{"pages":{"page":[{"@ID":25 "BOTTLING / FILLING 23 PETplanet Insider Vol. 25 for sterile air that perform SIP, reducing SIP time by about half. This not only reduces the amount of steam consumption and CO2 emissions, but also enables the aseptic filler to switch production in less than two hours. Increased productivity thanks to shorter SIP times and faster aseptic filling lines contributes to reduced TCO. The DNP aseptic filling system for PET bottles can be used for high-speed bottle production, for up to 72,000 bph. Changeovers can be done in less than 2 hours. It has a smaller footprint, higher production efficiency and less energy consumption through Kaizen (`big improvements`- a management system developed in Japan, based on the idea that employees should be involved in continually improving products, services, etc. to make the company as successful as possible. Kai: change and Zen: for the better). It is claimed to be a very reliable and sustainable aspetic filling system. DNP started to develop aseptic filling systems in 1972. DNP’s first aseptic filling machine launched in 1976 to produce single-use coffee creamer packs. The system was designed to allow the UHT sterilised coffee creamer to be filled and sealed in a hydrogen peroxide-sterilised lid and base within an aseptic chamber. This concept has been the basis for the development and sale of various aseptic filling systems (PET bottle, carton, cup, pouch, BIB, etc.) that use hydrogen peroxide sterilisation for the last 50 years. DNP will contribute to the development of an enrich and sustainable society by leveraging the aseptic technologies. www.dnp.co.jp/eng/group/aseptic-systems/ Synchonised system of an aseptic filler and a blow moulder with a preform decontaminator."},{"@ID":6 "PETcontents 4 PETplanet Insider Vol. 25 No. 03/24 www.petpla.net 03/2024 EDITOUR 10 PET bottles for food and non-food - Multiple designs produced in a one-step process 12 Mineral water bottler focusses on vertical integration - Deep water from the Hajar mountain region in the north-east of the Emirates MATERIALS / RECYCLING 14 From kerbside collection to sustainable packaging - Stadler and Krones install Las Vegas Polymer Center BOTTLE MAKING 17 Refillable PET bottle blowing - Sipa is pushing sustainable trends 18 Water and CSD bottling in China - Growing potential included BOTTLING / FILLING 22 Next generation of sustainable aseptic filling systems MARKET SURVEY 27 Suppliers of caps, cap systems & cap inspection systems EVENT PREVIEW 24 Chinaplas 2024 preview - part 2 32 Focus on green issues, recycling and energy efficiency 33 NPE 2024 preview - part 1 35 Meeting the market demand 36 Quality control and productivity improvement - Laboratory automation, precision bottle measurement and innovations in automated blow moulder control PACKAGING / PALLETISING 40 Delivering value – fast - Delta Engineering helps smooth the flow and boost efficiency of new bottle blowing lines 42 “The variability of rPET resin is a challenge for the packaging industry” - Interview with Jérôme Neveu, Packaging Product Manager at Sidel EVENT REVIEW 45 Challenging times - Review Petcore annual conference BUYER’S GUIDE 48 Get listed! INSIDE TRACK 3 Editorial 4 Contents 6 News 46 On site 47 Products 54 Outer Planet Page 12 Page 25 Page 40 EDITOUR"},{"@ID":51 "MATERIALS / RECYCLING PETplanet Insider Vol. 25 No. 03/24 www.petpla.net 14 Stadler and Krones install Las Vegas Polymer Center – the fi rst of its kind in North America From kerbside collection to sustainable packaging Stadler Anlagenbau GmbH, in collaboration with Krones, has designed and installed the new Republic Services Polymer Center in Las Vegas, Nevada, which processes plastic bottles, jugs and containers to produce plastic materials ready for use in new packaging. The first of its kind in North America, this facility aims to close the circular economy to meet the rising demand for high-quality and food-grade recycled plastic. Republic Services, a leader in the U.S. environmental services industry, has opened North America’s first vertically integrated plastics recycling facility, producing recycled resins for use in sustainable packaging. Krones, acting as general contractor in the project for the new Polymer Center in Las Vegas, worked hand in hand with Stadler, which was responsible for mechanical sorting on the PET and PO lines. The new plant will produce more than 100m lbs/a of recovered resin products that are returned to the circular economy. The new Polymer Center processes pre-sorted plastics collected by Republic Services across the Western United States to recover PET, which is converted into rPET flakes ready to be turned into new bottles, and polyolefins (PO) ready for use in the production of new bottles, jugs and containers. “The Polymer Center is the first facility of its kind in North America,” says Pete Keller, Vice President, Recycling and Sustainability at Republic Services. “It’s the first time a single U.S. company has managed the entire plastics recycling stream, from kerbside collection to production of high-quality recycled resins ready for use in sustainable packaging.” Dual Line plant closes the loop The Polymer Center in Las Vegas sorts and processes the materials, which are delivered in bales, on two lines: one for PET and one for mixed plastics, each with a capacity of 5 t/h. “This is the largest Dual Line plastics recycling plant in the USA,” comments Mat Everhart CEO, Stadler America LLC (a subsidiary of Stadler Anlagenbau GmbH). It is expected to put 100m lbs/a of plastics back into the circular economy by producing highquality, food-grade recycled material ready for use in packaging. The materials fed into the PET line undergo mechanical separation and the singulated material is cleaned of ferrous particles. A Stadler STT2000 ballistic separator sorts the material into rolling (3D), flat (2D) and fines fractions. The fractions go through sensorbased sorting with Near-Infrared (NIR) sorters. Caps, rings, and the 2D fraction go to compactors. The 3D fractions are directed to a Stadler Label Remover to remove the labels. The clear PET, caps and rings are directed to the Krones washing line, which granulates and cleans the material, while the colour PET is compacted into bales. On the mixed plastics treatment line, mechanical separation sorts the infeed into fines and sieve overflow – the latter further separated into light and heavy fractions. The heavy mixed plastics fraction is sorted into four polyethylene (PE) products – natural, white, red/orange/yellow, other/colour – and two polypropylene (PP) products – natural/white and other/colour. PET is sorted out of the remaining material and sent to the PET line. The products of the Mixed Plastics line are conveyed to storage bunkers where a semi-automatic feeding programme allows for materials to be discharged by grade to be fed into the baler. Vertically integrated plastic recycling facility (photos: RS)"},{"@ID":22 "BOTTLING / FILLING PETplanet Insider Vol. 25 No. 03/24 www.petpla.net 20 PROCESS PILOT+ Achieve Your Sustainability Goals and Produce Your Best Product TM Agr’s Process Pilot system provides personalized process control response to each unique bottle GHVLJQ EORZPROGHU ȴQJHUSULQW Ȃ VDIHO\\ DQG TXLFNO\\ 1R ELJ GDWD MXVW UHOLDEOH GDWD ZZZ DJULQWO FRP SMI Ecobloc Ergon 6-16-4 HC HEVF stretch-blowing/ filling/capping system. Containers worked: 4.5 and 6l PET containers of C’estbon natural water. Key facts: Compact solution for stretch-blow moulding, filling and capping large capacity PET bottles Does not require a rinsing machine and air belts between blower and filler Electronic control system of operations, motorised stretch rods and the use of high-efficiency valves controlled by flow meters Reduced energy consumption Energy-efficient IR preform heating lamps Two-stage air recovery system, which reduces energy costs for high-pressure compressed air production Filling valves that manage two speeds to fill homogeneously, without product spilling from the container. The duration of the filling cycles (slow or fast) can be managed in an intuitive way through the recipes in the human-machine interface (HMI Posyc) Reduced maintenance and management costs of the plant Easy-Cap: elevator and sorter Gravitational cap sorter, which takes the caps from a hopper and turns them correctly until they reach the bottling line. Key facts: Compact structure, made of AISI 304 steel, suitable for any layout solution Smooth and linear operation, that will only carry the caps that are in the correct position System suitable for different types of plastic caps User-friendly operator interface, which allows easy and efficient use of the machine by the operator ing 0.55 l PET bottles in 6x4, 5x3 and 4x3: this machine is currently installed in one of the two 48,000bph production lines of the Tianjin plant. The Chinese company extends over an area of about 100,000m2, of which 68,000m2 are occupied by bottling plants. The warehouse area alone occupies an area of 36,000m2 and allows Huihuang United (Tianjin) Food Co. to store more than 1.5 million packs of C’estbon-branded water, while ensuring its customers a daily delivery of 250,000 packs. Within the production area, six complete lines are currently installed for bottling and packaging various products in various pack formats. The new Ecobloc Ergon integrated system supplied by SMI, is part of a 6,000bph production line for 4.5 and 6 l PET containers branded C’estbon; the new plant is therefore added to the first stretch-blow moulder supplied by SMI in 2015 (in partnership with Sacmi), intended to produce the same bottle. While the SK 600 F shrinkwrapper supplied in 2013, dedicated to the packaging of 0.35 and 0.55 l PET bottles in film-only, is installed inside the 36,000bph line. Huang Gang, Plant Manager of Huihuang United (Tianjin) Food Co. Ltd. about the food & beverages market in the future: “I believe that in this sector there is a lot of room for development and innovation in China, given the constant growth of social well-being of increasingly large sections of the population and the improvement to people’s lifestyle. Companies operating in the food and beverage sector must pay more and more attention to the new needs of consumers, creating a wide and diversified offer of products made with advanced and sustainable processes for the well-being of the planet.” Huihuang United (Tianjin) Food and Zhuai Zhongfu are two industrial companies particularly attentive to the environment. Consequently, energy saving, and the reduction of carbon dioxide emissions have become one of the pillars of corporate social responsibility, which requires the increasingly massive use of new equipment and technologies designed to combine business efficiency and ecosystem protection. www.smigroup.it"},{"@ID":41 "BOTTLE ZONE EXHIBITOR LIST Booth # Booth # 1 Blow S16101 Koenig & Bauer Kammann (US), Inc. S21083 Acme Die Systems Pvt. Ltd. S10121 MAGIC MP SPA S13089 ! m|;um-ঞom-Ѵķ m1ĺ S12048 ;11-morѴ-vঞ1- \"uѴ S17097 Ѵhbm olru;vvक़u \"-mĺ ; $b1ĺ |7ĺ \"ঞ S18057 MHT USA LLC S19083 \" mvr;1ঞom S16089 MMC Packaging S13123 AND&OR AMERICA LLC S17049 NISSEI ASB COMPANY S19049 Atlas Copco Compressors LLC S16083 o o=v|;;u S12095 AutoTran, Inc. S13106 PETPlanet S12107 BENPAC Packaging S13107 $=oul $;1_moѴo]b;v |ĺ |7ĺ S16116 Ѵo oѴ7bm] $;1_moѴo]b;v S10104 Ѵ-vঞ1v -1_bm;u uor S17107 CAPrint Ltd. S20115 oѴhom u;=oulv S10119 COMPETEK S16097 PREVEN SRL S16077 Corvaglia Closures USA Inc. S13116 \" $;1_mb1-Ѵ !;vou1;v S10110 Custom Polymers, Inc. S10059 !ş Ѵ-vঞ1v -1_bm;u S19071 Danatronics S10076 !;vbm $;1_moѴo] Ő!$b Ѵo0-Ѵő S21075 Delta Engineering, Inc. S17061 !o0or-1ņ S19114 Dong-A Precision Ind. Co., Ltd. S12108 !o|_ );uh;]0- l0 S18076 Dyco Inc. S20089 \"_;m \r- m] oĺķ |7ĺ Ő -m]_oő S11123 m1ou; v|ol u;=oulv |7 S15117 SIDE America Corp. S16115 Ѵ; Ѵo Ő& $ ! \"ő S16107 \" _;lb1-Ѵv S17115 GDK S11071 \"ou1;Ѵbmh \"oѴঞomvķ S20083 -m]7om] ;v_-m m|;ѴѴb];m| tbrl;m| oĺķ |7ĺ S13101 $;1_Ŋ om] S10079 \t Ő ou|_ l;ub1-ő m1ĺ S20115 Tool Temp S12123 m|;um-ঞom-Ѵ -1h-]bm] o S18071 $ouv $;1_moѴo] uor Ő$ouv l;ub1-vķ m1ĺő S10071 -]lo_-m Ѵ-Ŋ -1_ |ĺ |7ĺ S12089 Uniloy S15057 \" l0 S19088 (-v-m|_- $ooѴ u-[v ($ |7ĺ S10107 u;v !;b=;m0;u] l0 ş oĺ S15115 Sigma Capseal S16071 olru;vvouv Ŋ ub-]- -v|-uub1- +ĺ b- \"ĺ ĺ S19106 KOKSAN PET PACKAGING S11115 \r olru;vvouv S18049 MARATHON HEATER PRIVATE LIMITED S10120 huom !00;u \t;;Ѵorl;m| -0ou-|ouķ m1ĺ S15111 METTLER TOLEDO S11118 Ѵr_-l-1 S13049 bm-|;1_ m1 S12111 American Tool & Mold, Inc. S10065 Movacolor S21111 ohb $;1_mb1-Ѵ -0ou-|ouķ m1ĺ S12071 \" ou|_ l;ub1- m1ĺ S13115 |ol-ঞom 7;-vķ m1ĺ S17083 ;| ѴѴ -m=-1|ubm] m1ĺ S15049 BBM America LLC S12056 $ $;1_moѴo]b;v l0 S11058 Big 3 Precision Products, Inc. S21089 Ѵ-vঞ0Ѵo \"uѴ S13065 oѴbm] \"|-];ņ ;;u -u7;m S10089 Ѵ-vঞv7 S15075 Compact Mould S13114 u;=oul \"oѴঞomvķ m1ĺ S15089 om|-bm;u |ol-ঞom \"v|;lv S18063 uo1o -1_bm;u m1ĺ S15097 CPS Resources, Inc. S17096 PTI S11107 + $ $;1_moѴo]b;v |7ĺ S16112 !;1_m;u Ѵ;1|uomb1v m7ĺķ m1ĺ S12106 Decosystem Srl S17100 RNA PRECISION INC S12115 Doloop (Putoksnis, UAB) S10118 !क़7;uv l0 S13100 Drinktec S12109 Sacmi USA S12101 ;\r $ !ƒķ S17089 SIAPI srl S18083 \"v|;lvķ m1ĺ S15083 \" ou|_ l;ub1-ķ m1ĺ S19096 Gatronova S11109 SMC Group srl S15113 u-r_b1v m|;um-ঞom-Ѵ uorķ m1ĺ S10052 Sukano Polymers USA S20107 ( Ŋ mmo-ঞ; mv|v|o@;u;7;Ѵm] l0 S16110 TECHNE S10049 -0;Ѵv S15119 $or -1_bm; uoh;uv \"ĺ ĺ S17077 Intravis, Inc S15063 $u-mvŊ |Ѵ-mঞ1 u;=oulv |7ĺ S10050 ş -1_bm;u )ouhv |7ĺ S12064 Urola S.C. S12119 KISAN PRECISION & IND S10074 );m|ou|_ $;1_moѴo]b;v S17071 Company Company"},{"@ID":28 "26 EVENT PREVIEW PETplanet Insider Vol. 25 No. 03/24 www.petpla.net Smart technology for caps and preforms Sacmi’s focus will be on its “digital revolution” in beverage cap and preform production. Offering ready-to-use solutions, the company emphasises tangible advantages in process efficiency, product quality, productivity and system user-friendliness. The latest generation of Sacmi CCM presses are claimed to achieve enhanced performance and user-friendliness, featuring predictive capabilities for both machine behaviour and process outcomes. In an exclusive preview, the company will illustrate how some of the key process parameters self-adjust on the basis of feedback from CVS control systems, designed and built by Sacmi. At the trade fair, Sacmi will showcase a CCM48 equipped with Smart Pack 2, enabling precise control over hydraulics, pellet insertion, and raw materials. Notably, a new ‘prediction’ button aids production drift anticipation and maintenance management proactively. Customers can leverage Cloud-based Sacmi Smart Care services to share machine data, while AI-enhanced vision systems facilitate the shift from quality control to process control. Sacmi’s AI-driven solutions address challenges such as problem anticipation, efficiency enhancement, and streamlined management. For instance, the IPS preform press range integrates the PVS156 vision system, while the CVs Software Suite has been developed to simplify defect classification, enhancing quality control efficiency. Sacmi ‘s digital developments prioritise monitoring machine and production process health and efficiency. The company offers solutions to facilitate customer transitions to new formats and standards, including tamper band slitting in post-processing downstream from compression moulding for swift adoption of tethered caps. These solutions, certified by major international brand owners, ensure profitability and future readiness. In cap and preform production, the company’s patented technologies like Cool+ mold in IPS presses have been developed to enhance productivity and long-term efficiency. On-site technical assistance and original spare parts available through Sacmi Shanghai are further claimed to guarantee optimal performance and return on investment for customers. www.sacmi.com polymetrix PET preform production in Swiss quality The Swiss family-owned company is a pioneer in the development and manufacture of PET preform moulds and continues to set standards in the industry. In over forty years, the company has built up extensive expertise in PET preform processes and technology. The experts at the high performance mould-maker share their knowledge throughout the entire production process, from the initial idea, through preform design and sampling, to mould manufacture and final product quality assurance. This is claimed to ensure that every customer achieves optimal results, enjoying an efficient design process, producing high-quality, cost-effective PET preforms and realising long-term savings in high-volume production. At Chinaplas, Otto Hofstetter AG will present its complete portfolio of high-quality injection moulds to industry professionals. This includes moulds for PET preforms from 2 to 192 cavities - for both top-entry and side-entry systems. The Swiss manufacturer also designs and builds moulds for medical applications, thin-wall packaging, cartridges, and in-mould labelling solutions. Sister company Otto Systems, focusing on special applications in the world of PET preforms, offers the PET Series and HOD Series turnkey production systems with clamping forces of 160 and 240t. The systems are claimed to meet high requirements for quality and energy efficiency. www.otto-hofstetter.swiss www.otto-systems.com Otto Hofstetter Hall 2.1 Booth C28 / Swiss Pavilion Sacmi Hall 2.1 Booth F61 Ot to Hofstet ter ’s 96-cavi ty side-entry PET preform moulds feature the advanced CavityLock technology, renowned for industry-leading performance and maximum availability. BEYOND THE HORIZON PROCESS SOLUTIONS FOR POLYMER RECYCLING AND SOLID STATE POLYMER UPGRADING Polymetrix, a Sanlian Buhler Company, provides process technology including EPCM services for the polymer recycling and manufacturing industry. Leading supplier of rPET systems and integrated rPET plants for single line capacities up to 70’000 tons per year. www.polymetrix.com www.slhpcn.com"},{"@ID":58 "PACKAGING / PALLETISING PETplanet Insider Vol. 25 No. 03/24 www.petpla.net 42 Interview with Jérôme Neveu, Packaging Product Manager at Sidel “The variability of rPET resin is a challenge for the packaging industry” At the BrauBeviale trade fair 2023, Sidel presented an impressive aseptic extra-light mini-PET bottle on a rather small area of its booth. This was of course due to the all-encompassing theme of beer at the trade fair. PETplanet Insider spoke to Jérôme Neveu, Packaging & Moulds Product Manager at Sidel, about current requirements, technical innovations, and the market situation of the PET bottle. PETplanet: The PET bottle is already a very