"MATERIALS / RECYCLING 13 PETplanet Insider Vol. 22 Through its working group, Petcore is developing studies to present data on the enhanced chemical recycling processes, where collected post-consumer PET from the market is depolymerised to starting materials, purified terephthalic acid (PTA) and mono-ethylene glycol (MEG) which can be used for making new polymers. Pilot plants have already given proof of concept, and demonstration plants are in construction and commissioning to exhibit scale up of operations. What is clear is that PET collected from the market is being re-used to create PET/polyester for the same end use giving a physically evident circular business model with recycled content in product placed on the market. Chemical recycling – Depolymerisation of PET to monomers – Claims and concerns Several scientific papers and NGO reports are expressing concerns that chemical recycling is overstating claims of lower GHG emissions and the improved LCA of recycled materials. Plus, the issue that chemical recycling could be bad for the environment due to byproduct waste management. Petcore supports the fact the any scientific data must be robust and comprehensible. Going back to the “licence to operate”, your sins will find you out if the overstatement of performance does not materialise. Add to this the EU Commission wishes to crack down on “Green Washing” so claims for performance will need to be accurate and auditable. Petcore agrees LCA analysis can be misinterpreted and can be misleading. The aspect raised in Zero Waste Europe’s Study “Understanding the Environmental Impacts of Chemical Recycling” makes sense to Petcore and we would encourage all NGO’s to work with the industry to bring our collective objectives together. At the start it was mentioned the value chain for PET wishes to comply with the requirement to address recyclability and increase recycling of PET to bring about a circular business model. In that, the industry wishes to ensure that all aspects of environmental and sustainable production are addressed, auditable and prove that the recycle business is the right alternative for the defined end use. Petcore encourages NGO’s and scientific researchers to approach us, as we will work with them to ensure the goal to bring circular business to PET is met along with meeting the conditions for a licence to operate. www.petcore-europe.org","@ID":15} "PETcontents 4 PETplanet Insider Vol. 22 No. 01+02/21 petpla.net 01+02/2021 TOP TALK 10 Full capacity despite the crisis - Interview with David González, Business Director of Novapet MATERIAL / RECYCLING 12 “Chemical recycling is a reality in the PET industry” by Stephen A. Short, President at Petcore Europe 14 Recycling in the U.S. - New edition of Plastics’ market watch series focuses on the U.S. plastic bottles market 16 From cup to cup - Organic yogurt in 100% rPET cups 18 Viscosity and homogeneity are crucial - Vacuum filter enables consistent viscosity for customised polyester CAPS & CLOSURES 21 Tethered caps inspection at a glance 25 Complex closures - Customised technology, flexibility and high-quality solutions 26 The Essential Guide to Tethered Closures 27 Understanding what the consumer wants and needs - Interview with Astrid Hoffmann-Leist, United Caps Chief Marketing and Innovation Officer & Business Director APAC 30 Convenient, comfortable, connected - Designing tethered caps 31 Ready-to-use tethered solution - Slitting solution for the manufacture of the new tethered caps presented ahead of the EU Directive that comes into force in 2024 32 Well dosed - Recycable valve for PET recycle stream MARKET SURVEY 28 Suppliers of resins & additives BOTTLE MAKING 33 From bottle supplier to OEM filler BOTTLING / FILLING 36 Reunion with a leading conversion and bottling company 38 The water mission - Russian company invests in three turnkey lines from KHS TRADE SHOW REVIEW 40 Rethinking the waste problem - Tomra webcast 43 Plastics Recycling Show Europe Virtual Event 2020 BUYER’S GUIDE 48 Get listed! Page 54 Page 36 Page 25 INSIDE TRACK 3 Editorial 4 Contents 6 News 44 Products 45 Patents 46 PET bottles for Beverage + Liquid Food 54 Outer Planet CAPS & CLOSURES","@ID":6} "CAPS & CLOSURES 27 PETplanet Insider Vol. 22 No. 01+02/21 petpla.net Interview with Astrid Hoffmann-Leist, United Caps Chief Marketing and Innovation Officer & Business Director APAC Understanding what the consumer wants and needs PETplanet: What trends are you observing in caps and closures for the food and beverage industry? Hoffmann-Leist: There are several key trends that we can observe: brands and consumers are demanding on-shelf stand-out and more sustainable solutions (lighter weights, bioresins, smaller neck sizes etc). With over 80 years working with plastics these are two areas where we have differentiating capabilities. Brands in particular work with us because of our ability to develop total packaging solutions that integrate seamlessly into the overall supply chain. PETplanet: What role does the consumer play in a company’s decision for a certain kind of cap or closure? Hoffmann-Leist: Everything starts with an understanding of what the consumer wants and needs - the value they are looking to obtain from a closure. As a closure manufacturer that means us taking the time and making investments to understand them better. We often talk about “Close to You” at United Caps. That’s as applicable to the consumer as it is to our direct customers. A great example is our 127 SafeTE closure for Infant Nutrition; at the very heart of that development was research that told us consumers in Asia wanted a premium solution for Baby Food containers that featured impenetrable security technologies. They wanted to be certain that the milk powder contained within hadn’t been touched since leaving the factory. That’s what led us to develop our industry leading Droplock and Flexband technology. PETplanet: What can you tell us about sustainability in the segment of caps and closures Hoffmann-Leist: There are a lot of exciting things happening in the world of caps and closures with regard to sustainability. A key driver is the EU’s Single Use Plastic Directive. The appetite for more sustainable solutions is growing. For beverages it requires that the closure is ‘tethered’ to the bottle to help ensure they are disposed of together. We fully expect that postBrexit the UK will implement tethering requirements and others will follow suit. California is considering it due to the impact of Chinese sanctions on the import of plastic waste for instance. Pace across different political environments may vary but ultimately this is the direction of travel. PETplanet: Turning now to materials, is there any news regarding sustainability? Hoffmann-Leist: As well as traditional petroleum-based plastics, we’ve developed a range of ‘Greener Closures’. They’re made from plantbased plastics, the beauty of them is CAPS & CLOSURES The EU’s Single Use Plastic Directive is certainly the key driver in the new developments that are currently propelling the caps and closures industry forward. Astrid Hoffmann-Leist shows in our interview the essential trends which also emerge when you listen to the consumer. Safety and sustainability play an increasingly important role here. that they’re developed from bio-based plastics like sugarcane or starch which absorbs CO2 and helps to reduce harmful greenhouse gases in our atmosphere. At the same time, they behave in exactly the same way as traditional plastics, completely indistinguishable in terms of performance. PETplanet: What are the challenges for the future? Hoffmann-Leist: Different sectors will have different needs and competitive advantage will go to those that emphasise integration and collaboration - by that we mean positioning to perform along the entire product journey, from in the plant to in the hand and for the planet. We anticipate an accelerating trend towards sustainable design and manufacture and an emphasis on product security. Of course, ultimately the economic environment for plastics must be a circular one. PETplanet: Thank you very much!","@ID":29} "BOTTLING / FILLING PETplanet Insider Vol. 22 No. 01+02/21 petpla.net 36 Reunion with a leading conversion and bottling company by Kay Barton It has been four years since we had an in-depth meeting with Keith Dai, Chairman of Taiwan Hon Chuan (THC), in Taichung, Taiwan in August 2016 (PETplanet Insider, Vol. 17, No. 10/16). The conversion giant and OEM bottler with 39 local and international plants and a company value of US$ 430m gave us a detailed insight into the company’s organisational structure and business activities. We visited one of its two local bottling plants next to THC’s headquarters with its integrated packaging museum which at that time was dealing exclusively with aseptic filling. With this year’s road show coming to Taiwan, we took the opportunity to follow up our initial visit and find out what THC has been up to since 2016. South-East Asia has been considerable during the last four years with the addition of seven production facilities. Brand new factories have been established in Indonesia, Myanmar, and Vietnam, specialising in the production of drinks and food packaging, as well as bottling. And there will also be a new plant in the Philippines in future. A new aseptic filling plant was opened in Taiwan and further expansions are planned. The company’s production area has increased from 738,000m2 to 888,134m2 and its value grown from US$ 430 million to US$ 540 million. THC achieved a 30% increase in turnover to US$ 727 million in 2019 compared to the 2016 figure of around US$ 550 million. Mr Dai explained: “We are constantly developing new products, for example in the closure sector. During PETplanet’s last visit, we talked about product visibility and interactive applications for end users. We had just developed the integrated QR code for closures which is now widely used on the Chinese mainland. As well as further work on this product, we have also produced holographic 3D aluminium and twin-coloured caps. We are also working on new barrier options for our packaging to make it more environmentally-friendly, depending on what the customer wants”. The use of rPET is particularly relevant here. Aseptic filling line in action “We have started to use rPET in some countries but respective regulations, especially in South-East Asia, often slow down further progress given rPET is still prohibited for use in food packaging”. Along with Taiwan and China, the THC group currently recycles around 300,000 t of PET and 80,000-100,000 t of PE. THC has also expanded capacity at its local Taichung plant by adding e.g. new injection-moulding, compresTour Sponsors: Chairman Keith Dai’s office with a view Taiwan Hon Chuan Enterprise Company Ltd. May 29, 2020 We met Mr Keith Dai, Chairman And there is much to report, with THC having steadily expanded its business both in Taiwan and on mainland China. Among other things, the company has now added food and dairy products to its business portfolio. Automation and exchange of information within THC’s many departments have been enhanced and internal processes streamlined. There have been other developments, particularly in relation to procedures, quality and food safety management issues. Shortly after our initial visit, a factory was established in Mozambique at the company’s first African location to produce plastic caps, preforms and PET bottles. A joint enterprise with bottled water manufacturer “Saida” in Algeria is currently in the pipeline. Although one factory has closed in mainland China, THC’s expansion in","@ID":38} "PETplanet Insider Vol. 22 No. 01+02/21 petpla.net 41 TRADE SHOW REVIEW Dr Volker Rehrmann, Head of Circular Economy at Tomra explained to host Claudia Fasse, Co-Founder & CEO von F+B Fasse und Bieger, the importance of immediate action with regard to holistic waste management, which would include long-term reductions in material usage and therefore waste generation, and improved recycling. He described the effects of coronavirus on current waste generation and the image of plastics in the pandemic as follows: “Basically we see increased generation of domestic waste as a result of increased home working or lockdowns. Overall however, it can be seen that the global negative image of plastics has sharply reversed, as the current situation has clearly exposed their necessity and their positive hygiene aspects.” In terms of plastic recycling, the currently low oil price means that virgin plastic material is somewhat cheaper than recyclate, as shown in the example of PET. However, continued Dr Rehrmann, many plastic manufacturers, converters and international or multinational brands are sticking to their line of maintaining the recyclate proportion in their packaging, despite any additional costs. The newly created department, the Circular Economy Division, will henceforth work towards holistic solutions for waste management. Its objectives are to reduce global emissions, increase the intentional collection of waste from 14% currently to 40% by 2030 so as to feed this into appropriate recycling streams, and establish a principle of closedloop recycling at 30%. Dr Dominic Hogg, Chairman at Eunomia Dr Dominic Hogg, Chairman at Eunomia, used a study to explain the impact of these holistic approaches to waste and recycling. This showed that in 2016, worldwide urban waste generation according to the World Bank amounted to 2.02 billion tonnes, which is comparable with ten thousand times the volume of the Empire State Building. A portion of this would never make it into the recycling stream, but would end up as landfill, in the environment or in the oceans. In 2030, waste generation is expected to amount to 2.59 billion tonnes. According to the International Resource Panel, the plastic and rubber industry contributes 1.5 gigatons of emissions annually. According to the World Resources Institute, an estimated 4.4-5.7 billion tonnes of overall emissions result from manufacturing things that later end up as urban waste. In 2030, it could even be 5.6-7.3 billion tonnes. “With the currently available options for optimised waste management, 1.58 billion tonnes of CO2 emissions could be saved by 2030, equivalent to around 3% of all global greenhouse gases. If we assume a higher waste generation of an additional 30%, which is likely, as it has been shown that the World Bank has set the data for several groups of countries too low, then potential savings of 2.17 billion tonnes would be realistic,” said Dr Hogg. This quantity would be comparable with renouncing twothirds of worldwide automotive traffic and all commercial flights. Stavanger pilot project The discussion group illustrated how a holistic solution could look by presenting a unique pilot project from the city of Stavanger in the southeast of Norway with a population of almost 144,000 residents. Besides comprehensive infrastructure for waste separation in Norway, systems like deposit schemes for containers already generate high recirculation. However, a great deal of additional potential was identified,” explained Dr Rehrmann. The municipality contacted us a few years ago with the aim of improving their already good collection and recycling system and increasing the April 13-16, 2021, Shenzhen at the Krones booth 10F23 German Technology Innovative hotrunner optiRun","@ID":43} "CAPS & CLOSURES 31 PETplanet Insider Vol. 22 No. 01+02/21 petpla.net design consultancy services. Working alongside customers, the experts at Sacmi’s Closures R&D Lab identify the best investment solution and provide the support needed to obtain the standard compliance certification required by major international brand owners. For tethered caps, Sacmi aims to partner with customers in order to transform the challenges of sustainability into opportunities, doing so by identifying the right slitting solution to be implemented on the existing line. www.sacmi.com Slitting solution for the manufacture of the new tethered caps presented ahead of the EU directive that comes into force in 2024. Ready-to-use tethered solution Tethered caps are a legal requirement promoted by the European Union to reduce the dispersion of plastic into the environment. All manufacturers must comply with this new standard by 2024 while simultaneously complying with other new regulations that require, for example, they make bottles from a minimum standard amount of resin obtained from recycling. More than four years before the EU directive is due to come into force, Sacmi already has ready-to-market tethered solutions available for both screw-off and snap caps that remain hinged to the bottle. Sacmi’s tethered cap development is closely linked to the development of new lightweight-oriented standards. The company has already developed a closure, Sacmi AB26CSDT1, suitable for the new GME30.40 neck standard. This neck-closure combination can save up to 2 g with respect to the common PCO1181 standard. The developed closure already has all the tethered features required to comply with the SUP standard. Implementation on existing lines The Italian company also offers the closures sector technical and Sacmi Delta hinged solution for a tethered closure on the GME30.26 applied on existing 29/25 Sacmi flap band closure Sacmi AB26CSDT1 solution for the new GME 30.40 for CSD application up to 5.2 vol and 3 l bottles Sacmi AB26CSDT1 with the tethered Delta hinged solution for GME30.40","@ID":33} "MATERIALS / RECYCLING 17 PETplanet Insider Vol. 22 removes the cardboard banderol and peels off the seal made from aluminium. What remains is the rPET cup itself, which is not printed nor laminated with other plastic types. Both print colours and multilayer material would contaminate the material and impede recycling for food packaging applications. Closed loop recycling PET-Man and Starlinger viscotec highlight the importance of efficient collection and sorting of packaging waste. It is a crucial prerequisite for recycling and for the circular economy to work. The project partners, therefore, initiated a regional collection system for the white rPET cups and installed collection points at recycling centres and supermarkets. Thousands of cups have since been collected and then recycled and reprocessed, to close the recycling loop. Packaging made from rPET has a low CO2 footprint and leaves reusable glass packaging and plastic packaging made from virgin material far behind in terms of emissions. To raise the consumers’ awareness, Starlinger viscotec and PETMan provide information for customers to allow a factual discussion about what constitutes an environmentally friendly packaging as not all customers were in favour of the switch from glass to plastic at