{"pages":{"page":[{"#text":"REGIONAL MARKET REPORTS 16 PETplanet insider Vol. 13 No. 10/12 www.petpla.net KHS Corpoplast Trading (Shanghai) “Assembly of the Blomax in China will be a quantum leap for KHS Corpoplast. That is our expectation”. Geoffrey Chan at the KHS Corpoplast off ce in Shanghai We met: Geoffrey Chan, Managing Director Back in 2006 – at the time of our last foray into the Chinese market – Corpoplast, a company headquartered in Hamburg, and Simonazzi, with head offices in Parma, were jointly venturing into China. Insiders will recall the barely disguised rivalry between the two companies under the umbrella of Swiss holding company SIG . Now – or so the joke goes – rivalry is once again to the fore, but this time exclusively in the German language since both KHS and Corpoplast have in the meantime been taken over by Salzgitter and they are both now part of that company’s strategic network. SIG Corpoplast has metamorphosed into KHS Corpoplast. In China KHS and KHS Corpoplast go their separate ways, with each individually accountable for its own acquisition activities involving stand-alone machinery and selling jointly imported combined PET lines. We met Geoffrey Chan from KHS Corpoplast in Shanghai to ask particularly about what has been happening over the past six years. How had KHS Corpoplast fared in this booming Chinese beverages market? Geoffrey Chan replied: “We have good reason to be satisfied with the role that we are playing today together with Sidel and Krones. The change from SIG to KHS was a logical move, it made old customers happy as well as generating new ones. The next step – namely, assembling the block machine in China for the mineral water market, which contain Blomax + filler + capper – will be a quantum leap for KHS Coroplast. Or, at least, this is our expectation“. Population of KHS Corpoplast blowers in China Already in service in China there are – according to estimates from KHS Corpoplast – 1,000 imported blow moulding machines as well as an unquantifiable number of machines manufactured in China. In the last three boom years an average of 80 to 100 blow moulding machines from Europe have been imported into China. In 2006 there were 90 Corpoplast blow moulding machines installed in China. Today – March 2012 – there are 150 Corpoplast blow mouling machines, including twelve Blomax in blocks with KHS (CSD and water) as well as five Blomax in blocks with Shibuya/Japan (aseptic). They are high end machines with outputs of between 20,000bph and 72,000bph, with the majority averaging out at over 40,000bph. Although the trend is moving in the direction of block installations, KHS Corpoplast supply stand-alone blowers, frequently on an exchange basis with old installations in the line. (This, for example, is the case with Swire, who have exchanged eight blowers for Blomax systems). “Fillers, especially, are less subjected to wear and tear . Blowers are more often subject to critical productivity checks within a five-year cycle”. KHS Corpoplast deliver 90% to bottlers / brand owners and 10% to converters. Major customers Swire (Coca Cola) (CSD) CCCIL (Coca Cola China Industrial Ltd.) (CSD) Ting Hsin (aseptic) Nongfu Spring (water and aseptic) President (aseptic) Huiyuan (juices) Recent references 23 sets of Blomax 24S for aseptic bottling of RTD tea in cooperation with GEA Procomac, 48,000bph each, for Tingshin (indirect sale via GEA Procomac). Three sets of Blomax 24C for aseptic bottling of peanut milk based product and RTD tea again together with GEA Procomac, for Yinlu Group (direct sale). Five sets of Blomax 28S, aseptic bottling of RMTea and juice), 54,000bph each, block together with Shibuya, for Nongfu Spring. Eight combi lines together with KHS, for CSD, 43,200 to 52,800 bph, for SWIRE and CCCIL (Coca Cola China Industrial Ltd.) Seven more combi lines together with KHS, for water, 43,200 to 72,000bph, for Nongfu Spring. Geoffrey Chan continues: “We enjoy healthy growth, our expansion is prudent. We consider ourselves as one of the three big players in our field – currently holding 15% of the market, and with hopes eventually of a 30% share.“ The Chinese market is important for the principles in Hamburg. In 2011 orders from China amounted to approx. 30% of KHS Corpoplast sales overall. Strategies The optimistic expectations for the market stem from an increasing self-confidence brought about as a result of the stable relationships in partnership with KHS. There is another factor and that is due to the decision to assemble Blomax blow moulding machines + filler + capper locally in China and eventually to manufacture components locally in the future. Funds of approx. US$ 7m are said to be available. The factory, situated in the vicinity of Shanghai, is poised to commence the assem-","@ID":18} "PETbottles 50 PETplanet insider Vol. 13 No. 10/12 www.petpla.net Home + Personal Care M&H goes ‘back to school’ M&H has announced the launch of a new collection of PET bottles, created in shapes inspired by science. The bottles are designed to be reminiscent of school science lessons and based on the flask, bottles and test tubes used by chemists. The range comprises the 300ml Florentine Flask; 300ml Erlenmeyer Flask; and 250ml Test Tube Bottle. M&H says that the bottle shapes are suitable for personal care products and for other market sectors such as pet care, automotive and food & beverages. www.mhplastics.com Odol-med 3 with waist GlaxoSmithKline is marketing its Odol-med 3 white velvet polar fresh mouth rinse for complementing the daily mouth hygiene routine in a waisted PET bottle containing 500ml of product. The clear bottle features a stylish embossed seal in the base area and a shrink sleeve label with a colour gradient acts as the vehicle for transmitting usage and retail information. The sleeve label, which is stretched over the dispensing screw cap, is torn off along perforations at the time of first opening, making it easy to establish whether there has been any prior tampering with the product. www.odol-med3.de Exotic hand soap Palmolive have expanded their successful range of fragrances ‘Ayurituel’ with a liquid hand soap. The variant shown here, which goes by the name of ”energy“, with extracts of Indian sandlewood and honey, is reported to have an invigorating effect. The transparent bottle made from PET is reminiscent of the shower gel bottle from the same product range, but is fitted with a lockable pump dispenser for extracting the liquid soap. A shiny metallic, teardrop-shaped label to front and rear, which gives an exotic effect, completes the 250ml content pack. www.palmolive.eu.com","@ID":52} "PETnews 6 PETplanet insider Vol. 13 No. 10/12 www.petpla.net Partnership for dry online cap sterilization Aptar Food + Beverage and Claranor have entered into a partnership to provide an alternative solution for the sterilization of sports caps. The pulsed light system developed by Claranor makes use of the bactericidal effect of UV rays, applied through very short and powerful flashes in order to decontaminate the surfaces. This system has the advantage of being clean, dry and chemical-free. With the Claranor system, the Original sports cap can be sterilized to Log 4 directly on production lines. Claranor pulsed light technology is an alternative to existing chemical and irradiation solutions and complies with industrial requirements and constraints. www.claranor.com PolyOne expands Innovation Centers PolyOne Corporation has made several customer-focused upgrades and enhancements to its collaborative Innovation Centers. The company operates eleven state-of-the-art Innovation Centers, located in seven countries and three regions around the world. Recent Innovation Center expansions and enhancements include the following: The launch of a new colour and additives Innovation Center in Seoul, South Korea Doubling the size of PolyOne’s Shanghai Innovation Center, including the addition of a training facility, design showroom and equipment that expands prototype capability to include textile and fibre applications; The launch of rapid prototyping equipment at PolyOne’s Avon Lake (Ohio) Innovation Center. This new technology provides customers with Fused Deposition Modelling capability, which makes use of computer drawings in order to directly manufacture working prototypes, thus eliminating the costly and time-consuming step of machining moulds from metal. This new 3-D printing capability also allows for on-the-spot experimentation with multiple-base materials; Increasing production capacity and expanding capabilities to support customers by prototyping film, sheet and injection moulding processes at PolyOne’s Suwanee (Georgia) Innovation Center. www.polyone.com Petainer plant expansion in Sweden Petainer, specialists in the development, design and manufacture of PET plastic containers, are strengthening their cutting-edge PET production systems at their production plant in Lidköping, Sweden. The company has agreed a multimillion Euro investment package over the coming twelve months, commencing with an initial order for a Husky HPP injection machine. This will be followed by additional investments focusing on growth and supporting the current customer base. www.petainer.com M&G plans PET plant in Texas M&G Group, producer of PET for packaging applications, has announced that it has purchased land in Corpus Christi, Texas where it will build its 1 million t/a PET plant accompanied by a 1.2 million t/a PTA plant. The property has been purchased by the M&G Group from the philanthropic organization, The Robert Driscoll and Julia Driscoll and Robert Driscoll, Jr. Foundation. According to M&G, the new plants will generate approximately 250 new jobs. The new PET single line plant will employ the same technology as M&G’s single reactor Suape (Brazil) PET plant, including M&G’s EasyUpTM SSP technology. Corpus Christi, Texas, is strategically located on the Gulf of Mexico. The Port of Corpus Christi is the sixth largest port in the United States in terms of tonnage, and is poised for significant expansion as a major trading gateway to Mexico and Latin America. www.gruppomg.com IVL opens up in Africa Indorama Ventures PLC (IVL) has commenced operations at its new 75,000t/a facility in Port Harcourt, Nigeria, the first PET plant in West Africa. It is equipped with Buhler SSP (Solid State Polymerisation) technology for production of bottle-grade PET chips, produced from polycondensed chips supplied by IVL’s facilities in Asia or Europe. Nigeria has an estimated demand of approximately 53,000t of PET and is one of the fastest growing economies in Africa. Port Harcourt, in Southern Nigeria, is the centre of the country’s oil and petrochemicals industry. IVL has 9,000 employees worldwide and 2011 consolidated revenue of US$ 6.1 billion. www.indorama.net Appe Poland goes for a Billion Appe, the packaging division of LSB, says building work at its new Polish factory in Tychy, near Katowice, is on schedule, with commercial production due to commence in December and the plant fully operational by January 2013. Three Husky injection moulding machines are being installed initially, to service the three major contracts that Appe Polska currently has in place. A DeepGrip blow-moulding machine will be installed in 2013. Appe Polska has put in place an ambitious five-year plan, which forecasts growth to 1 billion units/a. The site was selected for its proximity to Polish fillers and its capacity for expansion in line with growth forecasts. Fifteen operators are currently employed in the manufacturing plant and the workforce is expected to grow rapidly with planned production increases. Appe Polska will offer the company’s full product range, including DeepGrip, ActivSeal and its new hot-fill, pasteurisable jars. www.appepackaging.com","@ID":8} "TRADE SHOW PREVIEW 44 PETplanet insider Vol. 13 No. 10/12 www.petpla.net P.E.T. Engineering Hall 7 | Booth 236/237 Complete label-adhesive programme Having carried out further development activity relating to label adhesives cph has now completed its full programme. It includes casein-free- label adhesives, hybrids and casein varieties. All cph products offer a widened property- and performance profiles. These enhancements include high wet-adhesion capability even in the case of cold glass surfaces. All series of adhesives cover the full spectrum of requirements involved in the labelling of bottles. Products with higher resistance to ice- or condensate are available. Casein-free adhesives are bio-degradable and are free from heavy metals, formaldehyde or phenolic constituents. Zinc- and borax-free products are also available within the programme. The above-mentioned series of adhesives include many products which are suitable for the labelling of PET bottles and “No Label Look” applications. www.cph-group.com Cph Hall 4 | Booth 543 Increases output for blow-moulders SMI will be displaying a Smiform SR 6 rotary stretchblow. The output rate has been increased from 1,800 to 2,000 bph /cavity. This feature will be implemented as a standard feature on all new Smiform SR 4-6-8 and 10 (future) blow moulding machine models. Even pre-existing equipment of the same size can be retro-fitted in order to achieve the higher outuput rate prior feasibility analysis by Smiform’s technical department. The output rate increase from 1,800 to 2,000bph/ cavity has been made possible by a newly designed mould-holder’s opening/closure locking group that prevents the early wear of the locking group’s climb/descent cams. SMI SR series is designed for the production of plastic containers of different sizes and shape complexity. www.smigroup.it SMI Hall 7 | Booth 817 Labelling technology and extensive service package KHS is focusing this year on new developments in the field of filling and labelling technology as well as the extensive service offered for all its products. In the labelling area, the company is offering a new modular designbased labelling technology platform. Various labelling methods can be combined in one machine and oriented exactly to meet the requirements of the particular bottling operation. Platform system capacities range from 10,000 to 72,000 containers/h. The system is able to process both glass and plastic containers as well as cans. Moreover, KHS Service will be presenting an overview of the various upgrades available for the entire machine portfolio. www.khs.com Precision in labelling Gernep, manufacturer of rotary labelling machines, will be presenting its extensive range of labelling equipment and flexible applications. Even different labelling systems can be combined on one Gernep machine. All types of Gernep labelling machines can be equipped with servo driven bottle plates for the labelling of various container formats. www.gernep.de GERNEP Hall 7 | Booth 222 KHS Hall 5 | Booth 127 Ecological bottles P.E.T. Engineering will be showing its complete range of services and solutions for sustainable