"INSPECTION EQUIPMENT 42 PETplanet insider Vol. 16 No. 09/15 petpla.net ously shortened to its initial letters Agr. David Dineff explained: “The similarity in the measuring methods for glass and, after that, PET containers formed the starting point for conducting further research here and for adapting our machines for PET. Today we serve both sectors equally effectively”. A further important step in Agr’s history was the acquisition of Topwave Industries in 1999, which brought with it extended potential in terms of the product portfolio. After the acquisition of Topwave, during the years up to and around the turn of the century, Agr developed several other products such as Pilot Technology, which, as in the case of OLT, was used for the measurement of PET bottle wall thickness at production speeds with corresponding management of blow moulding lines. The Pilot System ensures, with its interactive control of the blow moulder, that wall thickness is managed precisely, on every bottle. This is true on difficult to process bottles, and especially those that have undergone aggressive lightweighting efforts. “At the moment there are 250-300 of these systems in use worldwide in the reheat stretch blow mouldings sector,” says David Dineff ”Many of the major beverage companies such as Coca-Cola, Pepsi, Niagara, AB InBev, Nestlé etc. form part of our customer base”. The main site at Butler has been retained with all its traditional and historic aspects. It is here, spread over several buildings with a total area of more than 12,000m2, that the complete production complex, plus the R&D Center, training and presentation rooms as well as the offices, is to be found. Agr has around 230 employees worldwide, 180 of whom are stationed in Butler. Agr’s global presence is split into four sectors: the Americas, Southern Europe/Northern Africa, Eastern Europe and Asia. These are independent locations with four regional directors offering a full range of services in addition to sales. “Our annual growth is between 4% and 6%”, says Robert Cowden. Agr is in private hands and has 15 shareholders. The main shareholder is Henry Dimmick Jr. What is it that makes Agr so special? “Well, we are currently the only company in the world that is able to supply machinery for real-time measurement and automated process control of PET container production at normal speeds”, replies Robert Cowden. “Our philosophy is to generate value-creating solutions. We employ an expert team of engineers, technicians and physicists whose job it is to develop ideas that do not occur to anyone else”. One of these is a machine add-on for the Process Pilot system by the name of Crystalview. This is intended to monitor and manage crystallinity/orientation. The aim is, by producing PET bottles with a consistent crystalline structure, to create more options within the lightweighting sector, improve the barrier characteristics and at the same time maintain the optimal wall thickness of PET containers. Certainly a meaningful idea when it comes to tackling the material savings side, especially considering that material is a significant portion of the total unit cost. “Our Chief Technical Officer Mr George Wolfe published some test results on crystalline structure in PET bottle manufacture using hot and cold moulds in 2014”, explains Robert Cowden. “As regards to CSD bottle manufacture in the cold moulding process, the tests showed, in the case of half litre and 2 litre bottles, that the time to stress cracking in relation to stretching temperature plays a decisive role”. (Fig.1) It is evident that the time to stress cracking improved significantly by maximising orientation in the cold process without any secondary effects. For bottle manufacturers this would signify good stress crack performance, minimum volume expansion under pressure, and maximum shelflife and burst pressure (Fig.2). For the cold mould process, the Crystalview product will enable the processing of preforms at the coldest possible temperatures for optimisation of the crystalline structure. In addition to improved bottle quality and performance this will offer the added benefit of significant energy savings that result from reduced processing temperatures. A version of Crystalview is also under development to regulate the hot mould process in a similar way. In this case, Crystalview will facilitate the processing of preforms at the hottest possible temperatures to maximise crystallinity/orientation without affecting the bottle clarity. The management of crystallinity/orientation in combination with maintaining the correct material thickness completes the process. Here Agr’s Process Pilot system comes into effect, which precisely controls and maintains material distribution, for either the hot or cold process, at a specified thickness to within ~0.0025mm and rounds off the overall process. Agr has announced that Crystalview will be released on to the market in the first quarter of 2016. www.agrintl.com F.l.t.r.: David Dineff and Robert S. Cowden in front of the Pilot Profiler","@ID":44}, "PRODUCTS 45 PETplanet insider Vol. 16 No. 09/15 Wellbeing in two glasses The Italian mineral water bottling company Ferrarelle SpA, owner of the Ferrarelle, launched a new mineral water Fonte Essenziale in March 2015. This mineral water is said to have beneficial effects on the hepatobiliary and intestinal systems, the most important of the waters administered at the Terme di Boario for hydropinic treatments. Fonte Essenziale aims to be a natural mineral water particularly suitable to clean the liver, stimulate bowel motility and thus facilitate proper evacuation. It is a mineral water intended for a selective individual consumption, not to the whole family-a product with a proper dosage. In order to feel the beneficial effects two glasses (400ml) are recommended, to be taken every day in the morning, preferably at room temperature and before breakfast. For this special positioning a packaging was needed able to express the core values of the product: the individual consumption at home and the specific functions for the liver and intestine, at the same time, communicate the fact of belonging to the category of mineral waters as well as the absolute purity and naturalness of the product. The choice was a 1l PET bottle usually tied to the on-thego consumption. The six pack bottles may allow an individual treatment of 15 days, a period in which the effects on the liver and intestines taking in through the recommended quantity of water, according to research done studies. That is why the designers of P.E.T. Engineering began sketching the packaging from the analysis of the context of use, the kitchen and the glass. Both become tools for drinking and a measurement unit for the proper dosage, as reported on the label. The designers were inspired by the simple geometry of tableware glasses coming to an essential and clean shaped packaging, with no decorations, elegant and delicate. The use of a transparent preform, thicker than common preforms of the 1l PET bottles on the market, has allowed obtaining a full gloss and a transparency similar to glass. The material used for premium bottles of the ho.re.ca sector, offering a consistency to the touch that enhances the distinctiveness of the new Fonte Essenziale. The purity of the material, its flat base, the thin label attached to the lower part of the bottle, enhanced by the creative look & feel of the brand developed by Life Communication, expresses the values and the preciousness of this water of a unique positioning. www.petengineering.com","@ID":47}, "Please order your copy at the PETplanet insider book shop: https://petpla.net/books Bottles, Preforms and Closures - A Design Guide for PET Packaging Second Edition by Ottmar Brandau € 115,00 180 pages © Copyright Elsevier 2012 CAPPING CLOSURES 40 PETplanet insider Vol. 16 No. 09/15 petpla.net Different applications, neck finishes for various, part 3 Closure for PET bottles PETplanet Insider is publishing extracts from successive chapters of Ottmar Brandaus’s “Bottle, Preform and Closures”, which was published by hbmedia. A newly revised version is reissued under the Elsevier imprint. 4.2.4 Necks for custom bottles Besides the three beverage categories discussed, there are now thou-sands of bottle types that do not fit into any of these. To give both bottle and cap producers a framework that guarantees that cap and bottle fit together, the Society of the Plastics Industry has devised a system that specifies both dimensions and tolerances. The data sheets give both metric and imperial dimensions, whereas nomenclature always refers to the metric number. The name of a neck finish of this type always starts with the letter “M” followed by the size of the neck in millimeters. After that come the letters “SP” followed by the numbers “400,” “410,” or “415.” These refer to 1, 1.5, and 2 thread turns, respectively (Fig. 4.7). Most bottles in this category are still extrusion blow moulded, but the injection process delivers a more precise and repeatable neck finish. Added to this weight savings that may be achieved by using PET and PET’s superior consumer appeal, it is understandable that many brand owners are looking for ways to convert into PET. Fig. 4.7 A large number of customised neck finishes are available through the SPI (Society of the Plastics Industry) system. Obstacles here are the greater flexibility of extrusion blow-moulded bottle designs, for example, with handles, and the higher tooling costs of the injection stretch blow moulding process. As many custom bottle necks do not feature an NSR, it becomes more difficult, though not impossi- * This article was published in Bottles, Preforms and Closures, Ottmar Brandau, Chapter 4.2 Copyright Elsevier 2012 ble, to guide preforms and bottles through blow moulding machines and conveyor systems. Therefore, many custom bottles are manufactured using the single-stage process, which is also more suitable considering the generally lower yearly volumes.","@ID":42}, "PREFORM PRODUCTION 23 PETplanet insider Vol. 16 No. 09/15 petpla.net Entering international markets by Kay Barton PETplanet in discussions with Yizumi: (f.l.t.r.:) James Zhang and Kay Barton We met: Mr James Zhang, Director & Deputy General Manager and Mr May Lam, Sales Assistant Yizumi Precision Machinery in Foshan City is a specialist in the manufacture of injection moulding machines. The company came into being in 2002, initially occupying a 2000m² site. The name Yizumi means “spring water” and aims to represents wisdom, strength and permanence. At the time the company was established, the management already had some 20 years’ experience behind it in the plastics sector. The PET sector constitutes a fundamental part of the company’s operations. The constant increase in demand for PET drinks packaging and the associated technical challenges prompted Yizumi to focus on the design and development of injection moulding machines for bottle production. 2005 saw the completion of the first stage of its new factory and a move into the National High-Tech Industrial Zone. Completion of the second stage followed in 2008. By 2010 two further plants had been built in the Foshan District of Shunde and in Wujiang. With the aim of opening up the US American market, in 2011 Yizumi took over HPM, a company from Ohio with a strong tradition behind it. This manufacturer of injection moulding machines, injection moulding moulds and hydraulic presses, with a history stretching back over 130 years and a good reputation in the USA, had been hard hit during the 2008 financial crisis and had been forced to close its doors. The decision to purchase on the part of Yizumi meant that the company was able to secure for itself, in addition to HPM’s forward-looking technology, any amount of potential in terms of its customer base. Another newly established firm that handles sales of HPM machinery locally is poised to pave the way into the North American market from now on. Since 2013 Yizumi has set up three production locations and two technology centres with a total of 1800 employees, including 63 sales offices in China and 25 sales agents spread across the globe. “To date we have designed and sold 200 machines, around 85% of which are on the Chinese market and the remaining 15% on the international market. Things are now really taking off!”, says James Zhang, Director and Deputy General Manager. “Taking into account potential opportunities in the global markets, we see, outside China, the best possible development opportunities for PET in India, Indonesia and the USA. Here population size and purchasing power play a decisive part”. We meet Mr Zhang on Yizumi‘s exhibition stand at Chinaplas, where the company is showcasing its new high-speed second generation PET preform in the IMS System “PET-72A2”. The update from the previous model PET-48A is a comprehensive remould in terms of design and architecture. Based on this system, Yizumi is supplying a turnkey solution inclusive of dryer, chiller and dehumidifier. The system is designed for sizes ranging from 48 to 96 cavities. Plasticising operations on the 2-stage are carried out electrically. “Here we offer our customers a considerable advantage in energy saving”, says Mr Zhang. The plasticising process saves them a minimum of 30% energy expenditure by comparison with similar systems. The clamping mechanism ensures high clamping force and rapid preform ejection; the hydraulic system incorporates a reliable pressure reservoir. In addition, preform unloading is carried out using robotics which ensures gentle handling of the materials. The line is operated by means of an imported controller complete with intuitive touchscreen. “The hot runners, the injection process and the robotics are controlled centrally from a computer. The cooling unit on the unloading robot cools the finished preforms to an ideal temperature”, continues James Zhang. “In the event of a need for modifications or maintenance works our team can step in and access the machine in real time by using remote maintenance facilities. They can also read off values and make the appropriate settings together with the customer”. “Our declared aim”, says James Zhang, “is to help our customers achieve improved rates of return and to give them a better experience. The current situation is that we have devised a 5-year Plan which is intended to put Yizumi on a world footing, primarily through working with international growth markets”. www.yizumi-group.com.hk Sample application: Product: water bottle preform Number of cavities: 72 Neck: 30/25 mm Weight: 12g Cycle time: 8.5s Daily Output: 731,859 pcs.","@ID":25}, "MARKET SURVEY 31 PETplanet insider Vol. 16 No. 09/15 petpla.net SMI S.p.A. PET Technologies Newamstar Packaging Machinery Co., Ltd. 1 Blow Via C.Ceresa, 10, 24015 San Giovanni Bianco (BG), Italy +39 0345 40 111 www.smigroup.it Mr Pietro Volpi Marketing Dept. Manager +39 0345 40 316 +39 0345 40 209 pietro.volpi@smigroup.net Grünlandgasse 5/1/12 2620 Neunkirchen, Austria +43 720 902 169 www.pet-eu.com Mr Maxim Poliansky Commercial Director +43 720 902 169 office@pet-eu.com East Xinjing Road, Zhangjiagang Economic & Technological Devl. Zone, Jiangsu 215618, P.R. China +86 512 5869 1111 www.newamstar.com +86 512 5867 3920 market@newamstar.com 23 ZA des Quatre Vents 95650 Boissy L'Aillerie, France +33 9800 820 70 www.1blow.com Mr Olivier Perche Sales Director +33 9800 820 75 +33 9800 820 71 operche@1blow.com S-Jar20l SR series (11 Models, SR HP 4-16c 3l; 1SR 20c 3l; 3SR HC 3-6 5-10l) APF-6004,APF3002, APF-4 APF-30, APF10, APF-5 RBM2D / RBM4D / RBM6D / RBM8D / RBM8M / RBM8 / RBM10 / RBM12 / RBM12M / RBM14M / RBM16M / RBM20 / RBM20M / RBM24 / RBM24M / RBM26 / RBM30S / RBM40S 1XL / 1XL Lab / 2L / 2LN / 2LO /2LHF / 2XLS / 4L / 4LN / 4LO / 4LHF / 1XXL / 2XXL / 3XXL 0,25l - 3l 0,2 - 2l 250ml-2500ml 0,15 - 12l 5.0-20.0 4l-10l 3,0 - 30l 15000ml 5 - 30l 20 4 cavities 1 to 2 cavities 20 8-40 4 1 nub 6 2 3 2.100bph (depending on the machine model) 1500 8000-80000 2000 2.000bph (depending on the machine model) 1500 4000-40000 1800 1.800-2.000bph (depending on the machine model and the preform weight) 1500 4000-40000 1700 200 jph/c 1.200bph (depending on the machine model and the bottle size) 1250 2000 1000 for 5l ; 600 for 20l 28 to 120 mm 200 for 30l 3.5x4.0x3.5 min 3.7x 3.7 x 3.1 (SR 4HP /SR 6HP) / max 4.8 x 8.6 x3.1 (SR20) 8.6 x 3.2 x 2.5 - 6.4 x 2.8 x 2.3 9.2 x 2.2 x 2.7 - 9.2 x 2.4 x 2.7 2,1 x 1,6 x 2,4 m Auto ejection semi auto 4 gallon 46 to 120 mm neck for oil, water and confectionary. Modular and compact design, reduced maintenance time, 40% savings in the compressed air consumption, quick changeover and mould replacement, Eco-friendly machines, enabled to stretch-blow lightweight preforms starting at 9.94g. oval / complex shapes 5 gallon bottles, 30l keg Efficient single mould capacity, perfect security system, quick-replaceable moulds, long-term continuously-running, energy-saving and lower consumption, capable for multi-type bottles, information processing system, remote monitoring and service module Preferential heating (oval bottles); Neck orientation (standard preforms); Hot Fill; Compatible with Sidel, Krones, KHS, Sipa, Side moulds; Recovery of blowing air; Power recovery Krones AG Sidel Group Boehmerwaldstr. 