{"pages":{"page":[{"#text":"EDITOUR PETplanet Insider Vol. 23 No. 04/22 www.petpla.net 29 PET packaging for drinks, food and pharmaceuticals Plastic containers for the Cypriot market by Kay Barton As part of our European Road Show, we visited the industrial estate of Frenaros in Cyprus, close to the tourist hotspots of Ayia Napa and Protaras. Here, we were told, there was an interesting plastic converter that provides various sectors of the local market and abroad, with flexible packaging solutions, sometimes using PET. We met founder and boss Yiannakis Kone and his son in their factory and formed an overview of their production processes and portfolio. Interview with YK Megaplast Ltd. March 1, 2022 We met: Mr Yiannakis Kone, Owner Mr Michalis Sideris, Business Development at Cypet Technologies From the outside, the double warehouse gives no reason to suggest it is the place we are looking for. Only a couple of large boxes marked “Megaplast” just being loaded by Gate 2 give any indication that we are in the right place. The workshop that we enter is unusually deserted apart from Yiannakis Kone, who is packing small bottles just created on one of his Nissei ASB machines. The six-person team is currently out of action due to coronavirus so he is simply doing the packing in his family business. “Such is the dedication and professionalism of this company to keep the production running, no matter what”, he says. Without him, the founder of Megaplast with a background in engineering, and his son George Kone with a background in economics, the local packaging market in Cyprus for pharmaceuticals, food and chemicals would presumably look very different. Mr Kone founded the business in 1994 specifically to develop and produce different types of packaging for different applications in the local market. Back then, he started production with one injection moulding machine and one extrusion blow moulding machine. cally. Mr Sideris explained: “Covid-19 presented many challenges, from health and safety in the work place, to supply chain logistics, to customer support, to project freezes globally. For each type of challenge, we had to get creative to work out solutions that would minimise workflow disruption. In the end, despite these challenges, we still delivered machines and moulds to customers, as well as continued to make additions to our order book.” In the future, Cypet intends to continue to invest heavily in R&D and continue its development of machine and container technology. The company is also planning to expand its plants in Cyprus and India. Furthermore, the business is investing in staff training in sales and marketing. In addition to its in-house sales department, the company works with several international sales agents, as well as in after-sales service. “We have a dedicated after-sales team, supporting customers on all five continents with a one hour response time for technical and processing support. We also have a stock of spare parts for immediate dispatch to customers. Cyprus is well connected by air to all continents for customer visits”, said Michalis. Cypet is operating one of their own machines on the floor below, which is used both for demonstration purposes as well as a proper production unit because the K28, which has two cavities, continually moulds 10 l water dispenser bottles for a local water bottler. www.cypet.eu Cypet’s production hall Michalis Sideris from Cypet (left) explains the features of the K16 to PETplanet editor Kay Barton. Tour Sponsors:","@ID":31} "PREFORM PRODUCTION PETplanet Insider Vol. 23 No. 04/22 www.petpla.net 17 on-line size recognition and changeover (PVS10 and Sacmi PLO030 positioner); this solution shriks size changeover times to under 1 minute, streamlining the operator’s work. The software platform offers the latest CVS 22 version and enables interoperability with the Sacmi Computer Vision family of PVS systems. Focus on moulds The new IPS 300 can mount moulds with 24 cavities for 48mm necks or as many as 96 cavities for 30mm necks. Thanks to the nanopitch patent, co-developed with partner company MHT, the Sacmi range features the ability to increase productivity on small formats as it allows as many as 144 cavities on the IPS 400 and 128 on the IPS 300. Productivity The IPS 300 combines short lock-to-lock times with 2.1 s with the Cool+, the inside cooling system; The cooling system improves the thermal efficiency of the cooler, especially with thick-walled preforms. The userfriendly press interface simplifies the worker’s tasks, especially start-up and changeovers. All auxiliary units can be controlled remotely and, thanks to the new Smart Care packages, machine data can be linked to Sacmi servers to implement proactive scheduled maintenance services. Integrated design services In its long history, Sacmi has developed over 500 cap and preform designs for customers worldwide. A sharp focus on design and personalisation provides further opportunities for customers, as the lab’s know-how lets them thoroughly test materials and solutions prior to actual industrialisation, ensuring their investment yields the anticipated results. Recently, the Sacmi Rigid Packaging Technologies BU established the new Packaging Center. This operates in concert with Sacmi Beverage to provide customers with close support for every aspect of preform design, in synergy with all the upstream and downstream aspects of the process and in keeping with today’s sustainability, quality and customisation goals. www.sacmi.com Preform Vision Systems: Featuring a patented polarised light inspection device and AI, the PVS systems have been developed to provide comprehensive production tracking. September 12-16, 2022 Munich, Germany Hall C5, Booth 440 Innovative solutions for special preforms PMC units for all major PET systems German Technology","@ID":19} "EDITOUR PETplanet Insider Vol. 23 No. 04/22 www.petpla.net 28 recently entered the highly demanding USA market. In the last two years, we have been expanding our sales efforts globally”. The company headquarters with its striking blue contours, very similar to the blue and white logo of Cypet Technologies, highlights the firm’s Greek roots. According to Mr Sideris, the industrial area of Dali offers good infrastructure, not only in terms of technology but also logistically, with access to local skilled workers in and around Nicosia and the port of Limassol only 40 minutes away from where the machines are shipped. There is still enough space next to the building, which has already been acquired for possible future expansion. Upon entering the premises, a staircase to the right of the reception area leads to the upper floor from where people get their first glimpse of Cypet’s assembly hall below through various glass panes. Up to seven machines can be shipped to international customers from here every year. The offices of the management and sales teams are situated opposite the glass panes. Moving along the corridor, we came to the hall itself where four machines were standing close to one another. “The two machines at the back have been ordered from the USA and Mexico”, Michalis explained, pointing to the opposite end of the hall. “They will be shipped to customers soon.” Using a one-cavity mould injection, the K53 machine intended for Mexico is going to produce stackable PET crates for fruit packaging. Another machine, a K38, is used in-house to develop the next generation stackable containers for cooking and engine oils made from virgin PET and rPET. Incidentally, we did learn in conversation that the machines can process up to 100% of recycled PET. “Our typical client base demands flexibility in terms of package size and design”, says Mr Sideris. The K53, with its ability to produce large-sized containers, or smaller ones with multiple cavities is Cypet’s best-seller. “Our customers are very cost-sensitive, but they are also pioneers who are willing to try new technologies or introduce new upgraded products in their markets, because they see the benefits”, said CEO Constantinos Sideris who holds a Chemical Engineering Degree from Cambridge University and an MBA from Carnegie Mellon University, as well as 37 years’ experience in the plastics industry. He summed up the advantages of single-stage technology by saying: “Our production costs per container are minimal, which is extremely important when it comes to price-sensitive products. Secondly, special container designs can be produced that stand out in the market and which are ideal in terms of weight versus quality. And given no preforms are required, there is no need for storage space, logistics and energy consumption for their conversion.” Twenty-seven people are employed at the Dali plant and 15 in India. The Dali workshop area measures 330m2 with production output twice as big. Another design and manufacturing facility has been added in India to support the local market. Individual parts and material are mainly supplied by well-known international providers, as are the moulds. “However, we do have the necessary equipment to produce the moulds ourselves and do so in some cases, depending on the situation”, said Michalis as he showed us around the workshop. Maintenance, refurbishment and upgrading of the moulds also takes place here. As we toured the plant, the issue of changes brought about by the pandemic was constantly cropping up so we asked about them more specifiF.l.t.r.: Constantinos Sideris with Michalis Sideris in the office with a PET drum produced using Cypet equipment Demonstration and water bottle production on a K28 machine A PET container produced on a K38 model for engine oil","@ID":30} "PREFORM PRODUCTION PETplanet Insider Vol. 23 No. 04/22 www.petpla.net 14 Sipa optimises cooling systems on preform tooling to cut customer costs and enhance sustainability Cool performance The sums are simple: productivity goes up, costs come down, carbon footprint gets smaller when you cut cycle time in preform production. Any reduction in specific energy consumption makes the process more sustainable. Plus, optimisation of water consumption leads to further falls, not only on this precious natural element but also in energy expenditure, as it reduces the electricity consumption of the pumps that feed the cooling circuits. This opens up the possibility of using smaller pumps, with another improvement in sustainability. Engineering and manufacturing in-house a huge number of PET preform moulds every year, Sipa claims to not only understand these sums, but to know how to put them into practice. The key elements that brought Sipa to a leading position on this application are the consolidated experience both on the engineering and manufacturing steps as well as the flexibility to engineer the tooling accordingly to the specific preform design and features. Considering all variables To provide maximum flexibility, Sipa engineers consider multiple variables, including the layout of the mould -- the number of cavities, horizontal pitch, vertical pitch, and so on. What results is a robust mould design that is suitable for whatever machines the customer has on their production floor. This concept of customisation is transferred into the complete mould development process, virtually from the moment the idea of the product is born, throughout the development of the application with the customer. Cooling circuits is one of the most important aspects that is considered right from the start. It goes almost without saying that the cooling system is designed not only in relation to the size of the mould and the machine, but also in relation to the geometry of the preform. Typically, based on the productivity objectives set by the customer, and the injection machine that they have available, reference is made to a specific layout (number of cavities, pitch and arrangement), each of which has a standardised architecture: this makes it possible to achieve various objectives of compatibility between the various components (between the mould cold half and the hot runner system, for example). Sipa, however, does not limit itself to applying a standard solution likely to provide satisfactory performance for any application. Instead it intends to create an optimal level of performance to meet every customer requirement. This requires checking that the cooling water distribution diagram is ideal for the specific application and, if necessary, applying corrective solutions in order to obtain a fully optimised result. In each and every case, one important job that is always carried out is optimisation of the stack cooling to ensure the best result in all its aspects. Results: 1) diagram of the water circuit always optimised for each plate in order to provide the right amount of water for each cavity, distributing it evenly; 2) cooling design of stack components always optimised, to obtain the best cooling performance with lowest energy consumption. Customised cooling design trough the FEA Dimensioning of every individual system is strongly supported by Finite Element Analysis (FEA) to evaluate the thermal and fluid dynamics of that system. Each plate has a PREFORMS","@ID":16} "36 PETplanet Insider Vol. 23 No. 04/22 www.petpla.net PETproducts Preform moulds, sampling and more Over the last 16 years, Petka has specialised in the production of PET p r e f o rm mou l ds and PET blowing moulds for all kind of machines. As a mould manufacturer, the company supports its customers in all phases. Before it comes to the production of the bottle, Petka designs suitable preforms based on the customers’ requests and needs. With its qualified and regularly trained design team, the company draws and creates the design of the preform according to the final bottle design. With its know-how, it knows how the preform behaves during the blowing process in the mould. The company is able to support its customers with preform samples at its facility. Due to the fast-changing times and trends, preform sampling has become a crucial and essential advantage for the market leading companies. Petka provides samples in its high-tech equipped laboratory with detailed quality reports that enable customers to make decisions on their future investments. In order to meet the expectations of its customers, Petka offers a customer service aimed at receiving and dealing with enquiries and comments, ensuring the repair of moulds, solving installation problems and helping with technical issues. By implementing the lean production and Industry 4.0 systems in its factory, the company has managed to take advantages of all its resources. Since its implementation, these systems have helped the company’s processes to increase efficiency and also to become more effective, flexible and competitive in the market. www.petkamold.com SmartMold injection mould monitoring system Mold-Masters SmartMold is a cloud-based software platform dedicated to the plastics industry providing real-time data to drive injection moulding innovation. Process data is collected from sensors embedded within the injection mould which offers feedback and insights that drive enhanced productivity. This solution is the first step towards predictive and autonomous capabilities within the facility. In addition to collecting sensor data, SmartMold software offers performance tracking, downtime tracking, scrap tracking, maintenance reminders, alerts, reporting, analytics, mould info, document storage and more. Although SmartMold is focused on the mould, it also has the potential to pull data from injection moulding machines. Real-time data is accessible 24/7 though a desktop online portal or on a mobile app. A major benefit of cloud-based systems is that they ensure the latest version is always available and do not require users to have their own IT team dedicated to support its functionality. SmartMold algorithms enables the path to predictive and other powerful capabilities. It offers unlimited data storage. Data collected through SmartMold is displayed on an intuitive desktop and mobile interfaces. However, users also have the freedom to pull data into existing ERP/MES systems through API’s. Additionally, data can be exported from the SmartMold system in various formats. Mold-Masters SmartMold is compatible with any brand of hot runner/mould. Additionally, users have the option to utilise the SmartMold infrastructure to obtain data from their injection machines. Users can connect moulds