"BOTTLING / FILLING 24 PETplanet insider Vol. 11 No. 01+02/10 www.petpla.net Intermediatebottle storage system (IBSS) Empty bottle storage and filling line feed is a regular problem for small to medium size filling companies who need maximum flexibility. Autefa automation GmbH of Friedberg, Germany, has developed a concept intended to change the traditional method of storing empty plastic and aluminium containers for future downstream processing. Known as an Intermediate Bottle Storage System (IBSS), it is claimed to be ideally suited for on-site or “through the wall” installations where bottle production and filling are carried out on the same site. blow mould area and the filling area with lanes of tabletop conveyor running parallel to the system. (Fig. 1) If bottles are intended to go directly to the filling lines, they bypass the IBSS on the tabletop conveyors and go directly to the respective filler. If bottles are to be placed into interim storage, they are picked and placed by tray loading/unloading robots (Fig. 2) into metal trays. These filled trays, which are totally self-supporting, are stacked vertically, then automatically placed into a storage system sized to meet the customer’s inventory requirements. When the bottles are needed for downstream processing, the stacks of trays are automatically retrieved, returned to the tray loading/unloading robot systems where each tray is unloaded and the bottles placed back onto the table top conveyor for delivery to the filling lines (Fig. 3). The main components of the IBSS are: tabletop conveyors (these may be obtained from preferred suppliers and adapted by Autefa), tray loading/unloading robots and special storage trays. Fig. 1: The IBSS is placed between the blow-mould area and the filling area. Fig. 2: Tray loading/unloading robots pick and place bottles into metal trays for intermediate storage. Traditionally, bottles that are not blown using an in-line SBM machine or a synchro system are palletized and held in stock to be retrieved when required. They are depalletized and sent “through the wall” to downstream filling, capping and labelling operations. This traditional method requires significant investment in packaging supplies as well as labour and capital equipment. The Autefa IBSS Concept: The Autefa IBSS drastically changes the above mode of operation with the primary aim of reducing costs for both the bottle producer and the filler (which may well be one and the same company). The IBSS is placed between the","@ID":26} "REGIONAL MARKET REPORTS 12 PETplanet insider Vol. 11 No. 01+02/10 www.petpla.net side Germany through acquisition. “Times of crisis also offer opportunities. If we see such an opportunity we will grab it!” That was their response to the idea of possible acquisition. PET-Verpackungen sees its future opportunities arising more in semi-industrial products replacing HDPE bottles and large containers up to 20l than only in niche applications within the wine bottle sector like for airlines. Uniplast Uniplast, with about 300 preform plants around Europe must be one of the biggest converters in the region. The story of their success began in the Ukraine where we have previously visited Yuri Khmara, who is still the chief executive of the group, at the plant in Dnepropetrovsk in the days when he had just a handful of machines to his name. (see issue 11+12, 2003 and issue 8, 2005). The rapid expansion of Uniplast has not only covered the other Eastern European states but also now includes Germany, where the group has been established for some months. At the end of 2007, with a truckload of preforms being shipped to Germany every working day, the time was obviously right for the company to set up its own operation in the country. Uniplast took over the bankrupt preform manufacturer Ecopack in Merseburg, together with their three Netstal systems. After only 6 weeks the team on site had production up and running. They increased the plant’s capacity with the purchase of two Husky Hypet 400 systems, and a third Husky is due for delivery about now. “We have effectively trebled the capacity of the plant which we took over here in Merseburg in just over a year,” commented the managing director Mr. Müller. “In the production bay we planned places for 12 preform systems, so we have plenty of room for expansion. We bring with us the know-how of preform production from the Ukraine and in the Ukraine they benefit from our organisational structure”. Sales in Germany is still carried out via the Uniplast office in Berlin. The material comes from the group’s own F.l.t.r: Alexander Büchler, Oliver Wiegand, CEO, PET Verpackungen, and Hubert Rebhan, Sales Manager PET Verpackungen F.l.t.r.: Alexander Büchler Ivo Müller, Plant Manager, and Bertolt Kämpfer, Technical Manager, Uniplast Merseburg tion of standard preforms for the beverage industry and one-way bottles. In recent years the preform sector hasn’t grown so much because big bottlers have increasingly moved to moulding their own preforms in-house. The speciality sector however grew much stronger and the company became market leader in Germany for multilayer preforms. Their major customers for multilayer preforms include the juice and beer industry as well as the CSD and mineral water bottlers who appreciate the tailor-made barrier properties of the preforms in order to enter new segments. The wide range of available preforms totalling more than 70 different designs as well as the expertise and know-how to offer an optimal solution for each bottle makes PET-Verpackungen one of the major suppliers for the filling industry in Europe. One of the strength of this PET expert is the use of recycled PET. The company has its own blending facility where they mix virgin resin and recycled PET according to the customer’s requirement e.g. for PETcycle preforms they use up to 50% recycled resin. For price-sensitive customers the percentage may vary depending on the price, availability and quality of R-PET. Even flakes can be used in various mixing proportions. To extend their product range, in 2005 the company nstalled Nissei single stage and Sipa stretch blow moulding machines. PET-Verpackungen was very pleased with the versatility and quick changeover times of the linear machines and are now able to supply customers with blown bottles - especially those filling companies who do not operate their own blowing machines. As the bottle business is growing further, last year the company expanded the production area by 2;500 m2 in order to build a stronger base to satisfy the continuous needs of this sector. Today they run 15 injection moulding machines from Husky, Kortec and Netstal, producing 2 billion monolayer and 300 million multilayer preforms. The warehouse has a capacity for storing 140 million preforms, making sure that enough preforms are available on short notice even in the peak season. PET-Verpackungen has moved from only being a supplier of standard preforms to a supplier of speciality and customized preforms as well as PET containers. Although the majority of the sales are currently generated in Germany, the owners Oliver and Nikolaus Wiegand do not exclude the possibility of expanding their sales area out-","@ID":14} "BOTTLE MAKING 16 PETplanet insider Vol. 11 No. 01+02/10 www.petpla.net The first foamed PET bottle from Coca-Cola in Denmark We had already seen the first foamed PET bottle from PTI at the NPE, and at the drinktec exhibition Coca-Cola showed us the practical application that they are running in Denmark, which prompted us to go back to PTI and ask them about the current situation with regard to this new bottle. normal bottles - there is no need for the bottle blower or filler to invest in new technology. Of course the preform manufacture is rather different. Here the plasticising unit is fitted with the MuCell gas injection process so that the foam can be introduced into the preform. It is possible to produce 100% foamed bottles where up to a 5% lightweighting can be achieved, but PTI believe that the main requirement will be for 2-layer bottles. Here, unlike the classic multi-layer process, the first component is injected, then the preform is transferred to a second mould and the second component injected over the first. At Coca-Cola the inner layer is solid, as we mentioned above, and the outer layer is foamed. However the opposite can also be achieved, with a foamed inner layer and a solid outer layer. This gives the opaque bottle a very high quality gloss. Additives for specific purposes, such as colours or scavengers, can be included in the different layers. However in many cases light-blockers are unnecessary, or can be significantly reduced, because the foam already blocks 50% of the light falling on the bottle. The following practical applications may be seriously considered: CSD Here, for the first time, opaque bottles can be produced without an additive, so that they are fully recyclable. And the density can be precisely adjusted by the solid inner layer to ensure that the PET flakes can be separated from caps and labels in the sink/float process during recycling. The foamed outer layer also helps keep the beverage cool for a longer time. Foamed PET bottles for CSD: without additives and fully recyclable PET and PTI go together like peaches and cream. For more than 25 years, PTI have been paving the way from the resin to the bottle and today many of the big names in the beverage business turn to PTI when it comes to developing a new bottle. PTI’s latest development is the foamed PET bottle, suitable for all kinds of applications. PTI Vice President Frank Semersky has launched the new technology with the name oPTI. The first practical application can now be seen on the store shelves. Coca-Cola are testing the bottle on the Danish market. “For the soft drinks sector it is important that the bottle can be recycled, so despite the foam we have to watch that the density of the material is still higher than water in order that the flakes from the foamed bottle sink like ordinary flakes during the sink/float separation process,” explained Frank Semersky. “The CSD bottle has a solid core and, as a second stage, a foamed outer layer. The foam gives the bottle a silvery opaque look without the use of additives,” he continued. The stretch/blow process and the machines are the same as for","@ID":18} "PET bottle-to-bottle recycling plants After more than 100 market surveys it is now time to turn our attention to machinery used in bottle to bottle recycling. We have for a long time been deliberating on whether to explain the technique used to transform used bottles into new bottles to you. We have decided not to bother. Because, at the end of the day, you are only interested in one thing and that is what goes in (material, energy, water) and what comes out (granulate with approval). As is so often the case in practice, something that sounds very simple to start with may turn out in the end to be not quite so easy after all. Ultimately, the input variable “Material“ is, to a major extent, dependent on the local circumstances. Systems ranging in size from 5 - 40,000t/a are particularly suitable for on-site installation, and depending on the local collection systems, the input variable “Material“can be highly differentiated. However, in order to make the systems comparable, we have opted by way of input variable for materials that are freely traded. When it comes to bottles it is almost a worst-case scenario - unsorted bottles in all colours and pressed into bales, whereas with the flakes it is a matter of slightly higher quality wares, clear with only a few contaminants. Whilst PETplanet Insider has have made every effort to ensure that the information in this new survey is up to date no claims are made regarding completeness or accuracy. All data is as supplied by the manufacturers. 