"PETplanet Insider Vol. 19 No. 05/18 petpla.net 65 TRADE SHOW REVIEW 65 TRADE SHOW REVIEW the longest possible use-by dates,” declared Müller. In a second production step, the previously injected blank is coated with a 1.4mm-thick, pure white outer skin. The colour is produced through the addition of the white pigment titanium dioxide. In contrast to single layer bottles, this process allows the volume of titanium dioxide to be consequently reduced from at least 10% to only 3% of the entire weight. “The market price for titanium dioxide is between seven and eight euros per kilogram. As such, the annual savings potential is considerable,” said Müller. Not least due to ecological aspects, the contemporary PET milk bottle also has the potential to force the outdated HDPE bottle out of the market in the long-term, states Nets-tal. PET raw material is around 30% less expensive than HDPE. This savings effect is underpinned by the fact that with Prelactia and its thin walls, bottles are around 20-30% lighter. “In contrast to an extrusion-blown process, no appreciable material loss occurs during the injection moulding process. Water and energy consumption is signicantly reduced.” explained Müller. As a result of the injection moulding process the thread is precisely dened, allowing the bottle to be reliably sealed with a screw cap even after opening multiple times. Any additional sealing with aluminium foil is superuous. “In point of fact the question of recycling coloured PET has not yet been fully addressed in many countries despite the increasing market shares. However, as one of the largest European countries, France has proved that the collection, separation and recycling of coloured PET milk bottles is indeed possible,” emphasised Müller. Customers in French supermarkets have been able to buy milk in lightweight Prelactia PET bottles throughout the country for a number of years. Cloud-based injection moulding “Industry 4.0 is a key theme for our Chinese customers. Under the term Plastics 4.0, Netstal develops innovative digital solutions with which our customers are able to achieve further increases in efciency in their production processes,” stated Müller. At the Chinaplas, the Swiss company were showcasing its new analysis app AnalytiX in Asia for the rst time. This cloud-based production monitoring allows users to keep track of their key machine parameters online, anytime, anywhere. “Our customers benet from automatic process and machine status analyses. This consequently saves a signicant amount of time and increases employee ef- ciency,” explained Müller. Supported by intelligent stability and productivity ratios, the user can identify individual machine trends or performance deviations at a glance. Data stored in Switzerland The important subject of data security is a priority at Netstal. All information is hosted in the secure Netstal cloud in Switzerland and is not accessible to third parties. User management and the granting of access rights are controlled entirely by the customer. A crucial prerequisite for the utilisation of AnalytiX is that injection moulding machines are equipped with the ‘iOT Ready Package’. The package comprises the NRS Connect module (Netstal Remote Support) and Euromap 15 interface. A machine’s connection to the Internet is facilitated either via cable (LAN) or wireless (WIFI, 4G). The basic version of AnalytiX itself is available free of charge as an app for iOS or Android. Fee-based subscriptions allow the functional scope to be exibly adapted to meet specic requirements. www.netstal.com info@hasplastik.com Tel: +90 212 695 50 00 Fax: +90 212 694 97 24 100815dmyR .com AnalytiX enables Netstal users to monitor their key injection moulding data, anytime, anywhere.","@ID":67}, "TRADE SHOW PREVIEW PETplanet Insider Vol. 19 No. 05/18 petpla.net 54 TRADE SHOW PREVIEW 54 Next generation stretch-blow moulder Since commencing production in 2010, 1Blow has been producing next generation stretch-blow moulding machine ideally suited for the custom PET bottle converter. And, in 2018, these limits are said to be pushed further with the commercial launch of the new 4LO stretch-blow moulder. The 4LO is built upon the same, efcient virtual-rotary platform that has been commercialised in numerous industrial applications around the world over the last six years. At its core, the 4LO possesses all of the superior 1Blow machine features and benets. S14089 TUNING UP YOUR PRODUCTION Mould & Matic Solutions GmbH Ziehbergstraße 2 4563 Micheldorf AUSTRIA T +43 7582 617 60-0 VѝJL'TV\\SKHUKTH[PJ JVT www.mouldandmatic.com LIVE ON DEMONSTRATION NPE 2018 7–11 May , Orlando, FL USA Hall B, W2727 BLOWLINER Injection Stretch Blow Moulding – customised to your needs Rotary motion is the key to achieving high-speed and low energy consumption in machinery through its unique Virtual Rotary Concept. Over 90% of the 4LO Machine Motions are rotary with a maximum mechanical output of 2,000bph and machine efciencies of +95% which are in-line. All of the main machine motions on the 4LO are affected by servo motors. Known for their repeatability and reliability, servo motors are most energy efcient motion system. 1Blow said that comparative operational testing to similar sized competitive machines has demonstrated that their machines can use up to 60% less energy and they are said to be the cleanest and quietest stretch-blow moulding machines. The 1Blow clamp format and stretch-rod pitch were designed for all blow mould formats currently being used. This research, combined an open architecture format allow 1Blow machines to accommodate blow moulds from virtually all other competitive SBM machines on the market. This ability allows customers to utilise existing blow moulds on a 1Blow machine, some of the company’s customers are using two or three different blow moulds. The 1Blow can be congured to accommodate the most widely manufactured and lowest cost blow moulds available. The 4LO was designed to minimise the number and quantity of change parts with the goal of reducing format costs for converting customers. Another benet of minimising the number and quantity of change parts is that it takes less time to do a machine changeover in some cases the machine has 50% less change parts. Despite its compact footprint, the 4LO has superior internal accessibility for technicians. Virtually every external body panel of the machine is actually a door which opens completely. The Virtual-Rotary Concept is spatially efcient and provides many open areas inside the machine large enough to comfortably accommodate a technician. Four technicians can be inside the machine at the same time. The 4LO machine goes to the Next Generation with its platform’s ability to accommodate all of the ve key technology kits with a maximum mechanical output of 8,000bph. 1Blow said that this is perfectly suited for the both the custom bottle moulding demands and production outputs of the North American Market. The ve key technology kits are: South Hall 14089","@ID":56}, "BOTTLING / FILLING PETplanet Insider Vol. 19 No. 05/18 petpla.net 37 BOTTLING / FILLING 37 important to us; it was also essential that we could fully rely on the technology to generate aseptic production conditions,” emphasises production manager Milka Tomanović. This quickly narrowed down the number of possible manufacturers. Nenad Delovski, head of the KHS ofce in Belgrade, had long been in touch with Nectar. “Five years ago we attended an aseptic presentation at the KHS factory in Bad Kreuznach together,” he remembers. “Since then we’ve been in constant contact, both locally and at various trade shows.” In the meantime the customer had become convinced that the high standard it required for its own products could only be achieved by using equipment of an equally top quality. This is even more important when it comes to securing a permanent supply to the European market. Above and beyond the basic requirements, the many opportunities offered by the system, its control setup and maintenance program and – above all – the recommendations from other companies ultimately persuaded Nectar to work together with the systems supplier. “With the new Innosept Asboll ABF 711 C Nectar has the rst aseptic ller of this kind for the production of fruit juice in all of Serbia,” explains Delovski – more than betting for the biggest fruit processor in the whole of southeast Europe. Boosting efciency The line has a capacity of 12,000bph and processes 500ml, 750ml and 1.5l PET bottles. Nectar not only invested in a ller but also in a stretch blow moulder by seizing the opportunity to acquire a used, fully overhauled system from KHS. Including all air conveyors, discharge to the packaging and palletizing section and an Innocheck FHC ll height control system the investment came to about €3.5 million – which Nectar believes is money well spent. What Tomanović particularly appreciates about the cooperation with KHS is the teamwork Nectar enjoys with KHS’ competent engineers. “These people share their knowledge with the customer,” she smiles. “This gives us security and the good feeling that we can easily clear up any problems which might arise in a straightforward manner.” Tomanović is also very pleased with the result. “With our new line we’ve been able to greatly boost our efciency – on the one hand thanks to the much higher capacity than on the old line and on the other through a reduction in downtime and larger production series.” www.khs.com Three questions for: Čedo Praška, director of Nectar What’s your company philosophy? Ever since its founding Nectar has attached great importance to product development and ensures that it produces consistent top quality. The growing enthusiasm of our consumers proves that we’re on the right track. What makes your company and your products so distinctive? The Nectar company is distinguished by its employees – especially by their expertise and high level of commitment. Our products are convincing not just thanks to their high standard but also through the wide range we offer, which includes something for everyone. What plans do you have for the future? We’ve made it our mission to become the market leader in the production of organic foods – and not just of beverages. We’re thus planning on making further investments and launching new packaging formats. We also want to offer consumers new products for all kinds of lifestyles, such as organic smoothies for people out and about and balanced breakfast snacks.","@ID":39}, "EDITOUR PETplanet Insider Vol. 19 No. 05/18 petpla.net 29 EDITOUR 29 Expanding PET business March 2018 We met: Kresten Hestehave, Vice President, Bomatic No, it is not the Vikings who have been running the Bomatic company in the picturesque city of Temecula, CA, over three generations since 1969. It is the Hestehave family from Denmark whose great enthusiasm and innovation have been instrumental in making US$20m in stretch-blowing moulding of containers, 70% of which is purely PET business. The company was originally set up as a mould maker. Blow moulding started in 1971 with manufacturing pill dispensers, made from polyolen. Nowadays, their PET processing is a two-stage process. The rm has been producing preforms, mostly in-house, since 2007. The mainstay was a Husky system which has now been supplemented by another 72 cavity line. A Cincinnati Milacron from the early days, built in 1981, is also still chugging along in the production of special preforms. The company started with linear systems, both 2 and 4 cavity to get their start in stretch blow-moulding. This is where Kresten Hetehave, Vice President comes in, having enhanced his machine capability with a new Tech Long CPX D06 stretch-moulding unit. This will make his business more efcient and produce at higher rates. And as things have all gone so well, Kresten will be getting another Tech Long machine within the next few months. The mould business has come on a lot since its early days. The company produces its stretch-blow and extrusion moulds in-house - allowing their customers to get to market faster. About 120 cavities come out of production each year. Kresten Hestehave sees himself as a one-stop provider. He helps to develop bottle designs, prototypes and pre-series for his customers as well, of course, as enhancing production. The drinks’ industry is currently his chief customer, although he would like to extend his client base to the cleaning and auto-care sectors. www.bomatic.com Tour Sponsors: Save RAW MATERIALS reduced plastic volumes Save ENERGY less energy consumption Save TROUBLE more quality and higher performance, guaranteed by a sole supplier Full INSPECTED online quality control / stand alone With Sacmi, the beverage specialists are always at your side. With our unbeatable technological know-how and continuous research we are creating new containers and closures designed to ensure outstanding performance. The new IPS injection system for preforms and the CCM compression press for caps, fully designed and built by Sacmi, allows for large-scale production with considerable advantages in terms of efficiency and flexibility. The outcome? Reduced plastic volumes, less energy consumption and lower running costs. All in a bottle: the one you’ll soon be making. Preform & Closure technologically together Kresten Hestehave, Vice President Bomatic, in conversation with PETplanet","@ID":31}, "MATERIALS / RECYCLING PETplanet Insider Vol. 19 No. 05/18 petpla.net 20 are better at source separation. Soft plastics are only recycled in small quantities in Australia. Polystyrene use is rampant, even in food packaging. China just stopped accepting Australian co-mingled recyclates, which caused a ‘recycling crisis’ in Victoria, where councils are telling people to ‘not recycle so much’. They don’t have anywhere to put those materials and might have to dump it in landll. I can’t imagine that would happen in Germany. On the more positive side, there is a massive grassroots movement underway to refuse-reduce-reuse. Australians are out there, cleaning up, opening repair cafés, going plastic-free in July, adopting a zero-waste lifestyle, restaurants are replacing plastic straws, and so on. I cannot keep up with all the Plasticwise, War-on-waste and Boomerang Bag groups popping up everywhere – all run by volunteers. I don’t know if that is happening at this scale in Europe; maybe European governments are doing more to reduce the impacts of plastics? PETplanet: With what difculties is the topic of plastics and plastics recycling associated in Australia, e. g. in terms of the sovereignty of the individual Australian states, for example? Annett Finger: What gets accepted for recycling, what goes into landll and what attracts a refund differs not only between states, but between councils. It is utterly confusing and frustrating. My own council, the City of Yarra, is probably one of the best in the country, they have a depot where you can drop off all sorts of materials for recycling: soft plastics, polystyrene, old X-rays, oppy disks, electronic goods, books, batteries and so much more. But still, the waste bins in my apartment block, just 200m from that depot, are lled with those materials. Next year, all the states other than Tasmania and Victoria will have a 10 cents refund scheme for containers. But there are differences in the way they are managed in each state. How much easier and cheaper would it be if we had a national system? PETplanet: In your opinion, how does the public feel about recycling in comparison with other countries? Annett Finger: People everywhere hate wasting resources and seeing their parks and waterways contaminated with litter. Australians widely support recycling but most are unaware that so much of it is/was sold to be processed overseas. Now that China has slammed their door shut on co-mingled recyclates, there is an opportunity to improve this ‘out of sight – out of mind’ mentality. Creating onshore recycling facilities will reduce carbon miles and create jobs. I’m not sure how Australian attitudes compare to European. How well would the Swedish system of separating out into 10 or so classes of materials be followed by Australians? I fear many would deem this too much effort at rst. But as I said earlier, there are many who focus on refusing and reducing. When I visit Germany I notice how over-packaged food and other consumer items are and how desensitised people are to singleuse plastics. This might be because they trust in effective recycling. Yet, I believe that recycling is not the ultimate answer to combating marine plastic pollution. PETplanet: Let’s turn to the topic of drinks. PET is the omnipresent form of packaging for drinks bottles here in Australia; some 17 billion plastic bottles are used here in Australia per year. As far as I am aware, if a deposit system were introduced here in Victoria an estimated 3 billion bottles could be sent for recycling. Some of the other Australian states and territories have already created successful deposit systems for the recycling of PET bottles and cans. Why hasn’t Victoria yet introduced such a scheme? Annett Finger: South Australia has had it for 40 years, Northern Territory since 2011, New South Wales since December last year. Queensland will start it a scheme in November 2018. Western Australia and Australian Capital Territory have not announced start dates yet but they are likely to be in 2019. The container deposit scheme has wide support in the population but it has been rejected by successive Victoria governments. The Napthine (Liberal) government promised to introduce a CDS if reelected in 2014 but was voted out. It’s hard to say where the opposition to CDS in Victoria comes from but Australia’s leading recycling company, Visy, has actively advocated against CDS in the past. They argued that it would have negative impacts on kerbside recycling and reduce their revenue. PETplanet: When is the implementation expected to take place in Victoria, and what is Boomerang doing in this respect? Annett Finger: We are hoping for an implementation of CDS in 2019. We will continue to raise awareness of and support for CDS in Victoria by collecting signatures, being present in social media and at local events. Next month, we are touring regional Victoria with the Big Bottle: a 4m Coke bottle with CDS slogans. The idea is to visit regional towns, connect with community and charity groups and talk to their local Members of Parliament. We will conduct clean-ups of drink containers on the road, store the containers inside the Big Bottle and deliver them at the end of the trip to the Victorian premier’s ofce. PETplanet: What projects and ideas do you want to address and implement in the future? Annett Finger: I would like to be involved in extending/improving onshore plastic recycling in Victoria. Furthermore, I’m passionate about directing our society towards zero waste. Boomerang Alliance have started a campaign called ‘Communities taking control’ in other states and I would like to do this in Victoria. There are so many great initiatives under way. Together, we can reach out and convert more people to a healthier lifestyle that is better for our oceans. www.boomerangalliance.org.au https://chuffed.org/project/big-bottle www.youtube.com/ watch?v=cJpD4DXwbv4&t=1s","@ID":22}, "11 NEWS PETplanet Insider Vol. 19 No. 05/18 petpla.net New technology converts PET waste back into virgin grade material Unilever has announced a partnership with start-up company Ioniqa & the largest global producer of PET resin Indorama Ventures to pioneer a new technology which converts PET waste back into virgin grade material for use in food packaging. Ioniqa has developed a proprietary technology that is able to convert any PET waste - including coloured packs - back into transparent virgin grade material. The technology has successfully passed its pilot stage and is now moving towards testing on an industrial scale. This new technology takes non-recycled PET waste - like coloured bottles - and breaks it down to base molecule level, while separating the colour and other contaminants. The molecules are converted back into PET which is equal to virgin grade quality at Indorama’s facility. If proven successful at industrial scale, in future it will be possible to convert all PET back into high quality, food-grade packaging. The three partnering companies believe that this fully circular solution could lead to an industry transformation, since the new technology can be repeated indenitely. www.unilever.com www.ioniqa.com www.indoramaventures.com Cannabis Science acquires Bottle It Inc. bottling manufacturing facility Cannabis Science, Inc. (CBIS), a U.S. company specialising in the development of cannabinoid-based medicines, announced the acquisition of Bottle It, Inc., located in Corona, California. Bottle It, Southern California’s premier manufacturer of PET bottles and containers, supplies preform and PET bottles to customers throughout North America and internationally. Established in 2014, Bottle It has reported approximately $1,500,00.00 in revenues each year for 2016 and 2017 consecutively. “Cannabis Science now has the in-house capacity to manufacture PET bottles and containers for Cannabis Science’s consumer products, as well as to manufacture bottles and containers for other manufactures of beverages, speciality waters, foods, cosmetics, and other products globally. This creates an important new revenue stream for Cannabis Science,” stated Raymond C. Dabney, Cannabis Science’s President & CEO, and Co-Founder. www.cannabisscience.com CEO Raymond C. Dabney at the CBIS Bottle It manufacturing plant","@ID":13}, "9 NEWS PETplanet Insider Vol. 19 No. 05/18 petpla.net WikiPETia.info New contents at wikipetia.info China’s bottled water market on decline, India on the rise While China remains one of the biggest bottled water markets globally, the latest research from global market intelligence agency Mintel reveals that retail volume sales are on the decline. In 2017, China’s bottled water market was forecast to reach sales volume of estimated 27 billion litres, up from 25 billion litres in 2015. However, sales volume growth has dipped from 5% in 2015 to 4.2% in 2017, and is predicted to fall further to 2.8% by 2021. In what is the world’s most populous country, the expansion of bottled water has been relatively fast, with per capita consumption rocketing from just 5l in 2007 to 20l in 2017. This is relatively low compared to more developed markets like Mexico (222l per capita) and the US (120l per capita). “Due to trends in premiumisation, China’s bottled water industry has seen rapid growth over the past decade. However, it was only a matter of time before market saturation started inhibiting growth potential for bottled water brands, especially amidst intensied competition in the wider beverage market. With more Chinese consumers drinking bottled water, brands are under pressure to differentiate themselves from rivals. Despite a saturated market, innovation opportunities still exist, and premiumisation remains key for value market growth,” said Loris Li, Associate Director, Food and Drink, at Mintel. Due, in part, to more premium options, Mintel research shows that half (50%) of Chinese consumers aged 20-49 drank unavoured sparkling water in 2016, up from 29% in 2015. Furthermore, three in ve (60%) drank avoured sparkling water in 2016, an impressive increase from 30% in 2015. Bottled water markets Bottled water remains one of the strongest performing sectors of the global non-alcoholic drinks market. The US is currently the largest bottled water market, with volumes forecast to reach 39 billion litres in 2017. The US is followed by Mexico (28.7 billion litres), China (27 billion litres), Indonesia (16 billion litres), and nally Germany (12 billion litres) - rounding out the list of top ve bottled water markets globally. India’s bottled water sector outpaced growth of any of the other major global markets between 2016 and 2017, recording an impressive 19% growth, although from a low base (4.8 billion litres in 2016 to 5.7 billion litres estimated in 2017). Also among the top ve fastest growing bottled water markets are Indonesia (13.2%), Vietnam (11%), the Philippines (10.6%), and finally South Korea (9.9%). www.mintel.com Package Integrity Knowledge Platform Ametek Mocon, a global leader in gas measurement technologies, announces the launch of a new website focused on packaging science, applications and standards. The website was created to assist packaging professionals in making better barrier material choices