"PRODUCTS 41 PETplanet insider Vol. 15 No. 05/14 Automatic dew-point and temperature control system Motan-colortronic have developed ATTN – an automatic temperature and dewpoint control system which maintains the dew-point of the granulate being dried constantly to a defined value in line with the process parameters of the part being moulded. ATTN is now a standard feature throughout the entire Luxor A range of dryers. ATTN is said to maintain a constant dew-point of the process air. It is suitable for materials that require predefined moisture content which would be damaged if over dried as a result of too low dew-points. The dew-point of the process air is constantly regulated and documented to ensure regulation precision within +/- 1°C. ATTN has been designed to maintain a constant dew-point of the process air for drying plastic granules. It is generally installed in the dry air generator and can only be set to one specific dew-point between -30°C and +5°C. This pre-set dewpoint value is then stored and maintained. This principle requires that the amount of moisture in the process return air is higher than the set dew-point. Under normal atmospheric conditions, this is the case with a control dewpoint between -30°C and -5°C. www.motan-colortronic.de Granulate temperature and dew-point control system Masterbatches for RPET Sukano has introduced a range of masterbatches that are intended to allow the integration of virgin polyester functions into RPET many times over . An optical brightener is said to reset the colour tone of the recycled material from yellowish to neutral. In addition, a melt strength enhancer reacts with broken molecular chains in the recycled PET and should restore them into almost their original strength. This increases viscosity and improves mechanical properties, making the material easier to process. The toughness of the material is claimed to be improved by impact modifiers which also improve antisplice properties for straps made from RPET. The company also offers slip/antiblock masterbatches for COF reduction at minimum haze increase as well as colour masterbatches and foaming agents. The functionalities can be combined in a single masterbatch or selected separately by the converter. www.sukano.com","@ID":43}, "TRADE SHOW REVIEW 38 PETplanet insider Vol. 15 No. 05/14 petpla.net Chinaplas 2014: Shanghai show attracts record numbers By the time Chinaplas 2014 closed its doors it had attracted a record number of visitors and delegates and had reinforced its claim to be the largest plastics and rubber fair in Asia. The show’s 28th edition was held at Shanghai New International Expo Centre (SNIEC), PR China, and ran from April 23-26. It attracted 130,370 visitors across the 4-day show, which was more than 14% higher than the previous show in Guangzhou and was the highest number ever. The total of overseas visitors also reached new heights, at 36,841 – nearly 20% more than in 2013 – from 143 countries, including India, Indonesia, Iran, Japan, Korea, Malaysia, Thailand and Russia. Domestic visitor numbers were also higher than ever, at 93,529; more than 12% higher than last year. Over 3,000 exhibitors from 39 countries and regions participated. Exhibitors occupied 13 outdoor halls and six exhibition suites, specially set up in SNIEC’s central square, in addition to all 17 exhibition halls. Total exhibition area exceeded 220,000m2 for this year. The showground accommodated 3,200 sets of machinery including energy saving, high performance and automation, and a diverse range chemicals & raw materials aimed at individual market needs. The exhibits were classified into eleven themed zones, including: Extrusion Machinery, Injection Moulding Machinery, Chemicals & Raw Materials, Auxiliary & Testing Equipment, Die & Mould, Film Technology, Plastic Packaging & Blow Moulding Machinery, Rubber Machinery & Equipment, Chinese Export Machinery & Materials, Bioplastics and Semi-finished Products. There were a number of advanced technologies including 3D rapid prototyping; micro-injection moulding; recycling; and technology for continuous fibre-reinforced composites. “Greenovation - Solution to Sustainability”, which ran concurrently, featured “The City of Tomorrow”, an open, semi-spherical structure portraying a sustainability model encompassing four aspects of manufacturing cycle: Green & Alternative Raw Materials; Energyefficient Machinery; Green Solutions for Customers; and Products and Recycling. The 29th edition of Chinaplas will be held on 20-23 May, 2015 at China Import and Export Fair Complex, Guangzhou, PR China. www.ChinaplasOnline.com Convey, blend and dry American company Conair presented web-enabled controls for dryers, blenders and material-handling systems, which can be accessed by a computer or smart phone and Internet connection to monitor conditions and change settings. The web-enabled and remotely-accessible equipment on show included a TB250 TrueBlend gravimetric blender with SB-2 control; W1000 Carousel Plus desiccant dryer with DC-T touchscreen dryer control; FLX central vacuumconveying system; and its DM3-e and TrueFeed gravimetric feeders. Conair Controls with data-gathering capabilities, like the Drying Monitor or SB-2 blender controls, can generate reports that can be immediately exported to reporting software. Also on the stand were MDA Series mould dryers, which deliver a flow of air dried to a -10°C (14°F) dew point. Conair says that the dry air prevents moisture from condensing out of warm humid ambient air onto cool mould surfaces. The system is designed for PET preforms and other products that require low-mould temperatures to maintain short cycle times and is claimed to be particularly useful in non-air-conditioned plants. China-manufactured Conair equipment on show included a mobile drying/conveying system and a BFSA volumetric feeder with stainless steel material hoppers as standard. www.conairgroup.com Anti-waste inspection systems German company Intravis GmbH, which specialises in vision inspection systems for the plastic packaging industry, believes that the Chinese plastic packaging market is in the process of transformation and that price pressures are leading to the drive to cut wastage of materials and energy. The company has opened a new subsidiary in China – Intravis Co. Ltd. – and has now sold nearly 50 units in the Asian markets. One of the new features demonstrated at Chinaplas was a user interface in Chinese. It is available on its preform and closure systems such as PreWatcher III, Sample-PreWatcher and CapWatcher III. www.intravis.de New underwater pelletising system Pump Solutions Group (PSG) launched its Automatik Plastics Machinery Sphero S underwater pelletising system at Chinaplas 2014. The company says that Sphero S has been specifically designed to be a costeffective alternative to larger and more customisable systems. The new machine incorporates a number of new developments and upgrades that are designed to be particularly suitable for compounding, masterbatch and recycling applications with medium throughputs of 0.7-3t. It features new pneumatic diverter valves, which are designed to optimise the flow channel and ease the cleaning of the cutting chamber. Improvements also make it easier to clean and to achieve quick knife changes. Its new frame allows it to be mounted on a single mobile structure, which is claimed to enable perfect alignment and a reduced footprint. The water bypass design has also been tuned for a faster start-up. www.psgdover.com","@ID":40}, "ONsite 42 PETplanet insider Vol. 15 No. 05/14 petpla.net With Sacmi, the beverage specialists are always at your side. With our unbeatable technological know-how and continuous research we are creating new containers and closures designed to ensure outstanding performance. The new IPS injection system for preforms and the CCM compression press for caps, fully designed and built by Sacmi, allows for large-scale production with considerable advantages in terms of efficiency and flexibility. The outcome? Reduced plastic volumes, less energy consumption and lower running costs. All in a bottle: the one you’ll soon be making. Preform & Closure technologically together Save RAW MATERIALS reduced plastic volumes Save ENERGY less energy consumption Save TROUBLE more quality and higher performance, guaranteed by a sole supplier Full INSPECTED online quality control / stand alone Growing appetite for edible oils The edible oil market in South Africa continues to grow. Wilmar Continental Edible Oil is one of the main domestic producers of sunflower seed oil and mixed seed oil and is responding to consumers’ new demands by continued investments. The company is well known throughout South Africa for the Excella, S’Lite, Pan and Canola oil brands and for the Conti mayonnaise, which are sold in retail stores and mass retail supermarkets. For the second time, it has invested in SMI’s packaging technologies for a PET line to fill edible oil. Less than a year into the modernisation project of the oil PET line in the plant in Randfontein, about 30km from Johannesburg, Wilmar Continental Oil has renewed its partnership with SMI for a new PET line for the 2l formats. Before completing the installation of the Smiflexi LWP 25 wrap-around case packer, the APS 3000 automatic palletiser and the Smiline conveyor belts for the expansion of the existing packaging plant for 350ml and 500ml bottles, new negotiations had been entered into between the two companies for the supply of a new “turnkey” line. In order to meet the growing market demand, Wilmar Continental Oil decided to invest in a new Smiform Ecobloc 4-24-6 VMAS integrated system for the stretch blow-moulding, filling and capping of up to 6,000bph of 2l PET containers and a Smiflexi combined packer of the LCM 30 series for the secondary packaging of said bottles in wrap-around boxes, tray+film and pad+film. Marketing Manager Asif Moosa comments: “The new investment is part of a multiannual plan of continued expansion of Wilmar’s facilities and market share made possible by the strong demand for our Excella-branded “premium” edible oil, which we sell in 2l bottles, from the domestic market and also from neighbouring countries”. www.smigroup.it","@ID":44}, "BOTTLE MAKING 34 PETplanet insider Vol. 15 No. 05/14 petpla.net SMI’s HSR stretch-blow moulder: Power reduced, savings up, production increased A golden thread Preforms heating module The company examined each of the machine sections in turn with a view to improving performance and efficiency. These included preforms feeding, heating module, stretch-blow moulding stations, bottle unloading. A particular feature involved simplifying the machine’s mechanical components by a mechanism for changing the pitch of the preform-holding spindles. This system has now been patented by SMI and the company claims cleaning and maintenance, as well as operating efficiency have been enhanced as a result. A further improvement, according to the company, involves the elimination of the spindle-holding chain inside the heating module, thus reducing the mechanical stress to which the machine is subject, and incidentally reducing machine jamming and downtime. When SMI investigated the preforms heating system, they devised a thermodynamic reflection system bringing high energy savings compared to conventional systems. This system heats the preforms using five infrared lamps on the front panel and only one IR lamp on the counter-panel. This means an average decrease of 40% installed electric power and a power consumption energy saving of up to 30% compared to conventional preforms heating systems, which require 10 or 11 IR lamps to achieve the same results. The modular design means that lamps are easy to remove and replace. Stretch-blow moulding carousel The preforms’ pre-stretching, stretching and blow moulding lock are mounted on the moulds. The valves unit, the stretch rod and the blow-moulding piston are grouped in a single integrated module, a technology developed by Swiss company Seitz. The company claims the motorised system will perform 25million cycles service-free). In addition, all the settings of the downward profile of each stretch rod can be changed. The grippers have also come in for some attention. These grip the preform and release the bottle during the stretchblow moulding process. By introducing a novel technical solution, the preform’s neck remains firmly anchored to the grasping gripper during the bottle’s entire production cycle, with advantages in terms of stretch-blow moulding operation precision and preform neck protection. Motor drive and man-machine interface The control panel is integrated into the system’s structure and a simple, user-friendly interface allows the operator easy control of all production operations, while also providing a full set of data in real time on machine running. Additionally, a single central motor transmits motion to the system’s various mechanical components. Smiform’s new stretch-blow moulders of the HSR series feature an automation and control system based on Sercos III fieldbus and Ethernet communication technology. www.smigroup.it SMI’s response to the pressing demands of the beverage industry for faster, more efficient and reduced power consumption production systems is the High-Speed Rotary (HSR) series. This is a new range of rotary stretch-blow moulders, offering an output of up to 2,500bph per cavity (0.5l bottles). According to the company, the new machine offers a reduction in power consumption of up to 30% compared to traditional solutions. SMI claims that the machine’s compact and ergonomic design greatly simplifies running, cleaning and maintenance and allows the user to save valuable space inside the bottling line.","@ID":36}, "BOTTLE MAKING 33 PETplanet insider Vol. 15 No. 05/14 petpla.net lised for new installations as well.This is the system we have installed in the Editourmobil. We have accommodated the kegs in what were formerly gas cupboards and fitted a small dispenser incorporating continuous flow cooling and compressor above the fridge. The manufacturer is Lindr. Having tapped the barrel, we can now leave the keg attached to the line for a number of weeks as we have no headspace and the lines are clean. The beer tastes just as it did on the first day. We collected the first keg from the Engel brewery. They work with 30l KeyKeg barrels, which are mainly exported to Italy. We were drinking the Kellerpils, a finely hopped, unfiltered beer. We didn’t need to push the shelf life to its limits because, after three days and, with the gallant assistance of friends and acquaintances, we had quaffed the lot. Afterwards we cleaned the lines with a flushing solution from a cleaning keg which was attached to the beer line instead of the normal keg. As nonwinter campers it was also advantageous for us to be able to purge the line so that the unit could be put into hibernation without any water in it. As for the second barrel, we then went off to the Brauhaus Neckarsulm to try out the self-service facility for the first time. This brewery only brews sufficient to meet the requirements of its own guest house. The master brewer is Karl Gruhler, a beer enthusiast who took us on a tour of his cellars. He was himself interested to see how the keg filling operation would go. Over to the storage tanks, everything properly disinfected and in no time at all the pipe was in the keg. This beer is also another unfiltered cloudy Pils. It has (had) a slightly hoppy taste; the higher CO 2 content in the beer ensures a delicate sparkle and at the same time a very fresh aroma. No doubt our forthcoming tour of Italy, North Africa and Spain will find us topping up our kegs with one local beer or another. www.dolium.be www.brauhaus-neckarsulm.de www.engelbier.de www.keykeg.com www.krones.com www.lindr.cz/en/ www.petainer.com","@ID":35}, "27 PETplanet insider Vol. 15 No. 05/14 petpla.net Preform equipment Caps and closures Bottle-to-bottle recycling plants Preforms Preform and single stage machinery Preform / stretch blow moulds Two-stage SBM machinery Compressors Resins / additives Filling equipment Closure systems Preform and single stage machinery Two market surveys are included in this issue of