"MATERIALS / RECYCLING PETplanet Insider Vol. 20 No. 12/19 petpla.net 11 It will be open to the general public for creating awareness, for interactive use by school going students and group excursions, NGOs and Public authorities in particular, to learn about plastics, as well as to the industry at large. With the provision of lectures and workshops on all aspects of plastic materials, as well as the handling and recycling of plastic waste, it will be a place where awareness of recycling will be raised and developed. This scale of project is unique in the Indian context and is seen and presented as a sensible step forwards, especially in terms of the current waste situation. In addition to its information and educating roles, the project will also focus on viral dissemination. Managing Director Vimal Kedia filled us in. “Recycling can only work if the big companies, especially those who make use of plastic packaging, can come together and tackle the issue as one.” he said. Depending on the overall marketing approach of Manjushree Technopack, Mr Vimal Kedia also hopes to create this venue as a tourist hotspot that would attract visitors from far afield. “With this project we want to demonstrate, above all else, the added value of plastics recycling as a resource, and make it clear that it isn’t just waste, and that new and other products can be made from old packaging,” Sanjay Balakrishna, GM Operations, explained, as he guided us through the shell of the building. Some of the feature areas are already taking shape but a fair amount of work remains to be done. The company is considering installing a mini showcase machine that would provide live demonstrations of how recycling works at the technical level. “The entire area of more than 1,800m2 and the landscaping around the building have been designed so that they are environmentally-friendly, as are the materials that we use,” he added. PETplanet will follow and report on the project as it develops. www.manjushreeindia.com Group picture at Manjushree Technopack’s Bommasandra plant (f.l.t.r.:) Manjushree’s MD Vimal Kedia, Yves Rebert (Husky), Kay Barton (PETplanet) and Ajith Sivakumar (Husky) Tree planting at Manjushree Technopack’s Bidadi plant with (f.r.t.l.) Vimal Kedia and the PETplanet team Rolf Sinkovec and Kay Barton Reliable high quality in plastic recycling thanks to HERBOLD Meckesheim’s modern washing systems www.herbold.com The increasing amount of plastic waste worldwide, along with legally stipulated recycling quotas, is making great technical solutions are therefore needed. The quality of the recyclate produced must be just right, so that it can be used in as many branches of industry as possible. HERBOLD has improved all process stages: Pre-crushing The new EWS 60/210 shredder has been designed for both dry and wet operation, and delights thanks to its high capacity and maintenance-friendly design. The pre-wash unit helps protect the subsequent machines and provides capacity for more material. Hydrocyclone separation stage: HERBOLD has optimised density separation in the hydrocyclone stage over the course of many years. Hydrocyclones achieve significantly better separation results than float/sink tanks. Hot washing (optional) With optimised temperatures and dwell times, and with the use of suitable cleaning agents, hot washing achieves better cleaning results compared to pure cold washing. HERBOLD has refined this process step, which has long been standard for recycling PET bottles, for use with PO film. The combination of hydrocyclone separation and hot washing forms the basis for quality levels never achieved before.","@ID":13}, "PREFORM PRODUCTION 35 PETplanet Insider Vol. 20 No. 12/19 petpla.net Eastern India’s largest PET converter on sustained growth course produces its own caps on a rotary compression moulding machine. More than 70 different preform designs are available, in weights from 8.7-700g and 25-120mm neck sizes, and a 5 gallon preform, too. Raw material is supplied by IVL Dhunseri (Aspet). Magpet’s wide customer base includes leading brands such as Adani, Bisleri, Diageo, Emami, IFB Agro and ITC. Professional management team in place Many private, fast-growing companies in India suffer from the problem that the organisational structure lags behind the growth; they remain locked into earlystage entrepreneurial business models, where the owner is involved in almost every aspect of the business. This is not the case at Magpet. The company, which is led by Mr Devendra Surana, has independent departments including Operation, Quality Control, R&D and Commercial Department, each led by its own head. Its SAP ERP system (enterprise resource planning) connects the different departments and provides comprehensive information and control over inventories, quality monitoring, efficiency and overall planning. Magpet’s embrace of this structure as the basis for high and sustainable growth has been justified by results. It has grown by an average of 30% annually since 2015, outpacing other converters in this region. A new production plant currently being built on its factory ground will add another 8,000t of bottle and preform capacity by the end of 2019. With this increase of 40% the cumulative Installed capacity would stand at 28,000t/a. Lightweighting and bottle development Magpet puts a strong focus on the development of new bottles for almost all applications and can be considered as the lightweighting pioneer in Eastern India. Magpet developments have been adopted by customers and competitors and have become standard design in the market. In 2006 it became the first company in Eastern India to introduce the 28mm Alaska neck. Five years ago, Magpet played a leading role in the development of a PET bottle to replace glass for local alcoholic beverages. Magpet’s customer-focused approach is illustrated by the fact that it can supply the same preform model in slightly different shapes in order to match customers’ particular machine types, whether they are automatic or semi-automatic units. www.magnumgroup.in Tour Sponsors: April, 2019, We met: Mr Devendra Surana, MD Mr Palash K Chakravorty, CEO Mr Arnab Basu, Technical Head It is not easy to impress seasoned PET insiders so the description of the way business is done at Magpet, Eastern India’s largest PET converter, as “highly professional” is praise indeed. 20,000 MTA of preforms and bottles The group’s first foray into plastic, in 1983, was with flexible packaging; its journey in PET began in 1999 with the launch of Magpet, which now produces preforms, bottles and caps. Its main factory is located in Hooghly, about 55km from Kolkata, and it has two additional factories in Guwahati, Assam which is the hub for fast-developing North Eastern region of India. With a total installed capacity of 20,000 t/a, it is the largest PET manufacturer in Eastern India. Magpet deploys ASB preform moulding systems, injection moulding machines from Windsor & Milacron, along with ASB single-stage and other two-stage stretch blow moulding equipment. It Devendra Surana (left) with Michael Maruschke in the selfie booth Arnab Basu the technical brain (right) explains quality control procedures to Michael Maruschke by Michael Maruschke","@ID":37}, "45 TRADE SHOW REVIEW PETplanet Insider Vol. 20 No. 12/19 petpla.net New hotrunner officially goes live after one-year test period MHT Mold & Hotrunner Technology AG, which has been part of Krones AG since November 2018, has launched a new hotrunner range that is targeted especially at recycled PET as well as PET flakes users and converters. The Optirun hotrunner range, which was developed over several years in collaboration with the Darmstadt University of Applied Sciences, was presented to the public for the first time at the K trade fair following a one-year practical test at an MHT customer’s premises. It aims to achieve a more efficient distribution of heat and materials, something usually associated with higher material flow, at the same time as optimising use of resources. The new range is fitted with the Vulcan II nozzle, which was launched in 2012 and achieves an energy saving of over 13%, compared with the nozzles in the company’s best-selling Legacy kit. According to MHT, maintenance intervals for the mould are also significantly longer. It is compatible with equipment from Niigon, Husky and Sacmi. “The K trade fair is basically our roll-out for the product range,” Carsten Lurz, Vice President Sales, Service and Marketing, explained. “In addition to its positive energy attributes, the mould also generates less PET dust. We are offering Optirun with 48 to a maximum of 144 cavities.” The two-plate hotrunner, which comes in a modular design to cater for different requirements, includes the option of individually controllable heating zones. Exhibited on the company’s stand was a 128-cavity hotrunner, with the cold half on display at Krones at the same time. Mr Lurz highlighted the fact that the company’s takeover by Krones continues to remain positive: “We’re set to end 2019 with a budget surplus.” www.mht-ag.com MHT’s booth at K show presenting the 128-cavity Optirun hotrunner Driving force for circular economy and technological leadership The circular economy and plastics recycling were the top themes at this year’s K, and Erema created a display platform in their Circonomic Centre where visitors to the trade fair were able to experience both themes live every day. With the recycling demonstrations and a large variety of products made of recycled plastic - which the plastics recycling machine manufacturer was able to exhibit thanks to their cooperation with 30 partner companies from the entire recyclates chain - the outdoor Circonomic Centre became one of the most popular visitor attractions at the whole trade fair. For Manfred Hackl, CEO of the Erema Group, this was confirmation of what they wanted to achieve with the Circonomic Centre: “Our goal was to work with our partners to draw attention to what is technologically possible in terms of recycling and the circular economy and what has already been implemented successfully and cost effectively. With this we wanted to provide a strong impetus to get new recycling projects on the road even faster in the future. The visitor interest and the high level of positive feedback we have received show that we have succeeded very well together with our customers and partners,” he says, drawing a positive balance. The huge interest in the recycling technologies from Erema Group companies is indicated not only by the high number of visitors to the Circonomic Centre and our trade fair stands, but also the very pleasing number of sales. This shows that the group of companies and its range of innovative products are ideally positioned to offer customers tailor-made solutions for a wide band of recycling requirements. Another topic highlighted at the K show: The U.S. Food and DrugAdministration (FDA) has recently approved the food contact compliance of post consumer recycled HDPE (PCR-HDPE) produced with the patented Intarema TVEplus RegrindPro extrusion system in combination with the ReFresher module. www.erema.com info@hasplastik.com Tel: +90 212 695 50 00 Fax: +90 212 694 97 24 100815dmyR .com","@ID":47}, "PREFORM PRODUCTION PETplanet Insider Vol. 20 No. 12/19 petpla.net 18 PREFORM Special 2014 At K 2013 Nissei ASB exhibited machinery featuring their 1.5-stage process. In their PF series, the preform is injection moulded, partially cooled, temperature equalised and reheated before being blown (issue 3). 2015 One year after the launch of the new model series with PET-Line 2400 and 4000, Netstal presented the new 5000 model for moulds with up to 144 cavities, featuring faster cycle times and energy savings compared to previous models, as we reported in issue 1+2. In issue 3 we reported about Sipa bringing together its preform compression moulding system with a stretchblow moulding unit in one machine. Xtreme Sincro claimed to produce preforms up to 10% lighter than any preforms produced by conventional injection moulding without losing any key properties. For the same issue, we visited Husky in Canada and learned that the recent trend towards smaller PET bottles could cause issues with shelf life in certain environments. So the time was considered right to launch a barrier module, built on the HyPET HPP5 platform. Several brands including Kortec and Mold-Masters were united under the Milacron banner. At NPE, a new servo-hydraulic PET system was presented with the M-PET 300. (Issue 4) Sacmi presented its new IPS 400 for up to 128-cavities in the same issue. It featured a post-cooling system with preforms unloading directly into boxes. On a demonstration in Imola, Italy, a 11 g preform was produced with a cycle time of 6.2 sec. on a 96-cavity MHT mould. For issue 9, we visited Yizumi Precision Machinery and its injection moulding machinery at Chinaplas. Their then new model PET-72A2 was designed for up to 96-cavities with energy-saving preform handling. Almost 300 different types of preforms for all neck finishes and weights were in the portfolio of Resilux when we visited them in Spain in 2014. Replacing aluminium with PET in the To what extent do you expect chemical recycling to change the preform landscape? Will we see more multi-layer in the future? Dave Morton, Vice President Multi-Layer Technology Solutions, Husky Injection Molding Systems: “Husky’s reinvention of multi-layer co-injection technology has opened up many new opportunities. With our ability to precisely dose the inner layer and our industry-leading systems, we’ve been able to help make packages more economical, reliable and sustainable. As new alternative materials are being developed (biodegradable, compostable, bio-based), we see a lot of interest in using multi-layer technology to help achieve sustainability goals and incorporate more recycled content in packages. This technology can help to unlock materials that are currently challenging to process, making this an exciting opportunity to help further drive the circular economy. Additive suppliers are able to utilise the accuracy of Husky’s multi-layer technology to ensure traditional materials are able to be separated in the recycling stream. Both chemical and monomer recycling can help our customers use materials that are currently challenging for mechanical recyclers to process, or have little to no end-market value. We see chemical and monomer recycling as a complementary technology to today’s thermo-mechanical recycling.” Moraldo Masi, Sacmi: “Chemical recycling can potentially turn around the preform landscape. This is so because if some of the many companies that are busy working on this process, searching for a feasible and economically-sustainable industrial process, will succeed, it will be possible to obtain again the chemical molecules that compose PET. This would be the real and complete circular economy, without limitations or compromises.” Pablo Fiorentini, Sipa: “Based on the latest directives and market projections, we expect a world that is increasingly respectful of rules and the environment; we expect that gradually the colour additives will be abandoned to get a similar scenario to that already existing in Japan where high levels of post-consumer flakes purity and clarity are available. In this regard, our Xtreme Renew system is the right solution at the right time because, thanks to mechanical recycling (much more advantageous than the chemical one) it is able to produce preforms for food contact in a single thermal cycle directly from simply washed flakes. Of course, the preform produced can be suitable also for non- food packaging. Considering the technologies developed and known so far, we cannot fail to note that there are strong constraints for the application of large-scale chemical recycling with justifiably acceptable costs. For the aforementioned reasons we expect multi-layer technology to be less and less required and tolerated.” spray container sector was on their agenda back then. The production of two-layer preforms manufactured using the overmoulding technique to protect light-sensitive content was presented in issue 11 by Netstal, offering a new PET line variant with, the 2C, with two injection moulding unites for this. Preforms could be fitted with a thin, dark-tinted inner layer. 