and design decisions. PackageIntegrity.com provides a platform for professors and other packaging thought-leaders to collaborate, learn and share packaging best practices. The website will feature articles, white papers, case studies, reference tools and research studies contributed by academics and industry peers. Readers and contributors will have the ability to share content and comment on social media. Designed to be a collaborative community, the website welcomes academic and industry researchers, packaging scientists, quality assurance/control technicians, and those interested in packaging integrity measurements to explore and contribute. www.packageintegrity.com Construction of a new factory building for caps and closures in Japan Nippon Closure Co., Ltd., a consolidated subsidiary of Toyo Seikan Group Holdings, Ltd., is constructing a new factory building on the site of its Japanese Komaki Plant, aiming to start operation in January 2019. Nippon Closure states that the decision to build a new factory to manufacture plastic closures has the purpose of securing manufacturing space which is scalable in response to growing plastic closure market, of reducing distribution cost through the realignment of production facilities producing plastic closures for beverage, and of improving productivity by introducing automated and labour-saving equipment. The total investment for the 13,200 building are is approximately 9.8 billion yen. The new facility is expected to start operation in January 2019. www.tskg-hd.com Petainer expands manufacturing capacity Petainer is expanding its operations in Europe and Russia to meet demand for its products and ensure it can support future growth. The company is building a new warehouse at its Aš plant in the Czech Republic to provide more on-site storage capacity to meet its current and future ambitious growth plans while also improving sustainability. The introduction of the new warehouse will remove the need for 1,740 truck deliveries per annum, reducing Petainer’s carbon footprint signicantly. The development follows a similar initiative at Petainer’s Lidköping plant in Sweden, where a new warehouse was built next to the factory to provide more storage capacity, reducing logistics and carbon footprint. At its Russian plant in Klin, Petainer has invested in injectionmoulding capability to localise supply of preforms for the Petainer keg. The Russian plant will also have additional warehouse capacity to improve supply chain efciencies. www.petainer.com","@ID":11}, "BOTTLE MAKING 31 PETplanet Insider Vol. 19 No. 05/18 petpla.net Stretch Blow Molding, part 9 - Oven section, transfer functions Machine details by Ottmar Brandau Ottmar Brandau has newly revised his book “Stretch Blow Molding”, rst published by hbmedia/ PETplanet Publisher, and now re-issued in a third edition under the Elsevier imprint. PETplanet Insider is publishing extracts from successive chapters in a series of articles. Different heating methods A completely different heating system has now been developed that uses microwave beams instead of infrared lamps (Fig. 4.5). Figure 4.5 Standard infrared emits favorable wavelengths below 1.5μm (1,500nm) only at high output rates of 3,500K whereas NIR delivers these over a larger range. Diagram courtesy of Adphos Group. Heating time is said to be around 3s, allowing the use of just 16 heating mandrels for an eight-cavity blow moulding machine compared to about 160 mandrels in a conventional oven system. This signicantly reduces changeover time for a different neck nish. Preforms absorb 95% of the microwave energy with excellent penetration independent of their colour, making fan cooling and equalisation time a thing of the past. Microwave stations are mounted in a rotating oven system rather than a linear one making the oven section very compact. Another advantage is that the neck nish does not need protection opening the door for improved wide-mouth container processing. A possible disadvantage is that proling the heat output is not possible. This means that the preform design has to be perfect so that an evenly heated preform yields a bottle with even wall thickness. This is an exciting step into lower energy consumption and better control over preform temperature and we will see how far it can go (Fig. 4.6). Figure 4.6: This system uses a rotary microwave oven system that drastically reduces heating time. Picture courtesy of Krones AG. product development caps & closures design high cavitation moulds multi-component moulds closure production systems after sales service competent – professional – inspiring Dr.-Walter-Zumtobel-Strasse 9 | 6850 Dornbirn | Austria | www.z-moulds.com NPE 2018 May 7th-11th meet us at booth S15070 Moulds at NPE 26mm 3-start water @ENGEL, booth W3303 @SUMITOMO DEMAG, booth W3045","@ID":33}, "imprint EDITORIAL PUBLISHER Alexander Büchler, Managing Director HEAD OFFICE heidelberg business media GmbH Bunsenstr. 14 69115 Heidelberg, Germany phone: +49 6221-65108-0 fax: +49 6221-65108-28 info@hbmedia.net EDITORIAL Kay Barton Heike Fischer Gabriele Kosmehl Michael Maruschke Ruari McCallion Waldemar Schmitke Anthony Withers WikiPETia.info petplanet@hbmedia.net MEDIA CONSULTANTS Martina Hirschmann hirschmann@hbmedia.net Johann Lange-Brock lange-brock@hbmedia.net phone: +49 6221-65108-0 fax: +49 6221-65108-28 LAYOUT AND PREPRESS EXPRIM Werbeagentur | exprim.de Matthias Gaumann READER SERVICES Till Kretner reader@hbmedia.net PRINT Chroma Druck & Verlag GmbH Werkstr. 25 67354 Römerberg Germany WWW www.hbmedia.net | petpla.net PETplanet Insider ISSN 1438-9459 is published 10 times a year. This publication is sent to qualified subscribers (1-year subscription 149 EUR, 2-year subscription 289 EUR, Young professionals’ subscription 99 EUR. Magazines will be dispatched to you by airmail). Not to be reproduced in any form without permission from the publisher. Note: The fact that product names may not be identified as trademarks is not an indication that such names are not registered trademarks. 3 PETplanet Insider Vol. 19 No. 05/18 petpla.net An Editour usually begins with a market overview interspersed with figures and background information, followed by a thoughtful look into the future. This time, by contrast, I found myself sitting in front of a blank screen because I had no idea what I should be writing about. The tour has been going on for some weeks now, the NPE show is almost upon us and we still do not have a clear picture of what is happening in the US drinks’ industry. At our editorial meeting, we joked about how to fill the required number of pages. Some not too serious suggestions ranged from “simply leaving them blank” to “colouring pictures”. Nevertheless, what follows are a few pages that serve as an introduction to the USA (see page 22) which I hope you will find interesting, even if what I have written is different from my usual style. My writer’s block was due to my inability to work out just what is going on in the USA at the moment, with increasingly critical voices being raised against plastics, accompanied by fanciful PET recycling quotas, punitive tariffs on packaging material and components, water shortages and contaminated drinking water in many parts of America. I outlined the reasons why any meaningful assessment of what might happen in the future is impossible at the moment. We will continue to collect figures and views during our tour and hopefully will be able to make a more informed prognosis in the summer. By then, we will have a better idea of what is happening in terms of punitive tariffs. At the NPE in Orlando in May, the Editourmobil and Bottle Zone will put us right at the heart of the North American plastics world, which will be hit just as hard by tariffs as the drinks’ industry. Here in our beer garden in the South Hall, drinking organic handcrafted beer from www.orlandobrewing.com, we can philosophise about the rights and wrongs of this world. As regards the quality of the beer, however, our visit to the brewery was very positive. Yours Alexander Büchler Dear friends of PETplanet Insider,","@ID":5}, "EDITOUR PETplanet Insider Vol. 19 No. 05/18 petpla.net 28 Durable bottles are back in fashion Boutique bottling Rivera Beverages, March 2018 We met: Mr Chris Solberg, General Manager Rivera Beverages from Garden Grove, California, is a ‘boutique bottling company’ that works exclusively with small to midsize high quality premium water brands. This is a growing trend in the USA. What a relief to go into the Rivera Beverages facility and nd actual quality water bottles that you can hold rmly in your hand and they do not crush or break when opened (spilling its contents all over your shirt, trousers or both). This trend has emerged in America, namely local premium water which, of course, comes in a high quality classic (durable) bottle with the classic heavy PCO 1810 cap. California has proven itself as the start market as the season here goes on throughout the year. On the east coast, the water market uctuates more, depending on the weather. Chris Solberg, General Manager of Rivera Beverages, tells us that Riviera bottles water on a contractual basis for premium brands. The rm choses to do business with this particular target group. Riviera produces and lls a variety of different styles of custommade bottles (all with the PCO 1810 neck nish) at their plant. Clients occasionally bring their own water with them. The furthest distance travelled is from Hawaii, to which it is then produced and shipped out under the “WAIAKEA” brand. It all started 12 years ago when the company was producing modest quantities for small private brands. Their customers included hotel chains among others. However, the premium brand business has become more and more prominent over the past ve years. Four years ago, in order to keep pace with increasing customer demand, Rivera invested in two new bottle blowing and lling lines from Tech Long. Riviera chose Tech Long because of the service, the quality of the equipment, and the support received. The old saying still applies today that the rst plant is sold by the seller and the rest by the service department. Riviera obtains its preforms primarily from Resilux in the USA. They have had mixed experiences with different preform suppliers resulting in too much variation in quality. The caps come from CSI. The bottles usually have a PCO 1810 cap on the neck, but can also sometimes have a PCO 28 ip top cap by using a second cap feeder. In short, this is a fantastic facility for this ‘boutique market’! www.rivierabeverages.com Tour Sponsors: Two eight-cavity bottle blowing machines supply both bottling lines. This unique water arrives in a tank trailer from Hawaii, is bottled at Riviera, then shipped to distribution centers. Chris Solberg, GM, Rivera Beverages, Garden Grove, California, USA.","@ID":30}, "69 BOTTLES PETplanet Insider Vol. 19 No. 05/18 Heat protection spray from dm “Long-haired girl”, a newly launched own brand from the German discount pharmacy chain dm, offers a young audience products and styling tips for long hair. A heat protection spray is included in the range. The two-phase product (one phase transparent, the other slightly red-coloured) is available in slim, clear 200ml bottles. The two phases must be mixed by shaking before applying to towel-dried hair. A lockable pump dispenser for application to the hair and a circulating paper label complete the packaging. www.dm.de Two-phase make-up remover A t wo - phase make - up remover for eye-lashes and eyebrows is sold to a young target group by new brand “#b.e. Routine” with the tagline “Can’t take my eyes off you”. The cleanser promises intense cleaning and care and contains papaya extract and allantoin. The clear bottle contains 125ml and clearly shows the two phases. The bottle must be shaken before application. Under the screw cap, an insert with a dosage opening for applying the remover is pressed into the container opening. A self-adhesive label offers product and handling information. www.beroutine.de","@ID":71}, "TRADE SHOW PREVIEW PETplanet Insider Vol. 19 No. 05/18 petpla.net 53 TRADE SHOW PREVIEW 53 Small and nimble injection-stretch-blow moulding machine Special formats for PET bottles Sipa, one of the world’s top suppliers of equipment for production of PET preforms and bottles, will show the latest version of its ECS SP injection-stretch-blow moulding (ISBM) system at NPE2018. The company, headquarted in Vittorio Veneto, Italy and with a major mould refurbishing center in Atlanta, GA, will also be illustrating its full range of equipment for one- and two-stage production of PET containers, its expertise in bottle design, mould development and construction, its equipment for bottle lling and packaging, and nally its turnkey system capabilities. Visitors to the Sipa booth will be able to nd out about just-introduced improvements to the ECS SP system.The Sipa ECS SP Hybrid system is designed for production of specialty products such as containers for cosmetic, dairy, personal care, pharmaceuticals products, and spirits, mainly encountered in sizes between 10 and 50ml. Larger size containers as wide mouth jar can be accommodated to if needed, up to 12.5l. I The systen can produce all sorts of shapes thanks to 40bar blow air pressure, within its chosen size range. Because production runs for these types of bottles are quite often fairly short, there is an important need to be able to change the injection and blow moulds quickly, so that down-time between runs is minimised. A new quick mould-change system on the ECS SP can slash changeover times by around a quarter. New features also add extra safety and user-friendliness for operators. With the words “circular economy” on everybody’s lips, Sipa will be talking about PET bottle recycling too. It will highlight Xtreme Renew, the system it co-developed with recycling technology specialist Erema, which enables direct processing of PET akes from post-consumer recycled bottles into food contact-compliant injection-compression moulded preforms in a fully integrated process. On Wednesday, May 9, at 12.15, Sipa’s General Manager Enrico Gribaudo will use his presentation during the Bottle Zone Technical Forum to addess PET preform manufacturing in the era of the circular economy, and how it can be accomplished in a nancially viable way. He will talk about how to use the “Three Rs” – Reduce, Reuse, Recycle – while dropping carbon footprint, saving energy and improving part quality. On Tuesday, May 8, at 12.15, Morris De Marchi, PET Packaging and Tooling Life Cycle Service Director at Sipa North America, will address the forum on the importance of a fast and costeffective response in the plastics industry. He will show how local refurbishing and conversion centers can provide a fast and efcient way of upgrading production without having to make a major investment in completely new tooling. Sipa North America has been ramping up its mould refurbishing activities in Atlanta since it moved its headquarters there in 2012. Atlanta serves customers in the east of the continent, while customers on the Pacic Coast are catered for from an operation in Los Angeles, Ca. Sipa has also been increasing its capabilities at its principal site in South America, in São Paulo, Brazil. www.sipasolutions.com South Hall 17085","@ID":55}, "BOTTLING / FILLING PETplanet Insider Vol. 19 No. 05/18 petpla.net 39 For the production and lling of PET bottles for ISM’s Cool Heaven water and Frutop juices in 500ml bottle format, the Sidel Matrix blow moulder was supplied to the Peruvian manufacturer in a Combi conguration, a competitive alternative to traditional lines. By integrating blowing, lling and capping, the Sidel Matrix Combi optimises line layout with a smaller, more compact footprint and ergonomic design. Additionally, by eliminating conveying, empty bottle handling, accumulation and storage, it ensures greater levels of hygiene. The solution offers an increase of up to 4% in efciency levels compared to standalone machines – featuring fewer pieces of equipment – and contributing to a reduction in operating costs of up to 12%, says the company. The Sidel Matrix blower offers 200 possible congurations to t production needs; it also manages to reduce the consumption of electricity, air and materials as well as downtime. Featuring a minimal environmental footprint, the Sidel Matrix blower with its patented ECO oven technology offers, according to the company, the best oven efciency on the market, reducing preform heating time, requiring fewer heating modules and lamps and thereby cutting electrical consumption by up to 45%. Furthermore, savings in compressed air of up to 30% are possible. Production of ISM’s bottled water and Frutop drinks naturally requires lling conditions of the strictest hygiene. The ller supplied to handle both water and fruit juices was a Sidel Matrix SF100 FM, which offers optimum uptime, high productivity, fully automatic changeovers and 30% less downtime needed for maintenance. Featuring magnetic owmeters, this solution is able to ll still beverages with precision, such as water, juices, nectars, soft drinks, isotonics and teas. Covering only the space around the valves and taking up 80% less space than traditional enclosures, the solution with its compact lling environment improves food safety and reduces the need for chemical agents. The solution supplied for ISM features nitrogen dosing, reducing the amount of oxygen at the top of the bottle and thereby ensuring the bottles are evenly lled, a feature that is particularly important in the case of juices. Use of nitrogen also improves the performance of the bottle throughout the whole value chain, offering greater rigidity and enhanced resistance to stress-cracking.","@ID":41}, "PETplanet Insider Vol. 19 No. 05/18 petpla.net 71 BOTTLES Promotional pack from bizzl To entice consumers in the drinks market to make a spontaneous purchase so as to enlarge the customer base or launch a new product, the Hassia Group brand “bizzl” is offering a three-pack of its lemonade/cola drinks at an attractive price. The different varieties are grouped in various ways and the consumer can select the mix most suitable for them. The image shows a three-pack with bizzl Passion, bizzl Caribic and bizzl Cola-Mix. The multi-use 1l bottles are typical of the brand with a foil label and a screw cap. The bottles are held together with a cardboard strip from which the individual bottles can be easily removed. www.bizzl.de Syrup with tea and lemon In the Czech Republic, drinks manufacturer Amin is selling a syrup for making up iced tea with a lemon avour. The concentrate comes in a square 600ml bottle with rounded corners. Horizontal ridges right around each corner stabilise the transparent bottle and make it easy to grip. The circulating paper label is printed with day, month and year and the best before date is indicated by a punch mark. The bottle is sealed with a white screw cap with guarantee band. Introducing the latest innovation in Tech-Long’s complete line of liquid packaging solutions: the CPX2 PET Stretch BlowMolder – featuring rotary processing performance in a stationary design. • Compact design, 2-cavity solution • Servo stretch • High performance, low energy usage • High versatility • Standard, oval shaped bottles • Application range from150ml to 1 gallon","@ID":73}, "TRADE SHOW PREVIEW PETplanet Insider Vol. 19 No. 05/18 petpla.net 57 Trendsetting technology for preform inspection Since its very rst participation in NPE, Intravis has been using the biggest plastics exhibition in North America to present its innovations to the public. This time, the company states that it is going to exhibit inspection solutions in their own booth, as well as in partner booths, that have the potential to revolutionise quality control in the plastic packaging industry - both in the short term and long term. West Hall, Level 2, 3391 Premiere: Innovation in preform inspection 17 cameras and up to 72,000 preforms per hour within a space-saving footprint of only 3m² (32 ft²) – these are the main features of the brand new PreWatcher 4, going public for the rst time. Its extensive inspection possibilities make it the perfect choice for all common types of preforms, e.g. for beverage, milk or cosmetics preforms with a narrow overhanging support ring - no matter if they are transparent, intensely coloured or even opaque. Thanks to its innovative adjustment approach, exchange parts become unnecessary. With its vast amount of individual inspections, the PreWatcher 4 leaves no inspection criterion to be desired and scores with its accuracy. Its numerous cameras and viewing perspectives gather more data to enable precise decisions. Operation of the system is further simplied with easy collection of reference samples, as well as the possibility to sort and arrange the preforms for further processing via an outfeed rail. Turnkey smart-camera-solution premieres in North America Another innovation to be exhibited in North America for the rst time is the IntraOne. With this system, Intravis offers a new single-camera-solution for bottles, closures and preforms as well as labels and decoration. The IntraOne is a turnkey system combining the advantages of a smart-camera with the well-established IntraVision software, and it will be available for demonstrations in the Intravis booth. Complete solutions for closure inspection at partner booths Intravis will demonstrate additional inspection solutions at their partners’ booths. At the Engel booth (W3303) the CapWatcher III with integrated print inspection for the control of printed closures will be presented, along with newly developed cross conveyor and Z-cooling-conveyor now available from Intravis. A second CapWatcher III can be found at the booth of Sumitomo (SHI) Demag (W3045). The highlight: Intravis’ IntraVisualizer software, which collects data, analyses trends, and even offers Estimated Time to Failure (ETF) warnings. This software allows operators to adjust parameters before defects occur, reducing scrap and signicantly increasing productivity. Space-saving inspection solution for pharmaceutical bottles Compact, comprehensive and costeffective – this is how Intravis describes the new product for bottle inspection, the SpotWatcher S. Within a footprint of 1m² (11ft²), this system offers high capabilities for the quality control of bottles. The SpotWatcher S is based on Intravis’ newest software version, which offers two particular highlights: Extensive user administration that allows the operation of the system to be adjusted to the individual requirements of each user, and an integrated reporting tool that records all parameters applied. These features enable customers to fulll GMP Guide Annex 11 and 21 CFR Part 11 regulations. With its small footprint and full scope of inspection, the SpotWatcher S offers ideal inspection capabilities for pharma bottle producers. www.intravis.com","@ID":59}, "TRADE SHOW PREVIEW PETplanet Insider Vol. 19 No. 05/18 petpla.net 52 Growth, investments, product news and Industry 4.0 Over the last ve years, the Piovan Group has recorded a signicant growth, as a result of acquisitions and the opening of new companies. In 2017, the group achieved a total turnover of €211m euros: its best-ever result, supported by a positive outlook for the current year along with an ambitious plan of investments. West Hall, Level 2, 1923 In the U.S., with its company UnaDyn, Piovan is looking forward this year to the completion of the hightech plant in Fredericksburg, VA. An important investment to support the development projects in North America. With this positive approach and with the brands of Piovan, Una-Dyn, Aquatech Fdm and Penta, the Piovan Group is attending this year’s NPE. Starting with Piovan, the new line of Quantum batch blenders – entirely made in the U.S. – expands further to cover applications requiring a very high degree of accuracy, along with the easylink automatic distribution solutions coupled with the Pureo lterless receivers. The complete line of granulators, Piovan branded, will be on display, including the models with the U&G disposable knives system, which allows signicant cost savings due to longer knife life with CPM10V tool steel. Under Una-Dyn brand, a wide array of drying systems fully equipped with loaders will be exhibited from Automate, the adaptive multiple hopper central drying system, to the energy efcient dryers of the Vantage series. A great deal of display will be given to Aquatech, the brand of the group for industrial cooling, which will show for the rst time in the United Stated: Easycool+, the new line of air and water-cooled chillers, along with Aryacool, the drycooler which can meet the needs of various industrial processes and DigitempEvo, the thermochiller unit for a exible heating or cooling solution. Nextherm is the absolute novelty for advanced mould temperature control. This system, Piovan claims, will signicantly reduce cycle time and guarantee a mould temperature that is accurate that waste is drastically reduced. As for powder and PVC treatment, visitors will see Fdm latest design solutions for precision blending and an innovative system by Penta, fully in operation, able to convey powders in a newly developed dense phase vacuum system which ensures a gentle handling of the most susceptible materials. Latest developments matching the Industry 4.0 requirements will be available at the booth on a special room equipped with touch screen monitors. Sound innovations in this respect will be represented by the launch of FACS 4.0, the state of the art and auxiliary equipment control and monitoring system, designed by Una-Dyn and the Winfactory 4.0, the Piovan’s supervisory software for the Smart Factory, OPC-UA compliant. www.piovan.com The Aquatech Araycool Drycooler and the Easycool+ Aircooled chiller will be shown at Piovan’s booth. Temperature control unit Nextherm by Aquatech","@ID":54}, "48 TRADE SHOW PREVIEW PETplanet Insider Vol. 19 No. 05/18 petpla.net South Hall 18155 South Hall 14053 Renewable-based products With North America set to become Clariant’s second largest global market by 2021 Clariant will zero in on the most relevant end-markets for North America’s plastics industry - transportation, packaging, healthcare, and industrial bres. Representatives from the Business Units Additives, Masterbatches and Pigments will be available discussing sustainable solutions for the industry. For example: Market-leading colours and effects for packaging, renewable-based products e.g. regional roll-out of rice bran waxes for automotive and E&E applications or “Future proofed” USP 661.1 compliant ingredients ready now to support the US pharmaceutical packaging and drug delivery device market ahead of May 2020. Other topics will be the support for the US’s growing electric car market by boosting performance, safety and aesthetics of plastic components and a host of textile solutions for carpets to bres for articial turf, seat belts and construction materials. www.clariant.com PET handleware production shifts into high gear The extrusion blow moulding of PET bottles integrating a true ow through handle identiable as #1 recyclable PET has long been a packaging goal for consumer products groups. The inherent challenge of parison formation with sufcient material hang strength resulted in the development of EBM-specic copolyester resins, such as PETG. Extrusion blow moulding grades of PETG have been commercially available for over 30 years, yet, unfortunately, these co-polyester materials are not readily managed in the established PET recycle infrastructure due to their lower drying and melting points. Several major PET material suppliers have recently developed high IV PET grades with hang strength, toughness and reduced crystallisation rates for extrusion blow moulding. In order to optimise the PET processing technology, Bekum partnered with both the PET material suppliers and a major North American converter to rene the EBM PET process to meet the PET handleware goals of the brand owner. From extrusion system design, mould construction, material drying, regrind reuse, and in-machine deashing, the EBM PET process was thoroughly analysed and validated. 