packaging. The range of services goes from the development of packaging based on the light-weighting design principle to the neck finish conversion, support for energy usage optimisation and maintenance optimisation, the upgrading of existing blowing machines and the restyling of blow moulds. The company says that its multidisciplinary approach encourages the close collaboration between designers, engineers and researchers to create an ecological bottle in every aspect, from its production to its disposal. www.petengineering.com","@ID":46} "BOTTLING / FILLING 34 PETplanet insider Vol. 13 No. 10/12 www.petpla.net Twin-flow hotfill process in Egypt *Based on an article by Jörg Mader, Krones AG Fruit drink with a real bite to it In the summer of 2011, Coca-Cola Bottling Egypt (CCBE) premiered a fruit juice featuring whole fruit chunks in PET bottles. The drink is being bottled using Krones’ FlexiFruit filling technology in the twin-flow hotfill process without using any preservatives. The Coca-Cola brand Cappy is familiar to Egyptians, but with “Cappy FruitBite” CCBE has broken new ground. The 300ml wide-neck PET bottle contains 4.3% of whole fruit chunks. The drink is available in four flavours so far, namely orange, mango, peach and cocktail (mango plus peach plus guava plus orange). The plant, located in the north of Cairo, houses the newly installed fruitjuice line, complementing a canning line and a non-returnable-glass line that were already operating here. On the hotfill line for non-returnable PET, CCBE is running its first fruit juice in Egypt. President & COO Salam El-Hammamy quantifies the market for still fruit juices and fruit-based beverages in Egypt at around 80 million Unit Cases (approximately 450 million l). Until August 2011, this was without any involvement on the part of CCBE: the market was served by a large number of small and mediumsized producers. Salam El-Hammamy still sees 10 to 15% of growth in this segment. Rigorous separation of juice and fruit chunks The crucial factor for gentle processing and structure retention of the fruit chunks is rigorous separation of the juice from the fruit chunks right from the start in the process section. The aseptic juice concentrate is handled separately from the fruit chunks themselves, which measure up to 6 x 6 x 6mm. They are delivered by fruit producers from Greece and Turkey as 10kg IQF (individually quick-frozen) blocks, and mixed with juice in two 5,000l tanks in a ratio of 40 : 60 in order to create what is called a “slurry” – without any crushing or maceration. The slurry is then pasteurised in a VarioFlash H shell-and-tube heat exchanger featuring interior cross-","@ID":36} "BOTTLES 49 PETplanet insider Vol. 13 No. 10/12 www.petpla.net Oval squeezer bottles PET Power is expanding its standard range to incorporate two oval grip bottles. Although the two shapes are very similar, they deviate slightly from one another in relation to measurements, curves and small details. The Ohadi Squeeze comes in a 300ml version and the Oregon Squeeze in a 285ml version. Both models feature a 38SP400 neck which is frequently used within the foodstuffs market. A number of dispensing caps are available for this type of neck. Because of the oval shape of this grip bottle it is particularly suitable for the foodstuffs industry. With a matching closure it is designed for dressings and other foodstuffs for measured dispensing. In addition to this, these models are also suitable for cosmetic products. Both models can be supplied in any colour required. A particularly attractive result can be achieved by fitting a coloured model with a matching label which precisely follows the contours of the presentation bottle. In addition, screen printing also imparts an individual character to these models. www.petpower.nl Post-exercise recovery drink Greiner Packaging International provides the packaging for Excel Milk Nutrition’s new 500ml packs. Xcel Milk is described as a post-exercise recovery drink based on fresh milk from a herd of pedigree Jersey cows. Additional ingredients are delivered by ‘Informed Sport’ registered suppliers, assured under the Femas certification programme. The company required a packaging partner with extensive experience of dairy products, geographical proximity to its British location in South Derbyshire, and appropriate technical expertise. Division Kavo of Greiner Packaging International, working with Excel, created what is claimed to be a functional and sustainable packaging solution. The 500ml package was designed by TGL Creative, design consultants, and references the classic and simple milk bottle shape and look, with a white and silvery finish. Embossed branding aids grip and multi-colour printing is intended to provide a ‘dynamic’ appearance. The bottle is made of food grade rPET. www.greiner-gpi.com The Leader in Dispensing Innovation Improved Convenience Greater Functionality Hygienic Shelf Appeal Customization Delivering solutions, shaping the future. www.aptar.com - infobev.gbl@aptar.com Visit us at Brau Beviale 2012 Hall 4 Stand 336","@ID":51} "PETproducts 46 PETplanet insider Vol. 13 No. 10/12 www.petpla.net R&D/Leverage Opti-Sim cuts time to market R&D/Leverage’s Opti-Sim virtual prototyping process is designed to help PET packagers to anticipate a bottle concept’s impact on engineering, operations and marketing. The company says that Opti-Sim’s capacity to perform a complete range of diagnostic, real-world simulations and incorporate multiple variables helps speed time-to-market, cut tooling and prototyping costs and enhance sustainability, for both new and existing designs. It incorporates historical data from the company’s 35 years of involvement in PET packaging, representing years of development and market experience. The objective is to enable customers to “test before they invest”, according to Dave Brunson, R&D/Leverage’s Vice President of Engineering. He added that the tool’s predictive analysis simulates variables such as top load and vacuum, light weight options to enhance sustainability, wall thicknesses, geometries and other factors in addition. R&D/Leverage’s services now extend from virtual pre-testing to prototyping, tool development and full production moulds. www.rdleverage.com DRT Nutraceutics renamed PurExtract DRT has rebranded its natural extract activities under the new name of PurExtract. The company’s natural extracts have been developed primarily for the health, beauty, well-being and nutrition sectors, and are used by leading companies in dietary supplements, nutri-cosmetics and dermo-cosmetics lines. The launch of the new name is being supported by the adoption of a new image and company style. The company’s product lines have been reorganised under three umbrella brands. Pur’Expert is aimed at the well-being and health sectors; Inbio-T targets nutria-cosmetics; and Derm’Expert is designed for the dermo-cosmetics industry. A new website was launched in July. www.purextract.fr One-touch control New England Machinery, Inc. (NEM) is now offering online recipe creation through the Human-Machine Interface (HMI) on all bottle unscramblers and capping equipment. Users enter bottle dimensions into the HMI recipe selected and PLC (programmable logic control) will automatically calculate the motor speeds and ratios necessary to run the particular container. Results are then automatically stored in the newly created recipe and displayed on the HMI, which allows the customer to add containers to the machine for future setups. All NEM unscrambler models come preprogrammed for line integration, which is achieved by either hardware interlocks or an Ethernet network. www.neminc.com Don’t call it hopper. Auxiliary equipment for plastics processing. This is your hopper internal material flow, don’t worry, we’ve got the solution. Conventional Drying system 7EV The hopper has become a machine, it is able to control the process according to the result to be obtained. Now we know what happens inside the hopper and we have improved the material flow inside it, fixing the exact treatment time for a polymer. 7 patents for unlimited advantages: the choice is yours. Original Turbo eXchanger www.moretto.com MATERIAL FLOW designed by Moretto HALL 7A STAND 519","@ID":48} "PET - THE NEXT GENERATION 23 PETplanet insider Vol. 13 No. 10/12 www.petpla.net The pavilion has no heating or air-conditioning instead relying on natural ventilation. To cool the space a section of the façade was left open to capture breezes and the water feature cooled the air as it passed into the building. Energy needs were kept low due to the large amount of natural light received through the Polli-Brick. The insulating properties reduce air-conditioning cost and the overall carbon footprint throughout the building life cycle. Waste recycling plant manufactured from by-products of ewaste recycling Miniwiz’ latest project is the architectural design and supply of the new Taiwanese electronic waste recycling plant and headquarters of Super Dragon Technology (SDTI). This electronic waste recycling plant claims to change the way e-waste is recycled. The building materials used to build the new factory are manufactured from by-products of ewaste recycling. www.miniwiz.com A total of 480,000 PolliBricks made of 1.5 million recycled PET bottles form the façade of the EcoArk pavilion. (photos. Miniwiz) ","@ID":25} "TRADE SHOW PREVIEW 43 PETplanet insider Vol. 13 No. 10/12 www.petpla.net Single-sourced throughout For decades, Krones has been offering complete systems for the entire beer production process: from raw-materials reception on to the brew house, then on to the fermentation stage, proceeding to the storage cellars and the bottling hall, and on top of all that, packaging, intralogistics and full-coverage automation – singlesourced throughout. With the CombiCube F for the filter cellar, Krones has now ntroducED another section in the brewing process: the CombiCube F is a TFS filter. The twin-flow principle has been retained, thus enabling the filtrate flow to be reduced down to 30% of the nominal output. All the other technological advantages of the TFS filter, of course, can also be utilised in the lower output range. The mid-tier filter is divided into five separate modules, which can be combined to suit the particular needs of the brewery involved. SitePilot is the umbrella brand for Krones’ IT products, and stands for a networked factory underpinned by integrated production and distribution logistics. The brand reduces complexities, and interlinks the various IT modules involved. The individual areas and products are connected to each other by SitePilot, but nonetheless function autonomously. They can be individually selected and combined, and each of them has been specifically designed to handle defined task categories at the client’s facility. www.krones.com Krones Hall 7A | Booth 206","@ID":45} "PETpatents www.verpackungspatente.de 52 PETplanet insider Vol. 13 No. 10/12 www.petpla.net Plastic container Europ. Award of Patent No. EP 2091824 B1 Applicant: Alpla Werke Alwin Lehner GmbH & Co. KG , Hard (AT) Date of Application: 15.10.2007 European grant of patent in respect of the structure and the process for manufacturing a plastic bottle with reinforcement grooves in the area of the shoulder. Tamperproof seal Disclosure No. DE 102009019362 A1 Applicant: Krones AG, Neutraubling (D) Date of Application: 29.4.2009 Improved plastic bottle Intern. Patent No. WO 2010 / 129402 A1 Applicant: Ball Corp., Broomf eld (US) Date of Application: 30.4.2010 A thin-walled bottle made from plastic is fitted in specific areas with ring-type reinforcements to absorb the forces that emerge during hot filling and subsequent cooling. Any tendency on the part of the bottle to become “oval“ is thereby prevented. Bottle fabricated in bio-plastic US - Patent No. US 2010 / 0288780 A1 Applicant: Green Planet Holdings Inc., Chicago (US) Date of Application : 23.4.2010 Bottle fabricated in plastic which takes account of enhanced requirements in terms of environmental compatibility, recycling and re-usability. The material is biologically degradable and is manufactured from biological base material, thus conserving resources. Improved guarantee strip Intern. Patent No. WO 2012 / 050759 A1 Applicant: Closure Systems International Inc., Crawfordsville (US) Date of Application: 20.9.2011 Weight-optimised screw closure with tamper strip. The guarantee strip has undergone improvements to the extent that any manipulation is made more difficult. Container closure Europ. Award of Patent No. EP 1666370 B1 Applicant: Closure Systems International Japan, Tokio (JP) Date of Application: 28.7.2004 Screw closure for a container. The closure is constructed so that, once a certain internal pressure is reached, it becomes elastically deformed and allows the pressure to escape to the outside. A bottle with a screw cap is secured by means of a sealing mark between the closure and the bottle. Unscrewing for the first time means that the seal will be irreversibly destroyed.","@ID":54} "MARKET SURVEY 30 PETplanet insider Vol. 13 No. 10/12 www.petpla.net 10/2012 MARKETsurvey Company name Kaeser Kompressoren GmbH Arizaga, Bastarrica y Cía, S.A. Postal address Telephone number Web site address Contact name Function Direct telephone number Fax E-Mail Carl-Kaeser-Str. 26, 96450 Coburg +49 9561 640 0 www.kaeser.com Wolfgang Hartmann Marketing Manager +49 9561 640-252 +49 9561 640-890 wolfgang.hartmann@kaeser.de Pol. Ind. Azitain 6, 20600 Eibar, Spain +34 943 820 400 www.abc-compressors.com Ignacio Azcuna Product Manager +34 630 751 355 +34 943 820 235 iazcuna@abc-compressors.com 1. Machine designation / model number Sigma PETAir Boosters 3THA-3-LT 4HA-4-TER-LT 3HA-4-LT 3HA-4-TER-LT 4HA-6-TER-LT 4HA-6-TRIS-LT 4HP-4-LT 3HP-4-LT 2. Number of models in range 25 14 3 4 4 2 4 4 5 5 3. Output in m³/hour 336 - 2,772 10,000 525 860 1,031 1,443 1,700 2,321 3,087 4,135 4. Compressor type Low pressure air Screw High pressure blowing air (up to 40bar) Piston Reciprocating Integrated system Reciprocating Reciprocating Reciprocating Reciprocating Reciprocating Reciprocating Reciprocating Reciprocating 5. Lubricated or oil-free Low pressure compressor Lubricated booster compressor Lubricated Oil-free integrated system Oil-free Oil-free Oil-free Oil-free Oil-free Oil-free Oil-free Oil-free 6. Machine layout V (2 cylinder), W (3 cylinder) 7. Number of compressor stages 1+1 1 or 2 3 4 3 3 4 4 4 3 8. Are special foundations required ? No No No No No No No No No No 9. Cooling system Air (water option) Water Water Water Water Water Water Water Water Water 10. Belt or direct drive Low pressure compressor Direct Booster compressor Belt Belt Integrated system Belt Belt Belt Belt Belt Belt Belt Belt Company name Siad Macchine Impianti Aerof on Engineers Private Limited Postal address Telephone number Web site address Contact name Function Direct telephone number Fax E-Mail