{"pages":{"page":[{"@ID":76, "PETplanet Insider Vol. 23 No. 09/22 www.petpla.net 71 BOTTLES PETbottles Beverage + Liquid Food Fine sauces from Aldi Süd Aldi Süd sel ls special food products under the label “Gourmet Finest Cuisine” as part of sales campaigns. Recent ly, several sauces were on sale, which were supposed to entice customers to buy them by using high-quality basic ingredients and interesting combinations. The two sauces or dressings shown - fig cream and mango cream with aceto balsamico as a base - were each filled in narrow bottles with 250ml contents. The bot t le was closed with a hinged lid with a dosage opening under the first withdrawal protection with a tear-off strip. The label and colour gave the bottle a high-quality appearance. www.aldi-sued.de Syrup from Hella In the context of sustainability, beverage manufacturers in Germany are increasingly relying on concentrates or syrups. These are only made ready to drink at home by adding water. In terms of logistics, this saves packaging, weight, loading and storage space. Also, the customer no longer carries so many heavy bottles. The most recent example is various syrup variants from Hella. The bottle made of 100% recycled material with a capacity of 500 ml produces six litres of readyto-drink beverage by adding water, which can also be produced with a fizzer. Under the two-colour dosing cap there is a sealing membrane that has to be removed before first use. www.hella-mineralbrunnen.de Isotonic drink from Alwa Under the name “alwa Iso Spritzer”, the German company alwa Mineralbrunnen GmbH fills 500ml of a low-calorie, isotonic sports drink made from natural mineral water with added fruit juice into a transparent, disposable deposit bottle. The bottle has a recess in the label area to fix the label. The transparent film label gives a clear view of the product. The picture shows the apple and grapefruit variants. An opaque screw cap with a guarantee band closes the bottle. www.alwa-mineralwasser.de Water from Tuscany Nestlé or San Pellegrino sells a natural mineral water from Tuscany under the name Acqua Panna in var ious container shapes and sizes and advertises it on the label with the name and the area of origin of the water. Among other things, the water is offered in a transparent PET bottle with a capacity of 500ml. The bottle as a whole evokes the feeling of a high-quality, lifestyle water with a glossy label and a screw cap with decoration. www.acquapanna.com"},{"@ID":4, "60 TRADE SHOW PREVIEW PETplanet Insider Vol. 23 No. 09/22 www.petpla.net Approach to circular economy, climate protection and digitalisation With the increasing focus on sustainability in plastic industries, Bariq shows their contribution to the hot topics of this year’s edition of the trade fair - circular economy, climate protection and digitalisation. As with the company‘s upcoming facility expansion (see page xy), Bariq aims to recycle 4 billion PET bottles per year, producing 35,000 t of food-grade rPET for new bottles and saving 80,000 t of CO2 that contributes to circular economy and climate protection. With its new digitalisation plan, Bariq is now able to trace all its products from supplier to customer. Also the new line will apply the latest technologies that uses AI, Robotics and machine learning for sorting and bottles identification. www.bariq-eg.com Circularity through plastics additives Milliken & Company showcases new measures to advance the circular economy through chemistry - part of the company’s 2025 sustainability goals. Additionally, Milliken is partnering with more than 30 partners in purposeful collaborations that will be on display throughout the K’ show, including its ongoing partnership with PureCycle Technologies, whose patented technology turns recycled PP into virgin-like material. Many of Milliken’s products are designed specifically to yield sustainability benefits. These qualities include: reduced energy consumption and lightweighting, better reuse potential, increased net use of recycled content, improved recycling and recyclability, and the replacement of less-sustainable resins. Milliken is actively engaging in several industry-spanning initiatives, including the Alliance to End Plastic Waste, The Recycling Partnership, the Association of Plastic Recyclers, the HolyGrail project to improve the sorting of waste plastics via digital watermarks, and the RecyClass recycled-content certification program for packaging, to name a few. www.milliken.com Swiss Made | www.imdvista.ch IMDvista NEURON Detailed 360° closure inspection with no need of closure orientation based on Artificial Intelligence Let’s talk about your solution Swiss Made | www.imdvista.ch Check out our latest innovation and visit us in hall B5 / booth 111 12. –16. September 2022 | Messe München PRODUCT LAUNCH Bariq Hall 7 Booth C27 Milliken Hall 6 Booth A27 SI Group to unveil new brand for plastics recycling SI Group, a global developer and manufacturer of performance additives, process solutions, pharmaceuticals, and chemical intermediates, will be introducing its new additives brand for plastics recycling. The company’s newest brand will encompass a comprehensive platform of additive solutions designed to accelerate the transition to a more circular economy and lead to a more sustainable plastics industry. PET stabiliser The first solutions to be introduced under the new brand name will be stabilisers for recycled polyolefins and PET that are specifically designed to allow customers to use more recycled materials without compromising performance in the end application. In addition to revealing the new brand, SI Group will be presenting its expanded portfolio and latest sustainability developments. Key product updates to be showcased include a new masterbatch grade of Weston 705 liquid antioxidant and Ultranox LC stabilisers. Since the last K’ show in 2019, the company has increased its focus on sustainability. www.siigroup.com SI Group Hall 6 Booth B08"},{"@ID":58, "TRADE SHOW REVIEW PETplanet Insider Vol. 23 No. 09/22 www.petpla.net 68 Review PETinar: Trends in the virgin and recycled PET market: How can recyclability, circularity and sustainability be realised? Spotlight on circularity of recycled PET The seventh PETinar organised by PETplanet Insider took place on May 6, 2022. PETplanet invited two experts to talk about trends and opportunities for recyclability, circular economy, and sustainability specifically for the PET industry. Casper van den Dungen, Vice President of Plastics Recyclers Europe and Dr Paolo Glerean, Chairman of RecyClass presented current facts, from legislation to market figures and initiatives to solve the problem of the shortage of recycled PET material. After a brief introduction of the two speakers, Ruari McCallion, editor of PETplanet, handed over to Casper, who began his presentation on promoting the circular economy in the PET industry in Europe. Casper spoke in behalf of Plastics Recyclers Europe. With 150 company members, various working groups on plastics recycling and the experience of over 25 years, Plastics Recyclers Europe (PRE) represents the voice of European plastics recyclers. Casper explained: “Recyclers are a very important factor in the circularity of plastics and the transition to a circular economy.” Regarding PET recycling Casper reminded: “Just a few years back, PET beverage bottles were recycled into fibres, for strapping or clothing. Today, the biggest outlet is packaging – making circularity real even for food contact applications.” He firstly presented on overview of the evolution on the PET bottles collection from 2018 to 2020 with the increase of 9%, from 51% to 61%. In the process, 4.6 million tonnes of rigid PET packaging ended their product life and were available for collection in 2020. 61% of PET bottles and 21% of trays were collected for recycling. There is still room for improvement for the collection volume. “Countries that have a Deposit Return Scheme (DRS) achieve a recycling rate of up to 83% or more. By 2025, the number of countries with DRS in the EU will have doubled. This means a significant increase in recyclabled material,” stated Casper. (Fig.1) Casper sees an increase in bottle-to-bottle recycling and fewer PET bottles being used for sheet production. “There was an increase of installed PET recycling capacity in 2020. Now we have reached a total of 2.8mt,” Casper continued. Due to new installed capacity, tray recycling will increase in France and Belgium. The end markets for recycled PET Casper summarised as follows: “A total of 27% is used for food contact application. 32% is processed for blow moulding and 33% in sheet production, finally 24% goes into fibre applications.” (Fig.2) “However, there are still some challenges with PET recycling that need to be addressed. These include the insufficient separate collection of PET, which results from a lack of investment. This in turn leads to poor quality of the collected material. There is also too little attention paid to design for recycling, and no harmonisation of systems or introduction of standards,” said Casper. In order to improve the situation, existing legislation such as the Plastics Strategy and the Single Use Plastic Directive will be supplemented by further PET-specific (Recycled Plastic in food-contact Articles Regulation) and packaging-related legislations (Waste Framework Directive, Waste Shipment Regulation and the Packaging & Packaging Waste Directive). “To meet the 90% collection rate and the mandatory recycled content targets, Europe will require an expansion in recycling (wash-) capacity of at least one third by 2029. (Fig.3) In thirteen other EU countries, politicians have decided to introduce DRS systems by 2025 at the latest. This will push more rPET into the market. However, it remains a balancing act between all stakeholders. But: as the EU is, on the global scale, the pioneer in terms of PET circularity thanks its extensive base of recycling companies, high-tech technologies and best practices it will have an impact on the countries across the globe by exporting its technologies and know-how,” Casper summarised. As Casper mentioned, the design for recycling is an important prerequisite to keep PET circular and thus highquality material in the market. Paolo Glerean is Chair of the RecyClass platform which aims to make plastic circular by ensuring all products are recyclable and by promoting transparent uptake of recycled content in new products in line with the circular economy. Paolo began by explaining: “The platform includes two major focus areas: recyclability and recycled content.” Fig.1 Fig.2 Fig.3"},{"@ID":60, "58 TRADE SHOW PREVIEW PETplanet Insider Vol. 23 No. 09/22 www.petpla.net Inline inspection and sorting During the online quality control of plastic pellets, Sikora’s Purity Scanner Advanced ensures that only pure material enters the further production process. Even small, critical contamination is reliably detected and automatically sorted out, says Sikora. Both the detection and the ejection behaviour of contaminated pellets are perfectly coordinated. Thanks to the modular system design of the scanner, different camera types can be used depending on the material being inspected. In addition to optical cameras, which detect black specks and discolourations, an X-ray camera can be installed to detect metallic contamination. Many systems on the market have a maximum of 2 optical cameras. According to Sikora, these quickly reach their limits due to a relatively low coverage as soon as the contamination are outside the field of view of the installed cameras. Therefore, the company offers its customers the possibility to have a third optical camera installed, if required. This camera setting offers a higher detection rate, so that more contamination can be detected. This is especial ly advantageous when the Purity Scanner Advanced is integrated directly into the production line as an inline system and multiple sorting with a typical 2-camera system is not possible. The Purity Scanner Advanced automatically sorts out the detected contamination via a blow-out unit. Thanks to the higher detection rate, more contaminants are sorted out with a 3-camera setting. Against this background, the optimisation of the by-catch becomes more important. Therefore, Sikora has developed the feature of “hybrid blow-out”. The customer can define in advance which impurities in the material represent uncritical contaminations and select a smaller blowout unit for these, so that their by-catch is reduced. These include, for example, small, light-coloured black specks that frequently occur in the material. On the other hand, a larger blow-out unit is specified for critical contaminants – for example, metal contaminants that can impair the functionality of the subsequent end product. www.sikora.net Sikora Hall 10 Booth F14"},{"@ID":36, "34 TRADE SHOW PREVIEW PETplanet Insider Vol. 23 No. 09/22 www.petpla.net Hall 14 Booth C03 Bekum Group Phone: +43 2783 4111 200 • sales@bekum.com • www.bekum.com DISCOVER OUR WIDEST RANGE OF INNOVATION OUR NEW 8-SERIES WITH 20 NEWMODELS SERIES New Small Electric Machines New Packaging Machine Line New Industrial Machine Line New Patented Drive Technology New Energy Saving Applications New Added Value Applications Labels for megatrends CCL Label will be showcasing its latest innovations with a focus on labels and sleeve solutions that support recycling and reuse of packaging to support a circular economy, intelligent label solutions and premium labels that stand out on the sales shelves. With the ‘Sustainable Label Family’ CCL has created a specifically engineered product range that is intendeed to cover all needs of brands that want to boost their recycling rates. For PET recycling, CCL offers EcoFloat shrink sleeves, EcoStream pressure-sensitive labels and Stretch Sleeve solutions that are floatable and detach automatically from the PET bottle in the sorting and recycling facility. The company’s ‘Sustainable Product Family’ portfolio include bio-based or floatable materials, wash-off solutions or ultra-thin sleeves that have a low carbon footprint. CCL also will have solutions for HDPE and PP containers on display as well as labels with special functionalities which support refPET bottle schemes as well as deposit schemes. In addition, the exhibits include label solutions for the beverage market that can transform packaging into a virtual communication channel. Other solutions are labels that include RFID and NFC technology which is the basis of intelligent labelling of the future to for example prevent food waste. Smart labelling technology can also be used to tackle the sorting and recycling challenges – by using digital watermarks on the packaging that are invisible to the eye but give the packaging a digital passport. This digital passport can be detected in the sorting facilities and so the package is sorted into the right recycling stream. www.ccllabel.com CCL Hall C6 – Booth 344 Caps solutions & an anniversary This year’s fair is something truly special for Corvaglia. With the company having celebrated its 30th anniversary last year, the show will give the company the opportunity to properly commemorate this milestone after it was delayed in doing so due to the pandemic. In addition, the company will be able to launch its new closure concepts for tethered caps, in which Corvaglia has invested intensive research. The company was able to develop a wide range of tethered caps solutions based on 30 years of experience in the development and production of one-piece caps with various types of tamper-evident bands and production technologies. Many of these solutions have now been implemented on an industrial scale, including the world’s first commercial production of an aseptic 38mm tethered cap. Sustainability is also integrated into the company’s own processes. For example, Corvaglia has been part of the Science Based Targets initiative (SBTi) since autumn 2021. This initiative supports companies in reducing their emissions in accordance with the Paris Climate Agreement. With its participation, the company committed to cutting its own emissions by at least 50% by 2030, which is in line with the goal of limiting the global temperature increase to 1.5 °C. Corvaglia is also proud to have achieved the gold medal in the EcoVadis sustainability rating, which puts it among the top five percentage of companies worldwide in the sustainability ranking. EcoVadis helps companies monitor their own value chain in regard to sustainability, and proposes measures to take to make improvements in this area. www.corvaglia.com Corvaglia Hall C5 – Booth 275 Range of Corvaglia tethered cap solutions"},{"@ID":2, "TRADE SHOW PREVIEW PETplanet Insider Vol. 23 No. 09/22 www.petpla.net 50 Sustainable and user-friendly closures More ECOnvenience Enhanced user convenience, climate friendliness, weight and material reductions are the key to success for future closure systems - Bericap is exhibiting solutions that already satisfy those requirements. Bericap committed long ago to ‘ECOnvenience’, i.e. eco-friendly convenience, and customisation. It particularly focuses on user-friendly and resourceconserving closure systems such as tethered caps for all relevant neck finishes and sport closures, all of which are customisable to customer requirements. Bericap | Hall C5 – Booth 375 Tethered caps According to a consumer study on tethered caps, which become mandatory in Europe in July 2024, consumers are willing to embrace eco-friendly closures if they also have handling benefits. The majority of consumers surveyed rated the Bericap tethered caps – which go by the name of ClipAside – more positively than conventional closures for their intuitive handling, their 180-degree opening angle and the fact that they are very hygienic. In addition to complying with EU Directive 2019/904 to improve recycling performance, beverage manufacturers who change over to ClipAside early can enhance their brand appeal and improve customer loyalty. Bericap designed ClipAside to allow customers to prepare for a fast and simple change-over to tethered caps while continuing to manufacture closures with the current TE band geometry (or to manufacture both types concurrently). When producing closures in designs that have been adapted to the future ClipAside height, Bericap can simply change the cutting geometry and switch between standard cut and tethered cap cut. It is then possible for the filling lines to conveniently switch between standard and tethered caps without any modifications being necessary, which fully reflects the current market situation. In other words, beverage manufacturers are ideally equipped for a flexible and efficient future change-over, says Bericap. Conserving resources Bericap has been pushing forward light weight initiatives across all product categories, because weight and material reductions improve sustainability. These initiatives include the development of new neck standards to reduce both bottle and closure material requirements, as well as the continuous optimisation of closure designs in conjunction with neck standard development. The company has played an instrumental role in the weight and material-saving evolution of the standard PCO 1810 neck finish to PCO 1881 and most recently the new GME 30.40. Bericap is currently working on the next ClipAside generation for the GME 30.40 neck finish, which represents another significant weight reduction compared to the recently launched version. Dynamic sport closures The existing secure and easy-touse Bericap sport closure programme for on-the-go products, which already includes Thumb’Up and Crystal, has been extended by new models Mayence and Biarritz, as well as the premium closure Monet. All Bericap sport closures are made of HDPE/PP materials and have a large opening for a better drinking experience. The The new sport cap model Monet"},{"@ID":78, "TRADE SHOW PREVIEW PETplanet Insider Vol. 23 No. 09/22 www.petpla.net 45 Moulding of returnable & refillable PET bottles Compared to their glass counterparts, returnable and refillable PET bottles are typically 90% lighter, with a 30% lower carbon footprint. Compared to single use PET bottles, returnable and refillable PET bottles weigh around twice as much, yet as a result of their reusability, they only consume around 8-10% of the PET material of equivalent single use bottles throughout their lifetime, which may extend up to 6 years considering a typical 3-month re-use cycle. Nissei ASB | Hall C5 – Booth 225 HSB-4N double blow heat-set reheat stretch blow moulding machine from Nissei ASB In a typical production scenario, a single HSB-4N machine will produce up to 20 million returnable & refillable PET bottles per year, and with each bottle having a lifetime of more than 25 cycles, this represents the equivalent of at least 500 million single use bottles. At end of life, refillable PET bottles are bottle-to-bottle recyclable or can be converted into other new products. Even when moulded with 100% virgin PET, the refillable bottle already has a lower carbon footprint compared to a single use bottle, but the ability to absorb 30% of recycled materials without any impact to performance, the carbon footprint of the container is reduced by around an additional 25%. Working with a famous brand filling company, Nissei ASB developed and launched the first returnable and refillable PET bottles for juices and soft drinks in the German market during the country’s first “green wave” way back in 1989. Shortly thereafter, ASB went on to supply similar systems to multiple companies in around 20 countries throughout the 1990s. cess via its HSB series reheat stretch blow moulding machines, Nissei ASB will demonstrate live moulding of a returnable and refillable PET bottle on an HSB-4N machine that are claimed to surpass current industry standards in all respects: A 1 l sparkling water with 1.5 gas vol. (design compatible with popular German industry standard for sparkling water), weighting 53 g (current industry standard 62 g), with reuse cycles greater than 25 times (current industry practice “up to 25 times”), with a rPET content of up to 30%, without reduction in performance (in laboratory testing ASB’s R&R bottles with 30% rPET actually achieved in excess of 30 times washing and pressurisation cycles). www.nisseiasb.co.jp Now, with the resurgence in interest and public demand for refillable packaging, not only in Germany but also globally, ASB is well placed to take advantage by utilising its broad packaging expertise as well as its capable moulding equipment. The double blow heat-set process that is the main feature of the HSB series machines, gives the ASB bottle significant advantages over other moulding methods, says ASB. The result is higher crystallinity (density) of the material, together with less stress in the moulded bottle. Both these factors combined result in improved thermal stability and greater resistance to environmental stress cracking, ensuring higher reusability rates at a lighter weight. At Drinktec 2022, using its wellestablished double blow heat-set pro1-liter returnable & refillable PET bottles as demonstrated at Drinktec, seen here with ASB developed preforms"},{"@ID":65, "63 TRADE SHOW PREVIEW PETplanet Insider Vol. 23 No. 09/22 www.petpla.net Drying system for rPET processing PET Solutions, part of Pegaso Industries Holding, is known for its auxiliary equipment and systems for preforms. Since 1994 the comapny is also established on the closures injection moulding market. The DRV Series is claimed to be an advanced drying system for pellets and flakes polymers in the market, being the final result of a 10 years R&D project including many PET Solutions branded patents. The company developed the system as the new excellence for rPET processing in cooperation with international leading beverage companies. Based on the continuous vacuum drying technology, it allows the extraction of contaminants (e.g. AA, Benzene) normally contained inside the rPET as result of the recycling process. This drying technology no longer requires the use of molecular sieves as current traditional standard drying technology and prevents the use of oil condensers to remove