2016 The IM process does not allow further reduction of material in the area of the injection point, resulting in a waste rate of 2-10% of PET material in bottle bases. This is what Creative Packaging Solutions (CPS) stated in issue 4. The solution Mint-Tec presented together with Netstal, Otto Hofstetter and MHT is a mechanically optimised base design of the preform, saving up to 4% material (photo next page, top).","@ID":20}, "MARKET SURVEY 29 PETplanet Insider Vol. 20 No. 12/19 petpla.net Erema Engineering Recycling Maschinen und Anlagen Ges.m.b.H. Gneuss Kunststofftechnik GmbH Tecnofer Ecoimpianti SRL Amut SPA Unterfeldstraße 3, 4052 Ansfelden, Austria +43 732 3190 0 www.erema.at Mr Christoph Wöss Business Development Manager, Application Bottle +43 732 3190 352 c.woess@erema-group.com Mönichhusen 42, 32549 Bad Oeynhausen, Germany +49 5731 5307 0 www.gneuss.com Via Calto 409 45030 Ceneselli (Ro), Italy +39 0425 849090 www.tecnofer.biz Mr Mauro Garbellini Sales manager +39 0425 849090 sales.dep1@tecnofer.biz Via Cameri 16, 28100 Novara, Italy +39 0321 6641 www.amutgroup.com Mr Piergianni Milani President +39 0321 664941 p.milani@amut.it Yes, washing done in cooperation with long-time partners Engineering of washing lines with long term partners Yes Yes No Up to 17,000 3,000-45,000 In function of size and stream quality FDA, ESFA, INTI, brand owners (conf.) Depending on bottle contamination Depends on stream quality Depending on input material 300-600 Vacunite- and Vacurema-Technology. Specification of input flakes: higher contamination can influence pellet quality but are basically possible to process, after discussion and agreed by Erema Yes FDA, EFSA (positive opinion issued), ANVISA, ilsi, BGBI, brand owners FDA, ESFA (pending), brand owners (conf.) No Up to 32,000 200-17,000 3,000-45,000 Depending on through-put and technology: 50-600 30-80, depending on size In function of size and stream quality FDA [cat. A-H&J]; EFSA (pending); brand owners (conf.); several national approvals (Austria, CH, Zona Mercursur, etc.) FDA, ESFA (pending), INTI, brand owners (conf.) Depending on application & technology type, there is a closed loop system no fresh water needed 1 Between 250-350 350 100-400 Specification of input flakes for MPR: Higher contamination can influence flake quality but are basically possible to process, after discussion and agreed by Erema Yes FDA [cat. A-H&J]; EFSA (pending); with Multi Purpose Reactor (MPR) Yes Up to 20,000 Amin. output capacity of 1,000 kg/h up to 4,000 kg/h 3,600-45,000 Between 20-60 Min. floor space from 700-800m² onwards, depending on layout type and hourly capacity. In function of size and stream quality FDA, EFSA (positive opinion issued) Respect the food grade parameters of the equipment dedicated to their use for food contact applications. Closed loop system Approx. 2,5-3 l/kg (2,5-3 m³/t), but it depends on layout type and production capacity 1 100 Between 0,58 - 0,62 kWh/kg (580 - 620 kWh/t), but it depends on layout type and production capacity 250-300 Detergent of different suppliers; quantity in function of the detergent Non disclose 50ppm To be defined in function of the contamination of the material Non disclose Yes, Vacurema Inline preform (Xtreme Renew) Yes, mainly thermoforming sheet lines in direct food contact Each washing line is customised as per customer’s final applications, so our lines can be applied and customised to each of the listed applications. Yes Yes, Vacurema Inline sheet Yes, several lines under operation worldwide Yes Yes, Vacurema Inline fibre; Yes, Vacurema Inline strapping Yes, several lines under operation worldwide Yes","@ID":31}, "PETnews 6 NEWS PETplanet Insider Vol. 20 No. 12/19 petpla.net SGT inaugurates its new Chalon-Sur-Saône site Société Générale des Techniques (SGT) inaugurated its new Chalon-Sur-Saône site in France. The specific feature of this factory is its integrated “SGR” plastics recycling line and its PET preform manufacturing unit. In opening the new SGT/SGR site, Frédéric Mignot, the Group’s Chairman, confirmed the Group’s commitment to sustainable development: “We are aware of everything that is at stake at the moment on both an economic and an environmental level and we have decided to make an active contribution to the development of a high performance circular economy in the packaging sector by proposing more recycled plastic”. The rPET, which SGR produces an average of 12,000 t/a, will have EFSA (European Food Safety Authority) and FDA (Food and Drug Administration) approval for food contact. “Our objective is to speed up the incorporation of recycled plastic into our preform production in accordance with new regulations”, he added. This means that the Group guarantees its customers not just the supply but also the quality of the rPET it provides. This project, which is supported by the Burgundy Franche Comté Region, Grand Chalon and ADEME (French Environment & Energy Management Agency), required significant investment to match the Group’s ambitions: 7 million Euro for the recycling unit and 21 million Euro for the preform manufacturing unit. With this 6th production unit, SGT is increasing its production capacity by one billion units/year. The site is equipped with the latest generation injection presses which combine technical and energy performance. It currently employs around twenty staff and is planning to recruit an additional 20 by 2021. www.sgt-pet.com Frédéric Mignot, SGT Group’s Chairman (on the right), is cutting the ribbon during the inauguration ceremony of the new site. drink technology India 2019 From December 12-14th, 2019, Delhi will host India’s biggest exposition for dairy, liquid food and beverage industry, drink technology India. It is the single-most platform that assembles and optimally represents the liquid food, beverage and dairy industry. North India is home to the largest dairy sector and the booming brewery industry of the country. The Indian dairy and brewery sector along with beverage industry is said to hold tremendous potential for value-addition and overall development. Drink technology India facilitates a befitting stage to exhibit innovations and solutions, custom-made for the Indian market. Mr Bhupinder Singh, CEO of Messe Muenchen India commented on the pre-registrations for drink technology India 2019: “The response we have received so far from exhibitors have superseded expectations. More than 90% of the exhibition space was already booked by early September. The list of international as well as national exhibitors wanting to be part of the trade show has seen a rapid upsurge since the last edition of the show.” Drink technology India exhibits all aspects of the beverage, dairy and liquid food industry – from filing plants, beverage additives, latest beer variation and various dairy products to innovative packaging concepts. The trade fair brings the entire industry together on one platform, empowering home-grown companies as well as connecting international market with Indian companies. www.drinktechnology-india.com KHS China to build new plant and service center in Kunshan KHS now intends to build a new plant and service center in Kunshan, enabling the company to respond more quickly to the local market. Kunshan’s deputy city mayor, party secretary and head of Zhangpu attended the groundbreaking ceremony of the KHS Kunshan plant on October 17, 2019. The executive management board of KHS GmbH and CFO Mr Martin Resch, Managing Director Mr Thomas Karell from KHS Corpoplast GmbH as well as Mr William Wu, KHS China CEO, were present and gave speeches during this milestone event. With a total investment of around €10m, the new around 10,000m² large factory will make engineering, production, logistics and service more efficient. KHS will be an important partner for the city of Kunshan and offer greatly enhanced support in the further development of the regional industry. “Kunshan is an attractive city for the beverage industry with skilled workers, well-developed infrastructure and widespread logistics networks for this kind of project,” said Martin Resch with great thanks to the deputy city mayor of Kunshan, Li Hui. “We are now able to produce a larger product portfolio including single blow moulders, fillers, and labellers as well as in various block versions, increasing the expertise in handling entire line projects,” claimed Mr Resch. Willian Wu is full of expectations for the future of the Kunshan plant and KHS China: “We will combine economic success with socially and ecologically responsible behaviour. Along with top technical performance, maximum sustainability is particularly close to our hearts.” www.khs.com","@ID":8}, "9 NEWS PETplanet Insider Vol. 20 No. 12/19 petpla.net “Choose Plastic” initiative by Amcor With a goal of educating consumers, customers and other stakeholders on the benefits of plastic packaging, Amcor recently launched a “Choose Plastic” marketing campaign. The multi-pronged initiative, which includes a new webpage, an informative brochure and other materials, is designed to: tell the “PET story” with truth, strength and conviction – clearing up common misperceptions regarding plastic packaging; demonstrate where PET stands versus other packaging types, including glass, cans and Tetra aseptic boxes; help customers educate their employees, legislators and consumers on the benefits of plastic packaging. Amcor states that PET bottles and jars are not only lightweight, shatterproof, transparent, recloseable and resealable, studies also show that they are infinitely recyclable, generate up to 70% less greenhouse gas emissions than other packaging types (compared to aluminium, glass and cans), require fewer fossil fuels to produce than aluminium cans and have fewer transportation costs than glass. Additionally, 90% of the PET that goes into recycling bins in the U.S. gets recycled (according to the Napcor Recycling Report), while only 49% of cans, 40% of glass and 16% of Tetra aseptic boxes get recycled. Eric Roegner, President of Amcor Rigid Packaging (ARP) noted that 97% of Amcor Rigid Packaging’s bottles and jars are designed to be recyclable. The company has pledged to develop all of its packaging to be recyclable or reusable by 2025. In addition, Amcor is working with associations such as The Plastics Industry Association, Napcor, and The Recycling Partnership to promote plastics, increase recycling rates and drive greater use of post-consumer materials. Amcor is also working with environmental organisations, such as the World Wildlife Fund and the Trash Free Seas Alliance to eliminate plastic waste. www.amcor.com www.sacmi.com Product design Product development Product validation Industrial production plant Process & quality control On-site and start-up assistance After-sales and Customer service SACMI 4.0 THE COMPLETE CLOSURE, PREFORM AND CONTAINER SOLUTION FOR YOUR SMART FACTORY Compression goes multilayer. Enjoy SACMI innovation. The new SACMI CCMMTM applies all the advantages of continuous compression technology to multilayer capsules, creating a barrier effect that protects aromas and makes production processes more and more sustainable. Barrier layer Tie layer Tie layer Main layer Continuous Compression Moulding with Multilayer technology. TM Main layer","@ID":11}, "imprint EDITORIAL PUBLISHER Alexander Büchler, Managing Director HEAD OFFICE heidelberg business media GmbH Bunsenstr. 14 69115 Heidelberg, Germany phone: +49 6221-65108-0 fax: +49 6221-65108-28 info@hbmedia.net EDITORIAL Kay Barton Heike Fischer Gabriele Kosmehl Michael Maruschke Ruari McCallion Waldemar Schmitke Anthony Withers WikiPETia.info petplanet@hbmedia.net MEDIA CONSULTANTS Martina Hirschmann hirschmann@hbmedia.net Johann Lange-Brock lange-brock@hbmedia.net phone: +49 6221-65108-0 fax: +49 6221-65108-28 LAYOUT AND PREPRESS EXPRIM Werbeagentur | exprim.de Matthias Gaumann READER SERVICES Till Kretner reader@hbmedia.net PRINT Chroma Druck & Verlag GmbH Werkstr. 25 67354 Römerberg Germany WWW www.hbmedia.net | petpla.net PETplanet Insider ISSN 1438-9459 is published 10 times a year. This publication is sent to qualified subscribers (1-year subscription 149 EUR, 2-year subscription 289 EUR, Young professionals’ subscription 99 EUR. Magazines will be dispatched to you by airmail). Not to be reproduced in any form without permission from the publisher. Note: The fact that product names may not be identified as trademarks is not an indication that such names are not registered trademarks. 3 PETplanet Insider Vol. 20 No. 12/19 petpla.net Amidst all the talk about the environment, it is sometimes easy to forget what we in the PET industry have managed to achieve over the years. By looking at our review of the preform process, people can see the rate at which we have been able to save material. In saying that, we are not just referring to lightweight discount bottles currently on the market, but we also mean bottles of the multinational brands. Otto Hofstetter illustrated this very clearly in their in-house magazine with the 2-litre Coca-Cola bottle from 1977. The same-sized Coca-Cola container can still be found on the market today, and you can see how innovation has led to reduced bottle weight over time. The bottle weighed 62 g in 1977 and had a cycle time of 30 seconds. The bottle had a cup base; 1990 saw the introduction of a new base without the cup, and a reduction in weight to 58 g; Improved stretch-blow moulding in 2000 was key in reducing bottle weight to 52 g and a further reduction to 47 g in 2004; In 2009, the 2-litre container acquired the 1881 neck, resulting in its current weight of 45.5 g. Over a period of more than 40 years, bottle weight has fallen from 62 to 45.5 g, i.e. a more than 25% reduction in weight. With today’s 13-second cycle time and 96-cavity mould, this amounts to more than 10 tonnes of PET saved per mould, per day. And on that note, we wish you all a peaceful holiday season. Your PETplanet Insider Editorial Team Dear readers, petpla.net D 51178; ISSN: 1438-9452 No. 9 2019 PETplanet is read inmore than 140 countries MAGAZINE FOR BOTTLERS AND BOTTLE-MAKERS IN THEAMERICAS,ASIA, EUROPEANDALLAROUND THE PLANET 09.09.19 Page 52 Page 28 MATERIALS MARKETsurvey Suppliers of ¿lling equipment & inspection systems Page 35 Page 10 No.10 2019 petpla.net D51178; ISSN:1438-9452 01.10.19 PETplanet is read inmore than 140 countries MAGAZINE FOR BOTTLERS AND BOTTLE-MAKERS IN THEAMERICAS,ASIA, EUROPEANDALLAROUND THE PLANET MARKETsurvey Suppliers of caps& closuresand inspection systems Page 43 Page 47 Page 26 No.11 2019 petpla.net D 51178; ISSN: 1438-9452 04.11.19 PETplanet is read inmore than 140 countries MAGAZINE FOR BOTTLERS AND BOTTLE-MAKERS IN THEAMERICAS,ASIA, EUROPEANDALLAROUND THE PLANET MARKETsurvey Suppliers of palletising& shrink ¿OPPDFKLQHU\\ Page 31 Page 10 MOULDMAKING Page 18 D 51178; ISSN D No.12 2019 petpla.net D 51178; ISSN: 1438-9452 09.12.19 PETplanet is read inmore than 140 countries MAGAZINE FOR BOTTLERS AND BOTTLE-MAKERS IN THEAMERICAS,ASIA, EUROPEANDALLAROUND THE PLANET MARKETsurvey Suppliers of recycling plants and washing units Page 27 Page 10 PREFORM Special Page 14","@ID":5}, "TRADE SHOW REVIEW PETplanet Insider Vol. 20 No. 12/19 petpla.net 43 PET preform and container measurements “The Pilot Vision+ system is a modular, vision-based inspection system that mounts inside high-speed SBM equipment with a special focus on containers with high amounts of rPET,” Marketing Director David Dineff explained. “The system is designed to handle operating speeds of up to 100,000 bph.” Inspection modules mount within the SBM and are available for preform, seal-surface, bottle sidewall and base. The Pilot Vision+ preform inspection module was developed to identify visible defects before the bottle is blown. Multiple colour cameras capture and generate images for 360º sidewall inspection, as well as end cap and gate. According to Agr, the optics, LED illumination and image analysis routines are optimised to identify preform defects that impact bottle integrity, particularly the black specs and particle contamination sometimes associated with rPET. “With the increased use of rPET, challenges related to colour consistency may also be an issue“, Mr Dineff continued. “The preform cameras check for acceptable colour ranges. This is particularly valuable with the variations in colour that can occur when higher percentages of rPET are used.