{"pages":{"page":[{"@ID":43 "No.1+2 2024 www.petpla.net D 51178; ISSN: 1438-9452 05 . 02 . 24 M A G A Z I N E F O R B O T T L E R S A N D B O T T L E - M A K E R S I N T H E A M E R I C A S , A S I A , E U R O P E A N D A L L A R O U N D T H E P L A N E T PETplanet is read in 159 countries MARKETsurvey Suppliers of resins and additives Page 24 EDITOUR CAPS & CLOSURESPage 16 Page 10"},{"@ID":28 "CAPS & CLOSURES 26 PETplanet Insider Vol. 25 No. 01+02/24 www.petpla.net opportunities to build up additional capacities, also in the future? Where are promising markets worldwide? Alpla: So far we have a strong demand in Eastern Europe. Based on our international network we check the demand worldwide by using our existing sales channels. Sales Manager Patrick Scherbanti added that the no-spill closure is included in the standard product range and distributed via the international network and that Alpla’s customers benefit from another innovation and can obtain the closure, including the bottle or preform, from one source. Depending on the market and application area, Alpla can also quickly and flexibly build up additional capacities. Customisation and sports version The no-spill closure is available for different neck finishes in a total of nine colours. Customised colours are also available above a certain number of units. The closure will also be available as a two-part sports version in the future – evaluations are currently underway. The alternative version dispenses liquid immediately after the cap is opened and does not require suction or pressure on the mouthpiece, making it easier to drink during physical peak performance. Further developments are already being planned and will be presented in early 2024. www.alpla.com Practical, intuitive, and child-friendly new closure solution Secure down to the last drop Alpla’s no-spill beverage closure has been designed to ensure not a single drop is lost. The new solution only dispenses liquid by vacuum or mechanical pressure on the elastic mouthpiece. Conversely, the closure keeps the liquid reliably sealed from the inside at up to 2.7bar bottle pressure. The secure valve closure system was developed by the Norwegian valve technology company Smart Seal and manufactured exclusively by Alpla from the outset. With the complete takeover of all tools and assembly lines at the Fußach site in Austria, Alpla is now setting the course for the further scaling of this new closure solution. At the same time, the company is intensifying the development of new tools, reducing material consumption through optimisation and investing in further product solutions. Daniel Gut, head of the Austrian plant in Fußach, says: “The history of the no-spill closure so far has been promising. Now, we are taking the next step and capitalising on our strengths as a global system provider. We want to exploit the enormous potential this offers us and can triple our production straight away.” PETplanet: May I kindly ask you to take one step back – why did you choose the Smart Seal solution? Alpla: So far Alpla had no own no-spill closures. The Smart Seal technology with its elastic mouthpiece and the innovative function that liquid is dispensed by suction is an ideal enlargement of our product portfolio. PETplanet: You mentioned earlier that there is still potential for a reduction of material at this closure. Can you please explain this in more detail? Alpla: The three-part valve closure offers a unique selling point compared to the two-part sports cap - the no-spill function. If the valve is not needed, the weight-reduced two-piece sports cap is the alternative. PETplanet: For what kind of application do you see most potential, you say that you will triple the production? Alpla: No-spill-proof drinks for children are a key application for which the technology is already available but still has room to grow. In addition, the easy opening and leakproof combination makes the closure ideal for travel and leisure activities as well as for hospital applications and use by the elderly where opening and closing without mess is very important. PETplanet: Plastic bottles and packaging must be produced with a certain percentage of recycled material. Are you planning to produce Alpla closures from recycled material as well? Alpla: At the moment there are no Efsa certified recycling material available for this type of plastic. As soon as there is, we will check the opportunities. PETplanet: As Alpla has an international network: Where do you see CAPS & CLOSURES"},{"@ID":7 "The worldwide round trip with PET world in the Middle East In a spectacular project taking us well into 2024, we will be travelling in a wide variety of ways to various countries and regions of the Middle East with different mobile editors. There we will interview machine manufacturers, the supply industry, bottle and beverage producers, as well as PET recyclers and everyone involved in the process chain. What market-specific trends are there now or will arise in the future? What developments and technologies are in vogue on the consumer and plant construction site in some of the hottest regions of the world? What special requirements are there? What role do topics such as food safety, shelf life and sustainability play in PET packaging and how are companies preparing themselves for the coming years? This, and much more we will be discussing face-to-face with all the key players and then our results will be presented to you in a series of must-read reports in PETplanet Insider. Please join on this enchanting voyage to the world of PET in the Middle East. We look forward to welcoming you on board! Our previous Road Shows at a glance 2010-2011-2012-2013-2014-2015- 2016-2017-2018-2019-2020-2022 Interested in being visited? barton@petpla.net Autumn 2023 - 2024 6 countries numerous interviews with PET companies Sponsors to date Editour The Middle East Roadshow"},{"@ID":24 "CAPS & CLOSURES 22 PETplanet Insider Vol. 25 No. 01+02/24 www.petpla.net The Clip Aside tethered cap solution by Bericap New standard cap in Eckes-Granini portfolio EU Directive 2019/904 mandates that all plastic caps must remain attached to beverage bottles with a capacity of up to 3 l after opening by July 3, 2024 at the latest. When it entered into force in 2019, the directive posed a significant challenge to the beverage industry. CAPS & CLOSURES Bericap, a well-known manufacturer of plastic and aluminium closures, is equipped to meet that challenge. The company said that more than six billion beverage bottles have already been manufactured and marketed with the Clip Aside tethered cap solution, and that figure continues to rise exponentially. The closures are available for all relevant neck fiishes from 26 to 38mm in all beverage categories, including carbonated soft drinks (CSD), water, juice and tea drinks, as well as milk products. The tethered cap solution is used on over 70 bottling lines in all beverage segments. One of these customers is Eckes-Granini, a leading supplier of fruit juices and fruit beverages in Europe. A new situation that calls for strong partners 2019 was an exciting year for the independent family-owned company based in Nieder-Olm, Germany, as it was for the entire industry. “We were busy setting up internal expert panels, analysing market studies and collaborating with established suppliers, such as our long-standing closure supplier Bericap,” recalled Tobias Schardt, Senior Expert Packaging & Technology at Eckes-Granini. “We soon identified the main priorities in the tethered closure development process. One was to ensure that disposable bottles were still easy to drink from, especially the popular bottle sizes of up to 0.5 l that people carry around with them,” summed up Thomas Henkel, Sales Director Beverage Closures at Bericap. “But it was also important for people to intuitively know how to open and close the bottles. Of the various design solutions initially pursued, the “Clip Aside” design was a clear winner in all criteria and from all perspectives: consumer, bottler and manufacturer.” Environmental protection meets technology To consistently implement the EU directive and think ahead in terms of"},{"@ID":5 "imprint EDITORIAL PUBLISHER Alexander Büchler, Managing Director HEAD OFFICE heidelberg business media GmbH Hubweg 15 74939 Zuzenhausen, Germany phone: +49 6221-65108-0 info@petpla.net EDITORIAL Kay Barton Heike Fischer Gabriele Kosmehl Michael Maruschke Ruari McCallion Anthony Withers Editorial & WikiPETia. info petplanet@petpla.net MEDIA CONSULTANTS Martina Hirschmann hirschmann@petpla.net Johann Lange-Brock lange-brock@petpla.net phone: +49 6221-65108-0 LAYOUT AND PREPRESS EXPRIM Werbeagentur Matthias Gaumann www.exprim.de READER SERVICES reader@petpla.net PRINT Chroma Druck Eine Unternehmung der Limberg-Druck GmbH Danziger Platz 6 67059 Ludwigshafen, Germany WWW www.hbmedia.net | www.petpla.net PETplanet Insider ISSN 1438-9459 is published 10 times a year. This publication is sent to qualified subscribers (1-year subscription 149 EUR, 2-year subscription 289 EUR, Young professionals’ subscription 99 EUR. Magazines will be dispatched to you by airmail). Not to be reproduced in any form without permission from the publisher. Note: The fact that product names may not be identified as trademarks is not an indication that such names are not registered trademarks. 3 PETplanet Insider Vol. 25 No. 01+02/24 www.petpla.net Credit: Cover illustration by Anja Stiehler-Patschan Dear readers, Sometimes two pieces of information fit together even though they actually have no connection with each other. This is definitely the case with my story today: the first happened in Mexico, the second in Lithuania. Both have to do with our new favourite topic, the Tethered Cap. In Ciudad Obregon, Mexico, my son visited the traditional restaurant El Bronco and, among other things, ordered water. A PET bottle came with a tethered cap. My son was puzzled. OK in Europe, maybe even in California but in Obregon? Upon closer inspection, he discovered that it was just a badly slit cap, so nothing to do with a tethered cap. And then we had a message from Retal in, Lithuania. When slitting, they removed just part of the knife and therefore the cap was only partially slitted. So actually the production error - found in Mexico - was dealt with in an orderly fashion. Retal has now found an EasyTether solution that costs practically nothing (photo below). Details can be found on page 33. Yours, Alexander Büchler"},{"@ID":34 "32 PETplanet Insider Vol. 25 No. 01+02/24 www.petpla.net PETproducts CAPS & CLOSURES Tethered cap inspection: full coverage The Heuft FinalView II Cap is fit for new challenges in the field of optical tethered cap inspections. A software upgrade makes it possible to roll out four individual camera shots each of asymmetrical tethered caps to a 360° view. Heuft said that this ensures gapless coverage. In addition, new lighting hardware facilitates all-around inspection of the tamper-evidence bands of rPET bottles. The cap angle detection reliably checks whether all containers are sealed correctly and tightly. Transmitted light is used to detect defects on the tamper-evidence band of all types of closures, combined with a realistic frontal inspection in incident light, particularly during asymmetrical tethered caps. Protruding hinges and unusual gaps in the tamper-evidence area no longer led to false rejections. The rotational asymmetry of some of these new types of closure caps can be precisely calculated with the intelligent Heuft Reflexx A.I. image processing, states Heuft. Where it was usual in the past to generate a black and white view four colour cameras with incident and transmitted light can now be integrated into the Heuft FinalView II Cap at the same time. The size of the faults detectable on the tamper evidence ring is reduced by a factor of three in comparison. Compared to its predecessors the Heuft FinalView II Cap offers twice as many colour cameras and six times the resolution. The maximum diameter of closures to be completely examined is increased by a factor of 1.5 and the possible height difference between the smallest and the largest full bottle which can be safely inspected increases to 30 cm. The audio-visual Heuft NaVi user guidance of the Heuft Spectrum II platform makes the complete inspection of the closures easy and realise gapless coverage with tethered caps, which will become mandatory throughout the EU in the middle of this year. www.heuft.com Tethered caps assembly – all processes in one machine An all-in-one machine from Contexo is claimed to allow for a fast and efficient assembly of tethered caps. The integration of the slitting process enables fast and reliable production. At the same time, the process allows many options when implementing new closures, says the company. The patented concept of the all-in-on system for single- and multi-part tethered caps was developed and designed to integrate all the necessary processes in one system: from assembly to folding and roll slitting of the TE band to closing and packaging. The advantages of the concept are a small footprint, reduced costs and less energy consumption. The system is based on continuous-motion rotary presses to guarantee maximum output rates. The integrated slitting unit eliminates the need to invest in expensive and highmaintenance injection moulds, says Contexo. Filigree inmould operations are replaced by simple, safe processes, as material no longer has to be pressed through narrow channels. The integrated folding and roll cutting of the TE strip is not only cost effective, but also stable in the production process: the TE bridges are not stressed or damaged during handling, the downstream process and assembly. This is claimed to eliminate high maintenance costs of the tools. At the same time, the high speed and repeatability in the production process is guaranteed, i.e. significant cost reduction with more safety. The camera stations used inspect the typical elements inside and outside the closure and enable 100% quality control. This ensures that only technically flawless products are sent for further processing. The user-friendliness of the machine has also been taken into account: 360° accessibility, changeable slitting unit and low maintenance thanks to mechanical components. The solution is also interesting for product development: it opens up many possibilities for product design. Whereas previously there were restrictions in terms of shape and appearance, innovative, eye-catching designs are now possible with the Contexo system. The vulnerability of the TE bridges is eliminated and the rotating mould axis makes unusual shapes possible. Even closures without TE bridges are feasible. www.contexo-automation.de"},{"@ID":42 "7 NEWS PETplanet Insider Vol. 25 No. 01+02/24 www.petpla.net ColorMatrix™ AAnchor™ Acetaldehyde Control Technology for PET can help you achieve sustainable and high-quality PET packaging by: • Reducing Acetaldehyde • Reducing Regulatory Risk • Improving Recyclability • Enhancing Bottle Quality Visit www.avient.com for more information about ColorMatrix™ AAnchor™ Acetaldehyde Control Technology for PET and