the contaminants, thus reducing the energy consumption impact of the drying process (reduced by 30 % compared to the traditional technology). Other advantages include low drying (reduced by 80% compared to the traditional technology), low changeover (reduced by 80% compared to the traditional technology), flexibility and the non-necessity of a connection to HTC water circuit. Main features: Production range up to 3,000 kg/h Supervision and management connectivity (e.g. Modbus, Ethernet, OPC UA) Remote connection User-friendly system www.pegasoindustries.com +44 78175 32087 +34 676 986 962 sales@petmachinery.com petmachinery.com Looking to sell your used PET machinery? We can help you. We offer a free valuation service, 50 years of industry experience, and a global network that guarantees you the best market value. Contact us today to find out more. THE INDUSTRY EXPERTS PET Solutions Hall 11 Booth I37"},{"@ID":11, "MARKET SURVEY 39 PETplanet Insider Vol. 23 No. 09/22 www.petpla.net 09/2022 MARKETsurvey Resins & additives Preform machinery Preform production & inspection systems Preform & SBM mould manufacturer SBM 2-stage Compressors Caps & closures & inspection systems Filling equipment & inspection systems Recycling machinery Palletising & shrink film machinery All about caps! For the third time, PETplanet decided to put all our surveys about caps & closures manufacturing together in one comprehensive overview - from mould maker, systems manufacturer, inspection systems provider to cap producer. Please find out about state of the art closure equipment. We thank all participants: z-mould, Corvaglia, Engel, Netstal (KM), Alpla, Has Plastik, IMDvista, Pressco Technology, Uner, Intravis, Sacmi and Sumitomo (SHI) Demag. Although the publisher has made every eff ort to make sure that the information in this survey is up to date, no claims are made regarding accuracy and completeness. AFM Active Flow Molding Core movement for less preform weight German Technology September 12-16, 2022 Munich, Germany Hall C5, Booth 440 Systems Company name Netstal Maschinen AG Engel Austria GmbH Sumitomo (SHI) Demag Plastics Machinery GmbH Sacmi Imola S.C Postal address Telephone number Web site address Contact name Function Direct telephone number E-mail Tschachenstrasse 1 8752 Näfels, Switzerland +41 55 618 61 11 www.netstal.com Mr Stefan Kleinfeld Product Manager +41 55 618 62 41 stefan.kleinfeld@netstal.com Ludwig-Engel-Straße 1, 4311 Schwertberg, Austria +43 50 620 0 www.engelglobal.com Mr Christoph Lhota Vice President, Packaging +43 50 620 3400 christoph.lhota@engel.at Altdorferstrasse 15 90571 Schwaig, Germany +49 91150610 www.sumitomo-shi-demag.eu Mr Arnaud Nomblot Director - Bus. Develpmt. Pack. +49 911 5061 625 arnaud.nomblot@shi-g.com Via Selice Prov. Le 17/A, 40026 Imola (BO) - Italy +39 0542 60 7111 www.sacmi.com Mr Stefano Severi Sales Area Manaer +39 335 659 4236 stefano.severi@sacmi.it Systems for cap/closure production Turnkey systems Injection moulding machine Model Elion Engel e-cap El-Exis SP CCM24SC /CCM32CM /CCM48SD/ CCM64MC Procession technology Injection moulding Injection moulding Compression Clamp force 1,200 - 4,200 kN 2,200 - 4,200kN 1,500 - 10,000kN Not applicable Cycle time (guaranteed 98% closure system effi ciency for): 2 - 20s 2 s (dry cycle times of 1.3 s with the e-cap 380) 26/22mm - up to 2,800 caps/min 29/25mm - up to 2,300 caps/min PCO1881 - up to 1,800 caps/min GME30.40 - up to 1,800 caps/min - High speed production: closure type/ weight/cavities: caps/min 26/22 / 0.8g / 96 / 2,298 29/25 caps / 1.3 g / 96 cavities / 2,880 caps/min (e-cap 380, Plastisud mould, HDPE) 29mm water/ 1.2g / 24 cavities: 1,000caps/min, 28mm CSD/ 2g / 32 cavities: 980caps/min, 29mm water/ 1.2g / 48 cavities: 2,000 caps/min, 28mm CSD/ 2.4g / 64 cavities: 1,600caps/min - Individual cap solution: closure type/ weight/cavities: caps/min 38 / 2.8g / 72 / 1,026 Drive concept Electric + hybrid All-electric Hybrid Electric / hydraulic Energy consumption (kwh/kg) 0.40 0.37 (e-cap 380) 0.40g, varying upon application Equal or more than 0.4 kwh/h Preferred mould makers Corvaglia, z-moulds, Plastisud z-moulds / Plastisud Sacmi Special features SmartOperation, twin-valve technology, high-speed toggle lever clamp myConnect Possibility to assemble only 12-32 moulds, inline quality control on all caps, cap weight adjustable from HMI, without mould change"},{"@ID":23, "MOULD MAKING PETplanet Insider Vol. 23 No. 09/22 www.petpla.net 21 Indian Railway brand. It created a new benchmark for the Indian water industry with a number of turnkey projects for very light preform and cap moulds for 200ml, 500ml and 1 l bottles, with non-nitro filled 26/22 necks. Acme supplies large-capacity bottle preform moulds, including the world’s first 12 cavity mould for five gallon/20 litre water bottles. The preforms have a 55mm bubbletop caps and weigh 750 g. The company has also supplied 72 cavity moulds, which are India’s largest, and, at the opposite extreme, it made the country’s fastest cap mould: a 48 cavity hot runner with a 4.4 s cycle time. The company developed and produced a dispensing pump (complete set of 7 moulds), making it the first company in India to offer a complete packaging and closure solution. In international markets, Acme Disys developed the world’s largest wide-mouth jar mould: a 12 cavity unit, producing 110mm necks, for the African market. In East Africa, it supplied a mineral water preform project to a leading international brand. The company can also claim another world first: a commercial mould for largecapacity preforms with handles, for Australia’s 2 l and 3 l juice market. In-house services Acme Disys’ inhouse resources include preform and cap product designs, prototyping and mould testing. Comprehensive in-house customer training is provided for mould assembly, maintenance and process optimisation. The company provides mould and hot half refurbishment of Husky, MHT, ASB, Sacmi and other international mould makers, as well as complete cold half and conversion kit serving of moulds of up to 96 cavities. Tethered caps are currently being developed and used in EU countries and elsewhere in the world. Acme Disys is already working to develop these caps in the near future, as required by individual markets. The company sees no major challenges with their development, having already worked on similar concepts. Neck finishes Acme Disys currently offers cap moulds for various standards, including: Water: 28mm Alaska, 26/22mm, 29/25mm, 30/25mm Juice and CSD: 1810 PCO,1810 PCO light weight,1881-pco,38mm Edible oil: CTC-26/10 with tamper evidence band for both right & left hand opening & then work as flip top Pickles and jar: 53mm with tamper evident band 20 l BT: 20 l bubbletop push-on cap with tear-off band PCO-2519, a standard similar to GME 30.40 (26mm) is in the development stage. Prototyping, testing and customer validation is under way. Product range PET preform moulds: 2-96 cavities for bottles & wide mouth jars Bottles - catering to beverages - water, carbonated, juice, liquor, pharma & personal care applications. Wide mouth jars - catering to FMCG and food applications Caps & closures: beverage packaging - water, carbonated, drinks, juices, pharma etc. Dispensing Pumps: Acme Disys is the first company in India to develop and offer complete sets of moulds to personal care & FMCG industries. Medical technology: blood collection tubes up to 48 cavities. www.acmedisys.com MORE DATA BETTER QUALITY LESS DOWNTIME BOOTH A4/410 VISIT US AT:"},{"@ID":32, "30 TRADE SHOW PREVIEW PETplanet Insider Vol. 23 No. 09/22 www.petpla.net Two-part stack A stack performs a variety of functions: to reproduce the contour of the preform, to ensure rapid demoulding by means of smart cooling, as well as the ability to adjust to changed preform geometries as easily as possible. MHT has made adjustments to all areas and is demonstrating its new OptiStack mould testing system. For the first time, the core is divided into two halves and has a patented contour-following inner cooling tube. The whole mould cavity has more uniform parts than before. For the customer, this means easier maintenance and assembly. For example, when converting the mould to a new preform shape, only mould-forming parts of the core need to be replaced. Furthermore, parts of the closure have been separated from contour-carrying components which means that refurbishments can be carried out easily and cost-effectively. The new stack can be seen in operation at the Netstal machine manufacturer stand (Booth 363, just opposite MHT). There, a 72-cavity mould produces lightweight 10.5g CSD preforms for 0.5 l bottles. A granulate is used which consists of 25% chemically recycled PET. The OptiRun MHT hot runner used here is ideally suited to the circular economy. During its development, the system was subjected to a lengthy test phase carried out under challenging production conditions (flake content up to 100%) with major packaging manufacturers. The post-cooling solution CoolMax exhibiting at the Netstal stand is claimed to guarantee short cycle times and good preform quality. It is suitable for all cavity numbers and can be individually adapted to special preforms, such as those for which no vacuum can be created. The GME 30.40 thread of the trade fair preform has already been designed for tethered caps. Matching bottles can be seen at the MHT stand. Like its parent company Krones, MHT is fully committed to recycling and the circular economy. This includes recycling-friendly preform design and technology such as AFM (Active Flow Moulding), which can be used to produce base geometries in a material saving manner. Krones (Hall B6) is presenting its own systems for washing and decontaminating PET flakes. Arranged in tandem, these facilities can convert flakes into food-standard PET feedstock. www.mht-ag.de Oil-free compressor range Indo-Air’s oil-free high pressure air compressor IAH series is a 100% oil-free compressor specially designed for the PET bottling industry. Its range is from 30 - 160kW, CFM from 110 - 545, pressure 32 - 40bar. The compressor features a silent canopy to reduce noise level. The IAH series air compressor comes with a specially designed controller with features such as pressure, temperature, alarms, history of alarms, service contact details etc. The company says that the compressor does not require any special foundations as it is mounted on anti-vibrating pads. The IAH series compressor is a water cooled air compressor which provides better cooling and an extended service life. At Drinktec, the compressor can be experienced in action at the Indoair booth. www.indoair.com ALL- IN- ONE-MACHINE ASSEMBLY FOLDING SLITTING TETHERED CAP CONTEXO GMBH Tel. +49 (0) 7181 / 606-100 info@contexo-gmbh.de www.contexo-automation.de VISIT US: DRINKTEC C5/175 MHT Hall C5 – Booth 440 Indoair Compressors Hall A6 – Booth 106"},{"@ID":8, "PETnews 6 NEWS PETplanet Insider Vol. 23 No. 09/22 www.petpla.net Innovations and sustainability in plastic bottles and containers The 6th edition of the Blow Moulding 2022 International Conference, Exhibition and Networking Event will take place in Brussels, Belgium, on 30 November - 1 December. This annual event brings together the entire supply chain: from brand owners and retailers to suppliers of raw materials and additives – not forgetting manufacturers of packaging and packaging components (preforms, bottles, caps & closures, labels & sleeves, etc.), equipment manufacturers, recyclers and sustainability experts, testing and certification agencies, academics and researchers. The 2022 edition features keynote speakers from Danone, Friesland Campina, Nestlé, Pepsico and the European Commission. The presentations will address a broad range of topics, including innovations, as well as insights, trends, developments and outlooks in this industry. Each presentation will be followed by a short Q&A session. The presentations programme is interspaced with networking opportunities, designed to enable participants to meet up, expand their network of industry contacts, discuss issues and explore potential new collaborations. The conference is accompanied by an exhibition, where suppliers will showcase their latest developments in terms of products, services and technologies. Registrations are accepted online, via the conference website: www.blow-moulding.com Manjushree Technopack acquires Hitesh Plastics Manjushree Technopack, India’s largest manufacturers of rigid plastic packaging backed by Advent International, has acquired Bangalore-based Hitesh Plastics. According to the agreement, MTL will acquire the business operations and manufacturing facilities of Hitesh Plastics. Hitesh Plastics is the leading manufacturer of plastic caps and closures in India. MTL enters the specialised caps and closure market with this acquisition, bolstering its position as an end-to-end integrated rigid plastic packaging player. Hitesh Plastics processes over 1,200 t/a of PP and PE to produce over 10 billion CSD, hot-fill, warm-fill, and water closures. It is a major supplier to companies like PepsiCo, Tata-Himalayan, Amul, and others. MTL will also add the acquired company’s two new plants in Jalgaon, Maharashtra, to its existing list of 21 plants in India. This will push MTL’s total manufacturing capacity beyond 200,000mt/a. Manjushree was advised by Khaitan & Co on this deal while HPPL was advised by Lumiere Law Partners. KPMG was the exclusive financial advisor to HPPL. www.manjushreeindia.com"},{"@ID":18, "EDITOUR PETplanet Insider Vol. 23 No. 09/22 www.petpla.net 16 Highest turnover despite pandemic July 26, 2022 We met: Josep Jimenez, Sales Manager Side S.A. Spanish plant manufacturer Side S.A. is a good example of lockdowns and pandemics not having to be the worst-case scenario for a company. Through pre-emptive action and close collaboration with customers, the company not only managed in 2021 to generate the best sales in its company history, but at the same time launched several innovations in the SBM and maintenance sectors. Side S.A. is known as a mediumsized supplier of blow moulding machines, especially those that produce bottles with complex technical refinements, e.g. oval bottles, bottles with complicated designs for cosmetics, or large-volume bottles with handles. But recently, in L’Ametlla del Vallès near Barcelona in Spain, a system series is also being produced that relies more firmly on speed and maximum efficiency. “We are a small company but we are listening to what our customers are saying,” says Josep Jiménez, Sales Manager at Side. “And bottle makers are interested in speed.” So the company has developed the new Series 3000, which comes with up to 8 cavities and has an output of up to 18,000 bph (see also Drinktec preview report p. 32). The company’s customer base, mainly in the water, edible oil/condiments and detergents sectors, is happily adopting the new product. Three systems from the 3000 range have already been installed for customers in Brazil, Spain and the Dominican Republic. Depending on customer requirements, Side also undertakes complete installation including blowing, rotary filler and capping monobloc systems. This customer base from the water / beverages filling sector is a particular target for the high-speed lines. But to the pleasant surprise of the company, simple bottle producers are also showing an interest in the new high-speed solutions for more niche customer orders. Innovations are also abundant in the existing machine park. As a further development of the 2-cavity machinery 1002e, on which bottles up to 2.5 l can be manufactured at an output of up to 3,800 bph, Side also brought onto the market the enhanced model 1022e 160 with an output of 4,000 bph and up to 80mm neck finish. Bottles up to 3 l in volume can be blown thanks to an increase in the centre distance of the moulds inside the machine. To meet the design demands of customers from the detergent industry, it has also been possible to enlarge the surface area. Also launched this year was the 2002eG XL system, which is driving the expansion of large-volume bottles for water coolers or edible oil. Bottles up to 25 l or up to 20 l as singleuse variants are manufactured on the 2-cavity machine at 2,500 bph. “This is the highest speed for these volumes currently available on the market,” says Jimenez. Using extreme situations correctly With so much desire to innovate, it’s no wonder that Side has generated the highest turnover in its company history with growth of 20% in the pandemic year of 2021. Of the 20 million euros, around 35-40% is attributed to the growing blow moulding department. With regard to electronic components, it plays into the company’s strengths that they can rely on inhouse products from the Side Automatización business unit; other companies are currently enduring long waits for these. “When Side was founded in 1974, it was a company for industrial electronics cabinets,” explains Jimenez. “And like never before, electronic components make up a significant Tour Sponsors: Josep Jimenez and Gabriele Kosmehl by Gabriele Kosmehl Josep Jimenez explains the double booster system which increases the diameter of the preform before blowing."},{"@ID":55, "TRADE SHOW PREVIEW PETplanet Insider Vol. 23 No. 09/22 www.petpla.net 44 No need for chemical decontamination Serac will be exhibiting at the Drinktec trade fair to present its sustainable packaging solutions enabling beverage manufacturers to reduce their consumption of water and virgin plastic. Reducing water consumption thanks to its chemical-free packaging sterilisation technology: BluStream. Serac | Hall B5 – Booth 340 Serac will present the BluStream chemical-free cap sterilisation module which has been in production for over a year at Sources Alma, a beverage manufacturer located in France. This module allows Sources Alma to eliminate the need for chemical decontamination of caps during the aseptic filling of sensitive beverages, such as flavoured waters, fruit juices or teabased drinks. By eliminating chemicals during sterilisation, the need for rinsing water is also eliminated. Indeed, as Romain Leclercq, Head of the Carbonated & Soft Drinks Division at Sources Alma, states: “BluStream technology contributes to the reduction of water and chemical consumption in our production site. Today we are very satisfied with the results we have obtained in terms of performance and decontamination efficiency”. 100% rPET opaque bottles The Serac booth will also feature a presentation of 100% rPET bottles, manufactured on Serac’s SBL blow moulding machine. Transparent bottles will be there of course, but also 100% recyclable opaque bottles used for light-sensitive products such as milk, and already on sale in French supermarkets. Adopting a “reuse, refill, return” model with glass bottles For beverage manufacturers who want to switch to a “reuse, refill, return” model, Serac offers visitors the opportunity to discover, or rather rediscover, its filling line for glass bottles, including intelligent inspection systems capable of meticulously controlling all parts of the bottle. Thanks to a complete range of decontamination technologies, the company is able to adapt its filling lines to the specific requirements of each company and to the reuse model in which they wish to participate, said Serac. Serac will be participating in the “Inspiration.Hub” series of conferences held in Hall A3 of the Drinktec exhibition: Delphine Gueguen, Technical Director Sensitive Products at Serac, will give a conference on Tuesday, September 13 from 10:00 to 10:30 a.m. in Hall A3 of the show. Conference title: How to remove chemicals from packaging sterilisation to make aseptic filling of drinks more environmentally friendly? www.serac-goup.com The one-stop-shop for all your needs. Hall A6 - 340"},{"@ID":81, "Sponsors to date The worldwide round trip with EDITOURS Back to Europe The second part of PETplanet’s bipartite Drinktec Editour is right ahead! After the successful first part “From Down Under to Japan” in 2020, our second stage of the project takes us back to the flourishing European hub where we will be exploring the latest technologies, news, innovations and developments that move our PET industry. It is time for a new start, for renewal and for developing new ways of thinking. During and especially after the pandemic, it will be vital to make every effort to get the global economy back on track in the medium term. Sustainability will be the key. Once again, PETplanet will be at the forefront. It will again be a partner in Drinktec, the world’s leading beverage trade fair, which is to be held in Munich from 12-16 September 2022. After the success of our previous Drinktec Road Shows, in 2017 in South East Asia and 2020 in Australasia, we will be back on the road in Europe for a whole year. Starting in Autumn 2021 with our Editourmobil, we will be ready for a new get-together with the industry. We will be revealing the results of our meetings and discussions at Drinktec with the leading thinkers in PET processing, packaging and recycling. Apart from new technologies we will be also taking stock of how things stand. We will be asking how global thinking might change as a result of Covid-19. How will bilateral business relationships cope with the aftermath of the pandemic? What opportunities will there be for the drinks industry and its suppliers? Our planning, in terms of precise timeframes and details of the countries to be visited will be flexible, in order to take account of the rapidly changing pandemic situation. However, this much we can confidently say: in these challenging times we, as the voice of the PET industry, will be at the very heart of the roadshow as usual and are already looking forward to welcoming you back on board the Editourmobil! Share this exciting experience with us! Interested in being interviewed? barton@petpla.net Let Your Inspiration Flow. 7KH (XURSHDQ 5RDG 6KRZ PART2 Empowered by drinktec Interested in becoming a Sponsor? sales@petpla.net Autumn 2021 - 2022"},{"@ID":48, "TRADE SHOW PREVIEW PETplanet Insider Vol. 23 No. 09/22 www.petpla.net 46 Preforms, labels and driving towards the circular economy Sacmi Beverage will present a range of products that focus on process sustainability, with ready-to-use innovations designed to support the creation of a returnable PET and food-grade resin recycling chain. The company’s new “Packaging Center” will also be demonstrated. Sacmi Beverage says that its range of beverage and food packaging technology incorporates sustainability at its core and features solutions designed to help its customers adapt to the sector’s “green deal”. Profitability and new standards are key concepts. They combine competitiveness of proposed solutions with the ease of making the technological switch towards a more environmentally friendly way of producing, while at the same time providing the best consumer experience for the customer, containing investment costs and facilitating the integration of new solutions on the standard machine range. Returnable and refillable PET The development of a returnable PET supply chain in the beverage industry requires a focus on the proper management of filling and labelling stages, including specific applications that can facilitate the recovery and cleaning of the container, which must be separated from the label at the end of the product life cycle. Sacmi Beverage’s range of labelling machines now includes a system for applying glue dots exclusively to the label and not to the container. This minimises the use of glue and facilitates separation of the label from the container during recycling. Within the RefPET (refillable PET bottles) project, Sacmi is proposing the use of special washable glues; substances soluble to soda at low temperatures. This solution is particularly suitable for returnable PET, where high washing temperatures could damage the container. This this solution, which is already available from Sacmi, as are the relevant special glues, involves the installation on the labelling machine of a special “Speed Coat” kit. This limits the application of the glue to a few well-defined points, favouring perfect adhesion but also easier detachment during the