01+02/10 MARKETsurvey PET bottle-to-bottle recycling plants Caps and closures Conveyers for preforms and empty bottles Preforms Preform moulds and SBM moulds 2-stage SBM machinery Preform and single stage machinery Resins and additives Filling equipment Compressors Company name Erema Engineering Recycling Maschinen und Anlagen GmbH Postal address Telephone number Web site address Contact name Function Direct telephone number Fax E-Mail Unterfeldstr. 3 A-4052 Ansfelden, Austria www.erema.at Christoph Wöss Vacurema Product Manager +43 732 3190-352 +43 732 3190-23 ch.woess@erema.at Bottle to Granulate cooporation with different wash plant manufacturers Input variable: collected pressed bottles, various colours Output: Granulate with approval Capacity [t/a] Floor space [m²] Which approvals Fresh water consumption per tonne output [m³/t] Consumption kWh per tonne output [kWh/t] Flakes to Granulate Vacurema - 3 models: Basic, Advanced, Prime Input variable: Flakes, coloured proportion max 5%, not much chlorine Basic flakes specification see below - Principle: Higher contamination levels are basically possible to process, after discussion and agreed by Erema, but could influence the quality of the pellet. Moisture max. [%] 0,7; Moisture variation [%/hr] +/- 0.1; Bulk density [kg/m³] 300 – 500; Bulk density variation [kg/m³/hr] +/- 50; Material Temp [°C] 15 – 50; Material temp. variation [°C/hr] +/- 5; Polymer density (amorphous) [kg/m³] 1,350 appr.; PET type Homopolymer; DSC Melting point [°C] 252 – 255; DSC onset for melting point [°C] 215; In case of Co-Polymers presence, the elements used for substitution like IPA, DEG or CHDM must be verified and its impact on processing has to be evaluated; PVC max. [ppm] 10; Glue max [ppm] 20; Aluminium max [ppm] 25; HDPE, PP max [ppm] 25; Total Polymer foreign particles total [ppm] 80; Coloured PET Flakes max [ppm] 50; PET dust max [%] 1 Output: Granulate with approval FDA, efsa (pending), Anvisa, ilsi, BGBI, and also from brand owners Capacity [t/a] up to 20,000 Floor space [m²] depending on throughput and technology type between 8 - 200 Which approvals FDA [cat. C-H]; some brand owners (conf.); some national approvals (Austria, CH, Zona Mercursur, etc.) Fresh water consumption per tonne output [m³/t] depending on application and technology type / closed loop system. Consumption kWh per tonne output [kWh/t] between 250 - 350 Bottles to Flakes MPR (Multi Purpose Reactor) Input variable: collected pressed bottles, various colours same as Flakes to Granulate Output: Flakes with/without approval FDA, efsa (pending) Capacity [t/a] up to 15,000 Floor space [m²] between 20-40 Which approvals FDA, efsa (pending) Fresh water consumption per tonne output [m³/t] Closed loop system Consumption kWh per tonne output [kWh/t] 100 Miscellaneous Company also offers systems for Bottle-to-film Vacurema Inline Sheet Bottle-to-fibre Vacurema Inline Fibre Bottle-to-strapping Vacurema Inline Strapping","@ID":19} "BOTTLING / FILLING 22 PETplanet insider Vol. 11 No. 01+02/10 www.petpla.net Jaipuria, Pearl Dinks, PepsiCo licensee “Let’s grow together” Interview with Mr Jaipuria regional brands are even further down. So we don’t regard Bisleri as a competitor. PETplanet: You nevertheless supply Bisleri with the same preforms that you use for Aquafina. Mr. Jaipuria: That’s right. We see from a production point of view that in India certain preform sizes are used by all of the fillers, such as the 22g for 1l water and the 25.5g for 0.5l CSD. PETplanet: But how do you manage to supply your customers in the high season? Do you give preference to your own factories? Mr. Jaipuria: If we did that we would not be where we are today with our preform business. We supply our regular clients, most of whom are in the north of India, with the preforms they need, even during the high season. We slow down deliveries to our own filling plants in the south and buy locally. So far the business and the logistics have worked out well. PETplanet: And what plans do you have for the future? Mr. Jaipuria: First of all we want to introduce new flavours onto the market. We see significant organic growth available here in India. In addition we are thinking seriously about setting up our own mango pulp plant. We don’t see any need to expand outside India for the moment, and in any case we want to increase our sales here to over 200 million US Dollars by 2012. This will mean that we are of a size that is of interest to the stock market. PETplanet: Many thanks Mr Jaipuria! PETplanet: Mr. Jaipuria, what do you have in mind with the motto “Let´grow together”? Mr. Jaipuria: Over the last three years we have grown by 20 to 25% per annum and this with Pepsi alone. We have now successfully launched mango juice and lemon juice in hot-fill PET, and it is here that we see huge growth potential in India alongside the classic CSDs and water, so our motto should prove justified over the next few years. C.K. Jaipuria Chairman, Jaipuria Group, New Delhi; sitting in the centre, and his son (right) are proud of 20- 25 % growth per annum over the last three years. Left: Viijay Walia, Deputy General Manager and Alexander Büchler. PETplanet: What percentage of your filling is done in PET? Mr. Jaipuria: At the moment about 50% glass and 50% PET. But I think that with the increasing distances between our filling plants PET will take a bigger share - say 60%. Glass bottles will continue to hold a strong position here in India. PETplanet: At Jammu you have built an ultra-modern preform line on the site of your filling line. You nevertheless therefore presumably see a strong demand for PET. Mr. Jaipuria: Certainly, it’s not a small plant. But we also produce preforms there that, in addition to our own needs, we have been supplying to other filling companies for a few years now. PETplanet: Mr. Walia introduced me yesterday to your customer Bisleri – theirs is the biggest water brand in the country. But don’t you compete with them with your Aquafina water brand? Mr. Jaipuria: PepsiCo, with all of its products, positions itself in the upper price sector. Bisleri, as a national brand, is positioned somewhere below this level, and the All good things come in t(h)rees! Alexander Büchler is planting his third tree in India (see issue 3/06), this time at the Jaipuria plant in Jammu. And there are most certainly more to come.","@ID":24} "NEWS 9 PETplanet insider Vol. 11 No. 01+02/10 www.petpla.net The brighter future for PET recycling? Post-consumer recycling of PET containers is gaining momentum. As the industry looks increasingly towards the opportunities for a cradle-to-cradle system, where containers are recycled back into new PET containers rather into other PET products, we need to consider the long-term effects of multiple recycling of the PET on the quality of final container aesthetics. Increasing volumes of containers entering the recycling stream already contain significant proportions of recycled material. The result of this current “success” in recycling is, however, likely to have a negative impact on the long term aesthetic quality of PET containers as the quality of the resin potentially deteriorates with each recycling trip. Consider also, that a large percentage of preform production contains faster reheat resin (for example for carbonated soft drinks), which can further compromise container aesthetics. Taking a common scenario, the first time that a container is recycled it could typically contain up to 30% recyclate. Through multi-trip processing a proportion of the recyclate will have gone through one or more process histories. Through multiple cycles it can become increasingly difficult to maintain good aesthetics of recycled containers. In order to withstand the rigours of multi-trip processing, PET resin will need to become more robust so that when it re-enters the recycling stream at each stage it is as “clean” as it possibly can be. Research into improving PET process capability through the recycling stream has developed a number of potential solutions to this problem. By improving the capability of reheat technology in PET preform processing, researchers at a colorant and additive dispersion specialist (a Petcore member) believe this issue can be overcome. Although reheat capability can be taken to extremes to create perfectly clear preforms, a balance needs to be struck between achieving an economically viable reheat process and optimised container aesthetics. This new reheat technology incorporates a high performance IR absorption component that has been shown to achieve greater reheat capability compared to currently available technologies whilst at the same time demonstrating a masking effect on any potential resin yellowing that may occur after multi-processing. The technology has by its very nature an inherent blue toning quality which results in a clear, bright container. This counteracts any yellowing that can cause a hazy effect in the final