"INSPECTION PETplanet Insider Vol. 20 No. 04/19 petpla.net 44 Integration of inline monitoring and offline inspection into preform manufacturing lines Preform Factory Concept 4.0 IMD Ltd offers preform manufacturers a flexible factory concept with inline monitoring and 100% offline inspection systems that can be integrated into existing production lines or entire production halls. The monitoring systems is claimed to ensure reliability on the entire production line via a portal that can be viewed from anywhere at any time. Acsur S.A. in Argentina has been using the IMDvista Factory Concept 4.0 for one and a half years now. Like many other preform manufacturers, Acsur S.A. is experiencing an increase in production error rates, as more and more recycled material and UV blockers are processed and process problems such as black spots, colour deviations, crystallisation and other errors in the production process occur and sometimes disappear again. Acsur S.A. has been manufacturing preforms and HDPE lids for the beverage, edible oil and detergent industries since 2002. They have nine production lines and a laboratory for quality control of the manufactured products. They use an Integrated Quality Management System (SGCI) supported by ISO 9001, FSSC 22000, ISO 14001 certifications. Three steps for higher preform quality Acsur’s existing production lines with several moulds and machines were upgraded in 2017 with the IMDvista Preform Factory Concept 4.0. The goal was to increase productivity and quality, and to learn more about sources of error in the production process in order to reduce or eliminate them. IMD Ltd. therefore implemented at Acsur S.A. a combination of: 1) Online monitoring of the entire production process and 2) Offline inspection of individual preforms if necessary (at high speed) and 3) A portal for all data, for the evaluation and processing of data from the entire process. First step: constant monitoring inline As it is of high importance to have the production chain under control the first step of the concept is constant monitoring inline of the production, so as to avoid scrap production over a long period. An IMDvista Peco Lux system for inline monitoring of PET preforms has been integrated into each of the eight existing preform injectionmoulding production lines. Monitoring of the whole process Monitoring the process in the Acsur plant is not only a monitoring of the product itself (preforms), but it is a monitoring of the whole production process, beginning with the resin (in mixed raw material) and ending with the finished preform. By examining these processes, the Acsur management was able to draw a conclusion over the quality of their raw material. On the resin – for example contamination and foreign particles inside the product – as well as of the master batch (colour drifts during the production). Going a step further to the storage room, whether humidity or dust is contaminating the resin while in storage. In the next step, the preform provides information on the process inside the machine. The operator is now able to conclude if the machine has a temperature or water and cooling problem (burn- /watermarks). If the tool/mould – or injection process has a problem, it can be seen in the finished preform, because of the short shot trend analyser software or because of evidence of long gates. Step two: offline post inspection at high speed The offline post inspection at high speed is carried out with the IMDvista Peco V3 with efficiency and precision. Only selected octabin boxes are inspected by IMDvista Peco Lux to make sure in the case of problems that only the bad preforms are sorted out while the good ones are used and sold. This factor guarantees Acsur S.A. a smooth production and quality management. The IMDvista Peco V3 can be used inline or offline. It is a compact preform inspection system. The preforms are kept in one straight line, no bends, no corners etc. Step three: one portal for all data Using these values, the final piece of the puzzle for the Portal (data for software data based systems) can generate all these data to a single Ricardo Berger, Quality Manager at Acsur S.A., Argentina.","@ID":46}, "MATERIALS / RECYCLING PETplanet Insider Vol. 20 No. 04/19 petpla.net 16 Using colours to add value to recycled packaging rPET in a premium look Two very public warnings issued in 2018 have to be taken to heart by the plastics industry. First, [if present trends continue] “…there will be more plastics in the ocean than fish by 2050”; second, “single-use packaging will be banned soon”. The plastics industry is under unprecedented pressure but singleuse packaging is unlikely to be banned completely; it is a convenient response to the metropolitan life style and has been spread very quickly, from industrialised countries to developing ones. Food safety, freshness and quality are all are provided by plastic packaging. There are, currently, no other real alternatives. The real challenge is to limit plastic waste going to landfill and into the oceans. An environmentally conscious culture, allied with effective collection strategies, are what is required. Claims and heated accusations that nobody cared about plastic pollution and waste until the publication of alarming pictures of congested rivers and dead wildlife is far from the truth. The plastic packaging industry has already reduced the amount of material used, through light weighting. We are now seeing the rise of the “EcoDesign” philosophy and the exploration of bioplastics – which have, so far, struggled to establish themselves. Olive green with virgin PET (left) and with 50% rPET (right) The keywords and main challenges for the coming years are: reuse – recycle – reduce – bio. Forecasts are that 50%, 75%, even 100% rPET will be used for single use packaging within the next five years. Critical issues will be sourcing, processability, safety and aesthetics. The last issue – aesthetics – might be considered less important but that is not the case. Is the market prepared to abandon attractive packaging? Will brand owners be prepared to see their products packaged in dull-looking rPET containers? Unlikely. Colour correction of rPET Colourants and additives could come to the rescue. Repi, which has more than 45 years’ experience, is working with brand owners and converters to find solutions that allow the use of more and more rPET, both by adjusting the polymer’s mechanical performance and correcting off-shade colours. Smoky black with virgin PET (left) and with 50% rPET (right) Repi’s Anti-Yellow Range (AY) uses different liquid additives to balance the appearance of incoming material. It is possible both to correct typical rPET greenish or greyish tones and to regain brightness. More recycled plastic content can then be used to produce good-looking preform and sheet. The mechanical performance of rPET must be also kept under control, to assure the quality and strength of a bottle. Repi’s IV Enhancer, which is normally added during the injection moulding process, attracts and binds oligomers to itself and increases IV back to the level of the virgin material. IV enhancer additive helps the mechanical performance of a rPET bottle increasing IV level from 0,05dl/g to over 0,10dl/g, depending on the LDR. Colours are also important. Repi’s Fumé range offers a wide choice of smokey shades that cover rPET material and can give a premium and delicate Recycling Special F.l.t.r.: 100% rPET, 100%rPET with AY 00015 @0.03% and same with AY 00201 with optical brightener @0.03% Antique rose with virgin PET (left) and with 50% rPET (right) Repi’s “Fumé shades” are intended to improve rPET aesthetics and help to increase the percentage of recycled material in packaging. Lucia Buffoni, Repi Marketing Manager, offers a personal perspective on the current state of recycling in plastic packaging and explains how colorants and additives can help overcome the challenges the industry is facing.","@ID":18}, "BOTTLING / FILLING PETplanet Insider Vol. 20 No. 04/19 petpla.net 47 rier PET and cap solutions with the Sidel aseptic filling packaging solution will allow reaching a 5-months yogurt shelf life, plus safety throughout the supply chain for distribution at room temperature. The team at Yili was impressed by the technical support given by Sidel in new product development, as well as in the variety of testing methods implemented to qualify the PET barrier solutions. A partner across the entire aseptic PET line Yili acquired two aseptic PET complete lines in the same year both including Sidel and Tetra Pak Processing Systems equipment. Every component was thus centred around one supplier, from process solution to PET packaging assessment, and from equipment definition and delivery to fast ramp-up. The lines, featuring a high-speed production capability to answer the growing Chinese market demand of liquid dairy products for Ready-to-drink (RTD) consumption, also offer Yili the opportunity to move from the traditional wet bottle decontamination technology they were previously using to the Sidel aseptic blow-fill-cap solution, equipped with dry preform and cap sterilisation technologies. For the top liquid dairy producer, this was another decisive factor in choosing Sidel. Traditional aseptic solutions use peracetic acid, which requires a rinsing of the bottles with chemicals or hot water while the Sidel Aseptic Combi Predis sterilises the preform by injecting hydrogen peroxide (H 2 O 2 ) vapour into the preform, right before the preform heating stage in the oven. This allows Yili to reduce waste and resources while benefitting from a competitive and cost-efficient solution. With no water and almost no use of chemicals for preform decontamination, it also addresses one of the most difficult challenges manufacturers are facing today when it comes to an optimal environmental footprint. In addition to greater production sustainability, it provides high levels of efficiency and bottles’ lightweighting potential, as these bottles do not have the thermal constraints associated with the traditional bottle-rinsing process. Designed to adapt production for future demands As Yili plans to diversify their portfolio with more value-added products to create and maintain a sustainable business, they required a versatile production line to vary the recipes of their products. This is why the Sidel Aseptic Combi Predis integrated as part of their complete lines are equipped with specific dosing valves with wider diameter and a low-high speed regulation to get prepared for the future market requirements. To match the increasing consumer demands, Yili recently invested in three new additional aseptic lines with the Sidel Aseptic Combi Predis to enlarge its production capacity. www.sidel.com l l l consumer bags textile packaging recycling rECO","@ID":49}, "MATERIALS / RECYCLING PETplanet Insider Vol. 20 No. 04/19 petpla.net 25 PETplanet talked to Roberta Gualtieri, Marketing Manager at Sipa PETplanet: This was the first time Sipa had taken part in the Petcore conference. What was the crucial factor that led to your decision? Roberta Gualtieri: It was the first time Sipa took part to the Petcore conference and the crucial factor behind this decision is Sipa’s aim to promote a different approach to the reuse and extension of plastic packaging life. Sipa in fact is engaged in a complete and coherent project for the reduction of environmental footprint of plastic and is highly committed to combine environmental sustainability and economic development. With Xtreme Renew, Sipa is ready with a technology that can close the loop for the Circular Economy. Not only it is 100% sustainable but it brings back countless advantages for the user: Energy savings: -30% (only 0.58 kWh/kg PET); CO ² emissions: -60% (compared to virgin resin); Advantage in logistics: -20% (logistics and transportation costs). PETplanet: What were you expecting from the conference and have your expectations been fulfilled? Roberta Gualtieri: Yes, expectations were fulfilled as we were searching for a more comprehensive understanding about legislation, collection issues and recycling production chain. PETplanet: What are the challenges you see in the PET bottling industry over the next 10 years? Roberta Gualtieri: Within the industry, we all know that plastic packaging materials, and PET in first place, offer major benefits with their abilities to keep foods fresh, reduce energy consumption in transport and handling, and improve safety. PET packaging is already more sustainable than many other forms of packaging, but graphic images that demonstrate the results of the irresponsible and unthinking disposal of plastics packaging – massive floating islands of plastics in our seas, despoiled beaches and countryside, suffering wildlife and so on – are leading to a public backlash. We need to improve the culture of bringing back more post-consumer PET as only in this way we can demonstrate the real value of the plastic packaging as it can undoubtedly become a source of wealth and not a source of environmental contamination with its misusage. In synthesis, proper collection and sorting together with education are the biggest challenges. www.sipasolutions.com motan-colortronic gmbh - info@motan-colortronic.de www.motan-colortronic.com ETA plus® considerably reduces energy consumption and protects materials. Drying has never been this efficient: ETA plus® LUXOR A Vist us: 09. - 11. 04. 2019 Hall 4, Stand 4-230 ture a milk bottle, closure and label all from sustainable sources, and fill it with organic milk The resulting pack is believed to be one of the first bio-based milk packages in Europe. The first production run at the dairy producer was made in autumn 2018, and the packs can now be found on the supermarket shelves already. We are currently in close contact with key resin suppliers and recyclers to understand and to align HDPE recycling activities/initiatives. In general we need to overcome the challenges, that HDPE passes food approval (odour, taste), that quality will be sufficient to ensure high performance of closures and colour varieties will be possible. www.bericap.com","@ID":27}, "MARKET SURVEY 31 PETplanet Insider Vol. 20 No. 04/19 petpla.net Inspections 04/2019 MARKETsurvey Resins & additives Preform machinery Preform production & inspection Preform & SBM mould manufacturer SBM 2 stage Compressors Filling equipment & inspection Caps & closures & inspection Palletising & shrink film machinery Recycling Supplier of preforms and inspection systems for preforms In this survey we would like to present you preform manufacturers and the inspection system suppliers who are taking care of the preforms before, during or after processing. We thank all the participating companies: Agr Int., IMD Ltd., Pressco Technology Inc., Resilux NV, PDG Plastiques, PET-Verpackungen GmbH, Hodmeter, Empacar, Sacmi Imola S.C., Retal, Chemco Group, SGT France, Intravis GmbH, Alpla Werke Alwin Lehner GmbH & Co KG, Plastipak, Gulf Pack, Novapet, Energo PET and Torus Measurement Systems. Although the publishers have made every effort to ensure that the information in this survey are up to date, no claims are made regarding completeness or accuracy. Company name Pressco Technology Inc SGT France Torus Measurement Systems Postal address Telephone number Web site address Contact name Function Direct telephone number E-Mail 29200 Aurora Road, Cleveland, OH, USA +1 440 498 2600 www.pressco.com Mr Tom O'Brien VP, Marketing, Sales & New Bus. Devlpm. +1 440 498 2600 sales@pressco.com 3 Rue de l'île Macé, 44112 Reze, France +33 0 2 4005 0937 ww.sgt-pet.com Mr Cyrille Pommerai Quality Control Specialist +33 0 2 4005 0937 c.pommerai@sgt-France.com Nedge Hill Science Park, Telford, Shropshire, TF3 3AJ, UK +44 1952 210020 www.torus-group.com Mr Spencer Whale Global Sales Manager +44 1952 219 972 spencer.whale@torus-group.com Preform inspection systems Yes, inside the blow moulder Sample Pre-Watcher B305 Auto Preform Inspection System Inspection speed Up to 2,500ppm 20ppm 10s/preform for:Auto alignment to thread start and dimensional neck measurement at two positions, 0° and 90° / 360° inspection for body contamination (8 positions) / 360° polarisation imaging (8 positions) / 3 tier classifcation (low, medium, high) Inspected parameters: Geometry / Body Unmelts, heat splay, burn marks, water spots, bent/ warped preforms, contamination, carbon streaks, bubbles/blisters, colour, crystallinity & clarity/hazing, gate length Body defect (including scratches, bubbles, contamination, burning, unmelted material, oil & water marks); gate height (legnth); preform height ; stringing; preform body diameter (@ 2 positions) Thread area Contamination, flash, dimensions, pulled threads Yes Measured features (including but not limited to): I, F, G, T, E, S, X, P, L, J, D, H, X,A, B, M, Z ; support ledge deformation; neck sinkage; ovality; station automatically aligns preform to thread start and performs measurements at both 0° and 90°; station contains automatically loaded UKAS traceable Master for calibration and qualification Mouth / Sealing surface Contamination, ovality and diameter, dirt & debris in the preform, nicks, gouges, short shots & dips Yes Sealing surface defect (including, scratches, notches, short shot, deformations) Gate / Dome Bent/warped preforms, dirt/debris, cracked gates Yes Gate area defect (including burning, tearing, casteling, voids, holes); multiple radial zones can be setup for customer defined areas of inspection; stringing (mentioned above); gate height (mentioned above) Colour Colour variations, incorrect colour Yes: L.a.b. / UV / IR Colour / measurement can include L, a, b, c, h, E, Ecmc etc.; provided with calibrated colour tiles for calibration and qualification, @ customer programmable positions; UV transmission, UV transmission @ selectable wavelengths (360nm - 420nm), @ customer programmable positions Cavity number No Yes Cavity recogntion capable of learning and reading different fonts; capable of recognising multiple fonts across different machines and tools; recognition scores for each character provided for analysis Measurement of absence or presence of barrier material Yes No Not yet available Layer thickness & position measurement at distinctive points No Yes (opacity / diameter / thickness / eccentricity / length / length injection points. Not yet available Layer thickness & position measurement at the complete body by scanning No No Not yet available Features: Installation: Stand-alone On customer-supplied starwheel Yes Yes Installation: Inline Mounting and installation inside major OEM blowmoulding machines; options available for stand-alone and inline systems Can be integrated in line in certain cases, but for batch inspection, not inspection at line speed · Side camera for cavity recognition Yes · Methode: destructive/non destructive Non destructive Rejections analysed by the quality control system non destructive · Data base connection Yes Yes Ethernet","@ID":33}, "48 PETplanet Insider Vol. 20 No. 04/19 petpla.net PETproducts Super-clean PET bottle recycling production line A new development from BoReTech is the Super-Clean PET bottle recycling production line (SCP). The SCP includes 18 completed processes, designed for food-grade bottle-tobottle project, with a standard capacity of 3,000 kg/h and a footprint of 2,000m² (height of workshop: 8m). The whole line adopts the modular design of standard equipment, with international spare parts availability. The rPET flakes thus produced can replace virgin material to blow bottles in 100% rPET and the IV of end product flakes is typically 0.7-0.78. BoReTech highlights especially the air pneumatic conveying and pumping connection between the various machine processes; the in-house developed automated DCS control system (one-button start & stop operation) as well as an easy to clean operation. The platform is movable and easy to assemble. Labels, powders & caps are collected online and recycled. The Super-Clean PET bottle recycling production line will be unveiled at the Chinaplas 2019 in Guangzhou. www.bo-re-tech.com Fine filtration An innovative FlexDisc filter for piston-activated screen changers substantially enlarges available filtration area without the need to increase machine size. It is claimed to enable processors and recyclers to achieve finer filtration, higher throughputs, longer filter service life, and reduced specific backflush volume. Nordson Corporation stated that the BKG FlexDisc is suitable for increasing productivity and enhancing quality in bottle-to-bottle PET recycling, PET fibre recycling, and battery separator film applications. The function of the hydraulic pistons, with which many BKG screen changers are equipped, is to insert screen cavities into the melt stream for filtration and to remove them for cleaning or replacement. In systems where FlexDiscs are used, each cavity contains a filter stack comprised of two to four FlexDiscs, depending on machine size. Each FlexDisc is equipped with two Nordson screen packs. As a result, there are two to 4.5 times more filtration area available for each cavity with the new FlexDisc than with conventional standard round screens, and 25% additional area (on average) when compared to the former FlexDisc version. The actual increase is dependent on machine size. Screen changers equipped with Nordson’s backflush technology include the BKG V-Type 3G and BKG HiCon K-SWE-4K-75/RS. Backflushing diverts the contaminant from the melt stream. The greater filtration efficiency of the new FlexDisc reduces the frequency of backflushing and thus the amount of specific backflush volume, states the company. As melt enters the filter stack from the upstream side, it is evenly distributed among the FlexDiscs, which are rheologically optimised to provide efficient filtration with minimal shear stress. At the same time, the structural integrity of the FlexDisc design enables it to withstand pressure differentials up to 130 bar (1,900 psi) during the backflush procedure. www.nordson.com Cut-away view showing distribution of polymer melt among FlexDisc filters and removal of