"PREFORM PRODUCTION 25 PETplanet Insider Vol. 18 No. 07/17 petpla.net Alok Parakh about National Polyplast’s PET preform range 60,000 tonnes of PET preform capacity The National Plastics Group is made up of three business units, serving PET packaging, automotive components and consumer electronics. The Group, which was established in 1951, is based in Chennai, India and has focused since its foundation on the production and sale of plastic products for a range of applications. The National Polyplast business, which was launched in 1991, focuses primarily on PET preforms. This particular line, which was first developed in the context of the company’s longstanding business relationship with PepsiCo, provided the basis for an unbroken history of expansion and a growth rate of 40% per annum in this segment until 2014. “Our advantage in the local market is our diversified nationwide presence,” explains Mr Sudershan Parakh who is the Group’s Managing Director besides Mr Alok and Mr Arihant who have day-to-day business responsibility. “National’s plants are located in Northern, Western and Southern regions of India, so that we are able to deliver our products to bottlers quickly and efficiently. As these are also situated near ports, we are able to import materials and export preforms in a cost-efficient manner.” The company’s market presence is a result of quickly adapting to changing market requirements and strong relationships built over decades with all key stake holders. The PET boom in the 1990s opened up several opportunities in packaging, driven by the growing purchasing power of the population. “When leading multinational beverage companies began activities in India in the early 90s, the soft drink boom and exponential growth was a foregone conclusion. With consumer preference shifting to PET in other global economies, it was only a matter of time before PET would supersede glass in India,” recalls Mr Parakh. At that time, National manufactured plastic crates for glass bottles. In 2003, the company decided to install its first Husky preform system, which had 48 cavities. Soon afterwards, it introduced its first Alaska neck-finish preforms for water applications, and the PCO 1881 for CSDs. Today, National manufactures on 12 preform production lines nationwide. The majority of preforms are made on the Husky HyPET HPP systems, including the first 144 cavity system in India. The lower volume products are produced on ASB PM lines. National’s manufacturing range extends to more than 30 preform variants, including 28mm PCO 1810 and 1881, Alaska 3 Start, Novembal 267, 38mm 2 Start and 30/25 Neck Finishes. It has the capacity to process more than 60,000 tonnes of PET preforms annually. According to the company’s own figures, it has the capacity to manufacture over 2.5bn preforms per year. The products’ key applications are water, CSD, fruit juices and milk. As well as PepsiCo, its customer base includes large brand owners such as Amul, Bisleri and many regional players. Standardisation of specifications has enabled National to move the moulds between their various sites and thus achieve the most efficient use of moulds and machinery. National employs over 750 personnel, over a total manufacturing and support area of more than 70,000m². The Group generated a turnover of over €50 million in 2016. “There are many preform suppliers in India but what makes us different are our customised and lightweight solutions, stringent food safety systems, customer proximity and above all the high level of trust and comfort built with each of our associates, in all three divisions of our Group,” Parakh said. “We will continue to invest in the future and attract new clients to our customer base for further growth, which will include the construction of another greenfield plant next year. We are also venturing into new packaging products so as to become a key point of contact in the field of packaging and exploring expansion opportunities in Southeast Asia, Middle East and Africa as well.” www.nationalgroup.in Alok Parakh, Director National Polyplast (India)","@ID":27}, "PETplanet Insider Vol. 18 No. 07/17 petpla.net 46 PETbottles Home + Personal Care Wash gel with active carbon Bioré, a “new” Kao Group brand which is part of Guhl Ikebana Ltd, is selling 200ml bottles of a wash gel in Germany with active carbon for poredeep skin cleansing. According to the manufacturer, the active carbon surrounds and removes twice as much dirt and impurities than an ordinary wash gel. The following promise is written on the folded adhesive sticker: “Every pore clean or your money back”. The almost black product comes in a clear elliptical bottle with a screw pump dispenser and locking function. www.biore.de A new size and range of “Real treasures” A new range of invigorating shampoo in Garnier’s “Real treasures” series comes in a newly introduced 400ml bottle. The shampoo does not contain silicones or parabens and relies on the virtues of green tea and five plants – eucalyptus, verbena, stinging nettles, lemon and aloe vera. The 400ml bottle is taller and slimmer than the 250ml version. The light green coloured bottle has a hinged cap and two clear self-adhesive labels on the front. www.garnier.de Hair care spray in two phases Procter and Gamble are selling a silicone-free hair spray as part of their Pantene Pro-V range for greasy hair called Micellar, Purity and Nourish. For its two-phase daily use, the product must be shaken well prior to each application. It should then be sprayed on damp or dry hair and can be left on without rinsing. The clear/blue product comes in a clear 150ml bottle with a screwed-on pump sprayer and secured by a protective cap. A no-look label explains how the product is to be used. www.pg.com .com 100815dmyL","@ID":48}, "MARKET SURVEY 28 PETplanet Insider Vol. 18 No. 07/17 petpla.net Systems for caps Suppliers of cutting plants Company name Starlinger & Co Ges.m.b.H Herbold Meckesheim GmbH Sorema Div. of Previero N. srl Postal address Telephone number Web site address Contact name Function Direct telephone number Fax E-Mail Sonnenuhrgasse 4, 1060 Wien, Austria +43 1 59955 0 www.recycling.starlinger.com Mr Paul Niedl Commercial Head Starlinger recycling technology +43 2674 808 3100 +43 2674 800 125 sales.nd@starlinger.com Industriestr. 33, 74909 Meckesheim, Germany +49 6226 932 0 www.herbold.com Mr Achim Ebel Vice President for Plastic Recovery Systems +49 6226 932 149 +49 6226 932 495 Achim.Ebel@herbold.com Via Per Cavolto 17, 22040 Anzano del Parco (CO), Italy +39 031 63491 250 www.sorema.it Mr Dario Previero General Manager +39 031 63491 250 +39 031 63491 217 sales@sorema.it Input/output Bales and/or single bottles Yes Output per hour From 500 to 10,000 kg/h Sorting Inclined belt conveyer with metal detector Yes Yes Additional techniques for impurity sorting Yes Yes Manual sorting possible? Yes Yes Granulator Wet or dry? Wet and dry Both according to process condition Cutting chamber setup With and without screw forced feeding Yes Size of granulat Depending to specs Customised Washing process Bottle to Granulate Four models: recoSTAR PET FG, recoSTAR PET FG+, recoSTAR PET iV+, recoSTAR PET iV+ Superior Input variable: collected pressed bottles, various colours Starlinger recycling technology offers the engineering of washing lines and / or a turn-key project with components and technologies available in the market Yes Output: Granulate with approval Yes (decontaminated for food-contact, IV increased, AA 1ppm, lowest VOC level) Yes Capacity [t/a] 6,000 - 26,000 t/a rPET pellets Up to 30,000 t/a Floor space [m²] Depending on design 1,000 - 4,000 m² Which approvals Several USA/FDA (C-H), Austria, Germany/BfR, Ilsi, France/AFFSSA, Finland, Australia, Canada, Egypt, Japan, Switzerland, several Latin American countries (Bolivia, Brazil, Chile, Colombia, Ecuador, Guatemala, Peru); follows EFSA requirements; brand owners Fresh water consumption per tonne output [m³/t] Depending on design 0.5 - 2 m²/t Consumption kWh per tonne output [kWh/t] Depending on design 545, depending on input material Flakes to Granulate Four models: recoSTAR PET FG, recoSTAR PET FG+, recoSTAR PET iV+, recoSTAR PET iV+ Superior Input variable: flakes, coloured proportion max 5%, not much chlorine Output: Granulate with approval Yes (decontaminated for food-contact, IV increased, AA 1ppm, lowest VOC level) Capacity [t/a] 1,500 t/a - 26,000 t/a (5 extruder sizes) Floor space [m²] 130 m² - 540 m² Which approvals Several USA/FDA (C-H), Austria, Germany/BfR, Ilsi, France/AFFSSA, Finland, Australia, Canada, Egypt, Japan, Switzerland, several Latin American countries (Bolivia, Brazil, Chile, Colombia, Ecuador, Guatemala, Peru); follows EFSA requirements; brand owners Fresh water consumption per tonne output [m³/t] approx. 0.15 Consumption kWh per tonne output [kWh/t] approx. 410 (depending on design) Bottles to Flakes Input variable: collected pressed bottles, various colours Starlinger recycling technology offers the engineering of washing lines and / or a turn-key project with components and technologies available in the market 1,000 / 10,000 kg/h Output: Flakes with/without approval Yes (decontaminated for food-contact, IV increased, AA 1ppm, lowest VOC level) 600 / 7,000 Kg/h with approval, according to project Capacity [t/a] 3,700 - 10,500 (5 sizes) Up to 30,000 t/a Depends on the different recycling plants Floor space [m²] approx. 150 1,000 - 4,000 m² Depends on the different recycling plants Which approvals FDA (hot-fill), follows EFSA requirements Accoring to project Fresh water consumption per tonne output [m³/t] 0.5 - 2.0 1 - 2 m³/t Consumption kWh per tonne output [kWh/t] 120 - 250 (incl. bottle washing to SSP) 250 - 300 0.20 - 0.27 kWh/t Drying Mechanical drying Hot air dryer (HAD) for higher moisture levels of the input material and/or for increased drying time and improved final material quality. Predrying unit (PDU) for optimum preparation of the material prior to extrusion. Supplied in different solutions Thermal dryer for final drying Post crystallisation unit (PCU) with hot air. To ensure constant crystallisation, this unit acts as hot storage buffer and provides the pellet temperature required for the subsequent solid stating process. Supplied in different solutions Filling station PET For rPET: Silo 1,000 - 5,000l in stainless steel, incl. platform scale, diverter valve and piping Yes Included PO Yes Included Metal/coloured PET Yes Included Labels","@ID":30}, "BOTTLE MAKING 12 PETplanet Insider Vol. 18 No. 07/17 petpla.net The use of PET is steadily gaining market share in FHPC markets traditionally dominated by HDPE (high density polyethylene) and PP (polypropylene). In 2016, PET packages accounted for 29 billion units for Food, 7 billion units for Personal Care and 8 billion units for Home Care, according to Euromonitor. These figures are expected to grow by an average of 3% for all three sectors by 2020. Sidel’s new SteadyEdge base, along with attractive PET package design variants, is said to ensure stable and cost-efficient production. Creative and distinctive package With SteadyEdge, brands will appear exactly as intended. The new base technology is designed to meet the challenge of producing flat, oval and rectangular containers in PET, which all require a specific production process that delivers the optimum material distribution of PET to achieve a top quality package. “It makes it possible to achieve premium-quality containers in PET, with sharper edges which have a radius as little as only 1mm, compared to a previous minimum of 2.5mm,” explains Pierrick Protais, Packaging Innovation Leader at Sidel. These sharper edges actually increase design freedom and facilitate the production of more elegant containers with bases which are less curved. Also, they open up particular marketing opportunities for containers with complex shapes and large labelling surfaces. The technology also ensures maximum container quality by way of accurate processing, optionally reinforced by a monitoring system of visual control of base movement on individual blowing stations. More stable package for optimum uptime The sharper edges possible on the package are used to effectively flatten and increase the ‘standing ring’ area of the base. “In this way the package is much more stable, preventing unwanted rocking and reducing the possibility of containers being knocked over,” adds Protais. “The application of SteadyEdge to any design can enhance the package’s stability by as much as 35%.” This is beneficial on the supermarket shelf and also in the home, as well as improving reliability on the production line. As packages are far less likely to fall while they are being conveyed between various machines, this results in fewer costly stoppages and greatly improved uptime. Cost-efficient and sustainable production This innovative packaging solution optimises productivity and low total cost of ownership (TCO) while product quality and reliability are maintained to a high standard. Benefits include lightweighting possibilities of up to 10% through the improved material stretch on the base. A reduction in blowing pressure decreases energy consumption by up to 20% during production when limitation is linked to base design. The solution has been achieving higher output rates which are also up to 10% faster - from 1,800bph per mould for flat containers with a standard base to 2,000bph per mould with SteadyEdge. Such greatly improved line performance typically contributes to a return on investment (ROI) in less than a single year, says Sidel. Smarter blowing and quick changeover The specific sharp base design is achieved using the new Sidel patented base mould system, Base OverStroke System (BOSS). BOSS is a piston activated in the blowing phase to stroke the base. This mechanical element allows for the raising and lowering of the base during the bottleforming process independent of the opening and closing of the two halfshells of the mould. BOSS is intended to provide flexible and versatile production with the option to implement quick mould changeovers and ensure maximum production uptime. A BOSS-to-BOSS change-over can be performed in just 3min; BOSS-to-other can be performed in 11min. Easy to implement and to retrofit, Sidel’s new BOSS solution is fully compatible with Sidel Universal blowing machines. It is currently in use by customers in different parts of the world, and will shortly also be available for Sidel Matrix blowing machines. www.sidel.com SteadyEdge