container and ultimately yields a higher quality recycled material. In studies through five process histories the reheat technology has been shown to maintain 100% of its IR absorption. In PET container recycling at least, moving towards cradleto-cradle “reincarnation” now appears to be a step closer to becoming a realistic solution for the future. Many Petcore members are investing in technology development to allow brand owners to package their products in recycled-content containers to give maximum shelf life and attractive aesthetics. Their ultimate aim is to produce PET recyclate of the best possible quality from existing bottle collection. A positive contribution from a sustainable industry. P E T C O R E C O L U M N","@ID":11} "MARKET SURVEY MARKETsurvey 01+02/10 Company name Zhejiang Boretech Co., Ltd. Sorema div. of Previero N.srl Krones AG Gneuss Kunststofftechnik GmbH Postal address Telephone number Web site address Contact name Function Direct telephone number Fax E-Mail 19K-1,07 Province Road, Pinghu Economic Development Zone, Pinghu City, Zhejiang, China www.bo-re-tech.com Alan Ou Sales Manager +86-573-85120186 +86-573-85113959 alanou@bo-re-tech.com Via per Cavolto 17, 22040 Anzano del Parco (Co) - Italy www.sorema.it - www.previero.it Mr Dario Previero Sales Manager +39 031 63491250 +39 031 63491217 sales @sorema.it Böhmerwaldstraße 5 93073 Neutraubling, Germany www.krones.com Peter Hartel Sales Dept. PET-Recycling + 49 9401 70-5448 + 49 9401 70-91-5448 Peter.Hartel@krones.com Moenichhusen 42, 32549 Bad Oeynhausen www.gneuss.com Dr. Axel Hannemann +49 5731 5307-0 gneuss@gneuss.com Bottle to Granulate Input variable: collected pressed bottles, various colours yes Output: Granulate with approval Capacity [t/a] 3,400t/a + 6,800t/a Floor space [m²] 800 - 1200m² Which approvals FDA - LNO Fresh water consumption per tonne output [m³/t] Consumption kWh per tonne output [kWh/t] Flakes to Granulate Input variable: Flakes, coloured proportion max 5%, not much chlorine cooperation with approved company for \"flakes to granulate\" yes yes Output: Granulate with approval yes Questions: Capacity [t/a] 3,400t/a + 6,800t/a up to 2,000kg/h Floor space [m²] 800 - 1,000m² 200 Which approvals FDA - LNO FDA Fresh water consumption per tonne output [m³/t] - Consumption kWh per tonne output [kWh/t] 400-800 Bottles to Flakes Input variable: collected pressed bottles, various colours Input variable: collected pressed PET/ HDPE bottles, various colours Output: Flakes with/without approval Output: High quality flakes for direct use in all main applications. Flakes are not food grade approved. with/without approval Capacity [t/a] 0.5~3 t/h Capacity[t/a]: (INPUT) From 3.000 to 40.000 3,400 t/a + 6,800 t/a with approval - 17,000 t/a without approval Floor space [m²] 700~1,200m2 Floor space [m²]: according to the lay out 600 - 1200m² Which approvals Which approvals: ? FDA - LNO Fresh water consumption per tonne output [m³/t] 2 Fresh water consumption per tonne output [m³/t] & Consumption kWh per tonne output [kWh/t]: Consumption kWh per tonne output [kWh/t] 100 Miscellaneous Capability to offer complete systems from bottle to flakes with closed loop water treatment Company also offers systems for Bottle-to-film yes yes Bottle-to-fibre yes yes Bottle-to-strapping yes yes","@ID":20} "imprint EDITORIAL 3 PETplanet insider Vol. 11 No. 01+02/10 www.petpla.net PUBLISHER Alexander Büchler, Managing Director HEAD OFFICE heidelberg business media GmbH Landhausstr. 4 69115 Heidelberg, Germany phone: +49(0)6221-65108-0 fax: +49(0)6221-65108-28 info@hbmedia.net EDITORIAL Doris Fischer fischer@hbmedia.net Ruari McCallion Tony O´Neill Ilona Trotter Wolfgang von Schroeter MEDIA CONSULTANTS Ute Andrä andrae@hbmedia.net Miriam Kiesler kiesler@hbmedia.net phone: +49(0)6221-65108-0 fax: +49(0)6221-65108-28 France, Italy, Spain, UK Elisabeth Maria Köpke phone: +49(0)6201-878925 fax: +49(0)6201-878926 koepke@hbmedia.net LAYOUT AND PREPRESS EXPRIM Kommunikationsdesign www.exprim.de PRINT WDW Druck GmbH Gustav-Throm-Straße 1 69181 Leimen-St.Ilgen Germany WWW www.petpla.net | www.pet-point.net PETplanet insider ISSN 1438-9459 is published 10 times a year. This publication is sent to qualified subscribers (1-year subscription 149 EUR, 2-year subscription 289 EUR, Young professionals’ subscription 99 EUR. Magazines will be dispatched to you by airmail). Not to be reproduced in any form without permission from the publisher. Note: The fact that product names may not be identified as trade marks is not an indication that such names are not registered trademarks. EDITORIAL dear readers, For ten years now you have been turning to the centre pages of each individual issue for the market overviews. For each sector we always try to identify the generally applicable characteristics that spell out the performance capability of the different systems so that you, as users, can compare one with the other. At the same time we are well aware that any system will only deliver its best once it has been fine-tuned to take account of the conditions on site, the raw materials available and the quality required. Such detailed information would be impossible in the context of a market overview. And, although we have now been producing them ever since our first issue, we are consistently finding it a challenge to compile a new market overview for each issue. It continues to be a relatively simple matter to put together a list of all the manufacturers for the corresponding machines. But not all reply or, if they do reply, their responses tend to be incomplete. We engage in a follow-up and try to find out why the companies are not cooperating or why there is something missing from their responses. It can’t be money because, by way of company policy, we will not on principle accept money for editorial reporting. One excuse that we often hear is that the technical data required is not available or, if it is available, it is not intended for the public domain. If, in due course, we update the market overview relating to a specific subject, talks with the machine manufacturers begin to flag. The companies acknowledge how important it is that they present their product range to you, our readers, together with the relevant performance characteristics. In this issue we have for the first time included the topic of Recycling Plants. And, just like in the other sectors, we have found that some of the manufacturers are not prepared to give detailed information or even to make any information available at all. In the final instance it is the market – and that means you yourselves – who must decide whether you will bear these companies in mind or not when it comes to awarding tenders. What we asked for was standard information. Anyone who is unable to supply this has no understanding of the recycling business; anyone who shies away from a direct comparison can only be offering systems that are considerably inferior to that offered by the competition. In my opinion, any other reasons are nothing but phoney. Let’s look forward to the next market overview in 2 years’ time and hope that the manufacturers of recycling machinery, along with their colleagues from the other PET sectors, will make up their minds to face up to competition. Yours, Alexander Büchler","@ID":5} "BOTTLING / FILLING 25 PETplanet insider Vol. 11 No. 01+02/10 www.petpla.net System Advantages: The primary goal of the IBSS is cost reduction with a secondary goal of improved quality control. Savings can be realized in the following areas: No storage materials: no pallets, layer sheets, top frames, strapping, stretch wrapping or labelling. Savings on capital equipment: no depalletizers, unscramblers, bins, strappers, stretch wrappers, labellers or fork trucks are required. Capital investment is of course necessary to buy the IBSS but this is a one-off cost and typically has a 2-3 year payback. Labour saving: The IBSS is designed such that there are no designated, full time operators required. Typically, an existing operator in an area close to the IBSS is assigned to oversee the system in case an alarm condition requires operator intervention. Quality: Suspect bottles or production lots can be identified, segregated and controlled thus preventing inferior quality production from being shipped. Flexibility: The system can be designed to have total flexibility between the blow moulders and filling lines. Any blow moulder output can be diverted to any filling line on short notice. Freight savings: The system is ideally suited for on-site and “through the wall” applications. Companies that had been purchasing bottles from off site suppliers and trucking pallets to the filler have elected to produce bottles on site utilizing the Autefa IBSS. Freight and handling costs have been eliminated. The Autefa IBSS is a patented, proven system currently in service in Europe and the United States. The design and fabrication of the system is based on a modular concept thus the IBSS can be expanded as requirements change. For smaller operations a small scale system can be installed and as the business grows, additional components can be added and integrated into the system. Fig. 3: The tray storage system is sized to meet the customer’s requirements. EREMA Engineering Recycling Maschinen und Anlagen Ges.m.b.H. Freindorf · Unterfeldstr. 