"TRADE SHOW REVIEW PETplanet Insider Vol. 18 No. 03/17 petpla.net 40 Bangalore conquers the north of the subcontinent - an interview with Manjushree Technopack The next Big Bang in India’s packaging industry by Kay Barton Manjushree catapulted its presence to a total of seven production sites for nearly the whole Indian market in a very short space of time. Its production level has risen to an annual output of 4 billion units, which corresponds to a share in the PET market of 15%. Its acquisition of Varahi has brought with it four new production sites, located in Baddi (Himachal Prades), Pant Nagar (Uttarakhand), Noida (Uttar Pradesh), and in the capital Delhi. The four plants contain more than 200 machines. With the takeover, Manjushree’s client base has grown by more than 100 companies; turnover for 2017 is forecast to be approaching USD120 million. PETplanet Insider: Rajat, we have known each other for a while now and I have witnessed quite a few developments in Manjushree Technopack. We met as recently as the spring of 2016 in Bangalore, with the intention of writing a story on your new preform facility in Bidadi. Now, just a few months later, you take over Varahi. How did this happen and what does it mean? Rajat Kedia: Yes, it’s a big deal! In our objectives for 2020 we had originally aimed for a turnover of USD180 million but it became clear to us that this target would not be reached with our existing locations in and around Bangalore. We have only supplied the south of India until now, so expanding and going to the north was the logical conclusion. Our old and new clients have, for some time, been longing for this in principle. PETplanet Insider: What do you mean longed for? Where did difficulties arise in the past? Rajat Kedia: Transport is the main problem. The distances and the related costs as well as the effort are naturally anything but trivial. Supplying the north from our headquarters in the south was not possible. We had already lost a few business opportunities because we were not a pan-India supplier with geographically strategic manufacturing locations. So it was a strategic decision; we now have a presence in both the north and south and, along with existing clients who want to process our products in their facilities in the north, we are confident of acquiring up to ten clients who will be entirely new to us. The first large client is already on board for the new facilities; this connection alone is expected to generate around USD7.3 million in the next half year. PETplanet Insider: This sounds positive on the one hand but, on the other hand, it also sounds like an insane amount of work for you and a huge change in a short space of time. How did the idea and implementation of a takeover come about? Why not just build from scratch? Rajat Kedia: We naturally discussed and deliberated for a very long time. Either way, we needed to open up to the north to grow. Building new facilities wasn’t an option – at least; not with our revenue target for 2020. When you build a new factory, you have to wait ten years before a plant can generate a turnover of USD10-12 million.The decision to go for the takeover developed from this situation. The idea incidentally came up one Sunday morning during a family discussion (laughs). We had the first meetings with the Varahi management team in October 2015. It took a year from then before we and they had finalised all the terms. PETplanet Insider: So now you have suddenly achieved an immense growth of directly applicable machines and can get started with production directly. Or will you simply carry on with your brands, almost without any great expenditure? For those who had not noticed or had not guessed, the news from Manjushree Technopack at the end of November 2016 caused quite a sensation. Manjushree, a PET processor from Bangalore, the capital of Karnataka in Southern India, announced that it had taken over its North Indian competitor Varahi Limited, a medium-sized company with 45 years of experience in the plastics processing sector. We met Director Rajat Kedia at drink technology India (dti) in December and took the opportunity to enquire further about the acquisition and to discuss the strategic background and objectives of this enormous step. Rajat Kedia, Director Manjushree Technopack","@ID":42}, "INSPECTION 19 PETplanet Insider Vol. 18 No. 03/17 petpla.net New bottle thickness measurement Torus always strives to improve rather than just match competitive inspection systems, one such casestudy is the development of the B300 bottle wall thickness gauge, (fig.1). The implementation of a new sensor technology with 4-axis motion control reduced R&R values by between 10-30%. Additionally, a solution to measure base thickness has solved a problem persistent in the industry for some time. New base designs and light-weighting techniques mean that measuring base thickness is more critical. The B300 gauge is a proven system operating in many plants worldwide. Speed versus information Plastic packaging production demands quick and reliable preform checks, whilst harmoniously working with the injection moulding process. All preform manufacturers face the following challenges; startup, tooling changeovers, small batches, trials and continuous production; thus requiring a comprehensive and flexible inspection system. Vision-based preform inspection gauges have been used within the industry for many years, typically inspecting each preform produced using online systems. Unfortunately with high frequency inspection, important and detailed information regarding the preform performance is compromised. Torus has developed the comprehensive and modular B305 preform inspection system (see fig. 2), comprising cavity ID recognition, neck, body and height measurement, body inspection, weight measurement, gate & seal inspection and polarised light. The advantages of the B305 preform inspection system include, but are not limited to, achieving true measurement through using patent-pending telecentric lenses and lights coupled with a traceable United Kingdom Accreditation Service (UKAS) master and verification artefacts; ‘start of thread’ is located to ensure measurements are taken at 0° and 90° for increased batch repeatability; and a variety of Cavity ID fonts can be reliably recognised using shape recognition, not limiting the customer to a single OCR font. (See fig. 3). Fig.2: Cavity ID station of the Torus B305 automatic preform inspection system IS STILL 50% TOO MUCH. ","@ID":21}, "INSPECTION 21 PETplanet Insider Vol. 18 No. 03/17 petpla.net SPCXplorer is suitable for single station application, through to full factory database-centric network installations. Designed with the needs of shopfloor data collection in mind, SPCXplorer can be interfaced to a large variety of manual instrumentation via RS232 connectivity, or for more complex gauging systems it can process bespoke ASCII data files via Ethernet. SPCXplorer offers a comprehensive array of data analysis tools, such as the example control charts in figure 7, which allows the end user to understand the measurement data and resultant effects on the production process. In addition, enabling data to be stored locally networked or exported to the customers preferred package. Flexibility and support The plastics packaging industry is continually evolving and has a vast array of differing processes, designs, technologies and requirements. To best answer the needs of the industry it is important to understand that each customer can have distinct and contrasting needs. To reflect this Torus not only works closely with customers but also offer a level of customisation and support. Customisation examples include; bespoke results screens, configurable network output, Shotscope integration and tailored batch set-up (see figure 8). Fig.8: Quick-start batch set-up Furthermore, the global service and support team of Torus offer a complete range of preventative maintenance contracts, on-site breakdown cover, recommended spares, verifications, re-calibration services and online remote support. The engineers travel around the world supporting over 400 systems and providing installation and training services. www.torus-group.com Fig.7: Torus SPCXplorer control chart","@ID":23}, "INSPECTION 22 PETplanet Insider Vol. 18 No. 03/17 petpla.net Unique sensor technology improves PET blow moulding processes News in online wall thickness measurement Wall thickness is one of the most important and frequently measured properties in PET bottles. This is easy to understand because material distribution, and how well it is monitored and controlled, is correlated with a wide variety of bottles’ critical performance characteristics. Vertical resistance, pressure resistance, creep, CO 2 retention, performance in filling, transportation and storage are all affected by a bottle’s wall thickness. Thickness measurement also plays an important role in bottle lightweighting. A new and unique thickness measurement technology solution that addresses these issues efficiently is now available. the process properly. Due to process drifts between sampling intervals, too many sub-quality bottles could be produced before the problem was detected. Hence, in the early 2000s, through-bottle IR absorption and camera based measurement systems began to appear on the market place. However, these methods have one important caveat; they combine thicknesses of a bottle’s two walls and cannot detect if one wall is too thin and the other is too thick. This means a through-bottle measurement system can report a bad bottle as a good one. Single-wall thickness measurement in real-time FocalSpec Ltd, headquartered in Oulu, Finland, is specialised in the development, manufacture and marketing of advanced optical sensors and systems for 3D and thickness measurement applications. FocalSpec’s management has a long history in the PET bottle testing field and was excited to re-enter the market with a completely new type of a product. The new Online Wall Thickness Measurement System was presented at the recent K 2016 in Düsseldorf, Germany. The FocalSpec system based on the company’s patented MCP 100 sensors, measures thickness of the nearest wall of passing bottles from one side of the flow. Having sensors on both sides of the conveyor enables the measurement of both walls individually. MCP 100 sensor The sensor that makes thickness measurement of individual bottle walls possible is based on safe IR light that was chosen because of its good penetration capabilities on pigmented materials. The sensor’s transmitter sends two IR beams into the bottle wall while the bottle is detected in the sensor’s capture area. A part of these beams is reflected from the bottles outside wall surface back to the sensor’s receiver. Some IR light penetrates the wall and reflects it to the sensor’s receiver from the inside wall surface. The sensor calculates the distance difference between these reflections which is adjusted for the material’s refractive index and is then sent out to a PC for processing and reporting. A little bit about history Since the invention of the PET bottle, manufacturers have been using various methods to measure wall thickness and applying the results in their processes. Micrometers were a logical first choice, and were soon followed by other manual methods such as section weighing, ultrasonic, capacitive and magnetic devices. The first semiautomatic laboratory instrument based on infrared absorption was introduced in the 1980s. As blow moulding machines became larger and faster, samplingbased off-line thickness measurement, combined with statistical process control methods, was often deemed inadequate for controlling FocalSpec wall thickness system INSPECTION S P E C I A L","@ID":24}, "INSPECTION 14 PETplanet Insider Vol. 18 No. 03/17 petpla.net Inspection systems at a glance Check first! As part of a holistic approach to quality control in preform production, PETplanet Insider showcases in its very first market survey this year (issue 1+2/2017) technical facts about preform inspection systems. On the following pages, our special on ‘inspection systems’ covers trends and practical methods of quality inspection systems relating to the PET bottle. The first article of Pressco Technologycovers new challenges in the all impacting PET bottle inspection; for the company these challenges include faster line speeds, light-weighting of bottles and closures, increased use of post-consumer regrind (PCR) material; and close-coupled blow-fill lines. At the K trade fair 2016, Dr Gerd Fuhrmann from Intravis told us about the LayerWatcher which is able to visualise the structure of layers in preforms, using measurements with infrared light. The non-destructive imaging device delivers an accurate picture of a virtual cut through the preform wall. Spencer Whale, Technical Sales Manager of Plastic PackagingTorus Measurement Systemssums up that the plastic packaging industry continues to push the boundaries of technology and innovation. The report focuses on the pressure on plastic converters to produce more environmentally friendly & low cost solutions resulting in advanced packaging designs. According to him this has increased the need for more stringent quality controls with a focus on traceability right the way through the process. Vertical resistance, pressure resistance, creep, CO 2 retention, performance in filling, transportation and storage are all affected by a bottle’s wall thickness: The companyFocalSpec introduces their unique sensor technology for wall thickness measurement. Sacmi shows their new and updated version of the high speed preform inspection system: PVS-3. The system uses polarised light for detecting any inclusions. The beauty & home, food & beverage and pharma packaging AptarGroup uses Sesotecmetal separators to protect its machines and avoid product contamination. Metal separators are used in the production of caps for beverages and other liquids. AGR inducts us in the core of its automated laboratory test cell which is a precision pick and place with an industrial robot that manages sample selection, placement of samples into the appropriate test station and the transfer of samples from one station to the next. The brand Rivella has been relying onTanner systems including the Ultra Clean Aseptic line containing the components for loading, conveying, sorting and inspection of the preforms. The line extends over two floors and feeds the aseptic blowing filling bloc with the checked preforms. IMDs team asks: how can a closure truly be 100% inspected without a conveying system hiding a part of it? Customers invest in a vision inspection system with five or even six cameras but they do not inspect the most visible aspects, namely the face of the closure. The solution: flying caps! INSPECTION S P E C I A L stf·sorting line stf·washing line professional plastic recycling solutions – made in germany The stf· group is the leading manufacturer of plastic sorting and washing machinery, especially for PET post-consumer bottles, with more than 60 turn-key plants and several single machines delivered worldwide. stf·group Industriestr. 