base for flat, oval and rectangular PET containers Sharper edges, increased design freedom SteadyEdge is a patented base solution by Sidel which offers Food, Home and Personal Care (FHPC) producers enhanced brand differentiation options and production efficiency. bottle making Example of a container with less curved base. Raising and lowering of the base during the bottle-forming process independent of the opening and closing of the two half-shells of the mould.","@ID":14}, "38 TRADE SHOW PREVIEW PETplanet Insider Vol. 18 No. 07/17 petpla.net TRADE SHOWpreview Drinktec: excitement mounts Around 1,600 exhibitors are participating in the leading trade fair for the Beverage and Liquid Food Industry. Drinktec will take place from September 11 to 15, 2017 in Munich. Exhibitors will be occupying a total hall space of over 150,000m2. The Innovation Flow Lounge (IFL) is one highlight of the supporting programme. Following its successful premiere in 2013, experts will be discussing the topical themes of importance for the future of the industry in the areas of product innovation, packaging and marketing. IFL and the special area New Beverage Concepts will have a joint space at the show, so that topics from the area of new beverage concepts, such as beverage ingredients and ideas, are also addressed and dealt with in the IFL. The IFL is focusing on product, brand and innovation managers, as well as decision-makers and managers in the fields of marketing and sales. Nearby, the PETpoint will be exhibiting in Hall 4A on 11,000m² dealing with all aspects of PET. As part of PETplanet’s close involvement with Drinktec, we have brought together an initial selection of companies whom we feel will be of significant interest to our readers. Hygienic retrofit of beverage filling line Claranor will be at Drinktec to present its latest innovations dedicated to the beverage industry. On top of its latest solutions: the Claranor Puls’Full Cap, a cap sterilisation for the most sensitive filling line. The cap is decontaminated not only inside, but also outside, adapted for ESL 60 days and more. Further on Claranor Essential, a cap decontamination equipment compact and cost attractive for lower speed lines (16.000 bph) will be shown. Claranor, with its new Puls’Combi PET, brings to the market a solution adapted for the hygienic retrofit of beverages filling lines enabling preform neck as well as cap sterilisation. This offer is for the soft drink market, moving ahead to products with lower CO2 protection, fewer preservatives, more nutrients, which are to be filled on existing lines. Consumers are looking for more natural and healthy beverages. For producers, these new needs often mean industrial challenges as the new products are more sensitive, require a much higher hygienic filling level, but on already existing lines. The new dry, on-line and without chemicals solution for the packaging sterilisation, offers a much higher level of hygiene between the filling and packing. Thanks to its experience with the beverage industry, with more than 180 units installed worldwide, including 60 in retrofit, Claranor has acquired the expertise to integrate its pulsed light cap and preform neck sterilisers into existing lines. www.claranor.com Hall A3 - Booth 111 Gernep GmbH labelling systems In order to meet the ever-increasing customer requirements in a wide range of markets, Gernep GmbH’s rotary labelling machines offer tailored solutions: Soluta for flexible selfadhesive, Labetta for universal cold glue and Rollfed or Rollina for rational all-round labelling with hot glue. Alternatively, Gernep labelling machines are designed modularly so that almost every special solution can be realised in addition to the standardised models. The units can be installed and dismantled easily and quickly. In addition, the company offers a wide range of additional equipment (e.g., camera-based or photoelectronic equipment). The company’s machine family thus offers the complete freedom of combination of wet, self-adhesive and the two hot glue systems in order to be able to tailor individual requirements perfectly and to be able to realise modern container configurations. www.gernep.de Hall A5 - Booth 302","@ID":40}, "BOTTLE MAKING 17 PETplanet Insider Vol. 18 No. 07/17 petpla.net Tour Sponsors: Local trade fairs gaining greater importance From Thailand to Vietnam by Kay Barton bottle making Meeting at Mahatanee’s booth during Propak Vietnam (f.l.t.r.): Yick Yu Lam and Kay Barton. Mahatanee Industrial Co., Ltd. March 21, 2017 We met: Mr Yick Yu Lam, Managing Director Thai machine manufacturer Mahatanee, which is better known under its “Great PET” machine brand name, exhibited at Propak Vietnam for the third time in a row in its 20-years history – and pronounced itself highly satisfied with the local market. In addition to its main business of blow moulding machines and ancillary equipment, Mahatanee manufactures sleeve-labelling equipment and cap counters. every year.” This level of demand is not coming solely from Tan Phu; nearly all drink, liquid-food and non-food products currently on the market in Vietnam are offered in PET bottles and cans. While they are manufactured on two-stage machines, manufacturers of them are almost non-existent in Vietnam itself. “There may be a small mechanic here and there, but no systems that are really to be taken seriously,” Mr Lam says. “The machines have all been imported up till now. That may change at some point in the future but it will be ten years before it does. At any rate, as of March we currently have exactly 100 blow moulding machines in the market here.” He dismisses concerns about any logistical challenges in exporting to Vietnam, from Thailand. “No complications at all. It maybe takes as little as two days to get a machine from our factory in Thailand to the customer in Vietnam. We will definitely continue to expand our future relations in Vietnam and we hope for new, interested customers.” www.great-pet.com www.stf-group.de ENGINEERING WITH THE COMPETENCE OF THE RECYCLER •Complete Plastic Sorting and Washing Lines engineered by Europe’s largest PET Recycler •Bottle-to-Bottle rPET Recycling •More than 60 PET Recycling Lines installed worldwide We spoke to Managing Director Yick Yu Lam about the company’s positive business relations with the Vietnam market, and about the way that local trade fairs in South-East Asia are gaining ever-greater importance. Our interview was held in front of the GPT-600 blow moulding line, which had pride of place and sole occupancy of its stand. With a capacity of up to 3,500bph for 600ml, it is among the faster systems in Great PET’s portfolio. It was the only machine exhibit at the exhibition stand. “We first came as an exhibitor to Propak Vietnam two years ago. At the time, admittedly, there was not an awful lot going on in the hall and we did wonder whether the decision to exhibit here was a good one,” Mr Lam recalls. “However, shortly after the trade fair, we received an e-mail with a purchase request.” That e-mail came from Tan Phu Plastic Joint Stock Company (TAPLAST), which became the company’s first customer in Vietnam. Its first order, which was for ten blow-moulding machines, was worth approximately US$700,000. Tan Phu became, and currently remains, Great Pet’s biggest client. It is purely a blower and has, Mr Lam advised us, four plants in Vietnam, of which the Ho Chi Minh City and Hanoi locations are the two largest. “They needed higher output equipment for their size segment and they turned to our fully electric machine models, which manage up to 4,000bph,” he says. “Since that first deal we have received orders for around an additional ten machines, from each factory,","@ID":19}, "BOTTLE MAKING 34 PETplanet Insider Vol. 18 No. 07/17 petpla.net Stretch Blow Molding, part 4 Material Basics / Behaviour in the blow mould by Ottmar Brandau Ottmar Brandau has newly revised his book “Strech Blow Molding”, first published by hbmedia / PETplanet Publisher, and now re-issued in a second edition under the Elsevier imprint. PETplanet Insider is publishing extracts from successive chapters in a series of articles. Property data for PET Since the strain-hardening phase of the process is so important for bottle performance, correct preform design, temperature profile, and blow air timing are all necessary to guarantee the best bottle. If the inflated preform reaches the bottle mould during the pre-blow phase, orientation does not occur to a sufficient degree and the finished bottle might fail any number of tests (see Table 2.2). 2.6 Acetaldehyde (AA) in PET bottles AA is a natural sweetener that is present in all citrus fruits and is often used as sweetener in beverages. It is also a by-product of heating PET, especially heating it to melt temRelevant parameters IV, temperature, and co-polymer content all play a role in determining how far the material stretches during yielding and what force is required to stretch it further (Fig. 2.17). Temperature conditioning allows the operator to improve the blow moulding process by making certain parts of the preform hotter or colder – changing the way in which they will stretch. The objective of preform design (or selection) and blow moulding processes is to properly match up the natural stretch ratio of the preform at the blow moulding conditions with the design stretch ratios of the preform/ bottle combination. Figure 2.17 Several factors at work, determining the natural stretch ratio.","@ID":36}, "BOTTLE MAKING 21 PETplanet Insider Vol. 18 No. 07/17 petpla.net before they are filled. Thanks to this dry sterilisation process, Konings’ production operation does not consume any water, and manages entirely without treating chemicals and generating sterile water. “The PET-Asept D dry-aseptic line offers maximised flexibility as far as format change-overs are concerned,” says Luc Nulens. A format change-over routine, including CIP/SIP cleaning, takes 2.5h. For comparison: the equivalent time for wet-aseptics is up to twelve hours. Konings calculates 30 minutes for a product change-over pure and simple, without intermediate flushing, and the figure is a mere ten minutes when the only thing required between two different products is to drain the pipes. Konings schedules one format change-over per day on average, and one product change-over roughly every eight hours. www.krones.com The PET-Asept D dry-aseptic line provides flexibility for format changeovers. Extended shelf-life The new container is coated with an oxygen barrier. To guarantee an extended shelf-life, Konings is reducing the product’s oxygen content: To start with, by deaerating the water down to less than 0.5 milligrams per litre; Then by putting it in interim storage in a sterile container with a nitrogen overlay; And finally by treating it with nitrogen during filling: here, the empty bottle is pressurised with nitrogen, thus preventing a vacuum in the container after filling, which would deform it. Thanks to the new PET-Asept D line, Konings has succeeded in tapping a new line of business: in future, the company can fill sensitive beverages without preservatives that do not need to be kept in the cold chain. “Our paramount goal is ensuring top quality for our products,” says Luc Nulens. 20,000 containers an hour The PET-Asept D line is rated at 20,000 containers an hour. It comprises: PET-Asept D aseptic block with preform feed, interior cleaning and inspection Contiform 3 stretch blow-moulding machine Injector D sterilising module Modulfill Asept VFJ aseptic filler Closure disinfection with gaseous H 2 O 2 Closer VarioClean CIP system for automatic cleaning VarioAsept J UHT system for thermal product treatment Checkmat unit for inspecting the fill level Linadry container drier Contiroll HS labeller Checkmat unit for inspecting proper placement of the labels Variopac Pro packer Modulpal palletiser PROCESS PILOT® makes producing a better PET bottle as easy as 2 3 1 MEASURE CONTROL OPTIMIZE every bottle for changes in material distribution process variation, inside the blowmolder material utilization and orientation to achieve maximum bottle performance CONTACT US TODAY TO LEARN MORE! AGRINTL.COM | +1.724.482.2163 | SALES@AGRINTL.COM see us at Booth A4-336","@ID":23}, "MARKET SURVEY 29 PETplanet Insider Vol. 18 No. 07/17 petpla.net Krones AG Böhmerwaldstrass 5, 93073 Neutraubling, Germany +49 9401 70 0 www.krones.com Mr Peter Hartel Head of Sales PET Recycling +49 9401 70 5448 +49 9401 70 91 5448 peter.hartel@krones.com Both possible Up to 4.5 t/h Yes, covered from sub-supplier Yes, covered from sub-supplier Yes Dry or wet, covered from sub-supplier 10 - 12 mm Yes, we produce the full washing process Depending on project Yes 3,500 t/a - 30,000 t/a 1,000 - 6,000 m² FDA-LNO, EFSA-LNO, brand owners 2.5 m³ / t Depending on design Depending on project Yes 3,500 t/a - 30,000 t/a 800 - 3,000 m² FDA-LNO, EFSA-LNO, brand owners Depending on design Depending on project Flakes with/without approval 3,500 t/a - 30,000 t/a 1,000 - 4,000 m² FDA-LNO, EFSA-LNO, brand owners Max 2.5 m³ / t Depending on design Yes Yes Yes Yes Yes Yes Suppliers of labelling and marking systems As supplement to the last issue of PETplanet Insider the companies P.E. Labellers S.p.A., Gernep GmbH and Heuft Systemtechnik GmbH present their state of the art labelling machinery! Although the publishers have made every effort to ensure that the information in this survey is up to date, no claims are made regarding completeness or accurancy. Company name P.E. Labellers S.p.A. Gernep GmbH Heuft Systemtechnik GmbH Postal address Telephone number Web site address Contact name Function Direct telephone number Fax E-mail Via Europa 25 - 46047 Porto Mantovano (Mantova), Italy +39 0376 389311 www.pelabellers.com Mr Luca Carollo Sales Director & Key Account Sales +39 0376 389311 +39 0376 389411 pelabellers@pelabellers.it Benzstr. 