"imprint EDITORIAL PUBLISHER Alexander Büchler, Managing Director HEAD OFFICE heidelberg business media GmbH Häusserstr. 36 69115 Heidelberg, Germany phone: +49 6221-65108-0 fax: +49 6221-65108-28 info@hbmedia.net EDITORIAL Doris Fischer: fischer@hbmedia.net Michael Maruschke Ruari McCallion Waldemar Schmitke Ilona Trotter Wolfgang von Schroeter Anthony Withers MEDIA CONSULTANTS Martina Hischmann hirschmann@hbmedia.net Roland Loch loch@hbmedia.net phone: +49 6221-65108-0 fax: +49 6221-65108-28 France, Italy, Spain, UK Elisabeth Maria Köpke phone: +49 6201-878925 fax: +49 6201-878926 koepke@hbmedia.net LAYOUT AND PREPRESS Exprim Kommunikationsdesign Matthias Gaumann | www.exprim.de READER SERVICES Heike Fischer reader@hbmedia.net PRINT Chroma Druck & Verlag GmbH Werkstr. 25 67454 Römerberg Germany WWW www.hbmedia.net | petpla.net PETplanet insider ISSN 1438-9459 is published 10 times a year. This publication is sent to qualified subscribers (1-year subscription 149 EUR, 2-year subscription 289 EUR, Young professionals’ subscription 99 EUR. Magazines will be dispatched to you by airmail). Not to be reproduced in any form without permission from the publisher. Note: The fact that product names may not be identified as trade marks is not an indication that such names are not registered trademarks. 3 PETplanet insider Vol. 14 No. 10/13 petpla.net dear readers, Many thanks to all of you who came to visit us on our stand at PETpoint. Our intensive discussions with you have demonstrated that we consistently have our finger on the pulse of the sector with our magazine and the regional reports based on our excursions in the Editourmobil. We were particularly delighted to renew our acquaintance on the stand with a number of the people we visited on our South America tour. There was invariably a cheery “Hello!“ Overall, our subjective impression was that we held more talks and established more contacts than in the crisis year 2009, the date of the last drinktec/ PETpoint. Our impressions were confirmed objectively by Messe München. The event closed with the number of visitors up by an impressive 13%. The international flavour of the show was underlined by the fact that visitors came from a total of 182 countries. Even the Managing Director of Messe München, Dr. Reinhard Pfeiffer, a man used to success, admitted that he was impressed “... that a good third of the foreign visitors came from overseas ...“. The absence of Husky and Sidel did not cast a shadow over the event: indeed competitors indicated that they were more than pleased with the show. This was confirmed by Dr. Golz, CEO of Netstal and KraussMaffei Injection Moulding, who informed us that, in view of its high level of popularity with visitors, he would be back again with two lines in 2017. It was evident that the majority of exhibits featured PET lines, even amongst all the companies offering complete systems, and this was not just confined to PETpoint Hall B3. What was striking was the high proportion of aseptic PET lines. We were able to admire a few systems - GEA Procomac, KHS, Krones and Serac. Also on view were a number of exhibitors showcasing solutions on the theme of the PET recyclable container. It would seem that beer in PET is now on its way following in the footsteps of PETkeg. We will be returning to the topic of beer in the keg in the coming issues, in preparation for which we will be kitting our Editourmobil out with a system. There’s nothing to beat hands on experience! Yours Alexander Büchler In the editorial for the last issue of PET Planet insider 9/2013 it was possible to get the impression that the heading “Lies, damned lies and ...” referred to the work of the respected market research companies Euromonitor International and Canadean. This was not the impression we intended to convey. The analysis provided by Euromonitor and Canadean has for many years been and continues to be of great help to us in compiling our regional reports from around the globe. We would also like to inform our readers that the Euromonitor data was inaccurately quoted in our article on Peru and Bolivia on page 15 of the last issue. We apologise for any confusion caused. PETkegs were a major topic at drinktec/PETpoint, here the”keykeg” Team, winners of the “Beverage Innovation Award” in the”Best Distribution Innovation” category. In order to conduct an in-depth test, we shall be installing Keykeg in the Editourmobil and carrying out some extensive tests on it during our 2014 Tour which is scheduled to take us through Italy, North Africa, Spain and France. 360° (Coverpage Photo: BASF/Emeco, 2013)","@ID":5}, "PETpatents www.verpackungspatente.de 72 PETplanet insider Vol. 14 No. 10/13 petpla.net Stackable bottle Utility Patent DE 202013000322 U1 Applicant: Marco Schupp, Schwollen (D) Date of Application: 15.1.2013 A rotationally symmetrical bottle is fitted with a number of peripheral recesses to enable safe and simple stacking. Hitherto, the bottles have incorporated snapin features on the outside and special mouldings in the base area in order to make them capable of being stacked parallel next to and on top of one another. Printed surface disclosure No. DE 102011082011 Applicant: Krones AG, Neutraubling (D) Date of Application: 1.9.2011 This Disclosure describes a means of printing the relief surface of a bottle in order to achieve optical effects or, by so doing, with a view to modifying the haptics of the bottle. Closing device European Award of Patent No.EP 2121466 B1 Applicant: Aptar Freyung GmbH, Freyung (D) Date of Application: 23.1.2007 Closing device for a container which may be exposed to differences in pressure. Opening the container first of all enables a pressure compensating channel. This prevents any escape of sizeable quantities of product in surges. Pack marking Disclosure No. DE 102011082972 A1 Applicant: Maschinenfabrik Gerd Mosca, Waldbrunn (D) Date of Application: 19.9.2011 Now that many packs are no longer held together by a plastic film wrapper but instead by means of straps or the like, the application proposes splitting up a large motif and affixing it to several container labels so as in this way to achieve a larger expanse on which advertising / information can be printed. Preform International Patent No. WO 2013 / 051601 A1 Applicant: Dai Nippon Printing Co. Ltd., Tokyo (JP) Date of Application: 24.9.2012 Preform for manufacturing a plastic bottle. The preform is specially moulded in the base area so as to enable a base of a particular shape to be created in the subsequent bottle. Plastic container International Patent No. WO 2013 / 052284 A1 Applicant: Graham Packaging Company L.P., York (US) Date of Application: 20.9.2012 A container to accommodate a product that is hot filled or which is heated after filling is fitted with specially moulded and aligned compensating surfaces to absorb the change in volume.","@ID":74}, "TRADE SHOW PREVIEW 63 PETplanet insider Vol. 14 No. 10/13 petpla.net SBM - Improved energy efficiency Urola, the Spanish manufacturer of blowing machines and moulds, will be presenting its Urbi 4L all electric blow-moulding in public for the first time. The company says that the new machine offers reduced energy consumption, higher efficiency in the heating systems and servomotor drives, air recovery from the pneumatic drives, and elimination of “parting lines”. Preforms heated in the oven are transferred directly to the mould and blown bottles are moved directly to the packaging exit. Preferential heating processes are available for asymmetrical bottle shapes and flat containers. The line can also be fitted with hot-fill technology. www.urola.com Scan & Measure Oxygen Ingress & Transmission Rates www.PreSens.de/ Fibox4 Fibox 4 Stand-alone fiber optic oxygen transmitter KHS Hall 13 Booth A75 Urola Hall 14 Booth B14 Lightweight thread During K 2013 KHS Corpoplast and KHS Plasmax will be presenting its PET bottle design solutions. For the first time at K 2013 the company will be showing its newest development: a ‘streamlined’ bottle thread. The objectives behind this latest development were not just to reduce weight but also to ensure that the bottle can be transported by an air conveyor, an option which can be retrofitted into existing lines and the performance of the stretch blow moulder is maintained. In addition, the setup must be able to continue to use the caps applied in the past. All of these criteria have been met. To date, classic threads for carbonated beverages weighed 3.7g. The new development now permits an extra 1.1g of material to be saved in this area which at a line output of 48,000bph results in a cost saving of approximately €385,000/a. PET experts at KHS are currently working on reducing the thread weight of PET bottles for still beverages. Another point of great interest will be InnoPET Plasmax barrier technology for PET bottles now in use worldwide and the new Plasmax+ process (See article on page 52). www.khscorpoplast.com www.khsplasmax.com Extruder equipment for PET recycling Extricom, the extruder manufacturer, will be presenting its RingExtruder RE XP/XPV series, which includes the RingExtruder RE PET bottleto-bottle PET recycling system. It consists of different modules – extrusion process section, vacuum, screen changer, melt pump and pelletiser – and converts postconsumer waste into high quality raw materials approved for food contact. Extricom says that 400,000t/a of postconsumer PET flakes will ultimately be recycled into pellets that meet FDA and EFSA requirements by its RingExtruder technology. The stand will also feature developments in the Extricom RingExtruder RE5XPV-28D; SideFeeder and Stuffer; parts for co-rotating twin screw extruder; and other developments in PET recycling. www.extricom.de Extricom Hall 14 Booth A36","@ID":65}, "BOTTLE MAKING 45 PETplanet insider Vol. 14 No. 10/13 petpla.net BOTTLE MAKING kegs are expensive, and time-consuming to produce, and the long distance transportation costs involved in returning the kegs are high.” The name Dolium, by the way, refers to the Latin word for an earthen vase or bulk container for wine or food. The idea of long distance transport is as such implicitly in our product name. Hole-through-the-wall production Beginning 2013, the first Dolium beer kegs were produced in Innocan’s Antwerp factory. The kegs are produced in a two stage blow moulding process. Innocan uses monolayer preforms, produced from a blended preforms mix of PET and active, passive barrier material and UV barriers. The beer keg targets to offer a high quality alternative for a competitive price which should stimulate beer exports. Alain Cap, General Director Innocan commented on the co-operation with Dispack: “This is a good example of our “holethrough-the wall”-principle. Dispack projects has its own assembly-unit in our factory in Antwerp. In that way we generate a close cooperation which results in tailor made innovation.” The Dolium beer keg is compatible with existing filling and draught equipment. A Pressure Relief Valve (PRV) ensures safe operation. The keg is equipped with a selfclosing valve which enables intermediate cleaning or disconnection. The keg can be stored and transported either horizontally or vertically. It can withstand dropping and can be rolled. In a further development, Dolium has recently been launched as a 20l oneway beer keg. Sustainable production processes Sustainability is regarded an important issue at Innocan. The company puts a lot of effort in a continuous analysis of internal and external logistic functions in order to develop more environmentally friendly production processes. Innocan aims to reduce its ecological footprint by producing 100% recyclable PET kegs either with its “holethrough-the wall” on-site production, or else by establishing production facilities adjacent to their customers. www.dolium.be www.innocan.eu","@ID":47}, "TRADE SHOW PREVIEW 60 PETplanet insider Vol. 14 No. 10/13 petpla.net Flexible delabelling Sorema, a division of Previero S.r.l., will be exhibiting its patent-pending Delabeller, which is designed to remove sleeve labels in post consumer PET bottle recycling lines. Sorema says that its system can be easily installed in any recycling lines processing between 600 and 12,000kg/h. The company states that it offers low energy consumption along with easy and cost-effective maintenance and spare parts. As well as delabelling, the Sorema technology can also undertake the dry pretreatment of mixed bottles or rigid packaging. The machine can open the materials and separate contaminants from the surface, as with sleeve labels, and it can be integrated with an aerodynamic separator in order to achieve efficient separation of light and bulky materials. The first Sorema delabelling system was installed early in 2013 in a US recycling plant. www.sorema.it Preform inspection system The Intravis PreWatcher III is the latest release in their line of highspeed preform inspection systems. With its space saving design this system can integrate into the production line to perform a comprehensive inspection of each preform for defects. Unlike its predecessor, the PreWatcher III is self-contained with a high-tech centrifugal feeding unit already included in the inspection system. By combining both the feeding unit and the inspection system, Intravis is able to fit the system into 8m² of floor space with a maximum height of only 2.5m. The new PreWatcher III can inspect preforms at speeds of up to 72,000ph. To ensure optimal preform presentation to the cameras, the preforms are separated by the VT wheel then picked up by individually rotating vacuum plates. The newly developed top sealing surface inspection with colour camera and bicolour multiangle lighting detects scratches and notches in the mouth area without being distracted by possible parting lines. While the technology of the predecessor was adapted for the inspection of the injection gate point, the device performs side wall and thread inspection with a total of 6 high-resolution cameras. These cameras take various precise images while the preform is rotating, thus creating a roll out image of the preform surface for the image processing system. The patented background suppression method suppresses the image from the rear side of the preform on translucent preforms, enabling the system to see and evaluate contamination, streaks, scratches, unmelts, oil splashes etc. At the same time the geometric characteristics, as well as the wall thickness, of the preform are being measured. Virtually all thread dimensions are measured by the cameras particularly aligned to the thread area. Simultaneously, the cavity numbers are being read, allowing for sorting of preforms by mould cavity numbers or creating cavity-related statistics. This works also for opaque preforms. To complete the inspection, detection of colour deviation in the l*a*b* colour space as well as the transmission in the UV and IR wavelengths is accomplished using a spectrometer. All references are taught through a training program. Tolerances for all measured values may be defined via the touch screen of the completely updated and cutting-edge user interface. Preforms that do not meet these requirements are removed from the production process and the remaining good preforms are counted. The PreWatcher III cannot only be integrated behind an injection moulding machine but can also be used offline for batch inspection of large preform batches. Intravis offers the necessary downstream equipment such as octabin or gaylord tipper, bunker and diverter for the packaging of the inspected good preforms. These components are optimally suited for the system and are controlled by the PreWatcher III interface. www.intravis.de Sorema Hall 9 Booth D41, D55 New drying control The Conair Group’s new DC-T TouchView control will be part of a central-drying cell that includes a W300 Carousel Plus desiccant dryer and a four-hopper ResinWorks system, equipped with the Conair Drying Monitor. The DC-T TouchView dryer control has an eight-inch-diagonal graphical touch-screen interface designed to provide operators with complete system information at a glance, including current and historical temperature data. The ResinWorks system combines multiple hoppers with integral air manifolds, ducting and wiring on a single platform. Conair is also exhibiting its FLX loading control, an entry-level plastic-resin-conveying system that was recently expanded to handle up to 128 loaders and 40 vacuum conveying pumps. Also networked at the K Show will be a TrueBlend TB-250 gravimetric blender, which offers throughputs of up to 431 kg/h. TrueBlend blenders are available in sizes to a maximum throughput of 5443kg/h. The four hoppers on the blender will be equipped with Access loaders and a Filterless loader. Conair’s new EP1 and EP2 Series of portable chillers will be represented by the EP1A-03 air-cooled model with onboard process fluid pump and tank. Another product making its first appearance at the K Show is an NCF-819 super-tangential granulator, part of a new line of machines with smaller footprints. An ATC dual-spindle coiler, which is designed for winding small, flexible extrusions, will provide an example of the company’s downstream solutions. www.conairgroup.com Conair Hall 10 Booth J59 Intravis Hall 11 Booth A58","@ID":62}, "BOTTLE MAKING 49 PETplanet insider Vol. 14 No. 10/13 in a matter of minutes. The blow-trim process allows the customised jar line to run at normal production speeds, in sync with the filling line. “The fact that the blow-trim process works with existing blowmoulder equipment allows us to be very competitive,” says Waud. Still, the through-thewall production process leaves scant margin for error in the jar finish. Despite its advantages, the blow-trim process is a demanding one, David Piccioli, Director, Global PET Technology Development notes. “This is no ordinary container. The process is more challenging than traditional reheat stretch blowmoulding. It is much more difficult to control the blown finish,” he points out. Concerns focus on material distribution in the body and thickness in the thread region. Jar finish is especially critical. Any interference or variation in the thread dimension makes it impossible to achieve the proper torque setting when applying the injection-moulded caps on the filling line. After capping and the hot-fill process, the jars are dipped in cooling water to hasten the drawing of a vacuum. A flaw in the finish can compromise the seal. The consequences, allowing cooling water into the jar, creating the potential for contamination, product spoilage, or leakage, are all unacceptable. To ensure that every jar on the conveyor to the filling line is defect-free, Graham Save money, save weight: withkronesLitePac and EvoLite. www.krones.com Graham Packaging uses the Agr OptiCheck inspection and measurement systems to ensure that every jar conveyed to the customer filling line will meet exacting expectations.","@ID":51}, "PETcontents 10/13 4 PETplanet insider Vol. 14 No. 10/13 petpla.net INSIDE TRACK 3 Editorial 4 Contents 9 News 67 Products 68 PET bottles for beverages and liquid food 70 PET bottles in health and beauty care packaging 72 Patents MARKET SURVEY 49 Suppliers of resins and functional additives for PET bottle production TRADESHOW PREVIEWS 56 K 2013 preview October 16 - 23, Düsseldorf, Germany 64 Drinktec review September 16 - 20, Munich, Germany EDITOUR REPORT 13 Chile and Argentina Go with the flow tour 2013 - part 2 MATERIAL / RECYCLING 30 Why does it work well? PET recycling in Switzerland 36 Better than new BASF introduces new additive for PET recycling BOTTLE MAKING 43 Hot enough Appe offers pasteurisable PET jar 44 Racked, stacked, launched Dispack projects, in partnership with innocan, launches Dolium, a one-way-beer keg 46 Moulds: Concepts, design and manufacture Bottles, preforms and closures - part 6 48 Peanut butter jar gets the vision treatment Graham Packaging uses Agr automated blowmoulder control and inspection for wide-mouth jars 52 Freshness made visible Plasmax+: Further enhancements in KHS Plasmax technology BUYER’S GUIDE 93 Get listed! Page 30 Page 56 Page 44","@ID":6}, "TRADE SHOW PREVIEW 56 PETplanet insider Vol. 14 No. 10/13 petpla.net It’s K time again In this issue we once again bring you details of a number of exhibitors with products of particular interest to the PET industry. There will be around 3,100 exhibitors. The exhibition runs from October 16 to 23, 2013. Opening hours are from 10 am to 6.30 pm. Hot stuff PETPlanet Insider published a full description of MHS - Mold Hotrunner Solutions’ Rheo-Pro iVG hot runner system in issue 4, 2012. The company will be exhibiting iVG2 at K 2013. It claims that iVG2 stack moulds produce a higher volume of parts in a smaller moulding machine, with a lower clamp force and a smaller footprint and that its new RheoPro iVG2 nozzle is the world’s most compact back-to-back valve gate hot runner system and the only internal valve gate currently on the market. The nozzle design closes the distance between the two parting lines to 285mm, with cavity spacing of only 63.5mm. A standard Rheo-Pro iVG2 48+48 stack mould, running in a 200t machine, can produce 96 light weight bottle closures every 3s or almost 3 million parts per day. MHS further asserts that it is the only valve gate hot runner that operates entirely without elastomeric seals or lubrication, and does not require any cooling. Its valve pin piston is located directly inside the hot runner nozzle body, which eliminates traditional pneumatic and hydraulic cylinders as well as external electric actuators. Compressed air for valve gate actuation within the nozzle is directly fed through the melt distribution manifold. Other injection moulding developments will also be shown on MHS’ stand. www.mhs-hotrunners.com MHS Mold Hotrunner Solutions Hall 1 Booth A09 Silver appearance With Symic C604, Eckart GmbH Germany will present a new pigment generation especially suited for application fields where metals cannot be used. This product combines highly brilliant metallic optics with the silky appearance of pearlescent pigments. The product is inert to acidic and alkali media as well as to oily