{"pages":{"page":[{"@ID":2, "19 EVENT REVIEW PETplanet Insider Vol. 23 mission, as recently there has been a veritable ‘tsunami’ of directives on plastics and recycling, making life difficult for recyclers activity. Then he stressed how successful was Petcore Europe’s campaign to explain to the general public and consumers how PET is a really a ‘different’ kind of plastic. Finally, Mr Philippe De Baer (Van Bael & Bellis) summarised all the current expected legislation from the EU Commissions, on SUP directives and also packaging waste directives. The effects of these new regulations may support the growth of the rPET market, increase demand and therefore exacerbate the imbalance between supply and demand of recycled material, in essence confirming what Mr Zanchi had discussed earlier during the morning session. Zanchi himself, in his closing statement, therefore insisted on this point, appealing to the EU Commission to make it easier to import flakes and rPET in Europe, for example by scrapping the need for reach certifications for these items. This point did not find Mr Bosmans open (yet) for discussion. He felt confident that the market would adapt to prevailing circumstances noting that the targets the EU have already imposed for 2025 and 2030 are likely to be increased! This argument will surely be on the table for a long time, and will inevitably be strongly debated again during the next PET Day event in 2023. www.gsiplastic.com"},{"@ID":42, "MARKET SURVEY 23 PETplanet Insider Vol. 23 No. 12/22 www.petpla.net 12/2022 MARKETsurvey Palletising and shrink film machinery To conclude this year’s market survey overview, the issue is dedicated to palletising and shrink film machinery. Please refer to the machine details for the state-of-the-art of the companies involved: Sidel, KHS Group, Krones AG, Jiangsu Newamstar Packaging Machinery Co., Ltd., Sipa, And & Or and SMI S.p.A. Although the publisher have made every eff ort to ensure that the information in this survey is up to date, no claims are made regarding completeness or accuracy. Company Sidel KHS Krones AG Jiangsu Newamstar Packaging Machinery Co., Ltd Postal address Telephone number Web site address Contact name Function Direct telephone number Email Rue du Commerce, 67116 Reichstett, France +33 388 183 880 www.sidel.com Mr Piero Zamboni PR Manager +39 521 999452 piero.zamboni@sidel.com Juchostraße 20, 44143 Dortmund, Germany +49 231 5690 www.khs.com Mr Ernst van Wickeren Product Manager Packaging +49 2821 503 200 ernst.vanwickeren@khs.com Böhmerwaldstraße 5 93073 Neutraubling, Germany +49 9401 70 0 www.krones.com Mr Andreas Fritsch Product Management Packaging Technology +49 8031 4040 www.info@krones.com No. 8 Xinjing East Road, Zhangjiagang Eco- and Technological Dev.-Zone, Jiangsu Province, China, 215618 +86 512 5869 1111 www.newamstar.com Mr Wesley Yin Marketing Manager +86 512 56993303 market@newamstar.com Shrink film machinery: Packagingoptions&output rate (packs/min) - print registered fi lm (yes/no; packs/min) Yes, up to 120 cycles per minute (PET bottles), 150 cycles per minute (cans) in 3 lanes Yes, 540 packs/min Yes, 150 x 4 = 600packs/min Yes, 60 - nested pack (yes/no; packs/min) Yes Yes, 80 packs/min Yes, 100packs/min No - label orientation (yes/no; packs/min) Yes No No No - carry handles (yes/no; packs/min) No Yes, 240 packs/min Yes, 80 x 2 = 160packs/min No - pad supported (yes/no; packs/min) Yes Yes, 110 packs/min Yes, 140 x 2 = 280packs/min Yes, 60 packs/min - tray supported (yes/no; packs/min) Yes Yes, 120 packs/min Yes, 120packs/min Yes, 60 packs/min - fi lm only (yes/no; packs/min) Yes Yes, 540 packs/min Yes, 150 x 4 = 600packs/min Yes, 80 packs/min - tray and fi lm (yes/no; packs/min) Yes Yes,120 packs/min Yes, 120packs/min Yes, 80 packs/min - pad and fi lm (yes/no; packs/min) Yes Yes, 110 packs/min NatureMultiPack 225 packs/min Yes, 140 x 2 = 280packs/min Yes, 80 packs/min Shrink process: - shrink tunnel with hot air or gas fi red opt. Yes With electricity or gas fi red (option) Yes Yes - oven Yes Yes No Yes - steam tunnel No No No Yes Footprint Depend on confi guration 4m, 6m or 8m long Depends on confi guration Number of possible lanes Up to 3 4 4 With 1 or 2 lanes Packaging material and possible thickness Low-density polyethylene (LDPE) from 27-100 μm Shrink fi lm 25-80 μm thickness; corrugated board: B,C, E and F-Flute, solid board Film, min 25-120 60 μm~80 μm Voltage/power/energy consumption NC Voltage: standard 3x400V; power: min. 22kW - max. 48kW; energy consumption: depending on requirements Depends on speed, package and material AC380V, 50Hz, about 110kW Film cutting and feeding system Yes Continuous feeding system from a roll Yes, fully automatic feeding, splicing, welding Yes Certifi cation CE certifi cation Compliant with 3c certifi cation Palletising machinery: Format changeover time Depend on confi guration Fully automatic changeover available - 0min operator time Depending on machine type, automatic changeover and manual changeover (5 to 10min) 20min Output rate (packs/min) Up to 12 layers/min Same as packaging machine 100-650lph (layers/hour) 120 Automatically intergrated: (yes/no) If necessary Yes Empty pack feeding Yes, empty pallet feeding Yes Yes Auto Insertion of interlayers Yes Yes Yes Auto Connectable to shrinkwrapper Yes Yes Yes Yes Special characteristics: i.e. low-level feed, cross conveyer barrier Available on high and low level infeed High speed with low level infeed Low-level feed, cross conveyer barrier Resins & additives Preform machinery Preform production & inspection systems Preform & SBM mould manufacturer SBM 2-stage Compressors Caps & closures & inspection systems Filling equipment & inspection systems Recycling machinery Palletising & shrink film machinery"},{"@ID":9, "7 NEWS PETplanet Insider Vol. 23 No. 12/22 www.petpla.net Coca-Cola HBC opens new recycling plant in Italy The Coca-Cola HBC Group inaugurated its second plant in Gaglianico, Italy, for the production of rPET bottles. The facility will transform up to 30,000 t/a of PET into new 100% recycled PET preforms. The company says that this will be enough to meet its beverage bottling needs in the country. Thanks to an investment of more than 30 million euros, Coca-Cola HBC converted a disused factory into an innovative hub which is powered 100% by electricity 100% from renewable sources. As a result, the plant will reduce the CO2 emissions of producing a preform by up to 70% compared with virgin plastic. The site, which will employ 41 people, and covers a total area of 18,000m2 is claimed to have among the first in Italy and in the world, some of the most advanced technologies to date. It is able to produce nine types of preforms, performing 4,700 quality checks per day. Speaking at the plant’s inauguration, Frank O’Donnell, General Manager of Coca-Cola HBC Italia said: “We want to keep investing and doing our part both to move toward a real circular economy in Italy and to contribute to the development of innovative projects in a region to which we are particularly close, despite the difficulties in our sector related to the rising cost of raw materials and energy. This renovated plant proves that giving companies the opportunity to do business and investment allows them to innovate and be more sustainable.” www.coca-colahellenic.com Faster and cooler than ever optiSTACK saves your time and money! German Technology Petainer: New manufacturing center in Tennessee, USA The global manufacturer of PET containers Petainer is kicking off a new PET blow moulding and custom designs facility in Tennessee, USA. The new center is intended to position Petainer’s supply chain closer to their customers to increase business performance and reduce carbon emissions. The new facility is located in Troy, Tennessee. The broad-based special ist team - materials scientists and engineers, injection moulding and blow moulding experts - is reported to provide packaging service and del iver solut ions wi th a ‘right f irst t ime’ mental i ty. For blow moulding, the site has two production lines operated by experienced engineers, enabling production from 250ml bottles to 30 l containers. From the new site in the United States, disposable PET drums and water cooling bottles can be delivered to the Midwest, reducing costs, delivery times and carbon footprint. www.petainer.com"},{"@ID":13, "EDITOUR PETplanet Insider Vol. 23 No. 12/22 www.petpla.net 11 mance of preventive maintenance. Our vision technology for quality defects at the preforms has a capacity of 27,000 pph. It is a real-time detection of any deviation from the established quality criteria,” Carlos finally explains and says goodbye at this point. We leave him to his machinery. We go outside in front of the production facility and after a short briefing by Ana we know what to expect next: the laboratory! R&D and quality Quality has a high priority at Novapet. Accordingly, there is a system that has grown since the company was founded, which adapts to new requirements and thus ensures quality. This integrated management system is called Lims. It includes ISOs for process quality, food safety, environmental and safety & health at work, as well as energy certification. The quality control of the produced resins and preforms takes place in the laboratory. Here we meet Olga, she explains that 15 people work in the lab 24 hours a day, 365 days a year. They test 11,000 samples per month. Their analysis service includes research, chemical and bacteriological analysis. The labor stuff examines the raw material, the end product and the environment. To ensure the quality of the working processes, Novapet places particular emphasis on the training and long-term employment of its employees. Continuous training keeps operations personnel trained in the use of the latest technologies in the sector. Recycled PET prduction As we leave the lab, our gaze falls on a part of the factory site that still looks a little like a construction site. However, some installations can already be seen. David explains that the production of Novapet’s own rPET will take place on this part of the factory site. A 15,000 t/a plant is to be put on production by January 2023. However, due to demand, capacity expansion to double the volume is already being considered. The rPET produced will not be available for sale but will be used exclusively to produce own rPET products. “We use the Vacunite technology from Erema. The Austrian producer of plastic recycling machines combines its Vacurema bottle-to-bottle process with Polymetrix’s recently patented Vacuum Solid State Polycondensation (SSP). What makes this combination so special is that all steps of the thermal process take place in a nitrogen atmosphere. The result is unique quality rPET pellets that more than meets all the requirements for food contact.” Sustainability and recent projects After the explanation of this construction site, we visit another highlight on the Novapet site: We drive by an off-road vehicle from the lower production area to a hill and look down on a 25 ha area with a photovoltaic plant. “This is our self-consumption photovoltaic field project. As you see we have already started.” From the hill we have also a look on the beautiful landscape around. From up here we can see a small stream meandering through the company grounds, as well as stork aeries on the factory buildings. “We try to support the storks, their aeries are very heavy, they weigh up to 500 kg,” David explains. “We live in harmony with nature here and try to reduce our environmental footprint through various partnerships and optimised transport routes, as well as at all points of our production. This starts with reducing the weight of the preforms, continues with an in-house biological wastewater treatment plant and continues with reducing emissions by shifting transport from trucks to rail. By switching transport alone, we were able to reduce CO2 emissions by 80%. And now we are expanding the photovoltaic system to use only our own produced green energy. Also, we do not create products that are not possible to be handled in a circular way,” David summarises. The morning has passed quickly and the heat on the photovoltaic field finally drives us back indoors. We ask David one last question: Where do you see serious challenges today and where do you see Novapet in 10 years? “Despite all the difficulties we face in the packaging market, we have shown that PET-producing companies have a great capacity to respond to the market in complex or emergency situations and this gives us added credibility and confidence in our clients,” David affirms. We thank Ana and David for their time, their patience, their conversations, and their willingness to provide information, and look forward to seeing them again soon - in Barbastro or at any other place where new, promising developments in the PET industry are being discussed. Novapet is a local company with a strong packaging culture, placed close to the market and close to its customers, and offers multitude of different PET solutions. Novapet has around 200 customers worldwide. It is located in 30 countries on 4 continents. The company has a total turnover of 400 mill €. It is integrated into the conversion process, injection, blowing and finally into special and adapted projects. The company manufactures resins, preforms and blows bottles. The PET resins and concentrates are for: still and carbonated drinks, hot fill, stretching PET, glass-like looking PET bottles, matt-or shining metal look, ovenable trays, PET for direct injection, for different mono- and multilayer bottles, and a family of resins for extrusion/ blowing bottles with and without handles. The preforms offer diverse types of mouths which cover the different needs of the current market. A second plant in Fuenlabrada near Madrid produces bottles for food and non-food products. www.novapet.com David González and Ana Chéliz driving with us up on the hill from where we have an overview over the plant and the the photovoltaic field."