In the supermarkets, the retail price is RMB 5 (EUR 0.67), whilst discount brands are RMB 3-4 (EUR 0.4-0.5). Foreign beers start at about RMB 10/0.5l (EUR 1.34). Beer production is virtually continual. Meura machine has a special kettle for every processing step. The recipe stipulates a mixture of 70% malted barley and 30% rice. The malt and rice are mashed and cooked in individual vessels, then mixed in-line, and continued dextrose and maltose steps in the following vessel. The spent grain is eliminated using plate filters. After the addition of hops and after cooking, the wort goes into a sedimentation tank, in which the hot trub is eliminated. Here, Lee would prefer more of a classic whirlpool, as the sedimentation process is not always stable. After this, the daily production reaches one of the fourteen 4,800hL large fermentation tanks. About 7% of alcohol is brewed in. The brewery’s yield is 80%.The green beer remains with the yeast for 18 days before it reaches a bottling machine through Pentair cross-flow membrane filters, in-line dilution with deaerated water to a reduced alcohol content of 3.5 to 4.5% (which is normal for China). Depending on the target market, the shelf life is either six months for the local market, or nine months for exports. www.martensbeer.com.cn F.l.t.r.: C.J. Lee and Alexander Büchler at the brewery house ent bottles with golden caps. The closures are the Super Shorties by Bericap, with their inserted liners which eat away the oxygen. Just before labelling in the Alfa Labeller, the bottle must be warmed up slightly so that no condensation will precipitate onto the bottle, which would interfere with the application of the paper labels. This is followed by two packers and one Sidel pal-","@ID":38}, "TRADE SHOW PREVIEW 62 PETplanet insider Vol. 17 No. 09/16 petpla.net Measuring layer thickness of bottles and preforms with terahertz-technology IMDvista provides a new measurement system based on terahertz technology. IMDvista’s Layer measures the layer thickness of translucent and opaque plastic bottles and preforms in a non-contact and non destructive manner. Layer is also able to locate and measure the costly, ultra-thin barrier layer within preforms or bottles. At the manufacturing stage of bottles and preforms, a quintessential step to ensure consistent quality involves the precise measurement of each layer of plastic. Current techniques for measuring the thickness of monolayer and multi-layer plastic bottles and preforms are often contact-based, destructive and time-consuming. Ranging from cutting the bottle and preform to alternative techniques that are limited in their ability to capture each layer in the structure, it is evident that a solution is needed to enhance current practices. Non-destructive way of measuring layers IMDvista’s Layer multi-layer thickness measurement system provides a quick, non-contact and non-destructive alternative to current measurement techniques for plastic bottles and preforms. This off-line system boasts unprecedented speed and accuracy to provide individual layer thickness measurements of multi-layer bottles and preforms. IMDvista Layer is capable of measuring up to ten layers ranging in thickness from 0.01mm to 5mm in a matter of seconds. Suited for cylindrical plastic bottles and preforms, Layer can be used to measure bottles with a maximum height of 300mm, a maximum diameter of 150mm and a neck diameter between 10mm to 100mm. Measures both transparent and opaque plastics IMDvista’s Layer is powered by TeraGauge; a core terahertz technology provided by measurement solutions company TeTechS. By leveraging the unique properties of terahertz waves, Layer can measure both opaque and translucent plastics in a non-contact and non-destructive manner. Determine individual layer thickness This turn-key system not only enables users to effectively determine individual layer thickness, but allows them to locate and measure the costly, ultrathin barrier layer within the preform or bottle. With a thickness measurement accuracy of 0.01mm, IMDvista’s Layer eliminates the need for destructive testing while providing users with precision, ease-of-use, and confidence in the quality of their plastic products. Powered by terahertz technology Terahertz waves fall along the electromagnetic spectrum between microwaves and infrared and possess unique properties that render them ideal for non-destructive testing of plastic bottles and preforms. Waterloo, Ontario based TeTechS’ TeraGauge is at the heart of IMDvista’s Layer system and works based on the terahertz time-domain principle. Essentially, short terahertz pulses penetrate the sample under test and are reflected back into TeraGauge at each layer. The reflected pulses then have their time-delay measured which corresponds to the thickness of the layers of the plastic bottle or preform. The difference between the time delay of two reflected pulses, allows for the calculation of the precise thickness of the individual layers within the plastic structure. The graph above depicts the process. www.imdvista.ch IMDvista Layer System can be seen at Milacron, Hall 15 Stand C06","@ID":66}, "NEWS 11 PETplanet insider Vol. 17 No. 09/16 petpla.net MHT MOLD & HOTRUNNER TECHNOLOGY AG Your Machine - Our Solution 1996-2016 20YEARS Booth 1C35 R&D/Leverage announces opening of updated design innovation studio Expertise in total packaging solutions including strategic structural brand development through production mould engineering and manufacturing puts R&D/Leverage as a full service provider for consumer products OEMs. To enhance the company’s services in upfront research, design and brand development for fortune 100 and 500 customers, R&D/Leverage announces the renovation and upgrading of its new design innovation studio. R&D/Leverage’s multiple facilities are located on a campus designed to provide access to the many value-added services the company offers. The newly updated design innovation studio is intended to provide a relaxed, informal and open “creative space” that infuses the energy required for collaborative brainstorming discussions as well as formal conference space and dedicated offices for the privacy of our customers. This design studio experience coupled with R&D/Leverage’s high-tech production expertise provides an integration of art, science and technology in a way that customers can achieve their goals. “Getting a group together in a relaxed space is conducive to a more open, free-thought process as opposed to sitting around a conference table,” explains Matthew Hutcherson, a Designer at R&D/Leverage. “That speaks a lot to the more open approach that designers and brand owners are taking nowadays. For creative people to have that open space and to not feel they have to be formal really helps the creative thought process and gives our customer’s confidence they’re with the right partner.” Shaun Markey, Brand Strategist for R&D/Leverage, explains that the challenge that many brand owners often have is finding a partner that can deliver a full package of services that includes creative product design and strategic brand integration at the front end of a programme along with innovative engineering and mould manufacturing at the back end. “That is R&D/Leverage’s unique value proposition,” Markey states. “Part of the catalyst for the new studio is our commitment to our customers to develop and deliver a collaborative and creative experience.” The beauty of R&D/Leverage’s process is the company’s wide-ranging expertise in all areas of helping brand owners take a product from concept creation to design development and finally to mould manufacturing. R&D/Leverage offers the flexibility to integrate product development, design and brand innovation as well as an understanding of what the consumers’ needs are. R&D/Leverage has the “soft” skills that brand owners depend on to innovate the brand as well as the technical knowledge to determine the ideal type of molding platform on which the product can best be executed. Over the past 40 years, R&D/Leverage has grown organically due to its vision and understanding of customer needs, connecting its expertise and strengths in brand development, product design, mould design and development and moulding technology to deliver a collaborative and creative experience. Providing the new Design Innovation Studio is further proof of R&D/Leverage’s commitment to the world of consumer products and the brand owners’ need for a single source partnership. “Customers typically require various resources for product design, mould design and build, and moulding processing, but the back and forth between different suppliers’ wastes time and money,” says Markey. “In the middle is the critical engineering portion with a line of sight to the manufacturing component of the programme. Foresight driven design is what we provide. What’s envision at the front end of the programme informs engineering and on to manufacturing.” “We want to continue that dynamic evolution and provide a customer focused base that will be a point of destination for our customers, collaboration with them and helping them envision product designs and incorporate the technology that maintain their leading-edge status with consumers,” says Markey. We are committed to driving innovation and collaboration to help the brands achieve their goals with a trusted partner.” www.rdleverage.com","@ID":15}, "TRADE SHOW PREVIEW 61 PETplanet insider Vol. 17 No. 09/16 petpla.net SMI Hall 14 Booth B69 New serie of fully electronic stretch-blow moulders EBS Ergon The new EBS (Electronic Blowing System) Ergon series is the result of a challenging two-year long research & development project which introduced concepts for the design and manufacture of SMI’s new machines. The first Ergon EBS model was presented to the sales network in October 2015 at the inauguration of the new showroom set up at the SMI headquarters in San Giovanni Bianco, Bergamo, Italy. The current Ergon EBS range includes seven models, from 4-16 cavities, suitable for the production of PET containers up to 3l running at the max. speed of 2,300bph per cavity for the 0.5l format (still water). There are also three HC models, from 3-6 cavities, for the production of containers up to 10l, running at the max. speed of 1,200bph per cavity for the 5l format. Top-notch reliability and efficiency The new Ergon EBS series originated from SMI’s twenty years’ experience in the manufacture of rotary stretch-blow moulders is claimed to be sturdier, more compact, more flexible and more technologically advanced. Its performance has improved with respect to its predecessor, thanks to a series of technical improvements applied to the stretch-blow moulding process. The blow moulding module of the Ergon EBS range is equipped with motorised stretching rods whose functioning is controlled by electronic drives with no need of mechanical cams. This technology enables a precise descent of the stretching rod, an accurate control of its position and energy savings. It enables to adjust the stretch-blowing speed without mechanical interventions (cams replacement), and reduces the vibration stress that the blow moulding carousel undergoes in the traditional solutions. The Ergon EBS series features high performance, low dead volume valves system which has reduced the pre-blowing and blowing times with the subsequent great advantage in terms of machine efficiency and quality of the final bottles. A fully “cam-free” stretchblow moulding process Another improvement implemented by SMI design engineers is the motorisation of the mechanical mould unit that has turned the Ergon EBS stretchblow moulders into a real “cam-free” system through its integration with the electronic stretching rod. This led to a greater kinematical accuracy, less maintenance, less vibration, less noise and longer system life. With one servomotor, the new configuration handles both the up & down movement of the bottom of the mould and the opening & closing of the mould-holding unit, reducing mechanical stress and noise, which this machine section is subjected to in the traditional cam-equipped solutions. Thanks to this new technology, the dead angle of the stretch-blow moulding carousel has