{"pages":{"page":[{"@ID":39, "TRADE SHOW PREVIEW PETplanet Insider Vol. 24 No. 03/23 www.petpla.net 37 TRADE SHOW PREVIEW 37 Omniboost recycling system including polyreactor Jump The Omniboost recycling system with a polyreactor Jump is designed to process PET waste into high-quality products. The integrated Jump can lift the IV value of a PET melt up to 0.95 dl/g. In the Jump the polymer passes over several slow turning elements which create a polymer film, the surface of which is constantly renewed. The reactor vessel is kept under vacuum, through which volatile substances are reliably removed. By regulating the residence time in the reactor, the vacuum, the fill level and the speed of rotation of the agitating devices, the polycondensation reaction can be altered to achieve the required product properties. Filtration technology The continuous rotary filtration systems are characterised by a filter disk on which the screen cavities are located in a ring pattern. Screens can be changed on the part of the filter disk that is not active in the melt channel, while the production process continues to run without any interruptions or disturbances. Gneuss’ top model, the RSFgenius, operates with an integrated back-flushing system offering self-cleaning for demanding applications and high quality requirements. Screens can be automatically re-used up to 400 times and filtration finenesses below 10microns/1,200 mesh are available. Measuring technology Gneuss provides flexible sensor solutions for pressure and temperature measurements, individually tailored to specific applications. The latest generation of Gneuss sensors and pressure monitors communicates completely digitally. Integrated RFID chips for digital gauge monitoring are available for all sensor models. www.gneuss.com Swiss Made | www.imdvista.ch IMDvista NEURON Detailed 360° closure inspection with no need of closure orientation based on Artificial Intelligence Let’s talk about your solution Patented rotary filtration system RSFgenius Gneuss sensors with digital gauge monitoring"},{"@ID":57, "1 The worldwide round trip with The Middle East Roadshow EDITOURS PET world in the Middle East New year, new tour! After our successful Drinktec tour, the PETplanet team is going to the Middle East in the last quarter of 2023! In a spectacular project taking us well into 2024, we will be travelling in a wide variety of ways to various countries and regions of the Middle East with different mobile editors. There we will interview machine manufacturers, the supply industry, bottle and beverage producers, as well as PET recyclers and everyone involved in the process chain. What market-specific trends are there now or will arise in the future? What developments and technologies are in vogue on the consumer and plant construction site in some of the hottest regions of the world? What special requirements are there? What role do topics such as food safety, shelf life and sustainability play in PET packaging and how are companies preparing themselves for the coming years? This, and much more we will be discussing face-to-face with all the key players and then our results will be presented to you in a series of must-read reports in PETplanet Insider. Please join on this enchanting voyage to the world of PET in the Middle East. We look forward to welcoming you on board! Our previous Road Shows at a glance 2010-2011-2012-2013-2014-2015- 2016-2017-2018-2019-2020-2022 Interested in being visited? barton@petpla.net Autumn 2023 - 2024 EDITOUR - THE MIDDLE EAST ROADSHOW 6 countries numerous interviews with PET companies Sponsors to date"},{"@ID":6, "PETcontents 4 PETplanet Insider Vol. 24 No. 03/23 www.petpla.net 03/2023 Page 14 BOTTLE MAKING 10 Igniting the next stage - Strategic plan for further growth in the Indian packaging market Bottle with glued-in handle for home care & food 12 “We need to work and move forward altogether. This is the only way to go.” - Interview with Maxim Poliansky, CEO of PET Technologies EDITOUR 14 Volvic, a very special natural mineral water - Carefully filled in PET bottles CAPS / CLOSURES 16 Perfect parameters - Interview with Federico Zannier, Arol Group Chief Strategy and Commercial Officer and Maca Engineering Managing Director 18 “Sustainability in production is essential for us” Interview with Michael Krueger, CEO of Corvaglia 20 Closures designed to meet the requirements of tomorrow 22 The closure inspection allrounders 24 High degree of customisation - Water brand Uliveto opts for GME30.40 and chooses ‘Asterix’ closure for its water bottles 25 Browning Motion - Brothers Make a business of saving the planet MARKET SURVEY 28 Suppliers of preform machinery CHINAPLAS PREVIEW 31 Chinaplas 2023 preview 36 Technologies for customisable recycling lines 38 Digital inside - Material and energy savings, ‘smart vision’ inspection & smart pack 39 Machines for food & beverage, pharma, consumer and industrial packaging EVENT REVIEW 40 Blow Moulding 2022 - 6th edition 43 Petcore Europe Annual Conference 2023 - PET value chain in a fast-paced environment for circularity, part 1 BUYER’S GUIDE 48 Get listed! INSIDE TRACK 3 Editorial 4 Contents 6 News 46 On site 47 Patents 54 Outer Planet CAPS & CLOSURES Page 47 Page 22"},{"@ID":2, "CAPS & CLOSURES 22 PETplanet Insider Vol. 24 No. 03/23 www.petpla.net The closure inspection allrounders CAPS & CLOSURES In the last decades, variations in closure designs have increased more and more. Nowadays, the market demands one-piece or multi-piece closures, sizes from 20 to more than 60mm in diameter, with or without printing, slitted closures, flip-top closures, tethered caps and much more. This wide variety of closure design variations poses different challenges for the inspection. In order to ensure high-quality vision inspection, Intravis GmbH developed a variety of different technologies for all types of closures. Standard closures The term “standard closure” is deceptive. Even though these closures are standardised and therefore produced in large quantities, they also have important elements on which the producers of the closures put a special focus. One priority of closure producers is, of course, the flawless functionality of the closures, especially in the thread area. Accordingly, Intravis has focused on a comprehensive inspection of the thread, for example with its CapWatcher Q-Line vision system. Thanks to special imaging developed in-house, the entire thread is captured with one camera and then inspected for defects in a roll-out image. Another crucial point in the production of standard closures is the closure dimensions. Intravis uses the CapWatcher Q-Line to inspect the external and internal dimensions, such as the height and diameter of the closure or even the diameter of internal sealing elements. Additionally, the CapWatcher Q-Line inspects defects like contamination, colour deviation and many more. Intravis also developed a patented temperature sensor that records the temperature of every single closure that is produced. It presents essential data for the CapWatcher Q-Line. Based on the temperature information, conclusions can be drawn about the shrinkage behavior of the closures which allows for the implementation of a precise capping process. A closure manufacturer can ensure that the closure has exactly the dimension that is needed at the planned time of application. The operator is able to monitor the cooling of individual cavities and ensure process stability. The next essential element of closure functionality is a flawless tamperevident band, which makes sure that a closure has not been opened already. Therefore, Intravis has created a technology to inspect the quality of the tamper-evident band. For slitted bands, additional attention is paid to the quality of the slit. For example, the technology inspects for deviations of the cutline or if the form is wavy. This makes it possible to detect worn knives or problems with the temperature of the blade at an early stage. Moreover, general defects like long and short shots or broken bridges are inspected at the tamperevident band. Multi-part closures In terms of inspection requirements, these multi-part closures (eg. push-pull or flip-top closures) are more challenging than standard closures. The production of the closures is significantly more complex and creates several challenges such as protruding flaps, damaged pull tabs, special geometries, and assembly faults. Each individual element of the multi-part closure as well as the assembled closure must be inspected in order to be able to guarantee 100% safety. To address this, Intravis has built up a team of qualified mechanical, electrical and software engineers who develop inspection solution for Flip-top closures present several challenges for inspection systems. The announcement of tethered caps prompted Intravis to develop some new technologies."},{"@ID":47, "PETplanet Insider Vol. 24 No. 03/23 www.petpla.net 45 TRADE SHOW REVIEW Happy 30th Birthday Petcore Paul Niedl, Commercial Head at Starlinger Recycling Technology “Congratulations to 30 years Petcore! We appreciate very much being an active member in this wide-spanning industry association that brings together and represents the whole value chain. The annual Petcore conference is THE meeting place of the European PET recycling industry and marked in our calendar every year. We look forward to supporting Petcore and to share our expertise on mechanical recycling especially in these challenging times with regards to climate change, plastics and recycling.” Sorema div. of Previero “Sorema div. of Previero N. srl congratulates with Petcore Europe for reaching this amazing goal. In these 30 years of activity, Petcore has demonstrated to be a unique occasion to connect all the major PET experts of the industry, and to be a great opportunity to share new points of reflections. Sorema wishes that Petcore Europe will continue with its work with the same dedication and commitment.” Christoph Wöss, Erema, Business Development Manager, Application Bottle “Erema Group is wishing you a very Happy Birthday. Out of the 30 years I had the great luck to see you growing and adapting for the last almost 16 years and I have to admit I am proud of what we have achieved! PET recycling is a benchmarking success globally and especially in Europe. Without cross- industrial alignment this would not be possible. Knowing what’s important for the next step in the complete production chain is key and that’s where Petcore is vividly important. Dear Petcore Europe: May the coming years be fruitful and creative for you. Let the changes in life be joyful, the achievements be grandiose, the dreams be realizable, the cooperation be benefi cial for all, and the diffi culties are carried out, leading to success and prosperity.” News from the Working Group - EPBP: Strengthening a Recognised Platform for the Circular Economy was presented by Co-Chair Antoon Spiessens, Coca-Cola. Antoon shortly introduced EPBP. The European PET Bottle Platform (EPBP) is a voluntary initiative supported by the European Federation of Bottled Waters (EFBW), the European Association of Plastic Recycling and Recovery Organisations (EPRO), Petcore Europe, Plastics Recyclers Europe (PRE) and the European non-alcoholic beverages association (Unesda). The Platform consists of technical experts in the field of PET production, design and recycling, whose objective is the evaluation of new technologies and providing an independent and confidential assessment of their impact on the PET recycling processes across Europe. EPBP has established several test procedures in order to assess the impact on recycling of new packaging technologies. Products that pass the tests should not cause any problems during recycling. To move beyond recyclability to the circular economy, the following should be considered. In the discussion, the members of the working group draw a conclusion: The entire bottle must be taken into account. What has been removed must also be recyclable, e.g. caps and labels. The effects on the recycling plants, e.g. due to the smallest deposits or impurities such as parts of a cap, are important to analyse. Also, there are substances that can pass EPBP protocols once, but if they pass multiple times, they can accumulate and become unacceptable. The group explained that in mechanical recycling, the industry must therefore agree on values for how high the proportions of these substances can be. 100 per cent mechanical PET recycling is not possible. The review of the second day will appear in issue 4 of PETplanet insider. www.petcore-europe.org"},{"@ID":37, "35 TRADE SHOW PREVIEW PETplanet Insider Vol. 24 No. 03/23 www.petpla.net High quality injection moulds and PET production systems from Switzerland The Swiss company Otto Hofstetter will present its products and services at an own booth. One focus of Otto Hofstetter is to inform customers about their complete portfolio of high-quality injection moulds. In addition to the well-known high-quality injection moulds, Otto Hofstetter offers all the services that start at the beginning of a project with a product idea, followed by the expertise to advise and design the product. Once the injection mould has been built, the After-sales service completes the overall package. Otto Hofstetter is known for PET preform moulds from 2 to 192 cavities, as well as injection moulds for thin-walled packaging, medical articles and in-mould labelling solutions. Complete PET production systems with clamping forces of 160 t and 240 t are offered under the “Otto Systems” brand. The systems are claimed to meet high requirements in terms of quality and energy efficiency. www.otto-hofstetter.swiss www.otto-systems.com 96 cavity side entry PET mould Otto Systems PET Series 160 OTTO HOFSTETTER Hall 7 Booth H51"},{"@ID":12, "BOTTLE MAKING 10 PETplanet Insider Vol. 24 No. 03/23 www.petpla.net Strategic plan for further growth in the Indian packaging market Igniting the next stage by Kay Barton Manjushree Technopack Limited from Bangalore, India, has set itself ambitious goals under the motto “MTL 2.0”, the company, which is one of the leading plastics processors in the subcontinent, announced as early as 2020 that it wanted to triple its turnover. Now, in the next step, a six- to seven-fold growth is planned by 2026. Reason enough to get to the bottom of the matter and have a conversation in a relaxed atmosphere with Technical Director Vijay Kumar Baheti and the Managing Director Thimmaiah Napanda. We visited: Manjushree Technopack Limited December 2, 2022 We met: Mr Vijay Kumar Baheti, Technical Director Mr Thimmaiah Napanda, Managing Director & CEO Manjushree Technopack currently has 23 factories across India. Since its acquisition by Advent International in 2018, the largest rigid plastic packaging producer has grown rapidly. We are sitting in the meeting room of the Phase 2 industrial estate in the Electronic City district, about 45 minutes from Bangalore city centre. Taking the seat across from us is the man who is rooted to the company like no other. Vijay Kumar Baheti has been with Manjushree for over 20 years. He has a degree in Chemical Engineering from the Birla Institute of Technology and Science in Pilani and can look back on 40 years of experience in the plastics industry. He began at Manjushree as Director of Operations, and has been in his current position since 2004. “Things have been going well for us over the last few years,” he explained. “The pandemic and now the situation with Russia have not really hurt us economically. It’s only the global price increases that we felt and still feel a little bit here and there.” Investments, he said, have continued steadily over the past few years, and energy and production efficiency have also been further optimised. Mr Baheti smiled and further explained, “The new target I want to announce to you today is to grow our sales six to seven times. It is a very pleasant challenge.” We ask what exactly the whole thing is expected to look like. “We want to further expand our capacities and implement new technologies. Existing equipment will be continuously upgraded accordingly. We also want to establish more locations, both through company takeovers and by establishing new factories. Possibly even on a global scale.” Currently, the company has a machine park of more than 20 Husky preform systems at various locations, more than 300 Nissei ASB single-stage systems, over 15 Sacmi compression moulding lines plus hundreds of IMM, IBM and EBM lines. With the recent acquisitions of Pearl Polymers 2020, Classy Kontainers and Hitesh Plastics in 2022, in-house production of caps and closures by multiple compression moulding lines also became an important feature.