Rapid IV build-up
NGR’s LSP technology has proven itself worldwide
Austrian company Next Generation Recyclingmaschinen GmbH (NGR) has been implementing sustainable recycling systems for PET since 2014. The core of the technology is polycondensation in the liquid phase along with highly efficient decontamination, rapid IV build-up and stabilisation of the IV value. In contrast to conventional systems, such as solid state polycondensation (SSP), NGR uses P:React liquid state polycondensation (LSP), which can process up to 3,000 kg/h. The process utilises PET’s tendency to rapidly condense in the melt phase, so that the IV value increases quickly and in line with requirements.
The process begins with the PET scrap being melted in a standard extruder, such as NGR’s own P:Gran. From there it is delivered to the P:React reactor vessel, where the melt is purified and decontaminated under high vacuum with a controlled residence time. Different modular filtration technologies are used according to the degree of particle contamination. In the reactor vertical section the melt is divided into numerous individual strands, which then drop through the high-level vacuum, with an extremely high surface area exposure. The increase in surface area allows the contaminants to be quickly removed. The melt collects in the horizontal section, where it remains for up to 30 minutes. A slow rotating augur further creates surface area exposure to the vacuum, where polycondensation is completed.
An example concept of a complete solution:
Fig. 1 LSP schematic diagram
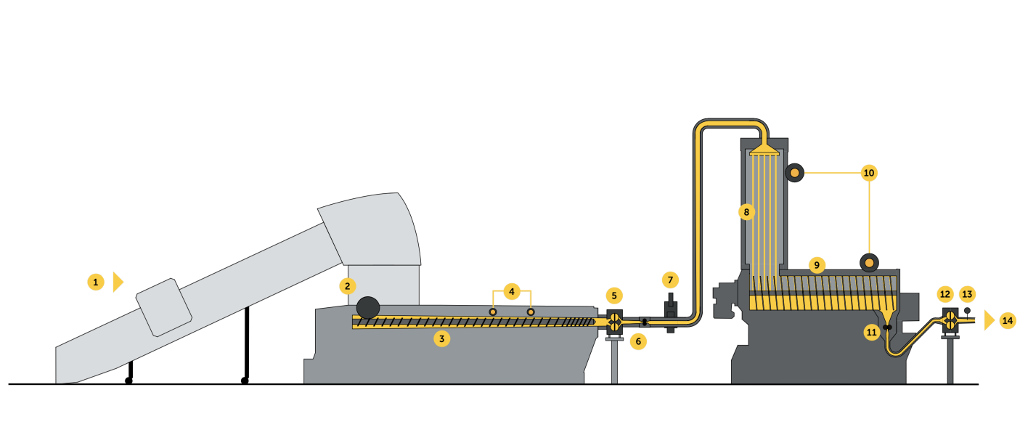
NGR’s high-level vacuum removes nearly 100% of all critical impurities found in PET waste. The filtered-out substances are collected in a redundant filter system, where they can be cleaned out without interrupting operations.
The LSP’s decontamination performance makes it open to a wider range of applications than other processes. The P:React has been successfully used in the film and fibre sector for several years already and NGR has installed several operating systems across the world for bottle-to-bottle recycling. More systems continue to being commissioned, as major beverage brand owners test, veryify and approve the LSP process for recycling post-consumer waste. LSP has also received food certifications such as FDA and EFSA. The main qualification that rPET must meet to achieve food-grade status is the extensive removal of all contaminants in a continuous process. The graph in fig. 2 shows that the decontamination levels achieved by the LSP exceed FDA requirements in all areas.
This ensures that both post-consumer and post-industrial PET waste is transformed into valuable rPET, with consistent IV value and consistent food safety, in the shortest possible time. The importance of quality and IV value of the input material is minimised as the LSP can achieve up to 30% IV increase. The entire process takes only minutes, rather than the hours required by conventional SSP methods.
Fig. 2 Decontamination performance, certified for 100% food contact
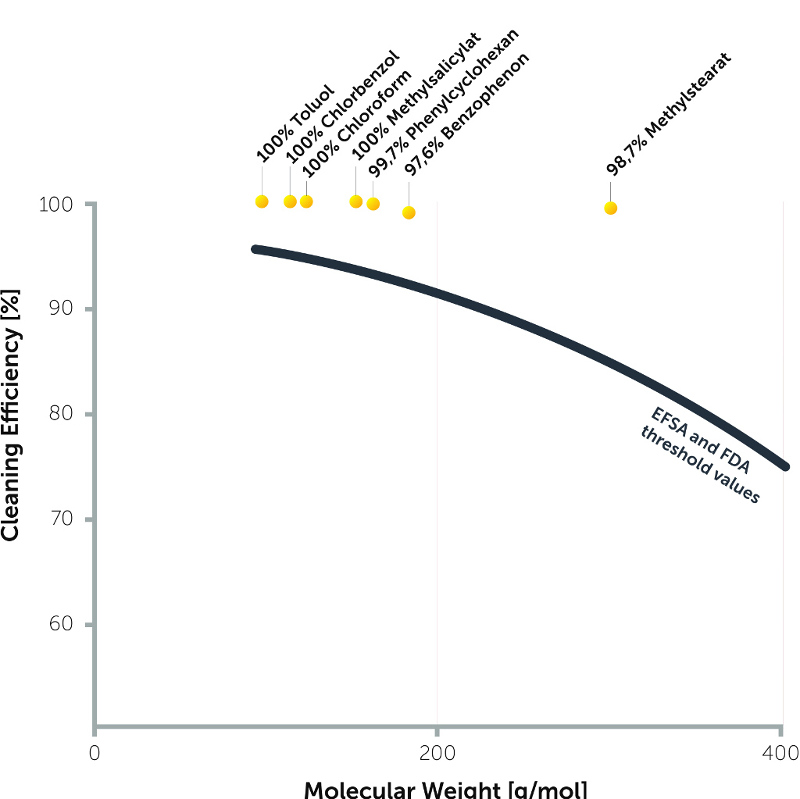
Consistent output IV and melt quality is achieved with two control parameters: 1) Vacuum pressure and 2) Residence time in the reactor. LSP production is a continuous (rather than batch) process and requires no process aids, such as nitrogen gas. Taking advantage of the energy efficiency associated with such a short residence time, while avoiding the high costs of nitrogen supply, helps to achieve very low overall operating costs. Increased demand and the sensitive price structure of input materials, such as bottle flakes, require that continuous process, along with a high flexibility in the technology. The SSP process is generally used to produce batches whose quality depends essentially on the input material. Analyses have shown that, within any given batch of post-consumer bottle flake, there is considerable variation in IV level and degree of impurity.