contaminants Recycling Special","@ID":50}, "49 PRODUCTS PETplanet Insider Vol. 20 No. 04/19 petpla.net Simple emptying of large refuse containers The compact horizontal baling press HSM HL 7009 MGB, with a pressing power of 700 kN, is claimes to be an economical waste disposal solution. It has been designed to empty large refuse containers filled with cardboard or plastic films and which have a capacity of over 1 x 1,100 or 2 x 240 l. The baling press is filled using the integrated hydraulic lifting/tilting device which enables a marked reduction in the number of people required to compress the material. Thanks to the large loading aperture, even bulky pieces of cardboard are not a problem. With a crosssection of 1,100x1,100mm and a bale length of about 1,200mm, the bales weigh up to 600kg. The hydraulic sliding door ensures convenient operation and safety for the operator when the bales are removed. The bales have 4-fold horizontal strapping and, thanks to their optimised dimensions and weights, achieve an optimum truck loading – this compact, horizontal counter-plate press is perfectly suited for larger waste disposal tasks and is an economical solution which provides a fast return on investment. www.hsm.eu We care about your performance. CAREFORMANCE STAY FLAKESIBLE. DIFFERENT INPUT. STABLE OUTPUT. ACUREMA® Inline Sheet and Preform Flexible for sure: from varying wall thicknesses, IV values and input materials such as PET bottle flakes, skeleton waste, edge trim or mixtures of them directly to the end product in stable, top quality. Food contact compliance included. That’s Careformance!","@ID":51}, "MATERIALS / RECYCLING PETplanet Insider Vol. 20 No. 04/19 petpla.net 10 Recycling Special PETplanet asked Mr Wim Hoenderdaal co-chairman of the Petcore Europe PET Thermoforms Working Group about the actual and future technology developments on chemical recycling. The chemical recycling process PETcore Europe has started the special PET industry group called “PET Monomer Recycling”. The reason for choosing the words “Monomer Recycling” instead of “Chemical Recycling” has to do with the fact that there is confusion about the exact meaning of the word Chemical Recycling of Plastics and if all processes falling in this category have a real environmental benefit. Feedstock recycling processes like gasification and pyrolysis can be applied for organic waste or mixed plastic What about chemical recycling? Looking back to the beginnings of plastics recycling, it becomes clear that since the 1980s, mechanical engineers have developed increasingly from general post-industrial plastics recyclers to highly specialised post-consumer PET recyclers. Making a name for themselves in particular are mechanical engineers in PET recycling from Austria, Germany and Italy. The specialising of PET recycling systems and the founding of individual PET business branches began around the turn of the millennium. To give three examples: In 1999, Erema receives FDA food approval for the Vacurema bottle to bottle system; continuous development of the Vacumera line specific to different needs; in 2018, Erema and Polymetrix develop a combination made from nitrogen and vacuum line: Vacunite waste and results in Syngas or oil like products. From these products new monomers can be produced. In some countries chemical recycling is considered as not acceptable because of “not enough” environmental benefits. In some cases no compensation is given for the collected mixed plastics when these processes are used. In case of Polyester, de-polymerisation leads directly to the required monomers and avoids a lot of processing steps and energy usage. This is highlighted by using the name “PET Monomer Recycling”. There are many ways to Rome, same count for the PET monomer recycling technologies that lead to purified monomers like PTA, Ethylene Glycol or BHET. After de-polymerisation a range of technologies can be applied for the purification, mostly a combination of filtration, absorption, distillation, ultra-filtration and crystallisation. Chemical recycling involved in the PET recycling market PET monomer recycling will always be complementary to mechanical recycling. When the feedstock (bales) have enough good quality, mechanical recycling can convert them into flakes or pellets that can perfectly be used in transparent bottle to bottle, film and sheet or to applications where colours are acceptable such as strapping. From the roughly 4.0 million tons of PET that is used in Europe for all bottles and thermoforms, only 1.2 to 1.3 million tons are recycled back from bottles into flakes or pellets, meaning that 2.7 million tons are not recovered. This is partly because of lack of collection and partly because of quality reasons. In case we would go to more deposit schemes in Europe, this would extract the good quality bottles enhancing mechanical recycling but at the same time is leaving us with the question of what to do with the rest. Applications that can absorb lower quality bales such as strapping are small and already saturated. It is just an estimation but let’s assume 50% of all PET packaging’s can be recovered by mechanical recycling and the other 50% for PET monomer recycling. PET monomer recycling is first of all solving the recyclability problem. Recycling starts with the recyclability of the packaging itself, design for recycling, colours, opaque, multilayer, AA scavengers, oxygen scavengers, etc. Starlinger 2004: Installation of the first recoStar PET 125 iV+ for regranulate approved by the FDA for use in food packaging; foundation of Starlinger Viscotec in 2012. In 2014, NGR brings P:React onto the market. The LSP process utilises the inherent capability of PET to condensate in the molten phase under vacuum. This condensation leads to an increase of IV. The high-performance vacuum effectively decontaminates the material from harmful chemicals, securing further use of the material for 100% food contact. The processes for PET recycling are constantly giving rise to new technologies. Recyclers have got to the point where they can supply their customers with the desired IV in flake form to suit the final application. Nevertheless, the PET recycling industry sees great challenges ahead. Because of the increasing demand for rPET and the lack of or insufficient collection systems, their customers receive varied, mostly poorer qualities of bales. Higher international quality standards are undercut by the poorer quality. Mechanical engineers therefore face even higher requirements to develop high quality solutions and to satisfy the increasing requests for systems. In addition to mechanical PET recycling, the last five years have seen the development of pilot projects in the field of chemical recycling. This method is seen as a solution supplementary to mechanical recycling and offers the possibility of converting ODRs and making them reusable. Over the coming pages of our Recycling Special, we have brought together several voices, opinions, conference reports and new developments in the sector. It is clear that the entire PET value creation chain is thrilled by the currently rapid developments in PET recycling! Recycling, a review","@ID":12}, "MATERIALS / RECYCLING PETplanet Insider Vol. 20 No. 04/19 petpla.net 38 dirt accumulate at molecule radicals on the rough surface resulting in a yellowing of flakes after thermal treatment. Since less alkali is necessary and soilings are emulsified by applying Tubiwash cleaning additives, extrusion filters are less contaminated (time and material saving) and PET flakes appear brighter. (Fig.3) Cleaning additive - further support Wherever hardening agents (lime) are dragged into an alkaline wet process deposits can reach machine parts such as heat exchangers which reduces the energy transmission. Due to the special composition most of the Tubiwash additives contain lime inhibitors to minimise lime deposits. Some PET recyclers are obliged to minimise the total dissolved solids concentration in their waste water. Therefore a cleaning with less alkali is preferred to reduce the ions in the water and a cleaning additive is welcome. Cleaning additive and alkali – the perfect combination Alkali has a certain cleaning effect and additionally cleaning additives can significantly improve the effect due to their cleaning and emulsifying power. Therefore a cleaning additive such as Tubiwash can be useful and valuable in PET recycling processes to fulfill also future requirements. www.cht.com The perfect combination for cleaning PET flakes - Sustainable and efficient process aids for PET bottle and tray recycling Cleaning additive and alkali CHT Group has supported the mechanical PET recycling process worldwide by focusing on efficient auxiliaries for quality improvements and process optimisations. As the actual recycling market is changing, the requirements on the cleaning process are also becoming different. Fig 3: PET flakes after roasting (220 °C, 30min) cleaned with NaOH (left) / NaOH + Tubiwash (right) Besides the rising demand for high quality recycled material, the increasing deterioration of input material (more non-food) quality requires an efficient cleaning that meets the highest quality demands. The cleaning is usually done with an alkaline liquor, based on caustic soda and a cleaning additive. What are the different roles of the liquor components and why the usage of a cleaning additive is absolutely worthwhile? Improvement of the recyclate quality Adhesive removal The adhesive removal can be an important factor in recycling process, depending on the input material. Therefore a high cleaning temperature (70-90°C) as well as alkaline salts and cleaning additives are used to remove the melt adhesives. The amount of alkali is limited because of a reduced friction among each flake resulting in a decreasing adhesive removal (fig. 1). The cleaning additive from Tubiwash range however increases the adhesive removal (fig. 2). Removing of organic substances Depending on the input material PET bottles and trays can contain oily and fatty substances. Alkalis degrade the native oils and fats into smaller molecules (alkaline hydrolyses / saponification). The cleaning additive Tubiwash removes them from the recyclate surface and emulsifies the molecules. Thus the emulsified organic substances cannot deposit on the PET flakes or the machine anymore. Improvement of flakes appearance Remaining substances on PET flakes often become yellowish after a thermal treatment (i.e. extrusion). Therefore removing soilings as well as taking away adhesives and organic substances are the main goals of the aqueous cleaning stage. Due to alkali the PET surface becomes considerably rougher (saponification) which supports the cleaning. On the other hand high amounts of alkali in combination with high treatment times and high temperatures cause a reduced brightness of the flakes. Oxygen and Fig 1: Dependency of adhesive removal on alkali and cleaning additive Fig. 2: Flakes incl. adhesive A cleaned at 70 °C with H 2 O / NaOH (25mS/cm) / NaOH + Tubiwash (right) Recycling Special","@ID":40}, "MARKET SURVEY 34 PETplanet Insider Vol. 20 No. 04/19 petpla.net Preforms Company name PDG Plastiques PET-Verpackungen GmbH Deutschland Chemco Plastic Industries PVT. LTD. Postal address Telephone number Web site address Contact name Function Direct telephone number E-mail ZI secteur 2 45330 Malesherbes, France +33 2 3834 6195 www.pdg-plastiques.com Mr Francois Desfretier General Manager +33 2 3834 6195 francois.desfretier@pdg-plastiques.com Gewerbegebiet 4 98701 Großbreitenbach, Germany +49 36781 48044 00 www.pet-verpackungen.de Mr Hubert Rebhan Business Development/Key Account +49 36781 48044 52 hubert.rebhan@pet-verpackungen.de 1412, 14th Floor, Maker Chamber 5, Nariman Point, Mumbai 400021, India +91 2222 821 777 www.chemcogroup.com Mr Vaibhav Saraogi Managing Director +91 2222 821 777 vaibhavsaraogi@chemcogroup.com Preforms Multilayer preforms (Yes/No) No Yes Yes PEN prefoms (Yes/No) No Upon request Upon request Preforms in alternative materials (PP/PLA/PEF) Which? BioPET - PP Upon request Upon request Preforms incorporating rPET (rPET content in %) Yes up to 100% Up to 100% 1 - 100% List of additives available Prelactia 100% light barrier for UHT sterilised long shelf-life milk, oxygen, UV, CO2 barriers, coloured preforms, preblow and Mint-Tec technology Colours, oxygen scavengers, UV-blockers, slipagents, AA-scavengers, brighteners, PA-based barriers All, as per customer’s requirements Preform range 29/25 shorty: 8-10.5-11.7-18.7-2122-23-23.5-24.5-28g; 30/25 high: 17.5-24.5-26-28-31-33-36-39-50g; 30/25 low: 17.5-24.5-26-28-31-33-36-39-50g; 38mm 3 start: 28-33.5-35-44-50g; Prelactia 38mm 3 start: 17-24-28-38g; 48/40: 47-55-62g; 27/32: 6.5g dairy and smoothies; 25/20: 6.5-8g dairy; 29/23: 24-27-33g chemical; PCO 1810: 20-33.6g; PCO 1881: 18.5-30-32-36.5g; ultra-lightweighting 2.4g preform; BVS 30H60: 50g wine (high oxygen barrier); 22H30: 19g Wine (high oxygen barrier) Complete range of preforms with 28mm PCO1810 and PCO1881 finish from 14.5g (e.g. for 0.25l bottles) up to 54g (e.g. for 2.0l bottles); for PETcycle customers in the German market, preforms with 28mm PCO1810 and PCO1881. The product range includes 38mm 2-Start and 3-Start Bericap preforms for wide mouth applications and 29-21 finish for flip top caps. Preforms for hotfill applications are available in a range from 23g up to 45g. For large containers 60g, 92g and 98g preforms with Bericap 48-41 are as well available as customised preforms with weights up to 481g. If the product requires enhanced barrier protection, the majority of the preforms are also available as multilayer with tailor-made barrier properties. Preforms for water, oil, dairy, CSD, 5,1020l, wide mouth preforms Chemco has an extensive range of preforms manufactured on Husky machines. Producing more than 3 billion preforms annually. Chemco has eight FSSC certified manufacturing facilities (6 in India, 2 in the Middle East). Inspections Company name Agr International Inc. Postal address Telephone number Web site address Contact name Function Direct telephone number E-Mail 615 Whitestown Road Butler, PA, USA +1 724 482 2163 www.agrintl.com Ms Karen Marcellus Marketing Coordinator +1 724 482 2163 kmarcellus@agrintl.com Preform inspection systems Pilot Vision (in blowmoulder system) Gawis OD Inspection speed Up to 100,000bph 45 preform/hour depending on measurements Inspected parameters: Geometry / Body Length, body diameters, lean; contamination, opaque spots (black spots), unmelts, bubbles/ blisters, burn marks, water spots, streaks Unlimited number of body diameters and wall thickness measurements, plus length, thickness accuracy to +/- 0.01mm Thread area No T, E, A, NR, H, L/D, ovality Mouth / Sealing surface No No Gate / Dome No No Colour No No Cavity number No No Measurement of absence or presence of barrier material No No Layer thickness & position measurement at distinctive points No Comprehensive thickness (monolayer) at any location over preform sidewall Layer thickness & position measurement at the complete body by scanning No No Features: Installation: Stand-alone No Yes Installation: Inline Yes · Side camera for cavity recognition · Methode: destructive/non destructive Non destructive Non destructive · Data base connection Industry standard Industry standard","@ID":36}, "MATERIALS / RECYCLING PETplanet Insider Vol. 20 No. 04/19 petpla.net 17 nuance to bottles and containers, for drinks and for cosmetic applications. This can be obtained by adding colour amounts as small as 0.05% to the PET/ rPET mix. The range extends from a light amber to light blues, greys, aqua-marine shades and antique rose. The Fumé range answers customers’ concerns about appearance of recycled material. It also offers the opportunity to reduce the amount of colour; several brands are moving from opaque/concealer shades to transparent. Some are even considering “going clear”, in order to help the recycling loop. This would have significant marketing impact, considering the iconic role of brand colours, in food and drink and cosmetic industries. Colour is crucial for brand recognition. It is easily memorised and recalls other feelings related to the product. Sometimes, colour is what prompts the “wow” at very first sight. It is able to compensate for revolutions in design, shape, weight or material of the packaging. Adding a small amount of a liquid colourant to PET/ rPET mix (between 0.02% and 0.6%) would not affect recycling. The protective characteristics of colours, even when transparent, in preserving packaged contents should not be underestimated. Vitamin or tonic water are both very light sensitive. When packaged in a transparent monolayer bottle, protection is best provided by a green or an amber colour, whose pigments protect contents even more than a transparent UV additive. Going clear would mean having to move to a full sleeve or to adapt the drink recipe.Repi’s Fumé range intends to offer the opportunity to launch new packaging, focused towards sustainability and circular economy, without affecting brand symbolism and recognition. There is nothing currently available to replace PET, with anything like the same properties. The packaging industry worldwide uses 70 million tonnes a year; production capacity is actually increasing. Polyester is not going anywhere, soon. PET’s recycling rate is high and its quality is improving. Colourants and dedicated additives are available to make it look and work even better. We should take advantage of them. After all: what would the world look without colour? www.repi.com ","@ID":19}, "PETplanet Insider Vol. 20 No. 04/19 petpla.net 53 BOTTLES 3 in 1 beard shampoo Under the brand name “Barber Club”, L’Oréal Men Expert is offering 200 ml of a 3 in 1 beard shampoo with essential cedarwood oil for the gentle cleansing of beard, face and hair in a slim, dark brown bottle. Two appropriately coloured self-adhesive labels describe product and application and a lockable, screwed-on pump dispenser enables dosed dispensing. www.loreal.com Limited edition from Pril To tie in with the end of winter, Henkel has brought a limited edition of its washing-up liquid Pril onto the shelves and impulse-buy areas of the shops. According to the manufacturer, the two specially aromatic varieties of the Power Gel - “be fresh” with apple and coconut water and “be happy” with strawberry and mint - are the best for dissolving grease and one teaspoon (3ml) is enough for 5 l of washing-up water. The washing-up liquid, coloured to match the fragrance, is available in transparent, slightly contoured 500ml bottles with a screwed-on hinged cap seal. A non-label-look label on the front and a printed label on the rear provide dosing and handling information. www.pril.de","@ID":55}, "MATERIALS / RECYCLING PETplanet Insider Vol. 20 No. 04/19 petpla.net 21 Using local sources for reuse in PET bottles Boost PET recycling in Austria The Austrian recycler ‘PET to PET Recycling Österreich GmbH’ recorded a plus of 9% in the recycling of PET bottles in 2018. With the growing demand for recycled material, the required capacity of the PET recycling line is increasing as well: together with manufacturer Starlinger recycling technology, the output has recently been raised by 20%. Recycling Special Located in Austria’s east, the recycling company PET to PET has processed about one billion PET bottles or 25,400 t in 2018 – a plus of 9% compared to the previous year. The five largest domestic beverage producers (Coca-Cola, Egger, Rauch, Spitz und Vöslauer) jointly operate the site with the aim of recovering recycled material from local sources for reuse in PET bottles. On average, domestic PET bottles already include 30-50% of recycled material. Vöslauer even lists a content of roughly 60% per bottle of mineral water and a planned increase to 100% in the coming years. The flagship of the company is the 0.5 l bottle, which is made of 100% recycled PET while using the same amount of material. Since 2010, PET to PET has been operating a Starlinger recycling line of the type recoStar PET 125 HC iV+. With this line, the pre-cut, washed and sorted flakes are processed into highquality regranulate. “With Starlinger’s technology, we have chosen one of the safest methods that guarantee thorough decontamination of the material according to the FIFO principle,” says Christian Strasser, Managing Director of PET to PET. “In this regard, the strict requirements of our owners, especially Coca-Cola, greatly influenced our decision when purchasing the line.” Geographical proximity – Starlinger and PET to PET are only about 30 miles apart – also played a role, as it allows short-term spare parts deliveries and swift technical assistance. The recycling of plastics is booming, not least because of the EU’s ambitious recycling targets – the circular economy package stipulates a recycling rate of 50% until the year 2025. Last year, the growing demand for recycled material prompted PET to PET to approach Starlinger recycling technology with the request for an increase in capacity of the recycling line. The customer was convinced that in cooperation with Starlinger’s specialists, an even higher throughput could be achieved. Through a detailed analysis, they jointly identified areas that showed potential for an increase in performance. Based on this analysis, Starlinger recycling technology compiled a package that was integrated into the line in several stages. The upgrade involved numerous process steps such as drying, extrusion, filtration, and energy recovery. “After completion of the revamp, the line runs at 20% more output with consistent quality and constant IV”, states Christian Lovranich, Head of Process Engineering of Starlinger recycling technology. “By doubling the capacity for energy recovery, we have not only made the line more productive, but also much more energy-efficient. The successful upgrade at PET to PET shows that even after many years of reliable operation, recycling lines can still achieve an increase in performance.” In PET recycling, the availability of input material is a limiting factor. At