Via Canovine, 2/4 – 24126 Bergamo, Italy +39 035 327611 www.siadmi.com Giovanni Brignoli Compressor Division +39 035 327609 +39 035 327694 giovanni.brignoli@siadmi.com B-505 Premium House, Opposite Gandhigram Railway Station, Ahmedabad 380 009, Gujarat, India +91 79 26589712 www.aeroflon.com Mitul Choksi Chief Operations Officer - Int. Business +91 79 40069715 +91 79 26586954 exports@aeroflon.com 1. Machine designation / model number BS line Tempo2 Af42 series 2. Number of models in range 19 18 8 3. Output in m³/hour 1,000 – 6,000 Nm3/h* (0°C– on sea level - r.H. 0%) 260 – 5,550 Nm3/h (0°C – on sea level - r.H. 0%) Up to 722 4. Compressor type High pressure blowing air (up to 40 bar) High pressure Low pressure air Screw 5bar High pressure blowing air (up to 40bar) Piston (booster) Piston 15bar Integrated system 42bar 5. Lubricated or oil-free Oil- free Oil-free Low pressure compressor Oil-free Oil-free Booster compressor Oil-free Oil-free Integrated system Oil-free 6. Machine layout V W Rectangular 7. Number of compressor stages 2 screw + 2 booster= 4 3 3 8. Are special foundations required ? No No Cement foundation required as per specification 9. Cooling system Water Water Water 10. Belt or direct drive Belt Low pressure compressor Direct V-belt Booster compressor Belt V-belt Integrated system V-belt","@ID":32} "PET - THE NEXT GENERATION 22 PETplanet insider Vol. 13 No. 10/12 www.petpla.net Recycled PET bottles for low carbon façade systems A PET brick in the wall “A product design company that got into architecture,” that is how Taiwanese company Miniwiz Sustainable Energy Development describe themselves. Founder Arthur Huang and his company conceptualised, designed, tested and manufactured a system made from recycled PET bottles. A total of 480,000 interlocking “bricks” were used for the façade at the EcoArk pavilion which forms the centrepiece of the 2010 Taipei International Flora Expo. The latest project is an architectural design and supply of a new electronic waste recycling plant. Polli-Brick is a building material made from 100% recycled polyethylene terephthalate polymer (PET). It is translucent, naturally insulated and durable. The modular 3D honeycomb self-interlocking units make it extremely strong without any chemical adhesives. Polli-Brick can be assembled into rectangular panels or any customised shape. It can be tailored to either a simple modular, quick to install, affordable cladding system or an interactive colour LED integrated animated building skin system. A Polli-Brick panel can bear up to 3,300Pa of destructive lateral wind force (up to Category 5 hurricanes) without any damage or water seepage and weighs only one-fifth of the material of the standard curtain wall system. The performance enhanced films enforce the panel strength while providing extra protection against UV, water and fire. The PC coating makes the Polli-Brick panel scratch-resistant and easy to clean. Polli-Brick can further enhance its environmental durability with biaxial-oriented metallised film to give the building façade and roofing a semi-translucent aluminium finish with an extremely low carbon footprint. The cross-industry R&D hybridisation keeps the recycling process economically efficient since Polli-Brick can be mass manufactured on site, reducing the carbon footprint when compared with conventional glass and steel structures. The system reduces energy consumption in both transportation and construction phases, but the dead load itself reflects cost saving potential within the building structure. The EcoArk project The nine storey tall EcoArk of the 2010 Flora Expo in Taipai, Taiwan is a steel construction and an envelope of Polli-Brick panels with an iPhone controlled lighting system of 40,000 LEDs. The roof features a large photovoltaic array to power the lighting, interior fans and a water feature. The structure of the Polli-Brick curtain wall was designed to be disassembled and reassembled in a new location after the Expo.","@ID":24} "REGIONAL MARKET REPORTS 15 The company Yinlu was established in 1985 as a fruit canning factory and was, until 2011, owned by the Chen family – first generation, today second generation. In 2011 Nestlé acquired a 60% stake in the enterprise for 10 billion RMB (corresponding to approx. €1.25bn) – and is exerting its influence in order to professionalise existing production and to collaborate in planning new installations. Three plants are running: in Xiamen (1.4 billion l), Shandong (0.7 billion l) and Hubei (1.1 billion l). One plant is under construction in Anhai, another plant is planned in Sechuan. Equipment installed Resin processed: 70,000t PET resin Injection moulding: 30 Netstal PET-Line systems (PET and caps inclusive) Two Huayan systems (local Chinese make) Blow moulding: 12 Sidel machines Filling aseptic 9 GEA Procomac lines One KHS Corpoplast line Compression moulding : Four Sacmi machines Innovation Don’t compromise on quality. For further information please contact: info@gabriel-chemie.com www.gabriel-chemie.com PremiumMasterbatches for Superb Products. Friedrichshafen Oct 16–20, 2012 VISIT US AT F AKUMA ! Huayan injection moulding system (local make) under maintenance Brief message from Tony Chen, typical of today’s China: “More beverages, more investments, more machines. With the growth of the beverage market, investment in machines must go on.” The product Milk based products such as peanut milk in various package formats – flower tea – juices – also water. In total 3.5 million t, corresponding to 3.5 billion litres 50% packaged in cans and cartons; 50% packaged in PET.","@ID":17} "BOTTLE MAKING 27 PETplanet insider Vol. 13 No. 10/12 www.petpla.net greatly reduced, because there is no conveying and the number of moving parts is limited.” Above all, this bottling line has enabled Refresco to increase its production volumes. After one year entirely devoted to the bottling of teabased drinks in different formats 1l, 1.5l and 2l – this line is now also used for fruit juices, thanks to an optimised schedule. The end of line includes a double palletising island to ensure even greater flexibility for palletisation. “Our line is equipped with two Sidel robotised end-of-line alternatives. They group bottles into batches of 2, 4 and 6, into four-packs with or without handles or into bulk pallets or half-pallets.” 100% dry With the start-up of this new bottling line in 2011, Refresco has gone all in with 100% dry aseptic bottling. This acquisition is based on experience with the aseptic line at the Nuits-Saint-Georges site, which was installed a year before and which also includes a Combi Predis/Capdis FMa with dry decontamination for preforms and caps. Similarly, Refresco wanted to make its technological leap forward complete at the Saint-Alban site, abandoning wet decontamination for cap sterilisation. “There was no reason to go with dry aseptic for CCT Creative Competence Technology GmbH Idsteiner Strasse 74 D-65527 Niedernhausen, Germany r.steinmetz@cct-systems.com www.cct-systems.com PET Molds Closure Molds Developments PET Systems Closure Systems ComPETCap® Designs powered by CCTSystems ® for further information please contact us Design and Patents CCTSystems®3025 for still water CCTSystems®1810 for CSD (carbonated soft drinks) current design CCT design 5,05g 4,10g 3,92g 3,05g current design CCT design bottles and keep a wet treatment for caps. We wanted a 100% dry Combi,” explains Frédéric Thoraval. “Compared to conventional wet decontamination systems, it has the advantage of requiring no water infeed. With this line, the use of sterilising agents has gone from 42t of peracetic acid to just 6.7t. One year after its start-up in March 2011, the results have been positive. The line is still being ramped up. It runs 24h a day, six days a week. The production cycle times have been validated up to 120h between two cleanings. Carbon footprint With the implementing of the new line the company cut their energy consumption by 30% versus a traditional aseptic line. The bottles produced contain 50% rPET. All in all, Refresco saves more than 1,700t of CO 2 , 38,000m² of water, 2.5 million kWh and over 400t of virgin PET each year. In late 2011, Refresco France and Sidel received First Prize in the “Economical and Clean Technologies” category at the French government’s Prix Entreprises et Environnement (Business and Environment Awards). www.sidel.com www.refresco.com ...ranging from mineral water and f avoured water to RTD teas, sodas and fruit juices.","@ID":29} "REGIONAL MARKET REPORTS 13 PETplanet insider Vol. 13 No. 10/12 www.petpla.net ers include the heavyweights Nongfu Springs, Yinlu and Wahaha. SOE in Xiamen is the model for the strengths of the merged group – there they have a KraussMaffei PETForm and two Netstal PET-Line lines in operation, in each case engaged in typical applications. PETplanet: You have undertaken a fundamental reorganisation which is not over yet. Your plans will require considerable investment in the coming years. Where is the money coming from – Munich or Switzerland? Michael Mueller: Funding will be made available by the Group. For me it is very important that we are able to offer our customers the best commercial solution on the market whatever the application will be. Additionally we will have a much bigger team to provide a first class service. Michael Mueller has been Vice President China for Sales/Service KraussMaffei and Netstal PET Group since September 2011. His career at KraussMaffei began in Project Management in 1997, subsequently in Sales. From 2002 to 2005 he worked in Key Account Management (Automotive plus Regional Representative). In 2006 he was appointed Vice President for the Injection Moulding, Extruding and PUR sectors in China. Bringing together the KraussMaffei and Netstal brand names – formerly fierce competitors – and forging them into a single operating unit presented a formidable challenge. An even greater challenge will be to ensure that both of these famous names prosper in the future. S.O.E .Group “Diversification through PET recycling\" We met: Universe Chen, General Manager (with David Tso) S.O.E. Group – Zhonghao Chemicals in Shantu, Guangdong – is active in polyester processing. 85 to 90% of sales relate to the manufacture of foils, including tapes for video and audio; 10 to 15% conversion of PET into preforms. As far as the PET business is concerned, S.O.E. is a classic converter who knows all about and limits itself to the supply of preforms. Are your standard PET preform molds making you as much money as they should? Ask how MPET with iFlow technology improves production and achieves greater quality results. Innovation doesn’t happen in isolation. It happens when blue-sky thinking meets down to earth knowhow and exceptional supply chain execution. The sort of innovation that Mold-Masters is known for, now applied to PET tooling for industry-leading results. Introducing MPET – the new PET preform tooling solution designed for the standards of tomorrow. Mold-Mastersand theMold-Masters logo are trademarksofMold-Masters (2007) Limited. © 2011Mold-Masters (2007) Limited.All rights reserved. Think about it. moldmasters.com/thinkaboutit info@moldmasters.com","@ID":15} "PETcontents 10/12 4 PETplanet insider Vol. 13 No. 10/12 www.petpla.net INSIDE TRACK 3 Editorial 4 Contents 6 News 46 Products 48 Bottles: Beverages and Liquid Food 50 Bottles: Home and Personal Care 52 Patents BOTTLE MAKING 26 A French tea party Dry aseptic line from Sidel at refresco 33 A playful bottle BTC Concept unveils stackable and lockable BottleClips BOTTLING / FILLING 34 Fruit drink with a real bite Twin-flow hotfill process in TRADESHOW PREVIEWS 38 Trade fair pairing in India packtech and dti India, November 6 - 8, 2012 42 Tradition, innovation and naturalness Brau Beviale Nuremberg, November 13 - 15, 2012 REGIONAL MARKET REPORT 10 China - Part 3 MATERIAL / RECYCLING 18 Food safety first! EFSA adopts first opinion on safe PET recycling 20 From bottle to sheet! Launch of ViscoSheet production line PET - THE NEXT GENERATION 22 A PET brick in the wall Recycled PET bottles for low carbon facade systems. PREFORM PRODUCTION 24 Wall thickness variation A rapid guide to perfect preforms - Part 33 MARKET SURVEY 29 Suppliers of compressor manufacturers for PET bottle blowing BUYER’S GUIDE 53 Get listed! Page 34 Page 20 Page 26","@ID":6} "TRADESHOW PREVIEW 41 PETplanet insider Vol. 13 No. 10/12 www.petpla.net turnover of US$15 bn in 2015. The main motor of growth is the food and beverage sector. The area of food processing could double within the next four to five years, which will lead to enormous demand for packaging material as well as for process technology.” The food and beverage industries generate the greatest demand for packaging, accounting for over 80%, followed by the pharmaceuticals industry and other sectors. The greatest demand is for flexible packaging materials such as films and laminates, followed by solid containers and packaging, tin cans, printed cartons, glass as well as closures and labels. Packaging with an annual growth rate of 15% – and rising In fiscal year 2011/2012 turnover in the Indian packaging industry will probably exceed €11bn, according to an analysis carried out by the Indian office of the VDMA. It has risen by 15% per year, on average, for the past seven years, and this rate of growth is likely to continue to accelerate, which is entirely logical if you look at the current per capita consumption of packaging material and compare it with levels worldwide. The average American consumes 13kg of packaging per year, while the average in Japan is 15kg and in India just 0.3kg. Indian consumers want simple and cheap packaging, on the one hand, but on the other are increasingly demanding attractive and hygienic forms of packaging and small portion packs, for example for household goods and toiletries. Trade fair pairing In 2010 the organisers of the two specialised trade fairs, Messe München (dti) and Messe Düsseldorf (International PackTech India) and their Indian subsidiaries, brought the two events together for the first time. In 2012 the total increase in exhibition space for both events will be almost 50%, thanks to the high uptake. Almost 300 exhibitors are expected on 12,000m2 exhibition space. www.packtech-india.com www.drinktechnology-india.com","@ID":43} "MATERIAL / RECYCLING 21 PETplanet insider Vol. 13 No. 10/12 www.petpla.net Engineering Excellence www.netstal.com Low production costs Maximum output At Netstal our aim is to help you produce the perfect PET preforms: at minimum cycle times you achieve maximum output with constantly high quality and energy efficiency. And that’s no coincidence: our team of experts are always there for you – with state-of-the-art systems. Brau Beviale, hall A7, booth 624/523 such as no melts or black spots 0.2mm in the final sheet. The food grade sheet was promptly analysed in the laboratory for any contaminants using gas chromatography in accordance with the Fraunhofer method. Regular quality control as defined by GMP (Good Manufacturing Practice) is essential. The viscoLAB makes it possible to track material and process quality continuously during the test runs and in the follow-up process. On the second day the IV increase of virgin pellets was shown. 