{"pages":{"page":[{"#text":"BOTTLE MAKING 40 PETplanet Insider Vol. 22 No. 07+08/21 petpla.net Combination of PET bottle blowing and pulsed light decontamination in one machine 3-log decontamination without chemicals Logarithmic scales are used to determine what percentage of a germ is killed by a certain procedure or disinfectant. The logarithmic reduction (log) stands for a germ reduction by a factor of 10. In Serac’s ESL Combox, a 3-log decontamination of containers can be achieved which corresponds to a 99.9% reduction of undesired organisms. This is accomplished by combining the blowing of bottles in a controlled environment just before filling and pulsed light treatment of necks and caps. This level of decontamination can be enough for several applications to significantly extend the shelf life. For example, Serac’s ESL Combox is used for fresh white milk with a 30 days shelf life, or for drinking yogurts with a 60 days shelf life in Asia. Pulsed light is a fast and efficient decontamination method. It destroys the cell membrane of microorganisms and degrades their DNA in less than a millisecond. Using neither water nor chemicals, pulsed light allows dairies to guarantee the absence of treatment residues in the packaging and to better manage water resources, both in terms of consumption and effluents. Small footprint The ESL Combox combines the blowing, filling and capping functions in a single unit with a footprint up to 25% smaller than that of a conventional filling line, says Serac. It is capable of blowing round, rectangular, oval or complex shaped bottles, ranging from 250ml to 2 l. And its patented positive neck transfer system allows different shapes and sizes of bottles to be filled on the same machine, with very short changeover times. The machine has been designed for low to medium output. www.serac-group.com BOTTLE MAKING ESL Combox Preform treatment by pulsed light in the ESL Combox In the new ESL Combox, the dairy packaging specialist Serac combines PET bottle blowing and pulsed light decontamination. This machine won over several dairy companies by enabling them to emphasise their commitment to sustainability while expanding the products’ shelf life. Cap treatment by pulsed light in the ESL Combox","@ID":42} "BOTTLE MAKING 35 PETplanet Insider Vol. 22 No. 07+08/21 petpla.net processing characteristics of rPET as well as less obvious factors, such as the increased level of powder that rPET processing creates. The company recently established the AWArPET brand to advance its environmentally conscious approach to the design and production of PET packaging. AWArPET helps to understand the impact of all packaging details, including preform colour, glue type and barrier options. Sipa says that this helps to, simultaneously, deliver on-shelf attractiveness and awareness of the role of recycling in a circular economy. AWArPET bottles are very light: SIPA has been involved in a design project for a 1l water bottle weighing just 16g, far lighter than most such bottles currently on the market. The cut-glass look Not so long ago, Sipa helped bring to market a new PET bottle for a premium mineral water that was, historically, packaged in glass. The challenge was to implement features such as sharp cuts and angles but in PET, to give the bottle a cut-glass look. New renderings were produced that satisfied the customer’s marketing needs as well as the bottle’s functional requirements. After the switch from glass to PET, the client gained 16% more market share while reducing the product’s carbon footprint by 65 per cent. www.sipasolutions.com Sipa’s CAD container design","@ID":37} "8 NEWS PETplanet Insider Vol. 22 No. 07+08/21 petpla.net Plastics Recycling Show Europe returns to Amsterdam in November The Plastics Recycling Show Europe (PRSE) returns to the RAI Amsterdam, The Netherlands on November 4-5, 2021, moving to the larger hall 12 to accommodate demand for a larger exhibition and conference space. The PRSE is a free-to-attend exhibition and a conference designed specifically for plastics recycling professionals. It brings together key players from the plastics and recycling sectors to showcase latest technology, share best practice, network and do business. A broad cross-section of the industry is represented at the event including plastics recycling machinery and equipment suppliers, plastic material suppliers and compounders, pre-processors, plastics recyclers, waste management specialists and industry associations. The latest trends in the plastics recycling sector will be explored throughout the free-to-attend two-day conference, which provides a holistic view of the whole plastic recycling value chain, drawing together political leaders, major brands, recyclers and the plastics recycling and manufacturing industry. Updating delegates on the latest political and legislative developments in plastics recycling in Europe will be the opening conference session entitled: Making Plastics Fully Circular: What’s Next? Materials focus sessions on the first day will explore the challenges, issues and opportunities within the sector for mechanical recycling, covering PET, PVC and technical plastics. The second day’s opening conference session is Closing the Circle with RecyClass and is followed by polyolefin material focus sessions which will examine the current status of polyolefin waste streams including LDPE and HDPE. The conference concludes with a final session looking at PP and PS recycling. The winners of all seven award categories at the Plastics Recycling Awards Europe 2021 will be announced at the event on November 5. All 55 finalists will be showcased in the exhibition, as will the winners of the 2020 awards, which were presented virtually. The hybrid event in November will allow people unable to visit the event in person to view elements of the two-day conference programme via livestream, including the announcement of winners of the Plastics RecyclingAwards Europe. Online-only visitors will also be able to interact directly with exhibitors. Organisers Crain Communications and Plastics Recyclers Europe are working closely with the RAI to ensure all visitors enjoy a covid-secure event. This will include following the latest guidelines from the Government of The Netherlands and the National Institute for Public Health and the Environment (RIVM). www.prseventeurope.com Associations claim priority access to recycled plastic material for beverage industry The non-alcoholic beverage industry in Europe, represented by the European Fruit Juice Association (AIJN), Natural Mineral Waters Europe (NMWE) and Unesda Soft Drinks Europe, calls on the European Commission for “priority access” to its recycled plastic (PET) material, or a similar mechanism that guarantees “right of first refusal”, to be incorporated in the upcoming revision of the EU Packaging and Packaging Waste Directive. As the beverage industry continues to invest in circularity and to put highly recyclable PET on the market, it needs to have priority access to its own recycled packaging material, the associations state. This will help the beverage industry produce new packaging with foodgrade recycled PET compliant with EU food safety standards, achieve its recycling targets and prevent its recycled PET being downcycled. Closing the bottle loop is required to ensure that the beverage industry meets the Single Use Plastics Directive (SUPD) targets and contributes to building a more circular economy for beverage packaging. The beverage industry is subject to several mandatory requirements under SUPD, one of which is that PET in bottles has to be foodgrade to comply with EU food safety standards. In addition to introducing mandatory collection targets for PET bottles, SUPD also mandates the beverage industry to use a minimum of 25% (by 2025) and 30% (by 2030) of recycled content. The beverage industry’s commitment is not only to achieve these EU targets, but also to go much further by creating a closed loop for its PET bottles. www.unesda.eu Investment in PET recycling facility in New South Wales, Australia The Clean Energy Finance Corporation (CEFC) has made its first investment under the Australian Recycling Investment Fund, committing up to US$12.05m (AU$16.5m) in debt finance on behalf of the Australian Government to a PET recycling facility in regional New South Wales. The new plant will recycle the equivalent of an estimated one billion PET bottles a year as well as create long term employment opportunities in Albury-Wodonga. The PET plastic will be used to produce more than 20,000 t/a of new bottles and food packaging. Circular Plastics Australia (CPA) will beAustralia’s largest PET plastic recycling plant and only the second facility of its kind in Australia to process PET endto-end into food-grade recycled PET. The plant is intended to increase Australian manufactured and sourced recycled PET by two thirds, reducing the country’s reliance on both new and imported recycled plastics. The announcement came just days after an export ban on sending mixed plastics overseas for recycling came into effect. The ban was agreed by Federal, State and local governments in 2019 after China and Indonesia blocked imports of waste from Australia and other nations. The project will draw on US$12.05m (AU$16.5m) in debt finance from the Commonwealth Bank of Australia, for a total debt finance package of US$24m (AU$33m), to build the US$33m (AU$45m) state-ofthe-art recycling facility. Construction is well underway, with the plant to be part powered by renewable electricity through the installation of solar panels. Recycled PET produced at the CPA facility will help fill a growing demand for green supply chains, displacing fossil fuel derived and carbon intensive virgin PET production. It comes asAustralia is required to take more responsibility for its waste and continue to develop the nation’s circular economy. www.cefc.com.au","@ID":10} "MARKET SURVEY 28 PETplanet Insider Vol. 22 No. 07+08/21 petpla.net 07+08/2021 MARKETsurvey Resins & additives Preform machinery Preform production & inspection systems Preform & SBM mould manufacturer SBM 2-stage Compressors Caps & closures & inspection systems Filling equipment & inspection systems Recycling machinery Palletising & shrink film machinery Compressors Compressors – not often in the spotlight perhaps, yet a vitally important component of PET production, and with significant potential of energy saving. Our annual market survey takes a closer look at these unsung heroes of the PET industry, featuring six compressor manufacturers and their product range: ABC Compressors, Kaeser Kompressoren SE, Siad Macchine Impianti, AF Compressors - Ateliers François S.A., Gardner Denver Ltd - Bellis & Morcom, Hertz Kompressoren GmbH and Nanjing Shangair Machinery Manufacturing Co.,Ltd. Although the publishers have made every effort to ensure that the information in this survey are up to date, no claims are made regarding completeness or accuracy. Company name ABC Compressors Kaeser Kompressoren SE AF Compressors, Ateliers François S.A. Postal address Telephone number Web site address Contact name Function Direct telephone number E-Mail Pol. Ind. Azitain 6, 20600, Eibar, Spain +34 943 820 400 www.abc-compressors.com Mr Gonzalo Gabarain Sales & Marketing Manager +34 647 413 760 ggabarain@abc-compressors.com Carl-Kaeser-Str. 26, 96450 Coburg, Germany +49 9561 640 0 www.kaeser.com Mr Henry Beyer Produkt Manager Kolbenkompressoren +49 9561 640 5017 henry.beyer@kaeser.de Ateliers François, Rue Côte d'Or 274, Liège B-4000, Belgium +32 4 229 70 10 www.afcompressors.com Mr Pascal Heyden Marketing Manager +352 26 95 66 28 pascal.heyden@afcompressors.com 1. Machine designation / model number Horizon | Horizon LP Sigma PETAir CE, L for 20 bar to 40 bar units, OPC for 7 bar to 10 bar units 2. Number of models in range 30+ models 25 High pressure units: 30 models, low pressure units: 22 units. 3. Output in m³/hour 250 - 6,000 336 - 2,772 300m³/h to 3,300m³/h for high pressure, 7.2m³/min to 58m³/min for low pressure (ISO1217:2009) 4. Compressor type Oil-free reciprocating piston compressor \"all-in-one\" skid Low pressure air Low pressure oil-free piston compressor Screw type L shape, 2-stage piston reciprocating oil-free air compressor (7 bar & 10 bar) High pressure blowing air (up to 40 bar) High pressure oil-free piston compressor (atmospheric up to 40bar) Piston type L shape, 3-stage piston reciprocating piston oil-free air compressor (20 bar up to 40 bar) Integrated system Atmospheric compressor including VSD with largest regulation range from 18% to 100% of the capacity All-in-One, 3-stage reciprocating piston oil free air compressor 5. Lubricated or oil-free 100% oil-free compressor class 0 Low pressure compressor 100% oil-free compressor class 0 Lubricated OPC range for oil free air 7 bar and 10 bar units. Booster compressor Not needed, it’s an atmospheric HP compressor. Lubricated 0-40 bar oil free reciprocating compressor Integrated system Atmospheric 100% oil-free compressor class 0 All-in-one system high and low pressure 6. Machine layout Horizontal opposed cylinders, forces balanced and virtually no vibrations \"V\" (2 cylinder), \"W\" (3 cylinder) L shape 7. Number of compressor stages 2 for LP and 3-4 for HP 1+1 2 stages, 2 cylinders for low pressure, 3 stages, 3 cylinders for high pressure 8. Are special foundations required ? No, virtually no vibrations No No 9. Cooling system Water cooled (closed cooling tower or aerocooler) Air (water option) Radiator cooler or evaporative closed cooling tower 10. Belt or direct drive Direct drive Transmission belt Low pressure compressor Direct drive Direct Low pressure 7bar 10 bar, transmission belt Booster compressor Not needed, atmoshperic HP direct drive Belt 0-40 bar compressor, transmission belt Integrated system Direct drive All-in-one system, transmission belt","@ID":30} "MATERIALS / RECYCLING PETplanet Insider Vol. 22 No. 07+08/21 petpla.net 43 hacker, General Manager of Starlinger recycling technology. Remote installation during the global pandemic Starlinger, like so many other machine and technology providers all over the world, tries to support its customers in every situation. “Machine installations and commissioning are definitely a challenge in these times”, continues Andreas Pechhacker. “With travel restrictions and quarantine periods in place in many countries we are glad that we have local technicians based all over the world. This bioPAC bioplasticsMAGAZINEpresents: Coorganized by supported by www.bio-pac.info #biopac Conference on Biobased Packaging 03 - 04 Nov 2021 - Düsseldorf, Germany Media Partner helped us already in the pandemic year of 2020 to get new equipment up and running as quickly as possible. In the case of EcoBlue, the technician from our Starlinger Thailand Office will be in charge for the installation of the new PET recycling line, with remote support from his colleagues in Austria, if necessary. All equipment has been tested and commissioned before shipment. Based on Starlinger’s plug & play principle, installation and commissioning of the recycling system at the customer’s site can be carried out quickly and smoothly. This way we ensure that EcoBlue can take up production as soon as possible.” EcoBlue’s 3D Pure rPET for bottles EcoBlue’s 3D Pure rPET for PET films EcoBlue Limited is a recycling company based in Thailand that offers high quality rPET, rHDPE and rPP made from post-consumer and industrial waste. It is a pioneer in offering high quality rPET with FDA approval for the PET film application which has been proven to work well for films with 90% rPET content. EcoBlue’s high-IV bottle-grade rPET can be used up to 100% for clear bottles suitable for food contact. EcoBlue also works towards Circularity of Resources by bringing difficultto-recycle materials like films and laminates into the recycling stream. This gives materials which would have otherwise ended up in landfills a second life and reduces their impact on the environment. www.ecoblue.co.th www.recycling.starlinger.com","@ID":45} "PETplanet Insider Vol. 22 No. 07+08/21 petpla.net 47 BOTTLES Organic honey in 100% recycled material dm Bio, the own brand for the pharmacy discount firm dm, is continuously extending its product range and switching to more sustainable packaging. The latest expansion of honey varieties includes the “blossom honey” version that comes in the now familiar squeezable headstand bottle. The organic honey product comes in a 350g bottle made from 100% recycled material. As with many other products, the closure is not “yet” made from recyclate. The cap has a tamper-proof strip which makes it easy to see if the bottle has already been opened. www.dm.de Ketchup with less sugar The German food manufacturer, Jütro and Co. Ltd KG, has brought out its own “Newmoji” ketchup with children specifically in mind and comes in a specially decorated bottle. It has matching printed motifs to encourage children or tempt