},{"@ID":36, "DRINKTEC REVIEW PETplanet Insider Vol. 23 No. 12/22 www.petpla.net 34 Magnetic fi lling valves increase product fl exibility of fi llers Filling valves for aseptic and ESL products Just in time for Drinktec, Gea expanded its portfolio of filling valves with new options that allow manufacturers to fill a wider range of beverages with one valve technology. The new generation of magnetic valves can be used for all filling platforms with a high hygiene level – in aseptic applications for dairy products, for example, as well as for ESL beverages with a longer shelf life. Demand dynamics and economic pressures on the beverage industry are turning flexibility into one of the core competencies of manufacturers. Faster changeovers for smaller quantities are also in demand in the filling sector. Gea’s filling specialists have developed a new generation of valves to ensure greater product diversity without compromising on hygiene. “Our customers want to implement product changes smoothly with as few operations as possible to work quickly and economically. This is reflected in the further development of our filling valves,” said Product Manager Massimo Nascimbeni, Filling & Packaging at Gea. “It was important to us to make the filling valves as flexible as possible so that producers can fill a wide variety of products with the same filling valves.” Gentle, precise and flexible filling The new generation uses magnetic actuators with seals that require less maintenance than the usual technical solutions. A pneumatic, or optionally a servo drive, refines the lifting and lowering movements of the control and shut-off valves. This means that beverages are processed gently and precisely, which is particularly important for viscous liquids or pressure-sensitive particles, such as fruit, cereals, nuts and seeds (up to 6x6x6mm) or fruit pulp (up to 3x20mm). To reduce the number of components on the new generation of filling valves, that would require service and warehouse logistics, Gea saved on the number of actuators without compromising on performance. In addition, the new filling system eliminates the need for dummy bottles by ensuring an efficient sterilisation position with only one magnetic joint. The new modules in Gea’s filling valve portfolio are suitable for all platforms designed for sensitive beverages. These include aseptic liquids such as dairy products and extended shelf life (ESL) beverages, which can be clear or contain fibres. Changeovers between the extremes of non- and highly carbonated beverages are possible without much effort. www.gea.com TURNKEY SOLUTION FOR BEVERAGE & NON-BEVERAGE PRODUCTS"},{"@ID":31, "DRINKTEC REVIEW PETplanet Insider Vol. 23 No. 12/22 www.petpla.net 29 average weight for sparkling wine is 720/750 g) and less likely to break – which is also great for changing supply logistics as sales via e-commerce and home delivery continue to rise. It is always useful to mention that this dramatic decreasing on bottle weight may surely have a positive impact on CO2 emission due to a more efficient logistic. Special powers At the center of the Sipa booth was an information area dedicated to packaging design, line integration, sustainability, filling and digitisation. Sipa says that one of its special powers is conceiving, developing, and delivering fully integrated production systems that exactly fit the requirements of its customers. A world premiere was presented at Drinktec, the Xtreme Renew Sincro Cube system for creating filled and capped bottles from 100% rPET flakes in a single step. It can be configured for all kinds of products: still and carbonated, cold-fill and hot-fill, with and without pulp, sensitive products (including CSDs without preservatives) and value products such as edible oil, milk and derivates, premium clear juices, home, and personal care products. Sipa also demonstrated solutions of its downstream equipment. A highlighted feature was a single Flextronic filling system that could be designed to handle PET and glass bottles. Sustainable and digital In the sustainability zone, the company showed multiple capabilities at the service of container producers, fillers and brand owners to reduce consumption of materials, energy, water, and compressed air, and to create containers that use the highest levels of recycled PET as well as alternative resins which are fully recyclable. Sipa also shined the light on AWArPET, the new brand to communicate the company’s approach in the design and production of primary and secondary packaging according to the utmost respect for the environment. Sipa’s product design experts are involved in the development of new packaging designs every year, and in all of these, the three Rs – Reduce, Reuse, Recycle – are constant guides. The zone on digitisation featured Sipa’s latest development in technical services package, called the Echo System. It makes it possible to have full control of system performance, increasing efficiency and optimising costs. It allows users to access information on any of their Sipa machines anywhere and anytime, summarised Sipa. www.sipasolutions.com Stretch blow moulder Xtra producing containers up to 12 liters in size. Connected wherever you like: the Echo System makes it possible to have full control of performance, to increase efficiency and to optimise costs."},{"@ID":24, "MARKET SURVEY 24 PETplanet Insider Vol. 23 No. 12/22 www.petpla.net Company And & Or Postal address Telephone number Web site address Contact name Function Direct telephone number Email PI El Limon, Av. de Europa, 6, 41928 Palomares Del Rio (Sevilla) - Spain +34 954 779 200 www.andyor.com Mr Caridad Ortega Suárez Sales Director +34 954 779 200 andyor@andyor.com Shrink film machinery: Packaging options & output rate (packs per minute) - print registered fi lm (yes/no; packs/min) No - nested pack (yes/no; packs/min) Yes, 15-900bpm - label orientation (yes/no; packs/min) No - carry handles (yes/no; packs/min) Yes, 15-400bpm - pad supported (yes/no; packs/min) Yes, 15-400bpm - tray supported (yes/no; packs/min) Yes, 15 -400bpm - fi lm only (yes/no; packs/min) Yes, 15-900bpm - tray and fi lm (yes/no; packs/min) Yes, 15-900bpm - pad and fi lm (yes/no; packs/min) Yes, 15-900bpm Shrink process: - shrink tunnel with hot air Shrinking pistols (hot air) - oven Footprint Several models depending on speed Number of possible lanes Max. length of the pack is 1,400mm Packaging material & possible thickness LDPE + LLDPE 40-60 μm Voltage/power/energy consumption Several models depending on speed Film cutting and feeding system Yes Certifi cation CE and UL Palletising machinery: Format changeover time 15-20min Output rate (packs/min) Up to 400bpm Automatically intergrated:(yes/no) Yes Empty pack feeding Yes Insertion of interlayers Yes Connectable to shrinkwrapper Yes Special characteristics: i.e. low-level feed, cross conveyer barrier Low-level feed; tray former possible to be integrated (display palletiser) Company Sipa Postal address Telephone number Web site address Contact name Function Direct telephone number Email Via Caduti del Lavoro n. 3; 31029 Vittorio Veneto (TV) - Italy +39 0438 911511 www.sipa.it Mr Matteo Tagliaferri Marketing and Communication +39 0521 548111 matteo.tagliaferri@zoppas.com Palletising machinery: Genius PTF Genius PTF/V Genius PTF/A Genius PTF - Active Layer Conventional automatic palletisers steady pallet type Conventional automatic palletisers steady pallet type, with double platform Conventional automatic palletisers moving pallet type Conventional automatic palletisers steady pallet type with innovative layer preparation Format changeover time 15min 15min 18min 10min Output rate (packs/min) Up to 330 layers/hour Up to 420 layers/hour Up to 700 layers/hour Up to 330 layers/hour Automatically intergrated:(yes/no) Empty pack feeding Yes, empty pallet feeding Yes Yes Yes Insertion of interlayers Yes Yes Yes Yes Connectable to shrinkwrapper Yes Yes Yes Yes Special characteristics: i.e. low-level feed, cross conveyer barrier - Operational fl exibility and further reduction in change-over times - Optimisation of cycle to increase performance, with improved control of the different movements using state-of-the-art electronic solutions - Customisation of the gripping system and layer transfer according to the product to handle - Designed to accept a variable number of product infeeds - Fully automatic system requiring limited operator intervention, operating in complete safety - Possibility to handle all main pallets on the market trouble-free, with highly customisable solutions - Operational fl exibility and further reduction in change-over times - Optimisation of cycle to increase performance, with improved control of the different movements using state-of-the-art electronic solutions - Customisation of the gripping system and layer transfer according to the product to handle - Designed to accept a variable number of product infeeds - Fully automatic system requiring limited operator intervention, operating in complete safety - Possibility to handle all main pallets on the market trouble-free, with highly customisable solutions - Operational fl exibility and further reduction in change-over times - Optimisation of cycle to increase performance, with improved control of the different movements using state-of-the-art electronic solutions - Customisation of the gripping system and layer transfer according to the product to handle - Designed to accept a variable number of product infeeds - Fully automatic system requiring limited operator intervention, operating in complete safety - Possibility to handle all main pallets on the market trouble-free, with highly customisable solutions - Operational fl exibility and further reduction in change-over times - Optimisation of cycle to increase performance, with improved control of the different movements using state-of-the-art electronic solutions - Customisation of the gripping system and layer transfer according to the product to handle - Designed to accept a variable number of product infeeds - Fully automatic system requiring limited operator intervention, operating in complete safety - Possibility to handle all main pallets on the market trouble-free, with highly customisable solutions - Linear axes layer preparation with active pack orientation and arrangement"},{"@ID":10, "8 NEWS PETplanet Insider Vol. 23 No. 12/22 www.petpla.net Repi appoints Dimitris Dounis as new Managing Director in Repi LLC Repi, a leading manufacturer of performance additives and colours for polyurethanes and thermoplastics, announces the appointment of Mr Dimitris Dounis as new Managing Director of the US based company to further support the growth in North and South America. Mr Dounis brings over twenty years of extensive experience in the chemical and polyurethanes industries. He holds a degree in chemical engineering and polymers science and has held various executive positions in multinational companies. Repi will leverage his extensive know-how and network in the chemical industry to boost its strategy to become a reference partner for liquid colour and performance additive solutions in the Americas. Repi entered the United States market with own offices, laboratory, and technical service department back in 2003 to introduce the colour ranges for polyurethane applications. The line of products for thermoplastic polymers followed soon after and in 2012 a new facility with state-of-the-art laboratory, manufacturing, as well as prototyping capabilities for PET packaging applications, was inaugurated in Gastonia, North Carolina. Today the American affiliate serves the Americas with the complete product range, directly or through established partners. www.repi.com Pact’s Australian billion bottle recycling project wins award Pact Group has won a major sustainable project award for bringing Australia’s biggest and advanced PET plastic recycling facility to life in just 370 days. Pact was awarded the Australian Institute of Project Management’s Sustainable Project Management Achievement Award for NSW for the $50 million Circular Plastics Australia (CPA) PET plastic recycling facility in Albury, New South Wales. The CPA facility is a joint venture between Pact, Cleanaway Waste Management, Asahi Beverages and Coca-Cola Europacific Partners (CCEP). A team from Pact project managed the build, which was delivered safely, on time and under budget on a greenfield site during a period of major global challenges, including the Covid 19 pandemic, supply chain pressures, and the blockage of the Suez Canal. Despite these challenges, it took one year and five days to establish the site, construct the facility, install the equipment and services, commission the machinery, and train a new team. The facility, which commenced operations in February 2022, has the capacity to recycle the equivalent of around 1 billion 600ml PET plastic beverage bottles each year into high-quality food-grade resin. Cleanaway collects, sorts and delivers PET plastic waste from kerbside collection bins and container deposit schemes to the Pactoperated facility for recycling. The recycled resin is then used by Asahi and Coca-Cola to manufacture new beverage bottles, and by Pact to make new beverage bottles and food packaging. Pact Group CEO Sanjay Dayal said it was a great honour for the Pact team to be recognised for its commitment to driving the circular economy in Australia. The CPA joint venture is building a second PET recycling facility with similar capacity in Melbourne which is due to commence operations in the first half of 2023. The CPA PET project in Albury was supported by a $5 million grant through the NSW Government’s Waste Less, Recycle More initiative, and the Australian Government’s Recycling Modernisation Fund. The award coincides with National Recycling Week, which this year has the theme “Waste isn’t Waste Until it’s Wasted.” www.pactgroup.com Florian Werner to become new CEO at Interzero Plastics Recycling Florian Werner will take over as CEO of Interzero Plastics Recycling, a segment of Europe’s leading provider of recycling solutions, Interzero. The focus of his activities will be on the further expansion of the segment, which is known for its plastics recycling and, with over 800,000 t/a, the largest sorting capacity in Europe. Florian Werner’s work will focus on the strategic development and the deepening of value creation. The measures already started to increase the performance and sorting quality of the plants, as well as the increase in the degree of recycling for plastics - for example, for the provision of plastic waste for chemical recycling - are a good starting position, on which it is now necessary to build further. In addition, the final integration process into the Interzero group of companies, which was newly created this year, is in full swing. “I am looking forward to the new tasks at Interzero. In many industries, the consistent closing of material cycles is moving more and more into the center of attention. Implementing innovative solutions together with the international Interzero team and our customers and thus contributing to a more sustainable use of raw materials is an exciting task on the pulse of time. As an innovation leader and Europe’s largest plastics sorter, with its people, team spirit and wealth of experience, the Interzero Group is excellently positioned for this,” Florian Werner emphasises. Florian Werner previously worked for the Swiss technology group OC Oerlikon AG, where he was head of the “Materials” business unit with locations in the USA, Canada, Germany and China and drove its successful turnaround. The CEO of Interzero Plastics Recycling GmbH, Stephan Schwarz, has left his position on November 1st 2022, to join ArcelorMittal. This step was planned and closely coordinated with Dr Axel Schweitzer, shareholder and chairman of Interzero, as a result of the sale of the former Alba International Recycling metal companies to the steel company. www.interzero.de"},{"@ID":33, "DRINKTEC REVIEW PETplanet Insider Vol. 23 No. 12/22 www.petpla.net 31 In order to help beverage producers, overcome all of these challenges and to provide options beyond manual operator intervention, Krones has developed Contiloop AI. The system is fully integrated into the stretch blow moulder, measures the wall thickness of each container at 32 points. During ongoing production, Contiloop AI responds to the slightest variations in material distribution and automatically adjusts the stretch blow moulding process in real time. It also considers additional parameters such as ambient temperature and humidity as well as preform feed and discharge temperatures. Any adjustments made are displayed on the HMI to give the operator a clear overview of the current process controls. Because production conditions are constantly changing, it’s not enough to have the controls revert to a specific, pre-set formula. Instead, various initial process settings are made for the system in an automated trial run and the resulting measurements are passed on to the Krones IIoT (Industrial Internet of Things) platform. There, the data flows into the Krones AI pipeline and is used to train the rule algorithm, the “intelligent agent”. When training is complete, the agent is loaded onto the machine’s Contiloop AI and is then available for use in production operations. Especially worthwhile when processing rPET In particular, when rPET is used, the available process window is usually very small and can sometimes be more variable than when virgin PET material is used. Even at high speeds and low container weights, this narrow window must be adhered to very precisely. Contiloop AI is climed to ensure a high level of quality in the finished containers and a low scrap (rejection) rate. But the advantages of Contiloop AI are not limited to material and process aspects – this technology also makes work considerably easier for operating personnel, says Krones. The automated controls mean far fewer manual interventions at the machine, and offline quality assurance can be reduced to a minimum. www.krones.com +44 78175 32087 +34 676 986 962 sales@petmachinery.com petmachinery.com Looking to sell your used PET machinery? We can help you. We offer a free valuation service, 50 years of industry experience, and a global network that guarantees you the best market value. Contact us today to find out more. THE INDUSTRY EXPERTS At Drinktec 2022, Jochen Hirdina, Head of Plastics Technology at Krones, explained the new Contiloop AI system which is fully integrated into the strech blow moulder. During production it measures the wall thickness of each container at 32 points and responds in real time. Any adjustments made are displayed on the HMI."