{"pages":{"page":[{"@ID":27, "MARKET SURVEY 25 PETplanet Insider Vol. 24 No. 06/23 www.petpla.net Kosme Gesellschaft mbH Sipa Gewerbestrasse 3, 2601 Sollenau, Austria +43 2628 411 0 www.kosme.at Mr Johann Gugler Managing Director +43 2628 411 125 johann.gugler@kosme.at Via Caduti del Lavoro, 3 - 31029 Vittorio Veneto, Italy +39 0438 911 511 www.sipa.it Mr Paolo De Nardi Project Leader/Stretch- Blow Moluders Development +39 0438 911 624 p.denardi@zoppas.com Rotary blowmoulder Linear blowmoulder EBS KL HC Ergon Linear Machines (5 models) Rotary Machines (7 models) Xtra: 6 to 24 (8 models) Rotary Blowmoulders SFL Performance 3H,4H,6,7,8; SFL Flex2; SFL Dynamic 2H,3H, 4,5; SFL Big 6,4; SFL Maxi 1,2,3; SFL WM (Wide Mouth) Linear Blowmoulders 0.05 - 3.0 (up to 4.0 l depending on design) 0.25 - 3.5 0.25 - 3.0 3 - 10 0.5 - 30.0 0.5 - 11.0 5 - 30 8 24 8 3 8 3 2,500 2,800 per cavity 1,800 bhc 2,500 2,700 per cavity 1,600 bhc 2,500 2,550 per cavity 1,800 bhc 1,200bph per cavity (*) Up to 1,250 for 5.0 l; 750 for 15.0 l; 700 for 20.0 l; 350 for 30.0 l 1,250 650 bhc 4.77 x 2.62x 2.35 min.: 4,500x1,830x3,100; max.: 5,100x1,850x3,100, (without preform feeding system) 6500 x 3500 x 3500 (without preform feeding system) Air recycling system, available also with PI, mould shells of linear machines are compatible with rotary machines, fast semiautomatic mould change within 10 minutes, preferential heating Active neck cooling, patented modular oven (low evergy consumption), block version with fi llers for all sizes available, all machines on one platform available Best output 2,700 bph/cav. with best process & Active angle: easy to blow. Reduced TCO: lower air and energy consumption (-25%). 30 sec to change blow mould (tool-less), simple use & maintenance. rPET Easy process. Bottles for water, oil, csd, heat resistant, oval simmetric and asimmetric, with preferential heating, neck orientation, with handle, wide mouth (up to 130 mm NF), large size (up to 30 litres), rPET, Tritan, PE, OPP Krones AG Boehmerwaldstr. 5, 93073 Neutraubling, Germany +49 9401 70 0 www.krones.com Mr Peter Christiansen Head of Sales Plastics and Block Technology +49 9401 70 4980 peter.christiansen@krones.com APF-6004, APF-3002 APF-10, APF-5 APF-30 Contiform Speed, 15 models available Contiform, 13 models available Contiform Heatset 13 models available Contiform Preferential Heating, 10 models available Contiform BigBottle 3 models available 0.2 - 2 0.1 - 2.0 0.1 - 3.5 0.1 - 2.0 0.1 - 3.5 3 - 10 15 - 40 4 28 28 22 2 1 1,500 2,750 2,500 2,000 (Heatset) 2,500 1,500 2,500 2,500 2,000 (Heatset) 2,500 1,500 2,400 2,400 2,000 (Heatset) 2,400 2,000 1,200 1,200 500 for 20-40 l 2,500 (still water/CSD) APF-6004: 8.6 x 3.2 x 2.5 APF-3002: 6.4 x 2.8 x 2.3 APF-10: 8.2 x 3.4 x 2.6 APF-5: 7.4 x 3.2 x 2.7 6.7 x 2.4 x 3.1 Depends on machine size Quick mould change, air recovery system, oval and complex shapes, space saving dimensions, hot fi ll option, patented mould closing system Lightweight containers for 3-6 l with 38mm preform, APF-5: 2 independent blowing units to produce two bottle formats/volumes by turns Possible to blow PET kegs and 4-5 US gallon returnable and one-way watercooler bottles on one blower Bottle design and mould manufacturing; bottle lightweighting concepts, Nitro-hot-fi ll; air-recycling systems for standard- and heat-set machines; rapid toolless product change-over systems; automated mould change-over systems (MouldXpress robot); integrated preform- and bottle inspection; Contiform Bloc (blower-fi ller-block); Contiform Bloc BL (blower-labeler-block); Ergobloc L and LM (blower-labeler-fi ller-block); Contipure Asept Bloc with integrated preform decontamination, Preferential Heating (PH) for non-round bottle production. Contiloop AI for automated process control."},{"@ID":15, "BEVERAGE INGREDIENTS PETplanet Insider Vol. 24 No. 06/23 www.petpla.net 13 all over the world and procuring and processing products locally, Doehler pursues a sustainable and qualityconscious approach to raw material procurement and the entire supply chain. This not only provides the basis for sustainable and high-quality products, but also secures reliable planning outlooks. Functional and healthy beverages As healthy lifestyles become more significant, natural and sustainable products – such as those that contain less sugar or that offer functional ingredients or a clean label declaration – have gained enormously in popularity. However, it is important that these health-related aspects do not cause the taste to be neglected. Working with an international team of experts, Doehler has developed an extensive portfolio of taste modulation products, such as for low-sugar products. These include natural sweetening, flavour, masking and texturising products and solutions that ensure good sensory properties in the respective applications and support a clean label declaration. Under its MultiSweet Plus umbrella brand, Doehler also offers an extensive portfolio of sweetening systems that are claimed to be ideal for reduced-calorie and calorie-free products in a host of different applications. This portfolio includes both artificial high-intensity sweeteners (HIS) like MultiSweet Classic and natural sweetening systems like MultiSweet Fruit and MultiSweet Stevia. MultiSense Flavours products can enhance the sensory properties of reduced-sugar products. MultiSense Sweet flavours, for example, help to reduce a product’s sugar content while still ensuring full taste. MultiSense Masking flavours, on the other hand, mask the aftertaste of sweeteners, proteins and other unwanted taste deviations, while MultiSense Mouthfeel flavours can improve the mouthfeel of calorie-free or reduced-calorie beverages. Functional beverages, which offer consumers added health value through natural vitamins or the use of botanical extracts, are also gaining in popularity. From functional energy drinks to sport drinks and beauty drinks, innovative concepts combined with exciting flavours give rise to diverse positioning options here. Doehler is setting new standards with its extensive portfolio of natural ingredients, such as those designed especially for functional beverages. The range includes health-promoting vitamin and mineral combinations, plant-based proteins and trendy botanical extracts like moringa, baobab, ginseng, green tea and guarana. These ingredients not only offer optimised nutrient quality, but also impress with their outstanding taste profile. www.doehler.com ALL- IN- ONE-MACHINE ASSEMBLY FOLDING SLITTING TETHERED CAP CONTEXO GMBH Tel. +49 (0) 7181 / 606-100 info@contexo-gmbh.de www.contexo-automation.de"},{"@ID":6, "PETcontents 4 PETplanet Insider Vol. 24 No. 06/23 www.petpla.net 06/2023 Page 39 BOTTLE MAKING 8 Cutting wine & beer carbon footprints MATERIALS / RECYCLING 10 Handling resin in the right way 12 Beverage ingredients: Trends and developments in 2023 BOTTLING / FILLING 14 The country of the five toasts - Water bottling in Georgia 16 Reaching new heights in water bottling - Sustainable filling lines in Poland 17 PET versatile aseptic lab filler 18 Processing demineralised seawater - Water treatment with new technology 19 Providing a 3R response for bottlers in PET 20 Inspecting closures on filled bottles 21 New tasks in bottle inspection PREFORM PRODUCTION 22 Efficient, safe and gentle loading - Company anniversary at Tanner, 50 years of preform handling MARKET SURVEY 23 Suppliers of 2-stage SBM machinery TRADE SHOW REVIEW 26 PETinar: Opening debate 2023 29 Chinaplas 2023, review part 1 32 Interpack 2023, review part 1 35 Market launch of PET sparkling wine bottle - Concept to prototype in less than a year 36 PRSE 2023 review, part 1: Support an organised value chain of rPET BUYER’S GUIDE 40 Get listed! INSIDE TRACK 3 Editorial 4 Contents 6 News 38 Onsite 39 PET bottles for beverage + liquid food 46 Outer Planet Page 35 FILLING Page 14"},{"@ID":31, "29 TRADE SHOW REVIEW PETplanet Insider Vol. 24 No. 06/23 www.petpla.net TRADE SHOWreview part 1 Chinaplas 2023 - a (record) return towards normality With the lifting of China’s years-long travel restrictions, PETplanet was finally back on site at Chinaplas, which took place this year in Shenzhen in southern China. The 35th edition of the fair on a whopping 380,000m2 of exhibition space and, according to information from the organisers, also the largest Chinaplas of all time, was not only very well attended on the four days of the event, we were also told of a very good quality of trade visitors as well as direct deals at exhibition stands. The mood of optimism was palpable. The focal points of the trade show were sustainability, circular economy and efficiency in plastics processing and also on digitalisation, food safety, ease of operation and, of course, the further development of all-electric machines. In parallel, a number of highly frequented forums, symposia and public trade meetings took place. Overall, a record 248,222 visitors attended the fair, of which 28,429 (11.45%) came from Hong Kong, Macao, Taiwan and overseas. On the exhibitor side, 3,905 companies from 38 countries publicised their news and presented their innovations. This year’s event thus exceeded the number of visitors from 2019 in Guangzhou by 51.99% and the 2021 event, also held in Shenzhen, by 63.16%. www.chinaplasonline.com ® Accurate. Fast. Intuitive. Simplified dimensional and thickness measurement of plastic containers and preforms featuring AutoJob®— automated attribute recognition and job setup in seconds. Visit us on social www.agrintl.com +1.724.482.2163 Injection moulding machine update for all-electric all-round processing Powerjet, the injection and blow moulding machine manufacturer based in Foshan, Guangdong, southern China, which we already reported on in our trade fair preview regarding its KPET series, showed another system at Chinaplas, which was mainly developed for the production of high-precision containers and parts, for example for medicine, but is also used in other non-food and food and beverage sectors. Mr Len Chen, CMO of the company, explained to us the details of the JT series, as the machine series is called. In this specific case, the JT-160E2 on display at the booth was an all-electric, energy-optimised injection moulding machine, with around 160 t clamping force and the ability to use moulds with heights of 180-520mm. The system at the show floor was equipped with a 32-cavity mould for the production of pipette tips from PP material. Also, according to the company, the system boasted a highperformance cycle time, low maintenance work and reduced operating noise. In addition to the production of precision PET medical parts, Mr Chen explained, the system would be also suitable for the production of PET containers or PE bottle caps. The different screws are part of the company’s portfolio, depending on the desired application. The model number E2, which has been available since 2022, is the successor generation of the model E, which was built from 2013 to 2017. www.powerjetmachine.cn F.r.t.l. Len Chen with Kay Barton in front of the JT System"},{"@ID":43, "BOTTLING / FILLING PETplanet Insider Vol. 24 No. 06/23 www.petpla.net 20 Inspecting closures on filled bottles Intravis GmbH is known for its vision inspection systems for plastic packaging. Many manufacturers of closures are familiar with the company’s systems such as the CapWatcher Q-Line. Not as well known is that Intravis also has a portfolio system explicitly for closure inspection in the wet area of filling lines: the CapWatcher FC. This posed exciting challenges to the CapWatcher development team of Intravis. The design First of all, it was clear that a specific system design was needed for an inspection behind the filling and capping process. Marius Pötting, Intravis product manager for closure systems, was involved in the development of the CapWatcher FC from the very beginning: “Post-filling and capping systems have to cope with completely different requirements. In particular, cleaning the system has to work conveniently and also in a fast and reliable way. Of course, the inspection system has to be resistant against standard cleaning processes on the market to entirely meet the customers’ hygienic demands.” The CapWatcher FC is equipped accordingly: A stainless steel housing which enables cleaning the system from the outside with a water jet; improved seals that can cope with aggressive cleaning methods, too and cameras that are protected from any contact to liquids thanks to transparent partition walls. All these features allow the system to be cleaned both externally and internally using typical cleaning methods for filling lines. This applies to the inspection unit and the control cabinet, which meets with the hygienic requirements of the filling companies accordingly. Inspection The inspection scope of a system for already applied closures differs compared to the scope of systems designed for the inspection in closure production lines, for example. In addition to inspecting for damage, presence and correct positioning of the applied closure, the fill level of the bottle is also examined. The highlight among the inspections, however, is the verification of the application angle. The CapWatcher FC uses index marks to inspect whether the closure is screwed down to its target position – or whether it is screwed down too far or not far enough. Therefore, marks on the closure and on the neck support ring that are barely perceptible to the end user are detected by the system. If the relative angular position of these marks is within a tolerated range, the system assumes that the closure has been completely and correctly applied, and the bottle is released for packaging. Handling the quality data collected As much as Intravis systems differ in their design and scope of inspection, they are similar with regards to handling the collected quality data: These are used for optimisation, especially for monitoring and improving the processes of upstream systems like filling and capping, to guarantee a flawless procedure. This means for the CapWatcher FC: Information obtained on the closure fit – e.g., on the closure position and application angle can be used to draw conclusions on the capping process. Defects can even be traced back specifically to each individual tool, offering the possibility of targeted intervention and optimised predictive maintenance. Additionally, the information obtained from the fill level verification can be used to draw conclusions about the performance of specific filling tools to ensure a smooth filling process. Even though the systems of the CapWatcher family at Intravis basically have the same focus for the inspection, namely closures, there are still many differences due to the challenges of their dedicated application areas. In both the design and the inspection scope of the CapWatcher FC, the Intravis development team has used previous experiences as well as completely new findings. Additionally, Intravis is already in the process of applying this knowledge to other products in the portfolio. As of this year, the LabelWatcher, an inspection system for the quality control of pressure-sensitive labels, is also available in a Washdown Design and thus available for wet areas. www.intravis.com FILLING The new CapWatcher FC of Intravis is specially designed for the use in the wet area of filling lines."