"8 NEWS PETplanet Insider Vol. 20 No. 11/19 petpla.net Sabic opens new caps & closures Technology and Innovation Center in the Netherlands Sabic, a global leader in the chemicals industry, announced the opening of its new Technology and Innovation Center dedicated to the caps and closures segment in Geleen, the Netherlands. Located in Sabic’s Global Technology Center for Europe on the Chemelot Campus, this investment is stated to be proof of Sabic’s commitment to the industry to develop new materials and technologies focused on caps and closures. The opening ceremony of the new facility was led by Sergi Monros, Sabic Vice President of Performance Polymers & Industry Solutions, Petrochemicals. The facility opening comes just a year after Sabic established its Caps & Closures industry segment organisation. Monros pointed to the growing need for creative solutions that are sustainable, cost-efficient and compliant. These solutions are coupled with the increased number of regulations governing product safety and consumer well-being. Sabic is pursuing cutting-edge technologies related to both new material development and to application testing. Polymers developed specifically for applications in this sector help enable, for example, lighter caps, and pumps and dispensing systems that are more efficient and easier to manufacture, all the while supporting customer efforts to improve overall sustainability. The center includes facilities that allow to simulate the real-life performance of finished products. The dedicated research laboratory has equipment for testing material characteristics such as mechanical properties, dimensional stability and environmental stress cracking resistance (ESCR). Cap specimens can be produced in-house for performance testing for potential applications and for the development of improved products. There will also be capability for developing and testing new product designs. www.sabic.com Space requests for NPE2021 outpacing previous edition The Plastics Industry Association (PLASTICS) officially kicked off the march to ‘NPE2021: The Plastics Show’ at K2019. Scheduled for May 17-21, 2021 at the Orange County Convention Center (OCCC) in Orlando, Fla., NPE2021 is expected to draw more than 55,000 attendees from more than 20,000 companies representing more than $ 100 billion in purchasing power. The trade show also features a brand new look, a new logo, a redesigned website, and a fitting tagline: Transform Tomorrow. In addition to the hundreds of machines operating at full capacity on the show floor, NPE2021 will also feature new educational opportunities and new Technology Zones to make it easier for attendees to conveniently find exactly what they’re looking for. “Every attendee can now customise their visit to make the most of their time at NPE. Plus, the zones allow exhibitors to aim to locate their booth in an area where the people in the aisles are interested in exactly what they’re selling,” said PLASTICS Vice President of Trade Shows and Marketing Susan Krys. The Plastics Industry Association (PLASTICS) announced that company requests for exhibit space at NPE2021 are already outpacing the demand for space ahead of the 2018 edition - a year in which the show sold out at its official Space Draw event for the first time in the show’s more than 80-year history. “More companies are requesting exhibit space and the amount of space being requested is more than was requested for 2018,” said Susan Krys. www.npe.org Alphamac & Side S.A. have reached a commercial agreement As of 1 October 2019, Alphamac & Side S.A. have reached a commercial agreement to combine efforts to market their systems for manufacturing PET and HDPE plastic containers.This agreement allows both companies to offer their international customers a wide range of systems and services, combining technology, knowledge and experience. This partnership will cover most of the demands in the liquid packaging market, offering complete solutions for PET and HDPE containers, providing turnkey services and products that meet customer requirements. Ms Judit Birosta (Managing Director of Side) and Mr Moreno Minguetti (Managing Director of Alphamac) have highlighted the synergy between the two companies, which has allowed them to achieve a worldwide presence for their products in a short time, having already been operating for many years as Side, and more recently as Alphamac in Russia and Italy. www.sidemachines.com","@ID":10}, "MOULD MAKING PETplanet Insider Vol. 20 No. 11/19 petpla.net 18 MOULD MAKING It is not working without: moulds Mould making, a review The PET bottle is a product that has been optimised over the last years and is constantly evolving. Different development steps have to be led back thereby on mould technology which made it over the years possible to fulfil producers and customers inquiries. The requirements to the mould makers are accordingly manifold. The following criteria are particularly important for closure and perform mould maker: a high degree of standardisation and modularisation of the tools, which allow a high degree of flexibility in order to quickly change the design or to expand the mould variation. High-precision production with guaranteed production cycles and production times; this in turn depends on material technology and processing. High surface and wear protection must also be guaranteed as well as minimal maintenance and a fast change over. A modern machine park must have a high degree of automation. This includes high-speed milling, electric discharge machining and CNC grinding. The peculiarities and challenges of the production of stretch blow moulds you can read on page 26. Closure moulds: z-mould’s high-cavity injection moulds have a high degree of standardisation and modularity which guarantees low-maintenance moulds, easy handling and flexibility. The patented z-slides mould technology for closures with tamper-evident band combines all essential market qualities in one product. Stack moulds, moulds with unscrewing function, flip-top moulds with in mould closing are produced on up to 144 cavities. Carbonated and non-carbonated drinks, water, juices and beer, as well as coffee & tea and dairy are filling application goods. Also edible oil, soy sauces and other fillings are possible. The lowest closer weight is 0.7 g. All single-piece standard closure dimensions for all neck finishes, sport closures, flip tops, push pulls, and multi component closures can be produced in HDPE, LDPE, PP or TPE on moulds with a cavity from 16-128. www.z-moulds.com Corvaglia has been offering closure solutions for PET bottles since 1991. A modular approach to injection moulding comes with significant advantages. It is flexible, whether to modify the mould or to replace certain parts. With a state of the art machine park, Corvaglia produces moulds with selected materials, an own cooling technology and special surface finishes. Closures can be produced for the following products: for still, carbonated, pressurised and non pressurised, milk, juice, tea, coffee, beer and energy drinks, and also for edible oil and detergents. Closures weight starts at 0.8 g. Made out of HDPE and PP for transparent parts, flat top and sport closures for beverage from 25-48mm neck finished can be produced. Corvaglia offers moulds with cavities from 24-96. www.corvaglia.com Preform and stretch blow moulds: GDXLPrecise Machinery was founded in 1993. It is a high tech enterprise of moulding equipment to the PET plastic industry. The company designs and manufactures PET moulds, including blow moulds, preform injection moulds and cap compression and injection moulds. Blow moulds are supplied to companies like Sidel, Krones, KHS, Tech-Long, Newamstar. The maximum size of the PET bottle has 5 l. The bottle design is optimised for light weight production, also with an optimised base for CSDs. z moulds 96 cavity z-slides","@ID":20}, "CAPS & CLOSURES 34 PETplanet Insider Vol. 20 No. 11/19 petpla.net CAPS & CLOSURES 34 Growth of a German closure manufacturer in India From strength to strength by Kay Barton International closure manufacturer Bericap, originally from Budenheim, Germany, has been operating in India since 2001. What started as a joint venture near Mumbai led to the establishment in 2007 of an independent production plant, located around 50km north-west of Pune, since when production has boomed. Initial output was 900 million closures annually; future output is set to be over 8 billion a year. This major increase in production, along with an active and growing presence in a wide range of segments in both the beverage and industrial sectors has enabled Bericap to establish a strong position on the local Indian market. Its medium-term strategy will see it building on that foundation by further increasing capacity. March 2019, Bericap India Pvt. Ltd. We met: Mr Rajesh Pantsachiv, General Manager Mr Kedar Chitale, Sales Head Tour Sponsors: Meet us at Brau Beviale in Nuremberg - Hall 7A / 7A - 301 Interview session with GM Rajesh Pantsachiv","@ID":36}, "PETplanet Insider Vol. 20 No. 11/19 petpla.net 53 BOTTLES Vitamins for women Olly, an American company for nutritional supplements to improve optimal physical functionality, is selling a variety of chews/gums with defined promises such as better sleep, stress resistance, improved appearance or simply more energy. The packaging for the gums is a squared, transparent plastic container reminiscent of a cosmetics jar. The lid must be pushed down to open and has brand embossing on three sides; the fourth side has shiny silver brand lettering. The lid is fixed using a type of bayonet seal with detents. A circulating self-adhesive label describes product and usage. The contents – 90 pieces – is intended for use over 45 days. www.olly.com ORGANISED BY: SILVER SPONSOR: SUPPORTING PARTNER MEDIA PARTNERS: BOOK NOW! Early bird rates available until 4 October 2019 Plastics Caps and Closures 2019 Conference 18-19 November 2019 • Beurs van Berlage, Amsterdam PROGRAMME ANNOUNCED! Key topics include innovation drivers, sustainability, the circular economy and tethered cap solutions. KEYNOTE SPEAKER: Hans van Bochove Vice-President Public Affairs Europe Coca-Cola European Partners Filip Vangeel Manager Circular Economy Valipac Augustin De Tilly Global Business Development Director Beverage Aptar Food + Beverage SPEAKERS INCLUDE: VIEW THE PROGRAMME AND REGISTER AT: PLASTICSCAPSANDCLOSURES.COM","@ID":55}, "TRADE SHOW REVIEW PETplanet Insider Vol. 20 No. 11/19 petpla.net 50 Summary of the 15th China International Recycled Polyester and PET Packaging Conference & Exhibition Facing external and internal challenges by Dr Ulrich Thiele, Co-Organiser The 15th China International Recycled Polyester and PET Packaging Conference & Exhibition was held on September 18-20, 2019 in Shanghai, China. During the conference it was interesting to see how the Chinese recycling industry in general and the Chinese polyester recycling industry in particular is on its way to digesting the drastic measures of the Chinese government to ban the import of any plastic waste from January 2018 on. While Europe is struggling with individual measures such as the ban on drinking straws, plastic bags or disposable tableware, the Chinese leadership has created eight ministerial administrative units covering the entire complex of environmental protection, renewable energies, circular economy including recycling and climate protection. There is still a substantial gap compared to European environmental standards but Chinese speed of progress in this area is impressive. More than 360 delegates from China and overseas heard about the latest results in polyester recycling technology, production and market and exchanged their recent experiences. Two contributions from governmental organisations and three from industry associations underlined the high administrative awareness of the recycling issue and loop economy in general. Zhang Deyuan, Dept. Director General of Institute of Economic System and Management NDRC outlined the basics regarding “China’s Policies for the Recycling Economy over the 13th Five-Year Plan-Recycled Plastics”. The pressures behind the environmental and recycling complex are China’s substantial fears that there is only a short time left to develop and introduce loop technology and economy. This new perspective is reflected in the establishment of eight different state councils, which cover the entire complex of environmental and recycling management. Most important among them are the NDRC, MIIT, Ministry of Environmental Protection, MOST and MOHURD. Li Deli, Secretary General of China Chemical Fibres Association Recycled Fibre Commission talked about “Green Fibre Certificate and Fibre Recycling”. The approved products and companies are of high product quality and production standards. The target is to substantially increase the number of approved companies to increase the acceptance of recycled products in the market. Wang Huansong, Senior Engineer Environmental Protection Research Institute of Light Industry explained the “Reformation of China’s Emission Permit System” which is similar to the European “Industrial Emissions Directive” or the BimSchG regulation in Germany. This new regulation has in particular the objective of reducing the ubiquitous air pollution in China’s major cities. Zhang Zhongjuan, Person in Charge of Energy Saving and Green Standard of Industry Dept., China National Textile and Apparel Council discussed “Green Factory Criteria for the Textile Industry”. This initiative introduced and promoted by MIIT is targeted to assess step by step the whole of Chinese Industry to improve","@ID":52}, "MARKET SURVEY 32 PETplanet Insider Vol. 20 No. 11/19 petpla.net Company SMI S.p.A. Postal address Telephone number Web site address Contact name Function Direct telephone number Email Via C.Ceresa, 10, 24015 San Giovanni Bianco (BG) - Italy +39 0345 40 111 www.smigroup.it Ms Daniela Dadda Marketing Department +39 0345 40.318 info@smigroup.it Shrink film machinery: Automatic machines for packing plastic, metal, cardboard or glass containers. Packs in film only, cardboard pad + film, tray only, cardboard tray + film Packaging options & output rate (packs per minute) Shrinkwrappers machines ; trayformers; overlapping cardboard sleeve multipackers; wrap-around casepackers and combined machines, provide performances from 30-450 packs/min (in triple lane), depending on the model or product to pack. - print registered film (yes/no; packs/min) Yes - nested pack (yes/no; packs/min) Yes - label orientation (yes/no; packs/min) Yes - carry handles (yes/no; packs/min) Yes - pad supported (yes/no; packs/min) Yes - tray supported (yes/no; packs/min) Yes - film only (yes/no; packs/min) Yes - tray and film (yes/no; packs/min) Yes - pad and film (yes/no; packs/min) Yes Shrink process: - shrink tunnel with hot air Smiflexi tunnel distributes hot air flows in an efficient and homogeneous way on the pack, thus ensuring its good quality at the end of the process. - oven Available tunnel methan heated Footprint Single lane: smallest AFW serie (10,060 x 1,774 x 2,450mm) till the bigger size SK 1200 HS (18,752.5 x 1,774 x 2,450mm) Double lane: smallest LSK 32 (9,820 x 1,974 x 2,450mm) till SK 1202 HS (18,752.5 x 1,974 x 2,450mm) Number of possible lanes 1-3 Packaging material & possible thickness film: 30-100μm depending on the production speed and pack collation, Cardboard: Low wave corrugated cardboard blanks: 3mm thickness. Voltage/power/energy consumption Depending on the machine model Film cutting and feeding system Manual sealing bar joins the films, film reels the machine is equipped with a dedicated reel truck, pneumatic blocking system and when the film ends, the machine stops, adjustment of the film length is electronic, equipped with a device for centering the printed film provided with reference mark. Certification CE Palletising machinery: Format changeover time The machine automation and control are entrusted to the Sercos Fieldbus technology, intuitive user interface for quick and easy management of end-of-line palletising operations, real-time machine diagnosis and technical support further enhance the machine control features. Output rate (packs/min) 35-100 packs/min (according to the size of the product handled and palletisation selected) Automatically intergrated:(yes/no) Yes Empty pack feeding Yes Insertion of interlayers Yes Connectable to shrinkwrapper Yes Special characteristics: i.e. low-level feed, cross conveyer barrier Swiftandprecisemovements:Thecentralcolumn isactuatedbybrushlessmotorswhichguaranteehighlydynamic,reliableandprecisemovementsofallaxesofoperation.Machine automationandcontrolareentrusted to theSercosFieldbus technology, featuringan intuitiveuser interface forquickandeasymanagementofend-of-linepalletisingoperations. Company Sipa Postal address Telephone number Web site address Contact name Function Direct telephone number Email Via Caduti del Lavoro n. 3; 31029 Vittorio Veneto (TV) - Italy +39 0438 911511 www.sipa.it Mr Matteo Tagliaferri Marketing and Communication +39 0521 548111 matteo.tagliaferri@zoppas.com Palletising machinery: Genius PTF Genius PTF/V Genius PTF/A Genius PTF - Active Layer Conventional automatic palletisers steady pallet type Conventional automatic palletisers steady pallet type, with double platform Conventional automatic palletisers moving pallet type Conventional automatic palletisers steady pallet type with innovative layer preparation Format changeover time 15min 15min 18min 10min Output rate (packs/min) Up to 330 layers/hour Up to 420 layers/hour Up to 700 layers/hour Up to 330 layers/hour Automatically intergrated:(yes/no) Empty pack feeding Yes, empty pallet feeding Yes Yes Yes Insertion of interlayers Yes Yes Yes Yes Connectable to shrinkwrapper Yes Yes Yes Yes Special characteristics: i.e. low-level feed, cross conveyer barrier - Operational flexibility and further reduction in change-over times - Optimisation of cycle to increase performance, with improved control of the different movements using stateof-the-art electronic solutions - Customisation of the gripping system and layer transfer according to the product to handle - Designed to accept a variable number of product infeeds - Fully automatic system requiring limited operator intervention, operating in complete safety - Possibility to handle all main pallets on the market trouble-free, with highly customisable solutions - Operational flexibility and further reduction in change-over times - Optimisation of cycle to increase performance, with improved control of the different movements using state-of-the-art electronic solutions - Customisation of the gripping system and layer transfer according to the product to handle - Designed to accept a variable number of product infeeds - Fully automatic system requiring limited operator intervention, operating in complete safety - Possibility to handle all main pallets on the market trouble-free, with highly customisable solutions - Operational flexibility and further reduction in change-over times - Optimisation of cycle to increase performance, with improved control of the different movements using state-ofthe-art electronic solutions - Customisation of the gripping system and layer transfer according to the product to handle - Designed to accept a variable number of product infeeds - Fully automatic system requiring limited operator intervention, operating in complete safety - Possibility to handle all main pallets on the market trouble-free, with highly customisable solutions - Operational flexibility and further reduction in change-over times - Optimisation of cycle to increase performance, with improved control of the different movements using state-of-the-art electronic solutions - Customisation of the gripping system and layer transfer according to the product to handle - Designed to accept a variable number of product infeeds - Fully automatic system requiring limited operator intervention, operating in complete safety - Possibility to handle all main pallets on the market trouble-free, with highly customisable solutions - Linear axes layer preparation with active pack orientation and arrangement","@ID":34}, "MARKET SURVEY 33 PETplanet Insider Vol. 20 No. 11/19 petpla.net Company Productive Systems (Pty) Ltd GEA Group Postal address Telephone number Web site address Contact name Function Direct telephone number Email PO Box 7643, Centurion, 0046 South Africa +27 12 661 1250 www.productivesystem.com Mr Stefan Schonfeldt Marketing Director +27 12 661 1250 prosys@iafrica.com Via Fedolfi 29, 43038 Sala Baganza, Parma, Italy +39 0521 839 0 www.gea.com Mr Alessandro Bello Vice President Head of Blowing, Filling & Packaging +39 0521 839 411 alessandro.bello@gea.com Palletising machinery: Semi automatic & automatic Yes Format changeover time 10-20min depending on differences in formats 5' (completely automatic) Output rate (packs per minute) 25,000bph (empty plastic bottles) 90pack/min 6x4 500ml (dia 56mm) Automatically intergrated:(yes/no) Empty pack feeding Yes Yes Insertion of interlayers Yes Yes Connectable to shrinkwrapper Yes Yes Special characteristics: i.e. lowlevel feed, cross conveyer barrier Yes Low level, high level, fully brushless palletiser permits smooth, precise movements and low energy consumption, predictive maintenance And & Or PI El Limon, Av. de Europa, 6, 41928 Palomares Del Rio (Sevilla) - Spain +34 954 779 200 www.andyor.com Mr Caridad Ortega Suárez Sales Director +34 954 779 200 andyor@andyor.com No Yes, 15-900bpm No Yes, 15-400bpm Yes, 15-400bpm Yes, 15 -400bpm Yes, 15-900bpm Yes, 15-900bpm Yes, 15-900bpm Shrinking pistols (hot air) Several models depending on speed Max. length of the pack is 1,400mm LDPE + LLDPE 40-60μm Several models depending on speed Yes CE and UL 15-20min Up to 400bpm Yes Yes Yes Yes Low-level feed; tray former possible to be integrated (display palletiser) Genius PTF - Fastlayer Genius PTF/A - Fastlayer Genius PP/PV Robby Pal Robby Pal with Fastlayer Conventional automatic palletisers steady pallet type with innovative layer preparation. Conventional automatic palletisers moving pallet type with innovative layer preparation. Conventional automatic palletisers steady pallet type for empty PET containers Robotic automatic palletiser Robotic automatic palletiser with innovative layer preparation. 10min 12min 15min 15min 10min Up to 330 layers/hour Up to 700 layers/hour Up to 330 layers/hour Up to 320 layers/hour Up to 320 layers/hour Yes Yes Yes Yes Yes Yes Yes Yes Yes Yes Yes Yes Yes Yes Yes -Operationalflexibilityand furtherreduction in change-over times -Optimisationofcycle to increaseperformance, with improvedcontrolof thedifferentmovements usingstate-of-the-artelectronicsolutions -Customisationof thegrippingsystemand layer transferaccording to theproduct tohandle -Designed toacceptavariablenumberof product infeeds -Fullyautomaticsystemrequiring limitedoperator intervention,operating incompletesafety -Possibility tohandleallmainpalletson the market trouble-free,withhighlycustomizable solutions -Layerpreparationwithactivepackorientation andarrangementwithrobots -Operationalflexibilityand furtherreduction in change-over times -Optimisationofcycle to increaseperformance, with improvedcontrolof thedifferentmovements usingstate-of-the-artelectronicsolutions -Customisationof thegrippingsystemand layer transferaccording to theproduct tohandle -Designed toacceptavariablenumberof product infeeds -Fullyautomaticsystemrequiring limitedoperator intervention,operating incompletesafety -Possibility tohandleallmainpalletson the market trouble-free,withhighlycustomisable solutions -Layerpreparationwithactivepackorientation andarrangementwithrobots -Operationalflexibilityand furtherreduction in change-over times -Optimisationofcycle to increaseperformance, with improvedcontrolof thedifferentmovements usingstate-of-the-artelectronicsolutions -Customisationof thegrippingsystemand layer transferaccording to theproduct tohandle Vacummheadavailble forwide mouthcontainers(i.e. jars). -Designed toacceptavariablenumberof product infeeds -Fullyautomaticsystemrequiring limitedoperator intervention,operating incompletesafety -Possibility tohandleallmainpalletson the market trouble-free,withhighlycustomisable solutions -Anextremelycompleterange to handledifferent typesofcontainersand products: layer,rowandmultiheadand looseproductpalletizingsystems -Extremelyflexibleandmodularsolutionwithreduced footprint -Customisationof thegrippingsystem and layer transferaccording to the product tohandle -Designed toacceptavariablenumber ofproduct infeeds -Fullyautomaticsystemrequiring limitedoperator intervention,operating incompletesafety -Possibility tohandleallmainpallets on themarket trouble-free,withhighly customisablesolutions -An extremely complete range to handle different types of containers and products: layer, row and multihead and loose product palletising systems - Extremely flexible and modular solution with reduced footprint - Customisation of the gripping system and layer transfer according to the product to handle - Designed to accept a variable number of product infeeds - Fully automatic system requiring limited operator intervention, operating in complete safety - Possibility to handle all main pallets on the market trouble-free, with highly customisable solutions - Layer preparation with active pack orientation and arrangement with robots","@ID":35}, "MATERIALS / RECYCLING PETplanet Insider Vol. 20 No. 11/19 petpla.net 36 Recycling marine plastics Ocean clean-up A partnership including Coca-Cola Corporation, Indorama Ventures, Ioniqa Technologies and Mares Circulares has successfully produced a PET bottle using recovered and recycled marine plastics. The partners say that this demonstrates that even ocean debris could be used in producing food and beverage packaging. The Coca-Cola Company has unveiled its first-ever bottles made using recovered and recycled marine plastics. In so doing, it has demonstrated that even ocean debris could, in future, be recycled for use in packaging for food and beverages. The ‘marine plastic bottle’ has been developed by a partnership between The Coca-Cola Company, Ioniqa Technologies, Indorama Ventures and Mares Circulares (Circular Seas). Around 300 sample bottles were made using 25% recycled marine plastic, retrieved from the oceans and beaches by volunteers who participated in 84 beach clean-ups in Spain and Portugal, and by fishermen in 12 ports across the Mediterranean Sea, as part of the Mares Circulares or “Circular Seas” project, which is partly funded by the Coca-Cola foundation and is a collaboration between the Coca-Cola system in Iberia; Spain’s Ministry of Agriculture, Fisheries, Food & the Environment; and three leading non-profit organizations: Chelonia Association, Ecomar Foundation and Vertidos Cero Association. Investing in technology In January 2019 Coca-Cola extended a loan to Ioniqa Technologies in the Netherlands, to help scale its proprietary enhanced recycling technology. The marine litter collected through Mares Circulares was recycled by Ioniqa Technologies, using its enhanced recycling processes, back into the building blocks needed to make foodgrade PET. Indorama Ventures, one of Coca-Cola’s suppliers of PET plastic and packaging solutions, subsequently converted this material into the PET plastic required to make the first Coca-Cola bottle (and the world’s first drinking bottle) made with marine plastics. Indorama is establishing a track record for taking on and completing very challenging recycling tasks. Earlier in 2019, Indorama announced that it would be opening a plant in Guadalajara, Mexico, that would be capable of recycling, to food-grade standard, plastic recovered from landfill. Proof of concept The marine plastic bottle has been developed as proof of concept for what enhanced recycling technologies may be capable of achieving. These technologies use newly-developed processes that break down the components of plastic and strip out impurities in lower-grade recyclables, enabling them to be rebuilt to ‘as new’ standards. This means that lower grade plastics, usually destined for incineration or landfill, can be reused. It also extends the reserves of materials available to make recycled content and helps to reduce the amount of virgin PET needed to be produced from fossil fuels, thus contributing to a lower carbon footprint. Scaling up In the immediate future, enhanced recycling will be introduced at commercial scale using waste from existing recyclers, including previously unrecyclable plastics and lower-quality recyclables. Bruno van Gompel, Technical and Supply Chain Director, Coca-Cola Western Europe, says the potential for the technology is huge. “Enhanced recycling technologies are enormously exciting, not just for us but for industry and society at large,” he said. “They accelerate the prospect of a closed-loop economy for plastic, which is why we are investing in them. As these begin to scale,","@ID":38}, "imprint EDITORIAL PUBLISHER Alexander Büchler, Managing Director HEAD OFFICE heidelberg business media GmbH Bunsenstr. 14 69115 Heidelberg, Germany phone: +49 6221-65108-0 fax: +49 6221-65108-28 info@hbmedia.net EDITORIAL Kay Barton Heike Fischer Gabriele Kosmehl Michael Maruschke Ruari McCallion Waldemar Schmitke Anthony Withers WikiPETia.info petplanet@hbmedia.net MEDIA CONSULTANTS Martina Hirschmann hirschmann@hbmedia.net Johann Lange-Brock lange-brock@hbmedia.net phone: +49 6221-65108-0 fax: +49 6221-65108-28 LAYOUT AND PREPRESS EXPRIM Werbeagentur | exprim.de Matthias Gaumann READER SERVICES Till Kretner reader@hbmedia.net PRINT Chroma Druck & Verlag GmbH Werkstr. 25 67354 Römerberg Germany WWW www.hbmedia.net | petpla.net PETplanet Insider ISSN 1438-9459 is published 10 times a year. This publication is sent to qualified subscribers (1-year subscription 149 EUR, 2-year subscription 289 EUR, Young professionals’ subscription 99 EUR. Magazines will be dispatched to you by airmail). Not to be reproduced in any form without permission from the publisher. Note: The fact that product names may not be identified as trademarks is not an indication that such names are not registered trademarks. 3 PETplanet Insider Vol. 20 No. 11/19 petpla.net Despite difficult conditions, the PET industry remains stable The K trade fair has closed its doors. We took the event as an opportunity to ask exhibitors with machines and moulds for our sector about their economic state. Overview: while the entire plastics engineering sector is affected by very sharp declines in new machinery business, the PET sector remains robust and stable. In detail: Mould manufacturers for caps are reporting a small dip in orders at the start of the year. After the EU decision about new caps, converters are ordering once again at a higher level. The new caps only become obligatory in three years, cap manufacturers have presented initial ideas and the current demand here is as high as ever. This is in line with statements from providers of capping machines. While generally in plastics engineering – especially in the automotive sector – declines of up to 40% have been reported, engineering for caps has remained steady. Providers of PET moulds report a similar situation. Since the capping industry presented new caps and closures that fulfil the new EU standards even on conventional neck geometries, business is continuing here as planned too, with lightweighting as an ongoing trend. So far, the sector has held its ground robustly in the face of Brexit, the US-China trade war and environmental activists, but there is uncertainty for providers as to whether the high level can be maintained into next year. Providers of bottling systems tell a different story. There are questions about how the plastics discussion affects PET bottles – perhaps more multi-use glass again or water from the tap. These are just a couple of issues that are unsettling bottlers. Even converting a bottling system to the new EU caps and closures in three years requires quite a substantial system conversion. This is why bottlers have put several projects on ice. We look forward to what we will hear at the Brau trade fair in November, where traditionally more bottlers than converters meet. Your PETplanet Insider Editorial Team Dear readers, 07+08 2019 petpla.net D51178; ISSN:1438-9452 29.07.19 PETplanet is read inmore than 140 countries ","@ID":5}, "39 TRADE SHOW PREVIEW PETplanet Insider Vol. 20 No. 11/19 petpla.net TRADE SHOWpreview BrauBeviale 2019 From November 12 to 14, 2019, Brau Beviale will take place in Nuremberg, Germany. The products and solutions showcased by around 1,100 exhibitors cover the entire beverage process chain. This year too, the main theme is the future viability of the beverage industry, and the challenges facing both equipment suppliers and beverage manufacturers will be explored. The popular BrauBeviale Forum offers its audience information, inspiration and the opportunity for interaction. Its highlights include high-calibre panel discussions with the who’s who from the beverage industry and political sphere on the two topics “Bottle deposit” & “Mineral water – a problem not a pleasure?” that are also hotly debated by the wider public. For details of the supporting programme please go to www.braubeviale.de/en/events Design for light-weight products Kiefer Werkzeugbau GmbH based in Schwaigern, Germany, has been active in the mould and die industry for the plastics processing industry for more than 30 years. As an independent mould maker, Kiefer is producing blow-moulds for all common rotary blow moulding machines and for linear blow moulding machines As the market demands savings in energy and lightweight products, new concepts in bottle design are required. There are various approaches such as the use of a new preform with a reduced thread, or a creative bottle design. The grip and shape stability on a thinner-walled bottle can be achieved by incorporating certain stabilising grooves, shafts, spirals. Here, the developer sets lines, waves and elements in such a way that the height differences haptically achieve a corresponding stability. Innovative bottom interpretations in the field of light-weight & low-pressure base design with the Pataloid-base and the flat base allow the bottler to reduce the blowing pressure by 30-50%, resulting in huge energy savings. The optimisation of the ventilation system between the bottle and the mould cavity enables faster exhaust of the air with a lower blowing pressure. Air moves in a homogeneous way: vent holes are replaced by lines. The finish of the bottle is improved, with a stronger, yet lighter base. These specifications of the light-weight & low pressure base design are common to all suitable blow moulding machines. www.kiefer-mold.de Kiefer Hall 7A | Booth 108 Speed-controlled all-in-one systems Boosters are needed when, for production-related reasons, compressed air is required at a higher pressure than network pressure. Kaeser’s new boosters provide the ideal solution for compressed air users in the brewery industry who require higher pressure air. As the first all-in-one booster system, the DNC series from Kaeser is now also available with variable speed control and with motor powers from 22-45 kW. As a result, the compressor flow rate is matched to actual air demand, which means that only as much energy is consumed as is needed to produce the supply of higher pressure compressed air. The system is therefore also especially efficient in the partial load range since the compressor switches to idle operation when air demand drops below the control range. Compressor operating speed and energy consumption are consequently kept to a minimum. With a motor capacity of 7.5-22 kW and flow rates of 2.3-12.2 m³/min, the CBS rotary screw blower provides the perfect solution for users, for example, who require air for wastewater treatment in operational clarification plants with a pressure differential of up to 1,100mbar. The blower also shines through with its many benefits when it comes to liquid aeration, flotation, fluidisation and bioreactor applications. It is stated to be up to 35 per cent more efficient than comparable conventional rotary lobe blowers and to offer significant energy advantages in the double-digit range compared with many other rotary screw blowers on the market. In fact, a rotary screw blower is so powerful that it can easily and effectively cover the control range of two to three rotary lobe blowers. www.kaeser.de 200ml bottle (left) and 330ml bottle (right) Kaeser Hall 4 | Booth 441 Rotary screw power for blowers, the Kaeser CBS series","@ID":41}, "42 TRADE SHOW PREVIEW Vol. 20 No. 11/19 petpla.net Bottle labelling Amongst this year’s exhibits, Sacmi will be highlighting complete bottle labelling solutions. These range from the ultra-high productivity Opera Modular series – designed for beers and spirits and capable of managing bottles of highly complex shape – to the Kube range, the Sacmi solution for medium output operations. The modular structure is claimed to ensure high versatility as it lets users operate in parallel on multiple labelling technologies/systems while making use and maintenance easier. More specifically, the Opera Modular solution on show at the fair will be equipped with a module designed to apply cold glue and self-adhesive labels on glass beer and other alcoholic drink bottles. Both the Kube and Opera Modular solutions are equipped with the automatic seal application system; they also feature LVS bottle positioning and Quality Control systems. The latest Sacmi products also include digital label printing systems. Labels are vital for bringing out the best in a brand and now, thanks to Sacmi D-Match - a versatile, economical solution that combines maximum personalisation with digital print quality, high speed and lower logistical and reel storage costs - they can be transformed into effective marketing tools. www.sacmi.com Sacmi Hall 7A | Booth 222/323 Solutions for avoiding micro-particles The specialist in cap feeding systems Gassner will be concentrating at Brau Beviale on avoiding micro-particles in bottled products, caused by contaminated closures. Anew addition to the range will be the SmartClean device, an ionised air cap rinser for the cleaning of closures just before the application. This compactly designed development is claimed to be capable of removing