"PETcontents 06/12 4 PETplanet insider Vol. 13 No. 06/12 www.petpla.net INSIDE TRACK 3 Editorial 4 Contents 6 News 38 Products 39 PETbottles: Beverages 40 Patents BOTTLE MAKING 22 Bumper harvest Amcor r´Rigid Plastics grows with PET wine bottles BEVERAGE PREPARATION 28 Weighing up the PET permeability rate P.E.T.proof Wild’s quick-test procedure BOTTLING / FILLING 32 Green for go! Krones NitroHotfill Line for Pago juices 34 Global beverage markets Rabobank’s market outlook sees five megatrends CAPPING / CLOSURES 37 Slimming down for hot-fill Bericap North America with DoubleSeal one piece hot-fill MATERIAL / RECYCLING 10 Biobased polyester - the next generation PREFORM PRODUCTION 12 Thread flow lines The rapid guide to perfect preforms - part 30 14 Cool running Puccetti amd Piovan’s PETchiller project EDITOUR REPORTS 16 Market opportunities in the wake of major upheaval - Armenia MARKET SURVEY 23 Suppliers of preforms BUYER’S GUIDE 41 Get listed! Page 32 Page 10 Bilder: S. 10 S. 23 Bild Person s. 32 Aufmacher sensitive BEVERAGES Page 22","@ID":6} "NEWS 9 PETplanet insider Vol. 13 No. 06/12 www.petpla.net drink technology India and International PackTech India getting bigger Almost 300 exhibitors are now confirmed for drink technology India (dti) and International PackTech India, which are taking place at the Bombay Convention & Exhibition Centre in Mumbai, India, from November 6- 8. Exhibitor numbers are up almost one-third since the last shows and organisers Messe Muenchen and Messe Duesseldorf anticipate that the shows will cover 12,000m2, almost 50% more space than previously. This is the second time that the companies have jointly organised the exhibitions and over 8,000 trade visitors are expected, a 30% increase. India represents one of the world’s fastest-growing markets for food and beverage, with the middle class on the subcontinent expected number around 580 million by 2025. Among the companies already registered as exhibitors are Clearpack India, KHS, Krones, Sidel and Siemens. PackTech will feature presentations from France, Italy, Turkey and Switzerland, while representatives from the industry in China and the UK will be presenting at dti. www.drinktechnology-india.com www.packtech-india.com New CEO for Mould Technologies Group and Schottli AG Mr. Thomas Anderegg has been appointed as Chief Executive Officer (CEO) of Mould Technologies Group and Schottli AG, with effect from October 1, 2012. He will succeed Martin Schöttli, who has led Schottli since 1986, and Mould Technologies Group since it was established in 2008. Thomas Anderegg holds a degree in machine engineering from the Swiss Federal Institute of Technology (ETHZ). He joins the company from Netstal-Maschinen AG, where he is a member of the executive Board of and Senior Vice President Sales and Marketing, responsible for all five business units, the marketing department and the company’s affiliations and representations. He was previously CEO of Corvaglia Closures AG. Mr. Schöttli will remain with the company as a board member and will be available for special projects. www.schoettli.com","@ID":11} "BOTTLING / FILLING 35 PETplanet insider Vol. 13 No. 06/12 www.petpla.net sensitive BEVERAGES Emerging markets lead growth The BRIC countries, along with other emerging economies, will be essential to growth in the next decade. In addition, Mexico, Venezuela, Colombia, Argentina, Indonesia, Thailand and the Philippines are projected to generate US$14 billion in retail sales of soft drinks between 2010 and 2015. China alone accounts for 24% of global beer sales – but it has the lowest per-capita consumption of the largest markets. It saw strong growth from 20052010, with rising disposable incomes and price competition helping affordability. The spirits market has seen 6% growth in Asia-Pacific and MEA (Middle East and Africa). India saw 12% growth in 2011, continuing the trend of the past five years and this is expected to continue, despite complex legislation and public pressure to raise the minimum drinking age. Rabobank views the Indian market as offering major opportunities for western spirits companies and expects M&A activity to accelerate over the coming year. Across the world, CSDs are second to bottled water in terms of volume, and leaders in total value. Global volume growth in CSDs was 2% in 2010, with the trend continuing through the next three years. Rabobank expects Asia-Pacific to displace N America as the largest market in 2012, driven by strong consumer demand for noncarbonated beverages such as RTD (ready-to-drink) tea and Asian speciality beverages, although these are smaller than the bottled water and CSD markets. Fastest growth has been in Eastern Europe and MEA, albeit from lower bases. South America also nearly doubled in size in the period 2005-2010. Juice and energy Functional drinks are showing signs of slowdown in developed markets, influenced by growing scrutiny by legislative and consumer groups of health claims. The market opportunity for energy drinks is Y O U R PA R T N E R F O R B L O W M O U L D S . Sidel • SIG • Krones • SIPA • MAG • ADS • Kosme • Nissei a. o. Röders GmbH / Scheibenstr. 6 / 29614 Soltau / Germany / www.roeders.de Telephone +49 5191-603-53 / Fax +49 5191-603-36 / E-Mail mold@roeders.de For our subsidiaries in China, USA and Latin America please check our website. PET STRETCH BLOW MOULDS Benef i t of 30 Years of Exper ience in Blow Mould Manufactur ing! shifting to SE Asia and China, where young consumers are switching from tea and coffee. Consumption is currently 25% that of N America. Global consumer demand for health and wellness beverages attracts companies such as Coca-Cola, PepsiCo, Suntory and Danone to convergence. Examples include Coca-Cola’s Minute Maid Pulpy in China, PepsiCo’s acquisitions of Russian companies Lebedyansky (juices) and Wimm-Bill-Dann (dairy), and joint ventures in the Middle East. It is expected that the global brands will continue their expansion into newer segments such as hot drinks, dairy and soy-based beverages, and new product creations will continue. Global juice consumption is expected to rise to 70 billion litres in 2012, led by China, Russia and India. However, value growth is lagging volume expansion in China. N America is expected to remain flat in volume terms but to account for 10% of the total value increase, as consumers trade up. Private label brands are","@ID":37} "MATERIAL / RECYCLING 10 PETplanet insider Vol. 13 No. 06/12 www.petpla.net Coca-Cola is taking PlantBottle-sized steps with a view to replacing petroleum-based PET containers with bio-based plastic bottles by 2020. This effort to commercialise a plastic bottle made entirely from plants builds on the Company’s introduction and roll-out of its first generation PlantBottle package. Since its introduction in 2009, the Company has already distributed more than 10 billion PlantBottle packages in 20 countries worldwide. Coca-Cola will continue to make investments in PlantBottle technology and aims to use PlantBottle packaging for the Company’s entire virgin PET supply by 2020. By the end of last year, agreements with Virent, Gevo and Avantium – three companies which develop plant-based alternatives to materials traditionally made from fossil fuels and other non-renewable resources - were signed following an in-depth two year analysis of different technologies by the Coca-Cola Company’s R&D team and technical advisory board. supported through strategic investors including Cargill, Shell and Honda. The company’s patented technology will also produce bio-based paraxylene - a key component needed to deliver 100% plant-based PET packaging.“ PET made from Virent‘s bio-based paraxylene features the same high quality and recyclability as materials used today, with the added benefit of being made from a wide range of renewable materials. The company is targeting early 2015 for the opening of its first full-scale commercial plant. Gevo Gevo is converting existing ethanol plants into biorefineries to make renewable building block products for the chemical and fuel industries. The Company plans to convert renewable raw materials into isobutanol and renewable hydrocarbons that can Coca-Cola’s commercial solutions for bio-based plastic bottles Biobased polyester – the next generation Virent Virent’s patented technology features catalytic chemistry to convert plant-based sugars into a full range of products identical to those made from petroleum, including gasoline, diesel, jet fuel, and chemicals for plastics and fibres. The development of Virent‘s BioForming technology platform is Earlier in 2011, Coca-Cola announced a partnership with H.J. Heinz Company that allows production of ketchup bottles using PlantBottle technology. The new packaging was launched in summer 2011 in the USA.","@ID":12} "Vol.6 PETplanet print PREFORM PRODUCTION 12 PETplanet insider Vol. 13 No. 06/12 www.petpla.net The rapid guide to perfect preforms - part 30 Thread flow lines Troubleshooting guides have suffered in the past from being locked away in offices and not being available to the people that actually need them. Considering the high cost of machine and tools high scrap rates can be a costly proposition eating away at already tight margins. PETplanet’s “Rapid Guide to Perfect Preforms” takes a different approach. It has been written for the people on the floor of injection moulding companies to support their daily work in making the best preforms possible. The product of two industry experts, Rick Unterlander and Ottmar Brandau, it gives concrete advice on 35 of the most common problems in preform manufacture, most illustrated by pictures. From high AA levels to wavy bodies processors can find help when they need it. Read chapter 30 of the guide. Symptom Translucent streaks on the outer surface of the neck finish. Usually found near a thread or neck feature. Cause The melt flow has been disturbed by the contour changes in the neck insert, causing gas / air to fold over and become trapped. This defect is exacerbated with polished neck insert surfaces. Table of Contents i........................ About the Authors ii.................................Introduction Chapter 1.............................. AA Level High 2........................ Accordion Preform 3....................... Air hooks / Streaks 4............................... Black Specks 5...................................... Bubbles 6..................................Burn Marks 7...........................Colour Streaking ................................... /Peeling 8..................................Crystallinity 9.................................Drool Marks 10.......................................... Flash 11......................... Gate Depressions 12............................... Gate Peeling 13..................Gate Voids / Pin Holes 14......................... Internal Gate Sink 15................................Internal Sinks 16........................................ IV Loss Solutions 1. Check injection time isn’t too low (injection rate too fast), especially in the last zones when the melt flows into the neck finish area, and adjust if necessary. Injection rate should be about 10 – 12g/sec/cavity. 2. Check to ensure hold (packing) pressure isn’t too low, especially near the beginning of hold time. Adjust higher if necessary to improve thread formation. 3. Ensure the mould neck insert and lock ring vents are clean. This will minimize gas entrapment at the TSS (Top Sealing Surface). 4. Ensure the neck inserts are clean. This will eliminate any obstructions when the melt is forming. 5. Check to ensure hold (packing) pressure isn’t too low, especially near the beginning of hold time. Adjust higher if necessary to fill out TSS contour. 17............................ Long Gate Nub 18...............................Milky Preform 19............................ Moisture Marks 20................Neck Finish out of Round 21....................... Parting Line Crease 22.................Parting Line Deformation 23......................... Preform Yellowing 24.................................. Short Shots 25.......................................... Sinks 26......................................... Splay 27........................... Stretched Necks 28..................................... Stringing 29......................... Surface Blemishes 30.. ....................... Thread Flow Lines 31...............TSS (Top Sealing Surface) ......................................... Sink 32.......................................Unmelts 33.................Wall Thickness Variation 34.................................Wavy Body 35.................................. Weld Lines","@ID":14} "PETnews 6 PETplanet insider Vol. 13 No. 06/12 www.petpla.net ColorMatrix reduces carbon footprint, gains recognition for recycling Liquid colorant and additive technologies ColorMatrix, now part of PolyOne, presented the results of an independent comparative study carried out by Sidel. It found that the company’s Joule RHB PET reheat additive, offers the largest carbon footprint reduction in PET preform processing compared with similar products, while maintaining performance and aesthetic qualities. The study compared resin containing 5ppm Joule RHB-2, an inert blue-shaded inorganic particulate, with a typical 5ppm carbon black commercial reheat resin and a commercial non-reheat resin. The Joule RHB-2 outperformed the other materials in terms of NIR absorption, L* luminance, reheat efficiency and energy use. Sidel tested the three materials in the form of 18.8g, 500ml carbonated soft drink (CSD) bottles and compared various qualitative characteristics. Using data from the Sidel study, ColorMatrix has determined that JouleRHB facilitates an energy reduction of 38% made possible when blowing one metric ton of PET. Joule RHB has FDA and EU food contact approved for use in PET bottle resins. ColorMatrix also exhibited the announcement by APR (Association of Post Consumer Plastic Recyclers) that its HyGuard oxygen scavenging system and Ultimate UV390 light-blocking technology achieve