Zero Cooling, multiple benefits
Nissei ASB, Hall 14, Booth B38
Nissei ASB Machine Co., Ltd., a leading manufacturer of machines and moulds for injection stretch blow moulding of PET and other plastics, intends to be making a strong impact with the target audience with live moulding demonstrations of five ASB-Series machines strongly showcasing ASB’s recently introduced “Zero Cooling” moulding process at its 712 m2 booth.
The major sectors of the PET container market that utilise one-step injection stretch blow moulding (ISBM) process are commonly those where containers are designed for market appeal and brand quality. This is particularly true for cosmetics, personal care, pharmaceutical, household or general food packaging. Zero Cooling – ASB’s advance in preform cooling technology – is claimed to suit the needs of these industries as it enables increased product quality at short moulding cycles. Taking full advantage of ASB’s proprietary 4-station, 1-step moulding method, the required preform cooling is now shifted away from the injection station and into the second, conditioning station to reduce injection cycle times.
Crucially, the Zero Cooling moulding method, first announced in 2018, enables short cycle times while avoiding the need for thin, compromised design preforms that are susceptible to several quality related problems, most notably the undesirable ‘fisheye’, ‘body ring’ and ‘orange peel’.
Now, with the preform designer able to freely focus on a shorter preform design with a thicker wall section that optimises stretch ratios, the result is improved quality as well as increased productivity, states the company, and continues: Actual results from typical Zero Cooling moulds have shown 15% or greater increase in stiffness and topload strength, improved control of material distribution and an average of 1.5 times productivity increases while improving on visual quality. In addition, since the container strength has now been improved by better orientation, more scope is available to apply additional light-weighting to the container’s specification.
The advanced cooling method also enables the moulding of heavyweight premium cosmetic containers in dramatically shortened cycle times exhibiting no haziness even when using standard, lower cost PET grades, rather than the higher priced specialised, low-crystallisation grades that are normally required. All this is intended to result in visual quality while saving cost and boosting productivity by 2-3 times over conventional moulding of these glass-like, premium designs.
ASB-12M – small size with vast capability
he model ASB-12M has established itself in the class of small, fully automated 1-step stretch blow moulding machines. Its Version 2 specification is intended to bring great performance and utility to the table. The Vision1 control system ensures that response & communication speed is 2.5 times faster than dedicated PLC systems enhancing machine cycle efficiency and control precision. The PC based system makes it flexible in use and compatible with Industry 4.0 for enhanced factory networking. Also, a larger, easy to read panel provides easier access to relevant information without changing pages. Other advantages include touchscreen operation, improved operator feedback and standardised interface across the model range assisting in operator training. Major machine functions can be added or updated via software installation only.
The revised ASB-12M expands the capabilities for production of a vast range of PET containers, including efficient lightweight bottles and wide mouthed jars. Key features include:
- Ability to process more than 20 resin types in addition to PET
- Moulds containers from 5 ml or less all the way up to 2.5 l capacity
- Variable cavitation for up to 15 mm neck diameter bottles in eight cavities through to 83 mm neck diameter jars in a single cavity
- Servo driven hydraulic pumps installed as standard, contributing to major energy savings and offering smooth and quiet operation
- Backwardly compatible with existing class mould tooling with minimal modifications
- Small size allows fast mould changeovers will minimal manpower, and minimal lifting equipment.
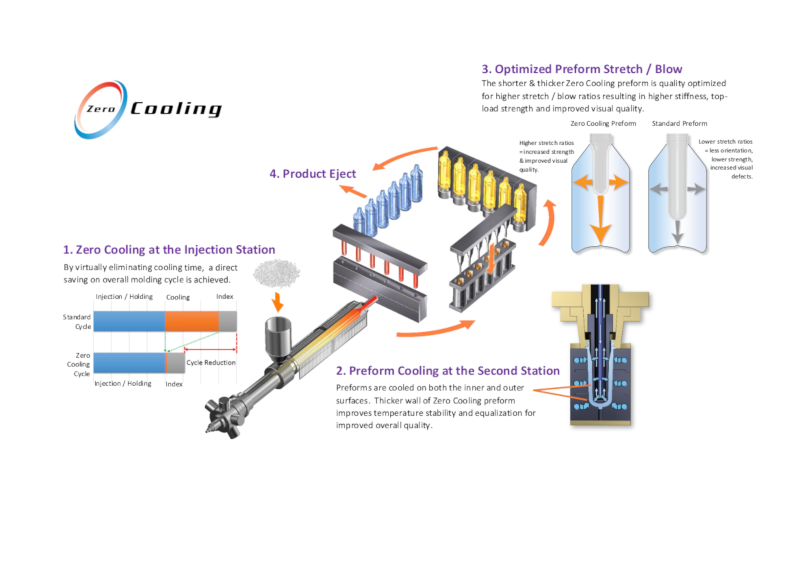
Overview of Zero Cooling (patented)
The model displayed at K’ will be fitted with the optional IU-10L long stroke injection unit that provides a 50% increase in available shot-size, expanding the scope for large containers, heavy-weight cosmetic bottles, or materials with lower density.