6, 93092 Barbing, Germany +49 9401 9213 0 www.gernep.de/en Mr Martin Hammerschmid General Manager +49 94019213 0 +49 9401 9213 29 martin.hammerschmid@gernep.de Am Wind 1, 56659 Burgbrohl, Germany +49 2636 56 0 www.heuft.com +49 2636 56 256 info@heuft.com Labelling machinery System Labelling machinery Flexible rotary for cold glue, hotmelt wrap around, holtmelt from reel, self-adhesive Rotary Type (rotary etc) Linear and rotary Rotary Rotary Modular installation Yes Modular installation No Application (cold glue, hotmelt wrap around, holtmelt from reel, self-adhesive) Yes, all Application (cold glue, hotmelt wrap around, holtmelt from reel, self-adhesive) Cold glue, hotmelt wrap around, self-adhesive Output rate From 60 to 1,300 bpm 800 - 40,000 per hour / 15 - 650 per minute Up to 72,000 per hour Number of labels/container Up to 7 PSL maximum 8 / others depends Various Footprint Footprint very flexible Various Container shape (cylindrical, rectangular, oval, square, etc.) All kind of containers Container shape (cylindrical, rectangular, oval or square) Various Label position and control on bottle (body, collar, back, neck ring, closure) Yes Label position and control on bottle (Body, collar, back, neck ring, closure) Yes","@ID":31}, "BOTTLE MAKING 20 PETplanet Insider Vol. 18 No. 07/17 petpla.net Co-packer opts for dry aseptics Juices, soft drinks, cider, beer, wine and spirits – so basically everything except milk and clear water: that’s the highly diversified range of products made by Konings for other beverage companies. The Belgian contract-filling firm has about a dozen key accounts, for whom it is something like a one-stop shop: Konings handles either the entire beverage production and filling operations, or it just fills the drinks as a co-packer. In a preliminary stage, the company processes apples and pears at its main facility in Zonhoven, and ferments these to make ciders. After these have been produced, they are stored in a warehouse with space for 20,000 pallets. Ten years ago, the founder’s family sold Konings. The four new owners then changed over the company’s structure with purposeful rigour step by step. Their intention was for Konings: to do entirely without house brands in the future, so as to be able to offer its contract-filling services more independently; to be expanded into a producer and filling company for any kind of beverage; to turn its back on short-term contracts and establish long-term alliances instead; to upgrade its product portfolio by deploying new technologies. From wet to dry-aseptics In four facilities at Konings, filling lines are up and running for returnable and non-returnable glass bottles, cans, cartons and PET containers. It is the sensitive juices, in particular, that demand gentle production and filling processes: in the English plant, wet-aseptics had already been used, and in the Dutch town of Breda two of these PET lines had likewise been running. But firstly no blow-moulder had been integrated into them there, and secondly the sterilisation rate was a mere log 4. This means that it was only possible to fill beverages in the cold chain. To be able to guarantee absolutely safe filling for all its customers’ sensitive beverages in future without adding any preservatives, the company decided to start using a dry-aseptic process from then on. Luc Nulens explains: “The advantages offered by dry sterilisation are obvious. Thanks to the high sterilisation rate of log 6, it’s possible to market the beverages outside the cold chain even when no preservatives are added. With the CIP/SIP cleaning procedure, format change-over times are significantly shorter and finally the consumption of energy, and processing and operating materials, meaning electricity, water, air and peroxides is reduced.” Lightweight PET container newly developed In this context, it was important that Krones, just like Konings, acts as a turnkey vendor and is able to supply the process technology involved as well, i.e. CIP and the product UHT system. Konings installed a stretch blow-moulder for the first time here. The new line has been up and running since January 2017, and includes a PET-Asept D aseptic block. It handles fruit juice, flavoured water, a whey-based soft drink, and a vitamin-enriched water. The latter had hitherto been hot-filled in Ireland in a 0.5l bottle weighing 27g. Together with Krones, Konings has developed a similar-looking container weighing a mere 22g. Thanks to aseptic filling, too, the best-before period has meanwhile be extended from six to nine months. Dry, sterile, efficacious The PET-Asept D process is made for safe filling of sensitive beverages without adding any preservatives. The sterilising agent used is gaseous hydrogen peroxide, which flows into the still-warm PET containers directly bottle making A high sterilisation rate, short format changeover times and low consumption of energy and processing/operating materials are reasons enough for Luc Nulens to opt for dry sterilisation.","@ID":22}, "41 TRADE SHOW PREVIEW PETplanet Insider Vol. 18 No. 07/17 petpla.net Blowmoulder automation tools Agr International, Inc. will be exhibiting an array of products for managing the production and quality of beverage containers. Featured will be the latest developments in advanced blowmoulder management, shelf-life control and pressurised container testing. The Process Pilot with CrystalView automated blowmoulder management system is ideal for beverage producers that PET bottles in-house. The Process Pilot product group offers precise material thickness distribution management on PET bottles, while offering hands-off blowmoulder control. With the trend towards ever lighter bottles, the Process Pilot system offers producers the ability to lightweight bottles to the absolute minimum while providing the confidence that material is distributed appropriately, with proper thickness in all critical areas, on every bottle produced. Whether the goal is to make the lightest bottle possible, process preforms of mixed lineage, improve bottle shelf-life and performance characteristics, save energy or just run a stable process 24/7, the Process Pilot product group offers a means to realise this goal profitably and with confidence. Shelf-life management is an important but tedious measurement. Agr will feature several products that provide immediate determination of the permeability and shelf-life performance of newly produced PET bottles. These products make it possible to effectively manage (in real-time) a bottle’s shelf-life performance for oxygen ingress, CO2 or water loss. Whether a final product is packaged in a PET bottle, PET keg, aluminium bottle or glass, accurate volume and proper pressure performance is paramount to the efficacy of the finished beverage container. The Agr PPT3000 offers a versatile solution for measuring volume expansion and pressure testing of containers manufactured from PET. Unlike other pressure testers, The PPT3000 actually simulates the rapid rise pressure profile that a container experiences during the filling cycle, providing valuable data that can be used to prevent filling line downtime due to premature pressure breaks. www.agrintl.com Agr’s Process Pilot blowmoulder automated control system Hall A4 - Booth 336","@ID":43}, "BOTTLE MAKING 16 PETplanet Insider Vol. 18 No. 07/17 petpla.net Tour Sponsors: Processing and bottling high-quality edible oils by Kay Barton bottle making Cai Lan Oils & Fats Industries Co., Ltd. (Calofic), part of Wilmar CLV March 31, 2017 We met: Mr Peh Ping Teik, Head of Technical, Wilmar CLV Mr Nguyen Tuan Anh, Plant Manager, Calofic Mr Trinh Tuan Anh, Consumer Pack/Deputy Manager, Calofic Mr Nguyen Van Son Em, Consumer Pack/Plastic/Deputy Manager, Calofic You can find vegetable cooking oils with the brands Neptune, Simply or Meizan everywhere you look in Vietnam. They are produced by Cai Lan Oils & Fats Industries Company Ltd (Calofic), a joint venture between Vocarimex (Vietnam Vegetable Oils Industry Corporation) and the Singapore-based Wilmar group which began in 1996. Calofic runs a refinery and packing plant in Ha Long, located around 170km to the east of Hanoi, as well as another factory in Ho Chi Minh City. Production began in the north just one year after their joint venture began, whereas production in the south began in 2007. Following our last visit in 2010, we have had yet another chance to get together with Mr Peh Ping Teik, Head of Technical in their Ho Chi Minh City office, afterwards taking a 20km journey to their factory. “Our capacities have more than doubled since PETplanet last paid us a visit,” Mr. Peh began. “90% of our consumer products are now bottled in PET and our edible oil sector is experiencing an annual growth rate of 10-15%.” Calofic produces and fills approximately 200 million bottles per year, as such, with a market share of 50%, they are the largest producer in the market in term of output. PET bottles are used in 0.25l, 0.4l, 1l, 2l, 5l and 10l sizes. A small proportion of their products is bottled in pouches or large containers with up to 25kg in HDPE containers. The company sources PET material from neighbouring countries tax-free. Their northern factory uses 2 x Sidel SBO 8, Sidel 2XL, Serac SBL (four cavities) and a Husky HyPET injection moulding line (72 cavities). According to Mr Peh, they work in close cooperation with Bericap in the cap sector. An example of their collaborative work includes the development of a new one-piece hinge cap which took place five years ago. In contrast to our last visit, Calofic are now setting their sights on hard preforms. In this way, they shifted their focus to producing bottles with a premium image. In their Ho Chi Minh City factory, 300 employees work across 85,000m2 of floor space. The premises have direct access to the river, meaning raw materials, such as palm oil, can be delivered by seaway. The material comes from countries including Malaysia, Indonesia and Argentina on a cargo ship and we had the chance to witness a palm oil delivery from Malaysia during our visit. Besides the brands mentioned above, Calofic also produces Cai Lan, Kiddy and Orchid on-site. There are some imports of cooking oil in consumer packs, but compared to the total edible oils market, the volume of imports is minimal. The company’s best-selling packaging is the 1l bottle. According to estimates, a typical family consumes an average of 2l of edible oil per month in big city, with an estimated annual consumption nationwide of around 9-10kg per capita. www.calofic.com.vn HCM plant info: Investment: US$ 91 millions Preform injection: Unique injection moulding 96 cavities (UPET) Blowing: Sidel SBO 2F, SBO 10, SBO 12, Sipa SFL 4/3, Serac SBL 4 cavities Filling: Serac and Techital. P.E. Labellers for hot melt label Palletising: PSS, Vepro Peh Ping Teik at his downtown office","@ID":18}, "BOTTLE MAKING 15 PETplanet Insider Vol. 18 No. 07/17 petpla.net esting. We are developing a pouch or brick replacement concept that is as cost effective, but also recyclable. We have demonstrated this concept to a number of end-users and brands who have found it extremely interesting. PETplanet: Very soon we will see the very first bottle commercialised which was manufactured with LiquiForm. Can you give us a hint as to what we need to be looking out for? Saxena: The first application will be launched very soon for the home and personal care market sector. So keep your eyes open for a soap or shamphoo, a detergent or a cleaning liquid. The reason why it is an HPC application is that the hygiene requirements are lower than those for beverage products. However, our licensees are working to realise launches in the beverage area as well. I expect that within the next 24-36 months, we should be able to see beverage products as well. PETplanet: Mr Saxena, thank you for your time! www.liquiformgroup.com Conventional blow moulding and filling operations (right) versus LiquiForm (left) LiquiForm","@ID":17}, "40 TRADE SHOW PREVIEW PETplanet Insider Vol. 18 No. 07/17 petpla.net Rapid automatic change-over The intense R&D activities which have been a feature of Lanfranchi in recent years have led to a new result in terms of technological developments applied to unscramblers: the automatic changeover. The Unscrambler 2.0 is capable of handling a wide range of containers of different shapes and size. This technology allows the Lanfranchi Unscrambler to reduce the bottle format change-over, without requiring the constant presence of an operator. The total change-over time is between 4 minutes to a maximum of 7 minutes. The machine working principles remain almost unchanged: Lift master system for bottle selection Single funnel or SR system Deformed bottles detecting system Bottle extraction with or without a vacuum star-wheel The orienting system has been replaced by the PRS system (Position Recognition System) With Unscrambler 2.0 the new configuration for the additional bottle size will be automatically created by the PLC, allowing a fast and easy change-over. During the change-over, the bottles can be fed easily into the machine. Each movement of the automatic change-over is also controlled by the machine’s PLC, thus permitting the operator to check the position of every component involved in this operation. The Unscrambler 2.0 has been around for one year now. The Lanfranchi Unscrambler 2.0 can be seen functioning in Spain, where it has been recently installed. www.lanfranchigroup.com • 28mm, 33mm and 38mm screw closures • Robust and trouble free capping • Established DoubleSeal™ technology - for secure sealing performance - for better protection against micro-organisms • Slit FLEXBAND® band technology for enhanced tamper evidence • O 2 barrier and scavenging options for screw flat caps supporting longer shelf life and fresher taste • Sports closures for aseptic filling and hot filling without aluminum foil • Special closures for syrups and carton packaging Unique range of screw and sports closures designed for cold fill and aseptic application BERICAP Technology for juices, RTD teas, health drinks www.bericap.com Hall A6 - Booth 103 24 caps in 2.7 seconds Arburg will demonstrate its injection moulding technology which has been specially optimised for the packaging industry, particularly for fast sequence and highcavity moulds. The exhibit, a packaging version of the hybrid Allrounder 570 H, has a clamping force of 1,800kN and a size 800 injection unit. Twenty-four drink bottle caps will be produced in a cycle time of only 2.7s on a high-performance mould from z-moulds. The weight of the HDPE moulded parts is 1.25g. A vacuum conveyor and a direct colouring device ensure a correspondingly high throughput. Quality monitoring is carried out in-line using an optical system. The hybrid Allrounders of the Hidrive series are intended to work cost-effectively and remain productive and energy-efficient. This is ensured in particular by the combination of high-speed servo-electric toggle, electric dosing and hydraulic accumulator technology. This facilitates accurate, dynamic injection at a high performance