“ The system is also able to learn multiple reference image sets for respective colour inspection, which can be useful for identifying different supply sources and preforms with slightly different colours. The Pilot Vision+ base inspection module incorporates a set of algorithms that can identify the smallest defects and anomalies, regardless of base size, shape or design. The base inspection module features a unique liquid lens, which adjusts focus for bottle heights from 127mm to 406mm, without mechanical components. The focus settings are saved with each job and are automatically adjusted for new container heights. The touch screen user interface provides comprehensive data access to the operator. The system features: pre-built tool sequences for each inspection type; the ability to adjust parameters using live and history images during production; and fullcolour preform imaging for colour management. “The system is part of Agr’s Process Pilot family and could be used along with the company’s longstanding Process Pilot blowmoulder management system,” Dineff said. This combination provides bottle producers with the ability to detect random occurring defects and to better manage material distribution, even in difficult bottle design situations. Agr also presented an update of their Gawis laboratory test series. The Gawis 4D provides enhanced levels of design, process and quality management for plastic containers and preforms. John McCabe, a design engineer on the Gawis 4D team, demonstrated the equipment in action on different containers and preforms, in a range of sizes and neck finishes. “The system can perform multiple measurements, on a wide range of plastic containers and preforms, with accuracy, repeatability and high operational throughput,“ Dineff explained. An updated, automated optical gauging and thickness measurement technology is designed to simplify container measurement operations for higher testing throughputs. The (patent pending) “Auto Job” function, incorporated in the device, is designed to simplify job setup and significantly reduce the time required for an operator to identify and configure finish measurements. It scans the bottle or preform and, utilising a form of AI, identifies standard finish measurements for that sample and incorporates them into the job with a single click, within 18 to 20 sec. The operator can make adjustments or additional measurements as necessary. By simplifying job creation, the Gawis 4D is claimed to be able to save hundreds of operator working hours each year. The system can process PET, PE and PP containers. It works with high pixel density camera components in combination with enhanced telecentric optics and lighting and undertakes 360º imaging, with frames captured up to 1º. This combination is claimed to achieve a precise image and dimensional data, while increasing throughput by 30%. A large library of industry standard finish measurement routines is provided with each system. These are customisable to meet the needs of the application. The equipment uses infrared light spectrometer technology to perform thickness measurements, without direct contact on the preform or bottle. It is also compatible with manual measurement and offers thickness measure at discrete points, or it can scan vertical or horizontal regions for material distribution analysis. Measurements can be performed at multiple locations and regions on the sample to get a full bottle profile. Once a job has been defined, measurements are performed in exactly the same way on every sample. The Gawis 4D features Industry 4.0 communication protocol and is backwardscompatible with previous versions. www.agrintl.com David Dineff (left) with Kay Barton next to the Gawis 4D Agr International, USA, exhibited the latest version of its Pilot Vision+ PET preform and bottle inspection system for in-line use in stretch blow mould (SBM) machinery, and premiered its new Gawis 4D laboratory system for precise container dimension and wall-thickness measurement.","@ID":45}, "PREFORM PRODUCTION PETplanet Insider Vol. 20 No. 12/19 petpla.net 33 tee perfect mould alignment; and LongLife treatment, which enables the expected life of this mould to exceed industry standards. “We are using open and available technology that can be mounted not only on Sipa XForm GEN3 and GEN4 production systems but also on other compatible platforms on the market, as long as they do not incorporate special protective software,” says Cavalet. www.sipasolutions.com 25-26 March 2020RAI, Amsterdam www.prseventeurope.com Incorporating The Plastics Recycling Show Europe will take place at the Rai, Amsterdam on 25th-26th March 2020 The Exhibition and Conference for the European Plastics Recycling Industry Register Now for free entry at prseventeurope.com","@ID":35}, "PREFORM PRODUCTION PETplanet Insider Vol. 20 No. 12/19 petpla.net 20 PREFORM Special Nissei ASB 1.5 step moulding For issue 12 we paid a visit to Retal Pennsylvania, where they were set up to produce, amongst others, three billion preforms on 400 or 500t machines. Our way led us also to Sipa’s Open House in Vittorio Veneto where the latest development was shown, the Xtreme blocked with a stretch blow moulding and filling line. So the process from PET flakes to bottles can be realised in one thermal cycle. The energy input in the preform injection-compression moulding is sufficient to produce the finished bottle. Sacmi widened their IPS machinery range to achieve 60,000 preforms/hour. Lightweighting could also be improved, resulting in preforms weights of 4.5 g (25mm neck). Retal explained in the same issue the adjustments which had been made to realise a 6 l container as a successor of a 5 l container, but with the same weight and improved performance. 2019 Nissei ASB moved preform cooling from the injection station to the conditioning station (issue 1+2). Called “Zero Cooling”, the injection station is ready for the next cycle without cooling waiting times, increasing productivity by a factor of 1.5. In issue 3 we reported on Huayan’s journey to the US. Many of their designs are intended to lightweighting, just as the then new 4.0 g preform for 250ml bottles (photo next column on the top). GDXL featured at Chinaplas its multi-layer co-injection solutions, allowing gradual colour change along the preforms. The solution can be achieved by modifying injection equipment into a co-injection system. (issue 5) How preform storage can affect a bottle’s performance was discussed in an article by PTI in issue 7+8. As a rule of thumb, the older the preform, the more difficult the processing; and while drier preforms stretch less, moisture is more impactful on the properties of larger diameter preforms. Stefan Bock, CEO of ReduPET explained in issue 10 why injection moulding and stretch blow moulding do not fit perfectly together, and how weak points can be overcome. During our Editour India we learned at Chemco that the trend towards small packaging sizes means that overall output is declining. The company manufactures preforms for Coca Cola’s 250ml bottle, and planned developments in the area of multi-layer. Nishant Mouldings from India manufactures almost 200 different preform designs, from 7.6 g to 735 g and 25-120mm neck size. Sustainable manufacturing was on the company’s top agenda (issue 11). Each preform manufacturing process has its advantages and disadvantages. How can a converter find the right process for his requirements? Moraldo Masi, Sacmi: “First of all, everybody should be aware of the various different technology existing in the market to produce bottles/containers. You may use single or double stage, injection, compression or a mix of different technologies. Although the main driver for the correct choice remains the TCO and operating costs, it is becoming more important every day to reach high quality standards, and this feature may change a lot from one technology to another and from one market to another. In our portfolio we have several technologies and we are quite accustomed to support our customer in their choice with this way of thinking.”","@ID":22}, "PREFORM PRODUCTION 34 PETplanet Insider Vol. 20 No. 12/19 petpla.net empowered by Drinktec New Zealand Australia Philippines Taiwan South Korea Japan Let Your Inspiration Flow. From Down Under to Japan It’s time for the Editour Road Show to hit the road again! The start of the new decade will see us undertaking a trip from Australia and New Zealand to Japan, via the Philippines, Taiwan and South Korea! With support from Drinktec, the world’s biggest beverages show, we will be shooting off to Australasia in April. Our journey from south to north will see our team visit a variety of locations, countries, cultures and climate zones, with different vehicles. From the legendary, biodiverse sceneries of Australia and New Zealand and with numerous interview visits in between, PETplanet and the Editourmobil will finish the Tour with a visit to Japan, the Land of the Rising Sun! Make sure you’re on board when we set off on our next adventure and get ready for in-depth analyses of the special features and trends in these bottle and beverage sectors! Interested in being visited? barton@hbmedia.net","@ID":36}, "TRADE SHOW REVIEW PETplanet Insider Vol. 20 No. 12/19 petpla.net 41 100% rPET Beyond Juice bottle Wide-neck containers for hot filling The third new product KHS presented at the K trade show was its latest development for hot filling: a wide-neck PET container that can be manufactured using the blow-trim process or from preforms with an injected, possibly crystalline, neck finish. The new process heats the blow moulds for thermal conditioning; later when the containers are filled and sealed, they should be able to withstand both positive and negative pressure. “The idea is that switching to PET in a market dominated by disposable glass for wide neck containers would result in significant CO 2 savings in terms of manufacturing, weight, transport and recycling,” Langhammer explained. Filling temperatures could also be a little lower than before as pasteurisation takes place at lower temperatures, due to PET’s good insulation. In the best case scenario, CO 2 emissions could fall by up to 90 per cent, especially when using rPET. KHS says that the container could also be provided with the Fresh Safe PET coating for oxygen-sensitive products. www.khs.com P R E F O R M M O N I T O R I N G PreMon® Powerful. Compact. Preform Monitoring. W W W . I N T R A V I S . C O M / P R E F O R M","@ID":43}, "PREFORM PRODUCTION PETplanet Insider Vol. 20 No. 12/19 petpla.net 24 Medium-sized company from Bangalore invests in new equipment Extension to the portfolio of preforms by Kay Barton April 2019, We met: Mr Madhav Jagani, Director Marketing Mr Harshit Vankani, Director Finance Fillenpac, which was founded as a converter, less than five years ago and is based in the north-west of Bangalore, specialises in preform and bottle production. Within a year, the company – led by Mr Madhav Jagani, Marketing Director and Mr Harshit Vankani, Finance Director – invested in a fully-electric Husky HP 180 with 40 cavities. It did so in the quest to win new customers, while offering existing customers added value in terms of quality. What started out as an experiment opened up new avenues for growth. It’s a decision that is now, clearly, paying off. Founded in 2015 as the sister company of Crystal Polymers, Fillenpac ultimately outgrew its subsidiary role and acquired its parent company in 2012. Change and expansion have continued; over the past two years it has seen revenues grow by approximately 200%. “This year, business has been very buoyant; we’ve had between 30 and 40 enquiries so far alone,” said Mr Jagani. While the size of Fillenpac in the Peenya Industrial Area in Bangalore is still currently manageable, it looked to us during our visit as if it using pretty much all the available space in its current premises. This was confirmed by the revelation that expansion is already planned to take place this year. The company has been using injection moulding equipment from Larsen & Toubro and Ferromatik Milacron in the manufacture of preforms and 20l water containers, from the day it first opened its doors. The decision to enter the world of the Husky was taken quite early in its existence. “We wanted to have a reliable preform production machine on board, whose products would provide high quality added value for our existing and potential customers,” Mr Jagani reported. “In 2016, we opted for a Husky system – not least, because of the accommodating approach they took during the negotiations, and the promise that we would benefit from three years’ after-sales service.” As we left the office suite and entered the production hall, we saw the latest baby in the machine park straight away. The Husky machine was undergoing scheduled maintenance and wasn’t running while we were at the plant but Mr Jagani told us that it is being used more and more. At first, it was needed only weekly; it is now being used every day. “We have six customers, all situated in and around Bangalore, who currently generate all of our workload,” Mr Jagani stated. The four machines from Larsen & Toubro and Ferromatik manufacture preforms in the 28mm Alaska range; the Husky machine produces 28mm preforms for CSD and hotfill. “The material savings in necks that we have achieved with the Husky have been welcomed very warmly by the customers. The preforms we are making are 0.3 g lighter in this area than comparable preforms from competitors, while maintaining the same quality,” Madhav Jagani explained. We were advised that the lighter preforms are now being tried out for the first time by customers in the state of Tamil Nadu. Since January, Fillenpac has also been able to offer hot-fill preforms. Around 75% of the preforms and PET containers it produces go to bottlers of water and beverages, 15% to the edible oil industry, and 10% to manufacturers of jars. Within the 930m2 facility, the company’s team of 32 processes approximately 8 t of PET material per day. “We are looking to the future positively and are now considering whether to open a plant in Gujarat in 2021,” Mr Jagani concluded. www.fillenpac.com Tour Sponsors: Wide-mouth preforms produced on Ferromatik Milacron equipment Short-neck preform production with (f.r.t.l.) Harshit Vankani, Kay Barton and Fillenpac staff","@ID":26}, "PREFORM PRODUCTION PETplanet Insider Vol. 20 No. 12/19 petpla.net 14 PREFORM Special A review of preform developments When designing preforms, a number of parameters have to be defined, like the overall shape, the neck finish and mechanical and barrier characteristics that need to be achieved. The length of the preform results from the bottle’s height (minus neck) as well as the axial stretch ratio, while the core diameter results from the Hoop stretch ratio and the bottle’s diameter. The preform wall thickness results from the bottle wall thickness multiplied by the biaxial stretch ratio. To produce PET bottles, preforms have to be manufactured and stretch blow moulded. Both processes can be carried out independently using different machinery (2-stage process) or in a single-stage process. In the 1-step or single-stage process, PET resin is melted and moulded into a bottle in one machine, using residual preform heat from the injection or injection-compression process to blow mould bottles into an equal number of blow cavities. In the 2-step process, preforms are manufactured on injection moulding machines as a first step by melting and moulding the PET resin. The finished preforms with a complete neck can then be re-heated and stretch blow moulded into bottles in stretch-blow moulding machinery in a second step. In 1995, Nissei ASB developed the 1.5 step moulding method, in which preforms are injection moulded, partially cooled to maximise stability and then temperature conditioned before being passed to a blow mould. This blow mould usually contains a third of the number of cavities of the preform mould (as it takes three times longer to injection mould preforms than to blow bottles). Each process has its advantages and disadvantages in terms of output or flexibility (amongst other factors), and preferences changed over the years. Enjoy the journey through 20 years of PET preform developments, the last topic of our jubilee year series! First of all, a look back over the past 20 years: What developments have been particularly influential to your activities in the area of design/system manufacturing for preforms? Moraldo Masi, PET Business Director Closures, Containers & PET BU Sacmi: “For many years the main driver was product light-weighting, one of the pillars of environmental protection and sustainability. Then, the focus broadened and achieving a circular economy became another tool for reaching real sustainability and protecting the environment. Everybody is working on new development based on re-use/re-cycle of products; we changed our designing drivers towards this new perspective. I believe that this is extremely positive and a big opportunity for companies strongly involved in PET products manufacturing systems, due to the fact that PET is the only fully multiple recyclable polymer and has perfect physical and mechanical features to make packaging.” Pablo Fiorentini, Global Sales Director, Preform Systems & Tooling Sipa: “As producers of preform systems, our main focus has always been trying to increase production capacity per installed unit with consequent benefits in terms of energy consumption and CO 2 emissions. Flexibility is our key word, we give customers complete freedom of choice thanks to the very high level of compatibility of our Xform Preform machines with moulds of different generations and different manufacturers. Always focused and attentive to the environmental impact of the industry to which we belong, we work tirelessly to propose ever lighter container solutions that meet the expectations and specifications required by our customers. Developing lighter preforms and thinner walls leads to multiple benefits, including a reduction in the total volume of processed PET, a reduction in cycle time, a reduction in the energy required to cool down the preform itself and a drop in the thermal power required during the heating process inside the blowing machine ovens.” by Gabriele Kosmehl","@ID":16}, "MARKET SURVEY 28 PETplanet Insider Vol. 20 No. 12/19 petpla.net 12/2019 MARKETsurvey Company name Starlinger Recycling Technology Boretech Environmental Engineering Co.,Ltd. Empacar S.A Postal address Telephone number Web site address Contact name Function Direct telephone number E-Mail Furtherstrasse 47, 2564 Weissenbach, Austria +43 2674 808 3101 www.recycling.starlinger.com Mr Paul Niedl Commercial Head - Div. recycling techn. +43 2674 800 3100 sales.nd@starlinger.com No.888, Jiuliting Avenue, Caoqiao Street, Pinghu, Zhejiang, China +86 573 85120 186 www.bo-re-tech.com Mr Alan Ou Senior V.P. +86 573 85136190 sales@bo-re-tech.com Parque Industrial 45, Santa Cruz de la Sierra, Bolivia +591 3 34655 25 www.empacar.com.bo Mr Carlos Limpias Elío General Manager +591 3 34655 25 climpias@empacar.com.bo Bottle to granulate Four models: recoStar PET FG, recoStar PET FG+, recoStar PET iV+, recoStar PET iV+ Superior Input variable: collected pressed bottles, various colours Starlinger recycling technology offers the engineering of washing lines and / or a turn-key project with components and technologies available on the market Output: Granulate with approval Yes (decontaminated for food contact, IV increased, AA 1ppm, lowest VOC level) Yes, for food grade, IV increased, AA 1ppm,lowest VOC level Capacity [t/a] 6,000-26,000 (rPET pellets) Up to 36,000 Floor space [m²] Depending on design Depeding on design Which approvals Several USA/FDA (C-H), Austria, Germany/BfR, Ilsi, France/AFFSSA, Finland, Australia, Canada, Egypt, Japan, Switzerland, several Latin American Countries (Bolivia, Brazil, Chile, Colombia, Ecuador, Guatemala, Peru); follows EFSA requiremens; several brand owners Flakes and Granulate FDA approval Fresh water consumption per tonne output [m³/t] Depending on design 1.5 Consumption kWh per tonne output [kWh/t] Depending on design 550 (including washing, pelletising, SSP) Flakes to granulate Four models: recoStar PET FG, recoStar PET FG+, recoStar PET iV+, recoStar PET iV+ Superior Input variable: flakes, coloured proportion max 5%, not much chlorine PET flakes 10ppm, PVC max content Output: Granulate with approval Yes (decontaminated for food-contact, IV increased, AA 1ppm, lowest VOC level) Yes: EFSA and FDA approved technology Capacity [t/a] 1,500-26,000 (7 extruder sizes) 8,000-20,000 8,000 Floor space [m²] 130-540 300-500, depeding on design 3,000 Which approvals Several USA/FDA (C-H), Austria, Germany/BfR, Ilsi, France/AFFSSA, Finland, Australia, Canada, Egypt, Japan, Switzerland, several Latin American Countries (Bolivia, Brazil, Chile, Colombia, Ecuador, Guatemala, Peru); follows EFSA requiremens; several brand owners Granulates with FDA approval Coca-Cola , Pepsico , Local Government Fresh water consumption per tonne output [m³/t] Approx. 