only, injection machines only or connect everything. Users can scale the system to their facility and budget requirements and only pay for what is used. Server facilities operating in all major regions offers compliance with local data privacy laws and enhances data response times. SmartMold offers global installation and technical support. www.moldmasters.com PREFORMS","@ID":38} "MATERIALS / RECYCLING PETplanet Insider Vol. 23 No. 04/22 www.petpla.net 11 MATERIALS / RECYCLING 11 to 2.2mt sent today). In that scenario rPET would reach 55% of total PET demand by 2030 (compared to 26% of today). The driving force for advancing both collection and recycling of PET is the legislative framework. The new EU Single Use Plastics Directive (SUP), which introduces specific targets on both collection and recycled material uptake, has already boosted the voluntary commitments and pledges of retailers, producers and brand owners alike. The value chain actors are, now more than ever before, focused on the integration of the recycled, food grade PET in their packaging products and declared a range of objectives to incorporate recycled content within their products. Driven by these pledges and with the mandatory recycled content targets – the share of foodgrade rPET in PET beverage bottle production is set to continue to grow rapidly. New trends and developments within the industry do and will continue to emerge. For example, capacity for PET tray recycling lines have increased in the past few years and it is estimated that the tray recycling capacity will reach around 100 kt of PET trays in the next 2 to 3 years, which is 10% of trays placed on the market and little less than half of trays currently collected. Recycling of this type of packaging will further add to the food grade volume, contributing towards the set targets. Moreover, by 2025 it is expected that 19 EU Member States will have DRS in place for PET bottles. Today, seven EU Member States with established DRS achieve sorted for recycling rates of 83% or higher. This implies that with the EU SUP Directive collection rate targets already in place, the collection figures, as well as quality, are likely to increase substantially in the lead up to 2025. As the EU is, on the global scale, the pioneer in terms of PET circularity thanks its extensive base of recycling companies, high-tech technologies and best practices it will have an impact on the countries across the globe by exporting its technologies and know-how. Concerning the technological development there will be more smarter packages appearing on the market which will allow for a better separation of different PET applications. Another important development will be making textile products more circular, as today PET recycling is focused on packaging. For this new stream chemical recycling will be the key technology. New infrastructure is, however, needed to handle the collection and feedstock preparation for this new circular path. Moreover, mechanical recycling with its best CO2 savings performance will remain the main practice for the industry in making PET circular, with chemical recycling being a complementary solution for new challenges to come. PETplanet: Thank you so much Casper. E N D L E S S I N N O V A T I O N S I N C E 1 9 1 9","@ID":13} "EVENT REVIEW PETplanet Insider Vol. 23 No. 04/22 www.petpla.net 33 Review of PETinar Tethered Caps: Design, Produce and Inspect! A well-tuned quartet by Heike Fischer On March 24th, 2022 PETplanet Insider presented its latest online conference. PETplanet invited speakers from three companies, Universal Closures, z-moulds and Intravis to talk about their experiences and assessments of the current situation of tethered caps. The three presenters, Mark Smith (Universal Closures), Michael Fink (z-moulds) and Sascha Baumanns (Intravis) know each other from joint projects that editor Ruari McCallion has already reported on in PETplanet Insider magazine. This well-tuned quartet gave a stimulating and highly informative performance at the event. Design tethered caps Mark Smith started his presentation with a brief introduction to the EU legislation (EU 2019/904), the Single-Use Plastics Directive (SUPD). He summarised that Article 6 of the SUPD sets rules for beverage bottles up to a volume of three litres. Specifically, he stated that unintended loss of caps or lids should be prevented from July 3rd, 2024 on, and that caps must be attached to the bottle. In concrete terms, this means that a 25N tear-off resistance must be given. Mark went on to talk about the pros and cons of existing closure sizes, such as PO 1881, most common for CSD, and the challenges of the new design for a tethered solution. Mark went on to say that in cooperation with Coca-Cola, Universal Closures has designed a solution for the new size GME 30.40, which can also be used for tethered applications. The GME 30.40 preserves the internal bore diameter of PCO 1881 but offers a weight reduction of ~1.2 g through external design optimisation and material elimination. Research on the GME 30.37 revealed that, despite the shortened neck, this design does not offer sufficient technical performance, especially regarding carbonated retension and opening performance, and it lacks the physical space required to accommodate ‘net zero’ closure tethering technology. Mark went on to ask if every closure and finish can be tethered? He pointed out that this is possible in principle, but that to design a tethered closure, the goal should be to find a zero-net solution that does not affect any key functions such as weight, capping application, manufacturing, tooling design and finally customer interaction. Universal Closures already have a lot of tethered solutions for many different applications. Mark presented two different closure solutions. First, he introduced the Eagle solution: a closure based on GME 30.40 with a screw top design, and which is useable for any beverage, including CSD. It meets requirements such as clearance to finish opening, a repeatable and intuitive operation as well as an opening self-holdback. Three principal challenges have been overcome: shell integrity for high CSD performance has been maintained, as have the finish clearance before tether articulation and the compatibility with capping system and cross closure. “A key part of achieving a Mark Smith, Technical Director & VP at Universal Closures Michael Fink, VP Sales & Marketing at z-moulds Sascha Baumanns, Head of Sales at Intravis PETINAR","@ID":35} "OUTER PLANET 46 PETplanet Insider Vol. 23 No. 04/22 www.petpla.net OUTER PLANET Think what you drink It is nothing new to state that scents, aromas and smells influence our perception of taste. What is new is to market these olfactory stimuli in the beverage sector. A young start-up company, Air up, has come up with the idea of scent pods. Cleverly combined with water, the scent pods, working with the human brain, detect the flavour. But how exactly does Air up work? It sounds a little like turning water into wine but the principle is very simple: the Tritan bottle is filled with 650ml of still or sparkling water, then one of 24 scent pods with a natural aroma is selected and placed in the top section. Sucking on the silicone mouthpiece draws up a mouthful of not only water but also air from outside through the scent pod. This brings retronasal olfaction into play. In the pharynx, the scented air rises from the water and is perceived as flavour by the olfactory centre. So the magic happens under your very nose. The scented air function can also be activated and deactivated easily via a slide mechanism. We asked Lena how they came to choose Tritan as a material. “Our aim is to make a healthy and sustainable lifestyle the most attractive choice. Accordingly, we use highquality materials in our products. For the bottle we use BPA-free Tritan to ensure our product has a long lifespan and is food safe.” Justifying the decision, she continues, “Also, Tritan is a lightweight material suitable for taking with you on the move and because of its transparency, you can keep an eye on your water consumption.” Almost two years of development time have gone into the bottle, which is manufactured at production sites in China. “Having said that, we are working continuously to bring the product closer to the customer and making transport routes shorter. One building block here is the development of new production sites. Already at the end of last year – and only a little over two years after our foundation – we opened a pod production site in Turkey, and another is being planned in Central Europe,” explains Lena. “Our production partners are selected on the basis of numerous criteria – including quality standards as regards the sustainability of processes.” www.air-up.com Currently, Air up customers can choose from a total of 24 pods to flavour their water. The foundation for Air up was laid by Lena Jüngst and Tim Jäger in 2016 when they were both studying Product Design at the Hochschule für Gestaltung [University of Design] in Schwäbisch Gmünd, Germany. In their Bachelor thesis on “Neuroscience meets Design” they analysed unhealthy diets as one of the greatest social problems of our time and also drafted a possible solution: based on neuroscientific findings, the pair developed a technique that aims to counteract the uptake of unhealthy drinks with the help of retronasal olfaction. They brought this technique into effect in the first prototype of the Air up bottle. A brief description: the brain differentiates between the smells it perceives orthonasally (via the nose) and retronasally (via the pharynx). While smells perceived orthonasally are also interpreted as such by the brain, retronasally perceived smells are perceived as flavours and are attributed to food or drink in the mouth. This interconnection in the brain enabled Lena and Tim to give water a variety of flavours simply using scented air. After completing their Bachelor degree, the two inventors received a great deal of positive feedback, had the idea patented and found themselves support from food technologists, business economists and industry experts. With their passion for the idea and the help of supporters, including EU financing from Climate KIC for particularly sustainable start-ups and the Exist business start-up grant from TU München [Technical University of Munich], the now five young entrepreneurs were able in 2018 to inspire three noteworthy investors to back their start-up. Through their financial support, volume production of the Air up starter set got underway in 2019. “Air up is now represented in a total of nine countries and this year, we are planning expansion to the USA,” says Lena Jüngst, explaining the latest company developments.","@ID":48} "PREFORM PRODUCTION PETplanet Insider Vol. 23 No. 04/22 www.petpla.net 15 personalised water diagram and each stack has a dedicated design. The reason, according to Sipa, is to make use of the best software systems currently on the market and customise them to provide high-speed mould analysis. This activity is incorporated into the engineering development flow, without having an impact on the lead time of the product. The impact that it does have is in the creation of a product with high performance, both in terms of cycle time and consumption in utilities that are all 100% tested internally before delivering the tool to the customer. Mapping characteristics Validation of the various analytical evaluations is carried out during the first stages of testing. Before conducting any functional testing, the moulds that are designed and built on the basis of these calculations are subject to measurements of the characteristic curves of flow rate and power on a special test bench. This activity is important, because it allows for validation of the project assumptions, and to increase the capacity of Sipa’s database through the acquisition of new experiences, further refining the calculation methods behind the company’s mould design capabilities. Sipa offers various adaptation kits that allow the installation of the same mould on different models of injection moulding machine to make customer operations as flexible and economical as possible. The benefits of the state-of-the-art Sipa toolings are accessible globally to all preform producers, since Sipa preform moulds can be interfaced with the vast majority of injection moulding machines that are used in this application. www.sipasolutions.com The number of cavities is one of the variables that has to be considered when optimising the preform production process. Cooling systems have to be designed in relation to the mould and machine size but also in relation to the geometry of the preform. ALL- IN- ONE-MACHINE ASSEMBLY FOLDING SLITTING TETHERED CAP CONTEXO GMBH Tel. +49 (0) 7181 / 606-100 info@contexo-gmbh.de www.contexo-automation.de","@ID":17} "EDITOUR PETplanet Insider Vol. 23 No. 04/22 www.petpla.net 26 The European Road Show in Cyprus Off the tourist track by Kay Barton The island of Cyprus lies in the eastern Mediterranean, just 70 km south of the Turkish mainland and 95 km west of Syria. The former British crown colony is divided into a northern, Turkish part, the internationally unrecognised Turkish Republic of Cyprus, and a southern part, the Republic of Cyprus. In addition, the two British military bases of Akrotiri and Dhekelia on the south coast are British Overseas Territories. Cyprus has been an EU member since 2004 and, with an area of 9,251 km², is the third largest Mediterranean island after Sicily and Sardinia in the western Mediterranean. The northern part of the island is inhabited by Turkish Cypriots, the southern part by Greek Cypriots. The division of the island also runs through the capital city, Nicosia. Today, it is the only divided capital in the world. A total of 1.2 million people live on the island, of which three quarters live in the southern part, where a total of more than 65% of cities and urban areas are situated. At 0.8%, population growth is stable, the average age is 38 and life expectancy is over 82 years. With regard to the economy, a financial crisis in 2012-2013 was partly triggered by strong economic ties with Greece and the crisis there. Since this was overcome, the economy has grown continuously with low taxes and high interest rates for foreign investors. In 2020, GDP was almost US$ 24 billion, around US$ 26,623 per capita. With imports to Cyprus of 21.6% and exports from Cyprus of 8.5%, Greece was first among all import and export countries in 2020. In 2020, the services sector formed the backbone at 75%, followed by industry at 13% and agriculture at 2%. At least until the pandemic caused a slump in tourism, which is so important for the country and contributes around 20% to the GDP, Cyprus had been recovering and this year remains on course. Industry experts estimate that the plastics market shows continual growth of around 5-10% annually since 2013. Currently, the field of pharmaceutical packaging in particular is said to be making bold strides forward. Overall, the local plastics processing industry is divided into around one third PET and two thirds PE and PP, where the trend in PET especially is on food packaging such as cans and containers. True figures are unfortunately hard to come by but we are told that the estimates reflect the local market. For the European Road Show we met both a machinery engineer and a user, and we investigated technology, procedures and activities. Macro-economic data Cyprus 2018 2019 2020 Population (millions) 1.2 1.2 1.2 Population growth p.a. 0.8% 0.8% 0.7% GDP (current prices, billions) US$ 25.3 US$ 25.0 US$ 23.8 GDP growth rate (real) 5.2% 3.1% -5.1% GDP per capita (current prices) US$ 29,334 US$ 29,206 US$ 27,528 Import (billions) US$ 18.8 US$ 19.4 US$ 19.3 Export (billions) US$ 19.2 US$ 19.5 US$ 18.7 National debt of GDP 98,4% 91,1% 115,3% Unemployment rate 8.4% 7.1% 7.6% Inflation 1.4% 0.3% -0.6% Kamara Tou Koraka Natural Bridge in Aiya Napa Left-hand driving in Cyprus Tourist hotspot Ayia Napa Tour Sponsors:","@ID":28} "EDITOUR PETplanet Insider Vol. 23 No. 04/22 www.petpla.net 27 PET container production made on equipment from the island of Cyprus Single-stage ISBM machines for flexible, special-sized formats by Kay Barton In the industrial area of Dali just under 20 km south of the Cypriot capital Nicosia, the medium-sized machine and mould supplier