particles with greatly improved efficiency. Other benefits include good access for the purpose of cleaning, robustness against aggressive detergents and reliability, even in wet and steamy conditions. Gassner claims that the system has low operating costs and does not need pressurised air. It can be integrated into existing lines. In addition, the Gassner strategy package includes a variety of further solutions to improve hygienic conditions at the cap transport. The company claims to be the only manufacturer who delivers all components of cap feeding from one single source, manufactured with in-house know-how. www.gassner.co.at Gassner Hall 7 | Booth 459","@ID":44}, "TRADE SHOW REVIEW PETplanet Insider Vol. 20 No. 11/19 petpla.net 46 ECS SP: Valve-gated hot runners The moulds mounted on the ECS SP are configured with valve-gated hot runners as standard, for production of premium quality containers. This solution gives users the opportunity to use, for any given number of cavities, the same hot runner system for different types of preforms, with only the cold half needing to be changed. This offers cost advantages, along with significantly reduced format changeover time. At K2019, the hot-fill option was fitted to an ECS SP80; the smaller ECS SP25 can also be equipped with it. The ECS SP systems are designed to offer compact dimensions, high energy-efficiency, best-in-class productivity through a combination of high cavitation and low cycle time, and premium quality container production. ECS SP in action: Production of ketchup containers The ECS SP80 HF, with 80 t injection clamp force, can produce containers as small as 10ml. The unit demonstrated at the K show was engaged in production of 420ml ovalshaped ketchup bottles, 167.5mm tall and weighing 28 g. The neck diameter was 38mm with an SP400 neck finish. These containers are resistant both to a filling temperature of 85 °C (±2 °C) and to vacuum forces that arise during cool-down. Sipa says that the second feature solves the problem of the label crinkling: partial or complete peeling off of the label, caused by container deformation. The ECS SP80 HF on show had six cavities and ran with a 14 second cycle time, producing 1,540 bph. Sipa says that the new hot-fill option for ECS SP machines is based on its experience in production of hot-fillable containers with both single-stage and two-stage technologies and that its new machines overcome the disadvantages of current low- to mediumoutput systems: the lower energy efficiency of two-stage technology; and the traditionally poor thermal resistance of hot-fill containers. The hot-fill option now provides ECS SP users with a lower-cost alternative to aseptic filling. Furthermore, if oxygen scavengers are used in PET containers it is possible to achieve a shelf life for ketchup as long as 12 months, without the need to add preservatives to the product. For new machines and retrofits Hot-fill capability can be retrofitted to existing ECS SP machines as well as supplied on new ones. The retrofit kit includes dedicated stretching rods, air valves, air vessel and piping that are required for the air recirculation in the container during the hot-fill process, an electrical heating system for the blow moulds that ensures the cleanliness of the blowing area (no oil is used), and upgrade of the machine’s control software in order to include the management of this option. XForm Gen 4 XP preform injection moulding New technology incorporated into the XForm Gen4 XP 250 and 350 t Debut of two new products at K2019 Hot-fill option for single-stage ISBM Italian PET machinery specialists presented its new hotfill option for ECS SP single-stage ISBM and unveiled the next-generation XForm 250 preform injection moulding platform. Sipa’s ECS SP machines’ hybrid drive technology uses servo-electric drives where precision and speed are required; hydraulics perform tasks where there is no particular need for high performance. This solution is designed to combine high performance and low energy consumption, and to offer a lower-cost alternative to aseptic filling. The new XForm Gen4 XP system incorporates the latest generation of preform injection moulding technology to deliver lowest conversion cost alongside market-leading speed, flexibility and ease of use.","@ID":48}, "43 TRADE SHOW PREVIEW PETplanet Insider Vol. 20 No. 11/19 petpla.net Retal Hall 4 | Booth 323 Patented performance Tethered closures are a hot topic in the packaging industry. Global PET, rPET and HDPE packaging producer Retal has invested considerable time and resources to creating innovative tethered closures that are both responsible and easy to use. Tethered closures from Retal are suitable for water, carbonated soft drinks and aseptic products. By ensuring that the lid is not separated from the bottle, they reduce contamination of recycling collections and help to support the circular economy by retaining materials and reducing waste. The Retal tethered closures are also intended to provide enhanced convenience for consumers thanks to the way in which it opens, creating a smooth contact. Aleksandr Kachanov, R&D director at Retal, explains, “We gained the patent certificates in June 2019 for our tethered closures; our unique solution allows the sharp edge to stay towards the bottle once it’s been opened, rather than towards the mouth of the consumer. Retal is one of very few closure manufacturers that has developed and invested in this special solution – it’s the embodiment of the Retal dedication to creating responsible solutions that are user-friendly. It’s not just a response to the EU SUP Directive; our tethered closures aide consumer convenience as they’re easy and comfortable to use.” The patented tethered closures have tested both injection moulded and a slit folded solution, with the design team lead by Kachanov creating prototypes that have been subjected to numerous strict tests. He says, “After extensive modifications to each solution, we focused on the injection moulded tethered closure as the majority of our closure moulds use this, making it a more cost-effective offer for our global food and beverage customers, particularly as our technical expertise is also more proficient in this area. Our brand owner customers and bottlers are unlikely to need investment in new solution when they chose tethered closures from Retal.” Retal’s packaging development expert Anton Sugoniaev shares how the intense testing phase has enabled the company to create an injection moulded tethered closure solution that addresses the core concerns of its customers and the consumer. Sugoniaev says, “There are limitations to the possible tethered closures, so they will all be similar, yet this is where the potential for differentiation is exciting; small changes deliver big advantages, particularly when it comes to consumer convenience. Our solution delivers a secure fixation of the closures next to bottle’s neck instead of allowing them bounce and turn around.” Initially created for the standard 1881 caps, the Retal tethered closure portfolio will extend across its range. www.retalgroup.com Tethered closures and more During Brau Beviale, Aptar will present its tethered closure solutions, which promote post-use recycling as the tethered closure stays attached to the bottle through its life cycle, while improving the consumer drinking experience. Aptar’s exhibits also include two other innovations by the supplier of packaging solutions, a new sports cap and a new instant mixing cap. www.aptar.com Aptar Hall 4 | Booth 129 GEA Hall 7 | Booth 600 Rapid changeover times Of particular interest to customers in the craft beer segment are space-saving, flexible and sustainable solutions that pay dividends at medium speeds and capacities. So GEA’s booth showcases the flexible, monoblock GEA Visitron Filler All-In-One, which can switch between filling bottles, cans and PET containers. It is claimed to be capable of handling the most varied formats, beverages and lid types with ease, but also to slash the filling block’s format and product changeover times from many to a mere 20 to 30 minutes. With these features, the filler is intended to respond to issues that are currently major preoccupations for beverage manufacturers. www.gea.com","@ID":45}, "PETplanet Insider Vol. 20 No. 11/19 petpla.net 51 TRADE SHOW REVIEW environmental issues, reduce CO 2 footprint and harmful emissions as well as raw material consumption. Zhang Feipeng, President Fujian Baichuan Resources Recycling Science & Technology Co., Ltd. introduced the audience to “Customisation and Green Development of Recycled Coloured Yarn”. To reduce the high water consumption during the wet dyeing of polyester yarn and fibre the application of colour masterbatch and spin-dyeing is the method of choice. Spin-dyeing of recycled fibre material is, compared to virgin polyester, more complicated because of the fluctuating discolouration of rPET. The way out is to increase colour lots by customer bundling and the availability of a large number of reproducible colours and colour shade recipes stored and organised in by a data base. Wolfgang Hermann, Business Development Manager Fibres & Textiles Erema Group GmbH discussed “Future requirements of the Circular Economy and Erema’s smart and flexible solutions”. Erema recognised the raw material producers as drivers of the plastic/polyester recycling and optimised its product portfolio accordingly. In this respect Erema is about to improve especially the uninterrupted running time of their recycling units from 12 to 24 months which is significant for the plant economy. Lin Jun, analyst of CHTC Landview Network (former CCFEI): The title of her contribution “Researches of rPET Industry Development in Current Macro-cycle” X-rayed in detail the economic development of PET recycling industry over the past ten years. Wang Zhijun, General Manager of Hebei Jinyi Polyester Fiber Co., Ltd. summarised with his contribution “Status quo and perspectives for the recycling industry” the tough situation of the Chinese PET recycling industry in all correlations like plant relocation to the Far East, low utilisation rates 50 -60%, US trade war and price erosion. Possible solutions include an increase of plant capacity and productivity as well as cooperation with important brand owners. David Hehenberger, Manager of Market and Business Development Department NGR Plastic Recycling Technologies updated the audience by talking about “Liquid State Polycondensation - Effectivity and Application Opportunities”. NGR’s LSP-unit to increase molecular weight of PET by melt phase polycondensation has now arrived in the recycling market with 16 units in film and fibre applications. A welcome side effect of the process is the decontamination during vacuum processing. Masanobu Ishikawa, PhD, Professor Emeritus Kobe University Councillor of The Japan Containers and Packaging Recycling Association: His contribution “PET bottle recycling in Japan: the history from the viewpoint of structural change to get future prospects” dealt with the scientific and social background of the consumption and recycling of plastic in Japan and worldwide. He explained the change from the linear to the circular economy and the underlying driving forces. Very important for the change to the circular economy are, according to Prof. Ishikawa policy and government as the leading forces of this process. Aldo Previero, General Manager of Sorema div. of Previero Srl presented the paper entitled “The State of the Art Sorema PET Washing Lines in China”. By producing PET flakes of superior quality using Sorema technology A. Previero claimed their pure rPET as unique and a product on its own, not as a replacement of virgin PET. Sun Yajun, General Manager Zhongxing Environmental Protection Technology Co., Ltd spoke about “Flake Recycling Leading Green Fashion” as an introduction and advertisement for his company. Zhang Lei, General Manager, Jiangyin Desel Environmental Protection Equipment Co., Ltd. His contribution was called “Cold Thinking on the Transfer and Development of the rPET Industry” and dealt with the general development of the PET recycling industry of China in comparison with other regions of the world, especially with problems of production relocation to Africa and the Far East. Qiu Binhong, Manager of Green Environment Department of Intertec Green Initiatives; the paper “GRS V4 Certificate - New Opportunities for Recycling Enterprises” advertised the application of the GRS V4 certificate as important tool to improve product quality of textiles based on rPET. Stewart Hardy, Global Manager Petrochemical Market Dynamics of Nexant Inc. analysed the rPET products and rPET raw material markets by its contribution “From Discount-toPremium: rPET Fibre in the Era of Sustainable Fashion”. Highly interesting is his prediction that the demand for recycled products will increase drastically in the near future. He analysed which market participants will grow and which will suffer during the area of conversion. The entrance of a substantial number of large brand owners and discounters in the recycling market will trigger a massive increase of rPET based products. The hitherto negative price gap between virgin and rPET will turn to positive in the near future. Ji Hui, Analyst CHTC Landview Network (CCFEI) closed the conference with her summary about “SWOT Analysis of rPET Industry against the Backdrop of Policy Change”. The analysis contains data of the Chinese rPET market and price development from 2017 till today and is providing a databased view of the drastic impact of the plastic waste import ban since 12/18. The conference book which contains most of the presentations is available on: www.polyester-technology.com or at www.ccfei.net","@ID":53}, "TRADE SHOW PREVIEW PETplanet Insider Vol. 20 No. 11/19 petpla.net 44 Krumbach cuts energy use and CO 2 with PET bottle disposal process Empty or full Mineral water company Mineralbrunnen Krumbach, which produces mineral water and soft drinks, calculates that it fills up to 150 million bottles a year, which it distributes to beverage wholesalers and retailers. It has recently invested in the installation of three Strautmann machines for the baling and compaction of used PET bottles, ready for shipping to recycling plants. In Krumbach’s previous process, full PET bottles were emptied through a perforator, then compacted in bales by a channel baler. The restricted availability of storage at the company’s site meant that bales had to be collected frequently. It was labourintensive and increasing transport and logistics costs, as well as bale handling and wear and tear on the perforator meant that the process became uneconomic. Alexander Diehm, Operations Manager, Mineralbrunnen Krumbach GmbH When it looked for an alternative collation, collection and disposal method, Krumbach sought a solution that could handle around 2,200 t of PET per year, with installations integrated into the production line and able to continuously compress PET bottles on-site. “The Strautmann concept, with two redundant briquetting presses and a dewaterer, offered logistical added value. The internal process is now much easier,” reports Alexander Diehm, Operations Manager at Mineralbrunnen Krumbach in Kißlegg, Germany. Empty disposable PET bottles are ejected on to a conveyor belt, which carries them directly into the briquetting presses. The high pressure BrikPress produces tightly compacted briquettes, at a rate of up to 45,000 bph (500ml). The bricquettes are then channelled away by gravity feed. Once outside, the briquettes fall over a two-way distributor into a two walking-floor semitrailers. “The high briquette density has enabled us to achieve 24 t capacity utilisation, compared with about 12 t before, and to reduce our CO 2 emissions,” says Alexander Diehm. BrikPress and channels The briquettes are then retrieved by a disposal company and processed into preforms, which Krumbach uses to rebuild PET bottles. Its recycling rate is 97 percent and represents a closed-loop cycle. Disposal PET bottles on the way to the compaction Discharged in the two walking-floor semitrailer Full PET beverage bottles are collected in small wells and placed in a LiquiDrainer by forklift. A feed rocker conveys the material to a rotor, which punctures the containers and empties them, at up to 10,000 bph (1 l) and with 99 per cent efficiency. The goods are pre-compacted and cancelled, to prevent potential abuse. The liquids collected run through a filter box and are discharged separately. The pre-compacted bottles are then discharged from the machine and carried by conveyer belt to the BrikPress and automatically compacted into briquettes. Mineralbrunnen Krumbach now has a fully automatic and reliable disposal system based on the Strautmann press system. Handling has been cut to a minimum and the company has greatly reduced its CO 2 emissions, also. www.strautmann-umwelt.de Strautmann Umwelttechnik Hall 8 | Booth 124","@ID":46}, "PREFORM PRODUCTION PETplanet Insider Vol. 20 No. 11/19 petpla.net 17 300 of which work in preforming. Here at the Bangalore site, Husky, Milacron and Conair equipment are in use. The part of the factory housing the Husky machines has been recently added. “We decided to invest in Husky systems in order to be more attractive not just to leading regional brands but also, beyond that, to be able to access more customers in the premium segment in the medium term,” said Nishant Bafna. Nishant Mouldings and its vision have already received several awards, including the India SME 100 Award 2018 and the Sir M. Visvesvaraya Manufacturing Excellence Award 2017-2018, from the government of Karnataka. “We are currently more dominant in the south and now also in the west of India. We are planning to expand in the north and east in the long term,” says Pankaj Bafna. “Accompanying this, we want to double our capacity to 60,000t. We also want to make our processes more automated, and will continue to invest in that area. We are also committed to reducing our carbon footprint.” During the past few years, Nishant has installed solar arrays in its factories; they are expected to reduce CO 2 emissions by 700t annually. The company is also aiming to set up more new, purpose-built factories in strategically different regions, in its drive to grow sales to US $150 million, in five years. www.fortunapet.com The Directors in front of a Husky HyPET 22h with (f.l.t.r.) Pankaj Bafna, Nishant Bafna and Kay Barton Staff preparing delivery bags for preforms","@ID":19}, "PETplanet Insider Vol. 20 No. 11/19 petpla.net 52 PETbottles Beverage + Liquid Food Topper in PET Gourmet Nut, a company founded ten years ago for healthy foods like nuts, fruits and herbs, is selling various toppings for salads under the brand “Modern Mill”. The range includes “Farm Fresh”, a mix of walnuts, almonds, pumpkin seeds, dried figs and cherries. 