"MATERIAL / RECYCLING 21 PETplanet insider Vol. 12 No. 03/11 www.petpla.net virgin material: intrinsic viscosity (iV) higher than 0.82 and more, acetaldehyde (AA) content of less than 1ppm, and excellent decontamination values, which allows packaging to be used with direct food contact. Customisation at investment The basic modules of Starlinger recycling technology are extruders for the mechanical recycling of PET bottle flakes and solid stating of flakes, pellets and others. The modular design can be varied according to application and the Starlinger machine concept covers the complete range of requirements for food contact and/or iV increase. The two budget versions of the recoStar PET line, recoStar PET FG and recoStar PET FG+, can be supplemented by an SSP (Solid State Polycondensation) reactor, either at outset or subsequently (graph 2). The recoStar PET iV+ solution for bottleto-bottle recycling has decontamination values that satisfy even brandowner requirements. In the high-tech solution for very exigent requirements, recoStar PET iV+ Superior, the material is decontaminated twice under vacuum, before and after the extruder, in order to achieve very high decontamination results. Flexibility is also important and a wide process window allows the modification of parameters in order to adapt to altered input qualities, while continuing to comply with food-grade requirements. Extrusion and SSP modules can operate in-line or standalone, which doubles capacity or enables the recycler to produce foodgrade flakes and pellets at the same time. IV level is adjustable by changing residence time in the SSP. Changing market requirements can be catered for by upgrades and modifications, such as: enlarging predrying volumes in case of decreased bulk density; increasing output by 25% by changing to high-capacity design; adding SSP volume for higher iV increase, etc. Steam and gas heating can be used to reduce electrical energy consumption. Following the markets’ demand for larger equipment, Starlinger recently increased the capacity of the recoStar PET line from 150 to 3,600kg/h. The SSP reactor series has also been extended, to include a new reactor with an increased volume of 18,000l and a solution for flakes only. Starlinger is just about to install the first line of its new solution for rPET in fibre production. Its specially-designed cascade filter system enables very fine filtration, down to 25μm, to meet the fibre industry’s particular requirements. Continuous cleaning of the production line filter could be reduced while the percentage of reused rPET could be increased. Starlinger is permanently offering test runs on the recoStar PET 65 iV+ line in the company’s recycling showroom at its Weissenbach, Austria, production site. The company also offers consulting and contracting for washing lines in addition to PET recycling lines. Reference lines for almost all kinds of plastics and for a wide variety of applications have been installed globally. Several bottle-tobottle projects will be installed across the world by Starlinger this year, including the first bottle-to-bottle project in Egypt and Peru which will be delivered within the next weeks. www.recycling.starlinger.com Graph 2: Flakes to pellets: the recoStar PET IV","@ID":23} "25 Bottle-to-bottle recycling plants Conveyors for preforms and empty bottles Caps and closures Preforms Perform moulds and SBM moulds Preform and single stage machinery 2-stage SBM machinery Compressors Filling equipment Resins and additives Suppliers of conveyors for preforms and empty bottles Last year, for the first time, we carried out a major survey covering conveyor systems. This is a broad market featuring a number of operators and, in our initial foray in 2010, we successfully included all the key players. Now, in our second survey, we have gone one better. Whereas last year just nine companies featured, this year no fewer than 12 manufacturers are included. On the following pages you will find detailed information on the range of conveyors marketed by Dimark, Europool, GEA Procomac, Intec Solutions, KHS, Krones, Mcon, Posimat, Sidel, Sismatico, SMI, Zecchetti. For further details readers are recommended to get in touch directly with the contact persons specified at the individual companies. Whilst the publishers have made aevery effort to ensure that the information is up to date, no claims are made regarding completeness or accuracy. 03/11 MARKETsurvey Company name KHS Corpoplast GmbH Posimat, S.A. GEA Procomac SpA Postal address Telephone number Web site address Contact name Function Direct telephone number Fax E-Mail Meiendorfer Str. 203, 22145 Hamburg , Germany +49 40 67907-0 www.khscorpoplast.com Frank Haesendonckx Director Competence Center SBM +49 40 67907 475 +49 40 67907 9475 Frank.Haesendonckx@khs.com Avda Arraona 23, 08210 Barberà del Vallès (Barcelona) Spain +34 93 7297616 www.posimat.com Maribel Rodríguez Sales Manager +34 93 7297616 +34 93 7188856 sales@posimat.com Via Fedolfi 29, 43038 Sala Baganza, Parma, Italy +39 0521 839411 www.procomac.it Fabio Borrini Product and Sales Manager Packaging Division +39 0521 333752 +39 0521 333823 fabio.borrini@geagroup.com Preform: From injection moulding machine into box: Box-filling system No No Maximum drop from conveyor belt to base of carton (in cm) In-line Control Preform: From box into SBM machine up to 60,000 preforms/h Dumper (Yes / No) Yes No Conversion to different neck diameters (No/mechanical/electrical) mechanical In-line control (Yes / No) Yes Bottle: From SBM to filler, air conveyor Air conveyor (incl. vertical) (Yes / No) No Yes Yes Purity levels Hepa filters DOP at 0,3 micras 99,99% efficiency 99.99 DOP – photometric test method. Bottle format conversion Yes Yes, automatic Conversion to different neck diameters Yes Yes, mechanical / automatic avaialable Bottle storage systems Bottle up-ender (Yes / No) No Yes No Buffer systems capacity (number of bottles from …to…) taylor made, can meet any requested capacity Storage systems capacity (number of bottles from... to…) taylor made, can meet any requested capacity Palleter and de-palleter for empty PET bottles No Yes Yes, depalletiser","@ID":27} "NEWS 7 PETplanet insider Vol. 12 No. 03/11 www.petpla.net Husky to acquire KTW Husky Injection Molding Systems has announced its intention to acquire closure mould maker KTW of Waidhofen, Austria. The sale is expected to complete in May 2011. The two companies have been working together for the past 14 years. From the completion of the acquisition, Husky will offer KTW-branded closure moulds as part of its fully-integrated turnkey systems, which include mould, machine, hot runner, temperature controller, and consulting and after-sales services. The current KTW leadership team, including Managing Directors Anja and Claus Ziegler, will continue to be involved in the business. KTW’s operations in Austria, the Czech Republic and Germany, will become Husky’s closure mould development and manufacturing centres. Husky plans to initiate a strategic review process of Injectoplast, KTW’s custom injection moulding division, in order to avoid any potential conflict of interest with Husky’s customers. www.husky.ca MachinePoint group launches MachinePoint Food Technologies MachinePoint Group has announced the launch of a new subsidiary company, MachinePoint Food Technologies. The new company is dedicated to offering complete turnkey projects and plant and process installation to processors in the agro food, beverage and dairy industries. The company intends to include the integration of used machinery into new projects in its offer. MachinePoint Food Technologies´ sister company, Machine- Point Used Machinery, controls 80% of the used equipment currently for sale in Europe; and has extensive logistics and engineering experience in transporting and integrating used equipment into new plant layouts. Machine Point Food Technologies has been created by a partnership between Machine Point Group and Gemina, a highly specialised process integrator that manufactures customised equipment for the agro food, beverage and dairy industries. Gemina is located in Murcia, southern Spain. It has been designing and building plants and process lines in its domestic markets and in Africa and Asia for liquid processing industries for 25 years. MachinePoint Food Technologies’ engineering centre, in Murcia, has more than 5000m2 of space for engineering, automation, manufacturing, finishing, assembling, testing and quality control of equipment to be installed at customers’ facilities. www.machinepoint.com","@ID":9} "BOTTLE MAKING 36 PETplanet insider Vol. 12 No. 03/11 www.petpla.net ing. The preform cartons are automatically unloaded, heated and blown out of round. In addition, two edges are pressed mechanically into the bottle in the blow mould. After the leakage check we move on to the actual new station for automatic handle fixing. Here the handles are loaded in the correct position via a hopper, compressed and snapped into place on the edges. After that we move on to the automatic packing station which is where we load the bottles on to pallets so that they are dust-proof. So you see, nowhere does a human come into contact with the preform or the bottle! This is the best we can offer our customer, too! PETplanet: An innovation of this sort has got to be maintenanceintensive? Mr Verma: It isn’t any more but you’re right, in the expansion phase it took us some time to get to where we wanted to be. But at this point I would like to say a big thank you to and express my appreciation of the team from Sipa they were always on hand and, when they needed to, they worked round the clock. I have been buying machines from a very wide range of manufacturers for 20 years and there are technical problems with every machine, but the service provided by Sipa is up with the best I have experienced. PETplanet: And you produce the handles yourselves too? Mr Verma: We have 8 injection moulding machines of different capacities in operation at our premises and these are primarily used for manufacturing the handles and the caps for our bottles. This means that we can always offer a complete system with bottle, cap and handle. PETplanet: Your boss, Anupam Lunavat, has said that JRD is aiming to be the market leader in South East Asia by 2012 and worldwide by 2015. Mr Verma: We are constantly expanding. Double figure growth rates in the higher range during the course of the year are normal. Each year we invest in new machines. Even in the last few years during which the industry in general has been reluctant to enter into any commitments. We do all this with our own money and with no help from the banks. Coming up are a further IML plant and another Sipa installation. So as to clear sufficient space for the new machines of plant we have, for example, moved all our old machines 500m further out into another bay. This is also where our bulk materials store is. But here at the parent plant things have once again become so cramped that the Sipa installation is having to sit alongside the old equipment. PETplanet: And what about your future plans? Mr Verma: We intend to expand into the sector of PP hollow plates for construction. As regards this, we have an exclusive agreement with an Italian engineering company. Only just round the corner from here a plant is being built at the moment which will accommodate four lines. PETplanet: Thank you very much, Mr. Verma, and I wish you every success. www.jrddubai.com www.sipa.com The new Illig plant shortly before commissioning. It is capable of thermoforming up to 600 million cups/a. Alessandro Piccino, Sipa and Alexander Büchler in front of the preform installation which produces oil preforms as well as preforms for juice bottles.","@ID":38} "NEWS 8 PETplanet insider Vol. 12 No. 03/11 www.petpla.net Indorama acquires Chinese assets, Investa N America businesses, looking at India expansion Indorama Ventures PCL, the Indonesian company that is the world’s largest producer of polyester and PET, has signed a definitive agreement to acquire PET polymer and resins manufacturing facilities located in Spartanburg, S.C. and Querétaro, Mexico from certain subsidiaries of Invista B.V., for US$420 million less certain assumed liabilities. The price includes $229 million for the net fixed assets and equity interests and $174 million for the net working capital of the business. The acquisition is expected to be financed from a combination of cash, existing credit facilities and additional debt, with completion in Q1 2011, subject to necessary regulatory approvals. The acquisition of Invista’s assets provides access to Latin America, which is a net PET importer with demand growing 7% a year on average. Indorama has also announced its acquisition of the PET and polyester polymer assets of Guangdong Shinda UHMWPE in China, with a combined capacity of 406,000t/y. Of the total cost of $93 million, $40 million will be spent to expand the plant’s capacity. The Guangdong base gives Indorama access to the Chinese mainland, which is the largest fibre and PET market in the world. Yearly demand for PET and fibre in China is expected to rise from 15 million and 31 million t in 2009 to 24 million and 48 million, respectively, in 2015. Invista’s Spartanburg, South Carolina facility produces polyester resins used in bottles for CSD, water, beer, juice, and wine; food and custom-container applications, and polyester staple fibre and speciality polymers for a variety of applications. The Spartanburg operation has a total capacity of 470 million t/a. The Querétaro, Mexico, facility produces polyester resins and polyester staple similar to the