PREFORM PRODUCTION PETplanet Insider Vol. 21 No. 10/20 petpla.net 22 A sideway gamechanger - New Netstal PET-Line with sideway removals system From up and over to side Krauss Maffei High Performance introduced its Netstal PET-Line with the sideway removal system in September which allowed us to take a close look at the new 4,000kN line along with Stefan Kleinfeld, Product Manager for the complete range of Netstal and Krauss Maffei PET Systems and Renzo Davatz, CEO of Krauss Maffei High Performance AG. Sideways removal has become the norm for all suppliers, with preform moulds and production facilities designed to accommodate this. Krauss Maffei High Performance, formerly known as Netstal, is the only company that prefers removing preforms up and over the machine. Their so-called PETLine, which is still sold under the Netstal product brand, is generally regarded by the industry as the most robust and energy efficient system on the market. In order to be active on the sideways removal market, three years ago the company decided to develop a completely new PET-Line as a sideways removal system. Moulds provided by suppliers since 2004 have been used with the machines. Not content with creating yet another standard system, the company was determined to improve on the energy efficiency capability and performance of previous PET systems. PETplanet: Are we seeing a completely new system here? Stefan Kleinfeld: During the development of each component, we always ask ourselves how we can increase productivity for the customer. Our key requirements have always been speed, energy efficiency, durability, ease of use and maintenance. The result is a system that has a lock-to-lock time of 1.9 seconds, with an energy consumption rate of 0.179 kWh/kg PET for the produced 18.6 g preform. In so doing, I believe we are setting new standards for the industry. PETplanet: Let us start with the lock-to-lock time. How have you been able to achieve this? Stefan Kleinfeld: A good example. From the clamping unit, you can see that we have put every component, or in this case, every assembly under the microscope. In order to achieve fast speeds we use the classic 5-point twin toggle lever, which accelerates and decelerates the moving panel that runs on large guide rails. This has been assembled with great precision and is wear-resistant. The toggle lever is driven by an electric motor which has transmission and steering rack. The electric motor generates the necessary speed. The steering rack is extremely durable and shows far less signs of wear and tear compared to spindles used elsewhere. For the user, this means that the precision and speed of the clamp will be just the same in 5-10 years’ time as it was on day one. By definition, the electric drive is more energy efficient than its hydraulic counterpart. This has enabled us to make additional savings as we are able to recuperate kinetic energy when braking. PETplanet: Is the plasticising unit just as well developed? Stefan Kleinfeld: The screw is certainly a very prominent feature of the system. The concept of the screw and shot pot is a proven success in our company and is the approach we decided to adopt. The screw was further developed, based on our experience with the PETForm and the PET-Line top-entry in order to obtain a significantly larger process window in the production environment. This is irrespective of the quality of the material; it can be 100% new or 100% rPET, something in between, or with additives. The screw has been extensively tested and is better than Stefan Kleinfeld, Product Manager PET Systems L-R: Stefan Kleinfeld (Product Manager PET Systems), Renzo Davatz (CEO KraussMaffei HighPerformance AG) and Eric Overbeek (VP Sales) present the new Netstal PET-LINE","@ID":24}, BOTTLE MAKING 29 PETplanet Insider Vol. 21 No. 10/20 petpla.net BOTTLE MAKING 29 bottles less attractive”, says Mr Clark in justification of this step. “In terms of caps, our disc caps for personal care products take first place.” Sustainability and environmental awareness play a central role in all our actions, explains John Clark. With this in mind, customers are also specifically sought that best suit Ant Packaging’s company philosophy. “Alternative culture is almost ubiquitous at our site. Simply because of this, it is immensely important for us that we fit in with that as a plastics processor. Production is therefore not only CO2 -neutral but bottles are manufactured from 100% recycled material, both PET and HDPE. Here, we are basically seeing a clear increase in the trend for using recycled plastics, mainly for products in areas with less sensitive pricing.” rPET is obtained from the local and Thai markets. Ant Packaging’s turnover is almost €3.5 million. Concentration is on the local market. Only 6% of annual turn-over is intended for export, primarily to New Zealand, but other overseas regions have been included in the past. Mr Clark describes his recipe for success as follows: “It’s possible that our 20/20 rule is responsible for this and we follow it consistently. Twenty main customers, who each make up more than 1% of our business, but no one customer is greater than 20% of our total turnover. It’s not about growth but about strategic partnerships with those who share our philosophy.” In contrast to other converters, the company is now facing particular challenges during the coronavirus crisis: sufficient production capacity. “We can hardly keep up with the high demand for hand sanitiser in Australia, like everywhere, so currently, we can only process orders from existing customers. Also, the administrative staff are mostly working from home throughout the crisis. Those who must go into work, like production employees, have their temperature taken when they arrive and undergo higher disinfection procedures in the production hall. These measures have been accepted well by our people,” says Mr Clark. “After the corona crisis, we want to invest in another single-stage PET system for bottles and an injection moulding system for caps. Furthermore, we are also planning to offer more products made from ocean plastic and are excited about the opportunities for chemical recycling.” www.antpackaging.com.au John Clark in his workshop","@ID":31}, FLIPPING THE WORLD OF PET UPSIDE DOWN AND EVEN SIDEWAYS. The All-New NETSTAL PET-LINE with Side Entry. kraussmaffei.com/new-petline The All-New NETSTAL PET-LINE comes with a variety of advantages to maximize output and minimize costs: - Side entry for maximum mold compatibility - Shortest cycle times for increased output - Lowest level of energy consumption to minimize the ecological footprint - Improved 100% rPET processing to enable the circular economy - New control unit including NETSTAL Smart Operation to ensure easy, fast and safe start-up and production","@ID":43}, PACKAGING / PALLETISING PETplanet Insider Vol. 21 No. 10/20 petpla.net 46 Optimised end of line packaging process Co-packing at its best Refresco Finland Oy is the leading bottling factory in Finland for co-packing juices, soft drinks, water, energy drinks and other non-alcoholic beverages for private labels - in addition to a wide range of products under its own brand. To automate and optimise the production process and respond to their customers’ requests for personalised “packaging” solutions while maintaining market trends, the Finnish company decided to invest in the purchase of a latest generation automatic packer CSK 50P Ergon supplied by SMI. Refresco Finland Oy from Kuopio is part of the Dutch multinational Refresco Group (the largest independent bottler in the world), which produces and sells a wide variety of private labels and offers its experience and professionalism within the industrial sector in Europe, North America and Mexico. In addition to managing the entire production chain, the Finnish company offers lots of services to the “private label” companies with which it works, from developing an idea to its implementation, from the development of the product to its bottling and packaging, from storage to logistics. At the same time, it keeps abreast of innovations in terms of products, packaging and scale, allowing the continual growth of its portfolio of products and the development of new systems to improve the production process in terms of offer quality, reduction of costs, energy savings and environmental safeguarding. In addition to the wide range of products produced for third parties, Refresco Finland Oy markets a wide range of its own brand. Made to measure solutions Refresco Finland includes a wide variety of customers and supplies bespoke solutions, able to satisfy not only global retailers but also private brand customers. Thanks to these ongoing collaborations, the bottler is able to put new products on the market in a very short time, to help its customers face new market challenges, respond to change and modernise continually. Thanks to the high technology of its plants, the variety of “packaging” solutions available, to the quality control system, which meets the highest national and international standards, and a structure that is strongly inclined towards “project development”, Refresco Finland Oy sees itself as the ideal partner for every industrial operator within the food & beverage sector who wishes to update the image of their products. The Finnish company has gained considerable experience in transforming the needs and requests of its customers with high quality proposals, guaranteeing the achievement of the objectives within budget and lead times. The food products that are produced in their plants are sold in a wide, diverse range of formats: PET, glass, can, brik and pouch. The innovative method for sterile bottling, for which the Refresco Group is well-known, is claimed to guarantee that the product has a long shelf-life, without compromising the quality of its food properties, in terms of authenticity, reliability and conservation. Compact wrapper The choice for the installation of a new, compact wrapper fell to the CSK range from SMI. For Refresco Finland Oy it seemed to be the most suitable choice to automate and optimise the end of line, secondary, packaging process as the range of these cutting-edge technology machines are claimed to stand out for their advanced automation, flexibility of use, low energy costs and respect for the environment. The CSK 50P Ergon installed at the factory in Kuopio, packs different types of bottles in PET in numerous pack formats in pad+film and film only. The CSK Ergon range includes single and twin lane models, with a compact and ergonomic design. Maximum speed for shrink wrapping is 50 packs/ F.l.t.r.: Ilpo Metso, Manager for Development Refresco; Carl B. Armstrong, F.A.T. Engineer SMI; Sami Kokkonen, Manager for Development Refresco","@ID":48}, MARKET SURVEY 32 PETplanet Insider Vol. 21 No. 10/20 petpla.net Filling inspection systems Company name Heuft Systemtechnik GMBH Pressco Technology Inc Sacmi Imola S.C. Newamstar Packaging Machinery Co., Ltd. Postal address Telephone number Web site address Contact name Function Direct telephone number E-Mail Am Wind 1, 56659 Burgbrohl, Germany +49 2636 56 0 www.heuft.com Sales requests +49 2636 56 0 sales.requests@heuft.com 29200 Aurora Road, Cleveland, OH USA +1 440 498 2600 www.pressco.com Mr Tom Murphy VP, Sales & Customer Service +1 440 498 2600 sales@pressco.com Via Selice Prov.le 17/A Imola (BO) Italy +39 0542 607111 www.sacmi.com Mr Stefano Severi Sales Area Manager +39 0542 607553 stefano.severi@sacmi.it East Xinjing Road, Zhangjiagang Economic & Technological Development Zone, Jiangsu 215618, P.R. China +86 512 5869 1111 www.newamstar.com Marketing Manager +86 512 5699 3303 market@newamstar.com Fill level control Infrared Yes No No Yes X-ray Yes Yes No Yes Gamma No Yes No Yes Camera Yes Yes, high frequency Yes Yes Contamination control Foreign object detection, low & high density, all types of foreign detection, unique pulsed X-ray & camera combined in one system No No Equipped with Recovery System Closure inspection Presents of cap Yes Yes Yes Yes Crooked cap Yes Yes Yes Yes Lifed cap Yes Yes Yes Yes Wrong cap Yes Yes Yes Yes Tamper evident band control Yes Yes Yes Yes Camera: 360° / sensor Yes Yes Camera with special peripheral lens to control 360° of the sidewall, real 3D technology for 360° precise inspection Yes Label inspection Torn label Yes Yes Yes, +/- 1° Yes Vertical / horizontal misalignment Yes Yes Yes, +/- 1mm Yes Best-before date control Yes No Presence / absence if printed in inkjet, OCR if laser printed Yes Camera: 360°/ sensor Yes Yes Camera 360° with real 3D technology Yes Pressure leak detector Yes No No Yes Applicable bottle type Diameter 30-80mm Up to 150mm Up to 150mm Up to 255mm Height 100-350mm Up to 400mm Up to 340mm Up to 500mm Rejecting bottle Yes Push reject and diverter reject options available Single or multi push devices Inspection speed Up to 72,000bph Over 3,000ppm Up to 72,000bph 72,000bph Monitoring Filling valves, closer heads, continous bottle tracking Filler valve, capper head correlation Panorama supervisor Filling Equipment Company name STM SP. Z O. O. SMI S.p.A. Sidel Postal address Telephone number Web site address Contact name Function Direct telephone number E-Mail Ul. Piaskowa 12, 78-520 Zlocieniec, Poland +48 94 367 14 71 www.stm-pack.com Mr Mateusz Kinda Sales Director +48 503036635 mk@stm-pack.com Via Carlo Ceresa, 10 24015 San Giovanni Bianco, Italy +39 0345 40111 www.smigroup.it Mr Pietro Volpi Marketing Dept. Manager +39 0345 40316 pietro.volpi@smigroup.net Via La Spezia 241/A, 43126 Parma, Italy +39 0521 9991 www.sidel.com Mr Stefano Baini Filling Product Manager stefano.baini@sidel.com 1. Machine designation / model number Arrow Blowing, filler and capping machine in Ecobloc configuration; rinser, filler and capper machine in Monobloc configuration Sidel Matrix SF 300 FM Sidel Matrix SF 100 FM 2. Number of filling heads (range: from/to) 12-72 9-126 32-216 24-144 3. Min to max bottle contents (in liters) 0.1-10 0.25-10 0.2-3.0 0.2-3.0 4. Filling speed: output (bph) (min to max): 1,000-68,100 4,000-81,000 (18°C) 5,000-90,000 specifiy: 1l bottle / still water (bph) 2,000-240,000 Up to 68,100 80,000 75,000 1l bottle / CSD (bph) 2,000-240,000 Up to 36,800 68,000 (18°C) 1l bottle / Milk (bph) 2,000-240,000 Up to 36,000 1l bottle / Juice (bph) 2,000-240,000 Up to 36,000 5. Filling process Pressureless (still drinks) Gravitiy filling / weight filling/ volumetric filling Yes Yes Yes Pressure filling (carbonated drinks) Isobaric filling Yes Yes Hot filling Gravitiy filling No Cold aseptic filling Weight filling No Juices with high pulp content Gravitiy filling / weight filling/ volumetric filling No Yes Yes 6. Type of filling valve and metering system Mechanical, electro-pneumatic, weight, flow Electronic volumetric filling valves Flowmeters (metering system) Electropneumatic volumetric filler with flowmeter volume control Electropneumatic volumetric filler with flowmeter volume control, with no bottle/valve contact 7. Special features (short description/keywords) Fast change of formats minimised up to 10 min., unique internal, neck-based transport of packages without necessity of setting the height, fast change of packaging formats with different diameters, user friendly touch panel with automatic diagnostic software, precise positioning of packages, operation limited to minimum Compact modular frame, with a wide choice of customisation options; operating and maintenance costs dramatically cut; easy and quick format changeover, with no need to replace mechanical components Fully automatic operating computer control; external beverage tank (no ring bowl); electropneumatic components integrated on filling valve For mineral and demineralised water ie R.O. (reverse osmosis) water; fully automatic operating computer control; external beverage tank (no ring bowl)","@ID":34}, 8 NEWS PETplanet Insider Vol. 21 No. 10/20 petpla.net PETinar: The Essential Guide to Tethered Closures In the EU, tethered closures will soon be mandatory for most single-use plastic containers. We expect other regions around the world to adopt similar legislation in the near future. How do you seize on that opportunity? What’s involved? Our PETinar has the answers. PETinar: The Essential Guide to Tethered Closures November 05, 2020 // 4p.m. CET Presented by Mike White of Husky Injection Molding Systems You will learn: Why switch to tethered closures: the basic requirements and opportunities Best practices in tethered closure design What’s involved and how to get started We will also share a gallery of real-world tethered closure designs for inspiration. Register free of charge at petpla.net/category/petinars Meeting 4.0 technologies The packaging machinery industry is often perceived as lagging behind latest technologies. To break with this, ABC decided to gain a new edge using modern automation as a standard. “Coupling reliability and smartness to their compressors gives a new breath to PET bottle manufacturers, providing a complete solution,” commented Victor Goncalves, Export Area Manager for French speaking countries and Italy at ABC Compressors. “ABC has been following the trend initiated by well-known PET blower manufacturers, offering real time communication and technical knowledge transfer through smart tools. For example: EVA, ABC’s augmented reality glasses, allow supporting maintenance tasks on compressors in real time, sharing technical drawings as well as audio and written content. We also implemented a synchronised monitoring solution to manage several machines on the same HMI screen. Today we can easily say customer technical teams are mastering ABC’s online tools just as well as mechanical ones,” states Goncalves and continues “After almost a year of Covid19 crisis, we’ve passed the test! 4.0 technologies enabled us to maintain high quality service by remotely monitoring maintenance works. Without any doubt, smart maintenance is our present, while ABC’s closest horizon is shaped by our new generation of low consumption motors.” www.abc-compressors.com PETINAR BERICAP Tethered Cap Solutions • Easy& intuitive handling • 180° opening • No change to - Neck finish - Capper - Filling line Approved and ready for line trials now!","@ID":10}, BOTTLE MAKING 40 PETplanet Insider Vol. 21 No. 10/20 petpla.net the amount of crystallisation reaches about 4%. Since crystalline material reduces many bottle properties, haze always causes bottles to be rejected and must therefore be avoided. As mentioned earlier crystalline haze may already be present in the preform and operators need to check their supply of preforms first when this defect occurs. Fig. 6.8 Thermo image of preform at the oven exit. Lower blowing temperatures yield better performing bottles. Photo courtesy of Husky IMS. Temperatures below 85°C (185°F) cause microcracks in the PET structure. These cracks show up as whitish rings, usually in areas with the highest stretch ratios and also cause bottle rejection. This type of failure is called pearlescense because of the pearl-like appearance of the defect (Fig. 6.8). Making bottles that show neither crystalline haze nor pearlescense still leaves a process window to