"EDITOUR REPORT 19 PETplanet insider Vol. 16 No. 05/15 petpla.net Supported by: is the quality issue first and foremost, combined with the difficulties encountered in opening up new markets, especially with closed borders and political unrest to take into account. Nevertheless, as Djamel Ouadah and Yacine Menguellat confirm, there is the political will this year to promote export as well as material imports. As Mr Menguellat says: “The Algerian authorities are ready to boost and support those local companies that have achieved such high potential and are very likely to allow them to enter the international market.” At PTD they agree that the closed Algerian market will open up and the company is keen to be ready for this when it does happen. Backed by credit from the BEA (Banque Extérieur d’Algérie), plans are afoot to implement the next big project by 2018, namely, the construction of a third site in Algeria. The administrative formalities for the expansion have already been completed and a 10ha plot has been purchased. The project involves the relocation of 60% of PTD’s production to the new site and both the re-deployment of existing and the procurement of new machines form part of the plan. www.ptd-dz.com Short cycle times, high shot-to-shot quality, low energy consumption and maximum flexibility. The new XFORM 300 with its unique 6-position post-mold cooling system boosts your output performance for the widest range of preforms. Cooling preforms faster and better, the 96-cavity platform is ideal for large runs and quick mold changes. And it lets you run any mold you want, old or new, OEM-built or not, in total freedom. From ultra-thin walled (with proprietary XMould™ technology) to wide mouth. XFORM 300, low transformation cost, high value. SIPA S.p.A. - Via Caduti del Lavoro, 3 - 31029 Vittorio Veneto (TV) - Italy Tel. +39 0438 911511 - Fax +39 0438 912273 - e-mail: sipa@zoppas.com www.sipa-xform.com Designed to adapt. Built to last. The new XFORM 300 IMAGINE THE LOWEST TRANSFORMATION COST. IN TOTAL FREEDOM. Next... In the upcoming issue you will read about our appointments in Morocco with: Chaouen Water June 16, 2014 PET Preforms Morocco June 17, 2014 Appe Morocco June 18, 2014 Les Huileries du Souss June 23, 2014","@ID":21}, "MARKET SURVEY 29 PETplanet insider Vol. 16 No. 05/15 petpla.net Appe S.B.E.C.M. Empacar S.A. Société Générale des Techniques (SGT) Novapet, S.A. Ellice Way, Wrexham Technology Park, Wrexham LL13 7YL, UK +44 1978 317 378 www.appe.com Ms Kinza Sutton Marketing Manager +44 1978 317 378 Kinza.Sutton@appe.com Rue de la plaine 47230 Lavardac, France +33 5 5397 4100 www.sbecm.com Mr Jean-Luc Didouan General Manager +33 5 5397 4100 +33 5 5365 8597 jean-luc.didouan@sbecm.com Casilia de Correo 2865, Santa Cruz de la Sierra, Bolivia +591 3 34 655 25 www.empacar.com.bo Mr Carlos Limpias Plant Manager +591 3 34 655 25 +591 3 34 618 83 climpias@empacar.com.bo 3 Rue de l’Île Macé 44412 Rezé, France +33 2 4005 0937 www.sgt-pet.com Mrs Le Claire Sales Administration Manager +33 2 4005 0288 +33 2 5170 0155 m.leclaire@sgt-france.com Zaragoza 50001 - Spain Paseo Independencia,21, 3rd floor + 34 976 216 129 www.novapet.es Mr Antonio Lázaro Preform Business Manager + 34 976 216129 + 34 901 021138 alazaro@samca.com Yes No No No No Yes Yes No No In project Yes, according to customer requirements Possible, according to the customer's needs No No Wide PET resins portfolio by Novapet Yes, from 1% - 100% 25% - 30% on regular request; could go up to 100% if it is the customer's request. Yes, 10% - 100% RPET content, clear and coloured 0% to 100% according to the client request 10-25% All colourants and barrier technologies AA scavengers, blockers, colouring agents (liquid or masterbatch), O2 absorbers, additives, blends, etc Activer barrier , O2 scavenger All colours, UV blocker, AA reducer, O2 scavenger, CO2 scavenger, reheat additive, white colour for UHT milk, gliding agent Concentrates (for milk and light sensitive products), colours, lubricants, nucleants, customer requirements Appe has a wide range of preform sizes and weights. Appe supplies preforms for use in bottled water, CSD, food, dairy, home and personal care, alcohol, industrial and other applications. Neck finish : 30/25 High and Low, 29/25, PCO 28 (1818, 1881), BPF, 38mm, 48/41, BVS, 21/29, 36/29, 28/400, 28/410. Preform customisation possible. Neck finish adaptation. Preform weight : 10g - 91g For any application and size: water, softdrinks, wine and spirits, oil, milk and dairy products, housecare, etc PCO 1810 (17,5g - 64 g) PCO 1881 (20.6, 23.1,46.6,54.6 g) Bericap 38 mm wide: 70,80g Bericap 48 mm wide: 85,94g 700 g preform for 5 gallon water bottle 29 mm edible oil : 18,21, 24 g 30/25 High neck and low neck: 13g - 44g 29/25 (without step): 8,6g - 35,8 29/25: 8,8g - 36g PCO 1810: 16g - 52,5g PCO 1881: 14,4g - 50g 28 BPF: 20,5g - 53g 38mm: 14g - 44g 38mm 43/36: 14g - 16g 38mm 43/36,5 (without step): 26g - 32g 38mm 43/36,5: 14g - 28,5g 48/40: 77g - 160g 21/29: 20g - 25g 28/22: 23g; 28/410: 19,5g - 40g 28/410 with anti back off system: 34g - 40g BVS 30 H: 40g - 53,5g CRC63: 445g Ø 29/25 W (short neck): 330ml to 2.000ml: 10.5g - 32g Ø 30/25 W (std neck): 330ml to 2.500ml: 12,5g - 35g Ø 48mm W: 5.000ml to 10.000 ml: 77g, 82g & 98g Ø PCO 1810 (std neck): 500ml to 3.000ml: 18,5g - 54g Ø PCO 1881 (std neck): 500ml to 2.000ml: 19,5g - 38,7g Ø 38mm: 500ml to 5.000ml: 23g - 68g Any other shape and weight under customer requirements Petainer UK Holdings Limited Alpla-Werke Alwin Lehner GmbH & Co. KG Tavistock House (North), Tavistock Square London WC1H 9HR, UK +44 207 3874 294 www.petainer.com Mr Clayton Black Product Manager +44 7833 324 428 clayton.black@petainer.com Mockenstrasse 34 6971 Hard, Austria +43 5574 6020 www.alpla.com Mr Hermann Riedlsperger Head of Corporate Sales - PET +43 5574 602 515 +43 5574 62017 515 hermann.riedlsperger@alpla.com No Yes Yes No HDPE, CPP, PET Yes up to 100% : refPET 30%; One way 25-100% Yes, on request colour, scavenger, easyfill, closure, barrier All customary additives 200ml - 30l Softdrink preform: 0,25-2,5l; various neck versions Water preform: 0,25-19l; various neck versions Edible oil preform: 0,5-10l Milk preform: 2-start, 3-start; various neck versions various neck versions for: preforms for personal care, home care, lubricants","@ID":31}, "EDITOUR REPORT 18 PETplanet insider Vol. 16 No. 05/15 petpla.net 2012 the company installed three Husky HyPETs, each with 72 cavities and, in 2013 and 2014, a further three Husky HyPET HPPs, each with 144 cavities. “Our 4th HyPET HPP with 144 cavities is scheduled for later this year. In addition, we have placed an order for a new Intravis PreWatcher“. PTD’s capacity is currently around 75,000t of material a year, although actual output is about 35%, around 26.000t, corresponding to some 550 million preforms. The portfolio features six weight categories between 15g and 34g in the 30/25 neck, in the case of PCO 1810 eleven types between 18g and 53.5g, in the PCO 1881 36g and 48g, as well as a size 38 neck, 28g, and two size 40 necks at 85g and 92g respectively. Closure production started in 2001. PTD produce 975 MT closures ranging from 1.79g to 3.10g annually on a SACMI 32 cavity compression machine, a Husky HyCAP with 48 cavities and a Netstal Synergy with 48 cavities. The company boasts a 153-man strong team at both locations, 20% of whom are currently completing a course of training at university. “It is here that the next generation can gain practical experience and then we take them on depending on their specialisation“, says Djamel. The company supplies around 100 customers in Algeria. “We have customers in all sectors“, he continues. “90% of our preforms go to bottlers of beverages and edible oils, cleaning agents and beauty care account for the rest”. PTD’s customer base includes water bottlers Saida, Guedila and Ifri, CSD bottlers Hamoud Boualem and Cevital in the beverages and edible oils sector. The net assets of the company grew from US$13.1m in 2010 to US$25.2m in 2014 with a balance sheet total of US$42.8m. The declared aim for 2015 is to increase output to 50-60%. Mr Yacine Menguellat says: “What we want in the medium term is to achieve a production quantity of 2 billion preforms and thereby significantly boost our export business. If we achieve this, we will become, along with our competitor SGT, the largest producers in North Africa. We envisage something like half of our products entering the local market and the other half going for export”. The company’s guiding principle is to concentrate exclusively on the theme of injection moulding whilst resolving other issues, such as, for example, that of transport with service providers. PDT has achieved certification to DIN ISO 9001:2008, less in the interests of achieving acceptance on the national and (in future) international business fronts, but rather in its own interests, as the team explained to me. This year they will also be applying for certification to ISO 22000. They confirmed that, up to now, export has been something of a closed book. There f.l.t.r.: Yacine Menguellat, Habiba Ouadah and Djamel Ouadah in front of the HyPET 500 PTD’s production hall","@ID":20}, "EDITOUR REPORT 15 PETplanet insider Vol. 16 Algeria A meeting with Algeria’s preform market leader SGT - Société Générale des Techniques | February 13, 2015 We met: Mr André Plotnikowa, Managing Director Mr Mohamed Yazid Bounoua, Human Resources Manager In Rouiba, around 30km East of Algiers is located the subsidiary company of the familyrun preform manufacturer group SGT (Société Générale des Techniques) France. Here we meet André Plotnikowa, Managing Director and Mr. Mohamed Yazid Bounoua, Human Resources Manager. The SGT group started operations manufacturing PVC compounds for the bottling industry in France in 1981. With the growing interest in PET bottles, SGT France eventually retrofitted in 1996, continued the PVC division until 2000 before discontinuing it. From then on, they concentrated on the production of PET preforms. SGT Algeria’s founder and Managing Director Mr André Plotnikowa remembers: “I came to Algeria at the end of the 90s because of a project in the water engineering sector for a water bottler and rapidly realised there was a future growing demand for PET preforms on the Algerian market. The trend here clearly indicated a new direction and a change","@ID":17}, "PETproducts 40 PETplanet insider Vol. 16 No. 05/15 petpla.net Penn Color launches frost-effect polymer colorants American company Penn Color, which is headquartered in Doylestown, Pennsylvania, has launched a new line of frost-effect colorants under the Pennacle Frost brand. They are intended for use in commonly-used blow moulding polymers. Penn Color says that the new line will provide brand owners with a vehicle to differentiate their beverage, personal care and household packaging products, and feature an “enhanced matte” finish that is designed to emulate the decorative spray process associated with cosmetic, ultra-premium spirits and other high-end consumer products. The company asserts that, by integrating the frost effect into the masterbatch, users can eliminate the ancillary costs associated with the secondary decoration process. Penn Color further claims that Pennacle Frost can be tailored to meet required levels of translucency or opacity and thus help achieve an “aesthetic continuity” – i.e., a common appearance – across various hues. The company says that the colours are formulated to be compatible with active and passive barriers and to comply with regulatory requirements, including those covering high alcohol content. The frost colours launched under the Pennacle Frost brand use Penn Color’s Pennacle (patent pending) carrier technology, which is claimed to provide consistent colour from bottle to bottle, along with improved reheat properties for two-stage platforms. Penn Color says that Pennacle Frost colours do not require pre-drying, and that they help to deliver cost savings when compared with traditional colour Masterbatches, by allowing higher pigment loading of the colorant for reduced LDR. The Pennacle Frost colour range includes Amethyst Blast, Ruby Ember, Frozen Sky, Emerald Ray, and Blazing Topaz. www.penncolor.com The first U-boat in a PET bottle The German company U-Boot Getränke has introduced a new “bottle-in-the-bottle” packaging concept to the beverage market, one that was available for decades only in selected restaurants and pubs. The classic “U-boat” is a schnapps glass filled with high-proof spirits that is dropped into a glass with soda. It had previously been impossible to order a U-boat in clubs, bars, or the like where drinks were dispensed only in bottles. Together with Greiner Packaging, U-Boot Getränke has now developed this new kind of packaging that pays tribute to the “mixed drink” concept. The new type of packaging provides U-boat drinks for the first time as filled, finished products and is particularly suited for skiing areas, as well as clubs and discos. Both bottles are sealed with the same cap which, when unscrewed, detaches the smaller inner bottle, the “U-boat”, from the seal. The U-boat then sinks in the bigger outer bottle. The inner bottle 30ml and outer bottle 140ml are both made from PET and produced by injection stretch blow moulding. The outer bottle is then screen printed with UV drying colours. The HDPE seal is injected and pad printed. One seal is used for both bottles. The small bottle comes with a snap-on neck and the large bottle with a screw-top neck. www.greiner-gpi.com The plastic closure company committed to your success BERICAP Technology Research and Development Mould Technology | Global Presence Capping Technology and Know-How Innovation and Flexibility www.bericap.com","@ID":42}, "imprint EDITORIAL PUBLISHER Alexander Büchler, Managing Director HEAD OFFICE heidelberg business media GmbH Häusserstr. 