},{"@ID":13, "PETnews 6 NEWS PETplanet Insider Vol. 24 No. 06/23 www.petpla.net PET imports to impact EU recycled content targets A major increase in PET imports threatens the competitiveness of the EU’s industry, along with its objective to improve the waste management of plastics, according to the organisation Plastics Recyclers Europe. Between 2021 and 2022 imports of PET have doubled reaching 1.9Mt, with India, China and Türkiye among the biggest exporters in terms of volumes and value followed by Indonesia, Egypt and Vietnam. With the increase, imports represented nearly 30% of the total demand for PET in Europe in 2022, compared to only 23% in 2020. Given the strong divergences in energy, labour and environmental costs in the EU compared to the rest of the world, this important market shift puts the European industry under a lot of pressure, states the organisation Plastics Recyclers Europe. “Following these concerning market developments, the EU has initiated an anti-dumping proceeding against China for the imports of PET throughout 2022”, said Herbert Snell, PRE PETWorking Group Vice Chair and Managing Director at Multiport GmbH – MultiPet GmbH part of the Veolia Group. “Among the allegations, the issued notice reflects a likelihood that increased dumped imports would have a negative impact on the performance of the EU industry”, he added. The growing imports could be explained by the heightened demand for rPET in the EU, driven by the 2025 recycled content targets of 25% for beverage bottles, and the consequent rise in rPET prices on the continent. “It needs to be ensured that recycled PET imported to the EU at significantly lower prices is compliant with the stringent EU food contact regulation, and therefore does not put at disadvantage the efforts made for creating a robust rPET industry in Europe”, stated Casper van den Dungen, Vice-President of Plastics Recyclers Europe. He continued: “This will additionally require full verification of the traceability of imported polymers by end users to avoid using self-declarations as the means of reporting recycled materials participating in the EU targets”. Consequently, ensuring the enforcement of EU rules for goods and materials from outside the continent is key to protecting the ‘Made in the EU’ and maintaining a level playing field for all actors. Otherwise, the circularity of plastic products placed on the market will be undermined, together with substantial investments in the recycling industry and its capacities, says the organisation. www.plasticsrecyclers.eu Indorama Ventures and Carbios reaffirm partnership to build first-of-a-kind PET bio-recycling plant in France Indorama Ventures Public Company Limited (IVL) a global sustainable chemical producer, and Carbios, a biotech company developing and industrialising biological solutions to reinvent the life cycle of plastic and textiles, announced the signing of a non-binding Memorandum of Understanding (MOU) to form a Joint Venture (JV) for the construction of the world’s first PET bio-recycling plant in France. Based on and subject to the comprehensive terms set out in the MOU, Indorama Ventures plans to mobilise about €110 million for the JV in equity and non-convertible loan financing, pending final engineering documentation and final economic feasibility studies. Both parties have acknowledged their mutual support for the implementation of the project and their intent to finalise contract documentation before end 2023. Subject to the successful performance of this first plant in France, Indorama Ventures confirms its intention to potentially expand the technology to other PET sites for future developments. Under the agreement signed, Carbios, which filed for plant permission in December 2022, is to acquire 13ha land from Indorama Ventures’ existing PET plant at Longlaville and expects to be granted permits by Q3 2023, allowing start of construction by end of 2023 and targeted commissioning in 2025. The land surface offers the possibility to double capacity. Pursuant to this MOU, Indorama Ventures shall ensure 100% of output repolymerisation and both partners shall collaborate to secure feedstock supply. The total capital investment for the new plant is re-estimated to be around € 230 million, taking into account recent impact from inflation. Project costs are to be financed by the sums mobilised by Indorama Ventures, the French State and Grand-Est Region subsidies available for the project, and by equity capitalisation of the JV by Carbios. Part of Carbios’ equity injection into the JV will be financed by a portion of Carbios’ current cash position (i.e. €86 million as of 30 April 2023). Carbios is actively examining the best options to finance its remaining equity injection into the JV and will choose the most appropriate solution and timeline based on market conditions. www.indoramaventures.com www.carbios.com Plastics Recycling Show Middle East & Africa opens in Dubai in September 2023 The launch edition of the Plastics Recycling Show Middle East & Africa (PRS ME&A) will take place at the Dubai World Trade Centre in Dubai, United Arab Emirates on September 5-7, 2023. The three-day exhibition and conference is the first and only event in the region specifically dedicated to plastics recycling and will run annually, starting in September. Visitor registration for the event is now open. The Plastics Recycling Show Middle East & Africa brings together key players from the plastics and recycling sectors to showcase innovative technology, share best practice, network and do business. A broad cross-section of the industry is represented at the event including plastics recycling machinery and equipment suppliers, plastic material suppliers and compounders, pre-processors, plastics recyclers, recycling and waste management specialists, regional government and industry associations. The latest trends in the plastics recycling sector will be explored in depth in the conference. www.prseventmea.com"},{"@ID":26, "MARKET SURVEY 24 PETplanet Insider Vol. 24 No. 06/23 www.petpla.net Company name 1 Blow SMI S.p.A. Postal address Telephone number Web site address Contact name Function Direct telephone number E-Mail 25 Chemin de Gerocourt, 95650 Boissy l'Aillerie, France +33 9800 820 70 www.1blow.com Mr Olivier Perche Sales Director +33 9800 821 80 operche@1blow.com Via C.Ceresa, 10, 24015 San Giovanni Bianco (BG), Italy +39 0345 40.111 www.smigroup.it Mr Pietro Volpi Marketing Dept. Manager +39 0345 40.316 info@smigroup.it 1. Machine designation / model number 1XXL / 1XXLN / 1XL / 1XL Lab / 2L / 2LN / 2LO /2LHF / 2XL / 2XLO / 4L / 4LN / 4LO / 4LHF / 4XLS / 5M-C / 6MO EBS K Ergon EBS KL Ergon EBS E Ergon 2. Bottle volume (from/to in litres) a) Standard machines 0.10 - 12 0.10 - 3 0.10 - 3 0.10 - 3 b) Machines for large containers 5 - 30 3. Maximum number of stretch-blow moulds (units) a) Standard machines 6 4 10 16 (20 for 0.75 l bottle) b) Machines for large containers 1 4. Output per stretch-blow mould for: 0.5 litres CSD bottle (units per hour) 2,000 2,500bph per cavity (*) 2,500 bph per cavity (*) 2,500 bph per cavity (*) 1 litre CSD bottle (units per hour) 1,800 2,500bph per cavity (*) 2,500 bph per cavity (*) 2,500 bph per cavity (*) 1.5 litres still mineral water bottle (units per hour) 1,700 2,300bph per cavity (*) 2,300 bph per cavity (*) 2,300 bph per cavity (*) Large capacity container 1,000 for 5 l ; 600 for 20 l Other (*) depending on the preform/ bottle features 5. Footprint / space requirement (L x W x H in metres) 2.1 x 1.6 x 2.4 2.32 x 3.28 x 2.3 without preforms hopper & unscrambler 4.77 x 2.62 x 2.35 Min: 5.8 x 3.9 x 2.55 - Max: 7.3 x 3.9 x 2.55 6. Special features (short description/keywords) Preferential Heating (oval bottles), neck orientation (with standard preforms), hot fi ll compatible with Sidel, Krones, KHS, Sipa, Side moulds; recovery of blowing air, power recovery 5M-C available as a Combi in cooperation with Ermi and Synerlink, integrated ink jet coding unit Sure Grip device for blow-moulded hand grip, BottleClips device available on 2 l & 4 l machines, selective access to HMI through bagde reader, all machines compatible with rPET preforms. High performances in the stretch-blow moulding of PET, rPET and PP bottles, solutions for producing plastic containers of different capacities, featuring various shapes, both simple and complex. Reduced maintenance and operational costs, quick changeover & mould replacement, reduced maintenance time, excellent quality/price ratio. High technological content of the solutions inspired by Industry 4.0 and Internet of Things (IoT), eco-friendly machines, enabled to stretch-blow lightweight preforms, easy to use thanks to the MotorNet System technology. The ARS (Air Recovery System) ensures up to 40% savings in compressed air consumption / reduction of energy costs. The ReduxAir optional kit enables to blow bottles with lower pressure compressed air. Company name Side S.A PET Technologies Postal address Telephone number Web site address Contact name Function Direct telephone number E-Mail Pol.Ind. Montguit, C/Llinars s/n, 08480 L'Ametlla del Valles, Barcelona, Spain +34938463051 www.sidemachines.com Mr Josep Jiménez Sales Manager +34677551928 jose.jiménez@side.es Grünlandgasse 5/1/12, 2620 Neunkirchen, Austria +43 720 775 196 www.pet-eu.com Mr Maxim Poliansky CEO +43 720 902 169 offi ce@pet-eu.com 1. Machine designation / model number 1002e-160e/c 2006e 2003eG 5001e 3008e APF-Max series 8 models avaliable 2. Bottle volume (from/to in litres) a) Standard machines Up to 3.5 Up to 2.5 - - Up to 2 0.2 - 8 b) Machines for large containers - - Up to 10 Up to 50 - 3. Maximum number of stretch-blow moulds (units) a) Standard machines 2 6 - - 8 8 b) Machines for large containers - - 3 1 - 4. Output per stretch-blow mould for: 0.5 litres CSD bottle (units per hour) 3,000 10,000 3,600 - 18,000 1,750 1 litre CSD bottle (units per hour) 3,000 10,000 3,600 - 16,000 1,750 1.5 litres still mineral water bottle (units per hour) 3,000 10,000 3,600 - 16,000 1,750 Large capacity container 3,000 600 16,000 Other 300 5. Footprint / space requirement (L x W x H in metres) 7x4.75x3.33 6.30x10x3.65 10.48x6.65x3.65 5.80x5.30x2.88 3.00x12x3.65 9.5 x 3.3 x 3.2 6. Special features (short description/keywords) Preferential oven, neck orientation, T-handle system, PP preform blowmoulding, online remote device 4.0, 5 Gallons returnable / one way, beer kegs, asymetric / oval bottles, air recovery system and hot fi ll. Modular system 6-8 cavities, fl exibility to produce 0.1 - 8.0 l bottles at one machine, NIR heating system, hot fi ll option, preferential heating option, quick changeover to other preform type, blow mould quick change, compatibility with rotary moulds"},{"@ID":5, "imprint EDITORIAL PUBLISHER Alexander Büchler, Managing Director HEAD OFFICE heidelberg business media GmbH Hubweg 15 74939 Zuzenhausen, Germany phone: +49 6221-65108-0 fax: +49 6221-65108-28 info@petpla.net EDITORIAL Kay Barton Heike Fischer Gabriele Kosmehl Michael Maruschke Ruari McCallion Anthony Withers WikiPETia. info petplanet@petpla.net MEDIA CONSULTANTS Martina Hirschmann hirschmann@petpla.net Johann Lange-Brock lange-brock@petpla.net phone: +49 6221-65108-0 fax: +49 6221-65108-28 LAYOUT AND PREPRESS EXPRIM Werbeagentur | exprim.de Matthias Gaumann READER SERVICES reader@petpla.net PRINT Chroma Druck Eine Unternehmung der Limberg-Druck GmbH Danziger Platz 6 67059 Ludwigshafen, Germany WWW www.hbmedia.net | www.petpla.net PETplanet Insider ISSN 1438-9459 is published 10 times a year. This publication is sent to qualified subscribers (1-year subscription 149 EUR, 2-year subscription 289 EUR, Young professionals’ subscription 99 EUR. Magazines will be dispatched to you by airmail). Not to be reproduced in any form without permission from the publisher. Note: The fact that product names may not be identified as trademarks is not an indication that such names are not registered trademarks. 3 PETplanet Insider Vol. 24 No. 06/23 www.petpla.net Dear readers, New horizon for packaging This year’s London Wine Fair, held at the Kensington Olympia Exhibition Centre, had a very strong theme of sustainability. A panel discussion on alternative packaging materials included representatives from Laylo, which sells premium boxed wines, Frugalpac, which makes bottles from recycled paper, and British retailers Tesco and Waitrose. Samples of cans and PET bottles were passed among the audience, which appeared to be quite open to ideas. A number of the exhibitors were actively seeking to change their packaging models. Shelf life is undeniably shorter in non-glass packages but, as most wine is bought by consumers for drinking the same day, is it really the major issue often claimed? Market considerations seem to be leading producers into actively consider different packaging for different markets. Handy 250 or 330ml cans of wine were promoted for relaxed, informal, social events. Laylo boxes offer six week life for red wine once opened. Petainer, who we spoke to (see separate article p. 8) talked of six to 18 months for PET bottles, depending on construction. However, shelf life is important for some. I spoke to a Cava producer from NE Spain, who present their wine as a premium product, are not considering PET. They cited the practicalities of packaging a carbonated product but there was also indication of strong cultural resistance. Help may be at hand. Sipa have developed a high-quality PET bottle specifically for sparkling wines (see article on p. 35). It weighs just 90 g – more than 80% lighter than the glass equivalent’s 750 g. Porto Protocol, based in Portugal, is a forum for exchanging ideas and innovations to improve sustainability, extending across 20 countries. One of its headline figures is that around 40% of the wine industry’s carbon emissions are from production and transportation of heavy glass bottles. Kakoulidis Vineyards, one of the new and growing wineries in Macedonia, Northern Greece, produces around 72,000 bottles of wine annually. Energy and transportation are two of their main costs but they said they cannot afford to be in the lead of developers of new technology but they are looking for ways to cut their costs and be more environmentally sustainable. An exhibitor who prefers to remain anonymous suggested that it will require the large producers, like LVMH, to change before the industry as a whole changes “but as long as they are making lots of money they have no incentive”. The impression I got was not so pessimistic. PET is gaining far more acceptance than was the case a decade ago. Retailers are putting pressure on their supply chain to be more sustainable and reduce carbon. Rocketing fuel and energy costs are concentrating minds. Weight savings of 85-90% and energy cost savings of over 70%, compared with traditional glass, cannot be ignored. Yours, Ruari McCallion “Export of wine in glass bottles, and their transport and limited recycling had the largest carbon footprint in Australian studies (68%). Grape growing, contributing 15% and wine making contributing 17% were similar and both minor components to the overall average fi gure.” Dr Richard Smart (Smart Viticulture) // www.portoprotocol.com"},{"@ID":42, "MATERIALS / RECYCLING PETplanet Insider Vol. 24 No. 06/23 www.petpla.net 10 Handling resin in the right way In the world of food packaging, the safety and quality of materials used are of paramount importance. Plastic resins are widely utilised in the production of food packaging, but not all resins are created equal. Two major regulatory bodies, the European Food Safety Authority (Efsa) and the U.S. Food and Drug Administration (FDA), provide guidelines and approvals for food-grade plastic resins. PET Solutions, known for plastic processing machinery, with more than 20 years of collaboration with the major producers of PET preforms, has recognised the need for tailored drying solutions based on the type of resin used. To address this, PET Solutions have developed two distinct dryer systems, each catering to different requirements. The first solution incorporates the use of an oil condenser, specifically designed for situations where non-Efsa certified resins are utilised. This dryer removes harmful substances during the plastic processing stage, ensuring product safety. While the inclusion of an oil condenser incurs energy costs, PET Solutions recognises its necessity in certain circumstances to maintain the integrity of the final product. Dryer The dryer features an automatic parameter setting that adjusts according to the IMM. It utilises a counter current regeneration system, which results in lower regeneration temperature and shorter regeneration time. With the smart start & stop function, it is claimed to prevent resin degradation. The dryer eliminates the need for cooling water during production and incorporates accurate process airflow control to minimise energy consumption. Oil condenser The oil condenser can be set up through the dryer without requiring an operator. It features automatic process airflow and temperature control, which ensures optimal performance and leads to energy savings. Additionally, there is an exclusive patented version of the oil condenser available that incorporates Activated Carbon for enhanced functionality, says PET Solutions. Ultra cleaning filter The Ultra Cleaning Filter is a patented catalytic filter specifically designed to reduce hydrocarbons. It is claimed to be effective in removing contaminants such as acetaldehyde, benzene, and limonene. With its specialised design, this filter ensures efficient purification of the airflow. Solution with food grade resin – new generation dryer with ultra cleaning filter On the other hand, PET Solutions has also developed a second dryer solution exclusively designed for Efsacertified resins. This dryer eliminates the need for an oil condenser, providing substantial energy savings. By leveraging the inherent safety and quality of Efsa-certified resins, this dryer ensures a more efficient and sustainable manufacturing process. New generation dryer The new generation dryer brings improvements to the quality of rPET materials. It boasts a remarkable +47% increase in filtration capacity, thanks to its double filter system, which also optimises maintenance operations. Additionally, the dryer achieves a -15% reduction