Cypet has been building single-stage ISBM machines for the production of standard and special PET containers and sizes since 2014. The family-run business has carved out a niche for itself in packaging production with an average annual revenue growth of 60% and now, after just a few years, is showcasing its technology on five continents using 27 machines and 66 moulds. Dedicated on-site service combined with digital support is able to provide prompt assistance to the customer. During the course of our European Road Show, we made a detour to Cyprus to visit the company founder and CEO Constantinos Sideris and his son Michalis, responsible for business development, to talk about technology, markets and growth potential. Interview with Cypet Technologies Ltd. March 1, 2022 We met: Constantinos Sideris, Director Michalis Sideris, Business Development Cypet is a spin-off of the previous family business M. Sideris and Son Ltd. founded in Cyprus in 1968 and which specialised in the supply of plastic packaging machines and equipment from manufacturers such as Haitian and Shini, as well as in plastic raw material. Initial sales markets were in Cyprus itself and Greece. The company subsequently patented a method for PET processing, built a prototype model and began marketing the technology with Cypet in 2014. In 2016, the first 50 l PET container was successfully developed and produced, followed by a 120 l version three years later. Last year, the firm introduced the second generation of its machines. “We are seeing clear growth potential in PET packaging and the replacement of HDPE containers by lighter and cheaper PET bottles, both in the food and non-food sectors”, said Michalis Sideris. “In addition, the advantages in terms of appearance, material properties, impermeability and recyclability outweigh those offered by HDPE. Our idea of having a dedicated machine company was not just born out of necessity, which of course it was, but more in light of our developments in the field.” Much of the equipment is currently used in the food sector (54%) with around 27% in beverages, and the remainder in nonfood applications. Even though the machines can make containers from 20ml up to 120 l, the most popular PET containers demanded by the market are in the range between 10 and 30 l. Customers include Keg King in Australia (see PETplanet Insider 10/20), Arma in Egypt, Savola Edible Oils from Sudan, BL Agro in India (see PETplanet Insider 07+08/2020), PET Innovators in the Netherlands, Oasis Water Company in Oman and PPI in the USA. According to Mr Sideris, the main markets are in the USA, Europe and India where the company also has a small-scale production facility and Africa. Mr Sideris explained the development: “Strategically, we first focused sales in Africa and India due to our machine’s competitive price point. Then demand from Europe came organically and finally we Tour Sponsors: A range of different PET containers made by the company","@ID":29} "EVENT REVIEW PETplanet Insider Vol. 23 No. 04/22 www.petpla.net 34 tethered closure on such a finish, is to make sure that you can raise the closure from its finish before you begin the articulation of the actual tethering. If you begin articulation too soon, you simply clash with the threads and it’s very difficult for the consumer to open cleanly,” Mark explained. The second closure Mark showed was a hinge-mould-closure (HMC) design. It does not work for CSD products, but is suitable for still beverages, water, and dairy. It is designed for short neck finishes like 29/25. In this closure a “natural tether” is given. It comes with a hinge tension in the design which gives the closure a natural spring effect that stays open over the centre at up to 220 degrees. There is no mechanical hold-back, it stays in that position. The challenge here which was successfully overcome, was to ensure that the cap is fully functioning on an existing threaded 29/25 finish. Mark concluded his presentation with a question: what’s next after tethering? He pointed out that tethering is just one way in which the plastics packaging industry could move towards reducing its environmental impact. He mentioned that a closure design from a single resin type will simplify recycling. In addition, he added that more recycled material should be used and more reusable packaging systems like RefPET bottles should be implemented. Moulds for tethered caps The second speaker was Michael Fink from z-moulds. Michael briefly introduced his company and proudly announced that z-moulds would have a sales and service team in the US from April 2022 on. z-moulds, as a mould making specialist for caps, helps cap designers like Universal Closures, to develop the best design for any tethered cap application. All global testing standards are possible in the approved z-moulds laboratory. Finally, after designing, testing, and developing, z-moulds supports the inline work at its customers’ premises. Michael explained the patented z-slides technology. It differs from other mould systems in the following aspects: the front of the mould has a complete flat parting line. Centring of the cavities is not necessary. The cavities and sliders are located inside the mould. The mould itself is centred with guiding bars; this results in an almost wear-free system. Each cavity is accessible from the front. The entire cavity stack can easily be pulled out so that each part of the cavity can be replaced (eg. core, cooling top, slider). The 70mm frame of the mould stays the same for all kind of closures. It is a completely modular system. Also, the cavity pitch remains the same, and in addition the same hot runner system can be used. New requirements arise for the tethered caps. Michael said that the z-slides technology is still used but it must be extended. The sliders need to be higher, because the parting line for a tethered cap design is moving up. By changing the angles on the demoulding face, where the height is increased to a distance of 15mm, it is possible, for example, to produce a 29/25 closure design entirely on the cold half of the mould. The extended z-slide technology can easily be implemented in the existing z-slides system. The extended z-slides system can be used for closures with an outer diameter of 25-33mm and a cap height in the slider of a maximum of 15mm. Most standard necks like PCO 1881, PCO 1810, 29/25mm and 30/25mm are compatible as well as new neck finishes like 26/22mm, GME 30.37, GME 30.38, GME 30.40, GME 30.41 and 25mm. Michael concluded that all z-moulds technologies like the z-slides, z-slides extended, and the z-folded system are compatible with each other. That means the systems have always the same pitch between the cavity, it is possible to use the same hot runner, and most mould plates are the same. In addition, they have the same mould accessories and last but not least the same cooling system. For Michael, the high flexibility of the systems is also a contribution to sustainability. He concluded: “It is better to use the existing equipment and cover the new requirements by making just simple changes.” Inspect tethered caps The last speaker to take the microphone was Sascha Baumanns. Sascha is Head of Sales at the German-based company Intravis GmbH. With a subsidiary in Atlanta, USA, as well as global service and sales points, Intravis is very well known for its inspection systems for the plastic packaging industry. Sascha pointed out that Intravis systems all over the world inspect an average of about 20,000 beverage closures – every single second. After this impressive statement, Sascha started to present Intravis’ inspection solutions for tethered closures. The new tethered closure designs which focus on compatibility with existing production equipment as well as on high added value in terms of user experience, result in new design features and therefore need new inspection solutions. The first of the three inspection systems presented by Sascha was the CapWatcher Q-Line, with the Q standing for Quality. This system is an inline solution suitable for the inspection behind an injection moulding or compression moulding machine. The CapWatcher Q-Line inspects 100% of the produced closures. The system is equipped with eight cameras, a micro-hole inspection, as well as a special temperature measurement. Altogether, the CapWatcher Q-Line gathers 144,000 cavity related product information every minute which helps to optimise the production process. As one example, Sascha explained, that the temperature measurement of each closure in combination with cavity number reading offers unprecedented possibilities in monitoring the performance of the mould. Sascha went on that a repeatable positioning and separation of the closures is both a fundamental requirement and the key for a reliable inspection. To assure the correct and soft separation, the CapWatcher Q-Line is equipped with a form fitting lateral star wheel. And for the positioning? Intravis now uses a newly developed Artificial Intelligence for its inspection modules which no longer needs a perfectly aligned closure for a properly done inspection. Another important feature is the contactless high-voltage inspection for detecting micro-holes in the injection point. These holes can lead to inconveniences for the end consumer since the bottle becomes leaky or foreign substances enter the bottle. A conventional micro-hole inspection still uses a metal wheel to dip into the closure, making it impossible to inspect fea-","@ID":36} "EDITOUR PETplanet Insider Vol. 23 No. 04/22 www.petpla.net 32 told me one or two anecdotes from his tour through Siberia in 2012. Very exciting... And what don’t I like? The blank patches on the world map, where PETplanet can’t travel because of the pandemic or for security reasons because of the political situation there. PETplanet Insider: No, we don’t like those either and we wish that one day we could travel to those parts of the world and build markets there. We’ve always had difficult situations or even corruption to deal with on our journeys, which is sometimes challenging but has always been manageable. With regard to challenges, what challenges does this kind of tour actually mean for you from a graphics point of view? Matthias Gaumann: Sometimes the greatest challenge is fitting a great deal of information onto a very small space. For example, when a route is to be illustrated with its many stops and these are geographically very close to each other - this can be very tight. Designers just love a big space to shape freely. Something else that can be challenging is collaborating with local service providers, for example when something has to be produced or printed on location. Then, there can be great differences in communication, the status of software or the typical workflow. But as the editor and tour manager, you are always at our side to manage communication and organisation perfectly. So everything has always gone very well. Thank you very much, Kay. PETplanet Insider: I do my best! I’d like to come back to our magazine, which is our main product, after all. From a graphics point of view, how does this kind of journal usually come into being; what are the processes? Matthias Gaumann: For me, it all starts with the issue plan that I receive on Monday from the editorial team. Then I know which text goes on which page. Next, I get all the texts and images. The artwork is checked for printability and converted to the required parameters. Then the texts and artwork are entered into the design grid and lined up. All finished pages are sent back to the editorial team for proofreading. Collaboration with Heike Fischer and Gabriele Kosmehl from the Editorial team is great – they really do a fantastic job. Thanks very much. Then the corrections come back and checks are made from a graphical point of view to ensure that the type area still fits after the corrections. I also get the files for the advertising spaces from the advertising department. These are also checked for printability and entered into the layout in accordance with the issue plan. For reasons of time, checking the printability of the adverts has to happen at least one week in advance. There’s no time for any correction of the data during issue production! Collaboration with Martina Hirschmann and Johann Lange-Brock from the advertising department is also really great. PETplanet Insider: I’ll be glad to pass that on! And is there more to do once all the corrections have been completed? Matthias Gaumann: After all the corrections – usually there are three “loops” – I then get “approval for printing”. I put together one whole printable file from all the files then I send this to the printers via FTP. Many thanks to our printer, Mr Frey at Chroma, for straightforward, friendly and excellent collaboration. After the printer starts the roll-out of the journals, PETplanet Insider is once again reconfigured into a web-optimised file version. On the Wednesday, this is then integrated into the website www.petpla.net using a special software tool and a workflow specially developed for PETplanet. This workflow was developed and introduced by Rolf Sinkovec and Felix Popp from the PETplanet team and it’s really fantastic. PETplanet Insider: On average, how many hours of work do you put into one issue? Matthias Gaumann: It’s usually around 50-60 hours on my side. PETplanet Insider: Can you try to show us a bit about how important the field of creativity is in your work and why or where it is particularly needed? Matthias Gaumann: Creativity is always essential! Even if journal typesetting with a fixed type area is predominantly good, old-fashioned tradecraft. Dealing with typography in running text has certain rules that you just have to learn. But you have to be creative, for example when compiling infographics or photo montages. Or with anything that is being newly created. Nothing at all happens without creativity, but the tradecraft that makes further processing possible in the first place is just as important. PETplanet Insider: OK, great! Have there been situations in the past where something went really amiss? Matthias Gaumann: Mistakes can always happen. The most frequent are spelling mistakes that can even have been missed by three or four people. It happens sometimes when you work on something for a long time. You get “professionally blinkered”. The most annoying thing is when it happens in short, large headlines and should be really obvious. Luckily, and thanks to the great team at PETplanet, I don’t have any spectacular stories for you! PETplanet Insider: Well, that’s a great reassurance to me! One last question for you: What else do you do at EXPRIM, apart from our work together? Matthias Gaumann: I’m able to work for very different sectors, companies and people. This includes medium-sized companies from various sectors including metal processing, plastic processing, machine manufacturers, automotive, tourism, trade, retail, property, healthcare, social and non-profit organisations, artisans, start-ups and many more. The range is wide and varied so I’m tackling new and exciting things all the time, both in theory and in practice. It’s fantastic and never gets boring. PETplanet Insider: Great. We wish you every ongoing success and we look forward to another great year of working with you and EXPRIM! Thank you for the interview, Matthias! www.exprim.de","@ID":34} "EVENT REVIEW PETplanet Insider Vol. 23 No. 04/22 www.petpla.net 35 tures inside of tethered closures - such as the re-closing functionality. In terms of the contactless variant, the closures slide under the inspection unit without the need for immersion or any contact. This is a great advantage in terms of process stability, and also a hygiene factor, Sascha said. Three cameras are used for the inner inspection of the closure. A large focus is placed on the important, functional elements. The scope of inspection includes the integrity as well as cosmetic aspects of the sealing surface, the seal cone, the closure aids, the thread, the area between the closure and the tamper-evident band, as well as the tamper-evident band itself. Moreover, functional elements, such as hinges or locking aids, are taken into account during inspection. To offer a complete outer inspection, the CapWatcher Q-Line transports the closures hanging on a vacuum belt. Four cameras inspect 360 degrees of every closure whereas the fifth