BOTTLING / FILLING PETplanet Insider Vol. 19 No. 09/18 petpla.net 35 PET bottle recycling tles and in 300ml, 500ml, and 1l returnable glass bottles (RGB). The company’s main competitors include Pepsi-Cola International (PCI) and RIHAM Harris International; its recent growth has been less than 0.38% p.a. Recycling procedures for plastic waste are centralised, and the need for recycling is urgent. Around 600t of plastic waste accrues each day in Kampala alone and more than half of it ends up in public spaces, according to the National Environment Management Authority (NEMA). This topic is now a serious political issue and CCBA works closely with authorities including NEMA; the United States Agency for International Development (USAID); the United Kingdom’s Department for International Development (DFID); and the German Society for International Cooperation (GIZ). Around 120 different waste collectors in total deliver recyclable materials to PRI each month but it can utilise only around seven tonnes of the 600t of the capital city’s daily waste. In terms of its own PET bottle products, CCBA currently collects and recycles 34% of the packages it sells; this is expected to increase 40% by the end of the year. There is still some serious persuasion needed so that recycling can become a reality across Uganda; the CCBA group has taken on the challenge. Alongside the positive environmental aspects, the collection process provides work to an estimated 600 – 1,000 people. In the coming two years a focus will be put on stimulating employment for women. Post-consumer plastic waste comes from landfill sites, public and private facilities, or just off the street. By 2030, Coca-Cola plans to recycle one bottle or can for every unit sold and wants to go beyond beverage production, developing Corporate Social Responsibility, environmental protection and recycling in the long term. PRI will be an important driver on a local level, where the goal is the same: to ensure that 100% of plastic packaging generated by Coca-Cola is within the recycling loop by 2030. Rwenzori Bottling Company entrance Century Bottling Company entrance CCBA’s CSD product line: Coca-Cola, Coke Zero Fanta Orange, Fanta Fruit Blast Sprite, Sprite Zero Schweppes Novida Pineapple, Schweppes C+, Schweppes Soda Water, Schweppes Tonic Water Stoney Tangawizi, Stoney Zero Krest Bitter Lemon Power Play Energy Drink Sparletta Pine Nut, Sparletta Cream Soda CCBA’s juice/RTD tea product line: Minute Maid Orange, Minute Maid Mango, Minute Maid Berry Blast Mazoe (Mango) Fuze Tea Lemon Grass Flavour, Fuze Tea Peach Flavour CCBA’s water product line: Dasani Rwenzori Pure Natural Mineral Water CCBA’s set-up Uganda: Century Bottling Company (CBC) Kampala: 4 bottling lines Supplier: 3x Krones lines: 2x PET,1x RGB 1x RGB mixed line: Krones, KHS, Filtec Century Bottling Company (CBC) Mbarara: 2 bottling lines Supplier: 1x PET line: KHS 1x RGB mixed line: KHS, Filtec, EBI, Chantec Conveyors Rwenzori Bottling Company (RBC) Kampala: 5 bottling lines Supplier: 3x SMI (SMI Form) 3x Mesal 2x Husky (HyPET 225 P85/95 E85, G-Line GL 300 PET P100/110 E120) 4x Smargon (SMPA-2G, SM 220 CS, SMP-65, SMP-90) 1x Kronce (C32-R45) Plastic Recycling Industries (PRI): PET flake recycling line Suppliers: 1x Zerma Granulator (GSH500/600) 1x Zerma Granulator (GSH-1000) CCBA‘s PCO 1881 preform range at Century Bottling Company Kampala (2x) and Mbarara (1x) PET preform lines 15.9g, blue 18.72g, clear 18.72g, blue 18.72g, amber 18.72g, green 18.75g, clear 18.75g, green 21.00g, hotfill, clear 21.47g, clear 21.47g, amber 21.47g, green 29.20g, blue 33.00g, hotfill, clear 44.71g, clear 46.60g, clear CCBA‘s 29/25 preform range at Rwenzori Bottling Company Kampala plant 12.80g, blue 19.50g, blue 20.00g, blue 26.70g, blue 38.70g, blue 95.00g, blue 415.00g, blue At the end of 2006 Plastic Recycling Industries (PRI) was acquired by Rwenzori Bottling. Its factory, located in the Nakawa district of Kampala, between the city centre and the Century Bottling Company, employs 46 permanent staff and up to 120 in total, depending on demand. This company, one of the largest recyclers in Uganda, now belongs to CCBA Uganda.,@ID:37}, BOTTLE MAKING 18 PETplanet Insider Vol. 19 No. 09/18 petpla.net New formula and a new rPET container for Ecover detergent A cleaner solution by Ruari McCallion When it changed the formula of its Ecover washing up liquid, People Against Dirty approached R&D Leverage to help it develop a new package that would clearly get across the message that improved cleaning performance is not incompatible with environmental responsibility. People Against Dirty, which was set up to create products that are sustainable and ecofriendly, is better known by the two brands it makes and markets: Method and Ecover. Method was founded in 2001, in California, USA. European company Ecover has a longer history, having launched the World’s first phosphate-free detergent in Belgium in 1979. The two companies merged in 2012. “People Against Dirty was set up to create products that are sustainable and eco-friendly,” said Ryan McSorley, the company’s EU Industrial Design Manager. What sets it apart in the household cleaning market is biodegradability. Its product formulas are all bio-based, and biodegradable. When Ecover began, in 1979, “green” cleaning wasn’t a major segment. Times have changed since then, environmental responsibility is very high on the agenda and it is now the leading green home care cleaner in Europe. It looks different from the established dishwasher detergent; while the best-known conventional brands tend to be green, Ecover is not. The company chooses to avoid using dyes in its products. While Green credentials are laudable, eco-friendly cleaning products also had the reputation of not being as effective as conventional, phosphate and chemical-laden competitors. That has changed. “We improved the formula a lot, in order to give a better experience to the consumer, to make it more efficacious,” McSorley said. “However, we recognised that a lot of people didn’t realise it had changed. So we thought: let’s use design as a way to reposition and allow the consumer to reconsider and reassess the brand.” Ecover detergent had previously been packaged in HDPE, blended with some plant-based plastic. As one of its main USPs (unique selling propositions) is purity and clearness, the decision was taken to design with PET in mind. “We did some work understanding that solution, the HDPE with plantbased plastic, or shifting to a 100% PCR (post consumer recyclate) PET bottle. The PCR PET bottle was the ecologically better option,” McSorley said. That may come as a surprise to some people, especially with the poor press that plastic bottles are getting at the moment. “It was a question of looking at the material properties of both. HDPE doesn’t degrade as quickly when you recycle. When we started adding plant-based plastic to HDPE we found that we struggled to achieve the technical specifications with 100% recycled HDPE, whereas we could with 100% recycled PET (rPET). The bottle we launched with R&D Leverage earlier in 2018 is made of 100% rPET.” Of course, it wasn’t as straightforward as simply switching from HDPE to rPET. Among the challenges was clarity; all rPET currently contains some impurities and it is extremely rare to get bottles made of it that are completely, crystal clear. “Part of the decision process for us was accepting those variations of colour, which can occur depending on the time of year and the source of the recycled material,” he said. Ecover turned this characteristic into an advantage. “We took the greyness and made it a feature in the design language of the bottle. The ribs almost accentuate the greyness but they make it look interesting, rather than a mistake.” People Against Dirty then approached R&D Leverage for help with the final design and for supply of production tooling. It already had some pre-CAD files, acrylic models and some 3D printed models. bottle making,@ID:20}, MATERIALS / RECYCLING PETplanet Insider Vol. 19 No. 09/18 petpla.net 11 this 3D information to understand how it works. During this study, they inadvertently engineered an enzyme that is a step better at degrading the plastic than the one that evolved in nature. “Although the improvement is modest, this unanticipated discovery suggests that there is room to further improve these enzymes, moving us closer to a recycling solution for the ever-growing mountain of discarded plastics,” Professor McGehhan said. The University of Portsmouth and NREL collaborated with scientists at the Diamond Light Source in the UK, a synchrotron that uses intense beams of X-rays, 10 billion times brighter than the sun, to act as a microscope powerful enough to see individual atoms. With help from computational modelling scientists at the University of South Florida and the University of Campinas in Brazil, the team discovered that PETase looks very similar to a cutinase (an enzyme that catalyses the chemical reaction), but it has some un usual features including a more open active site, making it able to accommodate man-made, rather than natural polymers, which suggested that PETase may have evolved in a PET-containing environment. To test that hypothesis, the researchers mutated the PETase active site to make it more like a cutinase; it was then that they found the mutated PETase was better than the natural PETase in degrading PET. The enzyme can also degrade polyethylene furandicarboxylate (PEF), a bio-based alternative to PET. The research team now intends to apply the tools of protein engineering and evolution to continue to improve it. The engineering process is reported to be very similar to that used in the production of enzymes currently found in bio-washing detergents, and in the manufacture of biofuels. As the technology already exists, the teams are optimistic that an industrially viable process could be developed to turn PET and other substrates back into their original building blocks for sustainable recycling. The research was funded by the University of Portsmouth, NREL and the UK’s Biotechnology and Biological Sciences Research Council. www.port.ac.uk www.nrel.gov PETase converts PET to MHET, with trace amounts of TPA and bis-TPA (BHET) as secondary products. The bacteria produces a second enzyme, MHETase (MHETdigesting enzyme), which further converts MHET into the two monomers, TPA and ethylene glycol (EG).,@ID:13}, PETpatents www.verpackungspatente.de PETplanet Insider Vol. 19 No. 09/18 petpla.net 48 Foldable base Europ. Patent No. EP 3257768 A1 Applicant: Sidel Participations, Octeville-sur-Mer (FR) Application date: 17.6.2016 The base of a plastic bottle is designed in such a way that after hot filling, sealing and cooling, a mechanical force pushes from within to regulate the internal pressure in the bottle and/or counterbalances the vacuum arising during cooling. Base shaping Intern. Patent No. WO 2018 / 005816 A1 Applicant: Amcor Ltd., Hawthorn (US) Application date: 29.6.2017 Plastic container with a base shape that takes on a previously defined deformation to reduce the volume after hot filling and cooling, without changing the visible outer shape of the bottle. Distorted bottle surfaces Intern. Patent No. WO 2018 / 008494 A1 Applicant: Toyo Seikan Co. Ltd., Tokyo (JP) Application date: 28.6.2017 A plastic bottle is shaped for stability and manufactured so that it looks like a series of quadratic pieces stacked on top of one another each at 45°. PET container with two openings Disclosure No. DE 102016008290 A1 Applicant: Sven Kopelke, Heidesee (DE) Application date: 1.7.2016 Container made from PET to hold liquid or viscose substances. To simplify removal from the container, it is proposed to provide both sides – top and bottom – with a stable base and resealable dispenser. It makes no difference which way up the container is; the product is always ready to dispense. Base shaping Europ. Patent issue No. EP 3013703 B1 Applicant: Sidel Participations, Octeville-Sur-Mer (FR) Application date: 22.4.2014 The shaping of a PET bottle and especially its base formation and/or shaping of the base surface and adjacent surfaces is issued a European patent. Plastic bottle Disclosure No. DE 102015003514 A1 Applicant: KHS Corpoplast GmbH, Hamburg (DE) Application date: 20.3.2015 Lightweight plastic bottle with specially shaped base and outer wall. Despite its “lightness”, the bottle is sufficiently stable and flexible so can counterbalance any forces caused by a vacuum.,@ID:50}, PETplanet Insider Vol. 19 No. 09/18 petpla.net 45 BOTTLES 50% less sugar – the light Limo Consumer health awareness and their desire for products that contain less sugar are forcing manufacturers to rethink their recipes and introduce appropriate products on to the market. The most recent example of this is a product made by EckesGranini Germany Limited – the light Limo – a further development of, or rather an addition to the “Limo” range but now with 50% less sugar, with its content reduced from approximately 9.0 to 4.5 g/100 ml. Two varieties, “Dark Berries Lemon” and “Lemon Mint”, are now available in the shops. The 1,000ml disposable deposit bottles have the typical brand surface structure of the granini bottles and are decorated with a clear, self-adhesive label which has details of competition prizes for its market launch. www.dielimo.de Rewe’s fruit tea The German discount d r ugs t o r e company, Rewe, has introduced a new drinks combination onto the refrigerated shelves under its own “Rewe to Go” brand. Rewe has comb i ned selected teas with fruit additives, i.e. a jasmine tea with strawberry and a rooibos tea with mango and passion fruit. The products do not contain flavours, preservatives or flavour enhancers. They come in slim, clear 500ml bottles with a large drink opening, decorated with a transparent plastic label. www.rewe.de Mueller milk with protein A recently market launched drink from the Mueller drinks range is helping to provide an adequate supply of body protein, containing 26g of protein in each bottle. Mueller milk protein is available in banana, chocolate and vanilla flavours. They come in white 400ml bottles with technically-cool designer labels. White screw tops with a tamper-proof strip and coloured printing on the top of the closure cap complete the packaging. www.muellermilch.de #ALL4PACK INSPIRE SHARE ACCOMPLISH (*) The new name of EMBALLAGE & MANUTENTION 26-29 NOV 2018 PARIS FRANCE Get your badge with the code PPPA4PALL WWW.ALL4PACK.COM,@ID:47}, MARKET SURVEY 29 PETplanet Insider Vol. 19 No. 09/18 petpla.net Sidel Serac Group Fogg Filler Newamstar Packaging Machinery Co., Ltd. Via La Spezia 241/A 43126 Parma Italy +39 0521 9991 www.sidel.com Mr Stefano Baini Filling Product Manager stefano.baini@sidel.com 12, route de Mamers, BP 46 72402 La Ferté Bernard Cedex, France +33 2 43 60 28 28 www.serac-group.com Mr Roland Nicolas Dairy & Aseptic Business Development Dir. +33 2 43 60 28 32 ronicolas@serac.fr 3455 John F Donnelly Dr. Holland, MI 49424, USA +1616 7863 644 www.foggfiller.com Ms Susan Lamar Media Ralations Manager +1 616 7863 644 slamar@foggfiller.com East Xinjing Road, Zhangjiagang Dvlp. Zone, Jiangsu 215618, P.R.China +86 512 5869 1111 www.newamstar.com +86 512 5867 3920 market@newamstar.com Sidel Matrix SF 300 FM Sidel Matrix SF 100 FM Sidel Matrix SF 700 FM Sensofill FMa Serac Aseptic System 5 (SAS 5) F series 32-216 24-120 