"NEWS 7 Are your standard PET preform molds making you as much money as they should? Ask how MPET with iFlow technology improves production and achieves greater quality results. Innovation doesn’t happen in isolation. It happens when blue-sky thinking meets down to earth knowhow and exceptional supply chain execution. The sort of innovation that Mold-Masters is known for, now applied to PET tooling for industry-leading results. Introducing MPET – the new PET preform tooling solution designed for the standards of tomorrow. Mold-Mastersand theMold-Masters logo are trademarksofMold-Masters (2007) Limited. © 2011Mold-Masters (2007) Limited.All rights reserved. Think about it. moldmasters.com/thinkaboutit info@moldmasters.com IVL reports increased Q1 sales and revenues Indorama Ventures Public Company Limited (IVL) saw sales volume of 1.2 million tonnes in Q1 2012, about 13% up from Q4 2011. The company said that this reflects re-stocking to meet consumer demand. Sales revenue of US$1.696 million was 21% higher than the previous quarter. Consolidated EBITDA for the quarter was 129% up on the previous quarter, at US$ 98 million, with core EBITDA 6% higher. Net profit of US$55 million, compared with a net loss of US$51 million in Q4 2011. PET sales revenue in Q1 2012 increased by 15% over Q4 2011 and 29% over Q1 2011, driven by the volume growth as acquisitions completed in Q1 2011 in China, Indonesia, Mexico, Poland, and USA were fullyintegrated for the first time. IVL says that it expects greater operational improvements in the first half 2012 in Thailand and Indonesia, with operational improvements at the company’s plant in China expected to lead to further revenue and earnings growth in 2012. The April 2012 restart of the company’s Lopburi site, hit by severe flooding in 2011, and the MEG acquisition in the USA, are expected to contribute significantly to 2012 performance. The acquisition of Polypet, in Indonesia is due to complete in Q2 2012 and to add to earnings in its first year of operations. www.indorama.net Husky growing in China Husky Injection Molding Systems has announced that it plans to establish a new manufacturing facility in the region of Suzhou. A series of investments are being made with the intention of strengthening local support, reducing lead times and providing more responsive reaction to the needs of its growing customer base in the country. The company recently signed an investment agreement with the Suzhou local government to purchase 53,000m² of greenfield land in the Suzhou New District, where it plans to establish a new manufacturing location that will increase local capacity, improve customer support and shorten lead times. The site is expected to be fully operational in 2014. Since first establishing a presence in 2004, Husky has more than doubled its footprint in the region and more than tripled its regional workforce. The Suzhou facility will complement Husky’s existing facilities, most notably the Shanghai Technical Center, which was opened in 2004 and has doubled in size since then. Husky has also recently invested in hot runner refurbishing, hot runner manufacturing and mould conversion capacity. www.husky.ca PETplanet insider Vol. 13 No. 07+08","@ID":9} "REGIONAL MARKET REPORTS 18 PETplanet insider Vol. 13 No. 07+08/12 www.petpla.net attempts to participate financially in their client’s, the bottler’s business, accepting operational and financial risk – by jointly investing and jointly running the bottling plants. Blowing and filling In this area, China is a veritable hot spot. The latest technologies find outlets in China and prime markets here. In today’s demanding PET world, blowing and filling and almost all related activities such as capping, labelling, palletising, transportation are interconnected, and in line and fully integrated. Supply of stand-alone machines for blowing is now the exception. Today’s China demands the most modern technology. Core equipment for fully integrated lines, especially for complex applications such as aseptic filling and hot filling are exclusively supplied by the hightech companies from Europe. The leading machinery suppliers: Sidel Krones KHS/Corpoplast According to Christian Blatt, General Manager of Krones in Taicang, who surely is an insider: “We all do extremely well – with different policies: Sidel with wholly local production. Krones with imported core machines and localised customer service. KHS in a joint venture with Guangdong Light Industrial Machinery Plant 2.” Right or wrong? We were to find out, when talking to the subsidiaries of the above “Big Three” on site. One more competent supplier is dedicated to challenging the “Big Three” – this is Sipa (blowing) after the merger with Berchi (filling). (In the June 2012 KHS announced their exit from the GLM2 joint venture. The company will invest in a production plant in Suzhou to build machines from the new EcoBloc range.) In addition to manufacturers of sophisticated high-end technology there is a large number of small companies that supply stand-alone machines with a lower performance profile. Some are international companies, but there are also some of Chinese origin. Customers include the small beverage producers, spread throughout the length and breadth of China, including municipalities, cooperatives. The Chinese market is no less vital and dynamic as far as these products are concerned but it is completely non-transparent and therefore not accessible for a classic, systematic survey. By contrast to the situation six years ago, there is no longer any demand for Single Step Injection Blow Moulding Machines. When it comes to the manufacture of PET bottles major companies like Wahaha and Tingyi have opted for the 2-stage technologies. Integrated blocked line systems: There is a total of approx. 