"MATERIALS / RECYCLING PETplanet Insider Vol. 21 No. 06/20 petpla.net 22 It is time to RE-focus by Lucia Buffoni, Marketing Manager, Repi Group For the plastic industry the year 2020 has been a major deadline for so many projects, pledges, activities at all levels. Goals were ambitious, but time was an ally. Already a couple of years back some goals started to be postponed to 2025, some even to 2030. Recycling Special With no doubt such a complexity like the Covid-19 one could not be imagined even remotely. So it happens that this year, that was meant to mark important acceleration of transition to an economy made of plastic alternatives have instead underscored that plastic is still the most reliable and affordable solution for personal protection. The pandemic is challenging everyone’s lifestyle, habits and daily life, even of those who are fighting for a reduction when not a ban of plastic. Many sustainability-conscious people may now find themselves with singleuse plastic items, such as disposable wipes and sanitary protective devices, but also plastic containers of hand sanitisers up to takeaway food containers and single serve drinks packaging. It seems now that not only giving up disposable plastic is not feasible but on the contrary plastic packaging the safest choice right now. If we look at the world consumption rates of last quarter, single use packaging is at a record high from north to south and this will last for a while, together with the demand of plastic disposable wipes, gloves, masks, etc. In such a context the best thing we can hope for is to this global black swan occurrence as a renewed push to boost a circular economy of which of course plastic recycling is the best example. Now more than ever the solution seems not to be the substitution of plastic, but a systems-level approach on a global scale to improve its recycling. Let us remain on the concept of “circular economy”. Reaching a “circular economy” means structuring economies on the virtuous closed loop of ‘make – use – recycle’ in which every product is designed to be used and then disposed leaving no traces, it means being re-used to generate other products and so on. All good so far but is this really the full picture? I mean if we recall the primary goal of a circular economy, that is to cut CO2 emissions as main cause of global warming, then the carbon footprint contribution of our activities should be the main driver. Instead, some solutions emerging and defined as 100% recyclable produce actually higher CO2 emissions than what they are replacing and can’t therefore be sustainable for the future. Looking in particular at the single use packaging sector, plastic packaging is the most attacked material and, as a consequence, we see a shift to other raw materials that are not automatically more carbon footprint friendly than plastics. This is often an emotional answer to social media attacks that could be even more harmful from a system point of view. As an example, replacing a PET bottle with a glass one is not the solution. Glass is defined as 100% recyclable and therefore eco-friendly. A consumer might not realise, however that to produce and recycle that glass bottle a huge quantity of energy will be required (melting process goes to temperatures as high as 1,500 °C). On top, logistics costs related to collection, transportation to the recycling site and then all the way back to the market again will have much more negative impact compared with a bottle made of PET. What if we try to let consumers learn what’s behind a packaging and why plastics in packaging have become so successful worldwide. The current health emergency is showing one of their unparallel advantages offered to consumers: safety. But plastic packaging does offer much more: light weight, a PET bottle is lighter than any other packaging and therefore consumers can practically carry their on-the-go snacks and drinks while commuting to job; more-over it hardly breaks, and its logistic is agile and safe all over the world; lastly plastics are highly recyclable (and recycled already) to enter the packaging value chain again or to be used for a number of other applications, not of lower value (textiles as an example). Coming now to the carbon footprint contribution, plastic packaging helps reduce CO2 emissions, especially when it involves recycling. A recent report of Plastics Europe shows that an increase in the recycling rate of 5mt of plastic packaging would make CO emissions falling by 7mt, corresponding to 2,4 million cars less on streets. A PET bottle made of 50% rPET has a lower environmental impact than a glass bottle (be it single use and reusable) or a tin can. The single use glass bottle is the least environmental unit, even behind aluminium tin which is almost always the runner-up to plastic packaging. Having said that, there are ways to make a plastic packaging even more sustainable. One way can be choosing additives and colours that add performance and aesthetics while having negligible impact on its recyclability. This is at the basis of the REFIT concept. Repi as a global colour and additive solutions supplier to the packaging industry has recently launched its REFIT vision, that adds a “R” to the three commonly accompanying circular economy statement: reducing, reusing, recycling, REFITting. REFIT means having an all-round approach to carbon footprint contribution. Protagonist is the liquid colour and additive technology that can be defined as a low carbon footprint technology. This can be proven in each step of the liquid lifecycle, as shown in the flowchart. The main reasons behind can be summarised as follows: Process - the manufacturing process of a liquid colour/additive is energy efficient since no high temperatures are needed to blend carriers (that are already liquid) with pigments or dyes. Regardless from the specific production cycle, all processes happen at room temperature. Logistics – the high concentration of liquids leads to less space needed for transport and therefore significant CO2 saving Stockage of liquids at the customer’s site is highly space efficient","@ID":24}, "MATERIALS / RECYCLING PETplanet Insider Vol. 21 No. 06/20 petpla.net 40 High-purity plastic flakes and increased productivity Meeting evolving requirements RCS is a company based in Werne, Germany, specialising in recycling management. With over 40 years’ experience, it provides companies solutions for the disposal of commercial waste with its three core competencies – waste disposal, raw material recycling and plastics. For a modernisation of the sorting plant, the company invested in Stadler systems. Sustainability and the environmentally friendly use of resources are the principles at the heart of RCS’s corporate philosophy. They run through every aspect of its operation, such as the advanced processes it uses to collect and transform waste into secondary raw materials, returning them to the production cycle. These core values also form the basis for its service to clients, as it works in partnership with them to develop a concept that is environmentally friendly and individually tailored to their needs. An important area of focus for RCS is the recycling of PET bottles to produce plastic flakes for a variety of applications and high-quality regranulate for the food sector. This activity is centred at its sorting plant, where it separates clear PET from colour PET – which account for 85% of the input – aluminium and ferrous cans, film and other materials. With a capacity of 7 t/h, the plant operates on a continuous shift system, processing used PET bottles into highquality food grade plastic flakes. The purity of the flakes is of paramount importance, as they are destined to the production of a variety of plastic products, from plastic fibres to films and packaging tapes, as well as products for the food industry. Every outgoing Big Bag is carefully checked for residual moisture, bulk density, incorrect colours and contaminants, as well as grain size distribution and adhesive residues to ensure the high quality of the output. A complete modernisation In order to achieve both the consistent high purity it requires and optimise the processes at its plant, RCS has relied on the expertise of Stadler Anlagenbau, a company dedicated to the planning, production and assembly of sorting systems and components for the waste disposal and recycling industry world-wide. “We had already purchased a ballistic separator from Stadler in 2005,” says Gerd Francke, joint CEO of RCS. “On the basis of the good experience with their technology, we decided again to choose Stadler for a new ballistic separator in 2014.” This was followed by a complete modernisation of the plant in 2017: “Stadler offered us the complete package, from project planning to the construction of the modernisation of the entire plant, managed and implemented by their staff,” explains Alexander Rimmer, joint CEO of the company. “We particularly appreciated their technical knowhow and the support during the entire project. Their advice was flawless and they offered us great technical experts who advised not only on the technology and processes, but also on the implementation possibilities specifically adapted to our technical requirements with good solutions to problems.” The completion of the project within very tight deadlines was a key requirement for RCS. The modernisation has brought multiple benefits to the sorting plant – not only on the quality of the output, but also on its operation and running costs, to the satisfaction of RCS’s CEOs: “The biggest advantage was a triple increase in quantity, quality, and yield. In addition, work processes have become easier for our employees. Recycling Special Alexander Rimmer (left) and Gerd Francke RCS PET sorting plant","@ID":42}, "TOP TALK PETplanet Insider Vol. 21 No. 06/20 petpla.net 14 The times they are a-changin’ by Heike Fischer One lesson you learn in the school of journalism, the one thing to be avoided at all costs, do not even think about - conducting an interview mainly via email. You lose the personal contact, the special atmosphere, the spontaneity in the course of the interview. But the current situation is teaching us all to rethink and what was previously unthinkable has now become the new reality. PETplanet spoke to a long-time friend, Alan Tolley, Managing Director of R&D/Leverage Europe. He is located in the UK, one of the countries most affected by the Covid 19 pandemic. We asked him for an assessment of the economic situation in his manufacturing plant, how their business in the US is being affected, and what steps his company is taking to adapt to the new conditions. PETplanet: Alan, how are things with you at the moment? How are people in the UK coping with the Covid-19 pandemic? Alan: At the moment it is quite surreal living in the United Kingdom where life goes on as normal with migrating birds returning to our shores, trees waking up after winter and flowers coming into bloom - and then you turn on the news and hear that hundreds of people have died the previous day from Covid-19. Thankfully the area where R&D/Leverage is located have been spared any major outbreak so all our staff are healthy and at work. Restrictions have made day to day life very different but it appears most people are coping with the pandemic well. PETplanet: In your view, how is the UK economy generally reacting to the crisis and more specifically what is the mood in the beverage and packaging industry? Alan: I believe the UK has handled the pandemic reasonably well in some areas but average at best in other areas, the United Kingdom Government promptly introduced a Furlough scheme to shield a large part of the United Kingdom population from losing their jobs but the question will be what happens when the Furlough scheme ends and the unemployment numbers increase. My concern was that we would see a closing down on all future project developments but quite the opposite has happened, we anticipated orders for hand sanitiser, hand soap and disinfectant bottle orders but we are receiving orders for personal care, home products and cosmetic projects. PETplanet: What changes have you had to make to your daily routine? Are you having to work from home? Alan: In line with the United Kingdom Government guidelines we have some of our employees working from home, we have also introduced a three shift pattern, mornings, afternoons and nights to reduce the number of staff we have on site at any given time to assist in the social distancing guidelines. One of our biggest challenges is to ensure the staff adhere to the regular hand washing followed by hand sanitiser and keeping to the 2 meter social distancing rule when life appears to be the old normal but we are in different times with this being the world’s new normal. PETplanet: Can you tell us about the situation in your production plant? Are all your employees working on site or have you had to develop flexible working models? Alan: Pretty much covered this earlier but at the moment we have a full healthy work force, we have implemented a three shift system to assist with social distancing which we have found to be more efficient for manufacturing. We have staff working from home where it is possible but as a manufacturing company there are limited numbers that can do this. One big difference is in the old normal we would have on average three different company representatives on site to oversee their tooling being qualified in our Product Solution Laboratory, currently no visitors are allowed on site so everything is being done via media or physically sending samples of the bottles for approval along with the inspection reports. PETplanet: Has R&D Leverage been able to maintain regular production? Have there been any problems with suppliers? Alan: We have been very lucky that most of our suppliers have stayed open and a few that closed we managed to find alternatives quickly without impacting on our ability to continue manufacturing. PETplanet: What feedback are you getting from your customers about the current situation? Have you been able to offer any special services to mitigate the effects of the crisis? Alan: Initially there was an urgency from our global customers for hand sanitiser, hand soap and disinfectant bottles with this first wave we supplied tooling with a 4 week delivery, we now receiving orders for a broader range of products with longer lead times. PETplanet: R&D Leverage is also a big player in the States. How do your colleagues in the US see the situation as regards business?","@ID":16}, "53 ON SITE PETplanet Insider Vol. 21 No. 06/20 Strautmann baler at the recycling center As a full-owned subsidiary of the Osnabrück district, Germany, Awigo Region Osnabrück GmbH is the central point of contact for all issues related to recycling and waste management in the region. As a certified waste management company, Awigo supports the approximately 360,000 inhabitants in the 21 cities, municipalities and integrated communities of the Osnabrück region as well as numerous commercial enterprises when it comes to environmentally friendly waste prevention, disposal and recycling. Due to the large amounts of different materials, it is very important to Awigo to dispose of the recyclables properly, environmentally friendly and economically. For hard plastics, Awigo tested Strautmann’s PP1208 - a press to compact the materials. The hard plastic was previously collected in loose containers at the recycling yards and taken to another location for baling. Due to the loose collection, many transport ways and costs were incurred. These were saved by using the PP 1208 directly at the recycling center. The PP1208 had grown through special adaptations to the task of compacting extremely large and bulky hard plastic parts with the highest pressing force. For example, trash cans, garden chairs and bobby cars were compacted into a directly marketable bale with a pressing force of 60 t. This saved a lot of space internally and reduced transport costs. Rolf Bringewatt, waste manager at Awigo, reports: “The material is really strongly compacted. The bale storage always looks good and we save transport routes due to the transport load. This is good for us in monetary terms, but also for the environment due to the reduced CO2 emissions.” www.strautmann-umwelt.de ONsite","@ID":55}, "MATERIALS / RECYCLING PETplanet Insider Vol. 21 No. 06/20 petpla.net 23 Now, coming to products, REFIT comprises additives and colours that are dedicated to plastic recycling and offer a broad-spectrum support in the form of aesthetics enhancers and mechanical boosters: Anti Yellow (AY) additives and IV enhancers. The colour of rPET varies a lot from supplier to supplier (and even from one batch to the other) and depending on the ratio of recycled PET used, the result can be anything from grey or pale yellow, to blue or greenish. The more recycled content the bottle has, the darker the end colour will appear. The AY range comprises different liquid additives able to balance the appearance of variations in material and to regain brightness, correct a greenish or greyish tone. Mechanical challenges, instead include a drop of the IV when using rPET. This happens because PET, after several production cycles, due to degradation, shows a reduction in the molecular weight: its chains are shorter, and the final product is mechanically weaker. Repi’s IV Enhancer combine shorter molecular chain to longer ones, thus increasing the IV of the material. Besides additives, colours can also come to the rescue. When a very dark rPET is used and an Anti-Yellow additive is not enough, corrections through colour may be crucial. Repi’s Fumé colour range is made of shades like ambers, light blues, greens or greys, that are used at very low dosages (as low as 0.05%) so not to impact the recycling stream. The entire value chain of plastic packaging has been working hard and constantly for many years on making plastic recyclable and recycled. Now more than ever, I like to think that the world after the pandemic will be wiser and more collaborative on a global scale. I want to believe that we are learning that blaming one solution against the other is not the right choice because, after all, each challenge has different facets and none of them can be overshadowed. Let’s REfocus instead on what “delivering the circular economy” means, without forgetting the carbon footprint impact of our choices. This is the only way to get to structured solutions, that will be effective and positive in the long run. Let’s be careful not to look at circularity with too narrow lens. www.repi.com RAW MATERIALS CARRIER SYSTEM Assuming pigments and active ingredients are similar, carbon footprint of carrier will make the difference COLOUR CONCENTRATION • Carbon footprint proportional to volume and weight being transported • High colour concentration (lower LDR) will lower the carbon footprint PROCESSING TECHNOLOGY • Energy efficiency depends on processing technology, e.g. polymer extrusion vs mixing & grinding • PACKAGING TECHNOLOGY • PACKAGING MATERIALS • Energy efficiency of packaging technology • Carbon footprint of packaging materials • Recyclability COLOUR CONCENTRATION • Carbon footprint proportional to volume and weight being transported • High colour concentration (lower LDR) will lower the carbon footprint • DOSING SYSTEM • COLOUR/ ADDITIVE CHANGE • Carbon footprint of dosing system (mass and materials) • Energy efficiency of dosing technology (faster change and therefore shorter transition time and production waste • Efficiency in setup and change of setup • LDR • Quantity of colour • Recyclability RAW MATERIALS TRANSPORT COLOUR/ ADDITIVE MANUFACTURING COLOUR/ ADDITIVE PACKAGING COLOUR/ ADDITIVE TRANSPORT PRODUCT PROCESSING PRODUCT LIFECYCLE UP TO WASTE DISPOSAL 1 2 3 4 5 6 7 PROCESS STEP DRIVERS RATIONALS Liquid colours vs masterbatches - carbon footprint comparison","@ID":25}, "MATERIALS / RECYCLING PETplanet Insider Vol. 21 No. 06/20 petpla.net 16 Recycling food packaging: the role of PET Packaging containing more than one type of plastic presents specific challenges that the industry must overcome. Increasing environmental awareness has placed a lot of pressure on the use of plastics in packaging. Companies like Unilever, Evian, Wal-Mart, Amcor, PepsiCo and L’Oréal have committed to making their products 100% recyclable by 2025. Top web Base web Structure Yield / gsm Structure Yield / gsm Original format 12/45 PET/PE.EVOH.PE 58.8 270/50 PET/PE 418.6 Mono-PET format 30 PET 42.0 270 PET 372.6 Weight saving 29% 11% Fig.1: Raw proteins–typical challenge, presented by Mark Dawes, DuPont Teijin Films at Petcore Europe 2020 Virgin PET is used widely in bottles, films and trays in the food and beverage/groceries market; recycled PET (rPET) is found increasingly in, for example, bottles, in fibre and strapping, and insulation products. The food & beverage sector recognises the need to increase its use of rPET and to address problems of recycling within its own supply chain. The issues were discussed at the Petcore European Conference 2020. Trays PET is the material of choice for the tray component in packages for fresh produce (especially in the UK); ready meals; and proteins – primarily meat but also non-meat alternatives. Lids Making lids and tops of PE film complicates recycling. If multiple elements are not fully separated, the recycling stream becomes contaminated. Closing the loop: recycling and circular manufacturing At the Petcore conference in February 2020, Mark Dawes, Market Development Manager, DuPont Teijin Films, acknowledged that the established practice of making trays of PET and lids of PE has worked well for a long time; the sealing