Since melting and decontamination happen in separate steps in the SSP process, the final IV result cannot be influenced during decontamination if the quality of the input material is not consistent. In fact, the detailed result is only known after the entire process has been completed. In contrast, P:React carries out the entire decontamination in the liquid phase, so that the control parameters described above can directly control the IV increase. If, for example, the input IV value drops, the vacuum level is automatically increased without operator intervention, keeping the output IV value very stable. This is particularly important because the IV value is first reduced in the extrusion process. The course of IV loss in the extruder, subsequent increase in the reactor and output stabilisation is shown below:
Fig. 3 IV value development
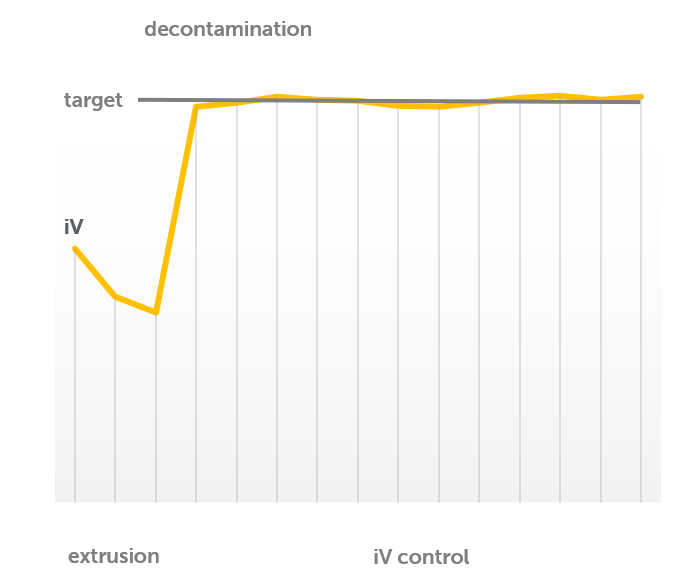
The stabilisation of IV value, which is not possible using solid state methods, allows other solutions for integrated processes. P:React has been used as upstream equipment for some time now and is directly coupled to the production of semi-finished products such as films, fibres and preforms. This results in further advantages and efficiencies on the manufacturer side. Energy-intensive heating and re-melting of rPET pellets is no longer necessary. More importantly, the recycling process does not need to overshoot IV buildup to account for subsequent IV loss in the re-melt step. As a result, the PET material is less stressed and the entire process is simplified in terms of costs and production time. A further advantage of the LSP process is its ease of use and high process stability. On the one hand, a standardised extruder without vacuum, but optionally with degassing stages, is used, and on the other hand, production interruptions do not affect the quality of the starting material. Since the vacuum is reduced when the material remains in the reactor for a longer period of time, the IV value remains constant at the desired level even during longer downtimes. In order to help operating personnel and to achieve a constant IV value, NGR has integrated an online viscometer. The measurement results are constantly reported to the plant control system. If minor deviations occur, the required control parameters are immediately adjusted to stabilise the output IV. Specifications of the input material thus take a back seat and manual intervention by operators is no longer necessary. A constant granulate quality with consistent IV value and the feeding of a constant melt specification into subsequent processes is guaranteed. It is possible to supplement the input material with additives or colour masterbatches, in order to optimise the output material. Corresponding feeding and dosing devices can be provided as an option at any time.
NGR operates a special PET pilot plant, with a fully instrumented test laboratory on site, where clients work alongside with NGR’s own experts to design their ideal process. Customers’ own material is processed in the required quantity and then subjected to a detailed properties analysis. In summary, NGR’s LSP process represents a major step in the ongoing struggle for sustainability. PET waste from both post-consumer and post-industrial resources can be reprocessed quickly and cost effectively. LSP can also be used to reprocess PET/PET-G or PET/PE composites, which have, previously, presented problematic challenges.
In today’s commercial environment, where many countries are establishing deposit and collection systems, PET reprocessing is already of special importance but it must also overcome economic hurdles and perform at high commercial levels. For this reason, numerous recycling companies and globally active producers of semi-finished products already rely on the NGR P:React series. All these companies can take advantage of the benefits for themselves and, simultaneously, reduce their CO2 footprint.
www.ngr-world.com