"EDITOUR REPORT 15 PET bottles. Here too there are two filler combinations available – monoblock and triblock. In the majority of cases the capping machine is equipped with a steam box for PET bottles which vaporises the inner compound and/or the sealing band. The Magic HF filler is based on electronic filling technology for still beverages. The fill point is very near to bottle headspace since in a secondary phase (through a tilting conveyor) the hot product sterilises the bottle neck and cap. To complete the line there are flash pasteurisers, cooling tunnel and tilting conveyor, where the filled PET bottles are placed on an oscillating conveyor belt at an angle of up to 90°. Craft brewery Finally, we come to another interesting topic, namely craft breweries in USA. Craft beer is enjoying increasing popularity over there and as a consequence also in other markets. Craft beer is local beer, brewed in smaller breweries with fill capacities of usually not more than 10,000 to 15,000 bottles per hour. This trend is hitting the big breweries, and craft beer is increasing its market share. There are, at present, more than 2,000 craft breweries in the USA. “It is here”, says Emanuele Piva, “that we see our strengths; in the supply of an entire line from the malt right through to the filled and palletised beer bottle in glass or in cans. Unfortunately, PET plays a subordinate role in this, we supplied the last PET filler there in 2009, whereas glass and cans are growing exponentially. As regards the process technology for beer, we had a stroke of luck. An Italian brewery fitter,“Velo“ in Treviso, had ceased trading and we were able to take over key employees and thus secure the brewing know-how for CFT. We have already supplied our first complete craft brewery to “ Birra del Ducato“ not far from here near Parma and are gaining some initial experience and three more are also on the way to customers. We envisage major growth potential with this product”, says Emanuele Piva. www.cft-group.com f.l.t.r.: Emanuele Piva, Beverage Sales Manager and Alexander Büchler, PETplanet in front of a can filler for beer. PETplanet insider Vol. 15","@ID":17}, "TRADE SHOW PREVIEW 45 PETplanet insider Vol. 15 No. 11/14 petpla.net Optical monitoring Berlin-based Dr. Thiedig GmbH & Co KG will be presenting Digox Optical, its process measuring device designed for the optical measurement of oxygen in the beverage industry, and Digox 6.1m, which is a portable analyser for measuring oxygen in laboratory situations and for calibration. Digox optical, an in-line measuring device, is based on the dynamic fluorescence quenching optical procedure. It uses neither a membrane nor an electrolyte and measurement is independent of the CO2 content and medium flow. It is directly installed in the pipe system and can operate in temperatures up to 130°C. Sensor replacement, which is required every 12 months, can be carried out quickly, directly in the line, without dismantling the device. The menu guidance system in the device software is supported through pictograms in the graphic display. Status information is displayed using different colours in the display illumination, which measure values through a graphic trend display. Intelligent diagnosis functions monitor wear. Digox optical is calibrated using the Digox 6.1 as reference measuring device, without removing the sensor. The measuring range of the new system is between 0 and 2,000 μg/l, the accuracy is +/- 1ppb. This system can be used in breweries for measuring tasks and process control including: water degassing, wort aeration, fermenting cellar, filtration, at separators, filling, and CO2 recovery. Digox 6.1 is used for measuring oxygen in laboratories and in-line situations such as at the storage tank, after filtration, at the filler and for inspection when receiving tank deliveries from third parties. www.thiedig.com Dr. Thiedig GmbH & Co. KG Hall 4 | Booth 318","@ID":47}, "TRADESHOW REVIEW 27 PETplanet insider Vol. 15 No. 11/14 petpla.net 4th edition Chips & Grapes 2014 PET in the vineyards by Wolfgang von Schröter Barbastro, 1st and 2nd October 2014. Here, among the vineyards of the Somontano Region at the foot of the Pyrenees, is where “Chips & Grapes“ took place, the 4th time the ”PET conference in the vineyards“ had been staged, once more organised and hosted by a committed team from Novapet, the leading Spanish manufacturer of PET granulate and also preforms. Chips & Grapes differs from PET conferences in other parts of the world by virtue of the unique way in which it endeavours to forge a link / relationship between man and nature, between individuals involved in the development and industrial production as well as in the bodegas and in vineyards of Barbastro. It involves people from the same region who share the same cultural background, the same capabilities, the same wealth of ideas both as regards Chips (PET granulates) and Grapes (the wine) and who instil each other with enthusiasm, as well as motivating and animating their colleagues. However, following a wine tasting in the Viñas del Vero to welcome the guests for the evening it quickly becomes clear that all this has less to do with philosophical, conciliatory idylls but is more a matter of hardheaded, strategic business dealings on the part of the organisers, their friends and customers assembled there to mark this, the 4th time that Chips & Grapes had been staged. The 3rd Conference in 2012 addressed the global topics of the PET value added chain overall from the granulate right through to the filled bottle, whereas the 4th conference had a narrower and more specific focus, namely, integrating into the value added chain those processes in which blow(ing) moulding plays a central part in the line. Other key topics addressed at the conference were specialisation and innovation, and in particular new applications and new materials. David Gonzalez, CEO of Novapet, summarised as follows: “All our efforts are directed towards identifying new perspectives and innovative applications for our PET material. The Novapet portfolio consists of 17 different formats based on 5 principle designs. We concentrate on serving niche markets and therefore smaller quantities, rather than the general commodity market. Commodities occupy something around 30% of our business. Naturally, research and developments and research for new materials are prime disciplines for Novapet.”","@ID":29}, "TRADESHOW REVIEW 30 PETplanet insider Vol. 15 No. 11/14 petpla.net Carmen Rus, Area Manager of P.E.T. Engineering It was what followed that made participants sit up and take notice as she explained “what we do”. Briefly but elegantly she talked her audience through packaging design – feasibility studies – prototyping - validation of the bottle in the laboratory – mould manufacturing – implementation on the filling line. She concluded – confidently: “P.E.T. Engineering is filling the gap, wherever needed and wanted, from the resin to the bottle.” Light barrier for sensitive products- Novapet Solutions Miguel Angel Arto, who delivered the talk, left his audience in no doubt that the Novapet strategy, as already formulated and presented in Chips & Grapes 2012 – has won recognition, that Novapet, together with DCU, had discovered the way into the milk and dairy market, is gaining market share: “A revolution on the shelf, which will continue“. The optimism appears to be justified when we consider the market data for milk and dairy produce, the potential for growth, in particular where dairy items are concerned and for PET (including DCU) compared with the alternative materials featuring by way of competition. Total global dairy market size in 2014: 783 tons Total milk dairy market size in EU28 in 2014: 159 tons Growth expectancy up to 2018: approx. 2% per annum Various ways to get to know... ... new developments in PET bottle... ... production and design.","@ID":32}, "It’s good to share Join in the debate and share knowledge at blog.KNOWLEDGEshare.com KNOWLEDGEshare is an industry forum comprising a digital community of senior industry players and thought leaders, supported by annual KNOWLEDGEshare Live events. The above articles are just a small selection of the many industry-wide topics that are being discussed right now. To learn more about these and other topics, or to share your own knowledge and join in the discussions, please visit blog.knowledgeshare.com. What do astronauts and beverage producers have in common? HACCP! No, it’s not a bad joke. Introduced in the 1960s, by the Pillsbury Company in the US, the Hazard Analysis Critical Control Point system (HACCP) was designed to ensure the highest quality food for astronauts in the space programme. Since then it has spread worldwide. Today following its principles is a legal requirement for all food and beverage producers in Europe and North America. In his latest post at KNOWLEDGEshare.com, Knuth Lorenzen (President of the European Hygienic Engineering & Design Group) explains why these principles are so important for today’s modern beverage producer. Read more at knowledgeshare.com/haccp Prediction: “We will see lights out bottling plants within the next 10–15 years” In a recent post from another KNOWLEDGEshare.com contributor, John Henry (CEO of changeover.com) explains why fully automated “lights out” beverage production could be a reality sooner than we think. If so, then according to Mr. Henry we need to start rethinking traditional changeover and clean-in-place (CIP) processes… Read more at knowledgeshare.com/lightsout Are consumers at risk from caffeine drinks? A recent World Health Organisation (WHO) study raised new concerns about caffeine levels in beverages, especially energy drinks. In a recent post on KNOWLEDGEshare.com Dr. Michaela Ellmann, a specialist lawyer for sraConsulting with many years of food industry experience, discusses the upcoming revision of the European Food Safety Authority’s (EFSA) opinion on the safety of caffeine. According to Dr. Ellmann, recent discussions highlighted WKH IDFW WKDW WKHUH ZLOO EH D VLJQL¿FDQW UHVWUXFWXULQJ RI WKH ()6$ RSLQLRQ on caffeine, and this will be the result of a review of more than 1,000 studies. Read more at knowledgeshare.com/caffeine Regulators are demanding more recycled PET in beverage bottles France could soon impose a recycled PET (rPET) usage goal of 25% in all PET bottles. In a post on KNOWLEDGEshare.com, Chris Dow (CEO of Closed Loop Recycling) discusses what we can do as consumers and as an industry to meet the increasing demand for rPET. Read more at knowledgeshare.com/rpet - Advertisement -","@ID":19}, "TRADE SHOW PREVIEW 46 PETplanet insider Vol. 15 No. 11/14 petpla.net Filling, consulting, kegs and decorating KHS’ stand will feature keg and decorating technology, along with the company’s consulting and other services. In the field of filling technology KHS will be exhibiting an electronically controlled, volumetric filler for cans in the form of the Innofill Can DVD, which has a capacity of up to 120,000 cans/h. Washing, cleaning and filling kegs The hallmark of the Innokeg Combikeg keg, washing and filling machine, with a capacity of up to 80 kegs/h, is its compact design. The systems for washing the kegs inside and out and for racking them are integrated into a single housing, as are the media tanks, controls and conveyors. The Combikeg is based on KHS’ established rotary principle. The target group for the product is small to medium-sized businesses in the brewing, soft drinks, mineral water, fruit juice and wine sectors. One of the features that has been optimised on the latest version of the machine is its safety panelling. Doors, which are are now half-height, make it easier to keep an eye on the valves and sensors. Faster responses are also possible and system availability is claimed to have been boosted. An additional caustic spray, which is tasked with removing the ink code on the keg fitting and shoulder, is incorporated into the exterior washer. New valves (seat valves with cup gasket) are used specially for the washing stations. KHS says that the valves have been designed to withstand severe conditions, including the use of chemicals and steam. The pneumatic rotor main drive in the Innokeg Combikeg has now been replaced with a servomotor, which is intended to ensure soft acceleration and braking of the keg when changing stations. Among the kegs to benefit from this are the particularly sensitive slim kegs and Petainer kegs, which are handled with adapters. The machine is also equipped for the new non-refillable keg from Petainer, which makes its premier appearance at Brau Beviale. Novel printing Direct Print, the new technology for direct digital printing of PET bottles, will be the subject of a major presentation and demonstrated by a sample printer on KHS’ stand. The printing process uses only UV inks; the company says they have low viscosity, dry in milliseconds, adhere well to PET bottles, have a high opacity, can be overprinted and ensure a brilliant colour image, with optical resolution of 1080 x 1080 pixels. They have been confirmed as suitable for use with foodstuffs and for unrestricted bottle-to-bottle recycling. Bottles & Shapes Packaging designer Claudia Schulte will be showing visitors how the specific properties of a PET bottle and cap concept can be successfully combined with high-quality design. Bottle decoration will be demonstrated with the use of the sample Direct Print printer. All development steps are carried out from a holistic perspective, incorporating economic, ecological and functional aspects of the packaging equally. All known influences are simulated and applied to the virtual packaging, including stress during conveying through the line up to and including the palletising process, and during shipment to the retail trade and points of sale. Coping with higher pH KHS says that beverages and liquid foods with a higher pH stand to benefit from its recently-developed Plasmax+ process. It is claimed to have a better long-term stability with higher pHs (4.5 or more) than the standard Plasmax process and offers better barrier effect when bottle material is subject to greater mechanical stress from high internal pressures, such as carbonated beverages. The new technology can be retrofitted into existing InnoPET Plasmax machines. www.khs.com KHS Hall 5 | Booth 127","@ID":48}, "MARKET SURVEY 34 PETplanet insider Vol. 15 No. 11/14 petpla.net 11/2014 MARKETsurvey Company name Sipa GEA Procomac Postal address Telephone number Web site address Contact name Function Direct telephone number Fax E-Mail Via Caduti del Lavoro n. 3 31029 Vittorio Veneto (TV) Italy +39 0438 911511 Mr Matteo Tagliaferri Marketing and Communication +39 0521 548111 matteo.tagliaferri@zoppas.com Via Fedolfi 29, 43038 Sala Baganza (PR) ITALY +39 0521 839411 www.procomac.com Mr Alessandro Bellò Head of Sales +39 0521 839490 +39 0521 833879 alessandro.bello@gea.com 1. Machine designation / model number Isofill P StillFills StillFill R\\HR Flextronic C Flextronic SE Flexotronic S ESL filling: Fill Star FX ESL filling: Fillstar DX Traditional Filling: Fillstar Lxi, Fillstar LXf, Fillstar DX, Fillstar PET 2. Number of filling heads (range: from/to) 20-160 20-120 20-120 50-160 20-160 20-160 15-140 15 to 140 Fillstar LXi 50 to 140, Fillstar LXf 50 to 140, Fillstar DX 30 to 100, Fillstar PET 45 to 140 3. Min to max bottle contents (in liters) 0.06l to 3l 0.06l to 3l 0.06l to 3.0l 4. Filling speed: output (bph) (min to max): specifiy: 1l bottle / still water (bph) 60.000 62.000 60.000 62.000 63.000 Fillstar LXf 10.000 up to 60.000, Fillstar PET 10.000 up to 60.000 1l bottle / CSD (bph) 51.000 55.000 (CMW) Fillstar LXi 10.000 up to 60.000, Fillstar PET 10.000 up to 60.000 1l bottle / Milk (bph) 62.000 62.000 6.000-60.000 6.000-48.000 Fillstar DX 6.000 up to 48.000 1l bottle / Juice (bph) 53.000 62.000 55.000 59.000 62.000 62.000 6.000-60.000 6.000 - 48.000 Fillstar LXf 10.000 up to 60.000 5. Filling process Pressureless (still drinks) yes yes yes yes yes yes yes yes yes (Fillstar LXf - Fillstar DX - Fillstar PET) Pressure filling (carbonated drinks) yes yes yes (Fillstar LXi - Fillstar PET) Hot filling yes yes yes Cold aseptic filling Juices with high pulp content yes yes yes specific filling valve (limits: FX P EVO 3x20 mm - FX C 5x5x5 mm) specific filling valve (limits: FX P EVO 3x20 mm - FX C 5x5x5 mm) yes 6. Type of filling valve and metering system isobaric mechanical level filling mechanical gravity filling mechanical gravity filling walve with recirculation isobaric volumetric filling valve gravity volumetric filling valve gravity volumetric filling valve Fillstar Lxi,Lxf,DX volumetric electronic filler with flowmeter; Fillstar PET mechanical counter-pressure filler Company name Sacmi Filling S.p.A Postal address Telephone number Web site address Contact name Function Direct telephone number Fax E-Mail info@sacmifilling.it +39 0521 695411 www.sacmifilling.it Mr Vezio Bernardi Manging Director +39 0521 695450 +39 0521 695401 vezio.bernardi@sacmi.it 1. Machine designation / model number EWS for still water in PET and still clear product ESF for carbonated soft drinks in PET EWF for flat product in PET Model EHF for fruit juice in hot fill in PET ELT for beer in PET 2. Number of filling heads (range: from/to) min 16 valves pitch 282 mm, max: 120 valves pitch 113 mm, 144 valves with pitch 94 mm min 32 valves pitch 141mm, max 180 valves pitch 113mm, 216 valves pitch 94mm min 16 valves pitch 282mm, max 120 valves potch 113mm, 144 valves pitch 94mm min 32 valves pitch 141mm, max 180 valves pitch 113mm, 216 valves pitch 94mm min 32 valves pitch 113mm, max 180 valves pitch 113mm, 216 valves pitch 94mm 3. Min to max bottle