3 · P.O.B. 38 · A-4052 Ansfelden/Linz · Austria Phone (43)732/3190-0 · Fax (43)732/3190-23 · erema@erema.at We know how. www.erema.at VACUREMA PRIME Up to 10% IV increase without energy intensive classic SSP process FDA approved, ILSI-conform Very low total energy consumption from 0,25Kw/kg pellet only More than 100 plants delivered worldwide YOUR MOST ECONOMIC WAY TO HIGH QUALITY BTB REGRANULATE PET BOTTLE RECYCLING BY VACUREMA","@ID":27} "REGIONAL MARKET REPORTS 10 PETplanet insider Vol. 11 No. 01+02/10 www.petpla.net Part 3 Germany The interviews and reports from the sector now follow in Part III of our Regional Market report Germany. As already stated in Parts 1 and II, it is practically impossible to get anything official out of the bottlers for the big discounters. So I am all the more delighted that the suppliers and a few brand name bottlers have agreed to make themselves available for a Q and A session. On the supplier guilds side, we have Alpla, PET Verpackungen, Uniplast and Bericap for you, whilst, as regards the bottlers, we shall be reporting on Romina, Hansa Heemann, Coca-Cola and Eckes Granini in issue 3. by Alexander Büchler Alpla For a report on Germany it is perhaps rather interesting to look at the market from the point of view of an outsider. We visited Alpla in Austria and asked the people there how they, as a company located outside the country, viewed Germany. We were able to talk to specialists from each of the key areas in the company - namely Sabrina Gerbault who covers dairy products, Rolf Jötten who covers soft drinks, Thomas Findeis who is the factory manager at Hard, and Rolf Hutz who looks after the closures business. In total Alpla have 8 factories in Germany and preforms are moulded at Kaiserslautern, Baesweiler, Berlin, VlothoExter and Lübeck. Alpla has actually been in Germany with several plants for 46 years - well before the arrival of PET - mainly with extrusion blow moulded HDPE containers. This finely tuned regional structure allowed Alpla, 15 years ago, to quickly take a share of the booming PET market across a wide geographical area. At that time Alpla had to make a key decision - whether to go for the single trip bottle or the returnable bottle business. A high percentage of the bottles required at that time were refillable bottles for Coca-Cola and the German mineral water association. Nevertheless the company proprietors, Lehner, decided to go full out for single trip business, including PETcycle. Today the company still supplies small Regional market reports Germany Part 3","@ID":12} "NEWS 8 PETplanet insider Vol. 11 No. 01+02/10 www.petpla.net New Mocon-certified testing opens in Mumbai, India Mocon, Inc. has partnered with Hemetek Techno Instruments of Mumbai, India to establish a certified test laboratory. Officially opened in January 2010, it is the first independent Mocon-certified site in the world. It will be providing barrier and headspace analysis, leak detection and burst testing for food, beverage and pharmaceutical/medical packaging. The Mumbai lab will be offering a two-day permeation/ packaging training program for people wishing to gain supervised experience on state-of-the-art Mocon testing equipment. The Mocon-certified lab will be able to provide results faster than Indian companies’ traditional testing institutions, helping companies cut development time and improve speed-to-market. The new lab provides a ‘test drive’ opportunity for companies considering buying Mocon testing equipment. New PET Engineering Vostok manager Italian company PET Engineering Srl has appointed Mrs. Yulia Valishina to the position of General Manager of PET Engineering Vostok, the company’s subsidiary in Moscow, Russia. She replaces Mr. Gianfranco Zoccatelli. Mrs. Valishina has held a number of positions in leading beverage industry companies, including almost 7 years as Area Service Manager for Russia and CIS at SIG Corpoplast Russia. Sustainable production of PET bottles Aachen University institute and industry partners research energy and resource efficiency Experts from different points along the chain have come together to establish a research project that is seeking to improve energy usage, sustainability and resource efficiency of stretch blow moulding PET bottle production. The project is especially tailored to small and medium-sized companies and is being financed with funds from the Federal Ministry of Education and Research (BMBF) in Germany. It is supervised by the Forschungszentrum Karlsruhe (PTKA); responsibility for coordinating the research activities and providing scientific supervision lies with the Institut für Kunststoffverarbeitung (IKV) at RWTH Aachen University. The IKV is also supporting the project through the consistent simulation of all the different process stages. Investigations are focused on a detailed analysis of the energy balance of the stretch blow moulding process. Methods are then developed for assessing the efficiency of industrial stretch blow moulding machines and components. Different approaches are being assessed to increasing the energy efficiency of the heating process and to increasing the resource and energy efficiency of the forming operation. Industrial partners are stretch blow moulding machine manufacturer KHS Corpoplast, Hamburg; AdPhos Innovative Technologies; and Bruckmühl-Heufeld, which specialises in thermal processes. Findings are sent to Okertaler Mineralbrunnen, Goslar (Weydringer Group), which adds application technology expertise. Results are implemented on an industrial stretch blow moulding machine, which produces alcohol-free beverages, and evaluated for energy utilisation. PET+ Drink Tech Asia 2010 with Pack Tech Asia The fourth PET+Drink Tech Asia international exhibition and seminar will be running from 27-29 August 2010 at Chennai Trade & Convention Centre, Tamil Nadu, India. It will showcase a wide spectrum of products in the PET drink and packaging related sectors. Exhibitors will include manufacturers and distributors of PET injection and stretch blow moulding machines; sheet extruding machines; recycling, washing and label separator equipment; refrigeration and ventilations technology; sterilisation systems; water treatment and automation and packaging technology. Visitors to the third edition, held in Mumbai in October 2009, included CEOs and heads of research involved in PET products and technologies; drinks industries; edible oils and spices; processed food; pharmaceuticals, cosmetics and chemicals. Pack Tech Asia 2010 which showcases developments, machinery and technologies in packaging, will run concurrenty with the PET+Drink Tech exhibition. Chinaplas 2010 Chinaplas 2010 will take place at Expo Centre, Pudong, Shanghai, P.R. China from April 19-22, 2010, integrating advanced technology into everyday life and accelerating development of plastics and rubber. The 24th International Exhibition of Plastics and Rubber Industries will showcase leading sourcing platforms and introduce innovative applications of plastics and rubber technologies for various industrial sectors. CHINAPLAS will host a series of concurrent activities under the theme of ‘Green Plastics – Our Goal; Our Future’. These will focus on how the 3Rs (Reduce, Reuse, Recycle) can be adopted to current and future plastics and rubber industries. An industrial forum on Green Technology will be held on the first three days. 1,900 exhibitors from 35 countries and regions, including 10 country/region pavilions, will welcome an expected 75,000 professional visitors from China and worldwide. www.chinaplasonline.com New Husky facility in India Groundwork has begun on a new facility in Chennai, India, for Husky Injection Molding Systems. When it is finished, the 3,300 square meter (35,520 sq ft) facility will accommodate sales, customer support, manufacturing and sourcing teams. It is intended to support Husky’s growing business in the region by providing local hot runner and mould refurbishing, to reduce lead times. Husky first entered the Indian market in 1999 and its local office was opened in 2001. The Chennai facility is expected to be operational within one year. Other recent investments in new markets include a larger technical centre in Yokohama, Japan, expansion of the technical centre in Shanghai, China and the establishment of a new PET and hot runner refurbishing centre in Moscow, Russia.","@ID":10} "PRODUCTS 27 PETplanet insider Vol. 11 No. 01+02/10 www.petpla.net PETproducts New energy-efficient grinders Die CentriCut grinders from Nuga AG of Switzerland, already claiming less energy consumption than many conventional grinders, now make the grinding of plastic residue and production rejects even more economical as the lifetime of the wear parts has been extended. Depending on the planned application the company selects the most appropriate materials and coatings for vulnerable wear parts to ensure maximum operational lifetime and user economy. Non-drip drinking system Menshen Innovations introduced the Sip’Core drinking system at drinktec 2009. Designed by Florian Wiplinger, the full Sip’Core system consists of a mouthpiece with protective cap, an adapter and non-split tube, a mount with spike for safe, non-spill closure opening and a pouch for liquids with assembly-part tube and nonspill valve. It can be attached to a pouch or bottle, with or without the tube. The one-way drinking system is light, can be operated hands-free and keeps liquids from exposure to air. It is designed for travellers, sports activities and for people with limited mobility (including geriatric patients), among other uses. Raised internal pressure will not cause spillage; liquid is released by external suction. www.menshen.com Natural tea infusions Wild, of Heidelberg-Eppelheim, Germany, a leading ingredients producer for the beverage industry, has developed new infusion-based concepts to meet the growing demand in Europe for RTD teas. According to the market research firm Canadean, the “ready-to-drink tea” category grew at an average of 9% per year between 2000 and 2008. The latest addition from Wild is an infusion based on rooibos (South African redbush tea), which will allow beverage producers to appeal to a broader target group. The rooibos plant is known to contain no caffeine, which makes rooibos-based drinks perfect natural thirst-quenchers for children. White and green tea drinks are among the most successful tea products in Western Europe and consumers perceive both varieties, as well as rooibos, as premium wellness products which, unlike iced tea, are not seasonal beverages. Volumetric filling system AMS Ferrari, of Modena, Italy, have developed a volumetric filler/capper system. The 52-valve Infinity system uses a Windows-based PC control for entering required capacity into the machine and shows three fills at once, to aid in monitoring and fault-finding. It is supplied from a pressurised tank, with electronic monitor, along a single pipe to the volumetric fillers. A second pipe controls the pneumatic valve opening and shutting. It is capable of handling a range of hot or cold fill beverages and liquids, from low-density water to highdensity products such as tomato sauce, ketchup and fruit preserves, as well as detergents and delicate fluids like milk. It is designed to respond automatically to changes in temperature and viscosity. www.amsferrari.it","@ID":29} "6 PETplanet insider Vol. 11 No. 01+02/10 www.petpla.net PETnews Coca-Cola Brazil PET Optimisation