recycling-reuse phase. In the case of wrap-around labels, the glue can be applied exclusively Sacmi Beverage | Hall B5 – Booth 101, 302-304"},{"@ID":57, "TRADE SHOW PREVIEW PETplanet Insider Vol. 23 No. 09/22 www.petpla.net 55 Turnkey solution for PET fillers Combined with the new improved version of the Heuft FinalView II Cap for a complete tethered cap inspection, the latest release of the Heuft squeezer II is a complete solution when it comes to sustainably safeguarding the integrity of filled PET bottles. Heuft presents the latest version of its FinalView II Cap solution for a complete tethered cap inspection. In combination with the latest release of the Heuft squeezer II, the components provide a complete solution for filled PET bottles. Now, not only the fill quantity and tightness of the containers themselves can be checked with precision, but also, among other things, the correct application, integrity, and functionality of their closures – up to the complete all-round inspection of asymmetrical tethered caps including rotation angle detection. The inspection path of the new Heuft squeezer II is flexibly extendable depending on the application for an even more precise detection of stress cracks and micro leaks which are hardly visible to the naked eye: The transport belt which guides the bottles and pressurises them in an exactly dosed manner for a comparative fill level check can now be integrated in different lengths for this purpose. At the same time, the sensitivity of the sensor system for the exact measurement of the internal pressure of the full containers has been further increased, says Heuft. The easy-to-connect Heuft FinalView II Cap enables a full-covering all-round inspection of the PET bottle screw caps. This also applies to tethered plastic caps. The smart Heuft reflexx A.I. image processing produces a detailed picture of new features; these include the unusually large gap between the cap and the tamper-evidence band of rotationally symmetrical tethered caps. This means that affected full containers are no longer rejected as faulty. In order to keep the false rejection rate at a very low level even with asymmetrical tethered caps, the FinalView II Cap has received specific software upgrades. This enables it to inspect both such closures which deviate from the usual rotational symmetry from one or more perspectives in a gaplessly and precise manner. In addition, Heuft says that the enhanced software masters another challenge in the detection of closures that are too high and possibly leaky: it can now reliably detect caps which exceed the targeted height by as little as 0.5mm. The cap angle detection system has also been enhanced. It verifies that the tethered caps are always correctly aligned and that they are actually screwed down as far as they should be. For mouths which are made of darker, less transparent rPET, the company has integrated a new special lighting system into the compact unit for the cap inspection of up to 72,000 bph directly on the running conveyor. Defective tamper evidence rings can thus be easily detected even under such conditions. www.heuft.com Heuft | Hall B4 – Booth 319/513 The right packaging solution for your product is essential for consumer acceptance and appeal. With Sidel experts, you can tune your line to improve long-term profitability and meet your circular economy goals without sacrificing efficiency. TRANSFORM TETHERED CAPS INTO A BUSINESS OPPORTUNITY sidel.com Meet us at September 12 -16 MUNICH Hall A6 - booth 339 DRINKTEC"},{"@ID":25, "BOTTLE MAKING 23 PETplanet Insider Vol. 23 ity (EPR) issued by the Ministry of Forest, Environment and Climate Change. Empty pouches are difficult for consumers to wash and thus avoid post-use odour. This, along with the high cost of collection of empty pouches, lead to PET bottles being considered as an ideal alternative, as they are reusable, re-sealable and easy to collect. The PET packaging sector itself is well established in India and, while the recycling sector is performing better than other types of packaging recycling, there remains plenty of opportunity for further improvement. The industry in India estimates that the rate of PET bottle recycling is about 75-80%, which is higher than other packaging materials such as paper-based multi-layered composite liquid cartons (50-55%) and glass bottles (45%). Advantages of PET over other packaging materials Dairy product manufacturers prefer PET bottles over other packaging materials for liquid packaging because it is 100% recyclable; has lower carbon emissions; has higher recoverability and recyclability; and are non-toxic and thus safe for food packaging. Infectious and sickness-causing biofilms – a broad category of microbial organisms, including fungi and bacteria – are more likely to be found in glass containers, in part due to poor sanitary conditions and low economic resources. PET is also up to 95% lighter than glass containers, which makes them easier to carry and leads to lower freight costs. Manufacture of PET bottles has a lower environmental impact, with much lower CO2 emisThe future starts in our heads Discover our line innovations at krones.com drinktec 2022 Munich 12-16 September Hall B6 sions. They can be manufactured in a variety of different shapes, sizes and capacities, can be made transparent, translucent or opaque. It costs less than glass, which makes PET packages more affordable for consumers. Chemco Plastics Ltd. is a leading Indian manufacturer of all kinds of PET packaging, from preforms to stretch blow-moulded bottles of different shapes, sizes, and capacities, and suitable for packaging liquid milk products. The company offers a single-source for all kinds of packaging solutions. www.chemcogroup.com"},{"@ID":19, "EDITOUR PETplanet Insider Vol. 23 No. 09/22 www.petpla.net 17 proportion of the company. Over the years, other activities have been added, such as motors, inverters and touchscreens, and also an in-house IoT service. And naturally, we also use this expertise in our blow moulding department.” This latter was added 28 years ago, when PET started playing an increasing role in the food and beverage industry in Europe in the early 1990s. Side’s owner at the time, Mr. Enric Birosta, decided to buy up a customer from the extrusion blow moulding machines sector and to refocus on stretch blow moulding machines. So the business unit Side SBM was founded. “This connection between business areas is now a great advantage for us. Most electronic components for our systems are available in our warehouse and we can also carry out certification ourselves. Our anticipatory stock management also avoid problems regarding availability and logistics, and we can maintain capacity of 25-30 SBM systems per year,” says Jimenez. If anything, increasing transport costs, a setback for many companies, have had rather a positive effect for Side, with bottle manufacturers preferring to open branches close to their customers to save on longer transport routes – branches that naturally need to be equipped with new Side systems. Close collaboration with the customer Side S.A.’s remote service system has also proved successful, particularly throughout the pandemic. Four employees supported customers in After Sales matters relating to the over 750 Side machines installed worldwide. Over 90% of servicing can be carried out remotely – a high proportion that also owes its acceptance to the lockdowns. “Basically, this is the normal evolution of things, but the pandemic has helped a lot to accelerate that,” says Jimenez and he adds: “We also offer our customers flexible maintenance contracts so that they don’t get into emergency situations in the first place. Via IoT, we check and optimise the system. This is a growing field that is very well accepted.” The app, too, which allows the customer operator to connect with the machine, relies on inhouse development. This not only provides all details for production but also data, for example about energy consumption. This is one of two hot topics among Side customers, and incentives to reduce energy consumption are being considered by Side in its new developments. This has resulted for example in the air recovery system, which is included as standard in the new 3000 Series and can be retrofitted for other models. Works with customers and the lab supplier regarding the oven are also targeting the reduction of energy consumption and these are reducing energy used by the oven by 20-25%. In its R&D Department, Side engineers are also implementing special bottle designs for customers, prototypes, and analysing the use of different materials. These can be organic-based plastics or different percentage levels of rPET – the second significant topic of concern for bottle producers. Besides the obvious reasons such as the circular economy or instructions from directives, Jimenez also welcomes the use of recyclates for another reason: “The use of rPET reduces the process power required. Many factors come into play here, for example the percentage proportion of recyclate or the use of additives, but at least 10% power can be saved in any case – simply because the darker colouring of the preforms better absorbs the heat of the infrared lamps.” Jimenez would view an rPET proportion of 80% as a good target and is regretful that “we are unfortunately still a long way from that.” www.sidemachines.com Assembly hall at Side’s premises near Barcelona"},{"@ID":26, "BOTTLE MAKING 24 PETplanet Insider Vol. 23 No. 09/22 www.petpla.net Wine in PET The wine market is looking at alternative solutions to glass containers, mainly because of the lack of raw material but not limited to it. So it’s a good time to enter the sector with PET bottles, thinks Gianfranco Zoppas, owner of Sipa and our interviewee. PETplanet: Hello, Mr Zoppas. When we last met two years ago, you were talking of “difficult times” during the coronavirus pandemic. How would you describe things now in view of the war in Ukraine, the exploding energy prices and the difficulties in procurement? Zoppas [laughs]: Even more difficult, of course. But we mustn’t forget that it’s these high energy costs that are giving us a boost in the PET sector. Producing and transporting PET bottles is now significantly more energy-saving - and therefore more environmentalfriendly - than glass bottles. This gives us the opportunity to break into sectors previously dominated by glass. PETplanet: Are you thinking of wine? Zoppas: Yes wine, and Prosecco of course. Here in Veneto, one billion bottles of Prosecco are filled each year. Last season, only 750 million glass bottles could be supplied. What are the wine growers doing with the remaining Prosecco? I think before the wine industry turns to substandard processing of their products, the PET bottle could open up new markets through innovative design. PETplanet: You think that a passionate wine drinker will buy wine in PET? Zoppas: I think so. And not only because of the lack of glass bottles but also a natural and progressive move from consumers since plastic bottles have been around for some time now, for example in planes or for spirits. Our packaging development team has recently developed a PET bottle perfectly replaceable to the current glass sparkling wine bottles ensuring filling on existing glass lines. The innovation focused on recreating the neck, typical of glass bottles, for the cork cap and cage closure. The bottles have been tested on glass lines ensuring perfect interchangeability with the current ones. The final consumer will live an experience in line with the containers currently on the market, from uncorking to pouring. The lighter container perfectly meets the needs of logistics, unbreakability and lightness increasingly required by new sales channels such as e-commerce and home delivery. Another example is the letterbox bottle from Garçon Wines (www. garconwines.com). These can be sent by post and delivered through the letterbox. There are many innovative examples. In our newly founded design lab for wine bottles, we are working on different ideas and how to implement them. PETplanet: Where is the cost benefit for the bottler as compared to a glass bottle with label and cap? Zoppas: I believe it’s not only the cost which is lower for PET bottles. From the viewpoint of the bottler, it’s also the availability of bottles, it’s about saving energy on each bottle both during production and of course in transportation, and it’s also a recyclable product - to name a few examples. Mr Zoppas and Alexander Büchler in front of the Xtreme with 100% rPET prefom manufacturing Sparkling wine bottle from the Sipa Design Laboratory"},{"@ID":37, "35 TRADE SHOW PREVIEW PETplanet Insider Vol. 23 No. 09/22 www.petpla.net Get critical answers faster Unique technology and research expertise At BMT we measure things others ignore and with these measurements we answer questions no one else can. With access to unrivalled data, we can harness the power of AI to make smarter decisions earlier in the product life cycle enabling faster times to market along with the ability to innovate freely. Talk to our specialist team info@bmt-ni.com C5.237 H14/C26"},{"@ID":27, "BOTTLE MAKING 25 PETplanet Insider Vol. 23 No. 09/22 www.petpla.net PETplanet: You have your own design department that develops innovative bottles. How are things looking on the machinery side? Zoppas: With our container design & engineering department we constantly develop new bottle concepts that perfectly fit market demands, but also on the side of our production systems we systematically update our offer to reach the highest performance. As an example, we have reworked our injection stretch blow moulding system ESC SP. With clamping forces of 25 t and 80 t, we are now offering a singlePicture of the new ECS SP stage production solution for smaller and medium-sized series production that is just as highly automated as our large systems. By running the preforms and the stretch blowing at one heat, we save 20% of the energy needed to run the usual 2-stage process. You can run the same hot runner for different cavities; the quick mould changeover saves on set-up time and we have increased output. I have to say, though, that in the last couple of years we have developed a lot of innovations on our systems. Integrations unthinkable just few years ago like Xtreme Renew Sincro Cube, a system that goes from the rPET hot washed flakes to the filled container, just to name one. Visitors at Drinktec show will touch all our new developments. And you are all invited! PETplanet: Many thanks, Mr Zoppas. www.sipasolutions.com Meet us at K in Düsseldorf | Hall 8A Booth 8AD50 | 19 – 26 October 2022 RECYCLING SOLUTIONS HIGH PERFORMANCE CLEANING ADDITIVES & SUPPORT How can your recycled product meet permanently increasing demands? With the CHT range of high performance process solutions with environmental relief for the wet cleaning and recycling process. We support you directly on site and ensure your quality controls in our laboratories with state-of-the-art equipment. Thus, your strong position in the growing market is confirmed day by day. More about us at www.cht.com"},{"@ID":39, "37 TRADE SHOW PREVIEW PETplanet Insider Vol. 23 No. 09/22 www.petpla.net The all-new PET-LINE comes with a variety of advantages to maximize output and minimize costs: • Maximum compatibility with legacy molds and PMC • Shortest cycle times for increased output • Lowest level of energy consumption to minimize the ecological footprint • Improved 100 % rPET processing to enable the circular economy • New control unit including Smart Operation to ensure easy, fast and safe start-up and production • Now available with 3000 and 4000 kN clamping force More details on www.netstal.com FLIPPING THE WORLD OF PET UPSIDE DOWN AND EVEN SIDEWAYS THE ALLNEW PETLINE WITH SIDE ENTRY. drinktec 2022 I 12-16 September I C5.363"},{"@ID":31, "29 TRADE SHOW PREVIEW PETplanet Insider Vol. 23 No. 09/22 www.petpla.net Our consultants aren’t good sales reps but they’re great at problem-solving. yellow.agency Drinktec 2022 Hall C5 Booth 335 3(7 SUHIRUP SURGXFWLRQ OLQHV HQJLQHHUHG E\\ 2WWR 6\\VWHPV URXWLQHO\\ VHW LQGXVWU\\ EHQFKPDUNV IRU SHUIRUPDQFH DYDLODELOLW\\ HQHUJ\\ HIƓFLHQF\\ and lowmaintenance costs. This is because the consultants and engineers at Otto Systems meet your production challenge with open minds, decades of experience and deep knowledge about PET production processes and techniques to ensure high quality at the best possible price. That’s why they are able to plan and implement production systems that are uncompromisingly tailored to your needs, independently selecting the best components from experienced manufacturers to achieve your goals. Call +41 55 285 22 11, otto-systems.com"},{"@ID":51, "TRADE SHOW PREVIEW PETplanet Insider Vol. 23 No. 09/22 www.petpla.net 49 TEM PLUS THE NEW SLITTING / FOLDING MACHINE FOR SPECIALTY CLOSURES. Tethered slitting, including oriented slitting feature Designed for large variety of speciality closures and speed demands Always identical high precision slit geometry Flexible machine concept for process sequence packsysglobal.com Swiss Engineered"},{"@ID":45, "TRADE SHOW PREVIEW PETplanet Insider Vol. 23 No. 09/22 www.petpla.net 43 Processing rPET without losing quality “Drinktec is back after five long years in which we have witnessed dramatic, never experienced before changes and evolutions worldwide. The packaging industry has had the chance to prove its crucial role in offering safety and hygiene in health emergencies like the one still ongoing. On the other hand, there is no doubt that the packaging world has been put under increasing pressure like never before by the tremendous push towards sustainability and recycling,” says Lucia Buffoni, Marketing Manager at Repi. Repi | Hall C5 – Booth 356 Repi, a manufacturer of liquid colours and additives for plastic packaging, will welcome visitors at the heart of the PET Point area to show its latest developments towards circularity and recycling. Repi has been focusing on advanced additive and colour solutions for PET and rPET for decades. Their ranges of anti-yellow, optical brighteners and IV enhancers have, over the years, represented a valid aid to rPET recyclers and packaging converters, offering a solution for anyone facing the challenge of including increasing rates of recycled material in their plastic packaging. Such additives can be used at different stages of the rPET value chain, ranging from recycling up to preform or tray manufacturing, with no impact on processes. It offers flexibility in its addition, which can be varied from one batch to another. The increasing demands for recycled percentages and the scarcity of food grade-PET flakes are presenting challenges related to quality and colour consistency between one batch and another. The main problem that both recyclers and converters struggle to manage is the drop of L* of CieLab numbers while respectively recycling and moulding or extruding the final Bottles of 100% rPET from mechanical recycling containing StabiPlus. Being a liquid formulation, concentration is high and related dosages minimal. packaging. The L*a*b* colour space describes all perceptible colours. It uses a three-dimensional colour space in which the brightness value L* is perpendicular to the colour plane (a*,b*). However, it is possible to correct off-shade rPET pellets with custom-made formulations that can act on both the a* and on the b*, where traditionally the darkening of material (precisely the drop of L*) is difficult to avoid. This is where StabiPlus additive comes in. The latest development by Repi: a liquid formulation acting specifically as a proactive stabiliser that prevents rPET from aging and discolouration, cycle after cycle. The additive can be used both at recycling stage, added to a mechanical recycling process with SSP, or directly by converters at their packaging production stage, providing flexibility in addition ratios. StabiPlus offers a new protection technology that does not affect intrinsic viscosity and therefore mechanical properties of the recycled PET, while widening the window for sustainable use of recycled PET. StabiPlus represents a valuable solution to boost the use of different incoming material quality since it improves aesthetics cycle after cycle. With its new StabiPlus additive, Repi shows how the technology of chemical additives can provide a crucial contribution to polymer recycling, and that it is necessary for the whole value chain of plastic packaging to closely co-operate and share challenges, ensuring that everyone is moving in the same direction, ever marked by the well-known key words, “reduce” (weight without losing performance), “reuse” (packaging whenever sustainable), “recycle” (thanks to the advanced technologies developed so far). www.repi.com rPET brightness and shade improves cycle after cycle. Each of the three cycles have been designed to highly stress material and show evidence of the additive’s performance: 1 lab cycle delivering double the stress of an industrial process. StabiPlus has been added to the 1st recycling loop only."