PETplanet insider: The first relates to suppliers of preform systems, the second covers suppliers of single stage machinrs. In alphabetical order they are for preform systems: Husky, Netstal, Nissei, Sacmi and Sipa for single stage machinery: Aoki, Cypet, Nissei and Sipa In the survey, the companies are shown in the order in which their details were received by the editors. Although the publishers have made every effort to ensure that the information in this survey is up to date, no claims are made regarding completeness or accuracy 5/2014 MARKETsurvey Company name Sacmi Imola Netstal Maschinen AG Postal address Telephone number Web site address Contact name Function Direct telephone number Fax E-Mail Via Provinciale Selice 17/A 40026 Imola BO, Italy +39 0542 607111 www.sacmi.it Moraldo Masi Director of Business Unit PET +39 0542 607888 +39 0542 642354 moraldo.masi@sacmi.it Tschachenstrasse 8752 Näfels, Switzerland +41 55 618 6111 www.netstal.com Stefan Bock Manager Application Technology +41 55 618 6156 +41 55 618 6070 stefan.bock@netstal.com Preform injection moulding systems PET-Line (Netstal brand) Machine model number / name IPS220 2400-4000 (110) 4000-4000 (110) 4000-6300 (135) 4000-7300 (150) Number of cavities (min/max units) 16 - 72 24 - 72 48 - 128 72 - 128 72 - 128 Maximum individual preform weight 140g 9 - 140g 9 - 70g 9 - 78g 9 - 91 g Max resin through-put (kg/h of PET) 625 740 740 1050 1350kg/h Standard features Injection cylinder (shooting pot); electrical drive for plasticizing screw; T-belt for preforms extraction; belt free robot linear motor with KERS; take out plate with 3 postcooling stations; HMI with control of all auxiliaries; double cylinder for preform ejection; digital valves for each actuator; water unloading system prior to mould changing; Complete system including material preparation, take out robot and post cooling Options / special features Fast change over system with plug-and-play mould fixing system; plug-and-play take out plate fixing system; water pumps for mould cooling assembled on main machine platform; secondary belts system for an easier collection of preforms sampling; quality control vision system with multiple camera Suitable for hotfill materials, wide mouth and big size preforms; *Calitec: intensive post cooling and shaping of produced preforms to reduce cycle time and increase productivity *Preblow: optimized preform design and post moulding process to reach thinner bottle bottom design and save material (light weighting preforms) *= available at PET-Line only","@ID":29}, "MARKET SURVEY 28 PETplanet insider Vol. 15 No. 05/14 petpla.net Preform equipment Single stage machinery 5/2014 MARKETsurvey Company name Nissei ASB Sipa Postal address Telephone number Web site address Contact name Function Direct telephone number Fax E-Mail 4586-3 koo, Komoro-shi, Nagano-ken, 384-8585 Japan +81-267-23-1565 www.nisseiasb.co.jp/en Katsuo Ishiguro Section Manager, Sales Coordination Team +81-267-23-1565 +81-267-23-1564 sales@nisseiasb.co.jp Via Caduti Del Lavoro 3 31029 Vittorio Veneto, Italy +39 0438911511 www.sipa.it. Pietro Marcati ISBM - Global Sales Manager +39 0438911511 +39 0438911694 pietro.marcati@zoppas.com Single stage ISBM machines Machine model / number ASB-50MB,ASB-12N/10,ASB-12M,ASB-15N/10E,ASB-70DPH,ASB-70DPW,ASB-150DP,ASB-150DPW,ASB-650EXHS, ASB-650EXHD, PF8-4B, PF6-2B, PF4-1BH, PF3-1BH, PF3-1BHLL, PF24-8B(24), PF24-8B(12), PF24-8B(12H) ECS FX 20 (6 models) ECS HS 12 (8 models) Bottle volume (from/to in litres) 0.003 - 20 0.25 - 3 0.25 - 7 Number of preform cavities 1 - 36 Up to 80 Up to 40 Number of stretch blow mould cavities 1 - 36 Up to 40 Up to 20 Max. preform/bottle weight in grams for the stated number of cavities 3 - 800 46.50 for the 80 injection cavities 37.50 for the 40 injection cavities Hourly output based on: 0.5l container 1,200 - 9,000 36,000 18,000 1l container 720 - 8,500 27,100 13,600 1l wide neck container up to 5,300 12,300 4,200 2l wide neck container up to 2,200 9,600 3,000 Other (e.g. containers for personal care products...) up to approx. 6,000 Machine footprint / space requirement (LxWxH in metres) 3.56x1.14x2.73 (ASB-50MB) 8.95x2.15x3.25 (PF24-8B) 18,000 9,000 Special features For wide range of resins including PET, PP, HDPE, LDPE, PLA, PES, PPSU, PC and others. ASB-12N/10 can operate in IBM or ISBM mode. ASB-12M uses servo driven hydraulics for exceptional energy efficiency. ASB-15N/10E: all electric 1-step ISBM machine. PF Series uses lower blow mold cavitiation and blows multiple times per cycle. PF24 models offer outputs up to 9,000bph for smaller bottles and 2,500bph for 5l bottles. Wide mouth - oval and asymmetrical - off-centred neck - hot Fillable & pasteurizables – aseptic & ultraclean - lightweight Company name Netstal Maschinen Postal address Telephone number Web site address Contact name Function Direct telephone number Fax E-Mail Tschachenstrasse 8752 Näfels, Switzerland +41 55 618 6111 www.netstal.com Stefan Bock Manager Application Technology +41 55 618 6156 +41 55 618 6070 stefan.bock@netstal.com Preform injection moulding systems PETForm (KraussMaffei brand) Machine model number / name KM1751900CV KM1753500CV KM3203500CV KM3204500CS KM3206100CS KM3503500CV KM3504500CS KM3506100CS Number of cavities (min/max units) 8-60 8-60 32-96 32-96 32-96 32-112 32-112 32-112 Maximum individual preform weight 30-228 58-442 36-110 42-128 71-215 31-94 36-109 60-184 Max resin through-put (kg/h of PET) 380 600 600 800 1050 600 800 1050 Standard features Options / special features","@ID":30}, "PETbottles 46 PETplanet insider Vol. 15 No. 05/14 petpla.net Home + Personal Care Refreshing simplicity PET Power is adding another new standard model to its comprehensive collection of shampoo and shower gel models. This elegant bottle has a volume of 250ml and, with a height of 146mm, is a relatively short model. This is amply compensated for by the 73mm width, which makes the striking and attractive Castalia Oval stand out on the shelf. The most striking feature is the fact that this model has two different sides. The right-hand side is largely straight whilst the left-hand side is curved. The model is produced with a 24Snap neck finish and can be combined with many standard closures. The most obvious product group for the Castalia Oval is the shampoo and shower gel segment. However, with a little imagination the model could also be used for other cosmetic product groups. One example would be the food industry, where a squeezable bottle with a dispensing cap is a desired option. The oval shape can easily be enhanced using most decoration techniques. A label which perfectly accentuates the asymmetrical play of lines will ensure an attractive finished product. The model can also easily be provided with a sleeve or screen print and can be produced in any desired colour. www.petpower.eu Vernel for sensitive skin Henkel have reworked their fabric conditioner Hautsensitiv, which has been developed specially for sensitive skin. This mild conditioner is free of artificial colourants and is said to help people suffering from allergies specifically through the selection of fragrance and content substances. The 2l bottle, which is made from PET, incorporates a recess at the back for a better grip and to enable the product to be poured into the screw cap. The cap is used for dispensing and is decorated with a re-designed sleeve label. This is hollowed out in the area of the grip recess and features a transparent section to enable a check to be made on fill level. www.henkel.com Gliss Kur in dual pack As part of a promotional campaign, Schwarzkopf & Henkel are marketing their “Million Gloss Shampoo”, part of the Gliss Kur Hair Repair range, in a dual pack at an attractive price. Two PET bottles, each 250ml, with a snapon hinge lid, are held together by means of a shrink label incorporating transparent areas. The labels on the backs of the bottles are printed on the inside with the sample reflections that are typical of this range. The sleeve label is printed in colour in the area of the barcodes. This is to avoid the price of the individual bottle being misread by the till scanners. The barcode for the dual pack is applied to the sleeve label using a self-adhesive label. www.glisskur.de","@ID":48}, "EDITOUR REPORT 16 PETplanet insider Vol. 15 No. 05/14 petpla.net There are also two further 32-cavity injection moulding machines on order for this application. The market for UHT milk packaging is also on the move. Bottling using PET bottles is increasing. Here too the company offers 1-piece HDPE closures featuring the DoubleSeal technology developed years ago, which does not call for an additional aluminium seal for the bottle and which is suitable for aseptic bottling. Danone has gone over to PET for packaging Activia yogurt and uses closure caps from Bericap featuring the DoubleSeal technology. When it comes to bottling milk in PET bottles, the pioneer was Leitíssimo, a company with roots in New Zealand, which bottles Premium milk. The cows do have New Zealand genes and feed exclusively on fresh grass. The product is unique in Brazil. Unsurprisingly, the milk is at the top end of the price range, but demand is constantly rising. It did not come as a surprise, therefore, that a premium milk, packed in a premium bottle, required a premium closure to “top it off”. Let’s leave the final word to Aurel Forgaci: “Since our early days, 15 years ago now, when we started doing business in Brazil, we did bet on HDPE 1-piece closures for the beverage industry. Time and patience proved us right. 1-piece closures are a reality and here to stay. They are more precise and thus perform better than their 2-piece counterparts. On top of that, they are more economical. They are just the best choice for bottlers. As simple as that.” May 16 and May 24, 2013 Ambev We met: Ricardo Rolim, Director of Institutional Relations, Sustainability and Communication Thiago Guedes Hackradt, Marketing Ricardo Rolim in front of Ambev’s historic picture gallery Bottle-to-bottle We encounter Ambev twice on our South America tour. On the first occasion we meet Thiago Guedes Hackradt from Marketing and the second time round it is Ricardo Rolim, Director of Institutional Relations, Sustainability and Communication who welcomes us. Here in Brazil, Ambev is made up of two divisions, the beer brewery and the CSD, non-alcoholic and non-carbonated sections. The Brazilian drinks market is dominated by CSD, followed by bottled water, isotonics and ready to drink teas. The flavours in the CSD market are, in order of popularity, Coca, Guarana, Orange and Lime. The majority of soft drinks are sold in supermarkets in the form of 2l non-returnable PET bottles for home consumption. Ambev‘s main CSD brands are Guarana Antarctica and Pepsi. In addition, there are other beverages such as Gatorade, H2OH and Lipton, all of which are marketed under licence from Pepsi Co. The mineral water market is serviced as part of a cooperation agreement with Nestlé. Our meeting with Ricardo Rolim begins with the company’s dream to be the Best Beer Company in a Better World. In line with the slogan we duly began at the beginning, taking a look at the training and education programmes for employees as part of their daily operations. Ricardo Rolim explains: “At an in-plant level we are focusing on waste recycling (up to 99%) and measures to reduce energy consumption and carbon emissions, making use of up to date technologies”. When we get on to the subject of recycled PET in Brazil, Ricardo Rolim claims: “One of our company’s most important external projects is the reprocessing of recycled PET into drinks bottles. The technology, which focuses on producing raw material from used PET that is suitable for re-use in drink bottles, is available on the Brazilian market. But the problem lies in the collection rates. A prime example here is cans. Here collection rates of 90% are achieved, with PET only just exceeding the 50% mark and even here there are pronounced regional differences”. Ricardo Rolim filled in the background: “One problem is the lack of support to cooperatives. Only 14% of municipalities in Brazil have PET recycling systems at their disposal. The used PET bottles end up predominantly in the household waste and it is from here that they are collected by the refuse pickers on the waste disposal sites”. He went on: “The general public don´t really know the high value of used PET bottles as a potential raw material. Education is the key. Separation of household waste at source would have the effect of significantly increasing collection rates”. To promote awareness of environmental issues amongst the general public, Ambev performs various actions such as active efforts at education and projects that benefit consumers, cooperatives, society and environment. One example is the project Ambev Recicla that contributes to the development of model cooperatives in several states","@ID":18}, "TRADE SHOW REVIEW 36 PETplanet insider Vol. 15 No. 05/14 petpla.net Interpack 2014 The triennial Interpack has attracted 175,000 visitors to Düsseldorf, engaged in the packaging sector and related processing industries. As with the previous fair in 2011, the exhibition centre with its 19 halls was booked out by about 2,700 exhibitors from industries ranging from food and beverages, confectionery and baked goods to pharmaceuticals and cosmetics, non-food consumer goods, industrial goods and related services. The companies came to Düsseldorf from about 60 countries and are occupying about 174,000m2 of net space. As usual PETplanet was present and investigated for those involved in the PET packaging sector. www.interpack.com Sterilisation with pulsed light Claranor presented a broadened range of applications for the sterilisation of packaging with pulsed light. The French company provides dry and non-chemical solutions for inline packaging sterilisation, based on the power of intense flashes of white light, or pulsed light technology. The portfolio includes machines for preform neck and aluminium lid sterilisation. Decontamination results are said to comply with industrial users’ requirements, and thus able to replace chemical solutions on ESL filling lines. www.claranor.com Lid and closure systems Procap, European supplier of plastic caps and closure systems, exhibited solutions for a variety of industries in the food and non-food sector. Featuring amongst the new solutions to be presented at the event is 38 Proline, a closure designed to assure reliable capping of non-carbonated beverages that helps to increase productivity, as well as saving time and cost. 29/21 Green1P is a monopiece closure for edible oils, vinegars and sauces. The lid has been optimised in terms of its weight on the basis of an existing model. For this lightweight solution less raw material is needed and less energy is required in production and transport. www.procap.com Shrink sleeve made from low density PET A low density PET (LDPET) has been developed by Sleever International with the objective of easy recyclability for beverage manufacturers. The solution is said to allow the separation of sleeves from bottles without any manual operation. The printed film uses inks that are specifically designed to withstand the materials segregation treatment with no risk of contamination for the PET flakes. The resulting recycled PET is claimed to meet most if not all the recyclers’ expectations. Thanks to a specific density, the LDPET can be easily sorted out in sedimentation tanks, according to the company. The LDPET flakes float whereas the PET bottle flakes sink to the bottom of the tank. The solution allows for the full or partial labelling of bottles ranging from 20cl to 2l with production outputs between 15,000 and 30,000bph. Developed for the beverage market, the LDPET also opens possibilities for other products packed in PET bottles, such as edible oils or detergents. www.sleever.com Wash-off pressure sensitive label CCL Label Meerane GmbH in Germany has developed a special wash-off pressure sensitive label. The label construction is said to be suited for easier separation of the label from the beverage container during the washing process for example whilst bottle-to-bottle recycling (B2B). The