{"pages":{"page":[{"#text":"8 NEWS PETplanet Insider Vol. 22 No. 05/21 petpla.net Engel live e-symposium 2021 will take place virtually in June Injection moulding machine manufacturer and system solution provider Engel is inviting customers to the live e-symposium 2021 from 22 to 24 June. For the first time, Engel’s traditional in-house exhibition will be a virtual event, enabling even more customers, partners and interested parties from all regions of the world to join in. Several thousand guests are expected. For three days, everything in Engel’s virtual world is revolving around the current and future challenges in injection moulding. How can the new possibilities of digitalisation be converted into opportunities? Which innovative technologies have the potential to increase competitiveness? And how can you reconcile sustainability and cost effectiveness? In keynote presentations and business talks – each with live moderated Q&A sessions – experts from Engel and other companies will provide answers to these and other burning questions. 25 machine exhibits in the virtual showroom as well as virtual tours through the Engel plants in Austria provide insights into innovative applications and development focuses. Engel’s Global Sales, Customer Service and Development teams are available for one-on-one meetings. All program items, such as the lectures and guided tours, will be offered in a total of seven languages. In addition, the presentations have been adapted to the individual requirements of each country and region. www.engelglobal.com New production site for Constantia Copenhagen The new site of Constantia Copenhagen in Ishøj, Denmark, is enabled with a fully automated production process which improves flexibility. In addition, the warehouse is now fully integrated within the site to enable further growth. The fully automated production site of Constantia Copenhagen covers a total area of 6,000m² where the flexible packaging producer can integrate more processes and products to expand its business. The new location uses a number of robotics technologies and a further increased level of hygiene measures. The packaging solutions produced at Constantia Copenhagen are claimed to meet high sustainability standards. In addition the site is entirely powered by greenelectricity. PimVervaat, CEO of Constantia Flexibles, states: “With more than eight million euros of investment we have built a state-ofthe-art facility which will serve our customers more efficiently with sustainable die cut lid products in the dairy market. Moreover, tripling our capacity through the enlargement of the site and the integrated warehouse ensures the best foundations for future growth and success. We are putting in place the highest health and safety standards for our employees, which remain our highest priority and asset.” www.cflex.com Wisecap welcomes new R&D Manager Wisecap Group has announced the appointment of its new R&D Manager Cristian Bugatti. This new entry is intended to drive the Group activities in the field of new developments and bears witness to the level of commitment and investments that Wisecap is dedicating to this activity. Cristian Bugatti has worked for a number of years in Product Design & Development in the field of plastic closures for both beverage and pharma application. His expertise and know-how are expected to give a strong push to the Group Innovation Team by leading current and future developments throughout the various markets that Wisecap presently serves. Sustainability, carbon footprint reduction and a renewed circular economy approach are also intended to be other main areas of focus in the activity of Cristian. www.wisecap.eu Indorama Ventures expands its sustainable brand platform with carbon neutral PET Indorama Ventures PCL (IVL), a leading chemicals and recycling company, is expanding its portfolio of sustainable solutions under its Deja brand. The global sustainable ingredients brand is a key part of the company’s commitment to meet growing demand for high performance products which will reduce impact on the environment, as IVL states. Deja Carbon Neutral PET pellet is claimed to be the world’s first certified carbon neutral PET pellet solution. It is an addition to the growing Deja portfolio, which includes sustainable PET, rPET, polymer and fibre range of products available across flake, pellet, fibre and filament ingredients. Deja Carbon Neutral PET pellet has been sustainably produced throughout its supply chain and helps environmentally conscious companies to achieve their sustainability targets by lowering their Scope 3 GHG emissions. Deja fibre and polymer products are claimed to offer high performance and versatility, with a lower carbon footprint. They can be applied to a wide range of applications across the hygiene, lifestyle, automotive and packaging sectors, while meeting the standards demanded by these specialist sectors. Deja Carbon Neutral is a PET proposition with neutralised raw material emissions, from cradle to IVL’s plant gates. It comes with an independently verified carbon neutral certification of compliance from globally established providers. Through a partnership with South Pole, a leading project developer and provider of global climate solutions, IVL offsets unavoidable carbon emissions through projects that help transform lives and protect the environment. www.indoramaventures.com","@ID":10} "TRADE SHOW REVIEW PETplanet Insider Vol. 22 No. 05/21 petpla.net 36 Chinaplas 2021 – PET exhibitor impressions Chinaplas 2021 was concluded at the new venue at Shenzhen World Exhibition & Convention Center on April 16 with a total of 152,134 visitors (149,771 local and 2,363 overseas). Though the total number of visitors this year dropped by 6.85%, the number of local visitors has increased by 23.46% compared to the previous edition in Guangzhou in 2019. In addition, the official live streaming platform has attracted 363,000 audiences. PETplanet was represented locally on site and was able to visit some exhibitors from the PET value chain for you.","@ID":38} "PETplanet Insider Vol. 22 No. 05/21 petpla.net 44 PETbottles Home + Personal Care Rose cleansing water Garnier has altered the packaging of its micellar All-in-1 rose cleansing water. The lightly coloured product now comes in a 375 ml instead of a 400 ml bottle which, according to the label, consists of 20% recycled material. The hinged press-down lid has been designed in such a way that it can no longer be unscrewed from the bottle. The inside of the reverse side label has a print of a rose blossom which is clearly visible through the transparent front sticker. www.garnier.de A bottle with a tag The Berlin-based company, Beautypunch Ltd, is selling various hair care products under its “Nature’s Paradise” label which come in eye-catching coloured PET bottles, 25% of which are made from recycled material. The products are 100% vegan including ingredients from exotic superfruits and superfoods and created using the latest technology. The pictures show two conditioners: one containing cranberry pulp and passion fruit, and the other cactus juice with Kakadu plum. The products come in a slim, long-necked 375 ml bottle and are applied via a disc-top cap which is secured with a snap-on action. A paper tag attached to the neck of the bottle highlights the products’ 98% natural ingredient content and attracts attention when displayed on the shelves. www.naturesparadise.de A foam bath with Thailand Feeling The German company, Vendoleo GmbH, has brought out a number of wellness products under its “Oriniq” label whose ingredients are associated with certain countries or regions. For example, the “Thailand Feeling” range features products such as orange blossom and bamboo, and “French Grape Luxury” containing grape seed oil. One product from the “Thailand Feeling” range is a soothing bubble bath that comes in a shiny, orange 500ml bottle. Two clear self-adhesive labels provide information about the product and its contents. A black screw cap completes the packaging. www.oriniq.de A refreshing facial toner Beiersdorf has brought out a refreshing facial toner product that offers the customer a thorough facial skin cleansing. It comes in a slightly bluish 200ml bottle that consists of 95% recycled material. The facial toner has been created to act in harmony with the skin’s microbiome for gentler care and protection. The product is applied via a hinged lid with a slanted top and dispensing spout. A small adhesive sticker on the cap explains the “microbiome” balance. www.nivea.de","@ID":46} "41 PRODUCTS PETplanet Insider Vol. 22 No. 05/21 petpla.net PETproducts Automating octabin assembly for preform packaging The use of octabin cardboard packaging for the handling and transport of PET preforms is becoming more widespread, because of a number of benefits and advantages compared over metal, wood, or plastic box packaging. These advantages include lower unit cost, good recyclability and lower environmental impact. The process of assembling octabins or other containers is, traditionally, a manual process and not always simple, with consequences for the operating cost of the final product. And&Or has developed a solution that offers the preform industry complete automation of octabin formation, transport to loaders and pick-up of filled boxes, as well as its labelling and wrapping. The automation of this process offers labour cost savings along with improvement in quality and traceability of the product during manufacture. Octabin forming work cells – or ‘islands’ – are custom designed for the floor space and specific requirements of each client. The process starts with the empty pallet dispenser, which can be complemented with metal or plastic box dispensers if required. The base or cover formation area, a cardboard forming machine, can work with hot glue equipment or a cardboard fitting system. The product is then moved to the body formation area, where a robot forms the unit into the required octabin format. At the next stage, a preformed, rollfed bag is inserted into the body by a machine that can work with different bag sizes, depending on the octabin presented to it. Body and base joints are then sealed by an automatic wrapping machine. Formed octabins are then delivered to the filling area, either by AGV or manually, with an electric stacker or truck; the filled packages are then transported to the collection area, manually or by AGV, labelled and readied for delivery to the warehouse. www.andyor.com Greiner Packaging introduces sustainable rPET cups for beer and other drinks Greiner Packaging has introduced sustainable rPET cups for beer and other drinks. Mechanical recycling of PET is already a viable option thanks to the high degree of purity and the material streams available. The cup concept will potentially allow for a dedicated recycling loop – for instance, at events. Greiner Packaging’s new plastic beer cup is currently made from 100% rPET, but can be made with 30 to 50% rPET if requested by a customer. The cups make an appealing visual impression thanks to attractive printing options and they are suited for embossing the required EU markings during mass production. Greiner Packaging has already produced an initial series of sample batches. www.greiner-gpi.com/en","@ID":43} "COMPRESSORS PETplanet Insider Vol. 22 No. 05/21 petpla.net 15 Sánchez: Unfortunately, the situation worldwide is going through a hard time. Our team works daily towards sustainability and efficiency. A few months ago, we launched a new system: SynchronizAir, a unique versatile and efficient optimisation system able to coordinate different compressor brands from a single place that avoids cascade regulation. We dedicate an important budget for our R&D department and new things are in the offing. PETplanet: On your homepage you have created access to a virtual showroom. Can you briefly tell us what interested people can find there? Sánchez: We created the virtual showroom with the idea of getting closer to our customers. Unfortunately, last year was an unusual situation and we tried to adapt as all exhibitions were cancelled. By visiting the virtual showroom, customers can get information about our products, services network, as it you would by visiting our booth in an exhibition. PETplanet: Should the showroom be a permanent addition to the trade fair business, also post-Covid? Sánchez: Most probably this showroom will be a permanent addition to the trade fair business, also post-Covid. The pandemic has changed many things and way of doing business and approaching our customers is one of them. PETplanet: In a former Q&A with ABC, it was mentioned that increasingly, desiccants have to be installed with the compressors, as gases from the refrigeration dryers become a concern for major players. What is the current situation? Sánchez: It is true, and some big players have literally forbidden refrigeration dryers. However, it is also true that new eco-friendly gases are coming along and are accepted in the industry. Luckily, we can offer both refrigeration and adsorption dryers. PETplanet: We can’t talk about compressors without addressing the issue of energy costs. What saving methods are currently being used and where might there still be scope for optimisation? Sánchez: Optimisation is a must for our customers. With the VSD (variable speed drive), adapting the air flow requests allow our clients to become more sustainable and efficient, being able to cut their energy cost up to 75% in unloading scenarios. We modulate the compressor capacity by regulating the motor speed, and therefore the piston strikes per minute, minimising the energy consumption. HRS (heat recovery system) is also regularly requested by our customers, where we can recover over 50% of the motor consumption in hot water. Our DUOO system (one compressor for both HP and LP simultaneous production) and the SynchronizAir, our latest releases, have been directly focused on energy savings. Our goal is to become the first compressor manufacturer that avoids unloading scenarios. PETplanet: VSD, HRS - the more regulation options a compressor has, the more complex the operation of the system becomes if you want to make full use of all the optimisation options. Has your training and service work changed over the years? Sánchez: We run ad-hoc training courses for our service agents and we arrange technical training according to their needs and characteristics of their compressor. This way, we ensure we cover not only the normal operation topic, but as well the different add-ons and features they have in the compressor. PETplanet: Mechanical engineering companies are increasingly complaining about higher steel prices and, above all, delivery delays. Is this a problem that concerns you? Sánchez: Not really. Luckily, our region is well-known for its manufacturing industry, and most of our suppliers are less than 150 km away. Even if it means higher raw material cost, it also means shorter deliveries, easyto-handle urgent situations and less transport contamination. PETplanet: Can you tell us about recently completed projects in the PET area? Sánchez: The Horizon range was launched in 2016 and currently there are around 1,000 units running across the world. Still we are expanding our business operations worldwide and ABC is recognised as one of the main players in HP compressors for the PET industry. Our International Commercial Team has been increased to reinforce our presence in the market, to enable us to be closer to our customers. Many players are now considering compressor updates or replacements due to energy consumption, and here is where we have something to say. Some of the latest projects have been turnkey ones, and we are good at tailor-made solutions. PETplanet: Which projects were particularly demanding to realise? Sánchez: There have been different challenges related not only to the plant location but also to the specific non-standard requests from our customers. As mentioned, our R&D budget is quite significant, and we like challenges. High altitudes, extreme temperatures, small spaces, irregular air demand, dual pressure ... PETplanet: In which regions and countries do you see the biggest potential for growth? Sánchez: Those where the population keeps increasing and production capacity lags behind: Africa, South-East Asia, the Middle East ... PETplanet: Thank you very much! Inmaculada Sánchez: “The pandemic has changed many things and especially how we do business.”","@ID":17} "PATENTS PETplanet Insider Vol. 22 No. 05/21 petpla.net 47 Underside shape Internal Patent No: WO 2020/ 081248 A1 Applicant: Pepsico Inc., Purchase (US) Registration date: 3.10.2019 This application describes the special geometric design of the underside of a plastic bottle intended for carbonated drinks. A robust bottle Internal Patent No: WO 2020/ 079122 A1 Applicant: Société des Produits Nestlé, Vevey (CH) Registration date: 18.10.2019 A thin-walled plastic bottle with specially shaped, graduated, reinforcing grills, designed to withstand lateral forces particularly well. Bottle with a bottom cap Internal Patent No: WO 2018/ 203146 A1 Applicant: Resilux N.V., Wetteren (BE) Registration date: 2.5.2018 The proposal is to clip on a suitably shaped bottle cap to enhance the underside area of a PET bottle for carbonated drinks in terms of its appearance, stability and resistance to breakages. Producing containers in a 3D printing process Internal Patent No: WO 2020/ 088944 A1 Applicant: Alpla Werke Alwin Lehner Co. Ltd., KG, Hard (AT) Registration date: 17.10.2019 The proposal is to create a supporting area of a container (side edges/ shoulder region) necessary for stability within the 3D printing process to withstand a wide range of materials. The thickness of the material in other areas is limited by the required barrier properties. A dual use bottle Internal Patent No: WO 2020/ 087142 A1 Applicant: Silton Batista Lima Bezerra, Brasilia (BR) Registration date: 27.9.2019 The outside of this plastic bottle has features into which the top side/thread of a similar bottle can be screwed. The bottle can be used in two ways: as a plaything or decorative item or for similar purposes. Plastic bottle European Patent No: EP 3216710 B1 Applicant: Suntory Holdings Ltd., Osaka (JP) Registration date: 29.10.2015 This European Patent describes the design of a light-weight plastic bottle whose underside and side walls are specially shaped to be sufficiently robust