},{"@ID":46, "DRINKTEC REVIEW PETplanet Insider Vol. 23 No. 12/22 www.petpla.net 28 State-of-the-art PET processing machinery Prepared for the future At Drinktec, Sipa demonstrated its expertise in PET processing know-how, from container engineering and design, preform injection, state-of-the-art blowing and filling systems, to sustainable solutions based on reducing the consumption of inputs and new fossil materials, as well as increasing the use of recyclates. Demonstrations and displays gave an insight into Sipa’s ability to deliver customised solutions with the flexibility to adapt to the rapidly changing market, across different technologies. Line integration, filling, sustainability, and digitalisation were the main focus areas on Sipa’s booth. Single- and two-stage technologies Sipa presented an SBM machine, an Xtra rotary system for the production of 100ml beverage containers. It can process 100% recycled PET with a total output of up to 65,000bph. A particular focus was given to a simple and fast mould changeover and to advanced controls, with Xtra HMI showing how easy it is the process set up, thanks to a Process Wizard. In its Xtra Big configuration, the Xtra rotary blow-moulding line can also produce containers up to 12 l and 48mm neck diameter. With an ECS SP80, a single-stage ISBM line, Sipa demonstrated how flexibly this machine can be used to produce a wide variety of containers. The ability to respond to rapidly changing customer and market demands is now more important than ever, especially given the current significant shortage in the availability of glass bottles, Sipa explained. Mould making for bottles and preforms Sipa develops and produces high-performance hot runner injection moulds with high cavity numbers. On display was a 180-cavity mould optimised for a high production rate of preforms. Sipa says this is important for the future to respond to customer requests for design changes resulting from changing regulatory requirements for bottle closures, which are likely to affect the design of bottle necks. Videos showed two new systems for keeping injection moulds clean when processing recycled PET: Xactive-Cleaning for hot halves and Xvacuum-Cleaning for cold halves. These systems have been developed by Sipa to avoid the accumulation of dust, which is mainly generated during the processing of rPET. New PET bottle designs At Drinktec, Sipa has presented for the first time a new premium bottle for HoReCA markets. Nothing strange about that, but this water is different. It’s a bottle that was conceived, designed, tested and produced inhouse by Sipa, then taken to an independent Sipa customer where it was filled and capped on Sipa equipment, given a label designed by Sipa, and then palletised with Sipa machinery. Sipa calls the product Bella. Bella, beautiful in Italian, signifies a new and progressive way of understanding packaging design and development. The project demonstrated how Sipa can partner with any customer, in all phases of a premium packaging project, from the original idea to design of the bottle and the preform best suited to make it; a bottle that catches the eye of the consumer with its elegant shape and beautiful label. Also the closure was purpose-designed by Sipa. PET bottle for sparkling wine A wine producer buying glass bottles today could easily pay 30% more than last year. The wine sector accounts for about 45% of the market for glass bottles, which until recently had seen a rapid increase - currently over 5 million tonnes, up from 4 million tonnes in 2016, worth over €2.4 billion. It is likely that sparkling wine producers paid much more for their bottles last year than they will in 2020. Just in time, Sipa has introduced its first PET bottle for sparkling wine. The company’s packaging team has developed a product that is a replacement for conventional glass bottles and can be used on existing bottling lines. An essential part of the Sipa design is the neck of the bottle, which looks like the glass bottle version, i.e. it adopts the classic mushroomshaped cork with its metal cage. The base also looks like the original. The design provides a top-load resistance of 3,500N. The PET bottles have already been tested on glass installations and have proven to be perfectly interchangeable with the glass versions. Sparkling wine consumers will enjoy the same experience with the new containers as they always have, from uncorking to pouring. They may notice that the PET versions are lighter at just 90 g (glass bottle Bella, the new premium PET bottle; design by Sipa"},{"@ID":12, "EDITOUR PETplanet Insider Vol. 23 No. 12/22 www.petpla.net 10 Spanish state-of-the-art PET packaging service Always in tune with the times by Heike Fischer The next part of our Editour starts in the north-east of Spain. 230 km from Barcelona, heading northwest, the Editourmobile reaches the Spanish province of Huesca, which belongs to the autonomous community of Aragon. Our destination is the Comarca of Somontano de Barbastro, with the district capital of the same name, Barbastro. In this small town of about 17,000 inhabitants, the history of the place is as vivid as its corporate culture. The Novapet company plant is located in the south of the city. We are warmly welcomed by Ana Chéliz, Marketing Manager at Novapet, and David González, General Manager of Novapet. Tour Sponsors: When we enter the company premises, we cannot yet guess the dimensions of this impressive production site. In the air-conditioned office, a commodity not to be underestimated in the Spanish summer, David starts directly with some details: “Novapet was founded in 1996 and belongs to the Samca Group. It started with a production of 30,000 t of bottle grade PET resin per year. The polymerisation plant was expanded in two steps with TechnipFMC Zimmer + SSP from Polymetrix technology. Today, we have a capacity of 260,000 t PET resin per year. After successive expansions of our injection plant since 2016, we produce 75,000 t of preforms a year.” After these impressive figures, David continues: “We are always in close contact with the bottlers and can therefore react quickly to demand. We don’t just produce standard PET resins, our special motivation is the challenge, the special. We are market oriented, accomplished to manage packaging supply chain, in direct contact and together with fast-moving consumer goods producers,” he emphasises. Production side But enough of dry figures, Ana and David take us on a tour of the factory. As we put on our protective clothing and reach the entrance to the production hall, we pass a small showroom. Novapet produces more than 30 different types of PET resins. “We want to meet the needs of our customers and are in close and continuous contact during a project,” David adds. The company offers its customers rapid prototyping and pilot production, as well as special contracts to ease the price risk management. An important service in times like these. In the anteroom of the production hall, we meet Carlos Álvarez, who is responsible for the management and control of the industrial injection moulding area. From a viewing platform, he proudly explains his machinery to us: in total we see 15 injection moulding machines. On the right, the red lettering PET on a blue and white machine catches our eye. Here are five Netstal PET Lines plus nine Husky-HyPET machines with clamping forces from 3,500 to 6,000 kN. “We get our moulds from Husky, MHT and Otto Hofstetter. We work with moulds up to 96 cavities from 10 to 98 g. A wide range of configurations, wall thicknesses, colours or weights etc. are possible, of course this is based on the customer’s needs. We have maximum flexibility thanks to the interchangeability of the moulds and direct production monitoring with absolute process control in real time. One special feature is our software Shotscope, which is dedicated for monitoring and controlling the number of cycles and ensuring the perforF.l.t.r.: David González, General Manger Novapet, Heike Fischer & Kay Barton, editors at PETplanet, in front of the Editourmobil at Novapet plant in Barbastro, Spain. Novapet is equipped with 9 Husky machines: 1 GL300, 3 HyPET 300, 2 HyPET 300HPP, 1 HyPET 400HPP, 1 HyPET 3005e+, 1 HyPET 4005e+ and 1 pilot line HyPET90 RS45/38. Further we see 3 PET-Line 3500/3550, 1 PET-Line 3500/6600 and 1 PET-Line 4000/6000 from Netstal."},{"@ID":39, "37 K SHOW REVIEW PETplanet Insider Vol. 23 No. 12/22 www.petpla.net Additive solutions The Texas-based chemical company SI Group from The Woodlands, north of Houston, launched its new “Evercycle” brand for PET and polyolefin processing at a press conference held at the K’ trade fair on October 20. It was unveiled by Robert Kaiser, VP Polymer Solutions and MD EMEA and Joey Gullion, Senior VP and CCO. The company, which has many years of experience in areas such as the manufacture of performance additives and antioxidant production with 20 manufacturing facilities worldwide, is responding to the industry’s growing need for improvements in circular economy and recyclability. As a result, Evercycle, which consists of five additive solutions, will in future help PET and polyolefin processors to have better control of product colour, process stability and acetaldehyde (AA) levels when producing and using recyclate. According to the company, two of the additives can be used in PET applications, PET-102D (granulate) and PET 103D (liquid). These are intended to control the colour of the actual container in bottle, tray and textile production during the production and processing of rPET. The other additives are intended to provide stabilisation in rigid HDPE and PP packaging (PP-101S), in flexible LDPE packaging (LD-101S) as well as improvement of mechanical performance in LDPE pre-consumer stretch film (LD-104P) respectively. The use of these technologies is expected to bring more plastics into a closed loop and value chain in order to support sustainability and profitability, as well as avoiding any downcycling into lower-value applications. Drawing on the results of a case study, Robert Kaiser discussed likely changes in the quality of PET material due to a steadily growing collection infrastructure for a wide range in quality of post-consumer waste with up to 30% rPET content. “For example, the resulting yellowing of the material could be offset by the use of blue pigments. The quality of material can also be addressed by using optical brighteners or AA scavenger technology if the values are elevated in the original material”, said Kaiser. All three issues could be addressed by the use of PET103D, according to SI Group. www.siigroup.com Robert Kaiser discusses the use of Evercycle in PET processing. Fewer rejects and more efficient control for bottle blowing At the trade fair booth of US engineering firm Agr, the company showed its automated blowing machine control system Process Pilot+, which it introduced at the end of August 2022. It is a combination of hardware and software that shall optimise the manufacturing of PET bottles and make the process more efficient and cost-effective overall, especially when using recyclate. The system is based on Agr’s control system Process Pilot, but according to the company, the blowing machine control’s reaction time during start-up, during changes to the ambient conditions or the control technology for the processed materials is improved while maintaining the same energy efficiency. Marketing Director David Dineff explained how it all works: “With the new system, we want to raise the usable productive capacity, i.e. the yield from the used material, while fundamentally minimising rejects and increasing overall efficiency and profitability.” The combination of software and hardware components, which operate a re-heat stretch-blowing machine in connection with the controls, should thus enable more comprehensive checks and a consequential optimisation of the blow moulding process. “The system contains algorithms that analyse the tiniest changes in material distribution and proactively adjust crucial settings on the blowing machine on the basis of these changes. This ensures that the correct thickness distribution is maintained consistently in the produced bottle,” said David. In this way, the system shall ensure that all produced bottles have the desired quality and performance properties, despite any deviations occurring in the environment, the systems, or the materials during the production process. “Our patented, ‘energy-efficient control technology’, as we call it, uses several control circuits and an adaptive prioritisation of rapid reaction controls to manage the blowing machine functions and control the blowing machine in such a way that the desired container properties are maintained within an efficient timeframe in a cost-effective way,” continued David. This approach enables the system to reduce the effects of process disruptions up to 40% more quickly and to achieve output material distribution up to 65% faster after start-up than earlier systems. This is particularly effective in the use of rPET and its variability. Agr reports that the system is compatible with all major two-stage system manufacturers and is no problem to retrofit. More than 500 Process Pilot systems are currently in operation in factories all over the world and the portfolio is to be further expanded. www.agrintl.com Agr’s K’ show booth"},{"@ID":20, "EVENT REVIEW PETplanet Insider Vol. 23 No. 12/22 www.petpla.net 18 PET production in China will be in surplus by 7 million tons. That means all margins will be squeezed further. And there will be a bigger push to export excess capacity from Asia. In Europe demand and production are steady. But manufacturers will have huge problems in 2023 to run at full capacity, due to the huge increases in energy costs and possible power outages. PET and raw materials will again become more competitive from China (and a few other countries like Vietnam, Indonesia and Turkey) as Indian producers will have to face a return to higher import duties from January. The situation of recycled PET is totally different. There is lack of material today and that will remain also until the 2025 deadline (for the target of 25% rPET in beverages). The estimate is that Europe will need 400,000 t/a by then! Hardly a negligeable amount. Zanchi stressed the point that, apart from improving bottles collection, it will be necessary to facilitate import of flakes and rPET from outside Europe and relax a number of regulatory constraints which, today, are stifling any increase in the use of recycled materials in the bottling industry. The