ingredients, and thus can be used for plastic bottles and packaging, e.g. for vinaigrettes or cooking oils, as well as for detergents and dish-washing liquids. Additionally, according to Eckart Symic C604 provides strong thermal stability and is thus suited for many packaging applications. www.eckart.net Eckart Hall 5 Booth E16 Liquid colours, additives and dosing systems At K 2013, Repi will be showcasing the complete product portfolio for packaging. Visitors will learn more about the Remap colours and additives, a wide range of products improving packaging aesthetics and enhancing product performance. The company’s technical team, providing support around the world, will explain the high technology performance of Repi U2011 dosing equipment and Repi Light Meter. Repi headquarters are located in Northern Italy. Distribution is provided worldwide through own organisations in Europe, Russia, North and South America, and a global commercial network. Repi provides full support to customers from initial idea to the final product realisation. www.repi.com Repi Hall 6 Booth B24","@ID":58}, "BOTTLE MAKING 44 PETplanet insider Vol. 14 No. 10/13 petpla.net 20l and 30l one-way Dolium beer keg. Dispack-projects nv, funded with Belgian private equity, started developing an inexpensive but sustainable alternative. Three years of intensive research, development and testing followed, in cooperation with several national and international brewers who were instrumental in defining an extensive list of specifications. Once Dispack has come up with the design, the next step was test production. Innocan plays a major role in developing and realising the production process of the Dolium one-way keg. Albert Wauters, CEO Dispack-projects: “Some time ago we realised that there was significant demand for a cost efficient solution to the export of beverages and in particular, for beer. Stainless steel Dispack-projects, in partnership with Innocan, launches Dolium, a one-way beer keg in PET Racked, stacked, launched Dispack projects and Innocan, both small and medium-size Belgian companies, specialized in packaging, have combined their expertise and introduced a 20l and 30l one-way beer keg in PET. The concept, called Dolium, is stackable and 100% recyclable. Innocan is a medium-sized company headquartered in Antwerp. It has two production sites in Antwerp (Belgium) and Roanne (Innocan France). There are two further in-house production-sites in Gent (Belgium) and Perpignan (France). Distribution partners are Adriaansen (Belgium), Houweling (Netherlands) , Invopak (UK) , and Manypack (France). The company was founded in 2010 by Alain Cap and Gust Gysen. Together they have over 50 years of expertise in the PET sector and in blow-moulding in particular. Their common goal was to find a more sustainable alternative for the existing HDPE-cans. One of the first developments is a stackable 20l PET-bottle, the first from a complete new generation of stackable and patented PET bottles. Innocan delivers a total concept, from PET-bottle to fitting caps and handles. After developing the first 20l PET bottles, other volumes of 10l, 15l and 25l followed quickly and the range is expanding continuously. Today, Innocan is developing the stackable version in 5l, for which there is a high market demand. In addition, Innocan is also busy developing a water bottle in PET. The Dolium concept For the most recent development, Dispack and Innocan forged a partnership for the production of the The Dolium keg is produced from monolayer PET preforms ... ... in a hole-though-the wall-priciple... ... at the Innocan plant in Antwerp. The blow-moulded Dolium keg","@ID":46}, "www.drinktec.petpla.net Supported by: Go With The Flow Tour Our successful South America tour is behind us! Our PETplanet Insider team, ever thirsty for knowledge, has been off on another tour of exploration. Starting in Lima, our longest tour so far in the Editourmobil took our editors, split into in four teams, through six countries in South America: from Peru via Bolivia, ChiOH DQG $UJHQWLQD DV IDU DV 8UXJXD\\ DQG XOWLPDWHO\\ %UD]LO DV D ¿QDO stop-off point. Three and a half months‘ travelling time, a distance of more than 12,000 kilometres and any amount of exciting interviews with the Great and the Good of the PET sector – the results of this year’s tour are once again an absolute highlight. Read all about the thrilling moments of the trip in our tour blog www.drinktec.petpla.net __________________________________________________ ¡Hemos dejado atrás nuestro exitoso Tour a Sudamérica! Nuestro equipo PETplanet Insider, cada vez más ansioso de conocimiento, ha salido en otro Tour de descubrimiento. El viaje comenzó en Lima, siendo el más largo hasta el momento en nuestro Editourmobil que llevó a nuestros editores, divididos en cuatro equipos, a través de seis países de América del Sur: de Perú a Uruguay, pasando por Bolivia, Chile y Argentina, para terPLQDU ¿QDOPHQWH HQ %UDVLO SDtV GH WUiQVLWR ¿QDO 8Q YLDMH FRQ XQD duración de tres meses y medio, un recorrido de más de 12.000 kilómetros y una gran cantidad de entrevistas fascinantes con la elite del sector PET: los resultados del recorrido de este año son una vez más de lo más destacado. Lea todo acerca de los emocionantes momentos vividos en el viaje en nuestro blog del Tour www.drinktec.petpla.net __________________________________________________ Nossa excursão de sucesso pela América do Sul terminou! Nossa equipe PETplanet Insider, sempre em busca de mais conhecimento, saiu para outra excursão de exploração. Partindo de Lima, nossa excursão mais longa até o momento na Editourmobil levou nossos editores, divididos em quatro equipes, por seis países da América do Sul: saindo do Peru, passando pela Bolívia, pelo Chile e pela Argentina, chegando ao Uruguai H ¿QDOPHQWH DWp D ~OWLPD SDUDGD QR %UDVLO 7UrV PHVHV H PHLR de viagem, mais de 12 mil quilômetros percorridos e uma quantidade enorme de empolgantes entrevistas com os Notáveis e os Talentos do setor PET foram o resultado da excursão deste ano e, mais uma vez, um sucesso absoluto. Leia tudo sobre os emocionantes momentos da viagem no nosso blog da excursão: www.drinktec.petpla.net Go with the flow The South-America round trip with 18th February - 24th May, 2013 18 de febrero - 24 de mayo de 2013 De 18 de fevereiro a 24 de maio de 2013","@ID":44}, "EDITOURS REPORTS 28 PETplanet insider Vol. 14 No. 10/13 petpla.net manufacturers pushing their way on to the market and the time had come to re-orientate. At the beginning of the 1990s a chance meeting with an Argentine employee of the North American company WTE (Waste to Energy) from Boston came to the rescue. They had been one of the first in what was at the time a PET recycling market that was still in its infancy and they were enjoying a positive sales trend as virgin material was still highly expensive. The number of PET bottles coming on stream was nevertheless still too small for WTE, which led to the idea of obtaining the necessary bottles through Coca-Cola Femsa and Pepsi Argentina, something which, taking into account the high cost of Virgin PET at the time, continued to represent a lucrative business. This left only the question of the most appropriate way of handling the logistics when it came to packaging and despatch – and this is where Marcelino / Reciclar came in with the experience he had gained from decades of operating in the retail market. Reciclar offered their services and were finally awarded the contract. The service enjoyed a boom until the price of virgin PET fell from US$4 at the time to US$0.75 per kg and the Americans withdrew from business in Argentina. Reciclar’s factory premises: Erwin Auspitz (Commercial Director, right) and Kay Barton surrounded by tonnes of compressed PET bottles Reciclar subsequently made a definite decision in 1995 to enter the recycling business themselves and their first 360° customer, Coca-Cola Femsa, was already on board, so to speak, as a result of their previous cooperation. After lengthy negotiations both parties resolved to sell CocaCola‘s used and faulty bottles to Reciclar, but this was to be just the start and later on it became a side issue. Instead they concentrated on the thousands of bottle collectors with whom Marcelino was likewise familiar from his old days as a dealer and who untiringly picked up bottles day in and day out, selling these to dealers who in turn sold the bottles on in part-sorted bundles to Reciclar. The first machines, as Erwin Auspitz explains, still tended to be simpler own-builds, imports from China or used machines from Brazil. From the material the machines produced the first flakes which were then exported to China in a dirty state. At the time, the price for 1kg bottles was around US$0.40, a feasible selling price to China merely a meagre US$0.12. However, Reciclar, fired with ambition at the idea of recycling, became involved in the business and, at the end of the 1990s, obtained support from CocaCola Argentina for just over two years. According to Auspitz, Coca-Cola was very interested in embarking on a project which would involve collecting the bottles from the streets. Coca-Cola invested US$0.20 per kg of street bottles collected in the project. The target was 100t per month, a figure that, in those days, was regarded as a colossal challenge. Today Reciclar recycles around 2,000t of bottles per month, made up almost exclusively of collected bottles plus a small ProTec Polymer Processing GmbH Headquarters Stubenwald-Allee 9 64625 Bensheim/Germany Phone: +49 6251 77061-0 E-mail: sales@sp-protec.com Web: www.sp-protec.com Trendsetting solutions to upgrade your virgin and post-consumer polymers! Düsseldorf Oct 16-23, 2013 Hall 9, Booth D60 Erwin Auspitz in front of a real company work of art: a Christmas tree made from old PET bottles and closures","@ID":30}, "TRADE SHOW PREVIEW 61 PETplanet insider Vol. 14 No. 10/13 petpla.net Air control Italian company Moretto SpA will be exhibiting a range of control, management and monitoring systems. Of particular interest to the PET field will be a dedicated variant of its Eureka dehumidification system, which is designed to use and monitor only the precise amount of process air required and thus optimise energy use. In the PET variant, the Flowmatik integrated automatic process air distributor, OTX thermal exchanger and Xmax dryers are calibrated to reduce airflow by over one-third, compared with standard systems, with consequent savings in process and heating energy usage. www.moretto.com HSM Hall 11 Booth F07 Error correction HSM’s stand will feature its new PET FluidEx 600, which empties full PET bottles, cans and Tetra Paks which have been, for example, incorrectly filled or labelled or that have exceeded the expiry date. Details of the machine appeared in PETplanet Insider drinktec preview earlier this year. The stand will also feature the HSM V-Press 860 P vertical baling press, which is designed for compressing opened or perforated PET bottles. A four-fold wire strapping keeps the bales of up to 230kg in shape with maximum bale sizes of 1,200 x 780 x max. 1,200mm. The PE 250 hydraulic label press, from HSM’s Pühler-HSM GmbH + Co. KG subsidiary, will also be on the stand. This press drains, compresses and conveys the medium through a press piston. www.hsm.eu Moretto Hall 11 Booth H57 ISBM and thin-wall cups Mould&Matic Solutions GmbH, Austria, will be found on two stands at the K Show. In Hall 12, Stand E49-5, the company will present an overview of its products and competences. One of the company’s pick-up stackers will be demonstrated on Amut’s stand in Hall 16, Stand D43. Mould&Matic’s range extends from tooling for the thermoforming and injection moulding of thin-walled cups and buckets, through peripheral equipment for thermoforming machines for packaging production, to its new “Blowliner”, a machine for single-stage injection stretch blow-moulding. The company says that Blowliner offers an economically attractive alternative for production of 100-500ml bottles and containers at annual quantities to around 50 million units. It can also be used for larger volume containers, of up to 10l, and is claimed to be customisable across a wide range. They can be operated as independent production cells or integrated directly into filling lines. www.mouldandmatic.com Mould & Matic Hall 12 Booth E49-5 Hall 16 Booth D43","@ID":63}, "MATERIAL / RECYCLING 33 PETplanet insider Vol. 14 No. 10/13 petpla.net HOLLAND COLOURSEurope BV | Halvemaanweg 1 | 7323 RW Apeldoorn | P.O. Box 720 7300 AS Apeldoorn | The Netherlands | T +31(0)55 368 07 00 | F +31(0)55 366 29 81 info@hollandcolours.com | www.hollandcolours.com Thousands of colour shades, a variety of product forms and a dedicated team at YOUR SERVICE to assist toYOUR SUCCESS. é Protective colourants with specific light and UV absorbance é Functional colourants for Oxygen Scavengers é High opaque white for dairy é AA Reducer é Tintmask-neutralising off-colour regrind é Blowing Aid é Optical Brighteners é Slip Additives é Matting Agents The IGSU interest group for clean environment IGSU volunteers Rhine riverbank in Basle land free of charge. Each year there is evidence of further growth in the number of operations that take back the PET bottles voluntarily, by an average of more than 2,000. Important voluntary partners also include the local authorities and the municipalities. Ecological benefits Closed-circuit bottling activities are not only climate-friendly but also save energy. A study commissioned by PET","@ID":35}, "NEWS 11 PETplanet insider Vol. 14 No. 10/13 petpla.net More efficient use of platen real estate increases the cavitation for a given machine size: s 72 vs. 48 Cavity with a 38mm finish in a 300T s 96 vs. 72 Cavity with a 28mm finish in a 300T s 128vs. 96 Cavity with a 28mm finish in a 400T + Proprietary iFLOW and iCOOL technology reduces cycle times while improving balance, lowering injection pressure and increasing dimensional repeatability + Tooling solutions to revitalize, recapitalize and rev up existing systems Get 50% more output from the same machine 96-CAVITY MICRO PITCH MOLD FOR 300T MACHINES Visit us at Hall 1 / A39 Contact us today at: mpeteurope@moldmasters.com Garrett replaces Rosenau at PolyOne Specialist polymer materials, services and solutions provider, PolyOne Corporation, has announced the appointment of Michael A. Garratt as Senior Vice President, President of Performance Products and Solutions. Mr. Garratt replaces industry veteran and respected PolyOne leader Robert M. Rosenau, who has decided to retire after a 37-year career. Mr. Garratt joined PolyOne from Marmon Utility, a Berkshire Hathaway company, where he served as president. He was formerly COO of Excel Polymers and previously worked with The Dow Chemical Company and DuPont Dow Elastomers. www.polyone.com Ferromatik Milacron India’s holds an ‘open house’ Ferromatik Milacron India demonstrated its ‘High Performance - New Generation’ injection moulding machine technologies and solutions during an ‘open house’ event at its Vatva, India facility, which ran from September 2 - 4, 2013. The event attracted over 800 visitors from the plastics moulding industry and various suppliers and partners took the opportunity to exhibit a range of solutions demonstrating improvements in cycle time and energy efficiency. On display were a two-component injection moulding machine – the first example of an Indian-built machine of this type; a 32-cavity PET production system, including peripheral equipment and associated conveying solution; an in-mould labelling system for thin wall containers; and a 550 t all-electric injection moulding machine – the largest built in India, to date. During the open house Ferromatik unveiled its new hydraulic injection moulding machines, which range from 100 to 450t. Ferromatik Milacron India is part of US company, Milacron LLC. www.milacronindia.com","@ID":13}, "PETnews 6 PETplanet insider Vol. 14 No. 10/13 petpla.net Petainer buys Sipa XForm Petainer has continued its investment in its Lidköping site with the purchase of a Sipa XForm 500 preform system. The new plant will enable the company to increase its production of preforms made with 50% R-PET material. The UK-based company has operations in Scandinavia, Czech Republic and Russia. Petainer and Sipa said that they are looking to build on their relationship with an ongoing focus on lightweighting, premium PET products and development of advanced solutions in commercial form. Both Petainer and Sipa were present at drinktec; Sipa is also exhibiting its XForm 150-300 at the K-show, Hall 13 B11. www.petainer.com www.sipa.it Americans buy in to Kreyenborg The Nordson Corporation, a mechanical engineering company based in Westlake, Ohio, USA, has acquired two of the five companies of the Kreyenborg Group. Jan-Udo Kreyenborg and Theodor Bruckmann, managing directors, have sold their shares in Kreyenborg GmbH and BKG Bruckmann & Kreyenborg GmbH and retired from the management of the companies. Kreyenborg manufactures screen changers and melt filters; BKG offers special processing technology for production of high-quality plastic pellets. Business managers Jan Hendrik Ostgathe and Ralf Simon will undertake management duties after the change in ownership of the company. Kreyenborg says that realignment with a larger, global partner is necessary for long-term corporate security and to remain competitive. The employment situation of the companies’ staff will remain unchanged. The two companies’ production facilities, at Coermuehle and at Hessenweg, in Muenster, have been leased to Nordson for an initial term of years. Nordson was established in 1954. It has over 5,000 employees and annual turnover of $1.5 billion. www.kreyenborg.de Indorama reports record sales revenues Indorama Ventures Public Company Limited (IVL) has reported total sales revenue of US$ 1.9 billion in Q2 2013, a rise of 9% over the same period last year. Margin gains in Asia have rebounded over the past twelve months, with core EBITDA achieving $144m (Q1 2013: $93m) but still below Q2 2012’s $150m. This was ascribed to lower output at the company’s glycols site in the USA, which was undergoing a planned turnaround. Mr. Aloke Lohia, Group CEO of Indorama Ventures, welcomed the results as encouraging signs that the trough of the last two years is now coming to an end, and that IVL’s differentiation and low-cost strategy is now showing positive returns. Price volatility continues to be high. Paraxylene and MEG feedstock prices dropped by 12% from Q1 to Q2, leading to an inventory loss of $38m. The PTA business is reported to have enjoyed moderate recovery, while margins in the HVA and PET businesses improved significantly. The Company’s North American businesses continues to outperform other regions despite the planned overhaul of its glycols business. German affiliate Trevira achieved its first net profit under IVL’s stewardship in Q2. The second half of 2013 is expected to see continued growth as operational excellence projects kick in and a new state-of-theart polyester fibre facility in Indonesia commences operation in Q4. This is expected to lower costs significantly. The company’s European business is currently undergoing brownfield expansion of PTA capacity in Rotterdam and debottlenecking of its PET plant in Poland. The Board has recommended an interim dividend payment for the first half of 2013 of Baht 0.14 per share or $22million. www.indoramaventures.com New Sales Director for PET Engineering PET Engineering has appointed Matthieu Tribot to the position of Sales Director. He will be responsible for expanding the sales of the company and for the promotion of the new products. PET Engineering has developed in recent years, such as the neck finish conversion service and the upgrading of old blowing machines through the Polaris Project. www.petengineering.com","@ID":8}, "EDITOURS REPORTS 16 PETplanet insider Vol. 14 No. 10/13 petpla.net Macro-economic data of Chile 2011 2012 2013 Population in million: 17.25 17.40 17.56 Population growth: 0.9% p.a. Gross domestic product: (billion USD)1 251.0 268.2 285.7* Growth rate gross domestic product (real) by comparison to previous year: +5.9% +5.5% +4.9%* GDP per capita (USD)1 14,552 15,410 16,273* Import in billion USD1: 74.9 79.3 no data available Exports in billion USD1: 81.4 78.8 no data available National debt: (of gross domestic product) 11.1% 11.9% no data available Unemployment 7.1% 6.5% 6.8%* Inflation rate by comparison to previous year: 3.3% 3.2% 2.8%* (Sources: OECD, Germany Trade & Invest, Federal Bureau of Statistics, IMF, World Bank) *estimate/1current dollar rate Macro-economic data of Argentina 2011 2012 2013 Population in million: 40.57 41.03 41.49 Population growth: 1.1% p.a. Gross domestic product (billion USD)1 444.6 474.8 495.1* Growth rate gross domestic product (real) by comparison to previous year: +8.9% +2.6% +3.1%* GDP per capita in USD1 10,959 11,573 11,932* Import in billion USD1: 73.9 68.5 no data available Exports in billion USD1: 84.0 81.2 no data available National debt: (of gross domestic product) 44.9% 45.2% 42.8%* Unemployment 7.2% 7.2% 7.2%* Inflation rate by comparison to previous year: 9.8% 9.9% 9.7%* (Sources: OECD, Germany Trade & Invest, Federal Bureau of Statistics, IMF, World Bank) *estimate/1current dollar rate","@ID":18}, "BOTTLE MAKING 47 PETplanet insider Vol. 14 No. 10/13 petpla.net modules for the respective make or type of stretch blow moulding machine and are combined to create a complete mould. The following discussion will thus be limited to the bottle-specific parts of a blow mould. Although the data on the bottle geometry will be used as a basis for the design of the mould in the CAD system, other aspects must also be considered. For example, a blow mould will usually comprise two cavity halves (which map the area below the bottle neck down to just above the base) plus the related base mould or insert. The first thing that must be decided is the position of the mould parting lines. In the case of a rotationally symmetrical design, the position of the vertical mould parting line in the body of the container is not a critical issue. But for design elements such as logos, recessed