removal performance of these labels is based upon the same principle as the WashOff labels available from CCL. Following the conventional method of reducing the returned PET containers into flakes, the hot water in the water bath causes the labels to shrink and then separate from the PET flakes without leaving any residual ink or adhesive. Whilst the PET flakes sink to the bottom, what is left of the labels floats to the surface enabling easy separation. A 2-layer construction is used for these labels which ensures that all inks are safely enclosed between the two plastic film layers. The result is that no contamination or discolouration of the water bath or the bottles/flakes is guaranteed. The LD-PSL labels can be applied by standard pressure sensitive labellers as commonly used in the industry today. www.cclbeverage.com","@ID":38}, "MATERIAL / RECYCLING 21 PETplanet insider Vol. 15 In addition, this proprietary titanium technology can be used to achieve all of the above benefits completely in the absence of any heavy metals and has been proven in both preform extrusion and bottle blowing following a successful 1,200kg/day PET chip continuous pilot unit trial. With typical addition levels of just 9-10 ppm Ti and 18-25 ppm phosphorous based on final polymer weight, replacement of antimony catalysts with CTL Ti638 UP is simple and requires no process control changes and only a minimal colour correction increase. This huge reduction in the amount of catalyst used dramatically reduces metal particulates in the PET polymer and also particulates that can cause fouling on the manufacturing plant. Favourable crystallisation properties of the Ti-PET allow manufacturers to decrease, or even eliminate, the more expensive isophthalic acid currently used for crystallinity control. On industrial scale The company’s UPTechnology platform is being exploited on industrial scale plants in Asia with further commercial trials scheduled and worldwide pilot unit testing on-going. The company has invested in a continuous pilot unit catalyst trial on Uhde Inventa-Fischer’s polyester 2R-MTR pilot plant. The trial enabled substantial testing of CTL’s new UP-catalysts by independent PET polyester production experts to demonstrate the benefits of the catalyst technology compared to the industry antimony reference. CTL’s products target the markets for mainstream, high intrinsic viscosity PET resin and sheet used for the production of bottle and packaging plastics. Their use is currently greater than 30 million t/a. Dr Alan Cooper, Technical Director, said: “The UP Technology platform can be modified to act as a drop-in replacement to current heavy metal catalysts for all PET production processes without any compromises. ” CTL has received the Queen’s Award for Enterprise 2014, in the Innovation category. The award recognises the commercial success of the company’s new polyester catalyst business. CTL have set the ambitious, but, in Dr Cooper’s opinion, “achievable” business target of taking over 50% of the PET resin and sheet market within the next five years. CTL now aims to apply their technology platform into other organo-titanium and zirconium areas, the timing of which has never been of greater significance as the use of toxic, restricted availability and often expensive alternatives comes under scrutiny. www.ctl8.com","@ID":23}, "BOTTLING / FILLING 31 PETplanet insider Vol. 15 No. 05/14 petpla.net of roughly 300 miles, the main sales areas being big cities like New York, Philadelphia, Baltimore and Boston. Approximately 130 trucks loaded up with freshly bottled water currently leave the company every day, with around 40 trucks delivering water from various springs in the region on a daily basis. Crossroads bottles spring water and also treated municipal water. With about 30 retail chains and casino operators, Crossroads has built up a broad customer base within a very short time. The company makes 80% of its sales with approximately 20% of its customers. Crossroads fills a diverse range of bottles and packs these into all kinds of shrink packs for retailers and casinos. Crossroads produces and fills 8, 10, 20 and 24 ounce and 0.5, 1.0 and 1.5l bottles, processing the 0.5l size only on the higher capacity lines. Crossroads make 90% of their sales with the latter. Kirk Richmond went on: “We can also take action as required on our multifunctional line when it comes to shrink packs; on the 72,000bph systems, however, we only program larger shrink pack units holding 24, 28, 32, 35 or 40 containers.” Something else Crossroads didn’t want to miss were the lightweight PET bottles Silver Springs had optimised together with KHS. For example, the 0.5l PET bottle for Silver Springs and Crossroads currently weighs just 9.1g. At Silver Springs the weight of the 13.2g bottle was cut down to 9.1g in two stages on application of KHS’ Bottles & Shapes programme. According to Kirk and Kane Richmond the next benchmark regarding PET weight is 8g, with the two brothers aiming for a maximum weight of around 7.5g for their 0.5l PET bottle in the long term. Essential line components On all three of its KHS turnkey lines Crossroads has opted for the InnoPET BloFill monoblock which consists of an InnoPET Blomax Series IV stretch blow moulder monoblocked with the Innofill NV filling system. This choice is also the result of the good experience Silver Springs has had; back in 2008 Silver Springs was the first beverage company in the world to invest in the then newly launched monoblock system which was kitted out with an InnoPET Blomax Series III stretch blow moulder. Silver Springs also ordered the world’s first InnoPET BloFill monoblock fitted with the InnoPET Blomax Series IV stretch blow moulder. On the newest line at Crossroads, which outputs up to 72,000bph, the InnoPET Blomax has 36 cavities, each of which can produce up to 2,250bph. The monoblock of the InnoPET Blomax Series IV and the Innofill NV filler has been kept as simple as possible. Removing bottles from the blow station and adjusting the distance of finished PET bottles to one another according to the configuration of the filling system is handled by just one modular transfer wheel. An airlock ensures that the dry area of the blow moulder is kept consistently separate from the wet area of the filler, thereby eliminating the risk of corrosion in the blow moulder. The logical consequence of gentle PET bottle handling is that bottles can be used which are lighter than those conveyed by an air conveyor. The filling system operates according to the principle of volumetric filling using electromagnetic induction flowmetering. Non-contact filling through a free-flow filling valve ensures microbiological and hygienic safety. The PET bottles are sealed by the classic Innofill SV screw capper. After they have been wrapped in film, the packs are directly conveyed into the shrink tunnel. The shrink tunnel is fitted with classic electrical heating and, like all KHS shrink tunnels, features hot air nozzle equipment which can be used in a variety of ways. Shrink packs are palletised on the Crossroads lines by an Innopal PB1HS with an upstream, inline robot grouping. This machinery is exceptionally well suited for palletising sensitive goods in particular, such as shrink packs. The inline robot grouping aligns the finished shrink packs with only minimal space requirements, after which a positive-fit gripper picks up, lifts, turns and places each individual shrink pack exactly in the programmed position. This gives Crossroads precision, exact reproducibility, precise alignment and gentle pack handling. The robot grouping enables all current and future container and layer requirements to be easily adapted by selecting the existing layer formation or programming a new container and layer formation. Crossroads is also planning on future success. It definitely has the space, with the option to buy the hired buildings and land secured. To close, Kirk Richmond says, “Considering that there’s a huge demand for bottled water in the northeast of the US, sales at Crossroads could be even higher than at Silver Springs in the near future. Together we already rank among the top five biggest bottling plants for water in the USA. In the family we can envision becoming a national presence in the water business in the medium to long term.” www.khs.com On all three of its KHS turnkey lines Crossroads has opted for the InnoPET BloFill monoblock which consists of an InnoPET Blomax Series IV stretch blow moulder monoblocked with the Innofill NV filling system, the Innopack Kisters SP Advanced shrink packer and the Innopal PB1HS palletizer with an upstream, inline robot grouping.","@ID":33}, "EDITOUR REPORT 12 PETplanet insider Vol. 15 No. 05/14 petpla.net In the penultimate stage of our tour of Brazil we took advantage of the opportunity to talk to machine manufacturers and suppliers of PET preforms and caps. We meet Husky on their World Tour 2013 conference in São Paulo. En route to São Paulo we visited Bericap, manufacturers of injection moulded plastic caps, the brewer and bottling company Ambev and also Logoplaste - Shefa, who have begun bottling UHT milk in PET bottles, thereby offering an alternative to the ubiquitous carton packaging usually used for UHT milk in Brazil. Interviews in this issue Husky Injection Molding Systems Bericap do Brasil Ltda. Ambev Logoplaste Shefa to follow: Döhler América Latina Ecoplaca Krauss Maffei do Brasil Ltda. Otto Hofstetter AG May 14, 2013 Husky We met: Keith Carlton, Vice President Global Sales Keith Carlton, Vice President, Global Sales, Beverage Packaging (left) and Waldemar Schmitke Lima Santiago La Paz Buenos Aires Montevideo Progresso São José dos Pinhais São Paulo Rio de Janeiro Lindóia Santa Cruz Sucre Quilmes Pilar Jaú Concepción Santa Fe Barueri Jundiai Sorocaba Amparoa Limeira Brazil Part 4 by Waldemar Schmitke and Florian Roscheck","@ID":14}, "EDITOUR REPORT 14 PETplanet insider Vol. 15 No. 05/14 petpla.net In the plastic closures sector, it is the 2-piece closures that have historically been dominant. This continues to be the case in the Brazilian market. All this diversity does not seem to faze Keith Carlton, who sees this as a challenge Husky is ready to take on. Up to now the bulk of overall business in Brazil has been in high cavitation preform systems. The potential offered by the niche markets is well-known. As far as preform manufacture is concerned, Husky offers a variety of solutions. One is the increased use of Husky’s H-PET AE (All-Electric) system, which offers an energy efficient, affordable solution for lower volume preform production. H-PET AE preform systems have already been sold in South America. The other approach, which has already been put into practice, is to upgrade existing preform systems to handle smaller cavitation moulds. In addition, there is the possibility of carrying out preform prototyping and testing for customer projects in Brazil. When looking at plastic beverage closures, two trends in particular are evident: the first is the increased adoption of 1-piece plastic beverage closures and the second is weight reduction. This latter is slowly becoming established. Both present considerable potential. According to Keith Carlton, this is an area where Husky, with its HyCap and HyCap HPP injection moulding systems for high output beverage closure manufacturing, is well-placed. In addition, Husky’s development centres for preforms and plastic closures work in close collaboration with the aim of achieving the best possible performance of the complete beverage package. In response to the question of just how high the potential for further weight reduction is, Keith Carlton replied, “We are only at the beginning. The potential for further weight savings in packaging (closure / PET bottle) is enormous, and this applies here in Brazil too. This is an initiative we, together with our customers, are actively working on.” May 15, 2013 Bericap do Brasil We met: Aurel Forgaci, Managing Director Fernando Seabra, Plant Manager Aurel Forgaci, Managing Director (left) and Fernando Seabra, Plant Manager in front of a Netstal Evos 72-cavity injection moulding machine for closures 1-piece closures - “the right choice, right from the start” Here at the factory in Sorocaba we are meeting Aurel Forgaci, Managing Director and Fernando Seabra plant Manager and we were delighted to be able to learn about the company here in Brazil and about the trends in the closure market. A member of a German family enterprise, Bericap do Brasil produces closure caps made from plastic in production workshops established throughout the world. The company’s head office is in Germany. The firm’s corporate programme also includes a central injection mould production plant in Hungary, which acts as a global supplier to all the plants. Excellence Centers in Germany, France, Spain and Turkey are all able to contribute their expertise in the development of closure caps. Specific market demands are, in some cases, developed locally. Bericap do Brasil is responsible for covering the Brazilian market, growing Bericap’s presence in South America and lately providing technological support for the plant in Argentina. The philosophy here, as indeed it is throughout the entire company, is to manufacture injection-moulded plastic closures. The plant has been established in Brazil since 1997 and today it employs 120 people. Plastic closure caps produced by the company are intended for a wide spectrum of the market: beverages, foodstuffs, the edible oil market, milk, agro-chemicals market, engine oil containers and metal cans. Drinks and foodstuffs packaging closures account for 65% of production. The fleet of injection moulding machines is made up of 32 machines from Netstal, Demag, Sumitomo and Arburg. The moulds used in injection moulding incorporate cavities ranging from 2 to 96. The production lines are fully automated. Inspection systems provide a full Quality Assurance function. Bericap do Brazil was the first closure cap manufacturer in Brazil to be awarded the FSSC 2200, a GFSI accepted protocol being a combination of ISO 22000 and PAS 223. Beverages closures Hitherto, the 2-piece plastic closure (closures with liner) was the norm in the beverages industry in Brazil, predominantly manufactured using the compression process. The 2-piece closure is made up of the actual closure cap and a liner made from EVA which is either placed in the compression moulding machine itself or in a subsequent station outside the compression moulding machine. The liner seals the PET bottle. The closure cap is made from PP. A serious disadvantage for the 2-piece closure is that the price of PP is rising more than PE globally and this affects prices in Brazil. The need for a liner adds to the cost base. The alternative is the 1-piece plastic closures made from HDPE. Aurel Fogaci: ”1-piece closures produced by injection moulding are more precise, providing narrower tolerances, than their compression moulded counterparts. Injection moulded closures are in high demand since a","@ID":16}, "EDITOUR REPORT 19 PackSys Global’s slitting machine easily meets the performance demands of the beverage industry. Slitting tamper evident bands is more efficient and accurate than molding bridges in the mold. With the option to process output of multiple injection molds on one folding/slitting machine, closure manufacturers have higher efficiency, faster cycle times, lower energy consumption, and use less floor space. PackSys Global – a cut above the rest. PackSys Global designs and builds full lines for manufacturing and decorating laminate and cosmetic tubes, plastic beverage caps, aluminum screw caps, aluminum tubes and aerosol cans. Its advanced packaging equipment is ideally suited for beverage, cosmetic, pharmaceutical and industrial markets. The world, s fastest plastic closure folding and slitting machine, capable of more than 60 parts/ second, designed and built using Swiss precision technology. Record-breaking Speed in Closure Production PackSys Global (Switzerland) Ltd. | Joweid Zentrum 1 | CH-8630 Rueti | Switzerland | T: +41 55 253 3831 | info@packsysglobal.com www.packsysglobal.com | @packsysglobal","@ID":21}, "BOTTLES 47 PETplanet