our full range of innovative polymer solutions for PET packaging. PET PACKAGING HOOKED ON SUSTAINABILITY"},{"@ID":39 "PETplanet Insider Vol. 25 No. 0/24 www.petpla.net 37 EVENT PREVIEW From AA reducers to UV blocking In 2014, Shanghai ColorWay New Material Co., Ltd embarked on a mission to serve the beverage and food packaging with the development of additive products. The commitment to innovation deepened in 2016 through strategic collaborations with university laboratories, reinforcing the company’s dedication to staying at the forefront of industry trends. Responding to business expansion, a new factory was established in Shanghai’s Fengxian district. At Chinaplas, the company will present is range of solutions for the global beverage and food packaging industry. UV blocker additives In the world of plastic packaging, protection is paramount. ColorWay’s UV blocker additives, UVS-392, are claimed to act as a formidable shield against light-sensitive components. These additives enhance product lifespan by preventing premature degradation and colour fading, reinforcing resilience against environmental stressors. Brew preservation The company’s PET beer packaging, OxyBLO2 1 & 2, addresses industry challenges with efficient oxygen scavenging, UV light protection, and a commitment to cost-effectiveness and sustainability. This solution is claimed to ensure efficient distribution and product integrity for breweries. Active O2 scavenger A key additive for the beverage industry, the company’s active O2 scavenger, OxyBLO2, aims to provide cost-effective oxygen barrier performance with minimal impact on bottle appearance. It is claimed to be ideal for aseptic cold filling and hot filling processes, extending shelf life by shielding products from oxygen exposure. Full light-blocker In balancing appearance and protection, ColorWay introduces DairyArmor, a full light-blocker in solid masterbatch form. It achieves a light-blocking effect equivalent to multi-layer packaging, preserving the quality of liquid dairy contents in monolayer PET bottles, says the company. AA reducer ColorWay’s AA reducer, PureGuard, is a specialised liquid additive designed for PET preforms. With up to an 80% reduction in acetaldehyde (AA) levels, it has been designed to prevent taste alterations and to ensure product consistency. The AA reducer supports sustainability goals by facilitating the use of recycled PET (rPET) and regrind materials, aligning with sustainability goals and offering universal compatibility with various PET resins and colours. www.colorwayglobal.com Colorway Hall 2.2 | Booth H51 The new Master in Closure Inspection IMDvista CAP MASTER First calibrated and validated in-line inspection In-line measurements with absolute values 100% repeatability Calibration tool with test certificate CERTIFICATE Calibrated System Solution"},{"@ID":33 "CAPS & CLOSURES 31 PETplanet Insider Vol. 25 No. 01+02/24 www.petpla.net The bottles, labels, caps and rings are shredded, and a sink-float process is used to separate the PET bottles from the PE and PP caps. The heavier PET sinks and the lighter polyolefins float and are skimmed off as a secondary recycling by product. Logic may dictate using PET for both bottle and cap to solve the issue, but Olsson explains it’s not that simple. “Mono-material packaging is a dream that a lot of recyclers, brand owners and chemical companies are striving for, but we are not there yet. Different polymers have different strengths and weaknesses,” he says. “Building in the threading on a cap that’s required to tighten and keep the container sealed is a property that polyolefins, PE and PP, lend themselves especially well too.” While some bottle recyclers see mixed polyolefins as a waste material, Castro sees opportunity. Because of their experience with a variety of materials and philosophy of one-stop solutions for his suppliers, Greenpath has extensive processing capabilities with different lines to sort diverse feedstock. The company is adept at mechanical, multi-material, and batch recycling processes. To realise the opportunity to close the loop on caps and offer a more sustainable market for polyolefins, Greenpath investigated various technologies to sort the mixed polyolefins. “PE and PP densities are very close to one another, so using float/sink tanks is not effective,” explains Castro. Alternative recycling technologies were also considered but didn’t offer the yield or recovery for both PE and PP resins that was desired. According to Castro, the cost-benefit analysis just didn’t justify the space and capital required. “The yields are low, and you have to consider the expenditure, space and waste generated from the separation process,” he says. Greenpath began to zero in on a mechanical solution using flake sorters. Company officials initiated conversations with Tomra, who had introduced a new type of flake sorting technology. One of the technology’s design parameters was to extract value from multicomponent plastic waste streams. Olsson mentions that the industry hasn’t begun to reach the ceiling limit for mechanical polyolefin sorting. “It’s best to pursue a path that introduces the least amount of change to the material and sorts in the most efficient way,” he says. “Mechanical and chemical sorting technology OEMs are just getting the first processes off the ground to produce materials resulting from the 2025 and 2030 circularity commitments made in the twenty-teens. Producing 95% or greater purity-by-polymer streams is critical for many types of downstream recycling processes, and flake sorting can get us there.” Flexibility in mechanical sorting Discussions related to Greenpath’s goals led down a path to selecting Tomra’s Innosort Flake sorter. As the sorter does not require a large footprint, it allowed an easy integration at the Colton, Calif. facility. After discussing the purity, yield and throughput necessary to meet Greenpath’s objectives, flake sorters were installed. Designed for flexibility, Innosort Flake incorporates a combination of sensor technologies, including colour cameras capable of identifying 16.8 million colour variations. With two-sided cameras, “one is positioned on each side of the chute where the materials fall through, so it can discern the difference between one side of the flake versus the other,” explains Olsson. It helps to identify in-mould labelling that can be a contaminant. “Features like this cater the machine especially well to the polyolefin recycling supply chain, which is in dire need of quality gap closure,” he adds. Its Flying Beam lighting system is claimed to offer fast and reliable material detection by the sorter’s near-infrared (NIR) sensors. Providing a homogeneous light distribution across the entire 2m machine width, it is claimed to ensure classification of PE and PP materials, as well as other polymers and materials. Integrated into the scanner box for protection against damage, the illumination technology offers up to 80% energy savings over conventional light sensors. Configuration flexibility allows for single or multiple step sorting with the same unit. “We can split the machine into multiple sorting tasks by chute and even split a chute into two different process streams or more,” explains Olsson. “We can do multiple passes through a machine or link many machines in series to achieve the results we need.” Castro admits the inconsistent feedstock Greenpath receives does present sorting challenges, but the company has been able to overcome these variations through years of experience to provide a good high-end recycled product. Still, the company ended up with a mixed polyolefin material. Optimising for consistency What makes Greenpath an asset for its suppliers also makes it a hindrance to polyolefin flake sorting. The inconsistent feed – plus the fact that this is the first operation in North America to attempt this type of mixed polyolefin sorting – has demanded special attention to detail with sorting optimisation. “These machines are themselves optimal in a steady state stream,” says Olsson, “and, thus, have to work together as a holistic process system, along with other types of processing equipment.” Getting it right to meet Greenpath’s high purity goals of mono-polymer PE and PP from inconsistent mixed polyolefin feedstock has both parties analysing the entire sorting process. While there is still some work to be done at the Colton facility, “mechanical viability is there,” confirms Olsson. The system is now to the point where the circuit can first sort by polymer with the Innosort Flake units and then by colour. “If a customer wants a natural or specific sorted colour such as red, white, blue orange, or green PE or PP product, we can purify and provide them a sorted colour that meets their specific application using PCR,” says Castro. www.tomra.com Greenpath processes a wide range of plastic materials."},{"@ID":40 "EVENT REVIEW PETplanet Insider Vol. 25 No. 01+02/24 www.petpla.net 38 PET blow moulds and machinery In the run-up to the Brau Beviale trade fair PETplanet took the opportunity to organise a PETinar on mould making and blowing machinery. PETplanet was particularly proud to enlist the support of the machine manufacturer 1Blow and mould manufacturer Röders Tec as speakers. These companies have been working together on a number of projects for many years. Olivier Perche, Sales Director at 1Blow and Steffen Lühning, Sales Manager at Röders Tec presented their technical and mould innovations. The PETinar was moderated by Ruari McCallion, Editor at PETplanet. 1Blow company Olivier first introduced the company 1Blow, a French machine manufacturer of PET bottles. He said that 1Blow has been growing steadily since the company’s founding in 2010. “We have sold around 215 machines so far,” he explained. Thanks to this growth over the years, the company relocated in 2014 to expand its production facilities and in 2016 built a factory hall dedicated exclusively to testing new shapes, new colours or new materials etc. for their customers. 1Blow also offers its customers the option of ordering their spare parts online, and an additional warehouse was built to meet expected demand. Online instructions, e.g. for preventive maintenance or changeover have also been made available on this special website thanks to several tutorials. Olivier went on: “As far as our offer is concerned, the company produces linear two-stage PET blow moulding machines.” The machines are available with one to five cavities, with a production speed of 1,000 to 9,000bph. Bottle sizes from 100ml to 30 l can be manufactured. The machines can produce typical PET bottles from round to oval shapes, using standard preforms, even with neck orientation which is achieved mechanically. Olivier cited a squeeze bottle with a flip-top closure for sauces as a typical application. All machines are equipped with servo drives. He added that this gives the operator control over the entire process within the machine. 1Blow exports its machines around the globe. Saving energy As an example, Olivier presented a 1Blow 2XL machine to explain special features for reducing power consumption and production costs. He began with the electric cabinet. “It has an integrated power recovery system. After every braking phase recovered energy is sent back to the other drivers in the machine. This saves 2-3%, a good starting point,“ Olivier stated. He went on to the heating. “There are three ovens on this 2-cavity machine. The operator can adjust each lamp in the ovens individually. With special Eco lamps, energy savings of up to 34% were achieved. These lamps focus the infrared energy on each preform.” Finally, Olivier explained the energy savings of the machine’s compressors. “Each bottle processes specifies the limitation of low air pressure. The compressed air can be adjusted with the reducer,” Olivier explained. He gave some figures: A reduction from 40 to 35 bar lowers air consumption by 12.5%: a reduction from 40 to 26bar requires 35% less compressed air. A compressor size of 40bar with an application of 30bar requires 20% less power. Further energy savings are achieved by the Air Recovery System. A fourth valve is added to the valve bloc. After blowing, the valves push the air to a 7bar vessel. Olivier also emphasised the excellent accessibility of the machine and the quick changeovers. Röders Tec Steffen then stepped up to the microphone to introduce the mould maker Röders Tec. The company is a sixth generation family business. Mr Jürgen Röders is currently Managing Director. Röders Tec was founded in 1814 and has been producing blow moulds since 1975. With around 500 employees in its three divisions pewter casting, blow mould manufacturing and high speed milling machines, Röders Tec produce around 6,000 moulds per year on three production sites covering 10,000m2. The company produces the blow mould inhouse. During the company’s history, numerous exclusive partnerships have been established with the most important machine suppliers such as Krones, KHS, Sidel and Sipa. Röders Tec developed the first quickchange solution in the 1990s and was the first German company to utilise 3D CAD/CAM technology. In 2001, Röders Tec opened subsidiaries in America and China, followed by Vietnam in 2012. Since 2019, Röders has been using a 1Blow machine to test new bottle projects from its customers. Any type of mould can be installed on the 1Blow machine. Energy-efficient blow moulds Röders has developed a low-pressure base mould that is available for bottle formats from 0.33 l to 2.5 l. It can be used for all petaloid and CSD types. The base has a special geometry with special venting holes and grooves, allowing the air to be expelled efficiently. The advantage of this technology is a better material flow, which means that the PET blow-moulding pressure can be reduced, and a lightweight bottle design is also possible. In addition, the venting channels do not affect the stability of the bottle. Steffen explained that with a 1.5 l mould only the base cup needs to be replaced without having to invest in a completely new mould set. In summary, he said that all potential results depend on local conditions. Röders also offers technical support on site to train customers’ operators to understand how stabilising the blowing process can result in reduced energy and material consumption. Steffen also shared some figures from previous projects with Coca-Cola and Pepsi. For a 330ml bottle of Coca-Cola, which was blowmoulded on a Krones Contiform Gen. 3 (2015), the pressure before the lowpressure base moulds were installed was approximately 25bar, afterwards it was approximately 17 bar. www.1blow.com www.roeders.de The video of this PETinar can be viewed on the PETplanet website. www.petpla.net/category/petinars/ PETINAR"},{"@ID":13 "EDITOUR PETplanet Insider Vol. 25 No. 01+02/24 www.petpla.net 11 safety to warehousing, logistics and the delivery fleet. His responsibilities also include sustainability and project planning, as well as the planning and implementation of this factory, where we met for the interview, and the company’s own distribution centres in various parts of the Emirates. He