“In the spirit of EPR and to complete the process chain in a meaningful way, we are now also expanding into plastics recycling,” explained Mr Baheti. Specifically, the company has been operating a recycling plant in Bangalore to process HDPE and PP under the “Born Again” brand since mid-2020. The capacity is 6,000 t annually. Plastic waste is collected, for example, in cooperation with the environmental and social enterprise Sahara Zero Waste, which collects plastic waste from various urban areas for further processing. The Indian government’s goal is to have 30% recycled content in new packaging by 2026. In the next big step, Manjushree now wants to tackle the issue of PET recycling. With the Bureau of Indian Standards (BIS) deciding in summer 2022 that rPET can also be used in beverage and food packaging in the future, which has been discussed for many years but is only now to be permitted by law, there will be immense opportunities to keep PET bottles in circulation by the time the legislation is expected to be finalised in 2025. Mr Baheti explained how the recycling project will work: “To get the process underway, we will probably start by working with recyclers. The possibilities are endless in the long run. Basically, every state in India would need ten recycling plants of its own to optimise the processing of waste from a logistical and economic point of view. In any case, we have plans to expand the recycling division in India, as well as to expand existing capacities. We are fully prepared to meet these challenges with confidence. Whatever it will take to implement our strategies and achieve our goals, we are committed to do.” www.manjushreeindia.com F.l.t.r.: Vijay Kumar Baheti, Kay Barton and Thimmaiah Napanda"},{"@ID":38, "TRADE SHOW PREVIEW PETplanet Insider Vol. 24 No. 03/23 www.petpla.net 36 Technologies for customisable recycling lines Gneuss’ MRS extrusion technology has proven itself as an alternative for the reprocessing of contaminated materials like polyester, polystyrene, polypropylene or polyethylenes. In combination with the Gneuss rotary filtration systems and optimised vacuum technology, customisable recycling lines tailor-made for a specific material can be engineered. Several Letters of Non Objection (LNOs) from the FDA, Efsa conformity and local approvals in Latin America confirm the decontamination efficiency of the technology. Omni recycling system for post-consumer fibre or thermoform reclaim The Omnimax recycling system processes industrial and post-consumer waste from all kinds of polymers and in all forms and shapes. It includes a 3C rotary feeder, an MRSjump extruder, a fully automatic melt filtration system RSFgenius and an online viscometer VIS. Gneuss says that the newly developed 3C rotary feeder makes it possible to use low bulk density materials without any external processing steps. A conveyor belt feeds shredded reclaim material into the hopper, where a fast-rotating disc with knives cuts, compacts and pre-conditions the material. The knives add energy into the material and start the heating and degassing process before the material is automatically fed into the MRSjump extruder. The MRS extruder is based on conventional single screw technology but is equipped with a multiple screw section for devolatilisation. It is claimed to enable efficient and gentle decontamination of PET, whilst achieving the requirements for direct food contact standards. The MRS extruder permits the processing of rPET directly into high quality end products without pre-drying, by using a simple and rugged vacuum system. This is achieved by means of its patented processing section. The multi rotation section is a drum containing multiple satellite single screws, driven by a ring gear and pinion transmission. Gneuss Omnimax recycling system with MRSjump extrusion system, rotary filtration system and 3C rotary feeder Omniboost recycling system with Jump polyreactor, MRS extrusion system, rotary filtration systems and 3C rotary feeder The satellite screws rotate in the opposite direction to the main screw. This disproportionately increases the surface exchange of the polymer melt. A large opening for venting, exposing the full length of the satellite screws, is under vacuum. This provides good and unrestricted access to the polymer melt, the surface of which is constantly replaced at a high rate by the action of the satellite screws in the multiple screw section. The surface area – and the surface area exchange rate – available for devolatilisation are far greater than in other extrusion systems, says Gneuss. As the thermal and mechanical stress on the polymer melt is minimised, PET processed on the MRS extruder has good optical and mechanical properties. The new MRSjump has a longer, modified version of the multi rotation section, which ensures both a longer residence time of the material and more surface area exchange under vacuum. The longer multi rotation section, coupled with a powerful vacuum system operating at 1mbar, can be used to boost the viscosity of rPET and to hold it at a stable level in spite of variations in the input material. Therefore, there is no need for any liquid phase (LSP) or solid state polymerisation (SSP). With the stabilisation and/or increase of the intrinsic viscosity in the extrusion process, the MRSjump is well suited to recycling e.g. PET film waste or fibre reclaim – applications for which direct recycling with one single extrusion step was previously impossible due to low intrinsic viscosity or variable input viscosities. GNEUSS Hall 10 Booth H31"},{"@ID":42, "TRADE SHOW REVIEW PETplanet Insider Vol. 24 No. 03/23 www.petpla.net 40 Blow Moulding 2022 - 6th edition The international conference, exhibition and networking event Blow Moulding focuses on innovations and sustainability in plastic bottles and containers. The 6th edition took place in Brussels, Belgium, on November 30 to December 1, 2022. Based on an article by Mr Noru Tsalic, Nortal Consulting Each year, the conference brings together the entire supply chain associated with this industry: from brand owners and retailers to designers, manufacturers of packaging components, providers of equipment and technology, suppliers of raw materials and additives, – not forgetting recyclers, sustainability experts, academic researchers and regulators to interact, explore new collaborations and accelerate progress and innovation. The event opened on November 29 with an evening Networking Reception – enabling the delegates to get together and interact socially and professionally in a relaxed atmosphere, over drinks and canapés. The next two days were dedicated to presentation sessions, interspersed with Q&A sessions and further social and networking opportunities. The presentations programme was opened by Conference Chair Noru Tsalic, who represented the organisers Nortal Consulting. Entitled ‘Trends & developments in the European Blow Moulding markets’, the presentation was designed to set the scene for all the other talks. In addition to quantitative market information, it included a series of assessments regarding the future outlook for this industry. The first Keynote Speaker was Felix Aymar, Manager Packaging Development EMEA at FrieslandCampina, Netherlands’ largest supplier of dairy products. Mr Aymar’s presentation was entitled ‘Trends and opportunities in bottles for dairy applications.’ Among other things, it demonstrated the use of the OBPPC Framework (Occasion, Brand, Price, Pack, Channel) to optimise packaging across the company. This was followed by another Keynote Speaker: Dr Guy Tantchou, Modelling and Simulation Engineer at Danone Packaging Research, who introduced ‘Numerical simulation of the stretch blow moulding process: new developments at industrial scale’. The presentation revealed novel, low cost capabilities for design exploration and lightweighting, the ability to anticipate potential manufacturing issues, as well as a new model of collaboration between R&D and industrial departments. Sebastian Wenderdel, Business Development manager PET at KHS, presented ‘Latest innova-"},{"@ID":3, "PETplanet Insider Vol. 24 No. 03/23 www.petpla.net 41 TRADE SHOW REVIEW tions in PET packaging technology’. He pointed at four main directions of innovation: process precision and flexibility, cost optimisation, time to market and environmental protection. As an example of innovation, he revealed a new series of PET containers provided with glued-in handles. Developed in 2021 by Nortal Consulting, V-Demos (Video Demonstrations) are a cost-effective and environmentally friendly alternative to ‘classic’ equipment demonstrations at trade fairs. The professionally-filmed videos enable the audience to view details and gain a better understanding of the technologies involved. One such V-Demo was presented by Krones and featured their Contiloop AI – a newly developed blow moulder process control system equipped with artificial intelligence. Unlike traditional control systems, Contiloop AI has ‘learning’ capabilities, enabling it to quickly adjust process parameters to compensate, for instance, for changes in raw material. This is particularly useful when rPET is used, as it enables the machine to manufacture on-spec, constant quality products based on raw materials with variable characteristics. Robert Aust, Head of Product Management Bloc and Plastics Krones, introduced this development and answered questions from the audience. Jorge Pucci, CSO of Moldintec, presented ‘PET label-less bottles’. This new technology replaces labels with information blown into the bottle itself, via etchings on the surface of the mould. The information is easy to read even on transparent bottles, thanks to light reflection and scattering effects. The environmental advantages are obvious. Innovation Leader Claudia Berardi presented Serioplast’s journey towards achieving circularity. Entitled ‘Recycling for good’, her presentation described in detail the various challenges posed by PCR (Post-Consumer Recycling), as well as the innovative ways used to overcome those difficulties. Achieving circularity was also the theme of the next presentation, delivered by Clemens Kitzberger, Business Development manager of Erema Group. Entitled ‘Another life for plastic’, his talk described a number of different technologies, which nevertheless have one goal in common: to deliver PCR material that is as similar as possible to virgin. In his presentation ‘Plastics – a battle of perception’, R&D/Leverage Global Marketing Director Robert Schiavone delivered a passionate appeal to the industry to organise and put together a better communications strategy, aimed at changing the negative perception of plastic packaging. The solution, he argued, is not to replace plastics, which – even where it is possible – would have deleterious results, both from a purely economic and from an environmental point of view. Rather, the solution to the issue of plastic pollution is better public policies and consumer education. (See also PETplanet 1+2/2023) The first day of conference ended with an interesting discussion, led by a panel of experts including Christian Müller (Managing Director, W.Müller EBM), Jochen Hirdina (Vice President Plastics Division, Krones) and Matteo Gaiardi (Global Sales Director, Serioplast). The theme was ‘What’s new? Learning points from the latest innovations unveiled at Drinktec and the K Fair’. The passionate discussion (with the participation of the panellists and the audience) revolved around two main innovation trends: digitalisation and sustainability. Among other things, the participants highlighted the essential role of brand owners, whose needs and expectations drive innovation along the entire supply chain. The proceedings opened again on December 1 with a joint presentation by Daniel Klein (simulation Modelling and Virtual Prototyping at Nestlé Waters) and Julius Petrausch (Lead Researcher, Leibnitz Institute of Polymer Research Dresden). Entitled ‘Novel methods and tools for predicting rPET processability’, their presentation revealed a methodology involving image processing and stress-strain calculations in order to build a ‘digital twin’. The latter can then be analysed in order to identify ideal materials and processes. Tom Palmer (Global Product Manager Plastics at Greif) presented ‘Latest Innovations in Blow-Moulded Industrial Packaging’. Using the 3R framework (Reduce, Reuse, Recycle), he provided examples of innovations for each of those imperatives. Miriam López Fernández, Blow Moulding Specialist at Repsol, followed suit with a presentation entitled ‘Circularity in industrial and household chemicals packaging: current and future solutions’. She revealed the company’s achievements in terms of mechanical and chemical recycling, as well as a new range of bio-based grades. ‘Extrusion Blow Moulding is the future’ was the confident title of a presentation by Andreas Kandt (Group Director Business Development, W. Müller GmbH). A wellknown figure in this industry, Mr Kandt detailed in a persuasive manner the many advantages offered by Extrusion Blow Moulding. Hans Videler (Asset manager PE Blow Moulding at LyondellBasell) presented ‘Advancing circularity for Extrusion Blow Moulded products’."},{"@ID":49, "PATENTS www.verpackungspatente.de PETplanet Insider Vol. 24 No. 03/23 www.petpla.net 47 PETpatents A cap with tethered strap International Patent No. WO 2022 / 184528 A1 Applicant: Closure Systems International España (Spain) S.L.U., Sant Cugat de Sesgarrigues (ES) Registration date: 23.2.2022 A screw cap with an anti-tamper strip and tethered strap. When opened for the first time, a fixed length tethered strap is “unwound” so that the closure and tamper-proof strip are “inextricably” connected in a way that does not interfere with the dispensing of liquid from the container. A container closure International Patent No. WO 2021 / 099358 A1 Applicant: Alpla Werke Alwin Lehner GmbH & Co. KG, Hard (AT) Registration date: 18.11.2020 A container cap with tamper-proof strip and tethered strap function. The application does not interfere with drinking or pouring from the container despite the presence of the tethered strap. A hinged top European Patent No. EP 4071078 A1 Applicant: Affaba & Ferrari S.r.l., Borgo San Giovanni (IT) Registration date: 4.4.2022 A hinged cap with a push-pull function, together with screw-on lid and tethered strap. A hinged lid European Patent No. EP 4089028 A1 Applicant: Nippon Closure Co. Ltd, Tokyo (JP) und Aptar Group Inc, Crystal Lake (US) Registration date: 7.1.2021 The European application shown here is a screw cap for a container. It has been designed in such a way that part of the hinge or tethered strap can be clicked into place, with the attached lid easily removable. A closure cap European Patent No. EP 4095064 A1 Applicant: Betapack S.A.U., Irun (ES) Registration date: 25.1.2021 A screw cap with antitamper strip and tethered strap. The cap stays in the “open” position when screwed on. A web-free locking device European Patent No. EP 4089030 A1 Applicant: Bericap Holding GmbH, Budenheim (DE) Registration date: 6.5.2022 The concept, design and method of manufacturing a closure mechanism with anchoring strap, anti-tamper strip and connecting feature are shown here. Traditional material web portions have been dispensed with in this application."