properties of PE are well known and have inspired confidence. Upcoming legislation, applying across the EU from 2025 and in the UK from 2022, will drive change. UK legislation will apply to plastic packaging with less than 30% recycled content and will affect all businesses that make or import packaging. The proposed measures will treat ‘easily separable components’, such as a lid and a tray, as two distinct and taxable items. Making trays and lids from the same material helps to mitigate the impact of the new tax. PET’s characteristics make it the most viable current option for closed-loop manufacture, for mechanically and chemically recycling back into itself with full food contact status. BoPET (biaxially-oriented PET) film offers the established PET characteristics of aroma barrier, protection, insulation, temperature resistance and mechanical strength. PET also offers potential benefits in terms of cost and packaging weight (see Fig.1) and the majority of applications can be converted immediately. PET: standalone product in recycling Dr Ana Fernandez, KP Films Corporation, pointed out that PET food packaging does not rely on other products in order to close the manufacturing loop and said that recycling thermoforms is the last step. 2016 saw a million PET sheets consumed in Europe, of which half was post-consumer rPET (PCR); 40% (400,000 t ) was virgin PET; 10% was industrial waste. Of those trays that contained more than 50% rPET, 40% were monoPET; 30% were PET/PE mix; and 30% were high barrier trays. Closed loop manufacturing will require the active co-operation of all stakeholders, including kerbside collections and recycling operations (see Fig.2). The industry has to stimulate demand for recyclable packaging and recycled content and design for sorting and recycling, which will be based upon the use primarily of clear and mono material. Coloured material must be NIR (near infra-red) detectable. Several projects addressing circular manufacturing and closed-loop recycling are currently in place across Europe, including: Thermoforming Working Group; Citeo Recyclage PB PET; CEUS “circular Economy for the Valorisation of Urban Plastic Waste”; PET Trays working group of the German Plastic Packaging Industry Association. The first “Holy Grail” research and development project achieved 70% efficiency in sorting monoPET and multiPET. It found that tray positioning affects detection rates but lids did not affect monoPET detection. Absorbent pads do, however; removal by final user should be encouraged. Holy Grail 2.0 achieved 100% detection in controlled tests at three metres/second, and upper 90% accuracy in mixed waste. It was also able to detect and account for inverted trays. The main recommendations are that trommels are useful for items of up to 40 mm diameter; shredders lead to low bulk density and generation of ‘fines’. Caustic washing at 95 oC for 10-15 minutes helps to Recycling Special","@ID":18}, "PETproducts 52 PETplanet Insider Vol. 21 No. 06/20 petpla.net Colors & Effects developed Sicopal Black K 0098 FK for smart recycling of dark plastics Recyclability is a decisive factor for plastics design. When coloured with carbon black, plastics go undetected by waste sorting machines. Even traces of carbon black can hinder the near infrared (NIR) sorting of polymer scrap due to the pigments absorbing properties. Consequently, the plastic cannot be detected for further recycling and the waste will be incinerated or landfilled. Therefore, replacing carbon black with the newly developed NIR-reflective Sicopal Black K 0098 FK contributes to smart recycling of plastics. Recyclability by design includes food contact compliance The new black offers high colour strength, opacity and food contact compliance, allowing its use in sensitive applications, like the colouration of food packaging. It is suitable for all commonly used plastics materials, including high heat polymers. Thanks to its good NIR-reflectivity Sicopal Black K 0098 FK allows the reliable detection of the polymer even at high pigment content. With its excellent processing stability, it can even be used for multiple processing steps and closed loop recycling. www.colors-effects.eu","@ID":54}, "MATERIALS / RECYCLING PETplanet Insider Vol. 21 No. 06/20 petpla.net 42 Pelletising and melt-delivery systems Producing virgin-like rPET by Frank Asmuss, Business Development Manager, and Stefan Wöstmann, Application Engineer, Nordson Corporation The worldwide boom in demand for recycled PET (rPET) has generated new challenges for polymer processing systems used to transform molten polymer from PET flake into highquality material for reuse. The biggest challenge involves bottle-to-bottle (B2B) recycling where regulatory and marketing mandates call for a dramatic increase in bottle collection and use of rPET in new packaging. Downstream of the extruder, the key equipment in rPET production lines includes so-called “melt delivery” components - gear pumps and screen changers; pelletising systems; and, as required, systems for crystallising pelletised material. Among the major post-extrusion challenges faced by processors of PET flake are intensifying requirements for: High levels of purity: Bottle flake feedstock includes considerable amounts of contaminants which must be filtered out by the screen changer. Melt pressure stability: A gear pump provides the uniform melt flow and pressure required for the process to operate efficiently and with uniformly high-quality product. The pressure requirements for each component downstream of the extruder must be calculated to determine the appropriate extruder drive rate and type of gear pump. Fineness of melt filtration: A fineness of 25-30μm is essential for bottle-to-fibre applications in order to extend the working life of the screen packs on the spinning line. In B2B recycling, finenesses are now increased from a typical former level of 60μm or more up to 40μm or less. By comparison, a young human eye cannot distinguish particles finer than 50μm. Minimal losses of polymer: The widely used “backflush” screen changer ejects some of the polymer melt as part of the process of removing contaminants. Over time, the amount of material loss can be substantial. One goal of development in screen changers is to reduce such losses. Energy efficiency: In conventional underwater pelletising systems, three phases where an energy input is required are 1) maintenance of the tempered water system circulating through the pelletiser; 2) drying of pellets; and 3) crystallisation. Reduction of energy consumption is one goal. High productivity: The maximum throughput now considered the state of the art in producing rPET pellets for bottle applications is approaching 5 t/h. For postextrusion components, achieving these rates depends on three factors: 1) component designs that yield streamlined flow properties; 2) enhanced control over melt pressure and temperature; and 3) reduction in downtime for troubleshooting and maintenance. Gear pump The gear pump shifts part of the job of building melt pressure from the extruder, thereby reducing stress on the extruder and on the processed material while delivering melt at the pressure level required by the screen changer and the following downstream equipment. In addition, the gear pump provides uniform flow, reducing surges and other process variations that can negatively affect the pelletising process and pellet uniformity. With use of a gear pump, the degassing system of an extruder can be made more reliable, and the extruder length can be reduced. Screen changer While typically deployed downstream of the extruder and upstream of the screen changer, the gear pump may be preceded by an additional screen changer that provides “prefiltration” at a level down to 1,000μm, removing large particles that can cause excessive wear to the gear pump. At this particle size, the contamination level is less than 0.1%, provided that there has been efficient washing and sorting prior to extrusion. Otherwise, the contamination level is larger. For the main filtration step in PET processing, a piston-actuated system with a self-cleaning feature based on a hydraulically powered process called backflushing is state-of-the-art. In a screen changer with four screen cavities, for example, melt flow is split into four streams. Backflushing starts when the pressure differential caused by contaminant build-up increases to a pre-set level. Melt is then compressed and discharged in reverse direction back through the screen, carrying away contaminant for removal from the system. The Recycling Special Gear pump","@ID":44}, "MATERIALS / RECYCLING PETplanet Insider Vol. 21 No. 06/20 petpla.net 19 cally possible under strict regulations and approval processes: mechanical or chemical. Mechanical recycling is currently the overwhelming reality in the industry. It is fairly simple since it is about shredding, washing and upgrading the original material. Chemical recycling, on the other hand, requires a longer cycle time. The molecules need to be broken up and the process of manufacturing the plastic from the very beginning needs to be restarted, creating additional costs. Nevertheless, at least three benefits are expected from chemical recycling technologies: the consistency of the quality of the recycled PET compared to virgin PET, absolute food safety and the possibility to mix the material with coloured and/or opaque PET. The willpower to push the packaging business towards a circular economy has revived chemical recycling. We are expecting to see it happen on an industrial scale in the next three to five years as a reasonable complement to mechanical recycling. For both mechanical and chemical recycling, collection and sorting are key regarding not only the quantity, but also the quality of the washed flakes, requiring adequate consumer behaviour, infrastructure and supporting regulation. However, if, as we assume, PET continues to be increasingly used in the future, the source of this PET remains an open question. Fossil-based vs bio-based vs bio-degradable Currently, the market is built on pure fossil-based PET with more than half of the world’s current synthetic fibre and bottle demand being met by PET. But when studying bio-based sources, we see that basically any kind of plastic can be made from them, raising the question as to whether we need to increase bioNO. ONE-WAY PRODUCTION. YES. TOP QUALITY RECYCLING. How can your recycled product meet permanently increasing demands? With the CHT range of high performance process solutions with environmental relief for the wet chemical cleaning. We support you directly on site and ensure your quality controls in our laboratories with state-of-the-art equipment. Thus, your strong position in the growing market is confirmed day by day. More about us at www.cht.com Mr Luc Desoutter Sustainability Officer at Sidel","@ID":21}, "MARKET SURVEY 32 PETplanet Insider Vol. 21 No. 06/20 petpla.net Company name Sidel Group Newamstar Packaging Machinery Co., Ltd. Postal address Telephone number Web site address Contact name Function Direct telephone number E-Mail Ave. de la Patrouille de France, CS 60627 Octeville sur Mer 76059 Le Havre cedex, France www.sidel.com Mr Stéphane Ménard, Mr Mathieu Druon Blowing Product Managers +33 232 858 687 stephane.menard@sidel.com; mathieu.druon@sidel.com East Xinjing Road, Zhangjiagang Eco. & Tech. Dev. Zone, Jiangsu 215618, P.R. China +86 512 5869 1111 www.newamstar.com market@newamstar.com 1. Machine designation / model number Sidel EvoBLOW Blower, 109 models Sidel EvoBLOW eHR (Heat Resistant) Blower, 38 models Sidel EvoBLOW PH (Preferential Heating) Blower, 18 models RBM2D/RBM6D/RBM8M/RBM8B/RBM10M/RBM10B/RBM12B/ RBM14B/RBM16M/RBM20M/RBM24S/RBM24M/RBM28S/ RBM28M/RBM30S/RBM36S/RBM40S 2. Bottle volume (from/to in litres) a) Standard machines From 0.25l to 3.5l From 0.25l to 2l From 0.25l to 2l (upon bottle dimensions) 0.16l - 2.5l b) Machines for large containers up to 5l Up to 3.5l Up to 3l (upon bottle dimensions) 3 - 20l 3. Maximum number of stretch-blow moulds (units) a) Standard machines From SBO 6 to SBO 34 (three frames, three oven pitches) From SBO 6 to SBO 28 (three frames, three oven pitches) From SBO 6 to SBO 22 8-40 b) Machines for large containers From SBO 6 to SBO 14 (one frame, three oven pitches) 2\\4\\6 4. Output per stretch-blow mould for: 0.5 litres CSD bottle (units per hour) 2,700 for XS mould size, 2,600 for M mould size, 2,400 for L mould size 2,000 for L mould size 2,000 for L mould size 12,000 - 81,000bph 1 litre CSD bottle (units per hour) 2,600 for M mould size, 2,400 for L mould size 2,000 for L mould size 2,000 for L mould size 4,000 - 60,000bph 1.5 litres still mineral water bottle (units per hour) 2,600 for M mould size, 2,400 for L mould size 2,000 for L mould size 2,000 for L mould size 4,000 - 45,000bph Large capacity container Up to 1,800 for L Jumbo mould size 1,800 for L Jumbo mould size 1,800 for L Jumbo mould size 2,000 - 6,000bph Other 2,000 for L eHR mould size for hot filled beverages 2,000 for L mould size 5. Footprint / space requirement (L x W x H in metres) MM model: 7.9 x 4.6 x 3.7 - GM model: 9 x 5 x 3.7 - LM model: 13.7 x 7 x 3.7 MM model: 7.9 x 4.6 x 3.7 - GM model: 9 x 5 x 3.7 - LM model: 13.7 x 7 x 3.7 MM model: 7.9 x 4.6 x 3.7 - GM model: 9 x 5 x 3.7 6. Special features (short description/ keywords) Maxi output smaller model / larger model: XS mould (up to 0.75l): 48,600 to 90,000bph; M mould (up to 2l): 15,600 to 67,200bph; L mould (up to 3.5l): 14,400 to 63,000bph; L Jumbo mould (up to 5l): 10,800 to 25,200bph Maxi output smaller model / larger model: L eHR mould: 10,800 to 56,000bph; electrical mould heating instead of oil mould heating Maxi output smaller model / larger model: 8,400 to 40,000bph; for flat and complex containers Efficient single mould capacity, perfect security system, quick-replaceable moulds, long-term continuously-running, energy-saving and lower consumption, capable for multi-type bottles, information processing system, remote monitoring and service module Company name Technopet Machineries Krones AG KHS Group Postal address Telephone number Web site address Contact name Function Direct telephone number E-Mail 14/15 ,Ground Floor,Shree Naman Plaza,S.V Road, Kandivali (west), Mumbai-400067, India +98 21040637 www.techno-pet.com Technopet Machineries Design, Engineering, Manufacturer & Exporter +98 2040637 sunil@technopet.in Boehmerwaldstr. 5 93073 Neutraubling, Germany +49 9401 700 www.krones.com Mr Peter Christiansen Head of Sales Plastics and Block Technology +49 9401 70 4980 peter.christiansen@krones.com Juchostraße 20 44143 Dortmund, Germany +49 231 569 0 www.khs.com Mr Marco Böhnke Product Manager +49 40 67907 483 marco.boehnke@khs.com 1. Machine designation / model number TP-OL 2400 AutoOL-3600 Auto-OL 6000 Jar 20L/ TSP 20L Contiform 3 Speed 12 models available Contiform 3 Pro 12 models available Contiform 3 Pro H 13 models available InnoPET Blomax Series V 2. Bottle volume (from/to in litres) 0.25 to 1 0.25 to 1 0.25 to 1 a) Standard machines 0.1 - 2.0 0.1 - 3.5 0.1 - 2.0 0.1 til 3.0 b) Machines for large containers 0.5 to 5 0.1 - 5.0 Up to 5.5 3. Maximum number of stretchblow moulds (units) 2 units 2 units 4 units a) Standard machines 30 28 28 6 til 36 (Regular station / 20 til 36 (Micro station)) b) Machines for large containers 1 units 12 4 til 8 4. Output per stretch-blowmould for: 0.5 litres CSD bottle (units per hour) 2,400bph 3,600bph 5400bph 2,750 2,500 2,000 (Heatset) Up to 2,800 1 litre CSD bottle (units per hour) 2,400bph 3,600bph 5400bph 2,500 2,500 2,000 (Heatset) Up to 2,500 1.5 litres still mineral water bottle (units per hour) 2,400 2,400 2,000 (Heatset) Up to 2,300 Large capacity container 200jpc/c 1,700 Up to 2,000 Other in ProShape & Contipure config. max. 2,300 in Multiprocess config. max. 2,500 Up to 2,000 5. Footprint / space requirement (L x W x H in metres) 1.5 x 1.1 x 2.5 2.2 x 2.0 x 2.5 3.1 x 2.5 x 3.0 from 5.4 x 6.5 x 4.6 to 6.8 x 12.8 x 4.6 from 5.4 x 6.5 x 4.6 to 7.5 x 12.8 x 4.6 from 5.4 x 6.5 x 4.6 to 7.5 x 14.0 x 4.6 5.69 x 3.45 x 3.75 up to 7.62 x 4.25 x 3.75 6. Special features (short description/keywords) Max 1 l, neck size:19-30 mm, Max.dia: 80 mm, max.height: 300mm, mould opening: 100mm; no. of cavity: 2 nos., type of mould: auto ejection, cavity distance: 110mm, preform; PCD in oven. 38 mm, mould thk: 170mm, preform neck cooling system: (360 degree, individul preform), IR heating system: 6 nos. ContiformBloc (Blower-Filler-Block); ContiformBloc BL(BlowerLabeler-Block); Ergobloc L& LM (Blower-Labeller-Filler-Block); ContipureAsept Bloc with integrated preform decontamination, ProShape (non-round bottle production). Bottle design and mould manufacturing; Bottle lightweighting concepts, Nitro-Hotfill;Air-Recycling Systems for Standard- and Heat-Set Machines; rapid product change-over systems (MouldXpress); automated mould change-over systems (MouldXpress Robot); integrated preform- and bottle inspection; Clever-Loc mould hanger: innovative mould hanger design for larger process angle and less complexity, Double Gate NIR oven for up to 50% less energy consumption, Focus Heater for better material usage and bottle light weighting, DuoCooling and Eco Dry for cooling energy reduction and higher hygiene due to less mould condensation","@ID":34}, "BOTTLE MAKING 50 PETplanet Insider Vol. 21 No. 06/20 petpla.net The Covid-19 emergency is likely to generate increased demand for personal hygiene and safety products, according to Sipa Small is beautiful Sipa expects the popularity of its ECS SP single-stage injection-stretch-blow moulding (ISBM) units will increase in the coming months as converters invest in equipment to manufacture small PET bottles that can be fitted with spray or dosing units for sanitising liquids. “The Covid-19 emergency is changing the way we live. When we emerge on the other side of the crisis, some things will return to the way they were but some things won’t. Generally, we hope we will learn from the experience and be better prepared for the future and for other crises, as yet unknown but as inevitable as the sunrise,” Sipa says. One of the issues that has been thrown into stark prominence is the importance of personal hygiene. Across the world, in all countries, whether they have been affected by the coronavirus or not, right at the top of the agenda is the injunction to “Wash your hands”. That message is likely to persist, well beyond the time when the emergency has passed. While regular washing with soap and water is the best way of preventing virus infection, that isn’t always possible. It is increasingly common for people to have a small liquid hand sanitizer handy, in a pocket or a handbag. Demand for smaller packaging As a result, Sipa expects the popularity of its ECS SP singlestage injection-stretch-blow moulding (ISBM) units will increase in the coming months, as converters invest in equipment to manufacture small PET bottles that can be fitted with spray or dosing units for sanitising liquids. The ECS range can be used to produce bottles as small as 10ml, which can be used for pharmaceuticals, cosmetics, food, liquor and nonfood products. Sipa has been involved with the design, development and production of ISBM systems for over 30 years. Its ECS equipment is capable of making a wide range of packaging, from miniature bottles through to large containers. The company says that they are popular with customers because costs associated with some elements of two-stage processing disappear – specifically, related to preform handling, storage, cooling and reheating. Flexible range of production Sipa’s range includes two models of four-station (injection, conditioning, blowing, discharge) ECS SP units specifically designed for small containers: ECS SP80 and ECS SP25 (the numbers refer to injection clamp force in tonnes). They are optimised for production of containers as small as 10ml but large tie-bar spacing enables the ECS SP80 to produce containers up to 12.5l in volume. ECS SP machines have compact footprints and are claimed to be energy efficient. They are designed to enable fast and straightforward changeovers between different product configurations; assembling and disassembling the neck-ring plate can be carried out by one person. The machines also handle preforms so as to enable moulding of neck and shoulder designs in ways impossible with two-step technology. The integrated production of preforms and bottles helps to eliminate scratches on finished products. Blow air pressure of up to 40bar can be used to produce sophisticated and complex bottle shapes. The ECS SP80 and SP25 can produce hot- fillable PET containers that withstand filling temperatures up to 90°C. Energy efficiency These ECS models are equipped use hybrid drives. They use hydraulics where large forces are required, such as in applying high clamp forces during preform production, for example. Fast, precise and energy-efficient movements, such as opening and closing of the blowing unit, plasticising screw and index rotation, are carried out by servoelectrics. This combination helps the machines to be more energy efficient and thus have a smaller carbon footprint than comparable equipment.","@ID":52}, "PREFORM PRODUCTION PETplanet Insider Vol. 21 No. 06/20 petpla.net 45 In-house preform production at Enrich Agro Food Products Strong growth with upward potential by Michael Maruschke Enrich Agro Food Products Pvt. Ltd., part of Kandhari Group of Industries, has been producing a wide range of soft drink products for over 30 years. Together with its group bottling associates, the company is presently one of the largest soft drink manufacturers in Northern India. It is a franchisee of Coke under a FOBO (Franchise