mature beverage packaging. Nevertheless, there are always new challenges for it. In addition to design trends, material savings and recycling, many other aspects must be considered. How do you approach developing a new bottle in general? Jérôme Neveu: Many current PET packaging developments are driven by consumer trends, and the industry needs to respond to both an increased expectation of eco-friendly packaging as well as having a bottle that stands out on the shelf to differentiate its brand. We support the industry by designing distinctive and appealing bottles that achieve high sustainability credentials and which also comply with regulations such as the European Packaging and Packaging Waste Regulation. Packaging circularity and reducing greenhouse gas emissions are both at the centre of our innovation’s roadmap. The 3R approach – reduce, recycle, reuse – underpins the development of our solutions. Firstly, reduction of raw material and fossil fuel use and secondly, supporting manufacturers to increase use of reusable and recyclable bottles. In conjunction, we strive to offer packaging formats that are also efficiently made, saving costs and lowering energy consumption. We also consider packaging logistics, carefully selecting the primary, secondary and tertiary packaging options to ensure final product remains undamaged when it reaches the supermarket shelves. PETplanet: When you look back over the past few years, which parameters were particularly decisive for a bottle design and why? Jérôme Neveu: There is no doubt that sustainability has been the driving force behind bottle design in recent years, not least because of new packaging regulations such as the Packaging and Packaging Waste Regulation and Single-Use Plastic (SUP) Directive, which have had a huge impact on the sustainability practices of the packaging manufacturing industry. At Sidel, we’ve introduced specific solutions to help beverage manufacturers reach their sustainability goals. For example, our advanced heating and blowing techniques have enabled bottle lightweighting and the use of rPET resin. Innovative mould technologies and dedicated bottle design has assisted manufacturers to utilise a high-end bottle made from 100 per cent rPET and our experts have also supported producers to embrace returnable PET and glass bottles. Tethered caps have also become an industry staple as a result of the SUP directive, and we’re supporting beverby Heike Fischer"},{"@ID":33 "31 EVENT PREVIEW PETplanet Insider Vol. 25 No. 03/24 www.petpla.net Devolatilisation and decontamination technologies for recycling applications Gneuss introduces its latest Omni recycling machines at Chinaplas, offering devolatilisation and decontamination technologies for various recycling applications. These machines, integrated with Gneuss MRS Extrusion Technology, are designed for closed-loop recycling. Accompanied by rotary filtration systems, advanced vacuum technology, and online viscosity measurement tools, these recycling lines can be tailored for specific materials, ensuring high-quality output. With FDA and Efsa compliance and local approvals, the efficiency of the decontamination process is validated. The Omni series handles various materials including PET scrap, PS, PP, PE, and PLA, with applications ranging from thermoformed sheet production to odour reduction in polymers. Its compact design and automated control ensure operational flexibility and energy efficiency, reducing both operational costs and CO2 footprint. The MRS extruder features a multiple screw section for devolatilisation. This design is claimed to increase the surface area exchange rate, resulting in thorough decontamination and good mechanical properties of recycled materials. Additionally, Gneuss’ proprietary vacuum systems extract volatile impurities, while the RSFgenius filtration technology offers self-cleaning capabilities and filtration finenesses below 10 microns (1,200mesh). The system can be retrofitted to existing lines, enabling the use of more contaminated materials without compromising quality. The inclusion of the Online Viscometer VIS enhances quality control by precisely measuring viscosity during processing. Gneuss also provides flexible and digitally integrated measurement technologies tailored to specific industrial needs, ensuring fast delivery and compliance with quality standards. www.gneuss.com Ink removal in plastics recycling plants Inks and coatings play a crucial role in packaging but pose challenges in transforming packaging waste into a valuable resource. The growing demand for high-quality recycled materials underscores the need for efficient ink removal processes in recycling plants. Sorema has introduced a de-inking process upstream of extrusion, ensuring minimal ink residues in recycled materials. This advanced washing system, developed by the company, combines several factors. These include the feeding of the incoming material with volumetric or gravimetric dosage, the controlled and independent dosage of chemical additives and a high friction of the material in hot water with a defined residence time adjustable to each specific inks and material. In this way, customers have the opportunity to wash rigid and flexible plastic materials on a single plant. The recycling process is then completed by one or more rinsing and drying phases of the flakes, before an eventual extrusion into granules. The de-inking process, primarily applied to post-industrial waste, is being explored for postconsumer waste recycling plants. The company’s laboratory in Alzate Brianza offers testing facilities for customers to validate the process with their products and optimise chemical formulations and washing times. These tests can also be completed with the “in-house” extrusion phase to verify the achieved results. Sorema provides complete turnkey washing and recycling plants, managing all stages of the process, including wastewater treatment. Collaborating with sister company Teknodepurazioni Aquae, Sorema offers integrated solutions for wastewater treatment, incorporating mechanical filtration processes with high-speed centrifuges, sedimentation with chemical adjuvants and purification with ozone and activated carbon treatments. www.sorema.it www.previero.it Sorema Hall 2.1 Booth C74 Gneuss Hall 2.1 Booth H26 product development caps & closures design high cavitation moulds multi-component moulds closure production systems after sales service +43 5572 7272-0 | sales@z-moulds.com | www.z-moulds.com z NEXT SHOWS CHINAPLAS 2024 Shanghai, April 23-26th, 2.1A52 NPE 2024 Orlando, May 6-10th, W7443C INSPIRING PARTNER WORLDS FIRST 128 CAVITIES BELOW 2 SEC. CYCLE TIME !"},{"@ID":57 "The worldwide round trip with PET world in the Middle East In a spectacular project taking us well into 2024, we will be travelling in a wide variety of ways to various countries and regions of the Middle East with different mobile editors. There we will interview machine manufacturers, the supply industry, bottle and beverage producers, as well as PET recyclers and everyone involved in the process chain. What market-specific trends are there now or will arise in the future? What developments and technologies are in vogue on the consumer and plant construction site in some of the hottest regions of the world? What special requirements are there? What role do topics such as food safety, shelf life and sustainability play in PET packaging and how are companies preparing themselves for the coming years? This, and much more we will be discussing face-to-face with all the key players and then our results will be presented to you in a series of must-read reports in PETplanet Insider. Please join on this enchanting voyage to the world of PET in the Middle East. We look forward to welcoming you on board! Our previous Road Shows at a glance 2010-2011-2012-2013-2014-2015- 2016-2017-2018-2019-2020-2022 Interested in being visited? barton@petpla.net Autumn 2023 - 2024 6 countries numerous interviews with PET companies Sponsors to date Editour The Middle East Roadshow"},{"@ID":32 "MARKET SURVEY 30 PETplanet Insider Vol. 25 No. 03/24 www.petpla.net Cap producer Company name Gulf Packaging System Co (3P GG) Retal Industries Ltd Alpla Werke Alwin Lehner GmbH & Co KG Corvaglia group Postal address Telephone number Web site address Contact name Function Direct telephone number E-Mail Post Box 20266, Jeddah 21455, KSA +966 12 6360099 www.3p-gulf.com Mr Mohammed Najmuddin VP-Operations info@gulf-pack.com Epimitheos St. 6, Industrial Area A, Limassol, 3056, Cyprus +357 25 270 500 www.retalgroup.com Fuat Karaev Global sales director +370 620 899 77 fuat.karaev@retalgroup.com Mockenstraße 34 6971 Hard, Austria +43 5574 602 0 www.alpla.com Michael Feltes Global Director - Business Development IM +43 5574 602 0 michael.feltes@alpla.com Hörnlistrasse 14, CH-8360 Eschlikon, Switzerland +41 71 973 77 77 www.corvaglia.com Mr Vaidotas Bucevicius Director Sales & Service +41 71 973 77 10 v.bucevicius@corvaglia.ch Product Range One-piece closures for beverages (Yes /No -If Yes, please specify material) Yes, HDPE Yes, HDPE Yes, HDPE Yes, HDPE Two-piece closures for beverages (with liner) (Yes / No -If Yes, please specify material Yes, PP with EVA liner No No No Applications relevant to PET containers (e.g. CSD, water, juice, beer, etc.) CSD, water, juice, milk, oil CSD, water, dairy, juice, CSD, water, juice, dairy CSD & carbonated bottled water, still bottled water (pressurised & non-pressurised), sensitive drinks (juices, teas, fl avoured waters, ...), sports & energy drinks, others (dairy, edible oil, …) Neck fi nishes available as standard 29/25, 1881, 30/25, 1816, 38mm, 48mm 1881, 1810, BPF, 48/41, 29/25, 38mm 3 starts, 26/22 GME30.40 26/22 (GME30.28, GME30.37, GME30.40); PCO1881; PCO1810; 38mm 2-start (GME30.29); 38mm 3-start (GME30.25); glass (MCA 7,5R); SPI-necks Several standard fi nishes from 25 to 48mm, e.g. Cetie standard necks GME 30.21 to GME 30.26, GME 30.28 to GME 30.33, GME 30.36 to GME 30.43, GME 32.03, GME 32.04 Printed caps available (Yes / No) Yes Yes Yes Yes Colour matching service (Yes / No) Yes Yes Yes Yes Child-proof closures (Yes /No) No No Yes No Push-Pull / sports caps (Yes / No) No No Yes Only in Mexico Special comments/special closures (e.g. tethered cap solution, fl ipt-tops, drinking spouts, lightest cap for 28mm PCO, 26mm for water etc including non-beverage closures...) Colour printing up to 3 colours, UV & IR laser engraving available; caps embossment upon request; tethered closures available for various neck fi nishes Non aerosol pumps in various neck fi nishes, buckets and canisters for various app., tethered cap solutions for 26/22, 1810, 1881, 38mm neck fi nishes; CRC caps; standard packaging for pharma app.; 2-chamber caps; bi-and multicomponent IM; custom-made closures Closure manufacturing sites in Switzerland, Mexico, USA. Corvaglia designed caps are available around the world via our partner network. Tethered caps for carbonated and non-carbonated drinks according to EU Directive 2019/904 Special patented closures or marketing features Yes Digital printing capabilities installed in our production sites Company name Uner Plastik AS Bericap Holding GmbH Has Plastik San Tic. A.S. Postal address Telephone number Web site address Contact name Function Direct telephone number E-Mail Gebze Plastikciler OSB 1.cad 11.sok No.3 41400 Kocaeli/Turkiye +90 262 751 3400 www.uner.com.tr Cumhur Filik Sales and Marketing Director +90 530 265 0663 cf@uner.com.tr Kirchstrasse 5, 55257 Budenheim, Germany +49 6139 2929 0 www.bericap.com Mr Thomas Schmidt Group Marketing Director +49 6139 2929 0 thomas.schmidt@bericap.com Firuzkoy Bulvari No 50 - 34325 Avcilar Istanbul, Turkey +90 212 695 50 00 www.hasplastik.com Unal Haspaylan Commercial Director +90 212 695 50 00 info@hasplastik.com Product Range One-piece closures for beverages (Yes /No -If Yes, please specify material) Yes, HDPE/LDPE/PP with recyclable content available Yes, HDPE Yes , HDPE Two-piece closures for beverages (with liner) (Yes / No -If Yes, please specify material No Yes, PP with EVA liner or HDPE with various liner types yes , HOD type only Applications relevant to PET containers (e.g. CSD, water, juice, beer, etc.) Beverages, CSD, bottled and 5G water, juice, dairy, edible oil, food, beer, industrial segments, etc. hotfi ll/aseptic/isotonic app. available Beverage: CSD, water, dairy, juices, energy drinks, teas, syrups, beer / Food: Ketchup, mayonnaise, spreadables, edible oil, soy & vinegar CSD, water, juice, energy drinks, beer etc. Neck fi nishes available as standard 28mm PCO-1810/1881, 29/25, 26/22, 30/25, 38mm 2/3 start hotfi ll/coldfi ll, 33mm 2 start hotfi ll, 29/21 1 or 2 pcs + 32/28 1 or 2 pcs snap-on for edible oil, 48/41, 55mm 5G, handles for 38mm+48mm+55mm or lean/lateral handles for edible oil bottles 26mm: PET 26/22 GME 30.28, GME 30.37, GME 30.38, GME 30.40, PET 26/21 GME 30.32; 28mm: PCO 1810, PCO 1881; 29mm: PET 29/25 GME 30.26, PET 29/21 GME 30.33, 30mm: PET 30/25 GME 30.21, 33mm: PET 33/12 GME 30.30, PET 32/2 GME 30.36, PET 32/15, 38mm: PET 37/32 GME 30.29, PET 37/16, PET 37/15, PET 38/33 GME 30.25, 48mm: GME 30.43 Tethered 26mm ( GME 30.40), tethered 29-25mm , tethered 1881, 26mm, 29-25mm, 30-25mm , 38mm, 48mm, 1810, 1881, HOD 55mm ( also non-standard solutions upon request) Printed caps available (Yes / No) Yes, printing available in up to 4 colours Yes (digital and tampon print) Yes Colour matching service (Yes / No) Yes, any colour can be matched with 99% accuracy Yes Yes Child-proof closures (Yes /No) No Yes No Push-Pull / sports caps (Yes / No) Yes Yes Yes Special comments/special closures (e.g. tethered cap solution, fl ipt-tops, drinking spouts, lightest cap for 28mm PCO, 26mm for water etc including non-beverage closures...) Design, improvement, and production of caps with our own Uner moulds. Tethered, light-weighted, digital printed, spouted caps, and many others - ClipAside tethered cap introduced for all relevant neck fi nishes across Europe - Mono-material sportscap range with special TE function (Biarritz, Mayence, Monet) - Bericap Falcon: Light-weight SnapCap for PET 26/21 necks - Extensive mono-material closure range for edible oil Tethered caps ( 26 GME 30.40, 1881, 29-25), fl ip top caps, lightest 1881 caps for high CSD, global technical service available Special patented closures or marketing features All closures designed and patented worldwide by Uner Plastik AS Silicone-free non-drip valve for sport caps and fl ip top closures HOD caps for 5 gallon, laser marking inside caps (alphanumeric codes, artwork etc), engraved logo designs"},{"@ID":3 "No.3 2024 www.petpla.net D 51178; ISSN: 1438-9452 25 . 03 . 24 M A G A Z I N E F O R B O T T L E R S A N D B O T T L E - M A K E R S I N T H E A M E R I C A S , A S I A , E U R O P E A N D A L L A R O U N D T H E P L A N E T PETplanet is read in 159 countries MARKETsurvey Suppliers of caps, cap systems and cap inspection systems Page 27 EDITOUR Page 24 Page 32 Page 10"},{"@ID":47 "EVENT REVIEW PETplanet Insider Vol. 25 No. 03/24 www.petpla.net 45 Review Petcore annual conference - The PET market under the microscope Challenging times The annual Petcore Europe conference took place in Brussels on February 7&8, 2024. The conference is becoming increasingly important and is growing from year to year. It is an important platform for European and international companies active in the PET plastic packaging and recycling industry to obtain international market analyses and the latest updates on EU regulations. This year has proved particularly challenging for Europe and global markets generally. Companies are still struggling with high energy costs brought about by the continuing conflicts in Ukraine and Gaza. Attacks on shipping in the Red Sea by Houthi militants have forced companies to divert ships from using the Suez Canal which has greatly increased costs of transportation. Consumers are cutting back on spending due to high inflation. Elections in the UK, EU and the United States are also expected to contribute to political uncertainty in the West. Finally, and more specifically, there is considerable concern in the plastic packaging and recycling sector that many EU regulations are unhelpful and not always sensible. As a result, there was a wide range of topics to discuss. After the 330 guests were welcomed by Roberto Bertaggia, Executive Director of Petcore Europe, and Antonello Ciotti, President of Petcore Europe, the first day began with Session1 - Market Dynamics. Patrick Bouzekri, Executive Vice President at SBA-CCI, Inc., offered his perspective on the worldwide PET packaging resin production growth rates in % p.a. from 20122027. From 2022 to 2023, the growth rate fell from 4.1% to 3%. The forecast from 2023 - 2024 - 2025 is steady growth of 2.3% until 2024 and 2.4% until 2025. From 2025, Bouzekri expects the growth rate to fall sharply by 3.8% by 2027. He puts the global nominal PET packaging resin capacity for 2023 at 45.5 million tonnes. It is expected to grow to 55.3 million tonnes by 2027. China in particular will see an annual increase (2023-2027) of 7,700kt and India an increase of 1,650kt. Bouzekri sees packaged water and packaged CSDs as important applications. He predicts a more relaxed situation in 2024. After a negative growth rate for packaged water in Western Europe of -0.9% in 2023, he sees growth recovering slightly to 0.3%. The average global growth rate for packaged water will be 3.3% in 2024. Above-average growth is seen in Asia at 5.9% and Africa at 4.1%. The percentage trend for CSDs is very similar, but not quite as high. The growth rate here is 0.7% in Western Europe in 2024 and 4.2% in Asia. The global average is 2.4%. These two beverage applications and the production capacities for PET resin show the clear trend in the growth markets of Asia and Africa. Bouzekri added that he expects a potential shortage of PTA in Europe as both Ineos and IVL shutdown PTA assets. In the event of a PTA shortage, brand owners will switch to recycled PET material on a large scale, which will boost the rPET market but also put pressure on it. This last piece of information was the perfect introduction for the next speaker, Nicholas Hodac, Director General of Unesda. He gave some interesting figures on Unesda before discussing the challenges of EU legislation for the soft drinks sector. He explained that 1.8 million people in the EU are directly or indirectly employed in the soft drinks industry, adding that the soft drinks value chain accounts for 1.29% of the EU’s GDP. Last but not least, he mentioned 34 billion euros in taxes paid to EU Member States