Spartanburg operation and has a total capacity of 535 million t/a. Invista’s Wilmington, N.C., site is not a part of the transaction, nor is its European Polymer & Resins business, which includes manufacturing operations in Germany. Indorama is also reported to be considering the construction of two new plants in India and the Middle East with a combined investment of $1.2 billion. www.indorama.com PET recycling increases in the USA The ‘2009 Report on Post-Consumer PET Container Recycling’, jointly published by the National Association for PET Container Resources (NAPCOR), The Association of Postconsumer Plastic Recyclers (APR), and the PET Resin Association (PETRA), found that PET recycling in the USA during 2009 achieved a rate of 28%, which is the sixth consecutive year of increase. The increase was despite an actual four % reduction in the total of PET bottles and jars available for recycling, by weight. The report also reveals the end uses for a record 937 million lbs (426 million kg) of recycled PET used in manufacturing applications. Strong increases in recycling over 2008 were identified in sheet & film, food & beverage bottles, and non-food bottles end-use categories. This is the fifth year that NAPCOR, APR, and PETRA have partnered to produce this report and the 15th year that NAPCOR has issued the report in its current format. The full report can be found on the APR and NAPCOR websites. NAPCOR and the International Bottled Water Association (IBWA) have produced two complementary studies, ‘2009 Post Consumer PET Bottle Bale Composition Analysis’ and ‘2009 Report on PET Water Bottle Recycling’, which analyse recycling of consumer products. The national recycling rate for PET plastic bottled water containers (500ml and three and five-gallon PET water cooler bottles) stood at 31% in 2009, up slightly from 2008, the studies found, which continues a trend of annual increases recorded since analysis began, in 2004, when the recycling rates for these containers were just over half the current levels. Data compiled from bale composition studies at 15 locations in 14 states determined that the total weight of all PET bottles and jars available in the USA for recycling in 2009 was 5.149bn lbs (2.34bn kg), a drop of four % from 2008. Just over one-quarter of the total (590 million kg) was represented by PET bottled water containers. The slight decrease in the total weight is attributed to adverse economic circumstances for consumers, light-weighting of bottles and jars and a 37% increase in the use of recycled PET resin (rPET) since 2008. In 2009, the gross recycling rate for all PET bottles is 28%, an increase of one % over 2008’s recycling rate. www.napcor.com www.plasticsrecycling.org DAK Americas completes acquisition of Eastman’s US PET business DAK Americas LLC, headquartered in Charlotte, NC, and a wholly owned subsidiary of Alfa S.A.B. de C.V. of Monterrey, Mexico, has completed the acquisition of the integrated PET and PTA business of Eastman Chemical Company. The acquisition brings DAK Americas’ total PET resin production capacity to more than 1.5 billion tons. The acquisition includes three production facilities in Columbia, SC, USA: two PET resin units and one PTA unit. The transaction includes the intellectual property for IntegRex PET and PTA. The PET resin production units have a combined annual capacity of 675,000t and the PTA unit has an annual production capacity of 600,000t. The Columbia site will be integrated into DAK Americas PET and PTA business units, which have operations in the U.S in Charleston, SC; Wilmington, NC; and Fayetteville, NC. The acquisition of Eastman’s assets in Columbia, SC, follows DAK’s purchase of Eastman’s PET International operations in Cosoleacaque, Mexico and Zarate, Argentina, which were completed in autumn 2007. www.dakamericas.com IV calculation app Plastic Technologies, Inc. (PTI) has launched a free iPhone/iPad app for calculating the final intrinsic viscosity (IV) for PET resin. PTI claims that the app is the first of its kind for the plastics packaging industry. The format, called a nomograph, uses a graphic representation of numerical values to produce a final calculation. PTI’s PET Hydrolytic Degradation Nomograph enables the user to indicate the starting IV by sliding a plot point on a vertical scale to the appropriate value. The same is done for moisture percentage. The two plot points are connected by a moveable line and the intersection of that line, on a third vertical plane, is the material’s final IV. PTI says that the nomograph calculates the final IV in a couple of seconds. The app can be found in the iTunes App Store by searching for ‘PET nomograph’. www.plasticstechnologies.com","@ID":10} "PETpatents www.verpackungspatente.de 44 PETplanet insider Vol. 12 No. 03/11 www.petpla.net Base structure International Patent No. WO 2010 / 078341 A1 Applied for by: Plastipak Packaging Inc., Plymouth (US) Application date: 29.12.2009 The base shape a plastic bottle for hot filling is intended to absorb the thermal expansion and subsequent cooling so as to avoid any permanent distortions of the bottle which may be visible to the user. Concave base International Patent No. WO 2010 / 061758 A1 Applicant: Kogyosho Co. Ltd., Tokyo (JP) Date of Application: 18.11.2009 Described is a plastic bottle with a base that is specially shaped to flexibly accommodate any change in volume that may occur as a result of hot filling without any change to the side walls. As the contents cool the base reverts to its original concave shape. Extra in the base International Patent No. WO 2010 / 063093 A1 Applicant: Antoine Becotte, Montreal (CA) Date of Application: 23.11.2009 A type of vent hole “whistle“ is integrated in the base of a bottle and this can be removed once the bottle is empty and subsequently used to generate noise, e.g. at a football match. Dispenser cap International Patent No. WO 2010 / 068633 A1 Applicant: Graham Packaging Comp., L.P., York (US) Date of Application: 8.12.2009 Closure manufactured as a single section with integrated dispensing chamber and hinged lid. Buffer area European Patent No. EP 2202163 A1 Applicant: Yoshino Kogyosho Co. Ltd., Tokio (JP) Date of Application: 15.10.2008 Plastic container with specially moulded buffer areas to accommodate changes in volume as a result of hot filling. Disclosure of the international application was made on 30.6.2010. Originality seal European Grant of Patent No. EP 1892194 B1 Applicant: Obrist Closures Switzerland GmbH, Reinach (CH) Date of Application: 9.8.2007 Multiple section closure with two lateral, easily identifiable lead segments that are cut off at the point of initial opening and can no longer be reinstated in their original position. This means that the consumer can easily recognise that the container has been opened. European Grant of Patent took place on 23.6.2010.","@ID":46} "MATERIAL / RECYCLING 16 PETplanet insider Vol. 12 No. 03/11 www.petpla.net 6th China international recycled Polyester Forum Hangzhou 2010 A conference selection Dr. Ulrich Thiele, of Dr. Thiele Polyester Technology, Bruchkoebel, Germany, reports from the 6th International Recycled Polyester Forum, which was held in Hangzhou, PRC, September, 15-17 2010. The conference was intended to provide insights into the dynamics of the whole polyester recycling chain, from bottle and waste collection to flake processing and product trading. It covered market development and process technology, especially low-carbon concepts. There is no more doubt: the polyester industry has returned to a healthy growth trend and polyester recycling is more vigorous than ever. China is the front-runner in polyester recycling, as in virgin polyester production. Pressure on hotel space in Shanghai during EXPO-2010 led to the Forum taking place in Hangzhou, as on several previous occasions, and was very well organized by the Chinese host organization CCFEI (www.ccfei.net). The conference was well received by the 222 participants from the polyester recycling industry, the majority – 80% - from China, with the balance from 16 other nations. International companies with businesses in China were represented by Chinese staff. A range of information The conference was a real mix of information about macro economic developments in the PET recycling industry in China and market development worldwide, plus presentations about new and further development of recycling technology and equipment. Li Shidong, secretary General of CCFA (China Chain Store and Franchise Association) Recycled Fibre Commission presented a detailed analysis of the current rPET market in China together with the targets for the coming years. The core developments supported by the Chinese government are energy and water saving in PET recycling; technology and equipment providers were called upon to intensify their efforts in these areas. The government supports recycling companies with subsidies of 100 – 200 Yuan/ton, under certification by national recognition systems. Zheng Yang, of SEPA´s (State Environmental Protection Administration) National Solid Waste Management Centre, focused particularly on the situation of imported plastic scrap and polyester. He highlighted the problem of unqualified waste imports and linked them to the Chinese government’s measures to fulfil the strict requirements of pollution prevention and control during recycling activities. Product development: cutting labour costs Steve Shen, Vice President of Zhejiang Boretech Co. Ltd demonstrated the significantly improved capabilities of Chinese engineering to deliver tailored recycling plants. He emphasised that, with increasing labour costs, the change from hand sorting to automatic sorting systems in unavoidable. One interesting aspect was his observation that bottle prewashing is included in Boretech lines, which significantly improves final flake quality. Gneuss Kunststofftechnik GmbH introduced a complete new line for processing bottle flakes; its Multi Rotation System – MRS – is combined with automatic filtration and inline-viscometer. The combination of its MRS and an NGR compact shredder provide a robust recycling unit for processing of all kinds of fibre and solid waste occurring as in-house-scrap during PET fibre and filament production. Dr Ulrich Thiele of Dr. Thiele Polyester Technology gave a lecture on prerequisites, organisation and needs of fibre in-house recycling. Di Gangli, Deputy General Manager of Longfu Recycling Energy Scientech Co. Ltd, reported on Longfu´s large scale rPET conversion to POY, DTY and FDY and a newly developed process to increase IV in melt phase for technical yarn spinning. A new sorting technology was introduced by Peter Mayer, sales manager of SE-Sotech GmbH. Its new system sorts flakes with higher efficiency and throughput than traditional processes; this new flake sorting technology might replace bottle sorting in future. Kurt Pichlmann, Area Sales Manager of Erema GmbH, centred his presentation around examples of how the applied technology impacts the economical success of PET recycling. Market analyses A highlight of the conference was the market analysis of Andrew Noone, Managing Director of PCI PET Packaging, Resin & Recycling Ltd. Verified figures on collection, import and processing of PET bottles from PCI´s cooperation with CCFEI authentic were provided, together with the global trends in collection and reuse. A quite remarkable figure was China’s supply trend to 2019, by which time China alone will undertake 5.8 million tonnes of PET recycling. Those market figures were supplemented by","@ID":18} "MATERIAL / RECYCLING 20 PETplanet insider Vol. 12 No. 03/11 www.petpla.net Recycling is growing rapidly and industry standards are rising; the technology is available to meet regulatory and market demands. Recycling: maximising use The growing use of rPET is not just a response to demand from bottlers for more recycled content, it is becoming an important marketing tool – but, at the same time, preform producers need to make sure they achieve the need for high quality by controlling material flow. The requirements of brand owners on rPET are actually much stricter than foodcontact certifications, so it is essential that adequate PET recycling technology is deployed. Starlinger recycling technology supplies high-tech recycling lines for bottle-to-bottle recycling and high-viscosity applications. Variables influencing PET recycling PET bottle recycling is driven by a number of factors, such as foodcontact issues, required quality and quantities of input and output. Other drivers can include the following: Political pressure that encourages resource conservation; education for waste avoidance; installation of systems to avoid land-fill; a promotion of the reuse of plastic waste. The most effective measure is the promotion of recycling through taxation or the threat of it. At the economic level, virgin resin price is the largest influence on recycling; rPET still needs to be cheaper, in order to be considered as replacement. The price for baled material and flakes is, therefore, driven not only by supply and demand but also by virgin resin price. Important social factors include wider acceptance of rPET in foodcontact packaging and employment opportunity for less educated workers in many countries. Beyond recycling technology availability, recyclability has to be considered when designing new packaging. A whole array of lifecycle analyses confirms the positive environmental impact of mechanical recycling. Export or import of PET packaging waste and collection and re-use rate are heavily regulated. Foodcontact approval is part of legal regulation in many