Owned Bottling Operation) agreement and has a strong focus on the CSD and juice segments. It has been growing strongly, in recent years especially; it doubled sales and almost tripled capacity in the past 48 months. Enrich Agro Food Products Pvt. Ltd. May, 2019 We met: Mr Pradeep Kumar, President Finance & Corporate Affairs Heritage Beverages, an associate of Enrich Agro Food, produces preforms. It has five Husky systems: two 32 cavity systems; a 72 cavity system and two 96 cavity systems. Total installed PET resin processing capacity is 21,000 t/a. In-house consumption of Heritage preforms accounts for 80% of output; the remainder is destined for other Coke bottlers. Versatile Polytech, another associate of Enrich Agro Food, has three Husky systems, with 56, 48 and 32 cavities, and has a PET resin processing capacity of 7,000 t/a. About 75% of its production is for in-house consumption. Vertical integration We asked Pradeep Kumar why the company decided to build up its own preform production. The answer is that Enrich Agro Food experienced severe shortages of preforms in the past and it wanted to be better positioned for further growth, so the owners determined to start inhouse production, something that Pradeep now sees as a fast-growing trend among Coca-Cola bottlers. He received a lot of support from Husky, who not only supplied the preform systems but also supported the company with necessary know-how. The market and the future Pradeep Kumar has been part of the company from the start; he signed the first registration deed and agreement for the production plants, he mentions with a smile. He continues to see very good growth potential for the Indian market. The consumption of soft drinks in India is still at a low level, at just 18-19 bottles per person annually; neighbouring Asian countries have up to 30. India’s population is still overwhelmingly rural; only 20-30% live in urban areas, which means there is huge potential in the 70-80% rural dwellers, which remains to be tapped. Pradeep Kumar in his office German Technology Tour Sponsors:","@ID":47}, "MATERIALS / RECYCLING PETplanet Insider Vol. 21 No. 06/20 petpla.net 20 based PET, which currently accounts for only 1% of the total PET production for packaging. In fact, this appears to be one of the most promising endeavours on the industry’s horizon as the big advantage of making bio-based PET is that we already have a whole industrial system set up today. The process and installation remain the same, and the PET material produced is strictly identical, still being 100% recyclable and compatible with existing and future recycling streams. We have to acknowledge that there is also a discussion about biodegradable plastics as an alternative to PET in the industry. As there is a lot of confusion existing between bio-based and bio-degradable materials, we want to clarify that there are fossil-based materials that are biodegradable as well as bio-sourced materials that are not bio-degradable and vice versa. The ratio of bio-degradable materials within the bio-based category is about 55%. However, we do not expect this development to catch on for two reasons: firstly, if degradation begins during the shelf life of the container, recycling would become complex, because you might collect and enter a container that is already degrading into the recycling stream. Secondly, Sidel and their customers see biodegradable claims as an incentive for consumers to throw away packaging, counting on the fact that it will simply disappear. In most cases the material will not degrade in an unsupervised, natural environment, for example a marine environment, but only under very specific conditions, such as industrial composting. In addition, biological degradation generates CO2 or even methane, contributing to GHG. PET collection, sorting and recycling are definitively the best solutions to minimise the environmental impact in all directions. Recycled PET and tethered caps For Sidel, there are other, more promising options out there to tackle the future challenges of packaging. The most significant one is rPET, as its carbon footprint is nearly five times lower than virgin PET. Its first intrinsic growth factor is consumer acceptance – people are ready to consume their beverages in 100% rPET bottles, something they may have been opposed to in the past. The second factor is the external regulation changes within the EU. The directive on SUP that was passed in early 2019 will have a massive impact on the packaging value stream of the future: by 2025, for example, the EU demands 25% of mandatory rPET content in bottles. This figure is intended to reach 30% in all plastic bottles by 2030 with key players in the industry opting for even more ambitious targets. Moreover, rPET content is not the only variable the EU intends to regulate. The European Commission is also speeding things up in terms of collection targets: for instance, a 90% collection target has been set for all member states by 2029. Converting to rPET is a significant change for the entire industry. Depending on collection methods and bottle origin, its quality varies. Therefore, Sidel is stating that it is their goal to develop technologies that are not affected by this inconsistency, but are ensured by designing different blower generations with re-heating and blowing wider processing windows. Under development is the laser oven technology as an alternative to the currently used infrared solution: a vertical-cavity surface-emitting-laser (VCSEL) diode extends the process capability and versatility of existing blowers for improved bottle design flexibility and greater packaging opportunities. The heating process is accurate and stable, allowing consistent material distribution for greater efficiency and a premium material for complex bottle design from the very outset of the production. This solution is claimed to have high potential for the future where Sidel might be able to deliver a blower that can handle up to 100% of rPET. Furthermore, Sidel’s rPET testing platform is contributing to this purpose, boosting the development and qualification of bottles with increasing rPET content. In a similar attempt to tackle plastic waste, the EU has also agreed to implement a mandatory tethered cap for all beverage containers up to 3 l by 2024 to keep the bottle and the cap attached to each other until both hit the recycling facilities, thus keeping bottle caps from freely floating in the oceans. While the law technically only impacts Europe, a global change is expected in the coming years due to European companies exporting their goods abroad, and Europe in turn importing goods from other countries, which will have to be compliant with this directive. It is unlikely that any key industry player will manage two different supply chains in parallel, i.e. one with and one without tethered caps. Additionally, we are seeing a similar push for tethered caps in some parts of the United States, with, for example, California striving for a similar law. Therefore, in the next decade, it is probable that anywhere in the world, PET bottles will have a tethered cap. Refillable PET bottles Besides rPET, there is another development on the beverage market looking promising: refillable bottles (ref-PET). In fact, relaunching ref-PET bottles is one of the top priorities for big players within the beverage market to lower the environmental footprint, using the bottles in the same way refillable glass bottles are used – minus the heavy transportation costs and fragility. Compared to one-way PET, it will depend on its effective number of uses and on logistics. The environmenVincent Le Guen, Vice President Packaging at Sidel","@ID":22}, "TOP TALK 15 PETplanet Insider Vol. 21 Alan: Our USA parent company are seeing pretty much the same results as we are in the United Kingdom with record sales, healthy workforce and working hard to meet customer demands. PETplanet: Of course, no-one knows how businesses will emerge from this crisis. In Europe some countries have started to ease the lockdown and are now talking about opening the borders. All very positive. In your view, how will your business and the economy fare in the last quarter of 2020? Alan: To answer that question I will need a Chrystal ball, this year is proving to be better than I anticipated and we have orders to fulfil through September but what the end of the year is going to bring is a guess with concerns about Covid-19 and also we have the not talked about Brexit. All we can do at R&D/Leverage is keep our workforce healthy and continue offering the World beating complete solution to the Injection Stretch Blow Moulding (ISBM) industry, thankfully in prior years we invested heavily in state of the art manufacturing equipment, latest technology inspection equipment and our 10 ISBM machines so we have everything in place to continue expanding through 2020 and beyond. Last year we secured our third facility at our Nottinghamshire site this gave us an extra 25% manufacturing and office space. PETplanet: In your view, what lessons will be learned for the economy and financial planning as a result of the pandemic? What plans are R&D Leverage developing for the post-crisis future? Alan: One topic that needs to be highlighted is that the dreaded plastic everyone wanted to talk about is now being recognised as a life saver in the fight against Covi-19. Plastic is not the problem, its people and governments who fail to recycle are the problem. Life is very different at the moment and this is probably the new normal where customers are not visiting R&D/Leverage, we are not visiting our global customers and we are relying more and more on technology to interface with not only our customers but also our families. I am not too sure life will go back to as it was before so trade fairs may become a thing of the past only time will tell. PETplanet: Thank you very much Alan! www.rdleverage.com","@ID":17}, "MATERIALS / RECYCLING PETplanet Insider Vol. 21 No. 06/20 petpla.net 38 Fit for recycled material thanks to retrofitted line components PET sheet lines “The demand for PET packaging sheet, which contains a high proportion of recycled material or is even made of 100% of it, has recently increased enormously due to public discussion and legal requirements.” states Gneuss and offers an economic approach. Recycling Special In order to be able to meet these requirements, many processors are confronted with high investment costs for equipment that can process recycled materials. After all, the quality of the end product must be good. A possibility to combine low investment costs with an extended processing window for recycled material is offered by Gneuss Kunststofftechnik GmbH from Bad Oeynhausen, Germany with a special retrofit service. One of the companies using this service is Cotnyl S.A. from San Martín, thus being the first company in Argentina to obtain local approval to produce packaging made of 100% rPET. On the one hand, the demand for plastic packaging is constantly increasing worldwide due to changing consumption and consumption habits, especially in the food and beverage sector. On the other hand, plastic packaging in particular has fallen into disrepute and has received new, often negative attention from the public. The call for waste reduction and reasonable recycling of plastic packaging is becoming ever louder. The European Union has drawn up legal directives which stipulate that by December 31, 2025 50% of plastic packaging placed on the market in an EU member state must be recycled. By the end of 2030 it should be 55% and from 2040 onwards all plastic packaging should be 100% reused or recycled so that a closed cycle is achieved. The market is already responding: according to a recent report by the British consultancy firm Eunomia, consumption of rPET in the EU in 2018 was around 1.4 million tonnes, accounting for 26% of the total demand for PET of 5.3 million tonnes. By 2030, experts expect an increase in demand for rPET of up to 55%. Approximately 20% of the existing rPET is used for PET trays throughout Europe, with the average proportion of recycled material already at 50% - and the trend is rising. This increased use of recycled materials poses problems for many packaging manufacturers. A recycling rate of up to 100% and the required recyclable design do not always meet the requirements for packaging, especially for food packaging. Food authorities and consumers expect the highest quality in terms of colour, purity, odour and mechanical properties. The desired properties often cannot be achieved with existing equipment designed for processing virgin materials. Investments in completely new lines, with which the processing of recycled materials is successful, are not always possible for economic or space reasons. An alternative is the Gneuss retrofit. Filtration system indispensable for high contamination levels Gneuss retrofitting is a good alternative for processing recycled materials. For example, Integrity from Chile has been using rotary filtration systems for several years now to produce PET thermoformed trays with 70% recycled content. This is possible thanks the patented filter disc technology, with constant pressure and fully automatically working. The high and fluctuating levels of contamination of the input material are a major problem in recycling processing. Especially due to the increasing demand for packaging with a high recycled content, the highquality recycled material, which mostly come from sorted bottle fractions, have become scarce and processors have to fall back on inferior recycled materials with higher degrees of contamination. This has enormous effects on the filtration process. Screens get dirty faster and as screen contamination increases, the pressure upstream of the filter increases, which in turn can lead to temperature and viscosity fluctuations, and finally the available area for the melt to pass through is reduced. This is where the RSFgenius filtration systems with back-flushing technology fully show their advantages. The screen cleaning is carried out fully automatically during the running production process via an integrated backflushing piston system, in which only a small portion of filtered melt is regularly shot through the dirty screen via a narrow gap by means of high-pressure pulses. The quantity required for this is freely adjustable and in practice corresponds to about 0.01 to 1% of the throughput. This means that the loss is significantly lower than with other systems available on the market, which operate with losses of up to 5%, which on the one hand reduces the margin and on the other hand leads again to","@ID":40}, "PETcontents 4 PETplanet Insider Vol. 21 No. 06/20 petpla.net 06/20 INSIDE TRACK 3 Editorial 4 Contents 6 News 52 Products 53 On site 54 PET bottles for Beverage + Liquid Food 55 PET bottles for Home + Personal Care 56 Patents TOP TALK 10 “When the emergency is over, we’ll all have to learn to live and work differently” - Interview with Vezio Bernardi, Sacmi 14 The times they are a-changin’ - Interview with Alan Tolley, R&D/Leverage MATERIALS / RECYCLING 16 Recycling food packaging: the role of PET 18 Is there a sustainable future for PET packaging? 22 It is time to RE-focus 24 High opacity, low TiO2 - New masterbatch offers “circular economy” design and zero TiO2 26 White, opaque, recyclable - Bottle-to-bottle recycling of light barrier white opaque PET 27 Reduced off-odour of plastic recyclates - Separate collection of packaging waste 28 From PET to protection against coronavirus 30 A plastic keg in a circular economy? 34 Closed plastics loop with sustainable systems - Recycled PET research since 2012 36 Doubling rPET capacity - Alpla expands PET recycling plant in Poland 38 PET sheet lines - Fit for recycled material thanks to retrofitted line components 40 Meeting evolving requirements - High-purity plastic flakes and increase productivity 42 Producing virgin-like rPET - Pelletising and melt-delivery systems MARKET SURVEY 31 Suppliers of two-stage SBM machinery PREFORM PRODUCTION 45 Strong growth with upward potential - In-house preform production at Enrich Agro Food Products 46 Preforms and closures for local brands BOTTLING / FILLING 48 Flavoured milk in aseptic bottles BOTTLE MAKING 50 Small is beautiful - The Covid-19 emergency is likely to generate increased demand for personal hygiene and safety products, according to Sipa BUYER’S GUIDE 57 Get listed! Recycling Special Page 36243648 Page 18 Page 50","@ID":6}, "MATERIALS / RECYCLING PETplanet Insider Vol. 21 No. 06/20 petpla.net 25 with the same opacity and whiteness. Depending on the target application, it could even be formulated with no minerals. The synergy between microstructured wall and light scattering is still at the core of pennaholt masterbatch. Its mechanism is created by a composition of inert particles and a highly engineered organic polymer, with high molecular weight and high thermal stability, that is FDA approved and REACH compliant. On the recycling side, Penn Color says that pennaholt meets the APR and EPBP guidelines on elutriation, extrusion, solid stating and material IV, with 50% rPET blend. When taken through multiple cycles of bottle-to-bottle closedloop recycling, PET bottles with the latest version exhibit no difference to clear PET bottles in terms of IV loss, either. Supporting the ‘circular economy’ The industry only puts on the market packages that are fully compliant with Health and Safety regulations. That requires the strict control of Non Intentionally Added Substances (NIAS) in the package. However, higher content of recycled material in packages and more recycling closed loops could risk NIAS build-up in the circular economy streams. Penn Color says that pennaholt is specifically formulated to reduce NIAS, with substances of higher level of purity and thermostability than found in conventional masterbatches. In a specific scenario of three closed loops of manufacturing, recycling and re-using with 100% rPET, analytical tests found 50% fewer NIAS with pennaholt than with a conventional TiO2 based masterbatch. Penn Color asserts that, as a platform technology, pennaholt allows the creation of bespoke formulations, for both monolayer and multilayer packages, to not just support but actually get ahead of global circularity and regulatory trends. www.penncolor.com MATERIALS / RECYCLING 25 E N D L E S S I N N O V A T I O N S I N C E 1 9 1 9","@ID":27}, "MATERIALS / RECYCLING PETplanet Insider Vol. 21 No. 06/20 petpla.net 34 Recycled PET research since 2012 Closed plastics loop with sustainable systems The debate on plastic is presenting the beverage and food industries with a number of big challenges. The KHS Group is clear that the increased use of recycled PET provides a significant partial solution to this problem. The Dortmund systems supplier is thus focusing on sustainable products and services which help to close the recycling loop. According to business magazine Forbes, around 140 PET bottles per head are circulated in Europe each year, with this figure more than twice that in the USA at 290. Despite all the criticism the plastic container is actually growing in popularity, with the number used increasing globally by around 4% per year. Awareness of the need to recycle is also on the rise, however; according to Forbes, an estimated 57% of all used PET bottles were collected worldwide in 2019. For 2029 the magazine forecasts that this rate will increase to 68% – albeit with major differences from region to region. While 57% of all bottles could be collected in Europe, in the USA this would only amount to 30%. China, on the other hand, could become something of a model student and in ten years achieve an impressive collection rate of 82%. Collecting does not necessarily mean recycling, however: in the USA 70% of all collected plastics end up at waste disposal sites – and in Europe 30%. Practically made for recycling: plastic Yet plastic can be very easily recycled, especially PET. It is the only plastic that, when recycled, satisfies the legal requirements governing food grade materials. Whereas with other materials, such as polypropylene, polyethylene and polystyrene, the loss of quality which occurs on application of the usual recycling methods is irreversible, recycled PET can always be brought up to the standard of new material. It is thus no surprise to learn that of the approximately 477,000mt of PET used each year to make bottles in Germany alone, about 93% of this material is recovered and reused. Only roughly a third of this is used to make new bottles; the rest goes into the manufacturing of films and especially textile fibres. This means that the bottle-to-bottle recycling loop is deprived of a large percentage of this raw material. There is also the development in price to be considered: while the cost of what is known as virgin PET is based on that of crude oil and benefits from the current low Recycling Special","@ID":36}, "MARKET SURVEY 33 PETplanet Insider Vol. 21 No. 06/20 petpla.net TES STM Group Sipa Street Magnacka 6, Kowale 80-180, Poland +48 583 017 181 www.tes.com.pl Mr Mateusz Kinda Sales Director +48 503 036 635 mk@stm-pack.com Via Caduti del Lavoro 3 31029 Vittorio Veneto, Italy +39 0438911511 www.sipa.it Mr Paolo De Nardi Project Leader/Stretch- Blow Molders Development +39 0438911624 p.denardi@zoppas.com Blue line hi-Tech series - linear machines Sidel EvoBlow Predis, 54 models Rotary Blowmoulders: XTRA: 6 to 24 (8 models) Linear Blowmoulders: SFL 6: 6/8, 6/6, 6/6 XXL, 6/4 XL, 6/4 XXL, 6/3 XL (5 models); SFL 4: 4/4, 4/3 XL, 4/2 XL (3 models); SFL 4 Wide Mouth: 4/4 WM, 4/3 WM XL (2 models); SFL 2/2 & SFL 1XL (2 models) 10ml - 3l; from 0.25l to 2l From 250ml to 3.5l From 250ml to 3.0l 3l - 10l; not applicable From 5l to 30l 8 from SBO 6 to SBO 26 (two frames, two oven pitches) 24 8 4 from SBO 6 to SBO 14 (one frame, two oven pitches) 2 2200 2,500 for XS mould size; 2,500 for M mould size; 2,400 for L mould size 2,550 per cav. 1,800bhc 2000 2,400 for M mould size; , 2,250 for L mould size 2,550 per cav. 1,600bhc 2000 2,400 for M mould size; 2,250 for L mould size 2,550 per cav. 1,800bhc 1,200; not applicable 650bhc Hot fill mould - 1,500 per cav., for juices, tea, sport drinks, milk-base products Up to 5.5 x 1.8 x 2.7 ( without preform feeding system); MM model: 7.9 x 4.6 x 3.7 Full electric sbm machines from 2 to 8 cav. with: air recovery systems for reducing consumption low and high pressure; hot air recovery system for preheating preforms in oven; Multiflex system - one machine many bottle necks diameter; hot filling version with electric mould heating; preferential heating - for difficult shapes oval and flat bottles; deep grip mould option Maxi output smaller model / larger model: XS mould (up to 0.75 litre): 45,000 to 60,000bph; M mould (up to 2l): 15,000 to 60,000bph; L mould (up to 3.5l): 14,400 to 57,600bph; dry preform sterilisation -Predis-, for aseptic bottling with no blower sterilisation Best output 2,550bph/cav. with best process & active angle: easy to blow. Reduced TCO: lower air & energy consumption (-25%). 