through the soft drinks value chain. He then explained Unesda’s sustainability commitments. He began by talking about their vision of circular packaging. Unesda supports the plan to have 50% recycled material in plastic packaging by 2025 and 100% recyclability of the packaging. By 2030, 90% of all packaging should be collectable and 100% rPET or renewable PET should be used for PET packaging. Finally he explained that Unesda also supports the increased use of reusable beverage systems. He then presented and commented on the most important EU regulations, starting with the EU Green Deal. This Deal has the ambition to make Europe the first climate-neutral continent and it includes many actions to reduce emissions, to decarbonise transports, and to improve energy efficiency. He stated that as a part of the Green Deal, the Commission developed an action plan to move towards a more circular European economy. A key element of the plan is the shift towards more sustainable packaging, including in the food and drink sector. Hodac also briefly mentioned the Single Use Plastic Directive (SUPD), which was implemented in 2021. Here, he emphasised the Recycled Content calculation and the litter clean-up costs. He added a proposal to ban recycled content not coming from the EU. Regarding the PPWR he called for a mandatory DRS. Priority access to food-grade recyclates in order to meet the recycled content targets. In addition he asked for the complementarity of reuse and recycling with well-designed exemptions from the reuse targets. In his view, refill is one of the solutions to achieve the reuse targets and he is opposed to a ban on single-use plastic grouped packaging. Regarding recycled content, he added that Unesda is calling for an open market with a level playing field (e.g. well-designed certification schemes for rPET, both for EU and non-EU feedstock, as an alternative to introducing limits for rPET). At the end of his presentation, he looked ahead to the coming year, noting that new EU Commissioners and a new European Parliament will be elected. “There is a lot of uncertainty about their priorities, but for us the main focus must be on the proper implementation of the transposition of the adopted EU legislation,” he concluded. www.petcore-europe.org Patrick Bouzekri, Executive Vice President at SBACCI, Inc. Nicholas Hodac, Director General of Unesda"},{"@ID":42 "PACKAGING / PALLETISING PETplanet Insider Vol. 25 No. 03/24 www.petpla.net 40 Delta Engineering helps smooth the fl ow and boost effi ciency of new bottle blowing lines Delivering value – fast by Ruari McCallion Califia farms invested in automation to save time, cut costs and boost environmental performance in its growing non-dairy drinks production. When Californian company Califia Farms decided to install KHS automated bottle blowing lines, it was recommended to contact Belgian company Delta Engineering for its bottle conveying systems. Delta had recently opened a facility in Georgia, USA, so it was able to design a system that integrated smoothly with the preform stretch blow-moulding line and provide in-country expertise and support. The strongly rising demand for plant-based alternatives to dairy milk, such as oat, almond and coconut milk drinks, has seen Califia Farms grow rapidly in recent years. Non-dairy ready-to-drink coffee and creamer sales spiked nearly 50 per cent in 2021, compared with the year before, and plant-based milk products are up 25 per cent from pre-Pandemic levels. Against this background, Califia successfully placed a multi-million US Dollar funding round in 2020, part of which it put to good use in modernising and upgrading its main production facility, near Los Angeles, California. Environmental responsibility Califia was founded in 2010 by the late Greg Steltenpohl and is now led by CEO Dave Ritterbush, has always had a focus on environmental responsibility. It does not grow its raw materials but sources them as locally as it can. Over 80 per cent of the almond milk it buys are grown and processed within 20 miles of its bottling lines, for example. The investment in the new lines is another step on the road. “The project involves the complete transition of our facility’s bottling lines, from using pre-blown bottles to blowing our own on-site. The objectives were two-fold: to achieve cost savings and to reduce emissions,” said Tyler Crow, Senior Plant Engineer. “Previously, we used a depalletiser to feed our packaging lines with the preblown bottles. As our volumes grew, this became more and more expensive – we were receiving double-digit truckloads of empty bottles each week.” Califia now fills approaching 60 million bottles a year, selling them on to its major markets in Los Angeles, New York, other parts of the USA and further afield. Transporting 60 million preblown bottles is an expensive and environmentally insensitive way of, essentially, moving fresh air, although installing a preform blowing line could be seen as adding complexity to an operation that had previously been simply about mixing and filling. Objectives: cut traffic, cut carbon, cut costs and improve supply security “When we ran the numbers, it quickly became clear that we could save a lot of money and carbon emissions by blowing bottles from preforms here, on site. We would be able to get 90 per cent of those trucks off the road,” Tyler explained. The discussion of possible gains from automation and blowing onsite became more urgent during the Covid pandemic period, when reliability of bottle supplies was severely impacted across the whole food and beverage industry. In the USA and across the world. Califia handled the situation pretty well and was able to maintain fill and delivery schedules at 98 per cent, according to an Delta Engineering South Hall, Level 1 Booth S17061 Bottle Zone"},{"@ID":7 "25 EVENT PREVIEW PETplanet Insider Vol. 25 No. 03/24 www.petpla.net Systems enhancing plastic industry efficiency Eisbär, a leading manufacturer of auxiliary equipment for the plastics industry, has unveiled a range of cutting-edge systems aimed at bolstering quality and productivity in plastic manufacturing processes. Specialising in solutions to prevent condensation on cooled moulds and facilitate the drying of plastic resin, Eisbär’s systems are engineered to handle high throughputs of up to 5,000 kg/h. As the demand for recycling post-consumer plastics continues to surge, Eisbär has developed specialised systems tailored to meet the unique requirements of recycled plastics. These systems efficiently process flakes, clean different materials, and contribute to the production of higher-quality regranulated plastics. The Eisbär Crystallizer: An essential component for processing amorphous PET flakes, the crystalliser treats flakes in a hopper with rotating stirring, achieving optimal results at temperatures between 130-140 °C for 1-3 hours. Eisbär dryer GDS: Crucial for residual moisture adjustment and material cleaning, the GDS dryer employs advanced drying technology with a slowly rotating adsorption wheel with honeycombed tunnels, achieving a residual moisture level of 30 ppm. Eisbär mixing and dosing units: Available in gravimetric or volumetric options and various sizes, these units are claimed to be essential for mixing virgin and recycled materials to achieve good product results, especially for converters using recycled materials. Eisbär conveying systems: The company’s expertise enables conveying of up to 5,000 kg/h for all free-flowing materials, accommodating variations in bulk density, flow properties, and dust content. Eisbär operates a state-of-the-art testing centre where customers can conduct comprehensive tests with granules or flakes. Materials are processed in a material dryer for a specific time and temperature, then analysed for contamination in a chemical institute. www.eisbaer.at Closure advancements for enhanced cycle times This year, Z-Moulds and Eisbär once again share a joint booth at Chinaplas. Z-Moulds will spotlight closure advancements and new technologies aimed at enhancing competitive advantage in cycle times and mould dimensions. In the realm of closure developments, the company is highlighting the 26mm GME 30.40, a solution poised to shape the future, alongside lightweight solutions for CSD closures. When it comes to novel technologies, Z-Moulds will be introducing their new pitch size. The 55mm Pitch, featuring patented z-slides, has enabled the construction of a 128-cavity mould measuring 696mm in width and 1.196mm in height. This reduced the closure’s fall height, compared to the market standard, by almost 500mm, resulting in a 0.12 second decrease in fall time. Additionally, the weight of the moving half was decreased by 45%, compared to market standards that contributed another 0.08 second reduction in opening/closing times. These advancements collectively enable Z-Moulds to achieve lower cycle times. For instance, the cycle time of a 26mm flat water closure could be reduced to 1.85 seconds. www.z-moulds.com Z-Moulds Hall 2.1 Booth A52 Eisbär Hall 2.1 Booth A50 PET crystalliser"},{"@ID":13 "EDITOUR 11 PETplanet Insider Vol. 25 from imports of recycled materials and increasingly towards local recycling. The Fujairah-based recycler Horizon Technologies FZC, for example, received authorisation for rPET for use in food contact this year. Aswin Puthran surmised that the upswing is likely to come primarily from a growing demand for PLA. “If PLA becomes established, the recycling infrastructure for PET will automatically change and improve. On the government side, the topic of recycling and the use of recycled material will also be pushed, albeit currently without a defined minimum percentage per packaging, but it will in any case support the customer-generated demand for packaging with a recycled content.” The only exciting thing that remains is the question of sorting by type, as there are currently hardly any options for this. But this is also set to change soon. www.petcogulf.com Only from KHS: freshness protection which is 100% bottle-to-bottle recyclable. With FreshSafe-PET® YG JCXG EQODKPGF VJG DGPGƂ VU QH 2'6 CPF INCUU DQVVNGU +VU YCHGT VJKP KPUKFG NC[GT QH INCUU MGGRU DGXGTCIGU HTGUJ HQT NQPIGT s CPF OCKPVCKPU VCUVG CPF XKVCOKPU 6JG EQCVKPI KU CNUQ HWNN[ EQORCVKDNG YKVJ '2$2 FGUKIP IWKFGNKPGU HQT TGE[ENKPI CPF KU TGEQIPK\\GF D[ VJG #24 6JKU KU [GV HWTVJGT RTQQH QH JQY YG CTG EQPUVCPVN[ TGKPXGPVKPI the PET bottle. RGV MJU EQO HTGUJUCHGRGV PET BOTTLE. THE REVOLUTION OF THE IT DOESN’T COMPROMISE ON RECYCLING EITHER. Aswin Puthran shows the finished rPET juice bottle. Aswin Puthran in production with a 5 l edible oil PET bottle"},{"@ID":24 "BOTTLING / FILLING PETplanet Insider Vol. 25 No. 03/24 www.petpla.net 22 Next generation of sustainable aseptic filling systems The Kirin Beverage Company Co., Ltd. (KBC) Shonan factory upgraded two PET bottle aseptic filling lines in 2022 and 2023 respectively. This new system utilised Dai Nippon Printing Co., Ltd. (DNP) Two-Step Sterilisation, which enables high productivity, low cost and reduced environmental impact while maintaining high aseptic quality for low-acid beverages. Relationship between KBC and DNP The KBC Shonan factory is located in a privileged location about 50km from the centre of Tokyo and has been producing beverages since 1973. In 1994, KBC and DNP jointly developed an aseptic PET bottle filling system that sterilises containers with hydrogen peroxide gas and began producing milk tea. Apart from this, KBC has manufactured a variety of products, including barley tea, green tea, lemon tea and functional beverages, and distributes them mainly in the Tokyo metropolitan area and to eastern Japan. In 2008, KBC and DNP developed a synchronised system that directly connects a blow moulder with an aseptic filler. This was the first system in the world to utilise the heat remaining in the bottle after the blow moulding process for hydrogen peroxide gas sterilisation of the bottle. This synchronised system has since become the standard equipment for aseptic PET bottle filling systems in Japan and has also been installed in China, South Korea and Southeast Asian countries. From 2021 onwards, the two PET bottle aseptic filling lines in operation at the KBC Shonan factory were to be upgraded sequentially. For this major equipment upgrade, KBC had three requirements. These were (1) highly productive high-speed lines, (2) energy and space savings, and (3) the ability to guarantee extremely reliable aseptic quality for low-acid beverages. To fully meet these requirements, Aseptic Systems (APS), the company in charge of DNP’s aseptic division, proposed a two-step sterilisation solution, which was adopted. Features of DNP two-step sterilisation The existing aseptic PET bottle filling line, installed in 2000, had a speed of 54,000 bph. The two-step sterilisation has successfully maintained this speed while reducing hydrogen peroxide, electricity, water consumption and footprint as well as saving manpower. There are five main reasons for this as follows: The stretch blow moulder and aseptic filler were integrated, and all air conveyors were removed. KHS’s stretch blow moulders were replaced by the latest energy-saving Series V. Utilising preform decontamination as the mainstay of container sterilisation and minimising bottle decontamination. As a result, hydrogen peroxide consumption for bottle decontamination was reduced by about 40% compared to the standard system. High sterility was achieved by decontaminating the preform and the bottle interior and exterior respectively. The total sterilisation effect of the two decontaminator is more than 9 LRV. It is also possible to adjust the sterilisation effect of preforms and bottles according to the guaranteed sterilisation level required for the product. For example, production can be carried out by preform decontamination only. Instead of a sterile water rinser, an inverted hot air rinser for bottles was installed. This hot air rinser simultaneously activates the hydrogen peroxide and removes foreign matter in the bottles. DNP’s new SIP (Sterilisation In Place) method ‘F0 Solution’ for the aseptic filler and liquid processing equipment was also installed. It was used in all aseptic tanks, UHT sterilisers, filling valves and filters KBC Shonan factory Aseptic filling systems for PET bottles"},{"@ID":5 "imprint EDITORIAL PUBLISHER Alexander Büchler, Managing Director HEAD OFFICE heidelberg business media GmbH Hubweg 15 74939 Zuzenhausen, Germany phone: +49 6221-65108-0 info@petpla.net EDITORIAL Kay Barton Heike Fischer Gabriele Kosmehl Michael Maruschke Ruari McCallion Anthony Withers Editorial & WikiPETia. info petplanet@petpla.net MEDIA CONSULTANTS Martina Hirschmann hirschmann@petpla.net Johann Lange-Brock lange-brock@petpla.net phone: +49 6221-65108-0 LAYOUT AND PREPRESS EXPRIM Werbeagentur Matthias Gaumann www.exprim.de READER SERVICES reader@petpla.net PRINT Chroma Druck Eine Unternehmung der Limberg-Druck GmbH Danziger Platz 6 67059 Ludwigshafen, Germany WWW www.hbmedia.net | www.petpla.net PETplanet Insider ISSN 1438-9459 is published 10 times a year. This publication is sent to qualified subscribers (1-year subscription 149 EUR, 2-year subscription 289 EUR, Young professionals’ subscription 99 EUR. Magazines will be dispatched to you by airmail). Not to be reproduced in any form without permission from the publisher. Note: The fact that product names may not be identified as trademarks is not an indication that such names are not registered trademarks. 3 PETplanet Insider Vol. 25 No. 03/24 www.petpla.net Dear readers, On March 3, Tuesday evening, the EU announced its plan to ban single-use plastic packaging by 2030. Food packaging is particularly affected. For the drinks sector, reusable systems in particular are to become mandatory. The member states are to set up deposit systems for single-use plastic bottles and beverage cans. The packaging industry is also to comply with mandatory reusable quotas in future. Packaging made of paper and other materials such as wood or wax, on the other hand, will remain permitted as far as possible. The industry is critical of this ban and has repeatedly pointed out that the ban will lead to a switch to other less environmentally friendly packaging materials. But will the industry be heard? The approval of the Member States for the new directive is not certain. Italy’s government is already voting against the law and the German government has not yet adopted a clear position on the new rules. If Germany were to abstain in the vote, the required majority would not be guaranteed. At the Petcore conference, which took place in Brussels in February, these considerations were noted with excitement. Read the first part of the follow-up report on p. 45. So, let’s wait and see and turn our attention to two very important trade fairs: Chinaplas is set to unfold at the National Exhibition and Convention Center (Shanghai) from April 23-26. Spanning an expansive exhibition area of over 380,000m2, this event is poised to host more than 4,000 exhibitors and attract over 250,000 visitors from around the world. The exhibits on display will range from raw materials to cutting-edge machinery and equipment. (p. 24 ff) And of course, the NPE show. It takes place from May 6-10, 2024 in Orange County Convention Center (OCCC), Orlando, Florida. With more than 1 million square feet of exhibit space, including six technology zones and over 2,000 exhibiting companies, NPE will bring the latest innovations in plastics, materials and manufacturing solutions designed to advance business together in one location. PETplanet has selected PET relevant exhibits, and you will find them on page 32 ff. We look forward to meeting you at our booth at the NPE! Stop by at the Bottle Zone! In addition to the two trade fairs, the PETplanet team is travelling worldwide, our Middle East Roadshow is in full swing and there are numerous other conferences taking place this spring. We’ll keep you updated, and in the meantime we wish you a good start to the season! Yours Heike Fischer Petcore conference, Brussels, Belgium"},{"@ID":40 "S10120 S10121 S11118 S10119 S12119 S15119 S15117 S16116 S16112 S15115 S15113 S15111 S16101 S16097 S17077 S18076 S17096 S17100 S16110 S12111 S12109 S13106 S12107 S13114 S12115 S13116 S10110 S11109 S12101 S13100 S12108 S11107 S12106 S10104 S10076 S10074 S10059 S10052 S10050 S10118 S10107 S16115 S21111 S21089 S16107 S15097 S15089 S15083 S15075 S16077 S16071 S17071 S16083 S17083 S18083 S18071 S18063 S18057 S18049 S19083 S20083 S21083 S21075 S16089 S10071 S11058 S11071 S10089 S12071 S19096 S10079 S19049 S19071 