5 93073 Neutraubling, Germany +49 9401 700 www.krones.com Mr Peter Christiansen Head of Sales Blow Moulding Technology/Block Technology +49 9401 70 4980 +49 9401 70 91 4980 peter.christiansen@krones.com Sidel International AG, Bösch 67 PO Box 6331 Hünenberg, Switzerland +41 41 785 23 60 www.sidel.com Mr Damien Fournier Blowing & Coating Product Management Director +33 2 32 8588 15 damien.fournier@sidel.com Contiform 3 Pro 11 models available Contiform 3 Pro SC 4 models available Contiform 3 Pro H 8 models available Sidel Matrix Blower 61 models available Sidel SBO Universal 2eco; 20 models available Sidel SBO Highspeed eco; 2 models available Sidel SBO Universal 2eco PH (Preferential Heating); 8 models available Sidel SBO Universal 2eco HR (Heat Resistant); 11 models available per range 0,1 - 3,0 (max. 3,78 i.e. 1 gallon) 0,1 - 0,7 0,1 - 2,0 0.25l - 3.5l 0.25l - 3l 0.20l - 0.7l 0.25l - 2l 0.25l - 3l 28 36 26 34 30 34 20 30 2.300 2.300 2.000 2,300 for XS mould size, 2,250 for M mould size, 2,200 for L mould size 2,2 2,000 for SBO 24 / 1,950 for SBO 34 1,400 1,800 / 1,700 for SBO 30 2250 2.000 2,250 for M mould size, 2,200 for L mould size 2,2 not available 1,400 1,800 / 1,700 for SBO 30 2250 1.800 2,250 for M mould size, 2,200 for L mould size 2,2 not available 1,400 1,800 / 1,700 for SBO 30 2,000 bph for Sidel Matrix HR blower 6,5 x 5,4 x 4,6 - 11,7 x 7,6 x 4,6 10,7 x 6,2 x 4,6 - 14,4 x 7,6 x 4,6 6,9 x 4,4 x 4,5 - 11,2 x 6,8 x 4,5 M model: 7.9 x 4.6 x 3.7 - G model: 9 x 5 x 3.7 - L model: 13,7 x 7 x 3.7 from 11.3 x 4.9 x 3.9 to 13.1 x 4.9 x 3.8 6.7 x 3.3 x 3.8 - 10.6 x 4.9 x 3.9 7.1 x 3.3 x 3.8 - 18.8 x 6.6 x 3.9 Bottle design & mould manufacturing; Nitro-Hot fill; Airrecycling systems for standard- & heat-set machines; rapid product change-over systems (MouldXpress); integrated preform- and bottle inspection; Mini output smaller model / Maxi output larger model: for XS mould (up to 0.75l): 26,400 - 78,200 bph; for M mould (up to 2 l): 12,000 - 54,000 bph; for L mould (up to 3.5l): 7,200 - 52,800 bph Mini output smaller model / Maxi output larger model: 6,000 - 54,000 bph Mini output smaller model / Maxi output larger model: 36,000 to 72,000 bottles per hour Mini output smaller model / Maxi output larger model: 8,400 - 28,000 bph; Speed up kit available on request Mini output smaller model / Maxi output larger model: 6,000 to 51,000 bph","@ID":33}, "COMPRESSION 34 PETplanet insider Vol. 16 No. 09/15 petpla.net dampers. It can be installed as a floormounted compressor with all ancillary equipment fixed on a baseplate, complete with all interconnecting pipework and electrical wiring; options for acoustic enclosures are also available. The WH35 uses the same crankcase casting as the WH29 and WH40 models, which means that the company can adjust its production to meet actual demand. The real lead time for the crankcase is around 26 weeks but customer lead time is around 12-16 weeks, depending on the model and required options. Sales of WH35 are expected to run at 10 to 20/yr, depending on market conditions. “At the start of the year we partner with our suppliers, to schedule the number of required crankcases. We will have the opportunity to ‘tweak’ throughout the year, in order to adjust the demand as the markets require”, Mr Perry explained. “We have deliveries every couple of months and hold a number in call-off. We add cylinders, motors, control panels, wiring, piping and other ancillaries here, at Redditch. The pipeline is under constant review and we have weekly sales calls with our sales partners.” Gardner Denver introduced Lean manufacturing a number of years ago. “The construction of the new facility in 2010 was the big catalyst for Lean”, he continued. “As you walk round the factory you will see issues boards and that everything is laid out clearly, working to 5S principles. Kaizen was introduced about 18 months ago and we have held a number of team-based kaizen events. We appointed Kane Marshall as Operations Director recently and we have a Continuous Improvement manager starting very soon. We see our approach as searching for continuous improvement, not just ‘kaizen blitz’ events – although we will hold them if we identify specific needs”. The effect of the introduction of Lean has delivered some surprises. The company now holds a larger stock of finished Hydrovane inventory, which is made up of smaller machines. This is in contrast to the typical Lean objective of reducing finished goods inventory, in order to deliver ‘just in time’. Gardner Denver operates a sales and operations planning (S&OP) program and what it has achieved is a shorter lead time, better response and lower component inventory, so that working capital and work in progress (WIP) has been reduced. The process also helps with the manufacture of the WH series. While the lead-time of the crankcases means that forecasting, rather than pure demand-led planning, is unavoidable, the amount of WIP has been cut and the process itself is more flexible. Added-value components are called off from suppliers in the UK, Eastern Europe and Asia, with UK suppliers being relied on to meet peaks in demand. The WH35 was ‘softlaunched’ at the ProPak exhibition in June 2015 and is reported to have received a positive response. The factory itself strikes the visitor as very clean and clearly laid out, and it doesn’t take long to spot how the work flows through it, even without our guide – Trevor Perry himself – pointing it out. But he was kind enough to do so anyway, in order to avoid any confusion. As we walked through the facility, the wide range and extent of equipment produced by the Gardner Denver brands and companies became apparent. We paused by a V130 compressor – a huge piece of kit that is used to stabilise oil rigs – before visiting the testing area, where every model is tested for up to 100 hours. The stores hold the full range of aftermarket spares and components. Moving along, we were introduced to a line of WH series crankcases that were awaiting assembly or in the process of it. A WH40 water-cooled unit, destined to be used by a major beverage producer for PET bottle blowing, was being assembled by, among others, Ben Sweet and Charlie Downes, two young men on the company’s apprenticeship scheme who were being ably supervised by Alec Whitehead and Anwar Din, 40-year Gardner Denver veteran engineers. The same beverage producer had already ordered a WH35 compressor, which will be delivered with an integrated aftercooler. “We have worked some of the major blow moulder manufacturers such as Krones, KHS and Sidel in order to ensure that our machine will align with their blowers,” Trevor Perry said. “The machine is computer-controlled in order to ensure repeatability. Better pressure control eliminates pressure losses”. Gardner Denver offers customers full service and maintenance contracts with their new machines. Another side of the operation that is growing is refurbishment. Gardner Denver WH series crankcases awaiting final assembly","@ID":36}, "MATERIAL / RECYCLING 15 PETplanet insider Vol. 16 No. 09/15 petpla.net MATERIAL / RECYCLING 15 Sorema adventure in Perpetual With its 40 years of experience Sorema is one of the leader in the design, construction and installation of plastics recycling plants worldwide. The activity covers all steps of the turn key project, from engineering, procurement and machine construction to the complete installation and plant startup. Since the early years Sorema developed strategic associations with customers around the world which were mostly requested by the local entrepreneurs. Following this strategical activity Sorema has joined Perpetual Recycling Solution in the USA - Indiana. This company, using Soremas wash line, is also equipped with machinery from other suppliers: in the feeding area, the sorting area, etc. One of the targets of this project for Sorema will be the harmonisation of the components changing and / or adding Sorema design-modules to obtain a fully integrated process. This activity foreseen multiple steps of implementation (improvement of the quality and the capacity) also considering the optimisation of the yield as the main objective of the intervention. The yield improvement should be found in the recovery of the products which includes PET fines, HDPE, labels, trays, etc. This approach at 360° of the PET recycling activity, using the US curbside material find justification in the present market conditions: 1) Provide higher added values to materials which drop significantly due to the reduced international demand. 2) Reduce the cost of waste material disposal. 3) Provide higher grade of flexibility on the input material acceptance due to the natural variability of the bale composition. 4) Improve the overall profitability of the mechanical recycling process. A new Sorema division (S.A.M. – Sorema assistant and management) was founded to provide the start up of a new project including the training of the operators, the definition of the production’s procedures, reaching higher manufacturing performance and for quality control (Q.C.), maintenance, logistic, etc. This all is integrated in a dedicated enterprise resource planning (ERP). The Perpetual Recycling Solution challenge is already providing positive results according to the expectation of all partners. www.sorema.it","@ID":17}, "MARKET SURVEY 30 PETplanet insider Vol. 16 No. 09/15 petpla.net 09/2015 MARKETsurvey Company name Technopet Machineries, India Postal address Telephone number Web site address Contact name Function Direct telephone number Fax E-Mail 14/15, Shree Naman Plaza, S.V.Road Kandivali(W), Mumbai- 400 067, India +91 022 28610 828 www.technopet.in Mr Vineet Bannore & Mr Sunil Bharkada Parters-Technology +91 9820346565 / 9821040637 vineetbannore@gmail.com/sunil@technopet.in 1. Machine designation / model number TSBM-3C/2l TSBM-2C/2l A-BJ1800 S-B1600 S-Jar 7l S-Jar15l 2. Bottle volume (from/to in litres) a) Standard machines 0.2-2.0 0.2-2.0 0.2-2.0 0.2-2.0 b) Machines for large containers 0.2 -7.0 2.0-15.0 3. Maximum number of stretch-blow moulds (units) a) Standard machines 3 nub 2 nub 2 nub 2 nub b) Machines for large containers 2 &1 nub 2 & 1 nub 4. Output per stretch-blow mould for: 0.5 litres CSD bottle (units per hour) 1400 1.400 1000 800 1 litre CSD bottle (units per hour) 1200 1.200 900 600 1.5 litres still mineral water bottle (units per hour) 1400 1.400 1.000 800 Large capacity container 400 jph/c 350 jph/c Other Neck dia 19 to 28 mm 19 to 28 mm 19 to 28 mm 19 to 28 mm 19 to 83 mm 28 to 120 mm 5. Footprint / space requirement (L x W x H in metres) 4.5x4.5x3.5 4x4x3.5 4x3x3 3x3x3 3.5x3.0x3 3.5x3.5x3 6. Special features (short description/keywords) Neck-up linear blow, neck down IR heating, Hopper feed, Servo 2-SPBM with 360* neck protection Eco and compact auto, Hand feed, servo driven,19-83 mm neck versatile bottle and jar SPBM Semi-Auto ejection manual feed 19 to 30 mm neck. Auto ejection semi auto, 2 gallon, 28 to 120 mm neck for water, oil & confectionary. Auto ejection semi auto 4 gallon 46 to 120 mm neck for oil, water and confectionary. Company name Serac Group MEGA Machinery Mould Co., Ltd. Urola S.C. UAB Terekas Postal address Telephone number Web site address Contact name Function Direct telephone number Fax E-Mail 12, route de Mamers, BP 46, 72402 La Ferté Bernard Cedex, France www.serac-group.com Mr Vincent Friart Blow Moulding Division Manager +60 3 7847 2228 vifriart@seracasia.com Xiayangao,Yanjiang, Linhai, Zhejiang,China +86 576 84020 122 www.MegaMachinery.com Mr Simon Sales Manager +86 576 84020 122 +86 576 84020 107 Simon@hymega.com Urola Kalea s/n, PO Box 20230 Legazpi, Spain +34 943 737003 www.urola.com Mr Iñaki Unanue +34 943 737144 iunanue@urola.com Vytauto g. 114A Kretinga LT-97134, Lithuania +370 445 51 431 www.blowmoulders.com Mr Gintautas Maksvytis Head of Export Department +370 445 77 868 gm@terekas.lt 1. Machine designation / model number Serac Blow Linear Lineal: URBI-2, URBI-4, URBI-6, URBI-8, URBI-2L, URBI-4L Rotary: SBM-6S, SBM-10S, SBM14S, SBM-20S, SBM-6, SBM-8, SBM-10,SBM-14, SBM-20 LITO 6/6 2. Bottle volume (from/to in litres) a) Standard machines 0,05 - 5l 2l 100ml - 2l 100-700ml 0.5l - 2.5l b) Machines for large containers 30l up to 10l 100-2500ml 5l - 40l 3. Maximum number of stretch-blow moulds (units) a) Standard machines 12 16 8 20 6 b) Machines for large containers 4 (1.5l - 5l) 2 4 20 4 4. Output per stretch-blow mould for: 0.5 litres CSD bottle (units per hour) 1.800 1600 1.600 1800 9000 1 litre CSD bottle (units per hour) 1.600 1500 1.600 1800 9000 1.5 litres still mineral water bottle (units per hour) 1.600 1200 1.700 1700 9000 Large capacity container 1200 (5l) 500 1.250 1600 5000 Other 5. Footprint / space requirement (L x W x H in metres) 6.2x2.2x2.7 Depended on the machine model URBI-2 (2.32x2.2x2.0) - URBI-8 (5.9x4.35x2.3) SBM6S(2.41x6x3.0) - SBM20 (4,5x3,5x3,24) 6x2x2.4 6. Special features (short description/ keywords) Fully integrated with with Serac fillers (Combox solution); No mechanical adjustement in change-overs; Significant economical savings with air recovery system and low electricity consumption provide the PHS for oval bottles, ARS, heat set blow moulds Fully electric, very compact, low energy consumption Options: preferential heating; air recovery, hot filling Short mould changeover time and high production flexibility","@ID":32}, "MARKET SURVEY 29 PETplanet insider Vol. 16 No. 09/15 petpla.net Caps and closures Bottle-to-bottle recycling plants Preform and single stage machinery Preforms Preform / stretch blow moulds Closure systems Two stage SBM machinery Compressors Resins / additives Filling equipment Suppliers of two stage stretch blow moulding machinery The companies are listed below in alphabetical order; in the table they appear in the order in which their details were received by the editors. 1 Blow, Amsler Equipment Inc., Krones AG, MEGA Machinery Mould Co., Newamstar Packaging Machinery Co., PET Technologies, Serac Group, Sidel Group, Sipa S.p.A., SMI S.p.A., Technopet Machineries, UAB Terekas and Urola Solutions. Although the publisher has made every effort to ensure that the information in this survey is up to date, no claims are made regarding completeness or accuracy. 09/2015 MARKETsurvey Company name Amsler Equipment Inc. Sipa S.p.A. Postal address Telephone number Web site address Contact name Function Direct telephone number Fax E-Mail 1245 Reid St., Unit 1, Richmond Hill, Ontario, Canada L4B1G4 +1 905 707 6704 www.amslerequipment.net Ms Heidi Amsler Sales and Marketing Manager +1 905 707 6704 +1 905 707 6707 sales@amslerequipment.net Via Caduti del Lavoro, 3 31029 Vittorio Veneto, Italy +39 04389 11511 www.sipa.it Ms Anna Horecica Csiki Project leader/Stretch-Blow moulders development +390438911511 +390438912273 Anna.Horecica@zoppas.com 1. Machine designation / model number Linear Series - 6 Models L12, L15, L22, L32, L407, L42 Linear Widemouth JAR Series - 2 Models L16J, L25J Linear Convertible Series - 2 Models L32C, L42C Linear Large Format Series - 3 Models; L110, LM120, L120C Rotary Series - 2 Models APT10, APT16 SFR Evo Cube: 6 - 8 - 10 - 12 - 16 - 20 -24 cavity (7 Models) Rotary blowmoulders SFL 6: 6/6, 6/6 XXL, 6/4 XL, 6/4 XXL , 6/3 XL (5 Models); SFL 4: 4/4, 4/3 XL, 4/2 XL (3 Models); SFL 4 WM: 4/4 WM, 4/3 WM, 4/2 WM (3 Models); SFL 2/2 & SFL 1 (2 Models); Linear blowmoulders 2. Bottle volume (from/to in litres) a) Standard machines 50ml - 5l 100ml - 6l 50ml - 5l 50ml - 3l 250ml - 3.0l b) Machines for large containers 4l - 23l 250ml - 3l 5 - 30l 3. Maximum number of stretch-blow moulds (units) a) Standard machines 4 2 16 6 b) Machines for large containers 6 2 24 2 4. Output per stretch-blow mould for: 0.5 litres CSD bottle (units per hour) 1800 1800 1500 2,250 - 50,400 1700 1 litre CSD bottle (units per hour) 1400 - 1800 1400 - 1800 1250 - 1500 2,250 1600 1.5 litres still mineral water bottle (units per hour) 1400 - 1800 1400 - 1800 1300 - 1500 2,250 1650 Large capacity container 300 (18.9l) 650 Other 800 - 1600 3000 (4l) 5. Footprint / space requirement (L x W x H in metres) 4.0x1.8x2.4 - 4.3x3.7x2.5 3.9x2.5x2.2 5.7x2.0x2.4 - 4.3x3.7x2.5 3.9x3.8x2.7 2.7x2.2x3.1 to 4.2x3.0x3.2 6. Special features (short description/keywords) Accepts MAG & other moulds; All servo-electric, servo stretch rods; Hot Fill, neck orientation; Air recovery system, handle insertion Accepts MAG & other moulds; Automatic loading of preforms; Up to 120mm neck size; Hot Fill Accepts MAG & other moulds; Flexible cavitation - run 1, 2 or 3 cavities in one machine; e.g. L32C in 3-cavity mode = 2l; L32C in 2-cavity mode = 3l; L32C in 1-cavity mode = 5l Accepts MAG & other moulds; L120C capable of 1, 2 or 3-cavity; Configuration & sizes from 4l to 18.9l Hot fill Polypropelene Output up to 2,250 bph/cav.;Flexibility: servo driven stretching rods, quick mould changeover, reduced TCO: lower air and energy Bottles water, oil, csd, heat resistant, oval sim-and asimmetric, preferential heating, neck orientation, with handle, wide mouth (up to 130mm NF), large size (up to 30 litres)","@ID":31}, "BOTTLE MAKING 27 PETplanet insider Vol. 16 No. 09/15 petpla.net three biggest producers in relation to its European competitors is rapidly substantiated. The customer has the choice between just under 300 different types of preforms for practically all CSD, water, beverages, edible oils, food and non-food applications in all weight and categories / neck finishes. Also on offer are 110 bottles and tubs, 82 of which are in non-metric US format. Different types of CO 2 , oxygen and light barriers can also be incorporated to meet customer requirements. The production ratio is around 70% for beverages / food and 30% for non-food applications. When it comes to catchment areas and product quality, the competitors are the same as the rest of Europe. 