Brazil is one of the biggest markets for Coca-Cola and non-returnable PET is the most important package, by sales volume. An optimisation plan, implemented in 2008 in Brazil, is being rolled out in neighbouring countries, particularly Brazil’s Mercosur free trade area neighbour countries of Argentina, Paraguay and Uruguay. The project is led by Coca-Cola Brazil packaging team as part of a supply chain efficiency program. The strategy is based on standard preform families, which were developed in collaboration with Husky and preform suppliers Amcor, Alpla, Cristalpet and Engepack. A platform of seven moulds now delivers 34 different preforms for a wide range of applications, from Contour 250ml up to 3l, for both still and carbonated beverages. All the preform bottle applications feature high stretch ratios, which enable lightweighting without compromising CO 2 retention and shelf life. The Contour 600ml bottle, for example, has been reduced from 28 to 20.6 , while still achieving approval under CocaCola’s standard quality process. Blow moulding capability has been modified in order to guarantee optimised wall thickness distribution and high PET crystallisation index. Implementation of the comprehensive optimisation programme is now being accelerated. The objective is to achieve lightweight options for all bottle families; 90% conversion to PC 1881 short height by December 2010; accelerated approval process through standardisation; cost reduction through supply chain and preform conversion efficiency; and reduction in environmental impact. Standardisation on just seven moulds will enable preform suppliers to invest in new generation high cavitation injection moulding machines. Asia helps bottled water ride global economic storm The Global Bottled Water Report from beverage industry intelligence specialists Canadean Ltd suggests that final year figures for 2009 may see expansion in the worldwide market for bottled water increase of just around 2%. North America (18% of the global market) fell from double-digit growth in 2007 to decline in 2008. Western Europe (nearly 30% of global) is also expected to show a decline in final figures for 2009, led by a slump in onpremise sales in Spain and broader downturns in France. Canadean’s Quarterly Beverage Tracker indicates that bottled water sales in China jumped by 18% in Q3 2009. Opportunities for expansion remain in Asia, where economies have continued to grow and per capita consumption is 40% of global average. The water market is expected to see growth rate of 5% after 2009, compared with 7% seen in 2007 and 9.5% in 2006. It anticipates every region in the world to be registering water growth in 2010. Simei-Enovitis holds up well despite recession With 51,545 qualified visitors to Simei (International Oenological and Bottling Equipment Exhibition) and Enovitis (International Vine and Olive Growing Technics Exhibition), held in Milan from November 24-29, 2009, the event compared well with the 2007 edition. Enovitis actually saw an increase in total visitor numbers. The number of foreign visitors was also stable, with the total of foreign delegations up 80%. This increase reflected intensive promotion activities carried out by the exhibitions’ organization secretariat in co-operation with ICE (Italian Trade Commission) and Promos (special Agency of the Milan Chamber of Commerce for international activities). Delegations came from a number of central and eastern European countries; from Russia and Kazakhstan; and from South Africa, the Americas, SE Asia, and the Middle East. Journalist representation, Italian and international, was up 50%. Sidel joins Napcor Sidel has joined Napcor (National Association for PET Container Resources), which is the trade association of the PET plastic industry in the United States and Canada. Its membership includes about 50 companies involved in different stages of the PET container life cycle, from preform manufacturers to packaging equipment makers, food and beverage companies and recycling operators. Among the issues that Napcor has been promoting for over 20 years are the use and recycling of PET packaging and communication of the attributes of PET as an environmentally sustainable material. Sidel says that Napcor membership will help the Group enhance its dialogue with other companies. “Sidel is committed to sustainability innovation and to making PET recycling easier, through both the design of its equipment and the design of packages,” said Luc Desoutter, Sustainability Manager for Sidel.","@ID":8} "NEWS 7 PETplanet insider Vol. 11 No. 01+02/10 www.petpla.net Eastman sues Indorama over Integrex PET manufacturing technology Eastman Chemical Company, headquartered in Kingsport, Tenn., USA, filed a lawsuit in December 2009 against Indorama companies located in the United States, Europe, and Thailand, which alleges unauthorised use of Eastman’s IntegRex PET manufacturing technology. In its announcement, Eastman said that it will “vigorously defend these intellectual property assets”. The patent infringement claims relate to PET manufacturing technology and Indorama’s alleged unauthorised disclosure and use of information covered by a license agreement between Eastman and several European Indorama entities. Beer market keeps growing despite downturn The global beer market has continued to grow despite upheavals in the world’s financial markets in 2008, according to a report from beverage research agency Canadean. However, the rate of growth slowed from 6% in 2007 to 2% in 2008. The report anticipates that 2009 results will show continuing slowdown, before demand begins to accelerate in 2010. Asia saw volumes increase 5% in 2008 and now accounts for around 1/3 of all beer sales. China accounts for 70% of all sales in the region and grew by 6%. Latin America saw sales up 3%, led by Brazil (4%). Western Europe has not seen growth since 2006; the Russian market saw its first decline in a decade, with sales anticipated to get worse. The picture in Europe is expected to be similar. The North American market is virtually flat. The fastest growth in the world has been in North Africa/Middle East but this market accounts for less than 1% of global sales. www.canadean.com Sports cap with optimised flow, wet and dry decontamination Cap manufacturer Bericap has started production of its new ‘Next Generation’ Push Pull sports cap, for launch to the marketing Q1 2010. The first version available will be for PCO1810 standard necks; PCO1881 and 38mm necks will follow. It conforms to all requirements for aseptic filling of beverages and is suitable for both wet and dry decontamination. Bericap describes the new product as suitable for ‘on the go’ consumption, combining attractive design with technical developments designed to provide the consumer with optimum flow rate, but without the need for complex treatment of the closure during the filling and closing process. It features Bericap’s DoubleSeal technology, already established in the company’s standard 28mm neck PCO1881 and PCO1810 closures, which do not use aluminium seals. The 3-piece cap is suitable for both still and medium carbonated drinks.","@ID":9} "MATERIAL / RECYCLING 14 PETplanet insider Vol. 11 No. 01+02/10 www.petpla.net PET prices: The “seasons rule” is losing its importance in Europe Global Service International (G.S.I.) is the European marketleading importer of PET into the EU. Since 2002 the company has organised the annual PET Day, aimed at providing extensive updates for their clients on PET market trends and price movements. At the 2009 PET Day, which took place in October in Florence, it clearly emerged that making reliable forecasts about the way that PET prices would move was becoming ever more complex and challenging. What are the principal factors responsible for the movements in PET prices? Just a few years ago this question would have been easy to answer, as the movements in PET prices in Europe followed a simple rule: demand and availability determined the price. The former increased in the months of February, March and April and at the same time the availability became more restricted, because preform manufacturers and beverage bottlers bought large quantities in order to produce in readiness for the forthcoming summer season. In the summer months, the so-called “high season”, there was a significant increase in the sales of mineral water and soft drinks (as there continues to be today), and for this reason the demand for PET to produce beverage bottles increased towards the end of the winter and during the spring. With the help of this overview, Sanjay Sinha has pointed out the influencing factors that control the PET price. One of the factors also included is the price of cotton. (Source: Reliance) The price of crude oil has also played a role for many years in determining the price of PET - although perhaps not as much as the seasonal factors. But extreme price differences, such we have seen as over the course of the last year, became more noticeable. As crude oil moved towards record levels in the first half of 2008, and in July of that year hit an unheard-of 147 US Dollars per barrel, the price of PET increased following this extreme movement in the price of oil. The beginning of the economic crisis had an equally rapid impact on PET prices, with the price of crude oil falling at times to below 40 Dollars per barrel. PET Day: an insight into complex relationships There is no doubt that observing the movements in the price of crude oil and taking note of the “seasons rule” will continue to be of help in forecasting PET prices, the demand levels in Europe, and availability, but for reliable forecasts regarding the way that prices will move these factors are no longer sufficient. Several new factors have come into play which must be kept very much in mind, commented Francesco Zanchi, CEO of Global Service International, Rescaldina, at the PET Day 2009 organised by his company. “Price volatility of 100 to 200 Euros per tonne, regardless of the season, will in future be the rule for PET - and 100 Euros/tonne is 10% of the average annual price,” said Zanchi (the average price during 2008 was 920 Euros/tonne for European PET and 1020 US Dollars/tonne FOB for PET from the Far East). PET Day thus provided G.S.I. with the opportunity to pursue their aim of giving their guests an insight into these increasingly complex