has 300 employees working under him. “This factory,” Mr Nehme continued, “is Industry 4.0-capable and a number of precautions were taken during construction to ensure that it also meets future sustainability and energy-saving requirements.” Several processes and filtration steps are used in the water treatment plant with a capacity of 150m3/h, including ultra filtration, carbon purification, reverse osmosis, microfiltration & UV disinfection. Aquafina also receives ozone treatment. For the water source, Dubai Refreshment mainly uses municipal water from the Dubai Electricity & Water Authority (Dewa). Cochran boilers can use gas or diesel fuel for steam generation, Gea ammonia compressors for the central cooling system, Atlas Copco compressors for low pressure air and AF Compressors for high pressure air. Krones equipment can be found in the syrup room. Here, the sugar and water is mixed with the concentrate and pumped directly into the bottling line. The water is treated using Veolia technology. “The production process and the lines are fully automated and run at 86% efficiency,” said Mr Nehme. The site covers a total of 140,000 m2, of which only around 50% - 50,000 m2 - is used for production and delivery and 20,000 m2 for waste water treatment, administration and staff areas. Five more lines could be added at any time. Syrup room with Krones equipment The company has a waste water treatment system and large-scale solar thermal and photovoltaic panels. The wastewater treatment plant has a nominal capacity of 1,100m3/h and is reused in utilities and for watering the outdoor greenery. Mr Nehme explained: “We can currently reuse around 85-90% of the wastewater produced in this way, around 500-600m3. Our solar system creates a capacity of 70m3/h for hot water and with the photovoltaic system, consisting of 11,000 panels, we cover more than 30-40% of the plant’s energy requirements with a capacity of of 3.7MW.” An optimised system for transporting and delivering goods is also used in logistics, with automatic route planning, digital mapping and utilisation of the 150 trucks, which reduces emissions and increases efficiency. In addition to this main plant and hub, there are also four warehouses in Sharjah, Ras Al Khaimah, Fujairah and Abu Dhabi. In total, the company has more than 1,000 employees and serves over 15,000 customers. The company’s expenditure has been recognised many times, both nationally and internationally. A hall of fame of these awards and certificates can be seen in the foyer, including the recently added Leeds Platinum Award, presented by the US Green Building Council (USGB) in recognition of the company’s sustainability achievements. “We also want to be more active in the snacks sector in future in order to develop from a pure beverage manufacturer into a beverage and food company,” said Wael Nehme, looking to the future. Format overview PET CSD: 0.3 l, 0.5 l, 1.25 l, 1.5 l, 2.28 l PET water (Aquafina): 0.33 l, 0.5 l, 1.5 l www.pepsidrc.com Plenty of space for further filling lines, currently used as an additional warehouse IMPROVEYOUR PRODUCTIVITY CONTACT USTODAY! info@moldmasters.com www.moldmasters.com Featuring ✓ High-performance 2-stage hot runner system. ✓ Enhance preform quality and productivity. ✓ Lower injection pressures to allow for faster cycle times and lightweighting."},{"@ID":8 "PETnews 6 NEWS PETplanet Insider Vol. 25 No. 01+02/24 www.petpla.net ArabPlast 2023: A showcase of innovation and sustainability in the plastics and petrochemical industry ArabPlast, the Dubai trade fair for the plastics, recycling, petrochemical, packaging & rubber industry, opened its doors from December 13-15, 2023. The three-day fair not only celebrated the latest advancements, and innovations, but also delved into sustainable solutions. A defining feature of ArabPlast 2023 was the participation of more than 750 exhibitors, representing 35 countries across the globe. The exhibition served as a stage for presenting the latest products, showcasing advanced technologies, and exchanging invaluable know-how. The diverse and global representation emphasised the interconnectedness of the plastics and petrochemical sectors, fostering collaboration and crossborder exchange of ideas that are vital for the industry’s evolution. In addition to the comprehensive displays, ArabPlast 2023 featured machine displays that captivated the audience. Cutting-edge machinery was showcased, providing attendees with a firsthand look at the latest innovations in plastic processing. In addition, on-the-spot machine sales added an element of practicality to the event, allowing industry professionals to acquire state-of-theart equipment right on the exhibition floor. The event also witnessed the unveiling of patented technology in plastic processing. This technology is claimed to represent a significant milestone in the global plastic industry, tick marking the first-time introduction of such advancements. Aligning with the global transition towards a more sustainable and environmentally conscious economy, exhibitors showcased eco-friendly solutions, sustainable practices, and innovations aimed at reducing the environmental footprint of the plastics and petrochemical industry. The commitment of these industries in the Middle East and beyond to sustainability was evident in the initiatives and products unveiled during the event, solidifying ArabPlast’s role as a driving force in fostering environmental responsibility. www.arabplast.info Krones announced it is to discontinue its digital container-decoration business The Krones Group has chosen to cease its activities in the field of digital container decoration by the end of 2023. The decision to cease the activities of the group’s subsidiary Dekron GmbH is the result of a careful review of Krones’ business strategy and the current market situation. Dekron informed its staff, customers, suppliers and business associates accordingly in November. Dekron GmbH has developed and manufactured machines from the DecoType series used for digitally decorating containers made of glass, PET and HDPE since 2018, with the group’s subsidiary KIC Krones supplying the matching UV inks. Krones has synergised in Dekron its own development activities and the business operations of Till GmbH, in which the company has had a majority holding since 2014. The subsidiary has been liquidated effective December 31, 2023 and the facility in Kelkheim closed down as part of the phase-out. A reconciliation of interests has been negotiated with all members of staff. www.krones.com La Spumante shines bright: triumphs at Worldstar 2024 Sipa’s La Spumante has secured two prestigious accolades at the Worldstar 2024. The popular awards were bestowed upon La Spumante in two significant categories: Alcoholic Beverages and Packaging Materials and Components. This success follows an important year for La Spumante in 2023, where it garnered widespread acclaim. In April, it clinched the Best Packaging Award in Italy, a testament to its exceptional design and functionality. Later in October, the PET bottle won at the SPE Blow Moulded Part Competition in Chicago, USA, showcasing its technological prowess and manufacturing excellence. Additionally, La Spumante earned a place as a finalist at the Food Bev Beverage Awards in November. La Spumante is lightweight, offers convenience to consumers and contributes to lower transport costs and a reduced carbon footprint. It is fully recyclable to meet environmental sustainability targets, emphasising its commitment to environmentally friendly packaging solutions. Sipa says that the PET bottle’s easy filling process streamlines production for manufacturers, ensuring efficiency without compromising on quality. Moreover, its remarkable 24 months shelf life adds a layer of practicality and convenience for both producers and consumers alike. Receiving the Worldstar 2024 award is not only a recognition of past achievements, but also a testament to the ongoing commitment to push boundaries and redefine standards in the world of packaging. The future looks promising for La Spumante as the company continues to make waves and set new standards in the industry, according to Sipa. www.sipa.com"},{"@ID":36 "34 EVENT PREVIEW PETplanet Insider Vol. 25 No. 01+02/24 www.petpla.net EVENTpreview Smart manufacturing and eco-friendly solutions at CBST and Chinaplas Newamstar is set to showcase its smart manufacturing techniques for eco-friendly products and engage in discussions on future industry trends at both CBST2024 and Chinaplas. During CBST2024, the company will present its comprehensive digital factory solutions and unveil new blockbuster products at their booth. In April, the spotlight shifts to Chinaplas, where Newamstar will feature its environmental, intelligent, and digital product lineup. The exhibi ted products aim to enhance production flexibility, efficiency, traceability, and control, while concurrently reducing overall production costs. Addressing market demands for customisation, multiple variants, fast cycles, and high-end products, the company says it is committed to meeting the diverse needs of its customers. At the core of its activities, Newamstar prioritises offering comprehensive service advice and personalised solutions to build high-quality and efficient smart factories for its clients, integrated in production and storage, and to help achieve high-quality growth in the food and beverage industry. https://en.newamstar.com CBST & Chinaplas - Leading trade fairs in Shanghai this spring In the upcoming spring season, our attention turns to two prominent trade fairs in Shanghai. The first is the 12th China International Beverage Industry Science and Technology Exhibition (CBST), scheduled to take place from March 6-8 at the Shanghai New International Expo Center in Halls N1-N3. This comprehensive exhibition encompasses all facets of the beverage industry chain, with special areas dedicated to blow moulding, filling, labelling, packaging, and more. Chinaplas is set to unfold at the National Exhibition and Convention Center (Shanghai) from April 23-26. Spanning an expansive exhibition area of over 380,000m2, this event is poised to host more than 4,000 exhibitors and attract over 250,000 visitors from around the world. The exhibits on display will range from raw materials to cuttingedge machinery and equipment. A select number of exhibitors will be previewing their highlights in this and the upcoming issue of PETplanet. www.cbst.com.cn www.chinaplasonline.com Sipa´s expertise on the Chinese Market Sipa will feature a comprehensive exhibition of its solutions for the production, filling and packaging of PET bottles as well as for preform production and the local production of injection- and blow moulds at the upcoming CBST. Preform manufacturing For the sustainable production of PET preforms, Sipa offers its well-known XForm system for preform production and the Xtreme Renew, an injection moulding preform system that uses hotwashed PET flakes to produce 100% rPET preforms. Preform moulds made by Sipa can hold 200 cavities thanks to the incorporation of high-performance hot runner systems developed and produced in-house. Repeat orders from major Chinese customers, as well as global operators with operations in the country, continue to come in for XForm systems. Bottle blowing The past year has seen remarkable strides in the rotary blowing system, Xtra. The company said that the linear blowers, the SFL series, expands the boundaries of linear blowmoulders, offering maximum flexibility combined with greater output and overall performance. Injection and blowing moulds Sipa produces its machines in Italy, but also has a mould-making and refurbishing operation in China, where it has a staff of around 200 employees. Sipa Machinery Hangzhou can produce up to 800 injection stacks and 300 blowing moulds every month. Additionally, a mould refurbishing service, a costeffective solution to restore mould productivity is offered. Full-service support Sipa has local service teams for all systems, whether injection moulds, preform systems, rotary or linear blow moulding machines or entire filling and bottling lines. Tailored packaging solutions The local design specialists own an in-depth understanding of the local packaging market in diverse sectors: beverages, mineral water, food, edible oil, cosmetics, and home and personal care products. www.sipasolutions.com Newamstar Hall N2 | Booth 2D01 Sipa Hall N1 | Booth 1A05 Newamstar Hall 8.1 | Booth D50"},{"@ID":35 "33 PRODUCTS PETplanet Insider Vol. 25 No. 01+02/24 www.petpla.net EasyTether solution The R&D team at plastic packaging producer Retal’s dedicated innovation centre in Lithuania has spent much of the last two years creating and developing a range of tethered closures that can partner with its preforms in different neck finishes. This has resulted in several tethered-ready options that meet all the rules, the company says. In addition to this careful R&D of technologically advanced tethered closures, the company has announced the discovery of a simple solution: a tethered closure solution that is claimed to be almost free to implement, to require only small machinery changes, and to result in a practical, comfortable tethered closure meeting the strict demands of many of Europe’s leading beverage brands. The head of Retal’s R&D department Anton Sugoniaev explains this solution: “We work closely with our compression machine supplier and they shared with us a small change inside the tooling that produces the caps. With this small but crucial change, we have been able to create what we call our Easy Tether solution.” This solution uses the same cap as its standard slitted cap; the only difference is that one bridge is not cut, thanks to the shorter blade that doesn’t cut the standard 360 degrees, but rather has a shorter blade that leaves one connection, which formed the ‘tether’. Sugoniaev continues, “It’s simple, strong and meets the legislation. As there’s practically no cost involved, with zero cost to the customer; they use the same cap shape as before and work exactly as they’re used to. It’s easy for us to share the solution with our customers and show them how it works and how it allows them to be in good time for the legislation at no downtime or investment to them or their production line.” These caps with a remaining connection would have previously been considered defective, he explains, while they are now in line with the new regulations and can be produced at high volumes with no additional costs, changes or downtime. Alongside the EasyTether, the company offers a range of technically complex tethered solutions for the popular 29/25, 1810 and 1881 neck finishes, with the team able to deliver a comparison of possible solutions to customers across Europe. www.retalgroup.com Pulsed-light technology helps beverage producers comply with EU regulations for tethered caps Mandatory tethered cap is a real challenge for the producers. The implementation requires to adjust their manufacturing processes. They have to work closely with the caps suppliers to redesign the cap and potentially with the capping machine manufacturers to review the filling line and adjust the cap chute. Claranor’s pulsed-light technology can decontaminate every kind of caps: flat, sport and also tethered caps. Recent microbiological tests have been run to confirm the performances on those new cap shapes. Producers could request this microbiological test results or ask to test their new caps. Compact, the equipment can be easily integrated on existing or new filling lines. Claranor offers a full range in terms of speeds - from Claranor Essential, a solutions up to 16,000bph to Inncap Evolution, a decontamination machine for high-speed filling line up to 120,000bph. The solutions are adapted for ultra-clean hot and cold fill ESL and preserved foods. The new Inncap Evolution machine is designed to ensure that their patented guidance channel could take over the technical constraints of those new tethered caps, especially their lightweight and thinner shape. Thus, the operation is jam-free, and the cap flow is continuous. Plus, Claranor helps beverages producers in achieving their sustainable goals: Their machines use no water, and no chemicals, and are sober in energy consumption. www.claranor.com"},{"@ID":18 "CAPS & CLOSURES 16 PETplanet Insider Vol. 25 No. 01+02/24 www.petpla.net Where is the limit? 