handles, etc., the position of the parting line must be agreed in detail with the customer. There may also be technical reasons that require a certain position of the mould parting line, e.g., if the number of venting bores is to be reduced or if such bores are to be fully avoided. To a certain extent, an appropriate positioning of the mould parting line may also be used to accommodate inevitable undercuts. Also the position of the parting line between the bottle body and the base must be carefully selected, which again is not only a matter of styling but also of engineering. For example, the height of the base and/ or the tapering between the feet of a petaloid base will clearly have an impact on the properties of the base of the bottle. Finally, the maximum bottom stroke of the blow moulding machine must be taken into account when determining the position of this parting line. Even if the spacer for the base mould is a relatively simple component, it must still be constructed specifically for each new container depending on the bottle height. One of the key aspects that should be considered when designing a blow mould based on the geometrical data of the bottle is shrinkage. Like all thermoplastics, PET will shrink when it cools down, so the cavity must be designed with an appropriate allowPlease order your copy at the PETplanet insider book shop: https://petpla.net/books Bottles, Preforms and Closures A Design Guide for PET Packaging Second Edition by Ottmar Brandau 115,00 € 180 pages © Copyright Elsevier 2012 ance. The actual shrinkage, which can amount to several millimetres in height and diameter, depends not only on the material and the geometry of the preform but also on the mould concept, the bottle size, the design elements, etc. These shrinkage factors are experimental values and part of the skill of the mould maker and ideally should be stored in digital form in an expert system. Also the design of the neck cooling must be taken into account for the mould design. In this respect, a difference is made between active neck cooling, with cooling bores in the neck plate, and passive neck cooling. For both passive and active neck cooling, a neck plate made of steel is used. For lower mould temperatures, passive cooling by a neck plate without cooling bores will be sufficient. If temperatures become higher, active cooling may become necessary. Here, the neck plate is cooled with water to keep the zone immediately below the neck ring as cool as possible. Other items that should be incorporated in the design of the mould cavity may include logos, the cavity number for quality control, country-specific PET recycling logos, etc., which are usually integrated in the bottom area of the bottle. Mould making With integrated CAD/CAM, the mould design data can be used to generate a full set of instructions for an NC milling machine for the production of the bottle-specific parts of the mould. In this respect, it will be necessary to decide whether design elements such as logos, textures, etc. permit milling the entire contour or whether certain parts may have to be produced by laser engraving or etching. State ofthe-art manufacturing methods and appropriate CAM systems today make it possible to create most textures and logos by milling. This eliminates the need for additional processes that would increase not only the costs but also the time needed to produce the mould. Ultimately, the mould maker will also consider his or her own capabilities, such as the available equipment, when making the decision. After the cavities have been produced by milling and/or other appropriate techniques, they are cleaned and finally polished, which can be done manually or by machine. Even today, most mould makers polish their moulds by hand because it is generally the less costly method. Machine polishing is expensive because for each individual bottle design a separate polishing body made of polycarbonate or a similar plastic must be produced. On the other hand, machine polishing will yield a higher surface quality, is a repeatable and dependable process, and is faster. Hence, for larger mould makers, where ancillary wage costs may be higher, an investment in a polishing machine would be attractive once annual production reaches about 2,000 – 3,000 moulds. After polishing, the complete mould is assembled and then fitted to the blow moulding machine for mould trials (see part 7). *This article was published in Bottles, Preforms and Closures, Ottmar Brandau, Chapter 1.6/1.7., Copyright Elsevier 2012","@ID":49}, "39 PETplanet insider Vol. 14 No. 10/13 petpla.net Caps and closures Bottle-to-bottle recycling plants Preform and single stage machinery Preforms Preform / Stretch blow moulds Two-stage SBM machinery Filling equipment Resins / Additives Compressors Closure systems PET bottle resins / colours and functional additives To complement the big plastics event of this year, K 2013, we are presenting the suppliers of PET bottle resins and the suppliers of colours/ functional additives in our market survey. The additives available include barrier improvement additives for sensitive beverages, UV blocker, brighteners and many other performance enhancers. Also included among the resin manufacturers, in alphabetical order, are: DAK Americas, Indorama, M & G, Neo Group and NovaPET In the additives range, there are nine global players among the suppliers: (in alphabetical order) Americhem, BASF, Clariant, Colormatrix, GabrielChemie, Holland Colors, NovaPET, Repi and Valspar. The suppliers are listed in the order in which their details were received by the editors. Although the publishers have made every effort to ensure that the information in this survey is up to date, no claims are made regarding completeness or accuracy. 10/2013 MARKETsurvey","@ID":41}, "EDITOUR REPORTS 29 PETplanet insider Vol. 14 No. 10/13 proportion of bought-in ones from all three Coca-Cola Femsa plants. In the meantime, there are also eight Reciclar employees working round the clock in these plants. As the years passed the requirement for increased quality grew and this resulted, in 2002/2003, in a technical upgrade with the purchase of three sorting plants from NRT, USA and later two Titech lines. Sorting equipment as well as cleaning process phases were incorporated and Reciclar has recently purchased a brand new Erema Vacurema Basic. This move means that Reciclar will, for the first time, be embarking on the production of 100% recycled PET granulate. A total of around half of the flakes remains in the home market whilst the other half goes for export. In the past this included customers such as Chile, Brazil, USA, Spain and Belgium, but the problem at the moment as far as export is concerned is the stagnating international price by comparison to the rising costs in Argentina. “Export“, says Auspitz, “is currently a loss-making operation in Argentina, but for us a necessary evil“. The problem is the limited size of the domestic market. In order to sell the quantities produced it is virtually essential to export. Nevertheless, in response to these unwelcome conditions, Reciclar have now also begun to cut back on production. Auspitz suspects that there is potential for the steady expansion of the internal market as part of the customer base and Reciclar is also anxious to work towards this. Of the projected figure of approx. 24,000t - 25,000t PET bottles per year, some 20% of material is lost in processing. The remaining 20,000t of flakes are cleaned, sorted and packed in bulk containers. The main customers in Argentina include Bandex, Treviplast and Paulini S.A., all operating in the PET packaging sector but with the exception of bottles, as Reciclar’s flakes are not authorised for use in bottle manufacture. Here their biggest competitor is Cabelma, a company that is going a step further and hence ranks alongside the classic bottle-to-bottle recyclers. Cabelma’s products are sold by this company, some back to Coca-Cola. Reciclar‘s long-term goal is the sustained improvement of quality and the associated new investments in technology aimed at further promoting the topic of recycling. www.reciclarsa.com","@ID":31}, "EDITOURS REPORTS 14 PETplanet insider Vol. 14 No. 10/13 petpla.net bright side, and her words lift my spirits. We need to look ahead, no point in moping. With no Editourmobil, we have to make alternative arrangements for our first appointment next day with CSD bottlers Embosur in Concepcion. The only option is to take the plane. Embosur bottles, amongst other things, one of the best known beverages in the country, the celebrated “Primeros” which they supply to some of the major discount chains. After an enlightening discussion, we have to rush off to the airport to catch our flight. The election of the new pope is underway and Chiraz and I watch with interest the live broadcast of the event. Our programme for the next few days is to fly to Buenos Aires, leaving the Editourmobil with Iveco in Santiago. Picking up the rest of our luggage from the vehicle, we head off to the airport. Shortly before midnight we arrive at our hotel in Buenos Aires. It is Saturday, the weekend it might be, but there is no rest for the wicked. We still have a lot of work to do. Our first impression of the city is Wow! this is really great! But we are already thinking of the week ahead: some interesting appointments in the offing. The first few days in the city simply fly by. Heidelberg’s meticulous original planning goes by the board, we need to start again from scratch. We can do the first appointments by taxi, and in the meantime, HQ will email me the revised programme. Refres Now, bottler of one of this country’s most famous brands “Manaus”, will be followed by Bericap, then PET recyclers Reciclar and finally Andina Empaques, the big Coca -Cola bottle- and preform manufacturer. Meanwhile no news on the Iveco/Editourmobil front. Let’s turn instead to Refres Now. The major bottler of the “Manaos” own brand happily combines, on its eight bottling lines, a total daily production of around 3m litres with Coca -Cola and Pepsi. We then move on to Bericap, based in Pilar, whose annual production totals some 1.3 billion closures. Today, Friday, our first appointment is with the PET recyclers Reciclar. We learn how around 25 tons of PET bottles are collected from the streets here, cleaned, sorted and recycled into flakes. by Kay Barton between the official exchange rate and real value, something which, in combination with the Mexico crisis of 1995, led to a fall in GDP of 4.6% while the unemployment rate rose to more than 18%. Corruption and the massive flight of capital to safer havens abroad exacerbated what was, to put it mildly, a chaotic situation. In 2001, the state declared bankruptcy. It was only the lifting of the currency peg in 2002 under the 17-months‘ presidency of Eduardo Duhalde and in the wake of stabilisation programmes on the part of the IMF that put Argentina, economically speaking, back on course during 2003. Nevertheless, imports have to be officially approved due to the shortage of foreign exchange. Under the presidency of Néstor Kirchner between 2003 and 2007 the economic state of deregulation was terminated and the debt management policy revised, although his methods aroused much controversy. The result was astonishing growth rates of around 8%. This course of action has been continued by Kirchner’s successor, his wife Cristina Férnandez de Kirchner. Since 2010 inflation has, officially, been of the order of 10%, but experts suspect that the real rate borders on 25%. In addition to this there are high export tariffs that constitute an additional burden hampering foreign trade. The lion’s share of Argentine industry is today accounted for by the service sector. Agriculture, stock breeding and mining are also assuming important economic positions alongside the processing industries. Agricultural products account for a proportion of around 34% of exports, whilst the level of industrial products is about 36%. Some of the most important industrial products are plastic products, machinery, automotive parts and steel. In addition, Argentina is one of Latin America’s largest steel producers. Their main trading partners when it comes to export are the Latin American member states of Mercosur (27%), followed by the EU (17%). The geography of Argentina is similar to Chile in its diversity, and is matched by hardly any other country in South America. With a total area of 2.78 million km2, Argentina is the eighth largest country in the world. Northsouth, it stretches for a distance of 3,694km, whilst from west to east it covers a distance of 1,423km. In the north the country borders Bolivia and Paraguay, in the north-east Brazil and Uruguay, to the east and south lies the Atlantic and in the west is Chile. The topography is as breathtaking and spectacular as Chile’s. With the high Andes to the west and the dry savannahs of Gran Chaco to the north, as well as the highlands in the interior of the country, the Sierras Pampeanas rising to heights of up to 6,250m and the Argentinian part of Patagonia in the south, the climate covers the whole spectrum from subtropical to sub-polar with everything in-between. The overall population currently stands at around 41.5 million, approximately, 12.8 million of whom live in the conurbation around the capital city of Buenos Aires plus the hinterland in the east of the country. The infrastructure situation is as varied as that of Chile. The congested urban areas are well served by rail, road and air, whilst other areas rely on coach and bus transport. For goods transport, gravel tracks and asphalted overland roads run side by side with well-constructed, dual","@ID":16}, "MATERIAL / RECYCLING 31 PETplanet insider Vol. 14 No. 10/13 petpla.net Measurement of PET quantities / quotas in 2012: Sales of PET bottles:100% (i.e. 46,341t and 1.5 billion bottles in circulation) Collection quota: 102% incl. misses, waste Recycling quota: 89% (Sorted PET excl. foreign substances) Utilization quota: 81% (Pure PET excl. lids, labels etc. i.e. 37,571t) Since 2009 the figures registered have been at approximately the same high level. 81% of the PET bottles filled and sold in Switzerland are in a closed circuit bottle arrangement. A total of over 90% of all PET bottles remain in Switzerland. The final output after collecting, compressing, sorting and repeat compressing into bales: Quality A (transparent): 43% (for bottles) Quality B (light blue): 17% (for bottles) Quality C (green/multi-coloured): 34% (for straps) Quality I (brown): 6% (for textiles) The qualities A and B undergo direct processing (without any further sorting by the recycler) to produce recyclate suitable for direct food contacs. The quality of the PET sorted is correspondingly high (99.8%). The associaton PET-Recycling Switzerland (PRS) At the heart of the Swiss recycling system is the association known as PET Recycling Switzerland (PRS), initially established in 1990 by the bottling firms, companies such as Coca Cola, Evian and Nestlé, who were directly affected by the new regulation relating to beverages packaging. PRS meets the obligation incumbent on the bottlers in relation to PET bottles which is enshrined in law, and acts on their behalf. The association PRS (PET-Recycling Switzerland) was established as a non-profit-making organisation. PRS is concerned with collecting PET beverage bottles. Virtually all Swiss beverage producers, importers, bottlers and the trade belong to the sector association. Today the Association makes a disposal network for PET bottles available for Switzerland as a whole. What this boils down to is a sector solution on a voluntary basis. The association formulates the challenging objectives and defines the standards. The members of the Association basically commit themselves to a voluntary solution geared to a market economy. This means that they are opposed to any state control on deposits or pre-levied disposal charges. According to PRS, the fact that measures can be adopted voluntarily creates enhanced incentives to build up an efficient recycling system. It is important that ecology and economics go hand in hand. Under no circumstances must they be allowed to be at odds with one another. The association embarked on its mission with a total of 19 members. At that time (1991) a total of 548t of PET was being collected. Quota for collection was 13%. In the second year (1992) a total of 3,300t was already being collected (quota 53%). In 1996 – with 14,448t of PET collected, the statutory quota specified for collection was exceeded for the first time. At PRS Switzerland there are 17 members of staff deployed in the office to organise, control and monitor activities. Approximately over 40 external companies are responsible for transport and sorting. First President is Eduard Suter, Acting Managing Director is René Herzog, with Jean-Claude Würmli (Deputy Managing Director). René Herzog puts the tasks of the PRS in a nutshell: “We organise the necessary logistics between all the people, companies and organisers involved in value creation. And we try to create public awareness about recycling. We were soon in receipt of the Marketing Award - in 1992. As regards the Logistic Award, we received this year (2013) and we are particularly pleased and satisfied about it“. ... at the golf course ... on site ... in front of the World Trade Center ... at the airport","@ID":33}, "MATERIAL / RECYCLING 30 PETplanet insider Vol. 14 No. 10/13 petpla.net PET Recycling - Why does it work well in Switzerland? by Wolfgang von Schroeter Discipline plays an important part in evaluating these high rates of recycling and this is basically to be attributed to the Swiss population, as well as the compact nature of Switzerland’s geographic features, the short routes and the comparably low quantities of PET that are moved about. Nevertheless, the model character of Swiss recycling is undisputed. It is always worth taking a look at the Swiss situation, at people and methods, logistics and organisation and, last but not least, at their marketing approach which is necessary to establish the concept of recycling in the mind of the consumer. In order to find this out we, that is, PETplanet Insider, travelled to Switzerland to find out, why PET recycling in Switzerland works so well. René Herzog, Managing Director of PET Recycling Swiss, is in no doubt: “The legislator – the Federal Office for the Environment – specifies the requirements. We, that is, the bottlers, the dealers, the recyclers as well as the consumers and PET-Recycling Switzerland (PRS) in their capacity as the organiser and motivator, we have committed ourselves to meet the legal requirements with a system that sets about establishing an interrelationship between all those involved in the process at a logistical level. We are all accountable at a mutual, joint and voluntary level, when it comes to achieving the target“. Caspar van Dungen, Managing Director of ITW Poly Recycling GmbH, as well as a member of numerous European recycling committees, adds approvingly: “Fairness is a precondition for the operation of the system. The Swiss perception of accountability is of something that is voluntary, fair and sincere“. The recycling (not recovery) quota that has been identified by the Confederate Department for the Environment, Traffic, Energy and Communication (UVEK) is 75%. 