550 integrated blocked line systems in the Chinese market. Sidel: over 300 complete lines (Doubled in last 6 years). Krones: approx.200 “blocked” lines (Market share dramatically increasing) KHS/Corpoplast: approx. 20 KHS with Blomax as well as Blomax in line with Shibuya/Japan. Beverage producers / bottlers: The largest beverages producers are also the largest bottlers in PET: Tingyi, Coca Cola Company, Hangzhou Wahaha Group, PepsiCo Uni-President. The four most important beverages producers/bottlers have undergone structural changes and further development over the last 6 years: Tingyi overtook Coca Cola in 2010 to take first place in the soft drink markets (including bulk/HOD waters). Tingyi und PepsiCo (23 bottling plants) as per company’s statement has entered into a strategic alliance - by Tingyi’s beverage subsidiaries becoming PepsiCo’s franchise bottler in China. Tingyi will partner with PepsiCo’s current bottlers to manufacture, sell and distribute PepsiCo’s carbonated soft drinks and Gatorade brands. PepsiCo and Tingyi will begin co-branding their respective juice brands using the Tropicana brand name under licence from PepsiCo. PepsiCo will retain branding and marketing responsibilities for these products. The alliance received regulatory approval in March 2012. Coca Colahas 32 bottling ventures and 41 production plants in China. Coca Cola has three strategic partners in China: Coca Cola China Industrial, Swire and COFCO Coca Cola Beverages. Coca Cola China Industrial – the former Kerry Beverages with 15 locations in China has been acquired by Coca Cola (B.I.G. = Beverage Investment Group)) and today operates as Coca Cola China Industrial Ltd. (CCCIL). Swire with licence from Coca Cola and 12 production locations, Cofco, a further licensee with 11 production locations. Hangzhou Wahahahas said goodbye to single stage technology in relation to the manufacture of PET bottles and over the last four years has been investing exclusively in equipment incorporating 2-stage technology. For the beverages market, the keyword is movement. As far as the market participants are concerned, they are being offered the chance to be part of the growth trend, but there is also exposure to risk. This is the reason for the agitation, the hectic pace, the constant realignment, the readjustment of strategy, the change of direction. There is and will be continued fierce competition for market shares and leading positions.“And certainly\" - as someone truly said - \"this show will run and run.” China part 2 PETplanet insider issue 9","@ID":20} "PATENTS 47 PETplanet insider Vol. 13 No. 07+08/12 www.petpla.net PETpatents www.verpackungspatente.de Dispensing cap Intern. Patent No. WO 2011 / 149501 A1 Applicant: Tap the Cap Inc., Encino (US) Date of Application: 11.3.2011 Universal-fit bottle cap incorporating a chamber which accommodates a powder additive. Pressure on the push-pull opens the chamber, mixing the powder with the contents of the bottle. Pulling the push-pull device upwards releases the opening and enables removal. Bottle base shape Intern. Patent No. WO 2011 / 154670 A1 Applicant: Sidel Participations, Octeville Sur Mer (FR) Date of Application: 14.6.2011 The base of a plastic bottle is specially moulded and fitted with special reinforcements. The specific shape is necessary for optimum absorption and onward transmission of the emerging forces. Hot filling Intern. Patent No. WO 2011 / 156145 A1 Applicant: Graham Packaging Comp., York (US) Date of Application: 26.5.2011 A bottle for hot filling is fitted with a base with four feet. The feet and the peripheral reinforcing grooves ensure improved stability of the bottle during hot filling. Reinforced bottle Intern. Patent No. WO 2012 / 002993 A1 Applicant: Johnson & Son Inc., Racine (US) Date of Application: 23.6.2011 A plastic bottle is reinforced in the relevant area in such a way that it displays maximum possible functionality. For example, the bottle is constructed so as to feature a greater wall thickness in the area where it is grasped so as to avoid any undesirable compression. Compressible plastic bottle Utility model DE 202011104709 U1 Applicant: Eschwin Schmidt, Köln (D) Application Date: 18.8.2011 A number of so-called rolling radii are featured on a plastic bottle and these enable the bottle to be compressed. The shape of the bottle and the size of the rolling radii must be chosen specifically in accordance with the materials in order to ensure optimum function. Reinforced bottom section International Patent No.WO 2011 / 157952 A1 Applicant: Sidel Participations, Octeville-sur-Mer (FR) Application Date: 15.6.2011 The