0.82IV bottle grade material was fed to the viscoStar reactor. Following application of the SSP process, final IV measurements showed a result of 0.95dl/g. The hot, dry pellets were fed directly from the reactor into the sheet line. Conference programme During the open-house event, the visitors had the opportunity to listen to presentations by international guest speakers. Among the guest speakers were Santiago Garcia-Gonzalez, Senior Consultant for PCI PET packaging, independent chemical engineer Allan Griff, Edward Kosior, Managing Director of Nextek Limited, an international consultancy dealing in plastics recycling which has developed new packaging technologies for the UK and Sion Stanfield who has spent over 25 years in the retail sector, holding senior positions at Tesco and Sainsburys. www.viscotec.at The new Viscotec production site and Technical Centre is extending to 20,000m² The Decon decontamination dryer","@ID":23} "MATERIAL / RECYCLING 19 PETplanet insider Vol. 13 kg in food would satisfy the above criterion for the default exposure scenario. In the case of the other exposure scenarios for adults and toddlers, the relevant migration criterion will accordingly be 0.75 and 0.15µg/kg food. Therefore if a recycling process is able to reduce an input reference contamination of 3mg/kg PET to a Cres not higher than a Cmod corresponding to the relevant migration criterion, the potential dietary exposure cannot be higher than 0.0025µg/kg bw/day and recycled PET manufactured with such recycling process is not considered of safety concern. The Panel considered appropriate that the proportion of PET from non-food consumer applications should be no more than 5% in the input to be recycled. The Panel’s conclusions for all three opinions included the statement that the recycling processes would not give rise to safety concerns if the proportion of PET from nonfood consumer applications does not exceed 5%. The Panel recommends that this is monitored periodically in line with Good Manufacturing Practices (GMP). EFSA evaluations only concern the safety of mechanical recycling processes, in which used consumer plastics are collected, ground into small flakes and decontaminated, before being processed into new materials for use in the food chain. Producers are required to demonstrate that their process can reduce chemical contaminants in the recycled plastic to such a level that potential migration of any residual chemicals does not pose a risk for human health. Applicants may be required to modify proposed uses and/or the proportion of recycled material to be in compliance with EFSA’s scientific methodology. These three opinions are the first opinions of a series to be issued over the next 18 months on applications for recycling processes to manufacture plastics for food contact materials. Once this series is completed, EFSA’s opinions will inform the decisions of the European Commission and Member States regarding the authorisation of the evaluated processes. Thereafter, recycled plastics used in food packaging, food containers and other food contact materials should only be obtained from EFSA assessed and authorised processes. EFSA publishes its opinions as they are adopted and not in any particular order of priority. An overview of all applications for authorisation received can be accessed on EFSA’s website. www.efsa.europa.eu SIPA S.p.A. - Via Caduti del Lavoro, 3 - 31029 Vittorio Veneto (TV) - Italy Tel. +39 0438 911511 - Fax +39 0438 912273 - e-mail: sipa@zoppas.com www.sipa-xform.com NEW PREFORM SYSTEM Designed to adapt. Built to last. Imagine using any preform mold in one system. Now you can. The new XFORM PET preform system gives you unprecedented flexibility combined with the highest running efficiency: it accepts the mostly used molds (old and new generation) present in the market. So you can feel free to innovate and grow without penalizing your existing assets.","@ID":21} "TRADE SHOW PREVIEW 42 PETplanet insider Vol. 13 No. 10/12 www.petpla.net Brau Beviale 2012: Tradition, innovation and naturalness Brau Beviale takes place from 13–15 November. Over 1,350 exhibitors (2011: 44 % international) will present a comprehensive spectrum of beverage raw materials, technologies, logistics and marketing ideas in the Exhibition Centre Nuremberg. A good 31,500 visitors (2011: 36 % international) from technical and commercial management in the European beverage industry are expected. We have put together a first selcetion from the many exhibits of interest to producers and fillers of PET bottles. More to follow in issues 11 and 12. www.ask-Brau-Beviale.de Carl Hirsch Hall 4 | Booth 442 Special edition bottles and crate decoration Carl Hirsch, Munich offers systems to re-decorate beverage crates or keg barrels as well as bottles for special editions of beer. The services comprise redecoration of old crates with new labels or sleeve or concepts to present a new brand on the market. The company also offers tailored solutions labels, machines which can be rented and even the personnel to manage a whole redecoration. In addition, the company offers a wide range of special bottles, tabs or labels for new types of beer. Nostalgic swing stopper bottles up to 3l volume and dark Champagne bottles packed in luxurious wooden boxes are further examples of the company’s range of products. www.carl-hirsch.de Integrated solutions Sacmi will be showcasing turnkey solutions from filling to labelling, from preform production to stretch-blow forming and systems to cater for everything from the raw material to the bottle. They will be featuring the IPS preform press: the recently developed system is characterised by flexibility and rapidity of size changeovers, ergonomic solutions, energy savings, reduced overall dimensions. The stand will also be dedicating plenty of space to the machines in the rotary SBF (stretch-blow forming) range, which have from 6 to 24 stretch-blowing stations and output levels of over 64,000bph in the standard half-litre format. Completing the fully integrated line Sacmi Verona provides labelling solutions for production lines that use several labelling, self-adhesive, hot glue or hot melt technologies. Sacmi will also be illustrating the latest developments in its CCM (continuous compression moulding) series. The compression presses feature output rates of up to 2,000caps/min and 1.6s cycle time along with low energy consumption. www.sacmi.com Sacmi Hall 5 | Booth 341 Kegs and more Petainer is a specialist in the design and manufacture of PET containers. The company delivers total packaging solutions ranging from design, supply and manufacture right through to supporting their products in use. Their product range extends from containers found on supermarket shelves to their latest development, an innovative, recyclable family of ‘one-way’ PET kegs and fittings for beer and other beverages. The Petainer keg can be used in various segments such as beer, wine, cider and others. www.petainer.com Petainer UK Holdings Hall 4 | Booth 236","@ID":44} "REGIONAL MARKET REPORTS 14 PETplanet insider Vol. 13 No. 10/12 www.petpla.net Universe Chen, General Manager S.O.E. Group Production Resin processed: 9,600t/a PET Number of preforms: 200 million, primarily heavy preforms Projected increase after investment into two more preform systems: Additional 7,200t/a PET Biggest customers are Pepsi (CSD) and Canten (mineral water). Locations in Xiamen (facility rented): one KraussMaffei PETForm system, 72 cavities in Guang Zhou one Husky system, one Krupp system, two Netstal systems with 128 cavities are on order. Long term policy: the Husky/Krupp systems are for CSD preforms, the KraussMaffei PETForm system for edible oil preforms, the Netstal systems for water. Project SOE has been concerned with the topic of recycling for the past six years. Talks have been held with the local municipalities about collection systems and with Chinese authorities about the use of rPET in food applications. Talks are also on the way with expert companies to supply equipment for re-processing bottles into pellets for bottle-to-bottle usage – such as Starlinger, Erema, Herbold and others. The capacity of recycling plant under consideration: between 25,000 and 30,000t of rPET. Quote from Universe Chen – probably referring to recent orders and addressed to Netstal: “We have no inventory, no preforms in stock. When the need arises with new orders, we rely on the timely response and the professional support of our suppliers.” Xiamen Yinlu Foods Group “More beverages, more investments, more machines.” F.l.t.r.: Tony Chen, Wolfgang von Schroeter, Michael Mueller We met: Tony Chen, Head of Purchasing (together with Michael Müller ) China’s PET sector speaks in hushed, reverent tones about Xiamen Yinlu Foods – or Yinlu for short, because the company’s image is totally at odds with the standards generally applicable to an industrial operation. This, however, does not make it any the less successful. Yinlu occupies grand and prestigious head office premises in the centre of the city of Xiamen – a high-ceilinged entrance hall with an impressive chandelier hanging from the ceiling, empty of people (unusual in China), marble columns and a marble floor. Here financial power and grandeur are displayed before which leaves the visitor from Europe awe-struck. The production operation takes place outside the city. In the company of David Tso, who represents the Netstal brand at the KraussMaffei Group in China, we visited the main plant, travelling across the open site, no fencing, no barrier, no need for the time-consuming identification process in order to gain access. David Tso knows his way around, he is, literally, at home here, as he navigates his way without hesitation into what is known as the ’Netstal Bay’ where a number of Netstal machines are working alongside a Huayan injection moulding machine. The maintenance people take a break from working inside the Chinese mould to say hello to us and, in particular, David Tso. The production facilities – aseptic bottling is a speciality at Yinlu – are spread over an extensive green area, with a lake and garden as well as villas for the owners (the Chen family) and management personnel on the same plot. Alongside the production bays is the company’s own conference centre. 20,000 employees are said to work here, 300,000 Chinese with a direct or indirect connection/ relationship with the Yinlu enterprise.","@ID":16} "REGIONAL MARKET REPORTS 12 PETplanet insider Vol. 13 No. 10/12 www.petpla.net Netstal’s best customers (estimate) These are the very big bottlers who work with Netstal PET-Line systems among others: Nongfu Springs with approx. 30 PET-Line installations Yinlu with approx. 30 PET-Line installations Wahaha: with approx. 9 PET-Line installations (order January 2012, delivery anticipated by September 2012) The biggest customer for closures is Tinghsin with approx. 70 units. Once the merger of the Netstal and KraussMaffei brands of PET systems has been completed and integrated into the KraussMaffei Group Organisation in China, there will be a much bigger team of service engineers on-site. At the Haiyan plant there are plans for a laboratory and a demo centre. Sources close to the company say there is talk of a possible integration of systems in Haiyan. David Tso – who has been with Netstal for twelve years – is relaxed about the small number of people employed in sales. There are only a small number of bottlers (albeit very big and important customers) with in-house production, and no converters, to look after. The watchword is “low key” – entirely in keeping with the Swiss character – direct and continuous dialogue with key managers and also with chiefs and owners, who dislike their time being wasted. David Tso: “Low key is essentially what I am about. I try to concentrate on the big picture.” In Xiamen we were fortunate enough to hold the following revealing discussion with Michael Mueller, Vice President China. PETplanet: Netstal and KraussMaffei have been run by a holding company in Munich since the 1990s yet were competitors for PET systems. Since October the same staff have been involved with both systems in China. What effects will this have and for which brand? Michael Mueller: The activities of the KraussMaffei Group in the PET sector now come under the Netstal umbrella – not only here in China but everywhere – and we are pursuing a vigorous commercial strategy. We have the commercial solution for every application - the Netstal PET-Line system with a horizontal injection unit for the quantity and volume market, the KraussMaffei PETForm system with vertical injection for the special applications (e.g. for heavy bottles, wide mouth bottles etc.). With this re-alignment of the product range, the KraussMaffei Group is now well positioned to exploit the opportunities offered by the Chinese PET sector. PETplanet: Your Netstal customers are noticing changes with concern such as: service centre in Pudong closed; at present no laboratory; no demo machines; fewer individuals for servicing the Netstal as well as the KraussMaffei machines installed. Customers must fly their operating and maintenance personal to Switzerland for training. How will KraussMaffei Group restore confidence and demonstrate commitment? Michael Mueller: Merging our activities now gives us a bigger team of Service staff, local engineers who will be trained in Netstal technology as well as in KraussMaffei technology. In addition, we are working close together with Netstal service and applications engineers from Switzerland. A laboratory is to be set up at the KraussMaffei Group Plant at Haiyan – complete with a Netstal system, 400t clamping force, a 6,600 plasticising unit to inject into 128 cavities, with a Hofstetter mould and pre-blow technology for lightweight bottles. The laboratory will be used for machine and process demonstrations as well as for training purposes. Sales of the classic KraussMaffei injection moulding machines, like our MX 850, which is now produced in China, will continue alongside sales of the Netstal systems. PETplanet: Are you planning to manufacture Netstal machines and systems in Haiyan following the example of Husky? Michael Mueller: Our plan is to be able to install systems in the existing factories and complement these with local peripheral equipment and ancillaries prior to commissioning. Our aim is to build up local expertise. The machines – these are at the heart of the systems – will be supplied from Switzerland in the future too. PETplanet: You come up against the dominant market leader in China – and elsewhere. What technological arguments do you put up in favour of products – Netstal and KraussMaffei – given the strength of the competition? How do the systems differ? Michael Mueller: I use three fundamental arguments: A Netstal development under the heading of ”Preblow“. By blowing the bottom part of the bottle in the robot system by air, Netstal can reduce the bottle weight by approx. 