"40 TRADE SHOW REVIEW PETplanet Insider Vol. 20 No. 03/19 petpla.net Top performances and low weights PET Engineering has been participated for the first time at the All4Pack show in Paris. The company presented the new version of Nova bottle, a light-weight solution for carbonated soft drinks. The PET bottle weights just 12.5 g for a half liter format with 4.2 gas volume pressure. The second highlight was the “Glow in the Dark”, a Multi-Layer bottle with a phosphorescent additive that glows in the dark or under a UV light. This lightweight bottle was developed in collaboration with Penn Color Inc. www.petengineering.com Looking for a challenge A lot of new products have been presented at the SGT booth at Paris. As a specialist in PET packaging industry for over 30 years, the Société Générale des Techniques has been offering high performance solutions for packaging liquids. SGT has invested in new HDPE injection moulding machines for caps in a new site in Setif, Algeria. This latestgeneration equipment will enable the SGT Group to increase its production capacity from 800 million to 2 billion caps per year, with new references for the necks: 29/25, 30/25 high ring, 33mm, 38mm, 38mm hot fill, 28mm, 48mm and 28 PCO 1881 and 1810. SGT proposes a complete and varied range of 260 PET preforms, 6 types of HDPE caps and 2 lightweight handles for 38mm and 40/48 necks. www.sgt-pet.com Smart packaging machines We met Pietro Vo l p i , Ma r ke t i ng Department Manager (photo on the right) at the All4pack in Paris. SMI p r esen t ed a model of the new LSK 30 SF Ergon. The machine is equipped with rounded safety doors made of anodised aluminium, which let all the motors, featuring low-energy consumption, be placed externally compared to the mechanical groups they activate. The door closing system is equipped with a slow-down device and accompanies the door smoothly in its final phase of closure. The LSK SF Ergon series arises from the need to provide an ad hoc machine for packing rigid containers in film only and consequently have available an extremely compact machine, easy to control and monitor. The process of packing in film is extremely fluid: on the machine infeed conveyor, equipped with low-friction chains made of thermoplastic material, loose containers are clustered in the desired format by a pneumatic device and electronically synchronised separating bars before accessing the film wrapping section and the shrink tunnel. www.smigroup.it Congratulations! PETplanet congratulates Comep Blow Molds & More to their 20 years company anniversary! Mr Vincent Barrett, Technico-commercial France, told us about some fundamental achievements of Comep for the blow moulding industry. Comep was one of the first in the low blowing pressure technologies and has developed the Low Pressure Base and the Super Vented Mold concepts. These patented technologies are a real revolution for all the bottlers, says Comped. The patents allow to reduce the blowing pressure from 30% to 50% and to generate significant energy savings. Thus, a 1.5 l water bottle is blown on high speed machine with 13.5 bars. 2 l flat & sparkling water bottles are blown on high speed machines with 21 bars in Europe on more than 8 bottling plants. The venting optimisation system between the bottle and the mould cavity allows a faster exhaust of the air with a lower blowing pressure. www.sa-comep.fr TRADE SHOWreview PART 2","@ID":42}, "BOTTLING / FILLING PETplanet Insider Vol. 20 No. 03/19 petpla.net 34 Bottles: recycled, produced, filled and shipped in a real cycle Water filling in 100% rPET On the most northerly part of our tour we met Sandy Gott of Ice River Spring in Feversham, Ontario. She told us the amazing story of her family-owned business which is the only beverage company in North America operating their own recycling facility, self-manufacturing their bottles out of 100% recycled post-consumer packaging. Tour Sponsors: As an introduction let me tell you some impressive hard facts: Ice River Spring has six plants for bottle producing and filling and one recycling plant in Canada. In the US there are five manufacturing plants. Each factory occupies roughly 100,000-600,000 square feet. Here in Feversham, the largest plant, they have six Husky preform machines as well as capping manufacturing equipment from the same company. Two Starlinger lines and a number of Krones machines for bottling, filling and packaging. We also recognised Sidel and IMDvista equipment. Every day they ship around 100 loads from this facility. We asked Sandy about how the idea to create this very successful business came about and the challenges that had to be faced: Sandy and her husband Jamie Gott founded the company in 1995, and two of their three children and other members of the family have also joined the business. Sandy also told us about their second business; they are organic farmers and originally their aim was to protect water sources. “We had a property with clean spring water, so we started selling tanker loads of water from our spring to bottlers in Toronto. Then we thought, why don’t we bottle the water ourselves? So Jamie built our first line in a 5,000 square feet bottling plant and it just grew from there.” The business model was easy, as it was focused exclusively on private label business. For the consumer that means having an alternative healthy beverage on the go. And the timing was good: “Here in Feversham we have the largest plant with about 600,000 square feet; there is a 5 km pipeline from our spring to the plant to limit the truck traffic. We expanded first in the West of Canada then in the US. At the moment we have six bottling plants in Canada and five in the US. Our recycling facility is located in Shelburne, Ontario. Caps collected from the recycling line are used at our sister company CRP Products to make outdoor furniture. All of our bottling plants are zero waste to landfill.” With an annual growth rate of 6-8% in the bottled water industry, especially in the private label sector, Ice River Spring has enjoyed continuing growth because consumers are really looking for a healthy beverage option. “This facility was built in 2000 and we added to it every year until completion in 2005. In the first five years of business we doubled our turnover every year. So we decided to build up a network across Canada to cut delivery times and to service the various regions more effectively. We have 800 team members in total and this increases enormously every year. Here we have Husky machines for preform injection, a number of machines for half litre and four litre bottles, 1.5 l bottles and the 15 l bottles. To give the complete overview: we have 6 preform machines in total, the Husky Hypet 500-144 cavity, and Hypet 400-96 cavity from Husky. The cap machinery is the Husky 6 Hylectric 300-72 cavity and Husky 10 Hylectric 300-96 cavity.” Sandy continues: “We have invested significantly in light weighting our product. When we started, our bottle weighed in at 20g now it’s 8.5g. It was at this point that we contacted Husky with a view to injecting our own preforms and producing our own bottles, and we also began injecting our own caps. We were sensitive to consumer concern about plastic in landfill and we start to think about what we could do to reduce our carbon footprint?” Ice River Spring tried two different options: “Initially we went with an aseptic packaging line which was paper based and learned very quickly that this is very difficult to recycle. We also worked with PLA resin but this was incapable of maintaining the integrity of a 2 year shelf life. We then began experimenting with recycled material and started to include it in our products, first 25% than 50%“. F.l.t.r.: Sandy Gott with her husband Jamie Gott, CEO of Ice River Spring and their daughter Crystal Howe, Sustainability Manger at Feversham plant Starlinger purification unit at Ice River Spring 5 km pipeline arriving from the source at the plant in Feversham Filling Special","@ID":36}, "MARKET SURVEY 28 PETplanet Insider Vol. 20 No. 03/19 petpla.net 03/2019 MARKETsurvey Resins & additives Preform machinery Preform production & inspection Preform & SBM mould manufacturer SBM 2 stage Compressors Filling equipment & inspection Caps & closures & inspection Palletising & shrink film machinery Recycling Suppliers of preform machinery In this issue we are proud to present our readers the very new developments in preform machinery. Please have a lock at the new cavity numbers, preform weight or the special features! These are the companies participating in this survey: Sacmi Imola, Sipa S.p.A., Netstal-Maschinen AG, Otto Systems AG, Husky Injection Molding Systems Ltd and Unique Injection Molding Systems. Although the publishers have made every effort to ensure that the information in this survey are up to date, no claims are made regarding completeness or accuracy. Company name Sipa S.p.A. Netstal-Maschinen AG Husky Injection Molding Ltd Unique Injection Molding Systems Co., Ltd. Postal address Telephone number Web site address Contact name Function Direct telephone number Fax E-Mail Via Caduti del Lavoro, 3 31029 Vittorio Veneto +39 0438 911 511 www.sipa.it Mr Stefano Baldassar Sales Director, Preform Systems & Tooling +39 0438 911 511 +39 0438 912 273 stefano.baldassar@zoppas.com Tschachenstrasse 8752 Näfels, Switzerland +41 55 618 6111 www.netstal.com Mr Stefan Kleinfeld Application & Product Manager +41 55 618 6241 +41 55 618 6605 stefan.kleinfeld@netstal.com 500 Queen Street South, Bolton, Ontario, L7E 5S5, Canada +1 905 951 5000 www.husky.co Mr Glenn Chessel +1 905 951 5000 sales@husky.ca No. 19 Shenzhou Road, HuangPu District,GZ, China +86 20 8226 5488 www.unique-pet.com +150 187 91820 +86 20 8226 5673 lzy@unique-pet.com Preform injection moulding systems Machine model number / name XForm 350 XForm 500 XTreme 72 XTreme 96 PET-Line 2400, PET-Line 4000, PET-Line 5000; PETLine 2C; PETForm 175 HyPET, HyPET HPP U-PET 500E 5000/8000 Number of cavities (min/max units) 8/128 8/180 72 96 32 - 144 Up to 160 Min 2 -144 cavities Max. individual preform weight (g) 750 750 60 60 Max shot weight 6,600 Not disclosed 38 to ~100 Max. resin through-put (kg/h of PET) 1,350 1,350 1,000 1,350 Up to 1,350 Not disclosed 1,100 Standard features (short description / keywords) XForm: available in GEN3 or GEN4 XP version (lower energy consumption, faster cycle time, redesigned HMI); XTreme: injectioncompression technology, ultra-thin wall capability, 2 preforms can be produced simultaneously Intrusion Clamping unit, injection unit, Siemens PLC closed loop control, hydraulic system, robot unit, remote supervision, turn-key engineering, hydraulic system Options / Special features (short description/keywords) XForm GEN4 XP: XP technology, LongLife tooling coating, XMold for ultra-thin preform injection capability, wide-mouth preforms capability; XTreme: built-in inspection system for 100% quality check, 100% recyled flakes processing capaibility, direct connection with Xtra SBM CPP = \"Controlled Production shutdown during a Power outage\"; NRS = Netstal remote Support, Energy Measurement Calitec Self cleaning Mould alignment Dynamic injection, compression injections","@ID":30}, "PREFORM PRODUCTION PETplanet Insider Vol. 20 No. 03/19 petpla.net 10 Huayan comes to America Light weight luggage by Mike Urquhart Guangzhou Huayan Company – known as Huayan – was founded in Guangzhou, China in 2002. Since its inception, the company has been focused on the PET preform injection moulding business. Much of Huayan’s early developments were with customers in China. Today, they have systems running throughout Asia and in Europe, North and South America, the Middle East and Africa. Huayan sold their first preform mould and machine in 2002 and since then have made a number of new product developments: 2004 – 48 cavity mould 2005 – 72 cavity mould 2008 – 96 cavity mould 2012 – introduced the Ecosys line of machines from 225 t to 500 t 2014 – introduced the Epioneer line of systems for 128 and 144 cavities 2018 – 176 cavity mould My Molding Solutions (MMS) team In 2017, My Molding Solutions (MMS) was founded and became the exclusive representatives for Huayan in the Americas, headquartered in Toronto. In 2018, they opened an office in Mexico and had a large booth in the Bottle Zone at NPE. Jackie Wei, president of MMS says “NPE was a major breakthrough for Huayan in the Americas. Most preform moulders in the Americas knew very little about Huayan. Once we informed them that we have over twenty 144 cavity systems in operation today, we received many inquiries. We offer complete system solutions with good parts and service support at a very competitive price.” New 4g preform development Huayan has also developed a number of new bottle and preform designs, many of them for light weighting. One such development is a 4 g 250 ml bottle with a 0.4 g closure. This design is claimed to provide: 3 stage sealing Easy capping Buckled lock structure Pilfer proof bridge Pilfer proof band The bottle and closure pass a stack test with 6 layers of 24 bottle cases. The cap is also designed to prevent tilting. The bottle has a non-threaded preform neck design that provides pressured seal closure for small water bottles, providing moulders light weighting with top sealing performance. As well as the standard finish, alternative designs are available including plastic foil sealing, 29/25 or 26/22 thread and a press on cap without a tamper-evident/anti-pilfer feature on the side. The main market for this has been water, but there are also enquiries for dairy and condiments. www.huayanamericas.com product development caps & closures design high cavitation moulds multi-component moulds closure production systems after sales service competent – professional – inspiring Dr.