},{"@ID":20, "CAPS & CLOSURES 18 PETplanet Insider Vol. 24 No. 03/23 www.petpla.net “Sustainability in production is essential for us” PETplanet spoke to Michael Krueger, CEO at Corvaglia and Chair at Cetie, about the current production situation and the standardised regulations on tethered cap. Michael Krueger, CEO at Corvaglia and Chair at Cetie CAPS & CLOSURES PETplanet: After the beverage industry had come through the pandemic relatively unscathed, new challenges followed due to the war in Ukraine. Did you have an impact on your business? Krueger: Yes, we had an impact on our business. The most important challenge was the sharp increase of energy prices, which obviously have a significant impact on the manufacturing cost of beverage closures in our Swiss production facility. The Mexican and US production facilities were not impacted on the same level. PETplanet: As a mould and cap producer and as the WG chairperson at Cetie, would you please be so kind and tell us about the current status of the SUP in relation to the tethered caps? Krueger: First, I wanted to thank every stakeholder involved in the process to create the proposal for the harmonised standard EN17665. Almost 100 industry experts worked together intensively in order to create this proposal. It was finalised by the group of experts in March 2022 and subsequently published by CEN. What is still pending before companies can refer to this standard for demonstrating compliance with EU directive 2019/904, Article 6 is the assessment of the EU commission, which took a bit longer than anticipated due to an uncertainty over a formality (the necessity of inclusion of the so-called Annex ZA) between CEN and the EU commission. The pathway to the standard becoming a harmonised standard should now be cleared and I expect the assessment by the EU commission to be finalised within the next 2-3 months. In the meantime, our working group works on a complementary document intended to clarify and provide guidance to users of the standard in its practical application. PETplanet: Since 2020, Corvaglia had increased the overall production of caps. Now the tethered caps have been added. What mould technology and what caps do you offer your customers in terms of a tethered solution? Krueger: A while ago, we introduced a new injection mould technology. We call it “adaptive flex-band technology”. This technology allows combining great applicability for bottlers with premium hinge functions for end consumers. This combination is unique and we see a high demand in the industry for it. Besides closure designs utilising adaptive flex-band technology, we also introduced closure designs with fully integrated hinges to the market. PETplanet: What were the challenges during development? Krueger: Generally, it is a challenge in itself to add a new functionality (tethering) that has not been requested before, while maintaining the normal requirements of the pretethered world, like good physical performance at the lowest possible amount of material consumed, good applicability and compatibility to existing bottling lines as much as possible. We also developed and implemented closures for new neck finishes (most notably the GME 30.40 neck finish) to further improve the carbon footprint as well as the economic effect of material savings. Our development department and implementation teams did a great job, and I am proud of what we have achieved! PETplanet: How much of your sales are in tethered technology at the moment? Krueger: Currently, about 40% of closures produced in our Swiss production site are tethered. Our Mexican and US sites have not yet switched to production of tethered caps. PETplanet: This closure solution is also being talked about outside Europe. Where do you see future markets for this closure solution? Krueger: We see a lot of general interest almost all over the world. However, I have the feeling that customers in most places outside of Europe – while interested - are rather waiting on how things turn out in Europe in terms of consumer acceptance of tethered caps as a whole and acceptance of individual solutions before making any final decisions to implement tethered caps on a large scale. PETplanet: What efforts are you making now and in the future for sustainable production processes? Krueger: As for probably every manufacturing company, sustainability in production is essential for us. This can for instance be seen by the fact that we have reduced our combined scope 1 + 2 GHG emissions in our European operations by more than 95% compared to 2018. The most important measure to achieve this was to change to 100% renewable energy sources. What also contributed to this drastic carbon footprint improvement are the continuation of the measures and actions we follow since decades, e.g. constantly lightweighting our products, investing in the most energy-efficient production means as well as in infrastructure improvements like modern heating concept, improved insulation and similar initiatives. PETplanet: Thank you very much Mr Krueger. www.corvaglia.com"},{"@ID":18, "CAPS & CLOSURES 16 PETplanet Insider Vol. 24 No. 03/23 www.petpla.net Interview with Federico Zannier, Arol Group Chief Strategy and Commercial Offi cer and Maca Engineering Managing Director Perfect parameters It might be thought that these days everything concerning the implementation of the EU regulation for the tethering of caps revolves around single use bottles. In fact, the conversion process is still ongoing. That apart, development work on other topics does not stand still, as Federico Zannier, Chief Strategy and Commercial Officer Arol Group and Maca Engineering Managing Director, explains. In their Closure Test Laboratory, developers and customers are working constantly on the best parameters to adjust the main characteristics that influence the capping process, to improve the interaction of the closure and preform and to adapt the capping process to the requirements of faster and faster systems. PETplanet: At Maca Engineering, which markets do you cover, geographically and by product segment, and in what volume range do your lines operate in the plastic closure sector for PET bottles? Zannier: We produce three types of equipment at Maca Engineering: complete lines to produce aluminium caps, complete lines for the assembly of plastic caps (for spirits, sports caps, etc.) and end-of- line for slitting folding of plastic caps. Thanks to the extensive Arol network, we cover all areas of the world. PETplanet: When we met at Drinktec last year, your company had just expanded with a new manufacturing facility in San Quirino, Pordenone, Italy. What made this step necessary and how are you positioned now? Zannier: From the acquisition [of Maca Engineering ME in January 2020] onwards we have tried to make available to ME the resources and the global presence of the Arol Group. This has allowed us to give a greater visibility to ME and consequently to stabilise the company on sales volumes that have made necessary the expansion of the plant. We have thus doubled the production capacity. With the new factory, the company occupies a total area of almost 9,500m2, of which 1,000m2 is office space and the remainder to produce components and to assemble machines that are shipped from San Quirino all over the world. But the amount of complete caps production lines is already saturating even this additional acquired capacity. In particular, aluminium and plastic assembly are driving the market but the tethered cap conversion is also giving an important boost to growth. PETplanet: You have also set up a Closure Test Lab for feasibility studies or sample runs. What can be tested and analysed here, in relation to plastic closures? Zannier: The modular Laboratory System produced in collaboration with Arol provides for the possibility to customise the cutting/folding of the plastic cap and then to test the application of the same on a preform. We are thus able to determine in a fully automatic way the most suitable application parameters for a new capping solution. In fact we can simulate any type of application. Our end-of-line systems for caps to be applied on PET bottles are up to a capacity of over 80,000 cph but we also have a range of laboratory solutions suitable for caps manufacturers. PETplanet: In what way do different masterbatch materials for the closures differ in handling? Zannier: The use of resins, colourants or special additives strongly influence the application torque and this is at the expense of the removal torque and therefore the customer experience. It is not uncommon to find two seemingly identical caps that behave differently in the production line and it is here that Arol’s experience with over 25,000 machines installed allows us to quickly identify the most suitable configuration for each application. The use of automatic laboratory systems also means we can identify in advance any problems caused using resins or particular CAPS & CLOSURES Federico Zannier Detail of the slitting/folding process by Gabriele Kosmehl"},{"@ID":56, "OUTER PLANET 54 PETplanet Insider Vol. 24 No. 03/23 www.petpla.net OUTER PLANET University of California Riverside method creates char from plastic and corn waste Turning plastic into a soil additive Based on an article by David Danelski, University of California, Riverside University of California, Riverside, scientists have moved a step closer to finding a valuable use for plastic waste: in a recent study, Kandis Leslie Abdul-Aziz, a UCR assistant professor of chemical and environmental engineering, and her colleagues detailed a method to convert plastic waste into a highly porous form of charcoal or char that has a whopping surface area of about 400m2 per gram of mass. Such charcoal captures carbon and could potentially be added to soil to improve soil water retention and aeration of farmlands. It could also fertilise the soil as it naturally breaks down. Abdul-Aziz, however, cautioned that more work needs to be done to substantiate the utility of such char in agriculture. The plastic-to-char process was developed at UC Riverside’s Marlan and Rosemary Bourns College of Engineering. It involved mixing one of two common types of plastic with corn waste — the leftover stalks, leaves, husks, and cobs — collectively known as corn stover. The mix was then cooked with highly compressed hot water, a process known as hydrothermal carbonisation. The highly porous char was produced using polystyrene, the plastic used for Styrofoam packaging, and PET. The study followed an earlier successful effort to use corn stover alone to make activated charcoal used to filter pollutants from drinking water. In the earlier study, charcoal made from corn stover alone activated with potassium hydroxide was able to absorb 98% of the pollutant vanillin from test water samples. In the follow-up study, Abdul-Aziz and her colleagues wanted to know if activated charcoal made from a combination of corn stover and plastic could also be an effective water treatment medium. If so, plastic waste could be repurposed to clean up water pollution. But the activated charcoal made from the mix absorbed only about 45% of vanillin in test water samples – making it ineffective for water cleanups, she said. “We theorise that there could be still some residual plastic on the surface of the materials, which is preventing the absorption of some of these (vanillin) molecules on the surface,” she said. Still, the ability to make highly porous charcoal by combining plastic and plant biomass waste is an important discovery, as detailed in the paper, “Synergistic and Antagonistic Effects of the Co-Pyrolysis of Plastics and Corn Stover to Produce Char and Activated Carbon,” published in the journal ACS Omega. The lead author is Mark Gale, a former UCR doctoral student who is now a lecturer at Harvey Mudd College. UCR undergraduate student Peter Nguyen is a co-author and Abdul-Aziz is the corresponding author. High surface area material “It could be a very useful biochar because it is a very high surface area material,” Abdul-Aziz said. “So, if we just stop at the char and not make it in that turn into activated carbon, I think there are a lot of useful ways that we can utilise it.” Plastic is essentially a solid form of petroleum that, when it accumulates in the environment, pollutes it and can kill animals that accidentally swallow parts or become entangled. Plastics also break down into micro-particles that, if they enter the human body, are suspected of causing inflammatory and immune reactions. As it often costs more to recycle used plastic than it costs to make new plastic from petroleum, Abdul-Aziz’s laboratory intended to take a different approach to recycling: It is devoted to putting pernicious waste products such as plastic and plant biomass waste back into the economy by upcycling them into valuable commodities. “I feel like we have more of an agnostic approach to plastic recycling when you can throw it in (with biomass) and use the char to better the soil,” she said. “That’s what we’re thinking.” www.ucr.edu Kandis Leslie Abdul-Aziz The char and activated carbon making process"},{"@ID":17, "EDITOUR 15 PETplanet Insider Vol. 24 it. This is not the case with a Combi or traditional line technology. Furthermore, there are five Sidel Combi, one Combi of Kosme, one Combi by SMI, Blower 5 SBO and some blower of Krupp. Volvic produces still water in 0.33 l, 0.5 l, 0.75 l, 1 l, 1.5 l, and 8 l, carbonated drinks in 0.75 l and 0.45 l bottles. Other flavoured drinks in 0.5 l, 0.75 l, 1 l, 1.5 l according to Michael. “In 2022 we have filled 1,430 billion bottles, which represent 1,770 billion liters in total; from 2017 to 2022 we got stable volumes. Volvic makes 98% of its sales in Europe and its main markets are France, Germany, and UK. Volvic is n°1 in mineral waters in France, n°1 in still mineral waters in Germany, n°1 in flavoured waters in United Kingdom and finally n°1 in flavoured waters in Switzerland“, Michael summarised. “For the future we will have major projects here in the production plant: The bottling lines 11 & 12 will be equipped with innovative technology from Krones, with the Ergobloc. These are lines without rinsing and more precise bottling technologies. From 2017, we have invested 30 million of euros in new lines and we have saved 13% of water. And finally, we have the Re-Use project. The objective of Re-Use is to treat the wastewater in order to obtain potable water quality and to reuse this treated water for equipment cleaning. This project is part of a larger plan for the rational use of water which was contracted between Volvic and the authorities on September 23, 2021. This plan is part of the voluntary roadmap carried out since 2017 to preserve this resource and act in a sustainable way, with a long-term and collective vision. This project could double the water savings achieved by 2025 and change industrial practices by paving the way for other companies,“ Michael states. As we come to the end of our tour through the factory, Michael mentiones that it is special to work for Volvic because the people grow up with the company and really love it. “We also got a beautiful natural resource that we preserved everyday with the Comité Environnement pour la Protection de l’Impluvium de Volvic (CEPIV) and other actors.” www.volvic.com The new Ergoblock L of Krones"},{"@ID":21, "TRADE SHOW PREVIEW PETplanet Insider Vol. 24 No. 03/23 www.petpla.net 38 Material and energy savings, ‘smart vision’ inspection & smart pack Digital inside Technological developments for energy savings and advanced controls for CCM and inspection systems ‘made in China’ are among the focus topics on Sacmi’s booth. But it’s not just technology that’s on show. Visitors to the stand can also see several Laboratory-made products, such as market-ready neck+cap and tethered-friendly solutions designed to aid the lightweighting transition: solutions already adopted by some of the industry’s major players. Sacmi has already installed more than 680 CCM machines on the Chinese market. At the show, the company is introducing numerous innovations on the latest generation of CCM presses. The press range now benefits from an integrated set of “smart vision” inspection systems, from the CHS (for closures), which has been manufactured directly in China since this year, to the PVS (for preforms), which can be integrated into the next-generation IPS 300 and IPS 400. The latest CCM machines are equipped with the brand new CMFlow extruder. Sacmi claims energy savings of up to 9% and up to 50% fewer black specks compared to the same resin processed with traditional extruders. CMFlow produces caps that have the same resistance to stress cracking as those produced with traditional extrusion technology and operates at lower temperatures. Because of its simple and compact design, maintenance is claimed to be quick and easy. Unlike a conventional extruder, the motor is coupled directly to the screw without any need for a gearmotor. CMFlow is as-standard on the new Sacmi CCM48SD presses yet can also be implemented on the CCM24SF and CCM32MC versions. Smart Pack All latest-generation CCMs – and existing versions such as the CCM24SF, CCM32MC, CCM48SD and CCM64MC – can be equipped with Sacmi Smart Pack. A digital control package that integrates advanced sensors and on-board controls, Smart Pack is claimed to simplify operation, increase machine availability and reduce the risk of errors or line stoppages. This is achieved by an automatic system that verifies correct dose insertion and positioning, through automatic (and predictive) hydraulic oil quality control and through cuttingedge thermoregulation to prevent onmould condensation. Smart vision To better support its customers, Sacmi has started production of its CHS cap inspection systems in one of its Chinese plants. The goal: to further accelerate delivery times and punctuality of service. The approach taken emphasises that inspection is no longer just about checking individual defects/caps, but about gathering valuable information to improve processes and predict deviations. Key innovations include a patented Sacmi solution that inspects tamper band slitting on the new tethered caps. The tethered standard is also of growing interest in China, and Sacmi offers a range of advantageous ready-to-use solutions, such as simple slitting of the tamper band in post processing. GME30.40 neck transition The new GME30.40 ‘multi-purpose’ 26/22 neck standard is gaining popularity in China and around the world as it offers a tethered-compatible solution that delivers net material savings of more than 30% without affecting performance. Through Sacmi Lab, each development is accompanied by a series of dedicated, customised, ready-to-use caps. Some of these will be showcased on the stand to illustrate their versatility, as they can all be customised to meet production requirements. The comprehensive technology spans from CCM presses to the latest-generation IPS