2017 saw the production commercialisation of ten Bekum HYBLOW 407D machines for the round-the-clock production of handled PET beverage bottles in fully #1 recyclable PET. www.bekumamerica.com Total bottle inspection system Air Logic Power Systems (ALPS) has joined forces with Swiss company IMD Ltd. to provide the blow moulding industry with the rst Total Bottle Inspection Solution. ALPS, a leader of high-speed leak testing equipment has combined its leak testing technologies with IMD’s state of the art IMDvista Vision Inspection Systems. By integrating both leak testing and visual inspection methods into one machine, the new Total Bottle Inspection Solution provides a range of quality-control checks, including the detection of leaks, contamination, cosmetic defects, measurement, ovality or other material issues. The combined, linear system can be integrated directly into the production line and enables containers that pass the set criteria to continue down the conveyor, while defective bottles will be rejected into a separate chute. Flex Pitch: multi-moving head leak tester with integrated visual inspection The ALPS Flex Pitch is a fast, tool-less, multi-moving head leak tester with the exibility to test a wide range of empty containers. The machine operates without a timing screw, reducing cost for tools and changeover time radically. The innovative new design maximises exibility as test heads can be pre-set to the required pitch enabling fast changeover between containers of varying diameters. The built in visual inspection unit enables customers to inspect the bottles at the same time, providing more efcient quality control checks. The machines on display will be the SC Linear, a general-purpose, single-station leak tester with an integrated table top conveyor and the NexGen 10, a rotary leak tester which handles high-speed applications up to 1,200 bottles per minute. www.alpsleak.com www.imdvista.ch ALPS South Hall 15045 IMD booth South Hall11057 Separating single-layer PET trays from PET bottles Tomra Sorting Recycling will showcase its latest plastic sensor based solutions including the new Sharp Eye technology, the new Laser Object Detection (LOD) system as well as the Autosort Flake. Tomra’s new Sharp Eye technology is for separating single-layer PET trays from PET bottles. This enhances the previous capability of its Autosort machine to separate multilayer trays. The processing is commercially signicant because small critical differences in the chemical properties of PET food trays and PET bottles mean that they have to be separated for equivalent-product recycling. Articial intelligence embedded in Tomra systems enables seamless analysis of sorted products, making the future plants even smarter. Tomra will introduce the new Laser Object Detection (LOD) system. Featuring laser technology that sorts based on the feed material’s spectral and spatial characteristics, new LOD technology detects material that near infrared technology (NIR) is incapable of identifying such as black plastic, glass and waste items. Unlike alternative methods that demand high-energy draw, the LOD system cost-efciently identi- es and sorts black objects from a variety of applications, boosting product quality. Foreground detection technology ensures the laser beam only identies material above the belt, reducing background noise and giving operations the exibility to use any type of belt feeder for the circuit. Tomra says that with this new technology customers can easily upgrade their installed Autosort’s and Finder’s for multiple applications. The result is an expanded application portfolio with a small initial investment. Autosort Flake is said to be the rst machine to successfully and simultaneously combine detection of colour, enhanced material information and metal objects. The result is a high purity and yield with one machine. Tomra Sorting’s Flying Beam technology, allows Autosort Flake to provide customers with continuous calibration translating into substantially, less downtime and greater output stability. Fourline technology leads to low maintenance needs and low energy consumption, conrming that it is indeed possible protect environmental resources while reducing operating costs. www.tomra.com South Hall 23202","@ID":50}, "67 ON SITE PETplanet Insider Vol. 19 No. 05/18 petpla.net High-capacity lling line for Hilwa mineral water Al Jouf Healthy Water in Saudi Arabia is relying on Sipa for its latest line for bottling Hilwa mineral water. The company, located in the city of Domat Al-Jandal in the Al Jouf area, obtains its water from a unique underground well, where the proportion of salts and the balance of water components are ideal for direct drinking without the need for any desalination or other treatments to remove contaminants. Domat Jandal is the oldest city on the Arabian Peninsula. It contains ruins and landmarks dating back to the seventh century BC. The area is also characterised by the cultivation of palm and olive trees, as well as heavy monsoon rains. The area is considered protected and far from any sources of pollution. Providing demanding customers across the peninsula with high quality water for 35 years now, Al Jouf Healthy Water has been developing its production capability ever since its establishment in 1982. Sipa has now become a partner, with the installation of a new high-capacity lling line. The Sipa line incorporates an SFR 24 rotary stretch-blow moulding unit directly connected in a Sincro Bloc to a Flextronic S 80.25 electronic volumetric gravity ller. Downstream from this Sincro Bloc is a CIP Unit 1S35, level, cap and label inspection systems, an Opera 400 33T labelling unit, an Altair 40 wrap-around packer, a Genius Active Layer palletiser, and nally an SPF stretch wrapper. The complete line has already proved itself with high productivity and reliability. It produces and lls bottles ranging in size from 200 to 600ml at a rate of 50,400bph – independent of bottle volume. The line also stands out for its low operating costs and exibility. With its special handling system that adapts to different necks, the Sincro Bloc requires little time for conguration changes when switching between bottle sizes. The rest of the line is designed with the same concept of fast and reliable changeovers. The entire Sipa line is designed to handle lightweight bottles, using the SincroBloc’s neck handling system which does not apply pressure to the container. The whole conveying system is designed keep the bottles in the best possible condition. And nally, the line incorporates the latest technology in palletising, with the Active Layer system. This brings a gentle touch to layer formation, ideal for lightweight bottles in shrink lm. www.sipa.it ONsite STAND S10196 – ONE for ALL","@ID":69}, "TRADE SHOW PREVIEW PETplanet Insider Vol. 19 No. 05/18 petpla.net 51 Custom-tailored inspection equipment Torus Measurement Systems will be visiting the USA this year and exhibiting for the very rst time at the NPE exhibition in Orlando. The Torus team will be offering regular demonstrations and information on Torus’ latest plastic packaging innovations, which are used extensively within industry for dimensional and destructive testing to meet the quality demands of customers. South Hall 10073 Torus pride themselves on their customer-centric philosophy and understand the importance of working together with customers to design and manufacture inspection equipment to suit their exacting requirements. The B302 Thread, Body & Thickness (TBT) gauge for plastic bottles and preforms was developed as a result of these customer discussions and combines the proven inspection capability of Torus’ B300 Bottle Wall Thickness gauge with the advanced technologies of the B305 preform gauge. The B302 is will be shown at NPE for the very rst time in America. The 6-axis TBT gauge combines automatic thread start and bottle alignment routines with the most recent non-contact confocal white-light technology to measure wall thickness, and the latest vision technology to measure neck nish, body dimensions and perpendicularity. This gives the operator the ability to take unrivalled, non-contact dimensions in one single operation without operator inuence. Thus providing savings in labour, time and material costs whilst at the same time creating a new standard for plastic packaging quality control. The B302 is designed with extended measurement range to deal with the latest industry needs with scope to measure lled and closed containers in round, oval, square/rectangle and non-symmetrical shaped bottles. Measurement results are presented to the operator in a clearly structured interface and can be exported to many leading data acquisition systems. The team will also be able to offer detailed information on the other equipment in the range – the B300 Bottle Wall Thickness gauge, B301 Semi-Automatic preform gauge, B303 Bottle Burst gauge, B304 Top Load & Volume gauge and the B305 Automatic preform inspection system. All Torus gauges are fully traceable to United Kingdom Accreditation Service (UKAS) standards and are supplied with calibrated masters, which have been measured in Torus’ own UKAS approved laboratory. Torus products are backed up with dedicated service and support from all over the world. The engineers and partner companies travel globally supporting over 400 pieces of automated machinery and providing installation and training services throughout the world. Spencer Whale – Technical Sales Manager for Plastic Packaging at Torus speaks about the show: “It’s an exciting time for Torus. Over the past ve years we have been developing a line of equipment and during this development period we have drawn on over 25 years of metrology experience to bring new, innovative ways of measuring all kinds of plastic packaging containers. This innovation has been very well received, therefore our customer base in this eld is growing rapidly. Torus can now offer the industry a full solution in terms of quality control equipment using the latest cutting edge technologies. I look forward to demonstrating our capabilities alongside our USA-based Service and Support team at NPE for the rst time in May.” www.torus-group.com","@ID":53}, "MATERIALS / RECYCLING PETplanet Insider Vol. 19 No. 05/18 petpla.net 15 Liquid colour technology alongside FMCG Colours with an extra Fast-moving consumer goods (FMCG) or consumer packaged goods (CPG) are normally sold quickly and at relatively low cost. Non-durable goods such as soft drinks, dairy products, fruits and vegetables, meat and baked goods are highly perishable and need consequently a package able to preserve them especially during logistics and distribution. At the same time, since those products are fast-moving, it is imperative for them to beat the competition: they need to be highly eye-catching and recognisable on shelves. The unit pack or primary package is critical for both product protection and shelf life, but provides sales incentives to consumers. The liquid technology of colours and additives has progressed so much that it is possible to combine trendy colours with speciality additives most of the time, states liquid colour and additive specialist Repi. An example of this is the powerful bright shades with UV protection used for kids’ juices or transparent shades combined with UV additives for vitamin and avoured waters. It also applies to special light shield whites used to protect fresh, ESL and even UHT milk from visible light and UV damage when packaged in a monolayer PET bottle. Repi UV absorbers create a barrier to the harmful UV-rays and visible light, which can damage the product inside. As the prot margin on FMCG products is relatively small, this means that production fails and scraps represent signicant costs for converters, who also have to factor in ever-shorter production cycles, thin wall thicknesses and high machine output. Liquid additives have an important role in this case too. The Repi SenzAA scavenger prevents acetaldehyde from building-up during the injection moulding of preforms, responsible for the unpleasant off-taste of waters bottled using PET. The reduction performance goes up to nearly 85% which means AA values of less than 1ppm can be obtained. Blowing additives are on the market to improve and control the absorption of infrared during the blowing stage of preforms; the line works in a smoother way, avoiding stops, reducing scraps and improving the output of blown bottles per hour. Process aid additives reduce sticking and create a better slip effect between preforms preventing surface scratches and at the same time optimising their storage up to +10% with consequent advantages in terms of storage and transport costs. The IV enhancer acts on PET intrinsic viscosity and stabilises the mechanical properties of PET containers. Such additives in liquid form can be blended with colours to make allin-one products which are dosed at very low percentages making for a cost-efcient solution. The above-mentioned challenges go hand in hand with the major sustainability and circular economy concepts: how to save the resources of our planet, or rather, how to use them intelligently and responsibly to secure sustainable future growth. In the packaging eld. This includes the need to radically raise recycling rates. Resin, colour and additive manufacturers play a crucial role in this context, evolving their know-how and providing solutions which satisfy brands, market managers and designers, packaging manufacturers and nal customers. Liquid technology is claimed to provide additives designed for postconsumer raw materials, like the Repi anti-yellow which corrects the offshade of rPET - whether it is greyish, reddish or greenish. The usable percentage of rPET increases up to 100%. In some cases, optical brighteners and colour toners further improve brightness and aesthetics. According to Repi, research and development in speciality additives and colours is the key for brands to package perishable products, with short shelf life in perfect looking and cost-effective plastic containers, offering advanced and smart solutions which production processes have not yet achieved. www.repi.com MATERIALS Special","@ID":17}, "BOTTLING / FILLING PETplanet Insider Vol. 19 No. 05/18 petpla.net 38 Peruvian beverage producer achieves energy savings Heavenly growth Peruvian company Industrias San Miguel (ISM) currently has seven lines producing PET bottles, ve of which are equipped with blow moulding machines supplied by Sidel. The most recent ISM installation is a Sidel Matrix Combi, bottling still water and avoured water at a rate of 36,000bph in the company’s Dominican factory. Energy savings of around 8%, compared to the previous ones, could be achieved at the new line. Industrias San Miguel produces soft drinks, fruit nectars and still water, all to the international standards ISO 9001, ISO 4001 and OHSAS 18001. Founded in 1988, when ISM’s original product, Kola Real, took the country by storm, the company strengthened its operations in January 2000, opening another soft drink manufacturing plant in Arequipa, Peru’s second biggest city. International expansion began with the appointment of two distributors in Chile in 2002 and took off three years later with the opening of two manufacturing plants overseas: one in the Dominican Republic in 2005 and the second in Brazil in 2012. A growing market In the Dominican Republic, in 2016, off-trade sales for bottled water rose by 2% in volume in that year, while sales gures rose by 5% in value - to reach 1.3 billion litres and DOP (Dominican Peso) 12.4 billion, respectively. Demand for bottled water in the region is expected to remain steady in the coming years, according to estimates by Euromonitor. Although the majority of still bottled water is typically sold in bulk, in large ve-gallon containers, and often delivered to apartments and residences of the Dominican consumers by their nearby independent grocery retailer, growth in the market was particularly fuelled by single-serve products launched that year. Higher than normal temperatures also played their part, causing an increased need for water consumption among the Dominican end users. In line with rising health awareness globally, consumers in the Republic are also shifting towards healthier options, including bottled water. Experiencing the biggest gain in market share in 2016, Industrias San Miguel continued to expand within the domestic bottled water market primarily under its Cool Heaven brand, increasing its sales in value by 17%. The organisation also continued to further consolidate its position within soft drinks. Following the sustained growth of its Kola Real brand, its Frutop brand - a refreshing drink with the combination of natural fruit avours enriched with vitamins A and C - its 360 energy drink and the introduction of a new passion fruit avour during the year, ISM intends to position itself as the leader within non-cola carbonated drinks. Savings in energy and bottle weight In 2005, ISM installed the rst Sidel blower. Angel Idone, Innovation and Engineering Specialist at ISM, particularly appreciates the Sidel solutions to be automated, efcient, fast and providing energy savings throughout the entire production process. He continues: “Since 2005, we have been acquiring Sidel blow moulding equipment. With the blow moulding of PET bottles being the most energyintensive process within the whole production line, they have helped us generate considerable savings over the years. The high uptime of Sidel equipment also enables us to achieve greater efciency from the production lines in which it is installed. Moreover, Sidel has helped us reduce our bottles’ weight, that’s why we have further minimised our TCO, which is key for our results.”","@ID":40}, "PETplanet Insider Vol. 19 No. 05/18 petpla.net 68 PETbottles Home + Personal Care Dispenser for body lotion Eos, previously known for lip care, is expanding its product range and has brought body lotion in three fragrance varieties onto the German market. “Berry Blossom”, “Gentle Petal” and “Vanilla Orchid” are available in both 200ml and 350ml sizes. The coloured bottles, which are bulbous to the front, are comfortable to hold. Consumers can choose between the flip-top 200ml bottle and the 350ml bottle with a pump dispenser. The pump dispenser is protected by a tamper-evident shrink sleeve with perforations for easy removal. The pump head must be twisted by 90° at the front so the dispenser can be pressed down. www.evolutionofsmooth.com Shampoo with aloe hydra bomb Under the name “Garnier Fructis”, Garner is selling a new kind of invigorating shampoo with an “aloe hydra bomb” additive in a transparent, green-coloured 300ml bottle. The slim conical bottle attracts attention on the shelf because of light reections from the rear label, which is silvery on the inside. The shampoo contains glycerine and aloe vera gel to invigorate the hair and to nourish it with moisture. The transparent hinged cap seal has an embossed dark-green cap surface. www.garnier.de Hair repair from Schwarzkopf With the slogan “Repair not haircut”, Schwarzkopf is advertising its new “Gliss Kur” shampoo for the repair and protection of long, damaged hair and the avoidance of a greasy hairline. The 250ml bottles are slim, easy-grip and conical with chamfered sides. The transparent, pink body has a rear label with a reective inner surface for optical effect. The product is easy to dispense through the square-shaped hinged cap. The advertising sticker with the slogan seals the product from unwanted tampering. www.schwarzkopf.de Unusual bottle from Ecover Ecover offers 450ml of washingup liquid with lemon and aloe vera in an up to 100% recyclable and up to 100% recycled plastic bottle with multiple circulating grooves in the upper area. The “kind to skin” product is made from plant-based and mineral ingredients. The bottle is sealed with a hinged cap seal with dosage opening. The transparent label on the front offers a view of the rear label, which is printed on the inside with lemon slices. www.ecoverdirect.de","@ID":70}, "PREFORM INSPECTION 30 PETplanet Insider Vol. 19 No. 05/18 petpla.net Preform colour control by Mr Ing. B. Hotting In the last years preform and cap colour quality controls have made big steps. Large multinationals in the food, beverage and cosmetics industry have been pushing the level up and up, demanding higher standards and smaller tolerances from preform manufacturers. When it comes to preforms, measuring colour with a standard spectrophotometer may not be the best way to guarantee a constant high quality. Apart from the fact that operating a spectrophotometer with its many settings is not easy to handle and asks for trained staff that may not be around 24hours a day, positioning a small round tube for the measurement port of a spectro is often impossible to do correct. Also