"EDITOUR REPORT 14 PETplanet insider Vol. 15 No. 04/14 petpla.net Other steps have been taken to increase the efficiency of the block lines and optimise material usage in the plastic closure by replacing the two-piece (liner) plastic closure with a single-piece closure. “This is a market change that was entirely initiated here at Coca Cola Brazil,” as Paulo Roberto Villas explains, adding the great benefits of linerless solution for CSD in the tropical weather enjoyed by the country. Plant bottle and supply of raw materials The term plant bottle encompasses a concept whereby PET bottles are manufactured either wholly or partly from renewable raw materials. PET is traditionally extracted from crude oil derivatives and is made up of 30% MEG and 70% PTA. The MEG component can also be manufactured from a vegetable base. Brazil is the biggest manufacturer in the world of bio-ethanol made from sugar cane. What could be more natural than to extract the bio MEG, as a derivative of bioethanol, from sugar cane? By comparison to other vegetable options sugar cane is particularly well-suited for the manufacture of bio-ethanol because there is no competition with existing agricultural land, and rain water is sufficient for irrigation. Since 2010, plant bottles have been used in smaller quantities in 600ml Coca Cola and the 0.5l still water pack. The MEG responsible for the green proportion of the plant bottles is made in India from bio-ethanol from Brazil. The conversion of PET resin to PET with a proportion of bio MEG (Plant bottle) doesn’t bring any change on the supply Chain, requiring only the fine tuning of the existing blowing lines; in addition, there are no changes required in the recycling chain. All of which are good reasons for speeding up the use of plant bottles. The supply of PET resin is the result of a partnership with M&G Brazil. Here the largest individual reactor in the world with an annual capacity of 650,000t is in operation. To give some idea of scale, Brazil’s annual consumption already accounts for 600,000t PET resin; what this means is that this reactor alone would be required to cover the domestic requirement and a further resin plant with an annual capacity of 700,000t (which is already at the planning stage) is unlikely to be sufficient. M&G is also the partner who will be using the bio MEG for the manufacture of polymers. Paulo Roberto Villas specifically points out: “At Coca Cola we do not develop any polymers, our concern focuses wholly on ensuring sustainability”. Asked about price trends, he is assuming that, although the price of bio-ethanol may fluctuate considerably in Brazil, the plant bottle material, once the planned bio-MEG capacities are installed, will flatline to the level of PET resin. As regards the next stage, the company is already looking at the option of extracting the PTA from natural resources. Plans for a pilot line are already underway. A not-unrealistic target for 2019/20 might be the ability to introduce a bio PET (100% biopolymer). Refillable PET bottles PET refill bottles were introduced in Brazil at the beginning of the 90s. Following some initial successes when the refillable bottles enjoyed a market share of 6%, there was a decline to approximately 2%, coinciding with the successful introduction of the disposable PET bottle. From 2008 onwards demand rose again and 15 new bottling lines installed/converted have increased over the past few years. The 2l refill PET bottle, with a weight of 98g, is the dominant product. Although authorisation allows 25 refill cycles, most operations run at 8-15 cycles. It is important that the consumer understands the difference in the non-returnable bottle, so one or two identifying marks (embossed logo + inside labelling) have been built in to emphasise the difference and avoid the returnable bottle being discarded (market price including deposit). Bottle to bottle recycling A further step towards mitigating the burden on the environment and ensuring sustainability is so-called ‘bottle to bottle’ recycling. However, its introduction in Brazil is constrained by a combination of strict legislation and excessive “small print”. For anyone who cares to read them, the labels on the bottles are printed with all the relevant rules and regulations. An authorisation for Brazil was granted in 2009 as a result of which CPR in Rio de Janeiro were authorised to supply the prepared PET material for the market launch by Coca Cola in 2011. We questioned Paulo Roberto Villas about the recycling rate in Brazil. “Currently, it stands at 56%. Aluminium recycling, by contrast, can reach up to 98%.” He continued: “We have kick started a programme in which everyone involved in the recycling chain assumes their own share of responsibility. This does not just apply to consumers, bottlers and supermarkets, but the government too has to accept some of the responsibility. The aim is to build up an infrastructure that creates value that can provide a living for the participating collectors and their families and where, in addition, recycling costs can be kept low. The target is to achieve collection rates of 75%.” We had one further question, which, though not directly related to matters in hand, was sure to have implications for the industry. What, we asked, were the likely prospects for capacity in Brazil in view of the World Cup and the Olympic Games which the country is hosting in 2014 and 2016. Paulo Roberto Villas’ perspective was interesting: “You have to remember, he said, that the Games will be taking place during the low season, so the effect on capacity should be beneficial. From our point of view, we do not envisage any new capacity expansion required to cope with this FWC event.” www.cocacolabrasil.com.br","@ID":16}, "PRODUCTS 51 PETplanet insider Vol. 15 No. 04/14 petpla.net Vision inspection systems and preform domes Several producers have developed new preform dome designs, the common ones being EcoBase with a rocket form or Capello Design with an oval dome design. Each of these preforms can provide weight savings. Further advantages include improved technical characteristics of the bottle or a better matter distribution on the bottle bottom and energy savings, with the preform domes being heated up more quickly. Yet for vision inspection systems these new geometric measurements represent a challenge as the previous inspection algorithms were all based on the conventional ball shape preform domes. Intravis, supplier of preform inspection systems, offers turn-key solutions for customers. Its preform inspection systems Sample PreWatcher and PreWatcher III are designed to be updated according to requirements and are able to integrate a new technical drawing of the customer’s preform into the algorithm. This enables accurate measurements of the new preform designs. The algorithm ensures the camera does not require re-alignment for every new preform length. Once set up, the software is also able to measure parameters like deviations and contaminations without changing the camera position. Updates for any geometric measurements can be integrated into existing systems in the field. www.intravis.com Past 28,000 Siapi says that it is the first company in the world to manufacture a two-stage linear blower that can produce more than 28,000 PET bph. The milestone has been passed on Siapi’s range of SDxx two-stage machines (xx indicates the number of cavities, from six to 20, arranged on two parallel presses). The machine’s star loading system sorts the heated preforms into the two presses and a new automation system runs and controls the machine movements that have been designed to be simple make it possible to produce PET containers at very high speeds. The range of two-stage linear blowers extends to eight models. They can be used to produce containers of 9l at a speed of 7,200bph, 4l at 10,600bph, 3l at 12,800bph, 2l at 15,200bph, 1l at 22,800bph, to half litre containers produced at over 28,600bph. It can process necks of up to 45mm and, exceptionally, up to 55mm for the larger 8l and 9l formats. Siapi says that the SDxx range can accommodate up to six of the 10 technology options available for its two-stage linear blowers. The new line extends Siapi’s model range to 36. www.siapi.it","@ID":53}, "BOTTLING / FILLING 40 PETplanet insider Vol. 15 No. 04/14 petpla.net Rexroth IndraMotion: Pre-defined function toolkits reduce programming effort Letting the software take the strain As the market for liquid food and beverages products continues to change with increasing rapidity, machine users in the beverage industry are increasingly demanding more flexible systems. This reinforces the trend towards more and more servo-drives in machines and the shifting of functions to software. Consequently, complexity is on the rise for the machine manufacturer. Rexroth now offers Open Core Engineering with pre-programmed function toolkits and new degrees of freedom for individual functions in its IndraMotion system solution. With its IndraDrive Mi cabinetfree drive technology, Rexroth is supporting the modularisation of flexible machine concepts. Machine manufacturers can therefore reduce the engineering effort required for the automation process, thus shortening the time to market. programming effort. Active vibration damping of the intelligent IndraDrive servo-drives increases dynamics while sparing the mechanical system and preventing liquids from spilling over. This motion control increases productivity and automatically compensates for fluctuations in process parameters. The machine manufacturer merely has to parameterise this prepared function. Bosch Rexroth claims that the FlexProfile adaptive system reduces the engineering effort needed for switching over to changed formats and recipes by means of software commands. This control function automatically establishes motion relations between connected drives. The OEM only has to set parameters to increase the flexibility of machines. The fact that functions are increasingly implemented in software extends modularisation in the machine building sector to also create modular softParameterising instead of programming Open Core Engineering integrates all the necessary software tools for efficient engineering. Rexroth has integrated its application experience in software in the pre-programmed function toolkits of its IndraMotion system solution. For example, “adaptive systems“ adjust the machine to changed conditions without additional Rexroth IndraMotion in applications associated with bottling: pre-defined function toolkits and new degrees of freedom for individual software functions shorten the time to market for machine builders.","@ID":42}, "EDITOUR REPORT 15 PETplanet insider Vol. 15 No. 04/14 petpla.net May 9, 2013 Andina Rio de Janeiro Refrescos Ltda. We met: Andre Braga, Production Director Sopro/TPM Ana Carolina Almeida, Industrial Supervisor Paulo Roberto Villas, Head of Corporate Packaging - supply chain, Coca Cola Brasil 22 years of bottling soft drinks for Coca Cola We are staying in Rio de Janerio and visiting Coca Cola Andina. Having learnt a huge amount about the market and the Coca Cola system at the Coca Cola Brazil HQ, we are now about to see what happens in practice. Paulo Roberto Villas is also with us at this meeting. Andina, a Chilean beverage company quoted on the stock exchange, is active in Chile, Argentina, Paraguay and Brazil. 80% of the company’s principal business activities relate to the bottling and distribution of Coca Cola soft drinks as franchise partners plus other beverages such as fruit juices, mineral water, beer, ready-to-drink juices and energy drinks, some of which are also manufactured and distributed under Coca Cola trademarks. The arrival of Embotelladora Andina S.A. on the Brazilian market came about with the acquisition of the Coca Cola bottler Rio de Janeiro Refrescos S.A. in 1994. It is in this plant in Taquara Rio de Janeiro that we find ourselves today. The company also has a second bottling plant on the east coast in a different Federal State.Here we are to meet the person responsible for production, Mr Andre Braga. The bottling section is dominated by Coca Cola soft drinks, which are bottled in cans, glass and PET bottles. The bottling volume at the plant is approximately 1.3 billion l/year. Andre Braga Coca Cola Andina (right) and Waldemar Schmitke in front of a bottling line for 2l PET bottles 2014","@ID":17}, "TRADE SHOW PREVIEW 45 PETplanet insider Vol. 15 No. 04/14 petpla.net Respecting values in effective dialogue www.krones.com interpack 2014 Düsseldorf, 8 – 14 May Hall 14 E29 Gea Procomac | Hall 07a Stand B09 Bottling sensitive dairy products GEA Procomac, the GEA Group’s bottling unit, will be presenting its technology and experience in the handling of pasteurised, Extended Shelf Life and UHT milk and liquid dairy products. The company will be presenting its new White & Safe bottles, designed specifically for ESL and UHT milk applications and featuring a range of light barrier additive concentrations. GEA Procomac will also be promoting two dedicated filling valves for liquid dairy filling for beverages with and without particulates. Additionally, the company has now developed two new filling machines designed for ESL applications: the Integrated Blow Fill ABF 4C and the WhiteBloc. The ABF 4C blows PET bottles from decontaminated preforms and fills them within the same machine. This technology is suitable for low, medium and highspeed applications with either screw cap or alufoil closures. As the process sterilises the preform, bottles cannot suffer from deformation/shrinkage and creative, ultra-lightweight designs can be produced. By contrast, WhiteBloc technology is suitable for use with either PET or HDPE bottles. Both technologies feature the GEA Procomac ‘Clean Box’ design that surrounds the whole filling bloc to keep optimum hygienic conditions. All components within this bounded area can be efficiently cleaned. www.gea.com","@ID":47}, "MARKET SURVEY 34 PETplanet insider Vol. 15 No. 04/14 petpla.net 4/2014 MARKETsurvey Company name Resilux Appe Société Générale des Techniques Retal Iberia, S.L.U. Postal address Telephone number Web site address Contact name Function Direct telephone number Fax E-mail Damstraat 4 9230 Wetteren, Belgium +3293657474 www.resilux.com Philippe Blonda Marketing & Sales Director +3293657476 +3293657475 philippe.blonda@resilux.com Ellice Way, Wrexham Technology Park, Wrexham, LL13 7YL, UK +44 1978 317 378 www.appe.com Kinza Sutton Marketing Manager +44 1978 317 378 Kinza.Sutton@appe.com 3 Rue de l’Île Macé 44412 Rezé, France 33 0 2 40 05 09 37 www.sgt-pet.com Martine Le Claire Sales Administration +33 2 40 05 02 88 +33 2 51 70 01 55 m.leclaire@sgt-france.com Ctra. Comarcal C-35, Km. 66,147 Sector 2 Parcela 5 - 17451 - Sant Feliu De Buixalleu (Girona), Spain +34 972865730 www.retaliberia.com Raquel Oller Bosch Sales Manager +34 696489901 +34 972865731 raquel.oller@retaliberia.com Preforms Multilayer preforms Yes Yes No No PEN prefoms No Yes No No Preforms in alternative materials (PP/PLA/PEF) Yes Yes, according to customer requirements No No Preforms incorporating rPET (rPET content in %) Yes - according to customer wishes Yes, from 1 - 100% dependent on requirements From 0% to 100% (according to the client request) 40 Additives available Oxygen barrier: ResiOx, CO2 barrier ResiC; Oxygen and CO2: ResiMid, ResiMax; Light barrier: ResiBlock All general additives including colourants, barriers for UV, O2 , CO2 , moisture All colours, UV blocker, AA reducer, O2 scavenger, CO2 scavenger, reheat additive, white colour for UHT milk, gliding agent Colour & slip agents Preform range Juice, milk: 38mm 2-start, 3-start CSD, water: 28 PCO 1810 / 28 PCO 1881 water: 29/25; 30/25; 48/40 oil: 48/40; 29/21; 39/21; 45/34 detergents: DIN28/410 Monolayer & multilayer preforms for water, soft drinks, juice, dairy, home and personal care, alcohol and food applications. Range of standard and non-standard preforms sizes / weights / necks & finishes / starts, including wide-mouth 30/25 high neck and low neck: 13g - 44g 29/25 (without step): 8,6g - 35,8g 29/25: 8,8g - 36g PCO 1810: 16g - 52,5g PCO 1881: 14,5g - 48g BPF: 20,5g - 53g 38mm: 14g - 44g 48/40: 77g - 95g 21/29: 20g - 25g 28/410: 19,5g - 40g BVS: 40g - 54g CRC63: 445g 9,3 - 100g Company name PET-Verpackungen GmbH Deutschland PET Prefroms Morocco NovaPET, S.A. Empacar Gastro PET Postal address Telephone number Web site address Contact name Function Direct telephone number Fax E-mail Gewerbegebiet 4, 98701 Großbreitenbach, Germany +49 3 67 81 / 4 80 - 4 57 www.pet-verpackungen.de Hubert Rebhan Head of Sales +49 3 67 81 / 4 80 - 4 53 +49 3 67 81 / 4 80 - 4 52 hubert.rebhan@wiegand-glas.de B 8-1 Zone Industrielle 13000 Benslimane, Morocco +212 5 23 29 88 78 www.petmorocco.com Rachid Nourredine Managing Director +212 5 23 29 88 78 +212 5 23 29 88 67 r.nourredine@petmorocco.com Zaragoza 50001, Office: Paseo Independencia, 21, 3rd floor, Spain +34 976 216129 www.novapet.es Antonio Lázaro Preform Business Manager +34 976 216129 +34 901 021138 alazaro@samca.com Casilla de Correo 2865, Santa Cruz de la Sierra, Bolivia +591 3 3649470 www.empacar.com.bo Carlos Limpias Plant Manager +591 3 3649470 +591 3 3461883 climpias@empacar.com.bo Kotna ulica 5 3000 Celje, Slovenia +386 3 425 80 32 www.gastropet.si Primož Agrež managing director +386 3 425 80 32 +386 3 425 80 31 info@gastropet.si Preforms Multilayer preforms Yes Yes No No No PEN prefoms Upon request Yes In project No No Preforms in alternative materials (PP/PLA/PEF) Upon request PLA Wide PET resins portfolio by NovaPEt No PLA preforms Preforms incorporating rPET (rPET content in %) Upon request No 10.0-25.0% 10%, 30%, 50%, 70% and 100% rPET clear and coloured Available according to customer requirements Additives available Colours, oxygen scavengers, UV-blockers, slip-agents, AA-scavengers, brighteners, PA-based barriers Concentrates (for milk and light sensitive products), colours, lubricants, nucleants, under customer requirements Active barrier , 02 scavenger According to customer requirements Preform range Standard preforms: 28mm PCO1810 and PCO1881 from 14.5g to 54g including preforms with 28mm PCO1810 and PCO1881 finish and typical octagonal neckring (PETcycle). 