S11123 S12123 S12095 S12089 S11115 S10049 S12056 S12064 S13123 S13115 S13107 S17115 S19114 S20115 S19106 S19088 S20089 S20107 S17107 S17097 S17089 S15063 S15057 S15049 S17061 S17049 S13101 S13089 S13065 S13049 S10065 S12048 BOTTLE ZONE, SOUTH HALL Supported by:"},{"@ID":2 "PETnews 6 NEWS PETplanet Insider Vol. 25 No. 03/24 www.petpla.net Eastman partners with mechanical recycler Dentis Group/Nord Pal Plast to unlock feedstock for its facility in France Eastman has announced a long-term agreement with Nord Pal Plast SA, part of Dentis Group, a leading Italian multinational company specialising in the recovery and mechanical recycling of PET packaging waste. Through their mechanical recycling sites in France (Nord Pal Plast SA), Spain (PET Companía Para Su Reciclado) and Italy (Dentis Recycling Italy Srl), Dentis will provide 30,000 metric t/a of rejected PET post-consumer waste to Eastman. These materials are planned to be recycled at Eastman’s molecular recycling facility in Port-Jérôme-sur-Seine, France. Eastman’s announced molecular recycling facility in Normandy is set to become the world’s largest material-to-material molecular recycling plant. At full capacity, after phase 1 and phase 2, the facility will have the capacity to recycle more than 200,000 t/a of hard-to-recycle polyester waste. Eastman’s molecular recycling technologies is claimed to allow for the breakdown of hard-to-recycle waste into its molecular building blocks. These building blocks are then reassembled to create first-quality materials without compromising performance. www.eastman.com MHT Mold & Hotrunner Technology AG and Z-Moulds GmbH join forces MHT Mold & Hotrunner Technology AG and Z-Moulds GmbH announced a collaborative effort aimed at advancing their respective businesses. MHT, headquartered in Hochheim am Main, Germany, is a well-known company renowned for its expertise in the field of packaging solutions. The company specialises in the development, manufacturing, and distribution of top-notch preform injection moulds and hot runners specifically designed for the beverage packaging industry. Notably, MHT has been a member of the Krones Group since 2018, solidifying its position as a key player in the industry. On the other hand, Z-Moulds, located in Dornbirn, Austria, has carved a niche for itself by delivering high-performance injection moulds tailored to meet the demanding requirements of the beverage packaging sector. Jeremie Cuny, Business Development Manager of MHT said: “MHT has diligently developed a premium hotrunner engineered to cater to the specific needs of this exacting industry. By combining Z-Moulds’ cold-half technology with MHT’s premium open gate hotrunner, we are confident that we will establish new benchmarks for top-quality closures.” www.mht-ag.com www.z-moulds.com Indicor announces acquisition of Agr Indicor, LLC., a diversified industrial company providing specialised, mission-critical technologies to customers across a variety of niche markets, announced the acquisition of Agr International, a provider of quality and process control technologies serving beverage packaging customers globally. Agr provides technology and services that support global glass and plastic packaging customers in ensuring their quality, productivity, and sustainability goals are met. The company’s technology includes laboratory and inline equipment and automated process systems that allow customers to meet the quality management needs of container manufacturers and brand owners. Agr’s management team will continue to lead the business from its Butler, PA, USA headquarters. Agr’s name, brands, and operational footprint will not change as a result of the transaction. The business will be led by Agr’s President, Sudha Jebadurai. www.indicor.com www.agrintl.com Visit us at our booth S20115"},{"@ID":34 "EVENT PREVIEW PETplanet Insider Vol. 25 No. 03/24 www.petpla.net 32 Focus on green issues, recycling and energy efficiency Pegaso Industries, the holding company headquartered in Borgoricco, Italy, and encompassing Plastic Systems, PET Solutions, Blauwer, Ergomec, and Steel Systems, is gearing up for active participation at both the Chinaplas in Shanghai and NPE in Orlando. Central to its showcase are innovation and sustainability, with a specific emphasis on green issues, recycling, and energy efficiency. Chinaplas serves as a pivotal platform to introduce developments in auxiliary automation for plastic material transformation across various sectors including automotive, medical, beverage, packaging, electronics, and cosmetics to the Asian market. Plastic Systems Shanghai Co. Ltd., founded in 2006, has emerged as a significant player in the Asia-Pacific region, boasting over 80 employees and an annual production of more than 100 systems. DR9 series new generation dryer The DR9 Series by PET Solutions represents a development in dehumidifier technology which particularly addresses the quality of rPET materials. Featuring a dual filter system, it achieves a remarkable 47% increase in filtration capacity, streamlining maintenance operations. In addition, the dehumidifier achieves a 15% reduction in energy consumption due to their new patented process design, with fans positioned after the drying towers. The larger size of the exchanger provides a 45% increase in cooling capacity. The dehumidifier’s efficiency is further accentuated by its ability to recover 25% of energy during rPET processing, eliminating the need for an oil condenser and contributing to overall system energy savings. DWC series rotor technology dryer Equipped with rotor technology, the DWC series by Plastic Systems is claimed to ensure high-level performance in dehumidification, catering to medium-scale productions with maximum efficiency and versatility. The DWCompact models employ rotor technology, offering capacities from 20 to 280m3/h and allowing for the management of hopper loading and machine transformation. Their sophisticated microprocessor control combined with a weighing system and intuitive operator interface make them ideal for various sectors, including optics and pharmaceuticals. At NPE, Pegaso Industries group will be present, along with all its companies, in the West Hall with a booth of approximately 400m2 where it will be possible to view the results of the latest patented developments. DRV series continuous vacuum drying system The DRV Series by PET Solutions integrates continuous vacuum drying technology, incorporating four hoppers and a hot air circulation system to accelerate dehumidification and ensure uniform processing. This system offers precise control over resin temperature, optimising material properties for injection moulding: 1st hopper: preheats the resin, gently removing surface moisture from the material. 2nd hopper: heats the resin to energise the material. 3rd hopper: using vacuum technology, creates a low-pressure environment favourable to moisture evaporation from the material. 4th hopper: increases the resin temperature for fine adjustment before injection moulding. SDS series dry-cooler Designed for closed-loop water cooling using ambient air, the SDS series dry-coolers from Blauwer feature high energy efficiency, contributing to reduced energy and water treatment consumption. With various models available, ranging from 60 to 1,600 kW, these dry-coolers are claimed to offer flexibility to meet diverse production needs. The main features of this solution include the high-efficiency finned aluminium heat exchanger with copper pipes, axial fans with speed control, and a microprocessor control with a 7” touchscreen display and alarm history. www.pegasoindustries.com Pegaso Industries Hall 2.1 Booth F81 Pegaso Industries West Building, Level 2 Booth W3331"},{"@ID":35 "33 EVENT PREVIEW PETplanet Insider Vol. 25 No. 03/24 www.petpla.net EVENTpreview NPE 2024 NPE2024 will open on Monday, May 6, 2024, at the Orange County Convention Center with 2,000+ exhibiting companies and more than 55,000 expected attendees from all sectors of the global supply chain. The Plastics Industry Association (Plastics) officially unveils more than 90 educational sessions ahead of the show. Attendees with the Expo Pass registration will have access to more than ever before with over 75 education sessions located on the show floor in the all-new Spark Stages. Highlighting advanced artificial intelligence applications, the future of plastics, business productivity & profitability, sustainability & advancement of the circular economy and more, attendees are encouraged to tailor their education schedules to meet their personal business needs. The three Spark Stages are as follows: Bottling Stage: Attendees will discover advancements in technologies for the beverage and non-food segments. Innovation Stage, sponsored by the Plastics Hall of Fame: Participants will witness the latest in electrification, Industry 4.0, thermoplastic alchemy, UV blockers, engineered thermoplastics and other exciting topics. Sustainability Stage, sponsored by Nova Chemicals: Explore how the entire plastics supply chain is developing solutions to improve efficiency, reduce materials loss, use less power and more. Off the show floor, and for the first time in its history, NPE will host some of the industry’s biggest and brightest speakers during: Industry briefings featuring thought leaders in the automotive, building and construction, consumer goods, and medical and packaging industries. Comprehensive plastics industry briefing that will include timely business updates from every market segment, including global insights on the economic impact of plastics, market trends, future forecasts on recycling and a review of the Global Plastics Treaty. Market Trends sessions with insights into the U.S. recycled plastics industry, the future of PE and PP and other leading topics. To attend these new off-floor sessions, an Expo Plus registration is required to unlock Market Trends with Icis, while Expo Premier gives attendees complete access to tailored industry insights and on-demand post-show recordings. www.npe.org Versatile stretch blow moulding equipment Flexblow, a leading manufacturer specialising in stretch blow moulding equipment, is gearing up to exhibit its solutions across various industries. The SBM equipment manufactured by the Lithuanian company is claimed to be versatile and to provide an extensive range of capabilities, including the production of cosmetic containers, hot-fill containers, jars, and large containers. According to the company, these machines offer one of the widest neck and size range capabilities on the market, allowing customers to achieve flexibility in their production processes. Flexblow also emphasises its record-setting complete mould and neck changeover times, ensuring efficiency and agility in manufacturing operations. During the exhibition, the company will unveil several features that are claimed to underscore its commitment to innovation and customer satisfaction. These highlights include a wall thickness assurance system, toolless changeover (including mould), hot fill capability, auto lamp positioning and preferential heating for oval containers. Representatives will be available to provide insights into the technologies, conduct live demonstrations showcasing equipment capabilities, and discuss tailored solutions to address individual manufacturing needs. www.fl exblow.com Flexblow South Hall, Level 1 Booth S16107 South Hall, Level 1 Booth S12107 Bottle Zone"},{"@ID":18 "MATERIALS / RECYCLING PETplanet Insider Vol. 25 No. 03/24 www.petpla.net 16 The Polymer Center in Las Vegas is part of Republic Services’ plans for a nationwide network to help customers achieve a true plastics circular economy, as Pete Keller explains: “The Polymer Center will help enable true bottle-to-bottle and packageto-package circularity for plastics, helping customers achieve their own sustainability goals. Our integrated regional hub-and-spoke model will ensure nationwide coverage. We’ve received an overwhelming response from the industry and potential customers, which has accelerated the development timeline for our second and third Polymer Centers.” Future plans The company plans to build three more Polymer Centers to address the gap between supply and the fastrising demand for recycled plastics driven by regulations and a shift in consumer preferences for sustainable packaging. A report by the Recycling Partnership estimates that the gap between the current US supply of rPET for use in bottles and the projected demand in 2025 is close to 500,000 t. Republic Services has decided to extend the collaboration with Stadler: “Our strong partnership with Stadler and Krones, the design and quality of equipment, and successful implementation in Las Vegas has given us the confidence to purchase systems 2 and 3 for our Centers under development,” concludes Pete Keller. www.w-stadler.de www.republicservices.com With Netstal’s leading preform injection molding technology. Our PET-Line impresses with broadest compatibility, maximum throughput, exceptional ĆďĆēĈĚ ĆħĄĊĆďĄĚ ĐđĕĊĎĂč đēĐĄĆĔĔĊďĈ Đć ē÷ìû Ăďą other challenging recyclates, and with its intuitive Axos control unit. Wemaximize your added value Preforms NPE 2024 I W223 Republic Services Polymer Center in Las Vegas"},{"@ID":56 "OUTER PLANET 54 PETplanet Insider Vol. 25 No. 03/24 www.petpla.net OUTER PLANET From the Himalayas During the trekking season, around one ton of waste is left each day in the Everest region. Nepalese non-profit project Sagarmatha Next and award-winning Dutch design firm Super Local announced the launch of the ‘Carry me back’ programme and the ‘From the Himalayas’ product collection. These initiatives offer sustainable solutions to remove, process, and transform waste from the Everest region. The majestic beauty of Sagarmatha National Park in Nepal, home of Mount Everest, draws over 80,000 visitors annually, offering tourists an unforgettable experience in nature. While this has brought considerable socio-economic benefits to the area, it has also resulted in tragic amounts of waste and pressure on the region’s delicate ecosystem during the last few decades. To address these environmental challenges, the Sagarmatha Next centre was built on the way to Everest Base Camp at an altitude of 3,775m. Sagarmatha Next aims to change the perception around “waste” by showcasing innovative solutions for solid waste management and demonstrating to locals and tourists alike that properly treated waste has value. Sagarmatha Next houses a visitor centre, art gallery, waste lab, recycled product shop, and cafe in its centre. ‘Carry me back’ programme During the trekking season, approximately one ton of waste is left each day in the Everest region. The high altitude, lack of connectivity, and limited recycling infrastructure make it challenging to remove waste, resulting in more than 80 open pits in the region in which waste is burned - contaminating the soil, water, and air and threatening biodiversity. Sagarmatha Next and Super Local partnered with a local waste management organisation to develop the ‘Carry me back’ programme. It is a crowdsourced waste removal system that harnesses the movement of locals and tourists from the mountains to lower regions where transported waste can be recycled. Waste is collected from the open pits, restaurants, lodges, and hiking trail waste bins. At the processing facility, waste is sorted, shredded, and packed in one kilo bags designed by Super Local. The filled bags are then offered to locals and visitors at a pickup station. The ‘Carry me back’ pouches are easily clipped onto backpacks and transported via the trail to the regional airport. Dedicated bins are available at the airport for the bags to be transferred by local private airlines to Kathmandu, where a partner facility recycles the waste. Locals and visitors alike have responded enthusiastically to the programme, with some people carrying up to 14 kg of waste on their way. Waste to product Once waste is transported via the ‘Carry me back’ programme to Kathmandu, it is further processed. While some materials, like water bottles and aluminium cans, are processed on a more industrial scale, for the processing of HDPE water bottle caps, Super Local was tasked with converting this waste material into unique products that tourists can buy, thus averting waste and financing Sagarmatha Next’s important work. Super Local developed an end-toend process including setting up an appropriate plastics workspace, building two hand-operated plastic injection machines utilising the open-source blueprints of Precious Plastic, and training the local staff through handson support during the first weeks of production. Super Local and Sagarmatha Next collaborated on the design concept, with Super Local developing the final designs and plastic moulds. The final output is the ‘From the Himalayas’ product collection, which consists of three different pebbleshaped plastic stones and a scale model of the Himalayas’ most iconic peaks. These colourful products use thousands of recycled bottle caps and are perfect items for tourists to remember their adventure, and hopefully their responsibility to the environment, even long after they have returned home. www.super-local.com www.sagarmathanext.com ‘Carry me back’ pouch filled with PET bottle caps Mould with Himalaya scale model Manual removal of labels and caps"},{"@ID":23 "34 EVENT PREVIEW PETplanet Insider Vol. 25 No. 03/24 www.petpla.net ‘Made-to-measure’ caps making equipment Maca Engineering – Arol Group, headquartered in Italy, specialises in manufacturing and globally supplying a comprehensive range of automatic machines and complete lines for the production and assembly of aluminium and plastic caps and closures. Each machine is tailored to meet specific customer requirements, offering highly technological solutions designed to address diverse production needs while optimising materials. Today, Maca boasts a skilled inhouse design team that conducts feasibility studies for new projects upon request. The company distinguishes itself with fully automatic production lines, encompassing planning, management, and process control. Over 80% of key components and structural parts, including machine units and dies, are manufactured in-house and stamped with an ID number, facilitating replacement part orders for customers. The company will present its expertise in providing complete lines and machinery for aluminium caps, assembly lines, machinery for both aluminium and plastic caps, and slitting/folding machines for plastic caps. The company offers solutions for various cap production needs, including