36 69115 Heidelberg, Germany phone: +49 6221-65108-0 fax: +49 6221-65108-28 info@hbmedia.net EDITORIAL Heike Fischer Gabriele Kosmehl Kay Barton Michael Maruschke Ruari McCallion Waldemar Schmitke Wolfgang von Schroeter Anthony Withers MEDIA CONSULTANTS Martina Hirschmann hirschmann@hbmedia.net Johann Lange-Brock lange-brock@hbmedia.net phone: +49 6221-65108-0 fax: +49 6221-65108-28 France, Italy, UK Elisabeth Maria Köpke phone: +49 6201-878925 fax: +49 6201-878926 koepke@hbmedia.net LAYOUT AND PREPRESS EXPRIM Werbeagentur Matthias Gaumann | www.exprim.de READER SERVICES Till Kretner reader@hbmedia.net PRINT Chroma Druck & Verlag GmbH Werkstr. 25 67354 Römerberg Germany WWW www.hbmedia.net | petpla.net PETplanet insider ISSN 1438-9459 is published 10 times a year. This publication is sent to qualified subscribers (1-year subscription 149 EUR, 2-year subscription 289 EUR, Young professionals’ subscription 99 EUR. Magazines will be dispatched to you by airmail). Not to be reproduced in any form without permission from the publisher. Note: The fact that product names may not be identified as trademarks is not an indication that such names are not registered trademarks. 3 PETplanet insider Vol. 16 No. 05/15 petpla.net dear readers, The crowds of attendees and the clamour of working equipment that filled the giant exhibit halls at NPE 2015 told the story better than numbers, but now there are statistics to make it official: NPE 2015 was the largest show in NPE history. The data shows NPE 2015 attracted 2,029 exhibitors over 104,813m² of exhibit space-exceeding the previous records of 2,009 exhibitors and 1,041,000 net 96,712m². In addition, registered attendance for NPE 2015 was 65,810 - 19% greater than three years ago. By comparison to this, the last K-Fair in Düsseldorf covered a net area of 171,000m² and registered some 217,000 turnstile movements or approx. 87,000 visitors (average duration of visit 2.5 days). International participation also set new NPE records. Nearly 44% of exhibiting companies and 26% of registrants came from outside the United States. This finally confirms that the decision to move the NPE from Chicago to Orlando was the right one. The target group from Central and South America now feel that they are also getting their fair share of attention. Nearly 5,000 registrants were from Latin America alone. All the names from the PET sector, great and small, were represented, not every company with a huge PET presentation. Milacron uses the fair to showcase its old and new PET activities and Husky has long regarded the NPE as a kind of in-house exhibition and pulled out all the stops. After its eventful journey, our Editourmobil had finally made it to the fair from the harbour in Halifax. And so, for PETplanet Insider too, it was a pleasant family get-together on the North American continent. We shall look forward to seeing whether this highly positive development is likely to be continued at the NPE to be staged from May 7-11, 2018. Yours Alexander Büchler","@ID":5}, "PREFORM PRODUCTION 38 PETplanet insider Vol. 16 No. 05/15 petpla.net Please order your copy at the PETplanet insider book shop: https://petpla.net/books Bottles, Preforms and Closures A Design Guide for PET Packaging Second Edition by Ottmar Brandau € 115,00 180 pages © Copyright Elsevier 2012 * This article was published in Bottles, Preforms and Closures, Ottmar Brandau, Chapter 3.8. Copyright Elsevier 2012 bottom cavities are colder than they need to be. Furthermore, preform parameters, especially in the gate area, will be different and may cause some preforms to be rejected. In order to balance the water flow to cavities or cores for that matter the supply and return path of the water should be equal. This can be achieved by the arrangement shown in Fig. 3.26. Although the bottom cavities receive water first and thus at the highest pressure and flow, the return flow path is longest, whereas it is the opposite for the top cavities, and so the total path of coolant is the same for each cavity. The way it is shown here would mean that water enters from the bottom and leaves from the top. This is often not practical because electrical connectors may be mounted on top of some tools. In this case, a third water line can be drilled that travels behind the two shown here, taking the coolant down to the bottom level. 3.9 Tool wear issues Preform tools have a number of wear parts such as heater bands or valve gate cylinders. These will be replaced during run times by maintenance personnel and are no reason to replace the tool altogether. However, when the taper locks wear out, it is usually time to either replace or at least refurbish the tool. Taper locks are the parts of the neck inserts (male side) and cavities (female side) that engage during closing and clamping and transmit the clamping force onto the tool. As these parts start to wear, they do not close as tightly and flash develops. When the flash exceeds a certain value [different for different geographical regions and brand owners but around 0.13 mm (0.005 in) per side as per the neck drawing], the tool is usually finished. There are several reasons why taper locks wear out even when they are properly hardened, assembled, and run. Tolerances in the manufacture of the injection machine platen, the tool plates, and the indi-vidual taper lock parts lead to slight misalignments, which do not allow all tapers in a multicavity tool to match perfectly. Clamping force is also not perfectly balanced (a difference in machine construction users should be aware of as there are differences between manufacturers), leading to some tapers receiving more clamping pressure than the others. Accumulation of dirt is another factor that forces tapers together unevenly. On horizontal machines, gravity also plays a role. Ninety degrees opposed to the closing action gravity leads to a slight sagging of the moving tool side after the bushings or linear bearings holding them have worn to some degree. Vertical machines do not suffer from this particular issue and feature indeed very impressive tool lives but have not been able to capture a lot of market share as they are more difficult to work on and require more energy to move the tools. With today’s fast-running machinery, tool wear has become a hot topic for users. Imagine a machine running a 7-s cycle time for a lightweight water bottle preform. If used 350 days/year and 24h/day, this machine will wrap up over 4 million cycles per year. Tools on horizontal machines are meant to last about 8 million cycles, which translates into a 2-year life for this tool. Some mould manufacturers now guarantee this number of cycles using the aforementioned flash value as benchmark. Figure 3.25 Top cavities receive less cooling than bottom cavities. Figure 3.26 The path of the coolant to and from each cavity is the same.","@ID":40}, "EDITOUR REPORT 10 PETplanet insider Vol. 16 No. 05/15 petpla.net Nuremberg Milan Rome Naples Palermo Tunis Algiers Rabat Casablanca Marrakech Seville Madrid Lisbon Bologna Monastir Agadir Tangier Valencia Cordoba Bilbao Oporto Andorra La Vella Venice Turin Florence Messina Barcelona Zaragoza North Africa Part 2 Tunisia and Algeria Continuing on our Go to Brau Beviale Tour 2014, we now arrive at the markets of North Africa. Here, as we already noted in PETplanet Insider 4/2015, we experience some interesting contrasts between the current situation and future ambitions. The effects of the different political situations and regulations in these three countries, as well as the undoubted potential, only serve as further inspiration to the local PET sectors. We started in Tunisia, where, between the end of April and the beginning of May 2014, we met recyclers Green Line and Sogedes, together with converters La Preforme and Omega Maghreb in the metropolitan area of Tunis. The next stop on our tour was intended to be Algeria; however, we had visa difficulties here in the early summer of last year with the result that it was February 2015 before we were able to catch up on our appointments with preform manufacturers SGT and PTD. by Kay Barton","@ID":12}, "INSPECTIONS / LABORATORY EQUIPMENT 32 PETplanet insider Vol. 16 No. 05/15 petpla.net Specified testing AGR Combitester for both capacity and top/side load measurements Tests on preforms and containers include numerous measurements for dimensional accuracy, mechanical, physical and chemical tests. Several functional tests for example of hot-fill distortion, stress cracking resistance, drop and leakage, as well as additional non-standard tests are possible. As far as materials characterisation is concerned, Sipa Lab has competence not only in PET, but also in polyolefins (PP, HDPE), polystyrene, and such biopolymers as PLA and PHA. For CSD applications, the Lab is equipped with a small filling line to pressurise the bottles and replicate industrial process. Versatile tests One particularly versatile tool that Sipa Lab has at its disposal is a FT-IR spectrometer. This can be used to determine the loss of CO 2 from bottles and is able to characterise a material by determining the functional groups it contains, helping to identify possible additives and analyse chemical compatibility. The FT-IR equipment can be used in an ATR (attenuated total reflection) configuration, which enables samples to be examined directly without special preparation to determine the characteristics of the surface layer of a product with near-infrared radiation. Tests for non-standard containers Sipa Lab is equipped with instruments, some developed internally, for the characterisation of non standard containers, such as large kegs for CSD and beer, as well as large containers for dispensers. Among other properties, handle resistance, top load and burst strength can be carried out. Out-of-the ordinary tests Sipa Lab finalises the measurement of acetaldehyde levels with gas chromatography by using the ground parison method. Measurement of moisture levels in granules, preform or container is completed by using a Karl Fischer titrator. The laboratory is even equipped with a UV-visible spectrophotometer. An additional application available is a small pasteuriser which technicians use to simulate sterilisation and pasteurisation cycles. The use of a data logger helps to monitor the temperature and pressure of the content during the process. A unique instrument that has been developed internally used principally for lightweighting research projects permits testers to determine the falling angle of a bottle and to observe the behaviour of the bottle during poring. CO 2 loss, O 2 gain Among the tests that the company regularly carries out in conformance to the normal protocols of the major players in the market, there are some rather particular ones that can be used to determine product shelf life. “We are able to determine the loss of carbon dioxide and, in the case of products susceptible to oxidation, oxygen uptake, using various techniques, depending on the protocols of various clients,” says Roberto De Luca at Sipa, who notes that the company is a certified laboratory for major players. Characterising barrier performance Sipa Lab is able to characterise existing containers and develop new barrier packaging, using oxygen scavengers, PET/PA co-injection, or special coatings. It uses a variety of tools to determine the mechanical and physical characteristics of coatings, including various devices to test for hardness, adhesion and abrasion resistance. www.sipa.it Sipa, the PETpreform and container producer, has comprehensive laboratory facilities that enable it to carry out an extensive range of tests for different shapes and sizes of preforms and containers, including jars, handled containers and beer kegs. Caps, closures and separate handles can be tested for the materials they are made. Mocon Oxtran for O 2 uptake measurement I N S P E C T I ON S & L A B O R A T O R Y E Q U I P M E N T","@ID":34}, "BOTTLE MAKING 23 PETplanet insider Vol. 16 No. 05/15 petpla.net SGT, naturally innovative The specialist in PET preforms and HDPE caps for over 30 years. +33 (0)2 40 05 09 37 /www.sgt-pet.com The Husky line is being launched in more and more areas. Next to the machine are the dryer and blender. Premium Sponsor Sponsors metal lid and then transferred into the pasteuriser. Here hot water at a temperature of 75°C trickles on to the container for 30min. The lid plays a critical role in this part of the process because it does in fact stay at this temperature for the whole period. The neck area is designed in a correspondingly complex manner to withstand the high temperature. For their own brand products, the manufacturer will use a 12oz square container. As a further stage in development, 10oz and 16oz round containers are scheduled to follow. These are intended for private labels. www.themonarchgroup.com www.globalformslimited.com","@ID":25}, "BOTTLE MAKING 22 PETplanet insider Vol. 16 No. 05/15 petpla.net Specialist custom blow moulder by Alexander Büchler For Monarch Plastics, Brampton, Canada, the customer’s requirements are always unique. They view every PET bottle as a new challenge. The latest highlight is a stretch blowmoulded, pasteurisable wide mouth container with injected neck for Maraschino cherries, complete with a standard tin-plate twist-off lid for glass containers. David Lewis, Director of Engineering at Monarch, is rather proud of this development- which is unique worldwide. The PET sector is handled by Fayyaz Khan. He produces preforms under the Globalforms brand name. Both companies belong to The Monarch Group with two plants in Canada and one plant in United States. In fact, pasteurising represents new territory for the company. For a number of years they have been producing containers from polyolefins. Their main customer here is S.C. Johnson. Target markets include the Personal Care, Home Care, Hair Care, Automotive, Food, Promotional and Pharmaceutical Industries. However, over the last few years, PET has become more widespread alongside the traditional blow moulding business. Initially containers were stretch blow moulded on Amsler and Automa and preforms for in-house use on Huarong - Taiwanese lines. Since then, three Sipa stretch blow moulders have joined a Husky Hypet 225 preform injection machine. Globalforms produces special neck finish preforms for variety of bottles and standard preforms for hot fill bottles. The new Maraschino