25% of all products are exported, chiefly to Portugal and the associated former Portuguese colonies, as well as to Morocco. “We have also been active in Latin America for a number of years but, due to the unfavourable dollar exchange rate, we are no longer sufficiently competitive in this market. However, we have on-going business dealings and good relations and are currently building up opportunities with different countries in Latin America”, reveals Ms Fabo. “The Latin American markets are still very exciting as far as we are concerned”. Depending on the application or requirement, Resilux also delivers to Italy from time to time, depending on, for example whether other plants (in this case the Greek plant in Patras) have the required moulds available. “Our strategy is flexibility, technological strength and proximity to the customer”. And what will the future bring? “Now”, explains Ms Fabo, “we envisage increasing interest in our AirOPack bottles in the future. We have secured a contract with a big manufacturer in this field and it is only a matter of time before this innovative form of packaging starts to become even more firmly established”. AirOPack, the result of a joint venture during the past decade between Resilux and Innovative Packaging Solutions AG, is aimed at revolutionising the spray container sector, e.g. in beauty and medical care, liquid food and detergent products by introducing PET packaging and replacing typical classics such as aluminium cans. This is claimed to improve visual appearance and recycling capability, and also has a patented compressed air method that ensures that the bottle is consistently emptied almost completely without losing any of the product. An innovation which could make aerosols redundant. “Our aim in the short term is to be able to offer a complete ready-to-go product, filled and labelled, with this trading partner”, summarised Fabo. www.resilux.com","@ID":29}, "NEWS 9 PETplanet insider Vol. 16 No. 09/15 petpla.net Logoplaste receives 2015 supplier award from SC Johnson SC Johnson announced Logoplaste as a recipient of its 2015 Customer Service Excellence Supplier Award. The company is being recognised for its best-in-class ontime/in-full delivery speed and flawless execution, while remaining agile and proactive in its supply chain. Winners were recently announced at an awards ceremony during an SC Johnson supplier recognition event in Chicago. The award honors the contributions of Logoplaste in establishing a solid, global partnership with its customer. SC Johnson applauded the company’s excellence in providing best-in-class, cross-functional collaboration both for day-to-day activities and new project developments. \"On behalf of SC Johnson, I’d like to congratulate Logoplaste on its exemplary customer service,\" said Marcelo Stefani, Vice President and Chief Procurement Officer, SC Johnson. \"This award recognizes the company’s proactive customer-oriented business attitude with long-term scope, and strong focus on partnership and continuous improvement.\" Logoplaste CEO, Filipe de Botton, reflected on the honor and immense pleasure in receiving such an award. \"It will increase the responsibility that weighs on Logoplaste when it comes to the quality of the relationship with SC Johnson,\" he stated. \"SC Johnson has the highest standards of FMCG companies worldwide. We have been able to deliver innovation along the supply chain thanks to the fantastic relationships that exist between both teams. We are strongly committed to continue growing our business relationship with SC Johnson on a worldwide scale.\" www.logoplaste.com Lightweight neck for edible oil on the rise It was a good 5 years ago when Bericap first brought the PET 26/21 bottle neck onto the market. This reduced bottle neck size allowed a weight saving of as much as 1.37g compared with the PET 29/21 then dominant on the market, enabling Bericap to make a major contribution to preserving natural resources and improving its carbon footprint. Bericap offers all standard closure variants for the PET 26/21 bottle neck, from a one-part closure through the two-part version to a variety of hinged closure variants. All closures can be configured with a top embossment. The higher closures allow brand individualisation through side printing. BERICAP sells more than 1 billion closures for the PET 26/21 bottle neck every year – and the trend is on the rise. www.bericap.com Foboha receive supplier excellence award Procter & Gamble (Cincinnati) have acknowledged Foboha (Germany) GmbH of Haslach as a preferred supplier for 2014. This is the second time since 2013 that the company has received this award. Together with a further 51 suppliers out of a total of 75,000, they were selected for the award at the beginning of 2015. The Excellence Award is made to companies who develop a special design that goes hand-in-hand with high quality, using innovations, technical know-how and creative problem-solving techniques. This is how A. D.Lafley, P&G’s Chairman of the Board, President and Chief Executive Officer, explained it at the Award Ceremony in Cincinnati, USA. Foboha have for many years been supplying Procter & Gamble with high-cavitation multi-component moulds with the technologies necessary to enable single face, multilevel or cube techniques. Over recent years P&G have been ordering cube moulds increasingly and in greater quantities. A decisive factor as far as the company was concerned was the high level of production output with shorter cycles. The moulds are used throughout the world in the production of plastic components for the Packaging und Health Care sectors. www.advaltech.com Rainer Armbruster, Managing Director Foboha (Germany) GmbH receives the P&G Award","@ID":11}, "MATERIAL / RECYCLING 20 PETplanet insider Vol. 16 No. 09/15 petpla.net PET resin manufacture and recycling by Kay Barton F.l.t.r. John Cullen, Ricky Lane and Joanna Ford next to the PET bottle tree We met: John T. Cullen, Director Resins Sales & Marketing; Ricky Lane, Director Public Affairs, Trade Relations & Corp. Communications; Joanna Ford, The Star Group, Sr. Vice President PR look at where we are now, we have grown more than 13 times in size”. DAK Americas‘ resin capacity currently lies at around 1.86 billion tonnes. Handling this quantity are around 1,500 members of staff who are spread over seven locations, four in North America, one in Central America and two in South America. We took a look at a sample of IntegRex PET (iPET), developed initially by Eastman Chemical, and now manufactured by DAK Americas for Grupo Petrotemex. The material is the company’s main driver with over 540kt sales each year. In contrast to traditional PET manufacturing, the special iPET architecture simplifies and eliminates several production stages in the manufacturing of PET Resin and saves significant energy and costs, such as omitting solids polymerisation. The idea is one part of the sustainability initiatives which DAK Americas has also embarked on at a corporate level, starting in 2006, focussing on ecological and economic aspects. DAK’s main PET product is branded under the Laser+family, which incorporates resins for various applications in the bottles, as well as the textile sector for carpets. An extrusion moulded bottle Resin manufacturer, DAK Americas, was founded in 2001 as a subsidiary company of the Mexican plastics producer Alpek S.A.B. de C.V. , under Grupo Petrotemex, a subsidiary of Alpek. Alpek is in turn a branch of the (also Mexican) business conglomerate Alfa S.A.B. de C.V. The activities of DAK Americas, which has its headquarters in Charlotte, North Carolina, are spread over the PET resin, PSF fibres, TPA monomers, speciality polyester resins and recycled PET sectors. The initial location for PET resin was Fayetteville, North Carolina and this heralded the beginning of what was to become the largest PET resin manufacturer in North America. At the NPE we spoke with Mr John T. Cullen, Director Resins Sales & Marketing and Mr Ricky Lane, Director Public Affairs, Trade Relations & Corporate Communications. John T. Cullen recalls: “Within two years of start-up we had already doubled the size of the company. If we DAK Americas‘ PET timeline: 2001-2007: company creation and expansion following initial acquisition of DuPont’s polyester fibres, monomers and resins businesses, new PET plant constructions and acquisition of the PET divisions of Eastman Chemical in Zarate, Argentina and Cosoleacaque, Mexico 2010: joint venture with Shaw Industries in setting up Clear Path Recycling in Fayetteville, North Carolina, one of the largest PET recyclers for post-consumer waste in North America 2011: acquisition of Eastman’s remaining PET resin division in Columbia, South Carolina: acquisition of Wellman, Inc’s PET resin in Bay St. Louis, Mississippi 2014: acquisition of PET recycling facility “CabelmaPET” in Buenos Aires, Argentina RECYCLING S P E C I A L","@ID":22}, "PACKING / PALLETISING 39 PETplanet insider Vol. 16 No. 09/15 petpla.net June 26, 2014 - We met: Mr Luís Rodrigues, Plant Manager Liquid Food in PET by Kay Barton F.r.t.l. Luís Rodrigues and Kay Barton at Mendes Goncalves’ front entrance The Mendes Goncalves Group which has its headquarters in Golega, also known as “City of Horses”, was launched in 1982 in the form of two separate and mutually cooperative companies, one concerned with bottling a vinegar mix and the other (in which the director at the time already held shares) with the production of the corresponding bottles. It was only very recently, in 2013, that the bottles division, in which production was based on 2-stage equipment from Nissei ASB, was purchased as a complete line and integrated in the form of a Group company. According to Plant Manager Luís Rodrigues who welcomes us in the main Plastics Division building which is currently undergoing renovation “At that time, the end of the 90s, bottle production was launched with an NSB20 from Automa, something that is now acceptable only in exceptional circumstances”. At the time when the bottle production plant was purchased, seven of the eight machines that feature today were already in situ. Alongside the old Automa unit, Mendes Goncalves runs a 2-stage operation focussing on the stretch blow moulding of 20 different types of bottles and these come in a total of around 5 different colours. In use are two PF8-4Bs from Nissei ASB, two 70-DPHs as well as one each PF41BH, 12M and 12N. The dispensers come from Piovan. At present there are 19 people employed in the Plastics Unit who work in three shifts. As a rule there may be up to four to five machines running at the same time here. “We only started in May 2013 but from May 2013 to May 2014 we managed to get through about 700t of PET material and manufactured 37 million bottles”. The company obtains the material from the Spanish company Cepsa. The bottles thus produced within the Plastics Division are used exclusively within the Group which has in the meantime started manufacturing other liquid food products in addition to vinegar within the bottling unit. Examples include ketchup and mayonnaise in squeezy bottles or spicy Piri-Piri with pineapple in a practical spray bottle. “Our products are available in big supermarket chains. For the “Continente, Pingo Doce e Jumbo” chain we even manufacture the “Paladin” brand on an exclusive basis. We buy in the ingredients for our brands as we need them and then formulate our own recipes. Depending on the customer’s requirements, we are also happy to provide support with the development of individually designed packaging and customised flavourings. Basically our customers receive an all-inclusive package as we make everything ourselves apart from closures and labelling (exclusively paper labels are used). For these we go to appropriate suppliers. Mendes Goncalves keeps the lion’s share of its liquid food products within the domestic market. As a result the export share in 2013 was only of the order of 20%. Luis Rodriguez concluded: “The current situation is that an order has just been placed for new moulds as we are at present in the development phase when it comes to new products and designs.” www.mendesgoncalves.pt","@ID":41}, "PETcontents 09/15 4 PETplanet insider Vol. 16 No. 09/15 petpla.net INSIDE TRACK 3 Editorial 4 Contents 6 News 44 Products 46 On site 48 PET bottles for Beverage + Liquid Food 50 PET bottles for Home + Personal Care 52 Patents MARKET SURVEY 29 Suppliers of two stage SBM machinery 36 Market survey USA / Canda, part 1 COMPRESSION 33 45 years of compression PACKAGING 39 Liquid food in PET CAPPING / CLOSURES 40 Bottles, preform, closures Different applications, neck finishes for various, part 3 INSPECTION EQUIPMENT 41 Test equipment for PET – inspired by glass bottle manufacturing BUYER’S GUIDE 53 Get listed! Page 44 MATERIAL / RECYCLING SPECIAL 10 Rethinking the next generation of PET recycling 12 Shipping multi-purpose reactors 13 Granulator for PET 14 Unifi plastics recycling facility 15 Sorema adventure in Perpetual 16 Recycling PET into pellets 20 PET resin manufacture and recycling 22 Panther Ultragranulator for PET bottle recycling PREFORM PRODUCTION 23 Entering international markets BOTTLE MAKING 24 As brilliant as glass …it could only be PET 26 PET preforms and bottles for the western Mediterranean and Africa Page 49 Page 33 RECYCLING S P E C I A L","@ID":6}, "PETnews 6 PETplanet insider Vol. 16 No. 09/15 petpla.net Newamstar Service Integration Brings Maximum Value for Customer Benefiting from fast development of China’s beverage and liquid products packaging industry, Newamstar Packaging Machinery Co., Ltd. has grown from a local enterprise to an important international player in packaging machinery. Presently, Newamstar provides several systems and lines for pretreatment, water treatment, blowing, filling, secondary packaging, robotic casing and palletising plus automatic warehousing for applications in beverage, dairy, alcohol, condiment, household and personal care. During the years the company supplied domestic and overseas customers like Coca-Cola, Pepsi Cola, Danone, Nestlé, Wahaha, Dali, Otsuka, Mayora, ThaiBev, Haitian etc. An important part of developments here is the blowingfilling-capping technology, which combines these processes in one combiblock and centers on digitization and system integration. This compact line handles all kinds of PET bottling activities for beverages, food and non-food products. Newamstar claims being the first in China each with its different outputs of the blowing-filling-capping combibloc of 36,000bph, 51,000bph and now 80,000bph ultra high speed systems. The new machine series in the different segments of the company’s portfolio are equipped with a remote service feature which can analyse equipment operation condition by data readout in case of need. www.newamstar.com Total integration for the beverage supply chain at the “Food & Beverage Plastic Day” On 15 September 2015 Sacmi holds the first “Food & Beverage Plastic Day” to showcase project H.E.R.O. - High Efficiency Resource Optimisation - applied to the beverage supply chain. Sacmi takes this opportunity to present the new IPS 400. This preform production machine is designed to handle moulds of up to 128 cavities. With low cycle times, IPS 400 adds technologies like automated unloading of the preform system and different circuitry inside the plasticising unit to the features of the previous range. Also new is the particular configuration of the cooling station of the preforms, where the kinetic energy of the gripper plate is recovered in the deceleration stage and reconverted into electrical energy. Furthermore Sacmi presents the CPB Link, a new automation dynamic buffer that enables the integration of cap and preform production in the bottling line. New developments of the Colora Cap system for high