1-3 94529 Aicha v. Wald – Germany fon +49 8544 960-110 mail contact@stf-group.de web www.stf-group.de scan for vCard stf ·group","@ID":16}, "BOTTLE MAKING 39 PETplanet Insider Vol. 18 Please order your copy at the PETplanet Insider book shop: petpla.net/book3 Stretch Blow Molding Second Edition by Ottmar Brandau € 130,00 320 pages © Copyright Elsevier 2012 2. Material Basics 2.1 Manufacture and states of PET Polyethylene terephthalate (PET) belongs to the group of materials known as thermoplastic polymers. The application of heat causes the softening and deformation of thermoplastics. In contrast, thermosets cure or solidify with the application of heat, and simply burn with continued heating. Like all polymers, PET is a large molecule consisting of chains of repeating units. The PET used for bottles typically has about 100–140 of the repeating units shown in fig. 2.1. Figure 2.1 The ring structure makes PET tough while the ethylene component gives it flexibility. A monomer is a single unit, which is repeated to form a polymer chain (Greek ‘mono’ one; ‘meros’ part). Polymerisation is the name given to the types of reactions where many monomer units are chemically linked to form polymers (‘polys’ many). A resin with only one type of monomer is called a homopolymer. Copolymer resins are the result of modifying the homopolymer chain with varying amounts of a second monomer (or comonomer) to change some of the performance properties of the resin. This can be represented by: homopolymer AAAAAAAAAAAAAAAAAAA co-polymer ABAAABAAAAABAAABBAA PET is manufactured as a homopolymer or co-polymer. Figure 2.2 An alcohol and an acid form the ester groups of PET that make it a polyester. IMAGINE USING ANY PREFORM MOLD IN ONE SYSTEM. AT THE FASTEST SPEED. XFORM 500 enters its third generation. The XFORM 500 GEN3 PET preform system gives you unprecedented flexibility combined with the fastest speed and the highest running efficiency: it accepts the widest range of legacy tooling present in the market. So you can feel free to innovate and grow without penalizing your existing assets. We made it happen. Designed to adapt. Built to last. SIPA S.p.A. - Via Caduti del Lavoro, 3 - 31029 Vittorio Veneto (TV) - Italy Tel. +39 0438 911511 - Fax +39 0438 912273 - email: sipa@zoppas.com www.sipa.it yesterday today","@ID":41}, "PETplanet Insider Vol. 18 No. 03/17 petpla.net 41 TRADE SHOW REVIEW This should go into production at the end of January. Since we are operating in this corner of India for the very first time, we expect that we will need half a year to win over the customer clientele there. PETplanet Insider: I wish you the best of success and thank you very much for the interview, Rajat! www.manjushreeindia.com Rajat Kedia: Yes, in theory. We need to gradually bring the newlyacquired plant, machinery and the factory overall to Manjushree’s standard, along with our people and the former Varahi employees. We will make some changes to the existing equipment and centralise the systems in order to increase output and input over the next several months. A few people from our management are already on site there, for this purpose. PETplanet Insider: Does this mean that you will continue to employ the Varahi staff under Manjushree? Rajat Kedia: Absolutely. Manjushree has not planned any changes in local management or site staff so far. On the contrary, we want their expertise to flow into the production in a targeted manner. PETplanet Insider: Will all processes be channelled through Bangalore? Rajat Kedia: All non-operative matters will remain centralised at our head office in Bangalore. We have established our Northern marketing office in the former Varahi office in Delhi. PETplanet Insider: Let’s talk briefly about the forecast outputs. What growth rates are expected with the acquisition? Rajat Kedia: We expect an approximate growth of 12,000 metric tons per annum of material in the blow moulding area. As Varahi only had a very small preform business, we will see material change of around 5,000 metric tons per annum. But this is not the only forecast increase in our output and capacities. It is worth mentioning that we are currently erecting a completely new factory in the northeast of India, in Guwahati in Assam. This is independent of the Varahi project and involves around seven or eight machines. W W W . I N T R A V I S . C O M Sample-PreWatcher® Comprehensive sampling analysis inline and offline High speed 100 % inline and offline inspection Color inspection right above the tooling plate Non-destructive layer inspection PreWatcher® III ColorWatcher® Integrated LayerWatcher® Preform Inspection Today.","@ID":43}, "INSPECTION 31 PETplanet Insider Vol. 18 No. 03/17 petpla.net loading, tracking and data reporting. Specialised bottle and preform trays that represent a complete mould round make it easy for operators to prepare sets of samples in advance and then load them into the system for hands-free processing. To enhance throughput, a pipeline approach is used for sample handling and testing, making it possible for concurrent operation of all testing devices. The robotic handling system ensures that samples are moved with efficiency and precision from one test station to another. Testing and throughput efficiency The Automated Laboratory test cell is designed to provide maximum testing throughput. It offers a solution to the challenges of an ever-increasing demand for sampling and testing to support ongoing production and manage quality. In addition to organising and consolidating critical testing operation in one compact area, the system offers a number of benefits including hands-free, walk-away operation, efficient management of samples and testing operations, documentation of results, and most significantly, an improvement in testing throughput of as much as 300%. Taking into account that each plant operation is unique, Agr engineers will work with companies to configure the Automated Laboratory test cell to meet the specific testing needs of that operation. www.agrintl.com Increased testing throughput in one compact area The automated laboratory The Agr Laboratory test cell provides an automated solution that tightly integrates multiple Agr testing devices. These include the Gawis, for thickness and dimensional measurements, the Combi Tester or TL2000 Topload Tester, for fill height and top load, and the PPT3000, for pressure and volume expansion. In addition to increased throughput, the automated cell approach also offers “cost-tooperate” savings. The Automated Laboratory test cell incorporates a heavy duty platform that can support up to three independent test stations. At the core of the cell is a precision pick and place industrial robot that manages sample selection, placement of samples into the appropriate test station and the transfer of samples from one station to the next. When tests on the individual sample are complete, the robot can either discard samples or return them to the sample tray for further analysis. Test results from each testing station are compiled with data correlated by sample and consolidated in a single test report. The rugged, compact design of this system makes it possible to locate it on the plant floor, near critical production operations, or in the traditional laboratory setting. Cell operations, including overall job setup, robot, sample coordination and tracking, as well as activation and control of individual test stations, are managed by a central computer housed within the test platform. A web-based user interface allows for maximum flexibility for job setup, job At the core of Agr’s Automated Laboratory test cell is a precision pick and place industrial robot that manages sample selection, placement of samples into the appropriate test station and the transfer of samples from one station to the next. INSPECTION S P E C I A L Today’s world of high-speed, light-weight PET bottle production has brought increased burdens on the QA team and the testing laboratory. As speeds increase and weights go down, laboratory testing throughput must also increase to provide comprehensive testing management and document quality. With limited personnel and equipment, laboratory throughput can be a challenge for many production facilities. Agr International’s Automated Laboratory test cell provides a solution for meeting the demands for increased throughput.","@ID":33}, "INSPECTION 15 PETplanet Insider Vol. 18 No. 03/17 petpla.net All around inspection for PET bottle production Rising to new challenges The combination of faster line speeds and lighter weight bottles and closures presents challenges for converters as well as bottlers. There is also an increased focus on seal integrity, particularly in the context of the trend to one-piece, plug-style closures. Inspection systems are, increasingly, being deployed at every step in the filling process. The closure is inspected on both the external side and the product side; the preform and empty bottle are inspected in the blowmoulder to examine the seal surface and inner bore for critical defects that may affect seal performance; and the filled/capped bottle is inspected for closure application defects, such as a rolled plug seal. Many of these individual defects become more difficult to detect at today’s higher line speeds. This has inspired Pressco to further develop and refine its software algorithms, which has helped to minimise false rejects and acceptances, alike. Its system now provides correlation of defects at the blowmoulder for mould, spindle, and transfer arm; and at the filler for filling valve and capping head. This speeds troubleshooting by clearly identifying which machine components are producing defective products. Bottles made using rPET/PCR have a much higher risk of foreign matter contamination, which can result in critical blowforming defects. Detecting these is very difficult once a bottle is blown; geometric features in some bottle designs can hide the contaminants from inspection systems. The key, then, is to inspect for these inclusions before blowing the bottle. In order to do so, Pressco has developed a solution for preform inspection inside the blowmoulder – an industry-first. The PW360 is a customdesigned module that provides full 360-degree inspection of the preform sidewall. This enables easier detection of foreign materials that may have become embedded in the plastic; a faulty preform can thus be detected and removed from the process before further value is added. As brand owners move toward selfmanufacture, a single production line can be blow-fill-label or blow-label-fill. This requires distributed inspections at the blowmoulder, cap feeder, filler, labeller and even case packer. It is the “preventable rejects” – filled bottles deemed defective due to a faulty component such as a bad bottle or closure – that often make up the greatest amount of scrap on a blow-fill line. A close-coupled line operating at a nominal 48,000bph will see a significant reduction of total cost by inspecting empty bottles in the blowmoulder and closures at the cap feeder. An ongoing initiative at a number of converters, as well as bottlers who self-manufacture, is to standardise and consolidate technology so that quality objectives can be achieved efficiently, without the challenge of mixed platforms, software, training, and so on. Pressco’s scalable, modular Intellispec platform allows each customer to deploy an integrated solution that facilitates inspection in multiple line locations, from a single control point. www.pressco.com Pressco Technology, which has recently celebrated its 50th anniversary, has been focused on addressing a range of trends that are impacting PET bottle inspection. These include faster line speeds, lightweighting of bottles and closures, increased use of post-consumer regrind (PCR) material; and close-coupled blow-fill lines. Any one of these is significant; having two or more in the same production environment can put severe demands on any inspection system. Pressco’s latest Intellispec platform has been designed to deliver high performance in defect detection, in the most advanced lines, including any or all of these conditions. Empty bottle inspection Full bottle inspection Preform inspection PW 360 INSPECTION S P E C I A L","@ID":17}, "CONVEYING PETplanet Insider Vol. 18 No. 03/17 petpla.net 34 Energy-efficient technology improves productivity Variable conveyor speed for optimal material handling Bergmann Spritzguss und Formenbau GmbH & Co. KG, which is headquartered in Telgte-Westbevern in Germany, was founded in 1989. It is an injection moulding company and system supplier that supplies a large number of customers from a wide range of industries. Bergmann offers a comprehensive range of services, ranging from the initial conception to the development and construction of plastic parts and relevant tools, as well as prototype construction, right up to the production process. The company’s portfolio also includes two areas of specialisation – Laser Radiation Welding and Direct Metal Laser Sintering – that are increasingly gaining in significance. Bergmann has two production sites. One in Telgte and, since 2000, one in Czaplinek, Poland. It currently owns 75 injection moulding machines with clamping forces of between 250 to 10,000kN, which include two 2-component machines, all equipped with parts removal devices. The company currently employs around 290 people. Each of the company’s production sites has a production area of around 10,000m² and is predominantly used to produce technical parts as well as assembled components over three shifts a day. The parts it produces range from extremely small precision parts with a part weight of 0.5g to large products weighing 5.8kg. The company processes around 4,000t of plastic annually, all of which are thermoplastics (with the exception of PVC). This means that Bergmann processes a wide range of different materials, which include 50 different types of material alone that require drying. On average, tools have to be changed five times a day. The company has 20 tool room staff who design and manufacture between 80 and 100 injection moulding tools with dead weights of up to eight tons for the company’s own production every year. Production expansion with central material supply system As the production facility in Telgte reached a stage where it could no longer cope with the increase in demand, Herbert Bergmann, founder and managing director of the company, decided to invest and extensively expand the facility. The comAs part of expanding its production facilities, Bergmann Spritzguss und Formenbau GmbH & Co. KG, which is based in Telgte-Westbevern, Germany, decided on a radical approach and equipped its entire production facility with a brand new material supply system comprising a central drying system, dosing systems and conveyors as well as a frequency-controlled conveyor control unit. Herbert Bergmann (left) and Frank Wortmann in front of the central drying system","@ID":36}, "imprint EDITORIAL PUBLISHER Alexander Büchler, Managing Director HEAD OFFICE heidelberg business media GmbH Bunsenstr. 14 69115 Heidelberg, Germany phone: +49 6221-65108-0 fax: +49 6221-65108-28 info@hbmedia.net EDITORIAL Kay Barton Heike Fischer Gabriele Kosmehl Michael Maruschke Ruari McCallion Waldemar Schmitke Anthony Withers WikiPETia.info petplanet@hbmedia.net MEDIA CONSULTANTS Martina Hirschmann hirschmann@hbmedia.net Johann Lange-Brock lange-brock@hbmedia.net phone: +49 6221-65108-0 fax: +49 6221-65108-28 LAYOUT AND PREPRESS EXPRIM Werbeagentur Matthias Gaumann | www.exprim.de READER SERVICES Till Kretner reader@hbmedia.net PRINT Chroma Druck & Verlag GmbH Werkstr. 25 67354 Römerberg Germany WWW www.hbmedia.net | petpla.net PETplanet Insider ISSN 1438-9459 is published 10 times a year. This publication is sent to qualified subscribers (1-year subscription 149 EUR, 2-year subscription 289 EUR, Young professionals’ subscription 99 EUR. Magazines will be dispatched to you by airmail). Not to be reproduced in any form without permission from the publisher. Note: The fact that product names may not be identified as trademarks is not an indication that such names are not registered trademarks. 