full recyclability under its Critical Guidance guidelines. www.colormatrix.com Stute commissions Krones PET recycling line Food company Stute Nahrungsmittelwerke, of Paderborn, is continuing its eco-friendly strategy with the commissioning of Germany’s first PET recycling line from Krones, which will commence operation a its beverage plant in August 2012. Stute already has three wind farms, a biogas system and several solar power installations that together provide more than 30% of its energy requirements and will soon be able to completely recycle PET material. The Krones PET recycling line, which features the company’s SuperClean-PET-flake process, is able to produce flakes that can be directly used for making new bottles. The recycling process washes and decontaminates the PET recyclate, guaranteeing its suitability for future food-grade applications. The recycling line is made up of a washing module, decontamination module, and peripherals. It is installed on two different levels: the washing module and the decontamination module are spatially separated, with the latter located directly next to the existing preform injection-moulding machines. Stute is shifting its container requirements progressively away from cardboard towards PET packaging and selected the Krones recycling solution because it is the only manufacturer currently able to offer a complete system, from container feed through to finished, decontaminated flakes. Using a high proportion of recycled PET enables the company to avoid the additional levy on non-returnable PET. www.krones.com Simei turns 50 in 2013 Simei, the International Exhibition of Machinery for Winemaking and Bottling, will celebrate its 50th anniversary with the 25th edition of the biennial show, which will run from November 12 - 16,2013 at Fiera Milano – Rho. The first Simei fair occupied 12,000m², hosted 170 exhibitors – 144 from Italy – and attracted 11,000 visitors; the 2013 show is confirmed for halls 9, 11, 13 and 15 at Fiera Milano. It will again feature the “technological innovation prize”, which began in 2011, which will be extended to the bottling and packaging of drinks in general. Other concurrent events will be announced in due course. www.simei.it Pramia Plastic opens rPET plant in Finland Pramia Plastic, a newly acquired subsidiary of alcohol manufacturing company Pramia, has opened in Toholampi, Finland, in an existing 7,000m2 manufacturing and processing facility that has now been reorganised. Pramia Plastic re-processes crushed recyclable bottles into renewed industrial raw material, such as rPET flakes, granulates and preforms. Starlinger equipment makes up the granulating line, and flake washing is undertaken by machinery from STF Maschinen und Anlagenbau GmbH. The company focuses on the production of 100% rPET with high IV. Output capacity for granulating and washing is 10,000t/a, which is in excess of current demand for rPET preforms. Pramia says that production will expand as opportunities arise. The plant has been organised in line with the parent company’s strategy of eco-friendliness and sustainability, and is a zero-waste facility. The company has integrated an internal system to ensure that quality is maintained at FDA standards. The opening of the facility means that Finland once again has domestic bottle recycling capacity, which had been absent for over a year. www.pramia.fi KHS exits Chinese joint venture KHS GmbH is divesting its 70% holding in the Guangdong Light Industry Machinery No. 2 Plant Co., Ltd (GLM2) joint venture. The shares, which were purchased in 2006, will be sold back to the minority shareholders. Prof. Dr.-Ing. Matthias Niemeyer, CEO of KHS, said that the joint venture had not achieved the company’s objectives in terms of profitability and sales growth. Spare parts and service for machines, lines and systems from the GLM2 joint venture will continue to be provided by GLM2. KHS intends to expand its activities in China and is to invest in sales activities. A production plant for line business is currently being commissioned for the Salzgitter Group in the Chinese city of Suzhou. It will build machines from the new EcoBloc range and will be oriented towards the requirements of the growing Asian PET market. The withdrawal from the joint venture is part of the company’s Fit4Future optimisation programme. www.khs.com","@ID":8} "BOTTLING / FILLING 36 PETplanet insider Vol. 13 No. 06/12 www.petpla.net sensitive BEVERAGES expected to continue to gain market share. Raw materials The soft drinks industry has been heavily affected by rises in raw material costs, along with energy, healthcare and insurance prices have also risen. Coca-Cola Corporation estimated that its raw material costs rose by more than US$800 million in 2011, leading to price increases by it and PepsiCo of up to 4%,in 2011. Large brand owners can pass higher costs on to consumers more easily than private label manufacturers, which is expected to lead to consolidation as additional savings are sought from scale and distribution efficiencies. Most growth in the juice segment comes from less-than-25%-fruit categories, and consumers are switching from traditional orange and apple flavours to new variations and exotic fruit flavours, as well as innovations such as smoothies. Bottled water continues to lead soft drinks volume, with 80% (14.5% carbonated) and annual growth of six per cent. Carbonated water continues to be supported by traditional markets but consumer pressure regarding sustainability is expected to continue. Alcohol Beer accounts for 78% of total alcoholic beverage volume and 45% by value. Growth has remained below its 10-year average since 2008. All MHT MOLD & HOTRUNNER TECHNOLOGY Dr. Ruben-Rausing-Str. 7 | D-65239 Hochheim/Main Tel. +49 (0) 6146-906-0 | www.mht-ag.de Make the most of your machine - with a high cavitation mold from MHT! For many machine types, we supply the mold with the highest cavitation, thereby enabling optimum preform output. For the Husky HyPET machine, we offer an upgrade set for 33% more preforms, without refitting on the machine! • 60 cavities for Netstal PETline 2000 • 96 cavities for Husky HyPET 300, • 112 cavities for KraussMaffei 350 Engineering made in Germany 128 for HyPET 400 Patent pending: MHTcoolMAX® post mold cooling five megatrends play a role in the beer sector, with M&A activity – largely, Western brewers buying companies in emerging markets. Global beer volume is expected to rise by 2%, to 196 billion litres, with China accounting for half the increase, followed by Asia and Africa, Beer volumes in established markets are declining, although niche products are performing well. Lager exemplifies bifurcation, with growth highest in the premium and economy segments, although standard lagers remain the largest category. Cider is forecast to trend up by 6% in 2012. Growth will come from all regions except Asia and S America. Malt-based RTDs have synergies with the brewing process and have attracted interest from beer producers. They are expected to grow by around 5% in Europe and N America. Consumption of spirits has seen strong growth in India and China especially. The market in India is an example of a megatrend in action, driven by new consumers with greater disposable income and greater aspirations. The premium end is growing fastest of all, and the larger players are growing at the expense of smaller companies. Five ‘megatrends’ in the global beverage market Volatility and rising commodity costs Emerging market growth Bifurcation (divergence) Strategic sourcing Convergence across segments Economics and markets: Future prosperity in growing BRICs markets Slower soft drinks growth in established markets Functional drinks slowing in developed markets - but growth in emerging markets Volatility in fruit drinks Recovery in bottled water Beer: potential in China, Asia and Africa Growth in ciders and RTDs ‘Premiumisation’ Foreign exchange volatility impacting on competitiveness *This article.is based on Rabobanks report ‘Best of times, Worst of times - Global Beverage Outlook 2012","@ID":38} "NEWS 7 PETplanet insider Vol. 13 No. 06/12 www.petpla.net Are your standard PET preform molds making you as much money as they should? Ask how MPET with iFlow technology improves production and achieves greater quality results. Innovation doesn’t happen in isolation. It happens when blue-sky thinking meets down to earth knowhow and exceptional supply chain execution. The sort of innovation that Mold-Masters is known for, now applied to PET tooling for industry-leading results. Introducing MPET – the new PET preform tooling solution designed for the standards of tomorrow. Mold-Masters and theMold-Masters logoare trademarks ofMold-Masters (2007) Limited. ©2011Mold-Masters (2007) Limited.All rights reserved. Think about it. moldmasters.com/thinkaboutit info@moldmasters.com Sidel invests in customer training In order to meet demand for targeted training Sidel has developed a new ‘competence audit’ program, which is claimed to look at operators and maintenance staff from both a theoretical and a practical point of view. Sidel specialists evaluate employees at their job, based on their performance and individual profile. Clients are provided with a report that includes detailed results for each employee and a custom-designed training plan. Training sessions are held either on-site or at one of Sidel’s seven worldwide training centres. It says that it trains over 5,000 people each year. Sidel recently inaugurated a new training lab in Parma, Italy, which houses two automation training stations, one room for training on aseptic fillers and one for different types of filling technologies and valves in a 150m2 extension to the existing facility. The Technical Training Centre in Beijing, which was opened in mid-2011, has already trained more than 150 people from 39 different clients, specialising in applications such as sensitive products, water and carbonated soft drinks. The 900m2 facility includes blow moulding machines, a laboratory with simulation benches for the configuration of standard and aseptic fillers, and a Combi automation desk for the reproduction of machine synchronization requirements. It has a fully equipped laboratory and three classrooms, including a virtual reality room where trainees can interact with projected models. Sidel has been offering training for 40 years and offers a range of programmes, from individually-tailored sessions to a portfolio of training courses and seminars. training-seminar.sidel.com www.sidel.com Bericap to expand production at Singapore site Bericap’s production site in Singapore, which was opened at the end of 2010, is to increase production of closures for customers in Thailand. Output in 2012 is expected to be double of the one achieved in its first year. The Singapore site was established with the intention of providing a central location for Southeast Asia and to assume responsibility for customer service in the region, which had previously been handled from China or other locations. During the plant’s first year, employees from China and Germany provided support to ensure that the facility achieved company standards. The plant manufactures closures for the chemical/ technical and edible oil sectors for export customers in Australia and Asia. The facility has 35 employees and capacity to expand beyond the former product program. www.berciap.com","@ID":9} "PETpatents www.verpackungspatente.de 40 PETplanet insider Vol. 13 No. 06/12 www.petpla.net Modular closing system International Patent No. WO 2011 / 128067 A1 Applicant: SHB GmbH, Crailsheim (D) Application Date: 12.4.2011 An adapter is snapped on to the shoulder of a plastic bottle so as to enable a very wide range of closure caps and/or screw tops to be used. This makes it possible to use one bottle for a very diverse range of products. Bottom of a plastic bottle European Patent No.EP 2374732 A1 Applicant: Yoshino Kogyosho Co., Tokyo (JP) Application Date: 24.12.2009 The bottom and the side walls of a plastic bottle are constructed in such a way as to enable them to be folded “inwards” as the level of content inside the bottle falls, thus reducing the volume. Improvements are being made to emptying the remaining contents of the container, which is fitted with a pump sprayer. Dispensing of detergent International Patent No. WO 2010 / 079023 A1 Applicant: Unilever Plc., London (GB) Application Date: 4.12.2009 Lid for mounting on a squeezable container for liquid detergent. Pressure on the container forces the product upwards via the uptake tube and at this point it is conveyed via guide rods into the dispensing chamber. The risk of any contamination during the dispensing operation is reduced. Foldable bottom section European Patent No.EP 2383205 A1 Applicant: Yoshino Kogyosho Co. Ltd., Tokio (JP) Application Date: 27.1.2010 A plastic bottle with a pump sprayer for deploying the contents is fitted with a bottom section that can be “pressed in“ as the level in the container falls in order to enable optimum delivery of the remaining quantity via the uptake tube. Improved sealing US - Patent Nr. US 2008 / 0245761 A1 Applicant: Graham Packaging Comp., York (US) Application Date : 9.10.2008 The selection of materials and the moulding of a plastic bottle are described. The bottle has been improved with regard to pasteurisation and the associated change in volume, deformation and leakage problems. Closure for beverage containers European Grant of Patent No. EP 1786693 B1 Applicant: Threadless Closures Ltd., London (GB) Application Date: 23.6.2005 Multiple section closure for a container with carbonated content. The closure is constructed in the form of a type of bayonet closure. The container does not require its own separate thread on the outside.","@ID":42} "MARKET SURVEY 24 PETplanet insider Vol. 13 No. 06/12 www.petpla.net 06/2012 MARKETsurvey Company name Retal Iberia SLU S G T PETform (Thailand) Ltd., Pramia Plastic Postal address Telephone number Web site address Contact name Function Direct telephone number Fax E-mail Ctra. Comarcal C-35 km 66, 147, 2º Sector, Parcela 55, 17451 Sant Feliu de Buixalleu (Girona) SPAIN +34972865730 (currently under renovation) Pere Plademunt General Manager +34972865732 +34972865731 pere.plademunt@retaliberia.com 3,rue de l'île Macé 44 412 Reze, France +33 (0)2 40 05 09 37 www.sgt-pet.com Martine Le Claire Sales administration +33 (0)2 40 05 02 88 +33 (0)2 51 70 01 55 m.leclaire@sgt-France.com 35th Floor Ocean Tower 2, 75/102-103 Sukhumvit Soi 19, Bangkok 10110, Thailand +662 6616661 www.indorama.net Pramod Narayan Dubey Marketing +66 819371978 +662 6616664 pramod@indorama.net Juustotie 25 69300 Toholampi, Finland www.pramiaplastic.fi Timo Nummikorpi Plant Manager timo.nummikorpi@pramiaplastic.fi Preforms Multilayer preforms (Yes/No) No No No PEN prefoms (Yes/No) No No No Preforms in alternative materials (PP/PLA/PEF) Which? No No No Preforms incorporating rPET (rPET content in %) Yes, 25% Yes - % adapted to customer's needs No 100% List of additives available Only colour additive (Repi) O2 Scavenger, UV blocker, gliding agent, anti-yellowing etc. Tailored to client's needs Preform range Neck/weight 29/21 Oil /22 -27 29/25 /10,0 - 29,5g 30/25 / 11,5 - 39g 48/40 / 79 - 100g BPF / 26 -51,5g Obrist 23g PCO 1810 / 20,5 -51g PCO1881 /38,7-43,7g Preform (mm) 100,6 66 - 115,1 69,84 - 142 142 - 158 99 /148 95,2 97,77 - 148 123 - 133,75 liters 1 0,33 - 2 0,33 - 2 5 -8. 