Consistent cap quality – Calibrated and validated in-line inspection
For over two decades, IMD has dedicated itself to expanding and optimising in-line and off-line inspection systems for beverage closures. Throughout this period, technological advances have shaped the landscape. The fundamental principle, however, has endured – the operator’s precise setup of the inspection system remains pivotal in guaranteeing closure quality before packaging and delivery to customers. This standard, IMD claims, could now be replaced by a new quality assurance system.
“To this day, the operator is a key factor in ensuring quality and system settings,” says IMD. “Globally, we have found it more difficult to find qualified operators who can set up and operate the production lines and the vision systems according to quality specifications. It is becoming obvious and imperative to be able to eliminate this uncertainty factor in the future.”
In response, the Swiss company introduces the IMDvista Cap Master – a vision inspection system that can be calibrated and validated for inline high-speed systems. If a system does not successfully pass the validation process, the production line cannot be started until re-calibrated in order to ensure customer quality. It actually should be already a standard process, the company says, as manual adjustments by operators can lead to variations in test tolerances and settings across different systems.
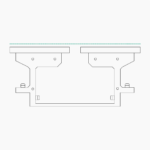
The calibration and validation process involves a reference tool which itself is calibrated and provided with a test certificate. Operators can use an automatic software process to calibrate the system, aligning factors such as lens, illumination, camera, software, and mechanics through a reliable and repeatable process.
A completely revised mechanical structure of the conveyor was required in order to calibrate the system in a very precise manner. IMD developed a new type of basic mechanical frame concept for this purpose. The so-called “backbone” is the solid and robust fundament of this new concept. The calibration concept can only be implemented if the mechanics are designed to ensure 100% repeatability during assembly, operation, maintenance and service. Through the backbone also the cameras, sensors and blow-out nozzles can be calibrated and set up into operation with a claimed 100% accurate repeatability.
Only if every vision system is calibrated, it can be ensured that all production lines are delivering 100% identical quality. This standardised approach enables uniform quality standards for the final product, irrespective of the experience level of local operators.
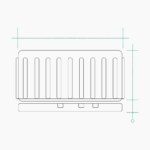
The in-line measurement system introduced by IMD is claimed to allow customers to measure closures with absolute values, a departure from the previous reliance on relative values. This significant change is intended to provide closure producers with new possibilities in production process planning. The potential impact on alleviating the quality laboratory’s workload remains to be seen.
Calibration also ensures that the quality and results at the production site align entirely with the feasibility study conducted by IMD’s laboratory. Following the completion of this study, the IMD application team provides customers with a new test program. This program, loaded onto the calibrated system, guarantees results identical to those obtained in the IMD laboratory, says the company. The program can be universally applied across all identical calibrated systems worldwide.
Operator level in the future
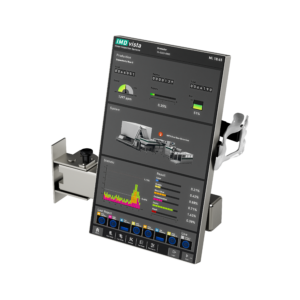
Looking ahead, the question arises: will camera specialists still be necessary in every production facility? Multinational companies have the option to create inspection programs for each product, defining tolerances and specifications in their global Quality Centre. These programs can then be easily uploaded to any IMDvista Cap Master worldwide. The market-ready technology and expertise in 100% calibration and validation position the industry to meet evolving market demands, ensuring quality independent of the operator’s technical know-how.
The Cap Master can be seen in action at the NPE in combination with the new Sumitomo (SHE) Demag all- electric Pac-E (booth W3343) or at the IMD booth (booth S20115).