contents (in liters) 12.000 to 64.000 10.000 to 72.000 (500ml bottles) 12.000 to 64.000 (500ml bottles) 12.000 to 60.000 (500ml bottles) 4. Filling speed: output (bph) (min to max): 250ml to 750ml: speed 36.000 250 ml: 25.800, 500ml: 18.400,750 ml: 15.200 250ml: 35.900, 500ml 27.700, 750ml: 21.200 250ml: 28.800, 500ml: 18.800, 750ml: 15.200 specifiy: 12.700 1l bottle beer 1l bottle / still water (bph) 30.000 13.200 1l bottle / CSD (bph) 1l bottle / Milk (bph) 12.000 1l bottle / Juice (bph) 16.900 5. Filling process Pressureless (still drinks) yes yes yes Pressure filling (carbonated drinks) Hot filling 96°C, min product conductivity: 20 μS/cm yes Cold aseptic filling Juices with high pulp content 6. Type of filling valve and metering system Filling system: time controlled, electronic-volumetric electronic-volumetric electronic-volumetric electronic-volumetric electronic-volumetric with long tube","@ID":36}, "TRADESHOW REVIEW 28 PETplanet insider Vol. 15 No. 11/14 petpla.net David González, CEO of Novapet Conference delegates represented the whole spectrum of the PET industry: converters, bottlers, brand owners - almost all of them from Spain. Apparently the topic of integration is significant for each of them, especially as growth in the PET market is Europe has ended - except perhaps in niche markets. Presentations Blow moulded bottles, market trends and opportunities for PET John Nash, director of AMI in the UK, spoke on the current status of the European PET markets. He pointed out some familiar and perhaps worrying trends in certain product areas, notably CSD, water, juice and nectars and still drinks. He went on to talk about potential measures to address these trends, such as technical developments of lightweighting and thin-walling, developments with recycled R-PET or bio-sourced and bio-degradable PLA. He compared PET with other materials, in so doing making special mention of the milk and milk drinks sector where there are forecasts of imminent growth in PET at the expense of cartons. John Nash, Director of AMI in the UK John Nash’s final rallying call – addressed to suppliers of material (and machines) – was a plea for cooperation through the value chain: ”Help brand owners to innovate their products and you will increase your business“. The message was certainly well received – especially by the prominent milk producers present in the audience. From polymerisation to container Jose Antonio Ramos, Head of Packaging Division, also picked up on the topic of integration. “Production of PET resin is the first and most important link to the delivery of the container for the final client. You need to understand the finished bottle to develop your material.” ”What is PET?” asked Jose Antonio Ramos, who began his talk with a reference to Leonardo da Vinci, the role model for “ideas, culture and strategy.” He discussed chemical formulae for PET, about quantities, about the – so to speak – almost magical characteristics of PET as a material. He highlighted what he considered to be the key concerns of the PET industry: reduction of weight in bottles – energy savings in process – increase in strengthening capacity – improvements in the technical behaviours of the bottles – improvement in thermal resistance – barrier effects – introduction of completely new resins for new markets. Participants of Chips & Grapes 2014 enjoy the good weather","@ID":30}, "40 PETplanet insider Vol. 15 No. 11/14 petpla.net about 100–120 bar on the screen of the machine (see Figs 3.6 and 3.8). 3.2.2 Injection Speed and Time Another point to note here is that injection time cannot be dialed in as well even though this time is displayed on the screen. As pressure and speed are interrelated, here are the factors that affect injection time: Speed setting Pressure setting Material viscosity Temperature This gives the operator excellent but only indirect control over the injection time. PET, like all other plastics, behaves mostly like a non-Newtonian liquid, i.e., its viscosity (its resistance to flow) changes with the shear rate. Shear rate is controlled by the injection speed. At very high shear rates PET would be oversheared and turn to a yellow/brown color. Therefore, the process window for injection speed is limited, and the operator has to take into account that changes to the injection speed will lead to changes in the material viscosity. Manufacturers recommend a fill rate of 10–12 g/s, and the graph in Fig. 3.9 is based on this rate while taking into account the fact that the rate needs to increase for heavier preforms to prevent the melt from freezing up during injection. There are usually three, four, or five settings for injection speed along the way the screw or shooting pot takes to push the required material into the cavities. The operator determines where the screw or shooting pod stroke starts, and the screw will end its travel when it comes to rest after injecting the material. The starting point of the screw is called shotsize, a slightly misleading name as we will see. Typical values for PET injection machines are 120–200mm. In most cases, the actually required amount of resin is less than the maximum and can be calculated as a ballpark figure using this formula: SS = W ×4/(D2 ×π×density) SS = shotsize in centimeters W = weight of one preform × cavitation in grams D = screw diameter in centimeters Density(melt) = 1.15 g/cm3. The operator should add 5–10 mm to the so calculated value because it is not advisable to let the screw or shooting pod bottom out at the end of the stroke. The small distance between the end of the stroke and the end of the barrel is called the cushion and is usually kept at around 3–5 mm. Longer cushions are possible but increase residence time. Some machines offer closed-loop cushion control where a cushion value is set and the machine determines the correct shotsize to achieve it. In order to get to the suggested injection time values, the operator has to try different speed settings. Most machines offer three to five different ones. Speed settings can be controlled in two ways: In an open-loop setting they are in percentage. Open loop means that there is no feedback between the settings and the actual speeds. The hydraulic valve opens at the set percentage and a certain speed is achieved. In a closed-loop system they are in millimeters per second. Here a feedback loop measures the actual speed and adjusts the valve to achieve the set speed. In a closed-loop system values at the screen may look like this: Screw speeds: 15 40 15 mm/s Screw positions: 25 55 65 mm In this three-point example shotsize is 65mm. The screw will then move from 65 to 55mm at a speed of 15mm/s, from 55 to 25mm at a speed of 40mm/s, and at 15mm/s thereafter. These values will then result in a certain injection time, and the operator can manipulate them to get to the desired time. Figure 3.8 The hydraulic force of 100 works on an area that is five to seven times the screw (or shooting pod) area. The force at the end of the screw is multiplied by the same factor as the difference in areas. Please order your copy at the PETplanet insider book shop: https://petpla.net/books Bottles, Preforms and Closures A Design Guide for PET Packaging Second Edition by Ottmar Brandau € 115,00 180 pages © Copyright Elsevier 2012 * This article was published in Bottles, Preforms and Closures, Ottmar Brandau, Chapter 3.2. Copyright Elsevier 2012","@ID":42}, "EDITOUR REPORT 18 PETplanet insider Vol. 15 No. 11/14 petpla.net during the last eighteen months. Arrangements are already in place for the follow-up. The 220t machine has been upgraded. The maximum mould size on this platform is at present 72 cavities and it is now also possible to use third party moulds. A further addition to the series is a 96-cavity preform system with a 400t clamping force already in the test phase and this will be introduced by the end of 2014.” According to Moraldo Masi: “With the 48 to 96-cavity preform systems we are able to access more than 60% of the market.” The percentage being exported is high, with the company supplying the Middle East, Northern and Central Africa and South East Asia. Some 50% of deliveries have also included an order for closure cap machines. Preform machine range (ISP) up to the end of 2014 ISP 220 up to 72 cavities Screw diameter 85/100mm Clamping force 220t IPS 400 up to 96 cavities Screw diameter 140mm Clamping force 400t Machine technology (Hybrid) Toggle lever clamping unit 2-stage injection with shooting pot, electric drive for plasticising and servo valve drive for the injection plunger Integrated unload system with post-cooling, arranged to side, with energy recuperation via the braking process. Cooling water and compressed air supply partly via the machine platens Ease of set up by inputting the main preform data Moulds from own mould construction incl. hot runners Cycle time 72-cavity, 0.5l water preform, 6.5sec Other PET applications The decision to build preform injection moulding machines does not mean that Sacmi has given up the idea of using compression technology for PET in stand-alone system. Moraldo Masi states: “We will continue with the development of PET lines for special applications where the preform needs to resist extreme conditions and where compression technology is advantageous (e.g. no gate, special resins where the IV is greater than 1 etc.” CCM closure cap machines Within the closure cap division at Sacmi there is one question that answers itself and that is, one piece or two piece closures? 90% of supplied closure cap lines are for one piece closures. A line for closure caps incorporating a tamper band consists of the actual compression moulding machine and a series-connected slitter which makes the slit in the tamper band. Depending on the design of the closure, a further module, the folder, may be required. Optionally, an inspection unit for inspecting the individual closures may be installed. Everything is from a single source. Approximately 100 plastic closure lines are supplied annually as well as seven to eight crown cork lines. As regards the plastics lines, 65 to 70% are for CSD, 30 to 35% for water and 2 to 5% for hot fill and juices. The company’s own mould construction facility supplies approximately 250 sets a year, either already installed in the lines or as sets for retrofitting, with an average of 32 cavities per set. There are five capacity volumes in the machinery range: 24 cavity up to 33mm cap diameter 24 cavity up to 63mm cap diameter as a special 32 cavity up to 43mm cap diameter 48 cavity up to 33mm cap diameter 64 cavity up to 43mm cap diameter 80 cavity up to 33mm cap diameter Extrusion capacities from 600 to 2.000 closures per minute. The best-selling line is the 48-cavity. Lightest closure: less than 1g water with 26mm cap diameter and olive plug. Massimo Gani sums up the situation on the closure market: “Some time ago, 2-piece closures in PP tended to predominate within our range of equipment. The development of the super-lightweight closures in the water sector ushered in a trend towards 1-piece closures. Nor did it stop with the CSDs. The development of lightweight 1-piece water closures came about during the implementation phase more in relation to the injection moulding process”. He continues: “Today the majority of applications for water closures are to be found in the injection moulding sector; in the case of CSD most are in compression moulding. Worldwide, the ratio of compression to injection moulding is 65 to 35%. We have already noted that some customers have in the past undergone a shift of orientation in regard to the manufacturing process. In terms of sales, however, this has not had any material impact because the strong growth has compensated for it. We responded and initially increased the mechanical speed of our lines. But, when it came to adapting process technology to the machine speed, it became necessary to Massimo Gani, Closures Sales Manager, in front of a CCM compression moulding closure caps machine in the assembly bay","@ID":20}, "PETproducts 52 PETplanet insider Vol. 15 No. 11/14 petpla.net Blow moulding machines get a complete makeover R&B Plastics Machinery LLC, a leading manufacturer of blow moulding and extrusion machinery and a specialist in machine modernisation, has announced the completion of major rebuild/modernisation projects for two leading U.S. original equipment manufacturers (OEMs). The rebuilding of three blow moulding machines for Cardinal Health and Amway are the latest examples which illustrate the advantages of machine modernisation versus the purchase of new capital equipment. For Cardinal Health, a leading manufacturer of medical devices, a used shuttle machine was purchased which was then stripped to the frame. R&B added the latest controls, mechanical and electrical systems, coolant, pneumatics, and hydraulics along with additional functionality and capabilities such as in-machine trimming for medical product manufacturing. The rebuild and upgrade provides the customer with a lower cost operation that yields the same output while utilising the latest technology and equipment available in the market today. For Amway, a leading manufacturer of consumer products, R&B upgraded two existing large wheel blow moulding machines, adding a range of new enhancements including new parison programming, open architecture control systems, and MAX extrusion screws for improved melt quality and increased production and performance. The upgrades enabled Amway to have the latest controls technology with a lower cost in-plant rebuild. The upgraded and refurbished blow moulding machines for Cardinal Health and Amway are currently in operation. Modernising and upgrading to today’s technology is said to provide measurable productivity improvements, faster cycle time, energy savings, improved quality, and greater efficiency and consistency, whilst also meeting the latest ANSI safety standards. Cost savings are measured by decreased labour, utility and materials usage. R&B performs rebuilds/modernisation on all makes and models, and provides the same warranty and performance guarantee that comes with new machinery. The company sells extrusion systems and blow moulding machinery, as well as performing extensive rebuild/modernisation of all competitive equipment. Customers represent diverse end-use markets including automotive, food/beverage, personal care, medical, motor oil/lubricants, household cleaners, detergents, and lawn/agricultural chemicals. www.rbplasticsmachinery.com Scan & Measure Oxygen Ingress & Transmission Rates www.PreSens.de/ Fibox4 Fibox 4 Stand-alone fiber optic oxygen transmitter","@ID":54}, "BOTTLES 57 PETplanet insider Vol. 15 No. 11/14 petpla.net Bittersprizz from bizzl Bizzl, a brand name of Hassia Mineralquellen GmbH & Co. KG, Germany, has recently launched a variant with a new taste in its range. The grapefruit lemonade is refined with a dash of bitter lemon to offer the consumer a new and interesting experience when it comes to taste. The bottle, which is manufactured from PET, is designed as a reusable bottle. It contains one litre and is decorated with a very wide range of embossed patterns and the brand logo. The label is a plastic label that is fixed by applying heat. www.bizzl.com New flavours beckon Odenwaldquelle, the regional drinks manufacturer operating in the area around Heidelberg, Germany has launched two new drinks on the market in identical PET bottles. One of these is an isotonic, low-calorie sports drink, “Iso Sport“, complete with six vitamins and a pink grapefruit juice content of 6%. The other drink is a rhubarb spritzer with a 10% proportion of fruit that is sweetened exclusively with fructose and free of added sweeteners and preservatives. The bottles (on which a deposit is payable) each contain one litre and feature embossing typical of the manufacturer, all-round adhesive labels made from paper and a screw cap with tamperproof guarantee. For reasons of weight, the support ring for the bottle is polygonal in shape. www.odenwaldquelle.de Your Cap. Your Signature. We inspect it. www.intravis.com","@ID":59}, "PREFORM PRODUCTION 39 PETplanet insider Vol. 15 No. 11/14 petpla.net Injection Parameters, part 16 Practical Guide to Injection Moulding of Preforms PETplanet insider is publishing extracts from successive chapters of Ottmar Brandau’s “Bottles, Preforms and Closures”, which was first published by hbmedia. A newly revised version is reissued under the Elsevier imprint. The parameters operators can control are: Injection pressure Injection speed Transition point Hold time Hold pressure Material “cushion” Most modern machines allow the operator to set all relevant values on the screen, whereas older machines may feature manual hydraulic and position controls. For this discussion it has no relevance how the pertinent values are controlled. It is important that readers understand the concepts. 