definition digital caps and closures will also be in focus. This system is now usable even on coloured caps, and fast graphic files loading and instant quick image change make it suitable for various capsule decorations. The company also studied Compression Blow Forming technology with an emphasis on green packaging, specifically the reduction of weights for dairy industry containers of up to 500 ml at equal performance. Finally, inspection solutions developed for the different businesses, machines and plant solutions of the Group will be presented as well. The presentation - followed by a gala dinner - will end with a visit to the R&S Beverage laboratory, where the solutions later industrialised and offered to the customers are developed and tested by Sacmi. The laboratory is a structure certified by the top global players in the beverage industry that can accompany products from the design stage onwards. It combines a guarantee on the final result with highly customised solutions in line with the most modern and diversified needs of the customer and the market. www.sacmi.com Polymetrix wins more PET projects with SSP technology Polymetrix AG, the former Bühler Thermal Processes AG, continues winning PET bottle grade projects with advanced SSP technologies. Two major Chinese PET resin manufacturers in Jiangsu Province and Zhejiang Province each ordered 600,000 tonnes per year of additional bottle grade PET SSP capacity using Polymetrix solid state polycondensation and pellet conveying technology. Recent Polymetrix SSP technology advancements are implemented for even more competitive production of PET resin. The plants will start production in the second quarter of 2016. www.polymetrix.com","@ID":8}, "PETbottles 50 PETplanet insider Vol. 16 No. 09/15 petpla.net Home + Personal Care Vivid colours at Balea The German discounter dm is selling under its own-brand name of Balea a new variation in fragrance in the “Dusche & Ölperlen” range. The shower gel incorporates small pearl-like beads that give off their fragrance when applied to the skin. The vividly coloured product with an apricot and jasmine flower fragrance is packaged in a transparent PET bottle with a content of 250ml and features a bright yellow, snap-on hinged lid complete with metering nozzle which can be operated with one hand and which acts as a closure. www.dm.de/balea Improved mouthwash In France, Unilever has overhauled its brand name Signal mouthwashes for protecting teeth and gums and has also updated the packaging. The alcohol-free Gel Liquide Actif envelopes the teeth in a permanent protective layer which is intended to prevent the formation and penetration of damaging bacteria. The product, which incorporates a glitter effect and is slightly violet-tinted, is bottled in a slightly waisted PET bottle with a content of 500ml. A shrink sleeve label transmits the retail information and a screw-on, opaque screw closure secured with an adhesive sticker and complete with measuring scale facilitates the dispensing of the mouthwash. www.missionsignal.fr","@ID":52}, "MATERIAL / RECYCLING 17 PETplanet insider Vol. 16 No. 09/15 petpla.net SIPA S.p.A. - Via Caduti del Lavoro, 3 - 31029 Vittorio Veneto (TV) - Italy Tel. +39 0438 911511 - Fax +39 0438 912273 - e-mail: sipa@zoppas.com www.sipa-xform.com yesterday today Short cycle times, high shot-to-shot quality, low energy consumption and maximum flexibility. The new XFORM 300 with its unique 6-position post-mold cooling system boosts your output performance for the widest range of preforms. Cooling preforms faster and better, the 96-cavity platform is ideal for large runs and quick mold changes. And it lets you run any mold you want, old or new, OEM-built or not, in total freedom. From ultra-thin walled (with proprietary XMould™ technology) to wide mouth. XFORM 300, low transformation cost, high value. Designed to adapt. Built to last. The new XFORM 300 IMAGINE THE LOWEST TRANSFORMATION COST. IN TOTAL FREEDOM. modest beginnings that Groupe Alma came into being, over the course of decades.” To market leadership with spring water and PET The now-78-year-old entrepreneur has created an empire supplying the whole of France with bottled water using a stringently rigorous concept. “My success is attributable to two things: firstly the exclusive use of pure spring water - nowadays, you see, many municipal utilities have got a problem with contamination as far as water supplies are concerned. And the second key to my success was the breakthrough achieved by PET for still water. This combination of spring water and PET containers is downright unbeatable”, explains Pierre Papillaud. Groupe Alma filled an estimated four billion bottles with spring water and mineral water in 2011, with a workforce of more than 1,600 people in 36 facilities. And in July 2012, Pierre Papillaud landed yet another coup: he purchased the mineral water bottlers Saint Amand, a company with around 400 million fills, which meant the group’s total sales were at a stroke propelled to more than 4.5 billion fills. Lightweighting and bottle-to-bottle recycling It was a few years ago that Pierre Papillaud started to give some thought to how the eco-compatibility of the containers he produced could be upgraded. Firstly, as in the USA, he opted for PET bottle lightweighting. And secondly he introduced bottle-to-bottle recycling of PET containers. At the Lesquin facility, in the vicinity of Lille’s airport, an opportunity arose some years ago to work together with a local recycling firm. Here, in a spacious recycling centre, the Nord Pal Plast company processes used PET containers so as to turn them into non-food-grade flakes for the textile industry. In a separate hall on the premises, Pierre Papillaud had the first bottle-to-bottle recycling line from Krones installed in 2009. The neighbouring Nord Pal Plast plant uses a 50-metre-long pipeline to supply this with just over 1,000 kilograms of nonfood-grade flakes an hour round the clock. Since there is no deposit on PET containers in France, Nord Pal Plast receives ample quantities of unsorted raw material that is mixed with wood, paper, many other plastics, aluminium, metal and further contaminants. So Roxpet decided to use the first recycling line for making pellets, because their production process, thanks to filtration of the PET","@ID":19}, "ON SITE 47 PETplanet insider Vol. 16 No. 09/15 petpla.net Carbonated soft drinks growth in Oman To meet the two-digit market growth from carbonated soft drink consumers, Oman Refreshment Company (ORC), a franchisee of PepsiCo International, has acquired a new production line from Sidel, provider of PET solutions for liquid packaging. ORC operates in different categories of the food and beverage market in Oman. The carbonated soft drinks category is the company’s main focus, which includes Pepsi, Mountain Dew and 7UP, to name a few. ORC has an 89% market share of this category. According to industry estimates, carbonated soft drinks were the most consumed beverage items in Oman with 362.4mill. litres recorded at the end of 2014, and a projected Compound Annual Growth Rate (CAGR) of 8.3% over the next five years. Since February 2015, ORC has been operating a Sidel Matrix Combi12 line which produces carbonated soft drinks in a 2.25l format at a speed of 18,000bph. The complete line, the latest generation of Sidel Matrix equipment, is said to help the Omani company increase its bottling capacity through the Sidel Matrix system. Mr. Youssef Ezzikhe, General Manager of ORC comments: “With the growing local demand for our products and carbonated soft drinks in general, we approached Sidel again to obtain a production line which will enable us to increase production, and eventually to achieve a stronger competitive edge.” Challenging the conventions of PET container production, the modular Sidel Matrix platform includes technological improvements to meet the needs of the liquid packaging industry. The line offers potential to reduce the consumption of raw materials and costs, particularly in terms of the amount of PET material required to produce the bottles. Despite the challenges presented by the carbonation process in terms of the bottle format, lightweighting has been applied to the 2.25 litre-bottles by Sidel’s Packaging Services team, part of the Sidel Service business unit. To produce the lightweighted bottles at high speed, an integrated blow-fill-cap solution - the Sidel Matrix Combi - was used. Because of the neck-handling and transfer of bottles between blow moulding and filling, the Sidel Matrix Combi is not bound by the limitations imposed by air conveyors. “In order for us to extend our equipment and services to a wider audience, we’ve established a solid presence in the region, and we are delighted to see the continuous success and growth that our customers are achieving. By providing innovative solutions, we are enabling beverage producers to keep up with the growth in the industry in their local markets and also at the regional and global levels,” said Harbinder Kathuria, Regional Commercial Director, Greater Middle East and Africa Zone at Sidel. www.sidel.com","@ID":49}, "MATERIAL / RECYCLING 21 PETplanet insider Vol. 16 No. 09/15 petpla.net is under discussion. “What we have here is an interesting example of material utilisation using a new methodology”, explains Mr Cullen. “One breakthrough for us was the development of PET resins that can be used on existing equipment by PP and PE users. This opens up entirely new perspectives in many extrusion blow moulding sectors. Users of polypropylene, polyvinylchloride or polyethylene, commonly used, for example, in the manufacture of containers for cleaning materials, now have the opportunity to change from their materials to PET. The concept is also feasible in the beverage sectors. There is a new EBM application that we are currently exploiting commercially together with a U.S. orange juice manufacturer, an interesting concept for larger containers with integrated handles”. Activities in conjunction with DAK Americas’ Clear Path Recycling enterprise and the question how to deal with the topic of PET recycling in principal are of particular interest to the company. As John T. Cullen says, “We have commoditised rPET in the USA and are keen to continue to keep green thinking alive and to promote it”. He went on: “In the CSD sector we produce a resin mixture with a 20% proportion of recycled material. We can safely say that our recycled PET material, once we have processed it, is on the same level as virgin PET”. The company’s recycled containing PET offerings have been certified by the Association of Postconsumer Recyclers (APR) that the material can enter the normal recycling streams. DAK Americas emphasise the importance of the quality of integrated recycled PET products as a rule for a better quality as if customers were to mix virgin and rPET resins by themselves. “The fact that customers are now coming up to us and asking proactively for material mixtures incorporating a proportion of rPET is still something of a novelty for us, but, currently, it is becoming increasingly evident that, for our customers too, the use of recycled material is important. Nevertheless, the current costs for recycled materials are a problem, in particular when the price of virgin PET is falling as a consequence of the drop in oil prices”. Currently some 30% of PET material is collected in the USA for recycling, according to DAK Americas. This corresponds to about 1 million tonnes of material, approx. 50% of which, it is reckoned, ends up in bottle-to-bottle recycling, divided up into approx. 10% beverages, 20% health and personal care and 50% household cleaning materials. DAK’s parent, Grupo Petrotemex will be licensing their IntegRex PTA (iPTA) technology to M&G Chemicals (Mossi & Ghisolfis Group), the builder of a new facility in Corpus Christi, Texas that claims it will be the world’s largest PTA/PET manufacturing facility. This facility is scheduled to start-up in mid to late 2016 and feature the high level of energy efficiency and competitiveness that iPTA Technology offers. Furthermore, DAK Americas claims a long term contractual right to 400,000t/yr of PET resin produced at the facility. www.dakamericas.com","@ID":23}, "imprint EDITORIAL PUBLISHER Alexander Büchler, Managing Director HEAD OFFICE heidelberg business media GmbH Häusserstr. 36 69115 Heidelberg, Germany phone: +49 6221-65108-0 fax: +49 6221-65108-28 info@hbmedia.net EDITORIAL Heike Fischer Gabriele Kosmehl Kay Barton Michael Maruschke Ruari McCallion Waldemar Schmitke Wolfgang von Schroeter Anthony Withers MEDIA CONSULTANTS Martina Hirschmann hirschmann@hbmedia.net Johann Lange-Brock lange-brock@hbmedia.net phone: +49 6221-65108-0 fax: +49 6221-65108-28 FRANCE, ITALY, UK Elisabeth Maria Köpke phone: +49 6201-878925 fax: +49 6201-878926 koepke@hbmedia.net LAYOUT AND PREPRESS EXPRIM Werbeagentur Matthias Gaumann | www.exprim.de READER SERVICES Till Kretner reader@hbmedia.net PRINT Chroma Druck & Verlag GmbH Werkstr. 25 67354 Römerberg Germany WWW www.hbmedia.net | petpla.net PETplanet insider ISSN 1438-9459 is published 10 times a year. This publication is sent to qualified subscribers (1-year subscription 149 EUR, 2-year subscription 289 EUR, Young professionals’ subscription 99 EUR. Magazines will be dispatched to you by airmail). Not to be reproduced in any form without permission from the publisher. Note: The fact that product names may not be identified as trademarks is not an indication that such names are not registered trademarks. 3 PETplanet insider Vol. 16 No. 09/15 petpla.net dear readers, It is rare indeed for me to be reporting on a product in this section of the magazine but what Next Generation Recyclingmaschinen GmbH (NGR) from Austria are currently showcasing is well worth a closer look. Theirs is a bottle-to-bottle recycling line that melts the PET and cleanses it sufficiently for the FDA to nod its approval and issue the appropriate permit. In fact, the concept is anything but new. Previously, PET shavings, and everything else, were thrown into the reactor during the PET manufacturing process, although this was more about saving money than actually putting bottle-to-bottle recycling into practice. These machines, often described as classics in the sector, chose the flake route, and were much less energy efficient than the NGR equipment. Transforming flakes and granulated material into new material that can be used for bottles is a time-consuming process, involving high temperatures and a vacuum environment. The new NGR system can do all that just a few minutes, at temperatures only slightly higher than the classical process. With a throughput of 2t/hr, the line is also just the right size for the decentralised treatment of PET shavings. So much for the theory. Practical application will reveal whether the theory is sustainable in the long term. Not for nothing have the established machine manufacturers been jumping through hoops for years in an attempt to achieve stable processes which are able to cover all eventualities. There is another consideration to take into account, namely, when it comes to recycling, not all countries are alike. Is it possible for one line to reflect all of these aspects? We are looking forward with eager anticipation to viewing the first commercial lines and having a look at how the new technology will stand the test of time on-site. Yours Alexander Büchler","@ID":5}, "COMPRESSION 33 PETplanet insider Vol. 16 No. 09/15 petpla.net 45 years of Compression by Ruari McCallion Gardner Denver, the global vacuum pump and compressor manufacturer, is celebrating 45 years of production at its site in Redditch, which is just south of Birmingham, in the English Midlands – the historical heart of the UK’s manufacturing industry. The company’s week-long series of celebratory events included the launch of a new machine: the WH35 high-pressure reciprocating compressor. Ruari McCallion took a tour of the factory and spoke with Trevor Perry, Product Director for High Pressure Solutions at Gardner Denver, about the market, products and the impact of Lean manufacturing. Gardner Denver proudly describes itself as “the only company in the UK to offer both vacuum and pressure solutions”. It is now part of Kohlberg Kravis Roberts & Co. L.P. (KKR), is headquartered in the USA and has 36 manufacturing facilities across the world. Its portfolio of brands includes Hydrovane, CompAir, Elmo Rietschle, Reavell, and Belliss & Morcom founded in 1852. The plant at Redditch, England, has been manufacturing for 45 years and now makes Hydrovane, Belliss & Morcom and Reavell products. It saw a major investment in 2010, with the opening of a brand new, purposebuilt facility for oil free compressors. Just over 300 people now work from the site, which also hosts a training school that caters for the needs of the company’s own employees, as well as distributors and customers, globally. “We make up to 2000 training