75% of PET bottles filled and sold must be recycled for new material usage. Should the recycling quota not be achieved, UVEK has the option of introducing a deposit on PET beverages packaging. Within 20 years of being set up, the amount of PET recycled in Switzerland has achieved 81% and thus exceeded the legal quota – a very good result indeed by international standards. Swiss ways of PET collection... ... on the beach ... at the supermarket ... at the museum","@ID":32}, "EDITOUR REPORTS 27 Finally the companies agreed to work towards establishing a Joint Venture in Argentina. Bericap imported the equipment to produce plastic closures for beverages. The bureaucracy and paperwork involved in importing and exporting is, according to Bericap Argentina, a horrendous and cumbersome headache. So much so that importing the plant into Argentina cost Bericap the loss of a good year’s production. “This delay cost us a substantial amount of money and we needed a fair amount of patience” says Günter Krautkrämer. Since then, the two Bericap lines, complete with integrated Netstal injection machines, have been installed with the help of Bericap technicians at Pilar and they are producing the 2.4g closure for the PCO 1881 neck finish in the CSD sector as well as the 1.8g still water closure for the PCO 3025 neck finish. Capacity here, amounting to around 700 million units per year, is to be expanded. On the remaining equipment, which dates back to the days of the crown corks factory, there are 1 billion 2.85g closures for the PCO 1810 and the 1816 neck finish and a fliptop cleaning agent cap for Procter & Gamble coming off the line in addition to the Bericap closures. Permanent technical support is given by Bericap do Brasil located at Sorocaba SP. Being used here in the areas of compression and slitting are machines from Nissei ASB, Ferromatik Milachron and Sacmi. The moulds come from Husky and Marlan, as well as from Bekomold, a subsidiary of Bericap in the two new lines. In the copolymer-PP sector the company Prepare for Life! Visit our booth 11/A58 at the K-Show and see our brand new preform inspection system PreWatcher III sources 70-80% from Braskem Brazil. The requirement for organoleptic HDP is met by Ineos. It is the intention of both joint venture partners to set up a totally separate stand-alone plant for closures in a couple of years. www.bericap.com March 22, 2013 Reciclar S.A. We met: Mr Erwin Auspitz, Commercial Director Added value for PET street refuse The story of the PET recycling company, Reciclar S.A. Buenos Aires, begins (as interview partner Mr Erwin Auspitz, responsible Commercial Director, explains), with its establishment by the Italian Marcelino Casella. These two gentlemen have been friends for more than 50 years. Around 1960 Marcelino embarked on an incarnation as a dealer in the glass bottles sector, such as, for example, wine and champagne bottles which he used to buy in and sell on. After around 30 years of operation, Marcelino had advanced to become one of the most important dealers in this sector. As time went on, however, the competition became fiercer and there were more and more glass bottle","@ID":29}, "BOTTLE MAKING 54 PETplanet insider Vol. 14 No. 10/13 petpla.net Plasmax technology PET bottles coated with SiOx applied by the InnoPET Plasmax 12D prevent the permeation of gases such as oxygen into the beverages and the loss of carbon dioxide from the products. The SiO x barrier is 100% transparent, which means the PET containers retain their transparent appearance. The coated PET bottles can be fully recycled, just like ordinary segregated PET in b-to-b processes. KHS Plasmax offers two machine types with the technology for bottle between 100ml and 1,500ml in size: InnoPET Plasmax 12D and InnoPET Plasmax 20Q. Current machines from the InnoPET Plasmax range can be retrofitted for the new Plasmax+ process. With these two machine sizes, KHS Plasmax covers the capacity range between 10,000 and 40,000bph. The InnoPET Plasmax 12D is equipped with twelve double coating stations and can coat up to 12,000bph; the InnoPET 20Q has 20 quadruple stations. It is designed for larger product lines and can process up to 40,000bph. The Plasmax technology with the FreshSafe-PET logo from KHS Plasmax, in 2012 was awarded the Italian packaging Oscar. Plasmax+ extends the range of applications form of the FreshSafe-PET solution with advantages such as higher quality and vitamin protection, longer shelf life, fresher taste and 100% recyclability. The study confirmed the very high acceptance of the PET barrier technology with the FreshSafe-PET logo. According to Bernd Kempa, CEO KHS Plasmax GmbH, it emerged from the study that 76% of all those interviewed would purchase drinks in FreshSafe PET bottles immediately on the basis of the specified advantages, even if it meant paying slightly more. “Our PET bottles with the glass barrier coating may cost a bit more than the non-coated PET bottles but they are still cheaper than other barrier solutions on the market. I am firmly convinced that we are poised to revolutionise the market for premium beverages with FreshSafe PET“. Plasmax+ The newly developed Plasmax+ process extends the range of applications for sensitive beverages (Fig.1). Areas of application are sensitive beverages (juices, soft drinks, hot drinks, tea, coffee, sauces, fruits, including beverages with a pH greater than 4.5). Special feature of the Plasmax+ technology is an additional topcoating. This is applied to the inside walls of the bottles after the silicon oxide coating applied in the Plasmax process. As a result, the product protection for beverages with a pH greater than 4.5 lasting for many months; KHS claims up to four times longer freshness versus the simple silicon oxide coating. In terms of costs KHS Plasmax claims a distinct advantage compared to other barrier solutions, such as multi-layer PET bottles. In the lower capacity range the cost per PET bottle is around 1.5 euro cents, falling to around 0.8 euro cents for lines with higher capacities. In the lower capacity range the cost per PET bottle is around 1.5 Euro Cents, falling to around 0.8 Euro Cents for lines with higher capacities. www.freshsafepet.khs.com www.khsplasmax.de www.khs.com InnoPET Plasmax: Break-down of coating costs - TCO","@ID":56}, "BOTTLE MAKING 43 PETplanet insider Vol. 14 No. 10/13 petpla.net Appe offers pasteurisable PET jar Hot enough Packaging solutions specialist Appe has launched a PET jar capable of hot-fill and/or pasteurisation. The ThermaLite jar is the result of the company’s previously-announced strategic partnership with Nissei ASB GmbH (Europe) This wide-mouthed jar can be hot-filled at temperatures up to 95°C. It can then be pasteurised for up to 20min. Previous technologies allowed PET to be filled at a maximum of 85°C and would not tolerate pasteurisation. Appe says the jar is up to 85% lighter than glass equivalents with a smaller footprint, delivering huge savings in transport costs both before and after filling. It also uses less energy during the filling process, as well as reducing noise levels and avoiding the risk of breakages on the line. The jar is currently available in six sizes from 370ml to 720ml in round and octagonal designs, with further shapes and sizes in development. The lightweight shatterproof construction offers safety throughout the supply chain. In the home, it provides easy handling and pouring for the consumer. It has a standard metal twist-off closure ensuring easy opening and closing. The jar is also fully recyclable. On-shelf impact In retail markets, the clarity of the PET creates excellent on-shelf impact for a wide range of products including cooking sauces, pesto, tomato-based products, pickled vegetables, relishes, chutneys, and fruit purées, jams and spreads. Equally important, thanks to the jar’s smaller footprint compared to glass, more units can be incorporated into the same shelf space, while its shatter-resistance offers new opportunities for product placement, for example inside the chill cabinets. The ThermaLite jar was named as one of Spain’s top 100 ideas by Actualidad Económica magazine. www.appe.com","@ID":45}, "PETbottles 70 PETplanet insider Vol. 14 No. 10/13 petpla.net Home + Personal Care Mouthwash with a waist Unilever is selling 500ml of alcohol-free mouthwash on the French market in a transparent bottle made from PET. The bottle, which is slightly curved to give a waisted effect, is decorated on both sides with No-Label-Look labels. On the back there is an arc-shaped recess which makes it easier to grasp and hold the bottle securely. The opaque screw closure serves as a measuring cup and is protected from tampering by means of an adhesive sticker. www.missionsignal.fr Concentrate capsules for all-purpose cleaner In the summer of 2013 SC Johnson GmbH launched a range of products on the German market under the brand name of “Mr. Muscle“. These included a concentrated allpurpose cleaner in a package made from water soluble foil. The method of application is simple – place a small capsule in 4l of hot water, wait 2min and the cleaning operation can begin. The capsules are supplied in packs of twelve, each including 4ml of concentrate, in a transparent, easy to handle PET container with a snap-on hinged lid. Before the lid can be opened, a closure segment must first be removed and then two tabs located opposite each other squeezed together. www.mrmuscle.de www.mas-aust r ia.com The MAS conical co-rotator for brilliant colours and highest quality","@ID":72}, "EDITOUR REPORTS 12 PETplanet insider Vol. 14 No. 10/13 petpla.net Get in touch with... economy & infrastructure As part of our Go With The Flow Tour through South America we visited the markets of Chile and Argentina. Our report starts with Chile. If we take the Latin American market as a whole, it is safe to state that Chile is undoubtedly one of the leading economies of the continent. Chile boasts the largest deposits of copper in the world, producing 27% of world requirements+ ; copper accounts for 20% of the country’s GDP and for 60% of its exports. Taking the per capita income in USD as a base, Chile is the richest country in South America. Chile is also a major exporting nation and its export quota is comparable with that of Germany. Between the end of the 1980s and the 1990s it achieved above-average high growth rates. The consistent upward trend, however, finally collapsed into recession in 1997/1998, intensified by the crises in Asia and Brazil. By 1999, copper prices had begun to increase again, and by 2000, the economy was once more on a stable footing. Copper, though dominant, is not Chile’s only resource: fruit, salmon, wine, wood, paper and methanol make up a substantial proportion of the country’s exports. The country has other noteworthy advantages. According to studies carried out by Transparency International, Chile is now largely free of corruption and, in 2005, according to the International Finance Corporation, it came first in the most enterprise-friendly countries in South America. Together with the USA, the European Union is an important trading partner of Chile. In 2012 State President Sebastián Pinera proclaimed 2013 to be the “year of innovation”. Experts are forecasting high levels of investment in high-tech products as a result of this initiative. In the machinery and plant segment in particular, Chile is looking to take advantage of the know-how of foreign suppliers. Geographically, Chile is one of the most fascinating countries in the world. It is a strip of land, 4,275kms long traversing 39 degrees of latitude, with an average width of some 180 km, which snakes its way along the west coast of the Pacific. With the Pacific ocean to the west and the Andes (which can rise to an altitude of just under 7,000m) to the east, Chile enjoys a diverse climate, from the arid wastes of the Atacama desert in the north west to the bitter cold of Patagonia in the south, a region still known as “the ends of the earth”. With temperatures varying by as much as 50°C, it is no surprise that machinery manufacturers face challenging times in supplying machinery to the materials producing sector. Chile shares its northern border with Peru, and in the north east with Argentina. The Atlantic lies to the south east. The infrastructure, and in particular the poor road network , presents a serious challenge as far as the transport of goods is concerned. Of the 80,000km of roads in the country, only a mere 20% is metalled. To alleviate the situation, work began in 1976 to construct a highway, known as the Carretera Austral 1976, to link Puerto Montt, in the north of the country, with Villa O’Higgins in the sparsely populated southern region. The final 100km of the total 1,240km of the highway, was finally completed in 2000. Access to the south is still difficult, involving a number of ferries, which operate only during two months of the year. The most practical way to the south is via Argentina. Generally, sea and air are the preferred options for transporting goods and materials, as we heard time and time again during our discussions with Chilean companies. Unsurprisingly our contacts were quick to point out Lima Santiago La Paz Buenos Aires Montevideo Progresso São José dos Pinhais São Paulo Rio de Janeiro Lindóia Santa Cruz Sucre Quilmes Pilar Jaú Concepción Santa Fe Barueri Jundiai Sorocaba Amparoa Limeira Chile and Argentina by Kay Barton (formerly Krüger)","@ID":14}, "EDITOUR REPORTS 13 PETplanet insider Vol. 14 No. 10/13 petpla.net We have arrived in Santiago. By “we”, I mean Team 2, consisting of my colleague Chiraz and me, Kay, and we are here to take over the Editourmobil from our colleagues in Team 1, Alex and Rolf. Immediately after the handover, our first task is to get to the Iveco workshop. The Editourmobil has suffered grievously on its journey over the Andes, and the engine is constantly stuttering and spluttering. Two of the Iveco mechanics take it on a test drive to see what’s wrong. They, and we, are in for a shock. Without warning, the vehicle stops on the motorway exit. The Editourmobil is as dead as a dodo, end of story. There’s nothing for it but to leave the vehicle to Iveco’s tender mercies, and make our way by taxi into the city, taking as much luggage as we can manage. Fortunately, Chiraz has a German friend in Santiago, and with her help, we locate a pleasant hotel where we spend the night. As an additional bonus, the hotel has a decent wifi so I am at least able to get a bit of work done. Next day, the first job is to get hold of Chilean SIM cards. Ominously, there is no news about the vehicle so it is a matter of waiting, and getting in touch with HQ in Heidelberg to establish some sort of Plan B for our upcoming appointments. Then comes the news from Iveco that we had been dreading: the Editourmobil’s transmission is completely knackered. No spare parts. Repair likely to take weeks. I feel sick to my stomach. Chiraz urges me to look on the Hall 9, stand 09A44 | 09A48 www.kreyenborg-bkg.com Screen changers. Melt pumps. Polymer valves. Underwater pelletizing systems. Centrifugal dryers. the heavy additional costs incurred by these two relatively expensive modes of transport which tend to be disproportionately high by comparison to the rest of South America, even in Patagonia itself. Something like half the 17.5 million Chileans live within the conurbation zone encompassed by the capital, the greater Santiago de Chile area, which itself accounts for around 6 million inhabitants. Away from Santiago and both to the north and south, settlements tend to be few and far between. Turning to Argentina, we once again find a similar pattern of economic highs and lows that have marked the country, the second largest in Latin America after Brazil. The industrialisation of Argentina back in the 50s stripped away large parts of what had, up to that time, been a predominantly agricultural economy. One significant change was the focus on the domestic market, so that the country, so to speak, was isolated from the outside world, with an economy that only looked inward. The country has a wealth of natural resources at its disposal along with deposits of oil and natural gas which are used in industrial applications. Different governments operated a strictly state-controlled economy right up to the beginning of deregulation and privatisation which began in the second half of the 70s. A military dictatorship and a huge rise in the national debt in 1976 resulted in multiple devaluations of the peso and led, after the reinstatement of democracy in 1983, to a period of hyperinflation, which President Carlos Menem halted in 1991 by putting the currency at parity with the US dollar and thus making Argentina attractive to foreign investors once again. The result was an average growth of 5% between 1991 and 1996. However, the long term consequence of linking the peso and the UD dollar was to make Argentinian exports more expensive on the world market, whilst foreign imports became cheaper. This resulted in many manufacturing plants throughout the country putting up the shutters. Consequently there was an increase in the imbalance","@ID":15}, "Variability costs you money. For the highest volume applications like preforms and closures, the injection molding equipment you invest in will make a big contribution to your bottom line. Investing in a complete Husky system ensures tighter process control, reduced resin consumption, lower scrap rates and increased production predictability—allowing you to consistently produce and ship higher quality parts. When compared to competitors, Husky preform systems are capable of delivering the highest rate of return, making them one of the best investments to grow your business. Husky helps you reduce variability in your injection molding process, so you can focus on what matters most—satisfied customers and a healthy bottom line. Working with Husky to reduce variability improves your bottom line variability Visit www.husky.ca/preform-solutions to learn more about the benefits of Husky’s complete PET preform systems. www.husky.ca/world-tour Husky World Tour 2013","@ID":2}, "MARKET SURVEY 40 PETplanet insider Vol. 14 No. 10/13 petpla.net Resins Additives 10/2013 MARKETsurvey Company name ColorMatrix BASF Color Solutions Germany GmbH Americhem Europe Ltd Holland Colours Europe BV. Gabriel-Chemie Gesellschaft m.b.H. Postal address Telephone number Web site address Contact name Function Direct telephone number Fax E-Mail Unity Grove, Knowsley Business Park, L34 9GT, UK + 44 151 6328800 www.colormatrix.com Claudia Finamore EMEAMarketing Manager +44 151 6328800 claudia.finamore@colormatrix.com Clevischer Ring 180, 51063 Köln, Germany +49 221 96498-0 www.basf.com/masterbatch Cawdor Street, Eccles M30 0QF Manchester, UK +44 161 789 7832 www.americhem.com Customer Service +44 161 789 7832 +44 161 787 7832 csseu@americhem.com 7323 RWApeldoorn, P.O.Box. 720, 7300 AS Apeldoorn, The Netherlands +31 55 368 0700 www.hollandcolours.com Wilfried Grob Sales&Marketing Director +31 55 368 0700 +31 55 366 2981 info@hollandcolours.com Industriestrasse 1, 2352 Gumpoldskirchen, Austria +43 2252 636 30-0 www.gabriel-chemie.com Ing. Manuel Hakel Key Account Manager Caps & Closures +43 2252 636 30-1641 +43 2252 627 25-1641 m.hakel@gabriel-chemie.com Additives and Colours for PET Liquid colours Yes No Yes No Microgranule colours Yes Yes Yes Masterbatch colours all colours possible, tailor-made Yes No Yes UV protection additive (solid) Yes Yes Yes UV protection additive (liquid) Yes No Yes No AA reduction (solid) No Yes (Specific markets) Yes AA reduction (liquid) Yes No No No Oxygen scavenger (solid) Yes Yes No Yes Oxygen scavenger (liquid) No No No Other PET additives in liquid or solid form Yes Solid: slip-, reheat-, RPETadditives High opaque white for light protection (solid), frost additive (solid), slip agent (solid), oxygen barrier neutral colorant, tintmask for recycled PET Yes Company name Neo Group Indorama Ventures Ltd Postal address Telephone number Web site address Contact name Function Direct telephone number Fax E-Mail Industrijos str. 2, Rimkai LT-95346, Klaipeda district ,Lithuania + 37046466710 www.neogroup.eu Gediminas Paulauskas Sales Manager +370 686 73401 +370 46466711 gediminas.paulauskas@neogroup.eu 75/102 Ocean Tower 2, 37th Floor Bangkok 10110, Thailand +662 661 6661 www.indoramaventures.com W.G. Hoenderdaal Technical Marketing and Development Manager +316 51809942 wim.hoenderdaal@nl.indorama.net RESINS Europe USA 1. Brand name of the resins NeoPET RamaPET Preformance PET Polyclear PET 2. IV Range a. of Homo-Polymers 0.56 - 0.64 0.71 - 0.95 0.58 - 0.95 b. of Co-Polymers 0.76 - 0.84 0.70 - 0.84 0.58 - 0.84 3. Speciality resins CSD NeoPET 80, NeoPET 82 R1, R182, R180 ES11, ES11 (A)-R10, 1101 Water Aqua NeoPET 76, NeoPET 78 N1, N1(S), N2, N180, W170 N2R, N2R (A)-R10, N2R-Ti, 3301 Beer NeoPET 80, NeoPET 82 N1, N1(S), N180 1708CC, 3302 Wine / Liquors NeoPET 80, NeoPET 82 N1, N1(S), N180 1708CC, 3302 Personal care /Pharmaceuticals NeoPET 80 N1, N1(S), N180 1708CC, 3302 Slow crystallisation P184 T-94, T-94-Ti Hotfill R1, HF 1708HS, 2201 Pre-coloured Fast reheat NeoPET 82 FR, NeoPET 84 FR R1, R182, R180 ES11, 1101 Other Ultra NeoPET R182 PlantPET, high IPAmodified resins 1110 (10% PCR) 4. Increased barrier properties Oxyclear barrier resin 5. PEN mixes available Yes 6. Recycled blends available Flake to Resin PET ES11 (A)-R10 7. Special comments Polyclear EBM PET for extrusion blow moulded containers Low IV and functionalized PET and copolyester polymers","@ID":42}, "BOTTLE MAKING 46 PETplanet insider Vol. 14 No. 10/13 petpla.net Bottles, preforms and closures, part 6* Moulds: Concepts, design and manufacture Depending on customer-specific criteria, such as the filling method (hot fill, aseptic, etc.), the general size of the customer’s bottles, the market positioning of the customer or the new bottle, the frequency of product changeovers, etc., there are different mould concepts that can be adopted. Some of the more common mould concepts are described below. After the bottle geometry and the mould concept have been determined, the focus shifts to the mould. *Ottmar Brandau’s “Bottles, Preforms and Closures” was first published by hbmedia. A newly revised version is reissued under the Elsevier imprint. PETplanet insider is publishing extracts from successive chapters. Shell moulds The most universal concept is the shell mould. With bottle capacities from 0.1l to about 2l, this type of mould is suitable for a very wide range of sizes. It comprises a mould housing that also incorporates the cooling channels, into which a shell, with the cavity itself, and the base mould are inserted using appropriate spacers as required by the bottle height. The base mould is cooled separately. These bottle-specific parts can be exchanged very quickly. Usually only a few screws have to be released to remove a shell. Hot-fill moulds Although shell, full-body, and small-cavity moulds are usually made of aluminium, hot-fill moulds are made principally of steel. The reasons are to be seen in the thermal elongation of the mould material and the problem of adhesion. Moulds for hot-fill bottles are heated to higher process temperatures (120–140°C) in the body area to permit a certain relaxation and so partly eliminate the internal tensions set up in the bottle during the stretching process. The neck area is always held at 20°C or lower to avoid deformation of the precision injectionmoulded preform neck finish, whereas the base mould temperature is around 60–80°C. This relaxation in the blow mould at inflation pressure prevents a subsequent relaxation, i.e., shrinking, when the bottle is in contact with the hot-fill contents, which sometimes have a temperature of up to 95°C. The higher mould temperatures result in a higher thermal load and thus a more pronounced elongation of the mould. Additionally, the PET material has a tendency to stick to aluminium at such high temperatures. As an alternative to steel, an aluminium mould with an anti-stick coating could be used but this would not solve the problem of thermal elongation. As a rule, hot-fill bottles have the so-called vacuum panels that, through controlled deformation, compensate for the partial vacuum that results from the cooling of the contents. Instead of such clearly visible panels, design elements such as grip areas have been developed that perform the same function but are not readily identifiable as vacuum panels. Another variant is the design of the bottle base such that it is able to compensate for the partial vacuum, again through controlled deformation. Under certain circumstances, moulds for bottles that will be filled with products at temperatures of up to 85°C may still be made as genuine aluminium shell moulds. In contrast to the true “hot-fill” process, this is referred to as the “relax” process. Other variants of heat-resistant bottles are used for applications where the bottles are sterilised with heated steam before filling or bottles are conveyed through a pasteurising system after filling. The related temperature load (temperature and duration) may result in other requirements for the selection of the mould concept. Mould design After the bottle geometry and the mould concept have been determined, as described in the previous sections, the focus shifts to the mould. At this stage, it is important that full use has been made of all the technical possibilities during the design phase to ensure a common understanding of design-related issues between the supplier and the customer. Because a 2D drawing can never give a 100% true impression of the subsequent appearance of the container, a photorealistic rendering will be much more meaningful. Depending on the selected mould concept, the complete mould will consist of different elements or assemblies that are usually available as ready-to-use","@ID":48}, "MATERIAL / RECYCLING 34 PETplanet insider Vol. 14 No. 10/13 petpla.net Recycling Switzerland with Carbotech and relating to the ”ecological benefits and optimisation potential of PET recycling” states: thanks to the Swiss recycling system, more than 3kg of greenhouse gases such as CO 2 are saved per kilogram PET recycled. PET is 100% recyclable. Every year the emissions of 140,000t of greenhouse gases (mainly CO 2 ) can be prevented. This corresponds to the emissions of all cars in the canton of Schaffhausen. with new products to be manufactured from the PET recycled in Switzerland, approx. 