"PETplanet Insider Vol. 18 No. 06/17 petpla.net 46 PETbottles Beverage + Liquid Food Aloe water with white grape In its domestic market, the American manufacturer L.A. Aloe LLC. sells 450ml Organic Aloe Water with white grape under the brand name “Aloe Gloe” in a square, transparent bottle. The water is gluten-free, low-calorie and does not contain preservatives. The sleeve has a matt white design - only the leaves of the aloe plant are printed in gloss. To suit the flavour, “White Grape” is the colour of the screw seal and guarantee band. www.aloegloe.com Vortex 9.5 in PET In the USA, increasing numbers of drinks are brought onto the market with pH-levels selected to ensure the optimum impact on processes in the body. The Canadian company Watermark Beverages Inc from Vancouver bottles fills a filtered and remineralised water with added potassium and a pH-level of 9.5 in a slim, clear 500ml bottle. A partly transparent sleeve and a screw seal with a guarantee band complete the packaging of the “H2O Vortex 9.5” at POS. www.vortexh20research.com Sugar-free tea from Asia The Singapore company Pokka Corp offers a variety of sugar-free tea drinks in Asian countries. The uniform bottle for 500ml is transparent and has slanted reinforcement ridges running around the bottle body and vertical ridges above and below this area. The varieties are differentiated by different sleeve designs that are adapted to suit each product. A white screw cap with guarantee band seals the drink. www.pokka.co .com 100815dmyL Low-fat kefir from Aldi Süd From its own organic range, Aldi Süd sells three different types of low-fat, mild kefir in an easy-grip, waisted, white-coloured PET bottle. The varieties are natural, lemon and raspberry. Each bottle contains 500ml of the organically-sourced product with a fat content of 1.5%. Each flavour has an appropriately printed sleeve and a tamper-evident screw seal to support its relaunch onto Aldi chiller shelves. The kefir manufacturer is Nöm AG from Austria. www.aldi-sued.de","@ID":48}, "BOTTLE MAKING 37 PETplanet Insider Vol. 18 No. 06/17 petpla.net Tour Sponsors: Go with the flow. South East Asia Road Show PET moulds and cap compression moulding systems by Kay Barton The company started life as a small workshop with three employees. By focusing on the design and manufacture of machine components, the company had grown to around 50 members of staff by 1996. Duy Khanh adopted its current trading name in 2004, the same year it attained ISO 9001-2000 certification. The company develops moulds for a variety of plastic applications and has invested in CNC and EDM equipment on a continuous basis; its manufacturing facilities are now equipped with over 100 machines, primarily from German, Japanese and Italian manufacturers. Production of moulds and precision components is complemented by mechanical engineering and the company now employs more than 100 staff. The largest share, 40% of its output, is precision manufacturing for machine components and cap compression moulding machines. Thirty per cent is devoted to the construction of plastic moulds (of which approximately half is accounted for by preform moulds, cap moulds and blow moulds) and 30% to stamping moulds for sheet metal. The PET moulds area is becoming more and more important, which is a leading reason why Duy Khanh makes a point of using high quality material. “In terms of our product quality, we certainly operate in a slightly higher segment because we buy most of our steel for our mould production from Germany and Japan,” explains Ms Do Ngoc Van Trang, right-hand-person to Mrs Truong Van Tien, the company’s managing director. “It is precisely this aspiration for high quality that is our key proposition.” Duy Khanh defines its target market as companies in the small and medium sized output segments. It offers preform moulds in 16, 24 and 48 cavities and cap compression moulding machine with 12, 16 and 24 cavities. “Our long experience and expertise has enabled us to develop a brand new product: The first ever Vietnamese compression moulding machine for sealing caps,” says managing director Mrs Truong Van Tien. With an average size of 30mm cap diameter, capacities are 6800 – 8500 units per hour for 16 cavity machines and 10,000 – 13,000 units for 24 cavity units. Depending on the mould, cap diameters of 22 – 65mm and heights of 10 – 40mm can be produced, with a power consumption of 18 – 24 and/or 22 – 28kW. While the construction of PET moulds is, currently, limited to the local market, customers for other areas of Duy Khanh’s manufacturing are located as far afield as north and south America, Japan, and Denmark. “It goes without saying that we want to push ahead and offer our PET and sealing cap moulds on a more international basis. Right now, however, our cap compression moulding machine is our priority,” Ms Trang explains. “We have sold four of these so far. We presented our new 24 cavity system to the general public for the first time at the Plastics Vietnam exhibition in February 2017.” Altogether, Duy Khanh manufactures approximately 10 – 15 preform moulds, 30 – 60 blow moulds and approximately 150 moulds for other applications per year. Its existing range is set to be joined by 5 – 6 compression moulding machines per year. The company’s annual turnover currently about US$2 million. Its current customers include the THP Group (RTD tea, energy drinks, fruit juice, water), Vinamilk and Lothamilk (milk products). “We will continue to grow,” Ms Trang concludes. “Our new factory in the HiTech Park in District 9 is planned to be ready by the end of 2018. We intend that the new factory will include new and bigger CNC machines for manufacturing larger moulds, with length of more than 2m.” www.duykhanh.com Interview with Duy Khanh Engineering Co., Ltd. March 24, 2017 We met: Mrs Truong Van Tien, Director Ms Do Ngoc Van Trang, Director Assistant Mr Nguyen Van Anh, Business Manager In the district of Tan Phu, Ho Chi Minh City, we visited Duy Khanh Engineering, a machinery and mould manufacturing company located between apartment buildings and momand-pop stores. This was an unusual experience for us as most of our interviewees are located in classic industrial areas. However, when the company was founded in 1989, the area was mainly wasteland; the current infrastructure has developed around it. Compression moulding machine with (f.l.t.r.) Do Ngoc Van Trang, Kay Barton and Truong Van Tien","@ID":39}, "TRADE SHOW REVIEW PETplanet Insider Vol. 18 No. 06/17 petpla.net 42 TRADE SHOW REVIEW 42 Health has become one of the most important trends in the food and beverage sector, as well as in personal and beauty care. Brand owners are responding to these consumer demands by replacing artificial colourants and preservatives with more natural ingredients, in everything from solid food, drinks and vitamins, to home- and personal-care products such as shampoos, dyes and cleaning chemicals. But this creates a new challenge; exposure to UV light can degrade these ingredients and negatively impact the appearance, fragrance, colour, flavour or nutrient value of the contents. To ensure product consistency – and, consequently, brand integrity – the contents of PET packaged goods must be protected from exposure to both sunlight and indoor lighting during storage, distribution, retail display and postpurchase storage. Milliken Chemical says that its ClearShield additives create a new UV protection performance standard for PET bottles and containers in personal care applications (shampoo, liquid soap and shower gels, as well as cosmetics); household cleaning products (detergents, hand soaps and dishwasher gels); various solid foods and spices; juices and energy drinks; and vitamin packaging, where such protection is vital, as most vitamins are very sensitive to light, heat and oxygen. “By incorporating the UV absorber into the PET package itself, this technology allows brand owners to reduce the often high loadings of UV additives that they previously had to include in the formulations of the packaged contents themselves,” Simon Bousquet explains. “ClearShield offers an alternative, simple way to protect against UV exposure.” ClearShield absorbers filter 95% of UV light at up to 390 nanometers and are effective at very low loadings, the company says. This enables the more extensive use of highly UV-sensitive natural essences, fragrances and colourants in the packaged products. In many cases, by reducing the stabilisers and preservatives needed as a result, it often is possible to also reduce formulation complexity; this, in turn, can reduce cost. Approved for food-contact applications by the European Food Safety Authority (EFSA), UV protected PET packaging At the Interpack 2017 show, Milliken Chemical demonstrated how its ClearShield colourless UV absorbers are protecting UV-sensitive contents from degradation, while maintaining the material’s clarity and transparency. PETplanet met Milliken’s technical manager Simon Bousquet and learned why the industry is becoming attracted to this product. www.bericap.com Unique range of light weight screw and sports closures for light weight PET neck standards for water • Closures for all common neck sizes 26/22, 28mm (PCO 1810, PCO 1881), 29/25, 30/25 • Light weight Hexalite range allowing light weight neck • Still water closures suitable for N 2 dosing • Sports closures fulfill BSDA requirements • Boreseal systems for excellent tightness • Consumer friendly opening forces BERICAP Technology for still water","@ID":44}, "BOTTLE MAKING 26 PETplanet Insider Vol. 18 No. 06/17 petpla.net preform design and process conditions. (Higher crystallinity levels are achieved in the heat-set process, see Chapter 7.) Figure 2.4 Different states of PET present in each bottle The finished bottle will have amorphous portions in the neck and gate area where the bottle was not stretched, oriented portions in the side walls, and sometimes thermally crystallised portions around the gate, a common preform defect that cannot be corrected during blow molding (Fig. 2.4). 2.3 Drying of PET Because PET is hygroscopic, it must be dried before it can be injected. The maximum amount of water in the resin when in the extruder throat is 50ppm. This residual moisture will react with the PET in the extruder and lead to an acceptable drop of 0.03–0.04 in IV (Fig. 2.5). Higher moisture levels will lead to much higher IV drops, rendering the material unsuitable for the application. Figure 2.5 Three moisturelevels, three resultingIV results.Amaterialof 0.82 IV will be reduced to an IV of 0.68 when processed with a moisture content of 200 ppm. The correct drying parameters are a combination of time and temperature at a certain airflow. Modern dryers are able to generate the required airflow of 4m3/h per kg per hour (1cfm per lb per hour). Under these conditions, processors must calculate or determine, by a practical experiment, the residence time of the resin in the hopper for a given job. To do this practically, a handful of color pellets is placed on top of the resin in the hopper with the time noted. The coloured pellets will eventually show up in the preforms and the time can then be measured. Depending on the position of the resin in the hopper, drying times differ, with the resin in the center of the hopper traveling up to 20% faster. Therefore, a median residence time must be chosen. Once this residence time has been established, the proper drying temperature can be chosen, for example, from the graph in Fig. 2.6. The maximum value of drying temperature is 171 °C (340 °F). Higher temperatures lead to oxidation, which manifest as a yellowing of the resin. Figure 2.6 Drying time must be chosen to match the residence time of the resin in the hopper. Improper drying and the resultant drop in IV change the inflation behavior of the preform in that the preform will inflate under lower pressure, because the natural stretch ratio is greater. In turn, this will lead to less orientation and weaker bottles. Preform designers should be aware of this connection in case problems that are all too easily blamed on preform design, arise during production. 2.4 Behavior in the injection mould We will not discuss the melting and visco-elastic flow of the material in the extruder barrel as they do not pertain as much to the preform design. But the injection part is important for designers to understand because of the particular opportunities and process limits, as well as possible defects that will then affect the blown bottles. Figure 2.7 Various components of a typical injection mould Injection moulds consist of the male core, the female cavity, and the neck inserts (Fig. 2.7). The latter have to move during ejection of the part to release the undercuts created by the thread beads. For this purpose, they are mounted on slides that are often cam-driven. Cores and cavities are always water-cooled; neck inserts may or may not be. Injection moulding of preforms is different from other forms of injection moulding as the preform wall is relatively thick, injection pressures are relatively low, and the injection speed is low to prevent shearing of the material. Figure 2.8 Empty cavity Figure 2.9 Injection 1 Figure 2.10 Injection 2","@ID":28}, "30 PETplanet Insider Vol. 18 No. 06/17 petpla.net Tour Sponsors: Go with the flow. South East Asia Road Show BOTTLING / FILLING Cherry-picking by Alexander Büchler Dynapack, Tangerang, Indonesia, February 20, 2017 We met: Dynapack, Tangerang: Tony T. Hambali, CEO Sanpak Unggul, Bogr: Tony Aviawan, Director Indo Kompresigma PT, Jakarta: Ohendry Husin Up to now, my visits to the Indonesian PET world were just like they always had been – a recycling firm here, a preform and cap supplier there, a bottling company just over the street. But my previous perceptions of industrial structure bit the dust after the meeting set in motion by Mr Ohendry Husin, local trade partner for Kaeser compressors, Indo Kompresigma PT, Jakarta. With 29 production centres in Indonesia, Thailand, China, Malaysia and Vietnam, Tony T. Hambali, CEO and owner of the Dynapack group is active in numerous domains: plastic packaging for food, beverage, cosmetics, pharmaceutical products, chemicals and lubricants as well as pails, bottle crates and precision plastic components for the automotive, home electrical appliances, consumer goods, electronics and computer industries. But it seems that is not enough: he wants to expand within the five countries where he currently has factories, both by setting up new businesses and acquiring others. “If a company fits into our structure, we pounce,” explains Tony. In the PET sector alone, he has facilities for injection moulding, injection blow moulding, blow-moulding, one and two stage processes, stretch blow-moulding and dry aseptic filling, as well as for a multitude of systems for post-production. There are also high-speed cap manufacturing equipment and rotary cube injection units for producing two part caps for 5 gallon water containers. For the beverage PET bottles, the caps are manufactured by its sister company called Uniplast totally based on a two-stage process. For non-beverage PET, Dynapast and its subsidiaries manufacture the products mostly based on single stage system. So how is this amalgamation of production processes achieved? In fact, the solution is rather simple – he listens to his customers. If they start manufacturing new products, he makes sure they have a new plant on-site, if they want to create a new product, his team searches for the most efficient option for its realisation, independent of the technology they have installed and procuring new technology where necessary. His biggest client Unilever is undoubtedly the driving force here, but Danone and Coca Cola have also taken note of his performance and flexibility. And he isn’t limited just to the PET sector – he also supplies other global brands, such as Tupperware, L’Oreal, GSK He runs the Dynapack Innovation Centre in Tangerang for these reasons. The heart of the company’s technology is located here. Every project is thoroughly evaluated and optimised to meet the needs of the client. He even manufactures his own moulds in-house to make sure he can achieve first-rate results. He relies on world class mould suppliers for moulds that the company cannot make. Tony T. Hambali, CEO and owner of the Dynapack group, has managed to cherry-pick from an extremely competitive Indonesian PET market. While bottling companies have to sell their products at almost cost-price, Tony is concentrating on taking orders with better margins. The catch: he has an infinite technological and product portfolio. But let’s take things one step at a time. Mr Ohendry Husin from PT Indo Kompresigma. State-of-the-art compressor installation by Kaeser High quality PET bottle produced by Dynaplack.","@ID":32}, "PREFORM PRODUCTION PETplanet Insider Vol. 18 No. 06/17 petpla.net 16 Sipa claims to break through barriers of preform mould design with advanced hot runner technology Non-standard cavity raises output PET processing technology specialist Sipa is using its expertise in hot runners with the intention of creating new preform moulds that exploits the potential of existing injection moulding machines beyond current limits. A new hot runner design concept allowed the engineers to manufacture the first 180-cavity preform tooling in the world. “We all know that there are moreor-less standard levels of cavitation for PET preform moulds running on regular injection moulding machines: 72, 96, 128, 144,” says Sipa’s Stefano Baldassar, Global Sales Manager – Preform Systems & Tooling. “These numbers were arrived at in order to stay within the design limitations of traditional hot runners. In fact, whenever anybody has tried to introduce moulds with different levels of cavitation – 56, 64 or 112 for example – they have failed. The moulds simply do not perform well enough.” That is why Sipa developed the new GEN4 hot runner design concept. It is said to overcome those limitations and to provide best-in-class balance, long maintenance intervals, and good ease of access when