when data shows there is something wrong, not many parameters can be changed to correct colour variations in the production process. Measuring transmission values with a standard spectrophotometer is an even a bigger challenge. Another reason is that the colour granulate is carefully checked by the supplier and the blow moulding process has very little effect on the colour as in shifts of green, blue, yellow or red, or a* or b* shifts when only one colourant is used. The main change in preform colour is in how much colour is added, changing the L* value or transmission % by tuning the dosing system. Image 1 shows a set of semi transparent preforms where more and more colourant is added in the startup process in order to get the correct preform, it is not the colour that changes its the L* value or transmission value. And although coloured, semi transparent preforms as in image 1 may be checked by the human eye, it is far from ideal. People are different and so are their eyes and with that their perception of colour. What one person judges as correct another may not. That is to say if the people are even trained to see small differences, leaving the quality control process prone to human error and claims by customers. For example, many may see the difference of the rst few preforms on the left, but the darker, more opaque preforms become, the more difcult it is for humans to see differences. Image 2 shows a set of preforms that are more opaque and differences between good and not good cannot be seen by the human eye anymore. Also simple tools like ashlights don’t work here anymore. For instance of the two red preforms in the image, one is good the other not hence on the outside they look identical. The P1 preform transmission instrument was specically designed for the preform industry. It measures accurately how much light passes through a preform, where 0% transmission means no light passes through the preform or cap and 100% transmission means all light is received (so no preform present). This instrument gives operators and quality control professionals an easy to use tool to guarantee a constant and high quality product. Opposite of a standard spectrophotometer, the preform can be placed very easily in the P1 instrument. See image 3, where the red preform is positioned in the middle of the instrument. The instrument can work stand alone or can be connected via ethernet to a company network to log measurements. It has been designed to keep operating errors to a minimum. It has only 2 buttons and the reection chamber has guides so it will be positioned in the same way every time. The instrument is designed so it gets more accurate the more opaque a preform is exactly there where the human eye has trouble distinguishing L* values. Small changes in transmission values are detected in an early stage, minimizing waste and valuable production time. Alternatively the instrument can be used to detect variations in transmission values due to preform position in the mould. www.colourconsult.nl","@ID":32}, "EDITOUR PETplanet Insider Vol. 19 No. 05/18 petpla.net 22 Tour Sponsors: The U.S. drinks industry in a tight spot Our current Editourmobil tour in the USA is taking place at a time of economic uncertainty. All previously made plans now have to be scrutinised by the U.S. drinks sector. The industry’s gures continue to reect outstanding growth but increasingly strident public attitudes on environmental issues over the years and the current trade war will bring about serious shifts in both the short and medium term. Current price rises affecting packaging and raw materials, together with a ruinous consumer price war, will lead to further consolidation in the drinks industry. A lot is said about Trump but what you can be sure of is his knack for illconsidered and ultimately damaging decisions. His deliberately conceived trade war launched in the last few weeks, principally directed at China, has given his “America First” slogan its very own dynamic which is already causing uncertainty on many levels, including in the U.S. drinks sector. Plastics Trump began his offensive by introducing punitive tariffs on metals in March. This is having a particularly signicant impact on the American plastics industry which already has several new major projects in the pipeline. Carl Dooley, President of the American Chemical Council (ACC), says that arrangements for new production facilities have been planned on a costed basis in terms of the free movement of goods. Strict tariffs on metals have resulted in revised economic appraisals which have led to a signicant slowdown in investment. In terms of products, the chemical industry has also been affected, with plastics included on a second list of Chinese tariffs introduced in April. Even though PET is not on the list, distortions in the U.S. plastics industry caused by Trump will also have repercussions for the drinks industry in the form of higher prices for materials in the near future. Colleagues in the can industry will certainly be badly affected with the price of material for drink cans having skyrocketed by 25% in March. The impacts on the plastics industry will be a topic for discussion at the forthcoming NPE in Orlando. With Editourmobil and Bottlezone, we are right in the thick of things.","@ID":24}, "MATERIALS / RECYCLING PETplanet Insider Vol. 19 No. 05/18 petpla.net 16 25% CO 2 emissions reduction in soft drink bottles Cutting carbon in PET recycling FtoP Direct Recycle Technology, developed by Suntory Holdings Limited jointly with Kyoei Industry Co., Ltd, Sipa SpA of Italy and Erema Group GmbH of Austria, is designed for use in soft drink PET bottle preform production. The producers claim that CO 2 emissions produced during manufacture are 25% lower per kg than previous recycling processes. Preforms using this technology will be manufactured at Kyoei Industry Co., Ltd, and introduced for part of Suntory Beverage & Food Limited’s PET bottle products from the summer of 2018 onward. FtoP (Flake to Preform) Direct Recycle Technology takes ake created by pulverising and washing recovered PET bottles, treats it at high temperature and low pressure for a xed period. After melting and ltering, the resulting recyclate can be used directly to manufacture preforms. In order to ensure preforms are of uniform quality, it is important to pour the melted ake into the moulding machine at a constant pressure. The development of FtoP technology involved the construction of actual facilities and their verication, over a protracted period of time. In comparison to the previous setup, which required a large number of processes including crystallisation and drying leading up to the manufacture of the preform, it is estimated that reductions in CO 2 emissions of approximately 25% will be possible, using FtoP technology. Suntory Holdings Limited and Kyoei Industry Co., Ltd have a track record in promoting activities to reduce the environmental impact of PET bottle manufacturing; they developed Japan’s rst bottle-to-bottle mechanical recycling system, in 2011. For this project the two companies entered into a joint initiative with two overseas equipment manufacturers, Sipa SpA of Italy and Erema Group GmbH, with the specic aim of achieving further reductions in environmental impact. www.suntory.com Kyoei Industry Co., Ltd, headquartered in Oyama City, Tochigi Prefecture, is a recycled materials manufacturer specialising in the recycling, processing and sale of synthetic resins. It has been involved in the recycling of PET bottles since 1986 and currently produces a total of 80,000t of recycled PET resin annually. Italian company Sipa SpA launched its “Xreme” rotary injection-compression moulding system in 2013, and introduced the rst machine of the series at Suntory Products Limited’s Haruna plant. Erema has produced more than 200 examples of its “Vacurema” PET bottle recycling system since it was launched in 1996, to producers around the world. Suntory Group has worked to develop PET bottles with a reduced environmental impact such as by introducing the lightest domestically manufactured PET bottle, 30% of which consists of plant-based materials, for use in the 550ml size of Suntory Tennensui. It is constructing a trial plant for PET bottles made entirely from plant-based materials.","@ID":18}, "TRADE SHOW PREVIEW PETplanet Insider Vol. 19 No. 05/18 petpla.net 61 face, and simultaneously transported from bottom to top by rotor paddles. Feeding is via a horizontal drainage screw, which eliminates most of the surface moisture before material enters the dryer. Energy savings are achieved by a reduction in motor size. A typical one or two stage drying system for PET akes with a 150 HP motor would yield a throughput of 2.5-3t/h. An HVT system can equal that performance with a drive motor of only 75 HP. Large doors on the HVT’s housing provide easy access to components simplifying routine maintenance. Rotor paddles and screens can be changed quickly and easily, and the unit’s housing is equipped with strategically located replaceable wear plates. Label Remover separates full wrap labels from PET bottles For plastic recycling plants, the Herbold Meckesheim Label Remover is said to be more effective than any other machinery for the removal of wraparound polyvinyl chloride (PVC) labels from polyester (PET) bottles, claims the company. Until now, removing and separating wraparound labels has been impossible at the prewash stages of bottle recycling and difcult and costly at subsequent stages, but the Label Remover is designed to be a game changer. The tightly clinging labels can be removed in a single step, early in the process and without the expense of generating extra steam. The machine separates bottles that are stuck together, reducing labor costs for manual separation. By removing almost all wraparound labels early in the recycling process, the Label Remover also saves money in another way: Down the line at the size-reduction stage, cutting blades will stay sharp longer because they won’t be dulled by many label remnants stuck to bottles. The Label Remover is available with two different capacities 4,500 or 8,000kg/h. Inside each machine, the removal of labels and adhesives from bottles is accomplished through friction between exchangeable ripoff elements bolted to the rotor and exchangeable pins tted to stator elements. All rip-off elements and pins are made of special wear-resistant steel. The design of the chamber ensures even loads and dwell times as bottles are advanced by the rotor. The chamber has no spaces where bottles might pass through the machine without undergoing full frictional contact, and likewise there are no surfaces to constrict the bottle ow, reducing the possibility of damage to the bottle. Wash line systems Herbold washing lines are built on a modular design which ensures all components function together in a seamless system. It also allows systems to expand as requirements change over time. From a simple wet granulator to sortation and separation equipment, pre-washing, washing, and drying, Herbold wash line systems can be congured to meet the specic needs of any application. Herbold Meckesheim USA, a subsidiary of Herbold Meckesheim Germany, designs, manufactures, and installs size-reduction equipment (shredders, granulators, etc.) and wash-line systems for the plastics industry, specializing in the recycling of industrial and post-consumer plastics. www.herbold.com IMPROVE LINE EFFICIENCY by 10% OR MORE CONTACT US TODAY TO LEARN MORE! AGRINTL.COM | +1.724.482.2163 | SALES@AGRINTL.COM 1MEASURE 2CONTROL 3OPTIMIZE PROCESS PILOT® Blowmolder management easy as . . . NPE.org VISIT US AT BOOTH S-16045","@ID":63}, "MATERIALS / RECYCLING PETplanet Insider Vol. 19 No. 05/18 petpla.net 12 High prices now the norm Since around the middle of last year, converters and bottlers companies have been confronted with a particular situation, one they are not familiar with. PET prices have been constantly moving, and only in one direction: upwards. Anyone betting on the PET market easing in 2018 would certainly have lost their money over the past three months. At the beginning of 2017, many processors would not have thought it possible that the price could still increase by €140 per tonne within 8 months. Last August, PET was fetching €1,578 per tonne; by March 2018, the price had risen to around €1,718 per tonne. There are many reasons to explain this upward swing. Blaming it solely on the increase in the price of feedstock alone would be a mistake. Feedstock prices off the scale Oil prices are also trending in one direction, namely upwards apart from few exceptional price reductions, but these did not disguise the overall trend. It has even happened with crude oil, something that many thought unlikely. In August, a barrel of Brent, located in the North Sea, cost around $US50. As of 18 April, Brent crude is fetching $US72 per barrel. Analysts suggest this is partially due to a reduction in American stock levels. Similarly, feedstock prices, essential in the manufacture of PET, have continued their upward trajectory. The market seemed to settle down in the autumn, but this did not have the promised effect, as a comparison over a longer timeframe reveals. From August 2017 to March 2018, paraxylene prices increased by €90 per tonne: over the same time period, MEG prices increased by €107 per tonne. These increases in feedstock prices cannot wholly be laid at the door of high oil prices. There are other factors: increased demand in Asia, tensions in the geopolitical arena, and even currency fluctuations are all helping to inflate prices. Limited availability boosts manufacturers Total European PET production stands at around 3.3 million tonnes, but current demand is at 3.6 million. As such, every production line that fails, regardless of the reason, impacts availability. Naturally, the price of goods which are in short supply increases. Since last year, this has also been the case for PET. The spot market had practically dried up. Anyone who had depleted their stocks in the hope that the market would settle down, and was still striking it rich in the spot market, paid for it with high prices. It is no wonder that PET manufacturers were in buoyant mood in 2017. They were able to achieve high margins in the second half of 2017 in particular and had already wrapped up their contracts profitably in the autumn. In addition, they reaped the benefits from gaining numerous new contractual customers who were banking on security and who were tired of depending on the unpredictability of the spot market. Shortages not recovered JBT Industries (India), to name but one, played their part in the shortages on the PET market. The business had to shut down their production plant in Geel, Belgium, halfway through 2017 due to problems with liquidity. This plant had a capacity of 430,000 tonnes and as such contributed over 13% of Europe’s active production capacity. Even the company’s plant in the United Arab Emirates could not produce more. Plants owned by other European PET manufacturers were not able to make up the resulting shortages. They did, however, benefit from the higher prices that they were able to charge due to market demand. Even when JBT Industries started to run one production line in November 2017, and later two, it did not have any impact on price or availability during the first quarter of 2018. The Mexican branch of the Mossi Ghisolfi Group going insolvent last year must have also played its part, with consequences also ensuing for the European PET market. The business was capable of producing 560,000 tonnes of PET and mainly supplied South and North America, yet they pulse PET price in *Euros per tonne, free delivered from March 2017 to March 2018 MATERIALS Special PETplanet Pulse, the PET price index, is e-mailed on a monthly basis to all subscribers of PETplanet Insider as a complementary service. pulse","@ID":14}, "EDITOUR 25 PETplanet Insider Vol. 19 A blocked Sacmi plant with a capacity of 44,000bph for the CSD “ICE” project is currently under construction. A new facility has been built next door which means that a production area of 179,000 sq. feet is now available to Fluid Forms. Preform machines are operated there. Given that Robert has worked for Husky for many years, it is no surprise that two Husky machines are used there. However, Sipa XForm has been introduced in the facility as a third injection moulding system which, for the last two months, has been producing preforms using 72 cavity tools. “I was sceptical in the beginning, especially about the toggle clamp, but as we did our initial feasibility study and actual production we are more then pleased with our decision. In particular, the quality of Sipa’s service is better than a small producer could possibly imagine”, said Robert. www.uidforms.net The new pride of the team: Sipa XForm Via Scodoncello n° 41/E - 43044 Collecchio (PR) - Italy - Tel.: +39 0521 541011 Everything and more... cooperating together All the solutions for PET bottles & for handling every type of plastic containers Design, construction & installation of: \" \" LANFRANCHI S.r.l. www.lanfranchi.it innovation plastic container ! IPC S.r.l. www.ipcsolution.it www.npeguestpass.org/588580 Visit us at Booth S15089 Free Ticket at: The Kuvée concept: A PET Hi Tech wine dispenser that increases the shelf life of wine after its opened. Kuvée Fresh Pour bottle and the wi-connected dispenser Kuvée Connect (right). The screen reveals, i.a. the story behind the wine, suggests food pairings, offers tips and tricks, and makes recommendations. (photos: Kuvée)","@ID":27}, "49 TRADE SHOW PREVIEW PETplanet Insider Vol. 19 No. 04/18 Improved productivity and next generation manufacturing Nissei ASB Machine Co., Ltd. one of the world leading manufacturer of machines for injection stretch blow moulding of PET and other plastics, will demonstrate live moulding featuring ve machine models together with a display of some of the most interesting recent updates in injection stretch-blow moulded packaging technology. Reecting consistent sales growth over the last three years, ASB will represented by its largest ever presence at NPE with a 740m2 booth and ve different machine models making live moulding demonstrations moulding a variety of products that showcase the versatility of the company’s technology and integration with the internet of things. Featured models will include: 1) ASB-12M v2 – Entry level & niche market four station one step injection stretch blow moulding machine featuring nextgeneration control system and radically shortened cycle time for heavyweight cosmetic containers using standard PET resin. 2) ASB-70DPH v4 – Superbly versatile mid-range four station onestep injection stretch blow moulding machine demonstrating visually perfect moulding of Tritan Co-polyester resin. 3) ASB-150DPX – World’s rst triple row, one-step injection stretch blow moulding machine moulding in 48cav and over 20,000bph. 4) HSB-2M/6 – 2-step re-heat stretch blow moulding machine featuring ASB’s double-blow heat-set technology for heat resistant large necked jars. 5) HSB-6N – 2-step re-heat stretch blow moulding machine featuring ASB’s double-blow heat-set technology for heat resistant beer bottles complying with the industry standard tunnel pasteurising process. The booth will also be exhibiting a full line of matched moulding ancillary equipment that ASB is able to supply, such as resin dryers, chillers, mould dehumidiers and mould temperature controllers. In-house custom designed pick and place take-out units with conveyor systems will also be demonstrated allowing prospective customers to easily install the moulding machines upstream of other processing equipment or a lling line. All models will be operating on a daily moulding schedule and the booth will include a wide range of samples and displays of other specialised technologies from ASB. www.nisseiasb.co.jp South Hall 19045","@ID":51}, "BOTTLING / FILLING PETplanet Insider Vol. 19 No. 05/18 petpla.net 36 Aseptic line for Nectar in Serbia Fruitful investment Serbian fruit juice producer Nectar is raising the level of its technical equipment to totally unprecedented heights with a new aseptic ller from KHS. This is not only of benet to the quality of its products but also to its efciency in production. When Nectar started up its rst production line for processing fruit juice in beverage cartons 20 years ago near Novi Sad in the northwest of Serbia, there was no telling just how fast the company would develop. Five years later a factory for the production of fruit concentrates and purées was procured in Vladičin Han in the south of the country. In 2005 a PET, a glass and a canning line were added to the machine park, with new beverage carton lines following soon after. In 2008 Nectar became the majority owner of the Heba mineral water bottling plant in Bujanovac, also in the south of Serbia, and since 2011 Nectar has owned Fructal, a Slovenian processor of fruit with over 70 years of tradition under its belt. Nectar is now a veritable model company as demonstrated among other things by it being awarded the title of best corporate brand in Serbia in 2013. No competitor covers all stages of the value chain as thoroughly as Nectar: from its own plantations through purchasing, fruit processing and cooperation with fruit farmers to the nished product. Its high standards are expressed by the Serbian ‘nije svejedno’ which translates into English as ‘it does matter’. The company, famous well beyond the Balkan region, makes good use of this slogan and its marketing campaign emotionally explains that it does matter what we drink and what we look forward to. As one would therefore expect, great attention is paid to product quality and food safety here. Until very recently sensitive products were pasteurised and lled with the help of ultraclean lling technology (UCF), where overpressure is applied to the lling and capping zone. The air is fed in through lters to prevent any possible microbiological contamination. In addition, the empty bottles are rst lled with nitrogen to improve the microbiological quality of the lling process. In order to satisfy its own growing demand for quality, Nectar has now opted for aseptic lling. This allows its range of products to be considerably expanded – both with regard to the fruit content and the various avours and product variants in all categories. “For us, the most important thing is that we can now carry out this process under sterile conditions,” smiles production manager Milka Tomanović. “This retains the natural properties of the fruit. We have a better quality of nal product and can offer greater microbiological quality over a longer period.” Safety rst Creating sterile conditions for aseptic llers is a tricky undertaking. It was thus soon clear to Nectar that the only technological partners to come into question were certied systems manufacturers proven worldwide. “Not only was the high quality of the components Nectar offers its customers a wide range of top-quality fruit beverages, one of them being the BUZZZ brand which is lled on the new aseptic line from KHS. The new PET bottle design for BUZZZ was developed by Nectar in close cooperation with the experts from the Bottles & Shapes program at KHS.","@ID":38}, "47 TRADE SHOW PREVIEW PETplanet Insider Vol. 19 No. 05/18 petpla.net Technical Forum at NPE 2018 hosted by PETplanet Insider Time Company Title Speaker(s) Monday, May 07, 2018 10:00 am ISBT Trends in beverage plastic packaging Ron Puvak 10:45 am Moretto USA LLC Eureka Plus: modular, energy-saving, resin dehumidication system for PET Eugene “Gene” Flockerzi, General Manager 11:30 am Husky Injection Molding Systems Ltd Unlocking opportunities with next generation engineered PET packages Sean Hoy, Director PET Tooling 12:15 pm tbc tbc tbc 1:00 pm Nissei ASB Containers for hot lling and pasteurising - A full overview of the challenges and ASB’s solutions tbc 1:45 pm tbc tbc tbc 2:30 pm tbc tbc tbc 3:15 pm tbc tbc tbc Tuesday, May 08, 2018 10:00 am ISBT Trends in beverage plastic packaging Ron Puvak 10:45 am Agr International, Inc. PET process automation - easy as 1-2-3 David Dineff, Global Marketing Director 11:30 am Conair Capture the future of PET: what will drying technology look like in 5 years? Chris Weinrich, Director, Packaging & Medical 12:15 pm Sipa The importance of a fast and cost-effective response in plastic industry Morris De Marchi, PET Packaging and Tooling LCS Director 1:00 pm Husky Injection Molding Systems Ltd How Multi-Layer