7.25oz or 206g of product is packaged in a slightly contoured, clear bottle with a screwed-on, easyopen hinged cap seal. A sleeve label with a window to show how much is left reminds the customer to re-buy the product. www.gourmetnut.com More protein, less sugar In the spirit of the times, Arlafoods is bringing a high-protein, low-sugar drink onto the market. The unchilled Arla brand drink is sold in Vanilla, Chocolate and Strawberry varieties and contains 25 g of protein per bottle and 40% less sugar than other comparable mixed milk drinks. The packaging for 500 g or 482ml is a slim, whitecoloured bottle with reinforcement ridges in the grip area. The packaging is completed at point of sale with a sleeve label suitable to each flavour and a screw cap with tamperevident seal. www.arlafoods.de Beet juice with a splash of lemon Trader Joe’s, a retail chain and brand in the USA belonging to the German Aldi Group, is selling a wide variety of products under its own brand, including a red beetroot juice. The 100% juice is finished with a dash of lemon juice and is available in a transparent bottle with compensation areas. The distinctively coloured sleeve label shows an illustration of red beetroot. The 20fl oz/591ml bottle is sealed with a green screw cap with guarantee band. www.traderjoes.com Ten cups of “greens” as a drink The company Forager Project from San Francisco focuses on plant-based nutrition with ingredients that are sustainably farmed and processed. Alongside products like milk and yoghurt from cashew nuts, they are also selling a large number of organic “functional drinks”. The “Greens & Greens” juice pictured contains celery juice, cucumber juice, kale juice, romaine juice, lemon juice, lime juice, parsley juice and a little cayenne pepper. The green drink is available in a slim, transparent bottle containing 12 fl oz / 355ml. A matt printed self-adhesive label provides information and a screw cap with guarantee band seals the bottle. www.foragerproject.com","@ID":54}, "PREFORM PRODUCTION PETplanet Insider Vol. 20 No. 11/19 petpla.net 16 How a preform and bottle producer from Bangalore is stepping on the gas Five years on and still going strong by Kay Barton In the western district of the southern Indian city of Bangalore, the Bafna family, led by Pankaj Bafna and his nephew Nishant Bafna, has successfully been producing preforms, bottles and jars for the Indian market for five years. The special thing about the two directors’ concept is, undoubtedly, their uncomplicated enthusiasm for what they do. Their products’ rather broad target market, which extends from small to large customers and includes everything in between, has enabled them to grow to roughly 30 times the company’s original size - within only six years. April 2019 - Nishant Mouldings Pvt. Ltd. We met: Mr Nishant Bafna, Director Mr Pankaj Bafna, Director With an outside temperature of 40 °C at the time of our visit, it was a relief to find ourselves sitting in Mr Nishant Bafna’s air-conditioned office, listening to him explain how the family company became successful. In 2001, Pankaj and his brother, Mahendra Bafna, founded a producer of PET jars for household goods under the brand name “FortunaPET” – a company that is still going strong today. The household goods sector is a specialised ‘niche’ market and it quickly became quite saturated with suppliers. The brothers still wanted to expand, however, and they identified the FMCG markets as offering opportunities to be tapped. This step proved to be the pathway to further success. “The final breakthrough arrived in 2012, when we had the idea of producing our own preforms and founded Nishant Mouldings,” explained Nishant Bafna, who was appointed as a director of FortunaPET in 2008. He ran his finger down the company’s portfolio, which incorporates approaching 200 different designs, from 7.6 g to 735 g and 25-120mm neck sizes with PCO 1810, 1881, Alaska ROPP or CTC finishes, among others. Its full product range extends to over 500 units, including bottles and containers. Its current markets are diverse, with customers in almost all sectors. “Our active base of regular buyers numbers around 600 companies. If we add the irregular buyers to that, then we are probably at around 2,000 customers,” he said. As well as beverages, the company’s products are used for cooking oils, pharmaceutical products, sweets, dairy products, spirits and home care applications. The corporate strategy involves being as close to the customer as possible. Nishant Mouldings operates two factories in Bangalore and two in Dadra, Silvassa, north of Mumbai, house a total of 39 preforming, 17 blowing, and four closure lines with an annual output of more than one billion pieces. The factory in Dadra has been completely rebuilt and went into operation in 2018. The company has 60 preform moulds at its disposal, with more than 1,500 cavities. 80-85% of the products are preforms, the rest are PET bottles, jars, and closures - exclusively wide-mouth. Total capacity for material processing is 30,000 t annually; utilisation is currently running at around 90%. Twenty warehouses, strategically located across India, hold stock levels amounting to between 50 and 100 t of material, in order to keep their respective regions appropriately supplied. Nishant Mouldings has a market share of around 2-2.5% and had a turnover of US$ 33 million in 2018. The target for 2019 is US$ 43 million. The company recently acquired its own HGV fleet, which (it says) has improved logistics enormously. The company’s annual growth over the past few years has been constant at 60%. It regards Manjushree Technopack, Sunpet (TPAC) and Chemco as its competitors. “We produce in India for India,” said Nishant Bafna. Exports account for less than five per cent of sales. Nishant Moulding as a whole has a workforce of around 500 employees, Tour Sponsors: Meeting in the office area with (f.r.t.l.) Nishant Bafna, Pankaj Bafna, Kay Barton and Ajith Sivakumar, Husky PET Sales Account Manager","@ID":18}, "TRADE SHOW PREVIEW PETplanet Insider Vol. 20 No. 11/19 petpla.net 45 empowered by Drinktec New Zealand Australia Philippines Taiwan South Korea Japan Let Your Inspiration Flow. From Down Under to Japan It’s time for the Editour Road Show to hit the road again! The start of the new decade will see us undertaking a trip from Australia and New Zealand to Japan, via the Philippines, Taiwan and South Korea! With support from Drinktec, the world’s biggest beverages show, we will be shooting off to Australasia in April. Our journey from south to north will see our team visit a variety of locations, countries, cultures and climate zones, with different vehicles. From the legendary, biodiverse sceneries of Australia and New Zealand and with numerous interview visits in between, PETplanet and the Editourmobil will finish the Tour with a visit to Japan, the Land of the Rising Sun! Make sure you’re on board when we set off on our next adventure and get ready for in-depth analyses of the special features and trends in these bottle and beverage sectors! Interested in being visited? barton@hbmedia.net","@ID":47}, "PETcontents 4 PETplanet Insider Vol. 20 No. 11/19 petpla.net 11/19 INSIDE TRACK 3 Editorial 4 Contents 6 News 52 PET bottles for Beverage + Liquid Food 54 PET bottles for Home + Personal Care 56 Patents BOTTLING / FILLING 10 0.25 litre CSD bottle with internal coating 12 Water for Bangalore and the region - India’s biggest water brand relies on sustainability - part 1 14 Increased shelf life, decreased weight - StrongPack and Sidel partner to create leading co-packaging hub for non-alcoholic beverages in Africa PREFORM PRODUCTION 16 Five years on and still going strong - How a preform and bottle producer from Bangalore is stepping on the gas MOULD MAKING 18 Mould making, a review 24 Process optimisation and prevention - Multifunctional device for greater productive capacity BOTTLE MAKING 26 Stretch Blow Molding, part 12 - Machine Details, Blow Moulds CAPS & CLOSURES 34 From strength to strength - Growth of a German closure manufacturer in India MATERIALS / RECYCLING 36 Ocean clean-up - Recycling marine plastics MARKET SURVEY 31 Suppliers of palletising & shrink film machinery TRADE SHOW PREVIEW 39 Brau Beviale 2019 44 Empty or full - Krumbach cuts energy use and CO 2 with PET bottle disposal process TRADE SHOW REVIEW 46 Hot-fill option for single-stage ISBM - Debut of two new products at K2019 48 13 countries in two days - 5th International Conference at PET Technologies 50 Facing external and internal challenges - Summary of the 15th China International Recycled Polyester and PET Packaging Conference & Exhibition BUYER’S GUIDE 57 Get listed! Page 36243610 Page 46 Page 39","@ID":6}, "TRADE SHOW REVIEW PETplanet Insider Vol. 20 No. 11/19 petpla.net 49 A cost-effective test mould is produced for the customer, design changes can be implemented very quickly and with this application small batches of up to 100 bottles can be produced. The company Thermo-Pack was presented by Dmitry Bogovik, Sales Director and Anna Tikhonova, Head of Production Services and Tanks department. The new company plant was visited on the second day of the event. A new 9,000m2 plant was opened in Bila Tserkva Kiev Region in 2017. Thermo-Pack was established in 1996. In 2003 the production of automatic packing machine of linear type for high-efficiency lines was started. At the Interpack trade fair in 2005 Thermo-Pack was exhibiting as one of three Ukrainian companies and presented to the European market. Today the Thermo-Pack machinery and packaging equipment is exported into 25 countries. With 165 employees and their own design departments it is well estabilshed on the packaging markt: from complete filling lines for PET bottle packaging format from 0.33 to 2 liters up to 19 l, with a capacity from 1000 to 15000 bph, depending on application. The Thermo-Pack lines including state of the art labelling, packaging and conveying systems. “The most frequently produced PET bottle in the Ukrainian market is the 1.5 litre PET bottle,” explained Mr Dmitry Bogovik. He continues: “We thank everyone for participation, as well as interesting and relevant reports. We are waiting for you at the 6th International Conference at PET Technologies, which will be held next year!” www.pet-eu.com www.tp-eu.com/en F.l.t.r.: Ms Valentyna Khmelnytska, Foreign-Economic Activity Expert and Dmitry Bogovik, Sales Director at Thermo-Pack Some bottle examples produced by PET Technologies are presented in a conference room as their Hall of Fame","@ID":51}, "MARKET SURVEY 31 PETplanet Insider Vol. 20 No. 11/19 petpla.net 11/2019 MARKETsurvey Resins & additives Preform machinery Preform production & inspection Preform & SBM mould manufacturer SBM 2 stage Compressors Filling equipment & inspection Caps & closures & inspection Palletising & shrink film machinery Recycling Palletising and shrink film machinery For the second time PETplanet Insider focuses on palletising and shrink film machinery to mark the occasion of Brau Beviale 2019. Here you find the machine details of state of the art technology from participating companies: SMI S.p.A., Sidel, Krones AG, Productive Systems (Pty) Ltd, Gebo Cermex, Jiangsu Newamstar Packaging Machinery Co., Ltd., GEA Group, And&Or and Sipa S.p.A. Although the publisher have made every effort to ensure that the information in this survey is up to date, no claims are made regarding completeness or accuracy. Company Sidel KHS Krones AG Jiangsu Newamstar Packaging Machinery Co., Ltd Postal address Telephone number Web site address Contact name Function Direct telephone number Email Rue du Commerce, 67116 Reichstett, France +33 388 183 880 www.sidel.com Ms Lucia Freschi PR Manager +39 521 999452 lucia.freschi@sidel.com Juchostraße 20, 44143 Dortmund, Germany +49 231 5690 www.khs.com Böhmerwaldstraße 5 93073 Neutraubling, Germany +49 9401 70 0 www.krones.com No. 8 Xinjing East Road, Zhangjiagang Eco- andTechnological Dev.-Zone, Jiangsu Province, China, 215618 +86 512 5869 1111 www.newamstar.com Mr Wesley Yin Marketing Manager +86 512 56993303 market@newamstar.com Shrink film machinery: Packaging options & output rate (packs per minute) - print registered film (yes/no; packs/min) Yes, up to 120 cycles per minute (PET bottles), 150 cycles per minute (cans) in 3 lanes Yes, 540 packs/min Yes, 150 x 4 = 600 ppm Yes, 60 - nested pack (yes/no; packs/min) Yes Yes, 80 packs/min Yes, 80 ppm No - label orientation (yes/no; packs/min) Yes No No No - carry handles (yes/no; packs/min) No Yes, 240 packs/min Yes, 80 x 2 = 160 ppm No - pad supported (yes/no; packs/min) Yes Yes, 110 packs/min Yes, 120 x 2 = 240 ppm Yes, 60 packs/min - tray supported (yes/no; packs/min) Yes Yes, 110 packs/min Yes, 100 ppm Yes, 60 packs/min - film only (yes/no; packs/min) Yes Yes, 540 packs/min Yes, 150 x 4 = 600 ppm Yes, 80 packs/min - tray and film (yes/no; packs/min) Yes Yes,110 packs/min Yes, 100 ppm Yes, 80 packs/min - pad and film (yes/no; packs/min) Yes Yes, 110 packs/min Yes, 120 x 2 = 240 ppm Yes, 80 packs/min Shrink process: - shrink tunnel with hot air or gas fired opt. Yes With electricity or gas fired (option) Yes Yes - oven Yes No Yes - steam tunnel No No Yes Footprint Depend on configuration Depends on speed Number of possible lanes Up to 3 4 4 Packaging material and possible thickness Low-density polyethylene (LDPE) from 27-100μm Shrink film 25-80μm thickness; corrugated board: B,C, E and F-Flute LDPE + ( LLPDE, MDPE, HDPE, PP) printed …., 25-120μm Voltage/power/energy consumption NC Voltage: standard 3x400V; power: min. 22KW - max. 48KW; energy consumption: depending on requirements Depends on speed, package and material Film cutting and feeding system Yes Continuous feeding system from a roll Yes, fully automatic feeding, splicing, welding Certification CE certification Palletising machinery: Format changeover time Depend on configuration Depends on machine type (non returnable, returnable) 20min Output rate (packs/min) Up to 12 layers/min 100 - 650 lph (layers per hour) 120 Automatically intergrated:(yes/no) If necessary Yes Empty pack feeding Yes, empty pallet feeding Yes Auto Insertion of interlayers Yes Yes Auto Connectable to shrinkwrapper Yes Yes Yes Special characteristics: i.e. low-level feed, cross conveyer barrier Available on high and low level infeed High speed with low level infeed Low-level feed, cross conveyer barrier","@ID":33}, "PETplanet Insider Vol. 20 No. 11/19 petpla.net 55 BOTTLES Cleansing foam in a pump dispenser Soap & Glory, the English manufacturer of cosmetic products, has brought 200ml of a liquid for gentle facial cleansing onto retailer shelves under the brand name “The Fab Pore”. The bottle is slightly coloured and has a screwed-on pump dispenser with a transparent protective cap. When dispensed, the liquid mixes with air to become foam. A transparent, self-adhesive label with motifs giving a retro look provides all relevant information. www.soapandglory.com Distinctive bottle for shampoo The American company “It’s a 10” is selling high-priced, specially developed products for professional haircare for men and women. Their products are available in distinctively designed plastic bottles. The “miracle moisture shampoo” is combined with ten component parts, such as Vitamin C, sunflower seed, acai, ginger, pomegranate and rooibos tea extract, and comes in a 295.7 ml / 10 fl oz dark blue, distinctive and directly printed bottle with a pump dispenser. To dispense the product, the upper part of the pump dispenser must be removed from the lower part by unscrewing several times to unlock it. www.itsa10haircare.com info@hasplastik.com Tel: +90 212 695 50 00 Fax: +90 212 694 97 24 100815dmyR .com","@ID":57}, "BOTTLE MAKING 11 PETplanet Insider Vol. 20 No. 11/19 petpla.net BOTTLE MAKING 11 conventional inline measuring methods which is why monitoring of process parameters is carried out. If these exceed a certain tolerance level, the bottles are rejected. Special attention has to be given to the vacuum pumps which are contaminated by residues sucked in via the vacuum. At each CIP (every 48 hours), the units must be thoroughly cleaned to ensure the process parameters remain within prescribed tolerance limits. HCCB are very pleased with their units. Soon after commissioning, they received an efficiency level of over 90% despite the sensitive nature of the plasma coating. It is therefore no surprise that two more have been ordered for the Indian market. In addition to the four already in India, the other two in Indonesia and Nepal, Coca-Cola now have eight in all. www.hccb.in/en Hindustan Coca-Cola beverage factory at Sanand, Gujarat, is now a Gold Certified Green Building The Indian Green Building Council (IGBC) has awarded the Gold certificate to HCCB newest factory at Sanand, Gujarat. The factory - a fully digital and worldclass facility, became operational in mid-2018. The Sanand factory is only one of nine Gold certified Green Buildings (factories) amongst the FMCG / Food industrial facilities in India. It is also the only factory run by HCCB, which employs more than 40% women. The Gold certification to the Sanand factory is based on an assessment of the site in the categories of sustainable site, water conservation, energy conservation, indoor environmental quality, material conservation and innovation. Initiatives such as prevention of soil erosion, group transportation and shuttle services, on site solar power generation & effective usage, rainwater harvesting, re-use of wastewater, vehicle charging facility, and several others, have been undertaken at Sanand to develop it into a green site. We took some shots in the first monsoon rains from outside the gates. In the picture, you can see Mr Girish Chhablani, the factory manager, with his assistant on the left.","@ID":13}, "BOTTLE MAKING 26 PETplanet Insider Vol. 20 No. 11/19 petpla.net Stretch Blow Molding, part 12 Machine Details, Blow Moulds by Ottmar Brandau Ottmar Brandau has newly revised his book “Stretch Blow Molding”, first published by hbmedia / PETplanet Publisher, and now re-issued in a third edition under the Elsevier Imprint. PETplanet Insider is publishing extracts from successive chapters in a serie of articles. Air Consumption Another important feature is air consumption and more specifically the so-called dead air volume. Air is the single-most costly part of blowing bottles besides the preforms and users do well to pay close attention to this issue. Air consumption is driven by the air pressure, the actual volume of the bottles produced, and the air that is not used in the blow process but needs to be exhausted every blow cycle. This air “hides” in the connection pieces between the blow valves and the cavity. When the exhaust valve is energised, all air that is between it and the cavity must be exhausted besides the actual bottle volume to make sure there is no pressure left in the blown bottle. Many manufacturers of blow machines do not publish this important information but users can calculate it by looking at the machine specifications. Let us assume a manufacturer specifies blow air consumption of 1,300 Nm3/h for the production of 20,000 b/h of 1.5 l volume at 35 bar. The volume that is actually inside the bottles is 20,000 b/h × 1.5 l × 35 bar/1,000 l/m3 = 1,050 Nm3/h. The difference of 1300-1050 = 250 Nm3/h is the dead air volume. This in turn is 367ml/bottle (250 Nm3/h × 1,000 l/ Nm3/h/20,000 b/h/35 bar). It is important to calculate this as a fixed number rather than a percentage as this lost air