been reduced by as much as 10° if compared to the previous range, making the structure much more compact. The mould-holder’s opening/closing movement has been optimised according to the effective diameter of the bottles to be produced. Since this leads to a gradual reduction of the opening/closing stroke, the stretch-blow moulding cycle is shorter as the container’s size decreases. New preform heating module The stretch-blow moulders of the Ergon EBS range feature a new preform heating module, characterised by compact dimensions, horizontal frame of the preform-holding mandrel chains (37mm pitch for bottles up to 3l and 54mm pitch for bottles up to 10l), and an optimised ventilation system. The concepts used in designing the new range of Ergon machines allow shortening the heating module by 50%, thus reducing the number of preforms that are in transit in front of the heating panels at a given time. The new preform heating module is equipped with heat-reflecting, energy efficiency panels made of composite materials positioned both on the front and to the rear of the heat lamps in charge of preforms heating. This solution ensures a high reflection of the heat generated by the lamps and its more uniform distribution on the preforms surface. The new configuration allow to eliminate the star wheel between the exit of the preform heating module and the inlet star of the stretch-blow moulding carousel, with advantages in terms of shorter preform transfer time, less heat dissipation and greater simplicity of the mechanical movements. Easy and economic running, cleaning and maintenance The stretch-blow moulding systems of the Ergon EBS series are characterised by their compact, ergonomic and functional frame, which considerably simplifies machine running, cleaning and maintenance operations. It is said to ensure space saving in the bottling line. Since the safety doors of the new Ergon EBS stretch-blow moulders have a rounded shape, there is more space inside the machine for cleaning and maintenance, which the operator can perform easily and safely. The ergonomics of SMI’s new stretch-blow moulders is further enhanced by the advanced technology used by the Motornet System automation and control system, which ensures the constant keeping of optimal working parameters during the whole production cycle and directly adjusts the machine’s settings, simplifying format changeovers. www.smigroup.it","@ID":65}, "72 PETplanet insider Vol. 17 No. 09/16 petpla.net PETbottles Beverage + Liquid Food Olive oil in small oil bottles The Hamburg company The Deli Garage is selling three high-quality olive oils that have been refined with hot peppers, lemon or rosemary in a bottle that stirs memories. The bottle with its 100ml content and the name Ölwechsel (oil change) is reminiscent in its shape of the small metal oil bottles that were used or still are used as containers for sewing machine or multipurpose oil. The clear containers are sealed with a screw cap that has a tip which can be unscrewed for exact dosing of the contents. The transparent self-adhesive labels are designed specifically for the products and imaginative silhouettes are printed on their inside back. www.the-deli-garage.de Clear apple cider vinegar by Verival Verival Pronurel Bio, a brand by the Vita+ Naturprodukte GmbH from Langkampfen, Austria, is bottling 750ml of “Bio-Apfel Essig Klar” (clear organic apple cider vinegar) into a clear plastic bottle. The bottle is imprinted with oval recesses in its neck area, which make the bottle more grippable and stabilise it in this area. The bottle is sealed with an attached screw cap with a detachable ring-pull as a safeguard for first use. A paper label that encircles the bottle communicates all necessary information. www.pronurel.com Tapered bottle for ice tea Under its own brand “Rewe beste Wahl” (Rewe best choice), Rewe sells different ice tea drinks with black tea base in a grip-friendly tapered one-way PET bottle. They each contain 500ml and thanks to the strong tapering can be held firmly and opened comfortably. The varieties on offer are decorated with a sleeve label and the original closure is labelled on the top with the variety description. www.rewe.de Strawberry lemonade in PET In addition to the familiar flavours for lemonades, there are new attempts time and again to offer the customers new fruit varieties. The German Hella Mineralbrunnen GmbH brought to market a strawberry lemonade with 6% fruit content which promises a fruity taste experience. 750ml are filled into a rather stocky, non-tapered bottle with encircling grooves. The weightreduced closure is fitted with a guarantee strip, and a shrink label complements its appearance on the retail shelf. www.hella-mineralbrunnen.de","@ID":76}, "PETproducts 68 PETplanet insider Vol. 17 No. 09/16 petpla.net www.stf-group.de ENGINEERING WITH THE COMPETENCE OF THE RECYCLER •Complete Plastic Sorting and Washing Lines engineered by Europe’s largest PET Recycler •Bottle-to-Bottle rPET Recycling •More than 60 PET Recycling Lines installed worldwide www.stf-group.de ENGINEERING WITH THE COMPETENCE OF THE RECYCLER •Complete Plastic Sorting and Washing Line engineered by Europe’s largest PET R cycler •Bottle-to-Bottle rPET ecycling More than 60 PET Recy ling Lines installed worldwide Booth 12 / F56 Kinder Cola shrink sleeve labels produced by Constantia Kinder Cola, the Dutch beverage line aimed at children, has tapped Constantia Flexibles to produce their new shrink sleeve labels. Made without caffeine and with significantly less sugar than traditional cola, Kinder Cola is the premier youth cola beverage in the region. Until recently, these products used a wrap-around label. Kinder Cola’s goal was to maximize their branding with a higher quality label. Constantia Flexibles’ shrink sleeve label was a good solution. It amplified their branding by providing a 360-degree messaging platform, more than doubling the amount of space available. Additionally, Constantia Flexibles’ technology includes multiple image printing, allowing for three designs per reel. Their bright and varied kid-friendly graphics pop off the bottle and visibility onshelf has significantly increased. The Kinder Cola team is very happy with the new label and is now using it on all of their kid-focused beverage products. www.cflex.com Water bottles for URC Philippines Universal Robina Corporation (URC) is a Philippine multinational with an established market especially in South East Asia in the food & beverage industry. URC Philippines requested a solution to produce new water bottles for mass consumption, having specific needs. The line speed should have a capacity of 50,000bph with a labelling machine speed of 55,000bph. The bottle shapes of 350ml and 500ml should be processed in ExtraLight on a blow moulding machine. The solution that P.E. Labellers proposed and installed is a Rollmatic with brushless motorised plate belt, reel-holders; servo-driven, dedicated brushless HS glue roller and automatic joiner. In addition, a special in feed solution with drive-break curve, long feed-screw and additional starwheel has been designed and implemented for the correct infeed of soft bottles into the machine. The low consistency of the bottles was a great preoccupation for the success of the project. However, with the right solutions described above, corrected and adapted during the FAT and the machine has been operating for over a year in three shifts with great customer satisfaction. www.pelabellers.com","@ID":72}, "NEWS 9 PETplanet insider Vol. 17 No. 09/16 petpla.net PROCESS PILOT® makes producing a better PET bottle as easy as 2 3 1 MEASURE CONTROL OPTIMIZE every bottle for changes in material distribution process variation, inside the blowmolder material utilization and orientation to achieve maximum bottle performance CONTACT US TODAY TO LEARN MORE! AGRINTL.COM | +1.724.482.2163 | SALES@AGRINTL.COM VISIT US AT BOOTH 11B40 Lightweight Containers to open new KeyKeg production line in Germany Lightweight Containers is opening a new production plant in Grossbreitenbach, Germany. The fully automated production line has a capacity of 400 KeyKeg Slimlines per hour and will be operational in the third quarter of this year. The line can produce all the members of the KeyKeg Slimline family of kegs. PET-Verpackungen Deutschland is the production partner and will manage the day-to-day production. The new production capacity will ensure that Lightweight Containers can meet the region’s sharply rising demand for the next few years. Anita Veenendaal, Chief Commercial Officer of Lightweight Containers, says, “We see service as a crucial element for our success. We aim to offer the best possible service, so we want to produce as close to our customers as we can. This new location and the extra capacity will reduce both delivery times and transport distances even more. In the last six years, our sales have grown more than 40% each year, and we’re seeing accelerated growth in the demand for our kegs almost everywhere in the world we serve. With this new production line, we can continue to serve our customers in this region at the level they’re used to.” Concentration on solutions for the total supply chain The new plant is being set up in close collaboration with production partner PET-Verpackungen Deutschland. Jan Veenendaal, CEO of Lightweight Containers adds, “Our oneway kegs have a lot of added value throughout the supply chain. They also fit in perfectly with trends like specialty beer exports and wine on draft, which partly explains why we’re growing so fast. We intend to keep concentrating on solutions for the beverage industry, and on crucial trends. We can do this by collaborating with a professional and flexible production partner like PET-Verpackungen, who completely shares our view of quality.” Two partner companies According to Oliver Wiegand of PET-Verpackungen GmbH, “Lightweight Containers has an international focus that fits in well with our international ambitions. Construction of the production line is going very smoothly. Lightweight Containers’ knowledge of and experience with production processes makes them a valuable partner. Both companies are also family-owned, which turns out to be a good foundation for an efficient and pleasant working relationship. We have all confidence that this line is just the beginning of a long and successful collaboration between two partner companies.” KeyKegs are currently produced in three locations: Schwerin (Germany), Den Helder (the Netherlands), and Joliet (USA). The line in Grossbreitenbach (Germany) will be operational in the third quarter of 2016. www.unikeg.com Reorganisation at Athena To better serve the expanding customer base, Athena is making organisational changes of the management team: Harold Luttmann has taken over as acting CEO, in addition to his current role of Chief Operations Officer. A Chief Commercial Officer (CCO) will be added to the management team shortly. Founder Robert Schad has temporarily assumed this responsibility. The CCO will be responsible for Sales, Marketing, Finance and Human Resources, as well as for growing the global sales and service network. A service representative is already stationed in the Pennsylvania-Ohio area, with Atlanta, Chicago, and Frankfurt am Main (Germany) to follow. Athena’s machine business has been on the rise since opening the new 155,000 square foot (14,400m2) facility in Vaughan, Ontario. This facility is said to allow Athena to compete on a global basis, due to automotive-style just-in-time assembly of machines. www.athenaautomation.com","@ID":13}, "BOTTLE MAKING 33 PETplanet insider Vol. 17 No. 09/16 petpla.net l l l consumer bags textile packaging recycling Test results provided conclusive evidence that PET performs as well as traditional kegs in terms of quality and taste; different beers were found to taste the same, whether stored in metal or in PET kegs. The conclusion was that both types of kegs have similar performance over the storage time. So what is driving the dramatic growth in PET kegs? Thanks to the lower total cost of ownership of PET versus metal, PetainerKeg is helping breweries and other beverage producers around the world enter and grow new