first. Leonhard Zaumer delivered his own verdict on the initiative: “We were prepared to explain our packaging choice to our customers in person, on our webpage and via social media. It is important to provide objective information for the discussion. In my opinion, the carbon footprint is a holistic measure to evaluate the impact of products on our environment.” www.viscotec.at Local collection points for rPET cups rPET yogurt cups","@ID":19} "MATERIALS / RECYCLING PETplanet Insider Vol. 22 No. 01+02/21 petpla.net 14 New edition of Plastics’ market watch series focuses on the U.S. plastic bottles market Recycling in the U.S. The Plastics Industry Association (Plastics) released a new Plastics Market Watch report, ‘Plastic Bottles Today: Innovating to Reach Today’s Consumer’, which shows that demand for plastic bottles continues to grow in the United States. In the report, the association throws light on the bottling market landscape; innovation with machines, materials and designs; demand and supply dynamics and on the current recycling situation. The U.S. market for plastic bottles IBISWorld reported in 2020 that the U.S. plastic bottles market size measured in revenue to grow at an annualised rate of 0.7% to US$ 11.9 billion over the next five years. However, estimates vary on the market size for plastic bottles. Assuming increased consumer demand for plastic bottles, Plastics’ new study is a timely look into the trends that shape the plastic bottling sector. The study provides insight for the entire plastics industry and supply chain, as well as brands and other stakeholders, into the growth and usage of plastics for bottling and containers. While bottles can be made with an array of polymers, PET is the leading plastic bottling material. Bottlers are using PET to develop lighter packaging that saves costs in raw polymers, energy and transportation. The PET bottle designs are also attractive to consumers in packaging and sustainability. PET is used for single-serving beverage choices and small or mediumsized food bottles while HDPE can mostly be found in larger gallon-sized bottles like milk or for vinegar and chocolate syrup bottles. PP is used in a variety of products, including medicines, maple syrup or ketchup containers. In total, the North American beverage industry expects a 4.5% growth rate in the years leading up to 2028, for a total value of $45.5 billion, according to the report. Plastics packaging will be used for 55% of the bottling needs in the years ahead according to PMMI, but competition between manufacturers of packaging materials will continue. PMMI predicts that aluminium cans and glass bottles will also undergo significant innovations. PET is the material of choice for water, carbonated soda, teas, sports drinks, and other beverages. American consumers want bottled water available for purchase where other beverages are sold, gaining market share at the expense of carbonated sodas or fruit drinks, according to the International Bottled Water Association (IBWA). IBWA reports wholesale dollar sales of bottled water grew 7.3% in 2018 to $18.4 billion; per capita, consumption rose 4.3% to 42.3 gallons, while soda and fruit drink consumption both declined in 2018. Information Resources Inc. (IRI) reported a 5.7% growth of bottled water in 2019.","@ID":16} "PETplanet Insider Vol. 22 No. 01+02/21 petpla.net 43 TRADE SHOW REVIEW Plastics Recycling Show Europe Virtual Event GAWiSD featuringAutoJob ™ – job set up in seconds +1.724.482.2163 AGRINTL.COM ACCURATE • FAST • REPEATABLE SEE GAWIS4D IN ACTION Dimensional and thickness measurements for plastic containers and preforms. ® Virginijus Sinkevičius, Commissioner for Environment, Oceans and Fisheries at the European Commission delivered the opening keynote and joined the panel for the opening session entitledThe New Reality for Plastics features . Fellow panellists included Ton Emans, President of Plastics Recyclers Europe (PRE) and Maria Ciliberti, Vice President at Borealis. They looked at the current state of the affairs and new developments of the plastics-related EU legislation and the industry’s answer to the ongoing legislative changes. Materials focus sessions on day one was covered PET (polyethylene terephthalate) and PVC (polyvinylchloride). Day two of the virtual conference started with the session entitledRevisiting Plastics Recyclability featuring Maja Desgrées du Loú, Policy Officer for Packaging and Packaging Waste at the European Commission, and Fabrizio Di Gregorio, Technical Manager of PRE. Moderated by RecyClass President, Paolo Glerean, this session focused on the revision of the packaging and packaging waste directive and the latest developments in the field of plastic packaging recyclability. The second day’s materials focus sessions covered the current status of polyolefin waste streams including high- and low-density polyethylene (LDPE and HDPE). Setting the tone for the final day of the conference was a session entitled Global Solutions and Regional Actions on Plastic Waste . Speakers included Hans Axel Kristensen, CEO of Plastix A/S, Philippe-Daniel Merillet, CEO & Co-Founder ofThe One Projectand Dorothea Wiplinger, Sustainability Manager – Strategy & Group Development at Borealis explored existing and developing worldwide solutions for combatting unwanted plastic waste in the environment. Materials focus sessions on day three was about polypropylene (PP) recycling and the latest trends in recycling technical plastics. The event featured five sponsored “Ask the Expert” Livestreams with industry experts from Erema, KraussMaffei, Vecoplan, Sesotec and Milliken, exploring a range of technical topics with in-depth presentations and Q & A sessions including: Driving the circular economy in plastic recycling: performance factors for post-consumer (PET/PO) applications and innovative lighthouse projects with Christoph Wöss and Clemens Kitzberger of Erema; Circular Economy & Compounding: Latest products, services and solutions with Carl-Philip Poepel, Ralf J. Dahl and Josef Art of KraussMaffei; Next level in plastics pre-treatment with Daniel Wienand and Philipp Güth of Vecoplan; How to tackle challenges in plastics sorting with Dominik Ebner, Benjamin Häusler and Franz Schaab of Sesotec; Enhancing the properties of recycled polypropylene resins in injection moulding with Tugce Asici-van Houselt and Marta Sans Peña of Milliken. All conference sessions are available for on-demand viewing on the PRSE Virtual website. www.prseventeurope.com Plastics Recycling Show Europe Virtual Event took place from December 9-11, 2020. Participation in all elements of the online event was free of charge. The PRSE virtual conference examined the latest developments in plastics recycling, practical solutions for the sustainable use of plastics, dealing with plastic waste and better design for recycling.","@ID":45} "8 NEWS PETplanet Insider Vol. 22 No. 01+02/21 petpla.net Avient ColorForward experts predict pandemic to influence colour preferences Avient Corporation, a provider of specialised and sustainable material solutions and services, announced that Avient ColorWorks has launched ColorForward 2022. This 16th edition of the annual colour forecasting guide for the plastics industry marks its debut within Avient, which was formed this year from legacy businesses PolyOne and Clariant Masterbatch. As in years past, ColorForward 2022 presents stories associated with four societal trends that are expected to influence consumers consciously or unconsciously over the next few years. Each trend theme also includes a palette of five associated colours that are predicted to elicit a response from consumers. This year, ColorForward 2022 trend watchers expect the effects of the Covid-19 pandemic to linger for some time, even if vaccines and treatments allow the world to return to some semblance of ‘normal.’ Naturally, they contend this will drive societal trends and consumer response to colour in the near- and mid-term future. “For 2022, the overall colour palette is dominated by shades of yellow,” explains Judith van Vliet, ColorWorks Senior Designer and leader of the ColorForward team, “and many of the other colours are joined to the yellow family. For instance, many of the greens, reds, oranges and some of the blues, have a high yellow influence, creating a sense of the warmth of human connections that are interrupted by the social isolation the pandemic forces on us. In addition, the yellowish greens are indicative of our need to reconnect with nature and avoid the synthetic, including all of the screens and digital connections we must now use excessively.” Avient ColorWorks also offers seminars at its four designs and technology centres around the world, as well as at selected conferences and customer sites. These can be conducted virtually and/or in-person when appropriate. www.avient.com Bericap’s recyclable 100% silicone-free BericapValve wins Sustainability Award 2020 BericapValve has won Packaging Europe’s Sustainability Award 2020 in the category “Recyclable Packaging”. The award recognises and awards the major sustainability impact behind the small visible change to a 100 % silicone-free valve. Unlike conventional silicone valves, Bericap’s product is made of TPE and does not contaminate the recycling stream with silicone. Its recyclability is top-rated and certified according to institute standards such as bifa Umweltinstitut and Fraunhofer. Bericap won the award against five finalists. In its statement, the jury highlighted that the BericapValve is “made for recycling”. Considering the entire recycling process, Bericap eliminated a weak spot that has a huge negative impact on the whole cycle: the contamination of the PET material by silicone valves. Bericap concluded that a change in material in the seemingly small valve away from the silicone would have significant positive effects on the entire process. The new product: BericapValve, is made of TPE, it recycles within the HDPE (high-density polyethylene) and PP (polypropylene) recycling stream without contaminating it while possessing the same properties as conventional valves. A small detail – but a game changer for recycling. The BericapValve is available in Bericap’s broad range of food closures and fits all common neck and standard flip-top closures. It can be utilised for sweet, sour and fat-containing products and ensures exact and clean dispensing. With this wide area of applications, the new valve is the sustainable alternative to conventional silicone valves which are currently used predominantly for ketchup, mayonnaise and other spreadables. The valve can be adjusted in material hardness and cutting geometry to any squeezable product. It is suitable for bottom-down or bottom-up usage. In order to adapt the valve material appropriately, the BericapValve has undergone numerous internal tests. It has been tested and certified according to the Commission Regulation (EU) No. 10/2011 of January 14, 2011 on plastic materials and articles intended to come into contact with food. www.bericap.com United Caps: Virtual event on ‘what you would have seen’ at Interpack With the Covid-19 pandemic continuing to ravage travel and trade shows, United Caps is working hard to ensure the industry has access to the information the company would have provided at Interpack. In line with that objective, the industry will be brought together for a virtual event on February 24-26, 2021 where there will be opportunity to learn more about the company’s latest innovations for key packaging sectors. During this event, United Caps will be showcasing the latest developments in the UCTC tethered closures range for beverages, new additions to the “Everything you need, nothing you don’t”- Edible Oils and Vinegars range as well as advancements in the sectors of Infant Nutrition and Agro & Petro chemical closures. Visitors will be able to watch videos, download white papers and organise 1-on-1 meetings with members of the United Caps key accounts teams for in-depth discussions. There will also be the opportunity to join seminars on how the company is approaching key issues impacting the industry from Sustainability and Differentiation right through to Innovation. Registration details will be soon announced on the United Caps website and through the company’s social media channels. www.unitedcaps.com","@ID":10} "MATERIALS / RECYCLING PETplanet Insider Vol. 22 No. 01+02/21 petpla.net 16 Organic yogurt in 100% rPET cups From cup to cup Starlinger viscotec, PET-Man and the dairy producer Biohof Zauner have together developed the first white yoghurt cup made from 100% rPET, which can be recycled after use and made into a yoghurt cup again. Line for rPET sheet extrusion at PET-Man Christina and Leonhard Zauner are Austrian farmers and producers of organic dairy products; they market their products under the brand ‘Biohof Zauner’. The couple wanted to pack yoghurts in the most sustainable way possible, and unexpectedly became pioneers of rPET packaging. The reasons Christina and Leonhard Zaumer were looking at sustainable packaging were clear. “In the past, we sold our yogurt in glass containers. These are heavy and the washing is timeconsuming and requires a lot of water and detergent,” Their requirements were clear, but none of the existing solutions met all of them, since “the packaging should be environmentally friendly, stable and lightweight. We wanted the packaging to be recyclable and to protect the dairy products from UV light - ideally, it is white.” Leonhard and Christina Zauner 100% recyclable In Europe, dairy products are currently packed mainly in polypropylene (PP) or polystyrene (PS), which according to the European Food Safety Authority (EFSA) cannot be reprocessed into recycled material for food contact. Strictly speaking, recycling these materials is “downcycling” rather than “recycling”. With rPET, Starlinger viscotec and PET-Man rely on upcycling. “For us, recyclable means that the same product can be made again after it has been used by the consumer and recycled.” Since there has been no packaging solution for yogurt which is recyclable according to food grade standards, they developed the first white cup made from 100% rPET. Organic yogurt cups made from rPET and designed to be recycled again The new rPET cup is not just made from recycled material, it is also designed for recycling. This assures 100% recyclability and turns the cup into valuable input material for recyclers after use. First, the consumer","@ID":18} "PETplanet Insider Vol. 22 No. 01+02/21 petpla.net 46 PETbottles Beverage + Liquid Food An eye-catching bottle for Fruity Touch The Italian drinks’ manufacturer, Sant‘Anna, has brought out a natural mineral water with a dash of fruit juice concentrate under the name, “Sant’Anna Fruity Touch”, which comes in a sharply tapered, clear 0.5 l bottle. The picture shows the variety containing strawberry and sour cherry. The surrounding grooves in the waist area, the dimple-like ridges above its base and narrow film label are interesting packaging features. The large bottle spout is secured by a screw cap. www.santanna.it A Rauch Juice Bar in 100% rPET The Austrian fruit juice company, Rauch GmbH, has brought out a passion fruit and peach white tea which comes in a 500ml bottle made from 100% rPET. The product contains 25% fruit juice and properly brewed tea but with no added sugar. The transparent bottle has a full-surface sleeve label with an unprinted area that allows the customer a clear view of the product. The brand logo is printed on top of the screw cap which has a tamper-proof strip. www.rauchjuicebar.cc Soda syrup in a tapered bottle MySodapop, soda pop manufacturers for making individual drinks at home, is also selling different syrup varieties of these fizzy drinks. One of them is the “Premium Soda Syrup” tonic water. The clear, tapered bottle contains 500ml of the product from which, according to the manufacturer, at least four litres of ready-to-drink beverages can be made. The sleeve label contains information on the product and how it should be dispensed. www.mysodapop.eu A healthy shot from I-Do Antidote Distribution GmbH from Munich has brought out an organically approved 60ml vegan shot under the I-Do label which comes in a handy, small, round bottle made from 100% rPET. In addition to the standard ginger content, the first of the two varieties shown contains aloe vera, apple vinegar, coconut and co, while the second shot comprises wheatgrass, moringa, baobab and co. Self-adhesive film labels provide information on the product with an opaque screw cap and tamper-proof strip that secure the bottle. www.ido.bio","@ID":48} "MATERIALS / RECYCLING PETplanet Insider Vol. 22 No. 01+02/21 petpla.net 18 Vacuum filter enables consistent viscosity for customised polyester Viscosity and homogeneity are crucial Further development of the circular economy for post-consumer or post-production waste is a particular priority, which means that the recyclability of PET products is especially significant. Modern, resource-friendly packaging would not be conceivable without manmade PET fibres and commodities made from chemicals, such as beverage bottles and cleaning materials. As a dominant raw material, along with polyolefins and polyamide, recycling of polyester is absolutely essential. In the case of PET bottle material, recycling of polyester materials and possibilities for converting the waste into new high-end products within the polyester filaments, fibres and nonwovens market are very advanced. Across the globe, consumers are demanding sustainable products and careful resource utilisation, in the textile sector increasingly, too. Leading fashion companies, sports apparel makers, furniture manufacturers and the automobile industry (e.g. for car seats and interior cladding) are increasingly focusing on sustainable products, including those made from recycled materials. They are already instructing suppliers of filaments, fibres and nonwovens that they will, in the near future, be switching their textile products from exclusively virgin polyester to as much as 100% recycle. Consumers’ social awareness has been the trigger. The original trend of manufacturing only sub-premium goods, e.g. insulating materials, using recycled polyester, is now seen as shortsighted. Recycled polyester has long been present within the high-end textile segment. Seeing polyester as a valuable resource rather than as waste is the correct perspective. Manmade fibres and filaments made from recycled bottle flakes require corresponding single-variety collection, pre-sorting and comprehensive cleaning of the material being recycled, before shredding into polyester flakes. They can then be spun directly into pre-oriented