is present for bottles of each size. A 500ml bottle has the same losses as a 1.5 l bottle; howFigure 4.19 During the “airback” phase, blow air is redirected to a distributor panel instead of exhausted to the atmosphere. Diagram courtesy of KHS Corpoplast GmbH.","@ID":28}, "TRADE SHOW REVIEW PETplanet Insider Vol. 20 No. 11/19 petpla.net 48 5th International Conference at PET Technologies 13 countries in two days It’s always nice to feel you’re in the right place at the right time! It is not only the enthusiasm for the PET material that inspired the participants at the fifth International PET Technologies Conference in Chernihiv, Ukraine. Above all the sincere discussions and interesting presentations by the company’s organisers and customers to the topic of modern trends of PET industry market were impressive. Of course this year is a very special one for PET Technologies. Like PETplanet, the company is celebrating its 20th anniversary. Since its founding in 1999, the company has grown into a global player with a sales and service network in 15 countries around the globe. PET Technologies blow moulding equipment and blow moulds can be found on five continents in over 45 countries. The quality of the company is not only confirmed by its steady growth but also by the confidence of long-standing customers and partnerships. In addition to numerous local brands, AB InBev, Olvi, Unibrew, CocaCola, Pepsi, Carlsberg and many more belong to its customer base. In keeping with the anniversary year, the company made itself a great gift: it opened a new workshop. A new, modern and well equipped blow moulds production hall operates now at full capacity. The first day of the event began with the opening speach and warm welcome words of Maxim Poliansky, CEO at PET Technologies. He emphasised the unified harmonious approach of production, landscape and way of life in the circular economy that PET Technologies is committed to. The opening presentation about the Circular Economy for PET bottles was held by Eduardo Martinez, CEO of Plásticos a la Medda, President of Plastics Recycling Association Mexico. Eduardo referred to the Ellen MacArthur Foundation and the three-step model of take-make-waste. This model has to be extended in the sense of the five R model: Rethink, Redesign, Reduce, Reuse and Recycle. Eduardo explained that after a short first-use cycle, 95% of plastic packaging material value, or USD80–120 billion annually, is lost to the economy and that a staggering 32% of plastic packaging escapes in collection systems. He poined out that the new Plastics Economy aims to overcome the limitations of today’s incremental improvements and fragmented initiatives, to create a shared sense of direction, to spark a wave of innovation and to move the plastics value chain into a positive spiral of value capture, stronger economics, and better environmental outcomes. For Eduardo recycling is the first option for plastic packaging waste. Eduardo explained, that the Mexican PET recycling rate is around 55.5%. He introduced PetStar the very large bottle-to-bottle recycling plant in Mexico, producing circa 50,000 metric tons of recycled resin annually. It is a merger of the companies Arca Continental, Coca-Cola de México, Bepensa Bebidas, Corporación del Fuerte, Corporación Rica, Grupo Bottler Nayar and Embotelladora de Colima. Valentina Sikdan, artist at PET Technologies presented her new design concepts for different PET bottle applications. Roland Steurer, Managing Director at PET Technologies GmbH, Austria, presented how these new concepts are implemented at PET Technologies. His vision begins with the development of a design idea for the customer, supported by CAD, up to the production of the mould and the blown bottle in 24 hours. To realise this vision, PET Technologies uses rapid prototyping with 3D printing machines. With this method the customer receives a fast and favourable result, also it offers a high flexibility in the production process, since one can react fast and uncomplicated to change requests, so Roland. Lightweight contructions und free-form geometries are possible. The production process is as follows: a bottle design is developed and a bottle dummy is produced with the help of 3D printing finally an inlet for the mould in which the bottles can be blown is produced. Roland summarises the key point of this project as follows: from the idea to the bottle it only takes 24 hours. Mr Eduardo A. Martinez from Plásticos a la Medida presenting his ideas on Circular Econony F.l.t.r.: Maxim Poliansky, CEO of PET Technologies and Roland Streuer, Managing Director at PET Technologies GmbH, Austria On the first day of the conference the 85 participants from 13 different countries were guided through the state of the art production hall of PET Technologies.","@ID":50}, "MOULD MAKING PETplanet Insider Vol. 20 No. 11/19 petpla.net 21 CEO Shurid Mody, PETform In addition, the new style features a reduced pitch size between cavities of as low as 40mm. “With this reduction, for neck diameters of 25mm and less, we can increase the cavitation by as much as 25% in the same machine”, said Mr. Mody. With the reduced pitch, the mass of the mould is reduced allowing for shorter lock to lock times and some saving in the energy used for platen motion. The lower mould pitch also results in lower pressure drop, preservation of material IV, energy saving and a wider process temperature window of 200-300 °C. This allows the usage of PET as well as biodegradable PET substitutes or PP likewise. www.petform.net Manjushree mould products: ASSP mould: This is a 9.68 gm capacity preform with 50ml pack. The specially designed preform with a neck for packing of carbonated soft drinks is suitable for use where carbon retention is an issue. The bottle made from this preform is known for its barrier properties. Mould for 2l bottle with handle: As know in ISBM process, bottles with integral handle cannot be produced; 2 l handle bottle, one half blow shell handle mechanism","@ID":23}, "BOTTLING / FILLING PETplanet Insider Vol. 20 No. 11/19 petpla.net 12 India’s biggest water brand relies on sustainability – Bisleri part 1 Water for Bangalore and the region by Kay Barton Bisleri water is, quite literally, on everyone’s lips. The country’s largest water bottler has its own plants in all conurbations, which means it’s always close to the shops and customers, ready to quench the thirst of the population of India. PETplanet has had the opportunity to visit various Bisleri plants several times in the past and to talk to the makers on site. We are now doing this on a grand scale, during the India Road Show; the production plant in Bangalore was the first of several scheduled factory visits. Here, we met Plant Manager Mr Vishwanath and his colleague Mr Sathyam Chaudhary, South Procurement Head, and talked about everyday business and water recovery. April 2019 - Bisleri Ltd We met: Mr G. N. Vishwanath, Senior Plant Manager Mr Sathyam Chaudhary, South Procurement Head On entering the premises of Bisleri, at some locations, we noticed signs on the buildings stating that photography was expressly welcomed – something rather unusual at a production facility. Bisleri aspires to be transparent to everyone, it seems. Indeed, as we found out in the interview, open communications are part of the company’s strategy. The Senior Plant Manager on site is Mr Vishwanath, who has been working for Bisleri Bangalore for 13 years. He and Mr Chaudhary who is responsible for the Devanahalli plant, welcomed us to the factory, which is situated approximately 30km outside the city, near the airport. “We launched the location here in Bangalore in 2000, and production started in 2001,” Mr Vishwanath explained. “In those days, PET was our direct starting point; alternative packaging was out of the question. The initial situation in Bangalore spoke in favour of this location as, at that time, clean water availability wasn’t good. Back then, we filled about 30,000 crates a year. Today’s figure is around 1 million; that’s about 500,000 litres per day, with our best seller being the 500ml bottle.” Turnover nationwide is USD 86.5 million, of which 35% is attributable to the activities in Bangalore. Water is the factory’s leading bottled product, with 90% of output. Carbonated fruit drinks and sodas account for the rest. The trend, we were told, is away from classic CSD beverages; not least because of the sugar tax. Bisleri’s share of the branded water segment is approximately 38% and its annual growth rate in the Bangalore area is around 30%. Tour Sponsors: Discussions on Bisleri’s activities with (f.l.t.r.) Mr Vishwanath, Mr Chaudhary and Kay Barton Bisleri’s drinks come in 250ml, 500ml, 1 l, 2 l, 5 l and 10 l disposable bottles with an Alaska neck finish, and in 20 l reusable containers. On site, technology from Mahavir is used for the treatment of the water. Three water filling lines, equipped with Kosme, Sidel and SMI machinery, are dedicated to the regular bottle formats. Two of the lines have an output of 100 bottles/minute each; one has a capacity of 200 bottles/minute.","@ID":14}, "PETplanet Insider Vol. 20 No. 11/19 petpla.net 54 PETbottles Home + Personal Care All-purpose cleaner with soda Frosch is selling 400ml of liquid all-purpose cleaner with soda in a “Maritime Edition” in a pot-bellied bottle made from up to 100% recycled plastic. The cleaner does not contain any microplastic. The bottle is decorated with a sleeve label with a window. Three different maritime motifs are available with turtles, seals or dolphins. The cleaner is dispensed via a screwed-on, transparent trigger with a lock function. An additional label indicates the benefits of the product and the packaging. www.frosch.de WC Power from Ajax Under the brand “Ajax” and the endorsement “WC Power”, Colgate-Palmolive has brought onto the market a WC cleaner that is stated to remove 99.9% of bacteria. The green-coloured cleaner is suitable for the inside and outside of the toilet. The 750 ml bottle has a lockable sprayer that also functions upside down; it is transparent and is decorated with a sleeve label. The label has perforations to enable simple separation of bottle and label during the recycling process. www.dm.de Scented glitter spray for hair Onivo Cosmetics from Narbonne / France is producing and selling scented cosmetic products in trendy packaging. For example, the company is selling a “Perfumed Hair Glitter Spray” for the brand “Unic Eau de Parfum” in a small 50ml bottle. The glitter particles in the product are distributed by shaking and then applied to the hair via the vertically operated pump sprayer. The lockable sprayer has a funnel-shaped nozzle to better distribute the product. A transparent self-adhesive label describes product and usage. www.onivo-cosmetics.com Organic cornflower for facial cleansing Garnier is selling 400 ml of an all-in-one micellar cleaning water for face, lips and eyes in the Garnier Bio range; it is available in a slightly green-coloured bottle with square shoulders. The cleaning water contains organically produced cornflower water and barley water and quickly and gently removes make-up residue. A screwed-on hinged cap seal with dosage opening that can be opened with one hand enables simple dispensing onto a cleaning pad. Two self-adhesive labels describe product and usage. www.garnier.de","@ID":56}, "PETnews 6 NEWS PETplanet Insider Vol. 20 No. 11/19 petpla.net Kreyenborg expanding manufacturing capacities and test facility Kreyenborg GmbH & Co. KG located in Senden, Germany, is keeping abreast of its growth with two new production halls, new machining centres and an extension of its test facility. The manufacturer of integral concepts for bulk handling applications for the foodstuff, chemical and plastics industries intends to convince with innovative solutions and a wide range of services offered. “We have more than doubled the volume of incoming orders over the past three years,” says managing partner Jan Hendrik Ostgathe, thus explaining the additional 2,200m2 of production surface at the company site in Senden. The construction of halls 4 and 5 has just been completed and the first new, modern machining centres “are moving in”. At the same time, the test facility has been extended substantially. Thus, the complete range of Kreyenborg products is available to customers who wish to test their applications as of now. This range of products includes all components needed for drying, decontamination, coating, heating-up, crystallising, storing, discharging, mixing and conveying of bulk densities. Growth in the plastics sector has been achieved not only thanks to the Infrared Rotary Drum long since developed to become a renowned product, used for pre-heating, crystallising, drying or coating tasks, but also as a result of the more recent, specifically developed machine components PET-Booster and IR-Clean. While the PET-Booster stands out due to its short drying times of around 10 minutes, the particular feature of the IR-Clean is the high decontamination performance; which is, when using recycling material, good enough to keep the required limit values imposed by EFSA and FDA, states the company. www.kreyenborg.com Erratum In issue 9/2019 there was an error in our article “PET - A review of material developments”. The second photo on page 34 left column should have been correctly assigned to the text section on page 33 below. These are bottles produced with the Polyone “Impress” high-gloss metallic effect colourant range. We thank Polyone for pointing this out! Official opening of United Caps manufacturing plant in Malaysia United Caps, an international manufacturer of caps and closures, reported that it held a formal grand opening for its new manufacturing plant located in Kulim, Malaysia. This plant is intended to position the company as a global player with continuing growth, opening new opportunities in the Asian market with its ‘Close to You’ strategy. During the event, United Caps launched a brandnew product designed specifically to meet the needs of the Asian market. 127 Safe-TE is intended to increase baby food safety and convenience with security features and a premium gold colour offering. “The decision to build this plant was part of our Close to You strategy to better serve the Asian market. This proximity enables us to shorten delivery times and focus on products that are the most relevant to this important market region, as demand for our products continues to grow. It was also an opportunity to launch a new product, 127 Safe-TE, our next-generation closure for infant nutrition. As we celebrate our 80th anniversary, we are also celebrating our transition from a European to a fully global organisation. The event was carried out live in all of our other subsidiaries throughout Europe as well.” said Benoit Henckes, CEO of United Caps. www.unitedcaps.com United Caps CEO Benoit Henckes (on the left) cuts the ribbon to mark the official opening of the Malaysian plant. K 2019 gives a signal for responsible handling of plastics K trade fair has drawn to a close in Düsseldorf after eight days on October 23, 2019. The 3,330 exhibitors from 63 nations proved that plastics continue to be an innovative, indispensable, future-oriented material. But they also unanimously underscored the necessity of having operational circular economies along the complete material chain and to this end already presented concrete solutions. Companies struck a nerve with people with this focus because the approximately 225,000 visitors from 165 countries took great interest especially in recycling systems, sustainable raw materials, resource-saving processes. Furthermore, K 2019 was characterised by a high propensity to invest as before. According to the organisers, the show was able to score points as a premiere platform where many trend-setting products and applications were presented to the world public for the first time. Many concrete negotiations were conducted and contracts signed. www.k-online.com","@ID":8}, "MATERIALS / RECYCLING PETplanet Insider Vol. 20 No. 11/19 petpla.net 37 we will see all kinds of used plastics returned, as good as new, not just once but again and again, diverting waste streams from incineration and landfill.” Targeting full recycling Coca-Cola has also announced that, across Western Europe, it is driving towards 100% recycled plastic in all of its bottles. In Great Britain, the company is on track to reach its target of moving to 50% in 2020. “While one of the challenges of moving past 50% has been the limited availability of food-grade quality recycled plastic, we hope that the new technology opens up new streams of material,” Mr van Gompel said. “We also believe that the introduction of a welldesigned Deposit Return Scheme in Great Britain will increase the feed of foodgrade plastic available and help us to reach this target, as well as reduce litter.” The Coca-Cola Company intends to roll out bottles including enhanced recycled content from 2020 and has publicly proclaimed clear goals in working towards a “World Without Waste”. Among the landmarks are the commitment to collect a bottle or can for every one it sells, by 2030. www.coca-colacompany.com www.ioniqa.com Diego Lugagne, Coca-Cola EMEA R&D - Packaging Innovation (left) and Jeroen Bulk, CFO Ioniqa Technologies (right) are examining the new concept bottles. www.krones.com The future is circular Can plastic packages be sustainable? Sure, if they’re resource-economically produced and efficiently recycled. KRONEShas the right technologies for this. Harness them, and become part of a closed-cycle economy that really pays off – for manufacturers, consumers and the natural environment alike. BrauBeviale 2019 Nuremberg, 12 – 14 November Stand 7A-510","@ID":39}, "40 TRADE SHOW PREVIEW PETplanet Insider Vol. 20 No. 11/19 petpla.net Steinfurth Hall 6 | Booth 107 UniKeg A is launched on the global market The new UniKeg A has been added to UniKeg’s range of products which are already available with Sankey-D and Sankey-S fittings. Like the rest of the range, the A-fitting, also known as German Slider, is compatible with existing MicroMatic universal coupling systems, so the kegs can be used anywhere in the world without additional cost. Following an extensive period that incorporated design, prototyping, trials and customer feedback, the UniKeg A-Type is now in full production. John Van Veen, head of R&D for UniKeg explains the key points of difference when comparing UniKeg A with other products currently available in market: “First and foremost, our double wall technology ensures that safety remains guaranteed, particularly in hot climates where a single wall keg may not deliver to the brand owner’s requirements. Secondly, the octagonal design of the handgrip and base cup made from 100% re-used material continues to deliver a robust performance in supply chain logistics. Finally, its circular credentials make it the more sustainable option as 63% of the keg is made from re-used, circular materials.” Annemieke Hartman - Jemmett, Chief Commercial Officer at UniKeg, said: “Now that we are able to offer the UniKeg A to the global market we are able to support producers of