At the trade show, this machine will be moulding a 4-cavity “family” mould featuring two separate premium grades, glass-like cosmetic container designs of 80 ml and 45 ml fill capacity sharing a common preform design. Thanks to the use of Zero Cooling, the cycle has been reduced from a typical previous time of up to 40 s down to just 12.5 s to achieve greater than 3 times increase in productivity. This revised cycle is being achieved using standard bottle grade PET.
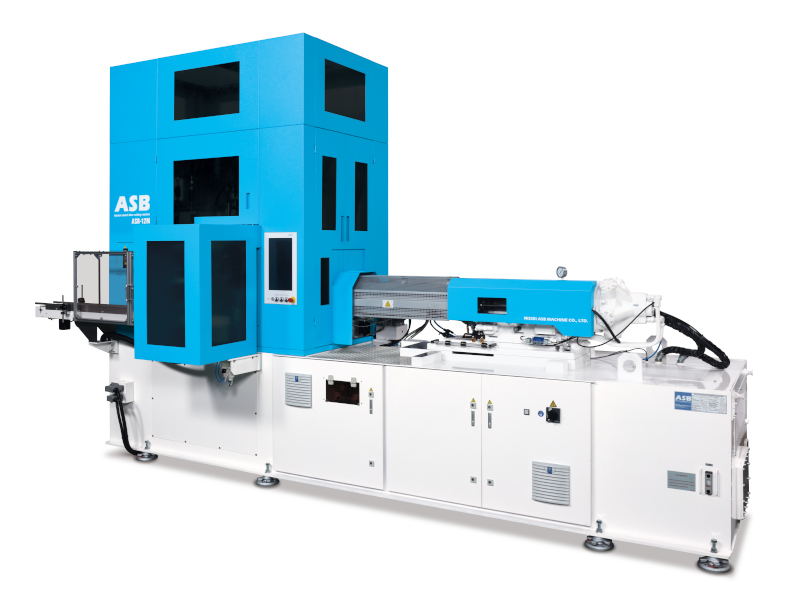
Versatile ASB-70DPH v4 model
With the ability to mould PET and up to 20 other resin types, combined with the capacity to mould up to 10 l capacity jars in a single cavity all the way through to sub-100 ml bottles in up to 12 cavities, the ASB-70DPH is a best-seller model of Nissei ASB. The ASB-70DPHv4 is a mid-range one-step injection stretch blow moulding machine that is claimed to offer moulding versatility in a “just-right” size with competitive investment costs and low cost of ownership. It utilises ASB’s renown 4-station moulding process to achieve moulding efficiency and stability of a wide range of moulding materials. Key features include:
- Ability to process up to 20 resin types in addition to PET
- Moulds containers from 50 ml or less all the way up to 10 l capacity
- Variable cavitation from 18 mm neck diameter small bottles in 12 cavities through to 149 mm neck diameter jars in a single cavity
- A wide array of factory options to tailor the machine to project-specific needs
- With no hydraulic components above the moulding area the risk of product contamination is eliminated

At the K exhibition, this version 4 model will be demonstrated moulding a 250 ml cylindrical shampoo / cosmetic container at a cycle of 13.4 s with 10 cavities producing over 2,600 bph. The demonstrated container design falls into a category that is often difficult to mould with perfect visual quality. Its small neck to body diameter ratio and a higher-than-normal weight as per the client’s requirement for a “quality feel” would cause moulding compromises with a standard mould. However, with the added benefits that Zero Cooling provides, not only is the productivity increased over a standard mould, the visual quality of the container becomes flawless, states the company.
Advanced version of ASB-70DPH
Although its external appearance is similar to the standard version on display, the ASB-70DPH Advanced Version has been fully re-engineered to demonstrate a variety of techniques to achieve reduced indexing time that fully complements the Zero Cooling process and to provide enhanced output, especially for smaller containers. Key points being demonstrated on this concept machine include:
- Revised hydraulic circuit for faster, smoother motion of clamping
- Adjustable stroke in all clamping stations reduces machine indexing time for shorter preforms, while adjustable daylight also allows longer preforms – a feature especially useful for many non-PET moulding resins
- Fully revised blow station to reduces index time, to simplify blow mould changeover and to reduce maintenance
- Compatibility with existing ASB-70DPH moulds
- Height adjustment system for injection unit reduces mould changeover times in high product mix moulding scenarios
With this Advanced Version machine giving a 40% reduction in indexing time, the demonstrated container using a short preform can be moulded at up to 2.4 s faster compared to a standard model. This saving is in addition to the reduced cycle time obtained from the use of Zero Cooling technology in the mould design.