0.15 No fresh water needed 1.5 Consumption kWh per tonne output [kWh/t] Approx. 410 (depending on design) 150-300, depending on design 333 Bottles to flakes Input variable: collected pressed bottles, various colours Starlinger recycling technology offers the engineering of washing lines and / or a turn-key project with components and technologies available on the market Pressed and loose bottles, clear, green and blue Output: Flakes with/without approval Yes (decontaminated for food contact, IV increased, AA 1ppm, lowest VOC level) Flakes with FDA approval Capacity [t/a] 3,700-10,500 (5 sizes) 4,000-72,000 12,000 Floor space [m²] Approx. 150 800-4,500 3,000 Which approvals FDA (hot-fill), follows EFSA requirements CE Coca-Cola , Pepsico , Local Government Fresh water consumption per tonne output [m³/t] 1.5 1.8 Consumption kWh per tonne output [kWh/t] 120-250 (incl. bottle washing to SSP) 350 Kind and quantity of detergents NaoH (2-3kg/t output), and brand detergent (1-1.5l/t output) 0.4kgrs/t Removal of the organic residuals up to which size [μm] Water filtration up to 1μm 1,000μm or 30 Mesh Presetting residence time in the process 360-400min in SSP @ 200-210°C Company also offers systems for Bottle-to-film Yes Yes Bottle-to-fibre Yes Yes, one stop solution from post-consumer bottles to PSF No Bottle-to-strapping Yes Yes, 100% rPET strap 8 -20mm width; yes, 700mm width, 0.1-1.5mm thickness","@ID":30}, "MARKET SURVEY 27 PETplanet Insider Vol. 20 No. 12/19 petpla.net 12/2019 MARKETsurvey Resins & additives Preform machinery Preform production & inspection Preform & SBM mould manufacturer SBM 2 stage Compressors Filling equipment & inspection Caps & closures & inspection Palletising & shrink film machinery Recycling Suppliers of recycling plants and washing units This time we close our annual market survey with a deeper look at suppliers of recycling plants and washing units. Find out more about new developments of the participating companies: Krones AG, Reciclar S.A., Previero N.- Sorema, Starlinger Recycling Technology, Boretech Environmental Engineering Co.,Ltd., Tecnofer, Amut SpA, Erema Group, Empacar SA. and Gneuss Kunststoff GmbH. Although the publisher have made every effort to ensure that the information in this survey is up to date, no claims are made regarding completeness or accuracy. Company name Krones AG Reciclar S.A. Sorema Div. of Previero Srl. Postal address Telephone number Web site address Contact name Function Direct telephone number E-Mail Böhmerwaldstrasse 5, 93073 Neutraubling, Germany +49 9401 70 0 www.krones.com Mr Peter Hartel Head of Sales PET Recycling +49 9401 70 5448 peter.hartel@krones.com Heredia 3220, Sarandi, Buenos Aires, Argentina +54 11 4205 0102 www.reciclarsa.com.ar Mr Nicolás Pell Richards Director +54 11 4205 0102 nico@reciclarsa.com Via Per Cavolto 17, 22040 Anzano del Parco (CO) - Italy +39 031 63491 250 www.sorema.it Mr Dario Previero General Manager +39 031 63491 250 sales@sorema.it Bottle to granulate Input variable: collected pressed bottles, various colours Depending on project; offering all kinds of solutions together with our cooperatioon partner Stadler 18,000 tons/year Variable quality of input material integrating bottles sorting Output: Granulate with approval Yes 9,600t/a Engineering and system integrated for complete system Capacity [t/a] 3,500-30,000 t/a 25,000t/a of flakes Up to 7,000 kg/h Floor space [m²] 1,000-6,000 22,000 According to sizes of plants and customer buildings Which approvals FDA-LNO, EFSA-LNO, brand owners FDA; local for food contact Depend on customer specifications Fresh water consumption per tonne output [m³/t] Max. 1.5 Depend on input quality Consumption kWh per tonne output [kWh/t] Depending on design Depend on sizes and plant configuration Flakes to granulate Input variable: flakes, coloured proportion max 5%, not much chlorine Depending on project No Output: Granulate with approval Yes No Capacity [t/a] 3,500-30,000 No Floor space [m²] 800-3,000 No Which approvals FDA-LNO, EFSA-LNO, brand owners No Fresh water consumption per tonne output [m³/t] Max. 1.5 No Consumption kWh per tonne output [kWh/t] Depending on design No Bottles to flakes Input variable: collected pressed bottles, various colours Depending on project; offering all kinds of solutions together with our cooperatioon partner Stadler Variable quality of input material integrating bottles sorting Output: Flakes with/without approval Flakes with/without approval Engineering and system integrated for complete system Capacity [t/a] 3,500-30,000 Up to 7,000 kg/h Floor space [m²] 1,000-4.000 According to sizes of plants and customer buildings Which approvals FDA-LNO, EFSA-LNO, brand owners Depend on customer specifications Fresh water consumption per tonne output [m³/t] Max. 1.5 1-2.5 Consumption kWh per tonne output [kWh/t] Depending on design 220-270 Kind and quantity of detergents Confidential Removal of the organic residuals up to which size [μm] Best results, values according to standards Presetting residence time in the process Confidential Company also offers systems for Bottle-to-film Yes Engineering and system integrated for complete system Bottle-to-fibre Yes No Bottle-to-strapping Yes Yes Engineering and system integrated for complete system","@ID":29}, "PETpatents www.verpackungspatente.de PETplanet Insider Vol. 20 No. 12/19 petpla.net 48 Pivotable bottle Intern. Patent No. WO 2019 / 030333 A1 Applicant: Maura Oerding, Berlin (DE) Application date: 9.8.2018 Drink bottle consisting of lower and upper part, which can be connected with each other to pivot and twist to enable a comfortable drinking position. Stackable bottle Europ. Patent No. EP 3431408 A1 Applicant: Brian Leonard Lodge, Milton Keynes (GB) Application date: 18.7.2017 A PET bottle with more than two litres of content is shaped so that two different handles can be slid over the bottle neck – depending on consumer wishes – but a good stackability is still guaranteed with both handles. Coated PET container Europ. Pat.issue No. EP 3218276 B1 Applicant: Graham Packaging Comp., Lancaster (US) Application date: 10.9.2015 Procedure for manufacturing PET containers with improved silicon dioxide coating. Divided container Intern. Patent No. WO 2019 / 030758 A1 Applicant: Johny Belah, Ramla (IL) Application date: 8.8.2018 To achieve sufficient freshness in a carbonated drink, it is proposed to divide the bottle into several areas / chambers that can be opened separately. Hot filling Intern. Patent No. WO 2019 / 040749 A1 Applicant: Graham Packaging Company L.P., Lancaster (US) Application date: 23.8.2018 Container for filling with hot products. The base is specially shaped to be able to absorb in a certain way the forces that arise during cooling. Small-volume wine bottle Intern. Patent No. WO 2019 / 054866 A1 Applicant: Creative Cloud Company B.V., Hilversum (NL) Application date: 13.9.2018 Small-volume, compact bottle made of plastic (PET) with screw cap for intake of wine. Preferred usage area is the catering sector in aeroplanes, trains or similar. One bottle is designed to fill one glass.","@ID":50}, "TRENDS PETplanet Insider Vol. 20 No. 12/19 petpla.net 36 How changing consumer preferences are influencing plastic packaging trends by Henry Zhang, Director of Marketing and Market Intelligence, Husky Injection Molding Systems In the rapidly changing world around us, food and beverage retail companies face a confluence of constantly evolving demographic shifts and consumer preferences. This constant change requires brand owners and packaging companies to move quickly to better align their offerings with consumer lifestyle interests and values. As a leading industrial technology provider to the plastics processing community, Husky Injection Molding Systems continuously monitors and assesses consumer trends and their impact on the food and beverage packaging markets. Based on research and collaborative partnerships with customers, suppliers, and industry partners worldwide, Husky has identified five consumer trends that have begun to transform the market. 1) Millennials want more personalised and customised offerings The preferences and buying habits of today’s millennials vastly differ from previous generations. This new generation of consumers desire products personalised to their unique needs, styles, or tastes. They are looking for an increased variety of customised offerings on the shelf. Building a strong connection between today’s millennials and brands requires providing something unique that aligns with the personal needs and values of these consumers. Doing so requires a significant number of new product varieties combined with the need for more flexibility in processing different package designs – shapes, sizes, forms, colours, flavours and messages. For package producers, it is challenging to provide a continual flow of products to keep up with these changing preferences. To help meet these challenges, Husky has developed a platform of flexible packaging solutions, from large-capacity, high-efficiency products to varieties that are customised and changing all the time. For example, for high volume, single SKU products, the company’s HyPET HPP5 system is engineered to deliver high productivity, quality, and consistency for driving down total cost of ownership. For the middle output, multiple package market, the company’s new NexPET system’s flexible design allows for shorter production runs and frequent changeovers while maintaining high-quality performance. 2) Increasingly discerning health-conscious consumers Today’s increasingly discerning health-conscious consumers are looking for more healthy products containing natural ingredients. Nutrition that supports both physical and emotional well-being is top of mind. Many consumers are moving away from processed foods containing additives and preservatives, reducing their intake of sugar, fat and salt ingredients, and favouring fresh foods, personalised nutrition solutions, and plant-based options. While a new generation is emerging, the market is also experiencing another demographic shift as a large portion of the global population ages. Ageing consumers who once regularly consumed two-litre carbonated beverages are now more health conscious and looking for food and beverages with more nutritional value. This older generation’s increased health consciousness creates unique needs for personalised consumer products. It also drives multiple changes to market The new NexPET Mold is a flexible mid-volume tool for shorter production runs and frequent changeovers.","@ID":38}, "PETcontents 4 PETplanet Insider Vol. 20 No. 12/19 petpla.net 12/19 INSIDE TRACK 3 Editorial 4 Contents 6 News 46 PET bottles for Beverage + Liquid Food 48 Patents RECYCLING 10 A step towards enlightenment - PET processor in India focuses on recycling awareness MOULD MAKING 10 PET moulds from Turkey PREFORM PRODUCTION 14 A review of preform developments 22 Diversity in plastic conversion - From household products to preforms and beyond! 24 Extension to the portfolio of preforms - Medium sized company from Bangalore invests in new equipment 25 Larger bottle, less weight - Delivering sustainability through lightweighting 31 Progressive preforms - Considerations when designing preforms 32 Raising the standards - Very high cavitation tooling 35 Eastern India’s largest PET converter on sustained growth course TRENDS 36 How changing consumers preferences are influencing plastic packaging trends MARKET SURVEY 27 Suppliers of recycling plants and washing units TRADE SHOW REVIEW 38 PET Day 2019 40 Sustainable technologies for beverage, food and non-food - KHS presents a bottle made from recycled materials, containers with clip-on handles, and wide-neck containers 42 A recycled vision in white - Light barrier white opaque bottles successfully trialled 43 PET preform and container measurement 44 K show review, part 1 BUYER’S GUIDE 49 Get listed! Page 36243610 Page 42 Page 40","@ID":6}, "PREFORM PRODUCTION PETplanet Insider Vol. 20 No. 12/19 petpla.net 31 Considerations when designing preforms Progressive preforms Producing the perfect preform is part of a work in progress; a circular and sustainable preform that allows consumers to enjoy convenience and brands to reduce their environmental impact needs stakeholders across the packaging value chain to take responsibility for their sphere of influence. For preform producers, understanding that their sphere of influence is active on both macro and micro levels means that producing the perfect preform is an exciting challenge. When it comes to develop preforms, global plastic packaging producer Retal draws in experts from design, recycling and production. These experts come both from within the company and from its vast network of multinational food and beverage brands. The core of a perfect preform lies in valuing the circularity of plastics packaging, states the company: rather than seeing the preform as a one-use unit, it should be seen as a potential source of ongoing value. To realise the preform design, Retal takes advantage of the latest CAD software from Dassault Systèmes, augmented with bespoke patches, to allow them to create precise information regarding performance relating to the distribution of the thickness and stretch ratio of the bottles without needing to produce a physical product. Designer Andzejus Buinovskis says, “Having 3D models of the preform and a bottle, we can simulate different stretch blow moulding settings, including preform temperature distribution, stretch rod movement, pre-blow and final blow pressure variations. It is a powerful tool that saves considerable time and money associated with prototyping. In one case, stretch blow moulding and top load simulations with two preforms of the same weight but different geometry showed us that one preform will produce a better, stronger bottle.” Design to recycle Practical advantages that contribute to the circularity and sustainability of its preforms, and to improve its overall environmental footprint have also to be taken into account. “Design to recycle” is increasingly important, with a crucial understanding that by designing products that can be easily and effectively recognised, directed to their corresponding recycling stream without disrupting the recycling process or hindering the quality of the recycled material collection. Lightweighting preforms means that less raw material is used to produce containers for the same volume of liquid/product, which also makes them cheaper to transport, reducing carbon emissions. Retal is committed to integrating design to recycle principles internally and by engaging with customers to raise awareness to ensure that its preforms can be turned into more easily recyclable PET bottles which is also reflected by a membership in the design for recycling platform RecyClass. The aim of this initiative is to improve the design of plastic packaging so