insider Vol. 15 No. 05/14 petpla.net The plastic closure company committed to your success BERICAP Technology Research and Development Mould Technology | Global Presence Capping Technology and Know-How Innovation and Flexibility www.bericap.com Beach style salt spray The German drugstore discounter dm is deploying for its new “Beach Style Salt Spray”, marketed under its own brand name Balea along with the tag “Trend it up”. The packaging used is a slim PET bottle, the upper half of which is tapered, containing 200ml. The white bottle is fitted with an all-round shrink sleeve label and the product is closed by means of a screw-on, opaque, orange-coloured pump dispenser complete with protective cap. The spray is intended to give the hair a matt, stranded but non-greasy look, reminiscent of the way it looks after a day on the beach. www.dm.de/balea Foam bath The German company tetesept is marketing 400ml gentle foam bath with orange blossom fragrance in a transparent, orange-coloured PETE bottle featuring a basic oval shape. The product, which is called “Schaumwelten” (“Foam Worlds”) is said to generate specially high levels of foam that last for a long time and which, thanks to the fragrance of orange blossom, have a particularly relaxing effect. The bottle closure is a white screw cap and the bottle is decorated with two self-adhesive labels. This new foam bath is available in five different fragrances. www.tetesept.de Beautiful skin oil Garnier is bottling 150ml of gentle regenerating oil with the product name “Beautiful Skin Oil” and the tag “Garnier body” in a tear drop-shaped PET bottle. The product, incorporating oils that are extracted from pomegranate, camellia, the jojoba plant and geranium, is designed to give mature skin an appearance radiating with youth. This gentle care product is applied via a tinted pump dispenser. The bottle has a slight purple tinge and is decorated with two labels and the rear label has a flower printed on it on the inside. For marketing purposes, a folded suspended label lists the advantages of the product. www.garnier.de Mini products in PET A huge number of branded products for weekend trips, for people travelling with only a small quantity of luggage or even for the jacket or handbag can be found on the supermarket shelves in shapely and brandtypical miniature bottles. Two examples of these are the hand disinfecting gel from Sagrotan in a transparent bottle made from PET with a content of 50ml, a screw-on hinge lid and, from Nivea for Nivea Men, a refreshing gentle shower gel with menthol for body, skin and hair. The bottle, with a content of 50ml, is made from PET and sealed with a snap-on lid which can be opened by twisting a few degrees from the longitudinal axis. To re-seal the container, simply snap the lid closed. www.sagrotan.de and www.nivea.de","@ID":49}, "MATERIAL / RECYCLING 20 PETplanet insider Vol. 15 No. 05/14 petpla.net PET Catalyst technology by CTL Heavy metal no longer in tune Catalytic Technologies Ltd (CTL) has developed a new titanium catalyst technology which eliminates the use of the heavy metal catalyst antimony oxide in PET production. The new technology has been tested by major industry players around the world. The company has announced the ambitious business target of taking over 50% of the PET resin and sheet market within the next five years. New titanium catalyst technology for the industrial production of PET is now being adopted around the globe as PET manufacturers and processors seek to eliminate the use of the heavy metal catalyst antimony oxide. The technology was developed by Catalytic Technologies Ltd (CTL), a company established in late 2010 on Teesside in the UK. To date the company has invested over £1million on research and development and in 2013 it launched its patent pending UP-Technology platform which exhibits performance unlike any other PET catalyst. UP is a catalyst technology platform that allows CTL to produce catalysts with a unique chemical composition. It also eliminates undesired side reactions in this application. In addition to eliminating antimony oxide, the catalyst offers high polymer thermal stability, improved brightness and clarity owing to lower impurity content. It also offers a net reduction in the overall process energy required to produce plastic packaging and, lighter bottles without compromising on bottle strength, according to the company. In 2012, and following the continuous PET pilot unit trial of CTL Ti638 UP in early 2013, the PET chip produced during the trial had been melt processed into 2l preforms and bottles. Product options for bottle grade PET CTL Ti638 can be used to produce PET fibre, film and resin at a range of intrinsic viscosities. The product contains 5% Ti on a weight basis and is a concentrated alternative catalyst to CTL Ti184. The active titanate catalyst is dissolved in a water solvent and can be used at 7-10ppm Ti in PET applications and, being more concentrated than Ti184, allows to reduce shipping and storage volumes by 2.5 times. The product needs to be diluted in MEG for addition to the PET process. CTL Ti638 Up is a catalyst designed for the production of high intrinsic viscosity PET 0.70 dl/g. While titanium catalysts for PET have been investigated for over three decades, limitations in the use of current Ti-PET as a result of thermal instability during processing at high IV are well known, and this has restricted existing catalysts to lower IV PET fibre and film applications. The industry has also suffered from the process limitations of titanate catalysts, particularly linked to solid state polymerisation rates. Catalytic Technologies claims that with the titane catalysts, manufacturers of polyester chip, bottles and A-PET sheet can experience improved thermal stability compared to antimony-PET lower chip acetaldehyde content and reduced AA generation during processing brighter polymer with reduced haze lower crystallinity chip allowing for up to 40% energy reduction on melt processing increase in PET crystallisation temperature allowing for higher temperature filling increased crystallinity in blown bottle side walls allowing for light weighting antimony free catalyst formulation full function for high IV PET, without compromise, in both solid state polymerisation and in melt to resin process technology.","@ID":22}, "PETbottles 44 PETplanet insider Vol. 15 No. 05/14 petpla.net Beverages & Liquid Food Quenches thirst Greater Than, an all-natural, thirst quenching functional beverage infused with coconut water and electrolytes, has chosen Closure Systems International (CSI) as the exclusive closure supplier for its 2.0 package re-design and national product distribution. Brothers Mark and Jon Sider created the drink which contains all natural ingredients, is low calorie and has twice the electrolyte content of mainstream sports drinks. The brand has enjoyed explosive growth since its introduction in 2010 in a single Chicago area store. Today, Greater Than is available in more than 200 locations as well as on-line from Amazon. In support of its expanded distribution and growth, the company has refreshed their brand, their formulations and their packaging based on consumer feedback. The redesigned package is now topped with CSI’s Extra-Lok V 38mm OD closure. This cap has been optimally designed to be the lightest weight two-lead, 38mm closure in the market while maintaining performance excellence. www.drinkgt.com Many multi-coloured marshmallows Via the German wholesale trade, Tri D’Aix GmbH, a company based in Alsdorf, is marketing 80 marshmallows in a transparent plastic container made from PET and around 30cm in height. The products, which come in various colours, are readily visible, due to the minimalistic size of the two labels and make an immediate visual impact. A metal screw-cap complete with a liner is used to close the container. Before opening for the first time there is a transparent self-adhesive strip that needs to be removed. www.tri-d-aix.com Iso Light in blue PET The German discounter Netto is selling 500ml of its Iso Light sports drink in a waisted, blue-tinted PET bottle under the brand name “Star Drink“. The bottle incorporates stabilising grooves in the waisted area which make the bottle easy to handle. An all-round body label made from foil conveys the necessary information and a screw cap in a contrasting colour with tamperproof guarantee completes the packaging. www.netto.de Green tea in green PET San Benedetto is packing 500ml of a drink based on green tea in a green-tinged PET bottle. The bottle incorporates a drinking aperture of adequate size and allround reinforcing grooves. A colour-matched foil label and a tamper-proof screw cap put the finishing touches to the product’s presentation at the PoS. www.sanbenedetto.it Black PET for energy drink The French supermarket chain Cora is currently using a PET bottle with an all-over black tint for its For-X energy drink containing taurine. The slimline, slightly waisted bottle is decorated with a foil label and a striking red screw cap complete with tamper-evident strip serves as a closure. Special emphasis is placed on the importance of consuming the drink well-chilled. www.coradrive.fr","@ID":46}, "NEWS 9 PETplanet insider Vol. 15 No. 05/14 petpla.net KraussMaffei Group driving company growth in China The KraussMaffei Group has officially inaugurated the second production hall at its manufacturing plant in Haiyan, China. Around 400 of its customers and business partners attended this event. As part of the expansion of the plant, the production space has been doubled and now covers 22,000m2. By doing so the company is continuing its expansion strategy in China, where it sees considerable growth potential for its KraussMaffei, KraussMaffei Berstorff and Netstal brands. To strengthen the local injection moulding portfolio, Netstal has also opened a new Demonstration and Training Center, which is also available for customers to visit. It is home to a fully electric Netstal Elion machine with a clamping force of 2,200kN, which is demonstrating sample production of PET blood collection tubes, and a complete PET-Line system, which is acting as a demonstration machine for the beverage industry. This system, which has a clamping force of 3,500kN, produces PCO28 preforms. The 96-cavity mould is supplied by Swiss company Otto Hofstetter AG, while the cooling equipment is provided by local manufacturer Shini Plastics Technologies Inc. www.kraussmaffeigroup.com www.netstal.com Demand for PET packaging material to reach $60 billion by 2019 The market report “The Future of PET Packaging to 2019” from Smithers Pira gives an overview of the state of the PET packaging industry in 2014, alongside global market forecasts to 2019, including key definitions and details of specific geographic markets. According to this, the global PET packaging market will be worth $48.1 billion in 2014, amounting to almost 16 million tonnes. Demand for PET packaging is expected to increase by an average of 4.6% annually over the next five years, and will amount to 19.9 million tonnes worth $60 billion by 2019. Within overall PET packaging consumption of 15.4 million tonnes in 2013, PET bottles for beverages accounted for over 80% of overall sales at 12.5 million tonnes (up 3.7% on 2012). In 2013, bottled water became the largest category for PET packaging; sales of PET water bottles grew by 7.3% reaching 5.45 million tonnes. Sales of PET bottles for carbonated soft drinks by comparison rose by 1.8% to 5.17 million tonnes. Slower growth of the latter is attributed to high penetration rates in major markets and a growing consumer preference for healthier drink options. According to Smithers Pira, in the key remaining packaging sectors, non-food PET packaging sales reached 804,328t (a 4.4% increase on 2012 levels), with thermoforming packaging consumption up 4.7% to 1.04 million tonnes. During the period 2014-19, the fastest growing end-use sector will be bottled water bottles with 6% growth in volume terms, followed by pharmaceutical and medical packaging and PET bottles for other drinks, both increasing by 5%. Key market drivers include rising incomes in developing markets of Asia Pacific, South and Central America and Central and Eastern Europe, with Asia Pacific becoming the largest regional market for PET packaging during the period 2009-13. www.smitherspira.com Erema expands global trial centres and technical support Erema customers now have a total of 13 facilities at their disposal for trial runs with the test materials they choose to provide. The trial centres are said to feature the latest technology thanks to the installation of the new plant generation Intarema with patented Counter Current technology. The test runs on these systems are carried out in realistic production conditions and thus provide the results with which the customer’s machine configuration is optimised on an individual basis. Currently some 400 tests are already carried out every year with a wide variety of customer materials. This number of test runs will continue to increase with the expansion of the trial centres. Seven systems are available in the Erema Customer Centre and three more in the R&D Centre at the company’s headquarters in Austria, two at the Erema North America (ENA) Trial Centre in Ipswich and one plant is at the trial centre in the Middle East. www.erema.at Avery adds Scottish recycling centre Avery Dennison has expanded its PET liner recycling programme with the addition of a new collection facility for brand owners in United Kingdom and Ireland. Waste PET liners can now be sold directly to PET Processors UK, Avery Dennison’s recycling partner in Dumfries, Scotland. PET Processors UK creates thermal forming sheets from the recycled liner, which are then used for food containers and as compounds for industrial use in automotive and construction applications. Brand owners in this region can engage with the Avery Dennison recycling programme with quantities from two tons upwards. The company says that its service can help customers to meet sustainability targets and also be a source of revenue. One million m² of liner waste is currently worth anything from GB£5,000 to GB£8,000 (€7-9,600; US$8-12,500). www.averydennison.com","@ID":11}, "TRADE SHOW REVIEW 37 PETplanet insider Vol. 15 No. 05/14 petpla.net Digital direct printing of containers Krones AG, Neutraubling, Germany, premiered the DecoType direct printing system for printing on plastic bottles. Compared to dressing containers in labels, direct printing of containers is said to offer more scope for individualised design of the containers. The use of updated decors or short-notice launches of newly developed products is intended to enable the client to react swiftly to changes and emergent trends on the market. Individualisation, small batch sizes, small print runs as well as printing barcodes or on uneven surfaces are claimed to be possible with enhanced affordability. With the new DecoType direct printing system, print heights of up to 200mm can be achieved using UV inks. Featuring a modular, compact construction, the machine is suitable for empty plastic containers made of PET, PP or PE, either cylindrical or special-shaped. A DecoType application for glass containers is in planning. Integrated printing units with ink supply and automatic pushbutton adjustment facilitate change-overs. The pushbutton-controlled cleaning process, too, has been automated. Ink topups function flawlessly, while arc emitters ensure reliable UV-drying of the printed containers, according to Krones. www.krones.com Hot melt wrap around labelling Gernep, manufacturer of labelling machines, presented its recently launched labelling machines for the packaging industry. The Rollfed and Rollina labelling machines are designed for the hot melt wrap around labelling for a variety of containers. The Rollfed model is used for the labelling of roll-fed plastic labels for bottles made from PET and other plastics, whilst Rollina is designed for magazine-fed paper labels for plastic containers. The glue application of both labelling systems comes from a closed hot melt unit. Thanks to this closed hot melt system, any contamination of glue