beer, wine, kombucha, coffee and other beverages with a product that already complies with the re-used materials content requirements; 30+% of the UniKeg is made out of re-used materials, ensuring that the brand owner is not presented with a tax levy on packaging following the introduction of new legislation in the coming years - offering the brand owner a suitable solution on price, quality and sustainability.” www.lightweight-containers.com Quality control on beverages and beverage packages The focus of this year`s trade show participation of Steinfurth is the improved and extended product line for combined monitoring of the quality parameters on beverages, closures and packages. Interconnection and automation in combination with easy and standardised operation and maintenance are intended for the modern beverages industry. The non-destructive CO2 tester CDA-OST is an optical instrument offered in the market with a standardised calibration and validation strategy. Together with the well-established and robust CDA family the complete range of CO2 measurement on packaged beverages is covered. The Compact PackageAnalyzer (CPA) as customised extendable Mini Lab covering measurement of CO2 , torque, brix, fill level, pH and conductivity delivers a time optimised and complete QAbeverage monitoring solution for application directly at the filling line. The patented and as measuring concept absolutely unique non-destructive handheld CO2 tester for packaged beverages (NICO) and the new automatic O2 headspace analyser are just two examples of dynamically growing number of the Steinfurth products. www.steinfurth.com +44 (0) 1254 584210 sales@petmachinery.com petmachinery.com Active for over 25 years, our global network and specialist knowledge makes us the go-to company for the sale or purchase of a PET machine. Commercially savvy, we work closely with our customers and our global network, to make sure everyone gets the best deal. Providing comprehensive advice throughout your sale or purchase; we can arrange dismantling, loading, packing, shipping, specialist insurance and commissioning. If you have amachine to sell or you’re looking to purchase, please get in touch. THE INDUSTRY EXPERTS Lightweight Containers Hall 4A | Booth 311","@ID":42}, "CAPS & CLOSURES 35 PETplanet Insider Vol. 20 No. 11/19 petpla.net The Bericap India plant is located in the Umbare Navalakh industrial estate, just over an hour’s drive from Pune. This is where the company produces closures for the beverage and edible oil segments, along with the automotive and agrochemical industries and other industrial markets. The installed capacity of its several dozen injection moulding machines stands at more than 4.0 billion closures per year. Its 120-strong workforce currently produces over 30 different types of closure, with further new developments in the process of being added. “Bericap Essel”, the joint venture from which this production site emerged, was between Bericap and tube manufacturer Essel Propack, one of the world’s largest manufacturers in this packaging sector between 2005 and 2010. “Bericap supplied the appropriate tube closure solutions until it became independent in 2007 and launched its own production site near Pune”, as Bericap India Pvt. Ltd. General Manager Rajesh Pantsachiv remembered what it was like in the early days. “We had a small team of 25 people, 12 injection moulding machines and an annual capacity of 900 million closures. We have grown considerably over the past 12 years!” he said. “We now have a total production area of around 5,000m², and a state-of-the-art injection moulding machines park, printing machines and laser marking machines, as well as several lines for finishing individual components.” The Bericap QMS (quality management system) was awarded ISO 9001:2008 certification in 2012; food safety system certification (FSSC) 22000 followed in 2015. The company produces 28mm and 22mm closures for CSDs; a range of closures for water in PET and HOD (home and office delivery) bottles; 28mm, 33mm and 38mm closures for juice and milk bottles; and other closures, including two-piece closures, for edible oils. For industrial market customers it manufactures closures for engine oil canisters, agrochemicals and for metal packaging, including complex models with integrated filling nozzles. Bericap identifies its principal competitors in the domestic, Indian market as compression moulding manufacturers Oriental Containers Ltd. (OCL) and Secure Industries. At the time of our visit, Bericap India had around 100 million closures in stock. There is space for 210 million but it was peak season for drinks bottling firms and stock levels had been reduced in order to meet demand. Further products for the liquor market have just been added to the beverages sector portfolio and, in 2018, it acquired many, many new customers. Mr Pantsachiv told us that, alongside the beverages industry, the engine oil business is also extremely important and similarly offers strong growth potential. The company is currently implementing tracking marks to be lasered into the lids as QR codes for the engine oil sector, as offered already from various other Bericap sites. The tour of the production facility illustrated the company’s continued growth. A second, new, 6,500m² production hall and warehouse is now connected to the existing production site. It is still largely empty but that will soon change. Further injection moulding machines and finishing lines are planned to be installed; Bericap is aiming to then break the 8 billion closure capacity mark. “We want to expand product and project development in all areas at the new plant”, said Mr Pantsachiv. “For over two years now, we have considerably stepped up our market scanning and penetration in various segments in order to introduce the established and advanced products from Europe and US product ranges to the Indian market. This will help us grow the business with a wider foot print & bring new technologies to India. If certain trends and demands prove lucrative, we may be able to launch local production of those closures.” In addition to the new capacity, the additionally equipped quality laboratory, mould workshop and maintenance section are to be expanded and given more space. www.bericap.com Closure moulding in action with Rajesh Pantsachiv (right) and Kay Barton Rajesh Pantsachiv showing a product display in the quality lab.","@ID":37}, "7 NEWS PETplanet Insider Vol. 20 No. 11/19 petpla.net Good prospects for drink technology India in New Delhi From filling plants, innovative beverage additives, new beer variations and dairy products to new packaging concepts: drink technology India shows all facets of the beverage, dairy and liquid food industry. The trade fair will take place in New Delhi from December 12 to 14. The list of national and international exhibitors is filling up: about 100 exhibitors will present themselves in December. Hence, about two months before the event, more than 90 per cent of the exhibition space at Pragati Maidan in New Delhi has been booked. In addition, the events pacprocess and food pex India will take place in parallel. The co-location of the trade fairs offers exhibitors and visitors a comprehensive all-round view. From beverages, liquid food to food and packaging solutions, the events cover all segments of the industry. Rising demand boosts packaging industry India is one of the most important sales markets in Asia for companies manufacturing machines for the production, processing and packaging of beverages and liquid food products. The forecasts for the coming years are also entirely positive. According to the VDMA Food Processing and Packaging Machinery Association, the demand of Indian consumers is rising in all sectors of the beverage and liquid food industry. According to the VDMA, the total demand for beverages is expected to grow by about 89 per cent by 2022. Rajesh Nath, Managing Director of VDMA India, also observes significant growth in the packaging sector: “The increasing demand for beverages as well as dairy and liquid food products is boosting the packaging industry. Automatic mould filling and sealing machines as well as aseptic Tetra Pak packaging machines for sterile filling and packaging of products are just some of the industry’s top topics.” In addition to solutions presented at the trade fair by the exhibitors, a new platform will also provide impetus for the packaging industry. The Packaging Design Innovation & Technology Conference will take place in New Delhi for the first time. Companies from the consumer goods industry will talk about packaging design, sustainability, food safety and smart packaging. Buyer-seller meetings The concept of the buyer-seller meetings, which have been an integral part of drink technology India in Mumbai since 2016, has proven to be successful. Exhibitors meet with potential customers to establish possible new business partnerships. With about 430 conversations at the last drink technology India 2018 in Mumbai, the concept received an enthusiastic response. www.drinktechnology-india.com/en 1st Aseptic blower FDA certified in USA ABF 1.2 is the Aseptic Blow-Fill system featuring the very first sterile aseptic blower approved FDA. The GEA ABF 1.2, installed and successfully validated in the USA, obtained the FDA certificate for shelf-stable, low acid beverages produced and distributed in the USA. Thanks to ABF 1.2 each single step of the sterilization process is monitored, whilst the aseptic blower, housed inside a microbiological isolator, avoids any potential risk of recontamination. Another milestone for GEA 10 years after the first FDA certificate received for its PAA based sterilization system.","@ID":9}, "PETpatents www.verpackungspatente.de PETplanet Insider Vol. 20 No. 11/19 petpla.net 56 Improved base optics Disclosure No. DE 102017120457 A1 Applicant: Krones AG, Neutraubling (DE) Application date: 6.9.2017 Light plastic bottle with circulating, rounded and uninterrupted base area. The base design does not have any ridges or straps in the side walls, making the appearance more similar to glass. Plastic container Europ. Patent No. EP 3453632 A1 Applicant: Krones AG, Neutraubling (DE) Application date: 28.3.2014 The European patent publication describes a reduced-weight plastic container (bottle) with specially shaped base and the blow mould for manufacturing the container. Plastic bottle with strapping Intern. Patent No. WO 2018 / 037052 A1 Applicant: Krones AG, Neutraubling (DE) Application date: 23.8.2017 So as to minimise the deformation in any direction of a pressurised PET bottle, crossed strapping is proposed to stabilise the bottle. Multi-layer bottle Intern. Patent No. WO 2019 / 069794 A1 Applicant: Hokkai Can Co., Ltd., Hokkaido (JP) Application date: 27.9.2018 Multi-layer bottle made from plastic with individual layers selected so that the quality/stability of the content (here soy sauce) is retained over a longer period. This is done by the deliberate delamination of individual layers and air penetrating in between. Plastic bottle Intern. Patent No. WO 2019 / 078042 A1 Applicant: Meiji University, Tokyo (JP) Application date: 5.10.2018 The shaping of the exterior of a plastic bottle with specially circulating lines. Large-volume plastic container Intern. Patent No. WO 2019 / 078305 A1 Applicant: Nissei ASB Machine Co. Ltd., Nagano (JP) Application date: 18.10.2018 Large-volume container for a liquid. The container has fold lines along which it is easily compressed – as the fill volume falls.","@ID":58}, "BOTTLE MAKING 29 PETplanet Insider Vol. 20 No. 11/19 petpla.net BOTTLE MAKING 29 surface of the rod cools the area it touches on the preform. Lightweight water bottles, for example, need the base totally stretched and a large rod diameter may prevent that from happening. On the other side, making a rod too thin would lend it to easy bending. As a consequence, rods are made to keep the larger diameter in the upper portion to prevent bending but are reduced in diameter in the area of the preform (Fig. 5.5). Figure 5.5 For lightweight water bottles and some soft drinks bottles stretch rods are slimmed down to prevent a cooling effect on the preform bottom. In single-stage moulding, stretch rods often have tips screwed on at the end. These could be made from aluminium or nylon. On machines without conditioning, they can also be used to cool the bottom of the preform, just the opposite function they have in two-stage moulding. This is useful because the bottom of the preform is often the hottest part and may lead to thin bottoms. A large tip made from aluminium can be placed into the preform a few seconds before the mould is closing. This does not lead to a cycle time increase as the blow cycle is always faster than the injection cycle. The timer “delay mould close” is used to achieve this effect (Fig. 5.6). Figure 5.6 In single-stage moulding a large stretch rod tip can help in cooling the bottom of the preform down to increase wall thickness in the bottom of the bottle. Please order your copy at the PETplanet Insider book shop: petpla.net/book3 Stretch Blow Molding Third Edition by Ottmar Brandau € 130,00 374 pages © Copyright Elsevier 2017, 2012 For more information about BERICAP TetheredCaps: BERICAP TetheredCap Easy handling Safe application No change to • Neck finish • Capper • Filling line Meet us at BrauBeviale Hall 4 / 4-515","@ID":31}, "PETplanet Insider Vol. 20 No. 11/19 petpla.net 47 TRADE SHOW REVIEW ADHESLEEVE® TECHNOLOGY THE BEST SOLUTION FOR ROLL-FED LABELLING EVEN ON CANS! ProMachBuilt.com | PELabellers.com LABELS APPLICATION WITHOUT HOT MELT GLUE. EASY LIKE SCOTCH-TAPE! EVEN MORE! The first eco-friendly linerless labeller using pre-glued films. 100% ecologic and recyclable product. Also for empty containers. Adhesleeve + thermal-shrinking system. More than a valid alternative to the sleeve application. HALL 7 | STAND #7-339 NOVEMBER 12 - 14, 2019 NUREMBERG, GERMANY cycle times and energy efficiency; and that it has the lowest maintenance cost in the sector. It accepts virtually all legacy tooling produced by any major mould maker. The new operator’s HMI features a large 21.5-inch touch screen with high-definition graphics and smartphone-style swipe functions; a multifunction control knob for one-handed operation; and fast response times, regardless of processor load. The HMI incorporates an advanced automatic process set-up and in-depth part quality troubleshooting tutorial, designed to help users improve machine uptime, cut scrap rates, and reduce dependence on highly-skilled machine operators. The XForm Gen4 XP, which is powered by the latest servo-driven hydraulic pumps, has a very low lock to lock time, along with an increased injection rate. Total energy efficiency has been increased: set up to full screw utilisation and PET with an IV of 0.80, the machine consumes just systems, which are capable of running with moulds holding up to 128 cavities, and the 180-cavity capable 500, has been designed to handle the most demanding applications. Sipa says that it delivers industry-leading short 0.195 kW of energy per kg of material processed. One of the reasons for the improvements in dry cycle time and energy efficiency is the introduction of a kinetic energy recovery system, acting on the toggle drive. Maintenance procedure has been greatly eased by a modified accumulator area layout. The accumulators are now mounted on a pull-out rack inside the machine frame and, in addition, the oil tank has been redesigned so that it does not need to be emptied to facilitate maintenance. It can also be used at altitudes of up to 3,000m without any modifications. “The net result of all these improvements is that our customers will be able to operate more consistently, at higher speeds, spending less on energy and maintenance, using a machine that will reduce conversion cost at record-low levels,” says Pablo Fiorentini, Global Sales Director, Preform Systems & Tooling at Sipa. www.sipa.it A 192 cavities hot runner displayed on the booth was sold to Western Container corporation","@ID":49}, "BOTTLING / FILLING PETplanet Insider Vol. 20 No. 11/19 petpla.net 13 BOTTLING / FILLING 13 Approximately 17 of the large 20 l containers are filled every minute. In addition to this proprietary plant, six additional contract bottlers use the facilities here in the south who fill exclusively for Bisleri, in particular the 20 l reusable containers. The giant water company pays meticulous attention to ensuring consistent, identical quality of water. “We obtain our preforms from the local converter, Manjushree Technopack. The lads there also make the 20 l containers,” Mr Vishwanath continued. The suppliers in the closures sector are Aglo Polymers, Bericap, Oriental Containers and Plenco. Around 300 employees work at the site on a three-shift pattern. In 2009, Bisleri changed its blue logo design to the green of today. Among other factors, this is intended to symbolise ecology and respect for the environment and nature. The bottler is putting its visual commitment into practice, having set up a small biotope on the factory premises. A water storage basin – stocked with fish – makes for an attractive demonstration of the water recovery system. Nestling in a park with a variety of plants, fruit trees and a large rabbit enclosure, the facility is designed not only to give company employees some relaxation, but to provide school groups and interested visitors with an understanding of the topic of sustainability, and to convey extensive learning content on plant and animal diversity at the same time. www.bisleri.com Bisleri’s very special format: the 5l “Rocking Bottle“ Bisleri staff packing boxes with “Bisleri 500“ www.sacmi.com Product design Product development Product validation Industrial production plant Process & quality control On-site and start-up assistance After-sales and Customer service SACMI 4.0 THE COMPLETE CLOSURE, PREFORM AND CONTAINER SOLUTION FOR YOUR SMART FACTORY Compression goes multilayer. Enjoy SACMI innovation. The new SACMI CCMMTM applies all the advantages of continuous compression technology to multilayer capsules, creating a barrier effect that protects aromas and makes production processes more and more sustainable. Barrier layer Tie layer Tie layer Main layer Continuous Compression Moulding with Multilayer technology. TM Main layer","@ID":15}, "MOULD MAKING PETplanet Insider Vol. 20 No. 11/19 petpla.net 22 MOULD MAKING so a bottle was designed in a way that a secondary handle can be fixed on it and it can work as an integral handle for holding bottles with high capacity conveniently. This development is primarily targeted at the liquor and edible oil segment. Bi-injection cap: This comprises of two colours in one single cap. This is not only aesthetically appealing but also acts as a deterrent for counterfeiting. This mould is a very special mould and the process is called Core Withdrawl. This machine comes with two barrels for zwo different colours. 