technology is enabling growth in PET packaging Dave Morton, Vice President Multi-Layer Barrier Solutions 1:45 pm Dow Chemical Caps and closures trends for 2018 Mandy Craig, Sr. Marketing Manager NA Rigid Packaging, Packaging & Specialty Plastics; John Sugden, TS&D Director NA Rigid Packaging, Packaging & Specialty Plastics 2:30 pm Tech-Long Packaging Machinery Preform and bottle manufacturing – A turnkey approach from Tech-Long Eddy Vuylsteker, Director of Commercial Operations; Fred Pinczuk, Business Development Manager 3:15 pm Nissei ASB ASB technical support center capabilities tbc Wednesday, May 09, 2018 10:00 am ABC Compressors Horizon 2019 Richard Zhang, Sales Area Manager 10:45 am W. Amsler Equipment Linear blow moulding of non-conventional barrier containers Bruce Coxhead, GM Operations 11:30 am Husky Injection Molding Systems Ltd Inherent closure features that enhance closure performance and appeal Mike White, Business Manager Beverage Closures 12:15 pm Sipa PET preform manufacturing in the era of circular economy Enrico Gribaudo, General Manager 1:00 pm Nissei ASB Guidelines and constraints for optimal ISBM container design tbc 1:45 pm Universal Dynamics AIBC Technology: PET preform quality and utmost constancy of production Giorgio Santello, Vice President Service & Sales 2:30 pm Frigel North America High efciency process cooling Lou Zavala, National Sales Manager 3:15 pm ISBT ISBT's online beverage institute Sara Shumpert Thursday, May 10, 2018 10:00 am tbc tbc tbc 10:45 am Husky Injection Molding Systems Ltd Improving overall efciency – how close collaboration and focus on the right KPIs can generate dramatic results John Quail, General Manager Customer Success Americas 11:30 am Nissei ASB One step ISBM 101 tbc 12:15 pm ISBT ISBT's online beverage institute Sara Shumpert 1:00 pm tbc tbc tbc 1:45 pm tbc tbc tbc 2:30 pm Lanfranchi North America Switch to PET: the best solution for most of your packaging Lucia Comper, Business Development Manager; Giovanni Renati, Sales Area Manager North America 3:15 pm tbc tbc tbc","@ID":49}, "MARKET SURVEY 41 PETplanet Insider Vol. 19 No. 05/18 petpla.net Company name Torus Measurement Systems Sacmi Imola S.C. IMD Ltd Pressco Technology Inc Agr International Inc. Postal address Telephone number Web site address Contact name Function Direct telephone number Fax E-Mail Torus House, Nedge Hill Science Park, Telford, Shropshire, TF3 3AJ, Great Britain +44 1952 2100 20 www.torus-group.com Mr Spencer Whale Technical Sales Manager +44 1952 2100 20 tms.sales@torus-group.com Via Selice Provinciale 17/A 40026 Imola (BO), Italy +39 0542 607111 www.sacmi.com Mr Stefano Severi Sales Area Manager +39 335 6594236 stefano.severi@sacmi.it Moosweg 1 2555 Brügg, Switzerland +41 32 366 80 66 www.imdvista.ch Mr Martin Gerber CSO of IMD Ltd. +41 32 366 80 66 +41 32 366 80 69 imd@imdvista.ch 29200 Aurora Road Cleveland, OH, USA +1 440 498 2600 www.pressco.com Mr Tom O'Brien VP, Marketing, Sales & New Business Development +1 440 498 2600 sales@pressco.com 615 Whitestown Road Butler, PA, USA +1 724 482 2163 www.agrintl.com Ms Karen Marcellus Marketing Coordinator +1 724 482 2163 +1 724 482 2767 kmarcellus@agrintl.com Preform Inspection Systems B305 Automatic Preform Inspection System PVS-2 PVS-3 Pilot Vision (in blowmoulder system) Gawis OD Inspection speed 10s per preform Up to 1,200 parts per hour Up to 72,000 parts per hour Up to 1,500 pieces per minute or 90,000 pieces per hour Up to 2,500/min Up to 100,000 bph 45 preform/hour depending on measurements Inspected parameters: Geometry / Body Body defect (including scratches, bubbles, contamination, burning, unmelted material, oil & water marks), gate height, preform hight, stringing, preform body diameter (2 positions) Contamination, shape, diameter, ovalisation, wall thickness, crystallisation, contamination, unmelts, bubbles, water marks, black specks, gate length, opacity, colour variations, scratches Contamination, shape, diameter, wall thickness, crystallisation, contamination, unmelts, bubbles, water marks, black specks, gate length, opacity, colour variations, scratches Black dots, burn marks, contamination, bended body, bubbles (air pockets), crystallised body, scratches, non-visible ow structures (low pressure while injection), total lenght, colour and colour deviation, long injection, unmelts Unmelts, heat splay, burn marks, water spots, bent/ warped preforms, contamination, carbon streaks, bubbles/blisters, colour, crystallinity & clarity/hazing, gate length Length, body diameters, lean Contamination, opaque spots (black spots), unmelts, bubbles/blisters, burn marks, water spots, streaks nlimited number of Body Diameters and wall thickness measurements, plus length, thickness accuracy to +/- 0.01mm Thread area Measured Features (including but not limited to): I, F, G, T, E, S, X, P, L, J, D, H, X, A, B, M, Z / Support Ledge Doformation / Neck Sinkage / Ovality Contaminations, cavity number recognition, diameters, ashes Contaminations, cavity number recognition, ashes Flashes on neck/ thread, scratches on neck area, support ring deformation, missing material on support ring Contamination, ash, dimensions, pulled threads No T, E, A, NR, H, L/D, ovality Mouth / Sealing surface Sealing Surface defect (including, scratches, notches, short shot, deformations) Diameters,ovality, thickness,scratches,short shots,ashes,notches, contaminations Diameters,ovality, thickness,scratches,short shots,ashes,notches, contaminations Ovality,diameter,ashes,shorts shots,ashingonparting line, deformationofsealingarea, coulorandcoulordeviation Contamination, ovality and diameter, dirt & debris in the preform, nicks, gouges, short shots & dips No No Gate / Dome -Gate Area Defect (burning, tearing, casteling, voids, holes). Multiple radial zones can be setup for customer dened areas of inspection - Stringing (mentioned above) - Gate Height (mentioned above) Crystallisation, contaminations, unmelt, bubbles, grooves, holes, cracks, position of the injection point Crystallisation, contaminations, unmelt, bubbles, grooves, holes, cracks, position of the injection point Gate defects, gate length (long gates), holes in gate and gate area, gate deformation, cracks in gate area, injection point out of centre, drip marks Bent/warped preforms, dirt/ debris, cracked gates No No Colour Measurement can include L, a, b, c, h, E, Ecmc; UV transmission, calibrated colour tiles Colour deviations, intensity deviations, LAB measurement Colour deviations, intensity deviations, LAB measurement Colour and colour deviation Colour variations, incorrect colour No No Cavity number Cavity recogntion capable of learning and reading different fonts. Capable of recognising multiple fonts across different machines and tools. Recognition scores for each character provided for analysis Cavity number recognition, cavity related statistics, sorting by cavity number Cavity number recognition, cavity related statistics, sorting by cavity number Cavity reading, self-learn cavity function for several cavity/templates, cavity related statistics and alarms, rejection of x cavity number, possibility to share information with injection moulding machine based of cavity number No No No Further criteria Preform weight: Weight module supplied with automatically loaded UKAS traceable master for calibration & Qualication Weight, patented grid inspection for detection of defects usually visible with polarised light Patented grid inspection for detection of defects usually visible with polarised light Non-visible ow structures (low pressure while injection) on body, extremely compact layout, less than 7m2 Additional inspection modules include: Neck support ring, inner barrel Preform weight No Measurement of absence or presence of barrier material No No No IMDvista BTIR Barrier Testing System Yes No No Layer thickness & position measurement at distinctive points No No No IMDvista Layer Testing System No No Comprehensive thickness (monolayer) at any location over preform sidewall Layer thickness & position measurement at the complete body by scanning No No No IMDvista Layer Testing System No No No Features: Installation: Stand-alone Yes Yes Yes Inline after injection moulding machine; before blowing and lling machine/line; complete line after injection and before blowing/lling. Production monitoring by IMDvista Peco Lux Mounting and installation inside major OEM blowmoulding machines No Yes Installation: Inline Can be integrated in line in certain cases, but for batch inspection, not inspection at line speed. Yes Yes Options available for standalone and inline systems Yes Side camera for cavity recognition Yes Yes No, patent pending cavity recognition with top camera 4 cameras with our newest intelligent software technology No Method: destructive / non destructive Non destructive Non destructive Non destructive Non-destructive vision inspection Non destructive Non destructive Non destructive Data base connection Suitable data output for Excel, statistical process control SQL database, possibility to extract data in XLS format, possibility of connection to ERP system SQL database, possibility to extract data in XLS format, possibility of connection to ERP system IMDvista Portal, connect all system on one central processing unit (operator panel) Yes Industry standard Industry standard","@ID":43}, "EDITOUR PETplanet Insider Vol. 19 No. 05/18 petpla.net 23 Components However, it is not just packaging that is affected as component suppliers are also having to reposition themselves in the USA. In the rst list, China has put agricultural products on the index, many of which are vital for drinks’ production. Farmers have to plan for the long term, particularly as regards perennial fruits. A collapse in the Chinese market would signicantly reduce vital income which cannot be made good very quickly by new sales markets. Fruit farmers are already under enormous public pressure as it is. Most fruit is grown in areas where water has been scarce for years. Households are obliged to save considerable amounts of water while farmers water their desert crops. This high consumption of water by farmers is attracting a lot of criticism from the public. The farmers ght their corner with slogans such as “No farms, no food” in order to win over the population. So it should only be a matter of time before the fruit markets begins to shift dramatically. Environmental awareness There is also trouble on the consumer side. While Trump does not care about the environment, having implied in a tweet on 6 November 2012 that global warming was a hoax created by and for the Chinese, designed to damage the U.S. economy, an “anti-plastics” movement has emerged among U.S. end-users. The plastic bag has become the symbol of environmental pollution to the consumer with around 100 billion of bags having been used in 2017. Disposable bags have been banned in several Californian cities. The U.S. drinks market will need to be careful that the huge quantities of plastic bottles which are routinely discarded in the countryside do not lead to anti-PET sentiments. PET recycling in the USA is shamefully low at 31%. Market gures The fact that, according to Euromonitor, the drinks’ market has grown by around 2% per year in recent times to 211 billion packages, of which 89 billion are PET bottles, 92 billion bottles made from polyolen and 86 billion cans (2013-2016, later gures are not available) means that all forecasts have become out of date. It is doubtful whether the 650 drinks packages per head in the USA in 2016 will remain at that level in 2018. The gure of 310 plastic bags per person should certainly be lower this year. The bottlers Ultimately, everything ends up with the bottlers. Higher packaging materials and component prices, a ruinous price war that has been going on for years and an increasingly critical public attitude towards plastics will not be without its consequences. If similar phenomena were to prevail in other markets (higher commodity prices, shrinking margins) this would lead to supplier concentration and consolidation with the big players gaining further scale. The medium-sized concerns will nd it increasingly difcult to consider this. As well as the very large enterprises, such a time is also an opportunity for the very small rms who are exible in their approach and have a clear idea of how to overcome the many stumbling blocks to provide a nancially strong target group with innovative products. On the rst part of our tour, we visited Rivera Beverages and Bomatic from the “small but beautiful” group, both of which are based in California (p. 28 and 29). It is to be hoped that the upturn will not stie the U.S. economy which has been in recession for many years.","@ID":25}, "TRADE SHOW PREVIEW PETplanet Insider Vol. 19 No. 05/18 petpla.net 50 Solution to serve all markets Husky, a leading industrial technology provider to the plastics processing community, announced that it will demonstrate its innovations for a variety of markets at NPE2018. In its 12,000 square foot exhibition space the company will also be showcasing a wide range of innovative applications and concept packaging developed in partnership with customers and industry partners. West Hall, Level 2, 1303 “Over the last several years, we have invested signicantly to further advance our already state-of-theart equipment. These investments have led to exciting developments in our Multi-Layer technology, our Hot Runner Valve Gate technology and in how we deliver complete tools, components, replacement parts and value-added services to our customers. We will always invest in research and development and in building valuable partnerships to be the innovation leader. It’s simply how we dene ourselves,” said John Galt, Husky’s President and CEO. Innovation Husky has been at the forefront of the injection moulding equipment industry for more than 65 years, remaining a leader by proactively building an unmatched understanding of shifting consumer trends, their impact on global markets and interpreting this to deliver novel and relevant innovations to customers. Now the company is looking beyond just offering more efcient processing equipment and toward the total endto-end lifecycle of injection moulding equipment and plastic moulded parts. Today and in the future, plastic packaging and moulded parts will require more exible and adaptive manufacturing solutions, as well as new business models, that support growth of both brands and plastics processors alike. The Multi-Layer technology Originally introduced at NPE in 2015, Husky’s Multi-Layer technology offers enhanced package performance, security and design, while using less material, to deliver a lower total part cost and a lower total cost of ownership. Momentum for Husky’s Multi-Layer technology continues, with now more than 30 systems sold around the world for a breadth of applications, including carbonated soft drinks, juice, sparkling water, beer, tea, dairy, food and personal care. “As an industry leader we are able to support our customers’ ability to design and deliver packaging that responds to the demands of a rapidly changing society. This includes the need for exible solutions that are more sustainable,” said Dave Morton, Husky’s Vice President of Multi-Layer Technology. “Our Multi-Layer Technology, paired with new recyclable barrier materials, delivers on this need by providing a functional package that protects the product more efciently from both a material and total cost perspective.” At NPE2018 the company will highlight the technology’s capability for various application requirements, including barriers for light, oxygen and carbon dioxide, as well as bottles with exciting new design and functional treatments that dramatically enhance shelf appeal. Application exibility with HyPET 225 system Husky will be running its fully integrated HyPET 225 preform manufacturing system which will be producing an 11g preform using a 48 cavity mould and running an 8.2s cycle time. The company is highlighting its PET Tooling technologies and services, which help reducing manufacturing risk while maintaining the highest levels of performance. The Bottle Zone Technical Forum, new this year at NPE2018, will feature presentations from Husky subject matter experts throughout the duration of the show. A signicant highlight of the Husky experience at NPE2018 will be its award-winning Valve Gate Hot Runner innovations, providing incredible gate quality over millions of cycles with reduced cost of ownership. www.innovation-everywhere.com","@ID":52}, "PETnews 6 NEWS PETplanet Insider Vol. 19 No. 05/18 petpla.net Amut and Erema hold Open House Amut and Erema are holding an Open House to present a sophisticated “Bottle to Packaging” process from 28 to 31 May 2018. Washed post-consumer PET bottle akes will be recycled live at the Amut headquarters in Novara, Italy, to make food contact grade thermoforming sheet in a direct process. This rPET sheet will be used at the Plast Milan exhibition – which is being held at the same time – to make thermoformed trays for the food sector. Interested producers will be able to process their own input material on the demonstration system in future to make plastic rolls. They can then test the samples later in their own thermoforming production to check the quality. The post-consumer akes are processed in the new demonstration facility – a direct combination of Vacurema technology and the Amut Inline Sheet plant in a single process. Thanks to the direct combination of recycling and production technology there is no longer any excess process stage. This is because the melt goes straight from the Vacurema to the Amut plant without the detour of pelletising. The post-consumer PET material is already decontaminated and pre-dried prior to extrusion in the vacuum reactor of the Vacurema Basic, with a throughput of up to 1,000kg/h. The newly developed Erema PET Laserlter processes input material with a degree of contamination of over 1% without any difculty and discharges the ltered particles continuously. Thanks to its unique pressure consistency this lter system is particularly suitable for inline production. Despite varying moisture, IV values and bulk densities in the input material, the melt has a constantly stable IV value and colour. Additionally, the process stands out through what is only a marginal IV drop. The melt then goes directly into the Amut Inline Sheet plant where it is processed into thermoforming sheet. The integrated online viscometer shows the user the actual viscosity of the melt. High-stiffness cooling rolls guarantee precise material planarity. Another boost in sheet quality comes from the fully integrated inline thickness gauge control. The hot lamination system represents an additional production benet and is particularly suitable for sensitive barrier lm thanks to the adjustable contact point. The wet coating at the end makes for an antistatic and anti-blocking solution. A free shuttle service between the trade fair in Milan and the Amut headquarters in Novara will be available for attendees. The demonstration facility in Novara will continue to be available for customer trials also after the Plast Milan show. www.erema-group.com Key process technology operating milestone for 100% bio-based PET bottle Anellotech, a sustainable technology company pioneering the Bio-TCat process for production of cost-competitive renewable chemicals and fuels from non-food biomass, announced a key operating milestone, achieving two weeks of continuous operation of its seven-story tall TCat-8 pilot plant, producing aromatics (primarily benzene, toluene, and xylenes) from loblolly pine feedstock. Anellotech also secured an additional $6 million investment from Suntory Holdings Limited, which was part of a previously announced $15 million package. Suntory’s total investment in Anellotech’s program is now more than $30 million. The Bio-TCat Process’s cost-competitive renewable aromatic chemicals are “drop in” replacements for their identical petroleum-derived counterparts, and can be used in manufacturing plastics such as polyester, nylon, polycarbonate, polystyrene, or for renewable transportation fuels. Having recently announced completion of commissioning of the TCat-8 pilot plant located in Silsbee, Texas, Anellotech has begun an extensive development program to optimise process variables, validate process economics, conrm catalyst long-term performance, and obtain the critical data for commercial plant design. As these studies continue, TCat-8 is producing evaluation quantities of renewable aromatic chemicals for conversion into bio-based polymer prototypes and for bio-fuel certication programs. “We have demonstrated continuous, stable operation of the TCat-8 pilot unit over a two week period as the rst key step in demonstrating Bio-TCat’s commercial viability,” said Dr Charles Sorensen, Chief Technology Ofcer of Anellotech. “In a relatively short time period, our pilot plant has generated a large amount of high-quality data which gives us condence that we will be able to achieve our longer-term operational goals. Continuous catalyst circulation, the injection of solid biomass feedstock into the reactor, and several internal recycle loops create numerous complexities that Anellotech engineers and scientists, together with our R&D partners IFPEN and Johnson Matthey, have successfully addressed.” The alliance with Suntory began in 2012 with the goal of enabling the development and commercialisation of cost-competitive 100% bio-based plastics for use in beverage bottles. Anellotech continues to seek additional strategic partners to support its development and participate in the future success of Bio-TCat technology, especially companies interested in using bio-benzene or toluene to reduce greenhouse gas emissions associated with the manufacture of polymers and products such as ABS, nylons, polycarbonates, polyurethanes, detergents, and other aromatic-containing products currently made from petroleum. www.anellotech.com","@ID":8}, "BOTTLE MAKING 34 PETplanet Insider Vol. 19 No. 05/18 petpla.net Figure 4.10 Layout of the various transfer functions of a Blomax Series III blow moulding machine. Diagram courtesy of SIG Corpoplast. This machine keeps the preforms on the mandrels throughout the oven and blow section, turning bottles right side up after blowing. In this way the diagram differs from machines that handle preforms in other ways. Preforms enter the machine at the loading station. Fed by gravity, worm drives, star wheels or scrolls, preforms are turned about 180 degrees when they go through the ovens neck down. Next they are pushed onto the mandrels, which is accomplished by either holding them in nests and moving the mandrels up from underneath or holding the mandrels and pushing the preforms into place. All machines have devices ensuring the preforms are rmly seated on the mandrels. Preforms that are not located rmly are removed from the machine by various means (g. 4.11). Figure 4.11 Preforms not properly seated on the mandrels are blown into an ejection pipe. Photo courtesy of SIG Corpoplast. The loading/unloading wheel turns clockwise as do the heating and blow wheels. The intermediate or transfer wheels turn counterclockwise. Loading of preforms onto mandrels and transferring blown bottles from transfer III to the turning wheel are both accomplished by this rst wheel. This dual functionality, that is found throughout rotary blow moulding machines, is possible because the neck support rings, that are already fully nished in the preforms, are used to hold both preforms and bottles (g. 4.12). Figure 4.12 The loading/unloading wheel is the heart of the various preform and bottle transfers. Diagram courtesy of SIG Corpoplast. Transfer I takes mandrels with preforms to the heating chain from where they travel through the oven section. Transfer II then moves them from the heating chain to the blow wheel (g. 4.13). Figure 4.13 Transfer wheels transfer preforms and bottles from one machine function to the other. Diagram courtesy of SIG Corpoplast. The elongated shape of the transfer arms or grippers is due to the fact that they must take the preforms to and from the centre of the blow clamp, clearing the mould halves. Transfer III nally takes the blown bottles from the blow clamps to the loading/unloading wheel. Because they are still upside down on this machine, they are then transferred one more time into the bottle turning wheel before they exit the machine. Linear machines These machines often have devices that turn a number of preforms and bottles