0.5g per preform compared to the best available competition solution. We have calculated an annual saving in materials of up to €400,000 – for still water using a 128-cavity system. As regards the vertical KraussMaffei PETForm systems – thick-walled preforms, wide mouth – cycle times can be optimised. By directly compounding with a Krauss Maffei Berstorff twin screw extruder, it is possible to use up to 100% recyclate, without the need for pre-drying. These are the foundation stones on which the KraussMaffei Group is building. PETplanet: Are there any indications so far that the new KraussMaffei Group strategy is paying off? Are we likely to be reading a success story any time soon? Michael Mueller: Despite the strength of the Swiss franc we are anticipating a large increase in our order intake and in the turnover of Netstal in China in the current financial year (as of September 2011). The custom-","@ID":14} "Vol.6 PETplanet print PREFORM PRODUCTION 24 PETplanet insider Vol. 13 No. 10/12 www.petpla.net The rapid guide to perfect preforms - part 33 Wall thickness variation Troubleshooting guides have suffered in the past from being locked away in offices and not being available to the people that actually need them. Considering the high cost of machine and tools high scrap rates can be a costly proposition eating away at already tight margins. PETplanet’s “Rapid Guide to Perfect Preforms” takes a different approach. It has been written for the people on the floor of injection moulding companies to support their daily work in making the best preforms possible. The product of two industry experts, Rick Unterlander and Ottmar Brandau, it gives concrete advice on 35 of the most common problems in preform manufacture, most illustrated by pictures. From high AA levels to wavy bodies processors can find help when they need it. Read chapter 33 of the guide. Symptom The range in preform wall thickness as measured around its circumference is above 0.15mm (0.006”). This is usually measured on the cylindrical body section of the preform near the end cap dome. Cause The mould core was not centered in the mould cavity during the moulding process. Table of Contents i........................ About the Authors ii.................................Introduction Chapter 1.............................. AA Level High 2........................ Accordion Preform 3....................... Air hooks / Streaks 4............................... Black Specks 5...................................... Bubbles 6..................................Burn Marks 7...........................Colour Streaking ................................... /Peeling 8..................................Crystallinity 9.................................Drool Marks 10.......................................... Flash 11......................... Gate Depressions 12............................... Gate Peeling 13..................Gate Voids / Pin Holes 14......................... Internal Gate Sink 15................................Internal Sinks 16........................................ IV Loss 17............................ Long Gate Nub 18...............................Milky Preform 19............................ Moisture Marks 20................Neck Finish out of Round 21....................... Parting Line Crease 22.................Parting Line Deformation 23......................... Preform Yellowing 24.................................. Short Shots 25.......................................... Sinks 26......................................... Splay 27........................... Stretched Necks 28..................................... Stringing 29......................... Surface Blemishes 30......................... Thread Flow Lines 31........ TSS (Top Sealing Surface) Sink 32.......................................Unmelts 33.. .............. Wall Thickness Variation 34.................................Wavy Body 35.................................. Weld Lines Solutions 1. Check injection time isn’t too low (injection rate too fast to cause core deflection) and adjust if necessary. Injection rate should be about 10 – 12g/sec/cavity. 2. Check to ensure injection pressure isn’t too high, especially when peaking at the transition point. 3. Check to ensure hold (packing) pressure isn’t too high, especially near the beginning of hold time. 4. Check hardware for worn, damaged or failed components, specifically the mould cores (bent), leader pins and bushings, mould level, core cooling tubes, neck ring tapers, cavity tapers, and lock ring tapers.. www.petpla.net PETplanet print vol.6 The Rapid Guide to Perfect Preforms machine no./name Order your copy now! www.petpla.net | info@hbmedia.net","@ID":26} "MARKET SURVEY 31 PETplanet insider Vol. 13 No. 10/12 www.petpla.net Ingersoll Rand Company 800 D Beaty Street, Davidson, North Carolina, USA +1704 655-4000 www.air.ingersollrand.com George Mankos Global Portfolio Manager +1 704 655-4311 +1 704 655-4039 george_mankos@irco.com 4HP-6-LT Centac C750-18, C750-20, C750-21, C1050-36 PETstar – booster / ps-2b 1250, 1470, 1980, 2290, 2840, 3340, 3850. PETstar –4 – 1500, 1700, 1900, 2100, 2300, 2500, 2800, 3000, 3300 3 5 7 18 6,004 3,085 - 6,360 Based on an inlet pressure of 8 bar-g: 1,195 - 3,696 1,497 - 3,298 Centrifugal design – 4-stages from atmosphere to 40 bar Primary booster system 4-stage from atmosphere reciprocating to 40bar Oil-free 2-stage screw or 3-stage centrifugal 2-stage reciprocating booster Reciprocating Oil-free. Oil-free Oil free Oil-free Horizontal Horizontal Balanced horizontally opposed layout 4 4 Primary + booster : 4 or 5 stages Primary + 2-stage booster : 2-3 stages 4 stages of compression all double acting. No No No No Water Water Water Water Direct Belt Direct Direct Belt Gardner Denver Ltd - Belliss & Morcom Leobersdorfer Maschinenfabrik GmbH & Co.KG Claybrook Drive Redditch B98 0DS England +44 0 1527 838600 www.belliss.com Trevor Perry Sales Director +44 0 1527 838606 +44 0 1527 838630 trevor.perry@gardnerdenver.com Suedbahnstrasse 28 2544 Leobersdorf , Austria +43 2256 9001 www.lmf.at Damir Pilipovic Sales Manager +43 2256 9001 339 +43 2256 9002 damir.pilipovic@lmf.at VH & WH range VC / VC-B / VCL-B 12 10 420 - 3,200 FAD 600 - 3,200 Reciprocating piston Xpiston Variable speed drive, air + heat recovery Oil-free Oil-free Air quality standard to ISO 8573-1 Single machine V and W configuration, complete with control panel, dryer, receiver, filters, cooling system. 3 3 + 4 No No Water Water Direct Belt and direct","@ID":33} "REGIONAL MARKET REPORTS 17 PETplanet insider Vol. 13 No. 10/12 www.petpla.net Sterilizer Rinser Filler Doser Dosing your Perfect MiX Let the fruit jump in! bly of blower filler capper block machines in June 2012. The new company is rebranded as Corpoplast Beverage Equipment (Suzhou) Company Ltd. This concept, i.e. building up a local production facility, has already proved itself elsewhere for KHS Corpoplast competitors in China and European machine manufacturers – such as: The components for the blower filler capper block machine are the combination of local supplied and the core components supplied from Germany. The design of the block machine is carried out completely in Germany while the factory handles the assembly only. Over the years, they have developed some local suppliers who were qualified to supply machine components for the Blomax assembled in Germany. The percentage of locally sourced components will be increased and optimised in future. This will help to reduce the cost and in other words, be more competitive in pricing. In the meantime they are accelerating their search for suitable suppliers. Factory capacity 20 to 30 installations per year Capacity ranges from 24,000 to 48,000bph Personnel on shop floor: 30 initially The new machines are targeting the mineral water market in China, which is extremely competitive in price. KHS has found it difficult to obtain a foothold in this market for this reason. Geoffrey Chan who happens to head up the new company as well claims: “Corpoplast Beverages Equipment (CBE) will enter new markets, and will not be taking business away from Germany. CBE with a specialised, optimised design will be more appropriate for a much bigger water market than we know today.” With Geoffrey Chan at the sharp end of KHS Corpoplast Trading and Corpoplast Beverage Equipment, we have an experienced manager with a total of 20 years’ experience in the Chinese plastics business, 16 of which have been for Corpoplast, first of all in Hongkong for Rieckermann Exporting and, since 2001, for SIG Corpoplast in Shanghai. There is no doubt that he is one of those charismatic characters who not only have an intimate knowledge of the PET business in China but have also put their own individual stamp on it. He has managed to navigate the company through critical situations, responded to changes both internally within the company and externally in the market place. In so doing he has enhanced the reputation of Corpoplast and certainly has confirmed his standing in the industry. Issue 11 China part 4","@ID":19} "PRODUCTS 47 PETplanet insider Vol. 12 No. 03/11 www.petpla.net Recycling line recoSTAR PET iV+ Ongoing PET recycling innovation, quality and state-of-the-art technology, a full range of consulting services – brought to you by Starlinger. Visit us at: PACK EXPO 2012, October 28 – 31, Booth N 5413 McCormick Place, Chicago, Illinois USA 6WDUOLQJHU +HDG 2IßFH 6RQQHQXKUJDVVH 9LHQQD $XVWULD _ 7 ) UHF\\FOLQJ#VWDUOLQJHU FRP ZZZ UHF\\FOLQJ VWDUOLQJHU FRP _ $ PHPEHU RI 6WDUOLQJHU *URXS Divide and conquer Cermex has announced the launch of the second lane divider designed and built in-house. Its DiviArm continuous lane divider follows the introduction of DiviSlat, at the end of 2011. Installed upstream from a case packer or shrink-wrapper, DiviArm is designed to distribute products at high speed without stopping the flow and without blocking/bumping products. It features a guiding arm for distributing primary packaging such as bottles, containers, cans and cartons into lanes. Cermex says that its objective is to build a range of machines and lane dividing solutions that will provide complete control over the lane divider/machine association, claimed to be one of the critical points of a packaging line. The company already has portfolio of case packers, shrink-wrappers and palletisers. It asserts that DiviArm integrates components that facilitate the interface with the case packers and shrinkwrappers and enable it to operate as a single supplier for installation and technical follow-up. The equipment is fitted with a guiding arm mounted on two axes. The transverse axis distributes products between lanes while the longitudinal axis synchronizes the product progression, so that products are guided at the speed of the lower conveyor without bumping. The system automatically empties the lane divider if the downstream machine stops, so that it can restart quickly, with no falling products and no loss in synchronisation. DiviArm is designed to offer product protection through a wide range of guide position adjustments and choice of material used to suit the product shape, resistance, label position, and so on. Cermex supplies complete turnkey solutions as well as individual machines and has developed DiviArm to integrate with its shrink-wrappers and case packers. However, the new lane divider is a stand-alone machine, which can be assimilated into any automated packaging line. It comes with its own independent electrical cabinet and several control systems and motorisations are available, depending on the customer’s line configuration and technical standards. A cantilever frame structure enables access to the setting points and speed is reported to be up to 60 cycles/min (350 prods/min). Although it can handle up to twelve lanes it has a compact footprint and is designed with modular architecture, in line with a TPM (Total Productive Maintenance) approach. It is also claimed to offer a low noise level. Following the completion of field trials and initial customer feedback, DiviArm is now entering commercial production. www.cermex.com","@ID":49} "MATERIAL / RECYCLING 18 PETplanet insider Vol. 13 No. 10/12 www.petpla.net EFSA adopts first opinions on safe PET recycling Food safety f rst The European Food Safety Authority (EFSA) Panel on Food Contact Materials, Enzymes, Flavourings and Processing Aids (CEF) has adopted three scientific opinions on the safety of processes to recycle PET for use in food contact materials. These are the first of a series on recycled plastic materials for food use and cover processes that are considered not to give rise to safety concerns if operated under well-defined and controlled conditions. They cover a total of ten recycling processes, grouped according to the applied recycling technology, and included processes based on Vacurema Prime; Starlinger IV+; and PETUK SSP technologies. EFSA Scientific opinion The scientific criteria used by EFSA’s CEF Panel for evaluating the safety of PET recycling processes was published in a scientific opinion in July 2011. This scientific opinion of EFSA deals with the criteria to be used for safety evaluation of a recycling process to produce recycled PET intended to be used for manufacture of materials and articles in contact with food. The principle of the evaluation is to apply the cleaning efficiency of a recycling technology or process, obtained from a challenge test with surrogate contaminants, to a reference contamination level for post consumer PET, conservatively set a 3mg/kg PET for a contaminant resulting from possible misuse. The resulting residual concentration of each contaminant in recycled PET (Cres) is then compared to a modelled concentration in PET (Cmod). This Cmod is calculated using generally recognized conservative migration models such that the related migration does not give rise to a dietary exposure exceeding 0.0025μg/kg bw/day, the human exposure threshold value for chemicals with structural alerts raising concern for potential genotoxicity, below which the risk to human health would be negligible. The default scenario, when the recycled PET is intended for general use, is that of an infant weighing 5kg and consuming every day 0.75l of water coming from a water bottle manufactured from 100% recycled PET. According to this scenario, it can be derived that the highest concentration of a substance in water that would ensure that the dietary exposure of 0.0025μg/kg bw/ day is not exceeded, is 0.017μg/kg food. Taking into account that generally