-Walter-Zumtobel-Strasse 9 | 6850 Dornbirn | Austria | www.z-moulds.com SAVE THE DATE Plastico Brasil March 25th- 29th, Sao Paulo Plastimagen April 2nd- 5th, Mexico City","@ID":12}, "BOTTLING / FILLING PETplanet Insider Vol. 20 No. 03/19 petpla.net 31 chose GEA to supply the aseptic filling technology with all its upstream equipment such as homogeniser, deaerator, UHT, aseptic tanks and CIP stations. “Thanks to the positive experience with the aseptic filling technology we were confident that GEA provided the best overall turnkey solution for us from top to bottom. We also included our milking parlour at the farm in the scope of supply.” To help manage the filling process, ABC Group commissioned the service of Uniplastido Interbuana (Uniplast). Uniplast was a pioneer of aseptic filling in Indonesia and has many years of experience working with the technology. “We chose a synchro aseptic system featuring a GEA EcoSpin2 sterilising technology fitted with a Fillstar FX-C filler,” said Edwin Gunadi, CEO of Uniplast. Developing the light barrier Uniplast then worked with its suppliers to develop a new light barrier for the PET bottles that would protect the fresh product adequately. The process took many months, but the outcome has provided a mono-layer light barrier that has the same functionality as common carton packaging. “It will provide protection for up to nine months, preserving the colour, taste and nutritional characteristics of the product without the need of a cold chain,” said Gunadi. The PET bottle is lighter and easier to handle than alternatives and provides the opportunity to design bottles in a variety of shapes in line with ABC Group’s marketing requirements. Integrated PAA sterilising system A key feature of the GEA EcoSpin2 is its robust and reliable bottle and cap sterilisation with a low chemical residual. The system uses only 1 PAA (Peracetic acid) sterilising solution to treat the bottle both inside and out simultaneously as well as the cap, without the need for wetting agents. The PAA solution is fully recovered and reused in a controlled loop. The PAA temperature does not exceed 65 °C so there is no risk of PET shrinkage when using lightweight containers. Caps are sterilised through immersion in a PAA solution to reduce and potential mechanical stress and achieve a proper bottle seal. The system at ABC Group fills up to 40,000 0.5 litre bottles/hour, however, GEA EcoSpin has a maximum capability of 72,000 bph. The Fillstar FX-C from GEA is a proven, high-speed, volumetric filler specially designed for filling still products, such as milk, with and without pulps, fibres and pieces with dimensions up to 6x6x6mm. (Image: GEA) ABC chose a synchro aseptic system featuring a GEA EcoSpin2 sterilising technology fitted with a Fillstar FX-C filler. A key feature of the GEA EcoSpin2 is its robust and reliable bottle and cap sterilisation with the lowest chemical residual. (Image: GEA) Preventing foaming The Fillstar FX-C from GEA is a proven, high-speed, volumetric filler specially designed for filling still products, such as milk, with and without pulps, fibres and pieces with dimensions up to 6x6x6 mm. This GEA aseptic system can extend filling to dose accurately particles with dimensions of up to 10x10x10 mm. The filler has an aseptic product tank, located on the top of the carrousel, that feeds the product through a linear path to reduce wastage during product changeover. Its dual-speed design – with a slow speed mode used at beginning and end of filling cycle – prevents foaming even when filling critical products. There is no contact between the filling nozzle and the bottle neck to avoid any cross contamination. www.gea.com","@ID":33}, "44 TRADE SHOW REVIEW PETplanet Insider Vol. 20 No. 03/19 petpla.net High performance systems for China PETplanet: Mr Keersmaekers: You are presenting your 1.5-step injection SBM machine in an upgraded version at CBB for the first time (see also PETplanet 10/2018 page 46f.). What have customers been saying about it? Keersmaekers: We developed the 1.5 step process back in 1995 and received great feedback over the years. The PF36/36600 shown here at CBB extends the productivity up to 15,00017,000bph and uses an advanced control system for even more precise control and enhanced machine cycle efficiency. PETplanet: You already have plants in Japan and India. Are you building machines for local demand in those countries? Keersmaekers: We are building machines for local demand as well as export to the same quality standards according to a range of different local requirements. PETplanet:Are the markets moving from low-cost to high tech? Keersmaekers: We are seeing a trend towards high performance systems here in China, hence the presentation of our 36/36 machine designed especially for water bottles. The growth of the cosmetics sector is also reflected in our business structure. We are increasingly selling highly flexible systems in this sector and have started promoting our newly developed zero cooling technology providing dramatically reduced cycle times whilst improving container quality. www.nisseiasb.co.jp Dongguan Longsun Machinery Co Ltd (Mr Perry Jiang) www.gdlongsun.com Linear SBM up to 6 cav; rotary SBM up to 20 cav.; moulds Jiangsu Huihe Packaging machinery Co Ltd (Mr Jerry Sun) www.huihemachinery.com Rotary SBM up to 48,000bph; filling for CSD, hotfill, liquid food and ultraclean Ribo Plastic Packaging Machinery Co. Ltd (Ms Felicity Huang) www.ribo-tech.com Linear SBM up to 12 cav. Jiangsu Jinrong Machinery Co Ltd (Ms Celya Qu) www.jinrong.cn SBM 6 to24 cav., 10,000 to 36,000bph Zhejiang Huangyan Ruiying Machinery Co Ltd www.rymould.com; www.ruiyingmachine.com Linear and rotary SBM from 2 -16 cav., blowing and mould TRADE SHOWreview PART3 Liao Ning Trueeasy Packaging Machinery Co Ltd (Ms Letizia) Linear SBM up to 6 cav. CBB Impressions - Chinese exhibitors of Stretch Blow Moulding Machinery Karel Keersmaekers-Michiels, Managing Director Nissei ASB GMBH and Alexander Büchler on the left","@ID":46}, "BOTTLING / FILLING PETplanet Insider Vol. 20 No. 03/19 petpla.net 22 Installation of an aseptic bottling line at Food Union’s Dong Ying dairy factory An entire line for dairy processing Serac’s engineering services were contracted to manage the conception and implementation of a full aseptic bottling line for dairy products, which commenced production in June 2018 in Dong Ying, China. Dong Ying is one of two liquid dairy plants that were simultaneously conceived, engineered and constructed for Food Union under the stewardship of SPX Flow. It makes use of advanced technology to set new standards for dairy processing in China, and to meet the Chinese government’s drive to enhance safety, quality and sustainability capabilities in national dairy production. From bottle blow-moulding to shrinkwrapping Serac led the development of the entire line, which is made up of a stretch blow-moulder; an aseptic fillercapper; label and shrink sleeve applicators; plus secondary and tertiary packaging units. The objective was to deliver the most advanced and upto-date solutions in terms of hygiene, efficiency and packaging to support Food Union’s (FUN) vision of innovation in China. The project included equipment selection, integration follow-up, factory acceptance tests and site acceptance tests, for which Serac assumed full responsibility and acted as FUN’s single point of contact. Serac’s assignment is a worldwide leader in low-acid products aseptic bottling solutions. It has 44 years of experience in the field and currently has over 78 lines running. A single line for viscous and liquid products The dairy bottling line in Dong Ying is used for UHT milks and other milk-based drink and, consequently, has to handle a range of viscosity. All the products are bottled on the same line through Serac’s Multiflow nozzles, which automatically adapt to viscosity and to three different bottle formats. Serac says the line benefited from Serac’s expertise in changeover management. It is designed to be highly flexible in order to maximise production capacity. Highly secure process The line has been validated according to European protocols for aseptic machines. The filling and capping unit uses the most advanced aseptic technology, to ensure no particles enter the sterile zone, which holds only the very minimum necessary amount of equipment. Particular attention has been paid to H 2 O 2 vapour bottle decontamination, which is highly secured and fully traceable. The process is defined and validated for each bottle format through challenge tests, and continuously monitored during production through Serac’s patented probe. Changing China’s dairy products landscape with premium products and attractive packaging Serac says that aseptic bottling is the final stage of an entire process dedicated to taste, nutritional value and food safety, which relies on breakthrough technologies to produce premium quality products. Designed to entice Chinese consumers and meet their convenience requirements, FUN products were to be presented in an appealing, reclosable packaging. White PET bottles, which are increasingly used on Chinese premium market segments, were chosen for packaging. Serac also provided support at the bottle specification stage. Although Serac has over 50 filling lines operating in China, Dong Ying is only the second fully aseptic solution. PET bottles are gaining market share compared with cartons; this trend, along with Food Union’s quest to play a leading role in the transformation of the Chinese dairy market, means that aseptic filling is also likely to see growth in the country. www.serac-inc.com Serac aseptic filler installed at Food Union Filling Special","@ID":24}, "BOTTLING / FILLING PETplanet Insider Vol. 20 No. 03/19 petpla.net 35 Almost everyone in the bottle business told them that a 100% rPET bottle was impossible, but Jamie and his team went ahead anyway and succeeded. “In 2008-2009 Amut and Starlinger could produce food grade recycled plastic on their lines. We decided to build our own recycling plant in Shelburne, Ontario. We installed Amut sortation equipment and 2 Starlinger purification unit lines, a Star 1 reco-Star PET 165 iV+ and Star 2 recoStar PET 165 HC iV+. From the blue box from Ontario (the Provinces’ recycling system) only 16% was PET, the rest was other plastics. We buy 85% of the PET plastics collected in the blue box in Ontario, and that was about right. We have created a steady demand for material, and this was important because previously it was not possible as waste plastic was shipped to China whenever domestic demand was low. With our own recycling plant we now have a total closed loop business.” Ice River Spring gave their consumers a real option: bottled water produced with a very low carbon footprint. “It is much more environmentally friendly because all bottles in every location in Canada are 100% rPET, from half litre and also the bigger 15 l bottle; we ship our rPET to all our plants in western Canada. In the US not yet every one of our partners is working 100%, but we are working on converting them. For private label producers, they now have the opportunity to advertise 100% rPET bottles and that is the best advertising.” “We do two different colours for the 100% rPET bottles, blue for most of our private label customers, and the green, recovered from the green PET in the stream, we use for our own brand. Ice River is sold exclusively in Canada in a green bottle. At the moment we are having to buy more green flakes to meet consumer demand for our product.” Sandy sees further growth on the recycling plastics side: “More of our US customers are converted to use rPET, and we are going to need a bigger supply and this will mean adding another recycling plant elsewhere in North America. The challenge here is to put it in a region where you have access to a consistent supply of material!” Sandy had one final comment to add: our main driver is to be the trusted provider of healthy beverages through innovative and responsible methods. We want to redefine bottled water and give consumers a sustainable option they can feel good about. We believe that closed loop business models will encourage other manufacturers and brand owners to do the same. www.iceriversprings.com for Pharma Applications 100% inline Inspection for PET, HDPE, LDPE, etc. for complex Shapes B O T T L E I N S P E C T I O N One of the Husky machines: A Hypet 400, 96 cavity","@ID":37}, "BOTTLE MAKING 15 PETplanet Insider Vol. 20 No. 03/19 petpla.net as well, are produced in-house, thus avoiding unnecessary journeys and reducing CO 2 emissions. So for a sustainable, efficient production operation, too, a partner like Krones was the choice. Two 16-part Contiform S machines produce a large bandwidth of bottles for products like washing-up liquid, household cleaning agents and detergents in sizes ranging from 100ml to 2 l. They are labelled on Krones Contiroll and Kosme Flexa labellers, and filled on Kosme weighing-cell fillers. The dry end additionally features Krones palletisers, the Robobox and the Pressant Uni. The most recent machine being used for container production, however, commissioned in 2017, features Krones’ ProShape technology: a Contiform 3 Pro with twelve cavities and a rating of up to 2,300 bottles per cavity and hour. Creating design eye-catchers with ProShape “With eye-catching bottle shapes, you can ensure consumers notice your product – since it’s the first impression that counts. In order to achieve this, we opted for an oval design of our containers,” explains Dr Wolfgang Gross, Managing Director of Fit GmbH. But it’s precisely this visual aspect that constitutes a challenge for standard machines, since the evenly heated preforms are not evenly shaped during the blowmoulding process: the long sides of the bottles, which are the first to come into contact with the compressed air, have a relatively high wall thickness. In parallel, this is reduced at the short sides of the bottle, since less material is available. To ensure that on these short sides the material thickness still suffices, a heavier preform can be used. But since this runs counter to the thrust for sustainability, and in addition a large proportion of the packaging costs depends directly on the preform’s weight, a different solution was needed. “With the ProShape module for selective preform temperature control, Krones has come up with a really persuasive proposition. The material is selectively distributed, either to create a uniform wall thickness, or to strengthen certain areas of the bottle. This enables eye-catching designs to be created, as well as facilitating the lightweighting of oval containers as part of the thrust for sustainability,” to quote Dr Wolfgang Gross. The ProShape module is integrated into the Contiform between a standard linear oven and a standard blowing wheel. Using aluminium moulds specially temperature-controlled to suit the requirements of the subsequent bottle, the requisite temperature profile is applied to the preform. This ensures that the preform is appropriately conditioned, after which it is passed to the mould following precise orientation. Selectively optimised material distribution is achieved during subsequent stretch blow-moulding of the bottle. For preform orientation, optical sensor technology is used that can detect orientation marks at the neck finish of highly disparate preforms. Once the orientation mark has been detected, the requisite angle is computed and the preform individually oriented accordingly in the treatment starwheel by means of servo-technology. This means, for example, that the preform can before conditioning be turned so as to ensure that later on the screw-cap always sits in the same position on the bottle. ProShape enables bottles featuring a prominent round-oval contour and a sophisticated wall thickness distribution to be flexibly produced with maximised efficiency, economical energy consumption levels and at low costs. In addition, the defined wall thicknesses in all container segments ensure optimal haptics and functionality, e.g. for the right rebound resilience when the bottle is squeezed. Hand in hand to create the perfect bottle In terms of bottle design, too, Krones supported company. Bottle, neck finish and closure were optimised, and customised to suit the application and the client’s stipulations. “Collaboration in the field of bottle development is excellent. Krones is able to offer comprehensive expertise for packaging development from a single source. This includes the well-versed design team, the technical competence and the experience gained in installing production lines. Combined with our innovative vigour and the equally great technical skills of my staff, solutions were created hand in hand that are truly impressive,” says an enthusiastic Dr Gross. www.krones.com Continuous expansion of the product portfolio: 1997: Fit launches the first 3-phase tabs on the market. 