{"pages":{"page":[{"@ID":25 "39 EVENT PREVIEW PETplanet Insider Vol. 25 No. 04/24 Solutions for food-grade recycled post-consumer PE, PP, PS and PET Super-cleaning and odour reduction solutions for the most popular consumer packaging materials: The two Starlinger business units Viscotec and recycling technology have joined forces to offer high-end solutions for producing food-grade recycled PP, PE PS and PET. The recyc l ing system cons i sts of a Reco Star dynamic recycling extruder with/ without degassing, a continuous melt filter or power-backflush filter, the Visco Zero melt phase decontamination reactor, a subsequent belt melt filter or power backflush filter before the underwater or water-ring pelletiser, and the optional PCUplus pel let flusher at the end of the process. Depending on the components in the line setup, the system produces recycled resin in various grades, ranging from food-safe to highly decontaminated and odour-treated. The Visco Zero reactor in combination with the PCUplus pellet flusher produces recycled PE, PP and PS that is claimed to meet the high standards for packaging with direct food contact. The Visco Zero melt phase decontamination reactor can also be installed as a turn-key stand-alone solution for decontaminating different types of high-viscosity materials fast and efficiently. During the decontamination process in the reactor volatile contaminants are claimed to be removed effectively and the material is cleansed and homogenised. Unwanted odours or substances such as spin finish are removed. When processing PET, it is possible to increase the IV to the desired level. At NPE, Starlinger is showing the RecoStar dynamic recycling extruder, PCUplus pellet flusher and Visco Zero melt phase decontamination reactor at their booth in the West Hall. www.starlinger.com Starlinger West Building, Level 2 Booth W5169 Expo Hall For a closed circuit: Krones recycling solutions We make a daily contribution to a global circular economy with our recycling innovations because we at Krones think beyond tomorrow and regard plastic waste as a valuable resource. Chinaplas 2024, 23-26 April, Shanghai Stand 2.1 H02 www.krones.com"},{"@ID":43 "41 EVENT PREVIEW PETplanet Insider Vol. 25 No. 04/24 www.petpla.net CHANGE YOUR PERSPECTIVE CUSTOMIZED COMPLETE LINES PREFORMS AND CONTAINERS PRODUCTION SYSTEMS SINCRO BLOC SOLUTIONS FILLING & SECONDARY PACKAGING SOLUTIONS TOOLING SOLUTIONS vbr-voѲࢼomvĸ1ol \" bv |_; omѲ vrrѲb;u om |_; l-uh;| -1ࢼm] -v - om;ňv|or v_orĶ 1-r-0Ѳ; o= o@;ubm] you a full range of vhbѲѲv vr;1bC1 |o |_; ;mࢼu; ruo1;vv ث =uol |_; 7;vb]m -m7 ruo71ࢼom o= ru;=oulvĶ loѲ7v -m7 1om|-bm;uvĶ r |o |_; u;-Ѳb-ࢼom o= 1olrѲ;|; Ѳbm;vĸ ); -u; -Ѳvo ;|u;l;Ѳ Y;b0Ѳ; bm ruob7bm] mbt; -m7 _b]_Ѳ 1v|olb;7 voѲࢼomv =ou |_; lov| 7b;uv; l-m=-1|ubm] u;tbu;l;m|vĸ $_; b7;-Ѳ r-u|m;u |o _-um;vv ou bl-]bm-ࢼom -m7 0ubm] ou ruof;1|v =uol r;ѲѲ;| |o r-ѲѲ;|ĸ PACKAGING DESIGN AND ENGINEERING"},{"@ID":20 "PREFORM PRODUCTION PETplanet Insider Vol. 25 No. 04/24 www.petpla.net 18 Optimising PET preform handling TB series conveyor belts PET Solutions’ TB series features meticulously engineered conveyor belts. These belts are designed to facilitate the seamless transfer of plastic products, particularly preforms, from transformation machines such as injection moulding machines, extruders, or blow moulders. These conveyor belts operate in close proximity to production machines, ensuring a smooth flow of preforms while minimising production waste. Constructed with high-quality materials, they feature polyurethane (PU) strips certified for food industry standards, ensuring durability and compliance with regulations. The PU strips are adept at handling high-temperature products, minimising the risk of material damage. Customisable options such as adjustable height, length, and variable inclinations, are claimed to ensure seamless integration into any production layout. Controlled by a state-ofthe-art microprocessor with a userfriendly touch display interface, these conveyor belts offer programmable functionality for easy configuration and monitoring. Standard features such as mobility wheels and inclinations at 30°, 45°, and 60° enhance versatility. Accessories like preform cooling systems, misting applications, and inverters for speed regulation complement the functionality of the TB Series conveyor belts, ensuring performance in various operational scenarios. SD series soft drop PET Solutions’ SD series introduces soft drop devices, pneumatic- driven storage units designed for preforms and plastic material exiting transformation machines. These devices receive material directly from injection machines through TB series conveyor belts, minimising handling damage. Controlled by a microprocessor with a user-friendly touch display, the soft drop series is claimed to guarantee precise material release at predetermined minimal heights, safeguarding against potential damage during unloading. Integrated features such as fixed screws prevent product contamination, while standard inverters ensure that the distribution inside the storage box is optimised by regulating the speed as needed. Accessories such as safety barriers and load cell applications enhance operational safety and efficiency. VB series vibrating tables The company’s VB series vibrating tables serve as an optional feature for soft drop and conveyor belts, ensuring uniform distribution of stored plastic products within containers. These tables with variable-intensity motors have been designed to optimise container capacity, eliminating central accumulation. Two variants are available, featuring either spring or anti-vibration buffer systems, catering to diverse operational requirements. By enhancing container capacity by up to 15%, these vibrating tables reduce storage volume requirements. PET Solutions offers a range of vibrating platforms compatible with various container types, including cardboard, metal, and plastic. The company says that the integration with soft drop or conveyor belt operator panels allows seamless operation, while customisable vibration modes ensure good performance tailored to specific needs. www.petsolutions.it PREFORMS TB series conveyor belt In PET preform manufacturing, precision and efficiency play vital roles. PET Solutions specialises in optimising the handling of preforms, streamlining production processes for enhanced productivity. SD series soft drop storage units receive the preforms directly from injection machines."},{"@ID":66 "40 EVENT PREVIEW PETplanet Insider Vol. 25 No. 04/24 www.petpla.net Energy-efficient material drying for low throughputs Eisbär will feature Plug&Dry, a complete solution designed for efficient material drying. With just a power connection and a material pipeline, the compact Plug & Dry offers material drying for PET granules, flakes, and of course, other materials. It consists of material drying, drying hoppers, and material conveyance. Plug&Dry is optimised for low throughputs, ranging from 25 to 200 kg/h. Despite its high efficiency, this system maintains a compact footprint, making it a space-saving alternative to conventional drying systems. A closed-loop system is used for rapid material drying. Plug & Dry is claimed to offer a continuous drying process, low energy costs, and a long lifespan. In addition, the absence of separate cooling technology or a cooling water connection enhances Plug&Dry’s flexibility, allowing for easy deployment and relocation. Key advantages of the solution include its simplicity of operation, low energy consumption, minimal maintenance requirements, and compact design. By eliminating the need for cooling water and additional cooling technology, Plug&Dry further emphasises its environmentally friendly approach. www.eisbaer.at Eisbär South Hall, Level 1 Booth S15083 Weima West Hall, Level 1 Booth W4781 + W4789 Booth 25 Tangerine Ballroom Recycling Zone Shredding, recycling & waste management Weima, a leading provider of size reduction equipment, is set to showcase its latest developments in plastic shredding, recycling, and waste management. With a focus on enhancing efficiency, promoting circularity, and maximising value throughout the plastics lifecycle, the company offers a diverse range of solutions tailored to meet the challenges encountered by plastics manufacturers, recyclers, and processors. Among the highlights at the Weima booth are the WLK 10, WLK 800 F+, and WKS 2200 single-shaft shredders. The WLK 10 single-shaft shredder offers versatility in processing a wide array of plastic materials, i.e. PET bottles. With its robust design and V-rotor technology, and its adaptable configurations, it is claimed to ensure optimal performance tailored to specific applications, while features such as a lift-up screen basket enhance convenience for operators. As an Official Recycler of NPE2024, Weima will showcase its shredders and granulators in action. Outside the main hall, visitors can witness the operation of the equipment as part of the Destroy Responsibly program, which aims to divert demonstration scrap from landfills by repurposing it. Realtime shredding of plastic scrap will take place in the Recycling Zone behind West Hall, with the material being reintroduced into plastic production processes by Commercial Plastics Recycling, Inc., in line with the goal of recycling 100% of the plastic scrap generated on the show floor in 2024. In addition to shredding, Weima offers expertise in draining and compression processes. www.weima.com Solutions for manufacturing, processing, conditioning and recycling plastics Maag Group has long been a leader in the development of die plates for underwater pelletising systems for compounding. With the recent acquisition of AMN, Maag expands its offerings to include die plates for virgin polyolefin production, leveraging the combined expertise of industry leaders such as AMN, Automatik, and Gala. Maag will exhibit the new Pearlo X Series pelletiser for throughputs of up to 40 t/h. Its high level of automation allows start-up and shut-down at the push of a button, while wear-optimised cutting tools maximise production times while minimising downtimes and waste. The company will also showcase its comprehensive range of filtration solutions spanning extrusion, virgin polymer production, and mechanical and chemical recycling processes. At the heart of the mechanical recycling portfolio is the high-performance melt filter from Ettlinger. The continuousrunning machines are specially designed for highly contaminated post-consumer recycling applications. The ERF and Eco series can deliver throughputs of up to 10 t/h depending on the application. On display at NPE will be an ERF 1000, the largest Ettlinger continuous filter available. For compounding and masterbatch applications, the company will feature the PrimoPlus 300 dry-cut pelletiser and a JSG pelletising system model. Maag also introduces Vectored Air Technology, a new mill housing that is claimed to enable throughput increases of up to 25% on the Rex Duo Plus pulveriser. Additionally, the company emphasises its commitment to customer service and after-sales support, offering roundthe-clock assistance globally, either in person or remotely. The recently launched MyMaag e-shop offers custom and plantspecific spares and wearing parts at the click of a mouse any time 24/7. www.maag.com Maag West Buidling, Level 2 Booth W3961 Expo Hall"},{"@ID":11 "9 NEWS PETplanet Insider Vol. 25 No. 04/24 Aldi launches first supermarket own-brand Packamama ‘flat’ recycled PET wine bottles Aldi has announced the UK’s first, supermarket own-brand flat rPET wine bottles. The Chapter & Verse Shiraz and Chapter & Verse Chardonnay are now available to buy in lightweight, fully recyclable PET bottles nationwide. Made from 100% rPET, the flat bottles weigh just 63g – making them nearly seven times lighter and stronger than a standard glass bottle, while being completely shatterproof. Removing 42 t of bottle weight for this launch alone, the next-gen bottles are claimed to be ideal for picnics and BBQs. The compact design means 30% more bottles can be loaded onto pallets and transported to supermarkets; and converting to these bottles compared to standard round glass, takes 30% of lorries off the road. What’s more, the packaging allows shoppers to stack and organise bottles in their homes, optimising storage space. Aldi has worked with Packamama on the supermarket-first initiative. With soft cherries and berries on the nose, the fruity Chapter & Verse Shi raz is claimed to delight tastebuds with a juicy palate. Aldi’s Chapter & Verse Chardonnay, by contrast, offers notes of honeysuckle and baked spiced apple, with nectarine and vanilla on the palate. Alongside the new plastic bottles, Aldi is reducing the average bottle weight of all its still wine products by 8%. The process has been started already and will be completed by 2025. www.packamama.com We will contribute to the realization of a sustainable low-carbon society by leveraging aseptic technologies. www MAXIMUM EXPERIENCE & QUALITY The world‘s largest supplier of aseptic filling systems for PET bottles of UHT tea. Aseptic Systems Your Solutions Provider Krones completes acquisition of Netstal In a press release dated February 7, 2024, Krones announced the signing of the contract for the acquisition of 100% of the shares in Netstal Maschinen AG (Netstal), based in Näfels, Switzerland. The acquisition remained subject among other things to regulatory approval. Krones has now received that approval with no conditions. The acquisition of the injection moulding technology company is thus final. Krones consolidates Netstal in the Filling and Packaging Technology segment as from March 28, 2024. Netstal will continue to manage its business self-responsible. www.krones.com"},{"@ID":29 "PACKAGING / PALLETISING PETplanet Insider Vol. 25 No. 04/24 www.petpla.net 27 How the “Greenwashed out” trend will impact the beverage PET market by Linda Lichtmess, Consultant at Euromonitor International Euromonitor’s annual “Global Consumer Trends” report reveals the most relevant trends for the upcoming year. It provides insights into consumer’s ever evolving values and explores how their behaviour impacts and shapes the FMCG industries. One of the top six trends identified is “Greenwashed Out” where consumers demand businesses to step up and prove their eco credentials. This article will take a closer look at this particular trend and its potential impact on the PET industry. In the past few years, consumers have not only worried about climate change, but tried to have a positive impact on the environment through their everyday actions (Euromonitor Voice of the Consumer Survey 2023, 64% of global consumers). This effort, however, seems to have little value as consumers realise that climate change is moving on, the world moves from one crisis to another. Even worse, consumers increasingly distrust many companies and their brands when it comes to their sustainability initiatives, as more greenwashing cases have made the news. This is a threat to companies and their long-term success. For the packaging industry and PET bottles in particular, this has certain implications, too. Transparent communication: no more greenwashing Consumers in 2024 are no longer won over by vague labels proclaiming “climate neutral” or “eco-friendly” without substantial evidence. They demand transparency and authenticity from companies, especially in the realm of sustainable packaging. In response, the PET bottle industry is undergoing a significant paradigm shift, emphasising clear communication about their environmental initiatives. More so, the EU’s Green Claims Directive is going to protect consumers by requiring companies to substantiate their sustainability claims. Besides the regulatory pressure, the higher frequency of natural disasters will impact businesses and economies too and makes immediate action even more urgent. A more transparent communication will be vital to not only educate consumers but also to foster trust and empower consumers to make more informed choices aligning with their environmental values. “45% of global respondents mentioned their company plans on investing in certifi cations to avoid greenwashing over the next fi ve years” Source: Euromonitor’s Voice of the Industry Sustainability Survey 2023 For the PET market, this is especially crucial as there has been a lot of attention on vague claims such as “climate neutral”, often found on bottled water brands. This has sparked various debates whether single-use PET bottles that travel hundreds of kilometres across European borders can be sustainable in the first place. Moreover, most brands have removed that claim after debates and even pending legal actions by non-profit organisations. This shows even more the need to back up such claims in order to not lose consumer’s trust. Sustainable packaging as a future investment It is crucial to understand that sustainability investments are not only a contemporary trend, but a strategic future investment driving longterm efficiency. There are long-term financial benefits when making such investments, e.g., investing in sustainable packaging technologies such as light-weight bottles. Energy-efficient manufacturing processes and the utilisation of recycled PET materials not only align with environmental goals but also lead to reduced production costs. This dual impact not only appeals to environmentally conscious consumers but also makes businesses bulletproof for the future. Source: Euromonitor’s Voice of the Industry Sustainability Survey 2023 Embracing the change As the “greenwashed out” trend gains momentum globally, the PET bottle industry in Europe finds itself at a crossroads. Embracing this shift with a commitment to transparent communication and sustainable practices is not just a necessity but a strategic imperative. Businesses that invest in genuine sustainability will not only weather the storm of consumer scepticism but also position themselves as pioneers in a future where responsible packaging is not just a trend but a way of life. www.euromonitor.com"},{"@ID":22 "Spherical pellets exiting an SSP reactor PREFORM PRODUCTION PETplanet Insider Vol. 25 No. 04/24 www.petpla.net 20 Influence of PET processing on preforms and bottles based on an article by Brent Culbert, Senior Process Engineer, Polymetrix AG Solid State Polycondensation (SSP) has been an integral part in the PET processing chain since the 1970s and is today considered a given in the manufacturing of PET bottles. It complements the melt phase by increasing the molecular weight of PET in the solid state above values that cannot be comfortably reached in continuous polymerisation, eliminates difficulties associated with the stirring of the viscous melt, limits degradation and removes byproducts such as acetaldehyde (AA) and oligomers. Process conditions, such as temperature and residence time, can vary considerably during SSP. This can be due to differences in the starting IV after continuous polymerisation (CP) or the final IV, which depends on the bottle grade targeted - mineral water or CSD for example, or equipment constraints and throughput variation. To illustrate the influence of SSP on preforms and bottles, four bottle