camera inspects the headplate from the bottom. The outside inspection pays special attention to the new features of tethered closures - no matter whether they are moulded hinges or slitted elements. Short shots, flashes or defects caused by worn blades can be identified at an early stage. All these inspections are summarised in a clear and intuitive software user interface which also displays the machine condition and provides deep, statistical analyses. The CapWatcher Q-Line brings the quality laboratory inline. Sascha continued by presenting the IntraOne. The smart camera solution is particularly space-saving. Thus, it can for example easily be integrated into the feeder of the capper before the filling process. With a dedicated inspection setup, the system is able to inspect closures for deformation, colour or dimensional accuracy, as well as the key functional elements inside the closure which could be damaged during the transportation and after the initial inspection at the closures producer. The third system presented by Sascha was the CapWatcher FC. It assures the quality of closures in the outfeed area of the filler after they are applied to the bottles. The system is equipped with seven cameras and inspects the filled bottles for proper closure fit, important features of tethered closures such as hinges and bridges, colour, the gap between the closure’s tamper-evident band and the bottle’s neck support ring, as well as the correct fill level of the filled bottle. As a highlight, the Cap Watcher FC also offers an inspection of the closure’s application angle on the bottle. At the end of his presentation, Sascha summarised how the presented vision solutions help at different stages of the production process: Whereas the CapWatcher Q-Line measures the closures with a repeatability of two-hundredths of a millimeter right after their production and the IntraOne supports the process right before the application of the closure to the bottle, the CapWatcher FC is used at the outfeed of the filling line to inspect the closures after their application to the bottle. Overall, Intravis offers a solution for every step of the closure process, and these solutions can be combined with the rest of the high-performance inspection systems. Intravis provides for the plastic packaging industry: From the preform, to the closure, to the PET bottle in the blow moulding machine, to the labelling of the filled bottle, and finally with the CapWatcher FC in the outfeed area of the filling line - all inspection systems are available from a single source. In connection with the IntraVisualizer, an analytics software for production quality data, this offers the possibility of traceability and documentation of the packaging quality in each individual production step. Finally, Sascha pointed out that all inspections are in accordance with Cetie Quality Guideline No.18. After these three very interesting presentations, a lively discussion began. The PETplanet Insider Team would like to thank the speakers and the numerous international participants for their interest. On the PETplanet homepage you will find all information: a video recording of the PETinar, as well as the presentations of the speakers for download. For further information, please do not hesitate to contact us! https://petpla.net/2022/03/25/ review-tethered-caps-design-produceand-inspect/?s=","@ID":37} "MATERIALS / RECYCLING PETplanet Insider Vol. 23 No. 04/22 www.petpla.net 10 How the industry continues to expand in Europe - Focus on PET Plastics recycling, part of the puzzle Interview with Casper van den Dungen, Vice President Plastics Recyclers Europe & PET Working Group Chairman PETplanet: What is the state of affairs in the plastics recycling industry in Europe? Casper: Polyethylene terephthalate (PET) is one of the most widely used recycled plastics and at the same time the most widely recycled polymer destined for food contact applications. Just 20 years ago recycled beverage bottles (PET) were used to produce fibres (for strapping or clothing, for example). Back then the technology was not developed to allow recycling into food contact applications and no framework was set in place to regulate that. Only in 2008, through Regulation 282/2008, a procedure for authorisation of recycling processes for PET in food contact applications was established. Following these changes, the market for recycled beverage bottles has been steadily growing and nowadays, the majority of PET beverage bottles are recycled via closed-loop systems back into packaging. The EU is the worldwide pioneer in terms of legislation on recycling and specifically on food contact recycling, as it has one of the most robust rules and standards, ensuring highest health and safety standards for this material. Many brands include recycled plastic to pack their mineral water bottles or soft drinks, as recycled PET can be used to make new food contact bottles with even 100% recycled content. Beyond recycled material being used in bottles it is used, for example, in trays. Already 1 out of 2 trays (used to pack ham, cheese, salads), or blister packs incorporates rPET. Both of these applications were possible largely thanks to the EU targets introduced in 1994, their consecutive revision back in 2008, the establishment of the regulation on the use of recycled plastic in food contact materials, and finally the introduction of the Circular Economy Package in 2015. Another important factor here, are massive advancements in recycling technologies, and, in general, within the value chain. The examples of technological developments include changes in the product design like intelligent labels which can indicate where to recycle the product. Additionally, sorting of products is no longer manual but has moved to more reliable automated systems which include robotic-like separation technology. These advancements helped overcome the limitations that were hampering the use of recycled materials in a broad range of applications including high value products. Some of these limitations include design for recycling of the products, their sortability or cleaning operations – to name a few. The optimisation of these processes at each step of the value chain started many years ago, paving the way towards PET’s circularity. Legislative incentives and technological advancements resulted in increased efficiency and effectiveness of the recycling processes, while increasing the sustainability of every new cycle. PETplanet: How is PET recycling performing currently? Casper: There is a steady move towards circularity of the PET industry in Europe. New study for collection, recycling capacity and production of PET for 2020 shows increases - in comparison to 2018 - in all measured factors. Major growth is observed, in particular, within the PET recycling market, with an overall 21% increase in the installed capacity, totaling 2.8mt in EU27+3. Main new capacities which have been installed recently are the decontamination lines to convert the washed bottles or trays to food grade pellets. Concerning the recycled PET market there is a potential shift away from virgin production towards recycled material production. In 2020, 1.7mt of recycled PET was produced, with a steady growth within trays and sheets application, which with a 32% share remain the largest outlet for rPET in packaging, followed by beverage bottles with a 29% share. On the collection figures 61% of beverage bottles were collected & sorted for recycling in Europe - a 9% increase in comparison to 2018. Concerning the food contact grade of recycled PET, mechanical recycling is the predominant process with the highest benefits when it comes to CO2 savings. It is clear as well that the legislative framework contributed to increasing an uptake of food contact rPET. The legal requirement to include 25% rPET content in mineral and soft drink bottles by 2025 together with the collection target for PET of 90% by 2029 are the main drivers. This growth is to continue developing rapidly in response to producers’ pledges and average recycled content targets. The new legislation impacted equally the developments of new Deposit Return Systems (DRS) which allow for a higher quality of collected material. This growth needs to be programmed inline to the what the current installed capacities can absorb. The availability of certified active statistical data is needed to help us in mastering this challenge. PETplanet: Where do you see our industry in 10 years from now? Casper: To reach the 30% recycled content target for beverage bottles by 2030, 3.6mt of PET will have to be sent for recycling (in comparison Casper van den Dungen, Vice President Plastics Recyclers Europe & PET Working Group Chairman","@ID":12} "MARKET SURVEY 22 PETplanet Insider Vol. 23 No. 04/22 www.petpla.net 04/2022 MARKETsurvey Suppliers of preforms & preform inspection systems In this issue PETplanet focus on new developments in performs and preform inspection system. We are very proud to present the brand-new data from the following perform manufacturers and preform inspection system manufacturers: Pressco Technology, Agr International, Intravis, IMD, Sacmi Imola, SGT, Hodmeter, Plastipak, Magpet Polymers, PDG Plastiques and Novapet. Although the publishers have made every eff ort to ensure that the information in this survey is up to date, no claims are made regarding completeness or accuracy. Resins & additives Preform machinery Preform production & inspection systems Preform & SBM mould manufacturer SBM 2-stage Compressors Caps & closures & inspection systems Filling equipment & inspection systems Recycling machinery Palletising & shrink film machinery Preform inspection Company name Pressco Technology Inc Agr International Inc. Postal address Telephone number Website address Contact name Function Direct telephone number E-Mail 29200 Aurora Road, Cleveland, OH, USA +1 440 498 2600 www.pressco.com Mr Tom Murphy VP, Sales & Customer Service +1 440 498 2600 sales@pressco.com 615 Whitestown Road Butler, PA 16001, USA +1 724 482 2163 www.agrintl.com Mr Martin Kuestner International Sales Director +1 66 2 73151 44 mkuestner@agrintl.com Preform Inspection Systems Intellispec Pilot Vision+ in-the-blowmoulder inspection system Gawis 4D laboratory measurement system Inspection speed Up to 2,500/min 100,000+ parts per hour 20 sec. per sample (dependent on complexity of actual measurement) Inspected parameters: Geometry / Body Unmelts, heat splay, burn marks, water spots, bent/warped preforms, contamination, carbon streaks, bubbles/blisters, colour, crystallinity & clarity/hazing, gate length Yes, contamination, opaque spots (black spots), unmelts, bubbles/blisters, burn marks, water spots, streaks Yes, diameter, length, gate length, out-of-round Thread area Contamination, fl ash, dimensions, pulled threads Yes, comprehensive fi nish measurement including horizontal measurement: vertical measurements, thread measurement, radius and angle Mouth / Sealing surface Contamination, ovality and diameter, dirt & debris in the preform, nicks, gouges, short shots & dips Yes, inspected after blowing - nicks, dents (V notches) and scratches in seal surface, surface irregularities, seal surface width (average), ovality, blown fi nish, choked neck, seal surface integrity, inner/outer diameter Gate / Dome Bent/warped preforms, dirt/debris, cracked gates Yes, contamination and position of injection point Yes, gate length and dome radius Colour Colour variations, incorrect colour Yes, colour and intensity deviations Cavity number Further criteria Additional inspection modules include: neck support ring, inner barrel Measurement of absence or presence of barrier material Yes Yes, barrier thickness and/or barrier presence Layer thickness & position measurement at distinctive points The Gawis 4D can perform thickness at any given pre-defi ned point Layer thickness & position measurement at the complete body by scanning The Gawis 4D scans horizontally and vertically at multiple location on a preform with graphic representation of results distribution over the scanned region Features: Installation: Stand-alone On customer-supplied starwheel Stand-alone, lab based, optional robotic systems available for walk-away testing Installation: Inline Mounting and installation inside major OEM blowmoulding machines; options available for stand-alone and inline systems In-line, in blowmoulder · Side camera for cavity recognition · Methode: destructive/non destructive Non-destructive Non-destructive Non-destructive · Data base connection Yes Yes, compatible with plant or system network Yes, compatible with plant or system network","@ID":24} "PETnews 6 NEWS PETplanet Insider Vol. 23 No. 04/22 www.petpla.net Pascal Lefèvre new Sidel global vice president food, home and personal care markets Sidel has announced the appointment of a new global vice president. Pascal Lefèvre will develop and drive Sidel’s food, home and personal care strategy, meeting the unique needs of these markets and delivering flexible, eco-friendly, and tailored-made solutions that will address the new and complex retailing and distribution challenges that customers face. Lefèvre will lead in the provision of innovative, eco-friendly, and ultra-flexible equipment to food, home and personal care customers. These feature a comprehensive range of blowers and end of line solutions, including packers and palletisers, for any type of primary and secondary packaging. Sidel also offers complete or partial integrated lines in categories like edible oil, sauces & dressing, coffee and more. Pascal Lefèvre explained that he will ensure Sidel can provide solutions that offer the flexibility, operability and product care demanded by these fast-moving and rapidly evolving market segments, while drawing on existing capability and expertise. Pascal Lefèvre joined Sidel in 2020. He attended ISG Paris Business School and has more than 20-years of experience working in senior positions within the packaging equipment industry. He said: “Sidel is supporting brand owners through the transition to fully recyclable light-weighted PET or rPET containers, leveraging our design capability and market-leading blow moulding solutions with its preferential heating technology for shaped containers.” www.sidel.com Extrupet doubling food-grade recycling capabilities Extrupet, one of the largest and advanced recyclers of plastics on the African continent, has announced a major expansion of their food-grade plastic recycling operations in South Africa. “Extrupet is proud to announce that we will double our food-grade operations by adding a fourth food-grade recycled PET (rPET) facility, which will increase our recycling capacity by an additional 33,000 tons per year,” said Chandru Wadhwani, Joint Managing Director at Extrupet. “The demand for food-grade recycling keeps on increasing, especially as retailers and consumers alike opt for more environmentally friendly options,” he continued. “Currently, only 60% of South Africa’s plastic bottles are recycled. With this increased capacity, we will be able to accommodate more of South Africa’s plastic waste and strengthen South Africa’s position as a circular economy leader in Africa and the world”. Phase 1 of this expansion is slated for Cape Town and is expected to be fully operational in 2023. The development will cost approximately R300 million (US$ 20.5 million) and will create additional jobs in the PET bottle collection industry. Extrupet, the first food-grade plastic recycler in South Africa, currently recycles more than 5 million PET bottles every day. The rPET is sold under Extrupet’s brand name PhoenixPET, which is certified by the European Food Safety Authority, Global Recycled Standard, BRC Packaging (AA rating) and ISO 9001:2015. The company was the first on the continent to use global FMCG approved technology to recycle PET bottles into resin for reuse in new carbonated soft drink bottles. www.extrupet.com Amcor Lift-Off initiative to offer seed funding for innovative start-ups Amcor, a global leader in packaging solutions, announced the launch of Amcor Lift-Off, an open-call initiative aimed at supporting seed stage start-ups that are focused on innovative packaging solutions and related technologies. Amcor Lift-Off offers these start-ups a chance to secure an investment of US$250,000, as well as operational guidance, to take their ideas to the next level. Amcor