adults to buy the product. According to the imprints, the product contains 30% less sugar due to the addition of apple juice and raw sugar, as well as being free of sweeteners. Under the screw-on hinged lid with silicone valve, the container opening is secured with a sealing lid that needs to be removed before opening. www.aldi-sued.de Caffeine water in PET Un d e r t h e b r a n d name “Viteau+ and active bio caffeine water”, the German food manufact u r e r, TSI Consume r Goods GmbH, is selling three varieties of a carbonated mineral water that has been infused with caffeine. This is a drink which aims to support hydration with a lemon, raspberry/basil and lime mint taste. The product comes in a clear, 500ml bottle made from 100% recycled material. Several eco-seals decorate the paper label which provides information about the product. A screw cap and tamper-proof strip complement the bottle. www.tsi.de Innocent juice with donations for butterflies A plea to “Save butterflies” decorates bottles of Innocent smoothies and juices as part of a promotion campaign. By entering a code that appears on the label or bottle tag, the buyer can choose one of three butterfly rescue projects online to which Innocent will donate 20 cents. The initiative is advertised prominently on the bottles. In the picture is a 900ml Multi-Mix Orange bottle that consists of at least 50% recyclate and is secured with an easy-to-grip screw cap. www.innocentdrinks.de www.netterling.com PETbottles Beverage + Liquid Food","@ID":49} "MOULD MAKING PETplanet Insider Vol. 22 No. 07+08/21 petpla.net 24 Pushing the boundaries of cavity numbers with upgrade moulds For many years, multi-cavity moulds represented the state of the art in injection moulding technology. The moulds manufactured by MHT AG in Hochheim, Germany, produce a large number of preforms in a single cycle. Their spectrum ranges from 2 to 192 mould cavities. However, injection moulders don’t allow for a free selection of the number of available cavities: The machine imposes clear limits on the mould design. The purchase of a new machine to increase output is often not a real option. So what alternatives are available to injection moulding companies to increase their production output in a significant way? Many years ago, MHT was the first mould manufacturer to introduce an upgrade for all common 3000kN and 4000kN PET systems. Exclusively for MHT’s partner Sacmi, MHT designed a patent-pending upgrade mould family that maximises the machine utilisation of the Sacmi IPS400 as well as the IPS300 – the novel Nano mould series. ANano upgrade for mould manufacturing For the first time, these upgrade moulds make it possible to operate a Sacmi IPS400 with a 144-cavity mould and a Sacmi IPS300 with a 128-cavity mould. This represents a new milestone in maximum machine utilisation. In order to realise the Nano pitch mould cavity spacing of 45mm x 111mm, the developers came up with an entirely new stack design. The greatest challenge was implementing all mould nest components in a significantly reduced space. Despite the minimised dimensions and the attendant thinner wall thicknesses, MHT offers users durable components, as usual. This is, among other things, guaranteed by the use of a material specially adapted for this application. In combination with this, MHT also relies on the guaranteed utilisation of the many advantages of a cavity with locking cones on both sides, the so-called core- or care-lock design. If the clamping pressure is distributed across two cones, users benefit from reduced component wear and a finer mould separation line. The development team also focused on effective heat dissipation in all its moulding components. Optimum cooling, even in the smallest space, is the basis for short cycle times and high-quality preforms. Reducing the ecological footprint In the preform design, the new mould design offers clearances up to 30mm in the support ring diameter, up to 26mm in the outer thread diameter and up to 21mm in the body diameter of the preform. This ideally positions these new upgrade moulds for many lightweight applications currently finding their way into the beverage industry all over the world. Even during transport, the upgrade moulds yield a reduction in CO2 emissions. Due to the reduced mould cavity distance, the weight of a 144-cavity upgrade mould is reduced to that of a 128-cavity standard mould. The loads on the machine remain constant due to the comparable total mass of all moving parts. This in turn has a positive effect on the cycle time. During production, the numerous cavities in a small space contribute to energy savings during each injection moulding cycle. All in all, 12.5% more preforms are produced in the usual production area. For the hot runner, this means less heating energy per preform, shorter flow channels and a lower pressure reduction. Producers can optimise their ecological footprint and reduce production costs at the same time. For precise melt guidance to the cavities, MHT relies on the latest generation of hot runners. Thanks to the cooperation with Sacmi, the OptiRun is receiving sufficient hot runner zones. Operators benefit from uniform heating of the melt with the associated increased process stability. Test results indicate a lower and uniform AA level (acetaldehyde level) in the PET. The cooperation between Sacmi and MHT offers IPS300 and IPS400 operators with a desire for higher output a comparatively cost-effective solution. Looking to the future, MHT aims to develop additional Nano upgrades in order to generate maximum output despite limited machine sizes. www.mht-ag.com A patent-pending mould family upgrades the Sacmi IPS400 and IPS 300 machine utilisation.","@ID":26} "BOTTLE MAKING 30 PETplanet Insider Vol. 22 No. 07+08/21 petpla.net Food grade sample bottles produced by a global consortium using enzymatic recycling process On the road to industrial scale A global consortium that includes French biochemical company Carbios, Nestlé Waters, L’Oréal Biotherm, PepsiCo and Suntory Beverage & Food Europe, has unveiled prototypes for food grade recycled PET bottles, produced as part of the project to support the industrialisation of a technology that allows plastic to be endlessly recycled while maintaining properties virtually equivalent to virgin plastics. Nestlé’s Research and Development Centre for Waters in Vittel, France, has produced the first Perrier 50 cl prototype bottles made from coloured recycled PET materials. The prototypes, which were thoroughly tested in terms of safety, quality, and performance, were adapted to withstand the pressure of carbonated water while incorporating the iconic design and green colour of the Perrier bottle. Nestlé’s R&D expertise and infrastructure was leveraged to create bottle preforms using the technology for other Carbios consortium members, who have produced demonstration sample bottles for products including L’Oréal Biotherm skincare range; PepsiCo Pepsi Max, and Suntory Beverage & Food Europe Orangina. Jean-Claude Lumaret, CEO Carbios Global consumer brands unveil world’s first enzymatically recycled bottles","@ID":32} "BOTTLE MAKING 26 PETplanet Insider Vol. 22 No. 07+08/21 petpla.net Quality control, fast-track material development and bottle prototyping Optimising bottle production Blowscan was developed to provide users with the capability to quantify the effects of blowing behaviour and understand variations in preform quality and material performance. It was born out of an EPSRC €1M collaborative partnership involving BMT, Queen’s University Belfast, Sidel, Logoplaste, Procter and Gamble, Husky and Pack 3.0. The machine has been designed to flexibly interchange between freeblow and mould-blow modes. This unique dual functionality is intended to provide a low-cost, efficient approach to troubleshoot preform manufacturing and bottle blowing problems, whilst at the same time enabling preproduction prototyping capability for new bottle development projects. How does it work? Blowscan has been developed as a lab-based stretch-blow machine that features bespoke instrumentation to investigate the complexities of the preform-to-bottle process. It utilises a pre-loaded batch feed system, as opposed to a continuous preform feed. This removes the need for ancillary equipment, such as conveyors, hoppers and unscramblers, considerably reducing the footprint. Oil bath or industrial-standard near-infrared (IR) heating are available as means of heating. The purpose of two heating methods is to isolate and assess the most influential properties of the preform, that being the mechanical and the optical properties. Oil bath heating disregards the colour of the preform and provides a consistent and reliable temperature profile that reveals the pure mechanical properties. The IR heating can be regarded as a more standard, industrial approach that provides a realistic temperature profile with the knowledge that it is influenced by preform colour. The desired blowing method can be selected prior to testing, with Blowscan offering free-blow and mould blow capabilities using a modular ‘roll-in, roll-out’ subassembly. With either set-up, the bottle is ejected from the blowing station and is deposited into a collection drawer for the user to retrieve and inspect. When the mould is removed, and the preform is allowed to deform freely, a considerable amount of detail can be extracted regarding the preform quality and material behaviour. During the free-blow process, the preform temperature, inflation pressure and blowing geometry can all be compared against a reference preform. To identify any changes in preform quality within a batch, evaluating the difference in blowing behaviour with BOTTLE MAKING Blowscan operational flow With growing environmental awareness, there is an increased uptake of sustainable materials by the bottle industry, such as recycled PET, bio-materials and additives. Their different compositions, when compared to typical polymers (e.g. virgin PET), means that there is a need to better monitor their influence on the blowing behaviour of the preform during stretch blow moulding (SBM) to ensure the quality of the final bottle. The latest state of the art instrument from Blow Moulding Technologies (BMT), Blowscan, has been specifically designed with this in mind. The technology became a valuable tool for BMT’s partners Logoplaste and PepsiCo for providing confidence for successful bottle production.","@ID":28} "TOP TALK PETplanet Insider Vol. 22 No. 07+08/21 petpla.net 15 Can you briefly explain to our readers the most important bills that affect the PET bottling/recycling industry? Radoszewski: There are two significant bills in California that we are keeping an eye on and it’s a bit confusing as to what the goal is here. AB 478 mandates recycled content in all thermoforms. This includes PET as well as the other resins such as polystyrene, polyethylene and polypropylene. Another bill we’re watching is SB 343. It would create a prescribed list of recyclable materials and would prevent the use of the chasing arrows symbol on any material not listed. Incredibly, PET thermoforms, which package so much of California’s fresh produce would not be considered recyclable and would instead be landfilled. There are strong, viable, and growing markets for this material in California and this legislation would prevent their recycling. In sum, one bill requires recycled content from materials that the other bill does not consider recyclable. PETplanet: What role do directives play for your members in the US market that, like the example of tethered caps, are currently becoming binding for the European market? Radoszewski: We continue to see legislation pushing tethered caps. These efforts are not as significant as has been the case in the past. However, Maine and Massachusetts both had bills introduced on the subject this year. Other directives we have been following are recycled content mandates in plastic bottles. Last year California passed a recycled content law, and this year Maine and Washington both passed similar laws. PETplanet: The challenging global situation entailed the shift of the NPE show to 2024. Which (strategic) changes, difficulties but also opportunities resulted from that for you? What possibilities are you going to tackle to strengthen the relationship with your exhibitors, visitors and of course your direct members, also in the interim period? Radoszewski: Organisations across the globe have found new meaning in the old idiom “necessity is the mother of invention.” The past 18 months or so have been jarring in so many ways, but our association has been more agile and adaptable than even I thought possible. We’ve accepted challenges as opportunities and have hosted numerous virtual events to maintain strong engagement with our members and stakeholders. At the same time, nothing can fully replace the in-person dynamics of a trade show of the size and scale of NPE. That’s why we’re laying the groundwork right now for the NPE2024 to be the best NPE ever. PETplanet: We are looking forward to it! Thank you very much! www.plasticsindustry.org The right tools and expertise to help with your rPETgoals! Agr is uniquely positioned to support your venture into rPET bottle manufacturing with a powerful combination of Process Control tools, Process Consultants, and decades of industry experience. AGRINTL.COM • +1.724.482.2163","@ID":17} "TRADE SHOW REVIEW PETplanet Insider Vol. 22 No. 07+08/21 petpla.net 44 “Post Covid-19 - Strategy and Trends for the Circular PET Economy” Petcore Europe annual conference 2021 part 2 The last three sessions of the second day of the conference covered the topics of “Trends in Design for Recycling”, “Monomer Recycling - where is circular PET headed?” and “Circularity of PET - opportunities beyond recycling”. The session of “Trends in Design for Recycling” started with a presentation byLuca Stramare from Corepla, who introduced the idea of a PET tray recyclability evaluation platform and continued with an update of the European PET Bottles Platform (EPBP). Luca mentioned the importance of focussing on design for recycling. He pointed out that the PET thermoforms platform is ready to take the challenge by “smartly cloning” of the EPBP concept for closing the loop on PET tray recycling. He explained that the full value chain is already represented under the umbrella of Petcore Europe. For building up the PET thermoforms platform the EPBP recyclability assessment model was adapted to the thermoforms value chain and its peculiarities. A steering and technical committee has already been appointed. Luca said that until today a toolbox with a main test protocol is defined and a first reference lab is identified. Only the quick tests still needed to be worked out. Design guidelines for the recycling of clear PET trays were published. Paolo Glerean from Aliplast introduced RecyClass with its new Recycled Content Traceability Certification. It contains the traceability evaluation of recycled material flows in a site producing products with rContent. Paolo explained that an independent certifi - cation body verifies the traceability of recycled content and the calculation of pre-consumer and post-consumer share in products. He added that the certificate validity is one year. The Audit Scheme of the certfication was developed according to a controlled blending model as described in ISO22095 Chain of Custody. The Audit Scheme was published in July 2020, the documentation can be found on the RecyClass homepage. The following session was about the topic of “Monomer Recycling - where is circular PET headed?” Mike Neal from Petkonseptemphasised the lack of a Monomer Recycling Legislation. He finally summarised that in the future the EU Commission is going to produce legislation to include chemical recycling. He pointed out that at the moment, the legislation is not even in draft stage. Martin Stephan, CEO of Carbios and Co-Chair of the Monomer Recycling SIG told about what the Monomer Recycling WG has initiated. The results are a Monomer NIAS evaluation program, a Technology Readiness Level (TRL) evaluation of the industry and a general specification for monomers/oligomers. In September 2021 the working group will present DG Santé first results of NIAS testing program, TRL, sector time to market. In a second step they will finalise the specification/ TRL/NIAS testing program and finally exchange with other Petcore Europe WG to structure feed stocks supply chain for monomer recycling. Jean-François Briois from Nestlé Watersexplained Nestlé’s vision for packaging sustainability. Nestlé’s long term vision is that none of their packaging ends up in landfill or as litter. By 2025, Nestlé intends to reduce its virgin plastic by 33%, and to make 100% of its packaging recyclable or reusable. Jean-Francoise highlited that PET packaging has the potential to become truly circular in 2030. After a comparison of mechanical and monomer