3.2.1 Injection Pressure Many operators are under the misconception that the injection pressure can be dialed in because there is a field on the screen with this name. However, this is not the case. Injection pressure is the result of how hard the machine pushes the resin and how hard the resin resists this pressure. The value on the screen merely determines the pressure at which the machine hydraulics will stop pushing and drain oil to the tank instead of sending it to the injection cylinder. The factors that determine injection pressure are: Injection speed settings: The faster the machine injects, the higher the pressure. Melt viscosity of the material (see the last chapter): This in turn depends on Temperature: The lower the resin temperature, the higher the required pressure. Intrinsic viscosity (IV) of the material: The higher the IV, the higher the required pressure. Pressures over 100 bar (1500 psi) are not recommended for PET. They tend to shear the material too much and this can lead to burn marks. Very thin (2.3 mm) preforms may require higher pressures, and this is one of the challenges in thin-wall moulding. Use of higher pressures during startup is a common practice when the mould is still colder compared to continuous production conditions. The hydraulic pressure controlled on the screen is not the pressure the material is subjected to. This is because the injection piston that is pushing the screw or shooting pod forward has a five to seven times larger area than the screw or shooting pod. This leads to pressure intensification by the same ratio. Actual material pressure should not exceed 700 bar (10,000 psi), and this equates to","@ID":41}, "TRADESHOW REVIEW 32 PETplanet insider Vol. 15 No. 11/14 petpla.net IMAGINE FILLING MULTIPLE PRODUCTS ON THE SAME LINE…NOW YOU CAN! Water, juice and soft drinks, all on a single machine? The Flextronic modular platform adapts effortlessly to still or sparkling, clear or pulpy and hot or cold-fill, and easily switches from one bottle neck-size to the other. A revolutionary filling technology that gives you extreme operational flexibility with minimal product loss and downtime at flavor switch. Clean, safe and versatile. Welcome to the new generation of fillers. carbonated still hot-fill cold-fill pulp non-pulp water juice soft drink SIPA S.p.A. - Via Caduti del Lavoro, 3 - 31029 Vittorio Veneto (TV) - Italy Tel. +39 0438 911511 - Fax +39 0438 912273 - e-mail: sipa@zoppas.com www.sipa.it Miguel Angel Arto, Business Development Director Novapet Novapet DCU – “monolayer light bottles, full light barrier, light weighting” - is one of the numerous innovative formats devised by the company and its partners, developed and manufactured for special niche applications. DCU is growing and acquiring ever greater significance in the Novapet portfolio and is the result of a successful strategy pursued consistently and with perseverance. Miguel Arto: “Even in difficult times it is possible to identify opportunities that will help the company and its customers to move forward. For Novapet, this particular opportunity goes by the name of DCU.” With this vibrant recommendation of DCU to the assembled milk producers, Miguel Arto brought his speech and also the conference to a conclusion. The subsequent concluding discussion between the experts will doubtless be continued at the next, the 5th Chips & Grapes, conference in 2016. www.amiplastics.com www.novapet.es www.procomac.it www.petengineering.com","@ID":34}, "PRODUCTS 53 PETplanet insider Vol. 15 No. 11/14 Inspection system for thin-walled caps & closures To achieve thinner walls of closures, the casting moulds and their channels have become thinner which might make the closure production process fault-prone. A frequently occurring error is a shortshot which makes, for instance, the security belts incomplete or even missing. To avoid this and ensure a high closure quality, the Intravis vision inspection systems such as the CapWatcher III are said to be able to deliver precise measurement data and inform the user constantly about the current status. They also offer a trend statistic that shows the user when the product quality moves towards waste during the production process. The user can subsequently realign the production systems to stay in the rated range. As a result, the vision inspection system avoids waste instead of producing it. www.intravis.de KHS establishes NMP Systems GmbH KHS GmbH has established a 100% KHS-owned subsidiary, NMP Systems GmbH, located at the offices of Salzgitter Trading in Düsseldorf, Germany. NMP Systems will bring two innovative technologies to market – Direct Print and Nature MultiPack. As a result of the technologies and materials involved, the business approach of NMP Systems will be to provide Machine and Consumables and Service in cooperation with the KHS global network. Direct Print is a technology for the digital printing of PET bottles – without the need for labels. This industrial solution for individually decorated bottles is claimed to ensure new consumer dialogue and marketing leverage for beverage industry brand owners. The KHS team has been working in codevelopment with global technology partners to formulate non-migrating digital inks in combination with rotating print heads. Today the Direct Print team is ready for market with a prototype customer installation, to be followed closely by the Direct Print equipment pilot series – bringing CMYK process colours + White at 1080 x 1080dpi (dots per inch) optical resolution for untreated PET bottles at production speeds of up to 12,000, 24,000 and 36,000bph. Nature MultiPack is a technology for multipacks – simply bonding containers together with specialised adhesives – creating packaging sustainability and new consumer convenience opportunities with multipacks for beverage industry brand owners. In comparison with printed film multipacks, Nature MultiPack has up to 85% less material, and saves up to 67% on energy for packaging equipment. The KHS team has been working in co-development with three global technology partners to formulate specialised adhesives, first for PET, next for cans and sometime in the future for glass bottles. The Nature MultiPack technology will collate and bond containers into single and double lane pack configurations, with the first target application now installed for a six-pack with 2 x 3 1.5l PET water bottles at a capacity of 42,000 bottles per hour. innovation@nmp-systems.com www.khs.com Creating value with powerful solutions www.krones.com BrauBeviale 2014 Nuremberg, 11 – 13 November Stand 7A-514","@ID":55}, "BOTTLES 59 PETplanet insider Vol. 15 No. 11/14 petpla.net Relaunch for Odol-med3 GlaxoSmithKline consumer healthcare has overhauled the appearance of its Odol-med3 mouthwash products. For packaging purposes, the waisted, transparent 500ml PET bottle continues to be used. In the area of the base it features a wave-shaped, peripheral groove that makes it easier to grasp and which also fixes the sleeve label in position. This has now undergone a design update and the effect is tidier, in fact it tends to be reminiscent of a medical product. The label is now stretched over the screw cap which has a dispensing function and acts as a tamper-proof seal. Along with the bluish, alcohol-free mouthwash its appearance on the shelf is now “fresher”. www.odol-med3.de Pril with grapefruit & cherry Henkel is constantly adding to its Pril range. Whereas a couple of months ago it was the ”power gel“ variants that were making an appearance on the market, this range is now being extended by a power gel with grapefruit & cherry which claims to remove fat and starch residue without any trouble at all. The red-tinted product is packaged in the familiar PET bottle with a content of 500ml and the screw-on push-pull closure with angled pouring spout. This range of fragrances can also be found on the shelves in the apple and lemon variants, which are tinted green or yellow to correspond to the colour of the fruit. www.pril.de CCT – SYS GmbH Idsteiner Strasse 74 D-65527 Niedernhausen, Germany a.schmitz@cct-systems.com www.cct-systems.com Portfolio Caps • Closure molds beverage field (produced under the brand “CCT Systems®)” - Completely new constructed and optimized molds for closures with slitted tamper evident band (SBT) - Completely new constructed and optimized molds for closures with slitted and folded tamper evident band (SFBT) • Devices and equipment for closure production Portfolio Preforms • Preform molds and preform molds cold halves • Conversion parts and spare parts for preform molds (here especially conversion parts for the weight reduction according to “ComPetCap®” construction) • Devices and equipment for preform production Consulting and supporting possibilities for • Closure development • Closure production • Closure processing • Preform development • Preform production PET Molds and Accessories Developments PET - Devices and Equipment Closure – Devices and Equipment New Range of Services Consulting und Support Closure molds and Accessories","@ID":61}, "TRADESHOW REVIEW 29 PETplanet insider Vol. 15 No. 11/14 TRADESHOW REVIEW 29 Cost effective 2-step process with machine direction print, lowering label costs + Roll count optimization + No seaming in label conversion: it’s done on the labellers + Storage space and shipping costs down thanks to higher roll and pallet quantities + Emerging lightweight micron film technology boosts productivity + Higher labelling speeds, up to 50,000 BPH + Weld seam applied during labelling process = COST REDUCTION UP TO 20% compared to traditional sleeve technologies Sacmi Verona S.p.A. Via Dell’Industria, 2/A 37060 Mozzecane (VR) Italy Tel. +39.045.6347511 sacmilabelling@sacmilabelling.it | www.sacmilabelling.com www.formsleeveplus.sacmi.com Quality +Cost Control in just one technology Jose Antonio Ramos, Head of Packaging Division of Novapet He concluded by drawing on his experience with Novapet: “We are totally dedicated to working with this wonderful material. Packaging is our core business and we handle all aspects from the chemistry to the final product.” PET Packaging: creating intelligently Carmen Rus, Area Manager of P.E.T. Engineering, adopted a committed, lively and highly specific approach to the problems that crop up in everyday practice in PET companies. According to Carmen Rus, many companies are overwhelmed by the constant procession of new challenges that characterise the PET market, where frequently only older, existing plants / lines may be available to meet these challenges. Not all companies – especially not the small and medium-sized ones – are in a position to maintain teams of development staff and technical personnel. However, even Pepsi avail themselves of the advice and cooperation of P.E.T. Engineering, in the same way as Husky and GEA among others and in particular Novapet – here in Barbastro for the development of new types of materials, for example, DCU in relation to milk packaging. In a section entitled “What we did,” Carmen Rus explained how P.E.T. Engineering had developed since its establishment in 1999; what success it has had in Italy and Russia, its investments and the awards it has received up to 2014. There followed by examples of successful bottle design – especially emphasising the Italian origin.","@ID":31}, "TRADE SHOW PREVIEW 47 PETplanet insider Vol. 15 No. 11/14 petpla.net Q Preform sterilization in the heating tunnel Q Protected conveying of preforms and bottles Q %QORNGVGN[ J[IKGPKE ƂNNKPI CPF ECRRKPI RTQEGUU The UCF BloFill monoblock from KHS – with fully enclosed hygiene housing Give your sensitive beverages more private space. Learn more at www.khs.com or scan the QR code. Multi-sensory monitoring The BBull Technology Group of Companies will be presenting a number new developments that have been introduced over the past year. The company’s exhibition this year will be focusing on checking and identifying the tightness of closures (on glass, PET and cans) as well as the soundness of containers (bottles, kegs). They will also be presenting their new distribution table for flat packs (cartons). Multikon EBI, BBull’s empty bottles inspection tool, is claimed to offer an outstandingly hygienic design, with hydraulic adjustment options throughout. This feature means that gear wheels, belts, spindles and servo motors have all been eliminated, as have corners that can harbour dust. The latest version of Multikon can monitor and inspect up to 70,000bph and can identify, detect and sort flaws, reliably. In the field of closures, BBull MAS is designed to acoustically detect CO2 leakages by taking an indirect measurement of the internal pressure in the container. A strong electromagnetic impulse will cause the closures to vibrate; the acoustic signal shows whether the internal pressure is correct and the closure is leakproof. BBull Pulse inspects flexible containers (cans, PET, plastic containers) with a telekinetic shock. The patented process provides precise information on the internal pressure and thus the security of the container. The company claims that BBull Pulse is up to 50% cheaper than systems currently available and, further, that it has a small space requirement. This means that it can be integrated into a line without any system modifications. It can be used as a stand-alone solution or in combination with a camera-based check on fill level and closure by equipment such as BBull Image 120. This enables 360° inspection of a container’s fill level and closure integrity to be carried out. With the use of a number of cameras, BBull Image Keg checks kegs after filling. The measuring bridge is installed on the conveyor belt and inspects the keg fitting from above and also from the side at the weld for any escape of froth, enabling reliable and definitive statements on the integrity of the kegs and that they are leakproof. Alongside BBull Image Keg Federspiel GmbH will be demonstrating its latest keg handling technology. The BBull XY Gate distribution table is used for distributing and bringing together flat packs, such as cartons and trays. Paxona, BBull’s Swiss subsidiary, will also exhibiting its latest barrel transportation and palletising options, as well as those for packing and unpacking. www.bbull.de BBull Technology Hall 7A | Booth 546","@ID":49}, "PETbottles 56 PETplanet insider Vol. 15 No. 11/14 petpla.net Beverage + Liquid Food Cocktail in PET Buzzballz LLC, a company based at Carrollton Texas,USA is marketing a number of ready-mixed cocktails in the USA under its own brand label and the “Tropic Chillerz” brand name. These feature an interesting packaging format incorporating a spherical PET container with a flat base and lid section and containing 187ml of product in each case. Depending on the product requirement and to suit the packaged product, the containers are brightly coloured with labelling directly applied. The container is closed by means of a beverage can lid made from metal which is opened in the same way as a beverage can using a ring pull. The container is completely recyclable, ideal for outdoor activities and can be placed in the freezer compartment. www.buzzballz.com Stacked wine tumblers A pack of four wine tumblers, stacked one on top of the other and sporting the tag “Zip / Snap / Sip“, are being marketed in America. These are interlinked to give a snap effect when one tumbler is removed from the other and the 4-pack is held together by means of common shrink sleeve label. A single, stand-alone tumbler (already filled) contains 187ml of wine. A total of four different types of wine is available. The tumbler is manufactured from transparent PET and sealed so as to be leakproof using a sealing membrane with a break-off clip. To protect the membrane on the topmost tumbler this is additionally fitted with a snap-on lid which can also be used as a lid for resealing purposes. The tumblers are also ideal to take along to parties, sporting events and on camping trips. www.drinkstack.com Müller Select in PET The Alois Müller dairy from Aretsried in Germany has extended its wellknown Müller dairy range to incorporate a variant called Select. Select is available in two varieties, one with melted dark chocolate and hazel nuts and one with melted white chocolate with coconut and almonds. Both types are packaged in smaller versions of the known bottle shape, with a content here of 263 or 268g or 250ml. The white bottles are sealed with tamper-proof screw closures and feature an adequately-dimensioned drinking opening. Rounding off the final packaging image are colour-matched shrink sleeve labels. www.muellermilch.de","@ID":58}, "BOTTLING / FILLING 23 PETplanet insider Vol. 15 No. 11/14 petpla.net Hall 7A | Booth 503 April 2013 saw APU commission the APW System C (Crane) high-bay warehouse from Krones, following eleven months’ construction. It is 83m long, 21m wide and 23m tall and has space for 9,240 pallet slots on twelve levels, with 70 two-deep slots on the longitudinal axis. The high-bay warehouse has been dimensioned for four serving aisles, three of which have already been equipped with one storage and retrieval unit each. The fourth aisle, incorporated in the layout so the warehouse can be extended to more than 11,000 slots, remains an option for the future. The warehouse has been equipped with specially-designed insulation, to enable it to cope with temperatures that swing from minus 40°C in winter to +40°C in summer. Ninetytwo automatically supplied order-picking workplaces on a descending roller conveyor are served by two transfer travelling carriages. An additional 82 manual workplaces handle order-picking C-articles. Dispatch orders and palletising are controlled by APU’s ERP (enterprise resource planning) system, with individual order-picking instructions transmitted to personalised handheld terminals via W-LAN. The fourth project, a “greenfield” 250,000hl brewery, was designed and constructed at the same time as the warehouse. It has been designed with the capacity to expand up to twice its current size, which will give APU potential brewing capacity of up to a million hectolitres. Its energy, environmental impact and and low operating costs were designed to meet ISO14001 standards. “Our strategic focus for the next five years is clear”, says Board Chairman Tseveenjav Erdenebileg. “We want to maintain market leadership in all our product categories, while also further upsizing our market share for soft drinks and milk. For beer, in particular, we’re anticipating