markets. To meet rising demand, PET Technologies has worked in partnership with Petainer to introduce a PET keg blow moulding machine at a beverages production plant, in order to reduce customer supply chain costs dramatically. The failsafe APF-30 automatic blower, which can produce 20-30l PET kegs from PetainerKeg preforms, was developed under an exclusive agreement as a result of close cooperation. Modified APF-30 blow moulder models with production capacities of 120 and 250 kegs per hour are now widely used by wine, beer, cider and juice producers to manufacture PET kegs and deliver their beverages to four corners of the world. The APF-30’s heater is equipped with 16 temperature-regulating zones to provide preforms with deep heating and uniform temperature distribution throughout the material. This feature is especially important for heavy and thick-wall preforms. The stretching unit has an embedded servo drive system, for easy control and stable rod speed. The blowing unit is equipped with original block of valves designed by PET Technologies’ R&D department. In conclusion, the APF-30 automatic blow moulding machine is a sustainable solution to for the production of PET kegs compatible with different filling lines at the plant, and helps to minimise logistics and storage costs. www.pet-eu.com www.petainerkeg.com","@ID":37}, "BOTTLE MAKING 28 PETplanet insider Vol. 17 No. 09/16 petpla.net Liaison of PET and PP for keeping liquids separated View the elements TricorBraun earned a Silver Award in the 28th DuPont Awards for Packaging Innovation for their novel and user-friendly packaging for Prestone Stop Leak. The packaging format contains three separate component parts combined into one to provide a simple and efficient use for car repairs. The liquid portion is contained by a 3oz PP bottle which sits in an 18oz clear PET bottle. The overcap does double duty as a jar holding the pellets portion of the product and is closed with a 51mm pinch and turn CRC closure. The stand out feature is the design aspect that keeps the liquid formula and pellets separate until use. Prestone Products Corporation’s patent-pending Triple Seal Protection Stop Leak family of products are intended to help eliminate expensive consumer auto repairs to radiators, head gaskets and engine blocks. To effectively deliver the value and easeof-use of this complex product and simplify the consumer experience, TricorBraun partnered with Prestone to develop a functional, transparent, three-compartment intuitive package design. This design allows the consumer to clearly see all of the elements of the product and engage with the product in a way that provides a more positive user experience. The product’s three active ingredients are beads and two liquid chemicals. The packaging brief called for a unified design that communicated to the consumer an “all-in-one system” while also providing storage for each of the ingredients in separate dosing chambers. First, the consumer adds the effervescent beads found in the top dosing chamber. Second, the consumer simultaneously pours the two separated liquid components from the inner preform tube and exterior bottle into the designated problem area. The resulting mixture seeks and finds the location of the leak and creates a web of fibres that bind to the metal around the leak while an acrylic polymer hardens and secures the seal. In spite of the fact that the Triple Seal Protection’s three ingredients must be stored separately, Prestone wanted them packaged as one convenient, transparent unit to enhance the consumer’s engagement with the new product. “We knew from the beginning how we wanted the packaging to look and work,” says Thomas Kalagher, Marketing Product Manager, Prestone Performance Chemicals. According to TricorBraun VP of Engineering & Technical Services, Jon-Paul Genest, “Prestone approached us with a complex and unproven design and what seemed like an impossible launch date. Our project management team responded with an actionable and manageable timeline and clearly defined deliverables. We maintained close collaboration and managed expectations throughout the process. From there, we engaged with one of our trusted development partners, Currier. Optimising our path to success was critical every step of the way.” Massimo Leone, VP Business Development, Currier Plastics describes what happened this way, “Working as a team with TricorBraun, we collectively managed to successfully finalise three different materials and four separate components with two different technologies. Both the injection moulding and injection stretch blow moulding process disciplines were needed. Also, three prototype injection moulds were launched concurrently with the injection stretch blow mould production tool. Timing was absolutely critical as the product was required to launch within three months from start to finish. Without the combined efforts of our mutual team, the aggressive launch date would never have been met.” Developing the package Kalagher’s concept for the package was a clear bottle with a smaller inner tube and a dosing chamber on top that houses the beads. TricorBraun defined a timeline of how they bottle making","@ID":32}, "PREFORM PRODUCTION 19 PETplanet insider Vol. 17 No. 09/16 petpla.net for a local syrup brand, who wished to continue using their original caps after converting to PET,” Mignot says. Part of SGT’s portfolio is the development, for the dairy segment, of monolayer PET preforms with characteristics of classical multilayer preforms. The resin formulation includes a full UV barrier, for example, and can thus be used by customers without further special conversions. This technology is currently available for SGT’s 38mm neck range, which includes more than 25 different preform models with volumes between 250ml and 2l. The 650g preform, mentioned above, features a 55mm neck and is used in the blow moulding of reusable 5 gallon water containers. The new building houses three Intravis prewatcher quality control systems and a vertical, fully-automated storage unit for moulds that, Mignot explained, hold 45t of single parts. On the storey above are two Piovan Genesys dryers for each new preform line, with the exception of the multilayer machine. “When demand is high, this arrangement enables us to guarantee rapid material change without downtimes. The next granulate is ready to use as and when it is required,” Mignot continues. The new water cooling treatment has delivered around 30% energy savings and is another step forward in the company’s ongoing ISO 50001 and 14001 certification process. The remaining 16 Husky machines, including HPP4, G-line and HyPET, have remained in the old part of the site. SGT obtains most of it raw material from Europe. “We are planning to invest soon in expanding our product storage facilities here at the headquarters,” Jolly tells us. “We also want to attain a recycling rate of about 12,000t of rPET. This way, we would double the current processing of recycled material for those clients who care about the rPET content of their packaging.” www.sgt-pet.com 19 PREFORM PRODUCTION CBB, October 11-14,2016 | Shanghai | China K 2016, October 19-26, 2016 | Düsseldorf | Germany CIBUS TEC, October 25-28 | Parma | Italy SITEVINITECH, October 27-29 | Mendoza | Argentina Pack Expo, November 6-9 | Chicago | USA With Sacmi, the beverage specialists are always at your side. With our unbeatable technological know-how and continuous research we are creating new containers and closures designed to ensure outstanding performance. The new IPS injection system for preforms and the CCM compression press for caps, fully designed and built by Sacmi, allows for large-scale production with considerable advantages in terms of efficiency and flexibility. The outcome? Reduced plastic volumes, less energy consumption and lower running costs. All in a bottle: the one you’ll soon be making. Preform & Closure technologically together Save RAW MATERIALS reduced plastic volumes Save ENERGY less energy consumption Save TROUBLE more quality and higher performance, guaranteed by a sole supplier Full INSPECTED online quality control / stand alone View into SGT’s new full automation production area","@ID":23}, "BOTTLE MAKING 27 PETplanet insider Vol. 17 No. 09/16 petpla.net A couple of design iterations were required to dial-in the proper neck finish. In addition, a small adjustment was made to the bottle’s shoulder height to accommodate the filling process. Unique hand grips require mould modifications Another major technical feat was the creation of a bottle with Method’s unique look, which could be stretch blow moulded and produced without a separate handle. Amcor’s design engineering team work closely with Method’s industrial design team to achieve the breakthrough. Method’s design concept called for ergonomic hand grips, which presented a mould making challenge, according to Lewis. The mould design problems were due to the cross corner parting line split and the highly functional ergonomic hand grips, which were to be moulded on the back side of the bottle. The difficulties were overcome by a variable radius parting line that reduced negative draft and allowed the part to release easily from the blow mould, thus preventing scratching or marring of the PET bottle if the mould was to drag on the panel wall. The 53oz container with 100% PCR PET content enabled Method, which was founded in 2000 on a strong environmental platform, to gain sustainability benefits. Analysis using Amcor’s Asset Life Cycle assessment tool showed that by using 100% PCR resin, the package’s life cycle energy consumption is reduced by 78% and its carbon footprint is lowered by 35%, compared with a virgin PET alternative. www.amcor.com www.methodhome.com","@ID":31}, "BOTTLES 75 PETplanet insider Vol. 17 No. 03/16 petpla.net Chocolate passion by Palmolive With the addition of “Palmolive Gourmet” Colgate Palmolive has launched several crème showers with special fragrance notes. The picture shows “Chocolate Passion” with cocoa extract. According to the manufacturer, this crème shower makes the skin smell delicious. The famous Palmolive PET bottle with 250ml was designed to match its contents. The shrink label and the twopart hinged lid closure take up the brown primary colour of cocoa and chocolate as a design element. www.colgate.de Laundry fragrance by Aldi The German discount store Aldi Süd had three different laundry fragrances on offer as promotional products under the trademark “Tandil”. The products are designed to lend a pleasant and long lasting scent to the laundry. 250ml of the liquid were filled into a conically top tapered PET bottle in a colour matching the product. A dosing aid is pressed into the container’s opening. A screw cap seals it all and self-adhesive labels communicate the directions for trade and use. www.aldi-sued.de","@ID":79}, "petpla.net D 51178; ISSN: 1438-9452 No. 9 2016 MAGAZ I NE FOR BOT T L E R S AND BOT T L E - MAK E R S IN THE AMERICAS, ASIA, EUROPE AND ALL AROUND THE PLANET 07 . 09 . 