logistics situation also is still an issue currently but, at least, freight rates are appearing to drop week by week. Zanchi pointed to some final questions worth considering. Among them, the evaluation of the effect of the sanctions on Russia, the Dollar/Euro rate, the increase in all production costs making Europe less competitive, and support for speeding up a circular economy. PET industry – production, converter & bottlers The afternoon session of the webinar opened with a first round table on the current situation facing the PET industry. Mr Hemant Sharma (Reliance) explained the efforts done in India to develop bottle and plastic collection and organise a PET recycling industry which is becoming a model for Asia and the world. Mr Hikoji Kosaka (Toyotsu PET Recycle S. – TRS) showed the activity of its new company, an investment of the Toyota Group into PET recycling, with a brand-new capacity of 40,000MT/a. Mr Christian Mayr (Alpla) underlined that the industry in Europe will be losing competitiveness but also consumers, and that increasing imports is merely a short-term remedy. Then Mr Dirk De Cuyper (Resilux) stressed how also his Group is already well into recycling activity, and called for more protection of the recycling chains in the old continent to make them sustainable and more competitive than virgin products. Distribution & consumers trends The second round table, on topics related to ‘Distribution & consumers trends’ started on a high note with the presence of Mr Hans Van Bochove (Coca-Cola). He explained that the limits imposed for 2030 on recycled contents in beverage bottles are just the minimum: people expect to get 100% of recycled material. But the fact is that there is not enough rPET in the market, and not of the right quality. Then Van Bochove brought some breaking news, disclosing that new regulations are coming soon from the EU Commission, particularly on packaging directives and collection. They will be game changers. There will be a more decisive push towards the encouragement of re-usable packaging (beverages will have an obligation for minimum 5% re-use). Most important is that the involvement of retailers towards collection will be considered an important necessary step forward, by requesting Member States to define how they propose to enact their own deposit return system rules. Mr Coert Michielsen (Refresco) agreed that it is possible to do more in Europe. Collection rates must be improved, and Japan and India are an example. The new rules of the EU, as explained by Van Bochove, will ensure better quality material for bottles too. In his opinion the EU should make it mandatory for retailers to accept collecting, making them more responsible on this issue. Closing this intriguing round table was Mr Philippe Gruyters (EMD, European Market Distribution), who is opening the way for the very first direct presence of retailer opinion in the PET Day. Gruyters explained that retailers already have their own policies on packaging and the use of recycled content. They are open to dialogue and to contribute to improve the system. However, it is necessary to study together with the small and big suppliers how to proceed, and the decisions must be for the long term, avoiding changing policies every one or two years. Circular economy The third and final round table examined the relationship between the circular economy and the current legislation in Europe. Mr Werner Bosmans (Policy Officer Environment, EU Commission) stated how the European Green Deal deals with the circular economy not underestimating the value of plastic, and PET in particular. The EU Commission is also working on a policy for bio-based and biodegradable materials, and on new rules for safe recycling in food contact materials. He finally declared that the Commission is most certainly not against plastics, but aims at tackling their unsustainable use. Mr Antonello Ciotti (Petcore Europe) criticised instead the Com-"},{"@ID":37, "PETplanet Insider Vol. 23 No. 12/22 www.petpla.net 35 K SHOW REVIEW Mold-Masters at K’ 2022 New inject to blow (I2B) system Mold-Masters’ new inject to blow (I2B) systems, developed in conjunction with its mouldmaker partner Cantoni S.r.l. (Lecco, LC, Italy), was presented at K’. Traditionally, bottle production made with injection blow moulding (IBM) or injection stretch blow moulding (ISBM) requires a dedicated production facility, special operator skills and high capital investment. The right tools and expertise to help with your rPET goals! Agr is uniquely positioned to support your venture into rPET bottle manufacturing with a powerful combination of Process Control tools, Process Consultants, and decades of industry experience. AGRINTL.COM • +1.724.482.2163 Moreover, if bottles need to be made as multilayer, then things become even more complicated. This is where Mold-Masters’ new I2B system enters the game. Moulders can use their existing injection moulding machines to make high-quality bottles and containers. The flexibility and lower capital investment requirements of this new system opens the door for many moulders to expand their project portfolio.Eliminating specialised IBM/ISBM equipment simplifies the production set-up. There’s no need to have a dedicated manufacturing call or to train operators for new skills. At the heart of this solution is Mold-Masters’ new I2B hot runner system, which is used to create the initial preform. From there, a servocontrolled shuttle moves the preform to the bottle cavity within the same machine for the bottle to be blown. The shuttle has two side-by-side cores and there are two bottle cavities on either side of the hot runner system. This allows the blow and injection function to happen simultaneously and finished bottles can be ejected at every cycle to improve productivity. The limitation of how many bottles can be produced each cycle depends on the size of the injection machine and the dimensions of the bottle. In addition, bottles can be produced either as mono-layer or co-injected. Co-injected bottles are produced without any penalty to cycle time and can incorporate either a high-performance barrier layer to extend shelf life of products or incorporate post-consumer recycled (PCR) material to meet sustainability targets. www.moldmasters.com Mold-Masters I2B system with co-injection e-multi auxiliary injection unit"},{"@ID":14, "EDITOUR PETplanet Insider Vol. 23 No. 12/22 www.petpla.net 12 Comprehensive restructuring from marketing to energy consumption Radical change for Acque Minerali d´Italia From before the coronavirus crisis, revenues at Acque Minerali d´Italia had halved. PETplanet insider spoke with the new CEO Alessandro Frondella, whose job it is to put this right. To do this, he is leaving no stone unturned – marketing, the team, customers, and technology. The energy consumption of the compressors was also checked. Tour Sponsors: Alessandro Frondella has been with Acque Minerali d´Italia (Ami) since mid2021 and has recently been appointed CEO to take the company forward. With its 8 factories and 27 bottling lines, Ami is one of the largest bottlers in Italy. Shortly before the coronavirus crisis, sales fell from 1 billion litres to 0.5 billion litres. This year, Ami is aiming for 0.7 billion litres. Alessandro’s task is to get Ami back on track. An analysis revealed that Ami sells 463 different products to around 1,000 customers. Alessandro wants to start by reducing the portfolio to around 270 products and the customer list by about 30%. The company will then focus on its three largest premium brands: Norda, Sangemini and Gaudianello, plus some local brands. In terms of technology, Alessandro is dealing with structures that have been established in perhaps a haphazard fashion in the factories. Bottling lines with individual machines are just as likely to be found there as modular systems. Filling speeds vary from 10,000 to 50,000bph. What they all have in common is the need for compressed air for stretch blowing. Here, too, Alessandro has found a mix of machines of various ages from various suppliers. An analysis showed that producing 1,000 l of compressed air consumes between 23 and 48kWh. The old 2-step compressors in particular, which first generate up to 7-10 bars of pressure then use a booster to increase this to the required 40 bars, have shown themselves to be energy guzzlers. In light of rocketing energy prices, Alessandro has decided on prompt action here. To carry out this strategic activity, he found in Siad Macchine Impianti, already an established supplier to Ami, where he developed a close cooperation with Marco Bassi, Italian Sales Manager for Food & Beverage Compressors. Based on the customers’ needs, Siad has created a product focused on sustainability and optimised for energy saving with complete service provision, their Vito Next. Alessandro says: “With the Vito compressors, we have simply constructed compressors that are easy to maintain, extremely energy efficient, and make only a minimum amount of noise and vibration. Full technical support is also fast and efficient.” Meanwhile, 6 Vitos are operating in the factories, 2 of which are from the new Vito Next range. In line with signed agreements, Siad’s software for the management of the entire compressor room will soon come into operation, which will allow Ami to optimise the production of compressed air and further increase efficiency and energy savings. Alessandro’s highly detailed knowledge of all technical and managerial aspects of production, systems and machines is impressive. It is rare for a CEO to know so much about every last nut and bolt – but a quick glance at his CV makes it clear why this is the case. Over 15 years, Alessandro has worked his way up through all departments, from machine operator to general manager of one of the first Italian mineral spring water companies. He brings together a wealth of knowledge from the front line, which he can now put to very good use. His primary concern however is the management structure. All the changes can only be implemented if they are dealt with by a team. Accordingly, Alessandro has built up appropriate structures in all of the eight factories. There are now organisation teams that are bringing the new ideas and radical changes to every nook and cranny of the workspace. Alessandro sees the predicament as a significant challenge. “The Italian water market is one of the most competitive markets in the world. Barely anyone can buy packaged water more cheaply than here, but consumers have understood that the price of water isn’t the only factor. So the goal is clear: concentration on premium brands with higher margins so that Ami can emerge once again in all its glory. We wish Ami every success. www.siadmi.com Vito compressors installed at the Norda production site in Primaluna, Lecco, Italy F.r.t.l: Alessandro Frondella, CEO of Ami and Marco Bassi, Italian Sales Manager for Food & Beverage Compressors of Siad Macchine Impianti"},{"@ID":6, "PETcontents 4 PETplanet Insider Vol. 23 No. 12/22 www.petpla.net 12/2022 Page 38 EDITOUR 10 Always in tune with the times - Spanish state-of-the-art PET packaging service 12 Radical change for Acque Minerali d’Italia - Comprehensive restructuring from marketing to energy consumption BOTTLE MAKING 14 Body and handle made entirely of rPET - Bottle with glued-in handle for home care & food 16 Inauguration of a PET water bottling plant in the midst of a war - A joint project of Avalon Group and PET Technologies EVENT REVIEW 17 PET Day 2022 - How to get out of the perfect storm? 20 PETinar: Technical highlights at Drinktec, day 2 26 Austrian PET recycler celebrates its 15th anniversary - Company growth enters its third phase MARKET SURVEY 23 Suppliers of palletising and shrink film machinery DRINKTEC REVIEW 28 Prepared for the future - State-of-the-art PET processing machinery 30 100,000 PET water bottles in one hour 32 Drinktec appearance at four locations 33 SoftBoost, a new split heating hopper 34 Filling valves for aseptic and ESL products - Magnetic filling valves increase product flexibility K’ SHOW REVIEW 35 New inject to blow (I2B) system - Mold-Masters at K’ 2022 36 K’ show review BUYER’S GUIDE 40 Get listed! INSIDE TRACK 3 Editorial 4 Contents 6 News 38 PET bottles for home + personal care 39 On site 46 Patents Page 12 BOTTLE MAKING Page 35"},{"@ID":4, "9 NEWS PETplanet Insider Vol. 23 No. 12/22 www.petpla.net"},{"@ID":44, "DRINKTEC REVIEW PETplanet Insider Vol. 18 No. 0/17 www.petpla.net 33 SoftBoost, a new split heating hopper Blow molds | Blow molding machines | PET bottle design | Packaging equipment APF-Max series All-electric FRQɍJXUDWLRQ 4XLFN FKDQJHRYHU IRU RWKHU SUHIRUP W\\SH %ORZ PROGV TXLFN FKDQJH NIR KHDWLQJ V\\VWHP Hot Fill RSWLRQ 6SDFH VDYLQJ RYHUDOO GLPHQVLRQV HEAD OFFICE PET Technologies GmbH Grünlandgasse 5/1/12 2620 Neunkirchen, Austria www.pet-eu.com tel.: +43 720 775 196 RIɍFH#SHW HX FRP Piovan presented its new hopper for up to 1,400 l. The hopper is designed for the rapid drying of regenerated PET with the aim of preserving the characteristics of the resin as much as possible, to obtain a highquality finished product and finally guaranteeing a high productivity. The new, patented air channeling system allows the granule to be heated to the core in just 40 minutes to quickly bring it from 120-180 °C. Completing the dehumidification directly or close to the injection moulding machine allows the main dehumidification hoppers to be used at temperatures between 120 and 140 °C, thus limiting heat loss. At the same time, this makes it possible to work along the plasticising screw of the press at lower temperatures, reducing further thermal stress during moulding and limiting the production of scrap. The reduced residence time of the material in the SoftBoost hopper, at the required working temperature, avoids unnecessary stress on the rPET and allows its mechanical, chemical and optical characteristics to be preserved. The small size and versatility of the system allows fast material changes even during mould changes, reducing downtime and maximising plant utilisation. www.piovan.com"},{"@ID":15, "PETplanet Insider Vol. 23 No. 12/22 www.petpla.net 27 EVENT REVIEW 27 EVENT REVIEW “Of course, switching from differently coloured to non-coloured transparent bottles is a major step forward which will gradually improve both quantity and quality. However, this is a lengthy process which the recycler cannot easily influence. We are putting a lot of effort into processing the main colours used on the market, namely blue and green, in a way that is suitable for food products and using them for beverage bottles. For this, we can point to several examples of 100% of coloured recyclates in Austria”, said Mr Strasser. In order to meet the needs of industry and to keep a recycling plant running in a commercially viable way, one cannot avoid purchasing a number of PET bottles locally which raises the question over the consistent quality of bottles from different sources. “We are mainly dealing with very small quantities, which are imported in compliance with the usual legal requirements. Adhering to specific quality standards is extremely difficult in practice and requires reliable business partnerships”, said Mr Strasser. The energy crisis is also playing a major role and poses considerable challenges for the circular economy. The use of and conversion to renewable energy is important but, according to Mr Strasser, will only result in a small reduction in energy costs. In fact, the price of food-grade recyclates is increasing and we are moving even further away from the price level for virgin material. Where do we go from here? Finally, we asked about future recycling possibilities and the requirement for tethered caps. Mr Strasser