intervention is finally required. This new GEN4 hot runner design allowed Sipa to engineer and manufacture the first 180cavity preform tooling in the world. “The geometry of the new mould provides excellent balance in melt flow,” says Stefano Baldassar. “No, it’s not the biggest preform mould in the world, but the filling characteristics are excellent, so the customer isn’t gaining quantity at the expense of quality. There are no penalties to pay in terms of cycle time and weight distribution.” Preform producers can now use moulds with non-standard cavity lay-outs to substantially raise output without putting extra stress on their machines. Sipa has just produced this 180-cavity mould that fits on a regular 500t machine that would normally run with moulds having no more than 144 cavities – providing the potential to raise productivity by 25%. More nonstandard moulds are in the pipeline, for use on smaller machines. Users of this new tooling can choose to increase output from their 500t machine, rather than running a smaller-cavitation mould at fast cycle times that stresses the machine, increasing maintenance costs and reducing its lifetime. Sipa achieved this while making no compromises on mould robustness: in fact, thanks to features like the SmartLock stack design (intended to deliver good component life), XGuidance (intended to guarantee good mould alignment) and its LongLife treatment, the expected life of this mould is expected to exceed industry standards. “We are using open and available technology that can be mounted not only on Sipa XForm GEN3 500t production systems but also on other compatible platforms on the market, as long as they do not incorporate special protective software,” says Baldassar. Sipa expects a high level of interest from key advanced markets, especially from North America and China. www.sipa.it PREFORM special","@ID":18}, "7 NEWS PETplanet Insider Vol. 18 No. 06/17 petpla.net Pro Mach strengthens decorative labelling capabilities with acquisition of P.E. Labellers Integrated packaging solutions leader Pro Mach, Inc. announced it has acquired global high-speed labelling solutions provider P.E. Labellers SpA. The addition of Italy-based P.E. Labellers is intended to expand Pro Mach’s capabilities to provide high-speed decorative labelling and integrated solutions worldwide. All global subsidiaries and management teams of P.E. Labellers join the Pro Mach team. Bruno Negri, co-founder and Chairman of the Board of P.E. Labellers, along with Nicola Schinelli, Vice Chairman of P.E. Labellers, will continue to lead the P.E. Labellers team, spanning over 400 employees across the world. P.E. Labellers has been a technology leader in automatic high-speed rotary and linear labelling equipment for more than 40 years. P.E. Labellers’ solutions are modular and include self-adhesive, hot melt, cold glue, roll-fed, and sleeve labelling technologies. P.E. Labellers’ Adhesleeve technology, which uses pre-glued films, has received industry-wide acclaim for its reliability, efficiency, sanitary design, and overall environmental friendliness, as well as reduction of costs and downtime. P.E. Labellers has more than 10,000 rotary and linear labellers installed worldwide. Pro Mach has grown into a leading single-source provider of high-performance packaging lines and integrated solutions. Since 2010, Pro Mach’s installed base of machinery solutions has more than doubled and sales outside of the United States have more than tripled. Pro Mach supports a global customer base with operations in North America, Europe, Middle East, and Asia. www.pelabellers.com www.promachinc.com drink technology India becomes an annual event as of 2017 drink technology India, the trade fair for the beverage, dairy and liquid-food industry in India, is switching to an annual format and will be held at various locations in the future - every two years in Mumbai, and alternating between New Delhi and Bangalore in the years in between. The objective of these regional spin-offs is to address the beverage, dairy, liquid-food sectors and their respective packaging industries in a more demand-oriented manner. Alternating between Delhi, Mumbai and Bangalore is intented to make it possible to better address and support customers in specific target groups in the various regions of India. For the first time ever, drink technology India will be held at the Pragati Maidan in New Delhi on October 26–28, 2017—together with IndiaPack and pacprocess India, formerly International PackTech India. Bhupinder Singh, CEO of Messe Muenchen India, is looking forward to this new challenge: “The foundation of the beverage industry in India is Mumbai, which is why dti will still be held here every two years. But in the years in between, we want to strengthen the presence and the range of attractions for our customers in India. Having dti alternate between New Delhi and Bangalore allows us to bring its knowhow to all of India and address specific needs in different regions.” Markus Kosak, Exhibition Director of drink technology India, feels that this new configuration has plenty of advantages: “Moving into northern and southern India satisfies the best prerequisites for serving India’s entire beverage, dairy and liquid-food industry. By continuing to develop this platform, not only are we giving our customers access to new potential, we are also making new networking opportunities available. In doing so, we give the beverage, dairy and liquid-food industry in India added value.” www.drinktechnology-india.com • Available in 3 sizes • Suitable for all dispensing systems • Unique base dispense feature, which reduces neck breakage of preforms • Eliminates production line contamination • Ecient fold ratio • Optimal transportation load of truck • High ROI (return on your investment) Stackabox™ Dispensing, Storage &Transport Collapsible Bulk Container Multipurpose Packaging System for PET Preforms Caps & Closures dssmith.com/stackabox ©2017DSSmith,PlasticsDivision,InjectionMouldedProducts","@ID":9}, "PREFORM PRODUCTION PETplanet Insider Vol. 18 No. 06/17 petpla.net 22 Polypropylene box for preform storage and transport Collapsible container for preforms by Tom Vander Sande Many brilliant innovations are not invented by technological geniuses who have an epiphany, but are based on a simple idea that takes root in the minds of people with hands-on experience. While on the job, they develop an improvement for a system that is not functioning perfectly. The Stackabox is a nice example of this grassroots technical development. The story of the Stackabox starts in 2007 at a Coca Cola Enterprise factory. Operators wonder if there is a better solution to store and transport preforms than in the classical cardboard bins or non-foldable boxes they use every day which entail all kinds of difficulties. For caps and closures the cardboard bins had to be ‘stabbed’ in order to make holes to dispense the products. Two colleagues, among whom current DS Smith employee Adrian Higgins and his partner Philip Bagley, began working on a prototype wooden, collapsible container. Their goal was to make a bigger, foldable container with multiple dispensing possibilities. Some traditional boxes could hold up only to two thousand preforms, but they hold only up to five to ten times higher. Other plastic packaging was as big empty as they were full, so the volume of the return transport equalled the original transport. Adrian and Phil strived to do three times better, with a fold down ratio of 1/3.5. The wooden prototype was a useful proof of concept, but a later polypropylene version got people across the industry really interested. Both preform manufacturers as well as big bottling companies saw the advantages of the collapsible container. Around this time, the concept crossed the path of DS Smith, and it was rapidly perfected and integrated into their larger product portfolio that consists mainly of bottle crates and pallets. This process was a natural symbiosis, since the larger part of the company’s clients are active in the beverage and filling industry. The final, perfected product boasts a number of advantages over previous storage and transport solutions. The sturdy polypropylene guarantees an almost endless lifecycle and allows for hundreds of journeys between the producers and their customers. In contrast to cardboard which requires a wooden pallet underneath, there is no risk for odour contamination, paper particles or wood splinters. The smooth inside of the Stackabox allows for easy and thorough cleansing and the built-in lids prevent dirt getting in. If the standards have to be even higher, the Stackabox easily allows for liners to be placed and removed. Transport and handling A single operator can erect the box in 30s before filling. Once full, the Stackabox is easily handled with FLT’s, without the need of separate wooden pallets. Moreover, the absence of a centre skid at the base minimises the possible damage done. Traditional pallets suffer most of the damage at the centre skid during automatic handling. A standard trailer will hold 52 full Stackaboxes. In most trucks and containers two large Stackaboxes can be stacked. But in order to fit regional variations in transport, the Stackabox comes in three distinct sizes: Maxi (1,350l), Medium (1,187l) and Compact (1,030l). The tare weight ranges from 78 to 72kg, and the pay load is with 500kg equal for all varieties. Maybe the most innovative aspect of the Stackabox is the perfect integration in the existing production lines of the beverage and filling companies. These global players are always looking for a faster pace of production and every segment of the line has to keep up. The new state of the art blowing and filling lines run at 40,000 bottles an hour. Considering a Stackabox will hold around 10,000 of 38g preforms or 60,000 closing capsules, a total of around four boxes have to be dispensed every hour per line. This is only feasible with a fully automated dispensing system and the Stackabox fits perfect in this concept. The patented design is the only bulk container that allows for both top- as bottom dispensing in a wide variety of existing dispensing frames. Bottom dispensing is becoming the overall preferred PREFORM special Loaded truck stackabox First prototype of the Stackabox","@ID":24}, "BOTTLING / FILLING PETplanet Insider Vol. 18 No. 06/17 petpla.net 33 Gebo Cermex upgrades Carola line in three weeks Great volumes to tight deadlines Mineral water producer Carola’s production line is now packaging its product in a new, lighter PET bottle, increasing output speeds by 3,000 containers per hour after a line upgrade by Gebo Cermex. Installation and ramp-up to full speed production was achieved in less than three weeks. Carola is one of the largest mineral water producers in France. Following the buy-out of the company by Spadel, the group focused on the bottling and marketing of natural mineral waters and a varied range of refreshing drinks. As part of its investment strategy, the Carola PET line facility in Ribeauvillé, Alsace, France, was the subject of a complete overhaul. The ageing line was causing problems because of restricted flexibility, restricted accumulation capacity, reduced speed due to the limitations of certain machines within the line, and poor working conditions. The line’s performance was preventing Carola from keeping pace with the fast-changing beverage market and fluctuations in consumer demand. The company was also eager to minimise bottle weight and to switch to more modern packaging formats. The strategy included a plan for the reduction of production costs. Renewed partnership built on proven experience Carola selected Gebo Cermex, part of the Sidel Group, to undertake the modernisation work, following the success of a returnable glass line project it previously executed at the plant. Thierry Klein, Director of Production Maintenance at Carola-Ribeauvillé, said that the company had been especially impressed with its expertise in line automation and project management. The project at the Carola-Ribeauvillé factory covered the whole production process, from bottle conveyors right through to the palletiser and presented the team in Gebo Cermex with several other challenges. The customer was seeking to upgrade the line without taking up any more room in a facility where floorspace was already at a premium. Everything had to be changed without creating a supply problem for the client. All the equipment had to be replaced and the entire line brought back into operation at full speed, in all formats, in no more than 21 days. Meeting targets, surpassing expectations José Lefort, Industrial Manager at Carola-Ribeauvillé said that the project had more than lived up to expectations. The new line has increased output rates by 3,000 bottles per hour for all packs. This increased productivity means that Carola can now produce greater volumes to tighter deadlines, enabling the company to respond to spikes in demand while reducing the stock managed for this purpose by an external storage provider. “Increasing output speeds by around 3,000 bottles per hour for all formats has allowed us to switch to two, eight-hour shifts, with barely any production now taking place at night,” José Lefort says. Customer supply uninterrupted The dismantling of the existing line and the assembly of the new equipment, which was the most crucial element of the project, took place well within schedule. The restart was successful across all formats, which now includes packs of 6, 8 and 24 bottles. Production was quickly ramped up; within a month the whole line was running at 75% of maximum capacity. All the machines and conveyors were reinstalled as close as possible to the ground, making them directly accessible and eliminating previous need to climb up on walkways. Line control is one of the major strengths of the new system, especially the advanced management of stoppages and restarts on the conveyors and the accumulation tables between the machines. Format changeovers on the new line are also much more efficient. The successful completion of the project has enabled Carola to introduce a new, lighter bottle design, as Lefort explains. “All the new bottles are perfectly stable on the conveyors. That meant that we were able to deliver our clients’ orders without interruption, while offering them new packaging options.” www.gebocermex.com www.carola.fr Pack conveyors Palletiser with robotic layer prepatation","@ID":35}, "PETnews 6 NEWS PETplanet Insider Vol. 18 No. 06/17 petpla.net Inside Bottling: Innovating to reach today’s consumer The Plastics Industry Association (PLASTICS) recently released a new Plastics Market Watch report, Plastic Bottles Today: Innovating to Reach Today’s Consumer, highlighting the demand for plastic bottles continuing to grow in the United States and Europe. This report forecasts positive growth for manufacturers of plastic containers and bottles. According to the report, the compound annual growth rate (CAGR) projection for this market segment is anticipated to rise 5.2% by 2020. This will allow revenue to grow $115.2 billion over five years. Some of the challenges, including dependency on softdrink producers, high capital costs, global competitive pressure, industry consolidation and questions of sustainability are off-set by continued increases across products and sectors, including beverage, food and water, household, pharmaceutical and automotive chemicals and fluids. Last year, for the first time ever, bottled water consumption exceeded carbonated soft drinks in sales in the United States according to the Beverage Marketing Corporation. Furthermore, a recent study from Zion Market Research forecasts bottled water consumption growing at a CAGR of 8.5% by 2020. The Plastics Market Watch report attributes the incredible growth of PET to the high ranking of bottling in terms of plastics industry employment numbers, dollar value of shipments and capital expenditures. With bottling’s rapid rise, its vital manufacturers stay on top of key issues, challenges and advances affecting bottling. To that end, PLASTICS has created the Bottle Zone covering more than 50,000 square feet on the exhibit floor at NPE2018 which will feature more than 40 industry leaders presenting the latest advancements, technologies and supplies in bottling manufacturing. The Bottle Zone will offer concentrated education sessions hosted by PETplanet that address those very topics to keep this important segment on the cutting edge. NPE2018, the triennial international plastics manufacturing exposition, returns to the Orange County Convention Center in Orlando, FL May 7-11, 2018. www.NPE.org/Bottle-Zone New preform quality control instrument For measuring the transmission value of preforms, Colour Consult introduces the new P1 desktop instrument for quality control. The instrument measures how much light passes through a preform or plastic cap. From transparent (100% transmission) to very dark, almost opaque preforms (0,1%). Small changes in transmission values are said to be detected in an early stage minimising waste and valuable production time. The instrument is easy to use and robust, says Colour Consult. It has only two buttons to operate, one for calibration and one to start a measurement. Measurement data is displayed on the instrument’s lcd or can be logged to a pc via Ethernet. www.colourconsult.nl/p1ad Erema extends production capacities and optimises fabrication The manufacturer of recycling systems is relying on new production processes with the optimum use of resources in its production of assembly groups. The new approach enables reduced production lead times for the individual assembly groups, such as melt filters and pelletisers, while at the same time increasing product quality. With the opening of its new assembly shop 4 at the Ansfelden location at the end of April Erema changed over to a production process which is geared towards future customer requirements. Customers benefit from lead times being significantly reduced, increased delivery reliability and a further increase in quality