16 MARKETsurvey Bottle-to-bottle recycling plants Page 41 The China Road Show Page 20 bottle making Page 21 Page 52 k-online.com Messe Düsseldorf GmbH P.O. Box 101006 40001 Düsseldorf _ Germany Tel. +49(0)211/4560-01 Fax +49(0)211/4560-668 www.messe-duesseldorf.de After 3 years, we’re ready to go again. K 2016 presents you the best that engineers, chemists and researchers currently have on offer: machinery, technology, materials, tools, applications, and forwardlooking products, processes and solutions. The best basis for global business, the perfect decision-making platform for investment. With some 3,200 exhibitors in 19 exhibition halls on more than 171,000 sqm of exhibition space, the world’s premier trade fair for the plastics and rubber industry will once again be presenting the entire range of products and services that the industry has to offer. Everything that will move the world in the future. Plan your visit now. I t ’ s K T i m e T i m e f o r D e c i s i o n s","@ID":1}, "TRADE SHOW PREVIEW 56 PETplanet insider Vol. 17 No. 09/16 petpla.net Milacron Hall 15 Booth C06 Hall 01 Booth A39 System solutions Milacron Holdings will be featuring Milacron, Ferromatik and Uniloy product branded injection, PET, blow and extrusion offerings in Hall 15 booth C06 and Milacron’s Melt Delivery and Control Systems will be in Hall 01 booth A39 (Mold-Masters, DME, Tirad and Cimcool). Amongst the exhibits of Milacron Holdings which are interesting for the PET industry are: PET preform system with co-injection barrier technology The M-PET 300, a servo-hydraulic PET system is said to combine key components across the company‘s product portfolio – machines, clamps, injection unit, end-of-arm tooling, hot runner, mould and robots – into a single solution. The system operates with Milacron’s Preform Tooling, as well as existing industry tooling solutions. Cell specifics: M-PET 300, 72 cavity, 37g preform, 14s cycle time, inspection system from IMD K-TEC machine platform The K-TEC injection moulding machine platform is said to ensure precision and repeatability, fast cycle times, high injection rates and pressure, parallel functions and easy maintenance. The K-TEC is available in full hydraulic or servo hydraulic configurations. It is suited for customised solutions for large production outputs. The K-TEC comes in eleven sizes from 60 to 450 metric tons clamping force, and is also available as a multi-component, monosandwich or cube machine. The cell utilises Foboha’s cube mould expertise and Trexel’s innovative MuCell system to produce a visually appealing cosmetic finish inside the PET preform. Cell specifics: 4 cavity, 30.5g preform, Mold-Masters 16 zone TempMaster hot runner controller, MuCell technology, Foboha cube mould High precision large mould bases Tirad product lines will feature Large Mold Bases with plate lengths up to 1.5 x 2.3m. The premier equipment used to make Large Mold Bases is said to reduce manual polishing and additional rework due to increased consistency in high quality finishes. The mould bases are intended for medical, pharmaceutical, food and beverage packaging and PET preform solutions. www.milacron.com","@ID":60}, "imprint EDITORIAL PUBLISHER Alexander Büchler, Managing Director HEAD OFFICE heidelberg business media GmbH Bunsenstr. 14 69115 Heidelberg, Germany phone: +49 6221-65108-0 fax: +49 6221-65108-28 info@hbmedia.net EDITORIAL Kay Barton Heike Fischer Gabriele Kosmehl Michael Maruschke Ruari McCallion Waldemar Schmitke Wolfgang von Schröter Anthony Withers WikiPETia.info Doris Fischer doris.fischer@hbmedia.net MEDIA CONSULTANTS Martina Hirschmann hirschmann@hbmedia.net Johann Lange-Brock lange-brock@hbmedia.net phone: +49 6221-65108-0 fax: +49 6221-65108-28 LAYOUT AND PREPRESS EXPRIM Werbeagentur Matthias Gaumann | www.exprim.de READER SERVICES Till Kretner reader@hbmedia.net PRINT Chroma Druck & Verlag GmbH Werkstr. 25 67354 Römerberg Germany WWW www.hbmedia.net | petpla.net PETplanet insider ISSN 1438-9459 is published 10 times a year. This publication is sent to qualified subscribers (1-year subscription 149 EUR, 2-year subscription 289 EUR, Young professionals’ subscription 99 EUR. Magazines will be dispatched to you by airmail). Not to be reproduced in any form without permission from the publisher. Note: The fact that product names may not be identified as trademarks is not an indication that such names are not registered trademarks. 3 PETplanet insider Vol. 17 No. 09/16 petpla.net Dear friends of PETplanet insider, Summer is drawing to a close, and I hope that you have enjoyed a successful season. This is now the moment for tidying up loose ends, to start thinking about new projects and of course, to catch up on our reading. With the summer fast becoming a distant memory, we embark upon our autumn tasks, from the K 2016 to the high point of which will be Brau Beviale in Nuremberg in November. In between is the Brew and Beverage exhibition in Shanghai, which has developed in recent years into an important meeting point for the beverage industry well beyond Chinese borders. This year we put China under the microscope with our Editourmobil tour of this vast economic powerhouse. The results were surprising. The market is in a consolidation phase, bottles have again become notably heavier over the past two years reflecting consumer demands for stable bottles (see issue 7+8, 2016). In this issue I report on my further visits to China. One of the most exciting highlights was certainly my discussions with Taiwanese Far Eastern Industries in the surroundings of Shanghai (p12 & p34). Far Eastern is well known as a PET producer and processor but much less well known is the fact that the Chinese company also manufactures and fills Suzhou beer in PET bottles in collaboration with Sino Belgium Beer Ltd, and if all that were not enough, also operates a brewery nearby. And so we arrived somewhat unprepared that morning for our interview where the beer was already flowing freely. Here we at last discovered the answer to the mystery of why the Chinese have a taste for very light beer. The reason is that next morning they can come into the office and proudly announce the number of beers they have downed the previous evening, and yet look at how fit they are! This only works with a very weak beer. Normal beer is therefore considered a bad beer. As I am reading PETplanet this evening, I shall of course be treating myself to a “bad” beer. Yours, Alexander Büchler","@ID":7}, "BOTTLE MAKING 32 PETplanet insider Vol. 17 No. 09/16 petpla.net PET kegs enjoy rapid growth bottle making PET Technologies and Petainer have recently developed a special solution to blow mould PetainerKeg, an increasingly popular alternative to traditional metal kegs for beer, wine, cider and similar beverages. Due to draught beverage sales expanding across geographic regions and the rising cost of natural resources, as well as increased supply change costs associated with transporting steel kegs, one-way PET kegs are enjoying healthy growth as a more cost effective alternative. Small and medium breweries, wine and cider producers, bars and restaurants are increasingly choosing a completely recyclable packing solution with no return logistics. Traditionally, materials such as ceramic, wood and metal were used to make kegs. For some in the industry, a move to PET raised questions about whether the material could offer the same attributes in terms of product quality. To provide robust scientific evidence that PET products could do the same job as traditional kegs, Petainer Czech Holdings turned to Versuchs- und Lehranstalt für Brauerei in Berlin, the renowned German association in the field of research, development and training for the brewing industry, to carry out a series of sensory evaluations comparing PET and metal containers. The examination and analytical process took place over a period of nine months. Petainer preform and keg The APF-30 automatic blow moulding machine","@ID":36}, "MATERIAL / RECYCLING 38 PETplanet insider Vol. 17 No. 09/16 petpla.net Reaching bursting point by Laurence Newman MEng. (Hons) Torus Measurement Systems, Telford, United Kingdom and contributions by Phil Brannon, ColorMatrix This article details the importance of understanding a PET bottle’s mechanical properties, particularly with the continued developments in lightweighting, recycled PET and barrier technology. It demonstrates how the data from a standard burst test can be used to explore stress-strain curves, fracture point, elastic & plastic regions, Young’s modulus and intrinsic viscosity to gain a more detailed overview of the finished bottle. Lightweighting, rPET and barrier technology PET is predominantly used in the manufacture of plastic bottles. It is relatively strong yet flexible with low permeability providing a suitable and costeffective packaging solution. During production it is important to understand the capabilities and limitations of the finished bottle design to ensure it is fit for purpose, with particular emphasis on the bottle’s mechanical properties. These properties are vital for ensuring the bottle maintains structural integrity during its lifecycle. With the rise in different manufacturing requirements, such as lightweighting, recycled PET and barrier technology it has never been more important to physically verify the bottle’s performance. Lightweighting is always a key area to save material costs, and due to recent advances in technology and design, there has been a heightened focus in this area. Inevitably as a bottle is lightweighted the wall thickness decreases and its strength is reduced. In the environmentally conscious society we live in, the use of recycled PET as a sustainable material is encouraged and as such is often used as a copolymer with virgin PET. Barrier technology within PET bottles has been another area of recent intense interest, with the addition of extra material at the injection moulding stage to prevent infrared, UV, oxygen and water ingress/emittance. Each of the manufacturing techniques detailed can have unknown effects on mechanical performance, with bottle integrity requiring reverification. While tensile and compressive testing can be carried out on preforms and thin PET sheets, these do not replicate the final bottle in its application and ignore any changes or defects that may occur during the blow moulding stage. Burst testing provides a real and physical representation of how the bottle performs under stress and what its limitations are. Furthermore, advanced analysis of the resultant data can provide a more detailed overview of the bottle’s mechanical performance and material properties. Basic burst testing An industry standard test to determine a bottle’s bursting point. The bottle is filled and primed before the pressure is increased at a controlled ramp rate, resulting in a corresponding volume increase, until the bottle bursts, as depicted in figure 1. Figure 1 Bottle burst sequence of Fill, Pressurise and Burst Typically, pressure and volume are both plotted against time to graphically represent the bottle expansion and burst, see figure 2. Measured features include burst pressure and volume expansion. Figure 2 Typical results graph from a standard burst test Advanced burst testing A number of important features can be identified by analysing the data obtained from the controlled burst test, to give an indication of the mechanical properties of the finished bottle. Stress-strain curve Stress (σ) is used to express the force acting upon a body and is defined by:","@ID":42}, "MARKET SURVEY 42 PETplanet insider Vol. 17 No. 09/16 petpla.net 09/2016 MARKETsurvey Company name Erema Engineering Recycling Maschinen und Anlagen Ges.m.b.H. Zhejiang Boretech Environmental Engineering Co. Ltd. Starlinger & Co. Ges.m.b.H. Postal address Telephone number Web site address Contact name Function Direct telephone number Fax E-Mail Unterfeldstraße 3, 4052 Ansfelden, Austria +43 732 3190-0 www.erema.at Mr Christoph Wöss Business Development Manager, Application Bottle +43 732 3190-352 +43 732 3190-23 ch.woess@erema.at No.888, Jiuliting Avenue, Caoqiao Street, Pinghu, Zhejiang, China +86 573 85120 186 www.bo-re-tech.com Mr Alan Ou Senior V.P. +86 573 85120 186 +86 573 85113 959 sales@bo-re-tech.com Sonnenuhrgasse 4 1060 Wien, Austria +43 1 59955-0 http://recycling.starlinger.com Mr Paul Niedl Head of Sales Division recycling technology +43 1 599 55 1310 +43 1 59955 25 sales.nd@starlinger.com Bottle to granulate Four models: recoSTAR PET FG, recoSTAR PET FG+, recoSTAR PET iV+, recoSTAR PET iV+ Superior Input variable: collected pressed bottles, various colours Yes, in cooperation with long-time partners Starlinger recycling technology offers the engineering of washing lines and/or a turnkey project with components and technologies available in the market Output: Granulate with approval Yes (decontaminated for food-contact, IV increased, AA 1ppm, lowest VOC level) Questions: Capacity [t/a] 6,000-26,000 t/a rPET pellets Floor space [m²] Depending on design Which approvals Several USA/FDA(C-H),Austria, Germany/BfR, Ilsi, France/AFFSSA, Finland,Australia, Canada, Egypt, Japan, Switzerland, several LatinAmerican Countries (Bolivia, Brazil, Chile, Colombia, Ecuador, Guatemala, Peru); follows EFSArequiremens; brand owners Fresh water consumption per tonne output [m³/t] Depending on design Consumption kWh per tonne output [kWh/t] Depending on design Flakes to granulate Four models: recoSTAR PET FG, recoSTAR PET FG+, recoSTAR PET iV+, recoSTAR PET iV+ Superior Input variable: Flakes, coloured proportion max 5%, not much chlorine Basic flakes specifications: Higher contamination can influence pellet quality but are basically possible to process, after discussion and agreed by Erema Output: Granulate with approval Yes (decontaminated for food-contact, IV increased, AA 1ppm, lowest VOC level) Flakes to granulate Capacity [t/a] 32,000 1,500 t/a - 26,000 t/a (5 extruder sizes) Floor space [m²] Depending on through-put and technology: 8-200 130-540m² Which approvals FDA [cat. A-H&J]; efsa (postive opinion issued); brand owners (conf.); several national approvals (Austria, CH, Zona Mercursur, etc.) Several USA/FDA(C-H),Austria, Germany/BfR, Ilsi, France/AFFSSA, Finland,Australia, Canada, Egypt, Japan, Switzerland, several LatinAmerican Countries (Bolivia, Brazil, Chile, Colombia, Ecuador, Guatemala, Peru); follows EFSArequiremens; brand owners Fresh water consumption per tonne output [m³/t] Depending on application and technology type but we have a closed loop system approx. 