work with. At very high stretch ratios there is often only one temperature the preform can be successfully blown at but most other times operators can blow at a certain temperature range. Bottles produced in this range might all look alike but when it comes to bottle properties such as carbonation retention, the bottles blown at the lowest possible temperature before pearlescense sets in are the ones that will perform best. This is because - as shown in chapter 3, section 3.2 - by lowering the preform temperature the maximum strain within the natural stretch ratio is reduced and the material is forced to orient more. It should now also be apparent that the optimal temperature profile within the preform wall (higher inside than outside temperature) leads to lower overall temperatures since the onset of pearlescense can be delayed: The further stretching inner parts do not fracture as early at the higher temperature. Please order your copy at the PETplanet Insider book shop: petpla.net/book3 Stretch Blow Molding Third Edition by Ottmar Brandau € 130,00 374 pages © Copyright Elsevier 2017, 2012 I should mention at this point that most bottles blown in this matter, that is, at the lowest possible temperature, require a minimum blow air pressure of 35bar with bar as a maximum. Compressed air takes up approximately 50% of bottle production energy cost (without the cost of preforms) and higher air pressure increases overall bottle cost. Sometimes a compromise between optimal bottle quality and economic considerations must be found. Recycling high-pressure air for preblow pressure is available on some machines and can reduce these costs.","@ID":42}, PACKAGING / PALLETISING PETplanet Insider Vol. 21 No. 10/20 petpla.net 47 minute in single lane and 50+50 packs/minute in twin lane (speed is variable according to the size of the container and the pack format). Packed products include bottle sizes of 0.33 l, 0.4 l, 0.5 l and 1.5 l in PET. Format changeover can be automatically regulated. The packer is equipped with a motorised system of oscillating laning guides at the machine infeed, which facilitate the correct laning of loose product on the conveyor which is made of low friction coefficient thermoplastic. As another advantage according to SMI is that grouping loose products in the format required is achieved continuously thanks to electronically synchronised fingers and separation guides. A cardboard blank magazine is situated under the infeed conveyor from where the sleeves are picked up by an alternate motion cardboard picker. Placed at the start of the cardboard ramp, it is equipped with a vacuum suction system set of suckers. The curved cardboard ramp at the beginning and at the end helps the layer to be inserted under the group of products at the outfeed of the electronic separator. A compact knife group, where the blade is managed by a “directdrive” brushless motor makes the cut precise and simplifies maintenance. The wrapper’s new ICOS motors, equipped with integrated, digital servo-driver simplifies the machine cabling to ensure greater energy efficiency, less noise and reduced component wear and tear. The CSK 50P Ergon features a shrink tunnel equipped with optional metal chain and lubrication that ensures that the film under the pack is joined perfectly. The machine is also equipped with a range of optional devices to guarantee a high level of quality of the final pack, such as a product stabiliser and an additional 1,150mm conveyor, placed at the tunnel outfeed which allow the packs to cool down. www.smigroup.it Refresco Finland Oy is part of the Refresco Group, producer of soft drinks and fruit juice for retailers and owners of private brands, which in January 2018 acquired the bottling activities of the American company Cott. It thus became the largest, independent bottler of the sector in Europe and North America and one of the top five in the world. With 59 factories and more than 250 production lines in Benelux, Finland, France, Germany, Spain, Italy, United Kingdom, Poland and the United States, the Refresco Group of companies, head-quartered in Rotterdam, possesses vast experience in the “supply chain” sector and has a reputation for innovation and development. The Dutch multinational group employs more than 9,500 people in Europe and the USA, produces 11 billion litres of beverages annually and in 2018 generated a revenue of around € 3.7 bn.","@ID":49}, imprint EDITORIAL PUBLISHER Alexander Büchler, Managing Director HEAD OFFICE heidelberg business media GmbH Vangerowstraße 33 69115 Heidelberg, Germany phone: +49 6221-65108-0 fax: +49 6221-65108-28 info@hbmedia.net EDITORIAL Kay Barton Heike Fischer Gabriele Kosmehl Michael Maruschke Ruari McCallion Waldemar Schmitke Anthony Withers WikiPETia.info petplanet@hbmedia.net MEDIA CONSULTANTS Martina Hirschmann hirschmann@hbmedia.net Johann Lange-Brock lange-brock@hbmedia.net phone: +49 6221-65108-0 fax: +49 6221-65108-28 LAYOUT AND PREPRESS EXPRIM Werbeagentur | exprim.de Matthias Gaumann READER SERVICES Till Kretner reader@hbmedia.net PRINT Chroma Druck Eine Unternehmung der Limberg-Druck GmbH Danziger Platz 6 67059 Ludwigshafen, Germany WWW www.hbmedia.net | petpla.net PETplanet Insider ISSN 1438-9459 is published 10 times a year. This publication is sent to qualified subscribers (1-year subscription 149 EUR, 2-year subscription 289 EUR, Young professionals’ subscription 99 EUR. Magazines will be dispatched to you by airmail). Not to be reproduced in any form without permission from the publisher. Note: The fact that product names may not be identified as trademarks is not an indication that such names are not registered trademarks. 3 PETplanet Insider Vol. 21 No. 10/20 petpla.net We have two reports on new preform machines to offer you in this issue. We visited Sipa to take a close look at compression injection moulding of preforms. There are now three machines operating at customer facilities and we were able to check out another four that we saw ready for shipment. The machinery is with the PET recyclers and destined for bottling plants, with Coca-Cola as the standout brand among those recipients. No less exciting has been the introduction of a new Netstal preform line, which offers sideways rather than the standard Swiss design of upwards removal. The machinery is quite new and has many innovative features. Most noteworthy is the fact that nearly all the moulds can be used on the new line in the conventional sideways removal process. The use of Netstal machines has been smoothly integrated in plants that operate IM machinery produced by other manufacturers. In discussions on up- and downwards removal, I have realised that the term “side entry”, which up until now has been a term used throughout the industry, is really thought from the machine developer’s perspective. The word “entry” implies that robotic devices penetrate the mould. However, every experienced developer knows that the main focus should be on the manufactured product, in our case, the preform, which is removed from and not driven into the mould. That is why we have taken the liberty of referring to it not as “side entry” but “sideways removal” as part of our contribution to the new Netstal range. Sipa has a simpler solution with its continuous preform production on carousels. This is correctly referred to as “transfer”. Whether or not you use side entry, sideways removal or transfer in your preform production, I hope you enjoy this issue. Yours sincerely Alexander Büchler Dear readers,","@ID":5}, PETplanet Insider Vol. 21 No. 10/20 petpla.net 54 PETbottles Beverage + Liquid Food Volvic launches a lemonade drink “Volvic Limotion” is the name that Danone Waters Germany has given to its product, which is now trading on the carbonated soft drinks’ market. Aside from fruit juice, the lemonades do not contain any additives. Depending on the variety, the fruit juice content is between approximately 7% and 9%, while the proportion of sugar is said to be 30% lower than other sweetened soft drinks in Germany, says the manufacturer. 100ml of lemonade contains around 4 g of sugar. The words on the bottle are aimed at a young target audience. The bottles are made out of 100% recycled material and have transparent, foil labels. The lemonade comes in new sized 0.45 and 0.9 l bottles. Appropriately coloured screw grip caps that match the product and tamperproof strip complete the product’s appearance. www.volvic.de New range from Vöslauer Vöslauer has launched a new, refreshing drink with a long history under the name “Balance Switchel”. The Switchel drink has been enhanced by the addition of vinegar, giving it a slightly acidic, thirst-quenching character. Vöslauer is currently offering two varieties: the classic version with lemon, lime, ginger and a little honey, and another variant (pictured) which contains blackcurrant, ginger, wild berries and honey. Both come in a distinctive, brand-typical bulbous bottle made from 100% recycled material. A hand grip screw cap with tamper-proof strip and transparent foil label complete the packaging. www.switchel.at Iced tea with no sugar Consumer criticism over the large amounts of sugar in popular iced tea drinks has not gone unheard. Many large manufacturers are now offering varieties that do not contain sugar. San Benedetto is also selling its own sugar-free, peach-flavoured iced tea. The slightly tapered 1.5 l bottles with embossed tea leaf design have a foil label. The conveniently sized large spout is secured by a screw cap with tamperproof strip. www.sanbenedetto.it Square bottle for an Aloe Vera drink Aleo, a brand of the Mega Baltic company based in Vilnius, Lithuania, is selling drinks with aloe vera content produced in Taiwan through various distribution partners. There are around a dozen different varieties, including those that have reduced calorie content. The 0.5 and 1 l bottles are square-edged shaped with a slightly greenish colour in the shoulder area and colour-matching screw cap. www.aleodrinks.eu","@ID":56}, PETnews 6 NEWS PETplanet Insider Vol. 21 No. 10/20 petpla.net Firmenich opens new pilot plant in Geneva Firmenich, a privately-owned P e r f ume a n d Taste company, announced the opening of its new biotechnology and naturals pilot plant and laboratory in Geneva, Switzerland. Benefiting from the latest digital technology, the facility opens a new era for the development of ingredients and clean label solutions by providing faster speed-to-market and greater flexibility for customer collaboration. Integrated into the Group’s flagship ingredients production site at La Plaine, Geneva, the facility operates to high safety and environmental standards, reducing waste and energy consumption. Operational this month, the pilot plant at La Plaine enabling the development of efficient and high-quality production processes through biotechnology or natural extraction. Harnessing digital technology for increased automation, the pilot plant is able to move from single to continuous batch process, increasing efficiency, speed and reducing the use of raw materials. In keeping with Firmenich’s recognised track record in sustainability, the new pilot plant benefits from efficient bioreactors, which minimises both the amount of waste produced and energy consumed. www.firmenich.com Alpla acquires facility of Amcor in India Alpla Group, a global specialist for packaging solutions and r e c y c l i ng , i s acquiring a facility in Western India for the production of preforms for PET bottles from the packaging company Amcor. Alpla Group has taken over a plant for rigid plastics in India from the global packaging specialist Amcor with effect from September 28, 2020. The plant in Alandi, West India, is in the immediate vicinity of the metropolis of Pune. It manufactures preforms for the production of PET bottles for the beverage industry. Customers include Coca-Cola and the Indian dairy company Amul. With this takeover, Alpla is expanding its core business in the PET area in India. All 50 employees will be taken over by Alpla. Vagish Dixit, Managing Director Alpla India: ‘The newly acquired facility near Pune will primarily help us to better serve the market in the Western Region of India and further expand existing partnerships with customers such as Coca-Cola.’ Alpla Pune is the ninth location of Alpla in India and the second in the west of the country. The contracting parties have agreed not to disclose any details of the contract. www.alpla.com Alpek announces M&G Mexico’s restructuring plan has been approved Alpek, S.A.B. de C.V. announced that the financial restructuring agreement between M&G Polímeros México, S.A. de C.V. and the majority of its creditors, including certain Alpek subsidiaries, has been approved on a definitive basis by the Mexican bankruptcy court. This approval would conclude the pre-agreed bankruptcy proceedings (“concurso mercantil preacordado”) initiated by M&G Mexico and its creditors in February 2019. Under the agreement, Alpek will begin recovering US $ 160 million in guaranteed debt, related to its first and second liens, as early as the end of this year. Based on the strong PET demand and margins seen in recent months, as well as the outlook for the global polyester industry, the company expects to recover the full amount of its guaranteed debt plus interest over the next five years. Alpek will also continue supplying the PTA needed by M&G Mexico’s PET facility. This will both ensure stable operations at M&G Mexico as Alpek recovers its debt, as well as a steady offtake for the PTA site in Altamira. “We are very pleased to see this process come to its successful completion under terms that are beneficial to all parties involved,” said José de Jesús Valdez, Alpek’s CEO. “Recovering our guaranteed debt will help Alpek continue pursuing valuegenerating opportunities while relying on a stronger free cash flow and financial position.” www.alpek.com And&Or Group buys the Madrid company Franco Dolfini Automation And&Or strengthens its position and offer of machinery and solutions for the blow moulding industry with the acquisition of the Madrid company Franco Dolfini Automation (FDA). Franco Dolfini Automation is a Spanish machine manufacturer for the automation of plastic botlles manufacturing processes. This 25 employees company, with a turnover of approximately € 2 million, fortifies And&Or’s offer in the blow moulding sector, and allows the group to establish itself more firmly in its position in the Spanish and international markets, increasing its product portfolio and improving its offer of products and services. FDA will work as a separate entity, and will keep its own brand, management team and strategy. Among other products, FDA adds quality control systems for PET bottles using high-voltage equipment to the And&Or portfolio, compact and flexible palletisers for empty bottles handling, tube-type baggers allowing plastic film consumption savings, dynamic weight systems, automatic cartoning machines, among others. The two companies follow a similar approach: offering simple and automatic solutions that improve the industrial processes of their clients. The sector’s demand and a close collaboration with its clients made both companies grow in solutions and products. www.andyor.com","@ID":8}, PACKAGING / PALLETISING PETplanet Insider Vol. 21 No. 10/20 petpla.net 48 Packaging with 33% material savings Thermoformed light-weight rPET Cardboard-plastic combinations as a sustainable packaging choice are helping to reduce plastic consumption, while at the same time ensuring high-quality appearance and stability. In addition, they offer extended marketing opportunities as the inside of the cardboard wrap can also be printed. Greiner Packaging’s K3 tub saves up to 33% plastic when compared to other pots of the same size, and is made with a minimum of 30% rPET. The K3 cardboard wrap can be produced with virgin or recycled board produced from sustainably managed forests, with full FSC (Forest Stewardship Council) chain of custody accreditation. The K3 light-weight thermoformed tub is made with a minimum of 30% rPET which can be increased to 100% rPET and is wrapped with a cardboard outer layer. The K3 pot is a popular lightweight alternative for many dairy brands and has already found its way into the instant snacking and cereal market. A K3 cup with a diameter of 95mm and a capacity of 500ml achieves a 17% reduction in CO2 emissions compared with a conventional direct-printed, thermoformed cup of the same size. Meanwhile, the cardboard wrap is produced from either virgin or recycled board and can be decorated with a wide range of finishes. Shelf impact Greiner Packaging’s K3 enhances shelf-impact through offering unique shapes and diverse finishing options, with a wide range of cup and tub sizes including the new fridge friendly rectangular pack. K3 is designed to maximise marketing potential for brand owners, as the cardboard outer can be printed on both sides, creating the opportunity for consumer engagement. While the outside can carry eye-catching graphics, branding and essential consumer information such as ingredients, the reverse can feature promotions and stickers. There is also an option to create product visibility through the addition of window apertures. K3 can be completed with a reusable lid which provides a secure seal for the product after it has been opened. The lid extends the product’s shelf-life, preventing it from absorbing odours, and ensuring it does not spill. “The development of K3 not only enhances a brand’s visibility, but also improves its sustainability credentials,” says Greiner Packaging Product Development Manager Lee McCauley. “Greiner Packaging Switzerland was the original pioneer of the K3 plastic-cardboard packaging solution which has been continuously improved for over 30 years and has been produced in Dungannon since 2013. Dairy customers were the first to capitalise on its environmental benefits and added-value marketing features, but K3 has now also being widely adopted for the food-on-the-go market with brands such as Symington’s.” Sustainable by design Thanks to its reduced plastic content, the K3 packaging solution has an improved CO2 footprint and it can be recycled efficiently, as the cardboard and plastic can be easily separated. “We are working hard to ensure that K3 is recyclable in every country where it is available, and in the UK, K3 has a ‘good’ recyclability rating,” says UK & Ireland Sales and Marketing Director Julie Eller. Digital watermarks can help to identify K3 products in sorting streams and K3 features an improved tear-off solution for easy separation of materials. The new, patent-pending tear-off system makes separating and recycling the two components clean and intuitive. “Sustainability is really important to Greiner Packaging. We have joined the Circular Plastics Alliance which aims to boost the EU market for recycled plastics to 10 million tonnes by 2025. We are also proud to have signed up for The Ellen MacArthur Foundation’s New Plastics Economy Global Commitment 2025. We are committed to the concept of a circular economy that keeps plastic in circulation as a material for as long as possible, and have