standards. Besides optimum tool selection for the respective assembly group, each workplace has access to modern fabrication infrastructure such as scissor lifts, slewing jib cranes and a fully automatic Kanban system. The necessary material and information processes are coordinated based on exactly timed planning of the individual workplaces. This ensures a smooth production process with upstream and downstream departments. www.erema-group.com","@ID":8}, "PREFORM PRODUCTION PETplanet Insider Vol. 18 No. 06/17 petpla.net 13 PREFORM PRODUCTION 13 Design to highlight product origin Deciding what drink to buy takes a customer only a few seconds. One of the crucial points in attracting a potential buyer’s attention is the appearance of the PET bottle. PET Technologies does its best to satisfy all the wishes of their clients, taking into account both the product and the region. Recently PET Technologies has implemented several national style projects. While cooperating with Akatsiya, a local mineral water producer in the Ukraine, the main task in the bottle design was to connect the trademark with the Ukrainian style, way of life, national traditions and customs. As a result an original design was developed for 0.5 and 1.5l bottles. The larger bottle was decorated with the authentic rhombic ornaments typical of Zakarpattia, a region in western Ukraine. These ornaments symbolises wealth and fertility. The rhomb with a point in the centre, shown on the bottle, stands for the crops in the field and wellbeing. The 500ml bottle ornament reflects success, wealth and personal growth. For the Zambian company Trade Kings, PET Technologies developed 500ml and 330ml CSD bottles prototypes by reducing the PET bottle weight whilst maintaining its high strength properties. For PET Technologies, prototyping of the bottle is very important because it is the only possibility for the customer to observe the new PET bottles right from the start and evaluate whether they meet the desired technical, visual and dimensional parameters. Reduction of the PET preform characteristics helps the manufacturer to save money and as a result can help make the final product price competitive. The Jermuk Group of Georgia told PET Technologies that they would like to switch from 48mm to 38mm Bericap preform to produce 3.0 and 5.0l PET bottles. The shift was done with PET Technologies automatic stretch blow moulding machine APF-5. Thus, the use of the 64g Bericap preform (38mm) instead of the 85g (48mm) saves up to 90t of PET material per year (amounting to US$ 135,000 according to the customer). With the automatic blow moulding machine APF-5 it is possible to produce 1600bph with a bottle volume from 3 to 10 litres. The two independent blowing units support both neck standards. As a result, the PET bottles decorated with pictures of mountains produced on the APF-5 blower highlight the natural origin and picturesque environment around the plant. PET Technologies experience in PET bottle designing, production and laboratory tests provides the possibility of implementing original projects that highlight product origins and at the same time reducing production costs. www.pet-eu.com PREFORM special","@ID":15}, "PREFORM PRODUCTION PETplanet Insider Vol. 18 No. 06/17 petpla.net 8 PREFORM special The challenge of providing adequate product protection increases as package sizes decrease. The rate of gas ingress (or loss) is proportional to the surface area of a package, while the total amount of gas that can be allowed to enter or leave a package is dictated by the product volume. Surface to volume ratio increases as package volumes decrease. This requires packages to have improved barrier properties to support the necessary product shelf life. Market trends, driven by a consumer preference for smaller packages and the ever-increasing need for brand owners to differentiate their products on store shelves, suggest that smaller volume packages will become increasingly more common. There are multiple approaches to extending the barrier properties of a PET package and the choice of technology will be dictated by multiple factors. Among those factors are the level of required barrier improvement, the need to maintain production flexibility, constraints placed by the logistics chain and of course, the total cost to produce. The easiest solution to improving the barrier properties of a traditional PET package is to blend PET at the injection system extruder with one of the many barrier materials available on the market. The resulting blend will have improved resistance to gas permeation (passive barrier) or may even actively trap oxygen molecules (active oxygen scavenger) in the polymer matrix. Not requiring any equipment changes other than the polymer dosing and mixing auxiliaries, this may be an appropriate solution in some situations. At the same time, the simplest solution, as often happens, has serious limitations or even penalties. The barrier improvement factor is directly proportional to the amount of barrier material added to the blend. As the additive level is increased, the clarity and transparency of a PET bottle typically suffers, placing a limit on how much improvement can be reached while maintaining the desired package appearance. Even more significant is the barrier material cost penalty of a blend solution and its potential impact on recyclability when compared to a multi-layer package. Bottle coating is another available option to improve the resistance of a monolayer PET package to gas permeation. A thin glass-like coating on the internal surface of a bottle can constitute an effective passive barrier to gas permeation. The coating is applied in a plasma treatment following the blow moulding process. Silicon oxide coating is clear and transparent, while amorphous carbon coating imparts a light yellow tint to a clear package. The effectiveness of such coatings may be limited by the bottle creep, which may disrupt its integrity and lower the net improvement of the barrier properties. In Unlocking PET packaging potential with Multi-Layer Technology Multiple layers extend barrier properties by Peter Yankov, Team Leader, Advanced Solutioning Process & Technology, Husky Injection Molding Systems In addition to the functions of containing and dispensing a product, as well as delivering a marketing message to the consumer, a package must provide necessary protection for its content, at least for the duration of the planned shelf life. Some simple examples include the need to keep the carbon dioxide content of a carbonated beverage from escaping, preventing oxygen from reaching sensitive juice and sauce products and limiting exposure to light for dairy applications, including visible, ultra-violet or infra-red. While PET provides a better gas barrier than many other packaging polymers, it is still permeable and some gas exchange takes place between the content of a package and the environment, often becoming the factor that limits product shelf life. Barrier requirements become more challenging as package volumes decrease. Husky’s Multi-Layer Technology positions the barrier exactly where it is needed. Pictured left is a biased black layer positioned away from the surface towards the core. Pictured right is a fully encapsulated dome.","@ID":10}, "PREFORM PRODUCTION PETplanet Insider Vol. 18 No. 06/17 petpla.net 12 An alternative to one-stage bottle production Injecting customised preforms Historically one-stage SBM machines were associated with speciality container production and the possibility of manufacturing a wide range of bottle necks and volumes on a single machine. However, the market need for higher production capacity and lower tool cost impelled two-stage machine producers to look for alternative solutions. One of the pioneers in the field, FlexBlow supplies both the versatile stretch blow moulding systems and dedicated PET preforms for hot-fill, light-weight bottle and custom bottle production. As raw PET absorbs moisture from the atmosphere, humidity has to be removed by drying before processing. There are four main factors relevant for the PET drying process: drying temperature, dew point, drying time and airflow. Dryer temperature should be set at between 177-182°C, and dried for approximately 4h. PET resin is supplied into the hopper dryer by the use of an autoloader that works on the principle of vacuum. Drying PET inside the machine throat minimises the possibility of contamination and moisture re-absorption. Before injecting the PET into the preform mould, the resin moisture level should be dried down to 0.05% or less in order to achieve fine non-crystalline and transparent preforms. Once the PET pellets have dried, they are forwarded for compressing and melting by rotating screw. The PET resin starts melting after it has reached the temperature of 254-256°C. A number of factors during preform injection process are in play including screw speed, injection speed and pressure, tube and nozzle temperature, switch mode speed as well as cooling and cycle time. Every single parameter mentioned above will influence the product quality, thus controlling them is fundamental. Recommended injection speed for preforms with a wall thickness up to 4mm should be 8-12g/sec/cavity, and it can be improved to 19g/sec/cavity if the thicker wall preforms are injected. The injection machine’s nozzle and front zone temperature should be close to 280°C, whilst the middle and rear zones should be around 282°C and 275°C. As preforms shrink from a melt density of 1.15g/cm3 to 1.33g/cm3 solid density, depending on the wall thickness, the hold time to cool the preforms should be adjusted: the thicker walled preforms should be held longer compared to the thin walled ones that cool down almost immediately after injection. The cooling time should not be less than 1.5s, and could be as long as 20s. In addition to the cooling liquid’s temperature which is normally 8-10 degrees inside the injection moulds, high-volume water flow is equally as important, and should be close to 5bar within the system, for optimal flow. Robotic take out is recommended for preform unloading from the mould as opposed to free-drop as this allows enough time for cooling and helps to prevent the preform surface from scratches, thus ensuring a smooth finish of the preform and blown bottle at the end of the process. PET preforms can be made both crystallisable and non-crystallisable by controlling the temperature and cooling time. The majority of PET resins are called copolymers due to the fact that a certain percentage of modifier has been incorporated in the polymer chain. Such blends improve crystallinity properties and the injection process in the mould is improved. Thus, manufacturing custom PET preforms in relatively small quantities for containers with non-standard necks, or for ultra-light and hot-fill bottles requires knowledge and precision in controlling the process. Hitherto, the traditional approach to preform supply used to be either cooperation with large preform manufacturers on the one hand, or one-stage machine producers on the other. Terekas now sees an alternative solution midway between these two traditional approaches. www.flexblow.com PREFORM special","@ID":14}, "PETpatents www.verpackungspatente.de PETplanet Insider Vol. 18 No. 06/17 petpla.net 48 Bottle with separate handle Europ. Patent No. EP 3056445 A1 Applicant: Nissei ASB Machine Co. Ltd., Nagano (JP) Application date: 7.10.2014 To improve handling, a separately formed handle is attached in the lateral indentation on a large-volume plastic bottle (more than 10 litres). Bottle container with handle Europ. Patent issue No. EP 2471719 B1 Applicant: Yoshino Kogyosho Co. Ltd., Tokio (JP) Application date: 20.8.2007 A plastic bottle with sidewall indentation for applying and fixing a separately formed handle is issued with a European patent. Base form Europ. Patent No. EP 3059175 A1 Applicant: Sidel Participations, Octeville-sur-Mer (FR) Application date: 13.1.2016 To make the base form of a plastic bottle sufficiently stable with the least possible use of material, this application proposes special, cross-running grooves / indentations. Plastic bottle FR - Patent No. 3012115 A1 Applicant: Sidel Participations, Octeville-sur-Mer (FR) Application date: 23.10.2013 Plastic bottle equipped with compensation areas can change its basic shape (rectangular - square). Reduced wall strength Internal Patent No. WO 2016 / 152456 A1 Applicant: Toyo Seikan Co. Ltd., Tokio (JP) Application date: 4.3.2016 Preform for manufacturing a plastic bottle. The preform is for the area that later becomes the base of the bottle; it is designed to have thinner walls here without impairing stability or impeding manufacturing. Sturdy plastic bottle Europ. Patent No. EP 3072825 A1 Applicant: The Coca Cola Comp., Atlanta (US) Application date: 21.11.2014 The shoulder area of a plastic bottle features several circular features that can compress when several bottles are stacked but this can be reversed when in their original position without damage to the bottle.","@ID":50}, "Decontamination dryer deCON50 PREFORM PRODUCTION PETplanet Insider Vol. 18 No. 06/17 petpla.net 24 PCR flake to preform made in Slovakia General Plastic, Plc. was founded in May 2002 with the main goal of PET bottle recycling in a state-of-the-art washing line and a bottle-to-bottle PET recycling plant from Starlinger. The food grade and iV increased pellets or washed flakes were sold on the open market. In 2010 the company expanded its activities into PET preforms for fillers of non-alcoholic drinks as well as wine, oil and the production of LDPE shrink film. General Plastic, based in Slovakia, is a well known processor of PET bottles and producers of PET preforms in Central Europe. The company’s business activities include: production of PET preforms for the producers of wine, non-alcoholic drinks and oils recycling of PET bottles into washed flakes production of PET re-granulate producing of LDPE shrink film recycling of non metallic scrap and remains PET preforms are designed for the production of bottles, mainly for foodstuffs. Coloured and colourless PET preforms are designed for blow moulded bottles made for direct contact with water, milk, fat food and alcoholic drinks (below 50% volume of ethanol) below 40°C. In light of a clear growth and sustainability strategy, the company decided in 2015 to dedicate a large investment for the “flake to preform” segment of which Starlinger viscotec’s deCON technology is an integral part. Jozef Ungvarsky, General Manager of General Plastic: “No other company could demonstrate a sufficiently high level of decontamination and suitable flexibility for this highly demanding application and this particular machine set-up. This set-up was the first and we could rely 100% on the professional support and expertise of the entire viscotec team, beginning with the sales process to the high level of technical support during installation right through to the end with the expertise for the EFSA application.” The hot-washed PCR bottle-flakes are conveyed into the viscotec decontamination dryer - where the flakes are treated at a specific temperature and under vacuum conditions. Crucial to this process is the first in first out (FIFO) principle to make sure that every flake is treated and hence decontaminated the same way. The dynamic vacuum in the unit ensures firstly, the decontamination to the highest possible standard in line with all important international regulations (e.g. EFSA, FDA, Health Canada). Secondly, in addition, dust from the bottleflake is extracted to avoid defects in the final product. A perfect drying under vacuum, which is the third advantage since moisture in the material is the biggest cause of iV loss. When processing PET it is essential to have the material super-dry to preserve the intrinsic viscosity as much as possible. After this pre-treatment, the material is conveyed into a dosing system which can mix various percentages of materials for the injection moulding stage. With this flexible setup and foodgrade without compromise preforms from 100% PCR flakes can be produced. The PCR flake to preform setup advantages include that less floor space and manpower are required and the simplified handling of materials. In addition, the overall lower investment cost in comparison to classic bottle-tobottle recycling in terms of machinery is probably the smallest one, according to viscotec. The most important by far are the comparatively low production costs as a result of cheaper input material on the one hand and the lower energy consumption on the other. PCR bottleflakes are supposed to be always lower in price than rPET pellets, since the complete step of drying and extrusion is not required. This also leads to a low energy consumption since the material is effectively pre-treated and melted only once before becoming a preform. Finally this process setup is the smartest and most efficient way to make preforms for drink manufacturers and still water fillers” summarises Jozef Ungvarsky this future oriented installation. www.generalplastic.sk www.viscotec.at PREFORM special At General Plastic in Slovakia preforms are made directly from PCR flakes. Jozef Ungvarsky, General Manager General Plastic","@ID":26}, "PREFORM PRODUCTION PETplanet Insider Vol. 18 No. 06/17 petpla.net 17 Go with the flow. South East Asia Road Show PREFORM special Tour Sponsors: Quality over quantity by Alexander Büchler two years there have only been three pieces of preform equipment in the newly opened factory in East Java. In total, PT Indo Tirta Abadi process approximately 42,000 tonnes of PET and 3,500 tonnes of HDPE annually. As mentioned above, Indo Tirta Abadi’s motto is quality over quantity. Therefore, all products are packaged in clean rooms; preforms are packaged in clean rooms in class 100,000, while closures are packed in rooms in the higher 10,000 class as they are no longer rinsed at the bottling plant, as such they require a higher class. So as to keep emissions as low as possible in the closure clean rooms, only one person