level. Simultaneous machine movements ensure reduced cycle times. The special combination of “distance between tie bars, clamping force and opening stroke” in the Packaging version is tailored to the efficient mass production of packaging articles. An important feature for high-speed operation is powerful ejection, which is synchronised with the mould movement and ensures the precise and reproducible falling of moulded parts. Special features are available for the production of thin-walled parts and screw caps, enabling the machines to be individually tailored to the relevant application. www.arburg.com Hall A4 - Booth 323","@ID":42}, "BOTTLE MAKING 23 PETplanet Insider Vol. 18 No. 07/17 petpla.net Let’s give the bottle the right look Have you ever wondered why you buy a certain product instead of another one? The answer has to be sough in a series of elements which influence the consumer’s purchasing behaviour: quality of the product, brand popularity, aesthetic aspect of the package, its position on the shelf and much more. bottle making For Italian company SMI, many statistical data have shown that the purchase decision is determined in 95% of cases by factors related to the emotions evoked by the product, so that we can openly speak of “emotional buying” or “impulse buying”. An essential role in leaving an impression on the consumers’ emotions and sensations is played by the package, thus the more captivating and original its shape, colours, conveyed messages are, the more you draw the consumer’s attention and interest. Nature moves The bottle designed by SMI for Al Saleh company (Iraq) is an example of a container that wants to create emotions. Everything started with the consumer’s idea of recalling natural elements to express their own feelings about respecting the environment; in this way a “green” bottle, with the reproduction of stylised leaves on its surface incites an emotional response towards the container and the brand. The accurate study of the incline of the bottle “shoulder” has permitted SMI designers to create on the surface an elaborate play of veins which allows the image of the leaf to acquire a three-dimensional aspect and at the same time to cover a function of support for the container so as to ensure a greater resistance to mechanical stress. SMI, thanks to a latest generation R & D laboratory, is able to design and develop graphically a wide variety of PET containers and to give the customer’s product design a new “emotional” face. The SMI design centre has to date created about 1,700 containers that differ in appearance, shape, weight and size. Quality moulds and accurate testing A great design is not enough to make a great looking bottle, the appeal of a container also depends on the accuracy and precision with which the moulds used to produce it are made. To ensure its customers of the highest quality containers, SMI created a specific department that produces aluminium and steel alloy moulds, suitable for use in its stretch-blow moulders and those of other manufacturers. The quality of the moulds is assured by employing an FMS line, consisting of 12 CNC machining centres. These are fully automated machine tools running nonstop 24/7, which follows computeraided manufacturing (CAM) programs. The company labs utilise vast resources for testing new technologies and applications, especially in the stretch-blow moulding of preforms made of PET and other materials. The use of sophisticated equipment allows testing and dimensional tests of the customer’s preforms, e.g. the thickness is measured accurately by cameras and parameterisation comparison software, while polarised light equipment is used to analyse the homogeneity of the polymer. SMI has a prototyping facility that ensures rapid quality sampling. The company uses testing equipment, such as the AGR International PPT3000 tester, which tests the quality of the bottles and ensures that they meet pressure resistance and volume expansion goals. www.smigroup.it","@ID":25}, "LABELLING PETplanet Insider Vol. 18 No. 0/17 petpla.net 36 Three questions for Vimal Kedia, MD Manjushree Technopack In-mould labelling in PET by Kay Barton MHT MOLD & HOTRUNNER TECHNOLOGY AG Your Machine - Our Solution Hall 4A, Booth 416 QUALITY MADE IN GERMANY Manjushree Technopack is becoming known for its adoption of in-mould labelling (IML) technology in PET packaging. Mr Vimal Kedia, the company’s Managing Director, about how in-mould labelling can be beneficial to PET packaging. PETplanet: Why is in-mould labelling a popular choice for thin-walled PET bottles? Vimal Kedia: IML is a fairly new concept for PET but is steadily becoming a popular choice. The challenge is in integration. Market players must ensure that they are able to effectively integrate machine, logo, label and bottle design. PETplanet: How has the in-mould labelling technology shaped the PET packaging industry? Vimal Kedia: The IML in PET industry has revolutionised decoration dynamics and will help premiumisation of client products, especially pharmaceutical products or liquor bottles. We will begin working with various companies to implement this from FY18 Q2 onwards. www.manjushreeindia.com PETplanet: How does in-mould labelling reinforce the PET container? Vimal Kedia: In-mould labelling in PET is a very new subject, although we have been working on this project for the last two to three years. The film used in manufacturing of a label is of a special quality which can be statically charged before fixing it on to the moulds. The labels are then stuck to the surface of the moulds with the help of vacuum pressure to ensure there is no bubble formation. After this, the mould is sealed and the preform is blown in accordance with the shape of the mould. Once the mould is sealed, the label is neatly embedded on the surface of the bottle. IML makes the packaging attractive with sharper graphics and photorealistic images. Vimal Kedia, MD, Manjushree Technopack receiving the Lifetime Achievement Award at The Economic Times Polymers Awards earlier this year","@ID":38}, "BOTTLING / FILLING PETplanet Insider Vol. 18 No. 07/17 petpla.net 31 Tour Sponsors: New soft drinks with German technology for Cambodia by Kay Barton Khmer Beverages Co., Ltd., Phnom Penh, Cambodia, April 3, 2017 We met: Mr Pov “Peter” Leang, President Khmer Beverages Mr Otdom Chhor, Training Supervisor Khmer Beverages Mr Sylyvann Borei, Corporate Communications Manager, Chip Mong Group Ltd. The Khmer Brewery in Phnom Penh, part of the Chip Mong Group, was just about to start its new soft drinks production when we met President Peter Leang for the interview. The family-led group was founded in 1982 and is active in Cambodia in various branches of industry. In addition to selling and producing international consumer goods in the field of drinks and food, it also trades in concrete, steel and ceramics as well as making cement for various fields of activity. Within just a few years, there has been huge investment in the highlymodern brewery and its “Cambodia Beer” is a familiar name in various countries. After previously filling beer into glass bottles, cans and kegs, they are now starting for the first time to fill various soft drinks into PET. The Khmer Brewery is the youngest member of the Chip Mong Group portfolio. After initially importing beer for the local market in 2005, in 2009 the company signed a contract with brewery equipment manufacturers Ziemann and filling specialists KHS for the first turnkey solution for its own beer production. The investment of US $60m into the project was to change the local market considerably from that moment. “We basically had no idea about production and filling and started from nowhere. But we saw clear opportunities in the Cambodian market so we simply took a chance”, explains Peter Leang in the brewery showroom. The first beer ran off the newly-installed equipment on November 1, 2011. In phase 1, Khmer Brewery started with 600,000hl and expanded just a year later into phase 2 - with capacity doubled. The end of 2013 saw phase 3, with yet another increase in capacity and further expansion into the production of soft drinks. At this point, the company decided on a Krones line for PET filling in this branch of the business and finally changed its name to Khmer Beverages. To date, the company has invested a total of US $220m and further expansions are planned. The current capacity for beer lies at 5 million hl, with current utilisation of 50%, almost exclusively for the home market, with less than one percent for export. In the soft drinks field, they started with 3 million hl capacity.The clean water supplied by the Phnom Penh Water Supply Authority used in production is a mix from various sources and is treated in different ways, depending on the drink for which it is used. Industrial water is cleansed in the in-house water treatment plant. During a tour of the brewery with the Training Supervisor, Mr Otdom Chhor, we came across quite a few Pentair Filtration and EUWA water treatment machines. Europe is everywhere. Apropos of Europe: a new canned stout beer called “Barrley Black” has just this March found its way into the portfolio. It also became clear during our tour that great store is set by open communication and closeness to clients. So a large part of the (new) production hall is laid out for the public to walk around and is there to guarantee visitors gain striking impressions in all areas. “Under our “Cambodia” brand, we shall in the future be filling water into PET. Our planned CSD brand will be called “Ize” and will be available in four to five flavours”. In the cans field, there will also be various juices and energy drinks without carbonisation. When it comes to the flavours, Khmer Beverages relies, inter alia, on sources such as Döhler and Wild. The packaging test runs were in the final phase at the time of our meeting and we got to see the first in-house manufactured PET bottles. The same preform CSD necks will be used for water and CSDs. The material comes from Indorama Thailand and is further processed on a Husky HyPET 300 HPP5. Here, there is a Husky 96 cavity tool for bottle sizes of 350ml and a 72 cavity tool for 500ml Peter Leang discusses the company’s strategy.","@ID":33}, "PETplanet Insider Vol. 18 No. 07/17 petpla.net 47 BOTTLES PETbottles Beverage + Liquid Food Alkaline black water A look along American and Canadian supermarket shelves reveals a wide range of spring water-based drinks which, by virtue of their origin, composition or additions, provide added benefits for the consumer. A striking example of this drinks’ range is a black water beverage under the protected brand name “blk”. This neutral tasting water does not contain sugar or carbohydrates, with the black colouring produced by adding fulvic acid, according to the manufacturer. Fulvic acid has long been used in the treatment of a variety of metabolic disorders. This particularly striking looking water which can be seen on the shelves comes in a slim 500ml bottle with a no-look label and screw cap. www.getblk.com An alternative to cream Aldi South has three different “Crème à la Cuisine” products on offer under their own Milfina brand as an easy alternative to cream. These vegetable fat varieties, whether they are used in cooking or for whipping, contain 7, 15 and 21% fat which is between 30 and 75% less fat content than cream. The products come in a 250ml bottle made from white PET. Sleeve labels and screw caps with a security strip are colour coordinated to ensure that the products are easily distinguishable. www.aldi-sued.de Vio Bio Limo with less sugar The Apollinaris brand which is part of Coca-Cola European Partners has extended its “Vio Bio Limo” range with the introduction of slightly sugared products. The three new varieties contain around 4g of sugar per 100ml which is approximately 50% less sugar content compared to traditional sugar lemonades in Germany. The products come in already familiar, clear and slightly waisted 0.5 or 1l bottles. The used bottle, or so-called plantbottle, consists of up to 14% renewable raw material, up to 35% of re-used plastic and is 100% recyclable. Colour matching sleeve labels and screw caps finish off the whole packaging for the retail shelves. www.vio.de Glucose syrup made from maize The Korean firm, Chung Jung One, has produced glucose syrup made from maize which comes in a strikingly designed, clear and easy to handle 700g bottle. There are oblique and horizontal grooves in the belly and lower parts and vertical indentations in the upper part of the bottle. A surrounding belly label transmits commercial data, while a screwedon hinge cap with dispensing spout makes the viscous contents easy to pour. Particularly striking is the figuratively designed dispensing spout which looks like a face, out of whose mouth the product is dispensed. www.nanuko.de","@ID":49}, "PETnews 6 NEWS PETplanet Insider Vol. 18 No. 07/17 petpla.net Alpla acquires South African Boxmore Packaging Boxmore Packaging, with headquarters in Johannesburg, South Africa, will become a fully owned subsidiary of the Austrian packaging specialist Alpla. Boxmore Packaging is specialised in PET preforms, PET bottles and closures, and currently employs around 1,000 members of staff at nine locations. “The African continent is an attractive growth market for us. With the purchase of Boxmore Packaging, we now also have a broad basis for entering the market in South Africa, in addition to our activities with Alpla Taba in North Africa’, says Alpla CEO Günther Lehner. Alpla has acquired 100% of Boxmore Packaging. All employees and locations are being taken on by Alpla, although it has been decided that the management structure will remain the same. The current board, under the leadership of Len Engelbrecht (Boxmore CEO), will continue to manage the existing Boxmore business, and in addition, take on responsibility for the integration and management of the existing Alpla SA business. For the foreseeable future the company will continue to operate under the existing name as a member of the Alpla Group. Founded in 1995, Boxmore Packaging is seen as the market leader for PET preforms and bottles (ISBM technology), as well as closures, in southern Africa. Around 1,000 employees currently manufacture approximately 4 billion of the aforementioned products each year at nine production locations. The customers of Boxmore Packaging are situated in more than 20 African countries, as well as on the islands in the Indian