38mm 2-start and 3-start Bericap preforms for wide mouth applications. Preforms for hotfill applications: 23g- 45g. For large containers 60g, 92g and 98g preforms with Bericap 48-41 / customized preforms up to 446g. For enhanced barrier protection, majority of the preforms also available as multilayer with tailor-made barrier properties Soft drinks/water Ø 29/25 W (short neck): 330ml - 2.000ml: 10.5g to 32g Ø 30/25 W (std neck): 330ml - 2.500ml: 12.5g to 35g Ø 48mm W: 5.000ml to 6.500ml: 77.0 and 82.0g Ø PCO 1810 (std neck): 500ml to 3.000ml: 18.5g to 54.0g Ø 38mm from 500ml to 5.000ml: 23.0g - 65.0g Any other shape and weight according to customer requirements CSD/water: PCO 1810 finish: 17.5g - 60g CSD/water: PCO 1881 finish: 20.6g - 54.6g oil, vinegar: 29mm edible oil finish : 18g - 24g water: 700g - 5 gallon preform For standard and special applications. PCO 1810: 18.2 - 24.5g PCO 1810: 32g - 48g Bericap 38mm 3-start: 16g - 41.5g","@ID":36}, "EDITOUR REPORT 18 PETplanet insider Vol. 15 No. 04/14 petpla.net petengineering.com info@petengineering.com P.E.T. Engineering: the one-stop shop for beverage packaging. Technology excellence, captivating design, ergonomic shapes: a product developed by P.E.T. Engineering is easily recognizable. Its technical know-how and experience have made of it a leader brand in the sector of PET containers. Design, prototyping, laboratory tests and the production of blow moulds: P.E.T. Engineering is the perfect partner, holding itself all the possible solutions. PACKAGING. EVERYTHING YOU NEED DESIGN The perfect shape for an easy handling. PROTOTYPING Bottles available just a few hours RESEARCH AND DEVELOPMENT New materials, innovative solutions and cutting edge technologies. PRODUCTION AND CUSTOMISING OF THE MOULDS High quality blow moulds for every kind of container and any type of blowing machine. STARTUPASSISTANCE AND TRAINING Supporting the client during the whole project. pure mineral water in PET bottles, carbonated and non-carbonated, bottle sizes ranging from 310ml up to 6l In OPP water dispensers, non-carbonated, container sizes 10 and 20l In OPP tubs, non-carbonated, tub sizes 200 and 305ml. Lindoya fruta fruit juices In PET bottles, non-carbonated, bottle size 400ml and 1l. Acquafibra and vitamin drinks In PET bottles, non-carbonated, bottle size 400ml and 1l The total filling capacity of the bottling lines is 100,000l/h. Andre Arlotti Gião, Head of Marketing, emphasises the important principle that all drinks are based on pure mineral water. Acquafibra Acquafibra has been bottled for six years and adheres strictly to the company’s guiding principle. Behind this name there is a prebiotic fibre which is mixed with the mineral water and then completely dissolved. There are also wonderful flavours added. The fiber is the energy source for the lactobacillus in the intestine mucus. A healthy mucus is responsible for a healthy digestion. Anyone, including children, need to consume pre-biotic fibre on a daily basis along with intestine hydration. In average, the human body needs 25g of pre-biotic fibre per day and lots of hydration, and the drink is able to provide both, 6g of pre-biotic in every bottle with adequate mucus hydration. The bottling process is carried out using 400ml PET bottles. The design of the bottle, developed by the company itself, is cylindrical and thus permits a label to be applied which covers the whole height of the bottle and which also acts as a defining feature, making it readily recognisable. Four flavours are available; these are created by the addition of aromatic flavouring. Liquid nitrogen is also used during the bottling process to provide additional stability for the bottle and to avoid oxidation. According to Andre Arlotti Gião, lightweighting is not of concern as far as this bottle is concerned. A PET bottle which is on the heavy side but still very stable helps to underpin the company’s claim to quality. This also applies to the plastic closure. However, Genuina uses all 100% recyclable materials. Today the breakdown for beverages production is 50% mineral water with decreasing share, 30% fruit juices and 20%Acquafibra and other healthy beverages, the growing share and the company focus. A breakdown of the bottle sizes reveals an even distribution. The delivery radius is 500km, servicing a market of 90 million people. Blow moulding of bottles and filling operations Genuina Lindoya purchases preforms on a regional basis from various preform manufacturers. The plastic closures are bought in from two suppliers. The in-house production of closures and preforms is not an issue here. The manufacture of the PET bottles is carried out on four Sidel stretch blow moulding machines. A total of eight bot-","@ID":20}, "BOTTLE MAKING 30 PETplanet insider Vol. 15 No. 04/14 petpla.net The Mexican soft drinks company Peñafiel, a subsidiary of the Dr Pepper Snapple Group, placed an order with Krones in December 2011 for a PET line featuring an ErgoBloc, which went into production in August 2012. When designing this line, Krones joined forces with the client to create the large-size bottles as well, which had to be able to cope with the extreme conditions involved. After commissioning had been completed, Peñafiel got together with Krones again, this time to design an entirely new still-water bottle with a special base. Low preform weights - high carbonation There were special requirements to meet for container design when it came to the large-size bottles up to 3.0l, and also the wide range of different formats, with 1.0, 1.5, 2.0, 2.5 and 3.0l. The flavoured waters being bottled also exhibit a high CO 2 content of up to 9g/l. At the same time, Peñafiel uses relatively low preform weights considering the high carbonation involved. Because of the extreme climatic and geographical conditions in Mexico, the company laid down stringent specifications and requirements for the packaging. During transportation, a bottle can be travelling on Mexican roads for 22h in the south-east, and for 20h in the north (up to 2,100km in each case). 85% of the country consists of mountain ranges, plateaus and valleys. In the middle of Mexico, the average elevation of the volcano belt is 6,600ft (2km). The Sierra Madre Occidental Krones and Peñafiel develop 3.0l bottles with a low preform weight and high internal pressure Extreme conditions - extreme design Based on an article by Inigo Marchal, Krones AG","@ID":32}, "PETnews 6 PETplanet insider Vol. 15 No. 04/14 petpla.net Husky reorganises Husky Injection Molding Systems has announced changes in its global organisation. Following the acquisition of Schöttli, the medical and closure mould maker, Husky has created a new combined business unit dedicated to medical and specialty packaging, which combines Schöttli technology, Husky’s specialty mould making facilities in Austria and the Czech Republic, aftermarket tooling and services, and the Hylectric system platform. Steve Lawrynuik, formerly Vice President, Customer Support, will head the new unit, as Vice President, Medical and Packaging Systems. John Galt, President and CEO, said that the dedicated medical and speciality packaging business will enable the company to provide greater focus on these markets and to offer customers a solution that covers mould, machine, hot runners, controllers and aftermarket services. Husky has also announced that Michael Urquhart, Vice President Global Sales, Packaging Systems, will retire after 33 years with the company. www.husky.ca Krones tips the light fantastic Krones’ superlight 500mm “PET lite 9.9 carbonated”, which weighs just 9.9g, was among the winners at this year’s iF Packaging Design awards in the beverages category and is now entitled to wear the “iF” label. It is divided into several functional areas with different wall thicknesses. Most of the PET material is located in the upper part of the bottle, where it is held and opened. The walls in the lower section receive only half as much material. Other weight savings are achieved with the special neck finish, which features a tear-off ring-pull closure. The company claims that PET lite 9.9 combines affordability with ecological awareness, as it uses less material than equivalent bottles, consumes less energy and has a lower environmental impact. PET lite 9.9 carbonated is now on display with other winners in the iF online exhibition and is part of the iF design exhibition in Hamburg. www.krones.com Bühler Thermal Processes installs 2.5 million t/a PET SSP capacity Bühler Thermal Processes AG (BPAG) and its partners in the Americas, Asia, Middle East and Europe have brought to fruition new projects for PET production using advanced SSP technology. PET producer Hainan Yisheng (China), a fast growing PET producer, has commercialised production of 1million t/y PET by the end of February 2014. Each of the four production lines was commissioned within less than three weeks and has achieved the nominal capacity and product quality specification. The state of the art SSP Process of BPAG has again demonstrated its robustness, energy efficiency and reliability. Reliance (India), PQS (Brazil), Sabic (Saudi Arabia) and Polyplex (Turkey) have also decided to expand their PET production capacity with the well proven SSP Technology of BPAG. These plants will be in production and deliver another 1.5million t/a of SSP production capacity within the first and second quarter of 2014. The SSP plants of BPAG are capable of reaching a single line capacity of 1,500t/d. One of Indorama’s SSP lines has reached a capacity of 850t/d and the new lines of Reliance with a nominal capacity of 900t/d are expected to reach 1,000t/day per line. For all plants BPAG supplied its energy-optimised SSP technology, basic and detail engineering, all plant components and supervised the construction and commissioning activities. www.btpag.com P.E.T. Engineering’s year of growth P.E.T. Engineering of San Vendemiano, Italy, which specialises in the design and manufacture of PET containers, has reported financial results for 2013 that show turnover (revenues) up by 45%, compared to 2012, and EBITDA up by 15%. Growth was led by countries outside the EU; 82% of total sales are outside Italy, with nearly 71% from outside the EU and led by Russia. The company reported that its staff numbers had increased by 30%. Product development is now being led by multidisciplinary teams, consisting of designers, engineers and researchers. PET Engineering received four design awards during 2013, led by the Oscar dell’imballaggio 2013 for its 5LW, its lightweight 5l container. www.petengineering.com Sidel takes Knowledgeshare to China The challenges and opportunities of the beverage market in China were the focus of Sidel’s two-day Know-ledgeshare Sanya 2014 event, which took place March 27 - 28 on Hainan Island, China. This was the second KnowledgeShare, following the launch event in Frankfurt in November 2013. The event attracted almost 300 participants from across the supply chain, including representatives from the China Beverage Industry Association and from Nielsen, the global market research and data specialists. They provided an insight into the fast-changing Chinese market. Subjects of the first day considered included how automation can help deliver higher productivity; greater efficiencies through smarter investments; reducing downtime by plant optimisation; and specific solutions for sensitive or particle filling beverage products. Day two’s headline topic was innovation to meet the challenges of tomorrow. Its breakout sessions looked at new product development; aseptic mixing and dosing solutions; reinventing packaging; and solutions in labelling. Fan Lidong, Vice President of Sidel Greater China observed that KnowledgeShare Sanya 2014 was a departure from the more conventional ‘conference’ approach, that the objective was to offer a collaborative forum in which the industry’s real issues could be openly discussed, with delegates benefiting from collective knowledge. After the event the discussions move online, supported by a dedicated KnowledgeShare blog, which is open to all in the industry. www.sidel.com","@ID":8}, "ONsite 54 PETplanet insider Vol. 15 No. 04/14 petpla.net Maag and Automatik upgrade Recron Recron Malaysia is a member of the Reliance Group, the world’s largest polyester and textile manufacturing company. Recron is a producer of both textile and bottle grade PET, which it manufactures in facilities in Nilai and Malaka. In its quest to raise production output it determined to upgrade and modernise its existing equipment, in order to sustain machine performance at the high levels, to decrease operating costs and to debottleneck its systems. Polymer pumps and pelletising equipment are, of course, key elements in polymer production and the wear of moving elements – rotors, counter knives and infeed rollers – has a considerable influence on the operating costs. The choice of profile or material for the rotor and adjustments for the pelletiser will directly affect both end product quality and material wastage rates. Close cooperation with machinery suppliers will usually help to reduce costs and extend equipment life. Recron collaborated with Maag Singapore, part of the Pump Solutions Group of Dover Corporation, and Automatik Malaysia to achieve its objectives. Maag’s new bearing material enables an improved clearance for existing polymer pumps and debottlenecking projects at Recron achieved uplift in production capacity of approximately 15%. This was done without changing other auxiliary equipment, such as universal drive shafts or drive units. The solution was devised jointly by Recron, as the machine operator, and by Maag as the gear pump supplier and the net result is that the plant is now producing more and with fewer interruptions or problems – with a further benefit that Mr Balasubramanian, Technology Manager, explained. ”Of particular notice is the fact that the positive results yielded have been achieved with little investment.” Automatik Plastics Machinery, a Maag subsidiary, supplied an under water strand pelletiser that played an important role in increasing pellet quality and reducing consumable costs. Initial discussions and on-site inspection of machinery and production processes identified potential improvements. New devices were put in place to reduce waste during startup. A number of old components were replaced in order to optimise the use and alignment of existing tools, such as rotors and bedknives, to actual product needs. Changes implemented on the machines, combined with operator and maintenance staff training, helped to increase productivity and to reduce maintenance time and costs. Mr. Balasubramanian observed that the local technical support and grinding service for the cutting rotors have helped Recron Malaysia to achieve equipment lifetimes significantly better than it had previously experienced. Chew Phenghuat and Seah Poh Siang, of Maag and Automatik, said that the companies’ approach of co-operation with customers, along with their technical support, enables both companies to provide commercial advantage. Maag Singapore was established in 2000; Automatik Plastics Machinery opened its service centre in Malaysia in 2009. www.maag.com SGT, naturally innovative The specialist in PET preforms and HDPE caps for over 30 years. +33 (0)2 40 05 09 37 /www.sgt-pet.com","@ID":56}, "PETpatents www.verpackungspatente.de 60 PETplanet insider Vol. 15 No. 04/14 petpla.net Container closure International Patent No. WO 2013 / 119781 A1 Applicant: Plastipak Packaging Inc., Plymouth (US) Date of Application: 7.2.2013 Screw closure with tamper-proof guarantee strip for mounting on a bottle designed for hot filling. The part of the closure that protrudes into the inside of the bottle in the form of a sealing lip stabilises the bottle and reduced headroom increases any possible internal pressure. Bottle for hot filling Disclosure No. DE 102012101738 A1 Applicant: Krones AG, Neutraubling (D) Date of Application: 1.3.2012 Sections of a thin-walled bottle designed for hot fill applications are enclosed by a holding fixture made from elastic material which exerts pressure on the bottle, promoting vacuum absorption during cooling and helping to reinstate the shape of the bottle. Integrated refill chamber International Patent No. WO 2013 / 154914 A1 Applicant: Microlin LLC., Salt Lake City (US) Date of Application: 4.4.2013 A container for holding a cleaning agent or disinfectant is equipped with an integrated additional chamber to accommodate a product concentrate in solid or liquid form. The product is released when required, the container is topped up with water and the finished spray product is ready for use. In-mould label International Patent No. WO 2013 / 161403 A1 Applicant: Yoshino Kogyosho Co. Ltd., Tokyo (JP) Date of Application: 11.3.2013 The material and the design of an inmould label are described. The label is also designed for applying to curved surfaces without any air bubbles or wrinkles forming. Container manufacture International Patent No. WO 2013 / 156532 A1 Applicant: Borealis AG, Vienna (AT) Date of Application: 17.4.2013 Customer preference for portable multipacks calls for stable and reliable outer packaging for several bottles. Proposed here is a type of strapping at bottle midriff level and an all-round shrink label. Bottom section shape International Patent No. WO 2013 / 156710 A1 Applicant: Sidel Participations, Octeville Sur Mer (FR) Date of Application: 10.4.2013 For PET bottles that are exposed to differences in pressure, a special bottom section shape is necessary so as to be able to compensate for the forces caused as a result of elastic deformation in the area of the base.","@ID":62}, "BOTTLES 57 PETplanet insider Vol. 15 No. 04/14 petpla.net Boosts energy, saves energy PET packaging specialist Appe has worked with Oji and Hero to produce an environmentally friendly 100% rPET bottle for Oji’s ‘sustainable’ functional fruit drink. The Oji drinks are available in four variants featuring different fruits and health benefits. All contain caffeine from green coffee beans to provide a mild energy boost along with a variety of nutrients including antioxidants, fibre, magnesium and vitamin C. The bottle is claimed to provide an ambient shelf life of six months for the preservative-free drinks, avoiding the energy consumption involved in keeping them chilled. Appe’s rPET material was the choice for Oji with its firm focus on sustainability. The new bottle enables the brand to achieve a ‘closed loop’ recycling system as the product can be recycled and then reused for a new 100% rPET bottle. This fits with Oji’s co-operation with the TerraCycle program that focuses on eradicating incineration and waste. The development and manufacture of the package has involved close collaboration with three of Appe’s sites. The company’s design team created the preform for the 100ml bottle and also had considerable creative input into its physical appearance. The rPET material is supplied by Appe’s recycling plant in Beaune, France, and to complete the process the bottle is manufactured at Appe Belgium, with bottles supplied to Hero’s filling operation in The Netherlands. Hero, a brand-focused consumerfoods group, interacted closely with Oji and APPE for the filling and shelf life aspect of the operation. www.appe.com Relaunch of Rewe The Rewe Group of Cologne has marked a proportion of its products with the phrase “Best Choice“ as a signal to the consumer that the item offers top quality at a reasonable price. At the same time the appearance of the products has also been changed. Two examples are the 1l PET bottle for multi-vitamin juice with a re-designed label that emphasises its premium quality and the PET bottle for whipped cream with a content of 500g, the label for which has also been re-designed. This results in a readily identifiable and distinguishable brand image on the shelf. www.rewe.de Big and beautiful PET Power’s bestknown family of widemouthed jars is probably its recessed Cylindrical range, and it has gained a new member. The newly-launched 3.5l jar has the same shapes as its siblings (round with a recessed label area), but differs slightly from them. It is a little narrower and taller and PET Power says that this gives a visual appearance that is a little more elegant than the other models. The 3.5l bottle is produced with the 100SP400 neck finish, which means that it can be used with a very wide range of standard aluminium or plastic closures. The cylindrical shape is claimed to be suitable for chemical or household products, food products such as sweets, sports supplements, and other products in powder form. While the shape is suitable for a wide range of decoration techniques, PET Power suggests that it is best suited to a label, which can be accurately applied to the recessed label area. The jar can be produced in a wide range of colours. www.petpower.eu","@ID":59}, "TRADE SHOW PREVIEW 48 PETplanet insider Vol. 15 No. 04/14 petpla.net GeboCermex | Hall 13 Stand C47 Robot-aided case packer Interpack 2014 will see the global premiere of Version 2 of GeboCermex’ FlexiCase top-loading case packer, which combines forming, loading and sealing functions to pack products that can be difficult to load into regular slotted containers (RSCs). GeboCermex says that Version 2 has been designed to be more compact than its predecessor and that it integrates lightweight tooling and a new robotic arm, designated E20. Overall machine length has been reduced by 1,100mm and the new compact robot arm is helpful in low-ceiling situations. The new gripping arm barely extends beyond the machine frame. Gripping heads are now available in honeycombed carbon and aluminium, which reduces head by 30%, compared with steel. The safety-head mechanism is claimed to be more sensitive to collisions and the numericalaxis gantry can handle payloads up to 260kg. Light loads can be handled at up to 30 cycles/min. www.gebocermex.com Sipa | Hall 13 Stand B73 Versatility and flexibility in modular fillers Sipa will exhibit four different configurations of its Flextronic electronic volumetric bottle fillers on its stand. Flextronic is