is looking to partner with innovative leaders that are working to create more sustainable packaging solutions, new packaging technologies or have developed a new business model. Applicants must be innovating in at least one of six strategic areas to apply: recycling systems, alternative barriers, paperbased solutions, smart and connected packaging, biomaterials, or new industry business models. Incorporated companies from around the world can apply for free. The Amcor Lift-Off program will proceed in three phases: Applications will be open online until May 15, 2022. (Applications received after May 15, 2022 will be considered for a second Amcor Lift-Off event in November 2022.) Applicants will then be screened and shortlisted, with up to 20 start-ups invited for a first call to pitch their ideas Five final start-ups will be invited to pitch on a first Lift-Off day toward the end of June before a team of senior Amcor leaders. Based on the ideas pitched, each of the five finalists could receive US$250,000 in the form of a convertible loan as well as Amcor support and resources to refine their products, build partnerships and scale across geographies. www.amcor.com/about/ventures","@ID":8} "PETplanet Insider Vol. 23 No. 04/22 www.petpla.net 38 PETbottles Beverage + Liquid Food Refreshing drink from Rettergut Rettergut, a company or brand, aims to reduce or avoid the waste of raw materials or parts of raw materials that do not meet the aesthetic or processing requirements of the food industry, such as “curved” cucumbers, deformed carrots or apples with “non-smooth” surfaces. Rettergut uses these flawless products and processes them further into products. For example, under the name “Des Sprudels Kern” there are several carbonated soft drinks, in the picture cucumber & mint and apple & sloe. The 500ml bottles are made of 100 % recycled PET, have an opaque screw cap and a paper label. www.rettergut.de Tea drink from Share The range of Share products to support people in need is becoming increasingly diverse. The latest example is a caffeinated tea drink made from organic Guayua tea with raspberry & blackberry. With the purchase of each bottle, the buyer donates one day of drinking water to a person in need. The 500ml bottle is made from 100% recycled material and sealed with a green coloured screw cap with a guarantee ring. The foil label explains the product and the Share initiative. The buyer can find out more about his donation via a QR code. www.share.eu Low-calorie vitamin drink In 2008, the story of the company Vitamin Well began in Sweden, which wanted to offer a healthy, low-calorie alternative to juices or lemonade. Today, the non-carbonated, lowcalorie soft drink with vitamins and minerals is available in various recipes and flavours in many countries, now also in Germany. Each 500ml is filled in a transparent disposable bottle with a paper label. On the label are the product instructions and a detailed list of ingredients. A silver screw cap rounds off the “clean”, almost medicinal look of the product. www.vitaminwell.com Sponsors to date Interested in becoming a Sponsor? sales@petpla.net The worldwide round trip with EDITOURS Interested in being interviewed? barton@petpla.net Let Your Inspiration Flow. 7KH (XURSHDQ 5RDG 6KRZ PART2 Empowered by drinktec Autumn 2021 - 2022 Back to Europe The second part of PETplanet’s bipartite Drinktec Editour is right ahead! After the successful first part “From Down Under to Japan” in 2020, our second stage of the project takes us back to the flourishing European hub where we will be exploring the latest technologies, news, innovations and developments that move our PET industry. We will be asking how global thinking might change as a result of Covid-19. How will bilateral business relationships cope with the aftermath of the pandemic? What opportunities will there be for the drinks industry and its suppliers? Our planning, in terms of precise timeframes and details of the countries to be visited will be flexible, in order to take account of the rapidly changing pandemic situation. We will be at the very heart of the roadshow as usual and are already looking forward to welcoming you back on board the Editourmobil! Share this exciting experience with us!","@ID":40} "PREFORM PRODUCTION PETplanet Insider Vol. 23 No. 04/22 www.petpla.net 13 PDG, François Desfretier, General Manager 1) I think reduction of weight is still a challenge. It will be done by preform design and dimensions, by new PET material properties, by bottle design and by blouwing process. We are working on all these subjects in order to improve LCA of liquid packaging. Novapet, Alázaro Ires, Preform Business Manager 1) To improve new references/moulds for new markets; as i t can be edible oils and housed hold, pharmacy and cosmetic products either. An rPET unit production is shortly added to Novapet to produce our rPET preforms. food liquids with a catalog of more than 260 references in mono and multilayer preforms. In addition, we are also more and more developing preforms for household products, hygiene, cosmetics and laundry industries where demand for PET and rPET packaging is growing. 3) SGT is investing into new cosmetic range of preforms like the 24/410 neck finish, in mono or multi-layer. Another area of interest is the chi l led dairy and spreadable markets for which we develop the preform “cup”. www.sgt-pet.com 2) We are specialised in preforms for UHT milk and dairy products. And it will continue. However, we also produce a lot of preforms in PET and rPET for all beverages and liquids in general. 3) All the beverage and liquid markets are intresting for us and we wi l l continue to invest in preform production because demand will continue to grow up for lighter packaging. www.pdg-plastiques.com 2) We are highly producing mineral water and carbonated soft drinks preforms. In the latest 2-3 years we have already highly entered into new markets as related. In a few months we will face as well preforms for returnable and non-returnable 3, 4 and 5 galons (from 12 to 20 l.). Common uses are edible oil, mineral water and also fertilisers. A new challenge. 3) Any of them can be interesting for Novapet. We are continuously improving the investment into preform production (current year 2500 MU) with the aim to relocate the production capacity into other location in Spain with new preform machinery units. www.novapet.com Chalon sur Saone, in Eastern of France. To answer cosme t i c cus t ome r s ’ requests, SGT will soon be able to propose new preforms with colouration effects based on a multilayer technology. 2) 80% of our production is dedicated to package Flexblow, Gintautas Maksvytis, CEO 1) Biodegradable packaging has been a big thing for a while. FlexBlow’s R&D packaging team is collaborating with partners and researching the usage of recycled biomass in packaging. rPET preform solutions are still one of the major needs. It’s related to the mandatory requirement to increase recycled material content by 2025, as well as to the global shift towards sustainable packaging. Our recent preform development projects concentrate on shelf-life extension for 100% rPET containers. 2) FlexBlow has launched special preforms as a response to the market needs. We specialise in designing and engineering custom preforms for niche projects, i.e. hot-fill product launch, conversion from glass, multilayer PP or HDPE to PET, l ightwe i ght i ng, opt imi s i ng preforms for very complicated design, etc. Our focus on customisation allows designing preforms that requi re no further adjustment of clients’ current filling, capping, palletising, or packing lines. Our know-how in preform, container, and mould engineering and dedicated in-house prototyping infrastructure enable us to provide custom preforms that are perfectly compatible for customers’ projects. Also, we have developed a tool dedicated to customising preforms - customers who consider custom preforms can receive instant offers through the self-service website. 3) We focus on developing customised preforms for var i ous produc t s : sauces, syrups, personal and home care, nutraceut icals and cosmetics, industrial chemicals, various beverages, oils, etc. FlexBlow’s in-house mould manufacturing and injection mould sharing strategy allows custom preforms with as little as 50,000 EUR on clients’ end. www.fl exblow.com","@ID":15} "PETplanet Insider Vol. 23 No. 04/22 www.petpla.net 37 BOTTLES PETbottles Aroma care foam bath by Tetesept The history of the German company Tetesept: begins more than 55 years ago with the first cold bath. Since then, the brand has developed into a provider of products related to well-being and health. The latest example of the brand expansion is an aroma care foam bath called “Switch off”, lavender and pomegranate oil provide relaxation and calm. The vegan product is free of microplastics. The stable bottle contains 500 ml and is made of 100% recycled material. The sleeve label has a perforation for easy detachment from the bottle. A corresponding notice requests that the bottle, lid and label be separated from each other in order to simplify recycling or make it possible in the first place. www.tetesept.de 2 in 1 from Schaum Kids Under the brand name “Schauma kids”, Schwarzkopf & Henkel fills 250ml of a 2-in-1 product specially formulated for children’s skin and hair - shampoo and wash gel with blueberry - into a special bottle. The bottle, made of 98% recycled material, is coloured blue and shaped like a trapezoid - flattened at the front and narrowing towards the back. This allows the bottle to face better on the shelf. The hinged cap, which is shaped to match the bottle and made of 25% recycled material, has a dispensing opening and can be detached from the bottle for recycling with a twisting motion. www.schwarzkopf.de Limited Edition by Fa According to Henkel & Schwarzkopf, Fa’s Limited Edition ‘Balancing Me Time’ with rose fragrance and argan oil - is designed to provide a relaxing shower experience. The bottle is made of 100% recycled material, of which 25% is social plastic. The almost transparent bottle makes it easy to see the colour of the product. 93% of the product ingredients are of natural origin. The colour of the hinged lid, the product and the label design give the product a rather colourful appearance. www.dm.de Home + Personal Care The right tools and expertise to help with your rPET goals! Agr is uniquely positioned to support your venture into rPET bottle manufacturing with a powerful combination of Process Control tools, Process Consultants, and decades of industry experience. AGRINTL.COM • +1.724.482.2163","@ID":39} "PATENTS PETpatents PETplanet Insider Vol. 23 No. 04/22 www.petpla.net 39 A bottle with a RFID label International Patent No. WO 2021 / 207323 A1 Applicant: The Coca-Cola Company, Atlanta (US) Date of application: 7.4.2021 An RFID label is integrated within a refillable bottle for carbonated drinks in order to determine the life cycle/refills of a bottle and to remove them from the cycle on reaching a certain age or to collect the required information. A container with delamination International Patent No. WO 2021 / 199925 A1 Applicant: Yoshino Kogyosho Co. Ltd., Tokyo (JP) Date of application: 5.3.2021 The structure and design of a double-walled bottle with the required delamination once the emptied bottles have been recorded. Double-walled preform International Patent No. WO 2021 / 202234 A1 Applicant: The Procter and Gamble Company, Cincinnati (US) Date of application: 25.3.2021 A double-walled preform consisting of two layers, or made from two preforms, inserted into one another to produce a doublewalled aerosol container. A double-walled container International Patent No. WO 2021 / 206088 A1 Applicant: Nissei ASB Machine Co. Ltd., Nagano (JP) Date of application: 6.4.2021 A container with pump dispenser made from a double-walled preform. When the inner container is emptied, it detaches from the outer one, allowing air into the vacuum space. A multilayer bottle International Patent No. WO 2021 / 207563 A1 Applicant: The Procter and Gamble Company, Cincinnati (US) Date of application: 9.4.2021 A bottle made from multilayered plastic material, including recycling layers, that create special optical effects. A reusable PET bottle for dairy products International Patent No. WO 2021 / 209561 A2 Applicant: Alpla Werke Alwin Lehner GmbH & Co. KG, Hard (AT) Date of application: 15.4.2021 A reusable PET bottle for dairy products. The container/interior is shaped in such a way that ensures there are no corners or edges that could cause product residues to stick to it.","@ID":41} "MARKET SURVEY 25 PETplanet Insider Vol. 23 No. 04/22 www.petpla.net PVS-3 PVS10L PLO030 - preform sorter/ feeder 90,000pph 72,000pph 40,000pph Contamination, shape, diameter, wall thickness, crystallisation, contamination, black specks, unmelts, bubbles, water marks, black specks, gate length, opacity, colour variations, scratches Contamination, shape, diameter, wall thickness, crystallisation, contamination, black specks, unmelts, bubbles, water marks, black specks, gate length, opacity, colour variations, scratches Contaminations, cavity number recognition, fl ashes Contaminations, cavity number recognition, fl ashes Diameters, ovality, thickness, scratches, short shots, fl ashes, notches, contaminations Diameters, ovality, thickness, scratches, short shots, fl ashes, notches, contaminations Crystallisation, contaminations, unmlet, bubbles, grooves, holes, cracks, position of the injection point, gate length Crystallisation, contaminations, unmlet, bubbles, grooves, holes, cracks, position of the injection point, gate length Colour variations, Intensity deviations, LAB measurement Colour variations, Intensity deviations, LAB measurement Cavity number recognition through advanced Deep Learning and AI algorithms to ensure the highest reliability even with those number with poor relief and/or poor contrast, cavity related statistics, sorting by cavity number Cavity number recognition through advanced Deep Learning and AI algorithms to ensure the highest reliability even with those number with poor relief and/or poor contrast, cavity related statistics, sorting by cavity number Patented polarised light inspection through advanced Deep Learning and AI algorithms Patented polarised light inspection through advanced Deep Learning and AI algorithms; DRIVA (Drive &Recognise through Intelligent Vision Algorithms): fully automated changeover. Automatic recognition of the new preform to inspect; changeover in about 1min, from a preform to another completely different (colour, diameter, neck and length) Yes Yes Yes Yes Yes No, patented cavity recognition with top camera and special lens Yes Non-destructive Non-destructive SQL database, possibility to extract data in Excel format, possibility of connection to ERP/MES system through supported transfer protocols such as: OPC/UA, MODBUS and HTTP SQL database, possibility to extract data in Excel format, possibility of connection to ERP/MES system through supported transfer protocols such as:OPC/UA, MODBUS and HTTP Magpet Polymers Pvt Ltd Sacmi Imola S.C. PDG Plastiques Novapet SA 36A Pratapaditya Road, Kolkata-700026 India +91 3340 71 5501 www.magnumgroup.in Mr Vaibhav Sethia Sales & marketing +91 983 0926 444 kol@magnumgroup.in Via Provinciale Selice 17/a 40026 Imola, Italy +39 0542 607111 www.sacmi.it Mr Moraldo Masi Preform Division Director moraldo.masi@sacmi.it ZI secteur 2, 45330 Malesherbes, France +33 2 3834 6195 www.pdg-plastiques.com Mr Francois Desfretier General Manager +33 2 3834 6195 francois.desfretier@pdg-plastiques.com Paseo de la independencia 21, 3. Zaragoza, Spain +34 976 2161 29 www.novapet.com Mr Antonio Lázaro Preform business manager +34 976 216129 alazaro@samca.com PP & PLA BioPET - PP Customer choice 100% Yes, up to 100% Yes, from 10-100% Prelactia 100% light barrier for UHT sterilised long shelf-life milk, Oxygen, UV, CO2 barriers Concentrates (for milk and light sensitive products); colours, lubricants, nucleants, under customer requirements Over 100 Sku's - PCO 1881, ROPP, Alaska, 5 gallon preforms etc. 5 - 140g Coloured preforms, Preblow technology, Mint-Tec technology; 29/25 shorty (8-10,5-11,7-18,721- 22-23-23,5-24-24,5-26,5-28g); 30/25 high (17,5-24,5-26-28-31-33-36-39-50g); 26/22 (10,5-17-23-28,5-30-34g); 38mm 3 start (18-22-28-32-33,5-35-44-50-62-64g); Prelactia 38mm 3 start (17-24-28-38g); 48/40 (47-55-62g); 21/29 (22,5g); 27/32 (6,5g dairy & smoothies); 25/20 (6,5- 8g dairy); PCO 1810 (20-33,6g); PCO 1881 (18,5-27-30-32-36,5g); 29/23 (24 -27- 33g chemical); BVS 30H60 (50g wine (high oxygen barrier)); 22H30 (19g wine (high oxygen barrier)); ultra-light weighting 2,4g preform standard and specifi c preforms for mineral water, dairy, juice, CSD etc.; overmoulding technology for 2 layers preforms Ø 29/25 W (short neck) 330-2.000ml (10-32g); Ø 30/25 W (std neck) 330 - 2,500ml (11,6-47g); Ø 48mm W 5,000-10,000ml (77, 82,98g); Ø PCO 1810 (std neck) 500-3,000ml (18,5-54g); Ø PCO 1881 (std neck) 300-2,000ml 17,5 & 25g; Ø 28/410 300-1,500ml (24, 30, 36,5, 42,5g); any other shape and weight (18-38,7g); Ø 38mm 500-6,000ml (27-75g); Ø 29/21 edible oil 0,5 & 1 l (22&25g); Ø 42/34 edible oil 3 & 5 l (75 & 85g); Ø Pilfer 28mm (small formats)","@ID":27} "PREFORM PRODUCTION PETplanet Insider Vol. 23 No. 04/22 www.petpla.net 12 Three question-survey on the current preform product situation and future challenges What’s new in preform production? PETplanet Insider gave preform producers the opportunity to describe their current situation and plans for the future. We are pleased to present the answers from Flexblow, Novapet, PDG, SGT and Plastipak. The companies answered the following three questions: 1) The last development steps in the production of preforms were the thin-wall-, the multilayer- and the use of rPET in a preform. What are the new challenges in the production of preforms? 