is said to be avoided in the hot melt circulation and this minimises cleaning and maintenance. The hot glue of the Rollina is economically applied onto the container by nozzles. The end glueing occurs through a stepless adjustable end-glueing edge at the end of the label magazine. In the Rollfed system, hot melt is applied contact-free to the label via nozzles while it is on the vacuum drum. The end glueing takes place by a stepless adjustable glueing edge and an end glueing plate on the transfer drum. The control of bottle rotation is said to reduce the changeover time to other container formats. www.gernep.de Liquid masterbatches One of the highlights presented by Clariant was the new HiFormer integrated system for liquid masterbatches, designed to enhance product properties and process parameters for customers. In addition to the improved efficiency of the manufacturing processes, the liquid masterbatches are said to be highly concentrated to achieve brilliant, vibrant hues. For packaging customers, the focus in recent developments has been on advancing EBM monolayer production processes. HiFormer EBM monolayer systems offer a reduction in masterbatches for lighter plastic packaging, according to the company. Another development showcased was a line of multicolour masterbatches that are used in combination with proprietary, patented, multilayer moulding process. The so-called Figaro Effect creates levels of opacity, translucency, gloss and special effects. www.clariant.com","@ID":39}, "PETpatents www.verpackungspatente.de 48 PETplanet insider Vol. 15 No. 05/14 petpla.net Pouring aid for larger containers International Patent No.WO 2013 / 176924 A1 Applicant: Procter & Gamble Company, Cincinnati (US) Date of Application: 14.5.2013 The trend towards ever larger containers for detergents, juices, milk etc. necessitates an increase in the use of materials required to produce a sufficiently sturdy container with a handle. This patent proposes using a separately manufactured pouring aid which is combined with a thin-walled bottle. Aerosol can made from PEF International Patent No. WO 2013 / 158582 A1 Applicant: Procter & Gamble Comp., Cincinnati (US) Date of Application: 16.4.2013 Application for the international registration of the design and process for manufacturing an aerosol can featuring a proportion of PEF (bio-based plastic). Plastic bottle European Patent No. EP 2644521 A1 Applicant: Krones AG, Neutraubling (D) Date of Application: 20.3.2013 A thin-walled plastic bottle for carbonated products incorporates a section between the thread and the shoulder which provides improved grip on the bottle for opening and pouring operations. The area (which may also be thicker-walled) features ridges/embossing. Secure closure European Patent No.EP 2653404 A1 Applicant: Robert C. Reinders, Las Vegas (US) Date of Application: 9.4.2013 The closure on a vessel is constructed and dimensioned in such a way as to incorporate openings that will prevent choking if swallowed accidentally. The openings allow a flow of air “through“ the closure and thus enable in- and exhaling. PET container for wine International Patent No. WO 2013 / 176833 A1 Applicant: Zipz Inc., Basking Ridge (US) Date of Application: 26.4.2013 Transparent container made from PET in the shape of a glass for holding wine. The container (already filled) is designed as a disposable container for use at large-scale events and is closed by means of a push-on lid. Prior to removal, the entire sleeve label with its tear-open perforation, the snap-on lid and a sealing membrane need to be removed. Plastic bottle European Award of Patent No. EP 2319771 B1 Applicant: Yoshino Kogyosho Co. Ltd., Tokyo (JP) Date of Application: 11.8.2009 Design of a thin-walled plastic bottle made from PET. Differences in pressure are compensated for by increasing the length of the bottle in the side wall and bottom section areas.","@ID":50}, "BOTTLE MAKING 32 PETplanet insider Vol. 15 No. 05/14 petpla.net Beer in PET - a never-ending story? Keg systems: A personal experiment For years, beer in PET bottles has occupied a niche position. Briefly fuelled by the introduction of the drink can deposit system in Germany ten years ago, it is becoming increasingly difficult to find the PET bottle being used for beer. Nevertheless, beer in PET seems to have an awesome future in front of it, namely, in the form of beer in the PET keg. To give it the once over, so to speak, we have installed a KeyKeg dispenser in our Editourmobil, and you are cordially invited to join us for a refreshing glass of beer. At drinktec we found a number of suppliers courting the favours of the breweries. Featured are the classic PET kegs with standardised bayonet fittings as can be seen in practically any bar taproom. The headspace in the barrel is pressurised with gas – as a rule CO 2 – which means that the beer can be conveyed under pressure into the dispenser line via a hose or pipe. Suppliers of these systems include, for example, Dolium, Petainer and PolyKeg. The advantages of these systems are clear. The keg is single-use, so there is no need to clean it, nor, more importantly, is return transport required. This represents a significant advantage for breweries whose beer marketing activities extend across national frontiers. Another key feature is that the range of different connections means that the bar owner is able to serve the beer via his normal tap system. Depending on the system, the disadvantage of all kegs, including the metal ones, is the need to pressurise the headspace with gas. Unless absolute cleanliness is scrupulously observed here, it will be possible for oxygen to get into the headspace – to the immediate detriment of the taste. Using a central tap system means that the existing beer lines are used. Generally, bar owner will need to ensure that these are cleaned regularly, otherwise the taste of the beer will be affected. Two PET keg systems: two different paths At drinktec, Krones presented the Bevkeg barrel system, in which the headspace is eliminated from the keg, both during the filling and during the emptying processes. The empty keg looks like a salad bowl. The whole of the top section is curved inwards. Filling pushes the upper section outwards without any headspace being formed. It is only when the keg is full that it assumes its typical shape. The process is reversed when emptying the keg: here a punch compresses the barrel mechanically so that the beer is forced out of the barrel. So as to avoid taking up the existing beer lines all at the same time, the keg is supplied with a single beer line only. The dispenser unit needs to be installed in the bar together with the keg. No provision is made for emptying via a central dispenser systems. Time will tell whether bar owners are ready to sacrifice valuable space in terms of refrigerator volume at the bar for just one type of beer. KeyKeg is the second system In this the PET keg does not come into direct contact with the beer. The beer is accommodated in an internal multilayer bag. Initially the bag is under vacuum. The bag is then filled with beer. The area between the bag and the PET keg is pressurised so that the bag is, so to speak, pre-tensioned. As the level of fill increases, it will be possible to release the pressure via a filler valve until the bag has been filled to capacity and is resting against the PET barrel. The emptying process then proceeds in the reverse sequence. A compressor is used to pressurise the space between the bag and the keg and the beer arrives at the dispenser. For simple bars the compressor is installed directly in the coolant dispenser, but of course there is no problem either in obtaining the pressure from a CO 2 bottle in the traditional manner. This makes the system available for use with already installed lines, although its CO 2 -free dispenser facility means that it can also be utiThe Krones approach: BevKeg","@ID":34}, "EDITOUR REPORT 18 PETplanet insider Vol. 15 No. 05/14 petpla.net Five years ago saw the inauguration of Shefa’s project to fill PET bottles with UHT milk. The project was subsequently implemented in December 2011. In response to my question to Paulo Vitor R.Mendonca of Shefa as to why PET bottles for milk and why UHT and not, for example, fresh milk, I received the following answers: “The market for milk is very large in Brazil, 67 billion litres are consumed each year. The packaging consists almost exclusively of drinks cartons with a shelf life of four months,” said Mendonca. ”What the market is looking for is an alternative which is more attractive to the user in terms of handling and appearance. PET bottles with the right barrier technology, a large diameter outlet, the appearance of a glass bottle and which were, in addition, also microwave-friendly promised to become the alternative we were looking for. PET is also readily recyclable.” He continued, “Something else that is helpful when it comes to decisions of this kind relates to the Brazilians’ shopping philosophy. They shop once a month, so buying fresh milk is something that simply never occurs to them because of its short shelf life. As far as container size is concerned, 1l bottles tend to dominate”. PET bottle specification 1l PET bottle, 2-layer, light (in the range of 400-580nm) - resistant min. four months Bottle weight: 26g Aseptic bottling Aluminium foil seal. The seal is, technologically speaking, not necessary, but is regarded as security against any unauthorised opening of the bottle. Plastic closure 38mm (1-piece) OPP label Packaging: six milk bottles in shrink film Fully automatic palletising Technology and machine systems The Prelactia Process developed by Netstal is applied as light barrier. The preform is manufactured with 2 x PET layers using the over-moulding- process. There is an external layer in white with limited light barrier; the internal layer is dark and blocks over 99.9% of the visible light. The Prelactia Process permits the use of a lower quantity of titanium dioxide for the light barrier and as a result of mould core stabilisation. It is possible for the inner layer to be injection moulded so that it is considerably thinner than the external layer. The preform wall thickness of approximately. 3mm that can be achieved by so doing results in a cycle time of 11.8s for a 24-cavity preform system. Currently in use are 2 x 24-cavity preform machines of the Netstal Synergy 2400 type as well as Piovan drying and materials handling systems. Paulo Vitor R. Mendoca in front of the Krones labellingmachine for PET milk bottles A further Netstal Synergy 2400 injection moulding machine incorporating a 32-cavity screw capping mould takes care of plastic caps production. A 38mm screw cap closure with a weight of 2.4g is running in a cycle time of 4s. The preforms are stretch blow moulded on a Sidel stretch blow moulding machine with a capacity of 18,000bph and transported through the wall of the factory directly to the aseptic Stork Holland bottler via an air conveyor section with a 2min buffer. The stretch blow moulding capacity is tailored to the filling capacity. Subsequently, the system proceeds directly to the aluminium foil sealing operation, screwing down the plastic caps, labelling and presentation in six-packs. Once in the six-packs, a fully automatic process transports the milk bottles via a tunnel into a different bay where they are palletised. The entire PET bottling plant operates 24 hours a day. In order to safeguard filling capacity, the company maintains a stock of preforms and screw caps amounting to 1 million parts of each item. Future prospects The first stage with a total capacity of 92 million PET UHT milk bottles per year is already inadequate. Demand is exceeding capacity. Today they are only servicing the Federal State of São Paulo with its population of 42 million. The next stage, which involves expansion to 200 million per year, is intended to go beyond this. A further Prelactia over-moulding preform machine is on its way to Brazil. Another PET bottle size, with a content of 0.5l is under discussion but is not a priority item.","@ID":20}, "23 PETplanet insider Vol. 15 No. 05/14 petpla.net MATERIAL / RECYCLING 13 marzo – 15 agosto 2014 Giro dell’Europa sudoccidentale e del Nord Africa con PETplanet Go to Brau Beviale – Esplorazione della regione del Mediterraneo occidentale Si parte per nuove avventure! Il nostro team di reporter di PETplanet Insider è di nuovo in partenza. L’Editourmobil è più grande e abbonda lo spirito di scoperta; questa volta il team esplorerà l’area del Mediterraneo occidentale. I nostri impavidi specialisti Alexander Büchler, Waldemar Schmitke, Kay Barton e Rolf analizzeranno i mercati PET di Italia, Tunisia, Algeria, Marocco, Spagna, Portogallo e Andorra. Il loro viaggio epico durerà 5 mesi, e comprenderà un arduo itinerario di 7.000 chilometri che attraverserà due continenti, durante il quale tre team di PETplanet incontreranno i principali esponenti del settore. E ancora una volta ci auguriamo di porgervi il benvenuto a bordo per condividere il viaggio con noi: seguite il blog del viaggio a www.braubeviale.petpla.net E potrete leggere le interviste con le aziende che visiteremo sul nostro stand alla Fiera Brau Beviale dall’11 al 13 novembre 2014 e successivamente in PETplanet Insider. www.braubeviale.petpla.net Supported by: Del 13 de marzo al 15 de agosto de 2014 Gira del Sudoeste de Europa y Norte de África con PETplanet Go to Brau Beviale – Explorando la región del Mediterráneo occidental ¡Nuevas aventuras a la vista! Nuestro equipo de reporteros de PETplanet Insider vuelve a poner rumbo hacia nuevos mares. Con un Editourmobil más grande y abundante espíritu aventurero, la gira explorará la región del Mediterráneo occidental. Nuestros intrépidos especialistas, Alexander Büchler, Waldemar Schmitke, Kay Barton y Rolf analizarán los mercados de PET de Italia, Túnez, Argelia, Marruecos, España, Portugal y Andorra. Ante ellos se abre un épico viaje de 5 meses con un extenuante recorrido de 7.000 kilómetros que les llevará a través de dos continentes. A lo largo del camino, tres entusiastas equipos de PETplanet entrevistarán a los principales jugadores del sector. Una vez más esperamos darles la bienvenida a bordo para que compartan el viaje con nosotros: siga la gira en el blog del viaje en www.braubeviale.petpla.net Descubra todas las entrevistas con las empresas que visitamos en el stand de la exhibición Brau Beviale del 11 al 13 de noviembre de 2014 y después en PETplanet Insider. 13 March - 15 August, 2014 Circular tour of South West Europe and North Africa with PETplanet Go to Brau Beviale – Exploring the western Mediterranean region Up and away on new adventures! Our team of reporters from PETplanet Insider are off on their travels again. Featuring a larger Editourmobil and the spirit of discovery in abundance, the tour this time is centred on and around the area of the western Mediterranean. Our intrepid specialists Alexander Büchler, Waldemar Schmitke, Kay Barton and Rolf will be analysing the PET markets of Italy, Tunisia, Algeria, Morocco, Spain, Portugal and Andorra. Before them is an epic journey of 5 months, involving a gruelling 7,000 kilometre itinerary covering two continents, during which three PETplanet teams will be talking with the major players. And once again we look forward to welcoming you on board to share in the trip with us: follow the tour by travel blog on www.braubeviale.petpla.net And you can find out all about the interviews with the companies we visit on our exhibition stand at Brau Beviale from 11 to 13 November 2014 and afterwards in PETplanet Insider. 