the new range of modular fillers designed to ensure high performance and reliability, and is the result of a long design period. In terms of flexibility, in particular, Flextronic fillers are ideal for packaging companies with a broad mix of products that they may need to run for relatively short periods, on a limited number of lines, as well as operators moving into new and fast-developing areas, where it is unclear at the outset what the major product will ultimately be, and where equipment adaptability is a priority. The modularity of the Flextronic system makes it easy to adapt to specific applications. The ‘C’ version is an isobaric filler for carbonated and non-carbonated beverages that can also handle hot-fill products. The Flextronic S gravity filler, with its simple non-contact membrane valve, finds its application area in the filling of water, milk, homogenised juices and clear products. The Flextronic SC, also a gravity filler, has a shuttered contact-type valve for hot and cold filling of smooth and pulpy beverages. A third gravity filler, Flextronic SE, with its non-contact shuttered valve, is designed for hot and cold filling of sensitive products such as premium juices with pulps. All four versions are on the Sipa stand. Flexibility makes its point as well with Sipa’s design of HotLight 28, a 28-mm short neck finish at just 3.8g. The HotLight 28 allows the production of hot fill and CSD containers on the same machine without any personalisation change. Flexibility is also evident in Sipa bottle production systems. A single SFR EVO 3 rotary stretch-blow moulding system, for example, can produce bottles for a wide range of drinks. Without changing the mould shells, it can be quickly converted from producing bottles for water or carbonated soft drinks to bottles for hot-fill applications. Additionally, Sipa’s Active Layer and Fastlayer palletising systems will be on show. No manual intervention is required in the Fastlayer area when there is a change in format of the product to be palletised - important when formats change frequently. www.sipa.it Finpac | Hall 13 Stand E84 Speed shrinking Finpac, Italy will be presenting its new model B4 machine, able to shrink up to 21,000 0.5l bph. With this machine it is possible to shrink two, three or four bottles with one sleeve to a multipack, with the same sleeve becoming a single label for each bottle. www.f npac.it PE Labellers | Hall 14 Stand D09 All-around view of labeling machines P.E. Labellers and Packlab will be showing four different types of labelling machines. PE Labellers’ Maya model sleeve applicator is designed for applying shrink sleeve labels on containers of any material, shape and size. Also on display will be Rollmatic, which (as its name implies) is a roll-fed labelling machine. Packlab’s Wing Rep FBW 60 linear self-adhesive rolling machine is equipped with self-adhesive stations with adjustable axles. Their motorised height and depth are controlled electronically from the LCD keypad on the adhesive unit. This configuration also allows for the optional adjustment of the automatic size change directly from the HMI panel. The stand will also commemorate P.E. Labellers’ celebration of its 40th anniversary. www.pelabellers.com","@ID":50}, "TRADE SHOW PREVIEW 47 PETplanet insider Vol. 15 No. 04/14 Bericap | Hall 10 Stand E67 Optimised closures Bericap will be exhibiting a comprehensive range of closures for the automobile, chemistry, pharmacology, agro-chemistry, and food and beverage markets. New solutions for protection against product piracy, including the use of laser technology, will also be presented. The new DIN closure range is approved for UN-hazardous substance in connection with different package types and/or suppliers and all sizes can be custom-made and equipped with a vent diaphragm. The SK 42/21 SFB closure is equipped with a new slitted strip and is available in two versions. The SK 42/21 SFB Mk is suitable for light packaging and containers without UN-hazardous approval. The SK 42/21 SFB MDS is equipped with a foamed PE-seal for containers with the relevant UNapproval. The BV 21/24 MAB ventilation valve is used primarily in agro-chemistry, chemistry and in the lubricating oils industries. Developments in the food segment include the EV28/26 press-on closure, which is suitable for standardised preforms for both cooking/salad oil and for sauces and syrups. It is available as standard screw-closure with special anti-drip pour-out, with and without flow regulator. The BericapValve dosing system will feature in various rigidity grades in solutions for ketchup, chocolate syrup, body lotion and pharmaceutical products. The still water market is served with the HexaLite 29/11 and 26/10, for 29/25 and 26/22 PET bottlenecks, respectively. The range has been extended with HexaLite 26/13 and 29/10, which are claimed to offer better grip. They also have an easy-to-open slitted and folded safety strip. A new and lighter 33mm closure for hotfilling will be on the stand, along with a lighter variant for the 38mm size. The novel 33/15mm closure for aseptic filling offers weight savings up to a claimed 30%. The PushPull sport closure and a sport closure variant for the PCO1810 thread will be on display, as will the LSK EV Galileo II 29/44 hinged closure, for PET and glass bottles and examples of the HC EV 29/21 edible oil closure, revised for syrup filling. www.bericap.com KHS | Hall 13 Stand A31 Faster liquid and viscous food packaging KHS’ focus will be on the KHS-Innopack Kisters TSP A-HTPFO packaging machine, which is designed to deal with all kinds of containers and packs, including plastics containers, individually formed packs and pre-packed product groups. The unit’s modular structure is intended to enable it to meet future demands and requirements; any additional functional modules can be added quickly and easily. An integrated conveyor belt, situated above the folding and setting station. When changing over to the formation of shrink packs only, this belt can be automatically lowered at the press of a button. It has been designed to reduce material consumption through cutting wastage, as well as cutting consumption of compressed air and energy. Film packs are shrunk in a shrink tunnel which is heated by either electricity or gas; energy savings of up to 50% are claimed. www.khs.com","@ID":49}, "TRADE SHOW PREVIEW 43 PETplanet insider Vol. 15 No. 04/14 petpla.net Starlinger | Hall W1, Stand B41 Masterbatch production from in-house waste Starlinger will be showing its recoBatch technology which, it says, enables in-house waste to be upcycled, as it makes it possible to add calcium carbonate (CaCO 3 ) during the recycling process. The waste becomes in-house produced masterbatch, which can be used to substitute part of the masterbatch needed in tape production. Starlinger recycling technology will be showing a recoStar universal 65 VAC recycling line with the recoBatch option. Starlinger viscotec will be showing its deCON 20 decontamination dryer, which is used for processing PET and HDPE flakes and recycled pellets, for use in food grade packaging. The deCON 20 is able to process input material in different forms, such as pellets, flakes and skeleton waste, simultaneously. The process is FDA and EFSA compliant. Starlinger viscotec’s recently-developed viscoSheet, which produces thermoforming sheets for food packaging from up to 100% recycled PET, will also be on display. www.starlinger.com Sacmi | Hall E2, Stand B45 Caps and more The star of the Sacmi stand will be the CCM48 cap manufacturing press. Developed by the Closures & Containers Division, this is the very latest in a series of presses. The CCM48 has already been exhibited at the Kappa and Drinktech 2013 fairs in Shanghai, and it will play a central role on the Sacmi stand. The machine can produce up to 2,000 plastic caps/min with just 48 moulds, a solution for the single-piece CSD, water, hot filling and cold aseptic filling cap-making market. The CCM48S will be equipped with a mould suitable for manufacturing single-piece AB29W caps in HDPE (high density polyethylene) with a diameter of 29mm and a weight of 1.35g. Featuring a compact design, the CCM48S can be smoothly integrated with the CVS in-line quality control vision system; made by Sacmi’s Automation & Inspection System Division. The latter is designed to ensure total cap control. Sacmi Automation & Inspection Systems will be presenting multiple inspection solutions, one of the most noteworthy being the CHS Lean. This modular solution offers inspection rates of up to 2,500caps/min / 150,000caps/h and has been developed for installation downstream from compression and injection lines. Chinaplas 2014 also offers an opportunity to showcase the results achieved – just two years after its market launch – by the IPS220 preform injection press. www.sacmi.com Husky | Hall E3, Stand F01 Hot runner and controller technology Husky Injection Molding Systems will focus on showcasing its latest technologies in hot runners and controllers, which it recently established as a strategic priority. Husky said that it is taking a targeted approach by displaying hot runner and controller technology designed to serve key markets, including consumer electronics, medical, automotive and closures. Among the technologies to be demonstrated are the Ultra SideGate hot runner; Ultra nozzles; and its latest developments in synchronised stem control applications. The stand will also be showing the Altanium Delta3, Matrix2 and other recent additions to the Altanium temperature controller product line. Husky will also be unveiling several new products at the show, which will address issues improved thermal uniformity, increased valve stem control, better gate quality and installation simplification. www.husky.ca","@ID":45}, "BOTTLES 59 PETplanet insider Vol. 15 No. 04/14 petpla.net Gesellschaft Wärme Kältetechnik mbH Friedrich-Ebert-Str. 306 · D-58566 Kierspe Tel. +49 2359 665-0 · www.gwk.com Perfect cooling and temperature control You will feel better having made the right decision. Reduce your energy consumption. System solutions Mould inserts Temperature control technology Water treatment Cooling technology Tailor made solutions Temperature controllers Chillers Energy saving cooling systems A breath of sea air Nivea is constantly expanding its shower gel range and adding yet another new variant to entice the customer to buy. The latest example is the “pure fresh“ shower gel with marine minerals and ocean-fresh fragrance. This viscous product is packaged in a slightly blue-tinged PET bottle containing 500ml and featuring a screw-on, dual-colour hinged lid. Two self-adhesive labels – the front one being a no-label look label – also contribute to the presentation. www.nivea.com Pre-wash gel from vanish Under their “Vanish“ brand name, ReckittBenckiser are marketing 200ml packs of spot remover for pre-treating stubborn spots prior to machine washing. The clear product is packaged in a transparent, easy-to-handle bottle made from PET. A dispenser/closure complete with an integrated silicone valve serves as a closure and this discharges product when pressed on to the bottle which is decorated with a tinted sleeve label. The outside of the closure incorporates features in other colours, the aim being to work the product into the surface of the piece to be cleaned. There is a cap to provide protection against operating errors during transport and storage and this also prevents any protuberance of the silicone valve. www.vanish.de Shapely bottle for hair oil Sporting the tag “Frizz Ease”, John Frieda is selling 100ml of hair oil that claims to tame unruly locks and make them silky smooth. The product is packaged in a slightly tinted, elegantly shaped bottle made from PET. With a view to enhancing its quality rating, one section of the hand-operated pump dispenser is presented with a shiny silver finish. A no-label look label on the front and a shaped self-adhesive label at the rear convey the customer information. The pump dispenser is protected by means of a transparent cap. www.johnfrieda.com Spray mist fertiliser for orchids The French company Carrefour was marketing 100ml of liquid spray mist fertiliser for orchids in a slimline, transparent PET bottle. The feed is applied via a coloured pump dispenser which is protected from damage during transport and storage by means of a plastic cap. The paper label incorporates detailed information about the application and the product. The product was only available for a short time as a promotional article.","@ID":61}, "NEWS 9 PETplanet insider Vol. 15 No. 04/14 petpla.net PET overcapacity ‘crisis’ PET markets globally are facing an overcapacity crisis as waves of new production resources come on stream in China, according to Francesco Zanchi, CEO of business services group GSI Global Service International. He delivered his analysis at the second ICIS PET Conference, held March 11/12, 2014 at the Hilton Amsterdam, The Netherlands. He that global PET demand in 2014 will increase 6% over 2013, to 19.7million t/a. However, he claimed that supply will increase by 20%, to 29.4million t/a, leaving the market around 50% over-supplied. The main source of the problem is asserted to be China, where local demand of 4.2million - 4.5million t is almost doubly catered for, with capacity of around 8million t. He forecasts a surge in Chinese exports, from 1.85million t in 2013 to 2.2milllion - 2.3million t this year. Chinese PET facilities will achieve operating rates of only around 65% during 2014. He further claimed that the situation in Europe is also deteriorating. While the region has traditionally been a net importer of PET because capacity lagged demand, two new projects scheduled to come on stream will change the picture. The additions of Lotte’s 200,000t/a plant in the UK and Indian group JBF Industries’ 440,000t/a facility in Belgium will be partially offset by closures at La Seda de Barcelona in Italy (180,000t/a) and Indorama at Workington (160,000t/a). Other projects have also been delayed or cancelled but Europe in 2014 will still have around 300,000t/a of new capacity, and facilities in Turkey and Egypt are also adding up to 900,000t/a of new capacity, which is mostly targeted at Europe. Furthermore, a new free trade agreement (FTA) with South Korea is lowering tariff barriers to zero, allowing it to export around 300,000t/a of PET towards Europe. Turkey, Thailand, Egypt and Indonesia all also have 0% duty arrangements, meaning a total of 2.4million t of PET capacity will be targeted on Europe. Mr Zanchi forecast that operating rates in Europe are likely to plummet from over 80% in 2013 to around 60-65% by 2015/16. On the other hand, he said that positive developments were likely to include reductions in the price of both PET and feedstock PTA, which will help European competitiveness and, consequently, stimulate demand. Earlier in the conference, Nexant Consultant Stuart Hardy, forecast that huge volumes of PTA capacity being added in China - around 17million tonnes from 2014 to 2017 - would lead to “terrible” margins, low operating rates and periodic plant shutdowns. www.gsiplastic.com Piovan’s golden year Italian company Piovan is marking its its golden anniversary. The company now known as Piovan was formally established in 1964, which means that this year – 2014 – marks its 50th year of the design, manufacture and supply of auxiliary machinery for the plastics industry. Over that time it has accumulated more than 50,000 customers worldwide. In fact, its roots go back even further than 50 years. In 1934, Costante Piovan & Figli was founded in Padua, Italy, as a metalworking shop - but its founder, Costante Piovan, had ambitions that went beyond merely producing moulds for other companies, no matter how prestigious they were. His customer-focused approach was unusual for the time, but this guiding principle has linked all three generations of the Piovan family. 1964 was the year when Piovan launched its first equipment on the Italian market - a granulator and a material loader. It now has five production facilities:in Italy, Germany, Brazil, China and the United States, 21 subsidiaries, agents in more than 70 countries, and a total of 900 employees, of which 140 are customer assistance engineers. Piovan’s range of products and services includes feeding, blending, drying and recycling systems, industrial chillers and temperature controllers. It integrates its wide array of equipment with proprietary production monitoring and control software. Piovan likes to claim that it continues to offer a customer-oriented approach as not just a supplier but as a partner, working alongside its customers. Piovan’s milestones: 1934: Costante Piovan & Figli (then Centro Meccanica), a specialist in precision mechanics, is established in Padua. 1964:Piovan produces its first granulator, followed by the Convair dryer and Convector feeder. 1970s: The first refrigeration line, in 1972, and its first central feeding, blending and drying system. A joint venture with Star, a Japanese robot manufacturer, gives life to Star Automation. Piovan Germany opens in Garching, near Munich, 1974. 1980s: Specialisation in PET, introduction of electronics, partnerships with key OEMs, further growth on foreign markets. Inauguration of the new facility in Santa Maria di Sala, near Venice, Piovan’s current headquarters. Piovan France opens in Brion, 1986. 1990s: Piovan extends into Automotive, Electronics and Textile, and opens new branches in Canada, Brazil and Asia. Acquisition of a software company to develop remote plant monitoring and control systems. 2000s: Two factories are started in Brazil and China; new branches opened in Mexico, UK, Austria, Hungary and the Czech Republic, India, Turkey, Thailand, Indonesia and Vietnam. In 2008, Piovan purchases US company Universal Dynamics, (UNA-DYN). In 2010, it acquires majority stake in FDM, a German company specialising in extrusion technology. www.piovan.com MachinePoint reports profitable 2013 MachinePoint, the European specialist in the sale of used plastic machinery, has reported increased revenues, sales and profitability in 2013. Its turnover rose by nearly 39% over 2012, which was itself 24% higher than the previous year. MachinePoint was founded in the early 1990s and was an early adopter of e-commerce. Around half of its business in 2013 came from returning customers. www.machinepoint.com","@ID":11}, "33 PETplanet insider Vol. 15 No. 04/14 petpla.net Caps and closures Bottle-to-bottle recycling plants Preforms Preform and single stage machinery Preform / stretch blow moulds Two-stage SBM machinery Compressors Resins / additives Filling equipment Closure systems Suppliers of preforms 20 companies from 16 countries participated in this year’s market survey of preform suppliers. They are shown in the order in which their details were received by the editors. In alphabetical order they are as follows: AMD (India) Alpla (Austria) Appe (UK) Empacar (Bolivia) Gastro PET (Slovenia) Gulf Packaging (Saudi Arabia) Kimex (Mexico) Manjushree (India) Novapet (Spain) PDG (France) PETform (Thailand) PET Preforms (Morocco) PET Verpackungen (Germany) Pramia (Finland) Resilux (Belgium) Retal Iberia (Spain) SBECM (France) SGT (France) Silver Spring (Russia) Terrachim (Bulgaria) Although the publishers have made every effort to ensure that the information in this survey is up to date, no claims are made regarding completeness or accuracy. 