ambitious targets for the use of recycled content. We have pledged to eliminate problematic or unnecessary plastic packaging and to ensure that 100% of plastic packaging we produce should be 100% recyclable, reusable, or compostable. When the cardboard and plastic parts of K3 are separated, the packaging is 100% recyclable, making it a perfect example of a circular economy product,” Julie Eller adds. www.greiner-gpi.com Greiner Packaging’s K3 cardboard-plastic packaging is proving popular for dairy and food-on-the-go brands.","@ID":50}, BOTTLE MAKING 28 PETplanet Insider Vol. 21 No. 10/20 petpla.net Interview with Ant Packaging Pty. Ltd. 20 April 2020 We met: Mr John Clark, Managing Director Sustainable bottle concept from New South Wales by Kay Barton Ant Packaging is a manufacturer of plastic bottles and other containers. The company is located in Bangalow in New South Wales, almost 100 km south of the famous Gold Coast, which hosted the 2018 Commonwealth Games that takes place every four years. After initial economic drought phases around the millennium, the company finally made a breakthrough with the decision to specialise in single-stage equipment for PET processing. Today, the manufacturer registers annual growth of 18% and works almost without exception in the non-food market. The company wants to set itself apart from competitors, not only through a conscious selection of customers, but also in its use of existing resources and in terms of sustainability. Together with Managing Director John Clark, we took a trip through company formation, philosophy and the status quo. The origins of Ant Packaging date back to 1998. Founder John Clark and a former partner did not want to fall in with a former employer’s relocation and they saw the situation as an occasion to found their own business. “At that time, there were several consolidations in bottle and container production in the Australian market,” explains John Clark. “We had the feeling that no-one was properly supplying containers for small and medium-sized companies, where a wide range of formats were often needed on a shortterm and flexible basis for premium products in small batches. So that’s what we did.” The company started with a Battenfeld Fischer K1-07 blowmoulding machine, with only moderate success. “At that time we had a customer from the hotel industry, for whom we manufactured PVC bottles,” reminisces Mr Clark. “With the Asian crisis around that time, tourists stayed away and beds were empty. Then we tried to win more clients. Two years later, we purchased a new extrusion moulding machine from a manufacturer in Thailand, after which we almost had our electricity cut off. A few more systems followed in subsequent years and we were able to carve out a market for ourselves in the sector for personal care and promotional bottles. Then, in 2006, we decided to expand our portfolio with PET.” This expansion was in fact an ASB50MB single-stage machine. A good decision, as it would turn out, as this enabled the company to quickly open up new customer networks. Packaging for laboratory consumables quickly became the most important market and soon, more equipment followed from Japanese engineering firm ASB. “Our business model is based around flexibility.” says John Clark. “Most PET manufacturers would be calculating how many machines they need to make a certain product, where we are always looking at how many different products we can get one machine to make. We offer customers a full in-house service from concept through design, prototyping, 3D printing, mould making and production. Only the mould making is something that we have outsourced.” Today’s portfolio includes caps as well as bottles and jars. Ant Packaging employs 20 employees, of which six work in the PET processing department. Here, three PET and four PE production lines are in use today, plus two cap lines. Alongside two ASB50MB, there is also an ASB-12N10 for PET; caps are produced on injection moulding machines from Demag with 100 t of clamping force. Wherever possible, the company strategy also involves excluding orders from the food sector and instead concentrating further on niche, non-food markets. The result of this is also the relatively small output of a total of around 14 million containers, of which 8 million are PET bottles and around 8 million are caps. With 25% apiece, half of this output finds application as laboratory consumables and beauty and personal care items, a further 20% in animal care products, 10% in promotional bottles and the rest in other, sometimes unknown sectors. Around 60% of customer enquiries relate to bottles, 20% to jars and 20% to caps. At 50% and 15% respectively, PET and recycled PET make up the majority of processing, both exclusively for bottle production; this is followed by 25% PE. PET bottles are produced in 15ml, 30ml, 50ml, 60ml, 100ml, 125ml, 200ml, 250ml, 375ml and 500ml volumes. Caps are available in 18mm, 24mm, 28mm, 38mm and 63mm diameters. “We have focused on 250ml and smaller as we are manufacturing in a regional area. Australia is a big country so transporting empty bottles around the country makes larger Tour Sponsors: Ant Packaging’s production and packaging area PETcast In our new Road Show podcast, PETplanet meets industry experts from Down Under to Japan and talks with them about their successes, decisions and current developments. Listen to the full conversation atwww.bit.ly/2HVwbAd","@ID":30}, COMPRESSORS PETplanet Insider Vol. 21 No. 10/20 petpla.net 14 Significant energy saving Green mechanics When designing the improved generation of the Vito Next compressor, the engineers from Siad Macchine Impianti (Siad MI) focused on efficient power consumption. The result is a sensible reduction compared to previous models. The world of industrial machinery is increasingly attentive to the environment as well as reducing consumption. Teams of engineers are working to create increasingly “ecofriendly” solutions. This focus is also very significant for Siad Macchine Impianti in Bergamo, Italy, where highpressure air compressors are made to inflate bottles used by lots of the mineral water and soft drink producers throughout the world, made from PET or also PLA. The types of Siad’s compressors are widespread and are also used to bottle milk, beer and wine. Less energy-intensive It starts right from the design phase: Siad’s aim is to produce machines that are more efficient (with identical energy consumption but producing more compressed air), more reliable - in terms of longer maintenance intervals and longer machine life - and offer better performance, such as lower noise and greater stability, compared to former generations. The first objective is to reduce energy consumption: “The cost of purchasing one of these machines represent only 11% of the total cost that the end user has to face in the life cycle of a compressor.” explains Gianluigi De Mitri, Siad MI’s Italian specialist in the Food & Beverage section of the compressor division, “Another 9% is represented by normal maintenance costs. So the rest, a full 80%, is represented by the energy costs of running the machine. We are talking about hundreds of kilowatts per hour: this is why Siad MI engineers have focused on this aspect, plus using inverters that regulate the frequency of the electric current, allowing the motor to work at variable speeds. The reduction in total consumption is significant.” Vito Next looks to the future Vito stands for “Value, Innovation, Technology, and Optimisation”. Moving on, the Next model points to a more sustainable future, as Siad points out. The Vito compressor was first launched in 2014: today there are 55 in operation in Italy and 200 worldwide. Totally made in Italy, it has a working life of at least twenty years and is offered in ten sizes to meet the numerous requirements of customers. Through regular dialogue with Siad MI, these same customers provide constant suggestions to improve performance and operation. The inclusion of a special anti-vibration system means that, for example, a Siad MI compressor can be installed on a second floor of a bottling company. Continuously evolving throughout seven years The first Vito compressor left the company’s factory in Bergamo seven years ago. Since then it has been continuously developed over time to adapt to the requirements of users, with whom the collaboration does not stop with the sale but continues throughout the working life of the machine. The new models in the Vito Next range are the result of this collaboration and the concentrated work of the engineers. Here are the four main new features of these machines. COMPRESSORS Energy efficiency starts with the design phase - Siad MI compressors at Bergamo, Italy.","@ID":16}, BOTTLE MAKING 36 PETplanet Insider Vol. 21 No. 10/20 petpla.net Fig. 6.1: Standard preform for carbonated beverages. The ring underneath the thread, called neck support ring (NSR) or transition ring, is used throughout the blow moulding machine to hold the preform in place. 6.1 Process overview While individual features differ between different types and brands of machines, they all load cooled, injection-moulded preforms, reheat them in an oven section, transfer them in a blow mould clamp, and stretch and blow them (for differences to the single-stage process see Chapter 8) (Fig. 6.1). Several questions arise that will be answered in this section of the book: What is the optimal blowing temperature? What is the optimal heat profile in the preform wall? How does polyethylene terephthalate (PET) absorb infrared energy and how can this knowledge be used to improve bottle properties? How do material properties and stretch ratios affect blowing behaviour? How can optimal wall thickness distribution be achieved? What amount of oven cooling should be used? How does blow air timing affect bottle properties? These are questions that machine operators are faced with daily and often a compromise between machine capabilities, output requirements, and bottle properties has to be found. It is therefore paramount that processors understand all relevant process charStretch Blow Molding, part 13 Fundamentals of the Blow Process by Ottmar Brandau Ottmar Brandau has newly revised his book “Stretch Blow Molding”, first published by hbmedia / PETplanet Publisher, and now re-issued in a third edition under the Elsevier Imprint. PETplanet Insider is publishing extracts from successive chapters in a serie of articles.","@ID":38}, 52 TRADE SHOW PREVIEW PETplanet Insider Vol. 21 No. 10/20 petpla.net TRADE SHOWpreview MIKE WHITE Business Development Manager for Beverage Closures The Essential Guide to Tethered Closures November 05, 4pm CET Register at www.PETpla.net Presented by Mike White of Husky Injection Molding Systems PETINAR Brau Beviale 2020 Brau Beviale will take place as a Special Edition at the Exhibition Centre Nuremberg from November 10-12w, 2020. Six lecture stages in the exhibition halls–BrauBeviale@stage–will provide plenty of space for discussion rounds on current trends and challenges. Tastings in the Craft Drinks Areas, competitions including the European Beer Star will be held. Brau Beviale will combine both in-person and online experiences. Trends from every segment In recent years, the Craft Drinks Area at Brau Beviale has become established as the preferred meeting place for trend scouts and people just wanting to learn more. This is the place for sampling inspiring products from the fields of beer, spirits, water, juices and non-alcoholic drinks. A smart and safe approach has been adopted to enable the extensive sampling to continue at this year’s Special Edition. Each of the three halls will covering all beverage segments and will have its own Craft Drinks Area. Following a short registration process, visitors can take a seat in the closed-off area, where the bartender will serve them with the tasting glasses. An exciting feature this year is that the tasting will come with digital support. A scan with the smartphone will put tasting notices, introductions and product info at the visitors’ fingertips –or they can opt to be inspired with no preconceptions. Sector’s leading thinkers on six stages On the agenda of the speeches consider the future viability and market opportunities for the beverage industry. Right on day 1 of the fair, the Center Stage will host discussion on the hot topic of “The Corona disruption and its consequences for the beverage industry”. And on a similar theme, the Marketing Forum held by K&A Brand Research on the same day will hazard a look into the future: “Drinks after the crisis: what will surprise people?” The Expert Forum German Beverages, previously positioned the day before Brau Beviale and part of the regular programme of the fair for the first time this year, will look at the “New normality in foreign trade”. And the lecture session on Italian Affairs will cast a special look at the market situation in Italy. In addition to the themes mentioned, the on-stage events will also cover topics such as sustainability, energy management and raw materials. The main focus for the last day of the fair will once again be on training and professional development, with information and contacts on the Center Stage for new talents and young professionals under the banner of #workforbeverages. www.braubeviale.de/en Illustrating bottle production Sipa will illustrate the last in bottle production, filling with all complete and versatile range of monoblocs to meet the most varied requirements in terms of both productivity (monoblocks with up to 160 valves) and products to process: still and carbonated water, soft drinks, milk and dairy products, beer, sport and energy drinks, tea and juice. www.sipa.it Sipa Hall 7 | Booth 358","@ID":54}, BEVERAGE INGREDIENTS PETplanet Insider Vol. 21 No. 10/20 petpla.net 19 Doehler provides individual taste solutions for a variety of beverages such as plant-based drinks with the ingredients derived from sustainable sources of high-quality raw materials. The portfolio ranges from solutions based on almonds to rice, or oats to coconut. The mild taste of oat drinks make them especially popular among consumers and distinguishes them from drinks such as those made from almonds or coconut, whose taste is rather sweet. Furthermore, oats contain important minerals such as potassium and magnesium, essential for building muscles and nerve cells. Alongside the increasing demand for plant-based foods and beverages, plant-based variations of traditional dairy products are also becoming popular. An increasing number of consumers around the world would like to avoid alcohol, according to a study conducted by Doehler Sensory & Consumer Science in 2019. Nearly half of those consumers surveyed (48%) stated a preference for non-alcoholic beverages over wine or beer, cocktails and long drinks. However, they are still interested in beverages with a convincing “adult” sensory taste profile. Hence, the taste, smell, consistency, mouthfeel and colour of nonalcoholic variants should hardly differ from alcoholic originals and should offer equivalent taste experiences. Non-alcoholic beers are now among the top market drivers in the beer category. While the consumption of alcoholic beers is only slightly increasing worldwide, nonalcoholic versions are gaining market share. This trend is clearly evident in Australia and New Zealand. The demand for non-alcoholic variants is also steadily increasing in the spirits sector; worldwide, non-alcoholic spirits are expected to grow at an annual rate of 7.5 per cent by 2024 (Statista, 2020). In addition to low alcohol, more and more consumers are also paying attention to drinks’ sugar content. In the case of spirits, consumers in Australia and New Zealand are increasingly focusing on sugar-free or reduced-sugar variants of products such as gin or vodka. Comprehensive portfolio As well as its portfolio of natural and authentic flavour extracts, Doehler also offers distillates of single plant substances for the traditional production of gin, as well as distillates from botanical mixtures. All distillates are “From the Named Source” (FTNS) and are produced by traditional batch distillation. Extracts or distillates such as ginger and hibiscus or herbal and tea infusions such as chamomile and hemp or green tea lead to individual flavours for distinctive non-alcoholic spirits. www.doehler.com PETcast In our new Road Show podcast, PETplanet meets industry experts from Down Under to Japan and talks with them about their successes, decisions and current developments. Listen to the full conversation atwww.bit.ly/2HVwbAd DNC boosters Turnkey all-in-one system • Compact powerhouse with a footprint of only 2.35 m² www.kaeser.com","@ID":21}, TOP TALK PETplanet Insider Vol. 21 No. 10/20 petpla.net 10 Georges Alard, Commercial Director AF Group, on the company’s 150th anniversary, the philosophy of looking forward and a look at developments in the PET compressors segment The beating heart of the bottling line When AF Compressors was founded in Belgium in 1870, the patent specification for the first PET bottles was still a hundred years away. Back then, the privately-owned company produced pneumatic hammers for the mining industry, i.e. for use in the construction of tunnels and galleries for coalmines. During the early 1980’s, AF’s first 40 bar oil free reciprocating air compressors were manufactured for blowing PET bottles – a market on which the company soon concentrated all its energies. PETplanet: First of all, congratulations on the 150 years of Ateliers François! How has the anniversary year gone for you so far? Alard: We started to consider this important milestone of the company during the Drinktec exhibition in 2018. Plans for our new larger service facilities to be situated close to Liège Airport were well advanced, together with a larger investment budget in research and development, so this coming jubilee year was to be the highlight of our company progress. Needless to say, who could have forecast the global impact of Covid-19 in 2020. However, we remain strong, our sales and service coverage is fully operational for all countries and customers that are themselves struggling to overcome the disruption of Covid19. Traditional sales and marketing methods for communicating our abilities and equipment such as trade fairs during our jubilee year have sadly been put on hold. No Gulfood Manufacturing, no Brau Beviale and others which we regularly attend. So 2021 will be considered as a recovery starting point. AF have experienced quite a few recovery starting points since 1870. PETplanet: In 150 years, the company has gone through some difficult times such as wars, world economic crises or even pandemics like the Spanish flu. How has the current Covid-19 crisis affected the company? Alard: Due to our long-term strategy of having daughter companies or sales and service agencies covering the majority of countries worldwide, the impact of Covid-19 has not been as severe as it could have been. Although international air travel is severely limited, our local technicians are still able to service the customers equipment on site; where there is a local lockdown