countries. A technology supplier wishing to have equipment recognised for foodcontact operation has to go through stringent testing, in order to prove cleansing capability. The letter of nonobjection from the FDA (United States Food and Drug Administration) is an essential requirement for any company to be considered as a supplier of super-clean recycling processes. As well as a challenge test, smell and taste tests might be required, in addition to migration or shelf-life tests. Precise definition and specification of input material is essential, as is a quality management audit of the recycler, in addition to the technology itself. In the case of the EFSA (European Food Safety Authority), it is expected that the current, initial authorisation phase will probably last until 2014. Commission regulation 282/2008 covers EU-wide harmonisation of regulations and standards but individual countries’ national law will at least partially apply until the end of the initial phase. A washing line, for example, has to adapt to the deteriorating quality of baled material unless one is prepared to pay a premium price. The presence of labels and glue are a challenge for separation, which is also the case with bottles made of PVC, PLA and other materials. Extrusion systems have to be flexible in order to handle bulk densities that are lower due to light weighting, and be able to change process parameters in response to additives in the packaging and other factors. The final application decides the required rPET quality. In order to satisfy consumers’ highest safety standards, many brand owners require more from their processes than simply being within detection limits. A requirement for ‘non-detectable VOC (volatile organic content) level’ is an increasingly common demand. A number of national and international certifications, including several FDA non-objection letters and brand owner approvals, confirm that rPET produced using the Starlinger iV+ process is suitable for packaging with direct food contact. Graph 1 shows a comparison of headspace gas chromatography of Starlinger rPET, compared with virgin resin. Starlinger launched its first PET recycling line in 2003 and has gone on to establish itself as a technologybased supplier of recycling lines for bottle-to-bottle and high-viscosity applications, amongst others. The total world-wide installed capacity for the production of rPET pellets used in direct food contact packaging may have been doubled in 2010, reaching over 180,000t/a. Starlinger’s recoStar PET iV+ technology yields recycled PET with properties similar to those of Graph 1: Headspace gaschromatography: virgin PET vs rPET (measured by Fraunhofer-Institut für Verfahrenstechnik und Verpackung, Germany).","@ID":22} "MATERIAL / RECYCLING 12 PETplanet insider Vol. 12 No. 03/11 www.petpla.net An innovative approach from Unisensor/Germany The power of sorting by Wolfgang von Schroeter The Powersort sensor system identifies the “good material” in a PET flake flow using high-speed laser spectroscopy, separating it from various contaminants in a single process step. Unisensor, the makers of Powersort claim that, depending on the type of impurity, separation levels of up to 98% can be achieved with a minimum loss of product. It is common knowledge that PET waste from clean bottles makes clean PET flakes or pellets. But collected bottles are by no means all clean. When collecting PET bottles all ingredients – visible or invisible - are collected as well. The visible elements are metal, labels, etiquettes and glue residue, caps screwed and unscrewed, external dirt and concrete material contamination. Non-visible elements include components integrated into the PET material like PVC, PC, PA 66, additives and blends. The number of possible impurities and material defects is on a permanent increase – one reason being a longer service life time, another the growing complexity of final applications and the repeated recycling of products. Thus the challenges for the industries involved are not going to go away. Most of these unwelcome ingredients - if not all - need to be removed for food contact approved PET flakes or pellets. The higher the contamination of collected bottles, the more complex the recycling. There is no single universal answer to solve the problem. Many individual proposals, mainly developed over long periods of trial and error, have resulted in the possibility of re-using recycled material. Some of these proposals are suitable for less demanding applications such as for fibre, sheet and strapping. Others require great effort to meet very particular applications, such as for RPET bottles for beverages. Nevertheless and despite numerous costly efforts – the recycling methods known so far were unable to identify and remove all of the unwanted contaminants. An innovative response to the problem recently came from Unisensor – Sensorsysteme GmbH, located in Karlsruhe, Germany. They brought to the recycling equipment market their Powersort sensor system which is able to detect and separate from a PET flake product flow invisible components, such as additives or PA 66, PVC or silicone and any other barrier substances used in food packaging. The first Powersort was sold in 2007. To date, the company has sold units to leading recycling firms in Europe, the US and most recently to Mexico. Powersort uses a measuring procedure based on high-speed laser spectroscopy. It identifies the “good material” in a PET flake flow on its specific opto-electronic spectrum, separating it in a single process step from various contaminants previously defined. The detection system excites the plastic particles with a powerful laser light, analysing the light spectrum that the individual part then emits. Each material has its own spectrum, or its own physical fingerprint. The sorting system separates out material whose spectrum differs from the reference spectrum of the “good” material. This means that","@ID":14} "MATERIAL / RECYCLING 19 PETplanet insider Vol. 12 No. 03/11 www.petpla.net The European PET Bottle Platform (EPBP) The European PET Bottle Platform was formed by the European Association of Plastics Recycling and Recovery Organisations (EPRO), the European Plastics Recyclers (EuPR), PET Containers Recycling Europe (Petcore), the Union of European Beverages Association (UNESDA) and the European Federation of Bottled Water (EFBW), with the main objective of evaluating packaging technologies and products and to facilitate PET bottle innovation, whilst minimising the economic and environmental consequences for recycling PET in Europe. It will do so by promoting the recyclability of PET bottles on the market by: Establishing European harmonised guidelines for PET bottles recyclability that will be accepted across the whole value chain. Encouraging industry to test new PET bottle concepts and/or materials before market launch according to the harmonised guidelines. Giving advice and recommendations to the different stakeholders. Sharing information and knowledge across the whole value chain. Members of the platform’s evaluation group are experienced technical experts from the whole PET value chain. They are tasked to evaluate novel technologies, materials and PET structures to verify their effect not only on the PET bottle recycling process but also on the PET chain. Companies developing new resins, additives, technologies and novel processes for PET bottles are urged to approach EPBP at the earliest opportunity so that their applications can be assessed in the most efficient and economic manner. The full EPBP protocol has been developed from the Petcore protocol and the US Association of Postconsumer Plastics Recyclers (APR) Critical Guidance Document and also takes into account learning from the industry. The protocol is split into quick tests and then more in-depth tests to ensure a speedy, accurate and economic outcome for both the applicant and for EPBP. The EPBP process can be viewed at: http://www.petbottleplatform.eu/technical.php More details and documents can be found on the EPBP website. Applicants are asked to discuss their application with EPBP in the first instance. To date EPBP has considered 17 applications. Many are ongoing but there are 6 so far on the positive list. www.petbottleplatform.eu","@ID":21} "MATERIAL / RECYCLING 14 PETplanet insider Vol. 12 No. 03/11 www.petpla.net Frédéric Blanchard, Plant Director APPE Beaune The system is running at 3t/h. Our goal is to set a new European standard with the highest quality PET flakes, which to date has been difficult especially given the numerous external contaminants that exist in the post consumer baled bottle stream today. APPE has a target to achieve fewer than 10ppm of external contamination (especially of PVC content) and only sophisticated sorting systems like the Powersort can meet our target. The installation of the Powersort in October 2010 has allowed APPE Beaune to significantly improve its quality of RPET resin suitable for direct food contact. It also allowed APPE to meet the requirements of its customers and - we believe – it sets the standard for others to follow. The sorter has now been running for 2 months (PETplanet: as at time of writing in December 2010) and we expect that following further finetuning and process stabilisation in the coming month our ultimate goal will be achieved.” Wellman Recycling plant / AE Spijk/Netherlands “Eventually, we feel, our quality will become evenmore reliable and our business solid and sustainable.” Wellman International with head quarters in Ireland is a global player in the development of fibre technologies, and also the largest European recycler of post-consumer PET bottles, with plants in the Netherlands and in France. The intake capacity of Wellman in Spijk/Netherlands is 60,000t in bales turning out 45,000t in flake form, of which approx 40% is supplied to the Wellman sister company in Ireland, where it is used for fibre. The balance goes mainly for sheet & bottle to bottle production to numerous external clients. Powersort was installed at the end of the processing line sorting flakes, further removing contaminants & additives mainly for supply to demanding external customers. At the Wellman plant in AE Spijk, Netherlands, the Powersort is installed at the end of the line. Ing. Will Dingen, Production Manager, commented: “The quality of incoming PET waste is unpredictable, since we buy from several sources. When we made the decision to buy Powersort, our existing customers had problems with additives in the flakes we supplied. We saw that the Unisensor machine was able to cope with the problems by eliminating the additives from the flow of flakes or at least by considerably reducing them. So we bought the machine, put it in place and started running. Of course with the new machine we also could separate from the PET flake flow other contaminants such as PA 66, PVC and coloured PET which we would then be able to sell as a by-product. The sorting system was installed in late 2009. We are very satisfied with the performance – running at a speed of 2.5t/h, sorting currently the majority of different additives out of those flakes which we separate for customers requesting a higher quality profile for sheet making and food packaging. We are still experimenting with the various machine and operational parameters, which require continuous optimisation. We also suffered from the influence of a very dusty environment.The critical issues are well on the way to being solved by both sides. Eventually – we feel - our quality will become even more reliable and our business solid and sustainable.” RecyPET in Frauenfeld/Switzerland “Powersort is in line - fully integrated.” Kornel Büsser, Managing Director and Production Manager, RecyPET The RecyPET company of Switzerland belongs to a group of international recyclers, together with Cleanaway PET International in Rostock/ Germany and Norköpping/Sweden, under the holding umbrella of Veolia Umweltservice. At RecyPET, Switzerland, the Powersort is fully integrated in the processing line. Swiss bales enjoy a high reputation for cleanliness. The intake capacity of RecyPET is 18,000t in bales containing beverage bottles only, which are collected, manually pre-sorted. The recyclate is returned to the markets in the form of CleanPET flakes – most of them with food approval for new bottles and sheets. The final sorting of flakes is receiving top priority at RecyPET. Three sorting systems are installed at the end of the processing line, one for sorting out metals and coloured flakes, one from Unisensor (Powersort mainly for sorting chemical elements integrated in PET such as additives, PVC, silicone and other defined contaminants) and one more optical sorter for even the slightest contamination of the flakes sorting out minor black and white crumbs. The flakes pass all three sorting systems, some of them even two or three times in order to minimise losses and ensure high quality.","@ID":16} "PETproducts 38 PETplanet insider Vol. 12 No. 03/11 www.petpla.net Post-consumer PET recycling Italian company Piovan manufactures and markets a line of auxiliary machines for production of flat sheet for thermoforming, profiles, fibres, hoses and wires and dedicated systems for the production of flexible films, both blown and cast. It has been addressing the particular issues associated with systems using post-consumer PET (PCR PET) flakes as the main raw material in the production of PET fibres for car interiors. PCR PET is amorphous, dusty and comes in flakes with variable granulometry, so that a specific treatment is needed in order to provide the mechanical properties required