32-108 27-100 8-90 1-120 filling valves 12-108 0.2-3.0 0.2-3.0 0.2-2.0 0.2-2.0 0.5-2 0.5-5 0.25-15 4,000-81,000 (18°C) 5,000-81,000 6,000-60,000 6,000-60,000 6,000-48,000 1,200-80,000 80,000 70,000 0-60,000 Up to 36,000 68,000 (18°C) 0-60,000 Up to 24,000 48,000 6,000-48,000 0-60,000 Up to 15,000 48,000 48,000 6,000-48,000 0-60,000 Up to 36,000 Yes Yes Yes Electronic net weigh filling Yes, gravity Yes Yes Yes Yes Yes Electronic net weigh filling Yes, gravity Yes Yes Electronic net weigh filling Cold extended shelf- gravity Yes Yes Yes Yes Yes Electronic net weigh filling Yes, gravity Yes Electropneumatic volumetric filler with flowmeter volume control Electropneumatic volumetric filler with flowmeter volume control, with no bottle/ valve contact Electropneumatic volumetric filler with flowmeter volume control Electronic volumetric filler Electronic net weigh filling; Multiflow (patented) magnetic valves with flow monitoring during filling process; pressure filler tank sterilisable with over-pressured water No metering system- gravity filling vales (to a level) Water valve, hot filling valve, isobaric valve, electronic valve, flometer, weight, liquid level inspection Fully automatic operating computer control; external beverage tank (no ring bowl); electropneumatic components integrated on filling valve; carousels (rinser, filler) and front base driven by servo-motors; available in Combi configuration (blow-fillcap system) For mineral and demineralised water i.e. R.O. (Reverse Osmosis) water; fully automatic operating computer control; external beverage tank (no ring bowl); all parts directly in contact with the beverage inAISI 316; carousels (rinser, filler) and front base driven by servo-motors; available inCombiconfiguration (blow-fill-cap) Quick changeover procedure; fully automatic operating computer control; food safety due to recirculation and CIP (Clean In Place) minimum flowrate control during operation; carousels (rinser, filler) and front base driven by servo-motors; all parts directly in contact with the beverage in AISI 316; flexible platform in terms of beverage category (limpid, with pulp, slurry with particles 10x10x10mm); available in Combi configuration (blow-fill-cap system) 165 production hours without cleaning/sterilisation; 3h downtime for cleaning; high efficiency and filling accuracy; quick beverage and format changeover; available in aseptic Combi configuration (blow-fill-cap system) with dry preform and cap decontamination (Combi Predis FMa Capdis) SAS 5 generation of aseptic filler with liquid PAA; dry controlled H2 02 or e-beam packaging sterilisation; bottle filling-closing with hygienic definition; filling: upfill net weigh filler Rinsers; fillers; cappers; cap sorters, sanitisers, skids,@ID:31}, COMPRESSORS PETplanet Insider Vol. 19 No. 09/18 petpla.net 26 Happy Birthday ABC Compressors! Striving for perfection COMPRESSORS We care about your performance. CAREFORMANCE STAY FLAKESIBLE. DIFFERENT INPUT. STABLE OUTPUT. ACUREMA® Inline Sheet and Preform Flexible for sure: from varying wall thicknesses, IV values and input materials such as PET bottle flakes, skeleton waste, edge trim or mixtures of them directly to the end product in stable, top quality. Food contact compliance included. That’s Careformance! VISIT US: FAKUMA Friedrichshafen / Germany 15 – 20 October 2018 Hall 6, Booth 6314 This year ABC Compressors is celebrating its 75th anniversary. The family owned company, based in Eibar, in the Basque Country, North of Spain, has been producing compressors for the last 75 years. Since its beginning in the early 40’s, ABC Compressors has developed different types of compressors for different types of markets with a well-known characteristic, its robustness. The growth of the company has been deeply designed. After several expansions within its facilities, by the end of the century, it took the plunge to a much bigger and well equipped new factory true to its roots in Eibar. Due to this step, a new horizon came up to the company and its internationalisation was virtually a necessity. The expansion plan started with different agents and services worldwide and reached its peak in 2010 with the opening of two assembly plants in China and Brazil. Since that time the company has developed a very strong and well-prepared service network with presence in more than 120 countries. This is why the company focuses on service as most of the customers claim. The added value are well-trained technicians placed worldwide and the original spare parts stocked closed to the customers. 2015 was a very important year for ABC Compressors with the launch of its new compressor range, Horizon. This range has rough up the compressor sector in the PET market. Thanks to its horizontal design to avoid any vibration, a direct couple motor and a state of the art technology ABC Compressors has strengthened itself in the compressors industry. In addition to this, ABC is focusing on investment in R&D. Thanks to an agreement with one of the famous engineering universities in Spain, ABC has been developing new products and new features to its portfolio. Due to its strategic planning, ABC devoted a significant amount of its income to R&D to keep being the market benchmark. The upcoming two years will be very exciting and important for the company. ABC has closed an alliance with another compressor manufacturer (will be announced soon). This agreement will help both companies to grow faster and keep developing. www.abc-compressors.com,@ID:28}, COMPRESSORS 25 PETplanet Insider Vol. 19 way, the in excess of 20-bar blowing air still amounts to 8-bar compressed air. System pressure is approximately 30-bar and was previously generated via a two-stage process. Compressors began the first stage. The second stage (booster) involved pumping compressed air into the pressure system. Here, Sant’Anna has replaced the old system with the first six Vito compressors of different sizes from Siad Macchine Impianti. Now it goes from ambient to system pressure. Energy savings are also considerable, amounting to 30%. However, savings were not the decisive factor in the decision to buy Siad Macchine Impianti compressors. Also significant in the bidding and rollout phase were an effective partner relationship and complete service provision, according to Dario Ferrero, who underlines the close partnership developed during these years of collaboration with Siad Macchine Impianti. The 18 and 19 filling lines are currently being assembled. This will not only mean an increase in capacity but also a step towards lighter bottles. The fast line, generating 82,000 bph, will in future, produce six-gram 0.5 l ones. This will make the new lines among the fastest PET lines anywhere in the world. “Only in the USA is there a comparably fast system”, says Dario Ferrero. www.siadmi.com,@ID:27}, imprint EDITORIAL PUBLISHER Alexander Büchler, Managing Director HEAD OFFICE heidelberg business media GmbH Bunsenstr. 14 69115 Heidelberg, Germany phone: +49 6221-65108-0 fax: +49 6221-65108-28 info@hbmedia.net EDITORIAL Kay Barton Heike Fischer Gabriele Kosmehl Michael Maruschke Ruari McCallion Waldemar Schmitke Anthony Withers WikiPETia.info petplanet@hbmedia.net MEDIA CONSULTANTS Martina Hirschmann hirschmann@hbmedia.net Johann Lange-Brock lange-brock@hbmedia.net phone: +49 6221-65108-0 fax: +49 6221-65108-28 LAYOUT AND PREPRESS EXPRIM Werbeagentur | exprim.de Matthias Gaumann READER SERVICES Till Kretner reader@hbmedia.net PRINT Chroma Druck & Verlag GmbH Werkstr. 25 67354 Römerberg Germany WWW www.hbmedia.net | petpla.net PETplanet Insider ISSN 1438-9459 is published 10 times a year. This publication is sent to qualified subscribers (1-year subscription 149 EUR, 2-year subscription 289 EUR, Young professionals’ subscription 99 EUR. Magazines will be dispatched to you by airmail). Not to be reproduced in any form without permission from the publisher. Note: The fact that product names may not be identified as trademarks is not an indication that such names are not registered trademarks. 3 PETplanet Insider Vol. 19 No. 09/18 petpla.net In times of globally increasing environmental awareness the acceptance of PET bottles is endangered. It can only be achieved if the negative environmental impacts of PET bottles are eliminated by an efficient recycling system. Otherwise, the PET bottle might suffer a similar fate as the plastic bag. Lacking any recycling system, the latter faces a growing rejection by the consumers. This is a fact I just came across when going grocery shopping with my children. As if this wasn’t stressful enough anyway my eldest daughter didn’t get tired of criticising me for-packing fruits and vegetables from the self-service area in plastic-bags. Her motivation is to protect the oceans instead of the washable goods. Ten days of vacation and according grocery shopping tours later I surrendered and accepted her prioritisation: I put a couple of unpacked peaches on the belt. By doing so, I reluctantly accepted any germs and bacteria which would now most probably contaminate the peaches. However, my daughter’s intentions to make the world a better place were undermined by the cashier: Without any comment she herself took out a plastic bag and packed the peaches in there. Not necessary to mention that my eldest immediately complained about this in total indignation. This anecdote underlines that the industry has to react in order to satisfy the demands of environmentally concerned as well as enlightened consumers. Therefore, the recycling of PET bottles in terms of collecting, sorting, washing and recycling options has to be improved. This issue of PETplanet presents various solutions which strengthen my confidence that the use of PET bottles is perfectly suited to soothe environmentally concerned consciences. Wishing that the next generation creates many critical minds! Yours, Alexander Büchler Dear readers,,@ID:5}, PREFORM HANDLING 12 PETplanet Insider Vol. 19 No. 09/18 petpla.net Quality and efficiency from the start of the process A fresh look at preform handling Preform feeding systems are installed worldwide on every blowmoulding machine used for sorting. Upstream of each feeding system is a tipper which transfers the preforms into the silo of the preform feeding system. Depending on the layout situation, it is also possible that the machines are located in different rooms. The main reason is to have a logistics area and a blowing/filling area. Although the function of the tipper is clear, it is an autonomous machine and is equipped with its own control system and cabinet. Moreover, tippers and their preform feeding systems are built by different manufacturers in most cases. Additionally, equipping the preform silo with a cover (protection against foreign particles) helps to further enhance the signal exchange between the two machines. There is no question that, in addition to technology, each machine also generates additional costs during the administrative process. That is why, towards the middle of last year, Tanner began to offer their customers different preform lines depending on performance and layout options - including also the possibility to install a pallet transport in front of the tipper for an efficient loading process. The tipper is no longer a standalone machine, but one component in the preform feeding system. In addition to reaping the technical advantages, costs have also been cut. The customer receives a complete solution from a single source. Tanner has also placed emphasis on optimising the efficiency and quality of preforms before the block. The concept of blocking the blow-moulding machine and filler, and in some cases the labeller too, means that machine downtime has an even greater impact on efficiency than before. What does this mean for preform handling? Efficiency of the preform line Irrespective of the preform design, layout possibilities, ambient conditions and operator experience, the preform line requires 99.8% efficiency. To date, most line stops are due to inadequate preform feeding systems. “The preforms are becoming lighter, the threads and support rings are smaller – all this makes handling more difficult. In order to achieve optimum efficiency, every detail of the system requires the right technical solution,” Marco Tanner, CEO M. Tanner AG, explained. Particularly with the block concept that is conventional today, which offers no possibility for regulation between the individual machines, efficiency in the first process step is of great importance. Upstream camera inspection To realise the aim of conveying the perfect preform into the blow-moulding machine, the camera inspection for ejecting of oval preforms, preforms with damaged mouths or banana-shaped preforms should take place upstream of the block. “Once a gap in the block has appeared, it can no longer be corrected. That is why we offer an extensive camera inspection upstream of the blow-moulding machine. The aim is to reduce downtime caused by defective preforms,” said Marco Tanner. This not only includes gaps caused by missing preforms, but also the effects caused by a gap. For this reason, the camera inspection at the inlet of the blow-moulding machine is only the second best variant, states the company. A clean preform after the first process step A clean preform is important for many reasons: Before block technology, water rinser was partially used between the blow-moulding machine and the filler. High-quality preform interior cleaning is not just a matter of choice; using ionised air to blow out foreign particles is much more cost-effective, water no longer necessary. “There are many concepts for preform cleaning. We are convinced that only an overhead solution that does not involve submerged nozzles can bring long-term success,” said Marco Tanner, adding, “Everything that can find its way into the preform must be able to get out again. Nozzles or lances are effective for dust removal, but are not suitable for larger particles.” The company is therefore offering an overhead air rinser solution to guarantee efficiency in cleaning out foreign particles as well as dust. Efficient preform cleaning is all the more important when preform/bottle sterilisation takes place in the downstream process. “The majority of germs are found on the particles themselves. Sterilisation without preform cleaning makes little sense. On the contrary we were able to demonstrably improve the results of sterilisation by efficient preform cleaning upstream of the blow-moulding machine,” said Marco Tanner. An overall concept Camera inspection and preform interior cleaning can be integrated into the preform line as well as final UVC irradiation. With or without additional components, the interface to the downstream process does not change. www.mtannerag.ch Marco Tanner, CEO M. Tanner AG An increase in machine blocking in PET filling lines involving machines such as blow-moulding machines, labellers and fillers has meant that quality and efficiency have taken on much greater significance in the first process step – preform handling. The Softhandling solution prevents damages on the preform.,@ID:14}, BOTTLING / FILLING PETplanet Insider Vol. 19 No. 09/18 petpla.net 34 Developments and goals of Coca-Cola Beverages in Africa Soft drinks and recycling in Uganda by Kay Barton With final regulatory approval from the Common Market for Eastern and Southern Africa (COMESA) Competition Commission