20l water can: This is a bottle made on a single stage ISBM machine with special technique of zero cooling giving advantage of higher production specially when the preforms are very thick; the strength is also claimed to be far better than bottles produced from normal ISBM process, with better mechanical properties and clarity. www.manjushreeindia.com 20l blown water packages 20 l water package mould Core plate assembly Nivea bi-injection flip-top cap, cavity side Core plate assembly Nivea bi-injection flip-top cap, cavity side Nivea bi-injection flip-top cap, core side","@ID":24}, "BOTTLE MAKING 27 PETplanet Insider Vol. 20 No. 11/19 petpla.net ever, in the case of the smaller bottle 73% more blow air is needed than would be if just the bottle needed to be supplied. Smaller dead air volumes will save significant money over the lifetime of the machine. Small machines particularly often feature high dead air losses and users should carefully examine manufacturers’ offerings (Fig. 4.19). There is one more source of needed air volume that is not mentioned yet. On some machines that use pneumatic cylinders for stretch rod activation, this air is actually highpressure blow air that is reduced to the 8 bar or so that the stretch rod cylinders are using. While compressing air to 35 or 40 bar and then reducing it to 8 or 10 bar is an expensive undertaking, this is done to avoid adding another line to the distributor inside the blow machine as this distributor for air, water, and electrical power is one of the most expensive parts of the blow moulding machine. The newest machines with servo or electromechanically controlled stretch rods do of course not use any air and will save money in the long run. Because of the cost of air consumption, most companies now offer air-recycling systems. These systems, instead of exhausting blow air into the atmosphere, pipe it back to a storage tank where it can then be used for preblow and stretch rod air, the machine air circuit, or other plant air requirements. Of course, pressure reducers in the systems allow the proper pressure for the various uses. In this manner, savings of 25–50% can be achieved. This not only reduces operational costs but also helps with capital expenses as fewer or smaller compressors may be needed. A small cycle time penalty is unavoidable because the air does not move as fast to the pressurised storage tank as it does to the lower atmospheric pressure. 5. Blow Moulds Blow moulds play a large part in making high-quality bottles. While the machine has to deliver preforms at the right temperature, it is the blow moulds that give containers repeatable features and a brilliant appearance (Fig. 5.1). Figure 5.1 Blow mould halves in and out of mould base and base insert. Highly polished aluminium is the most commonly used material for standard bottles. Photo courtesy of SIPA. 5.1 Design Neck and thread finish are already formed in the preform; so blow moulds form only the body and base of the bottle. In the reheat stretch blow moulding (RSBM) process they consist of three parts: two mould halves and one base insert (also called push-up). The base insert is necessary because the walls at the base of the concave container could not slide over the mould halves during mould opening if these were forming them. Instead, the vertically moving base insert is drawn out of the way before, or as, the mould opens (Fig. 5.2). Figure 5.2 Typical mould design for linear RSBM machine. The given details are followed by their descriptions: 1, Preform Retainer Insert; 2, S.S. Insert; 3, Mould Body; 4, Back Plate; 5, Base Insert/Pushup; 6, Locating Ring; 7, Push-up Holder; 8, Taper Lock Pins and Bushings; 9, Guide Finger. Drawing courtesy of Hallink Molds Ltd. While the three-piece design is common to all moulds, they are manufactured quite differently depending on the type of machine to which they will be fitted. Linear machines have all mould cavities mounted within two blocks where the cavities sit side by side. In rotary machines each blow mould is mounted to a separate carrier, opening and closing individually. Modern machines use so-called shell moulds whereby the actual mould halves are only 5mm thick and are assembled onto bases that are all the same for a family of containers. These bases carry all water connections and need not be touched during a changeover, thus reducing valuable time. Moulds are usually built from aluminium, which is chosen for its high heat transfer rate, easy machinability, and lightweight. The types of aluminium used are typically those used in the aircraft industry. AL 7075 T6, T-2024, or Alumenec 89 are some of the grades used worldwide for this application. Base inserts may be of the same material or made from beryllium–copper. Another material in use is stainless steel for hot-fill applications. While a polish to mirror-like quality is still the norm, some companies have quite successfully tried to leave moulds at a much rougher polishing state. This saves cost because the mirror polish is still applied manually while detracting only very slightly from the expected bottle surface appearance. The internal pressure of the blow air results in a considerable force against the closing mechanism of the blow mould. Blow moulds have guide pins and bushings as well as taper locks in the base insert that keep the mould in position during the blow process. Mould carriers feature locking mechanisms that keep them closed against the blow pressure. To alleviate these stresses and also make ever-lighter frames possible, “pancake” cylinders have become increasingly popular. These cylinders are very thin shells behind the blow moulds and are filled with the same air that blows the bottle. Since pressure is equal both inside and outside the mould there is no resultant force acting against the mould halves (Fig. 5.3). Figure 5.3 Blow mould with locking mechanism mounted inside a rotary machine. Photo courtesy of SIPA.","@ID":29}, "41 TRADE SHOW PREVIEW PETplanet Insider Vol. 20 No. 11/19 petpla.net SAVING UP TO 20% IN ENERGY IS A GOOD START. BUT BY NO MEANS THE END. November 12 –14 Hall 8 SMI Hall 7A | Booth 503 Strategic packaging Packaging helps to convey the qualities a product possesses and to provide consumers with interesting and relevant information. That is why Italian company SMI is keen to highlight strategic packaging. Format, colours, design, size and materials are elements used to ensure a brand stands out from the competition. More and more companies invest in innovative machines to increase their production capacity, in order to be able to satisfy the market needs and at the same time to differentiate products through attractive packs. Thanks to the design and production of machines with an innovative design, equipped with IoT technology, SMI provides solutions for the primary, secondary and tertiary packaging that ensure production efficiency, operational flexibility, energy saving, ease of use and bottling and packaging line monitoring. The packers from the MP Ergon range allow companies to compete, by leveraging on innovative packaging, without forgetting important elements, such as the practicality and the protection of packed products. The MP 150 Ergon overlapping cardboard sleeve packer, that will be showcased at Brau Beviale, is claimed to meet these needs. The machine that will be showcased packs in 1x3 in NT style 0.33 l glass beers by Via Priula brewery in San Pellegrino Terme, that are grouped in a pack equipped with a handle that serves as gift box. However, the packers from the MP range are suitable to pack a wide range of containers in many configurations, including PET. The continuous motion packaging cycle is claimed to ensure a smooth production flow, without jerky movements, which protects containers from knocks, ensuring product integrity, high quality of the pack and reduced mechanical wear of the machine components. The hot melt glue sealing of the pack bottom is precise and long-lasting, with the possibility of using different types of cardboard. Recognition and visibility of the product on the store shelves are key elements for the business success. For this reason, companies of the food & beverage industry invest strongly not only in secondary packaging, but also in the design of the primary packaging, by seeking shapes and sizes with a strong appeal and by using all the opportunities of customisation offered by a ductile and flexible material like PET. www.smigroup.it","@ID":43}, "MOULD MAKING PETplanet Insider Vol. 20 No. 11/19 petpla.net 19 In case of prefoms moulding GDXL offers for horizontal opening 32 to 144 cavities with standard and various neck finishes. Preform size ranges from pharmaceutical/cosmetic bottle to 5 gallon keg application (3.5-750 g). For a vertical opening GDXL offers cavities from 16-96. Various neck finishes are possible. The preform weight would be up to 69 g. www.gdxl.com While the company Röders Tec provided stretch blow moulds with a maximum size of 10 l in 2010, it now produces moulds for 20 l containers. Röders has been developing and producing stretch blow moulds for PET bottles and containers since 1975. Through the development of their own coatings for particularly hard and smooth surfaces, Röders has managed to qualify aluminium moulds for hot-filling production. It has cut the manufacturing costs and the wear in the blowing machine is minimised, because of reduced weight. Changing the mould is fast and easy. (RMC system) Röders has a quick and flexible bottle sampling. The company supplies moulds to Sidel, KHS, Krones, Sipa, Kosme, Nissei, Chumpower, Terekas and 1Blow etc. They have solutions for compatibility of moulds between different machine types. www.roeders.de/en/ Kiefer Mold has grown since its foundation in 1987 by Ulrich Kiefer, and became the specialist in manufacturing tools in the plastics transformation field. In 2010 Kiefer already produced moulds for all types of SBM machines. The maximum bottle size at that time was 10 l. Today the mould specialist produces mould for up to 30 l. Kiefer has a special design service with photochemical etching, milling, eroding and laser engraving. The moulds enable lightweight design and special designs for different products like functional drinks, juices, oil and vinegar. Moulds are also used for household products, cosmeticand petrochemical products. Kiefer supplied machine manufacturers like Kosme, Krones, Sipa, Sidel, ADS, Sacmi, KHS, Bekum, Side, SMI. www.kiefer-mold.de/en R&D Leverage was founded in 1976 serving the tool market. In the mid 1980’s R&D was already involved in the plastics industry. The company designs and build injections tools, ISBM, SBM, and extrusion blow moulds. In 1995 the UK division was build and there injection stretch blow tooling business stared. From 2000 on an expanded Product Solution Laboratory is running in the UK. In this laboratory they can trial products, colour, materials plus qualify product tooling on SBM machines. Today R&D Leverage supplies Sidel, Krones, Sipa, Side and Chumpower with stretch blow moulds. The maximum bottle size is 5 l. R&D also supplies retrofit moulds for existing SBM machines. Also prefom tooling belongs to R&D Leverage specialities. Preform mould for up to 96 cavities with perform sizes from 24mm through 63mm neck, with 12 g through 350 g weight can be produced. R&D Leverage builds moulds for Husky, BM Biraghi, Milacron, Engel, Krupp, Krauss Maffei. www.rdleverage.com Husky Injection Molding Systems Ltd. is a supplier of injection moulding equipment and services to the plastics industry. Husky design, manufacture and integrate a range of injection moulding equipment, including machines, moulds, hot runners, auxiliaries and integrated systems. It is known for its preform equipment which is used to produce a range of products for the beverage packaging, closures, thinwall packaging, medical, and consumer electronics markets. With more than 35 years of experience in the preform industry, Husky produces preform moulds with a cavity from 6 to 144. Threads were produced from up to 100mm in diameter and up to 205mm in length. Husky produces moulds to support all perform designs and output requirements. www.husky.co New generation of hot runners at MHT Since PET degrades quickly, both thermally and mechanically, the hot runner is highly significant in the manufacture of PET preforms. As a tool specialist, MHT Mold & Hotrunner Technology AG has developed a new generation of hot runners, optiRUN, that greatly reduces the formation of dust, a phenomenon feared by preform manufacturers. The dust is formed when a gaseous substance made of PET fission products precipitates on the metallic tool surfaces. With the new hot runner, the maintenance intervals are now longer. The hot runner was developed in collaboration with the Darmstadt University of Applied Sciences, which engaged in fundamental research on dwell times and the degradation of materials. The result is a conventional two-plate construction that is equipped with individual modular hot runner packages. This as well as the small-volume individually regulated heating zones makes very uniform temperature control across the entire system possible. Due to the division, it was also possible to re-design and improve the balancing and deflections of the melt flow with the help of simulations. The results of the short-shot test were excellent. The cooled adapter plates on the individual hot runner packages serve more than one purpose: They supply air, provide temperature control for the valve gate and can also make the use of different piston housings possible. This means that if the installation dimensions of future hot runner components should differ from the current Vulcan II series, one simply needs to exchange the adapter plates. Of course the new hot runner is 100% compatible with existing cold tool sides. One of optiRUN’s strengths lies in the processing of recycled PET as well as PET flakes. According to an EU directive, adding 25% rPET to fresh PET granules is prescribed as of 2025. From 2030, this proportion even goes up to 30%. It is important to be prepared for this with regard to MHT tools with a long service life. The focus will also be on the challenging processing of flakes. Starting immediately, information related to durability can be obtained from the cycle counter, which is installed by default, and the optionally available operating hours counter. Several prototypes of the optiRUN hot","@ID":21}, "BOTTLING / FILLING PETplanet Insider Vol. 20 No. 11/19 petpla.net 14 StrongPack and Sidel partner to create leading co-packing hub for non-alcoholic beverages in Africa Increased shelf life, decreased weight StrongPack Ltd. recently established its operations in the Nigerian market with the mission to become the number one, high-quality, non-alcoholic contract packaging company in Africa. As part of its greenfield project, they installed a total of four Sidel lines over the span of two years, including a can line, two regular complete PET lines and one PET line integrating Sidel’s Actis coating system. The latter was critical to increase the drinks’ shelf life, thus addressing some of the challenges in the local distribution chain. By choosing Actis, StrongPack could lightweight the bottles by 25% while redesigning their shapes. Carbonated soft drinks (CSD) are the second most popular beverage category in Africa, after bottled water. This segment continues to grow mainly due to the fact that the consumers’ purchasing power is steadily increasing on a continent with the youngest demography globally. However, distribution is complicated by long transportation routes and difficult road conditions, creating a large demand for bottled drinks with a longer shelf life. Within this emerging market, Nigeria is a very interesting case. With 195.9 million inhabitants and a population growth of 2.6% in 2018, it has been showing a healthy CSD performance over the last few years, even during economic slumps (with a volume growth of 11.1% CAGR from 2012 to 2017). This phenomenon was mainly driven by population increase, price competition and aggressive marketing campaigns from the major global CSD players. Tough logisitic conditions Witnessing these business opportunities in the CSD market, StrongPack started their operations in 2018 as a co-packer of non-alcoholic beverages with some ambitious goals: “In the next five years, we want to become the number one non-alcoholic contract packaging company in all of Africa,” explains Del Tupaz, Managing Director at StrongPack. “At the same time, we aim to be the leading high quality co-packer in Nigeria, whatever the brand. This is fundamental to our business approach and it is definitely paying us back. We have recently started co-packing 60 cl PET bottles for a leading global soft drink company,” he adds. When starting their operations in Nigeria, StrongPack needed to differentiate themselves and their capabilities from the existing players in the market, in a country that has historically chosen returnable glass bottles as the main packaging format. They did this by investing in state-of-the-art technology for PET and can production, therefore expanding the range of packaging options they could offer to their customers. PET, for example, is well renowned for the convenience, the reusability and the performance it can provide through the supply chain. However, given the hot temperatures and the tough logistics in Nigeria, handling PET packaging is more demanding compared to other parts of the world. Some products are displayed and merchandised outside on open marketplaces, often directly under the sun, a distribution set-up which leads to carbonation loss. Additionally, with poor road conditions, bottles are shaken during transportation, increasing the loss of carbonation further. The Managing Director of StrongPack adds, “We were looking for a solution that would help us overcome some of these challenges. After careful consideration, we found that Sidel and their Actis system – as integrated in a Combi configuration in one of our complete PET lines – was what would fit the local value chain conditions best.” This decision makes StrongPack the first and only beverage producer in Africa which has Sidel’s Actis technology installed and is able to provide coated PET bottles for CSD.","@ID":16}, "MOULD MAKING PETplanet Insider Vol. 20 No. 11/19 petpla.net 20 MOULD MAKING runner generation underwent a yearlong test phase under demanding production conditions (share of flakes of up to 70%) at major packaging manufacturers. Preform quality was analysed, and a special focus was placed on process reliability with very good results. After the product launch at the K trade fair, the new hot runner generation is available for tools from 48 to 144 cavities and all current mould cavity pitches. The current, proven generation of hot runners still an appealing choice due to its compact construction will remain in MHT’s portfolio, so that customers can choose a suitable solution depending on their machinery and tool size. www.mht-ag.com PET Technologies has finished project for Aqua-Premium LLC TM Voda UA is a combination of style, beauty and health. High quality of TM Voda UA spring water is confirmed by corresponding certificates; stylish bottle with poppy flowers emphasises the company’s image. It belongs to premium segment; its outstanding design makes the brand recognisable in the