128 cavities in a 1.85 seconds cycle time Today’s packaging requirements in the beverage sector are highly demanding, especially for still water. The packaging shouldn’t cost anything more, that’s why the requirements for the design, especially the weight, are enormous. But the requirements for the output of closure systems are also high, because the production costs can kept low. The Austrian company z-moulds has risen to this challenge and designed a 128-cavity closure mould system with a cycle time of less than 2 s. The existing 96-cavity moulds on the market operated with a cycle time of around 2 s, approaching their physical limits. The most important technical limitation was the dimensions of the mould in terms of height and mass, which reached the physical limits of the injection moulding machines. Gregor Degasperi, Business Development Manager of z-moulds, said: “Our initial idea was to stick with our existing pitch size of closure moulds at 70mm. However, this would have required a larger machine solely due to the mould size, although a 420 t injection moulding machine has sufficient clamping force. The second approach was to circumvent the laws of physics in order to decrease the closures fall time and reduce the weight of the moving half.” By introducing the 55mm pitch with the existing patented z-slides, z-moulds was able to build a mould with 128 cavities and a width of 696mm and a height of 1,196mm. This reduced the closure’s fall height, compared to the market standard, by 500mm, resulting in a 0.12 s decrease in fall time. In addition, the weight of the moving half was reduced by 45% compared to market standards, which contributed to a further reduction in opening/closing times of 0.08 s. These advances enable z-moulds to achieve a cycle time of 1.85 s. z-mould’s machine partner Netstal used its highspeed Elios model to achieve these results. A supplementary developPatented smart tool for cavity removal from the front ment was a smart tool to enable the removal and replacement of cavity inserts from front of the cavity plate within the machine, eliminating the need of pulling over the cavity plate to the cold side. This enhances efficiency and productivity. The development of these two patented innovations was made possible by the will to solve problems, to go beyond physical limits and to be inventive. They not only address specific challenges but also set a new standard for efficiency and productivity in mould development and plastic closure manufacturing. www.z-moulds.com 128 cavity z-slides mould for cap 26/22 with new 55mm pitch CAPS & CLOSURES z-moulds became its own legal entity in October 2023. The former Vice-President of Sales and Marketing, Michael Fink, was appointed as CEO."},{"@ID":3 "No.1+2 2024 www.petpla.net D 51178; ISSN: 1438-9452 05 . 02 . 24 M A G A Z I N E F O R B O T T L E R S A N D B O T T L E - M A K E R S I N T H E A M E R I C A S , A S I A , E U R O P E A N D A L L A R O U N D T H E P L A N E T PETplanet is read in 159 countries MARKETsurvey Suppliers of resins and additives Page 24 EDITOUR CAPS & CLOSURESPage 16 Page 10"},{"@ID":44 "EDITOUR PETplanet Insider Vol. 25 No. 01+02/24 www.petpla.net 10 Soft drinks, water and more snacks in the future Multinational brand on course for expansion in the UAE In 2016, the bottler Dubai Refreshment, franchisee for PepsiCo products, relocated to its new plant in Dubai Investment Park 2, just over 30 km south of the city centre. The new site, a greenfield project that currently employs around 700 people, was deliberately designed for continuous capacity expansion and, in addition to the state-of-the-art setup of European machine builders for its water and soft drinks bottling, not only offers plenty of space for additional equipment in the future, but has also taken a number of sustainability and environmental measures into account during construction and implemented them in a future-proof manner. In the foyer of Dubai Refreshment with Wael Nehme (left) and Kay Barton Interview meeting with Dubai Refreshment Company (DRC) December 5, 2023 We met: Mr Wael Nehme, VP, Supply Chain And Projects The history of Dubai Refreshment goes back to the late 1950s. It all began in 1959 with the establishment of a glass line for returnable Pepsi bottles and 20 employees in Deira in northern Dubai. In 1962, the company became an official Pepsi franchisee and delivered its drinks to customers with five trucks. Over the decades, many other products from the multinational brand’s range were added. One main product, Aquafina still water, has been bottled here since 2004 and was listed on the stock exchange in 2007. Five bottling lines are now in operation in the new factory, an investment of around US$ 200 million. A total of 15 different beverage brands roll off the production line here: Pepsi, 7Up, Mirinda, Shani, Lipton Iced Tea, Mountain Dew, Aquafina, Mathieu Teisseire, Ceres, Rockstar, Robinsons, London Essence, Evervess, Britvic, Gatorade, Life WTR and Ceres Juice. Pepsi and Aquafina make up the majority with more than 90%. In addition, the snacks Dofreeze Cakes, Edita Wafers and, more recently, Lay’s Crisps are also sold. The plant comprises two turnkey KHS lines for PET with 40,000bph capacity for 0.33 l to 2.25 l bottles, two turnkey KHS lines for cans with 90,000cph each for 0.15 l to 0.33 l, as well as a Simonazzi glass line with 24,000bhp for 0.25 l CSDs as well as for 0.33 l and 0.75 l Aquafina. These, as well as one of the PET and one of the canning lines, were taken over from the previous site and modernised. In addition to water and CSD, the two newly added lines can also hot fill. Preforms (PCO1881 in clear and green for CSD, 29/25 in clear for Aquafina) are bought in from various sources, and bottle blowing takes place on Sidel blow moulding lines (SBO12 for Aquafina, SBO8 and SBO14 for CSDs). The latest technologies in the range include 100% rPET bottles for the Pepsi, Pepsi Diet and Pepsi Black brands, which the company launched in October 2023 with the new legislation on the use of recyclate in food contact. PET accounts for 47% of total production. The plant currently has over 300 stock keeping units and produces over 60 million crates annually. “We are talking about one of the most modern production facilities in the Middle East,” explained Mr Wael Nehme, BSc and MBA graduate from American universities in Cairo & Dubai respectively, at the meeting. He has been working in operations and supply chain for more than 30 years. His personal career led him via Pepsi Société Moderne Libanaise Pour Le Commerce (SMLC) in Lebanon, Pepsi United Beverages in Kuwait and Pepsi Al Qahtani in Saudi Arabia to Dubai Refreshment in 2001. Here he started as Operations Manager and became responsible for the entire supply chain, from procurement, production, maintenance, quality control and 1.5 l bottles of Mountain Dew on their way to the palletiser EDITOUR"},{"@ID":26 "MARKET SURVEY 24 PETplanet Insider Vol. 25 No. 01+02/24 www.petpla.net 01+02/2024 MARKETsurvey Suppliers of resins & additives There is rapidly increasing demand for packaging materials that give even greater protection to their contents. Functional additives and resins are an important technology to fulfil this demand for more product protection and recyclability. A functional additive modifies the properties of packaging to impart desirable or beneficial functions. That is why we won’t stop a well-established tradition in opening our market surveys overview in 2024 with suppliers of resins and additives. Please find here the news of the companies: Avient, Repi S.r.l, Sukano AG, Köksan, Neo Group, Campine, Reliance Industries and Novapet, S.A. Although the publishers have made every eff ort to ensure that the information in this survey is up to date, no claims are made regarding completeness or accuracy. Resins & additives Cap producers, systems & inspection systems Preform machinery Preform production & inspection systems Preform, cap & SBM mould manufacturer SBM 2-stage Compressors Filling equipment & inspection systems Palletising & shrink film machinery Recycling machinery Additives Company name Sukano AG Repi Avient Corporation Campine nv. Postal address Telephone number Web site address Contact name Function Direct telephone number E-Mail Chaltenbodenstrasse 23, 8834 Schindellegi, Switzerland +41 44 787 57 77 www.sukano.com +41 44 787 57 77 media@sukano.com Via B. Franklin 2, 21050 Lonate Ceppiono, Italy +39 0331819511 www.repi.com Ms Lucia Buffoni Group Marketing Manager +41 79 9093 735 l.buffoni@repi.com 33587 Walker Road Avon Lake, 44012 OH, USA +1 440 930 1000 www.avient.com Mr Marco Schäfer Marketing EMEA +49 4102 487 158 marco.schaefer@avient.com Nijverheidsstraat 2, 2340 Beerse, Belgium +3214601511 www.campine.com Ms Rien Repriels Product Manager +32 1460 1624 rien.repriels@campine.com Additives and Colours for PET Liquid colours Yes Yes Microgranule colours Yes Yes Masterbatch colours Yes Yes UV protection additive (solid) Yes Yes UV protection additive (liquid) Yes Yes AA reduction (solid) Yes Yes AA reduction (liquid) Yes Yes Oxygen scavenger (solid) Yes Yes Oxygen scavenger (liquid) No IV Enhancer Yes Yes Yes Reheating Yes Yes Blowing additive Yes Yes Yes Slipping agent Yes Yes Yes Other PET additives: Antifog, antimicrobial, antistatic, antioxidant, compatibiliser, voiding agent, optical brightener, nucleating agent, matting agent, melt viscosity enhancer, mobility aid, mould release, slip/antiblock, light diffusor, impact modifi er, infrared, fl ame retardant, foaming agent, plasticiser, processing aid, NIR-detectable colours and blacks. Sukano is a distributor of ocean-bound rPET. Anti yellow, optical brightener, heat stabiliser for PET Recycling friendly toners, special effects, matting agent, slip additives, NIR black, light blocking additive for UHT milk bottles Catalyst for Solid State Polycondensation; Campine CD, Campine CS, Campine CB: All products can be delivered with or without MEG (Mono Ethylene Glycol) as wetting agent. The purpose of the wetting agent is to make the catalyst powder dustfree."},{"@ID":46 "CAPS & CLOSURES 20 PETplanet Insider Vol. 25 No. 01+02/24 www.petpla.net New challenges in sport caps making Attention to the environment, complex closures and ergonomics: the caps manufacturers are more and more raising the bar in their new developments. In this scenario, the Italian company Maca Engineering offers a complete range of automatic machines and systems for the production and assembly of aluminium and plastic caps and closures. capable of assembling up to three components with an output of up to 36,000 pph. The first flywheel is dedicated to folding body flap, the second flywheel for inserting ring and the third flywheel for inserting spout. For greater efficiency the ARV model provides some features such as ejection of defective pieces (for example, not assembled pieces), that occur without the machine stopping its process. Rejecting defective parts stations are located after each flywheel and consist of a sensor. If it detects an error (non-compliant piece for colour or incorrect assembly), it discards the piece, and this can happen at any stage of assembly. Model ITVE: continuous rotary slitting machine (also for tethered caps) The second model, ITVE, is a machine that cuts the bottom part of the cap. Thanks to the exit conveyor belt with the integration of a vision system, it checks for possible deformation of caps and ensures the correct presence of the components inside caps. Finally, it provides a straight end-line conveyor for cardboard boxes (four boxes in accumulation, one box in the filling position, and three boxes in discharge). Maca has the ability to assemble up to four components (body, ring, spout and valve) using the 3-Flywheel ARV and an additional ARV for inserting the valve. The machines can be supplied at low, medium and high speed, based on individual requirements. www.macaengineering.com CAPS & CLOSURES Maca Engineering has experience in tailor-made solutions to realise complex closures through fast, reliable and fully automated machines for over 30 years. Maca supports its customers with feasibility studies and design proposals in order to find the best possible solution in the initial phase of research or the market launch of a new product. Around 80% of key components and structural assemblies (including machine units, dies, etc.) are produced in-house and countermarked with an identification number. One of Maca’s main production areas is the assembling lines and slitting/folding machines for plastic caps and closures: not only pre-threaded flat plastic caps, but also pre-threaded sport plastic caps, complex closures for alcoholic drinks or pre-threaded agrochemical caps. One example, is a line for folding, assembling “TE ring” and spout and slitting for the production of sports caps. In particular, it is a flexible continuous rotary assembly machine model ARV and a continuous rotary slitting machine model ITVE. Structurally the ARV machine consists of three flywheels with 24 punches each Since a few years Maca Engineering became part of the Arol Group, which includes: Arol Closure Systems, the global point of reference in the design, manufacture and distribution of capping machines & capping turrets, caps feeding systems, caps orienting systems and caps sorters; Unimac-Gherri the specialist in filling and capping of glass, metal and plastic containers with twist-off and pre-threaded caps for dense, semi dense and pasty products and Tirelli, which develops and produce filling, capping and labelling systems mainly for home and personal care industry. Model ARV: continuous rotary assembly machine with an output of up to 36,000 pieces per hour Complex plastic closures (ex: sport cap)"},{"@ID":17 "MOULD MAKING PETplanet Insider Vol. 25 No. 01+02/24 www.petpla.net 15 96-cavity mould from Engel to Netstal Converting mould