cherries project is running on two Aoki SBIII500-150 lines with seven cavities each. Each project is not only a technological challenge for the Monarch team, it is also a logistical one. The customer may well come up with an idea, but that is no guide as to how the product will ultimately be received by the market. In such cases Monarch adopts a multilevel approach. In the case of the pill bottles project, Monarch initially produced stretch blow moulded containers from blow/trim neck in PET. The 250cc size bottle weighed 27g. With this the customer was able to conquer the market. As a second step they switched over to stretch blow moulding in PET with injected neck using a preform produced by Globalforms. The bottle looks the same from the outside but weighs a mere 17g. In total just under 400mill. containers leave the plant each year. The new cherry project means that some 50mill. of these are PET containers. This brings us back to the containers. The cherries are bottled warm in the containers, sealed with the The Aoki line with 7 cavities with adjacent palletising for the cherry project.","@ID":24}, "INSPECTIONS / LABORATORY EQUIPMENT 24 PETplanet insider Vol. 16 No. 05/15 petpla.net Preforms inspected all around Today’s production processes in the plastic packaging industry are faster and more elaborate than ever. They are driven by end-users’ continually increasing requirements, industry-wide pricing pressures and increasingly strict legal requirements, which demand that a higher proportion of material should be recovered and recycled. These factors – and the use of recycled material in particular – combine to make preform production more challenging. Black spots, bubbles, contaminates, colour variation and a range of other faults and errors can impair the quality of the end product, and quite visibly. Detailed quality inspection In order to avoid the quality of the packaging product being compromised in such ways, quality inspection – mainly inline, undertaken during the production process – is necessary. Furthermore, inspection should not add to production cycle time, faulty items should be sorted out automatically. Intravis, a leading producer of optical inspection systems for the plastic packaging industry, says that its PreWatcher III meets all these requirements. According to Intravis, the system incorporates “state of the art” inspection technology and has been optimised for integration into the production line. It undertakes 100% inspection of preforms, during production and according to defined error types, at rates up to 72,000 objects/h. Visitors to NPE 2015 in Florida were able to witness demonstration presentations and see for themselves how the PreWatcher III delivered on its promises. The PreWatcher III At eight square meters, PreWatcher III’s has a very small footprint. Intravis says that is made possible by an advanced process that adjusts and inspects the objects. Its newly-developed orientation mechanism uses centrifugal force. After a gentle adjustment, preforms are transported into a presentation device at controlled intervals. The preforms are first transported by the neckring, which enables both the mouth and the base areas to be visible from above. Then the preforms are sucked with their mouth opening towards the presenting device, so they are entirely visible from the side and can be rotated around their own axes, enabling inspections from all sides. Eight colour cameras provide 360° inspection. Six of them inspect the body and the thread and the other two inspect the mouth area and the injection point. There are no “dead areas” caused by conveyor belts or gripper arms. The system is constructed in order to ensure inspection of every area of the object. Defective preforms are sorted out by air pressure. Easy to integrate The PreWatcher III can be installed in-line behind an injection moulding machine. Off-line inspections can be provided in combination with a bunker, a dumper and an octabin diverter. Its versatility is yet Eight high-resolution cameras provide an all-around-inspection of the objects I N S P E C T I ON S & L A B O R A T O R Y E Q U I P M E N T","@ID":26}, "MATERIAL / RECYCLING 20 PETplanet insider Vol. 16 No. 05/15 petpla.net Petcore Europe organised a Recycling Rigid PET Thermoforms workshop on March 11, 2015, in Brussels. Brussels workshop shares best practice on PET thermoform recycling Petcore Europe’s workshop on the Recycling of Rigid PET Thermoforms involved fifty leaders and experts from across the European PET value chain. PET producers, converters, users, recyclers, technology providers and collection agencies discussed how the industry can work together to make PET thermoforms the best recyclable thermoformed packaging in its category. “The recycling of PET is a success story,” explained Indorama’s Wim Hoenderdaal, one of the organisers. “It is the only large-scale example in which the circle is closed at the highest level; new high quality packaging can be made out of recycled resin.” Recycled PET is used to make new bottles and thermoforms, particularly PET thermoforms – mainly trays. They are produced with an r-PET (recycled PET) content that is often above 70%, while fully complying with food contact regulations. The one-day workshop covered the current situation in various countries, including Germany, Belgium, UK and France, and was structured in three parts: Collection and Sorting; Packaging Technologies; and Recycling Technologies. Each session was followed by a panel debate where participants discussed and shared knowledge. “PET is the only value chain that takes care of the complete life-cycle of its products, including thermoforms,” said Patrick Peuch, Executive Director of Petcore Europe. “The goal of this workshop was to build and promote a working group to specifically update the state-of-the-art in PET thermoform lifecycle, including design-for-recycling, packaging technologies, collection, sorting and recycling technologies.” Petcore Europe believes that this workshop marks the establishment of a technical platform that will see the most important players of the industry working together to further improve the recycling of PET. Petcore Europe, which is based in Brussels, is the trade association that represents the whole European PET value chain. Its mission is to ensure that the industry and its associations are aligned to deliver increased value and sustainable growth of the value chain, to ensure that PET is positioned and recognised as an environmentally sustainable packaging material, to validate and support innovative packaging solutions from a recycling perspective and to work with all interested parties to ensure the sustainable growth of PET post-consumer collection and recycling. www.petcore.org","@ID":22}, "INSPECTIONS / LABORATORY EQUIPMENT 31 PETplanet insider Vol. 16 No. 05/15 petpla.net Error prevention in bottle manufacture by Kay Barton Air Logic Power Systems (ALPS), an engineering and manufacturing company headquartered in Milwaukee, Wisconsin, USA, have specialised exclusively in equipment to detect defects in containers and bottles. On the exhibition stand at the NPE I met up with Mr Scott D. Heins, Director of Sales & Marketing and Mr Jack Hughes, Marketing Coordinator. Their on-site highlight is the 8-station Speed-Glider, a new linear leak tester. Jack Hughes and Scott D. Heins in front of the Speed Glider A brief flashback. The company, which was set up in 1974, developed its first leak testing machine in 1978; the first high speed system for HDPE plastic containers came along in 1985. During the 1990s further developments in electronic technology followed and, from 2000 on, greater concentration on the changing packaging trend and high speed applications in PET. In 2000 ALPS became a part of TASI Group which, since the beginning of the 1980s, has been active in the test and inspection equipment sector as well as equipment for product measurement. A total of ten companies in the USA, Europe and Asia form the TASI Group. “Our success”, Mr Heins is convinced, “lies in the fact that we focus exclusively on test machinery. As things stand at the moment, we have supplied around 2600 leak testing machines to national and international customers. This corresponds to a total quantity of more than 50billion bottles and containers that our machines inspect annually. About half of these are PET bottle applications”. ALPS’ experience in test equipment extends to all bottle sizes, shapes and materials, from 3ml to 20 litres, from the beverages, food and non-food sectors. “One of the major markets started in the PET hot fill sector and checking for micro-holes. One ever-present problem was bottles that go through the entire filling process without these small defects being found. This is where our high speed rotary leak testers come in. Over the years we have also been focussing on developing a full range of products for high, medium and low speeds. In the rotary sector we are offering leak testers with 4 to 30 stations”. ALPS is also showcasing its NextGen Rotary Leak Tester on the stand. Currently, however, the company is selling more machines from the linear leak tester series. The Speed Glider, which ALPS claims to be the world’s fastest linear leak tester, can be seen in action. The measuring unit, with up to eight heads, is capable of managing up to 500 small-format bottles/containers a minute. The majority of activities today are in the medium and low speed lines sectors. Here ALPS is concentrating on extending the capacity of linear test machines. “Visual testing for PET bottles, as is quite common around the world, is a valuable tool but not fully effective for detection of the most critical defects. We see a growing trend for leak testing in all sectors as a simple and reliable means to detect defects that cannot be reliably found using other means. Market trends in our favour include the drive to zero defects, lightweighting and the use of rPET. In addition to micro-holes, our technology is also able to identify defects in the area of the neck and/ or seal. We use a very low measuring pressure in our machines to maximise the sensitivity for seal and body leak detection”. ALPS’ customer base incorporates all the well-known blow moulding companies and products without exception. One forecast for the company’s future predicts major potential in Asia due to inevitable increases in automation and quality demands as the markets mature. “Our business will grow there as the markets evolve towards quality standards similar to those in the USA or Europe. In the interests of improving presence and service”, Mr Heins goes on. TASI Group is combining the activities of the Advanced Package Test and Inspection Division with ALPS and the other two companies from this section of the Group (Bonfiglioli Engineering and Sepha) this year and merging the sales and service teams. Consideration is also being given, as part of a global expansion exercise, to a range of different production locations in the future. Currently ALPS offers service from its facility for the USA. Europe is serviced by the group companies and, from this year, a further local service facility will be inaugurated in Asia. “A global presence is what we want and this is what we are working on just at present”. www.alpsleak.com I N S P E C T I ON S & L A B O R A T O R Y E Q U I P M E N T","@ID":33}, "CAPPING / CLOSURES 34 PETplanet insider Vol. 16 No. 05/15 petpla.net International teamwork turns an idea into a point-of-sale product Dispensing Caps 2.0: Refillable packaging for additives or decorative closure for convenience beverages – the new-generation dispensing cap from Incap Ltd. offers a host of new possibilities for innovative product design. Developed by an international project team, the versatile dispensing cap was turned into a point-of-sale product by two companies: Hähl and Teamplast. Consumers are prepared to pay more for functional beverages enriched with nutrients or healthboosting additives. This trend allows beverage producers to move into a lucrative growth market, more so as their product innovations also cater to another emerging trend: convenience products. Enriched with vitamins, minerals or probiotics, the new beverages offer on-the-go solutions, which can be conveniently consumed directly after a workout or during lunch breaks. When dispensing caps become refill products In order to avoid the use of preservatives and prevent detrimental effects on or even loss of the effectiveness of additives after long storage, manufacturers have developed a dispensing cap that contains dry or even liquid additives in a separate chamber inside the cap. Twisting the cap, the consumer only triggers the mixing procedure when the product is about to be consumed. The patented, lightweight dispensing cap for PET bottles developed by Incap Ltd. now adds another benefit for beverage producers to the equation: maximum freedom of product design and additive options that can be tailored to individual consumer requirements. The dispensing cap is suitable for liquid additives as well as for granules, hot or carbonised bottled beverages. There is more: as the bottom of the cap is hermetically sealed, it can be sold in combination with the beverage or as an additive refill product. Athletes can conveniently carry their additives in their gym bags, children can mix in apple or orange flavours while they are travelling on the back seat of a car – there is no end to the creative potential of this innovative product, as Axel Hauck, co-owner of Incap Ltd. explains. Fine-tuning within an international teamwork This project is a perfect example of successful international teamwork. The German company Horst Hähl Kunststoffspritzguss & Werkzeugbau GmbH and the Dutch plastics specialist Teamplast supported Hong Kong-based Incap Ltd. at all stages of product development right through to market maturity. While the new Incap dispensing cap has a complex design, it also meets a wide range of optical, tactile, safety and hygiene specifications and provides the required ease of operation. Featuring wall-thickness levels of less than one millimetre and an extremely