recycling he summarised that monomer recycling needs support at R&D stage to qualify as many feedstocks as possible and to define relevant quality specifications. He added that there must be a support during scale-up to guide and fund industrial scale-up. The last session of the event was about “Circularity of PET - opportunities beyond recycling”. Carl-Eric Portaels from Petcore Europepresented Petcore’s communication campaign. The mission of the campaing is to achieve holistic recognition of the performance of PET to be a material of choice for packaging and other end-uses, meeting environmental, sustainability and performance criteria expectations of the consumer and other stakeholders. With websites, webinars and tests in France and Germany, the campaign End Waste, Recycle the Oneaims to present consumers critical knowledge on PET as a valuable resource and understanding on how to correctly recycle it. Eric Schaffner, CEO and Founder of Zeloopshowed a mobile application to reduce plastic littering. The application is characterised by giving incentives to the consumer for their pro- environmental behaviours with a first focus on plastic bottle collection. The whole Circular Economy Rewarding Platform has the aim to educate consumers in a smart way for sorting, resulting in more collection and better sorting quality. Sebastian Lemp from Alpla Groupintroduced a reuse model by Alpla. With a special designed PET bottle the consumer can refill the bottle at home or on the go. At a return drop of point the PET bottle is collected. Alpla’s PET pool bottles are a 1 l bottle with 55g and 500ml bottle with 38g (up to 10g less than comparable PET solutions). These bottles withstand a minimum of 15 cycles. by Heike Fischer www.petcoreeuropeannualconference.eu/presentations","@ID":46} "BOTTLE MAKING 38 PETplanet Insider Vol. 22 No. 07+08/21 petpla.net Designing for a closed loop PET market With the EU target to incorporate 25% of recycled plastic in PET beverage bottles from 2025, designing for sustainability is coming to the forefront. Avient’s ColorMatrix has a range of additives which can be part of the solution. Based on an article by Nick Ryan, Sales Director EMEA, ColorMatrix, Avient Corporation When the European Union announced a 25% rPET target for 2025, two key challenges were obvious - the availability and price of rPET. In response to the burgeoning demand for rPET, mechanical recycling has seen rapid growth in capacity and investment; however, deposit scheme feedstock alone can’t feed the appetite of this rapidly evolving market. In addition, other concerns - including aesthetics, fluctuating mechanical properties and Non-Intentionally Added Substances (NIAS) - have emerged. In this environment of rapid change and uncertainty, brand owners, converters and raw material suppliers are quickly adapting to balance the interests of their stakeholders, customers, legislators and recycling partners. Sustainability and brand protection PET packaging requires a full design process – aesthetics, additives with consideration for a content’s shelf-life and now the addition of rPET content. Avient states that the quality of recycled PET can be improved by its material science solutions such as additives, scavengers, and toners. Nothing is more damaging to a brand than a bad consumer experience like an off tasting, smelly or discoloured beverage. Content spoilage is also a significant contributor to overall carbon emissions, in many cases far more so than the packaging. This is why oxygen scavengers are widely utilised in juice, beer and wine applications. It is critical that the oxygen barrier protects the beverage right up to the time of consumption. When using rPET, this can be a challenge as rPET content greater than 25% can disrupt or deactivate existing barrier technologies. ColorMatrix Amosorb 4020R is an oxygen scavenger technology designed with the new rPET environment in mind, intended to help maintain full oxygen scavenging functionality, with no sign of deactivation even in bottles containing up to 100% recycled content. Bottles produced with this oxygen scavenger, in combination with rPET content, show minimal colour degradation when processed through existing recycle streams, says Avient. At the design stage, when adding rPET, by selecting a highly heat stable blue toner, such as Avient’s ColorMatrix Optica Toners, the material continues to tone out natural PET yellowing throughout its life leading to a cleaner, clearer rPET stream. These optical toners can also address the different behaviour of rPET compared to virgin PET due to fluctuating IV levels and variations in stretch. Their inorganic particles absorb and distribute heat more evenly throughout the preform inner and outer wall, overcoming much of the variation. In multiple commercial applications, this has enabled bottle blowers to regain lost efficiencies, improve bottle performance and reduce energy usage. Non-Intentionally Added Substances are also a challenge in the closed-loop PET market, where raw materials can be exposed to each other inadvertently with the potential risk of unintended impurities building up. Legislation is catching up with this and organisations have to be prepared. Avient has developed NIAS screening capabilities for standard colourants and additives designed to help brands manage compliance risks. Where PET bottles cannot return to the PET bottle stream, the outputs are ranging from fibre to food trays and even toy blocks. When decreasing chain length provides a challenge, whether that be in bottle-to-bottle rPET production or repairing heavily degraded PET solutions, Avient’s ColorMatrix RePrize is claimed to ensure that IV increases of up to 0.2d/l are possible. This has been successfully used to facilitate the use of 100% rPET in carbonated applications. The chain extender also allowed 100% tray to tray recycling and converted textile waste into reusable pellets. www.avient.com BOTTLE MAKING","@ID":40} "PETcontents 4 PETplanet Insider Vol. 22 No. 07+08/21 petpla.net 07+08/2021 Page 30 Page 18 TOP TALK 10 Brazil: PET helping a rollercoaster year for the package market - Interview with Auri Marçon, president of the PET industry association Abipet 14 “The long-term trend is upward” - After pandemic-related turbulence, the US PET industry is slowly recovering MATERIALS/RECYCLING 16 Optimised colour change for hot runner and injection moulding systems - Cooperation between two world-leading brands in material development and engineering 18 Preparations for competitive expansion at home - rPET an export hit and prospects for definite recycling regulations in China 22 FDA approval for Kreyenborg infrared rotary drums 42 Tackling waste problem in Thailand with PET bottle-to-bottle recycling line MOULD MAKING 24 Pushing the boundaries of cavity numbers with upgrade moulds MARKET SURVEY 28 Suppliers of compressors BOTTLE MAKING 26 Optimising bottle production - Quality control, fast-track material development and bottle prototyping 30 On the road to industrial scale - Food grade sample bottles produced by a global consortium using enzymatic recycling process 32 A new peak: APF-6004 blow moulder at Sairme Mineral Waters 34 From the seed to success - Bottle design and bottle making 36 Bottles designed around the product - Packaging that protects the product and looks appealing 38 Designing for a closed loop market 39 Rigid biodegradable containers 40 3-log decontamination without chemicals - Combination of PET bottle blowing and pulsed light decontamination in one machine 41 Designed for recycling TRADE SHOW REVIEW 44 Petcore Europe annual conference 2021, part 2 BUYER’S GUIDE 48 Get listed! INSIDE TRACK 3 Editorial 4 Contents 6 News 45 Products 47 PET bottles for Beverage + Liquid Food 54 Outer Planet Page 40 BOTTLE MAKING","@ID":6} "MATERIALS / RECYCLING PETplanet Insider Vol. 22 No. 07+08/21 petpla.net 18 rPET an export hit and prospects for definitive recycling regulations in China Preparations for competitive expansion at home The Chinese recycling firm, Guangxi Guolong Plastic Technology, is located just under 300 km north-west of Guangzhou near the city of Wuzhou in Guangxi Province. This privately-owned business was founded nine years ago by its Chairman, Guo Jiawan, and specialises in the production of food-grade rPET packaging and cups for food and drinks products, as well as rPET sheets and flakes. The company also uses high-end recycling equipment from Europe. Although the firm is not yet profitable, Mr Jiawan sees prospects for long-term success and potential. We talked to him about opportunities, goals and the current state of recycling in China. Guo Jiawan was previously active in the real estate business and managed the city’s only 5-star hotel before founding Guangxi Guolong Plastic Technology and deciding to move into the recycling industry in 2012. “Environmental protection is beneficial to future generations, and I am very enthusiastic about it”, said Mr Jiawan. And the ambitious entrepreneur has since invested quite a sum, US$ 124 million into his vision in the past eight years. “But we have not yet achieved profitability”, he added. We will soon learn the motivation behind this, but first, let us go back to the beginning. In order to gain a better understanding of the global recycling industry, the company founder and his team first travelled to different parts of the world, including Europe, North and South America, as well as Asia and south-east Asia, where they acquired valuable experience in local environments, and on the implementation of recycling practices and technologies. They visited test and development centres, including those of the plant manufacturer, Tomra, and ultimately came up with ideas and concepts for their own company project, with a focus on recycled material for food-grade applications. Over the years, the result has been the establishment of a machine park that, according to Mr Jiawan, sets itself apart from all its competitors in terms of its capabilities and technology. “Our province alone generates about 800,000 t of plastic waste annually, much of which is crushed and shredded by micro companies”, he says. “There have also been problems with existing, often outdated equipment and processing operations linked to all kinds of adverse ecological impacts that essentially breach China’s environmental protection regulations. We, on the other hand, have installed a comprehensive recycling system in Guangxi and established dedicated recycling centres in the cities where we can centrally process collected PET bottle waste that meets government standards.” According to Mr Jiawan, process issues are the main problem facing the Chinese recycling world today given the existence of disparate methodologies and physical recycling competing with its chemical alternative. In addition, there is still a significant proportion of biodegradable plastics. As a result, the company is still heavily export-driven, serving customers Chairman Mr Guo Jiawan Aerial shot of Guolong Plastic’s premises","@ID":20} "MATERIALS / RECYCLING 17 PETplanet Insider Vol. 22 tions on the procedure for using our granulate with their Altanium Controller, leading to cleaning processes being more standardised, simplified and especially more repeatable, with an overall lower use of Ultra Purge material and a time expenditure of just a few minutes.” According to ChemTrend, a case study with a customer shows a reduction of 85% in material waste and an 80% efficiency increase in the cleaning process. The work with Husky promises an expansion of customer potential for PET preform and PE end cap applications at a global level. But how did collaboration with the Canadian machinery engineer come about in the first place? “Chem-Trend’s relationship with Husky started several years ago with Husky first distributing Ultra Purge grades designed to purge PET preform applications alongside their systems designed for the same application,” explained Antje Scholl. “Based on the performance of our products and our level of service, the relationship grew over the years to expand Husky’s distribution of Ultra Purge grades for polyolefin application normally used in caps and closures.” Besides such intelligent solutions, the collaboration also sends out a signal of principle, which could certainly be applied to other collaborations as well. Ms Scholl says: “The vision of simplification and productivity increases for the customer is also a great opportunity to initiate further partnerships with other equipment suppliers in the future.” The pandemic has fuelled the need for packaging in all FMCG areas, which has also led to palpable demand worldwide for Chem-Trend’s cleaning granulate, although the company is keeping information on growth rates and sales of its products close to its chest. After all, alongside possible future collaborations, they want to continue developing their own products. www.chemtrend.com www.husky.co Chem-Trend headquarter R&D in Howell, Michigan","@ID":19} "TOP TALK PETplanet Insider Vol. 22 No. 07+08/21 petpla.net 10 Interview with Auri Marçon, president of the PET industry association Abipet Brazil: PET helping a rollercoaster year for the package market by Gabriele Kosmehl During the height of the Corona pandemic in 2020, companies in the PET value chain were also among those that stopped their operations as a precautionary measure - for a short time. It was not only the continuing high demand for PET bottles that had to be met, but also interruptions in the supply chain for other types of containers such as aluminium, glass or polyolefins which had to be absorbed with PET. And this high demand is not the only good news. There are also positive long-term developments to report in the opening up of new areas of application and the further development of the recycling industry. This is not least due to the work of the Brazilian PET association Abipet. PETplanet: Mr Marçon, Abipet is the non-profit Brazilian PET Industry Association. Can you please tell us what exactly you do and what your goals are as an organisation? Marçon: Yes, Abipet is a nonprofit organisation integrating the whole industrial steps related to the PET process: virgin resin manufacturers, preforms & bottles converters, sheets and thermoforming producers and recyclers. There is also the technology committee supporting all technical challenges including polymerisation, post-condensation, drying systems, injection, recycling, filtration, transportation, etc. International and local companies are our members: Alpek, Indorama, Amcor, Engepack, Gneuss, Husky, Krones, Piovan, Polymetrix, 3 Rios, ClearPET, GreenPCR, GlobalPET, Resipol, Lamina and others. PETplanet: What are the priority issues that are currently driving your agenda and that of your members? Marçon: Currently our main focuses are on environmental challenges and growing market segments. Just like all over the world the plastic industry is under attack here and not only by environmentalists but also by legislators, governors and other competitive materials. Even being the most recycled plastic with high end applications like bottle-to-bottle food grade, we, representing the PET industry sector, have a lot of things to do. Most issues we have been facing are related to the absence of information at several different levels of the society. Life Cycle Inventory and Circular Economy amongst others are concepts still unknown by the non-technical citizens, and mass communication is very expensive. Greenwashing from other materials competitors will not cooperate, of course. Concerning growing market segments, special attention is required from the new market segments for PET like beer, home and personal care, dairies, rtd juices and solid food. The challenge here is to identify the right moment when package producers or brand owners are reviewing their original production lines opening opportunities to show PET advantages. Technical support, market information and environmental performance of PET containers need to be provided. PETplanet: It is now several years since we took a close look at the Brazilian market in PETplanet (issue 1+2/2014 ff). At that time, the PET beverage market was showing a strong growth trend. How has it developed since then? Marçon: The local market has been following the world tendency with water rising faster during the last 10 years while soft drinks are reducing their share in the same period. Other beverages based on “healthiness concept” like teas, juices (concentrate or rtd), flavoured drinks, energisers as well as beverages for hydration are also growing. Brazil is a traditional agricultural country producing many kinds of meals and fruits at a favourable scenario for healthy beverages. It means that there is a significant amount of people drinking natural juices and this is a challenge for industrialised/ commercialised beverages that are supplying around 50% or 57% of the beverage’s consumption last year. The most important products bottled in PET containers are: soft drinks (43%), water (28%), edible oil (13%) (percentages estimated based on the last 3 years). PETplanet: Dairies in PET was seen as a particular growth market back in 2014. Can you say something about its performance in recent years? Marçon: Initially, about 5 years ago, the supermarket shelves were invaded by UHT milk brands bottled in PET containers, and now also yogurts and flavoured milk are replacing their original packages (polyolefin and cardboard) with PET. The low-cost production and the presentation of their products were originally their","@ID":12} "imprint EDITORIAL PUBLISHER Alexander Büchler, Managing Director HEAD OFFICE heidelberg business media GmbH Vangerowstraße 33 69115 Heidelberg, Germany phone: +49 6221-65108-0 fax: +49 6221-65108-28 info@hbmedia.net EDITORIAL Kay Barton Heike Fischer Gabriele Kosmehl Michael Maruschke Ruari McCallion Waldemar Schmitke Anthony Withers WikiPETia.info petplanet@hbmedia.net MEDIA CONSULTANTS Martina Hirschmann hirschmann@hbmedia.net Johann Lange-Brock lange-brock@hbmedia.net phone: +49 6221-65108-0 fax: +49 6221-65108-28 LAYOUT AND PREPRESS EXPRIM Werbeagentur | exprim.de Matthias Gaumann READER SERVICES Till Kretner reader@hbmedia.net PRINT Chroma Druck Eine Unternehmung der Limberg-Druck GmbH Danziger Platz 6 67059 Ludwigshafen, Germany WWW www.hbmedia.net | petpla.net PETplanet Insider ISSN 1438-9459 is published 10 times a year. This publication is sent to qualified subscribers (1-year subscription 149 EUR, 2-year subscription 289 EUR, Young professionals’ subscription 99 EUR. Magazines will be dispatched to you by airmail). Not to be reproduced in any form without permission from the publisher. Note: The fact that product names may not be identified as trademarks is not an indication that such names are not registered trademarks. 