through 180 degrees. This number is governed by the number of cavities that the machine blows (g. 4.14). Figure 4.14 The cylinder on the left centres and holds the mandrels while the preform turning device places two preforms. Photo courtesy of Amsler Equipment. Most machines use individual mandrels, combining them in front of the blow clamp and shuttling them in with a hydraulic cylinder. Mandrels may wear where they have hardened locating rings that t into cut-outs in the blow mould halves. Please order your copy at the PETplanet Insider book shop: petpla.net/book3 Stretch Blow Molding Third Edition by Ottmar Brandau € 130,00 374 pages © Copyright Elsevier 2017, 2012","@ID":36}, "MATERIALS / RECYCLING PETplanet Insider Vol. 19 No. 05/18 petpla.net 14 Growth areas for an established packaging material PET the Indian way It is almost 40 years ago that PET found its way into the Indian packaging market. Initially introduced for edible oil and jars for pickles and spices, the market quickly expanded to include bottled water, CSD, alcoholic beverages, fruit drinks, wellness drinks, personal care, agro-chemicals – and it did not stop there. Today all the milk variants as well as wine & beer are also packaged in PET. Now India is all set to reach the milestone of 1m TPA of PET consumption in 2018-19! Although PET has been an established packaging material in India for many decades, there are still segments where it is experiencing an upswing. “The emerging PET applications in India include fresh/ flavoured milk, UHT milk, chaas/ lassi, beer, paint, bulk edible oil packs.” explains Rajesh K. Gera, AVP Business Development – Reliance Industries Limited (RIL). He continues: “In addition to sparkling clear packs, opaque PET use is also growing due to the glossy pack finish in end-use sectors like paint, spices, edible oil among others.” Value-positioning is today encouraging an uptake in the use of PET and providing opportunities for non-Cola beverages in the health-wellness sector and this has resulted in the introduction of variants of fruit drinks, avoured water, nimboo paani and other beverages in PET. As far as soft drinks are concerned, Reliance estimates that the double-digit growth will continue, hovering at around 10% plus. Small size packs are especially in demand. After the successful rollout of 250ml and 300ml bottles by regional majors, 160ml bottles have now also been successfully launched. “These are able to reach the “bottom of pyramid” customers, and for this reason, one of the FMCG majors is intending to launch juices in aseptically lled PET bottles in different pack sizes” explains Gera. The alcoholic drinks market The alcoholic drinks market is also a growing one for PET. “In countries like India, one of the ways to effectively connect to consumers for alcohol products is also through appropriate and smart packaging including Interactive Packaging”, says Gera. PET bottles are extensively used for Indian-made foreign liquor (IMFL) and the growing trend is to further shift to PET for more and more liquor variants. The use of PET bottles in liquor has seen the emergence of niche shapes and colour effects. It has led to enhanced product appeal and increased sales for the said liquor variants in PET packs. Beer in PET is also enjoying great popularity. Brewery SAB Miller for example is using 1l and 1.5l barrier PET bottles, ash pasteurised, for three of their brands with a shelf life of two months. Non-beverage applications Besides food and beverage, the PET packaging market is growing exponentially: “Primarily, this includes the home and personal care market,” explains Gera. “The all-India PET consumption is 130kta in these sectors, and we are witnessing an ongoing shift from polyolens to PET for different pack variants. This is mainly due to improved bottle physicals and the cost-competitiveness PET offers.” The growing non-food market for PET also includes agro-chemicals and paints. For agro-chemicals, currently 10kta+ of PET is used, and this is increasing. As far as paints are concerned, Gera says that “PET is currently used for water-based paints, and there is interest for solvent-based paints. We foresee good potential for the use of bulk PET containers for this market in India”. There is an emergence of ‘Injection-moulded Items’ in PET, and RIL has developed special resins for this segment. Today PET trays, glasses and many other products in PET have been successfully launched in India. Blood collection tubes have been also successfully developed and other emerging markets for PET are EBM and thin wall mouldings. Outlook It is expected that the PET packaging market in India will continue the exponential growth it has shown in the past decades. In 2007-08, PET usage was 210kta and in 2016-17 it was 830kta, a growth of 300% in 10 years. Gera sums up: “India is now all set to reach the mile-stone of 1m TPA of PET consumption in 2018-19!” www.ril.com MATERIALS Special","@ID":16}, "MATERIALS / RECYCLING PETplanet Insider Vol. 19 No. 05/18 petpla.net 13 YOUR ADVANTAGE: •HIGHEST THROUGHPUT •HIGHEST ACCURACY •BEST REPRODUCIBILITY •100% NETWORK CONNECTIVITY WWW.EISBAER.AT MIXING AND DOSING SUSTAINABLE SYSTEMS FOR THE PLASTICS INDUSTRY also had clients in Southern Europe. As such, the loss of this PET production capacity has had permanent implications for the trade flows of European PET and means that the amount produced in JBT Industries’ second plant in Belgium has to be exported to the USA. The same goes for part of the PET produced by Alko Nafta in Kaliningrad. There is no indication that the PET market will settle down within the next few months either, bearing in mind how things developed in 2017. According to forecasts, the oil price is set to rise even more during the coming weeks, meaning that feedstock prices are also likely to increase, as oil is used in their production process. There has been a shortage of PET during the past months. It remains to be seen whether its availability improves in the near future. The drinks season is just around the corner, meaning the demand for PET will increase. Importing PET from Asia could be an option worth exploring for some processing plants, however many are afraid of the risk as they do not have any experience with imports, or because they are still hoping for prices to fall. As such, quotation prices should be tempting so that, on balance, opting to take this course of action would be worthwhile after consideration of all the risks. MEG & Paraxylene price in Euros per tonne, free delivered from March 2017 to March 2018","@ID":15}, "TRADE SHOW PREVIEW PETplanet Insider Vol. 19 No. 05/18 petpla.net 56 Sacmi adds value to the U.S. market Technology and design Sacmi will be at the NPE fair to present flexible, efficient, lightweight cap and container manufacturing solutions and complete cap-preform design solutions aimed at intercepting new high-added-value markets. Sacmi’s display area will go to the compression blow forming (CBF) range. Using a new container-making process that employs compression technology, these machines produce final products directly from pellets. Since the CBF range can be used with all the main commercially available resins, it offers precision and versatility. West Hall, Level 2, 363 South Hall 10051 Sacmi says that the CBF range actually combines the best characteristics of alternative technologies such as EBM, IBM and ISBM. This is the result of excellent thermodynamic stability throughout the process, no gate on container bottoms, high productivity and precisionmoulded necks. These factors, combined with using different resins and – in general – the ability to produce blown containers at lower cost (up to 20% less weight) have made a marked difference. Some thirty solutions have already been installed in China, Japan, the USA, India and other countries. The research on the closures front focuses on the repeatability and precision of continuous processes and on cutting weight and cost. This goes hand in hand with a capacity to respond to the burgeoning market demand for integrated solutions for high-added-value product lines. The Group’s latest cap manufacturing solution with the wellestablished continuous compression moulding (CCM) range, equipped with the COOL+ mould. The application on show at the fair – for the manufacture of a lightweight version of a popular CSD cap – is one Sacmi has designed for the strategic US market, which is constantly on the look-out for new solutions that combine lower weight, less environmental impact and innovative design. It is this capacity to design, together with the customer, the most suitable cap and preform solution – also with an eye to ‘green packaging’ – that makes Sacmi a partner, ensuring each new plant engineering project has everything covered from every angle: from technological consultation vis-à-vis the finished product (thanks to the advanced research lab, accredited by several key players in the beverage world) to the supply of complete production lines that integrate every aspect of manufacturing. The intrinsic advantages of this technology, which works at lower temperatures with respect to injection, is claimed to ensure excellent energy efficiency. Sacmi solutions allow finishing tasks (slitting, folding and non-destructive testing) to be performed on non-flat-top caps; this is thanks to a comprehensive range of slitting-folding machines that work in concert with cutting-edge inspection systems that allow control of every aspect of cap finishing. The advanced Sacmi H.E.R.E. (Human Expertise for Reactive Engineering) supervision system, which can be integrated along the entire plastic cap production line (of which the CCM is a part), allows Industry 4.0-type manufacturing plant control. All solutions on show in Orlando – CBF and CCM – will be equipped with a dedicated inspection system for in-line, high speed total quality control. www.sacmi.com","@ID":58}, "TRADE SHOW PREVIEW PETplanet Insider Vol. 19 No. 05/18 petpla.net 60 PET recycling equipment at NPE 2018 Herbold Meckesheim USA will have a signicant presence in Orlando. They offer a complete line of plastics size reduction and wash line products for use with PET. West Hall, Level 2, 7545 SB series granulators with screw feed A force fed granulator for size reduction of PET bottles, the model SMS 100/160-9-2 SB3 features a rotor that is 20% larger. The additional size and mass of the rotor allows the granulator to operate at higher throughput rates (up to 7t/h). Material is fed into the destruction chamber via a patented screw fed mechanism that utilises three vertically mounted feeding screws. This feeding method is intended to offer several advantages over gravity feeding including consistent, even feed rates, reduced power consumption, no material yback, quiet operation, less wear on the cutting chamber, and reduced nes and dust. The unique knife geometry which positions inclined rotor and stator knives at the same, but opposing angles provides a true double cross cutting action. HB series granulators with ram feed HB series granulators combine the best attributes of a shredder and a granulator for semi-automatic plastics recycling, states the company. They efciently reduce bulky items all the way down to particles 0.16 to 0.31 inches in diameter without any secondary size reduction. The HB series granulator has a powerful rotor with double-cross cutting action, a heavy-duty hydraulic ram, and a large feed hopper that can handle whole bales, cut-open lm rolls, mingled packs of sprue spiders, thick-walled purgings, carpet waste, pipes and proles, post-consumer bottles, and whole containers/crates without the need for dosed feeding or the risk of jams in the cutting chamber. Once the hopper is lled, the unit can be left unattended as the ram intermittently breaks pieces off the bottom of the load and pushes them into the cutting chamber. The particles produced are ready for further use. This one-machine size reduction also reduces electricity consumption and simplies cleaning, colour changes, material changes, and maintenance. The HB series granulator, constructed of sturdy welded steel, is available in four models with two rotor diameters (23.6” and 31.5”), four working widths (39.4” to 63”), four drives (45 to 200kW), and four throughput rates (0.5 to 6t/h). The design of the cutting chamber allows easy access for cleaning. The placement of the rotor bearings on the outside of the unit keeps nes out of the bearings and grease out of the product. Different rotor types are available. Energy saving HVT series dryer HVT series centrifugal dryers provide gentle energy saving drying of regrind, especially hollow bodies, PET bottles, polyolens and other plastics. The HVT’s distinguishing feature is its vertical rotor shaft, which ensures longer dwell time in the drying chamber. This vertical design offers the added advantage of signicant space savings versus horizontal systems. The renement of the HVT’s internal geometry, including the rotor and housing minimises the occurrence of nes and allows for greater yield. HVT dryers operate on the principle of centrifugal drying. Material is accelerated against a screened stator sur-","@ID":62}, "BOTTLING / FILLING PETplanet Insider Vol. 19 No. 05/18 petpla.net 45 Industry bodies reject Orb Media “Microplastics in bottled water” claims Plastics in bottled water? PETplanet Insider usually writes about liquids inside plastic packaging – beverages bottled in plastics. A study by an organisation named Orb Media has required that we look at things from the opposite side; it has claimed to have found plastics contained in beverages. Are there plastics in bottled water? In their responses, industry bodies IBWA and BSDA highlight awed methodology, unsubstantiated claims and lack of peer review in rebutting the media organisation’s reports of microplastic pollution in packaged water. In March 2018 Orb Media, a Washington, DC, USA based non-prot journalist organisation, issued a press release (“New Orb Media Reporting Finds Microplastics in Global Bottled Water”) claiming that “a single litre of bottled water can contain thousands of microplastic particles”. The press release related to tests on more than 250 bottles of water from 11 leading global brands, sourced from 19 locations in nine countries on ve continents including Brazil, China, India, Indonesia, Kenya, Lebanon, Mexico, Thailand, and the United States. The tests were supervised by Dr. Sherri Mason, a “leading microplastics researcher” and Chair of the Department of Geology and Environmental Sciences at the State University of New York at Fredonia. It claimed that its tests revealed “widespread contamination with plastic debris including polypropylene, nylon, and polyethylene terephthalate”, in 93% of the samples tested and with a global average of 325 parts/litre (ppl). It stated that implications for human health are “unknown”. Global packaging organisations were quick to respond and largely reject the implications and claims. Gavin Partington, Director General of the British Soft Drinks Association (BSDA), said: “There is no evidence or scientic consensus worldwide about the potential impacts of microplastic particles on human health. The study by Orb Media has not been through a scientic peer review and has a number of limitations.” The International Bottled Water Association (IBWA), headquartered in the USA and representing US and international bottlers, distributors, and suppliers, highlighted a number of claims in the report that were either unsubstantiated or misleading and stated categorically that “…this study’s ndings do nothing more than unnecessarily scare consumers”. “The particles below 100 microns had not been identied as plastic,” a spokesman told British news service, BBC News. “Since…alternatives would not be expected in bottled water, they could be described as ‘probably plastic’.” The IBWA pointed out that the ‘not-identied substances’ made up the vast majority of particles counted. The study acknowledged that the make-up of those particles was not conrmed. The research focused solely on bottled water product and did not look at any other food and beverage packaging, or make comparisons with levels of microparticles found in the wider environment, in soil, air and water. As Orb Media stated, the implications (if any) for human health are unknown. “To date, there is no applicable regulatory framework or scientic consensus with respect to the adequate testing methodology or potential impacts of microplastic particles, which could be found in any bottling environment,” IBWA said. “There is no scientic consensus on the potential health impacts of microplastic particles. The data on the topic is limited and conclusions differ dramatically from one study to another.” Because there is no scientic consensus about the potential health impacts of microplastic particles, the US Food and Drug Administration (FDA) has not issued any regulations concerning these substances in foods and beverages. Any regulatory action concerning microplastic particles would need to be based on sound science, including demonstrating a correlation between the levels of this substance found in foods and beverages and any potential adverse health effects. A recent scientic study published in the peer-reviewed journal Water Research in February 2018 concluded that no statistically relevant amount of microplastic can be found in water in single-use plastic bottles. (Analysis of microplastics in water by micro-Raman spectroscopy: Release of plastic particles from different packaging into mineral water by Schymanski et al.) IBWA went on to highlight that bottled water, as a packaged food product, is comprehensively regulated by the U.S. Food and Drug Administration (FDA) (and other regulatory bodies around the world). All bottled water products are produced utilising a multi-barrier approach, which helps prevent possible harmful contamination to the nished product as well as storage, production, and transportation equipment. Many of the steps are effective in safeguarding bottled water from microbiological and other contamination. Measures may include one or more of the following: source protection, source monitoring, reverse osmosis, distillation, micro-ltration, carbon ltration, ozonation, and ultraviolet (UV) light. “As always, the bottled water industry is committed to providing consumers with the safest and highest quality products and we are following any scientic developments on this subject closely,” IBWA concluded. www.bottledwater.org www.britishsoftdrinks.com www.orbmedia.org","@ID":47}, "BOTTLE MAKING 43 PETplanet Insider Vol. 19 “Within the local market, 250ml and 390ml bottles are extremely popular”, Mr Grant explains. “We see still water as a growing trend; our Mount Franklin and Coca-Cola’s Pump brand are very popular in this segment.” “Environmental considerations are an essential aspect of our philosophy,” says David Chalmers, as he describes Coca-Cola Amatil’s future business strategy. “The Sydney team works continuously on optimisation of processes for environmental and recycling issues. These range from reducing material to new packaging technologies and increasing the use of rPET in bottle production.” www.ccamatil.com Key data for Coca-Cola Amatil, Eastern Creek Site size: 142,000m² (of which 11,023m² is for PSD, 34,000m² for the DC) PSD Workforce: 39 Shift system: 4 shifts, 24/7 Portfolio preforms (Husky moulds) PCO 1881, produced on 144 cavities: 12.8g, 16.6g (15.84g), 19.8g (two moulds), 33g, 37.4g PCO 1881, produced on 128 cavities: 25.2g, 29g 38mm, produced on 128 cavities: 24g Portfolio closures (Z-Moulds) PCO 1881, produced on 96 cavities: 2.1g PCO 1881, produced on 72 cavities: 1.8g, 2.1g 38mm, produced on 48 cavities: 3.25g 38mm, Mercury 3 piece SC Available bottle sizes Water & CSD (PCO 1881): 250ml, 390ml, 450ml, 500ml, 600ml, 750ml, 800ml, 1l, 1.25l, 1.5l, 1.75l, 2l, 2.2l Warmll juices & sports drinks (both nitro and non-nitro), RTD, aseptic. 300ml, 500ml, 600ml, 750ml, 1l, 1.5l, 2l HyCap 2, including two new 300 and 400T HyCap 4-series models that were installed just at the end of 2017. The latest HyCap machines are to produce the Coca-Cola designed, Mercury 3-piece Sports Closure. The company’s bottling equipment is primarily from Krones, incorporating their turnkey blowll technology.","@ID":45}, "PETpatents www.verpackungspatente.de PETplanet Insider Vol. 19 No. 05/18 petpla.net 72 Plastic container European Patent issue No. EP 2653400 B1 Applicant: Suntory Holdings Ltd., Osaka (JP) Application date: 14.12.2011 A reduced-weight plastic container made from PET is furnished with special shapes so it remains sufciently stable even in case of impact or a “strong” longitudinal application of force. Plastic bottle European Patent issue No. EP 2962947 B1 Applicant: Yoshino Kogyosho Co. Ltd., Tokyo (JP) Application date: 17.12.2013 Hot llable plastic bottle made from PET with circulating brace ridges and a base shape that can elastically absorb the vacuum forces arising from cooling after hot lling. Preform with handle International Patent No. WO 2017 / 173477 A1 Applicant: Integrated Plastics PTY Ltd., Villawood (AU) Application date: 4.4.2017 The international application describes a preform with integrated handle for manufacturing a blown bottle. The procedure for manufacturing a bottle from this preform and the related aid for positioning in a machine are described. Folding container International Patent No. WO 2016 / 065486 A1 Applicant: First Element Packaging Inc., Calgary (CA) Application date: 30.10.2015 Folding plastic container designed as “disposable barrel” for beer. The container is equipped top and bottom with inserts for a frame to improve the stability and/or the folding and compression behaviour of the container. Plastic bottle surface European Patent No. EP 3216710 A1 Applicant: Suntory Holdings Ltd., Osaka (JP) Application date: 29.10.2015 A lightweight PET bottle has a special surface structure in the grip area to avoid any collapse of the bottle when gripping, locating, lifting or pouring. Improved opening procedure International Patent No. WO 2016 / 077517 A3 Applicant: Niagara Bottling LLC., Ontario (CA) Application date: 12.11.2015 PET bottle for carbonated drinks. Bottle and seal are perfectly suited to one another so any foaming or unwanted escape of the product is avoided when it is opened.","@ID":74}, "BOTTLE MAKING PETplanet Insider Vol. 19 No. 05/18 petpla.net 42 Soft drinks in Australia by Kay Barton Eastern Creek, just over 40km to the West of Australia’s leading commercial and business city, could be regarded as the ‘gateway’ to Sydney. It is also the location of one of CocaCola Amatil’s newest plants. With 36 plants in total, across Australia, New Zealand, Indonesia, Papua New Guinea, Fiji and Samoa, it is a true giant in the industry and one of the largest bottling companies in the Coca- Cola network globally. We met: Mr David K.L. Grant, Director Supply Chain, CCA Australia Mr David Chalmers, Operations Manager PSD, CCA Australia Mr Michael Ludemann, General Manager ANZ, Husky Injection Molding Coca-Cola Amatil employs around 13,000 staff, including circa 3500 in Australia. It maintains 126 production lines across its various national markets and, in 2017, it generated an underlying net prot after tax of AUD$416.2 million. Amatil stands for Allied Manufacturing and Trade Industries Limited; the acronym was rst used in 1977. The 142,000m² site in Eastern Creek has two facilities and houses production for PET preforms and HDPE closures, as well as the NSW Distribution Centre. The business was set up in 1904 and was involved in printing, agriculture and consumer products. The rm entered the packaging sector in 1960 and then the food and beverages sector in 1963. In 1965, the decision to purchase Coca-Cola Bottlers Pty in Perth paved the way for further business success. The change in name to Amatil in 1977 marked the start of an ongoing phase of strategic takeovers, and the establishment of plants in Southeast Asia and the Pacic region. Alongside non-alcoholic beverages, the company has also been bottling and distributing beers, spirits and alcoholic mixed drinks since 2006/2007, a segment which – along with coffee – is generating strong sales. At the Eastern Creek facility we were introduced to David K.L. Grant, Director, Supply Chain, with Coca-Cola Amatil, and David Chalmers, Operations Manager PSD. We were also joined by Michael Ludemann, General Manager ANZ for Husky Injection Molding Systems. Coca-Cola Amatil started using