agreed diffusion modelling overestimates migration by at least five times, a calculated migration less than 0.1μg/","@ID":20} "TRADE SHOW PREVIEW 45 PETplanet insider Vol. 13 No. 10/12 kronesFlexiFruit – doses fruit chunks as if they’re hand-picked. www.krones.com Brau Beviale 2012 Nürnberg, 13 – 15 November Hall 7A, Stand 206 Trends in beverage concepts At this year’s Brau Beviale, Wild is presenting beverage concepts with the focus on product ideas that emphasise naturalness. The highlights are beer mix drinks and malt-based soft drinks. According to Wild, the current trend goes toward unfiltered varieties that contain juice and feature a natural image. Products based on wheat beer and non-alcoholic options are also growing in popularity. Soft drinks that contain malt also give breweries and manufacturers of non-alcoholic beverages a way to expand their reach among consumers and appeal to new target groups. These slightly tart “brewed” citrus sodas are not too sweet; they are non-alcoholic and provide a good alternative to classic soft drinks and standard beer mix drinks. Altering the malt content in the beverage yields a wide range of different product options. A traditional (nonalcoholic) German drink known as a “Fassbrause” (Kegbrew) is yet another way to expand the target group and win over both younger trend-oriented consumers as well as more women. These non-alcoholic products are based on natural ingredients, and they are currently undergoing a large-scale renaissance. International favourites, especially in the Middle East, include varieties with a clearly defined malt note. Visitors can also learn more about new concepts for nonalcoholic soft drinks. Among other things, the company will present its new citrus-soda concepts featuring the innovative flavour of pomelo, as well as “energising” soft drinks based on guarana or maté. Wild’s concepts for soft drinks with a blend of fruit and mint also reflect the company’s activities in the field of natural mint flavours. Stevia, the nocalorie sweetener from natural source, can be used in all of these beverage categories. Consumer interest in steviasweetened products is growing stronger and stronger. Wild can also create low- or no-calories drinks. To improve the flavour profile of the sweetness the company uses its Taste Optimisation Technology. It also enhances the mouthfeel in the finished steviasweetened product, masking bitter offnotes. Stevia can be blended with Fruit Up, Wild’s natural fruit extract. www.wild.de Fassbrause, the German traditional drink, is in high demand among consumers – no matter whether lemon, elderberry or pink grapefruit. Source: WILD Wild Hall 1 | Booth 119","@ID":47} "REGIONAL MARKET REPORTS 10 PETplanet insider Vol. 13 No. 10/12 www.petpla.net China The third part of our Regional Market Report on China is dedicated to the interviews with KraussMaffei Group China, S.O.E. Group, Xiamen Yinlu Foods and KHS Corpoplast. KraussMaffei Group China “...the best commercial solution on the market whatever the application” Michael Mueller, left, and David Tso, right We met: Michael Mueller, Vice President China KraussMaffei Group David Tso, General Sales Manager China for the KraussMaffei and Netstal brand by Wolfgang von Schroeter The Netstal PET-Line system, featuring a horizontal injection moulding unit, and the KraussMaffei PETForm system with its vertical injection unit, used to be fierce competitors. However, since October 2011, they have been marketed in China by the same personnel / engineers under the auspices of a single department, their strategic aim being to pool their PET business interests. “...offering the best commercial solution on the market whatever the application“: This is is how Michael Mueller, Vice President China and the person responsible for the KraussMaffei Group’s injection moulding machines in China, sees it. His statement exudes commitment and conviction. The same goes for David Tso, General Sales Manager for China and the person responsible for the Netstal PET-Line systems on site (and, since October, also for KraussMaffei PETForm systems), a less ebullient personality perhaps and more reserved - qualities which have stood him in good stead during the dramatic events and changes in his career path – all this he has borne calmly and stoically. The off cial party line is as follows: “The PET activities of the Krauss Maffei Group with the products PET-Line and PETForm have now been brought together under the Netstal umbrella”. Regional market reports China Part 2","@ID":12} "BOTTLING / FILLING 37 PETplanet insider Vol. 13 No. 10/12 www.petpla.net ABC COMPRESSORS NEW PET RANGE THE MOST PROFITABLE AIR Safe Investment Total energy savings over 50% Efficient Consumption MinimumMaintenance · Up to 5 years guarantee. · Special financial terms. · Plug&Play. Complete set on base frame. · Up to 6.080 m3/h with a single compressor. · Built-in quality. The only manufacturer machining, mounting and testing the 100% of its bare compressors in Europe. · Proximity. Whole packages delivered through our sites in Europe, America and Asia. · ABC guarantees up to 15% saving thanks to our efficient design. · Save 50%of compression energy thanks to air reinjection in our 4 stage machines. · Additional 15% savingscoming from perfect adaptation to frequency converters. · Energy-audits to demonstrate it. · 8.000 hours of operationwithout any additional maintenance. · Life cycle services. From express spare parts delivery to special maintenance contracts and machine refurbishing. · 24Hx365D available worldwide for any service through our web platform. · More than 25 technical service hubs around the world to be closer. RELIABLE BEYOND LIMITS www.abc-compressors.com EXHIBITIONS 2012. Visit our stand at: DRINKTEC INDIA Mumbai (India), 6th - 8th November STAND E06 PROPAK INDONESIA Jakarta (Indonesia), 10th - 13th of October STAND D-8912","@ID":39} "2 PETplanet insider Vol. 13 No. 10/12 www.petpla.net Conveyors Bottle-to-bottle recycling plants Caps and closures Preform moulds and SBM moulds Preforms Preform and single stage machinery SBM machinery Compressors Filling equipment Resins and additives Suppliers of compressors for PET bottle blowing: Our annual market survey of compressor suppliers for PET bottle blowing gives a general overview of what’s out there in the market of compressed air systems. This year, eight companies take part. In alphabetical order they are: Aeroflon, Arizaga Bastarrica y Cía, Atlas Copco Crépelle, Gardner Denver Ltd. - Bellis & Morcom, Ingersoll Rand, Kaeser, LMF and Siad. In the survey they appear in the order in which their details were received by the editors. Although the publishers have made every effort to ensure that the information in this survey is up to date, no claims are made regarding completeness or accuracy. 10/2012 MARKETsurvey Company name Atlas Copco Crépelle Postal address Telephone number Web site address Contact name Function Direct telephone number Fax E-Mail 2 place Guy de Dampierre BP 29 59008 Lille Cedex France +33 3 20 52 47 11 www.atlascopco.com Sabine Wagnon Communications +33 3 59 01 05 02 +33 3 20 53 76 51 sabine.wagnon@fr.atlascopco.com 1. Machine designation / model number ZD ZD VSD P-compressors 2. Number of models in range 23 6 6 1 16 6 3. Output in m³/hour 792 - 4,108 FAD 792 - 1,177 FAD 529 - 1,152 FAD up to 1,584 - 3,957 FAD 626 - 1,119 FAD 163 - 786 FAD 890 - 1,372 FAD 4. Compressor type Low pressure air Screw Screw Variable speed drive screw Variable speed drive screw Screw High pressure blowing air (up to 40bar) Piston Piston Variable speed drive piston Variable speed drive piston Piston Integrated system Piston 5. Lubricated or oil-free Low pressure compressor Oil-free Oil-free Oil-free Oil-free Oil-free Booster compressor Oil-free Oil-free Oil-free Oil-free Oil-free Integrated system Oil-free 6. Machine layout Horizontal Horizontal Horizontal Horizontal Horizontal Horizontal 7. Number of compressor stages 2 + 2 2 + 2 2 + 2 2 + 2 3 1 + 3 8. Are special foundations required ? No No No No No No 9. Cooling system Water Air Water Air Water Water 10. Belt or direct drive Low pressure compressor Direct Direct Direct Direct Direct Booster compressor Belt Belt Belt Belt Belt Integrated system Belt","@ID":31} "REGIONAL MARKET REPORTS 11 PETplanet insider Vol. 13 No. 10/12 www.petpla.net With a helpful clarification: “With this step, the KraussMaffei Group is now well positioned to exploit the opportunities offered by the Chinese PET sector.” In plain English what this means is that the Netstal Service and Support Centre, opened in 2005 in the free trade area in Pudong, has been merged with the KraussMaffei Group offices in central Shanghai in October 2011 “to bundle the Groups strengths and expertise in a growth market”. The plan was to set up a lab and a Centre of PET Competence. Provision has been made in the plan for the installation of a demo machine and premises for education and training at the KraussMaffei Group Plant in Haiyan, approx. 1½ hours by car from Shanghai, where extruders have been manufactured locally for some years. According to the organisation chart, two divisions today exist as part of the KraussMaffei Group sales department for injection moulding machines and systems - one dealing with the classic range of KraussMaffei injection moulding machines (automotive and technical components in particular), the other covering the Netstal and KraussMaffei PET systems. Netstal products for caps and closures, medical and packaging applications, are being marketed by the divisions. Our meeting took place in Xiamen – where there are Netstal machines operating at Yinlu, and, on the following day, at SOE, where there is a vertical KraussMaffei PETForm machine in service. Netstal population in China We estimate between 80 and 90 PET-Line preform systems (in 2006 it was 30 to 40, i.e. stocks have doubled since 2006) and approx. 10 KraussMaffei PETForm systems in the Chines market. Netstal is the undisputed No. 2 in China. A similar number of 80/90 Netstal machines is estimated to operating in conjunction with closures applications. In the past, Netstal was estimated to reckon on an annual order intake of approx. Eight PET-Line systems and orders would be booked accordingly. This was very much in line with the typically Swiss conservative attitude – cautious, serious, and prudent - which they adopt when evaluating the market. It is a risk-free approach to business. However, since October 2011 (with a new structure in place, and a more dynamic strategy in a strong growth environment), we estimate that orders for more than 30 Netstal systems have already been booked and orders for several more systems are about to be finalised. China has become the strongest foreign market for the Swiss, accounting for approx. 50% of all PET preform systems currently supplied from Switzerland. One particularly remarkable feature is the ordering of several Netstal PETLine systems by one customer (Wahaha) in January 2012. Up to 2006, Wahaha had ordered Sipa single step systems exclusively and, since 2008, had chosen Husky preform systems, also exclusively. The fact that Netstal has achieved a breakthrough into Husky territory is nothing short of astonishing. Was it the constant, patient, professional canvassing of the market by David Tso? Or did Michael Mueller roll up his sleeves and start an aggressive sales pitch to win over new customers? Has the new structure of KraussMaffei and Netstal, the commitment to an enhanced Netstal presence, gone down well in the marketplace? It was probably a mix of all these factors combined perhaps with a feeling that maybe Husky was just too dominating in the market, and the time was now ripe for another company, Netstal, to make its presence felt. Only time will tell.","@ID":13} "BOTTLING / FILLING 35 PETplanet insider Vol. 13 No. 10/12 www.petpla.net INTERNATIONAL PACKAGING EXHIBITION - PARIS FRANCE 19 22 Nov. 2012 INNOVATIONS & SOLUTIONS Ev e r y t h i n g y o u n e e d t o KN OW ! * Code: P22107 Request your badge at www. emba l l ageweb. com COMEXPOSIUM - EMBALLAGE 2012 –Tel. : +33 (0) 1 76 77 12 80 – e-mail : stephanie.dryander@comexposium.com MORE INFORMATION? corrugated tubes, which increase the turbulent flow for an improved heat transfer with the medium-to-highviscosity products. Following a heatholding time of 21 to 30s, the slurry is passed directly to the pre-dosing filler in the bottling hall. The product is delivered by ultra-gentle, frequencycontrolled twin-screw pumps. Simultaneous juice treatment in the syrup kitchen begins with a continuously operating sugar dissolving station, which accepts the sugar from 1,000kg big bags and dissolves it at temperatures of 40°C at a rate of up to 15,000l/h (simple syrup) to create sugar syrup of 65°Brix, which is then cooled down. At the same time, pectin and other constituents such as citric acid are quickly dissolved using a special technology. The juice concentrate is removed from its aseptic packaging by two twin-screw pumps. The constituents are mixed with pretreated product water in two 40,000l tanks to create the finished beverage. The beverage is examined in the laboratory, and has to be approved by Quality Control before thermal product treatment and bottling. For highly viscous products like mango or guava, a homogeniser is also provided. The juice is pasteurised in a dedicated VarioFlash H heat exchanger, and is also passed through a product The slurry is then pasteurised in a VarioFlash H shell-and-tube heat exchanger featuring interior cross-corrugated tubes. From the Contiform H16 hotf ll stretch blow-moulding machine (far right), the containers are f rst passed to the predosing starwheel (back right) for the fruit-chunk slurry, then into the main f ller’s carousel for the juice (back left) and the capper (left).","@ID":37} "TRADESHOW PREVIEW 40 PETplanet insider Vol. 13 No. 10/12 www.petpla.net Hall: B1 Stand: B1-1111 16.