0,5 - 2 0,5 0,5 - 2 1,5 - 2 Between 10,5g to 450g for sizes of bottles between 0,15 and 20l Necks: 30/25 high and low neck, 29/25 with and without step, 28 PCO 1810, 28 PCO1881, 48/40, 28 BPF, 38mm, 28/410, 21/29, BVS 30H60, CRC63 17.02g 30/25mm PCO 28mm, 1881, 21.2 to 45 g PCO 28mm 1880, 40 and 45.6g 21,2g, 42,7g, 85g preforms using any additives and colours, tailored to client’s needs. Preforms use mainly rPET as raw material, with varying levels of rPET percentage up to 100 % rPET preforms, without deterioration of IV qualities. Company name S.B.E.C.M. Sunpet Ambalaj San. Ve Tic. As. Sundiapet Parle Agro Pvt. Ltd Postal address Telephone number Web site address Contact name Function Direct telephone number Fax E-mail Rue de la plaine 47230 Lavardac, France +33 (0)5 53 97 41 00 www.sbecm.com Jean-Luc Didouan General Manager +33 (0)5 53 97 41 00 +33 (0)5 53 65 85 97 jean-luc.didouan@sbecm.com 1. Osb. 10. Cad. No:4 Baspinar , Sehitkamil, Turkiye +90 342 337 12 30 sunpet.com.tr Hakan Cinkilic Export Manager +90 342 337 12 30 - 623 +90 342 337 12 33 info@sunpet.com.tr Plot No. 1 & 2 Khokhani Industrial Complex No.2 Vasai Kaman Road, Sativali, Vasai (E)401208. Mharastra India +91 250 3208849 www.sundiapet.com Sanjay Kothari +91 9820036748 sundiapet@gmail.com,diamec@gmail.com Western Express Highway, Andheri East, Chakala, Off Sahar Road, Mumbai-400099., India +91 22-67348000 www.parleagro.com Shailesh K Singhal Senior Manager +91 22-67348241 +91 22-66935050 consumercell@parleagro.com Preforms Multilayer preforms (Yes/No) No No No No PEN prefoms (Yes/No) Yes Yes No No Preforms in alternative materials (PP/PLA/PEF) Which? Possible No No No Preforms incorporating rPET (rPET content in %) up to 25% - 30% No 10 -15% No List of additives available AA scavengers, Blockers, Coloring agents, O2 absorbers, etc.. Biodegredable O2 scavenger / UV blocker Preform range Neck finish : 30/25 high and low, 29/25, PCO 28 (1818, 1881), BPF, 48/41. Study for special neck finish possible. Preform weight : from 15 to 91g 19mm to 120 mm & from 7 to 720g 30/25 3-start Obrist neck 28mm PCO - 1810 2-start short neck (27mm neck) 19mm ROPP 29/21 mm CTC 25mm ROPP 83mm jar preforms","@ID":26} "CAPPING / CLOSURES 37 PETplanet insider Vol. 13 No. 06/12 www.petpla.net Bericap reaches North American commercial market with its DoubleSeal one-piece hot f ll closure Slimming down for hot-fill Bericap North America announced in March that its exclusive DoubleSeal cap technology is now commercially available in the North American market. In itself, the system is not new. But now Bericap, in the shape of its DoubleSeal System, is also conducting hot fill operations with a reduced neck thickness, something which has up to now not been the case. Old, traditional wall thicknesses for 38mm necks are in the region of approx. 2.4mm; the wall thickness in the USA is approx. 2.2mm. Bericap’s successful tests in Latin-America show that a wall thickness of 1.5mm is possible, as a result of this some significant weight savings are emerging. The design is considered unique for hot fill applications since it will support, rather than distort, the finish when compared to traditional two-piece closures that cannot hold the finish when softened by the hot filled product. One piece closures with an integrated DoubleSeal-system provide significant higher seal and release angle. Only after a 160° turn of the closure the package will lose integrity where as a package closed with a two pieces closure will lose its integrity already after very few degrees of opening angle. “Traditional two-piece liner-andshell top seal closures require considerable torque in order to properly seal the container,” explains Volker Spiesmacher, Sales Director of Bericap. “In hot fill applications, the bottle neck is softened by the heat from the product itself. Consequently, the side and down-pressure from applying the closure puts considerable stress on the bottle finish. This can cause it to distort or ovalize, which can lead to leaking and product contamination.” The Bericap linerless one piece closure is featured with the DoubleSeal system, offering an outer and inner seal securing the integrity of the filled product. Furthermore, instead of down pressure during the sealing process, DoubleSeal caps provide lateral, opposing force pressure from both the outside and inside – effectively supporting instead of distorting the neck – which also results in a superior seal compared to the traditional two-piece method. As a result the Double Seal System allows to lightweight the neck walls of the hot fill bottle. The significant weight and cost savings are feasible. The chances of having a ‘leaker’ with DoubleSeal caps are virtually nil. That’s just one advantage of this product for industry users. The thicker walls employed to combat distortion from two-piece closures can be slimmed down dramatically. Currently, the neck finishes in a typical 20-oz. hot fill container are about 95/1,000 of an inch thick. Depending on the customer’s filling process; we could go down to 50/10,00 of an inch. This is nearly 50% less with no sealing problems whatsoever. The seal integrity for a product is another area where DoubleSeal offers improvement. With Bericap’s technology it breaks at a rotation point of up to 120%. According to Bericap, a 95 to 50/1,000-inch finish reduction will save about 3g of plastic, or 10% of the 30g total in a typical 20-oz. bottle. This means much less material going into bottles, and which needs to be dealt with post-usage. This achieves a reduction in the energy used to produce the bottles, resulting in a reduced carbon footprint and greenhouse gas emissions. Fits easily into existing lines The design, testing, validation and production of reduced plastic neck finishes won’t happen overnight, however, the system can fit easily into existing hot-fill operations. The changeover from two-piece equipment can be accomplished with very little production downtime, typically in less than a day. Although newly commercialised with an isotonic category leader in North America, Bericap’s liner-less technology is already proven in both hot fill, aseptic and cold fill applications. DoubleSeal caps are made with HDPE (High Density Polyethylene). www.bericap.com sensitive BEVERAGES","@ID":39} "#326-1, Taejeon-dong, Gwangju-si, Gyeonggi-do, 464-805, R. O. Korea Tel: +82 31 763 5621 Fax: +82 31 763 5623 E-mail: pnstech@pnstech.co.kr URL: www.pnstech.co.kr Machine Vision Inspection System PS-21GP S2 is connected on the production line directly. This machine inspect the PET bottle preform and reject the detected preform automatically. This operates from low to high speed which was designed based on the client’s production line. All of the preform checks for foreign substance by rotating the preform and using a specially designed mirror with a high degree of precision to check for the entire circumference of preform. In case of inspecting the long gate preform, the customer can put the gate cutting device in the PS-21GP S2, so the cost and the because the preform moving device is designed to gripper type, so customer doesn’t need to buy another change part. 3 Wheels Rotary Type Preform Whole surface Inspection System (PS-21GP Series 2) Basic Inspection Area 1. Neck Innerwall 2. Neck Finish 3. Basement 4. Screw Thread 5. Sidewall Available Options 1. Gate Cutting Device (2 in 1) 2. Mold Number Reading Machine Capacity 1. Low Speed: ~200 PPM 2. Middle Speed: 200~400 PPM 3. High Speed: 400~600 PPM Neck Finish Screw Thread Neck Innerwall Sidewall Upper Sidewall Lower Basement Gate Cutter Device (Option) Mold Number Reading (Option) Mirror Camera Rotation Illumination Mirror Scanner Mirror Scanner Preform Rotation Gate Cutting Infeed Reject Good Products","@ID":33} "PETproducts 38 PETplanet insider Vol. 13 No. 06/12 www.petpla.net Aseptic technology Modulbloc, is an aseptic filling solution offered by GEA Procomac, for the increasing demand for preservativefree beverages. With Modulbloc it is now possible to bottle sensitive, high- or low-acid beverages making them shelf stable without the use of preservatives. Modulbloc is a smart solution for low/medium speed filling lines. It uses Peracetic Acid (PAA) as the sterilizing medium to achieve up to 6 Log reduction in microorganism decontamination. It includes a sterilizer carousel, a rinser carousel, a filler carousel and a capper all on a single base frame. Rinsers are equipped with nozzles which reduce rinsing time, water consumption and maintainance costs. Filling is provided by a 33-valve aseptic filler from the FX range, featuring the high-flow filling valves, for clear products (not containing pulps and fibrEs). After filling the bottles move to an Arol 11-head capping machine, equipped with servomotors, to fit the bottles with 38mm caps. Also integrated into the system is a dual cap sorting elevator: one dedicated to sports caps; the second to standard flat caps. At Paradiso SpA, manufacturer of still and sparkling water and CSDs in Udine, Italy, a new Modulbloc aseptic filler handling teas, isotonics, and other beverages is notable for its compact layout. The line is manufacturing different kinds of ice teas at a speed of 12,000bph on 0.5l and 8,000bph on 1.5l bottles. GEA Procomac has also developed a low-medium speed version of its Aseptic Blow Fill (ABF) technology specifically to handle this market segment, introducing the Airstar 6 and 8 cavities. www.procomac.it High speed sensitive beverage production Sidel has refined its aseptic Combi Predis FMa technology to answer the growing demand of aseptic filling of teas, juices, nectars and isotonics. The new high-speed version will be capable of handling up to 48,000bph for small containers of up to 700ml, used mainly for on-the-go consumption. The new High Speed Combi Predis FMa is designed for markets that require high output and for countries where water resources are scarce. Predis is suitable for aseptic bottling of any kind of fruit juices, teas, isotonic beverages, carbonated soft drinks without preservatives, liquid dairy products and UHT milk. The Combi Predis FMa technology replaces bottle rinsing by dry preforms decontamination using hydrogen peroxide. The Combi Predis technology combines bottle blow moulding, filling and capping in a single system. The technology uses high standards of hygiene and offers water savings and minimized amounts of chemicals used as well as energy savings, a smaller footprint and the potential for lighter bottles. Quick format and liquid changeovers are possible, as well as 120h of non-stop production. www.sidel.com sensitive BEVERAGES","@ID":40} "23 PETplanet insider Vol. 13 No. 06/12 www.petpla.net Conveyors Bottle-to-bottle recycling plants Caps and closures Preform moulds and SBM moulds Preforms Preform and single stage machinery SBM machinery Compressors Filling equipment Resins and additives Suppliers of preforms In the overall preform market, suppliers range from players on the global stage to companies serving local markets. In this year’s survey, for the first time, we have asked which of the providers offer preforms using rPET content. 21 vendors are represented in our annual survey. Here they are, in alphabetical order: Alpla, Appe, GastroPET, Kimex, Manjushree, NovaPET, Parle Agro, PDG, Pearl, PETform, PET-Verpackungen, Plastipak, Pramia, Resilux, Retal Iberia, SBECM, SGT, Sundiapet, Sunpet, Terrachim and Westbridge. Although the publishers have made every effort to ensure that the information in this survey is up to date, no claims are made regarding completeness or accuracy. 06/2012 MARKETsurvey Company name PET-Verpackungen GmbH Deutschland IntraPac International - Westbridge Division Kimex SA de CV PDG Plastiques Postal address Telephone number Web site address Contact name Function Direct telephone number Fax E-mail Gewerbegebiet 4, 98701 Großbreitenbach, Germany +49 3 67 81 / 4 80 - 4 57 www.pet-verpackungen.de Hubert Rebhan Projects & Sales +49 3 67 81 / 4 80 - 4 53 +49 3 67 81 / 4 80 - 4 52 hubert.rebhan@wiegand-glas.de 3838E - 80 Avenue SE Calgary, Alberta T2C 2J7, Canada +1 403-248-1513 www.intrapacgroup.com Sharon Pokolm Sales Manager +1 403-207-7720 +1 403-248-1199 spokolm@intrapacgroup.com Querétaro,Tlalnepantla 54020 Edo. De México,México +52 55 5366 90 30 Jorge Larrañaga Comercial Director +52 55 5366 90 30 +52 55 5366 90 60 jlarranaga@kimex.com.mx ZI secteur 2 45330 Malesherbes, France +33 2 38 34 61 95 www.pdg-plastiques.com Francois Desfretier General Manager +33 2 38 34 61 95 +33 2 38 34 63 82 francois.desfretier@pdg-plastiques.com Preforms Multilayer preforms (Yes/No) Yes No No Yes PEN prefoms (Yes/No) Upon request No Yes Yes Preforms in alternative materials (PP/PLA/PEF) Which? Upon request No PP, PE, BioPET Preforms incorporating rPET (rPET content in %) up to 100% 20 % 100% for non-food up to 30% for beverages Yes from 10% to 100% List of additives available Colours, oxygen scavengers, UVblockers, slip-agents,AA-scavengers, brighteners, PA-based barriers Bio- degradable UV, oxygen scavenger, colour Uv Protector, O2 Scavenger, Nylon, Prelactia 100% light barrier for UHT steralized milk long shelf-life Oxygen, UV, CO2 barriers Preform range Standard preforms 28mm PCO1810 and PCO1881 finish from 14.5g (e.g. for 0.25l bottles) up to 54g (e.g. for 2.0l bottles). PCO 1810 and 1881 preforms are also available with octagonal neckring (e.g. for PETcycle customers). 