confirmed in mid-2015, Coca-Cola Beverages Africa (CCBA) was established as an entity created by the 2014 merger of the bottling interests of the Coca-Cola Company, SAB Miller (now AB InBev) and Gutsche Family Investments (GFI), the former Coca-Cola SABCO main shareholder. The three parties who had already been active in the African market for a number of years. The Coca-Cola Company now owns 65.5% of CCBA, and GFI owns 34.5%. The decadeslong experience of both partners in the sector of beverage production continues to influence CCBA and is expected to pave the way for further expansions. Currently, the company is considering the acquisition of AB InBev’s nonalcoholic beverage production plants in Botswana and Zambia, as well as other opportunities. CCBA has three bottling sites in Uganda, with 1,057 permanent employees including those at their subsidiaries. These include two Century Bottling Company factories and Rwenzori Bottling Company factor, which merged in 2016 to become the largest bottler in the country. In Spring 2018, US$8.35m was invested into one of Century Bottling’s factories in Nawanve, near the capital city of Kampala, for a new, German-manufactured water bottling line. The original factory was the first business to open its doors in the new Namanve Industrial Park, in 2001; Rwenzori Bottling is just next door. The second Century Bottling Company factory is 270km away in Mbarara, SouthWest Uganda. Alongside Coca-Cola itself, Fanta and Rwenzori Water are CCBA’s bestselling brands. Its total Ugandan output is 46 million cases, around 44% of which (13 million cases) are water. The remaining 33 million units are made up of CSDs, juices, RTDs, teas and sport and energy drinks. The drinks are bottled in 280ml, 350ml, 400ml, 500ml, 750ml, 1.5l, 2l, 5l and 18.5l PET botCoca-Cola Beverages (CCBA) is the largest bottler of soft drinks for the continent of Africa and the seventh largest bottling partner globally, in terms of revenue, and accounts for around 40% of all Coca-Cola sold in the continent. With over 30 production and bottling sites and 15,000 employees, the beverage giant supplies 550,000 businesses; they, in turn, serve around 249 million people in ten different countries: Ethiopia; the Comoro Islands; Ghana; Mayotte; Mozambique; Namibia; Kenya; South Africa; Tanzania; and Uganda. In many cases, CCBA is also the biggest employer in the country. In this article, we will be taking a closer look at production in Uganda. Collection and sorting point for postconsumer PET bottles,@ID:36}, Professor John McGeehan and colleagues inadvertently engineered an enzyme better at degrading plastic than the enzyme which evolved in nature (photo: Stefan Venter, UPIX Photography) Benjamin Luethi inspecting the I23 beamline detector at the Diamond Light Source which played a major role in the discovery (photo: Diamond Light Source) MATERIALS / RECYCLING PETplanet Insider Vol. 19 No. 09/18 petpla.net 10 A happy accident: PET-eating enzyme performance improved Researchers at the UK’s University of Portsmouth and the National Renewable Energy Laboratory in the USA ‘inadvertently’ engineered an enzyme to be even better at eating plastic than the one originally found in nature. Plastics generally and PET in particular have not been around very long but the impact of discarded, unrecycled plastics on the environment has been little short of disastrous. While nature is resilient and resourceful it is quite surprising to find that a life form – specifically, a bacterium – has already developed the ability to eat, digest and convert plastic back to its constituent components. The ability to enzymatically degrade PET had been thought to be limited to a few fungal species, which means that biodegradation has not been seen as a viable remediation or recycling strategy. A team of scientists, from the Kyoto Institute of Technology and Keio University, Japan, led by Shosuke Yokida, screened naturallyoccurring microbial communities in 250 samples of PET debris from sediment, soil, wastewater and activated sludge close to a recycling facility and, in 2016, isolated a novel bacterium, “Ideonella sakaiensis 201-F6”. When grown on PET, this strain produces two enzymes capable of hydrolyzing both PET and its reaction intermediate, mono(2-hydroxyethyl) terephthalic acid, and convert it back into its two environmentally benign monomers: terephthalic acid and ethylene glycol. The microbial colonies degraded PET film at 0.13mg cm–2 day–1 at 30 °C, which is neither fast enough nor on a sufficiently large scale to be commercially viable. While studying the bacterium discovered by the Yokida team, Professor John McGeehan at the University of Portsmouth, UK, and Dr Gregg Beckham at NREL, in the USA, solved the crystal structure of PETase - the enzyme that digests PET - and used PETase (PET-digesting enzyme),@ID:12}, BOTTLE MAKING 14 PETplanet Insider Vol. 19 No. 09/18 petpla.net Preferential heating for the manufacture of round and oval PET bottles A clean deal with new PET detergent bottles bottle making By investing in a KHS InnoPET Blomax Series IV stretch blow moulder the North Africans have now considerably boosted their capacity and at the same time lent their containers a modern design which saves on materials. Sarl Amir 2000 and its over 225 employees are headquartered in the town of Sidi Chahmi in Oran Province, where its range of products is filled into bottles manufactured on site. In 2017 the company sold 21,000 metric tons of detergent. As managing director Farouk Bordji considers the Algerian market to be more or less saturated, in the next few years he is planning to both develop new products and expand into the neighboring African countries in particular. Sarl Amir 2000 products are among the highquality brands found on the local supermarket shelves, with buyers prepared to pay a slightly higher price for a better constant quality. For the manufacturer it goes without saying that this must be manifested not just in the detergent itself but also in the packaging. In 2016 Bordji thus decided to modernise his production facilities and also increase capacity. At the time the stretch blow moulders the detergent manufacturer was using – three older machines with a respective capacity of up to 1,000bph – had been procured from a Chinese engineering company; Sarl Amir 2000 was increasingly dissatisfied with the bottle quality and system availability. Round or oval “Our PET containers are made by our wholly owned subsidiary Probimex which operates out of the same site. From here the finished bottles are counted into exact quantities and taken to the filling shop next door,” Bordji explains when outlining operations. This special logistics setup means that production reliability in the stretch blow moulding process is thus of great importance. “We therefore looked for a reliable machine which efficiently produces containers of a very high quality,” Bordji adds. Once initial contact had been established, KHS invited the businessman to Hamburg, Germany where he was impressed by the expertise which went into the design of high-quality PET bottles and by the KHS InnoPET Blomax Series IV stretch blow moulder. Personal talks on site soon revealed that the Algerians had found the right machine for their requirements, that KHS was able to give them a number of further benefits following extensive consultancy. As a result three bottle designs were also modernised with the help of the Bottles & Shapes program. The new stretch blow moulder in Sidi Chahmi passed its final acceptance test in November 2017 – and Bordji was very satisfied with the delivered machine. The KHS InnoPET Blomax Series IV is designed for the production of up to 12,000bph and enables both round and oval bottles to be processed using preferential heating (PH). This optional function is distinguished by the special construction of the preform heater. Fabian Partzsch, area product manager at KHS, is responsible for the customer and convinced him of the benefits of the technology. “With oval bottles the preform circumference has to be heated differently at various points to ensure optimum material distribution and thus a high bottle quality. Without preferential heating the preform circumference is heated evenly all round in the stretch blow moulder,” specifies Partzsch. “This means that the areas of the container which come into contact with the blow mould first cool down before the others.” The result is that the PET hardens at these points and the material is distributed unevenly. If, as is the case with preferential heating, a preform is heated selectively according to its later bottle shape, this undesired effect is compensated for and the perfect oval bottle is produced. Higher quality through active heating KHS has made this possible by installing a special heater section at the end of the heating segment. Here, the system first rotates the PET preforms through the heater to obtain a basic heating profile. In the downstream section rotation is stopped, giving the preform its selective heating profile. The new heater box specially developed for this application plays a big role here, transferring the required heating energy to the preform through two opposite heater levels. With this method KHS improves quality, especially regarding the material distribution and stability of the bottle. Another effect of preferential heating is that the intelligent technology allows material savings of up to several grams per bottle to be made. KHS offers preferential heating as an option on every new InnoPET Blomax Series IV; the PH variant can also be retrofitted into existing systems. Besides the machine’s unique technical selling point format changeSarl Amir 2000 in Algeria produces laundry detergents for the home market. To this end, it has now invested in the first KHS InnoPET Blomax Series IV stretch blow moulder with preferential heating for the manufacture of round and oval PET bottles. Sarl Amir 2000 produces some of the best-known brands in Algeria. It has several successful dishwashing detergents, window and bathroom cleaners and toilet cleansers. Amir Clean detergents for various applications,@ID:16}, 40 TRADE SHOW REVIEW PETplanet Insider Vol. 19 No. 09/18 petpla.net TRADE SHOWreview Gneuss presented the Processing Unit (GPU) for 2,000 lbs/h of rPET Gneuss Extrusion Technology showed a complete Gneuss Processing Unit (GPU) including a Multi Rotation System MRS 130 extruder, a fully automatic melt filtration system RSFgenius 150 and an online viscometer VIS, for the processing of 2,000lbs/h of undried and uncrystallised polyester (PET). The Gneuss Processing Unit (GPU) has been available for several years and has been proven itself for the reprocessing of bulky PET waste such as post-consumer bottle flake and industrial waste from fibre and film manufacture without pre-drying. A Gneuss Processing Unit consists of a Gneuss MRS extruder with its unmatched devolatilisation and decontamination performance in combination with a highly-efficient Gneuss Rotary Filtration System and an online viscometer VIS for intelligent dynamic viscosity control. The line on the show floor in Orlando was delivered to a customer in the U.S. to process 2,000lbs/h of rPET into a thermoforming sheet. Although originally developed specifically for PET, the MRS is also running in polyolefin and nylon applications, and being tested on a range of other materials and applications. Thanks to the patented combination of single screw extruder with a multiple screw section, the extruder is very sturdy and particularly well suited for recycling applications. www.gneuss.com State of the art closure manufacturing Sacmi’s research on t he c l osu r es front focuses on the repeatability and precision of continuous processes and on cutting weight and cost. This goes hand in hand with a capacity to respond to the burgeoning market demand for integrated solutions for high-added-value product lines. The Group’s latest cap manufacturing solution with the well-established CCM (continuous compression moulding) range, equipped with the Cool+ mould, offers a good example. The application on show was for the manufacture of a lightweight version of a popular CSD cap. It was just one of several Sacmi has designed for the strategic U.S. market, which is constantly on the look-out for new solutions that combine lower weight, less environmental impact and innovative design. All solutions has been designed with an eye to ‘green packaging’ – ensuring each new plant engineering project has everything covered from every angle: from technological consultation vis-à-vis the finished product (thanks to the advanced research lab, accredited by several key players in the beverage world) to the supply of complete production lines that integrate every aspect of manufacturing. It should also be pointed out that the advantages of this technology, which works at lower temperatures with respect to injection, ensure a high energy efficiency. Sacmi’s solutions allow finishing tasks (slitting, folding and non-destructive testing) to be performed on non flat-top caps; this is thanks to a comprehensive range of slitting-folding machines that work in concert with state of the art inspection systems that allow control of every aspect of cap finishing. www.sacmi.com Swiss Made | www.imdvista.ch IMDvista INOX Line Closure Inspection – 100% inline. Robust, compact and very flexible. One control center (HMI) for the whole line. IMDvista PECO V3 Preform Inspection. Less than 7m² and up to 90’000 pph. Cavity reading. IMDvista PECO LUX Preform Monitoring shot by shot. Requires no additional floor space. No preform orientation. Inspection Systems for the Plastic Packaging Industry F.l.t.r.: Dr Stephan Gneuss (CEO), Heike Fischer (PETplanet) and Monika Gneuss in front of the sold machine,@ID:42}, INSPECTION 37 PETplanet Insider Vol. 19 No. 09/18 petpla.net Fig. 3 Schematic presentation of noninvasive and non-destructive measurement of oxygen ingress into PET bottles Fig. 4 Equipment needed for oxygen ingress measurements Equipment (see Figure 4): 1) trace oxygen meter 2) light guide with the fixed metal fibre holder 3) oxygen-tight cap or any other tight closure 4) safety screw for fixing the oxygen tight cap 5) trace oxygen sensor spot 6) PET bottle The PSt6 (5) trace oxygen sensor spot is placed onto the transparent closure (3). Three seals ensure the closure’s gas tightness. A safety screw (4) is used to fix the closure (3). The reading is achieved by screwing the polymer optic fibre integrated in a metal holder on the outside of the package directly above the trace oxygen sensor. The sensor spot can, alternatively, be glued into the PET bottle, which then can be sealed with a standard closure and read out with a polymer optical fibre without a metal holder. Coated bottles should be transparent but measurement is possible through slightly coloured (e.g. greenish or yellowish) or turbid bottles. Dark brown PET bottles are not suited for direct sensor coatings; a transparent optical window or closure would be required. Filling procedure and measurement conditions Measurements with the final product (beer, fruit juice) in the bottle normally give the best ‘real life’ simulation but beer reacts with oxygen in a similar way to a scavenger. Carbonated water is used as an alternative for beer. A dosing pump fills the PET bottles in a nitrogenflushed glove box (Fig. 6) containing 