for optimal material processing in the extrusion line. Piovan has developed a solution with a crystallising, dehumidifying and dosing system with a capacity of up to 1,200kg/h PCR PET flakes and up to 1,600kg/h PET granules. Such large capacities are not conducive to easy changeovers or small production batches. In order to avoid material waste and long machine down-times, the company has developed a double dosing process and two separate parallel columns for crystallisation and drying, which allows the user to switch from PCR PET flakes to PET granules and to vary the percentage of the recycled material to a large concentration of PCR flakes, without affecting the system’s overall efficiency. Patented gas chambers heat up process air for the crystallising and drying systems. The entire production process can be managed via SVS, the company’s supervision software, from a remote PC workstation. Simple selection operations enable production to automatically adapt to different types of materials, depending on densities and capacities, with the intention of optimising energy usage and minimising waste. Piovan is developing its range of products specifically designed for the extrusion sector, including dryers, dosers, feeding and conveying systems, crystallisers, granulators and recovery solutions. It also develops customised systems in collaboration with OEM and extruder manufacturers. www.piovan.com Pre-reduction label remover from Herbold New designs for bottles and labels, including novel shapes and all-over sleeves, complicate the task of bottle recyclers, according to Herbold Meckesheim GmbH. Labels covering the whole surface of the bottle, for example, are an obstacle to optic sorting. If the labels are made of PVC then maintaining the expected quality standard with conventional technology cannot be guaranteed. Herbold claims to have overcome these problems with a new machine that uses friction to provide a preliminary treatment of the bottles before size reduction. The company says that the machine removes labels without unwanted side-effects, such as bottle-head breakage. Paper labels are removed and separated in a dry process, allowing easier separation of remaining paper fibres. The company says that all-over, shrink-fit labels can be almost completely removed and separated, which helps to prevent erroneous NIR identification during sorting. The pre-treatment machine’s technology is also said to enable removal and separation of bottle caps and silicone sealants. The process removes sand and foreign bodies at the same time as the label, which should help to increase the lifetime of cutting knives. www.herbold.com Piovan crystallising system Erratum! In the last issue of Petplanet we printed an unedited article on Messrs. PET Verpackungen Deutschland by mistake. Please see below the corrected version. We apologise for this error Preforms and new bottle designs to the fore The PET-Verpackungen Germany offers standard preforms with 28mm PCO 1810 neck finish and a range of new solutions in weight-reduced neck areas. The company also supplies a variety of new preforms PCO 1881 standard, as well as 38mm 2- and 3-start neck finishes. Furthermore, the company offers multilayer preforms with tailor-made barrier solutions, designed for sensitive-fill goods. PET Verpackungen are also producing PET bottles with capacities ranging from 20ml to 5l on five single-stage and two two-stage installations. Possible applications range from water, CSD and spirits as well as applications in the cosmetics and detergents sector right through to foodstuff applications. One new in-house development is a wide mouth jar for powdered milk/ coffee creamer. In the health and beauty care packaging sector PET Verpackungen has come up with a bottle family for hand sanitizer. A further new development that the people at PET Verpackungen have developed on their own initiative is a small 0.2l champagne ‘piccolo’ bottle. www.pet-verpackungen.de ALS compressed air-free automatic guide system Sidel’s ALS guide for air conveyors is an automatic adjustment system for side guides. It is designed to provide increased flexibility during format changeovers. It has no pneumatic cylinder, which is intended to enable it to automatically adapt to the majority of bottles currently on the market, on a single conveyor. The operator selects the desired format from the control panel, a gearbox transmits the appropriate movement to the side guides through a flexible shaft that follows the conveyor layout, and the guides are positioned by translation thanks to a worm gear. The system does not use compressed air, has a small number of parts and requires only one drive up to 30m per side. www.sidel.com","@ID":40} "BOTTLE MAKING 34 PETplanet insider Vol. 12 No. 03/11 www.petpla.net Automatic handle for edible oil It has been a constant source of frustration about stretch blow moulding that current technology was not able to allow handles to be incorporated on the same line. The result is that handles always have to be attached manually. Now, for the first time, we have seen an automated solution from Sipa at JRD in Dubai where the handles are fitted automatically using a Sipa machine. Briefly, JRD produces packaging for the water, dairy and edible oil market in Dubai. The company supplies thermoformed cups and plastic bottles. The preliminary products necessary for this, such as PET- and PP-sheets or preforms, are likewise produced in-house by the company. We met Mr. Sagar Verma, Business Head of JRD for 4 years. PETplanet: Mr Verma, there are innumerable companies producing cups and PET bottles for edible oil. Why should bottlers buy from you rather than anyone else? Mr Verma: You’re quite right, looking at the sheer volume of suppliers, but I think that we are, technologically speaking, very advanced and our prices are acceptable. Have a look at this for example. In the cups sector we are promoting the change here in Dubai from Polystyrene(PS) cups to environmentally-friendly polypropylene (PP) cups. PP can be recycled and keeps its shape even when filled with hot liquids. We offer everything, from elaborate in-mould labelling right through to the shrink sleeve and 8-colour printed labels. At the moment we are installing a new Illig RMD 75 K cups machine with a capacity of 600 million cups/a. It just doesn’t get any better than that. We also use Western European technology when it comes to decorating the cups. PETplanet: Yes and what about edible oil? Mr Verma: Our injection stretch blow moulding is conducted to a major extent on single-stage Aoki systems but for our Highlight we have, together with Sipa, devised a worldwide first in the shape of a 2-stage solution. Let’s start with the preform. Here we produce our own preforms on a Sipa system. These we store for 24 hours and then they go off for blow mouldEdible oil bottles: The handles are compressed by the new plant before being snapped into the edible oil bottle.","@ID":36} "PETbottles 42 PETplanet insider Vol. 12 No. 03/11 www.petpla.net Personal Care No-touch dispensing ReckittBenckiser is selling its 250ml “Dettol“ brand hand cleanser with a no-touch infrared dispensing system and PET refill bottle in the USA and England. The PET bottle with its special valve is placed headfirst in the dispenser and locked in position by applying slight pressure. In response to an infra-red trigger, the battery-operated dispenser then dispenses a dose of hand cleanser without the need for any physical contact. According to the manufacturer, 99.9% of bacteria are eliminated and your kitchen and bathroom stay clean. The aftermath of swine flu in Europe, which has led to enhanced hygiene precautions, is reinforcing sales of the product. The dispenser can be reloaded with a new PET bottle without any problems. The dispenser is sold in a high quality blister pack with pack inserts to provide the customer with further information. www.dettol.co.uk Sun protection The German drugstore discounter Schlecker of Uhingen is selling a range of pump spray products in PET bottles under the “AS“ brand name. These include, for example, the 150ml sun protection spray “Sun“ in a dark brown PET bottle with gold-coloured spray head along with 400ml room air fresheners in a transparent PET bottle with a secured spray trigger. Both bottles are decorated with modern no-label-look labels. www.schlecker.com Taft for designers Henkel Düsseldorf is offering 200ml spray gel under the “taft“ brand name in a blue-tinged PET bottle for the “Designer Look“. The bottle features no-label-look labels to front and rear that enhance the originality in terms of packaging impact of the light blue coloured bottle. A screw on, orange-coloured pump sprayer plus the safety cap round off this modern-look packaging ensemble. www.taft-looks.de Clearly high quality 100ml invigorating, blue coloured ice gel for regenerating tired feet is being sold by Yves Rocher of La Gacilly in a high quality PET bottle with an innovative shape and featuring a practical screw cap. The plastic screw cap– thanks to its easy to handle shape – presents no problems when it comes to opening and is reminiscent of the glass stoppers used in the past. Printed no-labellook labels to front and rear are also part of the decoration and convey the required trading information. www.yves-rocher.com Structuring shampoo Under its brand name of “Lavera“, the German company Laverana GmbH of Wennigsen is marketing 250ml structuring shampoo for regenerating stressed hair. The product is marketed in a round, dark brown PET bottle with a screw-on, black hinged cap and a content of 250ml. High quality printed front and rear labels provide information about the shampoo with its natural ingredients such as bio-aloe vera and bio-linden blossom. www.lavera.de Kneipp creates mood “Mood“ or “Time-Out“ – Kneipp Werke of Würzburg are selling a range of aromatic pamper foam baths in a round PET bottle containing 400ml of product and sporting a green screw cap. According to the manufacturer, the pamper foam bath is rich in naturopathic features, long-lasting foam and natural oils. The packaging is decorated with a high quality printed shrink sleeve label and it contains, if correctly dispensed, enough for eight relaxing baths. www.kneipp.de","@ID":44} "imprint EDITORIAL PUBLISHER Alexander Büchler, Managing Director HEAD OFFICE heidelberg business media GmbH Landhausstr. 4 69115 Heidelberg, Germany phone: +49(0)6221-65108-0 fax: +49(0)6221-65108-28 info@hbmedia.net EDITORIAL Doris Fischer fischer@hbmedia.net Michael Maruschke Ruari McCallion Ilona Trotter Wolfgang von Schroeter Anthony Withers MEDIA CONSULTANTS Ute Andrä andrae@hbmedia.net Miriam Kiesler kiesler@hbmedia.net phone: +49(0)6221-65108-0 fax: +49(0)6221-65108-28 France, Italy, Spain, UK Elisabeth Maria Köpke phone: +49(0)6201-878925 fax: +49(0)6201-878926 koepke@hbmedia.net LAYOUT AND PREPRESS Exprim Kommunikationsdesign Matthias Gaumann | www.exprim.de READER SERVICES Kay Krüger reader@hbmedia.net WWW www.petpla.net | india.petpla.net PETplanet insider ISSN 1438-9459 is published 10 times a year. This publication is sent to qualified subscribers (1-year subscription 149 EUR, 2-year subscription 289 EUR, Young professionals’ subscription 99 EUR. Magazines will be dispatched to you by airmail). Not to be reproduced in any form without permission from the publisher. Note: The fact that product names may not be identified as trade marks is not an indication that such names are not registered trademarks. 3 PETplanet insider Vol. 12 No. 03/11 www.petpla.net EDITORIAL dear readers, EDITORIAL The recycling of plastics is a matter of increasing and justified concern amongst the general public, involving as it does the use of finite resources and the burden it places on the environment. Undoubtedly PET recycling in particular is high on the list of priorities for the beverage and packaging industry. Producers of bottled water – using thousands of tons of PET - see recycling as a major element in the sustainability of their business and their long-term survival. This concern is shared by PETplanet Insider and our commitment to the subject will be extensively demonstrated during 2011 in a series of articles examining in detail the subject of recycling – we will be looking at the process itself, the equipment involved from a number of very different angles and of course to some rPET applications. Approximately 12 million t/a of virgin PET was globally produced in 2009 by chemical industries for use in the packaging sector. Approximately 4 million t/a (bottles) were collected for re-use – mainly in markets of developed countries. Only 20% of the recycled material are used for bottle-to-bottle due to the high quality requirements, 22% for sheets, 45% for fibre, 11% for strapping, 2% for miscellaneous – in 2009*. Data and figures must be taken with a little pinch of salt, since markets in the emerging world like Brazil, India and China are statistically unknown quantities. Some conclusions, however, are beyond doubt: The collection of post- consumer bottles needs to be improved. This is an obligation for everone – the general public, politicians and communities. One further, important point to be mentioned is that engineers and industries must face up to the challenge of improving the processing of PET waste to produce high quality food-approved RPET . Well established companies are focusing on PET bottle collection and waste separation, and in the production of flake and pellets, as well as the conversion of RPET flakes and pellets into final products. Big name suppliers have developed and produced machines to convert so-called “bad” PET waste to