0.15 Consumption kWh per tonne output [kWh/t] 250-350 approx. 410 (depending on design) Bottles to flakes Starlinger recycling technology offers the engineering of washing lines and/or a turnkey project with components and technologies available in the market Input variable: collected pressed bottles, various colours Yes, in cooperation with long-time partners Yes (decontaminated for food-contact, IV increased, AA 1ppm, lowest VOC level) Output: Flakes with/without approval FDA [cat. A-H&J]; efsa (postive opinion issued); with Multi Purpose Reactor (MPR) Bottles to flakes Capacity [t/a] 15,000 16,000 3,700 - 10,500 (5 sizes) Floor space [m²] 20-40 2,000 approx. 150 Which approvals FDA, efsa (postive opinion issued) FDA (hot-fill), follows EFSA requirements Fresh water consumption per tonne output [m³/t] closed loop system 1.5 Consumption kWh per tonne output [kWh/t] 100 150 120-250 (incl. bottle washing to SSP) Miscellaneous Company also offers systems for Bottle-to-film Vacurema inline sheet Yes Bottle-to-fibre Vacurema inline fibre Yes Yes Bottle-to-strapping Vacurema inline strapping Yes Yes","@ID":46}, "TRADE SHOW PREVIEW 52 PETplanet insider Vol. 17 No. 09/16 petpla.net K 2016 In October, some 3,100 businesses from almost 60 nations from the plastics and rubber industry will again be presenting trend-setting products, processes and practical solutions on more than 170,000m2 of net exhibition space. The strongest contingent of exhibitors comes from Europe, especially from Germany, Italy, Austria, Switzerland, France and Turkey, but there is also an impressive number of participants from the USA. At the same time, K is an indicator of changes in the global market: in recent years, the number of Asian companies and the exhibition space booked by them has been rising steadily, and this year, particularly China, Taiwan, India, Japan and South Korea will be showing a strong presence. Tailored materials, efficient use of resources, zero-defect production, generative production methods and digitalisation are only some of the many technological trends featured by this year’s trade fair. Our show previews in this and the coming issue of PETplanet will give you a flavour of what to expect from PET-relevant exhibitors at K 2016. K 2016 will be held from October 19-26 at the Düsseldorf fairgrounds. www.k-online.com Inspection systems 4.0 In the field of plastic packaging, industry 4.0 stands for the fusion of modern IT with current production technologies. The goal is to achieve better cost and time efficiency for production and excellent product quality. Especially the latter Intravis intends to support with advanced inspection technology of hardware and software. The IntraVisualizer is a newly developed software converting all measurement results of Intravis systems into simple and easy to read graphs. This way, the user can easily monitor all Intravis equipped lines side-by-side. Different time periods such as shifts or days as well as individual shots can be visualised. The development of different product characteristics can be precisely tracked on the screen. The software is operated on any standard internet browser and is touchscreen capable. The IntraVisualizer is also capable of creating trend statistics helping to minimise the reject rate. Selected product parameters are being measured and the progress of measuring results is analysed by the IntraVisualizer. It also indicates when a value permanently deviates from the desired nominal value. The Estimated Time to Failure (ETF) is shown on the screen and can be generated automatically via email. This is the time, estimated from trends, when products will start to be defective. The user now has the opportunity to intervene in production before the tolerance limit is exceeded. This prevention of scrap saves material and therefore enables increased productivity. Among the company’s exhibits will be the PreWatcher III, an updated inspection system for preform manufacturers (see PETplanet 3/2016, page 28-29). Intravis will exhibit other systems in cooperation with multiple partners. An IntraWatcher directly integrated into the takeout handling is shown at the Polymac Robotics booth (Hall 13, B59). At the Arburg booth (Hall 13, A13-1/A13-2) a CapWatcher is displayed performing inner and outer closure inspection. A SpotWatcher will be presented at the Kautex Maschinenbau booth (Hall 14, A16 / A18). www.intravis.de Intravis Hall 11 Booth A58","@ID":56}, "NEWS 8 PETplanet insider Vol. 17 No. 09/16 petpla.net COLOUR YOUR SUCCESS WITH US HOLLAND COLOURS EUROPE BV Halvemaanweg 1, 7323 RW Apeldoorn P.O. Box 720, 7300 AS Apeldoorn The Netherlands Tel.: +31 (0)55 368 07 00 E-mail: info@hollandcolours.com www.hollandcolours.com Thousands of colour shades, a variety of product formats: liquids, pastes, granulates, microbeads and additive solutions powered by our team of technical experts to ensure your success. Providing you with innovative, sustainable and cost effective solutions, fitting your requirements with our multiple product formats. Choosing or matching the right colour for your application. We offer a huge variety of solid and liquid colorants and additives like soft drinks, beer, dairy and many others for PET packaging applications with nearly four decades of experience: low dosage, high efficiency.","@ID":12}, "CAPPING / CLOSURES 44 PETplanet insider Vol. 17 No. 09/16 petpla.net Different applications, neck finishes for various, part 8 Closure for PET bottles & Resins PETplanet insider is publishing extracts from successive chapters of Ottmar Brandau’s “Bottles, Preforms and Closures,” which was published by hbmedia. A newly revised version is reissued under the Elsevier imprint. 4.5.1.1 Chemical Properties PP has excellent stress-crack resistance and tolerates higher temperatures quite well but does not fare as well at lower temperatures. Compared with HDPE, it has a lower density, has a higher softening point as it does not melt below 130 °C, and is also relatively hard and stiff. Additives are applied to all commercially produced PP resins to protect the polymer during processing and to enhance end-use performance. Maximum density is 0.915g/cm3 (fig. 4.32). PP comes in three grades: A general-purpose homopolymer. A block copolymer with 5–15% ethylene, which has a much improved impact resistance extending to temperatures below -20 °C. Its toughness can be further enhanced by the addition of impact modifiers, traditionally elastomers in a blending process. A random copolymer incorporating comonomer units arranged randomly (as distinct from discrete blocks) along the PP longchain molecule. Such polymers typically contain 1–7% ethylene and are selected where a lower melting point, more flexibility, and enhanced clarity are advantageous. Physical Properties Tensile Strengh 0.95 - 1.30 N/mm² Notched Impact Strengh 3.0 - 30.0 Kj/m² Thermal Coefficient of expansion 100 - 150 x 10-6 Max Cont Use Temp 80 °C Density 0.905 g/cm³ Resistance to Chemicals Dilute Acid **** Dilute Alkalis **** Oil and Greases **variable Aliphatic Hydrocarbons * Aromatic Hydrocarbons * Halogenated Hydrocarbons * Alcohols **** Key * poor ** moderate *** good **** very good Figure 4.32 PP properties at a glance PP’s high stiffness makes it unsuitable for one-piece closure applications. There are two reasons for this: In one-piece designs (see chapter 4.2) small cap protuberances con-","@ID":48}, "TRADE SHOW PREVIEW 59 New Eblow series The blow-moulding machine manufacturer Bekum is extending its electrical series Eblow. The newest addition is the Eblow 37 for packaging applications. It premieres at the K 2016 to specialists in the industry. The continual development of the machine range was followed by the introduction of the Eblow 07 series with patented C-frames. The newest development of the Berlin technology leader is the Eblow, a blow-moulding machine for high-performance production of blow-moulded articles, especially for canisters. With this model Bekum is looking to win points in the packaging sector, particularly from producers who are interested in an energy-efficient, flexible machine solution tailored for highperformance. The Eblow 37 design has its roots in the hydraulic machine range. The goal of the new technology was to take the experience from the manufacture of the Eblow electric packaging machine series and combine it with the advantages of the proven BA 34.2 hydraulic canister machine. The hydraulic BA 34.2 has been successfully positioned in the market with over 200 machines. Now Bekum is transferring this to an electric generation of machines, which offer a technically and economically attractive solution for producing articles between 10 and 35l. According to Bekum, the high-performance Eblow 37 provides canister manufacturers with the option of upping their added value through increased output volumes. www.bekum.de Bekum Hall 14 Booth C03 PETplanet insider Vol. 17","@ID":63}, "Hong Kong Chongqing Xi'an Taiyuan Shenyang Qingdao Nanjing Guangzhou Shanghai Beijing Jinan Sponsors The China Road Show The worldwide round trip with www.china.petpla.net 2016 is both the Year of the Monkey in Chinese astrology and the occasion of our first Editourmobil quest to sample the far-eastern culture of China. Our China Road Show Tour into the Middle Kingdom successfully began in Shanghai in April. Since then we have met many interesting PET companies, both machine and equipment suppliers and their bottling partners and customers. All the interviews with the people we met - and the travel experiences we have had so far - can be read along with photo material at our Editourblog at www.china.petpla.net The first interviews with the leading players in the market have already been published in PETplanet Insider and there are many more yet to come! We still have some way to go until we reach the China Brew China Beverage exhibition in Shanghai. There, we will be showcasing our Chinese Editourmobil, along with information about all companies that we have visited along the way. We look forward to our last stage of the Tour and to meeting you during China Brew China Beverage, October 11-14, 2016 in hall W2, booth no. 2Y445. Come and join us on an incredible exploration of the Chinese PET market! As the saying goes: ॹ䠂ҁ㺂θခ᯲䏩сȾ (A journey of a thousand miles begins with a single step). April – October 2016 Meet us at China Brew China Beverage, October 11-14, 2016 Hall W2, Booth no. 2Y445","@ID":67}, "TRADE SHOW PREVIEW 60 PETplanet insider Vol. 17 No. 09/16 petpla.net Direct post-crystallisation, processed for high efficiency Premiere at the K trade fair: PET CrystalBatch The new alternative to amorphous PET pellets is called PET CrystalBatch. In a new process developed by cpc, the material is directly post-crystallised and thereby subjected to less thermal stress. It retains its cylindrical shape and is claimed to have an excellent surface quality. To this end, PET CrystalBatch impresses with its homogeneous, stable product quality. It is dust-free and does not migrate. The PET pellets can be used universally, allowing