1999: the traditional Fit washingup liquid 500ml is given a fresh design and a new PET bottle. 2000: Fit purchases from the US Company Procter & Gamble the well-known brands Rei, Rei in the Tube and Sanso. 2015: the product portfolio is expanded with the acquisition of the Gard brand. 2016: acquisition of the Fenjal body care brand. Besides Fit, the company’s brands include Kuschelweich, Sunil, Rei (in the tube), Sanso and the hair care brand Gard, plus the body care brand Fenjal.","@ID":17}, "45 TRADE SHOW REVIEW PETplanet Insider Vol. 20 No. 03/19 petpla.net Shanghai Shangzhen Compressor Co Ltd (Mr Stephen Chao) www.szcompressor.com Piston compressor from 6 -25m³/h, 30 -40bar Adekom Kompressoren (Mr Stephen S L Chan) www.adekom.com.hk Piston compressor up to 30.5m³/min, 30-40bar CBB Impressions - Chinese exhibitors of IM Machinery/Moulds/Preforms CBB Impressions - Chinese exhibitors of Compressors Aoktac Precision Machinery Co Ltd (Mr Younis Zhou) www.aoktac.com Injection Blank, Blowing and Moulds Guangdong Friend Machinery Co., Ltd. www.friend-machine.com Injection Moulding, Blowing and Moulds GDXL Precise Machinery Co., Ltd. (Mr Billy Au-Yeung) www.gdxl.com Injection Moulding, Moulds Demark (Shanghai) Pack. Techno. (Mr Andy) www.demark-pet.com Injection Moulding, Injection Blow Hollow, Extrusion Blow Hollow, Moulds Qingdao Greenlong Machinery Co., Ltd. (Mr Henry He) www.greenlong.cn Injection Moulding, Moulds Guangzhou Huayan Precision (Mr Jason Lu) www.gzhuayan.com Injection Moulding, Moulds Unique Injection Molding System Co Ltd www.unique-pet.com IM and preform moulds, 1,300-5,000KN moulds from 8-144 cav. Techgen Machineries Ltd www.techgen.com.cn Injection Blank, Blowing and Moulds","@ID":47}, "BOTTLE MAKING 17 PETplanet Insider Vol. 20 No. 03/19 petpla.net Affordable meal in a handy bottle Complete nutrition on the go With a turnover of £ 14 million in 2017 and £ 40 million (~46m €) in 2018, Huel is one of the fastest growing companies in the UK. Turning the nutrition game in less than four years, it offers customers nutritionally complete meals with a mission surrounding convenience, affordability and lessening the impact on animals and the environment. Adding to their product line of Huel Powder, Huel Bars and Huel Granola, the Huel Ready-to-drink was launched in December 2018, in a practical 500ml PET bottle developed by PET Engineering in collaboration with GEA Procomac. The packaging design meets the brand’s two main requirements: coherency with the existing product portfolio and functionality. The first requirement was met by creating a simple shape, by choosing white to colour the preform, which is also useful to protect the bottle’s contents, and by using a full-sleeve to give the brand great visibility, as is also the case for the cardboard packaging and single packs already on the market. With regard to functionality, the large 38mm mouthpiece allows the bottle to be quickly used on-the-go in a practical way, making it perfect if time is of the essence and when there is no access to a kitchen to prepare a healthy and well-balanced meal. A complete and affordable meal in a handy bottle, the Huel Ready-to-drink contains all 26 essential vitamins and minerals, 20 g of protein, only 5 g of sugar and comes in two delicious flavours, Vanilla and Berry. Focus on the technology The bottle is produced on an aseptic line supplied by GEA, which includes a GEAABF 1.2 system. The GEA aseptic line – which obtained the FDA LONO certificate for producing and distributing in the USA ambient temperature shelf-stable low acid beverages – is based on an integrated aseptic blowing, filling and capping process and it is equipped with a 100% aseptic blower. The FDA clearance confirms that GEA’s ABF 1.2 technology ensures sterilisation efficiency and reliability during every step of sensitive beverage bottling. Thanks to the microbiological isolator extended also to the blower module, GEA ABF 1.2 aseptically blows preforms that have been previously sterilised with hydrogen peroxide vapour (VHP), treating simultaneously the inner and outer surfaces. The result is a single step preform sterilisation process that is claimed to grant a 100% process treatment monitoring and requires no rinsing water and significantly low chemical consumption. With ABF 1.2, which features continuous monitoring of each sterilisation process parameter as fully automated operation cycles, the risk of recontamination of any sensitive drinks during bottling is erased. www.petengineering.com BOTTLE MAKING 17 Visit us: www.bericap.com In addition to quality closures, BERICAP provides capping equipment and unique customer and technical service, globally. Experience from global business New product introduction Line / capping efficiency improvement Training for customers Troubleshooting on site (capper) Technical Service","@ID":19}, "DIGITALISATION PETplanet Insider Vol. 20 No. 03/19 petpla.net 36 Digitalised end-to-end manufacturing execution process provides both efficiency and flexibility A recipe for growth by Gabriele Kosmehl During a one-day event at its EMEA headquarters in Dudelange, Luxembourg, Husky Injection Molding Systems unveiled their Next Generation Operating Model (NGOM) program. This digitalised end-to-end manufacturing solution fulfils the purpose of serving customers with speed and quality through a more efficient and flexible business model. Continuing changes in consumer behaviour, such as the growing demand for customised products, prompted Husky to look for ways in which they could respond quicker and more flexibly to market trends. “People want to differentiate, and to provide that, you must offer a high degree of flexibility throughout your organisation,” explains Wesley Grove, Husky’s Vice President – Operations, NGOM to PETplanet. “The promise of digitalisation is exciting in that new technologies enable connectivity between traditionally siloed functions in a business. Designing processes across these functions, or end-toend, combined with technologies that connect our people to processes and tools enables us to react to our customers’ demands in a very fast way and with high quality. We see the ability to deliver fast with great quality and transparency as a very good recipe for growth.” It was back in 2016 when Husky defined the Factory of the Future concept and partnered with the Luxembourg Government’s Ministry of Economy & Luxinnovation, who made a €3.4 million contribution, to build a proof of concept to bring this new capability and value to life. A solution to the process-flow was developed the following year with Siemens who provided the automation and industrial software. NGOM has been in the validation phase since the first quarter of 2018, accepting orders from pilot lines. “Companies have been working to resolve wasteful processes since the beginning of time. Now digitalisation allows for new, breakthrough solutions with unprecedented flexibility in application and potential for scalability. What typically was a process redesign that accepted compromises can now be breakthrough approaches that resolve competing contradictions. We will create breakthrough capability in speed and flexibility at a very high quality that our customers will leverage for their growth. At the end of the day, we are striving to provide solutions with high added value and we believe that speed, quality, and flexibility are values that are great levers for growth that will continue to gain importance in the new economy,” said Grove. Cutting processes from several weeks down to several hours In the short term, a faster delivery with better quality is expected while the midterm goal is a delivery with greater efficiency. With time, digitalisation will fully integrate business process and product, enabling Husky’s customers to bring their product ideas to market with unmatched speed, confidence and design freedom. The NGOM process allows the company to cut hardware ordering and manufacturing from a process that takes several weeks down to a few hours. Through a web interface, customers can configure their order. Based on this criterion, a solution is calculated within minutes, ready to be produced within the completely automated process in a couple of hours. By evaluating all the generated data, processes and quality can be improved in real time . Husky’s sites in Luxembourg and Canada have been the focus to date. However, according to Grove, the NGOM is a global initiative involving all business units and functions within the company. For this project to succeed changes took place not only in digitisation processes and Industry 4.0 tools, but also and most importantly with team members. In addition to hiring new skillsets around digitisation, Husky is investing to ensure existing staff are fully preJean Christophe Witz with the first core produced using NGOM Wesley Grove, Vice President – Operations, NGOM, Gabriele Kosmehl, PETplanet and Jean Christophe Witz, Director of Digitization Husky Luxembourg (from left)","@ID":38}, "BOTTLING / FILLING PETplanet Insider Vol. 20 No. 03/19 petpla.net 12 Filling Special Acquisitions Market and technical data Sipa 1999 Introduction of rotary SBM 2000 SIG takes over Krupp Kunststofftechnik and therefore also Corpoplast SIG Plastics reports that the world market for 2-stage stretchblowing facilities is 1,590 units, for single-stage facilities 1,355 units and 1,150 preform facilities. In their view, in 2005, 17% of investment was in other drinks, 9% in oil and soya, 7% each in water and hotfill, and 4.4% in CSD. 2001 SFR rotary SBM, up to 1,750 b/h per cavity 2002 Packaging strategies reports over 2,125 million barrier bottles in 2001. Of these, 60% multilayer and 40% coated The first electronic filler Unitronic 2003 The EU Commission approves the purchase of Sidel by Tetra Laval Group. KHS takes over Allfill Canadean reports that the market share of PET in water packaging has risen from just over 40% in 1997 to 70% that year. The loser is the PVC bottle, which has fallen from 15% to 0% 2004 SIG Blowtec launched 2nd generation ISBMs, in the same breath, SIG announces sale of Blowtec Top Talk Fabio Firmani, CEO Sipa: “We are the only provider that delivers the entire process chain from preform to pallet”. Triple cavity blow moulder SFR 9/27 2005 SIG sells Simonazzi to Tetra Laval. KHS takes over majority at India production site Canadean reports that 40% of packaged drinks globally are in PET Top Talk Gianfranco Zoppas, Owner Sipa:\" I believe the best solution is single stage\". SFL linear SBM were redesigned (SFL 4 and 6) 2006 WCM as owner of the Klöckner factories is insolvent. KHS is later taken over by Salzgitter SIG reports that 60% of bottle costs are raw materials, 13% preform production and only 7% investment in SBM The first volumetric isobaric filler 2007 GEA takes over Procomac. Simonazzi fillers are now only sold under the name Sidel Canadean reports that almost 60% of all packaged water globally is in PET Redesign of the SFR EVO, now up to 2,000 b/h per cavity 2008 Salzgitter takes over KHS and SIG Beverages with Corpoplast. Brings everything together under the KHS umbrella. So KHS becomes a complete facility provider The lightweight 0.5 l bottle is here: Krones 8.85 g, Sipa 10.9 g, Sidel 9.9 g The first Sincro Bloc 2009 Kosme, provider of facilities in the low-spec range, is taken over 100% by Krones Sincro Tribloc: SBM filler and labelling 2010 2011 For 2015, Pira International envisages 7.7 billion PET beer bottles, of which around 50% without barriers, 1/4 multilayer, 10% coated, the rest with monolayer blends 2012 2013 Launch of Flexotronic: new filler platform with high flexibility 2014 2015 Sipa takes over Automa SBM and preform compression moulding Xtreme as a block in a facility. From granulate to finished bottle all at one heat 2016 LiquiForm partners with Krones as development partner. LiquiForm also cooperates with KHS Sidel reports on the reduction of the 0.5 l water bottle from 28 g in 1985 to 7.95 g in 2015 2017 Launch of Xtra rotary SBM with 2,550 b/h per cavity 2018 Sidel takes over PET Engineering GEA takes over Vipoll Gianfranco Zoppas, Owner, presents the Xtreme with blocked SBM and filler in Vittorio Veneto. \"In the past single stage plants were required. Today, it has become a two-stage technology\" 2019","@ID":14}, "BOTTLING / FILLING PETplanet Insider Vol. 20 No. 03/19 petpla.net 19 Cost-effective solution with significant savings The BoostPrime packaging solution is said to significantly reduce consumption of PET resin: it can decrease the current heat resistant (HR) bottle weight by up to 30% compared to regular HR PET bottles. It allows producers to save on label material by enabling to switch from a sleeve to a roll-fed label application. All the process parameters – air blowing pressure, air cooling – are optimised at maximum mechanical speed. When investing in the BoostPrime solution for a new hot-fill PET line to produce a 1 l hot-filled bottle, beverage producers can quickly reach a one-year payback when considering the additional investment versus a traditional line configuration. By shifting from regular HR bottles with vacuum panels decorated with sleeve labels to lightweighted BoostPrime bottles decorated with roll-fed labels, the bottle lightweighting potential is estimated to be between 3-7g, complemented with a ten-fold reduction in label costs. Top bottle quality and expanded package performances The complete packaging solution ensures a consistent blowing process and final bottle base profile for a top bottle quality. Although it is light, the bottle is just as strong when cooled because the inner bottle pressure stemming from the base inversion reduces risk of deformation. The quality of the label application is optimised as the container is stronger and the bottle wall surface is smoother. The large seating diameter of the base improves the bottle’s stability through the packaging line and on the pallet, thus contributing to line efficiency. BoostPrime hot-fill PET lines are running in Mexico The Sidel BoostPrime packaging solution has been validated with a key customer in Mexico, where industrial production successfully started early this year. With nearly 50 SKUs in production, this beverage producer has already achieved bottle weight savings up to 32%, according to Sidel. Those hot-filled drinks including juice, tea and isotonics are produced by using a variety of production configurations: off-line and in-line production, existing and new Sidel blowing and filling equipment, standalone Sidel blower and Sidel integrated blow-fill-cap Combi, SBO Universal and SBO Sidel Matrix blower ranges, contact filling and flow meter filling, applying roll-fed and sleeve labels. All the lines configured for BoostPrime can produce standard heat-resistant bottles with or without panels, which increases the versatility of this packaging solution. www.sidel.com","@ID":21}, "MARKET SURVEY 29 PETplanet Insider Vol. 20 No. 03/19 petpla.net Company name Sacmi Imola Otto Systems AG Postal address Telephone number Web site address Contact name Function Direct telephone number Fax E-Mail Via Provinciale Selice 17/A 40026 Imola (BO) Italy +39 0542 607111 www.sacmi.it Mr