places available each year and regularly train around 1200 people annually,” said Colin Mander, Regional Director for North Europe and the Middle East. Training and development is an important part of the company’s strategy for the future. “We currently have nine apprentices and five graduate recruits at this site and we have plans to increase the number of trainees in the future.” The company held a week-long series of events to celebrate 45 years of manufacturing at the Redditch site. It took the opportunity to launch an addition to its range of high-pressure reciprocating compressors, which are widely used in PET bottling plants. The new WH35 model sits between the existing WH29 and WH40 models in the Belliss & Morcom range. “We identified a gap in the market between our WH29 model, which has an output of 1800m3/hr and the WH40, with its output of 2300m3/hr, both at 40 barG,” said Trevor Perry, Product Director for High Pressure Solutions at Gardner Denver. The gap was identified at around 2100m3/ hr – the WH35’s output is stated to be 2120m3/hr at 40barG – and the company used the design process to respond to market demands for higher output, less power consumption and lower cost of ownership. “We talk directly to and visit our distributors and bottlers of water, still beverages and CSD – our ultimate customers, who use these machines in the process of blow-moulding PET bottles,” Mr Perry said. “We developed the WH35 as a result of hearing what they have to say”. Gardner Denver supplies all the major beverage manufacturers across the world and noted that demand for a machine that would sit in the 2100m3/ hr segment was particularly strong from bottlers in the Turkish, Asian and Middle Eastern markets. The WH35, which delivers oil-free air to ISO 8573-1 Class 0 standard, is claimed to be one of the most efficient PET compressors, in terms of power consumption, currently available. “This has been achieved with the use of the latest extended life materials along with key components such as variable speed drives and a highefficiency, water-cooled, shaftless motor, resulting in up to 20% savings on energy costs”, Mr Perry explained. “When we set about designing the new machine it was important to retain many of the key features and benefits of the successful oil-free systems developed under the Belliss & Morcom brand. Utilising the latest finite element analysis (FEA) and computational fluid dynamics (CFD), key features such as component interchangeability, low interstage pressure drops and low stress levels have all been added”. A particular feature highlighted during the presentation was the fact that the WH35 does not require special foundations. It is described as ‘dynamically balanced’, features cylinders inclined at an angle and is equipped with inbuilt anti-vibration Trevor Perry with WH series high-pressure reciprocating compressor crankcases","@ID":35}, "BOTTLE MAKING 24 PETplanet insider Vol. 16 No. 09/15 petpla.net BOTTLE MAKING 24 We met: Mr Kota Aoki, President & CEO, Mr Shigeo Yoshizawa, General Manager Sales and Marketing and Mr Takeshi Kochi, Section Manager Sales Coordination Section When the thoughts of an injection moulder turn to single stage systems, the supplier almost certain by coming to mind is Nissei ASB. The Japanese company, which has its head office in Komoro City, Nagano-ken, will be celebrating the 38th anniversary of its foundation at the end of the year and has maintained its position over the decades as one of the leading manufacturers of single stage PET lines worldwide. Right from the start, ASB focused on niche products and speciality formats in smaller quantities. The 1978 4-station single stage principle, better known today as the ASB series, is still a best seller, despite the fact that some new lines of machinery have been added, such as the 1.5 stage PF series, the 2-stage heatset PM, CM and HS systems in 1995, the ASB-50MB single stage in 2001 and, in 2007, the world’s first all-electric ISBM machine, the ASB-15N/10E. And, looking back, history confirms the company’s role right up to the present day as a lead supplier in many respects, such as in the introduction of multi-layer and PET bottle handles, to name just a couple of its firsts in the industry. On its exhibition stand at Chinaplas, ASB was showcasing its new thickbase mould development in the form of small cosmetics containers moulded on the compact ASB-12M machine. In talks with Mr Kota Aoki, President and CEO, Mr Shigeo Yoshizawa, General Manager Sales and Marketing and Mr Takeshi Kochi, Section Manager Sales Coordination Section, we discussed background factors and concept. “The competition has increased significantly“, explained Mr Yoshizawa. “Part of our corporate philosophy, however, is always to be one step ahead when it comes to technology. For this reason, we regard making a consistent effort to pinpoint ways of configuring the processing of PET and other plastics intelligently and efficiently in collaboration with our customers and their vision as an on-going aspiration and process within our company“. What started with a modest team of 20 employees has grown into a plant covering an area of 150,000m2 with around 1,450 global employees. The business achieved listing onto the First Section of the Tokyo Stock Exchange in 2013. The majority of shares are held by the founder family itself, which has enabled independence in decision-making processes. In 1997 the company established a plant in Mumbai, India. Today, this is one of the most important production locations worldwide, alongside the Japanese factory. In Japan, they concentrate on R&D and extremely customer-specific machines and As brilliant as glass… it could only be PET by Kay Barton","@ID":26}, "MARKET SURVEY 37 PETplanet insider Vol. 16 No. 09/15 is a focus on agriculture. All sectors of the economy are to a considerable extent dependent on export, the USA being by far the largest trading partner. Canada has enormous stocks of timber and water at its disposal. 46% of the land area is covered by forest. The land mass accounts for more than approx. 20% of the Earth’s fresh water reserves, 7% of which are considered renewable. In addition it boasts the world’s third largest crude oil reserves after Venezuela and Saudi Arabia, primarily in the form of oil sands in the province of Alberta. Additionally, Canada occupies fifth place in worldwide gas and oil prospecting. Since the beginning of the 1990s diamonds have been mined north of the Arctic Circle in the North West Territories and Nunavut. Today Canada is one of the largest producers of diamonds in the world. The country is also the second largest uranium producer in the world (18% of world production) after Kazakhstan. The large deposits of nonenergy raw materials such as iron ore, gold, copper, nickel and rare earths are becoming increasingly more important. Parallel to this Canada has a high-powered economy that is also oriented towards the technologies of the future. Important areas of the processing industry include automotive and aircraft construction, the metal industry, the food industry, timber and paper processing, the chemical industry as well as information and communication technology. 2012 2013 2014 GDP nominal (billions of USD) 1,821 1,825 1,768 GDP growth real (%) 1.70 2.00 2.30 Unemployment rate (%) 7.31 7.08 7.03 (Sources: Dept. of Foreign Affairs and Trade 15.03.2015, US economic statistics, Wikipedia)","@ID":39}, "BOTTLE MAKING 26 PETplanet insider Vol. 16 No. 09/15 petpla.net PET preforms and bottles for the western Mediterranean and Africa by Kay Barton June 26, 2014 - We met: Cristina Fabo Indurain, CFO and Estefanía Villalba Rivera, Head of Purchasing The Resilux Ibérica Packaging plant in the south western municipality of Higuera la Real, not far from the Portuguese border and 130km from Seville, was set up in 1997 as the first plant subsidiary of Resilux N.V. Belgium. We interviewed Cristina Fabo Indurain, CFO, and Estefanía Villalba Rivera, Head of Purchasing, who explained the history of the company and shared their vision for the future with PETplanet Insider. A mere two years after the establishment of Resilux Belgium, in 1994, the company was already looking for a location to expand that made sense from a strategic point of view. They quickly decided on Spain; at that time PET was experiencing immense growth here as the change from PVC to the new packaging material became established. January 1997 subsequently saw the construction of Resilux Ibérica’s first building as a 100% subsidiary, and this still forms part of the production facility today. The first two preform lines followed quickly in the following May. Three years later, in 2000, the remaining buildings were added including the warehouse. There are no problems with on-site expansion as Resilux owns around 60,000m2 of land. But why choose this particular location where we are now standing for a site? “Resilux wanted to be in the south of Spain, beyond Madrid, as the north would not have been a reasonable proposition for us“, says Cristina Fabo Indurain. “If we were based any further north it would mean that the range of our transport trucks would overlap with that of our Belgian headquarters. As things are at this location, both parties have a range reaching as far as the south of France without any further overlaps. In addition, we have sufficient space here in Higuera la Real, we are within striking distance of the Portuguese market with which we maintain a good relationship and also with Morocco, another key market as far as we are concerned”. Lisbon and Seville are more or less on their doorstep, and their proximity to Cadiz and Algeciras is advantagues for the import of materials and the export of their own products. Meanwhile, their fleet of machinery has been topped up to a respectable level, with the result that today there are eleven Netstal lines in the main factory area. There is also a dedicated test line. Resilux exclusively uses Otto Hofstetter moulds, the 96, 64 and 48 cavity models. According to Cristina Fabo Indurain, the trend is increasingly towards 96 and 64. In addition to the sizeable plot, there is still space on the factory floor. “We have been building with an eye to the long-term future of the company,” she continued, “and that means lots of space for new machines and offices”. Up to now they have been adding a line every other year. The lines are geared to Resilux’ requirements and incorporate influences and ideas that have been developed within the company. For metered dispensing purposes, equipment from among others, Piovan is used. Material dryers come from Somos and other specialized suppliers. Back in the days when the company started, the capacity was around 360 million preforms annually, whereas 1.2 billion are now possible. “We are consistently achieving 100% capacity” says Cristina Fabo. The number of bottles produced is currently around 40 million. If we compare the figures with the annual report for the company as a whole, the impact of the Spanish division becomes clearer: With growth a of 25% in 2010, Resilux sold 4.87 billion preforms in 2013; in the bottles sector it was 441 million bottles with a growth of 20.5%. The Spanish subsidiary has more than 120 customers at the moment. Depending on the season, there are around 70 employees working three shifts to ensure a smooth operation. In the outdoor area there are 10 silos, each with a material capacity of 100t. “We tend to rely significantly on local materials suppliers. Depending on the price of PET, we also order from the Middle and the Far East”, says Cristina Fabo Indurain. Looking at Resilux‘ portfolio, the fact that the company rates itself as one of the F.l.t.r.: Estefanía Villalba Rivera, Cristina Fabo Indurain and Kay Barton Editour2014","@ID":28}, "MARKET SURVEY 38 PETplanet insider Vol. 16 No. 09/15 petpla.net PET packaging North America North America is a typical converter market. Transport costs, especially in the USA, are still very low, not least because of the low cost of fuel. This means that the empty PET bottles are transported to the fillers. Inline operations (stretch blow moulding / filling) are in the minority. Further reasons for this are probably the frequent changes of format where the CSD products are concerned which would lead to significantly longer downtimes as regards inline operations. Also, there are in North America, in addition to the major converters, a large number of small blow moulding operations that naturally have no interest in abandoning their present structure. However, in the case of the mineral water bottlers, things are somewhat different; there is a preference for the inline operation especially where the weight optimised small bottle is concerned. Another example is the technique practised by the Portuguese company Logoplaste, which supplies the bottler with PET bottles exclusively by means of the “through the wall process”. This is possible by installing their own blow moulding machines in the customer’s bottling plant. In the CSD sector growth is very restrained or even in decline. Interestingly, the reasons for this lie in the fact that the Americans are becoming more and more health-conscious and increasingly limiting their consumption of soft drinks. At the same time drinking habits are also changing. Whereas, a few years ago, there was a predominance of the 2 litre PET bottles, the trend today is towards the smaller beverage bottles. Figures based on experience and obtained from major market players show that the average size of a bottle has already fallen to 1.2l. A crumb of comfort for the converters who are able, through higher quantities, to compensate to a degree. There is a diffrence to the mineral water sector. Here the figures have seen an encouraging rise over the last few years, even featuring two digit figures from time to time. However, according to Euromonitor, this trend is not set to last. Even now the market is having to content itself with growth rates in single figures and will have to go on doing so over the next few years. There has been some growth in the sector incorporating sports drinks, juices and tea-based drinks in PET applications, but this will also need to adjust to lower growth over the next few years. It is hot fill applications that are predominantly deployed in this area. There are scarcely any instances of aseptic bottling to be found. The reasons for this lie in the multiplicity of stretch blow moulding machines on the market where conversion to hot fill applications represents a considerably more attractive proposition than investing in new aseptic filling lines. PET jars may be described as a niche market. The volumes are relatively small and growth is only moderate. The reasons for this lie partly in the structure of the market itself; there are large numbers of extrusion blow moulding operations that supply the market with reasonably priced PP and HDPE bottles. Even though the PET material is very good value for money at the moment, it is unlikely that replacement will proceed at anything but at a very slow pace. Beverage packaging Canada and USA Retail/off trade unit volume in millions Type of packaging 2012 2013 2014 Canada Total packaging 18.005 18.124 18.241 Rigid plastic 4.174 4.396 4.537 PET bottles 4.028 4.228 4.350 PET jars 7.2 7.1 7 USA Total packaging 196.334 198.116 198.732 Rigid plastic 77.515 80.856 82.468 PET bottles 75.220 78.460 80.040 PET jars 89.2 89.6 86.3","@ID":40}, "PETproducts 44 PETplanet insider Vol. 16 No. 09/15 petpla.net Stretching the limits of PET processing Cypet Technologies Ltd. of Nicosia, Cyprus, manufacturer of single-stage PET processing machines has successfully produced on its Cypet K 28 machine a 50l flat-based container for the storage of liquids, powders or granular products. A 50l beer keg and a 35l conical-based container could be used as a fermenter for home brewing of beer. With the machine model Cypet K 53 it is possible producing up to 100l PET containers. Such containers can replace HDPE drums, especially for single-trip applications, resulting in weight reduction with the corresponding substantial savings in raw material cost. Cypets technology uses one clamping unit for both: the injection moulds for moulding performs and as well as for the blow moulds for stretch-blowing the bottles or jars. By using a strong clamping unit with ample space to house large moulds for big PET containers, Cypet machines are stretching the limits of PET processing to 50l and beyond. With their capabilities for container height, up to 850mm, as well as container body diameter, up to 450mm, Cypet machines are able to provide the PET industry the opportunity into new applications for the bulk packaging of foodstuffs, beverages, cleaning products and chemicals. The machines capabilities are also usable for taller bottles with a less diameter for equivalent volume, resulting in increased strength, allowing to optimise bottle weight in applications like