grade resins from four different commercial production facilities were compared in a standard preform trial at Packaging Technologies & Inspection (PTI) European headquarters in Switzerland. The resins, shown as 1 to 4 in Table 1, all target the mineral water market and do not contain a reheating agent. Their IVs range from 0.77 to 0.80 dl/g (ASTM); level modification varies from 3.9 to 4.6mol% (DEG+IPA). These differences do not significantly influence the preform results shown. Resins 1, 2 & 4 are all spherical pellets, crystallised directly from the melt; resin 3 is cylindrical and cooled below the glass transition (Tg) before storage and SSP processing. Generally, the longer residence time and the higher the temperature during SSP, the greater the IV increase. Resins 1, 2 & 3 were all processed under nitrogen N2 for between 9 h and 22 h at temperatures over 200 °C. Resin 4, from a Melt to Resin plant (MTR), has undergone a solidstate treatment (“conditioning”), which involves processing under dry air for an estimated 15-18 h at 180-185 °C, to remove AA while SSP also occurs. In Table 2, resin 4, the MTR resin, is clearly shown to differentiate from the other resins in several respects. It has a lower crystallinity, because of lower SSP temperatures, which is typified by a lower beginning of melting, although its melting point and PREFORMS Process parameters Unit Resin 1 2 3 4* Intrinsic Viscosity (IV) by ASTM** [dl/g] 0.785 0.768 0.779 0.800 Total modification (DEG+IPA) [mol%] 4.65 4.19 3.88 4.57 SSP processing Medium [-] N2 N2 N2 dry air SSP residence time [h] 22 9 17 15-18 SSP temperature [°C] 203 207 208 180-185 Pellet shape [-] spherical spherical cylindrical spherical Table 1: SSP processing conditions of various bottle grade resins *SSP conditions not known and therefore estimated **ASTM: American Society for Testing and Materials"},{"@ID":60 "PETplanet Insider Vol. 25 No. 04/24 www.petpla.net 43 EVENT PREVIEW Zero cooling allows a very thin, short injection moulded preform to be re-shaped for optimum stretch ratio at the blow station. The moulded cup will become a talking point at the event as the NPE exhibition’s official “Bottle Zone” will be serving beer and other refreshing beverages in this on-site moulded cup at its Beer Garden meeting area. ASB-150DPW Vision1 one-step double row ISBM machine The ASB-150DPW has the same general dimensions as the ASB-150DP but is engineered to provide double row moulding for higher output of medium sized bottles and jars in PET and a range of other resins. The live-moulded 900ml container with a weight of 40g is a typical PET jar for general food applications, however the inclusion of ASB’s Zero cooling technology enhances both the quality and productivity of the container to a significant degree over standard moulding methods, says the company. Servo-hydraulic drive provides smooth, quiet operation with reduced energy consumption compared to previous driving systems, while the optional NVES-150DPW-P/V take-out system will transfer the jars onto an output conveyor. Additional information The machines will be demonstrated with a wide range of matched upstream & downstream ancillary equipment including, such as bottle take-out units, chillers, resin dryers, mould temperature controllers, etc. ASB’s booth will also be exhibiting a wide range of new developments and packaging technologies including; Zero cooling, heat resistant PET containers, lightweight collapsible water servers, canted/tilted neck bottles, HDPE bottles by ISBM, thick wall / base cosmetic bottles, etc. www.nisseiasb.co.jp ASB-150DPW Vision1 with optional NVES bottle take-out unit ASB-150DP Vision1 with optional NVES type take-out unit installed The leading European exhibition, conference and awards for the Plastics Recycling industry. Discover the latest technologies and solutions, identify new business opportunities and network with the biggest names in plastics recycling. Visitor registration now OPEN! Register for your FREE entry badge at prseventeurope.com Organised by In association with MIDDLE EAST & AFRICA 10-12 September 2024 Dubai ASIA 13–14 November 2024 Marina Bay Sands, Singapore INDIA 4-6 December 2024 Mumbai, India Platinum Show Sponsor Gold Show Sponsor Silver Show Sponsors"},{"@ID":50 "EVENT PREVIEW PETplanet Insider Vol. 25 No. 04/24 www.petpla.net 48 Netstal’s Cap-Line system solution off ers performance and effi ciency on a small footprint 128 beverage caps every 1.9 seconds At the NPE, Netstal, together with their system partners and customer Alltrista, will be presenting a powerful production system for lightweight beverage closures. The 26mm water closures are produced in a mould with 128 cavities. The system runs with a cycle time of 1.9 seconds. With the Cap-Line, Netstal now offers injection moulding machines specifically pre-configured for closure applications. The exhibition machine is based on the high-performance Elios platform and is pre-configured with various equipment features for the efficient production of beverage closures. The Cap-Line 4500’s all-electric clamping unit with a dry cycle time of 1.4 seconds enables fast cycle times of less than 2 seconds. Thanks to the optimised barrier screw, a smaller injection unit is used. The new design ensures a higher plasticising performance and a better degree of homogenisation. Further options are available for individual optimisations, such as the four-key Smart Operation control panel or the adaptive system pressure reduction for additional energy savings. High productivity, low floor space requirement The complete system running on the Netstal booth with a 128-cavity mould from Z-Moulds and Intravis peripherals is identical to production systems used by the US contract manufacturer Alltrista. 26mm tamper-evident caps for still water are produced. Thanks to a new design, Z-Moulds was able to make the mould as small and light as a 96-cavity mould. This results in decisive advantages for closure manufacturers. Compared to previous 128-cavity moulds, the Z-Moulds mould fits into a machine with a smaller column distance. Due to the compact design, less mass has to be moved, which has a positive effect on the cycle time: “Running a mould with 128 cavities at a cycle time of less than 2 seconds is a world first,” says Netstal’s Head of Business Unit Caps and Closures, Horst Kogler. “Alltrista is the first in the world to produce with 128 cavities and a cycle time of 1.9 seconds. They produce more than 3.1 billion closures on two lines. More output per square metre of production area is currently not possible,” he added. The complete production system requires only around 50m2 floor space. In addition, there are further cost savings and a smaller environmental footprint thanks to the low power consumption of the more efficient and smaller machine. With 128 cavities, Netstal says, the line consumes around 12% less electricity than competitor machines operating with only 96 cavities. Furthermore, Alltrista was able to make the closures themselves more sustainable by reducing the weight of the closures by roughly 25% compared to previous industry benchmark, without compromising performance. Over the 3.1 billion closures per year that this program produces annually, the total amount of resin being removed from the product exceeds 930,000 kg/a. Downstream with in-line quality laboratory Downstream, the finished caps pass through the equipment of system partner Intravis until they are filled into octabins. The central element is the CapWatcher Q-Line, which enables a comprehensive 360° full inspection of the closures. With an accuracy in the hundredths of a millimetre range, the system checks up to 80 closures per second for more than 40 quality criteria. The cavity-related inspection is carried out with up to nine high-resolution cameras. Sophisticated tests, such as the patented temperature measurement and the non-contact micro-hole inspection, have been implemented for quality assurance of closure production. Alltrista - contract manufacturer from South Carolina At Alltrista, two identical system solutions for cap production are currently in operation. Alltrista Plastics LLC specialises in high-volume precision manufacturing. From rigid packaging and custom moulded solutions to assembly, filling, and kitting, Alltrista supports customers in the medical, healthcare and consumer goods industries with a wide range of products and services. Alltrista attaches great importance to continuously improving its own sustainability. The company was audited Netstal West Building - Level 2 Booth W223 Expo Hall The Cap-Line system solution from Netstal requires only 50m2 floor space."},{"@ID":49 "PETplanet Insider Vol. 25 No. 04/24 www.petpla.net 47 TRADE SHOW PREVIEW Vision inspection solutions for plastic packaging Intravis, a global provider of vision inspection solutions for plastic packaging, is ready to showcase its range of solutions at this year’s NPE. A total of six state-of-the-art quality control systems are brought to the forefront across four pivotal areas: Closures, bottles & containers, preforms, labels and decoration. They can be witnessed live on-site at the Intravis booth and the booths of various partners. Intravis South Hall, Level 1 Booth S15063 - Expo Hall Breaking boundaries with the LabelWatcher 360° A system for the 360° quality control of labels applied on both standard and uniquely shaped products, regardless of the rotational position of the products. Janina Orlowski, Head of Product Management and Marketing at Intravis, highlights: “With the LabelWatcher 360°, we’re pushing boundaries by inspecting even the most unconventional product shapes, elevating standards across the board. Inspecting a product with a square bottom and round top? This is easily possible with the sophisticated mix of adapted hardware and specialised software algorithms.” Apart from typical label quality inspections, the LabelWatcher 360° will also provide code reading and conduct various inspections at the bottle’s opening. The company explained that, thanks to its user-friendly and easy-to-handle user interface and the assistance of the Wizard software known as “Assistant 360°”, setting up new products can be done in a few simple steps by any machine operator. The compact footprint of the LabelWatcher 360° is a distinctive feature. Its sleek design allows for a seamless integration at any point behind the labelling machine, ensuring a flexible and space-saving solution. SpotWatcher Customized in new design The SpotWatcher Customized is the second system showcased at the Intravis booth at NPE. Recently, it has been upgraded with a sleek slash design which will make its deput at NPE. Intravis says that thanks to the new design, the SpotWatcher now boasts faster delivery times without compromising quality. Its modular profile frame and adaptable enclosure allow for easy adaptation to meet individual customer needs. The system offers a range of inspections for identifying material and contour defects, material inserts as well as colour streaks. It measures the dimensions in the thread area. The Intravis team will present the benefits of advanced software functionalities like such as person-based user administration, reject rate monitoring based on inspection criteria, and a longterm image memory. Fast closure inspection At the booth of Intravis’ partner Netstal Inc (W223), an upgraded inspection solution for plastic closures will be presented: The CapWatcher Q-Line has been optimised for faster production environments. The closure inspection system can now inspect up to 80 closures per second. This involves an all-round inspection of the closures for common defects and issues, including temperature measurement and contactless micro-hole inspection. In addition, the cavity number reading, paired with a cavity-related evaluation of the measurement results, allows customers to precisely localise potential for improvement and schedule their maintenance intervals with greater precision. The CapWatcher Q-Line can be observed in action, operating live behind a Netstal Cap-Line with a clamping force of 4,500kN, paired seamlessly with a CapLab from PackSys Global. The closures must also be sorted and fed, and octabins must be filled. Marius Pötting, Product Manager Caps & Closures at Intravis, states how this is accomplished by Intravis periphery for closure production lines: “Our cooling conveyor and CapFeeder ensure smooth sorting and feeding of the closures to the inspection system, while our AirDiverter fills the downstream octabins. Everything from a single source!” Thorough quality assurance of 5-gallon IML pails There is more excitement in the realm of in-mould label inspection at NPE. Over at the Milacron booth (W1601), a captivating production line for 5-gallon IML pails is showcased – a cooperation of Milacron, Beck Automation and Intravis. Another IMLWatcher will inspects every detail of the in-mould label and check for short shots at the pail’s edges. The system also conducts a thorough quality control inside the pail for defects such as blow-byes and contaminations. In addition to this, IML solutions for medical indutry will be presented. Intravis will also present a highlight in preform production and inspection with its partner Husky Technologies on booth W2801. www.intravis.com The LabelWatcher 360° inspects labels on any kind of product shape and in any rotational position."},{"@ID":30 "BOTTLE MAKING 28 PETplanet Insider Vol. 25 No. 04/24 www.petpla.net A distinctively eye-catching design and an unusual container type – Wine in PET bottles off ers a sustainable alternative to the traditional glass bottle A classic reinterpreted based on article by Peter Mörtl, Press Relations at Krones AG A wine bottle that is not only sustainable but also ideally suited for shipping: Cornelia Braun addressed that challenge in her bachelor’s thesis, which she wrote at Krones. She discovered great potential in PET – a material out of which she provided a modern Bordeaux bottle design to accompany her thesis. Wine has been sold in glass bottles since the 17th century. While the first of them were black, more colours like green and brown have been added over time. And several different bottle shapes have also been created. The various designs in common use today frequently denote the region where a wine is grown or the type of wine the bottle contains. Typical examples include the Franconian Bocksbeutel, the Burgundy and hock bottles as well as the best-known and most used bottle shape: the Bordeaux bottle. While working on her bachelor’s thesis at Krones, Cornelia Braun, a student at Ingolstadt University of Applied Sciences, examined the question of how the transport of wine bottles can be made more sustainable and more efficient. Her answer is: Use PET. Mario Casper, who has specialised in PET container design at Krones and mentored Cornelia Braun while she wrote her thesis, describes the current market situation as follows: “While this idea is in Germany still viewed with a certain degree of scepticism, it has become common practice in other countries such as France, Spain and Italy where supermarkets are already offering wine in PET bottles.” Weight reduction of up to 90% “PET offers several advantages over traditional glass bottles. One of them is the fact that less energy is needed to produce PET bottles, and another one their lower weight. A 0.75-litre glass bottle usually weighs at least 500 grams. So the use of PET can reduce the weight of primary packaging by up to 90 per cent. “And such savings also have a considerable effect on a company’s carbon footprint,” explains Cornelia Braun. “What’s more, it is possible to send a significantly larger number of PET preforms than empty glass bottles to the bottler in one delivery, which means fewer shipments are needed.” Use of PET makes for a reduction in packaging weight of up to 90% And PET is also a material ideally suited for recycling. “That was why development work was focused not only on the bottle as such but also on the capsule and the label. If one and the same material were to be used for all bottle components, that would simplify the recycling process even more,” says Mario Casper. But PET offers advantages not only in regard to sustainability and closing the plastics loop. For safety reasons, glass containers are not permitted during air travel and at many events. So unbreakability is yet another one of its positive aspects. Traditional bottle design - enhanced The design of the Bordeaux bottle made of PET provides for three different sizes, for a content of 750, 500 For the period from 2022 to 2027, the data analytics and consulting company GlobalData forecasts growth rates of around 6.7 per cent for wine in PET bottles."},{"@ID":61 "EDITOUR PETplanet Insider Vol. 25 No. 04/24 www.petpla.net 17 EDITOUR 17 comes from the unorganised waste sector due to the lack of collection and sorting infrastructure in Nigeria, is taken to collection points and eventually ends up at Polysmart, where it is processed thanks to the state-of-theart sorting and treatment, turned into pure form and sold through the Dubai office. Mr Wadhwani continued: “The difficulty in other parts of the world is often the expectation of recycled material. They want it to be as cheap as possible and there is often a lack of understanding about using recycled material when virgin material is much cheaper. Sometimes we have to face discussions in which customers try to push down the price of rPET by asking us to sell poor-quality material because they know that the end consumer wouldn’t notice the difference anyway. Of course, we can’t and don’t want to get involved in that in any way.” Mr Wadhwani suspected that the prices for recyclate will remain high for at least another three years and that Asian companies, especially Chinese companies, will likely dominate the pricing policy for virgin material in the future thanks to good technology and low general costs. “Of course, we are already seeing the extreme extent to which buyers often end up opting for Chinese virgin material and even that is sometimes too expensive for them,” said Girish Wadhwani. “Prices are being extremely dumped. It goes to the extent of selling material outright without any profit and adding X amount to the freight instead.” Despite the circumstances, he remains optimistic: “We cannot avoid recognising PET waste as a recyclable material. In my view, governments and brands should equally promote the issue of recycling, for example by setting minimum quantities in packaging, and educating the public on how to deal with it. www.shadpolymers.com BOTTLE TO BOTTLE RECOVERY MOISTURE CONTENT CONTROL PROCESS CONSISTENCY EXTREME BLENDING FLEXIBILITY moretto.com follow us MAKING THE DIFFERENCE ON PET. Booth W1743"},{"@ID":38 "36 EVENT PREVIEW PETplanet Insider Vol. 25 No. 04/24 www.petpla.net Oxygen scavenger technology for PET and technical seminars Avient Corporation is gearing up to dazzle attendees at NPE 2024 with a dynamic showcase of sustainability initiatives that promise to redefine the polymer industry’s approach to environmental responsibility. Highlights will include the announcement of a new facility in Ohio, the introduction of an oxygen scavenger technology for PET packaging to enhance product preservation sustainably as well as technical seminars at Avient’s customer centre. These seminars, which will explore carbon footprint reduction and sustainability strategies, include: 1) Understanding Carbon Footprint: Strategies for designers, processors, and OEMs that can help their customers be more eco-conscious during an entire product life cycle, from material selection to end-oflife considerations. 