complex closures, sport caps, plastic caps for mineral water or speciality caps. All Maca Engineering machines undergo testing in the presence of the customer so that smooth and correct operation can be verified at first hand. Total reliability of the after-sales service is assured since the technicians who assemble the machine are the same who will oversee commissioning on site. www.arol.com www.macaengineering.com Blow moulding with NIR heating system PET Technologies made its debut at the NPE exhibition in 2018, when it presented its APF-3002 blow moulding machine. Six years on from its first appearance, it is returning to the National Plastics Exhibition where it will showcase its latest addition to the APF-Max series: the APF-Max 3U. PET Technologies says that this machine exemplifies the technological and design advances that it has made over the past six years. Basic specifications include an output of up to 5,400bph and the capacity to cater to a wide range of bottle volumes, from 100ml to 8 l. It does this by being designed with the capacity to cope with a different numbers of cavities to suit various volume requirements. It also has the capacity to handle hotfill bottles, is equipped for preferential heating, has the ability to install rotary blow moulds and offers quick change for different preform types. The company particularly highlights its near-infrared (NIR) heating system, which enables the machines to more effectively work with different compounds in different ways. NIR penetrates PET perfectly, at consistent depth and thus reheats preforms consistently. PET Technologies says that the need for sustainable solutions is growing rapidly and that its incorporation of the novel NIR heating system means that it can easily handle rPET – the material that is shaping the future of sustainable bottle production. PET Technologies has become a reliable partner for a number of global corporations. It has achieved a strong market presence through, first, being able to create moulds for the majority of European blowing machine manufacturers. Second, its moulds are made of high quality duralumin alloys, with hardness reaching up to 100 HP. The third factor it highlights is its investment in advanced five-axis CNC machining centres from manufacturers such as Deckel, Maho of Germany, Doosan of South Korea and Micron MILL from Switzerland. The company says that use of fiveaxis machining centres removes the need for additional polishing, which has enabled it to reduce lead times for blow moulds to just two to three weeks. Shorter lead times enable swift transition to new product formats, which, in turn, enables faster market entry and saves valuable time. PET recognises that bottle shapes are brand owners’ signatures. It says that it specialises in crafting individual ident i t ies through a personal ised approach, to ensure that customers ideas are fully captured in bottle design as well as aesthetics. The company focuses on cost effectiveness, seeking ways to adapt designs to be lighter weight, without sacrificing quality. The design process includes 3D prototyping and lab testing to perfect bottle technology and appeal. www.pet-eu.com PET Technologies South Hall, Level 1 Booth S11058 Bottle Zone Maca Engineering West Building, Level 2 Booth W921C Expo Hall APF-Max 3U"},{"@ID":46 ""},{"@ID":20 "BOTTLING / FILLING PETplanet Insider Vol. 25 No. 03/24 www.petpla.net 18 Growing potential included Water and CSD bottling in China The consumption of bottled water is constantly growing in every part of the world and the forecasts of the major research institutes indicate that the trend will continue in the future. China is no exception, where, in the first quarter of 2023 alone, there was an increase in sales of bottled water of 10.9%. Faced with a scenario of strong expansion, the main Chinese brands in the beverage sector have launched a programme of investments in more modern and efficient production lines. The bottled water market in China Among the most important factors in the development of China’s bottled water sector, the constant growth both in terms of litres produced annually and in terms of the number of consumers are worth mentioning. Bottled water volumes increased by 10.9% in the first quarter of 2023, driven by the boom in retail sales. The increase in household consumption has fuelled demand for water in general and particular in large packaging. In addition, the recovery of tourism, following the lifting of post-pandemic travel restrictions, represented another strong boost to the recovery and expansion of the sector. It is estimated that during 2023, the sales volumes of bottled water will grow annually by 8.7%, a trend that should also be confirmed for the following years due to the increasing propensity of the Chinese population for healthier and more responsible lifestyles for the wellbeing of society and the environment. (Source: Globaldata 2023) The company Huihuang United (Tianjin) Food Co. Ltd. Huihuang United (Tianjin) Food Company was founded in 2011 as a subsidiary of Macau Huiyang International Investment Co. Ltd., a company belonging to the industrial giant Zhuhai Zhongfu Enterprises Co. The Tianjin-based company, which currently employs about 300 people, has distinguished itself since the beginning of its activity for the ability to manage large productions for third parties; since 2011 it collaborates, for example, with the US multinational Coca-Cola. The first supply of the Italian producers of bottling plants and packaging machines SMI to Huihuang United (Tianjin) Food Company dates back to the same year, with the installation of an SK 802 F shrinkwrapper for packMr Huang Gang, Plant Manager of Huihuang United (Tianjin) Food Co. Ltd. The Ecobloc EBS 04 HC C’estbon 6 l boxes"},{"@ID":1 "No.3 2024 www.petpla.net D 51178; ISSN: 1438-9452 25 . 03 . 24 M A G A Z I N E F O R B O T T L E R S A N D B O T T L E - M A K E R S I N T H E A M E R I C A S , A S I A , E U R O P E A N D A L L A R O U N D T H E P L A N E T PETplanet is read in 159 countries MARKETsurvey Suppliers of caps, cap systems and cap inspection systems Page 27 EDITOUR Page 24 Page 32 Page 10"},{"@ID":49 "47 PRODUCTS PETplanet Insider Vol. 25 No. 03/24 www.petpla.net High-pressure compressor Adekom, an established compressor manufacturer in Asia since 2003, with two decades of experience in the food and beverage industry, claims to understand the expectations of customers in the competitive world of PET bottle blowing. The KSP series screw+piston tandem high-pressure compressor represents a skid-mounted combination design, comprising a first stage oil-free screw and a second stage reliable oil-free piston booster. Together, they are meticulously engineered to create a stable and energy-efficient high-pressure compressor unit, capable of delivering 5.0-30.5m3/min at 40 bar of oil-free air continuously, adhering to ISO8573-1 Class 0 air quality standards. Oil-free air The first stage water injection screw fulfils four main functions of lubrication as well as cooling, sealing and noise reduction, thus providing 100% oil free air. No special treatment for the discharge water is required to meet environmental protection requirements. The screw air-end casing, the star wheel bracket and the whole system pipeline are of food grade stainless steel material. These components combine with an oil-free piston booster to assure the whole air system is free of oil. The screw air-end is made from corrosion resistant food-grade stainless steel to ensure durability. The lubrication water absorbs much of the heat from the compressor which itself runs at a low temperature. All components operate at a low temperature range which increases the machine reliability and prolongs the service life of the unit. The permanent magnet frequency inverter drive allows a wide regulation range whilst minimising energy consumption. Few consumables are required, so maintenance costs are low, and parts are easy to replace, says Adekom. The lubricating water is fitted with a fully automatic water changing device and it can be changed without stopping the operation of the unit. The advanced PLC ensures 100% digital control and automation from a single HMI point, with cloud monitoring and predictive maintenance. www.adekom.com.hk PETproducts"},{"@ID":29 "MARKET SURVEY 27 PETplanet Insider Vol. 25 No. 03/24 www.petpla.net 03/2024 MARKETsurvey Suppliers of caps, cap systems & cap inspection systems We are pleased to present the latest insights from suppliers and manufacturers in the cap industry. In response to our call, a wide array of companies have contributed their data, providing you with a comprehensive overview of their recent solutions. Please find here the new data of the companies: Alpla Werke Alwin Lehner GmbH, Bericap Holding GmbH, Corvaglia Group, Gulf Packaging System Co, Has Plastik San Tic. A.S., IMD Ltd, Intravis GmbH, Netstal Maschinen AG, P&S Technology Co Ltd, Retal Industries, Sacmi Imola SC, Sumitomo (SHI) Demag Plastics Machinery GmbH, Uner Plastic AS Although the publishers have made every eff ort to ensure that the information in this survey is up to date, no claims are made regarding completeness or accuracy. Resins & additives Cap producers, cap systems & cap inspection systems Preform machinery Preform production & inspection systems Preform, cap & SBM mould manufacturer SBM 2-stage Compressors Filling equipment & inspection systems Palletising & shrink film machinery Recycling machinery Cap systems Company name Sumitomo (SHI) Demag Plastics Machinery GmbH Gulf Packaging System Co (3P Gulf Group) Netstal Maschinen AG Sacmi Imola S.C Postal address Telephone number Web site address Contact name Function Direct telephone number E-mail Altdorferstrasse 15 90571 Schwaig, Germany +49 91150610 www.sumitomo-shi-demag.eu Mr Arnaud Nomblot Director - Bus. Dev. Pack. +49 911 5061 625 arnaud.nomblot@shi-g.com Post box 20266, Jeddah 21455, KSA +966 12 6360099 www.3p-gulf.com Mr. Mohammed Najmuddin VP-Operations +966 12 6360099 najm@gulf-pack.com Tschachenstrasse 1 8752 Näfels, Switzerland +41 55 618 6111 www.netstal.com Pascal Müller Product Manager CAP +41 55 618 61 92 sales.cap@netstal.com Via Selice Prov. Le 17/A, 40026 Imola (BO) - Italy +39 0542 60 7111 www.sacmi.com Mr Stefano Severi Sales Area Manager +39 335 659 4236 stefano.severi@sacmi.it Systems for cap/closure production Hysky Hycap system CAP-Line (based on Elion and Elios platform depending on clamping force) Model El-Exis SP / PAC-E Hycap-4 400 Elion series, Elios series CCM24SD CCM24SF CCM32MC CCM48SD CCM64MC Procession technology Injection moulding Injection moulding Injection Moulding Machines Compression Compression Compression Compression Compression Clamp force 1,500 - 10,000 kN 400 T 2,200 - 6,500 kN Not applicable Not applicable Not applicable Not applicable Not applicable Cycle time (guaranteed 98% closure system effi ciency for): 26/22 mm - up to 2,800 caps/min 3.0 sec 2 sec - High speed production: closure type/weight/cavities: caps/min 29/25 mm - up to 2,300 caps/min Min. water cap / 1.25g / 96 cavities / 2,133caps/min 26mm (GME 30.39); 0.75g; 128cav.; 4,042caps/min 28mm CSD / 2g / 24 cavities: 600caps/min 38mm CAF/ 2.6g / 24 cavities: 600 caps/ min 26 mm water / 0.9g / 24 cavities: 1,000caps/ min 28 mm CSD / 2g / 32 cavities: 980caps/min 26 mm water / 0.9g / 48 cavities: 2,000 caps/min 29mm water/ 1.2g / 48 cavities: 2,000caps/min 28mm CSD / 1.8g / 64 cavities: 1,920caps/min 38mm CAF/ 2.6g / 64 cavities: 1,600caps/min - Individual cap solution: closure type/weight/cavities: caps/min PCO1881 - up to 1,800 caps/min GME30.40 - up to 1,800 caps/min Min. water cap / 1.25g / 96 cavities / 2,133cpm Flip Top; 8.12 g; 48+48; 524 caps/min (IMC) Drive concept Hybrid / All-electric Hydraulic + electric Electric and hybrid electric / hydraulic electric / hydraulic electric / hydraulic electric / hydraulic electric / hydraulic Energy consumption (kwh/kg) 0.30-0.40 kWh/kg, varying upon application Product specifi c, as low as 0.37kWh/kg ±10% equal or more than 0.4 kwh/h equal or more than 0.4 kwh/h equal or more than 0.35 kwh/h equal or more than 0.35 kwh/h equal or more than 0.4 kwh/h Preferred mould makers Z-Moulds / Plastisud Corvaglia, Swiss Customer & project specifi c selection for best performance fi t Sacmi Sacmi Sacmi Sacmi Sacmi Special features MyConnect Break Then Leak feature Spindle-free high-speed toggle lever clamp, adaptive system pressure reduction (ASPR), responsive fi lling control (RFC), Axos 9 controller, Smart Operation, eService, Netstal remote control (NRC) Possibility to assemble only 12 moulds, inline quality control on all caps, cap weight adjustable from HMI, without mould change Possibility to assemble only 16 moulds, inline quality control on all caps, cap weight adjustable from HMI, without mould change Possibility to assemble only 24 moulds, inline quality control on all caps, cap weight adjustable from HMI, without mould change Possibility to assemble only 32 moulds, inline quality control on all caps, cap weight adjustable from HMI, without mould change"},{"@ID":54 "PETplanet Insider Vol. 25 No. 0/24 www.petpla.net 37 EVENT PREVIEW rPET, the Pilot Vision+ works seamlessly with today’s high-speed reheat stretch blow moulding equipment. The Pilot Vision+ system offers a modular approach to defect detection that works within the blow moulder. The open architecture of this system allows for simultaneous management of up to six cameras, in multiple locations. As part of Agr’s Process Pilot family of products, Pilot Vision+ can be combined with Process Pilot+ for a comprehensive bottle management solution, detecting random occurring defects and ensuring precise material distribution, even with the lightest and/or most difficult-to-process bottle design. In addition, Agr will have the newly released ThicknessPen handheld thickness measurement device available to try out on a variety of samples and materials. The device with its patent-pending dual-mode design, addresses various thickness measurement applications in the production environment. The ThicknessPen, used with or without a target ball, offers versatility for use in laboratories, plant floors or even in wet environments at a job site in the field while still providing the precision necessary for the laboratory and the portability, ruggedness and safety for use on the production floor. Agr measurement and processing experts will be available to discuss these products as well as their complete line of process monitoring and quality control equipment available for the plastic industry. www.agrintl.com Agr’s Process Pilot+ system incorporates a patented “Value Performance” technology that has been developed to improve blow moulder efficiency and profitability. The Process Pilot+ system allows operators to optimise the blow moulder based on performance, energy efficiency or operating costs."},{"@ID":43 "PACKAGING / PALLETISING PETplanet Insider Vol. 25 No. 03/24 www.petpla.net 41 interview Dave Ritterbush gave in August 2021, but achieving that level required a lot of agility and potentially expensive alternative sourcing, including airfreighting supplies. Automate to accelerate and update The decision was made to invest in two integrated bottle production lines, built around two KHS Blowmax B12 inline blow moulding machines. The bottles themselves were to be redesigned, to make the whole operation effective across KPIs including environmental performance and cost reduction. It was KHS that suggested Califia talk to Delta Engineering. “The project involved installing a high-speed takeout conveyor from the blow moulder and a chain conveyor buffer, to store bottles in case the downstream line goes down, for whatever reason,” said Danny Stevens, Senior Sales Engineer USA with Delta Engineering, based in the USA facility in Norcross, north-east of Atlanta, Georgia. Those two core machines were complemented with blow moulder take-outs, vacuum pumps and line controllers. The lines were also equipped with ionisers, to reduce static electricity, and Star Knobs on the guard rails to reduce changeover times. “They have to have room on the line to be able to store bottles, although it does have some internal capacity. Whenever a holdup occurs and is then cleared, the buffer will empty out and then the whole line will start up again.” Managing bottle blowing flow KHS was in the process of creating the line when Delta Engineering was approached. “We have bottles coming out of the machines at high speed and they need to transition to a table-top conveyor without falling over,” said Tyler. High speed conveying carries the risk of damage during operation, from falling over or jamming because of production interruption. The buffer capability maintains a smooth flow in the event of production stoppage. “Delta’s equipment is responsible for transporting the freshly-blown empty bottles from the blow-moulding machines to the fillers. Its solution uses a vacuum conveyor to help achieve a smooth transition. I was very pleased with the result.” Califia got in touch with Delta in May 2022 and they visited the factory to discuss the specific needs and layout requirements within a matter of days. Tyler specifically mentioned their quick turnaround of drawings and quotes for the equipment. The order was placed in July 2022; in December, just five months later, he flew over to Delta’s head office in Ophasselt, about 30km (19 miles) West of Brussels, in Belgium, for the factory acceptance test. Delta’s professionalism delivers value – fast “I was very impressed with their equipment manufacturing facility and on-site capabilities there,” said Tyler. Delta was so quick it had everything prepared from its side before the rest of the line was ready. Installation was finalised and completed in May 2023, with the new equipment fired up and put into production in June. It has been a major success. “The cost savings and carbon emission reductions have been in line with expectations. Current estimates are that we will save around 838 million tons of CO2 a year,” said Tyler, who is ready to place credit where it is due. “Delta has been responsive, professional and a joy to work with. They worked hard to ensure that everything was right before we installed their equipment. Their equipment is high quality and I attribute a large proportion of the project’s success to them.” www.califi afarms.com www.delta-engineering.be Tyler Crow, Senior Plant Engineer, Califia Farms At a glance: Califia Farms was founded in 2010 and fills over 60 million bottles a year with plant-based alternatives to dairy products, including milks and ready-to-drink coffee. Decision to update and automate cost control and environmental performance were key drivers. New equipment: two KHS Blowmax B12 in-line blow moulding machines. Delta Engineering equipment: ETN250 blow moulder take-out CD083 chain conveyors DBC202 chain conveyor buffer DLC421 line controllers DVP075 vacuum pumps Change/impact: over 830 million tons of CO2 eliminated from the supply chain; greater security of bottle supply; inward truck movements cut 90%; cost objectives met. Danny Stevens, Senior Sales Engineer USA, Delta Engineering David Ritterbush, CEO, Califia Farms"},{"@ID":17 "MATERIALS / RECYCLING PETplanet Insider Vol. 25 No. 03/24 www.petpla.net 15"},{"@ID":4 ""},{"@ID":12 "EDITOUR PETplanet Insider Vol. 25 No. 03/24 www.petpla.net 10 Multiple designs produced in a one-step process PET bottles for food and non-food by Kay Barton When it comes to format flexibility and high-quality special designs for often very different applications, manufacturers turn to single-stage lines. Petcogulf FZE, which we were able to visit in Dubai’s Jebel Ali free zone, is one such manufacturer. The company, led by Chairman and company owner Nabil Kanazeh and General Manager Aswin Puthran, specialises in PET bottle and container production for the beverage, food, personal care and home care sectors. It is part of the Petco Group, which consists of two independent companies, the local headquarters here and another plant in Jordan. Meeting with Petcogulf FZE December 6, 2023 We met: Mr Nabil Kanazeh, Chairman Mr Aswin Puthran, General Manager General Manager Aswin Puthran welcomed us in the foyer and took us past a large display case with countless different bottles and jars into the meeting room. He has been with the company since 2006, comes from the Indian state of Kerala, and is a Mechanical Engineer. Starting as a Plant Engineer, he later rose to his current position. He told us about the beginnings of the company. “The decision to set up the company in such a dynamic field was a logical one. At that time, there was so much demand and hardly any PET bottle manufacturers in the UAE, so the bottles had to be imported, which was laborious and costly. We therefore started with around three or four machines back then and now have 26.” 