further diversification as far as consumer tastes go, which we’re already helping along with Kaltenberg wheat beer, for example.” www.krones.com","@ID":25}, "BOTTLE MAKING 24 PETplanet insider Vol. 15 No. 11/14 petpla.net Edible oil PET bottle with a compression moulded T-hanDle Handling down to a T-hanDle Based on a report by David Birkby Side, blow-moulding manufacturer located in Barcelona, Spain, has collaborated with two other companies to launch a 3l PET bottle incorporating a moulded handle into the North American market. Demand for large-capacity containers of edible oils and other products is increasing across the world and especially in North America. Richardson Oilseed, Canada’s largest privately-owned agribusiness, challenged IntraPac, the Canadian division of IntraPac Group, to come up with a bottle that would meet market demand for a clear, 3l bottle with a consumer-friendly grip. The specifications for a clear, edible oil container narrowed material choices down to polypropylene (PP) or PET. While larger, blow-moulded PP bottles can be produced with integrated handles, the clarity, impact resistance and higher oxygen barrier qualities of PET would normally make it a better choice. However, PET technology had previously been able only to offer indented “easy grip” features on 32 and 64oz (950ml and 1.9l) juice bottles. This feature was not acceptable for larger packages, which often have a “snap-in” or even an integrated “moulded in” handle, normally made from PP. While this technology offers a developed by Pano Cap specifically for this application worked well, it placed some limits on preform design. After nearly a year and several iterations on both preform and bottle design, the 90g “T” handle mould made by Compact Mould was ready for production and market trials. According to the company, the finished article was positively received by consumers and has demonstrated good performance, as well as being cost-effective. Side has continued to evolve the T-hanDle system to apply to other market sectors, such as detergents, juices and bottled water and has developed lighter packages, including a T-hanDle for 2.5l bottles weighing just 54g. It has also developed the T-hanDle system for up to fourcavity machines and outputs of up to 4,000bph, depending on container sizes. www.t-handle.com www.sidemachines.com reliable commercial solution, it is considerably more expensive as it requires specialised tooling and equipment, resulting in higher unit prices. Side provided a vital step in developing the solution. It makes a machine that has the facility to compression-mould a “T” handle into larger-capacity PET bottles during the moulding process. Its idea and technology is already proven in Italy, Canada, Mexico, Chile, Spain, Morocco and other markets. Its automated equipment will produce up to 1,200bph per cavity, oriented towards the exit for easy palletising. Richardson required a design that would be compatible with their existing line, which would produce cartons at a competitive price point. Their specifications included top load capacity of at least 35lbs (15.9kg). The package requirements mean that design parameters would be very tight. While the 43mm thread finish","@ID":26}, "TRADESHOW REVIEW 31 PETplanet insider Vol. 15 No. 11/14 TRADESHOW REVIEW 31 Milk processed as liquid milk in dairies represents a small portion of 25% of total milk production – so far. Liquid milk packaged in carton 72% in HDPE 10% in PET 8% in glass 5% in others 5% Miguel Arto concluded from the statistical data: “Plastics (HDPE + PET) at almost 20%, is currently lagging behind carton, the market leader. But PET shows highest growth rates above all, since it has been proven, that monolayer white bottles offer suitable light protection and are a real and competitive alternative for packaging UHT milk.” Taking into consideration - weight – energy for production – sustainability – see-through – mechanical resistance – PET is best positioned with a high score in every key performance. PET for milk – according to Miguel Arto – is set to grow with the market, in particular by providing a substitute for cartons. “It’s a DCU bottle”, enthused Miguel Arto and presented examples, PET bottles for long life liquid milk – Novapet dairy and DCU proposal: DCU – resin by Novapet, bottle designed by GEA Procomac together with PET Engineering 1litre capacity, dia. 33mm; W=22 Gr full barrier for UHT milk – or DCU – resin by Novapet, bottle designed by PET Engineering 1litre capacity, dia. 33mm; W=19.5-21.5 g full barrier for UHT milk – Savings in weight due to lightweighting almost 50% - from 44g for a 1.2l UHT milk bottle in 2007 reduced to 23g for a 1l UHT milk bottle in 2014.","@ID":33}, "ONsite 54 PETplanet insider Vol. 15 No. 11/14 petpla.net Haiti bottler achieves 35% energy savings Energy savings of 35% have been achieved by Tropic S.A., a leading beverage manufacturer in Haiti, by introducing two blow moulders from Sidel. It is also claimed that the investment brought production improvements by replacing five existing blow moulders while still catering for the increased production of the company’s entire range of water, energy and carbonated soft drinks. The new equipment is running at 95% efficiency, backed by a maintenance contract from Sidel Services which is intended to ensure that the reliability and efficiencies continue to meet production demand. Tropic bottles eight different beverage brands that are sold in the Haitian domestic market and exported to surrounding countries. It was one of the first bottlers in Haiti to use PET. It introduced Aquafine purified water in PET bottles in 1996, and two years later moved into producing carbonated soft drinks, also in PET. The company prides itself on respecting all international manufacturing standards and using cutting edge production equipment. The company operates plants in two locations and was previously using five SBO2F blowers from Sidel. Tropic experiences peaks and troughs in its production schedules so recognised the need to manage this through greater flexibility. By talking to Sidel, the company realised that this flexibility could be achieved with just two Sidel blowers, including an SBO6U2 eco, backed by a maintenance contract. In addition to improved production efficiency, the Ecoven of the SB06U2 eco has achieved savings on Tropic’s energy bill. By requiring fewer lamps per module, as well as fewer heating modules, the Ecoven has enabled a 35% reduction in energy use, a considerable saving in Haiti where energy costs are high. www.sidel.com Yihai Kerry – Sipa partnership continues Vegetable oil producer Yihai Kerry is banking on Sipa in a new investment for its packaging lines. In its operations dedicated to edible oils, Yihai Kerry has been using Sipa+76pxs equipment for seven years, during which time it has accumulated a large number of linear stretch-blow moulding units, as well as preform injection moulding units. As a partner for a renovation project at its Kerry Oils & Grains (Tianjin) operation, Sipa will install four SFL6 systems for the production of bottles ranging in volume from 0.9l up to 10l. These will be brought into operation in the course of the current year. In addition, the Tianjin operation will be equipped with an XFORM 500/72 preform injection moulding system for production of 100g preforms. This system has a 72-cavity mould mounted on a 500t injection moulding machine. As far as the XFORM 500I concerned, Sipa guarantees a minimum of eight million production cycles before the first maintenance of the mould, and total energy consumption is best in class, according to Sipa. And if it chooses, Yihai Kerry can install any existing large mould on the XFORM 500, irrespective of whether that mould was made by Sipa or one of its competitors. The Shanghai-headquartered company Yihai Kerry, part of Wilmar International, Asia’s leading agribusiness group, produces edible oils, feed meals, rice, flour, bran, grains, specialty fats, oleochemicals and soy protein concentrate at over 170 large-scale integrated manufacturing plants located in 43 strategic locations. www.sipa.it","@ID":56}, "BOTTLE MAKING 43 PETplanet insider Vol. 15 No. 11/14 petpla.net are used for contouring applications which to an extent render time-consuming electrical discharge machining superfluous. Fitting of the tooling sets takes place here in-plant with the option, should the customer request it and the correct ISB is available, to test the tooling set.” Approximately 80 tooling sets are supplied per year. The average delivery time is eight weeks. James Ramsey felt that it was important to mention that an active risk management strategy is being implemented here which offers potential for identifying solutions to any faults or which can be taken into account when it comes to scheduling. He proudly shows me the scheduling sheets for shipments and payments which are put up in the factory and constantly updated, with the result that, so far this year and taking into account a specification of 98% for deliveries and payment receipts, the 99% mark has already been exceeded as regards both items. www.rdleverage.com","@ID":45}, "BOTTLE MAKING 41 PETplanet insider Vol. 15 No. 11/14 petpla.net From mould manufacture - tooling to service provider by Waldemar Schmitke R&D Leverage are much more than a mould builder, within their own specialist sector who are involved in the development of structural brand names. The American company, with a workforce of 322 in total, can look back on a 38-year development history. Their main plant is in Missouri, USA. For the past 17 years there has been a European branch in England, and then, 8 years ago, R&D Leverage UK moved into a new facility in Sutton in Ashfield, Nottinghamshire. workforce to build up and integrate quality, engineering and service management into the day-to-day life of the company. He went on: “We have developed from a toolmaker to a service provider for whom our customer service and advisory activities represent our highest priority. At the same time, what we understand by “customer service and advisory activities” is not only holding discussions but also actively assisting the customer with the design and development of the plastic containers, with prototyping and sample manufacture right through to small batches for a market test run. We have installed four single stage machines (3-off Nissei 70 DPH and 1-off Aoki 250 LL 755) specifically for this purpose. This total service solution has been very well received by our customers, so much so that we have decided to extend this division and accommodate it in a new building, together with the full complement of laboratory and test equipment. The building has already been completed and the move has started.” In terms of their mould making activities, they specialise in the sectors of consumer packaging for foodstuffs, beverages, household, bodycare and health, single stage tooling, IBM tooling, custom injection tooling, laser CD works Silicone tooling and moulding. The Leverage Division specialises in consumer packaging and offers service in relation to upfront research, ethnographic research, concept development validation (prototyping und sampling) as well as being home to R&D UK. R&D / Leverage UK Here in Nottinghamshire I meet the Managing Director of R&D/Leverage UK, Alan L. Tolley and his management team. The branch here in the UK is 95% geared to single stage tooling and employs a workforce of 82 on premises covering an area of 4.645,15m2 with a turnover of approx. £6.5m over the past year. “We are able to report encouraging growth over the past few years,” Alan L. Tolley tells us, and he attributes this to consistent efforts on the part of the Polishing the blow moulding moulds in the block by hand","@ID":43}, "TRADE SHOW PREVIEW 51 PETplanet insider Vol. 15 No. 11/14 petpla.net The plastic closure company committed to your success BERICAP Technology Research and Development Mould Technology | Global Presence Capping Technology and Know-How Innovation and Flexibility www.bericap.com Packaging, travelling and closures Husky Injection Molding Systems regards Western Europe as one of its largest and strongest markets and will be showing its wide range of beverage packaging solutions at Brau Beviale, including the latest versions of its HyPET HPP5 systems. It will also be exhibiting at PETnology as a lead sponsor of the event and is a lead sponsor of the PET Planet Tour, which will conclude at Brau Beviale. John Galt, Husky’s President and CEO, said that Husky will be discussing replacement strategies for ageing equipment that can help eliminate risk, reduce tooling costs, and allow for greater flexibility to adapt to changing market needs, offering a longer production time horizon. The company will also be speaking on PET business trends in the marketplace and growth opportunities within the industry and providing more insight into its latest beverage packaging and beverage closure solutions, including systems such as its HyPET High Performance Package (HPP5), tooling, software and services, which was launched late in 2013. Upgrades and enhancements such as intelligent Mold ID technology and improved ease-of-use with a larger display are claimed to reduce total cost to produce while providing high preform quality. Husky says that HTTP5 has shown up to 12% productivity improvement over the previous generation system for some applications. Husky also offers a turnkey H-PET AE (All-Electric) system, which is designed to produce both short and long production runs. The company says that it offers higher quality and improved productivity, along with market-leading energy consumption and labour cost efficiencies. Also on the stand will be Husky’s complete range of beverage closure solutions including its proven HyCAP system for high-output beverage closure manufacturing. www.husky.ca Husky Hall 4A | Booth 233","@ID":53}, "PETPLANET AWARD 2014 37 PETplanet insider Vol. 15 No. 11/14 petpla.net Fig. 6 How do you rate the performance of your preferred supplier in the following services? Fig. 7 Which is your most valued/best equipment? Fig. 8 What kind of services do you purchase from the supplier of this most valued equipment and how do you rate the performance of this supplier in this service?","@ID":39}, "MARKET SURVEY 35 PETplanet insider Vol. 15 No. 11/14 petpla.net Sidel International AG Bösch 67, PO Box 6331 Hünenberg, Switzerland +41 41 785 23 60 www.sidel.com Mr Stefano Baini Filling Product Manager stefano.baini@sidel.com Traditional filling: Fillstar HF Aseptic Filling: Fillstar FX, Fillstar CX, Piston Doser PX Sidel Matrix SF 300 FM Sidel Matrix SF 100 FM Europa WM Sidel Matrix SF 700 FM Sensofill FMa Fillstar HF 50 to 140 Fillstar FX 15 to 140, Fillstar CX 24 to 140, Aseptic Piston Doser PX 10 to 40 32-216 32-144 32-120 32-108 32-100 0.06l to 3.0l 0.06l to 3l 0.2-3.0 0.2-3.0 0.2-3.0 0.2-2.0 0.2-2.0 8.000-55.000 (18°C) 15.000-75.000 15.000-65.000 6.000-60.000 6.000-60.000 72.000 75.000 65.000 CX 5.000 to 40.000 55.000 (18°C) FX 6.000 to 60.000, Aseptic Piston Doser PX 6.000 to 48.000 45.000 Fillstar HF 6.000 up to 40.000 FX 6.000 to 60.000, CX 5.000 to 40.000, Aseptic Piston Doser PX 6.000 to 48.000 36.000 45.000 yes (Fillstar FX) yes yes yes yes yes (Fillstar CX) yes yes yes yes yes yes filling valve (limits: FX P EVO 3x20 mm - FX C 5x5x5 mm), For pieces up to 10x10x10: Aseptic Piston Doser PX yes yes yes Fillstar HF (gravity filling valve) Electronic volumetric filler flow meter, Volumetric piston doser with automatic dosing adjustment Electropneumatic volumetric filler with flowmeter volume control Electropneumatic volumetric filler with flowmeter volume control, with no bottle/valve contact Mechanical level Electronic volumetric filler, with Electropneumatic system with magnetic flowmeter volume control, with no bottle/valve contact Electronic volumetric filler Krones AG KHS GmbH Böhmerwaldstr. 5 93073 Neutraubling, Germany +49 9401 70 0 www.krones.com Mr Stefan Kraus Product Manager Filling Division +49 9401 3144 +49 9401 3056 stefan.kraus@krones.com Juchostr. 20 44143 Dortmund, Germany +49 231 569 0 www.khs.com Mr Thomas Niehr Product Management / Head of Aseptic filling +49 671 852 2901 thomas.niehr@khs.com Modulfill Aseptic Filling: Innosept Asbofill ABF Aseptic Filling: Innosept Asbofill ASR Aseptic Filling Innosept Asbofill ESL KHS Innofill DRV KHS Innofill NV 16 - 216 8 - 20 40 - 90 8 - 20 48 - 192 40 - 144 0,1 - 2,0 0,25 - 1,5 0,1 - 2,0 0,1 - 3,0 0,1 - 5,0 6000 - 24000 12000 - 36000 6000 - 24000 up to 72,000 6000 - 24000 12000 - 36000 6000 - 24000 70000 60.000 up to 65,000 no possible 12000 - 36000 60000 up to 60,000 6000 - 24000 12000 - 36000 6000 - 24000 up to 60,000 6000 - 24000 12000 - 36000 6000 - 24000 50.000 50.000 Volumetric filling system; Net weight filling system; Height filling system Contactless filling; Contactless filling; Short tube or long tube yes yes yes yes yes Volumetric filling system; Net weight filling system; Height filling system Contactless filling; Contactless filling; Short tube or long tube filling system optional for light carbonated yes Volumetric filling system; Net weight filling system; Height filling system Contactless filling; Contactless filling; Short tube or long tube yes yes PETAsept L / PETAsept D Contactless filling yes yes Height filling system; Pre-dosing system Long tube; Full bore filling / contactless / for pulp, fibres or fruit pieces yes yes yes yes Volumetric filling system; Net weight filling system; Height filling system Magnetic flow meter; Weighing cell; Electronic fill height measuring contact free filling with inductiv flow meter contact free filling (NCSD) with inductiv flow meter; contact filling (CSD) with inductiv flow meter contact free filling with inductiv flow meter short tube filling valve, volumetric freee flow filling valve, volumetric","@ID":37}, "MARKET SURVEY 33 PETplanet insider Vol. 15 No. 11/14 petpla.net Caps and closures Bottle-to-bottle recycling plants Preforms Preform and single stage machinery Preform / stretch blow moulds Two-stage SBM machinery Compressors Resins / additives Filling equipment Closure systems Suppliers of filling equipment: Traditionally we mark the occasion of the Brau Beviale exhibition with the publication of our market overview of filling equipment suppliers. This year nine companies from different countries will be taking part. They are: Fogg Filler (USA), SMI S.p.A. (Italy), Serac (France), Sipa (Italy), GEA Procomac (Italy), Sidel (Switzerland), Sacmi (Italy), Krones AG (Germany) and KHS Coroplast (Germany). The companies are shown in the table in the order in which their details were received by the editors. Although the publishers have made every effort to ensure that the information in this survey is up to date, no claims are made regarding completeness or accuracy. 