Combining technical know-how with customer needs
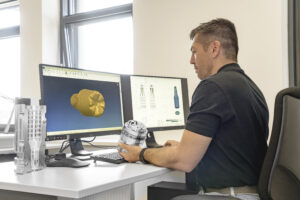
Creating the perfect bottle design
As a mould manufacturer, Röders creates its bottle designs from a technical point of view. After almost 50 years of bottle engineering and blow mould manufacturing, the company benefits from a huge experience of what is technically feasible and which details can be recommended to the customer.
Regardless of the technical equipment, a detailed design briefing is one key to achieving the design the customers are looking for. These briefings can vary – they can be very short, but already very clear. Or alternatively quite extensive, but confusing. In this article, Röders discusses the essential points needed to speed up the design process, make it as clear as possible for the technicians and most satisfactory for the customer.
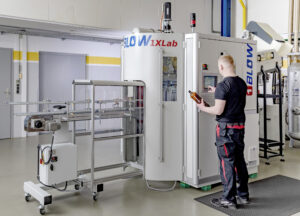
“Please provide a proposal for a 500 ml slim and elegant water bottle which would be unique in the market“– briefing completed. Röders has received many such requests in the past. So the question is asked: Still or carbonated water? Does “slim“ mean the client has a special diameter in mind? What is the individual understanding of “elegant”? What will be the preform weight for this bottle to take into account volume impact or haptic properties right from the start?
Other briefings are clearer as customers already know what they need to provide for the engineering team to get a quick drawing. No doubt it is easier to work with already existing ideas in mind. A frequent request is to increase or decrease an existing bottle to a new format, e.g. from 500 to 750 or 1,000 ml. The questions that need to be answered include: Are there fixed requirements such as the main diameter? Is the maximum height important to ensure proper presentation on the shelf later? Is the emphasis on cost saving by retaining customer’s existing preferred options on the line?
Marketing department vs. technical team – better together!
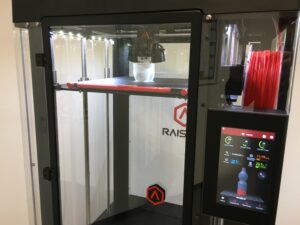
For sure it is important to have the right people involved in the design phase. Doing a bottle project from a marketing perspective will be very creative, but most likely not feasible on the production line without reducing efficiency. It is therefore very important to get the right know-how in the individual steps of the design phase. With the experience of more than 100,000 moulds manufactured, Röders always strives to balance the feedback between the different departments to guide the customer to a reliable solution.
Tools for testing new bottle shapes
In the laboratory equipped with a state-of-the-art 1Blow test blowing machine, Röders can check the properties of a bottle design in every detail. This offers the possibility, especially in the development phase, of enabling the most cost-effective and exact bottle development to achieve a functional bottle. In recent years, testing new moulds with a qualified laboratory report has proven to be increasingly useful for all parties involved. With the certified laboratory equipment, Röders is able to blow bottles with the desired preform weight and resin at short notice and, on the one hand, deliver them to the customer for test marketing purposes, line trials or palletising tests and, on the other hand, carry out all important tests itself.
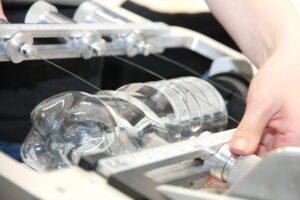
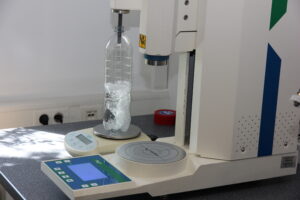
The client benefits from quick results and feasibility reports that show whether or not the design created meets all requirements. Röders utilises different tools and modern technology in the various stages of the process, including a 3D printer for bottle mock-ups. These mock-ups can be presented directly to the customer and accurately reflect the final product 1:1. In addition, the company uses state-of-the-art computer design programmes to develop even complicated design elements precisely and reliably. Through this process, the customer benefits not only from the exact results in the calculation of the bottle shapes, but also from detailed dimensions on drawings and special views of the prototypes, which are often used for advertising purposes due to their high quality.
Röder’s checklist to ensure a swift design process:
- Bottle size = required fill-level volume and required headspace
- Product to be filled
- CO2-level or use of nitrogen during the filling process
- Name of the bottle/project
- Preform neck finish + estimated weight, if available: preform drawing
- Requirements for bottle dimensions such as main diameter, total height, label area dimensions to meet existing customer preferred options
- Labelling: Sleeve or standard label etc.
- Base design: Petaloid, 6-feet, Champagne base, Star base, a reference type from an existing project or any other requirements – please let us know what you prefer
- Other details to share