in energy consumption on blowers, thanks to its new patented process design positioned after the desiccant towers. The larger exchanger size provides a +45% boost in cooling capacity. Furthermore, the dryer achieves a +25% overall energy recovery, eliminating the need for an oil condenser. Turbofan (option) The Turbofan is a patented solution that ensures a speed of +15,000 rpm. It is claimed to offer versatility, capable of handling up to 1,700 kg/h of material. With this advanced technology, the Turbofan provides enhanced performance and efficiency for a wide range of applications. PET Solutions’ commitment to providing customised drying solutions reflects the understanding of the varying needs within the bottling industry. By offering an oil condenser dryer for non-certified resins and an energysaving solution for Efsa-certified resins, enables companies to choose the most appropriate option based on their specific resin requirements and sustainability goals. www.petsolutions.it"},{"@ID":14, "BEVERAGE INGREDIENTS PETplanet Insider Vol. 24 No. 06/23 www.petpla.net 12 Multi-sensory taste sensations In the dynamic market of the beverage industry, products need to demonstrate their uniqueness and excite consumers in order to stand out. Consumers do not simply want to consume food and beverages, but to experience them. The way all its sensory properties work together is what distinguishes a product from the others. Doehler works hand in hand with its customers to create multi-sensory experiences that appeal to all the senses. This close collaboration makes it possible to create unique products that cater to everything consumers want and need. Younger consumer groups play an especially prominent role in shaping current trends in the beverage segment. Striking colours and exotic flavours are a key focus here – bright, intense colours make a product visually attractive and help it stand out at the point of sale. New beverages in striking colours like 2023’s Viva Magenta excite consumers and encourage them to make impulsive purchase decisions. These myriad fascinating impressions bring colour and taste together in new combinations and create unique sensory experiences. In the field of taste development, too, the desire for uniqueness and creativity continues unabated. Special, sometimes limited edition, products offer an exciting and interactive customer experience – such as “mystery” concepts, where consumers are encouraged to guess a hidden flavour and share their experience on social media. The limited cola edition “pixelflavoured”, which stands out with a 0% sugar content and a mysterious taste is a good example of this development, offering additional excitement and unmistakability. Traditional taste profiles vs new taste adventures Familiar taste profiles like traditional citrus fruits are as popular as ever. Associated with higher health value by 60% of consumers, citrus flavours remain the leading flavour on the market. Away from classic fruits, exotic citrus options like pomelo, yuzu and kumquat are also trending, adding exciting new taste notes to a broad spectrum of beverages from classic soft drinks to energy drinks, nectars and fruit juices. Doehler works with state-of-theart processing plants in the countries of origin in this field, such as Brazil. Together with an international network of specialists, they create bespoke and sustainable taste solutions. Doehler combines local expertise with global trends to deliver unique and authentic flavour solutions specially tailored to the needs of customers and their products. Alongside citrus, floral flavours have become increasingly important in the beverage segment, impressing with interesting new taste profiles – with hibiscus, jasmine, rose and elderflower leading the way. As functional beauty products enriched with plant-based essences become more popular, acceptance of and desire for beverages with the same interesting floral flavours are also growing, supporting the boom in the market. The sustainability factor In 2022, 58% of consumers demonstrated an increased preference for sustainable food and beverages as a way of expressing their commitment to an environmentally conscious lifestyle. As a leading provider of highquality natural ingredients, Doehler guarantees a transparent supply chain through its global procurement network – enabling access to a diverse portfolio of raw materials that are cultivated and extracted sustainably. By cooperating closely with partners Beverage ingredients: Trends and developments in 2023 The beverage industry is constantly coming up with new, surprising and innovative products to meet consumer tastes. As consumer preferences change ever faster and become ever more individual, the market is reacting with new product concepts full of innovative flavours, attractive designs and impressive functionality. Health aspects and sustainability are also playing an increasingly important role. The use of functional ingredients and natural, sustainably cultivated plant-based ingredients has made the beverage industry a key trendsetter in the food market."},{"@ID":29, "TRADE SHOW REVIEW PETplanet Insider Vol. 24 No. 06/23 www.petpla.net 27 holistic approach, Sipa has a comprehensive expert view of the complete PET bottle value chain, Paolo said. He described three production trends going on in the PET bottle market: First, there is an increasing demand for large-sized containers of more than 5 l. Secondly, and on this point Paolo confirmed Shankar’s statement, that there is a conversion from other packaging material to PET packaging. Especially glass, which is the most recent and interesting, Paolo stated. The third point Paolo drew attention to is the trend towards producing more sustainable packaging for a circular economy. In these three trends, Sipa saw a comprehensive protective performance of PET packaging. With a growth rate of 5.2% in the mineral water market and 1.3% for edible oil in PET containers by 2026, the large PET containers must not only protect the contents but also have good logistical properties. Sipa has developed more solid logistics for stable 20 l PET stackable containers. The 20 l solution is suitable for safe transport to remote locations worldwide. Thanks to in-house packaging development and implementation on the complete production line, the PET container could be supplied with a weight saving of 50% compared to the usual alternatives HDPE or aluminium. The empty container weighs 500 g and can be produced on the Sipa XForm or SFL XL machinery. Coming back to the second point of material conversion, Paolo explained the reason why the conversion from the material glass to PET has taken place and continues. Paolo referred to the high energy prices and thus the high production costs. This resulted in a great shortage of glass bottles, especially in wine but also in other industries like cosmetic packaging. Sipa has developed a patented solution for a sparkling wine PET bottle. This unbreakable, user-friendly PET bottle can conserve liquid for 24 months. It has a look-alike traditional cork neck-closure solution with a solid base to maintain the shape of the bottle. It can be filled on existing filling lines and offers benefits in terms of production costs, material savings and a reduced environmental footprint. Paolo pointed out that the market is ready to accept the light and smart solution for PET sparkling wine bottles. Another example of the conversion to PET packaging material was developed by Sipa for the cosmetics packaging industry. With all the advantages of PET packaging in terms of break resistance, colours and flexible design, Sipa presented a new PET perfume bottle. According to Paolo, it offers an excellent consumer experience and saves 80% in weight. With its easy transport properties and low greenhouse gas emissions, it is a cost-saving and environmentally friendly package. The third point Paolo made is Sipa’s contribution to the production of sustainable packaging solutions. Sipa refers to the three main topics reduce, reuse and recycle. By reducing the weight of a bottle, using refillable or reusable containers whenever possible and strongly encouraging recycling, Sipa is promoting its sustainable growth. Sipa accompanies its customers from the first design idea to the finished bottle to produce sustainable packaging. The concept is called AWArPET which pushes not only the design for recycling but also taking the upcoming regulations like SUP or PPWD into account. The use of rPET plays a major role. As soon as rPET is used, the CO2 emission is reduced. At every stage of the bottle’s development, Sipa pays attention to sustainable treatment, e.g., in terms of neck sizes, body & base design, label / labelless, tethered caps, use of resins and additives, colourants etc. Paolo added, that from a technical point of view Sipa has well established machine systems (XForm, Xtra & Xtreme Renew) to process 100% rPET paying special attention to rPET material, e.g. with a flexible oven or vision systems. Paolo mentioned that now 100% rPET is not sustainable, that it is an operational question which needs to be solved with the support of legislation and government assistance. Sipa also introduced a labelless rPET bottle fitting perfectly in the AWArPET concept. It is a new concept of bottle design which embedded the label. The more transparent container saves plastic material, colourants and glues. A new mould manufacturing is necessary to finally show all wanted and needed information on the bottle. Special attention should also be paid to blowing pressure management. Finally, Paolo summarised the full process knowhow to enhance the protection of Sipa’s PET packaging. “Sipa combines its knowledge of materials, its comprehensive packaging know-how - from preform to secondary packaging-, its flexible filling machine systems and its complete line capability - with its sustainable concept”, Paolo concluded. After the PET market analysis, the markets and trends of the PET bottle, a novelty from the preform manufacturing process rounded off the PETinar. PETplanet was very pleased to be able to welcome back an old friend, an absolute expert in preform production, for his presentation on the new ISO Technology that StackTeck incorporates in their preform mould hot runners, supplied exclusively by Yudo. Improving the moulded preform quality consistently – ISO Technology Rick began by explaining that the name ISO refers to isometric, a threedimensional representation of an object. With an isometric representaSponsored by"},{"@ID":2, "7 NEWS PETplanet Insider Vol. 24 No. 06/23 www.petpla.net Tomra and Plastretur sign joint venture to create Norway’s first dedicated sorting plant The global sustainable technology company Tomra has signed a majority ownership agreement with Plastretur, the Norwegian producer responsibility organisation responsible for recycling plastic packaging. The companies will pair up to create a plastic packaging sorting plant located in Norway. The € 50m joint venture (JV) will be split 65 per cent Tomra and 35 per cent Plastretur. In 2020, Plastretur initiated the ambitions to set up sorting infrastructure within Norway, as plastic packaging waste from Norway is currently being sent to Central Europe. Tomra’s investment will seek to close the gap in plastics recycling where there is a strong and growing demand from recyclers for high-quality plastic fractions. Joachim N. Amland, SVP Tomra Feedstock says: “We are recovering material that would have been lost to incineration, and using our existing Tomra technology, providing it to the market at very high quality, which has been missing until now.” This will be the first dedicated plastic packaging sorting plant in Norway, accepting municipal-sourced separated and mechanically recovered mixed plastic waste. The plastics will be sorted into seven types of plastic which will be processed into high-quality fractions that are ready to be used to produce new packaging and other high-quality products. In the JV, Plastretur will continue to take responsibility for sourcing plastic packaging waste from Norwegian municipalities, trade and industry, and deliver this to the plant as input. Tomra will be responsible for grading the fractions based on type and selling the plastic output. The total sorting capacity planned for the new site will be 90,000 t/a of plastics and it will be built in Holtskogen Næringspark, Indre Østfold Holtskogen, Norway (near Oslo). The capital investment consists primarily of machinery and equipment. The ground-breaking is planned to take place in mid-2023 and the plant is scheduled to be commissioned in Q4 2024 and to be fully operational by Q1 2025. www.tomra.com Plastics Industry Association announces NPE 2024 sold out show floor, breaking previous records The Plastics Industry Association announced that exhibit space at NPE 2024: The Plastics Show, the global platform for innovation in plastics, has completely sold out. With more than 1.1 million net square feet of exhibit space, this is a significant achievement 12 months ahead of the triennial trade show. NPE previously surpassed the NPE 2018 exhibit sales record in March at the NPE 2024 Space Draw. “More than 2,000 exhibitors will participate in NPE 2024: The Plastics Show in Orlando. Continued exhibitor enthusiasm reflects NPE’s importance to the global plastics industry,” said Matt Seaholm, President and CEO of Plastics. “We are excited to showcase the latest advances in plastic materials, manufacturing, recycling and processing – including innovations from more than 180 first-time NPE exhibitors.” With more than 55,000 attendees expected, NPE 2024 will be the largest plastics event in the Western Hemisphere. Registration will open on September 12, 2023. The latest advances in products and services will be highlighted in six sold-out technology zones, including an Advanced Manufacturing Zone, Bottle Zone, Materials Science Zone, Mould-making Zone, Recycling & Sustainability Zone and Packaging Zone. “With an end goal of diverting 100% of the recyclable plastic waste generated during the event, sustainability is not just a category at NPE2024,” stated Annina Donaldson, Chair of the NPE 2024 Sales and Marketing Committee. “Sustainability is a commitment incorporated into every detail.” Companies interested in exhibiting at NPE 2024 can visit npe.org/exhibit to add their name to the growing exhibitor waitlist. Should space become available, prospective exhibitors will be contacted in the order received, should space become available. www.npe.org Superior Tool Steel Enhanced Cavitation Prompt Tech Support Priority Development In House Testing YOU CAN HAVE FROM THE SAME RESOURCE Proven 500+ ISBM Molds Globally ACME DRINKTEC SOLUTIONS LLP CREATING MOLDS WITH A DIFFERENCE +91-9810418975 +91-9819020785 +91-9810631426 Sales@acmedrinktec.com www.acmedrinktec.com"},{"@ID":28, "TRADE SHOW REVIEW PETplanet Insider Vol. 24 No. 06/23 www.petpla.net 26 Review: PETinar Opening Debate 2023 by Heike Fischer When the first quarter of 2023 was over we took stock and looked ahead. What are the special challenges for the PET industry this year? How is the PET and rPET market developing, what are the trends in bottle design and what technologies can be used to meet new requirements? Reason enough to ask a panel of experts! On April 4, 2023, Srinivasan Prabhushankar (Shankar), CEO of Recycling at Indorama Ventures Public Co. Ltd. (IVL), Paolo De Nardi, Product Manager Stretch-Blow Moulding at Sipa and Rick Unterlander, General Manager PET StackTeck Systems Ltd. discussed these topics from the perspective of a material manufacturer, a machine builder, a bottle designer and a preform mould manufacturer. After a warm welcome and introduction by Ruari McCallion, Editor at PETplanet Insider, Shankar started his presentation with a brief overview of IVLs’ company goals and an outlook on the virgin and recycling PET market. Shankar stated that as a global chemical company Indorama creates sustainable products for society. With 140 production sites in 35 countries on six continents and more than 26,000 employees, IVL is a PETcentric company. IVL has a worldwide PET capacity of 6.2Mt/a which means a market share of 20%. In 2019, IVL pledged to the Ellen MacArthur Foundation to recycle 750,000 t of PET by 2025, which is an equal of 50 billion bottles per year. Today, Indorama already recycles 30-35 billion bottles per year. Virgin and recycled PET market Shankar went on to talk about the global production capacity of PET and rPET. He highlighted that Asia (23.03Mt of PET), Europe (4.9Mt of PET) and North America (4.6Mt) have the highest PET production figures. The global installed capacity is around 35Mt. The global PET line utilisation rate is at approximately 70-80%. The picture is similar for installed rPET capacity: here, too, Asia leads with 12.6Mt, followed by Europe with 3.3Mt and North America in third place with 2.4Mt. The global installed rPET capacity is 20Mt. Shankar pointed out that the utilisation rate of the installed PET recycling capacity is not as high as for virgin PET due to the low collection rate. The result is a limitation of the material contribution to recycling facilities. During the pandemic, IVL installed nine new mechanical recycling plants and is working to double its recycling capacity by 2030. Additional washing lines and more robots have been installed in existing and new recycling plants, especially in regions where labour is hard to find. To complement mechanical recycling, IVL is working on the commercialisation of new chemical recycling. In this area, Indorama is working with technology providers, such as Carbios in France, Europe, to set up a chemical recycling plant. The goal is to ensure that no more PET packaging ends up in landfill. Shankar summarised that PET is by far the most versatile polymer on the market. Whether it is used in packaging, textiles, automotive, etc., it always has great advantages such as its light weight, clarity, and transparency, and on top of that, it has the best carbon footprint, which is also greatly reduced when recycled. Due to the low carbon footprint of PET and rPET, which is demonstrated by a recent LCA study by Napcor, the industry is turning to PET over alternative materials like glass or aluminium. Due to this, the consumption of virgin PET is still growing, even in bad years. The growth rate is even higher than GDP growth. Finally, however, Shankar also drew attention to the challenges facing the PET industry. He sees the greatest challenge in the availability of feedstock. He pointed to three parameters: infrastructure, consumer behaviour and legislation. In terms of infrastructure, there is a lack of collection and sorting centres. In the area of consumer behaviour, IVL is committed to educating consumers, especially at a young age, to provide them with knowledge on how to deal with waste so that they adopt a desired behaviour. The project is called “Become a Waste Hero”. The third point is regulation. Shankar explained that in some countries, it takes a long time to set up deposit systems. A second point is that in some countries, recycled material is not allowed to come back into contact with food. In Thailand and India, for example, they are now starting to reconsider this. Finally, Shankar concluded that PET and rPET will have a bright and sustainable future. Markets and trends in PET bottle production Paolo took to the microphone to present PET bottle markets and trends observed by Sipa. With decades of experience in the PET industry, Sipa offers a complete service for PET bottle packaging, from pellets to pallets under one roof. Thanks to its"},{"@ID":7, "PREFORM PRODUCTION PETplanet Insider Vol. 24 No. 06/23 www.petpla.net 22 Company anniversary at Tanner - 50 years of preform handling Efficient, safe and gentle loading “Welcome to the World of Preform Handling” is written in large letters on the wall in M. Tanner AG’s in-house forum. Founded in 1973, the Swiss family company has been developing and producing preform handling systems for PET bottling plants and preform producers worldwide for 50 years. Over 4,000 systems are in operation, and in addition to feeding preforms into the blow moulding machine, many products and functions have been added over time. Today, the Swiss company supplies complete solutions from a single source with the Preform Line. The challenges in the production of PET bottles are constantly increasing, and the quality requirements are getting higher. Due to the increased use of rPET preforms, lighter preforms and higher output rates, the demands on preform handling before the blow moulding machine or the inspection system have increased significantly. For decades, M. Tanner AG has focused exclusively on the handling of the preforms. “In addition to high efficiency, today it is also about space-saving solutions, soft handling of the preforms and user-friendly and maintenance-friendly systems. The demands and focus on preform handling have increased significantly. “We offer our customers specific lines tailored precisely to their needs,” says CEO Marco Tanner. Where individual machines used to be required, today it is complete solutions that make the difference. From loading, sorting and feeding the preforms to complex quality optimisation, Tanner covers the entire preform handling process before the blow moulding machine or the inspection system. Safe and efficient preform loading is the priority. Whether manual, with an automatic feed or with a driverless transport system - Tanner offers various options, adapted to the logistical possibilities of the customer. Gentle handling of the preforms, especially when tipping, results in higher product quality and more process reliability. Soft handling is the future, especially due to the increased use of rPET. “The first process step has to be selected carefully, as it has a significant impact on the logistics and the focus time of the operator. This is where productivity can be increased,” explains Marco Tanner. Horizontally preform feeding Efficient orientation and feeding of the preforms at all speed ranges, regardless of the preform design, has been the claim of M. Tanner AG for decades. Thanks to the latest development “ErgoFlow”, it is now possible to feed the preforms horizontally close to the ground into the downstream machine, without air. An active belt guide replaces sliding by gravity and thus ensures high efficiency regardless of the preform quality. Space-saving, quick access and safe maintenance are just a few of the advantages. Hygiene tunnel Whether with the use of the unique overhead air rinser, including camera inspection, directly before the blow moulder to germ reduction at the mouth and thread, to a “hygiene tunnel” for the complete preform line – the Winterthur-based company offers a diverse portfolio. The product safety of the bottler is in the foreground. The cleaning efficiency is claimed to be guaranteed with the overhead preform rinsing and gaps in the downstream process can be prevented by means of camera inspection. www.mtannerag.ch info@petsolutions.it www.petsolutions.it THE rEVOLUTION IS HERE rPET new generation drying technology follow us DR series"},{"@ID":41, "PETplanet Insider Vol. 24 No. 06/23 www.petpla.net 39 BOTTLES PETbottles Beverage + Liquid Food Kola water from Switzerland Under the brand name “Knutwiler”, the Swiss mineral spring Bad Knutwil AG fills 500ml of Kola water, a caffeine-containing soft drink, in an easyto-grip waisted, transparent bottle. In the area of the waist, the bottle is provided with thread-like grooves. Compared to other colas, this variant is lighter in colour and contains only 4g of sugar per 100 ml. A screw cap with a guarantee band and a wrap-around foil label complete the packaging. www.knutwiler.ch Cola with tangerine flavour 500 ml Happy Cola Mandarine Flavour - Zero - is filled by the Swiss Holderhof Produkte AG in a longneck bottle made of plastic. The drink is described as a low-calorie lemonade with tangerine flavour. Colour-coordinated features such as an orange screw cap with a guarantee band and a paper label match the product description Mandarine Flavour. www.coop.ch Share with Fruit Infusion Water The well-known Share initiative, which donates or provides a certain amount of the same product to those in need for every product sold, has launched a low-calorie drink under the name Fruit Infusion. The drinks contain just over 3 g of sugar per 100ml and are filled in bottles made of 100 % recycled material. The labels and screw cap have been chosen to match the colours of the “Orange & Elderberry” and “Lemon & Mint” varieties. www.dm.de Lemon and cucumberflavoured drink The Acao GmbH from Wiesbaden, Germany sells various isotonic organic soft drinks in a bottle with a drinking cap under the brand name “Bio Iso”. The latest creation is the lemon cucumber-flavoured variant. The slim bottle is made of 100% recycled material. The bottle is closed with a two-colour sports cap with a first-draw safety device. A plastic label conveys the trade data. www.bio-iso.de"},{"@ID":18, "BOTTLING / FILLING PETplanet Insider Vol. 24 No. 06/23 www.petpla.net 16 Sustainable fi lling lines in Poland Reaching new heights in water bottling Polish producer of mineral water, Masspol is a supplier to one of the leading chain stores in the country. What allowed them to secure a long-term business partnership, was to expand their offering with a 5 l bottle. Answering the call for the upsizing trend, STM Group provided Masspol with a sustainable filling line, increasing the number of bottles on a pallet by 25%. It’s been a while since the pandemic has eased its grip on people. Now that countries are faced with post-Covid inflation, shopping for bargains has never been so important. Since value for money is sought after, buying in bulk and in big packages became a common practice in many households. On top of that, the unwavering convenience of home delivery has further solidified the habit of purchasing in large size containers and multipacks. As the era of social distancing came to an end, consumer focus shifted from safety and supply to green solutions. Sustainability has been the core influence in the packaging industry for some time now. Public awareness around the issue is reflected in the ever-changing retail landscape. According to West Rock - Pulse Packaging 2022 survey, we know how eco-friendly features impact consumer satisfaction. Notably, the packaging being right-sized is important for 63% of people; 62% pay attention to the fact that the product does not use excessive packaging; as much as 55% claim to look for packaging made from recycled materials; 54% are interested whether the manufacturing of the packaging produces fewer carbon emissions. When it comes to the mineral water industry, there is yet another issue one must take into account. Mainly, the dilemma faced by consumers on where and how to obtain drinking water. With numerous options to filter tap water at home, combined with lobbying against bottled water manufacturers, appealing to consumers’ preferences and conscience becomes a challenge. With new laws and regulations by EU and local governments to reduce waste and emissions, improve recovery and recycling, manufacturers have to make careful investment decisions. STM’s recent project for Polish company Masspol is the answer to these modernday market requirements. Masspol’s mineral bottling plant (manufacturing and water intake) is located in the town of Zubrzyk in the Beskid Sadecki region of Poprad Landscape Park. The company has been producing mineral and spring water packed in 500, 700, 100, 1,500ml PET bottles. Expanding their offering with 5,000ml water bottles, the company chose STM Group to build a filling line (another project for this client). Having received a return on previous investments (two blow moulding machines), Masspol hoped to make another profitable development. STM set itself the task of designing the whole production process in the most eco-friendly way. From PET bottle design to palletisation – every stage was conceived with sustainability in mind. Masspol needed energy-saving technology for the PET production to be eligible for EU funds from the Intelligent Development Programme. The project involved manufacturing a complete turnkey filling line for 5,000ml PET bottles. To meet the expected capacity of 4,000bph, STM suggested the STM Synchroblok Combifill 4/16/6 FlowMatic BIG. The machine features 4 cavity moulds, 16 filling nozzles and 6 capping heads. The first eco-innovation involved reducing preform weight from the standard 68g to 58g. This way, STM was able to lower the energy consumption down to 13W for blowing and filling one 5,000ml bottle (without nitrogen dosing). Secondly, TES STM Group patented and implemented an original system for recovering compressed air from the blow moulding machine. STM was able to capture 40% of the air (up to 10.5bar) and deliver it to all peripheral devices in both, STM line and an adjacent line for 1.5 l bottles at 18,000bph. 120Nm3 of compressed air every hour was saved. As a result, air compressors are in operation less frequently and the whole manufacturing plant is more energy efficient. The palletising stage was also defined by demands for sustainability. Although it is still a common practice in the industry, glueing the bottles together was out of the question for the client. Yet, by far the biggest engineering feat was to increase the number of bottles on the pallet: from 108 to 135. It called for a unique bottle design – taller and slimmer than the classic model – for higher packing efficiency. Wrapping was adjusted accordingly. The dedicated palletising system combines two rotating plate pallet wrappers and the process occurs right at the stacking places - without any transfer. This solution allowed a capacity of 25 pallets/hour to be achieved. www.stm-pack.com FILLING"},{"@ID":50, "BOTTLE MAKING 8 PETplanet Insider Vol. 24 No. 06/23 www.petpla.net Cutting wine & beer carbon footprints Petainer, who claim to “offer a wide range of lightweight, sustainable PET packaging solutions”, has been in business for over 35 years, designing and manufacturing “high-quality, cost-efficient products with circularity at their core”. It has manufacturing sites across the world, serving markets in Europe, the Americas and Asia. In Europe, it manufactures at sites in Lidköping, Sweden, and Aš in the Czech Republic, close to the German border. The Swedish site is certified carbon neutral. 2023 is the first time that Petainer has taken a stand at the International Wine Fair in London, held this year at London’s historic Kensington Olympia exhibition hall. It is big enough to host exhibitors from across the world but, at the same time, offers an intimate experience, where it is easy to visit the whole exhibition in a day. It was good timing because the theme of sustainability ran through the exhibition, across panel discussions and a wide range of stands from all over the world. We met: Petainer Craig Pope, European Commercial Director; Jake Mortiboys, Sales Manager, Western Europe Petainer was acquired in 2022 by Ara Partners, a Private Equity firm totally focused on investing in CO2 reducing Companies. It operates from offices in Houston, Texas, USA, and Dublin, Ireland. Large kegs, low carbon “Ara Partners specialises in decarbonisation investments and sees Petainer as one of the leaders in our industry, with the potential to scale up and take our solutions around the world,” said Craig Pope, Petainer European Commercial Director. “We have worked to create a diverse portfolio, with each product challenging traditional packaging formats and supporting decarbonisation. Whether it’s replacing heavy steel kegs with our lightweight PET keg solutions, replacing heavy glass in the beverage reuse market with RefPET, or in large format water replacing 5 Gallon polycarbonate bottles with our BPA free PET option, Petainer has a solution.” Petainer knows its market and its position very well and focuses on the niches where it is strong. “The alcohol sector is one of the markets where we have been expanding our product offering and we’re pleased to bring our PET wine bottle to the market. Glass bottles are carbon intensive, heavy and expensive to ship – all problems we can resolve using PET material. The trend for decarbonisation is seen at a brand level, but retailers are also starting to lead the way. For example, Systembolaget, Sweden’s state alcohol monopoly, specifies PET as a climate-friendly packaging choice for wine and spirits.” Lighter bottles, reduced costs The Petainer stand featured a few examples of the new PET wine bottles. “We have started in the wine market with two Bordeaux sizes: 1 l and 750ml, and we offer a Burgundy 750ml as well, each in green or clear PET,” he said. Craig explained further about the new range. “The wine industry is very much challenged by energy and transportation costs for glass and it is actively looking for alternative packaging formats to reduce its carbon footprint.” Studies show that a glass bottle represents the largest share - approximately 50% - of carbon emitted when making wine, he explained. “Glass bottle producers are targeting a reduction in weight from 550 g to 420 g by 2027, so the issue will prevail in the glass market. Our wine bottles weigh 49 g, without the closure and label. Being 90% lighter than glass and using much less energy to produce, PET wine bottles offer the potential for huge savings across the supply chain. Because it is lightweight, more wine can be transported in one journey, reducing costs and carbon emissions, along