38mm 2-Start and 3-Start Bericap preforms for wide mouth applications; 60g, 92g and 98g preforms with Bericap 48-41 finish for large containers. Majority of preforms available as multilayer with tailor-made barrier properties. 24mm 410 - 20, 23 28mm 400, 410, 415 - 36, 42, 47, 47g short taper 33mm 400 - 30, 36, 54 33mm 400 CRC - 46, 56 38mm 400 - 66 29mm Rical - 36, 41 32mm Rical - 48, 60 28mm Kerr - 39, 45, 86 33mm Kerr - 83, 90 33mm Kerr - 97g Long Kerr 38mm Portola SCIII - 59, 75, 83 30mm Stelvin - 65, 71 38mmAlcoa - 87 28mmPCO 1880 - 19, 24, 34, 42, 47, 55, 76 28mm PCO 1881 - 19, 24, 34, 47 Preforms for water CSD and hotfill from 12, 8g - 800g with different neck finishes : Alaska 26.6 short Corvaglia short Alaska Novenvall Corvaglia PCO 28 PCO 29 PCO30 PCO 31 48\" 38\" 38\" 38\" Standard and specific preforms for mineral water, dairy, juice, CSD..etc; coloured preforms; Preblow technology(also for leightweighting); 29/25 shorty : 8 - 10,5 - 11,7 - 18,7 - 22- 23 - 23,5 - 24,5 - 28g; 30/25 high: 17,5-25-26-28-31-33-36-39g; 30/25 low: 17,5-25-26-28-31-33-36-39g; 38mm 3 start: 26 - 33,5 - 35 - 44 - 50g; 38mm 3 start: 24 - 28g Prelactia; 48/40: 55 - 62g; 27/32: 6.5g dairy and smoothies; 25/20: 6.5 - 8g dairy; Ø28 BPF: 42 - 44 - 48 - 60g; 29/23: 24 - 33g chemical; BVS 30H60: 50g Wine (high oxygen barrier); ultra-lightweighting 2,4g preform; standard and specific preforms for mineral water, dairy, juice, CSD.etc; Overmoulding technology for 2-layers preforms","@ID":25} "EDITOUR REPORTS 21 PETplanet insider Vol. 13 No. 06/12 www.petpla.net two lines; a glass bottle line with a capacity of 15,600bph and a PET bottle line with capacity of 14,400bph, giving a total annual capacity of 60 million bottles per year. An additional facility, producing mineral water and carbonated soft drinks is due to open in September 2012. A further PET line will be added with a capacity of 35,000bph, which should be ready to produce for the 2013 season. As an addition to filling lines, there are two Husky systems used for manufacturing preforms; HyPET 120 with a 32 cavity mould for PET preforms and Hyelectric 160 with a 32 cavity mould for HDPE caps. The preforms are designed with 1810 PCO classic system hence they may be produced in 20g, 30g, 32g, 35g and 37g weights. Further improvements are currently being considered, including a proposal to switch to returnable PET bottles, as is happening in Germany, and this would bring ecological benefits.At present, the company is planning to install a 5l and 19l filling line using returnable and non-returnable bottles and for preforms for 19l bottles made of polycarbonate. The glass line will be for returnable bottles. For maximum control of quality and to make the production process less dependent on outside suppilers, the AraratGroup has installed a CO2 plant with a capacity of 500kg/h, which is easily able to handle 4,320 cases of carbonated soft drinks per day. These increased quantities have required improvements to the logistics systems and the loading bays have been enlarged to 1,000m2. A stationary washing system has also been installed for heavy trucks and other vehicles. As well as a growing domestic market the company is also targeting export markets not only to the north towards Russia, but also to Iran. *by Alexander Büchler Musheg Mkhitaryan, Nadezhda Gulaga, Sergey Hovhannisyan and Alexander Büchler","@ID":23} "Fig 1:The amount of oxygen which diffuses through the packaging into the beverages increases as the thickness of the packaging decreases. BEVERAGE PREPARATION 30 PETplanet insider Vol. 13 No. 06/12 www.petpla.net sensitive BEVERAGES BEVERAGE PREPARA well in bottles with higher permeability. It can be stated that the effect of oxygen on product quality is highly variable and depends on the formulation in question: the same oxygen ingress can have very different effects, depending on the flavour or product composition. Increasing the amount of ascorbic acid as an antioxidant in products A, B and C cannot always compensate for the sensory changes which occur during the product’s shelf-life. By contrast, the use of scavengers can offset or even overcompensate for the effects of lower weight. www.wild.de How P.E.T.proof works - results Wild developed the quick-test procedure P.E.T. proof in 2003. It is a comprehensive stress-test program which reproduces six months’ worth of real-time cumulative oxygen permeation within a period of four days. P.E.T. proof also makes it possible to depict real permeation data in a graph which shows the increases in oxygen levels inside the bottle. As a result, Wild can track values indicating the influence of the bottles, caps and filling processes on overall oxygen ingress. The method involves a non-invasive optoelectronic quantification of oxygen, the OxyTrace system, which is made by PreSens in Regensburg, Germany. In this context, non-invasive means that the bottle does not have to be opened to determine the necessary values: the values can easily be calculated into real permeation rates. In other words, P.E.T. proof is not a form of theoretical modeling; it documents real data. Every pattern on the graph can be supported by several hundred individual values, thus permitting high precision levels in the measurements. The samples also undergo parallel sensory analysis by a trained tasting panel using a difference-from-control test. P.E.T. proof was validated using several types of beverages: the results of P.E.T. proof tests and real-time tests were compared in analytical and sensory evaluations of products in different kinds of plastic bottles. In comparison to real-time tests, P.E.T. proof successfully yielded a very precise simulation of the effects that varying levels of oxygen permeability had on different types of bottles. Wild uses the process exclusively for products developed in-house. The process is internationally patent-protected and has become the company’s benchmark standard test procedure for new developments in the beverage sector. Fig 2: The oxygen ingress in the bottle which weighs 19.8 grams is 33% higher than in the 24g bottle. Fig. 3: In a test of the sensory stability of orange sodas, three different products were filled in seven PET bottles with different properties. The influence of the closure Wild can also use P.E.T. proof to isolate the influence of the closure and its impact on oxygen permeation. Another test sequence analysed a PET preform rather than a PET bottle. The thick and even structure of the preform gives it a reproducibly low rate of permeability; for the purposes of comparing the effect of the closure, this yields a constant “background noise“ which can be very easily distinguished from the fluctuating permeability rate of the closure. Wild compared the permeability of standard caps with that of barrier caps. Barrier caps feature a plastic lining of lower permeability. The results of the test show that the choice of closure can have a clear impact on the overall permeability of the packaging. Consequently, the closure must be included in the total analysis of a bottle’s permeability. Sensory stability Wild filled three different products into seven different kinds of PET bottles so it could attain robust data about the influence of the thickness on permeability and subsequently on the sensory stability of beverages(Fig. 3). The bottles were 21 and 24g monolayers (ML); 21 and 24g PET bottles which consist of 50% recycled PET and 50% new PET (RH), and three different scavenger versions with a bottle weight of 21g each. Products A, B and C were orange sodas with different flavourings but the same amount of sugar. During the filling process, 400mg/l ascorbic acid was added to each of the three. As part of the P.E.T. proof method, products also underwent a differencefrom-control test. The results were expressed on a scale ranging from 0 – 15 (0 = identical to the reference; 15 = very different from the reference): In comparison to the reference product in the taste test, no significant difference could be detected in the sample up to a value of 3, which was defined as the significance threshold. The rejection limit was set at 7.5, meaning products at that value or higher were deemed no longer marketable. The test results confirm that there are products which do not function 35 30 25 20 15 10 5 0 oxygen content [mg/l] 0 1 2 3 4 5 6 7 real time equivalent [m] 19,8 g/Fl. y=5,0201x R²=0,99244 21 g/Fl. y=4,3024x R²=0,99044 24 g/Fl. y=3,7723x R²=0,99016 15,0 13,5 12,0 10,5 9,0 7,5 6,0 4,5 3,0 1,5 0 Line scale value 21 g ML 21 g RH 24 g ML 24 g RH Scavenger 3 Scavenger 1 Scavenger 2 injection limit significance thresold prod. A prod. B prod. C","@ID":32} "BOTTLING / FILLING 33 PETplanet insider Vol. 13 No. 06/12 www.petpla.net sensitive BEVERAGES Fine-tuned 18,000bph line The Contiform H 12 is equipped with the Relax-Cooling (RC) process, a feature indispensable for the PET bottles’ base stability while being hotfilled. Both the mould base and the mould carrier are water-cooled, thus ensuring fast mould cool-down. The combination of the RC process with a lower mould temperature than that obtaining in a traditional heatset process permits the use of aluminium moulds, which significantly cuts the costs involved. After the stretch blowmoulding process, the bottles’ bases are water-cooled for fast stabilisation, with the bottles then passed to the Volumetic VODM-PET filler, where they are hot-filled at a product temperature of 82 to 84°C. A function for pressurising the bottles with liquid nitrogen has been directly integrated. This will evaporate immediately after the bottles have been closed, building up a pressure of 1.5 to 2bar in the head space, thus compensating for the PET bottles’ susceptibility to shrinkage during cool-down. This entails a slight drop in the fill level. After the yellow 38mm flatcap has been applied, the bottle’s head space is sterilised in a bottle inverter over a defined transport section. The downstream LinaCool cooling unit causes the temperature of the product in the bottles to drop from 87°C to around 35°C. This cooldown leads to a reduction of product volume, thus creating an underpressure in the bottles’ head space. The nitrogen added during filling prevents the bottle from contracting, ensuring the requisite bottle stability. Downstream of the cooling unit, further bottle handling takes place at ambient temperature and a residual pressure of 0.3 – 0.5bar in the container. The bottles are labelled with wrap-around labels with a Krones Contiroll. Process technology Krones also supplied the process-engineering kit required. The VarioFlash H flash pasteuriser, with a product tank, a shell-and-tube heat exchanger and a product deaerator, assures the correct quality and temperature of the juices. Here, the oxygen is easily removed from the juices, so as to prevent oxidation during heat-up and the heat-holding phase. One feature worth mentioning is the high spread in terms of the shell-and-tube heat exchanger’s output, ranging between 19,800l and 4,800l – in other words, precisely what the company needs for running a flexible production operation that handles both large and small containers and an ultra-wide beverage range, not least for relatively small batches. The product tank, holding 10,000l, decouples the product feed and the heat exchanger while also serving as a rework tank. During product changeovers the tank serves as a batch tank for the product that has been expelled with water. “A filling duration of three to four hours for our facility means a propersized batch”, explains André van Schuijlenburg. “And this was where the actual challenges for Krones were hidden, because, you see, we didn’t want to lose too much juice during product changeovers. When compared to beer, which consists of 95% water, juice is a very expensive product. This critical point received maximised attention during commissioning, with the result that today our product loss comes to around 1.5%, which is very good indeed. And this covers all the equipment involved, from product treatment and filler, right through to labelling and packing.” In fact, the huge output achieved, and the disparate parameters involved, such as a different propensity to foam during filling, for example, had to be given due attention during each step in the production and filling operations. What deserves a specific mention here is the interrelationship between the cooling unit and the flash pasteuriser: the warm water from the tunnel cooling unit, at approx. 