Moraldo Masi Director of Business Unit PET +39 0542 607888 +39 0542 642354 moraldo.masi@sacmi.it Zürcherstrasse 73 8730 Uznach, Switzerland +41 55 285 22 11 www.otto-systems.com Mr Stefan Zatti CEO +41 55 285 22 09 +41 55 285 22 44 stefan.zatti@otto-systems.com Preform injection moulding systems Machine model number / name IPS220 IPS400 PET-Series 120, PET-Series 160, PET-Series 250, PET-Series 350 Number of cavities (min/max units) 16 - 72 48 - 128 2 - 112 Max. individual preform weight (g) 140 140 Max. shot weight 5,410 Max. resin through-put (kg/h of PET) 625 1,250 Up to 1,150 Standard features (short description / keywords) Injection cylinder (shooting pot) Electrical drive for plasticising screw Injection cylinder (shooting pot) Electrical drive for plasticising screw Consulting & engineering of preform systems, complete preform production system including auxiliaries, full electric clamping unit, hybrid injection solution with shooting pot or electric injection with time safe unit TSU Options / Special features (short description/keywords) T-belt for preforms extraction Belt free robot linear motor with KERS Take out plate with 3 postcooling stations HMI with control of all auxiliaries Double cylinder for preform ejection Digital valves for each actuator Eater unloading system prior to mould changing Fast change over system with plug-and-play mould fixing system Plug-and-play take out plate fixing system Water pumps for mould cooling assembled on main machine platform Secondary belts system for an easier collection of preforms sampling Quality control vision system with multiple camera Direct preforms unloading from gripper plate Belt free robot linear motor with KERS Take out plate with 4 postcooling stations HMI with control of all auxiliaries Boosters on moving platen for first phase ejection Digital valves for each actuator Water unloading system prior to mould changing Mould interchangeability with most common existing solutions Boxes located in robot cabinet (less handling and contamination) Water pumps for mould cooling assembled on main machine platform On demand sampling system (up to 4 shots) Quality control vision system with multiple camera Extra large preform capability (up to 420mm), co-injection technology up to 72 cavities, integrated dust-evacuation (OH-Xtract), enhanced neck-cooling (OH-XCool), Wear-Protection Coating (OH-XTreme) IMPROVE LINE EFFICIENCY by 10% OR MORE CONTACT US TODAY TO LEARN MORE! AGRINTL.COM | +1.724.482.2163 | SALES@AGRINTL.COM 1MEASURE 2CONTROL 3OPTIMIZE PROCESS PILOT® Blowmolder management easy as . . .","@ID":31}, "42 TRADE SHOW REVIEW Vol. 20 No. 03/19 petpla.net Cradle-to-Cradle kegs Additional fittings for KeyKeg and UniKeg, global expansion of their production facilities and a clever tool for the home market are just some of the examples of innovations highlighted at Brau Beviale by Lightweight Containers. The UniKeg range of products is already available with Sankey-D and Sankey-S fittings. Lightweight Containers is now adding a non-alcoholic fitting to the KeyKeg and UniKeg as well as other fittings for the UniKeg. An A type fitting is coming soon. Annemieke Hartman (CCO) says “As you are aware, the market demand for lightweight kegs continues to grow. To support the demand of our customers and to grow our global presence, we need to expand. To be effectively able to do so we have just opened and are building state-of-the-art production facilities in Seaham, UK (2018), near Madrid, Spain (2019) and a location yet to be determined in Italy (2019/2020). Besides that, a number of other locations are under consideration in the short term.” To make drinks in keg available for everybody, the company has searched for an option to make home use possible. For the keg to be relevant in the home market they needed to reduce the entry barriers, which, in practice, meant they needed to eliminate complex, expensive dispensing systems. For that reason Lightweight Containers have introduced the manual dispenser. Using re-used plastic KeyKeg started to re-use plastics to create their griprings and base cups, made of 100% post-consumer recyclate. Today, KeyKegs are collected with the aim of creating new KeyKegs. For this reason, Lightweight Containers set up the OneCircle company, who were already involved in the collection of kegs used at festivals. The company has created fully operational collection networks in the Netherlands, Belgium, France and the UK, with programmes ready to roll out in the USA and Asia. In other markets such as Japan, the KeyKeg and UniKeg are processed by the local waste streams in accordance with local regulations. www.lightweight-containers.com www.onecircle.world Bianca Hofland, Senior Business Creator Marketing & Public Relations Lightweight Containers and Brett PA Lamont, OneCircle","@ID":44}, "41 TRADE SHOW REVIEW PETplanet Insider Vol. 20 No. 03/19 petpla.net BrauBeviale2018 GEA Vipoll launches latest monobloc filler for PET, glass and cans GEA’s January 2018 acquisition of Vipoll, the Slovenian manufacturer of filling systems and components for the beverage processing industry, has allowed the group to expand its end-to-end portfolio with the addition of flexible PET, glass and can packaging. The new range is marketed under the subsidiary brand, GEA Vipoll. The GEA Vipoll All In One, a multifunctional bottling machine for filling PET, glass bottles and cans, was presented at Brau Beviale 2018. The machine on display was developed for Norwegian brewery Mack, whose main production facility is at Nordkjosbotn, a location that makes it the northernmost brewery in the world. It is the most recent machine to have been produced from the All In One filling system range, which was commercially launched at the end of 2017. Depending on container size, the monobloc filler developed for Mack – one of Norway’s strongest beverage brands – can process approximately 8,000 containers per hour, including beer, cider and soft drinks; potential unit volumes are in excess of 20,000. Jakob Šalamun, Senior Sales Manager at GEA Vipoll, explains that these machines are the company’s response to growing market demand for filling and closing of different beverage containers via a single machine, as well as the demand for increased efficiency. Changeovers from PET to glass bottle or cans are possible in about 30 minutes, including cleaning. The rinser is equipped with universal grippers. The filler, which can handle hot and cold filling of still and carbonated beverages, features electro-pneumatic filling valves. The single, multi-function capping turrets can accommodate lids, bottle caps and plastic screw-on caps. Very low oxygen intake during filling is also a benefit that customers can rely on, according to GEA. The All-In-One machine can be connected to a SCADA system via a Human Machine Interface (HMI) and meets Weihenstephan standards for data transfer. The primary market for the All-In-One series today is breweries; however, the solution offers added flexibility for producers of soft drinks and other alcoholic beverages. Rinser-filler-capping blocks from this series are now in use at customers in Australia, Croatia, Sweden and South Africa. www.gea.com F.l.t.r.: GEA Vipoll’s Corporate Media & Press Manager Fanny Förster and Senior Sales Manager Jakob Šalamun Jakob Šalamun explains GEA Vipoll’s All In One bottling machine. Emptying and compaction of beverage containers Strautmann Umwelttechnik presented its waste disposal solutions. The LiquiDrainer allows insertion of full beverage containers. Cost-intensive manual opening of PET bottles is not necessary. Manually, by conveyor belt or forklift, up to 10,000 1 l beverage bottles can be inserted and emptied within 1h. A feed rocker feeds the material to the rotor. The rotor pricks into the beverage container so that liquid can escape. Due to the special rotor technique the beverage containers are not only emptied but also devalued. Thus residuals are destroyed and can’t get into circulation. The liquids are targetly drained and go through a coarse filter. They can also be sold to biogas plants. PET containers from t h e L i q u i Drainer can be compact e d w i t h a B r i k P r e s s . Through conveyor belts or a fork lift the press can be inserted 24/7. With a throughput of 50,000 bottels in 1h the material is compacted with 380kN. The result: high compacted briquettes. www.strautmann-umwelt.com TRADE SHOWreview PART2","@ID":43}, "PETcontents 03/19 4 PETplanet Insider Vol. 20 No. 03/19 petpla.net INSIDE TRACK 3 Editorial 4 Contents 6 News 39 Products 46 PET bottles for Beverage + Liquid Food 47 PET bottles for Home + Personal Care 48 Patents PREFORM PRODUCTION 10 Light weight luggage - Huayan comes to America BOTTLE MAKING 14 Green bottle, red tower - Eye-catching body shapes in the HPC category 17 Complete nutrition on the go - Affordable meal in a handy bottle BOTTLING / FILLING 11 A review of 2-stage SBM and PET filling 18 Active base inversion - New patented technology for hot-fill PET bottles 20 Automated filling of “local favourite” fruit blend drink - Kassatly Chtaura SAL adopts EBS K Ergon solutions 22 An entire line for dairy processing - Installation of an aseptic bottling line at Food Union’s Dong Ying dairy factory 23 Soy bean milk in PET - Aseptic PET bottle filling line for China’s VV Group 24 All-round worry-free filling 26 Blocking the elements - Linear stretch-blow and filling systems 30 From farm to customer in a single source - Drinkable yoghurt in Indonesia comes in PET 33 Setting up to the highest level technology - New hybrid system and in-house metal part production at FlexBlow 34 Water filling in 100% rPET - Bottles: recycled, produced, filled and shipped in a real cycle MARKET SURVEY 28 Suppliers of preform machinery DIGITALISATION 36 A recipe for growth - Digitalised end-to-end manufacturing execution process provides both efficiency and flexibility TRADE SHOW REVIEW 40 All4Pack Paris 2018 41 BrauBeviale Nuremberg 2018 44 China Brew China Beverage 2018 BUYER’S GUIDE 49 Get listed! Page 36 Page 42 243618 Page 24 Filling Special","@ID":6}, "DIGITALISATION PETplanet Insider Vol. 20 No. 03/19 petpla.net 37 pared for the digital age. “People feel nervous and excited at the same time. They hear in the news that robots are going to replace them when digitalising processes, but this is not at all how we see the future. It’s an opportunity to connect our people to our systems to enable breakthrough effectiveness, efficiency, and new capabilities. We are going to invest in our people, and they will benefit from this great opportunity to be well trained for these new types of jobs and to grow in the careers,” says Grove. “The Luxembourg Digital Skills Bridge Programme will help us in this journey to familiarise, train, and up-skill our team members to effectively interact and perform within the new system and to leverage the capabilities of speed, transparency, and flexibility that the NGOM offers .” www.husky.co Partnership with Siemens The Digital Industry Services offered by Siemens are designed to support customers as they work towards customised implementation of the Digital Enterprise, from consulting through implementation to data analytics. Industrial Edge is a concept devised by Siemens to enable data processing on the machine level as the optimal complement to cloud computing with the open IoT operating system MindSphere. Users are said to benefit from the integration and flexibility the system allows for the analysis of data either on the field level or in the cloud. Using digital twins of the product, the production process and performance, users benefit from shorter engineering and production times, from flexible, fully automated manufacturing concepts and efficient processes. At the same time, this technology provides the assurance of quality and adherence to strict security standards. And in turn, connection to MindSphere enables the continuous acquisition and analysis of machine data. This not only ensures increased machine productivity in running operation, but also enables the data gathered to be fed back into the digital machine model, so enabling further optimisation. On the basis of the gathered data, machine builders are also able to develop new services and business models such as “pay per use” concepts. www.siemens.com F.l.t.r.: John Galt, President and CEO Husky, Etienne Schneider, Minister of Economy Luxembourg and Klaus Helmrich, Central Board Member Siemens at Husky’s EMEA headquarters in Dudelange, Luxembourg where the press was introduced to the Next Generation Operating Model (NGOM) program.","@ID":39}, "PETpatents www.verpackungspatente.de PETplanet Insider Vol. 20 No. 03/19 petpla.net 48 Plastic bottle packing International Patent No. WO 2018/140569 A1 Applicant: Steven Klein, Danville (US) Registration date 25.01.2018 This application proposes sliding a separately manufactured thin-walled section over a “normal” plastic bottle bottom. This is shaped in such a way that enables the lid of another bottle to be pushed into it. This results in a relatively stable connection and the bottom being protected. Plastic bottle International Patent No. WO 2018/139536 A1 Applicant: The Coca Cola Company., Atlanta (US) Registration date: 25.01.2018 A plastic bottle for aseptic filling of a product. The bottle has uneven ribs, which both absorb vacuum forces and serve as an optical design mechanism. Bottles designed for hot liquids International Patent No. WO 2018/125967 A1 Applicant: Graham Packaging Company LLC., Lancaster (US) Registration date: 28.12.2017 The design and rationale for an asymmetrical plastic bottle are described in this application. The bottle is to be used for hot liquids and combines the handling area with compensatory surfaces. Twisted compensatory surfaces International Patent No. WO 2018/123944 A1 Applicant: Suntory Holdings Ltd., Osaka (JP) Registration date: 25.12.2017 Compensatory surfaces in the plastic bottle wall run diagonally over the circumference of the bottle. Bottom shape International Patent No. WO 2018/123368 A1 Applicant: Suntory Holdings Ltd., Osaka (JP) Registration date: 22.11.2017 A plastic bottle with a screw top and a special design of the base’s shape, or the joins from the side wall to its base. Illuminated bottle International Patent No. WO 2018/122333 A1 Applicant: Société Anonyme des Eaux Minérales D’Evian et en Abrégé, Evian-les-Bains (FR) Registration date: 28.12.2017 A bottle that is transparent/coloured in places can be displayed as a “work of art” using a smartphone and a picture of the bottle taken with individual lighting. To this end, the bottle is placed on the smartphone’s “light module”.","@ID":50}, "BOTTLING / FILLING PETplanet Insider Vol. 20 No. 03/19 petpla.net 25 For constructing and building up a machine, 20 to 30 weeks are required. Fogg has been growing steadily in recent months: around 40 people have been taken on. Fogg is also very proud of expanding its refurbishing area and it has integrated IT and R&D to its development programme. Fogg’s latest move towards technological improvement is the addition of a 3D printing lab and a new 44 magnetic capping head system. Fogg’s 3D printing lab is equipped with 10 printers that vary in capabilities. These machines range in size with the largest having the capability of printing parts