0.1% oxygen with nitrogen-saturated carbonated water (dissolved oxygen 10 ppb). A pressure tablet (3 g/l) containing sodium carbonate, sodium hydrogen carbonate and citric acid is used for carbonisation. Silver nitrate is added to prevent bacterial growth. Dissolved oxygen content after filling was 50 ppb. Fig. 5 Single-channel and multi-channel measurement set-up Filled bottles were placed on a shaker located in a climate oven. Measurements were taken in a controlled environment at 30 °C and 50% relative humidity. They were conditioned for one hour first and shaken during the process, to assure equilibrium in headspace and liquid. Up to 10 bottles were measured simultaneously.,@ID:39}, 42 TRADE SHOW REVIEW Vol. 19 No. 09/18 petpla.net Via Scodoncello n° 41/E - 43044 Collecchio (PR) - Italy - Tel.: +39 0521 541011 Everything and more... cooperating together global solutions for containers in PET and other plastic materials Design, construction & installation of: • Systems for handling & storing all types of plastic containers • Linear blow molders for PET bottles LANFRANCHI S.r.l. www.lanfranchi.it innovation plastic container Design, industrialization, blow molds & prototype sampling for PET containers IPC S.r.l. www.ipcsolution.it Linear and rotary options for inline blowing and filling with PET bottles With the SincroBloc, a fully integrated PET bottle blowing/ filling/capping systems based on SFL linear stretch-blow moulding units, beverage companies have the opportunity to choose the line that best fits their production requirement for formats of all sizes. This was the highlight on the Sipa booth at NPE. Linear blowers for bigger bottles, shorter runs, and more In the beginning, all SincroBloc models were based on SFR rotary stretch-blow moulding equipment. Some customers of Sipa, especially bottlers of water and edible oil, needed a system, clean and compact like the originals, for larger formats up to 12 litres. For this, only linear stretch-blowers will do. Some customers also want to produce only limited quantities, possibly at only 2,000bph and for this a linear machine is again more appropriate. Outputs from SincroBlocs account for all tastes. For example, rotary types can work at speeds of up to 54,000 small and medium-sized bottles per hour, while a system matching an SFL for large formats with a BigFill volumetric gravity-filling monobloc can push out 4,000 12 l containers over the same period. Versatility in linear and rotary formats The capabilities of the SFL SincroBloc units stretch well beyond big bottles and short runs. They can produce and fill small and large containers, in various formats, including bottles with handles. They can work with all types of liquids, whether they be still water, CSDs, milk, hot-filled products, or products with high added value such as oils, detergents and personal care. All SincroBloc systems are very versatile. For example, any one line, whether it is based on a linear or rotary blower, can produce and fill hot-fill and CSD drinks. Numerous Sipa customers have taken advantage of this feature. www.sipa.it F.l.t.r.: Johann Lange-Brock, PETplanet, Martina Bottarel, Sipa, Heike Fischer, PETplanet and Roberta Gualtieri, Sipa,@ID:44}, BOTTLE MAKING 19 PETplanet Insider Vol. 19 “Right from the first meeting it was obvious that R&D Leverage is really well versed in moulding PET and rPET in particular. They have expertise in making moulds that are really good quality and they were very helpful in solving some of the problems we were having, especially with the rib feature,” McSorley explained. “There was still a lot of challenge in the radiuses of the ribs. Some of them are quite small – 2.5mm or 3mm – and it was very important to get them right so that, when it was blow moulded, we would get the right detail and that it would look good. That was the result of a lot of collaboration with R&D Leverage.” The new Ecover bottle involved several changes from the previous package; in material, appearance and design, as well as the brand image and values that it seeks to convey. The whole process took around six months but the most intense piece was probably the bottle’s ribs. They had to be right; they could not look too flat and to be a clear feature on the design, which would work well with the colours of the rPET, the clear liquid within, the label and the cap. “R&D Leverage was really helpful in getting from the idea to reality,” McSorley said. “We wanted to make sure there’s enough clear space on the bottle, so that it could be detected as transparent PET as easily as possible and to make it as easily recyclable as possible. At the same time, I wanted it to be at home in your kitchen rather than looking like a big fat eyesore, which those bottles often are. Those ribs are a nice way to bring some light and refraction to the top of the bottle. From our point of view, our experience with R&D Leverage was a really solid collaboration.” www.ecover.com www.rdleverage.com 1st Aseptic blower FDA certified in USA ABF 1.2 is the Aseptic Blow-Fill system featuring the very first sterile aseptic blower approved FDA. The GEA ABF 1.2, installed and successfully validated in the USA, obtained the FDA certificate for shelf-stable, low acid beverages produced and distributed in the USA. Thanks to ABF 1.2 each single step of the sterilization process is monitored, whilst the aseptic blower, housed inside a microbiological isolator, avoids any potential risk of recontamination. Another milestone for GEA 10 years after the first FDA certificate received for its PAA based sterilization system.,@ID:21}, COMPRESSORS PETplanet Insider Vol. 19 No. 09/18 petpla.net 32 Monitoring and control devices integrated into the compressors allow users to choose between five different control modes. They minimise idle time and switching losses, depending on whether a compressor is used to cover base or peak loads. In larger compressed air stations, higher-level master control systems with management functions ensure the optimal interplay of individual compressors and perfectly coordinate their operation with the compressed air demand. Dry-compression rotary screw compressors with variable speed control using a frequency converter. When these systems are used in combination with constant-speed compressors, energy savings of up to 25% and more can be achieved. Analysis yields an optimal set-up Based on the air demand analysis (ADA) using Kaeser’s proprietary Kess software, the compressed air specialists concluded that the ideal system set-up for Christinen-Brunnen was two CSG 130-2 SFC aircooled, dry-compression rotary screw compressors (7.5 bar) with a two-stage screw compressor block. Each compressor feeds an energy-saving Sectotec TF 173 refrigeration dryer before the dried air is purified in an FE-177 D microfilter and released into the network. Asked about his new compressed air supply, plant manager Peter Wohlberg is all smiles. Now it takes just two compressors to match the performance of eight systems from another provider in the previous installation. As Wohlberg explains, that means more than energy savings when producing and treating compressed air. It has brought a 75% reduction in the maintenance and servicing costs, and has completely eliminated the costs for providing and operating the coolant system for the old water-cooled equipment. The Kaeser compressors are air cooled and require no elaborate additional installations. Moreover, the warm exhaust air is practically recycled. It is used to heat the production halls adjacent to the compressor station, thus saving heating costs. Peter Wohlberg is confident that the compressed air system will pay for itself in well under two years. www.kaeser.com D 16. – 20. OCTOBER 2018 a FRIEDRICHSHAFEN The Entire World of Plastics International trade fair for plastics processing @www.fakuma-messe.com B g +49 (0) 7025 9206-0 fakuma@schall-messen.de Organizer: P. E. SCHALL GmbH & Co. KG 26th Fakuma ! More than 1700 exhibitors from all over the world will present global offerings for technologies, processes and products made of plastic, as well as equipment and tooling for plastics processing, in 12 exhibition halls. You’ll be awaited by flexible, individualised solutions for current and future challenges faced by the automated, globalised economy. 4 Injection moulding machines 4 Thermal shaping technology 4 Extrusion plants 4 Tool systems 4Materials and components,@ID:34}, MARKET SURVEY 27 PETplanet Insider Vol. 19 No. 09/18 petpla.net 09/2018 MARKETsurvey Resins & additives Preform machinery Preform production Preform inspection SBM 2-stage Compressors Filling equipment & filling inspection Caps & closures and inspection Palletising & shrink film machinery Recycling Supplier of filling equipment and filling inspection systems It’s time to present some state-of-the art filling equipment and filling inspection systems in our PETplanet Insider. Have a look at the technical details provided by: Sacmi Imola, Sipa S.p.a., Krones AG, SMI S.p.a., Filtec, KHS GmbH, Sidel , Pressco Technology Inc, Serac Group, Fogg Filler, Heuft and Newamstar Packaging Machinery Co.Ltd. Although the publisher has made every effort to make sure that the information in this survey is up to date, no claims are made regarding accuracy and completeness. Filling Equipment Company name Sacmi Imola S.C. Sipa Postal address Telephone number Web site address Contact name Function Direct telephone number E-Mail Via Selice Provinciale, 17/A, C.P. 113 - 40026 Imola (BO), Italy +39 0542 607111 www.sacmi.com +39 0542 607111 sacmi@sacmi.it Via Caduti del Lavoro n. 3 31029 Vittorio Veneto (TV), Italy +39 0438 911511 Mr Matteo Tagliaferri Marketing and Communication +39 0521 548111 matteo.tagliaferri@zoppas.com 1. Machine designation / model number AWS/ESF IsoFill P StillFill EVO Flextronic C Flextronic SE Flextronic S Flextronic W BigFill 2. Number of filling heads (range: from/to) 32-192 20-160 20-120 50-180 20-180 20-180 20-96 12-24 3. Min to max bottle contents (in liters) 0.250-10 0.125-3 0.125-3 0.125-3 0.125-3 0.125-3 0.125-3 3-20 4. Filling speed: output (bph) (min to max): 10,000-80,000 specifiy: 1l bottle / still water (bph) 20,000-50,000 60,000 62,000 60,000 62,000 63,000 36,000 16,000 (3l) 1l bottle / CSD (bph) 20,000-50,000 51,000 (CMW) 55,000 (CMW) 1l bottle / milk (bph) 62,000 62,000 36,000 1l bottle / juice (bph) 20,000-50,000 53,000 60,000 59,000 62,000 62,000 36,000 5. Filling process Pressureless (still drinks) Yes Yes Yes Yes Yes Yes Yes Yes Pressure filling (carbonated drinks) Yes Yes Yes Hot filling Yes Yes Yes Cold aseptic filling No Juices with high pulp content Yes Yes Yes 6. Type of filling valve and metering system Electronic flowmeter isobaric mechanical level filling valve mechanical gravity filling valve isobaric volumetric filling valve gravity volumetric filling valve gravity volumetric filling valve electronic weight filler gravity volumetric filling valve 7. Special features (short description / keywords) Can filler AISI 316L SS valve; product deflection without deflector on the filling tube; quick changeover for different neck diameters AISI 316L SS valve; product deflection without deflector on the filling tube; quick changeover for different neck diameters AISI 316L SS valve; product deflection without deflector on the filling tube; quick changeover for different neck diameters AISI 316L SS valve; no contact between the valve and the bottle neck; quick changeover for different neck diameters AISI 316L SS valve; no contact between the valve and the bottle neck; quick changeover for different neck diameters AISI 316L SS valve; no contact between the valve and the bottle neck; quick changeover for different neck diameters AISI 316L SS valve; no contact between the valve and the bottle neck; quick changeover for different neck diameters,@ID:29}, INSPECTION 38 PETplanet Insider Vol. 19 No. 09/18 petpla.net Fig. 6 Glove box filled with nitrogen Bottles tested Several treated PET bottles (Table 2) were investigated for oxygen ingress rates: monolayer bottles with external coating (bottle type 1); monolayer with an additional active barrier (bottle type 2); internal surface coated bottles (bottle type 3); and three-layer bottles examples (bottle type 4). Bottle type Coating Weight Volume Scavenger 1a No 38 500 No 1b LC2a 38 500 No 2a No 38 500 2% 2b LC2 38 500 0% 2c LC2 38 500 1% 2d LC2 38 500 0.5% 3a No 31 500 No 3b Actis 31 500 No 4a three layers 28 500 No 4b three layers 28 500 Yes Table 2 Bottle types investigated Calculation of total oxygen and determination of the Barrier Improvement Factor (BIF): If two comparable bottles are tested but with different oxygen barrier layers, the BIF (barrier improvement factor) can be calculated by dividing the oxygen transmission rate (OTR) of the uncoated bottle by the OTR of the coated bottle. Results Bottle type 1: LC2 external coated PET bottles compared to an identical non-coated PET bottle Fig. 7 Composition of the external LC2 coating Figure 8 shows oxygen ingress into the LC2 coated and reference non-coated PET bottle, over a period of more than 25 days. In the first 48 h the increase of oxygen concentration in non-coated bottles and bottles with LC2 external coating is high and non-linear. The reasons for this are the migration of matrix oxygen dissolved in the PET bottle wall into the liquid; and the “steady-state” permeation stage, where oxygen molecules move through the PET bottle wall to the interior. Externally-coated PET bottles display similar oxygen ingress rates as non-coated reference bottles at the beginning of the measurement, up to the point when a new equilibrium is established. The LC2 barrier coating reduces the rate of subsequent permeation, illustrated by a significantly decreased slope. Fig. 8 Oxygen ingress into an externally LC2 coated PET bottle compared to non-coated reference bottle Total dissolved oxygen can be calculated from the slope of the curve; permeation in mg O 2 /l/day = ppm/day (or μg O 2 /l/day = ppb/day). Maximum oxygen concentration allowed in beer is 1mg/l (1,000ppb). Theoretical shelf-life can be calculated by dividing maximum allowed concentration by the slope of oxygen increase. Results are shown in Table 3. LC2coated noncoated Total bottle volume [ml] 518.00 518.00 Liquid [ml] 495.30 496.40 Headspace [ml] 22.70 21.60 Headspace [%] 4.58 4.35 Temperature [°C] 30.00 30.00 Z-value 2.64 2.55 Slope for dissolved O 2 a [ppb/day] 7.13 38.33 Slope total O 2 [ppb/ day] 18.80 97.90 Calculated shelf-life (days) 53.19 10.21 Table 3 Shelf-life increase of LC2-coated bottles A shelf-life of approximately 53 days is not sufficient. Bottle type 2: PET bottles with LC2 external coating and/or different contents of oxygen scavenger Matrix oxygen dissolved in PET can be removed by adding an oxygen scavenger into the PET material. Fig. 9 Oxygen ingress into treated PET bottles; (A) non-coated PET bottle with 2% scavenger, (B) LC2 coated PET bottle with no scavenger, (C) LC2 coated PET bottle with 1% scavenger, (D) LC2 coated PET bottle with 0.5% scavenger. The addition of 2% amosorb scavenger to the PET bottle (A) removes matrix oxygen. However, after eight days there is a significant increase of oxygen, which can be attributed to,@ID:40}, PETplanet Insider Vol. 19 No. 09/18 petpla.net 47 BOTTLES Bath time fun with pearls The discount drugstore firm, dm, is always looking to expand its “Sau Bär” brand, a range of bathing and hygienic products for babies and toddlers which grab children’s attention by their package design and product appearance. The most recent example of this is the pearl shower, a clear shower gel that contains washing agents derived from active plant-based ingredients. The children’s attention is not only drawn by the small coloured beads and air bubbles floating in the product but also by the scent which reminds them of sweets. The product comes in a clear 200ml plastic bottle with a partially transparent adhesive label and screwed-on hinged lid with dispensing spout. www.dm.de Mouthwash makes teeth white The new improved Colgate Max White Expert mouthwash promises instantly noticeable and permanently whiter teeth. According to the manufacturer, the alcohol-free mouthwash should be used twice a day for the best results. A dispensing cup is provided for use in gargling the contents. The mouth is then washed out with water. The white, easy-to-handle 500 ml bottle has two selfadhesive labels. The front one includes a slightly reflective, eye-catching layer. The top closure is covered with a shrink film with perforations for easy removal as a practical tamperproof protection. It also serves as additional advertising space. www.colgate.de,@ID:49}, PETcontents 09/18 4 PETplanet Insider Vol. 19 No. 09/18 petpla.net INSIDE TRACK 3 Editorial 4 Contents 6 News 43 Products 44 PET bottles for Beverage + Liquid Food 46 PET bottles for Home + Personal Care 48 Patents MATERIAL / RECYCLING 9 Future looking investment pays - rPET instead of virgin PET for producing food trays 10 A happy accident: PET-eating enzyme performance improved PREFORM HANDLING 12 A fresh look at preform handling - Quality and efficiency from the start of the process BOTTLE MAKING 14 A clean deal with new PET detergent bottles Preferential heating for the manufacture of round and oval PET bottles 16 6 g PET loss is a big win - Agr Process Pilot advances GEPP light weighting projects in Mexico 17 “The impossible, of course, may take a little longer!” 