55°C, is used for the first pre-warming stage in the VarioFlash H. www.krones.com The Contiform H 12 is equipped with the Relax-Cooling process, a feature for the PET bottles’ base stability while being hotfilled. Down the stream: The Modulpal palletiser.","@ID":35} "BOTTLING / FILLING 34 PETplanet insider Vol. 13 No. 06/12 www.petpla.net Rabobank’s Global Beverage Outlook 2012 sees volatility, divergence and convergence in a market inf uenced by f ve megatrends* Global beverage markets Rabobank International, the Dutch financial services company specialising in food, agribusiness and related activities, sees the global beverage market in 2012 and beyond as far from unified. It identifies five ‘megatrends’ that will influence the market in 2012 and beyond – and the common element is change. Different markets are behaving in different ways, and within regions, the mature areas of Europe and North America in particular, individual sectors are seeing erosion of the middle ground. Rabobank headlined its report ‘The Best of Times, the Worst of Times’, the opening lines of Charles Dickens’‘A Tale of Two Cities’, which was set in a period of turmoil, when old certainties were overturned and settled social structures were transformed. The company believes that the worst of the economic storm has passed although – as it points out – there are opposing forces, including consumer trends and commodity costs, that illustrate the conflicts facing the industry. The megatrends that Rabobank identifies are: volatility and rising commodity costs; emerging market growth; divergence – or ‘bifurcation’, as the company describes it; strategic sourcing; and convergence across segments. Five megatrends Volatility and commodity cost rises are on an unprecedented scale, leading to swings in prices of ‘soft’ commodities, including sugar, coffee and citrus. Growth in emerging market growth is led by spreading consumerism in BRIC (Brazil, Russia, India and China) markets. Bifurcation is the divergence of consumer demand; beverage consumers are drawn either by low prices and affordable quality, or by more expensive, premium brand positioning. Strategic sourcing reflects the need to establish and maintain more cost-effective global supply chains. Convergence cross segments sees soft drinks players moving into dairy; beer distributors acquiring wine and spirits businesses; and breweries buying soft drinks brands. It brings economies of scale across supply chains. Effects Not all segments experience the impact of these trends in the same way. CSD companies are less vulnerable to raw material price volatility than fruit juice producers; bifurcation is most apparent and influential in wine, although it is also apparent in beers. Convergence has just begun in the USA, while it is well-established in China, although American players are involved. The five megatrends have been evident across the global food and beverage industry for several years but their impact is modified in the wake and context of the global economic crisis and subsequent recovery. The rapidly-growing disparity between the ‘established’ economies and the fast-growing emerging markets amplifies their effect. Across the board, volatility will continue to be a risk factor. In the wine industry, for example, with fluctuating grape supplies and currencies, mitigating volatility across the supply chain will continue to be a key challenge. sensitive BEVERAGES","@ID":36} "BOTTLES 39 PETplanet insider Vol. 13 No. 06/12 www.petpla.net PETbottles Beverages Bottless: hot stuff Italian company Sipa has announced the launch of a new 500ml hot fill PET bottle that weighs just 13.1 g. Sipa says that it has introduced the new range, named Bottless, as part of the drive to reduce the environmental impact of PET containers. The company asserts that neither functionality nor aesthetic appeal have been compromised in the new design. The bottles are offered with different neck finish weights, according to customer requirements. A 28mm collar weighs 3.8 g, while the 33 and 38mm versions weigh 6.5 g. They can be produced on an SFR rotary blow moulding machine at a rate of 1,800b/h per cavity. www.sipa.it On the ball Special ball-shaped bottle commemorates Ukraine’s hosting of Euro 2012 Fans and visitors to the 2012 UEFA European Football Championship matches in the Ukraine were able to buy special ball-shaped Morshinka mineral water bottles from IDS Ukraine, as souvenirs of the fouryearly inter-nation competition. IDS Group Ukraine is part of IDS Borjomi International, one of the three largest producers of mineral water across the Commonwealth of Independent States (CIS) and the Baltic countries. It is a Ukraine mineral water producer; its Morshinska brand natural water is produced at the company’s Oskar plant in the west of the country, and sold in bottles made on Sipa equipment. Sipa has been doing business with IDS Group Ukraine since 2005, when it supplied the company with two lines for production of large bottles. One is in the Oskar plant, the other is in the Mirgrodskaya plant in the health resort of Mirgorod, in central Ukraine. IDS Group Ukraine designed a limitededition 2.5l water bottle to commemorate Ukraine’s biggest-ever sporting event. The bottles are made on a Sipa three-cavity SFL linear blow moulding unit and filled on a Sipa filling line. The preform was designed by a third party and Sipa provided analysis on optimum parameters for the reheatstretch-blow moulding sequence. It also collaborated on critical fine-tuning of the bottle’s design; the container’s volume is close to the upper limit of the blow-moulding machine used in production. Sipa also worked to ensure that labels could be applied correctly onto the bottle, which required minor modifications to the panels of the bottle to provide a suitable surface. www.sipa.it sensitive BEVERAGES","@ID":41} "PREFORM PRODUCTION 14 PETplanet insider Vol. 13 No. 06/12 www.petpla.net Puccetti and Piovan’s PETchiller project Cool running * Puccetti SpA – Plastics Division The company is part of the Puccetti Group, which is active in several industrial sectors. Following the requirements of an increasingly demanding market, the Puccetti Plastics Division has extended its product range by manufacturing preforms of different weight and with BPF-type of closures. Italian company Puccetti Plastics Division, founded in 1998 and a producer of PET preforms, is a member of the Puccetti Group*. When it went looking for optimised cooling systems for its preform production plant, the solutions found were developed in close collaboration with Piovan. The company was involved in all stages of the production process. The perform production process requires a high mould cooling capacity, so as to obtain preforms with suitable and constant mechanical characteristics. The original refrigeration system at Puccetti Materie Plastiche consisted of two centralised chilling units for low-temperature chilled water and one evaporation tower for high-temperature cooling water. The total thermal load, represented by moulds, robots, mould dryers, hydraulic system of the injection moulding machines and cooling for the PET dryers, is more than 1,500kW. According to an energy analysis of the total consumption of the two centralised refrigeration units, the evaporation tower and the pumping units, the amount of energy used each year was 2,313MWh. The location of the production plant has a characteristic temperature range between 5 and 25°C for 85% of the year. In the first stage of the project, which was aimed at studying and verifying the best solution, the working conditions of the existing system were analysed and possible alternatives assessed. Piovan proposed to replace the entire existing refrigeration system with the new PETchiller, a product offered by Piovan to obtain high energy efficiency from the chilled water system of any preform production process. PETchiller is offered in three possible configurations with integrated air cooling, with remote air cooling, or with water cooling. Energy savings Two high energy efficiency solutions were considered for Puccetti Materie Plastiche, both composed of free coolers and water-cooled chiller units. One solution involved a centralised PETchiller, the other individual PETchillers. The energy consumption analysis gave the following results: existing solution: 2,313 MWh/a centralised PETchiller solution: 1,762 MWh/a individual PETchiller solution: 1,272 MWh/a. The decision to choose the individual PETchiller solution, which offers savings of nearly 50% in electric power consumption, was made at quickly. This was the first step in a program to replace the entire system and was completed in spring 2010. www.piovan.com Piovan’s PETchiller installed above the injection moulding machine Piovan freecooler installation","@ID":16} "BOTTLE MAKING 27 PETplanet insider Vol. 13 No. 06/12 www.petpla.net PETplanet: Which sizes of PET bottle for wine are particularly popular in the USA? Piercy: The 187ml PET bottle is extremely popular, with most US consumers buying it in packs of four. If the consumer fancies a glass of wine, he or she opens one of the little bottles and consumes it at one sitting. The 187ml PET bottle thus also incorporates the idea of freshness. As we see it, there will be an increased move towards the 187ml PET bottle in the coming years. In the long term we expect that glass wine bottles of this size may no longer be available on the market, being instead replaced by the PET variety. Growing demand PETplanet: How high is the percentage of PET wine bottles currently consumed in the USA compared to glass wine bottles, and what percentage of these can be allocated to the 187ml PET bottle? Piercy: The current share of PET wine bottles in the USA is around 4%. Considering that wine in PET only really became relevant here about five years ago, this is a very good result. 90% of all wines filled in PET reaches the consumer in the 187ml PET container. For the future we can see clear growth potential for this size of bottle. At the same time, we also estimate that larger PET wine bottles, such as the 1l or 1.5l size, will attract more consumer interest. The target group for this larger type of PET bottle could be consumers buying wine for parties with friends, for instance. By the way, in the past few years Amcor has notched up an average yearly growth rate of approximately 10% for PET wine bottles. This again demonstrates that wine in PET is definitely a growth market. For 2011 we were forecasting sales of 150 million units for the 187ml PET wine bottle alone. Wine in PET pioneers PETplanet: Which wine companies are opting for wine in PET? Piercy: In the USA we mostly supply larger wineries, among them Sutter Home, the market leader for 187ml wine bottles. Sutter Home was a pioneer when in 2005 they began filling wine into 187ml PET bottles. The 187ml PET bottle was designed to look exactly like the 187ml glass bottle. In addition, the PET bottles could and still can be filled on an existing glass line. Sutter Home – and this is a clear signal to the US market as a whole – has since switched its entire 187ml bottle range over to lightweight PET containers. According to Wendy Nyberg, Marketing Director of Sutter Home, consumers are now confident that wine in PET bottles is of the same high quality and keeps as long as wine filled in glass bottles. They were also delighted that the 187ml PET bottle weighs just a sixth of the glass bottle and is smaller – although it contains an identical amount of wine – and has the added advantage of being unbreakable. Besides Sutter Home, other giants of the US wine industry we supply with PET wine bottles include Fetzer, Hopland, and Sonoma. Quality maintained PETplanet: Wine is a sensitive product that doesn’t tolerate any oxygen pickup in the container. What is Amcor’s approach to ensure the top quality to be maintained in PET bottles? Piercy: Amcor has taken great care to select a barrier coating for our PET wine bottles that upholds the quality of the wine to the fullest. We’ve made KHS’ Plasmax technology standard not just for wine but also for beer bottles, which on the US beer market still have an increasingly low market share. KHS gives us consistency, enabling us to always provide our customers with rapid solutions. As regards the Plasmax barrier coating process the insides of our PET wine bottles are covered with an ultrathin, completely transparent layer of glass. This glass layer prevents oxygen penetrating the PET bottles, ensuring that wine filled in a Plasmaxcoated bottle has just as long a shelf life as wine bottled in glass. The taste of the wine is also not affected. Another benefit of this process is that PET bottles coated with Plasmax technology are 100% recyclable, making the system sustainable. PETplanet: What are your expectations of growth of wine in PET? Piercy: We expect that in the next few years, the yearly growth potential for PET wine bottles could be approximately 10%. PETplanet: Mr Piercy, thank you very much for this interview. Fred Piercy, Director of wine and spirits at Amcor Rigid Plastics The Amcor PET bottles for wine are caoted with Plasmax barrier coating sensitive BEVERAGES","@ID":29} "BOTTLE MAKING 22 PETplanet insider Vol. 13 No. 06/12 www.petpla.net Amcor Rigid Plastics grows with PET wine bottles Bumper harvest Beyond the food and pharmaceuticals industries, Amcor Rigid Plastics supplies the beverage industry with plastic bottles for non-alcoholic beverages and also beer, wine, and spirits. Recently, the focus has shifted towards providing wine in PET bottles. In the following interview, Fred Piercy, Business Director for spirits, wine and beer, speaks about how this development came about, why wine in PET is being received positively, especially in the USA, how winemakers are profiting from the PET bottle trend, what the future could look like for wine in PET, and what specific requirements are necessary in the case of PET bottles for wine. Wine into PET? PETplanet: Mr Piercy, what do you think are the reasons for wine in PET bottles becoming more prominent with consumers in the USA? Piercy: First of all, there are the general advantages that come with the PET bottle. Consumers like the light, non-breakable bottles and often opt for this convenient type of container – once they’re convinced that the wine in PET bottle is of a good quality. Besides the lightweight and non-breakability of PET bottles, wine companies also consider the advantages in transportation and truck utilisation of the lightweight and smaller footprint containers. This provides for a sustainable solution. Incidentally, in the interest of sustainability we only supply our clients with PET wine bottles that are 100% recyclable. PETplanet: Who do you consider to be the main target groups for wine in PET? Piercy: Young adults are showing great interest in the