3 PETplanet Insider Vol. 18 No. 03/17 petpla.net Dear readers, Editour across Southeast Asia Edi-on-tour is off again, this year in South East Asia. First stop: Indonesia. Or to be more precise, we’re only visiting the greater Jakarta area in three stops, Bogor, Bandung and Jakarta. Just one sixth of the entire Indonesian population lives here, but it’s where a whopping 40% of packaged drinks are consumed. The per capita consumption amounts to under 70 litres per year within this region, meaning the fourth most populated country in the world has an enormous market potential, both in central zones, as well as increasing potential in more rural areas, as the population’s wealth also increases. However, sales remained stagnant last year and increases in electricity and fuel prices meant consumers were cautious. There were some sources indicating signs of growth, yet these were probably referring to turnover, rather than actual sales volumes. All market players have either increased their prices or reduced what they’re offering for the same price. The country is very price-sensitive: drinks on supermarket shelves priced at under 3,000 Indonesian rupees (IDR), equal to around EUR 0.20, are seen as reasonably priced. Those priced up to IDR 6,000 are seen as acceptable, whilst anything above is a pure luxury. I’m intrigued to find out how it’s possible to keep selling PET packaging, with a cap, label and contents, for 20 cents in the long-term. I was amazed to learn that manufacturers rely on high-tech, automated equipment to achieve prices within this range, in a country where manpower is available at such a low cost. And so, in somewhat disorganised country, I’ve seen some of the most modern factories in the world. I hope you’re looking forward to my reports from the tour in the forthcoming issues.* Yours, Alexander Büchler *Find the tour blog at petpla.net/drinktectour.php","@ID":5}, "Sponsors asia.petpla.net 2017 is Drinktec year! All over the world, the beverage and liquid food industry is preparing for the next edition of the great event, held once again in Germany. A new year also means a new road show - and a very special one. PETplanet is again partnering with Drinktec and we will be bringing our crew to South East Asia, under our new slogan: Go with the flow – South East Asia Road Show. From the end of January our editors Kay Barton and Alexander Büchler, along with “Flowy“, the Drinktec mascot, will be investigating the latest market-specific characteristics of distant countries as well as following welltrodden oaths, as always. With various “Editourmobil” vans we will travel to Thailand, Vietnam, Cambodia, Malaysia, Singapore and Indonesia. As our valued reader, you will once again get insider information and insights from the PET beverage and supplier industries, published regularly in PETplanet Insider. You can get even closer to the Tour experience by following us live on our travel blog at asia.petpla.net. Drinktec awaits us at journey‘s end. When we get there we will be presenting factsheets and product samples of all the companies we visited. We hope you enjoy “keeping up with the PETplanetarians“. We look forward to welcoming you on board once again! January – July 2017 Cambodia Laos Thailand Indonesia Vietnam Malaysia Singapore The worldwide round trip with Go with the flow. South East Asia Road Show powered by","@ID":32}, "BOTTLING / FILLING PETplanet Insider Vol. 18 No. 03/17 petpla.net 11 Nescafé, the instant coffee brand of nutrition company Nestlé. He went on to create the Tenwow brand in 1996. In 20 years, sales have grown to over 700 million Euros. Five beverage plants Tenwow initially produced several RTD tea beverages in PET hot fill containers using its first hot filling line at the main plant in Shanghai. Tenwow subsequently expanded the assortment to include an entire range of new products along with innovative taste variants. The company also developed new container designs. To this end, it expanded its filling capacities and installed a second and third PET hot fill line in Wuhan and in the newly constructed operation in Putian. These were joined by two beverage carton filling lines at the Shanghai site. At the same time, widely spread production locations helped facilitate the company’s distribution in this vast country. A further hot fill line was added in Chengdu in 2015. Subsequently, Tenwow began filling its natural mineral water Tribute Spring Water at the Changxing location. Tenwow now operates five beverage plants dispersed throughout China, and a sixth is planned for the north of the country near Beijing. Tea in summer, coffee in winter The year 2015 marked a turning point in the Tenwow filling philosophy and saw the company introduce aseptic filling of tea and coffee for the first time. Tenwow had produced RTD coffee for the first time just three years previously. At that time, consumption of this unfamiliar beverage variant was still marginal Filling philosophy has changed: Aseptic instead of hot fill Tea or coffee? Both! Following the growth recorded over the past few years, Euromonitor International predicts further growth of around 1.5 billion litres in the market for RTD tea beverages in China between 2015 and 2019. The popularity of coffee among Chinese consumers is also set to increase. Although sales of RTD coffee beverages are still at a low level, growth rates are significantly higher: Euromonitor expects sales to double within five years. These figures are likely to have struck a chord with Tenwow as well. After all, the company has a good instinct for the market. Founder and Chairman Lin Jianhua established the food trading company Nanpu in 1991 in Shanghai. Lin Jianhua was also one of the first Chinese importers of While ready-to-drink (RTD) tea beverages are already firmly established on the Chinese beverage market, RTD coffee beverages are only beginning to take hold. Tenwow International Holding distributes both products on the market. The company now wants to expand this segment further – while remaining true to a philosophy best conveyed by its slogan “from nature to love”. For this reason, Tenwow switched for the first time from the hot fill system to aseptic filling – with a high-performance PET Asept L2 line from Krones. Total consumption of ready-to-drink coffee and tea beverages (in million litres) Source: Euromonitor For Lu Ying, Vice President Tenwow International Holding, the benefits of aseptic filling compared with the hotfill process are obvious.","@ID":13}, "PETproducts 42 PETplanet Insider Vol. 18 No. 03/17 petpla.net Camera system for fill level and cap inspection The growing market for PET applications motivated Filtec to develop an inspection system for fill level and filler management systems. Currently many customers are using X-ray, gamma rays or HF high frequency (also called radio frequency) technology for the inspection of the correct fill level. All technologies have their pros and cons. While X-ray and gamma system have a very accurate measurement, these systems require a licence to operate the machines. HF systems are less accurate but do not require a licence. All of these systems are limited regarding cap inspections. The trend for lighter caps in order to save material costs increases the risk of high or tilted caps, causing a loss of pressure in the bottle. Using a standard sensor to detect a high or tilted cap is said to be not very reliable even if the smallest cap defects or broken tamper bands are detected. Thus Filtec developed the VISIONtec, a camera system for fill level and cap inspection. Using high-resolution cameras enables the system to detect – without any radiation or need of licences – the smallest variation of high fill and low fill as well as high/tilted caps and broken tamper bands. The optional filler valve monitor software informs the operator which filler valve caused a low fill and which capper head created a high or missing cap. This reduces the maintenance time of the filler significantly. Wizards for the changeover process, onscreen manuals and change parts lists are intended to facilitate work processes for operator and maintenance staff. The height adjustment for different bottle types is fully automatic, driven by servo motors at the touch of a button. The same modular machine can also be used for label inspection and sorting applications. This way the plant can standardise on one technology saving costs on operator training and spare parts. The simple tunnel design can easily be installed on existing filling lines. www.filtec.com Maximising packaging versatility For the brewing and beverage industries, flexibility in end-of-the-line packaging is an increasingly important consideration. Often individual containers have to be first placed in multipacks, and these then packed in an appropriate sales or outer package. Since both the multipacks and the endof-the-line packages are subject to changing consumption trends and will vary for different target groups, consumption occasions or export nations, maximised flexibility is imperative. The basic idea involved is that a single machine replaces up to six conventional individual machines linked by conveyors. With the Varioline of Krones, a combination conjuror, packaging processes involving up to three stages can be handled by a single machine. The consequence is space savings, reduced maintenance work and fewer operators. The modularised Varioline kit consists of three modules, which can be combined to form a customised packaging system. These three units, the cartoning, feed and basic modules, feature an identical basic construction, to create a modularised design concept that ensures flexibility for the future. The machine can handle up to 52,000cph. The Varioline packaging systems can also be block-synchronised with other machines, such as a Variopac Pro shrink-wrapper, so that besides carton packaging pure and simple the packs can also be wrapped in film. This option is already up and running at three clients, who have thus created maximised flexibility within a machinery block. www.krones.com The leakage check Greater precision when identifying minute leaks: the detection accuracy of the Heuft squeezer QL is claimed to be considerably higher compared with other Heuft systems for checking the tightness of plastic containers. The system is of particular interest to fillers of dairy products as the quality inspection focus is on sensitive products such as fresh milk, whey and yoghurt drinks or probiotic beverages. The Heuft squeezer QL even detects microscopically small leaks reliably, says the company. The detection accuracy is four times as high with regard to the size of the hole. This is achieved with a special belt drive which applies a precisely controlled amount of pressure to the containers. These pass through freely with belts which are three times as long as those of the other two versions of the device. This is in order to identify leaks by examining the internal pressure of the container using a comparative fill level measurement in a non-compressed and compressed condition. The longer inspection period provides more detection reliability. A servo control system adjusts the height and the passage width of the belt which is only on one level and the position of the measuring bridges for the fill level detection completely automatically. This makes it possible to inspect larger plastic containers and eliminates maladjustments during a brand change due to operator errors. The belt adapts itself independently to the changed container shape at the push of a button. All the brands which have been read in can be reproduced completely automatically. The Heuft squeezer QL also offers proven functions for a closure inspection. www.heuft.com","@ID":44}, "INSPECTION 17 PETplanet Insider Vol. 18 No. 03/17 petpla.net INSPECTION 17 Terahertz systems measure thicknesses at individual points at the preform; our technology, on the other hand, scans the whole preform. Thus, with a LayerWatcher system, a user can see the flow of the barrier material from the flow front to the trailing edge everywhere in the preform. Even the smallest irregularities are visible in the images. This is an invaluable advantage when setting up the process or ensuring the flawless all-over-quality of a preform with barrier layer. Gabriele Kosmehl: How does the assessment work? And what happens to the defective products? Gerd Fuhrmann: Sorting out defective products was yesterday. Today the aim is to produce 100% good quality right away. According to our slogan “We solve problems before they occur” the LayerWatcher will constantly monitor the quality of the barrier layer, taking into account a whole bunch of quality parameters. Feeding back this information into the injection moulding machine, an intelligent control will help to ensure a stable production process even in the presence of external perturbations. Gabriele Kosmehl: We saw the LayerWatcher at the Husky booth at the K. How does the collaboration with Husky work and at what stage is the development phase currently? Gerd Fuhrmann: We are linked to Husky through a long-term partnership. What we saw at the Husky booth is just the first step. Converters urge us to fully integrate the LayerWatcher into the production line ensuring the most efficient production of quality barrier preforms. We are working on that. Gabriele Kosmehl: Dr Fuhrmann, thank you very much for talking to us. www.intravis.de At K 2016 Husky was showcasing the Layer Watcher vision inspection system from Intravis in the context of a complete Multi-Layer Barrier experience centre. Husky’s latest PET release from the company is the new MultiLayer Barrier Technology, which offers the opportunity to explore PET as a packaging material for products requiring enhanced barrier properties that are traditionally packaged in materials such as glass, carton and aluminium. The technology is built on the company’s HyPET HPP5 platform. www.husky.co The LayerWatcher gives a clear image of a virtual cut of the preform wall. This enables the operator to discover all types of irregularities like a split of barrier layers as in this case. Full inspected! SAVE THE DATE PROPAK EAST AFRICA, 7/9.03.2017 #14H | Nairobi KENYA PROPAK VIETNAM, 21/23.03.2017 - K7 | Ho Chi Minh VIETNAM CRAFT & BREW, 10/13.04.2017 - #2155 | Washington USA ENOLITECH, 9/12.04.2017 | Verona ITALY DJAZAGRO, 10/13.04.2017 - #1K028 | Alger ALGERI","@ID":19}, "INSPECTION 18 PETplanet Insider Vol. 18 No. 03/17 petpla.net Inspection for advanced packaging designs No replication - no limitation by Spencer Whale, Technical Sales Manager – Plastic Packaging Torus Measurement Systems, Telford, UK The plastic packaging industry continues to push the boundaries of technology and innovation. Pressure on plastic converters to produce more environmentally friendly & low cost solutions has resulted in advanced packaging designs. This in turn has increased the need for more stringent quality controls with a focus on traceability right the way through the process. Leaders in the industry are realising the value of data recording to identify and resolve the source of quality issues. The industry is demanding a flexible and collaborative approach to meet their inspection requirements. It is imperative that the solutions are bolstered with reliable and efficient after sales support. Adopting this mind-set is imperative to meeting customers’ demands in an ever-changing industry. Two approaches to product development By researching the plastics market and listening to customers, it was evident to Torus certain areas of bottle and preform inspection had become stagnated. With the need for a fresh approach being apparent, Torus adopted a customer-centric philosophy, endeavouring to introduce new inspection systems and technologies to solve specific customer problems. Focusing on customer relationships, Torus aim to become a trusted partner rather than simply offering transactional exchange of equipment, creating a collaborative environment benefiting both Torus and their customer partners. Traceable and discernible metrology The importance of true metrology to the plastics industry is a growing trend. Existing controls have relied on process monitoring which is not an absolute procedure with traceable measurement. Process monitoring evaluates part to part variation, focusing only on the difference between one result and the next as opposed to determining the true value. Due to stable production requirements, the PET packaging industry originally implemented inspection systems based on process monitoring rather than metrology. With a strong emphasis now for true metrology, many plastic bottle manufacturers and fillers have commissioned Torus to help solve their inspection problems. Stringent testing and validation procedures are put in place to ensure that the stated repeatability, accuracy and R&R values are met with a technical specification which is shared with every customer. Torus’ experience of integrating various sensing technologies, contact and non-contact enables them to offer a complete quality control solution. Fig.1: Torus B300 bottle wall thickness INSPECTION S P E C I A L","@ID":20}, "MATERIALS / RECYCLING PETplanet Insider Vol. 18 No. 03/17 petpla.net 8 Bottle-to-bottle flakes with FDA approval The recycling company Invema commissioned a plant for the recycling of PET bottles in Honduras at the end of 2016 in order to produce bottle-to-bottle quality with Food and Drugs Administration (FDA) approval. In the first expansion stage the plant is processing 2,000t bottles per month. bold Meckesheim produced, installed and commissioned the plant. After regranulation the end product is sold to the local Coca Cola bottle producer. A second expansion step is in preparation. Its aim is to produce thermoforming PET film suitable for use in foodstuffs. Honduras already has a recycling rate of 84%, nevertheless, bottles have to be imported in order to use the plant to full capacity. The owner of Invema, George Gatlin, states in an interview: “Coca Cola is enthusiastic about the quality of the regranulate that we produce.” www.invemagroup.com www.herbold.com In Honduras the collection rate of PET bottles amounts to 84%. 