food grade RPET for re-use. But since the incoming “bad” PET often turns out to be a “bad” surprise for the recycler, the quality of the RPET that is produced is more a result of trial and error than expected. Thus the challenge remains for all parties concerned and involved to reduce the dependence of the good quality of PET intake as well as the unpredictable quality of outgoing RPET. In this edition of PETplanet we are looking at innovative equipment to do just that. Wolfgang von Schroeter * Recycling figures taken from PCI PET Packaging","@ID":5} "PREFORM PRODUCTION 31 PETplanet insider Vol. 12 No. 03/11 www.petpla.net Handling high levels of recyclate in PET preform machines Raising recyclate in preforms Sipa, the supplier of equipment for production of PET bottles and containers, has developed a range of solutions to produce preforms containing high levels of post-consumer recyclate in flake. Its preform injection moulding equipment designed for this function ranges from 96 down to 24 cavities. Sipa PPS Preform production systems produce preforms made with PET containing various levels of recyclate, up to 100%. The only change necessary to the standard configuration for handling flake at addition rates of up to 50% is the addition of an auxiliary gravimetric dryer. When recyclate content is in the 50-100% range, an upgrade to the plastification unit and filtration system is required. It is now possible to use as much as 50% recycled PET in bottles for mineral water sold in the European Union. In North America, several companies already produce bottles using exclusively 100% of rPET for their mineral water product. There are tight restrictions on the quality of recycled PET that can be used in new mineral water bottles. The material must be sourced from containers that were themselves approved for food contact applications. Sipa has presented the results of production on a standard-configuration PPS 72, equipped with 72 injection mould cavities and fitted with a 140-mm plasticating extruder with an output of 1200 kg/h coupled to a 6000g injection pot. In all cases up to a 40:60 virgin: recyclate content, no significant problems were observed in the productivity of the standard equipment, nor in the quality of the preforms. Processing temperature of 280°C was set for the extruder, injection pot, hot runners and nozzles. Dimensional controls were performed on the bodies of the preforms and also on the necks. Preform weight at various levels of flake, and levels of acetaldehyde within them, were measured. No significant dimensional difference between preforms made with 100% virgin PET and those containing recycled PET were observed, through to 50% addition levels. Acetaldehyde levels were actually seen to fall with increasing levels of recycled PET. www.sipa.com Sipa PPS preform machine detail Variation in preform colour depending on level of recyclate, from 0 to 70%. Variation inpreform col colour our dedepen pendinding og on lev levelel of of rec recycl yclate ate, from rom 0 to 70%. Table 1: Acetaldehyde levels as a function of recyclate: Falls measured in intrinsic viscosity are in line with virgin PET. The visual quality of preforms in terms of colour, presence of impurities and burnt specks depends on the quality of the flakes used. 0 1.0 2.0 3.0 4.0 5.0 6.0 Acetaldehyde [ppm] Number of cavities 66 63 9 7 PETALO A-10% PETALO A-20% PETALO A-30% virgin PET PETALO A-40% PETALO A-50% PETALO A-60%","@ID":33} "MATERIAL / RECYCLING 23 PETplanet insider Vol. 12 No. 03/11 www.petpla.net ment’s sense of responsibility for the country’s environment, and underpinned by another forward-looking perception from Sheikh Bashir Uddin, the Managing Director of the Akij Group. The Senior General Manager of the Akij Food & Beverage production facility, P. B. Barua, singles out three main reasons for the decision: “Firstly, the bottom line has to be right. And it is. At present, we’re already saving up to 30% of the price per container by using recycled flakes. Secondly, we don’t need so much foreign currency for importing PET granules – that is a crucial factor for a country like Bangladesh. And thirdly, we are able to help to significantly reduce the amount of garbage, specifically discarded PET containers, on the kerbside and in lakes and rivers.” This is why AFBL installed the first PET recycling line of its kind in Asia. In a new aisle of the hall in the Dhaka plant, Krones built a washing module with an output of 1,000kg/h, plus a decontamination module for 500kg/h. The washing module produces non-food-grade rPET flakes for use in the fibre, plastics or film industries. Full capacity utilisation is always dependent on the market price but Sheikh Uddin is already talking about converting the remaining 500kg/h of non-food-grade rPET flakes into polyester flakes, for use in the group’s own textile factory in a cotton-polyester mixture. One of the country’s many small plastic collection points. The material arrives in the beverage factory’s courtyard in big bags or already compressed and is in very poor condition. In a new aisle of the hall in the Dhaka plant, Krones built a washing module (left) with an output of 1,000kg/h, plus a decontamination module (right) for 500kg/h.","@ID":25} "MARKET SURVEY 27 Europool S.R.L. Dimark SP. Z O.O. Intec Solutions Inc Via G. Ferraris 13 - 43036 Fidenza (Pr) Italy +39.0524.528616 www.europoolengineering.com Mr. Marco Priero General Manager +39.0524.528616 +39.0524.520125 info@europoolengineering.com Lagiewnicka Street 2, 62-002 Zlotniki, Poland +48 618956002 www.dimark.eu Monika Mickiewicz Product Manager +48 618956002 Ext 17 +48 618956104 mickiewicz@dimark.com.pl 2382 Bolton Rd Atlanta, Ga 30318 USA +1 404 424 9451 www.intecsolutionsusa.com Arnold Manier President +1 404 424 9454 amanier@intecsolutionsusa.com No No Yes 25 cm with arm telescopic option No No Yes No No Yes No Yes, mechanical and speed control adjusted by PLC No No Yes Yes Yes Yes 99,9% up to 99% Hepa filter available Yes for 5l, 1,5l, 0,5l Yes Yes Yes Yes No No No No up 15,000 No up to 400,000 No No Yes Sidel Zecchetti Srl Avenue de la Patrouille de France, Octevillesur-;er, BP 204, 76053 Le Havre, France +33232858300 www.sidel.com Sylvie Rak Business Communication Manager +33 2 32 85 82 46 +33 2 32 85 81 34 sylvie.rak@sidel.com Via Galileo Galilei, 1-1/A 42027 Montecchio Emilia (RE) - Italy +39 0522 867411 www.zecchetti.it Francesco Parma Sales Manager +39 0522 867411 +39 0522 866034 f.parma@zecchetti.it preform conveyor in mass flow available No No Preform feeder Yes Yes Mechanical No Yes No Yes Yes GRAVI F5, OPA F8, DOP H12 3 levels : (a) 1-stage filtering : G4 – EN779:2002 - min 90% galvanometric (b) 2-stage filtering : F9 – EN779:2002 - min 95% opacimetric on 0,4 micron (c) 3-stage absolute filtering: H14 – EN1822 Hepa Fflter - 99,995 MPPS 0,12-0,17 micron – min 99,999 NaCI – 0,65 micron Filtered air class: 100 (according to the Federal Standard 209) - 5 (according to the ISO Standard 14644) Yes, different automatic side guiding + adapted regulation (a) automatic by means of pneumatic cylinders (b) automatic by means of unlimited position drives Yes (automatic change over) (a) automatic by means of pneumatic cylinders (b) automatic by means of unlimited position drives No Yes 1,000 - 50,000 ) No Yes Yes","@ID":29} "MATERIAL / RECYCLING 18 PETplanet insider Vol. 12 No. 03/11 www.petpla.net PETplanet speaks to Jean-Marc Rostagno – first President of Forum PET Europe Forum PET Europe launched The Forum PET Europe (FPE) was founded in Paris in November 2010 with the objective improving ad hoc communication on health & safety, recycling and innovation for PET packaging. The Forum PET Europe represents mainly the national PET converters (preforms, bottles, jars, containers and others PET packaging) and is a open source and collaborative platform of communication and action. This is in collaboration with Petcore, the European PET producer association which validates and supports innovative PET solutions from a recycle perspective, supports all PET recycling processes and facilitates sustainable growth for post consumer PET collection. The initiative for the Forum came from the PET associations of France (Elipso) and Germany (Forum PET within IK Industrievereinigung Kunststoffverpackungen) as well as from the Portuguese converter Logoplaste. Jean-Marc Rostagno, Managing Director of Artenius PET Packaging (APPE) Northern Europe, a leading European converter and also producer of recycled PET was appointed first president of Forum PET Europe. We asked Jean-Marc Rostagno for his comments on the new organisation. PETplanet: What is the policy of the FPE? Mr Rostagno: FPE will act as the spearhead for the national Forums. European counterparts want to see one single representative when considering discussions on matters of common interest. The Forum PET Europe is designed to fill that gap only. Some national Forums have already expressed an interest in joining and others will follow. Portugal for example has relatively few PET converters and will be represented initially by the main converter. PETplanet: Why yet another association amongst so many existing associations? Mr Rostagno: Quite simply because there is no such organisation representing PET converters. Our focus will be on key areas such as enhancing the sector’s reputation, acknowledging risks and opportunities and spreading a proper understanding of PET excellence in recycling (some converters are also recyclers). There is also a considerable amount of work to do on highlighting the untapped potential in PET innovation. PETplanet: What does all this mean in practical terms? Mr Rostagno: Let me give you a few brief headlines: First: Health and safety aspects – food contact information related to PET – in order to reassure stakeholders that our products are safe. Second: Recycling – integrity of recycling loop from bottle to bottle and the PET converter’s contribution in improving quality of the clear baled bottle flow (see last EPBP press release: FPE will help this approach with up to date input on recycling guide lines) Last but not least: Innovation, which means also caring for new and fast growing PET packaging : barrier bottles for beer, wine, milk, high end fruit juices to be recycled as well.. PETplanet: From what you are saying, it would appear that the interests of the converter come first and recycling comes second? Mr Rostagno: I’d prefer to put it another way: if attacks on the reputation of PET on supermarket shelves eventually succeed, there will soon be no PET to recycle. Recycling is a very high priority for the FPE. If I can put it this way: We can enhance the reputation of PET if we can show we are taking responsibility for recycling as well. PETplanet: Let’s turn to Petcore for a moment: don’t you share broadly the same objectives? Could there be areas of conflict? Mr Rostagno: No, both organisation complete and even reinforce each other. Our strength lies in our significant representation of the converting industry at a national level Also our focus is more on health & safety and fostering innovation. PETplanet: As far as recycling is concerned, is there any need to join both organisations or would there be a conflict? Mr Rostagno: Why would converters be in conflict with resin or additive producers? We talk to Petcore in order to improve the global “package” which we bring to our customers and hence to provide reassurance to the market. Thus: there is no disconnect either in communication nor in what we are doing – hopefully. PETplanet: What can we expect from Forum PET Europe in the near future? MrRostagno: We want to finish the job of contacting other European associations so that we enlist the support of those working within the PET supply chain. We are also working on the guidelines with European PET Bottle Platform (EPBP), representatives and supporting them as mentioned above. PETplanet: Who is joining next – to widen the platform for FPE? Mr Rostagno: The three topics that we have already mentioned: health & safety, recycling and innovation have received a broad welcome from those in the industry. We are hoping that this may encourage the formation of national PET forums, which could become at the same time members of the FPE. PETplanet: Thanks a lot, Mr Rostagno. www.forumpeteurope","@ID":20} "The food-grade flakes obtained at the end of this process are used by Akij directly for making PET preforms. MATERIAL / RECYCLING 22 PETplanet insider Vol. 12 No. 03/11 www.petpla.net Krones bottle-to-bottle PET recycling line* Bangladesh recycles *based on an article by Udo Lanzinger, Krones AG Production has now commenced on one of the first Krones bottle-to-bottle PET recycling lines in Bangladesh. Akij Food & Beverage LTD. (AFBL), a subsidiary of the multinational Akij Group and a newcomer to the soft-drinks market, recognised the opportunities offered by recycling PET containers from kerbside collections. In parallel with the installation of its fifth Krones bottling line, Akij invested in this high-tech recycling line with washing module and decontamination module and is already able to substitute recycled PET flakes for 30% of the PET raw material required in its in-house PET preform and container production operation. Cost savings and increasing independence of the global market for PET raw material are the direct consequences of this investment. A newcomer to the beverage market The Akij Food & Beverage Company was established as recently as 2004, and marked Akij Group’s first entry into a market that was new to the organisation. The company was set up “because we wanted to meet the demand for products made in Bangladesh