4/2014 MARKETsurvey","@ID":35}, "NEWS 10 PETplanet insider Vol. 15 No. 04/14 petpla.net Plastic Technologies goes Brazilian Plastic Technologies, Inc. (PTI), specialist in PET design, development and engineering services, has announced that it is to partner with the Brazilian Plastic Industry Association (Abiplast) to deliver a technical training course on PET package manufacturing. It will be delivered May 13-15 at Abiplast’s headquarters, São Paulo, Brazil. It will be supported by the Brazilian Packaging Association (Abre) and the Packaging Technology centre (Cetea). The course, entitled PET Packaging: Technology and Sustainability, will be offered in three consecutive one-day modules. The first will be devoted to PET Fundamentals (basic knowledge of PET materials, injection and blow moulding processes, quality assurance). It will be followed by Package Design (virtual modelling, FEA, additive/barriers/colorants and other design solutions) and will conclude with PET Sustainability (recycled materials and new biopolymers, energy conservation, solid waste management practices). Registration is $1,350 for the entire course or $500 for a one-day module. www.abiplast.org.br www.plastictechnologies.com Krones’ growth in 2013 Krones’ initial report on 2013 has stated that it achieved its targets for key financial performance indicators in 2013. Revenue rose 5.7%, from €2,664.2 million to €2,815.7 million, which was ahead of its target of 4%. The company specifically mentioned its competitive position in emerging markets as a positive factor. New orders improved by 3.2% year-on-year to €2,808.8 million and orders on hand totalled €992.5 million at December 31, 2013 (previous year: €999.3 million). Earnings before taxes (EBT) rose from €97.9 million to €169.7 million; 2012’s figure was affected by a one-time expense of €37.8 million, incurred as part of the Le-Nature’s settlement. EBT margin in 2013 was 6%, at the upper end of target (2012: 5.1%). The EBT margin for the company’s core segment actually reached 7.5% but the two smaller segments fell short of the prediction that they would break even in 2013. In the process technology segment, a writedown of approximately €5 million led to an earnings loss of €2.5 million, and losses at Kosme were €2.3 million after a weak fourth quarter. After taxes, Krones’ consolidated net income for the reporting period was €119.4 million (2012: €67.0 million), corresponding to earnings per share of €3.84 (€2.22 in 2012). Return on capital employed (Roce) increased to 16.7% (previous year, adjusted for Le-Nature’s: 13.6%), which was ahead of its 2013 target of 15%. Free cash flow rose from €30.6 million to €67.0 million. Including the €74 million in proceeds from the sale of treasury shares, cash and cash equivalents increased from €107.0 million to €239.9 million. Equity ratio rose from 38.5% to 42.6% in 2013. Krones plans a final dividend of €1/share, and a total of €2/share for the whole of 2013. The company expects increased momentum in 2014 and intends to continue with drives to increase efficiency along the value chain. It expects consolidated revenue to grow by 4% in 2014. Krones will publish its 2013 Annual Report and its report on the first quarter of 2014 on April 30, 2014. www.krones.com Nampak opens new closures line Nampak Nigeria has commissioned a new plastic closures line at its plant in Lagos, Nigeria. Bericap, of Germany, has a long-standing strategic partnership with Nampak South Africa and agreed to extend the manufacturing licence to include Nampak Nigeria. The initial product, closures for still water, will be followed by carbonated soft drink closures. The green field project included the installation of two Netstal 48 cavity injection moulders at the site in the Ikeja industrial area in Lagos state. Nampak Nigeria Lagos employs over 300 permanent and contract staff. The new lines’ initial focus will be on the local Nigerian market, supplying Coca Cola, Seven-Up, Nestle and SABMiller brands. Exports to Ghana and other neighbouring countries will be considered in the future. Nampak Closures in South Africa provided technical assistance. www.nampak.com Successful first fdt – food and drink technology Africa The inaugural fdt (food & drink technology) Africa trade fair and conference, which was held at Gallagher Convention Centre, Midrand, Johannesburg, South Africa, March 18-19, 2014, attracted 84 local and international exhibitors, who presented the latest technologies in the food and beverage processing and packaging industry. The conference programme, organised by the VDMA (Verband Deutscher Maschinen und Anlagenbau – the German Engineering Federation), focused on the hygienic, safe and efficient production of high quality food and beverages, and was presented with various case studies. Trade fair organisers Petra Westphal, Exhibition Group Director, Messe München International, and Elaine Crewe, CEO, MMI South Africa (Pty), said that they were delighted by the response to the first fdt, which attracted around 1,100 participants from countries across Africa. Senior corporate representatives including Steffen Manke, General Manager, Robert Bosch South Africa Limited and Emmanuel Rurema, Director Business Development – Africa, Pentair Filtration & Process, described the event as a success and a good opportunity to showcase current developments. fdt Africa marks a further phase in the internationalisation of drinktec Munich, which organises other events in India and China. The next fdt Africa will be held March 16-17, 2016. www.fdt-africa.com www.drinktec.com","@ID":12}, "PETbottles 56 PETplanet insider Vol. 15 No. 04/14 petpla.net Beverages & Liquid Food Premium water bottle As an independent mould maker, Kiefer, based in Germany, manufactures blow moulds made of aluminium for all rotary and linear blow moulding machines. A recent project was the implementation of a glass bottle design for PET bottle production for MBG International Brand’s product line Aqua Morelli, a premium water (still and carbonated) for the catering sector. The task was to maintain the popular design of the glass bottle and adapt this for the production of PET bottles. The elaborate logo engraved in the glass bottle had to be adapted to the PET bottle. The result is a PET bottle for 0.5l and 1.0l, the bottle being produced on a rotary stretch blow moulding machine. The bottle is made in dark blue PET and will soon find its use in the field of international premium gastronomy. www.kiefer-mold.de Water with Mg and Ca Adelholzener is now offering, as an addition to its Active O2 series, three drinks incorporating the tag function** which provide the daily requirement of calcium, magnesium and Vitamin B12 either wholly or in part. One of these three ingredients is added to the three varieties Apple/Lemon, Cherry/Cassis or Lemon/Nectarine. The clear, non-carbonated beverages are packed in transparent PET bottles with a content of 750ml. These are labelled with a wrap-around non-label look label which is additionally secured by means of a small paper sticker giving product information. A screw-on hinged lid with a self-closing silicone valve which is disabled when the lid is closed serves as a closure. Before opening for the first time a security device needs to be removed. www.activeo2.com Drinking yoghurt from Aldi Aldi-Süd is bottling 500g of its drinking yoghurt under the brand name “Desira“ and sporting the tag “Pure Enjoyment“ in a white tinted PET bottle. In order to be able to grasp the bottle securely it is waisted in the top third section. Reinforcement grooves are incorporated under the sleeve label and a white screw cap with guarantee strip rounds off the product’s appearance at the PoS. www.aldi-sued.de Vinegar in bottle with honeycomb structure Melfor, from Mulhouse in Alsace, France, is presenting its low-acid aromatic vinegar, which has been refined with honey, in an appropriately shaped PET bottle with a 1l content. The transparent bottle features raised embossing that is reminiscent of the honeycombs produced by bees. In the waisted area the bottle is decorated like an ornament. The closure consists of a screw cap with a pouring spout and a tamper-proof ring pull. www.melfor.com Cravendale goes PET Arla Foods, UK supplier of fresh milk and cream, processes over 2.2billion l of fresh milk each year through its six dairies and two creameries. The company has relaunched its Cravendale milk brand with the introduction of two new packaging formats. Its 1l retail units are now packed in PET bottles, after consumer research found that they were easier to use and re-close than gable-top cartons. The Cravendale brand is also being expanded into the food-to-go segment, with the launch of a new 500ml bottle. The new bottles have Bericap DoubleSeal DS 33/12 closures, which have tight sealing lids to ensure product integrity and are equipped with a folded tamper-evidence band. Bericap says that the DoubleSeal DS 33/12 range can be decontaminated with all standard decontamination methods currently available for aseptic filling. www.bericap.com","@ID":58}, "PETcontents 4/14 4 PETplanet insider Vol. 15 No. 04/14 petpla.net INSIDE TRACK 3 Editorial 4 Contents 6 News 50 Products 54 On site 56 PET bottles for beverages and liquid food 58 PET bottles in health and beauty care packaging 60 Patents MARKET SURVEY 33 Suppliers of PET preforms BOTTLING / FILLING 38 Raising the hygienic bar Sidel introduces Matrix modular hotfill machine 40 Letting the software take the strain Rexroth IndraMotion: pre-defined function toolkits for flexible machine concepts TRADESHOW PREVIEWS 42 Chinaplas preview April 23 - 26, Shanghai, China 44 Interpack preview May 8 - 14, Düsseldorf, Germany BUYER’S GUIDE 61 Get listed! Page 24 Page 40 Page 37 EDITOUR REPORT 12 Brazil - Part 3 Go with the flow tour: South America MATERIAL / RECYCLING 22 PET recycling takes a tumble Ohl process makes it safe for food PET - THE NEXT GENERATION 24 Beyond the bottle Ford and Coca-Cola collaborate in plastic recycling initiative PREFORM PRODUCTION 26 On the beat Upbeat gets into shape with Esterform packaging 28 Preform design Bottles, preforms and closures - part 11 BOTTLE MAKING 30 Extreme conditions - extreme design Krones and Penafiel develop 3.0l bottle CAPPING / CLOSURES 32 A dose of what you fancy does you good Vicap: sports cap with dosing chamber 37 Swing top lifts the spirit Amcor PET container for Vodka to use swing top closure","@ID":6}, "PREFORM PRODUCTION 28 PETplanet insider Vol. 15 No. 04/14 petpla.net Introduction to preform design PET preforms By Dr Laura Martin, formerly with Husky Injection Molding Systems and Ottmar Brandau, Apex Container Tech Inc. There is probably no subject in the PET industry shrouded in more mystery than the design of preforms. There is no handbook, no course, and very little other material that a prospective preform designer may peruse to get prepared for the job. The main reason is that preform design is still a “black art”, and no calculation or simulation can guarantee a perfectly suitable preform for a given bottle design and blow machine. PETplanet insider is publishing extracts from successive chapters of Ottmar Brandau’s “Bottles, Preforms and Closures”, which was first published by hbmedia. A newly revised version is reissued under the Elsevier imprint.","@ID":30}, "PRODUCTS 53 PETplanet insider Vol. 15 No. 04/14 Taste of Brazil With the Olympic Games in 2016 and the Fifa World Cup in 2018, Brazil is likely to be a regular feature in the world’s sporting and news headlines. Döhler, the specialist producer, marketer and supplier of technology-based natural ingredients and systems, has launched a new range of natural flavours, juice blends and customised compounds that it is calling “Taste of Brazil”. The portfolio extends from camu camu, caja and cupuaçu to lime and guaraná and açaí. The company says that such a wide variety of exotic flavours will enable the beverage and food industry to develop interesting positionings for seasonal and special edition products. The new range sits alongside and extends Döhler’s existing product ideas for carbonated soft drinks, liqueurs, desserts, and malt and milk mix beverages. www.doehler.com Low capacity shrink packing KHS’ new Innopack Kisters Primus SP shrink wrapper, which operates at up to 35 cycles/min, is aimed at low capacity users in the beverage, food and non-food industries. The newly-launched version now includes a number of features from the high performance range. The company claims that it offers improved ease of operation, sustainability in operation, and that the cube design, with more space within the machine, facilitates better access to individual components. Sliding doors with polycarbonate panes allow viewing of the inner workings of the shrink packer, even during production. The new construction has an open, hygienic design. The Innopack Kisters Primus SP now has a Siemens S7 controller and a total of four drives: the main drive, tunnel drive, film reel drive and feed conveyor drive. Identical servomotors are used for all function units. The switch cabinet has been moved from under the shrink tunnel to a position alongside the machine. KHS says that this both improves accessibility and deals with heating and ventilation problems previously experienced, especially in warmer climates. The company says that the machine can deal with a variety of shapes and sizes of containers and that both products and film are conveyed very gently. The shrink tunnel area uses variable hot air nozzle equipment and can be fitted with an optional energysaving package. The complete machine measures 9.7m by 1.95m. www.khs.com","@ID":55}, "EDITOUR REPORT 19 PETplanet insider Vol. 15 tling machines sourced from Brazilian manufacturers is available. Capacities extend from 1,500 20l water dispensers per hour up to 25,000 510 ml PET bottles per hour. The company operates nine bottling lines and co-packs and develops health drinks to many companies in Brazil and abroad.The 10l and 20l water dispensers made from OPP are washed and re-filled in house. And the way forward? New healthy products are coming on to the market. Other products: Fibre enhanced tea, 50% acai in PET (acai is a Brazilian fruit), vitamin enhanced waters with collagen, calcium, zinc and iron, and protein enhanced beverages are other examples of the company portfolio. New filling and blow moulding machines are on order to meet the requirement for on-going capacity increases. A happy byproduct of our visit was that we received a generous supply of the company’s products to ensure that we stayed healthy and hydrated on our onward journey. www.genuina.com May 13, 2013 Amcor Rigid Plastics South America We met: Ruben Melara, General Manager Enrique Raphael, Director of Business Development We are ready to convert Driving up to the Amcor plant in Jundiai in the Federal State of Sao Paulo we are struck by the number of well-known names in the immediate vicinity – names such as, for example, Coca Cola, Pepsi Co, Rexam, Husky, a high concentration of machine manufacturers, converters and bottlers. A PET business environment in a very small area. Arriving at the company we meet Ruben Melara, GenRuben Melara, General Manager","@ID":21}, "PET - THE NEXT GENERATION 24 PETplanet insider Vol. 15 No. 04/14 petpla.net Ford and Coca-Cola collaborate in plastic recycling initiative Beyond the bottle Interior fabric made from the same Renewable material used to produce Coke’s PlantBottle packaging is featured in this demo model of the Ford Fusion Energi The Ford Fusion Energi, Ford motor company’s plugin hybrid-powered passenger car, has taken a further step down the ‘green’ road with a collaboration that will see Coca-Cola’s PlantBottle technology used in the fabric interior of the seats, head restraints, and various liners and fittings. A demonstration model was showcased at the Los Angeles Auto Show, November 22 – December 1, 2013. Amid the high-profile unveilings of exotic supercars and eyecatching but barely-practical ‘concept cars’, Ford and Coca-Cola were showing a concept that is realistic, already features in a model available for sale, and extends ideas of sustainable manufacturing and plastics recycling into new areas. Recycled materials derived from PET bottles are already used in auto fittings but they are mostly tucked away out of sight, being deployed in such applications as noise and heat insulation. PlantBottle packaging is different: its visual appearance is perfectly acceptable, as are its comfort and wear performance levels. Scott Vitters, General Manager of the PlantBottle packaging platform at Coca-Cola, said the collaboration shows that the technology can be applied anywhere PET plastic is traditionally used, but with a lighter carbon footprint. The company’s first-generation PlantBottle packaging, used in fully-recyclable PET bottles, is made of two components: 30% plant-based MEG, and 70% PTA. In 2012 it signed an agreement with Avantium, of the Netherlands, to develop PEF, a 100% plant-based plastic. “We hope to drive awareness that PlantBottle Technology can be used across the entire polyester universe – in everything from the inside of a car, to carpet, to clothing,” said Vitters. R&D teams from Coke and Ford came together to discuss sustainable innovation during the course of 2011. Both companies use PET but in different applications. For Coke, it is (unsurprisingly) about bottles. Ford looks more to fabrics, including carpets and readily concedes that the discussions with Coca-Cola helped them to appreciate the opportunities of working together to develop a wider range of applications that would use sustainable, recyclable and recycled materials. While Ford maintains that it was already using environmentallyfriendly fabrics in its vehicles, it saw the technology as a further step along the road. Durable automotive-grade PET fabric Scientists and engineers at the two companies co-developed a fibre using PlantBottle material that could be woven into durable, automotivegrade PET fabric. Ford is evaluating the potential of using the material in other applications. The Fusion Energi was the obvious choice for a test vehicle, given its ‘eco-friendly’ presentation and image. Other renewable materials found in the car include carpet liner made from sound-absorbing denim and seat-cushion foam made from soybeans. www.coca-colacompany.com www.ford.com Ford and Coca-Cola showcased a demo version of the Ford plug-in hybrid Energi at the LA Auto Show– outfitted with the first-ever fabric covering for seat cushions, head restraints and more made with Coke’s PlantBottle Technology (photos: Coca-Cola/Ford)","@ID":26}, "BOTTLING / FILLING 41 PETplanet insider Vol. 15 No. 04/14 ware. Rexroth reflects this trend with its GAT Generic Application Template. This engineering tool accelerates the creation and linking of software modules to form complete automation solutions. In this way, machine manufacturers can shorten their time to market as the software share in automation increases. Individual functions Machine manufacturers can also realise, quickly and on their own, individual machine functions with real-time access with the high level languages of the IT world. This is now possible thanks to the new interface technology of Open Core Engineering with extended access to the control kernel. In this way, Rexroth now bridges the gap between the automation and the IT world. Additionally, machine builders can now implify operation and diagnostics with smartphones and tablet PCs. Open Core Engineering allows them to create application programmes for smart devices in the relevant target platform. These apps can access the control wireless and with all operating functions of these devices. Cabinet free drive technology On the hardware side, the IndraDrive Mi cabinet free drive technology supports the further modularisation of flexible machine concepts. By merging drive electronics and the motor to form an integral unit, electronics in the control cabinet are almost eliminated, and the required cabling for the connection of individual components is drastically reduced. The consequence is a maximum of flexibility and efficiency for both the machine builder and the machine user: The control cabinet volume, cabling effort and power losses in the control cabinet are reduced by up to 90%. Only a single cable is required for connecting drives that are connected in series. If drives are required in the system at a later point in time, for example due to an additionally installed machine module, these drives can easily be integrated at the desired position in the line – without affecting the control cabinet or the rest of the machine or production line. Rexroth complements the IndraMotion automation solution for bottling beverages and liquid food with components and mechatronic modules of hygienic design. The runner block of the linear guides with stainless steel cover strip are made of corrosion-inhibiting