complex geometry, the cap has to withstand high pressure and different temperatures. The sealing properties must not be jeopardised, particularly when carbonised beverages or hot liquids are being bottled. All project partners provided input for the processing-related finetuning. Hähl supplied expert information on prototyping and pilot moulds, Teamplast, certified expert for plastic closures, supported the manufacturer with constructive optimisation measures to ensure profitable and efficient large-scale production. Prototype and large-scale production on Sumitomo (SHI) Demag injection moulding machines In order to meet the product’s exacting precision and repeatability requirements, Hähl carried out the production mould optimization trials on an all-electric Sumitomo (SHI) Demag IntElect injection moulding machine. Teamplast also ran their large-scale production with injection moulding machines from the GermanJapanese manufacturer with headquarters in Schwaig near Nuremberg. The Dutch specialist operates a total of 30 Sumitomo (SHI) Demag injection moulding machines. Jürgen Mangold, Managing Director of Horst Hähl Kunststoffspritzguss & Werkzeugbau GmbH and Axel Hauck, Director Incap Europe talk about the different project stages and the special features of the new Incap dispensing cap: How did Hähl and Incap come to be project partners? Mangold: We knew Mr Hauck from earlier projects. After we encountered problems with our prototyping mould in China, he suggested that his company Hähl take on the development of the prototyping mould as well as the optimisation, construction and final design of the production mould. Together with Teamplast, we optimised the mould for large-scale production.","@ID":36}, "BOTTLING / FILLING 39 PETplanet insider Vol. 16 No. 05/15 petpla.net Saving energy, step by step Overheads for materials and the price of energy are among the biggest cost drivers in production. PepsiCo Deutschland GmbH charged KHS with the modernisation of their Punica PET bottle filling line at their site in Hamburg, Germany. When several hundred thousand PET bottles are manufactured and filled per day, a lot of electrical energy is used. For PepsiCo Deutschland GmbH electricity consumption is a relevant factor in its operating costs, a factor the company wished to minimise. Together, PepsiCo Deutschland GmbH and KHS therefore analysed the line’s energy-saving potential. As a result, KHS first modernised the blow air infeed on the KHS InnoPET stretch blow moulder from 2008 (a Blomax Series III Compact) in operation at the plant. With the help of KHS AirbackPlus system up to 35% of the blow air is now recycled, which has a positive effect on the process’ energy consumption. The next step involved KHS renewing the geometry of the line’s heater box in fall of 2014. The savings from this second optimisation measure are primarily achieved by the use of modern ceramic materials in the preform heater boxes. The reflective properties of the ceramic elements greatly improve the energy distribution in the heater box. The tunnel in the heater box has been made smaller so that less energy is needed for heating; energy can now be deployed when conditioning preforms in the heating process. Here, a more efficient unit comprising a reflector and infrared emitter prevents the sensitive bottle thread area being unnecessarily heated. The amount of cooling of this area can then be reduced. These technical features generate an energy saving of up to 30%. “At PepsiCo Deutschland we’re always trying to save energy to cut costs and protect the environment. We can check the heating profile of the modernised system on an energy monitor, allowing us to measure and document all significant savings. KHS converted our line quickly and competently without affecting system operation,” states Jens Hadler, project engineer at PepsiCo Deutschland GmbH. Heater boxes are converted in a maximum of one to two days. KHS process engineers make the small final adjustments during the startup phase so that disruption to production is kept short. “Through the amount of energy saved, investing in a modernisation of the durable InnoPET Blomax Series III pays off for customers after one to three years depending on the line’s capacity utilisation and the price of electricity,” explains Dirk Teschner, project manager at KHS Corpoplast. “We can retrofit any of our stretch blow moulders in the InnoPET Blomax Series III quickly and easily with cutting-edge preform heating technology.” For many companies, energyoptimised PET stretch blow moulders are an excellent way of reducing production costs. Teschner estimates that “After the successful conversion project at PepsiCo last year we’re expecting orders from other customers, too, for the upgrade of about 50 more lines in 2015.” www.khs.com www.pepsico.de","@ID":41}, "PETpatents www.verpackungspatente.de 48 PETplanet insider Vol. 16 No. 05/15 petpla.net Optimised manufacturing International Patent No. WO. 2014/127901 A1 Applicant: Alpla Werke Alwin Lehner GmbH & Co. KG, Hard (AT) Registration date: 02/15/2014 An improved method for making a container using the stretch blow-moulding process is described. The support ring integrated into the preform is “reused” as part of the container shoulder and is in close proximity to it. This allows for a more attractive container and closure design. Destruction of product capsules European Patent No.EP 2749502 A1 Applicant: Colgate-Palmolive Comp., New York (US) Date of Application: 21.4.2011 A disc similar to a filter with sharp edges is inserted into the neck of a container which stimulates/destroys the capsules inside the product that contain a second product. The two products are mixed together shortly before use and are able to react with one another. Bottom section mould European Patent No.EP 2752369 A1 Applicant: Yoshino Kogyosho Co. Ltd., Tokyo (JP) Date of Application: 29.8.2012 The shape of the bottom section of a hot fill bottle or a bottle containing carbonates needs to be specially designed and by definition capable of elastic deformation so as to be able to absorb differences in pressure without having a negative effect on the stability or external shape of the bottle. Pressure compensation opening European Patent No.EP 2752370 A1 Applicant: Yoshino Kogyosho Co. Ltd., Tokyo (JP) Date of Application: 8.8.2012 Multi-layer plastic bottle and process for manufacturing the said bottle inclusive of the insertion of an opening for pressure compensation (to allow air to flow in) in the neck area. As air flows in, one layer of plastic is delaminated and the product chamber formed by the internal layer is reduced in volume. Foam dispenser European Patent No.EP 2752374 A1 Applicant: Yoshino Kogyosho Co. Ltd., Tokyo (JP) Date of Application: 21.8.2012 Squeezable container for absorbing a liquid. Pressure on the container and a corresponding dispensing device generate a foam on output. Anti-drip closure International Patent No. WO 2013 / 041716 A1 Applicant: Maitrise & Innovation, Val de Reuil (FR) Date of Application: 24.9.2012 Structure and operation of an improved closure for a squeezable container. As a result of manual pressure on the container and thus on the product, the closure is opened and, when pressure is removed, is resealed so that it is once again tight and ”drip-free“.","@ID":50}, "Toronto Québec New York Atlanta Orlando Chicago Denver Las Vegas Seattle Calgary Montréal Los Angeles San Francisco Vancouver Dallas Houston Phoenix Washington, D.C. Boston Detroit Halifax Kansas City Oklahoma City Albuquerque www.npe.petpla.net , / 0 Premium Sponsor Sponsors NPE 2015 - The North American Road Show The first leg of our latest trip has been successfully concluded! From the busy harbour of the NPE 2015 our expedition crew has been reviewing all the meetings with the key players of the Canadian and US PET industries on the PETplanet exhibition stand in the South Hall. After resting at anchor awhile in Florida’s tranquil waters, our team of PET bottling Columbuses, consisting of Captain Alexander Büchler, Helmsmen Kay Barton and Waldemar Schmitke, together with Helmsman’s Mate and Able Seaman Rolf, is now steering a course towards the markets of Central USA. Wafted along by gentle zephyrs, the team is embarking on the second part of their voyage of discovery in Texas and will be sailing in a wide arc in the direction of Phoenix, before ultimately cresting the waves along the west coast of the USA, proceeding thence to the west coast of Canada. This is a tour where figures speak louder than words: a total travel distance of around 17,000 km and roughly six months of this thrilling adventure are out there just waiting for you! And, as always, you have the opportunity to accompany the crew interactively by following the entire tour on our weekly travel blog at npe.petpla. net. Please contact us if you would like our editors to make a detour to your own bottling, PET processing, closure cap, material manufacturing or recycling plant. YOU are our story. All aboard! Part 2 The worldwide round trip with","@ID":44}, "EDITOUR REPORT 16 PETplanet insider Vol. 16 No. 05/15 petpla.net from PVC to PET. At the time, I was already in contact with SGT France and suggested the idea of building their own location here in Algeria.” The well-known water bottler Ifri was a pioneer in the introduction of PET bottles in Algeria in 1996, located some 300km to the southeast. Major brands Coca-Cola and Pepsi later followed suit in 1999 and 2000. Due to the lack of an on-site preform supplier, Ifri obtained its preforms from SGT France until 2000. “After I had discussed everything with SGT France, we got going and started with the construction of the plant here in Algeria in 2001. Back then, the company had two Husky GL300 machines with 48 moulds each. At the start, output was around 180 million performs per year. In the following years more Husky systems arrived. SGT Algeria today produces on a total of 15 preform machines in Rouiba (1x LX225, 7x GL300, 5x HyPET300, 2x HyPET300 HPP 4.0), and six at the second plant around 300km away in Sétif (5x HyPET300 HPP 4.0, 1x HyPET300 4.0), a total of 2.8 billion units. Thus, in 2013, the company had a market share of 63% in the processing of preforms, only measuring pure converters and without considering fillers who produce their own preforms. Turnover amounted to €110m. Exclusive contracts exist with Coca-Cola, Pepsi, Nestlé and Henkel. “We are still away from the peak of our performance,” says Mr Plotnikowa. “At the moment, SGT is running at just about 70% of its capacity, there is still room left for improvement. Our current PET consumption amounts to 68,000 tons of resin.” SGT obtains the resin from the Middle and Far East. More than 200 different kinds of preform can be found in the company’s portfolio with 19 different neck finishes plus optional barriers available for applications between 125ml to 20l. In particular, SGT offers 80 preform types for water, 60 preform types for CSD, 26 types for both juices and milk products, seven for especially large filling quantities, five for wine and schnapps, ten for edible oils and ten in the household and cleaning products sector. Mr Plotnikowa went on: “One of SGT’s main advantages is the joint product development with customers which is beyond our own capacity here. We proactively integrate our clients and implement their ideas and suggestions throughout the entire process.” The site in Rouiba comprises of 1850m2 of floor space and employs 145 members of staff, Sétif occupies 1200m2 with 50 members of staff. Preform production was expanded with two Husky HyCAP lines in 2003 that currently produce 800 million caps per year. “We regard Algeria as a closed market,” Mr Plotnikowa continued, “We export to Tunisia and Libya, but only in small amounts. Mindful of the political situation, closed borders and civil unrest, our attention is on Algeria. Exports within Africa via road haulage make little sense, are far too unsafe and costly.” When we asked about environmental issues, it is obvious that we touch a nerve with Mr. Plotnikowa. “As the market leader, protecting the environmental is a major issue for us. We are organising ourselves here with other producers in the APAB (association of Algerian drinks manufacturers) in order to find ways of conserving resources and building an infrastructure for collection and recycling together. But at the moment, the collecting and separation of various post-consumer waste are the main tasks in order to deal with the pollution of the environment. “Our planning is long-term in nature, as bottle-2-bottle is far too expensive at the moment. Apart from that, we would first need the draft legislation in order to be allowed to use recycled materials in bottle production.” There is also a lot to be done with consumers, as awareness of using recycled materials in new packages has until now been low. According to surveys, consumers showed that they are reluctant to purchase recycled materials in the PET bottles of their choice. And just as we came across many times in our meetings with companies in Tunisia, Algerian legislation is also regulating the use of recycled PET materials exclusively to non-food applications. “Our vision,” Mr. Plotnikowa tells us, “is full commitment to matters of environmental protection and recycling. We are responsible for this as a company and want to promote the issue, as we increasingly must!” www.sgt-pet.com André Plotnikowa, Managing Director f.l.t.r.: Mohamed Yazid Bounoua and André Plotnikowa in front of the HyPET 300","@ID":18}, "PETnews 6 PETplanet insider Vol. 16 No. 05/15 petpla.net Karl Finke receives ISO 14001 and 50001 certification Karl Finke GmbH & Co. KG has received ISO 14001 and 50001 certification. ISO 50001 creates the basis for a sustainable policy of energy management. It systematically identifies the potential for enhancing energy efficiencies, thereby creating situations whereby energy-consumption levels and CO 2 -emissions are reduced. Standard ISO 14001 sets out the criteria that are to be met to maintain an efficient and effective system of environmental management. It provides a