2) Regulatory Navigation: Insights on navigating environmental standards, including PFAS and other chemicals, will be shared to help manufacturers stay compliant and competitive. 3) Enhancing Recyclability: Increasing bio and recycled content in polymers and enhancing recyclability through intelligent design to develop innovative approaches to brand differentiation and meet consumer demands for eco-conscious products. 4) Lightweighting Applications: Exploring the potential of foaming techniques and polymer substitutions to reduce weight and enhance efficiency, thus replacing traditional metal components. 5) Circular Composites: Pioneering approaches to making composites more circular, thereby reducing environmental impact and promoting resource efficiency throughout the product lifecycle. www.avient.com Solutions for challenges in packaging Sipa’s booth will offer a comprehensive display of expertise spanning packaging design and manufacturing, emphasising both economic viability and sustainability. The showcased solutions highlight the company’s approach to addressing various critical parameters such as weight reduction, container behaviour, filling line performance, storage, transportation, and cost-effectiveness. The focus is on delivering attractive bottles while optimising production costs. Two machineries will be running at the booth: Sipa’s Xtra rotary blowing systems are claimed to offer benefits such as the highest bhc output in the industry, a wide active process angle, high bottle quality irrespective of the preform material (rPET, bio-based resins), energy efficiency, and user-friendly operation. Sipa says that this combination of performance, speed, quality levels and saving leads to a reduction in total cost of ownership (TCO). On the booth, Xtra will be set in its PH (preferential heating) version producing very technical but attractive oval container for alcoholic beverages. In addition, the SFL Flex linear blow moulding system will be on display, producing a challenging asymmetrical bottle for chemical and household products. Sipa’s linear stretch-blow moulding systems have been designed as flexible and user-friendly systems for the production of a wide range of container types including standard, heat set, refillable, oval, large sizes, and wide mouth containers. The SFL Flex is ideal for business start-ups and lab environments. www.sipasolutions.com Sipa South Hall, Level 1 Booth S19096 Bottle Zone Avient South Hall, Level 2 Booth S210 Meeting Rooms STEPS TO THE PERFECT BOTTLE. www.roeders.de www.roeders.de Idea & Design Technology Manufacturing Blow Mould 100% Service Y O U R PA R T N E R F O R B L OW MO U L D S . Meet us at NPE 2024 South Hall Level 1 Booth S 13100g"},{"@ID":17 "EDITOUR PETplanet Insider Vol. 25 No. 04/24 www.petpla.net 15 “Sustainability is another element which is core in all our decision making. As a conscious decision, we are only working with resins which are 100% mono-material formats with proven mechanical recyclability (PET, PP & PE). On a continual basis, we are evaluating using rPET in production. One new project is a test series of jars that we have produced from Sun Packaging’s Nissei ASB department 100% rPET.” Mr Bhatia placed various sizes of these wide-mouth jars on the table between us. “My dream would be that in the next 24 to 26 months, we would produce at least 20% of our products here using rPET.” Nimit Bhatia has also been responsible for the plant in Malaysia as CEO since 2023. Combipack, the name of the brand that became part of the Group through acquisition in 2021, specialises in food and thin-wall packaging with IML technology, another area that Mr Bhatia finds exciting. “I am very excited about the new challenge in Malaysia,” he said with a laugh. SPS’s expansion strategy includes further growth in the MENA region with Egypt being a focus market, further consolidating its PET rigid packaging consumer business, and further penetration into the med-pharma space which complements the companies hygiene clean room manufacturing mindset well. www.tpacpackaging.com"},{"@ID":46 "EVENT PREVIEW PETplanet Insider Vol. 25 No. 04/24 www.petpla.net 44 Filling & packaging in a resource-saving way KHS will be presenting efficient and resource-saving solutions for filling and packaging processes. The focus will be on the latest generation of InnoPET Plasmax barrier technology and the InnoPET Blomax V stretch blow moulder with its double gate heating concept (DoGa). KHS will also be showcasing sustainable packaging options such as the KHS Nature MultiPack with universal adhesive. Barrier technology InnoPET Plasmax KHS consciously focuses on bottle sterilisation that – unlike preform sterilisation – can also be combined with the KHS FreshSafe PET coating system and thus offers additional barrier protection for sensitive beverages. On this variant all potential germs are removed from the containers directly prior to filling. This process gives bottlers more flexibility and greater availability during format changeovers than preform sterilisation, as here changing the stretch blow moulds disturbs the sterile state of the block. KHS will feature the latest generation of Plasmax coating technology. With this technique, a wafer-thin layer of chemically pure glass is applied to the insides of PET bottles, and bottle recyclability is claimed to be fully retained. This protects sensitive products such as fruit juice, wine, beer, soft drinks, ketchup, sauces and other liquid foods from oxidation and loss of CO2, meaning that they keep for considerably longer. KHS has continuously improved this procedure over the years and now brought it up to the next level. The result is better performance, quality and flexibility and a higher degree of efficiency. Stretch blow moulder InnoPET Blomax V with double gate heating concept (DoGa) The latest generation of the proven KHS InnoPET Blomax stretch blow moulders, the Series V, sets new standards in resource savings and considerably reduces the carbon footprint left by the production process. In addition to systems to save energy and cut down on the TCO and optimised features relevant to machine safety and ease of operation, the Series V provides with highly energy- and cost-effective plant engineering for the manufacture of plastic, bio-based or (r)PET bottles holding between 0.2 and 3.0 litres. It can be used to bottle water, soft drinks, beer or sensitive products. Thanks to the modular design with its supplementary micro blow station concept for special still water applications which can process containers of up to approximately 750 ml, it is highly flexible for targeted use and has six to 36 blowing stations with a specific capacity of up to 2,800 containers per hour and blow station. With the double gate heating concept (DoGa) based on tried-and-tested, highly efficient NIR heating technology, up to 40% in energy costs can be saved while taking up a minimum amount of space compared to single-lane stretch blow moulders of the same capacity, says KHS. Sustainable packaging option: Nature MultiPack with universal adhesive At the trade show, KHS will also be focusing on reducing packaging materials. Following the successful launch of a universal adhesive for beverage cans, KHS is now also offering this pioneering streamlined consumable for plastic bottles. Still one of the most environmentally-friendly secondary packaging styles on the market, PET containers of practically any shape, size or material thickness can now be joined together using just one type of adhesive. This is facilitated by a special process where the adhesive is foamed during application to the containers. The new system also increases the level of convenience for the consumer, as bottles are easier to separate. Moreover, the outer wall of the PET container is subjected to less stress when the pack is opened, meaning that even with lightweight bottles with a very low wall thickness overload and damage are more or less totally ruled out. www.khs.com KHS South Hall, Level 1 Booth S19088 Bottle Zone InnoPET Blomax V with double gate heating concept (photo: Joerg Schwalfenberg) PET containers of any shape, size or material thickness can be joined together using one type of adhesive (photo: Frank Reinhold)"},{"@ID":5 "imprint EDITORIAL PUBLISHER Alexander Büchler, Managing Director HEAD OFFICE heidelberg business media GmbH Hubweg 15 74939 Zuzenhausen, Germany phone: +49 6221-65108-0 info@petpla.net EDITORIAL Kay Barton Heike Fischer Gabriele Kosmehl Michael Maruschke Ruari McCallion Anthony Withers Editorial & WikiPETia. info petplanet@petpla.net MEDIA CONSULTANTS Martina Hirschmann hirschmann@petpla.net Johann Lange-Brock lange-brock@petpla.net phone: +49 6221-65108-0 LAYOUT AND PREPRESS EXPRIM Werbeagentur Matthias Gaumann www.exprim.de READER SERVICES reader@petpla.net PRINT Chroma Druck Eine Unternehmung der Limberg-Druck GmbH Danziger Platz 6 67059 Ludwigshafen, Germany WWW www.hbmedia.net | www.petpla.net PETplanet Insider ISSN 1438-9459 is published 10 times a year. This publication is sent to qualified subscribers (1-year subscription 149 EUR, 2-year subscription 289 EUR, Young professionals’ subscription 99 EUR. Magazines will be dispatched to you by airmail). Not to be reproduced in any form without permission from the publisher. Note: The fact that product names may not be identified as trademarks is not an indication that such names are not registered trademarks. 3 PETplanet Insider Vol. 25 No. 04/24 www.petpla.net Dear readers, The switch from Netstal to Krones is now official. The purchase follows a series of acquisitions that Krones has made in recent years. Examples include Gernep in 2015 (labelling machines) and MHT in 2018 (preform moulds). What all these takeovers have in common is that the acquired companies continue to operate on the market under their own label, largely retaining their independence. Another thing they have in common is that none of the companies has a global market presence yet and they certainly still have a lot of potential for the future. With Netstal, Krones has brought a technological market leader into the group that also has enormous growth opportunities in the market. With the new PET-Line machine generation and its side entry in particular, Netstal now has a product that can hold its own with the top dog, Husky. The circle that Netstal has not been able to break out of in recent years was certainly its low market share, selling only a limited number of machines and thus not generating sufficient resources to offer a full after sales service worldwide. No full service, so no new machines, which brings us back to the low market share. Let’s see if Krones can break the cycle and take Netstal into another dimension with its global presence. Yours, Alexander Büchler"},{"@ID":37 "35 EVENT PREVIEW PETplanet Insider Vol. 25 No. 04/24 www.petpla.net Side expands into the US market as Side America Corp. Side, a provider of PET blow moulding solutions, announces the establishment of Side America Corp. This expansion marks a pivotal moment for the company, aimed at enhancing accessibility and reaffirming its dedication to the US market. This strategic move is part of the company’s initiative to offer sales and service operations directly within the USA, ensuring seamless interactions for American clients and emphasising the company’s commitment to delivering support and tailored solutions. A highlight of Side’s US market entry is the debut of its advanced linear PET blow moulding machines, which are intended to push boundaries in terms of efficiency, precision, and production capacity in PET blow moulding. Additionally, the company is intensifying its focus on sustainability by prioritising eco-friendly packaging solutions, aligning with the preferences of 60% of bottle makers’ customers who seek environmentallyconscious options. Furthermore, the expansion into the USA underscores the company’s readiness to cultivate enduring partnerships and excel in the region, supported by a dedicated team equipped to navigate the complexities of the American market. Central to Side’s expertise is its adeptness in crafting intricate PET designs, showcasing its proficiency in shaping unique forms and structures within this versatile material. Moreover, Side remains steadfast in its commitment to operational efficiency and costeffectiveness, prioritising high production output while reducing costs to deliver tangible value to clients, thereby aiding them in streamlining operations and maximising returns on investment. At NPE, Side America Corp. will showcase cutting-edge solutions in PET preform blow moulding to the American market, alongside services and developments aimed at achieving toptier packaging solutions. Throughout the expo, Side America will exhibit a diverse range of PET blow moulding technologies and equipment designed to deliver efficiency, precision, and optimal performance in packaging production. Additionally, the company’s team of experts will be on hand to provide personalised guidance and tailored solutions to meet the specific needs of each customer. www.sidemachines.com Side South Hall, Level 1 Booth S16115 Bottle Zone"},{"@ID":55 "EVENT REVIEW PETplanet Insider Vol. 25 No. 04/24 www.petpla.net 53 Natthanun Sirirak, Managing Director of Envicco, also shed light on the Thai FDA system, which has stricter safety criteria than the US FDA and the European Efsa in terms of raw materials and contamination levels. For example, the Thai FDA prescribes a maximum contamination level of only 210ug/kg (US FDA 220ug/kg) and no raw materials from landfills are allowed. EcoBlue Ltd. Thailand, is another company that received rPET Thai FDA approval for food contact packaging applications. Made from 100% postconsumer waste, using state-of-the-art recycling equipment, including Starlinger’s Viscostar Solid State Polymerisation (SSP) system, and stringent quality controls, EcoBlue’s bottle grade rPET has also received US FDA and Efsa approval. The company also supplies specialty rPET for filaments, films, fibres and strapping, as well as foodgrade recycled HDPE and PP. No regulatory framework requiring the use of recycled content in packaging In addition to reliance on the informal sector, there is another major difference to the European and US recycling markets. There are no regulatory frameworks requiring the use of recycled content in packaging. Therefore, rPET has to be a cost effective alternative to virgin material, which it is not. As a result, the recycling sector is heavily reliant on major global brands committing to increase the amount of rPET in their bottles, either to meet the EU’s 25% target by 2025, as an internal corporate commitment or as a marketing strategy. However, the regulatory framework and consumer pressure are lacking. Bridging the circularity gap - PET through chemical recycling With a general lack of regulatory frameworks and higher operating costs compared to virgin material production, the capital-intensive chemical recycling process faces significant hurdles in SEA and NEA. But there are success stories. Japan’s Jeplan, founded in 2007, has been at the forefront of plastics recycling, with previous efforts in PET clothes-to-clothes recycling and commercial plant operations. In 2020, the company entered into a strategic partnership with technology provider and licensor Axens to develop an innovative recycling process called Rewind PET. In October 2023, Jeplan commissioned a 1,000t/a (1kta) PCR PET chemical recycling plant in Japan. The process can be used to recycle all types of PET waste, especially those that are difficult to recycle mechanically, such as dark and black PET materials, coloured and opaque bottles, multi-layer trays, packaging film and polyester textiles. Through continuous depolymerisation and deep cleaning, the process produces high quality BHET (bis(2hydroxyethyl) terephthalate) monomer, ensuring a virgin-like quality suitable for a wide range of PET applications, including food applications. The company’s chemical recycling efforts are also beginning to bear fruit. One of the first batches of rPET was immediately sold to a high-profile customer. Outdoor clothing specialist Patagonia is using its rPET to work towards eliminating all virgin polyester from its products by 2025. Others Participants and speakers were rather united when it came to DFR (Design for Recycling): No coloured bottles (clear or clear and light blue in a 70/30 ratio), mono-PET material, labels must be easy for the consumer to remove, no full-sleeve labels, no selfadhesive labels and no direct printing because of the risk of heavy metals in the colour pigment. PVC, but also PET-G, were mainly considered as problematic materials. The conference also covered topics such as legacy MSW (Municipal Solid Waste) Bio-mining (an environmentally friendly technique for separating soil and recyclable materials such as plastic, metal, paper and textiles) with an EPR perspective. www.icis.com"},{"@ID":9 "7 NEWS PETplanet Insider Vol. 25 No. 04/24 www.petpla.net SEE HOW MUCH YOU CAN SAVE MAINTENANCE COSTS 70% LESS ENERGY 90% LESS 70% REDUCTION IN CO2e 50% MORE PRODUCTIVITY Discover your potential savings. With just a few clicks, you’ll gain valuable insight into how ULTRA will positively impact your bottom line. 1. Go to ultra.maguire.com 2. Input your data. 3. Receive your customized PDF report of potential savings via email. The savings will vary based on your circumstances and should be reviewed with our sales team. USA Toll Free +1 888 459 2412 l Canada +1 905 879 1100 l Europe +44 1827 338 280 l Asia +65 6848 7117 l Taiwan +886 4 2658 1535 info@maguire.com www.maguire.com"},{"@ID":1 "No.4 2024 www.petpla.net D 51178; ISSN: 1438-9452 15 . 04 . 