Breaking barriers in PET recycling
Discussing the increase in recoverability by using magnetic coatings on shrink sleeves
by Gabriele Kosmehl
Shrink sleeve labels have long been identified as an obstacle to PET bottle recycling. With their patented magnetisable coatings, the start-up Magnomer aims to overcome these challenges. Their Magmark coatings, when applied to shrink sleeves, are claimed to allow efficient and economical separation – utilising existing infrastructure. The technology has garnered industry recognition and is poised to boost PET recycling rates.
PETplanet: Ravish, first of all, can you briefly introduce your company, please?
Ravish Majithia: Magnomer is a materials startup located in Framingham, MA, USA & Mumbai, India, introducing a patented magnetisable coatings technology called Magmark to transfer sortability features for recyclable packaging. Magmark coatings are printed using industry standard techniques as a transparent varnish to impart magnetisation on flexible films such as bottle labels. This complements widely used magnetic separators in plastics recycling to economically separate problematic labels. Magnomer’s coatings technology is a packaging design tool used to resolve long standing sorting issues in package recycling such as label contamination. Magnomer has received industry recognition from the Association of Plastic Recyclers (APR) on the basis of a first ever commercial scale recyclability test of shrink labelled bottles.
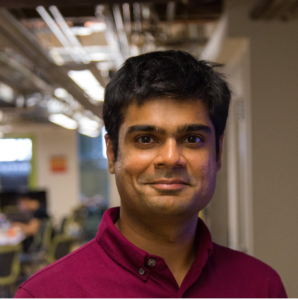
PETplanet: Which labels exactly belong to the “problematic” category when it comes to economic separation and how can companies implement your technology in practice?
Ravish Majithia: Shrink sleeve labels are simultaneously an excellent marketing resource – they are the fastest growing label category; and a significant deterrent to circular recycling of PET bottles. Major recycling associations like Recoup in UK, the Association of Plastic Recyclers (APR) in North America and European PET Bottle Platform (EPBP), Petcore and Recyclass in Europe have identified shrink sleeve labels and specifically PETG shrink sleeve labels as one of the biggest issues in PET recycling. The problem is sortation – sorting PETG shrink sleeve labels away from the PET bottles stream is the need of the hour.
Magnomer has developed a magnetisable coating which allows for easy sortation of shrink sleeve labels away from the PET stream. Magmark SS coating is a transparent, food-safe coating which can be printed on the labels using common high speed printing techniques like gravure and flexographic printing in high speed processes. The coating can be printed along with existing graphics requiring little to no modification to the printing operations, allowing for easy adoption with no capital expenditure required. We have proven our technology on a commercial scale. Over two metric tons of bottles with Magmark SS coated shrink sleeves were introduced into regular operations at two commercial PET reclaimers, Evergreen recycling and Indorama Ventures. More than 99% of the contaminating label flake was removed using magnetic separation. Based on the positive feedback from the reclaimers and their glowing testimonials the Association of Plastic Recyclers (APR) in North America awarded Magnomer the Innovation Recognition in June 2023. The coating itself does not impact any bottling process.
PETplanet: Do recyclers need additional equipment to achieve a good separation performance of magnetisable ink sleeves?
Ravish Majithia: Based on a survey conducted by the Association of Plastic Recyclers, PET reclaimers already have magnetic separators as a part of their flake decontamination process. Removal of metal contamination from PET is important and magnetic separators are commonly used to remove small metal pieces from PET flake. Magnomer’s coatings utilise this existing infrastructure to separate undesirable shrink sleeve flake as well.
PETplanet: What is the percentage of separation that can be achieved compared to conventional sleeves‘ separation?
Ravish Majithia: In the case of PETG, the most common sleeve resin used in North America and EU, more than 98% of sleeve flake was magnetically separated using Magmark SS coatings. This is compared to almost zero separation if our coating were not present for PETG removal.
PETplanet: You mentioned that the Association of Plastic Recyclers (APR) recently awarded you the responsible innovation award for the Magmark SS magnetisable coatings. How did the process work, what kind of tests were carried out?
Ravish Majithia: The Innovation recognition by APR is based on high volume commercial recycling tests. This includes:
- Printing over 250,000 “innovation“ bottles using standard PETG sleeves with Magmark SS coating
- Testing a subset of these bottles at three commercial MRFs to show that the use of Magmark SS coatings do not impact MRF operations;
- Introducing over 2 metric tons of “innovation“ bottles at two different PET reclaimers namely Indorama Ventures (facility in Alabama, US) and Evergreen Recycling (facility in Ohio, US) to showcase magnetic removal of sleeves.
As a part of the recognition process, the MRFs and reclaimers provided public testimonials to APR’s review committee which subsequently awarded the recognition to Magnomer.
PETplanet: Is Magmark limited to use on PET bottles‘ shrink sleeves or can it also be used for other types of packaging/labelling?
Ravish Majithia: Magmark technology can be applied to various categories of labels or flexible packaging – indeed anywhere where sorting of said flexible film is required. Our various current products and demo videos can be found on our website.
PETplanet: Thank you very much Ravish!