framework which serves to assist and support companies in their effort to evaluate all of the effects and impacts from the environmental point of view. www.finke-colors.eu IMDvista In-Line barrier inspection at the NPE show 2015 Barrier inspection is not only a life insurance for ensuring every single part has its barrier, but also used to optimise the process. To guarantee the quality of Milacron’s Kortec co-injected KlearCan, an IMDvista BTIR In-Line barrier inspection system was integrated. The fact that the IMDvista BTIR technology allows inspection for barrier content in-line and in motion,with no stop for the camera, made it possible to guarantee 100% production with one single camera. This technological advantage allowed CBW-Automation to integrate a cost effective and very compact single lane handling system. The crystal clear analysis of the IMDvista BTIR guarantees the existence of EVOH and offers the possibility to make fast and safe process adjustments during production and start up. This feature is of great importance for the operator of the injection moulding machine. These advantages of the IMDvista BTIR are a key factor for a fast, efficient and economical co-injection production line. www.imdvista.ch/en Tech-Long introduces G5 PET rotary stretch blow-moulding machine at NPE 2015 Tech-Long has introduced its G5 PET rotary stretch blow-moulding machine at the recent NPE 2015 in Orlando. The G5 machine features single-cavity outputs of up to 2,400bph available on machines ranging from 6 to 32 cavities, while reducing energy use by 10% to 15% compared to previous machines. In addition, high-compressed air recovery is improved to 40% to 55%. Improvements in machine speed result from the use of servo-motors instead of pneumatic stretch rods, an integrated gripper system for faster bottle discharge from the moulds and a new Programmable Logic Control (PLC) which also features a 15 inch touchscreen user interface. Lower energy consumption is achieved using an independently controlled heater, an advanced air circulating system and an optimised heating chain. Preforms are automatically inserted and discharged with less space between each. An integrated blowing unit reduces dead zone air and overall air use. Six valves are used for preblow, second blow, main blow, first cycle, second cycle and air exhaust. The machine requires no low-pressure compressed air. Mechanical seals replace previously used pneumatic seals, reducing air exhaust noise from 92 to 83 decibels. The new G5 PET blow-moulding machine’s unscrambler features an independent central processing unit (CPU), which provides more flexible operation. Programming changes can be made easily and quickly without affecting host machine (blower) settings or production. www.tech-longusa.com Plastipak progresses APPE acquisition PET packaging specialist, Appe, has confirmed that the agreement to purchase Group has now been completed. Plastipak Packaging’s intention to acquire the business, announced last November, is anticipated to be finalised on June 1, 2015. Plastipak Packaging, Inc. a global manufacturer of rigid plastic packaging, was selected by Forest Partners (administrators of La Seda de Barcelona) as the successful bidder to acquire Appe with a winning bid of €360 million. Martin Hargreaves, Appe’s CEO: “As Appe is the market leader for PET Packaging in Europe, the combined Appe and Plastipak business will further strengthen that position. Customers throughout our european locations will not only benefit from an extended geographical reach, but the deal will also see new cutting edge technologies broadening our respective product ranges”. www.appe.com I N S P E C T I ON S & L A B O R A T O R Y E Q U I P M E N T","@ID":8}, "PETcontents 05/15 4 PETplanet insider Vol. 16 No. 05/15 petpla.net INSIDE TRACK 3 Editorial 4 Contents 6 News 40 Products 43 On site 44 PET bottles for Beverage + Liquid Food 46 PET bottles for Home + Personal Care 48 Patents SPECIAL INSPECTIONS / LABORATORY EQUIPMENT 24 Preforms inspected all around 31 Error prevention in bottle manufacture 32 Specified testing MARKET SURVEY 27 Suppliers of PET preforms BOTTLING / FILLING 39 Saving energy, step by step CAPPING / CLOSURES 34 Dispensing Caps 2.0: International teamwork turns an idea into a point-of-sale product BUYER’S GUIDE 49 Get listed! Page 39 EDITOUR REPORT 10 North Africa part 2 MATERIAL / RECYCLING 20 Brussels workshop shares best practice on PET thermoform recycling BOTTLE MAKING 22 Specialist custom blow moulder 36 Bottles, preforms, closures Cooling issues, part 20 Page 40 Page 18 I N S P E C T I ON S & L A B O R A T O R Y E Q U I P M E N T","@ID":6}, "EDITOUR REPORT 11 PETplanet insider Vol. 16 No. 05/15 petpla.net Tunisia Downtown meeting with Green Line Bottle sorting at Green Line Green Line | April 29, 2014 We met: Mr Slim Baghdadi, Director The Green Line company, whose HQ is located in the centre of Tunis, is a company totally dedicated to the business of recycling, and in particular PET. Green Line, part of a multinational group, is itself made up of six recycling units and eight offices. The company originated in the collective experience of the waste management sector which began in Saudi Arabia and incorporated sorting lines from a company belonging to the same group and headquartered in Dubai. It was here that, in 2006, a major sorting unit for household waste was installed. At the time it was projected to handle a recycling volume of around 2,000 tonnes, a figure that has since doubled. “We were keen to apply the same operational principles in Tunisia and to concentrate on the process end of materials, i.e. the stuff that ends up on dumps or in the street“, said Mr Slim Baghdadi, Director of Green Line. A national promotional programme for recycling projects contributed to the decision. “Although it was difficult to obtain a licence from the government, we started with a couple of collection centres for PET and other plastics, as well as for cardboard packaging and paper. However, our focus was predominantly on PET“. The process begins with a preliminary sorting of the materials at the collection points. The next stage, which takes place inside the plant itself, is to sort the waste by colour. Around 5-6 tonnes of material end up at every Green Line collection point each day. This volume, although substantial, is insufficient to justify investing in automatic sorting, and this work is therefore carried out entirely by hand. If Green Line’s partners are included, the annual volume produced amounts to around 10,00012,000 tonnes. The overall condition of the incoming PET bottles is very good; contamination with dirt, the classic pollutant, is quite simply avoided. However, collecting, sorting, compressing and subsequent marketing is far from being the whole story. The export of bales made from materials that are essentially unmodified is really difficult and the only way to overcome this hurdle is to create added value. The company’s response was to acquire a crusher and shredder for PET bottles, and this process was complemented in 2009 by the purchase of a washing line that has been installed at another location, 140 km away from Tunis. All the machinery has been supplied by the Turkish company Ustin. Up to 2011, Green Line exported its flakes mainly to the Far East, with China the principal market, and also to Turkey, to a company that manufactures PET fibre from the recycled material. “Asian markets tend to prefer the unwashed flakes and, for reasons of cost, handle the wash process themselves“ says Mr Baghdadi. By contrast, the lion’s share of the hot-washed flakes is exported to Europe where it undergoes processing in countries such as, for example, the UK, France or the Netherlands. “Demand for good quality PET flakes is very high in these countries and these markets are becoming more and more important for us. However, we still produce a proportion of unwashed flakes to meet Asian requirements”. Are these exports financially viable? “In Tunisia“, Mr Baghdadi goes on, “there were historically no taxes on exports in the recycling sector. This year, for the first time, a comparatively low tax rate of 10% has been levied on this sector, but it applies only to newly established companies”. Green Line does have two local customers who process the material further to make PET straps, but this accounts for scarcely 2,000 tonnes of material per year. The use of PET flakes is still a relatively new idea and, because of a Tunisian ban on its use in food products, could only be considered within the extrusion sector for non-food products. The company’s current international customers use the material chiefly for the manufacture of sheets. Mr Baghdadi, with an eye to the future, is, however, already sounding out companies that are displaying an interest in processing the flakes for the manufacture of preforms. Is there much competition in the sector? “It is vital for us not to get involved in any rivalry with other recycling companies. We prefer instead to build networks. For example, we require PET bottles in sufficient quantities to ensure that the hot wash process is profitable. For their part, recycling collection companies want to sell their material. So there is the potential, once our needs have been met, to develop meaningful partnerships which can benefit everyone. A much bigger problem in the sector is the booming black market. There are companies that recycle without a permit, who are therefore operating outside the law, with a lower cost base. To cap it all, they pay no taxes. It means that, on average, we are immediately 30% worse off.” There has been a significant reduction in state controls on illegal transactions of this kind, Mr Baghdadi adds, particularly since the revolution at the beginning of 2011. Looking to the future, Green Line is currently exploring the possibility of setting up a parallel company with a UK partner to manufacture PET sheets using recycled material. “This is a sensible idea and we are, at this moment, busy working on the details together“. www.greenline.com.tn","@ID":13}, "ON SITE 43 PETplanet insider Vol. 15 No. 01+02/14 petpla.net Ultralight closure for Egyptian market Bericap introduces ultralight water closures HexaLite range fitting a 29mm neck The market environment and other current trends mean that cutting the cost of packaging is still of huge importance across all beverages. The fast-growing still water market is one of the markets looking for low-weight options. Bericap has extended its HexaLite range in response to market requirements with HexaLite UL 29/11 SFB, fitting a 29/25 mm neck size. The weight saving compared with a former 30/25 neck and closure combination is as much as 37%. Beside other Bericap locations, this closure is now being produced for water at Bericap Egypt and has since been introduced successfully onto the Egyptian market. A multinational player in the water market has opted for the closure, using it for different bottle sizes. The market introduction of the new ultralight closure, the lightest closure in the Egyptian market, started in January 2015 and gave new stimulus to the market. The HexaLite Ultra Lite UL 29/11 SFB is equipped with a slit flexband, supporting easy application and reliable tamper evidence functionality. Nitrogen dosing is feasible where bottlers want to use lightweight bottles and need to add nitrogen to stabilize the bottle. www.bericap.com ONsite See the dev iat ions? We do. 15 cameras . 36,000 bot t l es per hour. The SpotWatcher. W W W . I N T R A V I S . C O M V I S I T U S A T B O O T H 5 .1 C 0 8","@ID":45}, "INSPECTIONS / LABORATORY EQUIPMENT 25 PETplanet insider Vol. 16 No. 05/15 petpla.net info@hasplastik.com Tel: +90 212 695 50 00 Fax: +90 212 694 97 24 .com Caps & Closures Various software modules produce precise statistics to maintain an impeccable production process The PreWatcher III at a glance Up to 72,000 preforms/hr Eight square metres footprint Eight high-resolution colour cameras provide more data Cavity reading and colour inspection 100% inspection topped by the number of error types it can detect. The system inspects length, shape and diameter along with common error types including short shots, bubbles, oil spots, burns, deformations and contaminations in the mouth area. Additional inspection criteria such as ovality, flash at the parting line, scratches and sealing surface notches are also incorporated. Ralph Möller, unit leader at Hansa-Heemann, Germany, sees the advantage of these features. “The PreWatcher is making our start up with preforms from recyclate much easier”, Möller states about his two inline-systems from Intravis. Highlight cavity reading The proprietary Intravis cavity reading software identifies the preforms by defined cavity numbers, which means that it can trace errors to specific cavities. The colour cameras detect deviations in colour and intensity as well as coloured streaks in the body and the bottom. Their high resolution provides detailed raw data that can help operators to make better decisions, including when exactly an object will be identified as a bad part and be thrown out. The PreWatcher III can work to very fine specifications and thus only throw out bad parts if the deviations are recognisable and the products could not be sold to the end customer, thus minimising waste. The precise inspection enables the wider use of materials such as recyclate, without compromising end product quality. A newly-developed lighting technology, which is adaptable to the key features and characteristics of the object, enables a precise inspection with improved dynamics. www.intravis.de The PreWatcher III is optimized for an inline use","@ID":27}, "NEWS 8 PETplanet insider Vol. 16 No. 05/15 petpla.net RAL Quality Association endorses high grade PET recycling A further eight companies are awarded the seal of approval. At the 3rd meeting of members of the RAL Gütegemeinschaft Wertstoffkette PET Getränkeverpackungen e.V. (Registered Association RAL Quality Association - Recyclable Materials Chain PET Beverages Packaging e.V.) in March, 2015, a further eight companies were awarded the seal of