present, PET to PET can only partially cover its material needs from Austrian collection systems because the collected PET bottles are popular among manufacturers of other products as a secondary raw material. Examples of other products made from rPET are films for the food industry and strapping bands. In order to obtain enough raw material for new PET bottles, PET to PET purchases bales from neighbouring countries. At the recycling plant, transparent, blue, and green bottles are processed. The owners may exercise their pre-emptive right to the regranulate, the rest is sold to interested parties on the free market. With three out of four recycled PET bottles, PET recycling is already a prime example of a functioning circular economy in Austria. In future years, this rate will be increased even more in order to reach similar top values as Germany (90%). “The direction is clear; the technologies are available,” states Christian Strasser. “It lies within the responsibility of the manufacturers to close the circuits and design their products with an eye on recyclability.” Currently, the usage of many different kinds of plastics as well as multi-layered food packaging complicates recycling activities. “For PET bottles, excellent structures for collection and recycling are already in place,” Strasser emphasises. “Such structures must also be established for other kinds of plastic packaging so that the material streams can be returned to the production process. In addition, our society will need to undergo massive changes in terms of waste reduction and a more responsible use of our limited resources.” www.recycling.starlinger.com The recoStar PET 125 HC iV+ installed in 2010. Starlinger (Christian Lovranich, middle) and PET to PET (Gerhard Kammer, Christian Strasser)","@ID":23}, "PATENTS PETpatents PETplanet Insider Vol. 20 No. 04/19 petpla.net 51 Swivelling base section Intern. Patent No. WO 2018 / 171920 A1 Applicant: Krones AG, Neutraubling (DE) Application date: 13.12.2017 Procedure for optimised manufacturing of a container for hot filling. After hot filling and cooling, the specially shaped base area folds up to equalise the arising low pressure and stabilise the bottle. Flatter container Europ. Pat.issue No. EP 2814741 B1 Applicant: Sidel Participations, Octeville-Sur-Mer (FR) Application date: 7.2.2013 European patent issue describes shaping and procedure for manufacturing a flat, oval container with an arc-shaped base. Bottle for aseptic Intern. Patent No. WO 2018 / 164111 A1 Applicant: Suntory Holdings Ltd., Osaka (JP) Application date: 6.3.2018 A plastic bottle is specially shaped in its side walls and especially at the base so as to be able to absorb the forces arising from hot filling and subsequent cooling - without changing the visible shape. Stackable drink container Intern. Patent No. WO 2018 / 158326 A1 Applicant: IPET Technologies Ltd., Nicosia (CY) Application date: 28.2.2018 Upper and lower sides of a keg made from PET are shaped and combined with additional components so that they are easy to handle, carry and can be stacked together securely. Plastic container Intern. Patent No. WO 2018 / 159630 A1 Applicant: Suntory Holdings Ltd., Osaka (JP) Application date: 27.2.2018 Reduced-weight but sufficiently sturdy plastic bottle equipped with pressure equalisation areas for hot filling. Transparent keg Intern. Patent No. WO 2018 / 172913 A1 Applicant: Keg Solutions Srl., Verona (IT) Application date: 19.3.2018 A transparent / opaque pouch is inset into a transparent plastic keg. The choice of material prevents the penetration of UV radiation. The product and the remaining quantity are perfectly visible.","@ID":53}, "MATERIALS / RECYCLING PETplanet Insider Vol. 20 No. 04/19 petpla.net 14 The brand new Vacunite bottle-to-bottle recycling process for food contact grade rPET pellets Combining Vacuum and Nitrogen atmosphere is the key Erema is a leader in new technologies that shake up the recycling industry and is always new setting standards. With its new Vacunite system, a combination of the Basic Vacurema series, together with patented vacuum-supported nitrogen Solid State Polycondensation (SSP) by Polymetrix, Christoph Wöss, Business Development Manager for Bottle Applications at the Erema Group demonstrates his company’s role as an innovation pioneer. Recycling Special Almost in passing and with Austrian modesty, Christoph tells us that the Erema Group’s business is going extremely well and will achieve sales of € 180m by spring 2019. “Our growth will be driven by the commitments given by numerous brand owners. We are pulling out all the stops and are excited by the challenge!” he explains. The first three Vacunite systems have already been sold to France, Germany and India. A demonstration plant will be installed at Erema´s customer centre until the beginning of 2020. Never forget where you come from “In order to break new ground and develop innovative technologies, you must never forget where you come from. Our current Vacurema Basic, Advanced and Prime portfolio has been around for 20 years. In 1999, we achieved the FDA seal of approval for the first time with Basic, followed by Advanced in 2001 and Prime in 2006. A total of 225 systems have been sold, producing 1.6 million tonnes of food grade rPET worldwide”, says Christoph. Current contemplation Christoph keeps a close eye on the market. “One cubic metre of bale is becoming less and less good material. What is the reason for this? China´s plastic import ban and higher collection rates that are demanded by the EU and others, mean that everything possible can get into the bales. If you previously had 20% waste, the figure is now set at 25-35%: it varies from country to country. This means that I get a maximum of 700 kg of flakes from 1,000 kg of bale”. “In addition, Efsa stipulates that there should be a maximum of 5% non-food material in the flakes. There is also a wide range of colours: Americans in particular are confronted with this challenge. Although it is possible to blend to a degree, if the material really is to be recyclable, for perfect bottle-to-bottle grade you need to have transparent and clear flakes. Sprite, for example, has recently changed its colour from green to clear.” “There are EPBP and APR guidelines which should be observed: still some designers do not pay enough attention to recyclability of their products. However, there are also positive developments in this area. There are already new bottles which have gone through a whole range of tests without any problems. I was very pleased about that”, said Christoph. In- and output quality Input quality gets worse. Output quality is measured, among other things, by the residual content of the limonene in the granulate which assesses how effective the decontamination process has been. “Here too, there has been a change to the guideline values. The previous figure of 29 parts per billion has recently been adjusted to 19 ppb – ours is currently 10 ppb. A clear trend can be seen here. These values are becoming increasingly difficult to achieve. The adjustments, of course, stem from the fact that brands now want to use more rGranulate which, as a result, has brought this value into the spotlight”. An additional guideline that has to be adhered to is the so-called NIAS (Non-Intentionally Heike Fischer, PETplanet and Christoph Wöss, Erema, at the Petcore conference in Brussels","@ID":16}, "MATERIALS / RECYCLING PETplanet Insider Vol. 20 No. 04/19 petpla.net 15 Added Substances). These elements are formed when, for example, PVC or other additives are melted down. When melted at high temperature, the substances can produce all sorts of unwanted by products. Creating a solution Some brands has recently stated: More than 50% mechanically recycled PET cannot be used as this would result in excessive yellowing. In some countries it is possible to use 100% rPET, like Austria, Germany, Great Britain or Japan for example. The deposit system and the high in-put quality makes it possible. Colours are a problem, an enhanced, efficient decontamination, according to the limonene and NIAS value. All in all, a recycling system had to be robust as aluminium and steel or other abrasive contaminants could also be found in the post-consumer material. Last but not least, conversion costs had to be kept as low as possible. “We got together with Polymetrix. The name of the programme is Vacunite which unites vacuum andnitrogen (hence the name). The system has three main components: two from Erema and one from Polymetrix. Polymetrix has developed an SSP (Solid State Polycondensation) in line with our suggestions. It has already been patented and will be distributed solely by Erema”, said Christoph. The first step is a refined version of Vacurema Basic. Thanks to the energy input by mechanical friction, the Vacurema technology can handle dust and friction very well. The special feature of Vacunite technology is that the reactor is purged with high-purity nitrogen to further reduce yellow colouration. The first processing step has Efsa and FDA approval, so decontamination takes place already before the SSP. With further decontamination in the SSP, it has an enhanced safety capability, comparable with a car safety belt and airbag. The system has short meltpaths, high and constant viscosity and proven filtration. A flake input of 0.76 results in an output of 0.74dl/g. The second step is inline crystallisation. As a rule, all pellet SSP systems currently on the market require post-crystallisation before being integrated in the SSP. This involves additional aggregate and extra external energy. “We do not need that. We manage to achieve a high crystallisation value that enables us to directly feed into the SSP process, i.e. it is a compact system.” Christoph explained. The third step is the patented SSP. In the pre-heater which is nitrogen operated, the system heat to process temperature and transport the hot pellets with nitrogen into the SSP where the vacuum is employed at a gentle low pressure. The Vacunite process enables very high crystallisation rates without having to install an additional post-crystallisation. The nitrogen is purified with water pumps so that it can be returned to the upstream process steps, thus reducing overall nitrogen consumption. The material remains in the SSP. The system is designed for approximately nine hours operation which, can be adjusted according to need and residual contamination. “With a residence time of nine hours, we can achieve a viscosity rate of 0.83 dl/g in the final pellet which is ideal for bottle production,” Christoph stated. The technology was developed specifically for the requirements in the production of taste sensitive products such as water bottles. A water bottle places the toughest demands on the decontamination unit and colouring. Christoph went on “The PET water bottle has the highest market growth rate, according to Euromonitor: it`s shifting from CSD to water bottles.” Finally, a fluidised bed has been installed. Here, the pellets are cooled and dedusted to achieve a high degree of bottle transparency after preform production. The system’s dimensions are compact. Overall, Vacunite requires 40% fewer components than comparable systems. “An extra bonus is the pre-installation, i.e. we have a very limited installation time on site.” Christoph is pleased to report. In summary, Christoph says “We have a very well controlled process with double food-contact approval, as well as extremely low energy consumption. It is as low as our Vacurema Prime, now lying at 0.35 kWh/g. As an end product Vacunite technology produces rPET pellets which are unique in terms of quality and far exceed all legal food-contact requirements as well as the even higher requirements of leading brand owners”. Thanks very much to Christoph Wöss for talking to us at All4Pack Paris and the Petcore conference in Brussels in 2019. www.erema.com With HSM − turn your waste into valuable material! HSM Baling presses are specialised when it comes to compressing waste materials. Whether you opt for a horizontal baling press, a vertical baling press or a channel baling press – you will always select a quality machine „Made in Germany“. www.hsm.eu","@ID":17}, "MARKET SURVEY 32 PETplanet Insider Vol. 20 No. 04/19 petpla.net Inspections Company name Intravis GmbH Postal address Telephone number Web site address Contact name Function Direct telephone number E-Mail Rotter Bruch 26a, 52068 Aachen, Germany +49 241 9126 0 www.intravis.de Mr Markus Juppe CMO +49 241 9126 0 sales@intravis.de Preform inspection systems PreWatcher Offline PreWatcher Inline Sample-PreWatcher ColorWatcher Integrated LayerWatcher Inspection speed up to 100,000pph up to 72,000pph up to 1,200pph 8 preforms within 0.25s up to 144pph Inspected parameters: Geometry / Body Contamination; short shots; length; diameter; shape; unmelted material; oil & water marks; burn spots; scratches; opacity; crystallisation; streaks; bubbles Contamination; short shots; length; diameter; shape; unmelted material; oil & water marks; burn spots; scratches; opacity; crystallisation; streaks; bubbles Contamination; short shots; length; diameter; shape; unmelted material; oil & water marks; burn spots; wall thickness; inner wall damage; core shift; scratches; opacity; crystallisation; streaks; stress test with polarised light; bubbles Presence of barrier layers; thickness of barrier layers; position of barrier layers; structure of barrier layers; position of barrier leading edge; position of barrier trailing edge Thread area Contamination; thread dimensions; defects at the neck support ring; flash; pulled thread; Contamination; thread dimensions; defects at the neck support ring; flash; pulled thread Contamination; thread dimensions; defects at the neck support ring; flash; pulled thread Mouth / Sealing surface Diameter; ovality; short shots; flash; scratches and notches on the sealing surface; defects at the neck support ring; contamination Diameter; ovality; short shots; flash; scratches and notches on the sealing surface; contamination Diameter; ovality; short shots; flash; scratches and notches on the sealing surface; inner mouth wall inspection; contamination Gate / Dome Contamination; grooves; holes; cracks; crystallisation; postitioning of injection point; unmelted material; gate length; gate deformation; stringing Contamination; grooves; holes; cracks; crystallisation; postitioning of injection point; unmelted material; gate length; gate deformation; stringing Contamination; grooves; holes; cracks; crystallisation; postitioning of injection point; unmelted material; gate length; gate deformation; stringing Colour Colour and intensity deviations (ΔL*, Δa*, Δb*); presence of UV blocker; presence of barrier; presence of IR absorber (reheater) Colour and intensity deviations (ΔL*, Δa*, Δb*); presence of UV blocker; presence of barrier; presence of IR absorber (reheater) Colour and intensity deviations (ΔL*, Δa*, Δb*); presence of UV blocker; presence of barrier; presence of IR absorber (reheater) Colour and intensity deviations (ΔL*, Δa*, Δb*); presence of UV blocker; presence of barrier; presence of IR absorber (reheater); detection of trend of colour deviations Cavity number Cavity number reading; cavity related statistics; preform sorting according to cavity number; powerful cavity reading without need for learning for most fonts; possibility to share information based on cavity number with IMM; Cavity number reading; cavity related statistics; preform sorting according to cavity number; powerful cavity reading without need for learning for most fonts; possibility to share information based on cavity number with IMM Cavity number reading; cavity related statistics; preform sorting according to cavity number; enables collection of reference samples; powerful cavity reading without need for learning for most fonts; possibility to share information based on cavity number with IMM Cavity related statistics; powerful cavity reading without need for learning for most fonts; possibility to share information based on cavity number with IMM Cavity related statistics; powerful cavity reading without need for learning for most fonts; possibillity to share information based on cavity number with IMM Measurement of absence or presence of barrier material Yes Yes Yes Yes Yes Layer thickness & position measurement at distinctive points No No No No Yes Layer thickness & position measurement at the complete body by scanning No No No No Yes Features: · Installation: Stand-alone Yes Yes Yes No Yes Installation: Inline Yes, but optimised for offline Yes, optimised for inline after IMM and before blower and filler Yes, sampling Yes, integrated into injection moulding machine Yes, sampling · Side camera for cavity recognition Yes, 4 cameras Yes, 3 cameras Yes No Yes · Methode: destructive/ non destructive Non destructive Non destructive Non destructive Non destructive Non destructive · Data base connection Yes, all industry standards supported; ready for Industry 4.0 applications: XLS formats; SQL and several others; connectable to IntraVisualizer, ERP & QMS Yes, all industry standards supported; ready for Industry 4.0 applications: XLS formats; SQL and several others; connectable to IntraVisualizer, ERP & QMS Yes, all industry standards supported; ready for Industry 4.0 applications: XLS formats; SQL and several others; connectable to IntraVisualizer, ERP & QMS - yes, all industry standards supported; - Ready for Industry 4.0 applications: XLS formats; SQL and several others; connectable to IntraVisualizer, ERP & QMS; - yes, all industry standards supported; - Ready for Industry 4.0 applications: XLS formats; SQL and several others; connectable to IntraVisualizer, ERP & QMS;","@ID":34}, "MATERIALS / RECYCLING PETplanet Insider Vol. 20 No. 04/19 petpla.net 18 Recycling Special The 50/50 solution An interview with Rüdiger Löhl, Managing Director of E-proPlast, in which we discuss the increasing level of recyclate in PET bottles and why “100% rPET” is not sustainable. PETplanet: What are these issues that have to be borne in mind when using rPET? And which material mix of virgin/recycled material makes the most sense in your view, not only in terms of sustainability but also for processing technology and quality? Löhl: First of all, I should mention variations in colour. Due to the various input qualities in the recycling stream, PET regranulate has a different colouring. The natural colour of clear bottles can vary between grey, blue and greenish-yellow, depending on the input quality of the recyclate. The more recyclate is added, the darker the bottles become. Secondly, there may be visible black dots in the material as not all foreign particles can be completely filtered out during production of the PET regranulate. The third point relates to mechanical properties and wall thickness distribuPETplanet: Your company specialises in the design and manufacture of PET bottles for the beverages and HBC industries. To what extent has customer demand for new PET/rPET material shifted in recent years? Löhl: We have been manufacturing PET bottles which contain a proportion or as much as 100% rPET for many years. However, the number of orders has gone up dramatically in the last two years, nearly two-thirds of which are relate to the use of rPET. PETplanet: Does your customer markets (beverages/HBC) differ in this respect in terms of demand for a certain proportion of rPET/bottle? Löhl: We are not often involved in the classic beverage industry market (i.e. water, soft drinks etc.). We make a distinction between food and cleaning/cosmetic products. We produce PET juice bottles for cold and hot filling for the food sector, although demand for rPET in this area is still low. We also provide bottles for honey and sauces. Here, we are already using rPET on a large scale, with content ratios ranging from between 30% and 50%. With the advent of the Frosch brand from Werner & Mertz GmbH, demand for bottles with rPET is greatest for cleaning and care products. We produce a variety of products that comprise a proportion or up to 100% rPET. We are also seeing an increase in bottles for cosmetics products. Of course, customers always want the maximum percentage of rPET in their bottles. We discuss this in great detail with our clients in advance and highlight the various issues involved in the use of rPET. Rüdiger Löhl, Managing Director E-proPlast by Gabriele Kosmehl 100% rPET bottles PET bottle samples realised with 50% rPET","@ID":20}, "MATERIALS / RECYCLING PETplanet Insider Vol. 20 No. 04/19 petpla.net 23 NO. ONE-WAY PRODUCTION. YES. TOP QUALITY RECYCLING. How can your recycled product meet permanently increasing demands? With the CHT range of high performance process solutions with environmental relief for the wet chemical cleaning. We support you directly on site and ensure your quality controls in our laboratories with state-of-the-art equipment. Thus, your strong position in the growing market is confirmed day by day. More about us at www.cht.com PLASTIC RECYCLING SHOW | April 10 – 11 2019 RAI Amsterdam | hall 7 | booth B23 collection. Clarissa mentioned that Scotland, Malta, Portugal, Turkey, Romania, Slovakia and England are currently actively working on the implementation of Deposit Return Systems. The last presentation of the collection focused session was held by An Vossen from Plarebel and focused on the Belgian PET collection system. According to An, Belgium plans to achieve 90% of PET collection with curbside collection and improved sorting. Three presentations focusing on collection and sorting were followed by four presentations about trends in PET trays, textile and ODR recycling. Paolo Glerean (Aliplast) gave an insight in Petcore Europe’s PET Thermoforms Recycling Working Group. Paolo stressed the fact that chemical recycling on the one hand, and regional value chain alliances between packaging producers, recyclers and EPR schemes on the other hand, work synergistically to make PET trays truly circular. Paolo was followed by Karla Magruder from Fabrikology who presented the efforts of the textile industry to