13 mars – 15 août 2014 Tour de l’Europe du Sudouest et de l’Afrique du Nord avec PETplanet Go to Brau Beviale – À la découverte de la région méditerranéenne occidentale En avant vers de nouvelles aventures ! Notre équipe de reporters de PETplanet Insider reprend la route. Avec une édition de l’Editourmobil plus importante et une soif de découverte sans fin, le tour sera cette fois-ci centrée sur la partie occidentale de la région méditerranéenne. Nos intrépides experts, Alexander Büchler, Waldemar Schmitke, Kay Barton et Rolf , analyseront les marchés du PET en Italie, en Tunisie, en Algérie, au Maroc, en Espagne, au Portugal et en Andorre. Un voyage épique de 5 mois les attend, avec un éprouvant trajet de 7000 kilomètres couvrant deux continents tout au long duquel les trois équipes de PETplanet s’adresseront aux principaux acteurs du marché. Nous sommes là encore impatients de vous recevoir à bord pour faire ensemble un bout de chemin: suivez le tour sur notre journal en ligne www.braubeviale.petpla.net: vous trouverez tout ce qu’il faut savoir sur nos interviews avec les entreprises que nous rencontrerons sur notre stand d’exposition de Brau Beviale de 11 au 13 novembre 2014 et, après cela, à PETplanet Insider. Go to BrauBeviale The Western Mediterranean round trip","@ID":25}, "25 PETplanet insider Vol. 15 No. 05/14 petpla.net MATERIAL / RECYCLING to rearrange themselves. The rate of crystallisation is a function of the temperature, the IV of the polymer, and any comonomer content. Polymers are very rarely able to crystallise completely. The temperature range for crystallisation is between the glass transition temperature (Tg) and the melt temperature (Tm). Below Tg, the resin is described as being “glassy” because the mobility of the polymer chains is greatly reduced, and they are essentially locked in place regardless of whether they are in the amorphous or crystalline state. Above Tm, the polymer chains have too much energy to form stable ordered structures, and the molten resin is amorphous. Between Tg and Tm, the polymer chains have enough energy to rearrange themselves into the most thermodynamically favoured structure, so the resin crystallises. Thermally induced crystals are arranged in structures called “spherulites” because they start from a point source (nucleation site) and grow, radiating outward, in a spherical pattern. This must be avoided because the crystallised regions cause haze, destroying the clarity of the preform, and prevent proper stretch blow moulding. Mould cooling becomes essential and determines the quality of the preform at this stage. An increase in IV reduces the rate of crystallisation by lengthening the polymer chains, making it more difficult for a given chain to disentangle itself from other chains and form an ordered crystal. Copolymer content changes the molecular structure of the chains, inhibiting crystallisation by essentially introducing a unit into the chain that may not easily form crystals due to structural differences or disrupt the crystalline pattern. “Extended chain” or “oriented” crystallisation During stretch blow moulding, the amorphous chains in the preform are stretched and oriented, and a different form of crystallinity is developed. The chains are aligned in the direction of stress, orienting the chains and imposing a linear ordered structure throughout the area the stress is Please order your copy at the PETplanet insider book shop: https://petpla.net/books Bottles, Preforms and Closures A Design Guide for PET Packaging Second Edition by Ottmar Brandau € 115,00 180 pages © Copyright Elsevier 2012 applied. This “extended chain” or stress-induced crystallinity is necessary in the blow-moulded container for mechanical strength. Summary PET occurs in three different states: Amorphous, non-oriented, and clear, such as preforms and melted plastic resin; thermally (by means of temperature) crystallised, such as resin pellets: strain-induced crystals, such as bottle sidewalls. PET is transformed several times as it goes from pellet to preform to bottle. As resin pellets, PET is thermally crystallised to a level of 50–70%. Thermally induced crystals are arranged in large structures called spherulites, which reflect light. Therefore, PET appears white. During the injection process, these crystals are melted, resulting in an amorphous melt, which is injected into the preform mould cavities. The preform is rapidly cooled down to avoid recrystallisation. Preforms therefore do not have a crystal structure. This state is called amorphous. In the amorphous state the molecular chains show no orientation and no crystallinity, and their appearance has been compared with a bowl of spaghetti. There is nothing to reflect light and therefore the PET is clear. It also has little strength or barrier properties. In the reheat stretch blow machine, the material is forced by the stretch rod and blow air to orient in the axial and hoop direction, forming small, strain-induced crystals. These crystals do not reflect light and the bottle appears clear. It also has higher strength and barrier properties. Crystallisation levels of up to 25% can be achieved in the bottle sidewall given the correct preform design and process conditions (higher crystallinity levels are achieved in the heat-set process). The finished bottle will have amorphous portions in the neck and gate area where the bottle was not stretched, oriented portions in the sidewalls, and sometimes thermally crystallised portions around the gate, a common preform defect that cannot be corrected during blow moulding. * This article was published in Bottles, Preforms and Closures, Ottmar Brandau, Chapter 2.2. Copyright Elsevier 2012","@ID":27}, "24 PETplanet insider Vol. 15 No. 05/14 petpla.net MATERIAL / RECYCLING to the type of reaction where many monomer units are chemically linked to form polymers (“polys” many). A resin with only one type of monomer is called a homopolymer. Copolymer resins are the result of modifying the homopolymer chain with varying amounts of a second monomer (or comonomer) to change some of the performance properties of the resin. Manufacture of PET There are a few chemical routes to manufacture PET, but basically a compound with two acids, such as terephthalic acid (TPA), is esterified with a compound with two alcohols, ethylene glycol (EG). Because there are two functional groups on each component, they can continue to link up to form long chains. Water is a byproduct of this process. This esterification reaction is reversible, and this is the key to understand much of the behaviour of PET. Commercially the polymerisation is done in two stages. Melt phase condensation results in molten polymer with about 100 repeat units (intrinsic viscosity (IV), as explained subsequently, is about 0.6). The melt is pelletised and can be used for some applications such as in fibre at this point. To continue the polymerisation, a process called “solid stating” is needed. Solid stating produces high molecular weight PET needed for fabricating bottles. Catalysts Different catalysts are required for the two main chemical routes to manufacture PET. Special catalyst combinations can be used to influence the side reactions, to reduce the amount of diethylene glycol (DEG) or acetaldehyde (AA), or to improve the colour. Because the catalyst residues remain in the PET, they are still present during drying and processing. Therefore, different grades of PET from different manufacturers react differently if not processed at optimum conditions. For example, the dimethyl terephthalate (DMT) process (used chiefly by Eastman) requires an additional catalyst, which may result in a greater tendency of the resin to oxidise or “yellow” when overdried. PET- a linear condensation polymer PET does not branch: each molecule is a long “linear” chain. In addition, because it is formed by a reversible condensation reaction, it has a very simple distribution of molecular weights or chain lengths. The result as far as end users are concerned is that the chemical structure of a grade of PET can be described quite completely by only two measures: IV, which is a measure of molecular weight, and the copolymer content. In contrast, a polymer such as polyethylene can have unique molecular weight distributions and widely varying degrees and types of branching, which affect processing and performance profoundly. Intrinsic viscosity The properties of the PET polymer are largely dependent on the average molecular weight or the average number of repeat units of the polymer chains. This is usually determined by measurement of the intrinsic viscosity, or IV, as explained later. The relationship between molecular weight and IV is fairly linear. High-IV PET has a higher molecular weight than low-IV PET. The longer chains give the resin better properties in the final product but also affect the processing in predictable ways. The range of IVs used for PET bottle manufacturing is from about 0.73 to 0.86. Copolymer content PET copolymers are made by replacing a few per cent of one of the starting components with a different monomer. Eastman uses cyclohexane dimethanol (CHDM) to replace part of the EG. Most other resin manufacturers use IPA (isophthalic acid), which is also called purified isophthalic acid, to replace part of the TPA. DEG, a by-product of the polymerisation reaction, is another comonomer that lowers the melt temperature but is not as effective at slowing down crystallisation rates. DEG takes the place of EG in the chain. Several advantages are gained by using the copolymer especially in preform moulding applications: Copolymers crystallise more slowly than homopolymers, making it easier to fabricate clear preforms (see Chapter 2.2.4). Copolymers are easier to melt in the extruder as a result of the lower melting point and lower maximum degree of crystallinity. Copolymers impart better stresscrack resistance to the bottle. (Some of the generalised effects of IV and copolymer content are outlined in the book.) Crystallisation of PET PET is a semicrystalline resin. The word “crystalline” refers to a region of ordered chain arrangement, as opposed to “amorphous,” where the polymer chains lack order. Melted PET, by definition, is amorphous. When polymers are in an amorphous state, the molecular chains can be compared to a tangled web of spaghetti or springs. The analogy to tangled, stretched springs is particularly suitable for semicrystalline polymers because under certain conditions the polymer chains tend to coil into ordered structures, forming crystalline regions. The repeating units of the homopolymer chain fit together neatly, forming a close-packed array, which has a higher density than the amorphous state. Density measurement is commonly used to determine the degree of crystallinity. At room temperature, amorphous PET has a density of 1.335g/cc. The calculated density of a perfect PET crystal is 1.455g/cc. The density of a semicrystalline sample with x fraction of crystallinity is: 1 x (1-x) p = 1.455 + 1.335 The crystal structure has a lower energy state than the amorphous arrangement, so it is the favoured arrangement. Because polymer molecules are long and entangled, however, the amorphous state can be “frozen in” by rapidly cooling the PET melt. Crystallisation can occur at any temperature at which the polymer chains have sufficient mobility","@ID":26}, "EDITOUR REPORT 13 PETplanet insider Vol. 15 No. 05/14 petpla.net World Tour 2013 On May 15, 2013 the paths of the Husky World Tour 2013 and the PETplanet Go with the flow South America Tour coincided in Jundiai, São Paulo, Brazil. In Husky’s Brazil Technical Center in São Paulo I touched base with Keith Carlton, Husky’s Vice President, Global Sales, Beverage Packaging, who at the time had been recently appointed to this role. This is where the South America Beverage Packaging Conference is currently taking place. Regular readers will recall that Husky had embarked on a major World Tour 2013. After visits to South Korea and Europe, the Husky team moved to Latin America. According to Keith Carlton, a Beverage Packaging Conference traditionally takes place here in the Brazil Technical Center every year, and this year attendance has been particularly high. The number of participants is around 130, representing more than 70 companies. These range from small and medium-sized family enterprises to representatives from the major players, all from the beverage packaging sector. Husky created something of a stir within the industry when it decided to forego the big international plastics fairs in 2013 to organise its own world tour, meeting and talking with its customers face to face. I wanted to find out what Husky’s experience to date had been. According to Keith Carlton, the response to date had been very good, and the idea of having more intimate, local customer events had paid off. The tour had also proved an exceptional opportunity to network amongst industry professionals and has enabled richer, more focused customer interactions. I asked whether Husky would repeat the event. The answer was guarded, not surprisingly since a final judgement can only be made once the World Tour has been completed. Further stopovers for the Husky World Tour 2013 took place in June in Istanbul, Turkey, Bolton, Canada and Chicago, United States, which are being followed by further events in Delhi, India in August and Dudelange, Luxembourg in September, where Beverage Packaging was the focal point. Preforms and closures Brazilian style The Brazilian market is highly diverse. There are, inevitably, innumerable smallish companies for whom their own PET preform and/or bottling operation does not represent a paying proposition. Then there are the big converters who benefit from a global network. Just to add a few complications, there is a multiplicity of bottle sizes and geometries to take into consideration, which makes it all the more difficult to do like-for-like comparisons with other markets. Prepare for Life. From preform to bottle. We ensure a perfect process. www.intravis.com","@ID":15}, "ON SITE 43 PETplanet insider Vol. 15 No. 05/14 petpla.net Seven-up with Brandenburger Urstromquelle Brandenburger Urstromquelle, of Baruth, Germany, has invested in a new InnoPET Blomax Series IV stretch blow moulder, an Innofill DRV filling system, and an Innopack Kisters SP Advanced shrink packer. The KHS GmbH machines will be used primarily to bottle carbonated non-alcoholic beverages, such as water and apple spritzer, in 0.5l containers. The 28-cavity InnoPET can produce 63,000 PET bph. It is the 7th KHS blow-moulder to be installed in the factory and the third Series IV model. The new machine’s specially-developed heating module takes up only about half the space occupied by the equivalent unit in the Series III. KHS and Brandenburger Urstromquelle developed a concept for the Innopack Kisters SP Advanced packaging system that enables the processing of narrower film widths, with the help of an integrated web control. The system features hygienic design, operator-prompted format changeover, and hot air nozzles in the shrink tunnel area that can be adapted to different conditions. www.khs.com Romanian Quantum upgrades with Sidel Romanian company Quantum Mineral Trading Company Ltd owns and operates two mineral water springs (FH1 and FH2M) in the Harghita Mountains. The company bottles natural mineral water and partially carbonated natural mineral water from the wells under the ‘Spring Harghita’ brand name. The company’s daily production capacity of more than one million litre is bottled in PET formats ranging from 0.5 to 5l. Its three existing production lines originally comprised one Sidel Universal SBO6 and three SBO2F PET blow-moulding machines. After detailed discussion, it was decided to replace the ovens in the production lines with the more economical Ecoven, which cut electrical consumption by 45% while maintaining production capacity. At the same time, Quantum decided to adapt the existing bottle designs in order to reduce raw material consumption. The closure was changed from 1810 standard to 1881, which led to material savings of 1.5g on four bottle formats: 0.5, 1.5, 2 and 2.5l. Testing confirmed that the new design had not compromised the bottles’ mechanical properties or performance. Although it requires fewer heating modules and lamps, the Ecoven reduces preform-heating time and uses power more efficiently. Savings on compressed air consumption compared with the previous generation of blow-moulders are also expected to benefit Quantum Mineral’s Total Cost of Ownership (TCO). www.sidel.com","@ID":45}, "PETcontents 5/14 4 PETplanet insider Vol. 15 No. 05/14 petpla.net INSIDE TRACK 3 Editorial 4 Contents 6 News 40 Products 42 On site 44 PET bottles for beverages and liquid food 46 PET bottles in health and beauty care packaging 48 Patents MARKET SURVEY 33 Suppliers of PET preform systems / single stage machinery TRADESHOW REVIEWS 36 Interpack review Düsseldorf, Germany, May 8 - 14, 2014 38 Chinaplas review Shanghai, China, April 23 - 26, 2014 BUYER’S GUIDE 49 Get listed! Page 26 Page 34 Page 20 EDITOUR REPORT 12 Brazil - Part 4 Go with the flow tour: South America MATERIAL / RECYCLING 20 Heavy metal no longer in tune PET catalyst technology by CTL 22 Manufacture and states of PET Bottles, preforms and closures, part 12 BOTTLING / FILLING 26 Wetting the US appetite for water Crossroads Beverage Group runs three KHS turnkey lines for US water market BOTTLE MAKING 32 Keg systems: A personal experiment Beer in PET - a never-ending story? 