materials in conformity with FDA regulations. Complete linear modules simplify the construction and, with their smooth surfaces without gaps and bores, meet the requirements for a hygienic design. www.boschrexroth.com","@ID":43}, "BOTTLING / FILLING 38 PETplanet insider Vol. 15 No. 04/14 petpla.net Sidel has produced a new Sidel Matrix modular hotfill machine with a wide choice of possible configurations. Raising the hygiene bar Sidel’s modular Matrix hotfill system has been developed to ensure high levels of product safety and quality in the production of juices, nectars, still drinks, isotonics and tea (JNSDIT). The new Sidel Matrix hot filler has been developed to meet these standards for any kind of drink, of high or low acidity, that is to be bottled in PET containers in sizes ranging from 200ml to 2l. The filler is equipped with Sidel’s Integrated Slurry Dosing (ISD) and is designed to handle products with pulps or fruit pieces, sacs or fibres for products like pulpy juices, flavoured waters with fruit pieces, and new generation products such as Chinese Aloe Vera or coconut-based drinks. Electronic filling valves with individual flow meters have been installed in order to provide high levels of accuracy in dispensing appropriate filling volumes, while minimising product wastage. The new machine is capable of operating at production rates ranging from 6,000 to 60,000bph. Pulps and fibres Sidel says that its new Matrix hot filler can handle a broad range of products with or without pieces. In block-rinser configuration it manages still beverages, with a simple grid valve. Products with small pulps and fibres up to 1 x 10mm can be handled with the option of a plunger valve. It is also available for products with pieces measuring up to 10mm3, using a volumetric bits dosing turret. Any of these configurations can be utilised as the ‘filling’ module of an integrated ‘blow-fillcap’ solution within a Sidel Combi set-up. All the components that come into contact with the product are made from stainless steel. The fillers can be readily adapted to meet changing needs and the system’s upgradeable platform will enable customers to take advantage of new technical developments in the future. Hygienic solution Sidel says that its new Matrix hot filler will provide product safety by means of hygienic design and contactless filling valves, through the entire packaging process. The product never comes into contact with ambient air, and bottles are never brought into contact with filling valves, which reduces the risk of cross contamination. The filling environment can be tailored according to the level of hygiene required by the product being bottled. Alternatives include an open enclosure with the option of a roof with an air filtration unit, and a reduced enclosure, which has a filling area volume 72% less than the standard configuration. As fewer chemicals are required for cleaning, it offers even higher hygiene standards and less filtered air in the filling area. All effluents from its automatic cleaning system are drained into a single point, through collecting trays located around the base and the carousel. Flow management It is possible to control the flow rate from the tank to the filling valve throughout the filling process, without stressing the product being bottled. Any turbulence created by changing the flow rate remains within the tank, which acts as a buffer from the incoming product. This does not affect distribution and delivers a constant pressure on the filling valve, which helps to deliver high accuracy in the process. Dual-speed filling avoids the generation of any foam. The bottle and filling valve are both fixed during filling, to avoid any splashing and consequent product wastage. With the slurry dosing (ISD) integrated, the system undertakes a two-phase process. The first phase delivers the slurry (or particles) into the bottle, and the second fills the liquid juice. The slurry-dosing turret is also equipped with contactless valves. No parts enter the bottle, to maintain hygiene standards. The conic design of the valve for the volumetric doser is designed to prevent product leakage and waste. This dual-stream dosing by pistons is intended to ensure a constant and accurate delivery of pulp or slurry. Particle concentration can be adjusted from 20ml to 300ml, depending on the recipe and size of format being bottled, with a tolerance of plus or minus 10%. Sidel claims a particle damage rate of less than 10%. www.sidel.com","@ID":40}, "MATERIAL / RECYCLING 22 PETplanet insider Vol. 15 No. 04/14 petpla.net Ohl process makes it safe for food PET recycling takes a tumble At last year’s K trade fair in Düsseldorf, ProTec Polymer Processing was presenting the Ohl process in which flakes extracted from used PET bottles and washed are treated to create PET that exhibits material properties equivalent to those of virgin PET. The tumble reactor will also be presented at Chinaplas (see page 42). This bottle-to-bottle recycling is based primarily on two process steps: a continuous extrusion process and the subsequent discontinuous treatment of the extracted pellets in what is called the Ohl tumble reactor. This is supported by upstream, in-between and downstream auxiliary processes with the corresponding plant components. On display for the first time at the trade show is a new version of the tumble reactor featuring optimised energy consumption and drive technology. This coincides with innovations in the process control that aim to minimise the inevitable material degeneration (IV drop) in the extruder during treatment of the PET flakes. Energy consumption The Ohl tumble reactor, a rotation reactor that can be heated and evacuated, is a key system component in the multistage treatment process. PET recycling involves purging (decontaminating) the regrind of any volatile pollutants on the one hand, while allowing for simultaneous postcondensation (increasing the intrinsic viscosity IV) to occur on the other. For this purpose, the reactor consisting of a double shell is heated using heat transfer oil. The structurally optimised version of the reactor presented at the trade show uses a smaller volume of oil to achieve the heat transfer required to control the process. This also results in lower energy consumption. Together with the weight optimisation of the reactor container overall as well as the optimisation of the drive and control technology, energy consumption for this process step has been reduced by around 20%. Due to the general susceptibility of PET to hydrolysis, moisture is critical for the treatment in the extruder because of the associated material degeneration (IV drop). The flakes stored in silos or in big bags must therefore be pre-dried before entering the extruder. This cannot be compensated for by more intensive degassing of the extruder alone. Drawing on its many years of expertise in material processing, ProTec Polymer Processing has now enhanced this process step with a two-stage procedure. This is achieved by connecting a Somos dry air dryer downstream of the warm air dryer generally used to remove surface moisture from the washed flakes. This pre-drying of the material down to residual moisture in the ppm range significantly reduces IV drop during extrusion. Reducing the IV drop reduces the need to use large amounts of energy to post-condensate the material again afterwards. Consequently, the process duration required in the tumble reactor can also be shortened. Precise control over the parameters temperature, vacuum and time ensures that granulates – recyclates or new product – in the tumble reactor are individually processed to the required quality depending on the technical specifications and requirements of the intended use. As a result, PET pellets that can be reused to manufacture PET beverage bottles must meet minimum requirements particularly with regard to IV values: for beverages without carbon dioxide, these IV values are at least 0.75dl/g, for carbonated beverages, IV values of 0.78 to 0.82dl/g – and for technical applications, in part even significantly higher IV values are required. The rPET has an acetaldehyde content of ≤1ppm and is said to exhibit material properties just like virgin PET product. The non-objection letter from the FDA (Food and Drug Administration) verifies that the PET recyclates produced in this manner are safe when in direct contact with foodstuffs. Through batch operations, the entire content in the reactor has exactly the same retention time, through which reproducible, consistent product characteristics are attained. www.sp-protec.com","@ID":24}, "EDITOUR REPORT 13 PETplanet insider Vol. 15 No. 04/14 petpla.net May 8, 2013 Coca Cola Industrias Ltda. Brazil We met: Paulo Roberto Villas, Head of Corporate Packaging - Supply Chain Lucas Angelo Amendola, Packaging Specialist SR Paulo Roberto Villas, Head of Corporate Packaging - Supply Chain It’s not only the Brazilian countryside that is “green“ Coca Cola Latin America is the region that boasts the biggest turnover in the Coca Cola Group. There are 40 countries representing the Group, including Mexico. The Group is divided up into four business units, of which one is Coca Cola Brazil. En route for Coca Cola Brazil, we make the first stop in Rio de Janeiro. At the headquarters of Coca Cola Brazil in Rio de Janeiro we are introduced to the man responsible for Packaging, Mr Paulo Roberto Villas, and packaging specialist Mr Lucas Angelo Amendola. Coca Cola Brazil is the second biggest business unit in the Latin America Group. There are 15 bottling groups with 45 bottling plants and a total of 93 PET filling lines authorised to use the Coca Cola name under their Franchise Partner Principle. In Brazil alone the groups employ a total of 40,000 direct and 400,000 indirect employees. According to Paulo Roberto Villas, 12 billion litres are packaged each year (mainly of CSD), equal to a market share of 61%, using a particular method of operation which is regarded as a benchmark for the entire Coca Cola system. He explained: “Here in Brazil we monitor the overall supply chain from the polymer right through to the manufacture of the bottles and we are therefore very conscious of the impact we have on the environment and sustainability.” He went on: “We work in close cooperation and partnership with our suppliers. Together with them, we work on joint development projects, although at the end of the day Coca Cola becomes the owner of the product drawings. What this means is that all preform suppliers work with the same preform drawings from the “Coca Cola preform family“. Lightweighting In 2007, Coca Cola Brazil launched the first phase of their lightweighting programme for PET preforms keeping the PCO 1810 neck finish. However, before actually going into production, it was specified that the splitting lines in the injection mould also had to be suitable for PCO 1881. The idea behind this was to enable the mould to be rapidly converted, at reasonable cost, to the PCO 1881 format, which is significantly lighter in weight. In this way it was possible to introduce PCO 1881 finish step by step on the market. Nevertheless, lightweighting does not just apply to the neck finish, but a fresh look at the preform geometry itself was required. The reason is twofold: firstly, Brazil’s tropical conditions need to be taken into account and secondly, a shelf life guarantee is an essential requirement. It resulted in the 0.5l CSD preform: this weighs 20.6g and has a shelf life of 60 days (FTIR proven). The special features are a short preform with an aggressive stretch ratio which, by comparison to the European variant (longer with smaller stretch ratio) weighs in at around 2g less. Paulo Roberto Villas still recalls the reaction of his colleagues in whose opinion the preform was very difficult to blow and not recommended for implementation. Needless to say, for this preform, state of the art stretch blow moulding machines will be required which guarantee an optimal wall thickness distribution in the preform and are capable of working in the stretch blow moulding sector with a high crystallisation index. Only converters with the appropriate equipment are authorised by Coca Cola for this weight category. This also applies to the 2l contour bottle which, with a weight of 42.6g, also qualifies as lightweight under Brazilian specifications. A further step towards the use of lightweight PET bottles lies in the optimisation of the entire stretch blow moulding and filling line. Usually bottle silos are installed between the stretch blow moulding machine and the filler; however, these are not suitable for lightweight PET bottles (risk of damage to bottles and the efficiency of the line suffering as a result). The solution is systems in block format. The first block format stretch blow/filler line was installed in 2010. Today there are already 14 block lines operating for Coca Cola Brazil. Paulo Roberto Villas again: “There is a state of the art block line in Andina, Coca Cola Rio de Janeiro, which has an hourly capacity of 39,200 2l PET contour bottles. This makes it, by some distance, the largest in the world (for the family size bottle) in 2011. Previously”, he went on, “just 20,000 2l bph was the maximum.” Another state of the art block line is currently operating at Amcor/Femsa in Jundiai Sao Paulo, where they are filling 72,000 600ml PET bottles per hour, making this facility one of the largest of its kind in the world. The plastic closure is also part of the overall picture. In Brazil, the company operates a partnership with Bericap do Brasil in Brazil to produce a reduced weight plastic closure in parallel with the lightweighting preform programme.","@ID":15}, "TRADE SHOW PREVIEW 44 PETplanet insider Vol. 15 No. 04/14 petpla.net Mocon | Hall 05 Stand J03 Next generation oxygen permeation system Mocon, manufacturer of permeation instrumentation, has developed a new instrument which redefines oxygen transmission rate testing for all types of barrier materials. The new Ox-Tran Model 2/22 H will be available for demonstration at Interpack. The instrument is ideal for food, pharmaceutical, medical device and material producers who need to test packaging structures for oxygen permeation. The device is a fully automated system. When testing film with unknown characteristics, the auto test feature determines the optimal parameters and conducts the test to completion. Sequential testing allows for a film to be tested at multiple temperature/ relative humidity conditions with no operator involvement. Many safety features have been added to increase component lifetime. www.mocon.com More exhibitors, more premieres and a bigger supporting programme Interpack 2014, May 8-14, 2014, will feature about 2,700 exhibitors involved in packaging across food and beverages, pharmaceuticals and cosmetics, consumer goods, industrial goods and related services. Around 60 countries will be represented. The first-ever “Components for Processing and Packaging”, with daily lecture forum, will take place from May 8-10 in the Düsseldorf Stadthalle, Congress Centre South (CCD Süd). Around 75 exhibitors will show machinery, accessories, peripherals, auxiliaries and complete automation systems. The Save Food Congress, a joint initiative between the UN Food and Agriculture Organisation (FAO) and Messe Düsseldorf, running in CCD Süd May 7-8, will present the results of new studies on food loss and waste. InnovationParc Packaging will be located between Halls 2 and 3. The Interpack website includes the exhibitor database, personalised floorplan and matchmaking functions, and further information. Services can also be accessed by mobile. Admission tickets and exhibitor passes entitle bearer to free travel on the VRR regional public transport network, which serves the region around Messe Düsseldorf. www.interpack.com Strautmann | Hall 05 Stand 5J02 Managing material disposal German company Strautmann will be exhibiting its range of waste material management technology. The LiquiDrainer automatically empties filled PET bottles, Tetra briks and cans and separates liquids from outer packaging. The AutoLoadBaler has a collection trolley system with automatic baler filling. The BaleTainer is designed to handle large quantities of empty PET bottles, cardboard and foil, without preshredding. The StyroPress is an automatic briquetting press for the volume reduction of loose EPS (Styropor). www.strautmann-umwelt.de Bosch | Hall 06 Stand A31 – C58 Faster, more flexible liquid and viscous food packaging Bosch Packaging Technology’s stand at Interpack will feature its range of filling and packaging equipment for liquid and viscous food, including three new developments tailored to the dairy and baby food markets. The TFC 5532 thermoform, fill, label and seal machine’s 4x6 cup configuration can produce up to 43,200 cups/h and can handle cup sizes ranging from portion packs up to dessert cups. It is suitable for clean and ultra-clean hygienic packaging and can handle hot-fill applications and products with particulates of up to 25mm diameter. The new BLO linear PET container blowing machine allows dairy and beverage producers to package up to 35,000 containers/h, ranging in size from 60mm to 2l. Bosch says that it has been designed to minimise PET material and energy consumption. Rotation of preforms during heating ensures equal heat distribution on every material surface, which enables production of thin-walled containers. In combination with Ampack GmbH aseptic filling technologies, the equipment can be used for hygienic applications, including dairy-based yoghurt and coffee drinks, alongside mineral water and beverages. Ampack, which has been a Bosch Packaging Technology company since October 2012, has developed a new generation of its KF 2/4 carousel filling machine. The company says that it offers easier changing between bottle formats, cup formats and pack styles, as well as easy access for machine maintenance. It can handle cup and bottle sizes from 100-1000mm, at up to 10,000bph (200mm packages). The machine features a dosing system by inductive flow meter (IFM) and a filling valve developed and manufactured by Ampack. www.bosch.com","@ID":46}, "PETbottles 58 PETplanet insider Vol. 15 No. 04/14 petpla.net Home + Personal Care One squeeze - one dose = no mess - no waste Mr Propre is on the market since 45 years. Now in line with its sustainability goals, P&G launched the new Mr. Propre Liquid Gel in summer 2013 in the UK, and, at the end of last year, in France and Belgium. Additional market introductions are planned this year in the US and in more European countries. The packaging has a new performing dosing cap used originally in the food sector. By a simple squeeze of the bottle, the system, called “Auto-stop”, enables a quick and precise dosing of the right amount of product directly into the bucket. The proprietary system consists of a flip top cap with small timer mechanisms measuring the exact amount of liquid. Once this amount has been reached, the smart cap will shut off the fluid stream, preventing any overdosage. A small amount can still be applied directly on the stain or also on a sponge. Aptar developed the Smart Dosing cap. One of P&G’s prerequisites was to make the four components in one single material. PP was the answer. By contrast, most of the dosing systems or pumps currently on the market are made out of multiple materials, with the well-known consequences for recycling. Additionally, the P&G cap system is of a very small size. It can be easily adapted for any dosages between 5 and 50ml liquid, allowing future packaging possibilities. The new bottle is converted by Serioplast. The 600ml bottle is made out of PET 33g, allowing additional light-weighting of the pack. The previous 1,400ml container was in HDPE and weighted 78g . www.facebook.com/mrpropre Bottled haptics Johnson & Johnson are marketing their product “Wet Skin“, a transparent sun spray that can be sprayed on to wet skin, is water-resistant and non-greasy. Under the brand name “Piz Buin“, it is packaged in a 150ml PET bottle complete with pump spray and protective cap. The slightly bronze-tinged bottle is decorated using direct printing techniques. The