2,000t PET bottles per month are treated with the plant technology from Herbold Meckesheim. After sorting, the PET bottles are size reduced in two Herbold granulators with a capacity of 1,800kg/h. Secondary cleaning of the PO fraction during the hydrocyclone separation step from Herbold Meckesheim. Invema Group was founded 1994 with the idea of buying densifying aluminium beverage cans for recycling. Today Invema has 370 employees in Honduras and further 100 in El Salvador. They see to the collection, reception, sorting and treatment of plastic bottles. In a second step a plant was installed for treating the polyolefine fraction from the recycling process, i.e. the caps and labels of the bottles. Part of the energy needed for the recycling plants is produced on site: with 3,640 solar panels on the roofs of the plant location they are generating 1MW electrical power. In a multi-stage process, the bottles are pre-sorted, size-reduced, washed cold and hot and after drying forwarded to a flake sorting step. The German machine manufacturer Her-","@ID":10}, "INSPECTION 32 PETplanet Insider Vol. 18 No. 03/17 petpla.net Preform handling at Rivella Best selection Since 2015 all the PET brands of Rivella, a company based in Rothrist, Switzerland, are produced with a new Ultra Clean filling line. The products whose sizes vary between 0.33l to 1.5l are bottled at a maximum speed of 24,000 bottles per hour. With this investment, Rivella intends to send a strong signal highlighting process optimisation and quality improvement. From storage to preform inspection The Rivella production facility in Rothrist receives the preforms on the ground floor and loads them into interim storage. Depending on the production planning, the Tanner tipper will be loaded with the appropriate preform box. In the next stage, the preforms will be sorted and lined up to feed the inspection system. In this section, Tanner has integrated a preform inspection system from the Swiss based company IMD AG, one of the leading companies in inspection systems for preforms and closures. A full body inspection, a separate camera for the neck finish and a very precise support ring inspection guarantees a good quality. Defective preforms are separated out by the automatic blow-out without the need for any interruption to the preform feeding process. The system has a standard quantity of cameras. Out of a number of options, the camera inspection can be customised. Aseptic filling In the following stage, a 12m long elevator conveys the tested preforms up to the upper floor. A special design, conceived with experts from the local authority, has resulted in an especially constructed fire protection wall. Once on the upper floor, the preforms will be transported over the aseptic blowingfilling bloc to the roller sorter. Feeding the blowing machine In front of the aseptic blowingfilling bloc the preforms are again in The inspection system detects errors on the preform and incorrect ones will be ejected without halting production. For several years, the Swiss soft drink brand Rivella has been relying on Tanner systems including the Ultra Clean Aseptic line. The components for loading, conveying, sorting and inspection of the preforms are provided by Tanner. The line extends over two floors and feeds the aseptic blowing filling bloc with the checked preforms. Rivella’s company headquarters in Rothrist, Switzerland Preform feed Preform tipper the roller sorter and this will be sorted in line. Due to limited space, the roller sorter has been placed directly before the AseptBloc of Krones AG. The preforms reach the entrance of the blowing machine with a discharge rail including a 135 degree curve. www.mtannerag.ch INSPECTION S P E C I A L","@ID":34}, "BOTTLE MAKING 38 PETplanet Insider Vol. 18 No. 03/17 petpla.net In a wheel machine, each individual mould cavity opens and closes in sequence and machines of this type are called rotary machines. In the late 1970s, Sidel started experimenting by using this concept in the PET stretch blow moulding process. By 1980, Sidel had built the first prototype that would initiate unparalleled success in the blow moulding industry, propelling Sidel from a mid-size machine manufacturer to a billion dollar company. Today, companies such as Krones, Smiform, and Sipa have all developed rotary machines of their own and his competitive pressure has driven prices down, opening new applications for bottle blowing. Blow moulding speeds have also driven costs down: While 1,000 bottles/cavity/hour (b/c/h) was the benchmark for many years, today’s machines feature outputs of up to 2,200 b/c/h. The first ‘killer application’ for PET was the 2l bottle for carbonated soft drinks (CSD), introduced in 1978. The first bottles featured a domeshaped bottom ideally suited to sustain internal pressures that routinely reach 5bar (70 PSI). This required an additional plastic component, called a base cup, to be glued to the bottom in a secondary operation in order for the bottle to stand up. However, cost and recycling considerations (glue residue) encouraged the development of a one-piece bottle. The breakthrough came with the design of the so-called Petaloid base: a thick, mostly amorphous centre disk surrounded by five blown feet. Granted as patent to the Continental Can Company in 1971, it caused controversy with three other patents and litigation ensued for several years. It took until the early 1990s before one-piece bottles came off the conveyors of reheat stretchblow moulding machines and were completely replaced two-piece bottles within a few short years. By the mid-1990s, soft drink companies agreed to lower shelf-life requirements and so opened the way for the extremely successful launch of 20oz and 500ml containers. At the time of writing, water and a whole new line of beverages that did not even exist a few years ago, are the key drivers for PET growth. Hot-fill juices and the so-called Neutraceuticals have raised the demands imposed on today’s PET bottles and the industry has responded with a wealth of new technologies. Recent developments aim to eliminate the unsightly vacuum panels needed for controlled shrinkage of the PET bottle during cooling of a hot-filled product. Multilayer preforms and coating technologies increase shelf life and, therefore, open the way for even smaller CSD packages and the replacement of glass in a new set of applications. At this time, it is unclear whether coatings or multilayer technologies will prevail as the preferred choice of packaging, but it is this author’s opinion that a variety of methods will be required to meet an ever-increasing variety of packaging demands. On the horizon we can see PET entering the retort arena, used for packages that typically need exposure to 125°C (257°F) for a number of minutes and are currently all filled in cans and glass. The PET bottle’s crystallinity levels will have to be substantially increased to allow the use of PET here. At this time, the highest temperature PET is being exposed commercially is 95°C (203°F). Barrier enhancements will allow extended shelf life milk and other goods that require a long shelf life to be packaged in PET. Improved ways of injecting preforms and blowing bottles will extend the industry’s ability to deliver a safe, environmentally sound, and economical package to consumers. Figure 1.2 Rotary high-speed machines such as this blow moulder produce the bulk of PET bottles. Photo courtesy of KHS Corpoplast. .com 100815dmyL","@ID":40}, "INSPECTION 20 PETplanet Insider Vol. 18 No. 03/17 petpla.net Fig.3: Cavity ID recognition of different fonts Collaborations Having built up and continuing to build relationships and partnerships with leading plastic bottle and preform manufacturers, Torus have created a rewarding collaborative environment. Two examples of such collaborations are the advanced burst testing (see fig. 4) developed in collaboration with ColorMatrix and the single operation top load & volume gauge. Fig.4: Torus B303 bottle burst tester Advanced bottle burst results ColorMatrix required detailed information regarding material performance; specifically volume expansion & material yield data. Working with ColorMatrix, the research and development team understood the importance of why these features would be beneficial and created a specialised solution. The collaboration resulted in new features such as the stress strain curve shown in figure 5. Integrated top load & volume gauge With guidance from the team at Logoplaste, Torus developed a single operation top load & volume gauge, see figure 6. The system works by the user loading a bottle just once and performing both tests automatically. Torus researched the market and found that current systems were slow, with insufficient support. In many cases manual volume measurements were still being performed, draining manpower and often inducing measurement errors. The B304 top load & volume gauge combines both tests into one robust system, reducing operator intervention and increasing part traceability, saving testing time and improving accuracy. The complete solution It is important to understand the inspection process from start to finish. Beginning with the requirement and working with the customer to develop a reliable gauge, but also assisting with results analysis. To facilitate this, Torus offer statistical process control software, known as SPCXplorer. SPCXplorer can be configured for new Torus gauges and/or existing third party laboratory equipment. Using industry standard database platforms, INSPECTION S P E C I A L Fig.5: Stress strain curve Fig.6: Torus B304 top load & volume gauge","@ID":22}, "BOTTLE MAKING 37 PETplanet Insider Vol. 18 No. 03/17 petpla.net Part 1: A short history of stretch blow moulding / Material basics Stretch Blow Molding by Ottmar Brandau Ottmar Brandau has newly revised his book, first published by hbmedia / PETplanet Publisher, and now re-issued in a second edition under the Elsevier imprint. PETplanet Insider will be publishing extracts from successive chapters in a series of articles in forthcoming issues. 1. A short history of stretch blow moulding OPVC machines featured a double carriage where one side blew a preform from an extruded parison that was then transferred to the other side where the bottle was stretched and blown (see fig. 1.1). This yielded a lightweight bottle with superior properties and was successfully used to produce a variety of containers. However, PVC became environmentally suspect and PET is not suited to a process that requires what extrusion blow moulders call ‘hang strength’, the ability of the material to sustain shape at melt temperature against gravity. Another problem with the PVC process was its inability to be scaled up easily. Figure 1.1 Bekum’s double-sided extrusion stretch-blow machine for PVC where preforms are blown in the inner carriages and bottles in the outer ones. Photo courtesy of Bekum America Corporation. Meanwhile, several US-based companies had developed machinery to produce stretch-blown PET bottles. Cincinnati Milacron’s RHB-5 machine reheated preforms neck-side up, in four lanes, then stretched and blew them in a four-cavity mould. All moulds moved at the same time and machines of this type are referred to as linear or in-line machines. Initially, output was limited to 2,800 bottles per hour (bph) but later versions boosted output to 4,000bph before Cincinnati stopped producing them in the early nineties. Meanwhile in Europe, the German company Gildameister (later to become Corpoplast and today KHS Corpoplast) and the French company Sidel were developing machines for PET production (see fig. 1.2). Sidel produced extrusion blow moulding machines using horizontal wheels. The idea of reheating a thermoplastic material and then stretching it to enhance its properties was first employed in extruded sheet in the 1930s. However, it took until the 1970s for Nathaniel Wyeth and his staff at DuPont to blow the first polyethylene terephthalate (PET) bottle from an injection moulded PET preform. At the same time, Bekum Maschinenfabriken in Germany had commercialised a similar process, stretch-blow moulding an extrusion blow-moulded PVC preform in what is now known as a singlestage process. Oriented PVC has oxygen and water barriers, and even carbonation retention, similar to PET. Bekum’s","@ID":39}, "7 NEWS PETplanet Insider Vol. 18 No. 03/17 petpla.net U.S. caps & closures market for non-carbonated beverages The growth in the demand of single-serve beverages is currently the leading factor driving the market for caps and closures for non-carbonated beverages in the U.S. This is the result of a study by Transparency Market Research (TMR) which further argues that the demand for these caps and closures is also specifically on the rise due to a growing aversion to carbonated beverages amid the growing obesity crisis. The increasing number of consumers demanding smaller bottles and convenience packaging is also driving the U.S. caps and closures market for non-carbonated beverages. The market is being spurred by the increasing favourability of seasonal beverages as well. However, the U.S. caps and closures market for non-carbonated beverages is currently being restricted by the high costs of replacing manufacturing equipment and the switching costs associated with changing from two piece to one piece caps. Conventional manufacturers are also facing a solid competition from closure-less packaging. The U.S. caps and closures market for non-carbonated beverages is also being restricted by the stringent regulations by FDA and the high number of cases against companies regarding sealing breaches. The U.S. caps and closures for non-carbonated beverages market was valued at around USD2.64bn in 2016, registering a CAGR of 4.3% over 2016 to 2024. By the end of 2024, this revenue is expected to reach USD3.82bn. Among material types used in the manufacture of caps and closures for non-carbonated beverages in the U.S., PP accounted for leading market share of 60.2% in 2016 and is expected to retain its lead as well as gain a maximum incremental opportunity in terms of market revenue over the coming years. However, HDPE is anticipated to witness the leading CAGR of 13% over the forecast period from 2016 to 2024, due to the cost advantages of HDPE over others as well as its easier availability, and the increasing adoption