preform presses. The IPS 300 and 400 are the first solutions on the market to integrate, directly on the press, intensive preform inspection with the PVS 156 vision system. www.sacmi.com SACMI Hall 10 Booth H41 The vision system features advanced CVS 360 control software. Compression moulded tethered cap solutions, suitable for GME30.40"},{"@ID":45, "PETplanet Insider Vol. 24 No. 03/23 www.petpla.net 43 TRADE SHOW REVIEW PET value chain in a fast-paced environment for circularity Petcore Europe Annual Conference 2023 part 1 by Heike Fischer First day Antonello Ciotti, President of Petcore Europe, welcomed the participants and reaffirmed the solidarity of the 143 members representing the entire value chain. He emphasised the importance of the Petcore Europe association’s voice as the most important within the EU. He called for an improvement of internal and external communication, especially with regard to the ten Directives under debate this year. Dr Bruno Langlois, Carbios and Chair of the Depolymerisation Working Group, reported that there are currently four projects within and outside the EU. The companies involved are Eastman, Axens, Loop and Carbios. All these projects are still at different stages of development. Commercial scale is supported by the PPWR (November 2022), which provides for the reuse of materials and an increase in recycling. The textile feedstock is particularly important, Bruno added. An important issue, according to Bruno, is and remains the debate on mass balance. Mass balance is a widely used supply chain monitoring method in the depolymerisation industry. A “flat reallocation” is usually used over production batches. And guarantees confidence because of the ease of traceability. The debate revolves around reallocation and book and claim. Delphine Close, Policy Manager at Unesda Soft Drinks Europe and Chair of Petcore Europe’s Reuse Working Group explained that PET can play a key role in the circular economy for packaging by offering both recycling and reusable solutions that are safe and convenient for consumers while reducing packaging waste. She affirmed that recycling & reusing are two complementary ways to achieve packaging circularity, but the right conditions and enablers need to be set to ensure a positive integration of both solutions. Therefore, it was important to set up this new working group. The group works to provide information to stakeholders and decision-makers who want to better understand the recyclability of PET and share best practices among industry players, Delphine summarised. There were two updates on LCA: Lauren Laibach, Director of Data Services National Association for PET Container Resources (Napcor) and Stefan Frehland, Sustainability Consultant at Quantis. Lauren briefly explained that the new Napcor report will be authored by Franklin Associates (ERG). The study compares PET, glass and aluminium keg container systems and looks at multiple scenarios for each packaging format. The new report shows current life cycle assessments for virgin and recycled PET resin supply chains. However, Lauren has already been able to confirm that a PET CSD bottle weighs 9% less than a PET CSD bottle in 2009 compared to 2022, uses 25% less energy in production and ultimately produces 19% less greenhouse gas emissions. She concluded that PET bottle systems consistently have lower impacts than aluminium and glass alternatives in terms of cumulative energy demand, waste generation, global warming potential, acidification potential and smog formation potential. Stefan presented the Quantis method of a holistic multi-indicator approach to sustainability decision making. He explained Sphere, the so-called Packaging Sustainability The 30th anniversary of the annual Petcore conference was celebrated in Brussels on February 1+2, 2023. About 300 participants attended the hybrid conference on the topic “PET value chain in a fast-paced environment for circularity”. In addition to a festive evening event, Petcore set new accents within the conference programme structure. On the first day, short keynote speeches on technical updates were given by the different working groups chairs. This was followed by high-level panel discussions. The result was a series of exciting presentations on topics that are among the most pressing. On the second day, extensive presentations were held on the topic of the “PET value chain in a fast-changing environment”, including the annual update of the EU regulations for the plastics industry."},{"@ID":30, "MARKET SURVEY 28 PETplanet Insider Vol. 24 No. 03/23 www.petpla.net 03/2023 MARKETsurvey Suppliers of preform machinery In this issue PETplanet focuses on state-of- the-art perform machinery. We are proud to present the most exciting brand-new data from the following perform machine manufacturers: Sipa, Otto Systems AG, Sacmi Imola, Netstal Maschinen AG and Nissei ASB Machine Co. Ltd. Although the publishers have made every eff ort to ensure that the information in this survey is up to date, no claims are made regarding completeness or accuracy. Resins & additives Preform machinery Preform production & inspection systems Preform & SBM mould manufacturer SBM 2-stage Compressors All about caps Filling equipment & inspection systems Palletising & shrink film machinery Recycling machinery Company name Sipa Otto Systems AG Postal address Telephone number Web address Contact name Function Direct telephone number E-Mail Via Caduti Del Lavoro, 3, 31029 Vittorio Veneto, Italy +39 0438 911 511 www.sipa.it Mr Gianfranco Perricci Global Sales Director, Preform Systems & Tooling +39 0438 911 511 gianfranco.perricci@zoppas.com Zürcherstrasse 73, CH-8730 Uznach, Switzerland +41 55 285 22 11 www.otto-systems.com Mr Stefan Zatti CEO +41 55 285 22 09 stefan.zatti@otto-systems.com Preform injection moulding systems Machine model number / name Xform 250 Xform 350 Xform 500 Xtreme 72 Xtreme 96 PET-Series 160 and PET-Series 240 Number of cavities (min/max units) 96 128 200 72 96 2 - 96 cavities Maximum individual preform weight max shot weight 5,130 g Max resin through-put (kg/h of PET) up to 890 kg/h Standard Features (short description / keywords) Consulting & Engineering of preform systems: Complete integrated turnkey preform production system including auxiliaries, full electric clamping unit, two stage injection with shooting pot or injection with time safe unit (TSU) Options / Special Features (short description/keywords) Preform production: Xform 250: 69,000pph; Xform 350: 92,000pph; Xform 500: 147,000pph; Xtreme 72: 52,000pph; Xtreme 96: 69,000pph. Xtreme: injection-compression technology, ultra-thin wall capability, 2 preforms can be produced simultaneously. Xform Gen4 XP: XP technology, LongLife tooling coating, Xmold for ultra-thin preform injection capability, wide-mouth preforms capability. Xtreme: built-in inspection system for 100% quality check, 100% recyled fl akes processing capability, direct connection with Xtra SBM. Xform: available in Gen4 XP version (low energy consumption, fast cycle time, complete new HMI) Extra-large preform capability (up to 380mm), compatible to a selection of top-entry moulds, co-injection technology up to 72 cavtities, integrated dust-evacuation (OH-Xtract), enhanced neck-cooling (OH-Xcool), wear-protection coating (OH-Xtreme)."},{"@ID":55, "ONsite 46 PETplanet Insider Vol. 24 No. 03/23 www.petpla.net Indian Pepsi bottler set to expand outside India One of the world’s largest bottlers for PepsiCo outside the US has extended its Sipa machinery to expand its operations. Varun Beverages India Pvt Ltd (VBL) is an official bottler for Pepsi in India, where it has operations all over the country. Over the last few months, the company has been investing in XForm preform injection moulding systems, in Xtra rotary stretch-blow moulding, and in Sincro Bloc, thus integrating bottle blowing, filling and capping equipment in a single system. During 2022, three XForm 500 GEN4 XP systems, equipped with 180- and 144-cavity Sipa moulds, have been installed at different locations in India. All the machines are dedicated to the production of preforms for PepsiCo carbonated soft drinks, for bottles ranging in size from 250 up to 2,250ml. A Sincro Bloc 16-100-15 was installed in December 2022. VBL also works for Pepsi in other countries, including Zimbabwe, where it plans to grow its presence. It established a green field production facility in Zimbabwe four years ago, aiming to cater for what it said was “an untapped market with huge potential.” With a new Xtra 16, which went into operation in May last year, it clearly is on the way to realising that potential. The company listed high productivity and low energy consumption as two of the main reasons why VBL chose Xtra. Sipa states that Xtra can produce more bottles per cavity than any other stretch-blow moulding machine in its category, thanks in large part to its very wide active process angle (200 degrees), leading to a low TCO. VBL produces and distributes a wide range of carbonated soft drinks (CSDs), as well as a large selection of non-carbonated beverages (NCBs), including packaged drinking water sold under various PepsiCo trademarks. It has been associated with PepsiCo since the 1990s, and now has franchises for various PepsiCo products across 27 States and 7 Union Territories in India. VBL has 31 manufacturing plants in India and six more in other countries. www.sipasolutions.com BEYOND THE HORIZON PROCESS SOLUTIONS FOR POLYMER RECYCLING AND SOLID STATE POLYMER UPGRADING Polymetrix, a Sanlian Buhler Company, provides process technology including EPCM services for the polymer recycling and manufacturing industry. Leading supplier of rPET systems and integrated rPET plants for single line capacities up to 70’000 tons per year. www.polymetrix.com www.slhpcn.com"},{"@ID":53, "MARKET SURVEY 29 PETplanet Insider Vol. 24 No. 03/23 www.petpla.net 500+ Molds Proven Globally Acme Drinktec Solutions LLP Ph +91-9810418975, +91-9819020785, +91-9810631426 Email: sales@acmedrinktec.com Website: www.acmedrinktec.com #MOLD@70DPW MOLDS FOR ASB [50MB / 12M 70DPH / 70DPW], AOKI, SIPA, ETC Balanced HR System Creating Molds with a Difference YOU CAN HAVE FROM THE SAME RESOURCE Enhanced Cavitation Superior Tool Steel Company name Sacmi Imola Netstal Maschinen AG Nissei ASB Machine Co., Ltd. Postal address Telephone number Web address Contact name Function Direct telephone number E-Mail Via Provinciale Selice 17/A, 40026 Imola BO, Italy +39 0542 607111 www.sacmi.it Mr Moraldo Masi Director of Business Unit PET +39 0542 607888 moraldo.masi@sacmi.it Tschachenstrasse 1, CH-8752 Näfels, Switzerland +41 55 618 6111 www.netstal.com Mr Stefan Kleinfeld Product Manager +41 55 618 6241 stefan.kleinfeld@netstal.com 4586-3 koo, Komoro-shi, Nagano-ken, 384-8585 Japan +81 267 23 1565 www.nisseiasb.co.jp Mr Paul Atkin Manager, Sales Coordination Team +81 267 23 1565 sales@nisseiasb.com Preform injection moulding systems Machine model number / name IPS220 IPS300 IPS400 Side-entry systems: PET-Line 3000, PETLine 4000, PET-Line 5000 / Top-entry systems: PET-Line 2400, PET-Line 4000, PET-Line 5000 PM-70/65NII, PM-70/111N, PM170/111M Number of cavities (min/max units) 16 - 72 24-128 48 - 144 24 - 144 6 - 48 Maximum individual preform weight 140g 140g 140g max shot weight 6,600 g 240g Max resin through-put (kg/h of PET) 625 kg/h 900 kg/h 1,250 kg/h up to 1,600 kg/h approx. 250 kg/h Standard Features (short description / keywords) Injection cylinder (shooting pot), electrical drive for plasticising screw, T-belt for preforms extraction, Cool+ system (inside cooling), belt free robot linear motor with KERS, take-out plate with three postcooling stations IPS220 for IPS 300&400 four postcooling stations, HMI with control of all auxiliaries, double cylinder for preform ejection, digital valves for each actuator, water unloading system prior to mould changing, injection shot completition device (power failure). At IPS 300&400 digital valves for each actuator and water unloading system prior to mould changing. All PET systems: Intrusion function, automatic metering system; PETX-Screw (=optimised 100% rPET processing), side entry systems: smart operation (safe and guided operation) and energy recuperation (lowest energy consumption) Vertical clamping, built-in preform after-cooling stations, extremely compact Options / Special Features (short description/keywords) Fast change over system with plug-and-play mould fi xing system, plug-and-play take out plate fi xing system, water pumps for mould cooling assembled on main machine platform, secondary belts system for an easier collection of preforms sampling, quality control vision system with multiple camera, soft handling package walkway, high temperature environment package, cooling water sensoring kit. Injection shot completition device (power failure), water pumps for mould cooling assembled on main machine platform, quality control vision system with multiple camera, soft handling package, walkway, high temperature environment package and cooling water sensoring kit. Cycle guard (controlled production shutdown during a power outage), NRS (= Netstal remote support), energy measurement, preform inside cooling, staggered EOAT (= additional cooling station) and Q-vision control. Outputs are tailored to ASB's own range of 2-step blowing machines for hot fi ll application. PM-170/111M is designed for bottle and jar preforms with capability of neck size up to 120mm."},{"@ID":29, "CAPS & CLOSURES 21 PETplanet Insider Vol. 24 No. 03/23 www.petpla.net is silicone-free because it is impossible, or at least extremely difficult, to separate the silicone from the reusable PET in the recycling process. The Bericap valves that are used in various closures for the ketchup, mayonnaise and spreadables segments have obvious recycling advantages because they are made from a thermoplastic elastomer (TPE) that is 100% siliconefree. The new tethered caps also protect the environment because they are attached to and recycled with the bottle, thereby preventing environmental waste caused by discarded caps. European manufacturers and fillers of single-use beverage bottles with a capacity of up to 3 l have to change over to tethered caps by July 2024 when they become mandatory in Europe. The Bericap ClipAside allows the companies to continue manufacturing closures with the current TE band geometry at the same time, and to conveniently switch between standard and tethered cap bottles on the filling lines without the need for further modifications. Companies can change over their production lines in well ahead of deadlines for compliance with the new requirements. Bericap manufactures ClipAside closures for all relevant neck finishes. Reflecting the principle of ‘less is more’, Bericap is introducing weight and material reductions across all product categories and closure designs, from the sport caps that are now available in more variants to the new light weighting cap range for edible oils. The company is also involved in the development of new neck finish standards. The ‘made for recycling’ designs are based on a mono-material approach to eliminate material separation problems in the recycling process. Bericap will exhibit at the Interpack Trade Fair in Düsseldorf, Germany, from 4-10 of May 2023 under the slogan “Welcome to CapTown”. product development caps & closures design high cavitation moulds multi-component moulds closure production systems after sales service competent – professional – inspiring +43 5572 7272-0 | sales@z-moulds.com | www.z-moulds.com z With more than 4,000 employees at 26 production plants serving customers in over 100 countries across the world, Bericap is building on the positive development in 2022 and remains on track for growth in the region of 5 per cent this year. Bericap’s geographic expansion into new growth markets including Southeast Asia, Africa and South America continues, and it is planning to open new production plants in Vietnam and Kenya at the end of 2023. www.bericap.com F.l.t.r.: The latest Bericap sport caps: Biarritz, Mayence and Monet are designed to use fewer materials, improve recyclability due to mono-material and prevent littering (no loose parts). The new designs are available for all relevant neck finishes."