Ocean. The takeover was signed on July 5, 2017; implementation remains subject to the required legal and regulatory approval by the competition authorities. The contract parties have reached a confidentiality agreement regarding the financial details. www.alpla.com NGR strengthens its sales organisation in China and Southeast Asia The Austrian company Next Generation Recyclingmaschinen GmbH (NGR) develops and manufactures plastics recycling equipment for industrial and consumer waste. As part of the reopening of the three year-old Customer Care Center in Taicang, NGR is expanding its sales activities in China and Southeast Asia. With its move into the German Center Taicang, which is said to provide better infrastructure for customers and employees, the Chinese NGR subsidiary is laying new groundwork for China and the entire Southeast Asia region. The sales office will be led by the new sales director Jeffrey Tan, a native of Singapore. Jeffrey Tan has developed a strong technical background over his years working in the plastics industry, and will take over the appointment books for our customers starting in July. With Sven Heine, CEO of Anhui Green Recycling and Environmental Protection Research Center Co., Ltd., NGR has added an authorised partner for customer trials and technical support in Hefei. As a recycler of industrial plastic waste, Heine counts on NGR technology and also provides prospects the chance to carry out test series for customised recycling solutions with his company’s S:GRAN 85-70 V HD system. Technical support will be strengthened by a well-experienced service engineer. An expanded spare parts warehouse will provide more rapid customer support. www.ngr.at NGR recycling-line at Anhui Green Recycling and Environmental Protection Research Center for test runs Len Engelbrecht, CEO Boxmore (left), und Günther Lehner, CEO Alpla (right)","@ID":8}, "42 TRADE SHOW PREVIEW PETplanet Insider Vol. 18 No. 07/17 petpla.net Filling and packaging technologies Heuft will showcase technologies and modules for precise product tracking, fault detection and rejection, with the aim of setting new standards in terms of detection accuracy, operational reliability and price / performance ratio. F r om emp t y b o t t l e inspectors of the Heuft Spectrum II generation to a new category of slimline devices for an affordable introduction to a full container inspection up to Heuft’s programme standards, the company will present solutions for perfect packaging material and safe drinks. The complete range of products can be experienced on the Heuft booth on over 1,000m2 from the case check to the foreign object inspection. The more automated, networked and self-explanatory Heuft Spectrum II platform is regarded as the highlight. It is intended to make the reliable operation of modular inspection systems easier than ever before. New developments based on it for a continuous empty bottle inspection will be shown for the first time as well as several full container inspectors. A completely new device category is said to provide technologies which among other things carries out a reliable fill level detection or marking check in a confined space. www.heuft.com Hall B4 - Booth 315 Connecting Global Competence World’s Leading Trade Fair for the Beverage and Liquid Food Industry Processing + Filling + Packaging + Marketing September 11–15, 2017 Messe München, Germany, drinktec.com Fresh. Different. Personal. Take your business to the next level. In talks with experts from over 180countries. Explore ideas, innovations and investment at the No. 1global communication platform. Welcome to drinktec, the leading trade fair for the international beverage and liquid food industry. drinktec. Go with the flow. Get your ticket now! drinktec.com/tickets Follow us: Handle applicator The handle applicator SIAL6000 performs the insertion of (PP) lateral, colourable handles on PET bottles (from 2 up to 5 litres). This system allows PET bottles to be used for certain products when an easy pouring process is required. The machine is based on a rotary continuous system and it can be readily installed in the existing packaging line, on an existing conveyor and before the filling process. It allows the lateral handle to be inserted at speeds up to 15,000bph. www.andyor.com Hall A4 - Booth 202","@ID":44}, "39 TRADE SHOW PREVIEW PETplanet Insider Vol. 18 No. 07/17 Aseptic packaging treatment Serac amplifies its expertise in container treatment based on dry processes with an industrial sterilisation solution using ebeam technology. This is capable of ensuring a 5 log bacteriological reduction on Bacillus Pumilus without leaving any chemical residue in the container and eliminating the consumption of chemical agents to decontaminate a bottle. According to the company, BluStream is particularly interesting for manufacturers wishing to highlight production processes that respect both human beings and the environment as well as brands that follow natural trends and target sensitive consumers (babies, elderly people, people with allergies, etc.). Unlike peracetic acid (PAA) and hydrogen peroxide (H2 O2 ) treatments that rely on chemical principles, BluStream is based on a physical process. It uses an issuer which throws an electron beam over the container’s surface. Electrons quickly destroy microorganisms by breaking their DNA chains. This enables BluStream to achieve a 5 log bacteriological reduction on Bacillus Pumilus with a 1.5l bottle in about 5s. The BluStream process only depends on three critical easy to control parameters: voltage, current intensity and exposure time. BluStream treatment is also more economical in production because it requires no chemicals, no water, no compressed air, and a minimum increase in electrical consumption comparable to the H2 O2 treatment, says Serac. The unit is more compact than PAA and H2 O2 ones; the floor area is only 20m² for a rate up to 36,000bph. Bottles are treated on two successive carousels; the first one for the exterior treatment and the second one for the interior treatment of the bottle, continuously, at rates up to 36,000bph. BluStream treatment is compatible with all kinds of plastics; HDPE, PET, PP, PS, whatever their weight or shape. All bottle sizes can also be treated, provided that the neck diameter is above or equal to 30mm. Treatment efficiency allows this method to be used for highacid products (fruit juices) as well as for low-acid products (cow milk, soy milk, other vegetable milks and all nutritional products). www.serac-group.com Hall A5 - Booth 332","@ID":41}, "Sponsors asia.petpla.net 2017 is Drinktec year! All over the world, the beverage and liquid food industry is preparing for the next edition of the great event, held once again in Germany. A new year also means a new road show - and a very special one. PETplanet is again partnering with Drinktec and we will be bringing our crew to South East Asia, under our new slogan: Go with the flow – South East Asia Road Show. From the end of January our editors Kay Barton and Alexander Büchler, along with “Flowy“, the Drinktec mascot, will be investigating the latest market-specific characteristics of distant countries as well as following welltrodden oaths, as always. With various “Editourmobil” vans we will travel to Thailand, Vietnam, Cambodia, Malaysia, Singapore and Indonesia. As our valued reader, you will once again get insider information and insights from the PET beverage and supplier industries, published regularly in PETplanet Insider. You can get even closer to the Tour experience by following us live on our travel blog at asia.petpla.net. Drinktec awaits us at journey‘s end. When we get there we will be presenting factsheets and product samples of all the companies we visited. We hope you enjoy “keeping up with the PETplanetarians“. We look forward to welcoming you on board once again! January – July 2017 Cambodia Laos Thailand Indonesia Vietnam Malaysia Singapore The worldwide round trip with Go with the flow. South East Asia Road Show powered by","@ID":46}, "No.07 2017 petpla.net D 51178; ISSN: 1438-9452 24 . 07 . 17 PETplanet is read in more than 140 countries MAGAZ I NE FOR BOT T L E R S AND BOT T L E - MAK E R S IN THE AMERICAS, ASIA, EUROPE AND ALL AROUND THE PLANET MARKETsurvey Recycling: Cutting plants and Labelling & marking systems Page 27 bottle making Page 10","@ID":3}, "PETpatents www.verpackungspatente.de PETplanet Insider Vol. 18 No. 07/17 petpla.net 48 Container for hot filling Internal Patent No. WO 2015 / 069620 A1 Applicant: Amcor Ltd., Hawthorne (AU) Application date: 4.11.2014 A container for hot filling is furnished with compensation areas only in the base area so as to be able to absorb the pressure and vacuum forces arising from cooling. Improved base form Internal Patent No. WO 2015 / 071565 A1 Applicant: Sidel Participations, Octeville-sur-Mer (FR) Application date: 23.10.2014 The forming of the base in a plastic bottle has been modified by the manufacturer in terms of requirements in such a way that any arising production difficulties are reduced. Square plastic bottle Europ. Patent issue No. EP 2468649 B1 Applicant: Yoshino Kogyosho Co. Ltd., Tokio (JP) Application date: 25.8.2006 The shaping and manufacturing of a square plastic bottle with an integrated area for easier handling is issued with a European patent. Plastic container Internal Patent No. WO 2016 / 160424 A1 Applicant: Ring Container Technologies, Oakland (US) Application date: 22.3.2016 The application describes the manufacturing procedure for a wide-neck plastic container from a preform. After “blowing” the preform, the upper part is detached leaving a lightweight container with a large opening. Plastic bottle Internal Patent No. WO 2016 / 174831 A1 Applicant: Yoshino Kogyosho Co. Ltd., Tokio (JP) Application date: 8.4.2016 The reinforcement and/or pressure compensation areas of a container intended for hot filling are integrated below a certain degree into the container wall. Container with handle Internal Patent No. WO 2016 / 181850 A1 Applicant: Nissei ASB Machine Co. Ltd., Nagano (JP) Application date: 27.4.2016 A separately formed handle is placed in the tool for manufacturing a plastic bottle and is integrated securely into the bottle wall by the “blowing” of the preform.","@ID":50}, "BOTTLE MAKING 22 PETplanet Insider Vol. 18 No. 07/17 petpla.net Dairy industry to shift towards PET bottles Tasty, sweet, creamy, watery, savoury. We associate these words with liquid dairy products from our childhood. We used to know them in glass or HDPE bottles, plastic or carton containers. However, not so long ago, another type of packaging appeared and its demand has been continuously increasing: the PET bottle. The dairy company Organic Milk is not an exception. Not long ago the company installed an APF-3002 automatic stretch blow moulding machine for PET milk bottles. Supplied by PET Technologies they manufactured two sets of moulds for various bottle volumes. A preform heating system as well as an air-cooling system are intended to produce high quality bottles with original designs. Dairy product container development is not an easy process due to the chemical characteristics of a liquid product. Air, light or microbes can easily destroy them. So why does Organic Milk choose PET? On the one hand, it is an opportunity for a brand to stand out from similar products on the shelves: different designs, different volumes, and different bottle colours. On the other hand, PET’s hermetic cap capabilities, external odour protection barrier, lightweight nature and sustainability, all contribute to easier logistics and geographical sales expansion as well as total production and delivery chain cost reduction. The PET bottle market expansion rubs shoulders with the manufacturing cost reduction trend which is common for all industries. Now it is the dairy market’s turn to take a chance. Milky coloured or transparent, single-serve or half-gallon size, easy to hold and open, lightweight and sustainable: the PET bottle is becoming a reasonable alternative for both dairy products manufacturers and consumers. PET Technologies is among one of the few companies who started shifting milk plants towards PET almost 15 years ago. As a result, plenty of blow moulders in CIS countries produce well-designed and high performing PET bottles using PET Technologies machinery. www.pet-eu.com bottle making Injection moulding machines Thermal shaping technology Extrusion plants Tool systems Materials and components 25th Fakuma ! More than 1700 exhibitors from all over the world will present global offerings for technologies, processes and products made of plastic, as well as equipment and tooling for plastics processing, in 12 exhibition halls. 