11/2014 MARKETsurvey Company name Fogg Filler SMI S.p.A. Serac Postal address Telephone number Web site address Contact name Function Direct telephone number Fax E-Mail 3455 John F. Donelly Drive Holland, MI 49424, USA +1 616 786 3644 www.foggfiller.com Mr Mike Raczynski Sales Manager +1 616 738 0263 miker@foggfiller.com Via Carlo Ceresa, 10 24015 San Giovanni Bianco, Italy +39 0345 40111 www.smigroup.it Mr Pietro Volpi Marketing Dept. Manager +39 0345 40316 +39 0345 40209 pietro.volpi@smigroup.net 12 route de Mamers - BP 46 72400 La Ferte Bernard / France +33 2 43 60 28 28 www.serac-group.com Mr Roland Nicolas Dairy & Aseptic Business Development Director +33 2 43 60 28 32 +33 2 43 60 28 37 ronicolas@serac.fr www.dairy-filling-machines.com Mr Aymeric Vague Personal Care and Chemicals +33 2 43 60 29 55 +33 2 43 60 28 37 ayvague@serac.fr 1. Machine designation / model number Fogg Filler, 4 different sizes Ecobloc, blowing, filling & capping Serac Aseptic System 4 (SAS 4) Serac Aseptic System (SAS PL) Highly Hygienic Filler (H2F) Rotary Weigh Filler (R) 2. Number of filling heads (range: from/to) 12-90 Electronic volumetric fillers (18 - 126) 8 - 90 1 - 2 6-90 4- 90 3. Min to max bottle contents (in liters) 50ml - 10l 0.25 - 10l 4. Filling speed: output (bph) (min to max): 4,800 - 36,000 specifiy: 1l bottle / still water (bph) 60-600 4,800 - 36,000 1l bottle / CSD (bph) 4,800 - 36,000 1l bottle / Milk (bph) 60-630 4,800 - 36,000 up to 48 000 up to 1200 up to 48 000 up to 48 000 1l bottle / Juice (bph) 60-630 4,800 - 36,000 up to 48 000 up to 1200 up to 48 000 up to 48 000 5. Filling process Pressureless (still drinks) gravity fillers yes Electronic net weigh filling Mass flow meter fill Electronic net weigh filling Electronic net weigh filling Pressure filling (carbonated drinks) yes Hot filling gravity fillers Electronic net weigh filling Electronic net weigh filling Electronic net weigh filling Cold aseptic filling Electronic net weigh filling Mass flow meter fill Electronic net weigh filling Electronic net weigh filling Juices with high pulp content gravity fillers Electronic net weigh filling Mass flow meter fill Electronic net weigh filling Electronic net weigh filling 6. Type of filling valve and metering system Tri-Line Valves Electronic volumetric filling valves Flowmeters (metering system) Electronic net weigh filling Multiflow magnetic valves with flow monitoring Magnetic valves and flow meter Electronic net weigh filling Multiflow magnetic valves with flow monitoring Electronic net weigh filling Pneumatic valves","@ID":35}, "TRADE SHOW PREVIEW 44 PETplanet insider Vol. 15 No. 11/14 petpla.net Brau Beviale 2014, 11-13 November: The PET Selection: Brau Beviale is opening its doors in Nuremberg, Germany, at 9 a.m. on November 11, 2014. In our second trade show preview we have gathered a selection on the many exhibits of interest in the world of beverages in PET. Rinse, fill, cap The main attraction on Slovenian company Vipoll’s stand will be a Visitron VKR-ES-DN 24-24-6K(+6SA) complete rinser/filler/capper unit. A machine of this type has already been ordered by a brewery in Russia that produces unfiltered and unpasteurised quality beer, which requires high quality and hygiene standards. The filling module has 24 valves for carbonated and non-carbonated beverages. All drives are servo drives, including the infeed worm. A new outer cleaning system, which can be connected to the foam cleaning system, is designed to ensure total elimination of dirt and micro-organisms. A special cleaning attachment for the cap conveyer prevents the transfer of dirt from the equipment to the caps. External filling valves enable three-phases filling and can handle higher temperatures and less foam, for sensitive products. The filling valves have adjustable precision filling tubes, which is said to eliminate the need for equipment changeovers when varying filling levels. The rinser has 24 grippers/spray nozzles. Its stainless-steel frame is microbiologically designed and prepared for CIP. Specially manufactured grip heads do not have to be exchanged when the container format is changed. The capper’s six crown cork capping heads, which are installed at every second position, are intended to facilitate upgrades for screw caps without exchanging other capping heads. Vipoll will also be presenting its new line of process technology: pasteurisation units, mixers for non-alcoholic beverages, blenders for beer, carbonation and decarbonation units. www.vipoll.si Vipoll Hall 7 | Booth 233","@ID":46}, "PETPLANET AWARD 2014 36 PETplanet insider Vol. 15 No. 11/14 petpla.net PETplanet award 2014 – Service performance, developing countries Based on the After Sales study whose first part we published in our October issue, PETplanet insider has identified clear winners. We look forward to presenting them at Brau Beviale 2014 in Nuremberg, Germany. The award ceremony will take place on the first day of the trade fair, November 11, at 10 a.m. on our booth 7A-203. You are cordially invited to join us at the ceremony! The diversity of regional brands in particular, which are not significantly represented in the highly industrialised lead markets, stands out in rapidly developing markets. Subsequently a direct enquiry was made about preferred suppliers (fig. 5) and, linked to this, a question was asked about a wide range of services and how satisfaction with these services is viewed as far as the preferred suppliers are concerned (fig. 6). One of the striking features is that a number of services are rated as Very Good or Good but, in some sectors, there is still room for improvement – including where the preferred manufacturers are concerned. Here retrofit/overhaul services, spare parts consignment stock systems and 24/7 remote hotline support all deserve specific mention. The latter may well be attributable to the distance of the markets from the main suppliers, however, it certainly emphasises the need for a local presence in rapidly growing and highly diversified markets. Subsequently, participants were asked to “marry up” their preferred suppliers with the best equipment in their company’s own factory (fig. 7). It is interesting to note that supplier preference is not completely in alignment with the machines deemed to constitute the best equipment. As anticipated, the “global brands” The training facilities assessment will come as a particular surprise as far as the manufacturers are concerned. There appears to be a high potential for improvement as far as services of this kind are concerned, something which should not actually be surprising bearing in mind the characteristics of the markets surveyed and is slightly underestimated by manufacturers domiciled in the highly industrialised countries. The response to the final question in the results which are presented here in concise form should not be quite such a surprise. The aim of this question was to establish the criteria on which purchasing decisions (fig. 9) are based. Naturally, and this is reassuringly clear, “equipment performance” and “service performance” rank roughly the same when it comes to the highest level importance. It is good to find that there are fewer machine buyers buying purely on “price” - which is naturally important overall but is not categorised as pivotal. PETplanet A w a r d 2 0 1 4 as dominant suppliers and ”valued equipment” are represented in equal measure in the ratings, but with a relative shift. It is, however, interesting to assess which services are actually being purchased from the OEM machine suppliers who provide the best equipment (fig. 8). A further notable feature is the fact that the level of satisfaction is predominantly good but the potential for improvement is nevertheless increasing. There is a tendency for the services specified in fig. 6 to be assessed as even weaker. In addition to this there are incidental “Spare Parts, Maintenance and Repair Services”. Fig. 5 Which is your preferred equipment supplier?","@ID":38}, "Editour report 11 PETplanet insider Vol. 15 interruptions or speed fluctuations to the running of the line, whereas before, if there was a hitch anywhere, the team of operators used to run the filler slightly slower in order to mask the problem instead of fixing it. This is no longer an option - the problem has to be dealt with immediately, and a stretch blow moulder operates at fixed speed”. Patrizio’s 35 years of experience are very much to the fore. For example, all format components are placed clearly arranged on racks in close proximity to the line in order to minimize the change-over time. Summarising his activities overall: “You must never stop getting better, lighter and faster. In one of my previous 'professional lifes' I was a racing car engineer: As soon as you have achieved something the competition comes along and tries to claw back the advantage. One of the reasons for continuous stop and go was the 6-packs falling at the palletizer. This year the palletizer infeed has been upgraded by means of a two axis handling robot. Now every layer sits on the pallet 100% and there is no more trouble with 6-packs falling through”. The water Somewhat pushed into the background at the meeting was water. In fact, the water is a story in its own right especially when you are talking about natural sparkling water. Water from Nepi was a valued commodity even in ancient Roman times. It has its source in volcanic rocks and is naturally enriched with 2.2 grams/liter of natural carbonic acid. The proportion of minerals is low at around 600 mg/l. The water is served in restaurants around Rome in particular. So marketing activities also target its popularity with top chefs. The factory packs a total of 100 million bottles in PET containers. 25 million further reusable glass bottles are supplied to F.l.t.r.: Alexander Büchler PETplanet and Patrizio Dessi, General Manager, in front of the SIPA block line. PROVEN COST SAVINGS PERFORMANCE moldmasters.com Mold-Masters and theMold-Masters logoare trademarksofMold-Masters (2007) Limited. ©2014Mold-Masters (2007) Limited -AMilacronCompany.All rights reserved. Rely on our global support network for fast service and parts. North America 1-800-387-2483 | Europe 49 (0) 7221 5099-0 Asia 86 512 86162882 ALWAYS INNOVATING. + More efficient use of platen real estate increases the cavitation for a given machine size: • 72 vs. 48 Cavity with a 28mm finish in a 225T • 72 vs. 48 Cavity with a 38mm finish in a 300T • 96 vs. 72 Cavity with a 28mm finish in a 300T • 128 vs. 96 Cavity with a 28mm finish in a 400T + Proprietary iFLOW and iCOOL technology reduces cycle times while improving balance, lowering injection pressure and increasing dimensional repeatability + Tooling solutions to revitalize, recapitalize and rev up existing systems Get 50% more output from the same machine 96-CAVITY MICRO PITCH MOLD FOR 300T MACHINES Contact us today at: mpeteurope@moldmasters.com","@ID":13}, "PETcontents 11/14 4 PETplanet insider Vol. 15 No. 11/14 petpla.net INSIDE TRACK 3 Editorial 4 Contents 6 News 52 Products 54 On site 56 PET bottles for Beverages +Liquid food 58 PET bottles for Home + Personal care 60 Patents TRADESHOW REVIEW 27 Chips and Grapes 2014 PET in the vineyards 4th edition MARKET SURVEY 33 Suppliers of filling equipment After Sales Service 36 PETplanet award 2014 Service Performance, development countries Tradeshow Preview 44 Brau Beviale 2014, part 2 November 11-13, 2014 Nuremberg, Germany BUYER’S GUIDE 61 Get listed! Page 41 Page 44 EDITOUR Report 10 Single stage vs two-stage Acqua di Nepi 12 Own brands only Ferrarelle 14 We don’t have a stretch blow moulding machine for PET CTF Group 16 Moulding - Injection or compression? Sacmi Imola S.C. BOTTLING / Filling 21 Krones refreshes APU’s Mongolian operations BOTTLE MAKING 23 Handling down to a T-handDle 39 Practical Guide to Injection Moulding of Preforms Bottles, preforms and closures, part 16 41 From Mould Manufacture- Tooling to service provider R&D Leverage Page 56 PETplanet A w a r d 2 0 1 4","@ID":6}, "EDITOUR REPORT 16 PETplanet insider Vol. 15 No. 11/14 petpla.net Moulding - Injection or Compression? by Waldemar Schmitke Sacmi Imola S.C. Today we’re visiting the Sacmi Group in Imola. Sacmi has a long-standing corporate tradition; the company was launched in 1919 with a starting capital of 4.500 Lire (2 euros in today’s money) and just nine people and, despite economic and political turmoil, has succeeded in growing on a worldwide scale. It now has just under 4,000 employees and in 2012 reported a turnover of €1.243million. Its development has been driven by the core business of machines and complete production lines for ceramics (tiles), which still account for over 50% of trading volumes. Other mainstays are packaging machines for beverages and foodstuffs, machines for plastic closures and PET preforms, injection moulding machines and inspection machines. Of interest to us is what may be defined as the second biggest division at Sacmi, the beverage division. Here we find machines for preforms with conventional injection moulding, machines for plastic closures using the compression process, rotary stretch blow moulding machines with output capacities of up to 60,000 bottles per hour, filler lines complete with cappers with up to 216 filling valves, including some in block format with the blow moulding machine (combo), labellers, downstream equipment for packaging and palletising and the corresponding inspection systems. Here at this meeting we are confining ourselves to preform and closure cap machines. Of particular interest to us, especially as far as preform machines are concerned, is the use of injection moulding or the compression process and, as regards closure cap machines, we are keen to talk about the trend towards a move away from 2-piece closures to the one-piece variant. Here, at the Imola plant, we are meeting Moraldo Masi, Business Manager of the Beverages – PET Business Unit and Massimo Gani, the Closures Sales Manager. IPS preform systems Moraldo Masi explains: “At the start of the new century, Sacmi decided to diversify its business and identified the beverage sector as the one of greatest interest as it is, amongst other factors, also quite ‘close’ to the closures world. It was thus decided to boost the product portfolio via both takeovers and the development of new technology. The preforms sector was developed along two different lines: conventional technology, injection, by beginning a development programme that made use of the presses made by the recently acquired Negri Bossi group. the development of a totally new product, that exploited the principles used in the plastic closures sector – that is, compression”. Moraldo Masi continues: “This application of compression in PET preforms proved to be extremely difficult and complex for various reasons, not least because of the fact that the PET injection world has, during the last ten years, made enormous progress in terms of performance. Today, the project is still very much alive, albeit substantially revised since we are now preparing a rotary single-stage plant prototype which sees traditional rotary stretch-blow moulding applied to new preform compression technology, also rotary. The first plant will be installed in Italy in the Spring of 2015 and will be able to manufacture bottles starting from resin at a maximum output rate of 30,000 bph with 48 cavities”. Moraldo Masi went on: “A validated product that is currently selling on all markets is the new IPS preform injection press. “In 2012 the first preform injection moulding system (IPS) with a clamping force of 220t integrated unloading system and post-cooling and a 48-cavity preform mould from the company’s own mould output was launched on the market. “We made the right decision”, says Moraldo Masi, “as we have been able to sell 20 preform systems f.l.t.r.: Waldemar Schmitke, PETplanet, Moraldo Masi, Beverages & PET B.U. Business Manager and Alexander Büchler in front of an ISP Preform system in the assembly bay.v","@ID":18}, "PETPLANET AWARD 2014 38 PETplanet insider Vol. 15 No. 11/14 petpla.net We feel steel. Always with quality from the start. S+BIGROUP www.dew-stahl.com Plastic mould steels. We use them every day: PET bottles, caps, plastic packaging and other plastic parts. But scarcely anybody is aware that these products are manufactured in a tool or a mould made of specialty steel. Our plastic mould steels are easy-tomachine, corrosion-resistant, clean and wear-resistant – depending on what is required of them during use. That guarantees long tool service life, high productivity and efficiency. Which steel do you need? Personal contact between buyers and sellers of machinery continues to be very important and this leads us to conclude that it is precisely in the markets surveyed that a relationship of trust and reliability is regarded as a positive factor. Clearly, brand names do not attract an excessively high rating; however, it may be reliably concluded that the reason for the high demand for “global brands” has Fig. 9 How important is the overall service performance of an equipment supplier in after sales activity for future purchasing decisions from your perspective relative to other aspects? less to do with the wide distribution of these brands than their good/very good performance within the profile of what they have to offer: performance is right, price is competitive and reliability and service are at the highest level. This all testifies to a high level of benefit available to machine users today within a distinctive competitive framework. All in all they are satisfied with the service offered! Second Part of Service Performance - Key Measure for Equipment Sourcing by Prof. Dr Ing. Michael Koch, Technical University of Ilmenau, Germany. www.tu-ilmenau.de/en/ plasticstechnologies PETplanet A w a r d 2 0 1 4","@ID":40}, "PETbottles 58 PETplanet insider Vol. 15 No. 11/14 petpla.net Home + Personal Care Float away on a tide of hemp Kneipp are employing the calming powers of the patchouli and hemp plants in their aroma gentle foam bath which is being advertised as a special edition and which incorporates the tag “Float away on a tide of hemp”. 