works on the equipment, packing the closures into clean plastic bags. The products are then packed into cartons or boxes outside of this clean air zone. This is how Indo Tirta Abadi keeps its customers loyal. For Indo Tirta Abadi, this is a regular customer business. Indo Tirta Abadi strives to seek and pursue always a win-win solution with their customer. The company positions itself as packaging problem solver for its customers in Indonesia, offering an extraordinarily wide range of preform, bottle and closure. Whether its customers need them for still water, CSD, aseptic or hotfill, they can choose from various weights and neck size classes. So far, Indo Tirta Abadi has not offered their product consisting of regrind nor recycled materials. “We only use virgin material. In this way we can guarantee that our products are high-quality. The quality of rPET in Indonesia is not consistent enough at the moment,” Arief explains. This is the company philosophy even when some converters in Indonesia use certain percentage of non-processed regrind material to supply to their customers in order to cut down cost and increase profit. The principle of business at Indo Tirta Abadi is that they would like to absolutely ensure that the products going to their customers always 100% comply with customer’s specifications and requirement and to meet total customer satisfaction. www.indotirtabadi.com PT Indo Tirta Abadi, Tangerang, Indonesia, January 22, 2017 We met: Mr Arief Dewanto Mrs Jennifer Ali The preform and closure manufacturer, PT Indo Tirta Abadi, based in Tangerang, does not base its operations on price, rather they focus on quality and solutions for their customers. As such, the company can count multinational corporations and large-scale national brands amongst their clientele. “These companies want the best quality at a fair price,” according to Mr Arief Dewanto, Commercial Director of PT Indo Tirta Abadi. Founded in 2003, PT Indo Tirta Abadi began producing water preforms on 16 cavity equipment and they began to supply Coca Cola Indonesia using their new 56 cavity system as early as 2006, a year which also saw the company beginning to sell preforms for hotfill products. The company has also blow-moulded bottles since 2007, with Pepsi Cola as their first client. The next logical step was to expand their production to caps and so in both 2015 and 2016 the company expanded their cap and preform departments to include new installations. Sacmi supplied the four seal installations while the 13 preform systems are made by Husky and most of their equipment is based at their main factory in Tangerang. For F.l.t.r.: Arief Dewanto in front of the welltravelled Editourmobile with Alexander Büchler Packing preforms in the clean room Seals have even higher hygiene requirements here in the class 10,000 clean room.","@ID":19}, "PREFORM PRODUCTION PETplanet Insider Vol. 18 No. 06/17 petpla.net 10 PREFORM special right amount of barrier material for a given application while maintaining a robust productivity. It is well known that material cost is a major contributor to the total cost of a package. Barrier materials, while making up a relatively low (typically 2 -15%) percentage of a package’s weight are substantially more expensive than PET. This makes it critical to ensure the minimum necessary amount of barrier material is delivered to each mould cavity and distributed in the most effective manner within the preform. This level of advanced control is only possible with a fully integrated system that utilises a unique, stateof-the-art hot runner design. The hot runner is based on technology that enables an unprecedented level of balance, even before any controls are tuned for the application. This reduces the number of times melt flow is split in the hot runner, which is the single most significant contributing factor to hot runner imbalance. This hot runner technology also provides design freedom, optimising melt channel layouts of two material melt delivery systems for a high degree of thermal control. Many barrier materials have a lower melting point and are more temperature sensitive than PET. Overheating and excessive residence time may lead to material degradation. This not only impacts preform and bottle quality, but can also increase hot runner refurbishing intervals. Injection moulders familiar with co-injection will recognise that in the attempt to improve hot runner balance and ensure melt flow and temperature rates are as uniform as possible across multiple gates, the hot runner may be tuned by lowering and raising temperatures of manifolds and nozzle tips. Husky hot runners are designed to provide control flexibility through an increased number of manifold zones and individually temperature controlled tips. Traditional pneumatic actuation of valve gates has been upgraded to an electric servo, plate actuated synchronous valve gate system. At the same time, the high level of balance means that the range of temperatures used in further tuning the performance is reduced, further decreasing the maximum temperature experienced by barrier material. When running temperature sensitive barrier materials, purging both hot runner melt delivery systems with PET during system shut-down and restart is a good practice that has been automated. Even the best maintenance practices may leave room for unplanned events, such as contamination of source resin by foreign material. If a contamination particle finds its way into the hot runner, the most likely area for a blockage is the hot runner nozzle. It has been notoriously difficult to clean this area, often requiring complete hot runner disassembly. The HyPET HPP5 barrier system features a front removable nozzle design, which allows the maintenance or replacement of hot runner nozzles while in the press, by latching over the mould cavity plate to expose the tips. While co-injection moulding is still more complex than traditional monolayer injection moulding, the operation of the complete system is facilitated by Husky’s preform-centric control system, integrating all aspects of the injection moulding process and auxiliary equipment. Process setup for a new application begins with establishing a monolayer process for preform quality. When barrier material injection is enabled, the control system automatically adjusts the PET injection profile based on the barrier content and generates the barrier injection profile, which can be fine-tuned by the operator. Multi-Layer Technology offers a complete, integrated solution for manufacturing food and beverage products requiring enhanced barrier properties that is highly cost-effective, productive and flexible. It allows brand owners to rely on PET for more appealing packages that stand out on store shelves and support conversion from alternate materials, all factors that help to support the growth potential of PET packaging. www.engineeredpackage.com Husky’s Multi-Layer Technology is suitable for a variety of applications, including for carbonated soft drinks, mineral waters, juices, sauces, and now seeing expansion into dairy, beer and personal care products. Conventional manifolds split the melt channels many times, which creates shear related imbalance.","@ID":12}, "BOTTLING / FILLING PETplanet Insider Vol. 18 No. 06/17 petpla.net 32 Tour Sponsors: Go with the flow. South East Asia Road Show The world’s most sold bottled water by Alexander Büchler Danone Aqua, Bogor, Indonesia, February 21, 2017 We met: Mr Sultoni Atmaja, purchasing manager Mrs Oktarina Indrialaksmi PT Golden Mississippi was founded in 1973 in Bekasi and was one of the first businesses to enter the bottled water market. The first PET bottle was rolled out as early as 1985, whilst Europe was still using PVC bottles for their water. In Indonesia, the product was a 220ml PET. On 4th September 1998, the Aqua and Danone groups were merged. This step improved product quality and propelled Aqua to the biggest producer of packaged mineral water in Indonesia, with a market share of over 40%. Aqua comes from selected springs in Indonesia. The water is packaged into different sized plastic bottles; 330ml, 600ml, 750ml and 1500ml, with the most water being bottled in 32mm caps and 5 different flavours: Lychee Lemon, Liven Up Orang Lime, Dazzling Apple Guava, Passionate Passion Fruit, and Uniquely Your Mangga Kweni. Aqua Lastari was the new product, coming in 330ml bottles with 32mm caps. This juice supports health and life balance, as well as bridging the gaps between business and environmental sustainability. The 5.1ha site in Bogor has grown over the years, one hall joining onto the next. Every bottling production line has its own area, including the drying line. We visited the PET line with Sipa blow-moulding and Procomac bottling equipment for 600ml water bottles. This is where the newest product is processed – a 330ml contoured bottle covered in a sleeve printed with figures. Today the Star Trek range is on the production line. The bottle is rather heavy, weighing 16gr with a PCO 28 longneck. The product lines supermarket shelves at the same price as the original core product of the line – the 600ml shortneck water bottle. The water that Aqua uses in PET bottles is delivered by tankers from sources that are about 60km away, whereas the 5 gallon containers are filled with water from wells drilled on company premises. Aqua bottles a total of 160 million litres in gallon containers and a total of 180 million litres in PET bottles. Drinks in bottles with 32mm caps amount to 80 million litres per year. Preforms used for 600ml bottles and bottles with 32mm caps are produced in-house on Husky production lines. www.aqua.com Star Trek on PET water bottles by Aqua Danone The Editourmobile in front of the company logo Any idea what it is? Until recently, I didn’t know either. It’s Aqua by Danone in Indonesia and on average it has grown by at least 10% per year to reach the 13 billion litres sold in 2017. Their aim: to reach the 20-billion-litre mark in three to four years. Out of over 20 factories located in the country, we visited the site in Bogor which primarily supplies the greater Jakarta area. 5 gallon PC water containers. Aqua also packages in 240ml polypropylene cups. Besides water, they also produce the energy drink Mizone which comes in 500ml PET bottles with","@ID":34}, "43 TRADE SHOW REVIEW PETplanet Insider Vol. 18 No. 06/17 ClearShield is claimed to overcome the deficiencies of traditional technologies, including unwanted colour, migration and bloom. ClearShield UV absorbers are easy to handle and meter and, since they are incorporated into the PET itself, do not leach into beverages. PET preform producers and bottle converters will especially appreciate that the use of ClearShield-modified PET simplifies processing by resisting plate-out onto injection moulded preform and bottle moulding surfaces, the company asserts. The advantages also include clear sustainability benefits. Simon Bousquet says that formulators can obtain similar levels of protection to those offered by traditional absorbers from as little as one-twentieth the level of UV ClearShield absorber in the formulation. “This also eliminates concerns about toxicity or wastewater contamination by some of the chemicals traditionally used in other UV stabiliser,” he adds. “Better contents protection and extended shelf life help to reduce product waste. And by enabling greater use of more natural and uncoloured PET, ClearShield helps to reduce or eliminate the need to use dark or coloured containers to protect contents,” he explained. “Such opaque and coloured PET materials tend to make the recycle stream dark, which can make recycling more difficult and lessen the value of the reclaimed product.” This has prompted the Brusselsbased Plastics Recyclers Europe (PRE) trade group to sound the alarm bell about how the rise in use of coloured PET containers is “putting the future of PET recycling at risk.” If collected and sorted together, PRE noted, these numerous coloured containers will need extra sorting in the PET recycling plants. For recyclers to sell this coloured fraction the material will have to be tinted in black or grey, but no market currently exists for such a material in high quantities. These ‘colourful’ future trends will weaken the image of PET as a recycled product, the group warns. Milliken Chemical believes that these factors further strengthens the argument for using clear, uncoloured PET, and ClearShield UV absorbers allow this to happen, with no compromise in product quality. www.millikenchemical.com SIPA S.p.A. - Via Caduti del Lavoro, 3 - 31029 Vittorio Veneto (TV) - Italy Tel. +39 0438 911511 - Fax +39 0438 912273 - email: sipa@zoppas.com We make it happen. www.sipa.it Imagine taking your operating costs at the lowest level. Designed to adapt. Built to last. Preform Systems MAINTENANCE COST i stment Less than1%of the capital nve","@ID":45}, "TRADE SHOW REVIEW PETplanet Insider Vol. 18 No. 06/17 petpla.net 40 Benoît Henckes, CEO of United Caps, on balancing ease of use with lightweight design As lightweight as possible and compact as necessary by Gabriele Kosmehl The international Luxembourg-based exhibitor, United Caps, was demonstrating at this year’s Interpack trade fair how small improvements to caps and closures can enhance a product’s sale potential. Also, the company has just announced plans to expand into the South-East Asian market (see PETplanet 5/2017). A good enough reason therefore for PETplanet to drop in on United Caps and speak to its CEO, Benoît Henckes. PETplanet: Mr Henckes: What products are you tempting visitors with at this year’s Interpack trade fair? Henckes: We are offering a wide range of closure solutions for beverages, edible oil and dry food, which is something the food sector has been calling for. Special emphasis is being given to two particular strands which we use in the closure sector. The first is brand differentiation. Customers are increasingly offering to work with us to develop original closure solutions that visually distinguish a customer’s product on the merchandising shelves. To this end, we work with the client to create differentiating features that suit their particular needs, e.g. a special design, prints or engravings. The second strand is the issue of convenience. Improvements in handling have recently become the big talking point in the closure sector. PETplanet: Has light-weighting been superseded? And equally does that mean that closures are becoming heavier again? Henckes: Light-weighting has been a big issue in recent times. Theoretically, further weight savings are possible in the closure area but our current focus is on finding the right balance between light-weighting and convenience. In theory, we could produce caps weighing 1g but this would be pointless if it means the product can no longer be properly protected or if an older person is unable to open the bottle. To this end, we have come up with a really nice flower cap design. The petal flower design of this 1881 closure not only looks great on the shelf but also allows the end-user to open bottles with very little effort. An excellent combination of brand differentiation and convenience. PETplanet: How do you find out in advance whether a new closure will meet market requirements in terms of convenience and what are the constraints within which you have to operate? Henckes: The needs of the consumer are never overlooked in our developmental work; in fact we are putting large sums into market The easy-to-open flower design has been used for Wattwiller Mineral Waters Benoit Henckes, CEO, United Caps","@ID":42}, "41 TRADE SHOW REVIEW PETplanet Insider Vol. 18 No. 06/17 research. We need to keep in mind that our customers can simply adapt their filling lines to the new closure. Design it and make it work on our customer filling lines. This also includes support which we naturally offer as part of our service package. PETplanet: Turning now to your international business operations. At the beginning of May, you made it known that United Caps would be investing in a Malaysian facility to enable you to operate on the South-East Asian market. Can you explain the thinking behind this decision and say a little about how things stand at present? Henckes: Until now, United Caps has operated exclusively in Europe. Our multi-national clients have also been asking us to have a presence in the Asian region so we are really following our customers’ lead. That is why we are investing around €10m in a state-of-the-art manufacturing facility in Malaysia. Why Malaysia in particular? Firstly, it is a good source of people who have a highly skilled technical background. In addition, we have found a suitable location in Kulim High Tech Park which has first-rate logistical connections, being close to both a harbour and Singapore from where we can easily supply all the countries of South-East Asia. PETplanet: How will production be carried out on site and what manufacturing methods will you be using? Henckes: The intention is to move some of our production activities from Europe to Malaysia where we will use exactly the same manufacturing methods. Our aim is not to compete with local low cost suppliers but to provide expert support to our customers on the ground. For that reason, we will work exclusively with injection moulding just as we do over here, utilising the same, mostly fully electrical systems. We will move quickly to set up 10 mainly automated production lines which are expected to be completed by the beginning of next year. PETplanet: Mr Henckes. Many thanks for taking the time to talk to us. www.unitedcaps.com ChemTrend.com PROTECT YOUR ASSETS. Team up with Lusin® and Ultra Purge™ Lusin® and Ultra Purge™ form a winning combination Ultra Purge™ and Lusin®purging compounds, release agents andmold maintenanceproducts protect your assets by reducing downtime, increasing efficiency and extending the life of your tooling.","@ID":43}, "PETcontents 06/17 4 PETplanet Insider Vol. 18 No. 06/17 petpla.net Page 34 Page 16 Page 37 INSIDE TRACK 3 Editorial 4 Contents 6 News 46 PET bottles for