moulding of a weight-reduced lightweight bottle must be specially designed to take into account the need to withstand the raised internal pressure of a carbonated product. Reinforcing ribs and recesses are required to ensure an even and secure footprint when the bottle is standing upright.","@ID":49} "MATERIAL / RECYCLING 34 PETplanet insider Vol. 13 No. 07+08/12 www.petpla.net 3.6t/h bottle-to-bottle recycling 100% purified Pure bottle to bottle PET purification represents the peak of PET recycling activities. Because the material comes into contact with foodstuffs it is required to pass a series of official as well as internal tests. FDA is only one of a number of such tests. And it is here where Starlinger, with its PET recycling equipment, is most at home. The company’s latest development is a 3.6t/h system, the recoStar PET 330, with the first systems going to England to Continuum Recycling and to Australia to Visy Food Plastics. In the meantime the third system is under construction at the Weissenbach plant. To allow for the high throughput rates, the system works with two single screw extruders, each 165mm in diameter, which are constructed in parallel on one base frame. The advantage of this 2twosingle screw extruder concept is compact design and no technical risk as the 165mm extruder is Starlinger’s best seller and well proven at various PET bottle-tobottle recycling companies throughout the world. The two-stage preliminary drying of the flakes and the vacuum treatment of the granulate which follows extrusion, both of which are standard at Starlinger, are designed to take account of the high capacity. After the washing and the shredding comes the drying in two stages. In the first stage, hot air is applied to the flakes for about one hour to reduce the surface moisture. In the second stage, dry air is used for hygroscopic drying of the material in order to achieve a residual humidity of less than 50ppm. Many of the hazardous substances that need to be removed are already present in the exhaust air and are removed in the condenser. The exhaust air filters and condensers on the large system are so designed that they can be replaced during production. In the subsequent plasticisation process by means of the two extruders, the screws are vented and there is again the possibility that hazardous substances may escape. Following granulation, the required IV is set up in the vacuum vessel with continuous throughput over the length of the dwell period. Due to the defined grain size of the granulate, and the unique design of the first-in first-out SSP reactor the post-condensation process is uniform and reproducible. As this takes place at the end of the process, the IV value set is maintained and can no longer be changed by means of any subsequent operation. In addition, the AA content is very low as it is no longer able to build up by means of subsequent plasticisation and the associated thermal load. Despite all the possibilities inherent in the equipment, the input material is crucial to the quality of the recycled material. The better it is sorted and, (in particular), washed the better it is. The purified material is suitable for foodstuffs.Overall, Starlinger has an annual installed capacity of around 300kt for top-notch PET bottle to bottle recycling worldwide and additional capacity on PET bottle to sheet. Starlinger also supplies machinery for non-food application such as strapping and fibre/filament. Starlinger was founded in 1835 which means it has more than 175 years’ experience in building machines. The company’s roots are in textile packaging. It was Starlinger who engineered the circular loom for bags. As people had previously only been familiar with the flat loom, it used to be necessary to sew up the sides of the bags. Now the endlessly woven tube only needs to be sewn up at the top and bottom. Small bags are used mainly in Asia, S. America and the Middle East. There the infrastructure is not so well developed as in the industrialised countries and foodstuffs in bags fit very flexibly into the individual transport systems. At the heart of the 3.6t/h recoStar PET 330 system are the two compact extruders that are mounted closely together on one common base frame. The technical centre is open for customer trials throughout the year for both PET and non-PET applications such as PE, PP, PA, PS and others.","@ID":36} "REGIONAL MARKET REPORTS 10 PETplanet insider Vol. 13 No. 07+08/12 www.petpla.net China PET market driven by booming beverage sector A glance at the economic data for the years 2005 and 2010 / 2011 by way of comparison: GNP China 2005 2,226 billion US$ GNP 2010 5,500 billion US$ Growth over period of 5 years in total plus 165% Compared with Europe 2010 17,600 billion US$ USA 2010 14,400 billion US$ GNP per capita China 2005 1,714 US$ China 2010 4,330 US$ Growth over period of 5 years in total plus 153% Compared with Europe 2010 34,500 US$ USA 2010 46,500 US$ by Wolfgang von Schroeter PETplanet Insider reported from China approximately five years ago (see our Regional Reports in issues 04/2007 and 05/2007). Our objective in undertaking a further trip in March 2012 to explore the PET world in China was to update our PET