that is more easily recyclable into high-quality recyclates which can be reused again and again. RecyClass’ Chairman Paolo Glerean says, “We created our platform with a goal of harmonising the recyclability information across the plastics industry; we found that many actors of the plastics value chain, such as brands, converters and producers were keen to do more to make sure their products were in line with circular economy, yet the overwhelming and differing amount of information, on what is recyclability, is what made this task overly complicated. In our RecyClass tool, the A-F ranking provides a clear, reliable classification for plastic packaging, with clear suggestions on how to improve recyclability, in case there is room for improvement.” www.retalgroup.com PREFORM Special +44 (0) 1254 584210 sales@petmachinery.com petmachinery.com Active for over 25 years, our global network and specialist knowledge makes us the go-to company for the sale or purchase of a PET machine. Commercially savvy, we work closely with our customers and our global network, to make sure everyone gets the best deal. Providing comprehensive advice throughout your sale or purchase; we can arrange dismantling, loading, packing, shipping, specialist insurance and commissioning. If you have amachine to sell or you’re looking to purchase, please get in touch. THE INDUSTRY EXPERTS","@ID":33}, "PETplanet Insider Vol. 20 No. 12/19 petpla.net 46 PETbottles Beverage + Liquid Food Bulbous bottle for almond drink In the USA, company Califia Farms is selling 1.4 l of a vanillaflavoured almond drink in a bulbous, easy-grip bottle. The product is kosher, vegan and free from gluten, soya and milk constituents and carrageen. The transparent bottle is BPA free and is decorated with a milky sleeve label with a design typical of the brand. It is sealed with an opaque screw cap with detailing that also enables a secure hold on the bottle when unscrewing. www.califiafarms.com Triangular bottle area Company Alaska Glacier Products is bottling 500ml of water from a lake fed by a glacier in Alaska. The bottle is transparent and is round at the base then becomes triangular from around 2 cm from the base and then returns to a round shape above the label area. In places, the label has a no-label effect, giving a clear view of the “Clear Alaskan Glacial” water. A transparent screw cap with tamper-evident seal completes the packaging. www.alaskaglacier.com PETValue Chain Conference: Building a positive future Leading the change towards a sustainable industry with commitments to circularity NEW Recycled Polymers Training Course CLICK TO FIND OUT MORE INFORMATION 120+ ATTENDEES 90+ COMPANIES 32 COUNTRIES 22 SPEAKERS NUMBERS FROM 2019:","@ID":48}, "PREFORM PRODUCTION PETplanet Insider Vol. 20 No. 12/19 petpla.net 16 PREFORM Special In the following issue, Husky published a table that showed a 216cavity tool for the 65 t HyPET 650. 2007 Otto Hofstetter announced the next stage in the “more cavities, less tonnage” race (issue 7): 128 cavities on a 350 t system set a new benchmark. We recall, in 2001, 96-cavities on a 600 t system made headlines! Also in issue 7, Sacmi presented their PAM preform compression moulding system. Netstal announced their new, small 200 t preform system in issue 11, covering the range of 24-60 cavities. 2008 The continuous process of compression moulding preforms ensures that all preforms are exactly the same – as shown by Sacmi at an Open House in Italy at a prototype machine (issue 3). Processing the material at a 10-15 °C lower degree than IM eliminates the AA problem. In issue 5 we reported for the first time about Netstal’s Prelactia solution, the co-injected multi-barrier preforms for the dairy sector. 2009 Preform production taking place at an altitude of 5,000m: Husky reported the successful installation at Glacier Mineral Water in issue 5. Netstal managed to squeeze 60 cavities onto their small 200 t machines using an Otto Hofstetter tool (issue 9). Husky caught the eye in issue 10 with a special preform system for direct processing of PET containing a high percentage of flakes. 2010 For issue 3 we visited AMD in India which was then producing 18,000 t of preforms per year on a vertical KraussMaffei system. Netstal moved towards reducing energy consumption on their PETline systems (issue 4) but also towards achieving shorter cycle times. The newly developed Calitec system had been installed in Netstal systems with up to 192-cavities. In issue 7+8 GDXL featured its patented conical-base preform, saving weight and material. On the market since 2006, it had now come into operation at Coca-Cola in China. GDXL’s patented conical base preforms At K show, Netstal showed a new version of its PETline platform, operating with 60 cavities at 2,000 kN clamping force (instead of 3,500 kN previously). 0.5 l preforms were produced at a cycle time of 9 s (issue 9). Also at K, Husky launched its H-PET AE (all electric) preform injection moulding system (issue 10). The small system addressed the needs of consumers in emerging markets and low-volume producers. 2011 A new competitor in the preform tooling sector: in issue 1+2 Mold-Masters presented its complete preform system. Using their patented conformal cooling technologies called iCool, the company developed a complete mould solution for preform moulding. Issue 3 saw preform production containing up to 100% of PCR. Sipa’s preform injection moulding equipment designed for this function ranged from 96 down to 24-cavities. In the same issue, Husky introduced a recycled flake system, the HyPET RF, with an injection unit specifically designed for recycled flakes. Custom-made preforms were making a significant contribution to turnover for Retal Dnipro when we visited them in 2011 (see issue 4), and lightweighting was the need of the hour. For the 0.5 l bottle, the preform was slimmed down from 26 to 15.7 g. “Investing first, then getting orders” was the mantra of Rajat Kedia when we visited Manjushree in Bangalore (also issue 4). Being the first and then only company in India to have their own preform tools, they became the largest preform producer in India. In which areas do you see opportunities to further improve PET preforms and how do they influence your R&D work today? Moraldo Masi, Sacmi: “I think that many plastic packaging that until today have been produced with different material, could very soon be produced in PET. I’m referring to the dairy, food, pharma etc. sectors.” Pablo Fiorentini, Sipa: “Since we have been pushing towards unimaginable limits, the engineering of the preforms must be directly linked to the required characteristics of the final container. The study and application of the correct quality of PET material are increasingly the key to the success of projects.”","@ID":18}, "PETplanet Insider Vol. 20 No. 12/19 petpla.net 47 BOTTLES Coconut water in PET Zico Beverages LLC is bottling “natural organic coconut water“ in 400ml bottles. The liquid is bottled in Thailand and is kept chilled. The easy-grip bottle is slightly conical in shape but bulbous at the base to improve structural stability. All retail information is communicated via the sleeve label, which is reminiscent of sunshine and beach in colouration and design. The green screw cap is printed with the test stamp “USDA Organic”. www.zico.com Water with collagen The American manufacturer of collagen products – company Vital Proteins – also has a water with collagen in its range. Alongside 10 g of collagen and 1 g of sugar, the pictured variety also contains a dash of lemon juice to round off the flavour. The slim, transparent bottle holds 355ml/ 12 fl oz and is decorated with an appropriately designed matt sleeve label and a white screw cap with a tamper-evident seal. www.vitalproteins.com","@ID":49}, "TRENDS PETplanet Insider Vol. 20 No. 12/19 petpla.net 37 offerings, whether it’s smaller packages or more varieties of beverages with nutritious ingredients and supplements, such as coconut water, infused vitamins, etc. This requires packages to be designed and manufactured to better protect this sensitive content. Husky rates its multi-layer technology to serve this trend, as it is an integrated solution for plastic packaging that provides a barrier against oxygen and light to keep product contents fresh and nutrient rich. The ability to precisely dose the barrier layer and adjust the content range ensures seasonal variations are considered for enhancing package shelf life, while providing a potential savings of up to 50 per cent on barrier material costs for some applications – thereby reducing the total cost to produce per package. 3) Consumer preference for more convenient premium packaging More than half of the global population currently resides in cities, and the United Nations predicts this number to grow to 68% by 2050. This rapidly growing shift from rural to urban living is largely driven by a desire for economic empowerment. With urbanisation and wealth increasing, consumers are looking for premium products that are convenient. Packaging is usually central to the marketing of premium products, since it is often the package quality that signals a product’s high-end status. To make their products stand out against the competition, brand owners want creative package designs that catch the eye of consumers. Different dispensing systems enable the production of more userfriendly premium closures, such as flip-tops, sports caps, or extratall closures. With the capability to produce various colours, sizes and shapes, Husky’s multi-layer technology is claimed to allow for more creative decorative packaging solutions. For example, innovative materials added to packaging’s middle layer can enable phosphorescent bottles that glow in the dark, appealing colour gradients, or packages that react to temperature changes. 4) Growing interest in e-commerce and on-demand purchasing Many consumer habits are driven by convenience. Same-day home delivery, drive-up and pick-up grocery services, and other digital shopping services are becoming increasingly popular. It seems that the consumer preference for fast delivery and purchasing products online is quickly becoming the expected standard. This rapidly growing interest in e-commerce brings a wealth of new challenges and opportunities. Brand owners and plastic packaging producers must respond to market demands in a much faster way and change products more quickly to meet changing preferences. Faster package redesign and speed-to-market for new products are key to gaining a premium position and growing market share. The Next Generation Operating Model (NGOM), which is a digitalised, end-to-end manufacturing system is intended to offer enhanced capabilities to deliver solutions with unmatched speed and flexibility. Husky developed the automated manufacturing system to enable hardware to be configured through a web interface and then produced in a state-of-the-art laboratory through an automated process, ensuring that customers can more quickly respond to changing consumer preferences. 5) Demand for more sustainable, eco-friendly packaging Consumers are more environmentally conscious, placing more emphasis on the environment and recyclability. Demonstrating a commitment to sustainability is something consumers are increasingly demanding of the companies they choose to purchase from, and brands are responding with bold commitments to sustainable, eco-friendly products and packaging solutions. Sustainability has become a predominant theme in the plastics packaging industry. Maximising the use of recyclable and post-consumer resin (PCR) in packages and closures is in strong demand now and will continue to be in the years ahead. To meet this market need requires manufacturing systems with precise, controlled technology to ensure that high productivity and quality standards are maintained. Today, Husky is developing other high-precision systems for producing packaging with higher levels of postconsumer resin (PCR). This includes Husky’s HPP5e systems that can process 100% PCR and multi-layer technology solutions that can help increase PCR content for bottles, pails and other packages. With continued innovation in mechanical recycling, the company is also in the process of developing a new system focused on incorporating PCR in packages, intended to enable customers to bring more than 60,000,000 kg/a of PET into the circular economy. Working in conjunction with equipment that purifies the recycled material and eliminates intermediate steps of pelletising and re-melting, the system is stated to offer additional value in both operational savings and material quality. www.husky.co Launched in April 2019, HyPET HPP5e is Husky’s highest productivity system.","@ID":39}, "TRADE SHOW REVIEW PETplanet Insider Vol. 20 No. 12/19 petpla.net 42 Light barrier white opaque bottles successfully trialled A recycled vision in white While progress has been made across the board in recycling PET, the challenge of white bottles had remained. Can a white opaque masterbatch be used in PET monolayer bottles, including recycling rates of up to 100%, without impacting production and/or end product property like light barrier? Sukano and Sidel technically proved that Sukano-designed white opaque masterbatch formulations can be used in PET monolayer bottles, and still be processed at the same machine throughput. This was realised by using Sidel’s most recent generation of blow-moulders, EvoBlow, with no impact on colour, properties, functionality or production rates, according to the two companies. Sukano’s technical expert team started by formulating monolayer PET white bottles masterbatch and submitting them for recycling using the European PET Bottle Platform (EPBP) protocol. The melt viscosity, pressure and stability, were determined to be well processable. In addition, the high-quality melt filterability indicated its purity and consistency. The melt also showed very stable colour, with the end material remaining white at all levels, very similar to the initial virgin PET white bottles – also at 100% rPET. Finally, the IV was also reported stable, with a level of 0.65 at all stages of recycled PET. The Solid State Polymerisation (SSP) process evidenced a similar rate as for the virgin PET, with an IV level of 0.7/0.8. As one of the key factors, no agglomerations were found. Thanks to the formulation and ingredients used by Sukano technical experts, including selected raw material surface treatments that are compatible and stable during recycling. Michael Kirch, Global Head of R&D at Sukano stated: “We are convinced that the design guidelines for the recyclability of white opaque PET bottles can be enhanced to reflect the required technical requirements that enable bottle-to-bottle light barrier white opaque PET to come to life.” When design formulation expertise successfully meets top-edge blowing technology Sidel, a leading provider of equipment and services solutions for packaging food, beverage, home and personal care products in PET, can, glass and other materials, used the recycled material in its high speed PET blowing machine, to produce 25%, 50% and 100% light barrier white opaque rPET bottles. The light barrier was adjusted by adding a Sukano-designed white PET masterbatch formulation, except in the 100% rPET content bottle. In this case, the difference in terms of colour shade versus the original virgin bottle was barely noticeable, and the integrity of the light barrier was confirmed for extreme conditions, such as less than 0.1% light transmission at the 550nm wavelength. “We saw no measurable difference in processing conditions or blowing output while processing the 100% recycled white PET material from Sukanodesigned white masterbatches, even under the most challenging conditions,” said Naima Boutroy, Global Packaging Expert from Sidel. “While a few adjustments to the process may be needed to optimise the overall result, our joint achievement and proof of concept enables us to raise the bar, with great bottle mechanical and physical performances.” It is now clear that a routine can be established to create an official outlet for opaque PET bottles, and the impact on the environment could be relevant. The companies state that one of the greatest achievements of the collaboration is the demonstration that a light barrier white opaque PET bottle can indeed be up to 100% bottle-to-bottle recycled, going back to the same application or being upcycled and used for new added-value outlets. “Every local market is a key player to ensure that the circular economy does indeed join up. We are happy to announce we have taken another step forward by confirming the recyclability of light barrier white opaque PET bottles – and most importantly, offering an alternative end of life that goes back into its original application.” said Alessandra Funcia, Head of Sales & Marketing at Sukano. www.sukano.com www.sidel.com Sukano and Sidel recently teamed up to technically prove for the first time that making light barrier white opaque PET bottles from recycled material is possible – and can be done at the same throughput. Light barrier white opaque bottles (photo: Sidel)","@ID":44}, "TRADE