despite weighing very little. PETpatents","@ID":49} "TOP TALK PETplanet Insider Vol. 22 No. 05/21 petpla.net 10 to meet several needs in terms of competitiveness, efficiency, flexibility and ease of use for thousands of customers all over the world. IoT technology allows the operating data, for all of the equipment in a production facility, to be collected and clustered in a single management and control platform; thus provides a real-time continuous monitoring of industrial plant efficiency and the ability to intervene remotely on every decentralised system point, in the event of anomalies or problems. This makes it possible to get information in real time both from an aggregate point of view (production volume, mean production time, consumptions, inventories and stocks) and from each single machine. If there were any doubts about the necessity of digital transformation to business longevity, the coronavirus has silenced them. In a contactless world, the vast majority of interactions with customers and employees must take place virtually. With rare exception, operating digitally is the only way to stay in business through mandated shutdowns and restricted activity. This digital mandate isn’t new; it’s simply been brought into sharp focus. Just before the pandemic for example, SMI developed the new service of Augmented Reality smart glasses to make customer assistance smarter and easier. Through this system customers receive audiovisual support and it is possible not only to troubleshoot, but also to carry out installation and start-up of machines. Today, thanks to augmented reality technology, SMI customers can benefit from immediate technical support in real time, even if they are thousands of kilometres apart. This remote support service, inspired by the most recent innovations in IoT and Industry 4.0, uses augmented reality technology to create a “ virtual presence” communication system. Thanks to this system, SMI technicians can provide increasingly effective, timely and high-quality remote support to the customer’s operator, guiding him during repairs and maintenance by sharing useful and practical information. By wearing special glasses, called Augmented Reality Glasses, the machine operator can remotely send real-time images of the problem he is facing to an SMI expert at the Help Desk, in order to receive direct and immediate instructions on how to resolve the critical situation. This solution allows the reduction of both the length of the intervention and the related costs, as it does not require the physical presence of an SMI expert at the customer’s company and considerably reduces the “downtime” of machines and systems. PETplanet: Due to postponed or cancelled trade fairs and congresses many companies offer digital events directly from their production sites to stay present and in conversation. Are you planning such events? Paolo Nava: Nowadays we have been forced to change our habits, our behaviour, our consumption patterns and above of all we have been obliged to minimise social contacts. This has also led to the cancellation or postponement of exhibitions, events that have always been an occasion to create or consolidate social relations and to show innovations. Despite the physical distance we have had to keep, we have never stopped being by our customers’ side: AR smart glasses and online help desk services are just an example; however we’ve tried to go beyond online assistance and for this reason we have decided to create a “Virtual Expo”, a digital space dedicated to the interaction between us and our current and future customers. In this virtual space visitors can find our new developments and machine advantages through brochures, videos and pictures. Furthermore, visitors can ask for information through an online form and get in touch with our staff. Virtual tours aren’t new to SMI, since we already proposed it some years ago when we invited our customers to take a tour inside a complete water-bottling line. Using this technology we allowed visitors to step into the production sites of a SMI customer and take a close look at a whole bottling and packaging line without being on the spot physically. The virtual visitor could freely move within a range of 360° inside the facility and get detailed information over each single machine. We then realised that customers appreciated virtual events, as they save time and money - but, of course, they can’t replace face-to-face meetings. PETplanet: Due to the vaccination campaigns worldwide, the situation seems to be easing, although there are still exceptions, of course. What is SMI’s concept for restoring full capacity? Paolo Nava: Coronavirus has completely changed life and, while many hope those changes are temporary, the pandemic has unearthed weaknesses in the status quo. After every major crisis, humanity is forced to identify those weaknesses and evolve accordingly. I think that everybody agrees in the fact that Covid-19 will change life for a very long time. Vaccination campaigns worldwide will help solve the situation, but in 2021 we will continue to see changes as a result of the pandemic and this will involve technology, digitalisation, online and virtual services. Covid-19 forced companies, governments and social systems to change swiftly around the globe. Even prior to the pandemic, technology had become an increasingly important part of the workforce. Businesses were looking at technology as a helpful means of engaging with customers, allowing some workplace flexibility, and for a way to introduce automation and faster processes. However, the spread of the new coronavirus and the shutdown of in-person meetings for non-essential businesses accelerated these adoptions immensely. It forced companies to look into creative digital solutions, so that organisations could continue to function remotely and to serve their client base. Many changes have been made in response to the pandemic; anyway many of them are here to stay. Only when in-person meetings and work was limited in response to Covid-19, everybody quickly realised how powerful technology can be. The pandemic helped accelerate the digital transformation and created a landscape that will continue to encourage innovation and technological adoption moving forward. PETplanet: Where do you see potential in the packaging market and what are the strengths of SMI that you would like to develop further? SMI’s Ecobloc system","@ID":12} "OUTER PLANET 54 PETplanet Insider Vol. 22 No. 05/21 petpla.net OUTER PLANET Bio2Bottle: Biodegradable bottles made from bioplastics The Fraunhofer Institute for Environmental, Safety, and Energy Technology Umsicht is conducting research on bio-based and recyclable plastics together with four other partners. The aim of the joint project “Bio2Bottle” is to develop bio-based bottles that satisfy high standards and are biodegradable and recyclable at the same time. Target demonstrator products are bottles for the packaging of cleaning agents and agricultural soil additives. The permeability of plastics made from renewable raw materials available today is too high for this application and they do not meet all requirements. The environmental awareness that has arisen among both end consumers and industrial companies is leading to an even greater demand for sustainable products in the future. In their sales strategy, companies are increasingly focusing on recyclability and even biodegradability. The “Bio2Bottle” project, which is coordinated by Fraunhofer Umsicht, starts precisely here and has set itself the goal of developing a bio-based and recyclable plastic for the production of bottles. Requirements for biodegradable bottles Some marketable products already use bottles made from bio-based plastics such as polylactic acid (PLA). PLA is a bio-based polyester based on lactic acid with a high mechanical resilience, similar to PET. However, the material is not suitable for the intended applications due to an insufficient water vapour barrier. The focus of the “Bio2Bottle” project is the development of a bio-based plastic that is simultaneously suitable for the storage and transport of cleaning agents and agricultural soil additives, recyclable and biodegradable. Key requirements for these applications are high water vapour barrier, stability and melt viscosity of the material. Carbon dioxide and oxygen permeability, as well as gamma sterilisation, will also be considered in the development. In addition to these stringent requirements, the materials must be recyclable and biodegradable - even outside industrial composting facilities. “In the joint project, bio-based polymers are selected and their properties are modified by compounding with additional components in such a way that these high requirements are met,” explains Inna Bretz, head of the Department of circular and bio-based plastics at Fraunhofer Umsicht. “The goal of the project is to combine bio-based materials and recyclability,” she continues. Fraunhofer Umsicht already has many years of experience in the development of marketable plastic materials based on renewable resources. With the “Bio2Bottle” project, the institute ensures that the material development meets the special requirements of the customers for their application. Furthermore, the joint project aims to demonstrate that the bottle material can be reprocessed in a technically efficient recycling process, making it more competitive. The long-term use of the bottles as well as their reuse leads to less plastic waste and a reduced consumption of fossil raw materials for short-term products. In addition to this, the biodegradability of the bio-based bottles will be investigated and tuned under the coordination of Fraunhofer Umsicht. Project cooperation Four industrial companies and Fraunhofer Umsicht teamed up for the joint project “Bio2Bottle”. The cooperation partners include: Fraunhofer Institute for Environmental, Safety and Energy Technology Umsicht, Oberhausen Cleaneroo GmbH, Berlin UnaveraChemLab GmbH (Unavera), Mittenwald, Germany FKuR Kunststoff GmbH (FKuR), Willich Fritzmeier Umwelttechnik GmbH & Co. KG (FMU), Großhelfendorf, Germany - associated partner www.umsicht.fraunhofer.de In the twin screw extruder, compounds can be produced from biobased components, for example. This is what a durable biodegradable bottle could look like","@ID":56} "MARKET SURVEY 27 PETplanet Insider Vol. 22 No. 05/21 petpla.net 05/2021 MARKETsurvey Suppliers of preform and SBM moulds In this issue of PETplanet we are very glad to present you an update of mould manufacturing for perform and SBM moulds. Please have a close look at the companies showing their newest developments: PETform Technologies, Wentworth Mold, Sipa, Kosme, SMI, Röders, Krones, KHS, Hallink, Vitalii & Son, PET Technologies, GDXL, Moldintec, Sacmi Imola, MHT, Petka Kalip, Otto Hofstetter, StackTeck and Husky. Although the publishers have made every effort to ensure that the information in this survey are up to date, no claims are made regarding completeness or accuracy. Resins & additives Preform machinery Preform production & inspection systems Preform & SBM mould manufacturer SBM 2-stage Compressors Caps & closures & inspection systems Filling equipment & inspection systems Recycling machinery Palletising & shrink film machinery Stretch Blow Moulds Company name Röders Tec Sipa S.p.A. Hallink Moulds Inc. GDXL Precise Machinery Co., Ltd. Vitalii and Son Postal address Telephone number Web site address Contact name Function Direct telephone number E-Mail Scheibenstraße 6, 29614 Soltau, Germany +49 5191 603 53 www.roeders.de Mr Steffen Lühning / Mr Jani Rickert Sales Manager +49 5191 603 822 / +49 5191 603 340 mold@roeders.de Via Caduti del Lavoro 3, 31029 Vittorio Veneto, Italy +39 04389 11511 www.sipa.it Mr Paolo De Nardi Product Manager SBM +39 0438 911511 p.denardi@zoppas.com 284 Pinebush Road, Cambridge, Ontario N1T 1Z6, Canada +1 519 624-9720 www.hallink.com Mr Jason Warmington General Manager +1 519 624 9720 jwarmington@hallink.com No. 18 Changjiang Road, Guicheng, Nanhai, Foshan city, Guangdong Province, China. Postcode: 528251 +86 757 8677 7168 www.gdxl.com Mr Billy Ay Marketing Specialist +86 757 8677 7168 ext 8681 billy.auyeung@gdxl.com #276, bul. Vladislav Varnenchik 9009, City Varna, Bulgaria +359 887 978757 www.vitaliiandson.eu Mr Vitalii Marinyak Executive Director +359 888 518782 office@vitaliiandson.eu Stretch blow moulds Bottle size (max.) (in litres) Up to 30 30 20 Up to 5 0.02 to 20 Moulds supplied directly to blowing machine manufacturers Yes No Yes Yes Yes Do you supply retrofit moulds for existing SBM machines? Yes Yes Yes Yes, we supply moulds applicable to various brands of SBM machines such as Sidel, Krones, KHS, Sipa, Tech-Long, Newamstar, etc. Yes For which bottle maker have you already produced moulds Sidel, KHS Corpoplast, Krones, Sipa, Kosme, ADS, Nissei, Chumpower, Terekas, 1 blow and other major machine types Sidel, Krones, KHS/SIG/ Krupp, SMI, Siapi, Kosme, Side Sidel, Krones, KHS, Sipa, Nissei ASB, Aoki, Kosme, Siapi, Side, Urola, 1Blow, W. Amsler, ChiaMing, Aoli, etc. Bottlers/converters which supply bottle to beverage brands such as CocaCola, Pepsi-Cola, Danone, Nongfu Spring, etc.; as well as applications in food, cosmetic, pharmaceutical, home and personal care industries. Obolon, Ukraine; Geku Plastik GmbH; Precision Bottles Ltd, UK; Moulded Packaging, UK; Carlsberg, Bulgaria; Devin, Bulgaria; Eco bottles Ltd, Bulgaria; Nioro Plastics Ltd, RSA; Centro Fruta DOOEL, N. Macedonia ; RPC, France; and others Bottle design service Bottle design development Brandbuilding, product repositioning, marketing design, packaging engineering, lightweightening of existing bottles, technical feasibility; new AWArPET analysis (Design for Recycling), etc. Yes, services include preforms and bottle design, rapid prototyping, bottle sampling on a lab stretch blow moulder and on-site process assistance Yes, we design bottles according to customers' requirements on technical performance and appearance. Yes Specialities Quick and flexible bottle sampling and qualification in Röders laboratory with certified equipment Wide mouth, large sizes (up to 30 liters), asymmetrical, Nitrogen hot fill, containers with handles, HDPE to PET conversions, pharma & cosmetics Manufacturing stretch blow moulds and change parts (aka personalisation parts, handling parts and/or product dependant parts) for any make of 2-stage stretch blow moulder, un-scrambler and blow/fill/cap system Bottle designs for light-weighting, optimised CSD base, re-inforced structure, market-appealing styles and imitated texture, etc. All kind of moulds for rotary and linear machines Other Solutions for compatibility of moulds between different machine types, new Röders RMC-system for quick mould change to reduce changeover times and cut mould costs Manufacturing perso parts, descrambler, filler and capper change parts as well as blow mould/change parts custom tooling carts Design; 3D print; prototyping; bottle's shape analysis","@ID":29} "LABELLING PETplanet Insider Vol. 22 No. 05/21 petpla.net 31 guidelines and the free online tool. RecyClass offers recyclability certifications and recycled content traceability certification for plastic packaging. RecyClass publishes a new quick test for washing procedures for film and paper labels applied on HDPE & PP containers. The procedures were developed to determine whether onpack adhesive and label combinations are fully compatible with the post-consumer HDPE or PP recycling stream. They are destined for the label and adhesive industry as well as the recognised certification bodies which perform recyclability assessments of labelled packaging. These standard procedures were developed at a laboratory scale to allow companies to easily and quickly check the wash-off compatibility of their labels with recycling. The documents describe the steps that must be followed to carry out the analysis, as well as the assessment criteria to evaluate the behaviour of labels, sleeves, and adhesives during the washing process. As reported in the HDPE & PP Design for Recycling Guidelines, any label and adhesive combination must be water-soluble or water-releasable at 40 °C to get separated from the packaging during the recycling process. Additionally, paper labels must ensure no loss of fibres during the washing step to avoid wash water contamination and recyclate damaging. The Washing Quick Test Procedures were developed by the RecyClass HDPE and PP Technical Committees and, in particular, the adhesive and label manufacturers including Henkel, UPM Raflatac and Avery Dennison, that carried out internal testing to validate their feasibility. In the case of the non-removable adhesives in combination with film labels, they can be tested by RecyClass following a complete assess015*.*;& :063 -\"#&--*/( 130$&44 3&103550 :063 &31 2. 