with taking up less warehouse space”. The PET wine bottles Craig and Jake had on the Petainer stand were not the same as previous offers from other manufacturers, which felt firm and were made of composite materials. These felt more like heavier than usual carbonated soft drinks (CSD) bottles. “Product protection is essential, we have worked extensively with the Geisenheim University in Germany to predict the sensory quality and shelf life of wine with different barrier options. Our PET bottles are available with monolayer barrier protection for six months shelf life or multilayer barrier protection for 18 months,” said Craig. “Wine producers are grappling with recent cost increases and are more open to look at new ways to market their products and appeal to consumers. We see PET bottles as part of the packaging mix for wine, giving customers a familiar shape and look, and purchasing a 750ml bottle that they by Ruari McCallion Jake Mortiboys (left) and Craig Pope presenting the Petainer PET keg and PET wine bottle"},{"@ID":25, "MARKET SURVEY 23 PETplanet Insider Vol. 24 No. 06/23 www.petpla.net 06/2023 MARKETsurvey 2-stage SBM machinery What all types of 2-stage stretch blow moulding machines do have in common is that prior to the stretch blow moulding process, preforms must be injection moulded in a separate machine. However, there is a diverse range of models to choose from in 2-stage stretch blow moulding. Our market survey allows you to compare specific parameters of these state-of-the-art machines from some of the market leading manufacturers. We present a selection of up to five of their latest models! Although the publishers have made every eff ort to ensure that the information in this survey are up to date, no claims are made regarding completeness or accuracy. Resins & additives Preform machinery Preform production & inspection systems Preform & SBM mould manufacturer SBM 2-stage Compressors All about caps Filling equipment & inspection systems Palletising & shrink film machinery Recycling machinery Company name Luxber, S.L.U. Serac Group SAS TES STM Group FlexBlow Postal address Telephone number Web site address Contact name Function Direct telephone number E-Mail Av. de Azorin, 34-36, 03440 Ibi, Spain +34 96 555 3853 www.luxber.com Mr Ricardo Sanchez Export Manager +34 606 964 907 luxber@luxber.com 12, route de Mamers, BP 46, 72402 La Ferté Bernard Cedex, France +33 2 43 60 28 28 www.serac-group.com Mr Guillaume Fayard Blowing Division Director +60 12 418 1955 gufayard@seracasia.com Magnacka 6, Kowale 80-180, Poland +48 58 301 71 81 www.tes.com.pl Mr Mateusz Kinda STM Group Sales and R&D Director +48 503 036 635 mk@stm-pack.com Vytauto str. 114A, LT-97134 Kretinga, Lithuania +370 445 51431 www.fl exblow.com Mr Aurimas Ziausys Regional Manager, Europe +370 612 42946 blow@fl exblow.com 1. Machine designation / model number Tecnopet 1000, 2000, 4000, 6000 Serac Blow Linear Blue Line Hi-Tech Series - Linear machines FlexBlow 1, FlexBlow 2, FlexBlow 2-3, FlexBlow 3, FlexBlow 3 XL, FlexBlow 4, FlexBlow 6-4, FlexBlow 4 Hybrid, FlexBlow 6 Hybrid, FlexBlow 8 Hybrid, FlexBlow Multi 2. Bottle volume (from/to in litres) a) Standard machines 0.1 - 10 0.05 - 3 0.01 - 2.5 0.02 - 10 b) Machines for large containers 3 - 5 0.5 - 12 0.02 - 10 3. Maximum number of stretch-blow moulds (units) a) Standard machines 1, 2, 4 and 6 12 8 cavities 1 - 16 moulds b) Machines for large containers 4 4 cavities 1 - 16 moulds 4. Output per stretch-blow mould for: 0.5 litres CSD bottle (units per hour) 2,250 1,400 2,000 - 16,000bph 1,500 - 26,000 bph 1 litre CSD bottle (units per hour) 1,900 1,400 2,000 - 16,000bph 1,500 - 26,000 bph 1.5 litres still mineral water bottle (units per hour) 1,800 1,500 2,000 - 16,000bph 1,500 - 26,000 bph Large capacity container 1,000 1,200 - 4,400bph Up to 5,400bph for 5 l containers, up to 2,400bph for 10 l containers Other Hot-fi ll mould - 1,500 per cavity - up to 12,000bph 5. Footprint / space requirement (L x W x H in metres) 12.8x2.2x4.3 - 6.9 x2.2x2.7 up to 5.5x1.8x2.7 (without preform feeding system) FlexBlow 1 & 2 - 2.8 x 1.7 x 2.7 FlexBlow 3 & 4 - 3.6 x 1.7 x 2.7 FlexBlow 6 & 8 - 7.6 x 2.3 x 2.7 6. Special features (short description/ keywords) Preferential heating, air recovery system, wide neck, PP preforms Stand alone or in bloc with Serac fi ller for bottle or cups (Combox, Cupbox), full electrical motions, no mechanical adjustement during change-overs, signifi cant economical savings with air recovery system and low electricity consumption, preferential heating for fl at, oval and complex shapes, mould boxing on large capacities for handle insertion, clean options to run ESL or aseptic confi guration in bloc. Full electric stretch blow moulding machines from 2 to 8 cavities with: air recovery systems for reducing consuption of low and high pressure compressed air, hot air recovery system for preheating preforms in oven, multifl ex system - option of working with many bottle necks on one machine, hot fi lling version with electric mould heating, preferential heating - for diffi cult shapes oval and fl at bottles, deep grip mould option, moulds moving by servomotors, NIR and IR lamps system, mould change up to 10 min. Integrated blowing and packing systems, integrated quality control, wall thickness assurance, widest neck and size range capability, tool-less changeover systems, hot-fi ll integrations, wide-mouth capability (neck up to 120mm), preferential heating, neck orientation, compatible with Sidel, Sipa, KHS, Krones, Kosme moulds, compatible with stock and custom PET, rPET, PP, biodegradable preforms, downstream equipment"},{"@ID":44, "34 TRADE SHOW REVIEW PETplanet Insider Vol. 24 No. 06/23 www.petpla.net Practical digitalisation solutions The Fraunhofer Institute for Process Engineering and Packaging presented its new technologies and solutions for business in the packaging and food sectors. These new developments can help companies establish digitalised value creation processes and take their first step into the circular economy. Fraunhofer IVV is developing digital training systems based on virtual reality (VR) to provide support for vocational training and continued professional development for operating and technical staff. This enables the staff to master the steps involved in processes such as changeovers. The systems will also assist with developing in-depth process understanding as quickly as possible — a necessary step for eliminating and avoiding faults on a long-term basis. The training program can be run as a stand-alone application on VR terminals; there is no need for the machine itself to be present for the training activity. Learners are able to make mistakes and gather experience without impeding a machine’s availability for other uses or even risking damage. The VR training scenarios are based on a CAD model of the machine and the corresponding process model. When it comes to challenges such as ensuring the resilience of processes, implementing the circular economy or addressing skilled worker shortages, digitalisation can offer solutions. Fraunhofer IVV assists companies undergoing transformation processes — i.e., implementing concepts such as networked production, the industrial internet of things and data exchanges encompassing the entire value chain — by developing companyspecific technology and assistance solutions, individually tailored software for supporting system integration and AI applications for the production process. Fraunhofer IVV also demonstrated their AR-based technology CleanAssist, alongside two variants of their Mobile Cleaning Device. These technological applications enable efficient, resilient production processes that are claimed to ensure a high level of quality. Cleaning processes can be documented in a fully automated manner using intelligent sensor technology and a digital twin. This means that it is possible to genuinely validate cleaning processes. www.ivv.fraunhofer.de Intelligent cleaning robots for automated and reproducible cleaning of plants and production environments. Intelligent cleaning robots for automated and reproducible cleaning of plants and production environments"},{"@ID":3, "45 PETplanet Insider Vol. 24 No. 06/23 www.petpla.net BUYERS GUIDE Contact us Ask for your individual offer – call +49-6221-65108-0 or mail to sales@petpla.net 1 Line = 3,2 mm Example: 1,888.– EUR/year PETplanet Insider Hubweg 15 74939 Zuzenhausen, Germany Tel. +49-6221-65108-0 Fax +49-6221-65108-28 info@petpla.net www.petpla.net 32 mm 6.3 Line Conversion Packaging and Preform Engineering, Moulds and Line Conversion Tel: +33 (0)5 45 36 63 50 info@competek.com marketing@competek.com 7.0 USED MACHINERY T +44 (0) 1254 584210 T +34 676 986962 (SPAIN) E sales@petmachinery.com www.petmachinery.com 6.2 Design and Prototyping Locations in the US and Europe info@pti-usa.com info@pti-europe.com www.pti-usa.com Bottle and preform engineering rPET flakes and Hot fill solutions Training on Blow Moulding technologies (ISBM, SBM, EBM) www.gs4plastic.com BUYER´S GUIDE ENTRY - Print & Online Pricing Example: Placement in 10 issues plus online banner Pricing height (mm) x 5.90EUR x 10 Example 32mm=1,888 .00EUR/year Who’s Who in the PET market Stay permanently listed! Online in the corresponding news category and in the magazine’s Buyer’s Guide with your company logo and contact information."},{"@ID":21, "BOTTLING / FILLING PETplanet Insider Vol. 24 No. 06/23 www.petpla.net 19 BOTTLING / FILLING 19 Providing a 3R response for bottlers in PET The 3R approach (Re-duce, Re-use, Re-cycle) has become a “must” in the global beverage bottling market. And within this three-pronged pursuit of a circular economy, Sacmi has a wide range of solutions on offer for bottlers in PET. Less weight, same performance Sacmi has identified new standards for closure caps which reduce the weight and therefore the amount of plastic required by up to 50% or more. For the bottler, this means they can develop new designs while at the same time taking advantage of the opportunities offered by the shift to the green economy. The challenge of returnable PET In addition to weight reduction, returnable PET is another cornerstone of sustainability in the beverage packaging sector. Sacmi offers new labelling solutions with washable adhesives and/or a reduction in the number of adhesive dots that allow proper disposal and reuse of the container in a food-safe context. All the developments anticipate the various regulatory changes being implemented worldwide. Complete lines The Blo2Fill stretch blow/fill platform has been developed by Sacmi to optimise the process and achieve speeds of up to 81,000bph. The twin-cavity stretch blow-moulding machine, for example, doubles productivity for medium and small to medium formats. It is already available for the Combo solution, the new FEC (Full Electronic Capper) for the complete automation every single capping phase. All solutions can be combined with Sacmi Computer Vision systems for quality control of the complete container. The voice of the customer Every Sacmi Beverage technology and service is based on a VOC (Voice of the Customer) approach: This involves listening to and understanding the customer’s needs so that Sacmi always offers them the solution that suits their production requirements and their market best. Recent developments include new preventive maintenance plans for machines and equipment: these are designed to ensure efficient, worry-free production, so that customers get the best long-term results from their investment. In parallel with the maintenance plans, Sacmi will establish a new Packaging Centre, bringing together all the competencies of the Sacmi Group for complete product development. www.sacmi.com FILLING"},{"@ID":19, "BOTTLING / FILLING PETplanet Insider Vol. 24 No. 06/23 www.petpla.net 17 PET versatile aseptic lab filler Yili Group, Asia’s largest dairy company, received support and expertise from Sidel to install a versatile Aseptic Lab filler, which has been designed primarily for research and development and is situated in Yili’s specially constructed facility. It will enable the regional market leader to launch new products and adapt existing bottles, further enhancing its reputation for innovation. official launch of the PET versatile Aseptic Lab filler in Yili’s Shanghai innovation centre represents the further deepening of the strategic partnership between Yili and Sidel, from equipment supplying to all-round cooperation in packaging development, product development, resource and knowledge sharing. In relying on Sidel’s new PET versatile Aseptic Lab filler, Yili will not only continue to consolidate and expand its leading position in PET dairy packaging but also lay a solid foundation for further expanding its popularity and influence in the beverage industry. Yili’s choice also proves the value and contribution of Sidel in food safety, packaging innovation and sustainable development.” Innovation and sustainability are of mutual importance to both Sidel and Yili. The ongoing strategic partnership will enable Sidel to support Yili with the newly installed versatile Aseptic Lab filler providing the means to develop designs and products which maintain an existing level of sustainability. It will also be able to experiment and reduce energy consumption, in addition to reducing consumption and emissions, which can be shared to enable Sidel to further improve its service to customers. www.sidel.com BEYOND THE HORIZON PROCESS SOLUTIONS FOR POLYMER RECYCLING AND SOLID STATE POLYMER UPGRADING Polymetrix, a Sanlian Buhler Company, provides process technology including EPCM services for the polymer recycling and manufacturing industry. Leading supplier of rPET systems and integrated rPET plants for single line capacities up to 70’000 tons per year. www.polymetrix.com www.slhpcn.com FILLING Already in operation, compact in scale, the versatile Aseptic Lab filler was conceived to enable Yili to research and test product designs, enabling test runs consisting of a small number of bottles with different shapes and sizes. Entirely flexible, the line also allows Yili’s developers to customise any element of the test projects, ranging from the overall product to the specific neck, bottle format or capping. In addition to the several types of aseptic filling processes for both still and carbonated drinks, this lab line can handle other types of filling processes, such as hot filling. Additional benefits include huge flexibility, simplicity of operation, comprehensive maintenance and troubleshooting, said Sidel. As a provider of healthy food and a strong advocate of a healthy lifestyle, Yili aligns closely to its highest principle belief of quality being as precious as life itself. Yili has been supported by Sidel in meeting new demands for products, helping to maintain its leading position in the dairy market and to develop its presence in the market of other soft drinks. The delivery of Sidel’s versatile Aseptic Lab filler, along with a new EvoBlow eHR with six cavities, benefited from a combination of expertise, both in China and across the world. The impact of the Covid-19 pandemic created many challenges during the assembly of the line. However, Sidel and Yili cooperated very closely to ensure the successful completion of the project. The installation and technical assistance were delivered fully through professional guidance, conducted remotely via virtual calls by Sidel, and executed on the ground by experienced engineers based in Greater China. Sidel and Yili have forged a strategic partnership which commenced in 2017. Filippo Fu, Sidel Regional Sales Director China, said: “The Sidel installed a versatile Aseptic Lab filler at the premises of the Chinese dairy company Yili."