make polyester circular. With his second presentation of the day, Gian de Belder presented the work of Petcore Europe’s ODR Working Group in detail. Gian gave a summary of the sustainable sleeve and label workshop that Petcore Europe organised in October 2018. An important highlight of his presentation was the announcement of a 3-year temporary endorsement for perforated sleeves on Household and Personal Care (HPC) PET bottles by the European PET Bottle Platform. Following on, Johannes Burghaus, an associate of Gian at Procter & Gamble, shared an update from the PET Aerosol Recycling Special Industry Group that Petcore Europe and FEA are running in collaboration to conclude the session. Fabrizio Di Gregorio from PRE proceeded with a presentation on design for recycling. He presented RecyClass, an online tool that ranks the recyclability of a plastic package, as well as other Design for Recycling Guidelines such as protocols by European PET Bottle Platform (EPBP) and Petcore Europe PET Thermforms Recycling Working Group. Mr Martin Stephan, deputy CEO at Carbios Trends in chemical or back-to-monomer recycling The last session of this year’s Petcore Europe Conference focused on chemical recycling which was generally seen as one of the most important long-term solutions to make PET even more circular. Wim Hoenderdaal from Indorama Ventures Europe kicked-off the session with a general overview and stressed the following points:","@ID":25}, "PETplanet Insider Vol. 20 No. 04/19 petpla.net Appeal: bottle-to-bottle recycling has to be expanded significantly The recycled material is used in various areas. The most important of these is already the bottle-to-bottle recycling. Almost one third (32.6%) of the recycled PET material is used to produce new PET bottles. Nearly 30% of used beverage packaging goes to the film industry, which processes it into tray packaging for food, for example. More than 20% are used in the textile fibre industry. The remaining material is used in other areas. Schmidt takes stock “The various application areas show that recycled PET material is in great demand as resource. This, however, increases the price. As a result, the demand from non-food sectors makes it difficult for the beverage industry to further increase the share of recycled PET in new beverage bottles. The updated GVM study shows a 26.2% share of recycled material per bottle. Compared to the previous studies (2013: 24%; 2015: 26%), the rate is rising only marginally. “Increasing the share of recycled PET material is the goal of the beverage industry,” says Schmidt. The Forum PET therefore welcomes initiatives to increase the recyclate quota in beverage bottles, such as the new target mark of the RAL Gütegemeinschaft Wertstoffkette PET-Getränkeverpackungen. The association’s aim is for PET bottles with the RAL quality mark to have an average recyclate share of 50% by 2022. For a further expansion of bottle-to-bottle recycling, the market needs further impulses such as increased demand for PET beverage bottles with a high recyclate share from (discount) supermarket chains, says Schmidt. China import ban on PET bottles not relevant for Germany In the course of the discussion about import restrictions on plastic waste to China, the GVM study explicitly examines PET exports to the Asian country for the first time. The study shows that only around 3% of used PET bottles were exported from Germany to China even before the import ban. The fact that pictures of PET bottles were frequently shown in the public discussion about China’s import ban is therefore a deception, according to Schmidt. “In fact, China used to import used PET bottles on a large scale to process them into polyester yarns for the textile industry. For many years, however, German recyclers have been building up sufficient recycling capacities in Germany because the recyclable material is also in great demand in the local industry.“ The new GVM study refers to the data from 2017. It examined all relevant beverage segments in the deposit and non-deposit beverage sector. Not included in the analysis were the quantitatively insignificant PET beverage packages for milk, milk mix and milk-based beverages. www.forum-pet.de stf·sorting line stf·washing line professional plastic recycling solutions – made in germany The stf· group is the leading manufacturer of plastic sorting and washing machinery, especially for PET post-consumer bottles, with more than 60 turn-key plants and several single machines delivered worldwide. stf·group Industriestr. 1-3 94529 Aicha v. Wald – Germany fon +49 8544 960-110 mail contact@stf-group.de web www.stf-group.de scan for vCard stf ·group MATERIALS / RECYCLING 41","@ID":43}, "MATERIALS / RECYCLING PETplanet Insider Vol. 20 No. 04/19 petpla.net 40 Recycling Special Current study on the reusable material cycle Recycling rate for PET beverage bottles in Germany The German Packaging Act, which came into force on January 1, 2019, places higher demands on recycling and is intended to strengthen sustainable recycling management. The recycling of PET bottles in Germany is already at a high level: more than 93% of all PET bottles find a new field of application after use; the recycling rate of PET bottles with refundable deposit is even 97%. This is the result of the updated study “The emergence and recycling of PET beverage bottles in Germany” by the Gesellschaft für Verpackungsmarktforschung (GVM) on behalf of Forum PET. In particular, those responsible see potential in increasing the proportion of recycled PET material and the expansion of bottle-to-bottle recycling. “Compared with other countries, Germany leads the way in PET recycling as a prime example“, says Dr Isabell Schmidt, Managing Director at IK Industrievereinigung Kunststoffverpackungen e.V. “The updated study shows clearly that Germany is already recycling PET beverage bottles - especially in the deposit system - at almost the highest level.” In order to achieve the 90% quota for the separate collection of plastic bottles required at EU level, European countries such as France are currently discussing the introduction of a deposit system. “Thanks to the deposit system, the German recycling system already significantly exceeds this quota for PET bottles,” says Schmidt. The updated GVM study confirms this: Compared to the previous study, the recycling rates are at an almost unchanged level: 93% of all PET bottles were recycled in 2017 and the recycling rate of one-way deposit PET bottles is even 97,3%. Unique technologies, innovative solutions, comprehensive technical support, high expertise in all kinds of plastics applications. In others words: typical Gneuss. Continuously Constant gneuss.com Plastic Recycling Show Stand E 24 Pressure and process constantChinaplas Hall 5.1, Stand J36","@ID":42}, "9 NEWS PETplanet Insider Vol. 20 No. 04/19 petpla.net Swiss Made | www.imdvista.ch Inspection Systems for the Plastic Packaging Industry IMDvista INOX Line Closure Inspection – 100% inline. Robust, compact and very flexible. One control center (HMI) for the whole line. IMDvista PECO V3 Preform Inspection. Less than 7m² and up to 90’000 pph. Cavity reading. IMDvista PECO LUX Preform Monitoring shot by shot. Requires no additional floor space. No preform orientation. Chemical Recycling Europe officially launched On the 22nd of January, a new non-profit organisation, Chemical Recycling Europe, was created with the vision of establishing an industry platform for developing and promoting cutting-edge chemical recycling technologies for polymer waste across Europe. The new association aims to deepen collaboration with the EU Institutions and develop positive industrywide relationships throughout the whole chemical recycling value chains in Europe in order to boost specific polymer recycling. Chemical recycling of polymers in Europe will need to develop in order to reach the high level of expectations from the EU politicians. During the constitutional meeting, Carlos Monreal, CEO of Plastic Energy was elected President. Additional Board members are Jeroen Bulk (Ioniqa Technologies), Maurizio Crippa (Gr3n), Richard Daley (RENEW ELP), and Floris Geeris (IGE Solutions), all representing key European companies involved in chemical recycling. Chemical Recycling Europe is open to all companies across the value chain that want to ensure chemical recycling will truly find its way in the circular polymer value chains. For this purpose the first step is a major conference on chemical recycling in Brussels that will take place on June 4, 2019. www.chemicalrecyclingeurope.eu Husky names John Hafferty Chief Financial Officer Husky Injection Molding Systems announced the appointment of John Hafferty to the position of Chief Financial Officer. He will join Husky’s senior leadership team and will lead the global finance organisation. Mr. Hafferty has more than 35 years of financial and business experience with global companies. Prior to joining Husky, Hafferty was CFO for ElectroRent, a global rental equipment company that rents and sells test and measure equipment. He has also served as CFO for BlueLine Rental and has held numerous CFO positions with global transportation and logistics companies, along with being a CFO of a US Public traded company. Mr. Hafferty has a Bachelor of Science in Business Administration Degree with the major being in accounting from Kansas State University and holds a US CPA licence (inactive). www.husky.co Carlos Monreal, CEO of Plastics Energy, became first President of Chemical Recycling Europe Explore our newly designed website at petpla.net","@ID":11}, "8 NEWS PETplanet Insider Vol. 20 No. 04/19 petpla.net L’Occitane and Loop Industries sign supply agreement The L’Occitane Group and Loop Industries announced the signing of a multi-year supply agreement for Loop branded 100% sustainable PET. The agreement will see the L’Occitane en Provence brand start to incorporate Loop PET plastic into its product packaging as of 2022, enabling it to increase from its current 30% recycled plastic to reach 100% in its bottles by 2025 and place the Loop logo on all packaging containing Loop PET . As the demand for sustainable packaging solutions continues to grow, Loop Industries has emerged with transformational upcycling technology that allows plastic bottles and packaging, carpet and polyester textile of any colour, transparency or condition and even ocean plastics that have been degraded by the sun and salt, to provide brand owners a sustainable plastic product that helps solve the plastic pollution problem and meets FDA requirements for use in food-grade packaging. The L’Occitane Group says it is committed to limiting its impact on the environment at every possible step, from product formulation and sustainable packaging through to final product distribution. The company first introduced eco-refills in 2008 and currently proposes 15 eco-refill products. These not only use up to 90% less packaging than the original containers (representing a saving of 121 t in 2018), but also lower CO 2 emissions thanks to the reduced product transport. The group is working with specialised suppliers to design lighter packaging that prioritises recycled materials, and aims to increase its current 84% technically recyclable plastic in its bottles to 100% by 2025. https://group.loccitane.com E-book analysing the viability of using 100% recycled plastics Tomra Sorting Recycling has published an e-book examining the role that recycling can play in providing solutions to the world’s worsening resource crisis. It explores the technical feasibility and progress made towards 100% recyclability of plastics and highlights the opportunities of using high-quality recycled plastics for manufacturers of plastic products and packaging. The e-book points out that consumers’ concerns about waste bring opportunities for brands to demonstrate corporate social responsibility and build customer loyalty, to the benefit of their business results. New environmental targets and regulations across the world are putting the pressure on nations to improve their recycling rates. This will encourage investment and innovation in recycling, but more can be done now with the technologies that already exist. Tomra’s e-book explains how the significant progress in plastics recycling technologies, even for PET products, makes using 100% recycled plastics not only technically possible, but also economically worthwhile. The e-book begins by busting the misconception that PET packaging and products other than bottles can only be downcycled into inferior-quality products. In fact, PET bottle recycling has developed massively and it is possible to manufacture other PET products – and PET trays in particular – from 100% recycled materials, making sense environmentally and commercially, states Tomra. The e-book highlights the progress being made towards 100% recyclability with technologies such as the Sharp Eye and Laser Object Detection (LOD) systems recently introduced. The publication - titled ‘The Viability of Using 100% Recycled Plastics’ - is downloadable freeof-charge at https://hubs.ly/H0gYzDN0 www.tomra.com Acquisition of RPC – Berry global trumps Apollo bid Berry Global Group, Inc. announced a recommended superior offer to acquire all of the issued and to be issued ordinary share capital of RPC Group Plc for 793 pence per share in cash. Aggregate consideration will be approximately £5.0 billion (US $6.5 billion), including refinancing of RPC’s net debt. This offer trumps a former bid by Apollo Global Management who intended to buy RPC Group for £ 3.3bn (US $ 4.28 billion) in cash (782 pence per share). RPC is a leading international design and engineering company, providing plastic and recycled products for packaging and selected non-packaging markets with a focus on rigid and flexible packaging. The board of directors of RPC has unanimously recommended the superior offer by Berry. The proposed transaction, which is subject to customary closing conditions, is expected to close early in the third quarter of calendar year 2019. www.berryglobal.com From left: Sarah Pricaz, VP International Marketing, David Bayard, Technical Packaging Director, Raphaelle Archambaud-Sicot, CSR & Sustainable Development Director, Nelson Switzer, Chief Growth Officer for Loop Industries, and Corinne Fugier-Garrel, Packaging Design & Concept Director.","@ID":10}, "MATERIALS / RECYCLING PETplanet Insider Vol. 20 No. 04/19 petpla.net 26 Glass-coated PET bottles resolve juice production challenge Fully recyclable When the German Packaging Law came into effect on January 1, 2019, the new legislation set down binding rules to increase recycling quotas. The amendment will levy higher fees for packaging which is difficult to recycle. This includes non-returnable PET bottles with composite materials for juice and nectar, among other products. Juice and nectar producers are thus currently looking for solutions which will help them to avoid the ensuing increase in costs. The FreshSafe PET technology from KHS is claimed to present a viable alternative as it combines product protection with bottle-to-bottle recyclability. In view of the European Strategy for Plastics and other national legislation in countries outside Germany, KHS’ barrier technology is gaining in significance at an international level. When the new Packaging Law superseded the former Packaging Ordinance at the beginning of this year as the legal framework for the German market, it defined a new target quota of 70% for returnable systems. The new regulations also prescribe increased recycling quotas for all types of packaging – also for plastics. As of January, 58.5% of all plastic waste is to be recycled, i.e. the separate materials recovered and reused. From 2022 onwards this figure is to rise to 63%. At the moment the amount of plastic recycled in Germany totals around 36%. In this context the dual waste disposal systems responsible for the collection of recyclable materials, such as non-returnable juice and nectar PET bottles, will be obliged to significantly increase their recycling quotas in the future. The new law allows them to reduce costs for easily and effectively recyclable materials and to charge more for packaging which is difficult to reuse. In the future the participation fees calculated on this basis will be determined by a number of ecological criteria. The better a type of packaging can be segregated and recycled, the lower the fees for beverage producers and retailers. Additives in PET bottles complicate recycling In particular, this rule has an effect on all those beverages whose packaging materials cannot be easily recycled as they contain additives. Juice and nectar producers especially, who fill their products into PET bottles, are affected in some areas. Nonreturnable PET bottles are essentially fully recyclable; however, most of today’s juice and nectar bottles do not consist solely of PET. In many cases they contain multilayer, blended or scavenger materials which protect the sensitive beverages from external influences such as oxygen pickup. The composition of these PET bottles is such that it does not allow the materials to be collected by type and recycled together with PET bottles which fall under the one-way deposit system, thus hindering the establishment of a global recycling process. “One quarter of the clear rPET flakes from yellow recycling sacks contain scavengers which impair the quality with their yellowish colour, for example,” states Herbert Snell, managing director of the MultiPet GmbH recycling company. “Mixing PET bottles like these with other beverage bottles made of PET makes it more much more difficult to use these rPET flakes for bottle-to-bottle recycling.” “This is why at the moment they cannot be included in the German deposit system for one-way packaging,” says Snell. According to a current study by packaging market research institute GVM, about 10% of all non-returnable PET bottles do not carry a deposit, meaning that in 2017 38,000 metric tons of PET material bypassed the deposit system. At present the majority of such containers is used to bottle juices and nectars. If producers in this beverage segment fail to optimise their packaging portfolio with a view to full recyclability, they also face the threat of higher additional fees for placing classic PET bottles with additives on the market. FreshSafe PET juice bottles 100% recyclable Beverage producers can find one alternative in the FreshSafe PET Recycling Special","@ID":28}, "MATERIALS / RECYCLING PETplanet Insider Vol. 20 No. 04/19 petpla.net 12 Recycling Special Niedl: I can only speak about the growth numbers of PET bottle-tobottle recycling, as this is the market that Starlinger recycling technology is involved in. The market was good until 2013 but a bit slow in 2014-2016 until it grew again in 2017. Since 2018, the market has gone through the roof all over the world; I’d say our business in this segment has quadrupled and there is no end in sight. This development is due to changed consumer perception about recycling, but certainly recycling quotas set by individual countries further support this growth. PETplanet: There is more and more talk about what is called chemical recycling. How do you rate this technology? Would that be a field where Starlinger would be involved? Niedl: Chemical recycling has been around since decades, but what we see now is a kind of renaissance. In the past these processes have been too expensive to compete with mechanical recycling for regular applications. Now there are many new initiatives on a pilot scale. Such new approaches could complement mechanical recycling for difficult recycling applications such as multilayer or multi-material structures, but we will have to see once they get beyond the pilot scale if such chemical recycling approaches are cost-effective for a regular scale project. www.starlinger.com Dr. Stephan Gneuss, Managing Director at Gneuss PETplanet: Founded in 1983, Gneuss was initially specialised in melt treatment for the extrusion of profiles, pipes and plates and the production of compounds. When and why was plastic recycling a topic for Gneuss? Gneuss: As a manufacturer of filtration systems for polymer melts, recycling was a big topic from the beginning. The first focus was on industrial waste recycling. A big impact on the company started, when we broadened our focus to include post-consumer recycling, particularly PET from drinking bottles, which was already available in decent quantities and qualities at that time. In general you can say that the development of the company with regard to recycling was driven by customer demand as well as by technical developments made by Gneuss, such as the recycling filtration system RSFgenius and the degassing extrusion system MRS. PETplanet: The PET recycling industry has been very busy for quite some time now: the new EU directive of Plastic Strategy and the commitments of the big brand owners (Coca Cola / Nestlé / Pepsico etc.) to use more rPET in products are leading to a huge demand for rPET. One would assume that this also has a positive effect on the recycling system manufacturers - is this the case with Gneuss? Gneuss: There is a clear trend for growth in the bottle-to-bottle market segment driven by the relatively high prices achievable for rPET pellets. This is obviously a consequence of the new EU Directive of Plastic Strategy and the commitments of the big brand owners. However, the European bottle-to-bottle market is already quite mature. Inside the EU there are only few new players in the market. Most of the growth is taken up by the already existing big players. This situation differs a lot in the rest of the world since some markets are more and some less developed in this aspect. The consequences on the sheet market and also for fibre producers are not overall positive. The use of bottle flakes is quite common in these market segments, however it is tied to the availability of bottle flakes in a suitable quantity and quality. Due to the strong demand increase by the bottle-to-bottle market this is getting more and more difficult. Also, the