},{"@ID":34, "32 TRADE SHOW PREVIEW PETplanet Insider Vol. 23 No. 09/22 www.petpla.net A leap in quality monitoring for beverage ingredients as well as line parameters For years, the company Dausch Technologies, with its LiquiGuard programme, has been offering non-alcoholic beverage bottling plants the opportunity to precisely measure and visualise even small amounts of all relevant ingredients: total acid, caffeine, base material concentration, aromas, important sweeteners, B vitamins, Na benzoate as well as K sorbate or near water flavours. This is made possible by unique optical spectroscopy methods. The LiquiGuard Gen3 system continuously measures the beverage flow every ten seconds, processes the sample immediately and displays the result clearly in tables or charts on screens: smartphone, tablet or PC. This means continuous, fully automated quality monitoring of all relevant beverage parameters. However, what is completely new at Drinktec is that LiquiGuard Gen3, with the Quality Dashboard module, can not only process its “own” quality values, but also all data from all manufacturers involved: bottle weight, closure and torque, tightness of cans (seam parameters), carbon dioxide content, brix, conductivity, and much more. Consequently, the operating personnel on the line, as well as in the syrup room, in the quality assurance laboratory or even on the move, can query and check all values of the entire filling line at any time, in real time. www.dausch-technologies.de S3000 series: faster speeds, less energy Side S.A. says that its 3000 series blowing machines are designed to provide high production capacities for mineral water and soft drinks bottling in medium-sized facilities. The S3008 offers outputs in excess of 18,000 bph in 500 ml formats from eight cavities and is capable of producing containers of up to 2.5 l. It is the only machine currently available that can work with 38mm necks. The 3000 series includes three other blowing models. Two are aimed at large format containers for capacities such as five and eight litres. The five-cavity version has outputs up to 6,500bph; the four-cavity model can produce 4,000 10 l bph. Options such as preferential ovens for blowing oval bottles can be integrated. The new range allows blowing machines to be interconnected with filling and capping monoblocs, minimising machine footprint. Power and air consumption savings The reconfigured transport system and oven enable 3000 series blowing machines to deliver power consumption savings of over 20%, compared to previous models. The air recovery system is also more efficient, reducing consumption by 40%, the company says. Side offers the option of installing complete blowing, filling and capping systems for bottlers of water, soft drinks, juices, dairy products, oils and detergents or cosmetics. Other developments Side S.A. ’s new version of i ts 1002e+ 160ec blowing machine can blow wide-mouth containers up to 83mm, using a hybrid loading system. The new 2002eGXL blowing machine can produce up to 1,600 bph in 16 l formats and is capable of producing stackable 25 l one-way containers. The 5001eG’s newly developed preform pre-blowing stretching system provides capacities of 280-300 5 l returnable carboys per hour, even in containers with an inserted handle. This system can increase diameter without decreasing inside temperature, thus reducing the cycle time and improving material distribution throughout the container. www.sidemachines.com Dausch Hall B3 – Booth 357 Side Hall C5 – Booth 235 Label Lab Multi-Color Corporation (MCC) returns to Munich with the introduction of The Label Lab where their experts will inform about the latest developments and innovations in beverage labelling. A strong focus will be placed on sustainable label solutions including everything from recyclable PSL to floatable shrink sleeves and wash-off labels for returnable bottles. MCC‘s Sustainability Director, Stijn Billiet will be hosting focussed seminars and interactive discussions on sustainability. The company will also emphasise on how next-gen labels help products win the battle for the shelf. MCC will display a variety of interactive options for packaging that includes functional inks that react to UV/sunlight, black lights, heat/cold, etc. Inspiring examples of how labels can appeal to all of the senses using unique inks and materials will be highlighted. Smart packaging: the connected consumer Augmented reality, QR codes, and scannable labels are a great way to engage consumers and provide an interactive experience, as well as more efficiently and effectively manage a company‘s inventory. MCC will provide an industry update on the use of RFID and EAS tag use in packaging, including retailers demand and how MCC is positioning for the future. www.mcclabel.com MCC Hall C6 – Booth 326"},{"@ID":10, "8 NEWS PETplanet Insider Vol. 23 No. 09/22 www.petpla.net Help us shape the circular economy! Technically-minded and keen to protect the climate? Relish a challenge and want to help find the right people to do something about the plastic waste on our planet? Then Krones Recycling Solutions is the right place for you! For more than 20 years, we have been developing innovative technologies to keep valuable packaging materials within a closed loop – and to take our vision of a sustainable industry from Flensburg out into the wider world. There is more to do than ever, which is why we are now looking for committed individuals to join our team – for example in the following areas: Mechanical/electrical design and automation Process engineering Product management Erection and commissioning at customers' premises worldwide Employee management Maybe you share our vision of a waste-free world, but don't see your abilities reflected fully in any of these job areas? Then why not send us an unsolicited application? Because job titles are not what matters to us. What is important is who you are and what you can do. Any questions? Please contact Astrid Schwartz (astrid.schwartz@krones.com) for more information. We look forward to receiving your application (including all relevant documents). These can be uploaded in just a few clicks on our careers portal at www.krones.com. Amut completes recycling project in Romania Amut has completed the commissioning of a recycling plant for Pet Star Recycling, part of Pet Star Group, together with Pet Star Holding, a leading producer of preforms for PET bottles, in Romania. The company developed a customised solution aimed at delivering high performance. The new washing line fork PET processing with 3,000 kg/h total output is equipped with Amut’s patented De-Labeller together with the Friction Washer and presents the front-end sorting system sized to sort clear/light blue bottles from a stream including up to 14/15% of coloured ones suitable to treat 5,500 kg/h of inlet material. “From the very beginning, we have implemented the bottleto-bottle concept to increase the recycling potential of untapped plastic waste and its reuse in a new production process. That’s why we chose a strong partner, Amut, which provided us modern and innovative sorting and washing technology which allows us to be more efficient and to minimise water consumption for each kilo of high purity flakes we produce”, declared Mirela Dragoi, CEO Pet Star Recycling, Romania. www.amut.it Bariq to build a large rPET factory in MENA by 2023 In late 2021, Bariq was acquired by Intro Resource Recovery, a member of Intro Group, to strengthen its waste management portfolio. In February 2022, Bariq announced its sustainability strategy and plans to be the biggest recycler in the region by adding a washing and upgrading line to its portfolio. The new Starlinger recycling system, a RecoStar PET 215 HC iV+ including a ViscoStar 350 SSP reactor, reaches an output of 2,700kg/h and will enable Bariq to increase its total production capacity to 35,000 metric t/a of food-grade rPET pellets. The ViscoStar 350 SSP reactor (biggest size of the latest reactor generation) provides extended processing capacity and residence time while it keeps the footprint of the new recycling line compact like the first Starlinger PET recycling line Bariq installed in 2012. Bariq will also upgrade its existing Starlinger RecoStar PET 165 iV+ recycling line with a new melt filter doubling the filtration area allowing finer filtration through production and an additional SSP reactor ensuring high quality pellets. This setup increases the line’s output and allows the production of rPET types beyond the regular bottle-to-bottle grades, guaranteeing best decontamination results and 24/7 production of rPET with highest quality specifications, states the company. As the core strength of Bariq’s pellets is the quality, detection tools are one of the main assets of their laboratory. The laboratory is installing an Agilent GC-MS combined with a Markers Centri fully automated multimode extraction platform giving flexibility for efficient extraction and enrichment of VOCs. Bariq’s investment also includes the latest bottle & flakes sorting equipment from Tomra Recycling to ensure optimum quality of the input material. In addition to the sorting equipment, a Max-AI robot is added reaching a fully automated washing line from bales to flakes. Founded in 2011, Bariq is the first foodgrade rPET producer in Egypt and the biggest in the MENA region. The company started production of food-grade rPET recycling lines in 2012 and holds a positive EFSA opinion and an FDA Letter of NonObjection (LNO) among others. Exporting 100% to global players in the packaging sector for bottle and food container producers throughout Europe and North America. Bariq recycles 1.6 billion PET bottles per year on the foundation of two sustainability pillars of being economically justified and environmentally sound. The company has recycled approx.15 billion PET bottles into food and non-food grade pellets, which contributed to saving more than 250,000 t of CO2 and helping marine life avoid non-degradable plastic issues. www.bariq-eg.com Recycling plant at Pet Star Recycling, Romania (photo: Pet Star Recycling)"},{"@ID":29, "TRADE SHOW PREVIEW PETplanet Insider Vol. 23 No. 09/22 www.petpla.net 52 Closure solutions & smart drinkware Aptar Food + Beverage, a global leader in consumer product dispensing and active material science solutions, will showcase its latest closure solutions for dispensing beverages and other liquid products, from pouring to squeezing solutions, as well as new tethered closures in compliance with the upcoming European directive regulation for single-use plastics. The company will also feature an approach to the future of smart beverage containers, driving more adoption of recyclability and reusability. A planned unveiling of Aptar’s recently launched Food + Beverage new brand identity, ‘Create, Collaborate, Innovate’, is one more way for Aptar Food + Beverage to demonstrate the company’s passion and commitment to help companies achieve their environmental targets, while striving to create a more circular economy and make a positive impact in the lives of consumers around the world. Aptar will demonstrate its commitment to sustainability by showing new developments concerning tethering, linerless, and recyclable valve solutions; certifications such as ISCC+, partnerships with PureCycle, Rebo, Miwa, and others; and active collaboration with key organisations such as RecyClass, Wrap, APR, and WBCSD. Tethered solutions At the show, Aptar will feature its next-generation Rocket sports cap, a tethered solution for non-detachable, tamper evident visibility, featuring a wide opening angle for drinking comfort. Rocket is compliant with the upcoming European directive regarding tethered closures for single-use plastics scheduled to take effect in mid-2024. SimpliCycle recyclable valve As an industry leader in providing flow control dispensing solutions for more than 25 years, Aptar’s SimpliCycle recyclable valve is intended to drive sustainability to the forefront of packaging innovation. Made from a low-density material, the valve floats in the recycling tanks, allowing it to be easily separated from the PET stream, and then recycled right along with the PP/PE stream. When assembled into an Aptar closure, the SimpliCycle TPE valve provides a fully recyclable and high-performance solution for use with PET, PE, or PP containers. SimpliCycle was recently honoured to be awarded the best CSR/Sustainability initiative in 2021 by World Food Innovation Awards and in 2022 received the prestigious 2022 WorldStar Global Packaging Award for packaging innovation. Concepts & new solutions Aptar Food + Beverage will also showcase new concepts for pouring liquid beverages, including a prototype of the new Blue Evo Cap, as well as solutions for dispensing beverages in an inverted pouch format. Smart drinkware Aptar joined forces with Rebo, contributing its expertise in flip-top closures, sustainability and innovation to the partnership. Rebo manufactures a smart water bottle that is not only reusable but also features a hydration tracker to help users optimise performance and track their water intake via a linked smartphone app, as well as a light on the bottle, designed to help consumers increase water consumption by reminding them to drink. During Drinktec, visitors to the Aptar stand will have an opportunity to participate in a daily draw, with the lucky winners receiving a Rebo smart water bottle. www.aptar.com Aptar | Hall C5 – Booth 308 Aptar’s Rocket sports cap tethered solution features a wide opening angle for drinking comfort. Reusable smart water bottle that comes with a hydration tracker to help users optimise performance and track their water intake via a linked smartphone app. Aptar’s SimpliCycle recyclable valve is made from a low-density material, for floating in recycling tanks."},{"@ID":50, "TRADE SHOW PREVIEW PETplanet Insider Vol. 23 No. 09/22 www.petpla.net 48 Technologies for PET treatment Moretto is presenting three major systems at the fair: for the crystallisation of post-consumer materials, dosing systems and a drying system for high capacity production with self-adaptive technology. All of these products with a high technological content are intended to raise the quality standard, as well as increase production efficiency and deliver energy savings. A crucial process in PET recycling is crystallisation. MPK Moretto Krystallizer is a system designed to crystallise post-consumer materials - regrind and washed ready to be transformed. Treated in the right way, they can be used with virgin plastic polymers for new production processes. MPK boasts a number of important features such as the dropdown cone with assisted device that allows the operator to quickly proceed with cleaning and maintenance activities thanks to the easy opening which takes only two minutes. This is an exceptional usability factor in a machine that processes critical materials such as regrind and/or flakes, states Moretto. The internal mixer shaft with removable blades can be easily adapted to the various types of treated material. The blades have a wing profile that moves the material in a homogeneous way avoiding the formation of lumps during the crystallisation phase. The hopper – with the patented stainless steel shockproof coating Spyro – insulates the mixer body and limits heat dispersion, thereby increasing its energy efficiency. The control of the system processes is managed by a touch screen with a simple and intuitive interface. MPK is a latest generation product designed for the smart factory; it can be connected to other automatic equipment via web and remotely controlled through the supervision and management software Mowis which achieves total connectivity via Modbus, Ethernet, OPC UA. MPK is equipped with the Vortex filtration device, which eliminates the dust of the process circuit, thus increasing its autonomy. The Purex condensate separator filters the material flow back eliminating the volatile oily and/or resinous substances contained in the vapours, impurities typically present in post-consumer materials. Purex is intended to protect the environment and people. Dosing is another fundamental process in the plastic transformation to obtain a quality product that respects the design specifications. Having effective equipment is therefore essential. Moretto has a wide and complete range of dosers consisting of over 1,180 models. One of them is the DGM Gravix, a batch gravimetric dosing unit that ensures production flexibility and precision even in the presence of vibration thanks to the VIS (Vibration Immunity System). Modbus RS485, USB and Ethernet connections allow production to be monitored in real time and the composition of the recipes to be certified. At the fair a series 900 DGM specific for the treatment of flakes will be exhibited. Among other equipment to be exhibited, there will be a XD 800 X series dryer, a drying system for high capacity products and specifically adapted for technical polymers such as PET. This dryer, with self-adaptive technology optimises process conditions and reduces energy consumption by up to 42%. Thanks to the variable airflow, the dryer automatically adapts to production needs ensuring the correct supply of technological air to the material to be treated, preserving the polymer from thermal stress and viscosity variations. The turbo-compressor system combined with the energy recovery system from the regeneration process is claimed to offer extraordinary energy efficiency. It is a one power system that does not require compressed air or cooling water for its operation. The system configuration and operator control activities are facilitated thanks to the built-in touch screen with a simple and intuitive interface. Programming requires only two parameters to be set: material type and throughput. Once set, the machine handles all the process variables automatically. www.moretto.com Moretto | Hall C5 – Booth 234 DGM Maxi Gravix series MPK Krystallizer XD 800 X dryer touch controller"},{"@ID":80, "OUTER PLANET 78 PETplanet Insider Vol. 23 No. 09/22 www.petpla.net OUTER PLANET Designer polymers for easier mixed-material recycling Acknowledgement: This article is based on a report by Alison Hatt, published on Berkeley Lab’s Newsletter website. Plastics manufacturers and converters have made a lot of noise about increased use of recycled materials but there is another, rather inconvenient reality. Mixed-material products are very difficult to recycle. Trainers (aka sneakers), single-use bags, electronics and even food packaging films are made up of layers of different plastics. Once they are mixed, plastics become very difficult to recycle, especially by conventional, mechanical means. They cannot be recovered and reused, nor even downcycled into insulation or building materials. The likelihood is that they will end up in landfills, incinerators, garbage piles in the developing world or in the oceans. It’s another of the industry’s dirty secrets, one that is well past due to be effectively addressed. Scientists based at the Lawrence Berkeley National Laboratory – the Berkeley Lab, founded in 1931 at the University of Berkeley in San Francisco, California – have been engaged in work that has, they say, led to a new range of polymers that can be mixed, separated and recycled indefinitely. The material, polydiketoenamine (PDK), can be tailored to have different characteristics and performance standards, depending on the solution or application required. A study published in Science Advances demonstrated the Berkeley Lab team’s customised PDKs, tailored for mixedplastic recycling, and the method to fully recover the constituent plastics from products made of multiple materials. “An example might be a shoe, where textile is bonded to rubber. Conventional materials can’t be recycled for reuse, since they can’t be deconstructed independently,” said Brett Helms, of the Molecular Foundry, who headed the Berkeley Lab team. He said that, if they were made from specially designed PDK polymers, then they could be reclaimed, separated and recycled. Like other polymers, PDKs are made up of long-chain molecules, themselves comprised of small monomer units. The Berkeley team’s researchers demonstrated a variety of PDKs, each with a slightly different chemical structure, that could be ‘depolymerised’ – broken down into their monomers, with a high recovery yield. Those recovered monomers can then be used to make new PDKs. The process of breaking down the polymers is a chemical recycling process, using acids. Fig 1: Products made from two different PDK plastics can be deconstructed in acidic solution in stages, allowing for recycling of both plastic materials. (Credits: Brett Helms and Jenny Nuss/ Berkeley Lab) Fig. 1 shows two different PDK plastics in an acidic solution. It illustrates how each polymer can be easily broken down into individual monomers. The researchers demonstrated their system by creating blended plastics using molecules identified and optimised for particular applications. Each was made from two different PDKs, then completely depolymerised and the constituent materials recovered. The demonstration was repeated with PDKs of different colours; a slightly more complex process also delivered high yield levels. An ongoing challenge for recycling, especially in food packaging, is the long-term failure of the industry to produce easily-recyclable packaging film. The Berkeley Lab team showed how PDK can be used to make recyclable, flexible plastic packaging out of conventional plastics. They formed a multilayer film from PP and PET, using a “tie layer” of PDK. The researchers leveraged their control over the PDK layer to separate and fully recover the PP and PET. They also demonstrated an application for automobile recycling, with an object made of glass, steel and different PDKs. Helms said that the Berkeley Lab team has made a great stride in facilitating the recovery of polymers themselves, as well as materials bonded to them, enabling more circularity in manufacturing. The research was supported in part by the U.S. Department of Energy’s Office of Energy Efficiency & Renewable Energy and Berkeley Lab’s Laboratory Directed Research and Development programme. www.lbl.gov Each polymer breaks down into individual monomers in steps conducted at different temperatures."},{"@ID":49, "TRADE SHOW PREVIEW 47 PETplanet Insider Vol. 23 to the parts in contact between the two label edges, which can then separated at the recycling stage by a cutting accessory (also supplied by Sacmi). This eliminates problems with container cleaning. IPS range The recycling of resins for foodgrade use has also become increasingly important. Having first been achieved with PET, the concept is now, potentially, being applied to the entire capsule-container system. Sacmi has developed a set of solutions that can be integrated onto standard machines in its range. Sacmi’s range of IPS preform presses have been adapted to process up to 100% of rPET and up to 50% of PET in flake form. Latest developments to be presented at Drinktec include the potential to increase the proportion of rPET flake to 70-75% and to make the entire process more linear, with optimal management of flake and granule mixtures without the need to use two separate processing hoppers. The new Packaging Center, which operates closely with the Laboratory, means that Sacmi Beverage has the facilities and skills to work with customers at all stages from design to product and to identify the best production technologies, with solutions certified and approved by leading global players in the industry. More than 1,000 neckcapsule designs have been developed by the Laboratory in recent years. This approach, through the Packaging Center, aims to involve the world of bottlers more extensively, as they work in close contact with the market on a daily basis and perceive its constant demand for sustainable innovation. The international trade fair in Munich is also an opportunity for Sacmi Beverage to present its new package of advanced customer support services. These start with machine testing and extend to customised, lifetime maintenance and service plans along with a new set of high added-value digital services. www.sacmi.com THE PACKAGING OF THE FUTURE WITH US"},{"@ID":64, "62 TRADE SHOW PREVIEW PETplanet Insider Vol. 23 No. 09/22 www.petpla.net Plastics expertise and PET recycling As a sub-exhibitor of Oerlikon, BB Engineering presents itself as an expert in extrusion, mixing and filtration as well as an innovator for PET recycling with the VacuFil and VarioFil R+ systems. Extruders, mixers, filters As a joint venture of Brückner Maschinenbau and Oerlikon Barmag, BB Engineering took over the extruder division of Oerlikon Barmag in 2002. BB Engineering can thus draw on more than 60 years of experience in extruder construction and is constantly engaged in development work to further optimise its products. To date, approx. 