The faster the preform production, the more yield. The more durable the mould, the more the investment makes sense. This is even more the case if the tool can also be used on another machine. MHT Mold & Hotrunner Technology AG converted a 96-cavity mould from an Engel system to Netstal for Deltaplast, a Hungarian preform manufacturer, saving three seconds of cycle time. MHT manufactures high-cavity preform moulds for all PET lines on the market. The company has the expertise to adapt moulds from one machine type to another. MHT’s 96-cavity tool has been running reliably on an Engel macPET 330 at Deltaplast (Kecskemét, Hungary) since 2015. When this preform manufacturer purchased a Netstal PETline 4000 Side Entry model, it was worthwhile to rebuild the mould after 6.5 million cycles. Mr Zsolt Csengery, Deltaplast’s Chairman of the Board, commented: “We are happy to have MHT as a partner who not only supplies us with top moulds, but is also able to support us with special orders like this.” MHT has a wide range of adapter kits that can be used to convert moulds from one machine generation, machine brand or clamping force size to another. In some cases, it makes it possible to produce with more cavities after a conversion, with its upgrade kits. PROCESS PILOT+TM 2SWLPL]H %ORZPROGHU 3HUIRUPDQFH DQG 3URȴWDELOLW\\ ZLWK $XWRPDWHG &ORVHG /RRS &RQWURO Maximize rPET usability and processing Improve bottle performance and downstream operations Maintain lightweight, targeted material distribution Increase consistent production yield Overcome environmental and process variation 5HGXFH scrap with accelerated start-up +1.724.482.2163 agrintl.com In this particular case, MHT used an adapter set for the cold side and reconstructed the hot runner. MHT builds its own hot runners. The preform post-cooling (Post Mould Cooling) was brought up to date in Hochheim/Main, Germany. It includes a new removal plate as well as the patented CoolMax cooling solution, which combines the cooling and preform removal functions. CoolMax directs air flow efficiently to the thread and perform body, thus saving cycle time. The 96 prefoms at Deltaplast are now produced three seconds faster than before. The long-term use of PET moulds is not only financially attractive, it also reduces CO2 emissions, which is increasingly important in all areas of plastics processing. www.mht-ag.com"},{"@ID":23 "CAPS & CLOSURES 21 PETplanet Insider Vol. 25 No. 01+02/24 www.petpla.net An endless range o= ruo71ঞom rovvb0bѴbঞ;v with single-stage \" \"ĸrĸ ĸ (b- -7ࢼ 7;Ѳ -ouoĶ Ɛ ň ƐƎƍƏƔ (boubo (;m;|o Ŏ$(ŏ ň |-Ѳ $;Ѳĸ ƱƐƔ ƍƑƐѴ ƔƎƎƒƎƎ ň vbr-Şorr-vĸ1ol ň ĸvbr-ĸb| ECS SP models stand for a guarantee of quality based on 35 years of experience in Imf;1ঞom Stretch-Blow Molding technologies (ISBM) technology. Their robust system, produced in Italyķ -ѴѴov =ou |_; ruo71ঞom o= high quality containers in a b7; -ub;| o= 7b@;u;m| sizes, threads and shapes. Tooling investment can o[;m 0; orঞlb;7 by using one single (i.e. shared) hot umm;u b|_ lѴঞrѴ; 1oѴ7 _-Ѵ;vĺ \" \" l-1_bm;v _-; features that enable quick change-overs, accept legacy molds and are also characterized by their compact layouts and high ;m;u] ;L1b;m1. Imf;1ঞom Stretch BlowMolding System"},{"@ID":6 "PETcontents 4 PETplanet Insider Vol. 25 No. 01+02/24 www.petpla.net 1+2/2024 EDITOUR 10 Multinational brand on course for expansion in the UAE - Soft drinks, water and more snacks in the future MATERIALS / RECYCLING 12 Shifting focus - Starting with the end in mind for sustainable plastics packaging PREFORM PRODUCTION 14 Combined strengths for new wine packaging MOULD MAKING 15 Converting mould - 96-cavity mould from Engel to Netstal CAPS / CLOSURES 16 128 cavities in a 1.85 seconds cycle time - Where is the limit? 17 Navigating the transition 18 Weight savings combined with high performance - Boosting sustainability by lightweighting closures while maintaining performance and structural integrity 20 New challenges in sport caps making 22 New standard cap in Eckes-Granini portfolio - The Clip Aside tethered cap solution by Bericap 26 Secure down to the last drop - Practical, intuitive, and child-friendly new closure solution 27 Compact feeding solution 28 Consistent cap quality - Calibrated and validated in-line inspection 30 Closing the loop on bottle caps - Greenpath and Tomra pioneer mechanical sorting solution for separating polyolefins by polymer type and colour MARKET SURVEY 24 Suppliers of resins and additives EVENT PREVIEW 34 CBST & Chinaplas 2024 preview 37 From AA reducers to UV blocking EVENT REVIEW 38 PETinar: PET blow moulds and machinery BUYER’S GUIDE 40 Get listed! INSIDE TRACK 3 Editorial 4 Contents 6 News 32 Products 39 Patents 46 Outer Planet CAPS & CLOSURES Page 15 Page 10 EDITOUR Page 22"},{"@ID":16 "PREFORM PRODUCTION PETplanet Insider Vol. 25 No. 01+02/24 www.petpla.net 14 Combined strengths for new wine packaging In the ever-evolving landscape of plastic packaging, creativity remains a driving force behind transformative change. Sipa, the well-known plastic packaging specialist, designed the world’s first PET bottle specifically for sparkling wine. This new PET bottle has garnered significant attention within the wine industry and beyond. PET bottles for sparkling wine provide, in fact, numerous advantages, including lightweight design, durability, and sustainability. The pioneer PDG Plastiques: Forcing the packaging business in Europe The first player to recognise the potential of Sipa’s PET bottles for sparkling wine was the French preform, bottle and container manufacturer PDG Plastiques. The company converted Sipa’s new packaging solution into reality. Recognising the advantages the PET bottles offered, PDG Plastiques made a strategic investment in Sipa’s preform moulds with 32 cavities designed to produce sparkling wine preforms. PDG Plastiques invested in Sipa’s preform moulds as well as in the preform systems and blowing moulds. Their commitment to serving the wine packaging markets across Europe and their adoption of this sustainable packaging solutions exemplify their dedication to excellence. Expanding reach PDG Plastiques’ vision has enabled them to serve the wine packaging markets not only in their home country of France but also in Spain, Germany, and Italy, where the appreciation for fine wines runs deep. Their commitment has allowed them to make a significant impact on the wine packaging landscape. A sustainable future In addition to the advantages that PET bottles bring to wine packaging, PDG Plastiques produced the preform on Sipa’s XForm 350 GEN 4 preform system. The XForm platform, available in 250, 350, and 500 t, represents cost efficient PET preform production through conventional injection moulding. It boasts the capability to run moulds with up to 200 cavities, making it a versatile choice for various packaging needs. Sipa said that the advantages of the XForm are the high energy efficiency, low maintenance costs, and its ability to accept moulds from any manufacturer, showcasing its adaptability and value in the PET preform manufacturing industry. As the demand for available and sustainable packaging solutions continues to grow, Sipa and PDG Plastiques are offering PET bottle solutions that combine quality, sustainability, and design freedom. Together, they are redefining wine packaging, in a new, exciting, and eco-conscious way to enjoy the finest wines from around the world. www.sipasolutions.com www.pdg-plastiques.com The Sipa team and PDG management celebrate their success. The World Star-winning PET bottle for sparkling wine is launched on the international packaging market."},{"@ID":14 "MATERIALS / RECYCLING PETplanet Insider Vol. 25 No. 01+02/24 www.petpla.net 12 Starting with the end in mind for sustainable plastics packaging Shifting focus based on an article by Andrea Smith, Avient Increasing the amount of rPET can affect the processability, quality, and food safety of packaging. During the recycling of PET, it undergoes several remelting processes, which can cause thermal degradation and side reactions, resulting in rPET that is of a lower quality than virgin PET. This article will discuss the latest challenges and efforts from Avient to improve additives’ performance through recycling and design technologies with circularity in mind while maintaining functional performance. Today’s challenges Additives are added to PET to provide many functional advantages that can be particularly beneficial when using and processing rPET. However, as PET is recycled, it becomes increasingly important that these additives are designed to remain helpful and not adversely affect the quality, safety, and processability of rPET during the recycling process. This concept is of greater significance in closed-loop recycling systems, which are commonly used across Europe. Any negative impact from an additive could be enhanced due to the potential for accumulation in the closedloop system. Accumulation-related risks could be of particular concern, especially regarding regulatory or food safety. The accumulation of additives in recycling processes can lead to two potential issues. The first one is related to manufacturing and processability. For example, anthranilamide (ATA) based acetaldehyde (AA) scavengers are problematic due to high levels of sublimation. This issue manifests as deposition on the surface of the moulds in an injection moulding process, leading to downtime for cleaning the moulds, reducing efficiency and throughput. Deposition also occurs during the solid-state polymerisation (SSP) stage in the rPET manufacturing process when high levels of sublimation cause deposition on equipment, again leading to downtime for cleaning and reduced efficiency. If the levels of ATA in rPET keep accumulating, the processing issues related to ATA will also increase. The second issue is of higher concern and relates to regulatory compliance; the accumulation of ATAbased AA scavengers increases the risk of exceeding regulatory migration limits of ATA. This risk is well known and understood. However, when using ATA, there is a possibility of side reactions forming non-intentionally added substances (NIAS) components. These compounds also tend to accumulate over time despite being present at minimal levels and being undetectable until recently. As technology advances, the detection limits on analytical equipment have lowered, revealing the increasing concentration of these compounds due to the accumulation effect. This issue is now quickly becoming a concern for ATAbased products. Starting from September 2022, regulatory amendments have been imposed by Commission Regulation (EU) No 2020/1245 on Commission Regulation (EU) No 10/2011 regarding primary aromatic amines (PAAs). These compounds are present at minimal levels in PET-containing ATA-based scavengers and can now be detected by modern analytical devices. To remain compliant with the new regulations, it is necessary to provide additional toxicology data and migration testing for PAAs in PET articles containing ATA. PAAs are the first in a fast-growing list of other compounds detected in ATA-containing articles. Additional toxicology data and migration testing are crucial for these products to remain compliant. However, there is a significant risk of non-compliance that could result in a withdrawal of these products from the market in the future. Developing a solution To tackle today’s sustainability challenges, simulating the mechanical recycling process is necessary to design new additive technologies. Standard testing protocols at the European PET Bottle Platform (EPBP) and the Association of Plastic Recyclers (APR) are based upon one full recycle loop. However, as the use of rPET increases, the impact of two or more recycle loops is becoming increasingly significant. Therefore, it is more realistic to screen additive performance through at least two"},{"@ID":45 "CAPS & CLOSURES 30 PETplanet Insider Vol. 25 No. 01+02/24 www.petpla.net Greenpath’s vision is to create the same type of effective recycling system for bottle closures that exists for bottle recycling. Operating for more than 25 years with locations in California, Nevada and Texas, the vertically integrated Greenpath accepts a wide range of materials, and the flow of inbound materials can be somewhat inconsistent. However, this is where Joe Castro, President Greenpath Enterprises sees the company’s advantage in offering value-added services. Greenpath creates value being a one-stop solution for suppliers and customers alike by taking mixed trailer loads and variable supply streams and producing consistent, quality products. Materials received include paper, metals, and plastics. Considering only the polyolefin materials – low-density polyethylene (LDPE), high-density polyethylene (HDPE) and polypropylene (PP) – Greenpath accepts bottles, film, rigid plastics, and, of course, bottle caps. PE and PP have very close density characteristics and are challenging to separate into their different polymer types. That is why mixed polyolefins are primarily downcycled into more forgiving applications that allow for more contamination or a wider range of material specifications. “Alternatively, other companies use a ‘solution by dilution’ approach to include mixed polyolefins, using primarily virgin material and only a small fraction of recycled plastic,” says Joe Castro. With Greenpath’s focus on delivering value-added services to its customers, the polyolefin cap conundrum has kept Castro up at night for the last 15 years when they first started washing and processing recycled bottle caps. He had a vision for a sorting process solution to deliver high quality, consistent separation of HDPE from PP to give brand owners and manufacturing companies the flexibility to confidently include PCR in their injection moulding applications. “We are ultimately targeting 98% or greater purity levels,” offers Castro. The quest for cap to cap A beverage container commonly consists of four parts: the bottle, cap or closure, ring and label. States with recycled content laws for bottles have seen packaging companies and recyclers take the first step, focusing on the PET bottle, which comprises the bulk of the container’s weight. A more mature PET recycling infrastructure has led to brand owners incorporating up to 100% post-consumer recycled (PCR) material in their bottles. As regulations stiffen to increase the percentage of recycled content by weight, the next logical container component to address is the cap. “Following Greenpath’s approach, the industry can move toward a 100% PCR by weight package using only mechanical sortation,” says Eric Olsson, Area Segment Manager, Plastics, Tomra Recycling Sorting. For the cap to get to a recycler like Greenpath, the bottle is the carrier through the Material Recovery Facility (MRF). “Otherwise, the cap will get screened out in the front end of the circuit and more likely be landfilled,” mentions Castro. CAPS & CLOSURES Joe Castro (left), President Greenpath Enterprises, and Eric Olsson, Area Segment Manager, Plastics, Tomra Recycling Sorting Innosort Flake at Greenpath recycling facility Greenpath and Tomra pioneer mechanical sorting solution