400 ml of this foam bath with long-lasting foam are packaged in a handy white PET bottle complete with sleeve label and goldcoloured shiny screw cap. www.kneipp.de Double brazilian edition Some of the products launched on the market for the soccer world cup 2014 seem to be still selling even after the event. Two colourful examples are the “Guave Limette“, the brazilian edition of the dishwashing liquid in the “fit“range. Containing 500ml of product, this is packaged in the transparent PET bottle typical of the brand and also featuring a 2-colour push-pull closure. The other product with similar colouring is the Brazilian edition of “Kuschelweich” (“soft and cuddly”), another brand name owned by fit GmbH. The transparent PET bottle contains 750ml of product, is decorated with a plastic label and sealed with a screw cap which acts as a dispenser. www.fit.de Palmolive with passion fruit What a difference a year makes. Twelve months ago everyone was talking about passion fruit as a fragrance or flavouring for shower gel, now, one year on, it has metamorphosed into a scent for dishwashing liquid. Pressure on the part of consumers for pleasant, exotic fragrances familiar to them from the natural environment is forcing the manufacturers to come up with ever-new creations. The most recent example of this is Colgate-Palmolive with its dishwashing liquid incorporating the scent of maracuja (which is also known as passion fruit). 500ml of this product is packaged in a handy, transparent PET bottle with a screw-on push/ pull closure. The closure is moulded so that it matches the shape of the packaging perfectly and incorporates a raised edge to protect the push/pull from accidental operation. The bottle is decorated by means of a shrink sleeve label. www.colgate.com","@ID":60}, "imprint EDITORIAL PUBLISHER Alexander Büchler, Managing Director HEAD OFFICE heidelberg business media GmbH Häusserstr. 36 69115 Heidelberg, Germany phone: +49 6221-65108-0 fax: +49 6221-65108-28 info@hbmedia.net EDITORIAL Heike Fischer Gabriele Kosmehl Kay Barton Michael Maruschke Ruari McCallion Waldemar Schmitke Ilona Trotter Wolfgang von Schroeter Anthony Withers MEDIA CONSULTANTS Martina Hirschmann hirschmann@hbmedia.net Johann Lange-Brock lange-brock@hbmedia.net phone: +49 6221-65108-0 fax: +49 6221-65108-28 France, Italy, Spain, UK Elisabeth Maria Köpke phone: +49 6201-878925 fax: +49 6201-878926 koepke@hbmedia.net LAYOUT AND PREPRESS Exprim Kommunikationsdesign Matthias Gaumann | www.exprim.de READER SERVICES Till Kretner reader@hbmedia.net PRINT Chroma Druck & Verlag GmbH Werkstr. 25 67354 Römerberg Germany WWW www.hbmedia.net | petpla.net PETplanet insider ISSN 1438-9459 is published 10 times a year. This publication is sent to qualified subscribers (1-year subscription 149 EUR, 2-year subscription 289 EUR, Young professionals’ subscription 99 EUR. Magazines will be dispatched to you by airmail). Not to be reproduced in any form without permission from the publisher. Note: The fact that product names may not be identified as trademarks is not an indication that such names are not registered trademarks. 3 PETplanet insider Vol. 15 No. 11/14 petpla.net We have already visited many of you and you will have seen your photograph in PETplanet. Unfortunately not everyone gets in on the picture, so we have plans to take an enormous step forward on our exhibition stand at Brau Beviale. Have your photograph taken with our editorial team in front of our Editourmobil and paste your picture in right here on page 3. We look forward to seeing you! Yours Alexander Büchler dear readers, Visit us at the Brau Beviale Hall 7A Booth No. 203 and bring your PETplanet along together with your photograph!","@ID":5}, "Editour report 10 PETplanet insider Vol. 15 No. 11/14 petpla.net Single stage vs two-stage by Waldemar Schmitke Patrizio has been head of the operation for 3 years and has modernised it bit by bit. The block format line acquired a new stretch blow moulding machine a few weeks ago. The line has grown from 12 to 16 cavities. Now it is possible to get 32,000 b/h instead of the previous 24,000 b/h off the stretch blow moulding machine. The block format filler with 100 valves required a speed-up to adapt to the new output. San Benedetto has developed a tradition of dispensing with the support ring on the preform. This saves material and does not present any problems as far as the single stage equipment is concerned. As regards the 2-stage process, the handling of the preforms in the blowing machine requires some fine tuning and design tricks in order to ensure that the preforms - which have no support rings - run into the stretch blow moulding machine without jamming. Transport through the capper is also a special solution. In fact, the preform threads and cap threads are, for Patrizio, the parts on a block format line that are most susceptible to faults. “At the end of the day it is they that determine overall efficiency“, is what he says. Patrizio is in favour of block format lines. He pioneered this format in 2002, not only because they are of more compact construction and do not need any transporters, but also simply for a practical reason: “There are fewer Acqua di Nepi San Benedetto produces more than 3 billion PET bottles per year worldwide, around 85 % of these using the 1-stage process on Sipa machines. Says Patrizio Dessi, GM of Acqua di Nepi, a spring in the Acqua Minerale San Benedetto Group, “A lot of people consider 1–stage machines obsolete, but in certain conditions, once the processor is in control of the line, you get a highly efficient line that produces excellent bottles“. In his capacity as Plant Manager, Patrizio has acquired a lot of technical know-how over the years; he has been able to experience the 2-stage as well as the single stage world in all its manifestations. There is, nevertheless, a 2-stage item of equipment in his plant at Nepi. “It is certainly a good choice for those occasions when you have a lot of different bottles shapes and weights to be processed on the same line, and it is easier to operate when you can’t always rely on process specialists“, is his comment on the Sipa Berchi block format line installed. There is a long history of partnership between the San Benedetto Group and Sipa - the Zoppas family controls both the San Benedetto bottling company and Sipa. Nuremberg Milan Rome Naples Palermo Tunis Algiers Rabat Casablanca Marrakech Seville Madrid Lisbon Bologna Monastir Agadir Tangier Valencia Cordoba Bilbao Oporto Andorra La Vella Venice Turin Florence Messina Barcelona Zaragoza Italy Part 3","@ID":12}, "PETpatents www.verpackungspatente.de 60 PETplanet insider Vol. 15 No. 11/14 petpla.net Plastic container European Award of Patent No. EP 1886925 B1 Applicant: Suntory Holdings Ltd. und Yoshino Kogyosho Co. Ltd., (both JP) Application Date 2.5.2006 The process for shaping a thin-walled container in PET is described. The container is suitable for hot fill and incorporates adequate compensation surfaces during cooling. The tank can be constructed to make it visually attractive. Container base International Patent No. WO 2014 / 036516 A1 Applicant: Amcor Ltd., Hawthorn (AU) Application Date 30.8.2013 In order to ensure sufficient stability during changes in pressure, stability when standing upright and resistance to breakage, the base of a thin-walled plastic bottle made from PET must be formed in a particular way and fitted with ribs. Plastic bottle International Patent No. WO 2014 / 032730 A1 Applicant: SA des Eaux Minerales d’Evian Saeme, Evian-les-Bains (FR) Application Date 31.8.2012 Application relating to forming and the process for manufacturing a visually and functionally optimised plastic bottle from FDCA and / or MEG. Plastic container International Patent No.WO 2014 / 038921 A1 Applicant: Hyosung Corp., Seoul (KR) Application Date 10.9.2013 Forming of a “panel-free“ plastic bottle. In order to compensate for the change in pressure / volume during post-hot fill cooling, the shape of the base must meet specific requirements. Bottle without support ring International Patent No. WO 2014 / 053212 A1 Applicant: Alpla Werke Alwin Lehner GmbH, Hard (AT) Application Date 11.9.2013 This international application describes a preform for manufacturing a reduced weight plastic container which gets by without a support ring. The preform and the container manufactured from it meet the requirements as regards stability and can be sealed on traditional filler/bottling lines. Base form European Patent No. EP 2703307 A1 Applicant: Yoshino Kogyosyo Co. Ltd., Tokio (JP) Application Date 26.4.2012 In the interests of guaranteeing optimum compensation for differences in pressure that arise as a result of hot filling and subsequent cooling or due to carbonated contents, the shape of the base of a blow moulded plastic bottle is acquiring increasing importance. A number of variations are described.","@ID":62}, "PETnews 6 PETplanet insider Vol. 15 No. 11/14 petpla.net Husky further expands hot runners and controllers business Husky Injection Molding Systems continues to make investments to support the growth of its hot runners and controllers customers. Husky established its hot runners and controllers business as a strategic priority early in 2013 and is focused on developing products that solve key injection moulding challenges in areas such as gate quality, balance, ease of use and maintainability. Specific investments in 2014 include expanding Husky’s facility in Pudong, China with new manufacturing equipment and commencing hot runner manufacturing at its Chennai, India facility. This will allow Husky to achieve short lead times and to streamline the workload at its other manufacturing facilities in Milton, Vermont and Dudelange, Luxembourg. In the next twelve months, investments in the business will include increasing capacity to manufacture hot half plates, and introducing new manufacturing technology for manifolds at its Luxembourg facility. The company has also added more people to its sales support and customer service teams to give customers better support on mould and part design consulting, resin trials, start-up assistance and field troubleshooting. Husky has launched a number of products recently, including the hot runner and manifold systems Pronto and Ultra Sidegate, and the controllers series Altanium Matrix2 and Altanium Delta3, and the Unify pre-assembled manifold system. www.husky.ca Athena’s systems centre is taking shape The foundations and the building’s steel structure are finished, roof trusses, decking, and skylight frames are being erected. Athena’s new systems centre is taking shape as the company prepares to increase system integration and testing capacity. The new systems centre will also be the birthplace for Athena’s hybrid platform with integrated rotary table. A prototype will be shown at the NPE 2015. At this model the rotary table is integrated into the moving platen and suitable for conventional and rotary moulds. Earlier this year, Athena installed its first P120/E120 two-stage unit on an Xform 300 preform machine. The plasticizing screw diameter may optionally be increased to 130mm (E130). This machine features a throughput of 1,100kg/h PET (E130) and 900kg/h PET (E120). With this machine concept, Athena aims to become a leader in customization. The company is streamlining its current facility to reach a capacity of 4 to 6 machines per month in 2015. The new Systems Center will come on stream in early 2016 and significantly expand capacity. www.athenaautomation.com China Brew & China Beverage to move to Shanghai The next China Brew & China Beverage (CBB) will not be held in Beijing, but in Shanghai. In future the exhibition venue will be the Shanghai New International Exhibition Centre (SNIEC). The dates have already been agreed upon: October 11 to 14, 2016. The exhibition centre in Shanghai offers a better infrastructure. Another reason is that most of the beverage companies are based in this area. The change to the exhibition venue was agreed in cooperation with the VDMA, and the partners of drinktec. Dr. Reinhard Pfeiffer, Deputy CEO of Messe München International, and Richard Clemens, Managing Director of the Food Processing and Packaging Machinery Manufacturers Association affiliated in the VDMA (Germany´s engineering federation), spoke of a step in the right direction: “With this move to Shanghai, we want to make an already highly successful project even more successful. By being closer to the geographical heart of the beverages industry, we expect further synergy effects to be generated for the event,” said Pfeiffer. “The response we have had so far from our exhibitors and from the industry has been positive across the board,” emphasized Richard Clemens. CBB 2014 has got off to a successful start. A total of 708 exhibitors from 25 countries are putting on a presentation of their prodcuts and solutions at the New China International Exhibition Center (NCIC) in Beijing. 248 of these exhibitors are from outside China. The space taken up by non-Chinese exhibitors is 9,000m2 net, or 13% higher than at the last event. As such the international exhibitors account for around one quarter of the total exhibition space at this year´s CBB. More than 50,000 visitors are expected to come along to CBB 2014. www.chinabrew-beverage.com/english New leadership at Mold & Hotrunner Technology Scheduled change of leadership at MHT Mold & Hotrunner Technology AG: with effect from January 1, 2015, the supervisory board has appointed Christian Wagner to take over from Werner Plass the position of Technical and Sales Director. At the end of this year, Werner Plass, 63, will retire, but will continue to maintain close links with the company. In order to ensure a seamless transition within the management team, Christian Wagner, 42, will gradually take over all responsibilities over the next few months. With a postgraduate engineering degree (Dipl.