4:45&. -\"#&- 7*4*0/ */41&$5*0/ 888 */53\"7*4 $0. ment according to the RecyClass Recyclability Evaluation Protocols, to identify their impact on the quality of recycled HDPE & PP. Every component of plastic packaging must be considered when evaluating its recyclability. Labels and adhesives are just one of the examples. Making sure that they are compatible with recycling technologies is indispensable in driving high-quality recycling. By ensuring compatibility with the recycling process the quality of the recycled material increases and so does their potential for being used in high-end applications. www.recyclass.prezly.com/is-yourlabel-compatible-with-hdpe-ppcontainers-recycling-stream www.recyclass.eu","@ID":33} "TRADE SHOW REVIEW PETplanet Insider Vol. 22 No. 05/21 petpla.net 40 into transparent PET, coloured PET, white HDPE, coloured HDPE, other plastics and films. The high homogeneity of sorted materials lays the foundation for high-value recycling, said the company. At present, most recycling companies in China are mainly focused on downcycling, which is neither in line with the original intention of the circular economy nor can it provide a large number of high-quality recycled materials for brand companies. Kelly Xie mentioned that, currently, only 14% of plastic packaging is captured for recycling; and only two per cent of this is recycled in a ‘closed loop’, meaning that it can be reused again for the same purpose, without being downgraded to lower quality plastic. This proportion must be greatly improved. Tomra has announced a commitment for 40% of all plastic packaging produced worldwide to be collected for recycling by 2030. Ms Xie said that a group of leading consumer product brands and packaging companies are committed to using 100% reusable and recyclable packaging materials. “Through the joint efforts of source material manufacturers, brand owners and end consumers, plus policy support, we have confidence that this goal will be fully achieved. Tomra has been enabling this change through our technology and expertise for almost 50 years – we challenge others to join us and act now.” Tomra currently has more than 7,400 units installed around the world, of which nearly 300 units are in China, where its largest client uses 36 Tomra units. www.tomra.com Tomra’s booth at Chinaplas Creating Molds with ADifference BEST-IN-CLASS SINGLE STAGE ISBMMOLDS Acme Drinktec Solutions LLP Email: sales@acmedrinktec.com Website: www.acmedrinktec.com Phone +91-9810418975, +91-9819020785, +91-9810631426 Enhanced cavitation Superior tool steel Balanced HR system","@ID":42} "PETnews 6 NEWS PETplanet Insider Vol. 22 No. 05/21 petpla.net “Waste4Future” paves new ways for plastics recycling Asustainable society with climate-neutral processes requires significant adjustments in the value chains. Seven Fraunhofer Institutes are pooling their expertise in the lighthouse project “Waste4Future” to develop new solutions for this goal, from the raw material base to material flows and process engineering right to the end of a product’s life cycle. In particular, they want to increase energy and resource efficiency in the use of plastics and thus pave the way for a chemical industry that requires fewer fossil raw materials and produces fewer emissions. The carbon contained in plastics is an important resource for the chemical industry. If it is possible to better identify such carbon-containing components in waste, to recycle them more effectively, and to use them again to produce high-quality raw materials for industry, the carbon can be kept in the cycle. This not only reduces the need for fossil resources, but also pollution with CO2 emissions and plastic waste. At the same time, the security of supply for industry is improved because an additional source of carbon is tapped. The “Waste4Future” lighthouse project therefore aims to create new opportunities for recycling plastics in order to make the carbon they contain available as a “green” resource for the chemical industry. The outcome of the project, which will run until the end of 2023, is expected to be innovative recycling technologies for complex waste that can be used to obtain high-quality recyclates. Specifically, the development of a holistic, entropy-based assessment model is planned (entropy = measure of the disorder of a system), which will reorganise the recycling chain from process-guided to material-guided. A new type of sorting identifies which materials and in particular which plastic fractions are contained in the waste. Based on this analysis, the total stream is separated and a targeted decision is then made for the resulting sub-streams as to which recycling route is the most technically, ecologically and economically sensible for this specific waste quantity. What cannot be further utilised by means of mechanical recycling is available for chemical recycling, always with the aim of preserving the maximum possible amount of carbon compounds. Burning waste containing plastics at the end of the chain is thus eliminated. www.waste4future.fraunhofer.de World Packaging Organisation joins forces with members to create ‘WPO Packaging Database’ WPO (World Packaging Organisation) recently announced the creation of a ‘WPO Packaging Database’ that will contain global data such as regulations, safety, technology, sustainability, etc. all related to the packaging industry. “We have decided to take a step-by-step approach to collect important global packaging information. This is a project we have had in our agenda for a number of years but always lacked the resources”, states WPO President, Pierre Pienaar. “But thanks to WPO longstanding Chinese Board members, CPF (China Packaging Federation) and CEPI (China National Export Commodities Packaging Research Institute), we decided to join forces and offered to undertake such a venture along with the guidance of the WPO Executive team.” Pierre adds: “Due to this being in an infant stage and both parties in a learning phase, the intention is to commence ‘slowly and small’. We have discussed how this will possibly look initially and what we foresee over the next 3-5 years. Although we discussed global data such as regulations, safety, technology, sustainability, etc. we have decided to begin with simple but important global packaging market information.” The first topic to be explored in ‘WPO Packaging Database’ is the size of the packaging industry in WPO members´ countries. All the collected information will be displayed in the WPO platform database administered by CPF/CEPI where virtual address will be announced soon. www.worldpackaging.org www.cpf.org.cn www.pack-envi.com Company name revealed as CocaCola European Partners’ acquisition of Coca-Cola Amatil nears completion Coca-Cola Europacific Partners will be the name of the company as Coca-Cola Amatil (Amatil) and Coca-Cola European Partners (CCEP) join together following completion of the acquisition in May. Coca-Cola Europacific Partners will be the world’s largest Coca-Cola bottler and one of the leading FMCG companies in the world. The company will employ over 33,000 people, serving approximately 2 million customers in 26 countries. The proposed acquisition of Coca-Cola Amatil was announced in October 2020, and was approved by Amatil’s shareholders on 16 April 2021. Following the completion of the acquisition in May, the new company name will come into use. The company will continue to be listed on Euronext Amsterdam, the New York Stock Exchange, London Stock Exchange and on the Spanish Stock Exchanges, and will continue to trade under the symbol CCEP. www.cocacolaep.com The Petcore Europe Conference 2021 “Post Covid-19 - Strategy and Trends for the Circular PET Economy”: Petcore Europe is pleased to announce its annual conference from 2-3 June 2021 that will be held via virtual event platform. The first day will focus on perspectives and strategy for the PET value chain with presentations by the EU Commission and other trade focused experts. The second day is dedicated to trends in PET Collection, Sorting, Recycling and Circularity. Attendees will still be able to network thanks to a “Virtual Networking Room “, but they will also be able to visit “Virtual Exhibition booth”. Registration is already open. Find all information on topic and speakers at: www.petcore-europe.org/annual-conference-petcoreeurope-conference/304-save-date-register-now-petcoreeurope-conference-2021.html","@ID":8} "BOTTLE MAKING 23 PETplanet Insider Vol. 22 No. 05/21 petpla.net Figure 7.17 Air step 6. Before the exhaust valve can open, the high-pressure valve must close first. Figure 7.18 Air step 7. Now the exhaust valve opens and all air escapes. When troubleshooting the air pressure circuit, it is best to check the pressure diagram of the cavity that produces defective bottles. All modern rotary machines have these. A “sticky” preblow valve is often the cause of bottle problems and these screens show this very well. Please order your copy at the PETplanet Insider book shop: petpla.net/book3 Stretch Blow Molding Third Edition by Ottmar Brandau € 130,00 374 pages © Copyright Elsevier 2017, 2012 INDUSTRY- LEADING SOLUTIONS FOR SUSTAINABLE APPLICATIONS Mold-Masters’ industry-leading Co-injection Multi-Layer BarrierTechnology offers proven processing capabilities for your sustainable applications. This includes the use of high content post-consumer recycled materials (up to 50% of total part weight) and a wide range of Bio-Resins. For more information, contact co-injection@moldmasters.com Preserving Freshness • Maintaining Flavour • Extending Shelf Life","@ID":25} "COMPRESSORS PETplanet Insider Vol. 22 No. 05/21 petpla.net 14 COMPRESSORS 14 COMPRESSORS STEPS TO THE PERFECT BOTTLE. www.roeders.de www.roeders.de Idea & Design Technology Manufacturing Blow Mould 100% Service Y O U R PA R T N E R F O R B L OW MO U L D S . Interview with Inmaculada Sánchez, Area Sales Manager - Middle East at Arizaga, Bastarrica Y Cia, SA (ABC Compressors) Tackling energy costs and more by Gabriele Kosmehl ABC Compressor’s R&D department has its hands full even during the pandemic. The long-running concern in the compressor sector, energy costs, prompts many customers to update their machine park or to purchase new systems straight away. The compressor manufacturer’s team is particularly happy to solve tailor-made, non-standard requests. PETplanet: For PET bottle making, ABC offers various compressors from the Horizon range, with high and low pressure. Can you please briefly explain which model should the bottle maker choose? Sánchez: We have a wide compressor range to satisfy customer demand. In HP (high pressure), for small bottlers, our platform from 400 to 900m3 /h fits perfectly. For the big ones, we offer flexible solutions from 1,200m3 /h up to 6,600m3 /h. Our LP (low pressure) range is also as wide as the HP one, and many of the PET bottlers choose our LP units, as it is the same technology, and many parts are interchangeable. PETplanet: The Horizon comes with a layout of the cylinders with a horizontally opposed design. In your view, what advantages does this offer over dispositions like L- or V-shape? Sánchez: The horizontal layout makes complete sense in our case. In our compressors, cylinders are opposed, and the pistons are moving in opposite directions, balancing all forces and reducing vibrations to almost zero, that´s why we do not need antivibration pads like our competitors. This horizontal design means less wear, longer service cycle, smoother and wider regulation capacity and lower pressure drops. PETplanet: This year, ABC would certainly have been represented at some trade fairs. What would we have seen from you there? And are there any further improvements or modifications you are working on right now? The Horizon range was launched in 2016.","@ID":16} "MOULD MAKING PETplanet Insider Vol. 22 No. 05/21 petpla.net 12 Individual moulds technology from India by Kay Barton April 29, 2021 We met: Shurid Mody, CEO PETform has been manufacturing preform mould sets and PET hotrunners since 1999. The company, which is headquartered in Mumbai, operates a workshop in Nani Daman, about 180 km towards the north, along India’s west cost. As well as complete mould sets, PETform produces components and spare parts for well-known Canadian and European mould manufacturers. The company also offers prototyping services and has production capacity that can be used to supplement customers’ own preform production. We spoke with CEO Shurid Mody about the importance of precision and quality, and slow, but steady growth. PETform Technologies, privately held company, says that the owner’s mission is to provide high quality products and services with a competitive price model. The company is led by Shurid Mody, one of the better-known faces of the Indian PET industry. He holds a Bachelor of Science (BSc) in Chemical Engineering from Rutgers University, New Brunswick, New Jersey, USA, and has a history of innovation in the packaging and containers industry. His experience dates back to 1995, when he got into blow moulding because of the family’s beverage business. “I was looking after the blow moulding division”, Mr Mody explained. “Later, when we sold the business to Coca-Cola in 1999, we invested the proceeds into mould manufacturing and preform production. This was during the infancy of PET in India, so there was very good potential.” After a period of intense planning PETform Technologies was launched in 2012, independent of the existing family business and with a focus on the manufacturing of moulds for high-end preform systems and with an international approach. Mr Mody went on: “We ignored the low-end market in India, where customers, due to lack of technical knowledge, were taking decisions based solely on cost per cavity. Our focus was to provide tooling with minimum Total Cost of Ownership (TCO). This means using better designs, harder steels, finer tolerances on dimensions and better surface finishes for moulds to produce better preform quality, run faster and serve longer between refurbishing cycles.” When we, PETplanet, recalled our first meetings with Shurid Mody, this is probably the most significant statement linked to this company; one that has been burned into our minds: “We are an Indian company whose markets are primarily outside of India” - that is what Mr Mody confidently said a few times. But what does that mean in terms of business and the company’s approach? “The differences between us and other Indian manufacturers are, first, that we only offer preform injection moulds built to one standard, for instance”, Mr Mody explained further. “We grind all stack components to achieve fine tolerances and surface finish resulting in a significant longer service life, compared with a CNC turning process; and we always harden stack parts to 50-52 HRC. We use ultra-precision jig boring machines and grinders from Switzerland and Japan to manufacture the mould base plates. Jig borers are 3 to 4 times more accurate than standard CNC machining centres commonly used by other mould manufacturers.” For its raw material, PETform relies exclusively on steels manufactured by Deutsche Edelstahlwerke (DEW) in Germany. “We purchase the material directly through DEW’s subsidiary and not through dealers, so that we are guaranteed the source of the steel”, said Mr Mody. All finish machining and measurement is conducted in a temperature-controlled environment and all components are measured by high quality CMM (coordinate measurPETform’s CEO Shurid Mody Inspection of neck ring","@ID":14} "PETcontents 4 PETplanet Insider Vol. 22 No. 05/21 petpla.net 05/2021 Page 14 Page 46 TOP TALK 10 “Many changes have been made in response to the pandemic” - Interview with Paolo Nava, CEO SMI Group MOULD MAKING 12 Individual moulds technology from India COMPRESSORS 14 Tackling energy costs and more - Interview with Inmaculada Sánchez, Area Sales Manager Middle East, ABC Compressors 16 Sparkling performance - Chinese bottled water producer choses oil-free Atlas Copco compressor BOTTLE MAKING 25 One line for juice and dairy - India’s RJ Corp implements Sidel solution for aseptic filling 24 Reusing air - AirMaster technology in stretchblow moulding systems MARKET SURVEY 27 Suppliers of preform and SBM mould manufacturer LABELLING 30 Design for recycling - Is your label recycable? Test it! MATERIALS/RECYCLING 32 4. PETinar: The EU Directive’s impact for the PET value chain - The EU Single Use Plastics Directive EU 2019/904 and its implementation TRADE SHOW REVIEW 36 Chinaplas 2021 - PET exhibitor impressions 37 Solutions for extending shelf life of low-temperature fresh milk 39 Recycling in China - Technology and opinions from Tomra BUYER’S GUIDE 48 Get listed! COMPRESSORS INSIDE TRACK 3 Editorial 4 Contents 6 News 41 Products 43 On site 44 PET bottles for Home + Personal Care 46 PET bottles Beverage + Liquid Food 47 Patents 54 Outer Planet Page 10 LABELLING","@ID":6} "PETplanet Insider Vol. 22 No. 05/21 petpla.net 37 TRADE SHOW REVIEW Solutions for extending shelf life of low-temperature fresh milk by Song Junjie, Director, Cheng Wenjie, Deputy General Manager and Zheng Lishen, Manager, Tech-Long The rapid development of cities, the rise of fresh food e-commerce and the improvement of cold chain fresh food logistics have contributed to the rising popularity of low-temperature fresh milk, which requires refrigeration, in many regions in China. It has a flavour close to fresh milk, has a fresher taste and nutrient loss is lower than that of normal temperature sterilised milk. Low-temperature fresh milk currently accounts for about eight per cent of the entire domestic dairy product market, according to the Huajing Information Network; UHT normal temperature sterilised milk accounts for about 22%. As its nutritional and fresh characteristics meet consumer needs for healthy drinking, annual sales of fresh milk have been growing rapidly; at more than 10% since 2018. It has become a golden track that cannot be ignored in the dairy industry. Factors restricting development The shelf life of most low-temperature fresh milk on the market is limited by current production technology and is generally within three to seven days, with some up to 10 days or more. The short shelf life leads most low-temperature fresh milk sales to be regional. Production costs of traditional low-temperature fresh milk include packaging material, production equipment energy usage, sourcing, labour, product promotion and logistics. Disadvantages of traditional bottle dry production technology The traditional ultra-clean process sees the bottle sent first through the bottle loading platform/air duct/bottle unscrambler to the filling machine’s hydrogen peroxide sterilisation station. It then enters the hot air drying station to evaporate, dry and remove residue. The sterilised bottle then proceeds to the filling and capping machine. Cap sterilisation is usually by ultraviolet or pulsed light spectrum. Safety issues affecting shelf life The spectrum/ultraviolet method has a shadow effect, which means that sterilisation is incomplete, where light cannot be directly exposed to the thread of the cover. Light sterilisation has a poor killing effect on mould. As bottles can be loaded into the filling machine only by unscrambler, air duct, or manual bottle loading, it is difficult to avoid secondary pollution during the bottle transfer process. Dry sterilisation omits mechanical washing, which will affect the transfer process. Contaminated debris is difficult to remove, and there are safety hazards. The space and internal surface area of large bottles, with capacities of over one litre, mean that sterilisation efficiency is difficult to guarantee. External cleaning and disinfection of the equipment is usually done manually, which has been found to leave ‘dead’ corners, which have not been totally cleaned efficiently. The filling machine and capping machine are placed in the one-hundred-level space of the main machine. The filling environment inside the equipment is difficult to guarantee; it is easy for it to become to be