them to be easily integrated into various industrial manufacturing processes in various sectors. The search for greater efficiency determines the industrial production processes – for masterbatch developer cpc as well as for its customers. When PET is crystallised in a discontinuous process, the structure of the pellets suffers. It is subjected to high thermal stress in the successive process steps. Migration and dust represent additional obstacles for further processing. The solution lies in the so-called direct crystallisation. This enables optimisation of energy management, in which energy from the melting process is used for the crystallisation. Process stability and improved product quality are also additional resulting positive factors. The pellets no longer adhere. Known methods such as underwater strand pelletisation and underwater pelletisation are considered to be costly. cpc has developed a new method for direct post-crystallisation that further optimises the structure of the pellets. In this process, the crystallisation point is reached in a particularly gentle manner. The PET CrystalBatch produced by cpc is subjected to less thermal stress during direct post-crystallisation, retains its cylindrical shape and has a superior surface quality. To this end, PET CrystalBatch impresses with its homogeneous, stable product quality. It is dustfree and does not migrate. PET CrystalBatch belongs to the product range from cpc. Through direct post-crystallisation, it helps in reducing energy costs and improving processing efficiency. PET CrystalBatch can be used universally, allowing it to be easily integrated into various industrial manufacturing processes in various sectors. www.colorplasticchemie.de The color plastic chemie Albert Schleberger GmbH (cpc) family company, which was founded in 1968 and continues to be owner-managed, has been a specialist in the development and production of dye concentrates and additives for thermoplastics for over forty years. With over 100 employees, cpc is one of the leading masterbatch producers in Europe. Its products are available around the world. cpc has developed tailor-made solutions from dye samples and specifications, which can be integrated into modern production processes in an easy and safe manner. The company certified under ISO 9001:2008 is said to guarantee a consistently high quality of dye concentrates and additives produced at its site in Remscheid, Germany. In production, cpc processes traditional pigments and dyes of the highest quality and exclusively uses raw materials that are free of harmful heavy metals. Using renewable energy plays an important role for cpc as well as conscientious water and air conditioning. The independent family company is value-oriented and pays attention to the fair and respectful treatment of customers, partners and employees. The product range includes colour, additive and special batch for various ways of application in many industries, from building materials and toys to the food and cosmetics industries. In addition to dye concentrates and pigments, cpc also manufactures liquid dyes, dyes in granular form and dye compounds. cpc invites its customers to a personal consultation in a spacious and bright ColorLounge. Both the technical possibilities and trend aspects are included in the colour design of the products. For this, not only are colour chips presented but also real objects such as bottles and jars, creative injection moulding items as well as technical products from the automotive and pipe industry. In a separate light room, the selected colour design can be tested under various lighting conditions. After prior agreement, bottle prototypes can also be provided on site during the consultation. cpc applies co or mono extrusion for colouring or produces PET bottles in an injection, stretch, blow moulding process. cpc customers benefit from exclusive on-site service with the ColorMobil. CPC Hall 6 Booth D76","@ID":64}, "MOULD MAKING 20 PETplanet insider Vol. 17 No. 09/16 petpla.net MHT opens Service Centre in Taicang MHT China Team, f.l.t.r.: George Wang, Mario Franke and Helen Yang W W W . I N T R A V I S . C O M Sample-PreWatcher® Comprehensive sampling analysis inline and offline High speed 100 % inline and offline inspection Color inspection right above the tooling plate PreWatcher® III ColorWatcher® Integrated Preform Inspection Today. V I S I T U S A T 2 0 1 6 H A L L 1 1 , B O O T H A 5 8 May 27, 2016, MHT Taicang We met: George Wang, Service Engineer, Mario Franke, Sales Manager and Helen Yang, Sales Assistant It’s the next step into an interesting market: After the opening of a sales office in Taicang, China, in 2014 MHT Mold & Hotrunner Technology AG, Germany, a manufacturer of high-performance PET-moulds, has decided to add a service centre at the same location. This is to provide the Asian customers with local support and to underline the importance of the Chinese market. Sales Manager Mario Franke, Sales Assistant Helen Yang and Service Engineer George Wang will manage all the local sales and service activities. Recently mainly large moulds with up to 144 cavities have been ordered for well-known brands for PET preform high speed machines in China. Because of the current situation and in parallel the over-capacity in the market, there is a slow down for new PET lines currently in China. MHT is sure that the market will stabilise and grow further on a mid-term view. MHT has been selling preform moulds from Germany to China since 1999. Today about 100 MHT moulds are running in the country. www.mht-ag.com SPONSORS The China Road Show","@ID":24}, "CAPPING / CLOSURES 48 PETplanet insider Vol. 17 No. 09/16 petpla.net The China Road Show SPONSORS Focussing on caps Jian Ren, Business Manager at Plastisud Shanghai June 28, 2016 Plastisud, Shanghai We met: Jian Ren, Business Manager For more than 50 years in injection moulding industry, Plastisud has become an expert in “Injection Mould Engineering and Manufacturing,” mainly for closures, thin-wall packaging and medical parts. In China, the company focuses on caps. Jian Ren, Business Manager, is seeing little growth in this market, currently mainly affecting the machine manufacturers that sell new machines. For him as a mould maker, the situation is different. A cap mould needs to be replaced about every five to ten years, depending on market trends. Plastisud R&D Deparment is also helping customers to develop their own closures, with even more reliable and high production moulds, with high cavitation. For sure at some point there will be needs and requests for new tooling. As an example, an important market is conversion of the existing 30/25 cap to 29/25 caps. Jian Ren keeps meeting key players in China on a regular base to talk about new developments. Many Plastisud moulds are already producing for famous Chinese brands and confidence with the French technology is well established. www.plastisud.com FILLING MACHINES ARE NOT PRESSURE TESTING MACHINES Is your pressure testing doing what it needs to do? TheAgr PPT3000 is the only commercially available system | +1.724.482.2163 | SALES@AGRINTL.COM VISIT US AT BOOTH 11B40","@ID":52}, "BOTTLE MAKING 24 PETplanet insider Vol. 17 No. 09/16 petpla.net from KHS were already in operation at AGD. A new KHS InnoPET Blomax 10 S Series IV has been up and running at AGD’s bottling plant since December last year. “We’re convinced by the high quality of our new equipment, which is the latest generation of stretch blow moulding and filling technology, and its vast production capacity,” Lauría says. AGD can now produce up to 19,000bph square holding 0.9 or 1.0l bottles; up to 15,000 1.5l bottles can run through the machine every 60 minutes. By comparison, the old plant technology could only process a maximum capacity of 12,000 bottles in the two smaller formats and up to 10,200 of the larger size every hour. KHS has ensured this increase in efficiency through the lighter, the more stable bottle design. “Thanks to the lighter bottles – plus our new technology – we’re already benefitting from lower operating costs.” The combination of reduced consumption in energy and compressed air, fast format changeovers and improved system performance are the convincing arguments which speak for this system. The increased capacity and efficiency at its plant means that AGD is also able to pursue its international goals effectively; no less than 30% of Argentina’s exports in the edible oil segment are already attributable to AGD. The first months at the modernised production shop ran so smoothly that AGD promptly ordered a second KHS InnoPET Blomax 10 S Series IV, which KHS recently installed in General Deheza. It went into operation at AGD at the beginning of July 2016. www.khs.com www.agd.com.ar/en Optimisation through computer simulation: using its high-quality PET format database KHS came up with a new bottle design on the computer within a short time indeed. Aceitera General Deheza S.A. (AGD) was founded as an oil mill in 1948. In its founding years the output ran to 35 metric tonnes per day. AGD now positions itself on the market as a modern agricultural enterprise. It is capable of producing up to 20,000 tons of ground seed per day and has a storage capacity of 3.3 million tons. AGD employs over 2,500 people. Production is subdivided into various brands of valuable oil product from vegetable oil through gluten-free oil to biodiesel. AGD exports to 45 countries. New plant engineering: AGD has invested in a new stretch blow moulder from KHS to fill its new PET bottles. A second system went into operation at the beginning of July 2016. bottle making","@ID":28}, "CAPPING / CLOSURES 47 PETplanet insider Vol. 17 Please order your copy at the PETplanet insider book shop: https://petpla.net/books Bottles, Preforms and Closures - A Design Guide for PET Packaging Second Edition by Ottmar Brandau € 115,00 180 pages © Copyright Elsevier 2012 * This article was published in Bottles, Preforms and Closures, Ottmar Brandau, Chapter 4.5 and 4.6 Copyright Elsevier 2012 sports caps and other complicated configurations can be manufactured. Moveable inserts allow the creation of undercuts such as those necessary to slit tamper-evident bands right inside the mould instead of having them punched in a secondary operation. IM closure tools are sophisticated moulds that often cost more than the injection machine they are running on. To get the extremely low cycle times modern tools allow, water channels must be close to the plastic even in moving parts. This leads to significant manufacturing challenges that are costly to overcome. These tools also require a stringent maintenance programme especially when moving mould inserts are involved. A pressure difference of 5 bar (72 psi) between the supply and return water channels is also recommended to accomplish good turbulent flow that is able to extract heat quickly. Process control during injection and hold is most crucial for highest quality. Closed-loop controls on high-performance machines are recommended. Cycle times as low as 3.2s are possible, but other tool/machine combinations may run as slow as 14s.","@ID":51}, "BOTTLE MAKING 26 PETplanet insider Vol. 17 No. 09/16 petpla.net Amcor and Method overcome design challenges to develop first 100% PCR PET bottle for liquid laundry Clear containers for coloured concentrates Amcor has broken new ground with the development of the industry’s first liquid laundry bottle made of 100% post-consumer recycled (PCR) PET. The company helped San Francisco-based Method Products, the leader in eco-friendly household, fabric and personal care products, expand its liquid laundry offering. Its new 4x concentrated detergent product is packaged in a 53oz PET bottle made of 100% PCR PET resin. The breakthrough development, manifested in a sleek, transparent custom container with strong shelf appeal, did not come without resolution of some key process, mould, and design challenges, according to Matt Lewis, senior development engineer for Amcor Rigid Plastics. “Through our strong partnership with Method we have developed a long line of unique PET packages,” said Lewis. “We were able to again push the envelope and deliver an important