yarns (POY) filaments (DTY (drawn textured yarn) in the downstream process), staple fibres, nonwovens and BCF endless filaments. Technology is now so refined that many product applications achieve quality levels equivalent to virgin material. However, there are also many cases in which the material quality and/or property achieved does not meet market requirements. For numerous textile applications, parameters such as viscosity and homogeneity are crucial and must be subject to virtually no fluctuations. Enabling recycled polyester to be used in the first place requires pre-treatment. BB Engineering GmbH’s VacuFil recycling process enables the manufacture of outstandingly homogeneous, viscosity-stable rPET melt; a precisely definable and reproducible raw material for downstream processes, such as spinning plants. As an experienced manufacturer in this field, BB Engineering (BBE) is familiar with the dire impact that even the smallest viscosity deviation has on the spinning process. The company says that, with VacuFil, it has succeeded in aligning melt with process in a targeted manner, Matthias Schmitz, VacuFil Product Manager, and Dr Klaus Schäfer, Managing Director BB Engineering GmbH","@ID":20} "BOTTLE MAKING 33 PETplanet Insider Vol. 22 No. 01+02/21 petpla.net Target Plastic, May 25, 2020 We met: Mr Po-Chao Huang, Managing Director From bottle supplier to OEM fillerby Kay Barton The Huang family founded Target Plastic as PET was making its breakthrough into the Taiwan market in the mid-1990s. Located in Zhubei, about 70 km south-west of Taipei, it specialises in the production of PET bottles, particularly for hot fill applications and, more recently, ready-made ones for OEM drinks. Overseas exports, for example to Europe or North and South America, are a principal focus for the company’s efforts. We are not talking here about mass production but rather an emphasis on individual solutions and a flexible approach. We spoke to the founder’s son, Mr Po-Chao Huang, about the firm’s history, its day-to-day business and why Taiwan is such an excellent choice for international businesses. “My father founded the company as a plastic bottle manufacturer in 1994”, Mr Huang explains. At that time, Taiwan’s local market was dominated by glass and cans, with PET just starting to make in-roads. “My father liked the material’s attractive properties, in particular its light weight compared to glass and transparency in relation to cans. The potential for relatively lowcost processing also appealed to him”. When the company was established it staked everything it had on investing in a Nissei ASB machine. The first few years were to prove economically challenging before business finally picked up at the end of the 1990s. “We focused solely on bottle production for around 20 years, with PET processing making up 95% of our business strategy”, said Mr Huang. “The remainder comprised a small number of PP products”. Up until the mid-2010s, the company’s client base had been steady but rather modest. Then, two years ago, Target Plastic decided to bottle drinks for the first time and purchased a filling line. As Mr Huang explains “We wanted to expand our business model into an all-in-one solution as demand from industry was there. However, we did not have any brands, having become exclusively OEM bottlers. Nevertheless, we do supply products internationally”. It all started with a well-known flavoured water label with the company providing around two million bottles each month to ten different customers. A specially established subsidiary, which dealt exclusively with product sales, was also responsible for international marketing. “We then received a request for a tea drink, inititally from Hong Kong and started with 200,000 bottles which later went up to 300,000”. “We became interested in the Taiwan market’s potential early on”, Mr Huang explained. Today, exports make up 50% of the company’s drinks business which it intends to increase to 60-70% in the future. In terms of transport logistics, empty bottles remain ring-fenced in their own market. He adds “Over time, we have learned how to negotiate successfully with our international clients as business continues to grow”. The company uses differently-treated tap or groundwater in OEM drinks such as teas, juices and functional water, depending on the customer’s wishes. Target Plastic’s drinks are sold in North, Central and South America, Poland, Italy, Hong Kong, Singapore and, of course, in Taiwan itself. Blow moulded hot fill bottles with crystallised neck The machine inventory is growing all the time. We were told that Target Plastic has been buying one or two additional machines each year from Nissei ASB for the last decade or so. A number of machines obtained from the equipment supplier are now in producTour Sponsors: Some of Target Plastic’s bottles and beverages","@ID":35} "OUTER PLANET 54 PETplanet Insider Vol. 22 No. 01+02/21 petpla.net OUTER PLANET Bottles made of paper, houses built from PET bottles - in this new “Outer Planet” category, we will be presenting projects that you would not normally expect to see in PETplanet Insider. But bear with us, these projects are not quite as off the wall as you might think. Quirky they may be, and most may never get beyond the development stage, but some might just be the next big thing. Join us in some blue sky thinking that could energise our entire sector. Coca-Cola’s paper bottle prototype The perfect pulp? Houses built up from plastic African population stands at 1.4 billion people with an estimated 540 million people living in urban areas, and around 60% of them – 324 million people – live in informal settlements in inadequate homes. Assuming that on average five people live in one home, a deficit of adequate housing could be estimated at 64 million units today. Paper is not the very first material that comes to mind when packaging liquid-based contents. Nevertheless, several companies around the world are experimenting to produce 100% paper bottles. One of them is CocaCola Europe, which has presented the first prototype of a paper bottle - which, however, has not yet managed entirely without plastic. The concept has been developed with Coca-Cola’s partner, Paboco. The Danish company Paboco, which emerged from the start-up EcoXpac, is a joint venture between paper packaging material developer BillerudKorsnäs and bottle manufacturing specialist Alpla. “Our vision is to create a paper bottle than can be recycled like any other type of paper, and this prototype is the first step on the way to achieving this. A paper bottle opens up a whole new world of packaging possibilities, and we are convinced that paper packaging has a role to play in the future,” says Stijn Franssen, EMEA R&D Packaging Innovation Manager at Coca-Cola, who is working on the project. A lot of work still has to be done to achieve this vision of a recyclable paper bottle. The first-generation paper bottle still contains some plastic: “This firstgeneration paper bottle prototype still consists of a paper shell with a plastic closure and a plastic liner inside. The plastic we use is made from 100% recycled plastic that can be recycled again after use. But our vision is to create a paper bottle that can be recycled like any paper. The next step is to find a solution to create a bottle without the plastic liner,” Stijn says. Thorough testing going on Just like other types of packaging, a paper bottle of the future must adhere to the same high safety and quality standards for food packaging that currently apply. Stijn and this team are putting the bottle through comprehensive testing in the lab to see how it performs in the refrigerator, how strong it is, and how well it protects the drinks inside. “We also reflect on how our consumers will react to this paper bottle. Topics like when and where it could be sold and how it can be recycled are all being considered. The bottle must be explored from every perspective to ensure that we make the bottle the best it can be,” says Stijn. He is optimistic that future technological solutions will help achieve the vision of a paper bottle that is just as recyclable as paper – a type of packaging technology that can be part of CocaCola’s packaging and portfolio mix, and which could be used for a wide range of beverages. www.coca-cola.eu Between 1990 and 2017 African countries imported around 230mt of plastics. Most of these plastics has ended up in dumping sites across African cities after their uses and reuses and creating the biggest environmental concern as local governments are not equipped to process the waste. In 2019, Shelter Afrique stated that Africa needs 1.4 trillion USD to plug adequate and affordable housing deficit. The huge housing deficit on one hand and the huge amount of plastic waste in Africa can be seen as both a huge challenge and a tremendous opportunity to expand economic activity, create millions of jobs and promote environmental sustainability. UN-Habitat has been working with Othalo, a start-up company in Norway that has developed a technic to use recycled plastique to produce building components. Once plastic waste is recycled, it is shredded and mixed with other elements including non-flammable materials and used to produce building components like walls, floors and roofs. Othalo system can be used to build up to four floors. A 60m2 home will need 8t of recycled plastic. A factory with one production line produces 2,800 housing units annually. In partnering with UN-Habitat, Othalo wants to make sure that their technology responds to the needs of the final users. www.othalo.com","@ID":56} "PATENTS PETpatents www.verpackungspatente.de PETplanet Insider Vol. 22 No. 01+02/21 petpla.net 45 Plastic aerosol bottle Internal Patent No: WO 2020/ 053210 A1 Applicant: L’Oréal, Paris (FR) Registration date: 10.9.2019 This application describes a pressurised, one-piece plastic aerosol bottle which can meet specific requirements related to pressure stability and resistance to breakages if dropped accidentally. Pivoting underside section Internal Patent No: WO 2018/ 171920 A1 Applicant: Krones AG, Neutraubling (DE) Registration date: 13.12.2017 A specially produced hot fill bottle whose convex/folded base folds inwards after filling and cooling due to changes in volume. Stand sleeve Internal Patent No: WO 2018/ 172052 A1 Applicant: Alpla Werke Alwin Lehner GmbH & Co, KG, Hard (AT) Registration date: 6.3.2018 A stand sleeve for a container that is subjected to increased internal pressure, specifically a plastic aerosol container that has an appropriately shaped and stable base. Connectable bottles Internal Patent No: WO 2020/ 046228 A2 Applicant: Afsin, Türel, Denizli (TR) Registration date: 6.3.2019 The upper and undersides of the bottles are designed in such a way that allows several bottles to be connected in a liquid- and pressure-tight manner. Reinforced edges Internal Patent No: WO 2018/ 208903 A1 Applicant: The Coca-Cola Company, Atlanta (US) Registration date: 9.5.2018 A bottle for hot filling with specially shaped compensation surfaces and reinforced, stabilising corners/edges. Handle-equipped container European Patent No: EP 3623304 A1 Applicant: Nissei ASB Machine Co. Ltd., Nagano (JP) Registration date: 9.5.2018 A reusable bottle, e.g. for placing in a water dispenser, which has a handle that is specially integrated within the bottle’s shape to make it easier to wash/clean via the handle area with a cleansing agent.","@ID":47} "MATERIALS / RECYCLING PETplanet Insider Vol. 22 No. 01+02/21 petpla.net 15 Recycling & sustainability Spurred by consumers, government regulators around the world, nongovernment organisations and brands themselves, companies that use plastic bottles and packaging are making significant commitments and strides on sustainability. As the report shows, Europe is more advanced than the U.S. in recycling packaging and food service plastics: approximately 40% of overall plastics packaging is recycled by EU nations compared to 28% in the U.S. France, Germany, and the United Kingdom are leading the effort by establishing significant targets. When it comes to PET bottles specifically, approximately 37% single-serve PET bottled water containers are recycled, according to the National Association for PET Container Resources (Napcor). These rates exceed other bottle and plastic recycling rates; however, the bottled water industry and other beverage manufacturers recognise the need to improve recycling and usage of rPET bottling. Also in the focus of bottling design innovation is the tethered cap. A number of plastics companies have developed tethering designs to help brands meet the EU requirement and improve recyclability. In the U.S., tethered caps are expected to increase in usage as loose caps cause significant material loss when recycled mechanically and can leak into the environment. Plastics and its members believe the challenging factors in recycling are not insurmountable, but that current mechanical recycling efforts will not be able to meet the demand from businesses for quality recycled material. The report states that recycling infrastructure needs to improve and chemical recycling technologies will need to scale up and increase efficiencies in the coming years. With many major brands making packaging and bottling sustainability pledges that increase from 25% recycled content in 2025 to 50% or more recycled material content by 2030, more recycled content will need to be processed and made available to the market. The major issues hindering recycling in the U.S., according to the Recycling Partnership, are: 1) Packaging innovation has outpaced the capabilities of recycling systems. 2) Demand for recycled material outstrips supply. 3) Underlying challenges create a difficult environment to develop a sustainably funded and responsive recycling system. The International Society of Beverage Technologists (ISBT) is developing guidelines and recommendations for bottle designers to incorporate recycled PET material and improve packaging for current recycling stream companies to meet their sustainability goals. Brands are actively discussing the balance among sustainability, the recycling of the bottle, and marketing/ sales of product. Recycling challenges in the U.S. Virgin material costs vs. recycled material costs: Given current prices and supply of raw materials globally, the cost of recycled packaging material is more than virgin plastics. During tough economic times, costs influence purchasing decisions of both brands and consumers. Antiquated municipal recycling facilities (MRFs): Many of the recycling systems in metropolitan areas were designed more than 40 years ago; the kinds of materials being sent to MRFs have changed over the years (less newspaper/more plastic) as have technologies and capabilities, like laser sorting systems and improved landfill designs. Confusing/conflicting recycling rules and systems: The public and private sectors are promoting recycling and offering infrastructure, but rules can vary from one community to the next. Improved recycling consistencies, education, and enforcement can help increase and improve recycling. China’s “Operation National Sword”: In 2018, China enacted a national programme to ban (or dramatically limit) foreign recycling waste. For years, China imported 45% of the world’s plastic waste as well as other recycled materials. China’s new policy has overwhelmed America’s recycling system, changing the economics of recycling and management of waste. Local vs. state vs. national priorities for recycling/infrastructure: Recycling, compared to other infrastructure systems (roads, public transportation, water and sewage systems), is often overlooked and underfunded. Prioritising recycling at all levels of government and harmonising recycling systems will enhance recycling rates and the availability of recycled material. Evolving packaging design: Packaging systems for foods, beverages, and other consumer items can use a number of materials, including plastics. But some changes to packaging can improve their likelihood of being recycled, such as easily removed labels, inks and glues. Brands and packaging designs need to continue to focus on end-of-life issues to improve recycling rates. Contamination: The National Waste and Recycling Association estimates 25% of the nation’s recycling stream is contaminated material - significantly higher than the 7% contamination rate just 10 years ago. With 40% of Americans indicating they try to recycle “maybes” into their bins, conflicting rules and “wishcycling” add to contamination problems and rates. The complete report with all insights, data and market analyses is available at www.plasticsindustry.org Michael E. O’Leary, Senior Technical Services and Marketing Representative at DAK Americas and member of ISBT states: “The challenge that we see, even in reaching the 2025 recycled content goal, is the availability of recycled material. One immediate factor impacting these goals is Covid-19; many of the bottle deposit states are not collecting bottles right now. It is very difficult to get the necessary amount of content for producers to make the recycled PET and sell it to brand companies and converters,” O’Leary added. www.plasticsindustry.org","@ID":17} "CAPS & CLOSURES 32 PETplanet Insider Vol. 22 No. 01+02/21 petpla.net Recyclable valve for PET recycle stream Well dosed Aptar Food + Beverage, a global leader in dispensing solutions, offers a portfolio of dispensing closures for both the Food and the Beverage markets and is dedicated to creating solutions based directly on consumer feedback. One of these is a new valve designed to improve the recycling cycle. But Aptar also takes the tethered caps specifications into account with two newly developed closures. Aptar introduced a new valve, offering good flow control combined with clean dispensing. It is intended to ensure that consumers get a precise amount of product while avoiding drips, leaks, or spills. SimpliCycle valve is made from a TPE material with a low density that allows the valve to float, so it is easily separated from the PET stream, and then recycled within the PP/PE olefin stream. The SimpliCycle valve is claimed to offer recyclability while still maintaining all of the advantages of Aptar’s standard SimpliSqueeze and Swimming Silicone valves, including high repeatable performance and slit versatility to fit a wide variety of applications for food, beverage, and other product applications. By 2025, Aptar has committed to take action to eliminate problematic or unnecessary plastic packaging; to move from single-use toward reuse models where relevant; to have 100% of its plastic packaging be reusable, recyclable or compostable; and