30sec. to change blow mould (tool-less), simple use & maintenance. rPET easy process. Bottles for water, oil, csd, heat resistant, oval simmetric and asimmetric, with preferential heating, neck orientation, with handle, wide mouth (up to 130mm NF), large size (up to 30l), rPET, Tritan, PE, OPP Chumpower Machinery Corporation 1 Blow PET Technologies No.688-1, Sec. 3, Zhongshan Rd., Wuri Dist. Taichung City 414, Taiwan +88 6423 388 289 www.chumpower.com Mr Michael Lee Sales Manager +88 6905 363 828 sales@chumpower.com 25 Chemin de Gerocourt 95650 Boissy l'Aillerie, France +33 9800 820 70 www.1blow.com Mr Olivier Perche Sales Director +33 9800 820 75 operche@1blow.com Grünlandgasse 5/1/12 2620 Neunkirchen, Austria +43 720 775 196 www.pet-eu.com Mr Maxim Poliansky CEO +43 720 902 169 office@pet-eu.com CPSB - L1G/L1GM/L2GM/LS2G/LL3/L3M/LL4/L4M/L5M/LS6/LS6H/ LS7M/LS8/LSS8/LS8H/LS9/LS10/LSS10/LSS12/LSS12H/LSS14 1XXL / 1XXLN / 1XL / 1XL Lab / 2L / 2LN / 2LO /2LHF / 2XL NEW / 4L / 4LN / 4LO / 4LHF / 4XLS / 5M / 6MO APF-Max series 8 models avaliable APF-6004, APF-3002 APF-10, APF-5 APF-30 6 0.10 to 12l 0.2 - 3 0.2 - 2 20 5 to 30l 3 - 10 15 - 40 14 6 8 4 2 1 2 1 2,000 1,750 1,500 1,800 1,750 1,500 1,700 1,750 1,500 1,000 for 5l ; 600 for 20l 1,250 500 for 20-40l 2.1 x 1.6 x 2.4 9.5 x 3.3 x 3.2 APF-6004: 8.6 x 3.2 x 2.5 APF-3002: 6.4 x 2.8 x 2.3 APF-10: 8.2 x 3.4 x 2.6 APF-5: 7.4 x 3.2 x 2.7 6.7 x 2.4 x 3.1 Narrow-pitch mandrel chain to heat more preforms at one time, continuous rotation to achieve preform heating, neck shied throughout to prevent neck deformation during heating, ventilation system to ensure flat equilibrium temperature profile throughout prefrom thickness, infrared heat sensor for close-loop preform heating. Preferential Heating (oval bottles), neck orientation (with standard preforms), Hot Fill, compatible with Sidel, Krones, KHS, Sipa, Side moulds, recovery of blowing air, power recovery, 5M-C available as a Combi in cooperation with Ermi and Synerlink, integrated ink jet coding unit. New: Integrated leak tester, Sure Grip device for blow-moulded hand grip and selective access to HMI through badge reader Modular system 4-6-8 cavities, NIR heating system, hot fill option, quick changeover to other preform type, blow mold quick change Quick mould change, air recovery system, oval and complex shapes, space saving dimensions, hot fill option, patented mould closing system Lightweight containers for 3-6l with 38mm preform, APF-5: 2 independent blowing units to produce 2 bottle formats/volumes by turns Possible to blow PET kegs and 4-5 US gallon returnable and one-way watercooler bottles","@ID":35}, "MATERIALS / RECYCLING PETplanet Insider Vol. 21 No. 06/20 petpla.net 36 Alpla expands PET recycling plant in Poland Doubling rPET capacity A new rPET extrusion system went into operation in early May 2020 at the recycling plant PET Recycling Team in Radomsko, Poland. As a result, the capacity for rPET (PET regrind material) will be doubled from 15,000 to 30,000 tonnes per annum. In this article, Georg Lässer, Head of Recycling at Alpla, explains this new development. ‘A key target is the expansion of recycling activities by 2025.’ is the mantra running through every fibre of the Alpla organisation. At the end of 2018, the company signed the New Plastics Economy Global Commitment – an initiative of the Ellen MacArthur Foundation – which, amongst other things, commits to investing a total of 50 million euros in pursuit of this aim. “We take this voluntary commitment seriously and have initiated several international projects, such as the construction of a recycling plant in Thailand. We are also investing in the expansion and improvement of our existing recycling plants. We aim to process even more recycled material for the bottle-to-bottle cycle and make the production processes at our recycling plants more sustainable by means of modernisation.” explains Georg Lässer. New extrusion line in Poland At the beginning of May, a second rPET extrusion line went into operation at Alpla’s PET recycling plant in Radomsko. The 90 employees at PET Recycling Team Radomsko produce 30,000 tonnes of flakes a year from post-consumer material. Of this figure, 15,000 tonnes a year have thus far been extruded to produce regrind material. With the new system, the capacity will increase to 30,000 tonnes a year. As a result, the company is doubling the capacity for high-quality rPET, which can then be fed back into the bottle cycle. Downcycling (e.g. the use of flakes to produce film or their deployment in the textile industry) will largely be avoided. Instead, 30,000 t of regrind material will now be used solely to produce new packaging units for European customers – in keeping with the bottle-to-bottle principle. What’s more, all the input material – known as ‘post-consumer material’ – also comes from Europe, i.e. from Poland and neighbouring countries. Recycling Special Quality check in the PRT Radomosko laboratory Grinding and washing devices","@ID":38}, "MATERIALS / RECYCLING PETplanet Insider Vol. 21 No. 06/20 petpla.net 43 sequence is performed for each cavity one after the other. In normal operation, polymer is flowing through all four cavities. While one of the cavities is cleaned, production continues through the other three. There are two challenges to improving this type of screen changer: to reduce downtime by extending the working life of the screens and thus reducing the frequency of required screen changes; and, to cut back on material loss by reducing both the amount of polymer expended per backflush cycle and the number of cycles needed. With a ton of PET bottle flake selling at EUR920 ($ 1,000 USD), material losses with a standard backflush screen changer, operating on a 24/7 basis, can amount to more than EUR100,000 ($ 108,467 USD) per year. To address these issues, Nordson has developed a filter stack composed of multiple so-called FlexDiscs which replaces the standard screen in each cavity, substantially enlarging filtration area while decreasing the melt loss caused by backflushing. Each filter stack consists of two to four cassettes, with two screen packs in each cassette. clog in subsequent post-pelletising equipment as well as in hoppers and feed throats. Downstream of the pelletiser are the pellet dryer and the tempered water system. After process water has been used in the pelletiser cutting chamber and for transporting pellets to the dryer, it needs to be cleaned of fines and cooled to within a strictly maintained temperature range for reuse in the pelletising cycle. Finesremoval components in tempered water systems range from a woven wire mesh screen that periodically must be removed and cleaned manually, to systems that reduce downtime and operator intervention by providing continuous, automated filtration. Still more advanced is an automated, selfcleaning system that reduces overall pelletiser energy consumption by 10 to 17% by eliminating the need for a separate fines-removal system, which in standard systems requires a secondary, dedicated water pump. Reductions in downtime and material loss with BKG FlexDisc filter stack for screen changers Competitor (8 cavities) BKG HiCon V-Type-250-3G with BKG FlexDisc Throughput 1,800 kg/hr 3,968 lbs/hr 1,800 kg/hr 3,968 lbs/hr Filter fineness 30 micron 30 micron Filter area 1,814 cm² 4,000 cm² Screen changes per day 2 to 3 ---- Screen changes per week 14 to 21 2 Screen working life [hours] 8 to 12 110 Maximum number of backflushes 20 120 Material loss per backflush cycle 11.33 kg (25 lb) 9.97 kg (22 lb) Material loss per day 680 kg (1,500 lb) 239 kg (528 lb) Material savings ---- 65% Source: Nordson Corporation Backflush screen changer FlexDisc Underwater Pelletiser In PET recycling, backflush screen changers combined with FlexDisc filter stacks have provided filtration as fine as 25-30μm, increased screen lifetime, and exhibited more than 50% less material loss vs. comparable screen changers. Comparative data from trials at one recycling company appear in Table 1. Pelletising systems Two types of pelletising system are used in PET recycling: strand pelletisers and underwater pelletisers (UWPs). Widely used for recycling, UWPs are claimed to provide several advantages over strand pelletisers. The UWP can achieve great throughput rates and is more capable of automation, making possible linkage with the upstream process. Unfortunately a larger capital investment is required for realising these benefits. Unlike strand pelletising, underwater production of pellets is a closed process, minimising emissions as well as the generation of dust during production and in the final product. With constant melt flow (ideally ensured by a gear pump) and the flow uniformity provided by a round die plate, underwater pelletising yields the most consistent pellet size distribution. The spherical shape of pellets produced under water results in 5 to 10% greater bulk density compared to cylindrical pellets, and it reduces their tendency to","@ID":45}, "TOP TALK PETplanet Insider Vol. 21 No. 06/20 petpla.net 10 Interview with Vezio Bernardi, General Manager Sacmi Closures Containers PET QPC, on how to navigate a company through the Covid-19 crisis “When the emergency is over, we’ll all have to learn to live and work differently” by Gabriele Kosmehl The north is the region of Italy where the country’s engineering companies are located, and the north of Italy is also the first region in Europe where the coronavirus has struck fully. We would like to thank Vezio Bernardi for giving us a picture of the mood at the middle of May about Sacmi’s handling of the crisis situation, market developments and an outlook to the time after the crisis. PETplanet: First of all, where are you talking to us from right now? From your office desk or your home office? Bernardi: At the moment I’m working from home and just going into the office to deal with essential paperwork. Many national governments, including Italy’s, have imposed severe social distancing measures. These have, during this first phase, played an essential part in stemming the spread of a worldwide virus that is having inevitable repercussions on the way we live and work. Nonetheless, we’ve shown - by combining the advantages of IT with personal commitment - that it’s possible to carry on working at the highest level, keep in touch with customers and safeguard the efficiency and professionalism of our services as we await the time when we can get back to nurturing relationships directly with all our partners”. PETplanet: Northern Italy, where the headquarters of your company is located, was the first region after China that had to fight the coronavirus, and is still doing so. When did you realise that the virus could have a major impact and what measures did you take in response? Bernardi: At this stage, Sacmi’s motto was ‘Let’s move forward. Together’. Let’s take, for a moment, a closer look at what that means. True, Northern Italy, especially Lombardy, was where the virus hit hardest, with many people falling victim to it, especially among the most vulnerable. Fortunately, Italy is a developed nation with the ability to come together and deal with what is an epochal crisis, one that has, in fact, affected the country’s different regions in different ways. In this regard, I wish to point out that in Imola, a town of 70,000 inhabitants that’s home to Sacmi’s parent company, the situation has always been under the full control of the health authorities, with limited contagion and even more limited fatalities. Nonetheless, right from the earliest stages the Sacmi Group’s policy was one of scrupulous compliance with all the instructions issued by the health authorities, the government guidelines and, of course, common sense. Sacmi is already geared up for the reopening, also because the government immediately categorised the work done by Closures-Beverage as part of the ‘essential’ supply chains, so production was unaffected by stoppages”. PETplanet: What does this “gearing up” look like, what protective measures are currently still being implemented at your sites? Bernardi: As I said, our supply chain has not undergone any interruption. But the most important thing is that Sacmi as a whole - which works in various industries - immediately began to seek a way forward that would, first and foremost, protect our staff, suppliers, customers and partners’ health while allowing production and assistance services to continue. This is why it was essential for some workers to start working from home. At the same time, for personnel who still needed to come in to the company, we adopted every possible precaution, from PPE to sanitisation of premises, all under the daily control of a task force, specifically put together to cope with the emergency. PETplanet: Do you think that concepts like working from home will be firmly established on a larger scale at Sacmi even after the coronavirus crisis? Bernardi: I think this situation has accelerated what was already an ongoing process, often slowed more by bias and consolidated habit than","@ID":12}, "7 NEWS PETplanet Insider Vol. 21 No. 06/20 petpla.net In the current situation of social, health and economic challenges, the PET industry shows its innovative side. We receive a lot of news about short-term adjustments that ensure the continuity of production under increased hygienic standards. And there are also many projects that were realised with a lot of heart and soul in a very short time in order to provide support to the healthcare sector. PETplanet collects official statements from customers & companies in the PET value chain on how they cope with the situation on petpla.net (regular updates). Thyssenkrupp to build second polymer plant for Köksan in Turkey Thyssenkrupp’s plant engineering business has won a second order from the Turkish packaging producer Köksan for a new PET production plant. The plant will be built in Gaziantep, Turkey, next to an existing production line erected by thyssenkrupp in 2013. Its construction will double the site’s production capacity to 432,000t of PET resin per year. Completion and commissioning are planned for 2022. The plant will use the Melt-ToResin (MTR) process patented by thyssenkrupp’s subsidiary Uhde Inventa Fischer to produce various grades of resin. With this investment, Köksan intends to strengthen its market position both nationally and in the region. The PET will be supplied to the local market as well as to countries of the Middle East, CIS, America, Europe, andAfrica regions. According to Werner Steinauer, CEO of Uhde Inventa-Fischer, the plant can also be fed with a certain amount of recycled PET to meet the changing needs of customers and local authorities. The MTR process developed by thyssenkrupp is a continuous polycondensation process that obviates the need for the solid-state-postcondensation process steps in the production of PET resin. This leads to energy savings, reduced investment, operating and maintenance costs and a higher raw material yield compared to conventional technologies. The technology is claimed to meet today’s demand for sustainability by reducing the carbon footprint in terms of fuel and electrical energy by up to 30 per cent. A retrofitting of the plants with Thyssen-krupp’s FTR (Flakes-ToResin) recycling technology is also possible. www.thyssenkrupp-industrialsolutions.com","@ID":9}, "MATERIALS / RECYCLING PETplanet Insider Vol. 21 No. 06/20 petpla.net 18 Is there a sustainable future for PET packaging? by Luc Desoutter, Sustainability Officer Sidel and Vincent Le Guen, Vice President Packaging Sidel Packaging in general has come under a lot of fire in the past few years, with different types of plastics under intense scrutiny. Therefore, many brand owners and suppliers are taking increasing care when it comes to packaging and especially the type of packaging materials they opt for. Simultaneously, governments and regulators are attempting to decrease the overall amount of waste created on a global scale, sometimes going for quick fixes that can result in unintended consequences. In this article, Luc Desoutter and Vincent Le Guen from Sidel explain the paradox about PET bottles becoming the symbol of ocean waste and Single Use Plastics (SUP), while PET is the most recyclable and the most recycled plastic material. PET is a packaging material that has contributed to the development of the beverage industry by giving access to safe drinking water to billions of people. It is a great resource with many advantages: safe, lightweight, transparent, re-sealable, shapeable, 100% recyclable, having a very low carbon footprint, good mechanical as well as barrier properties at the price of a commodity. Plastics packaging like PET have a low environmental footprint compared to alternative non-plastic materials. The environmental costs of plastics in consumer goods are 3.8 times less than the alternatives. Bottle grade PET consumption is equal to less than 6% of total plastics production and far less than 1% of fossil resources, so banning this specific packaging material will not solve the environmental issues. In the packaging industry there is growing momentum to reduce waste by searching for alternatives to optimise primary, secondary and tertiary packaging, eliminating unnecessary plastics. In short, the problem that requires all our attention is the leakage of waste to the environment and especially into the sea. But this pollution is neither exclusive to PET nor to SUP. The focus should be on waste management, including the rationalisation of waste streams by favouring easy to recycle and higher value materials as well as concentrating waste streams to a lower number with higher volumes. 