waste streams regarding PET bottle flakes are more and more controlled by a small number of market players. This makes access to bottle flakes increasingly difficult for small and medium sized companies with little connection to the waste market, as it is typically the case for sheet producers. We expect this to be the main limitation for the future development of the PET recycling market: accessibility to bottle flakes. This is not only a EU specific situation. However, taking a global look, the situation differs very much from country to country. PETplanet: Gneuss offers a bottleto-bottle recycling system especially for PET recycling. What are the special features of this system? Gneuss: The bottle-to-bottle market was important for us from the very beginning with regard to our filtration systems. When we introduced the MRS extrusion system about 12 years ago, we were able to offer a new feature: decontamination of PET in one simple extrusion process without prior treatment of the flakes or an SSP. This system has been successfully implemented in a number of bottle-tobottle lines in the meantime. However, the main focus lies on thermoforming sheet where food contact approval plays an equally important role. Also, the fibre industry (which is still the main processor of PET bottle flakes) plays a very important role for our business. At the last K-show we introduced our “Jump” polymer reaction technology which allows an IV built up in the melt phase within just a few minutes. This offers new possibilities for the bottle-to-bottle recycling process. Due to the limited access of many companies to PET bottle flakes with a sufficient quality (e.g. little amount of foreign polymers), we, as a technology developing company, have been focusing in the last few years on technical improvements. New technologies, which allow the PET processor to work with low quality recycling materials and PET waste from alternative sources (such as post-consumer thermoforming sheet packaging). In the long term, we expect better collection and sorting logistics and technologies to be able to create a larger amount of well recyclable polymers in decent qualities. But in the short and medium term we need to focus on technologies which allow the processor to produce good quality products even with low quality input materials. www.gneuss.com","@ID":14}, "MATERIALS / RECYCLING PETplanet Insider Vol. 20 No. 04/19 petpla.net 24 Chemical recycling will not replace but complement mechanical recycling and will facilitate the recycling of PET thermoforms, opaque bottles and other difficult to recycle PET products. After Wim’s introduction, Martin Stephan from Carbios, Marco Brons from Cumapol, Frederic Favre from IFP Energies Nouvelles and Nelson Switzer from Loop Industries presented their companies’ chemical recycling projects in detail and answered the questions from the audience in a panel debate to end a highly successful conference. Carbios announced shortly after the Petcore conference in Brussels it has successfully produced the first PET bottles made with 100% Purified Terephthalic Acid (rPTA), through the enzymatic biorecycling of plastic waste. The company states that this milestone is a world-first, and confirms the potential of the technology to engage the whole industry in a responsible transition towards a circular economy. Alain Marty, Chief Scientific Officer at Carbios, comments, “We have successfully developed the first biological process with which all kinds of PET plastic waste can be broken down into its original components and reused to produce virgin plastic products for applications such as PET bottles. This new step shows the strong potential of Carbios’ enzymatic technology and provides a solution to help solve society’s growing waste problem.” Previously, Carbios demonstrated that its proprietary biorecycling technology, based on the use of bioengineered enzymes, had the ability to turn PET plastic waste back into its original components at a rate of 97% in 16 hours. It had also demonstrated that virgin PET can be made with 100% rPTA via its proprietary biorecycling process, which uses all kinds of post-consumer PET plastic bottles (clear, coloured, opaque, complex). By demonstrating now that 100% rPTA can be used to produce PET bottles that match brand and customer requirements, this technology proves to be a potential game-changer in the transition towards a circular economy that will benefit the environment and future generations. By decoupling the production of new plastic bottles from petrochemical feedstock and making waste collection economically more viable, the technology is intended to offer a sustainable and efficient solution to change the way some of the most commonly used plastic products are produced. Jean-Claude Lumaret, CEO of Carbios, adds, “The plastics industry faces fundamental challenges related to sustainability. Our technology, based on a circular model, reuses resources rather than consuming them. This new milestone takes us one step closer to bringing our technology to the market. With the construction of our demonstration plant to start later this year, we’re aiming to engage the whole plastics industry in a transition towards a circular economy and take a leadership role as a global license provider for the biorecycling of PET plastics and fibres.” www.petcore-europe.org At the Petcore conference we met Mr Christoph Thünemann, Group Director in Communications and Marketing at Bericap: PETplanet: Mr Thünemann, this was your first Petcore conference with Bericap. What were your reasons for participating? What was your special interest from a cap producer’s point of view? Thünemann: We see ourselves as partners of our customers who are manufacturers / brand owners as well as bottlers / converters. In order to act in a spirit of partnership and to add value - both technically and economically - for our customers, we constantly optimise the value chain. As a self-understanding of our service philosophy, it is important to gain a thorough understanding of trends, challenges and solutions in industries and our business environment. For me it makes sense to enter into dialogue with our partners at one of the leading European congresses on PET. Although we were already in very close personal contact with government officials on the EU Single Use Plastics (SUP) Directive, the implications of this for the entire beverage industry require a continuous exchange of information and ideas. The comments on the planned SUP were therefore very informative and helpful for me personally. We were also able to obtain confirmation that the tethered caps solutions Bericap has developed meet all the required expectations and requirements. PETplanet: Where do you see future challenges in the PET market? Thünemann: I see as one of the major challenges in the PET market the further optimisation of lifecycle processes for beverage bottles & closures. Deposit system for returnable and recycling bottles should be established in as many countries as possible, and hopefully similarly high return rates are achieved like with the German model. We are following the further development with great attention. PETplanet: The PET industry is currently making great efforts to make the required amount of recycled PET available to the market. Closures are usually made of PP or HDPE - is it a future topic for Bericap recycled material to be used in closure production? Thünemann: At Bericap we follow the Reduce, Reuse and Recycle approach. That is why we have been very active and successful in the last years for the weight reduction of closures and necks. With this approach, we have succeeded holistically in saving more than 50% of weight from PCO 1810 to 26/22. Therefore, the optimised use of materials is the first step in environmental protection. We just launched a project to meet our customer’s objective to manufacRecycling Special","@ID":26}, "MATERIALS / RECYCLING PETplanet Insider Vol. 20 No. 04/19 petpla.net 28 Consistently pursuing sustainability One of the pioneers of using recyclable plastic packaging is the Werner & Mertz Group, headquartered in Mainz, Germany. The company is very well known for its “Marke Frosch” logo, which stands for thorough cleaning in the home, and safety for people and the environment. Since the 1980s the company has been working on all its different brands e.g. Erdal, Emsal or Tana to improve the packaging and ingredients to make them recyclable and sustainable. Recycling Special For Werner & Mertz sustainability is not just a buzzword: Alexander Schau, responsible for packaging development, explained how they have taken a holistic approach to sustainability encouraged by managing director Mr Reinhardt Schneider. Mr Schneider started in the 1980s with environmentally-friendly products and kept faith with them even in the 1990s when public awareness declined. His visionary perspective has been amply vindicated today with the success of its brands. Emphasising the company’s commitment to sustainability and environmentally friendly construction, the roof of the Werner & Mertz HQ is dominated by an array of wind turbines. The wind turbines power a photovoltaic system coupled with a geothermal generator which provides 20% more energy than is needed for the ongoing operation of the building. Just as impressive as this ground-breaking system is the power supplied by the solar roof panels which is used to charge two electric Smart cars, part of the company’s fleet. The building has received numerous awards. To optimise working processes a new plant has already been completed and will be officially opened in May 2019. This plant is constructed on a circular model, from container production, to filling, and on to packaging and finally the warehouse, and the circular design reduces space and communication time. The result is an energy saving and a more cost-effective production. The plant will consist of several Alpla machines, amongst others, producing 100% rPET preforms made of 20% post-consumer PET collected under the Yellow Bag system and 80% PET from the European bottle to bottle collection. The filling capacity is about 5-9,000pph each filling line. The percentage of rPET increases in the Frosch plastic packaging. In 2008 it was 30%, from 2014 on 100% rPET. The 500ml bottles of the Frosch products were made out of 24g preforms. The weight of the preform results from the long life and often used products circle. The preforms have UV barrier protection, nothing more is needed. The design has remined pretty much the same over the years to promote consumer confidence in the reliability and quality of the product. Not only is the packaging environmentally-friendly, but also the formulations of the filling goods are continuously improved by using renewable primary products such a coconut fat, sunflower, olive or rape oil which are all bio-degradable. Beside the Frosch brand Werner & Mertz produces also for other brands. This is only a very small amount in the overall production, but it is important to carry out the use of recyclates in other markets sections. The key market for Werner & Mertz is Central Europe; some of their production goes to China and Japan. In total Werner & Mertz employs 1,072 staff. The awarded HQ of Werner & Mertz in Mainz, Germany One of the newest products in the market is a toilet deodoriser. The basket of this toilet freshener is currently made of 100% used plastic from PET bottles. In a joint project with The Green Dot and the affiliated companies Dannemann Global Extrusion and Berner Kunststofftechnik Werner & Mertz is developing a process to produce the basket from recycled PET trays obtained from the Yellow Bag household waste collection system. With this material source is the cleaning products manufacturer meeting its self-imposed standard of putting as much previously untapped material from the Yellow Bag as possible into its packaging. By using PET tray material, a closed-loop system is generated. www.werner-mertz.de by Heike Fischer Mr Alexander Schau, responsible for packaging development demonstrated the Frosch rPET bottle. State-of-the-art filling and packaging machinery at the new plant of Werner & Mertz","@ID":30}, "MATERIALS / RECYCLING PETplanet Insider Vol. 20 No. 04/19 petpla.net 29 W W W . I N T R A V I S . C O M / P R E F O R M controls 100% in- or offline Cavity relatedStatistics&Alarms clever Layout for small Footprint m² P R E F O R M I N S P E C T I O N up to100,000 Preforms/Hour Trouble with Contamination, Bubbles or Short-Shots? Find out more! PETplanet asked Mr Kay Reinhard Schneider, CEO of Werner & Mertz about future challenges and improvements for environmentally friendly plastic packaging. PETplanet: Where do you see future challenges in producing packaging made out of 100% rPET? Schneider: Quality, availability, lack of true innovation, unfit infrastructure, missing willingness to adapt/ change existing business models and processes and last but not least, price. Therefore a clear legal framework is necessary including tangible incentives for companies for early movers. PETplanet: Werner & Mertz is very well known for its sustainability strategy. Where do you see further improvements for an environmentally friendly plastic packaging? Schneider: We need to reduce complexity of plastic packaging (monomaterial). Less colour (pigments), additives (e.g. scavengers), no multi-layer from different plastics. Everything harmful to the quality of recyclates should eliminated or should be treated following the polluter-pays-principle. Werner & Mertz committed to have 100% of all consumer packaged products made from 100% PCR by 2025. This naturally includes 100% recycability.","@ID":31}, "MATERIALS / RECYCLING PETplanet Insider Vol. 20 No. 04/19 petpla.net 20 Recycling Special PET BOTTLE WASHING LINE SUPER CLEAN PROCESS (SCP) Capacity : 3000 kg/h/ 6000 kg/h Born for Food Grade Bottle-to-Bottle Modular Design for Flexible Layout considerable shortfall in demand, for PET at least. PETplanet: Which means that the post-consumer PET bottles which are not being recycled in open or closed loop systems will be transferred to thermal recycling. Löhl: However, the question must be asked as to what is actually so bad about thermal recycling? Around 87% of crude oil is directly converted into thermal energy (vehicles, aircraft, heating, power plants etc.) in Europe. Approximately eight percent is used for other purposes (building work, road construction etc.). Only around five percent is used in the production of all plastics, of which 40% is used for packaging. That means that only two percent of crude oil goes into the production of all types of packaging (foil, bottles etc.). No-one has yet been able to convince me why it is not sustainable to first manufacture products such as plastic packaging from crude oil, then protect their contents with packaging, bring the content with the packaging safely to the consumer before thermally recycling it . Here in Germany, residual waste is used in waste incineration plants. Gas and crude oil are frequently used as additional flammable agents to ensure the material actually burns. It would be much more sustainable to use a product such as old plastic for incineration purposes and generate energy before direct burning oil at these facilities. The talk of the socalled “plastic flood” or “mountains of plastic” is hard to bear. These do not exist at all! With the drink deposit for beverage bottles and the installed deposit machines (approximately 99% of which are returned to be processed again into recyclate) and yellow bag systems for packaging waste, Germany has the most efficient and best collection/utilisation regime anywhere in the world. It may well be time to reduce the discussion about the use and recycling of plastic packaging from the current emotional and populist level to a more factual and evidence-based approach. However, given the diverse interests of politics, so-called environmental organisations, the media, consumers and industry, this is likely to be difficult PETplanet: Thank you very much!","@ID":22}, "PETplanet Insider Vol. 20 No. 04/19 petpla.net 55 BOTTLES Smoothie for Valentine’s Day Around Valentine’s Day and for just a short pe r i od , t he Ge rman discount retailer Aldi Süd was selling various Smoothies, including strawberry-banana and apple-raspberry, under its own brand “rio d’oro” and the additional name “Schmusi”. The transparent bottles contained 250ml and were sealed with a screw seal with guarantee band. The sleeve labels were printed appropriately for the occasion with hearts and butterflies. www.aldi-sued.de Plant drinks from Innocent Following on from fruits and vegetables, the newest smoothie idea has recently come onto the market. Innocent has brought three plant drinks in the varieties of Almond, Oat and Hazelnut & Rice onto chiller shelves. Alongside the named ingredients, they contain only spring water and a little sea salt. There are no additives, stabilisers or additional sweeteners. The stable bottles contain 750ml and consists of at least 30% recycled PET. The transparent labels provide instructions on how the individual drinks can be enjoyed as additions to tea or coffee, on muesli, in cake or pancake batter or simply as a drink. Label and freshness seal are colour-matched with one another. www.innocentdrinks.de 10 -11April 2019 Organisers Event supporters established 1987 CONTACT: Matt Barber | mabarber@crain.com This free to attend conference and THORSTEN LEOPOLD Head of International Packaging Development Home Care Henkel AG & Co. KGaA GIAN DE BELDER Principal Scientist - Packaging R&D Procter & Gamble","@ID":57}, "imprint EDITORIAL PUBLISHER Alexander Büchler, Managing Director HEAD OFFICE heidelberg business media GmbH Bunsenstr. 14 69115 Heidelberg, Germany phone: +49 6221-65108-0 fax: +49 6221-65108-28 info@hbmedia.net EDITORIAL Kay Barton Heike Fischer Gabriele Kosmehl Michael Maruschke Ruari McCallion Waldemar Schmitke Anthony Withers WikiPETia.info petplanet@hbmedia.net MEDIA CONSULTANTS Martina Hirschmann hirschmann@hbmedia.net Johann Lange-Brock lange-brock@hbmedia.net phone: +49 6221-65108-0 fax: +49 6221-65108-28 LAYOUT AND PREPRESS EXPRIM Werbeagentur | exprim.de Matthias Gaumann READER SERVICES Till Kretner reader@hbmedia.net PRINT Chroma Druck & Verlag GmbH Werkstr. 25 67354 Römerberg Germany WWW www.hbmedia.net | petpla.net PETplanet Insider ISSN 1438-9459 is published 10 times a year. This publication is sent to qualified subscribers (1-year subscription 149 EUR, 2-year subscription 289 EUR, Young professionals’ subscription 99 EUR. Magazines will be dispatched to you by airmail). Not to be reproduced in any form without permission from the publisher. Note: The fact that product names may not be identified as trademarks is not an indication that such names are not registered trademarks. 