24 M A G A Z I N E F O R B O T T L E R S A N D B O T T L E - M A K E R S I N T H E A M E R I C A S , A S I A , E U R O P E A N D A L L A R O U N D T H E P L A N E T PETplanet is read in 159 countries MARKETsurvey Suppliers of preform machinery Page 32 EDITOUR Page 12 Page 34"},{"@ID":40 "38 EVENT PREVIEW PETplanet Insider Vol. 25 No. 04/24 www.petpla.net Recycling machine for post-consumer PET Gneuss will show a complete Omni recycling machine featuring a Multi Rotation System MRS 130 extruder, a water ring pump vacuum system, a fully automatic melt filtration system RSFgenius 150 and an online Viscometer VIS. This machine is designed for the processing of up to 1,000 kg/h (2,200 lbs/h) of undried and uncrystallised polyester (PET) reclaim. The line on display in Orlando will be delivered to a customer in Peru after the show to process rPET into a thermoforming sheet. In addition to its compact design, which requires little space and can therefore usually be easily integrated into existing premises, the Omni is flexible in use. The fully automated control of vacuum, extruder, dosing, degassing dwell time and filter exchange provides a consistent quality of the end product. With the tight and varying materials market, it is becoming increasingly important to be able to produce regardless of the properties of the input materials, especially in the case of varying and uncertain input qualities in the future. Gneuss says, that the compact design results in low energy consumption. Any energy used in the extrusion process is designed to be used in the next process step. This not only has a noticeable effect on electricity and gas consumption, but also significantly reduces the CO2 footprint of the recycling process. www.gneuss.com Gneuss Omnimax recycling machine with MRS extruder and RSFGenius filtration system Gneuss West Building, Level 2 Booth W5181 Expo Hall EISBÄR TROCKENTECHNIK GMBH Wuhrmühle 22 / A–6840 Götzis / T +43 5523 55558-0 / cool@eisbaer.at / www.eisbaer.at RECYCLING Conveying Drying Crystallizing Mixing&Dosing Decontamination Testing MEET US AT NPE Orlando, FL South Hall L1 S15083"},{"@ID":18 "EDITOUR PETplanet Insider Vol. 25 No. 04/24 www.petpla.net 16 Plastic material distributor in Dubai fi ghts against low-cost suppliers with quality promise Food-grade rPET from Nigeria for Europe, North America and beyond by Kay Barton The sales office for plastic raw materials, masterbatches and calcium carbonate, Shad Polymers DMCC, was founded in 2016 by our interview partner and Managing Director Mr Girish Wadhwani together with Mr Chandru Changrani and Vivek Changrani to administratively serve global markets from the Emirates, trade materials and ensure smooth supply. December 20, 2023 Interview with Shad Polymers DMCC We met: Mr Girish Wadhwani, Managing Director. The company is the exclusive distribution partner for rPET for the Polysmart Group, a synthetic fibre processor and recycling company based in Ota, Nigeria. Shad runs a local warehouse in Sri Lanka, CVG Resins & Polymers, one in Ethiopia and other warehouses in Nigeria. With the growing markets for rPET and the potential for post-consumer PET in Nigeria, Polysmart invested US$8 million and installed an Erema Vacurema turnkey recycling line, which has been producing rPET since 2022. We spoke to Mr Wadhwani about market trends, challenges and goals. Mr Girish Wadhwani is a Mechanical Engineer with a specialisation in Process Control Instrumentation and has lived in Nigeria for 18 years and in London for 20 years. The idea for the current sales office in the Jumeirah Lake Towers, around 25 km south of Dubai city centre, was born out of his long time spent in Nigeria. In addition to vPET and rPET, the products offered here include various other synthetic polymers, copolymers and terpolymers. Back in mid-2023, Mr Wadhwani gave us an insight into the fields of activity and the still young rPET project at the World Expo in Essen (see PETplanet 7+8/23, p. 32). We then accepted his invitation to meet during the Middle East Road Show in Dubai. “I find the new recycling project fascinating,” explained Mr Wadhwani over a cappuccino. “There is a lot of movement in the markets, but not always in the right direction, for example in terms of consistent quality or price expectations. Everything is determined by the core issues of availability, quality requirements and ultimately price. That’s why we are also focussing on sales in North America or, above all, Europe, where there is a constant demand for good quality, food-grade base material due to the minimum quantities of recyclate in PET packaging,” he explained. This source material is currently produced at Polysmart in Nigeria with an annual capacity of 6,000 t and is FDA and Efsa-certified. This makes it one of an estimated 15 to 20 significant recycling plants across Africa, of which around five to six produce around 80% of all recyclate on the continent. The largest of these are located in South Africa. The input material EDITOUR Managing Director Girish Wadhwani (right) with Kay Barton"},{"@ID":26 "MATERIALS / RECYCLING PETplanet Insider Vol. 25 No. 04/24 www.petpla.net 24 The Prevented Ocean Plastic Programme Plastic collected in coastal areas Prevented Ocean Plastic is a ground-up, vertically-integrated, fully certified recycled plastic supply chain solution, - connected from first collector to final product - that works at the scale required by industry with quality, traceability, and compliance. The brand is built by a small but formidable team working in offices on Richmond Green in London. The material, supplied by Bantam Materials UK Ltd, is high-quality recycled plastic collected from coastal areas at risk of ocean plastic pollution. The Prevented Ocean Plastic Programme offers an ongoing supply of this material while supporting local communities in the regions it sources from and driving long-term environmental solutions. Bantam has been a global supplier of recycled materials since 2011, successfully proving that sustainability and profitability are not mutually exclusive principles. In 2019, the team at Bantam recognised the need for a recycled plastics programme that specifically tackled the ocean plastic problem while building infrastructure, generating jobs, creating opportunities for brands to make a better plastic choice, and offering consumers a tangible, traceable alternative to virgin plastic. Since then, the programme has incentivised the collection of waste plastic around the world. This plastic is delivered to collection centres where it is sorted, cleaned, and ready to be recycled into new products with full traceability back to its coastline of collection. Quality is key Inside collection centres waste is hand-sorted - with caps, labels, and all other contaminants removed. It is then pressed into 99% PET bottle bales, exceeding regulatory requirements. By incentivising recyclers and collectors, the programme proves it is possible to encourage best-practices to ensure high-quality recycled material. Due to a lack of standards specific to the ocean-bound plastic supply chain, Prevented Ocean Plastic formalised their own. These look at practical fit-for-business practices, alongside internationally recognised ethical, social, and environmental trading requirements. The programme audits and then supports some of the world’s best informal recyclers to develop recycling infrastructure in coastal regions that have never had it before, which then operates to these elevated standards. Prevented Ocean Plastic lead the transformation of their industry and the building of a positive, transparent circular economy where everyone is respected. The programme has helped brands around the world, from Lidl to Louis Vuitton, meet their sustainability targets. Prevented Ocean Plastic material has now been included in almost 500 products across multiple categories, including fish, poultry, soft fruits, pet food, personal care, and home cleaning. In 2023, the National Health Service (NHS) in UK started using the material in some home testing kits. Prevented Ocean Plastic is built on a strategy of credibility first. The team is focused on a mission to recycle, clean, build and elevate, but will always welcome recognition for the Programme’s progress and achievements. In 2020, Prevented Ocean Plastic was part of the Retail Industry Awards ‘Sustainable Initiative of the Year’ winning entry in association with Lidl supermarket. In 2021, Bantam Materials UK Ltd. became the first recycled plastic supplier to join the Ethical Trading Initiative. They are the first recycled plastic business to be accepted to the leading alliance of companies, trade unions and NGOs that promotes respect for workers’ rights around the globe. In July 2022, USAID partnered with Prevented Ocean Plastic to open a centre in Indonesia. Another site, a direct result of an ongoing partnership with Singapore-based investment management firm Circulate Capital, opened in North Jakarta last October. In 2023, Prevented Ocean Plastic won a Zero Waste Award, and was invited to the Houses of Parliament to receive a Green World Award for commitment to environmental best practice. Also in 2023, the British Plastics Federation highlighted Prevented Ocean Plastic at the top of their list of innovations in plastics for the year. Prevented Ocean Plastic was an official nominee for the 2023 Earthshot Prize. More that can be done Last year, Prevented Ocean Plastic announced an ambitious new mission to open 25 new collection centres Sold at Lidl, plastic packaging made out of Prevented Ocean Plastic material."},{"@ID":33 "INSPECTION 31 PETplanet Insider Vol. 25 No. 04/24 www.petpla.net Purity Concept V: Reproducible optical laboratory testing of pellets, flakes and plates In the area of plastics, visitors can bring small quantities of opaque and amorphous pellets, flakes or plates to be inspected and analysed for impurities with the inspection and analysis system Purity Concept V during the exhibition. The system is suitable for reproducible laboratory applications and detects black and coloured contaminants from a size of 50 μm as well as discolourations. The analysis takes less than a minute, including test certificate and HSV colour chart of the detected colour deviations. The system thus contributes to increased product and quality reliability. Launch of new products At NPE 2024, Sikora will present new measuring devices that have been designed to redefine the segment of measuring technology for hose and tube extrusion lines. With Netstal’s leading preform injection molding technology. Our PET-Line impresses with broadest compatibility, maximum throughput, exceptional ĆďĆēĈĚ ĆħĄĊĆďĄĚ ĐđĕĊĎĂč đēĐĄĆĔĔĊďĈ Đć ē÷ìû Ăďą other challenging recyclates, and with its intuitive Axos control unit. Wemaximize your added value Preforms NPE 2024 I W223 Centerwave 6000: Measurement of tubes and pipes at a push of a button For measuring tubes and pipes with a diameter from 32mm to 1,600mm, Sikora will showcase the Centerwave 6000. All models of the Centerwave 6000 device series are characterised by their innovative measuring principle based on millimeter wave technology. Operation is intuitive at the push of a button, says Sikora. Once activated, the operator immediately receives continuous and precise measured values – without presetting the product parameters, without the influence of a coupling medium (water) and without any calibration. Right after the first vacuum tank, the system provides all product dimensions. A continuously rotating transceiver measures the diameter and wall thickness in 360 degrees across the entire product circumference. The extensive and precise measuring data enables fast centering of the extrusion tools respectively an automatic control to the minimum wall thickness for optimum material usage and overall sustainability as well as cost saving. X-Ray 6000 Pro: Material saving With the X-Ray 6000 Pro, Sikora presents a system based on X-ray technology that continuously provides measuring data on wall thickness, eccentricity and inner and outer diameter of hoses and tubes in extrusion lines. These are clearly displayed on the monitor of the Ecocontrol 6000 processor system. The X-Ray 6000 Pro can be used either after the extruder, between two vacuum tanks/ cooling sections, or at the end of the line for cold measurement. From the first day of commissioning, the system enables the wall thickness to be reduced to the smallest permissible value. This is claimed to result in material and cost savings for the user. www.sikora.net"},{"@ID":51 "PETplanet Insider Vol. 25 No. 04/24 www.petpla.net 49 EVENT PREVIEW Attend the 11th edition to hear from: Secure your place today: www.ami.ltd/event-closures Explore advances in materials and technologies to improve production efficiency and sustainability Headline sponsor Richard Novomesky The Coca-Cola Company Ingomar Henning Henkel Derek Hindle Aptar Closures Also sponsored by: Supported by: by Ecovadis in 2023 and received the silver medal for its sustainability performance to date. Alltrista ranked in the 88th percentile of all EcoVadis rated companies, and top 7% among its peers. Alltrista will be present at the Netstal booth during the NPE with its own staff to provide information from the customer’s perspective. For detailed information on all the company’s services, Netstal also recommend a visit to stand S22065 in the South Hall, where Alltrista will be showcasing their full offering of products and services in contract manufacturing and injection moulding. www.netstal.com The Netstal Cap-Line 4500 with 128-cavity mould from Z-Moulds produces 26mm tamper-evident water closures at a cycle time of 1.9 s."},{"@ID":63 "PETcontents 4 PETplanet Insider Vol. 25 No. 04/24 www.petpla.net 04/2024 EDITOUR 12 Visiting the drinking water department of the Sharjah government - PET bottle filling from the wells of Hamda region in Sharjah 14 Packaging with passion from Sharjah - Manufacturer from Thailand reaches for the stars 16 Food-grade rPET from Nigeria for Europe, North America and beyond - Plastic material distributor in Dubai fights against low-cost suppliers with quality promise PREFORM SPECIAL 18 Optimising PET preform handling 20 Influence of PET processing on preforms & bottles MATERIALS / RECYCLING 24 Plastic collected in coastal areas - The Prevented Ocean Plastic Programme 26 Differentiation in detail - AI-powered object recognition for sorting food-grade from non-food-grade plastics PACKAGING / PALLETISING 27 How the “Greenwashed out” trend will impact the beverage PET market BOTTLE MAKING 28 A classic reinterpreted - A distinctively eye-catching design and an unusual container type INSPECTION 30 Detecting contamination - Inspection and sorting of plastic pellets MARKET SURVEY 32 Suppliers of preform machinery EVENT PREVIEW 34 NPE 2024 preview - part 2 42 Set to boost product quality - Expansion of Vision1 model range & live demonstrations 44 Filling & packaging in a resource-saving way 45 Digital tools & AI - Sacmi will be highlighting human machine interaction based on new controls, digital tools & artificial intelligence 46 Dry ice cleaning solutions and the chance to win 47 Vision inspection solutions for plastic packaging 48 128 beverage caps every 1.9 seconds - Netstal’s Cap-Line system solution 50 Hot runner systems & more - Mold-Masters to present its latest systems EVENT REVIEW 51 2nd Icis Recycled Polymers Conference Asia BUYER’S GUIDE 56 Get listed! INSIDE TRACK 3 Editorial 4 Contents 6 News 22 Products 54 On site 55 Patents 62 Outer Planet PREFORMS Page 22 Page 12 EDITOUR Page 28"},{"@ID":32 "INSPECTION 30 PETplanet Insider Vol. 25 No. 04/24 www.petpla.net Inspection and sorting of plastic pellets Detecting contamination Sikora, a manufacturer of measuring, control and sorting technologies, will be exhibiting its wide range of technology for quality control and cost optimisation in hose, pipe and tube extrusion and material production and processing at NPE 2024. Sikora West Building, Level 2 Booth W5589 Expo Hall Purity Scanner Advanced: Modular system for flexible optical online inspection and sorting of plastic pellets Sikora exhibits the Purity Scanner Advanced that is used for inspection and sorting of plastic pellets. Even the smallest, critical contamination is claimed to be reliably detected and sorted out by the system. Thanks to the modular concept, different camera types can be used depending on the inspected material. In addition to optical 2μm high-resolution cameras, which detect black specks and discolourations, an X-ray camera can be installed to detect metallic contamination down to 50μm in the pellet. Common systems on the market have a maximum of two optical cameras. However, these quickly reach their limits due to relatively low coverage as soon as the contamination are outside the cameras’ field of view. The Purity Scanner Advanced automatically sorts out detected contamination via a blow-out unit. For optimising the bycatch, Sikora has developed a “hybrid blow-out” feature. The customer defines in advance which contaminants in the material are uncritical and select a smaller blow-out unit for these, so that their by-catch is reduced. Both reliable detection and hybrid blow-out ensure high material quality. At the same time, production processes are optimised, and the reduced by-catch contributes to costefficient and sustainable production. The Purity Scanner Advanced is used for inspection and sorting of plastic pellets. The worldwide round trip with Editour The Middle East Roadshow 6 countries numerous interviews with PET companies Follow us on www.petpla.net Autumn 2023 - 2024"},{"@ID":56 "ONsite 54 PETplanet Insider Vol. 25 No. 04/24 www.petpla.net Ganesha Ecopet and Sorema: a fruitful collaboration in plastic recycling Ganesha Ecopet, part of the Ganesha Group founded in 1994, is the largest player in post-consumer PET waste recycling in India with a total installed capacity of 150,000mt per year, giving new life to almost 9.4 billion bottles each year and saving 18% of India’s PET waste going into landfill. Additionally, it is the largest producer of recycled PET fibres and yarns (rPET), exporting certified products worldwide. With more than 30 years of presence, Ganesha Ecopet is now pioneering bottle-to-bottle recycling via its new brand “Go Rewise”, using recycled plastics in packaging solutions, thereby creating sustainable and circular solutions. Ganesha Ecopet offers sustainable packaging and textile solutions with FDA & Efsa approval, high-quality recycled PET resins, catering to the FMCG, and textile industries. In 2022, Ganesha Ecopet entrusted Sorema’s experience for the construction of a PET bottle-to-bottle recycling plant in India. A pioneering project, with a production capacity of 5,000 kg/hour of food-grade recycled PET material. This process involves the 100% use of locally collected PET plastic bottles, a Sorema washing system, followed by an extrusion and solid state Starlinger GmbH section. The finished product gained approval from industry giants like Coca-Cola & PepsiCo, and others, utilising the produced rPET pellets for 100% rPET bottle manufacturing. Established in 1974 in Como, Sorema is a result of a partnership with Previero, founded in 1922, and is now a division of Previero Srl. Sorema’s vision in the recycling plant production process ranges from material analysis to process optimisation and tailor-made plant and site design. The service includes design, production, commissioning, post-sales assistance, and long-term customer support. Since 2023, Sorema has been operating in partnership with Ambienta SGR Spa, tackling future challenges with increased opportunities. This collaboration represents a joint commitment to environmental sustainability and a model of how technology can lead the plastic recycling industry towards a greener and more responsible future. www.sorema.it"},{"@ID":57 "PATENTS PETpatents www.verpackungspatente.de PETplanet Insider Vol. 25 No. 04/24 www.petpla.net 55 A stackable bottle European Patent No. EP 4245679 A1 Applicant: Henkel AG & Co. KGaA, Düsseldorf (DE) Registration date: 17.2.2023 The base and top of a bottle with closure have been specially designed to enable several of these containers to be easily stacked. This is achieved by a cavity in the base area into which the cap positioned underneath fits perfectly. A plastic bottle European Patent No. EP 3763630 B1 Applicant: Suntory Holdings Ltd., Osaka (JP) Registration date: 28.2.2019 The shape and design of this lightweight PET bottle with angular compensation surfaces was granted a European patent on 5.9.2023. A container with corner support columns European Patent No. EP 3621888 B1 Applicant: The Coca-Cola Company, Atlanta (US) Registration date: 9.5.2018 A bottle designed for hot-filling with supporting corner columns was granted a European patent on 13.9.2023. A lightweight bottle European Patent No. EP 3347282 B1 Applicant: Amcor Rigid Plastics USA LLC., Wilmington (US) Registration date: 31.3.2017 A lightweight plastic bottle with a specially designed container neck/thread has been granted a European patent. A plastic bottle European Patent No. EP 3225562 B1 Applicant: Yoshino Kogyosho Co. Ltd., Tokyo (JP) Registration date: 23.2.2017 This European patent application dated 20.9.2023 is for a plastic bottle with a deformable base that absorbs changes in pressure that occur during hot-filling and the subsequent cooling process. A bottle with information International Patent No. WO 2023 / 191051 A1 Applicant: Otsuka Techno Corp., Tokushima (JP) Registration date: 31.3.2023 A plastic bottle that has a machine-readable code during mould production."