34 A golden thread SMI´s HSR stretch blow-moulder","@ID":6}, "imprint EDITORIAL PUBLISHER Alexander Büchler, Managing Director HEAD OFFICE heidelberg business media GmbH Häusserstr. 36 69115 Heidelberg, Germany phone: +49 6221-65108-0 fax: +49 6221-65108-28 info@hbmedia.net EDITORIAL Doris Fischer: fischer@hbmedia.net Gabriele Kosmehl Michael Maruschke Ruari McCallion Waldemar Schmitke Ilona Trotter Wolfgang von Schroeter Anthony Withers MEDIA CONSULTANTS Martina Hirschmann hirschmann@hbmedia.net Roland Loch loch@hbmedia.net phone: +49 6221-65108-0 fax: +49 6221-65108-28 France, Italy, Spain, UK Elisabeth Maria Köpke phone: +49 6201-878925 fax: +49 6201-878926 koepke@hbmedia.net LAYOUT AND PREPRESS Exprim Kommunikationsdesign Matthias Gaumann | www.exprim.de READER SERVICES Heike Fischer reader@hbmedia.net PRINT Chroma Druck & Verlag GmbH Werkstr. 25 67354 Römerberg Germany WWW www.hbmedia.net | petpla.net PETplanet insider ISSN 1438-9459 is published 10 times a year. This publication is sent to qualified subscribers (1-year subscription 149 EUR, 2-year subscription 289 EUR, Young professionals’ subscription 99 EUR. Magazines will be dispatched to you by airmail). Not to be reproduced in any form without permission from the publisher. Note: The fact that product names may not be identified as trademarks is not an indication that such names are not registered trademarks. 3 PETplanet insider Vol. 15 No. 05/14 petpla.net dear readers, A spanner in the works Our Editourmobil is once again on the move, this time around the western Mediterranean. Our focus last year was in planning our tour in North Africa and Italy. However the more we looked into it, the more options there seemed to be in Spain. Finally we made the decision to set up a team in Spain as well. It seems to be an interesting market. How are the bottlers and preform manufacturer actually coping in these troubled economic times for Spain? These were our thoughts. Since we were unable to get together a team, I finally decided to drive the Editourmobil solo to the Iberian Peninsula. Personal circumstances then obliged me to pull out at short notice and Waldemar Schmitke and Kay Barton stepped into the breach for a somewhat curtailed tour of Spain. For this, my grateful thanks. Hardly had they got underway when they had to consider cancelling the tour. As a general rule, an economic crisis usually sees an increase in the crime rate, and both members of the team were to find this out to their cost at the start of the tour in Barcelona. They happened to leave the Editourmobil unattended for two hours during the day and when they returned it had been ransacked. Cameras, laptop and all kinds of technical equipment had been illegally spirited away. We have travelled through many countries - even countries with higher crime rates, but we have never been cleaned out like this before. Odd items have gone AWOL, the monitor of the rear view camera went missing whilst on board ship, and in Brazil a solar panel disappeared from the roof. And that is the sum total, going back almost five years. The burglars got in through the cab and were able to get through the passageway to the rear of the vehicle. In the new Editourmobil currently being built, one thing is absolutely clear: there will be no way through. Safety glass windows are already on the agenda. It should all make it more difficult for the opportunist burglar. But it can never be 100% secure. I am relieved that Waldemar and Kay are physically unharmed, and hope that this is the first and last break-in for our Editourmobil. Yours Alexander Büchler","@ID":5}, "NEWS 10 PETplanet insider Vol. 15 No. 05/14 petpla.net Russia to triple PET capacity within the next few years PET production capacity in Russia is set to triple within the next few years. Two plants are scheduled for completion in 2014: two more, even larger, are at the planning stage. Currently there are four major chemical factories in Russia with advanced synthesis systems in which PET is produced. These companies are Alko - Nafta in Kaliningrad with a capacity of 230,000t, Senesch in Moscow with 100,000t, Sibur - PETF with 76,000t and Polyef in the Republic of Bashkortostan with 140,000t. In fact, if all plans currently being put forward are implemented, and this will depend inter alia on the supply of the basic constituents, terephthalic acid and monoethylene glycol (ethane), PET capacity in the next two to three years could triple - to 1.5 million tonnes per year. The biggest new project is being planned by Chemie Holding Onk. The Group is building a facility to produce 600,000t terephthalic acid and 600,000t/a PET. According to market expert Viktor Kernizki, the project is at the preliminary planning stage. Similarly, large plants are also planned in Kabardino - Balkaria. There, Etana is planning a new PET plant costing 15.7 billion rubles (about €320m). Etana plans to produce annually 486,000t PET, of which 15% will be PET fibres. At present, the planners are reportedly looking at Etana’s proposals relating to the infrastructure in and around the plant site. In the packaging industry, the main consumer of PET, there is still potential for growth. The market volume for PET in Russia is estimated at US$ 2bn. The growth forecast for the next few years is plus 4%/a. Actual growth will depend crucially on who comes out the winner in the long-running controversy over beer in PET bottles. Currently, about one third of PET production goes to breweries. Every second litre of beer sold in Russia is in plastic bottles. However, glass, metal and vodka producers are lobbying for a ban on the sale of alcoholic beverages in PET bottles. For their part, PET bottle producers and the breweries are supporting the status quo. In contrast to alcoholic drinks, demand is growing steadily for milk and bottled water. www.gtai.de www.creon-online.ru PTI announces oPTI PET technology partnership Plastic Technologies, Inc. (PTI) announces new technology partnerships to assist in the commercialisation of its overmoulded oPTI PET bottles. Foboha GmbH and Ferromatik Milacron GmbH have now joined PTI to improve speed-to-market and commercial viability for the lightweight foamed PET bottles. The Foboha cube mould system has been designed from the ground up to maximise cavitation and minimise cost for overmoulded parts. The goal was to increase production output criteria for the oPTI inner layer and an overmoulded traditional PET outer layer bottles. Coupling Foboha’s cube mould technology with Ferromatik Milacron’s injection moulding platform results in an increased number of cavities in the mould, thereby increasing the output. The oPTI process produces bottles with striking visual and tactile attributes, ideal for applications seeking brand differentiation. It is based on MuCell technology licensed from Trexel, Inc. Ideal applications are said to include foods, beverages (wine, spirits, beer, juice, nutriceuticals, etc.) health and beauty aids, cosmetics, etc. www.plastictechnologies.com Bühler Thermal Processes AG PET plants with SSP technologies Bühler Thermal Processes AG (BPAG) has introduced SSP technologies for strand cut pellets (ECOstrand) and underwater cut pellets (ECOsphere) which is said to reduce energy consumption by up to 50% compared to conventional technology. In addition the MEG consumption in polymer production can be reduced by 0.5kg/t of PET. The two leading PET producers Indorama Ventures and Far Eastern New Century have chosen the new BPAG Eco SSP technologies for their plant expansions in Europe and Asia. The Ecosphere technology will be commissioned by the middle of 2014 and the Ecostrand technology will be producing PET by May 2015. BPAG claims that the Eco SSP technologies allow a compact building structure and a lightweight building design with a minimum number of floors. The savings on the building structure costs are up to 50% compared to conventional design. www.btpag.com drink technology India and International PackTech India in Sept 2014 drink technology India and International PackTech India will take place under one roof in Mumbai from September 25-27 and present solutions for the international packaging, package labelling, processing, food and beverage industries. Six months before the start of the trade show double, the organisers expect an increase in sold floorspace of between 10 and 20%. A total of at least 260 exhibitors are expected for both events; they will present their products and services in Hall 1 of the Bombay Convention & Exhibition Centre. During the previous double feature in November 2012, the organisers recorded a total of 220 exhibitors. This year’s number of visitors is also expected to rise. A total of 7,500 specialists visited the last event; this year, the hosts anticipate about 8,500. For the first time, drink technology India will feature Round Table Talks: manufacturers from the beverage and food segment will present case studies to illustrate a specific topic. The presentation will be followed by a discussion with suppliers and the audience. The overall subject of this year’s Round Table Talks is “The Outlook for Beverages and Food in India 2020.” A second feature of the drink technology India supporting programme is the exhibitors’ forum with exhibitor presentations on the subjects of “Beverage” and “Food”. www.drinktechnology-india.com www.packtech-india.com","@ID":12}, "PETproducts 40 PETplanet insider Vol. 15 No. 05/14 petpla.net DRYING HAS NEVER BEEN THIS EFFICIENT: ETA plus® LUXOR - now available with ETAplus® ETAplus® considerably reduces energy consumption and protects materials. When it comes to drying, saving energy is a key concern. We have developed a system that combines airflow regulation with a temperature adjustment feature – that can be disabled if required –and efficient waste heat recovery. The result? A drying system that cuts energy consumption by up to 64%: ETAplus® . motan-colortronic gmbh info@motan-colortronic.de www.motan-colortronic.com Direct-cooled temperature control unit for up to 120°C The gwk company Wärme Kältetechnik, Kierspe, Germany has expanded its teco cs series to include a direct-cooled temperature control unit for the temperature range up to 120°C with heat outputs of 6 to 12kW. In addition, the facilities available with teco cs 140 t18 have been extended to include a wide range of options for the temperature range up to 140°C, such as a pump wear display, rotary field detection with automatic switchover and pump pressure display. Temperature control units in the teco series can be used for operation with water with direct or indirect cooling up to 95, 140, 150, 160 and 200°C, depending on the model. With heat outputs of up to 72kW, cooling capacities of up to 600kW and pump transfer volumes of up to 500l/min, the modular design series are said to be suitable for almost any application in the plastics processing industry. The models in the teco series which operate using heat transfer oils, are capable, depending on design, of accommodating temperature requirements of up to 180, 300 or 350°C in comparable performance categories. For cooling of mould segments where temperatures are difficult to control, gwk offer two models in the patented cold water tempering device range teco cw that can be operated glycol-free in the temperature range between 0 and 25°C. The standard equipment comprises leak stop operation, mould emptying, acoustic alarm, automatic filling and top-up, an additional facility for filling with conditioned water, dirt traps in the cooling water connection and parts in contact with the medium that are manufactured from corrosion-resistant materials. The circulating water is cooled down to the low temperatures directly in the device in proximity to the mould. www.gwk.com Takeaway items Hi-Cone has introduced a new carrier with takeaway items. The carriers are said to have minimal packaging compared to most types of packaging. In addition, they are waterproof, and removing one will not affect the integrity of the pack. All Hi-Cone carriers are made with photodegradable low-density polyethylene (LDPE). Over time, exposure to sunlight makes the carriers brittle. As a special feature, the takeaway carriers give companies options for implementing multipack promotional campaigns, designing them as bookmarks, wristbands, trading cards or stickers. www.hi-cone.com Takeaway carrier with takeaway items","@ID":42}, "BOTTLES 45 PETplanet insider Vol. 15 No. 05/14 IMAGINE FILLING MULTIPLE PRODUCTS ON THE SAME LINE…NOW YOU CAN! Water, juice and soft drinks, all on a single machine? The Flextronic modular platform adapts effortlessly to still or sparkling, clear or pulpy and hot or cold-fill, and easily switches from one bottle neck-size to the other. A revolutionary filling technology that gives you extreme operational flexibility with minimal product loss and downtime at flavor switch. Clean, safe and versatile. Welcome to the new generation of fillers. carbonated still hot-fill cold-fill pulp non-pulp water juice soft drink SIPA S.p.A. - Via Caduti del Lavoro, 3 - 31029 Vittorio Veneto (TV) - Italy Tel. +39 0438 911511 - Fax +39 0438 912273 - e-mail: sipa@zoppas.com www.sipa.it Busy bees A better base, a design for easier handling, and drip-free dispensing. Together with Breitsamer + Ulrich and a recognised closure manufacturer, Greiner Packaging International has modified the packaging of Breitsamer honey. Breitsamer honey products in the new PET bottles containing 350 or 500g have been in stores since January 2013. Greiner Packaging International produces the new honey bottles for Breitsamer from PET, using its Kavoblow stretch blow moulding process. According to Greiner, this process facilitates a highly efficient implementation of individual designs and combines flexibility with productivity. The look and handling of the bottle have been improved. Thanks to the new base design, the packaging is more stable during filling. The dose cap with membrane plays an important role here. It is equipped with an integrated, tear-off tamper-proof band and is made of PP. www.greiner-gpi.com PET bottle with a hat In conjunction with a promotion, Innocent has been asking its devotees to produce knitted hats for the wellknown bottles and to send these in to the company. For each hat submitted, Innocent donated 20 cents to the Red Cross to help with support for the elderly. The hats were then placed on the 500ml PET bottles with caps for shipping out to stores for subsequent use by the customer as egg cups, mobile phone covers or anything else that takes their fancy. www.innocentdrinks.co.uk","@ID":47}, "PETnews 6 PETplanet insider Vol. 15 No. 05/14 petpla.net Sale of Sacmi’s Plastics Division to Kingsbury The Sacmi Group has officially completed the transfer of its entire Plastics Division to the Kingsbury Group, Rochester, New York, USA. According to Sacmi Group’s General Manager Pietro Cassani, the sale is intended to underline Sacmi’s focus on the ceramics and packaging sectors. Cassani will, following this operation, become a member of the Kingsbury Group’s board of directors. The three business units concerned, the designer of injection moulding presses Negri Bossi, the manufacturer of very large presses Bi-Power and the provider of robotised solutions Robolino-Systrama of Vignate, currently worth some €100 million, are expected to experience new growth opportunities under the management of the new owner. The new owners have expressed their intention to maintain the current output facilities, especially in Cologno and at Sacmi Imola.Kingsbury Group is a global player in the automotive, aerospace and electronic components industries, doing business for over 120 years. www.sacmi.com Indorama Ventures acquires Sasa in Turkey Indorama Ventures Public Company Limited has announced the acquisition of 51% of leading Polyester and PET producer Sasa Polyester Sanayi A.