3 PETplanet Insider Vol. 20 No. 04/19 petpla.net I normally just flick through articles in the daily press on plastic waste and plastic bottles and on philosophical arguments about the benefits or otherwise of packaging. However, this time I actually found an interesting piece which discussed a study carried out by a certification company, Gutcert, based in Berlin, authored by Professor Dr Ing Jan Uwe Lieback and Sabine Schumacher. Using Berlin as an example, they looked at CO 2 consumption of water in glass and PET bottles as well as drinking water from the tap. What makes this study different from other similar studies is that it is not a universal theory for water that was being sought and subsequently not found, but rather a manageable framework, in this case Berlin, to show where and how much CO 2 is produced by water. Tap water has the best carbon footprint in Germany with the outstanding value of 0.02 gCO 2 /l. All the rest produce at least 10,000 times more CO 2 . The fact that tap water, which is not packaged or transported, has a phenomenal CO 2 balance comes as no surprise. But the authors continue. They have studied different types of water bottle packaging in Berlin, ranging from PET EW (disposable) to MW (reusable), glass MW and EW, as well as distance covered. From well springs near Berlin to expensive water from Italy. It has been shown that glass and PET have more or less the same carbon footprint for long distances greater than 1,000 km (around 300 gCO 2 /l). The different CO 2 emissions produced during production and transport are in roughly the same range for both package materials. Packaged water bottles originating from outlying areas (150 km) have a 50% less carbon footprint (150 km gCO 2 /l): whether they are in PET or glass, the ranges are similar. Emissions from water transported from these areas are not so significant. In conclusion. If microplastics are no longer at the forefront of politics and people’s minds when it comes to packaging, the spotlight will fall on society in terms of carbon footprint. And here is a microcosm of how Berlin goes about things – building bottling facilities near to the consumer. What has so far proved economically beneficial is also a big plus from an environmental protection perspective, along with water from the tap! Yours Alexander Büchler https://www.gut-cert.de/files/content/download/Nachhaltige_Entwicklung/ Wasserartikel.pdf?time=2019031507 Dear readers, The carbon balance between CO 2 and water","@ID":5}, "PETnews 6 NEWS PETplanet Insider Vol. 20 No. 04/19 petpla.net Dr Johannes-Thomas Grobe new head of Sales and Service at KHS Dr Johannes-Thomas Grobe is to be the new head of Sales and Service at KHS GmbH. This has now been confirmed by the company’s supervisory board. The 53-year-old will be moving from Dürr Systems AG, a machine and systems manufacturer for the automobile industry, to the Dortmund systems supplier. Dr Grobe joins chairman Kai Acker and Martin Resch on the KHS Executive Management Board. Dr Grobe has extensive knowledge as an executive manager of product and technological developments, innovative projects and production and manufacturing processes. The computer scientist, who obtained his PhD from RWTH Aachen University in 1998, initially held various posts at Bosch Rexroth AG, among them the vice-presidency of Sales for Industrial Management, Key Account Management and Application Development for Industrial Applications. Dr Grobe was then managing director of Bosch Rexroth in India. On September 1, 2015, he joined Dürr Systems AG as senior vice-president of Sales and Marketing for Paint and Final Assembly Systems. On April 1, 2019, Dr Grobe will take up his new position as head of Sales and Service at KHS. As the company states, the restructuring of the KHS Executive Management Board is now complete. www.khs.com DS Smith Plc – Sale of Plastics Division DS Smith announced it has reached agreement to sell its Plastics division to Olympus Partners for an enterprise value of $585 million, (approximately €519 million). The transaction is subject to customary closing conditions including regulatory approvals, with completion expected to take place in the second half of this calendar year. The Plastics division comprises the plastics operations of DS Smith, including flexible plastics, rigid plastics and foam products. Gross assets of the business as at 31st October 2018 were £ 223 million (€ 262 million) and profit before tax for the 12-month period to 31 October 2018 was £28 million (€ 33 million). This sale is intended to accelerate DS Smith’s programme of deleveraging, alongside organic cashflow. www.dssmith.com New Sidel Group CEO appointed The Tetra Laval Group Board has appointed Ms Monica Gimre President & CEO of Sidel Group, effective July 1, 2019. The appointment follows the decision by Mr Sam Strömerstén to retire from his position after more than three years as President & CEO and 36 years with the Tetra Laval Group. Monica Gimre is presently Executive Vice President Processing Solutions & Equipment in Tetra Pak. Prior to her present position she has had several managerial positions in the Group, including Vice President Marketing and Portfolio Management and Vice President Technical Sales and Service for Tetra Pak’s Processing business. She joined the Tetra Pak Global Leadership Team in 2016. Ms Gimre, who is 58 years old has a Master of Science in Chemical Engineering, Lund University, Sweden. www.sidel.com Indorama Ventures completes acquisition of Invista Resins & Fibers GmbH Indorama Ventures Public Company Limited (IVL), a global chemical producer, announced the completion of its acquisition of Invista Resins & Fibers GmbH, a speciality chemicals asset located in Gersthofen, Germany. The Gersthofen site has a combined capacity of 282,000 t/a, and employs approximately 140 staff. Indorama Ventures had previously announced its agreement to acquire Invista Resins & Fibers GmbH on December 20, 2018. This acquisition is aligned with IVL’s strategy to grow and support our customer’s needs with differentiated solutions in both packaging and in industrial fibres. It provides IVL with competitive advantages, obtaining the intellectual property rights of Polyshield PET and Oxyclear Barrier PET, Invista’s barrier technology, in all markets globally. Polyshield PET and Oxyclear Barrier PET brands are known for their oxygen barrier packaging, mainly used by the food and beverage industry, to extend the shelf life of juice, wine, beer, diary as well as ketchup. IVL currently has a leading market share in the North America oxygen barrier PET market. The company made its debut in this segment in 2011 through the acquisition of Auriga Polymers in South Carolina, USA, acquiring the rights to the technology for creating the Crystal Clear Oxygen Barrier Resin in certain markets in the Americas. This acquisition is intended to give IVL added momentum to address a growing demand for barrier resins, and reach both existing and new customers globally. www.indoramaventures.com","@ID":8}, "BOTTLING / FILLING PETplanet Insider Vol. 20 No. 04/19 petpla.net 46 Dry aseptic PET lines The world’s largest liquid dairy producer, Yili, strives to provide Chinese consumers with high-quality, nutritional, healthy, and innovative dairy products. Their continuously growing sales demonstrate how they manage to be successful in differentiating their brand with the help of premium dairies. PET packaging can help them advance as a business by offering new consumer experiences compared with the traditional carton format while allowing a more flexible production. Confidence in PET benefits Yili is a strong believer in the potential of PET as a packaging material, as it perfectly matches the Chinese consumers’ expectations by being user-friendly, shatterproof, re-sealable, and recyclable. It also provides freedom in bottle design to differentiate their dairy brand on the Chinese supermarket shelves. Perhaps more importantly, PET offers great benefits in terms of physical product and food barrier protection, therefore preserving nutritional and sensorial properties of yogurts at all stages – from production, storage, and shipment to distribution. Moreover, the closure tightness adds to PET’s convenience even without the use of aluminium foil. All of these reasons supported the Yili strategic direction to partially switch their production from carton to PET bottles with the aim of introducing innovative packages: a great pioneering move in the Chinese dairy market. As part of this change, the Ambrosial Greek Yogurt, packaged in PET single serve bottles, has been highly popular since its launch. Considering the growing market demand for this premium drinking yogurt, paired with a willingness to innovate the brand, Yili decided to invest in a couple of new aseptic PET packaging lines. This is when Sidel came in due to the solid and trustful partnership built between the two companies in the past. The team at Yili appreciated Sidel’s insights and inputs on beverage market trends, packaging design, and PET aseptic packaging expertise, all proving instrumental for the leading Chinese dairy brand. PET barrier qualified for 5-months shelf life With Sidel’s support, Yili was the first one to bottle Ambrosial Greek Yogurt in PET for ambient distribution – a product which had previously been offered in cartons. Sidel and Yili collaborated to fully qualify the PET barrier properties and make sure which type of PET bottles would allow Yili’s yogurts to retain their fresh taste and vitamin content. This is particularly important as this product’s quality can be easily compromised by the effects of light, oxygen, and temperature. All these considerations justified the requirement for full barrier opaque packaging. Sidel’s experts in liquid dairies and packaging performed a range of laboratory tests to determine the behaviour of different liquid dairy products (yogurt, UHT white milk) in several PET barrier solutions (PET multilayers and mono-layer with different rates of TiO 2 ). The scientists evaluated different caps’ opacity to achieve the optimal light and oxygen barrier and ensure the product’s stability without any alteration in terms of taste or colour. All these analyses confirmed that the combination of approved bar-","@ID":48}, "MATERIALS / RECYCLING PETplanet Insider Vol. 20 No. 04/19 petpla.net 27 technology provided by KHS. After the PET bottle has been manufactured, an ultra-thin glass coating is applied to its inside wall. These coated PET bottles are 100% recyclable, says KHS, as the coating is washed off during the recycling process, producing pure, fully segregated PET. This is confirmed by packaging expert Benedikt Kauertz, head of Environmental Assessment of Packaging at the independent Institute for Energy and Environmental Research (ifeu) in Heidelberg, Germany. “Glasscoated PET bottles allow juice and nectar bottles to be included in the pure PET cycle and their materials to be recycled together with other used PET bottles for water and carbonated beverages, for instance. To this end, however, the deposit-assisted return system must be extended to include these specially optimised bottles.” 97.9% of non-returnable deposit PET bottles are now recycled in this manner; juice bottles are not included in this figure. The first premium juice producers have realised this and are now already using the new FreshSafe PET technology worldwide. This can reduce the circulation of non-returnable PET bottles which are hard to recycle in the medium to long term, acknowledges Mario Dechent, director of Research and Development for the Eckes-Granini Group GmbH. “We directed our attention to the full recyclability of PET juice bottles very early on. With FreshSafe PET coating technology we’ve been using a sustainable system to fill our beverages for over ten years now, one which also permits pure-grade bottle-to-bottle recycling and thus increases the availability of useful recycling materials.” Barrier costs pay off thanks to lower fees Beverage producers naturally incur additional costs when they invest in barrier technology. However, as the overall operating costs are reduced, the procurement pays off quickly. With it juice and nectar producers can switch to less expensive standard PET preforms, relieving them of the obligation to source preforms from a specific manufacturer. In addition, compared to standard composite materials FreshSafe PET is claimed to provide a better barrier quality and to ensure much longer shelf lives. As they are fully recyclable, in the future FreshSafe PET bottles prove more favourable when it comes to the calculation of participation fees. KHS offers beverage producers an individual consideration of the total costs accrued when using this barrier technology. “Measured against the huge benefit of additional product protection and longer product shelf lives in particular, the costs per bottle are actually lower,” says Philipp Langhammer, product manager for barrier technology at KHS Corpoplast. “In view of the possible extra costs for the circulation of PET bottles which are tricky to recycle levied by the new Packaging Law, beverage producers should make their packaging portfolio future proof now and thus help to introduce a sustainable packaging system.” Possible full ban on plastics which are difficult to recycle Non-returnable PET bottles for juice and nectar which are difficult to recycle not only face the threat of higher fees due to their unfavourable properties. In the long term a complete ban on packaging such as the above could also even come into effect. The European Strategy for Plastics presented by the European Commission at the beginning of 2018 envisages all plastics having to be recycled by 2030. Various national initiatives in other countries of Europe are also promoting the reduction in plastic waste. In France, for example, the only plastics in use by 2025 at the latest should be recyclable. Moreover, in Great Britain new plastic packaging is to consist of an average of 30% recycled PET. International beverage producers have also begun to set themselves targets for a much higher recycling quota as a voluntary obligation. “By steadily ousting PET bottles for juice and nectar which are hard to recycle the market is increasingly opening up to recyclable packaging systems,” emphasises Langhammer. The growing demand for FreshSafe PET illustrates that barrier technology has hit a nerve among beverage producers. “The move away from composite materials which are difficult to recycle has already begun,” states Langhammer. “With the help of our technology the opportunities for processing pure PET are fundamentally increased.” www.khs.com Mario Dechent, director of R&D at Eckes-Granini (Source: Eckes-Granini Group GmbH) Herbert Snell, managing director of the MultiPet GmbH recycling company. (Source: MultiPet GmbH) Benedikt Kauertz, head of Environmental Assessment of Packaging at the independent Institute for Energy and Environmental Research (ifeu) in Heidelberg, Germany (Source: ifeu) Philipp Langhammer, coating technology product manager at KHS Corpoplast (Source: KHS Group)","@ID":29}, "MATERIALS / RECYCLING PETplanet Insider Vol. 20 No. 04/19 petpla.net 22 Petcore Europe Conference 2019 EU Plastics Strategy 2.0 Recycling Special Under the theme “EU Plastics Strategy 2.0 - Taking the PET industry to the next step”, the complete PET industry sector shared perspectives and strategies for a succesful and even more circular future. From PET resin producers, masterbatch producers, packaging designers and manufacturers, equipment manufacturers, label producers to major brand owners, EPR schemes, waste management organisations, recyclers, waste sorting and recycling machinery manufacturers - the entire value chain was represented. Additionally, speakers and participants from the European Commission (DG GROW), the European Parlimanet as well as ICIS shared their thoughts on the PET market as well as the plastics industry in the European Circular Economy. Mr Christian Crépet, Managing Director Petcore Europe Day 1 - PET market & strategy Susan Mair from ICIS gave an overview of the PET collection and recycling rates for 2017 as well as the key drivers of the market. According to ICIS “there is an under utilised PET recycling capacity of 300.000t due to a lack of material coming from collection processes”. Following the market assessment by ICIS, Alessandra Funcia, Head of Sales and Marketing Sukano, presented Petcore Europe’s programs of two major working groups: PET Thermoforms and Opaque & Difficult to recycle PET containers. After the introduction, experts from the PET value chain gave presentations detailing the market overview. Steve Scott, Chairman of the Committee of PET Manufacturers Europe (CPME), addressed the PET market from the perspectives of the European PET producers perspective. He stressed the importance of chemical or back-to-monomer recycling and the essential role PET producers will play to achieve it. Marc De Voogd, General Manager of Alpla France and Iberia, gave a converter’s vision for the future in his presentation. Accordingly the demand for post-consumer recycled PET will increase drastically by 2025 which is the challenge for the whole industry. Casper van den Dungen, Plastics Recyclers Europe (PRE) in the last presentation of this section gave an outlook on recycled PET up until 2030. The main points are firstly the Single Use Plastics Directive (SUP) will be the driver for the PET value developments and secondly the PET bottle collection is required to improve considerably to reach the 77% collection target in 2025. Casper concluded the presentation with a call to the recycling industry: “Use the momentum to create the difference.” Day 2 - Circularity and trends in recycling - EU Plastics Strategy 2.0 A significant highlight of the conference was the presentation of the European Strategy for Plastics in the circular economy by Laure Baillargeon from the European Commission - DG GROW. She gave insights in the newly launched Circular Plastics Alliance and stressed the fact that the European Commission is fully supportive of the plastics industry in delivering on the collection and reuse rates of plastics. It was also emphasised that the whole aspect of Life Cycle Analysis would be compared in decision making for preferred packaging alternatives. In summary, Christian Crépet, Executive Director of Petcore Europe, stressed the importance of collaboration between the industry and policy makers and congratulated DG GROW for the Circular Plastics Alliance initiative. Samuele Furfari (ULB) followed with a state-of-the-art presentation on the changing world of energy. According to the professor, who can look back at a long career in the European Commission where he implemented various energy policies and sustainable development, there is no new energy paradigm. The often predicted end of oil is not apparent. Mike Neal on behalf of CPME, followed Samuele Furfari with an enlightening presentation concerning the regulatory perspective on the PET value chain. Trends and solutions in PET collection and recycling In the afternoon session of day two, the focus shifted to trends and solutions in the PET post-consumer collection. First, Gian de Belder, Petcore Europe ODR Working Group Chairman, from Procter & Gamble presented the Holy Grail project on markers and digital watermarks. Gian also gave an interesting overview of the five pillars for a circular economy: design for recycling, access to collection, participation/education, separation and product innovation. Gian was followed by Clarissa Morawski from Reloop, who gave an update about the current developments in deposit Each year the European PET value chain meets in Brussels for the annual Petcore Europe Conference. Due to its continued success over recent past, this year the two day conference was held at a new venue to welcome more than 280 industry delegates. On February 6-7, 2019 more than 280 delegates from the entire PET value chain from Europe and beyond gathered in the Renaissance Brussels Hotel, adjacent to the European Parliament Area of Brussels.","@ID":24}, "PETcontents 04/19 4 PETplanet Insider Vol. 20 No. 04/19 petpla.net INSIDE TRACK 3 Editorial 4 Contents 6 News 48 Products 50 On site 51 Patents 52 PET bottles for Home + Personal Care 54 PET bottles for Beverage + Liquid Food MATERIAL / RECYCLING 10 A review of recycling developments 14 Combining Vacuum and Nitrogen atmosphere is the key - The brand new Vacunite bottle-to-bottle recycling process for food contact grade rPET pellets 16 rPET in a premium look - Using colours to add value to recycled packaging 18 The 50/50 solution - An interview with Rüdiger Löhl, Managing Director of E-proPlast 21 Boost PET recycling in Austria - Using local sources for reuse in PET bottles 22 EU Plastics Strategy 2.0 - Petcore Europe Conference 2019 26 Fully recyclable - Glass-coated PET bottles resolve juice production challenge 28 Consistently pursuing sustainability 30 Food safe PET recycling 36 A safety tightrobe walk - Post-consumer PET recycling in Ohio 38 Cleaning additive and alkali - The perfect combination for cleaning PET flakes 39 Clean results - Washing modules for the recycling of polyolefins 40 Recycling rate for PET beverage bottles in Germany - Current study on the reusable material cycle 42 Tackling PET recycling - Sesotec sorting systems at New Zealand’s first PET recycling plant MARKET SURVEY 31 Suppliers of preforms and preform inspection systems BOTTLE MAKING 43 Stretch Blow Molding, part 11 - Machine details: Changeover times INSPECTION 44 Preform Factory Concept 4.0 BOTTLING / FILLING 46 Dry aseptic PET lines BUYER’S GUIDE 57 Get listed! Page 36 Page 50 2436 Page 54 Recycling Special","@ID":6}, "MATERIALS / RECYCLING PETplanet Insider Vol. 20 No. 04/19 petpla.net 30 Food safe PET recycling Since the first “Letter of Non Objection” from the US Food and Drug Administration (FDA) in 2009, Gneuss’ recycling process based on the Multiple Screw Extruder (MRS) has received a number of national approvals for processing up to 100% post-consumer and industrial polyester reclaim into food contact products. Recycling Special Last year, Gneuss obtained food contact approval from Anvisa, Brazil’s equivalent to the FDA. This is the first ever approval in Brazil for making food contact sheet from PET reclaim. It is a significant contribution toward increasing polyester recycling in Brazil. In Latin America, Gneuss’ recycling process has also achieved the standards set by the Colombian food safety agency, Invima and its Argentinian counterpart, Senasa for processing 100% post-consumer PET reclaim to food contact products. In Europe, Gneuss received EFSA approval for the processing of 100% postconsumer PET on a thermoforming sheet line. One of these production lines is part of the technical center at Gneuss’ headquarters and available for customer trials. With the MRS sheet line undried PET reclaim material is processed directly into thermoforming sheet. The melt in the MRS extruder’s multiple screw section is devolatilised and decontaminated from impurities, oils and odours. Based on a conventional single-screw extruder, the multirotation section of the MRS extruder consists of a drum with eight satellite screws which have a ring gear and pinion drive. The degassing performance here is about fifty times higher than that of a conventional singlescrew extruder, while using a simple water-ring vacuum system with a vacuum of approx. 25-40mbar. A study by the British association for promoting recycling, “Waste and Resources Action Programme” (WRAP) in 2016 showed that with the help of the Gneuss Recycling Process, it was possible to take post– consumer thermoformed PET pots, tubs and trays from household waste and recycle them back into the same products, for food contact. Unlike the re-processing of PET bottle flake to sheet for thermoforming, this process is a truly circular one. The study was published under the title “Development and optimisation of a recycling process for PET pots, tubs and trays”. Thanks to the unparalleled devolatilisation performance of the Gneuss MRS extruder, contaminants such as oils, other harmful volatiles and also odours are efficiently removed from washed PET scrap without the need for pre-drying or any other heat treatment of the material prior to extrusion. Avoiding the need for heat treatment of the material prior to extrusion saves investment and energy costs, a whole inflexible process is eliminated, together with the risk of damage to the material. The polymer is processed gently in the low shear MRS extruder. The final product has excellent colour (low yellowing) and transparency, states the company. Gneuss’ research department is currently working on technical and innovative developments that will set new standards in PET extrusion in terms of performance, efficiency and product quality. These will be presented to the public at the K’ trade fair in October. www.gneuss.com CONTACT US TODAY TO LEARN MORE! AGRINTL.COM | +1.724.482.2163 | SALES@AGRINTL.COM MANAGE PREFORM VARIANCES Agr’s patented control technology precisely manages material distribution in PET containers to produce more consistent ERWWOHV UHJDUGOHVV RI GLHUHQFHV LQ SUHIRUPV PROCESS PILOT®","@ID":32}, "MATERIALS / RECYCLING PETplanet Insider Vol. 20 No. 04/19 petpla.net 11 PET monomer recycling can solve all these problems and make every PET packaging recyclable. Second, it will solve the waste problem, every packaging that is collected can be recycled, no reason to put it to incineration or landfill. Thirdly, it will increase recycling rates. Just assuming 80% of all PET packaging gets collected, mechanical recycling can bring back 40% and monomer recycling can top this up to 80%. And finally, instead of 2-3 times recycling, PET becomes 100% circular and can endlessly be recycled and even be “upcycled”. Not all PET monomer recycling processes will lead to 100% recycle content in one pellet or one bottle. Depending on the technologies and the size of the operations, the recycled monomers will be used over a large quantity of PET production. For solving the waste problem or for the environment, this is equally good. The current trend of claiming and targeting 35% to 50% and even 100% recycle content in some bottles can be challenged. Is there enough good quality rPET to do all this and what if the quality after 2-3 times recycling of a bottle with 50% rPET has gone down. We have to realise that specifying rPET content by governments is a tool and not a target. It tries to create a value to PET packaging waste and stimulate collection. Target is to solve the waste problem, waste on the streets, waste in the ocean and to re-use our raw materials as much as we can. Still a lot of work has to be done and high expectations have to be answered. This will take time. This year we may see the first semi-commercial scale production of 10.000 t recycled monomers and more will follow. Voices from the industry Mr Paul Niedl, Commercial Head at Starlinger Recycling Technology PETplanet: Since 2002, there has been a Recycling Division at Starlinger. 