environmentally compromised during the production process. Energy consumption The drying process after hydrogen peroxide sterilisation consumes a lot of electricity. Heat sterilisation and drying requires bottles to be heated, which restricts the latitude to reduce bottle weight and thus makes it impossible to reduce the amount (and therefore cost) of packaging materials. Total energy consumption for sterilisation and heating of large bottles is very significant. High production costs and short shelf life of current production technology are the main factors restricting the development of low-temperature fresh milk. Tech-Long launches a PET bottle solution PET bottles have the following advantages, compared with HDPE bottles: The cost of raw materials is lower than that of HDPE; bottle weight is less, for the same capacity. PET is tougher and stronger, has better sealing performance, no leakage of products, and less loss. The oxygen barrier is much better than HDPE, leading to better preservation of taste and flavour are better preserved. Shelf life is longer, under the same storage conditions. Colour masterbatch can be added to PET, for a good light barrier effect for some photosensitive products. Tech-Long’s exhibition specialist Xuxiao at Chinaplas","@ID":39} "MATERIALS / RECYCLING PETplanet Insider Vol. 22 No. 05/21 petpla.net 32 The EU Single Use Plastics Directive EU 2019/904 and its implementation 4. PETinar: The EU Directive’s impact for the PET value chain by Gabriele Kosmehl PETplanet’s fourth PETinar on April 22, 2021 welcomed Dr Rana Pant, Directorate-General for Environment, from the European Commission. In addition to explanations on the general content of the directive, the principal question to arise was: What effects will it have on companies in the PET value chain? A lively Q&A session revealed how much uncertainty there was in the industry - not least because exact guidelines from the EU are still some way off. Dr Rana Pant began by explaining the background to the measures in the Directive. “The basic principle on which these measures were based was the question: Are there more sustainable non-plastic or multi-use alternatives available right now on the market?” If so, market restrictions or market bans would be implemented. If there were no clear and more sustainable alternatives, then prevention measures would come into force such as requirements on product design, reducing consumption, improved customer engagement as well as better waste management (separate collection, extended producer responsibility + litter clean-up and in the case of beverage bottles, recycled content). Article 4 – Consumption reduction Dr Rana Plant went on to explain Article 4 which deals with a reduction in consumption covering food containers, cups for beverages including covers and lids. “It will be Member States’ responsibility to propose adequate measures to foster a sustained and quantitative reduction in those products. It is important to note while there is a requirement to have a measurable quantitative reduction, there will be no set quantitative target for such reduction. The baseline year is 2022, and the time frame for achieving the quantitative reduction is 2026.” National marketing restrictions are possible for the purposes of preventing those products from becoming litter in order to ensure that they are substituted with alternatives that are re-usable or do not contain plastic. Numerically, drinks bottles, caps and lids make up the largest proportion of the ten most common items of marine litter (source: Dr Rana Pant, EU Commission) Dr Rana Pant, DirectorateGeneral for Environment, European Commission The EU aims to become a forerunner in the global fight against marine litter and plastic pollution. Through the EU’s Directive on single-use plastics, different measures are being applied to the most common products found on European beaches as well as fishing gear. 1 Drinks bottles, caps and lids 2 Cigarette butts 3 Cotton buds sticks 4 Crisp packets / sweet wrappers 5 Sanitary applications 6 Plastic bags 7 Cutlery, straws and stirrers 8 Drinks cups and cup lids 9 Balloons and balloon sticks 10 Food containers including fast food packaging The most found marine litter items on European beaches by count","@ID":34} "TOP TALK PETplanet Insider Vol. 22 No. 05/21 petpla.net 11 Paolo Nava: There will be more than 300 billion extra pieces on the shelves of large supermarket chains by 2024. This is what emerges from the predictive analysis carried out by Mecs-Centro Studi Ucima on the growth prospects of packaging machinery. The market survey highlights that the most dynamic sectors will be those related to the production of soft drinks, dairy and confectionery and, as regards the packaging, those related to recyclable plastics. The research is a confirmation of the fact that the great worldwide debate concerning sustainability of packaging solutions has become a key factor in the growth strategies of food and beverage manufacturers. Environmental sustainability and innovation go hand in hand. Environmental protection is a primary objective, that can be achieved only through the joint action of companies and consumers. Companies are increasingly introducing technical innovations in order to produce in an environmentally friendly manner, while consumers are adopting lifestyles and behaviours capable of preserving the environment and enabling the collection and recycling of empty packaging. SMI has been at the forefront in the design of innovative and flexible packaging systems to handle packaging processes efficiently and in an environmentally friendly manner. For instance, shrink tunnels of shrink wrappers have been re-designed in a “green” key by implementing several technical innovations that allow to save on electricity and improve the quality of the packs produced. SMI stretchblow moulders, indeed, are designed to ensure high energy efficiency and the machines of the latest generation make use of cutting-edge technology, such as the Air Master double stage air recovery system; this latter technology enables to reduce HP compressed air consumption up to 40% compared to those systems that are not equipped with it. PETplanet: What future challenges do you see especially in the PET industry? Paolo Nava: Future is always full of challenges, especially for extremely competitive market segments like that of food & beverage. Companies, influenced by the trend of increasing product diversification, need flexible and efficient bottling and packaging plants in order to reach high levels of optimisation and competitiveness of their production lines. Furthermore, in an economic environment that is increasingly oriented towards eco-friendly solutions in the use of plastic packaging, a growing number of companies have chosen to use 100% rPET preforms, that allow to produce bottles with a high mechanical and aesthetic quality in a context with low environmental impact. Recent studies clearly show the advantages related to the use of PET plastic bottles, since those containers are unbreakable, safe, with great barrier properties, light and above all recyclable. When compared to other packaging materials, like glass or aluminium, traditional PET and, above all, its 100% recycled version (rPET), has a good environmental profile; in fact, thanks to its lightweight, in those bottles there’s less material to be produced, less material to be disposed of, less energy used to manufacture it and less fuel used for the transport of packed products. Thus, thanks to its recyclability and to its great weight/ capacity ratio, many producers choose this packaging material as the ideal solution in terms of environmental sustainability. Bottling and packaging solutions offered by SMI include a wide range of stretch-blow moulders from the EBS Ergon range that allow to produce rPET or PET containers; EBS machines can be supplied both as single unit or as part of integrated blowing-filling-capping mono-blocs of the Ecobloc Ergon range, complemented by different types of secondary and tertiary packaging machines capable of meeting just about any requirement in terms of pack format and production output. PETplanet: Where do you see SMI in the next 10 years? Paolo Nava: Further to the global pandemic and the associated travel restrictions, investments in machinery and equipment are temporarily in stand-by, waiting for a better economical scenario. However, there is a high level of interest in new technologies for efficient, hygienic and flexible beverage bottling and packaging plants like those supplied by SMI: hi-tech solutions inspired to Industry 4.0 and Internet of Things (IoT) concepts, which deliver more efficient, flexible, environment-friendly, ergonomic, easy to use and control systems. Although sustainability remains a top priority for packaging suppliers, experts also highlight the variables affecting the future of beverage packaging materials. The Covid-19 pandemic has demonstrated the value of plastics in general and plastic packaging in particular as the change in consumer behaviour toward more home-based activities and different beverages like teas, juices, soft drinks and water have all gained market share. Many of these products are packaged in PET. When it comes to the plastic containers markets, experts highlight how the industry is taking major steps to support the demand for sustainable solutions. Hundreds of millions of dollars are being invested in recycling and sustainability. Given the importance of packaging to the consumer experience, there is tremendous focus on choosing the right materials that will fulfil the sustainability needs while meeting the practical and economic demands of commerce. PET packaging has delivered sustainability, value and consumer appeal for over 40 years and continues to be the material of choice for many brands and retailers. Its lightweight, clarity, break-andtamper resistance and recyclability are all features that improve the consumer experience and help achieve a sustainable cycle. The future of plastic bottles in the beverage industry will move towards rPET and, therefore, most of operators are going to bet on this material. At the base of present and future developments stands the overall concept of the circular economy. The use of rPET for the production of new bottles is the core of this concept, since it allows to collect used material and process it so that it can be reused or recycled multiple times, avoiding waste and reducing the environmental impact, provided that efficient recycling and waste systems exist. Investing in a new bottling line for 100% recycled plastic containers (rPET) is the new frontier of sustainable growth and SMI investments in R&D will continue focusing on innovation, sustainability and flexibility to all new standards in the plastics industry like tethered cap solutions that comply with the EU directive, forbidding the use of single-use plastics. PETplanet: Thank you very much! www.smigroup.it","@ID":13} "BOTTLE MAKING 22 PETplanet Insider Vol. 22 No. 05/21 petpla.net this pressure to too low a value might allow movement of the preform bubble under the impact of high-pressure blow air and move the gate! Some machines offer a system to circulate high-pressure air through the blow mould further reducing cycle time. In either case blowing finishes around 300 degrees (Fig. 7.9) . Figure 7.9 High-pressure blow moves the preform the rest of the way to the walls of the blow mould. Mould opening The stretch rod moves out of the blow mould starting as early as 120 degrees venting is initiated with the end of blow. To facilitate this aspect, a venting valve allows air to escape via a large diameter hose or pipe ending in a suitable silencer to keep noise pollution in the plant down to a minimum. Venting finishes at 342 degrees and only then can the base be lowered. Lowering the base earlier would lead to the deformation of the bottle base known as rocker bottom. However, during venting, the clamp unlocks and at 320 degrees starts to open. This is possible because at that time pressure in the blow mould has significantly dropped. Remaining pressure may slightly bulge the bottle side walls outward but this will not lead to a permanent deformation. At 360 degrees the mould is open, the base insert is down and a new cycle begins (Fig. 7.10) . Figure 7.10 Pressure curve inside the blow mould here shown with optional air recovery. Diagram courtesy of Krones AG. 7.3 Air valve control At this point it may be beneficial to understand the functionality of the air valves that are so crucial to the proper timing of the blowing process. Today, most air valves used in blow moulding come in blocks of three or four: preblow, blow, exhaust, and a second exhaust valve or one used for air recycling. These valves are electrically triggered pneumatic slave valves as shown inFig. 7.11. Figure 7.11 Air to and from the blow cavity is a two-step process whereby an electrically operated valve switches an air-operated one. The valve on the left is electrically operated. When it switches, it opens the path of the air through the valve on the right. These valve blocks are mounted as close to the cavities as mechanically possible to minimise “dead air” loss. Modern valves contain pistons made from PET or other plastic that is durable and light to allow switching in milliseconds. This is one of the “secrets” of the faster machines! Here are the different stages of valve engagement throughout the cycle. P1 stands for preblow, P2 for high-pressure blow, and EX for exhaust (Figs. 7.12–7.18). Figure 7.12 Air step 1. At the beginning of the cycle P1 and P2 are closed and EX is still open from the previous exhaust cycle. Figure 7.13 Air step 2. The first event is the closing of the exhaust valve. Figure 7.14 Air step 3. Now the P1 opens and the preblow phase begins. Figure 7.15 Air step 4. To initiate highpressure blow, P2 opens at the same time as P1 closes. To prevent high-pressure air from getting into the preblow circuit, a check valve is mounted into the preblow line. Figure 7.16 Air step 5. The high-pressure valve is fully open and the container is blown to its finish dimension.","@ID":24} "TOP TALK PETplanet Insider Vol. 22 No. 05/21 petpla.net 9 Many changes have been made in response to the pandemic by Heike Fischer PETplanet Insider talked with Paolo Nava, CEO of SMI S.p.A. about the past Covid year, current developments in the beverage and packaging industry and SMI’s future investment plans. PETplanet: How did SMI manage the past year during the pandemic? Paolo Nava: Covid-19 has affected life of everybody. During 2020 and still now, the way we work, shop, eat, seek medical advice, socialise, participate in sport, and entertain ourselves will all be different. SMI has been obliged to reorganise the way of working, especially for sales meeting and after sale services. During this period we learnt that we must be ready for every new eventuality. Over the past year hundreds of millions of people have lived through lock-downs. The future looks uncertain. We don’t know when, or if, our societies might return to normal. Since the beginning of the pandemic, the SMI Group has always been strictly compliant with all official measures and safety precautions taken by national and local authorities to contain and contrast the spread of the virus and to safeguard all employees. Despite the health emergency, considering that most of our customers operates in the food & beverage sector, we never stopped giving them a technical support despite a lot of restrictions and limits imposed by the new pandemic. In fact, the SMI Group, as a manufacturer of bottling and packaging machines for food & beverage, household cleaning, personal hygiene, chemical and pharmaceutical products, belongs to the list of business activities that the Italian government authorised to go on working since it provided essential services and goods during the emergency. PETplanet: Italy was severely affected from the beginning and had to undergo several strict lock-downs. To what extent has the lock-down affected your infrastructure? Were you able to continue providing a response to demands from your customers worldwide? Paolo Nava: The area of Bergamo, where SMI is based, was among the most affected in the world by the pandemic. During that period there were a lot of difficulties in travelling to job sites, both SMI’s and our clients’ worldwide. Therefore we powered our staff of remotely-provided technical support, in order to satisfy our customer’s needs in terms of machine troubleshooting, overhauls, start ups and any other kind of needs. Both our production and office departments were always operative throughout lock-downs and restrictions, taking all safety measures and precautions set for by the national and local authorities. The SMI Group has defined significant measures aimed at fighting the virus and protecting the health of employees and contractors, such as: rearrangement of production layouts, sanitisation of the premises, purchases of personal protective equipment, temperature measurement, circulation of hygiene rules and social distancing and remote working. That’s why in that dramatic moment we wanted to give our own contribution to support, as far as possible, the improvement of the health situation in our country. Our organisation showed great empathy to the territory and to all those who were working hard to face this emergency; through a donation of € 120,000 our company SMIPack helped the municipality of San Giovanni Bianco to increase health measures aimed at reducing the spread of Covid-19, while a donation of € 200,000 by our company SMILab supported the well renowned Mario Negri Institute of Bergamo in the research activities aimed at defeating the virus. PETplanet: The word digitalisation is always mentioned in this context. Of course, this key term is not new in the plastics processing industry, but it is said that digitalisation has been strengthened by the pandemic. What developments do you welcome, that you already consider urgently necessary and where do you see no added value? Paolo Nava: In this period, characterised by restrictions to the freedom of movement in order to contain the spread of the Covid-19 virus, remote communication and digitalisation have become an even more important factor to maintain good relationships with customers and provide thousands of companies all over the world with quick and efficient technical assistance. We