to global quality standards, and we expected this market to offer us huge opportunities”, explains Sheikh Jamil Uddin, who is responsible for the group’s marketing operations. Akij Food & Beverage concentrated on soft drinks, water, fruit juices, milk and snacks, and grouped all of these divisions together in a new factory, located in Krishnapura, Dhamrai, 50 kilometres outside the capital, Dhaka. “For our founder, quality had always been the top priority”, Sheikh Uddin emphasises, which is why this visionary entrepreneur formulated the following maxim: “Uncompromising quality even in adverse market situations is the main force behind our success.” Recycling helps to reduce garbage The decision to install an in-house PET recycling line was finally arrived at after a long hard look at the pocket calculator, by heeding the manage-","@ID":24} "NEWS 10 PETplanet insider Vol. 12 No. 03/11 www.petpla.net DRYING HAS NEVER BEEN THIS EFFICIENT: ETA plus® LUXOR - now available with ETAplus® ETAplus® considerably reduces energy consumption and protects materials. When it comes to drying, saving energy is a key concern. We have developed a system that combines airflow regulation with a temperature adjustment feature – that can be disabled if required –and efficient waste heat recovery. The result? A drying system that cuts energy consumption by up to 64%: ETAplus® . motan-colortronic gmbh info@motan-colortronic.de www.motan-colortronic.com New CEO for Mold-Masters Mr William Barker has been appointed Chief Executive Officer of the Mold-Masters Group of Companies, effective December 6, 2010. Mr Barker has over 20 years of experience as a CEO/General Manager of high technology industrial manufacturing companies with a global footprint, most recently with Rexam PLC and Textron Inc. He has been a board member of both publicly traded and private equity owned companies. www.moldmasters.com 50th anniversary, New ‘Packworld’ centre for Greiner Packaging Austrian company Greiner Packaging International celebrated its 50th anniversary with the opening of its new ‘Packworld’ innovation and communications centre. The facility, located at the former Llosent & Forschner Korken GmbH factory in Oberwaltersdorf, near Vienna, offers conference and meeting rooms, a gastronomy sector and a lounge. The advanced facility is intended to be used for lectures, seminars, meetings and other communication and presentation events on the subject of packaging. The official opening ceremony, on September 30th 2010, saw a number of long-service and loyalty presentations to company employees. Greiner Packaging International employs a workforce of 2,878 employees at 28 production sites in Europe. The company achieved annual sales of €357 million in 2009. www.greiner-gpi.com Petainer acquires Rostiprimpac Specialist plastics packaging technology business Petainer has purchased PET packaging manufacturer Rostimprac AB, based in Norrkoping in Sweden, and Rostiprimpac Verpackungen GmbH based in Leinefelde, Germany, from A.P. Moller Maersk. Petainer intends to develop new products and markets following the acquisition. Petainer, a European designer and manufacturer of plastics (primarily PET) packaging has manufacturing plants at As in the Czech Republic and Lidkoping in Sweden, where it also has an R&D centre. The company has sales offices in Germany and the United Kingdom. www.petainer.com Indorama renames PET resins range Indorama Ventures has changed the names of the PET resins produced at its facilities in Rotterdam and Workington, because of the expiry of its Technical License Agreement with Eastman Chemical. Indorama emphasised that the move is purely a change of name and there is no change whatsoever to either the raw material make-up or the production processes used and does not indicate anything else. The changes took effect on March 1, 2011. The former and new names can be found on Indorama’s website. www.indoramaplymers.eu","@ID":12} "PRODUCTS 39 PETplanet insider Vol. 12 No. 03/11 www.petpla.net Compact inline crystallisation RPET pellets need to have the same parameters as new material, in order to produce preforms for food-standard PET bottles. This requires crystalline material and Erema is offering a solution with its Compact inline crystallisation (CIC) system. The company’s Vacurema system produces melt-filtrated strings that are briefly cooled in water and then cut into pellets. The material is fed into a container immediately afterwards. The latent thermal energy still contained in the pellets is used for crystallisation – without any additional outside energy required and without any process interruption. Downstream of the CIC, pellets with an AA content below 1ppm can be produced with a newly-developed pellet flusher, enabling production of rPET with the characteristics of new material. Erema claims that CIC can help to save up to €100,000 Euros at a throughput of 1,000 kg/h, with a low investment and machine footprint. www.erema.at Prefrom production with recycled PET Husky Injection Molding Systems’ sustainability solutions now include the company’s HyPET Recycled Flake (RF) system. It is specifically designed to support bottle-to-bottle recycling through the manufactures of preforms with high percentages of food-grade recycled PET flake, which is intended to enable significant increases to the amount of bottleto-bottle recycling. The consistent challenge has been increasing the recycled flake content in beverage packaging, while maintaining system performance and high bottle quality. The difference in physical properties and behaviour between flakes and pellets means that recycled flake adds to this challenge. Husky’s HyPET RF system has an injection unit that is specifically designed for recycled flake. Its mixing performance is designed to offer better material homogeneity, while continuous filtering reduces the presence of black specks. A shortened thermal process minimises thermal degradation. HyPET RF is based on Husky’s High Performance Package (HPP), and offers the same cycle time, throughput, shot repeatability and weight distribution. By addressing the specific issues in manufacturing PET bottles with the use of recycled PET flake, it is designed to allow manufacturers to introduce recycled PET flake into their products. Those already using recycled PET flake can eliminate some of the manufacturing and quality challenges while enabling an increase in flake content. Compared to food grade recycled pellets, the process for producing food grade flake does not involve melting or extrusion, which means a lower cost and lower carbon footprint. Husky says it has overcome the traditional disadvantage of food grade flake – the inability to melt filter – by implementing the continuous melt filter. The new extruder on the HyPET RF system is also claimed to eliminate the usual step of upsizing the extrusion screw. www.husky.ca","@ID":41} "PREFORM PRODUCTION 33 PETplanet insider Vol. 12 No. 03/11 www.petpla.net fax: +49 (0) 6221-65108-28 info@hbmedia.net www.petpla.net Order your copy now! PETplanet print vol.6 The Rapid Guide to Perfect Preforms machine no./name ol prices in EUR + VAT. 1- 3 exemplar each 129,- € 4 - 10 exemplar each 99,- € 10 exemplar each 69,- € .6 .6 .6 l. l ol Symptom: Faint white swirls and patches in various spots on the preform. Cause: Melt that has been thermally degraded by overheating in a specific zone (not oxidized). Solutions: 1. Check all temperature readings and correct if necessary. PET resin should be melted at about 280ºC (536ºF) +/- 10ºC (18ºF). 2. Check all %-controlled temperature settings and minimize if possible. %-controllers provide no temperature feedback and require fine tuning. 3. Check that all thermocouples are properly inserted and contacting the bottom of the wells. Having a thermocouple incorrectly seated in one zone has a major effect on this problem, especially if the melt stagnation time between cycles is long. 4. Make sure the extruder screw cushion is not excessive. This should be a minimum of 25mm to compensate for any fluctuations during screw recovery. (Two-stage machines only) 5. Check hardware for worn, damaged or failed components, specifically the machine and mould heaters, and thermocouples. 6. For prevention, always: a. Reduce temperatures by about 40ºC (104ºF) if the machine stops for more than 15min b. Reduce %-controllers by ½ if the machine stops for more than 15min c. Shut off nozzle tip heats if the machine stops for more than 10min d. Never exceed start up temperature soak times. Machine should be started within 15min of the temperatures reaching operating settings. Nozzle tips should only be turned on 5 to 7min prior to start up. IN EVERY BOTTLE THERE IS ALL OUR KNOW HOW.","@ID":35} "PETbottles 40 PETplanet insider Vol. 12 No. 03/11 www.petpla.net 40 Coffee enhancers Naples-based Saba, now part of the CO.DA.P group, has recently launched two new almond syrup product lines in PET bottles, which both use a standard non-drip 38mm cap from Aptar Food + Beverage. The line of almond syrup coffee enhancers comes in five flavours and is packed in a sleeved PET bottle with a partially transparent background. The products are offered in 700ml PET bottles, capped with a silvercoloured dispensing closure from Aptar. The 38mm PE flip-top closure has a tamper-evident ring-pull and a pouring beak to ensure drip-free pouring. Pizza spray complete with filling The French retailing giant Carrefour is marketing 250ml pizza spray in an original, transparent PET bottle filled with stuffed chilli peppers. The chilli peppers, which are bottled when dry and have the effect of ”turning up the heat“, are easy to see and catch the eye immediately at the POS. A pump spray (also transparent and featuring a snap-on lid and self-adhesive labels with a tear-off tamper-proof seal) puts the finishing touches to the appearance of the packaging. www.carrefour.fr The spirit of PET Antonio Nadal S.A. from Majorca is marketing an assortment featuring all kinds of high percentage alcoholic drinks in slightly curved PET 50ml volume bottles. As a result of their slightly curved shape, the bottles – one example being the ”Original Navy Rum“ – can be advantageously positioned on the shelf and the curved label has a pleasing appearance. The PET bottle features a printed aluminium screw cap with a tear-off tamper proof seal. www.antonionadal.com Striking Shape The Spanish company Solan de Cabras based in Cueno is marketing its 330ml MultiFruit Juice in a strikingly moulded PET bottle with a long neck.The bottle is decorated with a shrink sleeve label coordinated with the colour of the juice and features a generously proportioned drinking opening 32mm in diameter. A colourcoordinated screw cap with a tear-off tamperproof seal makes this modern beverage packaging complete. www.solandecabras.es","@ID":42} "MARKET SURVEY 26 MARKETsurvey 03/11 Company name Sismatico UK Ltd SMI S.P.A. MCon Conveyors Pvt. Ltd. Postal address Telephone number Web site address Contact name Function Direct telephone number Fax E-Mail Plumtree Farm Ind Est, Bircotes, Doncaster , DN11 8EW U.K. +44 1320 719738 www.sismatico-uk.com Duncan Griffiths Technical Sales Manager 01302 719222 duncan.griffiths@sismatico-uk.com Via Piazzalunga, 30 24015 San Giovanni Bianco(BG) Italy +39 0345 40.111 www.smigroup.it Pietro Volpi Marketing Manager +39 0345 40.316 +39 0345 40.209 info@smigroup.it Vishwachaya Indl. Estate, Sr. No. 322, Plot No. 2, Pirangut, Pune-412108. Maharashtra. India 0091-20-66749900/1/2 www.mconconveyors.com Mr. Shriram Rahalkar Director +91-9822615918 +91-20-667489903/4 shriram@mconconveyors.com Preform: From injection moulding machine into box: Box-filling system Yes No Maximum drop from conveyor belt to base of carton (in cm) 120 cm In-line Control Yes Preform: From box into SBM Machine up to 60 000 preforms/h Dumper (Yes / No) Yes Yes Conversion to different neck diameters (No/mechanical/electrical) mechanical/electrical mechanical In-line Control (Yes / No) Yes Yes Bottle: From SBM to filler, air conveyor Air Conveyor (incl. vertical) (Yes / No) Yes Yes Purity levels 99,997% G3/F9/H14 Bottle format conversion Yes Yes Conversion to different neck diameters Yes Yes Bottle storage systems Bottle Up-ender (Yes / No) Yes Buffer Systems Capacity Number of bottles from …to… depending on bottle diameter Storage Systems Capacity (Number of bottles from... to…) depending on bottle diameter Palleter and De-Palleter for empty PET bottles Yes Company name Krones AG Postal address Telephone number Web site address Contact name Function Direct telephone number Fax E-Mail Böhmerwaldstraße 5 93073 Neutraubling, Germany +49 9401 70-0 www.krones.com Reiner Kahl Vice President of Division Conveyor Technology +49 9401 70-3065 +49 9401 709-1-3065 Reiner.Kahl@krones.com Preform: From injection moulding machine into the box Box-filling system No Maximum drop from conveyor belt to base of carton (in cm) No In-line Control No Preform: From box into SBM machine up to 60,000 preforms/h Dumper (Yes / No) Yes Conversion to different neck diameters (No/mechanical/electrical) mechanical In-line Control (Yes / No) Yes Bottle: From SBM to filler, air conveyor Air Conveyor (incl. vertical) (Yes / No) Yes Purity levels F5, F8, H13(HEPA) Bottle format conversion automatic adjustable body guide rail via multi position cylinder (up to 12 positions) or stepless adjustment via linear motor Conversion to different neck diameters automatic adjustable neck-ring guide rail via pneumatic cylinders, also in curves Bottle storage systems Bottle Up-ender (Yes / No) No Buffer Systems Capacity Number of bottles from …to… Storage Systems Capacity (Number