14 machines are from Nissei ASB (models 12M, PF6-2B, PF4-1B, 50MB, 70DP). Production takes place in one to four cavities, with a container or bottle range from 50ml to 5 l. Around 260 different formats, both coloured and clear, can currently be produced, with an annual capacity of almost 110 million bottles and containers and over 90% capacity utilisation. Petcogulf obtains its raw materials from Reliance, Hainan Yisheng and Sabic, among others. In addition to a specific masterbatch, customers can also choose a UV barrier or a biodegradable additive for their packaging. Customers also receive the matching closures, which are supplied by Bericap. The manufacturer is certified in accordance with ISO9001:2015, BRC Issue 6 and HACCP. During our tour of the factory, we saw that production is divided into two sections - food items and non-food items. We also discovered two exotic machines in the single-stage machine park, namely a Haitian and a Joyson machine. “We currently produce rPET preforms for juices on the Haitian and blow the bottles on the Joyson, simply because it’s faster at the moment,” explained Mr Puthran. “Our typical customers include edible oil and juice bottlers, tea powder packers and personal and home care bottlers.” He then showed us some sample bottles. Shortly after the official approval of PET recyclate for food contact, Petcogulf acquired the corresponding confirmation for the use of rPET for this purpose. “RPET bottles are the hot topic right now,” said Mr Puthran and showed us one of his latest products, a fully labelled rPET juice bottle for the Carrefour food chain, the same bottle that we had previously been able to inspect virtually naked in production. The company, which recently generated an annual turnover of around US$ 8.2 million, is growing by an average of 10-15% and is focussing on organic expansion in line with the quantities required by customers. In the area of sustainability and recycling, the company saw great potential for the future, moving away EDITOUR The Editourmobil in the driveway of Petcogulf FZE All PET: an insight into the PET containers manufactured by Petcogulf Interview session with (f.l.t.r.) GM Aswin Puthran and Kay Barton Aswin Puthran shows one of the new rPET preforms for juice."},{"@ID":9 "7 NEWS PETplanet Insider Vol. 25 No. 03/24 www.petpla.net SEE HOW MUCH YOU CAN SAVE MAINTENANCE COSTS 70% LESS ENERGY 90% LESS 70% REDUCTION IN CO2e 50% MORE PRODUCTIVITY Discover your potential savings. With just a few clicks, you’ll gain valuable insight into how ULTRA will positively impact your bottom line. 1. Go to ultra.maguire.com 2. Input your data. 3. Receive your customized PDF report of potential savings via email. The savings will vary based on your circumstances and should be reviewed with our sales team. USA Toll Free +1 888 459 2412 l Canada +1 905 879 1100 l Europe +44 1827 338 280 l Asia +65 6848 7117 l Taiwan +886 4 2658 1535 info@maguire.com www.maguire.com"},{"@ID":48 "ONsite 46 PETplanet Insider Vol. 25 No. 03/24 www.petpla.net New PET recycling plant in Viet Nam After the successful commissioning of the post-consumer PET bottle washing and recycling plant at Commercial Plastics Co. - CPC in Yangon, Myanmar, Sorema recycling systems, a division of Previero N. SRL, is now preparing for the establishment of a second plant for the same company in Viet Nam. Andrea Villa, Senior Technical and Sales Engineer at Sorema, describes the newly- operational plant as follows: “After conducting a plant washing and recycling trial at our Recycling Research Center-RRC inAlzano Brianza with dirty bottles collected by CPC, we developed the parameters to design a 2,200 kg/h flakes production plant, which would make their material able to be reused to produce bottles again. The analysis of the material, conducted at Sorema’s laboratory, has verified that most of the local market collection consists of small-format bottles between 330ml and 1,000ml with a high-level of contamination from PVC labels, sand, and abrasive materials. Based on this analysis of the material to be processed, Sorema, known for its robust and efficient design, developed and produced a line for Myanmar, which features a number of customisations to be considered as standard for PET bottle recyclers in Southeast Asia.” The machines have been carefully built with high-quality components, starting with the prewash module for label removal and efficient cleaning of the material surface. This technology prepares the material for better bottle sorting and reduces the overall wear and tear on the entire line, without compromising the lifespan of the de-labeller, whose first maintenance is scheduled only after several months. Removal of PVC labels is achieved with a combination of de-labeller, wet elutriator and material detectors. Finally, the glue of the labels is removed. Mr Ryan, Technical Director of CPC - Commercial Plastics Co. Ltd. has confirmed the results: “The Sorema plant, which we chose after careful evaluation, was installed in Yangon and met our expectations. We ordered it to recycle post-consumer PET bottles from collection throughout Myanmar. With the Sorema plant, we have thus provided an industrial-scale solution to the problem of plastic pollution in Myanmar.” He continued, “Our main problem was the large amount of PVC labels in the incoming bales of material, and this contamination was brilliantly eliminated by Sorema. At the end of the process, the expected results in terms of product quantity and quality were achieved. High percentages of our recycled material can be reused in the production of new PET bottles.” www.sorema.it viscoZERO – processing PP, PE, PET & PS! ZERO contamination. ZERO odour. ZERO limits. foodgrade without compromise viscoZERO Upgrade your existing recycling plant with viscoZERO technology."},{"@ID":53 "MARKET SURVEY 29 PETplanet Insider Vol. 25 No. 03/24 www.petpla.net Intravis GmbH Rotter Bruch 26a, 52068 Aachen, Germany +49-241-9126-0 www.intravis.com Marius Pötting Product Manager Caps and Closures +49 241-9126-0 info@intravis.de CapWatcher Q-Line CapWatcher SC (Specialty Closures) CapWatcher B-Line CapWatcher FC IntraOne 80 cps / 4,800 cpm / 288,000 cph 80 cps / 4,800 cpm / 288,000 cph 40 cps / 2,400 cpm / 144,000 cph 20 caps on fi lled bottles/s / 1,200 bpm / 72,000 bph 50 cps / 3,000 cpm / 180,000 cph 3 cameras for inner insp. (sealing elements, thread, TE band), 4 cameras for outer insp., 1 camera for topwall/print insp., contactless microhole insp., temp. meas., 1 camera for cavity no. reading, sensor to detect concavity/ convexity of closures Fully customised insp. systems that are tailored to the needs and wishes of the customers Modular insp. system; 1 camera for inner inspection, 4 cameras for outer inspection, 1 camera for liner inspection/cavity no. reading Splash-proofed quality control of the fi lled end product; 5 cameras for outer inspection, the application angle and the TE band; 2 cameras for outer verifi cation of fi ll level and closure position Universally applicable single-camera-system (e.g. for OEM-integration into capper-, fi ller-, assembly-, laser- or printing-systems) Tethered caps, standard one-piece bev. closures, standard two-piece bev. closures (*CapWatcher Q-Line Slitter available for slitted closures, behind slitting machine) Tethered caps, standard one-and two-piece bev. closures, carton fi tment, fl ip-top, sports cap, push-pull, 3-piece closures, screw top cap, spout & dosing, beauty & home-care, food & bev., pharma, automotive, inserts, cutters, lids, dustcover Standard one-piece bev. closures, standard two-piece bev. closures, tethered caps (without tethered features) Standard one-piece bev. closures, standard two-piece bev. closures, metal closures (without meas. of application angle) Tethered caps, standard one-piece bev. closures, standard two-piece bev. closures, carton fi tment, fl ip-top, sports cap, push-pull, 3-piece closures, screw top cap, spout & dosing, beauty & home-care, food & bev., pharma, autom., inserts, cutters, lids, dustcover Meas. of inner seal cone diameter, thread insp., TE band insp., black specks, contamination, colour deviation, inner & outer seal cone, plug seal, constant distance and homogeneity between inner/outer seal cone, short shots, fl ashes, liner, protruding features, laser engraving, QR-/promotion codes, cavity no. reading Meas. of inner & outer seal cone diameter, thread insp., TE band insp., black specks, contamination, colour deviation, inner/outer seal cone, plug seal, constant distance between inner & outer seal cone, homogeneity between inner/outer seal cone, short shots, fl ashes, liner, protruding features, laser engraving, QR-/promotion codes, cavity no. reading Meas. of inner seal cone diameter, inner closure diameter, ovality, thread insp., TE band insp., black specks, contamination, colour deviation, inner/outer seal cone, short shots, fl ashes, liner, cavity no. reading Meas. of inner seal cone diameter, thread insp., TE band insp., black specks, contamination, colour deviation, inner/outer seal cone, plug seal, constant distance/ homogeneity between inner and outer seal cone, liner, laser engraving, QR-/promotion codes, cavity no. reading Meas. of outer closure diameter and height, long gate insp., slit quality for slitted closures, absence/damage of the TE band, colour deviation, black specks, contamination, ovality, short shots, fl ashes, angel hairs, colour streaks, fl ow lines/ cracks at injection gate, colour of injection gate, prints on head plate, tethered features, temp. meas. Meas. of outer closure diameter & height, long gate insp., slit quality for slitted closures, absence/damage of TE band, colour deviation, black specks, contamination, ovality, short shots, fl ashes, angel hairs, colour streaks, fl ow lines/colour/cracks at inj. gate, prints on head plate, tethered features, temp. meas. Meas. of outer closure diameter & height, colour deviation, black specks, contamination, absence and damage of TE band, short shots, fl ashes Meas. of application angle, TE band inspec., verifi cation of fi ll level, insp. for presence of closure, elevated closure, crooked/bent closure, domed closure (Bullnose) Meas. of outer closure diameter & height, long gate inspec., slit quality for slitted closures, broken bridges, fl ashes between bridges, colour deviation, black specks, contamination, ovality, short shots, fl ashes, angel hairs, colour streaks/fl ow lines/cracks at inj. gate, colour of inj. gate, prints on head plate High precision meas. of closure diameter and ovality, high precision meas. of inner & outer seal cone diameter and ovality, high precision meas. of outer closure height, missing or damaged TE band, height of the TE band, fl ap insp., vertical/horizontal/radial long shots, open and closed short shots, temp. meas. of every single closure High precision meas. of diameter and ovality (closure&seal cone), high precision meas. of closure height, assembly faults, missing components, damaged components, damaged seal cone, vertical/horizontal/radial long shots, open & closed short shots, height of TE band, missing/damaged TE band, damaged/turned up fl aps, damaged pull tabs, missing/damaged quality seal, temp. meas. of every single closure Diameter and ovality (closure, seal cone), closure height, damaged seal cone, missing or damaged TE band Missing closure, missing or damaged TE band, domed closure (Bullnose) Diameter and ovality (e.g. closure, seal cone), closure height, assembly faults, missing/damaged components, damaged seal cone, vertical long shots, open & closed short shots, horizontal/radial long shots, missing or damaged TE band, damaged/ turned up fl aps, damaged pull tabs, missing/ damaged quality seal Robust cavity reading with special illumination techn., cap-oriented imaging and machine-learning algorithms for cavity recognition. This enables the creation of real-time heat maps of moulds; problems in the temp. control of individual cavities or entire heating and cooling circuits can be detected and eliminated; microholes can be assigned to individual cavities; wear or defects in the tool can be detected at early stage; every defective closure will be assigned to its real cavity in the mould Robust cavity reading with machine-learning algorithms for outstanding cavity recognition. This enables wear/defects in the tool can be detected at an early stage; every defective closure will be assigned to its real cavity in the mould Robust cavity reading with machine-learning algorithms for outstanding cavity recognition. This enables wear/defects in the tool can be detected at an early stage; every defective closure will be assigned to its real cavity in the mould Contactless microhole insp. - no need to dip into the closure must-have for tethered caps with inserts Contactless microhole inspec. - no need to dip into the closure Missing components, weight, label, l*a*b values, barrier/label insp., tactile meas. Tethered & TE band features Filler and capper tracking (objects can be traced back to specifi c tool of fi ller and capper) Yes Yes Yes Yes Yes Yes Yes Yes Yes Yes Yes Yes Yes Yes Yes Data base connection; reject rate monitoring; product monitoring (upgradeable with IntraVisualizer); integrated control of up- and downstream equipment (one HMI for complete line); integrated trend statistics with pre-warning; industry 4.0 ready (IntraVisualizer & IntraRecommender) Data base connection; reject rate monitoring; product monitoring (upgradeable with IntraVisualizer); integrated control of up- and downstream equip. (one HMI for the Intravis sorter, insp. and packaging system / integration into line of customer possible); integrated trend statistics with pre-warning; industry 4.0 ready (IntraVisualizer & IntraRecommender) Data base connection; reject rate monitoring (via fi ller capper tracking, ejector available); product monitoring (upgradeable with IntraVisualizer); integrated control of up- and downstream equip. (ejector for fi lled bottles); integrated trend statistics with pre-warning; industry 4.0 ready (IntraVisualizer & IntraRecommender) Data base connection; reject rate monitoring; product monitoring (upgradeable with IntraVisualizer); integrated trend statistics with pre-warning; industry 4.0 ready (IntraVisualizer & IntraRecommender)"},{"@ID":15 "EDITOUR PETplanet Insider Vol. 25 No. 03/24 www.petpla.net 13 EDITOUR 13 sor side, equipment from AF Compressors, Bellis & Morcom and Atlas Copco is used. Three fully automated production lines from Krones with capacities of twice 44,000bph and once 18,000bph are used for the water retail market. Mr Younas explains: “There’s also a Krones hotfill line for juices with 12,000bph, but it’s not very busy at the moment, as it’s more of a side product. We had also produced flavoured water on this line for a while, but the market for flavoured water was rather subdued, so we put it on ice for the time being.” A second building houses a Kosme line for the 15.14 l containers and cap production. For the closures, the company works with Engel machinery. “We used to be able to export our water,” explains Mr Younas. “You could even get the brand in East Asia, Africa and Europe, but unfortunately these kinds of exports were banned around 2013, so we have been focussing on the local market ever since. However, our second plant in Oman does some exports. We share the market with the two big water brands Mai Dubai and Al Ain and all three brands have a similar average presence.” And the company wants to continue to grow and expand the brand in the future. “Masafi water has a long history. The fact that we differentiate ourselves from other major local brands through the way we produce water means that our water is well known and, above all, highly valued by the local population.” www.masafi .com F.l.t.r.: Fraz Younas and Mohammed Youssef at the Netstal preforming machine Freshly produced water bottle preform www.sacmi.com Product design Product development Product validation Industrial production plant Process & quality control On-site and start-up assistance After-sales and Customer service SACMI 4.0 THE COMPLETE CLOSURE, PREFORM AND CONTAINER SOLUTION FOR YOUR SMART FACTORY E N D L E S S I N N O V A T I O N S I N C E 1 9 1 9"},{"@ID":10 "8 NEWS PETplanet Insider Vol. 25 No. 03/24 www.petpla.net Generation Change at Sumitomo (SHI) Demag Management Board Gerd Liebig announced