we can send parts and assist remotely for maintenance thanks to UMI (User Maintenance Instructions) procedures. Of course, we are seeing a slowdown in new investments, however the aftermarket income is still holding showing that the PET industry is still in business. Meanwhile, sustainability and innovation management has been an integral part of AF since the 19th century - always looking forward to getting through challenging times targeting medium- and long-term achievements. PETplanet: Originally, when AF was founded in Liège, Belgium in 1870, the company manufactured compressors and motors for the mining and steel industry. Can you briefly outline how the path from the mining business to PET bottles took place and share a few milestones? Alard: In the early 1900’s AF was suppling heavy steel industry and other industrial activities. In the 1960’s the first oil-free compressors were produced, for chemicals, glass industry, breweries. One of the very first customers requiring a PET compressor was SPA Monopole S.A. in the Belgian Ardennes in Liège Province. And today, we are still proud to service and supply their mineral water facilities. PETplanet: It was oil-free compressors since the 1960’S and since then, for more than 30 years, AF has been producing the 40 bar oil-free piston compressors for blowing PET bottles. By light weighting the bottles, air pressure requirements fell. Also, some machinery manufacturers integrated air recovery systems in their stretch-blow moulding machinery. How has this affected the further development of your compressors? Alard: As you say, for 30 years we have been producing 40 bar oil free compressors for PET bottles. AF is perhaps unique compared to other compressor manufacturers in as much as we have concentrated virtually all of our energy into that market: working closely with the blowing machinery manufacturers, sometimes partnering joint development solutions, and closely following trends in drink consumption. Many of our earlier COMPRESSORS Georges Alard, Commercial Director AF Group, Georges Alard joined AF in 1983. by Gabriele Kosm hl","@ID":12}, PETproducts 56 PETplanet Insider Vol. 21 No. 10/20 petpla.net Chem-Trend showcases a preform coating system (PCS) for improved handling of PET preforms Chem-Trend participated in the development of a new preform coating system (PCS). This system enables preforms to be accurately sprayed directly after the injection-moulding process. The solution was developed by Bonino Group in collaboration with ChemTrend and Steidle. The system is installed directly after the injection-moulding machine and before the soft-drop or Octabin. It is designed to spray only the body of the preforms with extreme precision without applying any coating agent on the thread of the preforms. A specially designed “Safeguard” system installed around the neck area of the PET preforms prevents the coating agent from entering the preforms. The application method allows Lusin Lub O 32 F to coat preforms on the full body which results in a drastic reduction of scratches during the filling and unloading of the Octabins. Bonino Group was able to engineer a portable unit that can be easily integrated into production lines. Using Bonino’s technology, preforms are diverted into the PCS system after production, where they are then properly oriented and individually coated. The unit can be adjusted to accommodate virtually all preform designs and sizes in a few minutes. The seamlessly integrated process integrated coating (PIC) system developed by Steidle can accurately dose micro quantities of Lusin Lub O 32 F and ensure that the entire body of each preform is uniformly coated. The preform coating system was developed for use with Lusin Lub O 32 F made by Chem-Trend. This food contact compliant coating agent is a hybrid product that combines the effects of a lubricant and release agent, it ensures uniform coating of all PET preforms. The system provides the following benefits to manufacturers of PET preforms and end customers: A food contact compliant coating delivered by the integrated PCS safeguard that prevents Lusin Lub O 32 F from entering the body of PET preforms. Low dosing rate of Lusin Lub O 32 F on PET preforms thanks to the improved efficiency of the coating process. Reduces the number of scratched or scuffed PET performs. Maximises the quantity of preforms per Octabin thus reducing shipping and warehousing cost. 10-15%more PET preforms to be packed inside the Octabin on average. Improves bottle demoulding and bottle definition during the blow moulding process while not affecting the working life of heating lamps. Eliminates bottle jamming in conveying lines. www.us.chemtrend.com Quiet, more compact and with frequency control Kaeser boosters with drive powers ranging from 22 to 45 kW are now available in a new design: as compact and space-saving complete units optimised for low vibration and noise emissions. The option of frequency control and many additional enhancements, such as optimised cooling, serve to reduce overall system and energy costs even further. Previously this size of booster was only available in conventional versions – without Sigma Frequency Control (SFC). The new drive function ensures harmonisation of the booster on the input side with the upstream compressor output. This allows for reduction of the relatively high switching frequency characteristic of some booster applications. It’s precisely because applications do not always work with the same pressure that boosters must produce significantly greater pressure than is actually used in the application. The powerful SFC functionality helps adjust the free air delivery as consistently as possible to the needs of the system. This reduces switching differentials on both sides, as well as potentially resulting overpressure, leaks and machine load – all of which contribute to energy savings. Plug & run The new design saves space (the footprint has been reduced to just 2.3m² from 5m²) and makes maintenance more straightforward thanks to intelligent component layout. Despite their enhanced performance, the new boosters run noticeably quieter thanks to the enclosure with integrated after cooling as well as the low-vibration basic structure. For added convenience, the boosters are ready for immediate electrical connection upon delivery, minimising installation time and costs. Controller monitoring The integrated Sigma Control 2 controller is equipped with special booster software to ensure optimal system operation whilst also enabling convenient connection to master controller systems via Ethernet. Since all individual components can be perfectly coordinated with one another, the entire station can be optimised to provide maximum efficiency and performance. Integration is also possible within an Industry 4.0 environment. www.kaeser.de COMPRESSORS","@ID":58}, BOTTLE MAKING 26 PETplanet Insider Vol. 21 No. 10/20 petpla.net Coca-Cola Brazil recognised for refPET bottle Returnable, refillable & recyclable A PET bottle that can be reused 25 times is at the heart of Coca-Cola Brazil’s returnable bottle initiative. For this Universal Returnable Bottle, Coca-Cola Brazil and its partners have been awarded multiple times, most recently with the Bronze award at the World Star Packaging Awards 2020. The original Coca-Cola glass bottle was designed to be distinctive, immediately recognisable and reusable. Since 2000, the trend has been towards PET bottles, along with a wider range of designs, which made the handling of returnable packaging a complex and expensive activity. In 2018, Coca-Cola in Latin America established an Agile team, which included bottlers and key suppliers, to develop solutions to encourage and stimulate returnable packaging. A Universal Bottle with renewable labelling was a pillar for the relaunch of the Returnable Platform across Latin America. “This Returnable Platform is a E2E approach delivering a integrated solution balancing sustainability, consumer centric, supply chain efficiency and other key aspects that guarantee the successes of this initiative for Latam for next decades” said Paulo Villas, Technical Operations Director and agile team member. Goals: a range of refillable bottles The packaging solution begins with a refillable PET (refPET) 2 l bottle and evolve to include a range of refPET bottle sizes and glass, as well, and incorporate a labelling and label extraction system. By 2017, Coca-Cola’s Brazil packaging portfolio was already 100% recyclable (PET, glass, aluminium, HDPE etc) and the company had reduced the weight of PET packaging by 17% since 2008. Its sustainability goals included 30% refillable packaging by 2020 (35% by 2025), 100% effective disposal through trash collection channels and progressing to recycled resin comprising 50% of total material used. The strategy to achieve these goals and build a circular economy model, as defined by the Ellen MacArthur Foundation, includes investment in recycling cooperatives, redesign for 100% recyclability, and 20% of packaging being reusable (which the company already surpassed). TCCC packaging design guidelines has been adopted for many years and includes project covering all aspects, including choice of material, analysis of their recyclability, use of colour, and quantity of resin used etc. SIPA","@ID":28}, LABELLING PETplanet Insider Vol. 21 No. 10/20 petpla.net 50 An enduring partnership PE Labellers and Spumador, part of the Refresco Group, have been working together for nearly 40 years. Their successful relationship has been founded on collaboration and continuous innovation and improvement. Well-established Italian bottler Recoaro, which was founded in 1927, was acquired in 2016 by a company with an even longer pedigree: 132-year-old Spumador, a longstanding Italian beverages enterprise, with an international reputation. The two companies are part of Refresco Group, a Euronext-listed company, which is headquartered in The Netherlands and is the largest independent beverage bottling company in the world. It has a total of 60 sites in Europe and North America, focused on manufacturing fruit juices and soft drinks for retailers, and contract manufacturing for A-brands. Spumador alone produces 1.3 billion bottles a year in five plants in Italy, across 24 brand lines. Bottled products range from carbonated and still drinks to mineral waters, and from juices and soft drinks to alcoholic drinks. Products are offered across a range of packaging formats, including disposable and returnable glass, aseptic and standard PET, and bricks and cans. Its distribution extends across large-scale channels, the Horeca channel and discount stores. Recoaro Terme, in the province of Vicenza, is known for its mineral spring waters. They come from springs in the heart of the Small Dolomites, whose mountains protect the springs from pollution and impart a distinct chemical makeup, with a balanced mineral salt content and low levels of sodium. Recoaro brand water is packaged and distributed in bottles of various shapes and sizes. PE Labellers Group was established in 1974 and is headquartered in Porto Mantovano, Mantua, Italy. It has been known as a leading producer of automatic labelling machines for nearly 50 years; it has been working with Spumador for almost 40 years. The birth of the partnership Tullio Tiozzo, Managing Director at Spumador “The collaboration was born in the 1980s, when we felt the need to rely on a flexible and innovative supplier that could guarantee excellent after-sales service,” said Tullio Tiozzo, Spumador’s Managing Director. “Our companies have had a very similar development, targeting innovation, which the markets demand year after year. This way of doing business has rewarded both our companies, making them a point of reference in their sectors.” The relationship that has evolved is based on respect and sharing knowledge. Bruno Negri, Senior VP, PE Labellers “We are proud to play an important role in the Recoaro production chain,” said Bruno Negri, Senior VP of PE Labellers. “Listening to customer needs and meeting every production requirement have proven to be the most successful factors over the years. Even before being a winning business strategy, it was the PE philosophy. It’s in our DNA.” Among the innovative design solutions PE has created over the years are rotary labelling machines combined with independent self-adhesive stations; cold glue for fiscal and guarantee seals; linear sleeve models with thermo-retraction tunnels; special optional solutions such as optical orientation systems; label presence control; and correct position verification of applied labels. Machines are designed as ergonomic solutions and strongly oriented toward energy saving, as demanded by companies operating in beverage, food and dairy, personal and home care, and the chemical and pharmaceutical industries. Meeting changing demands Packaging method standards in the mineral water market and the beverage market in general have become highly demanding. Bottlers who use PET increasingly require lighter bottles, with rPET and new formats that are both ergonomic and with a strong appeal and image. Glass is also making something of a comeback, requiring new formats and attractive labels. “The market requires continuous development, both in the shapes of the bottles and in the labels, which should have increasingly greater impact on the eyes of consumers, says Tiozzo “Today, in order to meet the challenges posed by an increasingly competitive market, we must continue to invest in new technologies to enable the raising of the standards of productivity and reduce production costs. We require more flexible machines and faster format changeovers. Modular machines are the answer to current needs.” Two new P.E. Labellers S.p.A. Hall 7 | Booth 348 SL (Smart & Lean) – Modular Rotary labeller","@ID":52}, 7 NEWS PETplanet Insider Vol. 21 No. 10/20 petpla.net Manjushree Technopack acquires Pearl Polymers Limited Manjushree Technopack Limited (MTL), India’s largest rigid plastics packaging company backed by Advent International, announced that it was entering into a Business Transfer Agreement with Pearl Polymers Limited to acquire the commercial operations and manufacturing facilities of their B2B business. This transaction is subject to customary closing conditions and regulatory approvals. The proposed acquisition of Pearl Polymers’ B2B business will help MTL to consolidate their leadership position in the container segments, while reinforcing their technical strength. Speaking about the acquisition, Mr Sanjay Kapote, CEO of Manjushree Technopack Limited said “The acquisition announced is in line with our strategy to grow and diversify our business. Acquiring the B2B business from Pearl Polymers will allow us to consolidate our leadership position in the rigid packaging sector. We expect a seamless integration of the business with the rest of the MTL group given the success we have achieved in our acquisitions to date. Mr Chand Seth, CMD of Pearl Polymers Limited said “Pearl Polymers is the pioneer and was instrumental in creating the market for PET packaging in India. With its customer spread across India and in every segment of the market, we believe that this acquisition will bring great value. Our clients will continue to receive the same high-quality services that they have come to expect for the last 36 years. This deal will allow us to focus and grow the wellknown PearlPET brand to new levels. We expect to launch many new product lines in the future.” With the consummation of the proposed transaction, Manjushree will have access to four of Pearl Polymers’ production units and serve Pearl’s existing customer base that includes marquee clientele in the FMCG, liquor and pharma segments. www.manjushreeindia.com Ingersoll Rand awards $150 million equity grant to global workforce Ingersoll Rand Inc., a global provider of missioncritical flow creation and industrial solutions, celebrated its $150 million equity grant to nearly 16,000 employees worldwide with a virtual ringing of The Opening Bell at the New York Stock Exchange. “This is a $150 million investment in our employees,” remarked Vicente Reynal, Chief Executive Officer. “We are not aware of any other industrial company our size having done something like this; it’s a meaningful way to build an ownership culture where all employees can benefit from creating value as they all contribute to our success. Our employees have carried us through the beginning of a successful integration between Gardner Denver and the Ingersoll Rand Industrial segment, built a solid foundation and now position us to pivot to growth and achieve great things in the future. United by a common purpose and set of values, we believe our 16,000 employees around the world are unstoppable.” From an hourly assembly worker on the production line in Quincy, Illinois to a sales representative based in Shanghai, China, all eligible employees received a grant equal in value on the grant date to 20% of that employee’s annual base cash compensation. All permanent employees in good standing were eligible for the grant except senior management employees who are part of the company’s annual long-term incentive plan and employees in Vietnam and Philippines where local laws make granting equity prohibitive. Reynal continued, “If everybody thinks and acts like an owner, we all share in the benefits of any future value creation as the company continues its growth strategy and improves its profitability. Overall, we view this grant as a core strategy for increased employee engagement, an ownership mindset and sustainable long-term shareholder value enhancement.” ","@ID":9}, COMPRESSORS PETplanet Insider Vol. 21 No. 10/20 petpla.net 15 COMPRESSORS 15 Less consumption: The motors are designed to deliver high efficiency: according to the IEC/ EN 60034-30 standard, they are classified as IE3 (Premium) or IE4 (Super Premium Efficiency). In addition, thanks to the inverter that regulates the frequency of the electric current, they can work at variable speeds, resulting in an additional significant energy saving. They also prevent consumption peaks at start-up. Less maintenance: Vito Next compressors have taken a big step forward in terms of efficiency, reliability, component life, maintenance costs and adaptability to harsher environmental conditions, Siad states. The new systems provide moisture-free air and less vibration, ensuring longer component life and maintenance-free operation. No contamination: All compressors need to be lubricated, but not all in the same way. With Vito Next, oil is used only for the mechanical parts, those not intended for compressing the air that is used to inflate the bottles: this does not contain any trace of lubricant. In fact, the air is absolutely “oil-free” according to the ISO 8573 standard. Heat recovery: During operation, the Vito Next produces a lot of heat which comes from the coolers of the gas that is compressed. A specific and optimised solution allows for the recovery of hot water that can be supplied, up to 80 °C, such as, for example, for heating the working environment where the compressor is located or for heating