PET bottle for wine, for instance. They are particularly receptive to innovative container concepts. At the same time they’re always on the move and appreciate the convenience they have in a lightweight, non-breakable PET bottle. Furthermore, we count particularly convenience-oriented consumers of all legal drinking ages as part of our main target group. These include consumers who don’t want to carry heavy wine bottles back home with them after a big shopping trip, for example, or consumers who buy wine that they drink in venues outside the home. PET takes to the air PETplanet: Is retail the main sales channel for wine in PET bottles or is the hospitality trade also showing some interest? Piercy: Wine in PET is chiefly in demand with retailers. However, we are seeing an increase in demand from airlines. For example, the Cecchetti Wine Company from California supplies 187-ml PET bottles of their Red Tree brand wines to Air Canada, British Airways, and Continental Airlines. According to Roy Cecchetti, president of the Cecchetti Wine Company, airlines see the advantage of the lightweight PET wine bottle in the lower use of fuel – which in turn gives them sustainability and cuts costs. For air traffic the non-breakability of PET bottles is also a major criterion, and it’s important that Amcor provides PET wine bottles that preserve the quality of the wine as perfectly as traditional glass bottles do. This point of view is shared by Aldo Geloso, president of the Société De Vin Internationale Ltée. The Société De Vin Internationale Ltée is based in Canada and has recently started filling many of its fine wines into 1l PET wine bottles destined for airlines. It already works in close collaboration with Air Transat, one of the biggest charter airlines in Canada. Air Transat decided to start using the container after feedback from passengers during the test phase proved extremely positive. At 54g the 1l PET wine bottle for Air Transat weighs just an eighth of the 1l receptacle made of glass. Geloso reckons on more airlines showing an interest in his wine brands in the 1l PET bottle in the future. He is also thinking about bottling products such as cider in smaller 330ml and 500ml sizes of PET bottle and selling these through the retail trade. PET wine bottles are becoming increasingly popular in the USA. Of all wines filled in the USA, 4% reaches the consumer in the PET bottle. Sutter Home acted as a pioneer when in 2005 they began filling wine into 187ml PET bottles. The 187ml PET bottle is usually sold in packs of four. sensitive BEVERAGES","@ID":24} "EDITOUR REPORTS 17 PETplanet insider Vol. 13 No. 06/12 www.petpla.net the first time in Armenia’s supermarkets, the aspirations of the manufacturers have consistently been directed at PET. Today it is these manufacturers who dominate the local market which, in Soviet times, restricted itself to selling beverages packaged in glass only. The population’s preferences are overwhelmingly for CSD and carbonated water. Beverages Consumption in 2011 Carbonated Water 40 % CSD 37 % Still water 20 % Juice 2 % Beer 1 % Overall consumption of beverages in PET in 2011: approx. 180 million litres (Source: Hytex Plastic) As far as the beverage packaging market is concerned, until 1995 bottling activities in Armenia involved the exclusive use of glass containers. It was only as a result of the introduction of PET by two companies Jermuk (1995) and Hytex Plastic (1996) and the utilisation of PET bottles by Coca-Cola in Armenia that successive manufacturers, both large and small, were inspired to embrace the emerging market. Later, admittedly, the manufacturers who will benefit will be those who, through early investment and hence the acquisition of the corresponding capacity and technolengineering for a better world GEA Procomac S.p.A. The Aseptic Way ogy, secure for themselves the possibility of a long-term supplier cooperation with major brands. In the meantime, the current situation on the Armenian market reflects, in round terms, a proportion of 2/3rds PET to glass and the trend is rising. Looking at the individual PET beverages segments today, one striking feature is consumption in the CSD sector which is forging ahead, having undergone a continuous rise over the past few years. Based on this, a characteristic preference for the consumption of water with a CO 2 content may also be discerned. According to Hytex Plastic, based on a direct comparison of the years 2010 and 2011, market behaviour as regards PET consumption may be summarised as follows: CSD increased slightly by comparison to the previous year by 1% to 37%, carbonated water from 38% to 40%, whereas still water is down by 3% at 20%. Bringing up the rear are fruit juices and beer without any changes at 2% and 1% respectively. However, if anything, a rapid change may be expected in these figures as and when the market starts to expand in 2012/2013, resulting from the planned launch of a modern filling plant for water and CSD by the Ararat Group. Kay Krüger","@ID":19} "EDITOURS REPORTS 18 PETplanet insider Vol. 13 No. 06/12 www.petpla.net Armenia blog Here in Armenia, one feature dominates the landscape: the steppe. Yet again the time zone has changed. Confusing, to say the least. At about 5 pm, after a long journey, I arrive in Yerevan. Prior to finding a parking space for the Editourmobil close to my appointment tomorrow with Pepsi, I drop into a nearby filling station for water as the tank is now totally empty. The next morning I am starting to feel the effects of the last few strenuous days. However, the morning dose of caffeine restores the energy levels and I hasten to my appointment with Pepsi where Mrs Nune Stepanyan and Daniel Ghevondian answer my questions and take me round the modern bottling plants. There is no time to lose, for my next appointment takes me to the centre of Yerevan to Mr Hovhannes Azaryan of Grom LLC, a small family business producing PET bottles and filling beauty care products. After our meeting, it is lunch time and we enjoy a splendid meal in the private room of a sumptuous restaurant serving local delicacies. One of the minor sensations of the place is the tame brown bear besporting himself in the courtyard. An unpleasant surprise awaits me in the evening when eight burly policemen knock on my door, and take me briefly to the security office. It seems that the Editourmobil has attracted their suspicions. It all turns out for the best in the end, we manage to understand one another with much arm-waving and gesticulation, and after noting my passport number they bid me a friendly farewell. It is the morning of October 19, as I make my way to my next appointment with Hytex, fortunately not too far away from my parking spot for the night. I am welcomed by Mr Samvel Tumanyan and Mr Levon Meliksetyan, and over coffee and chocolate brandy beans (a local speciality) I learn a lot about not only preform production, but also about Armenia’s difficult situation with Azerbaijan and Turkey and the resulting concentration of companies in the purely national market. Around noon, it is time to take my leave of Armenia, and continue my journey to Baku. Getting into Azerbaijan is not so straightforward as it has to be via Georgia. And just to add to the complex border formalities it now starts to pour with rain again. - Kay Krüger - Pepsi Yerevan From water to CSD – how Pepsi is finding its way into Yerevan (f.l.t.r.) Nune Stepanyan, Kay Krüger and Daniel Ghevondian We met: Mr Daniel Ghevondian, Production Manager Ms Nune Stepanyan, Marketing Manager Pepsi’s site in Yerevan has a surface area of around 14,000 m2 and employs around 200 staff. It has its origins in the “Jermuk Group“ water bottling plant which has maintained a considerable share of the market for natural mineral water in Armenia for some years. Following the post-Millenium decision to collaborate with PepsiCo, initial agreements were drawn up for the sale of Pepsi products in 2001; these were imported from Georgia and sold in Armenia. Then there was the question of distribution and bottling; they decided over the following years to go for modern production lines from KHS with a view not only to taking over sales for Armenia but the bottling process as well. After final negotiations and corresponding laboratory tests carried out by Pepsi Ireland as regards product quality, initial production commenced in June 2011 once all the PET systems had been finally installed by KHS and all tests had been successfully rubber stamped and signed off by PepsiCo. The spring which is being used for the individual Pepsi products is located in the vicinity of the site. Pepsi Yerevan uses one of three technologies installed in Pepsi plants all over the world; this is known as Gen 2 Green - this means that no chlorine is used for treating the water here. Products bottled are (sorted by sales): Pepsi, Mirinda Orange, Mirinda Green Apple, Seven Up and Pepsi Light. Mr Ghevondian reckons that Mirinda Green Apple may well soon overtake Mirinda Orange in the rankings because Green Apple is experiencing a high level of popularity in Armenia. Pepsi’s filling operations comprise PET volumes 0.5l, 1.0l and 2l with the 2l bottle enjoying the lion’s share of sales. In the capping sector, the company operates with closures sourced from Bericap. As far as the future is concerned, a 1.5l bottle is also planned. In addition, the launch of a new beverages line for the Pepsi juice brands in cartons is scheduled by the spring of 2012. The identity of the carton suppliers is still at the discussion stage. www.pepsico.com","@ID":20} "BEVERAGE PREPARATION 28 PETplanet insider Vol. 13 No. 06/12 www.petpla.net sensitive BEVERAGES BEVERAGE PREPARA The trend toward PET packaging on the non-alcoholic soft drink market has been holding strong for years. The market share of disposable PET packaging was only 1.9% in 1999, but in 2004 it had reached 30.9% and by 2011 it had grown to 71.5%. In the course of this development, the weight of the bottle has fallen significantly. One of the distinctive properties of PET bottles is permeability. The extent to which atmospheric oxygen permeates the bottle can be critical, since in addition to temperature and light, oxygen is one of the main factors which contributes to the ageing process of foods. Permeability rises in inverse correlation to the weight of PET bottles falling: the thinner the packaging, the greater its permeability. Bottle weight and permeability This article discusses an experiment using P.E.T.proof to compare seven bottles with varying physical properties. This demonstrates the influence that the bottle weight and, by extension, the thickness have on permeability and subsequently on a beverage’s sensory stability. To date, the industry has had to add greater amounts of ascorbic acid as an antioxidant to bind the amount of oxygen which penetrates packaging. However, test results indicate that additional ascorbic acid cannot always compensate for the sensory changes a product undergoes during its shelflife. The use of oxygen scavengers can offset, if not overcompensate for, the consequence of lowering the weight of the bottle. Scavengers are substances or plastic systems which, when added to the PET compound, capture and oxidise the oxygen permeating the walls of the bottle. In the past several years, the weight of PET bottles has fallen dramatically: whereas a standard 0.5l bottle still weighed 27g in 2003, the figure fell to a mere 15.3g in 2007. The weight continued to fall to 12g by 2011. As a result, packaging has become thinner, and this in turn leads to higher gas permeability. (Fig. 1) P.E.T. proof provides a realistic simulation of oxygen permeation, thus permitting a comparison of the permeability rate of different bottle weights. In one test sequence, bottles weighing 19.8, 21 and 24g were compared. To rule out the effect of the cap, the mouths of the bottles were sealed with an aluminum foil. The oxygen permeation in the lightest bottle was 33% higher than in the heaviest. (Fig. 2) The 33% higher permeation rate accompanied by only 17.5% less material indicates that reducing the material does not have a linear effect. This can be explained as follows. The weight of the PET bottles was repeatedly reduced. However, if the overall reduction in material of the bottles which weighed a total of 19.8 or 24g is contrasted with the weight of each individual parts of the bottle, it becomes clear that the neck where the cap is screwed on remained at a constant weight of 6.15g. The weight is only lower in the body of the bottle, and correspondingly the material thickness was reduced there alone. This allowed the proportional weight to decline and thus the permeability of the body of the bottle to increase by 31% in the lighter bottle. In other words, reducing the amount of material is not a linear phenomenon: permeation increases disproportionately as weight falls. P.E.T. proof: Wild’s quick-test procedure Based on an article by Frank M. Spinner, Wild product development, Beverages Weighing up the PET permeability rate One of the distinctive properties of PET bottles is permeability. Conducting real-time tests in order to determine the impact that packaging has on beverage quality takes a great deal of time. The process can take several months, which means it is no longer viable for today’s market needs. Wild’s quick-test procedure called P.E.T. proof simulates the effects of oxygen on beverages in PET bottles and provides robust data after a mere 21 days.","@ID":30} "BOTTLING / FILLING 32 PETplanet insider Vol. 13 No. 06/12 www.petpla.net Krones NitroHotf ll line for Pago juices Based on an article by Ursula Danner, Krones AG Green for go! Green is the company colour of the Austrian fruit-juice producer Pago in Klagenfurt. The green bottles with their yellow lids have been for many years now the trademark of this company. The majority of the various juices they produce is sold in glass bottles for the horeca market but as drinks in PET bottles became ever more popular, the juice specialists from Carinthia were quick to tap into this segment as well. To start with, Pago had its products contract-bottled elsewhere. Since September 2011, the company has been bottling them in-house on their own NitroHotfill line from Krones. André van Schuijlenburg, Manager Supply Chain. 