of bottles from... to…) Palleter and De-Palleter for empty PET bottles Yes","@ID":28} "Vol.6 PETplanet print PREFORM PRODUCTION 32 PETplanet insider Vol. 12 No. 03/11 www.petpla.net Milky Preform Chapter 18 of the “Rapid Guide to Perfect Preforms” by Rick Unterlander and Ottmar Brandau Troubleshooting guides have suffered in the past from being locked away in offices and not being available to the people that actually need them. Considering the high cost of machine and tools high scrap rates can be a costly proposition eating away at already tight margins. PETplanet’s “Rapid Guide to Perfect Preforms” takes a different approach. Bound in laminated paper that is easy to clean off, the small format of the book of 108mm by 151mm (4.25” by 6”) allows easy storage in back pockets or tool boxes. It has been written for the people on the floor of injection moulding companies to support their daily work in making the best preforms possible. The product of two industry experts, Rick Unterlander and Ottmar Brandau, it gives concrete advice on 35 of the most common problems in preform manufacture, most illustrated by pictures. From high AA levels to wavy bodies processors can find help when they need it. Read chapter 18 of the guide. Recycling line recoSTAR PET iV+ Ongoing PET recycling innovation, quality and state-of-the-art technology, a full range of consulting services – brought to you by Starlinger. Visit us at: ANTEC 2011, Mai 1 - 5, Boston USA Hall C, Booth 212 www.starlinger.com 32","@ID":34} "MATERIAL / RECYCLING 15 PETplanet insider Vol. 12 No. 03/11 www.petpla.net EREMA Engineering Recycling Maschinen und Anlagen Ges.m.b.H. Unterfeldstraße 3 . A-4052 Ansfelden . Austria . erema@erema.at We know how. PET Extrusion System VACUREMA® Prime to produce BTB pellets that are EFSA, FDA and brand owner approved www.erema.at CIC compact inline crystallisation system • lower AA (1 ppm possible) • higher crystallinity • less equipment Batch process guarantees defined decontamination time for each PET flake Continuous software control for • food contact, IV and other parameters Efficient decontamination and IV increase . low energy consumption, 0.30 to 0.33 kWh/kg Output capacity from 500 to 2,600 kg/h 15 About Unisensor and Powersort Unisensor is a family-run high-tech company in the field of process analytics and control, more precisely opto-electronics and sensor systems technology. The senior owner - Professor Dr. Gunther Krieg - founded the company, which is close to and connected with the Karlsruhe Institute of Technology (KIT). Powersort is part of the product portfolio of Unisensor, which specialises in sensor systems technology for gas, fluid and solid material. Industries supplied include the beverage, gas, compressed air and recycling sectors. The first Powersort was sold in 2007. To date, the company has sold to leading recycling firms in Europe, in the US and most recently to Mexico. In December 2010 Unisensor/Powersort was one of three nominees for the German President’s “Award for Technology and Innovation”, which honours researchers and engineers who develop ground-breaking projects and products for the market. The award not only recognises scientific achievement, but also takes account of the marketability of the innovations and the associated potential for creating jobs. www.unisensor.de The developers of Powersort: J. Bohleber, Prof. G. Krieg, D. Fey (f.l.t.r) Kornel Büsser , Managing Director and Production Manager commented: „The most significant problem was silicone. In 2006 we installed the newly developed prototype of Powersort in our factory. The problem was instantaneously solved. We are now also able to recognise those foreign plastic particles, which are not PET, but have the same colour as PET, and eliminate same. In the last four years since installation, we have cooperated closely with Unisensor to adjust their sorting system to a factory environment utterly different from laboratory conditions. Unisensor has benefited from our experience. We have recently exchanged the prototype for a new Powersort.”","@ID":17} "PETnews 6 PETplanet insider Vol. 12 No. 03/11 www.petpla.net PlastID to develop detection and separation in recycle stream An industry group comprising Petcore, ColorMatrix, Pellenc, EPRO, EuPR, PlasticsEurope, UNESDA and EFBW has applied for a European R&D grant to fund the full scale-up of PlastID, a Petcore project intended to develop methods to detect and separate specific containers from the plastics recycle stream. The multi-million Euro project will focus on approved food-standard packaging polymers and it is envisaged that the technology developed through the PET recycle experience will be transferrable to HDPE, PP and PS. The use of novel materials in PET bottles can cause discoloration during the recycle process. One aim of the project is to facilitate the recovery of bottles containing novel materials from the clear bottle stream and divert them to higher value outlets. The PlastID project will develop an LCA (lifecycle assessment) on the collection, sorting and recycle processes and provide training in new technologies. The consortium is awaiting the outcome of its application and intends to present the project in greater detail in future editions of PETPlanet. www.petcore.org More exhibitors and services at 25th Chinaplas, May 2011 The 25th edition of Chinaplas, the International Exhibition on Plastics and Rubber Industries, will be held at China Import and Export Fair Pazhou Complex, Guangzhou, PR China, from May 17 to May 20, 2011. The confirmation of the India Pavilion brings the total of country and regional pavilions at the event to 11. Chinaplas will now be arranged under 12 themed zones, with the addition of the Rubber Machinery & Equipment; Industrial Services; and Bio-Plastics and Degradable Plastics zones. Over 20 enterprises have already reserved space in the Rubber Machinery & Equipment zone, in Hall 3.1. ChinaplasOnline.com, the official website, has been revamped and improved, with a search engine function that allows keyword searches in the website content and exhibitor’s data. The ‘Download Centre’ holds showrelated information, such as the visitor brochure, eNewsletter, etc. available for visitors to download. Japanese, Korean, Spanish, Italian, Russian and Arabic versions are now available. Latest show updates, transport and hotel information, and seminar details are available through WAP Chinaplas. www.chinaplasonline.com Mould Technologies Group acquires Magor Mold Inc. Mould Technologies Group (MTG) of Diessenhofen, Switzerland, which incorporates Schöttli AG, has acquired all of the issued shares in Magor Mold, Inc., of San Dimas, Ca, USA, as of January 2011. MTG also owns s-mouldtech, of Suzhou, China. Schöttli and Magor both specialise in the development and production of extremely high-output injection moulds. Schottli develops and produces injection moulds for the production of medical parts, caps and closures and thin-wall packaging and caters to medical disposables manufacturers and packaging and plastic cap producers. Magor injection moulds are mainly used for the production of transfusion systems, dialysis units, respirators and anaesthetic systems, drug applicators and hygiene products made from standard polymers and engineering thermoplastics. It predominantly supplies manufacturers of medical parts and disposables. Service and maintenance across MTG’s range of products will now be carried out by the local companies. Wolfgang Bühler and Martin Schöttli will both remain managing directors of Magor and Schöttli. www.schoettli.com www.magormold.com www.s-mouldtech.com Clear Path Recycling PET recycling facility operational Clear Path Recycling, LLC, the PET recycling joint venture company established by Shaw Industries Group, Inc., and DAK Americas LLC, in April 2009, has completed the first phase of its PET recycling facility in Fayetteville, NC and the plant is now operational. The facility produces recycled PET (RPET) flake from post-consumer PET bottles and now has the capacity to recycle up to 160 million pounds of PET bottles per year. This is estimated to save over 550,000 cubic yards of landfill space each year and over 1.9 trillion BTUs of energy annually, equal to the power needed for over 20,000 U.S. homes per year, according to Energy Information Administration data. Shaw and DAK will be the primary users of the RPET Flake (Recycled PET bottles) in their respective polyester based products including carpets, fibres and resins. The remaining product will be sold for merchant use. Plans for the facility include increasing throughput to 280 million pounds (127 million kg), about 5 billion bottles per year, which will make it the largest recycling facility in North America. www.clearpathrecycling.com New closures factory in South East Asia Bericap has recently opened a production facility in Singapore, which will be providing direct service to customers in the ASEAN zone. It is intended to be the nucleus for future expansion of sales and production facilities in South East Asia. The facility will initially manufacture closures for the non-food and non-beverage market, with beverage closures to follow in the near future, as well as a hinge closure for bottlers of soya sauce who require anti-drip features, tamper-evidence and a closure design allowing capping of hot-filled glass bottles. Bericap Singapore is preparing to introduce the DoubleSeal one-piece closure technology for carbonated beverages or hot-filling. A screw-cap with folded tamper evidence band for the agrochemical industry is also to be produced. The manufacturing process and other additional safety features make the closure difficult to copy and support anti-counterfeiting measures. and Bericap says that the new factory has space and capacity to enlarge the product range and increase output. www.bericap.com","@ID":8} "BOTTLES 41 PETplanet insider Vol. 12 No. 03/11 www.petpla.net Bio in PET The Swiss trading company Coop is marketing a 0.5l bio-cordial made from elderflowers in a practical, dark brown coloured PET bottle. The manufacturers of the cordial are Messrs. Lammann + Co. in Bi- schofszell, Switzerland. The bottle sports an allround paper body label and a snap-on dispenser cap with tear-off tamperproof seal. www.coop.ch Good health from Nestlé Under the brand name of “Nesfluid“, Nestlé France is marketing a range of 250ml drinks such as, for example, “Equilibre“ (with lemon / Vitamin C) or ”Protect“ (with pomegranate, zinc and selenium) in PET bottles for whenever you feel like topping up your fitness levels. The handy bottles have a square base and are decorated using shrink sleeve technology. A small, stick-on folding label on the cap provides information on the product advantages offered by the energy drink. A screw cap (diameter 32mm) complete with tear-off tamper-proof seal rounds off the profile of this PET bottle. www.nesfluid.fr Beaujolais goes PET APPE has announced that it doubled the amount of PET bottles it supplied for Beaujolais Nouveau Vintage. Other recent successes for the company in the wine sector include a major order for both 750ml and 187ml bottles for a South African winery and the supply of 187ml bottles for in-flight wines to two of Europe’s leading airlines. Total PET wine bottle production for APPE during 2010 has already grown by 45%, with stronger growth forecast next year. A 750ml bottle weighs 50g compared to the typical weight of a same size glass bottle of between 350g to 600g. APPE wine bottles also contain an active barrier system. The PET bottles echo the design of the traditional glass bottle, reinforcing wine’s premium image. They feature a stipple base, which prevents leaks during filling caused by conveyor friction, and incorporate a screw top closure for maximum convenience. They can be filled on the same filling lines and at the same speed as glass bottles. www.appepackaging.com","@ID":43} "PETcontents 03/11 4 PETplanet insider Vol. 12 No. 03/11 www.petpla.net INSIDE TRACK 3 Editorial 4 Contents 6 News 38 Products 40 Bottles 42 Personal care 35 Patents BUYER’S GUIDE 29 Get listed! MARKET SURVEY 22 Suppliers of conveyors for preforms and empty bottles PREFORM PRODUCTION 32 Milky preforms The rapid guide to perfect preforms, part 17 BOTTLE MAKING 34 Automatic handle for edible oil Automated solution from Sipa at JRD, Dubai RECYCLING SPECIAL MATERIAL / RECYCLING 12 The power of sorting An innovative approach from Unisensor, Germany 16 A conference selection 6th China International Recycled Polyester Forum Hangzhou 2010 18 Forum PET Europe launched PETplanet speaks to Jean-Marc Rostagno, First President of Forum PET Europe 20 Maximising use Recycling technology responding to regulatory and market demands 22 Bangladesh recycles First Krones bottle-to-bottle recycling line at Akij 30 From bottles to bags Outdoor specialist Vaude uses rPET for production of bags PREFORM PRODUCTION 31 Raising recyclate in preforms Handling high levels of recyclate in preform machines Page 12 Page 22 Page 30","@ID":6} "MATERIAL / RECYCLING 17 PETplanet insider Vol. 12 No. 03/11 www.petpla.net Caspar van den Dungen, Vice President of European Plastics Recyclers, in his overview about the development of PET recycling in Europe. Arnold Jahn, the new Managing Director of OHL Engineering GmbH presented an outline of the flexibility and capability of OHL´s recycling and decontamination technology. As last year, CCFEI Analyst Cao Wenting provided a detailed study on the economy of PET recycling in China. She underlined the problems caused by shortages of flakes, the narrowing price gap between virgin and R-PET and the need of