with 40” x 40” dimensions. These printers can print with a wide range of materials including rubber, nylon, PETG, polycarbonate, ABS, PLA, and IGUS. This range of materials make it possible for many different departments to utilise these machines. Before the printers, if Fogg was to make a back pocket (the part of the machine that holds bottles in place as they are filled) to test for a particular customer’s bottle, the engineers would have to draw it up, the machine shop would have to program the machines, and then they would machine the part on the router out of stainless steel. After testing the back pocket, if it is not perfect, everyone must go through the cycle again. With these 3D printers, the engineer draws up the part and just inputs the information and a prototype prints within hours in a cheaper material. According to Eric Meitz, a mechanical design engineer at Fogg, this process would take about 2 weeks to go through all the steps and be machined in the shop. With the help of the printers, an engineer can put the information into the printer and come back in about 11 hours and the part is printed and ready to test. Once the printed part is tested and finalised, it is sent to the machine shop and only must be milled once out of stainless. One more example of the clear time savings these printers provide is the difference in time it takes to The Model 44 magnetic capping head German Technology May 21-24, 2019, Guangzhou Hall 5.1, Booth S27 make a rubber gripper. Before the machines, the process would take 4 days and is now cut down to 6 hours. Due to the significant time savings, these printers allow Fogg to be more customer focused. Cutting down on the engineering release to production times, Fogg can greatly reduce lead times on custom parts. New magnetic capping heads The Model 44 magnetic capping head is the latest upgrade to the Fogg magnetic capping options. This newer version is easier to assemble and more user friendly. It is easier to take apart and work on for scheduled PMs. This model is a simpler design which allows customers to keep up on any maintenance or repairs inhouse instead of returning the clutch to the OEM/Fogg. The model 44 head is more robust to keep moisture out, allowing this capping head to perform better in aggressive washdowns. It is simple to adjust and features a more accurate torque as well. If one is looking for more torque, this new model is totally retrofittable to all Fogg designed cappers. This can be retrofitted to non-Fogg cappers through spartanparts.com. This Model 44 head can be set up for pick ‘n’ place, articulating, or random apply capping. www.foggfiller.com","@ID":27}, "8 NEWS PETplanet Insider Vol. 20 No. 03/19 petpla.net A special year starts with specialities! To celebrate its 20th anniversary, PETplanet has awarded itself a welcome present: our newly designed homepage is now online! The ebook features some of the key reports from the current issue, and is directly accessible online. Naturally, there is plenty of daily news from the industry, and on our twitter account you can follow the posts of our editors from around the world. Pack your bags and join us on our new Roadtrip to India! Delve into the Editour blogs to discover the adventures and market research from the various countries we have visited. Using the new event calendar you can easily locate all the important PET events and transfer them into your own schedule. Sign in for the brand-new Newsletter to be updated on events and other special features. In a new section called 20 years of PETplanet we will be presenting videos and a host of technology reports focusing on past, current and future questions! Also readily to hand you will find our WikiPETia database as well as the Pulse, the PET Price Index, to help you with your own research. Finally, with the new look, we are able to offer additional advertising formats offering you the ideal way to showcase your company! petpla.net Chem-Trend enhances R&D capabilities in Europe Chem-Trend, a market leader in the development, manufacturing, and marketing of release agents, purging compounds, and other process chemical specialities, announced the opening of an advanced research and development (R&D) laboratory space in Maisach, Germany. The new lab space will enhance Chem-Trend’s existing R&D capabilities and joins Chem-Trend’s network of innovative laboratories across the globe. Chem-Trend’s parent company, Freudenberg Chemical Specialities (FCS), has invested roughly € 40 million ($ 45.5 million) into the expansive new facility – spanning almost 10 acres. Various parts of the facility will be used by FCS’s Chem-Trend, Klüber Lubrication, and OKS business units. The integrated space includes areas for R&D, warehousing, training, dining, and administrative services. This major investment primarily aims to amplify excellent service, enhance technical support, and advance development capabilities for its customers over the long term. The expanded lab space - especially the new test field for product development, evaluation, and demonstration - is key to delivering elevated service to customers, with a special focus on Europe-based OEMs, states the company. www.chemtrend.com Retal celebrates solar powered facility Renewable energy was celebrated at the official opening of the largest roof-mounted solar powered plant in the Baltic States at global plastic packaging manufacturer Retal’s Lentvaris factory. Attended by many of Lithuania’s leading business people interested in green energy, the event, called “Solar Energy and Lithuanian Business: Good Practices and Challenges”, was held on February 7, 2019. Installed by contractors I + D Energias Lietuva in autumn 2018, the power plant is expected to reduce Retal’s CO 2 emissions by 733.6t/a. Giedrius Viederis, Director of Retal Lithuania, opened the event, where he explained that this project was driven by the obligation to both conserve the environment and consume clean energy. Thanking the partners and representatives of the Lietuvos Verslo Paramos Agentūra – Lithuanian Business Support Agency (LVPA) for financing the project, he said, “Today, Retal is also taking a step forward. The ceremonial opening of the largest roof-top solar power plant in the Baltic States is the result of a three-year project by many people to implement our idea.” Guests included Marius Skuodis, Deputy Minister of Economy and Innovation of the Republic of Lithuania, Rytis Kėvelaitis, Adviser to the Minister of Energy of the Republic of Lithuania, representatives of the Lithuanian Business Support Agency LVPA, Arnold Gaudiešius Ruta Jakubauskienė, Director of the Large Business Customer Department, and representatives from companies from across Lithuania interested in the use of renewable energy. Guests were given a tour of the roof-mounted solar panel plant and had the opportunity to learn about the technology used and ask questions of the suppliers involved in this project. Retal’s solar panel roof stands out for its exceptional safety and the quality of the materials used for its installation – all the solar modules have been manufactured in the European Union, giving the plant a twenty-year warranty. The power of the power plant is 1.4MW and the value of the project exceeds one million euros. www.retalgroup.com","@ID":10}, "BOTTLING / FILLING PETplanet Insider Vol. 20 No. 03/19 petpla.net 21 At a glance: Kassatly Chtaura’s integrated Ecobloc Ergon 2-9-3 K Ev system from SMI Stretch-blow moulding, filling and capping of 1 l and 2.65 l bottles in PET. Output up to 3,200 bph (1 l). The Ecobloc Ergon K series uses technological solutions inspired by the principles of Industry 4.0 and Internet of Things (IoT); Rotary, high efficiency stretch- blow moulding equipped with motorised stretch rods claimed to offer advantages compared to linear blowers; Compact plant groups stretchblow moulding, filling and capping of PET bottles in a single bloc and does not need a rinser or airveyors between blower and filler. For many years, Kassatly Chtaura had bottled their Jallab syrup by hand, buying empty PET bottles on the open market from a third party. Meeting increased demand during Ramadan with traditional, manual bottling was very difficult, so the company decided to automate the process, making it much easier to adjust production output according to market requirements. Its new, compact, integrated system from the Ecobloc Ergon K EV range was integrated in the existing line, to automate blowing, filling and capping operations in new PET bottles. While the other operations, such as labelling, are still carried out manually, the production process does not require secondary or tertiary packaging, as the bottles are sold loose. While the new PET bottle, which is blown and filled by the new line, is the same as that used in the past From left: Pierre Anid, General Manager of Novadim Food Technology; Nayef Kassatly, Managing Partner of Kassatly Chtaura; and Maurice Rassi, Technical Manager of Kassatly Chtaura. Jallab is a syrup made from carobs, dates, grape molasses and rose water. for manual production, SMI’s designers were asked to create a lighter bottle than its predecessor. This objective was achieved by optimising the preform material and working on the mechanical characteristics of the new container. The new design features improved material distribution and strengthening where needed. The outcome was a lighter bottle with economical and environmental advantages. www.smigroup.it Filling and capping process uses electronic control systems and high-efficiency, flowmetercontrolled valves. Preform heater module equipped with high-efficiency IR lamps and blow-moulding module equipped with a dual air recovery system helps to reduce compressed air and pre-heating energy costs. Weld-free modular structure, equipped with reinforced glass protection doors. Economical solutions allow the flow management of seasonal or bespoke production. Easy-Cap cap grabber Gravitational cap grabber collects the caps from a hopper, orientates them correctly and carries them to the bottling line. Made from AISI 304 steel, its compact structure makes it suitable for a wide range of layout solutions. It will only carry caps that are the correct way up; those that are misoriented will fall back into the hopper. The system is claimed to be suitable for a variety of different plastic caps. The interface is designed to allow the operator to use the machine easily and efficiently. The Kassatly Chtaura’s new Ecobloc Ergon K line was installed and will be serviced by Novadim Food Technology Company, which has represented the SMI Group in Lebanon for over 20 years. Its sixstrong team provides sales, service and technical assistance for over 200 SMI machines installed in Lebanon, Syria, Kuwait, Bahrein, Qatar, the United Arab Emirates, Oman, Yemen, Ethiopia, Sudan, Uganda and parts of Eastern Africa. Novadim, which is headquartered in Beirut, has a client list that includes Salassato Chtaura, Société Moderne Libanaise pour le Commerce (PepsiCo), National Beverage Company (Coca-Cola) and others. www.kassatly.net www.novadimft.com","@ID":23}, "BOTTLING / FILLING PETplanet Insider Vol. 20 No. 03/19 petpla.net 24 All around worry-free filling In Holland, MI, we arrived at the family owned company Fogg Filler. Ben Fogg, a third-generation member of the family is now leading the company. Fogg is very well known for its expertise in filling equipment for sensitive beverages such as dairy or juice. Susan Lamar, Media Relation Manager welcomes us in the new and well-designed building. We began by making a tour through the plant and were introduced to the workflow of Fogg Filler. Tour Sponsors: We met Susan Lamar, Media Relation Manager (photo left) Susan explained that the company was founded in 1956 by Clyde Fogg. He was one of the pioneers in modernising filling systems for plastic containers by adjusting valves, cappers and introducing special bottle handling for the new material. He incorporated it into existing dairy fillers. From this time on, the company was to develop state-of-the-art filling equipment. Susan went on to say that in 2000 Mike Fogg, the father of Ben, using all his engineering and management expertise, migrated Fogg Filler to the extended shelf life (ESL) industry, focusing efforts on clean, efficient filling for hot and cold applications. Before entering the production hall Susan tells us about the speciality in the hot-filling process: in hot-filling temperature management is always a concern. For this reason, Fogg Filler has created a unique temperature management system. A product evacuation tube inside the bowl pumps 5-50 gpm out of the bowl and sends it back to the kitchen for re-working when line stops occur. The product never comes into contact with the atmosphere so it can be re-processed in accordance with regulations. In the cold fill process of filling juices or other products with ESL, it is important to kill all micro-organisms for sanitation. Fogg offers Microb-blasters using UV light or chemicals to sanitise the caps and ensure the product stays safe. Fogg equipment fills flowable liquids (still, carbonated, flavoured or non-flavoured, with high ph) in PET bottles. In the manufacturing hall we see the production of rotary filling, rinsing and capping systems. Fogg is equipped with contoured stainlesssteel filler bowls from 2 ft. up to 12 ft diameter, 1-120 filling valves, integrated rinser and/or capping systems. Fogg offers gravity filling systems with speeds and bottle handling technology to assure optimum production rates possible to fill from 10 - 1,200 bpm on a single serve bottle. Fogg has designed a capper to ensure effortless operation. For multiple capping applications there is a large variety of closure systems: snap caps, snap-screw and screw caps can be run on the same machine. Fogg cappers feature quick-change capping chucks that add versatility in changing cap size and container. After getting to know the world of Fogg, Susan goes on to tell us also about their specially written manuals for each machine. These manuals should help machine builders and customers understand their Fogg machinery. This is necessary because Fogg produces 20-70 machines a year. by Heike Fischer Filling Special Fogg largest F 12 filler has an output of 1,200bpm on a single serve bpttle Cutting plastic templates for machine production","@ID":26}, "39 PRODUCTS PETplanet Insider Vol. 20 PETproducts Advanced thin-wall measurement for PET bottles Over the years, many PET bottle manufacturers have made great progress reducing excess material and moving towards lighter, more sustainable bottles. However, as weights continue to be reduced, the role of process variation and its effect on material distribution increasingly becomes a factor in the success of the weight-reduction program. Agr’s Process Pilot blowmoulder management system was developed to address this issue and offers manufacturers a tool to use in their weight reduction efforts. The Process Pilot system, with Agr Pilot Profiler measurement technology installed inside the blowmoulder, provides a means for manufacturers to accurately measure material distribution on every bottle (to 0.05 mm), in real time, and proactively adjust the blowmoulder to maintain proper distribution, countering the effect of process