-Ing.) in machine tooling, Christian Wagner has worked for MHT since its inception and has many years of experience in PET preform toolmaking and application technology. Until recently, he was running MHT’s US subsidiary as CEO. In 1998 along with ten partners, Werner Plass founded MHT, a specialist supplier of PET preform tools, and has since then been instrumental in shaping its development. Today, the medium-sized company has five production and service sites in Germany, North and South America and Asia and supplies customers in more than 100 different countries. Werner Plass is a well-known technical expert in the field of PET. It was under his direction that the first 144-cavity (year 2001) and 192-cavity (year 2004) tools were developed. www.mht-ag.de","@ID":8}, "TRADE SHOW PREVIEW 50 PETplanet insider Vol. 15 No. 11/14 petpla.net Pure, dry, energy-saving compressed air Quality compressed air treatment is more or less essential when working with foodstuffs. Kaeser Kompressoren will be presenting its Secotec series thermal mass refrigeration dryers, which are now available for a total range of 17 to 34 m³/min. the company says that its Secotec TF series dryers feature both low energy consumption and latent heat storage technology and offer 98% higher thermal storage density, compared to typically available systems with conventional thermal storage media. They also use 46% less space and are claimed to be around 60% lighter than existing systems, while consuming less than 87 watts per m³/min of compressed air to be dried. Also on the stand, the new Kaeser Filter products downstream from the dryer are designed to provide dependable removal of anything that shouldn’t be in the compressed air. They operate with minimal pressure differential, which remains virtually constant throughout the entire lifetime of the filter element. Low pressure differential leads to lower energy consumption. Kaeser filters’ performance characteristics were determined in accordance with ISO 12500 and were tested and verified by Lloyd`s Register, an independent testing agency. Visitors to the stand will be able to closely inspect Kaeser’s compact Airbox compressed air systems and CSG-2 and DSG-2 series dry-running rotary screw compressors, along with the energy-saving Secotec TF dryer with integrated Sigma Control. Kaeser says that it offers dry compressed air with reduced energy consumption. Its dry-running rotary screw compressors come with a ready-integrated i.HOC rotation dryer. www.kaeser.com Kaeser Hall 4 | Booth 429 Better-looking PET P.E.T Engineering has been working on projects which could help people to see PET as a valid alternative to glass, aluminium and HDPE, in both mechanical performance and appearance. The company will be presenting four projects, which have seen designers and engineers committed to developing packaging with a premium appearance using PET. The packaging proposed was born from a desire to ennoble PET by studying accessory elements such as labels and over packaging in order to create product systems capable of reconfiguring popular perceptions of PET bottles in the minds of bottlers and end consumers. PET Engineering says that the project outcomes – named Twins, Hero, Diva and Valley – will show that it is possible to make a container of great shelfappeal together with good mechanical characteristics that is also unbreakable and affordable. P.E.T. Engineering is a partner to Petnology, the yearly conference that is sub-divided into three themed cycles, and will be held concurrently with Brau Beviale. It offers experts in the supply chain and bottlers the opportunity to discuss the future of packaging and the challenges which the PET industry faces. Moreno Barel, P.E.T. Engineering’s C.E.O., will be making a conference presentation on PET’s future in alcoholic drink bottling in Russia in Stream B, the theme devoted to technical and innovation presentations. P.E.T. Engineering’s projects will also be found in PETArena within Brau Beviale. With its bottle developed for Devin, already a finalist in the Luxury Packaging Award, P.E.T. Engineering is also taking part in the World Beverage Innovation Awards @ Brau Beviale, organised by Foodbev Media. In conjunction with Unesda (the Union of European Beverages Associations) and Wafg, (the German non-alcoholic drinks trade association), P.E.T. Engineering’s Devin competing for Best Bottle in PET. www.petengineering.com PET Engineering Hall 7 | Booth 248-349","@ID":52}, "EDITOUR REPORT 14 PETplanet insider Vol. 15 No. 11/14 petpla.net We don’t have a stretch blow moulding machine for PET by Waldemar Schmitke CFT - Catelli Food Technology Our next visit takes us to a filling machine manufacturer in Italy with a broad range of applications - Catelli Food Technology, otherwise known as “CFT“, a company based in Parma. Here at the plant in Montecchio Emilia we meet Emanuele Piva, Beverage Sales Manager. We hope to hear more about the Group from him and the role played by PET in terms of corporate focus. The CFT Group has its roots in the Catelli family who have been producing and commissioning processing plants for handling tomatoes and fruits for almost 70 years. Not only process machinery is supplied but also turnkey factories under the name of Rossi & Catelli. CFT was set up in the wake of an expansion in 2006 which resulted from the merger with Manzini, who are also a major player in the food processing machinery and plant industry. Three years later CFT Packaging came into being with the purchase of SBC, Bottling & Canning, Comaco with filling machines for foodstuffs, edible and engine oils and Sima, also manufacturers of filling machines for foodstuffs as well as downstream items and palletisers. “What this means for us,” explains Emanuele Piva, “is that we are in a position to supply everything from a single source, from foodstuffs and beverages processing, packaging all the way through to palletising. With seven branches and agents in a further 43 countries, we are represented worldwide”. Sales in 2013 were around €120million, more or less equally divided between processing and packaging. In Italy there are two locations; one here in Montecchio Emilia and another in Parma with a total of 375 employees. Of these 165 people work in the Packaging Division and in Parma all the others work for Processing. However, by the end of 2014 this will no longer apply because both divisions will have been brought together under one roof in Parma. Packaging and Beverage Division “In the Filling Machine Division we take care of the entire sector, starting with foodstuffs, beverages, baby foods, edible oils right through to engine oils”, says Emanuele Piva. As far as the filling machines are concerned, the beverages dominate at 60%. In turn, the biggest share of this (50%) is accounted for by beer, which is somewhat unusual for an Italian company, as Emanuele Piva has to admit. The remaining 50% is divided up into juices, tea, energy drinks, spirit, still beverages and soft drinks. If we look at Packaging, we find that glass and cans tend to dominate. PET accounts for a share of only 15% of overall sales. The reason for this is the lack of a stretch blow moulding machine for PET bottles. “Today’s market calls for combined solutions (70% or more)”, says Emanuele Piva. There is an absence of any close cooperative relationship with blow moulding machine manufacturers because the major players have their own filling machines. “We missed out on the opportunity to purchase a very wellknown player when we had the chance. So we in PET tend to focus on the markets, such as, for example, the USA or applications where individual fillers are still in demand. In addition, we offer special solutions that call for a high degree of flexibility such as, for instance, fillers that are able to process PET and glass in one filling machine.” Emanuele Piva went on: “There is also the hot filling sector. Many people believe that this sector is being increasingly replaced by aseptic filling. That is not the way we see it. We have no aseptic lines in our range but are very strong on hot fill and ultra- clean applications and this applies to PET too. We have more than 175 lines on the market (predominantly in the Far East) and continue to look forward to an active stream of enquiries in this sector and that also goes for PET. Then there is a further sector, filling of soft drinks and juices using PET cans with an aluminium lid.” Although the price for the containers is quite high, Emanuele Piva nevertheless sees further potential for growth here, as he says “it also fits very well into our portfolio”. Ten to 15 lines as well as unit machines are delivered per year; this corresponds to a turnover of approx. €30million per year in the beverage sector. There are two main filling systems available for the PET filling operation. Master PET RS/SC for still and carbonated drinks Fill capacities from 5,000 to 60,000 bottles per hour Air separate return to avoid product oxidation Bottles up to a diameter of 125mm (Pitch 141mm) Soft drinks with four vol. of CO 2 at 15-17C° Still products filling without pressure Patented Filling Valve Opening Control Supplied as monoblock filler/capper or as triblock (rinser/filler/capper) Magic PET SC for still drinks only PET bottles up to 8 / 10l Air separate return to avoid product oxidation Pet bottles only Fill capacities from 5,000 to 60,000 bottles per hour Magic is also available as Magic HF for hot fill products such as juices, energy drinks, isotonic drinks and iced tea in","@ID":16}, "ON SITE 55 www.strautmann-umwelt.com | Auf dem Haarkamp 22 | 49219 Glandorf | Germany Since 20 years your partner for process reliability, safe emptying and disposal of Hall 6 | Booth 203 Six tonne flakes per hour C.Lic.Enrique Peña Nieto, the President of Mexico, the Board of Directors of PetStar and Coca-Cola Management participated in the opening ceremony held at PetStar premises at Toluca, Mexico, on the 16th of July. The occasion was the installation of the latest PET wash plant by Amut. This plant is the second to be supplied to PetStar, who wanted to double its existing capacity, thus demonstrating their commitment to recycling and their confidence in the reliability of the technology. This line completes Phase 2 of PetStar, owned by Coca-Cola and other Mexican investors, that today represents the largest Bottle-to-Bottle recycling plant in Latin America with an hourly net capacity of over 6.000kg/h, handling 1.5 billion PET bottles per year. The PET bottles recycling system is designed to convert post-consumer PET bottles into flakes suitable for processing by an SSP (solid-state polycondensation) system. The flakes produced are said to have a high level of purity and are suitable for Bottle-to-Bottle application. The plant has driven a change in Mexico’s waste management sector by converting the post-consumer bottles into usable and valuable manufacturing input. The non-biodegradable nature of PET bottles has always caused excessive waste disposal problems throughout Mexico but now they can enjoy a second life. The consumption of virgin PET involved in bottle production is consequently reduced. The plant includes a bottle pre-washing, detection, grinding, washing, drying and a final flakes detection in one integrated system running a continuous process. The washing systems enable the complete removal of impurities with a substantial saving of water and chemicals. The Friction Washer, connected with a water-flow recirculation and filtering system, removes any type of polluting material from the PET flakes. The system is a continuous process, not based on batches, where washing process, water temperature, friction level and resident time are automatically controlled and monitored. The supplying of this plant is part of a social responsibility programme to eradicate child labour: a reimbursement is provided to those families who collect waste bottles, giving them the opportunity of sending their children to school. Furthermore, the motto of PetStar “Recycling is giving PET new life” aims to have an educative function: awareness of recycling should start from childhood and children themselves can be an example to their parents and promote action to tackle pollution. www.amut.it","@ID":57}, "Editour report 12 PETplanet insider Vol. 15 No. 11/14 petpla.net restaurants and to households by an efficient door to door distribution organization. The supply radius for the company’s products is approximately 200 km, but in the last few years the distribution has reached Sicily and Sardinia, and the North and South of Italy. 53 to 65 people are employed here on site, depending on the season. Bottling takes place under two brand names – the historic and well known Acqua di Nepi and the new Fonte Vivia that is mainly distributed to hard-discount and/ or private labels. In 2013 turnover was around €18m. 2013 saw the filling operation rise to 125 million bottles - that is 95 million more than in 2002, when the company was purchased by the Zoppas family and PET investment was launched. The bottle sizes on the glass line are 0.5/0.75/1.0 and 2.0 litres. Running on the PET line are 0.5/1.0 and 1.5 litre PET bottles. The PET line is, as already mentioned, obtained from Sipa whilst everything else downstream is sourced mainly from Acmi Italy. The goods are packed in 6, 12 and 24 shrink film packs. Recycled PET is currently not used in Acqua di Nepi, but San Benedetto has the necessary know-how and capabilities. We extend our thanks for the interview and continue our journey (not without having imbibed a powerful slug of Acqua di Nepi to strengthen us for the road ahead). www.acquadinepi.it Own brands only by Waldemar Schmitke Ferrarelle Ferrarelle is a familiar brand name in Italy. The naturally carbonated mineral water comes from 13 springs on the company’s premises, which overall cover a total of 145 ha. Featuring somewhat fewer minerals is the Santagata brand of water distributed by Ferrarelle on the Italian market. In the still water sector, the company operates under the Natia brand name. For Giuseppe Cerbone, the General Manager, the private label route is not the way to go. “If we are forced to do that, we won’t earn any money any more“, is his view. As far as he is concerned, strong brands represent the guarantee for a future on the difficult Italian water market. He goes on: “We need to cultivate trends within society“. For him, one trend in society is the tendency towards health and anti-ageing. Bearing this in mind, he is trying to pinpoint additional niches through the medium of mineral water. One water with more minerals scored well in trial promotions. It is said to be healthy and to help eliminate waste products from the body. He is hoping for similar results in terms of a subsequent successful market launch. At the main plant in Riardo there are 4 PET lines and one glass bottling line for the main brands. The most recent installation dates back to 2013 and has a capacity of 40,000 1.5 litre bottles/hr. Responsible for palletising this volume is an impressive drying line from Acmi. Depending on their age, the stretch blow moulders are from Sidel and Krones. In total, Ferrarelle bottles 810 million litres (or 600 million bottles) a year. The proportion of glass is infinitesimally small. Although it says \"fill volume: 0.92 litres\" on the label on the glass bottle, the bottle in fact contains 1 litre. Giuseppe explains the reason for this as follows: “Previously the returnable bottles had a volume of 0.92 litres, today all bottles are 1 litre. Nevertheless, now and then vintage 0.92 litre bottles tend to find their way into the bottling plant. This is why we say 0.92 litres instead of 1 litre”. Weight reduction and energy savings are important goals for Giuseppe. Ferrarelle have reduced the weight of the 1.5 litre bottle from 37g in 2006 to 30g today and the energy consumption per cubic meter of water bottled from 51kW to 35kW. A characteristic feature of this significant level of progress is the fact that “these statistics are backed by investments amounting to a total of 15 million euros“. As regards energy consumption, they are anxious to make further strides. This year will see the compressors arriving on the test bench and they are looking forward to further efficiencies with these. At the moment they blow mould the bottles at 30 bar. Generally, Ferrarelle give the impression of being very environmentally aware. They have their own 1 megawatt solar plant which produces much of the factory’s electricity. 100,000 bees are producing honey on the gigantic site, and they also cultivate several varieties of organic wheat for pasta production and olives for oil. Also on the company premises is a farm dating back to the 18th century which the company has refurbished and restored to its original state. We thank our hosts for their friendly welcome and, with a couple of bottles of mineral water safely tucked away in our luggage, we leave Ferrarelle and head in the direction of Sicily. www.ferrarelle.it F.r.t.l.: Giuseppe Cerbone and Waldemar Schmitke in front of the Ferrarelle bottling plant in Riardo (CE) Italy","@ID":14}, "BOTTLING / FILLING 21 PETplanet insider Vol. 15 No. 11/14 petpla.net APU, Mongolia’s largest beverage producer, has been upgrading its facilities and production capacity in partnership with Krones Krones refreshes APU’s Mongolian operations APU, Mongolia’s largest beverage producer, operates a vodka distillery with an annual capacity of 200,000 hectolitres and an 80,000 hectolitre milkpowder-to-liquid plant, as well as production lines for fresh and UHT milk, yoghurt, soft drinks, fruit juices, still water and the country’s first carbonated water facility. Its range of twelve branded beers make it Mongolia’s largest brewer, with 52% market share. APU has expanded its business and broadened its product range significantly since 2009 and has undertaken four major projects, in partnership with Krones AG. APU has been producing its PET preforms in-house since 2012, on two injectionmoulding machines with a combined annual capacity of 80 million units. The first project was the design and installation of the country’s first canning line, in 2009. It is now running at its full 15,000cph capacity, on three shifts. APU already had a PET bottling line but, with an output of just 6.000bph, it was unable to keep pace with rising demand. Mongolia has embraced PET packaging with enthusiasm. “In rural areas, especially, PET containers are popular. They’re easy to transport, they don’t break and they can be re-used, for example, for storing fermented mare’s milk, Mongolia’s national drink”, Project Director Avirmed Mendbayar explained. Krones installed a complete Kosme line, rated at 12,000 containers an hour, combined with labelling technology. A rotary Kosme KSB 6R APU is Mongolia’s largest brewer. It has been using PET bottles for its beer since Q3 2012.","@ID":23}, "BOTTLE MAKING 42 PETplanet insider Vol. 15 No. 11/14 petpla.net He continued: “Our aim is to increase the existing four single stage machines to seven, space has already been assigned for installation with the appropriate footprint and sales negotiations for two further machines are underway. Our customer base is predominantly made up of converters, but we are also looking to talk to the brand owners with a view to offering them our design service and technological advice and consultation facilities and/or our own market and trend analyses. This in turn will help the converters to better understand and implement the requirements of their customers. Our aim is to win over customers by virtue of the service we offer and at the same time, of course, to ultimately win orders to ensure full capacity utilisation for our mould manufacture / tooling division.” Alan Tolley explained the company’s objectives: “We have a committed team available here on site with experienced employees, some of whom have already been actively engaged in this business for more than 20 years, plus a large number of young people who have found their own niche within the company based on an education and training programme sponsored by R&D.” Single stage tooling The range of single stage tooling extends from 1 to 24 cavities and, depending on the customer, is primarily designed to take into account existing Nissei and Aoki injection moulding/stretch blow moulding machines. “Every machine is different,” says Engineering Manager Gary Samson, “a challenge that our engineering team is happy to take up. For adapting a very wide range of interfaces we need, together with our customers, to define the interfaces and coordinate our mould manufacture / tooling technology with the required specifications, taking into account short delivery times. Our competitors are primarily the machinery suppliers who themselves have proprietary mould manufacture / tooling capacities at their disposal.” Gary Samson gave us details of the company strategy: “The local neighbourhood is helping us to reduce what are, as a rule, highly complex and expensive works and, together with our colleagues in mould manufacture / tooling, to meet delivery deadlines of eight weeks for a tooling set. Our sales strategy is also geared to this. Our Sales department consists of six employees who are site-based and thus have access to internal expertise and are in direct contact with Engineering. Application areas for our mould manufacture / tooling include Cosmetics, Pharmaceuticals, Household, Body Care, Beverageswith cosmetics reflecting the trend towards higher growth rates.” Although it is primarily PET that is processed (90%) there are also applications in the injection moulding/stretch blow moulding area for PP (baby foods) and PC. The markets for R&D UK are predominantly (85%) located in Europe but deliveries are also made to the Middle East, Africa and Brazil. The largest markets are, in order, the UK, Germany and Spain. Mould manufacture / tooling technology Hotrunners The hotrunner designated Genesis is an own product developed by the company. A thermal gate, in association with a hotrunner manifold balanced by means of pins, makes it possible to achieve a short sprue with a sprue height of approx. 