{"pages":{"page":[{"#text":"EDITOUR REPORTS 15 PETplanet insider Vol. 13 No. 05/12 www.petpla.net Facts and figures 2011* Reported 762 million unit cases of consolidated sales volume in 2011, was up by 15% (1 unit case equal 5,678l in average) compared with the previous year, i.e. approx. 4.3 billion liters Turkey sales volume was up by 11% in 2011 reaching 547 million unit cases, International Operations’ sales volume reached 215 million unit cases in 2011, up by 26% with strong performance in all categories of beverages. Production CCI has 20 plants in its operating geography – see above. In almost all plants PET bottles are blown and filled on integrated lines, where preforms are injection moulded. Preform moulding is a core business of CCI. In Turkey almost all preforms are injection moulded in-house – except the “dedicated” preforms for multi-layer and/or larger sized bottles. Equipment Injection moulding systems: Systems are mainly based on Husky equipment Blowing and filling: all prominent PET players are represented: Sidel, Krones, KHS and also Sipa For future investments (blowing/filling) block machines will be bought. Development efforts According to Selim Mizrahi: “Following the world markets, we do what every prime company does in terms of development and try to be the best in class.“ The main develoments are: Light weighting - by moulds up-grading and line refurbishing to achieve 10.5g bottles for 0.5l water. Energy savings - by low pressure blowing (reducing from 38 to 17bars) Resin handling - by optimization of cycle time and cavitations It is not only the technical topics that the CCI developers are concentrating on. The success of both product and company is constrained by the overall “Supply Chain”; this includes activities such as market research, decisions for formats, consultation, prototyping and testing, transportation and storage – all working together to provide a service to customer and end-user alike. Looking ahead Statement by the Engineering Service Director, Selim Mizrahi: “The future is bright for CCI. We are aiming to get bigger, by optimizing our systems, and promoting the service to our customers and to our consumers. *Facts and figures in this report were sourced from the official ‘Consolidated Financial Statements’ as published annually by the company. www..cci.com.tr","@ID":17} "EDITOURS REPORTS 12 PETplanet insider Vol. 13 No. 05/12 www.petpla.net Sunpet Turkey Gaziantep The re-scheduled meeting with Hakan Cinkilic at his stand at the NPE in Orlando We met: Hakan Cinklic, Foreign Trade Manager Expanding to the South-East Sunpet, with a maximum capacity of 9 million preforms per day, is one of the larger converters in Turkey. The company was launched in Gaziantep in 1998. It focuses on preforms for water and CSD bottling. In recent years the company has found favour with Coca Cola and Pepsi Cola. 70% of its preforms go for export to Iran and surrounding countries and the Gulf region. The reason for this is Gaziantep’s central position and good links to these regions. So it was almost a foregone conclusion that, in 2010, Sunpet should establish a second plant for itself in Amman, Jordan. With the company still in the same hands, a decision was made in favour of the name ‘Middle East’. “By concentrating production on site, we were able to circumvent a few restrictions and have been able to benefit from the favourable regional cost structures”, says Hakan Cinklic, Foreign Trade Manager of Sunpet. Capacity in Jordan is around 3 million preforms per day. At its home location the company has had very good experiences with Netstal equipment with the result that production is exclusively Netstal-based at the moment. The PCO 1881 too is scheduled for production at both locations this summer. www.sunpet.com.tr www.middleeastplastic.com Turkey blog – en route to Azerbaijan I reach the Turkish border at getting on for 4.30pm. A few hundred meters away is an absolutely huge mosque, from which the muezzin is calling the faithful to prayer. Gradually dusk begins to fall. On the outskirts of Istanbul, I turn off the motorway in search of a place to bed down for the night. I soon manage to find a place to park in a petrol station. Not far away is a main road, full of shops, where, thanks to the long opening hours, I stock up with food for the next few days. 8am the next morning finds me back on the road. Overnight, the weather has changed for the worse. Torrential rain and stormy skies give a grey, monotonous pallor to Istanbul. I am on the motorway, heading towards Ankara, where Mr Cem Altintas from Altintas Goldcap is expecting me that afternoon. I make excellent progress and cover the 450km in about four hours. The scenery en route is constantly changing and I greatly enjoy the wonderful views as the motorway snakes through the mountains. At length I arrive at Altintas Goldcap. After an in-depth interview and tour of the factory with Mr Cem Altintas, I am allowed to park the Editourmobil up for the night on the firm’s premises. It is still fairly early so I take the opportunity during the evening to write up the blog and ponder the next stage of my journey to eastern Turkey. From nearby comes the call of the muezzin. The next morning it is again an early start. At last the sky is blue again and the sun is shining. The journey, on new and well-engineered roads, is relaxing. A few hours later I reach the coast of the Black Sea, and for the next 700km I will be following this road to Georgia. - Kay Krüger - The return leg to Germany Gaziantep greets me with a balmy 20 degrees Celsius. After my initial difficulties with Turkish GPS systems, I prefer to rely on the help of locals, whose guidance ensures that I am on time for my appointment with the preform producer Köksan Lande. I am meeting Murat Kögoglu, the third generation of the family to run the company. Köksan boasts a total of 17 preform lines and currently a polymerisation line is being built on the site. About 1,050km lie ahead of me the next day as I head in the direction of Bursa to Eskapet. So far, the Editourmobil has acquitted itself very well on the 10,000 km Go to Brau Beviale tour: a few loose screws in the interior, problems with the steps and a broken water pump on the fresh water tank seem to be the only casualties of the arduous journey. Eventually I arrive at Eskapet, where Ramazan Akar takes me on a tour of the brand-new factory, which has an annual throughput of 50,000 tonnes of PET. The next stage of the journey is on to Istanbul, and a meeting with Hasplastik. En route, I am delighted to come across an amiable caravan manufacturer who is able to help repair the water tank, so at long last I have running water again. It is not until 10pm that I arrive at the Hasplastik HQ, where I am able to park the vehicle for the night. Next morning, I am picked up at the Editourmobil by Technical Director Murat Aner who takes me round the site with its 39 closure production lines. But now it is time to bid farewell to Turkey and move on to our next destination, Budapest, where Bericap awaits me on Sunday evening. - Alexander Büchler -","@ID":14} "NEWS 8 PETplanet insider Vol. 13 No. 05/12 www.petpla.net Mold-Masters and Plastec USA sign agent agreement Mold-Masters has signed an exclusive agency agreement with Plastec USA for product sales and service for most Central and South American regions, including Mexico, but excluding Brazil and Argentina, where Mold-Masters already has sales representation. Plastec has over 25 years of experience in the sale of plastic processing machinery in Latin America and is the largest export management company for the US plastics industry in Latin America. The group is headquartered in Miami, Florida, has a sister office in Mexico and additional offices throughout Central, South America and the Caribbean. It will offer the entire Mold-Masters product line. The agreement became operational on April 9, 2012. www.moldmasters.com Management changes at Corvaglia Romeo Corvaglia, founder and proprietor of Corvaglia Group, began streamlining in-house structures in the summer of 2011. The company says that this restructuring and remodelling process has now been completed. Thomas Marder, dipl. Ing. FH, became Group CEO on July 1, 2011. Romeo Corvaglia remains as Chairman of the Board of Directors but will gradually be stepping back from operational matters and devote his time to strategic projects. Dr Michael Krueger has been appointed CTO and manager of the Technology Department. Former CTO Roger Mueller left the firm with effect from April 2012. Peter Kistler, Eidg. Dipl. Techn. Kaufmann, will head the newly-created Process Improvement unit, which will analyse internal processes in the ongoing drive to integrate operations and refine workflow. In addition to his duties as Chief Sales Officer, Dr Peter Schkoda has taken over the management of Corvaglia Closures Eschlikon AG. Other Board roles and responsibilities are unchanged. www.corvaglia.ch Cermex acquires Newtec Cermex, a subsidiary of the Tetra Laval group, has announced that it is to acquire Newtec Case Palletizing from the Newtec Group. Cermex says that the acquisition represents a continuation of its growth strategy and will help to consolidate its resources in case packing, shrink-wrapping and palletising. The acquisition will bring Newtec Case Palletizing’s plant in Saint-Laurent-sur-Sèvre in France, into Cermex operations, including its layer-by-layer and roboticunit load palletizing activity. Cermex operates in the food, beverage, home care, personal care and health care sectors; Newtec Case Palletizing is also established in the liquid dairy products segment. The enlarged company will have a turnover of €120 million and nearly 800 employees. www.cermex.com PE reaches out to the Maghreb P.E.Labellers has opened a new branch in Algeria, which is to be known as P.E. Maghreb. It will be dedicated exclusively to the Maghreb – NW Africa, including Algeria, Morocco and Tunisia – which relies on locallyproduced labeling machines. The company’s objective is to provide effective after-sales service, technical support and spare parts production and supply. www.pelabellers.com www.pemaghreb.com Alpla and Sidel win 900 million bottle contract Alpla will be supplying 900 million empty bottles per year for the next eight years to ArcaContinental, the second-largest Coca-Cola bottler in Latin America. ALPLA turned to its long-term partner Sidel to acquire equipment and technical expertise. The bottles are produced on eleven SBO Universal2eco blow-molding machines and 1,200 moulds. Alpla will join its trade partner in its facilities and produce most of the bottles inline.with the objective of reducing shipping operations and stocking costs, optimising delivery times and ensuring optimal bottle quality. Small volumes of bottles will be produced in an offline production hall that will also be designated for palletising. The SBO Universal2eco blow-moulders delivered to Alpla are equipped with six to 26 cavities and will produce up to 2,200bph, in sizes ranging from 250ml to 3l. Some of the machines are able to produce up to 21 different shapes and sizes. There are 1,200 moulds equipped with Kohlox, a system made of thermo composite material that helps parts move freely without lubrication, thus reducing machine downtimes. The order was placed with Sidel in August 2011 and all were delivered by February 2012. The new machines are due to be installed in six plants across Mexico and will start operations in the coming weeks. www.sidel.com","@ID":10} "TRADE SHOW REVIEW 34 PETplanet insider Vol. 13 No. 05/12 www.petpla.net PET-Line on the platform 3500 On the exhibition stand of the KraussMaffei Group, the Swiss manufacturer Netstal presented its established overall PET system PET-Line based on the platform with 3500kN clamping force able to employ moulds with 48 to 128 cavities. This PET preform system features several improvements such as the simplified product removal, aftercooling unit and the increased injection pressure to shorten the cycle time. The machine model on show at Chinaplas was equipped with a 128-cavity mould of Hofstetter AG from Switzerland. Material handling and dry air for the inside of the mould were supplied by Eisbär of Austria who have developed the Drypack system especially for the PETLINE. At Chinaplas customers and visitors were also given the opportunity of inspecting the production plant of the KraussMaffei Group in Haiyan. www.netstal.com PET preform system Established as recently as 2002, the injection moulding machinery company Yizumi can be considered as a rising star in line with Chinese Haitian and Chen Hsong Group. Even during the 2009 financial crisis, the company achieved 25% growth. In 2010 the company launched 48 & 72-cavity PET preform injection moulding systems, focusing strongly on machines for PET preform production. 2011 was a year of surprises, with sales increasing over 30% again in a general market downturn, and the acquisition of the the intellectual property of HPM, a 135-year-old US company. This marks an important step in the company’s globalisation efforts. Currently, the company produces in two factories in China, while a third is under construction. 