relationships affecting the price of PET, as well as looking at some recent market trends. “Only","@ID":16} "PATENTS 35 PETplanet insider Vol. 11 No. 01+02/10 www.petpla.net PETpatents www.verpackungspatente.de Dispenser cap with rough surface finish Public Disclosure. DE 102008010085 A1 Applicant: Henkel KGaA, Düsseldorf (D) Date of application: 19.2.2008 The disclosure describes a dispenser cap for liquid or freeflowing granular detergent. The cap is made from PP, PE or PET and its outer surface has various rough areas to aid optimum grip and hold. Groove around the neck Public disclosure: DE 202009001417 U1 Applicant: Krones AG, Neutraubling (D) Date of application: 23.1.2009 To improve the handling, during forming and filling, of a bottle made from a preform, it is proposed that a groove is formed below the neck ring. The container becomes easier to hold in a precise grip and the amount of material, and hence the weight of the container, are reduced. Multiple additives International patent No. WO 2008 / 023981 A1 Applicant: Top Floor B.V., Delft (NL) Date of application: 22.8.2007 A resealable tube is incorporated into the neck of a bottle. The tube holds a number of water-soluble capsules. Thus sports drinks, as one example, can be easily and quickly be refreshed at any time. Cap for pressure equalisation International Patent No. WO 2009 / 089481 A1 Applicant: Ball Corp., Broomfield (US) Date of application: 9.1.2009 The screw cap of a container for hot filling has features that allow it to compensate for a reduction in volume when cooling, and so avoid deformation of the container. Bottle with additive International Patent No. WO 2009 / 103140 A2 Applicant: Teko Holding International C.V., Rotterdam (NL) Date of application: 20.2.2009 The outer wall of a bottle is recessed to accept an additive contained in a twopiece housing. The secondary container is held in place by a special retainer and protected against theft and tampering by a shrink sleeve. Sleeved bottle Public disclosure: DE 102008008151 A1 Applicant: Krones AG, Neutraubling (D) Date of application: 8.2.2008 A thin-walled bottle is covered in a sleeve made from an environmentally friendly, rigid, thermoplastic material. The sleeve is fixed to the container in a manner such that it can be removed and so is easy to dispose of when sorting refuse.","@ID":37} "4 PETplanet insider Vol. 11 No. 01+02/10 www.petpla.net PETcontents 01+02/10 INSIDE TRACK 3 Editorial 4 Contents 6 News 27 Products 28 Bottles 35 Patents BUYER’S GUIDE 29 Get listed! MARKET SURVEY 22 Suppliers of PET recycling plants for bottle-tobottle recycling BOTTLING /FILLING 22 Jaipuria, Pearl Dinks, PepsiCo licensee: “Let’s grow together” 24 Intermediate bottle storage system Page 24 Page 28 REGIONAL MARKET REPORT 10 Germany Part 3 MATERIAL / RECYCLING 14 PET prices: The „seasons rule“ is losing its importance in Europe BOTTLE MAKING 16 The first foamed PET bottle from Coca-Cola in Denmark 26 Austrian Technology Page 10 Page 22","@ID":6} "BOTTLE MAKING 21 PETplanet insider Vol. 11 No. 01+02/10 www.petpla.net Beer The beer bottle is the same as the CSD bottle in its construction, and so offers all of the same advantages. In addition an oxygen scavenger can be added to the inner layer and a UV blocker can be added to the outer foamed layer if required. For beer, an oxygen additive can be added to the oPTI bottle. Milk The oPTI bottle is ideal for milk and milk-based products. As a singlelayer, fully foamed bottle, advantage can be taken of the full weight-saving potential. The foam can block 50% of the light so that for some applications a light-blocker such as titanium oxide can be dispensed with altogether. If more effective light blocking is required the amount of titanium oxide can nevertheless be drastically reduced. This also means that a shrink sleeve is no longer needed for the purpose of blocking the light - fillers can now switch to cheaper “patch” labels. In the oPTI milk bottle the foam can block 50% of the light. Hot fill The oPTI hot fill bottle does not have to be reheated. Thanks to the foam evidence exists that the bottle not only more effectively isolates a chilled beverage but also retains the heat of a hot-filled beverage within the inner layer of the bottle during the filling process so that the outer layer does not reach the critical temperatures at which it begins to shrink in an uncontrolled manner. This makes the oPTI the first hot fill PET bottle that does not have to be reheated or to be made from a special hot-fill grade. Shampoo Tactile quality: Easy-to-grip shampoo bottle. A shampoo bottle does not normally go into the PET recycling stream so here too a fully foamed bottle is the most appropriate solution. The colours can be introduced at the preform stage. The big advantage for a shampoo bottle is its tactile quality. Even under the shower it is easy to grip and doesn’t slip through the fingers.","@ID":23} "REGIONAL MARKET REPORTS 11 PETplanet insider Vol. 11 No. 01+02/10 www.petpla.net to medium sized businesses, but does not shy away from the giants in the beverage sector. Whilst Lidl, the big discounters, produce their own preforms, and BUQ who fill for the discounters also make preforms, Alpla is producing prEforms and bottles for several German companies filling for major discount retailers. Clients who have their preforms or bottles produced in-house by Alpla appear satisfied with price and quality. Certainly no customers have as yet cancelled a contract in order to produce themselves or to buy on the open preform market. Which at last brings us to the specific subject of the German market - according to Alpla, German consumers are highly conscious of quality and price. For Alpla as a supplier that means, for instance, that water bottles not only have to contain an AA blocker but also that the client is prepared to pay the extra cost. Alpla also see the high quality demands by German consumers in their reaction to articles published in consumer test magazines, such as the “Stiftung Warentest”. If a mineral water or some other packaged beverage achieves a low score in a product comparison test then it will be almost unsaleable in Germany. Such a strong reaction is not seen in other countries. So with regard to quality the filling companies are very nervous, but they are normally reassured by suitable attestations and certificates. However, if anything were to go wrong the responsibility would rest with the supplier at the beginning of the chain - i.e. to Alpla. Despite stringent safety requirements set down by the filling companies the German market uses the lightest weight bottles. This may be in part due to the unusually high carbonation levels of up to 7 or 8 grams of CO 2 common in Germany, which produces a high internal pressure and in turn gives the package a high degree of inherent stability. Despite the low bottle weights Alpla have still not added the 1881 to their standard range. Apart from a few “inhouse” situations, where the 1881 is already being used, the market for small and medium sized bottlers has not yet developed that far. The investment required in converting the whole filling line is still too high relative to the achievable cost savings. In addition to water and CSD the other food and beverage sectors are also of course important at Alpla. In the beverage market they supply multilayer aseptic bottles for juices, which are supplied to the premium sector. The dairy business is also very promising. Because the distribution chain - once again in particular the discount retailers - is constantly pushing down the sales price of fresh and long-life milk, PET packaging for milk in Germany is not economically realistic. However the situation is different with higher priced yoghurts and mixed dairy drinks where, with the support of Alpla, there is a large amount of PET packaging in the 0.1 litre to 0.75 litre market. Smoothies, with a 38mm neck finish are making significant advances. Overall Alpla expects no real change in consumer tastes in Germany which would have an impact on other PET packaging. The main changes are expected to be seen as a result of legal requirements - principally changes to the Packaging Ordinance. The environmental studies currently being carried out should in fact present the single trip PET bottle in a more ecologically favourable light. For the same reason Alpla sees a negative impact on the use of PLA. If the whole production chain, including crop cultivation, is considered the consumption of primary energy is very high. PET-Verpackungen GmbH Deutschland The first documentary evidence mentioning Wiegand as a glass processor dates back to 1540. Since then the family was involved in the German glass industry. Today Wiegand-Glas supplies glass containers and other glass specialities for the food industry. In 1997 the Wiegands decided to invest in PET despite the fact that they were still one of the leading glass suppliers to the filling industry. They had recognised by that time that PET would ultimately drive out the glass bottle for CSD and water in Germany. Today, at Wiegand-Glas only a very few mineral water glass bottles are still produced and the company has grown to the market leader in the production of wine bottles. The new company set up to produce PET preforms and bottles was given a new name: PETVerpackungen GmbH Deutschland. Initially the new business grew at a rapid pace. Each year they doubled the number of machines that they operated. PET-Verpackungen concentrated on the producThe Alpla Board of Executives: F.l.t.r. Nicolas Lehner, CCO, Günther Lehner, CEO, and Georg Früh, CFO In addition to water and CSD the other food and beverage sectors are also important at Alpla","@ID":13} "MARKET SURVEY Herbold Meckesheim GmbH Starlinger & Co. Ges.m.b.H. Ohl Engineering GmbH - PET Recycling Technologies PTI Recycling Systems LLC Industriestr. 33, Germany-74909 Meckesheim www.herbold.com Mr. Siegfried Engel Vice President for Sale +49 (0) 6226 932 0 +49 (0) 6226 932 495 siegfried.engel@herbold.com Sonnenuhrgasse 4 1060 Wien http://recycling.starlinger.com Elfriede Hell, MBA General Manager recycling technology + 43 1 599 55 241 + 43 1 599 55 180 recycling.he@starlinger.com Gartenstraße 8, D-65549 Limburg www.ohl-eng.com Stefan Behnke Managing Director +49-6431-28099-147 +49-6431-28099-288 s.behnke@ohl-eng.com 1440 Timber Wolf Drive, Holland, Ohio 43528-0964 www.ptirecyclingsystems.com James M. Sheely V.P. Sales & Marketing +1 419.720.0450 +1 419.867.7700 j.sheely@plastictechnologies.com Engineering of washing lines and / or a turn-key project with technologies available in the market yes (Agglomerate) yes up to 36,000 t/a to be determined approx. 