PET bottles as far back as the late 1980s. In the 2000s and 2010s the company gradually made itself independent of external suppliers for PET bottles, preforms and closures, and launched its own complete supply division for bottle production. Today, the PSD (Packaging Services Division of Coca-Cola Amatil) produces 1.2bn preforms and 1.3bn closures in a state-of-the-art facility. Extensive use of fully-automated processes, robotics and automated vehicles mean that few human operators are needed. As well as supplying its own needs the plant also supplies other bottlers, with around 200 million preforms and as many closures. It is planned to develop this as a distinct business area. “Our model is highly competitive”, says David Chalmers. “Our injection moulding facilities can produce all models and we have, in principle, no restrictions on quantity. This means, for example, that even small volumes such as 1.5 million are feasible.” Coca-Cola Amatil currently uses ve Husky HyPET HPP4 and three Husky F.r.t.l.: David Chalmers and David Grant of Coca-Cola Amatil with Michael Ludeman from Husky Injection Molding Systems","@ID":44}, "EDITOUR PETplanet Insider Vol. 19 No. 05/18 petpla.net 26 Expanding the range of products into the global PET market Yudo goes global for PET by Kay Barton April 2018 Yudo considered expanding its product line to include PET moulds for many years before it did so. As customer demand for preform tooling increased, the recognition that Yudo’s existing product range naturally complemented the PET market made the decision inevitable. The result opened opportunities to deliver advanced performance technologies, with a commitment to fully service and support new PET customers across the world, the company says. Tour Sponsors: PiCOOL, Yudo’s patented post-mould cooling technology, uses a unique method to direct a spiral air stream onto the interior surface of preforms. This generates high levels of turbulence and more uniform distribution of cooling, making the process more effective. The company says that it achieves improved heat transfer during post-mould cooling and helps reduce cycle times, energy costs and tooling investment, as well as improving preform quality. It can be integrated into any machine equipped with post-mould cooling capability and works with all preform sizes and neck nishes. A privately-owned company founded in South Korea in 1980, Yudo designs and manufactures equipment for the injection moulding industry. It has grown from being a small hot runner manufacturer supplying local customers to a multi-national organization that’s approaching the US$ billion mark. It has over 3 million square feet (280,000sqm) of highly automated manufacturing space and employs more than 3,500 people, 235 of which are dedicated R&D engineers. Yudo maintains that the foundation of its growth is its record of developing and supplying leading edge hot runner technology for the automotive and consumer electronics industries. It claims that it is difcult to nd a hot runner in the consumer electronics world that is not produced by itself. A key element of its success is its patented and multi-award winning ISO Diffusion Bonding manufacturing process. A large portion of Yudo’s annual earnings is reinvested into research and development, in its drive to remain at the forefront of product advancement. Today, it has manufacturing centres in 24 countries around the world and sales and service representation in more than 60. The company is continuing to develop and expand its offerings beyond hot runners. It has an extensive line of supporting equipment that includes hot runner temperature controllers, complementary auxiliary equipment, in-mould labelling systems, high speed linear robots, integrated factory automation and logistics control, as well as customised intelligent management software packages for production monitoring and control. Yudo’s initial entry into the PET market was undertaken quietly, in 2009. It initially supplied only to the local market, with a small range of proprietary hot runner designs, and now produces complete mould tooling packages of up to 144 cavities. Yudo has taken the time to carefully prepare its entry into the global PET market and is now equipped to do so, according to Rick Unterlander, General Manager, Yudo ValuePro Lab Canada. Its entry strategy rests on two pillars: The company’s PETone range of PET products is designed to work with modern injection moulding machinery, as well as legacy platforms. These products include complete mould packages, mould conversion and replacement components, ISO Diffusion Bonded hot runners, and its patented PiCOOL post-mould cooling system. The second pillar is Otto Systems AG, which is a joint venture company with Otto Hofstetter AG. The Otto Systems team is focused on supplying and integrating turnkey systems, including moulds, hot runners, machines, take-out robots, post mould cooling automation, and all related auxiliary equipment. The synergies between Yudo and Otto Systems AG strengthen its manufacturing capabilities and expand its worldwide presence. Yudo’s ISO diffusion bonded hot runner technology, which is now available for all PET applications, utilises a solid-state diffusion process to construct its manifolds; wherein the atoms of multiple adjoining steel plates intersperse to become one. It was developed by Yudo speci- cally for hot runner manufacturing, to create a manifold system with inherent advantages for melt distribution. The process does not require solder, paste, brazing or welding; it facilitates the forming of precision machined and geometrically optimised melt ow channels without seams or edges. Jinho Yu, Engineering Manager, Yudo Co, says that it produces a more durable hot runner that does not use end plugs. Dead spots are eliminated, channel lengths minimised and channel surfaces polished, which all help to achieve reductions in colour changeover time, cavity to cavity weight variation, pressure drop, and AA generation. www.yudo.com","@ID":28}, "PETproducts 66 PETplanet Insider Vol. 19 No. 05/18 petpla.net Droplet-shaped lightweight bottle In many tropical countries, particularly in Asia, small water beakers made of PET are in widespread use. Sealed with a removable lm/foil, they supply the on-the-go market for a quick thirst-quencher betweentimes. Airlines like using these non-returnable beakers, too. Krones has now developed an attractive and practical alternative: a exible, reclosable small lightweight bottle. The droplet-shaped PET bottle holds 200ml, and with a weight of just 4.4g is extremely light. It can be produced using a standard blow-moulding machine that is also suitable for lightweight formats. Moreover, the container offers an option for pressurising it with nitrogen after lling, thus stabilising it for storage and transportation. In terms of dress the PET bottle offers abundant design versatility: different labelling processes enable different designs. This means the beverage producers can market the bottle in different price segments and retailing structures. The droplet shape is an eye-catcher, its geometry stabilises the lightweight bottle. The container features a 26/22 neck nish typical for water bottles, and can be closed with a normal screw-cap. The small, droplet-shaped PET bottle has been developed by Krones’ Packaging Development and Consulting Department. This unit creates new packaging designs and assists clients in translating an idea for a container/pack concept into technically feasible, marketable reality. Krones offers customised solutions, e.g. on the basis of nite-element analysis, or material-specic consultancy for complex packaging projects. Key facts: Weight 4.4g Stable thanks to nitrogen pressurisation Iconic design for mini- bottles Reclosable thanks to screw-cap An abundance of different labelling options Can be produced using standard blow-moulding machines www.krones.com Aseptic packaging by providing options beyond traditional at caps Aptar’s new sportc a p n ame d U n o 38mm is a 1-piece closure made of PP to suit the requirements and performance of the flip-top design and to provide the option of translucent or opaque colours. Uno provides one-hand opening and reclosing and is available in two 38mm neck nishes: 3-lead and 2-lead thread starts. The development in this larger, wide mouth neck nish is driven by the combination of three factors: the continuous growth of aseptically processed, shelf stable beverages such as juices, drinkable dairy, ready-to-drink coffees and teas, preservative free drinks and water - the dynamic growth of on-the-go beverage consumption in single serve packaging formats - and the increasing consumer demand for on-the-go beverage convenience, hygiene and resealablity provided by a ip-top sport cap with a larger neck nish for superior hydration. To address these customer and consumer needs, Aptar has developed Uno, a liner-less flip top, plug-seal sport closure for PET bottles, based on the success and market acceptance of the original sport closure family, offering a visible tamper evident and comfortable drinking spout. Uno 38mm is suitable for H 2 O 2 sterilisation for juice and dairy beverages, using the following aseptic equipment suppliers: Krones, Serac, KHS and GEA. Uno also ts Claranor Puls’Full Cap sterilisation with pulsed light. The closure perfectly passed the test and is therefore adapted for ESL>60 days and high acid aseptic lines. Uno 38mm is intended to provide safety and convenience for on-the-go beverage consumption for children and active adults alike. Consumers looking for natural and healthy beverages can now enjoy convenience, in today’s traditional premium water brand packaging. www.aptar.com","@ID":68}, "TRADE SHOW PREVIEW PETplanet Insider Vol. 19 No. 05/18 petpla.net 63 precision and energy efciency. The valve technology makes it possible to set the pilot and main blow pressures in increments of 0.1 bar. A customerspecic blow study determines the optimal material distribution in the blow mould during the proving process. Optionally, process monitoring can use pressure sensors to measure the main blow pressure while it is applied. If the pressure drops unexpectedly, the plastics processor immediately receives an alarm message. If a customer wishes, the Blowliner is available as a spray-blower without the stretching component. At the end of the blowing process, the vacuum gripper of the integrated linear unloading system removes the nished products from the tool and places them precisely on a conveyor belt or directly in boxes. Tool technology Many considerations owed into the tool technology during the conception of the Blowliner. Hornhuber recalls: “Our goal was to increase the number of cavities and thus productivity with additional optimised cycle time for existing plants. At the same time, we wanted to enable our customers to make optimum use of the machine. It should be possible to use the hot side of the tool to manufacture very different products in terms of size and thus number of cavities. This gives the user a very high level of exibility in their production.” The solution lies sary. The tool changes are easy. The operator uses the equipping carriage to move the tool to the machine and quickly and ergonomically changes the injection mould by means of a cable pull and roller conveyors. Satis- ed Hornhuber reports: “A complete tool change from good part to good part takes only ve to six hours for a trained technician. If only the blowform is being changed, this can be handled within 30 minutes.” Vertical integration One Mould & Matic customer produced four different items on his Blowliner M for the rst two years. Fast tool changes and high exibility regarding size and design of the preforming and blowing tools were essential. Then one of the articles was discontinued. He had to change from a 30ml vial to a 5l container. “No problem!” says Hornhuber. “This variety can be realised effortlessly with our tooling technology.” Except for the injection moulding machine and the hot channel system, all components of the Blowliners are from Mould & Matic. The entire machine control and software comes from Austrian Micheldorf and is programmed at Beckhoff. To optimise process reliability, camera inspection of the containers and a leak test are optionally available. The company advises on the choice of materials and the design of preforms and bottles. The preforms determine the cycle times of the stretchblow process, therefore the material distribution in the nal product and thus wall thicknesses. Hornhuber afrms: “Intelligent preform design saves money because we can realise material savings and higher cycle times.” The Blowliner M permits cycle times of 10s, the little brother Blowliner S can even manage less than 8s. The Blowliner M (double-row tool with twelve cavities) will be shown at the NPE, producing PET pill-packers. The containers have a volume of 250ml and weigh 30g. www.kiefel.com Three-row linear robot with a gripping mandrel in a balanced hot channel tool with a needle lock system. One question is primary to each new order: what products does the customer want to manufacture on the machine today and what does the future hold? Even if a two-rows 12-cavity tool is initially used for products with an article weight of 15g, the same hot side can later be used for products made of PET, PP or HDPE with, for example, 35g article weight. “The customer is prepared for future developments and can react quickly to new challenges”, claries Hornhuber. Before Mould & Matic manufactures the series tools, the company rst builds test tools and optimises the end product for them. The capacity for different product sizes and tool congurations, however, was by no means everything. Quick tool changes should be included, which can even be handled by a single operator if necessary. An air cushion tool carrier for the injection mould and one on rollers for the blow mould make the quick change possible. A hall crane is unnecesBlowliner Medium with a material throughput of up to 130kg PET per hour","@ID":65}, "PETplanet Insider Vol. 19 No. 05/18 petpla.net 70 PETbottles Beverage + Liquid Food Bulbous bottle for water The 330ml bottle of drinking water is specially adapted to the needs of babies and young children. It is sold by the Sanpellegrino brand “Levissima” under the tagline “issima” in a bottle especially designed for the target group. It attracts attention with its bulbous shape and its sleeve label printed with gures from the “Avengers” series. The label is drawn up as an additional seal over the easy-to-operate closure and must be partially removed before rst use using the easily visible perforations. www.levissima.it Skyr in the bottle 250ml Skyr Drink, a product manufactured in accordance with Icelandic tradition, is being sold by Arla Foods Deutschland GmbH via wholesale. The drink, available in Cherry and BlueberryBlackcurrant avours, is high in protein and low in fat. It is packaged in a white, contoured, stable bottle containing 250ml. A full sleeve label and screw cap with guarantee band enhance its appearance on chiller shelves. www.arlafoods.de Sports drink in PET Magnesia Go! is the name of the new natural non-carbonated mineral water from Karlsbad Mineralwasser GmbH. The water contains up to 170mg of magnesium per litre and supports the body’s metabolism. The blue multi-use bottle with ergonomic grip areas and an easy-open sports cap contains 750ml of water. A smooth foil label around the middle presents all necessary information. www.karlsbad-mineralwasser.de","@ID":72}, "TRADE SHOW PREVIEW PETplanet Insider Vol. 19 No. 05/18 petpla.net 58 A range of packaging solutions and mould making services R&D/Leverage, the independent packaging solutions and mould manufacturing specialists based in the Midwestern U.S., will showcase its latest accomplishments and complete range of services at the NPE 2018. R&D/Leverage introduces the Liberty IBM System. South Hall 32079 The Liberty tool is claimed to be a paradigm shift in IBM tool design. R&D/Leverage says that it has the following advantage: There is a faster, and safer start-up with less labor possible, resulting in a longer mould life, because of the patented Genesis IBM hot runner system which utilises the thermally insulated nozzles, onthe-y balancing, and elimination of further adjustments after initial mould set up. The production quality is said to be very high due to patented, selfadjusting cavities. These cavities are aligned perfectly on precision dowels, not key stock, to ensure a perfect cavity alignment. It eliminates mismatched threads, parting line mismatch, and gate damage. The Liberty IBM System can be started in only 3m, versus 45m or in some cases up to 2h for a traditional mould, after initial tool set up. R&D/Leverage is one of the most known manufacturer of stage PET tooling. It offers a complete solution for all PET converters. R&D/Leverage guarantees a free project evaluation by experienced tooling and processing engineers, an in-plant process support for new mould startup as well as an on-site process development for unit or production tooling. Customers are said to have a smooth transition of unit-to-production processing, a reduced time to market from project inception to production tooling and premium materials increase life of tooling and improves part quality. The Leverage group of R&D/ Leverage integrates an array of both creative and technical offerings: R&D/Leverage Packaging Solutions designs a strategy for each project. It begins with an alignment of internal and client stakeholders ensuring to provide creative packaging designs that can be manufactured. Teams of creative and technical experts working hand in hand to ensure a winning concept that is ready to move into production. There is also a technology and manufacturing research support through-out the design process to ensure speed to market. R&D/Leverage is happy to discuss new state of the art trends with their customers for example: In-house mould repair & refurbishment department, mould design analysis, opti-sim virtual prototyping as well as rapid prototyping and 3D part scanning. R&D/Leverage will also inform about its news projects such as: to keep the “Snap” in a new PET bottle for Snapple for Dr Pepper Snapple. www.rdleverage.com","@ID":60}, "10 NEWS Vol. 19 No. 05/18 petpla.net New Vice President of Packaging at Engel As of April 1, 2018, Frank Schuster is taking over as the Vice President of the Business Unit Packaging at the injection moulding machine manufacturer and system solution provider Engel, headquartered in Schwertberg, Austria. He succeeds Michael Feltes, who is transitioning to China within the group of companies. Frank Schuster has been with Engel for two years and, as the Sales Manager of Packaging, has made signicant contributions during this time to the successful development of the division and the continued strengthening of the Engel brand in the worldwide packaging industry, says the company. Prior to his time, Schuster was already active in leading sales positions in the eld of plastic machinery manufacturing with a focus on packaging. Michael Feltes, the previous Vice President of the Business Unit Packaging, is transitioning within the Engel Group of companies, becoming President Sales & Service for the Wintec subsidiary in Changzhou, China. www.engelglobal.com","@ID":12}, "PETcontents 05/18 4 PETplanet Insider Vol. 19 No. 05/18 petpla.net Page 54 Page 36 Page 66 INSIDE TRACK 3 Editorial 4 Contents 6 News 66 Products 67 On-site 68 PET bottles for Home + Personal Care 70 PET bottles for Beverage + Liquid Food 72 Patents MATERIAL / RECYCLING 12 High prices now the norm 14 PET the Indian way 15 Colour with an extra 16 Cutting carbon in PET recycling 18 “Recycling is not the ultimate answer” EDITOUR 22 The U.S. drinks industry in a tight spot 24 Always on the look-out for new markets 26 Yudo goes global for PET 28 Boutique bottling 29 Expanding PET business PREFORM INSPECTION 30 Preform colour control BOTTLE MAKING 31 Machine details - Oven section, transfer functions Stretch Blow Molding, part 9 42 Soft drinks in Australia BOTTLING / FILLING 36 Fruitful investment 38 Heavenly growth 45 Plastics in bottled water? MARKET SURVEY 40 Suppliers of PET preform inspection systems TRADE SHOW PREVIEW 46 NPE 2018 Bottle Zone oor plan 47 NPE 2018 Technical Forum 48 NPE 2018 preview 50 Solution to serve all markets 51 Custom-tailored inspection equipment 52 Growth, investments, product news and Industry 4.0 53 Special formats for PET bottles 54 Next generation stretch-blow moulder 56 Technology and design 57 Trendsetting technology for preform inspection 58 A range of packaging solutions and mould making services 59 Extended PET portfolio 60 PET recycling equipment at NPE 62 Full-blown bottles TRADE SHOW REVIEW 64 Milk joins the PET revolution BUYER’S GUIDE 73 Get listed! 