research activities dating back from that time. What developments there have been in China! What developments there have been in the markets – in particular the PEToriented markets associated with the linked group comprising of machine manufacturers, converters and bottlers. In 2005/2006 China’s economy was already well into an explosive boom. This development continued on an impressive scale. In the second half of the last year the emerging market of China metamorphosed into an industrial dynamo to challenge the world market leaders. Regional market reports China Part 1","@ID":12} "BOTTLE MAKING 36 PETplanet insider Vol. 13 No. 07+08/12 www.petpla.net According to Prof. Niemeyer who presented the 2011 sales figures to the trade press in Kleve, it is PET that is driving growth at KHS. With 10% growth in order intake, PET is definitely in the driving seat at KHS. With the expansion of the KHS Corpoplast site in Hamburg, the introduction of preform sterilisation as well as a PET bottling plant for still water specially developed for the Asian market, KHS is keen to further reinforce this trend. However, with a turnover of €917m, the 2008 pre-crisis level of €1012m has yet to be reached. Nevertheless, in view of the gap in the sales figures of €688 million in the crisis year of 2009, it at least shows that KHS is back. Despite the harsh competitive environment, Prof. Niemeyer stated that “...we (KHS) are growing faster and we are more profitable than our competitors”. The reason for this is, in his opinion, ”… our superior technology and outstanding service”. systems at Kriftel in Bad Kreuznach. The construction of transportation systems has migrated from Worms to the parent plant at Dortmund. As regards the other production plants, KHS has streamlined its production portfolio, regional lines have disappeared, instead the production of individual installations is being boosted in order to generate learning curves and scale effects in the production workshops. But even in the individual plants much has been going on, for example, the Kleve plant for the Kistler systems has been completely re-structured. The Kleve people have switched their plant over from workstation-based assembly to a continuous assembly line. At the same time it has proved possible to achieve a significant reduction in throughput times from 12 weeks to 5 to 7 weeks. The stock has been reduced by half, the assembly costs by 25%. All this has not been at the cost of quality either; on the contrary, the quality costs have similarly seen a reduction of 50%. www.khs.com KHS presents 2011 sales figures Growing with PET systems Worldwide sales are divided between Europe (30%), CIS and Asia (20%), America 29% and Africa and the Middle East 16%. An increase in order intake of approx. 17% was recorded for PET systems. Order intake as regards PET systems in 2010 was 41.4%; in 2011 it even got as high as 45.5%. In order to build machines in the required quantities, KHS laid the foundations in Hamburg in April 2012 to enable a 3,000m² expansion of the production facilities at Corpoplast to go ahead. In China the old JV in Shantou has been dissolved. KHS has not, in spite of considerable efforts, been able to achieve its targets in terms of sales and returns. KHS is now building its own plant in Shantou covering 5,000m², in which the new PET installation for still water – the CBE EcoBloc – is to be set up. Globally-speaking, KHS is working on optimising production. This, as far as Germany is concerned, means concentrating on fewer production locations. This has also involved the integration of the plant for KEG Prof. Dr-Ing Matthias Niemeyer, CEO of KHS GmbH: “We are growing faster and we are more profitable than our competitors”","@ID":38} "REGIONAL MARKET REPORTS 14 PETplanet insider Vol. 13 No. 07+08/12 www.petpla.net 60 50 40 30 20 0 2005 2006 2007 2008 2009 2010 2011* Soft Drinks (Per capita consumption) Volume growth in l * Forecast 20.6 28.3 33.6 38.7 44.2 50.3* 24.2 +18.7% +15.1% +14.2% +13.8% +17.5% +16.9% litres Development of per-capita-consumption in litres from 2005 to 2011 (Source Canadean) Consumption has more than doubled in the period under consideration, but is still very much below international standards – compared with: Mexico 361 litres per capita USA 335 litres per capita Japan 175 litres per capita Japan as the neighbouring Far Eastern state is considered as the benchmark for China. Soft Drinks - Packaging Mix Soft drinks packaging sales in China reached 137 bn units in 2011. 