1,000 m² to be determined all relevant approx. 0.5 - 1 m³/t approx. 545 kWh/t Flake to Sintered Pellet or Powder yes (Agglomerate) yes up to 13,000 t/a (1 unit) 1,500t/ pa - 26.000 t / pa (6 sizes) to be determined Pre-built systems at 5 MT/a to 10 MT/a (620 kg/h to 1,240 kg/h) or technology licensing approx. 64 m² 130m² - 540m² to be determined 250m” USA / FDA (cold-fill / hot-fill), Austria, Germany, via customer: France / AFSSA, Finland, Australia, Bolivia; follows EFSA requiremens; brand owners all relevant FDA, Canadian Health Authority, European Food Safety Applied, Major Global Brand Owner Approvals not required approx. 0.15 0.066887435 approx 125 kWh/t approx. 410 (depending on design) 585 kWh/t Starlinger recycling technology offers the engineering of washing lines and / or a turn-key project with technologies available in the market yes yes up to 5000 /a 3,700 - 10,500 approx 800m² approx. 150 FDA (cold-fill, hot-fill), follows EFSA requirements 0,5 - 1m³/t N/A approx 207 Wh/t 120 - 250 Material suitable for bottle, film, and extruded packaging yes yes size reduction and size reduction components. yes PET-bottles washing plants, turnkey systems, single components yes yes","@ID":21} "BOTTLE MAKING 26 PETplanet insider Vol. 11 No. 01+02/10 www.petpla.net Austrian Technology Stretch blow moulding plants up to 6,000b/h What does a stretch blow moulder need? This question (a no-brainer actually) has been re-interpreted by the two directors of the Austrian company PET Technologies Europe - Technical Director Roland Steurer and Walter Höbling, Managing Director. As far as Roland Steurer is concerned, there was no doubt about the requirement from an engineering angle: a machine that would operate reliably to produce reasonable bottles without any technical gadgetry. One operator should be able to master the machine inside a week, even if he has never seen a PET installation before. And, as regards the commercial aspect, Walter Höbling’s vision was similarly unclouded – it was to be cost-effective, at a price level that was pitched higher than Chinese and Taiwanese products, but substantially lower than the price of linear machines offered by the established machine manufacturers. Both know what they are talking about; Roland Steurer was with Alpla for almost 20 years and then spent several years as the engineer responsible for stretch blow moulding systems at Kosme, whilst Walter Höbling also has a Kosme background – he spent just over 12 years selling not only linear stretch blow moulding machines but also complete turnkey systems. They found a partner in the shape of a stretch blow moulding machine manufacturer with more than 10 years’ PET experience. Roland Steurer set about bringing the installations up to scratch technically. The heating oven and the blowing air components in particular have been newly developed. The production is being outsourced. So far the following types of machine have been supplied: the APF 3002 with 2 cavities and a capacity of 3,000b/h, the APF 6004 with 4 cavities and a capacity of 6,000 b/h for 0.2 – 2.0l bottles and the APF 5 with 2 cavities, which will also handle 5.0l and 10l bottles in addition to the 0.2l – 2l range. The plant is suitable for the beverage industry, the cleaning agents and cosmetics industries as well as food-quality oil bottles. As far as the beverages sector is concerned, the machines tend to be more suited to projects in the emerging countries of the world, because of the low output. PET Technologies Europe not only supply machines; bottle development and stretch blow moulds for all stretch blow moulding systems also feature in their portfolio. The machine control system has been kept simple – the operator will quickly find his way around. Complex functions such as, for example, adjustment of the pre-blowing pressure, are carried out directly on the machine by PET Technologies Europe, which means that there is no operator involvement. After little more than a year under development, 6 machines have already been sold. From left to right: Roland Steurer, Technical Director, Walter Höbling, Managing Director PET Technologies Europe and Alexander Büchler during the interview at the company’s head office in Wiener Neustadt, Austria.","@ID":28} "MATERIAL / RECYCLING 15 PETplanet insider Vol. 11 No. 01+02/10 www.petpla.net by knowing and understanding these relationships is it possible to recognise the right time to buy PET at the most advantageous price,” emphasised Zanchi. Crude oil: Increasing demand and higher shipping costs are driving prices In his presentation on “A Global Overview of Polyester Raw Materials” Sanjay Sinha from the Indian company Reliance Industries Ltd. of Mumbai, expressed the view that the price of crude oil would in future stabilise at a high level. His reason for this view is that he believes the demand for oil will continue to rise because the global Gross Domestic Product (GDP) will continue to grow. “The growth in global GDP may have been slowed down by the financial crisis, but by the end of 2009 the world will see a more stable situation and a sustained growth trend in the coming years, which would mean renewed growth in the demand for oil. There is a clear relationship between the global GDP and the demand for oil,” said Sinha. This scenario will impact on future oil prices, and in addition there is the difficulty of new oilfields which are often in inaccessible parts of the globe and so the extraction and transport costs will be higher. The difficult accessibility of new oil reserves and the continued growth in demand will lead, in Sinha’s opinion, to the price of a barrel of crude oil hovering at around 60 to 70 Dollars per barrel. Polyester, including fibres as well as PET resin for the production of film or bottles, will continue to enjoy strong levels of demand, believes Sinha. He forecasts the growth in demand at 4 to 6%, mainly based on demand in Asia, and in particular in China. The precursors too, which are used to produce polyesters, will see growing demand based on this prognosis. The substances in question here are paraxylene (PX), terephthalic acid (PTA) and monoethylene glycol (MEG). Polyester: Moderate growth in packaging applications - higher demand for fibres Roger Lee, Managing Director of Tecnon OrbiChem Ltd., London, put forward separate scenarios when looking at the demands for polyester for packaging and for the textile industry. He stated in his presentation that global production of PET for the packaging industry was growing by 9% per annum before the global financial crisis. In 2008 the growth rate was only 3.3% and during 2009 was expected to reach 4.4%. For 2010 Lee forecast a 6.3 growth rate. He also pointed out that in the Far East there was a lot of new production capacity, either already available or planned. In Europe and North America however the trend was in the opposite direction - more and more PET production capacity was standing idle, or permanently shut down for various reasons (technical or financial). Lee was of the view that PET for packaging applications would not grow so strongly and that only moderate rates of growth in relation to the global GDP were to be expected. He based this view on, amongst other things, the fact that the demand for virgin PET for beverage bottles was falling (e.g. a result of the light-weighting of bottles, and because distributors and drinks bottlers were demanding the use of a higher percentage of recycled PET for reasons of sustainability). Despite moderate growth of PET use in packaging applications the EU would in future be obliged to rely to a greater extent on imported resin. “The plant closures and the uncertainty surrounding European and American production plants, plus the new or planned capacities in the Far East, mean that in the next two years 48 to 49% of world PET production for packaging would come from the Far East. “The EU will therefore be obliged to import resin to cover demand, “ he explained. For polyester that is processed into fibres Lee sees a continued high demand. In the textile industry polyester will continue to be the preferred fibre. Cotton too has its impact “Today 70% of total polyester production is being used in the manufacture of fibres,” added Francesco Zanchi of.S.I. This fact in turn means that the price of other textile fibres, such as cotton, has an impact on the price of PET. Against this background, and above all with regard to the fact that PET imports into the EU will continue to increase, it is no wonder that movements in the price of, and demand for, PET in Europe can no longer be forecast based on the “seasons rule”, which in any case was only valid for the temperate countries in the northern hemisphere. The price of PET in Europe will be increasingly dependent on global factors. In 2009 China and North Eastern Asia’s contribution to worldwide PET production was more than 30%; its own consumption was considerably less than the quantity it produced. In Europe and America consumption is higher than production.","@ID":17} "REGIONAL MARKET REPORTS 13 PETplanet insider Vol. 11 No. 01+02/10 www.petpla.net year as a light weight line extension to the DoubleSeal SuperShorty, once again two years later, another 16% of weight saving was achieved. All this efforts save resin and therefore costs for our customers. And please note, these are all caps that were well accepted by the market - not prototypes that never came to market! You will see therefore that in this field we can talk about a two-year innovation cycle. PETplanet: As a global supplier and manufacturer of caps what do you see as typical features of the German market? Henkel: Nowhere in the world exists such a tough competition among retailers. The large number of hard discounters generates enormous pressure on prices for food and beverages which the individual producers pass to the packaging suppliers. The number of discount stores will grow even more in the near future. Only few beverage producers have had the capabilities to cope with these tough market conditions leaving behind a fragmentised water industry with many