to find solutions to increase recycled content across all plastic packaging used. Closures with benefits Caps and closures recently introduced by Aptar include the sport cap Rocket. It offers consumers visual safety through a yellowcoloured band that indicates whether packaging has already been opened. It provides further safety to consumers with its “no-dust”, double wall lid design that protects the spout from external contaminants, in addition to being designed to adhere to child safety standards (BSDA & EN 71*). CAPS & CLOSURES The sport cap Rocket offers consumers visual safety through a yellow-coloured band that indicates whether packaging has already been opened. A large finger recess and audible closing “click” sound makes opening and closing easy and reassuring to consumers. While most caps open at a 110-degree angle, Rocket’s hinge technology offers a comfortable 180-degree angle. The hinge functionality also ensures the elimination of the lid spring-back effect. The tamper evident band is tethered to the bottle with the Stay-With system, which keeps the closure attached to the bottle through its lifecycle, and therefore increases the likelihood of the closure being collected and sent through the recycling stream with PET containers. Rocket complies with upcoming regulations, including the Single Use Plastic (SUP) directive proposal in Europe. Maestro is Aptar’s new dispensing solution for edible oil that gives consumers an easy-to-open, portion control, and drip free benefits. Maestro’s wide finger recess allows consumers to easily open the lid with one hand, and the raised spout was thoughtfully designed to let consumers decide which flow to pour with. Thanks to its tethered cap and 100% recyclable material, Maestro is applicable to PET containers and is compliant with the PET recycling streams. www.aptar.com TPE valve +44 (0) 1254 584210 sales@petmachinery.com petmachinery.com Active for over 25 years, our global network and specialist knowledge makes us the go-to company for the sale or purchase of a PET machine. Commercially savvy, we work closely with our customers and our global network, to make sure everyone gets the best deal. Providing comprehensive advice throughout your sale or purchase; we can arrange dismantling, loading, packing, shipping, specialist insurance and commissioning. If you have amachine to sell or you’re looking to purchase, please get in touch. THE INDUSTRY EXPERTS","@ID":34} "MARKET SURVEY 29 PETplanet Insider Vol. 22 No. 01+02/21 petpla.net Resins Company name Indorama Ventures Polymers Germany GmbH Neo Group Reliance Industries Limited Novapet, S.A. Postal address Telephone number Web site address Contact name Function Direct telephone number E-Mail Philipp Reis Strasse 2 65795 Hattersheim, Germany +49 69 305 6025 www.indoramaventures.com Mr Christian de Lope Market & Business Development +49 172 652 6558 christian.delope@de.indorama.net Industrijos str. 2, Rimkai LT-95346 Klaipeda district, Lithuania +370 46466710 www.neogroup.eu Ms Justina Volček Product Development Manager +370 602 14 169 justina.volcek@neogroup.eu PETBU, Build. No. 8, BWing, 1st floor,Thane Belapur Road, RCP, Ghansoli, Navi Mumbai, 400701, Maharastra, India +91 22 7967 0000 www.ril.com P° Independencia, 21, 3°, PC 50001 +34 976 216129 www.novapet.es Mr Ricardo Monfil Head of Polymers Division +34 976 216129 rmonfil@samca.com Resins 1. Brand name of the resins Polyclear PET, PolyShield Resin, Xpure Polyester NEOPET Relpet and Relpet Green NovaPET 2. IV range a. of homo-polymers 0.60 - 1.05 0.56 - 0.82 0.76 0.58 - 0.96 b. of co-polymers 0.81 - 0.87 0.76 - 0.84 0.59 - 1.00 0.60 - 1.30 3. Speciality resins CSD Polyclear PET 1101 NEOPET 80, NEOPET 82 Relpet G5841 LBS Soft, CR Water Polyclear PET 1101, T94N Aqua NEOPET 76, NEOPET 78 Relpet G5761 MW Soft, CR, SPRIT Beer PolyShield Resin 2300 and Masterbatch 2520 NEOPET 80, NEOPET 82, NEOPET 84 Relpet B9845 Glasstar Edible oil Polyclear PET T94N CR, Glasstar Wine / Liquors PolyShield Resin 2300,2520; OxyClear Barrier Resin NEOPET 80, NEOPET 82 Relpet B9845 / Relpet G5801 Glasstar Personal care / Pharmaceuticals Polyclear PET T94N, XPure Polyester NEOPET 80 Relpet G5801 Glasstar, SPRIT Slow crystallisation Polyclear PET T94N, XPure Polyester Relpet S5841 (5 gallon returnable, thick sheet and thick moulded articles) Glasstar, SPRIT Hotfill NEOPET 82 HF Relpet H7761 HF Pre-coloured DCU, Luz Fast reheat Polyclear PET 1101 NEOPET 82 FR, NEOPET 84 FR Relpet QH5821 LBS Soft Other Next generation catalyst series Xpure Ultra NEOPET Relpet C1000 (CPET trays, high tenacity straps), Relpet IM5590 (thin wall products and injection moulded articles), Relept OP5821 (UHTmilk on aseptic filling line) CPET, HT, REX (for EBM), SOL (aerosol bodies), other nonpackaging applications 4. Increased barrier properties PolyShield Resin 2300, Masterbatch 2520, Oxyclear Additive 3500 Relpet B9845 barrier grade has both active oxygen barrier and passive carbon dioxide barrier Light barrier: Dairy, LUZ , DCU, Polygloss Gas barrier: GLASSTAR, SPRIT 5. PEN mixes available Yes, also PEN Copolymers with different PEN content 6. Recycled blends available Relpet Green (100% PCR) Yes, under customer requirements NEOPET CYCLE PET resins (with PCR content) 7. Special comments Extrusion Blow Moulding grade available: Polyclear EBM PET 5507 NPG modified resins under development Gradeshavebeendevelopedbasedonfinerrequirementsof end-use;customisedgrades(likeEBM)areavailableonrequest. Focused on innovation at the service of packaging Specialised in light barrier protection","@ID":31} "CAPS & CLOSURES 30 PETplanet Insider Vol. 22 No. 01+02/21 petpla.net Designing tethered caps Convenient, comfortable, connected The EU SUP Directive’s tethered closures rule for all beverage containers of up to three litres to have lids that ‘remain attached’ has pushed the effective design and manufacture of such closures up the priority list for plastic packaging manufactures. CAPS & CLOSURES Global plastic packaging manufacturer Retal is driven to meet and exceed EU targets to deliver on its beverage brand customers’ CSR targets as well as its own strict sustainability goals. Andzejus Buinovskis, design engineer at Retal, is at the heart of the company’s development of its tethered cap solutions, which is continually evolving as the brand owner requirements change. Buinovskis says, “The process of developing and changing has been interesting as we’ve been in close communication with our leading beverage brand customers. Their needs are evolving too as they put potential solutions to their test groups of experts and consumers, so sharing ideas has helped to create solutions that we’re really proud of.” Buinovskis and the team work on potential designs using 3D Experience software from Dassault Systèmes, which allows for ultra-detailed modelling of the tiniest details, which, for such a small end product, can make all the difference. Samples are then produced at its Lithuania plant and sent to customers for feedback. Buinovskis says, “We are continually developing and are open to other solutions, we have to be flexible in this changing landscape and, thanks to our R&D facilities, we can be nimble in response to our own findings and ideas and our customers’ demands. I am inspired by the feedback we get from our customers and also from the tight restrictions that the requirements and legislations demand.” Design process That balance of inspiration and legislation is where plastic packaging manufacturers are able to offer real advantage. The need to produce connected closures that offer brand differentiation while performing in a comfortable and sustainable manner is the very essence of the single use plastic industry for beverages. With the EU SUP Directive date fast approaching there is no alternative solution, or a possibility to just ‘stay as we are’, so integrating design inspiration with commercial understanding is an exciting opportunity. Buinovskis notes, “All the manufacturers have the same brief, we all know the brand requirements and we all know the EU legislation, so the task is to compound all our knowledge of closures and necks and pressure and weight and everything we know into a viable solution that can be commercially produced, allowing for the brand identity and the shelf differentiation.” Likes and dislikes The very personal nature of the tethered caps means that it is both the ultimate comfort of the end consumer and the environmental issue of effective collection and recycling that is at play. So the test groups offer crucial feedback on issues such as ease of opening in addition to the need for closures to stay connected in order to support efficient sorting of recycled plastic. Buinovskis concludes, “The effective design and manufacture of pleasing-touse tethered closures is an important chapter in our industry because it represents the future. We will always have to design tethered closures from now on as this legislation and the environmental needs of a circular economy will not go backwards.” www.retalgroup.com","@ID":32} "TOP TALK PETplanet Insider Vol. 22 No. 01+02/21 petpla.net 11 of projects at different levels of maturity which were already on their way. And we wrapped it all up in a single Strategic Plan for the company until 2030. The basic theme of this Plan is to create and to promote throughout the action of different divisions of the company a real and concrete circular economy for PET, which is, we believe, a wonderful material. For doing so, the Plan organises Novapet into three different divisions at the service of a unique strategic vision: Novapet resins and concentrates; Novapet packaging; and REnovaPET. PETplanet: With REnovaPET you are announcing a new subsidiary for recycled PET in addition to your virgin PET resins. Can you tell us more about this? González: REnovaPET has assumed and undertaken the fascinating mission to create real circular economy conditions for PET in the coming years. And this will be achieved not only because of the transformation of our industrial assets to produce PET with collected material (we expect to produce 120,000t in 2024), but because of our involvement as a company in the setting up of collection systems complementary to the existing integrated schemes. The installation of the first equipment to produce 15,000t of rPET will be done within this year and we expect to have it in operation in Q1 2022. We strongly believe in PET as a great material for the future. But “future” for this material means social and individual responsibility, adequate practices along the length of the chain, and the promotion of the right culture for it all. PETplanet: Mr González, during your Open House in 2016 you told me about your observations that your customers are increasingly outsourcing the injection moulding process but order the preforms from you instead. Your Barbastro plant was refitted from seven to eleven injection moulding machines by then in a record time. Now you have just announced that you are expanding the preform area even more. Can you briefly outline the developments for us? González: Our injection plant in Barbastro, close to the central Pyrenees, is equipped with eleven lines providing a total yearly output of two billion preforms. The new investments we have already announced involve new contracts signed with customers in France and northern Spain. These investments will lead to fourteen lines operating in Barbastro at the end of this year for a total output of 2,5 billion pieces a year. Moreover, nowadays Novapet Packaging is looking for locations for a new injection plant to be built in the South of Spain and with the plan to have it in operation at the end of 2022. We consider the installation of 4-5 injection lines in this second plant, for a total production of around 700 million preforms a year. PETplanet: Back in 2016, you also defined the dairy market as a major growth market for PET. How has this developed for you? González: Novapet has always considered the dairy market as one of the most important growing opportunities for PET as material. I do not think I need to insist on the convenience, functionality and shelf appealing virtues of PET compared with other traditional dairy packages. And these growing opportunities do not come exclusively from the plain clear bottles already widely used for fresh dairy products distributed under refrigerated conditions, but more importantly from the white bottles suitable for long shelf life dairies (ESL and UHT). Novapet was one of the very first companies dealing in this sector, and has today a global presence in it throughout the licence agreement upon our technology signed with Colormatrix (today Avient) four years ago. Today, our special PET technology for dairies is sold, under Avient’s brand Lactra SX, in four continents and is supporting the substantial growth of this market. PETplanet: Thank you very much! www.novapet.com Novapet restructures its business divisions Novapet, a Samca Group company, has undertaken a restructuring of its internal divisions which went into effect in January 2021. It is derived from the growth recorded in recent years in the company’s activities related to the production of containers, and from the approval of the company’s new Strategic Plan to the year 2030. Novapet will continue applying its strategy of progressive downstream integration of its activities in the PET market, with growth in the injection of preforms and in the design and production of finished PET containers. In the upcoming years a strong investment plan will serve this strategic line dedicated to: Reinforcing the production capacities of preforms in the plant in Barbastro, that is envisaged to pass the 2,500 million units in 2021. Consolidating the presence of the company in new functional markets. Creating a second injection plant in the south of the Peninsula. Making its subsidiary Farmaplás a leader in the market of finished containers of PET and polyolefins. To accomplish this, Novapet will concentrate all these activities in a new division with the business name Novapet Envase (Noven), which will be organised in two different branches of operations: Noven Preforms (for PET preforms as well as the technical, logistical and financial services associated with them) and Noven Farmaplás (including all the activities of the current Farmaplás). Secondly, Novapet has recently incorporated a new subsidiary, REnovaPET, which will concentrate all the assets and activities related to the production of rPET. In this regard, the company has already approved a first investments that will come on stream throughout 2021 to offer to the market, starting in 2022, 15,000 t/a of rPET. The company will continue the marketing strategy under the Novapet umbrella of virgin PET resines and concentrates, of the commodity resins and the wide range of speciality resins for sectors increasingly different from the traditional ones. www.novapetenvase.com","@ID":13} "INSPECTION 23 PETplanet Insider Vol. 22 Pressco Technology Inc., Mr Michael Coy, Director of Marketing PETplanet: Has your company already developed inspection systems for tethered caps? If so, what were the particular challenges during development and what are the new parameters of the inspection? Pressco Technology has already provided solutions to inspect tethered closures on filled PET bottles. Recently we supplied a system to be installed on an existing water bottling line in Europe; with some minor modifications to the inspection parameters, we were successful in deploying an inspection solution to meet the customer’s requirements for defect detection on the tethered closures. No major challenges were encountered. PETplanet: Can any design of tethered cap be inspected with one inspection system? Because this is an evolving issue, with different styles and designs of closures, a one-sizefits-all solution may not be realistic. Thus far, Pressco’s standard inspection system has been successfully adapted to the new tethered closure designs which we’ve been asked to inspect. Of primary importance is to carefully evaluate each individual closure design and to clearly define the inspection requirements. At Pressco, we are known for working closely with individual customers to develop and/or adapt our solutions to meet their particular needs. We always request that our customers submit samples of their closure and bottle designs along with their quality specifications and inspection requirements so that we may ensure a successful solution. The FHCP3X is Pressco’s full-bottle inspection system. It is capable to inspect many styles of tethered closures on filled & capped bottles in its standard configuration.","@ID":25} "MATERIALS / RECYCLING PETplanet Insider Vol. 22 No. 01+02/21 petpla.net 12 “Chemical recycling is a reality in the PET industry” by Stephen A. Short, President at Petcore Europe Petcore Europe is a Trade Association registered in Brussels, Belgium, and supports the value chain of the PET resin sector. Petcore is an active participant in the Circular Plastics Alliance sponsored by the European Commission to increase the recycling of plastic and create a circular business model by increasing the recycle content of plastics entering the market. To achieve this both aspects of mechanical and chemical recycling are evaluated to ensure end of waste criteria recognise the value of collected waste as a supply chain for reprocessed products. This article is related to PET resin as Petcore’s business focus, whilst recognising there is a wider picture for the total plastic sector. This article focuses on the chemical recycling of PET, a process known as depolymerisation. Mechanical recycling of PET has been commercially available for more than 25 years and continues to be a developing sector. Today chemical recycling is attracting attention by groups interested in the scientific and public area (NGO) seeking to understand the prospects and impact the process has on both the environment and overall sustainability of polymers. Petcore has a specialist working group established to work on common issues and inform the political, regulatory, and public interest whilst gaining an understanding of the chemical recycling of PET. Chemical recycling – Depolymerisation of PET to monomers - Basics To meet requirements both from political directives and public demand, both chemical and mechanical recycling of PET must grow. With a regulatory target of 30% recycled content for beverage bottles by 2030, the ability of the PET industry to achieve this requires significant innovation and investment. Chemical recycling is required along with mechanical, to displace non-sustainable fossil feedstock monomers in the virgin sector of the business and bringing