water dispenser bottles. Cypet has patented, designed, developed and commercialised a total of eight machine models ranging from 120t to 530t clamping force for the production of PET containers. Containers sizes from 50ml to 100l, with neck diameters of up to 220mm. Five of these machine models are based on servo-hydraulic technology for energy saving, while three are all-electric machine models, particularly suitable for clean room production of pharmaceutical or foodstuff containers. The Cypet machines are fitted as standard with an air regeneration system, recovering the high-pressure blowing air for re-use. www.cypet.eu Eco-sustainable solutions The Smi laboratories has led to the launch of the Ecobloc series featuring integrated systems of stretchblowing, filling/capping and labelling of PET containers with capacity up to 3l. The Ecobloc systems is said to be compact because of the modular frame, the application technologies ensures the synchronisation between the dry environment of the stretch-blowing module and the wet environment of the filling/capping module. Suitable for bottling lines of still and carbonated drinks, milk and edible oil, Smi’s integrated system of the Ecobloc series offers to the end user for example the machine’s modular and compact structure, which brings together the stretch-blow moulding, filling and capping modules in a single block and allows to eliminate the connection belts between blow moulder and filler and even, except in rare cases, the bottle rinsing machine. With this type of system, there is a reduction of water consumption, electricity, management and in maintenance care. The stretch-blow moulding module of Smi’s Ecobloc is equipped with an air recovery system (ARS), which recovers up to 40% of the high pressure compressed air used in the bottle production process to reuse it either during the pre-stretch blow moulding stage or in the machine’s utility systems. The Ecobloc reduces the risk of contamination of the bottles on their way from the blow moulder to the filler thanks to a star-star system enclosed inside a hollow joining cavity equipped with steel guards. The stretch-blow moulding, filling/capping modules integrated in an Ecobloc system are governed by a single automation and control system that allows the management of the system by one line operator through a simple and user-friendly man-machine interface. www.smigroup.it","@ID":46}, "BOTTLES 49 PETplanet insider Vol. 16 No. 09/15 petpla.net The plastic closure company committed to your success BERICAP Technology Research and Development Mould Technology | Global Presence Capping Technology and Know-How Innovation and Flexibility www.bericap.com Schweppes fruity in PET In the summer of 2015 Schweppes attempted to stimulate sales of the Fruity Range with a new advertising spot. The face of the advertising campaign was the German entertainer and presenter Anke Engelke. With this product range Schweppes was anxious to make inroads into the “sweet to bittersweet” taste range. The three types sporting the “non-bitter” tag, which are being advertised as ‘lemonade for grown-ups’, are packaged in transparent disposable bottles with a content of 500ml. Sleeve labels and colour-matched screw closures complete with tamper-proof strip round off the appearance of the pack at the PoS. www.schweppes.de/produkte The fresh tea shop The German company AFG GmbH is marketing various speciality teas under licence from “The Fresh Tea Shop”, a supplier of specialist teas set up in 2011. One of these is a herbal tea-based drink available in 500ml packs that uses no sweeteners or artificial flavours. By way of packaging the German company uses a PET bottle the entire surface of which is decorated with a sleeve label. The disposable bottle is tinted brown and features a drinking orifice of adequate size complete with tamper-proof screw closure. www.thefreshteashop.com Little miracles to drink “Organic Little Miracles“ is the name given by the Danish Power Brands Group A/S to its drink which consists of fruit juice, green tea, a hint of ginseng, acai extract and pomegranate and also contains agave syrup as a sweetening agent. The handy, transparent bottle holds 330 ml, is decorated, with the exception of an allround silvery strip, with a matt printed sleeve label and an opaque screw closure with tamper-proof guarantee and printed across the seal with the words “Drink to your health“. Additional information on the bio-certified drink can be obtained by means of a printed-on QR code. www.drinklittlemiracles.com","@ID":51}, "ONsite 46 PETplanet insider Vol. 16 No. 09/15 petpla.net ABF technology to Amul Dairy in India GEA aseptic blowing-filling (ABF) technology has been installed at Amul Dairy in India. GEA had previously supplied Amul with its first aseptic filling line for dairy products in PET bottles in India. That line improved productivity at the plant and changed the image of flavoured milk drinks, drinking yoghurt and milk shakes with young consumers in India. Amul Dairy in Gujarat has become somthing like a model producer for the Indian dairy industry. Its products are marketed under the popular Amul Kool and Amul Lassi brands. The possibilities offered by PET bottles pushed Amul to explore new flavours and products such as Amul Pro and Amul smoothies. PET bottles have made milk drinks fashionable and have allowed them to compete on equal terms with colas and other carbonated drinks on retail shelves. The ABF technology from GEA allows lighter-weight bottles to be used with complex designs that are not distorted during the sterilisation process. It takes a different approach to bottle blowing and filling by bringing both processes together in an aseptic environment. Instead of sterilising bottles after blowing, the system sterilises the preforms in an oven or with H 2 O 2 before blowing and keeps them in a sterile environment throughout the process. This process means that the bottle cannot be deformed by heat during the process and can, therefore, be lighter weight, further reducing PET consumption, allowing greater freedom in bottle design and reducing water consumption. This results in a lower total cost of ownership than traditional PAA systems. Less space is needed because there are no air conveyors, bottle sterilisation and rinsing carousels. “We were the first on the market with aseptic filling of milk products into PET bottles,” explained Mr. R S Sodhi, the Managing Director of Amul Dairy. “This allowed us to create a new market with young people in India for these drinks, increase our production and reduce our costs at the same time. The new ABF technology will keep us in our leading position and allow us to be even more creative with bottle design. I am very excited to see what the future holds for us.” The new ABF line is expected to be commissioned in the next few months. www.gea.com www.amul.com New stretch-blow unit for jars in the United Kingdom Esterform Packaging, headquarters in Tenbury Wells, England, produces an extensive range of PET preforms, bottles and jars for drinks, foods, household, garden and car-care applications. Last year it announced a significant increase in its preform production capacity, located at a second site in Leeds, and now it is extending finished container capacity, with the addition of a Sipa SFL 4/4 WM unit dedicated to the production of jars for food. The Sipa system, which was installed in March, will provide Esterform Packaging with significantly improved capability in high-volume two-stage production of PET food jars. Until now, most of the company’s jars were produced on lower-volume single-stage injection-stretchblow moulding units, as well as on a two-stage unit from another supplier. PET Jar sales had significantly increased, which prompted the purchase of a second two stage jar blowing machine. The SFL 4/4 WM (wide mouth) will make 360ml jars with 63mm neck finishes. With four cavities, it is capable of producing up to 6000 jars per hour. The complete system installed by Sipa also includes a set of blow moulds, a preform unscrambler, a “soft-drop” octabin preform dumper and an Air Recovery System for improved energy efficiency. “The customer told us that our preform unscrambler, preform infeed, oven, preform transfer system and blowing process are key improvements compared to their current line.” says Mauro Fibbia, Account Manager at Sipa. “The SFL 4/4 WM has a wider process window and a higher output than the current line, making the same jar from the same preform. Esterform appreciates the well thought-out design of our preform unscrambler as well.” www.esterform.com www.sipa.it","@ID":48}, "MATERIAL / RECYCLING 10 PETplanet insider Vol. 16 No. 09/15 petpla.net Rethinking the next generation of PET recycling Introducing new technology in the field of plastics recycling has always been the aim of Next Generation Recyclingmaschinen GmbH from Austria. The LSP process (Liquid State Polycondensation) for PET recycling combines increased of Intrinsic Viscosity (IV) and excellent decontamination properties with low energy consumption. The global annual PET consumption reaches some 20 million tons and the PET fiber business is approximately twice as big. Reasons enough to rethink the general approach of recycling the material and to start taking full advantage of PET’s properties by designing a new process. Improving PET properties in the liquid state PET, like all polymers, consists of polymer chains. The chains length determines the material strength and its viscosity (measured as IV). Each step in processing the material (fiber spinning, film extrusion, injection moulding, etc.), leads to “breaking” some of the chains apart, thereby reducing material strength and lowering the viscosity of the material towards easier flowing. The shotened polymer chains can be restored in length by polycondensation. The traditional method of achieving this is Solid State Polycondensation (SSP). Crystalline pellets or PET bottle flakes are heated to about 200 to 240°C and kept at this temperature for several hours, resulting in an increase of IV by approx. 0.01 to 0.02dl/g per hour resp. 0.05 to 0.06dl/g in the case of flakes. Liquid State Polycondensation (LSP), on the other hand, takes advantage of the material being at a higher temperature range (270 to 280°C) and therefore sports an increased reaction-speed of the polycondensation. The LSP process can increase the IV by 0.01 to 0.02 dl/g within minutes and keeps the desired IV within a narrow range of 0.015 dl/g. FDA non-objection-letter for 100% food application issued The backbone of the LSP process is P:REACT. In this reactor the surface/volume-ratio of molten PET is increased by forming strands and high performance vacuum is applied. This configuration enables easy decontamination of the material from harmful chemicals and makes the LSP process suitable for food-contact. A “challenge-test” conducted by Fraunhofer IVV / Germany provides the required scientific evidence for the decontamination performance of the process. In this test PET bottle flakes are purposely contaminated with various different chemicals. These flakes are then recycled by the LSP-Process and the remainders of the chemicals are analysed by Fraunhofer. The graph shows the cleaning capacity of the LSP process, being close to 100%. The yellow curve indicates the requirements by EFSA (European Food Safety Authority). Based on these tests FDA has issued a nonobjection-letter for applications in 100% food-contact in November 2013. P:REACT demonstrates outstanding performance The first P:REACT unit was installed in March 2015 and is producing rPellets from fibre scrap. The PET-fibres are collected from various points in the spinning process and contain up to 15% of spin oil. A shredder-feeder-extruder combination provides the PET melt and a first degassing. As the melt is introduced into P:REACT the IV is lifted from 0.56 dl/g to 0.66 dl/g within a variation of less than +/- 0.015 dl/g. The required elimination of the spin oil content comes automatically with the high decontamination performance of the unit. The equipment owner reuses the rPellets from P:REACT in his spin process simultaneously with virgin PET without any spin process adaption. Figure 1: PET process-comparison (data/graphic: NGR) SSP (Solid State Polycondensation) LSP (Liquid State Polycondensation) State of PET Solid / crystalline Liquid (melt) Environment Inert gas or vacuum Vacuum Typical Temperature (200-240) °C (270-280) °C IV – Lift-Speed (0.01 – 0.02) dl/g (rPellet) (0.05 – 0.06) dl/g (flake) per hour (0.01) dl/g per minute Figure 2: Decontamination performance of the LSP-process (data: Fraunhofer IVV, graphic: NGR) Recycling S p e c i a l","@ID":12}, "MATERIAL / RECYCLING 18 PETplanet insider Vol. 16 No. 09/15 petpla.net melt, offers an option for removing even more contaminants than that for flakes. Washing module and decontamination module A bottle-to-bottle recycling line from Krones basically consists of a washing module and a decontamination module. Pre-sorting, i.e. the process for removing foreign materials, can be handled either manually or automatically, and takes place in the neighbouring plant, as does bottle comminution. The ground flakes are then passed through a multi-stage washing process comprising prewashing, intensive washing, and postwashing. Before the material is dried, the closures, foreign substances and fine PET parts are removed. But what we are looking at here is still nonfood-grade flakes, which may well be used in the textile industry, for example, but definitely not for any applications where they come into contact with food and beverages. In order to qualify the recyclate for use in making beverage bottles, the next step is to remove all of the contaminants contained in the PET material. This decontamination process from Krones is performed in stages: two heat exchangers warm up the flakes, whereupon they are decontaminated in the downstream vacuum reactor. As the process continues, any coloured flakes still present, plus any metal particles, are removed, and any fine parts remaining are filtered out. It’s only after completion of this process that we’re looking at food-grade flakes. Additional sorting in the washing module The line installed for Roxpet contains some additional features: for example, Roxpet had one further unit installed upstream of the washing module, which removes a high percentage of all non-ferrous metals, such as aluminium. This unit processes more than 2,000kg/h, which means it’s big enough for both recycling lines. Each of the washing modules in the two lines, moreover, incorporates an all-metal sorting system, which serves yet again to remove any metal residues by means of magnets. And downstream of the washing module, a laser sorting system for the cleaned flakes has additionally been installed, likewise adequately dimensioned for serving both the recycling lines. It operates with four channels, two for each line, with one million measurements being taken per second. In this system, each flake is inspected for its material characteristics. Depending on the quality of the raw flakes supplied, the machine handles some umpteen thousand rejects per minute. Average wastage at Roxpet is between 7 and 8%. Plasticising and inline crystallisation The flakes, after having been cleaned and sorted in this way, are now passed to the decontamination module containing even more special features. An extruder screw has been linked up directly to the decontamination reactor, which serves to remove any contaminants from the flakes, thus creating food-grade quality. In this extruder screw, the material is liquefied and plasticised. Immediately downstream, the PET melt is passed through a filtration unit with 50-μm filter sheets, which arrest any particles still present. To ensure uninterrupted line operation, four filters have been installed here, which are backwashed at regular intervals with liquid PET. The flow of PET is now passed through a perforated plate, at the exit of which rotating blades cut it up into pellets. These pellets travel onwards into a mechanical centrifugal drier, removing the water, so that it can be re-used. The still-hot pellets continue to be amorphous, and are slowly cooled down in the inline crystallisation unit. It is in this step of the process that the so-important crystallisation of the PET pellets takes place, which is a vital precondition if they are to be successfully used in a preform injectionmoulding machine. A second identical line After the first recycling line had gone into operation, in late 2011, Roxpet installed a second identical line rated at 1,000kg/h, which was commissioned in April 2012. The two lines together provide an annual capacity totalling around 14,000 tons of food-grade pellets. This enables Roxpet to supply Groupe Alma’s preform-making operations in northern France, using silo-trucks. In total, throughout France, the group needs more than 100,000 tons of PET