87% of the machines are small to medium size, while 65% are servo machines. Yizumi has dedicated PET injection moulding machines and at the exhibition the company showed its PET-72A PET preform system with 72 cavity mould to produce 500ml water bottles (weight: 17.8g, size of bottle mouth: 3025) with a capacity of 518,400 preforms per day. The system was also equipped with a servo-driven robot. The mould was supplied by Chengdu Lianyu Mold Co., Ltd. It is claimed that by using servo pumps and insulation jackets, energy savings of 20-30% can be achieved compared to conventional hydraulic machines. In general, this company puts a strong focus on PET preform applications, and their newest brochure (currently available only in Chinese language) does already mention PET-96A and PET-144 preform systems. www.yizumi-group.com.hk One-step solution for two-stage PET preform moulding The ChenPET of Chen Hsong can be described as a one-step process for two-stage PET preform moulding production. This system integrates an injection moulding machine, hot runner mould, robotic take-out plate and pin conveyor, all controlled by a single master control supplied by Austrian company B&R. Currently systems from four to 72 cavities are available to produce up to 16,000 PET preforms/h. The CP-H93 at the show featured a productivity of 18,000 PET preforms/h with a 48 cavity (15g, 9.6s cycle time) and 23,000 preforms/h also with 48 cavity (12.5g, 7-8s cycle time). It is further claimed that the extruder screw design can reduce the acetaldehyde content of the PET preforms.The company also ran its Supermaster series of all-electric machine driven entirely by electric servo motors from Beckhoff. The patented non-linear injection system allows a combination of high speed, high pressure and long holding period. The company states that this machine can save up to 80% electric energy and up to 90% cooling water. The SM 160P on the show featured a high injection speed of 280mm/s (very suitable for thin parts) and high holding pressure of 120s at 1,500bar. Due to the use of the servo drives, a high injector positional control accuracy of up to 0.01mm can be achieved. www.chenhsong.com.hk Compression technology & stretch blow moulding CCM, which stands for “continuous compression moulding”, is currently still one of the most efficient cap production systems. The top of the CCM range is the CCM 48SB, which was showcased at the recent trade fair and capable of output rates of up to 1600 caps per minute with 48 cavities. The press was equipped with a mould suitable for the production of three types of HDPE S29W cap, 29mm in diameter and weighing just 1.25g. This very compact press was shown together with the CVS on-line cap quality control inspection system, developed by Sacmi’s Automation & Inspection System Division. Also an innovative CHS, a stand-alone machine with three video cameras for complete quality control of both the cap interior and exterior was presented. Sacmi is hoping to expand its product portfolio from caps to bottles. For example, the company now also offers blow-moulding machines with six to 24 blow moulding stations, able to produce more than 64,000bph in the standard half-litre format. A distinguishing feature of the Sacmi SBF machines is that there is the possibility to install a mould with one cavity for a large bottle (up to 3l) or with two for a small one (up to 600 ml) on each machine of the range. In this way, it is possible to process more than 2,700 small bottles per hour per station. The Sacmi SBF machine has also been designed to be integrated upstream of the company’s compression preform production system. www.sacmi.it","@ID":36} "PETbottles 40 PETplanet insider Vol. 13 No. 05/12 www.petpla.net Beverages Chilli sauce in PET The German company Kreyenhop & Kluge based in Oyten imports and sells 200 ml Thai Sriracha – hot chilli sauce in a direct print, transparent PET bottle with a green dispensing cap. On removal of the transparent protective cap, one output channel is released by turning the cap parts and the product is dispensed by the application of pressure to the side walls. www.kreyenhop.com Already a classic A classic among PET bottles is the hand-washing agent from Switzerland. The product, which is marketed through Migros, is presented in an orange, waisted PET bottle with a content of 750ml. A white screw cap with a coloured push/pull rounds off this iconic bottle. Commercial information and safety information are printed directly on the bottle. www.migros.ch 3-stage sports drink An optimally adjusted supply of nutrients is the promise made by albi GmbH with their 3-stage sports drink Enerjuice. The three drinks are specially designed to cater for the requirements of the athlete before, during and after exercise. Various combinations of juices and additives support the functionality of the drinks. “Enerjuice“ is sold in PET bottles each containing 500ml and featuring a belly label with a carbon fibre look. The surface of the bottle is rough in texture and fitted with stabilising grooves. A tamper-proof screw cap with a broad diameter makes it easier to drink straight out of the bottle. www.albi.de Premium juice Under the brand name “innocent“, the company of the same name from England markets carefully processed, unsweetened fruit juices in attractivelyshaped PET bottles each containing 900ml. The bottle, made from a minimum of 25% recycled PET, has an embossed brand logo. The label field is also visually offset by means of grooving. A paper label and a tamperproof screw closure round off the profile of this “ecologically correct“ product. www.innocent-international.com Italian iced tea San Benedetto S.p.A. of Scorze in Italy is marketing 500ml iced tea with fruit flavouring in a waisted, transparent PET bottle with a textured surface. A plastic label running round the bottle conveys the commercial information and a screw cap corresponding to the product variant – yellow for lemon, orange for peach – and complete with tamperevident band takes care of re-closure. www.sanbenedetto.it Home-grown fruits Eckes-Granini from Nieder-Olm, Germany, is continually expanding its Hohes C brand name with the addition of new flavours. One example of this is their “Home-grown Fruits“ – here apple and blackcurrant – in a no-deposit, 1-litre content PET bottle in the colours typical of the brand. There are three “Vitamin C guarantee” stamps incorporated in the neck of the bottle. A gold-coloured, tamper-evident screw cap and a paper level round off the appearance. www.hohes-C.de Tamper-proof tea 500ml black tea drink that you can drink either ice-cold as ice tea or also as a hot drink is being marketed by Refresco Deutschland GmbH in a teacoloured PET bottle with an opaque re-closable screw cap. “Arizona“ brand teas are available in different flavours, each of which is decorated with a sleeve label corresponding to the taste. The sleeve label which is pulled over the cap acts, in addition to the guarantee strip, as a second tamper-proof guarantee. www.drinkarizona.com","@ID":42} "TRADE SHOW REVIEW 28 PETplanet insider Vol. 13 No. 05/12 www.petpla.net Sipa meets the new preform system Prosecco Reception Prosecco reception with Gianfranco Zoppas (right), Enrico Gribaudo (left) and Alexander Büchler (centre) in front of the XForm It was at the NPE that the Chairman of Sipa, Gianfranco Zoppas, Sipa Corporate General Manager Enrico Gribaudo, and Alexander Büchler met up to celebrate the launch of XForm, the new preform system. Sipa’s intention is to shake up the market with this and to achieve the Number 2 spot in the preform equipment market within a short space of time. Their intention is backed up by a system that is both robust and fast. We have previously reported on the technical details in issue 3. At the Fair the Italians were showing a lightweight preform with a thickness of less than 0.8mm in the neck finish area. What this actually means is less than 1.8mm in the body area. They were showing this preform – which is difficult to inject – at the Fair within a production environment rather than under laboratory conditions. “Our intent is to demonstrate that the machine itself is capable of mastering difficult preforms of this nature without any problems”, says Gianfranco Zoppas. The equipment at the NPE Show concealed its power in its deceptively quiet operation. The mould closing movements could hardly be heard on the exhibition floor space. Production speed was very fast, with a cycle time below 6s. The visual impression of its power comes from the increased tie bar clearances of 1,050mm. This makes tool changes considerably easier. The job needs to be completed within three hours, says Gribaudo. The post-mould cooling unit has double the number of aftercooling stations as is the case with other suppliers. Instead of the usual three, Sipa manages, by rotating the take-out plate, to leave the preform in the robot arm for aftercooling for the equivalent of six cycles. This helps enormously in the case of the thick-walled preforms. The new XForm has a very robust mould design and is the first system in the market with mould life warranty. One of the major advantages of the XForm is the flexibility: it accepts the mostly used moulds (old and new generation) present in the market. The equipment can also cope with the processing of PET flakes, a process which is increasingly in demand. For instance, it can process 50% flakes with a reduction of only 10% in plastification capacity. Sipa stated that the interest raised by the presentation of the new preform system went beyond all expectations, while the feedback from all leading players has been excellent. A new 10,000m² building has been added to actual Sipa facilities dedicated to the production of the new XForm. Sipa was also exhibiting their new SFL WM for stretch blow moulding of wide mouth containers. “The wide mouth sector is experiencing above-average growth” says Gribaudo and he continues: ”More and more applications are migrating from glass to PET”. So logically speaking, simply re-tooling a normal linear system to wide mouth was a far from simple matter. Sipa have, with SFL WM, now launched an independent machine on the market. 130mm containers with, for example, four cavities, will go through the system. The system is primarily designed for converters who need to produce a number of different designs. “The 2-stage process is very well suited to flexible production; for large quantities and single-size formats we recommend the single stage solution”, is Gribaudo’s mission statement. As a sole supplier, he is happy that he is able to offer the customer single-stage as well as dual-stage, depending on the needs. www.sipa.it","@ID":30} "TRADE SHOW REVIEW 31 PETplanet insider Vol. 13 No. 05/12 www.petpla.net Lasersafe marking pigment has no heavy metals Eckart, part of Altana Group, describes its Lasersafe product as a new generation of laser marking additives based on heavy metal-free pigments, which it says makes them suitable for today’s eco-sensitive markets. It is able to produce high-contrast laser marking at high speed and with high quality. It claims that distinct clear types for uses including bar codes, UID or 2D can be achieved and that the durable markings produced by contactfree writing can be used for decoration, customisation, coding, part identification and traceability. It is suitable for laser marking with all standard lamp technology, such as the Nd:YAG laser system operating at 1,064nm. Eckart presented Lasersafe as an alternative to conventional products based on antimony oxide. www.eckart.net Americhem improves PCR for PET US-based Americhem, a global masterbatch and colour concentrate manufacturer, has added a PCR renewal additive for PET to its range, which it claims offers a number of advantages over existing PCR additives. The company says that it masks the yellowness typically associated with high use rates of PCR and improves ‘L-value’ and maintains clarity, without darkening. It does not increase haze and thus allows higher use levels in the final product. It comes in the form of cylindrical pellets, has a melting point in excess of 220OC and has a use rate of 0.2-1.0%, depending on the application. The new product is suitable for multiple applications, with both FDA and nonFDA versions available. americhem.com kronesFlexiFruit – doses fruit chunks as if they’re hand-picked. www.krones.com ProPak Asia 2012 Bangkok, 13 – 16 June Stand F1","@ID":33} "PETnews 6 PETplanet insider Vol. 13 No. 05/12 www.petpla.net Appe invests in Intravis automated inspection Appe, the packaging division of LSB, has invested €1.5m to develop and install Sample-PreWatcher technology from Intravis GmbH for the automatic inspection of the key quality parameters of preforms. The system has been deployed across all of Appe’s plant. The technology was developed by Intravis along with input from Appe’s pan-European quality team. The companies say that the system replaces manual inspection with an automated, rapid and in-depth analysis of preforms. Sample-PreWatcher carries out a complete visual inspection, colour analysis, cavity number recognition and neck dimension examination. The technology has been further developed to include weight control, thread-flash analysis and wall thickness variation. Other Intravis systems already used by Appe include a ColourWatcher system for preform colour consistency; PreWatcher for high-speed preform selection, and BottleWatcher for container inspection. www.appepackaging.com Danone Research and Avantium to develop PEF bottles for water Danone Research and Avantium have entered into a Joint Development Agreement for the development of PEF bottles for Danone, which is the world’s second-largest bottled water supplier. The agreement is the second in Avantium’s commercialisation strategy for co-development of its YXY (‘icksy’) technology for PEF bottles, which use bio-sourced material. YXY is a chemical-catalytic technology that converts carbohydrates produced from plants, grains, energy crops, lignocellulosic matter, waste streams, waste paper or agricultural residues into a variety of bio-based polymers. Aventium asserts that it does not compete with food supplies. The company says that a recent study by the Copernicus Institute at Utrecht University found that PEF has a 50-60% lower carbon footprint than oil-based PET. Finalizing the study is part of the Joint Development Agreement. Avantium is currently validating the use of existing supply and recycling chains with the aim of enabling a full transition to bio-based PEF bottles in three to five years. Avantium recently opened a pilot plant in Geleen, the Netherlands, with the capacity of producing 40t of PEF for application development. www.avantium.com www.yxy.com La Seda announces €40 million rights issue and corporate reorganisation In 2011 La Seda de Barcelona (LSB) successfully achieved refinancing of debt with its banks and redefined its core business by focusing on the plastic packaging sector. Consolidated turnover for financial year 2011 amounted to €1,172.4 million, which represents an increase of 17.6% over the previous year. All businesses within the Group made a positive contribution to its figures. EBITDA was €57.8 million, 15.9% less than 2010, and it reduced net consolidated debt by 42%, to €49.6 million. LSB has now announced a growth strategy for 2012, which includes a proposed €40 million rights issue to current shareholders. The strategic plan is intended to enable the plastic packaging division (Appe) to expand into new markets and focus on new materials and products. The company plans to create a new company that will integrate all the chemical businesses of the Group (PTA, glycol, PET, chemical PET recycling and technology) and facilitate the involvement of an industrial partner. The new division will have