advancement in bottle design, this time for the liquid laundry detergent market.” Method, which is well-known for its brightly coloured hand wash and all-purpose cleaning formulations showcased in clear PET bottles, achieved an industry first in a market that has previously been essentially limited to opaque highdensity polyethylene (HDPE) containers. This new PET offering in the liquid laundry segment resonates with the rest of Method’s brand portfolio in hand wash and all-purpose cleaners, according to Joe Hunter, director of packaging. Collaborative work solves three issues Amcor had to overcome three primary challenges, namely: colour stability of the laundry detergent in PET; hand grip design; and neck design. It worked in partnership with Method to tackle all of these issues. Method’s desire to offer liquid laundry detergent in a PET bottle required the company to address two fundamental problems: the lack of compatibility of its detergent products with PET packaging; and colour stability issues. Up until now, PET has struggled to enter the liquid laundry detergent market precisely because of these factors. First, Amcor set up a test protocol to assist Method in assessing its product formulas and compatibility with various clear PET bottle grades. This helped Method chemists in their formulation development and ultimately led to assurances of the package’s stability on the store shelf. Amcor did initial testing on preforms and further stability testing revealed no issues after numerous trials. Amcor also addressed the neck design, which presented challenges due to the two-piece polypropylene (PP) pour spout and cup closure. The pour spout required orientation to the front of the bottle and once in that location could not be rotated by the removal of the pour cup. This was complicated because the PP closure was designed for an HDPE bottle. PET is a more rigid and less flexible material and is less forgiving in terms of closure screw-on performance. The lug design on the neck finish went through a series of design trials and modifications in order to attain the positive stop in the thread finish. bottle making","@ID":30}, "BOTTLE MAKING 22 PETplanet insider Vol. 17 No. 09/16 petpla.net Greater economy from lower weight Save costs by reducing the weight of PET bottles: an increasing number of bottlers are prepared to cut down on the resources they use for packaging materials, for ecological as well as commercial reasons. But does less material mean a loss of quality for the individual bottle? The example of Argentinian edible oil producer Aceitera General Deheza S.A. (AGD) shows how KHS optimised the PET packaging design for AGD’s Natura brand – making considerable savings on materials in the process. which – along with the high quality of the oil – have made Natura a premium product. Cutting costs and boosting efficiency In order to reduce internal costs for its quality edible oil and at the same time promote sustainable use of resources, AGD aims to improve efficiency in its own processes. “Although our bottle to date had proved successful, we realised that we had to modernise the Natura bottle itself, along with its production processes,” says Mariano Lauría, bottling plant manager at AGD. “We aimed to reduce the weight of the bottle in the long term yet still boost the throughput in the machine.” For KHS, the most pressing task seemed to be almost ordinary: to develop a future-proof bottle shape with a high degree of stability. The special challenges this presented became evident on closer examination. These were determined by AGD’s design specifications as: to keep the square bottle shape established among end consumers; to include a recessed grip as an additional hallmark of quality; and to retain the size of the area for the bottle label. AGD also wanted to continue using the bottle’s typical jaycap. The top load, the determining reference value for the load-bearing capacity of the bottle during transportation, was clearly stipulated by the company. Three bottles holding 0.9, 1.0 and 1.5l respectively were to be optimised based on these requirements. Both the 0.9 and 1.0l PET bottle were to weigh between 27 and 27.5g, compared with the previous weight of 30g. A drop from 41.5g to a target value of between 38 and 39g was envisaged for the big 1.5l bottle. Computer simulation AGD has enjoyed a strong working relationship with KHS for many years. The solution KHS offered gave the Argentinians the headway they wanted. With its Bottles & Shapes PET bottle design concept, the KHS engineers kept more or less to the base of the existing PET bottle but designed a new, lighter thread for 0.9, 1.0 and 1.5 liters: applying its Bottles & Shapes programme KHS has optimised the weight of not one but three different PET bottles. bottle making Two newly-installed KHS InnoPET Blomax 10 S Series IV stretch blow moulders were able to deliver a higher production capacity even for the company’s square bottles. This, consequently, allows AGD to consistently pursue its strategy of growth. Natura brand has relied on PET as its container of choice since the late 1980s; it is now the market leader in its product category. In 1989 – when PET began to establish itself as an alternative packaging to glass – AGD was the first brand in Argentina to opt to fill vegetable oil into PET bottles. Over time, Natura advanced to become a leading brand of edible oil and it is now the top-selling oil in Argentina, Chile and other South American countries. The product can also be found on supermarket shelves outside its core markets. After starting off with a round bottle, AGD established a new design for its flagship product: a square PET bottle with stylish ribs and a consumer-friendly recessed grip. The brand’s success is inextricably linked to its special PET packaging,","@ID":26}, "MARKET SURVEY 43 PETplanet insider Vol. 17 No. 09/16 petpla.net STF Maschinen- und Anlagenbau GmbH Krones AG Polymetrix AG Gneuss Kunststofftechnik GmbH Herbold Meckesheim Industriestrasse 2 94529 Aicha v. Wald, Germany +49 8544 960 110 www.stf-group.de Mr Markus Ingenpaß Head of sales +49 8544 960 110 +49 8544 960 130 sales@stf-group.de Böhmerwaldstrass 5 93073 Neutraubling, Germany +49 9401 70 0 www.krones.com Mr Peter Hartel Head of Sales PET Recycling +49 9401 70 5448 +49 9401 70 91 5448 peter.hartel@krones.com Sandackerstrasse 24 9245 Oberbüren, Switzerland +41 7155 210 22 www.polymetrix.com Mr Karl Schoepf Product Manager Recycling +41 7155 210 82 karl.schoepf@polymetrix.com Mönichhusen 42 32549 Bad Oeynhausen, Germany +49 5731 5307 0 www.gneuss.com Industriestr. 33 74909 Meckesheim, Germany +49 6226 932 0 www.herbold.com Mr Siegfried Engel Vice President Sales +49 6226 932 133 +49 6226 932 495 siegfried.engel@herbold.com Engineering of washing lines with long term partners Yes Yes Agglomerate 3,500 t/a - 30,000 t/a 24,000 t/a Up to 17,000 Up to 36,000 1,000 - 6,000m² 5,000 1,000 FDA-LNO, EFSA-LNO, brand owners FDA, EFSA, Brand owner FDA, ESFA (pending), INTI, brand owners (conf.) 2,5m³/t 2.15m3/t Depending on bottle contamination 0.5-1 Depending on design 580KWh/t, 590kg steam/t Depending on input material 545 Yes FDA, ESFA (pending), brand owners (conf.) 3,500t/a - 30,000t/a 12,000-50,000t/a 200-17,000 Up to 13,000 (1 unit) 800-3,000m² 400-600m2 30-80, depending on size 64 FDA-LNO, EFSA-LNO, brand owners FDA, EFSA, Brand owner FDA, ESFA (pending), INTI, brand owners (conf.) 2.5m³/t 0.15m3/t 0, no fresh water needed Depending on design 290KWh/t 350 approx. 125 Various other plastics and contaminations Yes Flakes with/without approval 7,500-30,000 t/a output PET flakes 3,500t/a - 30,000t/a 24,000t/a 6,000-30,000 1,500 - 3,000m² 1,000-4,000m² 4,500m2 1,000-3,000 FDA / EFSA FDA-LNO, EFSA-LNO, brand owners Zero Emission Water Treatment 0m³/t max 2.5 m³/t 2m3/t 250kWh/t for sorting, grinding and washing Depending on design 290KWh/t, 590kg steam/t approx. 250-300 PET bottle washing plants, turnkey systems, single components, size reduction components Yes, mainly thermoforming sheet lines in direct food contact Yes, several lines under operation worldwide Yes","@ID":47}, "TRADE SHOW PREVIEW 64 PETplanet insider Vol. 17 No. 09/16 petpla.net FachPack 2016: Innovations aimed at sustainability BericapHall 6 Stand 6-418 Bericap will be showcasing new packaging solutions, such as the e-smoCap for e-liquids, alongside advances in its tried-and-tested closure solutions for canisters, metal packages, pesticides, lubricants, sauces & dressings, edible oil, food and beverages. Protection against product piracy Product piracy and the accompanying product counterfeiting are a sensitive problem with serious consequences when it comes to chemicals, especially in the agricultural sector. In order to protect refills from being adulterated or tampered with, all closures have a folded and cut guarantee strip which is said to be extremely difficult to manipulate and shows clear evidence of tearing when the closure is opened. Other safety options are customer-specific closure designs, possibly complemented by an additional security label connecting the guarantee strip to the closure, or the use of laser technology enabling, for example, the company name to be lasered across the security strip and closure, including on uneven surfaces. Bericap has developed a special counterfeit protection system for one engine oil manufacturer. The bottler’s logo is affixed to the side of the closure across the security strip. As soon as the closure is opened, the security strip breaks and the logo is “destroyed”, making it obvious that the bottle has already been opened. Closure for e-cigarette refill sets Bericap has developed the e-smoCap a childproof closure that makes it easier for millions of people throughout Europe to refill their e-cigarettes. The closure has ISO 8317 CRC certification from the Laboratoire National d’Essais, which is supervised by the French government. A sealing strip ensures that it is tamper-proof, thus providing protection and security for end consumers. There is a long, narrow drip nozzle inside the closure for easy refills. Of course, it is also possible to conceive of other applications for this product in which precision dosing is of paramount importance. www.bericap.com P.E. Labellers S.p.AHall 3 Stand 321 P.E. Labellers S.p.A is a company specialised in designing and producing labelling machines, using all the existing technologies - cold glue, self-adhesive, hot melt, roll-fed and combination systems - and suggesting new ones. For forty years P.E. Labellers is present in the Italian market with a high number of references, 95% of the sales revenue comes from exports. P.E. labelling machines are exported all over the world and P.E. is one of the worldwide leaders in the labelling sector. P.E. can boast more than 10,000 rotary and linear labellers installed on the international market, with a medium turnover of EUR 60 million per year. Also this year P.E. Labellers will take part to FachPack exhibition and the visitors could reach the news about P.E. Labellers for the company’s staff. www.pelabellers.it Tamper protection: Security label across the guarantee strip From September 27 to 29, 2016 Nuremberg will once again be the meeting place for inspiration and concrete solutions covering all aspects of packaging, technology, processing and logistics. At the last event, around 44,000 trade visitors entered an exchange here with 1,565 exhibitors on products and services in the packaging sector. FachPack is one of the most renowned packaging fairs in Europe. The exhibitors present solution concepts and innovations as well as services from the areas packaging, technology, processing and logistics. Trade visitors from Germany and the neighbouring countries come from all sectors involved with product packaging: food and beverages, pharmaceuticals-medicine-cosmetics, textiles, non-food, chemicals, printing, electrics/electronics, automotive, metal working, plastics processing, mechanical engineering/appliance construction, logistics, retail as well as media/advertising. An attractive support programme, the Forum PackBox together with numerous special shows and theme worlds, round off the range of products and services and