20,000 extruders have been delivered worldwide. The extruders are mainly used in film and synthetic fibre spinning lines for PP, PET, PA and PE. The portfolio also includes various continuous and discontinuous polymer filters from small to large (0.1-40m² filter area) as well as various polymer mixers. Recycling technology BB Engineering has been focusing its development work increasingly on recycling technologies for several years. In addition to extruders, filters and mixers that are suitable for both recycling processes and the processing of recyclate, BB Engineering offers a complete PET recycling plant called VacuFil. With VacuFil, BB Engineering has developed a PET LSP recycling process. It combines gentle large-scale filtration and targeted IV regulation for consistently good rPET melt quality. Thus, much more than simple “downcycling” is possible with VacuFil. VacuFil processes a wide range of input materials - post-production and post-consumer. The patented key component Visco+ vacuum filter removes volatile impurities quickly and reliably. VacuFil is a modular system that can be designed for different recycling applications. There are no limits to the downstream processes. Simple granulation is possible, but also direct feeding into further processing, e.g. in the synthetic fibre spinning mill. BBE offers VacuFil in combination with its own VarioFil compact spinning plant to produce polyester yarn. Open House This process can be visited during the K’ show at an open house of BB Engineering and Oerlikon Barmag. Not far from Düsseldorf, at the company’s site in Remscheid, BBE and Oerlikon Barmag will open their doors and give customers and interested parties an insight into the technical centre. Here, visitors can experience the VacuFil Visco+ recycling technology in operation with a connected VarioFil spinning plant and see live how high-quality recycling yarn is produced from PET waste. www.bbeng.de BB Engineering Hall 1 Booth D10"},{"@ID":13, "EDITOUR 11 PETplanet Insider Vol. 23 recycling was the first company worldwide to successfully integrate the recycling of post-consumer PET trays and containers into its own production process. This business segment of PET tray recycling will grow all the more the less multilayer products are used in the trays. Design for recycling should thus arrive in reality as soon as possible. PETplanet: The topic of PVC in PET comes up again and again. What does it look like today? Mr Heitzinger: As a rule, PVC gets into the PET quota via the labels. False PVC batches themselves are hardly to be found any more, or the pre-sorting systems have improved considerably in order to find more false batches in the process. This pre-sorting technology should be used as much as possible in order to be able to produce the necessary top quality in the end. We have already mentioned dyed PET. Another obstacle that can be solved is the direct printing of PET bottles and the direct printing of PE/PP caps on PET bottles. This is because this colour issue deteriorates the quality of the raw material, cannot be filtered out and remains in the recycling cycle or accumulates in the recycling cycle. PETplanet: You also produce systems for typical post-consumer plastic waste. What is the focus here? Mr Heitzinger: A simply question for a very diverse and large recycling area at Erema. We have seen a huge increase in orders for rPET systems, but the classic polyolefin share at Erema is still around 60% - 70% of the order intake. We are going in three main directions with our customers. One of them is to bring well-sorted, processed material streams in the film fraction up to the quality level of virgin material. Here, paper labels, tags and adhesives are the core problems that need to be worked on in processing. Perfect filtration and optimised pressures and mass temperaturs are essential here. The second main thrust goes into the reprocessing of classic post-consumer material, with varying degrees of moisture and contamination. Homogenisation capacity, power and filtration capacity of the plant are the key issues here. The third area is the professional processing of HDPE regrind with Regrind Pro Technology +Refresher for FDA approval. And the same applies to the polyolefin sector as to PET - no multilayers, please! PETplanet: A great finish. Many thanks for the interview. www.erema-group.com"},{"@ID":68, "TRADE SHOW REVIEW PETplanet Insider Vol. 23 No. 09/22 www.petpla.net 66 Petcore Europe annual conference 2022 part 1 Building up on the success of 2021 with more than 250 visitors, Petcore Europe annual conference took place in June 2022, at DoubleTree by Hilton Brussels City, Belgium. The topic of “Strategy and Trends for the Circular PET Economy” was discussed on the two days conference. The first day focused on perspectives, strategy and legislative challenges for the PET value chain. The second day was dedicated to trends in PET collection, sorting, recycling and circularity. After the opening speech by Antonello Ciotti (Chairman CPME), Christian Crepet (Petcore Europe) and Stephen Short (Petcore Europe), Mr Andy Grant, Technical Director at Eunomia Research and Consulting started with an overview of the current situation of the PET market. Andy reports that virgin PET production fell by 2.7% from 3.04mt to 3.00mt from 2018 to 2020. At the same time, the rPET production increased to 1.32mt. 70% of PET is used for the production of bottles (64% for beverages). The demand for trays has also increased, by 27% compared to 2018. Andy pointed out that over 70% of PET recycling capacity is distributed through Germany, Spain, Italy, France, UK and Ireland. He added that the recycled content in PET bottles and trays will increase. He summarised that collection and sorting must be focused on quality and that further improvements in design for recycling are needed that more rPET can be used within its own application cycle. Andy gave an outlook on depolymerisation. He told that this is still a young industry where the plants treating PET waste in Europe are at various stages of development with current input capacity of 68 kt p/a of prepared post-consumer PET flake. He explained that this technology is likely to see rapid growth over the next few years. Some of this will come from the expansion and construction of private facilities, and some will come from offering licences to use the technology. Andy closed with the statement that it can be assumed that by 2025, capacity for approximately 350 kt p/a of collected post-consumer PET flake could be available in Europe for depolymerisation processes, from which an estimated 345 kt p/a of virgin grade regenerated PET monomers or PET resin could be produced. Dr Stefan Kunerth, Technical Operations Director Western Europe at the Coca-Cola Company discussed a world without plastic waste in his lecture. He started by pointing out that by increasing the rPET content in the beverage bottles, this would be possible. Five global targets need to be considered: recyclability (100% by 2025), recycled content (50% by 2030), recycled PET (50% by 2030), collection (100% by 2030) and reducing virgin PET. The way to realise a world without waste is by closing the loop: this includes conscious design to minimise environmental impact. Likewise, collection must be increased in order to be able to recycle more efficiently, and finally, all stakeholders must be involved. Coca-Cola’s future PET bottle contains 70-80% rPET from mechanical recycling or polymer recycling. 20-30% is like-virgin material that comes from either the depolymerisation process or renewable sources. In 2030, the PET bottle will be 100% recycled or renewable. Maria Spyraki, MEP (Member of ITRE and ENVI Committees) gave an update on regulation and legislation for: Deposit for better collection and PET sorting system. Maria cited the global climate crisis and said that, according to the European Commission, circular transformation could lead to the creation of :700,000 new jobs and a 0.5% increase in EU GDP by 2030. According to the McArthur Foundation, redesigning plastic packaging could have a positive impact on the economics of recycling. She focused on the role of Deposit Refund Schemes in the circular transition in PET. The options are: well-designed and appropriate deposit refund schemes (DRS) have an impact on the circularity potential of PET. Deposit refund schemes can help facilitate waste collection, reduce littering and leakage and promote recycling, especially when combined with extended producer responsibility schemes. Extended producer responsibility (EPR) schemes can help finance waste management and materials recovery activities. It is therefore important to advocate for the creation of a pan-European business case for EPR and DRS. Similarly, the streamlining of the criteria applied to create a stable and predictable framework is necessary. Furthermore, the pressure on manufacturers towards the circular economy should be increased and incentives must be created to raise consumer awareness for behavioral changes. This enables the implementation of the dual objectives of the Packaging Directive Waste Directive: To improve the environmental performance of packaging and to facilitate the smooth functioning of the EU internal market and thereby the free movement of packaging and packaged goods in all Member States. These measures also offer the possibility of extending the directive on single-use plastics. This includes measures to reduce (over) packaging and packaging waste, as well as measures to improve the reuse and recycling of packaging and the use of recycled content. www.petcore-europe.org"},{"@ID":71, "PETplanet Insider Vol. 23 No. 09/22 www.petpla.net 69 TRADE SHOW REVIEW 69 TRADE SHOW REVIEW “RecyClass has many very well-known members and supporters from the brand & retailer, converters and raw material producer sectors. The platform provides lab testing protocols. These can be used to analyse the recyclability of packaging. As a result of the analysis, the product is classified in classes from A to F. A means recyclable to the highest level, F means the opposite. Numerous gradations are determined by taking external factors into account. With the help of the Design for Recycling Guidelines, packaging’s circularity can be improved, i.e. made more recyclable. Here, too, there are numerous recommendations and instructions. A recyclability rate assessment is also included.” Paolo continued: “After readjusting the individual areas that could still be improved in the product, the final step is certification. What must be taken into account is that the recommendations and analysis parameters are oriented towards the European market.” (Fig.4). In order to manufacture a product with rPET, certified material should be used. Therefore, RecyClass offers a tool for the certification of recycled material. Paolo went on: “Certification recognises the use of recycled plastics in products via an independent third-party audit. Certification is granted to a process linked to a product or group of products. The Audit Scheme verifies the traceability of recycled material in different process steps throughout the whole chain of custody of the recycled material. The Certification follows a controlled blending approach as a chain of custody model as described in ISO/IEC 22095:2020 (Fig.5) and the traceability principles stipulated in EN:15343, European Norm for Plastic Recycling. But there are some challenges and risks that have to be mentioned: the free allocation of recycled content must refer to real percentages, not credit systems between products, production lines, plants, etc.,” Paolo pointed out. He concluded: “The origin of the waste must be verified in case of a certification. And the RecyClass system has already received the accreditation from the EU according to EN:17065” https://petpla.net/2022/05/10/review-trends-in-thevirgin-and-recycled-pet-market-how-can-recyclabilitycircularity-and-sustainability-be-realised/?s= RECYCLASS TOOL RECYCLABILITY CERTIFICATION DESIGN FOR RECYCLING GUIDELINES • .$\") \"0$ о - *(( ) /$*). !*- +' ./$ + & \"$)\" • .$\") !*- 4 '$)\" җ ! Ҙ 0$ '$) . /- ).+*. $) /# /**' • .. ..$)\" *1 - '' - 4 ' $'$/4 *! !$)$.# + & \" • 4 ' $'$/4 '!Ҋ .. ..( )/ • 4 ' .. ( .0++*-/ HOW TO CLAIM RECYCLABILITY ? • 4 ' $'$/4 .. ..( )/ 4 - *\")$5 -/$!$ /$*) * $ . • -/$!$ /$*) !*''*2. *)/-*'' ' ) $)\" ++-* # . # $) *! 0./* 4 (* ' . . -$ $) \n ҝ\n сспшфѷспспѵ • # -/$!$ /$*) - ' / . /* - 4 ' +' ./$ . 2# ) ($3 2$/# */# - ( / -$ '. *- .0 ./ ) . - .0'/$)\" $) &)*2) +-*+*-/$*) *! - 4 ' *)/ )/ *! +' ./$ . $) *0/+0/ +-* 0 /.ѵ • * 0. *) /# +#4.$ ' +- . ) *! - 4 ' +' ./$ . $) /# *0/+0/ѵ CONTROLLED BLENDING CHAIN OF CUSTODY * 0( )/ /$*) 1 $' ' *)'$) /# - $)+0/ җ ѵ\"ѵ 1$-\"$)Ѷ !$'' -.Ѷ $/$1 .Ѷ / ѵ Fig.5 Fig.4"},{"@ID":44, "MARKET SURVEY 42 PETplanet Insider Vol. 23 No. 09/22 www.petpla.net Producer Company name Corvaglia group Has Plastik San Tic. A.S. Uner Plastik AS Alpla Werke Alwin Lehner GmbH & Co KG Postal address Telephone number Web site address Contact name Function Direct telephone number E-Mail Hörnlistrasse 14, 8360 Eschlikon Switzerland +41 71 973 77 77 www.corvaglia.com Mr Vaidotas Bucevicius Director Sales & Service +41 71 973 77 10 v.bucevicius@corvaglia.ch Firuzkoy Bulvari No, 34325 Avcilar, Istanbul, Turkey +90 212 695 50 00 www.hasplastik.com Mr Unal Haspaylan Commercial Director +90 212 695 50 00 info@hasplastik.com Gebze Plastikciler OSB 1.cad 11.sok No.3 41400 Kocaeli, Turkey + 90 262 751 3400 www.uner.com.tr Mr Cumhur Filik Sales and Marketing Director + 90 530 265 0663 CF@uner.com.tr Mockenstraße 34 6971 Hard, Austria +43 5574 602 0 www.alpla.com Ms Gabriele König Key Account Manager - Corporate Sales IM +43 5574 602 555 Gabriele.Koenig@alpla.com Product Range One-piece closures for beverages (Yes / No - If Yes, please specify material) Yes - HDPE Yes , HDPE Yes, HDPE/LDPE/PP with recyclable content is available Yes, HDPE Two-piece closures for beverages (with liner) (Yes / No - If Yes, please specify material) No No No No Applications relevant to PET containers (e.g. CSD, water, juice, beer, etc.) CSD & carbonated bottled water, still bottled water (pressurised & non-pressurised), sensitive drinks (juices, teas, fl avoured waters, ...), sports & energy drinks, others (dairy, edible oil, …) CSD, water, juice, energy drinks, beer, etc. Beverages, CSD, bottled and 5G water, juice, dairy, edible oil, food, beer, industrial segments, etc. and hotfi ll/aseptic/isotonic applications CSD, water, juice, dairy Neck fi nishes available as standard Several standard fi nishes from 25 to 48mm, e.g. Cetie standard necks GME 30.21 to GME 30.26, GME 30.28 to GME 30.33, GME 30.36 to GME 30.43, GME 32.03, GME 32.04 26mm, 29-25mm, 30-25mm, 38mm, 48mm, 1810, 1881, HOD 55mm (non-standard solutions upon request ) 28mm PCO-1810/1881, 29/25, 26/22, 30/25, 38mm 2/3 start hotfi ll/coldfi ll, 33mm 2 start hotfi ll, 29/21 1 or 2 pcs + 32/28 1 or 2 pcs snap-on for edible oil, 48/41, 55mm 5G, handles for 38mm+48mm+55mm or lean/lateral handles for edible oil bottles PCO1881; PCO1810; 38mm 2-start (GME30.29); 38mm 3-start (GME30.25); 30/25H; 48mm; glass (MCA 7,5R); SPI-necks; 26mm 3-start (GME30.28); 26mm 1-start (GME 30.37); 26/22 (GME 30.40) Printed caps available (Yes / No) Yes Yes Yes, printing is available in up to 4 colours Yes Colour matching service (Yes / No) Yes Yes Yes, any colour can be matched with 99% accuracy Yes Child-proof closures (Yes / No) No No No Yes Push-Pull / sports caps (Yes / No) Yes Yes Yes Yes Special comments/special closures (e.g. tethered cap solution, fl ipt-tops, drinking spouts, lightest cap for 28mm PCO, 26mm for water etc including non-beverage closures...) Closure manufacturing sites in Switzerland, Mexico, USA; Corvaglia designed caps are available all around the world via our partner network. Tethered caps for carbonated and noncarbonated drinks according to requirements of EU Directive 2019/904. Tethered caps, fl ip top caps, lightest 1881 caps for high CSD, global technical service is available We design, improve, and produce your caps with our own Uner moulds. Tethered, light-weighted, digital printed, spouted caps, and many others confi dentially. Non aerosol pumps in various neck fi nishes, buckets and canisters for various applications, tethered cap solutions for 1810, 1881, 38mm neck fi nishes; CRC caps; standard packaging for pharma applications; 2-chamber caps; bi-and multicomponent injection moulding; custom-made closures. Special patented closures or marketing features Digital printing capabilities installed at production sites HOD caps for 5 gallon, laser marking inside the caps (alfanumeric codes, artwork etc), engraved logo designs All closures are designed and patented worldwide by Uner Plastik AS. Mould Company name z-moulds Uner Plastik AS Corvaglia Mould AG Sacmi Imola S.A. Postal address Telephone number Web site address Contact name Function Direct telephone number E-mail z-werkzeugbau GmbH, Dr.-Walter-Zumtobel-Strasse 9, 6850 Dornbirn, Austria +43 5572 7272 0 www.z-moulds.com Mr Michael Fink VP Sales & Marketing +43 5572 7272-610 michael.fi nk@z-moulds.com Gebze Plastikciler OSB 1.cad 11.sok No.3 41400 Kocaeli, Turkey + 90 262 751 3400 www.uner.com.tr Mr Cumhur Filik Sales and Marketing Director + 90 530 265 0663 CF@uner.com.tr Hörnlistr. 14 8360 Eschlikon, Switzerland +41 71 973 77 77 www.corvaglia.com Mr Albert Brunner Director Sales & Service +41 71 973 77 52 a.brunner@corvaglia.ch Via Selice Prov. Le 17/A 40026 Imola (Bo), Italy +39 0542 607111 www.sacmi.com Mr Stefano Severi Sales Specialist Manager +39 335 659 4236 stefano.severi@sacmi.it Filling good: - beverages Carbonated and non-carbonated drinks, water, juices, beer, coffee & teas, dairy, etc. Still/sparkling water, CSD, beer, coffee, RTD CSD & carbonated bottled water, still bottled water (pressurised & non-pressurised), sensitive drinks (juices, teas, fl avoured waters,...), sports & energy drinks, others (dairy, edible oil, …) Still water CSD and sparkling water Juice, RTD tea, isotonic, cold /hot fi lled - other Edible oil, soy sauces and other fi lling goods possible on request Food, industrial, pharma Coffee, beer, detergents, other contents/ applications upon request Dairy, pharma & food - individial cap solutions Possible on request We design, improve, and produce your caps with our own Uner moulds Individual cap solutions are possible upon request Closure: -type All single-piece standard closure dimensions for all neck fi nishes, sports closures, fl ip-tops, push-pulls, multicomponent closures… 1 - 4 pieces in fl at/snap-on/fl ip-top/ push-pull/tethered caps Flat top & sports closures for neck fi nishes from 25 - 48mm, e.g. all Cetie standard necks GME 30.21 to GME 30.43 Flat top, 25-48mm Flat top, 26-38mm Flat top, 28-38mm / 48mm Flat top, child proof & stoppers -material HDPE, LDPE, PP, TPE, … PE/PP/PS/TPE HDPE (PP for transparent parts) HDPE HDPE and PP HDPE and PP PP, HDPE and TPE -weight Lowest from 0.7g 0.20g - 25.0g Starting from 0.8g From 0.8g up From 1.45g up From 1.65g up /1.95g up from 1.5-2.5g up Moulds: Clamping dimensions/ cavities 16 - 128 cavities 4x - 96x cavities 24 - 96 cavities From 12 - 64 cavities Preferred hot runner suppliers Mold-Masters and others Husky/Mold-Masters, and others Various Special features Several patented technologies for most effi cient closure production, with lowest downtimes and spare parts usage. All closures are designed and patented worldwide by Uner Plastik AS. Closure design approvals from all major beverage brand owners. Most economical closure designs for private labels. Tethered cap solutions for carbonated and noncarbonated drinks according to requirements of EU Directive 2019/904"},{"@ID":79, "61 TRADE SHOW PREVIEW PETplanet Insider Vol. 23 No. 09/22 www.petpla.net PET bottle-to-bottle technology Sorema, a division of Previero, is specialised in plastic recycling lines for the following plastic products: PO flexible packaging, PE stretch and bi-oriented films, agricultural film and pipes - PS, PP, PE and PET rigid packaging, HDPE, PET bottles and cans, fibres, and many others. Sorema’s upcycling concept encompasses the suitability of modifying the manufacture of a given packaging product like a PET bottle by replacing virgin polymer with a post-consumer collection material, in even larger percentages and which, after an appropriate recycling process, is available on an industrial scale. The company offers systems that start at 500kg/h up to the largest at 9,000 kg/h. Its proprietary recycling technology for sorting, grinding, and washing systems for PET bottles from post-consumer collection up to dried flakes include: The flow of the process water against the flow of the material so that the dirtiest water is used on the dirtiest material and the cleanest water is used on the cleanest material that enters the final rinsing process of the scale. The water is filtered and reused in an upstream cleaning phase. Use of mechanical friction and hot water washing (see photo), of chemicals products like NaOH, detergent and wetting agents. All combined at various stages achieving high levels of cleaning with a low usage of energy and consumables. Extraction of contaminants (e.g. alien plastics) also with detector systems to sort the diversity of plastics, colours, and containers before cleaning the material as a bottle and not as flakes, to the maximum extent. Human and on-line interface controls are available to allow visibility of the process parameters and production output, reducing management overhead costs. www.sorema.it Sorema Hall 9 Booth D29-D55"},{"@ID":30, "28 TRADE SHOW PREVIEW PETplanet Insider Vol. 23 No. 09/22 www.petpla.net TRADE SHOWpreview Drinktec 2022 preview part 3 This third instalment of our Drinktec preview once again highlights exhibitors that are of particular interest to those involved in the PET value chain. You can see the exhibits each day from 12-16 September, 09.00-18.00 Monday to Thursday and 09.00-17.00 on Friday. In addition to displays from 1,200 exhibitors, there is an extensive supporting programme, including lectures (excerpt below) and the following PET-related themes. September 13 / Hall A3: Sustainable production & sustainable packaging 10:00-10:30 - Delphine Gueguen, Serac: How to remove chemicals from packaging sterilisation to make aseptic filling of drinks more environmentally friendly? 10:30-11:00 - Martin Brown, Heraeus Noblelight: Modern day solutions for high speed and environmentally friendly disinfection of food and beverage packaging materials 11:30-12:00 - Dr Markus Grafen, Industrial Physics Steinfurt: Reliable non-destructive CO2 measurement - from lab to field Preform range SGT will highlight recent preform developments. Among those are a 3- and 5-gallon refill preform for water bottles which have been recently improved in terms of design and geometry. 33% shorter than most 5-gallon preforms on the market, it is claimed to optimise bi-orientation, to obtain a better stretching and blowing ratio and to prevent the bottle from crystallising. Its weight has been reduced from 730g to 650g for the 5-gallon version, and 450g for the 3-gallon one. The 55mm preform neck has been specially designed to guarantee a perfect seal. The ovoid preform base enables the bottoms of the bottles to be lightened after blowing. The integration of rPET content and of a handle is possible. Other developments which will be showcased are a recyclable alternative to polystyrene (PS) yoghurt and dessert cups that may integrate up to 100% rPET and multilayer preforms with a low opacifier rate (< 1%) dedicated to UHT milk packaging. The insertion of a layer of black PET close to the internal wall of the preform enables 99.95% of light transmission to be blocked out, says SGT. This technology enables the nutritional qualities of UHT milk to be preserved for longer and reduces the use of opacifiers which disrupt recycling flows. SGT also offers a new 24/410 neck preform dedicated to cosmetic and personal care applications (200ml). Body lotions, face creams, shampoo, conditioner and hand sanitiser are all claimed to be suited to this new cosmetic preform. The company has also increased its 38mm neck range with new preform weights, from 62g to 75g, for 3 - 5l still water or detergent containers. SGT has also developed a new CSD preform, the 26/22 neck finish, distinguished by low height and weight. All SGT preform ranges are suitable with tethered caps. www.sgt-pet.com September 13 / Hall A3: Consumer world & Product design 14:00-14:30 - Dr Peter Golz, VDMA: Measuring energy consumption of filling and packaging machines according to VDMA 8751 - experience and transferability of the measuring concept to processing units 15:30-16:00 - Vincent LeGuen, Sidel: Consumer appeal and wide-ranging performance in one design 16:00-16:30 - A new paradigm: sustainability trends and the plastic bottling industry September 15 / Hall A3: Sustainable production & sustainable packaging 10:30-11:00 - How Labels and Sleeves can boost packaging recycling 11:00-11:30 - Dr Elodie Bugnicourt, Steve Gould, Graphic Packaging International: Unlocking the potential of paperbased packaging and flexible automation to contribute to a more circular economy 11:30-12:00 - Paul Niedl, Starlinger: The art of PET recycling The full programme is available at www.drinktec.com SGT Hall C5 – Booth 240 Over 200 machines already installed Throughout Drinktec and K’ exhibitions, 1 Blow will reveal the latest development in its range of l inear blow-moulding machines: the 2XL. This machine offers a wide range of options: from 50 ml up to 12 l; either round, square, oval, or off-centred neck orientation; or hot fill bottles, all available for multiple applications and markets. The Sure Grip option (see picture) is also available on the 2XL, providing an easy-to-use bottle with an integrated handle. Without using any additional material in the handle, this eco-designed bottle remains in the PET stream and facilitates recycling. www.1blow.com 1Blow Hall C5 – Booth 201"},{"@ID":42, "MARKET SURVEY 40 PETplanet Insider Vol. 23 No. 09/22 www.petpla.net Inspection Company name Sacmi Imola S.A. IMD Ltd. Pressco Technology Inc Postal address Telephone number Web site address Contact name Function Direct telephone number Fax E-Mail Via Selice Prov. Le 17/A 40026 Imola (Bo), Italy +39 0542 607111 www.sacmi.com Mr Stefano Severi Sales Specialist Manager +39 335 659 4236 stefano.severi@sacmi.it Industriestrasse 37A 2555 Bruegg, Switzerland +41 32 366 80 66 www.imdvista.com Mr Martin Gerber Sales Director (CSO) +41 32 366 80 66 imd@imdvista.ch 29200 Aurora Road, Cleveland, OH, USA +1 440 498 2600 www.pressco.com Mr Tom Murphy VP, Sales & Customer Service +1 440 498 2600 sales@pressco.com Inspection system CHS102/202 PFMC Vision inspection systems for closures, preforms, bottles + barrier testing Intellispec Inspection speed Up to 4,500 caps/min Up to 200 caps/h Up to 4,500p/min - depending on closure type and geometry Up to 3,600ppm Inspection method Artifi cial computer vision algorithms, spark tester Mechanical and destructive breaking force test Non-contact inspection Vision Inspected objects Flat top caps, tethered caps, sport caps, hinge caps, multicomponents caps Flat top caps and tethered caps All types and shapes Food, beverage, pharma, specialty, dispensing, sport, plug seal or liner, injection or compression moulded Inspected parameters: -Inner inspection Inspection of the whole product side, including mouth, plug seal (one piece caps), gasket (two pieces caps). Dedicated algorithms for a precise thread inspection. Detection of small fl ashes and voids in Tamper Evident Band wings. Detection of colour variations, discolourations, contaminations, black specks, pulled threads, voids, fl ashes of material. Inspection of standard or tethered cut produced in the mould: fl ashes in the windows, windows partially closed, bridges, number of bridges, thickness of the bridges. 