PET production plants in Spain, Italy, Turkey and Greece; raw materials (Glycol) in Spain and in Portugal (PTA), as well as recycling plants in Spain and Italy. Future projects under consideration include a 400,000t PET production plant in Sines, Portugal, as well as a new Appe production facility in Poland. It also intends to build a new production facility in Italy and to increase the number of its TTW (‘through the wall’) service locations. Recycled PET production will be promoted in Italy (San Giorgio) and in Spain (El Prat), by the launch of Elite, a new product that is claimed to offer an equivalent quality to 100% virgin PET, with varying percentages of rPET. www.laseda.es Kortec moves house Kortec Inc., the supplier of turnkey co-injection systems, is moving its headquarters to a new location in Rowley, Mass, USA. The new headquarters, 3.5 miles (5.6km) north of its previous location in Ipswich, Mass, is 30% larger and will have additional capacity to accommodate engineering, mould assembly, and research and development activities. Effective May 7, 2012, the company’s address is: Kortec, Inc., 428 Newburyport Turnpike, Rowley, MA 01969. www.kortec.com","@ID":8} "MARKET SURVEY 26 PETplanet insider Vol. 13 No. 05/12 www.petpla.net One trade platform powered by drinktechnology-india.com drink technology India 2012 Your gateway to India’s future Supported by Forum organizer PackTech India 2012 Exhibition and Conference for Processes, Packaging and Printing www.packtech-india.com 7th International Supported by Sponsors and Conference Organizers Organized by The “who’s who” of two industries Contact drink technology India Messe München GmbH info@drinktechnology-india.com www.drinktechnology-india.com Phone+49 89 949-20114 Fax+49 89 949-20128 Contact International PackTech India Messe Düsseldorf GmbH info@messe-duesseldorf.de www.messe-duesseldorf.de Phone+49 211 45 60-7739 /-7741 Fax+49 211 45 60 -7739 /-7741 November 6–8, 2012 Bombay Convention and Exhibition Center Mumbai/India SBM Moulds Company name Moldintec SRL Kiefer Werkzeugbau GmbH KHS Corpoplast GmbH P.E.T. Engineering Srl Postal address Telephone number Web site address Contact name Function Direct telephone number Fax E-Mail Lamadrid 501 - Los Troncos Del Talar - Tigre - Buenos Aires - Argentina +54 11 6632 9999 www.moldintec.com.ar D.I. Jorge Pucci Commercial Director +54 911 4146 9894 jorgepucci@moldintec.com.ar Steinhäldenstraße 11, D-74193 Schwaigern, Germany +49-7138-9732-0 www.kiefer-mold.de Jörn Herget Project Manager +49 7138-9732-70 +49 7138-9732-90 joern.herget@kiefer-mold.de Meiendorfer Str. 203, 22145 Hamburg, Germany +49 40 67907 110 www.corpoplast.com; www.khs.com Arne Wiese Product Manager Bottles & Shapes +49 40 67907 113 +49 40 67907 9113 arne.wiese@khs.com Via Celtica 26/28 San Vendemiano Treviso Italy +39 0438 403069 www.petengineering.com Elisa Zanellato Marketing & Communications Manager +39 0438 403069 +39 0438 408420 e.zanellato@petengineering.com Stretch blow moulds Bottle size (max.) (in litres) 20l 10l 3l 10l Moulds supplied directly to blowing machine manufacturers Yes No, we are an independent mould maker All Corpoplast stretch blow moulding machines Yes Do you supply retrofit moulds for existing SBM machines? Yes No All Corpoplast machines, others on request Yes For which bottle makes have you already produced moulds Coca-Cola, Pepsico, Danone, Nestlé, Sacmi Coca-Cola, Pepsi, discounter, Henkel, Heineken, etc. Nestlé Waters, PepsiCo, InBev, Ferrero, Carlsberg, Efes Bottle design service Yes Yes Yes. Design matched to industrialization. Specialities CSD low pressure blow molding Lightweight design, special design for functional drinks, juices and household products Technical & marketing driven bottle optimisation, especially weight reduction with lab proven samples Neck finish conversion, upgrading of existing old blowing machines (Polaris Project), moulds Restyling (I.S.O.S.)","@ID":28} "PETproducts 36 PETplanet insider Vol. 13 No. 05/12 www.petpla.net ‘Natural colour’ rainbow Doehler has extended its portfolio of natural colours with the introduction of the Red Brilliance range. The colouring concentrates are produced from the black carrot in company’s plant in Akkent, Turkey, in keeping with its focus on the increasing demand for colours from natural sources. Its full range extends from “warm orange” to “shining ruby” hues, and on to shades of blues. All colours meet the requirements of Clean Labelling and can be used in a variety of food and beverage applications. The company says that both colour and ‘naturalness’ have important roles in the purchasing decision. The challenge for natural colours is the achievement of consistent quality, stability and long-term availability. Doehler says that it has been able to optimise the physical processing of the black carrot. The colouring concentrates gained from this processing are claimed to be superior to other colours containing anthocyanin, in terms of stability and cost-in-use. The colour concentrates are free of sulphur dioxide. The company has signed a number of agreements covering the cultivation of the carrot in Turkey, in order to secure access to consistent qualities and control of the entire value chain. www.doehler.com Injection blow moulding for developing markets The new Model 20 injection blow-moulding machine from Jomar Corporation, of New Jersey, USA, has been designed as a relatively lowcost machine and is aimed particularly at developing markets. The Model 20 is the smallest in the Jomar line but the company says that it can deliver high-quality bottles in large quantities. It has the capacity to produce 15 million 30ml eye-dropper bottles annually, assuming 6,000 operational h/a. Alternatively, short runs of two million bottles could be produced from a single mould in the same period or less. Jomar manufactures injection blow-moulding machinery for the pharmaceutical, health care, personal care, beauty, food, beverage and household products markets, with capacities ranging from 20 to 175t. www.jomarcorp.com","@ID":38} "Editour reports 11 PETplanet insider Vol. 13 No. 05/12 www.petpla.net Köksan PET Packaging Industry We met: Mr Murat Kökoglu, Member of the Board An affair of rapid growth With 17 preform lines and six closure lines, Köksan is one of the largest converters in Turkey as well as further afield. The rise from the first preform in 2004 up to an annual capacity of just under 100,000t of PET/a has been a rapid affair. This article sets out to track developments over the last five years in this company which is just coming up to its centenary. The initial situation was not particularly auspicious. The last occasion we visited Köksan (which was five years ago) it was just one preform manufacturer among a host of others in Turkey. Its head office and preform production centre were located at some distance from one another. Gaziantep, with a population of nearly one million, is situated in the remote South-East of Turkey, and is an important industrial centre. And the fact that Köksan’s product portfolio tends to be made up of standard commodities makes the company vulnerable to global competitive forces in the preforms sector. The company’s success cannot be ascribed to its favourable pricing structure because, had that been the case, Köksan would not have been consistently able to invest and re-invest in the expansion of its lines. So what is the secret of its success? This was the question we put to Murat Kökoglu, who is currently the 3rd generation of his family to manage the company. “We love our work, I don’t just go to work in the mornings, I actually run“ is how he sums up his enthusiasm for the company. This get-up-andgo attitude is infectious and acts as an inspiration to the other employees. Ali Ihsan Muhittinglu, Area Sales Manager confirms this: “We are a young team and look forward to the new challenges that each day brings“. And these challenges are legion. And these challenges were legion. The company had formerly run an operation bottling pickles in jars and graduated to PET via this route. The initial challenge as far as they were concerned came in 2006 with the decision to relocate their preform business, which had been established in Gaziantep only two years previously, to the main company site. Murat’s father told us five years ago that they ”needed one or two extra machines per year“. This has instead turned out to be two to three lines per year. There are currently 15 Netstal and 2 Husky lines which are supplied with PET from Piovan lines and the preforms are inspected by the IMD lines. The cap business represents a relatively recent development. It is Köksan’s intention, using the brand name Eurocap, to supply the industry with single serve bottles, but also 1.5l and 5 gallon bottles, together with CSD and edible oil caps. The cap lines in Gaziantep have been focusing on these. They now have a production capacity of 4 billion caps p/a on six lines - two Netstal and four Husky. Along with these are Forstag tools and Corvaglia closures for which Köksan has exclusive marketing rights in Turkey. The switch to lightweight water bottles and closures was successfully carried out in just a few months, almost all water customers are now going for the lightweight option. The next project is the lightweight 1881 neck finish. Here Köksan are planning to enter the market during the coming year. “50% of our products are sold in Turkey and the remaining 50% abroad. We get a number of enquiries relating to the 1881 from beyond our national borders. And if we produce the preform and closure with 1881 neck – here at our premises in Turkey it won’t be long before we find our local customers asking for it too“ is the strategy that Köksan is pursuing. The most ambitious project on which the Kökoglu family is now embarking is their own polymerisation plant with an annual capacity of 432,000t. The first half is due to go into production at the end of 2012 and the foundations are currently being laid. The plant will be sited directly adjacent to the preform hall. “Production of the 216,000t of PET will make Turkey independent of PET imports which means that it is not only good for us, it’s also good for the Turkish national economy“ explains Murat. And, by the time the second section of the plant commences operations in 2015, the Turkish market should have developed sufficiently to cope with it. This perhaps amounts to crystal ball gazing and identifying definite strategies will play just as great a part in achieving success as the enthusiasm described at the beginning of this article. www.koksan.com A new era for Köksan with the PET polymerisation plant. Murat Kökoglu in front of the foundations of the new facility. The company name cast in stone, solid enough for the 4th and 5th generation.","@ID":13} "Editour rEports 10 PETplanet insider Vol. 13 No. 05/12 www.petpla.net Turkey Part 2 The second part of our report on Turkey takes us to two of the major preform suppliers of the Turkish market: Sunpet and Köksan, both located in Gaziantep. And no report on the Turkish beverage market would be complete without visiting the Coca Cola Icecek head office in Istanbul. CCI has eight plants throughout Turkey. Due to time constraints we were not able to make time for the interviews with Sunpet and CCI during our Go to Brau Beviale tour. We rescheduled the meeting with CCI in Istanbul by beginning of 2012 and with Hakan Cinkilic of Sunpet at his stand at the NPE in Orlando. A market opens up Nuremberg Ljubljana Saedinenie Istanbul Baku Beograd Novi Sad Subotica Cegled Dulo Selo Mirna Peˇc Radenci Gorica Svetojansk Plovdiv Gaziantep Ingöl Ploiesti Ankara","@ID":12} "TRADE SHOW REVIEW 35 PETplanet insider Vol. 13 No. 05/12 www.petpla.net Recycling line recoSTAR PET iV+ Ongoing PET recycling innovation, quality and state-of-the-art technology, a full range of consulting services – brought to you by Starlinger. Visit us at: Starlinger recycling technology Open House, June 18-19 2012 Starlinger Factory 2, Furtherstrasse 47, 2564 Weissenbach, Austria 6WDUOLQJHU +HDG 2IßFH 6RQQHQXKUJDVVH 9LHQQD $XVWULD _ 7 ) UHF\\FOLQJ#VWDUOLQJHU FRP ZZZ UHF\\FOLQJ VWDUOLQJHU FRP _ $ PHPEHU RI 6WDUOLQJHU *URXS Blow moulding machine for 20l PET container Another company dedicated to PET is the Chinese company ZQ Machinery. Founded some 23 years ago, the machine supplier offers a wide range of rotary PET-stretch blow moulding machines to produce various containers, such as bottles for mineral water, carbonated drink, juice, milk, tea, edible oil, sauces, detergent, candy, and medicine bottles. The company claims to have delivered more approx. 