3 PETplanet Insider Vol. 22 No. 07+08/21 petpla.net Dear readers, The view from America You will find two top talks from America in this issue, first with Auri Marçon of Abipet, the non-profit Brazilian PET Industry Association, and then with Tony Radoszewski, President & CEO of the US organisation Plastics. Although the markets could hardly be more different, both report the difficulties of getting enough collected bottles for the production of rPET. In North America the problem is systemic. Waste is not separated in the municipalities and therefore PET bottles have to be laboriously separated from the waste stream. In Brazil, it was more of a corona-related problem. The essentially manual collection declined as people tended to stay at home shielding. Nevertheless, in both countries the demand for rPET is greater than the quantities produced. In Brazil in particular, the big brands with their rPET specifications have found a ready response amongst consumers, meaning that smaller bottlers now also have to follow suit. While in Brazil the recycling of bottles is already at the old level of 55% of used bottles, in the USA the recycling rate can hardly be increased due to the system. Deposit systems for PET bottles in the USA have only a small and sporadic impact. It is questionable how, in times of environmental debate, sustainability and the anti-plastic movements, the USA can allow itself to remain for years stuck at the almost constant 30% PET recycling quota. Yours sincerely, Alexander Büchler","@ID":5} "MATERIALS / RECYCLING PETplanet Insider Vol. 22 No. 07+08/21 petpla.net 42 Tackling plastic waste problem in Thailand with PET bottle-to-bottle recycling line EcoBlue Ltd., Thailand’s first bottle-to-bottle recycler, has set up a new recycling facility for PET and polyolefins. A new Starlinger PET bottle-to-bottle recycling line is going to be part of the expansion. “Our aim is to turn post-consumer and post-industrial waste materials into a sustainable substitute of virgin resin”, explains Pranay Jain, founder and Managing Director of EcoBlue Ltd. “In anticipation of the increased commitment of organisations towards sustainability, EcoBlue has invested in setting up a new recycling facility with technologies for PET and polyolefins recycling. By having Starlinger as a technology partner, we will ensure that we are able to provide consistent and high-quality bottle-grade rPET to our customers.” Starlinger’s RecoStar PET 215 iV+ bottle-to-bottle recycling system will be delivered to EcoBlue’s production site in Rayong Province, Thailand, in July 2021 and within the following weeks be assembled by the local Starlinger technician with remote support from Starlinger’s headquarters in Austria. The line reaches an output of 2,500 kg/h, equalling a total production capacity of about 20,000 t of bottle-grade rPET per year. High quality food-grade rPET made from certified 100% post-consumer recycled waste EcoBlue is Thailand’s first recycling company to receive the Letter of No-Objection (LNO) by the US FDA for its “3D Pure” rPET for use in foodcontact applications. The Starlinger technology will enable EcoBlue to provide superior quality rPET resin for bottle applications. EcoBlue’s “3D Pure” rPET can be traced back to 100% post-consumer PET waste material through its global recycled standard certification process. Providing sustainable recycled resin to brand owners for reducing their carbon foot print “We aim to work towards a circularity of resources by diverting post-consumer and post-industrial waste materials from landfills to the recycling stream”, explains Pranay Jain the motivation that drives the company. EcoBlue was founded in 2013 and has developed unique capabilities to produce high-quality rPET, rPP and rHDPE from post-consumer and industrial waste, providing a sustainable substitute to virgin resin. EcoBlue’s commitment towards sustainability does not only consist in providing high-quality recycled resin that can help reduce the carbon foot print of environmentally conscious organisations, but also in ensuring that it is produced in safe and equitable working conditions with no harmful impact on people and the environment. “With our portfolio of recycled products we provide a choice of sustainable raw materials for companies which look to reduce their impact on the environment”, says Pranay Jain. Bigger extruder sizes meet customer demands A special feature of the Starlinger PET recycling line is its special extruder size: With the 215mm screw the line reaches an output of 2,500 kg/h. “We sold the first PET recycling line with these extruder dimensions in 2019 and have witnessed a growing demand for this capacity since then. It is currently one of the most popular extruder sizes on the market and meets the existing trend towards higher extrusion capacities perfectly. The incoming orders for 215mm extruders for bottle-to-bottle applications exceed even our expectations”, explains Andreas PechStarlinger RecoStar PET 215 iV+ bottle-to-bottle recycling line","@ID":44} "7 NEWS PETplanet Insider Vol. 22 No. 07+08/21 petpla.net New facility in Indonesia to recycle 2 billion PET bottles annually Thailand-based Indorama Ventures Public Company Limited (IVL), producer of recycled PET for beverage bottles, announced it will build a facility in Karawang, West Java, to recycle 1.92 billion PET bottles a year in support of the government’s plan to reduce ocean debris. The facility, which is planned to launch in 2023, will create 217 new jobs. It is part of IVL’s global commitment to divert post-consumer PET bottles away from waste and back into the circular economy, supporting the Government of Indonesia’s National Plan of Action on Marine Plastic Debris. The recycling plant will provide the washed and shredded post-consumer bottles as PET flake feedstock to produce recycled resin that is suitable for food contact use. Indorama Ventures has six Indonesian sites across Purwakarta, Cilegon, Tangerang and Karawang. With this new recycling facility, IVL brings a circular business model to support our Indonesian operations. In 2019 Indorama Ventures announced it aims to recycle a minimum of 750,000 metric tons of PET globally by 2025, investing up to US$1.5 billion to achieve this goal. IVL’s new plant in Karawang, along with its other recycling facilities in Southeast Asia, will work with existing PET flake production facilities in Indonesia. www.indoramaventures.com ! %%% \" # \" #! !# \" \" &\" \" \"# $ #! ! % \" \" \" \" ' \" ! ! 9 !' \" #! \" # ! \" 9 \" ! 9 \" \" ! \" ! ! ! ! \" \" !\" \" % # 17th China International Recycled Polyester Conference & Exhibition The 17th China International Recycled Polyester Conference & Exhibition will take place from September 13-15, 2021 in the Holiday Inn Shanghai Hongqiao, China. For those who are not able to be present in Shanghai, the organisers are offering a global live stream. The Party Central Committee have proposed the major strategic targets to reach the CO2emission peak by 2030 and achieve carbon neutrality by 2060. Technological innovation to achieve the “dual carbon” goal has also become a market highlight. As a sustainable green lowcarbon fibre, recycled chemical fibre becomes an attraction for green investments, with a large amount of new capacity expected to come on stream in 2021. With more large-scale enterprises entering the recycling industry, small and medium-sized chemical fibre enterprises are facing increasing challenges from capacity expansions of industry giants. Meanwhile, the imbalance between excess recycling capacity and upstream raw material supply is becoming more evident. As a result, market competition has seen increasing disorder. In the face of the large expansion, how should companies identify their positioning and re-layout? What changes are taking place with quality standards and industry norms for recycling? Is there more room for breakthroughs in recycled raw material technology? Focusing on the themes of substitution and antisubstitution, positioning and breakthrough, necessity of market regulation, Recycled Fiber Commission of CCFA, China National Chemical Fiber Corp, China Chemical & Fiber Economic Information Network (CCFEI), Dr Thiele Polyester Technology, based on the successes in the past 16 years, are again to jointly present an event to support recycling economy and provide networking opportunities. www.www.ccfei.net","@ID":9} "BOTTLE MAKING 32 PETplanet Insider Vol. 22 No. 07+08/21 petpla.net A new peak: APF-6004 blow moulder at Sairme Mineral Waters Another APF-6004 blow moulder by PET Technologies has reached Sakartvelo, or Georgia, as it is known everywhere else. Sairme Mineral Waters Ltd brought the equipment and installed it in the very heart of one of the biggest spa resorts in Europe. It is the land of high mountains with picturesque valleys; the land of mountain rivers and springs. Sairme waters have been famous since 1893. In Georgian the name “Sairme” means “the place where deer dwell”. The bottling plant is located in Western Georgia, 950m above sea level, in the resort of Sairme. The modern Sairme Mineral Waters Ltd plant was inaugurated in 2006. Since then its spring water has become widely known for a unique balanced concentration of calcium, magnesium and sodium. It is shipped to 17 countries of the world. This is where packaging comes in. The role of the bottle increases with distance. The more kilometres that lie between the Sairme plant and the final destination of the water, the less vulnerable the container should be. For this reason, the company fills its products both in glass and PET bottles. Equipment developed by PET Technologies helps to produce the latter. Recently, Sairme Mineral Waters Ltd expanded its manufacturing facilities and installed an APF6004 blow moulder. PET Technologies supplied Sairme Mineral Waters with a turnkey solution; from the design of the PET bottles to start-up and final commissioning of the APF-6004 blow moulder. The training of Sairme technical staff and the aftersales service was an integral component of the contract. Thanks to a quick mould change Sairme is now able to produce the whole range of bottles from 500ml to 2 l. The company can switch from one format to another in 20 minutes. There is no downtime for maintenance, since the schedule allows any maintenance to be carried out during a shift change or days off. Bottle production The ergonomic bottle is transparent with a tint of green that highlights its natural origin, life and energy. The bottle shoulders resemble a drop of water that forms high in the mountains at the source of the river. This is where Sairme Mineral Waters Ltd collects water. Narrowing in the centre of the bottle gives the impression of a swift running mountain river. The applied technology played a crucial role in the manufacturing of this bottle. Intense preform heating and simultaneous air-cooling guarantee a uniform temperature distribution between the inner and outer wall. 8-zone heating and the facility to move the lamps in any position guaranteed that this complex bottle meets the predetermined characteristics, even if it is 100% rPET. Partnership The roots of the fruitful cooperation between PET Technologies and Sairme Mineral Waters Ltd go back to 2015. At that time, the bottling company was seeking a reliable supplier of blow moulds for 6-10 l bottles. PET Technologies seemed an attractive proposition due to the manufacturing facilities equipped with 4-, 5-axis machining centres and guaranteed terms of delivery. This first contact turned out to be successful. In 2017 the companies launched a second project together. This was also about blow moulds for up to 2 l bottles and Sairme Mineral Waters Ltd installed an automatic PET SBM machine of European manufacture. They perfectly matched the equipment. This second touch also turned out to be successful. In 2019 PET Technologies was again successful, when Sairme Mineral Waters Ltd chose PET Technologies as a supplier of SBM machines. The bottling company was looking for alternatives instead of the blow moulding equipment for small bottles that they were currently using. A previous successful project for 500ml, 1.5 l and 2.0 l moulds, carried out in 2017, was a strong point in favour of PET Technologies. Additionally, PET Technologies developed the design of these bottles taking into account the nature of the blowing process. Thus, Sairme Mineral Waters Ltd was able to achieve a functional and yet attractive PET bottle. www.pet-eu.com BOTTLE MAKING","@ID":34} "TOP TALK PETplanet Insider Vol. 22 No. 07+08/21 petpla.net 12 motivation, and recycling rate is now one important reason for the decision in favour of PET. Emphasising the recycling aspects, Brazil has also producers of polyester fibres working with rPET as raw material, and this created a natural destination for the white bottles of milk and dairies, and this is motivating many brand owners to review their package mix and reinforcing the tendency to move to PET as an environmentally friendly material PETplanet: Speaking about rPET – How strong is ‘design for recycling’ in Brazil? Marçon: Abipet has a strong interaction with the largest brand owners and other users of PET bottles, and in the past 15 years we have been helping them develop a better “eco-design” for the PET containers. Abipet developed and published the “Directives for PET bottles recyclability” that was disseminated in package design schools and within professionals from the packaging field around the country. PETplanet: How is the collection system for used PET bottles regulated in Brazil? And can you say something about the return rates? Marçon: Since more than 10 years ago, Abipet has been carrying out a PET Recycling Census with the objective of monitoring market and recycling performance in Brazil. More than a statistic search we interview almost 200 companies in different segments: recyclers, final user/application and integrated operations (from baled bottle to final product made of rPET). In 2019, Brazil recycled 311Kt corresponding to 55% of total disposed bottles in the urban solid waste. Many figures of the PET recycling performance can be found in the infographic ( page 11 ). The Brazilian recycling market has a relative maturity with 80% of approximately 48 recyclers operating for over ten years. There are at least eight large recyclers with bottle-to-bottle and food-grade plants producing more than 1,500Kt/month. All of them have suffered over the pandemic period since the automatised infrastructure supply chain for reclamation depended on people, many of whom were shielding of course. It is important to highlight that the big brands behaviour was important during the pandemic once they met their commitments regarding the rPET content into their bottles. This attitude kept recyclers working even during the difficult times. Unfortunately, there is still a large number of companies that have not joined the environmentally friendly design but from our point of view they are already being punished by final customers. “2020 is showing that virgin resin grew up 