of HDPE one piece injection-moulded closures. The U.S. caps and closures market for non-carbonated beverages is segmented on the basis of cap types, into screw caps, snap on caps, and push on caps. On the basis of material, the market is segmented into PP, LDPE, HDPE, PVC and PET. On the basis of application, the U.S. caps and closures market for non-carbonated beverages is segmented into bottled water, fruit beverages, ready-to-drink milk, sports beverages and others. Bottled water industry leads demand The bottled water segment is estimated to account for the leading share in the U.S. caps and closures market for noncarbonated beverages in 2016, and is anticipated to expand at a CAGR of 6.1% over the given forecast period. Bottled water is expected to witness maximum increase in basis points during the forecast period, expectedly accounting for 69.3% of the U.S. caps and closures market for non-carbonated beverages by 2024. The ready-to-drink segment was calculated to account for 8.4% in 2016 and is expected to expand at a CAGR of 9.8% from 2016 to 2024. Key players in the U.S. caps and closure market for noncarbonated beverages so far have included Closure Systems International, Inc., Silgan Plastic Closure Solutions, Bericap GmbH and Co KG, Global Closure Systems, AptarGroup, Inc., Berry Plastics Group, Inc., Amcor Limited, O.Berk Company, LLC, Blackhawk Molding Co. Inc., and Tecnocap S.p.A. www.transparencymarketresearch.com CHOOSE THE NUMBER ONE. BACK TO LIFE. VACUREMA® –FoodContact Approved Recycling Bottle-to-bottle Pelletising Inline Applications","@ID":9}, "INSPECTION 23 PETplanet Insider Vol. 18 No. 03/17 petpla.net or, if the installation space is limited for example due to a circular transfer table, the system design allows for a one-sided measurement with a single stack of sensors. The system is offered as “active” including real-time thickness monitoring and the automatic rejection of too thin/thick bottles or “passive” which provides real-time thickness monitoring and real-time automatic operator alarms for bad bottles by a light tower or a horn. The system is all-inclusive and mounted on a pedestal-style stand that can be equipped with casters which allows system mobility between production lines. A mobile system offers flexibility and cost savings to manufacturers that have several production lines. System operation The graphic user interface is operated via a touch panel monitor and the application software is recipe-based. Each bottle design has its own recipe that includes thickness specifications for each measurement location, cavity count, bottle image, etc. Sensor height level, distance and angle values in the recipe enable a quick alignment before the production run. While the system is running, thickness results from each sensor are plotted in real-time on its own chart that includes warning and specification limits. This makes it easy for an operator to instantly detect trends and other unusual process behaviour. The software reports mean thickness, standard deviation and process capability for each sensor. Bottles’ vertical thickness profile is displayed, too. The system PC can be connected to a LAN that allows remote access to the measurement results. Thickness data is available for closed-loop machine control. Filled bottles, preforms, glass The FocalSpec system’s singlesided measurement method enables the system to be used also on filled plastic bottles, monolayer and multilayer preforms, and empty and filled glass bottles. www.focalspec.com High speed, high accuracy Since modern high-capacity blow moulders have a very high output, designing the MPC 100 was a challenge. The sensor samples wall thickness at 10kHz (10,000 measurements per second) and the thickness resolution is 50 nanometres (2 micro inches). Since the sensor uses a pair of IR beams, it applies trigonometry to automatically correct thickness error that would otherwise affect readings from a non-perpendicular wall or tilted bottle. Modular design The FocalSpec system can be configured according to the manufacturer’s specific needs. The number of sensors on each side of the bottle flow can be selected based on the bottle size, design, and the number of desired measurement locations. Nonsymmetric designs may require an uneven number of sensors. If measurement of just one wall is enough Throughput: up to 120,000bph Materials: transparent and translucent PET, PP, PC, HDPE Colours: clear, green, amber, blue, red, etc. Thickness range: 0.05 – 5.00mm (0.002 – 0.197”) nominal FocalSpec MCP 100 sensor PROCESS PILOT® makes producing a better PET bottle as easy as 2 3 1 MEASURE CONTROL OPTIMIZE every bottle for changes in material distribution process variation, inside the blowmolder material utilization and orientation to achieve maximum bottle performance CONTACT US TODAY TO LEARN MORE! AGRINTL.COM | +1.724.482.2163 | SALES@AGRINTL.COM","@ID":25}, "MARKET SURVEY 29 PETplanet Insider Vol. 18 No. 03/17 petpla.net ProTec Polymer Processing GmbH Empacar Starlinger & Co. Ges.m.b.H. Polymetrix AG Herbold Meckesheim GmbH Stubenwald Allee 9, 64625 Bensheim, Germany +49 9251 77061 0 www.sp-protec.com Ms Karin Luxem Area Sales Manager Asia/Pacific +49 6251 77061 226 +49 6251 77061 81226 karin.luxem@sp-protec.com Parque Industrial PI-45, 2865 Santa Cruz de la Sierra, Bolivia +591 3 346 5525 www.empacar.com.bo Mr Carlos Limpias General Manager +591 3 346 5525 +591 3 3461 883 climpias@empacar.com.bo Sonnenuhrgasse 4, 1060 Wien, Autria +43 1 59955 0 www.recycling.starlinger.com Mr Paul Niedl Head of Sales Division recycling technology +43 1 599 55 1310 +43 1 59955 25 sales.nd@starlinger.com Sandackerstrasse 24, 9245 Oberbüren, Switzerland +41 7155 210 22 www.polymetrix.com Mr Karl Schoepf Product Manager Recycling +41 7155 210 82 karl.schoepf@polymetrix.com Industriestrasse 33, 74909 Meckesheim, Germany +49 6226 932 0 www.herbold.com Mr Siegfried Engel Vice President Sales +49 6226 932 133 +49 6226 932 495 Siegfried.Engel@herbold.com Four models: recoSTAR PET FG, recoSTAR PET FG+, recoSTAR PET iV+, recoSTAR PET iV+ Superior No own plants, cooperation with established washing system manufacturer Starlinger offers the engineering of washing lines and / or a turn-key project with components and technologies available in the market Yes (decontaminated for food-contact, IV increased, AA 1ppm, lowest VOC level) Agglomerate 6,000 - 26,000 t/a rPET pellets 24,000 t/a Up to 30,000 t/a Depending on design 5,000 1,000 - 4,000 Several USA/FDA (C-H), Austria, Germany/BfR, Ilsi, France/AFFSSA, Finland, Australia, Canada, Egypt, Japan, Switzerland, several Latin American Countries; follows EFSA requiremens; several brand owners FDA, EFSA, Brand owner Depending on design 2.15 Approx. 0.5 - 2 Depending on design 580 KWh/to, 590 kg steam/t Approx. 545, depending on input material Four models: recoSTAR PET FG, recoSTAR PET FG+, recoSTAR PET iV+, recoSTAR PET iV+ Superior Process for production of foodgrade pellets; special feature: flexible process which enables the reliable adjustability of customer specific values of viscosity PET flakes 10ppm PVC max content Pellets for direct food contact including IV increase and lowest VOC levels, AA1ppm Yes, EFSA , FDA approved technology Yes (decontaminated for food-contact, IV increased, AA 1ppm, lowest VOC level) 4,000 - 15,000 (other sizes possible on request) 8,000 1,500 t/a - 26,000 t/a (5 extruder sizes) 12,000 - 50,000 t/a 300 - 500 3,000 130 - 540 400 - 600 FDA, EFSA; Anvisa, brand owners Coca Cola , Pepsico , Local Gov. Several USA/FDA (C-H), Austria, Germany/BfR, Ilsi, France/AFFSSA, Finland, Australia, Canada, Egypt, Japan, Switzerland, several Latin American Countries; follows EFSA requiremens; several brand owners FDA, EFSA, Brand owner Only replacement of losses in pelletising and vacuum system 1,7 Approx. 0.15 0.15 0.35 520 Approx. 410 (depending on design) 290 kWh/t No own plants, cooperation with established washing system manufacturer Pressed and loose bottles , clear , green and blue Starlinger offers the engineering of washing lines and / or a turn-key project with components and technologies available in the market Yes (decontaminated for food-contact, IV increased, AA 1ppm, lowest VOC level) 12,000 3,700 - 10,500 (5 sizes) 24,000 t/a Up to 30,000 t/a 3,000 Approx. 150 4,500 1,000 - 4,000 Coca Cola , Pepsico , Local Gov. FDA (hot-fill), follows EFSA requirements 1,8 2 0.5 - 2.0 230 120 - 250 (incl. bottle washing to SSP) 290 kWh/t, 590 kg steam/t Approx. 250-300 0.4kg/t 1,000 μm or 30 Mesh 360 - 400 minutes in SSP, 200 - 210°C Yes Yes Yes PET bottle washing plants, turnkey systems, single components, size reduction components Yes No Yes Yes and drying and crystallising of PET, PLA etc., dosing and conveying systems Yes, 100% rPET Strap 8 - 20mm width, Yes, 700mm width , 0.1 - 1.5mm thickness Yes","@ID":31}, "INSPECTION 26 PETplanet Insider Vol. 18 No. 03/17 petpla.net Beauty+home, food+beverage and pharma company AptarGroup uses Sesotec metal separators to protect its machines and avoid product contamination Metal detection Aptar’s beauty+home production plant at Neubourg, France, is certified to ISO 14001:2004 for the development and production of spray and dosing systems, as well as small packaging solutions. It is part of the Group’s fragrances, skin care and cosmetics business unit and uses injection-moulding machines to produce components for perfume sprayers. Packaging systems for beauty products have to combine perfect function with attractive aesthetics. Before it used metal separators, magnet grids were inserted in the material feeders of the company’s injection-moulding production lines. The magnet grids suffered from two vulnerabilities: magnets attract only ferrous metals – any non-ferrous materials would not be detected and removed; and they were not 100% efficient at removing even all the ferrous material from the hot plastic. Aptar was advised to trial and assess an Aptar Protector system by French company Soufflet, which is best known for adding value to agricultural materials. These metal separators are installed directly above the material inlet of injection-moulding machines. They detect all magnetic and non-magnetic metal contaminants, including steel, stainless steel and aluminium, and can detect such contaminants even if they are enclosed in the product. Metal particles are removed by means of a “Quick Valve” reject unit. The six-month trial period was long enough to demonstrate that the Protector system offered a number of advantages to Aptar’s production processes. More effective removal of metal contaminants led to higher levels of quality output and, consequently, to a lower rejection rate and less machine downtime. The improved performance showed that the company could achieve an attractive cost/ performance ratio and a rapid return on investment. The Protector series are designed to detect and separate all magnetic and non-magnetic metals and can be used in the inspection of bulk materials; material flow; and bulk material columns. Sesotec says that they can detect and remove even the smallest magnetic and non-magnetic metal particles from regranulated and virgin material, thus helping consistent processing. The company further asserts that the Protector offers high scanning sensitivity for all metals and the highest possible immunity against vibration and electromagnetic interference. It also maintains that its proven separating unit guarantees safe and reliable operation even in applications with high throughput rates or with a high flake or regrind content, with minimal loss of good material. Its compact dimensions are intended to facilitate mounting of heavy conveying, mixing, and dosing units. Its preset parameters are designed to provide high levels of ease of operation and it also has “auto-learn” and manual compensation features. Sesotec says that the Protector metal separator is ideally suited for the packing industry in the production of caps for beverages and other liquids, or in the production of plastic articles for medical technology. Metal separators prevent malfunctions and thus increase the productivity of plastics processing machines. Aptar has now been using Sesotec Protector metal separators for over five years. The company’s plant maintenance engineer and production manager have said that they regard Sesotec metal separators as important components in quality assurance, and that daily performance tests demonstrate that the systems operate reliably, with fewer metal particles reaching the injection-moulding machines. Aptar has now installed more than 20 Protectors in its production lines. www.aptar.com www.sesotec.com Sesotec Protector AptarGroup, which is headquartered in Crystal Lake, Illinois, USA, is a leading manufacturer of dosing systems for a range of market applications, including solutions for the beauty+home and pharmaceutical business segments. Its product portfolio includes pump dispensers, caps and valves for skin care products, as well as spray pumps. It offers a standard range as well as bespoke packages and solutions. INSPECTION S P E C I A L","@ID":28}, "BOTTLING / FILLING PETplanet Insider Vol. 18 No. 03/17 petpla.net 12 among Chinese consumers. If at all, it was during the winter months that Chinese consumed coffee beverages because they were ideally suitable for boiling. This was not necessarily a disadvantage for Tenwow, as the main season for the finished tea products was during the summer months. Tenwow relied on the niche product coffee to offset weaker sales of tea during the winter months. Up to that point, the company had outsourced aseptic filling of its coffee products to a contract filler. However, the new finished coffee beverage Banuo is set to be available on the market all year round. Aseptic instead of hot fill Growing demand for coffee and tea coupled with the trend towards in-house production were the main reasons behind Tenwow’s decision to operate its own aseptic lines. One of these was installed by Krones at the Shanghai plant. For Lu Ying, Vice President Tenwow International Holding, the benefits of aseptic filling compared with the hot fill process are obvious: “For me, the aseptic process offers numerous advantages: The average costs of filling the containers are lower, the gentle filling improves the taste. And the aseptic process allows us to fill virtually all products whereas the hot fill process is confined to specific products. And finally, the aseptic process allows us a higher output of 48,000bph – compared with just 36,000bph using the hot fill system.” Reduced preform weight To preserve its brand identity, Tenwow uses the same bottle design as before for the coffee and tea beverages. This means that the aseptic filled containers have the same appearance as the hot fill containers. However, Tenwow has significantly reduced the preform weight. The 500ml bottle now weighs just 21g instead of 26.5g previously. “This equates to a saving of 5g of raw material per container,” explains Lu Ying, “a financial benefit that results in a clear reduction in overall operating costs.” This line marks the first cooperation between Krones and Tenwow. “When we began to analyse the area of aseptic filling, we became aware of the high-quality technology on offer from Krones. We were persuaded of the advantages of this technology based on customer references to other Krones lines. For us, Krones brings precision and quality, both in terms of the technology and its practical implementation. This was then also confirmed for us in reality with the new line,” explains Lu Ying. Two water lines with Contiform Bloc In the future, Tenwow wants to focus to an even greater extent on health-oriented products, thereby taking a further step towards meeting consumer demand. Specifically in the beverage segment, the company’s own R&D department wants to explore new market trends in order to meet consumer expectations with suitable beverage innovations. In 2017, Tenwow will also significantly increase filling