approval. Representatives of the beverages producer, PepsiCo Deutschland GmbH, the preform manufacturer PET-Verpackungen GmbH Deutschland (PET Packaging GmbH Germany), Varioform PET-Verpackungen Ges.m.b.H (PET Packaging Ges.m.b.H), Lübecker Kunststoffwerk GmbH (Lübeck Plastics Plant GmbH) and Plastikpak Luxpet, together with the PET recycling companies PET Recycling Team GmbH, Texplast GmbH and STF Recycling GmbH, accepted the certificate of quality approval. This brought the total of number of leading companies in the beverages industry and the plastics processing industry that have already acquired the RAL seal of approval to twelve. “Our members stand out because they consistently promote technical and product innovations at the various stages of production with a common aim of developing a closed circuit operation in terms of PET recyclables and continuing to improve the product-related ecological balance” says Andreas Normann, Chairman of the Board of the RAL Quality Association. PET lightweight bottles with the RAL seal of approval contain a minimum of 25% PET bottle recyclate. The member companies of the RAL Quality Association voluntarily submit to third party monitoring in order to achieve the seal of quality. The quality association is an initiative of the IK Industrievereinigung Kunstverpackungen (Industrial Plastic Packaging Association e.V.) and the Arbeitsgemeinschaft konsumenten- und ökologieorientierte Getränkeverpackungen (Working Party Consumer- and Ecology-oriented Beverages Packaging e.V.) (AKÖG). It is supported by an advisory committee on which the Fraunhofer Institute of Packaging (IW) and the Fresenius institute are represented. www.kunststoffverpackungen.de PETnology to cooperate with CCFEI for Polyester and PET Packaging Conference in China, Shanghai, September 16-18, 2015 PETnology and CCFEI have agreed to cooperate for the 11th China International Recycled Polyester and PET Packaging Conference & Exhibition being held in Shanghai on September 16-18, 2015. The focus of the well-established CCFEI event, attracting more than 300 participants, focused in the past on polyester recycling. With the cooperation, the range of topics will be enlarged to PET packaging. www.petnology.com","@ID":10}, "EDITOUR REPORT 12 PETplanet insider Vol. 16 No. 05/15 petpla.net Visions of structure and own fibre production Preforms for the market leader La Preforme | April 30, 2014 We met: Mr Mohamed El Mouldi, Plant Manager We meet the preform and crown cork manufacturer La Preforme, whose headquarters are 35km or so south of Tunis. The relatively small company with 100 employees and a production area of 20000 m2 is a subsidiary of the SFBT Group (”Société de Fabrication des boissons de Tunisie“), which has more production locations close to centres of population. “SFBT“, as Plant Manager Mr Mohamed El Mouldi, explains to us, “is the n°1 group in Tunisia in the manufacturing sector of beer and soft drinks. But to return to the story of La Preforme itself. The preform producer began life in 1983, initially manufacturing crown corks for the beer sector. In 1990 the company added preform production to its portfolio with the introduction of the PET bottle in Tunisia. Mr El Mouldi, who previously worked in beer bottling at SFBT, has since then spent ten years at the helm of La Preforme. “In the preform sector we currently manufacture exclusively for the CSD branch of SFBT. As for crown corks, we supply only around 40% to the group, the rest goes for export to central Africa“, explains Mr El Mouldi. On the technical side, the company uses Husky and Netstal machines, one of each. The 48-cavity machine from Husky has been giving good service since 1997. The line runs not only 26g preforms for 0.5 litre bottles but also 37g preforms for 1 litre bottles on two Husky moulds. The Netstal PET line was only acquired in 2013 which makes it virtually brand new. Here both 37g preforms for 1 litre and 45g preforms for 1.5 litre bottles roll off the production lines on 96 cavities and 2 moulds from Otto Hofstetter. All the preforms produced feature the PCO 1810 neck finish. Mr El Mouldi estimates that the total output today is around 180 million preforms per year, manufactured from around 7,000 tonnes of PET resin which La Preforme obtains exclusively from Korea, China and, to a lesser extent, Japan. “Since the arrival of our latest machine, output has grown so much that we now exploring a new project for the near future“, he says. “We are giving initial consideration to exporting a proportion of our production to Algeria“. Sogedes | May 1, 2014 We met: Mr Fadhel Belkhir, Plant Manager & Mr Feres Belkhir, Commercial Manager The emergence of Sogedes in Tunisia as a recycling company goes back to 2001. Even before it was established, Plant Manager Mr Fadhel Belkhir, had already acquired a good deal of experience in waste management and trading in the import and export of metal waste. Entering the plastics sector was an obvious step forward. His brother, Feres Belkhir, Commercial Manager, joined the company from Shell in 2006, but runs a parallel trading company specialising in Tunisian products, mainly in the food sector, such as edible oils. The two describe their vision as to how the Tunisian recycling market might be revolutionised. Sogedes specialises in recycling PET bottles. From the very beginning, the company manufactured PET flakes and exported them together with flakes bought in from all over the country. Sogedes obtains the bottles not only via collection centres but directly from collectors and also direct from the manufacturer in the form of scrap. Their condition on arrival can appropriately be described as a bit of a mixed bag, from reasonably clean to horribly dirty. Mr Fadhel Belkhier explains: “First of all, the waste goes through an initial sorting process, following which the bottles go into the crusher, with caps or labels still present. The next stage is washing when the labels and caps are removed. After further processing into flakes we are now left with virgin material, so to speak.” Sogedes currently has a capacity of around 500 tonnes of material per month, and at present between 250 tonnes and 300 tonnes are being processed. “We are currently assessing opportunities for recycling other plastics such as HDP, LDPE, PP or PE“, says Fadhel Belkhir. Depending on material input and season, up to 20-30 employees work in an area of 3,500m2. “The machines are made in China. Our hot wash line dates back to 2006, and at the time it was the first such machine in the whole of Tunisia“ says Fadhel Belkhir. “We export our flakes to Asia and Europe and sometimes the fact that the Asians may only want unwashed or cold-washed flakes we find a bit of a problem. Requirements in the European market are different. “And what about their own continent? The response was immediate. “There is no export activity in Africa; volumes are too small to be profitable. From the start, we saw Sogedes developing in three stages: first stage is the crushing of the bottles, the second either hot or cold washing and the final stage would be the installation of a PET fibre plant to enable us to recycle the flakes ourselves”. Plans are well advanced, I discover. All the","@ID":14}, "EDITOUR REPORT 13 PETplanet insider Vol. 16 overall planning measures were put in place years ago. These included feasibility studies, investigation of any financial support from the government, and finally potential geographical locations. The world economic crisis in 2009 put a damper on these ambitions, and for the present the idea of an in-house fibre plant remains on the back burner. “The investment would be substantial, but a plus point is that up to now, there has never been a fibre plant in Tunisia. All fibre is currently imported, so this is a hot topic”. Other areas to ponder are uniform capacity utilisation and material flow, both of which are preoccupying the brothers at the moment. They claim it would make much more sense for all those involved in the recycling process chain if the market were to be more meaningfully segmented by establishing rules and creating an end-to-end structure. In the opinion of Fadhel Belkhier, “Each company could then concentrate on a single sector and would be committed to passing on the product generated to the next stage in the chain. The collector delivers to the crusher, the crusher to the hot washer, the hot washer to an export company”. In this way – or at any rate this is the idea – material flows and price models would be more consistent than they are today. “For instance, the reason why we carry out the crushing, washing and comminution ourselves, is simply that we have no guarantee that the volume of material required for one of the processes would be adequate, or that prices would be more stable. If we had a fibre plant we could calculate the output using the quantity of PET we had produced ourselves and increase it appropriately, something which would be perfectly OK for us. But first of all we need to see details of how it is going to work in practice. What we are looking for here is another partner to participate in a joint venture, someone who will follow up this idea and develop it together with ourselves”. A new location would be part of the plan. “We would then need at least an area of 10,000 m2\". And Feres Belkhir adds: “What marks us out are quality and price, which we believe are the best in Tunisia. It is my firm belief that, with the help of a reliable foreign partner who supports our ideas, it would be possible for us to secure a significant market share for fibre with no problem whatsoever”. There is no challenge we will say no to. Because we know that with the widest range of products, technologies, expertise and services, there is no solution we can’t conceive. Contact us to see how our philosophy of Yes has reshaped the very fabric of our brand. Explore all that’s possible with injection, extrusion, blow molding, co-injection, hot runner systems, mold technologies, process control equipment and fluids. Visit www.milacron.com COME SEE WHAT YES BUILT. The new Milacron PET system can produce 10% more output. Available Now.","@ID":15}, "EDITOUR REPORT 14 PETplanet insider Vol. 16 No. 05/15 petpla.net Production hall of Sipa Closures, preforms and PET recycling Omega Maghreb, Sipa & Valorflakes | May 2, 2014 We met: Nessim Mami, Business Development Manager Not far from Zaghouan, some 50km to the south of Tunis, is where the three plants operated by brothers Mami and Nissim Youssef are to be found. We meet the latter for our interview. It was the beginning of the 1990s when the father of the two entrepreneurs started his business which they subsequently took over and expanded. The Youssef brothers‘ business consists of three companies: Omega Maghreb which manufactures closures, Sipa for the manufacture of preforms and Valorflakes in the PET recycling sector. Omega Maghreb: Omega Maghreb’s caps production started in 2001 and is based on machines from Husky, Netstal and BMB. A start was made in 2008 with two Netstal production lines, each with 48 cavities, for manufacturing 1.85g caps. In 2014 the third Netstal machine was added to the same specification. The output is around 360 million closures per year. Two BMB injection moulding machines each with 8 cavities generate 3.9g closures (around 25 million per year) and 6.9g closures (approx. 29 million p.a.). The Husky machine also installed in 2014 is operating, with 16 cavities for 1.3g closures, with an annual output of around 183 million closures. Sipa: In the Sipa preform plant the company’s production is based on Husky and Engel equipment dating back to 2006. Currently operating are the Husky GL300, LX225 and XL225 as well as two XL300s. 32g, 57g and 51g preforms run on the GL300 for use with 1,5 litre bottles in the CSD sector and mineral water. The LX225 produces 37g for 2 litre, 85g for 3 litre and 95g for 5 litre bottles which are filled with edible oil. They also have a fourth mould here for 37.5g preforms for 1 litre bottles of CSD. The XL225 is in an almost identical league with 37g, 85g and 100g for 2 litre, 3 litre and 5 litre edible oil bottles as well as 37.5g for 1 litre CSD. One of the Husky XL300 lines produces preforms for 0.5 litre mineral water bottles. The second XL300 is currently still in the test phase for 12.8g and 28.5g shortneck preforms, one each for 1.5 litre mineral water bottles together with 16.5g, 14.8g and 30g preforms for 0.5 litre and 1.5 litre mineral water bottles. The two Engel lines are identical in terms of their set up and produce 28g for 0,5 litre mineral water and CSD, along with 30g, 32g and 34g for 1.5 litre and 2 litre mineral waters. Valorflakes: Finally, the Group’s Valorflakes recycling unit forms what is, for the time being, the last stage in the valueadded chain as the brothers are currently thinking about setting up an additional fibre plant to utilise the recycled material. “This”, says Mami Youssef, „would mean that we had come full circle as far as PET recycling is concerned“. Valorflakes has opted for Sorema machines when it comes to its equipment and is currently manufacturing hot washed flakes, of which 60% are transparent and 40% blue. “We pay a great deal of attention to origin and quality and carry out consistent checks to monitor them“. www.valorflakes.com Production hall of Omega Maghreb","@ID":16}, "PRODUCTS 41 PETplanet insider Vol. 16 No. 05/15 petpla.net KHS presents very light PET bottles for milk and mixed milk beverages Ever lighter PET bottles have been KHS Gmbh’s PET team at its ”Bottles & Shapes” centre in Hamburg, Germany, have developed a lightweight 1l bottle for milk and mixed milk beverages that is now ready for market. Frank Haesendonckx, head of Technology at KHS Corpoplast, asserted that the ultralight bottle offers the milk industry an interesting alternative to the carton. KHS says that the bottle balances economic considerations, market acceptance and product quality. The milk industry, like the beverage industry, is subject to major cost pressures but must, at the same time, satisfy the highest demands for product safety. KHS claims that the