that he will be stepping down from the Management Board of Sumitomo Demag on August 31, 2024. After serving the injection moulding industry for 35 years, Gerd Liebig will complete the planned Sumitomo (SHI) Demag management transition, effective September 1, 2024. Mr. Liebig’s leadership tenure was characterised by his immense passion for the company and its employees, in addition to his steadfast allegiance to the plastics machinery industry. Mr. Liebig’s years in the industry has been marked by major changes in the market, applications, products and competition. “I have been honoured to fulfil this important role entrusted to me. Now it is time for me to pass the reins to the younger generation and step down from my operational responsibilities at SDG,” says the incumbent CEO. The next SDG management team will be formed from within the company’s own ranks. Currently serving alongside Mr. Liebig is CFO Christian Maget and COO Takaaki Kaneko. The new management team will be announced during the summer months. “Those who know me are aware that I am not going into retirement mode with this decision – rather, I will continue to support industry activities that give me the greatest pleasure. My commitment to combating climate change and to the energy transition is paramount,” said Liebig. “I won’t be retiring completely from the plastics industry, which has played an important role for more than half of my life and which I was also able to help shape to some extent. Rather, I will remain a part of Sumitomo and will continue to contribute to the Group to a limited extent and without operational responsibility.” www.sumitomo-shi-demag.eu CCL Industries: Official opening of sustainable sleeve label hub in Austria CCL Industries (CCL), a global leader in speciality label, security and packaging solutions, announced the official opening of its new sustainable sleeve label hub in Dornbirn, Austria - completing the move from its former site in Hohenems. The new facility represents a €50 million investment and is more than double the size of the previous site. Nearly 10,000 m2 are dedicated to production and a fully automated warehouse, including intelligent computer-controlled software to optimise storage space management and automate intra-logistics. At Dornbirn, CCL focuses on the latest sustainable shrink sleeve technology – made from floatable low-density polyolefin material. The sleeves easily separate from the primary container in the sink/float process at the sorters and recyclers, ideally supporting material separation and efficient recycling. Overall, CCL takes a holistic approach to sustainability, acting on the concept of “reduce, reuse, recycle” and even going one step further by actively supporting recycling with this solution. Heating is provided entirely by recovering heat generated by production machinery, compressors and the thermal oxidation system for solvents. A central distribution centre manages the distribution of heating and cooling. “There is also a PV system on the roof with more than 2,000 panels and a peak output of almost 900 kWp. The system produces the equivalent of 721,000 kWh per year, equivalent to the annual consumption of around 200 households. More than 80% of the electricity we produce is used internally, which saves 338 t of CO2 per year,” says Bernd Schmidle, Production Manager at CCLDornbirn, who led the planning and construction of the new bui lding and implemented the latest technology. www.cclind.com Moldmasters MODERNIZEYOURS INGLE STAGE BOTTLE PRODUCTION ✓ New high-performance single stage hot runner systems. ✓ Enhance bottle quality and consistency. ✓ Change color up to 4x faster. CONTACTUS TODAY! info@moldmasters.com www.moldmasters.com"},{"@ID":11 "9 NEWS PETplanet Insider Vol. 25 No. 03/24 www.petpla.net SGT invests €3 million in new material central facility Société Générale des Techniques (SGT), a manufacturer specialising in PET and rPET preforms, announced the installation and operational start-up of a new material central facility at its Rezé site in Loire-Atlantique, France, representing a major investment of €3 million. This installation enables the automatic supply of PET and rPET pellets to the injection moulding press park. Since the beginning of the year, this material central facility has been operating autonomously, eliminating the need for direct human intervention. It also contributes to improving ergonomics by reducing strenuous tasks and repetitive movements required for PET and rPET granule transfers. This simplification of logistical operations relieves employees from difficult manipulations and uncomfortable postures, resulting in improved working conditions. 4 km of pipes have been installed to optimise operational processes efficiently, ensuring continuous supply of raw materials. Thanks to an ultra-performing computer system, the installation deployed by MAT Techno-Logic offers precise management of all mixtures associated with each preform injection press. The flexibility of this new technology allows for automatic management of diverse mixtures, ranging from 0 to 100%, thus providing versatility in production. The implementation of this system is expected to bring several benefits: Firstly, to improve the efficiency of the production process, resulting in considerable time savings for the company. Additionally, the storage capacity of raw materials has been increased with the addition of 280 t of transition storage. Finally, the automation of the installation ensures a secure supply of PET to the presses, reducing risks associated with human errors. The new material central facility also emphasises complete traceability of preforms. Through advanced tracking systems, the company can guarantee the quality and origin of each product, thus meeting strictest requirements of its customers. By committing to this initiative, the SGT Group also demonstrates its adherence to environmental standards. In compliance with the Clean Sweep charter, the new material central facility helps prevent granule loss. www.sgt-pet.com We will contribute to the realization of a sustainable low-carbon society by leveraging aseptic technologies. www A BETTER FUTURE Through Advanced Filling Systems Aseptic Systems Your Solutions Provider"},{"@ID":14 "EDITOUR PETplanet Insider Vol. 25 No. 03/24 www.petpla.net 12 Deep water from the Hajar mountain region in the north-east of the Emirates Mineral water bottler focusses on vertical integration by Kay Barton If you drive from the hubs of Dubai or Abu Dhabi towards the port city of Fujairah on the north-east coast of the UAE, you will come across the southern foothills of the Hajar Mountains shortly before reaching your destination. A little further north and inland, about half an hour from Fujairah, lies the small village of Masafi, from which the water brand of the same name originates. It recently became part of the Hattan Group, which invests and operates in various sectors. The special thing about Masafi water is that, unlike other major brands in the country that obtain their water from municipal seawater desalination, the manufacturer extracts its water exclusively from wells up to 300m deep and then packages it in a vertically integrated process on plants of European origin. Plant Manager Fraz Younas and Engineering & Project Head Mohammed Youssef answered our questions about the details during a visit. Interview with Masafi Co. (LLC) December 12, 2023 We met: Mr Fraz Younas, Plant Manager UAE & Oman Mr Mohammed Youssef, Engineering & Project Head The way to Fraz Younas’ office is via a staircase on the first floor of one of the production halls. The “first water brand in the Emirates”, as we were told, has been in existence since 1977 and the founder himself, Mr Abdulla Al Ghurair, comes from the same area of Masafi. Masafi is currently chaired by Abdul Aziz Al Ghurair, a billionaire and Chairman of the Board of Mashreqbank. Until 1997, the company bottled in PVC bottles on a Sidel line with a capacity of 72,000 bph, after which Masafi switched 100% to PET. The company fills and sells three different types of mineral water, the Masafi “Pure” brand, the standard product with a pH value of 6.5-8.5, “Zero”, which is characterised by a sodium content of less than 1mg, and “Alkalife” with a pH value of 9. Masafi’s wide product portfolio includes drinking water, tissues, hygiene kits, oils and rice. Another Masafi plant is located in Oman. Today, Masafi is part of the Al Ghurair Group, a Dubaibased group of companies that is active in various industrial sectors as well as in the real estate and investment business. “We have seven wells here in the region for our water,” explained Mr Younas. He has a Master’s degree in Engineering Management, has been with the company for a year and a half and previously worked for Nestlé in Pakistan and Switzerland for over 15 years. “We have a constant supply of premium quality water here due to the special location of the wells,” says Mr Youssef, who has been working here for over three years and previously worked for Coca-Cola in Saudi Arabia for over three years. “The water continuously seeps into the groundwater here in the region via rainfall from the mountains. Rainfall is far more frequent here than anywhere else in the UAE.” Around 460 million bottles roll off the production line here every year, with the 0.5 l bottle making up the majority, accounting for around 40% of the total output. This is divided into the formats 0.2 l, 0.33 l, 1.5 l, all with 29/25 neck plus 5 l and 15.14 l containers for water dispensers. There are also 0.125 and 0.2 l thermoformed cups with a pull tab. The two estimate that around €50 million has been invested in the machinery and that the company has deliberately focussed on the highest quality suppliers from the outset. Two Netstal preforming machines with Otto Hofstetter different sets of 128cavity moulds and a 48-cavity mould are used for preforming, the latter for the long-life 0.5 l bottle. The material is dried using Gea dryers. A new Husky machine with six cavities for the special-format 15.14 l containers will be delivered shortly. On the compresEDITOUR Interview meeting at the Masafi office with (f.l.t.r.) Mohammed Youssef, Fraz Younas and Kay Barton Krones line for 1.5 l bottles in action Fraz Younas with a 1.5 l bottle of Masafi Pure"},{"@ID":30 "MARKET SURVEY 28 PETplanet Insider Vol. 25 No. 03/24 www.petpla.net Cap inspection systems Company name IMD Ltd. Gulf Packaging System Co (3P GG) Sacmi Imola S.A. P&S Technology Co., Ltd Postal address Telephone number Web site address Contact name Function Direct telephone no. E-Mail Industriestrasse 37A CH-2555 Bruegg +41 32 366 80 66 www.imdvista.ch Mr Martin Gerber Sales Director - CSO +41 32 366 80 66 imd@imdvista.ch Post box 20266, Jeddah 21455, KSA +966 12 636 00 99 www.3p-gulf.com Mr Mohammed Najmuddin VP - Operations +966 12 6360099 ext 105 info@gulf-pack.com Via Selice Prov. Le 17/A 40026 Imola (Bo), Italy +39 0542 607111 www.sacmi.com Mr Stefano Severi Sales Specialist Manager +39 335 659 4236 stefano.severi@sacmi.it 261 Daeji-ro, Suji-gu, Yongin-si, Gyenggi-do, 16882, Korea +82-31-763-5621 www.pnstech.co.kr +82-31-763-5621 pnstech@pnstech.co.k Inspection system IMDvista 100% closure inspection systems Camera vision inspection CHS102/202 PFMC Cap closure inspection Inspection speed up to 4,500 caps/min 2,400 caps/min Up to 4,500 caps/min Up to 200 caps/h Max 2,200 cpm Inspection method High resolution colour cameras Inline Artifi cial computer vision algorithms, spark tester Mechanical and destructive breaking force test Vision Inspected objects Any closure geometry and design Beverage closures Flat top caps, tethered caps, sport caps, hinge caps, multicomponents caps Flat top caps and tethered caps Aluminium / steel / plastic Inspected parameters: -Inner inspection Short shots, fl ash, colour defects, contamination, ovality, sealing lip defects, deformation, inside diameter Yes Insp. of the whole product side, incl. mouth, plug seal (one piece caps), gasket (two pieces caps); dedicated algorithms for precise thread insp.; detection of small fl ashes & voids in TE band wings; detection of colour variations, discolourations, contaminations, black specks, pulled threads, voids, fl ashes of material; insp. of standard/tethered cut produced in the mould: fl ashes in the windows, windows partially closed, bridges, no. of/thickness of bridges Ovality: ± 0.2mm, black particle: Φ 0.3mm, pinhole: Φ 0.5mm -Outer inspection Contamination outside wall, height meas., colour defects, deformation, outside fl ash, ovality, diameter Yes Complete insp. of the public side, including sidewall. Special CVS360-3Dmodule to unroll sidewall in a 2D image making a compensation of any deformation coming from lens deformation, perspective and spatial position of the object; insp. of the decoration with automatic recognition of colours and areas with a specifi c colour; colour variation (ΔE), wrong colour, colour planes registration, off-centre, stains, black specks and others Black particle: Φ 0.5mm, print: ≥30 gray level & ≥1.0mm offset -Geometry Any type Yes From a top view: ovalisation, indicative meas. on inner and outer diameter; from side views: outer diameters measured along the cap body, bulged caps, cap height -Cavity number reading Available Yes Yes, through AI algorithms for high reliability and performance; statistics of defects by cavity number, sorting by cavity number Yes, through CVScut vision system Save images by number with mould number reading function -Microhole inspection Available / high-voltage Spark system Yes Yes, with dedicated and integrated spark tester device -Additional inspection criteria for inserts Top plate inspection for colour, print and contamination N/A Yes (presence/absence, integrity, black specks, voids, fl ashes, contaminations…) Inspected diameter range : 12-53 mm; inspected height range 4-37mm Further inspection options New calibrated and validated system solution; AI inspection for tethered closure types - no false rejects Side inspection Breaking force test Cavity recognition, print colour, print damage Colour Camera: All colour cameras Yes CHS features up to 7/12 high resolution and high speed colour cameras to control the whole cap Yes Installation: Stand-alone (offl ine) Available No Yes CHS 102, no CHS 202 Yes Yes Inline Available Yes CHS family includes two machines: CHS102 (single vacuum conveyor belt) and CHS202 (double vacuum conveyor belt); both machines are compact and have been designed to match high production speeds (up to 4,500ppm) PFMC takes samples of plastic caps and performs destructive tests: breaking forces of the bridges and of the lugs that keep the cap tethered to the bottle; machine records detected values and provides a set of statistics; chart showing force as a function of time, export of data via Ethernet or USB Yes Softwarefeatures: AI tool - IMDvista Neuron; IMDvista Portal - Connects your IMD vision systems Software portal for process monitoring and control Graphical HMI translated in more than 20 languages, AI algorithms, colour analysis, special tools dedicated to a precise thread insp., runs under Windows 10 IoT"},{"@ID":26 "24 EVENT PREVIEW PETplanet Insider Vol. 25 No. 03/24 www.petpla.net EVENTpreview Chinaplas preview - part 2 The 36th Chinaplas International Exhibition on Plastics and Rubber Industries is set to take place in Shanghai, PR China, at the National Exhibition and Convention Center (Hongqiao) from April 23-26, 2024. From manufacturing techniques to sustainable practices, the exhibition will cover a wide range of topics that highlight the industry’s commitment to environmental responsibility and efficiency. You can find the first part of the trade fair preview in PETplanet issue 1+2. www.chinaplasonline.com Sustainable packaging solutions Avient Corporation will present its portfolio of materials and technologies that can help designers, brand owners, and manufacturers improve the sustainability, performance, and aesthetics of their applications, with a focus on enhancing recyclability in packaging. Avient will highlight the following solutions for applications in packaging, with a particular focus on bottle-to-bottle recycling developments: ColorMatrix Smartheat RHC Process Aid: an APR accredited, patent protected, liquid dispersion process aid, available to rPET producers and converters to help improve recycling and sustainability of PET bottles by enabling increased rPET content, improving rPET quality, and helping to reduce energy use and CO2 emissions. SmartHeat RHC is claimed to have minimal impact on final product colour or aesthetics. ColorMatrix Amosorb 4020R rPET Booster: an oxygen scavenging additive formulated for use with rPET. The solution has been developed to deliver full oxygen scavenging performance with up to 100% rPET content. It is also claimed to improve the aesthetics of the recycled bottle in terms of haze and colour. PCR Colour Prediction Service: a digital tool developed to illustrate the colour possibilities or limitations of certain postconsumer recycled material (PCR) before sample development to help simplify the overall decision-making process for brand owners and technical colourists. www.avient.com Avient Hall 8.2 Booth F31 Setting standards in PET recycling With the PET industry inAsia andAfrica expanding, theAustrian recycling machine manufacturer Erema is poised to address the rising demand for efficient recycling solutions at Chinaplas. The company will highlight its renowned Vacurema technology. This technology, introduced 25 years ago and continuously refined, forms the backbone of Erema’s PET recycling systems. The Vacurema machines feature SafeFlake technology, ensuring reliable decontamination, drying, and IV treatment of PET flakes prior to extrusion. This process maintains consistent rPET pellet quality, even with varying input material parameters. Moreover, the process is claimed to boast energy efficiency, making it a cost-effective and environmentally friendly solution. The Vacunite technology, another highlight at Erema’s booth, incorporates vacuum-assisted SSP in a nitrogen atmosphere. This solution is offering bottle-to-bottle customers improved technical performance and enhanced transparency. Recognising the importance of food-compliant rPET in industries beyond food, Erema has developed solutions for the textile industry. The Intarema FibrePro:IV machine, tailored for fibre-to-fibre recycling, produces high-quality rPET pellets suitable for fine fibre production. www.erema.com Erema Hall 2.1 Booth C55 Bottle-to-bottle pelletising system Aceretech, Jiangsu, China, introduces