surface of the bottle incorporates partial embossing reminiscent of drops of water cascading down it and thus reminds us of the application area. A spin-off from this embossing is good handling capability when the bottle is wet or touched with wet or sticky hands. The trading information on the reverse is also printed directly on to the bottle. www.pizbuin.com Easy-to-handle bottle shape Henkel Düsseldorf has carried out a general re-design of the shape of its spray bottle to include a hand-operated pump spray. The neck area of the PET bottle, which contains 750ml of product, is designed to be more ergonomic so that it sits better in the hand and the hand is automatically centred. The bottles with the brand names Bref, biff and Sidolin can be distinguished from one another by means of corresponding sleeve labels and pump dispensers with operating levers in various colours and their individual spray nozzles. www.henkel.com Attractive double pack A few years ago, transparent shrink wrap was only there to combine a number of products into a single sales unit offering a price advantage, today, by contrast, the labels are increasingly coming to be used as part of the overall packaging. Using a specially designed sleeve label, Colgate Palmolive is offering a dual pack consisting of two products from its ‘Aroma Therapy’ range packaged in PET bottles. The label is kept transparent at the front so as to show off the product and provides information about the product as well as other products from Palmolive on the sides and the rear. www.colgatepalmolive.com","@ID":60}, "MARKET SURVEY 35 PETplanet insider Vol. 15 No. 04/14 petpla.net Alpla-Werke Alwin Lehner Petform (Thailand) Silver Spring PDG Plastiques S.B.E.C.M. Mockenstrasse 34 6971 Hard, Austria +43 5574 6020 www.alpla.com Hermann Riedlsperger Head of Corporate Sales - PET +43 5574 602 515 +43 5574 62017 515 hermann.riedlsperger@alpla.com 35th Floor, Ocean Tower 2, 75/102-103 Sukhumvit Soi, 19 Road, Bangkok 10110, Thailand +66 26616661 www.indorama.net Pramod Dubey Marketing Head +66 819371978 +6626616665 pramod.d@indorama.net 630526 Russia, Novosibirsk, Proezd Avtomobilistov 12 +7 383 334 71 55 www.etalon-group.ru Durnov Petr Main Engineer +7 913 912 84 16 +7 383 334 64 70 p.durnov@etalon-group.ru ZI secteur 2, 45330 Malesherbes, France +33 2 38 34 61 95 www.pdg-plastiques.com Francois Desfretier General Manager +33 2 38 34 61 95 +33 2 38 34 63 82 francois.desfretier@pdg-plastiques.com Rue de la plaine 47230 Lavardac, France +33 5 53 97 41 00 www.sbecm.com Jean-Luc Didouan General Manager +33 5 53 97 41 00 +33 5 53 65 85 97 jean-luc.didouan@sbecm.com Yes No No Yes No No No No Yes Yes Yes No PolyShield 2300 k PP - PE - BioPET According to customer needs Yes, on request No No Yes up to 100% Up to 25% - 30%; according to customer's request. All customary additives Liquid colorants, Amosorb 4020 СМ, nylon Prelactia 100% light barrier for UHT sterilized milk long shelf-life, oxygen-, UV-, CO2 barriers AA scavengers, blockers, coloring agents (liquid or masterbatch), O2 absorbers, additives, blends, etc.. Softdrinks: Various neck versions from 0.25 to 2.5l. Water: Various neck versions from 0.25 to 19l Edible oil: from 0.5 to 10 ltr. Milk: Various neck versions (2-start, 3-start) Home, lubricants, personal care: Various neck versions 29-25: 14.3g - 28.5g 30-25: 17.0g 29-25 28 mm 1810: 25.5g - 45.6g 28mm 1881: 17.0g - 45.0g 2 BPF standard: 24g - 51,5g PCO standard: 20.5g - 52g PCO 1881 standard: 20.7g - 5.7g Bericap-38 standard: 18g - 27g, Bericap-48 : 85g, 89g 29/25 shorty : 8g - 28g 30/25 high: 17,5g - 50g 30/25 low: 17,5g - 50g 38mm 3 start: 28g - 50g 38mm 3 start: 24 - 28g Prelactia 48/40: 55 - 62g 27/32: 6,5g dairy and smoothies 25/20: 6,5 - 8g dairy PCO 1810: 33,6g 29/23: 24 -27- 33g chemical BVS 30H60: 50g wine 22H30: 19g wine Coloured preforms ultra-lightweighting 2,4g preform standard and specific preforms for mineral water, dairy, juice, CSD..etc Overmoulding technology for 2-layer preforms Preblow technology for lightweigthing bottles Neck finish : 30/25 high and low, 29/25, PCO 28 (1818, 1881), BPF, 38mm, 48/41, BVS. Study for special neck finish. Preform weight : 10 - 91g For any application and size: water, soft-drinks, oil, wine, dairy products, housecare, etc... Kimex Manjushree Technopack AMD Industries Limited Gulf Packaging System Terrachim 97 AD Pramia Plastic Oy Km. 26.5Autopista Mex-Qro., Lomas Boulevares, Tlalnepantla Edo. De México, C.P. 54020 +55 53 66 90 59 www.kimex.com.mx Jorge Larrañaga Director Comercial +55 53 66 90 59 +55 53 66 90 31 jlarranaga@kimex.com.mx 60 E, Bommasandra Industrial Area, Hosur Road, Bangalore - 560 099, India +91 80 43436200 www.manjushreeindia.com Rajat Kedia Director +91 80 43436200 +91 80 27822245 rajat.kedia@manjushreeindia.com FF-18, Pusa Road , Karol Bagh, New Delhi -110005 India +91 11 46830202 www.amdindustries.com Adit Gupta +91 11 46830202 +91 11 28753591 adit@amdindustries.com Post Box 20266, Jeddah 21455 Industrial City, phase 5, Saudi Arabia +966 12 636 00 99 www.3p-gulf.com Bader Abdullah General Manager +966 2 6360099 ext 101 +966 2 6082170 badr.abdullah@gulf-pack.com 6 Kupenite str., Sofia 1618, Bulgaria +359 2 955 63 22 www.terrachim.com Michail Kostov General Maneger +359 2 955 63 22 +359 2 955 63 25 terrachim@terrachim.com Juustotie 25, 69300 Toholampi Finland +358 400 187 826 www.pramiaplastic.fi Marko Mäkinen Entrepreneur +358 400 187 826 marko.makinen@pramiaplastic.fi No No No No No No Yes No No No No No No No No PET No No Yes 10% and 25% NO 50-100% UV-Pigments UV blocker, oxygen scavenger, slip agents, anti-yellow additive, AAA Nylon Amosorb According to customer requirements 13g - 62g 28mm PCO 1810: 12.5g - 48g 28mm PCO 1881: 13g - 52.7g PCO 1810 thick neck: 18.5g - 47g 3-start Alaska: 10.6g - 35.6g 20/25 3-start: 22g 28mm PCO neck (1810) – 54, 48, 48TN 44, 42, 39 ,28, 27, 27TN 30 TN & 25g 10.4g - 200g Preform weight 21.2g, 28g, 31.5g, 36g, 85g","@ID":37}, "EDITOUR REPORT 12 PETplanet insider Vol. 15 No. 04/14 petpla.net As described in the introduction to the Brazilian market (PETplanet Insider 1+2/2014), we came across more than 150 drinks bottling operations and breweries in Brazil, ranging from family businesses right through to companies with a global operation and featuring local as well as worldwide brands. Here in this issue we will be visiting the typical representatives of the beverages structure in Brazil, Coca Cola, Andina Refrescos and Genuina Lindoya, who could hardly be more different but who pursue identical strategies. On the one hand there is Coca Cola and their bottler Andina with its global reach and recognition value and, on the other, Genuina Lindoya, one of the numerous bottlers of mineral waters in family ownership, also readily recognisable by its own individual design bottle and label (Acquafibra), but with marketing activities restricted to a radius of 500km. From the packaging supplying part we will be meeting the preform and bottle manufacturer Amcor Rigid Plastics. Interviews in Brazil in this issue: Coca Cola Brasil Ltda. Andina Rio de Janeiro Refrescos Ltda. Lindoyana de Aguas Minerais Ltda. Amcor Rigid Plastics South America to follow: Husky Injection Molding Systems Bericap do Brasil Ltda. Ambev Logoplaste Shefa Döhler América Latina Ecoplaca Krauss Maffei do Brasil Ltda. Otto Hofstetter AG Lima Santiago La Paz Buenos Aires Montevideo Progresso São José dos Pinhais São Paulo Rio de Janeiro Lindóia Santa Cruz Sucre Quilmes Pilar Jaú Concepción Santa Fe Barueri Jundiai Sorocaba Amparoa Limeira Brazil Part 2 by Waldemar Schmitke","@ID":14}, "BOTTLE MAKING 31 PETplanet insider Vol. 15 No. 04/14 petpla.net and Sierra Madre Oriental mountain ranges run parallel to the coastal strips, rising to peaks of more than 9,900ft (3km). The coastal regions, by contrast, are only a few feet above sea level. Climatically, too, Mexico is a country of extremes, between subtropical, Alpine and desert regions. In the north, the prevailing temperatures lie between 10°C and 45°C. In the middle of the country, the average temperature for the year is 20°C. The climate in the south is tropical; temperatures can reach 40°C. 11bar internal pressure for 60s In order to take due account of these extreme conditions, Krones’ bottle development experts had to come up with something rather special in terms of design, consultancy and optimisation. For example, Krones optimised the 3.0l bottle design by giving it a special base for large-volume bottles, which had to pass stresscrack, thermal and burst-pressure tests without any problems. The biggest challenge of all was the internalpressure test. The 2.0l containers, for example, had to withstand an internal pressure of 11bar for 60s. Sampling and laboratory tests were handled in Krones’ PET Technology Centre. The client was present at almost all the sampling procedures in the laboratory, enabling him to verify in person that the bottles met the requirements involved. This was followed in each case by close consultations on the laboratory results between the client, Krones Applications Engineering and Krones Container Design. The overall design specifications were used to Peñafiel operates two production facilities in Mexico, at Guadalajara in the west of the Mexican highlands, about 500km west of Mexico City, and in Tehuacán in Mexico’s southern Puebla State. It is from there that deliveries are made to the entire country. Founded back in 1948, the family firm was taken over by Cadbury Schweppes in 1992. Today, Peñafiel belongs to the Texan Dr Pepper Snapple Group, a leading vendor of non-alcoholic beverages including soft drinks, teas, juices, mixed drinks, waters and other beverages.Their principal markets are North America and the Caribbean. In its portfolio, the group has more than 50 brands, such as 7UP, Canada Dry, Crush Orange, RC Cola, Orangina, Schweppes or Dr Pepper Cola and of course Peñafiel water. Peñafiel is offered as carbonated water which comes in six different flavours, ranging from strawberry and mandarin to pineapple. The plastic closure company committed to your success BERICAP Technology Research and Development Mould Technology | Global Presence Capping Technology and Know-How Innovation and Flexibility www.bericap.com define the test conditions, after which the bottle design and then the preform were optimised. Following the blow-moulding trials and laboratory studies, the test results were evaluated together with the client. Krones Applications Engineering made sure the client’s specifications were met, by providing the relevant process expertise and the appropriate machinery. Newly designed still-water bottle family After the line had been installed, Peñafiel had another task for Krones. For the first time, the company wanted to bottle not only carbonated soft drinks, but also still water. For this purpose, Peñafiel asked Krones to develop an entirely new still-water bottle. Due to the particular climatic and geographical conditions involved, this container was likewise required to be highly pressure-resistant, and suitable for passing the thermo-test, which with a still-water bottle cannot be taken for granted. For reasons of stability, filled bottles are required to embark on their extensive travels through Mexico with an internal pressure of 0.5bar. During the filling process itself, the bottle has to withstand a filling pressure of up to 11bar. For this purpose, Krones came up with a special still-water base, together with an entirely new container design for a bottle family featuring 0.5, 1.0 and 1.5l sizes in two variants. Following successful tests, Peñafiel opted for one variant, and the company can now deploy this family of bottles in the market, with the aim of conquering the still water segment, a new category for Peñafiel. www.krones.com","@ID":33}, "TRADE SHOW PREVIEW 49 PETplanet insider Vol. 15 No. 04/14 petpla.net SMI S.P.A. | Hall 14 Stand D12 Energy-saving line-end solutions Italian company SMI says that it had energy saving and environmental protection very much in mind during the design and development of its latest series of line-end packaging machines. The system displayed at Interpack 2014 is made up of a Smiflexi LWP 30 wrap-around casepacker with an APS 1550 P PLUS palletiser and is driven by brushless motors, which are claimed to offer reduced electricity consumption, maintenance costs and noise levels. The system’s conveyor belts are equipped with drives that regulate motor speed based on the machine’s actual operational needs and consume up to 35% less electricity. SMI says that the main feature of its APS Plus palletisers is the integration in the machine’s fixed column of all the mechanical components covering pallet layers construction, empty pallets feeding operation and interlayer pads insertion. www.smigroup.it Q Preform sterilization in the heating tunnel Q Protected conveying of preforms and bottles Q %QORNGVGN[ J[IKGPKE ƂNNKPI CPF ECRRKPI RTQEGUU The UCF BloFill monoblock from KHS – with fully enclosed hygiene housing Give your sensitive beverages more private space. Learn more at www.khs.com or scan the QR code. interpack 2014 May 08–14 | Hall 13 | Booth A31 Krones | Hall 14 Stand E29 Lightweights for hotfill, aseptics and carbonated beverages Krones says that its stand will be showcasing a series of developments aimed at creating lighter, more attractive packages with more energy-efficient, sustainable and affordable production operations. The company has developed a new base design for PET containers that has better resistance to heat and pressure and offers improved stability during transport. Krones asserts that the NitroFill process enables this new design and other hot fill bottles to be lighter. It’s PET lite 9.9 carbonated, a 500ml bottle that weighs just 9.9g, will also be on the stand, as will a new, square 500ml aseptic-fill PET bottle that weighs in at 12.5g and uses Contiform AseptBloc technology. The stand will in addition feature DecoType technology for printing direct onto containers, a redesigned Ergomatic cold-glue labelling station and its new Contiroll ED wraparound labelling station. Visitors will also be able to see Krones’ new LitePac packaging and palletising solution, which creates packs with an integrated handle and is claimed to offer cost reductions per pack of up to 74%. www.krones.com","@ID":51}, "PREFORM PRODUCTION 29 PETplanet insider Vol. 15 No. 04/14 petpla.net Our guess would be that to this day no 48 or more cavity system is built without first performing a trial run with a single-unit cavity. This is despite the fact that we understand material properties fairly well, and resin companies as well as independent laboratories offer material characterisations that detail stress/ strain graphs for a variety of material conditions. The unpredictable factor is that the formation of a bottle from a preform is literally explosive, and even tiny temperature variations affect the outcome. In addition, the parameters that control the inflation characteristics of a particular preform are manifold, still too many to make perfect predictions. Here is a partial list of the parameters that make the difference between failure and success: The preform temperature: PET can be blown at a range of 95–115°C (203–239°F). The temperature distribution: The profile of temperatures both in the vertical axis as well as through the preform wall is the result of many factors characterising the oven system in a reheat stretch blow machine or the hot runner system in a single-stage machine. We do not yet have models that can truly reflect them. Process conditions, such as stretch rod speed, and timing of primary and secondary air pressure result in different bottle wall thickness outcomes. Venting and the shape of mould corners affect preform inflation as well. Needless to say, even the best preform designs need experienced processors to dial in a specific blow machine. Two machines of the identical model using the same preforms and tooling will require slightly different setups to account for subtle differences in the machine characteristics, including such things as screw wear and infrared lamp age. This can only be accomplished by experimental development, and experience is invaluable. Please order your copy at the PETplanet insider book shop: https://petpla.net/books Bottles, Preforms and Closures A Design Guide for PET Packaging Second Edition by Ottmar Brandau € 115,00 180 pages © Copyright Elsevier 2012 In practice, less than perfect preforms are often used to make an acceptable bottle because preform designers typically add a few grams of material to allow for the factor of uncertainty and still make bottles which can be sold. The cost of the added weight is offset by a wider process window and lower scrap rates. Our guide sheds some light on the methodology that a designer might go through to come up with a preform suitable for a given bottle shape and wall thickness distribution. There are other ways of getting the same or similar results, and our methodology is by no means the only one. What most experienced designers do is to look up a similar bottle and then modify the preform to adjust for the slightly different shape of the new bottle. Rather unscientific but practical! Newcomers in the field do not have this luxury and are often stuck with whatever preforms they can buy from vendors. They then try a preform with the right or a similar weight and make adjustments to the design as necessary. With the help of our guide this task should become easier. We will explore all relevant material characteristics that are paramount to understand the inflation behaviour of the preform. We then take you through the design process step by step and point out differences between preforms for the single-and two-stage process. In any case, you should always make a trial cavity and perform blow moulding trials to determine whether your design works before committing to a multicavity tool! The next section gives some introductory information about PET that will help understand the terms used in the following sections. The section on behaviour in the blow mould is critical to understand the factors at play when designing preforms. The remaining sections in this chapter will help to give the designer and processor a feeling of the overall steps of the bottle-making process, which will be of practical use when developing or troubleshooting a container. The best practitioners of PET design and process development have to understand all the steps because every step has an influence on the properties of the final container. * This article was published in Bottles, Preforms and Closures, Ottmar Brandau, Chapter 2.1. Copyright Elsevier 2012","@ID":31}, "imprint EDITORIAL PUBLISHER Alexander Büchler, Managing Director HEAD OFFICE heidelberg business media GmbH Häusserstr. 36 69115 Heidelberg, Germany phone: +49 6221-65108-0 fax: +49 6221-65108-28 info@hbmedia.net EDITORIAL Doris Fischer: fischer@hbmedia.net Gabriele Kosmehl Michael Maruschke Ruari McCallion Waldemar Schmitke Ilona Trotter Wolfgang von Schroeter Anthony Withers MEDIA CONSULTANTS Martina Hirschmann hirschmann@hbmedia.net Roland Loch loch@hbmedia.net phone: +49 6221-65108-0 fax: +49 6221-65108-28 France, Italy, Spain, UK Elisabeth Maria Köpke phone: +49 6201-878925 fax: +49 6201-878926 koepke@hbmedia.net LAYOUT AND PREPRESS Exprim Kommunikationsdesign Matthias Gaumann | www.exprim.de READER SERVICES Heike Fischer reader@hbmedia.net PRINT Chroma Druck & Verlag GmbH Werkstr. 25 67354 Römerberg Germany WWW www.hbmedia.net | petpla.net PETplanet insider ISSN 1438-9459 is published 10 times a year. This publication is sent to qualified subscribers (1-year subscription 149 EUR, 2-year subscription 289 EUR, Young professionals’ subscription 99 EUR. Magazines will be dispatched to you by airmail). Not to be reproduced in any form without permission from the publisher. Note: The fact that product names may not be identified as trade marks is not an indication that such names are not registered trademarks. 