light PET bottle for milk and mixed milk beverages can be filled aseptically; provides product protection; reduces production costs; and is 100% recyclable. The 1l bottle has a neck thread diameter of 32mm and weighs just 20g; similar competitor bottles are usually around 10% heavier, at 22g. The material saving of two grams of PET per bottle can translate to a cost saving of €140,000pa, at a production rate of 50 million b/yr. Mr Haesendonckx says that KHS can see the potential for even greater weight savings to come. The company says that the bottles can also be easily processed as shrink packs, which eliminates the need for secondary packaging, such as trays, and their associated costs in materials and transportation. KHS observes that being light or ultralight is not enough in itself; the packaging must also convince the customer. To this end, the newly developed bottle is designed to offer convenient handling, with a staggered rib structure providing good grip. Milk products should, ideally, be protected by an ultraviolet light barrier, and KHS’ new product has two variants: it can be produced either as a transparent bottle which is enveloped in a protective sleeve after filling, or as a white bottle with a titanium oxide light barrier The typical vacuum created in bottles by the differences in temperature between hot filling and subsequent cooling has been taken into account by the Bottles & Shapes team. The bottles are manufactured with a FlipBase on a stretch blow moulder before being conveyed by their neck ring, aseptically filled and sealed. The FlipBase is designed to compensate for the negative pressure generated in the bottle. KHS claims that its new lightweight product offers producers in the dairy industry a lightweight, cost-effective and consumer-friendly bottle, which both protects milk products and is attractive on the shelf. www.khs.com","@ID":43}, "NEWS 9 PETplanet insider Vol. 16 No. 05/15 petpla.net Amcor announces acquisition of Nampak Flexibles Amcor announced the USD 22million (ZAR 250 million) acquisition of Nampak Flexibles, the market leader in flexible packaging in South Africa. Nampak Flexibles has extrusion, lamination and conversion capabilities across three plants, and generates sales of approximately USD 94 million per year. The business services multi-national and domestic customers in the beverage, food and home care end markets. www.amcor.com Netstal introduces 144 cavity preform system to the US Netstal has introduced the PET-Line 5000 to the US market. The preform production system is designed for moulds with 96 to 144 cavities and features an output of up to 100,000 preforms per hour. According to the company, high output levels are especially required in the US and Asia where the employment of 144 cavity preform moulds is appropriate. Netstal’s customers are generally large bottling plants that require a defined number of bottle variations. In these regions, the systems are horizontally integrated into the production process for example, the product is lining up directly alongside a blow-moulding machine. The PET-Line features several first-rate changes in the fields of energy consumption, control technology and machine control, such as an energy-efficient adaptive drive unit. It no longer operates with constant pump pressure, but rather adapts flexibly to the individual application and cycle requirements. In addition, all of the machine’s electrical drive motors are interconnected via an intermediate circuit to allow the braking energy being generated during operation to be used elsewhere. Overall, the system reduces the power requirement by around 10% compared to the preceding model, or up to 20% in comparison with the competition. The lock-to-lock time of the PET-Line 5000, from unlocking the mould to preform removal and locking, has been reduced by up to half a second. For standard applications with cycle times of less than 10sec, this equates to an increased output performance of tens of thousands of units per day. This was made possible by the new control technology: the exclusive use of digital controllers was combined with state-of-the-art valve technology. Shorter reaction times and increased oil displacement mean that the movement of the mould is swifter, while the dry cycle of the machine is reduced. wwww.netstal.com Full inspected! CHINAPLAS, 20/23.05.15 -#4.1 C41 - Guangzhou CHINA IRAN FOOD + BEV TEC, 26/29.05.15 - 38.01.10 - Tehran IRAN EXPOPACKMEXICO,16/19.06.15-#2636- CiudaddeMéxicoMEXICO PROPAK ASIA, 17/20.06.15 - HALL 1066G26 - Bangkok THAILAND ROSUPACK, 16/19.06.2015 - Moscow RUSSIA","@ID":11}, "MARKET SURVEY 28 PETplanet insider Vol. 16 No. 05/15 petpla.net 05/2015 MARKETsurvey Company name Manjushree Technopack PDG Plastiques Silver Spring Postal address Telephone number Web site address Contact name Function Direct telephone number Fax E-mail 60 E, Bommasandra Industrial Area, Hosur Road, Bangalore - 560 099, India +91 80 43436 200 www.manjushreeindia.com Mr Rajat Kedia Director +91 80 43436 200 +91 80 27822 245 rajat.kedia@manjushreeindia.com ZI secteur 2, 45330 Malesherbes, France +33 2 3834 6195 www.pdg-plastiques.com Mr Francois Desfretier General Manager +33 2 3834 6195 +33 2 3834 6382 francois.desfretier@pdg-plastiques.com 630526 Russia, Novosibirsk, Proezd Avtomobilistov 12 +7 383 334 7155 www.etalon-group.ru Mr Petr A. Durnov Chief Engineer +7 913 912 8416 +7 383 334 6470 p.durnov@etalon-group.ru Preforms Multilayer preforms (Yes/No) No No No PEN prefoms (Yes/No) No Yes No Preforms in alternative materials (PP/PLA/PEF) Which? No PP, PE, BioPET PolyShield Preforms incorporating rPET (rPET content in %) 10% and 25 % Yes up to 100% No List of additives available UV blocker, oxygen scavenger, slip additive, anti yellow additive, AAA Prelactia 100% light barrier for UHT steralised milk long shelf-life Oxygen, UV, CO2 barriers Colourants, MXD-6, blowing additive Preform range PCO 1810: 11,3g - 48g PCO 1881: 11,2g - 52,7g PCO 1810 Thick neck: 18,5g - 47g 3-start Alaska: 10,6g - 35,6g 30/25 mm 3 start: 22g 29/25 mm 3 start: 18,6g Colored preforms; Preblow technology; 29/25 shorty: 8g - 28g 30/25 high: 17,5g - 50g 30/25 low: 17,5g -50g 38mm 3 start: 28g - 50g Prelactia 38mm 3 start: 17g - 28g 48/40: 47g - 62g 27/32: 6,5g dairy and smoothies 25/20: 6,5g - 8g dairy PCO 1810: 33,6g PCO 1881: 32g 29/23: 24g - 33g chemical BVS 30H60: 50g wine 22H30: 19g wine ultra-lightweighting 2,4g preform; standard and specific preforms for mineral water, dairy, juice, CSD, etc.; Overmoulding technology for 2 layers preforms; Preblow technology for lightweigthing bottles Bericap 38: 18g - 27g Bericap 28: 86g - 89g BPF: 24g - 42g BPF/PCO: 32g - 51,5g PCO: 20,5g - 52g PCO 1881: 20,7g - 45,7g Oil: 25,5g Company name PET Prefroms Morocco SARL Resilux AMD Industries Limited Varioform PET Verpackung Ges.m.b.H. Postal address Telephone number Web site address Contact name Function Direct telephone number Fax E-mail B 8-1 Zone Industrielle 13000 Benslimane, Morocco +212 5 2329 8878 www.petmorocco.com Mr Rachid Nourredine Managing Director +212 5 2329 8878 +212 5 2329 8867 r.nourredine@petmorocco.com Damstraat 4, 9230 Wetteren Belgium +32 9365 7474 www.resilux.com Mr Philippe Blonda Marketing & Sales Director +32 9365 7476 +32 9365 7475 philippe.blonda@resilux.com FF-18, Pusa Road , Karol Bagh New Delhi - 110005 INDIA +91 11 46830 202 www.amdindustries.com Mr Adit Gupta Managing Director +91 981 1118 736 +91 11 28753 591 adit@amdindustries.com Industriestr. 5 3134 Reichersdorf, Austria +43 2783 7114 0 www.varioform.at Mr Ing. Werner Maurer General Manager +43 2783 7114 10 office@varioform.at Preforms Multilayer preforms (Yes/No) Yes Yes No No PEN prefoms (Yes/No) Yes No No No Preforms in alternative materials (PP/PLA/PEF) Which? PLA Yes No Hot Fill & Barriere solutions Preforms incorporating rPET (rPET content in %) No Yes, according customer wishes No 0 - 55% List of additives available Oxygen barrier: ResiOx, CO2 barrier: ResiC, Oxygen and CO2 : ResiMid, ResiMax; Light barrier: ResiBlock No please contact Varioform directly Preform range sorf drinks and water Juice, milk: 38mm 2-start, 3-start CSD, water: 28 PCO 1810 / 28 PCO 1881 water: 29/25, 30/25, 48/40 oil: 29/21, 39/21, 45/34, 48/40 detergents: DIN28/410 28mm PCO in 1810: 54g - 25g 28mm PCO in 1881: 52,7g - 23,7g 28 mm PCO Hot Fill in thick neck: 48,30g and 27g ECO base preforms in 1881: 25,1g and 21,4g 30/25 Neck Finish: 23g and 22g 29/25 Neck Finish: 20,3g 14,8g - 54g with PCO 1810 / PCO 1881","@ID":30}, "PREFORM PRODUCTION 37 PETplanet insider Vol. 16 No. 05/15 petpla.net mould metal is greatly jeopardised by the slow speed in the contact area. Systems with laminar flow show a large increase in coolant temperature through the system. Turbulent flow, on the other hand, allows frequent contact between coolant and mould metal. Because of the constant mixing of the coolant, its temperature does not spike up, keeping the important temperature difference between the coolant and the hot metal high. Turbulent flow is not so much dependent on a high inlet pressure but rather on the pressure difference between the inlet and the outlet. A pressure drop of 5 bar (70 psi) is sufficient to achieve this effect. Sizing return water line diameters to 25mm (1 in) bigger than supply lines often reduces back pressure that might be present in the system. A good sign of turbulent flow is a temperature difference of 1.5°C (3°F) between the inlet and outlet points. (Measurements must be taken by thermocouples inside the coolant flow and not on the pipes.) Increasing pump size in the central location or at each machine (booster pumps) is the most likely remedy for any deficiencies. If exact calculations are required, the so-called “Reynolds number” must be determined. This dimensionless number takes into account the viscosity of the fluid, the mass velocity, and the length of the pipes. A good resource for this can be found at: www.processassociates.com/process/ dimen/ dn_rey.htm. Reynolds numbers above 2000 indicate turbulent flow. 3.8.1 Antifreeze The use of antifreeze in cooling water deserves a special note. Anti-freeze has two functions in a water system. As the name implies, it reduces the freezing point of water. Water tem-perature at the contact point in the evaporator of the chiller will be several degrees lower than that at the exit point of the system. Hence, it may reach its freezing point even though the chiller is adjusted to a temperature well above it. The required antifreeze concentration will depend on the chosen water temperature. Recommended cooling water temperature for PET moulding is 8–10°C (46–50 °F). Antifreeze also has an anticorrosive effect. However, using antifreeze for corrosion protection requires concentrations of about 25%, which is the reason why this concentration level is recommended in some manuals. Unfortunately, the ability of antifreeze to absorb heat from mould parts is inferior to that of water, and the efficiency of the chiller system can be compromised. Furthermore, antifreeze is more viscous than water and so increases pump loads and electricity costs to run them. It is therefore preferable to adjust the antifreeze concentration only with respect to lowering the freezing point as necessary and to add corrosion protection by other means with regular water treatment. The best approach is to have the water tested by a certified laboratory and have qualified technicians proscribe a proper mix of chemicals that address corrosion as well as algae and mineral suppression. Antifreeze cannot be used in a cooling tower because the performance of a cooling tower is based on evaporation. Adding antifreeze continuously into cooling tower water would be expensive and is illegal in many jurisdictions as the evaporating antifreeze is an environmental hazard. Freeze prevention is accomplished instead by using a thermostat to cycle the tower fan and the tower recirculation pump on and off based on a temperature set point between 21 and 29 °C (70 and 85 °F). Antifreeze comes in two formulations: ethylene glycol and polypropylene glycol. The former is a controlled substance that may not be released into the municipal water system. The latter is environment friendly and should be used wherever available. 