-20.10.2012 DRYING HAS NEVER BEEN THIS EFFICIENT: ETA plus® LUXOR - now available with ETAplus® ETAplus® considerably reduces energy consumption and protects materials. When it comes to drying, saving energy is a key concern. We have developed a system that combines airflow regulation with a temperature adjustment feature – that can be disabled if required –and efficient waste heat recovery. The result? A drying system that cuts energy consumption by up to 64%: ETAplus® . motan-colortronic gmbh info@motan-colortronic.de www.motan-colortronic.com Dairy drinks India is the world’s biggest milk producer. Milk is firmly established in the daily diet. Dairy farmers have an annual output of over 100 million metric tons, most of which is directly consumed or sold informally. The dairy industry processes only about 13% of this milk yield. But this segment also is growing, from about 12.6 billion litres in 2011 to an expected 14.2 billion litres in 2013. In these two years alone additional capacity will be needed for the industrial processing of 1.6 billion litres of milk. Packaging markets and potential Although the supply of India-made processing and packaging machinery has increased in the past few years, demand for the latest foreign technology remains high, as International PackTech India and drink technology India (dti) show. For Rajesh Nath, Managing Director of VDMA’s Indian office in Calcutta, flexible packaging, including PET, is the fastest growing segment: ‘With the beverage and liquid food industry growing at around 14 to 15%, this will boost the demand in packaging and process technology. Hence this industry is gearing up to adopt scientific and functional packaging while keeping hygiene as important criteria.” Indian manufacturers, especially the export-oriented ones, therefore have a very strong high-tech focus in order to meet international standards and be competitive. Rajesh Nath sees the Indian packaging industry growing at an annual rate of 11%: “The industry is likely to reach a Graph 2: Packaging split for soft drinks in India in 2011 (Source: Canadean)","@ID":42} "imprint EDITORIAL PUBLISHER Alexander Büchler, Managing Director HEAD OFFICE heidelberg business media GmbH Häusserstr. 36 69115 Heidelberg, Germany phone: +49(0)6221-65108-0 fax: +49(0)6221-65108-28 info@hbmedia.net EDITORIAL Doris Fischer: fischer@hbmedia.net Michael Maruschke Ruari McCallion Ilona Trotter Wolfgang von Schroeter Anthony Withers MEDIA CONSULTANTS Ute Andrä andrae@hbmedia.net Martina Hischmann hirschmann@hbmedia.net phone: +49(0)6221-65108-0 fax: +49(0)6221-65108-28 France, Italy, Spain, UK Elisabeth Maria Köpke phone: +49(0)6201-878925 fax: +49(0)6201-878926 koepke@hbmedia.net LAYOUT AND PREPRESS Exprim Kommunikationsdesign Matthias Gaumann | www.exprim.de READER SERVICES Chiraz El-Goudi reader@hbmedia.net PRINT Chroma Druck & Verlag GmbH Werkstr. 25 67454 Römerberg Germany WWW www.hbmedia.net | www.petpla.net PETplanet insider ISSN 1438-9459 is published 10 times a year. This publication is sent to qualified subscribers (1-year subscription 149 EUR, 2-year subscription 289 EUR, Young professionals’ subscription 99 EUR. Magazines will be dispatched to you by airmail). Not to be reproduced in any form without permission from the publisher. Note: The fact that product names may not be identified as trade marks is not an indication that such names are not registered trademarks. 3 PETplanet insider Vol. 13 No. 10/12 www.petpla.net The success of PETplanet can be attributed to many things: its stylish design, an efficient mailing list and the support of our advertisers. Above and beyond all this, however, the key element of our success is down to the magazines’ overwhelming popularity with its readers.Our happiness will be complete only when PETplanet is the first item that you read in your morning post. You enjoy our reports from site, the well-researched technical articles and – last but not least – our market overviews. This consistently high standard does not come easily: we are fortunate in receiving many unsolicited, but expertly-written and authoritative articles from industry insiders, but we take particular pride in the stories that we conceive, research and write ourselves. It’s time now for the people involved to take a bow. In addition to the already familiar team made up of Doris Fischer, Wolfgang von Schröter, Gabriele Kosmehl, and Michael Maruschke, we are now pleased to report that we have succeeded in persuading one more specialist to make the daunting leap from industry to print. During the coming year, Waldemar Schmitke will be strengthening our editorial team. He boasts exceptional experience in the industry. He was responsible for the PET sector at Netstal for a number of years. He has designed, built and sold injection moulding machines. He understands the woes that beset processors worldwide and is completely familiar with the nuts and bolts of the injection moulding machine. Recently we embarked together on an editorial odyssey through the Ukraine and Poland (read the reports of the Go To Brau Tour in the upcoming issues of PETplanet insider, starting in issue 11/12) and were delighted to discover that Waldemar Schmitke took to technical journalism like the proverbial fish to water. Producing a good story often requires the persistence of a salesman to dig out the facts, the analytical faculties of a developer to understand the background, and the inspiration of an author to put the words on paper. All this Waldemar Schmitke brings with him. We know that you will extend a warm and sincere welcome to him, in the same way as you have always welcomed everyone in our team. I am confident that Waldemar Schmitke will contribute a wealth of new ideas to maintain the reputation of PETplanet. Yours Alexander Büchler EDITORIAL dear readers, EDITORIAL Waldemar Schmitke (right) at one of his first interviews at PET Technologies in Ukraine","@ID":5} "MATERIAL / RECYCLING 20 PETplanet insider Vol. 13 No. 10/12 www.petpla.net Launch of Viscosheet production line at Starlinger Viscotec open-house event From bottle to sheet 2 in 1 - Drying and decontamination of PET PCR f akes in a single step The Decon 50 decontamination dryer for post-consumer recycled PET flakes can be used as a stand-alone or in-line unit that both dries and decontaminates crystallized PCR flakes or skeleton waste in accordance with EFSA and FDA standards prior to the extrusion process. The Viscosheet line is designed for the production of 100% food grade rPET sheet. It can process up to 100% of undried material with minimized IV decrease. The main features of the line are: Conical twin screw extruder: Due to the high vacuum venting and the smooth processing in the co-rotating conical twin screw extruder, it is possible to achieve excellent colour and IV values even with undried PET materials. Optional co-extruder Power backflush screen changer: Specially designed for R-PET with a filtration fineness of 50μm, the power backflush filter eliminates pressure drops during backflushing and gives constant efficiency of filtration regardless of output. Gravimetric dosing unit Fully integrated operator interface Optional PE lamination PE film unwinder for laminating PE film on to the PET sheet. Fully automatic winder: Winder with fully-automatic roll change facility incl. cutting. Two individual rolls can be wound with a middle cut of the sheet on one shaft. Output up to 2000kg September 12 and 13, 2012 saw 200 visitors converge on the Viscotec open-house event in Upper Austria. Besides the conference programme, the main focus of interest as far as the visitors were concerned was the world premiere of the Viscosheet line which was being showcased under production conditions in the Technical Centre. The core competence of Starlinger viscotec, specialists in PET upgrading and decontamination technology, lies in food grade applications for recycled post-consumer PET and HDPE materials. The opening of the production site and Technical Centre on premises extending to 20,000m² has enabled Starlinger to expand their SSP (Solid State Polycendensation) Division. In the Technical Centre, where all viscotec products can be seen in production, customer tests can be run for any material configuration. At the open-house event, the Viscosheet line was producing 100% rPET sheet. The rPET flakes had been dried and decontaminated in the DecON module. According to Lisa Straub, Food Safety Manager at viscotec, “this is an integrated system that meets the new EFSA decontamination standard for infants which is the strictest in the world”. After the decontamination stage, the warm, dry flakes were run through a colour sorter, where the flakes, such as multilayer or PVC particles which changed colour after the thermal treatment stage in the Decon, can be sorted easily and inexpensively into the gravimetric feeding system on the sheet line. During the live demonstration forming part of the open-house event, the mixing ratio of four components varied in the course of full production between dry and warm granulate, cold granulate, undried in-house flakes and PCR flakes from the Decon unit without any perceptible property changes to the end product. Visitors were able to inspect the quality of the sheet using the integrated quality documentation system qualiTec, a development from Starlinger’s textile division which automatically measures, displays and fully documents important para-meters such as IV, thickness, colour L,a,b values and contaminants Viscosheet line under production conditions","@ID":22} "NEWS 8 PETplanet insider Vol. 13 No. 10/12 www.petpla.net Retal expands production range The Russian company. Manufacturer of Polymer Films (MPF), which belongs to the Retal Group, is to increase its production capacity of BoPET films. Starting from 2008, the company became a key player in the Russian market, with sales of more than 12,000t/a. An investment of about €40m in a new production line will allow the company to triple the volume of its production and sales, expand its product range, as well as consolidate its leading position in the Russian market, the CIS countries and Eastern Europe. Commissioning of the line is scheduled for the first quarter of 2015. www.retal.ru Resilux reports slower H1 2012, invests in capacity and R&D Resilux NV, the Dutch manufacturer of PET preforms and bottles, has reported lower sales volumes, revenues and profits in the first half of 2012 compared to 2011. Sales were down 3.6% and revenues by 8.5%, to €142 million. “Added value” declined by 9.8%, to €28.8 million; EBITDA by 24% (€13.7 million); and profit before tax was down by 30%, to €6.8 million. Resilux says that the performance resulted from poor spring weather in northern Europe compared with 2011, and the ongoing impact of the economic crisis in southern Europe. The biggest decreases in volumes were in Spain, France and Germany, while volumes increased in Greece, Switzerland, and East and Central Europe. Personnel costs increased, due to indexations, additional hiring and the strength of the Swiss Franc and US Dollar. Net financial debt (excluding subordinated loans) as at June 30, 2012 showed a decrease of €7.2 million, to €39.9 million. Net new investments in H1 2012 amounted to €6.8 million (2011: €11.5 million) and include the first part of a building in Switzerland, increases in production capacity and increases in new production tools. The company asserts that the new tools should allow it to offer solutions to customers to balance increasing raw material prices by means of lighter and more ecological products. Resilux says that its current cash flows allow it to invest in additional capacity and new products and to increase R&D. www.resilux.com Invista acquires La Seda IP and licensing Invista Performance Technologies has acquired intellectual property (IP) and licensing rights from La Seda de Barcelona SA, relating to its PTA, PET and related process technologies. The acquisition covers Europe, the Middle East and Africa (EMEA). The IP and licensing rights for the EMEA region were previously vested in a joint venture company established by predecessor companies of Invista and La Seda in 2000. www.invista.com “Big Five” announce formation of the Plant PET Technology Collaborative (PTC) Five of the world’s largest companies - Coca-Cola, Ford Motor Company, H.J. Heinz, Nike, Inc. and Procter & Gamble - have come together to form the Plant PET Technology Collaborative (PTC). It has been founded as a strategic working group focused on accelerating the development and use of 100% plant-based PET materials and fibre in the companies’ products. PET is used by all five companies in a variety of applications, including plastic bottles, apparel, footwear and automotive fabric and carpets. PTC is intended to build upon Coca-Cola’s PlantBottle packaging technology, which is partially made from plants and has a lower environmental impact than traditional PET plastic bottles. It will aim to drive the development of common methodologies and standards for the use of plant-based plastic including lifecycle analyses and universal terminology. www.thecoca-colacompany.com Erratum: Krones Contiform Medium output In the last issue we asked market participants, among other things, about the output per hour for the SBM mould for 1.5l still mineral water bottles. In the case of the Krones Contiform Medium the data was inadvertently omitted. We now wish to rectify this omission: the output of the Krones Contiform Medium is 2,250 units / h. www.krones.com Onex Corporation to acquire KraussMaffei Group Onex Corporation, a North American private equity firm, which sold Husky Injection Molding Systems in 2011, has agreed to acquire KraussMaffei Group. The firm signed the purchase contract to acquire the company from Madison Capital, the owner of KraussMaffei Group since 2006, for €568 million. The transaction is anticipated to close by March 31, 2013 subject to customary conditions und regulatory approvals. KraussMaffei is the first European-based investment for Onex Partners III. www.kraussmaffei.com www.onex.com","@ID":10} "BOTTLES 51 PETplanet insider Vol. 13 No. 10/12 www.petpla.net 730ml oval bottle in the standard range PET Power is expanding its standard range with a new oval bottle. This bottle, with its imposing appearance, has a volume of 730ml and appears quite tall as a result of its narrow shape. The model features two smooth presentation areas to front and rear. In addition to this, the sides and the neck have attractively rounded lines. The bottle is fitted with the popular 28SP410 neck version that can be conveniently combined with a large number of standard closures. The model is suitable for bottling both cosmetic products and foodstuffs as well as pharmaceutical products. It offers unlimited possibilities when it comes to decoration and can be fitted with a label, sleeve or screen printing. It goes without saying that this bottle can also be manufactured in a range of colours. www.petpower.nl Ajax in PET Colgate-Palmolive is offering its Ajax household cleaner in a pack specially designed for smear-free cleaning of windows and shiny surfaces. The tinted product comes in an easy to handle PET bottle. The product is dispensed by way of a lockable trigger which is screwed on to the neck of the bottle. A paper label printed on both sides incorporates all the retail information and usage details. www.palmolive.eu.com Cleanliness even with cold water Procter & Gamble GmbH of Schwalbach am Taunus have overhauled their Fairy hand washing up liquid. The formula has been changed and the product now boasts optimum effectiveness, even in cold water. A slightly greenish tinted PET bottle, shaped so that it is easy to handle and with a content of 450ml plus a screw-on hinged lid with an opening for dispensing serves as packaging for the product. The hinged lid can be raised slightly by means of an adequately dimensioned projection and then rocks into its final position via a pre-tensioned hinge. Three paper labels convey the necessary retail data. www.pg.com","@ID":53} "TRADESHOW PREVIEW 38 PETplanet insider Vol. 13 No. 10/12 www.petpla.net Demand for beverage technology and process and packing technology in India Trade fair pairing in India India is growing to become the second-most important market of the future, after China, for suppliers in the beverage and packaging industry. Many examples demonstrate India’s vast latent potential for any beverage manufacturers who serve the market with modern packaging such as PET, and equally so for the producers of packaging and process technology for beverages and foods. At Mumbai, from November 6 to 8, 2012, drink technology India (dti) and International PackTech India will offer a platform to bring together supply and demand for this sector. Retail trade regulation puts the brakes on growth A broad middle class acts as a motor for growth in any economy, According to a study by the McKinsey Global Institute (MGI), the Indian middle class, which numbered just about 50 million in 2007, will have grown to around 583 million by 2025. The factor that holds back growth the most, according to the Confederation of Indian Industry (CII), however, is the strict regulation of retail trade in India. Over 90% of perishable food is sold by local traders, for example from street stalls and little corner shops. Investment in modern super- and hypermarkets would also generate more investment in logistics, CII predicts. This change is bound to take place, and this would then result in a great increase in demand for individual packaging for foodstuffs, beverages and commodities. The establishment of a better organised structure in the retail trade industry is directly linked to a certain degree of Westernisation of the lifestyle and culture. The number of shops and supermarkets is rising, and with it the demand for packaging for the everyday goods they sell. Alcoholic drinks The consumption of beer at present is less than two litres per head per year. Euromonitor International expects the market in beer to double to a turnover of US$9 bn by 2016 alone. At present (2011) beer output is approximately 15 million hectolitres. 