sees the development of chemical processes as a way of complementing mechanical recycling. “Due to the currently expected higher processing costs, mono-fractions will be treated more cost-effectively in future by the use of mechanical systems, with more complex fractions being processed chemically. As far as tethered caps are concerned, the EU Directive ensures that caps remain attached to the bottle not only after consumption but also during sorting and manipulation, ultimately ending up at the recycling plant. There, the cap can be efficiently removed ready for a wide range of applications in the cycle economy. www.pet2pet.at PET to PET plant setup Washing plant - 3 t/h output Dryer section (Bezner/Heilig): Debaler, label remover, bottle sorting (automatic 2-stage colour, polymer, metal, manual). Wet end (B+B/Heilig): Wet grinding, hot washing, sink/float separation, drying, flake sorting (colour, polymer, each 2-stage) Food-grade processing: food grade flakes (URRC): 1.8 t/h Food grade rPET (2 Starlinger granulation plants) - 3 t/h Plant management: 24/7 Total capacity: 30,000 t/a Digital manufacturing line for plastic caps SACMI.COM Continuous compression molding solution: digital, smart, cost-effective. Conceived, designed and produced by SACMI. DIGITAL & PROFITABLE Line ready for advanced Smart Pack and Smart Care services to provide more effective synergy with HERE M.E.S. features. SMART & RELIABLE Reliable controls and immediate overview of the process via AI-based inspection systems integrated into all the processes. COMPACT &IWX MR GPEWW WTIGMƤG IRIVK] GSRWYQTXMSR CCM maximizes output rates per bay and is the most sustainable solution. momic"},{"@ID":41, "39 BOTTLES ON SITE PETplanet Insider Vol. 23 No. 12/22 www.petpla.net Handy bottle for shower gel 250ml Energy Kick shower gel by Adidas is filled in a handy bottle made of 100% recycled material. The product, which is combined with essential orange oil, promises fast skin regeneration, especially after sports. The bottle has grippy nubs in parts, while the right area of the bottle is rounded and smooth. The label is one-piece and wrapped around the rounded edge to provide more and easier-to-see information. The hinged lid with dispensing opening and embossing can be operated with one hand. www.dm.de Eye-catching bottle for dishwashing liquid The I tal ian supermarket chain Esselunga sells 500 ml each of a concentrated dishwasher detergent under the name Piatti in a bottle with recognition value. The transparent bottles have a constriction in the neck area that makes it easier to grip and handle the bottle. They are made of 50% recycled material. Colourful sleeve labels emphasise the shape of the bottle and echo the colour of the contents. A hinged lid with dosing function that can be operated with one hand rounds off the pack appearance. www.esselunga.it Alpla starts production at the new plant in Lanseria near Johannesburg In the new headquarters for Sub-Saharan Africa, Alpla is merging five previous locations in South Africa under one roof. All Alpla technologies, processes and materials are combined in the Lanseria plant and the first apprenticeship programme of Alpla in Africa will start at the beginning of 2023. 35,000m2 of covered production, administration and storage space, another 12,500 for future expansion, and 30,000m2 of roof area equipped with solar panels: with the new plant in Lanseria, Alpla is setting the course for further growth in SubSaharan Africa. After around two years of construction and relocation, the international Alpla celebrated the opening of the ultra-modern location in October 2022. The new location in the industrial area north of Johannesburg combines and builds on the five previous plants in Harrismith, Denver, Isando, Kempton Park and Samrand. The departments, employees and machines were relocated step by step. Around 350 employees will start working in Lanseria and their number is subject to further growth. The new plant will produce bottles, closures and special packaging for the food, personal and home care, chemical, cleaning agent and pharmaceutical industries – a total of around 3.5 billion pieces per year. Alpla uses six different technologies, including injection and compression moulding, injection stretch blow moulding and extrusion blow moulding. In addition to international corporations, Alpla supplies smaller local companies with plastic packaging solutions. The new plant with its modern equipment meets all international quality standards, is operated efficiently and increases flexibility. The company’s customers in the region are claimed to benefit from this service in the long term. With the new plant in Lanseria, Alpla is promoting its own training of specialists and has established a dual education and apprenticeship programme. This dual system of practical and theoretical training based on the Austrian model is already in operation at the Alpla locations in Germany, Mexico, India, Poland and China. From 2023, the first 12 South African apprentices are to begin their training in the plastics technology and machining technology trades in the ‘Future Corner’ training centre in Lanseria. www.alpla.com ONsite"},{"@ID":8, "PETnews 6 NEWS PETplanet Insider Vol. 23 No. 12/22 www.petpla.net Manjushree Technopack signs an MoU with IISc for recyclable plastic packaging Manjushree Technopack Ltd. (MTL) has signed a Memorandum of Understanding (MoU) with the Indian Institute of Science (IISc), Bengaluru, to create innovative and sustainable plastic packaging solutions. As part of the MoU, IISc will establish a Centre of Excellence for upcycling and recycling thermoplastics used in a wide spectrum of rigid plastic packaging present in everyday life, ranging from soft drink bottles to cleaning products such as washing tablets. This will see IISc and MTL developing solutions to turn waste into plastic packaging to allow repeated recycling of products. The organisations will also collaborate to develop a recyclable elastomeric material for all plastic pumps and triggers and also work to strengthen the caps of PET bottles, which are made from 100% recyclable plastic. One of the key aims of this MoU is to replace a number of non-recyclable packaging materials with recyclable monolayer materials, which is expected to help make transport cheaper and reduce breakage and damage. Another area of focus for the collaboration is the replacement of cardboard-based packaging, such as that used in pizza boxes, with foamed polyolefins, offering improved thermal insulation and weight reduction. IISc, established in 1909, has become India’s premier institute for advanced scientific and technological research and education and is an Institution of Eminence recognised by the Government of India, and MTL. With over 42 academic departments and centres, IISc collaborates with a number of technology giants to find scientific and technological solutions to some of the world’s most pressing challenges. MTL is South Asia’s largest PET bottle and preform manufacturing company. With 40 years of packaging expertise in India, the company caters to the packaging requirements of the FMCG, pharmaceutical and liquor industries, and works with some of the biggest brands in these segments. www.manjushreeindia.com www.iisc.ac.in Plastipak’s major recycling investment in Spain officially opens Plastipak, a global leader in the design, manufacture and recycling of plastic containers has announced the formal opening of a major recycling investment at its manufacturing site in Toledo, Spain by Don Emiliano García-Page, President of the Castilla-La Mancha Region. The new recycling facility converts PET flake into food-grade recycled PET (rPET) pellets suitable for direct use in new preforms, bottles and containers. The new recycling plant will produce 20,000 t/a of foodgrade recycled pellet and will eliminate recycled resin transport-related emissions since it is co-located at Plastipak’s current preform manufacturing site. The recycling plant is Plastipak’s fifth recycling facility, with other recycling plants located in USA, France, Luxembourg and the United Kingdom. In Europe, Plastipak is the largest producer of food-grade rPET, with well over 150,000 t/a of rPET capacity. Pedro Martins, Plastipak’s Executive Managing Director Europe, said “The use of rPET is a key tool in reducing our customer’s Scope 3 related emissions and forms an important part of their ESG-packaging related commitments. As well as supporting our customers to reduce their financial obligations under the planned Spanish plastics tax, the plant will also contribute to the meeting the minimum recycled content levels mandated by the Single Use Plastics Directive.” To support on-site energy generation, the state-of-theart facility incorporates advanced energy-saving technologies and equipment that includes the rooftop installation of over 1,800 photovoltaic (PV) solar panels. The PV panels are expected to generate more than 1,339MWh/a of electricity that will be consumed entirely on-site, saving more than 443 t/a of CO2 through the avoidance of consumption of electricity from the national grid. This is in addition to the CO2 avoided by using 20,000 t of recycled resin instead of virgin resin, says the company. www.plastipak.com"},{"@ID":16, "BOTTLE MAKING 14 PETplanet Insider Vol. 23 No. 12/22 www.petpla.net Bottle with glued-in handle for home care & food Body and handle made entirely of rPET KHS has further developed its rPET containers for the home care and food sectors. In addition to bottle handles slotted into place mechanically, the Dortmund company now offers a glued-in process: stretch blow moulded using the preferential heating method, the bottle is claimed to be more stable than the extrusion-blow-moulded polyolefin alternatives currently available on the market. Glued-in handles also require a simpler contour than the clip-in variety. The development of the 2.3 l PET bottle with a glued-in handle is the result of a one-and-a-halfyear cooperation between KHS and Logoplaste Innovation Lab. The aim was to design a bottle specifically for home care products with the smallest possible carbon footprint. With its ready-for-market system, KHS and Logoplaste Group wish to support the industry’s striving for greater sustainability. “Our adhesive technology enables us to cut down on the amount of energy and material used in production and manufacture a container that’s both more stable and visually more appealing than the standard products currently available on the market,” says Sebastian Wenderdel, PET sales business development manager at KHS in Hamburg, Germany. Direct comparison reveals that up to 30% fewer resources are used in the manufacturing process, with 10% in material saved over a clipin handle. Instead of producing the bottle on an extrusion blow moulder as is common, stretch blow moulding it is particularly energy efficient – a not inconsiderable advantage in view of the rising prices for energy and raw materials. In conjunction with preferential heating KHS claims to provide a precise and reliable piece of plant equipment. This tried-and-tested, energy-efficient heating method permits homogenous distribution of the material during the stretch blow moulding process in plastic bottles with an irregular and complex design, thus lowering the number of resources used and boosting bottle stability. Neck alignment with millimeter accuracy as an optional component allows precise product dosing with the help of oriented spout caps. Furthermore, as the new PET bottle does not have any seams – as opposed to those on standard containers made of HDPE or PP – it has proved convincing in rigorous in-house drop tests, claims Wenderdel. When selecting a suitable adhesive, the design team drew on the years of expertise accumulated by KHS during the Nature MultiPack project. The container provides a further plus when it comes to product marketing. “The transparent PET material makes the product visible,” Wenderdel states. Moreover, customers can have their very own bottle designed with the help of KHS Bottles & Shapes service program. Moving towards a circular economy With the development of its new PET bottle with a glued-in handle KHS is moving closer towards a circular economy. With this system, the company wishes to not only address manufacturers of home care products but also food producers. “We provide a circular container whose bottle body and handle consist of 100% recyclate and are themselves fully recyclable. This is still fairly unusual for containers with an integral grip,” emphasises Wenderdel. www.khs.com The new PET bottle with a glued-in handle from KHS reduces material consumption by up to 30%. Both the bottle body and handle are fully recyclable and made of rPET. Sebastian Wenderdel, PET sales business development manager at KHS in Hamburg, Germany BOTTLE MAKING"},{"@ID":7, "PETINAR PETplanet Insider Vol. 23 No. 12/22 www.petpla.net 20 Review on the PETinar series Technical Highlights at Drinktec 2022, day 2 PETINAR Sponsors Ueli Kobel, International Sales Manager, Product Manager Beverage & Specialties Division at PackSys Global, also fulfilled audience expectations and presented the new efficient and highly precise folding and cutting machines for the production of plastic closures. As part of the Brückner Group, Packsys Global has more than 300 employees and customers in 90 countries worldwide. Headquartered in Switzerland, Packsys Global currently has more than 500 machines on the plastic closure market. Ueli explained that all closure machines can be adapted for conventional or different types of tethered closures and that capLAB - the first inline system for quality testing of closures - can be used to comprehensively inspect tethered closures. To serve the tethered closure market, Packsys Global has developed three technologies: the smarTether, experTether and the CapCompass. SmarTether is a technology with a combination of various cutting segments to create perforation lines for the TE band and the tether function. This can be simple horizontal cutting, or it can be combined with multiple vertical or diagonal slit lines. smarTether purposely leaves a thin and controllable skin in defined sections of the separation lines. It supports during the capping process and will easily break at the first opening. Ueli states that smarTether can be applied on all existing major PET bottle closure applications. The technology delivers a high-performance tethered closure suitable for highspeed capping processes. The experTether is for lightweight plastic closures which require perfect and continuous support on both blades of the knives during the slitting process. ExperTether and smarTether can both be used for the same cutting line pattern. With experTether the entire slit contour is 100% cut through – including the vertical and diagonal section. This is done by the synchronisation of the rotating spindles to the fixed slitting knives. Independent of the machine speed, the synchronised inner and outer tooling provide unique slit accuracy for customised slitting patterns for the tethered feature. Both the TE band and the tethered feature are processed using the same mechanical cutting technology. CapCompass is the method to bring a closure, when first opened, to a position which is locked and does not disturb the consumer while drinking. Gable top or other carton packaging applications are major markets for this processing method. Whether it’s a pre-moulded hinge, a thread start, an embossing, or some other feature, the slit lines can be positioned for functionality and/or marketing purposes. CapCompass is made for cutting closures at the right place and could be combined with smarTether or experTether additionally to TE Band slitting. At Drinktec PackSys Global also presented its new TEM Plus, Ueli continued. This versatile machine is integrated into any production line due to independent control and optional vision inspection system. The TEM gives flexibility in the process sequence thanks to its modular design for S/F or F/S of TE band. It also allows a large variety of cap dimensions, including sport caps. Contour slitting and synchronised cutting enable tethered applications. The nominal diameter range is from 18mm to 90mm. Closures from 10mm to 48mm high can be processed at a speed of 800 ppm for heights up to 48mm and 1,000 ppm for heights up to 27mm, Ueli summarised. www.packsysglobal.com After this comprehensive insight into PackSys Global’s slitting and folding technology, Iacopo Bianconcini, Manager Marketing and Product Development at Sacmi, took over the microphone. He posed the question of how the digitalisation of closure manufacturing could be translated into a real economic advantage. Iacopo gave a brief introduction to Sacmi: with 4,720 employees worldwide Sacmi has a net worth turnover of more than €1,5 billion, with 86% being exported. It has 80 companies worldwide of which 10 are manufacturing facilities. He pointed out that Sacmi develops multi-material packaging solutions for the most diverse platforms, to meet the needs of beverages and food producers all over the globe. In so doing, Iacopo stated that Sacmi is at the forefront of the global transition to a circular economy in the packaging field. This is achieved using the 3Rs approach; Reduction, Expectations were again high on the second day of the PETinar series: the presentations by PackSys Global, Sacmi and Stack Teck were eagerly awaited. After the first day with presentations from z-moulds, who presented smaller, adapted mould sizes for the production of closures on smaller machine types, or the new high-quality tethered caps from Bericap, as well as the presentation of the new PAC-E machine generation from Sumitomo (SHI) Demag, the standard was high!"