2) Is there any specialisation in your company - what types of preforms does your company produce most often? Do you think this is the way you will continue? 3) Which markets are interesting for you, where will your company invest in the future in terms of preform production? Plastipak, Pedro Martins, Executive Managing Director Europe 1) The inclusion of rPET, with increasingly higher percentages of recycled material, often up to 100%, is still the dominant trend we see in our business. For Plastipak, a reprocessor and producer of food-grade rPET since 1998 in Europe, the inclusion of rPET in preforms is not the challenge as this has been a core capability for many years. With three recycling plants in Europe, one in the US and another one currently under construction in Spain, Plastipak is the largest producer of food-grade rPET in Europe. Reprocessing capacity is being developed at a high rate, however collection of post-consumer PET to feed the recycling plants remains a challenge, as does the leakage of material from closed loop bottle-to-bottle recycling in to applications such as textiles. Complete PREFORMS SGT & SGR Group, Frédéric Mignot, CEO 1) At SGT, we are focused on developing light weighting, sustainable and design-for-recycling preforms, three major trends for bottlers industry. Regarding light-weighting our preforms, we are currently working on a new range of ultra-lightweight PET preforms for food and non-foods applications. We are also developing a new range of preforms with the 26/22 neck finish specially designed for tethered caps. About increasing the incorporation of recycled PET, we are able to supply and incorporate 12,000 t of rPET per year in our preforms production thanks to our recycled unit - SGR - in closed-loop recycling is the ultimate goal, and so design-for-recycling is another critical component of the solution. For many years, the constant focus of our development team has been the design and creation of sustainable, fully circular packaging, and this philosophy is at the heart of every Plastipak innovation. Finally, our most important challenge is the production of the lowest carbon produc t s that we can. The design and production of low carbon preforms requi res the amalgamation of our key skills; design expertise, the latest light-weighting technologies, resin developments, inclusion of recycled content and best in class production. Underpinning this, 100% of the electricity Plastipak uses at its European plants originates from renewable sources. Our life cycle analysis service enables Plastipak to quantify environmental impacts, enabling our customers to make fully informed decisions on this basis. 2) With 15 plants across 12 countries in Europe, and many more in North and South America, Plastipak produces preforms and containers for the major applications of PET bottles and containers; beverage, food, home and personal care, industrial and more. Therefore, we cannot say that we specialise in any particular sector or in any particular product, apart from sustainable, innovative, high quality products. Our development centre looks at the whole life of the package and the requirements of the product that it destined to protect, so producing the lightest-weight, highest-performing package that is optimally designed to suit the filling platforms and logistical chains, right through to the end of life. This is the approach that has grown our business to the size it is today, and we anticipate that we will continue to follow this model. 3) Plastipak is customer-driven, and we develop long-term partnerships with our clients, many of which are multinational or leaders in their respective markets. This, combined with the contract-driven nature of our business, means that our investment is customer-centred, rather than speculative. Going forward, we anticipate this will not change, and we will grow with our customers. Plastipak will continue to make investment decisions on this basis, as well as with the long-term strategic intent of producing the lowest carbon, fully circular products possible, to support our, and our customer’s ESG aspirations and targets. www.plastipak.com","@ID":14} "EDITOUR PETplanet Insider Vol. 23 No. 04/22 www.petpla.net 30 Over the years, he has expanded the machine park and the customer base continually, not only because of the larger selection of containers and capacity but also, as Mr Kone tells us, through conservative planning and efficient economic management. The recently expanded 3,000m2 operation now houses 13 injection moulding and blowing machines from Aoki, Battenfeld, Fischer, Cypet, Haitian and Nissei ASB, of which five machines process PET. And there is still room for more equipment. Currently, more than 30 different bottles and containers make up the portfolio. Around 60% of these are used for pharmaceuticals, 30% for food and 10% for chemicals. Processing volumes are 30% PET, 60% HDPE in blow moulding processes and 10% HDPE, LDPE and PP in injection processes. In total, Megaplast manufactures around 20 million containers per year. Only three million of these are destined for the PET sector, of which 80% are for food, 10% for drinks and the remaining 10% for non-food applications. 10% of all products are exported, and for logistical reasons, these are exclusively very small containers. Company growth is said to be 10-15% annually. Mr Kone continues: “We have been able to see considerable growth, especially in the pharmaceuticals segment. Thanks to several precautions introduced both internally and by the authorities, we have seen few difficulties during the Covid pandemic, as yet in our day-to-day business.” Besides the standard portfolio, designing containers and determining market requirements are just as much a part of the business. Megaplast is certified to ISO 9001 and ISO 13485. “Our location here is right on the pulse of tourism,” explains Yiannakis Kone. “We are very close to our end customers that supply hotels, restaurants, supermarkets and hospitals. We are also close to the motorway, which allows us to reach customers in the rest of the country rapidly.” Incidentally, we learned that PET bestsellers are usually wide-mouth cans, which are manufactured on a Cypet K16 with 13 different moulds, which has been here since 2018. At the time of our visit, a two-cavity mould for 4.5 l jars was installed on the machine. “PET was and is a significant market segment for packaging in Cyprus and the market is growing continually, especially for wide-mouth containers. So we wanted to offer solutions here too,” says Mr Kone. In terms of raw material, they usually purchase Arya PET from JBF Europa; rPET isn’t even on the radar. “We still don’t use any PET recyclate because there is no demand for it on the market yet,” says Mr Kone. “However, we can start at any time because the Cypet machine is technically equipped for it.” In the future, they want to renew parts of the machine park, primarily to improve speeds and energy savings, and ultimately to reduce the carbon footprint; the Aoki machines, for example, are getting on in age. A proportion of electricity consumption can already be generated by the solar panels installed on the roof. “The quality of our products, the low production costs and rapid delivery with an eye on market demands are what set us apart,” says Mr Kone. Yiannakis Kone (right) together with supplier Michalis Sideris from Cypet","@ID":32} "PREFORM PRODUCTION PETplanet Insider Vol. 23 No. 04/22 www.petpla.net 20 Launch of the PM-100/111N series Compact vertical preform moulding Nissei ASB perhaps better known for its 1-step injection blow moulding machines (ISBM), is launching its new compact preform machine. The new PM-100/111N series is suitable for in-line, smallscale production of preforms for almost any type of container, including returnable and refillable bottles. Leveraging ASB’s long-term expertise with their 4-station, vertical clamping ISBM machines, the PM-100/111N model follows a similar rotary table structure but drops the blow station resulting in a 3-station layout made up of injection, cooling and eject functions. As with its 4-station ISBM models, preforms are held by the neck throughout the entire moulding process up to ejection with an integrated preform cooling. By application of ASB’s propriety Zero Cooling technology in the injection and cooling stations, preform designs can be optimised for thickness and stretch ratio achieving better or equivalent cycle times. Ejected preforms may be dropped onto a standard conveyor, or an optional 6-axis industrial robot can be installed to directly feed downstream moulding systems - or, in the case of heavier, special application preforms such as hot-fill or returnable and refillable, they can be fed to additional post mould cooling systems. Machine movements are hybrid with the hydraulic systems utilising servo driven pumps resulting in low energy consumption, together with smooth and quiet operation. ASB’s Vision1 PC based control system, quickly becoming standard across its complete line-up, is flexible in use and compatible with industry 4.0 for enhanced factory networking (IIoT). www.nisseiasb.co.jp PREFORMS Key facts: 18 to 36 cavities Up to 40mm thread diameter Preform weight from 6.5 g up to 80 g Up to 16,000 pph (500ml water) Compact, with less than 13m2 floor space +44 78175 32087 +34 676 986 962 sales@petmachinery.com petmachinery.com Looking to sell your used PET machinery? We can help you. We offer a free valuation service, 50 years of industry experience, and a global network that guarantees you the best market value. Contact us today to find out more. THE INDUSTRY EXPERTS","@ID":22} "PETcontents 4 PETplanet Insider Vol. 23 No. 04/22 www.petpla.net 04/2022 Page 46 MATERIALS / RECYCLING 10 Plastics recycling, part of the puzzle - How the industry continues to expand in Europe / Focus on PET PREFORM PRODUCTION 12 What’s new in preform production? Three-question survey on the current preform product situation and future challenges 14 Cool performance - Sipa optimises cooling systems on preform tooling to cut customer costs and enhance sustainability 16 Digital, rational, profitable - Sacmi’s Injection Preform System (IPS) 300 18 Automated quality assurance - AI and optical quality inspection solution for rPET bottles 20 Compact vertical preform moulding - Launch of the PM-100/111N series MARKET SURVEY 22 Suppliers of preforms & preform inspection systems EDITOUR 26 Off the tourist track - The European Road Show in Cyprus 27 Single-stage ISBM machines for flexible, special-sized formats 29 Plastic containers for the Cypriot market - PET packaging for drinks, food and pharmaceuticals 31 Inside PETplanet - Why the global mouthpiece for the PET sector is looking so good EVENT REVIEW 33 A well-tuned quartet - Review of PETinar Tethered Caps: Design, Produce, Inspect! BUYER’S GUIDE 40 Get listed! INSIDE TRACK 3 Editorial 4 Contents 6 News 36 Preform production products 37 PET bottles for home + personal care 38 PET bottles for beverage + liquid food 39 Patents 46 Outer Planet Page 27 Page 14 PREFORMS","@ID":6} "EDITOUR PETplanet Insider Vol. 23 No. 04/22 www.petpla.net 31 Why the global mouthpiece for the PET sector is looking so good Inside PETplanet by Kay Barton Since its start in 1999, PETplanet Insider has undergone several technical design alterations and developments – sometimes radical and sometimes subtle. And alongside the magazine, we have a digital presence online and countless other things that support our specialist information and make up our outward appearance. For almost 20 years now, this visual identity has been seen all over the world in the hands and on the screens of the most important decision makers in the PET sector. So we feel it’s high time to highlight the company that has (almost continuously) been behind PETplanet’s unique design: EXPRIM Editor Kay Barton made a small detour on our European Roadshow to drop into the village of Halver, around an hour’s drive northeast of Cologne. There, he spoke to “our” creative leader and agency manager Matthias Gaumann about him, us and our journey together. Interview with EXPRIM Advertising Agency, March 11, 2022 We met: Mr Matthias Gaumann, Owner and Managing Director PETplanet Insider: Matthias, it’s lovely that you’ve found the time to talk to us today about yourself and our work together. Tell our readers about your collaboration with PETplanet. Matthias Gaumann: I’ve been working with the team from PETplanet since 2001. At that time, I worked in a different advertising agency than I do today. When I left that agency in 2004, our paths also went separate ways but luckily not for long. In 2007, we found each other again. We met at the K2007 trade fair in Düsseldorf and remembered the positive and trusting collaboration of the past. It was rekindled from that moment on, and I’m still very happy about that. Thank you very much to Alexander Büchler for his courage, creativity and confidence! Many thanks for almost 20 years of collaboration with your fabulous, trustworthy, qualified and creative team that has come through so many highs and lows. PETplanet Insider: And thanks to you for your ongoing work on the graphical front! Tell us something about your personal background and how EXPRIM came into being. Matthias Gaumann: Coming from a generation that was lucky enough to experience computers finding their way into home offices and user interfaces becoming ever more intuitive, I was interested from an early age in shaping information simply and understandably in texts and images. Experiencing and shaping the development of the internet was and is still very exciting. I quickly made the decision to experience this fascination every day and study for a career as a media designer. Later, I also studied business management. The mixture of sound tradecraft, constantly changing technical requirements and creative challenges, as well as contact with great people and brilliant companies, still helps boost my motivation every day. EXPRIM means “expressing yourself” or “giving someone or something expression”. This is what we consider our task to be so this is why the agency has had this name since 2004. PETplanet Insider: Can you tell us about the range of tasks that can arise during a typical PETplanet day? Matthias Gaumann: My regular tasks include the design of and printable final artwork for the print media, such as PETplanet Insider. But sometimes, large-format layouts like tradefair stands, lettering for the Editourmobil or rollup banners are also part of my day. I also contribute graphics and layouts for digital media. PETplanet Insider: You mention the layout for the Editourmobil that you’ve always drafted. Everything else for the tour, in terms of graphics anyway, is also designed by you according to our basic ideas. What do you like, or even dislike, about this ongoing