offer additional value. This year FachPack will be focusing on resource-saving through recycling and greater energy efficiency through smart solutions. www.fachpack.de","@ID":68}, "TRADE SHOW PREVIEW 55 Corvaglia Hall 12 Booth A51-06 Measuring the actual moisture The Italian company Moretto, known for automation technology for the plastics processing industry, will present several exclusive solutions: Moisture Meter, a resin moisture analyser; XD 10, a high performance mini-dryer; DGM, a continuous batch gravimetric dosing unit; and Exa, a conveying system for up to six stations. Moisture Meter is an in-line resin moisture analyser. At Moretto’s booth there will be a working display of the system installed on a running injection moulding machine producing a standard medical device. With this instrument it is possible to certify the production of plastic parts and when installed directly on the processing machine, measures the actual moisture content of the plastic granules. No calibration is required and it is only necessary to select the polymer to be treated, from a materials database (included), and Moisture Meter will continuously control the process with sampling every 10s. Moisture Meter is claimed to represent the missing link in the overall drying process. With Moisture Meter it is possible to determine how much water remains in the process resin. Complementing this innovative instrument is also the availability for on-demand analysis to produce reports on production data by hour, minute, or, in the case of single cavity mould production, a report for every printed piece. Outside, it will be possible to visit Moretto’s 40t articulated lorry, Moretto in Motion, a laboratory of ideas which contain the latest news and innovations from Moretto. This exclusive area is dedicated to the most demanding customers and will be hosted by professional Moretto staff. www.moretto.com Moretto Hall 11 Booth H57 Closure systems Corvaglia’s participation in the exhibition will reflect the company’s expertise in creating tailor-made closure solutions to meet the challenges of its customers. Visitors will search in vain for standard products on the booth of the Eschlikon-based Swiss company which also has an additional manufacturing plant in Mexico. Instead, the display will be focused on the common exchange of closure solutions along the entire value chain. www.corvaglia.ch PETplanet insider Vol. 17","@ID":59}, "PETplanet insider Vol. 17 No. 09/16 petpla.net BOTTLE MAKING 30 Second 4l PET bottling line running for Nongfu Spring bottle making Following the success of the Sidel PET Combi line for 4 litre water bottles, which was supplied to Nongfu Spring in 2014, the producer has invested in a second Sidel bottling line, in order to further boost its production capacity. Nongfu Spring’s intention in the decision to switch from HDPE to PET for its 4l bottles was to create a bottle that would stand out on the supermarket shelf. It also wanted to achieve a more cost effective and sustainable production process for the family bottle format. The inherent properties of HDPE result in certain constraints in bottle design, reducing bottle appeal and, consequently, perceived value for consumers. The PET bottle is fully transparent and light, requires less material to produce and creates less waste than an HDPE bottle, which also lacks the clarity of PET. The new bottling line also offers lower total cost of ownership through its capacity for higher production output than an HDPE line. A dedicated Combi to boost productivity When Nongfu Spring decided to switch to PET it came with very precise and specific technical requirements for the bottling line. The company wanted to increase its production capacity and efficiency to meet growing market demand for the 4l bottle, while also reducing production costs; thus the specific request for high speed and line efficiency. Sidel proposed a bottling line at the required output of 14,000bph, integrating blow, fill and cap functions in a single machine. The Combi offers a reliable operational level that has enabled Nongfu to boost its overall productivity and maintain a competitive edge in supplying 4l water bottles. The Combi, manufactured in the Sidel Beijing plant, was fully tested in-house to ensure a fast installation and ramp-up in the customer’s production facility. This allowed validation of all the components and options specifically developed for Nongfu Spring. The Combi line is dedicated exclusively to the family bottle size. Sidel’s strong project management was instrumental to the success of what proved to be a complex process. There were several other third party companies involved, including the suppliers of the conveyor system, labeller and carton casers, which all had to be integrated into the line at the desired efficiency and output levels. Nongfu Spring water is one of the leading brands for natural mineral water in China. Drawn from natural water springs in various parts of the country, Nongfu Spring’s bottled water is one of the most well known on the domestic market. It held a 22% market share in China’s competitive bottled water segment in 2013. In addition to the regular 380ml, 550ml and 1.5l PET bottle formats, the company’s bottled water is also available in a 4l family size, which, until recently, was only available in High Density Polyethylene (HDPE). This was the starting point for its challenge to align the production of its bottles across the range, by switching from HDPE to PET for its largest bottle size. The company turned to Sidel to provide a packaging solution. Early in 2014 Sidel supplied the 4l PET bottle to Nongfu Spring, which runs at 14,000bph. This makes it the fastest-ever Combi water line.","@ID":34}, "AUTOMATION 49 PETplanet insider Vol. 17 No. 09/16 petpla.net Safe, sound and efficient Transfer arm for stretch blow moulding machines Properly designed and executed automation solutions increase efficiency, productivity, output and competitiveness. In order to deliver the advantages of automation, components need to be robust, as they will often be operating without human involvement or oversight. US company PHD, Inc, based in Fort Wayne, Indiana, says that it has developed solutions that take on these challenges and respond to the need for safe and reliable automation. “PHD has worked with container manufacturing and filling customers globally to support their initiatives to increase up time and lower cost,” a company spokesman said. It has worked independently and in collaboration with customers to design and manufacture both bespoke and standard equipment. It is particularly proud of its record of durability and reliability in service. “We have been able to develop products that have been in service for decades and have helped customers to eliminate the need for frequent refurbishment or annual disposal of equipment.” The manufacturer highlighted the examples of its stretching cylinders, which it maintains have longer running periods between rebuilds and can cope with multiple rebuilds, thus maximising service life. Within continuous extrusion blow moulding wheels, the increased exhaust capacity of its needle cylinders allow for extended run time between periodic cleaning intervals. Extended time in operation helps to reduce total cost of ownership and boost productivity, leading to improved profitability. It further claims that its transfer arms are more robust than its competitors and survive severe impact with no effect on production. “We recently worked with several customers to develop an improved transfer arm for blow moulders,” the company said. “The PHD arm provides significantly longer service life with increased bearing capacity. A typical 20mm ball bearing can wear out in months; the PHD 25mm recirculating roller bearing has more than twice the life. This rigid bearing reduces mis-feeds and damage to the preform caused by the original worn out linear rail drooping as it advances.” The PHD arm is also said to be much more robust because it incorporates a robust welded base, instead of the traditional cast base, which can bend and break under use. Typical features from PHD stretch rod cylinder for stretch blow moulding machines “When the original cast base bends the pivot bearing location is effected and parts are mis-loaded into the moulds, causing rejects and machine downtime,” the company continued. “Our robust weldment eliminates this problem. The arm also incorporates an optional threaded height adjustment that eliminates the tedious process of using shims to establish pass line height. The customer benefits from quicker and more accurate set-up, which improves machine up time and lowers cost of operation.” PHD has provided solutions for injection moulding, re-heat stretch blow moulding, continuous extrusion, package closure, labelling, validation, case packaging and palletising, as well as resin drying, preform transfer, stretching, nozzle solutions, trimming, and filling. www.phdinc.com Stretch rod cylinder for stretch blow moulding machines","@ID":53}, "CAPPING / CLOSURES 45 PETplanet insider Vol. 17 tact the neck finish to form a seal when fully torqued. This requires a certain softness on the part of the cap material. PP’s stiffness prevents this from happening. The unscrewing torque is an important measure for any applica-tion as consumers with low hand muscle power must be able to open the package easily. With a growing percentage of elderly people in all industrialized societies, unscrewing torque will gain even more importance in the coming years. Because of its stiffness, use of PP often results in unacceptable unscrewing torques when one-piece designs are used. This is because of the relatively large surface area of the cap that comes in contact with the bottle neck and the material’s “unwillingness” to give. Typical acceptable values for unscrewing torques are 10–18 in lb. Because of its high heat resistance, PP shines in hot-fill applications. Here two-piece designs are customary to circumvent PP’s incompatibility with one-piece closures. Developments are under way to use one-piece HDPE closures with a modified seal for hot-filled bottles, which brand owners consider for cost reduction. 4.5.2 Highdensity Polyethylene HDPE is the most widely used material for closure production. It is also the simplest polymer in terms of chemical structure. This “linear” poly-ethylene can be combined to a length that is appropriate for the applica-tion. Its relative softness allows the construction of a variety of one-piece designs. Slightly better heat transfer characteristics allow for faster cycle times than those for PP (Figs 4.33 and 4.34, page 46). We do more. Contiform AseptBloc #GermanBlingBling #ContiformAseptBloc Figure 4.33 HDPE consists of long chains or repeating CH2 units","@ID":49}, "BOTTLES 73 PETplanet insider Vol. 17 No. 03/16 petpla.net 100% juice by Rewe Under its own “Rewe Beste Wahl” brand, Rewe is selling 330ml of 100% whole fruit fresh juice that is bottled directly. The juice is not heated before bottling, and so according to the manufacturer it tastes “homemade”. A clear plastic bottle that is lightly conically tapered from its middle, with a sufficiently large drink opening and a screw cap with a safeguard for first use is used as packaging. It is decorated with a transparent self-adhesive label. For advertising purposes, some of the bottles are fitted with an attached cardboard sleeve to indicate its novelty and benefits. www.rewe.de PET beer barrel In some European countries, the beer group Heineken sells a beer dispensing apparatus for home use. In collaboration with a household appliance manufacturer, a dispensing apparatus called “The Sub” was conceived, in which a separately manufactured PET receptacle can be inserted comfortably, easily, and without the danger of being stained with beer. In reference to its torpedolike shape, this container is called “The Torp”. The container holds two litres and its surface is wrapped in a sleeve label. The system cools the beer to 2°C and it remains drinkable for up to 14 days. Currently 13 different types of beer are available for this system. www.global.the-sub.com","@ID":77}]}}
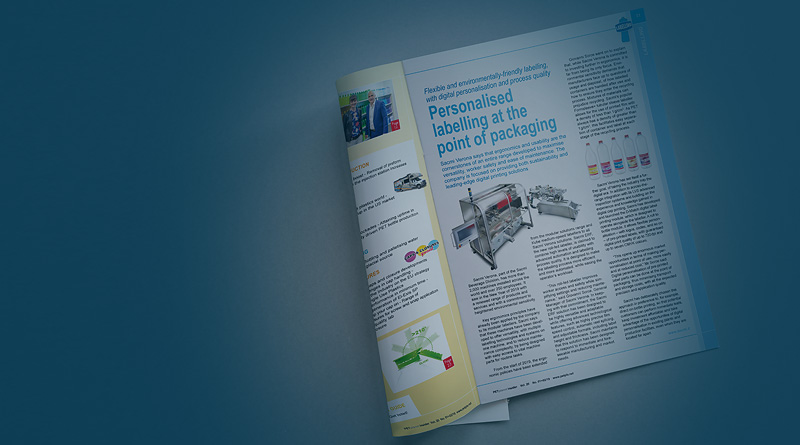