missed a lot, and still do, interpersonal interaction with our customers and partners, but at least geographical distance can be easily overcome with a series of communication tools based on telephone, email, videoconferencing and augmented reality. It’s true, in the plastic industry this digital technology isn’t new and at SMI, with more than 30 years of experience and know-how relating to the advanced automation of machines and equipment, we have developed increasingly innovative and efficient hardware and software control solutions. That’s why, well before pandemic, all of SMI products were equipped with IoT-embedded applications, able","@ID":11} "LABELLING PETplanet Insider Vol. 22 No. 05/21 petpla.net 30 Is your label recyclable? – Test it! Design for recycling For all plastic resins and container types, label selection should be considered carefully to find the solution most compatible with the recycling process that also provides the necessary performance characteristics. At a minimum, labels must be designed so that Near Infrared (NIR) sorting machinery can identify the polymer with the label attached, and labels should use adhesives that release from the bottle or packaging item. Metal foil or metalised labels may also interfere with automated sorting and testing is recommended. Removing adhesives is a significant component to the cost of recycling so the packages using the lowest quantity of appropriate adhesive are the most compatible. All labels should meet guidance for coverage and compatibility, and testing should be conducted in any areas where this is unclear. PETplanet presents three organisations pushing tests for the recycling of labels on plastic containers: Celab Europe, the Association of Plastic Recyclers (US), and RecyClass with a new quick test for washing procedures for film and paper labels applied on HDPE & PP containers. The mission of theAssociation of Plastic RecyclersFoundation based in the US is to drive sustainability solutions for plastics packaging in order to support the Circular Economy. Through education, research and collaboration, the Foundation seeks to enhance the value of plastic recycling as well as expand plastic recycling efforts at the state and national level. Established by the Association of Plastic Recyclers, the Foundation for Plastic Recycling is known for its commitment to enhancing and expanding plastics recycling efforts in order to garner economic and environmental benefits. Especially for the recycling of labels, inks and adhesives the Association of Plastic Recyclers offers guidelines and tests for: Evaluation of the Near Infrared (NIR) sorting potential of a whole plastic article; Evaluation of sorting potential for plastic articles utilising metal, metalised or metallic printed components; HDPE bleeding label test; Critical guidance protocol for HDPE natural bottles with labels; Critical guidance protocol for HDPE coloured bottles with labels; PET package component sink/float evaluation; Benchmark test for clear PET articles with labels and closures; Critical guidance protocol for clear PET articles with labels and closures. Additional guidance for choosing labels for PET bottles can be found: Film pressure sensitive labels on PET containers; Shrink sleeve labels on PET containers. www.plasticsrecycling.org/labelsinks-adhesives Finat, the European self-adhesive labelling industry association, announced the launch ofCelabEurope, a significant new initiative designed to create circular economy for self-adhesive label materials in Europe. By establishing a representative value-chain organisation, Celab-Europe works to identify and collectively scale recycling and re-use solutions for the self-adhesive label liner and matrix materials. The initiative aims to develop a sustainable and circular business model for over 75% of the used liner and matrix materials in Europe by 2025. Nearly 20 leading players from across the label value chain in Europe have since committed to support the initiative, including raw materials producers (papers, films, silicones, adhesives), label stock producers, and label companies. As the association with the largest interest group, Finat is proud to announce that it will host the project, with management undertaken by Sloop Consulting of The Netherlands (who were also involved in the foundation and management of the flexible packaging consortium Ceflex). Work streams Celab-Europe has created a set of deliverables to be completed by 2025 which have been assigned to four interconnected work streams: Data mining: Geographical ‘heat mapping’ of material usage to identify where materials become waste, and in what quantities; Recycling solutions: Identifying, proving, and supporting the development of sustainable end markets for repurposed/recycled liner and matrix materials; Logistics: Connecting with the European transportation and recycling sector to develop and optimise collection systems for liner and matrix; Legal framework: To monitor and advocate the development of regulations and guidelines that supports the development of a sustainable business model for recycling in Europe. www.celabglobal.org A third association comes with a new initiative: RecyClass is a comprehensive cross-industry initiative that works to advance plastic packaging recyclability and to establish a harmonised approach towards recycled content calculation and its traceability in Europe. Activities within RecyClass include the development of recyclability evaluation protocols and scientific testing of materials which serve as the base for the Design for Recycling LABELLING","@ID":32} "BOTTLING / FILLING PETplanet Insider Vol. 22 No. 05/21 petpla.net 26 line. This represents a major turning point for the companies in India, which were previously producing juices in PET bottles with the hot-fill process and milk in cartons. The adoption of Sidel’s Aseptic Combi Predis marks RJ Corp’s first step into aseptic PET bottling, as well as its first experience with dry preform sterilisation. The injection of hydrogen peroxide (H2O2 ) before the oven eliminates water consumption and can significantly reduce the use of chemicals. This is a lighthouse project for PepsiCo Inc. worldwide regarding the processing and bottling of its high-acid Tropicana juices products. The inclusion in the system of Capdis, a similar dry sterilisation for caps, helped to optimise the cleaning process and cap handling, to avoid deformation and ensure tightness between cap and bottle. “Sidel’s new line allows for up to 200 hours of continuous production without any stoppages for cleaning, keeping production running steadily and without any compromise on product quality. The equipment is easy to manage; operators find its functions intuitive and easily accessible,” says Rohit Sawhney, Sales Director for Sidel India. Aseptic PET packaging line The complete line at RJ Corp in Punjab includes flexible End of Line solutions: the medium-speed VersaFilm Access seamless shrinkwrapper; and the automatic PalKombi layer-by-layer palletiser. RJ Corp also invested in Sidel’s Efficiency Improvement Tool (EIT) in order to monitor Overall Equipment Effectiveness (OEE). It provides reports and analyses based on live and historical data, to better understand line flow, uncover sources of efficiency loss and achieve in-depth performance evaluation, and interfaces with inspection devices and business systems. Specific training was delivered to enable all RJ Corp technicians to gain complete understanding of aseptic PET packaging, including the Hazard Analysis Critical Control Point system (HACCP). Since its implementation and validation, the line has been working successfully with an output up to 36,000 bph. Overall, it expands production capabilities in terms of volume as well as a higher number of SKUs. Same bottle shapes and caps During the implementation of the packaging line, Sidel also shared its experience in PET packaging and helped design the new PET bottle, enabling the same shapes and caps to be used for both Cream Bell UHT milk and the Tropicana juices. The cap size for all bottle formats is 33mm, which is a common width for LDP but quite uncommon for juices. Sidel’s packaging experts developed and designed an iconic bottle shape in three formats – 200ml, 500ml and 1 l. All of the bottle shapes and formats underwent Finite Element Analysis (FEA) and on-site validations prior to industrial production, in order to ensure the bottles’ strength and performance across the supply chain. Produced in white monolayer barrier PET, the new packaging ensures a shelf life up to nine months for UHT milk. Furthermore, all the transparent Tropicana juice bottles passed the demanding PepsiCo validation protocols. Varun Beverages chose Sidel solutions again, for a plant located in Central-Eastern India. www.sidel.com Varun Beverages has installed Sidel’s Aseptic Combi Predis in its new plant in Punjab, India. Sidel’s packaging experts designed one bottle shape in three formats for both, Tropicana juice and Cream Bell UHT milk.","@ID":28} "42 PETplanet Insider Vol. 22 No. 05/21 petpla.net PackLab, labelling systems with self-adhesive technology The Italian company PackLab is specialised in the production of labelling systems with self-adhesive technology. PackLab produces labelling systems for many production sectors: from food to cosmetics, from chemicals to pharmaceuticals, and from packaging to personal & home care. The machines are modular and high precision linear labelling machines. The flexible and advanced technology maintains standards even in the presence of sudden variations in production speed, and can therefore easily adapt to the various usage needs. There is a vast range of offer, which includes 16 lines of linear machines with different characteristics and speeds, from 800 to 24,000bph. In addition to the labelling machines, the PackLab production range includes self-adhesive groups from 20 to 120m/min and freestanding applicators that can position the adhesive label on various points of the product. The company offers the well-known “Print & Apply” system for product traceability, with the printing and application of the label on the end of the line and on the pallets. PackLab machines are solutions for all types of cylindrical and shaped containers of various sizes, from vials to drums, from jars to bottles and flasks. Adhesive applications have practically no limits: front and back, side, enveloping, top and down, non-stop and many types of special applications. PackLab is part of the PE Labellers Group, a well known company producing fully modular automatic labelling machines. www.PackLab.it 3D printing material made from rPET Materials manufacturer Covestro introduces its first material developed by the additive manufacturing business recently acquired from DSM: a glass-fibre filled rPET for 3D pellet printing. Arnite AM2001 GF (G) rPET is made from post-consumer PET waste and fits Covestro’s vision for a Circular Economy. The glass-fibre filled pellet material brings structural performance to a part at a substantially lower carbon footprint than virgin material. The recycled PET has been optimised for 3D pellet printing. This technology, also known as fused granulate fabrication (FGF), allows for fast and economically viable additive manufacturing of large-size parts. Direct printing of applications lowers cost by reducing product development time. Plus 3D printing allows design flexibility, which can help reduce material cost. 3D printing is claimed to be an intrinsically more sustainable production method as it only uses the material that is needed. Arnite AM2001 (G) rPET‘s mechanical properties and broad processing window makes it suited for structural applications across a variety of industries, including pedestrian bridges, tiles for cyclist or pedestrian tunnels, architectural applications like cladding or partition walls, in- and outdoor furniture, small boats, packaging crates or tooling, says Covestro. www.covestro.com Covestro introduces its first product for 3D printing: a glassfilled rPET. It can be used to make, for example, furniture such as this chair, a design by Michiel van der Kley. (source: Covestro) LABELLING","@ID":44} "MARKET SURVEY 28 PETplanet Insider Vol. 22 No. 05/21 petpla.net Stretch Blow Moulds Company name Petka Kalip San. VE TIC. A.S. Moldintec UE - Solutions Center PETform Technologies Pvt. Ltd. Kosme Gesellschaft mbH Wentworth Mold Ltd. Postal address Telephone number Web site address Contact name Function Direct telephone number E-Mail Yesiloba Mah. 46075 Sk. No: 8 01100, Seyhan/Adana, Turkey +90 322 428 64 00 www.petkamold.com Mr Eyup Sivri Marketing Manager +90 534 243 42 00 eyup.sivri@petkamold.com Av. Ragull 50 1° 3A, 08173 Sant Cugat del Valles, Barcelona, Spain www.moldintec.com Mr Eng Xavier Palau Country Manager +34 659957897 xpalau@moldintec.com 51/54 Daman Industrial Estate, Kadaiya 396210, Daman, India +91 976 975 8634 www.petform.net Mr Amit Rathod Technical Sales Director +91 976 9758 634 info@petform.net Gewerbestr. 3, 2601 Sollenau, Austria +43 2628 411 0 www.kosme.at Mr Johann Gugler Managing Director +43 2628 411 125 johann.gugler@kosme.at 156 Adams Blvd., Brantford, ON, Canada N3S 7V5 +1 519 754 5400 www.wentworthmold.com Mr Tar Tsau General Manager +1 519 754 5400 ext 611 ttsau@wentworthmold.com Stretch blow moulds Bottle size (max.) (in litres) 0.1 - 19 20 30 30 10 Moulds supplied directly to blowing machine manufacturers No Yes No No Yes Do you supply retrofit moulds for existing SBM machines? Yes Yes Yes Yes Yes, also manufacture multi-platform compatible mould systems For which bottle maker have you already produced moulds Krones, KHS, Sidel, SMI, Sacmi, Sipa The Coca-Cola Company, Pepsico, Ambev, Danone, Envases Universales, Alpla, Otros Kosme, Krones, Sidel, KHS For all blow moulding machine platforms, e.g. Sidel, Krones, KHS, Sipa, etc. Bottle design service Conception of designs based on customer needs, 3D models, prototypes and bottles samples, lightweightning analysis, bottles neck conversion Yes Yes Yes Yes, container design, prototype sampling and bottle performance tests. Specialities Special designs for all type of bottles CSD, NCB, edible oil, commercial location Large bottles and jars Bottle development service free of charge, if blowmoulds are ordered Hot-fill/Heat-Set moulds with energy efficient system and multi-platform interchangeable quick mould systems Other FlexMolds, BaseMax (ultra low blowing petaloids and N2 bases) NoLabel (advanced laser decoration on mould skin) Joint development projects for special applications and new blow mould development. Preform Moulds Company name PETform Technologies Pvt. Ltd. MHT Mold & Hotrunner Technology AG Sipa S.p.A. Sacmi Imola Postal address Telephone number Web site address Contact name Function Direct telephone number E-Mail 51/54 Daman Industrial Estate, Kadaiya 396210, Daman, India +91 976 975 8634 www.petform.net Mr Amit Rathod Technical Sales Director +91 976 975 8634 info@petform.net Dr. Ruben-Rausing-Str. 7, 65239 Hochheim am Main, Germany +49 6146 9060 www.mht-ag.de Mr Carsten Lurz Vice President Sales, Service, Marketing info@mht-ag.de Via Caduti del Lavoro 3, 31029 Vittorio Veneto, Italy +39 04389 11511 www.sipa.it Mr Pablo Fiorentini Global Sales Director, Preform Systems & Tooling +39 04389 11511 pablo.fiorentini@zoppas.com Via Provinciale Selice 17/A, 40026 Imola BO, Italy +39 0542 607111 www.sacmi.it Mr Moraldo Masi Director of Business Unit PET +39 0542 607537 moraldo.masi@sacmi.it Preform moulds Horizontal opening Yes Number of cavities 144 2 to 192 cavities Up to 192 16-32-48-72-96-128-144 Preform sizes unlimited Up to 700g, for bottles up to 30l UP to 750g L 190mm Moulds already built for (makes) Husky, Netstal, Sipa, Sacmi Sacmi, Husky, Netstal, KraussMaffei HP, Sumitomo, Niigon, Arburg, BMB, Demark, Cincinnati, Unique, Negri-Bossi Sipa, Husky, Netstal, Krauss-Maffei, Sacmi Sacmi, Husky Vertical opening Yes Number of cavities 144 2 to 112 cavities Up to 96 Preform sizes unlimited Up to 600g, for bottles up to 30l Up to 150g Moulds already built for (makes) Sipa, Krauss Maffei, ASB Nissei KraussMaffei, Arburg Standard and custom, Sipa, Krauss-Maffei Do you produce single stage tooling sets? (Preform moulds AND blow moulds) Yes No Yes, for Sipa machines No Other - Preform moulds for PE, PP, PLA - Bag in bottle moulds - Wide mouth - Moulds for vacuum blood test tubes - Up to 5 gallon - Moulds for toner cartridges - 2K hotrunner (e.g. milk application) - AFM technology (Active Flow Moulding) Sacmi experience in the packaging industry is taking the lead also in the preform system manufacturing. One stop shopping to guarantee to our customer best quality on preforms and caps solution for any type of beverage application","@ID":30} "PETplanet Insider Vol. 22 No. 05/21 petpla.net 46 PETbottles Beverage + Liquid Food A single variety apple juice spritzer The German drink manufacturer, Gerolsteiner, has brought out a limited edition of a number of apple juice spritzers whose additives are made from one type of apple. The juices reflect the taste of the main ingredients, e.g. the juice from Braeburn apples is described as “sweet and sour”. The spritzers contain 50% juice and are mixed with Volcanic Eifel mineral water. The products come in a 500ml tapered bottle with sleeve label and easy-to-grip screw cap with tamper-proof strip. The colour of the cap matches the front label design. www.gerolsteiner.de A vitamin water in 100% recycled packaging The pharmacy discount firm, dm, is selling a limited edition of its new Vitamin Water Active product under its “Sportness” label which comes in a 500ml bottle. This low-calorie drink with magnesium, zinc and seven vitamins tastes of lemon and lime. The bottle and label are made from 100% recycled material. The slim bottle is secured via a yellow screw cap with tamper-proof strip. www.dm.de A vegan drink from Müller In launching its new drink, the German dairy company, Müller, is responding to the demands of many customers for vegan products. The new oat-based vegan drink comes in four flavours: chocolate, banana, caramel and vanilla. The drink comes in the brand’s trademark 400ml bottle, which has been customised for the new product with a natural-looking sleeve label and green screw cap which make it easily recognisable. www.muellermilch.de An immune shot from Life Fresh The German company, Live Fresh GmbH, has launched a spicy immune shot “Turmeric Power” with