81% in PET 4% in carton 9% in cans 6% in glass Packaging mix 2011 (Source Canadean) PET continues to take share from other pack types mainly due to growth in packaged water, RTD teas and still drinks. Since PET will remain the most important packaging type for soft drinks, new regulations by the Chinese Government in terms of recycling and reprocessing are pending. Carton still maintains a significant presence in juice, nectar and still drinks. Cans mainly in carbonates. Soft drinks - key players - leading soft drink trademark owners Ting Hsin International 22% Coca Cola Company 17% Hangzhou Wahaha Group 9% PepsiCo 8% Uni-President 5% How will the soft drink sector continue…? According to “Worldpress”: “The outlook for the soft drinks industry in 2011 and 2015 is that it will maintain a 12% - 15% annual growth rate. The overall size of the industry will continue to expand. The industry focuses on developing fruit and juice drinks, protein drinks and tea drinks. Bottled water will continue to show an upward trend, whereas production of carbonated beverages will gradually fall.” The four major categories We shall be looking only at the beverages that are predominantly bottled in PET bottles and which are of significance for the PET industries. These beverages are: Carbonated soft drinks Packaged water Juice, nectar, still drinks RTD tea drinks. The Soft drinks sector has a chequered history as far as China is concerned: 1979 to 1995: The first stage of beverage market was dominated by carbonated beverages like Coca Cola and Pepsi. 1996 to 2000: The second stage was marked by the triumph of bottled water from Master Kong, Wahaha, Nongfu and Robust. 2001 onwards: The third stage featured the rise of Master Kong’s tea beverage. 2002 onwards: The fourth stage: fruit juices – Uni-President gained popularity. In 2012 the four major soft drink categories – bottled in PET containers – are obviously at different stages of their commercial life cycle. Juice, nectar and still drinks are at the high growth stage, as is ready to drink tea: bottled water is hovering between the growth and mature stage, while carbonates have already reached the mature stage. Beverage life cycles in principle are significantly reduced as consumer tastes change. We shall be ignoring those beverages that, although they are also produced and consumed in large quantities in China, are today bottled predominantly in glass (e.g. beer) or in polycarbonates (e.g. bulk/HOD Water) and this is likely to be the case in the future as well. (And which consequently do not generate high sales figures as far as the PET industries are concerned). Packaged water 25 20 15 10 5 0 2007 2008 2009 2010 2011* Volume growth in bn l * Forecast 11.5 14.5 17.1 20.0 23.0* +26.0% +17.9% +17.0% +15.0% bn litres Volume growth in bn litres from 2005 to 2011(Source Canadean) Per capita consumption 2011*:16.9l","@ID":16} "PETcontents 07+08/12 4 PETplanet insider Vol. 13 No. 07+08/12 www.petpla.net INSIDE TRACK 3 Editorial 4 Contents 6 News 37 Products 38 Bottles 40 Personal Care 47 Patents PREFORM PRODUCTION 20 Top sealing surface sink A rapid guide to perfect preforms - Part 31 MARKET SURVEY 23 Suppliers of preform systems and suppliers of single stage machinery BOTTLE MAKING 36 Growing with PET systems KHS presents 2011 sales figures REGIONAL MARKET REPORT 10 China - Part 1 RECYCLING SPECIAL 27 Japan shows the way forward PET recycling from bottle to tray 30 A cut above Award-winning energy savings with spherical pellet 31 Bridging the gap New material combines virgin PET and rPET 32 Spanish water Appe’s award winning water bottles 33 Made to measure New developments in flakes to melt process 34 100% purified 3.6t/h bottle-to-bottle recycling BUYER’S GUIDE 41 Get listed! Page 36 Page 27 Page 38","@ID":6} "MATERIAL / RECYCLING 32 PETplanet insider Vol. 13 No. 07+08/12 www.petpla.net Appe’s award winnign water bottles Spanish water Appe has designed two mineral water bottles for the Spanish market. The custom-designed bottles incorporate 25% recycled PET (rPET), which result in a 12% reduction in carbon emissions compared to the use of virgin PET. The bottles are fully recyclable. Appe has won two Liderpack Awards in Spain for their mineral water packaging. The annual Liderpack Awards, organised by the Hispack exhibition and the Graphispack Association, celebrate the best in packaging and POS material manufactured in Spain. The Appe containers honoured at the 2011 awards were the 6.25l bottle for Font Vella and the 2.5l bottle for aquaBona. Font Vella bottle The Font Vella pack incorporates Appe’s Contcatip preform base which reduces the overall weight and prevents excess material accumulation at the bottom of the container combined with a reduction in wall thickness and enhancement to the bottle neck. This ensures material optimisation throughout the container to create a lighter pack while still retaining the required strength, performance and reliability. APPE says the lighter container achieves a reduction in carbon dioxide emissions that is equivalent to saving 15,000 trees per year.The 6.25l bottle was designed for Spanish mineral water supplier Font Vella y Lanjarón Waters. The new Font Vella Eco-Ligera bottle incorporates 25% recycled PET (rPET). This combination of light-weighting, use of recycled material and a logistically optimised design achieves a reduction of up to 29% in CO 2 emissions compared to other large container formats in 5 and 8l in the Font Vella range. As a result, says the company, less plastic per litre of water is used, and there is a clear eco-efficiency in its production and management. Font Vella became the first Spanish mineral water brand to include rPET into its packaging with the launch of its 1.5l bottle incorporating 25% rPET in July 2009. aquaBona The aquaBona bottle also features a lighter weight preform for further energy and carbon emission savings. The shape includes a recessed area that provides a convenient grip for easy handling and pouring. This design also enables the bottle to be placed on a table straight from the fridge without needing to decant the contents into a jug. The bottle can be stored in the fridge door as well as vertically or horizontally, helping to maximise available space. www.appe.com","@ID":34} "MATERIAL / RECYCLING 27 PETplanet insider Vol. 13 No. 07+08/12 www.petpla.net PET recycling from bottle to tray* *Based on an article by Thomas Gerstl, Krones AG Japan shows the way forward Japan has one of the most efficient PET bottle collection systems in the world. 