10 years later in 2012, the Viscotec division, which looks after entire rPET solutions, was founded. What was the deciding factor in founding Viscotec? Niedl: The business unit Viscotec was founded to better serve the market for PET solid state polycondensation and PET sheet extrusion. The business unit Starlinger recycling technology serves the market for PET bottle-to-bottle recycling along with other pelletising applications such as PE, PP, PS, and nylon, amongst others. Since PET solid state polycondensation and PET sheet extrusion is quite specific and a growing market, it did make sense to found a separate business unit for that. PETplanet: Over the past six months, Starlinger has seen an increase in installed plants and installed capacity of 5.4% and 5.3%, respectively. Do you see further growth in the field of PET recycling? If yes, over what period? MATERIALS / RECYCLING 11 SDWHQWV UHVHDUFKHUV DQG WHFKQLFLDQV LQVWDOOHG SODQWV EUDQFKHV ZRUOGZLGH ,I ZH KDGQêW JRQH VR IDU ZH ZRXOGQêW EH VR QHDU RXU IXWXUH VHHQ IURP QHDU","@ID":13}, "PETplanet Insider Vol. 20 No. 04/19 petpla.net 52 PETbottles Home + Personal Care Palmolive with mineral clay In the search for new, natural components for innovative shower creams, Palmolive is focusing on the long-known benefits of mineral clay and has brought several products containing mineral clay onto the market. The shower creams, advertised as “indulgent mineral clay” with rose oil and “cleansing mineral clay” with aloe vera extract, are available in a contoured bottle holding 250ml. Two shaped, self-adhesive labels provide all information and a hinged cap seal that can be opened with one hand rounds off the design, which is based on natural colours. www.palmolive.de Bottle up to 100% from recyclate The Henkel “Pro Nature” range has long been available in bottle bodies made from 100% recyclate; now the bottles from other brands, such as Sidolin, Biff etc, are made from 100% recyclate and are available on the shelves. Extra adhesive labels on the bottle necks draw attention to this innovation. To simplify correct sorting, the foil sleeve labels have a perforation around the bottle and the label can easily be taken off. www.henkel-reiniger.de Cream soap from Alverde With the headline “Home is...”, the German discount pharmacy chain dm has added three cream soaps to its growing, own-brand alverde Naturkosmetic liquid soap range: organic avocado/organic oat, organic orange/organic quinoa and organic almond/organic aloe vera. The products clean the hands gently without drying them out and offer subsequent care as they contain shea butter and vegetable glycerine. The brown-coloured bottles contain 300ml of creme soap, have a colourfully printed, stuck-on paper label and are equipped with a lockable pump dispenser. www.dm.de Hand soap from Dresdner Essenz Besides the fact that the product must satisfy the strict requirements of the consumer in terms of content, its acquisition and processing, natural cosmetic products must deal even more carefully with the issue of packaging. An example of this is the “Handschmeichler” hand soap sold in 280ml quantities from German natural cosmetic company Dresdner Essenz, which gently cleans and cares for hands with organic chokeberry and rice milk. The surfactants in the certified, vegan natural cosmetic are 100% plant-based and contain 100% natural fragrances. Furthermore, the recyclable bottles are made from 98% recycled material and the label from at least 70% renewable resources. The soap is dispensed via a lockable, screwed-on pump dispenser. www.dresdner-essenz.com","@ID":54}, "MATERIALS / RECYCLING PETplanet Insider Vol. 20 No. 04/19 petpla.net 37 the recycling rates, for instance, providing assistance for recycling carts in a community. “There is also a dialogue about EPR (extended producers responsibility) in the US, whether it will happen I’m not sure, but some things have to done differently in order for the supply to grow.” Challenges in local recycling The radius where Phoenix Technologies gets most material from is 500 miles: Michigan, Ohio, Kentucky, Indiana, and Illinois in the Mid-West. “Our customer base is also in a 500 mile radius. We think about collect and convert locally. 8 hours may not seem local, but for the US it is fairly local. It makes no sense to ship material from California here, the footprint is too big. Because bale quality is such that you might only recognise 65% good feedstock, it is not sensible to pay to ship that 35% that does not have much value. We really look where we source from and we keep a very close eye on the whole footprint. During the process we produce little that goes to landfill. Today, it is so hard to make all the pieces usable, we can find a home for everything, but it takes time to find such homes.” “We do not change our suppliers a lot because we spend so much time building up good relationships, trying all the time to make improvements. They want to send as much PET as possible, they know they cannot do 100% but they measure too, so our feedback is verification for their measurement system. We use our flakes to make resin and we know what we need to make our resin, so we can run different specifications of flakes. We also have green bales which are used primarily for strapping. For flakes, we can sack it up for shipping or put it in a silo and from there it is taken to our resin plant a kilometre away.” Recycling colours in the US In the US recycling of colour is clear, green and blue and amber; amber, for beer bottles. In total the market has many different colours outside of the green, blue, and amber. So what to do with these bottles? We have investigated Chemical Recycling: “Today (as of this interview) there is no independent commercial facility to my knowledge, they are in YOUR PARTNER IN RECYCL ING SYSTEMS WWW.SOREMA.IT FROM SINGLE MODULES TO TURNKEY PROJECTS startup, but as yet there is no commercial facility,” says Lori. In the end there is a lot of hope: “We hope to grow, hope to be more efficient, hope for development on the machinery because every human hand is hard to find. And there is work that should have not be done by humans, instead placing them where they can add more value. The city also hopes that we will grow.” Expansion plans: “Another plant is not out of the question but we like to see how stable the market turns out to be before we make any decision,” Lori said in conclusion. www.phoenixtechnologies.net The S+S Color Separator at the plant in Bowling Green, Ohio.","@ID":39}, "MARKET SURVEY 33 PETplanet Insider Vol. 20 No. 04/19 petpla.net Sacmi Imola S.C. IMD Ltd. Via Selice Prov. LE 17/A 40026 Imola (BO), Italy +39 0542 607 111 www.sacmi.com Mr Stefano Severi Vision SystemArea Manager +39 335 6594 236 stefano.severi@sacmi.it Moosweg 1, 2555 Brügg, Switzerland +41 32 366 80 66 www.imdvista.ch Mr Martin Gerber CSO of IMD Ltd. +41 32 366 80 66 imd@imdvista.ch PVS-2 PVS-3 PVS-5 PVS024 IMDvista PECO LUX IMDvista PECO V3 IMDvista PECO OEM Integration 1,100pph without weighing device, 600pph with weighing device up to 72,000pph up to 60,000pph up to 36,000pph According to the preform injection machine Up to 1,500ppm or 90,000pph Up to 4,000ppm or 240,000pph Dimensional measurement of diameters, thread area, wall thickness and perpendicularity lenght of the injection point, unmelt material, crystallisations, bubbles, oil marks, black specks, contaminations, burnt materials Indicative measurement of inner and outer diameters, lenght of the injection point, unmelt material, crystallisations, bubbles, oil marks, black specks, contaminations, burnt materials Indicative measurement of inner and outer diameters, lenght of the injection point, unmelt material, crystallisations, bubbles, oil marks, black specks, contaminations, burnt materials Indicative measurement of inner and outer diameters, lenght of the injection point, unmelt material, crystallisations, bubbles, oil marks, black specks, contaminations, burnt materials Colour variations, long gate / gate stringing, air bubbles, contamination, crystallinity, short shorts, short shot trend analyser Black dots, burn marks, contamination, bended body, bubbles (air pockets), crystallised body, scratches, non-visible flow structures (low pressure while injection), total lenght, colour and colour deviation, long injection, unmelts - depening on customer needs Black dots, burn marks, contamination, bended body, bubbles (air pockets), crystallised body, scratches, non-visible flow structures (low pressure while injection), total lenght, colour and colour deviation, long injection, unmelts - depening on customer needs Contaminations, flashes of material, black specks Contaminations, flashes of material, black specks Contaminations, flashes of material, black specks Contaminations, flashes of material, black specks Short shorts Flashes on neck/ thread, scratches on neck area, support ring deformation, missing material on support ring Flashes on neck/ thread, scratches on neck area, support ring deformation, missing material on support ring Notches, scratches, contaminations, ovality, external flashes, measurement of inner and outer diameters Notches, scratches, contaminations, ovality, external flashes, measurement of inner and outer diameters Notches, scratches, contaminations, ovality, external flashes, measurement of inner and outer diameters Notches, scratches, contaminations, ovality, external flashes, measurement of inner and outer diameters Ovality, diameter, flashes, shorts shots, flashing on parting line, deformation of sealing area, colour and colour deviation Ovality, diameter, flashes, shorts shots, flashing on parting line, deformation of sealing area, colour and colour deviation Lenght, voids, holes, crystallisations, black specks, bubbles, burnt material, unmelts Lenght, voids, holes, crystallisations, black specks, bubbles, burnt material, unmelts Lenght, voids, holes, crystallisations, black specks, bubbles, burnt material, unmelts Lenght, voids, holes, crystallisations, black specks, bubbles, burnt material, unmelts Long gate / gate stringing Gate defects, gate length (long gates), holes in gate and gate area, gate deformation, cracks in gate area, injection point out of centre, drip marks Gate defects, gate length (long gates), holes in gate and gate area, gate deformation, cracks in gate area, injection point out of centre, drip marks Colour intensity and deviation (ΔE) Colour intensity and deviation (ΔE) Colour intensity and deviation (ΔE) Colour intensity and deviation (ΔE) Color, Color Variations, Colour and colour deviation Colour and colour deviation Reading, sorting by cavity number, correlation of defects to cavity number yes, limitiations apply yes, limitiations apply Reading, sorting by cavity number, correlation of defects to cavity number Cavity reading, self-learn cavity function for several cavity/ templates, cavity related statistics and alarms, rejection of x cavity number, possibility to share information with injection moulding machine based of cavity number Cavity reading, self-learn cavity function for several cavity/ templates, cavity related statistics and alarms, rejection of x cavity number, possibility to share information with injection moulding machine based of cavity number No No No No No No No No No No No No Yes Yes Yes Yes Inline directly after injection moulding machine - does not need more floor space Inline after injection moulding machine. Before blowing and filling machine/line; complete line after injection and before blowing/filling and off-line stand alone Integrated into external handling or/ and automated systems Yes Yes Yes Yes Yes Yes, top camera Yes, top camera Yes Cavity recognition with easy self learn teach-in Cavity recognition with easy self learn teach-in Non destructive Non destructive Non destructive Non destructive Non destructive non-destructive vision inspection Non-destructive vision inspection Yes Yes Yes Yes Factory Concept 4.0 with IMDvista Portal: All system on one screen – A network solution for all your vision systems. Factory Concept 4.0 with IMDvista Portal: All system on one screen – A network solution for all your vision systems. Factory Concept 4.0 with IMDvista Portal: All system on one screen – A network solution for all your vision systems.","@ID":35}, "MARKET SURVEY 35 PETplanet Insider Vol. 20 No. 04/19 petpla.net Société Générale des Techniques (SGT) Alpla Werke Alwin Lehner GmbH & Co KG Gulf Packaging System, 3P Gulf Group Energo PET d.o.o. Novapet, S.A. 3 Rue de l’Île Macé 44412 Rezé, France +33 0 2 4005 09 37 www.sgt-pet.com Mr Pierre-Henri Jany Sales Manager +33 02 4005 09 37 p.jany@sgt-france.com Mockenstraße 34 6971 Hard, Austria +43 5574 6020 www.alpla.com Mr Jens Seifried Global Sales Director +43 5574 602 518 jens.seifried@alpla.com P.O.box 20266, Industrial City Phase 5, Jeddah 21455, Saudi Arabia +966 12 6360099 3p-gulf.com Mr Shadi Khan Key Accounts Executive, Int. Sales +966 547492027 gpssales@gulf-pack.com Bulevar Mihajla Pupina 12 11070 Novi Beograd, Serbia +381 222 391 334 www.energopet.net Mr Miroslav Popovic General Manager +381 222 391 334 office@energopet.net Paseo Independencia 21, 3rd floor, Zaragoza 50001, Spain +34 976216129 www.novapet.com Mr Antonio Lázaro Preform business manager +34 976 216129 alazaro@samca.com Yes Yes No No No No No No No No No Yes No No No From 0 -100% (according to the client request) Yes, on request No On customer request Yes, from 10-50% All colours, UV blocker, AA reducer, O2 and CO2 scavenger, reheat additive, white colour for UHT milk, gliding agent All customary additives Colourants, AA reducers, barrier additives Yes Concentrates (for milk and light sensitive products), colours, lubricants, nucleants, customer requirements Neck finish: 27/31, 45g; 55mm, 650g; 55mm S, 650g; 30/25 high neck and low neck: 13-44g; 30/25 BB Light, 22,50-28g; 29/25 (without step): 9.3-35.8g; 29/25, 9.5-36g; 28 PCO 1810, 16-52.5g; PCO 1881,14.4-50g; 28 BPF, 20.5-53g; 38mm 42/36, 14-44g; 38mm 43/36, 14-16g; 28/410 anti back off system; BVS 30 H, 40-53.5g; CRC63, 400-450g Softdrink preform: 0.25-2.5l; various neck versions; water preform: 0.25-19l; various neck versions; edible oil preform: 0.5-10l; milk preform: 2-start, 3-start; various neck versions; various neck versions for: preforms for personal care, home care, lubricants 7.9-30g, 29/25, 200-2,000ml for still water; 10.9-39.2g,30/25, 330-2,500ml for still water; 69g, 38mm, 5l for still water; 78g, 82.5g, 90.3g, 48mm, 5l for still water; 16-53.5g,PCO 1881 for carbonated soft drinks; 18-55g, PCO 1810/1816, carbonated soft drinks; 13.5g, 18g, 38mm, juice and milk 900 millions preforms: EnergoPET specialises in manufacturing of PET preforms, which are used for bottling of mineral water, soft drinks, beer, milk, chemical products etc.; including preforms with neck finishes: PCO 1810, Bericap 38mm, Twist-Off 30/25, Twist-Off 29/25 and PCO 1881. Implemented is the GFSI - FSSC 22000 Ø 29/25 W (short neck) 3302,000ml: 10-32g; Ø 30/25 W (std neck) 330-2,500ml: 11.6-47g; Ø 48mm W from 5.000-10,000ml: 77g, 82g & 98g; Ø PCO 1810 (std neck) 500-3,000ml: 18.5-54g; Ø PCO 1881 (std neck) 300-2,000ml: 18-38.7g; Ø 38mm, 500-6,000ml: 27-78g; customer requirements Preforms Company name Resilux Hodmeter Empacar S.A Retal Industries LTD Plastipak Packaging Postal address Telephone number Web site address Contact name Function Direct telephone number E-mail Damstraat 4, 9230 Wetteren, Belgium +3293657474 www.resilux.com Mr Philippe Blonda Marketing & Bus. Devlpm. Dir. +3293657476 philippe.blonda@resilux.com 140 rue Louis Pasteur, 76160 Darnétal, France + 33. 950 373 373 www.hodmeter.com Mr Antoine Brémilts Sales & Marketing + 33. 684 633 154 bremilts@hodmeter.com Parque Industrial - 45 Santa Cruz de la Sierra - Bolivia +591 3 34655 25 www.empacar.com.bo Mr Carlos Limpias Elío General Manager +591 3 34618 83 climpias@empacar.com.bo Epimitheos St. 6, Industrial Area A, Limassol, 3056, Cyprus +357 25 270 500 www.retalgroup.com Mr Milos Kuzman Vice President Sales & Service +357 25 270 500 sales@retalgroup.com Ellice Way, Wrexham Technology Park, Wrexham LL13 7YL, UK +44 1978 317378 www.plastipakeurope.com Mr Pedro Martins Sales Director Europe info-europe@plastipak.eu Preforms Multilayer preforms (Yes/No) Yes No No Yes Yes PEN prefoms (Yes/No) No No No No Yes Preforms in alternative materials (PP/PLA/PEF) Which? Yes, please contact us No No apllicable Yes - PLA, PEF Preforms incorporating rPET (rPET content in %) Yes, according customer wishes 0,00 % Yes, 10% to 100% rPET, clear and coloured Yes, rPET content 10 - 100% Yes, 1-100% List of additives available Oxygen barrier, CO2 barrier, light barrier, rPET No Activer barrier , O2 scavenger O2 scavengers; AA reducers; Slip agent; UV blockers; Brighteners; Various barrier additives. All colourants and barrier technologies. Preform range Juice, milk, CSD, water, oil and detergents 700 gr preform to blow 5 gallon refillable bottle 55 mm neck PCO 1810 (17.5 , 21,22,24.5,28,34 ,36,37,48,50,52,54,56,58,60,64 g) PCO 1881 (20.6 , 23.1,42.5,43.3,4 6.6,52.5,54.6,56.6,58.6 g) Bericap 38 mm wide (70,80 g) Bericap 48 mm wide (85,94 g); 700 g preform for 5 gallon water bottle; 29 mm edible oil : 18,21 24 g) Around 800 diffrent preforms designs with different weight (9,7 - 485g) and neck (PCO 1881, PCO1810, PET cycle Pco 1810, High PCO 1810, PCO HYBRID, BPF, 30/25, 29/25, Hexalite 26/22, Obrist, 34/29, 38 mm, 29/21, 28/410,etc. Plastipak has a wide range of preform sizes and weights too numerous to list. Contact us with your requirments; Plastipak supplies preforms for use in bottled water, CSD, food, dairy, home and personal care, alcohol, industrial and other applications.","@ID":37}, "MATERIALS / RECYCLING PETplanet Insider Vol. 20 No. 04/19 petpla.net 19 tion. Due to the fact that the regranulate has already passed through the production process once or several times the mechanical property does change. The bottles may have a reduced top load compared to new material. There is also the danger that sink marks may appear caused by different shrinkage properties. In addition, these properties can also fluctuate within a production batch of regranulate. This in turn affects the process settings and can lead to a degradation in wall thickness distribution. As regards processing and costeffectiveness, it should be said that when recycled material is used, it is fed separately through the production process. As with virgin material, the regranulate is dried and handled separately. This results in longer set-up times, higher energy consumption and more reject material. Last but not least comes quality and availability. We mainly use food-grade material as recyclate. Customers also demand this quality in cosmetic products. This is top quality recyclate but is more expensive than virgin material. Non-food recyclate is also used for chemical and industrial bottle products. The quality is not as good which leads to increased difficulties in production. Current very high demand and limited recyclate capacity could result in supply bottlenecks in the market. From a technical perspective, PET bottles can be produced using 100% rPET but for mentioned reasons we recommend 50% virgin and 50% recycled material. PETplanet: More and more bottles made from 100% rPET are now appearing on the drinks market, reflecting the tone of current debate on the issue of sustainability. Does 100% recycled material mean that it could not be more sustainable? Löhl: PET beverage bottles made from 100% recycled material are only used for niche products. Currently, an average of around 26% of rPET is used for bevarage drinks bottles in Germany. No industrial recycling process also with non-plastic materials exists in which 100% of an old material can always be converted into 100% of a “new” product. There are always process-related losses. This occurs as a result of sorting, grinding and associated dust generation, as well as start-up waste created during the production of regranulate etc. Waste generated during this process is used in Germany for thermal recycling. It can be assumed that a ratio between 5%-10% of the original material is lost due to the recycling process. In addition, the quality of the material is getting worse due to the permanent recycling. If only 100% recycled material would always beeing used for all “new” products, no material would