200 rotary PET blowing machines to about 180 customers from 36 countries around the world. At the exhibition the company displayed an automatic blow moulding machine for the production of 20l PET container (2 cavities, 600-800pcs/h). www.cnziqiang.com Injection moulded closure system The Husky HyCap HPP 300 produced a 1.2g 29/25 lightweight water closure at a 1.85s cycle using a 72-cavity KTW beverage closure mould. Husky’s next generation HyCap system was running a 26/22 application at NPE earlier in the month at a 2.2s cycle. HyCap HPP incorporates a number of features that focus on improving ease-of-use. Its SmartStart and SmartStop features provide faster and easier startup and shutdown, and with the latest generation of Polaris Control, enabling a greater degree of fine tuning, particularly benefiting faster cycling lightweight applications. The new system also features a single interface for central control of the entire system, including hot runner temperature control and auxiliary equipment. In addition, Husky demonstrated its H-PET AE (allelectric) injection moulding system for PET preform manufacturing, a complete,solution for lower volume preform production. The company also showed its new Ultra SideGate and UltraSync-E hot runners. Ultra SideGate provides an alternative for direct gating parts that cannot be effectively gated with a regular nozzle. UltraSync-E offers shot-to-shot and part-to-part consistency through precise stem closing to help eliminate variability from the injection moulding process. www.husky.ca High-speed cap printer The Italian company Moss has showcased what it claims is the world fastest printing machine for bottle cap decoration. MO 2062 is a rotary dry-offset printer which is potentially capable of reaching a production output of more than 300,000 caps/h. The machine can also be upgraded to up to 4 colours or can be equipped with Pre-Print, a colour unit for the application of a white background. The Mo 2062 can be described as decoration “in continuous motion” without alternate movements. This is possible due to a large central drum with capholders which works with a mechanical synchronism with the printing head. The system features magnetic plate-holding cylinders, central printing roller with ceramic coating and a rotary drum with integrated vacuum for cap-holders. All machine and accessory functions are controlled by a PLC with digital Bus Field control system. www.moss.it","@ID":37} "MARKET SURVEY 24 PETplanet insider Vol. 13 No. 05/12 www.petpla.net SBM Moulds Prefom Mould & SBM Moulds Company name Solent Mould Tools Ltd Sacmi RD/Leverage Petka Mold Industry Postal address Telephone number Web site address Contact name Survey Function Direct telephone number Fax E-Mail 1 Relay Road, Waterlooville, Hampshire, PO7 7XA United Kingdom. +44 023 9223 9950 www.solentmouldtools.co.uk Chris Smith Technical Sales & Service Manager +44 023 9223 9950 +44 023 9223 9951 chris.smith@solentmouldtools.co.uk Via Selice Provinciale 17/a 40026 Imola (Bo) Italy +39 0542 607111 www.sacmi.com Moraldo Masi Business Manager PET Division +39 0542 607888 moraldo.masi@sacmi.it Leverage House, Hamilton Road, Sutton in Ashfield, Nottinghamshire, UK +44 1623 556287 www.rdleverage.com Damon Sykes Sales Manager Direct telephone number +44 1623 552240 dykes@rdleverage.com Yeşiloba Mah.46075 Sok. No 8 Seyhan/Adana/Turkey +90 3224286400 www.petkamold.com Tarık Sivri General Manager +90 532 5248990 +90 3224282303 info@petkamold.com Stretch blow moulds Bottle size (max.) (in litres) 5l 3l 10l 19l Moulds supplied directly to blowing machine manufacturers Yes Yes Yes Do you supply retrofit moulds for existing SBM machines? Yes Yes Yes Yes For which bottle makes have you already produced moulds Sidel, Krones, KHS, Kosme, Siapi, Sipa, ADS, Nissei & Aoki Sidel, Krupp/Sig, Krones, SMI, Sipa, Mag, Siapi, Side, Kosme, Cincinnati, Chumpower Sidel, Krones, Siapi, Sipa, Kosme, ADS, SMI, Krupp, MAG, Bottle design service Yes Yes Yes Yes Specialities In feed / out feed change parts. Bottle esign after sales technical support . Flat and carbonated water, CSD, edible oil Supply of bottle prototype Preform moulds Horizontal opening Yes Yes Number of cavities 2 - 96 cavity Up to 72 Up to 96 From 2 to 96 Preform sizes Up to 450g Length up to 195mm 10g - 150g 14mm -110 mm neck finish Moulds already built for (makes) Husky, Nestal, Cincinnati, BM Biraghi, Engel, Krupp, Toyo Husky, Netstal, Krauss Maffei, Sipa Vertical opening Yes Yes Number of cavities 32 - 48 96 Preform sizes Pitch 50*130 Moulds already built for (makes) Do you produce single stage tooling sets? (Preform moulds AND blow moulds) Yes No Yes, for food, beverage, toiletries, household, pharmaceutical, healthcare and cosmetic industries. Yes Other Post mould cooling EOAT Company name Technopet Beaubury Precision Moulds Ltd. Comep S.A Postal address Telephone number Web site address Contact name Function Direct telephone number Fax E-Mail 15, Naman Plaza, S.V. Road, Kandiwali West, Mumbai 67, India 91 22 861 0828/ +91 9821040637 www.techno-pet.com Vineet Bannore Director +91 9820346565 +91 22 27453261 sales@techno-pet.com Telford Close, Rabans Lane Ind. Est. Aylesbury, Bucks. HP19 8DS UK +44 (0)1296 43 43 11 www.beaubury.co.uk Mark Sim Technical Sales Manager +44 (0)1296 43 43 11 +44 (0)1296 43 32 76 marksim.uk@gmail.com Z.A.E du Pont Neuf 16 130 Salles d'Angles (France) +33 5 45 36 63 50 www.sa-comep.fr Christophe Amarant Director +33 5 45 36 63 50 +33 5 45 32 08 08 christophe.amarant@sa-comep.fr Stretch blow moulds Bottle size (max.) (in litres) From 30ml to 20l and from 1 cavity to 6 cavities. 5l 30l Moulds supplied directly to blowing machine manufacturers Special purpose mould along with SBM machine directly to end user as a project. Yes We supply not only blowing machine manufacturers but also bottle fillers. Do you supply retrofit moulds for existing SBM machines? Yes Yes, moulds and perso parts, repairs and refurbishments Yes For which bottle makes have you already produced moulds Hot fill juices, natural water, cosmetic products for leading brands and beer bottle for Reliance Industries. Sidel, KHS, Aoki, Nissei, Side, ADS Nestlé, Danone, Coca-Cola, Orangina, Pepsi, Unilever, ColgatePalmolive,Roxane,… Bottle design service Transforming the new concept of PET container through PET engineering by providing design validation and simulatation services Yes Design, shape developments, prototyping, sample blowing, tests, serial moulds, setting up,process adjustments, repairing, spare parts and perso parts Specialities Iso-thermo crystallisation mould design for Hot and combo fill bottles. Duplex type mould for non concentric shape: Integrated handle mould design for edible oil container, non returnable 5 gallan jar mould. In mould handle place design. Bottle development, pilot and production mould manufacture with full perso parts package 05/2012 MARKETsurvey","@ID":26} "CAPPING / CLOSURES 21 PETplanet insider Vol. 13 No. 05/12 www.petpla.net there are thousands of manufacturers in the market. PETplanet: But now you are avoiding the question. For the Corvaglia Group, will you be able to keep your own head above water bearing in mind the alliances and acquisitions by the major machine manufacturers in the caps and closures sector? Corvaglia: We think of ourselves as closure specialists, rather than mould manufacturers. We also enjoy major success in operating our own production locations for closures. As regards the project business mentioned, I think that the machine manufacturers tend to take a superficial view and only see the actual production of the caps and not the subsequent stages. Our approach is different. We consider the production of the caps only as a part of the whole process. We have now been involved in this business for over 20 years and many times we have set benchmarks in this sector. PETplanet: What were for you these benchmarks as regards the overall concept? Corvaglia: Way back in 2003 we were undertaking initial trials with short necks for carbonated drinks, long before ISBT developed the 1881. As regards the optimisation of bottle neck standards it is us, I believe, who have laid the foundation stone for global change. Our last benchmark for non-carbonated water closures we set with the CSN-26 and a customer specific solution in the North American market. These closures are still undisputed overall concepts, not only as regards their weight but also in terms of their performance. PETplanet: It was something like less than 1g? Corvaglia: First of all it was 0.99, then 0.9 and now it’s 0.82g. These are the overall concepts I was talking about. PETplanet: At the NPE in Orlando we were viewing closure caps equipment from three manufacturers at the same time. And each one of them laid claim to having the fastest piece of kit. Which one of them is, in your opinion, the best injection moulding machine for a cap mould? Corvaglia: First of all we need to acknowledge that the injection moulding machine manufacturers and injection mould manufacturers have achieved a lot in the past years and that a handful to be continued on page 27","@ID":23} "PETbottles 38 PETplanet insider Vol. 13 No. 05/12 www.petpla.net Personal Care Gesellschaft Wärme Kältetechnik mbH Friedrich-Ebert-Str. 306 · D-58566 Kierspe Tel. +49 2359 665-0 · www.gwk.com Perfect cooling and temperature control You will feel better having made the right decision. Reduce your energy consumption. System solutions Mould inserts Temperature control technology Water treatment Cooling technology Tailor made solutions Temperature controllers Chillers Energy saving cooling systems Pantene Pro-V in new PET bottle Procter & Gamble took advantage of the opportunity presented by the re-alignment of the Pantene Pro-V hair care product range to revise the packaging. One example of the new design is the shampoo which cares for and strengthens fine hair. The transparent PET bottle, which is flattened at the sides and has a content of 250ml, has a non-label-look label at the front and a paper label at the rear which gives the commercial information. A snap-on, translucent hinged lid in PP with an opening segment coloured black makes it easier to open the pack. www.pantene.de Pictures on the inside Garnier’s revitalising shampoo “Olive Oil and Lemon“ comes with a promise of deep nourishment and silky shine and is marketed in a slightly tinted PET bottle with snap-on hinged lid. For ease of opening, the transparent cap features ribbing in a “leaf design”. The 300ml bottle sports a nonlabel-look at the front as decoration whereas the back incorporates the commercial information on the outside and is printed with an image showing an “olive branch with a lemon” on the inside. www.garnier.de Acid in PET The Italian company DAC S.p.A. is marketing 1l of 10% hydrochloric acid, under the Dedi brand name, in a PET bottle with a convenient, easy-to-handle shape and featuring a reinforced grip area. The bottle, which is manufactured from recycled PET, has a greenish tint. A recessed handle facilitates safe handling of the bottle and product. The bottle, which is secured by means of a tamper-proof strip, is fitted with a two-colour turn and push safety cap. The commercial information is conveyed by means of an all-round plastic label. www.gsgnet.it","@ID":40} "CAPPING / CLOSURES 27 PETplanet insider Vol. 13 No. 05/12 www.petpla.net of them today measure up very well to the compression system manufacturers. In the compression world, in fact we talk only about Sacmi today since the only competitor in Switzerland has withdrawn the product line from the market and the other one does not sell to third parties. In the past it was compression moulding that pitched the cycle times and the injection industry had long been chipping away at them. Looking at things from this angle, ‘THE’ closure production system probably does not exist today. There are certainly four to five injection machine builders who stand out conspicuously from the rest. Among these 5 top suppliers, good on-site service is an absolutely essential factor but this varies from region to region. Nevertheless, an integrated concept and a sense of responsibility are lacking as far as the majority of suppliers are concerned and therefore many such projects tend to fail. PETplanet: Who are the manufacturers, and what are the machines that Corvaglia use? Corvaglia: In the past we ourselves only used Husky and Netstal machines and we were looking at Engel for the next investment. Since Husky swallowed up our competitor KTW, and Engel signed a joint venture with Plastisud in China, thus becoming itself our competitors, we have had to look for alternatives. Here at our headquarters in Switzerland we have added to our stock of machinery some new Elion machines from Netstal. At our plant in Mexico we have chosen BMB from Italy because there are already 160 of their injection moulding machines in Mexico and the service is good there. However, in many countries this also applies to Netstal, Husky, Sumitomo and Engel. Nothing puts more pressure on the machine availability than inadequate service facilities, regardless of how fast it is. PETplanet: Many machinery manufacturers seem to have the closures sector in their sights. Why do you think this is? Surely the market is well catered for at present? Corvaglia: Good question. The best thing you can do is to ask the machine manufacturers themselves. As you said, by comparison to the preform, the market is considerably smaller in size. One mould for caps will produce about two to four times as many caps as a preform mould; this means that the market size for cap machines is only half and it will be split again when you consider that more than half of the soft drink closures still come in two parts and, purely because of this, are manufactured on compression equipment. This means that the market for closure equipment using injection moulding techniques may well be around a quarter the size of the preform machine business. As indicated above, you need to keep the overall life cycle of the cap in view all the time; a closure system is more complex and challenging than a preform system. This is, for example, also demonstrated by the fact that you need around twice as many people in the back office to handle a closure project than you need for a preform system. PETplanet: Keyword here is market size. You were one of the first to sell a complete closures system to China in 1992; in the meantime other toolmakers are overtaking you in the largest beverage market in the world. Corvaglia: China is a highly specific topic. We were the first company to assume overall responsibility from the development phase right through to applying the closure on the bottle. With this (at that time) unique concept, selling equipment was an easy matter. Sacmi from Italy, coming from the liner compression moulding business, reacted well here and developed a fully integrated programme based on compression moulding. Their start as far as two component closures were concerned made it possible for them to service this market practically on their own for a good long time. PETplanet: How has the market in China developed over the years? Corvaglia:The market has made a rapid transition to single-piece closures and it was precisely this that had been our specialised area since the foundation of the company over 20 years ago. Coinciding with this switchover has been an increasing demand for injection moulding systems. The reason lies in the fact that, in the injection moulding process, the closures are all set to go into the box once they have been extracted from the mould and it is precisely this that makes the injection moulding process very efficient. In the compression process you have the advantage of more efficient manufacturing since there is no hot runner distributor needed, but you always face subsequent processes such as slitting and folding of the tamper evident band. In this second process it is practically impossible to avoid any dust developing. The leading injection moulding machine manufacturers who were anxious to acquire a share in this market through collaborating or acquiring mould makers have not only eroded the prices for superior and efficient overall concepts but have also combined the two disadvantages of injection and compression moulding in a new system. The reason is that they use the injection moulding process to manufacture the body section and then cut and