100% inspection - guaranteed Available Yes -Outer inspection Complete inspection of the public side, including sidewall. Special CVS3603D module to unroll the sidewall in a 2D image making a compensation of any deformation coming from lens deformation, perspective and spatial position of the object. Inspection of the decoration with automatic recognition of colours and areas with a specifi c colour. Colour variation (ΔE), wrong colour, colour planes registration, off-centre, stains, black specks and many others. Available Yes -Geometry From a top view: Ovalisation, indicative measurement on inner and outer diameter; from side views: outer diameters measured long the cap body, bulged caps, cap height. Available Yes -Cavity number reading Yes, through artifi cial intelligence algorithms for high reliability and performance. Statistics of defects by cavity number, sorting by cavity number. Yes, through CVScut vision system Available No -Microhole inspection Yes, with dedicated and integrated spark tester device Available No -Additional inspection criteria for inserts Yes, (presence/absence, integrity, black specks, voids, fl ashes, contaminations…) Available - depending on your requirements Wide range of insert types and materials Further inspection options Side inspection Breaking force test Proven tethered closures inspection, slit inspection (after slitting machine), print inspection Colour, UV, print/deco, liner/wad, caps on fi lled containers Colour Camera: CHS features up to 7/12 high resolution and high speed colour cameras to control the whole cap Yes Available Installation: · Stand-alone (offl ine) Yes CHS 102, no CHS 202 Yes Flexible offl ine solutions out of one hand Yes · Inline CHS family includes two machines: CHS102 (single vacuum conveyor belt) and CHS202 (double vacuum conveyor belt). Both machines are very compact and have been designed to match the highest production speeds required by the market (up to 4,500ppm). PFMC takes samples of plastic caps and performs destructive tests: breaking forces of the bridges and of the lugs that keep the cap tethered to the bottle. The machine records the detected values and provides a set of statistics. It also produces chart showing force as a function of time, and can export that data via Ethernet or USB. Complete inline downstream solutions out of one hand Yes Softwarefeatures: Graphical HMI translated in more than 20 languages, artifi cial intelligence algorithms, colour analysis, special tools dedicated to a precise thread inspection, runs under Windows 10 IoT. IMDvista Neuron (AI based software for tethered and special closures) IMDvista Portal (one overview of all running IMDvista systems - connects your vision systems Industrie 4.0) Real-time trend data, last 100 images, defective image database/ archive, remote access, biometric user login, customisable reports, OPC connectivity"},{"@ID":20, "EDITOUR PETplanet Insider Vol. 23 No. 09/22 www.petpla.net 18 High speed assembly machines Contexo GmbH, February 2022 We met: Matthias Müller, Chief Commercial Officer (CCO) When assembly of multi-part caps is complicated and needs to be done quickly, Contexo claimes to offer a good solution. These are particularly suitable for complex cut and cap geometries for tethered closures. Up to 72,000 parts per hour can be produced on this machinery. We visited the plant in Winterbach, Germany. Tour Sponsors: The family business is run by three second generation brothers: Jürgen, Matthias and Steffen Müller. Their parents Heide and Karl are also on hand to offer advice and support to the three siblings. In the beverages sector, the company has made a name for itself for closures such as sports and carton caps, as well as providing assembly solutions for pouch closures. The assembly of trigger pumps and spray nozzles is a particular speciality. The company offers two basic machine designs: rotary and linear. Both are force controlled, the rotary machine via gear wheels and the linear via a main shaft that runs from the start of the assembly to the finished product. The shaft is fitted with cams that control the assembly units above it. Rotary designs with feed satellites are ideal for high processing speeds for closures. Up to 36 mould stations can be driven on the rotary machine. In addition to the standard assembly, the stations can also be designed as adhesive, welding, laser, cutting, folding, printing or testing units, depending on product requirements. The positive drive eliminates material buffers between the stations. It is very fascinating to witness the speed and precision with which parts pass through the stations. At the end of the process, a tested, finished and usually complex component emerges. Ten years ago, machines were producing 300 parts per minute, whereas now they can manage up to 1,200 parts per minute. While the linear and rotary machines and stations can be designed and built by CAD, the parts sorters involve manual work. The parts to be assembled are supplied in bulk and have to be transferred to the assembly station via the sorter in the correct position. While sorters for preforms and caps are now standard, Contexo does not shy away from complex part geometries. These geometries constantly challenge the company, particularly in the pump segment for bottles and sports caps. Here, eight work stations are constantly being built, welded, bent, tested, discarded and refined. A particular feature is the socalled vibration feed with TE-Proof. This makes it possible to feed hot injection-moulded parts directly and gently without the dreaded stress whitening. The forced control of the station means that even round parts can be aligned with precision. A small mechanical edge on the component is sufficient to fit it into the correct position. This function is especially important for beverage closures that have to open in a certain way. Matthias Müller, CCO Contexo GmbH Detail of Contexo’s patented all-in-one machine for tethered caps"},{"@ID":35, "TRADE SHOW PREVIEW PETplanet Insider Vol. 23 No. 09/22 www.petpla.net 54 News in index markings, wash-down design and separation methodology Vision inspection systems Intravis GmbH will present its wide range of vision inspection systems for the plastic packaging industry. The company will provide information on the CapWatcher FC, a system for use in the wet area of filling lines, which for the first time brings a new inspection technology as well as the washdown design for high splash water protection. “In recent years, we have further expanded our expertise in the wet area and developed our inspection systems based on our extensive project experience,” says Dr Gerd Fuhrmann, CEO at Intravis. Intravis | Hall C5 – Booth 135 The new CapWatcher FC With the CapWatcher FC, Intravis introduces for the first time a new inspection technology that uses index markings to inspect the application angle. With the help of five side cameras, the system detects whether the closure is screwed on in the target position or whether it has been screwed on too far or not far enough. The vision inspection system is guided by markings on the closure and neck support ring that are barely perceptible to the end user. If these markings are within a tolerated range of each other, the system assumes that the closure has been completely and correctly fitted and releases the bottle for packaging. The production line operator also receives comprehensive statistics correlating the average application angle with the capper’s tool. This allows malfunctions of a tool to be detected at short notice. In addition, the CapWatcher FC inspects the bottle for damage, presence and correct positioning of the closure, and records the fill level of the bottle. Washdown design for high splash protection The CapWatcher FC is completely designed in the new washdown design. Dr Gerd Fuhrmann: “The washdown design is intended for Intravis systems that are located exclusively in the wet area of the filling lines behind the filler. Thanks to the specific design, the inspection unit and the associated control cabinet are splashproof all around and meet the hygiene requirements of the fillers.” The design simplifies cleaning of the system as the exterior is designed to drain off any water. In addition, the interior of the CapWatcher FC is easily accessible. Besides the CapWatcher FC, the label inspection system LabelWatcher is now available in the washdown design. Janina Orlowski, Product Manager at Intravis: “With the washdown design on the LabelWatcher, we are once again significantly expanding its application possibilities. Each component is individually enclosed and thus optimally protected during ongoing operation and cleaning.” The LabelWatcher is already established on the market and is used for the comprehensive decoration inspection of bottles, jars, cans and containers. CapWatcher Q-Line Intravis will present its new and further developments of the CapWatcher Q-Line, which is tailored to the challenges of tethered cap inspection. Intravis will show an exhibit of this inspection system for caps at the hall C5 booth 319 of Sumitomo (SHI) Demag Plastics Machinery GmbH. Whereas the system previously used a star wheel to separate the caps from above, a positive, lateral star wheel separation is now selected. Gerd Fuhrmann: “The external shape and stability of tethered caps pose a challenge for separation, especially as the caps are becoming thinner and thinner. With our new form-fit, lateral star wheel separation, our systems ensure perfect separation and positioning of the caps even at the highest speeds. In the process, the closures are handled gently and carefully. Due to a software logic that has been optimised for the nonrotationally symmetrical outer appearance of the caps, the tethered caps no longer have to be aligned. This further simplifies the separation process.” Patented microhole inspection The CapWatcher Q-Line is designed to meet other specific requirements for tethered caps. For the inspection of caps with internal closure aids, so-called CAM’s, an electrode that is immersed in the cap is no longer required. Intravis’ patented non-contact microhole inspection detects microholes and thus prevents damage to the inner closure elements. The CapWatcher Q-Line can be used flexibly for numerous different cap designs - regardless of whether the caps are injection moulded or compression moulded, whether they are single- or multi-part, and whether the cap elements are moulded or cut. www.intravis.com The new CapWatcher FC in washdown design"},{"@ID":40, "ENERGY COSTS reduced by 15 %? UNLIMITED life time ! MAINTENANCE COSTS reduced by 50 %? Drinktec Munich Hall B5 / Stand 520 Messe München, 12-16 Sep. 2022 www.afcompressors.com sales@afcompressors.com YES! AF Compressors can provide sustainable and long life 8 bar & 10 baroil free air compressors! Can AF Compressors also supply 8 bar & 10 bar, oil free air compressors? AF COMPRESSORS"},{"@ID":72, "TRADE SHOW REVIEW PETplanet Insider Vol. 23 No. 09/22 www.petpla.net 70 Plastics Recycling Europe part 2 The Plastics Recycling Show Europe (PRSE) 2022 exhibition and conference, held in June in Amsterdam, The Netherlands, attracted visitors and exhibitors from across Europe and 80 different countries internationally. Over 4,700 attended the in-person event and over 500 more attended the hybrid event virtually. PETplanet selected some statements for you. Lucia Buffoni, Marketing Manager at Repi: ‘PRSE confirms that it is a strategic meeting point for all the players in the world of plastics recycling - a lot of people you would not have expected to meet during this period. This proves that the issue of sustainability is really taken seriously by the plastics industry. StabiPlus generated a lot of interest as it is a real answer to the need to protect recycled PET and allow it to be used in a higher percentage in packaging and for more cycles.’ www.repi.com Roberta Gualtieri, Marketing Manager at Sipa: ‘It was a very positive event with a large number of visitors and interest in our solutions for the design and manufacture of PET containers with rPET. We feel that the show is getting bigger every year, with more visitors and exhibitors, which shows the importance of the recycling process in our market. It was important for us to showcase our innovative approach to the circular economy. From design to recycle with our AwarPET solutions, which consider not only lightweighting solutions but also the right design for primary and secondary packaging. This also includes our traditional technologies for the production of preforms with up to 100% rPET content without modification compared to virgin material with our XForm preform systems, further the production of rPET preforms and bottles with our ECS SP ISBM systems, to our unique XTreme Renew technology from 100% rPET flakes to preforms or even bottles in a single system.’ www.sipasolutions.com Krones Recycling Team: ‘For Krones, the PRSE provided the perfect stage to get in touch with customers and inform them about the chances that recycling and of course about our recycling solutions offer. And we are happy to say: The fair not only met our expectations, but exceeded them. It was great to see, that the whole packaging industry is aware, that humankind has to deal with packages and recyclables in a sustainable closed-cycle economy.’ www.krones.com F.l.t.r. Markus Ingenpaß, Head of Sales PET Recycling Krones, Peter Hartl, Head of Sales Recycling Solution Krones and Michael Lässing, Head of Business Line Product Treatment & Cleaning Technology Krones Lucia Buffoni presenting the new StabiPlus at the PRSE show. For more information please see page 43. F.l.t.r.: Roberta Gualieri, Marketing Manager at Sipa and Gianfranco Perricci Converters Sales Director, Sipa."},{"@ID":77, "59 TRADE SHOW PREVIEW PETplanet Insider Vol. 23 No. 09/22 www.petpla.net Shredder solutions For use in plastic recycling plants, the demand for powerful shredders has grown. Especially those that can process entire bales at the beginning of the reprocessing chain. Modern washing plants in particular, such as produced by Herbold Meckesheim, require sophisticated shredder technology to be able to process high throughputs and challenging feed materials. At the same time, the machines should be largely wear-resistant and as simple as possible to operate and maintain. An example of a modern solution in recycling lines is the single-shaft shredder 60/210 from Herbold Meckesheim, which handles high throughputs and entire bales of plastic and is suitable for both dry and wet size reduction. It is claimed to combine a robust and durable construction with a maintenance-friendly design thanks to good accessibility through a large doublewing door and a hydraulically swing-away grinding chamber trough. In many washing plants, the EWS 60/210 serves as the first process stage. A special feature of the single-shaft shredder is the externally mounted and wear-protected rotor, which allows individual knife configurations in the cassettes and is equipped with screwed-on armour plates, making time-consuming hard facing obsolete. In addition, the rotor consists of also replaceable stator knives, and a second row can be fitted as an option. Thanks to its large flywheel masses, the double-sided belt drive is energy-efficient and requires little maintenance without a failure-prone gearbox. An overload clutch is used to protect against extraneous matters, which might cause damage to the machine. Another example is the double-shaft shredder DWS 45/160 by Herbold Meckesheim. Due to a large contact surface of the rotor, the machine has a salient ingestion performance and is appropriate for materials that could only be fed in batches with traditional shredders, such as big-bags or large voluminous containers. The shredding of the material, whether in dry or wet operation, to a uniform and constant granular size is determined by the selection of the screen. www.herbold.com Herbold Meckesheim Hall 9 Booth B34"},{"@ID":5, "imprint EDITORIAL PUBLISHER Alexander Büchler, Managing Director HEAD OFFICE heidelberg business media GmbH Hubweg 15 74939 Zuzenhausen, Germany phone: +49 6221-65108-0 fax: +49 6221-65108-28 info@petpla.net EDITORIAL Kay Barton Heike Fischer Gabriele Kosmehl Michael Maruschke Ruari McCallion Anthony Withers WikiPETia. info petplanet@petpla.net MEDIA CONSULTANTS Martina Hirschmann hirschmann@petpla.net Johann Lange-Brock lange-brock@petpla.net phone: +49 6221-65108-0 fax: +49 6221-65108-28 LAYOUT AND PREPRESS EXPRIM Werbeagentur | exprim.de Matthias Gaumann READER SERVICES Till Kretner reader@petpla.net PRINT Chroma Druck Eine Unternehmung der Limberg-Druck GmbH Danziger Platz 6 67059 Ludwigshafen, Germany WWW www.hbmedia.net | www.petpla.net PETplanet Insider ISSN 1438-9459 is published 10 times a year. This publication is sent to qualified subscribers (1-year subscription 149 EUR, 2-year subscription 289 EUR, Young professionals’ subscription 99 EUR. Magazines will be dispatched to you by airmail). Not to be reproduced in any form without permission from the publisher. Note: The fact that product names may not be identified as trademarks is not an indication that such names are not registered trademarks. 3 PETplanet Insider Vol. 23 No. 09/22 www.petpla.net Dear readers, On our current Editour, we visited many recyclers and found that the recycling rates for PET bottles within the packaging industry are very high. Of course, we don’t have a 100% cycle worldwide, but in whatever country in the world, the cycle is working, whether as a deposit system in some countries, or voluntary collection in Switzerland, for example, or as manual collection in emerging countries. The same applies to the polyolefin bottles. Where it doesn’t work at all is with multilayer packaging. As important as this is to the quality of the bottled product, multilayer packaging is not recyclable. Here the industry is producing a world full of litter with a vengeance. Collection and separation systems are plentiful, today’s technology can laboriously sort this packaging out of the trash, but in the end, at best, it goes to incineration. In emerging countries, it ends up in the environment more often than not. At the K fair, we will find many good approaches to packaging recycling, but no industrial solutions for multilayer packaging. Enzymatic recycling may offer a way forward - but only for PET - there are mealworms that eat plastics; then there are bioplastics from waste from the paper industry for packaging, such as from Tecnao, which can go in the compost bin, and so on. But the multilayer option is the cheapest for the industry because environmental pollution is not priced in. The association endofplasticwaste, representing the raw material and packaging industry, sweeps aside the problem thanks to its gigantic advertising budget. “The bad consumer just has to collect intelligently and then it will all work out” is the credo. Such problem-diverting measures by industry show that governments need to intervene as a matter of urgency. Politicians worldwide should only be promoting recyclable packaging in the sense of a closed cycle, they should release recycling materials for food packaging and should be setting binding quotas. Politicians must ban packaging that cannot be recycled or that can only be thermally recycled, or impose such high taxes on such material that it makes no economic sense to use it. The European Union’s circular economy package makes a start. From 2030 onwards, only plastic packaging that is one hundred percent recyclable will be allowed on the market. The international community has proved over and over that it can tackle environmental problems efficiently across continents. Against the will of the industry, it got the ozone hole and acid rain under control through bans and legal regulations. Why shouldn’t the same be done with packaging? I doubt whether banning plastic straws and mandating tethered caps will be significant or important enough steps to get us moving in the right direction. Yours, Alexander Büchler"},{"@ID":21, "EDITOUR 19 PETplanet Insider Vol. 23 Fig.1: Micky Mouse closures: the rotating tool axis allows the fast assembly of unusual cap designs. The machines also have solutions for new cut tethered caps that do not work on traditional sliders. As the cap rotates on the shaft, the closure runs past the knife, enabling bands to be cut that sit under noncircular caps. (Fig. 1) The fact that cap components sit on shafts and are not clamped from the outside means that even parts with sensitive surfaces, which are often required in the cosmetics sector, can be fitted without leaving any scratches. As well as the beverage industry, the machines are also used in the medical, beauty & home and consumer goods sectors. Contexo is currently focusing on sprayers for cleaning agents, an area in which the sons want to become global market leaders in the near future. www.contexo-gmbh.de Contexo is an international machine builder that designs and produces technical solutions for global brands and companies. Contexo specialises in building high-performance assembly machines for mass production. In 1982, Karl Müller, the family’s father, began building machines. His three sons have led the company since 2011. Contexo’s assembly machines are designed for good technical performance and versatility. Up to 65 production stages can be integrated in one system, for example: assembly, imprinting, joining, gluing, welding and lasering."},{"@ID":3, "No.09 2022 www.petpla.net D 51178; ISSN: 1438-9452 29 . 08 . 