50% of the energy amounting to 36 million tons of natural gas has been be saved each year (annual heating for all households in Canton Appenzell) Litter Even in Switzerland, a country where there is major emphasis on cleanliness, it is important to keep on reminding people that they need to get involved. PRS, together with the Igora Association (for the collection and recycling of aluminium), is conducting major campaigns against littering. Both collection organisations have combined their activities in “IG Saubere Umwelt” (IGSU = Interest group for clean environment), to which other organisations have also signed up, such as VetroSwiss, Tetra Pak, McDonald’s, Migros, Coop, the free newspapers “20 Minuten” and “Blick am Abend”, the Association of Swiss Media, Swiss Cigarette and the International Chewing Gum Association. Numerous volunteers, mainly young people and students, address “litterers” directly on the streets. A further Swiss invention which deserves a mention is the pay-as-youthrow sack (€2.00 per sack) into which households can put their left-over waste. The assumption behind this is that the thrifty Swiss, in order to save money, will participate in cost-free recycling and separate out their PET - as well as aluminium, glass, paper and compost. The pay-as-you-throw sack is a statutory requirement in all cantons, but only implemented yet in 80% of all municipalities. Usage of RPET Basically, the aim is to use the recyclate for manufacturing new bottles and in this way to complete the bottle-to-bottle cycle. Messrs. ITW Poly Recycling GmbH as well as RecyPET AG have been commissioned to salvage the sorted bottles and to produce a recyclate suitable for direct food contact which can be re-used in the production of beverage bottles. Both companies operate in close collaboration with the PRS which makes the arrangements for the used bottles to be collected and sorted by colour and quality, pressed into bales and delivered. Both companies process all collected qualities.","@ID":36}, "TRADE SHOW REVIEW 65 PETplanet insider Vol. 14 No. 10/13 Pet_Planet_Insider_Ottobre.eps 1 30/07/2013 10.34.39 New taste combinations Beside its wide range of ingredients for the food and beverages sector, Döhler unveiled many interesting new developments at Drinktec. The spectrum of product applications stretches from flavoured water and aqua plus beverages to a broad portfolio in the large carbonated soft drinks segment. Alongside classic products, the focus was on applications with a reduced calorie content, zero calorie and formulations with natural ingredients and a higher fruit content. Flavours such as brewed elderflower lemon and guarana-brewed teas, which use natural tea infusions instead of tea extracts, were waiting to be tasted on the Döhler stand. For the energy drinks market, the company offers ew taste applications, juicy energy beverages and natural caffeine sources, including the new flavours ginger and blueberry. In the sports drinks segment are new flavours such as lime mint guarana and functional protein drinks. In the segment of beverages containing fruit juices the newly developed product applications included aqua fruit beverages, fruit splashes, natural and still fruit juice beverages, nectars and fruit juices. As well as calorie reduction, the priorities are increased mouthfeel and entirely new taste combinations, such as uncommon fruits from Africa and Brazil. The range of innovations also includes beverages with malt extracts, ranging from Fassbrause (a non-alcoholic drink made from fruit and spices and malt extract, traditionally stored in a keg) and malt lemonades to malt & fruit and malt beverages with beer taste and 0.0% alcohol. For beer mixes Döhler was presenting new flavours such as blood orange, rum-honey and ginger. In the range of cider mix and wine mix beverages for low-alcohol beverages, new applications are cider mix with red fruits and chilli, wine mix with grapefruit and lavender and Asian flavours. For the spirits and liqueurs market, new on board were cream liqueurs in orange-cranberry, cocktail and whisky-honey flavours. For customers in the dairy industry, Döhler offered new applications such as malt milk, gelatine-free fruit preparations, bubbles and whipped fruit preparations. www.doehler.com","@ID":67}, "NEWS 10 PETplanet insider Vol. 14 No. 10/13 petpla.net petengineering.com info@petengineering.com P.E.T. Engineering: the one-stop shop for beverage packaging. Technology excellence, captivating design, ergonomic shapes: a product developed by P.E.T. Engineering is easily recognizable. Its technical know-how and experience have made of it a leader brand in the sector of PET containers. Design, prototyping, laboratory tests and the production of blow moulds: P.E.T. Engineering is the perfect partner, holding itself all the possible solutions. PACKAGING. EVERYTHING YOU NEED DESIGN The perfect shape for an easy handling. PROTOTYPING Bottles available just a few hours RESEARCH AND DEVELOPMENT New materials, innovative solutions and cutting edge technologies. PRODUCTION AND CUSTOMISING OF THE MOULDS High quality blow moulds for every kind of container and any type of blowing machine. STARTUPASSISTANCE AND TRAINING Supporting the client during the whole project. Gevo opens Texan paraxylene plant Gevo, Inc., currently the world’s only commercial producer of bio-isobutanol, has formally opened its demonstration-scale paraxylene plant in Silsbee, Texas, USA, with a ribbon-cutting ceremony. The facility is located adjacent to its existing jet fuel plant in the town. Gevo is working with The Coca-Cola Company to deliver a new production technology for renewable paraxylene, a key building block for producing fully renewable PET for beverage bottles, and with Toray Industries, Inc., to develop it as a building block for fully renewable polyester for packaging films and fibres used in textiles, clothing and other applications. R&D support for the plant was provided by the Coca-Cola company under a Joint Development Agreement; Toray provided funding assistance for its construction. Gevo and Toray have successfully produced fully renewable and recyclable PET fibres and films from isobutanol at laboratory scale in 2011. Toray is expanding its biomass-derived materials business and has signed an offtake agreement for paraxylene produced at the Silsbee facility. www.gevo.com Croda buys in China Croda International Plc has received Chinese regulatory approval to acquire a 65% equity interest in Sichuan Sipo Chemical Co. Ltd, a non-listed speciality chemicals manufacturer based in Mianyang City, Sichuan Province, China. The purchase consideration is RMB361.6m (£38.26m at an estimated exchange rate of RMB9.45/£). Completion of the transaction is subject to customary closing conditions, which are expected to be fulfilled within the next few weeks. Sipo, which was established in 1993, has approximately 300 employees and makes speciality derivatives from natural raw materials. Its products include primary amides, novel fatty acids and speciality esters. A custom-built production facility, opened in 2011, will provide Croda with additional capacity and increase improve proximity to customers in the region, helping to strengthen its existing operations across China as well as the Group’s overall position in Asia, the company says. Sipo will also consolidate Croda’s position in fatty acid amides (currently sold under the Crodamide brand) and add new technology that will enable the Group to expand its portfolio across a number of its core markets. Its intention is to grow sales into the polymer additives and lubricants sectors, with further opportunities in new markets expected to follow in due course. www.croda.com","@ID":12}, "EDITOURS REPORTS 18 PETplanet insider Vol. 14 No. 10/13 petpla.net EDITOUR REPORTS 18 CCT Creative Competence Technology GmbH Idsteiner Strasse 74 D-65527 Niedernhausen, Germany r.steinmetz@cct-systems.com www.cct-systems.com PET Molds Closure Molds Developments PET Systems Closure Systems Design and Patents CCTsystems®SST (Standard-Slider-Technology) CCTsystems®SBT (Slit-Band-Technology) CCTsystems®SFBT (Slit-Fold-Band-Technology) All Types available with: Design and Patents CCT O26 Series 0,9 g CCT O29 Series 1,2 g CCT O30 Series 1,8 g CCT O38 Series 2,9 g emerged about the market shares of the big CSD manufacturers: Coca Cola (with 60%), Pepsi (with 30%) and the discount brand Manaos (10%). One of our informants claimed that Manaos reckons it is ahead of Pepsi in terms of market share, but we failed to substantiate the story. A striking feature of the Argentinian beverage market is, here too, the high level of usage of the PCO 1810 neck finish. Following expert estimates, however, a large-scale conversion to the more lightweight PCO 1881 is likely to take place, probably in two years’ time. Largely due to the difficult economic situation, the majority of companies are not ready for major investments and are not likely to be so any time soon. With the technology in the PET sector that is already available in the market place, or so we kept hearing, Argentina finds itself at present at the limit, so to speak, where preform lightweights are concerned. As was consistently pointed out to us, if the present stagnation continues, investment in the PET packaging sector in Argentina is likely to lag behind from a technical viewpoint. For instance, cold air blowers are nowhere to be seen. As regards Argentine beer, basically the same situation exists as with Chilean beer. The customer has, without exception, gone for recyclable glass and cans. The bottle sizes are practically identical to Chile. With a 75% market share, the ”Quilmes“ beer (decorated in the country’s colours) is by far the brand of beer favoured by the Argentinians. Quilmes is a product of the Cervecería y maltería Quilmes brewery, part of the AmBev group. Between 2008 and 2012 consumption grew by 2.9% a year, and experts are forecasting an annual rise of 3.7% in the future. As is also the case in Chile, plastic closures are sometimes used. In his Editour report in PETplanet Insider issue 9/13, Alex Büchler drew attention to the Canadean and Euromonitor analyses of these markets. For our part, we have preferred figures from Anber Chile (Asociación Nacional de Bebidas Refrescantes), which are closer to the Euromonitor data. We have chosen this data for our analysis of the Argentinian market. Chile: Sales trends for non-alcoholic beverages in millions of litres (Source: Anber) 2008 2009 2010 2011 2012 CSD 1773 1,790 (+0.9%) 1,880 (+5.0%) 1,930 (+2.7%) 2,044 (+5.9%) Water 213 221 (+3.5%) 245 (+11.0%) 284 (+15.9%) 349 (+22.9%) Juices / nectars 159 173 (+8.6%) 197 (+14.2%) 228 (+15.7%) 268 (+17.5%) Sports drinks 7.2 8.7 (+20.4%) 11 (+26.1%) 15 (+36.8%) 22 (+46.0%) Tea No data 3.0 3.4 (+12.7%) 4.8 (+40.9%) 5.1 (+7.7%)","@ID":20}, "NEWS 9 PETplanet insider Vol. 14 No. 10/13 petpla.net CCC grows with Amsler Consolidated Container Company (CCC) has placed an order for three L42 4-cavity and one L32 3-cavity PET stretch-blow machines with Amsler Equipment Inc. The machines are being installed in two different facilities. The new, all-electric Amsler linear L32 and L42 machines feature an adjustable number of cavities. The L42 machines can be run in four-cavity mode for production of bottles of up to 2l, or in two-cavity mode for up to 5l bottles. The L32 machine can be run in three-cavity mode (up to 2l); in two-cavity for up to 3l; and single cavity for 5l packages. The Amsler machines have servo-actuated stretch rods, clamp, and preform in-feed to the moulds. At CCC’s request, the machines were equipped with Siemens user interfaces and controls systems. The machines will be used to produce a variety of containers for beverage, trigger sprayer and floor cleaner containers, among others. www.cccllc.com www.amslerequipment.net Döhler acquires 50% of fruit specialist Mais Fruta in Brazil Global ingredient company Döhler has acquired a 50% stake in the Brazil-based fruit specialist Mais Fruta Ltda. Since the 1990s Döhler has already been represented in Brazil and has a production site in Limeira. Mais Fruta Ltda. is a family-owned manufacturer and marketer of frozen fruits, fruit purees and juice concentrates for the food and beverage industry. The company is located in the city of Antonio Prado, in the heart of the grape growing areas in the South of Brazil. The investment secures Döhler’s access to high quality raw materials from a wide range of South American fruit varieties and opens up new potential for the development of innovative food and beverage applications. For the time being, Mais Fruta will continue to operate its business activities as before. www.doehler.com Netstal to focus on core expertise Netstal has announced that it will be focusing its activities on its core competency as a premium supplier of injection moulding machines. Its stated intention is to strengthen its international competitiveness and secure its longer term future. The Näfels site will be developed into a centre of excellence. The realignment will result in the activities of Research & Development, Sales, Systems and Application Engineering, Final Assembly and Service being based at the Näfels site, and broadened. The company has recently discontinued rotary parts manufacturing, while working to expand the scope of its product development and technological support for customers in the beverages and packaging industries, medical engineering and highprecision parts. The KraussMaffei PETForm product portfolio has been relocated from Munich to Näfels so that all PET-related technology areas will be concentrated on that site in future. Machining and module preassembly will be transferred to sister plants within the KraussMaffei Group in Germany and Slovakia, which will allow the final assembly area at Näfels to growth. The Netstal brand is to expand its core expertise in areas such as R&D, application engineering, and sales and service, with product launches at drinktec and K 2013. A full interview with Dr. Hans Ulrich Golz, CEO of Netstal, can be found in Issue 9 of PETplanet Insider, on page 34. www.netstal.com Amcor Packaging splits Amcor has announced that it intends to demerge its Australasia and Packaging Distribution (AAPD) business. Over the past six years, Amcor has invested more than US$1 bn in AAPD’s manufacturing capabilities, including a new recycled paper mill at Botany, a new furnace at the glass bottle plant at Gawler and a new beverage can line in New Zealand. Following the demerger, Graeme Liebelt will be Amcor’s Chairman and Ken MacKenzie will remain Managing Director and CEO. Chris Roberts will become Chairman of the yet-to-be-named new company; Nigel Garrard, the current President of AAPD, will be appointed CEO. The demerger is intended to be implemented through a capital reduction and Scheme of Arrangement. Further information in relation to the process of the demerger, financial profiles and capital structure of the new company and Amcor after the demerger will be provided to Amcor shareholders in the Scheme Booklet, which will be distributed in advance of the shareholder meeting that will be convened to vote on the demerger proposal. Amcor expects completion of the demerger to occur in December 2013, subject to requisite approvals. www.amcor.com","@ID":11}, "EDITOUR REPORTS 19 PETplanet insider Vol. 14 No. 10/13 petpla.net Off-trade volume sales trend Argentina for non-alcoholic beverages in millions of litres (Source: Euromonitor) 2008 2009 2010 2011 2012 Carbonates 6,369 5,839 (-8.3%) 5,433 (-6.9%) 5,326 (-2%) 5,444 (+2.2%) Water 4,533 4,556 (+0.5%) 4,736 (+3.9) 4,966 (+4.9%) 5,090 (2.5%) Juices 142 156 (+9.8%) 195 (+25%) 238 (+22%) 272 (+14.3%) Sports & Energy drinks 52.1 58.5 (+12.3%) 62.9 (+7.5%) 71.9 (+14.3%) 84.7 (+17.8) Tea No data Get in touch with... recycling When it comes to waste, Chile is the front runner in Latin America with around 6.5 million tonnes produced annually. A significant proportion of this is in plastic bottles. A mecca for the recycling industry, one might think. In reality, however, things look very different because there has so far been no attempt made to establish a large-scale recycling system. Efforts in the heavily populated areas around Santiago to collect disposable bottles using return systems currently exist only in rudimentary form. This is not the fault of the consumer, since there are many advocates for recycling. The stumbling block is the lack of an existing infrastructure. Nevertheless, last year saw the inauguration of a project in which the environmental authorities are also involved. The website www.sumaverde.cl incorporates details of the location of disposal stations in Santiago. However, there is also a grass roots movement which has taken the bull by the horns and made recycling part of the daily routine. They call themselves “cartoneros“ (waste picker) and there are said to be 30,000 of them. They go round the streets collecting and sorting any refuse lying about, sell it and are thus able, by demonstrating a bit of initiative, to earn themselves a little cash. There is a law, the “Ley de Residuos”, (Hazardous Waste Act) drawn up many years ago but still not enforced, but which will now be deployed in order to regulate how waste is dealt with. A significant point incorporated in this law is the newly regulated accountability in respect of waste on the part of the manufacturers of the packaging. At present, municipalities and local authorities bear the costs of disposal, but in the future the manufacturers of the packaging will be required to assume the costs themselves and, if applicable, offer to take back their waste products. Several companies are already making preparations for when the legislation comes into force and this, as our interview partners all agreed during our discussions, will have an effect on the entire production chain. The precise level of waste produced in Argentina is something we have not been able to find out, but we were able to get an approximate idea based on the fact that, every day, around 16,000t of waste are produced within the greater Buenos Aires area. As is also the case in Chile, there is no possibility of any officially organised recycling.","@ID":21}, "BOTTLE MAKING 48 PETplanet insider Vol. 14 No. 10/13 petpla.net Graham Packaging uses Agr automated blowmoulder control and inspection for wide-mouth jars Peanut butter jar gets the vision treatment Global packaging company Graham Packaging Co. L.P., York, PA, is accelerating the shift from glass, paper and metal to PET. One example is the development of the 30- and 32-ounce hot-fill, wide-mouth jars for peanut butter and other viscous foods for the branded product market. To make the speciality jars, which must meet demanding specifications, Graham has deployed its proprietary blowtrim technology in tandem with Agr International’s OptiCheck vision-based inspection and measurement system and Process Pilot automated blowmoulder control system. Blow-trim challenges The manufacturing challenge of the blow-trim jars is two-fold: with a range of 63mm to 83mm, the jar finish is too large for standard preforms and blowmoulders, yet it must be perfect for proper capping. Complicating the task is the mandate to use a single blowmoulder to produce both bottles with a 43mm finish and larger jars. “The spindles on our Sidel blowmoulder are 43mm. Normally, to make a jar with our larger finishes, you would need a dedicated machine with larger spindles, plus special preforms and different handling equipment like unscramblers,” explains Don Waud, Graham Plant Manager. “It can get very expensive.” The patented blow-trim process allows a single Sidel unit to fabricate both types of containers. When running the larger finish jars, Graham deploys a speciality mould inside the blowmoulder. The custom mould shapes a new set of jar threads along the side wall of the preform. The technique permits the use of traditional preforms with a 43mm diameter finish, thus eliminating the need for special preform manufacturing and handling equipment. In a secondary process, the portion of the jar above the newly blown threads - the moil, or excess area - is cut off by a trimmer downstream and subsequently recycled. Graham’s jar and bottle plant is co-located with the filling plant of an internationally known food processor. The arrangement saves shipping costs while offering the stability of a long-term supply agreement and the agility of just-in-time manufacturing. In the close-coupled operation, the containers are blown and immediately conveyed to the filling plant","@ID":50}, "EDITOUR REPORTS 21 PETplanet insider Vol. 14 No. 10/13 Valenzuela González, had