Beverage + Liquid Food 47 PET bottles for Home + Personal Care 48 Patents PREFORM PRODUCTION 8 Multiple layers extend barriers properties Unlocking PETpackaging potential with Multi-Layer Technologie 12 Injecting customised preforms An alternative to one-stage bottle production 13 Design to highlight product origin 14 Lighter preform, lighter bottle-Material savings focusing on the bottle neck, thread and cap 16 Non-standard cavity raises output 17 Quality over quantity Preform and closure manufacturer PT Indo Tirtra Abadi 18 Hodmeter replaces PCB with PET Preforms for 5-gallon refillable bottles 20 PET kegs for Russia-Retal JSC, Russia, enters the PET keg market 21 The preform experience The prefect bottle starts with the perfect preform 22 Collapsible container for preforms Polypropylene box for preform storage and transport 24 PCR flake to preform made in Slovakia BOTTLING / FILLING 30 Cherry-picking at Dynapack Group 32 The world’s most sold bottled water 33 Great volumes to tight deadlines Gebo Cermex upgrades Carola line in three weeks BOTTLE MAKING 25 Material basics / Drying of PET Strech Blow Moulding, part 3 GO WITH THE FLOW SOUTH EAST ASIA ROAD SHOW 34 Vietnam and Cambodia on their way up 37 PET moulds and cap compression moulding systems 38 Preforms, bottles and closures, all made under one roof! TRADE SHOW REVIEW 40 As lightweight as possible and compact as necessary 42 UV protected PET packaging 44 Creating a sustainable recycling society Plastics Recycling Show Europe, Amsterdam, NL 2017, part 2 BUYER’S GUIDE 49 Get listed! PREFORM special","@ID":6}, "Sponsors asia.petpla.net 2017 is Drinktec year! All over the world, the beverage and liquid food industry is preparing for the next edition of the great event, held once again in Germany. A new year also means a new road show - and a very special one. PETplanet is again partnering with Drinktec and we will be bringing our crew to South East Asia, under our new slogan: Go with the flow – South East Asia Road Show. From the end of January our editors Kay Barton and Alexander Büchler, along with “Flowy“, the Drinktec mascot, will be investigating the latest market-specific characteristics of distant countries as well as following welltrodden oaths, as always. With various “Editourmobil” vans we will travel to Thailand, Vietnam, Cambodia, Malaysia, Singapore and Indonesia. As our valued reader, you will once again get insider information and insights from the PET beverage and supplier industries, published regularly in PETplanet Insider. You can get even closer to the Tour experience by following us live on our travel blog at asia.petpla.net. Drinktec awaits us at journey‘s end. When we get there we will be presenting factsheets and product samples of all the companies we visited. We hope you enjoy “keeping up with the PETplanetarians“. We look forward to welcoming you on board once again! January – July 2017 Cambodia Laos Thailand Indonesia Vietnam Malaysia Singapore The worldwide round trip with Go with the flow. South East Asia Road Show powered by","@ID":29}, "PREFORM PRODUCTION 15 PETplanet Insider Vol. 18 No. 06/17 the standard only applies to the thread and not the closure. “On a lightweight version we can reduce the weight per thread with cap to 4.4g,” states Wiese. The 1.4g of material saved per bottle quickly make themselves felt to bottlers of CSDs. Those who buy in their PET preforms – and this is the majority of beverage bottlers – pay for them by weight and not per piece. Thus the more bottles produced each year, the lower the costs per container. The savings potential for still beverages is similarly large: on the lightest standard variant to date, what is known as the 26/22, the thread weighs just 0.95g, plus a further 0.7g for the closure. This amounts to less than a third of the PCO 1881 neck with cap. The development of new savings potential and especially the implementation thereof is an elaborate process where only a handful of manufacturers have the necessary expertise. At KHS this knowledge is pooled in its Bottles & Shapes program and through this made available to the customer. Focus on individual systems If a certain bottler wishes to further reduce the weight of his or her PET bottles and if the thread has been earmarked as a possible savings potential, the Hamburg experts of the systems supplier then scrutinise the demands the bottler makes of his or her bottles. The key questions here are: what internal and external pressure is exerted on the bottle? Which media are bottled? What does the customer expect regarding bottle handling? Based on these factors various performance specifications are drawn up which greatly reduce the number of possible selectable formats in advance. Together with the client the best possible solution is then chosen. In addition, the resulting developed bottle must ultimately be able to be processed on the plant equipment. A smaller neck ring is only beneficial if the filling system can also grip it, permitting the container to be safely guided along the production line. If the thread is reduced and less material used, it then needs less heat in the stretch blow moulding process so that it does not become deformed. The filled bottle would otherwise not close properly further down the line. KHS systems therefore make use of a special construction which ensures that in the stretch blow moulder heater no rays of heat from the infrared heater reach the preform above the neck ring. On newer systems users profit both from an optimised near infrared heater and an air recycling system (AirbackPlus), enabling only around 65% of the energy required to date to blow the PET bottles having to be used for the same production quantities. In combination with optimised containers, systems like these make for distinctly more sustainable and efficient production. www.khs.com repi.com A COLOUR IDENT I TY LIQUID COLOURS AND ADDITIVES FOR PACKAGING DRINKTEC 11-15 September 2017 - Munich, Germany Hall 4 Stand 500","@ID":17}, "No.06 2017 petpla.net D 51178; ISSN: 1438-9452 19 . 06 . 17 PETplanet is read in more than 140 countries MAGAZ I NE FOR BOT T L E R S AND BOT T L E - MAK E R S IN THE AMERICAS, ASIA, EUROPE AND ALL AROUND THE PLANET PREFORM special Page 8 Go with the flow. South East Asia Road Show Page 34","@ID":1}, "EDITOUR PETplanet Insider Vol. 18 No. 06/17 petpla.net 34 Tour Sponsors: Go with the flow. South East Asia Road Show Go with the flow - South East Asia Road Show: Vietnam and Cambodia Vietnam and Cambodia - on their way up by Kay Barton In the consumer goods industry there are two exciting fields of activity in which the expanding group of buyers, driven by rising levels of domestic economic activity and wealth, is becoming increasingly interested in buying new and innovative products. The food and electronics sectors are both playing an important and influential role. In both countries, wildly creative examples of PET packaging can frequently be seen on supermarket shelves; they provide a colourful, lively and attractive mix, just like Vietnam and Cambodia themselves. The ‘Socialist Republic of Vietnam’ is situated on the easternmost point of Indochina. With a total land area of approximately 333,000km2 it is a curve-shaped country, stretching some 1,600km from north to south and extending between 50km and roughly 600km from east to west. Vietnam borders China to its north, Laos to the north west, Cambodia and the Gulf of Thailand to the south west and the South China Sea to the east. In the 20th century it was subject to colonial rule by Japan and France, which was followed by the partition of the country into the anti-communist, free market South, and the communist North, with its planned economy. The failure of unification efforts in the 1950s led to the Vietnam war, which ended with the capitulation of South Vietnam in the spring of 1975. The country was formally reunified in mid-1976, as the Socialist Republic of Vietnam. The mid-1980 saw the government begin a gradual process of reforms towards an open market economy, which included allowing foreign companies to invest in the Vietnamese market. In 2006, the country’s official new alignment was decided, with the goal of developing into an industrialised nation by 2020 and achieving a constant rate of economic growth of between 8 and 8.5%. So far, this masterplan has been largely successful; the country’s gross domestic product (GDP) has achieved an annual growth rate of between 6-7%, making Vietnam one of the fastest growing markets in South East Asia. Its exports are led by US$34bn of mobile phones and spare parts for mobile phones (over US$ 34 bn), followed by textiles and shoes. In terms of imports, machinery and installations are out in front, accounting for over US$ 28 bn. In 1995, Vietnam became the first country in Indochina to join the Association of Southeast Asian Nations (ASEAN); it joined the World Trade Organisation (WTO) in 2007. With just over 92 million people, Vietnam is the third-most populous Asian nation, after Japan and the Philippines. Its tradition-steeped capital city of Hanoi, which is located in the northern part of the country, has a population of 7.6 million*. The largest conurbation in the country is the business centre of Ho Chi Minh City in the south, which is home to some 8.2 million* people (* 2015 estimates). Hanoi is also the oldest capital city in South East Asia; it celebrated its 1000-year anniversary in 2010. With an average age of just 30, Vietnam is a young country; however, this may change in decades to come, as Vietnam’s demographic profile is expected to age comparatively quickly, compared to other countries. Royal Palace Phnom Penh, Cambodia Macro-economic data Cambodia Population (2016) 15.8 million Population growth (2015) 1.6% p.a. GDP (2015) US$ 18.1 billion GDP growth rate (2016) 7.2% GDP per capita (nominal, 2016) approx. US$ 1,228 Import / export (2014) US$ 9.7 billion / US$ 6.8 billion Import / export (2015) US$ 10.7 billion / US$ 8.5 billion National debt (2015) 34% of GDP Unemployment (2016) 0.5% Inflation (2016) 1.2% The second stage of our South East Asia Road Show took us to Vietnam and Cambodia. These two countries have both suffered extremely turbulent and difficult political pasts; the after-effects are still being felt today, notwithstanding their current stability. Despite this, both countries are looking to the future and are banking on economic growth – although their economic infrastructures have significant differences, when directly compared.","@ID":36}, "PREFORM PRODUCTION PETplanet Insider Vol. 18 No. 06/17 petpla.net 20 Retal JSC, Russia, enters the PET keg market PET kegs for Russia Use of modern disposable high-volume PET packaging is a growing trend in the restaurant industry. This is why Retal JSC has started to produce preforms for 20, 30 and 35 litre PET kegs. Research shows only slight growth in beer production in Russia after four years of decline, but still it is less than 1% year on year. However, the PET keg segment is showing constant growth and Retal predicts that this market will double during the next year. PET kegs are growing in popularity all over the world. They can be filled even on the metal keg filling lines with the special adapter. In addition, PET kegs are convenient for transportation and the bottling of beer, kvass, wine, cider, sweet carbonated drinks and low-alcohol cocktails has a number of advantages. Disposable PET kegs meet all necessary environmental and safety standards and are much lighter and more economical compared to their metal counterparts. Also the use of PET kegs means that the whole chain of cost-based stages for the acquisition and turnover of kegs, such as return, washing and storage can be eliminated. This type of packaging works in accordance with the “ship and forget” principle. Retal entered this actively developing market taking production capacity in the Russian Federation into account, and special attention was given to material selection. Their partner in this project, as a developer and supplier of PET keg fittings is the Russian company “PET-Expert”, which also carries out blowing of PET kegs from Retal preforms. According to General Manager of PET-Expert Sergey Maximov: “We firmly believe that PET kegs are the future of the beer industry. Russian consumers are increasingly turning to live and craft beer, and the consumption culture is changing towards civilised consumption in bars, restaurants as in Europe. For this reason, the quality requirements for beer are becoming higher. This indicates that small and medium business sector in Russia is actively developing. We have been working with Retal for many years, and for us Retal is a very reliable supplier producing preforms with what we believe is the best quality on the market. We are making PET kegs together with Retal and we are sure that the project will be very successful.” In May 2017 Retal and PET-Expert presented its joint product during the XХVI international forum “Beer 2017” in Sochi, Russian Federation. “More than 100 beverage producers showed an interest in possible partnership. And already contracts were signed with some of them during the exhibition.” says Igor Golovanov, Deputy Sales Director Retal Russia. He continued “Retal successfully works with the beer segment in Russia, more than 15% of Retal’s production is shipped to beer customers. For more than ten years leading beer producers such as Carlsberg, Heineken or ABI have been our partners.” Product range growth with PET kegs is intended to further strengthen the company’s position in the Russian beer segment. www.retalgroup.com PREFORM special","@ID":22}, "PREFORM PRODUCTION PETplanet Insider Vol. 18 No. 06/17 petpla.net 19 PREFORM PRODUCTION 19 that the disadvantages could be largely overcome by good bottle design and specific washing processes. The first Hodmeter PET line started up in December 2012, at Defeaus. In January 2014, corporate water dispenser specialist Elis switched from Tritan to PET. Just over a year later, Hodmeter launched its first injection-moulded bottle with integral handle. Developments since then include: an 11l bottle with handle, launched in April 2015; a new neck, implemented in June 2016; Sipa homologation of Hodmeter’s preform in July 2016, with SMF following suit in November. Hodmeter supplies preform in 680 and 690g models, both with 55mm crown necks, and with a PET handle. Its range of large-capacity bottles extends from 10l to 5 gallons, with high co-polymer levels and IV values of 0.84, plus or minus 0.02. It meets all appropriate EU and US FDA certification standards. The 5-gallon PET bottles offer high logistical performance; 630 units can be carried on a 120 x 80 x 110cm pallet-box. 0ver 30,000 units – 48 pallet-boxes – can be carried in a standard 40-foot ISO container. The bottles are finished with Hodmeter’s MonoCap 2CE, which features a new, bi-injected seal for tightness and hygiene; and an internal valve for better cooler installation. It has three tamperevident layers: the label, inner valve and skirt. The single-piece construction ensures high hygiene standards and additional tamper evidence. The Hodmeter bottles are available in a range of colours. The company says that its PET bottles enable customers – from bottlers to end-users – to go completely BPA free. Established recycle channels for PET make it the preferred alternative to polycarbonate for the supply water in 5 gallon refillable bottles. www.hodmeter.com Hodmeter preforms for 5-gallon refillable bottles With Sacmi, the beverage specialists are always at your side. With our unbeatable technological know-how and continuous research we are creating new containers and closures designed to ensure outstanding performance. The new IPS injection system for preforms, the CCM compression press for caps and the quality control systems fully designed and built by Sacmi, allows for large-scale production with considerable advantages in terms of efficiency and flexibility. The outcome? Reduced plastic volumes, less energy consumption and lower running costs.All in a bottle: the one you’ll soon be making. SAVE THE DATE DRINKTEC, 11/15.09.17 | HALL B5 - 302| Munchen Germany SIMEI,11/15.09.17 | HALL C3 - 209| Munchen Germany PROPAK MYAMAR, 21/23.09.17 | Yangon, Myanmar PACK EXPO VEGAS, 25/27.09.17 | S-6249 | Las Vegas, USA SINGLE-SERVE CAPSULES 2017 | 10/11.10.17 | Cologne, Germany HOST, 20/24.10.17 | Milan, Italy GULFOOD, 31.10-2.11.17 | Dubai, UAE","@ID":21}, "PETplanet Insider Vol. 18 No. 06/17 petpla.net 47 BOTTLES PETbottles Home + Personal Care Improved spray head The German Henkel Group is replacing the familiar spray head on its brands such as Bref and Sidolin with a new development. The new spray head is bigger, sturdier and offers easier grip and handling. The activation lever is broader and better guided in its movement. The spray head can be locked by a 180 degree twist movement. By moving a whitecoloured side-slider across the opening, the consumer can select a spray-type product or a foam. The bottles remain the familiar PET bottles with different capacities and sleeves. www.henkel-reiniger.de/bref-power Ecological bathroom cleaner from dm Under their own brand name of “denk mit”, the German discount chemist dm sells 750ml bottles of bathroom cleaner with surfactant made from renewable resources. According to the manufacturer, the cleaner counteracts dirt and limescale, guarantees cleanliness and shine and is suitable for shower cubicles. The product has won several eco-labels and a bitter substance protects children from the risk of swallowing the product. The light green-coloured cleaner is supplied in an easy-grip bottle with a screwed on pump dispenser. Shaped labels on front and back describe product and handling. www.dm.de Pre-wash foam from Frosch Frosh has developed a lemon pre-wash foam and recently added it to its product range. The foam powerfully pre-treats dishes, effectively releasing crusted and greasy deposits and supporting and improving cleaning results in the dishwasher. The light-coloured, lemon-scented cleaner is available in 300ml bottles, the shape