17. –21. OCTOBER 2017 FRIEDRICHSHAFEN The Entire World of Plastics International trade fair for plastics processing +49 (0) 7025 9206-0 fakuma@schall-messen.de Organizer: P. E. SCHALL GmbH & Co. KG www.fakuma-messe.com You’ll be awaited by flexible, individualised solutions for current and future challenges faced by the automated, globalised economy.","@ID":24}, "TRADE SHOW PREVIEW PETplanet Insider Vol. 18 No. 0/17 petpla.net 43 Complete plant systems for the manufacture, bottling and packaging of beverages Global player in liquid packaging Since it was established in 1999 in Guangzhou, China, Tech-Long steadily expanded its product line as a manufacturer of large container water fillers. The now largest beverage packaging equipment manufacturer in Asia meanwhile operates facilities in the Americas as well as Europe. At Drinktec, Tech-Long will introduce the latest generation of it blow moulding machines G5 to the European market. In response to requests from a number of their customers, including global companies such as Coca- Cola, Pepsi Cola and P&G, Tech-Long expanded its operation to the Americas and established a base in the US in early 2012. To facilitate the growth of its Americas operation the company set up a 2,500m2 (27,000 square feet) facility in Duluth, Georgia, USA, to provide technical support, training and spare parts distribution. It has been in operation since September 2015 and now houses close to 2.0M in spare parts inventory, along with a North American Service & Service Operation that employs more than 20 people. TechLong has now installed equipment into more than 100 beverage bottling lines in North and South America, and sales in 2017 are expected to finish 300% above 2015’s outturn. Tech-Long products are now familiar in many markets outside China. In 2016 it reached the decision to establish a new European Headquarters, which is located in Vienna, Austria. Long-time industry expert Dominique Lipinski joined as the European CEO and the company has now taken on a number of experienced European Sales and Service personnel, to serve the local market. The company has steadily expanded its product line since it was established in 1999, in Guangzhou, China, as a manufacturer of large container water fillers. It offers complete plant systems for the manufacture, bottling and packaging of beverages, including water filtration, sugar dissolvers, tea extraction and ingredients mixing. It also provides PET blow moulders across a broad range of speeds and container sizes; fillers of various kinds; and post-filler operational equipment for conveying, labelling, packing and palletising. Tech-Long is the largest beverage packaging equipment manufacturer in Asia. It employs some 1,400 people and has sales approaching US$150 million. Blow moulding machines at Drinktec At Drinktec, Tech-Long will introduce its G5, Generation 5, blow moulding machines to the European market. The G5 machines are available in formats from four to 36 cavities, with a blowing rate of 2,250 to 2,400 standard bottles per hour per cavity, and with the capability to blow any PET container from 0.2l to 20l. Total Cost of Ownership (TCO) of G5 blow moulders is claimed to be reduced by a number of features incorporated in the design. Up to 50% air is recovered, the company says, which means that external low pressure air is not really needed. Standardisation of parts and elimination of the carrier chain reduces maintenance or in some cases totally eliminates regular part replacement. Tech-Long invests 6% of revenues in research and development activities each year and is awarded around 20 to 25 new patents annually; its intellectual property bank currently stands at two hundred and forty patents. The company says that its commitment to meeting customer needs and establish it as a global player in liquid packaging is demonstrated by its attention to high quality in design, engineering and manufacturing, along with the drive to create low TCO. www.tech-long-intl.com 䢮Fully electric mechanism 䢮Continuous preform feeding system 䢮Design for quick mold change 䢮Applications: water,CSD, juice, teas, oils, sauces, ketchup, cosmetics CPSB-LSS16 24000bph쨤Advanced efficiency Lower energy consumption Hall B5 - Booth 322","@ID":45}, "BOTTLE MAKING 14 PETplanet Insider Vol. 18 No. 07/17 petpla.net PETplanet: Mr Saxena, can you briefly describe the differences between the LiquiForm process and the classical 2-stage process? Saxena: In the classic 2-stage process, heated PET preforms are moulded into shape using compressed air and subsequently filled with a liquid. LiquiForm eliminates the compressed air and forms the bottle using the actual product. The output is a filled bottle ready to be capped, produced using less equipment, energy, labour and space. Beyond the energy and cost reduction, we are discovering that the bottle has superior definition and more uniform material distribution. Most importantly, whilst current technologies are resinspecific, LiquiForm has the flexibility to process different resins and sizes more easily on a single machine. This offers packaged goods companies an opportunity to simplify their supply chains and move packaging production closer to the market. PETplanet: Do the preforms have to be specially modified in order to be used with LiquiForm, or is any standard preform suitable for this purpose? Saxena: Standard preforms can be used in most instances. In fact, the vast majority of our work has been with standard preforms. But of course, as LiquiForm is a different process, there are opportunities for optimising the preforms to further improve the results. PETplanet: Clearly, the moulding process must also be carried out very quickly to avoid the liquid cooling the heated preforms? Saxena: You are right. One of the challenges using liquid instead of compressed air is that liquids have a much higher thermal conductivity and thus creates a cooling effect. So the forming process has to be carried out very, very quickly – our cycle time is a fraction of the time required for the compressed air process. Roughly 1-2/10 of a second (0.1-0.2s) for a standard 0.5l water bottle. PETplanet: To what extent does the viscosity of different liquids have to be considered? Saxena: We have been able to process a range of liquid products so far. Even very thick products such as a shampoo or conditioner which have a viscosity of up to 10,000 Centipoise, we have been able to do – and this, by the way, is an ongoing development. As we go along we add more and more products. The process is slightly adapted to suit each liquid’s condition. But the LiquiForm process is very versatile in handling not only various types of liquids but also different filling conditions. So for example you can have temperatures ranging from 10°C up to 87°C. PETplanet: Due to possible changes in a liquid’s volume, bottles are never fully filled. But if you are using the liquid to form the bottle, how do you form the neck area and below? Do you have to remove the liquid again after formfilling? Saxena: You are right, you don’t want the liquid all the way up to the neck and we have a number of techniques to have the liquid at the correct level at the head space. In some cases, the liquid may be removed, in some cases not. PETplanet: Does the additional weight of the liquid affect the cavities? Saxena: Indeed it does. A filled bottle is much heavier than an empty bottle and impacts the mechanism for taking the bottle out of the forming cavity. The equipment makers will have to design the outtake mechanism accordingly and ensure that the product doesn’t spill if the bottle is not already capped. So far we have successfully developed in our lab in Michigan anything from 200ml to 2l - simply because we designed the equipment that way. We are currently in the process of upgrading that equipment. We hope to be able to go as high as 4 or 5l in the future. PETplanet: You are claiming that LiquiForm could be used even without moulds in a low-budget so-called free blow approach. What is the reaction to that? Saxena: We are still continuing to work in this area. People in both developed and undeveloped markets find this free-blow process very interLiquiForm commercial debut expected with a bottle from the HPC sector by Gabriele Kosmehl The first bottle to be made using the LiquiForm process is expected to be launched soon on the market. PETplanet spoke with Ashish Saxena, Vice President and General Manager of the LiquiForm Group, about this and on-going projects and developments. Ashish Saxena, Vice President and General Manager of the LiquiForm Group bottle making","@ID":16}, "PREFORM PRODUCTION PETplanet Insider Vol. 18 No. 07/17 petpla.net 24 Reduced drop height of preforms into tipper brings benefits Gentle and quiet Less noise, improved quality: KHS Corpoplast GmbH has developed a new system for preform processing. With the InnoPET Silent TipTainer PET preforms are fed to the sorting unit especially gently. This results in a considerable reduction in the amount of noise around the tilter. “With the Silent TipTainer we’re achieving a much lower preform rejection rate than has been the case to date,” explains Alexander Heller, technical project manager and developer for preform conveying systems at KHS Corpoplast. The reason for this is that the drop height of the PET preforms into the tipper has been greatly reduced. Where the rejection rate was previously at 3%, just 0.25 to 0.3% of all preforms are now damaged during tilting or by bumping into one another as they fall. The lower drop height and smooth tipping in stages not only mean that preforms are handled more gently and that there are fewer breakages on the necks; the adapted tipping process also results in perceptibly lower noise levels. KHS measurements record a maximum of 80dB(A). The closed system also ensures that values of up to 110dB(A) are no longer standard. By reducing the amount of noise pollution occupational safety is improved further for operators working near the tipper. Best product quality is obtained by filling the optimised box tilter silo unit by up to two preform loads. At a higher preform density damage can be caused by the preforms falling onto one another. In the compact and hygienic Silent TipTainer the risk of contamination by dust or other foreign matter is reduced. Retrofits on existing lines possible The system is not just installable on new lines; it can also be retrofitted in existing and older plant engineering. All that the customer’s individual setup may require is a suitable software update. The Silent TipTainer is also flexible in its operation; the elevator can be connected inline or on both sides of the Silent TipTainer and operated from the right or left. At Gerolsteiner Brunnen GmbH & Co. KG the system has already been in operation for six months where the low preform rejection rate is especially appreciated. “Converting from the conventional box tilter to the Silent TipTainer reduces the number of rejections on downstream control units and upholds our high demand for quality while lowering rejection rates,” states Dieter Kuhl, head of Non-returnables Production at the mineral water bottling plant in Gerolstein, Germany. In addition, known flaws on the neck, which can lead to a loss of CO 2 among other problems, have also been reduced. www.khs.com In converting from the conventional box tilter to the Silent TipTainer Gerolsteiner upholds its high demand for quality while lowering rejection rates. Gerolsteiner also invested in KHS systems for efficient mineral water bottling in 2016. Gerolsteiner has been using the Silent TipTainer for more than six months now. The main features of the Silent TipTainer are its greatly reduced noise level and gentle preform handling.","@ID":26}, "PETcontents 07/17 4 PETplanet Insider Vol. 18 No. 07/17 petpla.net Page 38 Page 43 Page 20 INSIDE TRACK 3 Editorial 4 Contents 6 News 45 On-site 46 PET bottles for Home + Personal Care 47 PET bottles for Beverage + Liquid Food 48 Patents MOULD MAKING 9 Blow mould production in Vietnam BOTTLE MAKING 10 PET bottle prototyping Anwering the market’s need for rapid quality 11 Lower pressure for a more profitable production New generation of bases for CSD bottles 12 Sharper edges, increased design freedom SteadyEdge base for flat, oval and rectangu- lar PET containers 14 LiquiForm commercial debut expected with a bottle from the HPC sector 16 Processing and bottling high-quality edible oils 17 From Thailand to Vietnam Local trade fairs gaining greater importance 18 Process intergration to advance bottle production An integrated platform for bottlers and converter 20 Co-packer opts for dry aseptics 22 Dairy industry to shift towards PET bottles 23 Let’s give the bottle the right look 34 Material basics / Behaviour in the blow mould - Stretch Blow Moulding, part 4 PREFORM PRODUCTION 24 Gentle and quiet Reduced drop height of preforms into tipper brings benefits 25 60,000 tonnes of PET preform capacity Alok Parakh about National Polyplast’s PET preform range MARKET SURVEY 27 Suppliers of recycling cutting plants and suppliers of labelling & marking systems BOTTLING / FILLING 31 New soft drinks with German technology for Cambodia LABELLING 36 In-mould labelling in PET Three questions for Vimal Kedia, MD Manjushree Technopack TRADE SHOW PREVIEW 38 Drinktec 2017 preview 43 Global player in liquid packaging Complete plant systems for the manufacture, bottling and packaging of beverages BUYER’S GUIDE 49 Get listed! bottle making","@ID":6}, "imprint EDITORIAL PUBLISHER Alexander Büchler, Managing Director HEAD OFFICE heidelberg business media GmbH Bunsenstr. 14 69115 Heidelberg, Germany phone: +49 6221-65108-0 fax: +49 6221-65108-28 info@hbmedia.net EDITORIAL Kay Barton Heike Fischer Gabriele Kosmehl Michael Maruschke Ruari McCallion Waldemar Schmitke Anthony Withers WikiPETia.info petplanet@hbmedia.net MEDIA CONSULTANTS Martina Hirschmann hirschmann@hbmedia.net Johann Lange-Brock lange-brock@hbmedia.net phone: +49 6221-65108-0 fax: +49 6221-65108-28 LAYOUT AND PREPRESS EXPRIM Werbeagentur Matthias Gaumann | www.exprim.de READER SERVICES Till Kretner reader@hbmedia.net PRINT Chroma Druck & Verlag GmbH Werkstr. 25 67354 Römerberg Germany WWW www.hbmedia.net | petpla.net PETplanet Insider ISSN 1438-9459 is published 10 times a year. This publication is sent to qualified subscribers (1-year subscription 149 EUR, 2-year subscription 289 EUR, Young professionals’ subscription 99 EUR. Magazines will be dispatched to you by airmail). Not to be reproduced in any form without permission from the publisher. Note: The fact that product names may not be identified as trademarks is not an indication that such names are not registered trademarks. 3 PETplanet Insider Vol. 18 No. 07/17 petpla.net Dear friends of PETplaner Insider, Professor Dr. Michael Koch AN APPRECIATION Prof. Dr. Michael Koch sadly passed away on 15 June 2017 at the age of just 61. The PET pioneer had suffered a short but serious illness. His loss deprives his family with three daughters of its caring patriarch, the TU Ilmenau of a worthy professor, the PET world of one of its pioneers and me of a close friend of many years. From 1983 to 1995 he was a manager at Corpoplast – then still under the name Krupp Corpoplast – first in Development and later in Sales. During this time he was the driving force in the development of PET bottles from niche product to mass packaging for drinks. In his later professional career he worked for Tetra Pak PET packaging machines and also for Husky. His love for PET bottles has been a constant throughout his life. In his inimitable and highly motivated style and despite all university administrative barriers, he built up the specialist area of plastics technology from nothing in 2009 to the team of 16 full-time employees and 30 scientific assistants that it is today. And at all times his work included one or two PET projects. It was always a pleasure to drop in on him, to enjoy a beer or two together in the local student bars and thus contribute intellectually to the improvement of the PET world. Frequently, he interlinked different topics, juxtaposing them in a new way and coming to new and surprising conclusions. These were not always readily accepted - more often than not, he rubbed people up the wrong way and his ideas fell on deaf ears. But he was usually right. But it is not right that you - dear Michael - are not able to pursue your passion for science and PET bottles to a ripe old age. You will be sorely missed. Yours Alexander Büchler Univ.