Seamless and resource-saving recycling of PET bottles
Christian Strasser, CEO of PET to PET Recycling Österreich GmbH, on toxic trends in the raw materials market and how to ensure consistent material quality over the long term in the circular economy.
Pandemic-related lockdowns have changed beverage consumption, working conditions and the market for secondary raw materials. The recycling industry has also been greatly affected by economic developments. Nevertheless, thanks to coordinated efforts and strict adherence to its pandemic plan, the Austrian PET to PET Recycling company has not only managed to maintain a high volume of PET bottle recycling but even invested in plant expansion. Christian Strasser, CEO of PET to PET Recycling Österreich GmbH, tells us the secret of his success.
PETplanet: At the beginning of August, you drew a positive interim balance for the first half of 2021: 14,048 t PET beverage bottles were kept in the resource cycle. How did you manage this despite the special challenges posed by the Corona pandemic?
Strasser: The fact that we were able to maintain production and even achieve record levels of performance is mainly due to three factors. Firstly, having a detailed pandemic plan tailored specifically to production operations, including extremely strict hygiene measures and rapid Covid testing, enabled us to ensure the safety of our workforce. Secondly, the Austrian beverage industry continues to play a pioneering role in the use of recyclates in new PET bottles which has helped our sales. And thirdly, we are continually growing our business through on-going system optimisation, as well as expanding our facilities in the interests of the circular economy.
PETplanet: Have you noticed any pandemic-related changes in the last year, such as a different consumption of beverages or a change in the way consumers return empty bottles? And if so, have all the changes now settled down again?
Strasser: Major changes did indeed occur during the pandemic. If we look at consumer behaviour, it is clear that the partial disappearance of hospitality, tourism and limited leisure opportunities also resulted in a sharp decline in the use of small bottles. On the other hand, the number of large-volume packaged varieties, which are mainly sold via retail outlets, has grown strongly. The change in demand has also caused huge upheaval in the raw materials market. Primary raw material prices have fallen sharply, while at the same time, there has been high demand in the secondary raw material market, with a corresponding lower volume of bottles. This year in particular, prices for bales and the recyclates to be produced from them have risen to unprecedented levels.
In some cases, we have a situation where secondary material is being traded at almost twice the price of primary raw material. The term unhealthy is not sufficient to characterise this state of affairs – for a shift towards a circular economy a more appropriate word would be toxic.
I would characterise the behaviour of customers in relation to the separate collection of bottles as consistent even though there is great potential for a further increase in the amount collected.
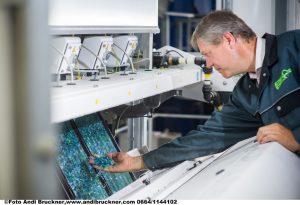
PETplanet: What development do you expect for the second half of 2021?
Strasser: The situation has improved as a result of the lifting of many restrictions. However, we will probably not be able to speak of normality for some time yet. The best outcome would be expecting sales figures to be similar to those of 2020.
PETplanet: During the pandemic, work was cut back and tightly managed in many companies. You, on the other hand, expanded. Can you please briefly explain what investments you have made and what might be next on the agenda?
Strasser: Increased demand for resource-saving recycling prompted us to invest in expanding our facilities despite the Covid crisis. This involved extending the outdoor and storage areas and increasing production capacity with a second granulation plant, which can produce 2 t/h of food-grade PET recyclate. An additional label removal system prior to wet washing helps in improving the cleansing process. In addition, the silo facility for washed flakes was expanded as a storage unit before food-grade processing. With these investments, we have not only ensured the seamless and resource-saving recycling of PET bottles but also created eight additional jobs.
PETplanet: From which area do you obtain the bale goods that are processed by you?
Strasser: The demand for recyclable PET bottles is very high throughout Europe. These recyclates can be used in all applications, even if high-quality recycling is no longer possible afterwards. Therefore, PET to PET must also source bottle bales from all over Europe, as far as transport costs will allow.
PETplanet: How long does a process take from the first processing step of the baled goods to the compounded rPET ready for delivery?
Strasser: The recycling operation takes 10-12 hours, depending on the process used. Two different techniques are used to convert PET bottles into PET flakes or PET granules. One plant thoroughly washes PET flakes using patented URRC (United Resource Recovery Cooperation) technology while in the second, PET is melted down and processed into granules. This produces quality that meets the highest food standards.
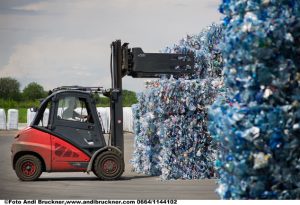
(Photo: Andi Bruckner)
PETplanet: In the EU, an average of 25% rPET content in bottles will become mandatory from 2025, with some brands pledging themselves to 100% rPET. In your eyes, what is the most appropriate recycled content ratio to ensure good material quality in the long term?
Strasser: Many manufacturers have increased recyclate usage rates in recent years, with new bottles now being produced from 100% recyclate. It ultimately all comes down to the average value that is fixed on the market as a whole. As is readily apparent, a 100% closed loop for all bottles is neither realistically achievable nor sustainable. Based on previous experience, we believe a sensible recyclate usage rate of 50% on average is reasonable in order to ensure consistent material quality over a long period of time. This includes very ambitious quotas of 100%, as well as very low ones of less than 30%. The average value that emerges on the market is relevant in all this.
PETplanet: When Europe switches to 25% rPET initially and 30% rPET from 2030 onwards, the demand for food-grade material will also continue to increase. Can you imagine opening more locations?
Strasser: Such options cannot be ruled out but there are currently no specific plans to do so. In any case, further expansion of the bottle-to-bottle cycle of the PET beverage bottle will require additional capacity for high-quality recycling plants.
PETplanet: Which “design for recycling” aspects, implemented in PET bottles, would make your work easier – or which additives, colourants, material combinations… are the most challenging to recycle?
Strasser: Any change or modification to the molecular structure of PET is problematic. This applies both to additives and, especially, to foreign polymers that change the material’s properties. In particular, if the added substances are thermally overloaded at PET processing temperatures, the optical and mechanical components are severely compromised. Last but not least, all elements used to manufacture and configure a beverage bottle must meet the criteria for full recyclability.
PETplanet: In 2009, Austria took PET returnable bottles off the market. Now the mineral water bottler Vöslauer has announced that it will revert to returnable PET bottles from 2022. How do you assess this changeover and does it affect you as a recycling company?
Strasser: Based on studies which show that the disposable PET beverage bottle when combined with a closed bottle-to-bottle cycle has the same ecological impact compared to the returnable glass bottle and that only a returnable PET bottle is better for the environment, I see the impact being relatively minor and would expect a slight decrease in returnable glass bottles.
PETplanet: Thank you very much Mr Strasser.
PET to PET Recycling Österreich GmbH was founded in April 2006 and is operated by leading companies in the Austrian beverage industry. Today, the 53,000 m² site is claimed to be one of the most modern PET recycling plants in the world. In 2010, a granulation plant was added to the recycling plant in Müllendorf. This was followed in the following year by the start of the new automatic bottle sorting stage and the installation of a silo plant, both of which were expanded again in 2017. In 2018, the PET to PET in-house laboratory was expanded, and in 2020 the handling areas and the granulation plant were extended.