72.1% of PET bottles are sent for recycling, an unheard-of proportion. 11% of the recyclates are bottle-to-bottle applications, 34% fibres, 49% sheets and 6% other, according to the Japanese Council for PET bottle recycling. Bottle-to-tray – producing food-grade trays and transport containers from used PET bottles: that’s the idea that the Japanese FP Corporation (FPCO) has recently been pursuing. In late 2010, the first bottle-tobottle recycling system from Krones went into operation at the client’s facility in Gifu-Hashima, enabling foodgrade PET recyclate to be obtained. A second identical Krones line went into production there during June 2012. FPCO uses the newly installed line to produce flakes, which in its own plants are processed together with virgin PET to make new, transparent trays and packages. FPCO has thus opened up a new recycling market for itself, and closed the circuit for part of the PET containers on the market. In 1990 FPCO was one of the first companies to have nailed its colours to the mast of food package recycling. The logistics are run on ecological principles: firstly, the network of collection points, sorting plants, recycling facilities and distribution centres is highly decentralised nationwide, which enhances the firm’s close-at-hand consumer-responsiveness. FPCO uses near-infrared technology to sort containers made of OPS, PET, PP, PVC and other materials. As with the PS trays, consumers are asked to wash the transparent containers and put them in the collection bins. The Japanese population cooperates splendidly with this system, with the containers arriving at the collection and sorting facilities having been thoroughly precleaned. Recycling in Japan operates with consumer education and PR work. A deposit is not charged. Japan possesses one of the world’s most exemplary PET recycling systems, with take-back machines and public collection sacks. There is an abundance of collection containers provided at public places and at the supermarkets. Some local councils arrange special PET collections in the households on certain workdays. FDA approval The collection rate for PET bottles is currently running at more than 70%. Most of them are recycled to make fibres, though predominantly not in Japan, but in China. Specifically, 596,000t of PET bottles were sold in Japan during 2009. Almost 430,000t of collected PET bottles were exported, the vast majority of them to China. In Japan itself, 200,000t were processed, predominantly for making co-extruded films and fibres. “Precisely because the export rates for PET containers were so high, we devoted considerable thought to processing both the PET packages and the PET bottles collected in order to make PET trays. It’s simply essential to put in place more Japanese recycling capabilities for utilising these resources. So we wanted to implement both trayto-tray and bottle-to-tray”, explains Yasuhiro Komatsu. “To enable the result to be re-used as food-grade PET, an FDA approval with a NoObjection Letter was required.” FCPO received this FDA approval line at the end of 2011. The first recycling line from Krones, is currently achieving an output of around 700t a month of finished flakes.","@ID":29} "REGIONAL MARKET REPORTS 15 PETplanet insider Vol. 13 No. 07+08/12 www.petpla.net Carbonates 14 12 10 8 6 4 2 0 2007 2008 2009 2010 2011* CSD Volume growth in bn l 10.0 11.3 12.0 11.9 12.5* +11.3% +6.2% +/- 0% +0.5% * Forecast bn litres Volume growth in bn litres from 2005 to 201! (Source Canadean). Per capita consumption 2011*: 9.2 litres Packaging: PET is key packaging with approx. ratio 128 (PET) to 322 (total) bn units. Can share is to drop. Glass remains a niche market The specialists inplastic recycling systems. VACUREMA® – PETextrusion technologies Choose the Number One. Packaging: pET share increasing: approx. ratio 188 (PET) to 224 (total) bn units. Glass remains a niche market Market participants: Tingyi Holding (Master Kong) 30% Hangzhou Wahaha 15% Zheijiang Nongfushanquan Waters 7% Coca Cola 7% China Resource Enterprises 6% Comments: A double-digit growth in recent years Within the waters sector, the mineral water gained market share.","@ID":17} "MARKET SURVEY 24 PETplanet insider Vol. 13 No. 07+08/12 www.petpla.net Preform Equipment 07+08/2012 MARKETsurvey Company name Sacmi Imola Sipa Spa Netstal Maschinen AG Postal address Telephone number Web site address Contact name Function Direct telephone number Fax E-Mail Via Provinicale Selice 17/A 40026 Imola, BO, Italy +39 0542 607111 www.sacmi.com Moraldo Masi Business Manager - B.U.PET +039 0542 607888 +039 0542 642354 