},{"@ID":49, "DRINKTEC REVIEW PETplanet Insider Vol. 23 No. 12/22 www.petpla.net 30 100,000 PET water bottles in one hour Whether it’s climate change, supplying the world’s population with enough food and drink, or responsible stewardship of packaging materials, humankind is currently facing major challenges which are also impacting the food and beverage industries. In Krones’ view, PET can help solve some of the pressing issues of our era. After all, this type of packaging can be sustainable – provided, of course, the process for producing the material is resourceeconomical and a closed cycle is maintained. In order to meet the rising demand for packaged water, filling companies need appropriate machine speeds. Contrary to commonly held opinion, a single larger line offers better performance in terms of both energy and media consumption per packaged unit than multiple medium-output lines. Krones’ response to this development with the first wet-end block achieving an output of 100,000 0.5 l water bottles per hour. The basic production sequence of this 100,000 bph block is the same as in a conventional ErgoBloc L. The preform feed unit passes the PET preforms into the Contiform 3 Speed stretch blow-moulding machine. With a rating of 2,750 containers per blowing station, it set new benchmarks for output and compressed-air consumption. In order to cope with the high output of the stretch blow-moulder, some additional, optimised components, functionalities and assemblies were incorporated in the Ergomodul. For example, the two Contiroll stations and the Multireel magazines for label reels feature a new buffer system which keeps the label tension at a constant maximum level, thus offering ideal preconditions for thin label films, a boon for sustainability. Another of the machine’s key features is the “no bottle – no label” function. If a service rejection in the blow-moulder causes a gap in the bottle flow entering the labeller, no label is transferred to the vacuum cylinder and the corresponding vacuum cylinder suction bars are retracted upon reaching the glueing unit. As a result, no label or glue is wasted and any gaps in the container flow no longer affect the efficiency of the line. Two filling units, two closing units – one machine The filler posed the biggest challenge for the development team because there are physical limits to the standard approach of “bigger carousel equals higher output”. At some point, the masses to be moved and the forces acting on them simply get too big to reliably maintain a stable process. To prevent this, the block features two modularised filling units and closing units. That may sound simple but was in fact difficult to implement because although the filling/closing of 100,000 bph is evenly distributed among two units each, these units are still constituent parts of a single integrated block with just one valve rack and one sorting system for closures. The Modulfill Dual features around 60 filling valves fewer than a one-filler solution would need for the same output. Thanks to its compact size, the filler takes up less space, but its output is still almost 20% higher. Smart process control system for the stretch blow moulder Steadily increasing production speeds present challenges: While the maximum output per blowing station was still at 1,600 containers per hour back in 2000, today’s stations can make up to 2,750 bottles per hour. So, a machine can turn out as many as 100,000 containers per hour. Of course, at such high speeds, even the slightest deviations from ideal conditions can quickly and significantly impact an entire production run. Two more important trends must also be borne in mind: First, consumers especially are calling for increased use of recycled PET material (rPET). But not all rPET is created equal. Any inconsistencies must be offset in the blow moulding process, to ensure that every container meets the specified quality criteria. The second trend is the continued effort among beverage producers to further reduce the weight of their bottles. PET (whether recycled or virgin material) is costly, and highquality rPET is a scarce commodity. And so it only makes sense to reduce the weight of the containers as much as possible – to save on materials in the production process and to further reduce the containers’ ecological footprint. The wet-end block achieves an output of 100,000bph 0.5 l water bottles."},{"@ID":19, "PETplanet Insider Vol. 23 No. 12/22 www.petpla.net 17 EVENT REVIEW How to get out of the perfect storm? PET Day 2022 The PET Day, an annual event organised by GSI (Global Service International) of Italy, has undoubtedly become, in the 20 years since its start-up, a defining moment where the policies of the main decision makers of the industry are forming the basis for all strategic decisions for the coming years. The information and the arguments discussed within the space of this single day, which has a special mark on the agenda of all involved in PET and the raw materials of the polyester industry, are thoroughly developed and dissected and are surprisingly precise, anticipating market movements. This 20th edition, for the third time in the form of webinar, took place on September 29, 2022. The turbulence that shook the world in 2020 has created unexpected challenges for all industries, and the industry is now urgently seeking a route map out of the storm. PET Day is the place where experts and top managers are looking at how to steady the ship out of the stormy seas and into calmer waters. Mr Francesco Zanchi, CEO and founder of GSI, began by welcoming the specially invited audience. He underlined the difficulties the sector is facing, but he also expressed confidence that these same difficulties can be transformed into opportunities: There is a way out of this ‘perfect storm’. The morning session was opened by Mr Paul Hodges, of New Normal Consulting, now a regular guest at the event, who addressed the economic situation, with particular regard to the inflation issue, or, better, the ‘Putinflation’ as he put it. When the unexpected happens, old models are no longer valid, he said. It is not possible to control the economy of billions of people just by acting on interest rates, as Central Banks used to do. Putinflation is taking us back to the ‘70s, he stated, but we should see the challenges ahead of us as opportunities. Hodges continued: The trends in the chemical industry were already revealing months ago what was about to hit us. A confluence of calamities, as the IMF said. Supply chain outages have caused major disruptions: we moved from ‘just in time’ stocks before Covid to ‘just in case’ stocks (on the expectation of problems). The Chinese economy, disrupted by the government’s zero-Covid policy is not helpful. To illustrate the situation, Hodges used the image of the four horsemen of the Apocalypse: war, plague (Covid), famine (food shortages), inflation. Finally, he went on, it will take another couple of years, according to past experience, to see overvalued stock markets bottoming out. But there are new opportunities. Hodges mentioned Elizabeth Kuebler Ross and her paradigm of loss model (in relation to Covid). It shows that people react to problems from denial to anger to bargaining, then to depression and finally acceptance. The latter opens the way to eliminating the earlier pessimism. It is necessary to transform the success factors, Hodges stated. More flexibility, solution-oriented policies, innovation, being closer to customers. And less global reach, size, locationoriented. Technology today must be greener. Sustainability, in the widest sense, is the great opportunity. So the economic recovery of industry needs to focus on the new risks (including energy and demographics). Risk management is clearly among the top priorities: increase in financial debts and environmental pressures must be rapidly managed today by the plastic industry. Eventually, Hodges summed up, investing in the future to make everything more sustainable is the key to survival and the only way out. Mr Zanchi, in applauding the analysis by Paul Hodges, sought to bring a ray of hope in the bleak picture of the scenario, by first introducing what GSI, through its Saint Lawrence Foundation and SBD (Social Business Development) is successfully doing in Sierra Leone to support the population of one of the poorest areas in the world. Thanks to the education of the local young generation, support in building a model poultry farm and, recently, establishing the growing of corn and maize, SBD is attempting to create a domino effect, to bring better food and health and to instil pride in local people to develop better living standards in their own homeland. Global polyester market Zanchi then started its analysis of the global polyester market: PTA has a big overcapacity issue, and next year it will be even bigger, MEG too."},{"@ID":45, "DRINKTEC REVIEW PETplanet Insider Vol. 23 No. 12/22 www.petpla.net 32 Good discussions, high quality of visitors Drinktec appearance at four locations The conclusion drawn by MHT Mold & Hotrunner Technology AG at Drinktec was very positive. The company took the opportunity to draw attention to itself at four locations. COMPLETE RECYCLING SOLUTION - FDA Approval - Low TCO (Total Cost of Ownership) - Energy Saving - Low Loss CONTACT US TO LEARN MORE ! WWW.BO-RE-TECH.COM | +86-573-85120186 | SALES@BO-RE-TECH.COM 3HOOHWL]LQJ /LQH 663 :DVKLQJ /LQH PET BOTTLE TO BOTTLE PLANT ENGINEERING AND CUSTOMIZED SERVICE Super CleanProcess At its own stand in hall C5, the company presented the technical refinements of its newly developed OptiStack. For the first time, it has a half-split core and the entire mould cavity is composed of more identical parts than before. For the customer, this means more ease of maintenance and assembly. When converting the mould to a new preform design, only the moulding parts of the core need to be replaced. Furthermore, wear elements have been separated from contour-carrying components, making refurbishments simple and cost-effective. Directly opposite, at Netstal, visitors could also experience the new development in action. A 72-cavity mould there produced 10.5 g light CSD preforms for bottles with a volume of 0.5 l. A granulate was processed that consisted of 25 per cent chemically recycled PET. The cycle time was 5.6 seconds. The GME 30.40 thread of the trade fair preform was already designed for tethered caps, which will be mandatory in the EU from 2024. In hall B5, Sacmi’s exhibits included the Nanopitch moulds from MHT. Thanks to very narrow mould cavity distances, 144 cavities fit in a Sacmi IPS with 400 t clamping force and 128 cavities on the IPS 300. At Krones in hall B6, various joint developments in the field of lightweighting and sustainability were on display. The presence with various topics on four Drinktec stands paid off for the MHT team. Customers came with concrete projects that now need to be implemented. www.mht-ag.com"},{"@ID":5, "imprint EDITORIAL PUBLISHER Alexander Büchler, Managing Director HEAD OFFICE heidelberg business media GmbH Hubweg 15 74939 Zuzenhausen, Germany phone: +49 6221-65108-0 fax: +49 6221-65108-28 info@petpla.net EDITORIAL Kay Barton Heike Fischer Gabriele Kosmehl Michael Maruschke Ruari McCallion Anthony Withers WikiPETia. info petplanet@petpla.net MEDIA CONSULTANTS Martina Hirschmann hirschmann@petpla.net Johann Lange-Brock lange-brock@petpla.net phone: +49 6221-65108-0 fax: +49 6221-65108-28 LAYOUT AND PREPRESS EXPRIM Werbeagentur | exprim.de Matthias Gaumann READER SERVICES reader@petpla.net PRINT Chroma Druck Eine Unternehmung der Limberg-Druck GmbH Danziger Platz 6 67059 Ludwigshafen, Germany WWW www.hbmedia.net | www.petpla.net PETplanet Insider ISSN 1438-9459 is published 10 times a year. This publication is sent to qualified subscribers (1-year subscription 149 EUR, 2-year subscription 289 EUR, Young professionals’ subscription 99 EUR. Magazines will be dispatched to you by airmail). Not to be reproduced in any form without permission from the publisher. Note: The fact that product names may not be identified as trademarks is not an indication that such names are not registered trademarks. 3 PETplanet Insider Vol. 23 No. 12/22 www.petpla.net Dear readers, We wouldn’t want to deprive you of the current market situation. We think the summary from Pulse, PETplanet’s monthly price overview, speaks for itself: Lower PET price despite higher energy costs In October, the high energy costs seem to have had no influence on the PET price. According to the available information, PET currently costs around 1,360-1,400€/t. PET is therefore around 95€/t cheaper than in September. “With the high energy costs, we need a sale price of at least 1,500€/t. Otherwise, production isn’t viable,” says one producer. Besides the high energy costs, transport costs that have increased by 20% are also a major cost factor. “We are bound to contracts that we agreed last year under quite different conditions.” Numerous European PET producers are therefore trying to reduce capacities with a shutdown and save energy that way. Four European manufacturers have announced shutdowns for the autumn. Later and later deals For several months already, it has been clear that price deals for feedstocks are being made later and later. Often, at the end of the month there has only been one or even no deal for feedstocks. This situation became particularly evident in October. Asian PET in high demand PET from Asia is currently especially cheap and therefore in very high demand. Compared to September, prices have fallen again. The Asian countries are profiting from cheaper oil from Russia and lower electricity and gas prices. No wonder more and more European processors are importing the necessary quantities of PET from Asia. At 930US$/t FOB, China is by far the cheapest provider. On average, Asian PET costs around 1,000US$/t FOB. As container prices have meanwhile also fallen sharply, Asian PET producers are amongst the winners in the current situation. Recyclate prices remain at a high level Also in October, prices for recyclate have moved very little. For flakes, prices of around 1,500-1,600 €/t have been quoted. Compared to last month, regranulate currently costs a little less, around 2,500 €/t. The major retail companies, especially discounters, are turning to their own closed circulation systems. The aim is to lower the costs for recyclate and to be independent of the market. With these impressions of the current situation on the PET market, we enter the new year with the hope of improvement! We look forward to accompanying you again next year and wish you happy holidays! Yours, PETplanet Insider Team"},{"@ID":38, "36 K SHOW REVIEW PETplanet Insider Vol. 23 No. 12/22 www.petpla.net TRADE SHOWreview This was K’ 2022 The joy of the plastics and rubber industry at finally being able to exchange ideas in person on a global level again after three years characterised K’ 2022 Düsseldorf and ensured a good mood among the 3,037 exhibitors (2019: 3,300 exhibitors). The companies reported good leads and a marked willingness to invest among trade visitors, mentioning promising new customer relations and the conclusion of numerous, in part, spontaneous business deals. 