variation. In the push for more sustainable bottles, weights are being reduced even further and, with that, the sidewall thickness of the bottle. In order to process these bottles effectively and control the material distribution, additional measurement accuracy is required. The new lightweight option, incorporated into the Pilot Profiler measurement component, offered with the Process Pilot system was developed to address this need for even greater measurement accuracy and control on very light bottles. With this option, a level of control is now available with the Process Pilot system that extends the measurement range to 0.025 mm, with an accuracy of +0.01mm for PET bottle sidewall material. Agr says that this added functionality delivers greater distribution control on bottles with very thin sidewalls or at specific locations on other types of bottles where precise material management is critical to meet performance and quality requirements. This capability removes one of the barriers to producing usable, lighter and more sustainable bottles. www.agrintl.com The Agr Process Pilot system with Pilot Profiler measurement technology helps ensure that the material in the light weighted bottle is distributed according to design and is consistent for the entire production run. ","@ID":41}, "43 TRADE SHOW REVIEW PETplanet Insider Vol. 20 No. 03/19 petpla.net Latest developments in empty bottle inspection Inspection techno l ogy spec i a l i s t Heuft used last year’s Brau Beviale trade fair to present equipment and systems for labelling; for the detection of foreign ma t t e r and o t he r defects in filled bottles; and for the analysis and sorting of empty PET, glass and can containers. PR editor Hilmar Wagner focused attention on the “In Line II” empty bottles inspection series, which now consists of three models: the “entry-level” IR; the standard IS; and premium IXS. The mechanical and physical design has been updated and the In Line II IS now features an open, compact design with “Clean Design” easy access for cleaning and maintenance. The company says that it can be easily integrated into existing filling systems. The In Line II system is designed for all-round inspection of empty bottles. Heuft says that all models in the range will reliably detect residual fluids, as well as checking bottlenecks, mouthpieces and sealing surfaces, as well as the bottle base. The system can complete side-wall inspections at a rate of up to 84,000 containers per hour. The IS additionally features individual, servo-controlled rotary transport plates for the rotation and fine adjustment of each individual bottle. The camera-based, double resolution, quadruple side-wall inspection system provides eight viewing angles and fully covers 360° of the container surface. Audio-visual user operation is by the in-house “NaVi” system. The machine is intended to be able to easily adapt to completely new containers by means of Heuft’s “Spectrum II” platform, and to readjust itself automatically. Changeover from PET to glass bottle inspection is, consequently, claimed to be achieved within a very short time. The IS now features technologies from the X-ray supported IXS. As with the premium system, all detection modules are fully integrated including fluid residual caustic detection, which was previously an external module. Mr Wagner added that Heuft’s “Lambda-K” container rejection system is designed to reject empty PET bottles, even if they are at risk of toppling over, at a rate of up to 60,000 containers per hour. The specially-designed compact conveyor belt mechanism and control system aims to remove containers that are either wrong or present problems. www.heuft.com In Line II IS inspection system Lambda-K rejection system Full inspected!","@ID":45}, "BOTTLING / FILLING PETplanet Insider Vol. 20 No. 03/19 petpla.net 13 Filling Special SIG Corpoplast, from 2008 KHS Corpoplast Krones Sidel Tech-Long Introduction of the SBM Series III Top Talk with Roman Boutellier, CEO SIG: He reports on the purchasing of various elements from Germany, Italy and Switzerland. Corpoplast (stretch-blowing, Germany) and SASIB (filler, Italy) should free SIG from dependence on drinks cartons Top Talk with Volker Kronseder, CEO of Krones. Presentation of ContiformS 2nd generation with suspended preform heating. 1,600 b/h per cavity. Presentation of Contiform Bloc SBM filler block Top Talk: Francis Olivier, CEO Sidel. At that time, Sidel had 2,800 machines on the market Introduction of Plasmax interior coating Top Talk with Gerard Stricher, new CEO of Sidel. Sidel is taken over by Tetra Laval. Contiform H: first heat-set SBM Top Talk: Rolf-Dieter Rademacher, CEO SIG Holding reinforces the concept with acquisition subsidiaries Corpoplast and Simonazzi as the direction for SIG in the PET world. SBM Blomax 24 Series III C with up to 1,800 b/h per cavity; KHS: launched third generation aseptic cold filling; cleanroom shrinks by 80% Top Talk Christoph Klenk, Krones. “We need facilities for the high-end market and also for the low-spec market.” Contiform S increases to 1,800 b/h per cavity TopTalk Olaf Weiland, CEO SIG Corpoplast: he reports on the 1,000th SBM, SIG Corpoplast appears independently for the first time at Interpack, Top Talk Ralf Bajorat, Head of SIG Beverage; KHS presents plastics-only filler SBM Contiform creates OPP bottles at the same speed as PET bottles; Krones F1 filler table-free filler only for PET SBO Universal. 3rd generation SBM 1,800 b/h per cavity. SBO first linear blower Top Talk: Rolf-Dieter Rademacher, CEO SIG: Sales increase, erosion of margins stops. KHS Till and Carlsberg launch the PET keg Krones reports a rapid rise in orders for blocked facilities Top Talk with Gerard Stricher, CEO of Sidel, about merger of Simonazzi and Sidel. Sale of 100th SBO Universal: Publisher Alexander Büchler, together with Subba Bangera, plants his second tree in India on the Sidel factory site Introduction of InnoPET BloFill, the first SBM filler block Sidel sells 20 water lines at 36,000 b/h to Ting Hsin, China KHS expands capacities for Corpoplast in Hamburg. So Anker goes to India, Allfill to Bad Kreuznach Top Talk Marcel Krauth, \"Mr. Beer\" by Sidel: “Beer is the largest packaging market worldwide after water; PET has a good starting point to gain a significant market share there.” Introduction of InnoPET Blomax Series IV Contiform S with 2,000 b/h per cavity. Sale of 1,000th Contiform. Presentation of ErgoBloc L SBM with filler and labeller Sale of 500th SBM Departure of Maternus Gemmel, CSO KHS, after 48 years in the company: “The takeover by Salzgitter was a sign for us” SBO Universal 2 2,000 b/h per cavity Sale of 100th InnoPET Blomax Series IV. Presentation of the dual concept aseptic filler Innosept Asbofill Contiform 3. Third generation, now with 2,250 b/h per cavity. Introduction of PET-Asept D Compact for low output range Awarding of the PETplanet After Sales Award Developing Countries for the categories \"They know me\" and \"pricing and volume discount on aftermarket\" Awarding of the PETplanet After Sales Award Developing Countries for the categories \"Supplier addresses me\", \"friendliness\", \"effective training\", \"Competence\" and \"Responsiveness\" Awarding of the PETplanet After Sales Award Developing Countries for the categories “Technician close to my plant\" and \"Reachability\". Liquiform, a JV between Amcor and Sidel to develop bottle forming and filling. Introduction of Sidel Matrix Hotfill filler from 200ml to 2 l Corpoplast celebrates 40 years of existence Contiform 3 Pro with 2,300 b/h per cavity. Volker Kronseder hands over operations to Christoph Klenk LiquiForm, the JV between Amcor and Sidel, is launched in USA Tech-Long presents 5th generation SBM. 2,400 b/h per cavity Introduction of the Triblock FreshSafe FormFill SBM and filling in one process Contiform 3 Pro now with 2,500 b/h per cavity 3G technology (laser heating of preforms) gives previously unheard of freedom in bottle design Kai Acker as new CEO makes it his primary goal to bring more structure and order to the KHS Group. InnoPET Blomax V with 2,500 b/h per cavity Contiform 3 Speed with 2,750 b/h per cavity","@ID":15}, "The new TEM machine offers new possibilities for slitting or slitting and folding of tamper evident bands for specialty caps. The TEM, a highly versatile machine for beverage, food, beauty & home, chemical and other products. Modular design machine for slitting/folding or folding/slitting of tamper evident band Large variety of cap dimensions, including sport caps All size parts located in the outside for easy adjustment and changeover Heating system for the blade. Blade position sensor Servo-driven infeed star wheel, integrated cap stop and sensor controlled upside down closure detection Operator friendly interface Match the output of associated moulding and downstream machines Easily integrated into any production line due to independent control and optional vision inspection system PackSys Global and its affiliated companies offer a wide product portfolio: Complete lines for laminate, extruded and aluminum tubes Plastic closures slitting and folding machines Cap printing lines Monobloc aerosol can lines Hot stamping solutions from Madag Printing Systems Tube, aerosol can and cartridge packing solutions from Texa Packaging Highly skilled R&D and production teams ensure constant development and integration of the latest technology on our equipment. We stand for Swiss engineered innovation and performance. Creating Packaging Technology. PackSys Global AG T +41 55 253 38 31 info@packsysglobal.com www.packsysglobal.com A Member of Brückner Group SPECIALTY CLOSURES TAMPER EVIDENCE","@ID":4}, "PETplanet Insider Vol. 20 No. 03/19 petpla.net 46 PETbottles Beverage + Liquid Food Sunny! new drink from Aldi Süd German discount retailer Aldi Süd has several NFC juices on its shelves with a fruit content of 70% under the name “Sunny!”. The Orange/Yuzu and Apple/Banana varieties come in easy-grip contoured 0.3 l bottles with slanted ridges to improve stability. A sleeve label and a colourmatched screw seal with guarantee band complete the packaging design. www.aldi-sued.de Volvic with mint and cucumber If Apple-Lemon flavour sounds a little boring, there are two new options in the Essence Range from Volvic: Mint-Cucumber and CitrusRosemary. The Mint-Cucumber bottle shown here contains extracts of mint, cucumber, basil and lemon. 1.1% organic lemon juice from lemon juice concentrate rounds out the flavour. The product is sold in a stable, transparent, 750ml bottle with rounded corners typical of the brand. A label, which is white at the upper part, describes the product and gives the bottle the appearance of a carafe with cucumber and basil leaves floating on the surface of the water. www.volvic.de Bringing together partners for the Southern African market in the analytics, food & beverage and environmental technology, we are proudly co-located with: food & drink technology Presented by Messe Muenchen South Africa Secure your space: Email: info@mm-sa.com Tel: 011 476 8093 Africa 2019 Connecting Global Competence Leading solutions across the full value chain","@ID":48}, "PETplanet Insider Vol. 20 No. 03/19 petpla.net 47 BOTTLES Home + Personal Care A bottle made from 100% recycled plastic Frosch, a brand of Werner and Mertz, has been investing in environmental products derived from sustainable, natural active ingredients since the mid-1980s and has increased the proportion of recycled plastic in some of its products to 100%. For example, the cap on the dishwasher detergent, “Frosch for clean seas”, is made from 100% recycled PP, while the bottle consists of 100% recycled PET. The bluish-coloured product itself is free of micro-plastics. A recommended dose is given according to how dirty the dishes are. The concentrate is dispensed by means of a push-pull lid, while the sleeve label has transparent windows and lettering. www.werner-mertz.de New scents for washing-up liquid The manufacturer of washing-up liquids for doing dishes by hand is bringing several different scent variants of its known product onto the market in quick succession. For example, the German discount pharmacy chain dm has put on sale two washing-up liquids, an ultra washing-up liquid “Botanic Dream” and “Nordic Berry”, which is particularly kind to skin. The drop-shaped, clear bottles hold 500 ml and have a screwed on, colourmatched push-pull cap and two shaped, self-adhesive labels. www.dm.de Shower creme with cola Shower cream that smells like cola is being sold by German manufacturer Vendoleo GmbH under the brand name “treaclemoon” in a stable, transparent bottle holding 500ml. The dark product “funny cola sparkle” is easy to recognise and is easy to dispense via a red screw seal with a hinged cap. According to the manufacturer, the shower cream provides plenty of fine foam. Alongside the amusing manufacturer instructions for application and effect, there is also a note that the product, which smells like a food, should not be drunk and should be kept away from children. www.treaclemoon.de “Nightly Reset” mouthwash The Johnson & Johnson brand Listerine is selling a mouthwash for daily use that is also effective overnight in a slim, contoured, clear bottle holding 400ml. In the contoured area, the bottle is shaped with “corners”. Two shaped self-adhesive labels emphasise the bottle shape and provide consumer information. The product, which remineralises tooth enamel, prevents the build-up of tartar and freshens breath, is dispensed via a childproof screw seal with dosing function and a shrink-wrap label, which provides a tamper-evident seal. www.listerine.de PETbottles","@ID":49}, "PETnews 6 NEWS PETplanet Insider Vol. 20 No. 03/19 petpla.net Loop Industries expands supply agreement with Danone for 100% sustainable PET Loop Industries, Inc., a leading technology company in sustainable plastic for packaging, announced that it has completed a multi-year supply agreement with Danone SA. Danone will purchase 100% sustainable and upcycled Loop branded PET from Loop’s joint venture facility with Indorama Ventures Limited in the United States for use in brands across its portfolio including Evian water. www.loopindustries.com Alpla completes takeover of Zamil Alpla The packaging solutions specialist Alpla, based in Austria, has completed a 100 per cent takeover of Zamil Alpla. Alpla and Zamil founded a joint venture in 2008, of which Alpla previously held a 49 per cent share. After ten years of close collaboration as part of a joint venture, Alpla has acquired all the shares of Zamil Alpla. The buyer will continue to run the company as before, and with all employees, under the name Alpla. Around 390 employees produce preforms and packaging made from HDPE and PET at three locations in Dammam, Jeddah (both Saudi Arabia) and Dubai (United Arab Emirates). The acquisition was signed on December 27, 2018 and will be completed in the first quarter of 2019. The contracting partners have agreed not to disclose any of the details of the agreement. www.alpla.com Temporary endorsement for perforated sleeves on HPC PET bottles Petcore Europe’s ODR Working Group has been working on increased recyclability of sleeved PET bottles as the use of sleeves can cause problems in sorting of PET bottles via Near Infrared (NIR) and