each year in order to produce preforms and PET containers for its water products. Pierre Papillaud would like to use up to 30% of recycled PET for bottle production. “Anyone contaminating the natural environment should be made to pay for it” There is still not enough raw material from collections available on the market. “Germany’s mandatory deposit has been the target of much The flakes are decontaminated in the vacuum reactor.","@ID":20}, "MATERIAL / RECYCLING 19 PETplanet insider Vol. 16 No. 09/15 petpla.net MATERIAL / RECYCLING 19 PETnology/tecPET GmbH | Regensburg, Germany Phone: +49 941 870 23 74 | Fax: +49 941 870 23 73 info@petnology.com PET Passion Week2015 NUREMBERG, GERMANY 09-12 NOVEMBER 2015 CONFERENCE 09-10 NOVEMBER www.petnology.com Free entry or VIP tickets End-User Special: PET AT BRAUBEVIALE 10-12 NOVEMBER www.petpassionweek.com INFORMATION PARTNER SUPPORTED BY ® S e n s o r s y s t e m e G m b H criticism from the country’s industrial sector. But it is in fact an excellent system, because it makes sure firstly that PET containers are returned at all, and secondly even pre-sorted. Unfortunately, we don’t have this wonderful system here in France, with a concomitantly low return quota, not to mention the bottles’ contamination”, says Pierre Papillaud. “My firm conviction is this: ‘Anyone contaminating the natural environment should be made to pay for it’. Our industrial sector does precisely that, by producing containers. It follows that responsibility for this has to be assumed, and the bottles have to be recycled. I don’t think there are very many companies in the world that stick to this philosophy as rigorously as we do. It is not first and foremost a question of money, it’s one of responsibility.” www.krones.com In the washing module, the flakes are passed through a multi-stage washing process comprising pre-washing, intensive washing, and post-washing.","@ID":21}, "PETpatents www.verpackungspatente.de 52 PETplanet insider Vol. 16 No. 09/15 petpla.net Container with gas feed option International Patent No.WO 2014 / 195339 A1 Applicant: Krones AG, Neutraubling (DE) Application date: 4.6.2014 The invention relates to a high volume PET container with a matching closure which enables the bottle to be integrated into a tap system. The bottle is designed to save on material without affecting functionality. Laminated bottle International Patent No. WO 2014 / 199555 A1 Applicant: Yoshino Kogyosho Co. Ltd., Tokyo (JP) Application date: 6.5.2014 Strips of material are integrated between the layers of a plastic bottle (minimum two layers) which modify the barrier characteristics of the bottle and/or adapt them to individual requirements. Bottom section shape International Patent No.WO 2014 / 207331 A1 Applicant: Sidel Participations, Octeville sur Mer (FR) Application date: 22.4.2014 Special shaping of the bottom section of a thinwalled PET bottle is the only way of guaranteeing sufficient stability to cope with pressure fluctuations resulting from hot filling or content incorporating carbon dioxide. Pack manufacture International Patent No.WO 2015 / 007532 A1 Applicant: KHS GmbH, Dortmund (DE) Application date: 3.7.2014 The application proposes combining a number of individual containers using an adhesive band or application of adhesive and a strap to create a “stable“ pack. The process and technical requirements such as heating elements for the adhesive and container positions are described. Multi-layer PET bottle International Patent No.WO 2013 / 112736 A1 Applicant: Plastipak Packaging Inc., Plymouth (US) Application date: 24.1.2013 This international application describes a PET bottle that is manufactured from two different PET variants. Improvements will be made to the bottle in terms of manufacture and recycling characteristics. Strengthened preform European Award of Patent No.EP 2630046 B1 Applicant: Sidel Participations, Octeville sur Mer (FR) Application date: 14.9.2011 A preform for manufacturing a PET bottle incorporates special peripheral bevels or bulges which help to stabilise the finished bottle.","@ID":54}, "PETbottles 48 PETplanet insider Vol. 16 No. 09/15 petpla.net Beverage + Liquid Food Want the secret to bottle light weighting? Process Pilot® automated blowmolder control system takes the guesswork out of material distribution management and can help ensure the success of even the most aggressive light weighting program. Featuring 24/7 blowmolder control, the Process Pilot system continuously maintains proper material distribution, on every bottle, to an unmatched level of accuracy. With the Process Pilot system, you have the means to push light weighting to the limit without sacrificing bottle quality or performance. Not convinced? Talk to one of our specialists today to schedule a free seminar and evaluation of the Process Pilot system on one of your blowmolding lines. Web: agrintl.com Tel: +1.724.482.2163 E-mail: sales@agrintl.com Visit us at the PETarena 4A-233 November 10–12, 2015 Nuremberg, Germany Spray gelatine The Italian company Fabbri 1905 are promising savings in terms of both time and product with their ready-to-use gelatine Fresca Frutta, which can be sprayed directly on to a fruit flan as well as also being suitable for decorating other sweet baked goods. The gelatine prevents any discoloration of the fruit as a result of contact with oxygen and gives it a shiny surface. A handy transparent bottle with a content of 150ml / 176gr serves as packaging for the product. A pump spray, which is secured by means of a shrink sleeve label with tear-off strip, enables metered application of the gelatine without any residual quantities remaining. www.fabbri1905.com/en Dressings in PET Tasty Secrets, a Dutch manufacturer of salad sauces, dressings and cheese dips, is marketing a proportion of its gluten-free salad sauces in small volume PET bottles via German supermarkets. The sauces, which are available in a range of variants (illustrated are Vinaigrette, Pesto and Honey Mustard) are free from flavour enhancers, preservatives, colorants as well as added fragrances and aromas. 120ml is packaged in bottles with a square base area and screw cap complete with tamper-evident strip. A self-adhesive strip features on three sides, the back permits a direct view of the product / its components. Juice spritzers from Rauch The Austrian fruit juices manufacturer Rauch has now included a juice spritzer in its range. Under the slogans “Make your day a happy day“ and “Sprizz“, the company is selling carbonated drinks with a fruit content of up to 20% in the trendy flavours of Cassis, Mango, Passion Fruit and Rhubarb. Each of the waisted, transparent bottles contains 500ml of product and is fitted with a screw closure with a tamper-proof guarantee. www.rauch.cc","@ID":50}, "MARKET SURVEY 36 PETplanet insider Vol. 16 No. 09/15 petpla.net Market survey: USA & Canada by Waldemar Schmitke For PETplanet insider 2015 has been the year of the North American Road Show. This is the year that saw us travelling through North America in our Editourmobil visiting firms that have found their niche in PET packaging. At the same time we are looking at the entire chain of development from the raw material stage right through to the filled PET bottle. Our journey starts on the east coast of the North American continent in the Canadian city of Halifax and finishes on the west coast of Canada in Calgary. This will be interspersed with a cross-country tour of the USA with the first stage destination being the NPE Show in Orlando Florida. Part 1: Canada The country covers the greater part of the northern half of North America (in total 41% of the continent) and is, in terms of its area, the second largest state in the world after Russia with an area of 9,984,670km2 (land: 9,093,507km², water: 891,163 km²). This extensive territory stretches as far as the Pacific Ocean in the west and the Atlantic Ocean in the east as well as from the Great Lakes and the 49th parallel in the south to the Arctic Ocean in the north. To the south lie the United States (continental United States), to the north-west the US Federal State of Alaska and to the north-east Greenland. The country’s only immediate neighbour occupying the territory is consequently the USA. The majority of the population live in the southern part of the country which is also where most of the cities are located. Important cities include Toronto, Montreal, Vancouver, Victoria, Calgary, Edmonton, Regina, Winnipeg, Ottawa and Halifax. The most northerly big city is Edmonton in Alberta. The most northerly, permanently inhabited human settlement in Canada (and also on Earth) is, however, Alert at the northern point of Ellesmere Island in the Nunavut Territory – latitude 82°28’ N which is situated at a distance of 834 km from the North Pole. Canada has ten provinces and three territories. The most populous province is Ontario, followed by Quebec and British Columbia. Capital city Ottawa in Ontario with a population of approx. 883,000 (metropolitan area approx. 1,236,000). State area 9,984,670km² Population and density Canada has a total of some 35 million inhabitants with a population density of 3.5 inhabitants per km2. This makes Canada one of the most thinly populated countries in the world. The majority of Canadians live either on the border with the USA or on the coasts. Eighty per cent of them live in the big cities of Montréal, Toronto, Vancouver and Ottawa. Canada is a country popular with immigrants from Europe, especially England, France, Germany and Italy, although a large number of immigrants also come from the eastern European countries. Today the highest numbers of immigrants to Canada are from the Asiatic states. At the head of the immigration queue is China. Land usage Agriculture 5% Pastureland 3% Forest 54% unproductive 38% Climate Temperate to arctic Terrain Mainly consisting of plains with mountain ranges in the west (Rocky Mountains). Lowlands in the south east. Natural raw materials Hydroelectric power, iron ore, fish, potassium salt, natural gas and oil, diamonds, lead, gold, silver, molybdenum and wood. Form of government Parliamentary monarchy with the British Monarch as the Head of State (represented by a Governor General). System of government Parliamentary democracy based on the Westminster System. Official language English and French Other languages spoken by original inhabitants, languages of other immigrant groups (Chinese, Italian, German etc.). Economy Canada is the world’s second largest state in terms of its area and the eleventh largest economy. It was a founder member of the G7 and G20 Groups. The commercial centres in the east and west are situated at a distance of up to 5,000km from each other. The country is thinly populated; broad swathes of the Canadian Arctic are practically devoid of people. Canada’s economy is based chiefly on raw materials, industry and agriculture. The productive economy and 85% of the workforce are concentrated inside a swathe up to 350km in width to the north of the US border. Most of the mining of raw material deposits takes place in remote parts of the country. Industry tends to be concentrated on the provinces of Ontario and Quebec as well as on the hinterland of Vancouver, in the southern parts of Saskatchewan and Alberta and in parts of Ontario there","@ID":38}, "PACKING / PALLETISING 41 PETplanet insider Vol. 16 No. 09/15 petpla.net Test equipment for PET – inspired by glass bottle manufacturing by Kay Barton www.stf-group.de ENGINEERING WITH THE COMPETENCE OF THE RECYCLER rComplete Plastic Sorting and Washing Lines engineered by Europe’s largest PET Recycler rBottle-to-Bottle rPET Recycling rMore than 60 PET Recycling Lines installed worldwide www.stf-group.de The gap between idea and feasibility in bottle manufacture is an ongoing topic within the sector. Appropriate instruments for measuring and analysis within the production process have become essential over the decades, in particular due to the advance of the trend towards savings in materials and lightweight applications. We visited the test equipment forging company Agr International in Butler, in the west of Pennsylvania, which, viewed on a global scale, has made a significant contribution to the further development of stretch blow moulding processes. Here in their present head offices we meet David Dineff, Global Product Marketing Director, and Robert S. Cowden, Chief Operating Officer. Agr originally stood for American Glass Research and was the historic root from which the company developed. The physicist and founder of the company, Dr. Frank Preston, moved to Pennsylvania in 1926, an event of global importance as far as the PET world is concerned. At that time West Pennsylvania was a glass manufacturing hotspot with a considerable proportion to glass bottles. Under the name of “Preston Laboratories” Dr. Preston embarked on research in the problem area of bottle manufacture. He subsequently developed measuring methods and instruments for early fault detection for what was at the time a market which was still in its infancy but already showing strong growth based on high demand. The first designs for a very wide range of test equipment started to emerge. At the beginning of the 1960s Dr. Preston, who was already getting on in years, sold the company to his employee Henry Dimmick Sr. and his partners. The sale involved changing the company’s name to American Glass Research. The company pushed ahead with setting up a division for the actual production of machinery for purposes of testing and analysis. New types of developments emerged for burst pressure and coating measurements of containers. The main development, however, that first made Agr famous, was a machine for real time measurement of the wall thickness of glass containers at manufacturing speed (OLT -on-line thickness). It was the OLT that actually kickstarted the commercial manufacture of systems of this kind in-house. Up to day, approx. 2,000 of these have been sold globally. With the start of the 80s and the rise of plastic packaging, the company simply adapted its technology to this new sector and, with the subsequent growth of the PET market, placed the focus fairly and squarely on the PET bottle and the manufacturing requirements typically associated with it. In order to prevent any confusion as far as the glass segment was concerned, the company brand name was simultane-","@ID":43}, "MATERIAL / RECYCLING 12 PETplanet insider Vol. 16 No. 09/15 petpla.net Shipping multi-purpose reactors Inspec t ion al l around. The Labe lWatcher 360. See i t l i ve at the Pack Expo, Las Vegas . W W W . I N T R A V I S . C O M V I S I T U S A T B O O T H S - 7 9 5 0 Vacurema MPR is easy to retrofil on existing PET extrusion sytem Erema is shipping three of the Multi-Purpose Reactors (MPR) at the beginning of summer 2015 to Latin America and Europe. Two MPR 1700s with a capacity of up to 1350kg/hr went to Latin America and Europe for the retrofitting of existing extrusion plants. Both customers already have an inline sheet system at their disposal which enables them to process washed post-consumer PET flakes directly to make 100% rPET flat sheet. Another MPR 2000 for throughputs of 1500-2000kg/hr as a stand-alone design for the production of decontaminated flakes likewise went to a customer in Europe. MPR enables to produce end products which meet the requirements for direct food contact in accordance with categories A-H/J of the FDA and EFSA. A total of 165 Vacurema systems are in operation throughout the world. The Multi-Purpose Reactor MPR uses high vacuum and high temperature for the effective decontamination, drying, dust removal and crystallisation of a variety of PET input materials in a single step. With the patented MPR technology Erema counts on crystallisation dryers which have proven their merits time and time again as components of the Vacurema PET extrusion systems, achieving a pre-drying level of under 100ppm moisture. The IV can be increased slightly. As a stand-alone solution the Multi-Purpose Reactor can produce food-contact grade and dustfree flakes – plus processing in high vacuum achieves better flake colour results, too. Washed PET bottle flakes, ground PET flat sheet waste and virgin PET material (plus mixtures of them) can all be used as input material. The bulk density of PET flakes and flat sheet waste can be increased by up to 80% at the same time, thus achieving constantly high throughput. It is also possible to process input materials with fluctuating residual moisture and bulk density. Additionally, the machine handles a wide variety of polymer types such as G-PET, PET/PE, multilayer and even PLA. www.erema.at RECYCLING S P E C I A L","@ID":14}, "BOTTLE MAKING 25 PETplanet insider Vol. 16 No. 09/15 petpla.net BOTTLE MAKING 25 Sample application: Container application: Cosmetic Cavities: 2 Cycle time: 42sec. Output: 170 pcs. per hour Container weight: 60g Container capacity: 100ml Neck diameter: 59mm Container height: 50mm