market. Main task of Glass-like bottles with traditional ornaments, realised by PET Technologies made the plant popular in Ukrainian culture. Combination of traditions, modern technologies and innovative standards marked another successful project completion of PET Technologies with Aqua-Premium LLC. www.pet-eu.com Reduced pitch, increased cavitation Indian PETform is a developer and provider of advanced preform moulds and hot-runner systems up to 144 cavities. At K2019 the Daman-based company introduced a new hot-runner development. Particular attention was paid to energy efficiency. Thus, the new hot-runner comes with an improved insulation. “By incorporating an advanced insulation made of titanium or ceramics between the hot manifold and the cold backing plates we are able to reduce energy consumption significantly. The new insulation made the system 15-20% more energy efficient, depending on the material used. Titanium, for example, has a third of the thermal conductivity compared with steel, ceramics only one tenth. And besides the energy savings aspect, better insulation also ensures shorter start-up times”, explained PETform’s CEO Shurid Mody. MHT new hotrunner generation optiRun the project was to adapt glass bottle design of TM Voda UA to the properties of PET material in three bottle volumes - 0.5, 1 and 1.5 l. At first sight it is hard to distinguish PET bottle from its glass prototype – the PET bottle bottom is flat and repeats the shape of the glass one. Bottle design contains poppy flowers that have rich history in Ukrainian culture - Ukrainians identify them with youth and beauty. Wide range of poppy flower symbolic meanings","@ID":22}, "BOTTLING / FILLING PETplanet Insider Vol. 20 No. 11/19 petpla.net 15 From greenfield project to four lines StrongPack first started their discussions with Sidel a few years ago when they entered the beverage bottling business, targeting a greenfield project with two complete lines, one for cans and the other one handling PET bottles. These lines started running in 2018 and back then were mainly dedicated to packaging RC Cola, one of the leading cola brands in the world, established in 1905. Their performance and reliability perfectly matched the co-packer’s expectations, and as a result, StrongPack invested in another two complete PET lines, one standard PET and one integrating Sidel’s Actis in Combi configuration. Planned on a new site of 8.4 ha and housed in a building of 32,000m2 in Agbara, an industrial area close to Lagos, this greenfield project was especially challenging. According to the Managing Director of StrongPack, at full development, 1.2 billion litres of non-alcoholic beverages per year will be produced at the site. CSD packaged in different container types and formats Thanks to the successful partnership with Sidel, the Nigerian co-packer now has a future-proof factory with four complete lines, where the equipment and processes are efficiently laid out, allowing them to do quick changeovers and fast CIPs for great production reliability and flexibility. The overall production capacity of the Agbara plant currently lies at 850 million PET bottles per year, including both standard and coated bottles. The two regular PET packaging lines are running at 36,800bph and 46,000bph. In addition, the versatile canning line produces 40,000cph. For the latter, the entire line layout and concept has originally been developed to support nonalcoholic malt production, a beverage which is quite popular in Nigeria. Lightweighted bottle saves 3 t of PET resin per day The complete PET line featuring Actis in a Combi configuration and handling two bottle formats (35cl and 50cl) is fuelling the unique production advantages offered to CSD brands by the Agbara site. Actis (Amorphous Carbon Treatment on Internal Surface) is Sidel’s proven plasma coating technology, promising to extend the shelf life of beverages by up to five times while enabling package lightweighting, yet with no compromises on recyclability. These benefits, paired with the ease of operations and the many Actis references installed globally, currently accounting for more than five billion bottles produced across CSD, beer, juices, tea and coffee, are exactly why StrongPack selected this solution. “The reduction of the 35cl bottle weight down to 15.5g allows us to roughly save about 3 t of resin per day. That is 3 t that are not going to the landfill,” says StrongPack. Helped by the Actis technology and the increased shelf life of the PET bottles, StrongPack plans to reach additional markets in West Africa that otherwise would not be available to them. Choosing Actis also offered the opportunity to develop a new bottle design for their 35 cl and 50 cl formats, which not only matches Actis’ requirements but also stands out at the point of sale – a key factor in the Nigerian market. www.sidel.com German Technology November 12-14, 2019 Nuremberg, Germany At the Krones Booth Hall 7A, Booth 510","@ID":17}, "MOULD MAKING PETplanet Insider Vol. 20 No. 11/19 petpla.net 24 Multifunctional device for greater productive capacity Process optimisation and prevention Otto Hofstetter AG is offering a new multifunctional device for its injection moulds. OH Xport helps manufacturers of packaging and preforms increase their production efficiency and further extend the longevity of their tools. During production, the device transmits crucial performance values to a cockpit, allowing for optimisation of production routines and error detection before malfunctions or quality loss become evident. Otto Hofstetter AG is upholding its tradition of maintaining close contact with its customers. The Swiss mould manufacturer thus realises the challenges that producers of packaging and PET preforms are confronted with on a daily basis. Significantly increasing annual productive capacity using an existing infrastructure is a formidable task. However, with OH Xport, Otto Hofstetter AG is confident of having created the prerequisite to do precisely that. Measured in terms of potential for improvement, an investment in the multifunctional device pays off even before the first year of use is over, states the company. OH Xport is a small, smart multifunctional device that supports packaging and preform manufacturers in numerous ways. It provides both a basis with which to optimise production routines and also identifies errors before malfunctions or quality losses are detected by the system operator. The entire process is defined by simplicity and security. Visualisation of relevant data OH Xport records the number of uses, system efficiency, cooling circuit and hot runner temperature, coolant flow rate, machine standstill times and the cause of a possible machinery stop. Based on the recorded data, the add-on device helps determine the right time for preventive maintenance. OH Xport gathers data on the tool and transmits it via a 3G data connection to an analysis site where it is automatically aggregated. The values are displayed as clear charts in a cockpit that can be controlled by all current internet browsers. Users who have been predefined by the operator can access the information necessary to prevent a machine standstill or improve production processes, for example. The cycle is complete once the plant manager learns of the increase in line efficiency thanks to the optimisations during the course of short-term, medium-term or even long-term reporting on the degree of process improvement. Retrofitting existing systems OH Xport is available immediately as an add-on for all new injection moulding tools from Otto Hofstetter AG. Existing systems can also be retrofitted thanks to its easy installation. Installation, commissioning and instruction are stated to be minimal and to require just two days. Likewise, the required machinery stop is negligible and lasts only two to four hours. Otto Hofstetter states that OH Xport provides major benefits such as higher annual production, increased longevity and preventive maintenance, and thus also more security during production - while being moderately priced. The benefits accrued in production should compensate for the investment before the first year of use is over. The Swiss mould producer provides an extended guarantee of either two or three years for new moulds equipped with OH Xport. www.otto-hofstetter.swiss Information gathered by the new OH Xport of Otto Hofstetter AG is presented in a cockpit, which is accessible via any standard internet browser. OH Xport is a new multifunctional device that helps to increase production efficiency and extend the longevity of moulds. MOULD MAKING","@ID":26}, "BOTTLE MAKING 28 PETplanet Insider Vol. 20 No. 11/19 petpla.net 5.2 Base Mould Today, all base moulds feature a small recess like a well in the center. This allows some room for the protruding injection gate on the preform. Keeping the gate in the center of the mould is probably the most important task in the blow process because any deviation from the center leads to uneven wall thickness variation. The well catches the injection gate and prevents it from slipping as long as there is enough pressure from the stretch rod. In many custom applications the bottle bottom is thicker than is really needed but because of preform design or machine insufficiencies it ends up like that. In these cases it is often the cooling of the bottle bottom that controls the cycle time. Proper cooling is therefore crucial to come to a cost-effective solution with fast cycles. Cooling lines should not be smaller than 6mm in diameter (unless of course there is no room in very small bottles) and the flow path should have no restrictions. High water supply pressure with low water return pressure are also helpful (Chapter 13, Section 13.2). 5.3 Making a Mould Today’s mould-making process starts with a three-dimensional (3D) computer model of the container itself. Physical models may be made by a variety of processes, the most popular still being stereo lithography with 3D printing catching up quickly because of the availability of low-cost printers. The model may be used to give marketing people a better “feeling” for a new container. Once approved, data of the computer model are then fitted in a new or existing mould base. At this point, shrinkage has to be added to the container dimensions. Polyethylene terephthalate (PET) shrinks approximately 0.08% but shrinkage is not uniform and it is the experience of the mould maker that determines how closely the capacity of the container matches specification. A variety of computer-aided design (CAD)/ computer-aided manufacture (CAM) programs allow the creation of machine cutter paths that are downloaded directly into high-speed machining centers. Machine operators load and center blocks of aluminium of suitable size and special cutters, spinning at up to 30,000 r.p.m., move at a speed of up to 20m/min. The resulting cavity surface is already smooth to the eye but most mould makers add a high, mirror-like polish, which still requires skilled, manual labour. The use of sandblasted surfaces that are common in other plastic processes has gained some ground as there is little difference in the appearance of the containers. Some mould makers then coat the cavity surfaces with various materials, often containing nickel and Teflon, to give it abrasion resistance. 5.4 Venting Venting is another area where the experience of the mould maker becomes extremely important. Because PET fills the mould cavity during blowing, the air inside the cavity must be exhausted. For this purpose mould makers add a variety of vents. Compared to other processes, such as injection moulding or extrusion blow moulding, PET is processed at a relatively low temperature in the RSBM process. Vent sizes are limited to 0.04mm (0.0015 in.) in injection moulding but vents of up to 0.5mm (0.020 in.) are used in RSBM with hole vents up to 1mm (0.040 in.). All moulds have vents on the contact surface of the cavities. One mould half is typically completely recessed against the mould base by up to 0.20mm (0.08 in.) or more commonly by 0.15mm (0.006 in.). Base vents are also common and are accomplished by leaving the base insert to move 0.25–0.3mm (0.010–0.012 in.) downward under the force of the stretch rod. The resulting ring-shaped gap between base insert and mould cavity allows air to escape. Hole vents up to 1mm are used in areas where air entrapment is suspected. Vents of this diameter may not show in areas where the material has stretched and consequentially strain-hardened but will show as small dimples where this is not the case. A common example of highly stretched material is the foot of a petaloid base for carbonated soft drinks (CSD) containers. Two small holes in each foot let air escape that might otherwise be trapped by the material flowing around it (Fig. 5.4). Figure 5.4 Hole vents up to 1mm in diameter can be successfully used as shown here in the panel area of a hot-fill bottle. Photo courtesy of Garrtech Inc. Another use of venting is to direct PET into hard-to-blow areas. In a highly oval bottle, for example, there is always the possibility of a ridge of higher wall thickness forming at the center of the narrow side of the container. Vent holes at the far side of the mould can attract PET to flow more quickly into these areas, thereby stretching out the preform walls close to the narrow side. A fine sandblast finish instead of the mirror-finish also helps to let the air move out of the mould. Due to low temperature in the RSBM process compared with uses in other processes, PET does not flow easily into small mould crevices. Minimum dimensions for female radii might be given as 0.8mm (1/32 in.) but it will depend on the stretch ratio of the PET flowing toward it whether it will fill out or form a greater radius instead. Male radii should be double that amount especially when used in bases. Here a sharp radius may cause a crease in the material and open the door to stress cracking. Venting in these areas can be attempted to reduce the risk of air entrapment stopping the advance of the parison but more often than not they do not seem to have much effect. We will simply have to live with the fact that PET benefits from more generous radii in this process. 5.5 Stretch Rod In two-stage moulding stretch rods are typically made of solid Stainless Steel with sizes 9–16mm (3/8–5/8 in.). Stretch rod diameters are often limited by the neck size and larger rods should always be used when the neck size allows it. This facilitates the exact placing and holding of the gate in the center of the mould. A downside of a large stretch rod diameter is that the","@ID":30}, "BOTTLE MAKING 10 PETplanet Insider Vol. 20 No. 11/19 petpla.net 0.25 litre CSD bottle with internal coating First production of the 0.25 litre CSD bottle with inner coating began nearly three years ago at Hindustan Coca-Cola’s plant in Hyderabad, India. There are currently four plants on the sub-continent with two more in the pipeline. So, it is time to drop in and get to the bottom of the technology. We met: Mr Girish Chhablani, Factory Manager HCCB Hindustan Coca-Cola Beverages Pvt Ltd (HCCB) was looking for an alternative to their returnable 0.2 l and 0.3 l bottles. Due to the long sales distances, a different option needed to have a shelf life of at least six months. To this end, an attempt was made to develop a PET bottle involving CocaCo l a A t l a n t a a n d KHS. The bottle still had to be affordable. That is why HCCB called the packaging affordable small sparkling package or ASSP. The lack of barrier properties in the small PET bottle size only achieves a 60 da y s e x p i r y date, which allows the Plasmax coating system to be used. A three-layer inner coating (adhesives, glass barrier, coating) can achieve the necessary shelf life. The original facility was built in Hyderabad in 2016. With a capacity of 36,000 bph, CocaCola was able to capture the Indian market. A second plant was built the following year in Vijayawada, which achieved a figure of 46,000 bph using similar technology. It differs from the original plant in that it is blocked (triblock), with unreliable air conveyors having been removed from the single machine layout. The stretch blow mould, Plasmax and shrink packer The process begins with a preform inspection. Preforms containing foreign matter (1 ppm or more) are removed. They then enter a 24-cavity SBM. The heating tunnel is not very long as only preforms weighing less than 10 g are heated. Each blown bottle has its own code which is later covered by a label showing cavity and production time. Air vents cool the floor area via several transfer stars and the Plasmax enters the unit’s main system. The bottles go into vacuum chambers in batches of four. On evacuation, three layers are deposited on the inner bottle wall via ignited plasmas. First there is an adhesive layer, followed by the actual glass barrier layer which is only a few molecules in diameter, and finally a protective layer. The glass layer is clear in contrast to the yellowish carbon colour of other coating processes. After evacuation, the bottle’s temperature is around 50 °C. It is cooled from the outside using a water aerosol to approximately 20 °C before being filled in a 144-cavity volumetric filler and secured by a 24-fold servocapper. Finally, there is another full bottle inspection, followed by further coding which can be used to make a decision on the filling valve and capper head. Production information is recorded in a text box which can be read by the customer. Preforms weighing between 9.61g and 9.68g are processed by the preform supplier. HCCB blows a total of three different bottle geometries for its 17 different products. The cap on the 22mm neck is supplied by Bericap. The unusual outer curvature for a CSD cap offers a high level of stability at low weight, thus providing a secure seal against loss of CO 2 . The chief component of the units is the plasma coating. The quality of the coating cannot be determined by Tour Sponsors: Until today running 0.2 l returnable glass bottles The ASSP 250ml bottle was introduced in 2016. components are supplied by KHS Germany while the capper fillers, transporters and palletising are provided by KHS India. Box kipper A completely new greenfield plant was built by HCCB in 2018 in Sananda, near Ahmedabad which we were allowed to visit. The plant manager is Mr Girish Chhablani who explained everything to us. There are two Triblock Freshsafe machines next to one another in the bottling building. In the filler zone, the control positions face each other, which means that just one operative is required in this area. As the blow moulding machine always rotates clockwise (from Blomax Series 5, anti-clockwise), the unit has been mirrored point-symmetrically. As a result, the preform material flow, bottle, filling and capping counter-rotate on both units. The two machines can be run by three operators on each shift. One is responsible for the filler area on both units, from the blowing stage to full bottle inspector and the second for the labelling and packing machines on both units. A third operative takes care of the palletising zone.","@ID":12}]}}
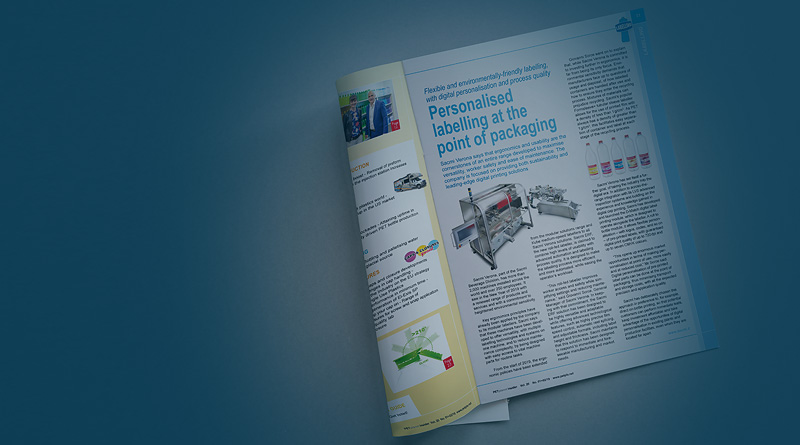