},{"@ID":39 "37 EVENT PREVIEW PETplanet Insider Vol. 25 No. 04/24 Swiss excellence in PET preform production Otto Hofstetter AG, a leader in the engineering and manufacture of PET preform moulds, will exhibit at NPE for the first time. With more than four decades of experience, the Swiss family business has extensive expertise in PET preform processes and technology. The highly experienced team of mould specialists share their knowledge across the entire production spectrum, from the initial idea and design of the preforms, through sampling and mould manufacture, to final product quality assurance. This meticulous process is claimed to ensure that each customer benefits from an efficient project workflow, produces high quality and cost effective PET preforms and achieves savings in high volume production over the long term. Otto Hofstetter AG will present its wide range of high-performance injection moulds to industry professionals. These include moulds for PET preforms with 2 to 192 cavities, suitable for both top-entry and side-entry systems. The Swiss manufacturer also offers high-precision moulds for medical applications, thinwall packaging, cartridges and in-mould labelling solutions. In addition to these products and services, sister company Otto Systems - which focuses on specialised PET preform appl ications - offers with its PET-Series and HOD-Series turnkey production systems with clamping forces of 160 and 240 t. These systems are claimed to meet high standards of quality and energy efficiency. www.otto-hofstetter.swiss Otto Hofstetter’s 144-cavity side-entry PET preform mould is engineered to Swiss standards of durability, cost-effectiveness and operational reliability. Otto Hofstetter AG South Hall, Level 1 Booth S12095 Bottle Zone Premium Sponsors Gold Sponsors Silver Sponsors 29th Strategy and Technology Conference for the PET Packaging Industry 12 - 13 June 2024 Lake Zurich, Switzerland www.petnology-conference.com PETnology's connecting comPETence PETnology Europe 2024 )XWXUH ƋW 3(7 VROXWLRQV Time to share visions organized by Lead Sponsor E N D L E S S I N N O V A T I O N S I N C E 1 9 1 9"},{"@ID":15 "MATERIALS / RECYCLING PETplanet Insider Vol. 25 No. 04/24 www.petpla.net 26 AI-powered object recognition for sorting food-grade from non-food-grade plastics Differentiation in detail Until now, food-grade sorting has proved a challenge for the industry as food and non-food packaging are often made of the same material and visually very similar which makes it difficult for sorting systems to differentiate and separate. Thanks to Tomra’s continued investment in a deep learning-based sorting add-on for its Autosort units, it is now possible for the first time to quickly and efficiently separate foodgrade from non-food-grade plastics for PET, PP and HDPE on a large scale. Tomra’s Gain technology, now rebranded Gainnext, resolves these challenges by further enhancing the sorting performance of the company’s Autosort units so they are capable of identifying objects that are hard and, in some cases, even impossible to classify using traditional optical waste sensors. Purity levels of over 95% By combining its traditional nearinfrared, visual spectrometry or other sensors with deep learning technology, Tomra has developed an accurate solution which achieves degrees of purity of 95% for the packaging applications in customers’ plants across UK and Europe. Tomra is also launching two nonfood applications that complement the company’s existing Gainnext ecosystem: an application for de-inking paper for cleaner paper streams, and a PET cleaner application for even higher purity PET bottle streams. Bottle-to-bottle quality Dr Volker Rehrmann, EVP, Head of Tomra Recycling, comments: “We have used AI technology to improve sorting performance for decades, but this latest groundbreaking application marks another industry first for us. AI has the power to transform resource recovery as we know it, and our latest sophisticated applications of deep learning and AI reinforce our position as a pioneer in this field. With its sophisticated use of deep learning, Gainnext enables food-grade sorting and bottle-to-bottle quality, tasks that have posed significant challenges for our industry for many years. The use of AI is driving material circularity at a time when it is needed most, with tightening regulations and increasing customer demand for technologically advanced solutions.” Indrajeed Prasad, Product Manager Deep Learning at Tomra Recycling, adds: “The use of deep learning technology not only automates manual sorting but also enables the industry to achieve high-quality recyclates through more granular sorting. Thanks to its ability to detect thousands of objects by material and shape in milliseconds, Gainnext solves even the most complex sorting tasks. Plus, with its integrated deep learning software, it offers the opportunity to adapt to future demands. We are delighted to be able to launch these innovative and muchneeded solutions to meet the ever more stringent quality requirements for sorting outputs, driven by the increasing demand from consumer brands for more high purity recycled content.” Field-proven technology Gainnext’s deep learning technology has been proven in the field for many years. Tomra introduced deep learning technology in 2019 with an application to identify and remove PEsilicon cartridges from PE streams. An application for wood chip classification soon followed in 2022. To date, more than 100 Autosort units with Gainnext are installed at material recovery facilities across the globe. Among the early adopters of the brand new applications are market-leading plants such as Berry Circular Polymers’ flagship facility in Leamington Spa, Viridor Avonmouth in Bristol, and the French Nord Pal Plast plant, which is owned by the European Dentis Group. www.tomra.com Leading global sorting solutions provider, Tomra Recycling, has announced the launch of three new applications to separate food-grade from non-food-grade plastics for PET, PP and HDPE. Following an invitation to the company’s site in Mülheim-Kärlich, Germany, PETplanet learned that the breakthrough was made possible by the company’s intensive research and development in deep learning, a subset of AI."},{"@ID":53 "EVENT REVIEW PETplanet Insider Vol. 25 No. 04/24 www.petpla.net 51 2nd Icis Recycled Polymers Conference Asia by Michael Maruschke The 2nd Icis Recycled Polymers Conference Asia was held in Bangkok on February 21-22 and focused on the challenges, regulatory developments and collaborative opportunities in the field of plastics recycling in Asia, including rPET. The conference was attended by 74 CEOs, senior professionals and market influencers from across the supply chain from 14 countries. General oversupply - weak demand for rPET Icis analyst Joshua Tan Chee Yong and senior editor Arianne Perez opened the conference with an overview of installed capacity, price trends and outlook for 2023 and 2024 in Asia. In APAC, mechanical recycling is a large market with over 18 MTPY of installed capacity, while the more complex chemical recycling is just starting to emerge with only 700 KTPY of installed capacity (figures include rPET, rPE and rPP). In 2023, the PET market experienced oversupply and weak demand for rPET. For most of 2023, there was a wide price spread between bottlegrade vPET from China and vPET in SEA (South East Asia), and an even wider spread between vPET from China and rPET in SEA and NEA. Increased PET production in China (an estimated 2-3 million tonnes of additional volume) contributed to this oversupply, flooding the market with cheaper PET and further reducing the attractiveness of rPET. In addition, rPET producers in SEA have also added new capacity, putting further pressure on prices. Weak demand from countries such as Thailand and Taiwan, where rPET is allowed in food packaging but not driven by sustainability targets or consumer pressure, has not helped. While brands and established rPET producers can cope with reduced margins and are expected to survive the current situation, smaller and mediumsized rPET producers have already reduced production rates and cut prices to attract buyers. Bottle grade material is and will remain the most traded grade from Asia. Most produced rPET is destined for products for the European and US markets. Polyolefins, especially rPE/HDPE, face a similar situation of price pressure due to the large volumes of virgin material entering the market. The outlook for 2024 remains weak: The general oversupply, the lack of sustainability targets or firm regulations in Asia on the mandatory use of rPET in packaging will continue to put pressure on the price of rPET. Currently, Australia, New Zealand, Japan, South Korea, Thailand, India, Taiwan, Hong Kong and other major economies have approved the use of rPET in food packaging. In China, there are several food grade rPET players involved in mechanical recycling, such as Ceville, Yisheng Petrochemical, Guolong, Incom Recycle, Veolia and Alba. In addition, chemical recycling (via depolymerisation) is well established with companies such as Zhejiang Jiaren (DMT), SK Chemical & Shuye (BHET), Fujian Cyclone (BHET) and Yinjinda (BHET to PETG). However, China remains one of the few countries that has not yet approved rPET for use in food packaging. Arnold Wang, Deputy Secretary General - China Packaging Federation, confirmed that many discussions and initiatives are underway and that people in the industry are eager to see progress. He expects something to happen this year. Collection and sorting - the challenges with the informal sector While countries such as Korea and Japan generally have some form of developed solid waste management system, countries in SEA and certain parts of the Indian subcontinent rely heavily on the informal sector and its waste pickers, bottle collectors, aggregators and possible middlemen. The particular challenges of sourcing raw materials from the informal sector were a key theme of the panel discussions and were also raised by several speakers. Christian Pranata, CEO of the Langgeng Jaya Group in Indonesia, knows the Indonesian plastics recycling market well. His company, Langgeng Jaya, started recycling post-consumer PET in 2006. “Never stop buying” (even on major holidays), Christian Pranata said during a panel discussion, mentioning that he would rather accept warehouses fuller than needed than interrupt the recycling chain. It is clear that people in the informal sector, especially bottle collectors, depend on a regular and continuous, albeit small, stream Price spread between Asia R-PET, PET stays wide 800 850 900 950 1,000 1,050 1,100 1,150 1,200 1,250 1,300 1,350 1,400 1,450 1,500 1,550 1,600 PET Bottle Grade FOB SE Asia PET Bottle Grade FOB China RPET Pellets, Bottle Grade FOB NE Asia RPET Pellets, Bottle Grade FOB SE Asia USD/Tonne • Price spread with China PET stays widest (incremental volumes 2-3 million tonnes/year) • Some R-PET producers lower prices to stoke buying interest • FMCGs lowers R-PET use, hikes PET in packaging mix • Weak support gained from Thailand, Taiwan approval of R-PET use in local packaging • New capacities worsen supply glut Bottle-Grade R-PET, PET Pellets in $/tonne Source: Icis"},{"@ID":13 "EVENT PREVIEW PETplanet Insider Vol. 25 No. 04/24 www.petpla.net 42 Expansion of Vision1 model range & live demonstrations Set to boost product quality Nissei ASB Machine Co., Ltd., a leading manufacturer of machines and moulds for injection stretch blow moulding of PET and other plastics, will demonstrate the live moulding of three ASB-Series moulding machines at NPE. A key highlight will be the global debut of ASB’s optional Vision1 control and monitoring system on all models. In addition, the PET moulding demonstrations will showcase the enhanced product quality and productivity made possible by ASB’s patented Zero Cooling technology. Moulding demonstrations Nissei ASB’s ASB-70DPW Vision1 one-step ISBM will be moulding a nonround 350ml HDPE container of 29.5 g in a double-row configuration, giving high output (1,550 bph). It is intended to make it a direct challenger in a sector of the market normally monopolised by traditional injection blow moulding. Additionally, the ASB-70DPW can simply and easily be adapted to mould PET, PP, COC, and a wide range of other resins including bioplastics that are beyond the capabilities of IBM systems. ASB-150DP Vision1 one-step ISBM machine The ASB-150DP 1-step injection stretch blow moulding machine is the largest capacity model in the ASB series, claimed to be perfectly matched for the North American market with robust sales since its launch. Although primarily designed for PET moulding, it is fully capable of moulding almost any thermoplastic resin into containers for both food and non-food-based applications. The live moulding demonstration of lightweight 475 ml PET cups (14.5g) with an output of 3,000bph is claimed to provide an easily recyclable, more cost effective and more resilient moulding solution over commonly used thermoforming or injection moulded cups of similar size and weight. Nissei ASB South Hall, Level 1 Booth S19049 Bottle Zone Example of free standing type Vision1 control panel Moulded product demonstrations by Nissei ASB (f.l.t.r.): 350ml (12oz) HDPE shampoo bottle, 475ml (16oz) PET cup, 900ml (30oz) PET jar Vision1 ASB’s Vision1 machine control & monitoring system is a proprietary software and hardware package fully compliant with the OPC UA global standard protocol for industrial network communication. Apart from control of the machine, the system can be networked into an existing factory management software package or set up with ASB’s standard “Vision1 for Factory” software solution included with every machine. Control of compatible upstream and downstream equipment can be integrated into the moulding machine’s control panel, while customisable real-time data can be accessed globally by the user’s management via any PC or mobile device. Additionally, remote off-site diagnosis can be conducted by technical staff or direct from ASB technical support. Zero cooling ASB’s patented Zero cooling technology leverages the second (conditioning) station of the four-station process to provide additional cooling or modification to moulded PET preforms, allowing the preform to be better optimised at the first (injection) station of the machine, resulting in good quality combined with high productivity. The North American ASB Technical Support Centre is of particular interest to ASB’s North American customers. Both the existing and planned support options in the Atlanta Technical Support Centre in the areas of sales, design, service, spare parts production, online parts ordering and on-site customer training will be presented in detail at the trade fair stand. ASB-70DPW Vision1 with optional NVES take-out system"},{"@ID":12 "10 NEWS PETplanet Insider Vol. 25 No. 04/24 www.petpla.net Inauguration of Circular PET plant in Japan Veolia, in partnership with a global trading and investment company Mitsui & Co.Ltd. and Japanese leading retail conglomerate Seven & i Holdings Co., Ltd., announces the inauguration of the Circular PET plant in Tsuyama, Japan. This state-of-the-art facility is claimed to mark a milestone in realising a circular business model that recycles used PET bottles into high-quality raw materials for PET bottles. This plant joins Plastiloop, a network of over 40 Veolia plastic recycling plants spread across the world. Veolia is the world leader in recycled plastic, with 500,000 metric tons of plastic recycled by 2023. PET bottles with caps or labels left on or leftover drinks have been considered difficult for bottle-to-bottle recycling in Japan. Using Veolia’s experience and know-how, the Circular PET plant has been designed to recycle such material and produce new food-grade PET bottles, contributing to a more sustainable future. The plant can produce 25,000 t of food-grade recycled PET resin per year, reducing 27,500 t of CO2 emission and meeting brand owners’ increasing demand. To ensure a steady supply of raw materials, Circular PET has established partnerships with key players in the industry, including the West Japan Railway Company and Kyushu Japan Railway Company. These partnerships enable the collection of used PET bottles, which are then sorted, crushed, washed, melted, and subjected to solid-state polymerisation to produce high-quality recycled PET resin. www.veolia.jp/en Dairy Gropper obtains independent certification for rPET Dairy Gropper has had the use of rPET recyclate in its PET bottle range certified by the independent seal “Flustix Recycled – DIN tested”. With the successful certification of rPET usage in bottles through this seal, the actor in the beverage and dairy industry intends to provide its customers with transparency for product labelling of their packaging in terms of responsible resource management. The customer base of the traditional dairy includes international retail conglomerates as well as the largest German retailers such as Lidl and Aldi. With the certification, the company, headquartered in Bissingen, Germany, ensures that a variety of packaging is produced as sustainably as possible and can be communicated to consumers at the point of sale as a more sustainable alternative to comparable products. “Our goal is the cycle. Plastic is ideal for preserving the safety and high quality of our food and is therefore an important resource. That’s why we have been working with recycled PET for years – out of conviction,” says managing director Heinrich Gropper. A particular advantage for retailers sourcing products from Gropper: If they wish to continue highlighting the use of recyclates in their own brands and communicate this to consumers, this can be done with a simple fast-track procedure. “Buyers can sub-certify their own brands