176,000 trade visitors (2019: 225,000) from all continents travelled to the event in Düsseldorf. At over 70% the proportion of international guests at K’ 2022 remained at a constantly high level, say the organisers. It was especially the wealth of new technology developments that raw materials producers, machine manufacturers and plastics processors presented for implementing the circular economy, resource conservation and climate protection that interested the trade visitors. Those travelled from 157 nations to the Rhine. Next to Germany, those European countries strongly represented on the visitors’ part included the Netherlands, Italy, Turkey, France, Belgium, Poland and Spain. With 42% of visitors coming from overseas, the reach of this year’s K’ was as high as usual among the international trade audience, state Messe Düsseldorf. While visitors from the East Asian region, in particular, were less well represented than at K’ three years ago due to the currently more difficult conditions in those countries on account of quarantine regulations, numerous visitors from the USA, Brazil and India were welcomed at this year’s event. For around two thirds of all visitors polled machinery and plant construction ranked first in terms of interest. 57% and, hence 5% more than at K’ 2019, said they were interested in raw and auxiliary materials, with recyclates and bioplastics being particularly popular. For 28% semi-finished products and technical parts made of plastics and rubber were the main reason for coming (multiple responses possible). The next K’ Düsseldorf will be held from October 8 to 15, 2025. www.k-online.com Stackable jerrycans, industrial drums & returnable handled bottles Cypet Technologies Ltd. showed its latest developments in injection stretch blow moulded PET containers. Three highlights can be mentioned: PET stackable jerrycans for foodstuff and industrial packaging: an example of this is the 10 l stackable bottle with integrated handle and recess for a funnel, for Ad Blue application. Cypet showed two versions of this product, one made from virgin PET and another made from 100% rPET. Cypet has calculated that the 20 l version of this jerrycan has 50% the carbon footprint throughout its lifecycle compared to the HDPE equivalent jerrycan. Industrial PET drums of different sizes: having demonstrated live production of 120 l drums back in K’ 2019, Cypet this year displayed drums of 50 l, 80 l and 120 l used for bulk packaging of goods around the world. PET returnable water bottle with integrated rigid handle: Cypet’s new ergonomic solution for the water industry was one of the most eye-catching displays, garnering attention not only from the water industry but from all visitors. As the world progressively transitions from PC water bottles to PET water bottles, Cypet is already getting ready to offer compelling solutions that offer the best economics, ergonomics and least carbon footprint. Cypet machines can produce this bottle in 4 cavities, resulting in the highest output of any single stage ISBM machine globally. www.cypet.eu Mobile near-infrared spectroscopy for plastics identification The BASF subsidiary Trinamix demonstrated an extension to its NIR spectroscopy solution launched in 2020 that offers rapid identification of a wide range of plastic types. The mobile and battery-operated handheld device, which can ident i fy more than 30 plastics at the touch of a button when held up to them, can also flexibly distinguish between PET-A and PET-G in relation to PET as an application extension. For example, this gives recycling companies the opportunity to quickly and randomly check received goods for purity and quality during increasingly complex waste flows. “Using the associated app, the analysis is relayed to a smartphone via Bluetooth and displayed directly or stored for later retrieval”, said Business Development Manager Adrian Vogel. “More detailed information on all measurements can also be accessed via a dedicated cloud-based customer portal if required”. According to the company, the device has a battery life of 6,000 measurements, with the app compatible with common smartphone operating systems. www.trinamixsensing.com/plasticsorting Business Development Manager Adrian Vogel at the BASF trade fair stand with the compact NIR spectroscopy device. The Cypet team at their booth at K’"},{"@ID":50, "PETplanet Insider Vol. 23 No. 12/22 www.petpla.net 38 PETbottles Home + Personal Care Micellar water with activated charcoal The range of micellar waters in a wide variety of designs is steadily increasing. The latest example is a gel-like all-in-1 micellar water with activated charcoal by Garnier Skin Active, which cleanses, removes makeup and visibly reduces blackheads. The activated charcoal contained in the micellar water slightly colours it, making the air bubbles contained in the product visually recognisable, and the gel-like consistency prevents the bubbles from rising. This look is immediately noticeable on the shelf. The 400ml bottle is made of 100% recycled material and comes in a brand-typical shaped, transparent bottle with a hinged lid and snap-on function. A non-label look label on the front makes the contents perfectly visible. www.garnier.de Liquid soap with aloe vera 250 ml liquid soap with aloe vera extract is sold by the Italian discounter md under the brand name “BotaniKa” in a square, transparent bottle. The gel-like product is dispensed via a greencoloured, lockable pump dispenser. The liquid soap is free of silicone and parabens. Two labels convey the trade data. www.mdspa.it Flushing of “no planet b” The German drugstore discounter dm launched a range of particularly sustainable products under its new own brand “no planet b”. Among them is a conditioner Intense Repair with apricot kernel oil and walnut extract. These two ingredients come from upcycling high-quality product residues from food and cooking oil production. The transparent bottle is made of 100% recycled mater ial , is decorated with a sleeve label and contains 300ml of conditioner. A screw-on disc-top closure allows the rinse to be dispensed in measured doses. www.dm.de Laundry perfume in the light variant For consumers who found the scent of the previous laundry perfumes too heavy, Procter & Gamble now launched the “Lenor Light Laundry Perfume”. This variant of the fragrance-enhancing pearls, in this case “Fresh Cotton Blossom”, contains no heavy perfumes and is intended to provide mild, long-lasting freshness. The packaging is the familiar, easy-to-grip, waisted bottle made of 100% recycled material and filled with 210g. The sleeve label is placed over the cap and protects against first use. www.lenor.de"},{"@ID":1, "PETplanet Insider Vol. 23 No. 12/22 www.petpla.net 21 PETINAR by light-weighting, Recycling while using new PCR resins and Reusing by producing returnable packages. In addition, Sacmi fulfils this objective by using rPET material in different packaging applications, by developing tethered caps which enable an easier recycling of the whole package. Returning to his question of how to translate digitalisation of closure manufacturing into a real economic advantage Iacopo explained it as generating, elaborating, and profiting from data. During the presentation of a compression moulding machine (CCM) for closures, shown at Drinktec, Iacopo explained how the data is generated. Sacmi has developed a new combination of hardware and software, called SmartPack, which generates the data. The hardware and software are designed to ensure fast, precise action on the production process. These features maximise flexibility, real-time precise adjustment during production, stated Iacopo. The SmartPack focuses on four aspects of the production process: pellet insertion, the material & thermic control and finally the hydraulic system. With SmartPack it is possible to get a graphic representation of the dose of molten material inside the mould during the production process. Through this and other devices the time for pellet cut and insertion adjustment is reduced by more than 50%. Process drifts are detected very quickly so that the operator can react before a problem occurs. It is also easy to detect any wear, because of the multiple checks enable the operator to predict wear related behaviours. This has an impact on the maintenance time of the machine, which schedule is adjusted according to sensors feedback, ensuring both process consistency and the longest life of the hardware in use. The second focus point is the material control where incorrect resin is detected. An algorithm programmed by Sacmi observes the change from one resin to another in real time. If the wrong resin is in production, the system issues an alarm first, then it stops the machine. The SmartPack also supports an assisted colour change, suitable for existing receipes and if the colour is already in the hopper. Soon as the colour change is started, the system starts deriving the previous colour and model in both the CCM press and the vision inspection system, until the new requested colour is detected, to be suitable for standard production. For a powerful and long-lasting machine system, it is necessary to ensure the good health of the hydraulic parts. In this case, the SmartPack checks the physical and chemical features of the oil, which, as Iacopo mentioned, is the life-blood of the machines. In addition, the hydropneumatics accumulators precharges are continuosly so that the operator can plan corrective actions in case of a loss of pressure. Thus, a huge package of data is produced, but how is it to be evaluated? The collected data is stored in the cloud and analysed using AI. For example, a comparison of two resins can be made for a desired application: which material is better suited, which resin saves material and engineering costs as well as machine maintenance. Iacopo concluded by summarising the features of the SmartPack care maintenance program; 22% less labour time, 20% fewer spare parts needed, and 55% more production efficiency is achieved over a two-year period, according to a case study, which resulted in 20,000€ savings for the customer. www.sacmi.com The last lecture in this PETinar series dealt with a new process during the production of preforms. Mr Jordan Robertson, VP of Business Development and Marketing at StackTeck presented the new PiCool technology, an advanced post mould cooling system for PET preforms. Jordan started by explaining existing conventional post mould cooling technology: In the preform moulding industry, there are 2 main technologies used for the cooling/transfer stations. Both provide internal convective cooling by introducing a stream of air into the preform, either by blowing air in, or in a reverse manner by drawing air out. Both methods have their advantages, and both offer improvements to cycle time and preform quality. So the question is: why did StackTeck set out to develop a new method that we now call PiCool? Because, said Jordan, we recognised thermal variations. We found through thermal imaging that preforms often have significant temperature variations, both lengthwise and circumferentially about the preform. This became a limitation when trying to accelerate cycle times, as certain sections of a preforms’ surface were hotter than others. These hot areas could result in deformation issues, contact marks, or sticking to one another. We then embarked on a project to improve the cooling uniformity at the final stage of moulding. With the PiCool concept the air stream enters the preform in a spiral direction, continuously wrapping around the internal surface picking up heat, then exiting through a centre exhaust tube. The spiral trajectory of the air stream forces the air over the internal curvature of the preform (concave shape). The concave shape creates extreme turbulence of the air flow: an effective “scrubbing” of the inner surface layer of the preform takes place, this creates a uniform cooling profile both axially and circumferentially and significantly improves the heat transfer to result in a colder preform temperature. There have been tests of the PiCool system on a 96 cavity 4-stage assembly in Netstal PET-Line 4000 system (side-entry). These tests show that with less cycle time and less temperature the same temperature is achieved as standard. www.stackteck.com With this lecture we closed the series of PETinars for this year with thanks to all our speakers and participants as well as our sponsors! Finally, a reminder that the lectures as well as the presentations are available online at: https://petpla.net/2022/09/06/ review-technical-highlights-drinktec2022/?s="},{"@ID":43, "MARKET SURVEY 25 PETplanet Insider Vol. 23 No. 12/22 www.petpla.net SMI S.p.A. Via C.Ceresa, 10, 24015 San Giovanni Bianco (BG) - Italy +39 0345 40 111 www.smigroup.it Ms Daniela Dadda Marketing Department +39 0345 40.318 info@smigroup.it Automatic machines for packing plastic, metal, cardboard or glass containers; packs in fi lm only, cardboard pad + fi lm, tray only, cardboard tray + fi lm SMI designs and manufactures a wide range of fully automated machines for secondary packaging: shrinkwrappers machines; trayformers; overlapping cardboard sleeve multipackers; wrap-around casepackers and combined machines. The models available provide performances from 30 to 450 packs/minute (in triple lane), depending on the model chosen and on the type of product to pack. SMI shrink wrappers and case packers can be integrated with a SMI palletiser to form a “Packbloc” compact end-of-line system. Yes Yes Yes Yes Yes Yes Yes Yes Yes Thanks to the precise analysis of thermodynamic phenomena generated by the shrink process, SMI tunnel distributes hot air fl ows in an effi cient and homogeneous way on the pack, thus ensuring its good quality at the end of the process. Available tunnel methan heated Single lane: smallest AFW serie (10,060 x 1,774 x 2,450mm) till the bigger size SK 1200 HS (18,752.5 x 1,774 x 2,450mm) Double lane: smallest LSK 32 (9,820 x 1,974 x 2,450mm) till SK 1202 HS (18,752.5 x 1,974 x 2,450mm) 1-3 Film: 30-100 μm depending on the production speed and pack collation; cardboard: low wave corrugated cardboard blanks: 3mm thickness Depending on the machine model Manual sealing bar joins the fi lms, fi lm reels the machine is equipped with a dedicated reel truck, pneumatic blocking system and when the fi lm ends, the machine stops, adjustment of the fi lm length is electronic, equipped with a device for centering the printed fi lm provided with reference mark CE The machine automation and control are entrusted to the Sercos Fieldbus technology; intuitive user interface for quick and easy management of end-of-line palletising operations; real-time machine diagnosis and technical support further enhance the machine control features. 