56 breweries produce beer under licence from the Indian Government. From 2009 to 2013 market forecasters reckon on an annual average rate of increase of 12%. The licensed liquor outlets and bigger restaurants offer gin, whisky, rum, arrak, wine, sparkling wine or toddy (palm wine). Even in the fiveyear period 2004 to 2008 sales of spirits rose by over half to 1.2 billion litres. From 2009 to 2013 a further average growth of around 10% per year may be expected – up to just under 2 billion litres of spirits. Soft drinks In 2011 about 1.5 billion litres of carbonated soft drinks were produced. Foreign direct investments in this sector so far amount to over US$1bn , among the biggest foreign commitments in India. Soft drinks are predicted to have an annual growth rate of almost 7% by 2013. Sales of bottled water are growing twice as fast, and also start at a much higher level, at around 4.5 billion litres in 2011. Graph 1 shows beverage consumption for beer and for soft drinks from 2007 to 2011. The beverage packaging split shows that PET has the largest pecentage share in the soft drinks sector (graph 2) Graph 1: Beverage consumption for beer and for soft drinks from 2007 to 2011 (Volume in million litres). (Source: Canadean)","@ID":40} "BOTTLE MAKING 26 PETplanet insider Vol. 13 No. 10/12 www.petpla.net Dry aseptic PET line from Sidel at Refresco, France A French tea party A year after production start-up, the first results are in for Refresco France’s latest aseptic PET bottling line, installed at its Saint-Alban-les-Eaux plant, for tea-based drinks. The Refresco Group produces and bottles refreshing non-alcoholic beverages, such as sodas, fruit juices, flavoured water and mineral water. Equipped with eight aseptic lines in all, its three production sites - Délifruits, Nuits-Saint-Georges and Les Eaux-Minérales-de-Saint-Alban – are the showcase for this European group’s core activity: aseptic PET bottling. The latest Sidel aseptic line started in 2011 at its SaintAlban plant. Refresco aims to serve major retailers and brands and offers support to conceive new recipes and reliable and sustainable packages for sensitive products. An example is the launch of aseptic bottling for carbonated drinks in 2010. As Frédéric Thoraval, Industrial Director at Refresco France, explains: “Our ambition is to promote and energise preservative-free carbonated drinks for retailers’ house brands and for the hard discount market.” Furthermore, the logistics platform at its Saint-Alban site enables Refresco to store more than 50,000 pallets each year, whether they come from that production site or from one of the other plants, with a view to distribution throughout France. The technological choice in favour of aseptic bottling in PET started in the late 1990s, at a time when it was not yet fully mastered. “For an industrial company, PET makes sense only with aseptic bottling,” comments Frédéric Thoraval. “Hot filling doesn’t make sense from an energy or money standpoint, since it requires more PET material in the bottle. The development of aseptic technology, combined with the growth of PET and recycled PET – versus other materials such as glass and cartons – shows that there are great opportunities for future innovations in the field of sensitive products.” Already convinced by the benefits of aseptic bottling, Refresco has chosen Sidel’s Combi Predis/Capdis FMa. For a large company, this integrated blowing-filling-capping system, which requires no air conveying, provides “a distinct edge in terms of floor space used. Maintenance is also Refresco has opted for 100% dry aspetic bottling. The Refresco beverage production... includes all kind of non-alcoholic beverages...","@ID":28} "BOTTLE MAKING 33 PETplanet insider Vol. 13 No. 10/12 www.petpla.net BTC Concept unveils stackable and lockable BottleClips A playful bottle BottleClips are based on a simple idea that has been a playground friend for generations: stacking and locking building blocks. The 500ml packs clip and lock simply, enabling both retailers to use space efficiently - and making it possible for consumers to create their own mix-and-match stack of flavours and textures, of beverages or other products. The heart of BottleClips is the clip-connect system that BTC Concept developed and has patented internationally. It can be integrated to bottles produced by injection blow moulding: PET, PE, PP, etc. The first examples of the new packaging are made of PET, as it happens. According to the inventors of BottleClips, Seiffeddine Bou-Mezrag and Yann Bassing, the idea came from the need to save space, to optimise storage utilisation and fill the spaces conventional bottles cannot reach. “Clipping bottles together emerged as a key feature, practical and fun for use at home, at the office or when on the go,” the inventors said. BTC Concept worked with PTI-Europe, a subsidiary of Plastic Technologies, Inc, on technical development and through to blow tests. The company claims that the result of the collaboration is a packaging solution that is practical, ‘playful’, and offers strong visual impact. This concept is designed to be suitable for beverages as well as other applications. It allows assembly of products, multi-brand or multiple-flavours without overpack, which means that consumers can customise the product by selecting their own flavours, or combine several associated products for “all-in-one” solutions, such as cereals, milk and fruit juice for breakfast, or for dietary programs. BTC has developed its prototypes with a reference volume of 500ml so that a combination of three bottles would be the height of a classic 1.5l bottle. The system is declinable to containers the volume of which can be up to 1l and with customizable shapes - identical or not. The company says that BottleClips can be produced at a similar cost to conventional bottles of the same volume and implemented on a standard production line, with moulds developed by the company. Seiffeddine Bou-Mezrag says that its progress in development has now enabled it to offer an industrial solution but a number of possible variants of BottleClips remain to be explored. “We are also working on the economic and environmental aspect in order to reduce the quantity of plastic,” he continued. “The 500ml non-carbonated BottleClips prototypes currently use 24g preforms. Our next objective is to go below 20g and to blow in BioPET.” The founders of BTC Concept filed the patent for their idea in 2007, incorporated in 2010 and attracted additional investment in 2011. They say that the company is now in touch with packaging and marketing teams from several large beverage companies. contact@btcconcept.com The stackable BottleClips is designed to be suitable for beverages as well as other applications","@ID":35} "BOTTLING / FILLING 36 PETplanet insider Vol. 13 No. 10/12 www.petpla.net de-aerator, so as to remove all the oxygen content. This de-aerator is fitted with an aroma recovery feature for preserving the full taste intensity of the juice. Pre-dosing The finished juice, still separate from the fruit chunks, is now also passed to the filling line, which is located in the separate bottling hall. Its heart is the PET monobloc, comprising a Contiform H16 hotfill stretch blow-moulding machine, a FlexiFruit filler with a pre-dosing starwheel for the fruit-chunk slurry, the main filler carousel for the juice, plus a capper. The monobloc has been dimensioned for handling 25,000 300ml bph or later on 18,000 1l bph. The pre-dosing machine has 33 valves. Each 300ml PET container is filled with 30mm of slurry. It is able to handle large fruit chunks measuring up to 10 x 10 x 10mm. The main filler possesses 55 valves, each of them fitted with a weighing cell which ensures an accurate final fill quantity with a deviation of plus/minus 0.5%. Before the bottles reach the juice filler, the weighing cells simultaneously measure the quantity of slurry dosed into each of them as well, and send this value as feedback to the pre-dosing filler, ensuring that the filling accuracy of each individual pre-dosing valve is continuously optimised. Thus each bottle is checked, making sure that the desired fill quantity of 300ml is complied with, irrespective of the slurry filling function. The PET containers are fitted with sterilised 38mm wide-neck plastic screw-caps with an O 2 scavenger. The hotfill monobloc features integrated automatic CIP (Cleaning in Place) and SIP (Sterilisation in Place) systems. Dry end The filled and capped containers are passed through a Linacool cooling tunnel, where in six stages, under minimised vacuum formation, they are gently cooled down within 40min to an ambient temperature of 27 to 30°. Dry-lubricated conveyors with a built-in buffering section holding 6,000 bottles then take the containers first to a blower-type drier and then to the labeller, a Sleevematic model that can dress the bottles both in full sleeves and in part-sleeves plus neck-sleeves. The drinks are packaged in as 3 x 2-, 3 x 4-, 6 x 4-, or 6 x 5-bottle packs. Technical Director Magdy Ismail explains “Production started on July 12, 2011, and by August 1, 2011 we were on the market. The bottling line’s performance is at over 80%.” The bottled products remain in the bay-type warehouse for five days, and are released when they have passed the microbiological examination in the lab. For the not-too-distant future, CCBE is not only examining additional flavours with fruit chunks, but also producing Cappy just with pulp, as well as larger containers holding up to one litre, and lighter containers than the 25g preform currently in use, by retrofitting the filler with a nitrogen droppler feature to run the NitroHotfill process. Since August 2011, the line has been up and running in two-shift operation, with six operators each for the process section and the bottling line, new staff hired specifically for this line. A service agreement with Krones has been in force since January 1,2011, with a term of three years, and covers the 20 Krones lines at CCBE in Egypt. www.krones.com The main f ller possesses 55 valves. Cappy FruitBite, as the only fruit juice so far being marketed in PET containers, with the additional benef t of the full-fruit content, is offered as a premium product at a higher price. Dry-lubricated conveyors with a built-in buffering section holding 6,000 bottles. End-of-the-line packaging is handled by a Variopac Pro TFS.","@ID":38} "PETbottles 48 PETplanet insider Vol. 13 No. 10/12 www.petpla.net Beverages + Liquid Food Energy without any compromise These days energy drinks often come in the shape of bulls or sharks and some other invincible creature. Fakeer took a different approach, with the aim of highlighting human strength and determination, together with an emphasis on living life to the full, with no compromises. Further, they wanted a complete departure from a traditional bottle shape. To help realise their vision, they consulted P.E.T. Engineering who came up with an innovative concept based on the human hand. The middle finger would point upwards, transforming itself into the neck of the bottle. The first challenge was to design the mould so as to allow the insertion of the stretch rod. Could such a complex geometry be blow moulded? A 3D prototype was produced. A second problem arose: could the finished bottle be successfully removed from the mould, a tricky operation with the undercut section on the hand. In the event the team succeeded and Fakeer’s energy drink now boasts one of the most distinctive bottles to be found anywhere. www.petengineering.com Pancake syrup 709ml (1.5 pints) of pancake syrup is being marketed by the American company Griffins Food Co. under the brand name Griffins in a shapely plastic bottle made from PET. The bottle, which is hexagonal in the neck area, is designed so that it incorporates lateral grooving in the grip area and has two consistently smooth surfaces for attaching the paper labels in the body area. Prior to initial opening the freshness membrane under the red hinged lid needs to be removed. www.griffinfood.com Revolution in PET-extrusion! Conical co-rotating MAS-extruder | perfect solution for A-PET, G-PET, PET Co-polymer … | prime pellet / melt quality (IV, b*, AA- content) | very low energy consumption | direct extrusion into sheet | stable melt pressure build up | small foot print paired with robust design | sizes available from 200 kg/h up to 1800 kg/h | suitable for food application M-A-S Maschinen- und Anlagenbau Schulz Gmbh A-4055 Pucking, Hobelweg 1 T: +43 7229 78 999, F: +43 7229 78 999 10 info@mas-austria.com www.mas-austria.com Halle/Hall: A6 Stand/Booth: A6-6409","@ID":50}]}}
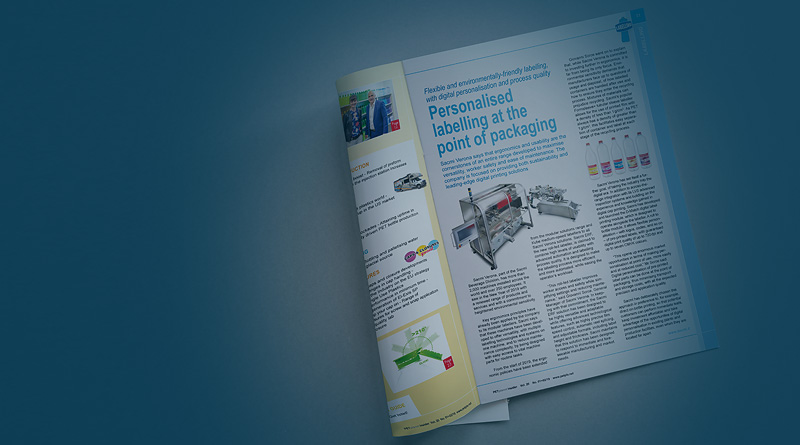