offices. ","@ID":17}, PREFORM PRODUCTION PETplanet Insider Vol. 21 No. 10/20 petpla.net 24 the previous versions in every respect in terms of material throughput kg/h, homogenisation, intake behaviour, start-up behaviour (usually lower granulate temperatures at the beginning), AA values and IV drop. PETplanet: There are some market traders who are convinced that using shot pot will always produce specks. Old PET residues from the pot generate black spots. Stefan Kleinfeld: This might well have happened in the past. Today, designs are much improved. The piston in the shot pot is essentially lubricated by the PET, thereby forcing out any older material lying between the piston and cylinder. This ensures that only freshly plasticised matter can enter the mould. PETplanet: The screw is electrically driven but transferring of the melt into the shooting pot is hydraulically. How did you attach the energy-saving pin to the hydraulic system? Stefan Kleinfeld: In principle, we have stuck to our model by using a controlled pump and hydraulic accumulator but have become much more efficient when it comes to the detail. One issue is the reduction of the hydraulic pressure which is needed when transferring the melt. Another issue, for example, is that of hydraulic oil. We now use HLP46 which has the necessary viscosity level at 40 degrees. Previously, that figure was 50 degrees, which means less heating and radiation energy. The oil is also available to users worldwide. A positive side-benefit is the hydraulics and its accumulators. In the event of a power failure, the oil will continue to flow through the pump from the accumulators. The pump’s electrical drive is then used as a generator with the machine able to complete the cycle in a controlled manner. The new 4,000 kN Netstal PET-Line. Sideways preform removal, 1.9 s lock-to-lock and highly energy efficient, as well as the potential to use existing moulds that are characteristic of the new concept. PETplanet: You can look back on decades of experience in using injection moulding machines. But the concept of sideways removal is a new one for you. Surely your competitors have the technology covered with patents? Stefan Kleinfeld: The first thing to say is that we have again made a thorough appraisal of the type of assembly, with cycle time and energy efficiency being key for us. The removal carriage recovers electrical energy during negative acceleration. By not connecting the placement arm to the moving panel, we have achieved greater freedom. Of course, we have studied the patent situation in great detail. However, sideways removal has been on the market for quite a while now, so some of the patents will have already expired. Internal preform cooling is one example. With our extraction system, we are able to handle all industry specifications, from internal preform cooling to the four post-mould cooling stations. PETplanet: Is the user interface also new? Stefan Kleinfeld: It’s not just the user interface – the whole control system is new. Better resolution of the parameters ensures that the machine can run smooth start-up and startdown curves at high speeds. But, you’re right, the user interface is a new innovation. The emphasis here has been on how easily the unit can be operated using only four buttons. We have had excellent results using this simplified approach when dealing with medical products. System failure due to operational error has been significantly reduced. Basic machine operators can be trained within a very short period of time. Specialists, of course, have full access to all set-up programmes. PETplanet: Have you also been able to bring your partners on board? Stefan Kleinfeld: Take Piovan. Control of the PET drying process can now be done from our interface or IMDvista. Preform control by a visual inspection system is integrated directly once the preforms have been discharged. PETplanet: With all the technical advantages, it is also important for attracting new sales that your system can be housed within existing production facilities in order to undertake sideways removal. How is this going? Stefan Kleinfeld: In spite of the toggle lever, our unit is several centimetres shorter and narrower in its size category than other suppliers. Our new Netstal PET-Line also fits into properly sized storage areas. Media connections are located in the plasticising area, i.e. where the user normally has their supply. And as energy consumption is low, the electrical feed should also be sufficient. PETplanet: You have installed a lot of new and more expensive machinery compared to the more traditional PET plants. Are you able to offer equipment at a marketable price? Stefan Kleinfeld: I mentioned this at the outset. We have always gone down the road of having the highest efficiency and durability. We have","@ID":26}, TOP TALK PETplanet Insider Vol. 21 No. 10/20 petpla.net 11 developments related to air recovery systems have been envied and copied by others. I must add that confidentiality and trust between AF and the blowing manufacturers is paramount, we are well known for keeping their confidences, which is one of the reasons we are able to work so closely with them. The compressor of course is the beating heart of the bottle line. If that fails, the line stops; if it cannot give pressure, the line stops; if the compressors ancillaries are not correctly matched or fail, the line stops. So we must look at every possible consequence when new developments are initiated. It is right that light weighting the bottles has resulted in lower blowing pressures. This meant compression ratios would be changed between compression stages. What effects had to be considered? The compresThe Atelier Francois team at the BrauBeviale 2019 sor cooling system had to be revised, could we lower the motor power? Lower pressures mean larger air dryers as more volume passes through them, which ultimately means more capital cost and more power to achieve the specification of air quality. So, everything must be taken into consideration before its introduction and we have encouraged close dialogue in the past, now, and in the future with those blow moulding equipment manufacturers who value environmental and sustainable developments. PETplanet: Can you also tell us what developments/improvements are next on the agenda? Alard: Over the last two years the plastic industry has faced a barrage of negativity, however common sense recognised that the plastic bottle was not the common enemy and PET bottle lines are still increasing worldwide. Beverage companies are now looking to use up to 100% recyclable material so we cannot see any market shift short term towards new technology or bottle material design especially in the Covid-19 era. Beverage companies will be looking at maintaining margins and keeping their customer base in a world where the hospitality / tourism industry is on its knees. I see for the immediate future a lower capital expenditure on new machinery but a higher income from maintenance and retrofits to keep the older machinery going. We already have installed a dedicated upgrade department and identified customers who can benefit from upgrades. PETplanet: When is retrofitting worthwhile and when do you recommend a customer to invest in a new compressor? product development caps & closures design high cavitation moulds multi-component moulds closure production systems after sales service competent – professional – inspiring Dr.-Walter-Zumtobel-Strasse 9 | 6850 Dornbirn | Austria | www.z-moulds.com L9 model PET compressor, 35bar, 500 kW, 3,300m³/h","@ID":13}, PREFORM PRODUCTION PETplanet Insider Vol. 21 No. 10/20 petpla.net 21 PETplanet: What is the savings potential in the design of a preform produced with Xtreme technology? Mr Narder: Xtreme technology overcomes current preform design limitations offering extensive lightweighting especially around the gate and under the support ring, areas which are not stretched during the bottle blowing. All this without compromising the mechanical performance of the bottles. PETplanet: Why Japan? In the IM sector, the Japanese rely on local products. Mr Narder: The Japanese believe in innovation and trusted our Xtreme technology. They have very high standards of quality and cleanliness, even in production. Here, with the 100% inline preform quality control and the fully electric Xtreme compared to IM with hydraulic components, we have been able to come up trumps. PETplanet: Here, in your factory, there are four more Xtremes for delivery. Mr Narder: This machine here is for Mexico. Here too, the Xtreme with 96 cavities is integrated with flake recycling. Another Xtreme starting from flakes is for a well-known multinational company for their facility in Poland and the other two stand-alone Xtremes running are going one in Korea and the other one in UAE. The latter has the option of producing two different preforms at the same time, which enables the customer to operate a large system even when item quantities of a preform are lower. This saves retooling time and cost. PETplanet: This means that all your Xtremes are going to or have gone to bottlers or, as Japan, to recyclers? Mr Narder: We can clearly see the focus on these customers. Ultimately, we want to offer the Xtreme integrated with the stretch-blower and filler. We have already one system running in Brazil since last year. Only bottlers would need this. Thanks to the fact that Xtreme technology can be connected upsteam or downstream, it opens new business models. In its Xtreme Renew configuration allows recyclers to increase the added value of their offer selling preforms instead of recycled raw material. Converters can take advantage of the combination of Xtreme preform production with stretch-blow moulders and operate a wall-to-wall selling bottles. PETplanet: Thank you, Antonio. Interview with Anna Horecica Csiki, Xtreme Product Manager PETplanet: Hello Anna. You have been Project Manager for the Xtreme for six years now. There has already been an attempt by another company to develop compression moulding for preforms. Are there no reservations in the market for your new technology? Mrs Horecica: The difference lies in the process. With the preform it is extremely important to be able to create reproducible conditions. The melt in particular requires a lot of attention. With us, the melt comes continually from the extruder at the relatively low pressure of 160bar and flows into the rotational hotrunner. Each cavity has its own dosing and injection unit which holds exactly the quantity of melt for the preform in the allocated cavity. Then we increase the injection pressure to max 300bar. This injectioncompression process is completely different to other developments and it guarantees to us that there is an optimum filling of the material in each cavity to produce a perfect preform. PETplanet: And each shot pot is individually adjustable? Mrs Horecica: Yes, so we can adjust each cavity optimally. We have further enhanced the concept and you can see on the system for the Middle East here that by adjusting the shot pots and of course using different stacks, we can also produce two very different preforms on the carousel at the same time. PETplanet: This means that individual cavities are mounted on the carousel? Mrs Horecica: Yes, the entire unit consists of two parts that the customer can quickly and easily adapt. The lower part is the hot side with the shot pot which does not require any changeover; the cold side (the injection stack) is above and no crane is needed for the exchange; the parts can be quickly removed by hand. This makes working at the machine much easier. PETplanet: How does this configuration influence the mould changeover? Mrs Horecica: Xtreme technology and special design of hot and cold parts allows the preform to preform changeover in less than 2 hours. PETplanet: How do the preform inspections work? Mrs Horecica: Here at the transfer station to preform cooling, we have two cameras that inspect neck geometry and injection point. Above, at the end of the cooling zone, there are three more cameras that check the outside body of the preform. A special software is able to identify the two different preforms produced simultaneously. PETplanet: Thank you, Anna. www.sipasolutions.com F.l.t.r.: Anna Horecica Csiki, Xtreme Product Manager, Alexander Büchler and Antonio Narder, General Manager at Sipa in front of Xtreme 72 cavities producing two preforms simultaneously.","@ID":23}, TOP TALK PETplanet Insider Vol. 21 No. 10/20 petpla.net 13 Working with us bears a risk and lowmaintenance costs. This is because the consultants and engineers at Otto Systems meet your production challenge with open minds, decades of experience and deep knowledge about PET production processes and techniques to ensure high quality at the best possible price. That’s why they are able to plan and implement production systems that are uncompromisingly tailored to your needs, independently selecting the best components from experienced manufacturers to achieve your goals.","@ID":15}, MARKET SURVEY 33 PETplanet Insider Vol. 21 No. 10/20 petpla.net German Technology KHS GmbH Newamstar Packaging Machinery Co., Ltd. Juchostraße 20 44143 Dortmund, Germany +49 231 569-0 www.khs.com Mr Manfred Härtel Product Manager Filling +49 231 569-0 manfred.haertel@khs.com East Xinjing Road, Zhangjiagang Economic & Technological Development Zone, Jiangsu 215618, P.R. China +86 512 5869 1111 www.newamstar.com Marketing Manager +86 512 5699 3303 market@newamstar.com Sidel Matrix SF 700 FM Sensofill FMa / FMac Innofill PET DRV Innofill PET NV Innofill PETACF-L XGF 32-108 27-150 48/216 32/144 20/40 20-120 0.2-2.0 0.2-3.0 0.1/3.0 0.1/3.0 0.1/2.0 0.1-15 6,000-60,000 6,000-60,000 Up to 90.000 Up to 90.000 Up to 28.000 1,200-81,000 Up to 90.000 Up to 90.000 Up to 54,000 36,000 Up to 82.000 Up to 36,000 48,000 Up to 50.000 Up to 28.000 Up to 36,000 48,000 48,000 Up to 60.000 Up to 60.000 Up to 28.000 Up to 36,000 Yes Yes Yes Yes Yes Yes Yes Yes No No Yes Yes Yes Yes No Yes Yes No No Yes Yes Yes Yes No Yes Yes Yes Electropneumatic volumetric filler with flowmeter volume control Electronic volumetric filler, magnetic filling valve Volumetric filling system; pneumatic cylinder; MID (inductive flow meter); Mass-flow (Coriolis) Volumetric filling system; pneumatic cylinder; MID (inductive flow meter); Mass-flow (Coriolis) Volumetric filling system; Inductive flow meter Water valve, hot filling valve, isobaric valve, electronic valve; Flometer, weight liquid level inspection Quick changeover procedure fully automatic operating computer control; food safety due to recirculation and CIP (Clean In Place) minimum flowrate control during operatio Up to 60,000bph (500ml bottle format); 200 production hours without cleaning/ sterilisation; flexible aseptic filling for a wide range of beverages, including still water, still and carbonated drinks, particles up to 6x6x6mm, viscous products, etc. CSD warm-filling up to 24°C; simple filling valve; compact unit; slow & fast-filling; gentle filling with low foaming; no beverage loss during production; PTFE-sealing technology prevents aroma transfer Contact-free filling Contact-free filling, slow & fast filling, gentle filling with low foaming; no beverage loss during production Intelligent Factory Management Platform","@ID":35}, PETplanet Insider Vol. 21 No. 10/20 petpla.net 55 BOTTLES Drinks with collagen The Italian drinks’ manufacturer, Aqua Sant’ Anna, has brought out a healthy drink with collagen and zinc as part of its “Beauty” product range. Both of these substances support the skin and promote skin renewal and are also supposed to eliminate and render harmless harmful products such as cell toxins and other similar substances. The drink comes in a clear 330ml bottle. Its design, colouring and closure colour are reminiscent of a product from the cosmetics industry. www.santanna.it “hohes C for kids” Some Eckes-Granini national organisations are offering products that are only currently available in their own countries. For example, in Austria, the company is selling two drinks with 55% juice content under the name “hohes C for kids”. In addition to vitamins C, D and E, folic acid is also added to the Red and Yellow Multis to ensure this target group derives the best possible nutrition from these drinks. No sugar is added. The 330ml bottle is secured by a tamperproof strip and resealable drinking cap to ensure that it can be easily handled by kids in schools and kindergartens. The bottles have printed sleeve labels, which are designed with children in mind. www.hohesc.at","@ID":57}, PREFORM PRODUCTION PETplanet Insider Vol. 21 No. 10/20 petpla.net 20 Sipa’s Xtreme up and running with customers Revolution, not evolution by Alexander Büchler Sipa introduce the injection compression process for preforms. Still in its secretive housing and with a limited view of the technology. Now, we have been allowed to put our heads in the machine in Italy and check out every screw. Interview with Mr Gianfranco Zoppas, Chairman PETplanet: Hello Mr Zoppas. We are standing here in front of an operational Xtreme. You have been coaxing this project along for six years. Finally the machines are with satisfied customers. How does that feel? Mr Zoppas: In these difficult times, it is great to see that our ideas really work. This is not one of those typical technical evolutions where we are making progress in the region of 1/10 of a gram. It is a revolution where we have completely reinvented the entire preform production. PETplanet: Revolution sounds a little bit extravagant. Mr Zoppas: Revolution is not just about technology; revolution is expensive but the result is what counts and I am very proud of what we have achieved. PETplanet: With the concept of the integrated Xtreme system from recycling through to the filled bottle, the so called Xtreme Renew Sincro Cube, the inefficiencies of the individual components add together so that overall efficiency would have to suffer. Mr Zoppas: We heard the same argument when we started around twenty years ago with integrated stretch-blow moulding systems, fillers, labellers and cappers. Today, it is impossible to imagine the market without these synchronised systems. Our investigations show that the technology runs in such a stable way that the overall efficiency of the entire line is above 90%, and the advantages of significantly lesser logistics and enormous energy savings from working with a single thermal cycle are overwhelming. PETplanet: Bottling systems are usually sold without profit and money is made on the subsequent servicing; preform systems usually contribute to company stability when sold. How have you placed the concept of the Xtreme? Mr Zoppas: At my age I think the money should flow right away but of course we tried to take other factors into account. PETplanet: Many thanks, Mr Zoppas. Interview with Antonio Narder, General Manager PETplanet: Hello Antonio. The first three Xtreme went to Japan. Two are with a flake recycling system from Erema. Why did the customer want this combination? Mr Narder: The customer is a PET recycler in Japan already producing PET flakes. He has expanded his supply