-Prof. Dr.-Ing. Michael Koch 1955 - 2017","@ID":5}, "7 NEWS PETplanet Insider Vol. 18 No. 07/17 petpla.net Virgin PET from plastic waste Carbios, a green chemistry company specialising in enzymatic bioprocesses applied to plastic and textile polymers, and TechnipFMC, a leading company in the fields of energy, chemistry and bio-sourced industries, announce the launch of a project for the industrial development of Carbios PET enzymatic recycling process. This will allow to produce virgin PET from plastic waste. This contract covers assistance to Carbios for the scale up of its process to ensure industrial competitiveness. Carbios’ proprietary innovation provides an industrial solution to fulfill sustainable development requirements of PET production processes. The global market of PET records a 4% to 5% annual growth according to Smithers Pira and Pira International, and represents a world production of 64 million tons each year (eq. $70 billion) (source: SRI Consulting in 2010, ICIS in 2009, Samsung in 2010, Tecnon in 2013 and IHS in 2014), split between one third of plastics and two thirds of fibres. In ten years’ time, the annual production of this market is expected to reach 100 million tons (eq. $110 billion). This process has been developed for the recycling of PET plastics, namely bottles, films and packaging. It enables to overcome constraints and limits of current recycling processes by the treatment of all kind of plastics containing PET (transparent, coloured, opaque and complex), and by the recovery of high-performance virgin PET directly from plastic waste. For the first time, a biological process paves the way to the recycling of PET following circular economy principles. The companies signed this contract to transpose Carbios’ process from the laboratory to the pilot scale. This assistance will further aim at supporting the development of the project and define the bases of the industrial process. www.carbios.fr www.technipfmc.com WikiPETia is growing Have you visited the PET knowledge management system WikiPETia recently? Major PET events for 2018 have already been included in our events calendar, so you can plan ahead. https://petpla.net/wiki?title=Events Additionally, more and more participants in the PET value chain from all over the world now appear in our system. You can find them by simply following the link https://petpla.net/wikipetia/ index.php?title=Companies or by reading our daily online news where companies already included in WikiPETia are directly linked. If your company is not yet listed, don’t worry! Simply ask us (petplanet@ hbmedia.net) to open up an account for you on WikiPETia where you can then expand your profile easily.","@ID":9}, "BOTTLE MAKING 10 PETplanet Insider Vol. 18 No. 07/17 petpla.net With the increasing need for non-standard packaging solutions that not only help to stand out in the fierce modern market environment, but also reinforces innovative product development, PET bottle prototyping is becoming paramount for launching new and rebranding existing products. As some bottling companies often demand an entirely customised PET bottle solution within a matter of weeks and sometimes days, the lead time for PET bottle prototypes is becoming shorter. There are several companies that offer a service from initial concept to actual bottle samples, and one of the key factors that enable rapid prototyping is the complete control of all processes along the way. One of the entrepreneurs in the field is Terekas. The company offers a comprehensive quality programme from design concept to injecting preforms and finally to blowing samples on the machines built inhouse FlexBlow – all under one roof. Bottle design New bottle development begins with the creative design session. The aim of this session is initially to define the customer’s needs and come up with a set of bespoke PET container visualisations with the help of bottle designers. The main advantage of having creative artists in-house is that technical limitations are not a restriction at this stage, and therefore coming up with ideas that are fresh and innovative in the market becomes possible. A number of visualisations can be prepared overnight, allowing the customer to choose their favourite option within 24 hours after the initial meeting. If the customer is unable to visit personally, a mobile design bureau service is available – bottle designers will come within a reasonable time period to discuss the design development possibilities. Technical drawing Subsequently, when the favourite artistic bottle design has been selected, a technical drawing is made. With the drawing in hand engineers carry out a container design and PET preform compatibility study to determine whether a customised preform is needed or an existing one is available for the particular bottle. An in-depth report highlights potential risks and recommendations are made should the initial design need to be altered to fulfil technical requirements. In the case of a specific neck finish, bespoke preform geometry or non-standard weight, a custom preform design is developed and single injection cavity is made for the prototype preforms that are injected in-house. Mould production During the process of choosing or manufacturing the correct preform, the PET bottle blow mould is manufactured by the use of 5-axis milling technology. After CMM precision testing, the readymade mould is fitted in the versatile PET blower that is capable of accommodating moulds from all blow moulding machine suppliers, and the prototype bottles are made. A wide range of different neck standards is available for prototyping, and no investment for additional tooling is normally necessary. The universal PET machine enables the production of hot-fill containers, wide-mouth jars, oval bottles, large-size containers, deep-grip bottles and much more. Bottle testing Blown bottles undergo comprehensive lab testing afterwards. Bottle samples are tested in the PET laboratory and an in-depth quality report is generated. Testing includes top-load check, complete wall, base and neck thickness measuring, vacuum chamber test, preform quality inspection, visual analysis, etc. Quality bottles are dispatched to the customer on the same day. Having the whole infrastructure under one roof enables some companies to offer a Quick Sample Program: customers receive a box of bottle prototypes delivered to their door within 7-14 days after the bottle drawing confirmation. All in all, the possibilities for nonstandard PET bottle prototype production are increasing, and Terekas claims to offer a speedy turnaround, quality and competitive rates for both blow mould and bottle prototype production due to the fact that all processes from A to Z are controlled in-house. www.flexblow.com bottle making Answering the market’s need for rapid quality PET bottle prototyping","@ID":12}, "BOTTLING / FILLING PETplanet Insider Vol. 18 No. 07/17 petpla.net 32 Husky installations ensure the preform supply and 1.51 water/CSDs. A HyCAP 300 with 72 cavities is installed for closing devices. “We want to start in the soft drinks field with 2.5 million hl”, says Peter Leang. “We might even be starting in April.” The operation sees itself in competition with the Heineken-owned Cambodia Brewery (CBL) and Cambrew (Angkor Beer). With its high-end technology from Europe and its high staff requirements and training standards from the 360 strong employee team, Khmer Beverages will be convincing above all on quality. “We are a drinks producer led by local people for the local population. The road for us in the soft drinks field will certainly not be a smooth one.” thinks Peter Leang. “But, as with the beer, where we set the bar high, not just on technology but also on ingredients from Europe (Note: the hops, for example, come Krones PET line 40,500bph No Name Type 1 Blow moulder machine Contiform 318 2 Preform feed unit Contifeed RS 3 Bottle filler Modulfill VFS (VODM PET) 2.520-77-103 4 Inspection machine Checkmat 731 FM-X 5 Warmer (heater-pasteuriser) Linatherm W6.4-244-31 6 Labeller (container labelling machine) Contiroll 720-18-HS-ED 7 Container dryer Linadry S2M 8 Inspection machine Checkmat 731 EM 9 Cap sleeve labelling machine Sleevematic M 2 10 Half tray packer Variopac PRO TFS-9 11 Palletiser Modulpal 2AC 12 RoboBox Robobox 13 Container conveyor Synco S 14 Container code/dating unit Imaje 15 Pack inspection (scale) Garvens (Mettler Toledo) 16 Mixer Contiflow 30/3 from Germany), we want to score here on quality and sustainability”. The current production site measures 1,872m2 for PET installation. With the further expansions planned, overall production will grow to 3,744m2. www.khmerbrewery.com W W W . I N T R A V I S . C O M Integrated inspection even on structured surfaces PETWatcher® Preform and PET-Bottle Inspection today. Non-destructive layer inspection Label inspection at up to 50 objects per second LayerWatcher® LabelWatcher® Sample-PreWatcher® Comprehensive sampling analysis inline and offline High speed 100 % inline and offline inspection PreWatcher® III V I S I T U S A T H A L L A 4 , B O O T H 3 4 4","@ID":34}, "BOTTLE MAKING 18 PETplanet Insider Vol. 18 No. 07/17 petpla.net An integrated platform for bottlers and converters Process integration to advance bottle production Sacmi Group presents the first integrated platform designed to bring bottlers and converters closer together. Introducing heroBlock, the all-new compact quadblock that combines stretch-blow moulding with labelling and filling. Plus new digital labelling solutions that allow testing, even on existing plants, with all the advantages of digital label customisation. With heroLine, the new dynamic cap and preform buffer, Sacmi has achieved total integration of the bottling process. heroLine is the first ‘all-in-one’ platform capable of integrating the two processes, thus offering potential added value in terms of logistics, efficiency and product quality. Developed as part of a wider Industry 4.0-focused integration policy that has, for years now, seen Sacmi lead the way with solutions that are ever-more integrated and automated, heroLine allows the Group to act as a partner both to bottlers who decide to internalise some production processes, and converters who choose to approach the market with in-house manufacturing solutions. Arriving at a certain point on our ‘industrial beverage journey’, that first began back in the‘70s when plastic bottles first began replacing glass containers, Sacmi heroLine brings us to the modern era of the wall-to-wall converter and all in one integrated processes, by merging the preform production (IPS, Injection Preform System) and cap production (CCM, Continuous Compression Moulding) lines with downstream stretch-blow moulding, bottling, labelling and packaging. Clean and linear, the configuration of the new Sacmi heroLine takes the development of the business model into account, providing major advantages in terms of quality, cost reduction, process and product safety (contamination risks always result in additional costs that heavily weigh on the bottler). Thanks to the automatic magazine and process integration, heroLine keeps caps and preforms at a constant temperature and humidity, and saves on the preform handling costs incurred during the traditional storage and conveying stages on stretch-blow moulding lines. Reduction and optimisation of intra-logistic costs, process traceability and a capacity to obtain higher-quality products while optimising and reducing raw material and energy costs are said to be the advantages of heroLine. Sacmi sees this as representative of its numerous technologies on the market that operate at every single line node, at high efficiency and effectiveness levels. Alongside the tried and tested IPS and CCM units that operate upstream from the CPB magazine, Sacmi has introduced heroBlock, the new quadblock that combines stretch-blow moulding, filling, closing and labelling - all in one machine. Providing compactness, efficiency and versatility thanks to the elimination of conveyors and intermediate stages, this solution allows process optimisation in terms of both efficiency and costs, says Sacmi. Making the most of the expertise already gained in digital cap printing with the proven ColoraCap, Sacmi is also presenting the new digital label printing module. Smoothly integrated into the labeller, this system allows ‘mass customisation’ of pre-printed labels. A clear choice, then, that allows potential customers to immediately test - with an easily, affordable investment - all the advantages of ‘digital personalisation’. www.sacmi.com bottle making","@ID":20}, "45 ON SITE PETplanet Insider Vol. 18 No. 07/17 petpla.net Starlinger line with Nordson Flex Disc melt filter: Bottle-to-bottle recycling results The Starlinger recoStar PET bottle-to-bottle recycling line which has been installed in April 2016 in the plastics recycling facility of the Canadian water bottler Ice River Springs in Feversham, Ontario, is said to deliver excellent production results. Due to Nordson’s BKG Flex Disc filter cartridge, which has been included for melt filtration, the production output is higher than the values guaranteed in the acceptance protocol. The purge rate has been reduced by 40%, and the melt loss due to backflushing is below the minimum values. The Nordson BKG HiCon K-SWE-250-4K-75/RS-FC screen changer is a backflush melt filter system for continuous operation with two screenbearing pistons and four screen cavities. With a total of approx. 