100% closed loop recyclable food-grade plastic PET is the only plastic suitable for direct food contact and for closed loop bottle-to-bottle recycling. A PET bottle’s journey doesn’t end after singleuse by consumers: used plastic bottles made of PET are recycled in such a way that the recyclate can be used for new PET bottles, thereby requiring fewer raw materials and reducing waste. Thus, it is the only plastic packaging material that is 100% recyclable, while meeting the tough standards in food contact regulations. The closed loop bottle-to-bottle approach leads to the actual task of recycling PET, where two main coexisting processes are theoretiRecycling Special Collection, sorting and recycling are regarded as the best solutions to minimise the environmental impact of PET bottles.","@ID":20}, "PETnews 6 NEWS PETplanet Insider Vol. 21 No. 06/20 petpla.net PETplanet launches its “PETinars” series of webinars The current coronavirus pandemic is highlighting the need for a fundamental global rethink. With the cancellation or postponement of international trade fairs, conferences, in-house events and the like, manufacturing industry has lost major venues for showcasing new technologies and innovative ideas. The global economy has largely shifted online and virtually as a result of homeworking during lockdowns, international travel restrictions or simply due to a personal and perhaps altruistic sense of safety consciousness. Professional cooperation between the mechanical engineering and end-user industries therefore needs alternative fora for traditional events which are still due to take place this year. And even once the crisis is over, experts already agree that these gatherings should continue, albeit organised in a different way and more digitally. Our PETplanet team is therefore introducing a new feature starting this month called “PETinars”, i.e. webinars created specially by and for our sector! We will be bringing together experts and key figures from across the sector for a series of annual online and interactive sessions consisting of technical presentations and discussions, information about products and systems, together with news from suppliers and end-users. Topics will be chosen based on particular PETplanet Insider focus themes, with participation free of charge for our readers. The theme of our first PETinar held on 28th May was “rPET in stretch blow moulded bottles”. Mr Christoph Wöss from Erema and Mr Arne Wiese from KHS discussed the effects of rPET on the design and production of preforms and PET bottles and how the associated bottle to bottle recycling might look. You can find the recording of the PETinar on our website. In our upcoming PETinars in June we will be discussing “Caps and closures manufacturing - injection versus compression moulding and tethered caps”. Participation for PETplanet readers is again free of charge. You can register for the PETinar via this link: petpla.net/petinars SGR recycling unit up and running Last November, Société Générale des Techniques (SGT) inaugurated its new site at Chalon-Sur-Saône in the east of France, which includes a preforms manufacturing plant and a plastics recycling unit, the SGR. The recycled PET produced by this new unit has been baptised CIRPET. The SGR unit has been up and running since the beginning of the year. It currently employs twenty or so workers and should eventually produce 12,000 t/a of recycled PET. “At present, the supply of recycled food-grade plastic does not meet the demand”, explains Frédéric Mignot, Chairman of the SGT/SGR Group. “To ensure we can supply the requisite volumes and quality rPET, we have decided to produce it ourselves”. This new unit features a unique regeneration line that can produce food grade recycled PET (rPET) via an extruding machine with underwater cutting and a decontamination system that produces rPET whose visible qualities (transparency and colour), mechanical qualities (viscosity) and organoleptic qualities are claimed to match those of virgin PET. Furthermore, the SGR uses a solid state polycondensation (SSP) system that offers the benefit of high industrial security, as all the stages of the thermal process take place in a neutral atmosphere. To introduce the concept of Circular PET, the CIRPET is currently pending approval by EFSA (European Food Safety Authority). www.sgt-pet.com Platform Packaging with Future On May 5th , representatives of the packaging value chain from Austria announced the launch of the “Platform Packaging with Future” (Verpackung mit Zukunft). This platform was founded by seven companies along the entire value chain - Greiner, Alpla Group, Nestlé Austria, Coca-Cola Austria, Interseroh Austria, Engel Austria and Erema Group. The cornerstones are the promotion of a functioning recycling economy, the creation of more awareness for the sensible use of packaging or the avoidance of packaging and thus the initiation of a constructive dialogue in the area of conflict in the packaging discussion with different stakeholders. Each member makes an important contribution to the success of these projects. The crisis shows the important properties of packaging “The four cornerstones of a functioning circular economy - Reduce, Replace, Reuse and Recycle - are already being implemented by the members of the platform in many areas. But together we can drive innovation even further. We want to position Austria as a model country in terms of sustainability in packaging and be a mouthpiece for this”, says Günther Lehner, CEO of the Vorarlberg Alpla Group, a globally active specialist for plastic packaging and recycling. “In the current crisis, important properties of packaging - transport protection, longer shelf life of food and the hygiene factor - have become clearly visible. In general, and especially in times like these, plastic packaging has the factual argument on its side - it would be good if it were to remain that way afterwards,” says Angela Teml, Head of Corporate Communications at Nestlé Austria, with a view to the future. Sustainability remains in focus in all considerations and projects. www.verpackungmitzukunft.at","@ID":8}, "MATERIALS / RECYCLING PETplanet Insider Vol. 21 No. 06/20 petpla.net 26 Bottle-to-bottle recycling of light barrier white opaque PET White, opaque, recyclable Bottles in opaque PET are increasingly replacing other material grades, especially in markets such as dairy and other sectors where demand is increasing. Thus far, a main concern was that the white opaque PET would lose one of the most important characteristics of PET, recyclability, but Spanish company Novapet is demonstrating that white opaque monolayer bottles can be separated and recycled into new bottles again. Recycling Special In addition to producing standard bottle grade PET, Novapet has for many years also been a manufacturer of speciality PET resins. The company is intending to incorporate the advantages of this material for new markets and, as a signatory of The New Plastics Economy Global Commitment, all the various grades must be 100% recyclable in practice. The company has significant experience in handling mechanical recycling projects, and has invested heavily in rPET production, using the material to manufacture preforms. Thanks to this experience, Novapet has been able to develop a recycling process for white opaque PET bottles. ODR - a growing market The use of monolayer white opaque PET bottles is growing rapidly because it provides the functionality and protection from light that UHT milk requires, an advantage other packaging options do not offer. Furthermore, it has the potential to achieve the sustainability aspects demanded by consumers and required by regulations. According to Plastics Europe Annual report (2018), the EU ODR market is 150 k tons, roughly 3-5% of total EU production. Around 6% of the PET recovered material in the EU16, a significant proportion, is not properly recycled. The reason is that there were limited end-use applications to absorb this material. There is also concern as regards the clear/light blue stream, because of the inorganic opacifiers included which reduce the yield. In order to demonstrate the feasibility and viability of the monolayer white PET recycling, Novapet has created, for the first time, a dedicated recycling stream of this material in a commercial recycling facility, sorting and recycling white opaque PET bottles into white flakes from standard bales collected in Spain. The recycling process is based on IR/VIS sorters, which are available in the majority of plants. It will require a detailed market study to assess the amount of input material and to adapt the configuration of the sorting system. Flakes, raw material in the circular economy The white flakes can be decontaminated according EFSA requirements and used again as raw material for the production of a recycled opacifier masterbatch or directly to rPET monolayer bottles. Various formulas would have to be applied depending on final use and light barrier requirements, to maintain the same machine throughput and without impacting properties, functionality and colour. Novapet’s specialist team have technically validated that it is possible to reprocess the white flakes, thus obtaining new white opaque resin and masterbatch formulations. All these formulations have been characterised along the entire process, controlling the key variables, in order to assure good processability and the decontamination conditions in the SSP reactor. Thus the process demonstrates that the recycling process to produce white recycled PET is able to be used for manufacturing containers in the food industry. Novapet Packaging division facilities produce the bottles using a regular injection-stretch-blow moulding process. The properties of the containers have been preserved in terms of colour, performance and light blocking properties. Novapet’s expertise in compounding production and recycling processes from the bale to the bottle, allows the company to claim that their recycling process meets consumer demand and observes the relevant directives. This new family of recycled products, rDCU and rDairy, will be commercially available by the end of 2020. www.novapet.com","@ID":28}, "8 NEWS PETplanet Insider Vol. 21 No. 06/20 petpla.net Further postponement and venue change of Chinaplas The 34th edition of Chinaplas cannot be held as scheduled and will be further postponed from 3-6 August 2020 to 13-16 April 2021, and the show venue will be changed from the National Exhibition and Convention Center in Shanghai to Shenzhen World Exhibition and Convention Center in Shenzhen. This was announced by the organiser Adsale Exhibition Services. In the announcement Adsale states that the coronavirus is largely under control in China, but poses a high degree of uncertainty globally. “China has now a formidable task of fighting against local rebound infections while preventing the next wave of outbreak from imported cases.” On 6th April 2020, the State Council of China issued the circular of “The Further Control and Preventive Measures of the Novel Coronavirus at Key Venues, Units and Groups”. According to “Preventive Suggestions” in the circular, it has clearly mentioned that all kinds of exhibitions have to be cancelled for the time being. Safety and health of all show participants are put as top priority. Regarding the participation or admission fee paid by exhibitors and visitors, the show organiser will make the necessary arrangements and notifications. www.chinaplasonline.com Open-source collaborative initiative for safety masks from PET PCR bottles Company Moldintec share their beverage industry-focused solution of a Safety Mask made from a PET PCR bottle. “There are many masks already shared on the web, we are aware of that. But we have tried to adapt the machinery we use every day to produce a suitable mask.” The Argentinian engineers prepared two versions starting from: PCO 1881 3 l bottle & PCO 48-41 6 l bottle. Recently, the CCU Group has deployed in Chile a facial mask made from a PET bottle: A total of 160,000 units will be produced that will be donated to the community throughout the country. Just over a month ago, Moldintec promoted an open-source collaborative initiative to the entire PET industry to design and manufacture a face mask to protect against the spread of Covid-19 using the technical and material resources available in their factories. The team of engineers working from their homes in preventive isolation developed the first model of a mask that can be cut from a PET bottle with simple office supplies (scissors, staplers, perforators). Moldintec quickly received the support of Syphon S.A., a preforms manufacturer in Argentina, who contributed with the blower, laboratory, the preforms, and, most importantly, the selfless collaboration of its engineers. The manufacturing team at Moldintec’s tool-shop in Buenos Aires coordinated the production of the first pilot mould that was completed just 24 hours later. After an intensive working month, CCU S.A. Chile presented the first industrial deployment of the mask. In the first stage, CCU plans to produce 160,000 units. Inmates will conduct the cutting and assembly manually in the penitentiary Colina-I which runs an educational and workcentre. “From Moldintec, we want to thank all those who selflessly contributed their knowledge and their skills working from home isolation to manufacture the first moulds.” said a company spokesman. “The design is open source, so if you want to make masks for donation, we are here to support you!” www.moldintec.com Wolfgang Steinwender becomes new CEO of NGR As of May 1, Wolfgang Steinwender took over as CEO of the Austrian plastics recycling machines manufacturer NGR. His predecessor Josef Hochreiter will devote more time to the further development of Next Generation Holding. Despite the worldwide uncertainties due to Covid 19, NGR is convinced it can continue the successful course supporting the plastics industry during its transition to the circular economy. Since joining the company in 2014, Wolfgang Steinwender has been serving as Managing Director of the NorthAmerican office inAtlanta, Georgia, where he headed the market penetration and customer support of theAmericas. Together with CTO Thomas Pichler and COOGerold Barth, Wolfgang Steinwender will focus on the further development of the circular economy. NGR offers a full range of post-consumer, post-industrial and PET recycling equipment. “About 400 million tons of plastics are being produced per year worldwide. It is key to put an emphasis on end-of-life plastics. Mechanical plastics recycling conserves resources, protects the environment and improves the CO2 balance. It is the key to sustainability. Therefore, it is crucial to achieve the highest possible quality of recycled materials by using innovative technologies and thus continuously increase the amount of recycled material in end products,” says Wolfgang Steinwender. Josef Hochreiter has been heading NGR for 12 years and grew it into one of the leading companies in its industry. Starting in May, he will focus on the further development of Next Generation Holding and, according to Josef Hochreiter, will continue to develop this global technology provider to support the transformation from a linear to a circular economy in plastics following the mission “Working for a better future”. www.ngr-world.com","@ID":10}, "MATERIALS / RECYCLING PETplanet Insider Vol. 21 No. 06/20 petpla.net 37 The new extrusion system itself is supplied by Austrian firm Starlinger, whose cutting-edge recycling technology Alpla has been using for many years. Hermann Adrigan from Starlinger also underlines the spirit of partnership: “Alpla is a long-standing and important partner for Starlinger. We are proud that we are able to contribute to the success of the Radomsko site by providing a further bottle-tobottle PET recycling system.” Green electricity improves carbon footprint In addition to the technical expansion of the plant, its energy supply has been switched fully to renewables. As shown by the carbon footprint calculation performed by independent consultancy firm c7-consult, the production of one kilogram of PET regrind material only generates 0.27 kg of carbon equivalent. This corresponds to 88 per cent (or eight times) less greenhouse gas than the production of virgin material (2.19 kg of carbon equivalent according to PlasticsEurope). Forward-looking strategy As an international developer and manufacturer of plastic packaging, Alpla recognised the importance of recycling at an early stage and was already entering into partnerships in the early 2000s. However, demand for recycled plastic has not always been as high as it is today. When the plant in Poland opened its doors in 2013, there was hardly any awareness amongst consumers and customers regarding the recycling of used materials. Nevertheless, the plant has been designed with foresight, enabling it to be upgraded quickly and without further construction measures. This approach is now paying off. “Over the years, PRT has held its own in a challenging market environment, helping to ensure that PET packaging units are seen as recyclables. Our market is now ready and, with the new set-up, we are in a strong position to make high-quality regrind material in the most sustainable way possible” explains Beata Szynkiewicz, Commercial Director at PRT Radomsko. Her colleague Marcin Jablonski, Plant Manager since 2014, adds: “By using green electricity, we are, in my opinion, taking the logical next step in our strategy. We are transforming used materials into recycled materials in the most energyefficient way possible for industry, helping to ensure a functioning circular economy, preventing litter and, at the same time, contributing to the fight against climate change”. www.alpla.com","@ID":39}, "PREFORM PRODUCTION 46 PETplanet Insider Vol. 21 No. 06/20 petpla.net Preforms and closures for local brands Is there a gap for a convertor to fill between multi-brand suppliers and simple preforms? Yes, according to Mr Ashutosh Gandhi, MD of Ahimsa Industries, Ahmedabad, who flew to Düsseldorf for the K trade-fair in 2010 and bought the then recently introduced, compact, fully automated H-PET AE 180 preform injection moulding system from Husky. The Greenpet brand was established and its work began. Greenpet Ahimsa Industries Ltd. June 2019 We met: Mr Ashutosh Gandhi, MD Mr Sanjay Agrawal, CEO It was, and still is, important to Gandhi that Greenpet supplies top quality products and is able to provide a wide variety of local fillers: from Alaska Neck water preforms to PCO 1881s for 150ml and 2-litre CSD and juice bottles, as well as offering a complete package that includes closures, together with first-class service. Nowadays, his customers can fill bottles at speeds of up to 12,000 bph, compared to 3,600 bph eight years ago. Greenpet has grown in step with its clients, with the result that one million preforms now leave the factory every day in a twin-shift operation. On request, he supplies the correct caps which he buys in and keeps in stock. “This is how we deliver our product to the customer within two hours of the request being received”, is his philosophy. He sells preforms in cardboard boxes and also in air-tight bags. “A bag is cheaper for our customers than a box”, explains Gandhi. Just as he always gives his utmost for his customers, so he also demands total commitment from his suppliers. His H-PET AE 180 was Husky’s first lower output, compact system to be sold to the customer. “To improve its control system Husky technicians came in”, recalls Sanjay Agrawal, CEO, of that time. “They helped us plan for three days and stayed for 18. After that, everything worked like clockwork.” Software development at Greenpet has ultimately benefitted all users of the compact Husky system. He opted for a Canadian manufacturer as the aftersales service is provided directly from India. Originally designed for 40 cavities, soon moulds for lower-weight preforms were being produced that increased this number to 48 cavities, thereby allowing him to produce 20% more preforms in one go. As the preforms have become lighter and thus more thin-walled, savings of an extra 10% of cycle time can be achieved. In 2013, a second H-PET AE system with a closure force of 230 t was added to the portfolio. The original plant now produces all water preforms (Alaska Neck) which are all new PCO 1881s. In all, Greenpet supplies a total of 11 different preforms, five for water and six PCO 1881s. In order to do this, he needs six mould sets. “Most of our capital is tied up here but we can only run two systems at the plant at any one time”, explains Gandhi. His idea is to build a second factory for his customers in the south and east of the country and regularly interchange the equipment so that four out of the six systems are always running. The team is also looking to maximise production and energy consumption. A change of machinery that took eight hours to complete some eight years ago now takes just 120 minutes. Whereas previously the cooling system needed 7,000 l per week, it is now able to achieve the same consumption over a period of two weeks. www.greenpet.in Tour Sponsors: Everything compact next to one another. Offices on the left, and the two Husky plants, with room for plant no. 3, on the right. Preforms can be packed in bags at the customer’s request.","@ID":48}, "MARKET SURVEY 31 PETplanet Insider Vol. 21 No. 06/20 petpla.net 06/2020 MARKETsurvey Resins & additives Preform machinery Preform production & inspection Preform & SBM mould manufacturer SBM 2 stage Compressors Caps & closures & inspection Filling equipment & inspection Recycling Palletising & shrink film machinery Two-stage SBM machinery What all types of 2-stage stretch blow moulding machines do have in common is that prior to the stretch blow moulding process, preforms have to be injection moulded in a separate machine. However, there is a diverse range of models to choose from in 2-stage stretch blow moulding. Our market survey allows you to compare specific parameters of these state-of-the-art machines from some of the market leading manufacturers. Although the publishers have made every effort to ensure that the information in this survey are up to date, no claims are made regarding completeness or accuracy. Company name Luxber, S.L.U. Kosme Gesellschaft mbH Sacmi Imola SMI S.p.A. Postal address Telephone number Web site address Contact name Function Direct telephone number E-Mail Av. De Azorin, 34-36 03440 IBI, Spain +34 96 555 3853 www.luxber.com Mr Ricardo Sanchez Export Manager +34 606 964 907 luxber@luxber.com Gewerbestrasse 3 2601 Sollenau, Austria +43 2628 411 0 www.kosme.at Mr Johann Gugler Managing Director +43 2628 411 125 johann.gugler@kosme.at Via Provinciale Selice 17/A 40026 Imola BO, Italy +39 0542 607111 www.sacmi.it Ms Monica Pedretti Beverage, Marketing & Com. +39 0521 695528 monica.pedretti@sacmi.it Via C.Ceresa, 10, 24015 San Giovanni Bianco (BG), Italy +39 0345 40 111 www.smigroup.it Mr Pietro Volpi Marketing Dept. Manager +39 0345 40 316 info@smigroup.it 1. Machine designation / model number TecnoPET 1000, 2000, 4000, 6000 Rotary machines (10 models) Linear machines (6 models) sbf The EBS (Electronic Blowing System) Ergon series of sbm machines, 13 models: N° 7 models, 4 to 16 cav., for bottles up to 3l. N° 3 HC (High Capacity) models, 3 to 6 cav., designed for high-capacity bottles (up to 10l). N° 3 EBS K (Electronic Blowing System Kompact) Ergon series of Kompact sbm machines, 3 models, 2 to 4 cav., for bottles up to 3l. 2. Bottle volume (from/to in litres) 0.10l - 10l a) Standard machines 0.1 up to 10 0.05 - 3.0 (up to 4.0l depending on design) 0.05 - 3.0 From 0.1 to 3 0.10l - 3l b) Machines for large containers 0.5 - 6.0 0.5 - 30.0 From 2 to 12 3.5l - 10l 3. Maximum number of stretch-blow moulds (units) a) Standard machines 1, 2, 4 and 6 8 4 18 16 b) Machines for large containers 6 3 6 6 4. Output per stretchblow mould for: 0.5 litres CSD bottle (units per hour) 2,250 2,500 1,700 4,500bph/mould 2,300bph per cav. (dep. on the preform/bottle features) 1 litre CSD bottle (units per hour) 1,900 2,500 1,650 2,250bph/mould 2,250bph per cav. (dep. on the preform/bottle features) 1.5 litres still mineral water bottle (units per hour) 1,800 2,500 1,600 2,250bph/mould 2,250bph per cav. (dep. on the preform/bottle features) Large capacity container 1,250 Up to 1,250 for 5.0l; 750 for 15.0l; 700 for 20.0l; 350 for 30.0l 1,200bph/mould 1,200bph per cav. (dep. on the preform/bottle features) Other 5. Footprint / space requirement (L x W x H in metres) 6.05 x 3.85 x 3.25 (without preform feeding system) Min.: 4.5 x 1.83 x 3.10 max.: 5.1 x 1.85 x 3.1 (without preform feeding system) Standard models: min 4.2 x 3.5 x 2.75 (EBS 4 &6 Ergon) - max 6.8 x 3.9 x 2.75 (EBS 16 Ergon). NB: without preforms hopper and unscrambler; K models: 2.32 x 3.28 x 2.3 mm; HC - High Capacity models: min 4.45 x 3.46 x 2.57 (EBS 3 HC Ergon) - max 5.55 x 3.46 x 2.57 (EBS 6 HC Ergon). NB: without preforms hopper and unscrambler. 