optical detectors used in waste plastic packaging sorting and recovery plants. In order not to lose material and include it in the right sorting stream, the group under the lead of Chair Gian De Belder, P&G, came up with the solution of perforated sleeves. These can be removed by the consumers of the Household and Personal Care (HPC) PET bottles. The Technical Committee of the European PET Bottle Platform (EPBP) has awarded a temporary endorsement to full body sleeves for a period of three years, provided the following conditions are met: The sleeve is equipped with double perforations which is designed to be easily identified and removed by consumers. The packaging industry develops a standardised perforation concept, both in terms of functionality (easy tearing off operation) and design (immediate recognition), irrespective of the type and content of the PET bottle. To support the above, PET bottles with perforated sleeves must carry a standardised message for the consumer asking them to remove the sleeve from the bottle, and then place both the bottle and the sleeve in the collection bin or bag for recycling. The packaging industry must support consumer cooperation with communication campaigns and provide data on the effectiveness of the consumer engagement. The PET bottle behind the sleeve must be compliant with the EPBP guidelines for transparent clear/light blue bottles and the sleeve should allow the recognition of the PET bottle, by polymer, if the sleeve is still present on the bottle before sorting. The sleeve design (materials and inks) must allow it to float in hot water and separate from PET flakes in a sink/ float separation step. Printed sleeves must not bleed inks into the washing water. Now that the conditional approval has been achieved, the industries involved will work together to meet the conditions. Meetings between the Petcore Europe ODR Working Group, A.I.S.E and Cosmetics Europe are already planned in the upcoming weeks. The three-year period will be used to assess the packaging industry commitment in adopting the solution and to measure consumer engagement in removing the sleeves. www.petcore-europe.org Acquisition of packaging business in Nigeria Indorama Ventures Public Company Limited signed through its indirect subsidiary, Indorama Netherlands B.V., a definitive share purchase agreement on February 6, 2019 with Church Street Trustees Limited as trustees of the SI Trust, BTI Overseas Limited and Capital Alliance Private Equity II Limited, for the acquisition of 100% of the share capital of Bevpak (Nigeria) Limited (“Bevpak”). Bevpak is one of the largest manufacturers of PET preforms in West Africa and is located in Ibadan, Nigeria, with a production capacity of 18,000mt per year. The value of the above acquisition, calculated in accordance with the regulations of the capital market supervisory board and the stock exchange of Thailand, as prescribed by the regulations of the Stock Exchange of Thailand Re: Disclosure of information and other acts of listed companies concerning the acquisition and disposition of assets, 2004 (as amended), is less than 15 per cent and the total size of all transactions in the past 6 months also does not exceed the 15 per cent threshold limits as prescribed in the regulations. This transaction is expected to be completed within Q1, 2019, subject to regulatory approvals. www.indoramaventures.com","@ID":8}, "No.03 2019 petpla.net D 51178; ISSN: 1438-9452 04 . 03 . 19 PETplanet is read in more than 140 countries MAGAZ I NE FOR BOT T L E R S AND BOT T L E - MAK E R S IN THE AMERICAS, ASIA, EUROPE AND ALL AROUND THE PLANET MARKETsurvey Suppliers of preform machinery Page 28 Page 24 Page 11 Filling Special","@ID":1}, "BOTTLING / FILLING PETplanet Insider Vol. 20 No. 03/19 petpla.net 30 Drinkable yoghurt in Indonesia comes in PET From farm to customer in a single source ABC Group is a major food and beverage company in Indonesia. The company has been in business since the 1970s and, in 2011 it decided to diversify to produce drinking milk, flavoured milks and drinkable yoghurt to meet a growing Indonesian market. In such a geographically expansive nation as Indonesia this was never going to be easy. What’s more, ABC Group decided to provide a product from farm to consumer from a single source. The aseptic technology has been provided by GEA. Warren Choo, CEO, ABC Group explained that he had wanted to enter the dairy business because of the market potential in Indonesia. “The first step was to find the land for the dairy farm and the milking parlour,” he said. The site chosen is in Bandung West Java. This achieved, Choo found a green field site close by at Garut, on which to build his milk processing factory. Construction began in 2015. But Choo knew that to make a real impact on the market in Indonesia he would need to do things differently. Indonesia is a nation of islands, more than 17,000 of them: the world’s largest archipelago, over 5,000 km from east to west. Moving goods to some of the more remote areas can take months by which time the shelf life of any normal fresh product would be compromised. However, Choo wanted to find a way to bring fresh, nutritious, great-tasting products to the country’s population. “We chose to use aseptic technology in PET bottles as the standard Tetra cartons can easily become damaged during transport and doesn’t offer the same flexibility as PET,” said Choo. “We wanted our product not only to taste great but look good as well. We have had experience before with PET and the new technologies available made us decide to go that route.” The technology in question is aseptic filling in which the PET bottle is sterilised, filled and capped in an aseptic environment. This, combined with utilising the latest developments in light barrier materials, allows ABC Group to create fresh dairy milks and drinkable yoghurt that have a shelf life of up to nine months giving ample time for the distribution process to take place, even in a country such as Indonesia. Aseptic filling technology In choosing his technology suppliers, Choo travelled to China for inspiration. “I went to China to research all the lines in several factories to see how the development of aseptic filling is going especially in the dairy segment. We also had our dairy consultants from Japan help us to make the decision.” After fully researching the market, ABC Group The line for Kin Bulgarian yoghurt at the ABC factory in Bandung West Java. ABC chose a GEA EcoSpin2 sterilising line fitted with a GEA Fillstar FX-C filler. (Photo: ABC Group) Filling Special","@ID":32}, "BOTTLING / FILLING PETplanet Insider Vol. 20 No. 03/19 petpla.net 26 Linear stretch-blow and filling systems Blocking the elements Sipa is now into its third year of production of the Sincro Bloc integrated linear PET bottle blowing, filling and capping systems. They were introduced in 2017 to complement the company’s existing offering in rotary systems. The company is very well known for its linear stretch-blow moulding systems with its SFL range, capable of highly cost-effective production of PET containers in all shapes and sizes. The SFL system continues to evolve, the most recent addition being the high-performance all-electric SFL 6/8 EVO featuring high-speed press movements and an improved blowing valve. The Linear Sincro Blocs were introduced in response to calls, particularly from companies bottling water and also oil, for a compact system that could produce and fill bottles in all formats up to 12 litres in size. The Linear Sincro Blocs are highly productive: a unit based on Sipa’s SFL 6 has a maximum output of close to 11,000 small bottles per hour, while a system configured for larger formats can produce and fill up to 4,000 12 l containers in the same time, or 6,600 5 l containers. Sipa says that the Linear Sincro Blocs are user-friendly, thanks to their relatively simple mechanical movements. This helps keep maintenance and initial investment costs down, leading to an advantageous Total Cost of Ownership (TCO). Simplicity helps with cleanliness and hygiene. There is no need for rinsing between blowing and filling, no need for external conveying systems, and total protection from the outside environment, from the moment the preform enters the feed shoot until the filled and sealed bottle emerges, ready for wrapping. On Sipa systems with integrated PET preform and bottle production, various options are available to maintain the cleanliness of the preforms between the injection moulding machine and the stretch-blow moulding unit. The collection hopper, lift and slide can all be enclosed and subject to over-pressure to keep out dust, for example; preforms can be blown with ionised air and subject to ventilation to remove possible dust; special ventilation filters can be installed in the reheat oven area. The filling system is extremely clean and easily sanitised, with advanced cleaning systems for both the production circuit (Clean-In-Place, CIP) and the total filling environment (Clean-Out-of-Place, COP). Automatic false bottle loading, together with the use of microbiological isolation around the immediate filling area, produce a high reduction in the space that needs to be kept under control, making it possible to use sanitising systems that are highly cost effective. “Our extended line-up means that bottling companies can now turn to Sipa for whatever line that best fits their production requirement, for formats of all sizes,” says Roberto Cucciol, Business Unit Director Specialties and Beverage. “Linear Sincro Bloc systems are ideal for large formats, and they are also the best choice for smaller runs. They can produce bottles with handles and widemouth jars and can also work with all types of liquids, water, oil, CSDs, milk, hot-filled products, detergents and personal care products. If necessary, the same line can produce and fill hotfill and CSD drinks. Numerous Sipa customers have taken advantage of this feature.” In the recent past, Sipa has installed various complete lines incorporating the SFL Sincro Bloc system for mineral water and edible oil in Europe, Turkey, and China some of them reaching the speed of 6,600 units an hour. In Turkey, to name but one, DSL Group chose the Sipa Linear Sincro Bloc after almost three years of positive experience with an earlier linear stretchblow moulding system, an SFL6/4XL, which is now integrated into a line producing and filling 10l still mineral water bottles. “Our satisfaction with the previous generation of Sipa equipment gave us the confidence we needed to go back to Sipa when we decided to make another important investment in blowing and filling,” says General Manager Kenan Dişli. www.sipasolutions.com Filling Special","@ID":28}, "BOTTLING / FILLING PETplanet Insider Vol. 20 No. 03/19 petpla.net 18 New patented technology for hot-fill PET bottles Active base inversion Sidel BoostPrime is a unique PET packaging solution, offering an alternative for hot-filled beverages in PET bottles. This patented solution is addressing the single serve market of JNSDIT (juice, nectar, soft drink, isotonics, tea) filled in PET bottles of up to 1.2 l at a temperature of 85-88 °C. The BoostPrime packaging solution removes the need for restrictive vacuum panels or gas addition into PET bottles normally required for the containers to resist hot-filling temperatures. The final bottle shape is achieved with an active base inversion and relies on three key features with minor impact on the packaging manufacturing line layout: The packaging design requires specific base geometry and specifications. The Base OverStroke System (BOSS) allows the mechanical forming of the bottle base during the blowing process. The inverter contributes to the base inversion. This step takes place after filling and capping, tilting and cooling and before labelling. It balances the negative pressure induced by the beverage cooling in the bottle from 85°C to ambient temperature. Increased packaging appeal to stand out on the shelf The removal of the technical constraints of the bottle vacuum offers total freedom of shape in order to attain premium and distinctive PET bottles. It allows a uniform look and feel for hot and aseptically-filled bottles for consistent brand image. Any iconic bottle shape with panels can be easily adapted without impacting the consumer perception. Besides that, it enlarges the branding opportunities as the bottles’ labelling surface with no vacuum panel is smoother and contributes to a greater and more impactful look and feel. The labelling quality for both roll-fed labels and sleeve labels is highly improved due to an inner bottle pressure during label application. Filling Special","@ID":20}, "BOTTLING / FILLING PETplanet Insider Vol. 20 No. 03/19 petpla.net 23 Aseptic PET bottle filling line for China’s VV Group Soy bean milk in PET VV Group, which was founded in 1992 and is based in Xuzhou, China, is one of the country’s leading producers of soy bean milk. It also produces Tianshan snow milk and Liuchaosong flour products. The company has a reputation within China as a pioneer that actively explores and seeks to expand the field of plant protein beverages. VV Group’s factory in Wuxi City has invested in a new aseptic filling line, provided and installed by Newamstar, to package liquid soy bean milk in PET bottles. Newamstar also lays claim to a pioneering reputation, as the leader in China in the adoption of aseptic filling technology for PET bottling. Once extracted from the bean, soy bean milk undergoes industrial processing to provide it with its colour, smell and taste. VV Group was originally known as a manufacturer of soy bean milk powder but has transferred its focus to liquid products. The flavour and nutritional qualities of the company’s soy bean milk have helped to make it popular with consumers. Its market share is reported to have grown and it has become a leading choice for workplace and domestic consumption. Newamstar and VV group signed a contract for an initial aseptic filling line, which has a capacity of 24,000 500ml bph. The line has been running smoothly from outset and has demonstrated the ability to produce good quality PET bottled soy bean milk, consistently and without major interruptions. The line’s performance has demonstrated the capacity of the product and the process to contribute to sustainable future development of the product within the VV Group. www.newamstar.com ADHESLEEVE® TECHNOLOGY THE BEST SOLUTION FOR ROLL-FED LABELLING EVEN ON CANS! ProMachBuilt.com | PELabellers.com LABELS APPLICATION WITHOUT HOT MELT GLUE. EASY LIKE SCOTCH-TAPE! EVEN MORE! The first eco-friendly linerless labeller using pre-glued films. 100% ecologic and recyclable product. Also for empty containers. Adhesleeve + thermal-shrinking system. More than a valid alternative to the sleeve application. BOOTH #L1 MARCH 19 - 21, 2019 HO CHI MINH, VIETNAM Filling Special","@ID":25}, "imprint EDITORIAL PUBLISHER Alexander Büchler, Managing Director HEAD OFFICE heidelberg business media GmbH Bunsenstr. 14 69115 Heidelberg, Germany phone: +49 6221-65108-0 fax: +49 6221-65108-28 info@hbmedia.net EDITORIAL Kay Barton Heike Fischer Gabriele Kosmehl Michael Maruschke Ruari McCallion Waldemar Schmitke Anthony Withers WikiPETia.info petplanet@hbmedia.net MEDIA CONSULTANTS Martina Hirschmann hirschmann@hbmedia.net Johann Lange-Brock lange-brock@hbmedia.net phone: +49 6221-65108-0 fax: +49 6221-65108-28 LAYOUT AND PREPRESS EXPRIM Werbeagentur | exprim.de Matthias Gaumann READER SERVICES Till Kretner reader@hbmedia.net PRINT Chroma Druck & Verlag GmbH Werkstr. 