capacities for its natural mineral water Tribute Spring Water. Following the positive experiences with the Krones PET-Asept L2 line, Tenwow placed an order with Krones for two water lines using Contiform Bloc, each of which can process 48,000 containers per hour. One of these water lines will be installed in Yifeng, and the other in Chang-xing. Tenwow switched for the first time from the hot fill system to aseptic filling – with a high-performance PET Asept L2 line from Krones. The aseptic filled containers have the same appearance as the hot fill containers. However, Tenwow has significantly reduced the preform weight.","@ID":14}, "PETplanet Insider Vol. 18 No. 03/17 petpla.net 46 PETbottles Home + Personal Care Washing up with plant power The You brand has brought the washing-up product “Mint Splash” with natural ingredients and scents onto the market. According to the manufacturer, the fresh product, smelling of natural mint, with 100% plant ingredients will wash crockery really well and safely, and in addition it is kind to the skin. The clear bottle contains 500ml, has a non-label-look self-adhesive label and push-pull closing device with a dosing opening allowing even the smallest amounts to be used. www.you-natuerlichstark.de Easy-to-grip bottle The bottle from “method” has optimum grippability in each area of the bottle for 739ml or 25 fl. oz. floor cleaner for sealed wood and laminate floors. The oval bottle has an easy-to-grip edge all round and a reduceddepth label area. The wax-free, plant-based product is poured, via a screw-on push-pull closing device with several fine output apertures in the bottle, directly onto the floor in order to clean and protect it and give it a pleasant aroma. www.methodhome.com El Vital against dandruff L’Oréal has closed a gap in the hair care programme and, since the beginning of 2017, has been selling an anti-dandruff range. The “Planta Clear Anti-Dandruff Gentle Shampoo“ is, according to the manufacturer, free of silicon, removes 100% of dandruff, is gentle on the head’s skin and leads to shiny and soft hair. Amongst other things, three essential oils help achieve this effect. The brand-typical bottle forming a cone shape upwards with 250ml contents was selected. Bottle and closing device fitted are coloured green, with the easy-to-open hinged top remaining white. The self-adhesive label on the front is lightly reflective. www.loreal-paris.de New brand in Germany Unilever has introduced a new brand onto the tooth care shelves in Germany. This brand has been known for some years in the Nordic countries. The origins of the product go back to the research results from a microbiologist in Scandinavia, who worked in the area of mouth hygiene and developed an improved toothpaste. In addition to various toothpaste variations, under the “Zendium” brand, there is also an alcoholfree mouthwash with proteins and enzymes to strengthen the mouth’s defences. The white-coloured, slightly waisted bottle contains 500ml of the blue-ish shiny product. The opaque screw cap which serves as a dosing point has a sticker to ensure first opening. www.zendium.de","@ID":48}, "PETpatents www.verpackungspatente.de PETplanet Insider Vol. 18 No. 03/17 petpla.net 48 PET bottle Europ. Pat.issue no. EP 2844570 B1 Applicant: Pet Engineering S.r.L., San Vendemiano (I) Application date: 24.4.2013 Thin-wall PET bottles are partially fitted with a kind of over-printing (filling with expanding nitrogen), in order for them to be sufficiently stable during transport or storage. In order to withstand this pressure without deforming, a particular shape is required. Coated PET containers Intern. Patent no. WO 2016 / 076944 A1 Applicant: Graham Packaging Comp., York (US) Application date: 10.9.2015 The improved process for coating a PET container with silica is described. The container’s barrier characteristics are improved by this coating. Reduced froth when opening Intern. Patent no. WO 2016 / 077517 A2 Applicant: Niagara Bottling LLC., Ontario (CA) Application date: 12.11.2015 A weight-reduced bottle is shaped in the opening area in such a way and with a matching screw cap that when opened, the froth and undesirable leakage of liquid from the container is reduced. Laminated bottle Europ. Patent no. EP 3009365 A1 Applicant: Yoshino Kogyosho Co. Ltd., Tokyo (JP) Application date: 8.5.2014 Some areas of a plastic PET bottle are fitted with an intermediate layer in order to improve the bottle’s barrier characteristics. The lamination is carried out in a way that prevents any undesirable shedding of the plastic layers / delamination. Plastic containers Europ. Pat.issue no. EP 2038183 B1 Applicant: Krones AG, Neutraubling (D) Application date: 2.12.2011 The European patent shows the special shaping of the bases of a PET bottle. The base is shaped in a new way to make the manufacturing process easier. Manufacture of wide-neck containers Intern. Patent no. WO 2016 / 097543 A1 Applicant: Sidel Participations, Octeville-sur-Mer (F) Application date: 10.12.2015 The international application describes the process for manufacturing a wide-neck container from a preform. A threaded insert is positioned in the tool for blowing the preform, which serves as the threaded part of the wide-neck container. The original bottle neck is severed.","@ID":50}, "The LayerWatcher at the K Show: inspecting preforms precisely and nondestructively all around The preform layers are measured all around by coherent infrared light within 25 seconds INSPECTION 16 PETplanet Insider Vol. 18 No. 03/17 petpla.net Inspecting barrier layers in transparent and coloured translucent preforms Non-destructive measurement Gabriele Kosmehl: Dr Fuhrmann, your new development, the LayerWatcher, is a system for the inspection of multilayer preforms. Can you please explain to us how the system works? Gerd Fuhrmann: The technology behind the LayerWatcher is based on the same principles as known from ultrasonic examinations. A pulse is sent into the material and the echo is analysed. But as we all know from our physics lessons at school, the lateral resolution is a function of the frequency of the probing wave; the higher the frequency the better the resolution. This is the reason for us to use infrared light. Gabriele Kosmehl: Other systems work with terahertz measuring. What are the differences to your system? Gerd Fuhrmann: Both systems are based on the same principle. However, terahertz radiation has a much longer wavelength than infrared light. While this affects the penetration characteristics, it also leads to significantly longer measurement times and a reduced resolution, for the reason mentioned above. A user will first recognise that the LayerWatcher system will give him a high resolution image like he would see it with a microscope when he cuts a preform wall. He will be able to see clearly even the smallest turbulences of the different materials which form the diverse layers. Terahertz systems measure layer thicknesses at just one point to finally spitting out some numbers. It stays obscure what a terahertz based system will measure in the presence of irregularities, for instance if the flow front of a barrier divides into two flows or shows turbulences. This is especially true as you have to tell a terahertz system for how many layers you are looking before you start. So the method thus involves a kind of guessing about the result before the measurement at all starts. Terahertz systems measure thick Dr Gerd Fuhrmann, managing director of Intravis GmbH The LayerWatcher by the German company Intravis GmbH is able to visualise the structure of layers in preforms, using measurements with infrared light. The non-destructive imaging device delivers an accurate picture of a virtual cut through the preform wall. Intravis presented the LayerWatcher at the K show at the booth of Husky Injection Molding Systems S.A.- a good opportunity for PETplanet to speak to the managing director of Intravis, Dr Gerd Fuhrmann. INSPECTION S P E C I A L","@ID":18}, "PETplanet Insider Vol. 18 No. 03/17 petpla.net 44 PETbottles Beverage + Liquid Food Conical bottle for smoothie Bolthouse Farms in California package the Green Goodness Smoothie, with apples, bananas, pineapple, mango, kiwi and spinach into a plastic bottle with a round base. Directly above the base rises a conical bottle with four side walls which are joined by rounded edges. A partially transparent sleeve label and a green screw cap with a guarantee band complete the packing design. www.bolthouse.com Happy Lithia Water Happy Water is a water from two Canadian sources. In addition to the “normal” minerals such as calcium, sodium, magnesium and potassium, the water also contains traces of lithium. 500ml are filled into a 100% biologically degradable transparent bottle. Two opaque self-adhesive labels explain the contents of the basic (alkaline) water with a pH value of 7.4. www.livehappywater.ca Coffee with almond milk Califia Farms in the USA sells coffee products which are cold and therefore gentle and low in acid and which, with the addition of various products, meet the popular trend. The image shows an unsweetened “Black & White” version with almond milk. 10.5 fl. oz. or 310ml are filled into a stable bottle with a sleeve label and screw cap with first opening security. www.califiafarms.com Mustard in PET The American firm Beaverton Foods displays 280ml Creamy Dill Mustard from the “inglehoffer” range in an eye-catching, clear and stable bottle. With the transparent bottle and the non-label-look label, the ingredients – dill – are visible. The output rim of the screw-on hinged top is designed as a narrow slit in order to simplify the flat look of the product. www.beavertonfoods.com • 28mm, 33mm and 38mm screw closures • Robust and trouble free capping • Established DoubleSeal™ technology - for secure sealing performance - for better protection against micro-organisms • Slit FLEXBAND® band technology for enhanced tamper evidence • O 2 barrier and scavenging options for screw flat caps supporting longer shelf life and fresher taste • Sports closures for aseptic filling and hot filling without aluminum foil • Special closures for syrups and carton packaging Unique range of screw and sports closures designed for cold fill and aseptic application BERICAP Technology for juices, RTD teas, health drinks www.bericap.com","@ID":46}, "INSPECTION 33 PETplanet Insider Vol. 18 No. 03/17 petpla.net Closure inspection system IMDvista Twin with new conveying technology Flying closure for accurate inspection After more than 15 years of experience in inline closure testing systems, IMDs team came to a point where advancing was only possible, after questioning everything they had done very successfully in past years: how can a closure truly be 100% inspected without a conveying system hiding a part of it? After the inspection “on the fly” bad closures are blown downwards, under natural gravity, with a small and fast air valve. Robust cavity reading independent of the surface quality The challenge in cavity reading these days is no more the reading algorithm (OCR) nor the inspection speed. It is more the changing contrast. The more the moulding tool is used, the more surface variations around the cavity number interfere with the reading. Cavity reading becomes more and more challenging. Adding a backlight for robust contrast A simply adapted backlight offers a stable contrast independent of the surface quality for cavity reading. The backlight offers even more options for inline closure testing: colour change, colour distribution and changes in the brightness can be detected with maximum resolution. Now drifts can be detected and corrected before they affect the quality of the closures, thanks to the addition of backlighting. To fulfil an all embracing inspection system the proven pinhole detection with the reliable high tension technology is integrated into the Twin system. The system saves significant energy because there is no longer any need for a vacuum pump and the maintenance work is reduced as well because no filters have to be changed. The noise level may thus be reduced to a minimum. For a compact layout IMDvista redesigned its waterfall feeder (WFS) to include a bunker. www.imdvista.ch/en INSPECTION S P E C I A L Closure production, especially in the beverage industry, is one of the most automated and optimised production processes in the plastic industry. Vision inspection systems are state of the art and well established. Customers invest in a vision inspection system with five or even six cameras but they do not inspect the most visible aspects, namely the face of the closure. New ‘flying closure’ conveying technology Two belts are used for spacing the closures and bring them into a controlled and stable flying condition. Dimension change can be done with simple spindle adjustments, no readjustment of the spacer required. Belt change takes less than a minute; it is no longer a time relevant maintenance factor. IMDvista Twin “flying closure”: there are no guides or conveyors hiding a part to be inspected. The inspection of the face from below is now integrated. Users, from operators to process engineers, are able to analyse and optimise the process with added backlight. Stabel contrast for reliable cavity reading and colour measurement.","@ID":35}, "PETnews 6 NEWS PETplanet Insider Vol. 18 No. 03/17 petpla.net EU Commission terminates anti-dumping measures concerning Chinese PET On February 7, the EU published a commission decision terminating an expiry review of the anti-dumping measures applicable to imports of certain PET originating in the People’s Republic of China. According to the European Commission, a further investigation on the 13-year-long trade remedy measures has not brought to light any considerations showing that such termination would be against the Union interest. Therefore the Commission considered that the present review proceeding should be terminated. The measures were supposed to expire in November 2015 but some European PET manufacturers asked for a review. Thereupon, interested parties were given the opportunity to make their views and to request a hearing. However, the Commission received no comments which would support the conclusion that such a termination would not be in the Union industry interest. The Commission, therefore, concludes that the expiry review of the anti-dumping measures applicable to imports of PET originating in the PRC should be terminated. www.eur-lex.europa.eu CarbonLite building PET recycling plant in Dallas Plastic beverage bottles will find a new life in a new $62 million plant being built in Dallas, USA, as CarbonLite gets ready to add a second facility to process 100 million pounds of postconsumer PET plastic bottles with the use of 100% green power. Construction is underway in a brand new 230,000-square-foot facility located in the city of Dallas. Start-up is planned for the end of the second quarter 2017, according to Leon Farahnik, chairman and CEO of CarbonLite. With the addition of the Dallas facility, CarbonLite will become the largest producer of food-grade PET in the world, processing over 200 million pounds of post-consumer beverage containers per year. The primary equipment suppliers for this project are BHS Group from the United States, Amut S.p.A from Italy, Erema Recycling System from Austria, and Pelletron from the United States. Nestlé Waters North America and Pepsico are the main consumers of CarbonLite raw material in pursuit of their sustainability efforts. www.carbonliterecycling.com Alpla expands its portfolio in Romania through new acquisition Alpla, a provider of plastic packaging, has acquired a 100% stake in the Romanian company Star East Pet SRL. The company, based in Brasov, specialises in the production of PET preforms for drinks, food and non-food products. With this acquisition, Alpla has expanded its production capacities in Eastern Europe. The product portfolio and customer base also complement its operations, with