of which is reminiscent of the large container. The packaging is completed by a screwed-on, lockable trigger, a foldable foam attachment and an adhesive label that better presents the innovation and its handling. www.dm.de/frosch Body oil from Balea 150ml body oil “relaxation”, also suitable for massage, is offered to customers as a product test by discount chemist dm under its own brand name Balea. The vanilla and lavender scented oil offers intensive skin care and is suitable for all skin types. The packaging is a conical, transparent bottle with a lilac-coloured screw seal and matching self-adhesive label. www.dm.de MHT MOLD & HOTRUNNER TECHNOLOGY AG Your Machine - Our Solution Hall 4A, Booth 416 QUALITY MADE IN GERMANY","@ID":49}, "BOTTLE MAKING 39 PETplanet Insider Vol. 18 No. 06/17 petpla.net from 2 to 20 cavities, of which 3 blowers are connected inline production at customers’ sites 15 Nissei ASB single-stage machines 8 compression moulding closure machines ranging from 32 to 64 cavities All the raw material used comes from Asia, including from Indorama Thailand. Around 70% of the products are channelled into the beverage industry, the rest into the food and nonfood sectors. Their customers include Pepsi and Vinamilk (see the company timelines), as well as Coca Cola, Unilever (whose factory is incidentally located right next door), Nestlé, almost every Vietnamese manufacturer of edible oil, as well as about 300 more. The manufacturer exports around 30% of preforms and 10-15% of closures, whilst 100% of the bottles they produce remain in Vietnam. Ngoc Nghia develops parts of their blow Company timeline: 1993 Ngoc Nghia was founded, becoming the first company in Vietnam to produce PET bottles 1998 First bottle factory was established in the Tan Binh district, Ho Chi Minh 2003 A second factory was constructed in Cu Chi to manufacture bottles and preforms 2005 PepsiCo production lines were set up 2007 A third factory, International PET (InterPET), was established in Tinh Tay Ninh, producing preforms and closures. Ngoc Nghia became a joint-stock company 2009 They officially became a public company. Their production lines for Vinamilk were set up 2010 A third factory producing preforms and closures was set up in Linh Trung 2012: Research and development began in advanced packaging for home and personal care, liquid dairy, beer and other sensitive products 2013: Ngoc Nghia products were now being used in 24 different countries worldwide 2015: Advanced packaging was introduced for liquid dairy, beer and other sensitive products moulding in-house, particularly for local brands, whilst Pepsi and Coca Cola supply their moulds themselves. After our tour of the factory the following day, we finally got to meet Mrs La Bui Hong Ngoc, or as she prefers to be known, Ruby, Vice Chairwoman and CCO of the PET Division at the new registered office in downtown Ngoc Nghia, housed in the nine-story Vietcombank Towers. She is part of the corporate family, owning a 75% share in the company. Of the remaining 25%, 14% is shared out chiefly among the employees. However, the company is not listed on the regular stock market, rather, the shares can only be traded over-the-counter (OTC). “Our turnover in 2016 amounted to US$60 million,” explains Ruby. “It was our worst year to date due to the numerous external factors affecting the beverage market. These factors included things such as scandals becoming public for one brand or another, shifts in consumer drinking behaviour, and an increased awareness of healthy beverages. As such, we have clearly identified our goals for the years to come and we can see a trend emerging: the population is consuming more and more bottled water. We’re also seeing an increasing demand for liquid food and nonfood, so we’re reacting accordingly by adapting our capacities and expanding our ranges here and there.” Around 75% of Ngoc Nghia’s products are currently used for drinks and liquid food, with 25% being employed within the non-food sector. “We’d like to improve our capacities for bottle blowing in the medium term, so we can cater for sectors not related to beverages, among others,” further explains Ruby. “Our aim for 2018 is to achieve a turnover of US$100 million.” www.nnc.com.vn Sacmi compression moulding installations Preforms made by Husky equipment","@ID":41}, "PREFORM PRODUCTION PETplanet Insider Vol. 18 No. 06/17 petpla.net 18 Preforms for 5-gallon refillable bottles Hodmeter replaces PCB with PET The 5-gallon refillable ‘water cooler’ bottle is a niche market and one that was under specific pressure with the Europewide ban on BPAs. Hodmeter responded with the development of a new, PET 5-gallon bottle, complete with integral handle and non-spill cap. French company Hodmeter S.à.r.l., which is based in Darnétal, on the outskirts of Rouen, is dedicated to the design, development, manufacture and supply of products and services for home and office delivery. One of its most visible products is the 5-gallon ‘water cooler’ bottle, the locus of countless office interactions in Europe and across the world. The familiar 5-gallon polycarbonate bottle has been under pressure to reform and be reconstituted. BPA (bisphenol A), a plasticiser used in PCB, has been identified as an “endocrine disruptor”; a compound found to produce adverse developmental, reproductive, neurological, and immune effects in both humans and wildlife. It has been determined to be harmful even at low concentrations and may pose the greatest risk during prenatal and early postnatal development, when organs and neural systems are forming in the developing child. It has been banned from use in baby feeding bottles in the EU, under Directive 2011/8/EU. It has been banned in France for use in any and all food packaging under Law 2012–1442. The ECHA (European Chemicals Agency) added BPA to the REACH (Registration, Evaluation, Authorisation & restriction of Chemicals) candidate list in January 2017. The search has been on for a replacement for PCB in large-capacity bottles for several years. Hodmeter narrowed down the alternatives to two: Tritan co-polyester, which has similar production processes and supply chain to PCB; and PET, in a heavy preform with local blow-moulding line. Neither solution provides a perfect replacement for PCB; each has its advantages and disadvantages. The company’s research and development program began in April 2012 with specialist washing and drop tests of PET prototype bottles, undertaken in collaboration with Defeaus S.à.r.l., a producer of mineral water. PET scored positively on its impact resilience; UV resistance; ease of assembly (blowing); logistics and supply chain; cost of production and recyclability. It fared less well on reaction to extremes of temperatures, rigidity, scratch resistance and the need for blow-moulding knowhow, which may not be present in the established suppliers of large-capacity bottled water. Hodmeter determined PREFORM special","@ID":20}, "BOTTLE MAKING 29 PETplanet Insider Vol. 18 No. 06/17 petpla.net Please order your copy at the PETplanet Insider book shop: petpla.net/book3 Stretch Blow Molding Second Edition by Ottmar Brandau € 130,00 320 pages © Copyright Elsevier 2012 rod and blow air provide the stress needed to transform the preform into a bottle. The top right of this and the following diagrams indicates the stage of the preform in the blow mould. Elastic deformation Figure 2.14 Elastic deformation occurs when the stretch rod starts moving mate¬rial toward theblow mould. The first stage is the area of elastic deformation, as seen in Fig. 2.14. Here, the material stretches but will retract if the stress is removed. This is similar to the way that metals behave, but the shape of the curve is slightly different. Looking at a preform, this stage can be compared to the stretch rod starting to push on the preform. If the stretch rod was retracted, the preform would shrink back almost to its original length. Yielding The second stage is yielding (Fig. 2.15). With no increase in stress, the material “gives,” elongating easily. This happens in the blow mould when the primary or pre-blow air partially inflates the preform. The preform will continue to inflate until it reaches the natural stretch ratio: the point after which higher stress is needed to achieve further elongation. Figure 2.15 At the yielding plateau, no further stress is required for additional strain. The third stage is called strain hardening (Fig. 2.16). Applied stress levels have to increase exponentially in order to force material to stretch further. This is the point in the blow process when high-pressure air enters the preform and forces it to stretch from a bubble to the blow cavity walls where it is rapidly cooled down. It is during the strain-hardening phase that the material achieves orientation. Figure 2.16 Highblow pressureforces the material to strain harden. PROCESS PILOT® makes producing a better PET bottle as easy as 2 3 1 MEASURE CONTROL OPTIMIZE every bottle for changes in material distribution process variation, inside the blowmolder material utilization and orientation to achieve maximum bottle performance CONTACT US TODAY TO LEARN MORE! AGRINTL.COM | +1.724.482.2163 | SALES@AGRINTL.COM see us at Booth A4-336","@ID":31}, "PETplanet Insider Vol. 18 No. 06/17 petpla.net 45 TRADE SHOW REVIEW In any case, networking in the niche “plastics recycling in Europe” sector is important. PETplanet: You were also present as exhibitors: what innovations did you or were you able to present at the conference? Meyer: On the one hand, we presented the new generation of the established Powersort 200 system, in which the core components were further developed: a new spectrometer unit, a new processor with increased computing power and a new high-performance laser system with a significantly higher output In addition, we presented Powersort 360. The main application area of this new product is the treatment of shredder fractions (8-75 mm grain size) with a high proportion of black plastics, such as e.g. in the processing of electronic devices or automobiles. PETplanet: A topic that is of great interest to many of our readers: are there any new developments at Unisensor in the PET recycling sector? Meyer: In 2016, we presented two new systems: The new generation of the Powersort 200 system, and the Powersort 360. It is important for our customers to achieve the highest degree of purity, especially in the final quality assurance at PET flake level, before everything is melted and the quality cannot be further improved. The performance stands out, among other reasons, for its very high resolution. Thus even the smallest impurities can be removed from the PET stream. In addition, the system detects PET flakes, which during further processing have begun to yellow and the system sorts them out. Despite the general caution in the PET recycling sector, leading recycling companies continue to optimise their processes through the use of our technology so that we can look back on a successful year in 2016 and look forward to a positive order situation in 2017. PETplanet: Was the conference successful for you? Meyer: For us, the conference was very successful, so much so that we intend to participate again in 2018. PETplanet: Thank you for your time and the informative conversation. To sum up, the PRS was a productive and essential show for the European recycling business. It was a vehicle for communicating the state of the art technologies and to discuss new opportunities for the economy. It will be exciting to read about the new Plastic Strategy report of the European Union and how this will go together with the experience and results of the PRS. A first intermediate result will hopefully be discussed at the next PRS in 2018! www.unisensor.de/en www.prseventeurope.com Injection moulding machines Thermal shaping technology Extrusion plants Tool systems Materials and components 25th Fakuma ! More than 1700 exhibitors from all over the world will present global offerings for technologies, processes and products made of plastic, as well as equipment and tooling for plastics processing, in 12 exhibition halls. 17. –21. OCTOBER 2017 FRIEDRICHSHAFEN The Entire World of Plastics International trade fair for plastics processing +49 (0) 7025 9206-0 fakuma@schall-messen.de Organizer: P. E. SCHALL GmbH & Co. KG www.fakuma-messe.com You’ll be awaited by flexible, individualised solutions for current and future challenges faced by the automated, globalised economy.","@ID":47}, "31 PETplanet Insider Vol. 18 No. 06/17 petpla.net BOTTLING / FILLING He only puts his trust in credible technology when it comes to machinery. Injection lines are up to 850t, fully electric and come from Japan and Europe. The Nissei ASB series systems also come from Japan and blow-moulding equipment is supplied by Kautex. He relies on Husky for preforms, Netstal for closures and thin wall products. Sidel for aseptic, and the two modular systems with rotary cubes come from Krauss Maffei in Munich. It is not maximum performance levels that are important to him, rather, it is making sure that service uptime is the best it can be, “What good are the best machines, if they’re left for 24h due to insufficient service? They can be as energy efficient and as productive as you like, and they can save as much material as you like, but just one day of downtime cancels out all these efforts,” explains Tony. In order to add some degree of structure to this plethora of processes, different factories concentrate on different technologies. To get a feel for how this works, we visited the Sanpack Unggul factor in Bogor. There are 29 blow-moulding machines, 11 stretch blow-moulding machines and 32 full-electric injection systems spread across two sites. As well as Kaeser compressors, of course. Ohendry has definitely been able to reap the benefits from Tony’s success story. Compressed air is needed in all the factories and his Kaeser compressors can be seen almost everywhere, whether it is a matter of 10bar that is needed for every facility, or 40bar for blow-moulding and stretch blow-moulding equipment. At Sanpak Unggul, a capacity of 40m3 for standard applications and 27m³ for up to 40bar of dry air to blow-mould hollow forms is installed in Factory 1. www.dynapackasia.com www.sanpak.co.id www.kaeserindo.com F.l.t.r.: Puji Widodo Ass., Mgr Technical and Mr Marcel Tjokrohartono Production Manager at Sanpak Unggul. Mr Tony T. Hambali, CEO at Dynapack. W W W . I N T R A V I S . C O M Sample-PreWatcher® Comprehensive sampling analysis inline and offline High speed 100 % inline and offline inspection Color inspection right above the tooling plate Non-destructive layer inspection PreWatcher® III ColorWatcher® Integrated LayerWatcher® Preform Inspection. Today.","@ID":33}, "PREFORM PRODUCTION PETplanet Insider Vol. 18 No. 06/17 petpla.net 23 system because it has the unique advantage to decrease damage to the bottleneck of the preforms, by smoothly sliding the preforms in the hopper of the filling line, but the flexibility of the Stackabox allows integration in every imaginable automated system. Even automated folding and erecting of an empty Stackabox by means of a folding robot is possible. Afterwards, 182 folded Stackaboxes, stacked seven high can make the return trip to the preform producers in one trailer. The Stackabox has been in use for 5 years, not quite long enough to make adequate conclusions about the maximum life span, but it will be possible to make hundreds of round trips with each box. And that is not the end of its lifecycle, because the polypropylene raw material is 100% recyclable and it can be used over again for the production of new containers or other plastic items. www.dssmith.com StackaboxMedium-1-stacked Stackabox dispensing: Dispensing of preforms ","@ID":25}, "imprint EDITORIAL PUBLISHER Alexander Büchler, Managing Director HEAD OFFICE heidelberg business media GmbH Bunsenstr. 14 69115 Heidelberg, Germany phone: +49 6221-65108-0 fax: +49 6221-65108-28 info@hbmedia.net EDITORIAL Kay Barton Heike Fischer Gabriele Kosmehl Michael Maruschke Ruari McCallion Waldemar Schmitke Anthony Withers WikiPETia.info petplanet@hbmedia.net MEDIA CONSULTANTS Martina Hirschmann hirschmann@hbmedia.net Johann Lange-Brock lange-brock@hbmedia.net phone: +49 6221-65108-0 fax: +49 6221-65108-28 LAYOUT AND PREPRESS EXPRIM Werbeagentur Matthias Gaumann | www.exprim.de READER SERVICES Till Kretner reader@hbmedia.net PRINT Chroma Druck & Verlag GmbH Werkstr. 25 67354 Römerberg Germany WWW www.hbmedia.net | petpla.net PETplanet Insider ISSN 1438-9459 is published 10 times a year. This publication is sent to qualified subscribers (1-year subscription 149 EUR, 2-year subscription 289 EUR, Young professionals’ subscription 99 EUR. Magazines will be dispatched to you by airmail). Not to be reproduced in any form without permission from the publisher. Note: The fact that product names may not be identified as trademarks is not an indication that such names are not registered trademarks. 