fold the tamper-evident band in subsequent processes. In a compression moulding process the cap shell goes oriented to the next station. Doing the injection as a first step you have to handle the closure with additional robotics or use sorting units between the processes. All this only happens because these companies are viewing the production of closures through the eyes of a machine manufacturer with the specific aim of selling their material. PETplanet:What are the implications for your projects in the Chinese market? Corvaglia: As regards projects for major brand owners, where actual performance is a stipulation, we have carried on implementing projects, also in China. Because actual performance in China today does not really count for everybody, either on the plant or in the filling process, the price of the equipment is the top priority. This, in my view, is set to change in the next few years and then the status quo will once again be different for us in China. PETplanet: Many thanks! www.corvaglia.ch","@ID":29} "Vol.6 PETplanet print PREFORM PRODUCTION 16 PETplanet insider Vol. 13 No. 05/12 www.petpla.net Surface blemishes The rapid guide to perfect preforms - part 29 Troubleshooting guides have suffered in the past from being locked away in offices and not being available to the people that actually need them. Considering the high cost of machine and tools high scrap rates can be a costly proposition eating away at already tight margins. PETplanet’s “Rapid Guide to Perfect Preforms” takes a different approach. It has been written for the people on the floor of injection moulding companies to support their daily work in making the best preforms possible. The product of two industry experts, Rick Unterlander and Ottmar Brandau, it gives concrete advice on 35 of the most common problems in preform manufacture, most illustrated by pictures. From high AA levels to wavy bodies processors can find help when they need it. Read chapter 29 of the guide. Symptom Scratches, random smudges, and elliptical marks that appear on the outside surface of the preform. Best observed under a polarized light fixture. Cause Preforms get marked when they contact each other (and other items) during handling. This consists of all forms of handling including part ejection, conveyance, bulk collection, transportation of finished production, and unloading for Table of Contents i........................ About the Authors ii.................................Introduction chapter 1.............................. AA Level High 2........................ Accordion Preform 3....................... Air hooks / Streaks 4............................... Black Specks 5...................................... Bubbles 6..................................Burn Marks 7...........................Colour Streaking ................................... /Peeling 8..................................Crystallinity 9.................................Drool Marks 10.......................................... Flash 11......................... Gate Depressions 12............................... Gate Peeling 13..................Gate Voids / Pin Holes 14......................... Internal Gate Sink 15................................Internal Sinks 16........................................ IV Loss subsequent processing. The marks may be amplified if the preforms are insufficiently cooled before handling begins, particularly if ejected above a 60°C (140°F) surface temperature. Solutions 1. Check water cooling temperature. This should be 7 – 10ºC (45 – 50ºF) for optimum cooling. 2. Check water cooling flow to mould and robot cooling receptacles. This should be at the mould manufacturers rating (for a given preform size and cavitation). 3. Check that the cooling time is sufficient for the preform being moulded. This typically ranges from about 1 to 3sec depending upon the preform wall thickness. Add time if necessary to increase solidification. 4. Maximize the cooling time of the robot. This should not be increased beyond the cycle time of the machine. 17............................ Long Gate Nub 18...............................Milky Preform 19............................ Moisture Marks 20................Neck Finish out of Round 21....................... Parting Line Crease 22.................Parting Line Deformation 23......................... Preform Yellowing 24.................................. Short Shots 25.......................................... Sinks 26......................................... Splay 27........................... Stretched Necks 28..................................... Stringing 29......................... Surface Blemishes 30......................... Thread Flow Lines 31...............TSS (Top Sealing Surface) ......................................... Sink 32.......................................Unmelts 33.................Wall Thickness Variation 34.................................Wavy Body 35.................................. Weld Lines","@ID":18} "NEWS 7 PETplanet insider Vol. 13 No. 05/12 KHS Corpoplast extending its assembly capacity KHS Corpoplast in Hamburg is extending its production space in order to meet continuing demand for its InnoPET Blomax Series IV generation of stretch blow moulders. Commencement of work on the building that will house its third production shop was marked by a groundbreaking ceremony at the end of April 2012. KHS Corpoplast is investing 3.2 million € in the new building. The production shop, which will provide approximately 2,500m2 of extra assembly space, is to be finished by October 2012. KHS Corpoplast’s Hamburg plant will then have about 11,000m2 of assembly space, around 3,500m2 for logistics use, and an office area of approximately 6,500m2. “In 2013 the offices are to be extended”, stated Thomas Karell, Managing Director of KHS Corpoplast, “and in 2015 we’ll be adding an extra 2,500m2 to the assembly area. Once everything’s finished, by 2015 we’ll have increased our production capacity by 100% compared to 2011.” www.khs.com Krones: sales up, EBT down, on target for growth in 2012 Krones’ first-quarter figures indicate that it is on track to achieve its 2012 sales target of 2-4% growth in the year as a whole. Q1 sales are reported to be 6.9% higher than the equivalent period in 2011, at €648.6 million. The largest contribution to growth came from Eastern Europe and South America. Earnings before taxes were €32.5 million, 7.7% less than the previous year’s €35.2 million. Pre-tax return on sales was also down, at 5% compared with 5.8%. However, Krones says that Q1 earnings are on target for 2012 as a whole. The company expects earnings performance in the upcoming quarters to exceed the corresponding 2011 levels. Consolidated net income after taxes of €22.3 million was €2.5 million down on the previous year. Earnings per share slipped from €0.82 to €0.74. Krones expects pre-tax return on sales, the ratio of earnings before taxes to sales will exceed 5% in 2012. It expects to return to its target sales growth range of 5% to 7% and to increase the return on sales in 2013. Mediation in the Le-Nature’s case in the USA has not been concluded. In March 2012, Krones warned that final settlement may affect 2011’s figures. www.krones.com DEUTSCHE EDELSTAHLWERKE, Obere Kaiserstr., D-57078 Siegen / Auestr. 4, D-58452 Witten Wer bringt PET-Flaschen in Form? CorroPlast® – der ultimative rostfreie Stahl für „All stainless“- Kunststoffformen.","@ID":9} "PRODUCTS 37 PETplanet insider Vol. 13 No. 05/12 www.petpla.net Dry, decontaminate and recycle Starlinger viscotec, the division of Starlinger Ges.m.b.h. that specialises in technology for IV increase and decontamination of PET PCR flakes and pellets, has been presenting its latest machinery to customers and at exhibitions. Its latest machine is the viscoSheet turn-key PET sheet line for the production of 100% food grade rPET sheet. It can process up to 100% of undried material with little or no IV decrease. The deCon 50 decontamination dryer for post-consumer recycled PET flakes uses the Fifo (first-in-first-out) principle to maintain consistency of treatment time and temperature for all flakes being processed, and can be used as a stand-alone or inline unit. It both dries and decontaminates crystallized PCR flakes or skeleton waste prior to the extrusion process and in accordance with EFSA and FDA standards. Starlinger recycling technology equipment has been approved for food applications with letters of non-objection from the FDA. www.starlinger.com Servo-driven Neco-Orientor for asymmetric bottles Nalbach Engineering has launched a new line of bottle orientors that are designed to uniformly orient asymmetric bottles quickly and simply. The NecoOrientor Inline “0/180° bottle orientor is a servo-driven system designed to turn nonround bottles into a common direction. Bottles are accepted from a single lane source and use a vision sensor. They are allowed to pass if they are oriented correctly oriented or spun through 180° if they are not. The Neco-Orientor is available as a fully-integrated option for the company’s line of plastic bottle unscramblers, or as a standalone product for a range of existing production lines. The Neco-Orientor and the unscrambler share a common HMI, vacuum conveyor and footprint. The standalone version includes a vacuum conveyor section, safety enclosure and controls that are designed to integrate into an existing production line. www.nalbach.com DRYING HAS NEVER BEEN THIS EFFICIENT: ETA plus® LUXOR - now available with ETAplus® ETAplus® considerably reduces energy consumption and protects materials. When it comes to drying, saving energy is a key concern. We have developed a system that combines airflow regulation with a temperature adjustment feature – that can be disabled if required –and efficient waste heat recovery. The result? A drying system that cuts energy consumption by up to 64%: ETAplus® . motan-colortronic gmbh info@motan-colortronic.de www.motan-colortronic.com","@ID":39} "EDITOUR REPORTS 13 PETplanet insider Vol. 13 No. 05/12 www.petpla.net Coca-Cola Icecek, Istanbul* *by Wolfgang von Schroeter Coca-Cola İçecek ranks 6th within the Coca-Cola system in terms of sales volume Coca-Cola İçecek (CCI) is a public company and ranks 6th within the Coca-Cola system in terms of sales volume. CCI’s core business is to produce, sell and distribute sparkling and still beverages of The Coca-Cola Company (TCCC). CCI employs close to 9,000 people and has operations in Turkey, Pakistan, Kazakhstan, Azerbaijan, Kyrgyzstan, Turkmenistan, Jordan, Iraq and Syria as well as exports to Tajikistan. CCI has a total of 20 plants and offers a wide range of beverages to a consumer base of more than 360 million people. In addition to sparkling beverages, the product portfolio includes juices, waters, sports and energy drinks, tea and iced teas. Coca-Cola İçecek (CCI) enjoys an outstanding ranking and reputation not only within the Coca-Cola system but also represents the gold standard on the Bosphorus for everything and anything to do with Turkish beverages: They produce the largest number of bottles, and the highest volumes, in monitoring the complete PET value added chain from the preform right through to the bottled, closed, labelled and palletized bottle. No wonder that practically all manufacturers of sophisticated PET machines are proud to count CCI among their references – companies such as Husky, Sipa, Sidel, Krones, KHS. Especially as they are all represented in the 20 factories that are managed and controlled from the central office in Istanbul; factories in Central Asia, the Middle East, Pakistan and Turkey. Factories that demonstrate year on year We Met: Selim Mizrahi, Engineering Service Director, CCI Metin Elsan, Packaging Manager, CCI Are your standard PET preform molds making you as much money as they should? Ask how MPET with iFlow technology improves production and achieves greater quality results. Innovation doesn’t happen in isolation. It happens when blue-sky thinking meets down to earth knowhow and exceptional supply chain execution. The sort of innovation that Mold-Masters is known for, now applied to PET tooling for industry-leading results. Introducing MPET – the new PET preform tooling solution designed for the standards of tomorrow. Mold-Masters and theMold-Masters logoare trademarks ofMold-Masters (2007) Limited. ©2011Mold-Masters (2007) Limited.All rights reserved. Think about it. moldmasters.com/thinkaboutit info@moldmasters.com","@ID":15} "TRADE SHOW REVIEW 30 PETplanet insider Vol. 13 No. 05/12 www.petpla.net MHT MOLD & HOTRUNNER TECHNOLOGY Dr. Ruben-Rausing-Str. 7 | D-65239 Hochheim/Main Tel. +49 (0) 6146-906-0 | www.mht-ag.de Make the most of your machine - with a high cavitation mold from MHT! For many machine types, we supply the mold with the highest cavitation, thereby enabling optimum preform output. For the Husky HyPET machine, we offer an upgrade set for 33% more preforms, without refitting on the machine! • 60 cavities for Netstal PETline 2000 • 96 cavities for Husky HyPET 300, • 112 cavities for KraussMaffei 350 Engineering made in Germany 128 for HyPET 400 Patent pending: MHTcoolMAX® post mold cooling How to make millions a day Sumitomo (SHI) Demag presented North America with El-Exis SP, a machine that is capable of producing over three million caps a day, every day, with energy efficiency The main attraction at Sumitomo (SHI) Demag’s stand at NPE was a series of two live demonstrations of its ElExis SP (for Speed Performance) 450/920-3000 moulding machine, which produced a ‘waterfall’ of over 150,000 bottle caps in an hour. The 500t (US) machine, which was making its first appearance in North America, was moulding 1g HDPE water bottle caps in a 96-cavity Schottli AG hotrunner, in 2.3s cycles. The actual production rate of 150,260 caps/h is equivalent to output of 3,606,260 over a 24h period. The demonstration also included an IMDVista vision inspection system, which checked the parts’ inner and outer diameters, seal area and tamper evident band. The El-Exis SP is available in model sizes ranging from 165 to 825t (US). The company says that it has been designed for high-speed production of applications such as thin-walled food packaging, closures for beverages, cartridges, plant pots and buckets. The hybrid machine is claimed to provide speed with performance through the use of ultra-high-speed injection by hydraulic accumulator and servo-valve, along with an energy-efficient electric screw drive designed to maximise plasticizing capacity and melt homogeneity. A