SHOW REVIEW PETplanet Insider Vol. 20 No. 12/19 petpla.net 38 PET Day 2019 The 17th edition of PET Day, the international event organised by G.S.I. (Global Service International, Italy), attracted over 100 registered participants from more than 70 companies, from 23 countries located on four continents across the world. Current challenges for the PET industry were discussed on October 3rd at Villa Medicae, on a Tuscan hilltop near Florence, Italy, overlooking the River Arno, which was built by the famous Medici family, four centuries ago. Participants, who attend by invitation only, were greeted by an opening lecture entitled “Preparing for the Downturn”, delivered by Mr Paul Hodges of International eChem. He explained why all indicators, especially those connected to world population and its progressive ageing, say that economies are now longer growing in the way or at the rates the world has been used to. Demographic trends in the developed economies in particular will lead to rapid reshaping of their economies. The challenges and opportunities presented by these changes will require business flexibility. PET is possibly the best placed of all polymers, as the most recycled plastic in a world where sustainability is a key requirement. India: filaments, fibres and recycling Mr Gunjan Sharma, CMO Polyester of Reliance Industries of India, gave a presentation on the evolution of polyester materials. Polyesters are the fastest-growing fibres in textile markets, particularly in Africa, China and India. The markets and supply of filaments are expected to grow faster than fibres. He described the capabilities of Reliance Group in meeting new consumer tastes and behaviours. Initiatives that directly respond to and address customer needs in sustainability and comfort and make use of new communications channels, such as social media, help to create high value across the chain and to raise Reliance’s visibility, giving it a positive image. Trade wars: economic instability and threats to the WTO structure Mr Philippe De Baere, of Van Bael & Bellis, Belgium, discussed the duties and tariffs in international trade, stating clearly that trade wars are threatening the viability of WTO agreements. Some countries have cited ‘national security’ in imposing duties that avoid WTO rules, retaliation ratchets up uncertainties and there appears to be no end in sight. There are pressures for change in methods of calculating duties, based more on labour rights and environment values, rather than pure trading or commercial considerations. The uncertainty of Brexit is unlikely to be resolved until January 2020. Global supply & demand and the growing role of China In his overview of the market, Mr Francesco Zanchi, CEO of GSI and the event’s host, analysed global supply and demand, highlighting China’s continuing huge surplus in PET capacity. He stated that Europe will have to maintain high import levels in 2020 to satisfy increased demand, especially for rPET and appealed to EU representatives to facilitate its import to meet strong demand. Stringent REACH requirements and food approval certifications hamper attempts to more fully utilise available rPET. GSI was recently invited to the 2019 International Futures Forum in Zhengzhou, China, to discuss its experience in the PTA future market (ZCE), where it started operating many years ago. Mr Zanchi handed over the stage to Mrs. Zongfang Wang, ZCE futures market promotion officer, to explain the basics of the Zhengzhou Commodity Exchange. It currently has 164 members; 29 overseas bankers can operate as brokers. Mr Zanchi concluded with a session on the circular economy and the need to accelerate collection rates all over Europe. RPET demand is rapidly increasing and its scarce availability is a matter of concern. Interlude: how the PET industry helps subsistence farmers in Sierra Leone Mrs. Chiara Zanchi, president of the Saint Lawrence Foundation, showed a film on its activities in Sierra Leone, where it provides practical assistance with sustainable farming production and business activity. The Foundation","@ID":40}, "TRADE SHOW REVIEW PETplanet Insider Vol. 20 No. 12/19 petpla.net 40 KHS presents a bottle made from recycled materials, containers with clip-on handles, and wide-neck containers Sustainable technologies for beverage, food and non-food Bottle made from 100% recycled material with coating for sensitive beverages Exhibiting its “Beyond Juice” bottle concept, machine manufacturer KHS presented a solution for sustainable bottle-to-bottle beverage packaging, in line with the “circular manufacturing” principle. The bottle’s distinguishing feature is that it consists of 100% recycled PET, with “Fresh Safe PET” silicon oxide (SiOx) barrier technology for sensitive products, such as fruit juice or carbonated beverages. This wafer-thin glass layer prevents change in the bottle’s contents caused by possible bidirectional influences and can be up to 10 times more effective than regular PET containers. This innovation means that manufacturers of higher sensitivity products should now be able to fulfil current and future environmental and sustainability issues and challenges. “The container was developed by KHS together with Interseroh, the Cologne-based environmental service provider, according to its latest design guidelines for recycling. It has been given the “Made for Recycling” seal,” Philipp Langhammer, Product Manager for Barrier Technology at KHS Corpoplast explained. “It is the first PET juice bottle to be awarded 20 out of the possible 20 points.” The SiOx coating, which is designed to avoid having a negative impact on the recycled material, played a decisive role. It can be separated exceptionally well in the recycling stream in comparison with other barrier products. “As long as it is converted in accordance with specifications, the technology can be used on the InnoPET Blomax stretch blow moulder followed by an InnoPET Plasmax coating machine, for example,” Mr Langhammer continued. “Beyond Juice” was demonstrated with a sophisticated texture design and small neck label which can be separated easily during the washing process, thanks to the use of a complementary adhesive. We were shown the bottle in the “Nature Multipack”, a six-pack carrier, the bottles of which were provided with one-way adhesive joints and a simple carry strap, instead of the classic all-round wrapping. Here, too, the company has continued to focus on sustainability and material savings. PET containers of up to 2.5 l with clip-on handle KHS unveiled a new PET container development with a clip-on carrying handle, designed for manufacturers of bigger containers in the beverage, food, and non-food sectors. It should be possible to manufacture the container in sizes of up to 2.5 l using existing equipment, such as the InnoPET Blomax Series V. KHS uses moulds with two additional moving mould elements, which can be activated pneumatically. This means that mounting points can be formed on the container during the stretch blow moulding process, onto which the handle is clipped in the subsequent manufacturing. According to the company, the precise synchronisation of the mould elements with the stretching system and the valve control is important in delivering optimum pack quality. The solution is designed to ensure that containers benefit from the positive material attributes of PET, the convenient handling of a gateway handle, and an energy-efficient system such as the Blomax Series V, which uses optimised near-infra-red heating and new double-lane technology, which combine to reduce energy usage by approximately 40 per cent. The air flow for the neck, reflector and lamps are separately adjustable, and the preforms will be cooled only at the necessary points. The machine is able to handle up to 2,500 containers per hour per blowing station and can process 100% rPET preforms. Christian Wopen, PR Editor of KHS’ press agency Sputnik (right), with Kay Barton and a levitating Beyond Juice bottle","@ID":42}, "PREFORM PRODUCTION PETplanet Insider Vol. 20 No. 12/19 petpla.net 19 In the same issue we depicted the M-PET 300 preform line, which Milacron was displaying at NPE. Rich Sieradzki, VP and GM of PET Systems defined the dairy market as the development’s main target, especially in conjunction with Milacron’s multilayer technology. For issue 9, we paid a visit to the French preform giant SGT. On its 21 preform machines, more than 200 different models could be delivered with 19 different neck sizes. At the time, SGT aimed at further investments and at doubling the rPET content in their preforms. In China, we visited machinery and mould manufacturer Guangzhou Huayan Precision Machinery (issue 10). With around 600 of an estimated 1,100-1,200 PET preform injection moulding machines in the market, it held a 55% market share. At the K show, Sipa demonstrated the production of ultralight preforms on its Xtreme injection compression moulding machinery. A 6 g preform for a 500ml container was claimed to be possible. For the production of preforms made from 100% postconsumer PET flakes, Sipa partnered with Erema, resulting in the Xtreme Renew. (Issue 12) 2017 How to act in a very price-sensitive market without compromising on quality was explained to us by PT Namasindo Plas in Indonesia (issue 5). To offer the “lowest preform prices in the world”, the company manufactured very high quantities of just a few standard preforms in three sizes. Thus, 390ml bottles as well as 535ml bottles are both produced from a 600ml preform. In issue 6, Husky gave an overview of technological approaches to improve barrier performance. One of them is their multi-layer technology where a preform is produced in sequential injection or a simultaneous co-injection process. The barrier layer is then sandwiched between inner and outer layer of the preform (photo below). In the same issue, KHS presented material saving solutions in the neck and thread area – especially important for those who buy their preforms per weight. With the GEN4 hot runner design concept, Sipa manufactured the first 180-cavity preform tooling in the world. Fitting on a regular 500 t machine that would normally run with 144-cavities, output could be increased without stressing the machine with fast cycle times. Large-scale preform manufacturer Chemco explained which factors have to be considered to define the perfect preform for customers. Besides light weight, other factors like installed equipment, required barrier qualities, country’s requirements or even geographical aspects have to be considered (photo below). In issue 9 we were introducing the joint venture between Otto Hofstetter and Yudo which enabled them to offer complete preform systems. In an interview with PETplanet, Robert Schad from Athena Automation (now Niigon) explained how they achieved industry-leading cycle times and low energy consumption. The trends he foresaw for the preform sector were diversification, quicker mould and tooling changes and smaller systems. At Drinktec, Husky presented its multi-layer technology for the first time live on a trade show. On the HPP5, a 17g CSD application was produced at 8.7s with a 72-cavity mould. Issue 10 saw the direct processing of washed PET flakes into food contact grade preforms in the PET Inline Preform system. The system combined Erema’s Vacurema technology with Sipa’s Xtreme preform production system. 2018 At NPE, Husky paired its multilayer technology with new recyclable barrier materials and highlighted the capability for various application requirements such as barriers for light, oxygen and carbon dioxide. (issue 5) At Chinaplas, Netstal had shown its Prelactia solution, dual-layer preforms for milk bottles. During the first step of the overmoulding process, a 1mm inner grey layer is injected. The dark colour creates the light barrier to protect the dairies. Netstal Prelactia The third generation of its Eco300/2500 injection moulding machine was presented by Demark at Chinaplas, as we reported in issue 7+8. Energy efficiency and closing times had been especially on the radar for improvement, resulting in a confirmation of acceptance by Coca Cola. Nissei ASB presented updated versions of its 1.5 step moulding machineries at CBB (issue 10). The model on stand was the PF36/36600, moulding 36 preforms/cycle, producing bottles of up to 600ml capacity (photo next page, top).","@ID":21}, "PREFORM PRODUCTION PETplanet Insider Vol. 20 No. 12/19 petpla.net 32 Very high cavitation tooling Raising the standards Sipa is a well-known producer of PET preform injection moulding systems with very high outputs. The Italian company designs and produces moulds and hot runner systems that fit in Sipa machines and machinery of other major producers. The company recently conceived, designed, built and delivered a preform mould hot runner system with 192 cavities for one of the world’s leading PET container makers, based in North America. Creating a hot runner system that consistently and reliably enables such large numbers of cavities to be filled identically, at high speed, without excessive force, is a serious design and engineering challenge. Key to Sipa’s successful range of high-cavity machines is its Xflow melt distribution system, which is now available for use on GEN3 and GEN4 (third and fourth generation) XForm 250, 350 and 500 high-performance injection moulding machines. Improved melt distribution Xflow incorporates a hot runner manifold design that provides industryleading levels of balance of melt distribution, along with the lowest pressure drop ever measured, states Sipa. The maintenance interval – five million cycles – is able to be so long because the system’s performance characteristics impose very low levels of wear and tear and Xflow is designed so that maintenance is easy to carry out, when it is required. This technology enables Sipa to create very high-cavitation systems without having to compromise on balance, pressure losses or the formation of acetaldehyde due to polymer degradation. Xflow can also be applied to moulds with more modest levels of cavitation, with similar benefits to operators. Advanced concepts in polymer rheology Sipa introduced Xflow technology in its hot runner systems for over five years in 2013. The company says that the solution applies the most advanced concepts of polymer fluid dynamics to hot runner engineering. By taking melt rheology aspects into account, it can obtain balancing results beyond the capability of traditional systems. When it first arrived on the market, Xflow halved the imbalance in melt flow compared with Sipa’s first generation of hot runners. Taking account of PET’s rheological properties all along the many flow paths to the individual cavities is critical, because PET preform walls have become so thin. Hot runners’ energy consumption has to be minimised, so that the injection unit can push the molten polymer as quickly and efficiently as possible into all the cavities. “Use of rheological balancing translates into minimum energy demand and a very low pressure drop,” says Andrea Cavalet – Global Engineering Manager Injection Moulds & Hot Runners. “Xflow can be applied to any application, to provide the best solution for high-speed injection of critical preforms.” Breaking down mould design barriers Sipa says that it is using its advanced expertise in hot runners is about more than just getting higher and higher cavity numbers; it is also creating new preform moulds that exploit the potential of existing injection moulding machines well beyond current limits. Its GEN4 hot runner design concept overcomes traditional limitations on cavity layouts. Most PET preform moulds have standard configurations of 72, 96, 128 or 144 cavities. Preform producers can now use moulds with non-standard cavity layouts to substantially raise output, without putting extra stress on their machines. World’s first 180-cavity preform mould The concept allowed Sipa to engineer and manufacture the first 180cavity preform tooling in the world. It runs on a regular 500 t press, which would usually be able to run with moulds with no more than 144 cavities. Sipa’s technology has provided its customer the potential to raise productivity by 25 per cent. “It’s not the biggest preform mould in the world but the filling characteristics are excellent,” says Cavalet. “The customer isn’t gaining quantity at the price of quality; there are no penalties in cycle time or weight distribution.” Maximising machine potential Sipa says that it achieved this improvement without compromising mould robustness. Features like the SmartLock stack design, which delivers improved component life; XGuidance, which is designed to guaranPREFORM Special","@ID":34}, "PREFORM PRODUCTION PETplanet Insider Vol. 20 No. 12/19 petpla.net 17 Issue 12 reported on Netstal taking over the PET activities from KraussMaffei. Whilst KraussMaffei had in its PETform series opted for vertical clamping, Netstal has built classic horizontal clamping into the PET-Line series. 