35 fruit-juice variants Christian Fruhwirth, the plant manager in Klagenfurt explains: “We have four different product groupings: the red fruits as potent health-boosters, citrus fruit products, our exotic line and the traditional fruit varieties.” The container range comprises the 0.2l glass bottle for the catering trade, with which the company leads the market in Austria and the neighbouring countries of Italy and Croatia. We also fill a 1.0l glass bottle. As the markets have changed, focusing more on at-home consumption and the PET bottle, we decided to include this type of container in our range as well.” Enjoying pure, unadulterated fruit juice, that’s the idea behind the brand, which means that no artificial flavourings, no preservatives are used. Pago in PET The company’s range of juices have been available in PET bottles since 2005. Today, as much as one third of its products is sold in PET bottles. To quote Christian Fruhwirth: “When we were considering the inclusion of PET in our container range, there was no doubt whatsoever that we would stick with the visual image of the bottle consumers have come to associate with the brand: green, orange-skin surface structure, yellow lid, wide-neck mouth. This quite clearly ruled out investing in the classical hotfill bottle in panel design right from the start. Hotfill bottles just don’t fit in with our image. This was why we had accepted – at least for as long as there was no alternative hotfill technology available – a situation where our contract bottler was filling our products in an aseptic process, likewise with kit from Krones.” As the PET bottle was a success on the market, they started an investment project for their own PET line at the Klagenfurt facility. With the newly installed Krones line, rated at 18,000bph, they produce 0.75l, 0.33l, 0.2l and 1.0l bottles, which are filled with a variety of juices. The whole line from the Contiform right through to the Variopac packer and the Modulpal palletiser is run by two operators. The present-day Pago company got started in the 1950s when the then owners, the Pagitz brothers, had the “Pago” brandname (combining “Pagitz” and “Obst”. (German for fruit) entered in the brand register. As from 1980, the company, in the meantime part of the big Austrian brewing conglomerate Brau Union Österreich, opened up new sales markets beyond the nation’s borders, with Italy, France, Spain and Croatia being the first markets targeted for the juice specialists’ exports. Since 2003 (when Brau Union was taken over by Heineken), the company has formed part of the world’s third-largest brewing conglomerate, and its biggest fruitjuice producer. As a premium brand, Pago complements the Dutch corporation’s portfolio perfectly, explains After the stretch blow-moulding process, the bottles’ bases are watercooled for fast stabilisation, with the bottles then passed to the filler. sensitive BEVERAGES","@ID":34} "PREFORM PRODUCTION 13 PETplanet insider Vol. 13 PETplanet print vol.6 The Rapid Guide to Perfect Preforms machine no./name 1- 3 exemplar each 129,- € 4 - 10 exemplar each 99,- € 10 exemplar each 69,- € prices in EUR + VAT. 6. Check all temperature readings and adjust higher if necessary. PET resin should be melted at about 280ºC (536ºF) +/- 10ºC (18ºF). Increase as necessary to improve melt flow. 7. Check for leaking core-air blow valve. Air pressure in the cavity during filling may restrict proper melt flow. 8. Ensure the core-air blow has a clean and moisture-free air supply to minimize the risk of contamination in the thread area. 9. Check to ensure that no moisture exists on the moulding surfaces, either from water leaks or condensation. This may obstruct normal melt flow and cause filling problems. The environmental dewpoint should be below the chilled water temperature to eliminate the risk of condensation. 10. Check hardware for worn, damaged or failed components, specifically the mould neck inserts (collapsed vents), lock ring vents, and lock ring / core parting line. www.petpla.net PETplanet print Vol. 6: The Rapid Guide to Perfect Preforms by Rick Unterlander and Ottmar Brandau fax: +49 (0) 6221-65108-28 info@hbmedia.net www.petpla.net Order your copy now!","@ID":15} "imprint EDITORIAL PUBLISHER Alexander Büchler, Managing Director HEAD OFFICE heidelberg business media GmbH Häusserstr. 36 69115 Heidelberg, Germany phone: +49(0)6221-65108-0 fax: +49(0)6221-65108-28 info@hbmedia.net EDITORIAL Doris Fischer: fischer@hbmedia.net Michael Maruschke Ruari McCallion Ilona Trotter Wolfgang von Schroeter Anthony Withers MEDIA CONSULTANTS Ute Andrä andrae@hbmedia.net Martina Hischmann hirschmann@hbmedia.net Ursula Wachter wachter@hbmedia.net phone: +49(0)6221-65108-0 fax: +49(0)6221-65108-28 France, Italy, Spain, UK Elisabeth Maria Köpke phone: +49(0)6201-878925 fax: +49(0)6201-878926 koepke@hbmedia.net LAYOUT AND PREPRESS Exprim Kommunikationsdesign Matthias Gaumann | www.exprim.de READER SERVICES Kay Krüger reader@hbmedia.net PRINT Chroma Druck & Verlag GmbH Werkstr. 25 67454 Römerberg Germany WWW www.hbmedia.net | www.petpla.net PETplanet insider ISSN 1438-9459 is published 10 times a year. This publication is sent to qualified subscribers (1-year subscription 149 EUR, 2-year subscription 289 EUR, Young professionals’ subscription 99 EUR. Magazines will be dispatched to you by airmail). Not to be reproduced in any form without permission from the publisher. Note: The fact that product names may not be identified as trade marks is not an indication that such names are not registered trademarks. 3 PETplanet insider Vol. 13 No. 06/12 www.petpla.net EDITORIAL dear readers, EDITORIAL Let PET be light PET bottles to light up 1,000,000 homes by the end of 2012 According to statistics from the National Electrification Commission of the Philippines in 2009, 3 million households still remain without power outside Metro Manila. And even in the city itself, families still continue to live in darkness. In addition, the Bureau of Fire Protection (BFP) has reported that a large number of fire-related incidents involve faulty electrical connections. Unauthorised settlements are high-risk areas, since the BFP does not conduct fire hazard inspections in these communities. The “MyShelter” Foundation wants to tackle this problem and aims to brighten up one million homes in the Philippines by 2012. The secret? Discarded PET bottles. “Isang Litrong Liwanag” - A Litre of Light “Isang Litrong Liwanag” (A Litre of Light) is the latest venture of the “MyShelter Foundation”, a lighting project which aims to bring the eco-friendly Solar Bottle Bulb to deprived communities nationwide. This is a programme developed by students from the Massachusetts Institute of Technology and inspired by many innovations from around the world. Many cultures have used glass bottles to allow lighting through the roof, and Alfredo Moser from Brazil began pioneering methods of experimenting with plastic bottles. The Philippines authorities took up the cause in a big way, using all the resources of the internet and social networks to spread the word and disseminate information. The step-by-step guide to making the PET bulb, for instance, can be found on Youtube, and then further discussed on Facebook. “Isang Litrong Liwanag” has now gone viral, spreading across the Philippines and around the world, lighting up thousands of homes with a simple formula; used PET bottles, water, bleach and pure Filipino ingenuity. The comprehensive 8-step guide on Youtube The process to make a PET solar bottle bulb is relatively easy and clearly explained in a 8-step guide on Youtube. Basically a PET bottle is filled with about 10ml chlorine and the rest with water. The filled and closed bottle is encased in a square galvanized iron sheet which in turn is then installed into the roof, bottle bottom downwards and the cap side towards the sky. In this process, the water refracts the light while the chlorine slows down evaporation. The solution is expected to last up to two years before it needs changing. The PE cap is additionally covered with a protective tube to avoid cracking caused by UV. It is said that each PET solar bulb emits the same amount of light as a 55-watt bulb and saves the planet about 64kg of carbon emissions a year. The foundation has just opened a new office in San Juan Manila where they will run training courses and issue community certifications. And they now take part in a variety of activities, for instance they participated in the United Nations Forum on Climate Change 2011 where they presented their grassroots solar lighting campaign to the world, under the eyes of SecretaryGeneral of the United Nations Ban Ki-Moon. www.isanglitrongliwanag.org Yours Michael Maruschke","@ID":5} "MARKET SURVEY 25 PETplanet insider Vol. 13 No. 06/12 www.petpla.net NovaPET, S.A. Manjushree Technopack LTD Plastipak International Holding Srl Gastro PET d.o.o. Zaragoza 50001 - Spain, Office: Paseo Independencia, 21, 3rd floor. +34 976 216129 www.novapet.es Mr Antonio Lázaro Preforms Sales Manager +34 976 216129 +34 901 021138 marto@samca.com /alazaro@samca.com No. 60-E, Bommasandra Industrial Area Hosur Road, Bangalore - 560099, India +91 80 43436200 www.manjushreeindia.com Rajat Kedia Director +91 80 43436200 +91 80 27832245 rajat.kedia@manjushreeindia.com Viale Azari 110, Verbania-Pallanza, 28922, Italy www.plastipak.com Marc Jacobs VP Sales & Marketing Plastipak Europe +352 358719202 +352 358719228 mjacobs@plastipak.eu Kotna ulica 5 3000 Celje, Slovenia +386 3 425 80 32 www.gastropet.si 3ULPRå general manager +386 3 425 80 32 +386 3 425 80 31 info@gastropet.si No No No No In project No No No Barrier Preforms using M&G Poliprotect and other barrier material. No PLA 10 - 25.% --- From 15% up to 100% Available according to customer requirements. All colours lubricants, nucleants, UV blocker, optocal brightener, quick rehaet additive, anti-static.liquid colours UV blocker, oxygen barrier, light barrier, AAblocker According to customer requirements. 29/25 W (short neck): 330ml - 2l (From 10.5 to 32g) 30/25 W (std neck): 0.33l - 2.5l (12.5 to 35g) 48mm W: 5l - 6.5l (77 and 82g) PCO 1810 (std neck):0.5l - 3l (18.5 - 54g) Any other shape and weight possible 28PCO 1810: 15g, 16.5g, 23.5g, 25g, 25.5g, 27g, 36g, 39g & 48g 28PCO 1881 short neck: 16g, 22.2g, 23.7g, 25.7g, 34.7g, 37.7g, 46.7g, 52.7g 28PCO hotfill thick neck: 18.5g, 24g, 27g, 47g 28mm 3 -Start Alaska: 10.5g, 13.6g, 15.6g, 21g, 22g, 35.6g 30/25 water neck: 22g 8 ECK 19.5 - 39g 10 ECK 18.5 - 33g PCO 1810 / 1816 14.8-52g PCO 1881 16.5 - 50.6g 29 / 25 25 - 27.5g 30 / 25 low 29 - 31g 30 / 25 high 15 - 35g Alaska 267 14.5 -35g Corvaglia 26 mm 14.8 - 37.5g 28mm BPF 23 - 39g 28mm BPFL 18.5 - 48g Bericap 38mm 2 starts 15 - 42g Bericap 38mm 3 starts 16 - 28g 38 mmAffaba Ferrari 25 - 37g 26 / 21 16.5 - 33g 29 / 21 28 - 69g 36 / 29 40 - 100g 48mm snap 85g PET preforms for various standard and special applications. PCO 1810: 18.5 - 24.5g PCO 1810: 33.3g - 48g Bericap 38mm 3-start: 16g - 41.5g Terrachim 97 AD Appe Pearl Drinks Limited Alpla-Werke Alwin Lehner GmbH & Co. KG Resilux NV 6 Kupenite str., Sofia 1618, Bulgaria +359 2 955 63 22 www.terrachim.com Michail Kostov General Manager +359 2 955 63 22 +359 2 955 63 25 terrachim@terrachim.com Ellice Way, Wrexham LL13 7YL United Kingdom +44 1978 317 378 www.appepackaging.com Kinza Sutton Marketing Manager +44 1978 317 378 kinza.sutton@arteniuspackaging.com 702,Ansal Bhawan, 16,K.G.Marg New Delhi-110001, India +91 11-46470200 www.jaipuria.co.in Vijay Walia Marketing +91 9811020870 +91 11-23327747 vijay.walia@ckjpearl.com Mockenstrasse 34 6971 Hard, Austria +43 5574 6020 www.alpla.com Hermann Riedlsperger Head of Sales - PET +43 5574 602 515 +43 5574 62017 515 hermann.riedlsperger@alpla.com Damstraat 4, 9230 Wetteren, Belgium +32 (9) 365 74 74 www.resilux.com Philippe Blonda Director of marketing and Sales +32 9 365 74 76 +32 9 365 74 75 Philippe.blonda@resilux.com No Yes No Yes Yes No Yes No No Yes No HDPE No Yes Yes up to 30% Yes 100% Yes, 50% and more Yes, up tp 50% Amosorb All Green colour all customary additives UV-blockers, colours, multiple barrier additives Preform weights:10.5g to 130g neck finishes: 30/25, PCO, 29/21, crown cork, 38mm and 48mm Design and manufacture of a huge variety of weights, finishes, gate designs, including wide mouth 22g 3-start Alaska 28mm for 1l water/edible oil 21.5g Three-start Alaska 30mm for 1l water 25.5g Three-start Alaska 30mm 1l water/edible oil 25.5g PCO 28 for 600g CSD 52g PCO 28 for 2l CSD 20.9g PCO 28mm for 0.3/0.4l CSD Soft drinks preforms: various neck versions from 0.25 - 2.5l Water preforms: various neck versions from 0.25 - 5l. Edible oil preforms:from 0.5 - 10l. Milk preforms with various neck versions (2-start, 3-start) Preforms for personal care, home care and lubricants: various neck versions Standard monolayer preforms: Barrier preforms (Monolayer & Multilayer): • ResiOx 3-6-9 • ResiC • Resimid & Resimax • Resiblock 0-2-4 Hot fill For filling at 85°C Refill Wide range of bottles available for immediate supply Bottle blowing & in-house blowing","@ID":27} "MATERIAL / RECYCLING 11 PETplanet insider Vol. 13 No. 06/12 www.petpla.net be directly integrated on a “drop in” basis into existing chemical and fuel products to deliver environmental and economic benefits. Gevo is committed to a sustainable biobased economy that meets society’s needs for plentiful food and clean air and water. “The agreement with Coca-Cola covers the development and commercialisation of the technology to produce paraxylene from bio-based isobutanol,” said Patrick Gruber, CEO of Gevo. Avantium Avantium is a technology company specialised in the area of advanced high-throughput R&D, and ‘spun out’ from petroleum company Shell in 2000. It has been working on bio-based material development since 