already experienced the advent of PET way back in the 90s thanks to Coca-Cola. The level of acceptance of and adjustment to the PET bottle on the part of consumers has been correspondingly high – PET represents the most widespread form of packaging in the non-alcoholic drinks sector and it was this that finally triggered Embosur’s decision. In 2004 the first Sipa SBM line came on stream in combination with filling equipment from Feijoo Argentina and a wrapping unit from Tecmi. In 2009 the company invested US$ 3,5 million in expanding its infrastructure and this led to the inauguration of a second production line. Buying in various ingredients and sweeteners which are refined for the various applications based on the company’s own formulas has meant that Primeros has currently seven different taste options available to it in the shape of CSD plus water and four kinds of juice. In addition to these there are other different CSDs such as the Iguazú series, isotonic drinks and, in the third party brands sector, the energy drink ‘Mr Big’. Overall Embosur’s bottling activities comprise five different size bottles - 0.5l, 1l, 1.5l, 2 and 3l. The water used in the production process is located on the company’s premises at a depth of 6-8m. Eight pumps are used to convey natural spring water from its source into the plant. A further spring at a depth of around 30m is also available as a fallback option. At present the company supplies an annual output of around 60 million litres inside Chile where it holds a 3% share of the market. Of this 84% is proprietary and 11% third party brand bottling. Two bottlers, who represent the primary competition, have a similar output. At a secondary level and with something like half the production output there are four other small competitors. Embosur’s core target group is chiefly discount chains, including Walmart and Unimarc, as well as smaller retail traders. The company uses the preform suppliers Amcor, Syphon, San Miguel and Cristalpet in Argentina and Peru. The preform sizes vary, depending on the application, from 22g / 24g for 0.5l, 21g for 1l, 44g for 1.5l, 48g / 50g for 2l and 58g for 3l bottles, all with neck finish PCO 1816. The closures come from Sinea, a company in Chile, as well as from CSI Closures.","@ID":23}, "TRADE SHOW REVIEW 64 PETplanet insider Vol. 14 No. 10/13 petpla.net Drinktec review On September 21, the doors closed on drinktec and the extraordinary number of more than 66.000 visitors who attended the exhibition. A brief review of some of the exciting new developments we uncovered at the show will surely whet the appetite for upcoming issues of PETplanet Insider, where all the highlights of drinktec will be featured. www.drinktec.com Cool running Lanxess has announced that its new Velcorin DT Touch dosing units for filling Velcorin as a cold sterilisation agent in non-alcoholic beverages and wine are now being sold worldwide. The units are manufactured in Germany and feature an aseptic design and connections to meet the strict purity requirements of the beverage industry. Lanxess says that they are designed to be both safe and easy to handle. Control and visualisation of the dosing process are enabled by a touch panel. The Velcorin range is designed to be effective against typical spoilage microorganisms such as yeast, mould and bacteria, which are present throughout the beverage filling process, but to act against them without compromising product taste. Lanxess says that Velcorin DT dosing units can be integrated into new or existing beverage production lines for a relatively small capital outlay. www.velcorin.com www.lanxess.com Stay-with Aptar Food and Beverage unveiled Micro, their new standard dispensing solution for water enhancers and liquid concentrates. Micro is a one-piece PP snap on closure, using an adapted SimpliSqueeze valve specifically developed to optimise performance of the flow control and the no-drip safety for out-of home consumer use. A smaller version of Aptar’s patented valve allows the stream of product dispensing to be precisely controlled by the consumer in order to obtain their preferred dosage. The closure orifice remains clean throughout usage, due to precise product cut-off. Their SimpliSqueeze valve always uses swimming silicone technology in beverages to ensure PET bottle recycling stream compatibility. The swimming silicone SimpliSqueeze valve has a density below 1 and therefore ‘swims’ to the surface to facilitate sorting. It was approved and certified in Europe by the Cotrep and the EPBP in 2011. With Micro there is said to be no mess and no drips for a neat package that can be safely and conveniently stored; even in a pocket or a bag for out of home consumption. A further point of interest was its new flip-top sports closure Avantage. Avantage is a monomaterial sports cap featuring a unique push-button tamper evidence. It has a 170° spring loaded hinge attaching the lid to the body of the cap, which enables consumers to drink uninterruptedly. These features are said to differentiate this closure from others in the market, and it also boasts an original tether design. Avantage is Aptar’s first closure featuring their Stay-With tether. Suitable for all neck sizes this proprietary tether permanently affixes the closure to the bottle and can be twisted and pulled away from the drinking orifice. It prevents misplacement of the cap. By preventing closures from being separated from the bottle, beverage makers will have a solution to meet new legislation already being passed in the EU and the UK requiring closures to be recycled with the bottle. www.aptar.com Barrier refined Invista has added new products to its barrier resin portfolio. The launch of PolyShield MB marks the latest extension to Invista’s barrier resins range. The new product offers makes the company’s established barrier technology available in a concentrated ‘masterbatch’ version. Invista says that it will allow converters and brewers to increase their sourcing flexibility and offer options to save on freight and duties. In the manufacture of monolayer beer containers, the masterbatch solution is prepared by blending PolyShield barrier resin with standard quality PET resin, along with the required amount of MXD6 nylon. The company claims that this enables producers to achieve an optimal balance between the cost of the packaging and the barrier performance needed to meet shelf life requirements of oxygen-sensitive food and beverages, including beer. Invista also exhibited a blend of PolyShield and MXD6 nylon developed for one-way beer kegs; OxyClear polyester barrier resin designed for the protection of oxygensensitive food and beverages such as juice, tea, wine and sauces; and Polyclear EBM, a PET grade that can be recycled in the clear PET stream. www.polymers.invista.com","@ID":66}, "MARKET SURVEY 41 PETplanet insider Vol. 14 No. 10/13 petpla.net Valspar Repi S.p.A. NovaPET, S.A. Clariant Masterbatches Europe 2000 Georgetowne Drive Sewickley, PA 15143 USA +1 800-873-5575 www.valsparpackaging.com Lynn Spataro Market Manager +1 724-940-3141 lspataro@valspar.com Via B. Franklin 2, 21050 Lonate Ceppino VA, Italy +39 0331 819511 www.repi.com Maurizio Amicabile Development Manager Packaging +39 0331 819511 +39 0331 819581 repi.italia@repi.com P° Independencia, 21, 3°, PC 50001, Spain + 34 976 216129 www.Novapet.es Miguel Angel Arto Business Development Director + 34 976 216129 + 34 901 021138 marto@samca.com Am Unisys Park 1, 65843 Sulzbach am Taunus, Germany +49 6196 757 6276 www.clariant.masterbatches.com Severine Wild Marketing Europe +49 6196 757 6276 +49 6196 757 6113 MB-MKTEurope@clariant.com Yes Yes No Yes No Yes No Yes Yes Yes Yes, SenzAA Yes Yes, SenzAA Yes valOR Activ and valOR ActivBloc No Yes No No valOR ActivBloc and valOR Bloc for passive barrier Anti yellow (liquid), process aid (liquid) IV enhancer (solid), blowing additive (liquid), optical brightener (liquid), colours for barrier solutions (liquid), white for monolayer UHT milk (liquid) DCU, Luz & Polygloss, the new generation of PET concentrates for (opaque and transparent) light barrier and metal gloss effects Slipping agent, reheating, matting agent and special effects Novapet, S.A. DAK Americas LLC DAK Americas LLC Specialty Polymers M&G Polimeri Italia SpA P° Independencia, 21, 3°, PC 50001, Spain +34 976 216129 www.novapet.es Miguel Angel Arto Business Development Director +34 976 216129 +34 901 021138 marto@samca.com 5925 Carnegie Blvd. Suite 500 Charlotte, NC 28209, USA +1 704 940 7500 www.dakmericas.com George Rollend Senior Technical Manager +1 603 672 6403 +1 866 833 5069 resinsinfo@dakamericas.com 223 Wilmington West Chester Pike, Suite 210, Chadds Ford, PA 19317, USA +1 610-558 7380 www.dakamericas.com John W. Jones Sr. Account Manager +1 215 794 7727 +1 215 794 7399 jjones@dakamericas.com Via Morolense Km 10 03010 Patrica (FR), Italy +39 0775 84.221 www.mg-chemicals.com Marilena Grecchi Area Sales Export and Marketing +39 02 82.273.242 +39 02 82.273.314 marilena.grecchi@gruppomg.com Mexico Asia Polyclear RamaPET NovaPET Laser + Array 9921M Cleartuf 0.80 - 0.95 0.62 - 0.96 NA 0.56 - 1.3 0.74 - 0.86 0.58 - 0.86 0.60 - 1.10 Laser+ 0.72 - 0.84 (dL/g) 0.56 - 1.3 0.76 ÷ 0.95 1101, 1111 S1, S2, R1, N1S Lbs Soft, Cr Laser + Cleartuf Ultra 3301 N2, N1 Mw Soft, Cr, Glasstar and X_treme Laser + W Cleartuf P76 - Cleartuf P82 N1 Glasstar Laser + Poliprotect N1 Glasstar Laser + Poliprotect N1 Glasstar, Sprit H 11, Sprit L01, Kera Laser + C Blow Fill Seal (BFS) Cleartuf P82 T-94 G1, SG1 Glasstar, X_treme,CLP (Sheet), Puro Laser + C 2201 H1 HF Laser + H Cleartuf P85HF Dairy, Luz R1, ES11 Lbs Laser+, Laser+ W, Laser+ HS Cleartuf Ultra PlantPET L1 (High flow blood tubes), film grades and masterbatches, Superbright low and high IV Chips (0.95-1.08) CPET, HT, REX (for EBM) Array 1.0 - 1.3 (dL/g) 9921 - non-medical; PETG 1) Barrier resins (i.e. Poliprotect) For different application (juices, beer, wine, dairy/milk based products, ketchup, mayonnaise….) 2) Cleartuf T95 (high viscosity). Main application: trays; Dairy, LUZ , DCU, Polygloss (light barrier). Glasstar (gas barrier) IPAmodified PETs Yes, with Poliprotect 2014 Yes Yes, under customer requirements Specialised in light barrier protection for long shelf life milk products (UHT, ESK, Milk shakes, yogurt) Batch processed specialty polymers available.","@ID":43}, "TRADE SHOW PREVIEW 62 PETplanet insider Vol. 14 No. 10/13 petpla.net Everything under control! Swiss company Olicorp will present its MCU series, a range of programmable embedded IP67 controllers tailored for the PET industry. Connected to the main PLC of the machine, the MCU ensures the real time control and the monitoring of the process. Being waterproof (IP67), the MCU can be installed directly on the machine close to the equipment to control. The MCU series is designed for the needs of, but is not limited to, the PET industry. Each MCU is designed to be quickly operational without any extensive engineering. MCU-Blow is an embedded IP67 programmable controller designed to enhance stretch blow process on each station of the machine and reduce the automation costs. It allows the angular position of the wheel to be read, and the stretch blow process to be synchronised with the angular position of the wheel. The device is designed for real time control of the complete stretch blow moulding process and allows online monitoring of the process parameters for each cavity. MCU-Injection is an embedded modular controller for injection machines. It is designed as a compact and ready to plug in solution, for full control of the injection unit (extruder, injection, cylinders, motors), of the clamping unite (closing, mould temperature, cooling robot) and for high speed motion control of the extracting robot. MCU-Thermocouple is a controller for the collection and analysis of the temperature information on machines and equipment. The MCU-Thermocouple is designed in two versions: 16 isolated inputs J type and 16 isolated inputs K type. Both solutions are in IP67 compact waterproof corpus equipped with Profibus DP slave and Bluetooth. Some of the benefits claimed by Olicorp for the MCU are: accuracy of measurement, elimination of intermediate connections. and reduction in cabling costs. www.olicorp.ch Olicorp Hall 12 Booth A51-6 Allrounders Arburg has taken a large, 1650m2 stand in order to present a range of machinery and the formal launch of new electric Allrounder units. The electric Allrounder 820 A will receive its world premiere at the K Show. It completes the company’s electric Alldrive series by bridging the gap between the 3200 and 5000kN machines. It incorporates a 4,000kN toggle-type clamping unit and a 2100 size electric injection unit, both of which have been newly developed for this machine. Arburg says that the new toggle size will also be available for the hybrid Hidrive range in future. The stand will also feature an Allrounder 370 E from the Edrive, integrated with a six-axis robotic system and an inline printing system from fpt Robotik into a production cell. An Allrounder 470 A equipped with a 64-cavity mould from Männer will produce high-precision, delicate dosage units in a cycle time of only 2s. A fullyelectric cube mould application for juice container closure production will be presented jointly with Foboha. www.arburg.com Arburg GmbH + Co KG Hall 13 Booth A13 Sacmi Hall 13 Booth A63 Caps, containers and preforms The Sacmi stand will showcase the company’s solutions for the manufacture of caps, preforms and containers and will include presses capable of producing large ‘one-step’ articles, along with others designed to combine the best of hydraulic and full-electric technology. A key exhibit will be the IPS 220 B, an injection preform press that was originally launched in 2012 and includes a control system that allows real-time control of process parameters, which Sacmi says enables greater flexibility in changeover. A very fast cycle time is achievable because of technical solutions such as the machine’s own KERS (kinetic energy recovery system). It can manufacture preforms of up to 190mm and at outputs up to 1,200 preforms/h. Sacmi’s stand will also have an upgraded version of the CCM 48 S, optimised for the innovative COOL+ mould. The version on show at the fair will produce 2,000 caps/ min. The new CHS Lean solution, which can inspect up to 150,000 caps/h allows 360° cap control, will also be on display, as will the CBF container manufacturing machine, another product originally launched in 2012. www.sacmi.com","@ID":64}, "EDITOURS REPORTS 26 PETplanet insider Vol. 14 No. 10/13 petpla.net Lemon, Grapefruit and Tonic Water flavours. Under the brand name “La Bichy Ahora“, seven further CSDs are also produced, as well as various waters and an additional cola product by the name of F-nandito-VII, Fernet Cola. All the syrups needed for the mixtures come from their own in-house production with added sugar and sweeteners. Refres Now, with an estimated annual output of around 1 billion litres and more than 1 billion bottles each year, has opted to use PET exclusively. “There was no question of any other packaging. It has proved successful because we now find ourselves ranked as the No. 2 behind Coca Cola and ahead of Pepsi “, says Canido. In the Manaos filling area at Refres Now, Walter and his interpreter Laura in front of the Sidel plant “In the final analysis, price and high quality are the purchasing criteria as far as the customer is concerned and we do the best we can to meet these requirements” says Production Manager Nestor Fischer. In addition to Argentina, Refres Now also supplies parts of Uruguay and Paraguay and plans are afoot to extend the catchment area even further. www.refresnow.com.ar 360° March 21, 2013 Bericap Argentina S.A. We met: Günter Krautkrämer, General Manager Expansion of closure production Bericap has been producing closures in Brazil since 1998 and has recently started to produce closures in Argentina as part of the company’s first geographic expansion in South America. Bericap’s Argentinean legal entity is Bericap S.A. The facility is located in the industrial zone of Pilar, some 65km North-West of Buenos Aires. This production facility is located in a separate section of the Inesa can factory. Bericap’s production hall When Inesa acquired this facility to produce metal cans they also acquired a plant manufacturing closures for PCO 1810 necks which was already in operation. For Inesa this was a relatively small sideline. Bericap’s interest in expanding their operations in Argentina matches Inesa’s interest to develop further the plastic closure business. While searching for a suitable cap for one of the cans, General Manager Ulises Porrier came into contact with Günter Krautkrämer of Bericap. The two of them rapidly realised that the two companies had much in common, and could develop their products to mutual benefit. development high cavity moulds technology centre production support competent – professional – inspiring Hoechster Strasse 8 · 6850 Dornbirn, Austria · T +43 5572 7272-720 · www.z-moulds.com multi-component injection moulds","@ID":28}, "EDITOUR REPORTS 17 EDITOUR REPORTS 17 carriageway motorways in metropolitan areas. Water is another important means of transportation, particularly for agricultural exports, making use of some 3,100km of navigable waterways. (Sources: Wikipedia, German Association for International Cooperation (GIZ)) Get in touch with... PET In terms of bottle production, PET in Chile has advanced since the initial imports which consisted of packaging for the beverages sector made by Coca-Cola during the mid-90s. However, one striking feature is the fact that this marked growth over the past few years relates almost exclusively to CSDs, non-CSDs, juices and water. The major brands here are indisputably Coca-Cola and Pepsi. The range, particularly as regards the B-brands, is wide and of great diversity, both in terms of taste as well as in terms of bottle sizes and design. And demand for CSDs is increasing. In per capita consumption of soft drinks in Latin America, Chile occupies second place with around 121l per year, behind the market leader Argentina with 131l. Likewise, juices and milk products in PET bottles are finding their way into the retail trade more and more frequently. By contrast, Chile’s beer market is characterised by the exclusive use of glass bottles (66%) up to 1l volume and cans (34%). In 2011, beer, in an overall comparison of all alcoholic drinks, represented a proportion of 53% of sales. Currently the sector is registering growth of between 8% and 10% per year, which enables us to state incontrovertibly that “beer is enjoying increasing popularity at grass roots level”. It is also a fact that, over the past few years, a trend towards higher quality beer has become discernible and for this people are prepared to pay higher prices. The leader in the beer market is the Compania Cerveceria Unidas (CCU) with a market share of around 75% and their strongest brand names are “Cristal“ and ”Escudo“. Apart from the occasional use of plastic closures on the large glass bottles, PET as a filler medium is not an attractive proposition for the consumer. On a number of occasions we heard about what was apparently an earlier attempt on the part of CCU to bottle the Cristal brand in PET, a move swiftly rejected by consumers. However, we have not been able to obtain confirmation of this story. In our discussions with market experts what came out was that the PET bottle tends to be favoured by smaller breweries rather than the majors. Now we come to the particular features that characterise Argentina. Here, too, it was CocaCola who popularised the use of PET. Based on our technical discussions with PET enthusiasts throughout the country, rough estimates","@ID":19}, "PETbottles 68 PETplanet insider Vol. 14 No. 10/13 petpla.net Beverages & Liquid Food Bio-lemonade The Austrian company IMS Höllinger is marketing its range of beverages with the suffix “bioorganic“ in slender PET bottles with a content of 500ml. The drinks contain less sugar than other lemonades and dispense with any artificial colourants. Each of the bottles features a sleeve label and is sealed by means of a screw closure (colour-matched) and a tamperproof strip. The caffeine-free cola incorporates a window in the sleeve label so that consumers can check how much there is left. www.hoellinger-juice.at www.juiceandsoda.at Gluten-free mayonnaise The Spanish company Conservas El Cidacos is selling 700ml of gluten-free mayonnaise in an elegant container made from transparent PET. The shape is strongly reminiscent of the glass containers with which customers are familiar. The container is sealed with a metal screw cap. The paper label on the front extends upwards to incorporate a tab and across the lid and thus acts as a tamper-proof guarantee or seal of freshness. www.cidacos.com Drinks that help you lose weight Under its brand name of Juva Ligne, the French company Laboratoires Juva Santé is offering a number of products for controlling or reducing weight. The sugar-free drinks are bottled in containers made from PET featuring an eye-catching shape. The content of the tall bottle in one of the signal colours is intended to boost metabolism. The bottle contains 500ml of product and is decorated with two shaped labels. The bottle, which has rather a squat appearance, contains various tea and coffee extracts and also incorporates a sleeve label which is pulled over the screw closure. www.juvaligne.com Cooking wine complete with dispenser cap Finding the right amount of wine to add to the cooking is not always easy. The French company “La Villageoise“ is selling three bottles of wine for cooking in small PET bottles, each with a content of 250ml. The tinted bottles, with their easyto-handle design, are sealed with a screw cap. Placed over this is a dispenser cap in the shape of a chef’s hat. The cap, which is secured by means of a detachable retaining strip, can be filled with 5cl of wine at a time. At the PoS three bottles linked by means of a cardboard cutout printed and featuring suggested recipes form a single sales unit. www.la-villageoise.com Edible oil with silicone