2012 Netstal’s LightBase process reduces weight while improving material distribution. Specially designed base geometries optimise preform surfaces for the heating process, thus better absorbing the thermal energy. Later in the blowing process this leads to thinner walls. (Issue 1+2). Preblow process depiction (Netstal), blowing the base area after IM Reducing thickness where the wall is at its thickest – Sipa concerned itself in issue 1+2 with bottle necks and produced light containers; the thickness and weight of the neck is determined by the preform injection moulding process. Sipa tackles the high output volume sector: At NPE, the company introduced a new PET preform moulding system. In issue 3 we introduced the new development, which accepted moulds from all leading mould makers. In the very same issue we reported that Sacmi had made a new start in the preform sector. IPS, standing for Injection Preform System, was presented at Plastmilano exhibition, sporting 48-cavities and a clamping force of 220t. Rapid mould change was a special focus. 2013 In issue 4, Jeff MacDonald, then Vice President Marketing at Husky, explained in an interview that the average number of cavities for preform systems has peaked. Instead he saw a decline, as the average number supplied was between 72- and 96-cavities per system. The basic reason for this: better technology equals improved performance per cavity. Netstal featured at Drinktec the PET-Line 2400 and issued an invitation to view the new PET-Line 4000, equipped with new features. The 72-cavity mould was provided by Otto Hofstetter. Cycle time was 5.4 sec. (Issue 7+8) In issue 9, Dr Golz, then President Krauss-Maffei and Netstal, spoke about plans to relocate KraussMaffei’s PETForm range of machinery to Netstal’s location in Näfels, Switzerland. Nevertheless, Netstal would continue to act independently in the market. A preform system based on injection compression moulding was presented by Sipa at Drinktec (issue 11). “Xtreme” was claimed to offer new design possibilities and weight savings as injection compression moulding allows for thinner walls and a thinner base area than injection moulding. On display at Drinktec was a 72-cavity solution, producing 8.7 g preforms (0.5 l). In issue 12, Husky announced the launch of HyPET HPP5 preform moulding system. A 12% increase in productivity was stated as well as a greater freedom in preform design.","@ID":19}, "MATERIALS / RECYCLING PETplanet Insider Vol. 20 No. 12/19 petpla.net 10 PET processor in India focuses on recycling awareness A step towards enlightenment by Kay Barton April 2019, We met: Mr Vimal Kedia, Managing Director Mr Ankit Kedia, Director; Mr Sanjay Balakrishna, GM Operations Following its takeover by US based PE investor Advent International in October 2018, the Bangalore (Southern India), based preform, bottle and container giant Manjushree Technopack has achieved strong growth, with no slackening of it in sight. As a leading supplier of Coca-Cola, PepsiCo and Bisleri, as well as numerous other national, multi- and international major brands, the business expects to achieve revenues of more than US$180 million in 2019, rising to $250 million in 2020; with a well thought out organic growth strategy and partly as a result of further acquisitions. of 14 Husky machines are mainly used to make over 100 variety of preforms in different weight categories, ranging from 9.6-675g. This includes the 22mm preform for the new 250ml bottle from Coca-Cola, which is a first in the world. A Sacmi CCM24 closure line was brought here from the northern plant in Baddi, Himachal Pradesh to complement the (relatively small) amount of bottle production at the location. It is important to mention that the company decided to start large scale preform manufacturing in its North unit and hence shifted two 96-cavity systems from this Bangalore plant to Pantnagar. The Bidadi plant currently handles around 70,000 of the 110,000 tonnes of material that Manjushree processes each year, across the seven plants it operates in India (see PETplanet Insider No. 3/2017, pp. 40 et seq). About 90% is PET processing and 10% PE. Advent International, which has invested in a total of seven companies in the Indian market alone, secured all of Kedaara’s 40% shares in Manjushree as well as 40% of all the shares held by the Kedia family, making it the majority shareholder of the company. “The shares were being traded at a reasonable price on the market at the time. When Advent became interested, we saw an opportunity to strengthen Manjushree over the long term and grow further. The transaction value was approximately US$375 million,” Vimal Kedia explained. “After this huge step forward, we now want to focus on new topics in the company – the topic of sustainability, above all else. In this project, we are working with CocaCola, PepsiCo, Reliance, Indorama, ASB and Husky, among other visionary front runners of the industry.” The Reuseum project This is an idea which was conceptualised three years ago, together with Coca-Cola. The “Reuseum” is currently being built on a site adjacent to the plant in Bidadi, at a cost of approximately US$700,000. When it is completed at the end of 2019, it will serve as a plastics reuse & recycling information centre. The building is a 1,800m2 circular complex, which will be home to an auditorium; exhibition space; digital and analogue information areas; a souvenir shop; and an atrium with a café and green spaces. Tour Sponsors: Construction site of the Reuseum The Kedia family is now engaged on a new project that is intended to communicate the benefits of recycling, reuse within the value chain and sustainability to the local population, on a wide scale in a practical way. We met Managing Director, Vimal Kedia and his team and got to find out about the “Reuseum”. A brief outline of what has happened since our last visit: We last visited their Bangalore preform plant, in Bidadi Industrial area, almost three years ago (see PETplanet Insider No. 11/2016, pp. 40 et seq.) On its opening in 2013, this plant completely took over the Injection Moulding division from its headquarters in Bommasandra - about an hour, as a new division. The business has expanded since, with four new Husky machines: two 400T – 4.0s, a 300T HyPET and a 180AE all-electric unit. The current total Vimal Kedia (left) welcomes Kay Barton at the Bidadi premises.","@ID":12}, "8 NEWS PETplanet Insider Vol. 20 No. 12/19 petpla.net Plastics press conference at K show The Plastic Industry Association (Plastics) press conference at the K Show covered the latest developments for the next edition of NPE: The Plastics Show in Orlando, Florida, 17-21 May 2021, Orange County Convention Centre. As well as a new profile in the form of new key visuals and website, the motto of the trade show is to be “Transform Tomorrow”. As the nonprofit organisation explained, this slogan intends to highlight the positive influence of, and changes in, plastic applications and products in everyday life - especially in the future - across all segments of industry. VP for Communications, Mrs Mia Freis Quinn, and VP Trade Shows and Marketing, Mrs Susan Krys, also explained the importance of the issue of global sustainability and recycling in the USA and from its perspective, and the management of plastic waste. According to Plastics, a variety of recycling projects are already being organised, including the Pacific Northwest Secondary Sorting Demonstration, and the participation in the promotion of educational projects on recycling was also highlighted. In addition to the objectives and topics for the upcoming NPE2021, the enthusiastic plastics expert and new President & CEO of Plastics, Tony Radoszewski, discussed the challenges and opportunities for plastics in the USA and in terms of the global import and export business. Radoszewski, who has some 40 years’ experience in the field, previously worked for Phillips Chemical; plastic pipe manufacturer Advanced Drainage Systems; and was President of the Plastics Pipe Institute. Together with Economics Chief Mr Perc Pineda PhD, the team provided an overview of the latest developments and trends for plastics up to the year 2021. According to a study conducted by Plastics with Probe Economics LLC, U.S. plastics manufacturing as a whole grew by 6% from 2017 to 2018, from US$ 306.2 billion to US$ 324.6 billion. Mexico and Canada were found to be the main export countries of the USA in 2018, with a total export volume of approximately US$30 billion. While China is the USA’s third biggest export market, it had trade deficit of US$ 14.3 billion in 2018 although, according to Mr Pineda, a trend towards reduced imports is expected by 2021. The USA saw an increase in the consumption of plastic products of more than 6%, from US $ 224 billion to US $ 238 billion. In comparison with 2018, the association predicts a fall in sales of machines and moulds in 2019, albeit with a positive trend over the next two years. In addition to the second edition of the “Bottle Zone”, the designated area for PET bottle production at the NPE, there will be new technology zones and a comprehensive supporting programme including information and training opportunities. The organisers are expecting more than 55,000 visitors and around 20,000 companies to attend the event. www.npe.org F.l.t.r.: Plastics new President & CEO Tony Radoszewski with Kay Barton That was Brau Beviale 2019 About 40,000 trade visitors (2018: 40,882), including around 18,000 from outside Germany, travelled to the capital goods exhibition for the beverage industry Brau Beviale to Nuremberg this year. With 1,088 exhibitors, 54 per cent from outside Germany, the exhibition provided an opportunity to learn all about the beverage manufacture process chain: raw materials, technologies and components, efficient and sustainable packaging, and creative marketing ideas. Once again this year, the exhibition had the key theme of “Future viability of the beverage sector”. The highly international make-up of the exhibitors and visitors was confirmed again this year, with exhibitors representing a total of 45 countries, mainly from Germany (504), Italy, China, the UK, the Czech Republic, Austria and Belgium. The approximately 40,000 trade visitors attended from 138 countries, with the majority, after Germany, coming from Italy, the Czech Republic, Austria, Russia, Belgium, Switzerland, the Netherlands, France and Poland. The themes in the supporting programme relating to the future of the sector were well received, as the organisers state. Discussions at the BrauBeviale Forum for instance ranged from open exchanges of opinion to highly contentious debate – not least in the issue of “Tap Water vs. Mineral Water” and the pledge question got the participants fired up, and vigorous discussion continued outside the forum. The event was rounded out with presentations on further topics of interest to the sector and top-level award presentations. The next edition of Brau Beviale will be held in Nuremberg from November 10-12, 2020. www.braubeviale.de/en","@ID":10}, "PREFORM PRODUCTION PETplanet Insider Vol. 20 No. 12/19 petpla.net 25 Delivering sustainability through lightweighting Larger bottle, less weight As the PET industry drives towards a circular manufacturing model, lightweighting helps to reduce the amount of post-consumer material that has to be recovered and reprocessed in the first place. Lightweighting plays an important role in reducing the environmental footprint of the packaging industry, as the hierarchy graph below illustrates. A lighter package, providing it still meets fundamental protection requirements, reduces the amount of material used and consequently cuts the amount of plastic than can potentially become litter or be improperly disposed of. Sacmi’s team was tasked to design and develop a new bottle that would provide competitive advantages in the marketplace, with no loss of performance. The specific project brief was as follows: 600ml bottle sleek design significantly lighter than competitors’ solutions, which weighed between 11.5 g and 12.5 g easy to manufacture top load similar to competitors’, which ranged between 26-56N (empty bottle, not vented) Focus on the neck Sacmi’s experts decided to change the neck finish, from 29/25mm to 25/22mm - a change that, on its own, delivered savings of about 1.4 g of PET. Total weight targeted was below 9 g. In order to achieve this and still be able to achieve suitable preform length and reasonable length to thickness ratio (L/t), Sacmi opted for an ogive tip bottom. The bottle’s sleek design followed the familiar look of other bottles already in use by the client company. Lighter but stronger The stretch ratio: AXIAL = 3.35 HOOP = 4.11 PLANAR = 13.75 allowed for relatively wide blowing processing windows, though being high enough to produce a sturdy bottle. It features a non-vented top load value of 47N. This is better than most other bottles already on the market despite being significantly lighter, states the company. www.sacmi.com The Ogive tip allows lengthening of the preform in order to have a wide process window in terms of stretch ratios and keep a relatively low L/T = 40.2. The cap weight was kept at 0.8g despite featuring an extended height for convenience. PREFORM Special IMDvista INOX Line Closure Inspection – 100% Inline – Complete solution out of one hand. – Robust, compact and very flexible. – One control center (HMI) for the whole line. IMDvista PECO LUX Preform Monitoring – Shot by Shot – Requires no additional floor space. – No preform orientation necessary and no moving parts. – Up to 80% part inspection. Inspection Systems for the Plastic Packaging Industry IMDvista BOCO SCAN We scan and measure your Bottle Inline – Transparent, opaque, shiny and matte bottles in one system. – Calibrated measurement +/- 5 μm. – Fast automatic product change. Swiss Made | www.imdvista.ch","@ID":27}, "PREFORM PRODUCTION PETplanet Insider Vol. 20 No. 12/19 petpla.net 22 From household products to preforms - and beyond! Diversity in plastic conversion by Kay Barton April, 2019 We met: Mr Alok Parakh, Director The National Group, which is based in Chennai, Tamil Nadu, is engaged in several areas of plastics processing. National Polyplast undertakes the production of preforms; the group also manufactures beverage crates and IML containers and produces a wide variety of plastic parts for white goods, consumer electronics, the IT sector and leading brands in the automotive industry, at a total of 12 plants across India. For organisational reasons, we met with Director Alok Parakh to talk about the company’s PET activities at National’s automotive plant, which is situated approximately 55km southwest of Chennai city centre. It is this kind of expertise, across different segments, that has contributed significantly to the success of this 100% privately owned company over the past decades. The history of the family business goes back a long way. The “National” brand, one of the first plastics processors in the country, was founded as long ago as 1951 by Mr B.R. Parakh. Due to the superior economic opportunities in the south of India at that time, he decided to move from Rajasthan to Tamil Nadu where, until then, there had been no real plastics industry. From there, Mr Parakh started producing PS and PE household goods for the whole of India and later, in the 1980s, National manufactured plastic frames for tube TVs. In 1990, the company began to manufacture plastic beverage crates for glass bottles for PepsiCo, the soft drinks giant. When the PET boom hit India, the company jumped on the bandwagon, establishing the National Polyplast segment. As it turns out, it was the right decision. Alok Parakh remembers the beginnings. “We started preform production in 2003, with our first 48-cavity Husky machine, and shortly thereafter successively made the popular Alaska preform neck for water applications. It is now omnipresent in India,” he said. “At the time, PepsiCo needed a preform type at very short notice and we had three months to offer a finished solution. We ultimately secured the order. Over the years, we have grown closely together and we now develop best in class preforms jointly with PepsiCo R&D, in India and USA.” While National Polyplast was initially completely dependent on PepsiCo, new customers have gradually come on board. Today, PepsiCo accounts for a healthier proportion of 20% of sales. As well as bottles for water and for Pepsi beverages, a Husky unit also produces aseptic preforms for Amul, in a clean chamber. The plants are equipped with Husky systems exclusively; 96-cavity machines are currently in operation in the three facilities. The moulds are supplied by Husky & MHT, and alternate from plant to plant, which allows Parakh to get the most out of his machines. National Polyplast’s product range in India has changed, from mass market to individual bottle sizes. For example: Pepsi beverages were originally packaged in three bottle sizes: 0.5 l, 1 l and 1.5 l. Today, there are 0.25 l, 0.3 l, 0.4 l, 0.6 l, 0.75 l, 1 l, 2.0 l and 2.25 l. This expansion of the range demonstrates that the company has to be much more flexible as a converter than in the early days. The service life of a preform design has also reduced considerably. The weight of preforms for still water has decreased, from 22 to 