2005 and around 50% of its business activity is now bio-based. The company develops and commercialises YXY - its brand name for the technology to produce chemical building blocks for bio-based materials with exceptional product properties at a competitive price which is designed to enable 100% PEF bottles. The agreement with Coca-Cola includes the development of PEF (polyethylene-furanoate). Avantium says that various functional properties of PEF make it a suitable alternative to petroleum-based PET for future beverage packaging. YXY technology converts biomass into Furanics building blocks, such as FDCA (2.5-furandicarboxylic acid), the monomer that can be used for the production of PEF, which is claimed to be 100% recyclable. YXY uses carbohydrates as feedstock, which can be obtained from biomass such as sugarcane, agricultural residues, plants and grains. The company says that its chemical-catalytic technology can be implemented in existing chemical production assets with some retrofitting. This is claimed to represent a much lower investment than a new plant. CCT Creative Competence Technology GmbH Idsteiner Strasse 74 D-65527 Niedernhausen, Germany r.steinmetz@cct-systems.com www.cct-systems.com CCTsystems®-40 Cav. Mold ≥ 160 to Clamping force CCTsystems®-60 Cav. Mold ≥ 240 to Clamping force PET Molds Design and Patents Developments PET Systems All Closure types with CCTsystem®- BPT Best Performance Technology Closure molds Closure Molds Closure Systems Avantium says that it has already made bottles with what it claims are exceptional barrier and thermal properties. It further asserted that its production process fits well with existing supply chains. Commercial production of PEF is anticipated to commence in three to four years. The company opened a pilot PEF plant on December 8 2011. It has a capacity of 40t/a and will produce PEF material for application development. Avantium does not currently plan to build, own or operate PEF production plants and it is actively discussing partnerships with other leading brand owners to develop PEF bottles, fibres and film. The company intends to license its YXY technology to enable large scale, world-wide production and use of its biobased plastic materials. According to Avantium Chief Technology Officer Frank Roerink PEF has oxygen barrier properties six times better than PET, and carbon dioxide and water barrier properties twice as high. PETplanet insider reported that Danone Research and Avantium have entered into a Joint Development Agreement for the development of PEF bottles for Danone. The agreement is the second in Avantium’s commercialisation strategy for co-development of its YXY technology for PEF bottles, which use bio-sourced material (see PETplanet insider issue 5, page 6) Coca-Cola: extending range and collaboration The Coca-Cola Company already uses recyclable bottles that contain up to 30% bioplastics. Its first-generation PlantBottle packaging, used in fully-recyclable PET bottles, is made of two components: 30% plant-based MEG (mono-ethylene glycol), and 70% PTA. www.avantium.com www.yxy.com www.thecoca-colacompany.com","@ID":13} "EDITOURS REPORTS 20 PETplanet insider Vol. 13 No. 06/12 www.petpla.net Grom LLC Yerevan Care and household products with PET from the House of Grom We met: Mr Hovhannes Azaryan, General Director Hovhannes Azaryan (left) and KAy Krüger (right) The family firm of Grom LLC started life in 2001 and right up to the present day, has been managed by Mr Hovhannes Azaryan and his brother with a workforce of around 40 employees on the edge of the city of Yerevan. This small company, which is currently expanding and moving from its original site of around 3,000m2 to occupy premises with an area of 18,000m2 in a different part of Yerevan, produces PET bottles and jars in the household and beauty care sector, along with their contents such as soap and shampoos, most of which are packaged in bottles of their own manufacture. A further branch activity of the business consists in buying in bottles from outside which are filled with their own filler products. Due to the political situation and for reasons of infrastructure, Grom has made up its mind over the course of the years to manufacture its products itself and to halt the import of products from Russia. Accordingly, Grom was working with a Chinese blow moulding machine; however, the results achieved with it did not come up to expectations and it was not long before they had to opt for two ASB machines, one for each location. Grom, as Mr Azaryan showed me, currently has the facilities to blow mould around 12 different bottles. The various closures are bought in from Turkey but, in the future, the intention is to also manufacture these on site. As Grom is currently only active on the Armenian market, Mr Azaryan is toying with the idea of exporting his products to Georgia too. Mr Azaryan is likewise interested in the production of PET bottles for mineral water, because – in his words – the Armenian market is experiencing constant growth in the still water sector. CJSC Hytex Plastic Pioneers on the preform front We met: Mr Levon Meliksetyan, Chairman Mr Samvel Tumanyan, General Director In Yerevan I visited Mr Samvel Tumanyan, General Director and Mr Levon Meliksetyan, Chairman of preeform manufacturers Hytex Plastic, both of whom have been readers of PETplanet since 2004. Hytex Plastic, specialists in the manufacture of preforms, run a production operation at two plants: since 1997 at the Armenian location and, since 2007, at a second site in Georgia. Hytex is the first company to introduce PET on to the Armenian market as a material for bottles. Each year a total of approximately 140 million preforms are created in seven different formats using two Husky HyPET machines which have been in operation since 2004. In front of a Husky HyPET 120at HyPET: Levon Meliksetyan, Kay Krüger and Samvel Tumanyan (from left to right) The final decision in favour of the Husky machines was made on the occasion of the K-Fair in 2004. It was here that the contracts for the purchase of the HyPETs were concluded, the machines which were subsequently destined to assume the place formerly occupied by a Korean machine and a second hand Krupp and DemagMannesmann machine that had been acquired at a later date. In addition to the two HyPETs in Yerevan, Hytex Plastic have a further HyPET at the Georgia plant. Here a second additional HyPET is currently in the procurement phase. In 2005 the company in Yerevan, having met all the necessary pre-conditions, concluded the supplier contracts with Coca-Cola Armenia. At present Hytex Plastic supply Coca-Cola with more than 50% of the preforms produced, whilst the remainder is spread across other processors in Armenia and Georgia. Ararat Under construction* We met: Nadezhda Gulaga, Marketing Manager Musheg Mkhitaryan, President Sergey Hovhannisyan, Project Manager Mineral water under the brand name Ararat was bottled in Armenia from 1964 till 1988, and the majority of it was exported. Following the collapse of Soviet Union and the subsequent war the bottling plant was destroyed. The rarat Group was created in 2007 with the task of building the new factory for bottling Ararat mineral water.A brand-new facility was built from scratch on a green field site. . It has","@ID":22} "NEWS 8 PETplanet insider Vol. 13 No. 06/12 www.petpla.net US bottled water consumption rises The International Bottled Water Association (IBWA), in conjunction with Beverage Marketing Corporation (BMC) has released bottled water statistics for 2011. The data complied by BMC a research, consulting, and financial services firm dedicated to the global beverage industry, shows that the overall consumption of bottled water has increased by 4.1%, building on 2010’s growth. In 2011, total U.S. bottled water consumption increased to 9.1 billion gallons, up from 8.75 billion gallons in 2010. All other major beverage categories such as carbonated soft drinks, milk, and fruit beverages experienced continuing declines in consumption. Per-capita consumption is up 3.2% in 2011; every person in America drank an average of 29.2 gallons (US – 110.5l) of bottled water last year. The bottled water industry is using a variety of measures to reduce environmental footprint. Between 2000 and 2008, bottled water companies reduced the weight of PET resin plastic single-serve bottles by 32% . www.beveragemarketing.com Sacmi and Sipa collaborate in preform and closure project The two companies Sipa and Sacmi have joined forces to develop a new system that combines PET preforms and closures. The development team for this collaboration is headed by Enrico Gribaudo (Sipa) and Giuseppe Lesce (Sacmi) respectively. It is said that the new solution, under the acronym “S.U.P.E.R.” ( Sustainable, Unique, Productive, Easy, and Reliable), will be a special combination of preform neck finish and lightweighted caps that is intended to eliminate problems associated with the operation of a cap on the neck of a PET bottle. The two companies state that this new system, protected by patents, will include closures that will be lighter than the average of alternatives available on the market today. And it is said that the system aims to be highly productive, especially when switching between containers of various types, including water, soft drinks, and aseptically filled drinks, and that very little modification of the lines is required for either preforms or closures (the latter produced with Sacmi’s compression process). According to the two companies, there will be a new “easy-to-open” design of the bottle, i.e. the leak angle is greater than the bridge-break angle, a feature not available on the market today, according to the development team. Specific information or details about this new system have not been disclosed.","@ID":10} "www.braubeviale.petpla.net fon: +49-6221-65108-0 | info@hbmedia.net | www.petpla.net Go to Brau Beviale - The Russia-Germany round trip with 13.-15.11.2012, Nuremberg, Germany 25 June - 31 July, 2012 С 26-го по 31-е июля 2012 г. Supported by: Go to Brau Beviale - A trip to visit friends The Editourmobil is back! Episode Two of this successful touring project will see the intrepid team from PETplanet Insider making their way this time from the start point at the Nuremberg Exhibition Centre to Russia and on to the Ural mountains. Yekaterinburg marks the halfway stage, from where the Editourmobil returns to Germany via the Ukraine and Poland. In two stages, with three teams, and involving a round trip of some 10,000 km, the Insider experts will be interviewing the most interesting and innovative PET producers and meeting key companies, large and small, in these fastdeveloping beverage markets. Join us during the tour at braubeviale.petpla.net Meet us, live!, after the tour at the Brau Beviale Nuremberg, Hall 7A, Booth 720 - where the clover grows! Kay Krüger Alexander Büchler Waldemar Schmitke 03. - 11. September, 2012 C 3-го по 11-е сентября 2012 г. Michael Maruschke Посещение выставки Brau Beviale - Российско-германская экскурсионная поездка совместно с организациейPETpla.net","@ID":28} "EDITOUR REPORTS 16 PETplanet insider Vol. 13 No. 06/12 www.petpla.net The landlocked state of Armenia is of interest not only from a political but also from a geographic angle. The country gained its independence with the collapse of the USSR in 1991. It has a total area of around 30,000m² and a population of 3.26 million inhabitants. This mountainous country, nestling in the heart of the Small Caucasus and bordering on Georgia to the north, Azerbaijan to the east, Iran to the south-west, the Independent Republic of Nakhchivan in the south and Turkey in the west, was the first country in the world to introduce Christianity as its state religion back in the year 301. Bearing in mind this traditional anchorage, it is scarcely surprising that today around 94% of the Armenian population is Christian. Two key factors play a role in the Armenian economy. The first is the continuing dispute with Turkey relating to recognition of the Armenian genocide during the First Market opportunities in the wake of major upheaval World War. The second is the dispute with Azerbaijan over the post-1994 occupation of the Bergkarabach region in the south-east of Armenia which, in the opinion of the United Nations and the Council of Europe, is part of Azerbaijan. Thus, Armenia’s importing and exporting activities inevitably focus on Georgia (situated in the north) as well as, in individual cases, Russia and to an extent on new business with Iran. Business dealings with Turkey or even Azerbaijan are practically impossible. A situation is emerging where Armenia is becoming to a major extent self-sufficient in the manufacture of products and concentrates a great deal on its own market. The beverage market The Armenian beverages market is confined within its own borders due to political and geographical peculiarities. Since the mid-90s when PET bottles became available for Armenia Nuremberg Ljubljana Saedinenie Istanbul Yerevan Baku Beograd Novi Sad Subotica Cegled Dulo Selo Mirna Peˇc Radenci Gorica Svetojansk Plovdiv Gaziantep Ingöl Ploiesti Ankara","@ID":18} "BERICAP Technology for juices, RTD teas, health drinks Committed to serving the juices, RTD teas and health drinks industry unique range of screw and sports closures designed for aseptic cold and hot fill 33mm and 38mm screw closures – for robust and trouble free capping – DoubleSeal™ technology for safer tightness and better protection against micro-organisms – unique FLEXBAND®, band for enhanced tamper proof efficiency, though without decontamination liquid retention O2 barrier and scavenging options on all screw flat caps of the range, for longer shelf life and fresher taste Sports Closures for aseptic filling without aluminium foil NEW 33mm BERICAP S.A. Poligono Industrial Can Font E-08430 La Roca del Vallés (Barcelona) · Spain Tel.: +34 93 842 4722 · Fax: +34 93 842 2025 info.spain@bericap.com · www.bericap.com","@ID":21}]}}
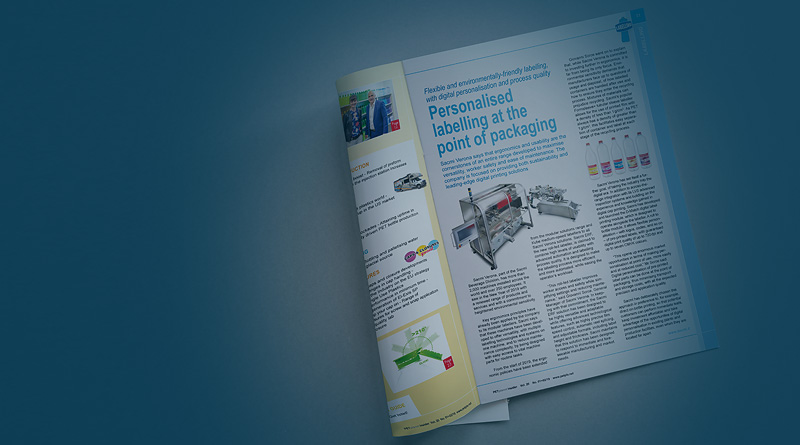