valve The French foodstuffs group Lesieur has redesigned its PET bottle for 375ml ”Isio 4“edible oil and fitted it with a dispensing closure. The waisted, transparent bottle features burls to the side which make for improved handling. There is an automatic closure silicone valve incorporated in the screw on hinged lid. For metered dispensing of the oil with no spillage, the bottle is turned on its head and squeezed. Underneath the screw cap there is a sealing membrane that serves as a tamper-proof guarantee. www.lesieur.fr Evian for kids Evian are selling their 0.33l PET water bottle in France in a 12-pack made from cardboard. The product is suitable for children from six months of age. The bottle, which is shaped so that it is easy to grip, is fitted with a screw cap instead of a sports cap and features a demountable suction device enclosed in the pack which can be used to replace the cap ready for use. The bottle is fitted with a peripheral body label that incorporates a picture showing an infant plus corresponding explanations to illustrate correct handling. www.evian.fr","@ID":70}, "EDITOURS REPORTS 24 PETplanet insider Vol. 14 No. 10/13 petpla.net The fact that the company is very well prepared to face the future is also demonstrated by its fleet of machines which is shown and explained to me by Production Manager Ahmed Usen on a tour of the plant. During the past three years alone, five new machines have been purchased so that today there are eleven blow moulding machines and eight injection moulding machines gracing the production areas. This is another reason for the outstanding relationship between the company and the machine manufacturers. The Husky HyPET 500 machine, which was the first to be purchased last year, is the largest machine on site. The next scheduled investment is a preform inspection machine with a throughput of 20,000 preforms per hour. Eight injection moulding machines run in the high season, on Saturdays too if required. It is not only at Plasco that people are giving some thought to protecting the environment. The Chilean government is this year discussing the implementation of a recycling guideline for national industry. With an eye to the future, the Chilean company is already assessing the possible effects on production so as to ensure that it stays true to its environmentally aware profile. What is Plasco doing that is so exceptional, I ask, before downing the last drop of Espresso left in my cup. “We are constantly debating how we can achieve further reductions in the weight of the bottles. Doing this helps to take care of the environment. We are very efficient and bring out approximately seven new bottles every year with this in mind. Innovation is our corporate philosophy!” www.ccu.cl March 21, 2013 Refres Now We met: Walter Canido, Managing Director Nestor Fischer, Production Manager The CSD and water bottler Refres Now, located in the south of Buenos Aires, is today one of the most important bottlers in the discounter segment. In conversation with Managing Director Walter Canido and Production Manager Nestor Fischer, we find out how the company has got to where it is today. (F.l.t.r.) Production Manager Nestor Fischer, Managing Director Walter Canido and Laura (linguistic support) To begin with, and prior to the establishment of Refres Now, day-to-day business was taken up with the distribution purely of beverages and this went on for many years. Family member and Managing Director Orlando Canido, so Walter Canido tells us, embarked on the successive opening up of his market beyond the confines of Buenos Aires, first on a small scale and later expanding to bigger things. However, at a certain moment, it became evident that obstacles within the sales chain were restricting further opportunities for development and growth. “To put it bluntly, we were the new kids on the block, with no track to boast of“, says Walter Canido with a smile. “At the time, the decision to establish our own bottling plant was frankly a gut feeling that it was the right thing to do”. If nothing else, it was also the discovery of a drinking water well on the present company’s premises that got the show on the road. In 2005 Refres Now was finally set up by Orlando Canido, with three production lines to start with and technology partially salvaged from the 70s, before modern technologies came on the scene in 2009. Today the company premises cover around 54,000m² and the company has 192 employees. Refres Now’s bottling line for “Manaos Soda” The nine bottling lines and production units from Sidel, Sacmi and Acmi produce beverages bottles in 0.5, 0.6, 1.25, 1.5, 1.75, 2, 2.25 and 6l sizes using 17g to 84g preforms with a PCO 1810 neck finish. The closures are supplied by Sinea Enterprise. Their undisputed flagship product is “Manaos Cola“, whose name honours the town of Manaus. The beverage is also available in Orange,","@ID":26}, "MATERIAL / RECYCLING 35 PETplanet insider Vol. 14 No. 10/13 petpla.netUsing 100% PRS bottles creates a Swiss quality PET feedstock. ITW Poly Recycling was set up in 1992 and was operating the first PET recycling plant in Weinfelden, Switzerland. Input capacity 20,000t/a, of which 10,000t/a are returned to the PET recycling circuit for bottleto-bottle application. The balance of recovered PET material is for foils, textile and straps. ITW Poly Recycling produces RPET for the fillers in form of granulates. RecyPET AG was set up in 1998 and has been operating the PET recycling plant in Frauenfeld, Switzerland, since September 2000. Input capacity is approx. 18,000t/a. RecyPET AG produces RPET for the fillers in form of flakes. Caspar van Dungen apparently positions the Swiss situation in an European overview: “Certainly we are sandwiched between PRS and Switzerland has a PET recycling quota of 89% (2012) fillers – regarding quantities and price – since we exclusively receive from PRS collectors and exclusively supply to Swiss beverage fillers. There is a financial risk. And sometimes there are Challenges. But there is also a living partnership between all participants in the PET circuit.” And he adds a personal rejoinder: “I live and work here because of this mutual accountability which is part of our joint perception“.","@ID":37}, "EDITOURS REPORTS 22 PETplanet insider Vol. 14 No. 10/13 petpla.net EDITOUR REPORTS 22 (F.r.t.l.) General Manager David Fierro Salazar, Controller Sergio R. Valenzuela and Kay Barton talking about the Tecmi Wrapping Unit Embosur, according to Fierro Salazar, has a total quality base and he backs up his statement by referring to the certified HACCP Standard and pending certification to BRC (British Retail Consortium) as they are planning to export beverages for the first time in the near future, specifically to France. www.embosur.cl April 16, 2013 Plasco We met: Marco Dall’Olio, CEO Ahmed Usen, Production Manager Growing with its customers Since 1991 Plasco, based in Santiago, Chile, has been producing and selling bottles made from its own preforms. In 2007 the company started selling preforms in addition to bottles and four years after, in 2009, started to produce plastic closures. Plasco develop an average of seven new bottles per year, working intensively also to achieve reductions in weight. As a company in the CCU Group Plasco produces preforms, bottles and caps for water, soft drinks and juices. Plasco’s CEO, Marco Dall’Olio, who originally hails from Italy, explains to me over an original Italian Espresso the impressive development of this 165-employee strong company which today produces 500 million preforms a year and also blow bottles, roughly half of these in-house. Originally Plasco, based in Santiago, Chile, was producing and selling bottles made from its own preforms. In 2007 the company commenced selling preforms in addition to bottles, because it was more efficient for customers to blow bottles themselves. Hot fill products today account for around one third of Plasco’s production. Marco Dall’Olio is particularly proud of the fact that Plasco has been producing preforms and caps for short neck products since 2009. Over a period of just eleven months he succeeded, in his capacity as Project Manager at the time, in converting Plasco’s entire, one way PET production, from BERICAP the plastic closure company committed to your success www.bericap.com Research and Development Developing closure solutions to meet your specific requirements Mould Technology A detailed understanding of mould design with in-house mould making facilities in Hungary and Germany Global Presence Local production in 21 strategically located factories. An on-going strategy of stregthening our global presence Capping Technology and Know-How Special advice on capping technology with on-going technical support Innovation and Flexibility Our broad range of plastic closures is the basis for generating new innovation. Our expertise covers aseptic, hot fill, barrier, anti-counter- feiting TE-systems, consumer convenience and child resistance","@ID":24}, "BOTTLE MAKING 50 PETplanet insider Vol. 14 No. 10/13 petpla.net installed Agr’s OptiCheck as “the last line of defence” before the containers go through the wall to the customer facility. The compact OptiCheck is an inspection and measurement system that offers both in-line gauging of critical finish dimensions and defect detection for seal surface-related problems. With its ability to measure finish dimensions inline to an accuracy of 0.002 inches, OptiCheck is well suited to the needs of blow-trim containers. Its finish gauging module uses a proprietary configuration of multiple cameras, LED-based backlighting, and high-speed imaging to measure the critical dimensions. Robust image analysis algorithms accurately identify flaws and blemishes, such as whiskers left from trimming, which had been a frequent but hard-to-detect defect on the Graham line. “We are looking at the diameter of the neck, the height of neck, and A, T, E, and H dimensions of the wide-mouth jars so after filling the cap and tamper band can be fully engaged,” Graham process technician Josh Chesley points out. Fine-tuning blowmoulder control To neutralise the inconsistencies in bottle manufacture, be it environmental conditions or variations in preforms, Graham installed Agr’s Process Pilot system to gain additional control over the blowmoulding process. The Process Pilot incorporates interactive software along with a series of sensors providing high-precision wall thickness measurement. These work in conjunction with the blowmoulder controls to proactively manage material distribution in the bottle or jar. Because the system adjusts multiple blowmoulder parameters simultaneously - lamps, blow pressure, and timing, for example - the plant can maintain tight process control limits to produce jars that meet or exceed customer expectations with minimal operator intervention. “You initially set up the blowmoulder to make the bottle with the desired thickness properties, the baseline,” Waud explains. “The Process Pilot system manages it from there, continually adjusting the blowmoulder every one to two minutes to maintain the baseline thickness distribution as the process changes throughout the day or night.” Being able to accurately monitor and manage material distribution of the container is a key benefit for this application. To withstand the customer’s higher filling temperatures, the hot-fill jars must be more rigid than traditional bottles. The Process Pilot’s sophisticated algorithms analyse minute changes in material distribution, using the feedback to adjust critical blowmoulder settings so proper thickness distribution is maintained. Before the blowmoulder control system was installed, Graham operators would monitor the reject rate on the OptiCheck for thread dimensions. When an issue was detected, they would make adjustments to correct the blowmoulder. Now, with the Process Pilot in place, adjustments for material in the thread region are performed automatically. During the Process Pilot installation, the Agr engineer used the system’s graphical data display to illustrate variations in blowmoulder performance and the impact of operator adjustments while the machine was running without the automated controls. Waud comments that the graphic depiction of the process on the full-colour process management screen was especially useful in helping operators understand the impact of their changes to blowmoulder settings. According to Graham, installing the automated control system has generated many measurable benefits for Graham’s blow-trim operations: In just one year’s time this approach has generated 52.7% improvement in waste reduction. Factoring in productivity improvements and reduction in waste, the payback on the equipment investment is estimated at less than a year. “We don’t run our jar line without the Agr systems,” Waud concludes. www.grahampackaging.com","@ID":52}, "BOTTLE MAKING 52 PETplanet insider Vol. 14 No. 10/13 petpla.net Plasmax+: Further enhancements in KHS Plasmax technology Freshness made visible With its improved Plasmax process, called Plasmax+, KHS Plasmax offers new opportunities for a number of different applications. At the same time, its FreshSafe campaign is promoting a new coating solution for PET bottles for sensitive beverages. FreshSafe PET is also giving KHS the ideal opportunity of making a threefold approach to manufacturers, bottlers and the end consumer. In light of the market requirements for high-quality, fresh beverages, Hamburg-based KHS Plasmax, a member of the KHS group and 100% subsidiary of Salzgitter AG, is focusing on improving the barrier characteristics of PET bottles and other containers by further enhancements in their Plasmax technology. The coated bottles offer improved protection of sensitive beverages, thus giving beverages a longer shelf life, and the taste is retained for longer than in conventional PET containers. No additives are used. The FreshSafe PET logo on the coated bottles will visually demonstrate to consumers the improved protective properties, thereby emphasising the enhanced freshness of the product. It enables producers to highlight the benefits for consumers offered by the bottles. In addition to high-quality fruit juice, Plasmax-coated bottles can also be used for wine, beer, soft drinks, ketchup, sauces, and other liquid foods. The glass coating of PET bottles can be easily separated from the base material and the PET raw material during recycling. Even the coating itself is sustainable, since the InnoPET Plasmax packaging machines operate in a particularly resource-conserving manner: The barrier coating of the PET bottles uses a minimum amount of silicon oxide and can in fact even reduce PET consumption. 1g of silicon oxide is sufficient for coating around 500 bottles. In addition, thanks to their non-permeable coating, FreshSafe-PET bottles are lighter than conventional PET bottles. Consumer study In late 2012 KHS commissioned a consumer study to realistically assess the acceptance and thus the market opportunities for the FreshSafe-PET solution. The survey was based on a representative sample of about 1,000 people. It started off with general questions on the criteria which are regarded as important for beverage packaging, leading to what motivates people to buy a particular beverage, and finally to checking consumers’ subjective views on whether certain beverages are associated with specific packaging shapes and styles. PET bottles emerged as clear favourites, with glass containers lagging well behind. Outstanding plus-points that were repeatedly mentioned were lower weight, unbreakability, and convenient handling. Advantages of glass bottles included quality, better taste of the beverages, hygiene, and environmental-friendliness. The respondents were then introduced to the Plasmax coating technology in the Bernd Kempa, Managing Director of KHS Plasmax","@ID":54}, "TRADE SHOW REVIEW 66 PETplanet insider Vol. 14 No. 10/13 petpla.net As sharp as a knife British company Secomak, which is headquartered to the north-west of London, launched its latest development at drinktec 2013. Its Powerstrip air knife drying system has been designed to operate in the latest high-speed production lines. Secomak says that its latest drying solutions reduce downtime, cut costs and optimise efficiency. In PET bottle configuration, it can process between 12 and 60,000bph. Its configurations include date coding, labelling, cap inspection, camera orientation and complex bottle shapes, and the makers assert that it is designed to be fitted over a clients’ own conveyor. The Powerstrip is a modular system that is claimed to eliminate issues related to excess surface water such as rusty crown caps, label adhesion or alignment failures and illegible date codes. Access is by gullwing doors, which are designed to save space. Acoustic packs are supplied as standard. The machine, which is manufactured from high-grade stainless steel, contains dispersed water and directs it to ground level via an integral drip tray and drain, which also serves to isolate and protect the blower, which is available in four, eight and 15kW configurations. Secomak says that ongoing support, provided throughout the equipment’s lifecycle, includes performance optimisation and can also monitor the parent system and flag up preventive maintenance issues before they become critical. www.secomak.com Packers ITW Global Packaging Solutions chose drinktec 2013 to demonstrate the extent and reach of its product portfolio and range of brands. The group includes a number of well-known suppliers of production equipment, packaging materials, systems integration and warehouse automation. ITW has acquired companies in Spain, Germany, Brazil and the United States in recent years and many of them have, individually, attended drinktec in the past. This year marked the first time that ITW physically located its major suppliers to the beverage industry in one stand. The exhibit featured working demonstrations including ITW Warehouse Automation’s Storfast cart-based AS/RS system; a pouch packer from the Meurer Gruppe of Germany, announced as ITW’s most recent acquisition in June this year; a functioning “Dynac-centric” line design loop from Hartness; and stretch film from Mima and Haloila. ITW now has a presence in 58 countries and employs around 60,000 people. www.itwpackagingsolutions.com Fruits of union Gebo Cermex launched EvoFlex palletiser. Conveying and line engineering specialist Gebo merged with overwrapping and end-of-line company Cermex in early 2013 and presented the new product launch from Gebo Cermex at drinktec 2013. The EvoFlex high-speed palletising range is claimed to be flexible enough to any and all types of products and secondary packaging. It features a single-column design, double lifting unit and floor level infeed and the company says that it is the fastest palletising system in its category. It is capable of processing up to twelve layers per minute and is the first in a new range of end-of-line solutions. Gebo Cermex says that the system is designed to enable one person to operate and control the entire end-of-line area. The single-column arrangement enables the machines to switch between different product and packaging formats in under 1min and with no manual adjustment. The company says that this minimises changeover time and line downtime. Gebo Cermex asserts that EvoFlex has the functionality of robotic systems with reduced total cost of ownership, including operational and maintenance costs and reduced energy consumption because of servomotor technology. www.gebocermex.com","@ID":68}, "TRADE SHOW PREVIEW 57 PETplanet insider Vol. 14 No. 10/13 petpla.net Lubricate and release Chem-Trend will present its full range of processing aids for the thermoplastic segment. Of particular interest to the PET market will be the company’s new Lusin Lub O 32 F, which has been developed particularly for the manufacture of PET preforms and PET film. Lusin Lub O 32 F is a hybrid product that acts as both a lubricant and a release agent. Chem-Trend claims that the dual-purpose compound prevents surface scratches on PET preforms in conveyer systems and prevents large PET bottles sticking to each other during production. Its minimal residue formation characteristic means that it helps to ensure a higher quality when manufacturing blown film. Chem-Trend says that its lubricating performance and release properties help to reduce scrap rates, increase tool-life, and cut machine downtimes. Lusin Lub O 32 F contains no solvents, silicone, or halogens; overspray can be removed by using water. The new product is NSF H1 registered and EU (2002/72/EG) certified, which means that it can be used in the manufacture of products which are subject to food hygiene requirements. www.chemtrend.com Chem-Trend Hall 7.2 Booth E09 CHOOSE THE NUMBER ONE. K 2013 / 16-23 October 2013 Düsseldorf / Germany / Hall 09, Booth C05 TOTHE NEWDIMENSION Flexible dosing Colormatrix will exhibit Amosorb, its active oxygen scavenger with enhanced clarity characteristics. in Hall 8A. Active oxygen barrier delivers high-level product protection for oxygen sensitive beverages and foods packaged in PET. The company will be also showcasing its next generation FlexCart liquid dosing system. The company says that the latest version incorporates a range of global packaging and pump variations, with the intention of eliminating the need for additional dosing equipment. The company claims that FlexCart enables clean and spill-free operation, offers improved metering accuracy and minimises waste. The system achieves its flexibility through the use of easily-interchangeable dosing pumps, transfer pumps and packaging types that are suitable for a variety of applications. New packaging cassettes and pump connectors enable quick, spill-free product changeovers without the need for special tools. www.colormatrix.com Colormatrix Hall 8A Booth J13","@ID":59}, "PRODUCTS PETproducts 67 PETplanet insider Vol. 14 No. 10/13 petpla.net Hot runner temperature control Husky Injection Molding Systems has announced the launch of Altanium Delta3, which is an addition to its family of hot runner temperature controllers. It is