18 A cleaner solution - New formula and new rPET container for Ecover detergent COMPRESSORS 20 Getting into shape - Every day, one AF compressor is shipped somewhere in the world 23 Shaftless motors - The bottom line on drive efficiency 24 “When you live high up you can see for miles” 26 Striving for perfection - Happy Birthday ABC Compressors! 31 Clean compressed air - Best quality goes into the bottle MARKET SURVEY 27 Suppliers of filling equipment & filling inspection BOTTLING / FILLING 34 Soft drinks and recycling in Uganda - Developments and goals of Coca-Cola Beverages in Africa INSPECTION 36 Six months shelf life for beer and CSD - Non-destructive testing of oxygen transmission in PET bottles TRADE SHOW REVIEW 40 NPE 2018 review, part 2 BUYER’S GUIDE 49 Get listed! Page 24 Page 36 Page 12 18 bottle making COMPRESSORS,@ID:6}, COMPRESSORS PETplanet Insider Vol. 19 No. 09/18 petpla.net 20 Every day, one AF compressor is shipped somewhere in the world Getting into shape Every day for the past 10 years someone, somewhere in the world, has taken delivery of a new AF Compressor. Belgium enterprise Ateliers François S.A., the privatelyowned company better known as AF Compressors, is rapidly approaching its 150th anniversary; for 30 of those years, since the early 1980s, it has been a leader in the manufacturer of compressors specifically designed for the needs of PET bottle production. Its share of the blow-mould market is now estimated at 60%; it produces 400 units a year, 95% of which are destined for PET blow moulding applications. It has a global turnover of € 100 million annually, and has a client list that includes Coca-Cola, Pepsi-Cola, Danone, Nestlé Waters, and Ting Hsin, as well as major blow mould machinery manufacturers. COMPRESSORS PETplanet Insider (PP): What is it that distinguishes AF Compressors from its competition? Pascal Heyden, Sales & Marketing Manager, AF Compressors (AF): The three-stage PET compressors built by Ateliers François feature a distinctive ‘’L-shape’’, for optimum efficiency while using fewer moving parts, and enabling slow operating speeds. The initial compression of the air is carried out in the first stage by one large, double acting, vertically arranged piston. Final compression up to 40 bar pressure takes place in the second and third stages by two horizontal pistons mounted on the same piston rod, each of which is single acting. The compressor is driven by a centrally mounted crankshaft and by an electric motor up to 550 kW. Shaft power requirements for all AF Compressors are below the nominal rating of the installed motor, which means that all motors are provided with a service factor of 1.0. PP: How did AF Compressors get to its leading position in the market? AF: The company has diversified its product portfolio over the years, in response to customer demand, to include two-stage, oil free, piston compressors providing 7-10 bar oilfree air utilising the same “L-shape” design and turn-key package as offered with their high-pressure PET compressors. The “OPC series” of compressors, with capacities from 7.2m³/min up to 58m³/min, can be equipped with the same optional energy efficient solutions offered on the 20-40 bar compressor packages. With hundreds of OPC references now installed, mainly in the PET and beverage industry, AF Compressors is established as a complete system provider for both high and low pressure compressed air applications, with full global aftermarket support and service capability to the customer. PP: How does the company support its customers in the field? AF: Our Belgium HQ is the heart of our operations and, in January 2018, we inaugurated our brand new Service Headquarters, located near our main factory in Liège, close to Liège Airport and just one hour from Antwerp port by truck. This facility provides rapid response of replacement parts needs direct to customer’s facilities around the world. Orders placed before 3 p.m. Belgium time can be shipped the same day, by via air freight. The new Service HQ manages the storage, preparation, and shipping of all completed compressor packages produced in the factory. PP: Does AF deliver all global support from Belgium? AF: Definitely not! Global expansion requires global presence, in order to deliver the levels of support our customers expect. AF now has three production centres: in Belgium, in China, and in India. It has 15 subsidiaries, two distribution centres, 20 official agencies and multiple spare shops. No less than 150 of our 400 (or so) employees are specialised service engineers, specifically trained for 40 bar compressors. Official training centres, available to clients for improving the skills of their in-house personnel, are located in Belgium, China, India, South Africa, Dubai and the USA. PP: AF has a reputation for high levels of reliability in use. However, the market is changing and new technologies are emerging, in the PET industry as much as any other. How is the company changing to meet the demands of the industry, such as from emerging economies? AF: AF has evolved its mindset from being “just another manufacturer”,@ID:22}, COMPRESSORS PETplanet Insider Vol. 19 No. 09/18 petpla.net 23 The bottom line on drive efficiency Shaftless motors PET bottle blowing is an energy intensive process. It is therefore important that the compressors powering the bottle blowing machines are operating as efficiently as possible. Bellis and Morcom’s range of shaftless motor drives claim to eradicate inefficiencies which can occur when using traditional drive systems for PET compressors. COMPRESSORS Oct. 24-26,2018, Mumbai German Technology One of the benefits claimed for the shaftless motor is that it is connected directly to the compressor crankshaft, transmitting 100% of the motors output power directly into the compressors running gear. According to the company, this solution results in fewer wearing parts and a reduced machine footprint. Other benefits, states the company, relate to the transfer of power from the compressor motor. Even the smallest issues here can have a large impact on energy consumption. For example, a single 500 kW PET compressor may cost over $ 400,000 a year to run. However, even a 1% loss of efficiency on the drive system can add over $ 4,000 in energy costs. Many conventional compressors use inefficient belt drive systems, which operate with inefficiencies of between 5-7%. This can rise to as much as 12% after belt wear and friction losses, depending on the maintenance schedule that a plant has in place. As a result, a drive belt drive system could be costing as much as $ 50,000 per compressor every year in wasted energy. By contrast, the company claims that their shaftless motor reduces absorbed power and can eliminate the losses that may be incurred by a belt drive system. The company offers its shaftless motor technology as standard on compressors rated above 110 kW. A further benefit which the company claims for its shaftless motor is reduced maintenance. Regarded as a necessary evil by most operators, the shaftless motor requires no maintenance, thus eliminating the routine maintenance required by traditional belt drives, such as belt tensioning, replacement, motor alignment and coupling checks, are eliminated with shaftless motor technology. Another factor is that businesses have become increasingly wary of purchasing a compressor for a low upfront capital cost, only to find maintenance issues arise further down the line and any initial capital purchase savings are lost to unscheduled repairs. Finally, the company points out that in the forty years they have been supplying the PET market, the savings due to improved motor performance and reduced maintenance can yield considerable cost savings and improve the bottom line. www.gardnerdevner.com/ shaftlessmotors The shaftless motor factory View from the top: a shaftless motor,@ID:25}, 7 NEWS PETplanet Insider Vol. 19 No. 09/18 petpla.net PTT Global Chemical, TOC Glycol and Mitsui Chemicals sign JV in Thailand PTT Global Chemical PLC (GC) together with TOC Glycol Co., Ltd. (TOCGC), a subsidiary of GC Group, announced the signing of joint venture agreements with Mitsui Chemicals Inc. (MCI), to cooperate in managing Siam Mitsui PTA Co., Ltd. (SMPC), a PTA producer, and Thai PET Resin Co., Ltd. (TPRC), a PET producer. GC and TOCGC will hold 74% of the shares in SMPC and TPRC, while Mitsui Chemicals will hold 26%. Under the joint venture, GC will supply the feedstock Paraxylene (PX), a key raw material for PTA, and TOCGC will supply Mono Ethylene Glycol (MEG), a key raw material for PET. MCI will provide technology know-how, technical support as well as the marketing and sales network. GC, the chemical flagship of the PTT Group, operates in eight areas of businesses. It has a combined chemical and petrochemical capacity of 10.2mt/a and a crude oil and condensate distillation capacity of 280,000 barrels per day. PTTGC is expanding its business into performance and speciality chemicals. MCI is one of the leading petrochemical companies in Japan as well as globally, with turnover of approximately 1,329 billion Yen in 2017 with approximately 17,277 employees. MCI maximises the group’s strengths by focusing on a truly global platform and diverse human resources and a technological progress to produce material to meet customer needs including creating high-value-added products and services. www.pttgcgroup.com With Sacmi, the beverage specialists are always at your side. With our unbeatable technological know-how and continuous research we are creating new containers and closures designed to ensure outstanding performance. The new IPS injection system for preforms, the CCM compression press for caps and the quality control systems fully designed and built by Sacmi, allows for large-scale production with considerable advantages in terms of efficiency and flexibility. The outcome? Reduced plastic volumes, less energy consumption and lower running costs.All in a bottle: the one you’ll soon be making. SAVE THE DATE http://www.sacmi.com/en-US/Events/Packaging From left: Patiparn Sukorndhaman, Chairman of the Board of Directors of TOC Glycol Co., Ltd.; Mr Supattanapong Punmeechaow, President and CEO of PTT Global Chemical PLC (GC); and Mr Tsutomu Tannowa; President and CEO, Mitsui Chemicals Inc.; were on hand to sign the JV agreements.,@ID:9}, BOTTLE MAKING 16 PETplanet Insider Vol. 19 No. 09/18 petpla.net Agr Process Pilot advances GEPP light weighting projects in Mexico 6g PET loss is big win bottle making This impressive weight decrease has been accomplished against a backdrop of shifting environmental conditions that add an extra layer of complexity to the blow moulding process. Despite temperature swings of 40°C or more throughout the day, Line 1 at GEPP’s Hermosillo plant, in the northwestern Mexico state of Sonora, turns out PET bottles that consistently hit the new light weighted target as it operates around the clock. Successful light weighting demands rigorous adherence to the material distribution recipe developed for the bottle type. That is a lot harder to do when working with less material, observes GEPP Corporate Technical Manager Jesús López. Introducing a new level of control over bottle blowing, the Agr system provides the acute precision necessary to offset the impact of Hermosillo’s fluctuating temperatures. As López explains, “You don’t want to put the same amount of heat on a 90-degree preform as a 70-degree preform.” Pilot’s high-precision sensors, deployed in the blowmoulder takeout area, measure the thickness of each bottle at 12.5mm intervals along the sidewall. Agr’s proprietary algorithms instantaneously analyse the measurements and compare them to the recipe. If material distribution starts trending out of spec, Pilot adjusts the appropriate blowmoulder function control - for example, tweaking the preblow setting or lamp temperature - to maintain consistent production. Eliminating the need for manual intervention, which is frequently an exercise in guesswork even for skilled operators; this automated fine tuning makes sure the right amount of resin is distributed to the right area of the bottle, regardless of ambient conditions.The bottom-line impact of less material consumption, the Agr system has enabled GEPP, the exclusive bottler of PepsiCo trademark beverages in Mexico, to make other major productivity gains, especially when it comes to changeover. Hermosillo’s Line 1 produces a mix of no-, low-, and high-carbonation bottles for six different products: Pepsi, 7UP, Mirinda (an orange-flavoured soda), Manzanita Sol (apple flavour), Limonada (lime), and Epura (water) in multiple sizes: 600ml, 1l, 1.5l, 2l, 2.5l, and 3l. Changing from one container to another used to take an average of 2h - about 1.5h to replace the moulds in the 16-station blowmoulder, and then another half-hour for process verification and quality checks. Now, with the Process Pilot installed, the blowmoulder produces good bottles on start-up, with no need for sampling and tweaking, making each changeover 25% faster, while also saving 6,000 bottles from scrap. The benefits of robust bottle production also show up downstream in the integrated bottle-making and filling plant. López has noted far fewer disruptions in labelling, capping, and shrink wrapping due to non-conforming bottles. On the infrequent occasions when jams occur, “Pilot