improved proximity to existing customers. “We are gaining access to a strong distribution network. Star East Pet is a good strategic partner, which will help us to achieve our targets in Romania and beyond,” says Alpla CEO Günther Lehner. Star East Pet was founded in 1997 under the leadership of Dan Moldovan and has developed into one of Romania’s leading manufacturers of PET preforms. The company employs 70 people and specialises in the production of PET preforms for drinks, food and non-food products, for both local and international customers. Alpla itself has been involved in the Romanian market for many years. Its focus is on bottles and closures for the personal care and home care market segments. The deal is expected to be concluded by the middle of 2017, subject to the required legal and regulatory approval by the competent authorities. The contracting parties have agreed not to disclose the financial details. www.alpla.com Intravis: 4th International user meeting Intravis once again welcomes the plastic packaging industry to its International User Meeting. The well-known producer of vision inspection systems announces the fourth issue of this event, to be held once again in Aachen, Germany. From 10 to 12 of May 2017, the participants discuss the topic of “Industrial Internet of Things – Where’s the Beef?” At the event, they have the chance to not only receive first-handinformation from presentations but also take actively part in discussions and workshops. “The user meeting is an essential information experience to our participants”, says Gerd Fuhrmann, managing director of Intravis. “Together, we want to network and share ideas for the future of the plastic packaging industry.” www.intravis.de WikiPETia.info New contents at wikipetia.info","@ID":8}, "CONVEYING PETplanet Insider Vol. 18 No. 03/17 petpla.net 36 The concept is based on a machine-specific conveyor system, which means that every processing machine has its own material supply line. This principle is particularly suited for production processes that involve a high number of materials, frequent material changes and a large number of machines. Machine-specific systems are very suitable for supplying dried materials when used with a dry air supply system and discharge valves for the supply lines. When long distances are involved, dry air supply systems with discharge valves have the advantage of preventing the material in the supply lines from being re-moisturised. The drying hoppers and several separate service tanks are connected to the material lines leading to the machines through a coupling station through which several machines can be supplied at the same time. The coupling station is equipped with suction lances that can be connected to an additional back-up dryer or a service tank as required when processing small quantities of materials. One of the drying hoppers and two supply lines are reserved for transparent and white material. This drying hopper is also fitted with a high efficiency particulate air (HEPA) filter between the heater and hopper. The coupling station is operated, i.e. the lines are connected and disconnected, by personnel. For safety, the system also features a material path selection system (target-source assignments), where personnel have to enter the address of the source (drying hopper) and target (machine) at the control. Provided the lines have been correctly connected, the material will subsequently flow accordingly. If one of the two addresses is incorrect, the material will not flow, because only the material slide gate of the correct drying hopper will be opened. This principle ensures that materials are not mixed up. Starting from the coupling station, a near 1,000m of pipes were laid throughout the rest of the production hall. The pipes leading to the machines are made of wear-resistant stainless steel, while the pipe bends are made of borosilicate glass. The flexible connections between the material lines and machines were realised using highquality PUR ducting. Higher productivity – higher energy efficiency The vacuum is generated by two frequency-controlled blowers inside the system that are coupled to one another. One of these supplies the drying system and the other is for the material supply to the machines. In order to safeguard production, both of the blowers’ performance has been selected such that each one of them could take over all of the supply processes in the system in the event the other fails or has to be serviced. In that case, the switch will happen automatically. To make sure that the material is transported in a careful way, the blowers can be operated at variable speeds, which is a way to affect the speed at which the material is transported. This means that every machine and its conveyor – as well as every material – can be assigned an optimum conveying speed. This solution is designed both to protect the system components from wear and to protect the material itself. Thanks to the throughput-dependent drying process and associated use of frequency-controlled pumps, the production system has become significantly more energy efficient. Even though actual electricity consumption has not yet been determined in detail, initial rough estimates indicate significant energy savings. The automated material supply system also means that production processes are more reliable and less material is being used. The system’s operation is supported by a database stored in the dryer control that contains the drying parameters for more than 70 standard materials. This means that the only action required by personnel is to select the correct material. The corresponding information is also displayed on a terminal in the production hall. If necessary, the system can also be protected by setting up password protection for different operating levels. www.spritzguss-bergmann.de www.motan-colortronic.com www.flinkundwortmann.de A central material supply system with a decentralised colour dosing system ensures that processes are reliable and low energy and material consumption.","@ID":38}, "PETplanet Insider Vol. 18 No. 03/17 petpla.net 45 BOTTLES Creamy horseradish from Canada Lynch, a well-known food manufacturer in Canada, fills 375ml gluten-free Creamy Horseradish Sauce into a newly-designed, transparent bottle which is flattened in the side wall area with a full-surface sleeve label and a screw-on hinged closing device with a dosing opening. The label is transparent in some areas in order to show the product. Before first use the closing device must be unscrewed and a seal membrane removed. www.lynchfoods.com Elegant bottle The Canadian firm Cyoni fills 296ml various freshly-pressed juices into bottles with wavy side walls. The sides are designed in such a way that several bottles can be stacked next to one another and thus form a unit. At the same time, the waves make the bottles easier to hold. A nonlabel-look on the front and a white label on the back provide the trade data. A screw cap with a tamper-proof band is used for closing. The curved bottles are also available in the 1l format. www.cyoni.com A NONCOLOUR TECHNOLOGY","@ID":47}, "BOTTLING / FILLING PETplanet Insider Vol. 18 No. 03/17 petpla.net 13 Tenwow International currently employs more than 3,000 people. The company is a manufacturer of packaged foodstuffs and beverages. It is one of the largest Chinese importers of fast-moving consumer goods (FMCG) in these areas. The product groups include alcoholic beverages, foodstuffs and snacks (including dried fruit, muesli, oat flakes, nuts and dried pork), non-alcoholic beverages and other FMCG. Tenwow carries trade goods from renowned international manufacturers such as Nestlé, Martell, Hennessy, Unilever and Wrigley – in total around 5,000 different products from 70 different national and international manufacturers. In China, there are 142,000 sales outlets in 30 provinces and autonomous districts. The highly popular fruit juice series “VitC&VitE” generated growth of 42%, although fruit teas recorded a slight drop primarily due to poor weather. The newly introduced water brand Tribute Spring as well as Tenwow Natural Water performed in line with management expectations. The packaging for the fruit tea series was redesigned and a new fruit juice variant added. Modufill Asept VFJ volumetric filler with 110 filling valves and flow meters The Chinese Krones subsidiary in Taicang will also redesign the container shape for Tribute Spring Water to further boost the mineral water’s presence in the market. By focusing on quality and performance, Tenwow is following a consistent strategy with regard to its beverage filling operations. www.krones.com www.ir.tenwow.com.hk The aseptic line with an output of 48,000bph comprises: Contiform 3 blow moulder with 22 blowing stations Aseptic steriliser for container disinfection with peracetic acid Modulfill Asept VFJ volumetric filler with 110 filling valves and flow meters Process Control System (PCS) for controlling process parameters during production AquaAsept sterile water UHT line Checkmat FM-X for fill level inspection with X-rays Linadry dryer Sleevematic labeller for full and partial sleeves Steaming tunnel Checkmat E for label inspection and Checkmat D for code/date inspection Variopac Pro W packer (wraparound packaging) and Modulpal 2A palletiser Line networking and LDS line documentation system product development caps & closures design high cavitation moulds multi-component moulds closure production systems after sales service competent – professional – inspiring Dr.-Walter-Zumtobel-Strasse 9 | 6850 Dornbirn | Austria | www.z-moulds.com Plástico Brasil March 20th-24th meet us at booth D251","@ID":15}, "INSPECTION 24 PETplanet Insider Vol. 18 No. 03/17 petpla.net High speed preform inspection system updated Polarised light is the key The PVS-3 preform vision system, developed by Sacmi’s Automation & Inspection Systems Division has given its first market showing at the last edition of the international K’ 2016 fair in Düsseldorf, Germany. Performance and flexibility are the key elements. The system can be equipped (on request) with the automatic centrifugal positioning unit which makes it suitable in terms of compactness and efficiency for the downstream installation of any injection press, new or existing. of particular interest: it enhances efficiency and is nicely compact, making investment decisions regarding existing lines easier. For offline installation the traditional roller positioner is available, while the in-line solution can be equipped downstream with the “soft drop” system that delicately sets down preforms exiting the vision system in octabins. on line efficiency and extending monitoring, also remotely, to every stage of production. Thanks to the software platform, it is possible to equip the Sacmi PVS-3 with both black and white video cameras and ultra-high resolution colour acquisition devices; the latter are designed for thorough inspection of preform colour. Adding yet further value is Sacmi’s capacity to include allround solutions, personalised according to the individual customer’s manufacturing requirements and the target market. Solutions that range from complete plant engineering design (injection presses, stretch-blow moulding and filling lines, robotised handling systems and Sacmi-built end-ofline systems) to a fast, efficient spare parts and after-sales service that is guaranteed by the Sacmi Global Network. www.sacmi.it After the trade fair ten machines have been installed and sold worldwide, from Spain to Vietnam. This demonstrates the market has been quick to respond to a solution that offers inspection rates of up to 72,000pph and a flexibility that the system can be installed both in-line with the press and offline. In case of in-line operation, the upstream automatic centrifugal positioner is INSPECTION S P E C I A L Sacmi’s PVS-3 spans from standard checks such as inspection of the preform mouth to the finish (especially the thread), the body and the bottom. Optional features include the patented Sacmi “grille” method to intercept defects that can only be detected with polarised light, such as on-material stress, surface irregularities and watermarks etc. The PVS-3 installs the latest CVS 3000 64-bit software system developed by Sacmi and shared by all vision systems in the range. It ensures interoperability between machines and a fully integrated approach that Sacmi calls total quality control. The interconnected system is able to provide precious additional information","@ID":26}, "CONVEYING 35 PETplanet Insider Vol. 18 machines that needed to be supplied with material. However, as part of this ongoing expansion, another four machines were added to the project as planning was still under way. On completion, the project comprised the design and construction of a material supply system with ten Luxorbin drying hoppers, six of which with a volumetric capacity of 400l each, and two each with volumetric capacities of 250 and 150l. In this system, the dry air is supplied by a Luxor 1200 dry air generator with DryingOrganizer to protect material from being over-dried and hygroscopic polymers from being insufficiently dried. The dry air generator’s control unit can control and monitor up to 16 drying hoppers, associated conveyors and discharge valves, as well as 24 materials handling units. Every drying hopper is assigned a storage tank. pany subsequently built two new halls – one for production and another for a central material supply system and material storage – with the aim of optimising material flow. Up until then, the material supply system had been located inside the production hall, which had resulted in corresponding disadvantages because it took up much needed space, created a lot of noise and heat, as well as granulate residues on the floor. The aim had subsequently been to keep the two systems completely separate and keep the production area free from any stand-alone units, sacks and containers with granulate and colouring agent. All machines will be equipped with new conveyors and their own colour dosing systems, as well as adapters to make it possible to use the systems interchangeably should the need arise. At this stage, the materials handling operations had also required full-time attendance by three members of staff who were urgently needed elsewhere. Bergmann commissioned the Northern KFW office of Kunststofftechnik Flink & Wortmann GbR (KFW) – a Motan-Colortronic distribution partner – to design and build the new system. The entire design and construction process, from the first contact from Bergmann to the date the system was commissioned, took no more than six months. When it came to designing the system, there were two key considerations that had to be taken into account: one was that the machines had to be directly supplied with material and the other was that dried material had to be always available. This required finding a balanced and economical solution regarding the size and number of drying hoppers. Initially, there were 16 injection moulding","@ID":37}, "BOTTLE MAKING 10 PETplanet Insider Vol. 18 No. 03/17 petpla.net Increased resistance and stability for CSD bottles CSD in harsh conditions The new StarLite Tropical base enlarges the family of StarLite bottle solutions originally developed by Sidel packaging experts. This latest addition to the range is designed to offer a flexible solution for CSD, in all packaging sizes from 0.25 to 3l. Additionally, it is applicable to the different standard levels of carbonation. It is specifically designed for CSD bottles undergoing harsh conditions - for instance when produced and distributed in the supply chain at very high temperatures or in environments which are particularly humid. The end result is a PET bottle that offers improved resistance in terms of stress cracking and creeping, as well as better stability throughout the supply chain, says Sidel. It is also intended to avoid material waste during production and