produced at Gropper and now pre-certified. This offers, for example, the LEH the opportunity to use the recognised seal and thus communicate their sustainability commitment to consumers, also within the framework of the upcoming EU Green Claims Directive, with a certified seal,” says Malte Biss, founder of the Flustix initiative. “In a time when consumers are increasingly sceptical of self-declarations, the independent certification implemented by us simplifies the offering of credible and recognised sustainability claims for our customers’ own brands,” explains Wolfgang Hoff, managing director of Gropper. “With this step, we are preparing: even before the EU Green Claims Directive comes into effect, we offer a fast and easy-to-implement sub-licensing system with Flustix. This minimises the effort for our customers.” The Flustix Recycled certification covers the rPET (PCR) content of 50% and 100% in all transparent and light blue rPET bottles of Gropper products in 14 sizes ranging from 90ml to 1,500ml. www.gropper.de www.fl ustix.com PROCESS PILOT+ Achieve Your Sustainability Goals and Produce Your Best Product TM Agr’s Process Pilot system provides personalized process control response to each unique bottle GHVLJQ EORZPROGHU ȴQJHUSULQW Ȃ VDIHO\\ DQG TXLFNO\\ 1R ELJ GDWD MXVW UHOLDEOH GDWD ZZZ DJULQWO FRP "},{"@ID":10 "8 NEWS PETplanet Insider Vol. 25 No. 04/24 www.petpla.net Triple success in Australia’s circular plastic projects Circular Plastics Australia (PET), a joint venture between Pact Group, Cleanaway Waste Management, Asahi Beverages, and Coca-Cola Europacific Partners (CCEP), has selected Amut as the preferred partner for designing and constructing its “Duet and Symphony” recycling projects in Albury and Melbourne. The Italian recycling company was also chosen by the Circular Plastics Australia (PE) joint venture between Pact and Cleanaway for the “Choir” project, also in Melbourne. These integrated, custom-engineered sorting and washing plants ensure that the bottles are part of a closed cycle, where they are used, collected, and given another life. While Duet and Symphony are intended for sorting and washing PET bottles, Choir focuses on HDPE and PP. The Duet recycling line, in operation since 2022, was initially designed for a total output of 3,400 kg/h. After one year of operation, it now reaches a total output of 4,000 kg/h. Amut expresses pride in the acceptance of their specialised technology provided to the Symphony project last November. The opening ceremony of Symphony took place in the presence of Federal Environment Minister Tanya Plibersek and Victorian Minister for Environment Steve Dimopoulos. In December, Amut received approval from the client for the Choir project as well. The Symphony plastic recycling facility is the largest of its kind in Victoria and is furnished with state-of-the-art equipment capable of producing up to 20,000 t/a of recycled PET resin. When fully operational, Symphony can convert the equivalent of up to one billion 600ml PET plastic beverage bottles annually into high-value food-grade PET pellets, which are then used to make new rPET beverage bottles and food packaging. Additionally, the Symphony plant has the capability to process low-viscosity PET tubs and trays. Amut’s washing lines are equipped with technical solutions claimed to ensure the high purity of the final PO/PET flakes, particularly in removing organic and inorganic contaminants and separating PSA labels and glue. These highly automated washing systems are claimed to ensure low operational costs by reducing power and water consumption, as well as chemicals.” www.amut.it +49 7584 9226-0 info@w-stadler.de www.w-stadler.de STADLER Anlagenbau GmbH Premium machines, smart solutions From cutting-edge engineering and complete solutions to single-machine brilliance: Discover STADLER’s smart solutions for every need! US recyclers recovered over five billion pounds of post-consumer plastic for recycling in 2022 Recyclers recovered just over five billion pounds of post-consumer plastic for recycling in the United States in 2022 with the vast majority staying in North America to be processed and remanufactured into new products, according to new data released by the Association of Plastic Recyclers (APR), ISRI, and the U.S. Plastics Pact. Prepared by Stina Inc., and based on surveys conducted by Stina Inc. and the National Association for PET Container Resources (Napcor), the 2022 U.S. Post-consumer Plastic Recycling Data Dashboard details U.S. sourced post-consumer plastic recovered for recycling. North American reclaimers acquired 93.7% of plastic recovered for recycling in the U.S. while exports overseas fell to 6.3%. Although total volumes recovered were down by 1.4% (71.2 million pounds), U.S. reclaimers acquired 21.4 million pounds more U.S. sourced post-consumer plastic over 2021, for a total of 4,307.8 million pounds or 85.9% of the total. Bottles: largest decrease of 107.1 million pounds The 2022 data shows that the five billion pounds of plastic recovered in this year include Bottles (2,784 million pounds, 55.5% of total); Non-Bottle Rigids (1,111.8 million pounds, 22.2% of total), Film (1,110.3 million pounds, 22.1% of total) and Other Plastics (11 million pounds, 0.2% of total). While the volumes reported as recovered for recycling in Non-Bottle Rigids and Film categories held steady or increased in 2022, as compared to 2021, the volumes in Bottle and Other Plastics categories decreased. Bottles had the largest decrease of 107.1 million pounds with a decline across all bottle categories. www.plasticsrecycling.org"},{"@ID":65 ""},{"@ID":52 "EVENT PREVIEW PETplanet Insider Vol. 25 No. 0/24 www.petpla.net 50 Mold-Masters to present its latest systems Hot runner systems & more Mold-Masters will showcase new products including hot runner systems, temperature and motion controllers, an auxiliary injection unit, a gate seal, and sustainable processing solutions. The new hot runner systems include the Fusion Series G3 and the Ecoone Series. The Fusion Series G3 hot runner system comes pre-assembled and features compound nozzles; a heated nozzle flange; quick change headless valve pins; and waterless actuators with passive actuator cooling technology. The Ecoone Series 1-8 drop hot runner system is a highly economical, standardised solution suitable for processing commodity resins. MoldMasters says that it is a simple, costsensitive solution for applications such as consumer goods, small home appliances, basic automotive components, electronic peripherals/accessories. Its wide range of standard components includes nozzles with a shot range capacity from less than 5g up to 3,500g, in lengths from 50-300mm. Manifolds are available with custom pitch ranges. On display will be a Temp Master M4 hot runner temperature controller and an M-Ax mould motion controller. The Temp Master M4 features MoldMasters’ new HR-connect technology, which replaces conventional mould thermocouple and power cables with a single lightweight cable connection to the control head unit. Mold-Masters describes this as a “new standard” for temperature controller design.The new M-Ax mould motion controller features a simplified user interface. Special features include preprogrammed mode functions and energy monitoring, which allows moulders to measure and track energy consumption of their motion controls, and torque monitoring, which can be used for a variety of user-determined purposes. Visitors will also see the company’s E-Multi auxiliary injection units, including the E-Multi mini, described as a compact, lightweight unit designed for small shot weights. It can be attached directly to the mould and mounted in nearly any orientation. A pivoting hopper can move laterally, to accommodate challenging installation positions. Mold-Masters West Building, Level 2 Booth W1601A West Hall The Sprint Apex gate seal minimises flow lines and is claimed to improve stress crack resistance of CSD caps by up to 40%. It is also designed to enhance part quality, improve colour change and minimise maintenance costs by eliminating the insulation cap. Mold-Masters’ co-injection multi-layer systems allow moulders to incorporate recycled content up to 50% of total part weight, as the core layer positioned between two layers of virgin resin. The technology is compatible with small to large packaging products and a range of other applications. A system producing 5-gallon pails with recycled cores on a 950t machine will be on display and running live. Various processing solutions for bio-resins and recycled materials will also be on display. Mold-Masters offers both complete system solutions and retrofit packages to convert conventional single shot injection machines to co-injection. www.moldmasters.com The Sprint Apex gate seal minimises flow lines and improves stress crack resistance of CSD caps."},{"@ID":21 "PREFORM PRODUCTION PETplanet Insider Vol. 25 No. 04/24 www.petpla.net 19"},{"@ID":54 "EVENT REVIEW PETplanet Insider Vol. 25 No. 04/24 www.petpla.net 52 of income. If this is not forthcoming, people will turn to any other kind of work to make a living. Laurent Besson, General Manager of Veolia Services Indonesia, also recognises the challenge of collecting raw materials. In Asia, Veolia operates 14 plastics recycling plants with an annual capacity of 250,000t for PET, HDPE, LDPE, PP and ABS. In Indonesia, the company recycles 1.2 billion bottles per year to produce 25kt/y of food-grade rPET. The company’s PlastiLoop sustainability programme is designed not only to secure raw materials but also to support the informal sector by providing social and financial services (e.g. savings accounts), training, PPE equipment and uniforms to promote social recognition. To prove the origin and impact from raw materials to finished products, the company uses an end-toend traceability system using blockchain technology. Another sustainability programme in Indonesia is the Mahija Parahita Nusantara Foundation, a joint initiative between Coca-Cola Europe Pacific Partners Indonesia (CCEP Indonesia) and Dynapack Asia. It was the first closed-loop, food contact-approved PET bottle recycling facility in Indonesia. In the Philippines, Coca-Cola and Indorama Ventures have launched the Tapon to Ipon initiative to supply clear PET plastic bottles to their joint venture, PETValue Philippines. The collection programme uses pop-up booths for post-consumer PET plastic bottles. Consumers can drop off (tapon) their used clear PET plastic bottles of any brand and receive incentives (ipon) in return. The development of the rPET market in Thailand has only just begun. In 2022, the Thai Ministry of Public Health issued Notification No. 435, or “MOPH 435” for short, setting the standard to allow the use of PCR PET for food contact packaging. In 2023, three companies were approved and listed on the Thai FDA’s positive list. The first company was Envicco. Envicco is a joint venture between PTT Global Chemical Public Company Limited, Thailand’s largest petrochemical company, and Alpla, the global rigid packaging specialist. The majority of the feedstock is sourced from the informal sector: drop points, local communities, schools, brand owners, waste community centres and micro-waste collectors. The project covers more than 45 provinces in Thailand. The installed capacity is 30,000 MTA of PCR PET (US FDA, EU EFSA and Thai FDA) and 15,000 MTA of PCR HDPE. Weak end market demand for recycled polymers Source: ICIS virgin and recycled polymer reports, 2024 600 1000 1400 1800 Feb 23 Jun 23 Oct 23 V-PET vs R-PET Prices in Asia (USD/ Tonne) PET Bottle Grade FOB Asia SE Assessment Spot 2- 6 Weeks Full Market Range Weekly (Mid) RPET Pellets, Bottle Grade FOB Asia SE Assessment Container Spot 0-6 Weeks Full Market Range Weekly (Mid)"},{"@ID":23 "PREFORM PRODUCTION PETplanet Insider Vol. 25 No. 04/24 www.petpla.net 21 end point of melting remain similar to the other resins. It is darker (lower L*colour), due to the very high Sb content (300 ppm) and is yellower (higher b* colour) due to processing under dry air at 180-185 °C for long periods of time. Yellowness is an indication of thermo-oxidative degradation. It is assumed that the high Sb content is required to boost reactivity in both the CP and SSP, for making higher IV in the CP and compensating for lower temperatures in SSP, which indicates a lack of flexibility during processing. Generally, the level of contaminants tends to decrease with increasing IV across SSP. Both Resins 1 & 3 easily reach the industry standard for residual AA of 1 ppm indicating sufficient SSP treatment. Resins 2 & 4 have AA values 1 ppm, due to reduced SSP treatment. 2-Methyl-1,3-Dioxolane (MDO) is referred to as “hidden AA”, as it can be converted back to AA and ethylene glycol in the presence of water. The MDO level in the MTR resin is around 10 times higher than the other resins; this is thought to be caused by processing under dry air. Preforming 43 g preforms were made at PTI in Switzerland on an Arburg 370C mono-cavity moulding machine. Process parameters were kept the same for all resins: drying for 5-6 h at 160 °C to less than 10 ppm and injection moulding at barrel temperatures of 280 °C. The preform results in Table 3 can be used to compare the behaviour of the different resins, but the results cannot be compared directly to results from production scale preforming. All resins melted out without any issues during preforming. Neither the differing modification levels nor the level of crystallinity level influenced the melt out behaviour of the resins at 280 °C. No significant difference was observed in the melting behaviour of spherical and cylindrical pellets. An IV drop of around 0.02 dl/g was seen in all resins, regardless of solid-state treatment, which is typical during preforming as the resins were all well dried. This would suggest that moisture content, which was the same for all samples, had a more significant effect on IV drop than any difference in molecular weight distribution (polydispersity) between the samples. The influence of SSP processing can be seen when comparing the combined AA and MDO (mmol/ kg) loading of the preforms. Resins 1 & 3, with the longest SSP residence times and highest temperatures, have a much lower overall AA & MDO content, by 25-40%, compared to resins 2 (lowest SSP residence time) & 4 (lowest SSP temperature). A shift in Preform quality Unit Resin 1 2 3 4 IV (ASTM) [dl/g] 0.765 0.747 0.759 0.778 IV drop (ASTM) [dl/g] 0.019 0.023 0.019 0.021 Haze [%] 8.89 8.60 8.17 10.69 Colour L* [-] 82.03 81.56 84.28 76.10 Colour b* [-] 2.60 3.69 2.70 4.85 Residual AA [mg/kg] 6.2 9 6.2 6.7 Residual MDO [mg/kg] 5.9 8.4 8.1 9.9 Total MDO & AA [mmol/kg] 0.21 0.30 0.23 0.26 Table 3: Preform measurements - Note: Haze and colour measurements made directly on preform; glass preform used as zero reference for haze. Resin quality Unit Resin 1 2 3 4 Pellet crystallinity (av.) [wt%] 56.3 55.5 58.8 49.7 Colour L* [-] 88.0 87.9 90.6 83.7 Colour b* [-] -2.3 -2.73 -2.14 -0.31 Residual AA [mg/kg] 0.90 1.4 0.61 1.1 Residual MDO [mg/kg] 0.67 1.0 0.82 7.7 Antimony (Sb) content [ppm] 208 240 188 316 Table 2: Bottle grade resin measurements the MDO and AA balance can also be seen; this is due to equilibration. The colour of the preforms is directly influenced by bottle grade resin quality. The MTR resin, with a long residence time under air and very high Sb content, results in darker (lower L* colour) and yellower preforms (higher b*). It also has a significantly higher haze level than the other resins; this could be caused by either the high Sb content or, possibly, degradation reactions from the long residence time under air at high temperature. Summary SSP continues to prove its value in the PET processing chain. Better management of the IV split between CP and SSP can allow more process flexibility, such as lower Sb contents, and improve preform and bottle quality. Longer SSP times and higher SSP temperatures under N2 produce a cleaner resin, resulting in lower overall AA and MDO content in preforms and bottles while still maintaining good colour and low haze. SSP processing under dry air has limitations and leads to yellowness, an indication of oxidative degradation, as temperatures increase above 180 °C and residence times are extended to increase IV. www.polymetrix.com"},{"@ID":58 "No.4 2024 www.petpla.net D 51178; ISSN: 1438-9452 15 . 04 . 