Ş in Turkey through its wholly-owned subsidiary Indorama Netherlands B.V. from Hacı Ömer Sabancı Holding A.Ş. Sasa is a publicly listed company on the Borsa Istanbul and IBV will be conducting a mandatory tender offer for the remaining 49% of Sasa’s share at Borsa Istanbul in accordance with the requirements of Turkish Capital Markets Legislation. Sasa incorporates integrated feedstock and polymer facilities producing DMT, staple fibres, filament yarns, PET, PBT polymers and speciality chemicals with a total plant capacity of 600,000t/a. Sasa supplies both Turkish and European markets, serving over 54 countries with 150 different types of products. www.indoramaventures.com Octal reports more than US$ 3 billion in sales The PET producer Octal has surpassed the US$ 3 billion dollar mark in sales, a record in the company’s six-year history. The company also claims to have recorded its highest quarter production volume of PET in Q1, 2014 with March 2014 being its second best month ever of PET production volumes. The latest capacity expansion of its state-of-the-art PET complex in Salalah, Oman has increased production of bottle grade PET resin by 40% with a monthly run-rate of US$ 100 million. Octal accounts for approximately 15% of Oman’s non-oil exports, which equates to about 1.5% of the national GDP. www.octal.com Greiner Packaging starts in the US Greiner Packaging International is moving to new offices in May 2014 at its first US site in Pittston, Pennsylvania. Production will start in July, and initial machine operation should start by the fourth quarter of this year. The focus is on premium packaging for the dairy industry. A 10,000m2 area is available for the first development stage in Pittston, Pennsylvania. Greiner Packaging International will use it primarily to manufacture high-quality premium packaging (cardboard-plastic combinations as well as printed cups). The new site is said to lie in a logistically accessible and geographically favourable location. From the packaging industry’s point of view, the Pennsylvania region is among the most attractive in the US. Around 40% of the US population lives in the country’s Northeast and Midwest. Many milk-processing plants are also based here. Most of the employees will come from the region. www.greiner.at Arburg expands central production plant On April 28, 2014, Arburg held the official groundbreaking ceremony for a new assembly hall in Lossburg, Germany, which will expand the central production location by 13% to just under 165,000m2. Initial excavation work began in March 2014 and the completion date has been set for the autumn of 2015. With the new building section, Arburg is responding to the increasing demand for large injection moulding machines up to a clamping force of 5,000kN and complete production cells. The capital investment for the new building section, to the tune of many tens of millions of euros, is said to demonstrate a clear commitment to Lossburg as a production location. www.arburg.com","@ID":8}, "EDITOUR REPORT 17 PETplanet insider Vol. 15 No. 05/14 petpla.net of the country through improvements in management and equipment donation. The project also encourages networking activities with other cooperatives and facilitates access to the recycling industry. In 2012, Ambev launched packing Guarana Antarctica (2l) with 100% rPET. The launch represents an important boost for recycling in the country. Only in 2013 were saved 8,210t of virgin material with the creation of 100% rPET. Also in 2013, more than 230 million bottles were taken from the trash. Currently rPET is used in 2l and 1,5l painted bottles for own products such as Guarana. The intention is to expand this technology. However, everything depends on what happens as regards increasing the availability of rPET. “Our aim is to expand the use of recycled PET. But we are aware at the same time that the company will also need to make a considerable contribution towards ensuring material availability. Nevertheless,” says Ricardo Rolim, “a contribution of this nature will not only stand us in good stead but will also help the environment in Brazil”. May 17, 2014 Logoplaste Shefa We met: Fabio Salik, Managing Director Ricardo David, Operations Director Vitor Vila Verde, Brasil R&D Manager Leandro Sponchiado, Manufacturing Manager Paulo Vitor R. Mendonca, Shefa Area Sales Manager PET Systems Netstal Italo Zavaglia, Head of the Netstal Division of KraussMaffei Group do Brasil Netstal Prelactia over-moulding preform-systems with 24 cavities PET packaging for milk takes hold in Brazil Surrounded by the farmlands of Amparo, better known as the “flower of the mountains,“ is the homeland of Shefa, a company whose business is bottling UHT milk and juices. The unimpressive walls that surround the plant disguise the fact that this company makes use of the very latest technology and operates with a meticulous attention to detail. They cooperate with a Portuguese company, called Logoplaste, well-known for manufacturing PET preforms and bottles. Logoplaste produces PET bottles and screw caps in a neighbouring facility prior to transporting them via an air conveyor (through the factory wall) to Shefa for filling with UHT milk. We were welcomed by a reception committee made up of staff from both companies. UHT milk in PET bottles: the project Shefa packages UHT milk and juices spread over the following lines: 8 x Tetra Pak 3 x SIG 1 x PET aseptic bottling line from Storck","@ID":19}, "EDITOUR REPORT 15 large brand owner has started a migration process from two- to 1-piece HDPE closures. Due to its inherent higher precision, weight reduction is possible, addressing current sustainability trends. Furthermore, HDPE can be produced from ethanol, not yet economically possible with PP. “Green” HDPE is a potential additional driver in the future, to completely rid the market of PP, 2-piece closures. Bericap do Brasil basically only converts PE, no PP is currently being consumed. And last but not least, 1-piece HDPE closures do perform well on filling lines. Those bottlers that have already been fortunate enough to convert, do not want to be reminded about the past. Line performance has drastically improved since using Bericap 1-piece closures, all of them recognise this as a fact!” The 1-piece HDPE closure Right from the start, Bericap do Brasil, as soon as it was incorporated and producing its first closures, followed what the group was doing already in other countries and introduced injection moulded 1-piece plastic closures. Aurel Fogaci again: “Our competitive edge in terms of know-how enables us to service the market more professionally. Injection is in Bericap’s DNA. 1-piece beverage closures is what Bericap has been successfully doing for almost 20 years now”. The first 96-cavity injection moulding system for 1-piece closures is currently being commissioned. Up to now the injection moulding systems used by Bericap do Brasil have been a maximum 72 cavity. The fastest screw cap system is a 72-cavity Evos injection moulding machine from Netstal. The closure weighs 1.7g, is targeted for still water for PCO 1881 finish, the material is HDPE and the cycle time is below 3s. The current installed 1-piece beverage closure capacity surpasses 1 billion yearly closures, of which 40% are used for mineral water. The edible oil market is undergoing further growth. The Editourmobil standing in front of the factory in Sorocaba SP PETplanet insider Vol. 15","@ID":17}, "MARKET SURVEY 29 PETplanet insider Vol. 15 No. 05/14 petpla.net CyPET Technologies Aoki Technical Laboratory, Inc. Lefkosias 45, 2540 Dhali, Nicosia, Cyprus +357 22 610 700 www.cypet.eu Constantinos Sideris Director +357 99 693 923 +357 22 610 800 info@cypet.eu 4963-3 Minamijo, Sakaki-Machi, Hanishina-Gun, Nagano-Ken 389-0603, Japan +81-268-82-0111 www.aokitech.co.jp Hiroshi Chino President's Office +81-268-81-1368 +81-268-75-8114 h.chino@aokitech.co.jp K 16 K 28 K 53 K 19E K 30E SBIII-500LL-50 0.05 - 5 0.05 - 20 0.5 - 50 0.05 - 10 0.05 - 20 0.25 - 2l 1 - 12 1 - 16 1 - 24 1 - 16 1 - 24 9 ~ 16 1 - 12 1 - 16 1 - 24 1 - 16 1 - 24 9 ~ 16 280 - 16 760 - 38 1600 - 65 360 - 18 760 - 32 5 ~ 50 1,800 2,600 4,800 2,600 3,400 Approx. 8,600 900 2,600 4,800 1,700 2,600 Approx. 4,400 800 1,600 3,000 900 1,700 Approx. 3,600 on different model 400 1,600 3,000 800 1,700 Approx. 2,400 on different machine model 900 1,700 3,200 1,700 1,700 Approx. 2,000 ~ 5,000 5.2x1.4x3.4 6.8x1.9x3.8 10.3x2.2x4.4 6.1x1.8x3.7 7.5x1.9x3.9 6.38x3.55x3.49 K 16, K 28 & K 53: Servohydraulic, energy-saving models. K 19E & K 30E are all-electric models. Nissei ASB Machine Sipa Husky Injection Molding Systems 4586-3 koo, Komoro-shi, Nagano-ken, 384-8585, Japan +81 267 23 1565 www.nisseiasb.co.jp/en Katsuo Ishiguro Section Manager, Sales Coordination Team +81 267 23 1565 +81 267 23 1564 sales@nisseiasb.co.jp Via Caduti Del Lavoro, 3 31029 Vittorio Veneto, Italy +39 0438911511 www.sipa.it Stefano Baldassar Preform System Global Sales Manager +39 0438911511 +39 0438912273 stefano.baldassar@zoppas.com 500 Queen Street South Bolton, ON, L7E 5S5, Canada +1 905 951 5000 www.husky.co David Matts Director, Business Development, H-PETAE +1 905 951 5000 x 5092 dmatts@husky.ca Erin Fortin Product Manager, Business Development +1 905 951 5000 x 2605 +1 905 951 5358 efortin@husky.ca PM-70/65NII, PM-70/111N, PM-170/111M XForm 150 XForm 300 XForm 500 H-PETAE HyPET HyPET HPP5 6 - 48 from 2 to 48 from 2 to 96 from 48 to 144 2-48 6/144 (in standard matrix) 48/144 (in standard matrix) 240 1508/62 3000/60 156/52 Dependent on number of cavities and preform design 83 (dependent on number of cavities and preform design) 102g (dependent on number of cavities and preform design) 250 580 900 1,400 448 1,470 1,700 Vertical clamping, built-in preform aftercooling stations, compact XForm 150/300: energy efficient, small footprint, servo-driven clamp, cooling robot, can install legacy tooling, fast mould change, wide-mouth capability, XForm 500: new Evo robot for faster cycles, can accept legacy moulds and EOATs, fast mould change All-electric, complete preform moulding system (including machine, mould, robot, full auxiliaries). Low energy consumption, capable of =20,000bph depending on preform design, simple factory installation with consolidated utility connection points, up to 3 stage cooling take-off plate, auto lubrication, 3 year limited warranty Performance enhancement, energy efficiency, system robustness, faster controls Performance package, increased uptime and tooling life, maintenance package with alignment features, preform sampling, Altanium inside, system integration, auxiliaries integration, ease of use enhancements, system-based HMI, CoolPik DH2 Outputs tailored to ASB's own range of 2-step blowing machines for hot fill application. PM-170/111M designed for bottle and jar preforms with capability of neck size up to 120mm. XForm 150/300: Duo I & Duo II PostMold Cooling, LongLife, Xmold for ultra-thin preform injection capability XFORM 500: LongLife, XMold for ultra-thin preform injection capability Integrated auxiliary controls through single machine HMI, quick mould change with split gate & magnetic platen option, stripper ring mould technology for wide mouth applications, able to produce from 30mm to 180mm neck finishes as standard Adaptive post-mould cooling, performance packages Flexibility package, high cavitation option, compatibility packages, 30mm performance package, injection completion during power outage","@ID":31}, "22 PETplanet insider Vol. 15 No. 05/14 petpla.net MATERIAL / RECYCLING Bottles, preforms and closures, part 11 Manufacture and states of PET By Dr Laura Martin, formerly with Husky Injection Molding Systems and Ottmar Brandau, Apex Container Tech Inc. After having gathered some insights into the basics of PET preform design in part 11, we now follow down the road and take a closer look at PET material properties and how they are being influenced during the transformation process from resin pellets to preforms and finished bottles. PETplanet insider is publishing extracts from successive chapters of Ottmar Brandau’s “Bottles, Preforms and Closures”, which was first published by hbmedia. A newly revised version is reissued under the Elsevier imprint. PET belongs to the group of materials known as thermoplastic polymers. The application of heat causes the softening and deformation of thermoplastics. In contrast, thermosets cure or solidify with the application of heat and simply burn with continued heating. Like all polymers, PET is a large molecule consisting of chains of repeating units. The PET used for bottles typically has about 100–140 of the repeating unit. A monomer is a single unit that is repeated to form a polymer chain (Greek “mono” one; “meros” part). Polymerisation is the name given","@ID":24}, "BOTTLING / FILLING 26 PETplanet insider Vol. 15 No. 05/14 petpla.net Crossroads Beverage Group runs three KHS turnkey lines for US water market Wetting the US appetite for water Based on an article by Georg Zuzok, Head of Market Zone Americas, KHS GmbH, Bad Kreuznach, Germany / Jon Elward, Head of Stretch Blow Molders, KHS USA, Inc., USA Crossroads Beverage Group shares the same lineage as the founders of Silver Springs. The Richmond family established the Silver Springs Bottled Water Company in 1991 at a time when the bottled water business was still in its infancy in the United States of America. Kirk Richmond’s parents Karl and Margaret saw great potential for this segment of the beverage industry and were to prove correct in their assumptions. They began bottling with just six employees, filling 5l gallons with spring water. The company started its operations with two KHS PET systems, one a multifunctional line outputting 36,000bph and the second solely reserved for the processing of 0.5l bottles at a rate of 72,000bph. Silver Springs in Florida is now a permanent fixture on the bottled water market, filling an ever smaller percentage of its total output into 5l gallons and dealing chiefly in water in PET bottles. The President and CEO of Silver Springs and Crossroads Beverage Group is Kane Richmond, the founders’ son and Kirk’s brother. Keith Richmond, another brother, acts as CIO of Silver Springs. Kirk Richmond smiles, “We assumed that these two lines would initially do us for one or two years. However, as the market wants much more of our quality water than first expected and as our two KHS lines were running at almost maximum capacity only six months after they were commissioned, in 2012 we ordered a second 72,000bph, KHS turnkey line to fill 0.5l bottles. This now operates 24/7 and is already running at half of its full capacity.” The idea of setting up a second bottled water company alongside Silver Springs arose about three years ago. Kirk Richmond tells us more. “We’d known for quite a while that the market in the northeast of the US was undersupplied with bottled water, especially as far as distribution through the retail trade was concerned. We had lots of enquiries at Silver Springs from this region and when this number became considerable we decided to open a second bottling plant in the Northeast.” Core businesses Crossroads’ core area of business is to supply retailers and casino operations with their own private label bottled water. If required, the company also assists in the creation of bottle designs, labels and shrink packs. At present Crossroads distributes the majority of its product within a radius In 2012 a new bottled water company was opened in the US state of Pennsylvania: the Crossroads Beverage Group. The first bottle of water rolled off the conveyor belt on April 16, 2012. Today, the company runs three KHS bottling lines. Approximately 130 trucks loaded up with freshly bottled water currently leave the company every day.","@ID":28}]}}
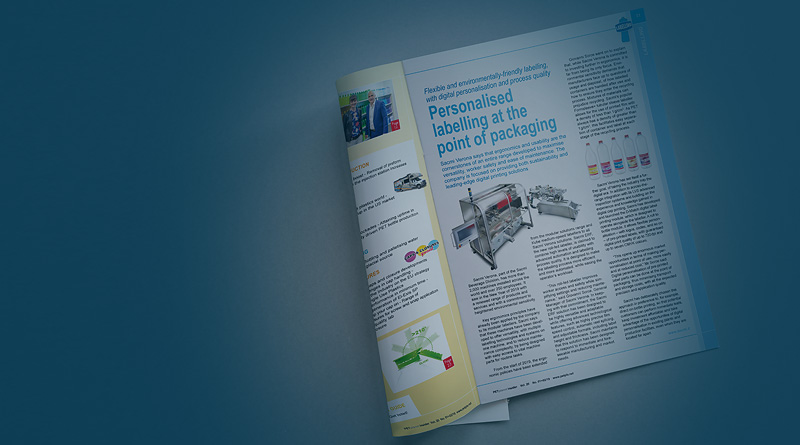