3.8.2 Water flow balance Equally important is the fact that cooling water reaches each core and cavity at the same time and flow rate. Examining Fig. 3.25, it is easy to see that the top cavities will receive less water flow and pressure than the bottom ones because the pressure drops when the water flows up to them. As a result, cycle time will have to be adjusted so that the warmer top cavities can be demoulded while the Want the secret to bottle light weighting? Process Pilot® automated blowmolder control system takes the guesswork out of material distribution management and can help ensure the success of even the most aggressive light weighting program. Featuring 24/7 blowmolder control, the Process Pilot system continuously maintains proper material distribution, on every bottle, to an unmatched level of accuracy. With the Process Pilot system, you have the means to push light weighting to the limit without sacrificing bottle quality or performance. Not convinced? Talk to one of our specialists today to schedule a free seminar and evaluation of the Process Pilot system on one of your blowmolding lines. Web: agrintl.com Tel: +1.724.482.2163 E-mail: sales@agrintl.com","@ID":39}, "PETbottles 44 PETplanet insider Vol. 16 No. 05/15 petpla.net Beverage + Liquid Food MHT MOLD & HOTRUNNER TECHNOLOGY AG Your Machine - Our Solution German Technology 5.1 C10 Volvic – Angel or Devil? For Volvic Touch, Danone Waters Deutschland GmbH has launched two new flavour variations with an unusual composition and an appropriate marketing concept. One of these soft drinks, sporting a ”Devilish“ tag, is made from natural mineral water with strawberry, cherry and ginger flavours, whilst the second drink is called ”Heavenly“ and tastes of blueberries, cassis and vanilla. The products are packed in transparent PET bottles each containing 1.5l and reinforcement grooves running all round the bottle. The name “Touch” is omitted on the transparent plastic labels and a devil/angel symbol acts as an aid to orientation. The bottles are sealed with colour-coded screw closures complete with tamper-proof guarantee. www.volvic.de Ti expands its product range “Ti“, a brand name of the German company Teeküche GmbH, has expanded its existing range, which has until now been made up of three types, by a new variant consisting of the basic ingredient – black tea – and a proportion of blueberry and pomegranate juice. All types of the beverage, manufactured from freshly brewed tea are packaged in elegant PET bottles containing half a litre or one litre, with the brand name in the form of a tea leaf in the neck area, an all-round paper label and a screw closure complete with guarantee strip. All four types display the bio-seal in accordance with the EU Eco Regulation. www.ti-erfrischungstee.de fruit2go in PET “fruit2go“ is Franken Brunnen’s name for their non-carbonated series of soft drinks, each with a fruit content of approx.12%. There is a total of six different drinks in the range. The illustration shows grapefruit/raspberry and citrus/ pomelo. As a rule the products attract immediate attention due to their intense, almost luminous colour and their visually attractive packaging. The 0.75l bottle is waisted to make it easier to grasp and hold, featuring slight impressions and decorated with a plastic label. www.frankenbrunnen.de","@ID":46}, "CAPPING / CLOSURES 35 PETplanet insider Vol. 16 No. 05/15 petpla.net Securing value for a strong future www.krones.com IPACK-IMA 2015 Mailand/Roh, 19 – 23 May Hall 4, Stand E03/F10 Why is precision such an important requirement for injection moulding machines? Mangold: The mould optimisation trials quickly revealed that the production of Incap dispensing caps required maximum precision in terms of dimensional stability and geometry of the carrier components, in order to ensure that the sealing properties of the membrane and the assembled carrier components were never jeopardized. The process safety had to be guaranteed at all times. This is why the 8-cavity production mould design was optimised –during pilot trials on an all-electric Sumitomo (SHI) Demag IntElect injection moulding machine. What makes Incap dispensing caps so special? Hauck: With their special design, Incap dispensing caps are in a category of their own among competing products on the shelf. While consumers using our product feel that they are contributing to their health and wellbeing, they also experience this cap as a fun novelty item as these caps allow them to add the ingredients themselves and watch them dissolve in their beverage. Bottlers are impressed with the product’s versatility, which is why our caps are ideal marketing material. A beverage is so much more interesting if consumers can prepare their very own special drink. www.kunststoffspritzgusswerkzeugbau.de www.incap.hk www.teamplast.nl www.sumitomo-shi-demag.eu","@ID":37}, "BOTTLES 45 PETplanet insider Vol. 16 No. 05/15 petpla.net Aptar makes a Better Bottle Aptar Food + Beverage, part of the AptarGroup, has announced that is collaborating with The Better Bottle Company in the commercial production of a turnkey “water enhancer” drinks solution that is designed to enable producers to service the trend towards water as the drink of choice among increasingly health-conscious consumers. The Better Bottle Company is a Dutch manufacturer of soft drinks, compact, portable, concentrated dilutable drinks and drinks enhancers. It produces solutions for liquid water, dairy drinks, coffee, tea and beer enhancers. The new bottle uses Micro, Aptar’s dispensing closure solution, which provides a spill-proof package and a straight directional dispense, by means of its flip-top closure and its internally-mounted SimpliSqueeze silicone valve system flow control. The design of Micro provides a side-opening system that is suitable for either left- or right-handed users. Consumers can squeeze out as much or as little enhancer and add it to their water, according to personal taste. www.thebetterbottlecompany.com www.aptar.com Identify the flavour and reward your good taste As part of a promotion, Müller Dairies are selling four different Müller Dairies drinks, asking customers to guess the components of the flavouring and promising a prize to successful participants. Participants can register at www. hast-du-geschmack.de and submit their suggestions as regards product composition. At the end of the competition there will be a draw among the successful participants for 100 prizes. The four types are packaged in the familiar PET bottles with a content of 400ml / 424g. Each of the bottles is decorated with an individually designed sleeve label which is pulled over the screw closure, giving additional protection and making the bottle stand out. www.hast-du-geschmack.de","@ID":47}, "BOTTLES 47 PETplanet insider Vol. 16 No. 05/15 petpla.net Hair gloss oil in PET Schwarzkopf and Henkel have launched a hair gloss oil, known as “essence Ultime“ which has been developed in collaboration with Claudia Schiffer. This oil is said to endow coloured and highlighted hair with spectacular brilliance and also protects it from the sun. The edges of the bottle are rounded with generously-proportioned radii; the bottle is comfortable to handle, made from PET and can accommodate 75ml of product. The product is dispensed via a white pump dispenser which is protected from accidental operation during transport and storage by means of a superimposed protective cap. An all-round, partially transparent plastic label enables the user to see the colour and consistency of the product. www.essence-ultime.de Pril ushers in the spring Henkel has been marketing two new Pril variants as part of a time-limited campaign. To bring the fragrance of spring into the kitchen, 500ml of power gel with the scent of blue gentian or crocus flowers were being sold. According to the manufacturer, the fragrance did not adhere to the dishes but instead only scented the rinsing water. The products were tinted turquoise and lilac, thus ensuring a spot of colour in the kitchen. Used as packaging was a waisted, transparent PET bottle with a screwon push-pull and “slanting” output orifice. The transparent front label was designed to match the particular product. www.pril.de","@ID":49}, "PREFORM PRODUCTION 36 PETplanet insider Vol. 16 No. 05/15 petpla.net Cooling issues, part 20 Practical guide to injection moulding of preforms PETplanet Insider is publishing extracts from successive chapters of Ottmar Brandau’s “Bottle, Preforms, Closures”, which was published by hbmedia. A newly revised version is reissued under the Elsevier imprint. 3.8 Cooling issues PET preforms feature relatively thick walls, and the material melts at a high temperature. The combination of these two attributes requires a massive amount of chilled water in order to cool preforms down to demolding temperature. As shown in Chapter 2.4, rapid cooling is also paramount to avoid crystallisation of the material. To better understand how to best cool, we need to look at how the cooling medium flows through the various channels to the machine and in the tool. Process heat flows to the chilled water in three different ways: 1) PET to mould metal 2) Mold metal to coolant in cooling channel 3) From outside of the mold (shop air) to the non-PET side of the cooling channel (so-called “mould sweating”). The first step is controlled by the heat conductivity of the mould material. The second step depends on how much contact the cold cooling agent makes with the PET side of the cooling channel. This in turn is controlled by the way the cooling agent flows and its distance from the hot PET. We distinguish two flow modes in liquids: laminar and turbulent. Laminar flow is characterised by the highest speed in the center of the channel, where there is little friction, decreasing to zero at the wall of the cooling channel, where friction is highest Heat exchange between cooling agent and Figure 3.24 Velocity profile in laminar flow. Longer arrows indicate higher speeds.","@ID":38}, "EDITOUR REPORT 17 PETplanet insider Vol. 16 Q Preform sterilization in the heating tunnel Q Protected conveying of preforms and bottles Q %QORNGVGN[ J[IKGPKE ƂNNKPI CPF ECRRKPI RTQEGUU The UCF BloFill monoblock from KHS – with fully enclosed hygiene housing Give your sensitive beverages more private space. Learn more at www.khs.com or scan the QR code. Entering the International market PTD Plastique – Transformation & Distribution Sarl | February 14, 2015 We met: Mr Djamel Ouadah, General Manager Mrs Habiba Ouadah, Sales Manager Mr Yacine Menguellat, Financial Manager My trip took me from Algiers to Blida, some 50km away. This is where the head office of PTD, Plastique – Transformation & Distribution, is located; the company is the second largest preform manufacturer in Algeria with an associated caps production facility. They are a direct competitor of SGT. My discussions are with Djamel Ouadah, General Manager, Yacine Menguellat, Financial Manager and Sales Manager Habiba Ouadah. As is so often the case, the link with plastic here has its roots in the family. Djamel Ouadah‘s father had, along with his brother, already been playing an active part in the Algerian polystyrol sector since 1965. In 1978 the two businesses were split and, because Mr Ouadah Senior was anxious to avoid entering into competition with his brother, he launched a new business in the packaging sector for cleaning materials and cosmetic items. By 1997 PET was gaining an increasing foothold and subsequently, Mr Ouadah Senior made the decision to invest in PET injection moulding technology. From that moment on, the focus was on establishing the strategic direction of PET as the company’s main product within the plant. The original plastics production facility continued to run in parallel right through until 2006, but without any new investments. Djamel Ouadah took over the PET production-related businesses following the death of his father in 2008 and has consistently continued to develop these further. “Our first injection moulding machine in 1997 was an Aoki“ Djamel Ouadah recalls. “At the time it was the very first PET installation on the Algerian market”. I subsequently learned that, in 1999, PTD purchased another machine namely a Krupp Premax with 48 cavities. The years that followed saw PTD opting for Husky and Netstal machines. In 2002 the first Husky G-Line with 56 cavities was commissioned, in 2004 two Netstal PET Line machines, each with 96 cavities, were added and in 2007 the third 96-cavity machine came on stream. In 2011 and","@ID":19}, "PETbottles 46 PETplanet insider Vol. 16 No. 05/15 petpla.net Home + Personal Care Interesting Insights Under the Gliss Kur label, Schwarzkopf is marketing its “Dream Hair – Weightless Oil“ hair care product in a slightly tinted 150ml PET bottle. One particularly striking feature of the bottle is the label at the back which, on the side facing the bottle, incorporates surfaces that intersect to reflect the incoming light like a lens. At the PoS this means that effects emerge that attract the interest of the customer. A colour-matched, screw-on pump dispenser with protective cap and two labels add the necessary finishing touches to the appearance of the pack. www.glisskur.de Hair perfume in PET German drugstore discounter dm’s own-label product “Balea Trend it up“ which targets young and trendy customers now includes a hair perfume in its range. 100ml of the product, advertised with attributes such as “glamorous hair perfume” and “bewitching fragrance experience”, is packaged in a slim-line and easy-to handle PET bottle. This transparent bottle is decorated with an all-round shrink sleeve and a pump dispenser ensures straightforward spraying of the contents on to the hair. www.dm.de Special cleaner from Sonax Sonax, the German manufacturer of automobile care products, is offering a special cleaner for removing insect residue from paint, glass, chrome and plastic. The product, called “InsektenStar“, is in signal colours which might almost be described as luminescent. It is sprayed on to the dirty surfaces prior to actually washing the car, partially dissolving the insect residue and softening it so that it can be easily removed in the subsequent wash. A transparent PET bottle with a content of 750ml which is easy to grasp and hold serves as packaging. The product is extracted from the product via a lockable pump dispenser. www.sonax.com Loyalty generates rewards at L’Oreal As part of a special promotion, L’Oreal has been marketing a shampoo from the Elvital Fibralogy range in a relatively large bottle with a content of 400ml at an attractive price. The bottle, which is advertised as a “Loyalty Pack“, is similar to the 250ml volume bottles and is, despite its size, easy to handle and user-friendly. The slim PET bottle is tinted and sealed by means of a snap-on two-colour hinged lid. Adhesive labels to front and rear convey the information and the words “Loyalty Pack” promote the sales campaign. www.lorealparis.com","@ID":48}, "MARKET SURVEY 27 PETplanet insider Vol. 16 No. 05/15 petpla.net Caps and closures Bottle-to-bottle recycling plants Preform and single stage machinery Preforms Preform / stretch blow moulds Closure systems Two stage SBM machinery Compressors Resins / additives Filling equipment Suppliers of PET preforms 14 companies from 9 countries participated in this year’s market survey of perform suppliers. They are shown in the order in which their details were received by the editors. In alphabetical order there are as follows: Alpla (Austria) AMD Industries Ltd. (India) Appe (United Kingdom) Empacar S.A. (Bolivia) Manjushree (India) Novapet (Spain) PDG Plastiques (France) Petainer (United Kingdom) PET Preforms (Morocco) Resilux (Belgium) S.B.E.C.M. (France) S.G.T. (France) Silver Spring (Russia) Varioform Pet (Austria) Although the publishers have made every effort to ensure that the information in this survey is up to date, no claims are made regarding completeness or accuracy. 05/2015 MARKETsurvey","@ID":29},
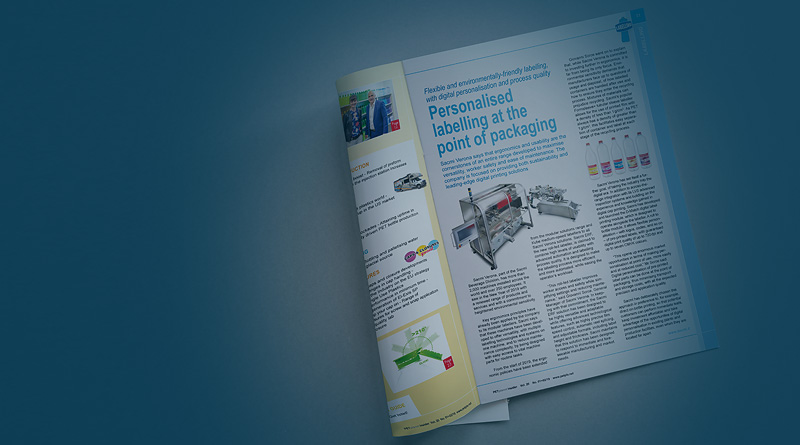