rejuvenation to the resin. Mechanical recycling cannot be the only supply as the performance of the higher percentage mechanically recycled product decreases over time. A synergistic balance of both processes brings the total performance. The chemical industry is highly regulated to ensure that occupational health, environmental impact, input and output product safety and other targets are met to provide a “licence to operate”. There are several processes of chemical recycling which are in development today. To depolymerise PET back to its components, the standards for operating a chemical plant must be met. We support the request by NGO’s for the legislators to scrutinise these developments to ensure they meet the required standards. The industry wishes to comply with reaching the targets, safely and with reduced impact on the environment. This is true of not only in the product but also the whole value chain. However, the balance between negative reinforcement such as plastic tax and/or total ban on plastic products and the ability to have investment in the right innovation, plant and production must be considered to ensure that chemical recycling develops into a sustainable industry meeting the need for the circular economy. This is related to waste management development given that the apparent directive is a reduction in waste, rather than focusing on turning the waste industry into a feedstock sector. If the “end of waste “objective is common for both public and industry turning waste into a valued feedstock the circular economy will blossom and grow. Chemical recycling – Depolymerisation of PET to monomers – Path forward The observations and critique by the NGO’s and scientific studies that raised concern over the suitability and overstated claims by industry referencing chemical recycling is worthy of consideration. It is a common fact that the main objectives of chemical recycling require proven facts. Only by driving innovation can we test these objectives, develop the facts, and prove the concept. It is during the initial phase that most innovative ideas die a death as investment is required without guarantee of pay back. As the value chain for PET, the sector clearly understands there are unknowns which can only be removed by laboratory testing, through a pilot plant, then scale-up to demonstration. Typically, it takes years to go through this process during which failures can and do occur. Chemical recycling is a reality in the PET industry. Today, mechanically recycled flake that has EFSA opinion for safe use as food contact material, is injected into the primary reactor of the virgin PET plant. Using excess glycol (monomer) the melted flake is mixed with the traditional virgin prepolymer starting materials. The flake breaks down to lower molecular weight oligomers and then re-combines with the starting materials to give a homogeneous low polymer that goes further through the process to produce the final PET resin. The process is limited to the percentage of recycled flake can be mixed with virgin feedstock.","@ID":14} "7 NEWS PETplanet Insider Vol. 22 No. 01+02/21 petpla.net Sacmi: RigidPackagingTechnologies B.U. established All of Sacmi’s closure, preform, container, computer vision system and post-processing operations are being brought together in a newly formed Business Unit RigidPackagingTechnologies. This operation is part of a wider Sacmi strategy of developing technologies and solutions for every stage of the production process, with applications ranging from post-processing to research into new materials. General Manager of the B.U. is Vezio Bernardi. The new B.U. aims to take a sector and technological trend-based approach by setting up new, effective internal synergies. Moreover, it aims to merge cores businesses (such as cap, preform and container-making technologies) with new ones in post-processing, an area strengthened in 2020 by the acquisition of Velomat, a specialised designer and builder of high-speed assembly machines for cap closures, micro-pumps and medical devices. Lightweighting, tethered caps, integrated capsule-preform design, in-line computer vision systems that use predictive and A.I. algorithms: these are just some of the things the Business Unit will focus on during 2021 as it seeks to strengthen its technologies for each business area-sector. This will begin with areas such as the latest generation of single and multi-layer CCM compression presses and technologies for the production of PET preforms (IPS) and PET, PP and HDPE containers (CBF, blow moulding, form-fill-seal, with synergies extending to the Sacmi beverage world). That strengthening will also involve, together with plastics, the metal packaging production/quality control sector, the search for alternative materials to plastic and other future developments the international packaging industry might need to face in the coming years. www.sacmi.com Krones virtual showroom online The Krones virtual showroom serves as a communication platform to secure and build customer relationships even in times of travel restrictions and cancelled trade events. Especially during the Covid-19 pandemic, new forms of communication have become increasingly important, with virtual interaction replacing many face-to-face meetings. This is true not only for the private sphere but also for the Krones sales department, which is having to manage without trade fairs at a time when visits to customers are severely restricted. Back in April 2020, Krones created a digital trade fair stand as a platform for customer meetings and at the same time started working on a larger-scale solution: a virtual showroom, which has been online since November 30, 2020. “This showroom is not intended as a trade fair replacement but as an enhancement to trade fairs and also as a long-term communication platform, even when trade fairs are able to resume again in their usual format,” explains Peter Moertl, Press Relations Krones AG. MetaPure Recycling System The showroom includes 3D models of machines that have been made virtually accessible – an advantage illustrated especially by the recycling system for PET and Polyolefin, Krones MetaPure. Although in reality this is several hundred cubic metres in size, interested viewers can inspect it from all angles online and even go right into the system, without having to travel. Everything from the separating of the baled product, the delabeller, the sorting tower, the individual washing modules and the decontamination module MetaPure S can be seen by the viewer conveniently on the screen. Alongside the 3D models, the virtual showroom also includes its own conferencing tool, through which customers can find out more about the Krones portfolio in personal meetings with sales consultants. www.krones.com/en/the-virtualkrones-showroom.php BERICAP Tethered Cap Solutions • Easy& intuitive handling • 180° opening • No change to - Neck finish - Capper - Filling line Approved and ready for line trials now!","@ID":9} "CAPS & CLOSURES 25 PETplanet Insider Vol. 22 No. 01+02/21 petpla.net Customised technology, flexibility and high-quality solutions Complex closures Increasingly complex closures, attention to the environment, ergonomics: caps manufacturers are continuously raising the bar in their new developments. The Italian company Maca Engineering manufactures and supplies a complete range of automatic machines and lines for the production and assembly of aluminium and plastic caps and closures, meeting new challenges in cap design and production. The manufacture of complex closures through fast, reliable and fully automated machines has been the hallmark of Maca Engineering’s experience for over 30 years. It is an ability recognised by the market to the point that often in the initial research or prototype stage of a new product, companies are consulting Maca on the feasibility of the proposed designs as well as requesting Maca to come up with the solution that offers the best performance. One of Maca’s main production areas is the assembling lines and slitting/folding machines for plastic caps and closures. This includes prethreaded flat plastic caps and prethreaded sport plastic caps, complex closures for alcoholic drinks or prethreaded agrochemical caps. To take one example, Maca points to a line for cutting the tamper evident ring, folding the inner flap of plastic caps and inserting pre-cut liners. The ITVE-MRR machine consists of two flywheels; the first cuts the tamper evident ring, the second (optional) folds the inner flap. The machine is fitted with loading and discharging stars synchronised with the main flywheel and photocells and an external slitting blade which can be easily replaced. Caps of different diameters can be processed without changing the gears. The second Bite-Mark IRV-type machine type IRV inserts pre-cut liners inside the cap. The machine can process either loose liners or it can be customised to work with liners pre-stacked in a tube for specific products (such as agrochemical caps). It is equipped with an exit conveyor belt with the option of installing a vacuum system to allow a vision system to be integrated. Finally, the machine offers a box diverter for loading 2 boxes. Sports caps The Maca product range also offers a continuous motion rotary assembling machine with 3 flywheels with 24 punches each for sport caps for assembling up to a maximum of 3 components with an output up to 36,000 pcs/hr. More than 80% of key components and structural assemblies (including machine units, dies, etc.) are produced in-house and countermarked with an identification number to simplify re-ordering. All Maca Engineering machines are tested in the presence of the customer so that smooth and correct operation can be verified at first hand. Reliability of the after-sales service is assured since the technicians who assemble the machine are the same technicians who will oversee commissioning on site. Recently Maca Engineering joined Arol Group, which includes Arol Closure Systems, the global reference point in the design, manufacture and distribution of capping machines & capping turrets, as well as cap feeding, orienting and sorting systems. The two companies are joined by Unimac-Gherri, a specialist in filling and capping of glass, metal and plastic containers with twist-off and prethreaded caps for dense, semidense and pasty products; and Tirelli, which develops and produces filling, capping and labelling systems mainly for the cosmetics industry. www.macaengineering.com CAPS & CLOSURES Processing of plastic closures Maca Engineering’s facility in San Quirino, Italy","@ID":27} "BOTTLING / FILLING PETplanet Insider Vol. 22 No. 01+02/21 petpla.net 37 BOTTLING / FILLING 37 sion moulding and label printing machines from Husky, Sacmi or Bobst. This is in addition to the new aseptic Gea filling line mentioned earlier. Injection moulding machines from Husky The Taiwanese market is dominated by RTD drinks. Coca-Cola’s “Real Leaf” and Uni President’s “Chai Li Won” are the most popular brands in this sector, according to THC. Regular CocaCola is ahead when it comes to CSD drinks. 580ml – 600ml bottles are THC’s best sellers, with most preferring 600ml bottles. “A total of around 504 million bottles a year can now roll off the production line company wide”, explained Mr Dai. “Exports in 2019 also increased by 18% compared to the previous year”. However, sales of PET preforms, bottles, caps and labels still dominate, comprising a 63% share of the company’s business while OEM drinks account for 31%. The rest accounts for cigarette and beer packaging material trade. According to Mr Dai, THC is not expected to experience any significant changes in 2020 despite the effect of Covid-19 as Taiwan is still the main market and the situation here being more stable compared to the rest of the world. Logistics and supply chains have also been functioning well with business unaffected by the distribution of products to various international markets. We want to know if anything has changed since then. “We see PET packaging as an on-going mainstream trend given the many advantages the material offers. Outstanding recycling properties are now gradually being added to rPET”, he said. “Taiwan has also done a lot of work in this area in recent times and greatly expanded its recycling infrastructure, with recycled material now finding its way back into products. Recycled PET is used in Taiwan’s textile industry as the government still prohibits recycled material content in packaging related to food or beverages. Less pleasing, however, is the fact that the global image of plastic is leading to some companies reverting back to glass or cans which would be disastrous for the environment. THC wants to further expand its global sales network at some point, particularly in relation to the work we are doing on the use of rPET and compostable PET material” said Mr Dai. www.honchuan.com www.sacmi.com With 30 years of experience and 15,000 stacks a year, SACMI is the world’s biggest producer of moulds for the beverage industry. Product design, mould development and direct testing on SACMI machines ensure an all-round service of unrivalled quality. Product design Product development Product validation Industrial production plant Process & quality control On-site and start-up assistance After-sales and Customer service SACMI 4.0 THE COMPLETE CLOSURE, PREFORM AND CONTAINER SOLUTION FOR YOUR SMART FACTORY 30 years of putting things together perfectly to create" "INSPECTION 24 PETplanet Insider Vol. 22 No. 01+02/21 petpla.net PETplanet: What must users be prepared for? Are the new systems easy to integrate into existing processes? What is the technical and financial expenditure? Closure manufacturers as well as bottlers should work closely with the vision supplier to carefully review the particular closure designs and the quality requirements. In many cases, this process will be no different than it would be with a standard closure, with similar costs and installation requirements. However, more complex closure designs and/or customer requirements could indicate a need for additional development work to produce a satisfactory inspection solution. www.pressco.com Sacmi Imola, Mr Stefano Severi, Sales Specialist Manager, Rigid Packaging Technologies BU PETplanet: Has your company already developed inspection systems for tethered caps? If so, what were the challenges during development and what are the new inspection parameters? This subject actually covers two different situations: tethered caps with the cut made inside the mould and those on which the cut is made externally with a scoring machine such as a Sacmi SFM. If the cut is made inside the mould, it is large enough to be inspected with standard CVS systems. Sacmi has, for many years, been designing vision systems for the inspection of complex caps such as sport or hinge caps. Our globally renowned CVS360-3D applies 3D algorithms that can accurately ‘unroll’ the sidewall of a cap, whatever its shape, to create a 2D image, dynamically compensating for any deformation that may stem from the object’s spatial position, perspective or lens deformation. This builds a perfect image on which we can apply all our inspection algorithms. Already successfully applied in hundreds of applications, this technique has also been used in the inspection of tethered caps. If, instead, the cut is made externally with a scoring machine (e.g. an SFM), it is very thin (a few hundredths of a mm) and is very difficult to inspect with conventional vision systems. For this type of application, Sacmi recently presented a new machine called PFMC (Pull Force Measuring-CVS machine) which performs a mechanical breakage test of the tamper-evident band. This machine periodically takes a number of caps from production and performs mechanical breakage tests. It also incorporates a CVS system (called CVS-CUT); the latter is configured with an ultra-high-resolution camera that unrolls the cap sidewall and ensures the cut is controlled to perfection. Among the numerous checks performed by CVS-CUT, the most interesting for cap manufacturers are: cut quality (thickness and straightness), measurement of the bridge section, marks on the knurls, misaligned cut joint, etc. Of course, PFMC is also suitable for inspecting tethered caps with tamper-evident bands produced in the mould, providing additional information on the breaking force related to each single cavity and more precise inspection of cuts and bridges. PETplanet: Can all tethered cap designs be inspected with just one inspection system? Yes, the flexibility of our Sacmi Computer Vision Software easily lets users create dedicated inspection recipes for different cap types. PETplanet: What must users be prepared for? Are the new systems easy to integrate into existing processes? What levels of technical effort and financial expenditure are involved? As mentioned above, the approach to tethered cap inspection differs depending on the type of cut (in-mould or external). Sacmi can provide simple vision systems (CVS – Cap Vision Systems), inspection solutions that integrate vision and handling (CHS machines), or dedicated machines specifically designed to test the pull force needed to break the tamper-evident band (PFMC machine). CVS and CHS can be configured or expanded according to customer requirements. While CHS machines are usually delivered with the CVS360-3D module pre-installed, which makes them ready for the inspection of tethered caps, standard CVS models are usually configured as per the customer’s requirements, so it may be necessary to add the CVS360-3D module: this requires only a small investment and some additional space in the conveyor. Both solutions (CVS and CHS) feature the same software platform (our well-known Sacmi Computer Vision Software), so operators do not have to learn something completely new, they just have to learn how to use the CVS360-3D. Moreover, a Wizard greatly simplifies this operation, which can be completed in just a few steps. The PFMC machine, instead, incorporates a CVS-CUT Vision System. This means that workers who already know how to use the Sacmi CVS can immediately operate this new machine too; in addition, untrained workers can learn easily via the software platform’s user-friendly HMI. www.sacmi.com","@ID":26} "BOTTLING / FILLING PETplanet Insider Vol. 22 No. 01+02/21 petpla.net 39 recycling and use recycled PET in our containers. We’re also trying to continuously reduce the weight of our bottles. At the same time we’re lowering the impact on the environment by cutting energy and media consumption in production.” In order to so do IDS Borjomi has invested a considerable sum in the consistent modernisation of its bottling