},{"@ID":14, "BOTTLE MAKING 12 PETplanet Insider Vol. 24 No. 03/23 www.petpla.net “We need to work and move forward altogether. This is the only way to go.” Russia’s war against Ukraine, which is contrary to international law, has been going on for a year now. PETplanet spoke to Maxim Poliansky, CEO of PET Technologies, about production conditions, challenges and his assessment for the coming six months. PET Technologies plant is located in Chernihiv, in north-eastern Ukraine, about 80 km from the Belarusian border and 140 km north of Kyiv. PETplanet: What is the current economic situation of the PET and plastic packaging industry in Ukraine? Poliansky: The PET container market in Ukraine is keeping pace with the global trend: consumption is growing. This might seem surprising as several bottlers have ceased operations, but their share of the market has been taken over by other producers. In addition, humanitarian demand has actually led to this market growing. The PET container is still the most economic and at the same time most effective type of packaging. We are continuing to see a higher percentage of rPET in bottles and a trend towards reducing PET bottle weight. Milk and vegetable oil is one of the top growth sectors. The beer market was a little sluggish in mid-2022, but by the end of the year it was beginning to move and Inbev, Carlsberg and some middlesized breweries are now coming back to us with their projects. PETplanet: What are your current production conditions? Poliansky: Manufacturing facilities of PET Technologies are in full operation. The number of employees has not significantly reduced since the war started. Some people are still abroad, but 80% of pre-war numbers are working and that percentage is OK for us. Indeed, in some professional sectors we are hiring again. When the Russians began their full-scale invasion of Ukraine, we did our utmost to hold on to our staff and we have achieved this goal. As for production conditions we immediately implemented additional measures at our manufacturing facilities: industrial generators were installed to ensure we had enough electricity in the case of power cuts, and we created alternative supply chains. In this way, all equipment was produced on time; we have kept to the lead-times agreed with the customer. It’s worth highlighting that currently PET Technologies´ lead-time is about average for the market average or even shorter. Usually, we use the western border of Ukraine to export equipment. In this sense, nothing has changed and delivery times have been unaffected. We are still selling in Ukraine and exporting. Even in 2022 we shipped 3 blowers to the USA. PETplanet: What are your strategies to lead your company through these difficult times? Poliansky: It is now evident that the Ukrainian economy has not come to a halt, despite the war. Local manufacturers of food and beverages have invested hundreds of thousands of US dollars in PET stretch blow-moulding machines since February 2022! Ukrainians and Ukrainian business have a clear vision – we need to work and move forward altogether. This is the only way to go. Our customers worldwide continue to place orders with PET Technologies, trusting in Ukraine. Some of the regions where we have sold our machines and moulds include Europe, the Middle East (Saudi Arabia takes a lot of our moulds) and the Americas. PET Technologies GmbH, Austria (part of the PET Technologies group) participates significantly in these projects. This March we will be commencing manufacture and commissioning of another machine in the United States, followed subsequently in Mexico. PETplanet: What are the biggest challenges in general and how do you see the next six months? Poliansky: People are our principal resource and our biggest challenge is to look after them in whatever way we can. These are people in our company, together with their families, as well as our city and country itself. We consider our mission to maintain the economic balance of the country. PET Technologies is not just staying fully operational, but we are also continuing to invest in research and development! We have recently extended our newest APF-Max series of blow-moulders with smaller 2 and 3-cavity machines. Soon they will be launched on the market. PET Technologies is continuing to develop into new business directions, expanding its manufacturing facilities and we have already invested in new equipment! PETplanet: Thank you so much Maxim. www.pet-eu.com by Heike Fischer"},{"@ID":9, "7 NEWS PETplanet Insider Vol. 24 No. 03/23 Construction of the largest recycling plant for food-grade PET/HDPE plastic in Vietnam Alba Group Asia, a provider of waste management and recycling solutions and VietCycle, a nationally established waste collection and plastics recycl ing company in Vietnam, announced the launch of a cooperation to jointly develop the largest plast ics recycl ing plant for food-grade PET/HDPE in Vietnam. At the signing of the cooperation agreement in the capital Hanoi, high representatives of the government of Vietnam and the German embassy confirmed contribution of the project to one of the most urgent environmental problems in the country and pledged their support. They are aware that Vietnam is one of the biggest polluters of the world’s oceans, according to the World Bank. Every year, Vietnam discharges about 3 million tonnes of plastic waste on land and an estimated 0.28 to 0.73 mi l l ion tonnes of plastics waste into the ocean. Across Vietnam, local governments are struggling to collect, transport, treat and dispose of their growing waste streams. Rapid urbanisation combined with increasing economic and population growth will further increase the volume of waste, according to Dr Alex Schweitzer, Chairman Interzero. Together wi th Vi etCyc l e, Interzero wants to tackle this challenge: The investment sum for the planned plant will be up to 50 million US dollars. Interzero aims for a capacity of up to 48,000 t/a. The first phase of operation is expected to start in 2024/2025. The project will use modern technologies to produce food-grade PET/HDPE following international standards set by the EU. Through this partnership, VietCycle’s network can grow and offer a significantly larger number of informal waste collectors an upgrade of their work, which is so important for Vietnam. Gender equality and social inclusion in the collection system and in the plastic recycling sector are among the key objectives of the partnership. Hoang Duc Vuong, Chairman of VietCycle Joint Stock Company, said: “Working with Alba Group Asia helps us realise our dream of recycling plastic waste based on advanced technology, contributing to sustainability and humanity.” In addition to the promising partnership and significant contribution to combating climate change in Vietnam, the expansion of the network will enable Interzero and VietCycle to reach many of today’s still very disadvantaged collectors and improve their lives by offering training and social security services. www.interzero.de/en/"},{"@ID":33, "31 TRADE SHOW PREVIEW PETplanet Insider Vol. 24 No. 03/23 www.petpla.net TRADE SHOWpreview Chinaplas 2023 - Concurrent Events Chinaplas 2023, Asia’s leading plastics and rubber trade fair, to be held from April 17 to 20, will bring together more than 3,900 prominent exhibitors from all over the world to present cuttingedge and practical solutions. The show will also organise a series of concurrent events addressing the industrial needs in the hot green trends of carbon neutrality, circular economy, and sustainable development. Plastics recycling & circular economy conference and showcase What kind of technologies will make the circular economy work? The 2025 commitment to sustainable development of enterprises across the plastics and rubber industries is being gradually fulfilled with the advance in materials and technologies. To keep abreast of new trends, the conference will cover recycling classification from experienced countries and regions, technological achievements of plastics recycling and applications, and outline the pattern and prospects of the plastics recycling industry in Asia and other regions. Besides the main conference, parallel sub-forums will be held for industry elites to share their insights, introducing the hot topics such as “Green Design and Cross-Value Chain Collaboration”, “Energy Efficient and Low Carbon Supply Chain” and “Value-added Mechanical Recycling and Chemical Recycling”. Sustainability Resonator – art installation An installation art - Sustainability Resonator will be set up at the trade show, to disseminate the ideas of “environmental protection, recycling, jointly shaping the future of the plastics industry, additive manufacturing, crossover innovation, biodegradation and sustainable development”. The organiser of Chinaplas is collecting voice messages of participants who shared their views on environmental protection and sustainable development from different countries and regions. With the help of 3D printing, parametric design and green material, the collected sounds can be presented in a piece of “voice cell” and assembled to a crowd-generating installation art. 1,500+ voice contributors have already participated in the creation of the installation with their voices. Tech Talk Visitors can attend Tech Talk to learn more about green and leading technologies and its applications. Over 30 of the latest technologies will be revealed in a series of open forums and more than 20 industry experts will present their hottest and highly advanced products and technologies under five different themes: eco-friendly solutions, medical plastics & antimicrobial solutions, surface treatment solutions, lightweight solutions, innovative materials. Professional speakers will drill deeper into the practicability of sustainable and green solutions while audiences will quickly capture the industrial trends of plastics and rubber industries facilitating agile business decisions. Applications in focus Awide spectrum of brands from enduser markets, universities and research centres will be gathering at Applications in Focus to share high performance plastics and rubber applications, such as photovoltaic, plastic and rubber antibacterial technology, sterilisation packaging, green low-carbon and circular economy, etc. More than 70 hot topics will be shared by renowned brands, industry leaders, experts, universities, associations etc. There are in total 12 thematic seminars including in-depth talks on the experiences and technology prospects of the application industries. www.chinaplasonline.com"},{"@ID":10, "8 NEWS PETplanet Insider Vol. 24 No. 03/23 www.petpla.net Specials at Interpack open up new perspectives At Interpack from May 4 to 10, 2023 in Düsseldorf, Germany, there will be numerous new special areas and promotions to complement the offerings of the approximately 2,700 exhibitors. I n t erpack s t ands f or produc t launches, technological news and packaging innovations, according to the organisers. These will be highlighted this year through award ceremonies. The “WorldStar Packaging Awards” 2023, which will be presented by the World Packaging Organisation, WPO, at Interpack. A total of 228 award winners demonstrates the innovative strength of the industry. The “PackTheFuture Award” of the German IK Industrievereinigung Kunststoffverpackungen and its French partner Elipso will also be handed out during interpack. This year’s Interpack also features new categories: Gift Packaging, Digital Packaging and the special category Accessible Packaging. There will also be a new Start-up zone in hall 15, where innovations from software solutions for recycling or the supply chain, sustainable materials or packaging will be presented. “Spotlight talks & trends” at Interpack means seven days of input around the most important topics and trends in the industry, best practices, exciting applications and their drivers for innovation and growth. Deutscher Fachverlag is the partner of the lecture forum. Each day of the trade fair will have a different focus topic and will feature presentations, case studies and interactive sessions with top industry experts. The focus will be on topics related to logistics, circular economy, sustainability, digital technologies, product safety and e-commerce. Companies such as Siemens, Schütz and Markem-Imaje have already announced their attendance for presentations. www.interpack.com Alpek shutdown of PET resin operations at its Cooper River site Alpek, S.A.B. de C.V. announced the shutdown of its PET resin operations at its Cooper River site near Charleston, South Carolina, USA for an indefinite period. The site was built in the early 1970’s, has an installed capacity of 170,000 t of PET resin, and represents approximately 2% of Alpek’s total assets. Alpek is consistently looking for ways to create value by optimising its footprint and increasing its cost competitiveness. As such, it has been growing with more efficient assets that maintain the company as one of the leaders in its industry. Alpek will transfer Cooper River’s PET resin production to its other sites, enabling cost reductions of approximately U.S. $20 million at an annualised rate and improvements in capacity utilisation. www.alpek.com STF America announces the sale of what will be the first PET bottle washing plant in the Dominican Republic STF Group of Germany and Zimmer America Corp. announce the sale of an STF PET bottle washing plant in the Dominican Republic, the first of its kind in the country. The line will be installed at Cilpen Global Business s.r.l., a major waste and plastic recycler on the island. The line has a capacity of 2.5 metric t/h (5,500 lbs/h) output of PET flakes and features STF machinery manufactured in Germany, such as the screening trommel, label scraper, star screen, grinder, washing, drying, and flake separation machinery, as well as a complete water re-circulation system. Installation of the line will begin in the first quarter of 2024. www.stf-group.de"},{"@ID":16, "EDITOUR PETplanet Insider Vol. 24 No. 03/23 www.petpla.net 14 Carefully fi lled in PET bottles Volvic, a very special natural mineral water Coming from the west of France, we reach the AuvergneRhône-Alpes region. The Massif Central welcomes us. From a distance we can already make out the volcanic landscape of the Chaîne des Puys with its 1,465m high volcano Puy-de-Dôme. This Chaîne des Puys is represented by the silhouette of the Puy Pariou on the label of the water bottler Volvic, and this is our next stop on this tour! Sponsors Arriving at the Volvic factory, we are greeted by Project Manager Michael De Macedo. He is responsible for installing two new PET production lines at Volvic. With enthusiasm and verve, he tells us about the features of this special place and the Volvic source. “Volvic natural mineral water is drawn from the heart of the Auvergne volcanoes. At the heart of the Volvic catchment area, the rainwater infiltration zone, water trickles and percolates for nearly five years in contact with ancient rocks. Throughout its journey in this vast natural filter, water acquires its mineral composition and unique taste. Collected at a depth of between 50 and 100m, the water is bottled directly. It is therefore pumped and transported to the bottling plant through a stainless-steel pipe. Its original purity is maintained from its emergence to its bottling: from the volcanic depths to home, without any chemical treatment. It is never in contact with ambient air until the first time the bottle is opened. Volvic natural mineral water has a low mineral content (= dry residue 500mg/l), so the whole family can drink as much as they like every day with no limits.” The Volvic production site covers an area of 125,000m2, with an area of 309,000m2 free for further growth, the equivalent of 60 football fields. Around 850 employees with permanent contracts working in the plant. While Michael reports we are guided through a small exhibition area about the history of Volvic company. Finally, we reach the production halls, the heart of the factory. “Today, we have eight production lines for the bottling of Volvic natural mineral water. Seven lines for PET bottles and one for glass bottles in Volvic still water plant. On Volvic Fruit’s plant there are five production lines we are bottling Volvic fruit drinks, while one of them can fill PET bottles and bricks. We produce rPET and vPET preforms on six Husky and one Netstal machines, in a lot of different combinations of resin, dyes and percentage, with neck sizes of 29/25 and 30/25. Our ambition is to produce the whole product range of Volvic out of 100% rPET by 2025.We need to modify all our lines to be able to use tethered caps by the end of the year for Volvic plant and by the end of 2024 for Volvic Fruit plant. We are in a period of big modification on the plant in order to change and modify the machines to be able to implement tethered cap on all our products.” In another production hall we see one new Ergoblock L from Krones as the new line 12. Michael tells us that Volvic chose this technology because it is the most efficient in terms of the quantity of water and air used and in terms of “waste”. For example, there is no more rinsing, if a bottle has a labeling defect, we can eject it before filling Michael De Macedo, Project Manager at Volvic and Heike Fischer, PETplanet Insider The best-selling rPET bottle is the 1.5 l bottle for the German market."