3 PETplanet insider Vol. 15 No. 04/14 petpla.net dear readers, Closures, closures, closures … We are currently on our travels in Italy with our Editourmobil and already we have held a number of meetings with bottlers, preform producers and suppliers. They are all moaning about the high costs, in particular for electricity and diesel. According to them, they are the highest in the world. The economic crisis is still a thorn in the side of the Italian consumer and the beverages market overall is shrinking year by year. Despite this, every company we visited has managed to find its way through the crisis. The priority topic at every meeting was how to reduce energy and materials. And, probing more deeply, the closure very often emerged as the source of inspiration for significant savings. It is the one-piece closure that, time after time, is ushering in new savings here. The dividing line is sometimes nothing more than the payback period for the changeover. It is only after this that we find the weight factor going down by leaps and bounds. Although annual preform consumption in Italy remains fairly consistent at 10billion, materials usage is falling at a rate of between 5 and 8% a year. The Italian machine manufacturers are also following this trend. For example, Sacmi has again made some definite gains in cycle time thanks to better cooling. Moreover, 80% of the installations supplied are compression systems for single-piece closures. A few years ago things were different. At that time the two-piece closure was the dominant feature. However, this is a trend that is not just in evidence in Italy. On our last tour in the Editourmobil we visited Coca Cola in Brazil. At the time the proportion of two-piece closures was 80%; today the ratio is reversed. Now it is the turn of the one-piece closure to assume the 80% share. Once again it is becoming clear that the trends in closures are exerting pressure on the whole of the PET sector. Yours Alexander Büchler","@ID":5}, "EDITOUR REPORT 21 PETplanet insider Vol. 15 No. 04/14 of 82,000t of PET. By contrast, according to Ruben Melara, only 75,000t were needed for 2.5billion preforms in 2012, with a comparable preform mix, and they are continuing with the weight reduction in small steps. The production program is still focusing on the beverages sector and now expanded into containers for food and other segments. Along with the light weight program for one way containers, there is encouraging development in the refillable PET bottles for CSD, where once again growth is being registered. One focus of development within the group is hot fill PET bottles. However, here in Brazil the market tends to be modest. “Even though we have the lightest hot fill PET bottle with a crystallised neck finish on the market,” says Ruben Melara, “the majority of bottles deployed are restricted to isotonic and ready-to-drink teas.” Bottled juices do not feature here in Brazil. The reasons for this probably lie in the plentiful supply of local fruits. A typical breakfast consists of coffee, freshly pressed fruit juice and bread. In addition, here in Brazil the topic of aseptic bottling is still in its early stages, which is actually unusual for such a large beverage market, says Ruben Melara. The manufacture of heat set preforms with 33 and 38mm neck finishes is carried out in Manaus and the stretch blow moulding machines for this are installed at Jundiai. Although the company is geared to the major beverages bottlers, the smaller operations are not neglected. There are joint projects with selected firms that do not have sufficient knowledge of PET processing at their disposal. “In this way,” Ruben Melara went on, ”we are following a trend in the market, namely, the individualisation of smaller beverages companies through the medium of their product.” Machinery Preform production is carried out on Husky injection moulding systems with cavities ranging from 48 to 144. Tendency is to focus all new investments in high cavitation moulds and top of the line injection machines. In the 2-stage stretch blow moulding machine sector, Sidel blow moulding machines dominate the current platform installed in Amcor Brazil.The single stage sector is covered by Nissei and Aoki injection stretch blow moulding machines. The PET resin is mainly supplied by local M&G operation located in Suape. In response to the question as to whether BioPET is being processed or a proportion of recyclate, Ruben Melara responded that “we only process new product. BioPET (PET made from sugar cane) is what everyone wants, but the price difference in relation to PET resin is still too high. However, should we be required to use BioPET, then we are ready to convert.” www.amcor.com","@ID":23}, "PETproducts 50 PETplanet insider Vol. 15 No. 04/14 petpla.net DRYING HAS NEVER BEEN THIS EFFICIENT: ETA plus® LUXOR - now available with ETAplus® ETAplus® considerably reduces energy consumption and protects materials. When it comes to drying, saving energy is a key concern. We have developed a system that combines airflow regulation with a temperature adjustment feature – that can be disabled if required –and efficient waste heat recovery. The result? A drying system that cuts energy consumption by up to 64%: ETAplus® . motan-colortronic gmbh info@motan-colortronic.de www.motan-colortronic.com HexStack for bigger bottles Hexacomb, part of Packaging corporation of America and a manufacturer of paper-based protective packaging and graphic display boards, has developed what it describes as an improved casing method for the transportation of larger-sized liquid bottles. The company claims that customer feedback has indicated cost savings of up to 75% as well as improved load containment, compared to traditional secondary packaging methods. The HexStack packaging system features a single layer of Hexacomb honeycomb material, which is custom-die cut to accommodate the specific bottle neck. The pad is laid on top of a layer of bottles, with the closures and necks inserted into the die cut orifices, which surround the bottle ecks and rest on the shoulder, immobilising the container. A secondary process can punch die-cut a shallower, wider circular channel under the hole to accommodate an optional carrying handle ring. For bottle designs with concave bases, the slightly protruding closure above the die-cut orifice can nest into the base of the container above it, further stabilising the load. The final step is shrink wrapping. Hexacomb says that this development enables larger liquid bottles to be stacked three layers high for transport and retail display, and claims that the system both saves secondary packaging costs savings and helps to minimise product damage during transport. The company further maintains that HexStack can enable more product to be merchandised in the same amount of space. Hexacomb HexStack pads are made primarily from renewable wood fibres, contain recycled content and are recyclable in corrugated recycling streams. www.hexacomb.com","@ID":52}, "EDITOUR REPORT 16 PETplanet insider Vol. 15 No. 04/14 petpla.net PET bottles When we get to the PET bottling section we are struck by the wide diversity of Brazilian bottle sizes. In addition to the traditional bottle sizes such as 0.5, 1.0, 1.5 and 2.0l, we find here a host of intermediate sizes such as, for example, 0.25, 0.5, 0.6, 1.75, 2.25, 2.75, and 3.0ls. The latter is popular during the Christmas season, for example. In addition there are straight wall, contour and refillable applications. Typical PET bottle weights are: 3.0l (straight wall) 56.4g 2.0l (contour) 42.6g 2.0l (refill) 98.0g 0.6/0.25l (same preform) 20.6g PET equipment The first installations go back to 1991 with an initial KHS bottling machine that is still in operation. Over the course of the years further installations from KHS, Krones and Sidel followed, together with bottling lines and stretch blow moulding machines from Sidel and Krones. Overall there are six PET lines here, the most recent having been installed in 2011/13, from Krones and Sidel, in block construction (stretch blow moulding machine and bottler on-line) in accordance with the latest state of the art technology. The bottling capacities are up to 39,200 2l Coca Cola contour PET bph. These are marshalled ready for despatch in trays of six bottles. Preforms are predominantly purchased from Alpla and Amcor in Brazil and not stretch blow moulded by the company itself. In the case of refillable PET, the situation is somewhat different; for this the 600ml and 2l PET bottles are bought in. The growing requirement has made it necessary to replace one glass line with a new PET refillable line.As regards the quantity bottled at the plant, the 2l PET bottle dominates. Worthy of mention is the 600ml PET bottle where all the possible material options are deployed here such as virgin material, recycled PET, plant bottle material from 30% bio-ethanol and copolymer for refill. Beverage processing The concentrate comes from the Coca Cola Latin America concentrate centre at Manaus. The water and the unrefined sugar are processed here in this plant and blended fully automatically on the bottling lines and mixed with carbonic acid. Energy Here too, saving energy in the factory is a prime concern. In the last five years a range of projects have been launched. For example, a new generator is just being installed that can get by with only a few emulsions and which works more efficiently than the present day system. A further project lies in the provision of compressed air for the stretch blow moulding machines. In the manufacture of PET bottles, the greatest demand for energy comes from the compressed air compressors. For the stretch blow","@ID":18}, "PRODUCTS 52 PETplanet insider Vol. 15 No. 04/14 petpla.net Draw the Attention! Systems for Decoration Inspection Booth E1T09 Winding instead of shrinking In collaboration with Polifilm Extrusion and the Italian company Al.Ma.C. Packaging, Antalis Verpackungen has developed a system, which has been launched under the ”Cyclepacker“ label, packages bottles together by wrapping them in heavy duty Twistex PE film. In addition to a saving in materials of approximately 60%, eliminating the energy-intensive shrink tunnel in this new technology brings reduction in costs. Lower film consumption as a result of the use of winding technology simultaneously reduces the licensing fees for disposal by up to 60%. Using the Cyclepacker system means that the CO 2 emissions can be reduced by almost 80%. The Cyclepacker incorporates two winding rings per module with a total capacity of up to 6,000bph. Because of its modular construction, the system can be expanded as required to suit the capacity requirement. The low weight roller (12kg) and roller bracket make for easier changing of the film rollers. According to the manufacturer, the special Twistex film with its brilliant clarity offers particular compound stability and more robust loading units. www.cyclepacker.eu Improved shelf-life estimates Agr International, in conjunction with Container Science, has launched an update to its PPT3000 testing systems. The company says that the M-Rule shelf-life model will provide more accurate shelf-life estimates compared with current, time-consuming methods. The PPT3000 has the ability to directly enter wall thickness data. Along with other improvements, this feature is claimed to provide a more consistent and accurate estimation of shelf-life on current bottle production. Temperature, humidity, volume, carbonisation levels and other variables that can affect shelf-life are pre-defined as part of the model and reproduced for every test. Results can be obtained within the current production window, which means that the data can be used in process management. Pressure and volume expansion data on a given bottle is captured by the PPT3000 tester and analysed by a version of the M-Rule software. This data is used to map material utilisation in relation to shelf-life for the bottles being tested. In addressing the unique attributes of individual bottle designs, a custom “fingerprint”, created by Agr, holds the recipe for shelf-life testing of a particular bottle. Fingerprints can be built for specific end-use requirements, such as CO2 egress on CSD bottles, oxygen ingress, or water loss on lightweight water bottles. Fingerprint information is incorporated into the job for that bottle on the PPT3000 and called upon when testing bottles of the same type to determine material utilisation and shelf-life performance. www.agrintl.com","@ID":54}, "TRADE SHOW PREVIEW 42 PETplanet insider Vol. 15 No. 04/14 petpla.net China calling - Chinaplas 2014 “The 28th International Exhibition on Plastics and Rubber” – better known as Chinaplas 2014 will be staged at Shanghai New International Expo Centre, China, April 23-26, 2014. The organisers of say that this year’s edition is expected to attract more than 2,900 exhibitors and will occupy an exhibition area of over 220,000m2. It will feature international pavilions from countries in Europe, the Far East, Turkey and the USA. Bayer MaterialScience, Dow, Kolon Plastics, and Sunshow, Uniplas have confirmed their attendance. In order to help delegates to find their way around the large exhibition area, some products will be classified into particular zones; Chemicals and Raw Materials, Colour Pigment and Masterbatch will be located at additional exhibition hall C10, with Additives in hall C11. www.chinaplasonline.com Gneuss | Hall E1, Stand C21 Next round of rotary filtration systems Gneuss will be presenting a number of new developments in their range of rotary filtration systems. The RFSgenius M is designed for the processing of highly contaminated materials. Its synchronisation of the drive and back flushing systems enable a major increase of the screen area exchange rate. The SFXmagnus R debuts the option of an integrated self-cleaning, back flushing system, which can be switched off when not needed. Gneuss’ range of screen changers is being extended with the addition of SFpvc, which is aimed at the PVC market as its name implies. The KR discontinuous screen changer is designed to be rugged and compact. Gneuss will also be exhibiting its MRS Extruder, which processes reclaimed PET without pre-drying; speciality sensors and transducers; and safety cut-out sensors and systems. www.gneuss.com ProTec | Hall E1, Stand E43 Solid state reactor and long-fibre plastics Highlights on ProTec Polymer Processing’s stand will include the new, optimised solid-state Ohl tumble reactor, which is a solid-state polycondensation (SSP) reactor that can be heated and evacuated. It is available in coordinated modular sizes, from 50l for laboratory through to 44m³ containers for manufacturing plants. ProTec maintains that it uses less oil in heat transfer than its predecessor, as well as less energy. The company’s plant technology for manufacturing long-fibre thermoplastics is claimed to be suitable for manufacturing a broad range of materials using a diverse polymer matrix and different types of fibre reinforcement, using the pultrusion process jointly developed by ProTec Polymer Processing and PolymersNet. The company’s Somos TF 40 eco auxiliary dryer will illustrate the Somos range’s flexibility and energy efficiency. www.sp-protec.com Netstal | Hall E1, Stand K41 New closure machinery Netstal, the precision injection moulding company, is offering the opportunity to witness live production during an “open house” event at its production plant in Haiyan, Taishan, Guandong province. The event will coincide with Chinaplas. PET blood collection tubes will be manufactured on an all-electric Elion with a 2,200kN clamping force. Netstal installed a complete PET-Line system with cooling and drying units at its demonstration plant for the beverage industry in China in September 2013. This system, which has a clamping force of 4,000kN, will also produce PCO28 preforms in time for the opening of the extension to the Haiyan plant. Netstal has reported rising demand for custom caps and closures and, in particular, for its PET-Line 2400 and 4000 ranges, along with Elion 4200. The open house event will also provide the opportunity to see examples of technology from KraussMaffei and KraussMaffei Berstorff. www.netstal.com Schöttli | Hall E4, Stand B01 Medical and speciality closure mould making technology Schöttli, Husky Injection Molding Systems’ recently acquired subsidiary, will be hosting its own stand at Chinaplas 2014. It will focus on showcasing the company’s latest mould technology for select medical and speciality closure applications including syringes, infusion/transfusion products, diagnostic systems and feminine care items. Husky’s Easycube mould technology will also be featured. www.schoettli.com","@ID":44}, "CAPPING / CLOSURES 37 PETplanet insider Vol. 15 No. 04/14 petpla.net Custom 1.75l PET bottle for McCormick Distilling’s eco-friendly 360 Vodka from Amcor uses swing top closure McCormick Distilling, a Weston, Missouri, USA based manufacturer and distributor of premium spirits, has converted its eco-friendly 360 Vodka 1.75l line from glass to lightweight PET bottles from Amcor Rigid Plastics. The custom 1.75l container delivers distinctive styling and consumer handling and supports a swing top closure. ture a swing top closure. Adapting the closure to PET was a major design challenge for the bottle manufacturer, according to Myles Graybill, Amcor project engineer. Amcor’s Advanced Engineering team performed Finite Element Analysis (FEA) modelling to predict the container’s performance behaviour and adapted the metalbased closure to the 23mm finish diameter, thus creating a bottle that would be fully functional. “The neck design was critical as we undertook many iterations and hours of trial and error to adapt the existing closure to PET,” said Graybill. The design also incorporates a tamper-evident band strip. Amcor also reduced the bottle’s height, enabling the container to be better displayed on retail shelves. Previously, retailers either didn’t carry the product or were forced to place it on a top shelf or lay it down. McCormick uses PET containers in various sizes for a range of spirits products. 