1.3mm instead of the usual 3-4mm. Preferential heat pots The use of a preferential heat pot is possible in the conditioning station for the manufacture of PET bottles. In the case of uneven wall thicknesses within the preform, preforms may be inclined to bend as a result of the different cooling speeds that ensue. The result is an uneven distribution of wall thicknesses in the blow moulded bottle. With the preferential heat pot there is the option of heating only the cooler half of the preform and thus of achieving a uniform preform wall temperature. Stretch blow moulding unit Featured here is a special development for broad neck containers, namely the expandable blow core seal. This incorporates a high savings potential for compressed air with neck finishes of up to 40mm in diameter. The low-level blow moulding station has a rapid installation system with fixing pins on a universal back plate. The blow moulds are not fitted individually but milled in a block. This means a reduction in the components required for construction and the time required for mould changeover. Mould and tooling manufacturing General Manager James Ramsey: “Mechanical component manufacture takes place here on the premises. We make almost everything ourselves, only the surface annealing and heat treatments are sent out to companies in the area. Our fleet of machine tools comprises the most modern machinery in this category. For example, 5-axis high speed milling machines Alan L. Tolley, Managing Director R&D/Leverage UK","@ID":44}, "TRADE SHOW PREVIEW 48 PETplanet insider Vol. 15 No. 11/14 petpla.net PET Technologies at Brau Beviale PET Technologies are going to exhibit a new automatic stretch blow moulding machine APF-30, which is intended for 30l PET-kegs and 5 gallon one-way and returnable PET bottles production with the output 200bph. New APF-30 is said to be a perfect match of modern design and high quality, which efficiency and long-term operation is guaranteed by PET Technologies highskilled technical team. PET Technologies invite to visit them on booth 7A-321, hall 7A for more deep discussion of their products and services. www.pet-eu.com PET Technology Hall 7A | Booth 321 Automated hygiene Jürgen Löhrke GmbH, which is headquartered in Lübeck, Germany, will be presenting its wide range of products for automated process hygiene. A highlight of its stand will be its Cleenius cleaning robot, which has been designed to clean hard-to-access or dangerous areas of production facilities, including the insides of tanks, particularly those with complex agitators, as well as operating machinery. Also on the stand will be examples of Pulsed Light technology, which uses high-intensity flashes of light to sterilise packaging material, without water or chemical products. Löhrke’s product portfolio includes, in addition, solutions for CIP (clean-in-place), filling hygiene, disinfection with chlorine dioxide and electrochemical activated water (ECA) and chemical storage. www.loehrke.com Loehrke GmbH Hall 4 | Booth 315","@ID":50}, "NEWS 9 PETplanet insider Vol. 15 No. 11/14 petpla.net Fi-Cell bottle technology now available in the U.S. A new foamed polyethylene terephthalate (PET) bottle technology will give carbonated beverages, wine, spirits, cosmetics, personal care and other applications, physical and visual properties not previously available in a monolayer bottle. It is also suitable for certain asepticallypackaged products. The Fi-Cell (fine cellular) foamed PET bottle is the first technology being made available to the U.S. marketplace under the recently announced representation agreement between Plastic Technologies, Inc. (PTI) and Toyo Seikan Co. Ltd. The technology has already been commercialized by Toyo Seikan in Japan for a line of coffee drinks. One of the Fi-Cell’s key attributes is that the process produces monolayer bottles with a smooth inner and outer wall surface. Other foamed bottle technologies usually require an overmoulded bottle to achieve a similar result. The introduction is particularly significant for carbonated beverage applications that require a smooth inner wall for an accurate fill. A rough interior surface subjects the liquid to mechanical action. This causes the CO 2 to come out of the liquid and turn into gas or froth. Tricked by the froth into thinking that the correct volume has been filled, the filler stops the process resulting in an underfilled container. Fi-Cell bottles have smooth inner walls which prevents that from happening. In addition, the Fi-Cell process produces a visually-exciting metallic finish without the use of expensive metallic colorants. www.plastictechnologies.com International PackTech India and Drink Technology India set visitor record The trade fair duo International PackTech India and Drink technology India were very successful with a visitor increase of 37%. From September 25 to 27, 2014, around 10,250 trade visitors came to the Bombay Convention & Exhibition Centre to gather information about new developments for international packaging, package printing, processing, beverage and food industries. International PackTech India and Drink technology India took place together under one roof for the third time already. The trade fair duo confirmed its reputation as a business platform that provides customised solutions for the Indian market. A total of 230 exhibitors presented their products on the three trade fair days. The area of food processing was represented at both trade fairs for the first time and is to be expanded further in the future. The organisers, Messe Düsseldorf and its Indian subsidiary for International PackTech India as well as Messe München International and its subsidiary MMI India for drink technology India, also drew a positive balance. “We have achieved a completely new level with this result,” declared Dr. Reinhard Pfeiffer, Deputy Chief Executive Officer of Messe München International. “Following three joint events, drink technology India and International PackTech India have finally become established in the India market.” Werner M. Dornscheidt, Chief Executive Officer of Messe Düsseldorf, underlined: “Companies meet well prepared customers here who are ready to invest. Exhibiting companies reported very concrete business negotiations.The visitors put up with long travel distances in part to experience new technologies of international and domestic suppliers live at this trade fair. The very positive result of the trade fair duo makes us optimistic for the future.” Managing Director Richard Clemens of the association Food Processing and Packaging Machinery in the German Engineering Federation (VDMA), a sponsor of International PackTech India and drink technology India, stated: “Our expectations with respect to the number of visitors and competence have been considerably exceeded.” The next International PackTech India and Drink technology India is expected to take place from April 28 to 30, 2016, again in the Bombay Convention & Exhibition Centre in Mumbai. www.packtech-india.com www.drinktechnology-india.com New CEO of Sukano AG The Board of Directors of Sukano AG has elected Michael de Braaf as Sukano AG’s new CEO. Michael de Braaf has been Sukano’s Head of Sales since March 1, 2014 and has several years of experience in large international chemical and plastics companies. In addition to his new tasks as CEO of Sukano AG, Michael de Braaf will continue to head the sales team. www.sukano.com Global Closure Systems launches bicolour flip top closure for the personal care market Global Closure Systems has introduced the flip top closure Diamond for shampoos, shower gels and skin care applications. The new closure is produced by Obrist, one of GCS’ plants in Spain. Since 2009, Global Closure Systems’ Spanish facilities have provided products based on bi-injection technology. The group was the first manufacturer in Spain to design standard bicolour flip top closures and is a leading provider of both standard and customized bi-injected closures for leading personal care companies. Following the recent success of Rubi and Perla, GCS is launching Diamond, a new oval bi-injected snap hinge closure, available in different colour combinations, including translucent. With its rounded shape, its matt base and glossy lid, the Diamond closure shall meet the expectations of the beauty and cosmetic industry in terms of aesthetics, convenience and on the shelf differentiation. The closure is easy to use for consumers who just need to slide a finger up to open the closure. The headstand pack option ensures that the content can be dispensed and accessed more easily and efficiently to the last drop. The closure is suitable for PET, PE and PP bottles and has been designed for a push-on application and its PCO 28mm neck finish offers a material savings in the bottle neck itself. www.gcs.com","@ID":11}, "BOTTLING / FILLING 22 PETplanet insider Vol. 15 No. 11/14 petpla.net + 33 (0)2 40 05 09 37 SOCIÉTÉ GÉNÉRALE DES TECHNIQUES 3 RUE DE L’ÎLE MACÉ - 44 412 REZÉ - FRANCE www.sgt-pet.com SGT, Naturally Innovative The specialist in PET preforms and HDPE caps for over 30 years. Meet us at EMBALLAGE PACKAGING EXHIBITION Paris Nord Villepinte 17th to 20th of November 2014 HALL 4 / STANDA 014 WWW.SGT-PET.COM stretch blow-moulding machine with six stations and an integrated preform rinser supplies an Isoblock filler with containers. APU has a choice of three concatenated labellers: a Contiroll for applying wrap-around labels, a Sleevematic with a shrink tunnel for full-length sleeves, and a cold-glue machine for shoulder and back labels. The new PET line started operation in Q3 2012 and is now running in one to three shifts, filling beer and soft drinks; the proportions vary according to seasonal demand. The older PET line is now used solely for filling table water. Krones also installed a new syrup kitchen, as part of the PET project. It is made up of sugar-dissolving station, powder-dissolving, and mixing stations, and supplemented by a Contiflow mixer. Sugar-dissolving is undertaken in batches of up to 2,000l in two vessels, a sugar tank and a heat exchanger with a syrup cooling capacity of of 8,000l/h. The filter system comprises four strainers and two bag filters. The powder-dissolving station consists of a concentrate station and a tank with a screw-type agitator. The mixing station has three tanks, each holding 15,000l. The carbonation unit’s throughput is 10,000l/h; the flash pasteuriser’s speed that can be varied between 5,500 and 13,750l/h and can handle beer, juice and carbonated beverages, using plate heat exchangers. The syrup kitchen possesses its own CIP system with three tanks and two separate admission units. The third APU/Krones project was the construction of Mongolia’s very first high-bay warehouse in Mongolia. The country has vast areas of open, sparsely-inhabited landscape, extending 2,400km west to east across two time zones and over 1,200 km north to south. APU supplies its beverages to more than 7,000 sales outlets, about 60% directly from headquarters; the balance is served by wholesalers. The furthest distribution depot, a small town called Ölgii, is around 1,700km west of Ulanbaatar. APU’s purpose-built high-bay warehouse project managed by Krones, has three serving aisles currently in operation and has space for a fourth.","@ID":24}, "EDITOUR REPORT 20 PETplanet insider Vol. 15 No. 11/14 petpla.net EDITOUR REPORT 20 Meet us at Brau Beviale in Nuremberg – Hall 5 / 5-427 reduce the cooling times in the cavities. In order to do this, however, close contour cooling in the cavities (Cool+) was required, but this entailed considerably higher manufacturing costs (35%) than the traditional approach.” Massimo Gani also talked about the increase in capacity. “Today, however, we achieve high mechanical speeds on our plants by means of improved cavity cooling and in this way have been able to increase line extrusion capacity by between 45 and 50%. The additional costs of the cavities as reflected in the investment costs for the overall plant only amount to 14%.” In the case of 1-piece closures, it is HDPE that is used in processing applications because PP is too viscous for the thin walls in the closure. “The fact that the proportion of compression moulding is very high in the case of CSD closures is no coincidence,” Massimo Gani continues. In order to avoid stress cracking they use materials with a low melt flow index or / and increase the process temperatures. By contrast, the compression process permits operation at a lower melt index compared to injection moulding at cooling temperatures of 20°C and thus not only has a positive impact on stress cracking but also on energy consumption. The biggest market for CCM plants is China with 35%, followed by South America, Mexico, India, Africa and the Far East. To date, five CCM 80 lines have been installed on the premises of a large bottling enterprise in Germany. Massimo Gani looks to the future with confidence. “One important point as far as we are concerned is the preform systems. We are strongly represented among the ranks of the converters, but when it comes to bottlers who had made the decision in favour of vertical integration, we did not have the preform system in the past. This is one aspect in which we have now taken a step forwards”. We extend our thanks for the detailed talks and the opportunity to enrich our knowledge and resume our journey in the direction of Rome. www.sacmi.com","@ID":22}, "TRADE SHOW PREVIEW 49 PETplanet insider Vol. 15 No. 11/14 petpla.net Quality Association PET Beverage Packaging e.V. The aim of the Quality Association is to close the loop relating to recyclables in PET as a packaging medium and thus to increase the proportion of PET recyclables in drinks bottles. This will encourage the further sustained development of PET beverage bottles from an eco-logical viewpoint and make a positive contribution to resource efficiency and to protecting the environment and the climate. In addition, through the deployment of uniform quality specifications, a high level of consumer protection will be ensured. The RAL Quality Association covers the entire supply chain starting with the recycling of used PET drinks bottles and culminating in the manufacture and filling of PET drinks bottles. The Guidelines, which apply to all members, are set out in the RAL quality and test regulations. The members of the Quality Association voluntarily agree to submit to the quality and test criteria of RAL Quality and Test Assurance and are thus permitted to use the recognised RAL quality mark. The following are currently eligible for membership of the Quality Association: Recyclers of PET for manufacturing recyclates which come into contact with foodstuffs (food grade) Preform producers Drinks producers (bottlers/ fillers) for mineral waters and soft drinks Supplementing the group of individuals with an interest in these activities and the member base are sustaining mem-bers. In terms of their technological production expertise, the members are leaders at a national and international level. A specialist committee monitors the work of the Quality Commission so as to ensure consistent high quality. Checks on the quality criteria are carried out by a recognised test institute. www.wertstoff-pet.de Wertstoff PET Hall 4A | Booth 210","@ID":51}]}}
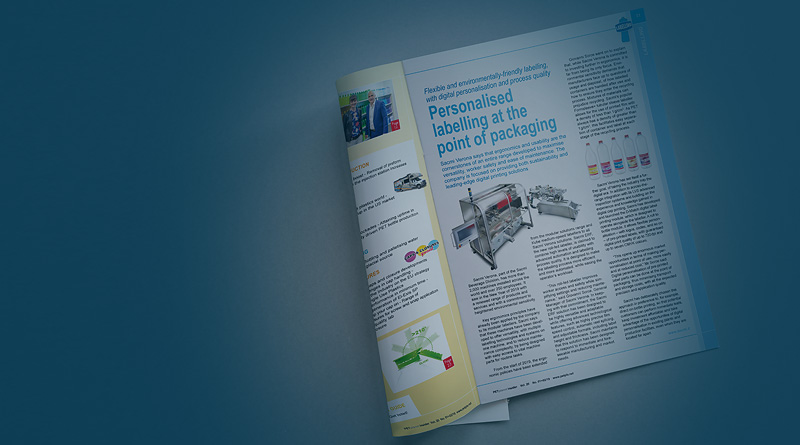