8% supplying the domestic market, exporting and covering the lack of rPET during the difficult period” PETplanet: Brazil is one of the countries with the highest number of cases of coronavirus in the world. What other impact has this had on the economy so far - especially as far as the PET value chain is concerned? Marçon: Brazil has currently around 200 million inhabitants and proportionally the number of people infected was obviously significant. On the other hand, in terms of cases/millions of people, the Brazilian index was smaller than many developed countries even during the pandemic peak. Considering the negative aspects caused by coronavirus for the economy worldwide perhaps Brazil has not faced the worst scenario as agrobusiness and other important segments didn’t stop during the pandemic period. For 2021, the GDP is expected to reach 4.5%. PET industry performance was not so bad. Final figures are not finalised yet but our estimate for 2020 is showing that virgin resin grew up 8% supplying the domestic market, exporting and covering the lack of rPET during the difficult period when reclamations was not able to supply recycling businesses. Another important aspect regarding packages is the rupture in the supply chain observed for aluminium cans, glass bottles and polyolefins. During the second semester of 2020 and now in 2021, many brand owners changed their mix of packages increasing the PET bottles in their lines. PETplanet: Did your members also experience any pandemic-related interruptions in supply chains, besides the recyclers’ infrastructure? Marçon: During the worst period in 2020 (March/April) many companies stopped or significantly reduced their operations for a short period of time as a precautionary measure but it was quickly resumed once demand for beverage didn’t stop. We observe the change in the demand profile with reductions in soft drink consumption and growth in water, edible oil, detergents, alcohol-gel, cleansers and many different containers for food delivery, the majority in thermoformed trays. An interesting experience is related to the available capacity of virgin resins that supplied all the domestic demand and exported to other countries including the USA. The total capacity of PET virgin resin in Brazil is 1,000Kt/a, and the regular demand last year was between 600700Kt/a. As I mentioned, the recyclers were significantly affected in 2020 because reclamation did not work regularly over the entire country and their raw material (disposable/baled bottles) was not enough to supply recycling plants. PETplanet: Did you notice any changes in consumer behaviour which have had a particular impact on PET packaging during the pandemic, but also on the long term? Marçon: All PET converters realised the change in the size of PET bottles demanded. Due to the lockdown in the cities the “on the go” consumption (small containers) was replaced for home consumption (larger bottles). Another change was the increase in PET trays used for food delivery that took advantage to increase their market share due to the lack of polyolefins to supply the converters. The same happened with detergent and other cleansers when many brands increased PET packages in their portfolio. PETplanet: Thank you for your insights! www.abipet.org.br","@ID":14} "OUTER PLANET 54 PETplanet Insider Vol. 22 No. 07+08/21 petpla.net OUTER PLANET Bacteria transform terephthalic acid into vanilla flavouring Tasty transformation A recipe that starts with “Take one half of an empty PET bottle”? Although unlikely to happen, PET bottles have become the focus of attention for some scientists who managed to convert post-consumer bottles to vanillin. A decisive contribution to the miraculous transformation is made by the bacterium Escherichia coli (E. coli). Researchers from the University of Edinburgh have discovered that the bacterium E. coli, naturally found in the human and animal intestine, can be deployed as a sustainable way to convert post-consumer plastic into vanillin, a new study reveals. The scientists hope that their discovery could boost the circular economy, which aims to eliminate waste, keep products and materials in use and have positive impacts for synthetic biology. The scientists Joanna C. Sadler and Stephen Wallace from the University of Edinburgh’s Institute of Quantitative Biology, Biochemistry and Biotechnology used a laboratory engineered E. coli bacterium to convert the monomer terephthalic acid (TA) directly into the high value molecule vanillin, via a series of chemical reactions, using a single engineered microorganism. According to the researchers, the reaction is mild, uses a whole-cell catalyst produced from renewable feedstocks and occurs under ambient conditions (room temperature, pH5.5–7), in aqueous media, requires no additional cofactors or reagents and generates no hazardous waste. Maximum vanillin titres of 785μM (79% conversion) were achieved after extensive process optimisation studies. The team also demonstrated how the technique works by converting a used plastic bottle into vanillin by adding the E. coli to the degraded plastic waste at ambient temperature and in aqueous conditions: they therefore selected a thermostable enzyme as a biocatalyst to aid hydrolysis of PET into TA. This enzyme released TA directly and did not require an additional enzyme to hydrolyse mono-2-hydroxyethyl terephthalate (MHET) for release of TA. The reaction was cooled to room temperature and freshly prepared E. coli and a biotransformation buffer concentrate were added, and reactions were analysed after 24h. Without any process optimisation, vanillin was detected. The researchers say that the vanillin produced would be fit for human consumption but further experimental tests are required. Vanillin is widely used in the food and cosmetics industries, as well as the formulation of herbicides, antifoaming agents and cleaning products. Global demand for vanillin was in excess of 37,000 t in 2018. The demand for vanillin is growing rapidly and is projected to exceed 59,000 t by 2025. Natural vanillin can be produced by extraction and isolation from vanilla beans or rice bran. However, over 90% of the vanillin used worldwide is produced synthetically - by microbial fermentation via a non-natural, engineered pathway. The aromatic substance Vanillin is a cheaper alternative to natural vanilla, whose prices had overtaken even the price of silver in recent years. Future studies will focus on intensifying this process through further strain engineering, process optimisation and extension of the pathway to other metabolites. The study, published in Green Chemistry, lays the foundation for further studies to maximise vanillin production towards industrially relevant levels and the extension of the pathway to other metabolites. The research was funded by a BBSRC Discovery Fellowship and a UKRI Future Leaders Fellowship. www.ed.ac.uk www.rsc.org Vanillin can be extracted from natural ingredients like vanilla pods, which belong to the orchid family, or synthetically. This is where PET could join the game.","@ID":56} "TOP TALK PETplanet Insider Vol. 22 No. 07+08/21 petpla.net 11 Census of PET Recycling in Brazil a b i p e t . o r g . b r 11º 314 2014 2015 274 2016 250 2017 260 2018 278 2019 311 PET post consume (in kton/year) The research in numbers Where does raw material come from? How is recycled PET sold? Final applications for recycled PET How to increase collection volume? Build Large Centers for Waste Collection and Sorting Increase the selective collection Increase the number of Cooperatives USERS (70%) Only consumes recycled PET INTEGRATED (8%) recycles and utilizes recycled PET RECYCLERS (22%) PET packages recycling only 23% 22% 15% 17% 10% 13% Textile Preforms/ bottles (in volume) (in volume) Sheets/ Thermoforming Strapping Others 68% Recyclables dealers 57% Flake 17% Cooperatives 43% Pellet 6% Selective Collection (Kurbside) 6% Other 3% Waste pickers Over 160 companies classified in 3 groups 311 thousand tons Total volume of post consume recycled PET in 2019 Chemical Circular Economy boosting PET Recycling 55% of disposable packages +12%","@ID":13} "MATERIALS / RECYCLING PETplanet Insider Vol. 22 No. 07+08/21 petpla.net 20 in other Asian and south-east Asian countries, as well as in America and Europe. “The physical recycling of foodgrade applications has made great technological advances over the years to a level which, I believe, offers considerable benefits which is why we chose this area. However, standardised regulations would be needed for a breakthrough in China itself”, explains Mr Jiawan. Meanwhile, his company’s technical equipment portfolio includes Tomra systems for bottle and flake storing, namely the Autosort for pre-sorting of bottles and Autosort Flake and Innosort Flake, both for flake purification, several three-layer co-extrusion ABA structure rPET sheet production lines, a Buhler SSP line, a PET extrusion and granulation production line, five high-speed thermoforming production lines, a Kiefel KTR6.1 high-speed cup making machine with the largest output, an HDPE bottle cleaning line and an HDPE granulation production line. “The waste source or condition is obviously critical to our processes and requires a centralised solution. With the introduction of the 2017 Waste Ban, under which solid waste can no longer be imported into the country for recycling, China now has an opportunity on a broad scale for us to develop and install a proper recycling system that incorporates many improvements in terms of waste separation and collection”, says Mr Jiawan. Coming back to the point on motivation and his continuing investment, he explains: “I am very optimistic about the development space and prospects of the waste plastics recycling market” and takes us on a short excursion into the current state of recycling in China. “China is a large consumer of plastics and is also an energy-intensive country, and demand for plastics can never be satisfied by imports”, says the Chairman. “China is also in the stage of pollution control, banning the import of waste plastics. After the 18th National Congress of the Communist Party of China (CPC), “Lush mountains and lucid waters are as valuable as gold and silver.” has become an important national policy. The Chinese government has promulgated a large number of policies to promote the development of circular economy. Apart from that, brand owners for recycled plastics will also promote the growth of the recycled plastics market in China. Apple, Foxconn, Huawei, Unilever, Procter & Gamble and other companies have already been seeking high-quality recycled plastics suppliers in China. Therefore, plastics recycling is a general trend with rosy prospects. He went on: “The recycling of plastics is generally encouraged all over the world. Both market and government measures are being introduced in this regard. Some large international brand owners have increased the proportion of recycled plastics in their products. The demand in the high-end chemical fibre industry for example is pretty high and supply cannot keep up. Also, the demand for food-grade recycled plastics is growing in Europe and America, Japan, South Korea and Southeast Asia.” Difficulties also emerged during the pandemic. Although China was able to have Covid-19 under control quite quickly, the company was forced to adjust its original plans due to disrupted supply chains and export business issues. “Recycling channels have been under restrictions after the Spring Festival, crippling our recycling and production efforts for a long time”, says Mr Jiawan. “Our imported equipment arrived at the plant in 2019. Because of the pandemic, it was impossible for engineers to come from Europe to install and commission the production line. The equipment was only installed in October and then officially put into production in November 2020, which has greatly affected our production plan. However, since production inauguration in November 2020, we have seen orders increasing day by day. Our products are very popular in Europe and America. And while forming a closed loop of the whole industrial chain, our company achieves the independent sale of products in each link, improving our competitiveness in the market. Thanks to eight years of investment, 2021 will be the year when Guolong begins to prosper and really enter the fast lane of development. Nevertheless, our company has adjusted business objectives and development strategies to cope with the impact of the Covid-19 pandemic. We hope that the Chinese government will promulgate policies to vigorously support the development of the plastics recycling industry. For example, China can consider the mandatory requirements of Europe and America for manufacturers to increase the proportion of recycled plastics in their products, and formulate container packaging standards, thus encouraging the recycling of waste plastics.” Plastics have attracted an unwarranted negative image globally in recent years, mainly as a result of misinformation and conflicting opinions regarding responsibility for waste Recycling plant infeed","@ID":22} "45 PRODUCTS PETplanet Insider Vol. 22 No. 07+08/21 petpla.net PETproducts Handle applicators And&Or, a leader in the manufacture and marketing of handle applicator machines for PET and PE bottles, provides solutions for the automatic insertion of various types of handles. They are adaptable for low, medium or high-speed lines, as well as for multiple types of operation, including rotary, interval linear or continuous linear. The use of the company’s handle application technology enables the manufacturing of a handy and easy carry handle-ware for a large PET container (3 to 5 l) with either a lateral, umbrella or neck handle. And&Or says that traditionally, the move from the classic HDPE handle-ware to a more attractive PET handle-ware container has been challenging, largely due to the lack of precise and specialised handle application technology. In addition, And&Or specialises in the manufacture of a carton collar applicator which automatically inserts the carton collar to single bottles or packs, from 300ml to 5 l. The advantages of this technology are, the flexibility to work with different carton and packaging types, the security by PET fairing, and the easy to use touch screen. With this growing demand for automatic handle application technology, And&Or supports the customer by providing a complete solution from initial concept and design of the handle, bottle & preform specs right through to the successful development of a cost effective final product, offering brand advice along with their professional expertise. www.andyor.com BOTTLE MAKING Bottle design services Producer of specialised preform and blow moulds Petka holds its own design department to create customised bottle designs on demand. The processes offered by their design department and highly qualified designers range from a first evaluation to a prototype before the production of the final product starts. The bottle designs are conceived in accordance with the dimensions of the preform to be blown, specified by the client. After a detailed analysis of the preform concept, Petka’s designers produce a selection of appropriate designs. Once a 3D drawing has been finalised, the designers create a 3D mockup to provide an accurate visual representation of the design. The mockup allows the company to highlight the key functions, attractive features, and unique details of the bottle. This innovative part of the process ensures Petka can demonstrate the final shape of the bottle to the client, prior to any sign-off. To further improve the customer experience, the next step is prototyping. Producing a prototype helps to truly understand the future product and also allows customers to test the design’s accuracy before starting the production process, explains Petka. The main advantages this offers the clients is the possibility to trial their design in “real-world” scenarios and interact with it more effectively. The main objective is to identify potential abnormalities or issues and have the possibility to modify certain aspects of the design if there are any uncertainties, prior to launching a finalised product. In their R&D department, Petka are always working on new features. Their latest development relates to the design of the bottom mould and works on blowing the base with low pressure to produce a more stable base. www.petkamold.com","@ID":47} "BOTTLE MAKING 27 PETplanet Insider Vol. 22 No. 07+08/21 petpla.net respect to a reference is vital — this is the principle of Blowscan. The difference in blowing behaviour is quantified and a verdict on the preform condition can be made. Additionally, with the mould kit, the operator is able to test the desired bottle design while maintaining the same heating and blowing parameters. This allows for rapid bottle prototyping without interrupting the production lines. Who benefits? Blowscan