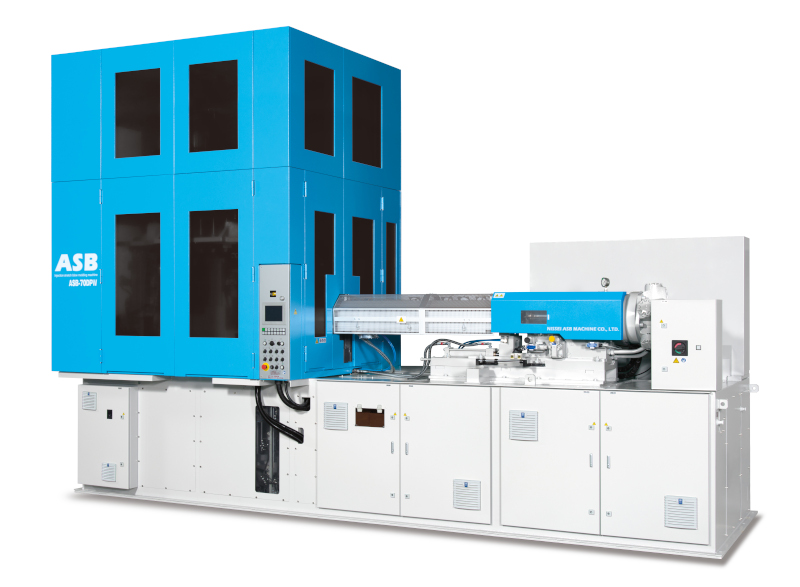
Combining the aforementioned machine revisions with ASB’s Zero Cooling mould technology, the 8-cavity, single row mould producing a 30 ml, 3.8 g, 19 mm screw neck container for medical or toiletry use will cycle at 4.4 s to provide over 6,500 bph. The double-row moulding equivalent to the ASB-70DPH is optimised for production of smaller bottles in moulding configurations from 8 to 24 cavities for high productivity of containers up to 1l capacity. Assisting with energy saving, the servo hydraulic system provides power consumption savings of 30-40% compared to the same mould and cycle time running in a conventional machine, while an optional blow air recycle system has the capability to take exhausted blowing air back into the machine system for air cylinder operation.
Now fitted as standard, an enhanced mould changing system in all stations permits reductions in overall mould change time. For a blow mould change, just 30% of the previous time is required while for a total and complete preform and blow mould change, around 50% of the previous time is required. At K, the machine will be moulding an oval 300 ml shampoo container in 14 cavities at a cycle time of 13.6 s to generate over 3,700 bph using a 100% recycled rPET.
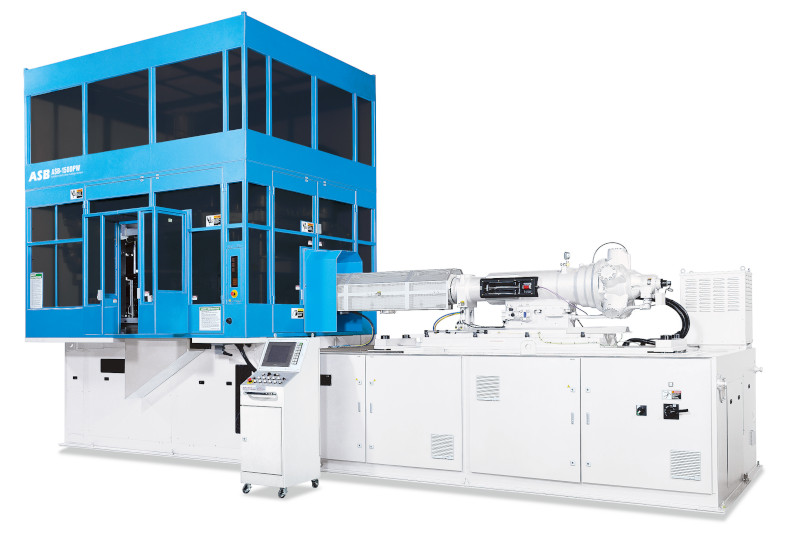
ASB-150DPW: for small & medium bottles & jars
The largest model on display is part of the ASB-150 Series that operate using single, double or triple row moulding. Despite being a high productivity machine for small to medium sized containers, the double row layout of the ASB-150DPW also has the versatility to mould a wide variety of bottles and jars in PET and other resins. Output is typically around 2.5 times that of the smaller ASB-70DPW.
With its design based on the shared ASB-150DP / ASB-150DPX mechanical architecture, operation, maintenance and spare parts share many common features, thereby reducing total cost of ownership where its “siblings” are also in use. Energy consumption is maintained low due to the adoption of standard variable displacement or optional servo driven hydraulic pumps.
The ASB-150DPW is capable to mould containers from 1.5 l jars with 94 mm necks to sub-150 ml bottles ranging from 8 to 36 cavities. At K, the machine will be demonstrated moulding a 900 ml, 70 mm neck diameter general food jar in 14 cavities. The adoption of Zero Cooling offering a cycle of 9.4 s means that productivity will exceed 5,300 bph while moulding strong containers in 100% rPET.