6. Special features (short description/keywords) Preferential heating, air recovery system, wide neck, PP preforms Active neck cooling; patented modular oven (low evergy consumption); block version with fillers for all sizes available Air recycling system, available also with PI; mould shells of linear machines are compatible with rotary machines; fast semiautomatic mould change within 10 minutes; preferential heating Compact frame, ensuring significant space saving in the bottling line; Ergonomic and functional design, simplifying its running, cleaning and maintenance operations; High technological content of the solutions inspired by Industry 4.0 and Internet of Things (IoT); New preform-heating module, featuring compact dimensions, horizontal frame of the preformholding mandrels chain and a ventilation system that optimize the preform heating process","@ID":33}, "TOP TALK PETplanet Insider Vol. 21 No. 06/20 petpla.net 11 any real limits imposed by the technology. Of course, we mustn’t forget that some limits do remain: for some staff it will always be essential to be able to go into the company, or visit a customer, albeit with all the necessary precautions. What I think, in all conscience, is that when the emergency is over, we’ll all have to learn to live and work differently. We’ll need to place greater emphasis on relationships, skills and initiative, on our ability to build well-being for our companies, customers and communities while making use of new tools. PETplanet: You mentioned that your supply chain has not undergone any interruption. Does that mean that all deliveries are timely and complete? Bernardi: Out in the field, major difficulties still persist. Not all suppliers were able to keep production going. Sacmi has broad shoulders, but this is not so for everyone. Some of our partners are experiencing the inevitable economic difficulties that stem from quarantines and production stoppages. Moreover, we can’t deny that implementing all the necessary safety measures lowers, in the short term, the efficiency of the companies. This is reflected in a slowdown of the entire supply chain which, at times, demands prompt corrective action. Fortunately, Sacmi has selected its suppliers carefully over the years; hence our confidence that the moderate delays being experienced in some cases will soon be corrected and regular supply and assistance services re-established. PETplanet: How can you support your customers especially in countries with closed borders and severe travel restrictions? Is it ‘business as usual’ for your support services? Bernardi: If we take pre-Covid service and assistance levels as a benchmark, the answer is no. It would be dishonest to argue otherwise. However, we’re doing everything possible to adapt our support and assistance capacity to fastchanging scenarios. As early as the beginning of March, we sent many of our Italian technicians to strategic locations in various parts of the world, thus strengthening our presence in areas already manned by local technicians. In addition to the provision of routine Customer Services, Sacmi is also using virtual reality for both Factory Acceptance Tests (FAT) and Start-up and Acceptance Tests (SAT) on customers’ premises. Day by day, we’re steadily improving and implementing technical/ technological solutions that expand our remote operations capacity. With the support of locally placed technicians and the help of the customers themselves, we’re able to keep operations ticking along satisfactorily. It is, I wish to reiterate, a challenge that we are fully equipped to cope with: but victory will only be achieved through teamwork. Hence, I repeat, the slogan that has accompanied us so far: Let’s move forward. Together. PETplanet: In addition to maintaining operations, EU directives, such as tethered caps, have to be developed and implemented. Is © Universal Closures Ltd. info@uclltd.com www.universalclosures.com","@ID":13}, "imprint EDITORIAL PUBLISHER Alexander Büchler, Managing Director HEAD OFFICE heidelberg business media GmbH Vangerowstraße 33 69115 Heidelberg, Germany phone: +49 6221-65108-0 fax: +49 6221-65108-28 info@hbmedia.net EDITORIAL Kay Barton Heike Fischer Gabriele Kosmehl Michael Maruschke Ruari McCallion Waldemar Schmitke Anthony Withers WikiPETia.info petplanet@hbmedia.net MEDIA CONSULTANTS Martina Hirschmann hirschmann@hbmedia.net Johann Lange-Brock lange-brock@hbmedia.net phone: +49 6221-65108-0 fax: +49 6221-65108-28 LAYOUT AND PREPRESS EXPRIM Werbeagentur | exprim.de Matthias Gaumann READER SERVICES Till Kretner reader@hbmedia.net PRINT Chroma Druck & Verlag GmbH Werkstr. 25 67354 Römerberg Germany WWW www.hbmedia.net | petpla.net PETplanet Insider ISSN 1438-9459 is published 10 times a year. This publication is sent to qualified subscribers (1-year subscription 149 EUR, 2-year subscription 289 EUR, Young professionals’ subscription 99 EUR. Magazines will be dispatched to you by airmail). Not to be reproduced in any form without permission from the publisher. Note: The fact that product names may not be identified as trademarks is not an indication that such names are not registered trademarks. 3 PETplanet Insider Vol. 21 No. 06/20 petpla.net Dear readers, With coronavirus restrictions practically the new normal, we at PETplanet have increased our online activity with the launch of our first PETcast as part of Editour. This has been produced by John Clark, Managing Director of Ant Packaging Pty Ltd, Bangalow, NSW, Australia. In it, the converter describes his business model and the impact coronavirus is having on the company. Our first webinar will take place on 28 May entitled “rPET in stretch-blow mould bottles” with special reference to EU Directive 2019/904. Under this legislation, bottlers must use 25% rPET in drinks’ bottles by 2025 and 30% rPET by 2030. The Directive also establishes quotas for fixed recycling and tethered caps. The webinar will examine how rPET influences the design and production of preforms and PET bottles and what bottle-to-bottle recycling looks like in practice. The event will be chaired by recycling expert, Mr Stefan Bock from ReduPET. Christoph Wöss from Erema will talk about bottle-to-bottle recycling and Arne Wiese from KHS Corpoplast will outline the challenges posed by rPET in stretch-blow moulding. We are already looking forward to our next PETinars on Inspection and Caps. Despite all the online activities, it is always nice to hold a printed version in your hands! Enjoy our June issue on recycling. Yours sincerely Alexander Büchler","@ID":5}, "MATERIALS / RECYCLING PETplanet Insider Vol. 21 No. 06/20 petpla.net 41 Also, the Stadler equipment is very durable, and therefore requires less maintenance. As a result of the modernisation and the simplified maintenance, costs and workflows could be optimised.” An upgrade with a label remover The recycling industry is in constant evolution, as the packaging used by manufacturers changes over time. This is the case of PET bottles, which are increasingly packed in ‘full-body’ sleeves: “To optimise sorting and achieve better quality for our customers, the separation of label and PET bottle must take place before sorting,” explains RCS’s CEO. “with the Stadler label remover the labels are stripped off and the PET bottles are less damaged than with other manufacturers. As a result, we can register less fine abrasion,” concludes Alexander Rimmer. Stadler’s label remover – launched in 2019 with the name Delabeler – removes labels from bottles of all types, achieving a quality standard of up to 80 per cent of labels removed. It processes a mass flow of up to 9Tn/h – depending on the particle size and material composition. It is claimed to stand out for the robust construction that is the hallmark of Stadler equipment and is highly resistant to impurities. These features result in durability and a consistently high performance throughout its long-life cycle. The Stadler label remover has been in operation at the RCS PET sorting plant, where it has proved to be an effective solution: “We are very satisfied with the label remover because it requires less maintenance and its throughput is geared to that of our plant. With this machine, there is less wear on the knives and the machine is not very susceptible to impurities such as foil or wood. In addition, it does not cause any damage to the PET bottles. With the label remover, we can separate the labels from the bottles before sorting, which enables us to guarantee a consistently high level of purity,” concludes Alexander Rimmer. www.w-stadler.de motan-colortronic gmbh - info@motan-colortronic.de www.motan-colortronic.com The energy-saving crystalliser. Easy on the environment, easy on your budget. Reliable Crystallisation CRYSTALLISER Label remover","@ID":43}, "PETplanet Insider Vol. 21 No. 06/20 petpla.net 55 BOTTLES PETbottles Home + Personal Care Two-phase eye make-up remover Beiersdorf has launched a “doubleeffect make-up remover” on the market. The product quickly and thoroughly removes even extremely waterproof make-up and protects the eyelashes. The bottle holds 125ml of the two-phase liquid, which is mixed with cornflower extract. The phases are mixed by shaking and can be applied using a cleaning pad. Two transparent foil labels provide application instructions. Under the screw cap, a dosing insert is pressed into the bottle opening. www.nivea.de Fairy in 100% recyclate At the end of February 2020, Fairy, a Procter & Gamble brand, brought three new washing up liquids with the tagline “100% natural aroma” onto retailer shelves. These contain 100% natural ingredients, and one variety is free from perfume and colourant. The image shows the “Lavender & Rosemary” variety in the bottle typical of the brand, here containing 625ml and with the screwed-on hinged cap with dosing function. The bottle is made from 100% recyclate, only the cap and label are not. The inside of the rear label is printed with sprigs of rosemary and lavender. One teaspoon of the light purple product is enough for 5 l of washing-up water. www.for-me-online.de","@ID":57}, "MATERIALS / RECYCLING PETplanet Insider Vol. 21 No. 06/20 petpla.net 27 Separate collection of packaging waste Reduced off-odour of plastic recyclates Plastic recyclates produced from waste packaging have to meet high sensory requirements in order to be used for new products. Plastic recyclates often have off-odours, some of which have not hitherto been identified. Recycling Special The Fraunhofer Institute for Process Engineering and Packaging IVV has analysed the sensory properties of post-consumer shopping bags made of low density polyethylene (LDPE) and originating from different collection systems. More than 60 odorous substances were identified using combined chemo-analytical methods. The information gained provides a targeted strategy for avoiding off-odours. The results of this collaborative study with the Chair of Aroma and Smell Research at the FriedrichAlexander-Universität Erlangen-Nürnberg and the University of Alicante have now been published. In order to meet the targets of the new EU Packaging and Packaging Waste Directive concerning the recycling of packaging waste, new markets for recyclates produced from waste plastic packaging must be found. Recyclates produced from waste plastic packaging must have no off-odours if they are to be used as secondary raw materials for the manufacture of high-quality consumer products. Indeed, the off-odours in plastic recyclates prevent a closed cycle for the recycling of plastic packaging materials. Currently, there is a particularly high reusage rate for recyclates produced from polyethylene terephthalate (PET) bottles. LDPE packaging waste in focus The Sensory Analytics department at the Fraunhofer IVV characterises and optimises plastics and recyclates. The odorants in HDPE waste and the recyclates produced from packaging from bodycare products and detergents have already been analysed. Low density polyethylene (LDPE) is one of the most commonly used plastics. It is widely used for packaging materials such as plastic shopping bags. Via various collection systems these bags end up as packaging waste. Part of the current study on post-consumer LDPE shopping bags concerned the effect of the collection strategy on the sensory impairment of the waste. Identification of odorants - the key step Identification of the substances causing off-odours is essential in order to be able to take measures for odour optimisation. Most of the odorants identified in the study are typical metabolites of microorganisms. Many of these metabolites had a cheeselike or feceslike odour. The odorants included carboxylic acids and sulfurcontaining and nitrogencontaining components. The chemical structures of the odorants gave key insight into their origin. Using this information, the pathways into the packaging waste and via the recycling process into the recyclate were identified. Depending on which process step cannot remove an odorant or even results in a new odorant, targeted measures can be taken to reduce odorants or avoid the formation of new odorants. Odorant reduction via separate collection in the yellow bag The study showed that the way the packaging waste is collected has a large bearing on the odour quality of plastic shopping bags. There are significant benefits by separate collection in the yellow bag. Waste collected in this way had a significantly lower overall odour. In contrast, the waste fraction collected in the general household waste had more intense cheesy-like, sulfur-like, and feces-like odours. The higher organic fraction in the general waste favours the formation of these microbial degradation products. It was also demonstrated that the post-consumer LDPE shopping bags from the separate collection that were washed at 60 degrees had fewer odorants and a reduced overall odour than the unwashed bags. Methods for odour identification in plastic waste The Fraunhofer IVV scientists used sensory analytics to identify the odours. Sensory evaluation of the sample materials was first undertaken by a trained sensory panel. The odorants were then identified using chemo-analytical methods such as gas chromatography - olfactometry and with two-dimensional coupling with mass spectrometry. This enabled the chemical structures to be determined and also possible formation pathways and sources of the odorants to be identified. These key findings can now be used to develop customised solutions for optimisation of the odour of plastic recyclates, starting at the waste collection stage. www.ivv.fraunhofer.de/en","@ID":29}, "BOTTLING / FILLING PETplanet Insider Vol. 21 No. 06/20 petpla.net 49 played into his own hand by producing caps for his two filling systems only. This meant that the injection moulding process and the sealing system on the filling line could be adapted to one another so that the capping system ran smoothly. For the distant future, he is thinking about his own preform production for the 13.2 g preform. “When we have four aseptic systems with a total of 2 million bottles per day, then we can also build up a profitable preform production system,” says Bayati. Another unsolved issue is that of recycling. “We have to take back and process the empty bottles,” he says with certainty. The bottle is also covered with a PVC sleeve, which makes recycling more difficult. But Amul is working closely with other major players of PET to come out with long term sustainable solution. www.amul.com AmulFed Dairy, Gandhinagar is a unit of Gujarat Co-operative Milk Marketing Federation Limited (Amul Federation). GCMMFL which markets the popular Amul brand of milk and dairy products is owned by 3.6 million milk producers of Gujarat. Amul spurred India’s White Revolution, which made the country the world’s largest producer of milk and milk products. Amul meant different things to different people : To a milk producer: A life enriching experience To a consumer: Assurance of having wholesome milk To a mother: A reliable source of nourishment for her child To the country: Rural development and self reliance Our Editourmobil is parked in the middle of lush Green AmulFed Dairy. Herbold Meckesheim GmbH Your Partner for Plastics Wash Lines www.herbold.com As a one-stop supplier, we provide all relevant process components : Pre-washing units Hydro-cyclone separation systems Friction washers Mechanical and thermal driers Water treatment As a specialist for plastics recyclingwe are your contact forcomplex applications . We have the long lasting expertise in washing, separation and drying - to recycle new, used and contaminated plastics waste. Thanks to our modular technology, we are able to develop customized overall concepts or to optimize your already-existing plant. Key points for your profitability: Best flake quality High energy efficiency Minimized fresh water quantities Low downtimes and labour utilization Durable equipment made for tough applications","@ID":51}, "TOP TALK PETplanet Insider Vol. 21 No. 06/20 petpla.net 12 development work even possible under present circumstances? Bernardi: Without a doubt, albeit with the necessary precautions. All those who can conduct their business from home will still continue to do so. For those who work in the lab where we develop and test all new capsule developments - including work on tethered caps - we’ve divided the work into two 8-hour shifts so we can work in complete safety on all the development projects included in the original program. PETplanet: What about your order books? Do you feel that your customers are currently holding back on purchasing decisions? Bernardi: Unfortunately, the crisis is a global one that extends far beyond the borders of Italy and Europe. In its truest meaning, the word ‘crisis’ signifies change: in the way we work, consume, live. In China, for example, where the recovery has already begun, our customers are manufacturing at 80% capacity and the curtailment of in-country travel is shifting consumption from small-format drinks to public vending machines or larger formats. In any case, the fact that Chinaplas - a longstanding plastics fair held in April, the ideal time to understand the production needs of the Chinese market - was cancelled, leads us to view the ongoing recovery with a degree of caution. In India, the total lockdown, now expected to last until early May, has also shut down production in the beverage supply chain. Here, our customers kept on manufacturing while warehouse stocks lasted, then closed their factories. Even in Africa - affected to a lesser extent by contagion as such - travel restrictions prevent people from buying drinks from the street stalls that constitute the bulk of the continent’s ‘retail outlets’. Moving on to the United States, millions of people have been placed under lockdown and lost their jobs in the space of just a few short weeks. This will inevitably impact consumption and, consequently, the investment choices made by the industry’s multinationals, triggering a cascade effect that reaches our customers. In any case, we believe it’s too soon to assess the real impact of the situation on our sales. A lot will depend on the how long the recovery takes and how it unfolds, on when investors - and, more importantly, end consumers - start to feel confident again. PETplanet: In Germany, more than half of all companies applied for short-time working. Does this possibility exist at your company locations and if so, do you make use of it? Bernardi: In Italy too, many companies, ours included, are taking advantage of the social safety nets provided for by current legislation. These include cassa integrazione, which provides payment for furloughed workers, and the use of backlogged holidays as we seek, in every way possible, to compensate for the production slowdown or, in many cases, partial or total production stoppages. Clearly, such emergency measures are not sustainable in the long run, as company resources are limited and even state coffers are not bottomless. Hence the need to prepare for a safe restart as soon as possible. PETplanet: What other supporting measures would you have liked to see from your government or the EU? Bernardi: I am, with good reason, worried that, even after any recovery, all the companies in the supply chain will have liquidity and volume issues and that it will take a long time to get back to preCovid levels. During this Phase 2, it may simply be unfair to apply the usual economy and company performance indicators. Of course, in the short term it will be essential to make good use of all the available tools, such as the export financing support plan (SACE), in a broader, more streamlined way than in the past. PETplanet: When do you expect the economy to recover? Bernardi: I’m no expert in macroeconomic analysis. However, I do read in-depth studies on our industries on a daily basis. My own opinion is that we’ll see an economic recovery in the last quarter of the year, but if we’re looking at a ‘return to normal’ we’ll have to wait until at