ginger, turmeric, lemon, orange and vitamin C which comes in a small 60ml bottle made from 100% recycled PET. The juices are coldpressed, never heated and kept at high pressure. The square-shaped bottle has rounded side edges which are then transformed into a round shape under the neck ring area. A generously large spout is secured via a screw cap and tamper-proof strip. Two labels contain product and retail information. www.livefresh.de","@ID":48} "PETplanet Insider Vol. 22 No. 05/21 petpla.net 39 TRADE SHOW REVIEW Technology and opinions from Tomra Recycling in China Ten years ago, in 2011, Tomra Recycling Business entered the Chinese market to develop products tailored for local demands. Tomra China set up a testing centre, supply chain centre and, crucially, a customer service centre, in order to alleviate Chinese customers’ concerns about time-consuming and costly maintenance of high-end equipment imported from Europe. Localisation became the top priority. Near Tomra’s technology exhibits at the show, Ms Kelly Xie, Head of Tomra Recycling China, shared some comments on and insights in the current recycling situation in China. At this year’s Chinaplas, Tomra highlighted its Innosort Flake sorting solution. The current version, launched in January 2019 after indepth market research, is a costeffective solution tailored to the Chinese market. It is also exported to other markets such as Southeast Asia. Designed for recovery of even the smallest flakes, Innosort Flake removes polymers, coloured flakes and metals across various applications, including PET and PO, according to the company. It uses Tomra’s Flying Beam technology and a dual full colour camera to remove large amounts of impurities, as small as 2mm grain size. With a sorting width of 2.000mm it is able to process up to 6 t/h, conducting multiple sorting steps to achieve the purest end product. Talking about the current situation of plastic recycling technology and the market in China, Ms Kelly Xie, Head of Tomra Recycling China, said that she had contacted and exchanged ideas with many customers and industry professionals at Chinaplas. The increasing demand for high-quality recycled plastics was emphasised by the fact that most people she talked to wanted to learn about the latest technology and market information on waste plastic recycling. She is very confident in the prospects of the plastic recycling industry. People from world-leading brands of household products visited the Tomra booth for in depth discussions. They were concerned about whether the average Chinese consumers would accept recycled plastics in household products packaging, and whether they would be willing to pay the higher prices resulting from the use of recycled materials. In her opinion, the reuse of plastics in the FMCG sector has improved but the quality, cost, and cleanliness of recycled plastic packaging are still controversial in the industry. More efforts should be made to promote consumer trust in recycled materials. Ms Xie offered some advice to encourage greater acceptance and to take pride in using and consuming recycled packaging. She suggested that the household products and beverage industries should strive to tell the story and explain the process. After efficient sorting and cleaning, recycled materials have the same quality as virgin materials and can be recycled in production and consumption. Recycling plastic has a great role to play in saving the already overwhelmed earth. She also suggested that brand owners partner with competent recycling companies to drive technology upgrades and to enhance the supply of high-end materials. The recycling industry has an excellent opportunity for growth and this offers a significant benefit for Tomra. However, Ms Xie pointed out that although the plastic recycling industry is regarded as a sunrise industry, with unlimited business opportunities, its development will not happen overnight. There will be no explosive growth in the short term; it will go through an extended period of evolution, despite all the hype. You can’t make something out of nothing, as the saying goes. Although the processes of sorting, washing, and extrusion of waste plastics are technically mature, recycling companies are encountering significant problems in obtaining waste materials. The establishment of a scientific and standardised waste plastic collection system, covering transportation, terminal disposal, resource recovery, and information management, is essential. Ms Xie shared the successful example of Tomra helping to build the Shanghai Xupu Two-Network Integration Distribution Centre. The amended Law on the Prevention and Control of Environmental Pollution by Solid Wastes, which was introduced on September 1, 2020, requires “strengthening the integration of the Sanitation System and the Recycling System in terms of planning, construction and operation”: the “Integration of the Two Networks”. Shanghai has been at the forefront of this process in China and has built a series of pilot projects. A dedicated plastic sorting line was created in Shanghai Xupu Two-Network Integration Distribution Centre to recycle all kinds of plastics in household waste and reduce plastic pollution. Tomra’s NIR sorting machine, Autosort, detects and sorts mixed waste plastics according to their material and colour characteristics. They are sorted Kelly Xie, Head of Tomra Recycling China","@ID":41} "PETplanet Insider Vol. 22 No. 05/21 petpla.net 45 BOTTLES Toothpaste in a PET headstand bottle Colgate-Palmolive has brought out three new toothpaste products in innovative, recyclable packaging under Colgate’s “elixir” label. Three varieties have been developed for whiter teeth, to eliminate discolouration and protect gums. The packaging removes the distinction between a cosmetic and dental care product, as well as between a tube and headstand bottle in terms of packaging. The products come in a fairly stiff 80ml container with a tube-shaped shoulder on which a lid with dispensing spout and sealed cap is placed. The packaging is sealed and secured by an interlocking transparent screw cap with an insert to ensure the dispensing spout is properly secured. Any residues remaining in the tube are likely to be minimal. www.colgate.de Do-it-Yourself liquid soap The Munich-based company, Sause GmbH, has launched a new sustainable liquid foam soap product under the name “Sause - Die Seifenbrause”. Customers can choose between a glass flacon or a dispenser made from recycled PET as a soap bottle. Both have a lockable pump dispenser. The concentrate tablets that produce the soap are packed into cardboard tubes with interlocking lids. The liquid soap is created by pouring water into marked bottles, then adding the requisite number of tablets. Wait until the tablets have dissolved, by which time the soap will be ready. Varieties are available with or without added fragrances. www.seifenbrause.de A refill system for dishwashing detergent The buzzwords “sustainable” and “environmentally-friendly” are causing new innovations and companies in the cleansing product sector to spring up like mushrooms. Only time will tell which one prevails. Here, the German company, Blaue Helden, is focusing on a reusable bottle made from PET that can be purchased empty. By adding water and the appropriate tablet, the customer can create a dishwashing detergent, as well as a glass, bathroom or all-purpose cleaner. The individual power tabs come in a 100% plastic-free sealededge bag that can be disposed of in waste paper. When you buy one of these bottles in a shop, it comes with a tag to which a starter tablet is attached. The bottles come in different sizes depending on the product and are fitted with suitable triggers or pump dispensers. www.blauehelden.de","@ID":47} "43 ON SITE PETplanet Insider Vol. 18 No. 0/17 petpla.net Melt filtration system brings efficiency dividend for Spanish bottle-to-bottle recycler The processing of PET bottle flakes presents particular challenges for melt filtration systems. On the one hand, the post-consumer material source typically has a relatively high contamination level, on the other, the quality requirements (fine filtration) are very high – especially when the material is to be put back into transparent bottles for beverages. To avoid the need for constantly changing the filter elements by hand, the ideal melt filtration system should be self-cleaning. Typically, the principle of back flushing is used. A proportion of the melt flow is diverted so that it flows in the reverse direction across filter elements which are not in use in order to wash out the contamination. The cleaning efficiency of the back-flushing and the quantity of material needed for back flushing vary greatly between the different systems available on the market. With the Gneuss RSFgenius Melt Filtration System, the high-pressure sequential cleaning system is claimed to ensure that the filter elements are completely cleaned with a minimum of polymer. Nosoplas in Spain decided in favour of the RSFgenius Rotary Filtration System due to the high efficiency and the rapid return on investment which it promises to offer. Nosoplas manufactures bottle grade pellets (chip) from PET bottle flake. The pellets (chip) are supplied to other companies, where they are injection moulded to preforms which are later blown into high quality bottles for beverages. Nosoplas decided to replace their existing, conventional filtration system due to problems with back flushing and high polymer losses. They replaced this conventional system with a Gneuss RSFgenius 175 for a throughput of 1,500kg/h and a filtration fineness of 56μm. In fact, the customer is even able to operate with 30μm for special products. And all this with a constant, steady melt pressure, minimal losses due to back flushing and without any production variations, even during replacement of the filter elements. Nosoplas says that the expectations placed on the retrofit with a Gneuss Rotary Filter are fulfilled. Immediately after commissioning the units, a drastic reduction in in material loss due to back flushing was observed and, at the same time, the quality of the rPET granulate produced was noticeably improved. The Gneuss Rotary Filtration Technology is claimed to ensure an uninterrupted production process under constant conditions – even when post-consumer recycled material is processed. Gneuss Melt Filtration Systems are well suited for retrofitting to existing extrusion lines. www.gneuss.de ONsite Fully-automatic, process and pressure constant RSFgenius Back Flushing Filtration System The right tools and expertise to help with your rPETgoals! Agr is uniquely positioned to support your venture into rPET bottle manufacturing with a powerful combination of Process Control tools, Process Consultants, and decades of industry experience. AGRINTL.COM • +1.724.482.2163","@ID":45} "MARKET SURVEY 29 PETplanet Insider Vol. 22 No. 05/21 petpla.net PET Technologies SMI S.p.A. Krones AG KHS GmbH Grünlandgasse 5/1/12, 2620 Neunkirchen, Austria +43 720 775 196 www.pet-eu.com Mr Maxim Poliansky CEO +43 720 902 169 office@pet-eu.com Via C.Ceresa, 10 24015 San Giovanni Bianco (BG), Italy +39 0345 40.111 www.smigroup.it Marketing department +39 0345 40111 info@smigroup.it Böhmerwaldstrasse 5 93073 Neutraubling, Germany +49 9401 70 0 www.krones.com Mr Moritz Vowe SA LCS Retrofits and Products +49 9401 70 5250 moritz.vowe@krones.com Juchostr. 20, D-44143 Dortmund +49 231 569 0 www.khs.com Mr Dennis Jacobi Manager Service Sales +49 40 67907 225 dennis.jacobi@khs.com 40 10 5 Depending on individual bottle geometry: - typically 100ml-2,500ml with regular moulds, inner shell & outer shell system (requires additional maxi pencake at approx. 1,500ml to hold the mould closed) - up to 3,900ml with compact moulds (outer=inner shell, still usable at standard blowmoulder) - up to 5,500ml with compact large moulds (only applicable at special compact large blowmoulder) Yes Yes Yes KHS manufactures blowing machines Yes Yes Yes Yes Rotary and linear blow moulders: Sidel, KHS, Krupp, Sipa, SMI, Krones, Kosme, Siapi, Mag Plastic, ADS, Lonza, Side, Chumpower etc. Up to now, SMI engineers have designed about 1,700 containers, featuring from the most simple to the most sophisticated shape. Krones, Kosme, Sidel, Sipa, KHS (SIG) Corpoplast etc. Hundreds of customers from different branches (softdrinks, water, beer, non-food, food, …), including global key accounts such as Coca-Cola and PepsiCo Creation of unique bottle design, branding, product naming, logos and labels, 3D models, prototyping, bottle sampling, PET containers laboratory tests Yes. SMI design, develop and virtually prototype a wide range of packaging solutions in rPET and PET, according to the customers' specific requirements. Yes Yes: preform and bottle design (technical/ marketing), finite elements analysis, 3D modelling, … Moulds for 100ml - 40l containers, filling line conversions, bottles for chemicals and detergents, sanitisers, hot fill, wide neck jars, lightweight designs, laboratory tests The moulds are manufactured using a special aluminium alloy. SMI relies on a special laboratory for the production of moulds and mechanical components, equipped with an FMS line consisting of 12 CNCmachining centres: highly automated machines, running 7 days a week round the clock, even operator-less, according to pre-set production programmes (CAM).The 12 machining centres can achieve an output of more than 15,000 moulds/a; they are equipped with linear motors with a speed rate up to 80 meters/minute and mandrels achieving a speed rate of 30,000 rounds/minute.As a result, top-level quality standards are constantly provided. Bottle development customised to filling and packaging lines with performance commitments; preform-/bottle light weighting for standard- and heat-set process; low blowing pressure mould design; “Mould quick change” systems; automated mould change-over systems Light weighting, low pressure, complete PET line optimisation, carbon dioxide calculator, global key account certified laboratory, … Short lead time The “ReduxAir” system allows to carry out stretch-blowmoulding operations at lower pressures than usual. By an innovative design and specific technical solutions this system allows for the air in between the bottle's outer walls and the mould's surface to be more quickly released; thus, the PET bottle manufacturing process can be carried out with compressed air pressure at 15-20 bars (such a value depends on the preform and bottle features and on the stretch-blowmoulding process conditions).The great advantage the ReduxAir's user can benefit from in terms of lower power consumption of the compressor requires a few design limitations in the bottle's shape and features. Petka Kalip San. VE TIC. A.S. Otto Hofstetter AG GDXL Precise Machinery Co., Ltd. StackTeck Systems Ltd Husky Injection Molding Systems Yesiloba Mah. 46075 Sk. No: 8 01100, Seyhan/Adana, Turkey +90 322 428 64 00 www.petkamold.com Mr Eyup Sivri Marketing Manager +90 534 243 42 00 eyup.sivri@petkamold.com Zürcherstrasse 73, 8730 Uznach, Switzerland +41 55 285 22 11 www.otto-hofstetter.swiss Mr Markus Feldmann Division Manager PET +41 55 285 22 97 fen@otto-hofstetter.ch No. 18 Changjiang Road, Guicheng, Nanhai, Foshan city, Guangdong Province, China. Postcode: 528251 +86 757 8677 7168 www.gdxl.com Mr Billy Ay Marketing Specialist +86 757 8677 7168 ext 8681 billy.auyeung@gdxl.com 1 Paget Rd, Brampton, Ontario, L6T 5S2, Canada +1 416 749-0880 www.stackteck.com Rick Unterlander GM PET +1 416 749 0880 runterlander@stackteck.com 500 Queen Street South - Bolton, ON L7E 5S5 - Canada +1 905 951 5000 www.husky.co Mr Daniel During PET Tooling Business Manager dduring@husky.ca Yes From 2 cavities to 144 cavities 2 up to 192 From 32 to 144 cavities 2 - 144 6 to 144 14mm - 110mm neck finish Up to 500g Various neck finish standards including 1810, 1881, 30/25, 29/25, 26/22, 38mm, etc. Preformweight from approx. 3.5g to 750g (for applications from pharmaceutical/cosmetic bottle to 5gallon keg) neck size 13-120mm DIA, weight 4-710g Threads up to 100 mm in diameter and up to 205 mm in length Netstal, Husky, Sipa, Sacmi Netstal, BMB, Husky, Arburg, Husky, Netstal, Niigon, Krauss-Maffei, Sipa, etc. All major PET preform machine suppliers We have moulds to support all preform designs and output requirements - we have designed moulds for preforms with a thread diameter up to 120 mm and lengths over 400 mm long From 2 to 128 cavities 2 up to 112 From 16 to 96 cavities 14mm - 110mm neck finish Up to 500g Various neck finish standards including 1810, 1881, 30/25, 29/25, 26/22, 38mm, etc.; preform weight up to 69g KraussMaffei, Sipa Arburg, KraussMaffei Sipa, Krauss-Maffei, etc. No No No Yes, preform moulds (cold halves and hot runners) Husky does not currently produce blow moulds. - multilayer moulds up to 72 cavities - moulds for PP - moulds for thinwall packaging - moulds for cartridges and tubes - moulds for medical products We also provide engineering solutions together with our partners for: - multilayer co-injection containers with barrier properties to gases, moisture and light; and market-appealing elements such as colour gradation and imitated texture; - complete preform production systems Manufacture robot end of arm tooling and PiCool post mould cooling transfer stations Husky's HyPET preform injection moulding systems deliver reduced variability and increased part quality; and the lowest energy consumption per part produced. Backed by Husky's more than 35 years of preform equipment experience, our preform systems offer industry-leading technology that is proven and reliable.","@ID":31} "BOTTLE MAKING 18 PETplanet Insider Vol. 22 No. 05/21 petpla.net Stretch Blow Molding, part 14 Fundamentals of the Blow Process by Ottmar Brandau Ottmar Brandau has newly revised his book “Stretch Blow Molding”, first published by hbmedia / PETplanet Publisher, and now re-issued in a third edition under the Elsevier Imprint. PETplanet Insider is publishing extracts from successive chapters in a serie of articles. In this chapter, we will be examining what actually happens inside the blow mould during the blowing of bottles. This description is based on materials science, practical experience gathered by interrupting the blow process at various stages, and blow mould simulation software. 