chain from the processing of waste PET bottles to include preform production. Now, with the Xtreme Renew technology he bought, after the flakes have been decontaminated to food grade quality and the IV raised to the required level, the melt from the extruder goes straight into the hotrunner of the Xtreme for the production of preforms. As the flakes are only plasticised once, this saves energy and reduces the material degradation. Therefore the production cost of a recycled preform with 100% rPET from flakes is greatly reduced. PETplanet: Why is there a melt pump installed between the recycling extruder and the hotrunner? Mr Narder: Because it is important that entry to the Xtreme is at equal melt pressure. In contrast to classic injection moulding, this is very low at max. 300 bar. And that is one reason why the material is not placed under great stress and the IV drop is kept to a minimum. F.l.t.r.: Alexander Büchler and Gianfranco Zoppas in front of the Xtreme Renew System The Xtreme Renew System at Sipa’s factory in Italy","@ID":22}, COMPRESSORS PETplanet Insider Vol. 21 No. 10/20 petpla.net 17 Kris Vermeulen: As you mentioned, the ZD is on a concrete base frame, which indeed eliminates the need for special foundations nor special anchoring, and in addition, it also absorbs the little vibrations that a Balance Opposite Piston (BOP) or “boxer” type of piston set-up already has, making our ZD the machine which in our view, has the lowest vibration in the market. The canopy enclosure also reduces noise levels significantly. These two features allow customers to install the machine at any location in their plant, even in the production area, and even better, next to the blow moulding machine. This not only eliminates the need for having a (separate) compressor room, but also removes the need for having long high pressure piping in between the compressor and the blow moulding unit. PETplanet: Things have moved on since 2004. How has the ZD range developed since then? Kris Vermeulen: All our ZDs in the range have 4 stages to achieve high pressure. These 4 stages deliver the additional advantage that you have 3 interstage pressures to choose from (one at every stage and the 4th one, the final discharge pressure) and this offers great flexibility. The second stage pressure is typically between 6 and 10bar, and every plant has a need for (low pressure) air within that pressure range somewhere else in their factory, whether it is for their labelling machine, transportation and/or packaging. We can supply both low and high pressure from our ZD unit in one solution and so eliminating the need for an (additional) low pressure compressor. PETplanet: In these difficult times, companies are wary of making significant investment in new machines. Is this something Atlas Copco has considered? Kris Vermeulen: We are very aware of the possible effects of the Covid pandemic on investment and business confidence and we are therefore offering three versions of the ZD family to meet the specific needs of our customers: ZD Premium delivers a high pressure flow at the desired pressure. ZD Xtend additionally offers a low/ medium pressure tap-off of dry oilfree air. ZD Flex is our top of the range compressor delivering air at all pressures to all the machines in our customers’ factory. The ZD Flex can be designed for the minimum total Capex, the most optimal Opex (lowest energy consumption), and/or reducing our customers’ Risk (and so lowest liabilities); a well balanced combination of these three is evidentially also possible. PETplanet: Do all your compressors work with energy recovery systems? Kris Vermeulen: Energy reduction is at the core of our design. So, of course, energy recovery systems are available. In fact, if we look at our ZD solution, we can offer energy recovery at different levels, either only for the first 2 stages, the last 2 stages or on all 4 stages, where the amount of heat that is recovered is about the same as the total electric power the ZD consumes. Another advantage that our ZD offers is the fact that the first 2 stages use screw technology, which allows higher discharge temperatures, allowing the highest water temperature possible for the energy recovery system and this enables the highest energy recovery percentage in the market. Another energy recovery system is the re-use of “waste” compressed air from the blow moulding machine, where again our 4-stages enable the highest pressure recovery as it can be re-inected at higher pressure and thus deliver the highest energy recovery. PETplanet: How else can the customer reduce the cost of compressed air on an existing installation? Kris Vermeulen: Good question. Feedback from our customers has indicated that our ZD Flex offering is an excellent solution both for new (greenfield) plants, but even for existing installations as well. Our ZD Flex can be configured to meet customer demands to ensure it meets energyand cost-saving goals, and this not only for this year but also for future expansions to come. Another important element, the cost of an installation is not only the cost of the equipment: you have seen that with our low noise, low vibration ZD unit, you have the possibility to install the unit next to the blow moulding machine, offering flexibility and cost savings, as this reduces the need for expanding the high pressure piping or adding additional high pressure piping, but also removing the need for a high pressure compressor room fets eliminated. Saving our customers’ money on the total project cost for expansion. PETplanet: Flexibility and customisation are becoming increasingly important in bottle production. How can a compressor handle different bottle and production volumes and at the same time be energy efficient? Kris Vermeulen: This point is precisely the reason why we have our ZD Flex solution. With different bottles and different bottle sizes, comes of course different air volume requirements. After all, a small bottle needs less volume of air than a big bottle to be blown. This is the main reason why we have our VSD version available, as this regulates the rotating speed of the ZD and so the flow. Our aim is to supply a system that meets our customers’ specific needs. PETplanet: To conclude, a question on the current situation. Als Mats Rahmström, President and CEO of the Atlas Copco Group, in his report for the second quarter of 2020, pointed out that the group is withstanding tough market conditions and keeping profitability and cash flow at good levels. With the pandemic still very much with us, how is the situation today, a few months later? Kris Vermeulen: We need to be flexible in meeting our customers’ and the market’s changing needs. We remain optimistic that our ZD family will be able to provide the right response to this crisis and it is vital that we keep in constant virtual contact with our customers especially using our global sales and operations teams who are fully trained in virtual tools from demos on real time to factory acceptance tests. PETplanet: Thank you very much! www.atlascopco.com","@ID":19}, BOTTLE MAKING 35 PETplanet Insider Vol. 21 No. 10/20 petpla.net Mr Fiala. With a bag-in-keg design, Keg King is also aiming to attract another target group, the wine industry. Furthermore, continues Will Fiala, our 35 l and 60 l fermentation containers are really catching on with home brewers, not only in Australia, but also internationally. These are also used as containers for loose goods like nuts or grains and they set themselves apart from the competition with their excellent material clarity, stability and integrity. There are still challenges to produce these containers cost effectively. “By having a container which is made with a handle system as part of the process cost savings are achieved as well as a stronger product. The moulds for this sort of keg are extremely complex and with this design we are pushing the envelope significantly. Getting the highest burst pressure is obviously the main desirable feature.“ According to the company, Keg King’s market share here is 70%. At the moment, the company has seven different moulds, of which three are used for the PET containers and kegs mentioned here. At full capacity, around 2,000 PET kegs can be produced, which corresponds to around 50 t of material annually. This makes the PET business around 30% of the overall revenue. Another 30% of all PET products are sold outside of Australia, with the focus on the European, Asian and American markets. The company obtains its raw materials from Chinese supplier Jade. According to CEO Will Fiala, capacity will soon double. “We are about to order a second K53 from Cypet, so that in future we have a dedicated machine specifically for ongoing PET keg production. We want to make this investment within the next two months,” says Mr Fiala. Keg King currently employs around 25 employees on its 5,000m2 site. In 2019, overall turnover was US$ 5.2 million of which around US$ 1.6 million was from PET products. In future, the supply chain to end customers and breweries that use Keg King’s kegs is to undergo further systematic expansion. Keykeg/Unikeg and Dolium are among the strongest competitors in the sector. www.keg-king.com.au Keg King’s production with Will Fiala (right), employee Nick and a 60 l keg check it out: check.","@ID":37}, BEVERAGE INGREDIENTS PETplanet Insider Vol. 21 No. 10/20 petpla.net 18 Natural, healthy and low alcohol drinks are popular in Australia and New Zealand Beverage Trends in Australia & New Zealand Across the range and across the world, the soft drinks, energy drinks, sports drinks or RTD coffee drinks beverage market has been showing consistent growth. This trend is expected to continue in the coming years, which means that the industry will be challenged to pick up on current and emerging trends and respond quickly to consumer wishes. As well as new and innovative flavours, consumers worldwide are increasingly looking for more healthy, reduced sugar and plant-based variants of their favourite drinks. improving joint health. With an estimated turnover of US$ 129.7 million (according to findings published in the Sydney Morning Herald), production of kombucha is one of the most booming industries in Australia. Kombucha as a major winner Mostly produced from sweetened black or green tea, kombucha is promoted as a drink that provides consumers a completely new taste experience, with a low calorie content. The essential element is “scoby” (Symbiotic Colony of Bacteria and Yeast), also known as “kombucha culture”. It contains various bacteria and yeasts that help to ferment the tea, resulting in a soft drink with slightly vinegary taste profile and containing some alcohol; usually below 0.5 per cent. As the sugar content of the beverage is significantly reduced during the fermentation process, kombucha aligns with the continually growing demand for refreshing, reduced sugar beverages associated with a healthy lifestyle. Doehler supplies its customers with natural ingredients required for the production of kombucha from a single source and with a kombucha base that allows customers to formulate individual recipes without needing to ferment. The kombucha base is available in conventional and in organic quality. While it is originally from China, this novel drink has now found its way onto supermarket shelves around the world and it has quickly become one of the most important drinks of the beverage scene in Australia. In 2019, the secondhighest number of new kombucha product launches in the world were made there; only the USA had more (source: Mintel Global New Products Database). Plant-based diet on the rise Around 10% of Australia’s population of just under 25 million consume plant-based food only (Roy Morgan Market Research, 2019). The beverage industry is adapting to the changing preferences and habits of consumers and increasingly providing plant-based products that create a unique taste experience. In Australia and New Zealand, naturalness, health and plant-based nutrition are among the biggest trends in beverages. Kombucha, a modern and natural fermented tea drink, has emerged as a particular new favourite. The trend towards beverages based on fermented tea has gained high consumer acceptance not only because of its taste, but also for its versatile health benefits. Kombucha is claimed to contribute positively to detoxification of the body and to strengthening the immune system and Tour Sponsors: +44 (0) 1254 584210 sales@petmachinery.com petmachinery.com Active for over 25 years, our global network and specialist knowledge makes us the go-to company for the sale or purchase of a PET machine. Commercially savvy, we work closely with our customers and our global network, to make sure everyone gets the best deal. Providing comprehensive advice throughout your sale or purchase; we can arrange dismantling, loading, packing, shipping, specialist insurance and commissioning. If you have amachine to sell or you’re looking to purchase, please get in touch. THE INDUSTRY EXPERTS","@ID":20}, BOTTLING / FILLING PETplanet Insider Vol. 21 No. 10/20 petpla.net 44 Improved filling technology More performance, less space Two years after the introduction of the Super Combi to the industry for compact lines’ solutions, Sidel presents a next-generation solution Super Combi Compact that is even more compact. Allowing up to 30% footprint reduction compared to the previous model, the solution excites with an efficiency enhancement it assures for still water production thanks to the new filling technology embedded in the Sidel EvoFill HS Still that guarantees a 30% faster performance. Growing demand for packaged water “We see that the water category has been seeing an unprecedented growth fuelled by a worldwide increase in demand. Due to consumers’ rising health consciousness paired with the trend towards so called “better-for-you drinks”, the packaged water category has remained at the forefront of consumer purchasing decisions since 2018,” explains Stefano Baini, Product Manager Filling and Super Combi at Sidel, identifying why the company has invested in the development of a compact line solution for still water production. This green trajectory throughout the water category was globally influenced by a large hike in tourism along with extremely warm weathers not only in warm climate countries, but in parts of Western Europe too. Enhanced performance and productivity Similarly to its predecessor, Super Combi Compact is integrating five process steps – preform feeder, blower, labeller, filler/capper and cap feeder – into an all-in-one, smart system. What describes the new solution the best is the continuous top-level performance it provides up to 54,000bph in a reduced space. Furthermore, its ergonomics and the latest technologies support easy access, operation and maintenance while ensuring high end-product quality. The overall higher level of efficiency of the solution is achieved by providing maximum uptime and consistent production output at medium to high speed. Maximum productivity of the line is reached particularly due to improvements at the blowing, filling and labelling stages. The blower can produce up to 2,700 bph per mould. A robotic arm solution for automatic Next-generation Sidel Super Combi Compact allows up to 30% footprint reduction and promises a 30% faster performance compared to the previous model.","@ID":46}, BOTTLE MAKING 39 PETplanet Insider Vol. 21 No. 10/20 petpla.net thermocouple is mounted and how many lamps are used. If the lamps closest to the thermocouple are at a high percentage, the reading will be higher just because of this and not because the temperature is actually higher. If the thermocouple was mounted some distance away from the lamps, let us say, somewhere in the exhaust duct it would give a more reliable reading of the temperature we are interested in when it comes to preform heating but would then not give us a good picture of the heat inside the oven. In short, this reading should be regarded with caution. There are two features a blow machine must have so that air cooling can be effective: a thermocouple in one oven measuring the oven temperature and a variable speed motor for the air exhaust fan. The thermocouple must be protected from lamp radiation and be in the air stream, cooling the preforms, not in the one cooling the lamps. The fan should effectively blow warm air out of the system so the oven temperature can be controlled under a variety of process conditions. The reading of this thermocouple must be taken with caution. Depending on how high in the oven it is mounted and whether the top lamps are on or not, readings can differ by a significant amount. The reading is useful to check for differences once a suitable oven temperature has been established but it is not possible to give a recommendation that fits all circumstances. Equilibration time is another way of evening out differences in temperature through the preform wall. Equilibration happens when preforms leave the oven section on the way to the blow moulding station as well as between ovens. Time spend in equilibration depends on the physical length of track between heating and blowing and the throughput rate. Due to more exposure to the environment outside the ovens, outer preform walls tend to cool down more than inner walls thus contributing to the optimal temperature profile. Some machines have extra space in the heating section to allow ovens be moved for optimal equilibration. It is the lack of sufficient equilibration time on some small, linear machines that often leads to inferior bottle quality. 