3 PETplanet Insider Vol. 18 No. 06/17 petpla.net Dear friends of PETplaner Insider, Summer has now begun in our part of the world. For us and for the beverage industry, we hope it will be warm and long! Almost the entire PETplanet team has flown to Spain, Italy, Thailand and Laos - and not just on holiday... The final of our Go with the flow Editour is almost upon us! In the fifth and last part of our South East Asia Roadshow, around 20 suppliers, machine manufacturers and bottlers are being visited in Laos and Thailand. The detailed interviews and market overviews will appear in future issues of PETplanet Insider, and you can follow our journey and all its challenges and excitements on our tour blog. The grand finale where we will be holding an exhibition featuring all companies we visited will be showcased this year at the most important trade fair event for our sector: Drinktec 2017 in Munich, which opens its doors from 11th to 15th September. The trade fair has grown since 2013 and new ideas have been incorporated in its programme. Not only has the world’s leading wine technology trade fair SIMEI been integrated; there are also numerous innovations, including the creation of a special area for new beverage concepts. Similarly, KHS and Sidel have stepped forward to sponsor a lecture series called 5 o’clock Theme, in which on three afternoons, stimulating talks will be presented on future scenarios and new market and business ideas. And beer-lovers are not forgotten either: the beer highlights will be showcased in their own appropriately named hall, place2beer. We will be keeping you up to date with all PET topics set to feature at Drinktec in the next three issues. In this issue, our special focus will be on preform production. We have researched the current state of the industry in extensive reports and interviews so we can provide you with comprehensive information about the latest developments and applications of multilayers, about creative mould design, the production of kegs and about transportation options. Rounding off this summer edition are two interviews on the subject of packaging that came about in the aftermath of the Interpack trade fair, the second conference report from the Plastics Recycling Show Europe in Amsterdam, a first contribution on Cambodia and Vietnam and the first tour interviews from these countries. I hope you enjoy reading, perhaps whilst relaxing on the beach? Yours Heike Fischer","@ID":5}, "BOTTLE MAKING 38 PETplanet Insider Vol. 18 No. 06/17 petpla.net Tour Sponsors: Go with the flow. South East Asia Road Show Preforms, bottles and closures, all made under one roof! by Kay Barton The outside temperature registered over 35°C with a humidity of 60%, but inside the halls, the air conditioning ensured the temperature was a maximum of 28-30°C throughout our visit. Mr Musa pointed to a dryer located above a HyPET: “This material dryer we have installed does all the hard work, because the humidity in the country can cause problems for the converter.” The new division of the factory was first opened in 2016, with a HyPET 400 and even newer Sacmi compression moulding lines. Significantly, it has space for future growth. “ This year, we’re planning to expand this section of the factory by installing new machines and moulds. This way, we can meet the increasing demand for PET,” explains Mr Musa. In the second factory located in Cu Chi, an area which is mainly known for the Cu Chi Tunnel dating back to the Vietnam War, we were met by Mr La Son Ha, Deputy General Director who has been with the company from the very start. This local factory focuses on producing bottles and preforms. The only exception is the single production line for closures. 300 employees work across the threehectare company premises. “Our market share is 40% for PET packaging in Vietnam,” explains Mr Musa. “Our main competitors are Taiwan Hon Chuan, Sri Thai and Bavico.“ The technical set-up: 16 injection machines ranging from 32 to 96 cavities 8 rotary blowing machines ranging Interview with Ngoc Nghia Industry March 28-29, 2017 We met: Mrs La Bui Hong Ngoc, Vice Chairwoman & CCO PET Division Mr Musa, R&D Officer Mr Tran Quang Huy, Deputy General Manager at International PET (Ngoc Nghia subsidiary) Mr La Son Ha, Deputy General Director La Bui Hong Ngoc in the HQ’s entrance area Seven years have passed since our last interview with allround producers Ngoc Nghia (see PETplanet Insider No. 6/2010). Over these seven years, a lot has happened on the Vietnamese market, as well as in the company itself, and besides the food trade, PET is their main business. Their management underwent significant internal changes to ensure they are prepared for the long haul in terms of local demands and challenges in the packaging domain. The manufacturing company currently employs around 800 staff in the PET domain. We have given ourselves two days to visit both the two factories located around Ho Chi Minh, as well as the current company headquarters in the city centre. We also plan to participate in some lengthy discussions about the current state of play, the PET market situation and their strategical focus for the future. On our first visit to the InterPET factories in Tinh Tay Ninh, we met Mr Musa. He was for six months R&D Officer, and he accompanied us both here, as well as during our subsequent visit to the factory in Cu Chi. “I actually work at the company headquarters in the city, but I regularly travel to our factories to check how our projects are getting on,” he explains. We also got to meet Mr Tran Quang Huy at InterPET, the Deputy General Manager. InterPET employs around 300 staff across its four-hectare premises. Husky’s HyPET 300 and the Sacmi compression moulding machines are housed in the older of the two factory divisions. Meeting at InterPET with (f.l.t.r.) Mr Tran Quang Huy and Mr Musa","@ID":40}, "Editour 36 Tour Sponsors: Go with the flow. South East Asia Road Show Vol. 18 No. 06/17 petpla.net over the previous year. The proportion of non-Asian companies responding to local demand is also high. Röders, a German company, has recently started blow-mould manufacturing here and now wishes to expand. Unfortunately, figures on local consumers or the distribution of PET across the different drinks segments have proven to be impossible to obtain, or lack the required level of detail and differentiation. But according to Euromonitor, PET bottles’ share of the retail market in Vietnam increased almost 48% over two years, from 2013’s total of 3.76bn units to 5.55bn in 2015. The packaging market in Cambodia Similar challenges apply to Cambodia. There is, basically, no data on the local packaging and drinks scene in the country – at least, there wasn’t when this article was written. Even well-known sources of business information do not have any reliable points of reference on the situation here. Discussions with Coca-Cola (Cambodia Beverage Company), frequently a dependable source of good data, also failed to yield any specific figures or market information. Our visit to the giant brewery owned by the Khmer Brewery (Cambodia Beer), which has just finished installing its brand new Krones PET soft drinks system, provided some interesting insights into what is a brand new, high-end project for the company. During our interview, however, we were again advised that no historical values or solid data for fact-finding were yet available against which to compare the performance of new soft drinks, or PET. This murky situation makes it difficult or even impossible for small and medium sized companies to make investments in the drinks industry. We will continue to monitor developments and hope to be able to provide some dependable data in the future. Beverages Packaging Vietnam: Retail/ off-trade in million units (Total Packaging 11.043,80 in 2015) Source: Euromonitor Beverages Packaging Vietnam: Retail/ off-trade in million units, year-over year growth in % (Total Packaging 10,10 in 2015) Source: Euromonitor","@ID":38}, "BOTTLE MAKING 25 PETplanet Insider Vol. 18 No. 06/17 petpla.net Stretch Blow Molding, part 3 Material Basics / Drying of PET by Ottmar Brandau Ottmar Brandau has newly revised his book “Strech Blow Molding”, first published by hbmedia / PETplanet Publisher, and now re-issued in a second edition under the Elsevier imprint. PETplanet Insider is publishing extracts from successive chapters in a series of articles. During the injection process, these crystals are melted, resulting in an amorphous melt which is injected into preform mould cavities. The preform is rapidly cooled down to avoid re-crystallisation. Preforms, therefore, do not have a crystal structure – this state is called amorphous state. In the amorphous state, the molecular chains show no orientation and no crystallinity, and their appearance has been compared with a bowl of spaghetti. There is nothing to reflect light and therefore the PET is clear. It also has minimal strength and barrier properties. In the reheat stretch-blow machine (RSBM), the material is forced by the stretch rod and blow air to orient in the axial and hoop direction, forming small, strain-induced crystals. These crystals do not reflect light and the bottle appears clear. It also has higher strength and barrier properties. Crystallisation levels of up to 25% can be achieved in the bottle side wall, given the correct “Extended chain” or “oriented” crystallisation During stretch-blow moulding, the amorphous chains in the preform are stretched and oriented, and a different form of crystallinity is developed. The chains are aligned in the direction of stress, orienting themselves and imposing a linear ordered structure throughout the area of applied stress. This ‘extended chain’ or stressinduced crystallinity is necessary in the blow-moulded container for mechanical strength. Summary PET occurs in three different states: Amorphous, nonoriented, and clear, such as preforms and melted plastic resin Thermally (by means of temperature) crystallised, such as resin pellets Strain-induced crystallized, such as bottle side walls PET is transformed several times as it goes from pellet to preform to bottle. As resin pellets, PET is thermally crystallised to a level of 50–70%. Thermally induced crystals are arranged in large structures called spherulites, which reflect light, making PET appear white.","@ID":27}, "PREFORM PRODUCTION PETplanet Insider Vol. 18 No. 06/17 petpla.net 9 contrast, the multi-layer co-injection barrier solution provides a greater package design freedom, since the package creep and deformation levels are less critical or even inconsequential for the barrier performance. It further allows active oxygen scavenger materials to be introduced, preventing oxygen ingress and lowering oxygen content in the headspace. A multi-layer structure providing a barrier to light can also be created when required. On the operational level, coatings are attractive due to a low cost of consumable materials. At the same time, a plasma coating system represents an additional process step between bottle blowing and filling, which can pose a challenge to preform moulders supplying multiple blowing sites. Multi-Layer Technology A multi-layer preform is produced in a sequential injection or a simultaneous co-injection process. In both cases, the resulting preform contains a distinct layer of the barrier material sandwiched between the inner and outer layers of PET. Even though barrier materials are typically approved for food and beverage applications, as an added benefit this results in only PET being in direct contact with such products. Preform blowing and filling steps subsequent to injection moulding do not require changes to the existing production lines. This means that, when desirable, a producer is able to maintain the flexibility of operating a central injection moulding facility supplying multiple blowing and filling locations. Husky’s Multi-Layer Technology is an integrated system solution building on the monolayer preform performance of the company’s HyPET HPP5 product line. Simultaneous co-injection results in faster cycle times and the ability to inject thinwall preforms, since both PET and the barrier materials flow into the mould cavity through the gate at the same time. The multi-layer melt flow is formed in the nozzle of the coinjection hot runner, while the standard mould cold half can be interchanged between the monolayer and the multilayer systems, assuming the same hot runner pitch and nozzle interface is maintained. Both passive and active barrier materials are more effective when used in a concentrated layer in a multi-layer package, compared to a monolayer blend with PET. The same barrier improvement factor can be achieved in a multi-layer barrier package using approximately 50% or less of the blended barrier material. The effect has been reported with co-injection systems and confirmed in laboratory studies. This holds true for both the oxygen scavenger applications, where oxygen must be prevented from reaching the product, and for passive barrier applications, where carbonation must be kept inside the package, although the mechanism differs. In the case of a passive barrier layer, the gas permeation rate is reduced by creating a denser “fence” for gas molecules. In the case of an active scavenger, the useful capacity of the scavenger material is extended by ensuring only the oxygen molecules that reach the barrier layer are reacting with the scavenger and are trapped. Even though light barrier applications do not involve gas diffusion mechanisms, similar material cost and package performance advantages are derived from a multi-layer technology. Shelf life of dairy products (such as UHT milk) processed for long shelf life at ambient temperature is limited, among other factors, by the breakdown of riboflavin (vitamin B2) and oxidation of proteins and lipids triggered by exposure to light, leading to a loss in nutritional value and off-flavours. Monolayer preforms containing significantly above 12% of a TiO2 master batch (titanium oxide commonly used to produce a strongly opaque white) are difficult and at some point impossible to stretch blow, thus limiting the extent of light barrier that can be achieved. In contrast, multi-layer preforms containing a black PET layer hidden within an opaque white PET achieve signicantly lower light transmission, blocking up to 99.99% of light up to 650nm wavelength, while reducing the amount of expensive opaque white additive that is needed. The ability to provide uninterrupted barrier layer coverage through the preform dome improves package barrier performance and is especially important for oxygen and light sensitive applications. In particular, some food types (i.e. pasta sauces) do not readily mix inside the package, creating a potential for local oxidisation of the product in segments of the package not covered by the barrier layer, causing spoilage. The Husky hot runner design and control system allow moulding of the multi-layer preforms with either closed or open dome tips (with or without barrier layer in the bottle base), in the former case providing outstanding control over the termination (trailing edge) or the barrier layer. An important factor to lowering the total cost to produce is the ability to precisely dose and distribute just the Husky’s Multi-Layer Technology combines the benefits of the company’s proven HyPET HPP5 system with a revolutionary new hot runner to enable the most precise and controlled dosing of barrier material.","@ID":11}, "PREFORM PRODUCTION PETplanet Insider Vol. 18 No. 06/17 petpla.net 14 On the one hand a PET bottle must stay stable so that customers can continue to use it comfortably and it remains unbreakable. On the other a carbonated medium in the bottle requires a certain wall thickness in order that only the stipulated amount of CO 2 is diffused and the bottle can withstand the internal pressure. The preform must also safely survive the production process both in the stretch blow moulder and then as a bottle on the filling system. There are thus many reasons why the material and consequently the weight of the PET bottle cannot be reduced any further. With more efficient bottle shapes and ever thinner wall thicknesses KHS has nevertheless been able to make considerable savings in weight in the past. “We’re increasingly noticing that current containers are now reaching their limits when it comes to wall thickness. We’re thus turning our attention to other parts of the bottle,” says Arne Wiese, product manager for Bottles & Shapes at KHS. He and his team still see potential in the bottle thread area in particular, yet here, too, there is a lot to be taken into consideration. The best-known and most widely used thread is what is known as the PCO 1881. This is a voluntary standard with a thread diameter of 28mm which is chiefly used by beverage producers for carbonated beverages. The diameter is measured at the widest point of the thread. Directly below this is the neck ring which is usually the widest point of the bottle neck. The thread diameter thus does not always allow conclusions to be drawn regarding the size of the bottle opening. On a PCO 1881 this is 21.74mm, for example. Looking at the International Society of Beverage Technologists (ISBT) website, a scientific and technical society for the beverage industry, one can find countless voluntary standards these can greatly differ when dealing with still beverages compared to hot fill variants, for example. There is also a range of non-standardised models produced by various suppliers. One good example of how confusing this development can be is the persistent use of the PCO 1810 which preceded the PCO 1881. There are also reduced and light versions of this type of bottle neck. All of these types of closure have one thing in common, however: they should close the bottle securely and easily, thus the newer standards are using less and less material and growing lighter and lighter. Savings potential According to KHS, in numbers this means that users can reckon on a standard PCI 1881 thread, including the cap, weighing approximately 5.8g. Without the cap this is about 3.7g. Precise figures cannot be given, as Material savings focusing on the bottle neck, thread and cap Lighter preform, lighter bottle The KHS Group keeps finding new ways of optimising containers for carbonated or non-carbonated beverages, with developers currently focusing on the bottle neck, thread and cap. A number of adjustments enable further savings to be made in this area - without the bottle body sacrificing any of its convenience for the consumer. PREFORM special Neck, thread and cap often offer potential for material savings. Arne Wiese, product manager Bottles & Shapes at KHS","@ID":16}, "TRADE SHOW REVIEW PETplanet Insider Vol. 18 No. 06/17 petpla.net 44 Plastics Recycling Show Europe, Amsterdam, NL 2017, part 2 Creating a sustainable recycling society by Heike Fischer The Plastics Recycling Show (PRS) featured a pan-European exhibition and conference sessions designed specifically for the plastics recycling industry. The event in Amsterdam held in March 2017 brought together key players from the plastics and recycling sectors to