18.6g. Seven years ago, a CSD bottle weighed 27.7g, today it is 21.5g. These changes require continuous investment in production equipments. Their latest project is IML (in-mould labelling) for containers. Although thinwall injection with label inlays is still not, currently, very common in India, the packaging industry is increasingly insisting on it. As a result, National Polyplast now has three IML units operating at the PET plant. A new facility, being built right next door, will provide space for 10 preform and 20 IML machines. This investment demTour Sponsors: Alok Parakh (left) and team in front of his 96-cavity Husky machine in Silvassa Alok Parakh (left) interviewed by Kay Barton","@ID":24}, "44 TRADE SHOW REVIEW PETplanet Insider Vol. 20 No. 12/19 petpla.net TRADE SHOWreview Heat-set upgrade for Lithuanian SBM machine It was very late in the run-up to the K show that Lithuanian machine manufacturer Flexblow decided to present “DoubleBlow”, the latest version of its well-known Freedom range of models. The compact two-stage SBM machine is based on the company’s established frame design and is capable of making containers with a neck finish of 18mm to 120mm; this means that one single system can be used on a flexible basis for a wide variety of applications. The exhibit on display is designed to be of particular interest to hot-fill bottlers, as highlighted by the prominent “Hot-fill freedom” lettering on the machine. CEO Gintautas Maksvytis explained the key innovations. “Like the other models from our company, the system is fully electric,” he said. The specialist heating and cooling design results in an increased degree of crystallisation “This model manufactures bottles with a high degree of crystallisation for product fillings of up to 93 °C with, if required, oval bottle geometry; the oven comes with preferential heating zones. As well as virgin PET, the stretch blow moulding machine can processes rPET or PLA, at a maximum output of 2,800 bottles per hour.” Flexblow claims that Double-Blow has a power consumption of approximately 30 kW/h. The exhibit at the trade fair booth worked with a four-cavity system. As with other models from Flexblow the moulds aim to allow for a rapid change of less than ten minutes or a complete system change in approximately 30 minutes. “Our integrated inspection system is also new,” Mr Maksvytis explained. “Temperatures are monitored and leak tests are carried out during the manufacturing process and the machine also measures the correct wall thickness of the containers, while they are being made.” The company is increasingly focusing on sustainable production at its Kretinga location. “Six months ago, we converted our manufacturing facility to green energy and we want to continue pursuing and expanding on this principle.” www.flexblow.com Moulding machine manufacturer goes PET Egg Harbor Township in New Jersey, located around one hour’s drive south-east of Philadelphia, PA, in the USA, is home to the head office of machine manufacturer Jomar. The company, whose history dates back to the late 1960s, has built and sold more than 2,000 injection blow moulding machines worldwide for a variety of plastic applications in the small and medium output range, primarily for non-food applications. External markets are particularly important for the company: around 80% of its production is destined for export. PET processing is not new for the company but, due to its increasing popularity in personal, beauty and health care packaging, i the logical next step was to expand their capabilities with PET. At the K trade show, Jomar presented the Technodrive 65 PET, its new, variable three-station IBM model. “We generally have a lot of customers who come from the extrusion sector and are looking for alternatives, or want to add IBM equipment to their production facilities,” Sales Manager Ron Gabriele explained. “The machine on the stand here is being publicly presented for the first time in Europe. It is specifically designed to process PET and then revert to more traditional IBM materials such as PP or PE.” The Technodrive 65 PET is the first Jomar machine to focus on PET. The model on display featured six cavities, producing 50ml perfume containers with a wall thickness of 0.7mm at a cycle time of 12 seconds and at an output rate of approximately 1,700bph. A maximum of eight cavities is possible; the smallest neck size is 8mm diameter. Full changeover, including screw exchange, takes approximately 4½ hours. The compact machine (L: 292 x W: 198 x H: 341 cm) has a drying cycle time of 1.8 sec and an average consumption of 24.7 kW. In addition to PET, the system can also process other plastics, such as HDPE or PP. www.jomarcorp.com F.r.t.l.: Aidas Vizgaudas, lmantas Maksvytis, Gintautas Maksvytis and Kay Barton Sales Manager Ron Gabriele in front of the Technodrive 65 PET","@ID":46}, "PREFORM PRODUCTION PETplanet Insider Vol. 20 No. 12/19 petpla.net 23 onstrates National’s strategy: PET will always be an integral part of National Polyplast but growth will come from IML as well. Three preform plants, one located in Northern India at Roorkee, one in West at Silvassa and the third in South at Pondicherry, have a total capacity of over 60,000 t of material. Raw material is supplied primarily by Indorama and Reliance. As stated above, 20% is destined for PepsiCo; other major customers include Bisleri, Big Cola, Indian Railway Catering & Tourism Corporation (IRCTC) and Nourishco Beverages. “We’re clearly going for Husky equipment,” said Alok Parakh. “Many customers have, in the past, experienced difficulties with inexpensive preforms and they approach us looking for new, reliable products. Roughly 85 to 90% of our preforms are destined for the domestic market, while the rest are for export, mainly to African countries or the Middle East.” The turnover of the National Group has grown by almost 63% to US$70 million since our last meeting, in 2017. Some 20% is attributable to the preform business alone. “We see the boom in local brands as the trigger factor behind this,” he continued. “This year, we also had the Cricket League games, with a lot of beverages being consumed everywhere. The elections that are currently under way may also make a contribution.” In addition to the planned expansions in the future, the last two to three years have seen a stronger focus on product development with customers. Alcoholic Beverages and Edible Oil segments are also to be added, with two new production lines already in operation. www.nationalplasticsgroup.com Director Alok Parakh in the entrance area of his automotive plant near Chennai","@ID":25}, "MOULD MAKING PETplanet Insider Vol. 20 No. 12/19 petpla.net 12 PET moulds from Turkey by Kay Barton October, 2019 Meeting with Petka Mold Industry during K We met: Mr Tarik Sivri, General Manager Petka was found in 2005 by a group of five people, experienced in the PET industry, with the intention of building a company that would be recognised for its expertise and specialist knowledge. From outset, Petka focused exclusively on the production of PET preform and blowing moulds and spare parts for them. The company’s five shareholders own the company equally, with 20% each, and they each have a specific managerial role: general manager; projects; production; technical; and purchasing. Petka employs a total of 116 people at its 3,700m2 factory, located in Adana, which is the administrative capital of Adana Province, in south-central Anatolia. The company exports 80% of its production, to over 55 countries across the world. At K show we met General Manager Mr Tarik Sivri to learn more about the manufacturer. The company launched its first 32-cavity preform mould in 2006, just a year after its foundation. Its debut 48-cavity preform mould followed a year later and a 72-cavity full cold half unit was presented in 2009. Three years after that, in 2012, the company increased its capacity and working space with a move to a new plant. As well as launching new products, the company has a track record of existing product improvement, weight reduction and improving performance in operation. Mr Sivri explained: “Petka works with leading brands in the PET industry, producing a range of mould types that are suitable for various injection and blowing machines of the well-known brands. It uses high-precision European and Japanese machines for manufacturing. More than 400 Petka preform moulds are currently running in over 180 different companies. The company currently has the capacity to produce 30,000 stack parts for preform moulds and 1,500 blowing mould sets per year.“ Since it was established, Petka has invested in new technology and is committed to continuous improvement. Mr Sivri sees his company clientfocused, from the selection of their suppliers and raw materials to delivery and aftersales technical support. “We provide ongoing training to our staff, to ensure it clearly understands customer requirements, complaints if they arise, and to propose and deliver efficient solutions“, he said. He makes a point of maintaining up to date and in-depth knowledge of the market and technical developments, which enables it to advise, guide and co-operate with customers in understanding market demands and trends, and developing the best solutions to meet them. “Our vision and objective is to “become a top three globally preferred and reliable mould supplier for the PET industry“, Tarik Sivri added. Within Turkey itself, Petka enjoys a market share of 35-40%. It is the largest domestically-owned company in the country for PET moulds; its competitors are the leading international mould producers, both locallybased and as importers. It has averaged growth in the region of 40% a year, consistently. The manufacturer has responded to market pressures to address issues of sustainability by, in particular, research and development of lighter and fully reusable packaging. It is also developing moulds that are suitable for the new age of rPET. www.petkamold.com Tarik Sivri, General Manager Petka (left) with Kay Barton","@ID":14}, "PREFORM PRODUCTION PETplanet Insider Vol. 20 No. 12/19 petpla.net 15 PET preforms – some highlights 1999-2019, as reported in PETplanet Insider 1999 In our first issue, a 3-layer preform system was presented by Demag and installed at Kulleborn & Stenström in Sweden. Recycled material was used for the inner layer. At that time, the Swedish company produced 70 million preforms for 0.5 l bottles for Coca Cola. 2000 In issue 6, Husky presented a 60-cavity Quad Index machine as a further development of the Index range introduced in 1997. With this, a 7 sec cycle time could be achieved for 0.5 l preforms. 2001 PETplanet’s first book “Dressed to fill” was published. Cycle times of 14-16 sec for preforms with wall thicknesses of 3.0-3.6mm were by then standard. Issue 6 saw Netstal’s new 144cavity preform system with a cycle time of less than 11sec for a 20.8g preform. The machine was shown at that year’s K show. The tool came from MHT. We featured the first vertical Krauss-Maffei preform system for many years in issue 8, with a 24-cavity tool from Otto Hofstetter. In issue 9 Robert Schad, back then CEO of Husky, expressed hesitation with regard to taking up the 144cavity challenge laid down by Netstal. At the following K trade show, a 144cavity micro-pitch tool (at least a display model) was shown on the stand (as reported in issue 11+12). Also in issue 9, MHT presented the micro-pitch tool in detail. It allowed 72-cavity tools to be run on a 300 t machine rather than the usual 48 cavities, and a 144-cavity run on a 600 t machine which previously could run only 96 tools. Arburg featured the vertically orientated Preliner in issue 11, with 130 t and 220 t versions for up to 16 cavities. 2002 We saw the first Krupp preform system in issue 10, under the Engel name. The range, rebranded as MacPET, had undergone a major overhaul by Engel and covered machines from 250-500 t. 2003 Husky presented the new developments of the Index machine in issue 8. The machine now went up to 600 t and 144 cavities. Cycle time for lightweight preforms was 5.7 sec. Of even greater importance for the future was the presentation of the HyPET preform systems, which were to slowly replace the fully hydraulic G range. 2004 A Husky advertisement announced for the first time that in addition to the standard 300 t and 600 t machines other sizes were available. In issue 9, Netstal talked about their 96-cavity system for 20 g preforms with a 9.66 s cycle time. Some of the big names talked about the need for a 196-cavity system in issue 12. Mike Urquhard, at the time at Husky, saw his 144-cavity system as sufficient for big quantities. Otto Hofstetter posed some critical questions concerning the economics of such a system, and Waldemar Schmitke, then at Netstal, presented for the first time the Netstal 196-cavity system, asking whether that would now be the end of the “cavity race”. 2005 Manfred Lausenhammer of MHT said in an interview in issue 1+2 that they had built a 196-cavity tool and reported sales of over eighty tools with 144 cavities. He believed in a market for the 196-cavity system, too. Another machinery manufacturer appeared on the horizon: Chen Hsong who had been at the 2004 K show edition presented their 48-cavity system in issue 1+2. 2006 Netstal showed their 196-cavity system for the first time at NPE (issue 5).","@ID":17}, "PETplanet Insider Vol. 20 No. 12/19 petpla.net 39 TRADE SHOW REVIEW is supported by GSI and by generous donations from businesses and individuals. Every penny raised is destined for Sierra Leone, where the money is used to develop sustainable business managed by competent professionals from the Makeni University’s Faculty of Agriculture, which was founded and is supported by Saint Lawrence Foundation. By helping the people building their future in their homeland, Saint Lawrence aims at creating the base for a better future for these deprived communities. Pollution and greenhouse gases In the afternoon Mr David Bucknall, of Heriot-Watt University, Edinburgh, Scotland, explained why why banning plastics completely may actually damage the planet. The pollution impact of the production and related logistics of glass and paper would increase CO 2 emissions by at last four times compared with PET, which still has great potential and is a decidedly better choice than its competitors and alternatives. The industry must keep working to correct waste mismanagement and increase rates of collection and clearly establish the ‘circular economy’ that will transform PET from a perceived problem to the leading solution. The circular economy Mr Werner Bosmans, DG Environment, explained how the circular economy is already a subject of discussion within the EU commission. Actions taken to deliver the goal of 100% reusable plastic packaging by 2030 include support for alternative feedstocks and banning single-use items, which have been proven to be the prime source of marine littering. The EU will be pushing to have all PET containers and bottles to have 25% of recycled content and 77% collection rate by 2025, with the goal of 90% in 2029. Mr Gunjan Sharma of Reliance presented papers on behalf of Mr Vipul Shah. Reliance Group’s circular economy was extended first into the textile market, and with plastic waste promoted for use in road surfacing. The company has launched a high profile awareness campaign in India, in both rural and urban areas. It has created a global alliance with more than 25 other Companies called AEPW (Alliance to End Plastic Waste) put a full stop to waste. Conclusion The concluding round table talk provided a platform to a number of leading figures within the PET indusGerman Technology January 28-31, 2020 Moscow try. Mr Christian Mayr (Alpla) underlined that PET companies have been investing in recycling for 15 years. Mr Coert Michielsen (Refresco) said there is not enough rPET available and it is expensive. Mr Carlo Galli (Nestlé) explained how his company is looking at alternatives in line with consumers’ preferences. Refillable bottles are growing strongly in Asia but customers must be aware that they are the focal point of the circular economy. Mr Satoshi Soda (Toyota Tsusho) explained how Japan achieved 90% collection rate and is still trying to improve. Mr Renato Zelcher (Crocco and EuPC) said that communication on plastics must be improved. The whole industry is ready for the circular economy; improved collection rates are needed. Mr Darrel Collier (Napcor) complained about poor collection rates in the US and what Napcor is trying to do, using all media, from social to broadcast news networks, to push people to take responsibility. Mr Zanchi concluded the discussions by underlining how the PET global industry is working hard on recycling issues and moving towards solutions quickly, by reacting promptly to indiscriminate attacks of various media. It is undeniable that much progress has been achieved within the polyester community to face the situation, without avoiding discussion of the real problems; on the contrary, by seeking to transform them into opportunities. www.gsiplastic.com","@ID":41}]}}
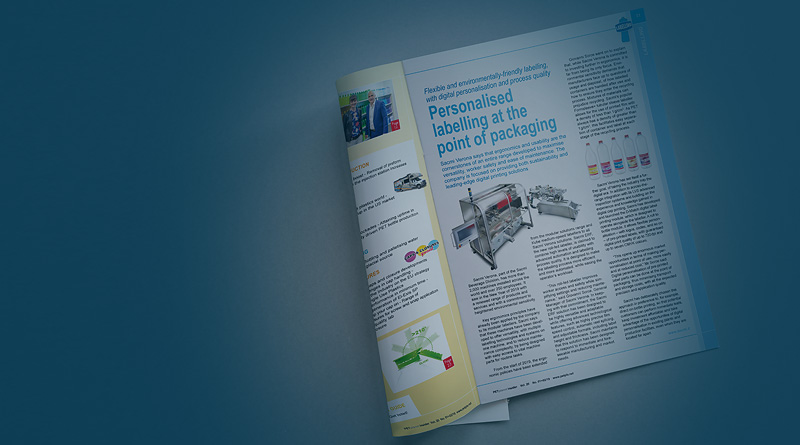