},{"@ID":11, "BOTTLE MAKING 9 PETplanet Insider Vol. 24 No. 06/23 www.petpla.net aren’t planning to lay down. For value and standard price point wines, which are designed to be enjoyed young, it makes sense for both the producer and consumers to use PET. For the producer, PET is financially attractive compared to other alternative packaging formats as it can run on their existing filling equipment, and for the consumer it gives them flexibility to take a PET bottle where glass can’t go. The carbon credentials of wine in PET bottles can be shared by brands at the point of purchase against glass providing consumers with an informed choice,” said Craig. Single use large kegs: an environmentally friendly solution? Petainer is very well known globally for its beer kegs. The 20 l example on its stand for wine on tap, which Craig and Jake are clearly proud of, is a one-way container, which prompted the question: how is “single use” environmentally friendly? “You have to look at the carbon footprint of draught beverages from cradle to gate,” Craig replied. “In the case of beer kegs, we focus on two main markets: export and smaller, craft brewers. Smaller scale operators prefer not to invest in steel kegs as they grow their business. We make it possible for craft brewers to enter new markets without heavy outlay on kegs, transport and cleaning infrastructure. For export, PET is light weight – nowhere near as heavy as steel and you can transport your beverage anywhere in the world. If you imagine the volume of beer being exported from Europe in steel kegs, the cost of lost kegs, of collecting them, returning, and washing, some export routes can be very inefficient making one way kegs the clear choice. This gives brewers the opportunity to access global markets without the need to manage costly return logistics. We can model the carbon footprint of our kegs vs steel to demonstrate that our kegs really are the climate smart option.” Whilst our Hybrid keg is non-returnable, the chimes at the top and bottom, are made with 100% recycled polypropylene which can be easily removed from the keg and reused. We are seeing a growing number of brewers reusing these components to save cost and reduce their carbon footprint. “The Hybrid keg can be conveyed and filled on steel kegs lines so there is real opportunity for brewers to switch between steel and PET to access new draught markets and save a lot on operating costs. Steel keg losses can be as high as 10 to 15% in some cases,” Jake Mortiboys added. The Hybrid keg can be collected and disassembled for recycling, post use. The snap fit nature of the chime components ensures it’s easy to separate these components and reduce the volume of waste. Bottle to bottle recycling is not yet possible but a closed loop solution for PET kegs is clearly on the horizon. Petainer is working with a major brewing brand to use clear 20 l kegs packed inside a cardboard outer box, which is itself totally recyclable and will give the required UV & light protection. www.petainer.com Over 10,000 drinks industry professionals attended the London Wine Fair in May."},{"@ID":45, "1 The worldwide round trip with The Middle East Roadshow EDITOURS PET world in the Middle East New year, new tour! After our successful Drinktec tour, the PETplanet team is going to the Middle East in the last quarter of 2023! In a spectacular project taking us well into 2024, we will be travelling in a wide variety of ways to various countries and regions of the Middle East with different mobile editors. There we will interview machine manufacturers, the supply industry, bottle and beverage producers, as well as PET recyclers and everyone involved in the process chain. What market-specific trends are there now or will arise in the future? What developments and technologies are in vogue on the consumer and plant construction site in some of the hottest regions of the world? What special requirements are there? What role do topics such as food safety, shelf life and sustainability play in PET packaging and how are companies preparing themselves for the coming years? This, and much more we will be discussing face-to-face with all the key players and then our results will be presented to you in a series of must-read reports in PETplanet Insider. Please join on this enchanting voyage to the world of PET in the Middle East. We look forward to welcoming you on board! Our previous Road Shows at a glance 2010-2011-2012-2013-2014-2015- 2016-2017-2018-2019-2020-2022 Interested in being visited? barton@petpla.net Autumn 2023 - 2024 EDITOUR - THE MIDDLE EAST ROADSHOW 6 countries numerous interviews with PET companies Sponsors to date"},{"@ID":48, "OUTER PLANET 46 PETplanet Insider Vol. 24 No. 06/23 www.petpla.net OUTER PLANET First PET resin made from waste carbon LanzaTech Global, Inc. a carbon capture and transformation (“CCT”) company that converts waste carbon into materials such as sustainable fuels, fabrics, packaging, and other products that people use in their daily lives, and Plastipak Packaging, Inc. well known for the design, manufacture, and recycling of plastic containers, announce they have successfully produced PPK Natura, the first PET resin made from captured carbon emissions. The resin is claimed to be suitable for food, personal care, and pharmaceutical packaging, as well as non-packaging applications. Leading Swiss retailer Migros and its subsidiary Mibelle Group were the first to use this PET in in-house brand packaging, including in creating PET bottles for smoothies and the containers of household cleaners that also contained LanzaTech ethanol as a key ingredient. “LanzaTech’s commercial technology is designed to enable our partners in diverse industries to reduce their carbon footprint and overall environmental impact,” said Jennifer Holmgren, Chief Executive Officer of LanzaTech. “Our partnership with Plastipak is critical to demonstrating what is possible today. Today, we are producing food- and pharmaceutical-grade packaging and are well on our way to creating a more sustainable future for all.” Producing PET with lower environmental impacts LanzaTech’s CCT technology works like a brewery in which proprietary bacteria consume pollution and convert it into CarbonSmart chemicals. Those chemicals are then turned into products ranging from clothing and laundry detergent to sustainable aviation fuel. Using a variety of waste feedstocks, LanzaTech’s technology platform is creating a future where consumers are not dependent on virgin fossil inputs for everything in their daily lives. “We are delighted to partner with LanzaTech to achieve early progress in our ambition to produce PET with lower environmental impacts. The use of CarbonSmart MEG is a first and important milestone in our journey toward this goal, and combined with use of renewable electricity in the production process, has contributed to significant progress in indicators such as carbon reduction and use of fossil resources. PPK Natura resin is one element of Plastipak’s ESG program, which among other initiatives, targets the extension of our product circularity with the intent of supporting customers in reducing their Scope 3 emissions. We look forward to a long and mutually beneficial partnership with LanzaTech as we work together to achieve our long-term goals.” said Pedro Martins, Executive Managing Director Europe of Plastipak. “The use of fossil fuels must be avoided. Where this is not possible, it makes sense to include greenhouse gases in products so that the gases do not contribute to global warming and climate change,” says Christoph Meili, a specialist in life cycle assessments at WWF Switzerland. www.lanzatech.com www.plastipak.com PET resin comprises 30% monoethylene glycol (MEG) traditionally derived from petroleum. PPK Natura leverages CarbonSmart MEG from LanzaTech’s CCT process. It retains the technical properties of virgin fossil PET while carrying a lower carbon footprint. PPK Natura resin reduces greenhouse gas emissions, and its production process does not require land or food resources. In addition, packaging made out of this material can be fully recycled at the end of its life, keeping the carbon in a circular material cycle."},{"@ID":34, "32 TRADE SHOW REVIEW PETplanet Insider Vol. 24 No. 06/23 www.petpla.net Interpack 2023 review - part 1 Sustainability has long been heralded as THE top issue in the industry. At this year’s Interpack, one could see for oneself that it has really arrived on a broad scale. Whether it’s the use of lightweight solutions, resource management or the recycling cycle - the industry can supply what the customer demands. In addition, new digitalisation solutions in particular can help determine the new technological developments. Under the heading “Welcome Home”, the trade fair welcomed approx. 143,000 visitors from all over the world in Düsseldorf, Germany. Alongside many European countries, the largest visitor nations were India, Japan and the USA. Around 75% of visitors came from middle or top management to experience technologies and solutions of 2,807 exhibitors from 155 countries. The next Interpack will be held in Düsseldorf from May 7 to 13, 2026. www.interpack.de KHS, Andreas Klages, Project Processing – Product Support, Barrier Coating Technology 1) Overall, what were your impressions of Interpack? Sustainability and circular packaging are the major topics of the exhibition. This can be seen, for example, in relation to savings in material which in the PET sector is limited not just to lightweight bottles but is also relevant to secondary packaging. 2) What aspects of your company offer were you highlighting? When it comes to material savings, KHS offers solutions that replace shrink film with carrying handles for multipacks. Here, however, we can offer some improvements: the Nature MultiPack attaches beverage containers to a solid pack not by using shrink film but by means of easily detachable adhesive dots that have already achieved up to 90% savings in packaging material. By reducing the number of glue dots in the MultiPacks we are also continuing to address the issue of material savings. Another recent development is the introduction of a cardboard carrying handle. The new packs are processed on the modular KHS Innopack Kisters NMP packaging machine. A newly developed unit feeds in the alternative cardboard clip and slots it onto the PET containers. Former process steps such as distribution among different lanes, buffering and pack turning are no longer required. 3) What will be the coming trends in PET bottles? The amount of rPET in bottles will certainly continue to further increase in the future. Consumers and brands would very much like to use 100% rPET but at the moment this would come at a high cost for the material. Due to this and the currently limited availability of high-quality material some producers are temporarily reducing the actual rPET percentage. Another cont inuous trend is the demand for increased energy efficiency in bottle production. With DoGa in the KHS InnoPET Blomax Series V, the innovative two lane preform heating oven, energy savings of up to 30% are achieved compared to modern single-lane ovens. This will significantly reduce both the cost of energy and the CO2 generation. www.khs.com United Caps, Benoit Henckes, CEO 1) Overall, what were your impressions of Interpack? We are very pleased. It was a bit quieter at the weekend but we made many excellent contacts and had productive discussions on all the other days. 2) What aspects of your company offer were you highlighting? Sustainability! This is a big issue for us, as well globally, that we want to promote in our work. All our European plants are now operating with 100% renewable energy which has led to us signing an agreement with a wind farm operator in Sweden. We also want to use renewable or recycled plastic in as many caps as possible which will reduce our carbon footprint and help our customers to do the same. Another focus for us is tethered closures. We are nearing the EU deadline [July 2024] but many companies have yet to make the switch or even reached a decision. 3) What will be the coming trends in PET bottles? PET bottles comprise around 30% of United Caps’ Business. The tethered closures I have just mentioned are, of course, a major work area for us. There are customers in the EU who are shying away from extra investment, preferring to wait and see if and when the Directive is actually implemented. At the same time, companies from outside the EU are watching the situation extremely closely, particularly in terms of customer approval. Here, we are able to offer a variety of solutions, including moulded and slitted tethering styles that are consumer-friendly and can be handled intuitively. Further developments in the PET bottle closure sector can be seen by the increased use of PET bottles for edible oils for which we can also offer solutions. www.unitedcaps.com"},{"@ID":37, "PETplanet Insider Vol. 24 No. 06/23 www.petpla.net 35 TRADE SHOW REVIEW Concept to prototype in less than a year Market launch of PET sparkling wine bottle F.l.t.r.: Susanne Kretzschmer, Head of Strategic Marketing, Indorama Ventures Polymers Germany; Antonio Narder, General Manager Sipa S.p.A.; Alexander Büchler, Publisher PETplanet; Dr Patrik Amrhein, Managing Director, Indorama Ventures Polymers Germany and Marco Brusadin, Global Packaging Development Director, Sipa S.p.A. The empty 750ml PET container weighs only 90 g compared to 750 g of a glass bottle, thereby saving 660 g. The 90 g material has a glass-like feel to it. Marco Brusadin, Global Packaging Development Director at Sipa S.p.A., was keen to ensure that the new bottle could be filled on existing glass lines without any modifications. The neck finish, the height of the bottle and waist circumference are identical to those of the glass version. The filling pressure can be left at 5.5 bar without any problems and the bottler can retain the bottle with the label and mushroom-shaped cork with its metal cage etc. Plus, the costs per PET bottle are lower than for glass. The CO2 footprint is significantly lower compared to that of a glass bottle. Glass is processed at 1,400 °C and PET at 260 °C. When you also consider the 7-times weight of a glass bottle, it quickly becomes clear that a lot is saved in the production process alone. As Antonio Narder, General Manager of Sipa S.p.A., explains: “If 24 pallets of filled glass bottles normally fit on an articulated lorry with a loading capacity of 27 t, all 32 pallet spaces can be used to stack the lightweight PET bottle. This also has a positive effect on our CO2 footprint”. To keep the sparkling wine in the PET bottle for longer, Sipa has worked in collaboration with global Indorama Ventures, the world’s largest producer of PET and recycled resin used in plastic beverage bottles, in partnership with the brand’s Specialty Polymer’s business in Germany. “When we were choosing the material, it was important for us to get as close as possible to a glass bottle, both visually and in terms of barrier features,” explained Dr Patrick Amrhein, Managing Director, Indorama Ventures Polymers Germany. “We use our modified PET as the polymer and OxyClear as a barrier material. This gives us 24 months of pure, unadulterated drinking pleasure.” Susanne Kretzschmer, Head of Strategic Marketing at Indorama Ventures Polymers Germany, added “It is rare to complete a project from the prototype stage to market launch in less than six months. In this case, it was made possible thanks to the close and excellent cooperation with Sipa, and the potential this bottle represents to the wine market.” Sparkling wine consumers will enjoy the same sensual experience with the new PET bottles as they always have done with glass ones, from uncorking to pouring. But they will most likely notice that the PET versions are much lighter and virtually unbreakable. That is also great for operators throughout the ever-changing supply chain, as sales via e-commerce and home delivery continue to rise. www.sipasolutions.com www.indoramaventures.com Against the background of sharply rising energy prices and the resulting increase in the cost of glass bottles, in 2022 Sipa began developing a high-quality PET alternative to the sparkling wine glass bottle. Ready in time for Drinktec held in Munich last September, where they showcased the prototype of the premium bottle, and then later showcased at Interpack 2023 where Sipa displayed the version that has now been launched to market in collaboration with Indorama Ventures. The PET sparkling wine bottle from Sipa won the top prize in the 2023 Best Packaging contest held during Milan Design Week in April. The award came from a panel headed by Professor Valeria Bucchetti, coordinator of the Communication Design course at Milan Polytechnic University. The panel concluded that the bottle led the field in meeting strict criteria for Quality Design."