25 67354 Römerberg Germany WWW www.hbmedia.net | petpla.net PETplanet Insider ISSN 1438-9459 is published 10 times a year. This publication is sent to qualified subscribers (1-year subscription 149 EUR, 2-year subscription 289 EUR, Young professionals’ subscription 99 EUR. Magazines will be dispatched to you by airmail). Not to be reproduced in any form without permission from the publisher. Note: The fact that product names may not be identified as trademarks is not an indication that such names are not registered trademarks. 3 PETplanet Insider Vol. 20 No. 03/19 petpla.net There are things you cannot believe… Are we making life too difficult for ourselves in the plastics industry? Is talk about microplastics in our oceans just a side issue? Will we ever see the tethered closure that does away with plastic waste? Are discussions about disposable PET bottles fake news? This is the conclusion I had to draw when I saw a letter from one of our readers, secondary school teacher Hans-Jörg Schmidt, in Bad Fallingbostel, Germany. “Our school has been receiving copies of PETplanet from you for about 10 years. However, the study of plastics has now been removed from the secondary school curriculum as it is not seen as being “of everyday importance”. As I therefore will no longer be able to teach this subject, I have (unfortunately) no further need for your magazine. Once again, many thanks for all the valuable material you have provided which I have used both in the classroom and on a personal level”. And then there are things that please you… This year, we are celebrating 20 years of PETplanet Insider. And we are particularly delighted to have received video congratulations from the industry. Take a look at our newly designed homepage (petpla.net) to see greeting messages from Flexblow, Retal and Erema. Yours, Alexander Büchler Dear readers,","@ID":5}, "BOTTLING / FILLING PETplanet Insider Vol. 20 No. 03/19 petpla.net 11 20 years of stretch-blowing and filler technology in PETplanet Insider Dear friends of PETplanet, I would like to give you my subjective summary of the last 20 years of two-stage SBM and filling. I’ve been working on this for a long time because my thoughts have digressed so many times. The many people we have got to know throughout our 20-year journey, the interviews, the site visits, the travelling. For me, it’s been 20 years full of emotions. In this overview, I have tried to sketch out the history of the main protagonists, the companies and the technology. Corpoplast has always been a tower of strength. Sold many times (Krupp, SIG, KHS) and even more frequently trying to integrate, the company has continually developed and under today’s KHS umbrella, it is enjoying what may be its golden era. Which brings us to the just as chequered history of KHS. A continually changing CEO - I won’t bore you with all their names - bankruptcy of the parent company WCM and now finally, structured expansion under Salzgitter. Things were not always so changeable at KHS and this was shown in our interview in 2010 with Maternus Gemmel, who retired as CSO after 48 years in the company. Two further old hands that must get a mention here are Gianfranco Zoppas, owner of Sipa and, of course, Volker Kronseder of Krones. Both have promoted and supported the development of PET drinks technology with clear vision. Over 20 years ago, Volker Kronseder recognised that stretch blowing belonged in filling and he has continually driven forward his own Contiform development. The first facilities may have raised a smile but today they are among the market leaders. Gianfranco Zoppas is a technological visionary. Regardless of what had gone before, he has always addressed the question of what the market needs. In Top Talk Filling Special 2005, he was still convinced that single-stage was the right way to go but in a 2018 interview, he reinforced the 2-stage procedure. But what does he have in mind? The blocked Xtreme from granulate to finished bottle all at one heat. But isn’t that the signature feature of the 1-stage process? So Zoppas statement in 2005 has proven to be well-founded, although in quite a different way than first thought. Enjoy the overview. Perhaps you’ll be mentioned somewhere too. Yours Alexander Büchler","@ID":13}, "BOTTLING / FILLING PETplanet Insider Vol. 20 No. 03/19 petpla.net 20 Kassatly Chtaura SAL adopts EBS K Ergon solutions to cope with surges in demand for Jallab Juice Automated filling of “local favourite” fruit blend drink Lebanon is where Europe meets the Arab world; where Beirut’s Corniche is just a few blocks from the bazaar and the souk. The country’s food and beverages reflect the mixture of influences, where meals centred on Turkish and Arab ingredients are presented with French refinements. One of the most popular drinks in the country is “Jallob Juice”, which is made from carob, fruit syrup, dates, grape molasses and rose water, incense smoked. Kassatly Chtaura, founded in 1974 by current CEO Akram Kassatly, was the first company to bottle this syrup in modern production plants and make it commercially in a modern way. The company now offers a wide variety of beverages in addition to fruit syrups like Jallab, including liqueurs, alcoholic and Buzz and Freez brands of non-alcoholic beers. In 2015 the company launched Beirut Beer. Throughout its existence, Kassatly has continually invested in upgrading and modernising its machinery. Its most recent investment, necessary in order to meet high market demand for Jallob, has been to completely automate the bottling process. It now has installed a system of the Ecobloc Ergon 2-9-3 K EV range, provided by SMI, which combines stretch-blow moulding, filling and capping of 1 l and 2.65 l PET bottles in a single machine, at up to 3,200 bph. Kassatly Chataura has worked with SMI since 1997. It currently has more than 10 SMI packers from the WP, SK and MP ranges, used to secondary pack a wide range of wrap-around boxes, shrink-wrapped bundles and card multi-packs. Originally from the Middle East, Turkey and Iran, Jallab is a syrup served diluted with water, ice, Zibibbo wine and pine nuts. It is presented as a delicious, refreshing beverage, which can be consumed on its own or with a meal. The combination of fruits, rose water and incense gives it a unique, sweet aroma. It is traditionally a summer drink but it has seen a significant rise in popularity as a drink to break the fast during Ramadan, the great Muslim period of fasting and penance. During Ramadan, Muslims are not allowed to eat or even drink while the sun is up. The fast is broken at the end of each day with dates and jallab syrup. The word Ramadan derives from the Arabic “ramiḍa” or “al-ramaḍ”, which means “burning heat” or “dryness”. It begins with “l’hilal”, which in Arabic means “new moon”, in the ninth month of each year and lasts 29 or 30 days according to the waxing moon. As the Islamic calendar has 354 or 355 days (10 or 11 days fewer than the Gregorian solar year), the month of Ramadan falls at a different time of the solar calendar each year. It gradually moves backwards against the Western solar year and changes season, sometimes falling in summer, when the days are longer and hotter and fasting becomes even more demanding. Drinking jallab syrup at the end of a day of fasting becomes an important way to replenish energy and re-hydrate. This tradition sees sales increase significantly during Ramadan. Lebanese Kassatly Chtaura’s product range includes liqueurs, beers and syrups. The 1 l and 2.65 l bottles are stretchblow moulded, filled and capped in a single machine. Easy-Cap cap grabber Filling Special","@ID":22}, "BOTTLING / FILLING PETplanet Insider Vol. 20 No. 03/19 petpla.net 33 New hybrid system and in-house metal part production at FlexBlow Setting up to the highest level technology FlexBlow, machine manufacturer of versatile two stage PET SBM technology, further strengthens its position in this fast-growing PET market by moving towards Industry 4.0. In building a new 3,500m2 manufacturing facility in addition to the existing 10,000m2 site in Kretinga, Lithuania the company expanded its capacity and improves its technology. FlexBlow’s early vision of demandresponsive PET bottle blowing has gone a long way since this familyowned company first began operations in 1994. Close observation of market development with shrinking PET bottle production batches and increasing demand for greater in-house PET container production flexibility, has led the company to focus their strategic progression on continuous technology improvement in anticipation of their client’s needs for in-house versatility. Today, with the FlexBlow series enjoying a reputation as the two-stage PET SBM machines capable of huge versatility, the think tank at FlexBlow has come up with plans to turn up the volume once again. A new investment has been secured for a new modern manufacturing plant to be built in addition to the existing 10,000m2 site. The vision for FlexBlow’s new site is set to transform the company’s processes and operations by introducing a complete manufacturing environment that operates based on real-time data collection and localisation during production. To achieve this, FlexBlow‘s technical director and his team have worked together to optimise processes by combining relevant physical and digital technologies, including intelligent robot units programmed to make decisions based on real-time data collected from the production floor. An on-site dedicated testing laboratory, 3D printers for both plastic and metal components, as well as a topnotch working environment designed to foster employee motivation and engagement will form the complete picture of FlexBlow’s new production site. The new production site is set to start operations as soon as July 2019. Long-term committed advocates for progressing versatility and responsiveness of their client’s operations by providing them with adequate tools in a shape of FlexBlow machines, recently the company discovered that continuing to push the leading edge of technology meant embracing a commitment to self-sufficiency themselves. The company’s decision to start volume production of the new 8-cavity FlexBlow 8 Hybrid systems for increased production capacity of up to 12,000 bph, with bottles sizes from 10ml to 1.5 l, neck finishes from 18-38mm, meant moving away from limited supplier capabilities. It is the way of becoming self-sufficient as far as being able to fabricate all necessary metal parts, including heavy duty metal PET SBM machine components in-house. Today FlexBlow’s off-site largescale metal parts manufacturing site stands complete with a new generation high-precision 5 axis Hyundai milling machines, 2-ton 360-degree overhead cranes, a large-scale sheet metal plasma bending machine, and an industrial large equipment (8,000x4,000x2,600mm) paint spray booth for that trademark quality finish. Flexblow’s says that its success is set to continue as the business is wellequipped and ready to move towards advanced digital technologies whilst continuing to draw from its strength of profound knowledge and understanding of the packaging market. www.flexblow.com Sheet Metal Bending machine in the new prodcution hall of Flexblow Filling Special","@ID":35}, "BOTTLE MAKING 14 PETplanet Insider Vol. 20 No. 03/19 petpla.net Eye-catching body shapes in the HPC category Green bottle, red tower At retail outlets, consumers are faced with a huge choice of different products in the HPC (Household and Personal Care) category – and nevertheless they decide within a fraction of a second to buy a particular product. But how is this done? Besides the decision made on the basis of the product and the brandname, the bottle design and the label always play a vital role, too. The container’s look serves simply as an eye-catcher. Fit GmbH, headquartered in Zittau, Germany, realised this decades ago. One of the company’s best-known products is the green original variant of the Fit washing-up liquid in a striking, angular bottle. The shape of this bottle is modelled on a historical landmark: the Red Tower in Chemnitz. The corporate history of Fit is an eventful one, and begins 65 years ago in what is now called Chemnitz with the Fit-liquid brandname. Just one year later, the Fit washingup liquid was launched. Following German reunification, falling sales figures and the concomitantly critical financial situation almost bankrupted the company. The reason: Fit had not been listed by most of West Germany’s new retail chains. But instead of giving up, trucks were loaded with Fit’s products and sold from the loading bed in front of the supermarkets. In 1993, the graduate chemist Dr Wolfgang Gross purchased the plant in Zittau, and founded the presentday Fit GmbH. The take-over came as a breath of fresh air for the company. With substantial investments, in a first step the production lines were expanded and modernised. And certification under DIN ISO 9001 had back in 1995 already enhanced the transparency of the firm’s operational procedures, reducing the defect rate and thus saving costs as well. Even more important, however, was the return of an R&D-driven mindset and a resolve to innovate. In addition to the main product, the East German classic Fit washing-up liquid, the product portfolio was steadily expanded in subsequent years. There followed cleaning tabs, washing powder and laundry perfumes, plus body care products. It didn’t take long for the measures to produce success: today, the mid-tier company’s sales figures, at € 165m gross turnover, are 27 times as high as in 1993. And the biggest setback in the firm’s history has also been overcome: in August 2010, the River Neisse burst its banks, overflowing into the company’s entire premises. The disastrous flooding destroyed stocks, and paralysed the entire production operation. The loss and damage ran into millions, and complete normality was only restored many months later – even though production was resumed quite quickly. Besides Fit, the company’s brands meanwhile include Kuschelweich, Sunil, Rei (in the tube), Sanso and the hair care brand Gard, plus the body care brand Fenjal. Traditionally sustainable by conviction For more than 25 years now, Fit GmbH has prioritised responsible dealings with the natural environment, coupled with high product quality. Many products are manufactured on the basis of sustainable raw materials, are phosphate-free and completely biodegradable, and bear the European Eco-Label. But it’s not only in the portfolio and the constituents that Fit displays its corporate commitment to the natural environment, it’s in the entire production process as well. An in-house solar installation supplies power amounting to almost 135,000 kWh a year. Preforms, and sometimes closures ProShape can be integrated not only in Krones’ machines, but in Kosme’s as well. With the ProShape module, preforms can be selectively temperature-controlled, so as to subsequently blowmould them into perfectly shaped containers.","@ID":16}]}}
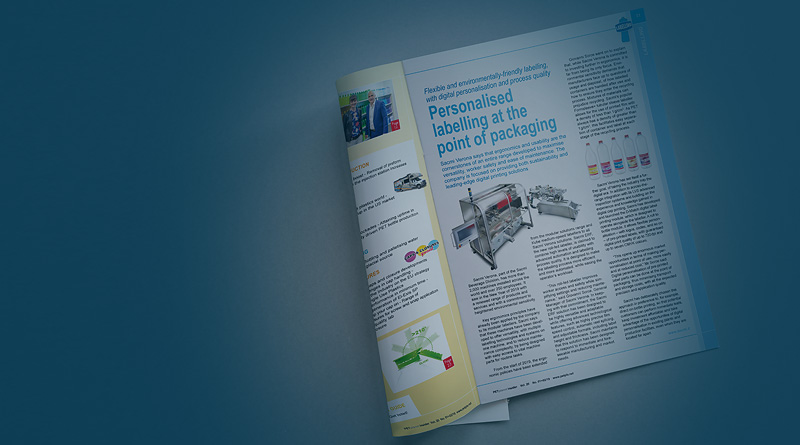