for separating polyolefi ns by polymer type and colour Closing the loop on bottle caps The full-service recycler, processor and manufacturer Greenpath has partnered with Tomra Recycling Sorting to install and optimise a plastic flake sorting production line designed specifically to identify and separate polyolefin caps from carbonated and non-carbonated beverage bottles. Mixed polyolefin bottle caps"},{"@ID":31 "CAPS & CLOSURES 29 PETplanet Insider Vol. 25 No. 0/24 www.petpla.net Standardised test systems and results within one production site or worldwide in different plants Only if every vision system is calibrated, it can be ensured that all production lines are delivering 100% identical quality. This standardised approach enables uniform quality standards for the final product, irrespective of the experience level of local operators. In-line measurement system with calibrated absolute values of +/- 10 μm The in-line measurement system introduced by IMD is claimed to allow customers to measure closures with absolute values, a departure from the previous reliance on relative values. This significant change is intended to provide closure producers with new possibilities in production process planning. The potential impact on alleviating the quality laboratory’s workload remains to be seen. Calibration also ensures that the quality and results at the production site align entirely with the feasibility study conducted by IMD’s laboratory. Following the completion of this study, the IMD application team provides customers with a new test program. This program, loaded onto the calibrated system, guarantees results identical to those obtained in the IMD laboratory, says the company. The program can be universally applied across all identical calibrated systems worldwide. Operator level in the future Looking ahead, the question arises: will camera specialists still be necessary in every production facility? Multinational companies have the option to create inspection programs for each product, defining tolerances and specifications in their global Quality Centre. These programs can then be easily uploaded to any IMDvista Cap Master worldwide. The market-ready technology and expertise in 100% calibration and validation position the industry to meet evolving market demands, ensuring quality independent of the operator’s technical know-how. The Cap Master can be seen in action at the NPE in combination with the new Sumitomo (SHE) Demag all- electric Pac-E (booth W3343) or at the IMD booth (booth S20115). www.imdvista.ch The calibration tool (top) and Vision Control Center V5 (below) for validation ALL- IN- ONE-MACHINE ASSEMBLY FOLDING SLITTING TETHERED CAP CONTEXO GMBH Tel. +49 (0) 7181 / 606-100 info@contexo-gmbh.de www.contexo-automation.de"},{"@ID":19 "CAPS & CLOSURES 17 PETplanet Insider Vol. 25 No. 01+02/24 www.petpla.net Navigating the transition In an era marked by evolving standards and sustainability imperatives, the shift towards new cap and neck formats can be a daunting challenge for producers. Balancing innovation with the need to protect investments requires a strategic approach. Sacmi asserts that a seamless, profitable, and future-proof transition is achievable through a triad of strategies. The ongoing transition towards new neck and cap formats, designed to comply with standards and sustainability requirements while keeping pace with consumption habits, can be bewildering for producers as they strive to innovate while safeguarding their investments. Sacmi suggests that a simple, profitable, and future-proof transition can be accomplished in three ways: by providing complete product solutions via the Rigid Packaging Lab, through close collaboration with major international certification bodies such as Cetie, and by adopting a win-win approach that expedites the uptake and diffusion of new standards. The 26/22 mm neck/cap transition Globally, there is an installed capacity of 39 billion caps for 26/22mm necks per year. From Africa to the Americas, from Europe to South-East Asia, an increasing number of producers are seizing this opportunity or planning to do so. This change commenced with the transition from the PCO1810 to the PCO1881, currently the world’s most commonly used cap. Over the last 10-15 years, this transition has resulted in raw material savings of more than 50%, enhancing plant profitability and environmental sustainability. Now, Sacmi is aiming higher with new solutions that are already on the market and certified by the major international brand owners. Future-proofing (tethered) The enforcement of the EU Directive on single-use plastics, which imposes the new tethered standard on European markets, raises questions about what manufacturers who operate in parts of the world where tethered caps are not (yet) mandatory should do. The technological approach Sacmi is offering involves slitting the tamper band in post-processing, downstream from compression moulding (CCM); this is claimed to allow the transition to be completed swiftly, flexibly and with limited investment. Secondly, Sacmi says that the switch to tethered caps can be combined with new neck standards. All the latest caps in the 26/22mm ‘family’ are available in both tethered and non-tethered versions. This enables producers to prepare themselves for future regulatory changes and adapt production setups to a variety of market contexts, countries and consumption styles. The Rigid Packaging Lab In addition to substantial installed output capacity globally, the company has chosen to pursue its business goals through technical-technological dissemination. The UAE, Nigeria, South Africa and India are just some of the places where Sacmi has organised country-specific seminars and provides comprehensive consultancy services. Ranging from the product and the technology to design, these services draw on a database of over 1,000 cap-neck designs that the lab has created for customers worldwide in recent years. 35% less plastic Every solution in the new 26/22mm family, for example the new multi-purpose caps such as the AB26 CSDT-5 for GME 30.40, is claimed to offer a specific advantage with respect to the ones already in use. The first, most general benefit is a reduced need for virgin resins while maintaining equal functionality, strength and sealing performance. On the tethered front, according to the company, there is no need for heavy investment in the mould, which would, among other things, lower line productivity and jeopardise the anticipated sustainability benefits. From a technological perspective, extensive digitalisation of each stage simplifies and upgrades the production process, with all the intrinsic bonuses of compression technology. www.sacmi.com CAPS & CLOSURES GME 30.40 neck finishes 26/22 AB26 CSD15"},{"@ID":27 "MARKET SURVEY 25 PETplanet Insider Vol. 25 No. 01+02/24 www.petpla.net Resins Company name Novapet, S.A. Köksan PET Packaging Industry Neo Group Reliance Industries Ltd Postal address Telephone number Web site address Contact name Function Direct telephone number E-Mail P° Independencia, 21, 3°, PC 50001, Zaragoza, Spain +34 976 216129 www.novapet.es Mr Ricardo Monfi l Head of Polymers Division +34 976 216129 rmonfi l@samca.com 4.Organize Sanayi Böglesi 83422 Nolu Cadde No: 10 Şehitkamil, Gaziantep, Turkey +90 342 357 03 30 www.koksan.com Mr Serhat Tümer Board Member +90 532 696 55 86 serhat.tumer@koksan.com Industrijos St. 2, Rimkai, Dovilai eld., LT-95346 Klaipėda district, Lithuania +37 0464 66 710 www.neogroup.eu Mr Gediminas Paulauskas Sales Manager +37 046466 710 Building 8B, Reliance Corporate Park, Ghansoli, Navi Mumbai 400701, India +91 22 79670000 www.ril.com Mr Bharat B Mehta VP Marketing +917710022861 bharat.b.mehta@ril.com RESINS 1. Brand name of the resins NovaPET K084 - K080 - K076 NeoPET Virgin PET \"Relpet\", rPET \"Relpet Green\" 2. IV Range 0.76 - 0.80, 0.84 0.56 - 0.82 0.59 - 1.00dl/gm a. of Homo-Polymers 0.58 - 0.96dl/g Homo polymers 0.76 - 0.84 0.76dl/gm b. of Co-Polymers 0.60 - 1.30dl/g 0.59 - 1.00dl/gm 3. Speciality resins No NeoPET Cycle Opaque grade for milk, Relpet OP5821 CSD LBS Soft, CR Available NeoPET 80, NeoPET 82 Relpet QH5821, Relpet G5841, Relpet Green B84 Water MW Soft, CR Available NeoPET 76, NeoPET 78 Relpet G5761, Relpet Green B76 Beer Glasstar + Sprit No NeoPET 80, NeoPET 82, NeoPET 84 Relpet B9845 (Barrier resin) Edible oil CR, Glasstar Available Relpet G5761, Relpet G5801 Wine / Liquors Glasstar, , LBS Soft No NeoPET 80, NeoPET 82 Relpet G5801, Relpet B9845, Relpet Green B80 Personal care / Pharmaceuticals Glasstar, Sprit Available NeoPET 80 Relpet G5801 Slow crystallisation Glasstar, Sprit No Relpet GL5000 Hotfi ll HF No NeoPET 82 HF Relpet H7761 Pre-coloured DCU, Luz, Polygloss No Fast reheat LB Soft Available NeoPET 82 FR, NeoPET 84 FR Relpet QH5821 Other CPET, HT, REX (for EBM), Sol (aerosol bodies), PET grades for other non-packaging applications Ultra NeoPET Relpet IM5590 for blood collection tubes 4. Increased barrier properties Light barrier: Dairy, Luz , DCU, Polygloss Gas barrier: Glasstar, Sprit No Relpet B9845 5. PEN mixes available No 6. Recycled blends available Yes, under customer requirements Yes NeoPET Cycle PET resins (25-30% PCR content) 100% rPET under Relpet Green brand 7. Special comments Focused on innovation at the service of packaging; specialised in light barrier protection; committed to create new markets for PET. MTS ( Melt-to-Resin) NeoPET Cycle - Innovation dedicated to sustainable future Customised grades can be developed"},{"@ID":38 "36 EVENT PREVIEW PETplanet Insider Vol. 25 No. 01+02/24 www.petpla.net Three questions for Boretech What recent developments in the PET market have significantly influenced your ongoing R&D initiatives? In recent years, we have observed several changes in the packaging market with the gradual increase in the application of recycled PET. Many countries have also progressively relaxed regulations on the use of recycled PET in food contact applications. Such measures have played a positive role in promoting the development of the PET recycling industry. On the other hand, there are new requirements for the design of PET bottles to facilitate better recycling. Some brands have introduced PET bottles without labels, contributing to improved recycling efficiency. Examples include the global launch of the first-ever “label-free Coca-Cola” in South Korea by Coca-Cola, 100% recyclable PET bottles without labels introduced by the Thai mineral water brand C2, and the redesigned labelfree green tea packaging from Suntory in Japan. These designs are being wellreceived by the PET recycling industry. We are pleased to see this series of changes, as they are crucial for us to adjust PET bottle recycling and cleaning processes. Furthermore, PET recycling industry players are expanding globally. Companies are aligning with ESG (Environmental, Social, and Governance) goals, demanding unmanned operation for recycling equipment, and presenting new requirements for water usage, energy consumption, and space utilisation. In the aspect of equipment development and improvement, Boretech is optimising operations concerning personnel, energy consumption, and space. The scope of PET recycling has broadened, and diverse solutions are proposed for different forms of PET containers. As we approach this year’s Chinaplas in Shanghai, we are eager to learn about your expectations for the event. What specific goals or outcomes are you anticipating for your company? Last year at Chinaplas, there was a noticeable lack of overseas attendees. In 2024, with travel restrictions completely lifted and the implementation of unilateral travel facilitation policies by the Chinese government, it is expected that the number of overseas visitors will increase, contributing to a more vibrant Chinaplas this year. We are eagerly anticipating the upcoming exhibition and have made thorough preparations. We will showcase our latest generation ES process recycling solution for PET bottles on-site to meet the evolving demands of the market. We look forward to the opportunity to connect with industry professionals and demonstrate our commitment to addressing the changing needs of the market. Could you please share a preview of what visitors can look forward to in terms of highlights on new products, technologies, or interactive experiences that will be showcased. Built on the enhancement of equipment performance and functionality, the new generation process, formed through the integrated design of the process, is streamlined for efficient operation. It features high-quality recycling and cleaning, with a production line characterised by advanced levels of automation and informatisation, low manpower requirements, low production costs, high product recovery rates, and a high costeffectiveness ratio. Occupying a smaller footprint with approximately a 25% reduct ion compared to traditional processes, Boretech system maximises cost savings for customers in terms of land use and factory construction for equivalent processing capacities. Highly modular, it achieves synergistic effects where 1+12, integrating processes seamlessly to reduce space requirements and enhance overall efficiency. Delivering high-quality finished products with virtually zero residual chemicals, our system exhibits exceptional cleaning performance, ensuring stable product quality suitable for both bottleto-bottle and ultra-fine fibre production. With low production costs and a reduction of approximately 1/3 in online labour requirements, the system emphasises machine automation, ease of maintenance, and high levels of efficiency, optimising unit energy consumption. Environmental ly sustainable, the system incorporates a 13.3% reduction in average energy consumption per ton of output through precise online filtration of chemical water, minimising overall resource usage. www.bo-re-tech.com Boretech Booth NF07 SMI enhances China presence at CBST Embracing a strategy centered on the ongoing enhancement of customer service, SMI has established a longstanding presence in China through SMI Machinery Beijing Co. Ltd. This strategic move enables SMI to effectively reach and serve key industrial hubs across the country, elevating the quality of technicalcommercial services provided to their customers. During the CBST event, SMI Machinery will be represented by their dedicated Beijing-based staff, showcasing the company’s portfolio. www.smigroup.it SMI Hall N1 | Booth 1E07"},{"@ID":15 "MATERIALS / RECYCLING PETplanet Insider Vol. 25 No. 01+02/24 www.petpla.net 13 MATERIALS / RECYCLING 13 full recycle loops. Avient has developed the “Heat Stability Protocol,” which involves screening new additive solutions for PET packaging for impact on colour and NIAS through two full recycle loops at 100% recycled content. With the use of high-tech analytical equipment for minimal impact on colour shift, so there are no adverse effects on impurities or product safety. In the case of AA scavengers, replacing ATA was essential to avoid processing and regulatory issues caused by recycling and product accumulation. A new molecule had to be designed to provide effective acetaldehyde reduction