brings the process back to baseline two to three times faster,” he says. A seasoned bottle veteran who was heavily involved in GEPP’s transition to PET from glass in the mid-1990s, López is responsible for all PET operations across the company’s 25 plants. Hermosillo, with its long-established history and operations team, represents the first site to mount a light weighting initiative in conjunction with the Process Pilot. The success of that effort, in tandem with faster blowmoulder start-ups, shorter changeovers, rapid jam recovery, and reduced scrap, has generated an attractive return on investment, not only on the 2l container but other sizes and types as well. It gives GEPP the confidence of improved bottle quality, which for López is the “paramount” consideration. Looking ahead, López would like to “standardise as much of the equipment and process as possible.” He nurtures the vision of installing the system on Hermosillo’s second blowing line and establishing the plant as the training site for all GEPP blowmoulder operations throughout the country. “Process Pilot manages how the blowmoulder makes the bottle so it always comes out the same,” López concludes. www.agrintl.com www.sidel.com With an Agr Process Pilot automated blow moulder control system mated to a Sidel SBO 16 universal blow moulder, Mexican beverage producer GEPP has trimmed the weight of its 2 l low carbonation PET bottle from 52 g to 46 g. Given blow moulder operating speeds of 24,000 bph, the 6 g reduction is saving the company approximately 7 t of resin over each 48 h production run.,@ID:18}, COMPRESSORS 33 PETplanet Insider Vol. 19 To ensure top-quality compressed air, the company operates a state-of-the-art compressed air system with dry-compression rotary screw compressors, energy-saving Secotec driers and the corresponding filters. To further optimise the energy efficiency, the heat produced by the compressors is used to heat the adjoining rooms. The SAM 4.0 is a compressed air management system that not only monitors the individual components of a compressed air station, but also coordinates their operation to keep energy consumption as low as possible. Kaeser Kompressoren, a family-owned company, is one of the leading manufacturers and providers of compressed air products and services. Established in 1919 as a machine workshop, Kaeser currently has two manufacturing sites in Germany. The company employs approximately 6,000 people worldwide. Kaeser offers the following products and services: rotary screw compressors, reciprocating compressors, road-going portable compressors, dental compressors, compressed air management systems, vacuum pumps, blowers and filters, dryers. As well as compressed air tools and accessories, consultation and planning, compressed air demand analyses and finally contracting (operator models for compressed air stations). Tech-Long offers a complete line of high-speed packaging solutions to deliver BOTTLE MAKING 15 PETplanet Insider Vol. 19 No. 09/18 petpla.net overs can be made in a short space of time. Operators can switch from the PH function for oval bottles to standard heating and back at the press of a button. New bottle design for more success at the POS On its current generation of machinery Sarl Amir 2000 now produces one round and two different oval bottles. All three were redesigned AF COMPRESSORS HIGH & LOW PRESSURE OIL FREE AIR SOLUTIONS THE WORLD LEADER OF PET COMPRESSORS +6000oil free piston PET compressors in+175 countries www.afcompressors.com when the old plant engineering was replaced. In its Bottles and Shapes program KHS designs containers to suit the individual demands of manufacturers and consumers. KHS’ designer first submitted handdrawn suggestions to the Algerian detergent manufacturer which the partners then jointly put into practice following the assessment thereof. The more modern designs not only appeal to buyers at the point of sale but also save on resources by using less material. In combination with new stretch blow moulder, Sarl Amir 2000 is thus lowering its costs per bottle. “Our InnoPET Blomax Series IV runs at more or less top capacity from 8a.m. to 4p.m. every day,” states Bordji. “In a very short time indeed we’re thus producing more and higher quality bottles than before.” Thanks to the machine’s high availability personnel planning has also become much easier. As manual infeed is now a thing of the past and fewer operators are required, the manufacturer has been able to free up capacities for other tasks. “However, what’s far more important than all of these advantages is that we’re also noticing an effect on the shelves,” says Bordji. Customers have received the new designs very well which contribute to the positive, high-quality image of the entire brand. “With this we’re also setting ourselves apart from the competition – which can help us to achieve further growth on a saturated market,” concludes Bordji. www.khs.com,@ID:17}, MARKET SURVEY 30 PETplanet Insider Vol. 19 No. 09/18 petpla.net Filling inspection systems Company name Sacmi Imola S.C. Filtec Europe GmbH KHS GmbH Pressco Technology Inc Fogg Filler Heuft Systemtechnik GmbH Postal address Telephone number Web site address Contact name Function Direct telephone no. E-Mail Via Selice Provinciale, 17/A, C.P. 113 - 40026 Imola (BO), Italy +39 0542 607111 www.sacmi.com +39 0542 607111 sacmi@sacmi.it Osterrade 56, 21031 Hamburg, Germany +49 40 7393350 www.filtec.com Dr Joachim von Meyer Dir. Europe Africa Middle East +49-40-7393350 jvonmeyer@filtec.com Juchostraße 20, 44143 Dortmund, Germany +49 231 569 0 www.khs.com Mr Helmut Schmitt Project Man. Inspection Tech. +49 231 569 10124 helmut.schmitt@khs.com 29200 Aurora Road, Cleveland, OH USA +1 440 498 2600 www.pressco.com Mr Tom O'Brien (VP, Marketing) Sales & New Business Dev. +1 440 498 2600 sales@pressco.com 3455 John F. Donnelly Dr. Holland, MI 49424, USA +1 616 786 3644 www.foggfiller.com Ms Susan Lamar Media Ralations Manager +1 616 786 3644 slamar@foggfiller.com Am Wind 1 56659 Burgbrohl, Germany +49 2636 56 0 www.heuft.com Fill level control Infrared Yes Yes No No Gravity fill - it fills to a specific level Yes (over- and underfill + quantifiying and statistics per filler valve) X-ray Yes Yes Yes No Yes (over- and underfill + quantifiying and statistics per filler valve) Gamma No Yes No No No, because old technologie with no advantages compared to x-ray Camera Yes Yes Yes, all possible in high frequency Yes Yes (over- and underfill + quantifiying and statistics per filler valve) Contamination control Yes Foreign substance inspection (sniffing) for empty ref PET bottles No Full exended shelf life line options; UV sanitising for bottles and caps; chemical rinsing for bottles and caps; multiple enclosure options with optional HEPAair system; machinery comes standard with Fogg Sanibar systemwith additional enclosure wash options Detection of foreign objects and dirt in filled containers, detection of foreign objects, dirt and residual liquids in empty containers Closure inspection Presence of cap Yes Yes Yes Yes Yes (camera or sensor technologie) Crooked cap Yes Yes Yes Yes Yes (camera or sensor technologie) Lifted cap Yes Yes Yes Yes Yes (camera or sensor technologie) Wrong cap Yes Yes Yes Yes Yes (camera or sensor technologie) Tamper evident band control Yes Yes Yes Yes Yes (with 360° all around view) Camera: 360° / sensor Yes Yes Yes, both Yes Yes (with up to 16 cameras) Label inspection Torn label Yes Yes No Yes Yes (with 360° camera inspection) Vertical / horizontal misalignment Yes Yes Yes Yes Yes (with transmitted light or 360° camera inspection) Best-before date control Yes Yes Code presence inspection No Yes (presence check with sensor, or verification with camera) Camera: 360°/ sensor Yes Yes Camera and sensor Yes Yes (sensors for label presence check or multiple cameras for 360° label verification in several levels) Pressure leak detector Yes squeezer No Yes (active or passive pressure/leakage check) Applicable bottle type Diameter 114 Per customer requirement 40-110mm Up to 150mm 8\ All usual diameters Height 363 Per customer requirement 150-360mm Up to 400mm \18 All usual heights Rejecting bottle Yes Yes Into bin and onto collecting table Push reject and diverter reject options available Yes (various rejection systems for different rejection tasks) Inspection speed Up to 80,000bph Per customer requirement PET: up to 86,000bph Over 3,000ppm Up to 100,000 containers/h, 2,000mm/s Monitoring Yes Per customer requirement Filler-/Sealer Management Filler valve; capper head correlation Yes (self explaining device interface which gives all needed information about the inspection, additionally counters, messages and statistics can be transferred to data aquisition systems),@ID:32}, MATERIALS / RECYCLING PETplanet Insider Vol. 19 No. 09/18 petpla.net 9 rPET instead of virgin PET for producing food trays Future looking investment pays EstPak Plastik is a family-owned enterprise founded 1999 in Hiiuma, Estonia, where the business started with one small thermoforming machine. Due to exports to the Scandinavian markets, EstPak reached a further development stage with the installation of a new advanced production plant in Harjumaa, where the company employs around 40 people. EstPak extended their production area up to 10,000m2, just south of Tallinn. “The capacity amounts to 145 million trays with an export rate to the Scandinavian market of approximately 80%,” says Marek Harjak, Managing Director at EstPak Plastik. Forecasts point out that especially recycled PET will be a main resource for thermoformed food trays in the years to come. Plastic is an essential material in everyday life, one that is hardly imaginable without it. The recently adopted EU plastic strategy considers the ability to reuse and recycle plastic to promote an European transition towards a circular economy which adheres to the global climate commitments. Currently the PET collection rate in Europe is up to 52%. By 2030 all packaging shall be based on reusable or recyclable material. An inevitability that EstPak Plastik early recognised. EstPak Plastik is responsible for guaranteeing that their thermoformed food trays are safe when they are in direct contact with food. As one of the leading PP and rPET specialist, EstPak Plastik is able to offer monolayer and laminated sheet to the thermoforming or Form-Fill-Seal market due to the latest investment in Starlinger-viscotec at the end of 2017. Before that, the company relied entirely on virgin PET material. “We were looking for a solution which is able to produce rPET film that can get in touch with any type of food – including water applications,” explains Marek Harjak. Considering higher costs, and especially the lack of sustainability, virgin material was no longer an appropriate option for EstPak. Using post-consumer recycled PET flakes for the production of packaging containers for the food industry is a delicate topic. In order to guarantee food safety, rPET material needs to be decontaminated beforehand, which is done by the deCON – decontamination module of Starlinger viscotec. In the next step the viscoSHEET extrusion line uses the super-cleanest material to produce sheet with the highest degree of purity. This project funded by an Estonian environmental program pushed EstPak Plastik into a leading position on the Scandinavian market. Besides their innovation capacity, skillful and dedicated employees are the main forces to gain customer satisfaction, the organisation’s most important asset to expand their client base. This investment even captured the attention of the Estonian government. The environment minister of Estonia, Siim Kiisler, attended the opening ceremony of the new production building and in his speech he pointed out the importance of sustainable approaches. Steps towards a green economy, including safe consumption and a better protected environment should be guaranteed. Therefore concepts, such as producing plastic packaging based on rPET, are indispensable for future investments. “EstPak Plastiks goal is to be the first choice to contact regarding packaging questions in Nordic Countries. Hoping to boost our sales in trays and rPET sheet in the future, investments in thermoforming and rPET extrusion lines need to be done soon. EstPak is a smart, innovative and suistainable producer, where design and production fully respect the needs of reuse and recycling,” reveals Marek Harjak. www.viscotec.at www.estpakplastik.ee Starlingers viscoSHEET extrusion line at EstPak Plastik workshop The new production plant of EstPak Plastik in Harjumaa, Estonia,@ID:11}, INSPECTION 39 PETplanet Insider Vol. 19 No. 09/18 petpla.net INSPECTION 39 the scavenger being consumed. After 20 days it has been completely consumed and the ingress slope is identical to that of the non-coated reference bottle in Figure 8. A combination barrier system involves addition of Amosorb DFC oxygen scavenger to the PET layer of LC2-coated PET bottles. Locating the scavenger in the inner PET layer protects it from ambient oxygen. This inner-layer scavenger reacts with oxygen that has permeated through the outside coating and is available to diminish the headspace and dissolved oxygen integrated by the filling process. Adding 1% scavenger to a coated PET bottle results in an ingress rate significantly below 1,000 ppb over a period of six months (C). Even after 180 days the scavenger is still active and total oxygen ingress is below 1,000 ppb. Reducing scavenger content from 1% to 0.5% (D) results in increased oxygen ingress but it is still well below 1 ppm. Bottle type 3: Inorganic coatings can be applied to the inside of the bottle after blowing. Sidel Actis coating technology produces a thin layer of amorphous carbon, typically 100 to 200 nm thick, on the inner surface. Fig. 10 Comparison of oxygen ingress into an Actis coated bottle and the respective non-coated reference bottle The inner coating provides an efficient barrier and prevents oxygen desorption from the PET bottle wall into the product during the first few days of storage. A BIF factor of 9.9 was determined by comparing the slopes of oxygen ingress of coated and non-coated bottles. For both bottle types, sampling rate was adjusted to 30 s; mean value was taken from seven bottles. Fig. 11 Common multilayer structure Bottle type 4: Multilayer bottle containing oxygen scavenger Fig. 12 Oxygen ingress in multilayer bottles; (A) without active barrier, (B) multilayer bottles containing proprietary scavengers in the PA innerlayer. The sampling rate was adjusted to 30 s. The combination of a multilayer structure, incorporating an active barrier within the middle layer, decreases oxygen ingress significantly. To sum up, the best performance is shown by those bottles which use an active barrier (scavenger) additional to the passive barrier which is also acting as a protection layer to prevent the reaction of the scavenger with atmospheric oxygen. A shelf-life of more than 180 days can be reached even when the amount of scavenger has been reduced. www.presens.de www.bericap.com Unique range of light weight screw and sports closures for light weight PET neck standards for water • Closures for all common neck sizes 26/22, 28mm (PCO 1810, PCO 1881), 29/25, 30/25 • Light weight Hexalite range allowing light weight neck • Still water closures suitable for N 2 dosing • Sports closures fulfill BSDA requirements • Boreseal systems for excellent tightness • Consumer friendly opening forces BERICAP Technology for still water,@ID:41}, COMPRESSORS 21 PETplanet Insider Vol. 19 No. 09/18 to one that can produce compressors with dynamical customer solutions, to further reduce operating costs. Optional innovations now available include fully integrated Heat Recovery System and Smart Inverter Starter to reduce peak inrush during starting. The Adjustable Air Flow System, for example, optimises on and off load ratios from 50% to 100%, depending on air demands. These options help to maximise energy savings and reduce customers’ overall carbon footprint, which helps them to achieve their sustainability goals. PP: That is great for today’s market; what sort of developments are you preparing and launching for the future? AF: In anticipation of future PET market changes, and in order to meet the current market trends of lower blow pressures, to 20bar, Ateliers François started an R&D program at the University of Louvain-La-Neuve in Belgium, to improve and maximise its compressors’ efficiencies. The research conducted at the university, as well as with other scientific associations and additional R&D centres within the global AF organisation, led to the development of a complete new range of compressors. While the new range uses the same proven and reliable “L-shape” design, the compressor cylinders themselves have been redesigned, new piston ring technology has been introduced, and improvements to the interconnecting pipework and intercoolers have increased air capacity and output. PP: Will the new “L Series” of compressors replace the existing range? AF: Not at this time. The new “L Series” is in addition to the existing “CE Series”. It will complement and increase the number of models and capacities within our compressor range. This means that customers can be completely confident that the compressor selected will perfectly match the air blowing requirements for every application. In the future, as market and technological changes effect the compressed air requirements in our industry, our equipment may need to be adapted to sustain the current high efficiency of our compressors. AF will continue to innovate in a continuous way to anticipate these market changes. PP: What ancillary equipment do purchasers have to buy? AF: Each AF Compressor is complete with refrigerated air dryer, receiver, starter/control panel, antivibration mounts, and 40 bar piping to between the compressor skid and air dryer for ease of installation. Optional equipment available includes closed loop cooling systems; and compressor package can be equipped to meet local certifications and climatic conditions for any location, anywhere in the world. www.afcompressors.com From the preform to the packaged PET bottle, our lines not only considerably save on energy but also on materials and maintenance costs. One such system is our compact InnoPET TriBlock Aqua INSPECTION 36 PETplanet Insider Vol. 19 No. 09/18 petpla.net Non-destructive testing of oxygen transmission in PET bottles The study sought to determine the feasibility of achieving a shelf-life of 180 days with a total oxygen concentration (dissolved and headspace) of less than 1 ppm. The non-invasive and non-destructive technique uses optical-chemical sensors that can detect 1 ppb (part per billion) of dissolved oxygen. It measures oxygen ingress continuously, under real conditions and over a long period of time. Fig. 1 Factors affecting shelf life of products in PET bottles Experiment details Measurement is based on the effect of dynamic luminescence quenching by molecular oxygen (Figure 2). Fig. 2 Principle of dynamic quenching of luminescence by molecular oxygen (1) Luminescence process in absence of oxygen (2) Deactivation of the luminescent indicator molecule by molecular oxygen Collision between a luminophore in its excited state and oxygen results in collisional or dynamic quenching: radiationless deactivation. Energy transfer takes place from the excited indicator molecule to oxygen. The indicator molecule’s total measurable luminescence signal decreases. The oxygen meter uses a bluegreen light source for excitation. An optical polymer fibre is used as signal transducer and leads the emission light to a photodiode. The technique measures the luminescence lifetime as the oxygen-dependent parameter. Decay time does not depend on fluctuations in intensity of the light source and sensitivity of the detector. It is not influenced by signal loss caused by fibre bending or by intensity changes caused by changes in the geometry of the sensor and is, to a great extent, independent of the concentration of the indicator in the sensitive layer. Photobleaching and leaching of the indicator dye and variations in the optical properties of the sample have no influence. Optical chemical sensors measure in both liquid and in gaseous (headspace) areas. They perform through transparent materials up to 10 mm thick and through turbid (cloudy) packaging. Oxygen levels can be detected in parts per million (ppm) to parts per billion (ppb) ranges. Dissolved oxygen Gaseous & dissolved oxygen Measurement range 0-2mg/l (ppm) 0-56.9 μmol/l 0-5% O 2 0-41.4hPa Limit of detection (LOD) 1ppb of dissolved oxygen 0.002% oxygen Resolution ± 0.0003mg/l at 0.001mg/l ± 0.0006mg/l at 0.09mg/l ± 0.010 μmol/l at 0.03 μmol/l ± 0.020 μmol/l at 2.8 μmol/l ± 0.0007% O 2 at 0.002% O 2 ± 0.0015% O 2 at 0.2% O 2 ± 0.007hPa at 0.023hPa ± 0.015hPa at 2.0hPa Accuracy (+20 °C) ± 1ppb or 3% of the respective concentration; whichever is higher Response time 40 s 6 s Calibration Conventional two-point calibration in oxygen-free environment (nitrogen); second calibration value, optimally between 1 and 2% oxygen Temperature range From 0 °C to +50 °C Long-term stability 100,000 data points without drift Table 1 Technical data of the PSt6 type sensor Six months shelf life for beer and CSD Oxygen causes chemical processes that impair shelf life, flavour and quality of beer and carbonated soft drinks (CSD). To protect the product, monolayer bottles can be coated with high–barrier material on either the inner or outer surface. One or more high-barrier layers can be incorporated in a multilayer structure, and oxygen scavenger materials can be incorporated in the bottle wall. Determining the barrier improvement factor (BIF) compared to non-treated bottles requires precise measurements of oxygen permeation under real conditions. Traditional analysing techniques do not operate in real conditions and/or require destructive measurement processes. Presens Precision Sensing GmbH undertook a study using an analysing method based on an oxygen-dependent measurement of luminescence decay time.,@ID:38}, MARKET SURVEY 28 PETplanet Insider Vol. 19 No. 09/18 petpla.net Filling Equipment .com 100815dmyL Company name Krones AG SMI S.p.A. KHS GmbH Postal address Telephone number Web site address Contact name Function Direct telephone number E-Mail Böhmerwaldstr. 5 93073 Neutraubling, Germany +49 9401 70 0 www.krones.com Mr Philipp Schön Product Manager Filling Division +49 9401 4567 philipp.schoen@krones.com Via Carlo Ceresa, 10 24015 San Giovanni Bianco, Italy +39 0345 40111 www.smigroup.it Mr Pietro Volpi Marketing Dept. Manager +39 0345 40316 pietro.volpi@smigroup.net Juchostraße 20 44143 Dortmund, Germany +49 231 569 0 www.khs.com Mr Manfred Härtel Product Manager Filling +49 671 852 2644 manfred.haertel@khs.com 1. Machine designation / model number Modulfill EcoBloc Ergon & Electronic volumetric fillers DRV-VF NV 2. Number of filling heads (range: from/to) 16 -216 9-126 48/216 32/144 3. Min to max bottle contents (in liters) 0.1-5 0.25-10 0.1/3.0 0.1/3.0 4. Filling speed: output (bph) (min to max): 1,000-68,100 5,000-82,000 5,000-82,000 specifiy: 1l bottle / still water (bph) Up to 72,000 Up to 68,100 17,000-82,000 17,000-82,000 1l bottle / CSD (bph) Up to 65,000 Up to 33,600 13,000-80,000 1l bottle / milk (bph) Up to 60,000 Up to 36,000 10,000-50,000 1l bottle / juice (bph) Up to 60,000 Up to 36,000 17,000-80,000 10,000-60,000 5. Filling process Pressureless (still drinks) Volumetricfillingsystem;netweight system;heightfillingsystem Yes N-process Yes Pressure filling (carbonated drinks) Volumetricfillingsystem;netweight system;heightfillingsystem Yes VF-process Not possible Hot filling Volumetricfillingsystem;netweight system;heightfillingsystem No H-process Yes Cold aseptic filling PETAsept L/PETAsept D/ Contiform AseptBloc DN/DA, contactless filling systems No Other filling system available Other filling system available Juices with high pulp content Height filling system, pre-dosing system asepctic & hot mode No Yes 6. Type of filling valve and metering system Volumetric filling system; net weight system; height filling system Electronic volumetric filling valves; Flowmeters (metering system) Computer controlled, pneumatic cylinder, MID, inductive flow meter Mass-flow, Coriolis 7. Special features (short description/ keywords) Monotec; cap disinfection; clean room cover; foam cleaning system; nitrogen droppler; automatic CIP- caps; Capcade; bloc solutions Compact modular frame, with customisation options; operating and maintenance costs cut; easy and quick format changeover, with no need to replace mechanical components; high hygiene and easy maintenance and cleaning CSD warm-filling up to 24°C; simple filling valve; compact unit; slow & fast-filling; gentle filling with low foaming; no beverage loss during production; PTFE-sealing technology prevents aroma transfer Contact-free filling 09/2018 MARKETsurvey,@ID:30}, BOTTLE MAKING 17 PETplanet Insider Vol. 18 No. 0/17 petpla.net “The impossible, of course, may take a little longer!” PET Technologies has recently released the last generation of its PET stretch blow moulder APF-Max on the market. Its output varies between 6,000-14,000 bph, whilst the bottle capacity is between 0.2 and 3.0 l. There are eight modifications for producing water or CSD, dairy products or beer, juice or sauce, oil or vinegar, chemicals or cosmetics. bottle making KOMPRESSOREN Visit us: Hall 4, Stand 441 from the 13th - 15th of November 2018 in Nuremberg, Germany DNC booster – turnkey all-in-one system • Compact powerhouse with a footprint of only 2.35 m² ,QLWLDO SUHVVXUH XS WR EDU ² ÀQDO SUHVVXUH XS WR EDU • Plug and Play: ready for immediate operation • IE3 motor for optimum performance and energy savings 6,*0$ &21752/ FRQWUROOHU H[FHSWLRQDO HˣFLHQF\\ DQG QHWZRUN FDSDEOH ,QGXVWULH www.kaeser.com Nuremberg, Germany, 13th - 15th of November Quick change and flexibility To transform 4-cavity modification into 8 cavities a 7,000 bph modification APF-Max 4 is available and this increases the output up to 14,000 bph. It is also possible to install extra mould cavities, several ovens on the heater to get an upgrade to the APF-Max 8. All the mould cavities are separate for easy installation and removal. PET Technologies states that 15min are needed to change the blow- mould to produce a different PET bottle format. Two hours are required for the APF-Max changeover to a different preform neck standard which can be between 18 and 48mm. The APF-Max is also designed for hot filling. NIR heating system and low total installed power The APF-Max blow moulder is equipped with a special short wave near infrared heating system (NIR). This is a fairly unusual method for PET blow moulding machines market, but has evident benefits, according to PET Technologies. Preform heating is more efficient and fewer kilowatts are consumed. The heater itself is significantly shorter. Thus, the APF-Max design is more compact. All-electric configuration The automatic PET stretch blow moulder APF-Max has 6 servo drives to guarantee stable PET bottle manufacturing and high output. They are embedded in the mould closing unit, preform stretching, heater, preform transfer to the blowing part and bottle outfeed system. Automatic temperature regulation and preblow are controlled via a PLC form B&R. New design and user-friendly interface This is now the fourth generation of APF-Max blow moulders. At a superficial level, it is different from the PET Technologies product range. This new generation of blow moulders boasts a number of features including a streamlined design, corporate electric cabinet and communications connected via the top of the machine. To change all 108 mandrels in the heater take 15min. PET Technologies R&D developed the APF-Max blow moulder from scratch. The first machines have been successfully installed at customers and are manufacturing PET bottles for water and dairy products. www.pet-eu.com,@ID:19}, COMPRESSORS PETplanet Insider Vol. 19 No. 09/18 petpla.net 31 Best quality goes into the bottle Clean compressed air At the Christinen-Brunnen mineral water plant in Bielefeld, Germany, two dry-compression rotary screw compressors combined with two refrigeration dryers and various filters produce food-grade control air and supply air for the treatment, mixing and bottling of mineral spring water. COMPRESSORS L IGHTWE IGHT WI TH CONF IDENCE CONTACT US TODAY TO LEAR MORE! AGRINTL.COM | +1.724.482.2163 | SALES@AGRINTL.COM PROCESS PILOT® Blowmolder management easy as . . . Highly accurate material distribution guarantees that even WKH OLJKWHVW FRQWDLQHU PHHWV \\RXU VSHFLȴFDWLRQV In many industrial applications, it is important for the compressed air to be as clean as possible. One example is the beverage industry. Franz Bunte went into the beverage trade in 1895. His business grew rapidly and he was soon well known across the region of eastern Westphalia. In 1932 Franz Bunte’s son-in-law Paul Gehring took over the business, which has since operated under the name GehringBunte. After securing a licence in 1934 to make and sell Coca-Cola within a 30 km radius of its headquarters, Gehring-Bunte expanded into the beverage production business. The third generation assumed control of the family business in 1955, when Paul Gehring’s sons Dr Paul Gehring and Werner Gehring took the helm. They made the company what it is today: a leading seller of brand-name beverages. This success was built on Christinen-Brunnen, a mineral water plant in Ummeln, Germany. The new company’s first bottle, labelled “Teutoburger Mineralbrunnen”, left the production line on May 1, 1966. Today “Christinen” is among Germany’s most recognised mineral water brands and is also very popular across Europe. Since 1994, the company’s activities have been complemented by a bottling operation in the town of Wiesenburg am Fläming in the state of Brandenburg and the products of the Erkrath mineral spring near Cologne. In 2011 Gehring-Bunte had a total output of 155m litres bottled in 300m containers by approximately 220 employees. Compressed air – food-grade and economical As an energy source and control medium, compressed air is used everywhere in a bottling plant. However, these applications are subject to stringent air purity standards. A basic air supply is also needed for the boosters of the two PET bottle production lines. Consequently, when it came time to replace the entire compressed air system, it was clear from the outset: the new rotary screw compressors would have to be dry compression models. Moreover, the compressed air treatment equipment would have to ensure the necessary quality on a reliable basis. Compressed air stations often generate more compressed air than is actually used, as the end users’ requirements vary