22 PETplanet is read in more than 140 countries MAGAZ I NE FOR BOT T L E R S AND BOT T L E - MAK E R S IN THE AMER ICAS, AS IA, EUROPE AND AL L AROUND THE PLANET MARKETsurvey All about caps: cap producer, supplier of moulds, machinery and inspection systems Page 39 Page 10 Page 26 Page 57"},{"@ID":6, "PETcontents 4 PETplanet Insider Vol. 23 No. 09/22 www.petpla.net 09/2022 Page 12 EDITOUR 10 “No multilayers, please!” - Post-consumer PET tray recycling 12 Multinational drinks giant expanding its capacities - Increased PET bottle production with technology from Neutraublingen 16 Highest turnover despite pandemic 18 High speed assembly machines 64 Automatic adjustments MOULD MAKING 20 A growing Indian company with international interests BOTTLE MAKING 22 PET milk packaging in India 24 Wine in PET MARKET SURVEY 39 All about caps: cap producer, supplier of moulds, machinery and inspection systems TRADE SHOW PREVIEW 26 Drinktec 2022: floorplan 28 Highlights at Drinktec 2022, part 3 43 Processing rPET without losing quality 44 No need for chemical decontamination 45 Moulding of returnable & refillable PET bottles 46 Preforms, labels and driving towards the circular economy 48 Technologies for PET treatment 50 More ECOnvenience - Sustainable and user-friendly closures 52 Closure solution and smart drinkware 54 Vision inspection systems - News in index markings, wash-down design and seperation methodology 55 Turnkey solution for PET fillers 57 K’ show 2022, preview part 1 EVENT REVIEW 66 Petcore Europe annual conference 2022 68 PETinar: Spotlight on circularity for recycled PET 70 Plastics Recycling Show Europe 2022, part 2 BUYER’S GUIDE 72 Get listed! INSIDE TRACK 3 Editorial 4 Contents 6 News 71 PET bottles for beverage + liquid food 78 Outer Planet Page 34 Page 64"},{"@ID":66, "EDITOUR PETplanet Insider Vol. 23 No. 09/22 www.petpla.net 64 Automatic adjustments June 14, 2022 We met: Dr Johannes Kilian, Vice President Process Technology and inject 4.0, Engel Ivica Puskaric, Sales Director Packaging, Engel What happens when cap moulds are frequently being changed and the ideal machine mould combination is not always achieved? And what if the energy efficiency of an entire facility, which has been designed and built at great expense, declines dramatically? And what if the raw material includes recycling material and causes process instabilities? We spoke to Dr Johannes Kilian, Plasticising Systems and Recycling Development and Ivica Puskaric, Sales Director, Packaging, both of whom work for Engel. As an innovation leader when it comes to injection moulding machines, Engel is a key player in the cap production sector. The e-cap series, which has been specially developed for cap manufacture with its water-cooled electric and hydraulic nozzle drives, as well as hybrid ejector, can achieve cycle times of less than two seconds. Perfect alignment of the mould size and the injection moulding machine can secure energy savings of up to 50% compared to other machine designs. However, experience has shown that the perfect mould does not always fit on the best machine. Large caps with few cavities and small cap diameters with many cavities are often produced on the same mould tables, particularly in companies where many mould changes occur. And if there is no machine available, a small mould may well be fitted to a large unit. In addition, due to the upcoming amount of recycling material the raw material viscosity changes much higher compared to virgin material production. This leads to process instabilities and necessary process adaptions. An experienced machine setter can overcome these challenges and still produce high-quality caps. However, this tends to result in a significant reduction in performance. Generally, little attention is paid to the lowest possible clamping force. The rule of thumb here will be to get the machine producing whatever is possible. This leads to increased capping and an unnecessary use of energy. A similar approach is taken in relation to cooling. “A lot goes a long way”. Of course, this also results in needless energy consumption. With Engel’s new iQ clamp control, the machine automatically optimises the clamping force. Using injection pressure and mould breathing signal, the machine is able to quickly find the lowest possible clamping force to produce high-quality caps within the shortest time cycle without any additional sensors in the mould. A manual approach to achieve the minimum required clamping force would need several cycles and additional measurement equipment. It is a similar picture when it comes to cooling. Here too, “full power” is normally used. The iQ flow control measures differences in pressure for each cooling cycle and makes adjustments where necessary. In combination with other smartly regulated cooling equipment, this results in optimum cooling results with significantly reduced energy consumption and little or no adverse impact on cooling times. Tour Sponsors: Hall 15 Booth B42-C58 “The results of the test series are unambiguous and repeatable. Thanks to the iQ weight control software, weight fl uctuations were reduced from 0.02 g to 0.003 g. This is equivalent to a weight constancy improvement of 85%. We are now totally satisfi ed with a reject rate of 0.047%. Based on this, we have been able to re-duce the quality control overhead, and improve the effi ciency of the manufacturing process.” Frank Breunig, Initiative, Project & Process Engineer, Procter & Gamble Manufacturing GmbH The Editourmobil at Engel, Schwertberg, Austria. Above: Dr Gerhard Dimmler; left: Alexander Büchler, Publisher of PETplanet Insider; right: Ivica Puskaric, Sales Director, Packaging; below: CEO Stefan Engleder"},{"@ID":75, "TRADE SHOW PREVIEW PETplanet Insider Vol. 23 No. 09/22 www.petpla.net 51 TRADE SHOW PREVIEW 51 one-piece Bericap Biarritz is claimed to unite modern design with intuitive handling. It is suitable for dry and wet aseptic filling. Two-piece sport closure Bericap Mayence can have a bi-colour design and is suitable for wet aseptic filling. Bericap Monet, a two-piece dryand-wet-aseptic-fillable premium closure, features a high-visibility tamper evidence ring different colour between the body and cap – and the distinctive window on the closure clearly indicates if the closure has already been opened. Integrated portfolio This year Bericap is presenting a fully comprehensive range of closures for the beverage industry to Drinktec visitors. It was completed in 2021 by aluminium roll-on closures when Mala Verschluss-Systeme GmbH of Bad Liebenstein, Germany, became part of the Bericap Group, uniting plastic and aluminium closures under one roof. Today, Bericap has a uniquely comprehensive range of closures, enabling it to cater to individual customer requirements and preferences with even greater precision and efficiency. Bericap also offers numerous individual decoration and design solutions for all of its closures to improve shelf visibility or communicate marketing activities. They are available on a mass-produced basis or in small production batches for promotions and other special projects. www.bericap.com Digital manufacturing line for plastic caps SACMI.COM Continuous compression molding solution: digital, smart, cost-effective. Conceived, designed and produced by SACMI. DIGITAL & PROFITABLE Line ready for advanced Smart Pack and Smart Care services to provide more effective synergy with HERE M.E.S. features. SMART & RELIABLE Reliable controls and immediate overview of the process via AI-based inspection systems integrated into all the processes. COMPACT &IWX MR GPEWW WTIGMƤG IRIVK] GSRWYQTXMSR CCM maximizes output rates per bay and is the most sustainable solution. momic The ClipAside cap with parallel tethers"},{"@ID":33, "31 TRADE SHOW PREVIEW PETplanet Insider Vol. 23 No. 09/22 www.petpla.net Energy-saving cap feeding system Gassner, a specialist company for closure feeding systems, is presenting the FlexiLiner, a flexible conveyor for feeding already oriented bottle caps, closures or cans. Wi th this solut ion, each cap is gripped gently only once, as it goes onto the conveyor line (SoftGrip). It then remains in the same position throughout the whole conveying process without any relative movement to the conveyor, without rubbing against the guides and without the risk of getting tangled or jammed. Routing can be handled uninterrupted on one machine. The continuous conveyor line can run vertically, horizontally, diagonally, upwards, downwards, to the left and/or to the right in any order. This means that the conveyor line can be flexible in adapting to the customer’s requirements and to the situation in the filling plant. Sensitive and abrasion-producing transitions and connecting channels are no longer needed and can be discarded altogether. All this enhances operational safety and avoids faulty closures on the capping machine. Reduced downtime increases the system’s efficiency and the costs incurred by preform rejects due to faults in the closures are now a thing of the past, says the company. Hygiene is improved by the absence of abrasion and angel hair with the FlexiLiner and there is no disruptive air turbulence. The closures do not collide with one another, nor is there any other type of interference or frictional forces present during the smooth transport. This means that the FlexiLiner can continue to move caps that have already been quality-tested in routing without the risk of them being crushed. As the SoftGrip elements automatically adjust to different diameters, it is possible to process caps for a range of spouts, e.g. closures for 28mm and 38mm neck finishes. Likewise, a variety of cap sizes can be transported, e.g. flat caps and sports closures. Height and diameters can also vary. For example, 28mm flat caps can be combined with 38mm sports closures without any conversion effort. www.gassner.co.at product development caps & closures design high cavitation moulds multi-component moulds closure production systems after sales service competent – professional – inspiring +43 5572 7272-0 | sales@z-moulds.com | www.z-moulds.com Visit us @DRINKTEC Munich, Sept. 12-16th Hall C5 Booth 207 Gassner Hall B4 – Booth 123 Cap solutions Has Plastik will be exhibiting its new plastic cap solutions. The company will showcase its new tethered caps and lightweighted 5 gallon solution developed together with its long term business partner Corvaglia AG in Switzerland. Other highlights at the exhibition will be their UTC laser marking applications with QR codes as well as alphanumeric fonts (photo above). No need for manual registration - any phone camera can read them easily. All caps will be available with Has Plastik’s proven customer support. With more than 42 years of experience, Has Plastik has been a leader in introducing lightweight solutions into the market whilst reducing their environmental footprint. www.hasplastik.com Has Plastik Hall C5 – Booth 248"},{"@ID":28, "26 TRADE SHOW PREVIEW PETplanet Insider Vol. 23 No. 09/22 www.petpla.net HALL PLAN hall C4 (excerpt) C5 C5 B4 GALEB METAL PACK UBC GROUP NEW BOX CLEMENTE RIGAMONTI ECOCAP’S GOGLIO PELLICONI MAJOR DRAFT BEER MICRO MATIC KEG SOLUTIONS CHART MISA KEGSTAR NCC EUROPE CARTOBOL TEFEN BTWATZKE TRIVIUM CANMAKER GEVAPLAST ARDAGH DRINKOTEC BINARY EDF WORK & MEET LOUNGE VBS OBERHOFER LANKER PACK BELVAC WEILI RUIAN ES PROCESS on energy consumption, PET RECYCLING PLANT Compact process, modular design equipment space. CONTACT US TO LEARN MORE ! WWW.BO-RE-TECH.COM | +86-573-85120186 | SALES@BO-RE-TECH.COM"},{"@ID":69, ""},{"@ID":12, "EDITOUR PETplanet Insider Vol. 23 No. 09/22 www.petpla.net 10 Post-consumer PET tray recycling “No multilayers, please!” June 2022 We met: Michael Heitzinger, CEO at Erema When Erema talks about plastic recycling in the sense of “cycling”, i.e. a circulation system, it’s pretty credible. For 39 years, the company has been manufacturing recycling systems. We spoke to CEO Michael Heitzinger about the latest developments in more than just the rPET field. Tour Sponsors: PETplanet: Mr Heitzinger, Erema has been building recycling systems for almost 40 years? For how many years have you also been active in the rPET sector and where is the trend going? Mr Heitzinger: We have been working on the rPET product application for a good 20 years. Plastic recycling is booming overall, especially PET recycling. We notice that the shift to ever larger plants is progressing very rapidly. A few years ago, recycling plants were in the range of 1 t/h and 2.4 t/h per machine. Of course, this varies from PET to polyolefin. Now, in early summer, we have just finished testing and delivering our first 6 t/h PET line in our factory hall and the machine is now already installed at our German customer. Besides the great political pressure to build up recycling capacities, securing the material flows is the first big barrier or gateway for recyclers to be able to grow. The processing logistics for used PET bottles are already lagging behind the required and desired rPET volume and the lack of mass flow is already limiting larger investments. Only those who can secure the material have the opportunity to earn money with rPET. In parallel, the processing of rPET material is becoming increasingly important and intensive. The progress in technical processing, pre-sorting, sorting, washing (hot or cold) has been implemented and only needs to be used more. PETplanet: The proportion of recyclate in bottles is increasing. What does this mean for the system manufacturers? Mr Heitzinger: Today we are talking about up to 100% recyclate in a bottle, which means that yellow and grey haze must be avoided. For this reason, in Vacunite, our rPET system, the material is never heated above 150 °C if atmospheric oxygen is still present. Above that, only nitrogen mixture is used to prevent yellow discolouration of the material, because this discolouration property cannot be reversed. In addition to discolouration, material quality in terms of constant IV and cleanliness is becoming more and more important, because the weight of PET bottles (0.25 l) is moving from 24 g/bottle to 8 - 9 g/bottle as at Niagara Waters in the USA, which increases the challenge in production. The separation of the coloured bottle flakes is an important part of the processing, prior to extrusion, and is usually carried out on our own extruder lines. Due to higher recycling rates and increased awareness, more and more PET bottles are being made transparent and the “colour” is applied to the label. Basically, coloured rPET granulate still finds good sales markets in the staple fibre industry. But also in the fibre industry there is a growing awareness to use more recycled material. So we already have more than 30 plants processing PET bottle flakes into high-quality POY fibre. Unfortunately, this is a “material loss” for the real closed loop process from bottle-to-bottle. PETplanet: Your latest project is the processing of PET trays? Mr Heitzinger: Yes, this is a material stream that is still difficult to handle and must be specially prepared and processed. A thoroughly difficult product niche, since the material cannot be collected so easy by type like the PET bottle and has a high potential for multilayer components. Nevertheless, a material stream of the future. “From niche existence to musthave.” These are just a few words to describe the development that plastics recycling has undergone in recent years. The plastic packaging manufacturer Faerch from Denmark and Erema customer in the field of Michael Heitzinger, CEO at Erema Alexander Büchler enjoys the overview of a large Vacurema system."},{"@ID":59, "57 TRADE SHOW PREVIEW PETplanet Insider Vol. 23 No. 09/22 www.petpla.net TRADE SHOWpreview K’ 2022 preview Every three years, and this autumn again, the world of plastics meets in Düsseldorf: from October 19 to 26, 2022, the trade fair K’ presents new products and innovations from all sectors of the industry – from production to processing, to mechanical engineering. Once again, the central point of contact for the critical exchange of information, thoughts, and opinions is represented by the Special Show “Plastics shape the future” in hall 6. The focus of the special show under the auspices of Plastics Europe Deutschland (PED), the plastics producers’ association, and Messe Düsseldorf will be on the three ground-breaking hot topics of K 2022: climate protection, circular economy, and digitalisation. In entertaining formats, high-level guests from the world of politics, science, and the industry, as well as NGOs will share information about and discuss economic, social, and environmental challenges and solutions around the leading themes of K’ 2022 – thus connecting the trade fair presentations of the companies with the societal agenda of K’. These core themes are also taken up by many exhibitors. We have compiled some of the items on display in this first part of our preview. www.k-online.com Innovative series with over 12 new machine sizes The focus of Bekum’s trade fair presentation is the market launch of the new machine series for packaging and industrial containers. At the last K’ fair, Bekum presented the machine Concept 808. With the newly developed machines of the 8-series, Bekum intends to set the benchmark for future extrusion blow moulding machines. New features include the multiple awardwinning machine design, energy-efficient HiPEx 36D extruders, spiral mandrel die heads for uniform melt homogeneity, Bekum’s Industry 4.0- capable BC 8.0 machine control system and the patented C-frame for good clamping force distribution. Depending on the size, the EBlow machines of the 8-series are available as single- and double-station versions. The sizes EBlow 208D, 308D and 408D form an independent, modular construction kit as components of the 8-series platform. The robust design has been optimised for a small footprint and is characterised by flexibility and maximum efficiency. Reduced moving masses allow short dry cycle times. Mould changes, maintenance and service are simplified by easy accessibility to the extrusion head and the blow mould. The new small blow moulding machines, in the 8-series are designed for small packages and have clamping forces of 60-120 kN. New blow moulding machines up to 20 l The modular, flexibly configurable extrusion blow moulding machines of the 8-series include the machine sizes 508, 608, 708, 808, 1008 and 1208, all of which are available as double-station machines. The 508, 608, 708 and 38 sizes are also offered in single-station versions. The series offers clamping forces from 200-500 kN and has been designed for maximum productivity and ease of use. With the e-Twin toggle, Bekum presents a new, unique clamping drive system for short clamping force build-up times, which, in conjunction with the patented C-frame, guarantees platen parallelism. Thus, covering the most diverse production and material requirements for packaging and handled canisters up to 20 l in an efficient way. www.bekum.com Bekum Hall 14 Booth C03"},{"@ID":16, "EDITOUR PETplanet Insider Vol. 23 No. 09/22 www.petpla.net 14 eight years. In 2018, he finally moved as Operations Manager to Karlsruhe. “I was attracted by the exciting task of expanding the site, the large-scale production and the opportunity to build a new team fit for the future,” he remembered. Part of being fit for the future included the single-use PET line, just coming into operation. “Initially, we combined the investment in the site’s new line with production capacities,” said Dederer. “At the CCEP site in Liederbach, near Frankfurt in Hesse, we couldn’t see any expansion options and so decided to bring the single-use PET line there dating from 2013 into line with the latest technology and relocate it to Karlsruhe, where the necessary expansion options were available. The plan was to further extend the factory for strategic reasons, with the aim of expanding PET manufacturing, but nevertheless to keep production in the south of Germany, which was possible through this relocation. Here in Karlsruhe, this enabled us to increase the overall efficiency of the company, i.e. greater volumes and more staff, and we created around 70 new jobs,” summarised Andreas Dederer. Currently, a total of 248 employees work on the 56,000m2 Neureut production site, where there are further expansion possibilities. Production, products, key figures Coca-Cola and Coke Zero account for about 80% of the overall production, some 15% for Fanta Orange, Sprite, Mezzo Mix, and Coke Light and circa 5% for other products - all in 1.25 l PET bottles. Up to 36,000 bottles pass through the bottling system every hour. Almost 2.5 million leave the factory each week for the south and west of the country. For its upgraded Liederbach lines, operation relies on blowing and bottling technology from Krones. PCO1881 preforms of 31.5 g are produced inhouse on six Netstal PET-Line systems, not at the Karlsruhe site but at the site in Halle. Blowing in Karlsruhe is on a Krones Contiform Bloc C316. CCEP purchases the caps from Bericap and these are to be gradually replaced by tethered caps. Mr Dederer said: “In Karlsruhe, we are planning to adapt the PET line accordingly in calendar week 9. This line conversion should take place on site over 2.5 weeks.” To supply the new production lines and so we can produce more on the can lines, production-related supply areas have also recently been modernised and expanded. This includes the tanks in the Coca-Cola syrup room that can now supply two production systems at once with syrup for drinks bottling. Water treatment has also been reworked and expanded so two production lines can be operated at once. Six new loading ramps have been constructed in logistics, which should ensure that from now on, twice as many lorries can be loaded at the same time. Furthermore, the company fills 330ml sleek and standard cans, as well as the Monster Energy range in 500ml and 568ml. A total output of 342 million cans and 115 million PET bottles is planned for this year. Mains water is used and in 2021, consumption was around 2.377 litres per finished drink, we were told. Trends, sustainability and coronavirus lessons Compared to last year, water consumption has increased slightly, Mr Dederer explained. “This was caused by installation, new process techniques and validation processes. But the aim in 2022 is to reduce water use by 25 per cent. Furthermore, we have our own mineral well available, which currently isn’t in operation. However, this will also be used in future for reasons of sustainability and efficiency,” continued Mr Dederer. “We are also pursuing the aim, besides converting to tethered caps, of manufacturing our entire CocaCola bottle portfolio from 100% rPET in the upcoming years.” In 2019, the company responded to a generally stronger demand in the glass sector by investing US$5.3 million in a new 1l glass multi-use line in Deizisau. The Neureut site offers the opportunity to expand further in future but there are no expansion plans, at least for the moment. The pandemic that started in 2020 was an endurance test for the drinks manufacturer. “We’ve learned to work more flexibly with regard to time and location. But it was a challenging time overall for the factory,” said Dederer. “However, we’re proud of our employees because they all pulled together, which has had a positive effect on team spirit. As the only factory in Germany producing the Monster products, we were under particular pressure to maintain production and"},{"@ID":9, "7 NEWS PETplanet Insider Vol. 23 No. 09/22 www.petpla.net Sidel expands in East Africa with new Nairobi office opening Sidel has expanded its presence in Africa with the official opening of a new office in Nairobi, Kenya on July 28. The move is intended to increase its support for its customers in East Africa, a key market for Sidel and one of the continent’s fastest-growing regions. Sidel has been serving the African market for many years. Building on this, the new East Africa office will enable it to drive development in the region by working more closely with customers to provide them with dedicated engineering capability and on-the-ground customer service. The East Africa region is made up of 15 countries, from Eritrea in the north to the island of Mauritius. Tanzania, Uganda, Kenya and Ethiopia have some of the highest levels of GDP and disposable income growth on the continent, indicating significant potential for years to come. The new Sidel office is located in the heart of Nairobi’s central business district alongside sister company TetraPak as well as the African head offices of other international companies. Africa is home to the world’s youngest and fastesturbanising population and has the potential to become one of the major sources of global growth. At more than one billion, sub-Saharan Africa’s population is currently growing at around 2.7% a year – more than twice as fast as South Asia and Latin America. www.sidel.com Gerhard Ohler new CEO of Next Generation Recyclingmaschinen GmbH (NGR) Next Generat ion Recycl ingmaschinen GmbH saw a personnel change at the top management. Gerhard Ohler took over the role as CEO of Next Generation Recyclingmaschinen GmbH (NGR), based in Feldkirchen, succeeding Wolfgang Steinwender, who has held this position since May 2020. Ohler, a 54-year-old industrial engineer, has many years of internat ional experience in extrusion technology and plastics recycling. Among other positions, he served as General Manager of Krauss Maffei in Shanghai and