is claimed to offer a number of benefits across all sectors of the supply chain. Through the use of the instrument, material producers can quickly and efficiently assess the blowing potential of novel materials, without the need for cumbersome industrial equipment. Preform manufacturers can identify the quality of preform batches as they are produced, which in turn provides converters with confidence. Finally, both converters and brand owners have the added benefit of producing small runs of bottle prototypes without interrupting production. Case studies Case study 1 – Recycled material type Blowing geometry (rPET and flake) Case study 2 – rPET content For this case study, an investigation was conducted for PepsiCo to examine the difference in blowing behaviour between different rPET resins, by varying the post-consumer resin (PCR) percentage. Virgin, 25% PCR and 100% PCR preforms were analysed using Blowscan. Effect of PCR increase on blowing behaviour relative to virgin As the % PCR content was increased, there was a significant change in the blowing behaviour for both IR and oil bath heated preforms. The 100% PCR preform demonstrated a 31.9% and 27.2% shift in blowing capability for oil bath and IR heating, respectively, when compared to virgin preforms. This indicated that, in this instance, the increase in PCR material influences both the mechanical properties and optical properties of the preform, and as before, a change in blowing behaviour will result in a change in bottle performance. Knowing how a change in material composition (be it PCR content, amount of additives, colour, preform age, moisture etc) influences the blowing behaviour allows the user to make informed decisions as to how best to implement the blowing process and ultimately, benefit production. PepsiCo’s Max Rodriguez, Sr. Manager, Global Packaging R&D, concluded, “BMT compliments PepsiCo’s Global Packaging R&D’s internal capabilities, by providing structural FEA support, SBM PET material characterisation, and package development research collaboration. The Blowscan unit will allow us to expand our internal capabilities across several areas, including packaging innovation, sustainability, productivity, and brand stewardship. www.bmt-ni.com Working with Logoplaste Innovation Lab, BMT’s Blowscan was used to investigate the difference in blowing behaviour between rPET preforms manufactured from resin and from flake. Logoplaste Europe R&D Director, Francisco Alves, stated, “At the end of 2019, we challenged BMT, with Logoplaste’s assistance, to develop a lab version of their Indicate machine to use as a quality control and development tool. This allowed us to address characterisation needs that we can’t meaningfully access today with conventional characterisation techniques”. The preform geometry, heating conditions (oil bath and IR) and blowing parameters were fixed for both materials. From the trials, the preform temperature, inflation pressure and blowing geometry (via edge detection) were analysed. Oil bath trials revealed that there was no difference between the mechanical properties of the two preform types. However, the IR heating process produced two different temperature profiles and as a result, the blowing geometry exposed a difference in blowing behaviour. The result of the ‘hotter’ rPET preform during IR heating was a free-blow bottle that had a 12% larger deformation. In addition, the increased temperature created an earlier onset of deformation by 30ms. In a process that takes a fraction of a second, this can be significant for the bottle properties, particularly material distribution and as a result, the inservice performance. Blowscan was used to examine the change in material properties and quantify the shift in process parameters required to produce the same blowing behaviour as the reference preform. In this study, a 5% oven power increase allowed the flake preform to blow with the same behaviour as the rPET preform. This finding is vital for bottle production when implementing new materials and identifying an appropriate process window. Alves summarised, “This equipment will be a strong complement on the preform quality control plan for our operation’s most challenging applications. This will improve our ability to link new preform and bottle designs to material properties, allowing higher efficiencies, enabling lighter weights and providing more sustainable solutions to our customers.”","@ID":29} "BOTTLE MAKING 34 PETplanet Insider Vol. 22 No. 07+08/21 petpla.net Bottle design and bottle making From the seed to success Italian company Sipa says that it deploys an array of tools in supporting PET bottle makers create attention-catching designs that can be produced quickly, economically and sustainably. Prototypes are developed with 3D printing as well as more traditional laboratory machines; software simulation is used to anticipate thermal profile, thickness distribution, cooling optimisation, and final bottle performance. Knowledge of legal aspects These technical capabilities are complemented by understanding of, and adherence to, current and upcoming regulations relating to consumer packaging, especially single-use plastics. In the immediate future, EU legislation will impact the PET bottle sector with the requirement for tethered caps, which will affect all bottles up to 3 l in volume. By 2024, new solutions will need to be in place, which means there will be significant changes to production lines. Sipa is already testing new cap and neck designs. The EU is also requiring higher PET recycled percentage on new bottles, along with higher waste collection rates. … and technical Sipa is already proposing new lightweight versions of some of the most widely used neck finishes in the market for waters, CSDs, edible oils and hot-fill liquids. The aim is to achieve material savings without any loss of performance, using the same closures and without any changes to handling on the production line. A new neck ring is the only change needed by preform producers in order to switch to the new designs. Five steps to design heaven The company’s design and engineering experts consider not only the look of a container but also how the look fits with the identity of the packaged product, how the container feels and behaves, how easy it is to produce, how it performs on the filling line, in storage, and in transport; and – last but not least – how much it will cost. A typical design project can be separated into five steps, starting with the marketing brief from the client, using a proprietary Sipa interactive document to share ideas, inspirations and expectations. Step two covers sketches, concept ideas, and computer-generated 3D proposals. Step three is production of prototypes, for which Sipa has been using 3D printing for several years. The company maintains that this technology delivers a look and feel very close to that of the final product. Sipa employs various printing technologies to create prototypes in sizes from 10ml all the way up to 4l. Stereolithography (SLA), enables the use of a clear, almost water-white, photopolymer in creation of hollow parts. Engineering aspects Step four tackles the feasibility of the product, including preform development, technical specifications, stretch ratio calculations and shelf simulation. The mechanical performance of the bottle is assessed with the help of Finite Element Analysis (FEA). In Step five, technical drawings are finalised. Preform and bottle production can be tried and moulded products put through rigorous laboratory testing, to confirm computer predictions. Once this has been carried out to the customer’s satisfaction, full production can begin. Use of rPET The use of post-consumer recycled PET (rPET) in bottle design and process technologies requires appropriate expertise. Sipa’s designs take into account differences and variations in BOTTLE MAKING rPET bottle design","@ID":36} "BOTTLE MAKING 39 PETplanet Insider Vol. 22 No. 07+08/21 petpla.net Rigid biodegradable containers Spanish company Noven Farmaplás, subsidiary of Novapet, is launching a new line of biodegradable containers for applications in different food, pharmaceutical, parapharmaceutical and cosmetic sectors, and for hygiene and cleaning products. This launch is a result of the company’s technical cooperation with Novapet’s sister company Nurel; both are part of the Samca, producer and owner of Inzea resins technology. Combining traditional production processes, eco-friendliness and performance, Inzea polymers are a leading material for compostable bottles or jars. They are claimed to offer the same functionality as conventional polymers but they have the advantage of reconverting the container into compost after use. Two grades of Inzea resins are offered by Noven Farmaplás for this new line of rigid containers. Inzea F38, a grade specially designed for extrusion blow-moulding gives containers a good visual appearance, with a pearly finish. It is certified by TUV with the Ok Compost seal (EN 13432 compliant) for industrial composting. With a maximum thickness of 1mm, it is a grade approved by FDA and is compliant with EN 10/2011 European standards on plastic materials and articles intended to come into contact with food. With more than 70% of its material content is from renewable sources, it has mechanical properties comparable to PP and good chemical compatibility. Inzea F29 TR is a special grade for injection blow-moulding that provides good transparency, depending on thickness. It, also, is certified by TUV with the EN 13432-compliant Ok Compost seal for industrial composting and has a maximum thickness of 1.5mm. Again, it is an FDA-approved grade for food contact and is compliant with EN 10/2011. More than 95% of its content is from renewable sources and it shows good chemical compatibility. Noven Farmaplás is equipped with both extrusion blow-moulding and injection blow-moulding production lines. Noven Farmaplás says that this initiative reinforces its environmental commitment with two ranges of sustainable containers. The PET containers are both recyclable themselves and produced with up to 100% recycled PET, in a fully circular manufacturing structure. Biodegradable containers complement the range for market segments in which PET has less presence. www.novapet.com BOTTLE MAKING GAWiSD featuringAutoJob ™ – job set up in seconds +1.724.482.2163 AGRINTL.COM ACCURATE • FAST • REPEATABLE SEE GAWIS4D IN ACTION Dimensional and thickness measurements for plastic containers and preforms. ®","@ID":41} "MATERIALS / RECYCLING PETplanet Insider Vol. 22 No. 07+08/21 petpla.net 22 FDA approval for Kreyenborg infrared rotary drum Recycling and Circular Economy are highly topical issues among both end consumers and legislators today, while plastic package and wrap are regarded critically in the food industry in general and in particular. When using PET post-consumer recycling ware for packages with direct food contact, however, a so-called Super Clean Process authorised by the FDA and / or EFSA is currently required and will be needed all the more in future. With its IR-Clean System, Kreyenborg offers an attractive alternative for the subsequent use of PET post-consumer ware - this system allows direct decontamination without any kind of vacuum technology. On the basis of the experience gained with manifold installed IRD crystallisation and drying systems, the focus in the development of the IR-Clean (R) was in the first instance focused on the requirements and ancillary conditions prevailing in PET sheet extrusion processes. In these applications, a fairly high portion of recycled material originating from in-house and post-consumer flakes in the form of ground PET bottle flakes has always been fed into the process. PET post-consumer recycling ware, however, is used at 100% on very few occasions. This is due to the given circumstances in film production cycles, where edge trim and skeleton scrap from the thermoforming process are fed into the extrusion process on a regular basis. These are classified as post-industrial ground stock and do not need any Super Clean Process. In establishing standards and collecting systems even for PET trays, it is foreseeable that these will be available as post-consumer ware in the near future as well and will thus be a useful complement to the rPET bottle flakes which are used almost exclusively today. As a result, this so-called tray-to-tray recycling process will open up even more potential for the use of rPET and, thus, for the R-Clean system. However, Super Clean Recycling Processes applied for the decontamination of PET flakes are in most cases based on the technically complex bottle-to-bottle processes, which do not only require food suitability, but also the development of intrinsic viscosity (iV) by Solid State Polycondensation (SSP). The vacuum technology required for this purpose is relatively expensive and requires intensive maintenance, though, due to the high complexity of the equipment needed. But as PET sheet extrusion requires much lower viscosities as compared to pre-form production processes, the increase of the Intrinsic Viscosity (IV) is in principle unnecessary. Even in preform systems, direct processing of rPET flakes has meanwhile become possible from a technical point of view - but in these cases, the portion of recycled material remains in the lower range of double-digit percentages, so that the impact on viscosity is insignificant here as well. These special aspects of PET sheet extrusion have been taken into account consistently in the development of the IR-Clean concept, aimed at offering an effective, but at the same time easily and cost-efficiently manageable solution to end users, which can also be applied and retrofitted independently of the extruder type. Optimisation of a proven principle The IR-Clean represents an optimisation of the well-proven and already successfully used Infrared Rotary Drum (IRD) in terms of process technology. The standard process of crystallisation and drying of PET post-consumer bottle flakes in the IRD has been modified by a number of development features inside the machine and new process parameters - this has resulted in remarkably good decontamination results, which have been proven in several challenge tests carried out in collaboration with the Fraunhofer Institute IVV, Freising, Germany. The key to the good results lies in the general functional principle of the Infrared Rotary Drum - the small quantity treated in the process and the continuous movement of the material ensure a permanent surface exchange of the recycling material to be treated. At the same time, the material is continually circulated in the helical flights of the rotary drum and is in this way conveyed towards the surface by a repetitive movement. Additionally, the helix welded inside the rotary drum guarantees an accurately defined flow of material (first-in / firstout) - which is an important aspect as regards the process monitoring and documentation requirements. This good mixing behaviour inside the rotary drum then combines the IR-Clean with the quick and direct heat input by infrared radiation. High temperatures can be achieved within just a few minutes thanks to the halogen radiation used, for the material is heated up directly without resorting to the influx of hot air. These are two of the most important criteria to fulfil for an efficient decontamination process: surface and temperature. Throughout this process, the IR-Clean basic concept can completely do without cooling water or pre-conditioned process air and - above all - without any expensive and high maintenance vacuum systems.","@ID":24} "TOP TALK PETplanet Insider Vol. 22 No. 07+08/21 petpla.net 14 After pandemic-related turbulence, the US PET industry is slowly recovering “The long-term trend is upward” by Gabriele Kosmehl As President & CEO of the Plastics Industry Association, Tony Radoszewski experienced first-hand the light and dark sides that the pandemic had in store for the US plastics industry. In our interview, he reports on the advantages that the material was able to demonstrate for the health sector, but also on the adverse effects that the pandemic had on the recycling market. PETplanet: Plastics Industry Association is supporting the entire US plastics chain. How have you and your members experienced the last 18 months, in the wake of the pandemic? Radoszewski: Plastic is everywhere, but its positive contributions have tended to hide in plain sight. The pandemic really brought to light how essential plastic is to modern societies. Plastic gloves, face masks and barriers have been essential in preventing and treating Covid-19. Put simply, plastic has proven to be irreplaceable, and no doubt saved countless lives during this challenging period. PETplanet: What precautions had you taken in your organisation regarding the pandemic, and which are still active? Radoszewski: I have a very real responsibility as the