plants. Two new filling lines from Dortmund systems provider KHS were installed and commissioned at the production sites in Novosibirsk and Lipetsk at the beginning of 2018 and at the end of 2019 the production shop in Kostroma was brought up to date. Here, too, this has resulted in the output being doubled in the first quarter of 2020. The lines, which have a capacity of up to 44,000 0.5 l bph, are identical in their design and feature a blending system for nearwater products with a stretch blow moulder, labeller, filler, shrink packer and palletiser. At all three bottling plants a uniform, high standard of quality, production and logistics has thus been created which also allows for future growth. Light and stable KHS has been able to score on the bottle weight. With the help of KHS’ Bottles & Shapes experts the container design has been further developed so that the base is lighter – without making any concessions regarding stability. This means that the weight of the 0.5 l bottle has been decreased from 20.5 g to 18.8 g, thus also reducing the amount of materials used and cutting CO2 emissions. One can imagine that an investment project like this wasn’t without its challenges. “There were sometimes a few language or cultural barriers to overcome yet this was absolutely no problem thanks to our highly professional and friendly cooperation,” emphasises Evgeny Vturin, operational director for IDS Borjomi Russia. In some respects the climatic conditions actually proved more demanding. “It’s not that easy to ship a line to Novosibirsk and install it there in the winter. It was so bitterly cold that even the heat exchanger froze during transport. In the end everything turned out well, however, and the line went into operation on time.” www.khs.com Easy transport: The finished PET bottles travel from the stretch blow moulder to the filler on transfer stars.","@ID":41} "BOTTLE MAKING 35 PETplanet Insider Vol. 22 No. 01+02/21 petpla.net It is possible that Target Plastic will be adding its own brand to the company’s portfolio at some stage because as Mr Huang explained “We currently have one hot fill line and would like to add one or two more at some point. And we have other ideas for the future. Maybe we will make our own caps, create a private label for water or venture into aseptic filling – we will see. Nevertheless, we can already combine all aspects of packaging, production and bottling and so offer a range of different solutions. We regularly receive excellent feedback whenever customers visit our site to look at our production facilities. We want to show how much Taiwan can offer technologically and across cultures and will be pulling out all the stops in this endeavour”. Finally, how has Target Plastic been affected by Covid-19? “Well, business was excellent prior to March 2020. However, we were able to bring in a lot of stock in advance of the pandemic”, said Mr Huang. “April was not a good month for us but we recovered in May because Taiwan had the virus under control quickly. However, we can see that customers from other countries are being very wary in their behaviour or not around at all because their factories have been closed. On top of that, the situation surrounding the number of victims is naturally adding to the uncertainty”. www.tctarget.com Beverage production in full swing","@ID":37} "MARKET SURVEY 28 PETplanet Insider Vol. 22 No. 01+02/21 petpla.net 01+02/2021 MARKETsurvey Additives Suppliers of resins & additives There is rapidly increasing demand for packaging materials that give even greater protection to their contents. Functional additives and resins are an important technology in meeting this demand for greater product protection in the plastic packaging market. A functional additive modifies the properties of packaging to impart desirable or beneficial functions. That is why we won’t stop a well-established tradition in opening our market surveys overview in 2021 with suppliers of resins and additives. These companies participated: Addform Limited, Avient Cooperation, Repi S.r.l, Sukano AG, Indorama Ventures Polymers Germany & Indorama Ventures Ltd, Neo Group, Reliance Industries and Novapet, S.A. Please notice: Since July 1st 2020, PolyOne is renamed as Avient. At the same time, Clariant MB broke away from Clariant, and merged to become part of Avient. Although the publishers have made every effort to ensure that the information in this survey is up to date, no claims are made regarding completeness or accuracy. Company name Addform Limited Avient Corporation Repi S.r.l. Sukano AG Indorama Ventures Polymers Germany GmbH Postal address Telephone number Web site address Contact name Function Direct telephone number E-Mail Unit 21, Skypark Industrial Estate Liverpool, L24 1YL, Great Britain +44 151 659 1102 www.addform.co.uk Mr Richard Glen Sales Manager +44 151 659 1102 richard.glen@addform.co.uk 33587 Walker Road Avon Lake, 44012 OH, United States +1 440 930 1000 www.avient.com Mr Marco Schäfer Marketing EMEA +49 4102 487 158 marco.schaefer@avient.com Via B. Franklin 2, 21050 Lonate Ceppino VA, Italy +39 0331 819511 www.repi.com Ms Lucia Buffoni Marketing Manager l.buffoni@repi.com Chaltenbodenstrasse 23 8834 Schindellegi, Switzerland + 41 44 787 57 77 www.sukano.com +41 44 787 57 77 media@sukano.com Philipp Reis Strasse 2 65795 Hattersheim, Germany +49 69 305 6025 www.indoramaventures.com Mr Christian de Lope Market & Business Development +49 172 652 6558 christian.delope@de.indorama.net Additives and Colours for PET Liquid colours Yes Yes Yes No Microgranule colours No Yes Yes Masterbatch colours Yes Yes Yes UV protection additive (solid) Yes Yes Yes UV protection additive (liquid) Yes Yes Yes No AA reduction (solid) Yes Yes - SenzAA No AA reduction (liquid) Yes Yes - SenzAA No Oxygen scavenger (solid) Yes No Oxyclear Additive 3500 (requires additional components) Oxygen scavenger (liquid) No No IV enhancer Yes Yes Yes Yes Reheating Yes Yes No Blowing additive Yes No Yes (liquid) Yes Slipping agent Yes Yes Yes (liquid) Yes Other PET additives: Anti Yellow, Antiblock Matting Agent, Toners, Special Effect, NIR Black, Light Blocking Additive for UHT milk bottles Anti Yellow (liquid), Process Aid (liquid), Optical Brightener (liquid), Colours for Barrier Solutions (liquid), Whites for monolayer UHT Milk (liquid), blacks with no carbon black Antioxidants, Antistatics, Melt Enhancer, Voiding Agent, Optical Brightener, Nucleating Agent, Mould Release, Matting Agent, Slip/Antiblock, Light Diffusor, Light Barrier, Impact Modifier, Flame Retardant, Antimicrobial, Plasticiser, Pinning Agent, Foaming Agent Resins & additives Preform machinery Preform production & inspection systems Preform & SBM mould manufacturer SBM 2-stage Compressors Caps & closures & inspection systems Filling equipment & inspection systems Recycling machinery Palletising & shrink film machinery","@ID":30} "TOP TALK PETplanet Insider Vol. 22 No. 01+02/21 petpla.net 10 Full capacity despite the crisis In our interview, David González, Business Director of Novapet, reveals how reliable continuity still exists even when everything is upside down and why the summer of the pandemic year 2020 was the right moment for implementing strategic plans up to 2030. PETplanet: Mr González, how Novapet coped with the past year? González: It’s been quite a challenging year, indeed. No need to comment on the depth and the rapidity of the changes and disruptions we all had to face in our markets and sectors of activity because of the pandemic. From the basic supplies of our raw materials, to the end point of our marketing activities, almost everything had to be reinvented from one day to the next, while ensuring, at the same time, the normal continuity of our production, technical assistance and deliveries. We cannot forget that from the very first day of our Spanish lockdown, our company was considered “strategic”. I can now say that this situation has demanded an important extra effort from our team in terms of concentration, dedication and personal responsibility. Luckily, Novapet had previously paid special attention to our Business Contingency Plans in all our divisions, you know, the kind of provisions you make in ordinary times when you don’t even think this might be ever used. It has been used! And now we can say that thanks to these plans, Novapet has maintained its activity at full capacity during all these difficult months, and we have even been able to fulfil an extraordinarily high demand in our three markets: PET resins, PET preforms and bottles. PETplanet: Spain imposed strict contact restrictions early on. How did the customer support succeed at a distance? González: Mostly via virtual tools. But our technical assistance team has kept travelling around when and wherever a customer really needed them. And this has been the case even in the hardest moments of the lockdown. Obviously, we have adopted the strictest safety protocols for these travels, but I repeat: we have always been very aware of our responsibilities as a strategic industry. The other day, out of curiosity, I checked the number of kilometres covered by our technicians during the pandemic. And I can assure you, it’s quite an impressive number. PETplanet: Were your logistics influenced by the lockdown? González: Not that much. All the transportation sector was considered strategic as well, and I personally think society should recognise the very special effort this sector has deployed to keep all our industries and the shelves of our supermarkets fully supplied. Of course, we have had some minor disturbances affecting basically transportation by road, but with a negligible effect on sea, rail supplies and freight transport. PETplanet: Digitalisation is one of the buzzwords associated with the pandemic. In our industry, too, the pressure is growing, for example to build digital trading platforms for commodities or to ensure better networking. You have already mentioned digital tools to keep in touch with your customers. Besides this, how are you positioned digitally, or how urgent are such developments on your agenda? González: My personal vision is that, from both ends of the value chain, the PET or the PET packaging market, were already highly “digitalised” in virtually all the operations (supply, planning, production, logistics, technical assistance, etc.). This is, no doubt, our case as a company. Obviously, this trend is becoming more and more intense, and you cannot stop benchmarking and updating your tools. PETplanet: Have you also taken advantage of offers such as digital trade fairs and congresses? González: Yes, certainly, we have attended several congresses and conferences in their virtual editions. We think it is always important to keep updated on what is going on in our sector. Most especially during these uncertain times. PETplanet: Did you benefit from the fact that the pandemic has shown plastics in a good light, and helped dispel negative criticisms of the sector? González: No doubt! From the first moment, plastics in general, and PET in a very particular way, were widely identified as a basic means of fighting the pandemic and its effects on our lives. From the most visible medical, sanitary and protection equipment, to the omnipresent bottles of handwashes, or other hygienic and food articles, plastic has shown in the clearest possible way that it is an irreplaceable material to provide safety, cleanliness, lightness and ease of use. Let me add that the plastic industry has also proven its amazing capacity for response and adaptation to a world in disruption, because of its technological flexibility, training in fast decision-making, and the robustness of the value chain. PETplanet: It is often said that the pandemic has acted as a driving force, accelerating developments that would have happened sooner or later anyway. If this is the case, what changes have been implemented in your company that you expect to last? And are there also any programmes that you had to abandon, or cuts that you were forced to make? González: This last summer, once the first impacts of the sanitary crisis were more or less under control, we started a strategic reflection on the moves the markets and society were expecting from us to make in the coming years. We were helped in this process by the political and public debate on the priorities for the future, and obviously by a long series by Gabriele Kosmehl","@ID":12} "BOTTLE MAKING 34 PETplanet Insider Vol. 22 No. 01+02/21 petpla.net tion, including 12 preform units and nine crystallisers for hot fill application containers. A small number of preforms are also sold to third-party consumers. “We have been producing bottles with PCO1810 necks for a long time but have now switched 70-80% of our production capacity to PCO1881s”, said Mr Huang. “We also bought a machine for producing 38mm bottle necks three years ago. Our moulds and cavities are designed for a wide range of bottle types. We currently use 16, 24 and 32 cavities in our preforms, and 4, 6 and 10 for blowing purposes”. Caps are not made by the company but purchased exclusively from local firms. Bottles range from between 250ml to 2 l in size. Mr Huang estimates that around 30-40 different moulds are used. The 500ml square bottle is the company’s overseas best seller which can be packaged and easily stacked on pallets. Target Plastic sells mostly 600ml, 650ml and 1.5 l cans on the local market. Total production is 350 million bottles a year, of which 50 million are filled. Among the firm’s biggest customers are Kaishi Oolong in Taiwan and the Polish Biedronka supermarket chain. PET material is sourced from Shinkong, Nanya and Far East who can sometimes supply preforms in rare and exceptional circumstances. Target Plastic’s most recent turnover was US$ 30 million and has been growing considerably since last year. 100 out of its 160 employees work in blowing and 60 in filling activities. Bottling and downstream equipment come from local suppliers. “We are considering investing more in European machinery in the long-term”, said Mr Huang. “We are also looking at integrated inline systems for blowing, filling and capping, e.g. from Sidel, Krones, KHS or CFT”. Hot filling in-house Hot filling is the company’s main in-house application. Mr Huang estimates his own share of Taiwan’s market for hot fill products to be between 50-55% which includes genuine light weight varieties. “We have achieved real savings in material compared to bottles that were one and a half times heavier in my father’s day. I can say that our hot fill bottles are among the lightest available internationally. Our strengths here clearly lie on the technological side”. One reason for the high demand for his hot fill drinks is probably savings in material of approximately 26-30 g in heavy packaging. Here, the target is only 20-22 g. The concept of hot fill drinks is an extremely important one but local equipment is often outdated, he added. At the same time, however, this may also offer promising investment opportunities. In addition, rPET will be used more in future to meet customer expectations. Managing Director Po-Chao Huang in front of Target Plastic’s filling area “American and European customers in particular want to see more rPET in bottles”, said Mr Huang. Far East is currently the only firm in Taiwan which can provide recycled PET. It is very expensive and you can only get it when combined with new material under the terms of supply contracts. However, Nanya and Shinkong will probably be able to offer solutions here soon. In Taiwan itself, rPET cannot be used in drinks packaging by law but we hope this legislation will be amended soon. In the meantime, we are keeping a close eye on developments in the USA and Europe and will react as we see fit. Recycling is also becoming increasingly important locally and is something that NGOs in Taiwan are actively promoting. The population is open to this idea, with further measures assuming greater significance for all kinds of material”. Taiwan Honchuan is Target Plastic’s largest competitor in terms of products and Mr Huang freely admits his company is in a different league when it comes to volume. “Our main areas of expertise are in providing flexible solutions for smaller customers which we also support when entering the market. The same drinks recipes can be used in different countries which enables customers to get started quickly using their own private labels”. 500ml square bottle “Aloe”","@ID":36} "TRADE SHOW REVIEW 42 No. 01+02/21 petpla.net sorting and recycling rates for paper and domestic waste.” For cardboard, paper and unsorted domestic waste, Tomra and the municipality developed a unique recycling facility, the IVAR Sorting Plant, which was constructed around 15 km to the south of Stavanger in Sandnes. It has been operating since January 2019 and it processes waste from the municipal districts of Sola, Gjesdal, Randaberg, Finnøy, Kvitsøy, Klepp, Hå, Time and Ryfylke, as well as Stavanger and Sandnes. The facility achieves an annual throughput of 25,000 t of paper and cardboard and up to 70,000 t of domestic waste. Alongside machinery from Sutco Recyclingtechnik, various types of Tomra Autosort technology are used. Besides sorting, there is also a washing and extrusions line in the same space. “It has been possible to quadruple the recovery of plastics from domestic waste,” said Dr Rehrmann. The Stavanger study by Eunomia showed that the previously established recycling system produced a recycling rate of 50.8%, explained Dr Hogg. This corresponded to a reduction of greenhouse gases by 67.3%. The possibilities of the new facility should bring the recycling rate to 64.7%. This is already very close to a future EU directive of 65%, which would correspond to an effective emissions reduction of 75.2%. A webcast viewer asked about the subsequent quality of the recycled material and Dr Rehrmann was able to give a positive response. He said that depending on material quality, e.g. for PET and PS plastics, it was technically possible to process these into foodgrade packaging, even after sorting from domestic waste. We at PETplanet asked how materials suppliers and converters could best be incorporated into the circular economy, for example through own recollection of packaging or by installing inhouse recycling systems. Dr Rehrmann explained that chemical companies, for example, could basically no longer ignore the waste situation, which is why many of these companies are relying increasingly on their own recycling facilities. www.tomra.com Sponsors to date Spring – Autumn 2021 TOUR SPONSORING PACKAGE Company logo on the Editourmobil Full page Tour advertisement featuring sponsor company logos in PETplanet magazine Sponsor companies descriptions and logos featured in the Tour sponsorship brochure Square banner small on the petpla.net website* Logos of sponsors in the Tour section on the petpla.net website Company logo under every tour article published in PETplanet magazine Roll-up display banner with sponsor logos featured in photo shoots at various locations during the Tour The Tour and sponsors will be promoted at Drinktec, Munich, October 4-8, 2021 Participation fee: 5,950€ The worldwide round trip with Back to Europe After our last Editour “From Down Under to Japan” PETplanet will be continuing its journey this year in a second stage of its Tour bringing news and exploring the innovations of technology hub Europe! 