24 M A G A Z I N E F O R B O T T L E R S A N D B O T T L E - M A K E R S I N T H E A M E R I C A S , A S I A , E U R O P E A N D A L L A R O U N D T H E P L A N E T PETplanet is read in 159 countries MARKETsurvey Suppliers of preform machinery Page 32 EDITOUR Page 12 Page 34"},{"@ID":8 "PETnews 6 NEWS PETplanet Insider Vol. 25 No. 04/24 www.petpla.net The And&Or Group acquires Icebel The industrial automation company And&Or, headquartered in Palomares del Río, Spain, announced the acquisition of Icebel, a leading Portuguese company specialising in machinery and technologies for the glass industry. This operation reflects the continued growth and expansion of the And&Or Group in the market, further solidifying its position as a leader in automation solutions for the industry. The acquisition of Icebel represents a key strategic step for the And&Or Group, as it combines its expertise in handling plastic packaging (PET, HDPE) with Icebel’s analogous experience in glass packaging. This is intended to complement the product and service portfolio of the And&Or Group, allowing both companies to leverage synergies and collaborate in creating comprehensive solutions for the industry. The integration is expected to enable the Group to offer a wider range of solutions, increasing its manufacturing capacity to address the growing demands of the market and provide greater value to its customers. “We are delighted to welcome Icebel to the And&Or family. This acquisition reflects our ongoing commitment to excellence and innovation in the field of industrial automation,” said Antonio Ortega Suarez, CEO of And&Or. “Together, we are better positioned to provide comprehensive and advanced solutions to our customers across Europe, strengthening our position as industry leaders.” Alfonso Cardeira, Managing Director of Icewbel, stated, “This integration into the And&Or Group is a great opportunity to drive the company’s growth and progression. We are focused on ensuring that our relationship with all stakeholders is strengthened with this acquisition.” Both companies will work together to ensure a smooth transition that benefits both employees and customers. It is expected that this acquisition will strengthen the Group’s international presence. www.andyor.com Eastman plans to invest in two additional molecular recycling plants Eastman announced it has achieved on-spec initial production and is generating revenue from its new molecular recycling facility in Kingsport, Tennessee, USA. The company expects to ramp up production of the new facility over the coming months and enable growth across a wide range of markets. Achieving this critical milestone enables the company’s pathway to deliver approximately $75 million of incremental EBITDA in 2024 from this facility as it builds momentum in its circular economy platform. “By demonstrating molecular recycling at this scale, we have solidified our position as a leader in the creation of a circular economy. Demand for recycled material at virgin-quality levels from our new facility remains strong, and we are excited to announce this significant next milestone in our journey,” said Mark Costa, Board Chair and CEO. In addition to this recently completed facility in Kingsport, Eastman plans to invest in two additional molecular recycling plants, one in France and another U.S. site. The location of its second U.S. molecular recycling facility will be Longview, Texas. The selection of the Longview site was based on several factors, says Eastman, including existing infrastructure and operations synergies, favourable energy supply, access to feedstock pools in the western and central U.S., and ample space for renewable energy generation. The Longview facility will have the capacity to recycle approximately 110,000 metric tonnes of hard-to-recycle plastic waste. Eastman’s proven polyester renewal technology recycles hard-to-recycle plastic waste currently bound for landfill or incineration. The company’s technology allows this waste to be broken down into its molecular building blocks and then reassembled to become virginquality material without compromising performance. Eastman is enabling the potentially infinite use of materials by keeping these valuable molecules in production, in a material-to-material high-yield loop. Eastman can transform waste plastic into virgin quality food contact polyesters with lower greenhouse gas emissions than traditional methods. www.eastman.com Change in the CHT management board As of April 1, 2024, Eva Baumann takes over the posi t ion of CEO of CHT. Together wi th Prof Dr Klaus Müller, who acts as CFO, she forms the management of the internationally act ive Group. Unt i l 2020, Eva Baumann had worked for many years in a leading global company in the chemical industry. She has been part of the CHT Group since January 2020 and, as Group Vice President, has headed the Business Field General Industries at Group level. As CEO, she is now responsible for Marketing, Sales, Corporate Strategy, Human Resources and Sustainability. Eva Baumann has ambitious plans for the future of the CHT Group: “We are facing challenging but promising times of change. As a foundation-owned company, we have a strong backing. Nevertheless, we bear an immense responsibility for the continued existence of the company and for our employees all over the world. As a player in the chemical industry, we are also particularly committed to preserving our planet. Having been part of the CHT Group for many years, I know the character of the company and the people who make it up very well.” www.cht.com"},{"@ID":34 "MARKET SURVEY 32 PETplanet Insider Vol. 25 No. 04/24 www.petpla.net 04/2024 MARKETsurvey Suppliers of preform machinery In this issue, PETplanet focuses on state-of-the-art preform machinery. We are proud to present the most exciting brand-new data from the following preform machine manufacturers: Sipa, Otto Systems AG, Sacmi Imola, Netstal Maschinen AG and Nissei ASB Machine Co. Ltd. Although the publishers have made every eff ort to ensure that the information in this survey is up to date, no claims are made regarding completeness or accuracy. Resins & additives Cap producers, systems & inspection systems Preform machinery Preform production & inspection systems Preform, cap & SBM mould manufacturer SBM 2-stage Compressors Filling equipment & inspection systems Palletising & shrink film machinery Recycling machinery Company name Sipa Otto Systems AG Netstal Maschinen AG Postal address Telephone number Web address Contact name Function Direct telephone number E-Mail Via Caduti del Lavoro, 3, 31029 Vittorio Veneto (TV), Italy +39 04389 11 511 www.sipa.it Ms Anna Horecica Csiki Preform Systems Product Manager +39 04389 11 511 anna.horecica@zoppas.com Zürcherstrasse 73, 8730 Uznach, Switzerland +41 55 285 22 11 www.otto-systems.com Mr Reto Bamert Chief Sales Offi cer +41 55 285 22 69 reto.bamert@otto-systems.com Tschachenstrasse 1, 8752 Näfels, Switzerland +41 55 618 6111 www.netstal.com Mr Stefan Kleinfeld Product Manager +41 55 618 6241 stefan.kleinfeld@netstal.com Preform injection moulding systems Machine model number / name Xform 250 Xform 350 Xform 500 Xtreme 72 Xtreme 96 PET-Series 160 & PET-Series 240 Side Entry Systems: PET-Line 3000, PET-Line 4000, PET-Line 5000 & Top Entry Systems: PETLine 4000 Number of cavities (min/max units) 96 128 200 72 96 4 - 96 cavities 24 - 144 Maximum individual preform weight up to 780g max. shot weight 6,600g Max resin through-put (kg/h of PET) up to 890kg/h PET up to 1,600kg/h Produced preforms per hour (min/max) 69,000 92,000 147,000 50,000 69,000 up to 65,000 max. 100,000 Standard Features (short description / keywords) Otto Systems is a supplier of integrated PET preform production systems with a modular and standardised design. The systems feature a high level of fl exibility, functionality and compactness. The PET-Series gives producers a high-performance system for small production batches that is compatible with selected top-entry moulds and, as a variant, capable of producing preforms up to 400mm in length. All systems: Intrusion, PETXScrew (=optimised 100% rPET processing) Side Entry Systems: smart operation (= safe and guided operation) and energy recuperation (low energy consumption) Options / Special Features (short description/keywords) Xform: available in Gen4 XP version (low energy consumption, fast cycle time, legacy tooling compatibility); Xtreme: injection-compression technology, ultra-thin wall capability, two preforms can be produced simultaneously; Xform Gen4 XP: XP technology, long-life tooling coating, Xmold for ultrathin preform injection capability, wide-mouth preforms capability; Xtreme: built-in inspection system for 100% quality check, 100% recycled fl akes processing capability, direct connection with Xtra SBM. The HOD-Series from Otto Systems is the fi rst highperformance preform production system tailored specifi cally to the HOD market. With a 160- and 240-ton system, the HOD-Series meets all the demanding technical requirements for producing large and heavy preforms. The PET-Series system with its special confi guration of the tie bar spacing, ensures compatibility with the most important top-accessible moulds. Cycle guard (= controlled production shutdown during a power outage), NRC (= Netstal remote control), energy measurement, preform inside cooling, staggered EOAT (= additional cooling station) and integrated Q-monitoring system."},{"@ID":24 "22 PETplanet Insider Vol. 25 No. 04/24 www.petpla.net PETproducts A bigger extrusion unit for ultra-high output preform production Sipa has expanded its lineup of extrusion units compatible with the Xform 500 injection moulding system. The EE155 extra-large extruder is designed to provide added convenience for processors utilising the company’s unique 200 cavity PET preform moulds for high-speed production. The EE155 is an addition to its range of extrusion units that fit on the Xform 500 injection moulding system. Sipa says that sales of its Xform systems are growing yearon-year and around 15% of current purchases of the Xform 500 are for use with 180 or 200 high-cavitation moulds. The company describes the introduction of the higher capacity machine, with a capacity of around 1,700 kg/h, as a “logical step”. The capacity is much higher than its previous top-of-the-range unit and is intended to offer customers more flexibility when making preforms with higher weights, across the full range of mould cavitations. Sipa started 2024 producing new Xform 500 systems equipped with the EE155 extruder, scheduled for delivery in April. The company now offers three sizes of Xform, with clamp forces of 250, 350, and 500 tonnes; each model can be equipped with at least three different sizes of extruder. There are now four extruder options for the Xform 500: the existing EE100, EE120, EE140 and the latest addition, the EE155. www.sipasolutions.com Quality control for flawless preforms Sacmi’s PVS156 vision system offers continuous, in-line quality preform control without interrupting machine operation. Offering real-time data analysis and user-friendly reporting, the system is claimed to empower preform producers to elevate both quality standards and production efficiency. The PVS156 features a comprehensive camera system, utilising six cameras to inspect preforms from every angle. Camera 1 focuses on the top seal area, detecting defects like dents and short shots, while also measuring inner diameter and ovality for precise shape control. Camera 2 examines the preform bottom, identifying issues such as crystallisation, gate flash, and pinpointing holes through the gate. Camera 3 is dedicated to dimensional analysis, capturing 44 images during a 360-degree preform rotation to measure critical dimensions like neck diameters and support ring heights, customisable to specific requirements. Camera 4 utilises polarised light and artificial intelligence to differentiate good preforms from bad with accuracy. Camera 5 provides an unrolled view of the neck, detecting inclusions, black spots, and reading cavity numbers with dual lighting. Camera 6 analyses the preform body, measuring diameters, gate length, wall thickness, concentricity, and colour variations, ensuring adherence to colour standards and rejecting preforms showing signs of excessive yellowing (indicative of RPFT degradation). Beyond inspection: empowering data-driven decisions Beyond inspection, the PVS156 delivers valuable data and comprehensive reports, including defect types, defects per cavity, measurement statistics, weight distribution, and historical performance data for informed decision-making. Operators can fine-tune the inspection process to their specific requirements by adjusting sensitivity, focusing on specific columns, and permanently rejecting problematic cavities. At NPE 2024, Sacmi will be showcasing its PVS156 vision system incorporated in the IPS 300 press (see also page 45). www.sacmi.com PREFORMS"},{"@ID":31 "Cornelia Braun (left) and her Prof Erik Schneider (right); Cornelia was awarded the Prize of the Association of German Engineers for her Bordeaux bottle design. BOTTLE MAKING 29 PETplanet Insider Vol. 25 No. 04/24 www.petpla.net or 200ml. It is reminiscent of the traditional wine bottle made of glass but a crystalline pattern gives it quite a different visual appeal. The Bordeaux bottle’s design marries the traditional shape with the indentation in the base to contemporary elements. The new design also features a concave base (punt), just like the traditional Bordeaux bottles. That shape has proven its worth ever since it was developed: When wine is stored, tannins and colourants polymerise over time, resulting in a sediment (or deposit) which can be detected in the liquid either as solid or turbid matter. The indentation in the bottle’s base produces a groove where such matter can settle, so it is not swirling around in the wine when it is poured. Prize-winning design Cornelia Braun was awarded the 2023 Prize of the Association of German Engineers (VDI) for the design she developed. What particularly impressed the jury was the technical and design-related solution she found in answer to the multifaceted challenges involved, not least the consummate combination of high-quality wine with a container material that may seem a bit unusual at first glance. www.krones.com"},{"@ID":47 "PETplanet Insider Vol. 25 No. 04/24 www.petpla.net 45 EVENT PREVIEW Sacmi will be highlighting human machine interaction based on new controls, digital tools and artifi cial intelligence (AI) Digital tools & AI Sacmi says that the primary goal of digitally advanced controls is to protect customers’ investment by making it easier for operators to manage machines and plants. Its stand at NPE will present and demonstrate ‘digital inside’ technologies from three perspectives. Smart Pack 2 includes Sacmi’s latest and most advanced control package and is available from 2024 on its CCM cap presses. Its goal is deep control of everything on the machines from hydraulics to consumption, bringing systems ‘self adjustment’ capabilities and feeding valuable functional information back to process control. New for 2024 is the ‘prediction’ button on the press, which forecasts machine behaviour over time, anticipating production drifts and expediting proactive maintenance. Smart Care service provides secure, in-Cloud sharing of main operating parameters. This helps to ensure optimal decision making on the line and feeds customers real-time suggestions and assistance from the Sacmi team. Smart Care augments the opportunities offered by Space, the gateway to Sacmi assistant services, which is provided in synergy with the Sacmi USA team. Classy AI is part of the Sacmi Computer Vision systems (CVs) suite. It automatically classifies defects, making it easier to run plants and perform process control. Sacmi will also be presenting Gilda AI, which it describes as a ‘chatbot-like tool’. It will be playing a lead role on the exhibition stand and visitors will have the opportunity to see live demonstrations. In the event of a machine malfunction or process drift, operators can simply ‘ask Gilda’ to obtain prompt customised AI-powered answers to their queries. Visitors to the Sacmi stand will have a great opportunity to see a CCM64 cap press and IPS 300 preform press in action. As well as advanced controls and integration with quality control, the latest solutions also offer the prospect of working with fully recycled materials. The CCM on the stand can be fed with HDPE from recycled sources, including PCR foodgrade material acquired on the market in accordance with FDA regulations. This has opened up new opportunities for the recycling of HDPE caps and the same is the case for the IPS press; the machine that will be demonstrated at the show has already been sold to a leading American customer who aims to feed it with 100% rPET. Sacmi will also be showcasing an enhanced solution that takes next towards the new 26/22mm standard. Its compliance with the new standard is guaranteed, Sacmi says, as it has been working in close collaboration with major international certification bodies, including Cetie, the International Technical Centre for Bottling, headquartered in Paris, France. Sacmi says that the solutions that will be on display at NPE will demonstrate how it is providing customers with close support, helping to identify solutions that best match their product production requirements while factoring in consumption habits for individual segments countries or markets. The company says that it currently offers the market’s largest family of caps for 26/22mm necks and a wide range of opportunities and choices in tethered caps, as well. The IPS on the stand will be equipped with a 72-cavity MHT mould, set up to produce light preforms. www.sacmi.com Sacmi West Building, Level 2 Booth W1243 The CCM on the stand has already been sold to a leading American customer. 2024 Training Schedule Technology&Application of PET Plastic Packaging for Hot-Fill &Aseptic Beverages Join our expert team for small group training on a variety of subjects - from materials to recycling. Scan to learn more & register for classes! ©2024 Plastic Technologies | 1440 Timberwolf Drive, Holland, Ohio USA 43528 www.pti-usa.com"},{"@ID":59 "EDITOUR PETplanet Insider Vol. 25 No. 04/24 www.petpla.net 12 PET bottle fi lling from the wells of Hamda region in Sharjah Visiting the drinking water department of the Sharjah government by Kay Barton Zulal was founded in the village of Hamda, part of the Emirate of Sharjah in the United Arab Emirates, under the patronage of H.H. Sheikh Dr Sultan Bin Mohammed Al-Qasimi, Member of the Supreme Court and Ruler of Sharjah. His vision was to provide clean, pure drinking water from the Hamda wells for the general public of Sharjah and other emirates of the United Arab Emirates. December 12, 2023: Interview with Sharjah Electricity, Water and Gas Authority, Zulal Water Department (SEWA) We met: Mr Padubidri Shridar Niranjan, Production Manager Ms Hamda Bukhatir, Chemical Engineer Zulal Water Factory was established in 1995 as a government organisation under the Sharjah Electricity and Water Gas Authority (Sewa). Our interviewee Mr Padubidri Shridar Niranjan, the Production Manager in charge, is relatively new to the factory and has many years of professional experience in the FMCG industry, having managed various projects throughout his career. His colleague Hamda Bukhatir, Chemical Engineer, also took part in the interview. Sewa (Zulal) sits on a number of wells in and around the Hamda region, at an average depth of 150 to 350 metres, from which it extracts water, treats it with modern technology and bottles it in various PET bottle sizes. We sat on a comfortable couch opposite the man who has worked in every branch of the FMCG industry for 37 years and can look back on a remarkable wealth of experience. Mr Niranjan, originally from Bangalore, India, has a mechanical engineering background and has been passionately dedicated to the Authority and Hamda water since Q3 2022, having previously worked in various industries and packaging sectors such as can, PET, HDPE, or glass filling for beverages. His professional experience includes stints at tin can manufacturer Sapin in Saudi Arabia, the edible oil manufacturer Savola in Bharain, the German plant manufacturer Krones, the water bottler Masafi, which is around 50 km away from here, and the water bottler Mai Dubai. He also worked as a freelance consultant for a preform project. Now he is part of Zulal, where he reports directly to Mr Majid Abdulaziz Alowais, Director of the Zulal Water Factory. Zulal is headed by His Excellency Abdalla Abdelrahman Al Shamsi, Director General of Sewa. As we learnt, Zulal is said to be the purity of the natural beauty of the Emirates from the Hamda wells. The water is characterised in particular by its low sodium content and pH value of 7.5. “Zulal Water,” explained Mr Niranjan, “switched completely to PET from 2004 onwards. Our current setup is fully automated across the board, from pumping the water from the numerous wells to the finished bottle. We are talking about a purely natural sourced product from the Hamda wells.” The plant covers nearly 11,150 m2 and is currently running at around 70% capacity. The company is using a complete Sidel line with 45,000 bph capacity for 0.2 l, 0.33 l, 0.5 l and 1.5 l, all with standardised 29/25 neck finish. Two Bosch packaging systems, each with 16,000 bph, produce small-format drop bottles. 