clamping unit with AC servo drive and hydrostatic transmission provides quick mould opening and closing, with low energy usage. The machine features a number of developments over its predecessors. It is designed to be up to 30% more energy-efficient than other highspeed hybrids and offers an increase in injection speed of up to 30% over Cumitomo’s El-Exis S model. The company says that it can achieve up to 1,000mm/sec, depending on configuration and can accelerate from standstill to 800mm/sec in 25 milliseconds. A position-regulated servo valve, combined with a high-resolution path measuring system, has been created to support fast and precise transfer from injection to hold pressure. The machine’s new NC5 Plus control system has been redesigned and features a number of proprietary functions for high-speed operation and efficient energy use. The 330 to 500 US ton models offer an expanded opening stroke, in order to meet requirements for moulding deeper containers, such as buckets. Sumitomo manufactures a range of high-precision IM machines for various applications. Its all-electric platform extends from eight to 606 US tons, including micro to midsized, high-speed, high-duty, vertical, insert, high-speed multi-shot and disc moulding machine series. It produces ultra-high-speed hybrid machines for packaging and other thin-wall applications. www.sumitomo-shi-demag.com","@ID":32} "23 PETplanet insider Vol. 13 No. 05/12 www.petpla.net Conveyors Bottle-to-bottle recycling plants Caps and closures Preform moulds and SBM moulds Preforms Preform and single stage machinery SBM machinery Compressors Filling equipment Resins and additives Mould tools for PET bottle production On pages 23 - 26 our market survey gives an overview of suppliers ofmould tools for PET bottle production. The supplliers are divided into three groups, (in alphabetical order in each case), as follows: Suppliers of preform moulds: Hofstetter, Husky, MHT, Mold-Masters, Steelmades and Thaizhou Sica Suppliers of stretch blow moulds: Beaubury, Comep, KHS, Kiefer, Kosme, Krones, Moldintec, PET Engineering, Röders, Sidel, Technopet and Wentworth Suppliers of both preform moulds and stretch blow moulds: Nissei ASB, Petka, R+D Leverage, Sacmi, Simex, Sipa Molds, Solent Mould Tools (SMT), Tooling Preform Systems (TPS) The suppliers are shown in the table in the order that their details were received by the editors. Although the publishers have made every effort to ensure that the information in this survey is up to date, no claims are made regarding completeness or accuracy. 05/2012 MARKETsurvey Preform Moulds Company name Taizhou Sica Mould Co.,Ltd Otto Hofstetter AG MHT Mold & Hotrunner Technology AG Steelmades Husky Injection Molding Systems Mold-Masters Europa GmbH Postal address Telephone number Web site address Contact name Function Direct telephone number Fax E-Mail Qili Industry Zone,Huangyan, Taizhou,Zhejiang, China +86-13857621725 www.sicamould.com Jason King Sales Manager +86-13857663163 +86-576-84360607 sicamould@126.com Zürcherstrasse 73, 8730 Uznach Switzerland +41 55 285 22 11 www.otto-hofstetter.com Stefan Zatti Division Man. Sales &Marketing +41 55 285 22 09 +41 55 285 22 44 zat@otto-hofstetter.ch Dr. Ruben-Rausing-Str. 7, D-65239 Hochheim/Main, Germany +49 (0) 6146-906-0 www.mht-ag.de Volker Jährling VP of Sales and Service +49 (0) 6146-906-122 +49 (0) 6146-906-399 vjaehrling@mht-ag.de B/14, Ghatkopar Ind. Estate, LBS Road, Ghatkopar (W), Mumbai - 400 086, INDIA 91 22 25007774, 67550450 www.steelmades.com Mr. Vipul mehta Director +9323907774 +91 22 67969001 steelmades@gmail.com 500 Queen Street South, Bolton, Ontario, L7E 5S5 +1 905 951 5000 www.husky.ca Robin Lovell Product Manager +1 905 951 5000 rlovell@husky.ca Neumattring 1, 76532 Baden-Baden Germany +49 7221 5099-0 www.moldmasters.com Manfred Lausenhammer Director, Operations +49 7221 5099-0 +49 7221 53093 mpeteurope@moldmasters.com Preform moulds Horizontal opening Yes yes Yes Number of cavities 1 up to 96 2 up to 192 2-192 cavities UP TO 72 CAVITY 2 to 196 up to 144 Preform sizes Neck diameter 16 - 300mm; preform weight 6 - 750g. up to 500g up to 600 grams, for bottles up to 30 litres All - accomodated preform lengths from 28 mm to 310 mm up to 5 gal / 20 l moulds already built for (makes) Nawakheth, Cello, Kmp, Hpl, Coca Cola, Pepsi, Netstal, Netstal, Arburg, BMB, Husky Netstal, Husky, Engel, Arburg, Cincinnati, SIG, BMB Yudo, Husky Hot Runners For All The Indian Machines. H-PETAE, HyPET, HyPET HPP, HyPET RF all major brands of PET systems Vertical opening No yes Number of cavities 2 up to 96 2-112 cavities Up to 96 Preform sizes up to 500g up to 600 grams, for bottles up to 30 litres up to 5 gal / 20 l Moulds already built for (makes) Arburg, Krauss-Maffei KraussMaffei all major brands of PET systems Do you produce single stage tooling sets? (Preform moulds AND blow moulds) No.Only for double stage preform molds and blow molds. No No No Axiom hot runners for single stage IBM & ISBM Other Multilayer moulds up to 72 cav. Moulds for PP Moulds for thinwall packaging Moulds for cartridges and tubes Wide mouth, high performance moulds, up to 8 gallon, trigger moulds, moulds for vacuum blood test tubes Cold half and interchangeable spares for branded imported moulds. 96 drop moulds for 300t machines iFlow hotrunner systems; rapide system (fast tool changes), iCool conformal mould stack cooling technology, iFlow inside: hot runner manifold upgrade program; hot runner refurbishing/upgrade programs","@ID":25} "BOTTLING / FILLING 18 PETplanet insider Vol. 13 No. 05/12 www.petpla.net Lipetskpivo Brewery invests in a fully automatic KHS Petainer keg line A pioneering performance Based on an article by Dr. Felix Wagner, Manager, Filling and Keg Technology Competence Centre, KHS GmbH, Germany. Jörg Lauer, Petainer Keg Project Manager, KHS GmbH, Germany. Alexander Burenin, Sales, KHS Russia Lipetskpivo Brewery in Russia, formerly a state-owned enterprise, transformed in 1992 into a co-operative, produces beer but also non-alcoholic beverages. In 2002, production amounted to 160,000 hectolitres, but rose in 2011 to over one million hectolitres of beer, soft drinks, juices und water. Now it has become the first brewery in the world to invest in a fully automatic KHS Petainer keg line. Lipetskpivo sees itself as a brewery from the region and for the region, its distribution radius being around 500km from its own doorstep. Lipetskpivo holds second place in the brewery ranking for this area, with BBH holding the top spot. The brewery in Lipetsk supplies both retailers and the hospitality trade with beer and non-alcoholic beverages. This – and this is a decisive factor, according to Vyacheslav Markov, who took the helm as the brewery’s Managing Director in 2002 – is what the average Russian employee can afford, the mean monthly wage being around € 550 or 22,500 rubles. Lipetskpivo firmly adheres to its concept of providing consumers with a quality product at what it considers a fair price. A 1.5l PET bottle of Lipetskoe or Priyatel beer, for instance, the two brands produced at Lipetskpivo, can be purchased at a retail store for about 90 rubles. The annual per capita consumption of beer in the Lipetsk region amounts to approximately 70l. Today, 68% of the company’s sales are attributable to the brewery’s two aforementioned beer brands. Soft drinks and fruit juices account for a further 14.5%, with water clocking up 13% of the total sales and kvass 4.5%. Markov believes that these figures will change in the near future. “With our technical setup we’re now prepared for all eventualities,” Markov claims. “If more water, soft drinks, fruit juices, or kvass and less beer are required, we’ll simply change our production schedule.” The non-refillable PET bottle has the top slot in the range of possible containers. The 1.5l PET bottle makes up about 50% of total production. Another type of choice packaging, especially for Lipetskpivo’s brand beers, is the 30l and 50l keg varieties. To date 12% of the brewery’s filling volume has been fed into the classic refillable steel keg. The biggest disadvantage of such kegs, in the eyes of Lipetskpivo, is the amount of economic effort involved in handling them. Costs for return, storage, and washing play a significant role here. The question was whether a nonreturnable PET keg system would be feasible and whether it would help to avoid such expense. Petainer kegs are non-refillable, disposable kegs that do not have to be returned to the brewery and which are 100% recyclable. This saves not only on logistics for keg return to the brewery but also on outgoings for keg washing. The kegs can be ordered entirely according to local market demand or even manufactured inline on a special Petainer keg line. StorVyacheslav Markov, Managing Director, and Roman Lizunov, Manager of the Engineering Department at Lipetskpivo","@ID":20} "EDITOURS REPORTS 14 PETplanet insider Vol. 13 No. 05/12 www.petpla.net growth and consistently deliver improved results for their owners and investors. In our Regional Market Report in 2005, we at PETplanet Insider had already established that the Turkish market had the potential for strong and sustained growth and had made the corresponding forecast. The crucial drivers for the growth market at the time were: political stability, an emerging middle class, a proportion of young people growing up, and, at the same time and in particular, the major need to catch up as regards the relatively low per capita consumption of more sophisticated beverages. All in all, good and typical reasons for increased consumption of beverages and an increase in the associated packagings – all of which are still valid today. This positive trend is readily discernible if we take the development of the Gross National Product (GNP) per capita: GNP per capita 2004 – approx. US$ 4.100 GNP per capita 2010 – approx. US$ 10.000 But it is not just the economic environment and the Turkish market, the fact that a vital and committed local industry exists has also contributed to this development – including the packaging industry overall, the producers of PET materials and processors in particular. CCI – 54,3% owned by Turkish investors; 20,1% in the ownership of the “Coca-Cola Company“ and with the remainder quoted on the Stock Exchange (Istanbul Stock Exchange under CCOLA.IS) – is wholly in line with current (macro) economic trends in Turkey, something which the trends in terms of volume and annual sales go to prove. Selim Mizrahi, Engineering Service Director of CCI, with whom we spoke on 24th January 2012, makes the following claim on his own account as well as on behalf of his company – with no false modesty: ”Certainly the market exists and is there. But our outstanding success is due to the best brand we have and the best people we employ – who are fully focused on customers and their individual desires – whether small or large.” Products CCI has the right to exclusively produce, sell and distribute The Coca-Cola Company (“TCCC”) beverages in authorized packages with TCCC’s trademarks, including Coca-Cola, Coca-Cola Zero, Coca-Cola light, Fanta, Sprite, Cappy, Sen Sun, Powerade, Burn and Damla throughout Turkey and adjacent international markets. Additional indigenous products are energy drinks, tea and iced teas. Bottle sizes vary between 0,2l and 3,0l. Majority products in 2,5l Contour PET bottles 51.5g with PCO1881 neck finish. Trend towards PET substituting glass in all markets and categories continue. According to Selim Mizrahi: “PET is picking up. Almost every new investment is directed into PET packaging.”","@ID":16} "TRADE SHOW REVIEW 32 PETplanet insider Vol. 13 No. 05/12 www.petpla.net Chinaplas: centre stage for new applications According to statistics and statements from plastics processors, the Chinese plastic industry is slowing down. But “slowing down” in China means that the recent record years may be over, but that there is still healthy growth mainly driven by the packaging and automotive industry. With a total of 110,000 visitors the annual Chinaplas exhibition, now the second largest plastic trade show in the world, closed its doors for 2012. While the overall number of visitors was slightly higher than last year in Guangzhou (2011: 94,084 visitors), the number of foreign visitors increased significantly again (28,110, up 25.59%). As happens every year, new Chinese companies appeared on the scene, frequently showing copycat versions of machines from established European companies. Every machine on show, whether from overseas or from local manufacturers is festooned with a “Please NO Photography” sign, which are widely ignored. Photographing machines with the aim of copying them is widespread. Because of this and also the high costs of displaying machines on an annual basis, some overseas exhibitors refrain from exhibiting machines to protect their intellectual property. Caps and closures was one of the hot topics this year. Around the globe, demand for caps and closures is expanding by around 5%/a and China is the world’s largest market in terms of volume. Husky presented its Hycap system, which they had already launched at NPE. At the same time Engel and mould maker Plastisud announced the “Green Cap” joint venture and presented also their high speed cap injection moulding system with a capacity of around 130,000caps/h. With these two innovations, both manufacturers challenge Sacmi, the compression moulding specialist.The competition has just begun. So it seems that machinery manufacturers increasingly use China and the Chinaplas exhibition to showcase new applications and areas. Compression moulding specialist Sacmi presented stretch blow moulding machines, preform specialist Husky introduced a high-speed cap production system, directly competing with automotive specialist Engel. There are two main reasons for global operating machinery manufacturers to choose Chinaplas as the world stage for their innovations. In China output matters, i.e. high-output machines are in demand. And Chinese processors are somehow more open to buy a production system from a reputable manufacturer, even if the company is not well-known for this particular application. Double feature “Decentralised production guarantees short delivery times to our customers in Asia” says Gero Willmeroth, President Sales and Service of Engel Machinery (Shanghai) Co., and inaugurated the new factory in Shanghai during Chinaplas. The company started production in China in 2005 and now employs about 210 people in Shanghai, Shenzhen, Chengdu and Beijing. Currently about 100 large-capacity “Engel duo” injection moulding machines with clamping forces from 450-3,200kN are produced annually. Now, with the recent expansion more than 200 machines can be assembled. Although robots are imported from their Austrian plant, the automatisation of the complete production cell is then done locally in China. Today, Engel has a market share of about 20% in China for injection moulding machines of the larger size. Also on Chinaplas, Engel and Plastisud announced their ‘Green Cap’ Joint Venture (see PETplanet issue 4/12, page 10. “The Chinese market is very demanding. Chinese customers request nothing but the best”, says Walter J. Jungwirth, Director New Business Development at Engel Austria. The two companies will offer turnkey solutions for the production of sealing caps for water and soft drinks containers in China. Greencap has set up its base in Shanghai in the premises of Engel to bring a complete and fast service to the Chinese customers. Green Cap unveiled the new con cept: an all-electric Engel e-cap 3440/420 injection moulding machine with a 96-cavity mould made by Plastisud that can produce nearly 130,000 sealing caps per hour, reaching a cycle time faster than 2.8s. With cycle times of under 3s and injection speeds of up to 460mm/s, Engel’s all-electric e-cap injection moulding machine is designed to handle high output rates. Green Cap total solutions promise energy consumption of 0.75kWh/kg of granules.The system can be equipped with 32 to 96-cavity moulds as standard along with machine clamping force of 200 to 420t, as a further option, 500t machines are available. www.engelglobal.com www.plastisud.com Inauguration ceremony at the new Engel factory in Shanghai","@ID":34} "imprint EDITORIAL PUBLISHER Alexander Büchler, Managing Director HEAD OFFICE heidelberg business media GmbH Häusserstr. 