4,000cm², the filtration area is 2.4 times larger as using standard screens, filtering the melt with a fineness of 56μ. There is a high process stabilisation of 75% in the filtration area during screen change and backflushing. The recoStar PET 165 HC iV+ recycling line is the second line Ice River Springs installed after purchasing the first PET recycling line from Starlinger recycling technology in 2010. The new line has a production capacity of 1,900kg/h and recycles prewashed PET bottle flakes from curb side collection in Canada. Ice River Springs has set up plants in Canada and the US. The bottled water producer is running its own PET bottle-tobottle recycling operation, Blue Mountain Plastics in Shelburne, which is equipped with washing and recycling lines and produces bottles made of up to 100% recycled PET. In 2011, Ice River Springs received the ‘Letter of Non-Objection’ for its bottles produced from rPET from the Bureau of Chemical Safety/Food Directorate, Health Canada. The company runs a vertically integrated operation that also includes preform production and bottle filling plants, which complete the system for closed loop PET bottle recycling. Ice River Springs is the only beverage company in North America to operate such a system. www.starlinger.com ONsite","@ID":47}, "MOULD MAKING PETplanet Insider Vol. 18 No. 07/17 petpla.net 9 Tour Sponsors: Investment in the growth of the local PET market Blow mould production in Vietnam by Kay Barton “One of our main customers here in Vietnam is a European company working in the shoe industry. The company comes from Germany, but also has a factory here. We create the form parts for them”, explained Thomas Schröder. “We also supply, for example, a machine manufacturer from Hamburg in Germany, which also has a representative office in Kuala Lumpur.” The principle idea behind the establishment of a branch office in Vietnam was the wish to shorten the delivery times within Asia and to use the possibilities offered by the growing markets there. Röders initially began in the area of precision-parts manufacturing and mechanical engineering. In order to get started, a Vietnamese business consultant with a German background was brought on board, and it was he who suggested the location, particularly due to the infrastructural advantages offered by having an airport and port nearby for exports. Blow mould production itself was only added as a new area six months ago due to the industrial prognoses for PET, in particular for the local market. The company invested approximately US$ 1,000,000 in this part of the production. “The very first reason for going to Asia was simply to shorten the delivery times to those markets. Vietnam is certainly one of the most exciting”, said Thomas Schröder. “By setting up a facility here, we also wanted to be able to win new customers in Asia on a fully independent basis. Our core markets in addition to Vietnam are Thailand, Taiwan and possibly also Japan in the future.” The low operating costs in Vietnam is something that the machine manufacturer passes on to their customers, and in this way also wants to keep pace with the competition when it comes to prices, but still providing the same level of high quality. The facility is currently manufacturing blow moulds on three high-performance milling machines, one of which was taken over from the machine components for the mould production and two were acquired new. “We are planning to add four further machines over the coming 24 months”, explained Schröder further. The production building has a production area of 1,600m2 and has 55 employees working on a threeshift basis. Due to the requirements with respect to precision production, the production area is cooled to 24°C and diverse filter systems ensure that humidity is removed from the air. In keeping with its expansion plans, the company has just rented a further production hall on the neighbouring site with a production area of 2,000m2. “This building was just a warehouse; this means that we are currently in the process of putting the necessary infrastructure in place in order to then be able to install the machinery. We want to exclusively concentrate on the blow mould area here.” The Vietnamese facility turned over US$ 2.8 million in 2016; the goal for 2017 is US$ 3.8 million. Schröder is optimistic: “With the market potential on offer for PET, we should be able to achieve this goal.” www.roeders.de The South East Asia Road Show meets Thomas Schröder of Roeders Vietnam Thomas Schröder in his manufacturing area Interview with Roeders Vietnam Co., Ltd. March 30, 2017 We met: Mr Thomas Schröder, Deputy General Director Röders GmbH, a company with a long tradition from the North-German town of Soltau, opened a representative office in Vietnam in April 2013 with the goal of serving the Asian market from there, and growing its sales, particularly in the area of blow-mould manufacturing. The company is known for its milling and grinding machine and blow mould manufacturing, among other products. Vietnam was chosen not least due to the very good growth prognoses for PET packaging in the upcoming years. We spoke with Thomas Schröder who is responsible for the factory in the Binh Chanh District, Ho Chi Minh City, and who regularly travels between the company’s German headquarters and Vietnam.","@ID":11}, "BOTTLE MAKING 11 PETplanet Insider Vol. 18 No. 07/17 petpla.net New generation of bases for CDS bottles Lower pressure for a more profitable production The blowing of CSD beverage bottles is increasingly challenging in terms of speed and energy consumption, especially for blow moulding tool manufacturers. From the milestone of 28bar of blowing pressure achieved in 2008, the energy efficiency of the blow mould and the high physical performance of the bottle have been the driver for the engineering team of the Argentinian company Moldintec. The development of the technology applied in these high efficiency moulds was monitored closely by Paulo Villas, Regional Technical Director at CocaCola Brazil BU and Orlando Diz, Industrial Director at Coca-Cola Reginald Lee SA (Relesa). Relesa has tested and implemented in its bottling plant in Buenos Aires the successive generations of Moldintec’s bases to optimise its bottle manufacturing. The recently introduced BaseMax was industrially tested and applied earlier this year during the regional launch of several new bottle shapes and sizes, including the company’s new asymmetric bottles. Low pressure, stable container The capability of the mould to have sharper geometry in the container while blowing pressure decreases enhances the physical performance of the petaloid even after lightweighting. It is claimed to improve reliability of the bottle, making it more stable and attractive in the market. Benefits include the capability of lightweighting up to 10% thanks to a better stretching of the base material. The advanced geometry of the BaseMax petaloid is said to be repeatable although at extremely low pressures. Test runs have shown 100% repeatability of the standing and heel area, even with final blowing pressure of 15bar. It turns into a more stable container and less susceptible to falling on the line, the shelf of the supermarket or the consumer’s home. BaseMax prevents unwanted rocking if the shape of the bottle body is slim, complex or asymmetrical. It also minimises the possibility of falling when being transported between equipment, reduces expensive stoppages and improves the operational efficiency. The reduction of the final blowing pressure translates into multiple savings: lower energy consumption, less maintenance, reduction of the carbon footprint, and more environmental friendliness. Moldintec states that the solution is easy to implement and to retrofit, fully compatible with new and existing moulds, even if they were manufactured by other tooling suppliers. The improved energy consumption might contribute to a possible ROI in less than a year. Redesigned multibrand blowing mould platform Moldintec will be announcing more developments in the upcoming months, particularly in the materials and manufacturing processes of their moulds. These developments are expected to increase the design freedom of Moldintec’s engineers. Brands will appear exactly as intended by use of laser machining technology allowing sharper edges and unlimited decoration design freedom, says the company. Thus the development is providing bottlers within highly competitive market opportunities to differentiate their products and increase their market share with PET. Moldintec’s multi-brand platform concept provides flexible and versatile production to implement quick mould changeovers between machines from different manufacturers. The design approach is not only about optimising the blowing process as a source of savings for the bottle manufacturer, the total cost of ownership (TCO) is being constantly reviewed, while maintaining a high standard of mould quality and reliability. www.moldintec.com.ar bottle making Bottle base realised with BaseMax at a final blowing pressure of 15bar BaseMax is a patented solution for ultra-low blowing pressure of petaloid CSD bottle bases. This new generation combines advanced geometric design with thermodynamic mould engineering that allows blowing processes at very low pressures, 15 to 20 bar, and a 100% copying rate of the shape even at high speed depending on the specific process conditions. BaseMax full mould","@ID":13}, "MARKET SURVEY 27 PETplanet Insider Vol. 18 No. 07/17 petpla.net 07/2017 MARKETsurvey Preforms & preform inspection Recycling plants & washing units Palletising & shrink film machinery Caps & closure systems & CC inspection Labelling & marking systems Recycling: Cutting plants Filling equipment & filling inspection Resins, additives Compressors SBM machinery & quality inspection Suppliers of cutting plants To complete the overview of recycling plants in our Market Surveys for this year, we will present you for the first time some additional information related to cutting plants for PET recycling. Please find below the technology of the participating companies in detail: Neue Herbold Maschinen- und Anlagenbau GmbH, STF Maschinen- und Anlagenbau GmbH, Starlinger & Co Ges.m.b.H, Herbold Meckesheim GmbH, Sorema Div. of Previero N.srl and Krones AG. Although the publishers have made every effort to ensure that the information in this survey is up to date, no claims are made regarding completeness or accurancy. Company name Neue Herbold Maschinen- und Anlagenbau GmbH STF Maschinen- und Anlagenbau GmbH Postal address Telephone number Web site address Contact name Function Direct telephone number Fax E-Mail Wiesenstraße 44, 74889 Sinsheim-Reihen, Germany +49 7261 9248 0 www.neue-herbold.com Mr Bernd Humpa Sales Manager +49 7261 9248 54 +49 7261 9248 99 b.humpa@neue-herbold.com Industriestr. 2, 94529- Aicha v. Wald Germany +49 8544 960 129 www.stf-group.de Mr Markus Ingenpass Sales Director +49 8544 960 129 +49 8544 960 130 contact@stf-group.de Input/output Bales and/or single bottles Both possible Bales, single bottles, briquettes Output per hour 500-1,500 kg/h 1 - 4 t/h Sorting Inclined belt conveyer with metal detector Yes Yes Additional techniques for impurity sorting Starscreen, zigzag sifter, windsifter, float-sink-tank Removal of film, paper/cardboard, metal, plastics, colour, screening of small pieces, complete sorting-lines Manual sorting possible? Yes Yes Granulator Wet or dry? Both possible Wet and dry cutting Cutting chamber setup Horizontal rotor Different rotors available, complete exchangeable wearing protection of cutting chamber Size of granulat By customer's choice 6 - 100 mm Washing process Complete (hot-) washing lines available Bottle toGranulate Input variable: collected pressedbottles, variouscolours Output: Granulate with approval Cap i acty [t/ ]a Floor space [m²] Whichapprovals Fresh water consumption per tonne output [m³/t] Consumption kWhper tonne output [kWh/t] Flakes to Granulate Input variable: flakes, coloured proportion max 5%, not much chlorine Output: Granulate with approval Capacity [t/a] Floor space [m²] Whichapprovals Freshwater consumptionper tonne output [m³/t] Consumption kWhper tonne outp tu [kWh/t] Bottles to Flakes Input variable: collected pressed bottles, various colours Deposit, curbside, MRF/PRF-collection, loose or baled, all kind of colours, other plastics Output: Flakes with/without approval PET-flakes with approval (FDA, EFSA) Capacity [t/a] Depending on the number of shifts From 1 t/h up to 6 t/h Floor space [m²] Approx. 400 m2 (max. height 7-8 m in a few areas) 1,000 - 2,000 m2 Which approvals FDA, EFSA, brand-approvals Fresh water consumption per tonne output [m³/t] Approx. 10-15 m3/h Different water circulation and treatment systems, from 1 m³/t to 0.1 m³/t fresh water (zero discharge) Consumption kWh per tonne output [kWh/t] 433 kW 200 kWh/t - 250 kWh/t sorting, grinding + washing line total Drying Mechanical drying Yes (standard) Friction dryers/centrifuges 0.8 % Thermal dryer for final drying Yes, if the customer's specification requires a low residual moisture Thermal dryers with gas or heat-exchanger 0.3% Filling station PET Yes Filling stations, single and double, with filling sensors, stuffing devices and scales PO On customer's demand Metal/coloured PET Depends on the chosen sorter Labels Yes","@ID":29}, "BOTTLE MAKING 35 PETplanet Insider Vol. 18 No. 07/17 perature. Its significance in the PET industry relates to the production of water bottles. Still water taste is very sensitive to even small AA concentrations while the sugar content of carbonated drinks and juices masks any flavour contributed by AA completely. Producers of preforms for other beverages may still monitor AA content as a way of keeping track of the maintenance state of screw and barrel, because, when these parts wear, shear stress, and with it the AA creation, is increased. Please order your copy at the PETplanet Insider book shop: petpla.net/ book3 Stretch Blow Molding Second Edition by Ottmar Brandau € 130,00 320 pages © Copyright Elsevier 2012 Property Non-oriented Oriented Thickness (mm) 0.36 0.36 Water vapour transmission rate (g/m3 × 24h) 3.4 2.3 Oxygen permeability (cm3 × mm/m2 × 24h × atm) 2.9 2.2 Carbon dioxide permeability (cm3 × mm/m2 × 24h × atm) 15.7 14 Tensile modulus of elasticity (Mpa) 3170 4960 Tensile stress @ yield (Mpa) 82 172 Table 2.2 Virtually all properties of PET benefit from a high degree of orientation. NBĔ H?Q ;AĔ I@ INNFCHĴ GREAT TECHNOLOGY ...IN A SMALL BODY NEW EBS ERGON BLOWERS EBS ERGON VIDEO ...scan & discover it! Compact and ergonomic design, cutting-edge technical solutions, top performances, high energy saving: that’s the new EBS ERGON series of fully electronic rotary stretch-blow moulders for manufacturing PET containers from 0.10 to 10 L up to 35,200 bottles/hour (0.5 L format). Available as stand-alone equipment or integrated into an ECOBLOC® ERGON compact systemof bottle blowing, filling and capping. I COMPLETE LINES I ROTARY STRETCH-BLOW MOULDERS & FILLERS I I PACKERS I PALLETISERS I www.smigroup.it","@ID":37}]}}
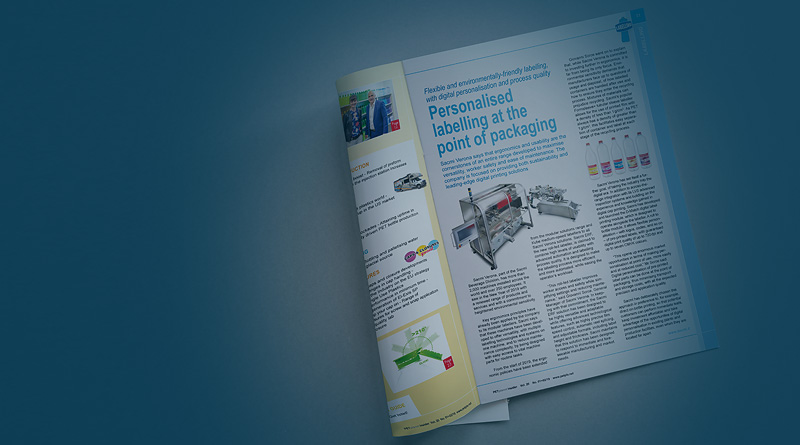