network and capitalise on the business opportunities plastic recycling offers. The two-day conference programme was divided into three parts: sessions focusing on materials, challenges for the plastics recycling industry and the plastic recycling process. The PET session was opened by Casper van den Dungen, Vice President and PET WG Chairman at Plastics Recyclers Europe. Read about his presentation in PETplanet 5/2017. On the second day there were two focus topics during the conference: challenges for the recycling industry and the plastics recycling process. The first session was chaired by Clarissa Morawski, Managing Director of Reloop. Roger Bayham discussed the problematic image of plastic. Lucie Charbonel, Marketing Leader of DuPont Performance Materials, Recycling and Industrial Segments explained the DuPont view of using the difficult- to-recycling streams and their new series of Entira EP copolymers. These high performance compatibilisers, based on ethylene copolymers, are able to boost the performance of recycled polyolefins to a similar level as virgin resins. In the second session Jim Armstrong, Managing Director of Kermadec chaired the topic of the Plastics Recycling Process. On this panel there were presentations from NRT Next Generation Group on the topic of Inline melt characterisation of rPellets, from Interseroh with a presentation on finding new markets for recycling materials and a concluding presentation from KraussMaffei Berstorff explaining their EdelweissCompounding for producing highquality compounds from plastic waste. Jan Meyer, Business Development Manager of Unisensor Sensorensysteme GmbH, discussed the purification of PET flake streams with laser spectroscopy. After the show PETplanet took the opportunity of discussing this technology with Jan Meyer. PETplanet: What were the reasons for the participation of Unisensor at this conference? Meyer: Principally, because it was the first PRS. We were one of the companies that has supported the conference from the outset, determined to push through this format and committing ourselves at an early stage to taking part. It is important that there is also an open, central event for the plastics recycling industry in Europe - similar to the very successful format of the “Plastic Recycling Conference” in the USA. PETplanet: Did you meet many customers here? Meyer: As an established and highly innovative manufacturer of high-performance sorting systems, we also met experienced customers who would like to further optimise their processes using our technology. PETplanet: Is it a conference where views can be exchanged? Mr Jan Meyer, Business Development Manager at Unisensor The new generation of the Unisensor Powersort 200","@ID":46}, "EDITOUR PETplanet Insider Vol. 18 No. 06/17 petpla.net 35 Over the years since 2011, the economy has been growing at a constant rate of 7%, a trend which appears to be continuing. So far, so good, although it is possible that this could become a problem in the medium term, as the apparent stability and success has led to some degree of complacency. Urgent structural irregularities have not been addressed, including the development of a legally binding framework for the market economy; the fight against high levels of government corruption; everpresent skills shortages; and very high energy costs. The long-distance transport of goods is also challenging. Cambodia’s transport infrastructure is fairly basic and many of its roads remain unmade. The capital, Phnom Penh has a population of around 2 million, including its suburbs. It is also the country’s tourist hub, although many of its visitors also travel to the world-famous Angkor Wat temple complex, some 330km away. In addition to its growing tourism industry, Cambodia’s key economic sectors are agriculture, textiles, shoe making and construction. In terms of international trade, the textile industry’s US$6bn value make it the country’s most valuable export sector. (Sources: World Bank, Trading Economics, WKO, OEC) The packaging market in Vietnam According to a report by the German Engineering Federation (VDMA), the economic upswing in Vietnam has led to a higher standard of living, superior standards of education, and a huge increase in demand for food packaging. It is forecast to increase by 38%, from 3.9m. tonnes in 2015 to 5.4m. tonnes in 2020, with milk products accounting for the biggest overall share; this segment alone is expected to increase by 45%. The packaging segment showing the strongest growth is rigid plastics, primarily PET bottles, which is forecast to grow by 50% by the end of the decade. Metals are expected to grow by 31%, cartons by approximately 10% and glass by around 25% (see VDMA table below). Consequently, demand for high-end processing technology is high. According to the analysts, 2015 saw imports of machinery reach a value of US$426m – an increase of 10% over the previous year. With imports to the value of US$148m, China was the leading country of origin, followed by Germany (US$84m) and Japan (US$32m). The figures and positive forecasts matched those of the businesses that we visited with here. For example, Duy Khan, a manufacturer of machinery and moulds, is expanding into a bigger plant. PET processor Ngoc Nghia currently has a 40% market share and is forecasting a huge increase in demand for packaged water, liquid food and non-food products over the coming years. In 2016, one of its customers, a leading water brand in Vietnam, recorded a 127% increase in volume Cambodia lies to the south west of Vietnam. With a total land area of approximately 181,000km2 it stretches roughly 450km from north to south and up to 580km from east to west. Across the border to the north lies Laos; Thailand is located to the north and northwest; and the Gulf of Thailand washes its south coast. The country is home to some 16 million people; the average age of less than 25 makes it even younger than Vietnam. Over the past 150 years Cambodia has, like Vietnam, experienced periods of bloodshed and instability. It was controlled by Thailand and Vietnam in the 19th century, before France established a protectorate in 1863 and then officially colonise the country in the 1880s. After being occupied by Japan during the Second World War, Cambodia first declared its independence in 1945; the French then returned and the country didn’t gain full independence until 1953. From the mid-1950s onwards, political differences led to the development of at least two, armed, opposing camps: a Communist faction, and a government oriented to western values. The civil war that erupted in 1970 lasted for five years and ultimately involved North Vietnam, South Vietnam and the USA, in support of various parties within the country, bringing the Vietnam war to Cambodian soil and contributing to the strengthening of the ultra-Communist Khmer Rouge, which took power in April 1975. Its “Year Zero” declaration led to the emptying of the cities, in pursuit of a radical attempt to transform Cambodia into a peasants’ state. The project had appalling consequences for the population; it is estimated that between 1.7 and 2.2. million people died at the during this period. In 1979, when the regime was overthrown with help of the Vietnamese Army, the People’s Republic of Kampuchea was founded. It has been officially known as the “State of Cambodia” since 1989. This still wasn’t the end of Cambodia’s turmoil. Intermittent conflict and the existence of a virtual ‘state within a state’ to the north of the country continued until the Paris Peace Accords of 1991, which saw the disarming of the Khmer Rouge and ushered in the country’s transformation and move from a planned economy to a market-oriented, westernised economy. Membership of ASEAN and the WTO enabled Cambodia to gain access to global markets. Vietnam: Packaging demand by material 2015-2019, Source VDMA. Macro-economic data Vietnam Population (2016) 92.6 million Population growth (2015) 1.07% p.a. GDP (2015) US$ 193.6 billion GDP growth rate (2016) 6.1% GDP per capita (nominal, 2016) US$ 2,164 Import / export (2014) US$ 148 billion / US$ 150.2 billion Import / export (2015) US$ 165.7 billion / US$ 162.1 billion National debt (2015) 58.3% of GDP Unemployment (2016) 3.7% Inflation (2016) 4.7%","@ID":37}, "PREFORM PRODUCTION PETplanet Insider Vol. 18 No. 06/17 petpla.net 21 The perfect bottle starts with the perfect preform The preform experience Whether one is running a high-speed bottle blowing line reaching speeds of 1,000bpm or a single cavity manual blowing machine, one of the most important factors that will define success is the quality of the PET preform and the capability of the supplier to adapt to everchanging requirements. Large scale global manufacturers of PET preforms like Chemco have been able to provide customers with previously unavailable tools that are intended to make it easier and financially more economical to switch from other forms of packaging. Companies supplying blowing and filling lines to customers often ask for samples of preforms in order to ensure that the promised running speed can be achieved. Designing and delivering the perfect PET preform starts with understanding the customer’s requirements at a technical level. This is where Chemco applies its knowledge of designing, prototyping, manufacturing and running PET preforms in suggesting the best fit from its huge existing selection or design a completely new preform. Having several blowing line engineers and experts on its pay role in addition to the technical tie ups with various filling and blowing line companies, Chemco helps the customer in achieving high efficiency rates from their current or new lines. The weight of the preform, though very important in terms of the commercial viability of any project, cannot be the only defining factor. Other considerations are important such as the customer’s installed equipment and manufacturing capability to the product’s shelf life requirement if any, the barrier qualities required to safeguard the product, etc. The goal is to achieve the perfect balance between performance of the product without compromising on quality and without driving the price up by increasing the weight of the PET preform. Preforms for India – focusing on the country’s requirements Many large customers who have been using preforms as the primary source of packaging their products, have their own designs that have been tried and tested for decades. These designs evolve over time based on the geography of the product placement and with the availability of better manufacturing technology and equipment. A good example of this is Coca-Cola in India. Coca-Cola has a huge database of global knowledge and experience of which PET preform to source. Yet in India they have developed new preforms with Chemco that are unique to the country’s requirements. After receiving all the necessary inputs, the company provides computer simulations of the blowing process that helps the customer understand what to expect with the preform they will source. This however is no longer enough. It is important for the customer to not only see what to expect on a computer screen but also experience the same practically in their facility. For this very reason, there is the option of prototyping that will allow the customer to get the preform in their hands and up and running on their machine before they go ahead with large scale commercial production. For prototyping Chemco can use one of its many smaller sized testing machines with a low cavitation preform mould to produce a test batch. In cases where the customer requires a high level of accuracy between the final product and the prototype preforms (more common on high output lines), Chemco can make change parts to replace a few cavities in an existing high cavitation tool to produce a large batch. These preforms are automatically segregated with an online vision inspection system. The future sees the Mumbai-based company investigating and automating the manufacturing of preforms with Industry 4.0, and is already embracing this vision. According to the company, it is not enough simply to invest in high speed lines for preform manufacture but to provide the customer with all the tools required under one roof. www.chemcogroup.com PREFORM special PET preform production capacity: 60,000 MT Locations: 10 Workforce: 1500+ PET preform range: over 100 different PET preforms","@ID":23}, "BOTTLE MAKING 28 PETplanet Insider Vol. 18 No. 06/17 petpla.net Figure 2.11 Injection 3 Figure 2.12 Injection 4 Figure 2.13 Injection 5 We begin injection with the tool closed, forming an empty cavity as shown in Fig. 2.8. Material enters the cavity through the gate (Fig. 2.9). Despite the rela-tively low injection pressure, the material pressure may bend the injection core to one side and cause what is known as ‘core shift’ with the resulting preform wall thickness becoming uneven. This is especially true for thin cores (below 17mm) but may also happen for standard ones when guide bushings are worn out, for example. As the hot material hits the cold mould walls, the resin in direct contact with the wall freezes off and forms a boundary layer (Fig. 2.10). The material in this layer will not change during injection. Its thickness restricts the mould channel and is one reason why a minimum wall thickness must be maintained in the preform gate area. As more material enters the cavity, the boundary layer expands along the length of the preform. Its thickness stays the same as long as hot material is flowing through (Fig. 2.11). The air that is present in the mold cavity must have an escape path, otherwise, trapped air would lead to sink marks in the preforms. Four to eight vents with depth of approximately 0.001– 0.0015mm are machined into the face area of the preform neck, allowing air to vent to the outside. Sink marks are also prevented and the flow of material improves by giving cores a finish in the direction of material flow rather than radially. This is achieved by special machinery that turns the cores while simultaneously moving a polishing stone back and forth on the longitudinal axis of the core. At this point, the cavity has been filled during the injection process (Fig. 2.12). The added resistance causes the hydraulic pressure to increase and it is here that the machine needs to be switched from injection to hold or packing pressure. This can be done by using the actual pressure as the setting to trigger the hold pressure but, for PET, a position-based trigger has proven to be more consistent and is therefore used almost exclusively. The point at which this occurs is called the transition or switch-over point and can be dialed in on the screen. During the hold phase material that is now starting to shrink as it cools is replaced through the stillopen center of the melt stream (Fig. 2.13). This is necessary to avoid sink marks. During cooling time, the material cools quickly and shrinks onto the core in the process. It is noteworthy that the gate area of the preform always stays warmest as it is the last part of the preform to receive hot material. Most preform defects such as cloudiness are located here, for that reason. In single-stage stretchblow molding, the warmer gate area limits the pro¬cessability of the preform as the temperature cannot completely be dialed in but is a result of wall thickness and injection parameters. When problems with a particular preform arise, designers should be aware of the various aspects of the injection molding process and drying parameters and first ensure that preforms were processed correctly before making changes to their shape. 2.5 Behavior in the blow mould Natural Stretch Ratio (or Natural Draw Ratio) The stretch or draw ratio of a polymer is the ratio of the resulting length (in the direction of applied stress) to the original length. When PET is stretched, for example, during blow molding, it reaches a point at which an increase in the force is required to continue stretching. The point at which the PET requires this extra force is called the natural stretch ratio (NSR) for a particular set of stretching conditions. The NSR is reached when strain (or work) hardening occurs on the stress–strain curve for materials. Recall that before a material yields, once the applied force is removed, it can return to its original dimensions. Stretching beyond the yield point results in permanent deformation, and further stretching will result in fracture. In some materials, including PET, strain hardening can occur before fracture, which is essentially the aligning (or orienting) of the structural regions of the material in the direction of the applied stress which can result in improved physical properties of the material. The design of a PET preform is such that during stretch blow, the optimum orientation is achieved just as the stretched walls meet the mould. This point occurs just beyond the NSR. Proper stretching results in longer shelf life and less gas permeability, e.g., higher carbon dioxide retention for soda. Overstretching results in a “pearlescent” appearance to the bottle signifying microcracks (fracture) and excessive deformation. A resin with a low IV has a higher NSR than a resin with high IV. The polymer chains in a low IV resin are shorter and, therefore, less entangled and can be easily stretched more than those in a high IV resin. In the high IV resin, chain entanglement limits the amount of stretch; this is, similar to trying to pull one end from a tangled ball of string where the knots limit the length that can be pulled out. For this reason, preform designs differ when considering low IV or high IV PET. The figures in the following sections illustrate the material stretching in the blow mould without relating to actual data. Strain (elongation) is plotted on the horizontal axis and the corresponding stress on the vertical axis. To obtain these data, a heated test strip of PET might be pulled on a special machine that records the pulling force and the elongation of the strip. In the RSBM process, the stretch","@ID":30}]}}
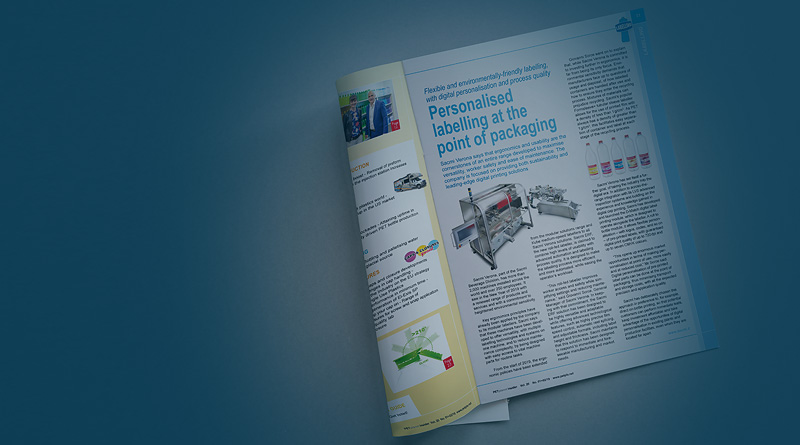