2021 will be the year of the new start, of renewal and for developing new ways of thinking. During and especially after the pandemic, it will be vital to make every effort to get the global economy back on track in the medium term. Sustainability will be the key. Once again PETplanet will be at the forefront, as partner in the world’s leading beverage trade fair Drinktec to be held in Munich from 4-8 October 2021. After the success of our previous Drinktec Road Shows 2017 in South East Asia and last year in Australasia, we will be back on the road in Europe this spring with our Editourmobil for a new gettogether with the industry. We will be revealing the results of our meetings and discussions at Drinktec with the leading thinkers in PET processing, packaging and recycling. Apart from new technologies we will be also taking stock of how things stand. We will be asking how global thinking might change as a result of COVID-19. How will bilateral business relationships cope with the aftermath of the pandemic? What opportunities will there be for the drinks industry and its suppliers? Our planning, in terms of precise timeframes and details of the countries to be visited will be flexible to take account of the rapidly changing pandemic situation. However, this much we can confidently say: in these challenging times, we as the voice of the PET industry will be at the very heart of the roadshow as usual and are already looking forward to welcoming you back on board the Editourmobil! Share with us this exciting experience! Interested in being interviewed? barton@hbmedia.net Let Your Inspiration Flow. 7KH (XURSHDQ 5RDG 6KRZ PART2 Empowered by drinktec Interested in becoming a Sponsor? sales@hbmedia.net","@ID":44} "INSPECTION 22 PETplanet Insider Vol. 22 No. 01+02/21 petpla.net come up with complex outside hinge structures, we simply need to add our AI software tool IMDvista Neuron. PETplanet: What must users be prepared for? Are the new systems easy to integrate into existing processes? What is the technical and financial expenditure? Our customers can continue working with existing standard IMDvista vision inspection equipment without expensive system modifications for a wide range of tethered closure designs. Our IMDvista Neuron software is much more cost-efficient than a custom-made mechanical orientation station, especially for closure designs with special hinge structure designs. The IMDvista Neuron is able to inspect the closures much more precisely without any risks of closure jams or false rejects within the whole process! www.imdvista.ch Intravis, Mr Christoph Wynands, Productmanager for Preform and Closure Inspection systems PETplanet: Has your company already developed inspection systems for tethered caps? If so, what were the particular challenges during development and what are the new parameters of the inspection? Yes, with the CapWatcher Q-Line we responded very early - in spring/summer 2019 - to the first indications of expected changes in closure design. Since then, we have been in close contact with our customers and partners. In addition, as an active member of the Cetie, we are always up to date with the latest developments and thus learn very early on what requirements can be expected from our partners. About our solution: The CapWatcher Q-Line is an inspection system for the end-ofline inspection of closures, which is also ideally equipped for the requirements of tethered caps. Three inspection stations with different optics for inspecting the inside of the closure, as well as five cameras for inspecting the closure from the outside, provide a complete all-round view of every detail - at production speeds of up to 3,600 closures per minute. The special features of tethered caps pose no problem for the CapWatcher Q-Line. Take, for example, the closure aids/ CAM’s located inside the closure: With our patented non-contact microhole inspection, we do not have to dip into the closure to be able to exclude microholes with 100% certainty. A normal HV inspection dipping into the closure quickly reaches its limits of reliability here. The external shape and dimensional stability of tethered caps are also challenges our CapWatcher Q-Line can handle. Our form-fitting, lateral star wheel separation copes with external features such as hinges as well as with the increasing sensitivity of the ever thinner closures - and does so with high precision even at the highest speeds. And for our software, the rotationally invariant tethered caps do not need to be aligned either - our software logic masters any alignment for a reliable inspection. In addition, temperature measurement, cavity reading and testing of the slitting quality of the guarantee band are some of the other advantages of the CapWatcher Q-Line, which has now proven itself in various applications for over two years. PETplanet: Can any design of tethered cap be inspected with one inspection system? Basically, there are no limits to what the CapWatcher Q-Line can do. We have solutions for injection moulded as well as for closures from compression moulding; inspect closures with cut as well as closures with moulded tether features; inspect standard PCO1881 beverage closures as well as multi-part closures for beverage cartons in assembly handlings. PETplanet: What must users be prepared for? Are the new systems easy to integrate into existing processes? What is the technical and financial expenditure? Customers with a CapWatcher Q-Line are already well prepared today. Here, the technical and financial effort is very low and an adaptation can be implemented very quickly. Customers with older system generations have to invest more effort here. But we also offer options and solutions for this. Customers who do not yet have an Intravis inspection system have a wide choice of solutions. Here, we are happy to support you in selecting, setting up and implementing a complete downstream concept tailored to your specific needs. www.intravis.com","@ID":24} "imprint EDITORIAL PUBLISHER Alexander Büchler, Managing Director HEAD OFFICE heidelberg business media GmbH Vangerowstraße 33 69115 Heidelberg, Germany phone: +49 6221-65108-0 fax: +49 6221-65108-28 info@hbmedia.net EDITORIAL Kay Barton Heike Fischer Gabriele Kosmehl Michael Maruschke Ruari McCallion Waldemar Schmitke Anthony Withers WikiPETia.info petplanet@hbmedia.net MEDIA CONSULTANTS Martina Hirschmann hirschmann@hbmedia.net Johann Lange-Brock lange-brock@hbmedia.net phone: +49 6221-65108-0 fax: +49 6221-65108-28 LAYOUT AND PREPRESS EXPRIM Werbeagentur | exprim.de Matthias Gaumann READER SERVICES Till Kretner reader@hbmedia.net PRINT Chroma Druck Eine Unternehmung der Limberg-Druck GmbH Danziger Platz 6 67059 Ludwigshafen, Germany WWW www.hbmedia.net | petpla.net PETplanet Insider ISSN 1438-9459 is published 10 times a year. This publication is sent to qualified subscribers (1-year subscription 149 EUR, 2-year subscription 289 EUR, Young professionals’ subscription 99 EUR. Magazines will be dispatched to you by airmail). Not to be reproduced in any form without permission from the publisher. Note: The fact that product names may not be identified as trademarks is not an indication that such names are not registered trademarks. 3 PETplanet Insider Vol. 22 No. 01+02/21 petpla.net Are one-way refundable deposits a German thing? As a global leader in collection, Germany is extending the scope of its bottle deposit system. According to PET Forum, 94% of all PET drinks containers, with or without a refundable deposit, are already being recycled in Germany of which 37% is bottle-to-bottle with the remainder going into fibre or other elements. The refundable deposit is 25 cents per bottle. Assuming a bottle weighs on average 25 g, the value of post-consumer 1 kg PET bottles is around 10EUR. Quite a remarkable difference to the price around 1EUR/kg of virgin PET. Supposedly environmentally-friendly carton drinks containers are not eligible for a single-use refundable deposit. At the start of the year, the Environmental Action Germany (EAG - DUH) organisation determined that the 76% recycling rate claimed by the manufacturers was purely window-dressing. This figure includes moisture, dirt, aluminium, plastics and paper, some of which is incinerated. If all these elements are excluded, you are left with a recycling rate of just under 30%. So, although a PET container has a demonstrably better collection and material recycling rate, a drinks carton does not qualify for a redeemable deposit according to a new regulation on the deposit on non-refillable containers in Germany. Hard to understand but that’s politics I guess. One interesting aspect of the EAG study is that up to 50% of a drinks carton’s weight is made up of plastic which makes me wonder what would happen if we wrapped thick paper labels around PET bottles. We would then have a material mix of 50% paper and 50% plastic. Would this make the container deposit free? Also of note in this context is the work of Paboco (Paper Bottle Company) which, as a joint venture of BillerudKorsnäs and Alpla, is developing a paper container using recycled fibres. The barrier layer is still made from plastic. Despite being in the experimental stage, CocaCola Europe is already going public with the bottle (see page 54). Other brands include Carlsberg, the Absolut Company and L’Oréal. It will be intriguing to see how the paper container will ultimately be launched on the market and whether it will be deposit or deposit-free in Germany only. Yours sincerely, Alexander Büchler Dear readers,","@ID":5} "TRADE SHOW REVIEW PETplanet Insider Vol. 22 No. 01+02/21 petpla.net 40 Tomra webcast Rethinking the waste problem by Kay Barton On November 11, 2020, Norwegian recycling equipment manufacturer Tomra held a webcast on its newly founded Circular Economy Division, on global warming and waste generation, and on a solution-oriented recycling study. Together with British sustainability consultancy Eunomia and German communications company F+B Fasse und Bieger, the discussion covered matters such as the current levels of waste and emissions, the long-term trends of these, and all-encompassing recycling concepts. A pilot project from the Norwegian city of Stavanger was presented as a case study. Claudia Fasse, Co-Founder & CEO of F+B Fasse und Bieger Dr Volker Rehrmann, Head of Circular Economy at Tomra Stavanger recycling plant","@ID":42} "PETplanet Insider Vol. 22 No. 01+02/21 petpla.net 47 BOTTLES A cannabis shot in PET The German company, LiveFresh GmbH, producer of various juices and shots that contain superfood additives, has brought out a fresh and cold-pressed cannabis shot with orange, lime, turmeric, ginger, hemp juice and macha. The product comes in a square, 60ml bottle made from 100% recycled PET. The supporting ring that protrudes over the bottle’s outer area and large drinking spout are particularly eye-catching. The bottle is secured by a green cap. www.livefresh.de Kefir with high protein content With its new kefir with added protein, the Ehrmann Dairy, founded 100 years ago, is combining two consumer demands, namely an exotic, healthy drink with an added benefit. The low-fat drink does not contain lactose or gluten but includes 20% protein. The kefir comes in tapered, white-coloured 350g or 339ml bottles with the taste of passion fruit. The bottle has a bilingual, full-surface sleeve label, with “Milk Drink” being the English name of the product. www.ehrmann.de Shenzhen World Exhibition & Convention Center, PR China 350,000 sqm Exhibition Area 3,600+ International Exhibitors 3,800+ Machine Exhibits 90,000 sqm Plastics & Rubber Raw Materials Zone","@ID":49} "MATERIALS / RECYCLING PETplanet Insider Vol. 22 No. 01+02/21 petpla.net 19 depending on the intended end application. Macro- and microscopic melt homogeneity is achieved by means of homogenisation drying, controlled plasticising, gentle filtration and controlled vacuum degassing. In the downstream processes, melt can either be granulated first, or fed directly into the product manufacturing process. Recycled polyester, produced using VacuFil, can even be used for more challenging downstream processes, including the manufacture of FDY filaments. In the FDY single-stage process, material is subjected to extreme loads throughout manufacturing; filaments are drawn at speeds of up to 4,500m/min. BBE, headquartered in Remscheid, Germany, is a joint venture between Brückner Group GmbH, of Siegsdorf, Germany, a leading manufacturer of machines for the polyester foil industry, and Oerlikon Textile GmbH & Co. KG, a leading producer of systems for the manmade fibre industry, also of Remscheid, Germany. BBE is a pioneer in the development of processes for recycled materials, particularly polyester flakes, and converting them into contemporary, market-appropriate products for filaments, fibres and nonwovens. “What Oerlikon Barmag brings to the table as a technological leader in the field of filament yarn spinning systems, BBE complements with considerable know-how in the area of extrusion and filtration and in systems construction and engineering”, says Dr Klaus Schäfer, CEO of BBE. BBE is the exclusive supplier of extrusion filter technology for various manmade fibre industry polymers, particularly polyester, for its parent companies. Its association with the Brückner and Oerlikon Textile groups means that BBE is very much aware of industry requirements for granulate and melt made from recyclate. The further development of post-consumer PET material and post-production PET material is of special interest to BBE’s parent companies and the driver for bundling their recycling expertise into the BBE joint venture. BBE is co-located with Oerlikon Barmag in Remscheid and is an established manufacturer of compact and flexible systems for the manmade fibre industry. VarioFil R spinning systems have been used for converting rPET granulates and flakes into POY/DTY for both textile and carpet applications. VarioFil systems are also used in production of spin-dyed products made from rPET granulates. The development, construction and assembly of VacuFil and VarioFil units are carried out exclusively in Remscheid, in line with the company’s ‘Made in Germany’ philosophy. VacuFil premiered at ITMA 2019 in Barcelona. Numerous tests have subsequently been conducted on the pilot system at Remscheid, using waste material supplied by customers; the recycled polyester has been successfully spun into POY and FDY. Target viscosities and starting materials are achieved with the use of the Visco+ vacuum filter; a reactor is not required. The VacuFil blends largescale filtration and swift intrinsic viscosity build-up for consistent melt quality. The attached vacuum unit, which is automatically regulated between 1 and 30mbar, removes volatile contamination, ensures a controlled IV increase and delivers melt homogeneity, which is vital for downstream spinning performance. An inline viscosity measuring unit connected to the vacuum system continuously monitors and adjusts IV. This enables producers to generate the specific recycled polyester required for their application. The company says that VariFil’s degasification performance reduces the need for energyintensive pre-drying. With a modular structure and a performance spectrum from 300-3,000kg/h, VacuFil systems offer a range of possibilities for processing polyester waste. Bottle flakes, agglomerated spinning waste or a mixture can be processed into high-quality rPET granulate or fed directly into downstream processes. The entire recycling process is controlled and monitored by Oerlikon Barmag’s Guide system. The optional 3DD mixer, manufactured by BBE, enables producers to include additives and easily change rPET ratios in the main melt from between 5 and 50%, to comply with legal standards. Customer requirements can be catered for with different system configurations. “Close collaboration between potential operators of the system and our experts ensures that projects are successful. Tests carried out using customers’ raw material in our small-scale production system guarantee a sophisticated process that complies with requirements. Our process visualisation system ensures customers always have a close eye on the broad operating window and the optimum operating point. Our software provides essential process optimisation information. This saves costs and increases productivity,” says Matthias Schmitz, VacuFil Product Manager. Throughout the Covid-19 pandemic, BBE has offered digital videoconferencing to continue providing access to their technology for customers across the world. www.bbeng.de Visco +filter components – the heart heart of the BB Engineering’s VacuFil recycling system","@ID":21} "INSPECTION 21 PETplanet Insider Vol. 22 No. 01+02/21 petpla.net Tethered caps inspection at a glance CAPS & CLOSURES In July 2019, the EU commission published the Plastic Strategy paper to reduce plastic waste, including a regulation with regard to closures on plastic beverage bottles: Plastic closures must remain attached to the bottles from July 2024 at the latest. This poses major challenges for the industry. Several cap solutions have already appeared in the market. As a logical consequence, PETplanet Insider is therefore asking about the inspection options for these closures. Find out here about the inspection solutions for tethered caps from: IMD, Intravis, Pressco and Sacmi. IMDvista, Mr Martin Gerber, Sales Director (CSO) PETplanet: Has your company already developed inspection systems for tethered caps? If so, what were the particular challenges during development and what are the new parameters of the inspection? IMD was already in a good position to fulfil the expectations regarding the inspection of the new tethered closure features. More than 4 years ago, IMD started a project with a major European closure manufacturer to inspect complex assembled sport closures with a hinge and tethered functions. At that time, we faced the same challenges we are now facing once again with the new tethered designs: testing