},{"@ID":11, "9 NEWS PETplanet Insider Vol. 24 No. 03/23 www.petpla.net Napcor releases Life Cycle Assessment for beverage container systems The National Association for PET Container Resources (Napcor) released a Life Cycle Assessment (LCA) that compares PET, glass and aluminium carbonated soft drink (CSD) and still water beverage container systems. The assessment found that PET plastic bottles, when compared to aluminium cans and glass bottles, are significantly better for the environment. The study was completed by Franklin Associates, a leading LCA consulting firm and pioneer in the field, and went through an extensive peer review and verification process. Findings show that when it comes to the best beverage packaging for the environment, the answer is PET. Compared to glass and aluminium beverage containers, PET plastic bottles create less solid waste, use less water during production and generate fewer emissions that contribute to acid rain and smog. If U.S. consumers selected PET plastic bottles instead of glass bott les for their soda beverages over the course of one year, it would be the same as: The amount of GHG emissions avoided by recycling instead of landfilling nearly 53,000 garbage trucks of waste; The carbon sequestered by adding almost 1.3 million acres of U.S. forest. Similarly, if US residents choose PET plast ic bott les instead of aluminium cans for their soda beverages over the course of one year, resulting impacts would be the same as: Conserving 4.4 billion liters of water; Remov ing 688,000 gas powered cars off the road annually; Diverting 138 million bags filled with trash for recycling versus landfills. The LCA compared the most commonly used beverage containers for carbonated soft drinks and still water and found that a 16.9 ounce PET plastic water bottle compared to a standard-size 12 ounce aluminium can: Creates 80% less solid waste; Uses 53% less water during production; Has 74% lower global warming potential; Generates 68-83% fewer emissions that contribute to the formation of acid rain and smog. The cradle-to-grave LCA looked at commonly used PET plastic, glass and aluminium beverage containers for CSD and still water. It found that glass tends to have the highest environmental impacts, followed by aluminium and then PET bottles. PET plastic bottles are a more sustainable beverage container option and have a lower impact on several key environmental metrics, including greenhouse gas emissions, energy demand, water consumption, smog, acid rain and eutrophication potential. www.napcor.com"},{"@ID":36, "34 TRADE SHOW PREVIEW PETplanet Insider Vol. 24 No. 03/23 www.petpla.net Injection and blow moulding machinery Powerjet will showcase its latest products, including PET preform injection moulding machines, all-electric injection moulding machines, two-platen injection moulding machines, and blow moulding machines. Powerjet states that their products not only have good performance and flexible operation but also can meet the needs of customers in different fields. KPET series for PET bottle preforms The Powerjet KPET series is claimed to be a highefficiency injection moulding machine designed specifically for PET bottle preform injection moulding, with the KPET4505L-E6 being an important model within the series. Based on the PET series platform of Powerjet injection moulding machines, this specialised model combines Powerjet’s technical advantages with product innovation and iteration, providing customers with good performance and stable production capacity. Claimed benefits include good performance in terms of repeat accuracy, plasticising speed, and power consumption during the production process. The KPET series is also claimed to have advantages in terms of energy consumption and cost control: the electric melting glue system offers reduced energy consumption and improving production thoughput. Moreover, the KPET4505L-E6 model uses a PET-specialised screw with an ultra-long L/D ratio that improves product shrinkage issues, enhancing product precision and appearance quality. During the exhibition, preforms for water bottles will be produced on-site using the KPET4505L-E6 model, which features 96 cavities, a cycle time of only 13s, and a weight of 13.6 g per preform, with a daily production capacity of up to 630,000 pcs. www.powerjetmachine.cn 10,000g PET injection system for the production of jumbo PET preforms Kronce, a manufacturer of equipment and solutions for the production of PET preforms, presents its advanced preform production system designed for profitability and efficient production. As its latest contribution to the PET industry, Kronce has launched a new generation PET injection moulding system, KSPET8/135STD, for jumbo PET preforms of 900g and a mould with up to 8 cavities. The professionally designed PET screw with a diameter of 135mm ensures that the system achieves an injection capacity of 10,000 g - one of the largest PET toggle types PET injection system in the industry. A top-entering cross-axis preform pick-up robot and servo-driven system have been integrated into the Kronce system to help realise automated production with energy-saving performance. In the 5-gallon drinking water industry and mariculture field, this system has a much wider application and advantage than the normal system with the traditional cavity mould, states the company. www.smargon.com Mechanical recycling solutions for PET and more Sorema, as a division of Previero, has a consolidated experience in the Chinese market, where the company has maintained a constant presence even during recent years when travelling was more complex. The company will be present at the fair with its experienced staff to present its new developments in mechanical recycling of plastics like PET, PP, PE and fibres. It will also show a special Drying Centrifuge Model DCE 10/20 (see photo). Sorema plastic recycling lines up to 10,000kg/h are designed for plastic products from post-industrial or post-consumer collection as of flexible packaging in PP, PE, BOPP & BOPET, agricultural films, rigid packaging in PS, PP, PE and PET, bottles and cans in HDPE or PET. “In China, as in the rest of the world, we believe that the PET industry will develop as it has over recent years. The large producers of bottles for mineral water, soft drink or thermoformed trays for fruit and vegetables and the main producers of fibres for sports garments will take enormous advance from the availability in the market of recycled materials in high quality and in high quality”, says Sorema. www.sorema.it POWERJET Hall 11 Booth A31 KRONCE Hall 11 Booth F01 SOREMA Hall 10 Booth F41"},{"@ID":58, "TRADE SHOW REVIEW PETplanet Insider Vol. 24 No. 03/23 www.petpla.net 42 Based on internal development but also on a series of joint ventures and collaborations, his company’s new offering includes materials recycled mechanically and chemically, as well as grades based on renewable feedstock. Blow moulded containers are just one component of the complete packaging solution we call ‘plastic bottles’. Other components – such as caps and closures, labels, etc. - are just as necessary and are also covered by the conference. For instance: through the Single Use Plastics Directive, the EU Commission has mandated a complete transition to tethered caps by July 3, 2024. Bericap is one of the suppliers providing solutions in this area. Group Technical Sales Director Andreas Brem detailed that offering and the technologies behind it, in his presentation ‘Innovative tethered caps meet blow moulded containers’. Which gave Sjoerd van Laar, Product Manager at Heuft, the perfect opportunity to introduce ‘Futureproof closure integrity: inspection of tethered caps’. The company’s inspection system creates a standard histogram and identifies deviations from that pattern. One of the well-known challenges of recycling is the labels attached to bottles and jars. In his presentation entitled ‘Labels in the context of recycling’, McBride’s Packaging Process Engineer Klaas Geneyn explained the holistic approach adopted by his company, which placed it well on its way to achieving the 2025 recycling targets. For brand owners like PepsiCo, time to market is one of the most important metrics of success. Senior Manager Global Beverage Packaging R&D Max Rodriguez explained how his team has achieved an amazing breakthrough in this respect: ‘Concept to Manufacturing in 5 Days: Utilizing Advanced Capabilities at PepsiCo’. This methodology is colloquially known as ‘Concept on Monday – product on Friday’. Last, but by no means least: the organisers invited Policy Officer Dr Wolfgang Trunk from the European Commission DG Environment to review the impact of Europe’s brandnew regulatory framework for packaging and packaging waste. Fortuitously, the Commission’s debate finished the day before the presentation, enabling Dr Trunk to reveal the main points of the new regulation at the conference. His review was met with keen interest by all participants. The next (7th) edition – Blow Moulding 2023 – will take place on 12-13 December, in Cologne, Germany. www.blow-moulding.com"},{"@ID":8, "PETnews 6 NEWS PETplanet Insider Vol. 24 No. 03/23 www.petpla.net Danone North America to invest up to US $65 million to create a new bottle production line Danone North America announced it will invest up to US $65 million over the next two years to create a new bottle production line in Jacksonville, Florida. The investment is intended to support Danone North America’s long-term growth strategy and to deliver key benefits across the U.S. business, including advancing operational excellence, enabling flexibility in bottle design, accelerating the company’s sustainability goals, and driving cost efficiencies. This multi-million-dollar investment will increase production of several of Danone’s coffee and creamer brands in the U.S., including International Delight, Silk and Stok. It also serves to meet consumer demand in these categories while supporting the company’s sustainability goal by reducing overall water consumption, decreasing carbon emissions and accelerating the company’s goal of packaging circularity. The expansion will also create up to 40 new full-time jobs with competitive wages and benefits. New employees will be eligible for Danone North America’s parental bonding leave policy, enabling all manufacturing employees with one year of tenure to take up to 18 weeks of paid time off after the birth or adoption of a child. www.danonenorthamerica.com Berry and Coca-Cola collaborate to implement tethered caps in EU markets Berry Global Group, Inc. is the first plastic packaging manufacturer in Europe to supply The Coca-Cola Company with a lightweight, tethered closure for its carbonated soft drinks in PET bot t les. Bolstered by EU Single-Use Plastics Directive, Berry’s new tethered closure for Coca-Cola is designed to remain intact with the bottle – making it less likely to be littered and more likely to be recycled. In 2019, Coca-Cola held a supplier event to brief for this project. Berry – who has had an existing supply relationship with Coca-Cola for more than 20 years – was short-listed as a supplier in January 2020. Over 400 million closures have been applied to date on Coca-Cola bottling lines in Germany, Spain and the UK, with the rollout to continue to the company’s other European plants. Maintaining a convenient and comfortable user experience, in addition to product safety and security, Berry’s new tethered closure for Coca-Cola features a special tamper-evident band that, once broken, does not impact the closure’s ability to remain attached and is positioned out of the way for drinking but can easily be reclosed. When open, it is claimed to provide a wide angle for easy access to the beverage and comfortable on-the-go drinking. Berry’s closure for Coca-Cola is based on its patented CompactFlip hinge solution which unscrews and flips-open intuitively, according to Berry. It is the first to be used in conjunction with the new lightweight 26mm GME30.40 neck, developed by Cetie (The International Technical Centre for Bottling) Single-Use Plastics Group, of which Berry is a member. The new neck finish is claimed to deliver an over 1 g saving in PET compared to the current PCO-1881 neck. Combined with a 10% weight reduction from the Berry closure, the new pack is now around 20% lighter than the PCO-1881 version, states the company. Berry says that the production process remains the same, however, the filling line needed fine-tuning – with adjustments to feeding lines, capping chucks and cameras. www.berryglobal.com ALL- IN- ONE-MACHINE ASSEMBLY FOLDING SLITTING TETHERED CAP CONTEXO GMBH Tel. +49 (0) 7181 / 606-100 info@contexo-gmbh.de www.contexo-automation.de"},{"@ID":26, "CAPS & CLOSURES 24 PETplanet Insider Vol. 24 No. 03/23 www.petpla.net Water brand Uliveto opts for GME30.40 and chooses ‘Asterix’ closure for its water bottles High degree of customisation Wisecap has developed the ‘Asterix’ closure for the new GME30.40 neck, adding a new member to the family of the 26mm neck finish in its closure portfolio. The Italian premium brand Uliveto has decided to be the first on the market to use the new GME30.40 neck finish in combination with the Asterix closure - among other things because this offers a high degree of customisation. Asterix has been specifically designed to offer a low weight, high performance alternative for different types of beverage products. The high degree of customisation results from attention to the smallest details. This was particularly important for Uliveto to ensure effective communication even through the cap in use. This combination of neck and closure is claimed to perfectly meet market needs while ensuring compliance with EU and national standards. It is also available in the tether HO2 version. The development of a new neck-closure system represents an important opportunity to match the search for high performance with the reduction of packaging weight, says Wisecap. “The Wisecap Group range responds to all market requirements for compliance with European and national regulations,” explains Luca Nanetti, CCO of the group. He also underlines that HO2 is Wisecap’s answer to the requirements for CAPS & CLOSURES Blow molds | Blow molding machines | PET bottle design | Packaging equipment APF-Max series All-electric FRQɍJXUDWLRQ 4XLFN FKDQJHRYHU IRU RWKHU SUHIRUP W\\SH %ORZ PROGV TXLFN FKDQJH NIR KHDWLQJ V\\VWHP Hot Fill RSWLRQ 6SDFH VDYLQJ RYHUDOO GLPHQVLRQV HEAD OFFICE PET Technologies GmbH Grünlandgasse 5/1/12 2620 Neunkirchen, Austria w .pet-eu.com tel.: +43 720 775 196 RIɍFH#SHW HX FRP a tether closure which is the result of intense research and development work to ensure an optimal consumer experience while maintaining a simple and intuitive opening system: The cap is connected to a tab that ensures it cannot be separated from the bottle. It is a versatile solution that can be adapted to the different closures in their catalogue. www.wisecap.eu"},{"@ID":13, "TRADE SHOW REVIEW PETplanet Insider Vol. 24 No. 03/23 www.petpla.net 44 Framework by Quantis. It provides a platform for multi-criteria decision making for companies with simultaneous LCA and circularity targets. It offers a packaging system perspective combined with a market perspective to fully identify packaging system and market-specific improvement opportunities. Sphere and other initiatives like MariLCA (Marine Impacts in Life Cycle Assessment) are important steps on the way from parallel LCA and circular economy accounting to full integration of circular economy attributes into LCA, Stefan ended. Alessandra Funcia, Sukano and Chair of the O&F Working Group, spoke about White Opaque PET - from a recycling problem to a value chain opportunity. Alessandra reported on the results of the 2022 working group: The EPBP design-for-recycling website for white, opaque and coloured PET bottles was updated after technical review and approval by expert panels from O&F and EPBP. In addition, the EPBP pop-up website for opaque PET bottles and for coloured PET bottles was published. A proposal for an rPET specification for recyclers and outlets was also made. In addition, Alessandra mentioned that Recyclass was asked to include the EPBP website updates in their assessment scorecard for opaque white PET bottles. She added that a webinar on sorting is planned but has been postponed due to priorities and staff shortages. A planned LCA peer review for white opaque milk bottles is still pending due to budget. This year, the webinar and LCA analysis focusing on white opaque PET bottles should be carried out on a smaller scale if possible, with a focus on CO2 emissions. Two important issues to work on are, firstly, the work on the DfR guidelines and EoL preferential options for functional bottles and, secondly, the collaboration with WG Thermoforms to evaluate PET trays and coloured PET bottles as a stream. The WG - The Label of the Future was presented by Sofiane Mameri, Sustainable Development Manager at Sleever and Laurent Foldès, Market Development Manager at KP (seen on picture). The working group defines three criteria for the label of the next generation. 1. The label needs to inform and/or protect the container and the consumer whether for technological, or regulatory reasons. 