Managing Director at Greiner Packaging International. Before joining NGR, the native Upper Austrian was responsible for the management of the Greiner Extrusion Group as CEO since 2013. In his private life, Gerhard Ohler is married and has two grown-up children. Josef Hochreiter, CEO of Next Generation Group: “I am delighted to have gained an experienced manager for us in Gerhard Ohler. With this appointment, we will not only be able to successfully continue along the path we have chosen, but also to break new ground in plastics recycling. We have now created the best conditions to realise our mission ‘working for a better future’ together with a highly motivated team and to continue to develop and build highly efficient recycling machines for our customers in the future.” www.ngr-world.com Gerhard Ohler, new CEO at Next Generation Recyclingmaschinen GmbH"},{"@ID":38, "36 TRADE SHOW PREVIEW PETplanet Insider Vol. 23 No. 09/22 www.petpla.net GAWiSD featuring AutoJob™–job set up in seconds +1.724.482.2163 AGRINTL.COM ACCURATE • FAST • REPEATABLE SEE GAWIS4D IN ACTION Dimensional and thickness measurements for plastic containers and preforms. ® VISIT OUR BOOTH AT THESE SHOWS: drinktec Sep 12–16 Munich C5.121 K 2022 Oct 19–26 Düsseldorf 11C40 Lightweight in recyclate KHS‘ focus will be on the filler/seamer block SmartCan by KHS/Ferrum. But the machine and plant manufacturer also has something on show for the PET industry: with its new Loop Lite PET bottle concept, KHS is further helping to optimise the eco balance of beverage packaging and promoting closed recycling loops. In addition, the turnkey supplier will also be exhibiting a modular automation concept for PET lines as well as its full range of services that include both on-site assignments and remote digital solutions. With its Loop Lite packaging concept, KHS presents a very light 0.5 l PET bottle made entirely of recyclate. The specially developed design of this packaging for highly carbonated beverages allows up to 25% less material to be used compared to standard market CSD bottles and has been developed to be fed into the closed recycling loop. Its thin interior coating of glass claims to ensure long-term product protection. As well as environmentally friendly packaging, more and more consumers want to be able to choose from a wide range of products. Bottlers are therefore having to frequently expand their portfolios, with the number of stock keeping units, or SKUs, constantly on the rise as a result. In order to keep line availability and efficiency at a high level, they require fast product changeovers. KHS caters for this demand with its new, modular automation concept for PET lines. With fast, reliable, and reproducible changeovers, it boosts the overall equipment effectiveness. In ideal conditions, format changeovers from one SKU to another can be performed in 30 minutes – including running the system empty and restarting it (value refers to a non-returnable PET line). The new KHS setup reduces all manual activities by up to 80%. KHS will also be showcasing their digital services. The intelligent ReDiS and augmented reality remote diagnostics and remote maintenance services as well as the web-based Basic Line Monitoring system have proved to be of immeasurable value during the pandemic, KHS says. www.khs.com Solutions to industry challenges Sidel, a global provider of packaging solutions, is inviting customers to its booth to discuss industry challenges and discover packaging solutions of the future. Sidel will showcase systems and services, line engineering, and digital and eco-solutions, including aseptic production, sustainability, packaging optimisation and holistic turnkey solutions. Digital evolution: Digital solutions enabling customers to face challenges, and reach peak production performance without compromising operational costs, product quality or environmental impact. The Evo-On software suite is claimed to offer powerful cloud computing and data analytic technologies. Sustainable transformation: Eco-friendly packaging alternatives, from 100% rPET and light-weighted primary packaging with tethered caps, to optimised secondary and tertiary packaging alternatives. Aseptic: With 47 years’ experience in aseptic packaging equipment technology, Sidel will be premiering a new development. Complete line solutions: Sidel has a comprehensive portfolio of services in every related field including line concept, engineering, line control and automation, packaging technologies and equipment. Sidel’s acknowledged experts in packaging solutions for beverage, food, home and personal care products in PET, can, glass and other materials will be available at the show, meeting customers at the event to discuss future solutions to their challenges. www.sidel.com Sidel Hall A6 – Booth 339 KHS Hall B4 - Booth 336"},{"@ID":15, "EDITOUR PETplanet Insider Vol. 23 No. 09/22 www.petpla.net 13 An endless range of production possibilities with single-stage SIPA S.p.A. - Via Caduti del Lavoro, 3 - 31029 Vittorio Veneto (TV) - Italy - Tel. +39 0438 911511 - sipa@zoppas.com - www.sipa.it ECS SP models stand for a guarantee of quality based on 35 years of experience in Injection Stretch-Blow Molding technologies (ISBM) technology. Their robust system, produced in Italy, allows for the production of high quality containers in a wide variety of different sizes, threads and shapes. Tooling investment can often be optimized by using one single (i.e. shared) hot runner withmultiple cold halves. ECS SPmachines have features that enable quick change-overs, accept legacy molds and are also characterized by their compact layouts and high HQHUJ\\ HIĆFLHQF\\. Injection Stretch BlowMolding System"},{"@ID":24, "BOTTLE MAKING 22 PETplanet Insider Vol. 23 No. 09/22 www.petpla.net PET milk packaging in India India has been increasing its availability of milk and dairy products for over 20 years and is now the world’s largest producer and consumer of dairy products. Its rural economy is heavily dependent on the dairy sector as a source of jobs and revenue. While it has the world’s highest population of cattle, milk production per animal is much lower than other major dairy producers. Almost all dairy products are consumed domestically in India, with the majority sold as fluid milk. There is thus a lot of room for growth and added value in the Indian dairy business. Dairy products in India are available as liquid milk, UHT milk, flavoured milk, curd, flavoured & frozen yogurts, lassi, buttermilk, probiotic dairy products, buttermilk, table butter, ghee, cheese, khoya, cream, skimmed milk powder, dairy whiteners, sweet, condensed milk, ice cream, whey, organic milk, milkshake, and dairy sweets. Liquid milk has the highest market share of other milk-based products or dairy products. A recent study says that the dairy market in India reached a value of INR 13,174 billion (€160.46 bn) in 2021 and it is expected to touch INR 30,840 billion (€375.63 bn) by 2027; a CAGR of 14.98% from 2022-27. Milk is considered to be the complete food as the composition of milk consists of 87.7% water, 4.9% carbohydrate, 3.4% fat 3.3% protein, and 0.7% minerals. The composition of milk may vary slightly, depending upon the animals - cow, buffalo, goat - and the type of breed but milk is very much susceptible to the attack of micro-organisms and can become spoiled within an hour when exposed to some ambient conditions. Because of this, all kinds of fresh liquid milk can be subjected to heat treatment to eliminate micro-organisms and extend shelf life. Treatments include pasteurisation, sterilisation and ultra-high temperature sterilisation (UHT). Liquid milk is generally sold in glass bottles, high-density polyethylene (HDPE) and PET bottles, paper-based multilayered composite liquid cartons, and plastic pouches. Global trends in the packaging of milk products According to a market study by Euro Monitor, the use of PET as a packaging material is expected to continuously grow within the liquid dairy sector globally. Liquid milk products packaged in PET were forecast to reach 16.2 billion units worldwide by 2022. Bottle sizes up to 500ml represent more than two-thirds of those PET packages and were projected to reach 10.35 billion units in 2022. The growth of PET bottles for milk packaging can be credited its 100 per cent recyclability, excellent barrier properties, and secure closures systems, which ensure food safety. Moreover, from transparent to opaque solutions, PET packaging can deliver extended shelf life without the need for aluminium foil, enabling a more sustainable business. PET packaging for liquid milk in India Many state-level dairy products manufacturers in India are planning to package liquid milk in PET bottles rather than plastic pouches, in order to comply with the notification on Extended Producer ResponsibilLiquid milk is generally sold in glass bottles, HDPE and PET bottles, paper-based multi-layered composite liquid cartons, and plastic pouches. PET as a packaging material is expected to continuously grow within the liquid dairy sector globally."},{"@ID":22, "MOULD MAKING PETplanet Insider Vol. 23 No. 09/22 www.petpla.net 20 A growing Indian company with international interests Acme Disys, which was established in 2002, is headquartered in New Delhi, India, where its manufacturing and sales organisations are also based. The company’s 70-plus employees work in a modern production facility equipped with in-house design and engineering resources. It uses advanced high precision machine tools, sourced from leading German and Japanese suppliers, to manufacture high performance injection moulds. Its factory complex also houses mould testing resources, equipped with contemporary injection moulding machines from leading global companies. Acme Disys sells PET preform, caps and closures moulds across India and to more than 30 countries in Asia, the Middle East, Africa, Turkey, Cyprus and other countries. It has capacity for most light weighted preforms and caps, along with the latest neck finishes for water, juice, CSD, edible oil and wide-mouth jars for customers in India. Trends in moulds for preforms and caps Suppliers in India are working to become specialists in particular industries and offering dedicated, light weighted neck finishes. The latest varieties of necks and sizes are widely available for water, juice, CSD, edible oils and wide mouth jars for FMCG markets. Fridge bottles for household industries are also trending upwards. Decentralisation of production in India is accelerating, along with greater market spread and reach. Companies are establishing multiple production locations across the country, including in rural areas. The trend for PET preform moulds is towards higher cavitation, hot runner systems and quick interchangeability of stacks for various varieties and sizes to be offered. “In the cap and closure segments, we are observing a shift from compression moulding to injection moulding, with light weighting & tamper evident features as the key drivers. Adopting the post-moulding operation into the mould enhances the value proposition,” says Harbir Singh, Acme Disys’ Managing Director. Industries and market share Acme Disys serves packaging industry customers across all the main drinks sectors, including beverages, water, CSD, juices, food and FMCG. Although the fragmented nature of the industry makes it difficult to be absolutely precise, the company’s pan-India market share is estimated at 30-40% of the PET preform mould beverages segment. Preform and cap mould projects Acme Disys has delivered a number of special projects, in recent times. Among the highlights of recent projects were the delivery of a prestigious preform mould project for Parle Drinks in Nepal, to cater for their market for juice & CSD products, including Frooti and Appy Fizz, with PCO 2519 neck finishes. It also supplied one of the Indian market’s lightest preform and cap solutions, to a large mineral water company in Gujarat. Its 1 g cap for 26mm neck finishes, catering for 6.5 g, 9 g and 16.5 g preforms, is now an industry benchmark. The company supplied a high speed, productive solution for water preforms to a company in Gujarat that is an exclusive supplier to the Patanjali brand and the Rail Neer Mould assembly at Acme Disys Mr Harbir Singh, Managing Director Acme Disys"},{"@ID":43, "MARKET SURVEY 41 PETplanet Insider Vol. 23 No. 09/22 www.petpla.net Intravis GmbH Rotter Bruch 26a, 52068 Aachen, Germany +49 241 9126 0 www.intravis.de Marius Pötting Product Manager Caps and Closures +49 241 9126 0 +49-241-9126-100 info@intravis.de CapWatcher Q-Line CapWatcherSC (specialty closures) IntraOne! CapWatcher B-Line CapWatcher FC 60cps / 3,600cpm / 216,000 cph 80 cps / 4,800 cpm / 288,000 cph 50cps / 3,000cpm / 180,000cph 40 cps / 2,400 cpm / 144,000 cph 12 caps on fi lled bottles per second / 720 bpm / 43,200 bph 3 cameras for inner inspection (sealing elements, thread, tamper evident), 4 cameras for shell inspection, 1 camera for topwall inspection, contactless microhole inspection, temperature measurement, cavity reading Fully customised inspection systems that are tailored to the needs and wishes of our customers The perfect system for OEMintegration into capper-, fi ller-, assembly-, laser- or printingsystems Modular inspection system which can be confi gured with the basic modules of the closure inspection. 1 camera for inner inspection, 4 cameras for outer inspection, 1 camera for liner inspection/ cavity number reading Splash-proofed quality control of the fi lled end product. 5 cameras for outer inspection of the application angle and the tamper-evident band. 2 cameras for outer verifi cation of the fi ll level and the closure position. Tethered caps, standard one-piece beverage closures, standard two-piece beverage closures Tethered caps, carton fi tment, fl ip-top, sports cap, push-pull, 3-piece closures, screw top cap, spout & dosing, beauty & home-care, food & beverage, pharma, automotive, inserts, cutters, lids, dustcover Tethered caps, standard one-piece beverage closures, standard twopiece beverage closures, carton fi tment, fl ip-top, sports cap, push-pull, 3-piece closures, screw top cap Standard one-piece beverage closures, standard two-piece beverage closures, tethered caps (without tethered features) Standard one-piece beverage closures, standard two-piece beverage closures, metal closures (without measurement of application angle) Measurement of inner seal cone diameter (σ = 0.02mm), pulled thread inspection, tamper evident band inspection, black specks, contamination, colour deviation, inner seal cone, outer seal cone, plug seal, constant distance between inner seal and outer seal, homogeneity between inner seal and outer seal Measurement of inner seal cone diameter, pulled thread inspection, tamper evident band inspection, black specks, contamination, colour deviation, inner seal cone, outer seal cone, plug seal, constant distance between inner seal and outer seal, homogeneity between inner seal and outer seal, liner, laser engraving, QRcodes, promotion codes, cavity number reading. Measurement of inner seal cone diameter, inner closure diameter, ovality, thread inspection, tamper- evident band inspection, black specks, contamination, colour deviation, inner seal cone, outer seal cone, constant distance between inner and outer seal cone, short shots, fl ashes, liner, cavity number reading Measurement of outer closure diameter (σ = 0.02 mm) and height (σ = 0.02 mm), long gate inspection, slit quality for slitted closures, broken bridges, hinges, fl ashes between bridges, colour deviation, black specks Measurement of outer closure diameter & height, long gate inspection, slit quality for slitted closures, broken bridges, fl ashes between bridges, colour deviation, black specks, contamination, ovality, short shots, fl ashes, angel hairs. Measurement of outer closure diameter, measurement of outer closure height, colour deviation, black specks, contamination, absence and damage of the tamper- evident band, short shots, fl ashes Measurement of the application angle, tamper- evident band inspection, verifi cation of the fi ll level, inspection for: the presence of the closure, elevated closure, crooked/bent closure, domed closure (Bullnose) High precision measurement of the outer closure diameter: accuracy σ = 0.02mm, high precision measurement of the inner seal cone diameter: accuracy σ = 0.02mm, high precision measurement of the outer closure height: accuracy σ = 0.02mm Diameter and ovality, height, assembly faults, missing & damaged components, damaged seal cone, vertical long shots, open & closed short shots, horizontal/ radial long shots, tamper evident band, damaged fl aps, turned up fl aps, damaged pull tabs, missing or damaged quality seal. Diameter and ovality (e.g. closure, seal cone), closure height, damaged seal cone, missing or damaged tamper-evident band Missing closure, missing or damaged tamper-evident band, domed closure (Bullnose) Robust cavity reading with special illumination technology, cap-oriented imaging & machine-learning algorithms for cavity recognition. No time-consuming teaching or learning procedure necessary. This enables the creation of real-time heat maps of moulds. Problems in temperature control of individual cavities or entire heating & cooling circuits can be detected & eliminated Robust cavity reading with specially developed illumination technology, caporiented imaging and machine-learning algorithms for outstanding cavity recognition. No time-consuming teaching or learning procedure necessary. Unique, robust cavity reading with machine-learning algorithms for outstanding cavity recognition. No time-consuming teaching or learning procedure. This enables: - Wear or defects in the tool can be detected at an early stage - Every defect closure will be assigned to its real cavity in the mould New contactless microhole inspection, no need to dip into the closure -> must-have for tethered caps with inserts New contactless microhole inspection - no need to dip into the closure Missing components, closure height, diameter and ovality, fl ow lines, weight, Label, l*a*b values, barrier inspection, layer inspection, tactile measurement Pull-off test, TE-features Filler and capper tracking: Objects can be reliably traced back to the specifi c tool of the fi ller and capper. For example, defects of a tool can be detected at an early stage Yes Yes Yes Yes Yes Yes Yes Yes Yes Yes Yes Yes Yes Yes Yes Data base connection, reject rate monitoring, production monitoring, integrated control of up- and downstream equipment, integrated trend statistics with pre-warning. IntraVisualizer - data analytics to improve production quality visualises the data of all Intravis systems on site simultaneously. Most importantly, it helps to investigate defective product (Root-cause analysis) predicting and avoiding quality failures and material waste. In addition, it detects negative trends before faulty products are produced. It is possible to integrate data from different production machines with a robust OPC-UA interface according to Euromap standard. Data base connection, reject rate monitoring, production monitoring, HMI for the Intravis sorter, inspection system and packaging system integrated trend statistics with pre-warning, industry 4.0 ready Data base connection, reject rate monitoring, production monitoring, multistep rejector for fi lled bottles integrated trend statistics with prewarning, industry 4.0 ready"},{"@ID":17, "EDITOUR PETplanet Insider Vol. 23 No. 09/22 www.petpla.net 15 CCEP’s chronology 1981 New-build “Im kleinen Bruch” and installation of a KHS line for 330ml and 500 l multi-use glass bottling 1996 Adoption into CCE AG 2013 Upgrading of the KHS multi-use glass line to 1 l PET RR (glass and PET combi-line) 2015 Uninstalling of the KHS line and, after nine months of conversion time, start of the new KHS can line with capacity for 120,000 cans/h and reorganisation of the production area 2016 Start of Monster production with 4 flavours on the KHS can line, bottling of Monster and Coca-Cola products 2017 CC export business to Italy 2018 CC export business to Norway 2019 Start of Monster Mega Can 568ml production 2020 Start of standard 330ml can for Denmark with 6 flavours Increase of Monster flavours to 17 Monster export business to Denmark 10-pack Monster 500ml for Germany 2021 US$16 million investment in production, supply areas and logistics, creation of a total of 60 new jobs Installation of a second line (normal resistance PET), relocated from Liederbach to Karlsruhe Introduction of 24/6+ shift system (20 shifts/week) in Q2 2022 Introduction of 24/7 shift system on Jan 01, 22 Start of second line (normal resistance PET) therefore the supply for Germany. We managed well. Even during the coronavirus pandemic, the energy category experienced very strong sales growth. In the last 12 months, the category has seen double-digit growth in sales compared to the previous year so is stronger than all other categories of non-alcoholic soft drinks, such as juices. The drinks are very popular primarily with young and affluent adults, who are also very open to innovation. In the last five years, Monster Energy has been a growth driver in the energy category and grew even more strongly than the energy drinks category overall.” www.cocacolaep.com"},{"@ID":14, "EDITOUR PETplanet Insider Vol. 23 No. 09/22 www.petpla.net 12 Increased PET bottle production with technology from Neutraubling Multinational drinks giant expanding its capacities by Kay Barton June 2022 Coca-Cola Europacific Partners (CCEP) Deutschland GmbH We met: Mr Andreas Dederer, Operations Manager In Neureut, a district of Karlsruhe in Baden-Wuerttemberg in the south of Germany, the local site of Coca-Cola Europacific Partners Deutschland – CCEP for short – is celebrating its 40th anniversary. Produced here are the 1.25 l Coca-Cola PET single-use bottles and other drinks cans. It supplies CSDs not only to the state of Baden-Wuerttemberg itself but also to neighbouring states, with some of the soft drinks also going to other countries in Europe. Tour Sponsors: Besides Coca-Cola, the brand’s “Monster” range of energy drinks are exclusively produced here for all of Germany. At the same time as the anniversary celebrations, the manufacturer is also launching its newly created capacities for drinks production, materials supply and logistics. The beating heart of the almost US$16 million expansion is a technologically completely reworked PET line, which is making the anniversary site fit for the future. Operations Manager for the site, Mr Andreas Dederer, spoke to us about origins, technologies and plans. Then to now In March 1980, the then CocaCola concession Getränke Troullier GmbH & Co. KG began construction of the factory at a cost of 18 million German marks. After its completion in November 1981, it was inaugurated in May 1982. The new factory was located on the “Kleines Bruch” industrial estate, where we find ourselves today. But before its construction, Coca-Cola had been bottled in Karlsruhe-Neureut since 1969 in a factory in Unterfeldstrasse. Relocation took place then because there was no option to expand there. “However, the connection between Coca-Cola and Karlsruhe dated back even further,” explained interviewee Andreas Dederer. “Their common history began over 85 years ago, when the Karl Troullier concession sold its first bottles of Coca-Cola in Herderstrasse in Karlsruhe. In the first year, they achieved sales of 9,000 cases.” Mr Dederer has been employed in the drinks industry for 25 years. In Deizisau, to the south-east of Stuttgart, he began his career as a Shift Manager at the Urbacher Mineralquellen glass and multi-use container site, a branch of Coca-Cola Erfrischungsgetränke AG (CCEAG), as it was at the time. After nine years, he transferred to the Urbach site to work there as Production and Maintenance Manager. In 2006, he was promoted to Operations Manager, initially provisionally, and from 2007 to 2010, he was made permanent in that role. He returned to the Deizisau site in that role and ran it for the following Freshly filled Coca-Cola PET bottles Andreas Dederer in his office"}]}}
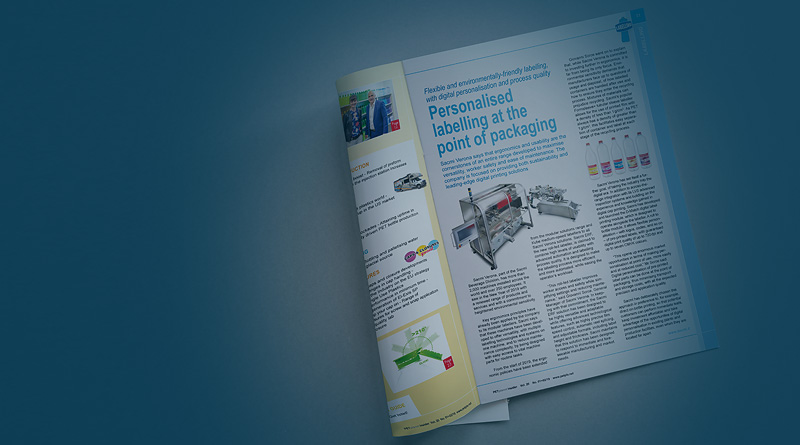