storage while not compromising on the safety standards of the beverage inside. Improved bottle resistance and stability The StarLite Tropical base has been designed to improve performance in terms of resistance. Its optimised geometry reinforces all the zones which are more susceptible to stress cracking due to mechanical constraints. This avoids potential breaking of the PET bottle walls and base which can be caused by interactions with fluids or chemicals during the conveying stage. The base has been evaluated and qualified under rigorous test protocols which are internationally recognised. It successfully completed a demanding creeping test conducted over 72h under 38°C and 50% moisture conditions. This proved a good base roll-out resistance when the bottle is under pressure at high temperature and demonstrated that it is less likely to burst during production or to deform during transportation. Also, Sidel packaging experts conducted various trials through computer simulations, followed by real-world physical tests, to achieve optimum bottle strength. In those tests the StarLite Tropical design resulted in improved bottle stability and, again, more resistance to extreme temperatures (hot and cold). The Sidel StarLite Tropical base is already in production in far-eastern countries. The improved bottle stability is achieved through the enhanced base standing surface. High surface contact of the base’s feet ensures easy bottle transportation and smooth conveying, an efficient solution for even high-output lines. This prevents bottles falling when passing through machine interfaces within the PET bottling line and results in a higher production uptime. Base moulds for all production configurations Having an enhanced venting design, the new Sidel StarLite Tropical base moulds are offering an optimised cooling capacity to further improve bottle base performances. Available for all Sidel moulds, they are easy to implement in PET production lines and can even be retrofitted to existing Sidel CSD moulds to adapt bottle designs, says the company. The new base can be applied to all lines equipped with any generation of Sidel blowers, in standalone - with an additional post-mould cooling base device - or Combi configurations. www.sidel.com Environments with very high temperatures or a particularly humid climate can have an impact on the resistance of PET bottles. The latest addition to Sidel’s StarLite range of bottle bases is intended to ensure better bottle performance for carbonated soft drinks (CSD) produced and distributed in extreme environmental conditions.","@ID":12}, "MARKET SURVEY 27 PETplanet Insider Vol. 18 No. 03/17 petpla.net 03/2017 MARKETsurvey Preforms & preform inspection Recycling plants & washing units Palletising & shrink film machinery Caps & closure systems & CC inspection Labelling & marking systems Recycling: Cutting plants Filling equipment & filling inspection Resins, additives Compressors SBM machinery & quality inspection Suppliers of recycling plants and washing units As one of the first market surveys this year we decided to show our readers new developments of the recycling industry. Detailed information about plants and some new added question regarding washing units conclude this survey. This year 12 companies took part, they are shown in the order in which their details were received by the editors: Gneuss Kunststofftechnik GmbH, Erema Group GmbH, Previero N. srl - Sorema div. of Previero, Amut Spa, STF Group, Ko Win Yang Industrial Co.Ltd, Krones AG, ProTec Polymer Processing GmbH, Empacar S.A., Starlinger & Co. Gesellschaft m.b.H., Polymetrix AG and Herbold Meckesheim GmbH. Although the publisher have made every effort to ensure that the information in this survey is up to date, no claims are made regarding completeness or accurancy. Company name Gneuss Kunststofftechnik GmbH Erema Engineering Recycling Maschinen und Anlagen Ges.m.b.H. Postal address Telephone number Web site address Contact name Function Direct telephone number Fax E-Mail Mönichhusen 42, 32549 Bad Oeynhausen, Germany +49 5731 5307 0 www.gneuss.com Unterfeldstraße 3, 4052 Ansfelden, Autria +43 732 3190-0 www.erema.at Mr Christoph Wöss Business Development Manager, Application Bottle +43 732 3190 352 +43 732 3190 23 c.woess@erema-group.com Bottle to granulate Input variable: collected pressed bottles, various colours Engineering of washing lines with long term partners Yes, washing done in cooperation with long-time partners Output: granulate with approval Yes Capacity [t/a] Up to 17,000 Floor space [m²] Which approvals FDA, ESFA (pending), INTI, brand owners (conf.) Fresh water consumption per tonne output [m³/t] Depending on bottle contamination Consumption kWh per tonne output [kWh/t] Depending on input material Flakes to granulate Input variable: flakes, coloured proportion max 5%, not much chlorine Specification of input flakes for Vacurema: higher contamination can influence pellet quality but are basically possible to process, after discussion and agreed by Erema Output: granulate with approval FDA, ESFA (pending), brand owners (conf.) FDA, EFSA (positive opinion issued), ANVISA, ilsi, BGBI, brand owners Capacity [t/a] 200 - 17,000 Up to 32,000 Floor space [m²] 30 - 80, depending on size Depending on through-put and technology: 50 - 600 Which approvals FDA, ESFA (pending), INTI, brand owners (conf.) FDA [cat. A-H&J]; EFSA (pending); brand owners (conf.); several national approvals (Austria, CH, Zona Mercursur, etc.) Fresh water consumption per tonne output [m³/t] no fresh water needed Depending on application & technology type, there is a closed loop system Consumption kWh per tonne output [kWh/t] 350 Between 250 - 350 Bottles to flakes Input variable: collected pressed bottles, various colours Specification of input flakes for MPR: Higher contamination can influence flake quality but are basically possible to process, after discussion and agreed by Erema Output: flakes with/without approval FDA [cat. A-H&J]; EFSA (pending); with Multi Purpose Reactor (MPR) Capacity [t/a] Up to 20,000 Floor space [m²] Between 20 - 60 Which approvals FDA, EFSA (positive opinion issued) Fresh water consumption per tonne output [m³/t] Closed loop system Consumption kWh per tonne output [kWh/t] 100 Kind and quantity of detergents Removal of the organic residuals up to which size [μm] Presetting residence time in the process Company also offers systems for Bottle-to-film Yes, mainly thermoforming sheet lines in direct food contact Yes, Vacurema Inline preform (Xtreme Renew) Bottle-to-fibre Yes, several lines under operation worldwide Yes, Vacurema Inline sheet Bottle-to-strapping Yes, several lines under operation worldwide Yes, Vacurema Inline fibre, Yes, Vacurema Inline strapping","@ID":29}, "PETplanet Insider Vol. 18 No. 03/17 petpla.net 47 BOTTLES Mouthwash with whitening effect Under “CB12“ brand, Meda Pharma S.p.A, through its German subsidiary, distributes an alcohol-free mouthwash which gives pleasant breath for 12 hours and with longer use – two weeks – can make the teeth whiter. Unlike the more expensive competitor’s product, it is filled into a 200ml bottle with an all-round self-adhesive label. To distance itself further from the competition and to be eye-catching, the bottle has a metallic shiny screw cap with a tamper-proof band. www.cb12.de Washing up with orange and cinnamon Aldi Süd is selling a hand wash with high grease-removing properties based on the natural effect of orange and cinnamon on offer under its ”alio” own brand. A litre of the orange-coloured product is packed into a clear bottle made from 100% recyclable material and has an integrated gripping area. The screwon, two-colour push-pull closing device makes it easier to dose small amounts of the highly-effective hand wash. Two self-adhesive shaped labels round off the item’s look. www.aldi-sued.de Connecting Global Competence World’s Leading Trade Fair for the Beverage and Liquid Food Industry Processing + Filling + Packaging + Marketing September 11–15, 2017 Messe München, Germany, drinktec.com Fresh. Different. Personal. Take your business to the next level. In talks with experts from over 180countries. Explore ideas, innovations and investment at the No. 1global communication platform. Welcome to drinktec, the leading trade fair for the international beverage and liquid food industry. drinktec. Go with the flow. Get your ticket now! drinktec.com/tickets Follow us:","@ID":49}, "43 ON SITE PETplanet Insider Vol. 18 No. 03/17 petpla.net PET Technologies to install its blow moulding machine at Bear Beer plant Bear Beer is the market leader in Kyrgyzstan and produces over 38l/minute - 25 bottles à 1.5l - both of soft drinks and beer. This is where technologies and equipment play a key role. PET Technologies installed and integrated its automatic stretch blow moulding machine APF-6004 with the output 6,000bph for up to 2l with the filling line of the European provider. The customer has chosen this solution due to the need to produce nine formats from 0.5l to 1.5l. According to Bear Beer representative, they have chosen this blower due to its technical features: easy control and maintenance, low rejection rate, intensive heating system with IR lamps and eight temperature regulation zones with independent deactivation to form bottles with original shape. PET Technologies R&D Department also developed nine mould sets to produce bottles for different types of beverages. www.pet-eu.com ONsite","@ID":45}, "PETcontents 03/17 4 PETplanet Insider Vol. 18 No. 03/17 petpla.net INSIDE TRACK 3 Editorial 4 Contents 6 News 42 Products 43 On-site 44 PET bottles for Beverage + Liquid Food 46 PET bottles for Home + Personal Care 48 Patents MATERIAL / RECYCLING 8 Bottle-to-bottle flakes with FDA approval BOTTLE MAKING 10 CSD in harsh conditions Increased resistance and stability for CSD bottles 37 Stretch blow molding Part 1: A short history of stretch blow moulding & material basics BOTTLING / FILLING 11 Tea or coffee? Both! Filling philosophy has changed: Aseptic instead of hot fill INSPECTION 14 Check first! Inspection systems at a glance 15 Rising to new challenges All around inspection for PET bottle production 16 Non-destructive measurement Inspecting barrier layers in transparent and coloured translucent preforms 18 No replication - no limitation Inspection for advanced packaging designs 22 News in online wall thickness measurement Unique sensor technology improves PET blow moulding processes 24 Polarised light is the key High speed preform inspection system updated 26 Metal detection AptarGroup uses Sesotec metal separators to protect its machines and avoid product contamination 31 The automated laboratory Increased testing throughput in one compact area 32 Best selection Preform handling at Rivella 33 Flying closure for accurate inspection Closure inspection system IMDvista Twin with new conveying technology MARKET SURVEY 27 Suppliers of recycling plants & washing units CONVEYING 34 Variable conveyer speed for optimal material handling Energy-efficient technology improves productivity TRADE SHOW REVIEW 40 The next Big Bang in India’s packaging industry Bangalore conquers the north of the subconti- nent - an interview with Manjushree Technopack BUYER’S GUIDE 49 Get listed! INSPECTION S P E C I A L Page 8 Page 18","@ID":6}, "MARKET SURVEY 28 PETplanet Insider Vol. 18 No. 03/17 petpla.net Company name Sorema div. of Previero N Srl. Amut SPA STF Maschinen- und Anlagenbau GmbH Ko Win Yang Industrial CO., LTD Krones AG Postal address Telephone number Web site address Contact name Function Direct telephone number Fax E-Mail Via Per Cavolto 17, 22040 Anzano del Parco (CO), Italy +39 031 63461 250 www.sorema.it Mr Dario Previero General Manager +39 031 63491 250 +39 031 63491 217 sales@sorema.it Via Cameri 16, 28100 Novara, Italy +39 0321 6641 www.amutgroup.com Mr Piergianni Milani President +39 0321 664 941 p.milani@amut.it Industriestr. 2, 94529 Aicha v. Wald, Germany +49 8544 960 110 www.stf-group.de Mr Markus Ingenpaß Sales Manager +49 8544 960 110 +49 8544 960 130 contact@stf-group.de No. 81, Ln. 56, Chung Chow Rd., Long Jing Dist., Taichung City, Taiwan 43451, China +886 4 26300 888 www.kowinrecycle.com Ms Joanna Liang Sales +886 9 21724528 +886 4 26300 869 sales1@kowinrecycle.com.tw Böhmerwaldstrasse 5 93073 Neutraubling, Germany +49 9401 70 0 www.krones.com Mr Peter Hartel Head of Sales PET Recycling +49 9401 70 5448 +49 9401 70 91 5448 peter.hartel@krones.com Bottle to granulate Input variable: collected pressed bottles, various colours Yes Bottle sorting with long time partners; engineering, washing technology and decontamination technology from Krones; turnkey solution Output: granulate with approval No Yes Capacity [t/a] 3,000 - 45,000 500 - 600kg/h 3,500 t/a - 30,000 t/a Floor space [m²] In function of size and stream quality 900 1,000 - 6,000 Which approvals Tüv Rheinland certificate, DUNS registered certificate & The 21st Taiwan SMEs Innovation Award FDA-LNO, EFSA-LNO, brand owners Fresh water consumption per tonne output [m³/t] Depends on stream quality 16 Max 2,5 Consumption kWh per tonne output [kWh/t] 300 - 600 744 Depending on design Flakes to granulate Input variable: flakes, coloured proportion max 5%, not much chlorine Yes Engineering and washing technology and decontamination technology from Krones; turnkey solution Output: granulate with approval No Yes Capacity [t/a] 3,000 - 45,000 500 - 600kg/h 3,500 t/a - 30,000 t/a Floor space [m²] In function of size and stream quality 700 800 - 3,000 Which approvals Tüv Rheinland certificate, DUNS registered certificate & The 21st Taiwan SMEs Innovation Award FDA-LNO, EFSA-LNO, brand owners Fresh water consumption per tonne output [m³/t] Depends on stream quality 11 Max 2.5 Consumption kWh per tonne output [kWh/t] 300 - 600 647 Depending on design Bottles to flakes Input variable: collected pressed bottles, various colours 1,000 - 10,000kg/h Yes Deposit, curbside, MRF/PRF-collection, loose or baled, all kind of colours, other plastics, other contaminations Bottle sorting with long time partners; engineering, washing technology and decontamination technology from Krones; turnkey solution Output: flakes with/without approval 600 - 7,000kg/h Yes Flakes with/without approval: PET flakes with approval (FDA, EFSA) Flakes with/without approval Capacity [t/a] Depends on the different recycling plants 3,600 - 45,000 1 t/h up to 6 t/h 500 - 1,000kg/h 3,500 t/a - 30,000 t/a Floor space [m²] Depends on the different recycling plants In function of size and stream quality 1,000 - 2,000 600 1,000 - 4,000 Which approvals Depends on the different recycling plants FDA, EFSA, brand-approvals Tüv Rheinland certificate, DUNS registered certificate & The 21st Taiwan SMEs Innovation Award FDA-LNO, EFSA-LNO, brand owners Fresh water consumption per tonne output [m³/t] Depends on the different recycling plants 1 Different water circulation & treatment systems, from 1 - 0.1 fresh water (zero discharge) 14 Max 2.5m³/t Consumption kWh per tonne output [kWh/t] Depends on the different recycling plants 250 - 300 200 - 250 sorting, grinding & washing line total 321kw Depending on design Kind and quantity of detergents Non disclose Caustic soda, detergent from various brands. The quantity of detergent depends on the brand, approx. 0.5-1l/t 1) Customer can buy suitable detergent in the local market 2) Detergent quantity : Adjust according to the actual washing situation; Ko Win washing machine can recycle and reuse the detergent so as to reduce the detergent consumption Removal of the organic residuals up to which size [μm] 50ppm Total removal of residual organics on flakes, filtration of water 0,015μm possible Up to 5ppm for the final product Presetting residence time in the process Non disclose 45 - 60 minutes, continuous fall system It will be 30 - 45 minutes Company also offers systems for Bottle-to-film Yes Yes Bottle-to-fibre Yes Yes Bottle-to-strapping Yes Yes","@ID":30},
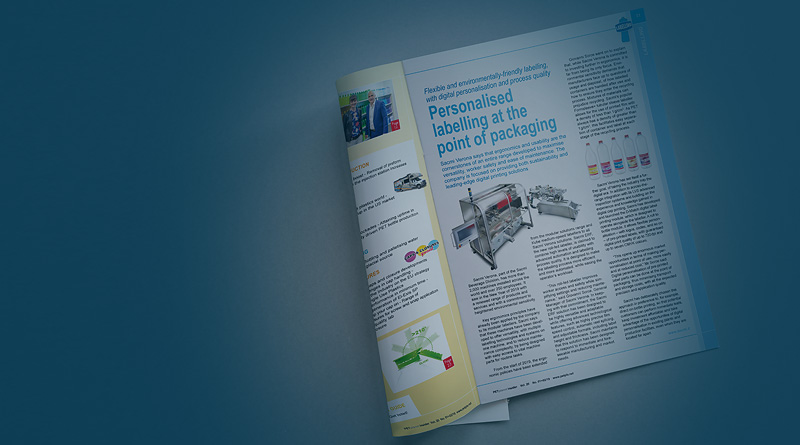