36 69115 Heidelberg, Germany phone: +49(0)6221-65108-0 fax: +49(0)6221-65108-28 info@hbmedia.net EDITORIAL Doris Fischer: fischer@hbmedia.net Michael Maruschke Ruari McCallion Ilona Trotter Wolfgang von Schroeter Anthony Withers MEDIA CONSULTANTS Ute Andrä andrae@hbmedia.net Martina Hischmann hirschmann@hbmedia.net Ursula Wachter wachter@hbmedia.net phone: +49(0)6221-65108-0 fax: +49(0)6221-65108-28 France, Italy, Spain, UK Elisabeth Maria Köpke phone: +49(0)6201-878925 fax: +49(0)6201-878926 koepke@hbmedia.net LAYOUT AND PREPRESS Exprim Kommunikationsdesign Matthias Gaumann | www.exprim.de READER SERVICES Kay Krüger reader@hbmedia.net PRINT Chroma Druck & Verlag GmbH Werkstr.25 67454 Römerberg Germany WWW www.petpla.net | india.petpla.net PETplanet insider ISSN 1438-9459 is published 10 times a year. This publication is sent to qualified subscribers (1-year subscription 149 EUR, 2-year subscription 289 EUR, Young professionals’ subscription 99 EUR. Magazines will be dispatched to you by airmail). Not to be reproduced in any form without permission from the publisher. Note: The fact that product names may not be identified as trade marks is not an indication that such names are not registered trademarks. 3 PETplanet insider Vol. 13 No. 05/12 www.petpla.net EDITORIAL dear readers, EDITORIAL The charm of Chinaplas The 26th annual Chinaplas has just closed its doors. Compared to last year, 25% more overseas visitors participated in what is the 2nd largest plastic show in the world. Unlike the K-Show and NPE, Chinaplas takes place every year, alternating between Shanghai and Guangzhou. Displaying new machine every year is a virtual impossibility. And costly. A few years ago members of the influential VDMA (German Engineering Federation) tried to persuade the organisers to move away from an annual show, but to no effect. Ignoring this for a moment, what makes Chinaplas really different from the K-Show and NPE? First of all, signs carry different meanings in China. On practically every machine on display the crossed-out camera sign is ubiquitous. It seems to be subject to many interpretations. “No photography”, however, is one interpretation that definitely does not apply. They also do things differently in China as regards the services offered. At the entrance to the exhibition centre, freelance agents promise cheap admission to the fair by selling exhibitor passes of companies that do not even exist. Some “photographers”, with a strong engineering background, take detailed pictures of machines for undisclosed purposes. Other people, with a strong plant engineering background, attempt to gain access to one of the popular Open Houses operated by European machinery manufacturers, and the reason is not entirely due to the delicious Chinese food on offer. And then there are the attractive hostesses, working on commission, who make up in looks what they lack in engineering know-how, luring unsuspecting foreign customers (“you are looking for moulds?”) into certain Chinese tooling companies. Another startling difference is the fact that every year new Chinese machinery manufacturers appear out of nowhere, and exhibit machines that look amazingly similar to existing European designs. While senior management debate whether to sue the Chinese company for copyright or patent infringement, other freelance agents equipped with cameras and i-phones have meanwhile taken enough detailed photos to bring their own machines to a new level. This kind of “Chinese R&D” at the fair is only scratching the surface. Some companies do some more “basic research” and invest money. They buy machines and tooling from European competitors in order to dismantle, measure and copy them. European machinery manufacturers are well aware of this situation. But they are also aware that China is one of the fastest growing beverage markets. It simply cannot be ignored. For full coverage of Chinaplas, see our special feature on page 32. Yours, Michael Maruschke","@ID":5} "PATENTS PETpatents 41 PETplanet insider Vol. 13 No. 05/12 www.petpla.net Dispensing device Disclosure No. DE 102010009797 A1 Applicant: Inotech Kunststofftechnik GmbH, Nabburg (D) Date of Application: 1.3.2010 Dispensing device for free-flowing products which can be manufactured easily and from a small number of components. The dispenser has no metal spring and this simplifies the processes of disposal and checking for foreign bodies in the end product. Pouring aid Disclosure No. DE 102010012218 A1 Applicant: Jörg Haberland, Uchte (D) Date of Application: 19.3.2010 Integrated pouring aid for bottles made from all types of plastics. This design prevents any “gurgling“ when the liquid is poured out as well as the associated release of carbon dioxide. Even the product in the bottle releases less carbon dioxide. Flexible base European Award of Patent EP 2173637 B1 Applicant: Sidel Participations, Octeville Sur Mer (FR) Date of Application: 29.7.2008 The base of a PET bottle with reinforcing ribs and a large opening diameter is so formed that it is able to absorb any change in volume that may occur during hot filling and subsequent cooling by means of elastic deformation.","@ID":43} "CAPPING / CLOSURES 20 PETplanet insider Vol. 13 No. 05/12 www.petpla.net Interview with Romeo Corvaglia, owner of the Corvaglia Group, headquartered in Switzerland Closure moulds – a complicated issue For most machinery manufacturers, it couldn’t be simpler. First, take a fast machine, add a mould and problem solved, you have a ready-to-go cap production unit. We talked with Romeo Corvaglia about the market for closure production systems and why, despite sounding so simple, it is not really that simple at all. In his opinion the closure is not just a matter of machine and mould. The entire approach has to be more holistic. PETplanet: Husky has bought up KTW, Engel has the JV Green Cap with Plastisud in China, and during the Euro crisis the Swiss Franc has been so high that the Swiss National Bank has had to intervene. Do you still see any potential when it comes to selling your Corvaglia closures moulds ? Corvaglia: Strictly speaking, we are not in the business of merely selling moulds but offering overall concepts for “closure solutions” to our customers. As a rule moulds are included in the contract. But, clearly, we earn our living by taking a holistic view of the closure. PETplanet: What exactly do you mean by “closure solutions“? Doesn’t every machine manufacturer claim to offer their customers “solutions”! Corvaglia: A closure is something that is highly dynamic. There is a lot of intellectual property in each closure design to guarantee high performance at lowest cost. First of all it needs to be manufactured and then it has to be applied onto a bottle. And this is the big difference from the preform. Neck finishes are standardised. The body of the preform is defined by the shape of the final bottle and the expertise of the bottle blower. An order for a preform is considered completed once the correct tolerances have been achieved, and that’s where the story ends. A closure, by contrast, not only has to be designed and produced, but also has to go through the capper without any problems and then withstand possibly tough conditions for many months before it even reaches the consumer. PETplanet: It doesn‘t always happen like that though, does it? It’s no coincidence that bottlers sometimes buy equipment with two cappers on one unit so as to ensure that the faults attributable to closures do not adversely affect the performance of the production lines. Corvaglia: As is now becoming apparent, a closure is disproportionately more complex and, above all, more multifaceted than a preform. Unsurprising then that there are only a handful of closure manufacturers operating on a supra-regional level. In the preform sector, in contrast, Romeo Corvaglia, owner of the Corvaglia Group 28mm CSN sports cap 38mm Mercury cap 28mm Flexgrip Corvaglia 38mm Sensocap","@ID":22} "TRADE SHOW REVIEW 29 PETplanet insider Vol. 13 No. 05/12 www.petpla.net The specialists inplastic recycling systems. VACUREMA® – PETextrusion technologies Choose the Number One. Interview with Oriol Vives, MD Side Spain and Josep Jimenez, Export Manager, Side Spain The Specialities At the NPE in Orlando we met Oriol Vives, MD and Josep Jimenez, Export Manager, both from Side Spain. They were exhibiting a 2l container with a moulded recess handle strongly reminiscent of the complete through-handle featured on the traditional HDPE bottles. PETplanet: These are the first handles on stretch blow moulded PET bottles that you can get a reasonable grip on, even if the handle does not go all the way through. Jimenez: Yes, we always try to come up with good solutions for our customers. This handle is one of those solutions. We mould the handle within the stretch moulding operation. The finished bottle can be readily removed from the mould for direct filling. Any further steps, such as where you would normally expect an additional stage for mounting the handle, are omitted. Our customers like the solution. And we only need 90g worth of PET material in order to implement it. PETplanet: You are well known for individual customer solutions; I believe Tupperware also work with your equipment? Jimenez: Yes, here we have developed equipment to manufacture stretch blow moulded bottles from PP for the company. The bottle is refillable. The plants that operate in Germany and India are based on the same design. The bottle is suitable for use in the microwave, it is dishwasher-proof and it can also be filled with hot liquid. This has been a very nice as well as a very sophisticated project. PETplanet: Thank you very much. www.sidemachines.com Oriol Vives (left) Managing Director Side Spain, and Josep Jimenez (right), Export Manager Side","@ID":31} "MARKET SURVEY 25 PETplanet insider Vol. 13 No. 05/12 www.petpla.net TPS - Tooling Preform Systems BV Nissei ASB Machine Co., Ltd. Simex SRL Sipa Molds C Houtmanstraat 42, NL-7825VG Emmen +31 591 679768 www.tps.nl Richard Tempel Sales Manager PET +31 6 25041136 +31 591 630616 info@tps.nl 4586-3 Koo, Komoro-shi, Nagano-ken 384-8585, Japan +81 267 23-1565 http://www.nisseiasb.co.jp/en/ Katsuo Ishiguro Manager - Sales Coordination Team +81 267 23-1565 +81 267 23-1564 sales@nisseiasb.co.jp Via M.Biagi e M.D'Antona ,5 60025 Loreto (AN) Italy +39 071 7500214 www.simexitaly.it Graziano Giuggiolini Sales Manager +39 071 7500214 +39 071 7501958 giuggiolini@simexitaly.it Via Caduti del Lavoro 3 - 31029 Vittorio Veneto Italy +390438911511 www.sipa.it Peter dal Bo Molds Division Director +390438911511 +390438911694 peter.dalbo@zoppas.com 50l 22l 20l (5gallon) 30l no Only for own machines Yes No yes Only for own machines Yes Yes Sidel, Siapi, SIG Krones Chum and others Moulds are customized for each customer Sidel, Krones, KHS/SIG/Krupp, SMI, Siapi, Kosme Yes Yes: brandbuilding, product repositioning, marketing design, packaging engineering, etc.; Large preforms and containers. 5 Gallon to 50l Handled, non-round, wide-neck, hot fill, non-round neck, offset neck, heavy weight cosmetic, etc. Containers for mineral water, carboneted soft drinks, milk, edible oil, wine, beer, cosmetics and other Wide mouth, large sizes (up to 30l), asymmetrical, nitrogen hot fill, containers with handles, HDPE to PET conversions. Yes Yes Yes 96 Up to 144 Up to 144 Up to 750g/110mm All sizes and finishes Up to 30l Husky Netstal SIG/Engel Arburg Battenfeld Demag FCH and others Mineral water Husky, Netstal, Krauss-Maffei, Krupp, BMB Yes Yes No Yes 196 8-32 up to 96 Up to 750g/110mm Up to 180g up to 10l KM Nissei ASB machines only Sipa, Krauss-Maffei No Yes - main business is single stage Yes Yes, for Sipa systems Design, development and prototyping for various applications. In-House preform and blowing machinery up to 50l; Lab facility for all preform/container tests available. Blow moulds for extrusion blowing Air recovery systems, rotary blowmolder and filling lines spare parts Sidel Blowing & Services Wentworth Mold Ltd. Krones AG Kosme GmbH Röders TEC Avenue de la Patrouille de France, Octeville sur Mer, BP 204, 76053 Le Havre cedex - France +33 2 32 85 86 87 www.sidel.com Laurent Charrier Tooling Product Manager +33 2 32 85 80 63 +33 2 32 85 81 69 laurent.charrier@sidel.com 566 Arvin Ave., Stoney Creek, Ontario, L8E 5P1, Canada +1 905-643-9044 www.wentworthmold.com Tar Tsau General Manager +1 905-512-0072 +1 905-643-5406 ttsau@wentworthmold.com Böhmerwaldstr. 5, 93073 Neutraubling, Germany +49 9401 70-0 www.krones.com Peter Christiansen Sales Director Blow Moulding Techn. +49 9401 70-4980 +49 9401 70-914980 peter.christiansen@krones.com Gewerbestr. 