2. The label placed on household rigid PET packaging placed in the EU market needs to be compatible with the mechanical recycling streams in place. 3. The label should contribute to efficient recycling of packaging waste at high rates and produce high quality secondary raw materials to enable a true circular economy. The companies Celab, Avery Dennison, Sleever and KP will work on design and style guidelines for recyclable labels. For example Celab will establish a PET liner recycler network across Europe, Avery Dennison will do research with the focus on glues for PSL or wrap around labels. With a CAGR of 6.2% by 2027, the full body shrink sleeve labels market needs to be taking care of to ensure sorting and recyclability of the bottles. Sleever will set up guidelines to anticipate this evolution and guide European brands. KP will evaluate the impact of crystallisable PET (cPET) film and washable nonbleeding inks on: Water contamination, NIAS and the rPET quality. The working group also has some recommendations to the EU following the revision of the Packaging and Packaging Waste Regulation (PPWR): The group calls for European standards instead of certification bodies per member state. The second demand is for a European packaging policy, can be done by exploring multiple solutions and that requires the full value stream collaboration including packaging professionals and considering technical innovation on a European and global scale. In addition, the group calls for the European packaging industry and Member States to deliver lasting and effective change for the better by 2030 through a collaborative dynamic with European partners. The NIAS working group, represented by Casper van den Dungen, Plastics Recyclers Europe, Maria Zaccarias, Logoplaste and Robert Geser, Alpla, gave an update on the development of the database ‘GEneral NIas’. Casper started with a presentation of Ping, which was founded seven years ago. The aim was to drive value chain collaboration to comply with Commission Regulation (EU) No 10/2011 of January 14, 2011 on plastic materials and articles intended to come into contact with food and its subsequent amendments on non-intentionally added substances (NIAS). Therefore, the Ping published recommendations for the assessment of NIAS in February 2020. They are freely available to any member of the PET value chain. The Ping operates in strict confidentiality to ensure that sensitive industry information can be managed to benefit the PET Supply Chain. Essential to the production of accurate data on the NIAS is a harmonised approach, explained Casper. The aim is to centralise data on NIAS studies in the value chain and track trends using the test method guidelines developed by Ping. NIAS entering the value chain must also be identified and monitored (commitment 2022/1616 in October ‘24). A risk assessment of the identified NIAS must then take place, summarised Casper. He continued by explaining how to proceed with database building. The WG approach the value chain and ask them to participate in the project by providing data and funding the project. As we know that data collection requires a third party to anonymise, aggregate and risk assess the data, funding from participants is required. Ping will support the participating members and Petcore will take care of the administration, budget control and project tracking."},{"@ID":27, "CAPS & CLOSURES 25 PETplanet Insider Vol. 24 No. 03/23 www.petpla.net Brothers Make a business of saving the planet Browning Motion by Ruari McCallion The seaside city of Bournemouth, Southern England, has a dual personality. It has been a much-loved holiday and short break resort since the 19th Century but it also has a long and distinguished manufacturing history. Away from the beaches, tucked away down a rutted lane on the northern outskirts of the city, is a collection of large barns and warehouse-style boxes, which house a range of start-ups, cottage industries and small businesses. We met: Matt Browning, Director and Co-Founder Brothers Make probably qualifies under all three headings. As its name indicates, it was founded by two brothers: Matt and Jonny Browning. They started with (and still produce) a series of ‘how to’ videos on YouTube, showing subscribers how to recycle bottle tops and waste plastic into something new – signs, stool seats, pens, pots, cutting boards, combs and even jewellery. Their YouTube channel, which has been running for five years, now has over 250,000 subscribers. They sell their products in Bournemouth, further afield in England’s southern counties and to international customers, as well. Matt, who greeted me at the door of their small workshop located in a corner of one of the large units, reckons they have sold something to someone in most countries across the world. He was working as a teacher at a secondary school (high school) until only a few months ago, when he went full time with the business. Matt and Jonny want to keep plastic from landfill and to show what is possible, even at a small scale. The first thing Matt made was a plasticheaded mallet, which he still has in the workshop. The impetus to turn what was an interesting side-line into a business came from the Sixth Form (final two years) students at the school where he was teaching. “The students came up with the idea of making some pens. I had never made a pen before but I was prepared to try it,” he says. “We made some pens out of recycled plastic and the kids loved it. We made a YouTube video, even though I was a bit hesitant because I was worried we weren’t very good at it but we did it and it turned out to be our most successful video up till then. We went from 6,000 subscribers to 60,000 in about two weeks.” Brothers Make’s products all have a marbled appearance. This is deliberate; far from trying to conceal the use of recycled plastics or to make them look as much like virgin material as possible, the look is part of the image. They deliberately set out to make clear to users that their cutting board, jewellery, signs, coffee tables or whatever are reusing plastic, not exploiting natural resources. Brothers Make still makes pens from recycled plastic but now uses stainless steel mechanics that are finished with a plastic external barrel. They aren’t bargain bucket prices but each one is hand made and unique: no two patterns are the same. It’s like having your very own NFT (non-fungible token) and being able to hold it and write with it! The majority of sales are through Brothers Make’s online shop, with about a third of total revenues generated by direct sales at street markets, fairs and trade shows. Sales to businesses are actively pursued and promoted. A big order is already in: 64,000 beads for a local jewellery company. “We can work with businesses to either make products for them to sell or for branded products as promotion items or for use within the company,” Matt explains. “We can make that for them CAPS & CLOSURES Brothers Make recycle bottle caps and other plastic waste to make new items, like these jewellery pieces."},{"@ID":28, "CAPS & CLOSURES 26 PETplanet Insider Vol. 24 No. 03/23 www.petpla.net using our own 100% recycled plastic, or we can work with them and take some of that waste from them as well.” Caps, lids and tubs are sorted by colour and shredded The production process is almost entirely manual. Caps, lids and tubs are sorted by colour and shredded. The range of colours have exotic names reminiscent of science fiction stories and movies. The change to white for all milk bottle tops isn’t an immediate threat; they have about half a tonne already collected and waiting to be used although they will be cutting the number of colours, from 15 to the most popular eight. They have expanded their range of materials to include DVD cases, which they already have two giant boxes full of. When the brothers started, they used a sandwich press machine but, two years ago, invested in two small injection machines with built-in heaters that extrude into steel moulds. The moulds are made by a business just a few miles from their workshop – they really are serious about minimising transport miles. Collect, recycle & reuse The machines are manually operated; while I was there, one of the part-time staff members was producing combs by turning a wheel that pushed warmed and ductile plastic down through a nozzle into the die, and maintained pressure by hand until the moulding process was complete. It takes time and is obviously labourintensive but the point is not peak efficiency; it is to demonstrate the principle of collection, reuse and recycling. That the business makes enough money to now support the Browning brothers full time, along with a small number of part-time staff, is a bonus. “When we started, we worked just one day a week. That day would start at 9.00 am and go on till midnight but it was just one day!” Matt says, with a cheerful chuckle. He showed me some examples of raw materials: bottle tops from milk bottles, shampoo and cosmetic containers and domestic cleaning materials. “We get our materials from the local community. About 75% of our supplies come from local schools and the rest from coffee shops, hair salons and companies who want to see their waste genuinely recycled. A lot of it isn’t, in fact; it goes to landfill. Recycling rates in the UK are pretty poor,” he says. The schools especially are enthusiastic; the recycling message is well established. Businesses join in when they realise that, by giving their waste to Brothers Make, they don’t have to pay disposal costs. “It’s a win-win; we get our materials for virtually nothing and they save on collection costs,” Matt explains. “We are a bit specific about what we will take but, once we do, we use all of it. We rigorously separate the different types of plastic – PP from HDPE, for example; we mostly use HDPE – and we collect and reuse our own offcuts and mis-moulds.” Matt cheerfully accepts that Brothers Make is a ‘cottage industry’ at present but demand is strong and rising and the Browning boys have plans to expand. “We have two machines currently and we are looking to grow to six, eight or ten. We will also be looking to hire more people. We want to get people in and learning the ropes on how to do it,” Matt says. “I would love it if we ran out of plastic to recycle but something like 300 million tonnes of plastic are produced every year. What we are doing is just showing people there is a way to turn the tap off.” www.brothersmake.com CAPS & CLOSURES The right tools and expertise to help with your rPET goals! Agr is uniquely positioned to support your venture into rPET bottle manufacturing with a powerful combination of Process Control tools, Process Consultants, and decades of industry experience. AGRINTL.COM • +1.724.482.2163"},{"@ID":34, "32 TRADE SHOW PREVIEW PETplanet Insider Vol. 24 No. 03/23 www.petpla.net Xform equipped with high cavitation preform mould Sipa will present its complete technology and service offering for PET rigid packaging. Highlights include production equipment and moulds for preforms and containers, as well as assistance for customers in development of highperformance packaging. The company offers expertise in production equipment and support in container development to PET packaging companies in China and around the world by providing local consultancy on bottle design and engineering. Emphasis will be given to Xform PET p r e f o rm i n j ec t i on moulding systems. The machines, now in their fourth generation, are claimed to stand out with their performance in output rates and qual ity, energy efficiency, reliability and low maintenance costs. M o u l d s m a d e by Sipa can hold as many as 200 cavities – something no other company can offer, according to the company – thanks in part to the incorporation of high-performance hot runner systems developed and produced in-house. Repeat orders from major Chinese customers, as well as global operators with operations in the country, continue to come in for Xform systems. The Xform platform covers three machine sizes, with clamp forces of 280, 350 and 500 t, each of them enabling cost-efficient production of PET preforms. Sipa says that they excel when running with their on-house produced moulds, but they can also accept moulds built by any other major manufacturer. While Sipa makes its machines in Italy, it has also an important mould-making and advance refurbishing operations successfully serving the bigger players in the Chinese market. Among its latest innovations is the AWArPET brand, developed to communicate the company’s approach in the design and production of primary and secondary packaging that involves the utmost respect for the environment. Sipa’s product design experts are involved in the development of thousands of new packaging designs every year, and in all of these, the three Rs – Reduce, Reuse, Recycle – provide constant reference points. www.sipasolutions.com BOTTLE TO BOTTLE RECOVERY MOISTURE CONTENT CONTROL PROCESS CONSISTENCY EXTREME BLENDING FLEXIBILITY MAKING THE DIFFERENCE ON PET. moretto.com follow us SIPA Hall 11 Booth P51"},{"@ID":25, "CAPS & CLOSURES 23 PETplanet Insider Vol. 24 No. 03/23 www.petpla.net the individual needs and situation of each customer. Dr Gerd Fuhrmann, CEO of Intravis, comments on this: “With us, customers always receive a system developed and built specifically for their request. Of course, this is especially needed for projects with multi-part closures or even unusual dimensions of the closure. We rarely have any one project that is like the other, because every system and every order brings its challenges. Production line space is usually very limited. And sometimes special inspections have to be developed for a closure. With a standard solution, limits are quickly reached.” In addition, Dr Fuhrmann continues, the company has been investing in a large service network for years in order to supply customers with turnkey systems that are ready to run after installation. Tethered caps With the EU Directive 2019/904 Single Use Plastics (SUP), the need arose that caps are permanently connected to the bottle. As a result, this led to the development of an inspection solution for tethered caps. Even though these are similar to standard caps in many requirements, they do have some challenging elements, for example the CAMs located inside the closure. To avoid damaging them during micro-hole inspection, Intravis produced its patented, non-contact HV inspection. As the name indicates, this inspection no longer dips into the closure during inspection to find microholes in the head plate of the closure. The external shape and dimensional stability of tethered caps are further challenges that the inspection system must handle. Practice has shown that Intravis’ form-fitting, patented lateral star wheel separation copes well with external features, such as hinges. Moreover, the separation technique precisely handles the high sensitivity of increasingly thinner closures even at the highest production speeds, states the company. In addition, Intravis uses software that can cope with any orientation of rotationally asymmetric closures like tethered caps. Specifically, this involves equipping individual modules with a new core algorithm based on Deep Learning. Marius Pötting, product manager for closure inspection systems at Intravis, describes it this way: “The heart of our systems is the IntraVision, our self-developed software. It has been using Deep Learning algorithms for some time. As a result of our constant development efforts, we have succeeded in applying Deep Learning to the detection of anomalies.” Anomalies are any deviations from a pre-defined, optimal standard including deviations that are difficult for the customer to describe in advance. Whereas previously a large number of samples were needed for each type of defect to be found, the new logic changes the approach completely. The software is first trained based on a pool of good parts, and thus learns how the optimal closure appearance looks like. This pool of good parts is necessary to evaluate natural variations as “OK parts” on the one hand, but also to evaluate small, real defects as “not OK parts” on the other hand. The quality of what has been learned is then checked and optimised based on bad part samples. In the subsequent real world production process, everything that does not correspond to this trained optimum is sorted out. By means of the adjustment options, the operator still has the possibility to influence the sensitivity of the inspection and, thus, the ratio between efficiency and object quality. “The special feature of this software technology is its fast-learning capability. For example, if I teach the software with closures in different rotational positions, I do not need to align asymmetrical closures during inspection. And if I teach the system with other closure designs, it can also immediately inspect these as well,” says Marius Pötting, summarising the possibilities of the technology. Applied closures Closures are naturally intended to be applied to filled bottles – and thus in the wet area of a production line. To enable customers to use Intravis systems as well in this area, the company developed a washdown design for its CapWatcher FC system. Marius Pötting mentions, “The CapWatcher FC is an Intravis system developed exclusively for the wet area of the filling line behind the filler and capper. We have already been able to gain experience in the wet area in various projects over the past few years, which we have used and transferred to this stand-alone product.” Based on this experience, the CapWatcher FC – both the inspection unit itself and the related electrical cabinet – is completely splash-proofed according to the IP65 standard as well as designed in accordance with the bottlers’ hygienic measures. This makes cleaning the system easy and uncomplicated, even with aggressive methods and means. One important inspection in this area is the quality control of the application angle of the closure. With three side cameras, the CapWatcher FC uses index marks to inspect whether the closure is screwed down to its target position – or whether it is screwed down too far or not far enough. Marks on the closure and on the neck support ring that are barely perceptible to the end user are detected by the system. If these marks are within a tolerated range to each other, the system assumes that the closure has been completely and correctly applied – and the bottle is released for packaging. This new technology is used for the first time. Of particular interest to the production line operators are the comprehensive statistics that correlate the average application angle with the capping head. Thus, the operator can detect a malfunction of a capping head at short notice. www.intravis.com With the CapWatcher FC, there is now also a separate Intravis system available just for the wet area."