moraldo.masi@sacmi.it Via Caduti del Lavoro 3, 31029 Vittorio Veneto, Italy +39 0438 911511 www.sipa.it Stefano Baldassar Preform Systems Sales Manager +39 348 5298868 stefano.baldassar@zoppas.com Tschachenstrasse 8752 Näfels, Schweiz +41 55 618 6111 www.netstal.com Stefan Bock Manager Application Technology +41 55 618 6156 +41 55 618 6070 stefan.bock@netstal.com Preform injection moulding systems Machine model number / name IPS XForm 128 PPS 300 PETline 2000-3700R (95) PETline 3500-3550R (110) PETline 3500-6600R (135) Number of cavities (min/max units) 16-96 72/128 16/48 32 - 60 64 -128 72 128 Maximum individual preform weight up to 140g 83 240 9 - 86g 9 - 86g 9 - 86 g Max resin through-put (kg/h of PET) 1,000 1,200 500 560 750 1,050 Standard Features Centralized control panel for the whole system; Integrated take out plate and post cooler system XForm: can use existing moulds, mould life guarantee, 15°C cooling Complete system including material preparation, take out robot and post cooling Options / Special Features Fast mould change over Integrated cooling water and thermoregulator system Hybrid machine with energy recovery system 5-points toggle for optimized lockto-lock time IceCool stack design for improved cooling and cycle time reduction Suitable for hotfill materials, wide mouth and big size preforms Calitec: Intensive post cooling and shaping of produced preforms Preblow: Optimized preform design and post moulding process for light-weight preforms Single Stage Machinery Company name Sipa SPA Nissei ASB Machine Co., Ltd. Postal address Telephone number Web site address Contact name Function Direct telephone number Fax E-Mail Via Caduti Del Lavoro 3 31029 Vittorio Veneto, Italy +390438911511 www.sipa.it Machinery Division Director +390438911511 +390438911694 sipa@zoppas.com 4586-3 koo, Komoro-shi, Nagano-ken, 384-8585 Japan +81-267-23-1565 www.nisseiasb.co.jp/en Mr. Katsuo Ishiguro Section Manager, Sales Coordination Team +81-267-23-1565 +81-267-23-1564 sales@nisseiasb.co.jp Single stage ISBM machines Machine model / number ECS HS 6 (6 models) ECS FX 20 (6 models) ECS HS 12 (8 models) ASB-50MB, ASB-12N/10, ASB-15N/10E, ASB-70DPH, ASB-70DPW, ASB-150DP, ASB-150DPW, ASB-650EXHS, ASB650EXHD, PF8-4B, PF6-2B, PF4-1BH, PF3-1BH, PF3-1BHLL Bottle volume (from/to in litres) From 0.25 to 10l (up to 30l with special configuration and reduced cavitation) From 0.25 to 3.8l From 0.25 to 7l (up to 30l with special configuration and reduced cavitation) 0.003 (3ml) - 20l Number of preform cavities Up to 20 Up to 80 Up to 40 1 - 36 Number of stretch blow mould cavities Up to 10 Up to 40 Up to 20 1 - 36 Max. preform/bottle weight in grams for the stated number of cavities 75g for the 20 injection cavities 46.50g for the 80 injection cavities 37.50 g for the 40 injection cavities 3g - 800g Hourly output based on: 0.5l container 8,000b/h 36,000b/h 18,000b/h 1,200 -7,000bph 1l container 7,200b/h 27,100b/h 13,600b/h 720 - 5,300bph 1l wide neck container 3,000b/h 13,500b/h 4,000 /h Up to 5,300bph 2l wide neck container Up to 2,000bph Other (e.g. containers for personal care products...) Up to approx. 6,000bph Machine footprint / space requirement (LxWxH in metres) 3.56 x 1.14 x 2.73 (ASB-50MB) 7.66 x 3.12 x 3.89 (ASB-650EXHD) Special features (short description/ keywords) Lightweight containers big size containers (up to 30l) asymmetrical containers - off-centred neck- hot fill containers pasteurizable containers aseptic PET containers for cold filling ultra clean PET containers Lightweight containers asymmetrical containers off-centred neck- hot fill containers pasteurizable containers aseptic PET containers for cold filling ultra clean PET containers Lightweight containers big size containers (up to 30 l) asymmetrical containers off-centred neck pasteurizable containers aseptic PET containers for cold filling ultra clean PET containers For PET, PP, HDPE, LDPE, PLA, PES, PPSU, PC and others. ASB-12N/10 can operate for IBM process. ASB-15N/10E all electric 1-step ISBM machine. PF series uses lower blow mould cavitiation and blows multiple times per cycle for excellent efficiency.","@ID":26} "REGIONAL MARKET REPORTS 11 PETplanet insider Vol. 13 No. 07+08/12 www.petpla.net The comparison shows the enormous growth of the Chinese economy. The per capita income (GNP per capita) is increasing dramatically. At the same time, however, there is a clear gap i.e. the need to catch up in terms of per capita income by comparison with Europe and the United States. China – as the economists at the relevant institutes predict – has a dazzling future before it and they are talking of a “major transformation by 2030“. The Asian Development Bank (ADB) forecasts a GNP of 21,700 billion US$ by 2030. Economic output and purchasing power are increasing. In addition, China is becoming the largest outlet for international capital. ADB is talking of an epicentre of global growth in the 21st century. (At the same time, the bankers at ADB are leaving unanswered the question of whether our planet earth will still possess the necessary resources). China’s significance as far as the world economy is concerned is undisputed, it is endorsed in the economics pages of the international press. The