its bottle-to-bottle food-grade pelletising system. The continuous SSP (solid state polycondensation) production process consists of several key components. These components are claimed to seamlessly integrate with preceding granulation equipment to achieve continuous crystallisation and viscosity enhancement of rPET pellets. This system is capable of achieving approximately 0.02 dl/g/H viscosity enhancement, removing acetaldehyde to ensure its content is ≤1 ppm, and reducing the levels of both polar and non-polar toxic volatile compounds (such as 3-acetone, benzophenone, etc.) to less than 200PPB. www.aceretech.com Aceretech ND18"},{"@ID":52 "EVENT PREVIEW PETplanet Insider Vol. 25 No. 0/24 www.petpla.net 36 Laboratory automation, precision bottle measurement and innovations in automated blow moulder control Quality control and productivity improvement Laboratory automation, precision bottle measurement, and innovations in automated blow moulder control are key focuses for Agr’s array of products designed to assist container producers, converters, and fillers in staying competitive while meeting the increased quality demands of today’s world. The company will be showcasing several new product developments, alongside quality management and process control equipment for plastic containers. One of the highlights will be the Gawis 4D, Agr’s all-in-one automated laboratory measurement system, which streamlines laboratory measurement operations by performing a multitude of critical dimensional and thickness measurements in one simple operation. The Gawis 4D features Agr’s patented AutoJob, enabling the creation of complicated job setups in a matter of seconds. When paired with the robotic handling system, up to 128 bottles or preforms can be measured, hands-free, with accuracy, repeatability, and operational throughput. The focal point of Agr’s display will be the Process Pilot+, representing the latest advancements in automated blow moulder control for PET bottles. Built upon Agr’s well-known Process Pilot automated blow moulder management system, the Process Pilot+ incorporates a patented technology that is claimed to enhance blow moulder efficiency and profitability. This system allows operators to optimise the blow moulder based on performance, energy efficiency or operating costs. By continuously measuring material distribution on every bottle, the Process Pilot system proactively manages the blow moulder to maintain optimal material distribution, even amidst environmental and material variations, particularly those associated with rPET production. AGR says that the Process Pilot+ system is an indispensable tool for PET bottle manufacturers committed to incorporating rPET into their product mix. Pilot Vision+ is claimed to be Agr’s latest and most powerful in-the-blow moulder vision system. Specifically designed for quality management of bottles with high percentages of Agr’s Pilot Vision+ system is designed to meet the inspection challenges of PET bottles made with higher percentages of recycled material. Agr South Hall, Level 1 Booth 12048 Bottle Zone"},{"@ID":37 "PETplanet Insider Vol. 25 No. 03/24 www.petpla.net 35 EVENT PREVIEW Meeting the market demand ABC Compressors, a global leading provider of compressed air and gas solutions, is set to unveil its latest advancements at NPE. With a steadfast focus on energy efficiency and reliability, the company has introduced two transformative products that promise to redefine industry standards. Both solutions can be seen in the bottle zone. Horizon Synchro - PET synchronous compressor At the forefront of ABC Compressors’ latest achievements is the Horizon Synchro range. This line of compressors are claimed to offer a range of benefits that enhance efficiency and performance on high-speed production lines. The PET synchronous compressor range is equipped with state-of-the-art permanent magnet motors, delivering superior energy efficiency compared to conventional models, ABC says. This advanced technology not only reduces energy consumption but also lowers maintenance costs. Additionally, with variable speed drives, these compressors can adapt to specific application needs, ensuring precise control and significant energy savings under varying load conditions. The compact design of the Horizon Synchro compressors optimises floor space in beverage production facilities, allowing for space-saving installation. Enhanced intercooling processes are claimed to ensure improved performance and extended equipment lifespan, ensuring high-quality compressed air and increased reliability. The range also boasts advanced digital management systems for remote monitoring and control, allowing operators to optimise compressor operation for efficiency by tracking performance or receiving real-time alerts. ABC Compressors will be exhibiting a unit of the Horizon Synchro compressor at their booth. X-PET – all-in-one containerised high-pressure compressor Another product introduced by ABC Compressors is the X-PET range. Born from the technology utilised in its larger sibling, the Horizon Synchro, it has been designed for clients in the beverage and plastic bottling industries with lower-speed lines. The X-PET series is claimed to be the market’s first atmospheric compressor boasting oil-free piston technology and pressures of up to 580 psig, all within a container ready to operate without the need for external cooling equipment, as it is air-cooled via a built-in fan. The air-cooled feature not only maximises savings on water consumption but also on the energy required for water temperature regulation, having a double impact in the total cost of ownership. The X-PET series features a compact design that allows installation in any production plant corner, eliminating the need for a separate compressor room and facilitating easy relocation. While incorporating the technology from the Horizon Synchro, the X-PET also features a direct-coupled motor that eliminates losses associated with other transmission methods, a variable speed that adjusts compressor usage to match the plant’s requirements and a digital compressor that centralises the operation from a single HMI point. ABC Compressors will be exhibiting two units of the X-PET that will be providing air to various Aoki Technical Laboratory lines at the bottle zone, booth S12071. www.abc-compressors.com Plug&play high-pressure air solution X-PET Horizon Synchro ABC Compressors South Hall, Level 1 Booth S19106 Bottle Zone 2024 Training Schedule Technology&Application of PET Plastic Packaging for Hot-Fill &Aseptic Beverages Join our expert team for small group training on a variety of subjects - from materials to recycling. Scan to learn more & register for classes! ©2024 Plastic Technologies | 1440 Timberwolf Drive, Holland, Ohio USA 43528 www.pti-usa.com"},{"@ID":45 "PACKAGING / PALLETISING PETplanet Insider Vol. 25 No. 03/24 www.petpla.net 43 age manufacturers to make sure they are ready for the switch in July 2024. However, alongside an increased demand for the sustainability, sales of high-end products have rocketed, particularly in the sensitive juices, teas and flavoured drinks market, and bottle design has had to adapt to stand out in one of the fastest growing and competitive beverage segments. So in Sidel we have responded by creating dedicated solutions that combine the highest eco credentials with an appealing drinking experience, such as our 1Skin concept. PETplanet: Sidel offers a wide range of PET bottle packaging. From still to carbonated beverages, from sensitive to hot-filled products, also for non-food applications such as household or cosmetics. Sidel has developed two new sustainable PET bottle designs for beverages, StarLite R and 1Skin. Can you tell us more about these two bottles? Jérôme Neveu: StarLite R and 1Skin are a result of our continuous packaging optimisation programme and both bottles are designed to reduce greenhouse gas emissions while offering new marketing opportunities and high production performance for manufacturers. StarLite R for carbonated soft drinks (CSD) is a 100% rPET bottle featuring packaging circularity and ultimate packaging quality. This solution offers greater protection against deformation, increased resistance to bursting and optimum stability, thereby ensuring a transition to rPET bottles with no fear. It leverages improved process technology including an advanced mould base profile and stretch rod end design. StarLite R CSD also utilises an ultra-efficient bottle base cooling method with innovative dual external and internal cooling to ensure a perfect shape. StarLite R CSD can be easily installed on existing production lines and adapted to fit current bottle designs as it is compatible with Sidel’s signature blow moulders, EvoBlow, Universal and Series 2 and is suitable for high-speed productions. The 1Skin concept is a breakthrough both in sustainability and in its streamlined design to drive sales of high-end products within the sensitive juices, teas and flavoured drinks market. It features comfortable pouring and drinking thanks to an ergonomic grip and attached cap lock feature to keep the open bottle top away from the consumer’s face. This bottle provides a minimalist, premium, label-free design with multiple font and texture options and attractive natural light and shadow play with the bottle transparency. QR or bar codes can be printed on the bottle closure to provide information to consumers or enable individual unit sales. Combining a tethered cap and a label-free bottle design, 1Skin can immediately enter the recycling stream with no need to separate additional raw materials such as ink, glue, labels or sleeves. We can add the 1Skin solution into new equipment or add it to existing lines using our dedicated line conversion services. PETplanet: In which applications do you see growth opportunities for the PET bottle and where? Jérôme Neveu: The use of recycled PET content in packaging has increased, driven by regulations across the world and brands’ commitment to packaging circularity. It’s clear that the market for rPET is evolving as more beverage and food manufacturers look to embrace a sustainable material that is compatible with their existing manufacturing equipment. For sure, combining lightweight and recycled PET is the fastest way for brands to reach carbon neutrality. Using our deep understanding of recycled PET resin characteristics, its variability and its impact on bottle production, we’re continuing to innovate and find more breakthrough solutions for rPET bottle production so we can achieve consistent production performance and bottle quality with rPET. Our packaging optimisation services for bottle weight reduction help to significantly offset rPET resin costs. On top, in June last year, we launched our RePETable offer, the 360° one-stop shop for recycled PET, it supports on one hand to secure bottle production efficiency and quality whatever the rPET percentage, and on the other hand it supports the industry in developing design for recycling packaging. With the RePETable offer, we’re committed to creating a virtuous closed-loop process for foodgrade rPET bottles which will help grow the market for recycled PET further in the future. PETplanet: What does the future PET bottle look like for you? Where do you see challenges for your customers? How does Sidel support its customers with additional services? Jérôme Neveu: The main trend for PET is to increase its circularity this is why there is a growing desire to use recycled PET in bottle production. The variability of rPET resin is a challenge for the packaging industry, due to both the seasonality of products entering the recycling stream and the vast range of suppliers. The different PET collection models mean that postconsumer PET material bales will vary from region-to-region and the recycling process and equipment used will also influence PET resin. The varying characteristics for rPET resin could lead to a narrower process window and a lower bottle quality, especially when it comes to carbonated beverages. In addition to common CSD bottle manufacturing challenges such as stress cracking, roll out and bursting during blowing, a higher temperature may also be required to process rPET bottles. Consequently, packaging manufacturers can experience reduced control over rPET material stretching and distribution in the bottle-making process. However, with our deep understanding of recycled PET resin characteristics, its variability, and its impact on bottle production, we developed solutions for bottle manufacturing equipment to have a process that address rPET characteristics. This is part of our RePETable offer that includes machine upgrades and dedicated packaging solutions such as StarLite R which uses leading technologies to ensure efficient rPET bottle production by restoring a much wider process window. Establishing a virtuous closed-loop process for food-grade rPET bottles also means to design the primary packaging with the view of making it easily recyclable. Through our RePETable offer we also aim to support robust primary packaging circularity by helping the market innovate with new materials for primary packaging (closures, sleeves, glues, labels, additives and colouring…) while ensuring they are designed-for-recycling. For this we leverage a unique asset, our small-scale PET recycling pilot line that recreates every step in the recycling process. PETplanet: Thank you so much Mr Neveu. www.sidel.com"},{"@ID":21 "BOTTLING / FILLING PETplanet Insider Vol. 25 No. 03/24 www.petpla.net 19 Wedon’t focus on clients’ problems EXW RQ ƓQGLQJ VPDUW VROXWLRQV IRU WKHP yellow.agency Swiss-engineered Preform Systems At Otto Systems we focus on solutions for special applications in PET preform production. We provide you with the most economical answers to your needs. Our unique system concept is based on smart modularity, proven performance, IXOO LQWHJUDWLRQ DQG PD[LPXP ŴH[LELOLW\\ )URP LGHD WR RSHUDWLRQ 2WWR 6\\VWHPV JLYHV \\RX D GHFLVLYH FRPSHWLWLYH HGJH with your satisfaction as our guiding principle. Jump-start your PET preform production with us. otto-systems.com NPE 2024 ORLANDO,FL MAY 6–10 South Hall Level 1 Booth S12095"},{"@ID":55 "BOTTLE MAKING 17 PETplanet Insider Vol. 25 No. 03/24 www.petpla.net Sipa is pushing sustainable trends Refillable PET bottle blowing The popularity of refillable PET bottles is growing fast. Governments are pushing for them, all sorts of technologies are increasingly enabling them, major brands are keener to make them, and multiple markets around the world are pulling them. Sipa is prepared with its RefPET bottle blowing system. offers several features for downstream partners involved in RefPET bottle and also preform production. It has, for example, significant experience in special preform design and production. For the bottle moulding itself, it has developed electric heating of blow moulds, to improve bottle performance and also special base designs, for which it has a patent pending. Sipa says that processing equipment is available for production using between two and six cavities. Diverse blow moulding systems are in use for RefPET bottle production. For high output – up to approaching 8,000 bph – of bottles around 2 l in volume, there are the Xtra 6 and 8 rotary systems. Linear SFL systems – performance 6, Dynamic 4 and Dynamic 3H, as well as Flex 2 types, are for lower outputs and larger bottle volumes. These feature stretching capabilities, ease of use and maintenance, clean operation, and excellent energy efficiency. The global market for PET bottles is changing, and RefPET is on the up. www.sipasolutions.com By the end of this year, the global market for refillable PET bottles should be close to $10 billion, and in ten years’ time it could be worth well over $15 billion. Refillables are emblematic of the circular economy, but they also represent another circle. Back in the 1960s and 70s, refillable glass bottles were extremely popular in Northern Europe and North America in particular. But then return schemes all but disappeared during the 1980s and ‘90s, as metal cans and singleuse PET bottles gained dominance. Now, sustainability issues are pushing drinks packaging to return to its roots. Under the European Green Deal, new regulations say the market share of bottles for non-alcoholic beverages in reusable/refillable packaging should reach 10% by 2030, rising to 40% by 2040. In Europe, there have been widespread rollouts of new deposit return schemes (DRS). National governments are developing their laws to mandate more sustainable plastics packaging. France for example banned the sale of single-use plastic water bottles in public places in 2020. In the USA, the number of specialist refillable water stations has increased by 50% over the last five years. In parts of Latin America, returnable bottles never left the mainstream. Improving bottle-to-bottle circularity Sipa has for many years been in the vanguard of the “3Rs” movement: Reduce, Reuse, Recycle. It regards refillable PET – RefPET bottles as one important answer to solving the global packaging sustainability problem. RefPET bottles combine the advantages of one-way PET bottles and multi-use glass ones. Logistical limitations to their adoption are being addressed. Independent Life Cycle Analyses (LCAs) have shown that RefPET bottles perform better, and are more sustainable, than reusable glass bottles. However, considerable changes in manufacturing processes, inputs, and logistics required for PET containers will be necessary, since RefPET bottles are quite different from one-way types, and industry-wide change in the manufacturing of PET packaging will be necessary. In a RefPET system for example, the bottle needs to be filled and washed at high temperatures multiple times, in order to meet hygiene requirements. This means RefPET bottles are more than twice as heavy as in one-way. That puts extra demands on preform and bottle production, including cooling systems. Sipa has therefore successfully developed preform and container design for refillable bottles with special focus on lightweighting all bottle sizes designing a new base for the 3 l that improves base forming and washing cycles. The company also worked on RefPET bottles in collaboration with various downstream partners. This includes very large water bottles for water coolers, where results are very promising, Sipa stated. Sipa’s SFL Maxi 1 machine yields considerable advantages in both Opex and Capex, compared with competitors. Sipa RefPET bottles produced on SFL Dynamic 4"}]}}
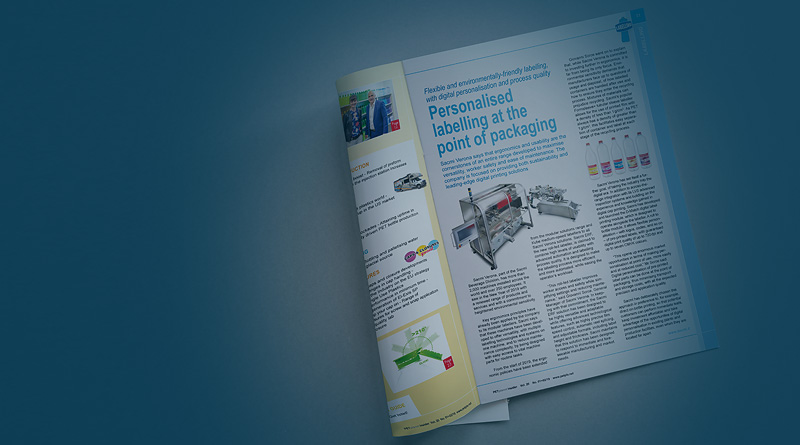