Latest generation of XForm preform injection moulding platform and hot-fill option for single-stage ISBM
Sipa, Hall 13, Booth B11
Sipa’s new XForm GEN4 XP system incorporates the latest generation of preform injection moulding technology to deliver the lowest conversion cost alongside unmatched speed, flexibility and ease of use.
New technology incorporated into 250, 350 and 500t system, capable of running with moulds holding up to 128 cavities and 180 respectively, has been designed to handle the most demanding applications. It delivers leading short cycle times in the industry; it offers industry-leading energy efficiency; and it has the lowest maintenance cost in the sector. As with all other XForms, the XForm GEN4 XP accepts virtually all legacy tooling produced by any major mould maker.
The XForm GEN4 XP provides a totally new operator experience, delivered through an HMI with a large 21.5-inch touch screen with high-definition graphics, swipe functions just like a smartphone, a multi-function control knob for one-handed operation, and fast response times unaffected by processor load. The HMI incorporates an advanced automatic process set-up and an in-depth part quality troubleshooting tutorial, which together will help users improve machine up-time, lower scrap rates, and depend less on highly skilled machine operators.
Powered by the latest servo-driven hydraulic pumps, the XForm GEN4 XP has record-low lock to lock time, paired with an increased injection rate. Total energy efficiency has been increased by a similar amount: in a typical set-up with the machine set-up to full screw utilisation and PET with an IV of 0.80, the XForm GEN4 XP consumes just 0.195 kW of energy for every kg of material processed. One of the reasons for the improvements in dry cycle time and energy efficiency is the introduction of a kinetic energy recovery system acting on the toggle drive.
Sipa’s XForm platform has already gained a reputation for its ease of maintenance, but on the GEN4 XP, it is easier than ever, Sipa says. That’s because, for example, the company has modified the accumulator area layout so that the accumulators are now mounted on a pull-out rack inside the machine frame. In addition, the oil tank has been redesigned so that it does not need to be emptied in case of maintenance (it can also be used at altitudes of up to 3,000m without any modifications).
“The net result of all these improvements is that our customers will be able to operate more consistently, at higher speeds, spending less on energy and maintenance, using a machine that will reduce conversion cost at record-low levels,” says Stefano Baldassar, Global Sales Director, Preform Systems & Tooling at Sipa.
Hot-fill option for single-stage ISBM
Sipa will also showcase the new hot-fill option for ECS SP single-stage injection-stretch-blow moulding machines.
ECS SP machines have a hybrid drive technology. Servo-electric drives are used where precision and speed are required, while hydraulics perform tasks where there is no particular need for high performance. This solution provides the best combination of high performance and low energy consumption.
Valve-gated hot runners
The moulds mounted on the ECS SP are equipped in a standard configuration with valve-gated hot runners for production of premium quality containers. An additional advantage of the moulds solution provided by Sipa is that it gives users the opportunity to use, for any given number of cavities, the same hot runner system for different types of preforms, with only the cold half needing to be changed. This has obvious advantages in term of costs and significantly reduces the time required for format changes.
At K2019, the hot-fill option will be fitted to an ECS SP80, the larger of the two models in the ECS SP family (the smaller ECS SP25 can also be equipped with the hot-fill option). The ECS SP systems stand out for their compact dimensions, high energy-efficiency, for the best-in-class productivity (thanks to a combination of high cavitation and low cycle time), and the premium quality of the containers they produce.
Production of ketchup containers
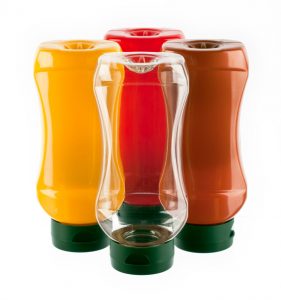
The ECS SP80 HF, which has an 80t injection clamp force, can produce containers as small as 10ml. At the K show, the containers being produced will be rather larger than that: 420ml ketchup bottles with an oval shape that weigh just 28g. Other bottle features include a height of 167.5mm and a neck diameter of 38mm with a SP400 neck finish.
These containers are resistant both to a filling temperature of 85°C (±2°C) and to vacuum forces that occur as they cool down. This second feature is very important, because it solves the long-standing problem of the label crinkling, that is, the partial or even complete peeling off of the label, owing to deformation of the container.
The ECS SP80 HF on the stand will have six cavities and will run with a cycle time of around 14s, resulting in a productivity of 1,540bph.
Years of experience in hot-fill at Sipa
The new hot-fill option for ECS SP machines stems from Sipa’s extensive experience in technology for production of hot-fillable containers with both single-stage and two-stage technologies. This has enabled it to tackle the two major downsides of the solutions currently available on the market for low-output systems (producing from a few hundred to a few thousand parts/hour): on the one hand, there is the lower energy efficiency of two-stage technology; and on the other, there is the poor thermal resistance of hot-fill containers produced so far with single-stage machines.
The hot-fill option now provides ECS SP users with a lower-cost alternative to aseptic filling. In addition to that, if oxygen scavengers are used in the PET, it is possible to achieve a shelf life for the ketchup as long as 12 months without needing to adding preservatives to the product, therefore providing a healthier product in line with the latest trends of the market.
For new machines and retrofits
Hot-fill capability can be retrofitted to existing ECS SP machines as well as supplied on new ones. The retrofit kit includes dedicated stretching rods, air valves, air vessel and piping that are required for the air recirculation in the container during the hot-fill process, an electrical heating system for the blow moulds that ensures the cleanliness of the blowing area (no oil is used), and the upgrade of the machine’s control software in order to include the management of this option.
Sipa, whose experience in the single-stage technology now stretches back over more than 25 years, also offers ECS SP users the opportunity to leverage its wide expertise in developing optimised preforms that enables very high productivity and premium container quality.