least the second half of 2021. PETplanet: In our last editorial in PETplanet 5/2020 we published a guest article by Erik Eichler, the production manager of Hansa-Heemann AG, Germany. In it, he highlighted the efforts of the PET bottling industry and at the same time pointed out that this situation should be used as an opportunity to improve the public image of the PET bottle. How do you think the image could change, and the hygiene and logistical advantages of plastics could become the focus of public attention in the long term? Bernardi: I fully agree with Mr. Eichler, for a clear reason. Our problem is not plastic, but its dispersion into the environment and incorrect recycling-disposal methods. We should take this opportunity to make people more aware that plastic, especially PET, is crucial to the survival of 10 billion people, that is, the number of people who will, in the space of a few decades, soon be living on earth. In such a scenario, developing a circular economy is a must, a strategy vital to the survival of our species and the protection of our shared home, planet Earth. Hence our belief that plastic can and should play an essential role on account of its low cost, the ease with which it can be recycled-reused and, in essence, the possibility of its reintegration into the chain of environmental resources that are essential to our lives, health and well-being. PETplanet: Thank you very much, Mr Bernardi!","@ID":14}, "MATERIALS / RECYCLING PETplanet Insider Vol. 21 No. 06/20 petpla.net 24 New masterbatch offers “circular economy” design and zero TiO2 High opacity, low TiO2 In early 2018, white opaque PET bottles for milk narrowly escaped being banned in France, on the basis that they were “non-recyclable”. The issue attracted a lot of negative media coverage and became a high-profile political topic. Ultimately, the bottles were allowed to remain on the French market, conditional on the industry driving a drastic reduction of TiO2 (titanium dioxide) content. The following year, Penn Color introduced pennaholt, a white masterbatch containing 50% less TiO2 . The company says that it enabled the design of white PET bottles with very low TiO2 but, at the same time, maintaining the highest levels of opacity and whiteness for maximum shelf-life and shelf appeal. The original pennholt enabled typical 8% TiO2 content in a PET bottle for long life white milk to be cut to below 4% in monolayer PET bottles and below 2% in multilayer packages. This helped to improve white opaque PET’s compatibility with the non-clear recycled PET stream, where high content of TiO2 had previously been identified as hindering both the recycling process and the manufacture of end-products using non-clear rPET content. A changed approach to reduce TiO2 Opacity drives consumer’s experience of the quality and safety of the product, as light blocking protects organoleptic properties and nutrients. High opacity (99.5% at 550 nm) and premium whiteness (87L) are required to package longlife white milk. Whiteness, with its implications of cleanliness, freshness, purity and safety, sends a message that plays a critical role in the success of the product. Conventional white masterbatch technologies exploit the light scattering property of TiO2 , dispersed in a plain package wall, to provide opacity and whiteness. Pennaholt uses a different mechanism. Its patent-pending technology generates micro-structured interfaces within the PET bottle wall, using high reflective characteristics to create a barrier to light. High opacity and premium whiteness result from a synergistic effect between the micro-structured wall and the light scattering effect of inert particles. Compliance with new legislation TiO2 now faces another critical challenge. In February 2020, the EU CLP (classification, labelling and packaging of chemical substances) classified it as a suspected carcinogen (level 2), by inhalation of powders or dust. The effective date of restriction is confirmed as October 2021. As the classification is “by inhalation”, it does not apply to packages, where TiO2 is “locked” in the polymer. Packagers should, however, be aware that it is the combination between the CLP and the EU waste directive that is a concern. Any waste containing more than one per cent of a carcinogenic substance is considered hazardous. The waste directive applies regardless of the form of the substance so it means any recycled PET bottle with more than 1% TiO2 is hazardous waste. The EU has recently published its “new circular economy plan” with even stricter regulations on the presence of hazardous substances in the recycling streams. White opaque PET will face a challenging situation from October 2021, additional to its technical compatibility with the recycling stream and the Single Use Plastic directive. Penn Color says that it can help customers with its technological development of pennaholt. Its latest variants are now available with only one per cent or even zero TiO2 but Recycling Special","@ID":26}, "MATERIALS / RECYCLING PETplanet Insider Vol. 21 No. 06/20 petpla.net 35 market price thereof, the charge for recycled PET has continuously risen over the last three years. Companies now have to pay about 20% more for rPET than for the original material – also because the supply cannot meet the growing demand. High standards of quality Not only do hurdles have to be overcome at the raw materials end; some beverage producers also have reservations. They often fear that the rPET material may discolour or that the level of intrinsic viscosity may drop. Another issue is safety standard and thus the harmlessness of the material. Time and again the question is raised as to whether multiple recycling can affect the quality. Although this has not yet been fully researched in practice, one thing is clear: as the polymer chains reform, no compromises must be made as regards the material quality as long as the additives can be completely separated off. The European PET Bottle Platform (EPBP) is just one of the institutions that helps to assure high standards of quality with its clear specifications and certifications. Whereas just a few years ago experimentation was rife and the beverage and food industries gained their experience with recycled PET through sheer trial and error, from a technical standpoint there is now nothing preventing the global use of high percentages of recycled PET. More and more beverage producers and brands are even opting to use bottles made of 100% recyclate. Where this is not yet the case, voluntary commitments are being publicised; Poland Spring, one of the biggest water brands in the USA, and Evian want to use recycled PET only by 2025. The other brands by Danone Waters, Pepsi and Coca-Cola plan to introduce a worldwide quota of 50% by this date. Their objective? They would like the consumer to interpret the slight graying that can occur when PET bottles are recycled several times over as a hallmark of quality for sustainable packaging. Sound expertise: studying rPET since 2012 The KHS Group has been examining the use of recyclate for some time now – in fact since 2012. KHS’ Bottles and Shapes service program focuses on the practical application thereof on the stretch blow moulders and indeed all of the filling and packaging lines engineered by the Dortmund systems supplier. “We run tests to qualify recycled PET so that we can tell our customers in advance which impact the material will have on the blow moulder and bottle quality,” says Arne Wiese, product manager for Bottles & Shapes at KHS Corpoplast. The aim is to be able to quantify the various different qualities. In doing so, KHS must work closely with preform manufacturers. They are ultimately often the companies which subject the washed PET flakes or rPET granulate to further thermomechanical processing and prepare them for injection moulding. “We’re consulting with all of the major plastics processors in Europe on this topic,” Wiese emphasises. KHS is liaising with various engineering companies on preform manufacture. Thanks to this close cooperation, data from the injection moulding process can be used just in time to adapt the stretch blow moulding process. Adaptations needed “With recyclate the colour can vary from batch to batch, for instance,” is how Wiese outlines one of the challenges faced. “Darker material absorbs heat better. The lower heating capacity requires less energy. This makes production more efficient yet means that adaptations must be made to the blow moulding program on the stretch blow moulder.” It is therefore essential that the effects are quantified, he continues. Another challenge is the intrinsic viscosity (IV). “The longer the recyclate is boiled under vacuum, the longer the polymer chains become. This means that the IV increases and the quality improves. However, this results in additional costs which not everyone is prepared to invest,” Wiese adds. “Here, we have to come up with ways of redistributing the material from uncritical areas – the bottle base in the case of still water – to more critical zones.” Experience shows that manufacturers of premium brands – whose containers have thicker walls – have less cause for adjustment than discounters, where all of the lightweighting options have often been exhausted. This is where recyclate can reach its limits. In this context a technology developed by KHS in cooperation with inspection technology manufacturer Agr International scores points: Unit Mold Control, a digital, automated control system which regulates the blow stations on the InnoPET Blomax individually. It helps to control material distribution more precisely, reduces variations in the wall thickness by up to 30% and lessens any fluctuations in quality during stretch blow moulding. “This is especially relevant when using recycled PET,” explains Frank Haesendonckx, head of Technology at KHS Corpoplast. “Here, the quality of the material can vary, meaning that the lower the preform weight, the greater the fluctuations in material in the bottle and the more unstable it becomes.” During continuous wall thickness inspection the new system identifies any unwanted material displacement and automatically counteracts this, states Haesendonckx. “Unit Mold Control combines weight reduction with bottle stability and is thus one of the many sustainable and effective answers KHS has to the challenges thrown up by the current packaging debate.” According to Bottles & Shapes expert Arne Wiese there are no convincing arguments against the use of recycled PET in beverage bottles. The only relevant difference he sees between virgin PET and recycled material is the slightly darker colour. This is a question of sorting, however – and only really visible in water bottles. With other beverages, such as the Beyond Juice bottle developed by KHS which is made entirely of recyclate, the consumer would not even notice the difference once the bottle is filled. As far as the mechanics are concerned, there is nothing to stop companies converting to rPET, providing ideal conditions for the creation of a functioning circular economy. www.khs.com","@ID":37}, "PETplanet Insider Vol. 21 No. 06/20 petpla.net 54 Shampoo with 93% natural ingredients The Procter & Gamble brand “Herbal Essences” is bottling 225ml of sulphatefree shampoo with aloe and bamboo in a slim, light green bottle, which is 100% recyclable but, according to the label, is made with only 25% recycled product. The shampoo is free of silicon and colourant and provides hair with strength and moisture. A transparent self-adhesive label on the front allows a view of the shampoo; the label on the rear describes application and ingredients. It is dispensed via a screw-on hinged cap with dosing function. www.for-me-online.de Dairy free yogurt Under the brand Califia Farms, the American company of the same name has a range of plant-based vegan products in its range. These include several probiotic yoghurt varieties, which are available in contoured bottles. Alongside “10 billion living cultures per serving”, these hold a total of 240ml of yoghurt. The bottles are decorated with a sleeve label typical of the brand and are sealed with a transparent screw cap with guarantee band. www.califiafarms.com Rose bloom lemonade in 100% recyclate German manufacturer Voelkel GmbH is selling 0.43 l of organic rose lemonade under the label “the fair lemonade” in a transparent, long-necked bottle. Certified with the Fairtrade seal, the vegan product contains raw sugar and a proportion of an extract of rose bloom alongside mineral water. The screw cap and label are of a suitable colour for the slightly pink-coloured lemonade. www.sei-mit-uns-fuer.de Turmeric shot from Aldi Süd As a consequence of the constantly changing trends in foods, providers are forced to react and to offer suitable products. In a promotional campaign, Aldi Süd has expanded its own brand “rio d’oro” with a turmeric shot as an NFC juice. Alongside orange, ginger and turmeric juice, the shot also contains cayenne pepper. The brightly coloured juice must be stored in the refrigerator and shaken before consuming. The clear bottle holds 150ml, is decorated with a transparent sleeve label and is sealed with an opaque screw cap. www.aldi-sued.de PETbottles Beverage + Liquid Food Mystery flavour from Sparkling Ice Each year, American company Talking Rain Beverage Company brings a specially designed bottle onto the market as a “mystery flavour” in conjunction with a competition. The lightly sparkling water is mixed with natural aromas; consumers are encouraged to identify the flavours and to register them. This bottle is from 2019 and the main prize was a cruise. The slim bottle contains 17fl. oz. (502.8 ml) and has a colourfully printed circulating foil label. The bottle is sealed with an opaque screw cap with guarantee band. www.sparklingice.com","@ID":56}, "CAPS & CLOSURES 47 PETplanet Insider Vol. 21 No. 06/20 petpla.net empowered by Drinktec New Zealand Australia Philippines Taiwan South Korea Japan Let Your Inspiration Flow. )URP 'RZQ 8QGHU WR -DSDQ G’day and Konnichiwa! Editour Road Show goes virtual This year’s Editour Road Show was planned to be our next big international editorial project. That is now impossible. For the safety of others and our own, we are all working from home during the lockdown period. But it’s still time for the Editour Road Show to hit the road – it’s just that we won’t be doing so physically, not at the moment. The start of the new decade will see us undertaking a trip starting in Australia, moving on to New Zealand and then Japan, via the Philippines, Taiwan and South Korea. With support from Drinktec, the world’s biggest beverages show, we will be ‘virtually’ shooting off to Australasia in April. The first weeks will see us interviewing PET companies along the route via Internet and phone. These encounters will appear not only in PETplanet Insider but also in a completely new way – new to us, anyway: as podcasts on our website, for the first time ever! We will keep monitoring the situation closely to decide if, how, when and where we can still go personally with our Editourmobil, later in the year, while complying with governmental rules. We will present a comprehensive review of our Tour experiences both at China Brew China Beverage in Shanghai, China, in October and at Drink Technology India in Mumbai, India, in December 2020. Make sure you’re on board when we set off on our next adventure and get ready for in-depth analyses, special features and reports of trends in these bottle and beverage sectors! Enjoy our first-ever Virtual Editour! Stay safe and healthy! Interested in being interviewed? barton@hbmedia.net April - December 2020 Powered by","@ID":49}, "MATERIALS / RECYCLING PETplanet Insider Vol. 21 No. 06/20 petpla.net 17 improve elimination of high organic loads. Sieving at 0.8 mm eliminates lower density contaminants, including labels. Rinsing through a 0.8 mm sieve at 250-750 litres of water/t and gentle drying avoids material losses and fine generation. Avoiding fine separation can lead to increased PVC presence. The Ecosense Certification mark is aimed at those products that require multilayer packaging. The principal DFR requirements are for: clear materials; adhesives soluble in 80oC caustic washes; no PU; and barrier materials incorporated in the PET layer. The Ecosense circular model ensures traceability from tray waste along the value chain. PET in thermoforms The Recycling Thermoforms Working Group goal is to increase PET’s market share in Europe’s thermoforms by providing sustainable and reliable end-of-life recycling solutions. Three task forces have been established. One is developing DFR guidelines; a second will report on sorting and recycling of PET thermoforms. The third group is tasked with and communications to the industry. The industry wants to show that properly designed packaging, separate collection, good sorting and recycling of PET trays makes tray-to-tray recycling realistic, although a separate PET trays recycling stream is probably required. Petcore Europe publishes and regularly updates recyclability evaluation protocols for PET trays and wash-off of adhesives and labels. France presses forward France is aiming at a complete ban on all single-use plastic packaging by 2040, in stages. The new ‘banned’ list will be updated every five years. By 2030, all packaging must be recyclable and plastic beverage bottles will have been reduced by 50%, compared with 2019. All ambient fruit and vegetable packaging will be banned by 2022. Citeo, which is an officially regulated not-for-profit private company, is charged with organising collection, sorting and processing of waste packaging and paper; managing research programmes to develop eco-design and industrial processes; and raising public awareness of separating and sorting. Opaque PET bottles, primarily used for dairy products, account for three per cent of all PET bottles on the French market, amounting to 12,000 tonnes. As they contain Titanium Dioxide (TiO2 ), they can block spinning processes and damage machinery. Opaque bottle recycling is now managed at plant entrances and opaque-only bale recycling began in January 2020. Bottle-to-bottle recycling is being developed with Paprec and French milk consortiums; enhanced recycling is being undertaken with Soprema. MonoPET trays in France now amount to 50,000 t/year, with a further 30-40,000 t/year of PET/PE trays. There are now several PET tray projects and Citeo has worked with Petcore on specifications for eco designs to facilitate tray to tray and enhanced recycling. The move is to monoPET on the base with floating lidding film, avoiding PET/PE combinations; PET foam; PET blister and GAG trays; and aluminium metallisation. Innovation in packaging is still possible, with the following provisos: Recyclability must be addressed before launching any new package. Recycling streams and partners must be clear from outset. Recyclability must include sorting, recycling and outlet quality Full recyclability test protocols must be accepted by all the value chain Tests must be conducted on pilot lines, rather than as laboratory trials. The commitment of each element in the value chain is essential in achieving closed loop manufacturing. www.petcore-europe.org Fig.2: The collobaration of all stakeholder, by Dr Ana Fernandez KP, presented at Petcore Europe 2020","@ID":19}, "MATERIALS / RECYCLING PETplanet Insider Vol. 21 No. 06/20 petpla.net 30 A plastic keg in a circular economy? ability and innovation. One focus is on circular design and the use of reusable raw materials. Due to their functionality the kegs are made from a compilation of different kinds of plastic. These plastics, when sorted, are fully recyclable mono materials. However, because the multi-material and voluminous kegs do not fit in existing reverse logistic systems and are relatively low in numbers, the big waste collectors are not yet keen on organising their collection and recycling. For that reason, it has been challenging to get the materials back in a closed loop via existing waste recycling streams. Since 2017, in addition to the existing waste streams, OneCircle has focused on building a community in several different countries to arrange collection and recycling of the kegs. The great advantage of this is that OneCircle keeps control of the raw materials and can therefore use the kegs as raw materials to reuse in the production of new kegs. KeyKegs are the only kegs that fit in a circular economy, states the company. OneCircle facilitates the contact between brewers, distributors and even endusers (restaurants and bars) through its KeyKegUsers.com platform. To close the loop, the same platform can be used to make the connection to local recyclers. These community members take care of local collection and temporary storage. They compress the empty kegs in bales to reduce the volume for transport. OneCircle is supporting these initiatives with lease programs for balers. As soon as reasonable quantities of used kegs are ready for transport, OneCircle takes over and organises transport to partners offering the recycling facilities. For (Western) Europe KeyKegs are recycled in large numbers during quarterly campaigns in Germany. The main mono-materials PET and PP (approx. 