6.5 Optimal preform temperature Now that we have established the optimal temperature profile within the preform wall, it is time to consider the overall temperature of the preform. PET has a temperature process window from 90 to 115°C. Higher temperatures cause the material to crystallise. This becomes first visible as cloudiness or haze when www.krones.com The future is circular Can plastic packages be sustainable? Sure, if they’re resource-economically produced and efficiently recycled. KRONEShas the right technologies for this. Harness them, and become part of a closed-cycle economy that really pays off – for manufacturers, consumers and the natural environment alike.","@ID":41}, BOTTLING / FILLING PETplanet Insider Vol. 21 No. 10/20 petpla.net 43 half of the year. Sales of Coke Classic rose by 11.4% in 2-litre and 3.6% in 600ml bottles; Mount Franklin 600ml bottled water sales grew four per cent. New products with reduced sugar content recently added to the portfolio include: Rekorderlig Cider Botanicals (an alcoholic ready-to-drink product available in various flavours); Powerade Active Water; and Nutriboost dairy drinks. Sustainable packaging The use of virgin PET is being reduced and replaced by recycled material in the production process. At the end of 2019 Amatil announced that it would be making seven out of 10 of its single-serve bottles in Australia from 100% rPET. This amounts to around 18,000 t/a of material. “In response to the high global demand for rPET, we joined forces at the end of last year with Veolia, the environmental service provider, to explore the possibility and viability of establishing a recycling plant for rPET in Australia”, Mr Chalmers said. Veolia is a global company that provides and maintains water, wastewater, energy and waste management services, as well as having waste management operations in 35 countries. “Amatil’s Packaging Services Division and our Futureworks team, responsible for developing sustainable packaging, are currently exploring ways of using more rPET in the medium term,” he continued. Increased use of rPET depends on its availability. “We are definitely seeing trends towards the increased use of recycled material as well as increased demand for PET recycling. This will have a long-term bearing on our packaging work in the pre- and post-consumer market.” Amatil recently received two prizes at the 2020 Australian Packaging Innovation and Design Awards ceremony for its 100% rPET CSD bottle. It was awarded Best Australian Sustainable Packaging Design and recognised for Packaging Innovation and Design in the ‘Beverage’ category. The company’s Eastern Creek, Sydney, plant has seen some changes since our previous visits, in the extent of automation especially. Robot cells have been incorporated into a fullyautomated production process, erecting the Orbis style bulk bins (gaylords), inserting a plastic bag before filling with either preforms or closures and then, once filled, being sealed and labelled. The three-part SyLon Mercury Sports Cap, which was introduced in 2018 and made entirely from HDPE has been widely accepted in the market and proved to be particularly effective in difficult applications, such as nitrodosed hot fill. The company continues the active development of caps and closure designs, so that it can be fully prepared for the introduction of new EU standards, such as tethered caps (which will be compulsory in the EU from 2024) if the Australian market decides to also enforce this type of packaging change. It already has cap designs that will meet the basic requirements. A number of measures have been taken at the Eastern Creek plant and throughout the Amatil group to protect employees, suppliers, customers and products from Covid-19, including comprehensive hygiene plans and contact restrictions, both in B2B and B2C operations. Events and larger-scale gatherings have also been completely scaled back. www.ccamatil.com Mercury Line - Final part inspection via the IMD Vista inspection system","@ID":45}, PETcontents 4 PETplanet Insider Vol. 21 No. 10/20 petpla.net 10/2020 INSIDE TRACK 3 Editorial 4 Contents 6 News 54 PET bottles for Beverage + Liquid Food 56 Products TOP TALK 10 The beating heart of the bottling line - Interview with Georges Alard, Commercial Director, AF Group COMPRESSORS 14 Green mechanics - Significant energy savings 16 Meeting changing needs - Interview with Kris Vermeulen, Global Product Manager PET Compressors & Service, Atlas Copco BEVERAGE INGREDIENTS 18 Beverage trends in Australia & New Zealand - Natural, healthy and low alcoholic drinks are popular PREFORM PRODUCTION 20 Revolution, not evolution - Sipa’s Xtreme up and running with customers 22 From up and over to side - A sideway gamechanger, New Netstal PET-Line with sideway removals system BOTTLE MAKING 26 Returnable, refillable & recyclable - Coca-Cola Brazil recognised for refPET bottle 28 Sustainable bottle concept from New South Wales 34 PET kegs in special formats 36 Stretch Blow Molding, part 13 - Fundamentals of the blow process MARKET SURVEY 31 Suppliers of filling equipment and inspection systems BOTTLING / FILLING 42 Softdrinks with less sugar in bottles made from rPET 44 More performance, less space - Improved filling technology PACKAGING / PALLETISING 46 Co-packing at its best - Optimised end of line packaging process 48 Thermoformed lightweight rPET - Packaging with 33% material savings TRADESHOW PREVIEW 50 An enduring partnership 52 Brau Beviale 2020 BUYER’S GUIDE 57 Get listed! Page 26 COMPRESSORS Page 20 Page 34","@ID":6}, BOTTLING / FILLING PETplanet Insider Vol. 21 No. 10/20 petpla.net 45 mould changeover is available to reduce change-over time and improve safety conditions by not requiring any human intervention. Labelling is assured by a single-aggregate labelling system, ensuring reliable production as well as fast and easy label-reel auto splicing. The Super Combi Compact’s labeller technology features faster changeovers and easy replacement of parts as well as an automatic label vacuum extractor for maximised uptime. In addition, the labeller can accommodate different labels and technologies (Roll-fed, PSL). Sidel’s EvoFill HS Still filling technology Sidel EvoFill HS Still is the new filler with proportional filling valves, controlled by electro-magnetic actuators, guarantees a 30% faster filling with total control and accuracy when it comes to dosing the liquid into its designated container. The improved and completely dynamic filling technology allows high precision in modulating the beverage flow, as the plunger inside the filling valve can individually be moved to an infinite number of positions, resulting in maximum freedom in terms of different beverage types to be filled and different optimum filling speeds and levels. The new hygienic valve design with no beverage membrane assures beverage quality with no flavour carry-over. EvoFill HS Still is a simplified solution characterised by fewer components and functions, resulting in less maintenance costs, and a highly reduced filler footprint with less filling valves. Additionally, the filler features an onboard beverage tank further contributing to minimise the required floor space. It might also be equipped with an Integrated Cleaning System (ICS), cutting down on water and chemical consumption for internal cleaning as well as on floor space by rendering the need for an external cleaning in place system and additional tanks unnecessary. In total, with saving up to 30% of precious floor space while, at the same time, boosting production efficiency by another 30%, and delivering maximum speeds of up to 54,000 bph, the new Super Combi Compact is for producers of PET bottled water. Stefano Baini concludes: “Its new, compact design and innovative filling technology makes it an ideal solution for maximising production and increasing line efficiency at the best TCO per square foot – allowing producers to make the most of their existing space or new greenfield projects.” www.sidel.com The improved and completely dynamic filling technology allows for high precision in modulating the beverage flow, resulting in freedom in terms of different beverage types to be filled, and different optimum filling speeds and levels BOTTLING / FILLING 45 DISCOVER MORE ON WWW.CHPLUB.COM MicroDry ® AIR is a tailor made dry 1o-ঞm] voѴঞom =ou -bu 1om;ouvĺ m1u;-v;7 Ѵbm; ;L1b;m1 b|_ 70% !;71;7 ;m;u] 1ov| b|_ 40% ROI Ѵ;vv |_-m Ɛ ;-u JAM FREE AIR CONVEYORS A microdrop of ou r-|;m|;7dry 1o-ঞm] ru;;m|v fromvঞ1hbm] -m7 f-llbm] ĺ","@ID":47}, COMPRESSORS PETplanet Insider Vol. 21 No. 10/20 petpla.net 16 Interview with Kris Vermeulen, Global Product Manager PET Compressors and Service Atlas Copco Meeting changing needs by Gabriele Kosmehl Low noise, low vibration, low energy consumption and last but not least high flexibility – Atlas Copco is steadily expanding the range of its popular ZD series over the last 15 years, to meet all compressed air requirements their customers might have. The core of all new developments is energy reduction. PETplanet: Could you start by telling us a bit about your product portfolio in the PET sector? Kris Vermeulen: First, I would like to mention that at Atlas Copco, we have been serving the PET industry for many years. We have built our expertise thanks to the close interaction with our customers and this resulted in our approach reflecting the PET industry requirements. A new addition to our solutions is our PET compressor that doesn’t need water: The ZP range delivers a capacity varying from 200m³/h up to 800m³/h. The ZP is a plug and play machine, requiring only an electrical connection to deliver high pressure compressed air. The ZP is also available as fixed speed and variable speed drive (VSD). Our best known solution however is our ZD FF (FF = Full Feature), which delivers a capacity varying from 800m³/h up to 4,100m³/h and can deliver a working pressure up to 42bar. Wehave also expanding this range up to 100bar. The ZD FF is available as a fixed speed unit, but also as a Variable Speed Drive (VSD) unit which we believe helps reduce our customers’ energy costs. PETplanet: Could you explain what you mean by “Full Feature”? Kris Vermeulen: The ZD is always delivered as a Full Feature version, meaning it always includes an adsorption dryer which by the way does not require additional energy. In order to always have a good (pressure) dewpoint at any working pressure (25-42 bar), we dry the air at interstage pressure with our rotary drum heat of compression adsorption dryer, this down to -20°C PDP, enabling at the final high discharge pressure always dry air (PDP 3 °C). This even when the working pressure is lower than 40 bar, as at lower pressure our PDP only improves, where at 30 bar we even have a negative PDP (PDP 0 °C). PETplanet: When you launched the ZD line in 2004, a first in PET compressor design was the piston compressor’s integral concrete base plate which eliminated the need for special foundations of any type. COMPRESSORS","@ID":18}, BOTTLING / FILLING PETplanet Insider Vol. 21 No. 10/20 petpla.net 42 Interview with Coca-Cola Amatil June 8, 2020 We met: David Chalmers, Operations Manager, PSD Ideas and initiatives from Down Under Softdrinks with less sugar in bottles made from rPET by Kay Barton In 2018, we visited the Coca-Cola Amatil (Amatil) plant in Eastern Creek, near Sydney, on Australia’s East Coast and discussed the company’s operations and plans, including its newly-developed SyLon cap (see PETplanet Insider 05/18 and 10/18). A lot has happened in the two years since then, especially global developments in ‘better-for-you’ drinks, sustainability and environmental issues and, of course, Covid-19. Back in 2018 we interviewed David Chalmers, Operations Manager of the Packaging Services Department (PSD) at Amatil and were able to speak to again this year as part of our Road Show. Amatil’s financial performance in 2019 was positive, with EBIT (earnings before interest and tax) up 0.8% to AU$ 639.3 million (US$ 444.8 million). Its Australian Beverages business accounted for 57.7% of the total, with the balance generated by operations in New Zealand & Fiji, and Indonesia & Papua New Guinea (PT Coca-Cola Bottling Indonesia, jointly owned with The Coca-Cola Company Ltd). Market uncertainty regarding the duration and impact of the Covid-19 pandemic meant that the company decided to withdraw forward-looking market guidance in March 2020. Two sustainability issues in particular continue to be the focus of Amatil’s attentions going forward: the use of recycled material in PET bottles and the reduction of drinks’ sugar content. Sugar reduction initiatives Amatil is targeting a reduction in sugar content of 10%/100ml in its non-alcoholic beverage portfolio in Australia and New Zealand by 2020 and is aligned with industry peers in Australia to achieve a 20% reduction by 2025. By 2019, the company had reduced sugar content (measured in g/100ml) by 8.8% in Australia, 5.3% in New Zealand and 13.5% in Indonesia. Twenty-five beverage products have been reformulated in Australia since 2015, along with eight in New Zealand. Mr Chalmers gives one example: “Last September, we introduced a new version of our popular Sprite carbonated soft drink that contained 40% less sugar than the original, to cite just one example,” he said. “This sugar-reduced product now contains 4.9 g/100ml, compared to the previous 8.6 g, without compromising on taste”. While there is a definite trend in the industry towards overtly ‘healthy’ ready-to-drink beverages, Coca-Cola proved Amatil’s most popular brand in 2019, particularly during the second Tour Sponsors: David Chalmers in front of a Husky HyCap IMM equipped with a closure mould from Z-Moulds Project Pristine new Orbis bin erector","@ID":44}, BOTTLE MAKING 38 PETplanet Insider Vol. 21 No. 10/20 petpla.net a higher temperature. In order to understand how this can indeed be accomplished, we need to understand how the oven lamps heat up the PET preforms. 6.3 Types of heat transfer There are three ways of conveying heat and all three are present in a reheat stretch blow machine: conduction convection radiation Conduction occurs when two parts touch each other and heat flows from the warmer to the colder part. An example of this is a warm mandrel transferring heat into the preform neck. Conduction is not suitable for use as a means of reheating because PET like most plastics is a poor conductor and it would take too long to reheat preforms this way. Convection is heat transfer with participation of air. Heating up of air in the ovens of the blow machine takes place and depending on the temperature of this air it can either heat or cool the outside of the preforms. Air heating is difficult to control, highly dependent on environmental conditions and furthermore heats the outside of the preform more than the inside; just the opposite of what is required. The output of the oven lamps radiates to the preforms in the form of waves. These waves can be readily absorbed by the PET or penetrate with little absorption. When surface absorption takes place, a large amount of heat is transferred directly to the outside surface of the preform. From there it would then travel by conduction to the inside. This behaviour is undesirable since the outside wall would overheat with the inside wall staying colder. Therefore a high degree of surface absorption is not suited for optimal reheating. 6.4 Light absorption characteristics of PET Oven lamps can be adjusted in a voltage range of 0–220V. On some machines a percentage setting of 0–99% indicates this. One less understood feature of this control is that voltage output affects both temperature andwavelength. We measure wavelength for this part of the electromagnetic spectrum in either micrometers (one millionth of a meter) or nanometers (one billionth of a meter) and 1000nm make up 1μm. While these lamps all work in the infrared spectrum, this spectrum ranges from 0.7 to 100μm and it depends on the voltage setting, which wavelength the lamp is emitting. It should be noted that while the lamps work mostly in the infrared spectrum, they also emit wavelengths on either side of this range. Shorter waves of 400–700nm are in the visible spectrum (Fig. 6.3). Fig. 6.3 Typical range of emitted wavelengths of infrared lamps. Diagram courtesy of Philips. Fig. 6.4 shows how PET absorbs the output of the infrared lamps depending on the wavelength of the emitted radiation. It was recorded by emitting the different wavelengths shown as the horizontal axis through a strip of PET and measuring the wavelength after it bounced off a reflector. To the left of the horizontal axis are the short waves. Here PET absorbs up to 50% of the emitted radiation. Between about 1,000 and 2,200nm absorption is about 20% with 80% of the heat being lost. At longer waves to the right of the axis absorption increases again. Fig. 6.4 Lamp settings change both heat flow and wavelength. Optimal wavelength is indicated between the two black arrows. High absorption rates would lead to an overheating of the outside skin of the preform, which is detrimental to an optimum heat profile. Therefore the majority of the lamp output should be between 1,000 and 2,200nm. This is the output the lamp emits at a voltage of 220–110V or 100–50%. While this is admittedly a wasteful process, it allows the heat waves to penetrate the preform walls evenly, heating inside and outside walls to roughly the same degree (Figs. 6.5–6.7). Fig. 6.5 Summary graph of empirical temperature data of preform inside and outside wall at 40% lamp output. Inside temperature lags. Graph: Mr. Bonnebat Fig. 6.6 Summary graph of empirical temperature data of preform inside and outside wall at 70% lamp output. High absorption at outside wall leads to great difference. Graph: Mr. Bonnebat Fig. 6.7 Actual temperature data of preform inside and outside wall at 100% lamp output in one position. Inside temperature increases faster due to ideal radiation wavelength and convective cooling of the outside. Graph: Bonnebat Now that the preforms are reheating evenly, the next step is to cool down the outside wall of the preform. This is accomplished by blowing air into the ovens at a rate high enough to lower the temperature to below blowing temperature. This air will absorb heat more from the outside of the preform wall than the inside since it comes more into contact with it. An oven temperature of 85°C (185°F) has been proven to be sufficiently low to facilitate this effect. However, oven temperature readings are highly dependent on where the","@ID":40}, MARKET SURVEY 31 PETplanet Insider Vol. 21 No. 10/20 petpla.net 10/2020 MARKETsurvey Resins & additives Preform machinery Preform production & inspection Preform & SBM mould manufacturer SBM 2 stage Compressors Caps & closures & inspection Filling equipment & inspection Recycling Palletising & shrink film machinery Supplier of filling equipment and filling inspection systems It’s time to present some state-of-the-art filling equipment and filling inspection systems in our annual market survey. Please have a look at the up to date technical details provided by: Sacmi Imola S.C., SMI S.p.A., Sipa S.p.A, Pressco Technology Inc., Sidel, KHS GmbH, Newamstar Packaging Machinery Co., Ltd., STM S.P. and Heuft Systemtechnik GmbH. Although the publisher has made every effort to make sure that the information in this survey is up to date, no claims are made regarding accuracy and completeness. Filling Equipment Company name Sipa Postal address Telephone number Web site address Contact name Function Direct telephone number E-Mail Via Caduti del Lavoro n. 3 31029 Vittorio Veneto (TV), Italy +39 0438 911 511 www.sipasolutions.com Mr Matteo Tagliaferri Marketing and Communication +39 0438 911 511 matteo.tagliaferri@zoppas.com 1. Machine designation / model number Isofill P Stillfill EVO Flextronic C Flextronic SE Flextronic S Flextronic W Bigfill 2. Number of filling heads (range: from/to) 20-160 20-120 50-180 20-180 20-180 20-96 12-24 3. Min to max bottle contents (in liters) 0.125-3 0.125-3 0.125-3 0.125-3 0.125-3 0.125-3 3-20 4. Filling speed: output (bph) (min to max): specifiy: 1l bottle / still water (bph) 60,000 62,000 60,000 62,000 63,000 36,000 16,000 (3l) 1l bottle / CSD (bph) 51,000 (CMW) 55,000 (CMW) 1l bottle / Milk (bph) 62,000 62,000 36,000 1l bottle / Juice (bph) 53,000 60,000 59,000 62,000 62,000 36,000 5. Filling process Pressureless (still drinks) Yes Yes Yes Yes Yes Yes Yes Pressure filling (carbonated drinks) Yes Yes Hot filling Yes Yes Cold aseptic filling Juices with high pulp content Yes Yes 6. Type of filling valve and metering system Isobaric mechanical level filling Mechanical gravity filling Isobaric volumetric filling valve Gravity volumetric filling