},{"@ID":19, "CAPS & CLOSURES 17 PETplanet Insider Vol. 24 No. 03/23 www.petpla.net CAPS & CLOSURES 17 additives. Arol also continuously runs tests in its own laboratory to support its customers in identifying the most suitable application specifications. PETplanet: The switch to tethered caps for single use bottles has created some buzz in the industry. Has the changeover to tethered solutions already been completed with your customers? Zannier: We are constantly receiving test requests for new solutions, and it would appear that this changeover process is far from being completed. PETplanet: What special challenges do tethered caps have to overcome when it comes to the cutting process? Zannier: If the tethered is oriented, the biggest problem is to find the right solution to put the cap in the most suitable position. If instead it is a matter of 3D cutting, the most critical is to identify the most correct shape for the cutting blade. Here, too, years of experience in the sector has allowed us to better manage, even with innovative solutions, the requirements of the most demanding customers. PETplanet: Besides tethered caps, what other developments are you observing in the field of PET bottle caps? Zannier: The trend is for a faster and faster throughput rather than for lighter sports caps and this can make the assembly stage more challenging. PETplanet: Thank you very much! Italian Arol Group includes Arol Closure System, specialised in the design, manufacture and distribution of capping equipment, feeding and cap orientation machines, Unimac-Gherri, specialist in filling and closing glass containers with twist-off tops for food, Tirelli, focused on packaging equipment for the cosmetics, home and body care industry and Maca Engineering (ME), specialist in designing and manufacturing machines and complete line for the production, assembly and cut of aluminium and plastic caps and closures. www.arol-group.com ITVE-MRR-IRV line for cutting the tamper evident ring, folding the inner flap of caps and inserting pre-cut liners www.sacmi.com Product design Product development Product validation Industrial production plant Process & quality control On-site and start-up assistance After-sales and Customer service SACMI 4.0 THE COMPLETE CLOSURE, PREFORM AND CONTAINER SOLUTION FOR YOUR SMART FACTORY E N D L E S S I N N O V A T I O N S I N C E 1 9 1 9"},{"@ID":52, "CAPS & CLOSURES 20 PETplanet Insider Vol. 24 No. 03/23 www.petpla.net Closures designed to meet the requirements of tomorrow Product integrity, user convenience, customisation and sustainability are the features modern closures must have to meet today’s demands of the beverage and liquid food industry. Ideally, they are backed up with consumer and application expertise, mould making and production capacities as well as a global network providing local support and technical service along the entire ‘closure process’: From idea to high performance of the filling line. CAPS & CLOSURES Bericap, a global manufacturer of plastic and aluminium closures, made timely forward-looking investments in these areas – and its decision has proved to be right. Bericap is reporting revenue of EUR 1.2 billion at the end of its successful 2022 financial year. Strong growth in demand for new developed closures that are tailored to customer needs and sustainable efforts drove up Bericap’s annual production output last year to 95 billion closures for the different industries. Product integrity and consumer convenience An elementary aspect of all Bericap closure solutions is the focus on product integrity and user safety, from protection during transportation or storage to leakproof re-closing and tamper resistance and a strong impact on sustainability. Consumers will only choose ecofriendly closures over conventional caps if they offer handling advantages. That’s why the Bericap product development teams focus on optimising customer convenience with products that are easy to open, can be closed again without leaking and offer a comfortable drinking and drip-free pouring experience. Bericap conducts studies and field tests to obtain consumer opinions about its products. A ClipAside consumer survey delivered convincing results, with the majority of users rating the Bericap tethered caps more positively than conventional closures for their intuitive handling, their 180-degree opening angle and the fact that they are very hygienic. The Bericap sport caps also have a 180-degree opening angle, and can be intuitively opened using one hand, offering genuine ‘convenience to go’ to the user. Customisation Packaging is an integral part of the product, especially in the consumer goods segment, so a unique and flexible packaging design contributes to brand differentiation and provides the basis for marketing activities. Bericap offers numerous individual print, decoration and design solutions for closures and has the necessary competence in the different production processes. These solutions help customers make their products stand out on the retail shelf and in marketing activities. Sustainability Light weighting – weight and material reductions – and enhanced recyclability are central to closure sustainability. Bericap geared its product portfolio to sustainability a long time ago. New developed closures are also regularly rolled out to further optimise the company’s environmental track record. For example, it has entirely dispensed with silicone. Unlike most of the valves found in closures for spreadable products, the BericapValve Recycling advantage: Silicone-free BericapValve Bericap Hexalite 29/13 CA, ClipAside tethered cap for PET 29/25 neck finishes"},{"@ID":5, "imprint EDITORIAL PUBLISHER Alexander Büchler, Managing Director HEAD OFFICE heidelberg business media GmbH Hubweg 15 74939 Zuzenhausen, Germany phone: +49 6221-65108-0 fax: +49 6221-65108-28 info@petpla.net EDITORIAL Kay Barton Heike Fischer Gabriele Kosmehl Michael Maruschke Ruari McCallion Anthony Withers WikiPETia. info petplanet@petpla.net MEDIA CONSULTANTS Martina Hirschmann hirschmann@petpla.net Johann Lange-Brock lange-brock@petpla.net phone: +49 6221-65108-0 fax: +49 6221-65108-28 LAYOUT AND PREPRESS EXPRIM Werbeagentur | exprim.de Matthias Gaumann READER SERVICES reader@petpla.net PRINT Chroma Druck Eine Unternehmung der Limberg-Druck GmbH Danziger Platz 6 67059 Ludwigshafen, Germany WWW www.hbmedia.net | www.petpla.net PETplanet Insider ISSN 1438-9459 is published 10 times a year. This publication is sent to qualified subscribers (1-year subscription 149 EUR, 2-year subscription 289 EUR, Young professionals’ subscription 99 EUR. Magazines will be dispatched to you by airmail). Not to be reproduced in any form without permission from the publisher. Note: The fact that product names may not be identified as trademarks is not an indication that such names are not registered trademarks. 3 PETplanet Insider Vol. 24 No. 03/23 www.petpla.net Dear readers, The European Commission has published its Technical Report on Plastic Waste* which looks at all plastic waste streams from shredded electrical equipment and flexible plastic packaging to PET bottles and trays. It then explores mechanical, physical and chemical recycling using case studies, industry data and reference material. After 73 closely-printed pages and hundreds of illustrations, the mechanical recycling of PET packaging (bottles and trays) comes out best of all 27 plastic fractions, with 2,000 kg of CO2 savings per fraction of a tonne! You as readers and we as editors have always known this and it is encouraging that the European Commission now agrees with us. The report meanders its way through the waste mountain for another 50 pages of small print and colourful graphics. An assessment of the future highlighted in a number of scenarios is exciting. Physical and chemical recycling in particular consumes a lot of energy and with it CO2 and, as a result, will be unable to compete with mechanical recycling for many years to come. Conversely, the costs involved in mechanical recycling are reasonably stable (collection, transport, processing) while other processes are dependent on the price of energy and consequently very likely to become more and more expensive. Not even optimised reactors and plants will be able to negate major increases in prices. So, dear readers, we will still be meeting at flaking mills many years from now. Best wishes Alexander Büchler *The full report ‘Environmental and economic assessment of plastic waste recycling - A comparison of mechanical, physical, chemical recycling and energy recovery of plastic waste’ is available at https://op.europa.eu"},{"@ID":51, "TRADE SHOW PREVIEW PETplanet Insider Vol. 24 No. 03/23 www.petpla.net 39 Machines for food & beverage, pharma, consumer and industrial packaging Bekum, machine builder and specialist in extrusion blow moulded packaging, will provide information on 20 new machine models for small to large container volumes. Bekum’s new 8 series, first introduced at last year’s K’ 2022 trade fair, highlights energy-efficiency, flexibility and short delivery times. The presentation of many exclusive technical solutions, the expansion of digital service support, the processing of recycling materials and the calcium carbonate (chalk) in a three-layer technology are the focus at the trade show. With the market launch of the new 8 Series, Bekum now also offers allelectric small blow moulding machines with a 60/120kN clamping force and 280-520mm carriage stroke for small bottles. The new all-electric long-stroke machines with 500kN clamping force and 1080/1280mm carriage stroke for maximum output complete the packaging machine line for bottles, canisters and containers, which starts with 150kN clamping force and 520mm carriage stroke. Another highlight is the newly developed XBlow large blow-moulding machines, featuring a new industrial machine design for large canisters, (L-ring) drums, and IBCs with hybridelectric clamping unit up to 3,000kN clamping force (patent pending). The packaging and long-stroke machines are equipped with the new e-twin-toggle all-electric clamping drive via double toggle lever with a unique bearing system and with low wear, available exclusively from Bekum. The globally standardised control platform Bekum Control 8.0 with industry 4.0 package and AI health monitoring is claimed to provide maximum system availability, also available as retrofits for existing Bekum machines. In the 8 Series, efficient HiPEx 36D extruders in new sizes up to 720 kg/h throughput with high melt homogeneity and 20% energy savings are achieved. With the expansion of service support in Traismauer, Austria, Bekum customers profit from shorter response times, digital technical support via smart glass (augmented reality), tablet, smartphone and a digital spare parts catalogue. In addition, Bekum is pursuing a complete approach to customer consultations for extrusion-blown containers with the name “contours and containers”. Based on a customer’s packaging concept, Bekum and its partners offer feasibility testing, FEM and extrusion simulation, as well as 3D prototyping through the development and design phase of a container. This accelerates time-to-market and reduces costs. Material savings with tri-extrusion technology For many years, Bekum has been committed to the circular economy and has been delivering solutions for the cost-effective use of correctly sorted PE or PP post-consumer recycled materials. By using tri-extrusion technology and Bekum’s simulationbased newly developed 3-layer spiral mandrel heads for packaging and industrial lines, resource-efficient blow-moulded containers are created. During this three-layer process, the recycled material (PCR) is embedded in the middle regrind layer between thin-walled inner and outer layers, which are manufactured from virgin materials. Of particular ecological concern is the ability to achieve the highest possible PCR loading in the middle regrind layer, taking into account the geometry of the moulded part, in order to reduce the overall consumption of the virgin plastic within the production cycle. The ability to guarantee that the plastics have been correctly sorted is crucial for this process. If the inner layer, the outer later and the regrind layer are made of the same material, it is only then possible to easily recycle the three-layer product at the end of its useful life and reintroduce it into the circular economy. In addition, the use of PCR in the middle layer can often bring about a reduction in the cost of container production. www.bekum.com BEKUM Hall 10 Booth H31"},{"@ID":4, "33 TRADE SHOW PREVIEW PETplanet Insider Vol. 24 No. 03/23 www.petpla.net 5IF SJHIU JOTQFDUJPO TPMVUJPO '03 &\"$) $\"1 $-0463& QSPEVDUJPO BQQMJDBUJPO 888 */53\"7*4 $0. Polymer production and processing The Maag Group is presenting its product portfolio on pump & filtration systems, pelletising & pulverising systems, recycling systems and digital solutions. The Ext rex gear pumps GA are designed for common thermoplastic extrusion applications and are claimed to offer a high overall efficiency and minimum abrasion due to leading gear and bearing technology. They feature with low pulsation pump action also in cases of high differential pressure and a simple and compact design. The Extrex recycling pump has been newly developed to ensure rel iable extrusion in the recycling process. It features an optimised geometry that, in many cases, eliminates the need for an upstream protective filter, saving space and reducing the energy required for heating and drive power. Maag Ettlinger ERF 350 is a highperformance melt filter for the filtration of heavily contaminated polymer feedstock. The filter is self-cleaning with a rotating, perforated drum, through which there is a continuous flow of melt from the outside to the inside. A scraper removes the contaminants that are held back on the surface and feeds them to the discharge system. This enables the filter to be used fully automatically and without any disruptions over long periods and without having to replace the screen. The advantages: reliable melt filtration, ultra-low melt losses and good mixing and homogenising of the melts. The Baoli-3 strand pelletiser is outfitted with German-made core components and has been designed for use with both hard and soft pelletising materials. The most noteworthy highlights are its compact design that features height-adjustment, left-side/right-side control capabilities that provide greater operational flexibility, and reduced noise generation during operation. At the same time it offers easy access for cleaning, making it easy for maintenance, material changes, and colour changes. The Zhuli system is a flexible underwater pelletising system designed for use with standard products, such as filled polyolefins, polyesters and thermoplastic elastomers. Zhuli’s cutting tools are claimed to deliver spherical pellets of high quality that are suited for further processing, with throughput rates of up to 1,200 kg/h. The pelletising system has a small footprint and is simple to operate. www.maag.com MAAG GROUP Hall 10 Booth F11"}]}}
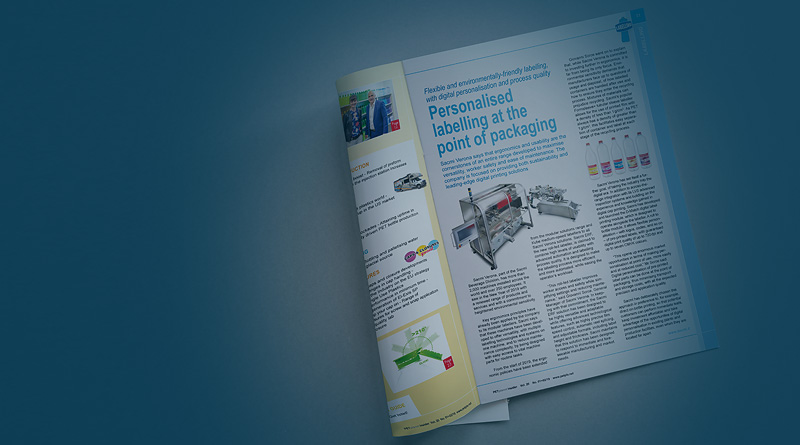