24 MATERIALS Special","@ID":6}, "MARKET SURVEY 40 PETplanet Insider Vol. 19 No. 05/18 petpla.net 05/2018 MARKETsurvey Resins & additives Preform machinery Preform production Preform inspection SBM 2-stage Compressors Filling equipment & lling inspection Caps & closures and inspection Palletising & shrink lm machinery Recycling Preform inspection As part of a holistic approach to quality control in preform production PETplanet Insider showcases for the second time an overview of preform inspection systems. Even the smallest faults in PET preforms have a signicant impact in bottle production and bottle quality. In the most severe cases, faulty preforms can even lead to malfunctions in the blowmoulder. With ever increasing outputs in the blow moulding systems, perfect preforms are indispensable. This is where preform inspection systems come in: preform inspection systems check the preform’s quality and reject faulty preforms immediately from the production line. Thus preform inspection becomes an essential part of process quality control. These are the participants: Intravis GmbH, Torus Technology Group, Sacmi Imola S.C., IMD Ltd. and Pressco Technology Inc. and Agr International Although the publishers have made every effort to ensure that the information in this market survey is up to date, no claims are made regarding completeness or accuracy. Company name Intravis GmbH Postal address Telephone number Web site address Contact name Function Direct telephone number Fax E-Mail Rotter Bruch 26a, 52068 Aachen, Germany +49 241 9126 0 www.intravis.de Mr Markus Juppe Director Sales & Marketing +49 241 9126 0 +49 241 9126 100 sales@intravis.de Preform Inspection Systems PreWatcher 4 PreWatcher III Sample-PreWatcher ColorWatcher Integrated LayerWatcher Inspection speed Up to 100.000 objects/hour Up to 72,000 objects/hour Up to 1,200 objects/hour 8 preforms within 0.25s Up to 144 objects/hour Inspected parameters: Geometry / Body Contamination, length, diameter, shape, short shots, gate length, unmelted material, bubbles, oil & water marks, burn spots Contamination, length, diameter, shape, short shots, gate length, unmelted material, bubbles, oil & water marks, burn spots Contamination, length, diameter, shape, short shots, gate length, unmelted material, bubbles, oil & water marks, burn spots, wall thickness, inner wall damage, core shift Presence of barrier layers, thickness of barrier layers, position of barrier layers, structure of barrier layers, position of barrier leading edge, position of barrier trailing edge Thread area Contamination, thread dimensions, defects at the neck support ring, ash Contamination, thread dimensions, defects at the neck support ring, ash Contamination, thread dimensions, defects at the neck support ring, ash Mouth / Sealing surface Diameter, ovality, ash, scratches and notches on the sealing surface, defects at neck support ring Diameter, ovality, ash, scratches and notches on the sealing surface Diameter, ovality, ash, scratches and notches on the sealing surface, inner mouth wall inspection Gate / Dome Contamination, grooves, holes, cracks, crystallisation Contamination, grooves, holes, cracks, crystallisation Contamination, grooves, holes, cracks, crystallisation Colour Colour and intensity deviations (ΔL*, Δa*, Δb*), presence of UV blocker, barrier, nylon blocker and IR absorber (reheater) Colour and intensity deviations (ΔL*, Δa*, Δb*), presence of UV blocker, barrier, nylon blocker and IR absorber (reheater) Colour and intensity deviations (ΔL*, Δa*, Δb*), presence of UV blocker, barrier, nylon blocker and of IR absorber (reheater) Colour and intensity deviations (ΔL*, Δa*, Δb*), presence of UV blocker, barrier, nylon blocker and of IR absorber, (reheater) detection of trend of colour deviations Cavity number Cavity number reading, cavity related statistics, preform sorting according to cavity number Cavity number reading, cavity related statistics, preform sorting according to cavity number Cavity number reading, cavity related statistics, preform sorting according to cavity number, enables collection of reference samples Cavity related statistics Cavity related statistics Further criteria Sorting possibility due to several reject stations Stress test with polarised light, high precision weight measurement, high precision dimension measurement Early warning stage, fast reaction time because inspection results available parallel to preform cooling Visualisation of barrier layers in 3D images Measurement of absence or presence of barrier material Yes Yes Yes Yes Yes Layer thickness & position measurement at distinctive points Yes No No No Yes Layer thickness & position measurement at the complete body by scanning No No No No Yes Features: Installation: Stand-alone Yes Yes Yes No Yes Installation: Inline Yes, but optimised for ofine Yes, optimised for inline Yes, sampling Yes, integrated into injection moulding machine Yes, sampling Side camera for cavity recognition Yes Yes Yes No Yes Method: destructive / non destructive Non destructive Non destructive Non destructive Non destructive Non destructive Data base connection Yes Yes Yes Yes Yes","@ID":42}, "TRADE SHOW REVIEW PETplanet Insider Vol. 19 No. 05/18 petpla.net 64 Cost-efcient milk packaging and Industry 4.0 Milk joins the PET revolution Swiss injection moulding machine manufacturer Netstal showcased dual-layer Prelactia barrier preforms for milk bottles at Chinaplas in Shanghai. Primarily, Prelactia can be used to package liquid dairy products with a long shelf life safely, economically and with a visually appealing result. The new cloud-based analysis app AnalytiX helps injection moulding companies to further increase efciency. Maximum freedom of design for milk bottles Swiss injection moulding machine manufacturer Netstal presented its Prelactia packaging solution for liquid dairy products at Chinaplas. In addition to fullling numerous technical functions, modern-day packaging also needs to be an attractive advertising media and purchasing incentive. Brand owners in the carbonated soft drinks segment have long since exploited the broad freedom of design offered by PET bottles in an endeavour to stand out from the competition at the point of sale with increasingly unconventional bottle shapes. This phenomenon is less common in relation to the lling of liquid dairy products due to the signicant limitations of conventional HDPE and carton milk packaging. “Prelactia PET preforms provide llers of liquid dairy products with new opportunities to distinguish themselves from the competition with customised bottle shapes,” explained Stefan Müller, Sales Director Asia at Netstal. Improved light barrier The double-layer structure of the patented barrier preform offers an economic benet compared to other packaging processes. During the rst step of the overmoulding process, a 1mm-thick, inner grey layer is injected. The dark colour effectively creates a light barrier. “A good comparison would be with early milk bottles made of dark-brown coloured glass, Prelactia blocks out virtually 100% of the visible light spectrum. As a result, the bottles are particularly well-suited for milk products with South Hall · S21085 German Technology Barrier packaging for liquid dairy products The PET-Line 2C is a high-performance injection moulding system for two-component preforms.","@ID":66}, "MATERIALS / RECYCLING PETplanet Insider Vol. 19 No. 05/18 petpla.net 18 PET recycling in Australia – a discussion with Boomerang Alliance campaigner Annett Finger “Recycling is not the ultimate answer” by Kay Barton In February, we visited the Sustainable Living Festival in Melbourne, which celebrated its 20th anniversary in 2018. Over the years, something that originated with a small group of local activists has developed into an event that has gained international recognition and now attracts more than 100,000 visitors every year. It is here that we met with PhD Annett Finger, who works for the Boomerang Alliance NGO as its sole campaigner in the Australian state of Victoria. Annett is ghting for a better understanding of the handling of plastic waste, for nationwide recycling and for the container deposit scheme, and doing so also at a political level. For NGOs, reformers and activists and for all other interested visitors, the Sustainable Living Festival is an annual highlight. It is the major opportunity to nd out about Australian projects, to initiate collaborations or to simply exchange views and experiences, to talk about their own contributions and to take part in discussions on the subject of sustainability. As well as numerous information stands on a variety of different concepts, the event includes workshops, discussions and presentations by experts. PETplanet: What were the factors that led to the founding of the Boomerang Alliance Initiative by Dave West in 2003? Was there some kind of trigger? Annett Finger: He was working with the Ecos group and key NGOs on introducing product stewardship and container deposits. These schemes were driven by the overuse of packaging, the litter they produced and the resources that were wasted. It became clear that we needed a coalition. PETplanet: How did Boomerang become part of TEC (the Total Environment Centre)? Annett Finger: TEC provides logistical and strategic support to Boomerang Alliance. PETplanet: When did you join Boomerang Alliance, and why? Annett Finger: I joined Boomerang Alliance in August 2016. After years of research in marine ecotoxi-","@ID":20}, "TRADE SHOW PREVIEW PETplanet Insider Vol. 19 No. 05/18 petpla.net 62 Injection stretch blow-moulding technology for a variety of bottles Full-blown bottles With the development of the single-stage injection-stretch blow moulding machine Blowliner, the plastics specialist Mould & Matic from Austria, a Kiefel subsidiary company, has opened up a new market. Although they were newcomers to the blow-moulding industry, success has not been slow. Honey, ketchup, detergent bottles, cosmetic and pill packaging or baby bottles - the product variants that are created on the Blowliner are just as diverse as their design. Bernhard Hornhuber, sales manager for blow-moulding technology, about the Blowliner: “Customers really appreciate the fact that they get the complete line - from granulate to packaging - from a single source.” The machine is available in three sizes. The bestseller is the Blowliner Medium with a material throughput of up to 130kg PET per hour. Like its smaller and larger siblings, it also processes PET, PP and HDPE. Thanks to its intelligent concept, it can be upgraded to multi-layer applications at any time. Above all, the premium sector, which attaches great importance to the high quality and transparency of packaging, and where the quantities are between three and 20 million, values the 1-stage system. Hornhuber gets to the heart of the reasons: “Our clients produce sophisticated packaging. They must meet high quality requirements regarding transparency and dimensional accuracy. Most customers produce medium quantities and they want the exibility to produce different containers with volumes between 10ml and 5l on the same machine. The Blowliner fulls all of these wishes and thus contributes to sustainable high plant utilisation at our customers.” But how does the system meet the requirements of the market? A closer look at the design of the Blowliner reveals the answer. The injection moulding unit is at the beginning of the linear machine. This is a vertical hydraulic Engel machine with up to 4,000kN clamping force and a clamping surface of up to 800 x 1000mm - depending on the size of the system. The plasticising unit processes PET, PP and HDPE. Here the preforms are created; depending on the product, these range from eight to 64 cavities. Each machine can be upgraded with a unit for the production of multi-layer preforms. This permits production of preforms made of PP with barrier layers of EVOH or PET with PA. Still warm, they are removed by a linear robot with a gripping mandrel and the preforms are transferred to the stretch-blow unit with a clamping force of up to 400kN. The machine works with one to four-rows blow tools that accept preforms with diameters from 10 to 150mm. Each series of cavities has its own pre- and main blow valve so that the pre- and main blow pressures can be set individually. This makes it possible to run different product variants on one tool. The entire stretch-blow unit has servo motor drives that provide exact repeatability, Blowliner product samples Bernhard Hornhuber, Area Sales Manager Blow Moulding, Mould & Matic Solutions GmbH West Hall 2727","@ID":64}, "TRADE SHOW PREVIEW PETplanet Insider Vol. 18 No. 0/17 petpla.net 59 Extended PET portfolio South Hall 12045 The perfect image High precision closure caps decoration. Up to five colors. At a speed of 250,000 caps/h. Visit us at the NPE – Orlando, Florida USA May 7–11, 2018 West Hall Level 2, Hall D, Stand W6847 www.tampoprint.de “A clear trend can be detected within the beverage industry,” says Frank Haesendonckx, head of Sales and Technology at KHS Corpoplast in Hamburg, Germany. “The demand for single-serve packs holding between 250 and 800ml is on the rise. We’ve thus developed a new version of our tried-and-tested InnoPET Blomax stretch blow moulder especially for this segment.” The system is more compact and at the same time more powerful. The central new feature is its small mould carriers which enable up to 2,500 containers per hour and station to be manufactured. It is available as a modular design. Depending on user requirements it can be blocked with other KHS systems – such as the Innosept Asboll for the hygienic lling of sensitive products, for instance. The new KHS chunk dosing unit for exible product design can also be integrated into the system. This permits fruit, vegetables or cereals up to 10 x 10 x 10mm in size to be added. “We’re vastly expanding the application options and are thus supplying systems for new markets,” claims Haesendonckx. KHS will also present its extremely light packaging solutions. The systems provider expects its Factor 100 0.5l PET bottle for still water to attract plenty of attention. With its expertise in lightweighting KHS offers its customers holistic consultancy from the design through the technical engineering to the production of their PET bottles. This produces individual containers tailored to suit the required functionality and load. Precise neck handling Further developments as regards preferential heating will also be in focus at the trade show. This setup enables the production of oval containers with an efcient distribution of materials and wide-neck containers with openings measuring up to 70mm and permits extremely precise neck handling – while ensuring a high bottle quality and low energy consumption in the SBM process. “Wide-neck systems and special packaging forms are also gaining in signicance,” explains Haesendonckx. The reason for this lies in the known advantages over glass: unbreakability, a lower weight and the option of inline production, as containers no longer have to be supplied to the plant but can be produced on site. Protection for sensitive products Another KHS development which will be on show is FreshSafe PET. This gives sensitive juices and carbonated soft drinks perfect protection by covering the inside wall of the PET container with a wafer-thin layer of silicon oxide. “With our innovative barrier technology beverages have a shelf life which is comparable to those bottled in glass,” says Haesendonckx. This coating method also protects sensitive foods such as tomato sauce, fruit and vegetables – even in transparent PET containers. www.khs.com Extremely light single-serve formats, wide-neck and oval packaging solutions and powerful, compact machines: the KHS Group will presenting its extended PET portfolio NPE Plastics Show.","@ID":61}, "EDITOUR PETplanet Insider Vol. 19 No. 05/18 petpla.net 24 Tour Sponsors: March 2018 Fluid Forms Inc., Colton, California, We met: Robert Mauricio, General Manager Always on the look-out for new markets Penta is at the high end of the premium water market, i.e. costing more than one US Dollar for a halflitre bottle. What makes this product so special is a 11-hour process that removes all minerals from the water which, according to Mauricio, allows the pure taste of the water to come through. Penta has found its place in the American market. Finding niches is a fundamental strategy employed by both companies. United Beverage has other drinks besides the aforementioned Penta brand, e.g. carbonated soft drinks for Cosco, puried water, alkaline water, and many more which all come in PET bottles. Fluid Forms has made its own special contribution to United Beverage’s success. As well as producing bottles for its sister company, Fluid Forms operates as a bottle supplier on the open market. In so doing, Robert Mauricio is setting his sights on niches in the alcohol industry. “Here the volumes are smaller and the margins better than commodities such as water bottles”, said Mauricio. Projects involving up to one million bottles per year or more t best with his idea. His target market is the whole of the south-west. He has also managed to attract a great deal of interest from four bottle llers within an immediate 50-mile radius. He sees himself not as a bottle supplier but more like a partner who is involved from the initial idea to the nished bottle. His company is also prepared to invest in the necessary machinery. One of his PET projects is the Kuvée wine packaging system which enables the contents of an opened wine bottle to keep fresh for up to 30 days and more. The idea is to t a PET wine capsule with a high tech dispenser (Smart Bottle) and pour the wine through a special check valve system into the wine glass. There is a microchip in the capsule neck which reads out information to the Smart Bottle, e.g. wine history, reordering, how much has been consumed etc., which is then displayed on an inbuilt screen. The PET capsule and Smart Bottle for wine could one day be as popular as Keurig is to coffee. Fluid Forms machinery is as varied as their projects are diverse. The two lling lines are currently being fed in alternation from a single blow-moulder. The link is made via conveyor belts and an unscrambler at a particular bottling plant. Robert Mauricio, General Manager, Fluid Forms, Colton, California, prior to Editourmobil F.l.t.r.: Maria Salazar, Quality Manager, Sergio Benavides, Injection Supervisor, and Evelyn Soto, POC Fluid Forms Inc. and United Beverage plants are located in Colton California southeast of Los Angeles. The companies operate as separate business units belonging to the same ownership: Fluid Forms produces preforms and bottles while United Beverage lls and manages its own brandname “Penta”.","@ID":26}, "TRADE SHOW PREVIEW PETplanet Insider Vol. 19 No. 05/18 petpla.net 55 TRADE SHOW PREVIEW 55 Preferential & offset neck heating This technology kit produces opposing longitudinal heating bands to the preform to optimise production of oval or oblong bottles.This technology goes one step further by also allowing for these heated bands to be moved offaxis from the preform centerline; so that offset neck bottles can be produced. Neck orientation This technology kit puts all the neck nishes on each and every bottle to be in the same orientation. This is invaluable for containers that use a ip-top cap so that it aligns in the proper position for opening and pouring. 1Blow can do this alignment without the need of a tab or V-notch on the preform. The 1Blow servo-driven mechanical system relies only on the thread start, and thus can use standard preforms; opening up the spectrum of preforms that can be used. Heat set This set combines heated blow moulds with recirculating high pressure air cooling to induce higher crystallinity into the bottles. This higher crystallinity allows the resultant bottles to have heat resistance to the hot ll process. • 28mm, 33mm and 38mm screw closures • Robust and trouble free capping • Established DoubleSeal™ technology - for secure sealing performance - for better protection against micro-organisms • Slit FLEXBAND® band technology for enhanced tamper evidence • O 2 barrier and scavenging options for screw flat caps supporting longer shelf life and fresher taste • Sports closures for aseptic filling and hot filling without aluminum foil • Special closures for syrups and carton packaging Unique range of screw and sports closures designed for cold fill and aseptic application BERICAP Technology for juices, RTD teas, health drinks www.bericap.com Base inversion This technology kit is a multistaged mould base system that allows for the base push-up of the blow mould to be moved up in two or more increments and allows for the creation of a diaphragm base. On heat set bottles this acts to absorb the vacuum created after the liquid contents cool in hot ll bottles. Sure grip This technology kit allows for the production of bottles with a hyper-extended grip into the bottle that could not be produced in standard stretch-blow moulding processes. It utilises software and hardware on the machine combined with a multi-staged mould insert system that allows for both opposing handle grip contours to be moved inward during the stretch-blow moulding process. 1Blow invites the visitors to its booth to experience the 4LO rst hand and to see and learn of all of its features, benets, and advantages, and why it also just might be the greenest stretch-blow moulding machine on the market today. www.1blow.com","@ID":57}, "BOTTLE MAKING 32 PETplanet Insider Vol. 19 No. 05/18 petpla.net Another new approach is heating with laser beams. Beams created by diode lasers are emitted in the NIR spectrum directed very precisely onto the various areas of the preform with limited convectional heat. This oven system can be linear or circular as shown in Fig 4.7. Figure 4.7 Circular oven with laser heating. Picture part of patent #8, 330, 290. Lamp control There are a variety of control mechanisms present depending on machine manufacturer and year of manufacture. Modern machines allow adjustment from control screens while older machines use a number of control devices. Voltage regulators control all lamps from 0 to 220V. On some control screens this is expressed as a percentage from 0 to 99%. Machines differ in how many voltage regulators are in use (Fig. 4.8). Figure 4.8 Modern machines offer lamp control right on screen. Diagram courtesy of KHS Corpoplast. In addition there is often a master module allowing the adjustment of all lamps in one oven up to the maximum voltage. Individual lamps can also be switched off completely either right on the screen or by pulling the plug in the control cabinet (see chapter 10 on how these features are used in the process). Most machines monitor current ow to the lamps and warn operators if the current falls below a lower threshold because of lamp burnout or cable-breakage. Fan cooling Besides cooling the lamps and reflectors oven systems must also provide preform cooling (chapter 6). Designers use air blowers for this task exclusively and machines differ in the number, size, location, and control of these. Simpler methods are fans with fixed speed motors while more sophisticated machines offer variable speed motors to control air flow. In the latter case thermocouples in one oven provide a means of correlating the effect of the fan to the oven environment (see chapter 6, section 6.4 for possible problems). Close-looping of fan speed and oven temperature may or may not be available and is not always advised. Consider this scenario: Preform temperature is set to 90°C and oven temperature to 85°C, both being close looped. Let us say the plant temperature increases during the day as is common in the summer months in Northern climates. The effect on preform and oven temperature is not the same though. If the preforms become warmer the machine regulates the lamps down. This leads to a drop in oven temperature. If this drop is larger than the increased air temperature the fan will decrease its speed leading to increased preform temperatures and the lamps will be further decreased to compensate. The two regulatory circuits would basically fight each other unless the increase in environmental temperature change affects both parts by the same percentage, which could actually lead to overregulation when the lamp output drops and the fan speed increases at the same time. It is therefore often better to closeloop the preform temperature only and control oven temperature manually. Choose at least three times the number of cavities as the moving average for lamp control, that is, on a 20-cavity machine it should be at least 60. Choose a small proportional factor (the rate at which the lamp output will be changed) as well, typically 0.3. This will avoid overregulation (fig. 4.9). Figure 4.9 Air ow in oven with preforms right side up. Diagram courtesy of Adphos Group. 4.2 Transfer functions Rotary machines One variable speed DC or AC motor drives all machine functions through a combination of gears, chains, or linkages, ensuring that all physical movements are synchronised whether preforms are in the machine or not (except the stretch rod). Brakes and clutches on the main wheels prevent overloads or unwanted movements (spinning) during a sudden stop. An electronic rotary indicator signals the main drive position to the programmable logic controller (PLC) during each rotation. The PLC manages all nonsynchronised machine actions such as blow air. A hand crank allows manual machine rotation for adjustment or clearing of preforms. Transfer functions vary a great deal from machine to machine. Fig. 4.10 will give an idea of the components involved.","@ID":34}, "MATERIALS / RECYCLING 19 PETplanet Insider Vol. 19 cology, I was aware of the immense task of reducing marine plastic pollution. It appealed to me to work with an organisation that used reputable research, worked as an alliance and applied targeted campaigns to effect legislative changes on all levels of government. PETplanet: What are your precise tasks and responsibilities as a campaigner in the Australian state of Victoria? Annett Finger: I am running two campaigns. The first, ‘Ban the Bag’, aims to get single-use plastic bags banned in Victoria. We have been promised that bags will be banned but have seen no details yet from the Victoria government. The second campaign is the ‘Container Deposit Scheme’, which is seeking to get Victoria to implement a 10 cents per container refund scheme and harmonise it with other states. My work includes research and litter data analysis, issuing of reports and media releases, contact with ministerial and department staff, and presentations at schools, festivals and community gatherings. My work is incredibly diverse. As I am the sole representative of Boomerang Alliance in Victoria I do it all, pretty much. I work closely with our Victorian allies, such as Friends of the Earth, Plasticbagfree Victoria, Sea Shepherd, Beach Patrol and other like-minded groups, such as the Port Phillip EcoCentre, the Marine Mammal Foundation and Zero Waste Victoria and many others. One of the best things we achieved in the past 18 months was co-founding the Plasticfree Victoria Alliance. It is a ‘supergroup’ of over 80 (and growing rapidly) organisations and businesses, who want to tackle the challenge of plastic pollution in Victoria. PETplanet: You emigrated to Australia as a German citizen in 1998. You have a doctorate in ecological sciences and you will soon be gaining dual nationality. How do you find the handling of post-consumer waste in Australia, compared with Western Europe? Annett Finger: Australians are both better and worse in regard to post-consumer waste. The worst rst: the recycling infrastructure is worse than in Europe. Much less is recycled and even less of that is processed onshore. Of course, some European reports include waste to energy under recycling, so the recycling rates might be overstated but Germany and Sweden, for instance, repi.com A COLOUR IDENT I TY LIQUID COLOURS AND ADDITIVES FOR PACKAGING NPE - Orlando, FL - South Hall - Level 1 - Booth S19103","@ID":21}]}}
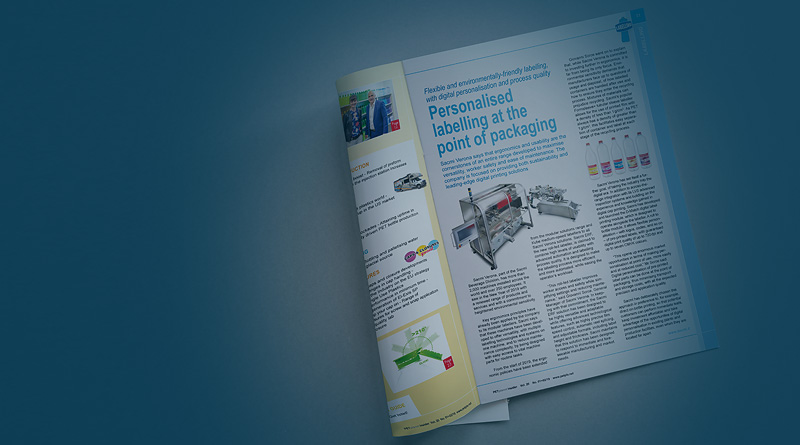