leader of our association to keep my people safe. I take that responsibility very seriously. We’ve consistently adhered to guidance and protocols from federal and local public health agencies. We’ve been very successful in adapting to virtual operations since last year. That being said, I very much look forward to getting back into the office for regular in-person meetings with my staff later this year. It’s tough to replace the ability to drop into a colleague’s office with a quick question. Those quick brainstorming sessions can often times lead to big ideas. PETplanet: Regarding the PET/ bottling industry in particular - how do the production figures currently compare to the last few years? Radoszewski: The long-term trend is upward and production has partially recovered from the shock that resulted from the pandemic last year. However, various near-term supply chain bottlenecks have prevented a full production recovery compared to past years. PETplanet: During the pandemic, the consumption behaviour of many consumers changed. In Europe, for example, there was an increase in sales of PET packaging in larger containers. Have you also observed new trends in the USA - a country where larger containers are more important anyway - with regard to PET bottles? Radoszewski: The data really doesn’t point to a strong shift to larger containers in the United States. Consumption of essentials rose significantly during the pandemic, which was reflected in both small and large PET containers. During the peak of the public health crisis, consumers purchased what was readily available. PETplanet: During the lockdowns, many recyclers complained of not getting bottles back at the usual rate. How have the recyclers among your members been doing? And are the plants now running at full capacity again? Radoszewski: Our members also experienced the availability issue. Interestingly, this happened most noticeably in those states with bottlereturn policies since the deposit centres stopped taking them back. New York even waived the requirement for retailers to take them back. Some kerb side collection was impacted, but not as drastically. Most plants currently are back to operating at full capacity. However, the bale price is significantly higher than last year at this time and in some places almost double 2019 prices. PETplanet: In your view, how does the American recycling industry compare internationally with regard to PET? And what adjustments could be made for further improvements? Radoszewski: The US differs from most of the world because we do not have a single system to collect plastics, especially PET bottles. This complicates access to recycling and is influenced by a number of local factors including container-deposit policies, attitudes, and infrastructure. These all impact the economics of recycling. Unlike other types of plastic products where there may be technical challenges in their recycling, the issue with PET bottles is one of consumer participation. Recyclers could – and want – to process more PET bottles. There is a strong market for recycled PET. Increased consumer education and an increase is recycling infrastructure would go a long way to improving the recycling system and rates overall. PETplanet: California is in the headlines often at the moment because of new packaging and recycling bills, and your association has specifically positioned itself against the California Labelling Bill SB 343.","@ID":16} "BOTTLE MAKING 37 PETplanet Insider Vol. 22 Belgium-based Resilux produces PET bottles and preforms in Europe and the USA as well as operating a PET recycling plant in Switzerland. Although listed on the stock exchange, Resilux is still a family business offering customised products and services to customers in the food, drinks and nonfood sectors. “This allows the customer to choose the most suitable one for their process and do a ‘real life’ test on their production line,” explains Resilux. Delivery: either preforms or blown bottles When designing a bottle for a customer, Resilux aims to add value through the speed and quality of the design process. In addition, they can deliver either preforms (if the customer has a blower of their own) or finished blown bottles from one of their production units. www.resilux.com ‘Real life’ test on the customer’s production line: Sample bottles are blown with different preform designs and weights.","@ID":39} "MATERIALS / RECYCLING PETplanet Insider Vol. 22 No. 07+08/21 petpla.net 21 MATERIALS / RECYCLING 21 ENDLESS INNOVATION SINCE 1919 handling which we also touched on. How does Guolong Plastics currently see and position itself as a recycler? “First of all, plastics are the only viable option in the most diverse areas. However, it is vital that these materials are recycled properly in order to prevent environmental pollution. Governments in Europe and the USA have been increasingly addressing this issue, with wellknown corporations gradually following suit by raising awareness and promoting responsible recycling. Here, the Chinese authorities are also increasingly managing the circular economy issue by taking the measures I mentioned earlier and this will become a life-long opportunity for us that will bring exceptional growth opportunities”, said Mr Jiawan. Mr Jiawan explained what these will be, mainly with the use of figures: “This year, Guolong will continue to expand the recycled ABS project with an annual output of 200,000 t and the recycled PP project with an annual output of 80,000 t. Guolong plans to recycle and treat 530,000 t of waste plastics annually by 2022. The annual output of over 400,000 t of recycled plastic products means over US$ 620 million of yearly sales revenue. Given favourable policies and a thriving economy, China’s domestic plastics recycling market will embrace a huge development opportunity. Like an ambitious young man, I remain optimistic about Guolong’s growth prospects. I will lead Guolong to further tap the local markets in Guangxi Province, and gradually expand our business operations across China.” www.guolongplastic.com www.tomra.com Tomra Autosort for bottle sorting","@ID":23} "MATERIALS / RECYCLING PETplanet Insider Vol. 22 No. 07+08/21 petpla.net 23 Modular concept even as a retrofit solution for existing PET systems Crystallisation and drying are the key elements of the IR-Clean concept. While various required residual humidity rates are already distinguished in the drying process, delimitation of the performance is to be regarded as a possible feature depending on the specific application in the food grade process as well. The IR-Clean as a basic component consists of a continuously working infrared system alone and - by reducing the residence time to significantly less than one hour - achieves the values imposed by the FDA within one single process step. The residual humidity levels of 300 ppm achieved simultaneously are perfectly adequate for multi-screw extruders or single screw extruders including a degassing facility. If lower limit values are required, as they can for instance partly be imposed by the European EFSA, it will be possible to extend the system by installing a downstream finisher, thus creating an IR-Clean+ system. This equipment allows an even greater reduction of the residual quantities of contaminants with high boiling points such as benzophenone and achieving drying values of 50 ppm as a side effect. These features even allow the strict limits specified by the EFSA for bottle-to-bottle applications to be achieved. Depending on the portion of recycled material, this reconditioning process can still be kept very short, not exceeding a total residence time of between 1.5 to 2.5 hours. Exactly like in IRD Drying Systems, the overall energy use can be reduced by up to 30% as compared to conventional systems. This is due to the fact that the material pre-dried and perfectly pre-heated in the IRD is transferred into the second drying or decontamination step, whereby the air volume and the heating capacity in the after-drying system / finisher can be considerably minimised. Both IR-Clean variants achieve the required values imposed by the FDA / EFSA already during the solid phase, i.e. independently of the plasticising or extrusion processes. Consequently, retrofitting of existing extruders (single screw, twin screw or multi-screw systems) is possible without any problems. What is more, possibilities do not just open up in the extrusion sector, but in PET preform applications as well. Meanwhile, the latest developments in the area of plasticising units of injection moulding machines even permit the direct admixture of rPET flakes to the virgin material. As a pre-drying process of several hours is also indispensable in any case, a combination of the IRClean basic unit with existing preform systems is the ideally suited solution. Apart from conveying and transport technology, filtration units and demisters, the package developed by Kreyenborg includes a comprehensive set of control systems that allow complete process monitoring, including the documentation of process parameters. Results of the challenge test In the first step, commercial PET bottle flakes were used, which were contaminated with pre-defined model contaminants deliberately. The flake material so prepared was exposed to a customary washing process (15 min at 75 °C with 1% of sodium hydroxide), then flushed with cold water and pre-dried mechanically. This washing process is part of the recycling process to be contemplated, but is already performed by the supplier of the PET flakes. The washed flake material was treated in the IR-Clean process, then analysed and submitted to a migration evaluation procedure. The results have shown a cleaning efficiency of the IR-Clean process of 96-99% depending on the surrogate. On the basis of these values, a Letter of NonObjection was issued by the US Food and Drug Administration FDA, which certifies the safety and soundness of the use of packaging material with a 100% rPET portion under the criteria C-G using the IR-Clean. The results may also be used within the bounds of the limit values determined by the European Authority for Food Safety, EFSA. To make its assessment, however, the EFSA specifies 365 days at 25 °C for use of a packaging material, which corresponds for instance to a PET bottle for mineral water. In addition, EFSA’s evaluation makes distinctions with respect to consumers and admissible values for babies, toddlers and adults. According to the company, the IRClean is an efficient and cost-effective concept which can be retro-fitted to existing PET systems. www.kreyenborg.com","@ID":25} "PETnews 6 NEWS PETplanet Insider Vol. 22 No. 07+08/21 petpla.net Erema Group joins Chemical Recycling Europe Erema Group is a member of the Chemical Recycling Europe association as of July 2021. The Austrian plastics recycling machine manufacturer and provider of services related to the recycling process has been committed to improving networking and intensive cooperation within the plastics industry for many years. Erema’s aim is to integrate recycling know-how into the value chain in such a way that benefits the environment, the industry, and society. The company states that in order to achieve the European Union’s targets for plastics recycling and the use of recyclates, the technical capabilities of mechanical recycling need to be exploited to the full by expanding collection, sorting and recycling infrastructure and by further developing the technologies and end applications. For material flows where this recycling route is approaching its limits, it is important to regulate and apply additional processes. Chemical Recycling presents a viable option to recycle the maximum volume of plastic waste, and is the shared interest of the companies in the association, says Erema. “In many cases, mechanical processes are at the beginning of the process chain for Chemical Recycling in order to prepare input streams and ensure a reliable, continuous and energy-efficient material feed,” explains Mr Klaus Lederer, Technology Research Manager, Chemical Recycling at Erema Group GmbH. Erema extrusion technologies adapted to meet these specific requirements are already being used in existing chemical recycling plants. As a member of Chemical Recycling Europe, Erema Group would like to contribute the know-how of the group of companies to the further development of Chemical Recycling processes, broaden the group’s own understanding of the needs of plant operators and promote cooperation. www.erema-group.com Largest mechanical sorting plant in Brazil Stadler recently signed an agreement with Orizon Valorização de Resíduos to build the largest mechanical sorting plant in Brazil. The accord aims to ensure the processing of 500,000 t/a of solid waste, in a country where the potential for recycling is growing. The agreement is claimed to represent a technological breakthrough in the operations of the Jaboatão dos Guararapes Ecopark in Pernambuco, northeast Brazil, which will allow a greater reuse of recyclable waste. In 2020, the plant received 1.5 million tonnes, equivalent to the waste generated by 3.7 million people. This will be the largest mechanical sorting plant ever built in the Brazilian market. Stadler has designed and implemented the entire project with two overarching objectives: to modernise and to strengthen Orizon’s plant for the sorting process and select the recoverable products with highest value to serve increasingly demanding domestic and international markets. At the new sorting plant, 150 people will be employed, who will carry out this work in the project, which will start its operation in 2022. This plant has been designed to process a large volume of material with initial separation of the coarse and heavy fraction through mechanical sorting and final separation of thefines by hand. In addition, the plant layout already envisages the possibility of extending the line to increase its capacity, as well as increasing the automation of its processes. Orizon Valorização de Resíduos operatesfive ecoparks in Brazil, and its waste management and processing facilities receive approximately 4.6 million t/a of waste, serving approximately 20 million people and more than 500 business customers. www.w-stadler.de ABC Compressors appoints new sales manager for Eastern Europe Spanish company ABC Compressors has announced the appointment of Mr Eriz Cristóbal as its new International Sales Area Manager for Eastern Europe. His predecessor, Mr Nacho Urbistondo, has moved to a new ABC office in Miami, USA. Eriz graduated on Mining Engineering with a specialisation in Energy Resources. He also holds a Master´s degree in Sustainable Energy Engineering. A native of Bilbao, he has lived and worked in the UK and Mexico, as well as Spain. He started his professional career as an engineer in the oil & gas and steel industries before moving on to sales management positions in the solar photovoltaic and steel industries. www.abc-compressors.com","@ID":8} "BOTTLE MAKING 41 PETplanet Insider Vol. 22 No. 07+08/21 petpla.net Designed for recycling Creating PET bottles that offer sustainability, reliability, shelf appeal and are in accordance with regulation requires a combination of expertise, technical equipment and suitable materials. Global plastic packaging manufacturer Retal develops and produces PET and rPET preforms, closures, containers, and films. Its R&D, design and sales teams work closely together to create solutions that meet brand owners’ demands. Food and beverage brand owners’ need for on-shelf differentiation must be blended with CSR (Corporate Social Responsibility) targets. Julius Barniskis, design engineer at Retal, explains how the company works with dedicated software: “Preforms, closures and containers evolve to solve as we go deeper into the technical capabilities of our design software,” he says. “We can virtually simulate stretch blow moulding, including wall thickness distribution and stretch ratio. From that we can analyse the results or use later. Other scenarios can show how much pressure the bottle withstands and the location of failure when filled with carbonated drink. In drop load analysis, an initial velocity is applied to the bottle, corresponding to drop height and gravitational acceleration when the bottle collides a rigid floor. Damage regions in the label area or other parts can be visualised with applied clamping force. Top load simulation determines how many bottles can be placed on top of each other before collapsing, which is key information for packing and palletising. We can thoroughly test key parameters without costly production changes, reduce lead time for prototyping and free up valuable resources.” Simulation enables customers to see how bottles will perform without the time-consuming expense of creating physical prototypes and thus speed up decision making. “By inputting material properties, temperatures required for blowing and the