7.1 Reheating preforms Throughput rate, air flow, and lamp settings all determine the temperature of the preforms before blowing. Throughput rate may be dependent on preform wall thickness if the heating capacity of the machine is limited, or by the required blow process time. For example, a 2 l bottle requires a longer venting time than a 500ml bottle. Although throughput rate can be adjusted while the machine is in production, it is easier to set the machine at a speed derived from experience with similar bottles before starting up. On rotary machines blow wheel movement and mandrel chain speed are coupled and output rate determines process time that the processor can then subdivided into the different process stages within the confinements of the machine cycle. On some linear machine a process time can be selected and the machine adjusts the output to suit. Air flow is best left at a medium level and adjusted once some bottles have been blown. The first step in lamp adjustment is to adjust the height of the oven bank to suit the particular neck design. For this purpose a cold preform is placed on a mandrel and the oven heat shield positioned such that it is just above the neck support ring of the preform. Most oven banks are mounted on adjustment blocks that can be vertically moved with threaded rods (Fig. 7.1). Figure 7.1 Modern ovens allow easy access for adjustment and maintenance. Photo courtesy of Krones AG. The next step is to examine the preform to be blown. Preform wall thickness ranges from 2 to 5mm (0.080–0.200 in.) for standard bottles up to 5 l and might not be evenly distributed. Preform designers strive to create an even body wall thickness but bottles such as those with a champagne style base (e.g., beer bottles) need extra material close to the base. These preforms have 4–5mm wall thickness in the lower fifth of the body, requiring extra heating there. The initial heat profile will always have a high setting for the first, and sometimes the first two lamps. This will depend on where the transition area between the neck of the preform and body ends, and the shoulder angle of the bottle. Steep angles in the bottle shoulder require less material and the preform must be heated more in the area that will form them. The remaining lamps will be adjusted to suit the preform body wall thickness. As stated earlier, there are rotary and linear ovens. Rotary and single-line ovens heat up preforms","@ID":20} "BOTTLE MAKING 24 PETplanet Insider Vol. 22 No. 05/21 petpla.net Air Master technology in stretch-blow moulding systems Reusing air The production process of PET and rPET containers by means of stretch-blow moulding systems requires the use of high pressure compressed air produced by a compressor powered by electricity. SMI stretch-blow moulders are designed to ensure energy efficiency; in particular, the machines of the latest generation using the technology of the Air Master double stage air recovery system, that enables compressed air consumption to be reduced by up to 40% compared to the systems that are not equipped with it. GAWiSD featuringAutoJob ™ – job set up in seconds +1.724.482.2163 AGRINTL.COM ACCURATE • FAST • REPEATABLE SEE GAWIS4D IN ACTION Dimensional and thickness measurements for plastic containers and preforms. ® Air Master: what it is The double stage air recovery system is configured as follows: the first stage recovers the air that is then used for the pre-blowing and the machine service phases. The second system, that complements the first one, takes part of the exhaust air and uses it exclusively for the blowing phase. Air Master: how it works On every stretch-blow moulding station, two exhaust valves are installed: the first feeds the recovery system, pumping air into the recovery line, while the second discharges the air that cannot be recovered. The air recovered is taken and used for feeding the pre-blowing and the machine service circuits. Some extra air is used for feeding the low pressure line of the machine external utilities. The second stage allows a further saving, as it uses the exhaust air for the blowing phase. SMI stretch-blow moulders of the previous generations can benefit from the advantages of this recovery system, by installing an upgrade package. Air Master upgrade The upgrade ensures recovering the compressed air that would otherwise be released to the environment. By reusing the air of the stretch-blow moulding process the reduction of high pressure air and electricity consumption of up to 30% results in an eco-sustainable production process. As a positive side effect, there is less wear and reduced maintenance costs of the compressor. An example of calculation: savings can be achieved by installing the Air Master upgrade on a stretch-blow moulder with 8 cavities, producing 1.5 l PET bottles at 2,250 bph, with a blowing pressure of 33 bar and a production of 4,000 h/a. With an upgrade, 30% air savings can be achieved, the consumption is about 784Nm3 /h, resulting in energy costs at 43,903 € per year. Without the upgrade the air consumption is about 1,120Nm3 /h with energy costs at 62,720 € per year. www.smigroup.it","@ID":26} "TRADE SHOW REVIEW PETplanet Insider Vol. 22 No. 05/21 petpla.net 38 outside the machine, leaving only essential components in the 100-level environment and thus reducing the possibility of contamination of the filling environment. Automatic COP/SOP means there is no need for manual cleaning and disinfection of the inside of the machine, which reduces or completely eliminates the risk of manmade pollution and extends the continuous operation cycle of the equipment. The PET solution extends shelf from three to seven days to 21 days. Equipment selection Although capital costs of traditional ultra-clean equipment are small, the safety and production costs are poor. Aseptic equipment can meet the requirements of low-temperature fresh milk to extend the safe shelf life of low-temperature fresh milk in terms of safety, but initial investment cost is high, but the production costs have no advantages. Tech-Long ultra-clean preform dry sterilisation blowing-filling-capping monobloc is available for a moderate capital cost. It competes by offering advantages in terms of safety and equipment production costs. It can greatly improve the shelf life of lowtemperature fresh milk products while reducing energy consumption in production. It is the first choice for major dairy companies to produce long-shelf low-temperature fresh milk products. www.tech-long.com Tech-Long ultra-clean preform dry sterilisation blowing-filling-capping monobloc sterilisation of full-size bottles. Using the heat of the bottle blower to heat and evaporate the hydrogen peroxide in the preform removes residues without additional heating and air drying. Dry bottle sterilisation has to adapt to bottle thickness. If it is too thin, it will be thermally deformed. Preform sterilisation does not need to consider heat deformation. The sterilisation efficiency of the bottle can be stabilised to 3~5 log, according to demand. As a gas, hydrogen peroxide eliminates dead corners. The sterilisation process has a broad spectrum, with efficiency stable to more than 3 log. The blowing-filling-capping mode controls bottle pollution from the source. The ready-to-use mode prevents secondary pollution during bottle transfer. The whole unit is equipped with 100-level purification. The main filling and capping machine have a liquid seal. The flowmeter, electrical components, valves and other parts that are not easy to clean and are likely to cause secondary pollution are located New equipment combination, new process route Tech-Long ultra-clean preform dry sterilisation blowing-filling-capping monobloc process flow: Preforms are first processed through the closed unscrambler. The neatly ordered preforms first pass through the bottle mouth UV sterilisation section before entering the bottle blowing machine. Ion dust removal eliminates debris particles in the preform. The preforms are sterilised with hydrogen peroxide, using the heat of the heating mechanism of the bottle blowing machine for drying, and then blown and moulded by aseptic high-pressure air. They are then sent for filling and capping. Reduce equipment energy consumption, improve product safety, and extend shelf life Dry preform sterilisation is relatively fixed, at 2~6ml/min, offering considerable savings compared with November 7-9, 2021, Dubai At the Krones booth A1-34 German Technology Innovative hotrunner optiRun","@ID":40} "MATERIALS / RECYCLING PETplanet Insider Vol. 22 No. 05/21 petpla.net 34 raising consumer awareness. The impact of inappropriate waste disposal and littering as well as information on alternatives, reuse systems and waste management options shall be provided. Implementation The commission has to come up with two sets of guidelines, the SUP Guidelines (what is to be considered a single use plastic product, definitions) and guidelines on EPR (criteria on costs of litter clean up). Two standardisation requests are both ongoing concerning tethered caps and lids, according to Art. 6 (plastic bottles); and circularity of fishing gear, Art. 8(9). There will be a range of implementation acts regarding Marking, beverage bottles separate collection, reporting of fishing gear and waste collected; measuring and reporting consumption reduction by Member States; reporting of post consumption waste tobacco products; measuring and reporting of recycled content of SUP beverage bottles. Transposition and Implementation Member States have two years to bring into force national laws and regulations to comply with the Directive - by July 3, 2021 Article 5 (market restrictions) – from 3 July 2021 Article 6 (1) (product design) – from 3 July 2024 Article 7(1) (marking) – from 3 July 2021 Article 8 (EPR) - by 31 Dec 2024 Evaluation of the Directive (Article 15) by July 2027 Responsibilities of Member States EU Member States are obliged to enshrine the stipulations contained in the Directive into national law. Bottle manufacturers may have to adapt to different requirements in different end markets. For example, one member state may decide to only allow bottles that each contain at least 25% rPET in order to achieve the required quota, while another country may opt for a mixed calculation and aim for an average value of at least 25%. However, evidence must be provided and a control and reporting system must be maintained. The EU is to provide rules for the calculation and verification of the targets of rPET that also provides information on how to deal with moisture content, biobased contents etc. Implementation of that verification will be up to Member States. This also includes how to monitor the flow of imported goods for a certain market. Possible sanctions on companies in the event of non-compliance with the State’s own requirements are also subject to the member states. rPET specifications and availability Most of the questions that most concerned the 300 or so registered participants in the PETinar related to rPET and in particular to availability, price movements and monitoring. Dr Pant indicated that the 25% recycled content in PET bottles by 2025 should be achievable. According to the Commission’s calculations, it should be even possible to achieve the target of 30% in 2030 with only PET bottles using recycled content (while the target is set for all bottles). A concern from the auditorium was that, as rPET is more expensive than virgin PET, manufacturers of preforms and bottles could face competition from non-EU countries that do not comply with the Directive. But as compliance is not at the EU level, but wholly on individual Member States, it will be up to Member States themselves to monitor compliance. The recycled content target is not necessarily related to each bottle, each member state must ensure 25% rPET on average in the bottles sold in their market. However, the target is of course applicable to products whether produced within or outside the EU. By reaching the target above an average value, Member States could help small to medium-sized companies avoid a price war over rPET, which could increase if significant numbers of large companies advertise the fact that they use 100% rPET in their products. Support from the EU will be given in terms of continuing research projects or in the recycling infrastructure to support high quality collection, high quality sorting, high quality recycling and finally a high-quality recycled input back into the value chain processes. Digging deeper, a participant asked if the directive could ruin Europe’s recycling industry by stimulating an increased import of recycled material from outside the EU. Dr Pant answered: “It is correct that the rPET content in European bottles on the European market does not have to come from Europe. But of course, we look at the whole value chain and with the separate collection, for recycling, of those bottles which are placed on the European market, we hope to improve the situation and availability and as well the price of this recycled material.” Dr Pant pointed out that the Commission’s intention is not to encourage huge import flows of recycled plastic from outside. On the contrary, there are ambitions to speed up the authorisation process of FCM (food contact material) recycling regulations within the Commission’s DirectorateGeneral for Health and Food Safety (DG Santé) and the European Food Safety Authority EFSA. ”I am confident that by 2025, this will no longer be an issue for PET”. http://ec.europa.eu/environment/ circular-economy/index_en.htm Missed our PETinar? The presentation and a video recording is available at petpla.net","@ID":36} "imprint EDITORIAL PUBLISHER Alexander Büchler, Managing Director HEAD OFFICE heidelberg business media GmbH Vangerowstraße 33 69115 Heidelberg, Germany phone: +49 6221-65108-0 fax: +49 6221-65108-28 info@hbmedia.net EDITORIAL Kay Barton Heike Fischer Gabriele Kosmehl Michael Maruschke Ruari McCallion Waldemar Schmitke Anthony Withers WikiPETia.info petplanet@hbmedia.net MEDIA CONSULTANTS Martina Hirschmann hirschmann@hbmedia.net Johann Lange-Brock lange-brock@hbmedia.net phone: +49 6221-65108-0 fax: +49 6221-65108-28 LAYOUT AND PREPRESS EXPRIM Werbeagentur | exprim.de Matthias Gaumann READER SERVICES Till Kretner reader@hbmedia.net PRINT Chroma Druck Eine Unternehmung der Limberg-Druck GmbH Danziger Platz 6 67059 Ludwigshafen, Germany WWW www.hbmedia.net | petpla.net PETplanet Insider ISSN 1438-9459 is published 10 times a year. This publication is sent to qualified subscribers (1-year subscription 149 EUR, 2-year subscription 289 EUR, Young professionals’ subscription 99 EUR. Magazines will be dispatched to you by airmail). Not to be reproduced in any form without permission from the publisher. Note: The fact that product names may not be identified as trademarks is not an indication that such names are not registered trademarks. 3 PETplanet Insider Vol. 22 No. 05/21 petpla.net rPET and tethered caps have been occupying the industry for some time now. In the last PETinar we were able to oblige Dr Rana Pant, Directorate-General for Environment, from the European Commission, dear friends of PETplanet, to answer your questions. While the cap topic hardly got a mention in the question and answer session, the audience pounced when the topic of the proportion of rPET in the bottle came up. It should be 25% by 2025 and 30% by 2030. But already then the first discussions began. The percentage should be achieved on average and member states can set their own requirements. So each bottle must contain at least 25% - or 25% on average across all bottles. The doors and gates are once again open to diversity. Woe to anyone who wants to import a bottle from one country to another. The control of the recycled material and its supply chains is also in the hands of member states. Fears were voiced in the auditorium that cheap rPET from non-EU countries will flood the market, to the detriment of the strictly regulated European recycling industry. Dr Pant was unable to rule out this possibility but considered it unlikely. He pointed out that the relevant authorisation process of FCM (food contact material) should finally be completed quickly. To summarise the event, the EU has set a framework that the member states now have to implement. They have so much freedom that it is unlikely that we will get uniform regulations across national borders. We already have these kinds of different regulations today. It is a shame that the new EU guidelines have not improved the situation and have left the smaller countries exposed. Yours sincerely, Alexander Büchler Dear readers,","@ID":5} "MATERIALS / RECYCLING PETplanet Insider Vol. 22 No. 05/21 petpla.net 33 MATERIALS / RECYCLING 33 Article 5 – Market restriction (bans) Article 5 covers those single-use plastic products for which more sustainable and readily available alternatives have been identified. Products not using such alternatives will be banned as of July 2021. Article 6 – Product design requirements The tethering of caps is part of article 6 and stipulates that caps and lids remain attached to beverage containers and bottles up to 3 litres. The auditorium was particularly interested in the publication of a formal standard. In response, Dr Pant stated that work on standardisation is ongoing and acknowledged that this is now “work in progress”. The two organisations responsible for the design standardisation are CEN, the European Committee for Standardisation and CETIE, the international association publishing technical reference documentation on bottling and related subjects. However, Dr Pant pointed out that it is not that the standard itself which is mandatory but the provisions and the Directive. Manufacturers are obliged to observe the terms of the Directive and show compliance to enable them to introduce their product on the market. Compliance with the standard will give presumption of compliance with the Directive. The same article also covers the binding target for Member States to ensure compliance with the recycled content of single-use plastic beverage bottles placed on the market: at least 25% of recycled plastic for singleuse PET beverage bottles from 2025 at least 30% of recycled content for all single-use plastic beverage bottles from 2030 (covering all bottles, not only PET bottles) Article 7 – Marking requirements This article is related to the marking of products. Products have to be labelled to inform consumers that this product contains plastic and should be disposed of safely. The label should warn the consumer