LEADING TECHNOLOGIES Messehinweise etc. www.gneuss.com FOR POLYESTER RECYCLING • Unmatched Devolatilizing Efficiency with Gneuss MRS Extrusion Technology • Reliable Melt Filtration and True Process Consistency with Gneuss Rotary Filtration Technology • Permanent Accuracy and Quality Assurance with Gneuss Measurement Technology Naturally with up to 100 % Recycled Material and for Direct Food Contact Applications. See you there! Fakuma 2015 Friedrichshafen, Germany Hall A6, Stand 6501 moulds, whereas Mumbai is predominantly responsible for the types of machine offering higher outputs and featuring more strongly standardised technology. The ASB-12M has also been manufactured here since the end of 2012. This machine is basically a further development of the popular ASB-50 model introduced in 1981, which was followed by the ASB-50MB and ASB-12N/10 models, finally culminating in the ASB-12M. Main applications include cosmetics, pharmaceuticals and small liquor bottles. “This machine is highly economical in operation, and that makes it popular with start-up companies. At the same time the containers produced are of very good quality. In addition to the start-up companies we also have a number of customers who continue to invest in additional ASB-12M’s as they grow to extend their fleet” says Mr Yoshizawa. Together we take a look at the thick base PET jar. One of its striking features is its design which is so close to that of competitors in the glass industry that initially it is not possible to identify any differences in terms of optics and haptics. Only the fact that the surface feels warmer and the injection point give the game away. Kota Aoki chips in: “What you see here is the result of years of experience in the area of machinery and moulds in different materials for the cosmetics industry. This kind of product is the complete opposite of lightweight and mass production PET and caters for groups of users in the high end product range whose requirements and margins make packaging of this sort a necessity. The thick base jar represents the next step when it comes to imitating glass”. Nissei ASB showcased the concept for the first time at the IPF2014 in Japan and is now doing so for the second time at Chinaplas. One essential part of the technology behind the thick base is the cooling concept, as well as the movable injection core during injection moulding and optimised cooling during conditioning and stretch blow moulding. “Because mould technology is involved here, it can also be utilised on many of ASB’s other models“, adds Mr Aoki. www.nisseiasb.co.jp","@ID":27}, "MATERIAL / RECYCLING 22 PETplanet insider Vol. 16 No. 09/15 petpla.net Panther Ultragranulator for PET bottle recycling CHOOSE THE NUMBER ONE. BACK TO LIFE. VACUREMA® –FoodContact Approved Recycling With highly efficient decontamination BEFORE the extrusion process. Bottle-to-bottle Pelletising Inline Applications Pallmann Maschinenfabrik GmbH & Co. KG from Zweibrücken, Germany, has extended its range of “Panther” recycling granulators, by adding the “Ultragranulator” which has been specially designed for recycling reusable materials from PET bottles. Individual PET bottles are continuously fed into the cutting chamber by means of a conveyor belt. Angled rotor knives work with a very close cutting gap against opposing slanted counter knives and cut the bottles into flakes. The special rotor cuts diagonally, which saves energy. The lower part of the housing is fitted with a large screen, which holds the PET flakes in the cutting chamber until they are discharged through the screen holes. The mesh size can be selected, which determines the size of the flakes and throughput rate of the granulator. Throughput rates of up to 3.5 t/h are possible with a flake size of approximately 14mm and an appropriate by sized machine. After being cut, the material is pneumatically suctioned and transported into a cleaning system. The Panther Ultragranulator is designed for easy access to the cutting chamber for cleaning operations and parts replacement. The rotor and stator knives can be re-sharpened many times and adjusted from the outside. The screens are even reversible, so that both sides can be used. The Ultragranulator is designed for continuous operation and can be integrated into existing recycling lines or used as a stand-alone machine. www.pallmann.eu RECYCLING S P E C I A L","@ID":24}, "COMPRESSION 35 PETplanet insider Vol. 16 No. 09/15 petpla.net Recycling line Sonnenuhrgasse 4, A 1060 Vienna l consumer bags textile packaging Assembly workstations in Gardner Denver’s purpose-built factory at Redditch West Midlands England “We have developed the refurbishment side in response to customer needs”, Trevor Perry explained. “Budgets have been hit very hard in recent times and, while companies may want and need to replace or upgrade their equipment, financial restraints have prevented them. What we can do with the refurbishment programme is provide them with a machine that has been stripped right back to its component parts and then completely rebuilt, at a substantial saving in capital expenditure”. The 45th anniversary celebrations at the Redditch plant seem to have been well received and the company intends to hold other events in the future. With the development of machines like the WH35 and a wide range of vacuum and compressor equipment, 45 years may just be the first few chapters for Gardner Denver in England. www.gardnerdenver.com","@ID":37}, "BOTTLES 51 PETplanet insider Vol. 16 No. 09/15 petpla.net info@hasplastik.com Tel: +90 212 695 50 00 Fax: +90 212 694 97 24 100815dmyR .com Purple rain from Zekol As part of an advertising campaign and sporting the tag Purple Rain, Aldi Sud are selling one litre of shower cubicle cleaner from their Zekol range in a transparent PET bottle shaped so that it is easy to handle. The product is claimed to get everything sparkling clean – all the customer needs to do is spray, leave to work in and then rinse off. In addition, it has a delayed effect on re-soiling and makes it more difficult. The slightly tinted product is discharged via a screw-on, 2-colour trigger with actuation lock and spray adjustment. www.aldi-sued.de Limited edition bodymilk spray In a pack marked Limited Edition, the German discount drugstore dm is selling, under its natural cosmetics brand name of alverde, 150ml of bodymilk spray in a drop-shaped white PET bottle. This bodymilk contains bio almond oil, bio jojoba oil, bio shea butter, glycerine, water mint and extract of seaweed. The care product, described as hydrophilic, is said to make the skin soft and promote moisture conservation. The milk is applied to the skin via a screwed-on pump sprayer which is protected against accidental activation by means of a transparent cap. www.dm.de/alverde Lenor in the form of a superconcentrate Procter & Gamble are selling 1.35l of Lenor Superconcentrate, enough for 54 washes, in a dark green tinted bottle. Since, according to the manufacturer, the concentrate makes 30% more washes possible per litre, a customised metering facility is recommended. The appropriate markings are incorporated in the shiny silvery screw closure. Underneath its all-round foil label the bottle is fitted with slanting reinforcement grooves which make grasping and holding the bottle safer during the pouring operation. www.lenor.com","@ID":53}, "MATERIAL / RECYCLING 16 PETplanet insider Vol. 16 No. 09/15 petpla.net Recycling PET into pellets based on an article by Dr. Thomas Friedlaender, Krones AG and Mr Jean Renson, Krones AG Belgium It’s a spring-water empire: Cristaline is France’s best-selling packaged water. Behind this brand is the Groupe Alma conglomerate, behind which, in turn, is one man: Pierre Papillaud, who in his Roxpet subsidiary has commissioned the second MetaPure PET bottle-to-bottle recycling line from Krones, for making food-grade PET pellets to be re-used in container production. These are the first two Krones lines of their kind, which serve to make not flakes but pellets. A variety of different processes id Krones PET recycling are on the market. In Bangladesh, Akij Food & Beverage Ltd. is operating a bottleto-bottle recycling line from Krones where used and pre-sorted PET bottles are turned into food-grade flakes, which serve to make preforms: bottle-to-bottle. In Japan, FPCO also runs a Krones recycling line to produce food-grade flakes from old PET bottles. These, however, serve primarily to make foodgrade films used by the company as packaging for ready-to-cook meals and fresh foodstuffs as well, and are turned into preforms and new PET containers only as a secondary benefit. Food-grade pellets from non-food-grade flakes The French Roxpet company in Lesquin, a suburb of Lille, not far from the Belgian border, is adopting a different approach: it purchases nonfood-grade flakes from a neighbouring plastic recycling facility, cleans them so as to render them food-grade, and makes them into pellets, which are then directly used for preform production to make PET containers. This is the first recycling line from Krones where the end product is pellets, not flakes. Consequently, the process sequence in some steps deviates from the one familiar in the bottle-tobottle recycling lines Krones has built so far. Roxpet is the PET-recycling subsidiary of the French Groupe Alma, which operates quite a few bottling plants for mineral and spring water: 36 in France, two in Italy (Courmayeur and Contursi), plus one each in Spain (Aquadeus) and Luxembourg (Beckerich). The euphonious, prestigious names of the French mineral waters are very well-known the whole world over, most of them belonging to multinational conglomerates. However, the market leader in the French water segment, with its impressive per-capita consumption of around 135 litres, is not to be found among them. It is Groupe Alma, with its Cristaline brand. And the majority shareholder is a man who has built up this group for more than 50 years: Pierre Papillaud. “I’m very proud of my life and of what I’ve achieved”, says Papillaud. “I grew up as a farmboy in Saint-Émilion, the worldrenowned wine-growing village to the east of Bordeaux. I was running around barefoot until I was seven. When I was 24, that was in 1959, I hired four employees and started to fill spring water and soda, at 600 bottles an hour. And it was from these RECYCLING S P E C I A L","@ID":18}, "MATERIAL / RECYCLING 13 PETplanet insider Vol. 16 No. 09/15 petpla.net Granulator for PET Herbold Meckesheim provides customised solutions for the recycling of plastic waste in the fields of shredding, grinding, pulverizing, agglomerating, dry and wet cleaning, processing of compounds and metal separation. One example delivered to a French mineral water producer: A Herbold granulator of the C-series with integrated sound insulation for size-reducing PET bottles and preforms from the production of these hollow bodies. The scrap components are collected in containers that are emptied with the help of a tilting device onto a sorting table upstream of a conveyor belt. This sorting table is especially equipped with several cavities enabling the evacuation of foreign bodies such as small screws, wooden pieces or other extraneous materials – the bottles and preforms are forwarded to the conveyor belt by the operator. At the same time the special belt design makes a dosed feeding of the granulator inlet possible. The parts touching products are made of stainless steel. An integrated metal detector stops the feeding belt in case of detected metal foreign bodies in the feeding material to make their easy removal. Magnetic foreign bodies,stainless steel and other non-magnetic metal parts are detected. The Herbold granulator type SML 45/70 works with the double cross cutting geometry. The rotor and stator knife are mounted at inclined angles opposed to each other, thus ensuring a “true scissor cut” and generating little dust and noise and reducing the power input. With a power of only 37 kW a throughput of 1500 – 2000 kg/h of PET preforms is yielded. The outboard rotor bearings are completely separate from the grinding chamber, and no fines from the grinding material can destroy the bearings. The screen and the upper part of the housing can easily be hinged open. The knives can be adjusted outside in a jig supplied with the machine. The regrind is evacuated by the suction unit, freed from dust and can be reused for the production of new bottles. www.herbold.com Herbold Granulator RECYCLING S P E C I A L","@ID":15}, "MATERIAL / RECYCLING 11 PETplanet insider Vol. 16 Now Lanfranchi is able to support its customers with a complete range of Linear blow moulding machines for PET containers, from 0,25 lt to 40 lt. Possibility of supplying bottle and preform drawings to the costumers Linear blow moulding machine range goes from 1 cavity up to 12 cavities for any kind of bottle in terms of shape and design. Linear blow moulding machines are designed especially for big containers, special shape bottles and wide mouth containers. The simplicity of P:REACT involves only two parameters of control: The level of vacuum and the residue time of the molten PET inside the equipment. The IV is measured inline and provides a signal for the automatic control of the machine parameters. This together with a simple reactor configuration ensures easy operation and low maintenance costs. Figure 3: input material PET scrap from spinning / rPET-pellets after recycling (Images: NGR) Highest energy efficiency P:REACT works extremely energy efficient, as the reactor basically only requires energy for maintaining the temperature of the molten PET. Energy measurements show a specific consumption of only 0.12 kWh/kg including pelletising. These figures reflect the processing of PET fibers at IV of 0.62 dl/g, an output of 350 kg/h on a shredder-feederextruder combination. The rPellets are showing an IV of 0.70 dl/g. Versatile application of P:REACT for recycling of PET products from various sources In the upcoming months more P:REACTs are to be installed. For example, one unit for in-house recycling of thermoforming skeletons with an output of 2,000 kg/h and another stand-alone unit for used PET-carpet recycling. Extensive tests on the processing of bottle flakes, preforms, PET woven fabric, etc. have demonstrated the versability of P:REACT. In the case of recycling PET-bottle flakes, tests have shown the system to be suitable for exceeding brand owner specifications. www.ngr.at Figure 5: P:REACT (Images: NGR)","@ID":13}, "MATERIAL / RECYCLING 14 PETplanet insider Vol. 16 No. 09/15 petpla.net Unifi plastics recycling facility Engineering Excellence Low production costs Maximum output At Netstal our aim is to help you produce the perfect PET preforms: at minimum cycle times you achieve maximum output with constantly high quality and energy efficiency. And that’s no coincidence: our team of experts are always there for you – with state-of-the-art systems. www.netstal.com Fakuma, hall A7, booth 7303/7304 Unifi Manufacturing, Inc. has selected Amut S.p.A to assist in the design, construction and assembly of a new PET recycling system for the conversion of post-consumer PET bottles into quality fiber. The new system will be utilised in the company’s Reidsville, N.C., facility. The approximate $25mill. investment in a bottle processing plant will help Unifi achieve its intent of backward integration for its Repreve recycled fiber product line. Amut’s patented Dry De-Labelling system removes the full body shrink sleeve labels from the PET bottles separately in a “dry” phase that will allow for the recovery and collection of labels, prior to the Amut patented PET flake washing process. “This is an important step in the processing of municipal waste stream post-consumer bales,” said Anthony Georges, president of Amut North America. “We are excited to work with Unifi and be a part of their bottle processing plant and the durable, sustainable products they’re creating.” “Unifi’s Repreve brand demonstrates the company’s commitment to improving the environment through recycling efforts, converting post-consumer materials – like recycled plastic bottles – into high-quality fibers that can be used for a variety of applications. Since 2009, Unifi has recycled more than 4 billion recycled plastic bottles into Repreve fiber that is used in products made by some of the world’s favorite brands, including Haggar, Ford and Quiksilver, among others.” “After evaluating a number of technologies, we chose to utilize the proven Amut PET processes to ensure that Unifi’s high production standards are met,” said Mark McNeill, vice president of technology and business development for Unifi. Unifi’s new bottle processing plant will produce an estimated 75mill. pounds annually of r-PET materials, in addition to the caps and label streams. Operations at the new plant will begin June 2016. www.amut.it Amut De-labeller RECYCLING S P E C I A L","@ID":16}]}}
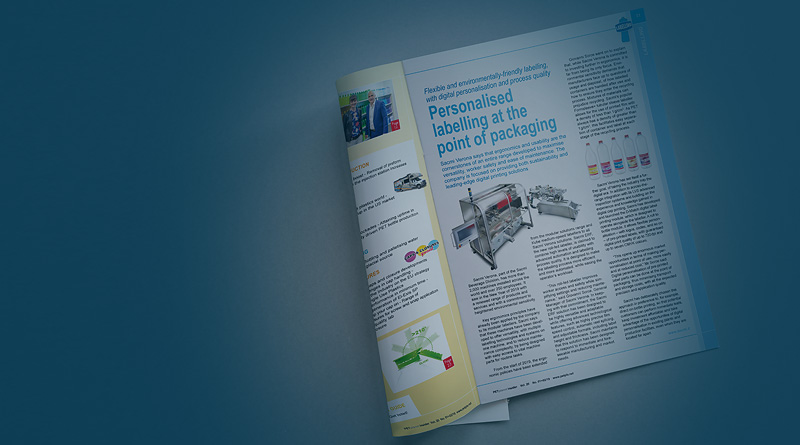