renovation and innovation in China´s polyester recycling industry. The progress in technology was further demonstrated by Li Zunde, General Manager of Shanghai Machine Sorting Technology Co. Ltd. His company is focused on all kinds of automatic sorting, which is a key factor in reducing labour costs and improve R-PET quality. The final presentation, held by Bjoern Walter, Head of Process & Application Technology Centre at Coperion Najing Corporation, provided an insight on the conversion of bottle flakes to stable fibre without pre-drying, by applying twin-screw-extrusion in combination with automatic filtration. In conclusion, one can say that the 6th China International Recycled Polyester Forum Hangzhou 2010 has evolved from a national event to an international and well-regarded conference that presents wide-ranging information on a quickly and robustlygrowing polyester recycling industry. Anyone interested in purchasing the preprints of this conference should send their request to drthiele@polyester-technology.com or order directly from the web site of CCFEI. www.ccfei.net","@ID":19} "MATERIAL / RECYCLING 30 PETplanet insider Vol. 11 No. 03/10 www.petpla.net From bottles to bags Outdoor specialist company Vaude is taking PET down the route of fashion - it is using recycled plastic PET bottles to create a new collection of bags. After the bottles have gone through their first use, they are cleaned, shredded and turned into fibres. This material is then used in the manufacture of seven bags and two backpacks in the company’s Recycled range. Fashionable bag made from PET bottles These bags are a long way from the image of an old, beat-up PET bottle. The modern designs with quilted seams give either a clean streamlined business look or a gracefully curved wave format. The material used feels like real fabric, with a fine and soft touch. The material used to line the bags and packs is 100% post-consumer recycled PET bottles. The outer material is made from 55% PET fibres interwoven with 45% polyester fibres. Each bag, depending on its size and features, uses about 12 recycled bottles. Prior to their rebirth as a bag, the bottles must first be properly cleaned and caps and paper labels removed. A shredder processes the plastic into chips, which are then used to make the fibres. These can be interwoven with other materials, such as polyester, or used on their own to make, for example, the lining for bags and packs. Built-in raincovers and padded laptop compartments The new bags and packs offer a variety of advantages along with their environmental contribution: the haPET and torPet bags, for example, come with built-in raincovers, padded laptop compartments, and can be slipped on to the handle of a rolling bag for easy transportation. The PETon and PETrik backpacks can carry 23 and 24l of volume, respectively. All the products, including PETula, PETeris and PETje, the three laptop and business bags, are available in a variety of colours. The small agaPET shoulder bag is an ideal pick for city outings; the larger PETronella bag offers expandable volume capacity and two carrying handles, for successful shopping sprees. www.vaude.com Revolution in PET-extrusion! Conical co-rotating MAS-extruder | perfect solution for A-PET, G-PET, PET Co-polymer … | prime pellet / melt quality (IV, b*, AA- content) | very low energy consumption | direct extrusion into sheet | stable melt pressure build up | small foot print paired with robust design | sizes available from 200 kg/h up to 1500 kg/h | suitable for food application M-A-S Maschinen- und Anlagenbau Schulz Gmbh A-4055 Pucking, Hobelweg 1 T: +43 7229 78 999, F: +43 7229 78 999 10 info@mas-austria.com www.mas-austria.com","@ID":32} "MATERIAL / RECYCLING 29 PETplanet insider Vol. 12 No. 03/11 www.petpla.net Akij Group The Akij Group is a heavyweight in Bangladesh with its population of around 150 million. Named after its founding father, Sheikh Akij Uddin, the company achieves a turnover of just under €400 million, with a payroll of about 50,000 people. In the 1940s, when the country was still under British colonial rule, Sheikh Akij Uddin had built up the group from the smallest of beginnings: as a trader in jute, the ‘golden fibre of Bangladesh’ into a conglomerate of enterprises operating in 24 lines of business, which today is managed by his ten sons. Akij is a major player in the cement, printing, chipboard and tobacco industries and operates the world’s biggest jute mill, which employs 7,000 people. Akij is involved in five non-profit-making institutions, including a hospital, an orphanage and a college. The target ratio is 50 : 50 The washing module can be run for as long or as short a time as the client prefers. The downstream decontamination module, which refines half of the non-food-grade flakes, uses relatively high process temperatures and should run with as few interruptions as possible, in order to make best use of energy – which is what it does. The food-grade flakes obtained at the end of this process are used by Akij directly for making PET preforms. The three Sipa and Husky injection-moulding machines for in-house preform production are located in an adjacent hall and specially equipped for processing flakes. At present, AFBL is working with a mixing ratio of 30 - 40% RPET flakes and 60 - 70% new material (granulated). The target ratio is 50:50. The 30:70 / 40:60 mixture is used to make white preforms for cola, juices and water and green ones for two lime-based soft drinks. In future, P.B. Barua also aims to produce brown bottles from recycled flakes, for the company’s ’Speed’ energy drink. Kerbside collections The Akij Group obtains the starting material for the recycling line exclusively from kerbside collections in Bangladesh. It requires at least 12t/day in order to ensure the decontamination module is constantly working to capacity. About 50 sizeable collection centres and many more smaller contact points have covered about half of the nation’s territory, so far. The plans are to extend the catchment area step by step to include all of Bangladesh. Akij buys the merchandise by weight from subcontractors. Since the project was started, the price per kilogram has already doubled, from around 20 to 40 eurocents, because Akij finds itself bidding for the raw material in direct competition with foreign recycling companies. So the PET recycling line’s cost-efficiency is all the more important. The material arrives in the beverage factory’s courtyard in big bags or already compressed. It is in very poor condition, which presents a real challenge. It is mixed with containers made of different types of plastic, and collected at a host of different locations in Bangladesh. The proportion of dirt and sand is very high and the oil content is far from negligible, as beverage bottles are in Bangladesh often misused as oil storage containers, with consequent difficulties downstream. Pre-sorting is very important in order to ensure the requisite starting quality of the material for the recycling line. This separation function, sorting out non-plastic materials, different types of plastic (including multilayer), or sorting into the different colours encountered, can be handled automatically, semiautomatically or by hand. Akij has opted for manual presorting. FDA approval “Approval by the FDA was particularly important for us”, explains P. B. Barua. “We do, of course, monitor both flake quality and bottle quality on a permanent basis, with checks on IV value, moisture, density, crystallisation and colour. What’s interesting for us is the fact that the system runs fully automatically. For the Krones process, the intrinsic viscosity doesn’t have to be as high as for other technologies, which is a definite advantage. The recycling line is high-tech kit, which is why we have to be able to rely on the manufacturer; we need fast feedback and good service support.” Akij recycles; Bangladesh profits. www.krones.de www.akij.net The bottle-to-bottle decontamination module has at Akij been installed on an area of just under 190m². Decontamination proper is handled in a vacuum reactor.","@ID":31} "NEWS 11 PETplanet insider Vol. 12 No. 03/11 www.petpla.net Coca-Cola China award for Husky Husky Injection Molding Systems was presented with the Best Innovation Award at Coca-Cola China’s Supplier Sustainability Summit, which took place in Shanghai, China, November 23-24, 2010. The award was for the development of Husky’s EcoBase preform, which helped Coca-Cola China in its development of lightweighting initiatives. Coca-Cola China used the summit, attended by nearly 150 representatives, to present its 2020 Vision to suppliers, which focuses on addressing sustainability, environmental and social issues. www.husky.ca www.thecoca-colacompany.com Gabriel-Chemie Group expands in Russia Gabriel-Chemie Group’s Russian subsidiary, GabrielChemie-Rus-2, which has production facilities approximately 80km SW of Moscow in Dorokhovo, has completed a number of projects that have increased production capacity from 1,000t to 2,500t. During 2011, capacity will again be increased, to 5,000t. The company has also invested in lab equipment and has increased its Russian-manufactured product range of white masterbatches and additives. Gabriel-Chemie-Rus-2 has appointed anew sales director, Dmitry Grigoriev, a new plant manager, Yury Gribanov, and continues to invest in developing its Russian personnel, with training at Group production sites in Austria, Germany and at other plants. www.gabriel-chemie.com Long-term trends re-emerge in new beverage packaging report Beverage industry information specialist Canadean’s latest special interest report, ‘Innovation in Beverage Packaging 2010’, indicates that the global economic downturn, financial squeeze, volatile raw material prices and declining consumer spending has resulted in a slowdown or complete reversal of longer term beverage packaging design trends. The focus shifted strongly towards cost and cost-related factors, such as materials reduction and improvements in line efficiency, filling techniques and cost-effectiveness. As some countries began to emerge from recession during 2010, longer-term trends towards increased use of added-value and convenience features, more sophisticated packaging materials, smaller ‘onthe-go’ packs and more elaborate shapes, designs and prints, reflecting economic, demographic and consumerled changes, have re-emerged. The last two years have seen discount retailers gain market share from supermarkets, who have responded by extending their own ranges towards the ‘value’ end of the market. Key global trends include continued PET growth in most beverage categories, including refillable PET gaining share in carbonates and packaged water; increased use of hot-fill PET for nectars and juices; a general shift to lighter, more flexible packages and pouches; and greater emphasis on environmental issues. China is now the biggest single source of packaging demand and consumption, with other emerging markets beginning to take off strongly. www.canadean.com","@ID":13} "MATERIAL / RECYCLING 13 PETplanet insider Vol. 12 No. 03/11 www.petpla.net the sorting system can evaluate up to a million spectra per second and can detect accurately even the finest particles. Materials to be eliminated are identified individually, detected at the threshold and blown out. Unisensor claim that “depending on the type of impurity, separation levels of up to 98% can be achieved with a minimum loss of product”. Powersort was exhibited at K2010 in Düsseldorf. We saw the machine in the Unisensor Technical Centre in Karlsruhe in an impressive demonstration. But laboratory conditions in general differ from the tough conditions found on the shop floor. So we visited three customers of Unisensor to ask them about their experience and listen to their comments. They are given below. References We first asked Artenius Packaging in France for an opinion. Then we went to Wellman International in the Netherlands and finally to RecyPET in Switzerland. We saw Powersort in action and we asked questions such as the following: Why Powersort and for what particular purpose? Where – in an established operating recycling line – is the optimum location to install the sensor system, so that it operates efficiently and economically? And, most importantly, how good is the quality of the end product? We heard the following comments: Artenius PET Packaging Europe (APPE) recycling plant/ Beaune/France “Stabilising quality in an established line” APPE, part of La Seda de Barcelona, has been pioneering PET recycling in Europe. APPE in Beaune has an intake capacity of 31,000t in bales and supplies 24,000t in pellet form to the markets, of which approx. 17,000t are so called high quality SuperCycle pellets with food contact approval. A significant portion of pellets are for APPE inhouse conversion into new preforms for demanding customers such as Danone and Coca Cola. Powersort was placed within an existing operating line to improve and stabilise the quality of flakes before extrusion into pellets. Frédéric Blanchard, Plant Director at APPE Beaune, commented: “APPE recycling in Beaune invested in a Powersort from Unisensor last year. The flakes sorter from the German company – with a laser detection system - is able to sort PET flakes at a high output rate. We have installed the system just before the extruder. This amazes even the professionals: oval shapes can also be blow-moulded. Using ProShape – the latest module for the krones Contiform. www.krones.com interpack 2011 Düsseldorf, 12 – 18 May Hall 14, Stand D14/E29","@ID":15}]}}
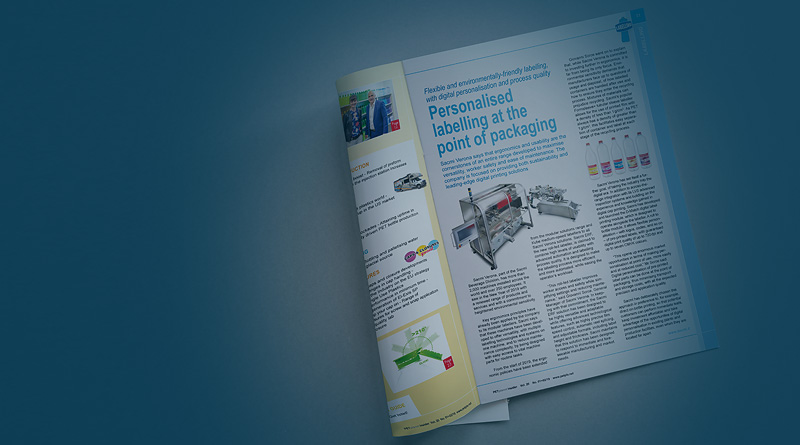