},{"@ID":4, "BOTTLING / FILLING 15 PETplanet Insider Vol. 24 tling lines side by side: one for 0.33 l and 0.5 l glass bottles and the other for 0.5 l, 1 l and 1.5 l PET bottles. The logistic configuration of the two lines side by side allows space and costs to be optimised, due to the fact that both use the same area for raw materials and the same unloading and storage area for the finished pallets ready for distribution. Production line for PET bottles: Ecobloc Ergon integrated system for carbonated products – production up to 10,800 bph Containers worked: 0.5 l, 1 l and 1.5 l bottles in PET for carbonated water LSK 40F Ergon shrinkwrapper – production up to 40 packs/min Packs created: bundles in film only in 3x2 (1 l and 1.5 l bottles) and 4x3 (0.5 l bottles) formats SMI solutions for SNO The growing demand for SNO natural water has required new investments, for the expansion and modernisation of two end-of-lines at the Misaktsieli plant. Working in close collaboration with the Aqua Geo team, SMI engineers designed an automatic solution for secondary and tertiary packaging optimised for the production needs of the Georgian company’s plant; the primary objective of the new intervention was to increase the production efficiency of the lines for the bottling and packaging of 0.5 l and 1.5 l PET bottles of SNO water. www.smigroup.it Complete end of line - PET 24,000bph including: CSK 50F Ergon shrinkwrapper – production up to 50 packs/min Products worked: 0.5 l and 1.5 l bottles in PET Packs created: bundles in film only in 6x4 and 4x3 (0.5 l ) and 3x2 (1.5 l) formats Conveyors to carry the loose product from the out feed of the filler monobloc, accumulation conveyors before and after the labeller and conveyors to carry the packs between the packer and the palletiser Handle applicator HA 60 APS 1550 Ergon palletiser with rotating arm wrapper Packs worked: bundles arriving from the CSK 50F Ergon packer Pallets created: europallet 800 x 1,200 and 1,000 x 1,200"},{"@ID":30, "TRADE SHOW REVIEW PETplanet Insider Vol. 24 No. 06/23 www.petpla.net 28 tion, engineers can effectively design a network of hot runner distribution channels to optimise flow characteristics. The ISO technology makes use of a state-of-the-art diffusion bonding process. Put simply, diffusion bonding is a process where the atoms of separate surfaces intersperse to become one, resulting in the formation of a single inseparable object. A distinctive characteristic of diffusion bonding is that it does not use any form of brazing, soldering, or welding. There are no pastes, no flux or bonding elements used at all. Adjoining plates are simply in direct contact with each other during the entire process. The next phase involves applying a high pressure and heat to the adjoining plates. This is maintained for a defined period of time, depending upon the plate size used. During this time a molecular exchange takes place across the plates, and just as gases and liquids diffuse, solids do as well under the right conditions. Once the process is completed the result is the creation of a single piece manifold which is robust, accurate and has no risk of separation. Rick explained that they do this because traditional manifolds are manufactured using gun drilled linear channels that interconnect within a steel block. Lines are drilled from the sides that intersect each other, then plugged, to form a series of melt channels directed to each drop. By contrast, diffusion bonding allows the entire channel arrangement to be simplified without the complications of using end plugs so there is no risk of leaks. The melt channels can be contoured and shaped to provide an optimised flow path to each cavity. As an example, Rick showed a 96 cavity ISO hot runner layout as manufactured by diffusion bonding. The process permits smooth level transitions and eliminates any sharp corners and edges with no dead spots. This helps to enhance flow characteristics and minimise pressure drop throughout the entire channel layout. It is a characteristic that benefits PET and other heat sensitive materials. Rick asked: “How does this impact performance and part quality?” In a back-to-back comparison of a short shot test with a conventional hot runner and the ISO hot runner from a 96 cavity 28 g preform mould, StackTeck stopped the injection when the preforms were filled to 50 per cent. The resulting fill pattern showed the weight distribution of the plastic injected into each cavity, helping to highlight imbalances in the hot runner. In this example the weight variation was reduced from 46 per cent to 19 per cent when comparing conventional to ISO. The improved uniformity with ISO translates into a larger processing window for moulding, minimising the need to adjust and tweak parameters for the outlier preforms that may be on the edge of acceptable quality. This makes setting up the process conditions easier and quicker such as when speeding up cycle times or when starting up a new mould. There is less need to make adjustments to fix quality problems on the outlier preforms. As a downstream benefit the customer in this example reported fewer bottle-to-bottle quality variations at the blow moulder. Rick also presented a back-toback comparison showing a reduction in pressure drop using the ISO hot runner. In the same 96 cavity 28 g preform mould two injection rates were set up with the conventional hot runner at 10 and 13 g per second per cavity, resulting in a 680 and 780 bar peak injection pressure respectively. The ISO hot runner achieved a 16.9 g per second per cavity injection rate yet still registered a slightly lower peak pressure than the slowest injection rate using the conventional hot runner. The preforms made in each case were checked under a polarised light to confirm that no changes in stress pattern were visible. The end result was a significant injection time reduction which reduced the overall cycle. These two characteristics; improved balance and reduced pressure drop enable technologies such as over-moulding and thin wall preforms to be accurately and consistently moulded. Over-moulded preforms tend to have very thin layers with high L/T ratios and this requires both a tight cavity to cavity balance and a low pressure drop throughout the hot runner to ensure the layers are accurately and consistently formed with no risk of short shooting the very thin layers. This also benefits monolayer preforms, most notably with flat water applications especially as they become thinner and thinner due to light weighting programs. In another example, a 144 cavity application with a conventional hot runner was compared with an ISO hot runner. The comparison revealed the peak injection pressure was reduced by 19 per cent, the preform weight variation halved, and the average acetaldehyde level reduced by 24 per cent. Finally, Rick introduced KoolTrack, another way to take advantage of the diffusion bonding technology which also helps to improve product quality and cycle time but now on the cold half side. The KoolTrack can simply be described as conformal cooling similar to how ISO diffusion bonding changes the way hot runners are designed and manufactured. KoolTrack is currently being successfully used in a variety of PET and non-PET applications. We thank all speakers and participants and point out that a video and the presentations can be found on our homepage! Sponsored by https://petpla.net/2023/03/10/petinar-2023-opening-debate/"},{"@ID":39, "PETplanet Insider Vol. 24 No. 06/23 www.petpla.net 37 TRADE SHOW REVIEW 37 TRADE SHOW REVIEW the pace for the recycling industry’s growth and will oblige all stakeholders to professionalised and industrialised all steps of the value chain. PETplanet: What is your expansion strategy? Are you building more factories for the mechanical recycling of PET or are there other processes you are considering? Aloxe: In France, the new plant starts production at the beginning of July, and by 2024 will have a capacity of 50,000 t of food-grade rPET pellets. In Italy, we are doubling our rPET pellet capacity to 30,000 t. And our Polish project is set to produce 40,000 t of rPET pellets by spring 2024. With these capacities, we are the independent leader in rPET pellets in Europe. We aim to keep expanding in the market and consolidate our position by considering acquisitions and greenfield projects. PETplanet: What suggestions do you have for establishing an industrial value chain for rPET? What challenges do you see at the moment and in the future? Aloxe: Our customers’ main expectations are to guarantee highquality product, standardised and consistent with time. In today’s economic context, excellent processability of rPET in applications is a key. In other words, by gradually replacing virgin PET with recycled PET, we ensure a high level of material mastery for our customers. We draw on the best assets and skills to commit to our customers. www.aloxe.one E N D L E S S I N N O V A T I O N S I N C E 1 9 1 9 Two new Erema Vacunite systems are installed in France."},{"@ID":40, "ONsite 38 PETplanet Insider Vol. 24 No. 06/23 www.petpla.net ONsite 38 PET soft drink bottle recycling plant in Myanmar Sorema Division of Previero N. Srl set up a PET post-consumer bottle washing and recycling plant at Commercial Plastics Co. - CPC in Yangon, Myanmar (Burma). Andrea Villa, Senior Technical and Sales Engineer of Sorema describes the newly started up plant as follows: “After conducting a wash and recycle trial on the plant at our Recycling Research Center - RRC in Alzate Brianza with CPC collected dirty bottles, we developed the parameters to design a 2,200kg/h flakes output plant, which would make their material able to be reused to produce soft drink bottles again”. He continued: “The material test, conducted at Sorema’s RRC laboratory, has verified that most of the local market collection consists of small-format bottles between 330 and 1,000 ml with a high-level contamination from PVC labels, sand, and abrasive materials. Based on this analysis of the material to be processed, Sorema has developed and manufactured a bottle-to-bottle line for SEA, which features a series of customisations to be considered as standard throughout all South-East Asia (SEA) PET bottles recyclers.” The following machines have been built up: the pre-washing module for removing labels and for optimal cleaning of the material surface. This technology prepares the material for a better sorting of the bottles and reduces the overall wear the whole line. The delabeller has an expectation of its first maintenance after several months. The efficient removal of PVC labels is achieved with a combination of delabeller, wet elutriator and material detectors. Because the SEA market is quickly evolving from PVC to PP labels, Sorema technology has focused on removing the glue of the labels. Sorema has also paid particular attention to the possible wear conditions due to local collection where the level of sand in the input bales is elevated. www.sorema.it Blow Moulding 2023 7th Edition INTERNATIONAL CONFERENCE, EXHIBITION & NETWORKING EVENT INNOVATIONS AND SUSTAINABILITY IN PLASTIC BOTTLES & CONTAINERS 11-13 December 2023 Cologne, Germany Bringing together the entire supply chain: raw material suppliers to brand owners, retailers, recyclers – and everything in-between. Join the Conference. Get updated on latest trends and innovations. Network with key opinion leaders and industry experts. Register at www.blow-moulding.com For additional information email us at info@blow-moulding.com"},{"@ID":16, "BOTTLING / FILLING PETplanet Insider Vol. 24 No. 06/23 www.petpla.net 14 Water bottling in Georgia The country of the five toasts In the heart of the Caucasus region, Georgia is one of the richest nations in mineral and thermal waters, even if its large-scale marketing is a fairly recent activity, entrusted to leading companies such as Aqua Geo. In this state of the former USSR, on the border between Europe and Asia, squeezed between the mountains of the Caucasus and the Black Sea, one is struck by the richness of the waterways and the fertility of the land, which is almost entirely cultivated, with the exception of the highest peaks in the Svaneti region, which reach up to 5,000m above sea level. Not surprisingly, the name “Georgia” derives from the Greek term “georg”, used to indicate agriculture. Georgia has an ancient history for the cultivation of vines and the production of wine, as evidenced by the archaeological finds of the oldest winery in the world with some traces dating up to 8,000 years ago. In the last decade, however, the Georgian economy has come on in leaps and bounds, moving from an almost exclusive dependence on wine production to a diversification into new sectors, such as the production of beverages and carbonated waters. Thanks to investments made by the food & beverage companies, Georgia today boasts excellent production of lemonade and beer, while the mineral water sector is constantly expanding. This phenomenon requires the use of increasingly advanced bottling and packaging technologies, such as those used by the company Aqua Geo Ltd in its carbonated water production plants under the “Kobi” brand and natural water under the “SNO” brand. To automate the bottling and packaging process, the Georgian company turned to SMI for the supply of numerous turnkey plants, which include a line for PET bottles and one for glass bottles in the Kobi plant and two end-of-lines for the secondary and tertiary packaging of SNO natural water at the Misaktsieli plant, near the village of Natakhtari, a few kilometers from the capital Tbilisi. The two brands of mineral water marketed by Aqua Geo, SNO and Kobi, owe their name to the geographical position of the two springs from which the product flows. SMI solutions for Kobi The Kobi water bottling plant is a demonstration of the large investments being made in the beverage and natural mineral water industry in Georgia; a great challenge, in a country where history and culture are deeply linked to wine production. Since its foundation, the Aqua Geo company has always had the main aim of equipping itself with modern technologies, to create a high, quality, product capable of equaling the mineral waters present on the main European markets. This is an objective that the Georgian company is able to achieve everyday thanks to severe laboratory tests on the water from the source and the finished product, modern and sophisticated control systems for the entire production process and continuous monitoring of the packaging and distribution process. SMI, which has been collaborating with Aqua Geo since 2011, has been involved in the important development project of the Kobi brand and has designed, built and installed two botFILLING"},{"@ID":32, "30 TRADE SHOW REVIEW PETplanet Insider Vol. 24 No. 06/23 www.petpla.net Closure production with high output Plastic closure producer Guangzhou Jeepine, based in Guangzhou, Canton, showed its 54-cavity CCM-JP54 rotary machine for the first time at Chinaplas. The company, which was founded in 2008, has since sold more than 500 machines and holds more than 130 patents, offers complete solutions for various requirements, including inspection units and sorting and slitting folding units. The manufacturer places particular emphasis on production capacity in combination with energy efficiency, ease of operation and a low investment. While its little brother CCM-JP24 with 24 cavities, which Jeepine has had in its portfolio for some time, scores more in the area of flexibility with small and large closure formats at 24,000 closures per hour, the new JP54 offers a maximum output of 100,000 closures. “The advantage of the JP54 here is clearly the ability to mass produce small closures for water bottles, for example, such as the 30/23, or the PCO 1881 for carbonated beverages,” says Mr Lomen Yao, International Sales Director (South-east Asia). “We quote an ROI for the machine within two years at full production use, as it is around 60%-65% below comparable imported compression moulding machines from Europe.” Intelligent energy and material management should ensure savings in ongoing operations. For example, low-temperature heating is used in the material melting process, which saves about half the energy used by injection machines in the heating and cooling process. Furthermore, according to Mr Yao, the rotary machine is equipped with a dual-pump hydraulic system and PID control for low-pressure closing and highpressure moulding. The system also has industry-standard process monitoring on board and is said to reduce manpower requirements accordingly. “The machine can be integrated into existing production lines inline. We also offer dedicated transport channels to the system to protect the closures from any contamination.” Internationally, the machine is currently receiving more orders from America, India, the Middle East, Indonesia, Malaysia, Myanmar, Vietnam, Korea, etc., according to Jeepine. “Some JP54 systems are currently finished and ready for transport,” Mr Yao said. In the future, the company started deploying local service teams in different parts of the world to be closer and faster to the customer. In addition, a solution for the production of tethered caps is already in the starting blocks and is thus also fit for future markets outside Europe, where the topic is not yet very present, at least not at present, but is likely to come in the medium term. www.capmakingmachine.com Preform injection moulding with integrated handle Since 2019, GDXL has been working with the patent holder of the Integrated Moulded Handle (IMH) technology to bring to market engineered solutions for PET preforms and bottle products with integrated moulded handles. The handle and bottle body are integrally moulded during the preform stage, eliminating the need to