over the course of the day. As a result, there is often an imbalance between production and consumption. The best approach is therefore to start with an analysis of the actual needs and then to build a system based on the results. In 2011, Christinen-Brunnen bottled 155m litres of beverages in 300m containers.,@ID:33}, PETplanet Insider Vol. 19 No. 09/18 petpla.net 44 44 PETbottles Beverage + Liquid Food Switchel ready-to-drink mix As with many trends, this year’s European summer drink comes from the USA. The vegan drink, which has been popular in the States for decades, consists of maple syrup, apple vinegar, ginger and water. It is lauded as a health elixir and is supposed, among other things, to help with weight loss. It is very easy for people to make, although the manufacturers also sell it as a readyto-drink mix. Under the “Für” label, which is the name of its sustainable agriculture campaign, the German company, Voelkel Limited, is selling several varieties of Switchel in clear, easy-to-handle 200ml plastic bottles. The suitably sized large drink opening is secured with matching-coloured screw tops with a tamper-proof strip. www.sei-mit-uns-fuer.de Monster Hydro in PET While Monster Beverage sells most of its drinks in cans, the company is launching its carbonated “M Hydro” energy drinks range with dextrose in clear, slim 550ml PET bottles. Three different varieties are currently available: mean green, tropical thunder and manic melon. A transparent sleeve label provides product information, as well as emphasising some of the drink’s advantages such as being triple-filtered, low in sugar and including vitamin additives. A screw top with a typical brand logo secures the suitably sized large drink opening. www.monsterenergy.com A classic now in a bottle San Pellegrino is selling its popular carbonated fruit drinks, Limonata and Aranciata, which have previously been mainly available in cans, and more recently in 500 ml PET bottles. The bottles are coloured to match each product and have a rough surface and star-shaped embossing in the neck area. According to the manufacturer, the reasons for their introduction were the potential for resealing and consumer-driven demand for this type of packaging. A matching screw cap and wrap-around plastic label complete the packaging. www.sanpellegrino.com BOTTLES,@ID:46}, PETplanet Insider Vol. 19 No. 09/18 petpla.net 46 PETbottles Home + Personal Care Frosch relies on raspberry vinegar For more than three decades, the Frosch brand has offered cleaning and laundry detergents with active natural ingredients. The newest and lightly luminous pink product is a raspberry vinegar cleaner for calcium and urine deposits, which simultaneously removes unpleasant odours and spreads the scent of raspberries. The bottle is up to 100% recycled PET and contains 750ml and the angled neck simplifies application of the cleaner. The screwed-on seal with application assistance is covered with a childproof, transparent screw cap. www.frosch.de Hydro Boost from Neutrogena The Neutrogena brand from Johnson & Johnson is bringing a body spray onto the German market with the name Hydro Boost; its composition and effects are based on findings from face care. The spray contains a hyaluron gel complex, which is absorbed immediately and cools the skin. The milky product is sold in a 200ml slim, blue-coloured bottle with a plastic label and screwed-on pump dispenser with a transparent protection cap. www.neutrogena.de braubeviale.de MAKING YOUR BUSINESS SUCCESSFUL. BrauBeviale is where you cultivate success – in dialogue as an equal partner, with experts in the sector, with innovations that give you a competitive edge. Everything you need for tomorrow – in a single venue. For exhibition highlights and important information for your visit: braubeviale.de/Your-Success Good business. Good conversations. Nuremberg, Germany | 13 – 15 November,@ID:48}, PETnews 6 NEWS PETplanet Insider Vol. 19 No. 09/18 petpla.net The versatile supporting programme of fdt Africa From resource conservation and energy efficiency, new raw materials to forward-looking developments in processing and bottling and packaging, food & drink technology Africa (fdt) presents solutions that are tailored to the particularities of the South African market. The supporting programme of the exhibition is equally geared to the needs of the local industry and will shed light on the future topics of the industry. From September 4-6, the food, beverage and packaging industry will meet in Johannesburg. The platform for the market in Southern Africa covers the entire process chain – from raw materials to processing, bottling, packaging and logistics. This year’s fdt Africa supporting programme will shed light on the future of the food and beverage industry in Southern Africa, will pick up on current topics and show practical solutions for the industry. The second day of the exhibition offers symposia with the industry leaders Bosch Packaging, Bühler, KHS Manufacturing and Pentair, offering participants an insight into the trends, challenges and opportunities in the areas of water management, packaging and process technology. On the first and third day of the exhibition, the Speakers’ Corner will provide an overview of topics that are shaping the industry. Experts will assess the developments on the South African market and offer new stimuli for the industry. There will be presentations and lectures by companies and associations including Brewsters Craft, Centec, Pall, the South African Association of Fragrances and Flavour Industry (SAFFI), Sphere Foods Africa, the VDMA Food Processing and Packaging Machinery Association and many others. The presented topics will be very diverse and thus cover a wide range of areas within the industry, such as consumption patterns for soft drinks in the sub-Saharan region, quality management systems for food safety and de-gassers for feed water. www.fdt-africa.com Gea receives accolade for aseptic blow-fill-cap technology with FDA certification In July 2018, the U.S. Food and Drug Administration (FDA) awarded Gea a letter of no objection (LONO) for its ABF 1.2 technology, an integrated blowing, filling and capping solution featuring a fully aseptic rotary blowing machine. It is the only system equipped with a 100% aseptic blower that is allowed to produce shelf-stable low acid (LA) beverages free from preservatives for distribution at ambient temperature in the U.S. market. The FDA testing is considered one of the most comprehensive validation protocols available in the aseptic beverage market. Their stringent requirements ensure enhanced product safety, and their approval is highly valued even outside the U.S. The FDA clearance confirms that Gea’s ABF 1.2 technology ensures maximum sterilisation efficiency and reliability during every step of sensitive beverage bottling. Gea successfully passed the validation tests which were performed on an ABF 1.2 system installed in the U.S. – and which is now already producing and delivering shelf-stable liquid dairy products to the North-American market. The Gea solution is based on an integrated blowing, filling and capping process that runs within a 100% aseptic environment. Thanks to the microbiological isolator, Gea ABF 1.2 aseptically blows preforms that have been previously treated with hydrogen peroxide vapour (VHP). The result is a single zone sterilisation process that requires no water and fewer chemicals. www.gea.com In-house services for preforms, containers and caps Chemco announces that its research and development department provides tailored solutions to meet the demands of the container market. Transparency and sustainability of the project the customer is envisioning is the ultimate objective for Chemco. This is realised by partnering with brand owners and providing services at all levels of development. These include development work such as R&D and prototyping, material chemistry and design up to mould tooling, production, efficiency improvements or packaging. The in-house services allow the company to provide fast development times. The company emphasises that these services - many are offered either at minimal or free of cost to clients - opening the way for innovation rather than just copy-pasting sometimes obsolete ideas. Chemco believes that adding the additional financial burden to every aspect of development will only strain the client and often force them to compromise on their vision for their product, limiting the product’s chances of success. Chemco’s journey in bottle-making started with a small machine that could produce fewer than 2 bpm. Today, Mumbai-located Chemco owns and operates many hundreds of wholly automated machines manufacturing PET preforms and a wide variety of blow mould PET containers as well as caps and closures. www.chemcogroup.com,@ID:8}, 43 PRODUCTS PETplanet Insider Vol. 19 No. 09/18 petpla.net PETproducts Conformal cooling vs standard cooling by Jay Vang, Customer Success Engineer at Moldex3d With the acceleration of 3D printing technology, the realisation of complex (non-conventional) cooling designs is quickly gaining ground in the injection moulding industry. Additive manufacturing such as direct metal laser sintering (DMLS) can almost print any imaginable complex cooling circuit design, within the printer platform and print angle limitations, to help control part quality and cycle time.In today’s economy, time is money. In the injection moulding industry, the cooling phase typically determines the length of the overall cycle time. This may be due to factors such as (but not limited to) controlled cooling rate requirements or simply due to the part(s) not reaching safe ejection temperature. Since complex channels can be created, near the part surface and hard to reach areas, potential reduction in cooling time and improvement in part quality can be achieved. Using additive manufacturing for conformal cooling, not only can the designs be complex and contour along the part surface, but it can also potentially be built quicker than conventional machining. This is even truer for multi-cavity moulds utilising additive manufacturing to build conformal cooling channels. In conjunction with knowing how conformal cooling can help potentially reduce mould build time, reduce cycle time, and increase part quality, utilising plastic simulation software can help put a relative value in determining the reduction of cycle time and in the improvements of part quality such as distortion. In Fig. 1, direct temperature comparison in the tool can be analysed to determine cooling efficiency and uniformity between a conventional and a conformal spiral cooling channel. Due to conventional cooling design constraints, heat is not removed from the insert and part as efficiently and as uniformly as the conformal cooling design. One factor in minimising warp is to minimise differential shrink. With better mould temperature uniformity, differential shrinkage can be reduced which again helps minimise warp. Fig. 2 compares simulation results at sensor nodes placed on the part surface to determine the temperature profile through an injection moulding cycle comparing the two cooling channels above. The temperature profile indicates a max ∆T of approx. 2~3°C for the case with the conformal cooling design compared to a max ∆T of approx. 5~7 °C for the conventional cooling design. Because the differential temperature of the part is reduced, the rate that the material of the part freezes and shrinks are closer and in turn, should yield a part with less warpage. In summary, the utilisation of today’s technology such as vacuum brazing or additive manufacturing to create complex water design to help reduce cycle time and increase part quality is rapidly growing. Coupling conformal cooling design with simulation software can help to prove the validity of conformal cooling in injection moulding and help determine potential ROI. www.moldex3d.com Fig. 1 Conformal cooling simulation Fig. 2 Conventional cooling,@ID:45}, COMPRESSORS PETplanet Insider Vol. 19 No. 09/18 petpla.net 24 “When you live high up you can see for miles” Is not just an old farmer’s saying, it also describes the company philosophy of Alberto Bertone, owner of the Sant’Anna bottled water producer in Vinadio, Italy, which has springs up to 2,000metres above sea level. For him, this means looking far into the future: total sustainability. While “sustainability” is often used by many as a marketing term, you can experience sustainability for real at Sant’Anna. It begins with small things in the factory. For example, all lamps are powered using energy-saving LED technology. However, sustainability is also evident on a larger scale as Alberto has had new halls built out of wood. As he says “For me, wood is a sustainable building material – more maintenance-intensive than concrete, as well as being a natural building material”. With an annual production capacity of 3.5 billion bottles on 18 bottling lines, Sant’Anna is one of the world’s largest bottling plants. Transport within the facility is undertaken by 40 automated laser-guided carts. Trucks arrive at the plant by the minute and transport 11,000 pallets a day to the nearest railway station. This is sustainability in action because rail is more sustainable than truck transport, says Marco Balbiano, member of Sant’Anna’s Innovation Team. Looking far into the future, Bertone is putting his faith in PLA bottles. PLA (polylactic acid) is a material defined as sustainable because it is produced from renewable resources, through processes of corn fermentation, separation and polymerisation and degrades in the soil in about 12 weeks. His innovation team has been working on the roll-out for over ten years. What sounded simple at the outset has become more complicated as the project has progressed. “We have had to rethink the whole process”, says Dario Ferrero, Sant’Anna’s Plant Manager. Lower temperatures, blowing pressures, handling of material – everything had to be tested. Through lower temperatures and pressures, the plant is able to save 60-70% of energy used in production – an aspect of sustainability which is often overlooked with PLA bottles. Meanwhile, they are proud to be the first and only plant in Italy to have a significant bottling line based on a compostable PLA bottle. They are also currently working on producing labels and caps using compostable materials. This means that the consumer will be able to dispose of the whole bottle through compost waste with a clear conscience and not have to separate both label and lid as they have previously. Sustainability is not just about natural building materials and degradable PLA bottles – it also means making meaningful energy savings. One of the biggest energy guzzlers during the stretch-blow moulding and PET bottle filling process is undoubtedly the production of blowing air. In order to keep the required amount as little as possible, the stretch-blow moulding machines operate using compressed air recirculation. This COMPRESSORS Alberto Bertone (left), owner of Sant’Anna bottled water, and Marco Bassi, Siad Macchine Impianti Compressors Div. Food & Beverage Key Account / Italian Sales Sant’Anna replaced the old systems with six Vito compressors of different sizes from Siad Macchine Impianti, enjoying now energy savings of up to 30%. by Alexander Büchler,@ID:26}]}}
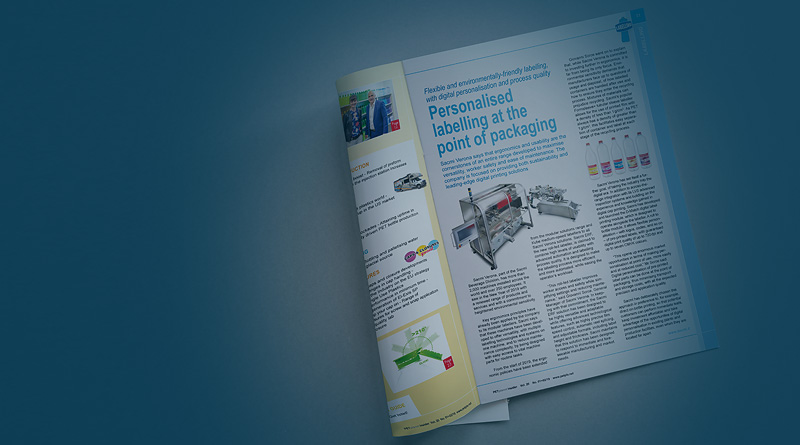