and full circularity. After stringent performance validation testing, extensive recycle and NIAS testing using the heat stability protocol, and multiple beta customer tests, Avient is offering a new patented AA scavenging technology called ColorMatrix AAnchor. It is designed with recycling in mind and is claimed to have much lower levels of sublimation than ATA-containing products. Furthermore, it does not cause deposition on moulds or equipment, and the potential for migration of this molecule is much lower than ATA, reducing the risk of exceeding regulatory migration thresholds, even in closed-loop recycling systems. Being ATA-free, ColorMatrix AAnchor does not cause the formation of PAAs. It is a liquid dispersion that can be added to an injection moulding or extrusion process using standard ColorMatrix liquid dosing systems. Implementing sustainable solutions for plastic packaging As the European Union sets new, mandatory targets to increase the amount of recycled content in plastic packaging and ensure its recyclability, new measures to safeguard the quality of rPET will also be required, especially for its use in food contact packaging applications where, besides being easy to process and having good mechanical properties, it’s important to avoid the creation of unwanted substances during repetitive processing. Further optimisation of the process and packaging composition will help the industry to overcome these challenges. It’s also necessary to develop existing solutions further to ensure the suitability of packaging for specific applications. The primary focus of new developments should be on eliminating gaps that limit the circularity of packaging. These criteria have become mandatory for packaging design in recent years. Understanding these gaps also requires a robust development process for new solutions. This process should involve simulating the recycling process multiple times to identify any potential accumulation of unwanted substances. Ultimately, this will help eliminate critical substances before a product launches and becomes part of the rPET stream. www.avient.com"},{"@ID":21 "CAPS & CLOSURES 19 PETplanet Insider Vol. 25 ronmental and commercial. The 25/22 variants offer reduced cost of production and weight savings of up to 1.85 g, compared with 29/25 (GME 30.26). Husky has developed a portfolio of 25/22 solutions that enable brands to achieve weight savings without compromising the consumer experience (see Fig. 5). An extended height 25/22 (~8.7mm) offers more grip than the typical 29/25 (~8.2mm) closure. This extended grip offers a good balance between weight savings and preserving the consumer experience. The above example is one of many innovative closure designs that Husky offers to help brand owners and closure manufacturers improve their sustainability efforts while improving profitability. The company says that all of this can be realised without compromising the consumer experience. www.husky.co Fig. 5: 29/25 & 25/22 dispensing system (neck + closure) comparison Fig. 4: Popular neck finish options (still water)"},{"@ID":25 "CAPS & CLOSURES 23 PETplanet Insider Vol. 25 No. 01+02/24 www.petpla.net its environmental footprint, EckesGranini focused on another aspect besides tethered caps: the modification of the neck finish to achieve significant material savings. The company opted to switch over its leading brand “hohes C” to bottles with the PET 26/GME 30.40 neck finish. “That was obviously a bold business decision that reflected our willingness to invest in the conversion of our filling systems,” said Céline Bacigalupi, Senior Manager Packaging & Technology at Eckes-Granini. The investment delivered impressive results because the quantity of plastic pellets required to manufacture the bottle and closure has been significantly reduced. Support in every detail In the future, Bericap’s Clip Aside tethered caps will be used with all the major Eckes-Granini brands – from hohes C and granini to Joker, Pago, Rynkeby and Brämhults. Line by line, joint project teams handled the preparations to switch over to the new closure generations, and custom solutions were developed for the different closure types on bottles of various sizes and designs. This meant developing detailed solutions for numerous sub-variants, all based on the general Clip Aside concept. “We have always been committed to providing our customers with comprehensive support,” said Thomas Henkel. “So we brought our technical upstream suppliers on board. Millions of euros of investments in moulds and processing equipment were essential to meet future demand for Clip Aside at the Eckes-Granini bottling plants.” Next steps The work is almost finished: the new tethered caps have been validated on each of the filling lines, the new moulds have been put into operation at Bericap and production has been ramped up. The focus is now on optimising line efficiency and ensuring the technically correct application of the closures. The Bericap technical service team is providing on-site support to establish the optimum settings together with bottlers and machine manufacturers. “The last lines are scheduled to be converted in May,” said Tobias Schardt. “Thanks to Bericap’s innovative Clip Aside caps, we’ll be compliant with the EU’s tethering requirements before July 2024. At the same time, it’s great to know that we’re helping to reduce plastic material usage in every Eckes-Granini bottle we sell.” www.bericap.com www.eckes-granini.com Packaging Closures þĊĕĉ õĆĕĔĕĂč Ĕ čĆĂąĊďĈ ĊďċĆĄĕĊĐď ĎĐčąĊďĈ ĕĆĄĉďĐčĐĈĚ ćĐē ĉĊĈĉ½ĔđĆĆą ĂđđčĊĄĂĕĊĐďĔ Wemaximize your added value NPE 2024 I W223"},{"@ID":30 "CAPS & CLOSURES 28 PETplanet Insider Vol. 25 No. 0/24 www.petpla.net Calibrated and validated in-line inspection Consistent cap quality For over two decades, IMD has dedicated itself to expanding and optimising in-line and off-line inspection systems for beverage closures. Throughout this period, technological advances have shaped the landscape. The fundamental principle, however, has endured - the operator’s precise setup of the inspection system remains pivotal in guaranteeing closure quality before packaging and delivery to customers. This standard, IMD claims, could now be replaced by a new quality assurance system. “To this day, the operator is a key factor in ensuring quality and system settings,” says IMD. “Globally, we have found it more difficult to find qualified operators who can set up and operate the production lines and the vision systems according to quality specifications. It is becoming obvious and imperative to be able to eliminate this uncertainty factor in the future.” In response, the Swiss company introduces the IMDvista Cap Master - a vision inspection system that can be calibrated and validated for inline high-speed systems. If a system does not successfully pass the validation process, the production line cannot be started until re-calibrated in order to ensure customer quality. It actually should be already a standard process, the company says, as manual adjustments by operators can lead to variations in test tolerances and settings across different systems. The calibration and validation process involves a reference tool which itself is calibrated and provided with a test certificate. Operators can use an automatic software process to calibrate the system, aligning factors such as lens, illumination, camera, software, and mechanics through a reliable and repeatable process. The “backbone”, a new mechanical structure and essential concept A completely revised mechanical structure of the conveyor was required in order to calibrate the system in a very precise manner. IMD developed a new type of basic mechanical frame concept for this purpose. The so-called “backbone” is the solid and robust fundament of this new concept. The calibration concept can only be implemented if the mechanics are designed to ensure 100% repeatability during assembly, operation, maintenance and service. Through the backbone also the cameras, sensors and blow-out nozzles can be calibrated and set up into operation with a claimed 100% accurate repeatability. CAPS & CLOSURES /' The IMDvista Cap Master has been designed to guarantee quality assurance across all test systems, regardless of who sets it up."},{"@ID":2 "CAPS & CLOSURES 18 PETplanet Insider Vol. 25 No. 01+02/24 www.petpla.net Boosting sustainability by lightweighting closures while maintaining performance and structural integrity Weight savings combined with high performance Beverage brand owners and/or packaging manufacturers are working to reduce the impacts their businesses have on the environment. The motivations for these efforts can legislative, or to better align with the values of their stakeholders (e.g. ESG compliance). Husky’s beverage closure business is helping to enable the circular economy with its manufacturing technology. While significant focus on lightweighting is placed on the PET bottle, the closure can also make a meaningful contribution to further improve the sustainability of the overall package. Husky has developed a leading portfolio of closures in terms of weight and performance. Weight optimisation is achieved using sophisticated simulation tools backed up with a deep knowledge base. The basic concept of lightweighting is simple. Remove as much resin from specific closure features as possible without impacting performance or the user experience. A lower part weight requires less time to manufacture thereby improving productivity. Reducing the amount of resin used in each closure may involve the modification of feature specific geometry. These geometric modifications are subject to multiple simulations, to ensure performance is at least maintained or improved. An iterative simulation approach is applied until the performance criteria are satisfied. Fig 1: A 29/25 still water closure broken out into its fundamental elements. Simulation tools are used to predict how much material can be removed from each feature without negatively impacting performance/usability. Husky says that it has developed a leading portfolio of ultra-lightweight closures leveraging extensive use of mechanical and melt flow simulation tools. The process involves breaking the closure down into its specific features (Fig. 1), and focusing on material removal without compromising performance or usability. Simulation tools are used to predict performance behaviour. The features are modified accordingly until the target weight is achieved and simulation outcomes are favourable. Fig. 2: Popular neck finish options (CSD) The introduction of new industry standard neck finishes presents an opportunity to develop higher levels of performance at a lighter weight. Fig. 2 identifies the most common neck finishes used for CSD applications. While other CSD neck finishes exist, these tend to have a regional focus and are not as widespread on a global level (e.g. PCO1873). The recently introduced 26/22 CSD family (GME30.37, GME30.40, & GME30.41) of neck finishes offers opportunities for weight savings combined with a high level of performance. PCO1881 (3.81 g) is the most common CSD finish globally. The next generation 26/22 CSD neck finishes range in weight from 2.30-2.70 g. Fig. 3 identifies the critical dimensions of PCO1881 compared with the new 26/22 CSD options. All three 26/22 CSD finishes feature the same inner bore diameter of 21.7418mm (same as PCO1881), thereby preserving the drinking experience. The GME 30.40 and GME 30.41 finishes offer a higher performance rating for gas carbonation at 5.2 vol, compared with 4.5 vol for the PCO1881 finish. GME 30.37 offers an even lower rating at 4.2 vol. but with a slight weight savings benefit. GME 30.40 is compatible with tethered caps; GME 30.41 is designed for non-tethered applications. Fig. 4 identifies the most widely used neck finishes for still water. The 25/22 (GME 30.39) and 26/22 3-Start (GME 30.28) have emerged as viable alternatives to the 29/25 (GME 30.26) standard in recent years. The 25/22 and its variants have expanded beyond North America and have seen brand adoption in other regions including Europe, Middle East, SAARC, and Southeast Asia. The key drivers for this adoption are both enviCAPS & CLOSURES Fig. 3: PCO1881 & 26/22 CSD neck finish variants"},{"@ID":10 "8 NEWS PETplanet Insider Vol. 25 No. 01+02/24 www.petpla.net Petcore Europe – Annual Conference 2024 The conference, being held in Brussels from February 7-8, 2024, will take place against the background of the finalisation of the EU’s landmark Packaging and Packaging Waste Regulation (PPWR). Day One will consider the impact that the regulation will have on businesses operating both upstream and downstream, with industry experts and representatives from the European Commission. This year Petcore Europe will gather three DGs: DG Sante, DG Grow & DG Env, namely, Bastiaan Schupp – Legislative Officer – Food Contact Materials for the European Commission (DG Health and Food Safety), Stefano Soro – Head of Unit – Green and Circular Economy at European Commission (DG Grow) and Wolfgang Trunk – Policy Officer at European Commission (DG Environment) are coming together to debate and explore market developments shaping the sector. The agenda will cover reams of legislation and impending regulation, and address the challenges and opportunities facing those in the PET industry. Petcore Europe is launching a new working group, Advocacy, to cope with these challenges. The President of Petcore Europe, Antonello Ciotti, explains that the association has “a lot to say” on these issues and adds that Petcore Europe needs to be more agile in promoting its ideas when it has a common position among all its members. On Day One, the latest updates on textile and the ongoing PET Communications Campaign 2024 will be revealed. “Communication is important, and we must show how the PET bottle is being recycled,” says Antonello. “It can only be done if the consumer takes the first step. In countries without deposits, we do campaigns to increase the consumer’s understanding that recycling starts with them. The value of rPET is important and there must be an incentive for companies to start collecting.” During Day Two the experts from the entire PET value chain will share their updates on LCA, reuse, labels and other insightful topics, covering all the challenges and innovations, embraced by Petcore Europe Technical WGs throughout 2023. www.petcoreeuropeannualconference.org Reliance Industries becomes first in India to use chemical recycling for circular polymers Reliance Industries Limited (RIL), operator of the world’s largest integrated refining and petrochemical complex, has become the first Indian company to chemically recycle plastic waste-based pyrolysis oil into International Sustainability & Carbon Certification (ISCC)-Plus certified circular polymers. RIL shipped its first batch of ISCC-Plus certified circular polymers, named CircuRepol (Polypropylene) and CircuRelene (Polyethylene). RIL paves the way in India by using new technology to recycle plastic by converting plastic waste into special circular polymers, thereby making a positive impact on the environment. RIL’s commitment to