valve Gravity volumetric filling valve Electronic weight filler Gravity volumetric filling valve 7. Special features (short description/keywords) AISI 316L SS valve, product deflection without deflector on the filling tube, quick changeover for different neck diameters, automatic dummy bottle insertion, mobile vent tube, centralised remote fill level adjustment AISI 316L SS valve, product deflection without deflector on the filling tube, quick changeover for different neck diameters, seperated bottle air return, hot fill kit for product recirculation, constant and controlled recirculation rate in bottle, centralised remote fill level adjustment no bottle no fill system AISI 316L SS valve, product deflection without deflector on the filling tube, quick changeover for different neck diameters, automatic dummy bottle insertion, magnetic flow meter product control, filling speed control, XFill configuration without tank on board, dry pressurisation separated bottle air return AISI 316L SS valve, no contact between valve and bottle neck, quick changeover for different neck diameters, ultra clean version available, magnetic flow meter product control, filling speed control, automatic dummy bottle insertion, XFill configuration without tank on board AISI 316L SS valve, no contact between valve and bottle neck, quick changeover for different neck diameters, ultra clean version available, 3 positions membrane valve filling speed control, automatic dummy bottle insertion, XFill configuration without tank on board AISI 316L SS valve, no contact between valve and bottle neck, quick changeover for different neck diameters, load cell integrated in the bottle neck support, 3 positions membrane valve filling speed control, automatic dummy bottle insertion AISI 316L SS valve, no contact between the valve and the bottle neck, quick changeover for different neck diameters, ultra clean version available, 3 positions membrane valve filling speed control, automatic dummy bottle insertion, high flow performance","@ID":33}, BOTTLE MAKING 27 PETplanet Insider Vol. 21 No. 10/20 petpla.net Single, distinctive bottle shape Historically, Coca-Cola adopt a different bottle shape for each Brand in its portfolio, including Coke, Fanta, Sprite and juices. A single bottle design for returnable bottles eliminates the need for changeovers and facilitates savings on the production line and helps to reduce empty bottle stock levels. The Universal Returnable Bottle is the same silhouette and distinctly Coca-Cola family, whatever the contents. Individual products are distinguished by removable renewable labelling. In pursuit of its strategy of affordability, flexibility and reliability, the company opted for modular, flexible labellers with label extraction at bottle washing stage as the preferred solution. Renewable paper labelling offers a ‘clean’ look and the ability to work with different marketing campaigns. “This solution development required lot of collaboration between bottlers, machinery and label suppliers in order to achieve a efficient and optimised solution including high speed labelling on all around labelling (wrap around). Several parameters must be tightly controlled. Coca-Cola is now developing BOPP and RGB paper labelling on the same equipment.” said Paulo Villas. Delivering the solution The design project developed technological solutions that enabled more reuse/ refill cycles with the RefPET material. Each refillable PET bottle can be reused 25 times and can be 100% recycled, including labels, so there is no waste. The Universal refPET bottle was launched in the first half of 2018 and later implemented the renewable labelling system. The lightweight refPET packages are: 2 l/91 g; 2,500ml/110 g; and 3,000ml/125 g bottles. Additionally, returnable glass bottles with ACL (applied ceramic label) was launched completing bottle family. The renewable labelling is now being validate also for returnable glass bottles. Since 2018, Coca-Cola Latin America operations began installing the labelling/extraction system. It now has 12 lines in Brazil and 25 lines across the Latin America region, accounting for around 17% of all production lines in the region. Full implementation across all lines is targeted as part of a five-year plan requiring approximately US$ 250 millions of investment.","@ID":29}, PREFORM PRODUCTION PETplanet Insider Vol. 21 No. 10/20 petpla.net 25 set new standards in terms of speed and energy efficiency. When you look at the overall cost of preforms, the machinery investment is only a small part. And I believe that once this unit is on the market, customers will be able to see for themselves just how realistic the costs are for them. After all, they can now compare empirical values of their moulds from previous lines with the actual cost of the new Netstal PET-Line. This might be a good opportunity for you as editor to research on site. PETplanet: Has the market pushed you to enter the side entry technology? Renzo Davatz: Let’s put it this way: many of our customers have encouraged us to take this step. Even a technically good unique selling point such as removal from the top can be a limiting factor for market access if the market moves in a different direction. PETplanet: With the new system you want to reshuffle the cards in the market. What are your concrete goals? Renzo Davatz: Due to the lack of mould compatibility, we have had little access to the growing market for high-performance side entry systems. With the new Netstal PET-Line we provide a relevant alternative for many users worldwide. Accordingly we want to achieve significant growth in the coming years and double our sales of PET machines. www.kraussmaffei.com","@ID":27}, BOTTLE MAKING 37 PETplanet Insider Vol. 21 No. 10/20 petpla.net acteristics. Only then are they able to find the optimal solution to a multifaceted problem. 6.2 Stretch ratios To better understand what the process needs to accomplish, we need to study how stretch ratios between bottle and preform are calculated and how temperature differences in the preform wall affect them. While there is no accepted standard in the industry how stretch ratios are calculated, it is safe to say that they represent the ratio of bottle dimensions to corresponding preform dimensions. There are two types of stretch ratios (Fig. 6.2): Axial stretch ratio dividing the length of the bottle by the length of the preform as measured from underneath the neck support ring (NSR) to the end of bottle and preform. Hoop stretch ratios can be measured in three different ways: 1) Dividing the outside bottle diameter by the corresponding outside preform diameter. 2) Dividing the inside bottle diameter by the corresponding inside preform diameter. 3) Dividing the average bottle diameter by the corresponding average preform diameter. Taking Fig. 6.2 as an example, here are three calculated stretch ratios: Outside hoop stretch ratio (max.): 74.98/22.2 = 3.38 Inside hoop stretch ratio (max.): 74.58/15 = 4.97 Axial stretch ratio: 199.63/92.05 = 2.17 It becomes apparent that the inside stretch ratio is significantly (47% in this particular case, others may be lower or higher depending on the wall thickness of the preform) higher than the outside stretch ratio. This is the result of the bottle wall thickness being so much smaller than the preform wall thickness, so there is only a small difference between inner and outer bottle diameter but a large difference between inner and outer preform diameter. Intuitively, it is understood that warmer areas stretch easier than colder ones. Since the inner preform walls must stretch further, we can postulate that they should be at a higher temperature than the outside walls. However, heat enters the preform from the outside by means of the infrared lamps, so it seems a rather difficult challenge to get the inside wall to POWER UP YOUR LINE! READY TO SHINE? To make the most of what differentiates you, our complete solutions are based on future-proof technology, disruptive concepts and human ingenuity. Our goal: to bring you performance all along the line. You are unique, so are our solutions. sidel.com Fig. 6.2: Stretch ratios can be calculated from preform and bottle dimensions.","@ID":39}, LABELLING PETplanet Insider Vol. 21 No. 10/20 petpla.net 51 PE Labeller machines were installed in the Recoaro factory in 2019-20. A new PE machine was installed on the PET mineral water line, with the primary objective of replacing paper labels with plastic and increasing the overall efficiency of the line. The requirements for the new machine were that it should produce 30,000bph in OPP with four different formats. The objectives were: to increase the productivity and flexibility of the line, replace paper labels with plastic and, going forward, increase efficiency while reducing maintenance costs. “The machine had to be made with format changes in mind and to be interchangeable with the other two already installed on other production lines, and with the guarantee of a low annual maintenance cost,” said Negri. “We understood the needs and regard meeting them as a joint success.” Equipping for the future “The future will be affected by the negative impact Covid-19,” says Tiozzo. “We expect to see consolidation in all sectors, with takeovers by large groups. Only those who are quick to understand and react to rapid changes in the market will overcome the complex challenge that lies ahead.” Recoaro will seek to consolidate its market share and expand into new areas, such as co-packing seltzer alcohol beverages. Sustainability, in production and distribution, will be among the highest priorities. PE Labellers will be part of that future, challenged to propose and develop innovative, high performance labelling solutions. www.pelabellers.com Simpl-Cut machine is an ergonomic labelling solution Building the future in every moment of your business 40 Bar Oil-Free Piston Compressors for PET Applications. hertz-kompressoren.com The Simpl-Cut is ideal for many different sectors: Beverage (mineral waters and soft drinks), Food & Dairy, Home Care or Chemicals.","@ID":53}, 53 TRADE SHOW PREVIEW PETplanet Insider Vol. 21 No. 10/20 KHS Hall 7a | Booth 320 Reliable technology and digital service for the beverage industry The exhibition focus will be on KHS’ new and further developments in filling technology, especially those for the can and glass bottle segments. The KHS Group will also be presenting its broad portfolio of digital services that give customers numerous benefits, particularly in view of the current social and travel restrictions. Digital systems prevent production loss When social distancing and travel restrictions greatly hamper the maintenance and repair of machinery, creative solutions are called for. “With our comprehensive range of digital services we’re showing which efficient measures can help minimise downtimes and prevent production stops,” Dr Johannes T. Grobe, CSO for the KHS Group, states. Thanks to its proven ReDiS remote diagnostic service and augmented reality service KHS also reliably helps its customers to remedy faults quickly and directly by remote access – without a KHS service engineer having to be on site. The digital monitoring of entire lines is just as smart, this made possible by the web-based Basic Line Monitoring software that assesses the line’s efficiency and pinpoints any possible errors. The German turnkey supplier also proves a reliable partner to its clients with its 24/7 Service HelpDesk. This is available round the clock for spare parts inquiries and to process any technical problems that might arise. Numerous optimisations in filling technology With its further developments for beverage cans KHS is meeting the growing market demand for this container segment. For instance, the KHS Innofill Can DVD can now fill beverages while they are warm. Another important upgrade is the new pneumatic lowering device for the centering bells that further boosts the standard of hygiene already inherent on the can filler. ‘Little brother’ Innofill Can C, on the other hand, has had its production capacity optimised. Instead of 5,000 to 15,000 cans an hour, the machine can process up to 50,000 containers in the same time. Furthermore, with its Innofill Glass platform KHS is expanding its portfolio for the filling of sensitive beverages such as beer and fruit juice. The long-tube filler is especially convincing here with its high degree of flexibility and modular design. www.khs.com","@ID":55}, TOP TALK PETplanet Insider Vol. 21 No. 10/20 petpla.net 12 Alard: That is not such an easy question to answer. Piston compressors can go on for decades with the correct maintenance regime unlike other types of compressors which can have a finite lifetime. We have compressors still operating after over 30 years in adverse conditions. However, the longer the compressor is operational (we are talking years), the more difficult it becomes to satisfy the consumable spares supply, likewise also electronics quickly become obsolete compared to mechanical parts. Another reason for a company to keep its compressor running is familiarity, they don’t want to change, the owner loves it, the maintenance staff don’t want to learn about a new machine…. Many excuses. So we take the view that 10 years is a good time period to review with the customer the options open to him. We would recommend a system audit. Can it be improved by a new management system for example? Would a new compressor take the place of two older units? It’s the closeness, the partnership, with our customers that AF pride themselves on, that we not only can have these types of discussions whilst maintaining and expanding our customer base. PETplanet: If retrofitting is the customers’ choice to update an older compressor in an energy-efficient way - what options do they have? Alard: We have several options. It could be mechanical, by retrofitting the latest designs of mechanical compression parts, or cooling systems. Electrical, by replacing old PLC’s with the latest versions. Systems, by looking and analysing operational loads and powers. Heat recovery systems, either retrofitted or plug and play. Management control systems. As I have said previously, we have a dedicated department whose sole function is looking at customer upgrades. PETplanet: As you mentioned earlier, this year AF will not be attending Brau Beviale due to Covid-19. What would you have presented if you had been in Nuremberg this year? Alard: Recently AF has re-designed and developed our two stage industrial compressors into a larger, more energy efficient range based on our phenomenally successful PET compressor for 3 to 15bar units for specialised applications. Low pressure units, two stage oil-free compressor for 8 and 10bar (from 3 to 15bar). So apart from presenting our OPC range we would be promoting more prominently our new “All in One,” a system which can deliver simultaneously high and low pressure from a single 3 stage compressor. This multi flexible use compressor is a creative opportunity for customers to reduce Capex and Opex in a significant way. This system is protected by an international patent. PETplanet: AF currently has installations in more than 175 countries. Geographically speaking, what is the focus in terms of expansion? Alard: To begin with, there is the “traditional” Greater Middle-East. AF Middle-East was already settled in the Jebel Ali Free Trade Zone but last year AF became owner of its own facilities, with spare parts components to market and service the Greater Middle East, Eastern Africa, and the 5 Stan (Kazakhstan, Kyrgyzstan, Tajikistan, Turkmenistan and Uzbekistan). So, next to the “traditional” Greater Middle-East, Asia, and Africa mature markets, Europe and Africa are presently very active … But each and every country and regions require a quick and rapid service, and therefore we cannot afford to neglect any zone, there is no such thing as a “small” customer, there is no “second category” geographic sector. PETplanet: Thank you very much for Mr Alard, and all the best to AF and its 150 years jubilee! www.afcompressors.com COMPRESSORS New oil free piston reciprocating air compressor OPC-110 – 8bar and 10bar Yesterday and today - AF’s former production halls and the new warehousing facilities in Liège, Belgium frames. Highly competitive power to capacity rates make the reciprocating compressor very desirable to own and operate when electrical energy costs are rising. These two-stage oil free compressors marketed as our OPC range can operate in the normal 7 to 10bar industrial standard and we have options","@ID":14}, BOTTLE MAKING 34 PETplanet Insider Vol. 21 No. 10/20 petpla.net Interview with Keg King, MCH Australia Pty. Ltd. 20 April 2020 We met: Mr Will Fiala, CEO PET kegs in special formats by Kay Barton In the Melbourne suburb of Springvale, the Keg King brand manufactures large-format kegs and PET containers. The company began its PET activities in 2015 as a reaction to the booming craft ale scene in Australia, not only with PET kegs but also with a wide variety of products in the field of brewing equipment and for the brewing process. We got to know CEO Will Fiala back in 2019 at the Brau Beviale trade fair in Nuremberg and inspected several PET exhibits. Now we spoke to him about the background and the technological challenges of his keg developments. Back at Brau Beviale, we could see that Will Fiala was an extremely pleasant and creative guy. He leads the company together with Managing Director Dr Maggie Hu, who has a medical background. Mr Fiala himself is a qualified electrical engineer. “In 2004, Dr Maggie Hu founded the company as an import business four years before she finally specialised in 2008 in the field of home-brewing equipment. I’ve been on board with the company since 2017,” explains Mr Fiala. Low cost alternative for brewers The reason for manufacturing PET kegs lies in a growing demand for lowcost alternatives which mostly comes from smaller breweries who need to avoid the high costs of acquiring and maintaining steel kegs. However the early days here were challenging. “Because of various factors, the market acceptance of the kegs we manufactured before 2018 remained somewhat behind expectations. It was only after investing in a K53 singlestage system from Cypet and their Zeg technology for manufacturing very light single-use PET kegs with a fill volume of 20 l that we gradually made a name for ourselves. We still have no market share for these kegs but we are about to start mass production. We are still waiting for further feedback from the breweries that are currently using and testing our kegs.” The kegs should then be provided with both A-style and D-style couplers. The reason for choosing the K53 model was economics. “We are able to blow our containers on one machine rather than two“, explained Tour Sponsors: Will Fiala showing kegs in front of his company. 20 l keg PETcast In our new Road Show podcast, PETplanet meets industry experts from Down Under to Japan and talks with them about their successes, decisions and current developments. Listen to the full conversation atwww.bit.ly/2HVwbAd","@ID":36}]}}
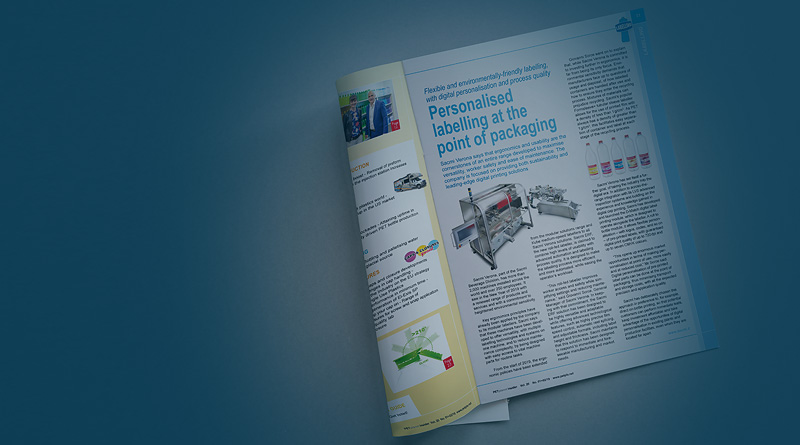