360 Vodka comes in a wide variety of flavours and is available in retail establishments throughout the U.S. www.mccormickdistilling.com www.amcor.com McCormick Distilling, located in historic Weston, Missouri, is the oldest continuously operating distillery in the U.S. McCormick is a spirits maker with a new mix of products, based on nearly 150 years of experience. The bottle for 360 Vodka was designed to impart the look and feel of glass. At the same time, the lightweight PET container delivers the well-known sustainability advantages, reduced shipping and transportation costs, and a reduced carbon footprint. The containers are 1/10 the weight of glass bottles, unbreakable, and recyclable. As part of its sustainability focus, McCormick also uses reusable closures and recycled paper printed with water-based eco-friendly inks. Since organic grain leaves a larger footprint, 360 Vodka uses local grain grown less than 95 miles / 153km from the country’s most energy efficient distillery where 360 Vodka is crafted. This gives the brand its distinctive, smooth taste that has been awarded with multiple platinum and gold medals for taste from international spirits competitions. Amcor claims that the PET container for McCormick is the first to feaSwing top lifts the spirit","@ID":39}, "EDITOUR REPORT 20 PETplanet insider Vol. 15 No. 04/14 petpla.net It’s Wednesday and we are crawling through the rush hour traffic in Rio towards our meeting with Coca Cola. At their offices, we are welcomed by Paulo Roberto Villas, Head of Supply Chain for Packaging, and Lucas Angelo Amendola, Packaging Specialist. Both tell us a lot of interesting facts about the company’s current and future projects. The next day and together with Paulo Roberto we have our next appointment with Coca Cola franchisees Andina. André Braga, bottle blowmoulding production manager, and Ana Carolina Almeida, Industrial Supervisor bid us welcome and take us on a tour of the plant. Before we leave, our hosts kindly help us fill the Editourmobil water tanks. The next stage of the journey, according to the itinerary prepared by our colleagues in Heidelberg, is a mere 200km away – or so we were led to believe. But sad to say, having driven for an hour it turns out that Lindóia, where we have our next interview, is nearly 500km away. Something seems to have gone badly wrong here. Naturally we would not be able to manage this distance even if we drove all day and all night, especially as we have only a couple of energy drinks to keep us going. In the morning, on the way to Lindóia, we come across a shopping centre and although it is not fully open, we manage to find a coffee shop to recharge our batteries before finally reaching Genuina Lindoya. In an interview with Julio Almeida, Administrative Director, and Andre Arlotti Giao, Head of Marketing, we get a lot of information about the health-oriented drinks company. The week was, to say the least, full of ups and downs. There’s no shortage of excitement on an Editourmobil tour! The following week begins early Monday morning in the car park of a shopping centre in Barueri in the district of São Paulo. Our upcoming visit, to Grupo Ravi, is first on the list. Grupo Ravi produces, amongst other products, closures for PET bottles in South America. Director Aurelio Silva welcomes us together with Erica Rodrigues from the research and development department and accountant Claudia Mello. In the course of a most interesting interview we learn about the company’s broad portfolio of products and their coverage of the South American market. (by Florian Roscheck) eral Manager of Amcor Rigid Plastics Brazil. In response to a question about location, proximity to the customer was the argument presented. Here in Jundiai Amcor have two blow moulding plants for PET bottles. One plant is directly linked with an important CSD PET bottler. PET bottles are passed through the wall and collected ready for filling. The other plant next door (where we are) produces PET bottles for CSD and hot fill applications using the 2-stage process. Amcor operates a total of six plants in Brazil, among the two blowing plants located in Jundiai, a third blowing plant located in Goiania is dedicated to blow food containers for an important multinational company. Two preform injection plants, one located in Manaus in the Federal State of Amazonas; and Amcor’s newest plant in the industrial and port area of Porto de Suape in the Federal State of Pernambuco. The sixth plant in Louveira (São Paulo State) is dedicated for pharmaceuticals, personal care and home care sectors. By contrast to all the other plants in Brazil, this plant in Louveira produces a wide range of containers and closures with different production platforms and technologies, as well as different resins according to market requirements. One step machines, extrusion blow, injection blow and injection moulding machines are in perfect alignment with decorating machines capable of fine printing containers. Particular features of the Brazilian market Brazil is by far the largest market in South America with a population of more than 190 million. In this market we find more than 150 beverages bottling companies and brewing operations, from the family firm through to enterprises boasting a global presence, from local to global brands. According to Ruben Melara “there’s a special place in the market for each and every option. As a result, however, an enormous diversity of geometries and sizes is developing where bottles are concerned, together with a range of different specifications. A challenge that can only be overcome by means of innovation and technology.” Nor is the growth of the market currently of much help. 2012 brought with it a growth in the sector amounting to 2% by comparison to a normal growth rate in the past of 6-7%. The root cause of this is attributed to the sluggish growth of the Brazilian economy over the past year. Lightweight preforms Amcor is continuously working on programmes aimed at reducing the weight of preforms and bottles from an early stage. Their philosophy here is to manage the various stages in development themselves before presenting them to the market. To this end, Amcor Brazil tend to fall back on the development departments within their American headquarters who, with their extensive experience and test facilities, are able to offer the required support. The largest customer in Brazil, has, in their own factories in Brazil, an important migration to the 1881 neck finish for beverages bottles with the aim of achieving 100% in a very near future, causing an important weight reduction of the container. This migration, combined with the most innovative program to reduce weight on the body of the containers, has caused enormous savings in terms of total PET resin tons demanded: in 2009, 2.1billion preforms were being manufactured using a total weight","@ID":22}, "ON SITE 55 PETplanet insider Vol. 15 No. 04/14 petpla.net Sidel’s bright ideas cut energy consumption PepsiCo Deutschland has reduced energy use by 19% and lowered costs by 16% on a Sidel blower at its plant in Rodgau, near Frankfurt, Germany, after installing Eco lamps. The lamps, which consume around 90-95% of the total electrical power used by a blower, were installed to support the customer’s eco-friendly approach at the facility. PepsiCo Deutschland’s portfolio includes Pepsi, Pepsi Light, Schwip Schwap, Mirinda and 7-Up, Gatorade, Rockstar energy drink, K-Fee ready-to-drink coffee, Punica and other fruit and vegetable juices. Data collected on-site shown that the lamps generated a return on investment (ROI) in 12 months. Consumer awareness of environmental issues in Germany is particularly high and PepsiCo says it has responded by striving to achieve a balance between pure commercial success, in the form of solid financial results, and social responsibility. It has adopted a commitment to sustainable growth, which it has named “Performance with Purpose”. Sidel’, Sidel helped the customer to identify the right solution to save money, targeting savings of 15% for the installation of the Eco lamps. Measurements taken before and after the fitting of the lamps, confirmed that the savings were actually as high as 19%. Sidel says that the lamps combine sustainability and economic performance and are available for its SBO Series1 and Series2 blowers. They have a life expectancy of 5,000 hours and, in some cases, can be fitted with no modification of the existing oven or blowing process. The Eco lamps also enable better stability through the preform heating process, which leads to a more optimised production output. The PepsiCo machine in Rodgau is an SBO 18 Series2, which produces 1.5l and 2l PET bottles for the Pepsi, Schwip Schwap and Pepsi Max brands. The machine was, in 2008, fitted with Sidel’s air-recycling system, in order to reduce blow-moulding air consumption by 16%. In 2011 another joint collaboration reduced package weight and improved blowing pressure, which was subsequently reduced to 28-30bar. Performance of the finished bottle was retained. www.sidel.com","@ID":57}, "CAPPING / CLOSURES 32 PETplanet insider Vol. 15 No. 04/14 petpla.net Vicap: a sports cap with dosing chamber A dose of what you fancy does you good At first glance, Vicap looks like a normal sports cap. But Vicap is hiding a little secret: 12.5mm of liquid or 7g powder opens up the possibility of creating mixed drinks or energy drinks with dietary supplements. For 2014, the plan is to launch the product in a number of countries. The question that Vicap Systems, a company set up in 2006, asked itself was simple enough: how can water be enriched both in taste and with vitamins, without both losing their effectiveness? Vicap systems and Gerhard Priewe put their heads together and pretty quickly came up with the answer. Keep the vitamins, flavour carriers or sources of energy separate from the water, and they will retain their effectiveness. With this flash of inspiration, Vicap was born. So beautifully logical is it, that three Swiss investors subsequently showed interest in this innovative closure. For the system to work, the vitamins must be housed in a light-proof chamber. In addition, the chamber needs to be protected against any moisture that might seep up out of the beverage. The vitamins, flavourings or other added products need to be in both liquid and powder form. A number of these requirements were met thanks to the chamber being secured by means of a copyright-protected aluminium foil. Roger Wilfinger, CEO of Vicap, recognised the potential when he first came across the firm as an investor in 2008. After 2010, when he took over at the helm of the company, he implemented a complete turnaround. He created an interdisciplinary network with strong and well-established partners. He also positioned the company in the market as an innovative packaging manufacturer for functional beverages closures. Today Vicap is being produced and assembled fully automatically in the Vicap factory at Koblach in Austria in collaboration with Monfort Kunststofftechnik (Plastics Technology). The filling operation takes place under cleanroom conditions at Humana Pharma International, a subsidiary of the German DMK, and the product is subsequently marketed in twelve European countries. A further production facility is taking shape in Izmir in Turkey aimed at satisfying the strong demand in this region where food and drink has to be prepared in accordance with halal custom and practice. Handling is very simple. All the consumer has to do is remove the overcap and push down the “spike”. This penetrates the aluminium foil and the flavouring or vitamin mixes with the drink in the bottle. The Vicap is capable of absorbing 12.5ml liquid and 7g powder. Currently the closure can be supplied in a 38mm, 3-start version. The following versions are under development: PCO 1810 and 1881 for still and CO 2 . www.vicapsystems.eu","@ID":34}, "TRADE SHOW PREVIEW 46 PETplanet insider Vol. 15 No. 04/14 petpla.net CCT Creative Competence Technology GmbH Idsteiner Strasse 74 D-65527 Niedernhausen, Germany r.steinmetz@cct-systems.com www.cct-systems.com PET Molds Developments PET Systems Closure Systems Closure Molds Blow Molds Your complete Project Partner for: • Closure Molds • Preform Molds • Blow Molds Blow Molds Sacmi | Hall 8a Stand E03 Complete lines Sacmi Imola S.C. will be presenting its latest CCM developments, its new Colora Cap decorating system, quality control solutions for caps and preforms, the Formsleeve+ by Sacmi Verona, and a new TF 12 tray forming machine from Sacmi Packaging. Machines on the stand will include the 32-cavity CCM, a compression press for the manufacture of plastic caps, characterised by the low temperatures at which the extrusion process takes place. Equipped with a ‘Cool+’ mould, which is designed to take the efficiency of the cooling process even further, the CCM32 will be making soft drink closures with cycle times of approximately 2s. It will also demonstrate an integrated two-camera Sacmi CVS3000 Quality Control system integrated. Colora Cap is a on-cap digital printing system that allows high-definition images to be printed directly on the production line. Real-time decoration changeovers can be made by simply switching to a different graphics file. The Sacmi CVS3000 Quality Control system, stationed both upstream and downstream, ensures that only flawless caps are decorated and only those with fault-free images are used in bottling. Formsleeve+, a new modular labeller, is designed to form the sleeve directly in the machine from the roll using natural bonding liquids and to reduce costs. Product quality is maintained by the LVS36, which has updated software. The PVS and CHS quality control vision systems are designed for direct installation on the line, next to the press. PVS can check up to 36,000 units/hr; the CHS cap control system is equipped with HD video cameras that can check every side of the cap. Sacmi Packaging’s TF 70 modular tray former, made up of magazine, press and corner modules, will also be on the stand. www.sacmi.com RPC Group | Hall 10 Stand D21 Polymer products and processes Exhibits on RPC Group’s stand will include different solutions for single-serve beverage systems; airless dispensers, cream jars, deo sticks and lip care packs; barrier technologies for extended ambient shelf life for food products; and technical developments in pharmaceutical dispensing and dosing systems. RPC Bebo Plastik’s Bebo Swing, developed to integrate easy-opening, reclosing and tamper-evidence for spreadable products such as cheese, margarine and butter, can be manufactured in monolayer or multilayer PP for protection against oxygen ingress and a light barrier can also be incorporated. RPC Formatec has introduced a new system that enables users of PMDIs (pressurised metered dose inhalers) to count down the number of doses taken and alert them when the unit needs replacing. RPC Emballages Moirans has launched a UN-certified 20l container that weighs just 700g. SuperLock from RPC Superfos combines an oxygen barrier on all surfaces with a membrane seal, and a new pet food pack that can replace aluminium trays. During Interpack, RPC Superfos will be officially presented with a WorldStar award for its custom oxygen barrier packaging for Bornholms’ seafood. www.rpc-group.com HSM | Hall 10 Stand E52 More efficient, lower-energy baling press HSM of Frickingen, Germany, will be presenting three vertical baling presses from its V-Press range. All three will be equipped with the company’s “rapid reverse technology”, which helps to reduce energy consumption while increasing throughput and cutting cycle time. The HSM V-Press 860 L bundles bales by weight at up to 460kg, regardless of the material, and bound 4-fold with wire strapping as a standard. Polyester strapping is also available as an option. HSM says that special profiles in the bale ejection door, the filling hatch and in the press ram form recesses in the bales, which eliminates the need for pallets. The entry-level HSM V-Press 504 can process up to six 50kg (maximum) bales/h, depending on the material. www.hsm.eu","@ID":48}, "EDITOUR REPORT 17 PETplanet insider Vol. 15 PROVEN COST SAVINGS PERFORMANCE moldmasters.com Mold-Mastersand theMold-Masters logo are trademarksofMold-Masters (2007) Limited. © 2014Mold-Masters (2007) Limited -AMilacronCompany.All rights reserved. Rely on our global support network for fast service and parts. North America 1-800-387-2483 | Europe 49 (0) 7221 5099-0 Asia 86 512 86162882 ALWAYS INNOVATING. + More efficient use of platen real estate increases the cavitation for a given machine size: s 72 vs. 48 Cavity with a 28mm finish in a 225T s 72 vs. 48 Cavity with a 38mm finish in a 300T s 96 vs. 72 Cavity with a 28mm finish in a 300T s 128vs. 96 Cavity with a 28mm finish in a 400T + Proprietary iFLOW and iCOOL technology reduces cycle times while improving balance, lowering injection pressure and increasing dimensional repeatability + Tooling solutions to revitalize, recapitalize and rev up existing systems Get 50% more output from the same machine 96-CAVITY MICRO PITCH MOLD FOR 300T MACHINES Contact us today at: mpeteurope@moldmasters.com moulding process and depending on the size of the bottle up to 40bar is required in the first blow moulding station and, where a number of stretch blow moulding machines are being operated, pressure is supplied via a central compressor station. The project consists in finding, once for each consumer (stretch blow moulding machine featuring a range of bottle sizes), the optimum set point for the blowing pressure level and also to delegate the compressed air. Deploying these measures it proved possible to reduce the overall pressure level first of all to 32bar and then to the present 27bar. For a 2l Coca Cola contour bottle the requirement for blowing pressure today lies at around 25/26bar. The aim is: get close to a blowing pressure of 20bar, says Andre Braga. www.koandina.com May 10, 2013 Lindoyana de Aguas Minearis Ltda. We met: Andre Arlotti Gião, Head of Marketing Julio Almeida, Administrative Director Health above all “Health Above All” is the guiding principle of Genuina Lindoya. 20 years ago this mineral water bottling operation came under new ownership, but this guiding principle has continued to this day. The company, which is under private management, places great emphasis on sustainability. This is also evident in its dealings with suppliers and service providers who work together like one big family. The commodity on which the business is founded is pure mineral water from this region of Serra da Mantiqueira, which is conveyed from the company’s own springs into two filling plants. The bottling operation comprises the following: From right to left: Julio Almeida, Administrative Director and Andre Arlotti Gião, Head of Marketing","@ID":19}, "PREFORM PRODUCTION 26 PETplanet insider Vol. 15 No. 04/14 petpla.net Upbeat gets into shape with Esterform packaging On the beat Esterform Packaging is a converter of PET in the UK with production sites in Tenbury Wells and Leeds. Its preform range also covers lightweighting solutions. Typical customers are companies filling juices and juice drinks, bottled water, dairy drinks, still and sparkling soft drinks and food products. Another significant group of customers are producers of liquids for personal care, household, DIY and car applications. Most customers buy standard off the shelf bottles; or customised designs in volume. A small number of larger customers buy preforms to blow in line. Esterform is having a full materials laboratory for in-depth testing. Production is primarily based on two stage and single stage injection stretch blow moulding, with the capacity to produce up to 1.5 billion units a year (PET preforms, bottles and jars). Lighter weight options According to national UK statistics, the numbers of single person households are increasing dramatically in Western Europe – and there is growing demand from elderly consumers and students for consumer packaging that is lighter in weight and easy to carry. Esterform already produces Innocent’s 1l carafes along with a wide range of bottles and preforms for all types of beverage, ranging from water and sparkling drinks to dairy, juice and functional drinks. Last year, the company introduced short neck 28mm 1881 PCO neck preforms for soft drinks and water in bottles from 250ml to 2l. These save on expensive PET resin and conserve precious resources – so meeting consumer and retailer demands for sustainability. A wide choice PET bottles from Esterform are suitable for juices (especially fresh pressed), juice drinks, dairy beverages and smoothies. The 38mm necks are offered with 3-start and single start finishes, to match a wide range of closure options. Recently, Esterform used these skills to turn the bottle design concepts into an exciting contemporary product that won ‘Best New Brand’ at the Beverage Innovation Awards at Drinktec 2013, organised by FoodBev Media. Discussions between Volac’s and Esterform began in April 2012 and following the suggestion of the waisted design in the original brief, the initial concept design for a customised 250ml bottle was presented in May. The resulting design appeals to Volac’s key target market of health conscious consumers. The first production run took place in November with bottles delivered in time for the initial trials and for the full product launch at the beginning of March 2013. Designed so that consumers can drink straight from the bottle, Upbeat uses a 38 UCS with a 38mm UCS tamper evident cap. Essential UV protection A UV barrier is essential to protect the whey-based Upbeat product. It was suggested that a clear or opaque white master-batch be added to the monolayer PET to add a UV barrier to the bottle. Ultimately Volac decided to go for a sleeve incorporating a UV lacquer. This provides a good UV barrier while enhancing the aesthetic appeal of the pack design. The product is not aseptically filled, so requires refrigeration in shipping, display and storage. www.esterform.com When UK based Volac’s company was looking for a unique shape to give their new protein rich drink ‘Upbeat’ a creative identity with an outstanding presence on the store shelf, it approached Esterform. The shapely, curvy design appeals to Volac’s key target market of health conscious consumers","@ID":28}]}}
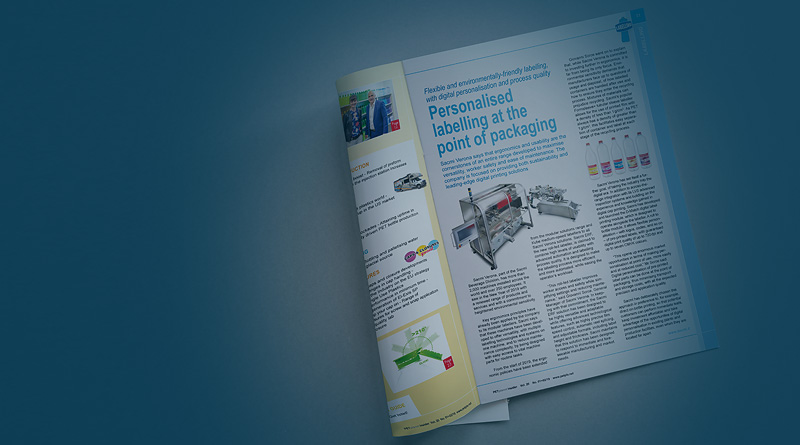