be available within a short period of time anymore! This means that the use of 100% rPET is not sustainable. The desire to use as much as 100% recycled material is essentially driven by marketing. Everyone would like to write 100% rPET on the label to suggest a sustainable product to the end consumer. Although this reflects the spirit of the times, it is not technically feasible in the long-term. As with any other material, for plastics it is vital that new material is added into the process; otherwise it will not function indefinitely. Comparison preforms made from virgin PET (on the right) and made from 50% rPET About E-ProPlast E-ProPlast is a medium-sized company based in Schmalkalden, Germany. It has been producing standard and individual customer PET bottles for start-up businesses and well-known manufacturers in the food, chemical and cosmetic industries since 2002. Many bottles are manufactured for niche products. It hardly ever produces classic bevarage bottles such as those used for CSD, mineral water and soft drinks. The company supports its customers from the initial design development stage through the mould making process till the production of preforms and bottles. The size of PET bottles produced today range from between 10-1,500ml. Production takes place on two -stage stretch-blow moulding lines. The required preforms are manly made at the company’s own production facilities. www.e-proplast.eu PETplanet: Are you able to comment on current availability of recycled PET? Löhl: As demand increases so availability becomes more critical and rPET prices rise. The quality also suffers rather than improve. PETplanet: What in your view can be done to improve the current market situation? Löhl: We can only assess the market from the point of view of a bottle manufacturer. A study conducted by GVM (Gesellschaft für Verpackungsmarktforschung mbh) in 2018 showed that around two-thirds of the PET recyclate produced is used in the production of foil and fibres, while only one-third goes back to bottle to bottle production. However, foil and fibres hardly provide any input to the recycling stream! Good quality rPET currently comes almost exclusively from bevarage bottles. Here, the German bottle deposit system plays an important role. However the recycling stream of dual systems (yellow bag) has still a","@ID":21}, "MATERIALS / RECYCLING PETplanet Insider Vol. 20 No. 04/19 petpla.net 42 Sesotec sorting systems at New Zealand’s first PET recycling plant Tackling PET recycling 20,000 tons of virgin PET is imported to New Zealand annually. New Zealand government’s Waste Minimisation Fund supports the project to reduce that environmental harm. A grant enables the parent company Flight Group Ltd to open New Zealand’s first PET recycling plant in Wellington and spend NZ$ 12 million (US$ 8.8 million) on a full upgrade at its facility including a wash plant for PET bottles. Flight Group was established in 1907 and initially made leather luggage. It is still privately held by members of the original Osborne family owners. Flight moved into plastic production in the 1970s. It also has PET product manufacturing plants in Adelaide, Australia, and Romsey, UK. Keith Smith, CEO of Flight Plastics Ltd in Wellington said the wash plant and other work at the facility enables Flight Plastics to produce thermoformed packaging from recycled PET bottles. The company installed extrusion equipment to use recycled PET flakes starting in 2014, using imported flake to prove the process and establish a customer base. They had very encouraging results, so the next step was to install their own wash plant. Flight Plastics has the capacity to recycle 6,000 metric tons of PET a year. It gets feedstock from kerbside collections around the nation, which collect about 8,000 t annually. Sorting bottles and flakes As a part of the investment in a wash plant, Flight Plastics installed a multi-sensor sorting line including two bottle sorters and a flake sorter. These three systems secure the output quality as well as a continuous supply of PET flakes to the production line. After the upstream process steps such as bale breaking the bottles are fed to Sesotec‘s Varisort MN multisensor sorting system. This system was installed for the separation of PET bottles from other polymers (near infrared sensor N) as well as metals (metal sensor M). Flight Plastics also decided to install a further Varisort CN. This second Varisort is equipped with colour sensors C and near infrared sensor N for material identification and sorts as well as cleans the PET bottles into a transparent clear and a coloured fraction. Those sorted bottles are fed into a cutting mill where they are cut to the desired flake size and passed through a washing and drying process. In the next step Sesotec‘s Flake Purifier multisensor-sorting-system is used for a final cleaning of the PET flakes. Here the remaining off-colours, wrong polymers and small sized metal pieces will be removed. This multi-sensor configuration equipped with a high resolution outblast system is claimed to allow highest possible sorting efficiency combined with lowest possible material loss rates. Depending on the application the three sensors can be used individually or in combination. www.sesotec.com Sesotec‘s Flake Purifier multisensor-sortingsystem is used for a final cleaning of the PET flakes. Flight Plastics installed a multi-sensor sorting line including two bottle sorters. Recycling Special","@ID":44}, "INSPECTION PETplanet Insider Vol. 20 No. 04/19 petpla.net 45 Data for closed loop control and Industry 4.0: SPC for trend analysis; production & quality monitoring; remote access to vision systems and preventive action for high efficiency via the IMD vista Portal IMDvista Peco Lux Process monitoring shot by shot Main performance quality drifts and colour variations can be monitored in a continuous mode. Easy integration into any production system Requires no additional floor space No preform orientation needed High speed inspection camera – speed according to your production line speed. Inspects a great variety of preform formats with a single set-up IMDvista V5 software, based on self-learn functions (AI) IMDvista Peco V3 Easy and fast product change (no mechanical size parts) Whole line easy to access (floor level) Cavity detection Conveyor belts only (no star wheels) Integrated bad part bin (half octabin on pallet) Bad and good part boxes easy accessable Box filling directly after conveyor Taking up less than 7sqm including the sorter High output speed of up to 90’000 p/h control centre. The IMDvista Portal with a large touch screen connects all IMDvista vision systems and provides a complete overview of production, system setup, inspection and statistical data. Deviations and alarms are easy to understand and analyse. Further, immediate corrective actions can be taken directly on the systems. The navigation is intuitive and the system easy to use. All the data generated during the process, the Acsur plant is now able Inside the Acsur factory to use in closed loop circuits, reports, statistic, time and date and other relevant information. The Peco Lux Monitoring system is intended to provide Acsur with all the essential data they need to guarantee a precise production process without wasting time and energy on cost consuming post inspection of hours of production of preforms. Since the installation of these systems, the two companies Acsur S.A. and IMD Ltd. have been exchanging experiences and are continuously optimising the systems. The technical and commercial support is provided remotely, or personally directly at the factory, by the globally available service technicians. www.imdvista.ch www.acsur.com.ar","@ID":47}, "BOTTLE MAKING 43 PETplanet Insider Vol. 20 No. 04/19 petpla.net German Technology May 21-24, 2019, Guangzhou Hall 5.1, Booth S27 Strech Blow Molding, part 11 - Machine details: Changeover times Machine details by Ottmar Brandau Ottmar Brandau has newly revised his book “Strech Blow Molding”, first published by hbmedia / PETplanet Publisher, and now re-issued in a third edition under the Elsevier Imprint. PETplanet Insider is publishing extracts from successive chaperts in a serie of articles. Changeover times Changeover times are important for those factories that do not have the luxury of running the same product 365 days/year but have to change 2–5 times per week. When the same necks are used, the steps involved are as follows: disconnect water hoses replace blow moulds replace bottom inserts replace stretch rod stops or dial in new stop values change PLC recipe change preform supply. All blow machine manufacturers have now quick-change systems (fig. 4.18) that make this task much less time consuming. Water hoses are equipped with quick-disconnects or eliminate the disconnection completely by feeding water through the carriers with the moulds being outfitted with O-rings that do not require anything to be disconnected. Blow moulds used are mounted with two screws holding each half. Modern systems feature locking mechanisms that allow mould removal with one twist of a special tool or no tool at all. Same for the bottom inserts. Stretch rod stops are also easily replaced or not necessary when servomotors are used instead of cam-driven pneumatic cylinders. Taken all measures together may reduce changeover time from 5 min/cavity to less than 1 min/ cavity. On a 20-cavity system, this would result in time savings of 80 min/changeover, allowing an additional production of over 53,000 bottles if the machine runs at a speed of 2,000 bottles/cavity/h (b/c/h). Even if the margin was only 0.5 cents/bottle, an additional revenue of $ 250 per changeover could be achieved. Figure 4.18 This tool-less system allows mould changeover in less than 1min/ cavity. Picture courtesy of Sidel Inc. Please order your copy at the PETplanet Insider book shop: petpla.net/book3 Stretch Blow Molding Third Edition by Ottmar Brandau € 130,00 374 pages © Copyright Elsevier 2017, 2012","@ID":45}, "MATERIALS / RECYCLING PETplanet Insider Vol. 20 No. 04/19 petpla.net 36 Post-consumer PET recycling in Ohio A safety tightrope walk June 2018, We met Lori Carson, Director Commercial Operations at Phoenix Technologies Running a full capacity of 60-65 million lbs a year and established for 25 years in recycling plants, Lori Carson, Director Commercial Operations, at Phoenix Technologies has gotten to know many of the problems that can crop up in the post-consumer recycling industry. Starting up the plant in the first place that was the big challenge. In 1993 the company was founded as a resin plant producing 5 million lbs of resin, quickly expanded and now has two plants: one sorting, one resin plant with 100 staff. Recycling Special Right from the beginning Phoenix kept in close contact with the sustainability department of the city’s government in Wood County, where Lori also sits on the solid waste board. They are the only recycler representatives together with people representing the collection side. The county seat is Bowling Green, where a collection centre is located just across the street from the plant. This is also the drop-off centre for waste collections from surrounding towns, and for other venues such as trade fair waste. According to Lori, the system works well because everyone knows everyone else. “We are constantly asking ourselves how we can improve and we try to be good neighbours. We work hard to achieve this because it’s the only way to ensure we get good cooperation.” “We still buy clean flake material from the outside. The line is undercapacity for our resin plant, a deliberate decision, as this enables us to go into the marketplace and buy any special quality we might need. We had some partners to whom we made commitments, and it just made sense to keep relationships with them.” STF is the equipment supplier, and they installed their largest line. Lori told us that they chose STF because they operate their own lines, so they are very much aware of all the challenges that can occur. The sorting equipment is a combination of S+S and Buhler, who were recommended by STF. “We sent our material to Germany, to undergo trials, because US bales are different to European, to make sure the line could process them acceptably.” Market situation In the US, PET and HDPE are the materials which are mainly recycled, and Lori sees these streams continuing to grow. For two years, it has been an extremely challenging market: virgin resin has been very competitive economically, pricing has been extremely challenging for recyclers especially in the United States to meet. “The positive to our startup period was learning when raw material pricing was low!” she states. In the US, the recycling rate is very low at 28 or 29%. These rates are reported in cooperation with the APR (Association of post-consumer plastic recycling) and the ACC (American Chemistry Council). Lori explained “Every year, the commission carries out a study which collects and compiles the data from the entire industry, and that’s how we get the recycling rate. It could be slightly off if they don’t have all the recycling data, but the rate has been constant at around the 30% mark for quite a while now.” There is lots of discussion how to get the recycling rates up in the US. In about 8-10 of some of the bigger States, a bottle deposit scheme exists, e.g. New England states, New York, Michigan, Oregon, and California among others have enacted some bottle deposit laws, and Hawaii also has bottle deposit laws. “In those states, the recycling rate is 70%, which just goes to show how awful the average 30% rate really is! That’s where the challenge lies!” Lori pointed out. “It is not the ability to recycle, because we can - there are companies like us in the market, the problem is the collection side, how can we grow more supply?” How to improve collection “30% is used to support the industry: the problem with it is economics. If there is not enough material and supply is always limited than it’s about the price. Quality is key objective, but when demand is higher than supply, it’s a lot about price. That makes your recycling resin get out of kilter with the price of virgin material. If the price is too far out, demand begins to shrink as users revert to virgin material.” Lori explained. Big brands, like Coca Cola, Pepsi and Nestlé are trying to work on the supply side. In the US there are industry supported organisations like The Closed Loop Fund and the Recycling Partnership. The idea of these entities is to be able to assist communities, recyclers and others with investment that helps increase by Heike Fischer F.l.t.r.: Heike Fischer, PETplanet and Lori Carson, Director Commercial Operations at Phoenix Technologies Tour Sponsors:","@ID":38}, "PETplanet Insider Vol. 20 No. 04/19 petpla.net 54 PETbottles Beverage + Liquid Food Bottle just with rear label Under the brand name “Eternal”, American company Eternal Water is selling its “Naturally Alkaline Spring Water”, obtained from artesian sources and free from additives, in three sizes of plastic bottle. The contoured bottles have floral embossing and feature branded lettering in the grip area. The unusual feature is a flat area on the rear, where the only metallic, shiny, printed label is applied to the inside of the bottle. This generates a 3-D effect when looking at the bottle from the front. www.eternalwater.com Alcohol-free cocktails Under the brand name “Flirt”, Refresco Deutschland GmbH is selling several alcohol-free, ready-to-drink cocktails such as Hugo, Moscow Mule and Strawberry Daiquiri in a transparent, slightly contoured PET bottle holding 750ml. The bottle is decorated with circulating, stabilising, wavy embossing. A circulating shrink-wrap label provides product information and an appropriately coloured screw seal with guarantee band seals the bottle. www.refresco.de Salad dressing in PET Ge r ma n c omp a n y Feinkost Popp GmbH is offering 210 ml of chilled, ready-to-eat salad dressing in the varieties of HoneyMustard, Sylter Style, Garden Herb and Chives in its own retail chain. The slim bottles are found on the chiller shelves and are decorated with two self-adhesive labels and a screw seal made from metal with an adhesive sticker as a freshness indicator. www.popp-feinkost.de Teabag in PET The tea manufacturer/tea processor “Teavana”, which is part of Starbucks, is selling various varieties of its speciality teas over the counter in a transparent plastic beaker with snap-on lid - both made from PET. Under the lid is a removable membrane as a freshness and tamper-evident seal. The container holds 15 tetrahedron-shaped bags each holding 4 g. The bags are made from a type of material, have no additional packaging and the content is clearly visible. The beaker is decorated with a sleeve label with perforation to enable easy removal from the container. www.teavana.com","@ID":56}, "50 PETplanet Insider Vol. 20 No. 04/19 petpla.net 50 ONsite Indorama Venture selects Amut Technology to clean ‘Dirtiest PET bottles ever recycled’ Indorama Ventures has announced that it is to open a new recycling facility in Guadalajara, Mexico, at its Ecomex JV facility, close to its production site. The new plant will be operational in Autumn 2019. It has selected Amut Group to provide processing equipment and to upgrade an existing unit at the Ecomex plant. The new capacity means that the factory will be capable of producing over 13,000 pounds per hour of high- quality PET flakes from postconsumer PET bottles, which will be coming from landfill. According to the company, these are the dirtiest bottles ever seen in this market. Amut technology has been selected to convert the material into premier value clean PET flakes, which will be used to produce new resins for a variety of sustainable products. Indorama Ventures’ goal is to close the loop on recycling and increase the sustainability of the PET containers. “The new plant will process more than 100 million pounds of plastic bottles annually into clean PET flakes for our FuTuRe-PET,” said Mr Yash Awasthi, Vice President of Indorama Ventures North American Operations. The new washing plant has been specifically developed to process very dirty post-consumer, landfill-recovered PET bottles. The de-labeller removes the labels, especially the full body shrink sleeves, to make the bottles ready to go through cleaning operations. The 4,000 kg/h washing section has seen the friction force of Amut’s turbo and friction machines increased, to remove fine pollutants, labels, glue and soil. Pre-washing and de-labelling are carried out in cold water; the turbo and friction washer have hot water flow. The Amut technology reduces fresh water usage to the very minimum. Water is continuously filtered and can be re-used. Consumption of energy and cleaning agents is also maximally restrained. www.amut.it Recycling Special .com 100815dmyL","@ID":52}, "MATERIALS / RECYCLING PETplanet Insider Vol. 20 No. 04/19 petpla.net 39 Washing modules for the recycling of polyolefins Clean results Demand from customers, as well as the increasing number of criteria required for the recycling of re-usable materials from the waste flow, have inspired Krones to develop a washing technology for polyolefins, too. This was recently launched on the market under the name of MetaPure W-PO. The MetaPure W washing module from Krones was developed and built for continuous operation in the recycling process of PET containers. During this time, there have also been demands in the market to recycle polypropylene (PP) and polyethylene (PE), in order to render them suitable for high-grade re-use. One of the key characteristics of polyolefins is that their density is lower than one, hence they float on the water’s surface. PET, on the other hand, is significantly heavier than water, and therefore sinks to the bottom (table 1). Polyolefins: 1 PET: 1.38 to 1.40 PP: 0.90 to 0.915 LDPE: 0.915 to 0.935 HDPE: 0.94 to 0.97 Table 1: Comparison of density (in g/ cm3) PET vs polyolefins The polyolefins’ relatively low density, and thus their ability to float, are very helpful in the washing process for PET when it comes to separating the cap material from the PET itself. In the washing process for polyolefins, this material characteristic did require some procedural adjustments. However, the overall concept continues to be based on the experience gathered in the field of PET washing technology. Individually tried-and-tested units were adapted to suit the PO-specific traits, but the process-engineering features of Krones’ washing technology remained unchanged. The high quality washing achieved during inhouse trials was validated in external laboratories, and confirmed by the production of test specimens. Odour-neutrality One problem encountered with polyolefins is material collection, and the resultant side-effects. Generally speaking polyolefin packaging is that which is collected in household rubbish, or in separate bins or sacks for plastics. Since this material is usually not cleaned before recycling, it is invariably in contact with organic residues. This creates an enormous biological and chemical loading, which leads to an unpleasant smell. It is then relatively difficult to make sure the end-product is odour-neutral. However, with the standard washing module used in the in-house pilot plant, optimum results in regards to cleanliness and odour-neutrality could indeed be achieved, says Krones. In the future, the washing modules for PET and polyolefins will be available under the names of MetaPure W-PET and MetaPure W-PO respectively. www.krones.com Recycling Special Visit us: www.bericap.com Total development of neck and closure • New 26/22 1-start PET neck: weight savings for closure and neck of 50% compared to their predecessors Consumer convenience • Good grip: closures easy to handle for consumers • Slit and folded TE band: safe application, easy first opening Suitable for aseptic, carbonated an non-carbonated drinks REDUCE IT We call it optimized material usage Optimized neck and closures: • 1810 • 1881 • 26/22","@ID":41},
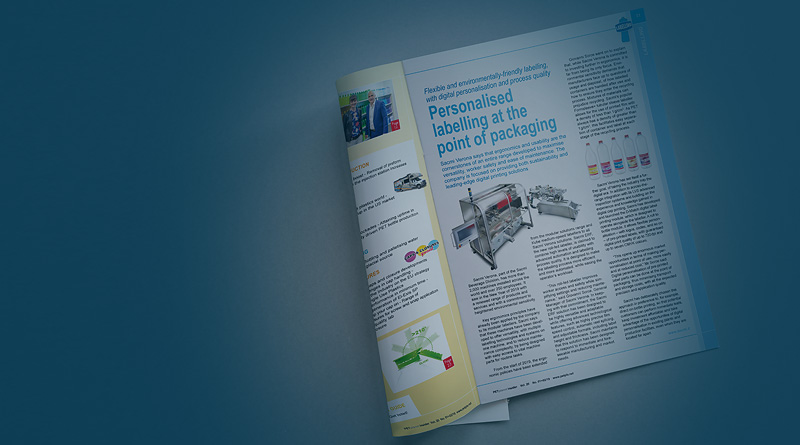