3, 2601 Sollenau, Austria +43 (0)2628 411-0 www.kosme-austria.com Johann Gugler Managing Director +43 2628 411 125 +43 2628 411 4125 j.gugler@kosme-austria.com Scheibenstrasse 6, 29614 Soltau, Germany 0049 5191 603 53 www.roeders.de Friedo Böhling sales manager 0049 5191 603 53 0049 5191 603 36 mold@roeders.de 10l 10l 3 30l 10l Yes No No No Yes Yes, moulds and personalization parts, repairs and refurbishment Yes; also multi-platform quick change moulds. Yes Yes Yes Sidel, Krones, KHS Corpoplast, Sipa Yes, for all stretch blow moulding machine platforms, cold fill or hotfill or two-stage wide mouth Krones, Kosme, Sidel, Sipa, KHS (SIG) Corpoplast Kosme, Krones, Sidel, KHS Sidel, KHS Corpoplast, Krones, Sipa, Kosme, ADS, Nissei and other major machine types Yes, design, prototypes, sensitive products centre Yes; also bottle sampling and performance tests. yes Yes Bottle design & development & test blowing & full laboratory available Full packaging solution provider including packaging design, preform/bottle lightweighting development, blow mould and personalization parts engineering Hot-fill/heatset mould. Bottle development services, customized to filling- and packaging lines. Preform/bottle lightweighting developments for standard- and heat-set process. \"Mould quick-change\" solutions. Bottle development service free of charge, if blow moulds are ordered Solutions for compatibility of moulds between different machine types, new Röders RMC-system for quick mould change","@ID":27} "TRADE SHOW REVIEW 33 PETplanet insider Vol. 13 No. 05/12 www.petpla.net Rotary bottle surface inspection system The Korean specialist for testing and surface inspection displayed several machines on its booth, including the PS-21RP rotary surface inspection system for bottle sizes of 0.5 to 2.0l and a maximum capacity of 24,000bph. This rotary type of inspection machine rotates the PET bottle 360° to fully check for deficiencies during the PET bottle production by inspecting the mouth top crack, oval, substances in & out, the sidewall and the bottom. In addition, the image grey scale of the CCD camera allows accurate filming and is able to detect unknown surface particles of 0.5mm at an accuracy of 99%. The system also collects data retrieved during the inspection process and enables monitoring of the data for statistical quality management. A self diagnostic feature that is installed in the system immediately alerts problems thus preventing failure of inspection. The mechanical structure of the system allows a 24/7 operation. Another version of inspection systems, the PS-21RPL, is also able to detect pin holes starting from the size of 0.5mm. This system can handle 350ml to 1.5l bottles. In general, the company is also in a position to install inspection systems for bottom and sidewall in Sidel SBO blow moulding machines, as already realised in SBO10 and SBO16. www.pnstech.co.kr Y O U R PA R T N E R F O R B L O W M O U L D S . Sidel • SIG • Krones • SIPA • MAG • ADS • Kosme • Nissei a. o. Röders GmbH / Scheibenstr. 6 / 29614 Soltau / Germany / www.roeders.de Telephone +49 5191-603-53 / Fax +49 5191-603-36 / E-Mail mold@roeders.de For our subsidiaries in China, USA and Latin America please check our website. PET STRETCH BLOW MOULDS Benef i t of 30 Years of Exper ience in Blow Mould Manufactur ing! Oil cap with changeable insert The Austrian company htw molds- and manufacturing technology specialises in the design and production of injection moulds for screw caps. The product portfolio includes soft drink caps, sport bottle caps, oil caps, flip-top caps, shampoo caps and cosmetic caps. 1-cavity pilot moulds as well as 96-cavity series moulds can be supplied. The company also holds patents on different kinds of screw caps and grants licences for production. The company also offers Toolstar hotrunner systems and gammaflux hotrunner controllers in connection with their moulds. At the exhibition different caps were shown, including a patented oil cap with a drop stop feature and changeable inserts for oil, soya or vinegar. www.htw-werkzeugbau.com Hydraulic PET preform system The Chinese company Hwamda exhibited and ran a PET injection system for the production of PET preforms combining a fully hydraulic injection moulding machine with toggle clamping unit, mould, robot (with drives from Lenze Germany) and auxiliary machines. The M8-DH injection machine with single cylinder and servo motor has a two-stage injection unit in order to reduce the preplasticising cycle time and to shorten the whole moulding cycle time. It is also equipped with a two-circuit oil piping system and close-loop servo injection valve. The power system of the machine is all hydraulic and the main components are from brands such as Bosch, Intermot, Vickers, Yuken and Atos. www.hwamda.com","@ID":35} "BOTTLING / FILLING 19 PETplanet insider Vol. 13 No. 05/12 www.petpla.net age costs are considerably reduced – and costs for keg repairs become a thing of the past. The kegs, available in sizes of 15, 20, 30, and 40l are currently available and come with a compatible flat fitting and a basket fitting. One 40-foot standard container can deliver 40,000 fittings sets and preforms. 15l or 20 l kegs weigh 250g, with 30l kegs slightly over the 400g mark. Logistics costs for deliveries are reduced by between around 20% and 30% per hectolitre of beer. The keg fittings are fully compatible with standard tapping apparatus and can be connected up to existing systems for draught beer in the same way as classic steel kegs. This means that bar staff do not have to undergo special training. Recycling is said to be straightforward. After being relieved of pressure, the empty kegs can be easily folded and disposed of as recyclable waste. The keg makes use of modern barrier technology. An oxygen scavenger prevents oxygen from penetrating the container; nylon particles protect the product from CO 2 loss. Pigments in the polymer also help to guard the contents against infiltration of UV light. The minimum shelf life of beer racked in a Petainer is nine months – with the quality of beer comparable to beer in steel kegs. Lipetskpivo invested in a fully automatic, KHS Innokeg Till PETLine F8 Petainer keg system which also includes an Innopro pasteuriser and Innopro CIP system. The output of the line can reach 240 kegs/h. At present the line is set up to rack 30l kegs only. Markov comments, “In our view the 30l keg best combines all the economical and ecological advantages. Our current plan is to limit ourselves to processing this size of keg. However, it’s good to know that should we make any changes at our end, our KHS system can be adapted to suit.” Lipetskpivo manufactures its containers inline. The preforms and fittings are supplied by the manufacturer. The preforms are blown in a blow moulder which has an automatic preform intake. The blown kegs are sent off to the fitting inserter on a conveyor enclosed in Plexiglas for ultra hygienic transportation. Here, Moretto S.p.A. Via dell’Artigianato 3 35010 Massanzago (PD) ITALY Tel. +39 049 93 96 711 Fax +39 049 93 96 710 www.moretto.com designed by Moretto The most ambitious project in the history of dehumidification. Drying Revolution a handling robot first grips the fitting and attaches it to the rinser pipe. This robot then inserts the assembled elements into the keg. The kegs then travel to a filling and packaging area specially tailored to Lipetskpivo’s requirements. Four Innokeg Till PETBoy F2 racking segments, each with two racking stations, are arranged in a semicircle. A robot with a radius of 240° feeds the eight racking heads with kegs. The robot has a swivelable gripper head which can transport two kegs at once. After each keg has been racked, the robot places the racked kegs in packaging cartons. When packed with one keg apiece the cartons then travel on to the carton sealer and carton coder. An Innopack CV carton sealer downstream of the racking and packaging process ensures flawless glue application and perfectly sealed cartons. An Innopal PBL1N1 column-type robot, equipped with a low pack infeed, is responsible for palletising the cartons. Lipetskpivo will begin marketing the Petainer keg in spring. By then all test phases in the hospitality and food trade will have ended and marketing concepts developed. First response from the market has been extremely encouraging. “By next summer at the latest we’re reckoning on our keg line running in two shifts at full capacity” states Markov. If Lipetskpivo’s forecast turns out to be right, in the future the brewery also plans to rack soft drinks in the kegs beside beer and kvass. The brewery is planning to modernise the plant and extend their production capacities up until the end of 2013, with capacities of up to 2.5 million hectolitres. The kegs are handled in the Innokeg Till PET Boy F2 racking stations by a robot.","@ID":21} "BOTTLES 39 PETplanet insider Vol. 13 No. 05/12 www.petpla.net CCT Creative Competence Technology GmbH Idsteiner Strasse 74 D-65527 Niedernhausen, Germany r.steinmetz@cct-systems.com www.cct-systems.com PET Molds Closure Molds Developments PET Systems Closure Systems Design and Patents CCTsystems®SST (Standard-Slider-Technology) CCTsystems®SBT (Slit-Band-Technology) CCTsystems®SFBT (Slit-Fold-Band-Technology) All Types available with: Design and Patents CCT O26 Series 0,9 g CCT O29 Series 1,2 g CCT O30 Series 1,8 g CCT O38 Series 2,9 g Scented bleaching Under the brand name Silvan, the Italian company GSG is marketing 2l of scented bleaching / cleaning agent in a yellow-tinted PET bottle with a two-colour safety cap complete with tamper-proof band. The bottle, which features peripheral reinforcing ribs and two recessed handles, is decorated with two paper labels. www.gsgnet.it Mouthwash for kids Listerine Smart Kidz is what the German subsidiary of Johnson & Johnson, McNeil Consumer Healthcare GmbH from Neuss, calls its fluoridecontaining mouthwash with berry flavours. This alcohol- and sugar-free rinse colours any food residue and this becomes visible on rinsing into the wash basin, thus making it clear to the ‘Kids’ how they benefit from the product. This coloured product is packaged in a waisted, transparent PET bottle with a content of 500ml plus dispensing system. Exerting pressure on the container has the effect of filling a dispensing chamber which is subsequently emptied. Prior to use, protection is provided by a pre-perforated shrink film over the screw cap. www.listerine.de Number 7 M&H Plastics has worked with UK health and beauty manufacturer and retailer, Boots and its design agency, Two Create, on the new packaging for its collection of products in the No. 7 Everyday Skincare range. Boots commissioned M&H to manufacture a bespoke bottle with the overall brief to produce a contemporary shape that was in line with the existing No. 7 brand identity. M&H produced a 100ml and 200ml clear PET bottle featuring foil blocking of the No. 7 name in gunmetal grey in an off-centre positioning. A twopiece colour coordinated screw cap was also produced in conjunction with MBF Plastiques, with the intention of giving the product a premium appearance. Aptar supplied the slimline two-colour pump for the lotion bottles. www.mhplastics.com","@ID":41} "PREFORM PRODUCTION 17 PETplanet insider Vol. 13 No. 05/12 www.petpla.net PETplanet print vol.6 The Rapid Guide to Perfect Preforms machine no./name 1- 3 exemplar each 129,- € 4 - 10 exemplar each 99,- € 10 exemplar each 69,- € prices in EUR + VAT. 5. Check that the hold (packing) time isn’t too little for the preform being moulded. Increase as necessary to improve solidification. 6. Check that the hold (packing) pressure isn’t too low. Higher pressures will improve cooling by maintaining good contact with the moulding surface and by increasing the melt density. Increase as necessary. 7. Check all temperature readings and correct if necessary. PET resin should be melted at about 280ºC (536ºF) +/- 10ºC (18ºF). Reduce as necessary. 8. Check that the mould core half (moving platen side) doesn’t drop slightly during the unclamp and initial mould open sequence. This could scratch the bottom surface of the preforms. 9. Check that no anomalies are present on the moulding surfaces and robot cooling receptacles. Repair if necessary. 10. Ensure the mould / robot alignment is accurate. 11. Ensure preform handling is not congested at the deposit locations and collection bins. 12. Ensure no abrasive objects contact the preforms during handling. 13. Check hardware for worn, damaged or failed components, specifically clogged core / cavity cooling channels, robot receptacle cooling channels, conveyor obstructions, and turbulent downstream handling. www.petpla.net PETplanet print Vol. 6: The Rapid Guide to Perfect Preforms by Rick Unterlander and Ottmar Brandau fax: +49 (0) 6221-65108-28 info@hbmedia.net www.petpla.net Order your copy now! With a long story in packaging engineering SIPA can support its customers on lightweight preform development as well as preform lightweight conversions on existing mold. SIPA has developed specific neck ring design solutions for an optimal cooling and cycle time, even in case of short preform and neck finish conversion. SIPA provides complete preform mold for any PET system (up to 96 cav.), cold half for existing hot half (up to 144 cav.), hot half for existing cold half (up to 96 cav.); furthermore it provides conversions of existing mold (full or partial kits), mold spare parts and refurbishment. All SIPA preform molds feature LongLife™, a new design engineered to extend the mold service life. LongLife™ PET preform molds with strong focus on lightweight. www.sipa.it","@ID":19} "PETcontents 05/12 4 PETplanet insider Vol. 13 No. 05/12 www.petpla.net INSIDE TRACK 3 Editorial 4 Contents 6 News 36 Products 38 PET bottles: Personal care 40 PET bottles: Beverages 41 Patents MARKET SURVEY 27 Suppliers of mould tools for PET bottle production TRADESHOW REVIEW 28 Prosecco reception Interview with Gianfranco Zoppas and Enrico Gribaudo at NPE 29 NPE review 32 Centre stage for new applications Chinaplas review EDITOUR REPORTS 10 A market opens up Turkey Part 2 PREFORM PRODUCTION 16 Surface blemishing The rapid guide to perfect preforms - part 29 BOTTLING / FILLING 18 A pioneering performance Lipetskpivo Brewery invests in a fully automatic KHS Petainer keg line CAPPING / CLOSURES 20 Closure moulds - a complicated issue Interview with Romeo Corvaglia, Owner of Corvaglia AG Page 20 BUYER’S GUIDE 42 Get listed! Page 38 Page 28 Page 16","@ID":6}]}}
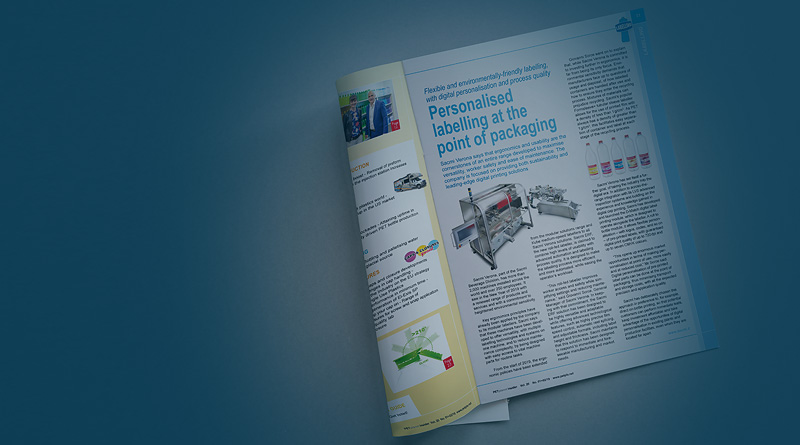