18.9 l containers are produced on a Bardi machine and small thermoforming cups on Novopack equipment. The preforms and closures are sourced locally. “We attach great importance to high-quality packaging, which is why the preforms and closures come from Husky, Netstal, Sacmi and Engel machines”, said Mr Niranjan. www.zulal.ae EDITOUR Production Manager Padubidri Shridar Niranjan Zulal employee blowing bottles on a Sidel SBO18 0.5 l bottles on their way to the shrink tunnel"},{"@ID":48 "EVENT PREVIEW PETplanet Insider Vol. 25 No. 04/24 www.petpla.net 46 Dry ice cleaning solutions and the chance to win Cold Jet will be showcasing five new machines at their booth, all operational for live demonstrations. Visitors will have the opportunity to witness or participate in live mould cleaning demonstrations using a dry ice blaster. Additionally, guests can observe the manufacturing process for producing dry ice pellets at designated daily demonstration times. Embracing the NPE 2024 ‘Made For You’ theme, Cold Jet is offering visitors a chance to win a newly designed i3 Microclean 2 smart dry ice blaster valued at $40,000. Cold Jets dry ice blasters provide a variety of solutions that touch numerous applications in the plastics industry, including cleaning injection moulds in-situ at operating, blow moulds, extrusion dies, de-flashing and deburring parts, surface preparation (cleaning) parts prior to painting, post-processing 3D printed parts, etc. It is a dry process, non-abrasive and does not generate any secondary waste. Among the machinery on site will be the new 2024 PCS 60, an automation-ready 3mm pellet-based system allowing plastics processors to selectively control 28 different pellet sizes from 3.0mm down to 0.3mm particles. This flexibility in adjusting and storing particle size in memory enables customised cleaning aggressiveness tailored to various substrates, recognising the diversity in tooling geometries. Also featured will be the new Icerocket 3mm pellet-based system, a lower priced solution with the ability to make some minor particle size adjustments via a fragmenting nozzle. Its 3mm platform make it a popular choice for screw cleaning applications. Cold Jet West Hall - Booth W5371 The new i3 Microclean 2 is a dry ice block system, shaving a 5x5x10 dry ice block, is complementing the most popular blaster in the plastics industry, the i3 Microclean. With its capability to clean moulds, de-flash and/or deburr parts, it is claimed to be a versatile choice. The new block system can also utilise 3mm pellet in addition to block dry ice. The PE 80 pelletiser, a low-volume dry ice production machine, has been designed for those processors who choose to make their own dry ice, ondemand when needed. Cold Jet will also be demonstrating its CJ Connect monitoring system bringing Industry 4.0 principles to the maintenance function. This system enables remote monitoring of cleaning operations, scheduling, and reporting of cleaning times and costs. Existing customers will have the opportunity to meet with Customer Service, which will be exhibiting a variety of new parts and accessories and service contracts. Cold Jet emphasises that cleaning with dry ice is environmentally favourable, replacing traditional solvent-based methods. Dry ice is recycled CO2, thus not contributing to greenhouse gas emissions, as recognised by California Air Resources Board (CARB) and exempted from reporting requirements by the Environmental Protection Agency (EPA) under the Greenhouse Gas Reporting Program (GHGRP). www.coldjet.com Icerocket MODERNIZEYOURS INGLE STAGE BOTTLE PRODUCTION ✓ New high-performance single stage hot runner systems. ✓ Enhance bottle quality and consistency. ✓ Change color up to 4x faster. CONTACTUS TODAY! info@moldmasters.com www.moldmasters.com Dry ice block system i3 Microclean 2"},{"@ID":35 "MARKET SURVEY 33 PETplanet Insider Vol. 25 No. 04/24 www.petpla.net Company name Sacmi Imola Nissei ASB Machine Co., Ltd. Postal address Telephone number Web address Contact name Function Direct telephone number E-Mail Via Selice Provinciale 17/A, 40026 Imola BO, Italy +39 0542 607 111 www.sacmi.it Mr Moraldo Masi Director of Business Unit PET +39 0542 607 888 moraldo.masi@sacmi.it 4586-3 koo, Komoro-shi, Nagano-ken, 384-8585, Japan +81 267 23 1565 www.nisseiasb.co.jp Mr Paul Atkin Manager, Sales Coordination Team +81 267 23 1565 sales@nisseiasb.com Preform injection moulding systems Machine model number / name IPS220 IPS300 IPS400 PM-70/65NII, PM-70/111N, PM170/111M Number of cavities (min/max units) 16-72 24-128 48-144 6-48 Maximum individual preform weight 140g 140g 140g 240g Max resin through-put (kg/h of PET) 625kg/h 900kg/h 1,250kg/h 250 (approx) Produced preforms per hour (min/max) Standard Features (short description / keywords) Injection cylinder (shooting pot), electrical drive for plasticising screw, T-belt for preforms extraction, Cool+ system (inside cooling), belt free robot linear motor with KERS, take-out plate with three post-cooling stations, HMI with control of all auxiliaries, boosters on moving platen for fi rst phase ejection, double cylinder for preform ejection; digital valves for each actuator, water unloading system prior to mould changing and injection shot completition device (power failure). Vertical clamping, built-in preform after-cooling stations, extremely compact Options / Special Features (short description/keywords) Water pumps for mould cooling assembled on main machine platform; quality control vision system with multiple camera, soft handling package, walkway, high temperature environment package and cooling water sensoring kit. Outputs are tailored to ASB's own range of 2-step blowing machines for hot fi ll application. PM-170/111M is designed for bottle and jar preforms with capability of neck size up to 120mm. .FFU VT BU 4PVUI )BMM\r 4 -*7& */41&$5*0/ %&.0/453\"5*0/ 0/ 4*5&"},{"@ID":27 "MATERIALS / RECYCLING PETplanet Insider Vol. 25 No. 04/24 www.petpla.net 25 by 2025. Of this new infrastructure, 20 centres will be high-capacity collection centres capable of processing 100 t of discarded plastic waste per month, and five will be bigger ‘aggregation centres’, able to process up to 500 t per month. By 2025, Prevented Ocean Plastic expects to be collecting 50,000 t/a of plastic waste across the 25 centres. Additionally, the 25 centres will support approximately 1,000 direct jobs and create income opportunities for thousands more bottle collectors in the informal waste sector. Raffi Schieir, Director of Prevented Ocean Plastic, said, “At a time when there’s a lot of negative talk about the future of the planet, it’s good to be doing something that has an immediate, positive impact on people and their local communities. By choosing recycled and looking for the Prevented Ocean Plastic logo, we can all support responsible sourcing through these substantial, brick-and-mortar builds.“ Also in the future, in addition to a focus on collecting PET plastic, Prevented Ocean Plastic will expand into other types of plastic, including HDPE and PP, potentially preventing an extra 10,000 t of ocean plastic over the next three years. The Prevented Ocean Plastic mission is to explore a viable circular economy for all ocean-bound plastic waste. Since its inception, Prevented Ocean Plastic has generated over 500,000 bottle collector workdays, created almost 2,000 direct jobs, and prevented more than 2.5 billion bottles from entering the ocean. www.preventedoceanplastic.com www.bantamltd.com MATERIALS / RECYCLING 25 E N D L E S S I N N O V A T I O N S I N C E 1 9 1 9 Prevented Ocean Plastic plant in Bali, Indonesia"},{"@ID":7 "EDITOUR PETplanet Insider Vol. 25 No. 04/24 www.petpla.net 14 Manufacturer from Thailand reaches for the stars Packaging with passion from Sharjah by Kay Barton When talking about the packaging market in Asia, it is impossible to ignore the listed company Thai Plaspac (TPAC), Asia’s fastest growing packaging company. The manufacturer of predominantly food and pharmaceutical packaging (focused on rigid mono-material packaging formats) is headquartered in Bangkok, Thailand. December 14, 2023 Interview with Sun Packaging Systems FZC We met: Mr Nimit Bhatia, CEO UAE, CEO Malaysia, and India export business Today it boasts 16 world class production facilities, four of which are in Thailand, nine in India, one in Malaysia and two in the UAE. A 17th plant will soon be added, which is currently under construction in the Philippines. The Group uses technologies from Sidel, Netstal, ASB, Husky, Arburg and Sumitomo Demag, among others. Its customer base comprises over 1,500 companies, including almost all the well-known multinational brands. TPAC employs around 3,000 people and exports to ~ 50+ countries. Back in 2019, we visited the TPAC plant Sunrise Containers in Mumbai as part of the India Road Show (see PETplanet 10/2019, pages 30-31) and learned a lot of interesting facts about the company. Since then, the company has grown and evolved considerably. We spoke to the CEO responsible for the UAE and Malaysia business, Mr Nimit Bhatia, at the Sharjah site, about what this means in concrete terms for activities in the MENA region. Sun Packaging Systems (SPS) was founded in 2004 by three individuals and has plants located in Sharjah Airport International Free Zone. Nimit Bhatia, now CEO of SPS, has been with the company since inception i.e. 2004, when he joined as Business Development Manager. The passionate 40-yearold and father of two was born in Bahrain and grew up in Dubai after his family emigrated here from India. He attended Indian High School Dubai, later completed his bachelor’s degree at Indiana Bloomington University, USA, eventually returning to Dubai, starting his career where we visited him today, 19 years later. “Unlike probably most managers in this industry, I only learned the packaging business and all the technical details when I was on board at Sun Packaging, strongly believing that practical experience is the most effective way to learn. In addition to guidance from my father, I am fortunate to have a mentor (Mr K L Mundhra) who has played a significant role as a father figure, imparting valuable lessons in integrity and business complexities. These teachings have been instrumental in shaping my journey to where I stand today”, explained Nimit Bhatia. “Over time, we wanted to expand our fields of activity beyond food and also gain a foothold in other applications,” says Mr Bhatia. “Around 2009, we started single-stage production. Our sales target was the Gulf Cooperation Council states.” Additional storage space became necessary and so the company built a warehouse nearby in 2012. In 2019, SPS agreed a share sale with TPAC, which was aiming to expand its market presence in the Middle East. With this partnership, and now stronger backing and commitment behind Mr Nimit, a new bolder more aggressive vision was set out for the company. Today, Sun Packaging Systems employs 200+ people from six nationalities and uses state-of-theart technologies with a no compromise philosophy when choosing vendor partners. SPS provides various packaging solutions such as injection stretch blow moulding, extrusion blow moulding, PET preforms and injection moulding to cater for the needs of customers. SPS offers an extensive range of common mould portfolio (500+ products), keeping in mind market demands and serving global customer requirements. TPAC Group has a world class R&D team which co-create products with its customers (help with curating of packaging from birth to delivery of final product) for any of their specifications. Within the group, more than ten people are involved in R&D,” explained Mr Bhatia. These custom-made designs account for around 40% of the SPS local business. “Our mindset and our curiosity are also important for our success, we are a young, creative team and what that means is reflected in the figures: from 2019 to 2022, the company doubled its capacity thanks to customer loyalty and growth,” continued Mr Bhatia. EDITOUR CEO Nimit Bhatia shows the new jar series made of 100% rPET Pooja inauguration ceremony of a brand new Nissei ASB 12M machine with (f.r.t.l.) Nimit Bhatia, Kay Barton and employees"},{"@ID":62 "OUTER PLANET 62 PETplanet Insider Vol. 25 No. 04/24 www.petpla.net OUTER PLANET Putting an end to bio-based plastic anxiety Bio-based plastics such as polylactic acid (PLA) came from a great idea: they were invented to help solve the plastic waste crisis by being constructed so as to break down in the natural environment. Unfortunately, they can make waste management more challenging because they look and feel the same as conventional, petroleum-based plastics. As a result, many products are added to the recycling stream by well-intentioned consumers, get shredded and melted down with the recyclable plastics and bring down the quality of the mixture, making it harder to manufacture functional products out of recycled plastic resin. The only solution, currently, is to try to separate the different plastics at recycling facilities. Yet even with the most high-end, automated sorting tools, some biobased plastics end up contaminating the sorted streams. Scientists at Lawrence Berkeley National Laboratory (Berkeley Lab) and the Joint BioEnergy Institute (JBEI) are collaborating with X – the moonshot incubator led by Alphabet, Google’s parent company (not to be confused with Elon Musk’s company) – to skip the separation step and make a better product. The team has invented a process to break down mixtures of petroleum- and bio-based plastics, using naturally-derived salt solutions paired with specialised microbes, in a single vat. The salts act as a catalyst to break the materials down from polymers into individual molecules (monomers), which the microbes ferment into a biodegradable polymer that can be made into fresh commodity products. The process is described in a One Earth paper published last October. The paper describes a series of laboratory-scale experiments with mixtures of PET and PLA, the most common bio-based plastic, using an amino-acid-based salt catalyst and a strain of Pseudomonas putida, engineered by scientists at Oak Ridge National Laboratory. This combination successfully broke down 95% of the PET/PLA mixture and converted the molecules into a type of biodegradable polyhydroxyalkanoate (PHA) polymer. The team’s approach could enable bio-based manufacturing of other valuable products, with the same bacteria. Biofuels or even medicines could be made from plastic waste. “We foresee the potential to replace sugars, traditional carbon sources for microbes, with processed hard-to-recycle mixed plastics that can be converted to valuable products through fermentation,” said Zilong Wang, a UC Berkeley postdoctoral researcher working at JBEI. The team is searching for an organic salt catalyst that is both highly effective at breaking polymers down and can be reused in multiple batches, to lower costs, and is also modeling the process in large scale, real-world recycling facilities. This chemical recycling process is currently proven only for mixtures of PET and biodegradable PLA but it is claimed to be beneficial for diverse plastic streams typically encountered in real recycling facilities and can be completely integrated with them. This would be very helpful in dealing with commercial products such as fleece jackets, which comprise PET-based polyesters alongside polyolefins or polyamides. The one-pot process can separate the polyester component from that mixture and convert it into a bioplastic. The monomers are soluble in water but polyolefins or polyamides are not, which means that they can be easily removed by filtration and then sent off for a traditional mechanical recycling process. Chemical recycling has been difficult to achieve at commercial scale, because the separation steps are so expensive, according to Ning Sun, staff scientist at ABPDU, lead author and principal investigator of this project. “By using a biocompatible catalyst in water, the microbes can directly convert the depolymerised plastics without extra separation steps,” he said. Co-authors Nawa R. Baral and Corinne Scown, experts in technoeconomic analysis in JBEI and Berkeley Lab’s Biosciences Area, also demonstrated that, once optimised with a reusable salt solution, the process could reduce the cost and carbon footprint of PHAs by 62% and 29%, respectively, compared with today’s commercial PHA production. www.lbl.gov A graphic showcasing the scientists’ streamlined one-pot process. (Credit: Bianca Susara/Berkeley Lab)"},{"@ID":36 "34 EVENT PREVIEW PETplanet Insider Vol. 25 No. 04/24 www.petpla.net Injection moulds in action Z-Moulds will showcase two of their injection moulds in action, each paired with a partner’s injection moulding machine. Firstly, the 72-cavity mould designed for a lightweight 1.00g 26/22mm closure will be running on Sumitomo Demag’s newest electric Pac-E machine (booth W3343). Of particular note on this machine is the collaboration between Z-Moulds and their partner MHT, a member of the Krones Group, in developing a hot runner system - a successful collaboration the company is eager to highlight. The highlight, at least in terms of moulds, will be the latest innovation, a mould featuring 128 cavities, which will be demonstrated on Netstal’s Elios 4500 machine (booth W223). This system is claimed to offer unmatched capacity and boasts a cycle time of 1.85 seconds and to set a new standard for high performance. This combination of machine and mould is expected to yield an output of around 2 billion 26mm still water closures, each weighing just 0.74 g. www.z-moulds.com South Hall, Level 1 Booth S12107 Bottle Zone Z-Moulds West Building, Level 2 Booth W7443C Expo Hall Let’s meet at the Bottle Zone - Join us live on stage in Orlando for the special three-day PETinar edition! The NPE show is just around the corner! Without a doubt, the NPE is the most important event for the global plastics processing industry this spring. To enrich your visit to the fair, the PETplanet team has organised a three-day conference! As a special edition of the PETinars, PETplanet has put together the following programme for you on the event stage in the Bottle Zone from Tuesday to Thursday, May 7-9 from 11-12 pm: Opening the three-day PETinar conference series on May7, Icis will provide you with the latest updates in the US virgin and recycled PET market. This will be followed by Erema talking about its PET recycling technologies and observations on the US market. The day will be rounded off by the Italian machine manufacturer Sipa, who will be presenting its new high-end preform and bottle equipment. The second day of the conference, Wednesday, May 8 from 11-12 pm, is dedicated to the production, fi lling and capping of PET bottles. Mould manufacturer Röders Tec will be presenting its new bottom moulds for SBM. Industry heavyweight Krones will present its latest fi lling technologies, and Sacmi, a supplier of machines and complete lines for the ceramics, metal, packaging and plastic container industries, will discuss its new capping technology and explain its AI-based production processes. The last day of the conference, Thursday, May 9, 2024, will be dedicated to sustainable and high-performance packaging. Here, PTI will report on its latest PET bottle design projects. KHS, a provider of fi lling and packaging solutions for glass and PET bottles, cans, drums and pouches, will report on the diffi culties for PET bottlers and bottle manufacturers to maintain a sustainable and profi table business and present its solutions. Maguire will conclude with its technology for perfect material handling to meet the current challenges in the plastic processing industry. www.petpla.net PETINAR SPECIAL EDITION"}]}}
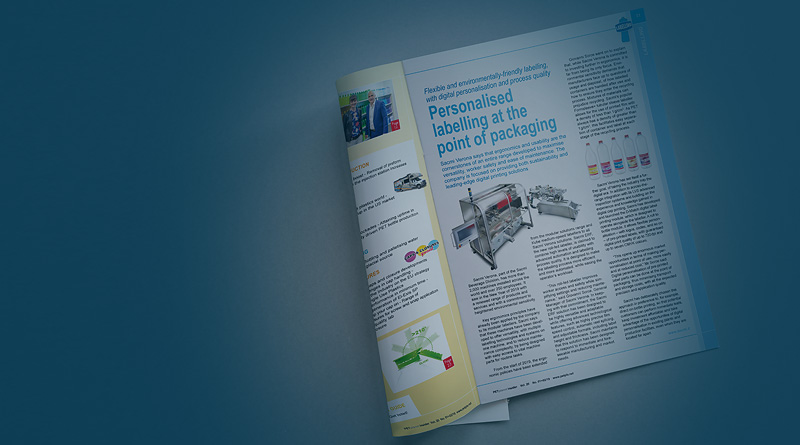