Improved hotrunner insulation with ceramic components
Swedish company Heatlock, pioneers of ceramics in hotrunners, demonstrates clear advantages in heat loss and consequent energy usage by using ceramics in key components.
Heatlock Co Ltd, which was originally founded in Sweden and remains in the hands of the second generation of the Helldin family, has been manufacturing hotrunners for over 30 years. It sold its first hotrunner system in 1977 and, in 1982 it introduced ceramics as insulation for hotrunners – the first company in the world to do so. It made a very strong statement about its future when, in 2003, it entered the Chinese market by establishing a joint venture, LKM Heatlock, with Chinese company LKM. Six years later it established its own operation, as Heatlock Co Ltd, with facilities in Hong Kong and at three locations in the People’s Republic of China (PRC): in Foshan City, Quandong; 40 km West of Shanghai in Suzhou City, Jiangsu Province; and in the NE of the country in Qingdao, Shandoing Province. In 2014, Heatlock opened Tech Centres in the USA (Detroit, Michigan) and in Germany (Erbach).
In 2007, four years after it entered the Chinese market, the company patented a new generation of ceramic technology, which offered improved performance compared to previous generations. Its all-in-one A3 series was launched in 2011 and remains a strong seller today. Heatlock says that its ‘workhorse’ series is “built to last, durable, with hot to cold or direct gate solutions, including valve gates”. A floating manifold system is also available; it features modular design that can be adapted to suit a wide range of mouldings. Its hot runners are designed to be easy to use, the company says. Among the standard features of Heatlock’s caps and closures hot half range are built-in flash memory with complete mould details, and a Digital Project Book that includes all documentation for individual projects, including service information.
Superior insulation for energy savings
The key feature and attraction of hotrunner ceramic components is their superior heat-retaining and insulation performance, compared with titanium and steel. Its ceramic parts have demonstrated performance between five and seven times better than titanium and eight to 12 times better than steel, at compression strengths of 2,100 M/mm2, and the ability to withstand temperatures of up to 1,400 °C. The improved performance is demonstrated in Fig.1.
It shows the different levels of manifold heat losses in comparable moulds that are each supported by four spacers: steel in one case (the red line) and ceramic in the other (the blue line).
Over the period measured – three hours/180 minutes – the ceramic spacers saved 0.33 Wh for each square millimetre of contact surface, compared with steel. In the case of Heatlock’s KE0200305 spacers, four of which have a combined surface area of 490 mm2, heat loss savings would total 160 Wh.
The benefit to operating companies that use ceramic rather than steel spacers is to save energy on heating, give better hotrunner temperature control, improve recovery and give less work for the chiller to undertake, all leading to better part control and quality consistency. The greater insulation properties mean that more supports can be employed, with greater support area, improving mould rigidity and without high levels of heat loss.
Heatlock says that its latest generation CE-FIX ceramic clamp technology, delivered within 5 micron height tolerace, offers increased sustainability, ease of installation and adjustment.
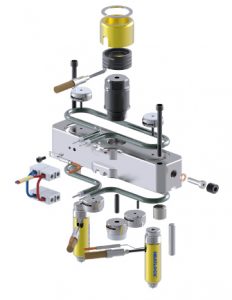
small heat input from the
manifold into the mould plates. The
heating elements on both sides ensure a good and even temperature in the manifold.
Tailored hot half systems
Heatlock’s hot half systems are tailored for specific customer requirements. At Plastimagen Mexico 2019, the company announced its first partnership for caps and closures moulds, with TK Mold Shenzen, of China. Heatlock says that the partnership is dedicated to “providing high quality moulds of 32 cavities and under”, which it has identified as an opportunity gap in the market. The company claims that its hot half systems, which are all manufactured from P20 or stainless steel, are more affordable than equivalent systems from established global suppliers.
As well as built-in flash memory with complete mould details and a Digital Project Book that includes all documentation for individual projects, including service information, Heatlock’s hot half systems come with a full range of standard fittings and features. Insulation plates, high tolerance location elements, built-in service tools and service interval counters are all included as standard.
Total quality commitment and global network
Heatlock’s production processes are constantly monitored and improved using TQM (total quality management) Lean Sigma and TPM (total productive maintenance) BPM/BPR (business process management/business process re-engineering) techniques and tools.
Its distribution network includes presences in most countries across the world with mould making or injection moulding manufacturers.