manufacture and assemble separate handles and saving operating and energy costs. In addition, the integral handle is made of PET material, just like the preform, to ensure full recyclability and better environmental performance compared to conventional bottles with insert or clip-on handles. The preform with integrated handle can also be made from rPET materials, according to GDXL, and its performance can meet the general technical standard required for conventional bottles with non-one-piece handles. When designing the mould, the structure must be modified accordingly when an integrated handle is added. For example, the neck rings in each cavity are lengthened to accommodate the integral handle. Corresponding adjustments to the cavity spacing and the thickness of the mould plates are also required. Depending on the design of the IMH preform, a maximum of 24 cavities per mould can generally be achieved. Since there is no special cooling after ejection for this type of preform, the expected output for a typical injection moulding machine equipped with 24 cavities of mould is 2,000 pieces per hour for a 100 g preform. Since the handle is integrated into the preform on SBM machines, protection must be provided for the handle while the preform is being heated. www.gdxl.com F.l.t.r.: Sales Director Patrick Lam and Marketing Specialist Billy Au-Yeung showing preform and bottle samples with IMH technology The handle is made of PET and is moulded at preform stage. F.l.t.r.: Lomen Yao with Kay Barton in front of the CCM-JP54"},{"@ID":33, "31 TRADE SHOW REVIEW PETplanet Insider Vol. 24 No. 06/23 www.petpla.net Preform moulds from Zhejiang At the booth of Chinese mould maker New Thinking Mould, General Manager Mr Louis He showcased two new injection moulds for bottle preform and PET jar preform production with wide-mouth. The company, which was founded in 2015, has been exporting strongly to foreign markets for some time, we were told. Various moulds are already in use in North and South America, some Maghreb states and within Asia. The areas of application range from beverage applications to milk and edible oil products to food and non-food segments. In addition to hot and cold halves, stack and hot runner parts are also offered. “We rely on reputable sources for our products,” explained Mr Louis He. In manufacturing, for example, the steel would come from ASSAB and the heating element and nozzle tip is imported from European companies. The current portfolio include moulds with up to 96 cavities, each with energy-optimised, individual voltage regulation and up to 5 million closing cycles, according to New Thinking Mould. The moulds on display at the stand were a 48-cavity mould for 9.5g preforms with 29/25 neck for 250ml bottles, and a 12-cavity wide mouth mould with 110mm neck at 75 g. www.newthinkingmould.com Wide-mouth preform mould Mr Louis shows the new 48-cavity mould."},{"@ID":23, "BOTTLING / FILLING PETplanet Insider Vol. 24 No. 06/23 www.petpla.net 21 New tasks in bottle inspection Additional operating modes, extended functionality, new machine connections: The Heuft One expands its range of applications. From now on the entry-level device can not only be used for checking full containers but also as a smart distribution system, for detecting downtimes and serial faults on master machines or for localising the cause of quality defects in good time. A new thermal sensor even makes it possible to check lasered best-before dates and markings on PET bottles. Space-saving detection and direct evaluation of defects on the conveyor. The slimline control terminal can be flexibly accommodated in the filling line, even further away from the actual detection units. Combining a smart detection technology such as the X-ray measuring bridge for the simultaneous detection of underfilling and overfilling with a maximum of one further simpler function in order to check the presence of the closure at the same time, for example. This concept has made the Heuft One the standard for entry into the full case check. It quite deliberately provides for a device to fulfil only one or two individual basic tasks at a time. For instance, the use of an intelligent colour sensor camera with a directly integrated image evaluation is possible as an alternative to the fill level check with infrared, high frequency or X-ray technology. This can then be used for detailed label inspection, for example, which in turn can be supplemented by simple sensor technology, such as for checking the internal pressure of the container. Or it verifies the colour or coding of the closures in a top-down arrangement, which can also be checked for overheight by means of a photo cell. This compact entry-level device is already ready for a wide variety of applications. The latest release brings new possibilities so that the range of individual tasks which the Heuft One can fulfil in each case has been extended even further: the new “Large containers” mode now also makes it possible to check the quality of voluminous full containers. Another alternative mode of operation turns the Heuft One into a smart distribution system which controls the distribution of full containers to two different lanes in order to ensure a uniform supply to leading machines or other important filling areas. Because the device can now also be connected directly to the respective filler, closer or labeller it can – without an additional conveyor area – adapt itself exactly to the timing of such leading machines, detect downtimes as well as serial faults and integrate detection modules directly into them. Freshly applied labels, for example, can be checked within the labeller, bottle bursts or filling tubes that have become entangled in the full product can be detected and managed while still in the filler, and sealing faults can be identified immediately after sealing. A locator identifies in good time those filling valves and capper heads which repeatedly cause incorrect fillings and closure faults. The Heuft One can also control random sampling and realise production data acquisition and remote maintenance in real time via an online connection. And as an alternative to the bbd and code verification with the intelligent Heuft reflexx A.I. camera a special thermal sensor can now also be connected which checks the presence of product markings lasered into PET full bottles directly behind the coder on the basis of their ambient temperature. Designed as an affordable entry-level device a Heuft One device can usually only be equipped with a maximum of two detection modules or can only carry out one of the different operating modes available in contrast to more powerful full container inspection and fill management systems from Heuft. This has not changed with the latest release. However, the individual standard tasks which it can now take on have been considerably expanded. www.heuft.com FILLING"},{"@ID":35, "33 TRADE SHOW REVIEW PETplanet Insider Vol. 24 No. 06/23 Flexible and sustainable capping On Arol‘s booth, visitors experienced the latest capping technologies on product safety, a view on circular economy and on more sustainable packaging materials: spindles and heads for ROPP aluminium caps on glass and can bottles, smart instrumented bottles (wireless Bluetooth torque and top load tester for off and on-line dynamic measurements), decappers, decrowners. The company also presented tests on paper caps, thanks to the Arol LabV, a laboratory capper able to measure: approach angle, screwing stroke and angle, flat angle, total cam stroke. Arol also presented everything they have on offer for PET bottlers from an environmental point of view: from the laboratory phase – with the robotic station ClosureXpertLab, where new ultra-light and/or tethered caps are tested, including extra-light bottles with different percentages of recycled plastic- to the caps feeding phase with visual quality control, up to the de-dusting phase (pre-capping), and to the fully servo-controlled capping cycle (Equatorque IQ- Evo). The Arol capping technology is based on a special direct drive technology that is fully software modelled. This approach allowed the implementation of a “Torque Virtual Sensor” as well as a new non-invasive control of all parameters of the capping head during its lifetime. New algorithms for “position approach” and “application angle detection” at each capping cycle (Arol Thread Engage Technology) are available. New sensors have been developed for automatic, non-invasive wear detection of plastic rollers and for machine monitoring, such as temperatures and vibration of critical parts or detection and prediction of mechanical anomalies (Arol Node Sensors Wireless Technology). Great attention is paid to flexibility: for example, the ability to handle different combinations of closures on the same machine, such as plastic threaded closures, crown caps and ROPP closures. Special attention is also given to full quality control such as microplastic or the packaging using RoboQCS and subsequent feedback to the capper and the entire capping process to keep it stable and measurable. www.arol.com Laboratory capper for capping tests and small production batches able to set up different values for cam profile; on site, the application of a paper cap on a PET preform was shown."},{"@ID":38, "TRADE SHOW REVIEW PETplanet Insider Vol. 24 No. 06/23 www.petpla.net 36 Support an organised value chain of rPET Recycled PET is and will be an increasingly sought-after material. Due to EU directives and the obligation of numerous packaging manufacturers to use a high proportion of rPET in their products, but with less demand at the moment, the rPET market is becoming increasingly stressed. Numerous circular economy initiatives, recycling-friendly product design, certificates that guarantee the origin and quality of rPET are important individual building blocks for shaping the rPET market. At the PRSE 2023 in Amsterdam all hot topics of the plastics recycling industry were discussed. There is still no organised value chain for rPET in Europe (or worldwide). The producer of high quality recycled material company Aloxe was founded in 2020 by Arnaud Piroëlle and Clément Lefebvre, two wellknown experts in the PET and chemical industry. PETplanet spoke to Aloxe about the current rPET market situation, the company’s growth strategy and the challenges of establishing an rPET value chain. PETplanet: What was the trigger for founding Aloxe? What reasons were important for you and what is your goal? Aloxe: The two founders, Arnaud Piroëlle and Clément Lefebvre drawing on their experience at leading companies in the sector (BASF, Veolia) and in entrepreneurship decided to found Aloxe to address a the fast-growing sustainable packaging market in Europe. They identified a strong demand in the food-contact rPET market, with customers looking for standardised high volumes and demanding quality in the face of a market that was still fragmented and offering inconsistent quality; the project started from this observation, to establish a leader who could guarantee large volumes with high and consistent quality. PETplanet: You currently produce in three countries: in Italy, France and (two factories) in Poland. How much rPET do you produce pre year and what equipment do you use? Aloxe: In 2024, Aloxe will have a 120,000 t rPET pellets output capacity in Europe. We run state-of-the-art recycling lines like Erema and Starlinger in brand new plants, allowing optimum industrialised processes. Our core business is high quality and food contact rPET pellets to supply the beverages, food containers, cosmetics, pharmaceutical, and home & personal care packaging industry. We supply standardised products with good processability for our customers. PETplanet: What kind of flakes and pellets do you produce? Where do you see more demand – from the packaging- or from the textile/technical industry? Aloxe: We mainly supply the foodgrade packaging industry and foster circular economy such as bottle to bottle. Demand is driven by European regulations and some local taxes on the incorporation of recycled plastics, and also by companies’ commitments to the plastics circular economy, hence reducing their carbon footprint. We supply different markets: CSD bottle with Orgop clear P rPET pellets with high IV, non-CSD bottle, trays and food containers with Orgio clear rPET pellets, cosmetics and pharmaceutical containers with Orgio Crystal rPET pellets meeting the high transparency requirements, and milk bottle with Orgio Olive. We produce flakes for our own pelletising lines and also offer food grade flakes (Efsa approved) to meet customers’ needs. PETplanet: Where do you buy your bales, your material from? Are there reliable partners? What is your approach to be able to process enough material? Aloxe: At Aloxe, we buy bales and flakes; we are partially integrated to guarantee a secured and steady supply. To achieve this, we benefit from a wide network and long-standing partnerships built over time; our feedstock is secured to meet our customers’ requirements in terms of quality and origins. PETplanet: What do you find useful about the EU directives and what could be improved? Do they strengthen the European rPET market? Aloxe: Establishing concrete recycled target contents for bottles in the EU has boosted the recycling industry! Today, as the industry moves to meet these targets in Europe, the rPET value chain has become a showcase not only in Europe but worldwide and proves that the plastics circular economy is on the move. We still face many challenges, of course, but the momentum is there. Being realistic, future regulations will set F.l.t.r.: Aloxe team at the PRSE: Stefano Petrucci - Sales Manager Europe South; Tomasz Czerwinski - Project Manager Europe; Paul-Pierre Piolé – Sales Director; Kira Laudy – Executive Assistant; Miguel Alfaro Neira – Raw Materials & Energy Procurement Manager and Dariusz Lanski - Account Manager Europe East"},{"@ID":46, "BOTTLING / FILLING PETplanet Insider Vol. 24 No. 06/23 www.petpla.net 18 Water treatment system with new technology Processing demineralised seawater The Saudi-Arabian drinking-water producer Makkah Water Company has, for now, finished updating and expanding capacity at its main plant in Jeddah. The new, high-performance water treatment system from Krones passed final acceptance testing in October 2022. Before that, acceptance testing on two new high-speed filling lines was completed in the spring of 2022. Makkah Water Company began operations and production in 1975. The main plant in Jeddah now has seven complete lines from Krones up and running. In its second plant, Al Janoub in the city of Gizan in southern Saudi Arabia, Makkah Water is still working with mix-and-match lines that include a variety of blow moulders, fillers, and labellers from Krones. Whereas the Jeddah plant produces Safa water, the Gizan plant is focused on the Mozn brand. In this project phase, Makkah Water had the existing wet end of an 81,000 bph line replaced with an ErgoBloc L. Later in the update project, the company then decided to swap out two more existing lines for Krones systems. Each of the three ErgoBloc L lines fills still table water at 81,000 containers per hour. Treating demineralised seawater The water treatment system is among the largest of its kind that Krones has built to date, rated at three times 110m3/h. The system, which actually comprises three units, each equipped with ultrafiltration, reverse osmosis, and electro-deionisation, processes demineralised seawater. With the new electro-deionisation (EDI) module, whose debut installation is this one at Makkah Water, the result is ultrapure, deionised water to which the desired minerals can then be added. The addition of the EDI module is especially important for producing still table water whose mineral content has no tolerance for deviation, as is the case at Makkah Water. In addition, the scope of supply also included an activated-carbon filter and modules for remineralisation and ozonisation: The Hydronomic MDS mineral-dosing station uses a mass flow meter to deliver precise quantities of various minerals. The Hydronomic OZ water ozonisation system stabilises the product microbiologically prior to filling. “The new water treatment system replaced our existing equipment. Installation and commissioning went according to plan,” explains owner Sheikh Ali. “For this water treatment project, we chose to work with Krones based on the new technology and our long and excellent partnership – and that has so far served us well,” he explains. www.krones.com FILLING The Hydronomic MDS mineral-dosing station uses a mass flow meter to deliver highly precise quantities of various minerals. At the Jeddah site, Makkah Water now fills its Safa brand with an ErgoBloc L."}]}}
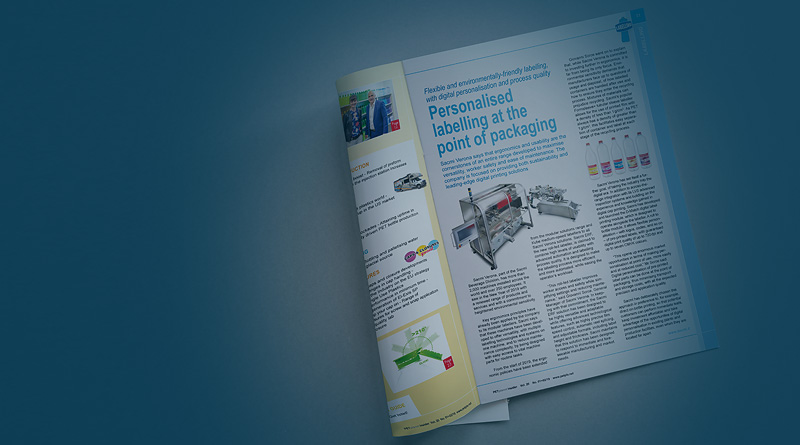