complex structures with no rotational orientation of the closure when they are presented to the vision system. Working very closely with brand owners, converters and market leaders, we have over 25 running systems or prototype lines inspecting tethered closures in the European market. As the tethered designs are very different, some are simple to inspect and do not require a special camera setup or additional software changes. Others turned out to be a challenge because of the complexity of the design. Imagine if we have to inspect a tethered closure design with a complex outside hinge structure. Rotational positioning is not an option because of the speed and the requirement for inline inspection. A simple “panorama view” does not solve the problem… our new IMDvista Neuronsoftware tool could solve it. Neuron is a vision tool using AI (Artificial Intelligence) technology. IMDvista Neuron was the break-through and key factor to guarantee a true 100% inspection of complex tethered closure designs. A “new star is born” in IMD’s closure inspection portfolio. PETplanet: Can any design of tethered cap be inspected with one inspection system? Yes! There are different manufacturing processes in order to produce closures with the new tethered and the warranty band functions. Injection moulding: Complete realised by injection moulding process Slitting and folding equipment after injection moulding process Moulded warranty band and tethered feature in combination with an external folding equipment Compression moulding: Slitting and folding equipment after compression moulding IMD is able to cover all the various production processes and tethered closures designs with our well-known and market proven standard camera and sorting equipment.If our customers","@ID":23} "PETproducts 44 PETplanet Insider Vol. 22 No. 01+02/21 petpla.net PET preform that helps to extend shelf life Global plastic packaging manufacturer Retal is actively working with a leading food and agri-business to manufacture a PET preform that helps to extend the shelf life of its popular refrigerated drinking yoghurt in Africa. To achieve this, Retal is adding ColorMatrix Lactra SX Light Blocking Additive to its monolayer PET bottles for the multinational producer’s refrigerated drinking yoghurt specifically for the Nigerian market. The PolyOne additive is claimed to block 99.9% of light, thus protecting the dairy product. Jiri Nydrle, Sales manager at Retal Czech, is working directly with the customer and said “Light blocking is a particularly hot topic in the African dairy market and, at present, we only export this monolayer PET preform with the Lactra additive as there is not the current demand for dairy milk in PET bottles in Europe as cartons have a clear dominance in the UHT sector.” He continued: “The brand owner in Nigeria had a break in their supply chain so we were asked to help by our valued long-term partner Caraway Africa Nigeria Ltd. Our sales director got the initial contact and he was able to quickly close the deal. The whole offer was discussed online and we were able to agree prices and arrange for ten containers to be sent to Nigeria. It was a very effective method of communication and kept everything moving quickly; it shows a new way of working.” With all the constituents of the solid masterbatch ColorMatrix Lactra SX Light Blocking Additive certified as food safe, it offers a good way to extend shelf life without impacting the product quality; drinking yoghurt in Lactra preforms has a six month refrigerated shelf life. Lactra does not need to be dried before processing; it is solid state pellets that are added as close as possible to the extruder entrance, and it creates an opaque white preform with an almost total light block. Retal expects to see continued demand for preforms with Lactra in other countries as it delivers good refrigerated shelfstability for dairy products without adding weight as monolayer PET is used. www.retalgroup.com Tethered caps solutions On July 3, 2019, the EU published a far-reaching regulation. According to the legislative text, plastic closures must remain attached to the bottle during consumption by July 2024 at the latest. As an experienced company for the development of plastic closures, CCT Systems has started the development work on these international requirements. The following objectives have been defined internally as guidelines for this development: Uncompromising compliance with the EU’s specified requirement, especially the fixing of the closure to the bottle should be stable and can only be overcome with aids. The existing handling of the consumers for opening and closing of the closure should not be negatively affected. The solution found should work on all different bottle neck sizes up to 48mm in diameter. The solution found should work for non-carbonated as well as carbonated beverages. Investment in the industries concerned should be as low as possible. Already on May 10, 2019, a patent for the corresponding tethered caps could be filed with the German Patent Office. On April 9, 2020, the patent was granted with Patent No. 10 2019 112 259 and the grant of the patent was published. An international patent application PCT/EP2020/061353 was filed on April 23, 2020 and published under the publication number WO2020/229134 on November 19, 2020. Characteristics of CCT tethered cap solution: Usual & easy handling Safe application Stable connection of the cap to the plastic bottle No change to: Capper, filling line, slitting technology Closures can be produced in injection moulding and compression technology Only a 2mm increased distance between the holding ring of the tamper-evident band and the transferring ring is required at the neck of the bottle. Due mainly to the global pandemic, CCT Systems is no longer able to market the existing international property rights or related products worldwide on its own. For this reason, CCT Systems is looking for cooperation partners or alternatively interested parties for the worldwide marketing of the existing property rights and the necessary documents and constructions. www.cct-systems.com CAPS & CLOSURES","@ID":46} "CAPS & CLOSURES 26 PETplanet Insider Vol. 22 No. 01+02/21 petpla.net The Essential Guide to Tethered Closures With 179 attendees from 39 countries the third PETinar organised by PETplanet Insider took place on November 5, 2020. PETplanet invited Michael White of Husky to present: the Essential Guide to Tethered Closures. Fig 1: Threaded. Compatible with all beverage types Michael White is the Director of Business Development for Closures at Husky Injection Molding Systems. The webinar begins with an overview of the EU Single Use Plastic (SUP) Strategy, which was approved by the European Parliament in March 2019. It specifies that by July 2024, all SUP beverage containers with a volume ≤ 3 l requires the closure to remain on the bottle. Based on market interest, Michael believes that it is only a matter of time before this directive is adopted in other countries outside of Europe. Husky sees the directive as an opportunity for brand owners to enhance their product on the shelf while communicating a message of sustainability. Husky’s tethered development program began with an intensive study on the consumer interaction. By looking at each interaction point with the application, from selection on the shelf, to the re-closing experience, Husky has been able to optimise their designs. These designs are intuitive, and enhance the consumer experience through the use of audible and tactile feedback. Fig 2: Snap. Well-suited for still water Husky sees the tethered designs falling into two primary buckets: the snap neck finishes (Fig.2) and the threaded neck finishes (Fig.1). The snap neck is best suited for light weight still water applications. A snap sealing is insufficient to retain the internal bottle pressures created by CSD and JSDT (juices, sports drinks, and tea) beverages. Threaded necks are compatible with all beverage types. Husky is actively working on different tethered designs. A key aspect is balancing legislative compliance while minimising tooling investment. Husky’s standard tethered design has the shell connected to the tamper evident band (TEB) via a member segment. While this concept satisfies the legislative requirement, it detracts from the user’s drinking experience. Husky’s premium tethered solution provides the best of both worlds. It ensures legislative compliance while promoting an enhanced consumer experience by enabling locking of the shell in the open position. By enabling locking, the closure shell will not interfere with the pouring experience and/or when drinking direct from the bottle. (Fig.3) The moulded-in bridge approach to closure manufacturing enables more complex geometry to be injection moulded without any downstream secondary operations to be performed. Once the closure is ejected from the mould, it is ready to be applied on the capping line (Fig.4). Fig 3: Fixed shell position in the open position Fig 4: Moulded-in bridge: Ready for capping line, no secondary operations required Fig 5: Integrated hinge. Promotes positive consumer experience by enabling shell locking There is not a one size fits all as different neck finishes offer their own unique set of challenges. That is why Husky is working on a portfolio of solutions including: Snap-on flip top closures Flip Lid flip top closures Standard tether Premium tether Contact Husky for any questions on their tethered cap solutions and download the Essential Guide to Tethered Closures free of charge. The PETinar is available on the PETplanet Insider homepage. We thank Michael for his very interesting presentation of Husky Technology and all participants for their interest and stimulating questions. www.husky.co Husky Download Guide: https://campaigns.husky.ca/TetheredClosuresGuide Listen to PETinar at PETplanet: petpla.net/2020/11/10/ review-the-essential-guide-to-tethered-closures/?s CAPS & CLOSURES","@ID":28} "BOTTLING / FILLING PETplanet Insider Vol. 22 No. 01+02/21 petpla.net 38 Russian company invests in three turnkey lines from KHS The water mission IDS Borjomi has made it its mission to help the people of Russia lead healthy lives by drinking water. This calls not just for a clever strategy but also for a pioneering tecahnological infrastructure, with KHS contributing three new turnkey lines to the latter. IDS Borjomi is pursuing its noble objective with much success: since 2002 the domestic market for bottled water has more than doubled and with annual growth rates of around 7% there’s no end to the boom in sight. IDS Borjomi has made a considerable contribution here. In 2009 the company procured the Svyatoj Istochnik or Saint Spring brand. This bottled water brand has been available in Russia since 1994 and was the first on the market. Originally from Kostroma, the brand has also been bottled in Lipetsk since 2010 and since 2017 in Novosibirsk, over 3,000 km from Moscow. Production at the latter site has ensured that Svyatoj is also available in Siberia and the Urals, thus catering for the entire Russian market. This has proved a successful concept: with a financial share of almost 11% Svyatoj Istochnik is now market leader in Russia – by a large margin. Pioneering a healthy lifestyle Part of the strategy is to inform consumers of the health benefits of bottled water. “We tell our target groups how important it is to maintain their intake of fluids,” explains Alexander Zhadanov, CEO von IDS Borjomi Russia. “We want our customers to get used to drinking at least three 0.5 l bottles of water a day. This means that they consume the recommended amount of 1.5 l needed to stay healthy. We even provide recommendations on when it’s best to drink water: for example in the mornings, right after waking up to activate your organism, or half an hour before meals to stay in shape. Or throughout the day in order to be able to tackle important tasks with the necessary concentration.” It helps that the Russians have long followed the trend of adopting a healthier way of life, increasingly rejecting carbonated, sugary beverages, juices and even coffee and turning instead to water. The brand is also reaching out to consumers through a number of major advertising campaigns. Commercials featuring prominent figures as reformed water drinkers set an example in front of the camera. The brand also passes on the message to children of all ages (and their parents) that it’s fun to drink water – and it’s good for you. To this end, as a contract filler for Disney Svyatoj Istochnik fills its water into special bottles that are extremely popular with kids. Care for the environment Accepting social and ecological responsibility is also an aspect of the company’s philosophy. “We’re always looking for ways of striking a balance between the use of PET and the protection of the environment as part of our sustainability strategy,” states Zhadanov. “We use eco-friendly packaging, promote the collection of PET bottles and packaging for Alexander Zhadanov, CEO of IDS Borjomi: Converting their country to a nation of water drinkers with great success: IDS Borjomi Russia and CEO Alexander Zhadanov have a lot to be pleased about. Shrink packer: The bottles are formed into packs on the KHS shrink packer and wrapped in shrink film.","@ID":40} "PETnews 6 NEWS PETplanet Insider Vol. 22 No. 01+02/21 petpla.net Demand for PET recycling technologies continues to grow Austrian Erema Engineering Recycling Maschinen und Anlagen Ges.m.b.H announced that the demand for its PET recycling technologies is growing worldwide across the entire PET segment. “Despite declining sales of beverages due to the Corona pandemic and a tense situation in the recycling industry accounted for by the fall in the price of virgin material, interest in our PET recycling technologies remains high,” reports Christoph Wöss, Business Development Manager at Erema. Erema estimates the total capacity of all PET recycling machines sold to date for various applications at 2.6 million t/a, with the recent trend pointing clearly towards large-scale systems processing 2,000 kg/h upwards. A recycling system installed in Mexico this year is outstanding in this respect. It consists of two Vacurema Basic T machines with a throughput capacity of 4,000kg/h each and Solid State Polycondensation (SSP). “The customer is planning an annual production of up to 60,000 t of food contact compliant rPET. These are the largest systems we have ever built, but our order books already have an order for an even larger one,” says Christoph Wöss. Erema is particularly satisfied with the market success of the innovative Vacunite technology, which redefines the benchmark for performance in bottle-to-bottle. In just under two years, the energy-efficient system, developed in cooperation with Polymetrix, has already been sold to 13 customers worldwide. The Vacunite process is claimed to combine vacuum and nitrogen technology, to ensure maximum decontamination efficiency and, with the best rPET colour values, also to ensure that higher proportions of rPET are possible in the bottle end product. Growth is driven by more than the positive development of the bottle-to-bottle sector. Processing PET flakes directly into preforms (flakes-to-preform) or film in a single processing step – made possible using the MultiPurpose Reactor, which can be installed as an upgrade to existing film extrusion lines (bottle-to-sheet) – and especially into recycled pellets for the textile industry (bottle-to-POY) also boosts demand in this segment. As a service to customers, Erema specialists take on the task of applying for assessments of the respective recycling process by the European Food and Safety Authority (EFSA) and provide advice and support in the preparations for the approval procedures required for the production of food contact compliant rPET. Finally, following the expansion of manufacturing and office space, the customer centre at the company headquarters in Ansfelden is also currently being expanded. Material tests using the Vacunite process will also be carried out on-site at Erema, expected to start during the first half of 2021. www.erema-group.com NPE 2021 cancelled After consultation with medical and legal experts, the Plastics Officers of the Board, the NPE executive committee, exhibitors, and the association membership, the Plastics Board of Directors decided, and is announcing, the cancellation of the in-person components of NPE2021, scheduled for May 17–21, 2021, in Orlando, Florida due to the ongoing coronavirus pandemic. After extensive review, it has been determined that it is not possible to hold the planned event and also provide a safe environment at that time and location, and therefore the in-person show must be cancelled, as the organiser announced. The Plastics Industry Association (Plastics) places the health and safety of the members, exhibitors, staff, and the attendees as its highest priority. The Association states “While we are disappointed by the circumstances that led to this decision, we know that the plastics industry is strong and resilient. Over the past ten months, it has been leading the transformation of manufacturing processes and supply chain operations that deliver medical equipment and supplies to pharmaceutical companies, medical supply manufacturers, and healthcare workers, protecting first responders and frontline workers against the coronavirus. By bringing companies at the forefront of plastics manufacturing together in other ways, Plastics will continue to provide opportunities for the industry to unite to solve today’s needs and reimagine how to meet tomorrow’s challenges.” www.npe.org The date for Interpack 2023 is set The next Interpack will take place from May 4-10, 2023 at the Düsseldorf Trade Fair Centre. Messe Düsseldorf set this date in agreement with its partners and committees. Interested companies from the packaging sector and the associated processing industry will be able to register online from the end of March/beginning of April, provided all goes to plan. Exhibitors who were approved for Interpack 2021, which was cancelled due to the pandemic, have already been able to reserve their stand positions for 2023 and will now be able to rebook when they register. Components will take place in parallel with Interpack. It is oriented towards the supplier sector for the packaging and processing industry. Both Interpack and Components will regularly provide information on industry trends and innovations up until the next edition of both trade fairs. The online presence of the upcoming Interpack and Components 2023 is also being built up and expanded. www.interpack.com","@ID":8}
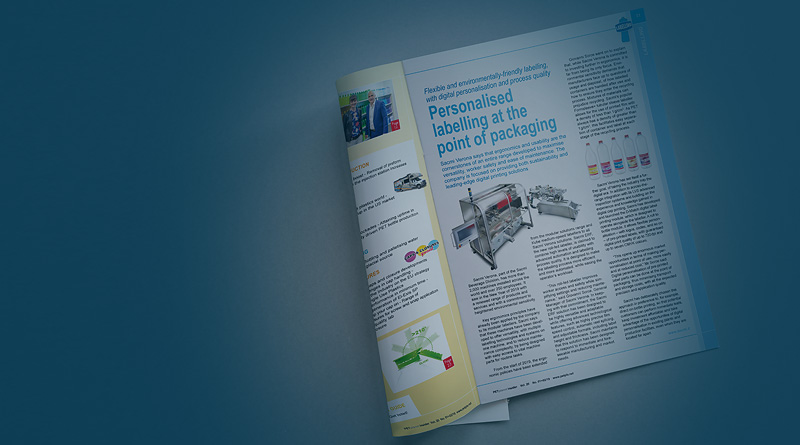