86% of the product’s raw materials) are recovered. These materials are then processed to be reused in new KeyKegs. At present, approximately 30% of a KeyKeg and UniKeg is made from recycled material. In the second part of 2020 this percentage will be increased to approximately 45%. By achieving this, the products already by far exceed the European targets for 2025. However, the percentage of recycled materials in KeyKegs and UniKegs is set to grow considerably before the year 2025 to reach the goal of circularity. For other parts of the world, OneCircle is striving for the same concept. However, because logistics are sometimes challenging, and recycling facilities are limited, a special tool has been developed: The tool easily disassembles the kegs, separating the main mono materials PP and PET to facilitate local recycling of these materials on available local facilities. www.lightweight-containers.com Recycling Special OneCircle, a Dutch family-owned company runs a growing, global business committed to sustain","@ID":32}, "MATERIALS / RECYCLING PETplanet Insider Vol. 21 No. 06/20 petpla.net 21 MATERIALS / RECYCLING 21 tal impact of the bottle is divided by the number of uses. Moreover, it depends on the return rate and life span: with a 95% return rate, a seven-year life span and three cycles per year, the average refilling number per bottle will be 11. Even after these various filling cycles, the bottles can be recycled. This makes it a unique system in terms of ease of recycling and reintroduction with ref-PET revealing itself to be a huge opportunity, especially for short distance distribution in big cities with satellite filling sites. The recipe for a sustainable transformation To meet these challenges, Sidel states that collaboration is key, across and beyond the plastic industry. The circular economy is the new paradigm, aiming at closing the loop to avoid leakage to the environment by favouring recycling as well as reduction and reuse with PET having a unique position. Leading brand owners are convinced that the right answer to reduce their packaging GHG impact is recycled PET and refillable PET. To support the transformation towards sustainability, besides the industry stakeholders’ commitments, four ingredients are required to support it: correct consumer behaviour, extended collection infrastructure, innovative technologies across the value chain and intensified regulation with mandatory collection targets and recycled content. www.sidel.com","@ID":23}, "MATERIALS / RECYCLING PETplanet Insider Vol. 21 No. 06/20 petpla.net 29 made from recycled PET. Sheets for the usage as protective packaging (lu´um) or face shield (Invemask) need to be free of any contamination causing coloured spots or wholes in the sheets. Decisive for the use of recycled PET is that it must be processed in the purest form possible and optimally cleaned in the recycling process. Therefore, Invema uses a cleaning system from its long-term partner CHT Group. The combination of an effective cleaning machine from Herbold and a powerful cleaning liquor consisting of caustic soda and Tubiwash enables Invema to reach the best transparency for the trays and face shields. Besides this, Tubifoam and Tubiwet support the separation of the materials resulting in the needed material purity of PET. CHT Group can contribute its strength from individual recipes and strong technical service to support Invema not only to make the actual process most efficient, but also to save important resources such as energy and water, thus protecting the environment. Other than the recycling process the CHT Group makes further important contributions to interrupting the infection pathways of the coronavirus. Disinfectants for hand and surface hygiene are produced to help at various locations worldwide as well as special coatings for so-called “textile face masks” and professional medical workwear partly made from recycled PET. Thus, PET provides strong assistance to make our everyday life more comfortable and safer. In times like we are in now, the advantages of circular economy are obviously and the effort to give a PET bottle or tray a second life is worthwhile. www.cht.com","@ID":31}, "BOTTLING / FILLING PETplanet Insider Vol. 21 No. 06/20 petpla.net 48 Flavoured milk in aseptic bottles Amul has hit upon a new field for PET in India. It is filling PET bottles with 200ml of flavoured milk. The market for aseptic packaging is booming. Amul already have three aseptic PET bottle filling lines, while a fourth line had been ordered to start production before the end of 2019. We met: Mr Anil Bayati, GM Gandhinagar, June 2019 With the present handling of 20 to 25 million litres of milk per day, Amul has become one of the largest milk processors in India and Gujarat Cooperative Milk Marketing Federation Limited (GCMMF) (Amul Federation), which markets the popular Amul brand of milk and dairy products, is the fastest growing dairy organisation in the entire world. As per latest report by IFCN (International Farm Comparison Network - a leading, global dairy knowledge organisation) Amul ranks 9th among the largest milk processors of the world. Being a co-operative Amul is well supported by the association of 3.6 million farmers and hence Amul always ensures a sustainable income to their farmers. Amul processes the milk into every conceivable dairy product, from classic milk to cheese to chocolate to ice cream. To do this, Amul relies on the latest production technologies with the highest standards of hygiene. This is why, early on, Mr Anil Bayati GM installed pasteurisers and aseptic equipment for dairy products. Particularly for flavoured milk in single serve 200 ml packaging, Amul has gone beyond the pasteurised can and beyond the aseptic Tetra Pack. In 2013, the first aseptic system for PET from Gea Procomac was installed in response to the boom for flavoured milk. The system provides the market with 30,000 bph. Just like the can and the carton, the flavoured milk need not be cooled for transport; the BBD is 6 months. Flavoured milk viz. Saffron (Kesar), Elaichi, Rose, coffee etc. are different in colour and the customer can see through the transparent PET bottles to make their choice from a distance. In total, the milk beverage range in PET consists of 30 different products. These have a screw cap on a 38mm wide mouth, from which the consumer can drink directly, comfortably. Later in 2017, second and third line (One each from GEA Procomac and Krones) were installed. Now Amul could produce 1.5 million packs per day. Further to meet the increasing demand, Amul has ordered a fourth line, this time an aseptic linear filling system from KHS. Even these additional quantities of products were no problem for Amul to sell. Crucial to the selection of KHS was the dry aseptic process, while Gea Procomac uses the wet aseptic procedure. “We must work very sustainably. Here in Gujarat, the use of water in particular is of immense significance. We recycle all the water we use and when it is no longer useful for processing, we water the green spaces and then it comes back sometime as rain,” says Bayati in his statement. Amul already processes around 2,700 MT of plastic per month into packaging (poly film) for the food sector. So it was only a matter of time before Amul started producing the preforms and caps themselves for the aseptic lines. “First, we decided on caps. Our calculations showed that there was a higher hidden profit in cap manufacturing than in preforms, so we started with those.” Amul has bought one Husky closure injection moulding system and planning for another closure system by the 2019 year end. At 38mm and 3.1 g, the closures provide superior safety to protect the product’s sensitive contents. Bayati Tour Sponsors: Anil Bayati, General Manager AmulFed Dairy (right) in the AmulFed Dairy entrance area along with Rohan Shahane from Husky Injection Molding (left). Between them the father of the white revolution Dr Verghese Kurien (left) and Founder Chairman of Amul Shri Tribhuvandas K Patel (right).","@ID":50}, "MATERIALS / RECYCLING PETplanet Insider Vol. 21 No. 06/20 petpla.net 39 scrap production that has to be recycled or disposed of. Even with high degrees of contamination, the screens of the RSFgenius can be reused up to 400 times, depending on the filter fineness, and allow fully automatic production without the need for personnel for several weeks. Retrofit extruder allows food contact There are many factors involved in the processing of PET in general, and of recycled material in particular. In addition to the mechanical cleaning of the melt by the filtration system, the extruder has the task of thermal cleaning. Here, the processing unit should work gently in order to exert as little mechanical stress as possible on the sensitive polymer. Through simultaneous vacuum degassing, low-molecular components such as monomers, oligomers or decomposition products can be removed from the plastic melt on the Building the future in every moment of your business 40 Bar Oil-Free Piston Compressors for PET Applications. hertz-kompressoren.com one hand, while on the other hand moisture escapes here, which would initiate chain degradation and thus viscosity reduction. Finally, more happens in the vacuum zone: contaminants that can never be ruled out in recycled goods, such as solvents, stabilisers, acetaldehyde scavengers or oils, must escape. The Gneuss Multi-Rotation System (MRS) extruder based on a single screw extruder. This extruder processes PET melt gently and provides a particularly large melt surface in the multi-screw section with degassing zone. In this way, with a simple vacuum of 25 to 30mbar degassing and decontamination performance is ensured. The American FDA authority to grant Gneuss MRS Extrusion Technology a Letter of Non-Objection. As well as in Europe, where the Gneuss recycling process received EFSA approval for the processing of 100% post-consumer PET on thermoforming sheet processing line. Online viscometer completes retrofit solutions It measures a small partial flow of the melt during ongoing production and determines melt temperature and pressure via a precisely manufactured slit capillary. Based on internal calculations, the online viscometer constantly provides the representative shear rate and dynamic viscosity. Depending on the values determined, the vacuum in the degassing zone of the MRS extruder is readjusted to keep the melt viscosity within the specified tolerances. Regardless of which key component, MRS extruder, melt filtration system or online viscometer, a processor chooses, the ability to process recycled material and still produce high-quality PET sheet is therefore possible. Gneuss states that in combination with the company’s consulting services, an optimum solution can be found for almost any application. www.gneuss.com","@ID":41}, "MATERIALS / RECYCLING PETplanet Insider Vol. 21 No. 06/20 petpla.net 28 From PET to protection against coronavirus A drink anytime, anywhere. Easy to go, easy to dispose of. The drinking bottles at hand do not only characterise city scenes and cultural events but are also a synonym for our consumer society. Worldwide, more than 22 million tons of PET bottles are currently being produced (trend + 4% per year) and today only around half of these drinking bottles are taken to the recycling process although it is simple and sensible to give a used bottle a second life. Recycling Special For example, the recycling process can save up to 70% of water compared to new production and reduce CO2 emissions by up to 50%. Furthermore, the recycling saves crude oil and consumes approx. 45% less energy. In the event of proper disposal an already used PET bottle can be used in a more versatile way than almost any other product. It can serve as a raw material for new products such as textiles (approx. 48%), new bottles (approx. 27%) and sheets (approx. 18%). Next to the existing applications, there are new ways to make life a bit safer and more comfortable. Especially in a difficult time as we are in now, the advantages of PET material are obvious. Sheets made from recycled PET are protecting our food and give them a longer life which helps us to deal with the increased time at home. Invema, a PET recycler in Central America, collects millions of beverage bottles, recycles them and produces 100% food-grade recycled PET sheets. These sheets are used for food packaging and in the face of this health crisis against the actual coronavirus, further ideas arise which has launched the initiative of building face shields as a humanitarian response against corona viruses. The protective face shield project now called Invemask, helps protect the face, eyes, nose, mouth and ears and is exclusively for bio sanitary use. Designed to be a support weapon to prevent the spread of corona viruses anywhere in the world. Invema currently works only with 100 of the more than 300 people it has on its staff. This work team is totally focused on the production of 100% recycled PET sheets following their transformation to the food-grade packages (lu´um) and face shields (Invemask). Invemask is an example that recycling helps the world and that projects like this are part of a practical and sustainable circular economy, where the range of CHT Group products help to ensure an optimal quality and the necessary technical results for the sheets","@ID":30}, "BOTTLE MAKING 51 PETplanet Insider Vol. 21 No. 06/20 petpla.net Adjustable, adaptable, accurate The ECS machines have adjustable strokes for injection and stretch-blowing, according to preform length and bottle diameter, which help to optimise cycle time and energy consumption. While they have been designed to work with Sipa moulds, they can be adapted to run with moulds from other OEMs. Sipa recently undertook a significant redesign of the operator interface (HMI), which incorporated lessons learned from the experience in practice of machine operators. The company analysed operating procedures and created a set of shortcuts, with the aim of simplification. The result is an HMI that is designed to enable the operator to get where they need to be, quickly and with the minimum of actions. Individual preform cavities can be provided with their own conditioning parameters, determined according to the design of the preform. In the bottle blowing section, it is also possible to manage conditions separately in each cavity in the bottle-blowing section, to maintain quality across any number of bottles in a production run. Short maintenance times The use of needle valve gates with simple geometry in hot runners in the preform injection section enables them to be purged quickly, which helps to cut set-up time. The hot runner system can feed up to 10 cavities. Loading and unloading the preform core plate is an automated procedure. The system incorporates additional sensors to ensure that the mould opening stroke is adjusted correctly to the preform length. Sipa says that changing the blow moulds is an easy procedure and claims that the ECS SP 25 and ECS SP 80 have a best-inclass lock-to-lock time. Value for money According to Sipa, the ECS range offers converters a higher cavitation capability than rival machines of a similar size, claiming a level at least 25% higher for the same size of container. Their ceramic heaters offer fast heating and good material distribution for oval shaped bottles, without having to rely on complex shaped injection tools; and robust construction and smooth operation for durability and repeatability. Sipa summarises the ECS SP range as offering competitive output for the level of investment and consequent bottle cost and presents it as an excellent solution for converters wanting containers with high-quality appearance and non-standard necks, in limited production batches and in various colours, appropriate to personal care and pharma, cosmetics, food, liquor and miniatures businesses. www.sipasolutions.com ECS SP single stage ISBM moulds l l textile packaging","@ID":53}, "PETpatents www.verpackungspatente.de PETplanet Insider Vol. 21 No. 06/20 petpla.net 56 Base shaping Intern. Patent No. WO 2018 / 065691 A1 Applicant: Sidel Participations, Octeville-Sur-Mer (FR) Application date: 21.9.2017 International application is made for the special geometry of a base shape for a reduced-weight plastic bottle intended for hot filling and/or carbonated drinks. Thin-walled plastic bottle Intern. Patent No. WO 2019 / 192974 A1 Applicant: Societé Anonyme des Eaux Minerales D’Évian et en Abrege, Évian-les-Bains (FR) Application date: 2.4.2019 The application proposes an especially thinwalled bottle to be placed or screwed into a type of casing. The consumer can then grip the bottle securely over this casing without risking the collapse of the bottle; this prevents any unintentional escape of the product when opening. Base shaping US - Patent No. US 2018 / 0127137 A1 Applicant: PepsiCo. Inc., Purchase (US) Application date: 4.11.2016 Application is made for the special base shaping of a plastic bottle to hold a carbonated drink. The base should retain its shape and stability under increased internal pressure. Various ridge depths Europ. Patent No. EP 3536623 A1 Applicant: Niagara Bottling LLC., Ontario (US) Application date: 4.12.2012 Application is made for a plastic bottle with circulating ridges of varying depths. This should provide advantages for labelling, handling and joining several bottles together “packaging-free” using bands, film etc. Light bottle Intern. Patent No. WO 2018 / 089908 A1 Applicant: Amcor Group GmbH, Zürich (CH) Application date: 13.11.2017 The base of a reducedweight bottle must be specially shaped so as to remain sufficiently stable even at lower weights and prevent misshaping through pressure or stress during handling. Container with reinforcement Europ. Patent No. EP 3539889 A2 Applicant: P.E.T. Engineering s.r.l., San Vendemiano (IT) Application date: 5.3.2019 The application proposes a light bottle to be assembled from two parts. The upper part is the bottle with a hemispherical base (cannot stand) and a second, separately manufactured part is joined to the bottle by gluing or notches to provide a standing base.","@ID":58}, "MATERIALS / RECYCLING PETplanet Insider Vol. 21 No. 06/20 petpla.net 44 Energy-saving inline crystallisation For the bottle-to-bottle recycling process, systems have been developed that reduce energy costs by combining the pelletising and crystallisation step in a single integrated process. This technology uses the thermal energy of the molten polymer in PET pelletising for subsequent crystallisation, avoiding the need to cool PET after pelletising and then reheat it for crystallisation. The inline crystallisation system developed by Nordson, called CrystallCut, is designed to work with the spherical pellets generated by UWPs and is an integrated network incorporating pelletiser, dryer, and crystallising unit. rPET pellets achieve a crystallisation level of up to 32% (in production of virgin polymer, by comparison, the figure is approximately 40%, depending on the initial quality of the material). Subsequently, a solid state polycondensation (SSP) reactor raises the IV of the polymer and carries out a final decontamination step by removing trace substances like acetaldehyde, which have a deleterious effect on taste in food applications. Pellet temperature in the CrystallCut system is maintained at 140180 °C. The system eliminates the intervening step of holding pellets in a silo at a maximum 60 °C (to avoid pellets sticking together) and a separate pre-crystallisation step before the pellets are transferred to the SSP reactor. Alternatively, by adjusting process parameters, it is possible to bypass the CrystallCut step or to produce amorphous polymer. Compared with a traditional operation with UWP and SSP operating at 2.5 t/h, the CrystallCut system provides thermal energy savings of 30 to 50 kWh/t, electrical energy savings of 10 kWh/t, a reduction in cooling water of up to 40%, and a reduction in fresh water for refill of up to 90%. As energy costs vary from region to region globally, plant operators need to calculate their cost savings individually. The system can be used to yield rPET with near-virgin properties. Because process heat is retained in the core of the pellets, crystallisation takes place uniformly from the core to the outside surface. By means of process optimisation, it is possible to achieve this crystallinity at small pellet sizes, making the rPET more compatible with virgin PET when blended. At the same time the higher bulk density of the rPET increases SSP capacity and reduces costs for transportation and packaging. Complete polymer processing systems Polymer processing systems for PET recycling are available individually, but there are benefits in sourcing them from a single company. Apart from the obvious one of reducing the number of interfaces during the engineering and purchasing phase, single-sourcing enables the supplier to design a system to maximise the efficiency with which the various equipment components interact. For example, the pressure demands of the screen changer and pelletiser affect the selection of the gear pump. Another advantage of working with a single supplier is that of using a single control or software solution to integrate the entire post-extrusion system. With UWPs, the operator can use a single interface on the pelletising system to access the extruder, feeding equipment, screen changer, and melt pump. To meet the surge in demand anticipated for rPET, the recycling industry will have to achieve massive increases in new capacity. Along with the extensive equipment needed for producing high-quality flake from postconsumer PET bottles, recycling companies will have to invest in extrusion and post-extrusion systems capable of yielding rPET with properties as close as possible to those of virgin material. In helping these companies to supply a fast-growing market for rPET, new-generation post-extrusion systems will be key to increasing productivity and profitability. www.nordson.com Spherical pellets CrystallCut installation","@ID":46}]}}
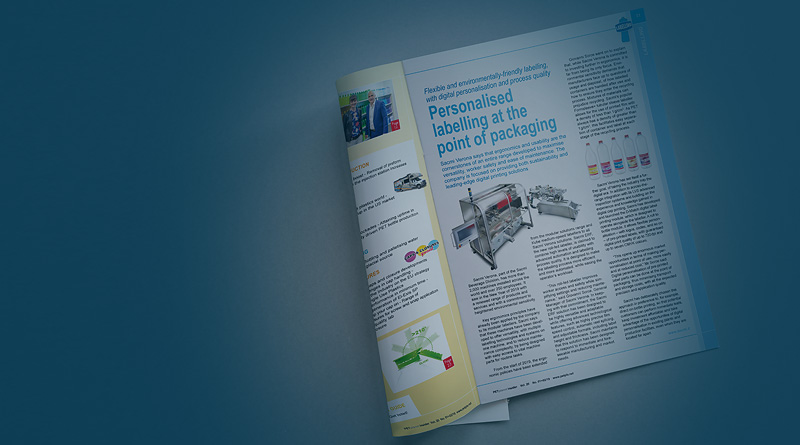