design elements into the software, we can make an expert judgement as to what will perform better. We incorporate the technical information with the design requirements. Retal incorporates Design for Recycling wherever possible to increase recyclability and also lightweight with different grips, stronger but lighter elements, and clever use of branding elements such as laser engraving inside the closures. www.retalgroup.com BOTTLE MAKING +44 (0) 1254 584210 sales@petmachinery.com petmachinery.com Active for over 25 years, our global network and specialist knowledge makes us the go-to company for the sale or purchase of a PET machine. Commercially savvy, we work closely with our customers and our global network, to make sure everyone gets the best deal. Providing comprehensive advice throughout your sale or purchase; we can arrange dismantling, loading, packing, shipping, specialist insurance and commissioning. If you have amachine to sell or you’re looking to purchase, please get in touch. THE INDUSTRY EXPERTS","@ID":43} "MATERIALS / RECYCLING PETplanet Insider Vol. 22 No. 07+08/21 petpla.net 16 Cooperation between two world-leading brands in material development and engineering Optimised colour change for hot runner and injection moulding systems by Kay Barton With its headquarters in Howell, Michigan, USA, Chem-Trend recently announced its cooperation with injection moulding plant manufacturer Husky Injection Molding Systems from Bolton, Canada. Compound manufacturer Chem-Trend cites more efficient and costeffective procedures for colour changes within production processes in PET processing as the basis for cooperation. In use here is the cleaning granulate Ultra Purge, which ChemTrend has had in its range since 2016 and forms the basis for cooperation. We spoke to Ms Antje Scholl, responsible Global Business Development Director for Thermoplastics, about the new partnership and technology. Chem-Trend, which was already offering cleaning granulate in the late 1980s, took over the Ultra Purge segment of Italian manufacturer MPI Moulds Plus International in 2016 to further strengthen its own market position. The product line has been and continues to be further developed and should see application in the widest range of materials, processes and technical environments for manufacturing the widest range of products. The granulate is used in fields like packaging and end cap manufacturing, automotive, homewares, electronics and medical plastic products. According to company statements, the customer base is growing continually, although precise figures and customers are not mentioned by name for reasons of company policy. “We produce Ultra Purge in different parts of the world to guarantee rapid supply chains,” says Antje Scholl, “including in Europe, North and South America and Asia.” With particular regard to classical methods, she explains the specific merits of using the cleaning granulate as follows: “An established method for a colour change, for example on a high cavity mould, is simply the use of more virgin material to switch the colour. This leads naturally not only to longer downtimes, which can sometimes last hours, depending on application and material, but also to all kinds of avoidable material use and product defects. In cooperation with Husky, we are combining our instrucUltra Purge compounds Antje Scholl, Global Business Development Director for Thermoplastics, Chem-Trend","@ID":18} "BOTTLE MAKING 31 PETplanet Insider Vol. 22 No. 07+08/21 petpla.net The announcement and demonstrations come after 10 years’ research and development by Carbios to create a process using an enzyme that naturally occurs in compost heaps, which normally breaks down leaf membranes of dead plants. Carbios adapted the enzyme and fine-tuned the technology to break down any kind of PET plastic, regardless of colour or complexity, into its basic building blocks, which can then be turned back into like-new, virginquality plastic. The new material can be used in food-grade rPET; plastics that would otherwise go to waste or be incinerated, can now be brought back into a continuous circular system of recycling. The breakthrough biotechnology succeeds in breaking down 97% of plastic in 16 hours, which is 10,000 times more efficient than any biological plastic recycling trial to date. While recycled PET bottles already exist in the marketplace, this technology, when developed at industrial scale, will help increase the amount of PET plastic that can be recycled. The brands involved in the consortium will work to scale the new process to help meet the global demand for sustainable packaging solutions. In September 2021, Carbios will break ground on a demonstration plant, before launching a 40,000 t capacity industrial facility, by 2025. Enzymatic recycling overcomes the issue of degradation in conventional recycling and can be used on any type of PET plastic. Because Carbios’ recycling process works under mild conditions, it could also lower the carbon footprint of PET waste treatment by saving 30% of CO2 emissions compared to a conventional end of life mix of incineration and landfill, taking virgin PET production substitution into account. “In a world first, we have created food-grade clear bottles from enzymatically recycled coloured and complex plastic, with identical properties to virgin PET,” said Carbios’ CEO Jean Claude Lumaret. “In partnership with the Consortium, we have proved the viability of the technology with the world’s leading brands. This is a truly transformational innovation that could finally fully close the loop on PET plastic supply globally, so that it never becomes waste.” November 7-9, 2021, Dubai At the KRONES booth A1-34 German Technology Innovative hotrunner optiRun Jean-Francois Briois, Head of Packaging Material Science and Environmental Sustainability for Nestlé Waters global R&D also welcomed the success of the 10-year project. “It is very exciting to see that the quality of the prototype bottles made from 100% coloured recycled PET materials is virtually identical to clear virgin PET,” he said. “When we reach industrial scale, this enzymatic recycling technology will enable us to produce highquality rPET bottles and help Nestlé in its journey to reduce the use of virgin plastics.” L’Oréal has been working with Carbios on the project since 2017. Jacques Playe, L’Oréal’s Global Head of Packaging and Product Development, described it as a promising innovation for the coming years and a demonstration of the company’s circularity initiative that was embarked upon more than 15 years ago. “The global issue of plastic waste requires transformational thinking, creative partnerships and innovative brands coming together to seek out new solutions,” observed Ron Khan, Chief R&D Officer, Suntory Beverage & Food Europe, which has the ambition of achieving 100% sustainable plastic. Carbios intends to license its technology to PET manufacturers worldwide, with the intention of accelerating the global adoption of enzymatic recycling for all kinds of PET based products. www.carbios.com www.nestle.com The technology aims to endlessly recycle plastic while maintaining properties that are equivalent to virgin material.","@ID":33} "46 PRODUCTS PETplanet Insider Vol. 22 No. 07+08/21 petpla.net Bottles with built-in handles An increasing number of food companies are embracing PET bottles with built-in handles, as they provide an easy dispensing solution. Pouring oil from a container with handles is a different experience than pouring it from a standard bottle without them. Not only do handles provide a more comfortable and precise, hassle-free dispensing experience but their eye-catching design is an effective tool to stand out on the store shelves. Today, there are many types of bottles with built in handles to choose from. SMI manufactures both pre inserted handles and post inserted handles with their state-of-the -art stretch blow moulding machines. Preinserted handle bottles are made through special moulds that ensure the easy insertion of the handles into the bottle. Rotary stretch-blow moulders For large-scale production of PET and rPET containers, SMI offers a wide range of rotary stretch-blow moulders from the EBS Ergon range, available both in stand-alone and Ecobloc version. In the Ecobloc combi version, stretch-blow moulding, filling and capping are integrated into a single bloc that does not require a rinser or the conveyor belts between the stretch-blow moulder and the filler. The equipment design reduces energy costs thanks to a preform-heating module with high-efficiency IR lamps and a doublestage air recovery system. SMI says that the fast format changeovers and mould replacements were a special focus when designing this modular technology. www.smigroup.it New bottle design and water line for Durrat AI Khaleej in Iraq Established in 2007, Durrat Al Khaleej is one of the leading bottled water producers in Iraq. Inspired to improve production to ensure they meet stringent standards, Durrat Al Khaleej has a laboratory that systematically checks the water produced, guaranteeing high levels of quality and safety throughout the supply chain, from raw materials to the point of consumption. To optimise bottle design as well as line performance, Durrat Al Khaleej chose Sidel to deliver a complete water line. As the site for the line was a greenfield project, the collaboration between Sidel and DaK was key to the successful development of a new PET bottle design as well as managing the installation and commissioning of the equipment. Following a meeting in Dubai, Sidel’s packaging experts proposed a lightweight solution, which could also incorporate the bottles’ original premium look, fully meeting the client’s expectations. Weighing only 10.5 g, the lightweight PET bottle in the 500ml bottle format, also has high stability and has so far proved to be successful in the market. The line operates with a speed of 24,000 bph for 500ml. Not only has it helped the client save water on bottle cleaning, but also no air conveyer is needed. “Sidel provided extra support well beyond the scope of delivering the equipment to Europe, by choosing trusted shipping companies and recommending approved experts for installation and commissioning of the line in Iraq. This ensured that the entire logistic flow was well planned and smoothly implemented,” explains Mr Ibraheem Ghudaib, CEO at Durrat Al Khaleej. The installation and commissioning was successful, achieving 98.1% line efficiency during the customer acceptance validation (CAV). Thanks to Sidel’s great teamwork, the project kick-off was in March 2020, and the first sellable bottle was launched in December 2020. www.sidel.com BOTTLE MAKING","@ID":48} "BOTTLE MAKING 36 PETplanet Insider Vol. 22 No. 07+08/21 petpla.net Packaging that protects the product and looks appealing Bottles designed around the product Belgium-based Resilux offers a design service to create bottles which are sustainable, attractive and functional to give consumers the best product experience. In this article, the company takes us through the steps of the design process, from initial concept to the finished product. The evaluation process “Initially we carry out extensive research into our customer’s precise needs to ensure the final design meets all their requirements and expectations,” says Resilux. The key to a good design is understanding the product that is being bottled: what production process treatment will it need? What shelf life will it have? At this stage, it is also crucial to take into consideration the final product’s distribution channel - will the product be transported chilled or at ambient temperature? Or will there be restrictions due to palletising? Another important aspect is the ergonomics and how the product can be made as user-friendly as possible? Clear answers to all these questions have to be evaluated before the design can begin. From concept to draft design The process begins with an initial idea from the marketing department. From that initial concept, the Resilux R&D department will study the project and make the initial draft design. Recently, as companies have become focused more and more on sustainability, rPET solutions can be set up for any product. When it comes to designing a new bottle using rPET, particular attention has to be paid to the influence it has on the bottle colour, stretching ratios and stability during the blowing process and in the final bottle. Another key part of the design process is to consider how the new bottle can contribute to minimising storage and transport costs while leaving as small a carbon footprint as possible. In this way, the desire to do what is right for the planet continues throughout the process, states Resilux. First design proposal It takes just three days for the company’s R&D department to optimise all the project variables, including: The customer´s requirements Evaluating the different preforms available in the Resilux portfolio Evaluating different resins Checking stretching ratios of the preform/bottle Based on all these inputs, Resilux produce a 3D image using CAD 3D software. Resilux will initially offer a customer its first proposal including a 2D drawing, a 3D pdf, a rendered 3D image and a palletising proposal. The rendered image and 3D pdf can also be customised with the customer’s own label design and be simulated to show what the final, filled product will look like on the shelf. Further design changes can be made in consultation with the customer until all aesthetic and functional needs are aligned. The next step includes producing a mock-up of the approved design so that the customer can see the physical bottle complete with its label to better appreciate the bottle’s shape and to compare the design with others. This mock-up of how people will actually experience the final product gives the customer a chance to touch and feel the new bottle and it helps the R&D team evaluate if any further improvements are necessary. Weeks 4-5: first production After a customer has accepted the design proposal, a pilot blowing mould is ordered to produce actual PET bottles. The blowing mould is manufactured within 4-5 weeks of the initial design approval. Sample bottles will be blown with different preform designs and weights. BOTTLE MAKING After evaluation, the design process can begin.","@ID":38} "MARKET SURVEY 29 PETplanet Insider Vol. 22 No. 07+08/21 petpla.net Company name Gardner Denver Ltd - Belliss & Morcom Siad Macchine Impianti Hertz Kompressoren GmbH Nanjing Shangair Machinery Manufacturing Co., Ltd. Postal address Telephone number Web site address Contact name Function Direct telephone number E-Mail Claybrook Drive, Redditch, Birmingham B98 0DS +44 1527 838 600 www.gardnerdenver.com Mr Trevor Perry Sales Director +44 1527 838 601 trevor.perry@gardnerdenver.com Via Canovine, 2/4, 24126 Bergamo, Italy +39 035 327611 www.siadmi.com Mr Giovanni Brignoli Compressors Division, Food & Beverage Product Leader +39 035 327609 & +39 035 327694 giovanni_brignoli@siad.eu export@hertz-kompressoren.com +49 951 9643 13 88 www.hertz-kompressoren.com Mr Ercan Asmaz Sales Manager / Europe +49 533 962 64 22 ercanasmaz@hertz-kompressoren.com No.1, Xiyan Road, Binjiang Economic Development Zone Jiangning District, Nanjing, China +86 25 86408239 www.shangair.com Mr Edward Zhou Overseas Sales Manager +86 1519595 1347 rusia@shangair.com 1. Machine designation / model number VH7 to WH50 Vito Next BS Line Pet Master VSD 180 (PET Master Series & PET Master VSD Series) WM 2. Number of models in range 13 32 19 PET Master 50/75/100/125/150/18 0/220/270/300 & PET Master VSD 75/125/180/220/300 2 3. Output in m³/hour 417 - 3,229m3 /h FAD 100 - 6,000 1,000 – 6,000 810 60 ~ 72 4. Compressor type 3 stage Reciprocating High pressure blowing air (up to 40bar) High pressure blowing air (up to 40bar) Low pressure air Yes Low pressure screw High pressure blowing air (up to 40 bar) Yes Piston High pressure piston (booster) Reciprocating Integrated system Yes 60m3 /min, 72m3 /min, air tank 150 l 5. Lubricated or oil-free Oil free Oil free Oil-free (high pressure compressor) Oil splash lubricate Low pressure compressor No Oil free 30bar Booster compressor No Oil free Integrated system Yes Yes Yes 6. Machine layout VH and WH V and H (horizontal) V 4,192 x 1,977 x 2,814 7. Number of compressor stages 3 3 2 screw + 2 booster = 4 total 3 2 8. Are special foundations required? No No No Yes No 9. Cooling system Yes Water Water Water-cooled Air cooling 10. Belt or direct drive Direct Drive via Shaftless Motor Belt drive Belt Low pressure compressor No Direct drive Belt Booster compressor No Belt drive Integrated system Yes The worldwide round trip with EDITOURS Let Your Inspiration Flow. 7KH (XURSHDQ 5RDG 6KRZ PART2 Empowered by drinktec Autumn 2021 - 2022 Interested in being interviewed? barton@hbmedia.net Interested in becoming a Sponsor? sales@hbmedia.net","@ID":31}]}}
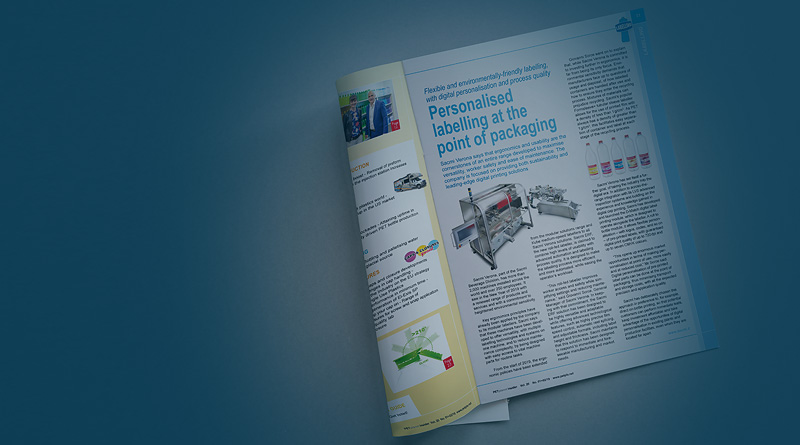