sustainability is demonstrated through its innovative methods like chemical recycling which help create a circular economy. The company firmly believes in finding smart solutions to reduce plastic waste and inspire others to join in this journey towards a greener future. CircuRepol and CircuRelene have been designed to lead the way in circular economy practices. RIL’s Jamnagar refinery became the first refinery to get the important ISCC-Plus certification, proving that it can produce circular polymers through chemical recycling. The ISCC-Plus certification guarantees that traceability and rules are followed in making circular polymers. RIL has developed a technology that turns different types of plastic waste, including single-use and multi-layered plastics, into pyrolysis oil. The company is working with trusted partners to increase the production of this oil and turn the yield into circular polymers. Chemical recycling has many benefits, including turning plastic waste into high-quality materials for new plastic. These materials can be used for packaging that comes into contact with food. www.ril.com Hungary launches new deposit return scheme for drink container recycling Starting from January 1, 2024 Hungary has implemented a new deposit return system (DRS) for recycling singleuse drink containers. Manufacturer of reverse vending machines Tomra has partnered with Mohu (MOL Hulladékgazdálkodási Zrt.), the central system administrator for the DRS, to roll out a collection infrastructure aimed at making drink container returns as convenient as possible for recyclers. This DRS covers ready-to-drink or concentrated beverages (except milk and milk-based beverages), in singleuse aluminium cans and glass/plastic bottles, ranging from 0.1 l to 3 l in size. Consumers pay a deposit of 50 Hungarian forint (approximately 0.13 €) when purchasing an eligible drink, which is refunded to them once they return the empty drink container for recycling. Drink containers in Hungary can be returned to grocery retailers over 400m2 in size, and the growing number of voluntary and manual sites. This initiative aims to integrate recycling into consumers’ existing shopping routines. Tomra has installed more than 1,000 high-volume reverse vending machines (RVMs) for medium and large locations like supermarkets and hypermarkets in urban settings across Hungary, with the roll-out of further RVMs to continue in 2024. When a consumer inserts drink containers into an RVM, it automatically identifies and sorts the containers, and pays out the correct refund, more efficiently and securely than with a manual return of containers. Hungary’s DRS follows closely after a new deposit return systems launched in the Australian state of Victoria on November 1 and in Romania on November 30, and comes ahead of Ireland’s launch next month on February 1, 2024. www.mohu.hu www.tomra.com"},{"@ID":11 "9 NEWS PETplanet Insider Vol. 25 No. 01+02/24 www.petpla.net ClipAside, drink, love! On an exponential growth path: Tethered ClipAside passes the 6 billion mark. Contact us and arrange your line trials now! www.bericap.com PET 38 PET 29/25 PCO 1881 PET 33 PET 26 PET 26 GME 30.40 A consumer real-life study conducted in France found a high level of acceptance among consumers for our innovative new closure. After just one or two experiences, even the youngest and oldest users could handle the smart closure without difficulty – often with one hand. What’s more, many praised the eco-friendly nature of the cap, which remains on the bottle neck and avoids creating additional plastic waste. Best of all for you, this premium product can be integrated into most lines for any popular neck finish without major modification of your production equipment - proven by more than 70 successfully converted filling lines across Europe."},{"@ID":37 "35 EVENT PREVIEW PETplanet Insider Vol. 25 No. 01+02/24 www.petpla.net Three questions for GDXL What recent developments in the PET market have significantly influenced your ongoing R&D initiatives? For the commodities which PET packages generally apply, including beverages, food, personal care and household products, we observe recent trends of consumers looking for healthy, cost-effective and individualised products. There also have been growing concerns about sustainability and corporate responsibility. All these have subsequently driven our development direction for PET packages. As a PET package engineering solutions provider, our R&D focus on optimising PET preform and bottle design, as well as their corresponding mould design and structure to achieve improvements in performance, light-weighting, productivity, as well as saving raw materials and energy costs. These raise the value of the resulting products. We have also been working with our partners on new industrial applications such as multi-layer co-injection and containers with integrated moulded handles, to deliver individualised packaging solutions. As we approach this year’s trade shows in Shanghai, we are eager to learn about your expectations for the event. What specific goals or outcomes are you anticipating for your company? This year we don’t plan to take part in Chinaplas, but will take part in CBST to be held in early March which focuses on various aspects of beverages. We utilise CBST as an ideal platform to enhance relationships with our domestic customers who continuously support us, and to discuss any on-going and potential projects. Besides, compared with the event last year when China had just opened up its borders after the pandemic, this year we expect there would be more foreign visitors participating in the event. This is good news to us, as foreign markets have been our growth driver in recent years, particularly in the South Asia region. Could you please share a preview of what visitors can look forward to in terms of highlights on new products, technologies, or interactive experiences that will be showcased. For CBST, visitors can look forward to the latest industrial developments across the beverage production chain in China from raw material processing, food additives, sterilisation, packaging & labelling, filling & sealing, beverage innovation and marketing. i.e. key aspects on which a beverage business needs to focus. Major stakeholders in the China beverage sector will take part in CBST. Moreover, the event’s organiser, the China Beverage Industry Association, will also host an annual conference and innovation forum during the event to discuss the latest industrial trend and development of the beverage industry in China. On the other hand, Chinaplas covers raw materials, injection and auxiliary equipment across major plastic-related industries including automobile, building, medical, electronics, general packaging, daily life commodity, as well as recycling & circular economy. And it covers various types of plastics, PET is just one of them. Visitors can expect there will be emphasis on innovation on sustainability and applications of artificial intelligence. As the scale of this four-day event is huge, we would advise visitors to plan ahead for any interested targets. www.gdxl.com GDXL Hall N1 | Booth 1E03"},{"@ID":48 "OUTER PLANET 46 PETplanet Insider Vol. 25 No. 01+02/24 www.petpla.net OUTER PLANET Bottle made of compostable material The bottle that disappears In the realm of sustainable design, Tomorrow Machine, a Swedish design studio, has worked extensively to develop packaging solutions that replicates the life cycle of fresh products. In collaboration with the global juice company Eckes Granini and their premium brand Brämhults, a bio-based juice bottle made from potato is now being developed. 21-22 February 2024 AVANI Sukhumvit Bangkok — Thailand 2nd ICIS Recycled Polymers Conference Attended by key market influencers and senior professionals, the 2nd ICIS Recycled Polymers Conference | Asia allows delegates to gain critical insight into the recycled polymer industry and learn how to overcome pain points stakeholders are having. The conference is also the perfect place for you to meet potential business partners and customers, so you can collaborate with the entire value chain to enhance the plastics circular economy. Advancing plastics recycling through development and collaboration To find out more, visit the conferencewebsite: www.events.icis.com/recycledpolymersasia the unique design approach, “With a bottle designed to be torn apart after it has been used, by peeling it like a fruit, the idea is that oneself can speed up the decomposition process. When you break the packaging and put it in contact with water, a natural reaction starts to break down the bottle immediately – and that’s how we created a bottle with the ability to disappear by itself.” GoneShells is a research project aiming to replace fossil-based materials as well as to question the lifespan of today’s packaging. Supported by the strategic innovation programme BioInnovation, a joint venture by Vinnova, Formas and Swedish Energy Agency and with expertise from Rise Research Institute of Sweden and F&B Happy, development is carried out along with the design of prototypes. The initial phases of the testing process show great potential. Eckes Granini and Tomorrow Machines are excited to continue their shared journey of developing a sustainable packaging for Brämhults. www.goneshells.com degrade it. The uniqueness of GoneShells lies in the speed and multiple alternatives of degradation. The material has been developed with the ability to break down under different conditions and work in symbiosis with what is inside. So, when the project is ready for the market, the bottle can be eaten, home composted or even dissolved under your water tap in the kitchen sink, says the design studio. Anna Glansén, Founder at Tomorrow Machine, explains Tomorrow Machine highlights the need to challenge existing packaging norms, emphasising that while the contents inside may spoil within days or weeks, traditional packaging solutions often endure for years or even decades. Furthermore, many currently available biodegradable packaging materials necessitate industrial composting processes. So the special feature of bottle is not just the bio-based material it is made of, but the multiple possibilities to"},{"@ID":41 "PATENTS PETpatents www.verpackungspatente.de PETplanet Insider Vol. 25 No. 01+02/24 www.petpla.net 39 Closure with retaining strap European Patent No. EP 4140914 A1 Applicant: Closure Systems International Espana S.L.U., Barcelona (ES) Registration date: 10.10.2019 A closure with retaining strap, which can be easily twisted and secured by the consumer. Retaining strap International Patent No. WO 2023 / 057742 A1 Applicant: Creanova Universal Closures Ltd., Bath (GB) Registration date: 3.10.2022 A screw cap with tamper-proof strip that “unrolls” when first opened, then acts as a retaining strap long enough for the screw cap to easily fit under the neck ring. Cap with support ring Application No. DE 102021125520 A1 Applicant: Bericap Holding GmbH, Budenheim (DE) Registration date: 1.10.2021 The closure cap is attached to the lower section which, when opened, does not flip back during pouring or drinking from the bottle, thereby avoiding any inconvenience to the consumer. Container closure International Patent No. WO 2021 / 245218 A1 Applicant: Alpla Werke Alwin Lehner GmbH & Co. Kg, Hard (AT) Registration date: 4.6.2021 A container closure to which a screw cap is attached via two retaining straps. The lid should be handled carefully to avoid any dirt created by product residues from the cap getting on to the bottle or consumer. Screw cap International Patent No. WO 2023 / 085211 A1 Applicant: Toyo Seikan Group Holdings Ltd., Tokyo (JP) Registration date: 4.11.2022 A screw cap with tamper-proof strip made from up to 94% biodegradable/organic material. Fixed closure International Patent No. WO 2023 / 081880 A1 Applicant: Silgan White Cap LLC., Downers Grove (US) Registration date: 7.11.2022 A closure with tamperproof/retaining strap. When opened, the lid is fixed in a certain position so as not to get in the way when the product is being poured or drunk. CAPS & CLOSURES"},{"@ID":4 "CAPS & CLOSURES 27 PETplanet Insider Vol. 25 No. 01+02/24 www.petpla.net CAPS & CLOSURES 27 Compact feeding solution Intravis GmbH presents a new, space-saving solution for feeding closures to an inspection unit. Bunker and feeder are combined on a very small footprint with the same performance as before. Intravis has been known primarily for its vision inspection systems for the quality control of plastic packaging. In recent years, however, the Aachen-based company has also made a name for itself with feeding solutions for plastic closures. Intravis launched its first in-house sorter – the CapFeeder – back in 2018. Over the last six years, it has been characterised by the fastest feeding performance on the market. In the meantime, Intravis expanded its portfolio of feeding solutions to include cooling and cross conveyor belts, which can be adapted to the respective production line layouts of customers. Intravis is now presenting a new, compact, and space-saving solution for the feeding area. The so-called Tower Bunker is arranged vertically above the CapFeeder on a footprint of just 3 m². The bunker serves as an intermediate buffer and forwards the closures to the CapFeeder. The CapFeeder orients the closures and transfers them to the inspection system. Developed for a major customer this solution addresses one of the biggest problems in modern production facilities. Marius Pötting, Product Manager Caps and Closures at Intravis, is responsible for closure inspection systems and therefore also feeding solutions. He reports: “We often hear, especially from our customers in industrialised nations, that they lack space at their production sites. They try to make maximum usage of their production area and eventually reach the natural limits of their premises. With a customer-oriented solution in mind, Intravis has also optimised the space utilisation of the feeder by arranging the Tower Bunker vertically above the CapFeeder. This has significantly reduced the footprint. In most production halls, on the other hand, there is sufficient space in height. The result is a space saving of up to 40% compared to previous layouts.” The performance of the CapFeeder remains unaffected by the small footprint. In combination with the Tower Bunker, the feeding unit achieves the same feeding speed – i.e. up to 288,000 closures per hour. With a capacity of 400 l, large quantities of closures can be conveyed at highest production speeds. The Tower Bunker measures 2.30m in height. “The Tower Bunker in combination with our CapFeeder offers the same performance in a very small space. The Tower Bunker’s first customer is actually very impressed.” reports Marius Pötting. www.intravis.com Shall we? %X 7%'1- TEVXRIVWLMT MW JSVIZIV Choose everlasting excellence for your tethered cap production plant. With SACMI ]SYƅPP ƼRH E JYXYVI VIEH] WSPYXMSR XLEXƅW designed to stand the test of time. sacmi.com E N D L E S S I N N O V A T I O N S I N C E 1 9 1 9 CAPS & CLOSURES"}]}}
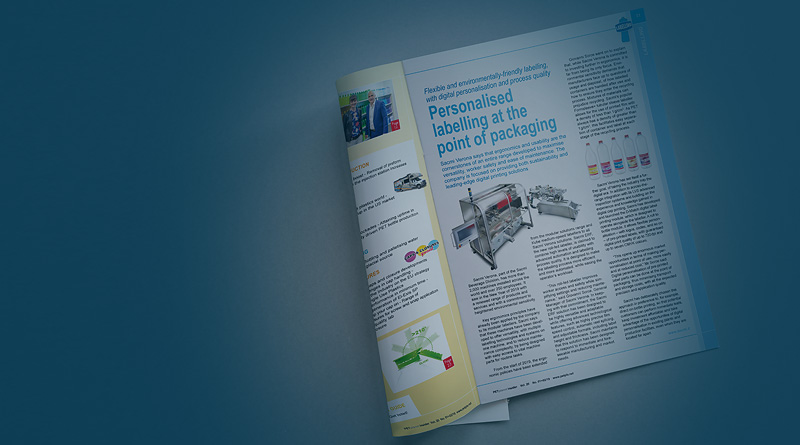