project? Matthias Gaumann: After a while you get to know the major players in the PET sector, even as a sector outsider. But through the Editour, you get to know the smaller companies and the hidden champions. I find the different company locations interesting too. You also get an insight into the companies and learn a bit about the people behind the big names, as well as the technology. Of course, the stories from countries I’ve never travelled to are also interesting. For example, Rolf Sinkovec (Editor’s note: former PETplanet IT officer and occasional tour participant) recently Tour Sponsors:","@ID":33} "MARKET SURVEY 23 PETplanet Insider Vol. 23 No. 04/22 www.petpla.net Preform inspection Company name Intravis GmbH Postal address Telephone number Website address Contact name Function Direct telephone number E-Mail Rotter Bruch 26a, 52068 Aachen, Germany +49 241 9126 0 www.intravis.com Mr Markus Juppe CMO +49 241 9126 0 sales@intravis.de Preform Inspection Systems PreWatcher Offline Sample-PreWatcher PreMon LayerWatcher ColorWatcher Lab Inspection speed Up to 100,000 objects/hour with 18 cameras Up to 1,200 objects/hour with weight check Up to 72,000 objects/hour with 5 cameras Up to 144 objects/hour Manual feeding, handling time: up to 5 sec. / object measurement time: up to 10ms/object Inspected parameters: Geometry / Body Contamination; short shots; length; diameter; shape; unmelted material; oil & water marks; burn spots; scratches; opacity; crystallisation; streaks; bubbles; colour and colour deviations; barrier; stress test with polarised light Contamination; short shots; length; diameter; shape; unmelted material; oil & water marks; burn spots; wall thickness; inner wall damage; core shift; scratches; opacity; crystallisation; streaks; stress test with polarised light; bubbles; colour and colour deviations; barrier Colour and colour deviations; contamination; unmelted material; oil; burn spots; opacity; yellowness Presence of barrier layers; thickness of barrier layers; position of barrier layers; structure of barrier layers; position of barrier leading edge; position of barrier trailing edge Colour and colour deviations Thread area Contamination; thread dimensions; defects at the neck support ring; fl ash; pulled thread Contamination; thread dimensions; defects at the neck support ring; fl ash; pulled thread; tactile inspection of inner wall diameter Mouth / Sealing surface Diameter; ovality; short shots; fl ash; scratches and notches on the sealing surface; defects at the neck support ring; contamination; Diameter; ovality; short shots; fl ash; scratches and notches on the sealing surface; inner mouth wall inspection; contamination Short shots; scratches/notches; contamination Gate / Dome Contamination; grooves; holes; cracks; crystallisation; postitioning of injection point; unmelted material; gate length; gate deformation; stringing Contamination; grooves; holes; cracks; crystallisation; postitioning of injection point; unmelted material; gate length; gate deformation; stringing; wall thickness Length of injection point; contamination Colour Colour and intensity deviations (ΔL*, Δa*, Δb*); presence of UV blocker; presence of barrier; presence of IR absorber (reheater) Colour and intensity deviations (ΔL*, Δa*, Δb*); presence of UV blocker; presence of barrier; presence of IR absorber (reheater) Colour and intensity deviations (ΔL*, Δa*, Δb*); yellowness Colour and intensity deviations (ΔL*, Δa*, Δb*); presence of UV blocker; presence of barrier; presence of IR absorber (reheater) Cavity number Cavity number reading; cavity related statistics; preform sorting according to cavity number; powerful cavity reading without need for learning for most fonts; possibility to share information based on cavity number with IMM Cavity number reading; cavity related statistics; preform sorting according to cavity number; enables collection of reference samples; powerful cavity reading without need for learning for most fonts; possibility to share information based on cavity number with IMM Cavity related statistics; powerful cavity reading without need for learning for most fonts; possibillity to share information based on cavity number with IMM Further criteria Precise separation and positioning of preforms due to star wheel separation; second ejector for easy collection of sample preforms; space-saving design on less than 4m²; 100% quality control without blind areas; for transparent, translucent and opaque preforms Precise and extensive measurement of weight and dimension; cavity-correlated information about every detail of the preform; reference sample collection based on defect and/or cavity Comprehensive octabin or time related statistic dashboard; bad part ejection with ejection compensation; high precision through preform orientation; easy reference creation due to PreMon Wizard Visualisation of individual barrier layers in 3D images in less than 30 sec.; inspection of up to 100,000 measuring points; layer measurement with OptoSonix scan technology; cavity-related information High precision colour inspection with spectrometer; for translucent, transparent and opaque preforms; analysis of even small colour nuances; no change parts required Measurement of absence or presence of barrier material Yes Yes Yes Yes Layer thickness & position measurement at distinctive points Yes Layer thickness & position measurement at the complete body by scanning Yes Features: Installation: Stand-alone Yes Yes Yes Yes Installation: Inline Yes, but optimised for offl ine Yes, sampling Yes, optimised for inline after IMM Yes, sampling · Side camera for cavity recognition Yes, 4 cameras Yes, rollout of the complete thread area Yes, rollout of the complete thread area No, but manual input · Method: destructive/non destructive Non-destructive Non-destructive Non-destructive Non-destructive Non-destructive · Data base connection Yes, all industry standards supported; ready for Industry 4.0 applications: XLS formats; SQL and several others; connectable to IntraVisualizer, ERP & QMS Yes, all industry standards supported; ready for Industry 4.0 applications: XLS formats; SQL and several others; connectable to IntraVisualizer, ERP & QMS Yes, all industry standards supported; ready for Industry 4.0 applications: XLS formats; SQL and several others; connectable to IntraVisualizer, ERP & QMS Yes, all industry standards supported; ready for Industry 4.0 applications: XLS formats; SQL and several others; connectable to IntraVisualizer, ERP & QMS Yes, all industry standards supported; ready for Industry 4.0 applications: XLS formats; SQL and several others; connectable to IntraVisualizer, ERP & QMS","@ID":25} "7 NEWS PETplanet Insider Vol. 23 No. 04/22 www.petpla.net Coca-Cola: New PET line in operation at the Karlsruhe Germany plant Coca-Cola Europacific Partners Germany (CCEP DE) has commissioned a new PET line in Karlsruhe, Germany. With this addition, the plant can now fill up to 36,000 PET bottles/ hour, each containing 1.25 l of beverages such as Coca-Cola, Fanta or Sprite. To achieve this, the beverage manufacturer has expanded the Neureut site, also in the production-related supply areas and logistics. CCEP DE has invested 15 million Euros and created more than 60 new jobs. The new PET line, which was inaugurated at the beginning of the year, strengthens the supply of the production network around Karlsruhe five days a week after the successful relocation. In addition, up to 120,000 cans are produced every hour. The production times have been extended: from now on, the canning line will run around the clock. In addition to the new PET line, other changes at the plant include six loading ramps implemented for faster truck handling. Further innovations can be found in the water treatment and syrup room: the water capacities required to supply the two lines were doubled to supply the new line, and the tanks in the syrup room were replaced and expanded. The conversion was rounded off by a new concentrate station and purification plant. www.cocacolaep.com Tomra celebrates 50th anniversary Tomra, a global provider of advanced collection and sorting systems, is celebrating its 50th anniversary. Tomra was founded in Norway on April 1, 1972 by brothers Petter and Tore Planke. After seeing a local grocer struggle with the manual collection of empty bottles in their store, the brothers developed the first fully-automated reverse vending machine (RVM) in their family’s garage. This invention was ground-breaking for recycling processes and its concept is used today around the world. Over the years, Tomra’s technology expanded to include advanced sorting systems for the food, recycling, and mining industries. Today, Tomra employs more than 4,600 people around the world and has annual sales of €1bn. Twenty per cent of the group’s workforce and eight per cent of its revenues are dedicated to research and development. To meet Tomra’s ambition of increasing global recycling collection to 40 per cent and increased plastics in closed-loop systems to 30 per cent by 2030, the company plans to continue its growth and increase headcount. The expansion will explore new business opportunities, develop solutions to mitigate climate change, and in doing so, preserve natural resources for future generations. Tove Andersen, Tomra’s president and chief executive officer, said: “Fifty years after its humble beginnings, Tomra can be proud of the fact that it is a highly respected global market leader. This is living proof of our ability to adapt, innovate, and provide the solutions our customers really need. This is also a time to look forward because we are now opening a new chapter in Tomra’s story where we step up our role leading the resource revolution.” Digital transformation is at the heart of the company’s vision for the future with Tomra Insight, a cloud-based data analysis platform with remote service capability. It offers recyclers a state-of-the-art approach to improve sorting performance and reduce operating costs. Tomra Recycling is a leading global supplier of sensorbased sorting solutions and connected digital services that transform waste into valuable secondary raw materials. The company has installed over 8,200 sorting units for waste and metal recycling in more than 100 countries worldwide. Designed and built to maximise recycling yields, Tomra machines can be put to the test at any of its seven test centres worldwide. www.tomra.com","@ID":9} "8 NEWS PETplanet Insider Vol. 23 No. 04/22 www.petpla.net Erema establishes new R&D centre for recycling technologies Construction machinery rolls into action again at the Erema site in Ansfelden, Austria. The ground-breaking ceremony on April 6 signals the start of work on a new R&D centre. Two halls with a total area of 1,550m2 and a new office building with 50 workplaces will be built. The centre will offer cross-departmental and cross-company test machines and laboratory for research and development of plastics recycling technologies to further advance the circular economy. Completion is scheduled for February 2023. In recent years, approximately 5 per cent of turnover has been reinvested annually in R&D. Employees from different departments handle process engineering challenges, developments in mechanical engineering and automation technology, and special technologies with a view to further improving the quality of recycled pellets. They also focus on new recycling technologies for waste plastic materials for which there is currently no satisfactory circular economy solution. The decisive factor here is also to exploit the potential of digitalisation. By collecting and analysing machine data, not only can recycling processes and product quality be further improved, but the digital service offering for customers can be developed. Such offerings include customer-specific information tools that feature plant and process data, predictive maintenance and online support as well as commissioning via remote access. For material tests, an expanded machine park will be available following completion of the new centre. Here, the recycling process can be evaluated end-to-end, including upstream and downstream processes such as shredding and further processing of the recycled pellets. The material tests are supported by analysis in the professionally equipped laboratory, which will be relocated to the new premises and upgraded where necessary with the latest lab equipment. “The necessity of investing in the circular economy and in plastics recycling is clear from the current crises, which will be with us for some time to come,” says Manfred Hackl. “Both coronavirus and the consequences of the invasion of Ukraine have shown us the reality of the EU’s dependence on resources. Our mission “Another life for plastic. Because we care.” is more relevant today than ever before.” www.erema-group.com From left: Markus Huber-Lindinger Managing Director Erema GmbH, Markus Achleitner Upper Austria´s Minister for the Economy, Manfred Hackl CEO Erema Group GmbH and Christian Partoll Ansfelden´s Mayor (photo: Land OÖ/Kauder) Tony Radoszewski departs Plastics Industry Association Former President and CEO Tony Radoszewski is no longer with the Plastics Industry Association. Radoszewski’s last day was March 25, as announced by Tad McGwire, Chairman of the Board: “Tony Radoszewski is no longer with the Plastics Industry Association. His last day as President and CEO was Friday, March 25. We are grateful to Tony for his service to the plastics industry. Tony served our association during a period that included significant challenges, but Plastics remains as strong as ever. We extend Tony our best wishes in his future endeavours and extend our sincere thanks for his commitment and contributions”, McGwire stated. Radoszewski had assumed the role of President and CEO in 2019 after the death of his predecessor Bill Carteaux. Radoszewski’s successor has not yet been announced. www.plasticsindustry.org","@ID":10} "PREFORM PRODUCTION PETplanet Insider Vol. 23 No. 04/22 www.petpla.net 18 AI and optical quality inspection solution for rPET bottles Automated quality assurance Doloop, a leading European PET packaging producer, has partnered with high-tech company Sprana to create a new quality inspection solution for beverage bottle preforms. The technology is claimed to allow the use of higher percentages of recycled material, while ensuring high product quality. This new system can inspect PET preforms at very early stages of production and provide information on quality before they are blown into bottles. Used inline, it allows detection of any defect that may have occurred during the production process. AI (artificial intelligence) driven technology enables automated, continuous quality assurance. PET bottles and increasing interest in recycled PET CO2 emissions created during production processes have a significant environmental impact; which can be reduced by greater use of recycled PET derived from collected post-consumer bottles. The EU Single-Use Plastic Directive requires PET bottles for beverages to include 25% of recycled materials by 2025, and 30% by 2030. These requirements create a need for methods and tools that can improve and guarantee high quality control and accurate analysis in the manufacturing process. The greatest challenges in increasing usage of recycled PET in preforms are: maintaining high product quality; guaranteed efficient production; and ensuring optimal performance of PET bottles in later phases. Quality control during manufacturing is thus becoming increasingly crucial in the plastics sector. Quality inspection solution Doloop has already invested € 7 million in the last seven years in quality assurance, including new inspection technologies. The use of recycled material increases colour variations. It can be difficult to ensure consistent production and product quality as recycled PET colour tends to differ from batch to batch. This is because of different sources of PET bottles, collected in different markets, being used as inputs in the recycling process. Doloop has been able to overcome this challenge by partnering with Sprana, an expert in visual inspection technologies and AI. This R&D project was supported by the EEA and Norway Grants Program for Business Development, Innovation and SMEs. During the project, the company carried out research and experimental activities to improve the control of PET preforms