35-100 packs/min (according to the size of the product handled and palletisation selected) Yes Yes Yes Yes Swift and precisemovements: The central column is actuated by brushlessmotors which guarantee dynamic, reliable and precisemovements of all axes of operation; machine automation and control are entrusted to the Sercos Fieldbus technology, featuring an intuitive user interface for quick and easymanagement of end-of-line palletising operations. Genius PTF - Fastlayer Genius PTF/A - Fastlayer Genius PP/PV Robby Pal Robby Pal with Fastlayer Conventional automatic palletisers steady pallet type with innovative layer preparation Conventional automatic palletisers moving pallet type with innovative layer preparation Conventional automatic palletisers steady pallet type for empty PET containers Robotic automatic palletiser Robotic automatic palletiser with layer preparation 10min 12min 15min 15min 10min Up to 330 layers/hour Up to 700 layers/hour Up to 330 layers/hour Up to 320 layers/hour Up to 320 layers/hour Yes Yes Yes Yes Yes Yes Yes Yes Yes Yes Yes Yes Yes Yes Yes - Operational fl exibility and further reduction in change-over times - Optimisation of cycle to increase performance, with improved control of the different movements using state-of-the-art electronic solutions - Customisation of the gripping systemand layer transfer according to the product to handle - Designed to accept a variable number of product infeeds - Fully automatic system requiring limited operator intervention, operating in complete safety - Possibility to handle all main pallets on the market trouble-free, with customisable solutions - Layer preparationwith active pack orientation and arrangement with robots - Operational fl exibility and further reduction in change-over times - Optimisation of cycle to increase performance, with improved control of the different movements using state-of-the-art electronic solutions - Customisation of the gripping systemand layer transfer according to the product to handle - Designed to accept a variable number of product infeeds - Fully automatic system requiring limited operator intervention, operating in complete safety - Possibility to handle all main pallets on the market trouble-free, with customisable solutions - Layer preparationwith active pack orientation and arrangement with robots - Operational fl exibility and further reduction in change-over times - Optimisation of cycle to increase performance, with improved control of the different movements using state-of-the-art electronic solutions - Customisation of the gripping systemand layer transfer according to the product to handle vacuumhead available for wide mouth containers (i.e. jars). - Designed to accept a variable number of product infeeds - Fully automatic system requiring limited operator intervention, operating in complete safety - Possibility to handle all main pallets on the market trouble-free, with customisable solutions - Complete range to handle different types of containers and products: layer, rowandmultihead and loose product palletising systems - Flexible andmodular solutionwith reduced footprint - Customisation of the gripping systemand layer transfer according to the product to handle - Designed to accept a variable number of product infeeds - Fully automatic system requiring limited operator intervention, operating in complete safety - Possibility to handle all main pallets on themarket trouble-free, with customisable solutions - Complete range to handle different types of containers and products: layer, rowandmultihead and loose product palletising systems - Flexible andmodular solutionwith reduced footprint - Customisation of the gripping systemand layer transfer according to the product to handle - Designed to accept a variable number of product infeeds - Fully automatic system requiring limited operator intervention, operating in complete safety - Possibility to handle all main pallets on the market trouble-free, with customisable solutions - Layer preparationwith active pack orientation and arrangement with robots"},{"@ID":28, "EVENT REVIEW PETplanet Insider Vol. 23 No. 12/22 www.petpla.net 26 Company growth enters its third phase Austrian PET recycler celebrates its 15th anniversary by Kay Barton On September 23 this year, the firm PET to PET based in Müllendorf, Austria, celebrated 15 years of company and recycling history. On the occasion of the anniversary, the recycler invited guests to an open house event that took place in perfect weather. As well as tributes from the management and a trip through the company’s success story, guests from the world of politics, business and investors from the drinks industry also had their say. This was followed by a tour of the recycling plant for processing post-consumer PET bottles during which PETplanet joined in the discussions. Anniversary celebration, history and the latest news Founded in 2006 and launching its operations in 2007, no-one could have imagined the success and growth that PET to PET has managed to achieve. Since then, the company’s estate has increased fivefold, said Managing Director Christian Strasser to invited guests on a stage set up in the courtyard. The company has so far processed 325,000t of PET and consistently invested in technological and sustainable development and expanded its facilities over the years, as well as overcoming lean periods caused by the pandemic. This has been achieved largely through its own efforts as Hanno Mandl from Rauch Fruchtsäfte (Fruit Juices) pointed out given Coca-Cola HBC Austria, Egger Getränke (Drinks), the S.Spitz company and Vöslauer Mineralwasser (Mineral Water) as well as Rauch also hold shares in the company. After a downturn last year, PET to PET was able to report successful interim results, achieving new record figures for the first half of 2022: 15,131t of PET beverage bottles kept in the resource cycle, an increase of 5.3% compared to pre-pandemic level (2019: 14,329t). 30,000t of PET material are estimated by the end of the year, the equivalent of 1.2 billion PET bottles. PET to PET currently employs 81 staff on a 72,000m2 site that has a 3,300m2 production facility and a 4,050m2 warehouse. The third phase of the company’s expansion took place this year, with its estate growing by 19,000m2 in order to provide additional on-site storage capacity. The newly created area is to be equipped with a photovoltaic system with approximately 12,000m2 of panelling for providing around 15% of the required electrical energy for the company’s future production. The total investment is €30 million. Archaeological finds from a Bronze Age burial ground which were discovered by chance during the expansion were displayed publicly for the first time at the event. Bottle procurement, the state of the market, constraints and ideas for optimisation The huge global demand for highquality rPET for use in food packaging requires the secure collection and procurement of used PET bottles for recycling at a time when the market situation is anything but rosy. As Christian Strasser explained. “The strong desire for food-grade recyclates for beverage bottles is also leading to an excessive demand for collected and sorted bottles for many other applications. Consequently, we have witnessed an unprecedented price development which has led to a steady growth of procurement markets within and, to a lesser extent, outside Europe”. Strasser explained what mechanisms he believes are necessary to improve the situation. “PET beverage bottles are the only form of packaging under current EU law for which mandatory use quotas have been set. However, no prioritisation is currently envisaged that would regulate access to raw material. As a result, all applications that use PET as a material have equal access to these quotas, even if it then immediately leaves the cycle in lower-value applications. This often leads to imbalances, particularly in non-food applications. In my opinion, a structural framework needs to be put in place here. For example, new deposit systems developed in a number of European countries could help in improving both the supply and price situation which would guarantee not only higher quality but also greater quantities. The volume of returns and prioritisation in the use of beverage bottles could be fixed by lobbying brand owners and policy-makers. At the same time, it would also be possible to determine the required recyclability as part of a deposit approval system.” Another mechanism for enhancing the quality of post-consumer material would be colour purity. Leading brands such as Coca-Cola have responded and are increasingly dispensing with coloured PET bottles from their products in order to have a positive impact on the recycling loop. However, the system is to a large extent still in its infancy. Company tour with Managing Director Christian Strasser"},{"@ID":48, "PETpatents www.verpackungspatente.de PETplanet Insider Vol. 23 No. 12/22 www.petpla.net 46 A thin-walled container International Patent No. WO 2020 / 208243 A1 Applicant: Société Anonyme des Eaux Minérales d’Evian et en Abrégé, Evian-les-Bains (FR) Registration date: 10.4.2020 A specially shaped, thin-walled PET container consisting of at least 50% recycled material. The wall thickness ranges from 50-150μm. A bottle with twisted levels European Patent No. EP 3483081 B1 Applicant: Toyo Seikan Co. Ltd., Tokyo (JP) Registration date: 28.6.2017 A plastic bottle with an angular base in which various sequential levels are each twisted by 45°. A bottle with a handle International Patent No. WO 2020 / 234125 A1 Applicant: Sidel Participations, Octeville-sur-Mer (FR) Registration date: 14.5.2020 A waisted plastic bottle that has a recess into which a specially prepared handle can be inserted. A double-walled preform International Patent No. WO 2022 / 074885 A1 Applicant: Toyo Seikan Co. Ltd., Tokyo (JP) Registration date: 6.7.2021 A partly double-walled preform for creating a special exterior or optic of the outer surface that can be used in the making of a container. A disposable lid International Patent No. WO 2022 / 096047 A1 Applicant: Schropp GmbH & Co. KG, Gundelsheim (DE) Registration date: 14.10.2021 A disposable lid designed for a hot drinks container that consists of at least 60% rPET which is an improvement on PS-based lids in terms of sustainability and recycling. An improved bottle International Patent No. WO 2022 / 103992 A1 Applicant: Niagara Bottling LLC., Diamond Bar (US) Registration date: 11.11.2021 A lightweight bottle made from a specially shaped preform with reinforced grooves that are arranged in a way that makes it difficult for a bottle to be deformed during transport or storage."},{"@ID":17, "B309 internal diaMETER Non-contact internal diameter measurement for varying sized and shaped containers, from small vials to large jars, with a two-axis camera system for automated neck centralisation. COMPLETE QUALITY CONTROL SOLUTIONs Scan the QR Code to view our full range of plastic packaging inspection systems www.torus-group.com MATERIAL DISTRIBUTION FINISHED DIMENSION BOTTLE STABILITY BOTTLE CAPACITY & WEIGHT BOTTLE INTEGRITY FINISHED DIMENSION B300 Wall thickness Material thickness measurement using non-contact white light technology to provide process control and quality assurance for material distribution from the blow-moulding process. B302 THREAD, BODY, THICKNESS A combined material thickness and dimensional measurement gauge where external dimensions are made possible by intelligent and adaptive machine vision. B303 BURST Destructive burst test with automated critical pressure, expansion volume and hold-time measurement. B307 top load Destructive vertical and horizontal load test adhering to ASTM D2659. Programmable customised tests available with automated graphical and numerical reports. B304 top load, volume & weight Critical load, volume and weight testing is combined into a fast single cycle inspection system. This can process empty, filled and capped containers as well as sealed and vented test types. measurement systems"},{"@ID":47, "BOTTLE MAKING 16 PETplanet Insider Vol. 23 No. 12/22 www.petpla.net A joint project of Avalon Group and PET Technologies Inauguration of a PET water bottling plant in the midst of war Water is a real miracle without which we cannot imagine life on earth. Water is life; it is a unique combination of simple and complex. It consists of only 3 atoms - 2 hydrogen and 1 oxygen. But it still remains a mystery how they interact with each other. To begin with the period of implementation: martial law in Ukraine, turbulent times for both companies, the partial destruction of the newly built Avalon plant, the newest enterprise in Eastern Europe, equipped with modern production lines. Despite all the difficulties, the company persevered, rebuilt the premises and is now providing people with water. The Avalon plant is equipped with domestically produced equipment, in particular with PET Technologies blow moulding machines: an automatic blow moulding machine APF-6004 and semi-automatic blow moulding machine UPF-10. Avalon uses them to produce 500ml, 1 l, 2 l, and 6 l PET containers. The history of Avalon Group begins with the spring. It has been sought for a long period of time, and once finally discovered, the extracted water delighted and surprised with its naturally balanced composition and mild taste. Avalon natural water is crystal-clear, pleasant-tasting and nutritious artesian water from a spring 108m deep in the Cenomanian water horizon (Kyiv region). It is a perfect thirst-quencher, ideal for daily use. The finished product complies with national certification standards and has taste qualities that are highly prized by consumers. Consumers can choose the water they like best: still, slightly carbonated or strongly carbonated. All of it is enriched with calcium, magnesium, potassium and sodium. Avalon chose the APF-6004 to produce bottles with a volume of up to 2 l. This machine model is reliable and very easy to use, perfectly suited for a first-time user. Furthermore, according to PET Technologies, it guarantees the production of 6,000 bph. PET Technologies also brought its knowledge to bear on the design of a new bottle. The PET bottle encapsulates the idea that Avalon is an ideal form of water. It is elegant and ergonomic, attractive from the outside and convenient for the consumer. The decorative line on the walls of the bottle curves like a flowing and gurgling stream. The line that wraps around the walls of the bottle is dotted with small elements – the shagreen. It resembles the uneven surface of water, with its fast and turbulent currents. This decorative element also adds to its ease of use. PET Technologies manufactures moulds on 4- and 5-axis CNC machining centres, which allows an array of complex surface designs, - from completely flat to the most elegant curved elements. The absence of reverse osmosis during filtration preserves the original structure of Avalon water molecules, and PET Technologies blow moulding equipment gives it a perfect shape. Such symbiosis became the key to the success of the project, which successfully faced the challenge of conflict and emerged triumphant! www.pet-eu.com BOTTLE MAKING"}]}}
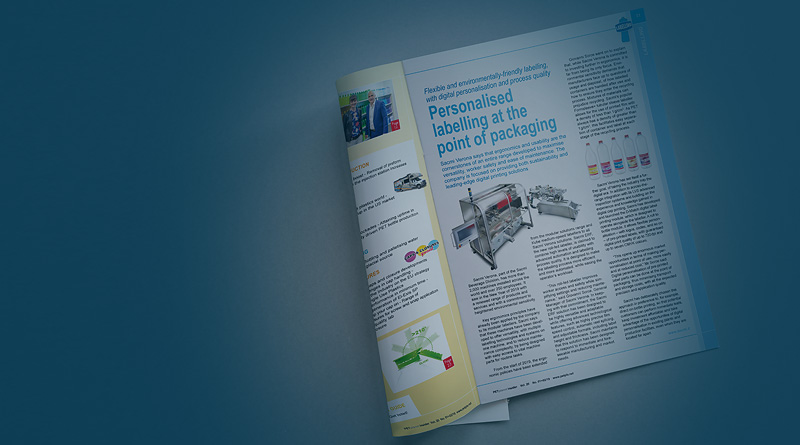