intended to “bridge the gap” between the functionality of the existing Neo2 and Matrix controllers. Husky says that Delta3 offers an integrated, intelligent platform for from two to 128 zones of control and helps customers achieve increased part quality and improved uptime. Delta3 is equipped with an improved, intuitive navigation method that is coupled with a large, full-colour touchscreen. It is intended to be easy to learn and to achieve fast and consistent start-ups. Automatic storage and recall of set-ups ensure the same processing parameters are used for a mould without operator intervention. Multilingual support is available and historical event auditing and improved process monitoring help to achieve faster troubleshooting. Delta3 is also claimed to have advanced monitoring capability, which will further help to eliminate the risk of bad parts entering the downstream process. Integrated mould protection is intended to prevent material degradation and to address issues before part quality is compromised. Real-time power deviation monitoring enables the automatic detection of signs of possible plastic leakage and impending heater failure. Delta3 has been designed on a platform that supports network connectivity and close integration with other Husky products. Remote monitoring capabilities are available through the Altanium dashboard application. Husky claims that having one control card for all Altanium models, including Neo2, Delta3 and Matrix, maximises interchangeability and reduces the number of parts to stock and maintain. www.husky.ca Into the future with e-calc Austrian plastics processing machinery manufacturer Engel has announced that it has launched a new calculation app for mobile devices. The app, called e-calc, will automatically supply the values required for material and component-dependent design of injection moulding machines, as well as critical setting data, after the entry of certain parameters. The stated intention is to ensure that the injection moulding machine perfectly matches the application in hand. Relevant materials data are stored in the software and optimum values for the required stroke volume, filling pressure, resulting clamping force and the screw speed and cooling time are computed. Engel claims that the app also offers improved safety, as less-experienced plastics processors can rely on the software to find the right solution, and the machine setter benefits in terms of process settings in on-going operation. The app removes the need for a calculator and manual entry of materials data manually. Materials data for typical thermoplastics, which were previously grouped on a slide rule, are now stored in the app and include melt, mould and pre-drying temperatures and times, viscosity and wall thickness factors, temperature conductivities and de-moulding temperatures, permissible peripheral screw speeds, enthalpy values and guidelines for processing loss. The new software includes a glossary of technical terms. The app is currently available in German and English for Android smartphones; versions for iOS and Windows Phone are under development. www.engelglobal.com","@ID":69}, "EDITOURS REPORTS 20 PETplanet insider Vol. 14 No. 10/13 petpla.net Waste is dumped on the street, in gardens or in dumps. The cartoneros earn themselves a little cash by collecting and sorting it. Around 1/5th of the waste is plastics and most of it tends to be PET bottles. As we discovered, the municipal and provincial authorities only came to appreciate some two years or so ago that they needed to March 13,.2013 Embosur We met: David Fierro Salazar, General Manager Rodrigo Gutiérrez López, Commercial Director Sergio R. Valenzuela, Controller One of Embosur’s CSD best sellers: the Iguazú Cola The Buenos Aires obelisk erected in 1936 on the Plaza de la República 360° Interviews in Chile: Embosur (by Kay Barton) Plasco (by Florian Roscheck) Interviews in Argentina: Refres Now (by Kay Barton) Bericap (by Kay Barton) Reciclar (By Kay Barton) Andina Empaques (By Kay Barton) Quilmes (by Kay Barton) Estambul (by Florian Roscheck) Druetta (by Florian Roscheck) do something about recycling, although nobody here is venturing to make any precise time estimates. Without the cartoneros the situation would probably be even worse, as towns and cities are absolutely dependent on these waste pickers. B-brands with quality Embosur, a company with around 50 employees, has, since its foundation in 2004, maintained its corporate head office in the Coronel Industrial Park in Concepción, approximately 500km south of Santiago. The history of this small bottling plant is in essence derived from two factors, namely, a logical consequence of further development as well as a bold approach and a dash of flair. The idea of Embosur came to Managing Director David Fierro Salazar for the first time in 2003. Before Embosur came about he had also been Managing Director of the supermarket supplier “Cadesur“. He made use of that year to make all the preparations necessary for starting the business. For its part, Cadesur was established in 1989 and subsequently continued until 2009 parallel to Embosur before Mr Fierro Salazar finally closed the operation down. Using his experience in retail with Cadesur, Fierro Salazar, together with local beverages producers, developed his first proprietary beverage under the brand name of Primeros. This was in 2002. Subsequently, in 2003, he decided that he wanted to concentrate on producing his own beverages. Fierro Salazar used that year to put in place the infrastructure for his idea. The Chilean market, according to Sergio","@ID":22}, "EDITOUR REPORTS 23 PETplanet insider Vol. 14 No. 10/13 petpla.net DRYING HAS NEVER BEEN THIS EFFICIENT: ETA plus® LUXOR - now available with ETAplus® ETAplus® considerably reduces energy consumption and protects materials. When it comes to drying, saving energy is a key concern. We have developed a system that combines airflow regulation with a temperature adjustment feature – that can be disabled if required –and efficient waste heat recovery. The result? A drying system that cuts energy consumption by up to 64%: ETAplus® . motan-colortronic gmbh info@motan-colortronic.de www.motan-colortronic.com Halle: 9 Stand: 9B24 16.-23.10.2013 long to short neck and in installing a production line for caps. At this time the preform manufacturer was one of the first companies on the South American market capable of manufacturing short neck products. Today the company is still working intensively and in close collaboration with its customers to reduce the weight of the bottles. Marco Dall’Olio presents a selection of products manufactured by his company Plasco in Santiago. December is an important month for Plasco. It is when more than one tenth of their annual business is generated. In order to be able to handle the high demand in the high season from December to March the Chilean company puts sufficient preforms into store to enable it to tide it over a peak sales period. A flexible approach to bottle production allows Plasco to supply customers on a just in time basis. The 120 production employees who work in the 3-shift system even work on Saturdays in the high season if the requirement dictates. When I tackle him about the future prospects for his company, a broad smile spreads over Marco Dall’Olio‘s face. In the last year alone the amount produced in PET tonnes has grown by approx. 25%. Much of this growth is due to increased sales of new beverages products of his customers who needed new preforms, bottles and caps. In addition to preforms, bottles are also produced at Plasco and packaged for onward transport.","@ID":25}, "TRADE SHOW PREVIEW 58 PETplanet insider Vol. 14 No. 10/13 petpla.net Maag Hall 9 Booth A04 Compact screen changer Maag Filtration’s new screen changer will be shown and demonstrated at K 2013. The company says it is the most compact of its type in the world. The new model has up to four times more filter area than conventional systems. It adapts the patented design of Maag’s large-area polymer screen changer to the special needs and filter requirements of the extrusion industry. The pistons are now fitted with curved breaker plates. 75% of the active piston surface acts as an filtration area and this is claimed to give a filtration area up to four times the size for any given footprint area, which also leads to longer screen life, low pressure differential, a lower flux rate, and an increased filtration level. Its technology was described in PETplanet Insider issue 05/2013. Also on display will be Maag Pump Systems’ new Maax 400S, an automation solution targeted at co-extrusion lines. It complements the company’s existing maax 100S and 600S models and features a new controller, based on the latest Siemens Simatic HMI generation, with a high-resolution 16 million color widescreen touch panel display. Maag group company Automatik Plastics Machinery will be showing its Duro 2000, which is designed for the cost-effective drying of abrasive and sensitive compounds. www.maag.com Dryers and more Motan Colortronic GmbH will be exhibiting its new range of Luxor CA S dryers with hopper volumes of 0.75, 1.5, 3 and 5l, which has been developed for the production of small and micro parts, is among the highlights. The dryers are small and light enough to be mounted on all processing machines. They take factory-supplied compressed air and expand it to atmospheric pressure, which produces dry process air with a very low dew point. Motan’s ATTN automatic temperature and dew point levelling system option is now available for the whole Luxor A dryer range. ATTN has been specially developed for applications with which drying of materials needs to take place within a narrow dew point “window”. Also on the stand will be Ultrablend gravimetric dosing system for pharma, medical and cleanroom applications; new Spectracolor G dosing and mixing stations designed for yarn fibre applications, including PET yarns; and Gravinet GP Light control systems. www.motan-colortronic.de Motan Hall 9 Booth B24 Erema Hall 9 Booth C05 Under wraps? Erema, supplier of recycling equipment from Ansfelden/Linz, Austria, which this year celebrates its 30-year anniversary, has announced the presentation of a new core technology at K 2013. The company is keeping everyone guessing as regards the technological details which will only be unveiled at the Fair. www.erema.at Recycling heavily contaminated waste Starlinger will have two stands at K2013. In hall 9, Starlinger recycling technology will launch a new development, which allows the recycling of highly contaminated post-consumer and post-industrial plastic waste such as washed household waste, agricultural films or similar, as well as heavily printed material. The technology will also demonstrate very good compounding capability for upgrading the final product. During the exhibition a RecoStaruniversal 65 VAC will process highly printed PE film and demonstrate the high-quality melt degassing and cleansing capacity needed for high-quality regranulate that can be used in different applications. Starlinger viscotec will stage the world premiere of the new Decon reactor in hall 9. A ViscoStar reactor will be set up in hall 16, where a video wall will also show the recently launched ViscoSheet PET sheet line. The new sheet line is able to process up to 100% recycled PET, virgin PET, and PIR (post-industrial regrind) at guaranteed IV levels, meeting FDA/EFSA levels for food-grade applications. www.starlinger.com Starlinger Hall 9 Booth D21 Hall 16 Booth B47 Market segmentation Italian company Piovan will be presenting “Industry Expertise” which is taking it towards industry sector specialisation. The company says that Industry Expertise refers to eight fields of application: packaging, automotive, industrial & electronics, building & construction, textile, furniture-toys-housewares, medical & pharmaceutical, recycling & compounds. Each of these fields can be further subdivided into additional specialised sectors. Packaging, for instance, includes sectors such as PET preforms, thermoforming sheets, cap production, vial blowing, blown film extrusion, plastic bands and so on. The consolidation of technological advantage, achieved through drying systems like Genesys and Modula, cooling systems like PETchiller and Ecosmart and the expansion into new fields of application with Ryng, Winfactory and other new products in the future, will form the backbone of Piovan’s development in coming years. www.piovan.com Piovan Hall 9 Booth C59","@ID":60}, "MATERIAL / RECYCLING 32 PETplanet insider Vol. 14 No. 10/13 petpla.net The likelihood that the successful development of PRS and the recycling system as a whole may also have something to do with the personalities of the directors and the management, as well as their professional tenacity, diplomatic skills and continuity ongoing over a number of years cannot be ruled out. René Herzog, who has been discharging the duties of Managing Director for more than 20 years, will be retiring in 2013. His successor, Jean-Claude Würmli, has committed himself to carrying on the tradition. Bottling in closed circuit Call it a Swiss phenomenon if you will, this closed circuit bottling with the emphasis on the word ’closed‘. The target agreed by all those concerned is to ensure that this closed circuit solution is applied to as many PET bottles filled and used in Switzerland as possible. 60% of all bottles are being collected, sorted and recycled before they find their way into new PET bottles in the form of flakes or granulate and are subsequently reabsorbed into the same cycle. The remaining 40% end up as raw material for secondary markets. Over 90% of the PET material stays in Switzerland. Clean goods are supplied and returned. At the beginning and end of the bottle-to-bottle cycle are the bottling companies. Up to a maximum of 40% recyclate (RPET) is added to new virgin for manufacture of new PET bottles. The unavoidable waste has left the circuit already in the early sorting processes. PRS is responsible for the comprehensive collection of used PET beverage bottles and for compressing, sorting and re-compressing them, for supplying sorted PET beverage bottles to the recyclers RecyPET AG and ITW Poly Recycling GmbH who supply RPET to the bottlers. René Herzog says: “From the point of view of quality, it is important to us that the cycle in Switzerland should take place with materials that have been processed exclusively in Switzerland. Once filled in Switzerland, the PET bottle stays in Switzerland, it is collected up and returned to the cycle. It is only in this way that we can ensure proper management of quality control”. Financing arrangements Since 1991 PET Recycling Switzerland has been levying a pre-paid contribution to recycling on PET disposable bottles. This contribution, together with the proceeds from the sale of collected material to the recycling factories, serves as a straightforward financing instrument, with no profit or market control objectives, for financing collections, transport, administration and communication. (i.e. 2/3 of cost from pre-paid contribution, 1/3 from sale of collected PET). Collecting the PET bottles Collecting PET is a straightforward affair and yet it is during the process of collecting the PET bottles that the success of the Swiss system overall is judged. At the same time social acceptance and how to motivate everyone to join in is just as important as collecting the bottles. PRS is responsible for organising the collection of the PET bottles. PET beverage bottles can be handed in at sales points selling beverages in PET bottles in more than 7,000 locations. In addition, public collection containers are available. With 7,000 locations obliged to collect the recycling quota of 55% is achieved. Growth potential is nearly exhausted. And then there are operators of collection booths with a total of approx. 30,000 operations in the work and leisure sector. These account for more than 2/3rds of the overall network of collection points: offices, schools, inns, hotels, filling stations, railway stations, sports grounds, hospitals and homes. Here 26% of recycling quota is achieved. Growth potential exists for new voluntary collection. In total 55% plus 26% equals to 81%. Despite the cost the recycling quota above 75% is being achieved with voluntary collection only. The PET bottles, once collected, are picked up by PET Recycling SwitzerRené Herzog, Managing Director (left), and Jean-Claude Würmli, Deputy Managing Director of PET Recycling Switzerland (PRS) Caspar van den Dungen, Managing Director of ITW Poly Recycling GmbH","@ID":34}, "BOTTLES 71 PETplanet insider Vol. 14 No. 10/13 Push-pull with collar Colgate-Palmolive demonstrates, through its bottles of washing up liquid, how a screw-on push-pull closure can be integrated in the design of the bottle. The transparent PET bottle containing 500ml of washing up liquid is fitted with a closure that features a collar underneath that covers part of the shoulder of the bottle and ensures a visually appealing transition from bottle to closure. The push-pull, tinted green, is fitted in such a way into the sides of the closure (which is slightly extended upwards) that it cannot be pulled out by accident. www.colgate.de Washing gel Neutrogena is marketing its 200ml skin-conditioning wash gel with lemon and mandarin extract with the additional epithet “visibly clear“ in a clearview PET bottle. The product reportedly cleanses the pores of the skin, protects against new impurities and ensures a more matt appearance to the skin. No-label-look labels to front and rear convey the necessary trade data and a rotate-to-lock pump dispenser made from transparent plastic is used to close the bottle. www.neutrogena.de Supple curves for fabric conditioner The German discounter Lidl is packaging, under its trademark Doussy, 2l of fabric conditioner in a purple-tinted PET bottle. The side contours are designed in sweeping curves, featuring embossing in the shape of waves and/or droplets whilst there are two side recesses which act as handles. The silvercoloured screw cap serves as a dispenser cup. There are two shaped labels which convey the necessary trade information. www.lidl.de","@ID":73}, "MATERIAL / RECYCLING 37 PETplanet insider Vol. 14 No. 10/13 petpla.net At its K 2013 press conference, BASF Plastics Additives introduced an additive designed to be used in the recycling of PET. The additive, known as Joncryl ADR, is claimed to help recyclates to achieve high performance characteristics, superior even to virgin product: The keyword is upcycling instead of downcycling. Downcycling through processing and re-processing The polymer chains of a recycled plastics material are exposed to harsh conditions, not just at the reprocessing stage but even the original compounding and processing can lead to a reduction in the average molecular weight. There are the further stresses to which they are exposed during their “active life”, for example, reactions due to ageing , hydrolysis and contact with acids, laundry detergents or other aggressive media. For these reasons, neither fresh recyclates nor even scrap and faulty batches from the manufacturing process have generally been able to compete with the material properties of virgin material itself. A special case is PET, a plastic not actually produced by BASF. All over the world PET bottles are collected, comminuted, washed and pelletised on a huge scale. The pellets obtained are remarkably uncontaminated with other types of plastic. This is why mechanical PET recycling makes a lot of sense compared with some other plastics where this level of purity can only be achieved at significantly greater expense and inconvenience. Nonetheless, even the use of recycled PET polyester was for a long time limited to simple applications such as fibre production; melt strength was not sufficient to manufacture high-grade packaging because of the shortened chain lengths of the molecules. The result is downcycling of the material which means that it is only suitable for use in applications of lower quality. The problem with insufficient melt strength of PET recyclates can be solved by using functional additives from BASF such as Joncryl ADR. These are chain extenders, i.e., molecules that attach to the ends of broken polymer chains. They act like an adhesive which sticks the split polymer chains back together again and so repairs or “heals” them at a molecular level. Not only are the original chain lengths and hence melt strengths restored as a result; the molecular chains produced can be even longer than in the original material, depending on the amount of additive incorporated. Consequently, the restored material can be used not only to make bottles again, but it can also be processed into sheets that are thermoformable into packaging - such as cups for the food industry. In addition, Joncryl ADR additives can also endow the recycled polyester with completely new and desirable properties. Chain extenders having multiple reactive sites can link polyester fragments together to form highly branched polymers of high molecular weight which are completely unobtainable initially via conventional poly-condensation reactions; they then also display correspondingly interesting mechanical properties. Joncryl ADR 4300 equips recycled PET for example with increased tensile strength useful in packaging straps or high-tenacity fibres. PET with glass fibre Exclusively in the USA, BASF offers Petra 7030, a special easy-flow injection-moulding PET with 30% glass fibre content, based on recycled material. Petra 7030 combines high strength and stiffness with very good dimensional stability, low creep and good high-temperature properties. Because of its good flow properties, the products fabricated from the material have a high-quality surface finish even without painting. Petra 7030 has already come to be used in the 111 Navy Chair, manufactured by the furniture maker Emeco and presented during the design competition of the North American plastics fair NPE 2012. It is made from recycled PET bottles. www.plasticadditives.basf.com","@ID":39},
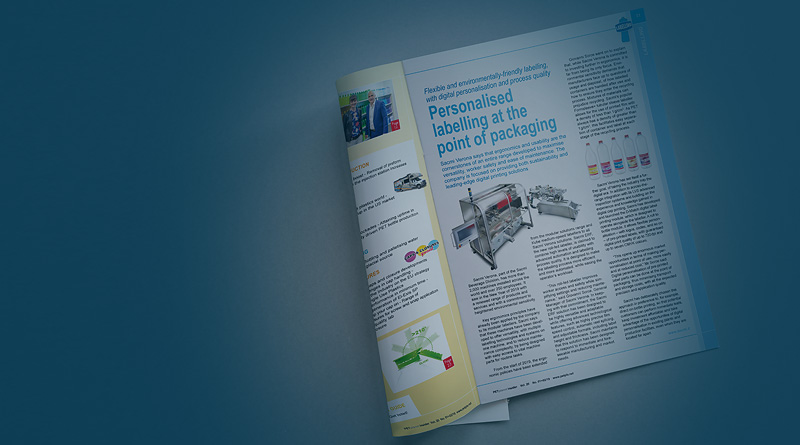