using artificial intelligence technologies, while increasing the use of recycled materials. Realtime monitoring and analysis allowed much faster and more efficiently inspection. Manual inspection of PET preforms is inefficient, time consuming and increases the possibility of defective production. Doloop maintains that, by optimising and improving quality control at preform stage, manufacturers are able to reduce human involvement in quality assurance and move personnel to more demanding production processes. The project aimed not only to increase the use of recycled PET in packaging products, but also to take another step towards the goal of a circular economy in the plastic packaging industry. Image recognition systems and artificial intelligence-based quality control systems and inline colour analysers have been installed in nine Doloop injection lines. Finished preforms’ colour can now be analysed and evaluated continuously during the production process. Automating the quality inspection process with the new technology saved up to 89,760 manhours of labour per year, according to Doloop’s CEO. Since introducing the technologies in 2019, the number of quality claims due to discolouration have been reduced by as much as 50 per cent, states the company, and add that clients have found that: bottling lines could work with high efficiency and had few stoppages, due to better quality of preforms with rPET content; PREFORMS Different PET preforms with different percentages of recycled materials (f.l.t.r. 25-50-75-100%) (photo: Krones)","@ID":20} "PREFORM PRODUCTION PETplanet Insider Vol. 23 No. 04/22 www.petpla.net 16 Sacmi’s Injection Preform System (IPS) 300 Digital, rational, profitable Recently boosted by the launch of the new IPS 300, Sacmi’s platform incorporates a new approach to the vision concept, paving the way for total quality control. This is achieved via software-controlled systems that make full use of the latest AI, states Sacmi. PREFORMS Preform production Sacmi is well known for its rigid packaging solutions. In 2012, Sacmi started diversification in the preform field by developing the IPS platform. The first solution in the family, specifically designed for bottlers, was the IPS 220. This was followed by the IPS 400, developed for converters and designed to maximise performance in terms of productivity and versatile utilisation of different mould types. Now, 10 years later, 140 Sacmi systems running worldwide. The new IPS 300 The decision to develop the IPS 300 was driven by a need to optimise the process on current needs of the industry. Like the IPS 400, what makes this machine special is the interchangeability of the moulds, including those produced by third parties, provided they are equipped with external air and coolant connections. Flexible and modular, the machine can mount the plasticising unit that best suits the preform type being produced (from 625 to 1,220 kg/hour). It has also been designed to drive down specific consumption, which remains below 0.2 kW/kg. Several options are available to design solutions based on individual production needs; these include the dye and additive mixer, the injection cycle completion kit (in the event of a power outage) and the piping and water filtration process control sensor kit. Automation The latest generation of IPS machines feature a Beckhoff TwinCat architecture with EtherCat fieldbus. This ‘infrastructure’ takes process control to advanced levels, opening the industry to IoT opportunities (selflearning and predictive checks). The solution adopted for the aftercooler allows the vision system - the PVS 156 from the Sacmi computer vision range - to be installed directly on the machine. This results constant product quality monitoring, for example on the 96-cavity solution the check time for an entire moulding is cut to about 5 minutes. This latest development aims to increase the coverage and accuracy of routine checks. It performes in a set time according to the quantity of preforms present and the complexity of inspection and allows the company to integrate preform quality control directly on the line. This differs from the common practice of post-production inspection, which carries the risk and relative cost of having to re-check entire, potentially faulty batches. Preform Vision Systems (PVS) Featuring a patented polarised light inspection device and AI, the PVS systems have been developed to provide comprehensive production tracking; this allows users, for example, to read the cavity number and correlate statistical data concerning potential defects. Hence, alongside the new PVS156, Sacmi provides the PVS002, a comprehensive unit designed to help technicians carry out routine production checks in quality control labs. It can perform all-round inspection of the mouth, finish, bottom and body, measure weight and read cavity numbers. The PVS003, instead, is an in-line solution downstream from the press that provides inspection rates up to 90,000 pph. The PVS10 off-line unit, operating at up to 72,000 pph, complements the new self-guided Sacmi D.R.I.V.A. system, which performs automatic","@ID":18} "imprint EDITORIAL PUBLISHER Alexander Büchler, Managing Director HEAD OFFICE heidelberg business media GmbH Vangerowstraße 33 69115 Heidelberg, Germany phone: +49 6221-65108-0 fax: +49 6221-65108-28 info@petpla.net EDITORIAL Kay Barton Heike Fischer Gabriele Kosmehl Michael Maruschke Ruari McCallion Anthony Withers WikiPETia. info petplanet@petpla.net MEDIA CONSULTANTS Martina Hirschmann hirschmann@petpla.net Johann Lange-Brock lange-brock@petpla.net phone: +49 6221-65108-0 fax: +49 6221-65108-28 LAYOUT AND PREPRESS EXPRIM Werbeagentur | exprim.de Matthias Gaumann READER SERVICES Till Kretner reader@petpla.net PRINT Chroma Druck Eine Unternehmung der Limberg-Druck GmbH Danziger Platz 6 67059 Ludwigshafen, Germany WWW www.hbmedia.net | www.petpla.net PETplanet Insider ISSN 1438-9459 is published 10 times a year. This publication is sent to qualified subscribers (1-year subscription 149 EUR, 2-year subscription 289 EUR, Young professionals’ subscription 99 EUR. Magazines will be dispatched to you by airmail). Not to be reproduced in any form without permission from the publisher. Note: The fact that product names may not be identified as trademarks is not an indication that such names are not registered trademarks. 3 PETplanet Insider Vol. 23 No. 04/22 www.petpla.net Dear readers, You and I, who work with PET bottles on a daily basis, are often met with quizzical looks and good-natured ribbing when we display our expert knowledge of bottles amongst friends and acquaintances. For example, as I reflect during a break for coffee and cake on the savings made in material over the years and the challenges involved in labelling, or the sheer volumes produced by cap and preform machines, I realise that more can be done to address the public’s perception of packaging and PET in particular. In addition, we are now faced with the introduction of the tethered cap in 2024 and when I mention this in private conversations, some people shake their heads in disbelief at what they see as political over-regulation. Nevertheless, we as an industry need to rise to this challenge and bring the customer along with us. An incident that occurred during a private function convinced me that we cannot afford to wait. During this season’s first barbecue, Coca-Cola was served as well as beer and wine. Quite by chance, our host brought along new 0.33 litre bottles from the Berlin plant. Coca-Cola European Partners Berlin are one of the first German companies that have dared to offer tethered caps to their end customer. The words “Leave me on for recycling” are written in large letters on the cap. Unfortunately, none of the guests at the barbecue noticed these words. Two men pulled the cap off completely while two women only removed one attachment, which meant that the closure was still hanging on one strip. I naturally took advantage of the situation to interview these four individuals. All of them found the attached cap annoying, believing that a production fault was responsible for the cap not coming off properly. The women were also not too pleased that the partially attached cap was dangling in their faces whilst drinking. No-one realised that the cap can be folded to the side. Surely the consumer will have learned how to handle the cap better by 2024 but after the evening’s barbecue, this seems to be a distant hope. I have to say that I applaud Coca-Cola’s bold move on behalf of the whole industry and that we can all benefit from their experience when operating on the market. I will hopefully have better experiences to report after closing the barbecue season in late autumn. Yours sincerely, Alexander Büchler","@ID":5} "PREFORM PRODUCTION 19 PETplanet Insider Vol. 23 almost one day per year is saved in hours spent administering discolouration claims; clients develop and deliver to market new products with rPET easier and faster, as less time is spent optimising production and adjusting quality; Bottles on the shelf appear visually much more consistent, with less colour variation. Future challenges Doloop is aiming to become carbon-neutral. The company is achieving this by offsetting the CO2 emissions generated during production with renewable energy projects. It is also making all of its products recyclable or compostable. The automated quality inspection is now moving to the second stage of development to tackle another quality issue: black specs, which are small, dark fractions or particles found in blown bottles, resulting from increased use of recycled materials. They do not harm product itself but the appearance is affected when the bottle is blown. Doloop and Sprana plan to upgrade the existing base of the PET preform inspection system and adapt to detect black specs during in-line production. In 2021, Doloop produced almost 1.5 billion PET preforms and 35 million PET bottles. The company has expanded its range of sustainable packaging solutions and started producing PET rigid film in late 2021. Its customers include well-known brand-owners, international and local companies. 90% of the company’s production is exported to more than 20 countries around the world, including Germany, Norway, Finland and Sweden. www.doloop.com Inline quality control and PET preforms inspection technology","@ID":21} "MARKET SURVEY 24 PETplanet Insider Vol. 23 No. 04/22 www.petpla.net Preform inspection Company name IMD Ltd. Sacmi Imola S.C. Postal address Telephone number Website address Contact name Function Direct telephone number E-Mail Industriestrasse 37A, 2555 Brügg BE, Switzerland +41 32 366 80 66 www.imdvista.ch Mr Martin Gerber Sales Director (CSO) +41 32 366 80 66 m.gerber@imdvista.ch Via Selice Provinciale 17/A, 40026 Imola (BO), Italy +39 0542 607111 www.sacmi.com Mr Stefano Severi Sales Specialist Manager +39 335 6594236 stefano.severi@sacmi.it Preform Inspection Systems IMDvista Peco V3 - 100% Preform Inspection System IMDvista Peco Lux - Preform Monitoring System PVS002C Inspection speed Up to 90,000 pph According to injection moulding machine speed Up to 1,200pph Inspected parameters: Geometry / Body Black spots, burn marks, contamination, deformation body, air bubbles, scratches, non-visible fl ow structures (low pressure while injection), total length, colour defects, too long injection points, unmelts Colour defects and deviation, contamination, burn marks, air bubbles, scratches, too long injection points Contamination, shape, diameter, ovalisation, wall thickness, crystallisation, unmelts, bubbles, water marks, black specks, gate length, opacity, colour variations, scratches and many other Thread area Flashes on neck/thread, scratches on neck area, support ring deformation, missing material on support ring Contaminations, cavity number recognition, diameters, fl ashes, black specks, diameters measurements Mouth / Sealing surface Ovality, diameter, fl ashes, shorts shots, fl ash on parting line, deformation of sealing area, colour defects and colour deviation Short shot trend analyser Diameters, ovality, thickness, scratches, short shots, fl ashes, notches, contaminations and black specks Gate / Dome Gate defects, gate lenght (long gates), holes in gate and gate area, gate deformation, cracks in gate area, injection point out of center, drip marks Too long injection point Crystallisation, contaminations, unmlet, bubbles, grooves, holes, cracks, position of the injection point, black specks, gate length Colour Colour defects and deviation (L*A*B*) Colour defects and deviation (L*A*B*) Colour variations, Intensity deviations, LAB measurement Cavity number Cavity recognition and reading, cavity related statistics and alarms, rejection of X cavity numbers Cavity number recognition through advanced Deep Learning and AI algorithms to ensure the highest reliability even with those number with poor relief and/or poor contrast, cavity related statistics, sorting by cavity number Further criteria System on operator level: “IMD is proud to offer exclusively the most compact solution in the market together with our partner M. Tanner Ltd. Switzerland” No additional fl oor space required - simple and fast integration onto specifi c injection moulding machine Weight check, patented polarised light inspection through advanced Deep Learning and AI algorithms, fast manual changeover through intelligent guided procedure, measurement of thread and body, perpendicularity, wall thickness and fl ash in the parting line Measurement of absence or presence of barrier material Layer thickness & position measurement at distinctive points Layer thickness & position measurement at the complete body by scanning Features: Installation: Stand-alone Yes Yes Installation: Inline Yes Yes Yes · Side camera for cavity recognition Included Yes · Methode: destructive/non destructive Non-destructive Non-destructive Non-destructive · Data base connection IMDvista Portal / Customer ERP System IMDvista Portal SQL database, possibility to extract data in Excel format, possibility of connection to ERP/MES system through supported transfer protocols such as:OPC/UA, MODBUS and HTTP Preforms Company name Société Générale des Techniques (SGT) Hodmeter Plastipak Postal address Telephone number Website address Contact name Function Direct telephone number E-mail 3 Rue de l’Île Macé 44412 Rezé, France +33 2 40 05 09 37 www.sgt-pet.com Mr Pierre-Henri Jany Sales Manager +33 2 40 05 09 37 p.jany@sgt-france.com 140 rue Louis Pasteur 76160 Darnétal, France +33 950 373 373 www.hodmeter.com Mr Antoine Brémilts Sales & Marketing +33 684 633 154 bremilts@hodmeter.com Ringlaan 7, 2960 Brecht, Belgium +32 3 330 08 12 www.plastipak.com Mr David Albeniz Sales & Marketing Director - EU info@plastipak.com Preforms Multilayer preforms (Yes/No) Yes Yes PEN prefoms (Yes/No) Preforms in alternative materials (PP/PLA/PEF) Which? Yes, BioPET & PEF Yes, PLA & PEF Preforms incorporating rPET (rPET content in %) 1% to 100% (upon requests), own food grade rPET: CIRPET Yes, up to 100% List of additives available All colours & barrier technologies: UV blocker, AA reducer; O2 & CO2 scavenger, reheat additive, white colour for UHT milk, slip agent All colourants and barrier technologies Preform range Preforms for use in bottled water, CSD, food, dairy, juices, oil & vinegar, sauces & condiments, home and personal care, wine & spirits, industrial and other applications. 27/31 (36-66g); 27/32 (25,10-50,10g); 55mm for 5 gallon (refi llable application 450-650g); 30/25 (high&low neck 13-44g); 30/25 BB light (22,50-28g); 29/25 without step (9,3-35,8g); 29/25 (9,5-36g); 28 PCO1810 (16-52,5g); PCO 1881 (14,50-50g); PCO 1881M (13-17,50g) 26/22 (17-30g); 28 BPF (20,5-53g); 38mm 42/36, 38mm 43/36, 38mm 43/36,5 (without step), 38mm 43/36,5, 38mm hot fi ll (14-70g); 33mm (12-26g); 45/52 (yogurt cup 11g); 48/40 (77-160g); 21/29 (20-52g); 28/22 (23g); 28/400 (20g); 28/410 (19,5-52,50g); 28/410 with anti-back-off system (34-40g); 22H30 (18g); BVS 30 H (40-53,50g); CRC63 (385-450g); 38/400 (18-28g); 24/410 (24g); 26/22 CSD (28-29,50g); 29/23 (30,50g); 48CH (90g); 63/54 (385g) 700g (55mm neck) Plastipak supplies preforms for use in bottled water, CSD, food, dairy, home and personal care, alcohol, industrial and other applications. Plastipak has a wide range of preform sizes and weights too numerous to list.","@ID":26}]}}
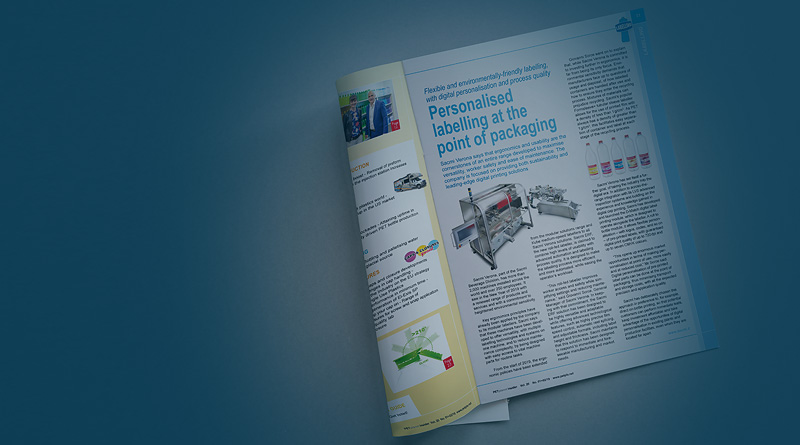