of the negative environmental impact if the product is disposed of inappropriately. Article 8 - Extended producer responsibility (EPR) The extended producer responsibility is enshrined in Article 8. For food and beverage containers, bottles, cups, packets and wrappers, lightweight carrier bags and tobacco products with filters, producers will help cover the costs of waste prevention (awareness raising); waste management (collection and treatment costs of on-the-go waste in public areas); litter clean-up and data gathering. Article 9 – Separate collection The target for the separate collection for recycling of plastic beverage bottles is defined as 77% by 2025 and 90% by 2029. Member States can decide themselves whether to address these targets through EPR or through deposit refund schemes. The idea behind this is to support high quality recyclates and the uptake of secondary raw materials, and indirectly also support the enlarged and heightened plastic packaging recycling target of 55% by 2030 in accordance with the Packaging Waste Directive. Article 10 – Awareness raising measures The aim of this article is to achieve a reduction in littering of single use plastic products and fishing gear by","@ID":35} "BOTTLING / FILLING PETplanet Insider Vol. 22 No. 05/21 petpla.net 25 India’s RJ Corp implements Sidel solution for aspetic filling One line for juice and dairy Varun Beverages Ltd, part of Indian company RJ Corp group, one of PepsiCo Inc’s largest franchises, has installed Sidel’s Aseptic Combi Predis in its new plant in Punjab, India. This project aims to expand PET bottling capacity and provide production flexibility for the Cream Bell private label milk brand, as well as Pepsi’s Tropicana juice range. This is RJ Corp’s first commercial release in India of liquid dairy products (LDP) in PET. Privately-owned RJ Corp has, since the early 1990s, established itself with strong business presences in beverages, fast food restaurants, retail, ice cream, dairy products, healthcare and education. Through Varun Beverages Ltd., the group is one of the largest bottling partners for PepsiCo in the world. It currently operates 36 plants on the Indian subcontinent and in Africa, producing CSD, water and hot-fill juices as well as LDP. Production flexibility Responding to Indian consumers’ trend towards nutritional beverages, RJ Corp decided to diversify its portfolio and put more emphasis on 100% juices with pulp and ultra-high temperature (UHT) LDP and to seek to produce both on the same production line. The only way this could be done, while meeting PepsiCo’s high standards for food safety and hygiene, was with aseptic technology, according to Mr. R.J.S. Bagga, Director Technical & Operations at RJ Corp. After visiting a French copacker that has used and trusted the technology to handle both juices and milk for more than 10 years the company decided to install Sidel’s Aseptic Combi Predis, including dry preform sterilisation. The Sidel technology, which has been approved by the FDA for lowacid production since 2017, allows the producer to switch easily and safely between four UHT milk flavours (white UHT milk, coffee, chocolate and mango) and various kinds of juice recipes (eg, orange delight & 100% orange juice with pulp, mixed fruit delight and 100% mixed fruit juice, guava, apple delight and 100% apple juice, and lychee delight) on the same","@ID":27} "MOULD MAKING PETplanet Insider Vol. 22 No. 05/21 petpla.net 13 ing machines) and other instruments, multiple times for 100% quality control. PETform says that the company is the only preform mould manufacturer in India with in-house preform systems from Husky and Krauss Maffei for testing moulds up to 96 cavities. The company currently serves clients in over 100 countries. Its primary markets are North America (35%), Latin America (35%), Europe (10%) and North Africa (10%); the balance is spread between the Middle East and the rest of Africa. Its revenues in 2020 totalled US$ 4 million, with a year to year compound growth of 20% since it was founded in 2012. The workshop extends to 4,000m2 and has a workforce of 120 people. It houses eight CNC turning/turn-mill centres; six ultra-high precision jig boring machines and four CNC machining centres; surface grinders; and universal cylindrical grinders; one deep hole boring machine and two CNC EDM machines. For prototyping, the company uses a Husky lab machine with two or four cavities. For mould testing, PETform employs Husky and Krauss Maffei preform systems, as well as two optical and tactile scanning CMMs, made by Carl Zeiss. “For moulds and hot runners to be reliable, besides the use of good quality steels and heat treatment, it is also necessary to maintain tolerances of well under 10 microns and to have a good surface on mating or sliding surfaces”, he went on. “This requires the deployment of highly accurate machine tools that are well maintained and regularly calibrated, in a temperature controlled environment, operated by experienced machinists using internally-developed work holding methods, tool selection, cutting processes and in-process and post-process measurement techniques. PETform excels in all departments and is therefore able to deliver excellent value for money, low TCO injection tools that produce good parts for over 8 million shots before the next refurbishment cycle.” Mr Mody determines his portfolio as a reasonably-priced alternative to the well respected Canadian and European mould manufacturers. “We actually grew by 35% last year, despite Covid-19, and expect to grow this year also”, he said. ”We will grow even if the market shrinks, as we are able to take market share from the high end mould producers with our intrinsic competitive advantage.” PETform has the capacity to handle turnover three times last year’s, we were advised; so future plans are pretty much already in place. The company plans to invest later this year in a new preform system that will be able to test moulds of up to 144 cavities with horizontal pitch of 100mm or less, and up to 96 cavities with horizontal pitch of 140mm or less. Its manufacturing and inspecting equipment is going to be continuously upgraded. PETform has successfully supplied, complete mould refurbishment packages for moulds up to 144 cavities. “Our interests lie in producing the best value for money product and having happy customers. We are not in a hurry to grow or to claim market share at any cost. It takes time to develop and educate personnel thoroughly in manufacturing, quality control, testing, service and application support. We will restrict our business volume to what we can support promptly and effectively. We want to be able to sleep peacefully at night knowing that our moulds in the field are reliable performers,” Mr Mody concludes. www.petform.net www.petequip.net 72-cavity preform mould for Husky machine 72-cavity preform mould for Netstal machine","@ID":15} "BOTTLE MAKING 19 PETplanet Insider Vol. 22 No. 05/21 petpla.net in one continuous motion, whereas linear ovens may feature a U-shaped track system with no oven module in the turnaround section. The latter arrangement leads to two increments of equilibration time as shown later. The possibility of overheating the outer preform wall is minimised with the addition of the second equilibration period. 7.2 Blowing bottles Fig. 7.2 is a cycle diagram of a typical rotary stretch blow moulding machine. Black arrows indicate the duration of the machine function. In rotary machines, all times are actual degrees of rotation of the blow wheel rather than time increments. This has the advantage that certain process characteristics can be described without referring to varying cycle times. A disadvantage of camcontrolled movement comes into play when the machine has to be adjusted for throughput. This might be the case when a thicker-than-usual preform wall has to be blown and the existing oven banks are not able to reheat these at the faster cycle time. For optimum performance it becomes necessary here to adjust the cams for mould opening, closing, and so on since the same number of degrees now means longer times and there is no process reason to slow down the mould closing simply because the machine is running slower. Cam adjustment is more time-consuming and so adds to the changeover time of the machine. Figure 7.2 Rotary blow moulding machine cycle diagram. Rotary machines use increments of one rotation of the blow wheel to control machine functions. There are two important points that require careful mechanical adjustment: The point where the stretch rod just touches the bottom of the preform without stretching it, the so-called “0” point. The end position of the stretch rod, the “10” point. This position must leave approximately 1–2mm (0.040–0.080 in.) between stretch rod and base insert for the preform gate depending on the wall thickness in the gate area of the preform. Both adjustments must be made with cold preforms while the machine is operated manually. Exact adjustments are important for proper processing. For the process it is irrelevant whether the preform is neck up (as in the following drawings) or upside down. Mould closed Figure 7.3 An O-ring may seal the preform from the environment. Use and placement of O-rings are particular to each machine manufacturer. At the start of the blowing cycle is a temperature-conditioned preform located on a mandrel or placed in the blow mould via grippers (Fig. 7.3) . An O-ring situated at the inside of the neck or at the top thread surface inhibits air exchange between the inside of the preform and the environment. On machines where the preform is taken off the mandrel for blowing, a blow nozzle is pushed into the neck of the preform for this purpose. The mould cooling water temperature will be between 8 °C and 65 °C (45 °F and 150 °F) with higher temperatures being more favorable to the process with the caveat that they may increase cycle time. At 12 °C in the cycle the base insert starts lifting. It has to be in position to interlock with the blow mould. To save time, the mould starts closing at 14 degrees and is closing around the base insert at 39 °C. Once the blow mould has closed at 49 degrees and locked at 57 degrees, air pressure inside and outside the preform is equal and the stretch rod DNC boosters Turnkey all-in-one system • Compact powerhouse with a footprint of only 2.35 m² ,QLWLDO SUHVVXUH XS WR EDU ² ÀQDO SUHVVXUH XS WR EDU • Plug and play: ready for immediate operation 3UHPLXP HˣFLHQF\\ ,( PRWRU GHOLYHUV LPSUHVVLYH SHUIRUPDQFH DQG HQHUJ\\ VDYLQJV • Sigma Control 2 controller: RSWLPXP HˣFLHQF\\ DQG QHWZRUN FDSDELOLW\\ ,QGXVWULH www.kaeser.com","@ID":21} "BOTTLE MAKING 20 PETplanet Insider Vol. 22 No. 05/21 petpla.net tip has moved to a position very close to, but not touching, the inside of the preform base. The locking is often checked with the help of a switch at 69 degrees (Fig. 7.4) . Figure 7.4 Mould assembly at the start of the blowing process. Stretch rod engages Both blow nozzle (if present) and stretch rod start moving at 51 °C. The preblow pressure may start as soon as the blow nozzle is fully down but there are some delays before full preblow pressure is actually acting on the preform. For example, the blow valve has a certain delay because mechanical parts in the valve must physically move before air can actually pass through. The air has to cross the distance between the valve and the cavity and the closer the valve is mounted the faster the process can start. Once inside the cavity, the inrushing air will have slightly decreased in pressure and it is a fraction of a second before pressure is built up again. These delays combined, take approximately 0.05– 0.15 s, mostly dependent on the distance between blow valve and cavity. Stretch rod action may be delayed to allow pressure to enter at the same time as the stretch rod moves. Depending on the preform temperature the stretch rod may stretch the gate section of the preform first because of mechanical stress acting on this surface before reaching other parts of the preform (Fig. 7.5) . Figure 7.5 The stretch rod engages the lower part of the preform and may pull it out before stretching other parts. Preblow engages As the stretch rod travels further preblow pressure reaches its maximum value of 5–20 bar (70–290 psi). The rubber-like state of the polyethylene terephthalate (PET) will now be inflated into a bubble at the weakest point. This is usually one third to halfway down the heated length of the preform. With properly designed preforms, this yielding phase (Chapter 3, Section 3.2) will come to an end before the bubble reaches the mould walls, thus allowing room for the material to orient more later. As the material extends and reaches the end of its natural stretch ratio the ensuing molecular orientation increases the mechanical strength of the stretched areas. Now areas bordering on the already stretched part are weaker and will therefore start to extend. If the preform is at the same temperature throughout the walls, the bubble will develop from the top down (Fig. 7.6) . Figure 7.6 Preblow pressure creates a bubble not unlike the way a balloon inflates. The stretch speed is an important aspect of proper bottle blowing. Too low a speed can lead to preforms cooling down to a temperature approaching the glass transition temperature where they will not stretch evenly. Higher speeds also improve molecular orientation. Stretch rod at base insert Figure 7.7 When the stretch rod has fully extended the bubble has grown to fill most of the cavity. As the stretch rod races toward the base insert of the mould, more and more sections of the preform start yielding, thereby enlarging the bubble. The speed of development and the extent of the bubble depend on the material’s intrinsic viscosity (IV) and temperature. (Fig. 7.7) . The stretch rod reaches the end position at approximately 90 degrees in the cycle depending on the length of the bottle. It is advantageous in some cases to hold the preblow pressure for another 0.05–0.1 s allowing the bubble to extend further down and so pushing more material to the outer rims of the bottom of the bottle. For many other bottles it is best to trigger the high pressure as soon as the stretch rod is fully extended. On some machines there is a special timer called “temporisation” which delays the onset of high-pressure blow. Other machines feature simply an adjustable switch indicating the stretch being fully extended, and otherwise rely on the slight delay of the start of blow for the reasons described earlier. The preform is now ready for orientation (Fig. 7.8) . Figure 7.8 The bubble can be extended further by slightly delaying the onset of highpressure blow. High-pressure blow Blowing may start as early as 95 degrees or as late as 120 degrees depending on the air delay or the amount of temporisation. The impact of air at 40 bar (580 psi) pressure is dramatic: it takes only around 0.02 s to change the bubble into a fully formed bottle. Air pressure forces the material against the cooler walls of the mould cavity. The material must be cooled below the glass transition temperature and another benefit of running cooler preforms is that the required cooling is minimised, allowing faster cycle times. It should be noted that the stretch rod has to hold the preform gate firmly in the center of the base insert. Any deviation will result in uneven bottle wall thickness. Some linear machines use the air pressure to the stretch rod cylinder as speed control. Reducing","@ID":22} "COMPRESSORS PETplanet Insider Vol. 22 No. 05/21 petpla.net 16 Chinese bottled water producer choses oil-free Atlas Copco compressor Sparkling performance Ever since Shanghai-based bottled water producer Yanzhong Beverage Co. Ltd. was founded in 1996, their salted soda water has been a favourite summer drink of Shanghai residents. In 2016 the company invested in a new manufacturing facility in the district of Boshan to meet an ever-increasing demand. Their aim was not only to scale up production, but to upgrade to a higher manufacturing standard, for increased safety, efficiency and energy savings. Yanzhong Beverage chose to install an Atlas Copco oil-free compressor to ensure that every bubble in its popular drink is safe and healthy. Eliminating all risks of oil residues In beverage production it is critical to eliminate all risk of oil residues polluting the product. If oil from the air compressor enters the PET water bottle, it can affect the taste and smell and at worst, be a health risk. Air power is needed for bottle blowing, filling, capping, labelling and packaging. Oil pollutants can block up the parts, creating unplanned downtime. What’s more, emissions from these parts can contaminate the workshop, which could also pollute the end product. With all these risks in mind Atlas Copco was the bottler’s choice for the purity of its 100% oil-free compressed air. Already back in 2008, Atlas Copco states that it was the first supplier in the compressor industry to obtain the ISO 8573-1 class 0 oil-free air technology certificate. Finding the best solution for the plant A sales supervisor at Atlas Copco’s oil-free air division worked together with Zhang Lingfeng, Chairman of the Board of Yanzhong, to find the best solution for the new plant with regards to its manufacturing techniques, air demand and overall budget. An Atlas Copco ZDXtend integrated compressor now provides both low-pressure and high-pressure oil-free air for the production line. An ZR110FF unit provides medium pressure air for packaging and instruments, and an DX45 booster increases the medium pressure air to 40 bar to provide high-pressure air for bottle blowing. “So far, the machines are running very stably and smoothly, helping us achieve new sales records,” Zhang Lingfeng says. www.atlascopcogroup.com COMPRESSORS ipr +44 (0) 1254 584210 sales@petmachinery.com petmachinery.com Active for over 25 years, our global network and specialist knowledge makes us the go-to company for the sale or purchase of a PET machine. Commercially savvy, we work closely with our customers and our global network, to make sure everyone gets the best deal. Providing comprehensive advice throughout your sale or purchase; we can arrange dismantling, loading, packing, shipping, specialist insurance and commissioning. If you have amachine to sell or you’re looking to purchase, please get in touch. THE INDUSTRY EXPERTS","@ID":18}]}}
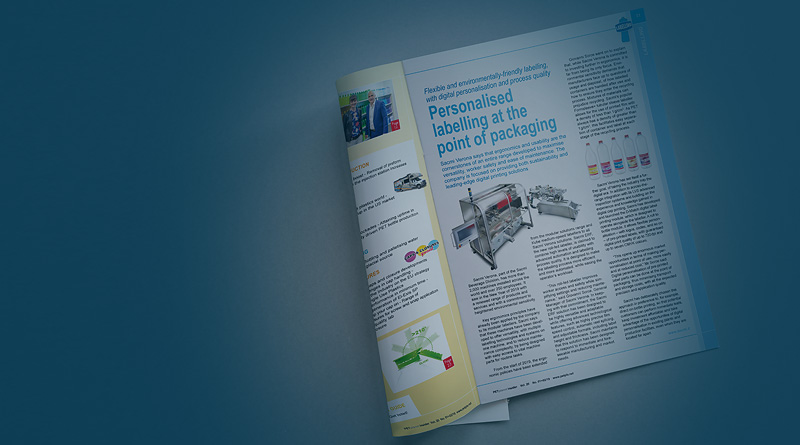