mid-sized companies. PETplanet: Many thanks, Mr Henkel! plant in Lithuania. In Germany they produce standard PCO 28 preforms with weights from 17.5 to 36g. Now, in the quiet season they are switching part of the production in Merseburg over to the new lightweight preforms. Uniplast Germany still imports other preforms from various of the group’s plants. The next major move can already be seen in the production bay - in-house production of PCO 28 caps on a Husky Electric 800t machine fitted with a 144 cavity mould tool. Bericap Interview with Thomas Henkel PETplanet: Good morning Mr Henkel. In Germany we are increasingly seeing that beverage fillers are producing own preforms. Lidl have already gone a step further and now make own closures. Do you think that in future more fillers will make own closures, or is this a unique case? Henkel: You are right. I came from a manufacturer of plastic pots and tubs, and originally the pots and the lids always came from the same supplier. The idea of the pot and the lid coming from different sources was a new concept at the time, but nowadays reality. But if we look more closely at the matter it quickly becomes clear - even if preforms and caps are both injection moulded the production of caps is considerably more complex. Just think of all the different colour changes for caps, and then the printing. A beverage filler can enjoy a considerable degree of product differentiation at the point of sale through the design of his cap, even if the bottles are all the same. This variation doesn’t apply to that extent to preforms. PETplanet: The current trend towards light weighting of preforms is also to a large extent a success for caps. I’m thinking of the 1881. Henkel: We have certainly achieved a lot in recent years with regard to light weighted caps for still water and CSDs, but we shouldn’t forget that Germany, with its multitude of small fillers, is still a big market for classic 1810 caps. For small companies it is not an economical proposition at the moment - despite the savings in material. We as cap manufacturers are required to supply the new lightweight caps and the traditional, well-proven beverage caps. PETplanet: And just how rapidly does the innovation cycle move in the closures business? Henkel: As a good example I would like to take you through our development programme for beer caps. In 2003, when beer was starting to be filled in PET in appreciable quantities, we had our one-piece “DoubleSeal O 2 S” on the market, just two years later we had developed a lightweight version - the “ECO O 2 S” achieving a weight reduction of 12%. Again, just two years after that in 2007, we launched the “DoubleSeal SuperShorty” for the 1881 neck, crown design, based on a request of the beer industry. And in case you think that was the end, take a look at our “DoubleSeal SuperShorty Eco“ which followed this Some of Bericap’s beer closure developments: DoubleSeal O 2 S (right) and DoubleSeal SuperShorty O 2 S (left and second) DoubleSeal Supershorty O 2 S for the 1881 neck","@ID":15} "BOTTLING / FILLING 23 PETplanet insider Vol. 11 No. 01+02/10 www.petpla.net are also running three shifts, another blower from another part of the business supplies the extra bottles. Mr Bedi is particularly proud of the water treatment plant, installed three years ago. “This enabled us to reduce the water usage in production from 30 litres per case down to 11.8l per case”. He is generally very environmentally aware and conscious of the need to save energy. “For our preform production we have to generate our own electricity, which costs twice as much as electricity supplied by the government, but it is only at the beginning of next year, after 5 years, that we will be able to link up to the main supply. In future we will also have to significantly reduce our consumption of oil, which includes using less oil-based PET and focussing more on glass”, he says. We asked whether PLA would be an alternative. “In India we have over 15% of the world population, living on 2.14% of the earth’s surface. We need our productive land to provide food and not to produce packaging”. He made it quite clear. In the air-conditioned PET hall there are three 225 ton Husky HyPETs. Six different mould tools, each with 48 cavities, are enough to cover the whole of the beverage range. In total 1 million preforms per day can be supplied. Of these there are about 450,000 x 22g, 350,000 x 25.5g and 250,000 x 52g. There are a total of 50 employees in the preform plant working on a 3-shift basis. 1322 x 22g preforms are packed in small handy cartons and then stacked onto pallets. A forklift takes the cartons to the truck where, as is normal in India, they are loaded by hand. The truck leaves the plant and goes directly to the filling plant. For customers in That is the motto of the Jaipuria Group, who, as a PepsiCo licensee, supplies around 40% of the Indian market with soft drinks from the American group. Jaipuria is broken down into various divisions depending on the job which they do. Preform production operates under the name of Pearl Drinks, and the filling lines under the Pearl Bottling name. C. K. Jaipuria oversees the whole operation. Visit to the plant in Jammu, India Delhi the preforms are delivered within 24 hours, but for those in the south the truck-drivers plan for a 3-week journey. A positive aspect to the use of the cartons is that the preforms coming off the conveyor do not fall very far into the small cartons, and so any damage is largely avoided. Because in the off-peak season the preform factory supplies Jaipuria’s own plants in the south of India it runs right through the year at a very high level of capacity utilisation. Each line has its own material feed system - two delivered by Plastic systems and one by Piovan. Whenever Mr. Bedi talks about his views of PET and PLA, he comments on the material feed equipment. “I prefer the Plastic systems equipment,” he says, “but as a company Piovan is in front”. Mr Bedi also pays special attention to the cooling systems, as the temperature reaches as high as 44°C. But alongside monitoring the technical aspects of the plant he has one more highly responsible task: I was allowed to plant a tree in his company garden and he has promised to care for it and look after it for me. Alexander Büchler As well as producing preforms the plant at Jammu fills the whole of the Jai Beverages and Jai Juices range of drinks: CSDs in glass and PET, water in PET and juices in hot-fill glass. There is also a Tetra pak line for 0.2l packs of juice. In total the whole plant runs at over 1,000 fills per minute. The plant is managed by the ever-anxious Mr. Bedi. It was he who created a flourishing beverage plant 10 years ago on an industrial site that had been empty for 5 years. “When we started this was all an overgrown wilderness”, he said talking about how the plant began. PET bottle blowing is done on various linear MAG and Sidel machines and filling is done using mechanical fillers. To ensure that the production facilities are as flexible as possible the blowers are not directly linked to the filling machines. This means that the blowers can run three shifts, delivering the bottles into silos. In the high season, when the fillers Mr Uday Bhan, centre, C.E.O. of the PET preform division of Pearl Drinks, and Deputy General Manager Vijay Walia (left), have established PDL Preforms as a new brand within the company. F.l.t.r.:Alexander Büchler; SK Gupta, AGM Pearl Drinks, Jammu; Tejbir Singh Bedi, Vice President Jai Beverages, Jammu, and Vijay Walia at their visit of the preform production site.","@ID":25} "28 PETplanet insider Vol. 11 No. 01+02/10 www.petpla.net PETbottles Yellow PET for lemons The French company Pletercil Interco of Le Bourget du Lac are selling 500ml packs of pure lemon juice in a round, easy-to-grip PET bottle. In its upper half the yellow bottle has prominent moulded ribs for stability. It carries a wrap-around paper label. The tamperevident screw cap in a suitable green colour nicely finishes off the pack. Recycling line recoSTAR PET iV+ Ongoing PET recycling innovation, quality and state-of-the-art technology, a full range of consulting services – brought to you by Starlinger. Visit us at: Plastimagen, Mexico City, Centro Banamex, March 23-26, 2010, Booth 1700-05 Plastic Recycling Conference, Hilton Austin, TX, March 2-3, 2010 www.starlinger.com Another way to pack sugar! The “Sucrisse” liquid sugar from the Aarberg + Frauenfeld sugar plant in Switzerland is described by the company as the “modern way of sweetening”. The special hinged closure, developed by German tooling and plastics processing company Krallmann, incorporates a K-squeeze TPE valve adapted for liquid sugar and so enabling controlled dispensing. The crystal clear PET bottle, supplied by Gizeh PET, is formed to look rather like a sugar crystal and is suitable for table use. Dextropur in a handy “can” For a fast energy boost the German company Dextro Energie GmbH of Krefeld now offer a 190g pack of “Dextropur Plus“ powder in a handy can-shaped PET container. The concave form of the can is decorated with a modern shrink sleeve label and sealed by a screw-on dispenser lid. The lid has two resealable hinged flaps with orifices for shaking the powder or serving it onto a spoon. An aluminium seal over the mouth of the container provides tamper evidence and security. Double role cap with kids’ drink The Austrian drinks manufacturer Vöslauer Mineralwasser AG of Bad Vöslau is marketing a kids; drink (0.33l of non-carbonated mineral water) in a PET bottle with a secondary feature: if the handy push-pull drinking cap is unscrewed and one blows through the open cap it produces a noise like a trumpet. Voslauer call it the dual-role “Blaster “ cap, and describe its benefits on the bottle label. Both the screw cap and the push-pull section are tamper proofed on this modern kid’s pack, and a wrap around paper label carries the required product and commercial data. Sangria in PET Bodegas Salzillo S.A. of Jumilla in Spain are marketing 1l of sangia (a Spanish red wine punch) in a PET bottle. The rectangular bottle is decorated with bright front and rear labels and carries a red aluminium cap with a tear-off tamper-proof feature. The shape of the bottle looks very similar to their competitors’ glass bottles on the store shelf.","@ID":30}
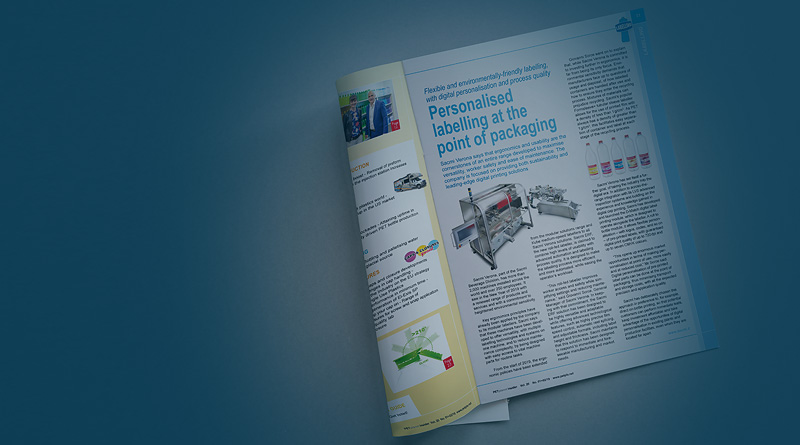