fact that differences exist in the perceptions of the East (China) and the West (including Europe) as regards the pursuit of business interests and in particular as regards ”intellectual property“, likewise provides a field day for inventive journalists. With our PET industries in mind we at PETplanet Insider would remind readers of the statement of our report from 2007 which has lost none of its applicability: No enterprise that considers itself a global player can afford to ignore China. China is the largest and most important global PET market. Having said this, we will now turn to the subject of our article, namely the beverages sector in China and packaging; growth since 2005/2006; the situation in 2012 as we see it today and finally the forecast. There is no doubt that the explosion in macroeconomic growth in China has not left the beverages sector unscathed. Indeed the sector has been particularly marked and this has also caused ripples in the subsequent development of the PET industries. The parameters for positive development in the beverages sector are not difficult to define: Economic growth; The stable political system; The large number of people and their increasing needs; The consistently growing and consuming middle class; The urbanisation (government programme that provides financial support to the rural population who work in the cities and raises the standard of living). All the above will boost people’s demand for beverages. In addition: The Chinese leaders have declared their intention to speed up commerce internally so as to become less dependent on export and on the unpredictable cycles of world commerce. Which means the promotion of products manufactured in China and a focus on consumption by a growing middle class. Good times, therefore, for the beverages sector and its suppliers, also for the PET industries and, in particular, for the suppliers of the PET processing machines – as we shall discover in the course of our research. To enable us to understand what is happening here in China, what we need to do is to calmly compare sales and volumes in relation to beverages as well as packaging in 2005 and 2010 and allow this information to sink in. It was Shao Jin Rong, one of the directors of the beverages giant Wahaha in Hangzhou, which we had visited in 2006, who treated us to an impressive lecture on the very direct relationships between GNP, consumption of beverages, market share and the resulting requirement for machines from the point of view of Wahaha. To quote: “Experience shows that the beverages market is growing at a rate at least twice the speed of the gross domestic product. GNP in 2012 up approx. 8% Growth of beverages market up 2 x 8% = 16% Wahaha market share approx. 10%, i.e. Wahaha therefore needs to participate in the growth to the tune of 1.6% A bottling line with an output of 40,000bph corresponds to a market share of 0.05%. Assuming that the plants and all the systems installed at Wahaha are already working to full capacity, Wahaha will need to invest in 30 new lines each year and also in 30 preform systems in order to keep its market share of 10% – and that is what we are doing“. And it is only in this way – applying this formula – that it is possible to explain the investment fever that has gripped Wahaha in the last three to four years. Shao again: “… since 2008 we have bought almost 100 new preform injection moulding machines and similar or same number of combi lines for blowing and filling, just in order to maintain our share in the growing beverage markets …”. Shao was right in his assumption that the beverages market for both alcoholic and non-alcoholic drinks would see an annual growth of twice GNP. But Shao’s business – Wahaha’ soft drinks – has seen repeated growth of almost double of the considerable beverage percentage. Wahaha is only one of the very big boys in the Chinese beverages business. The other major players – including Ting Hsin International, Coca Cola Company, Nongfu Springs – have not been idle and have committed themselves to investing aggressively and no less enthusiastically to a similar extent. Of course, China is not so transparent and straightforward always and everywhere. It is however an amazing and sobering fact that the trends recorded in the market data have already become reality.","@ID":13} "REGIONAL MARKET REPORTS 12 PETplanet insider Vol. 13 No. 07+08/12 www.petpla.net The first part of our research (in this issue) consists of a comparison of the volumes of beverages in the period from 2005 to 2010 and the forecast up to today and beyond. We will be establishing just how many tonnes of PET have been and will be converted, as well as by which Chinese companies and with which PET processing machines and how many. (Some of the data has been accurately determined, other data has been estimated.) The unusually strong demand has led to strong competition within the industry and among all participants. How the machine manufacturers, converters and bottlers will cope with this challenge, and the measures and strategies they will employ, is a subject that will be explored in future issues. In 2006 we met and discussed with the leading players how they saw the Chinese beverages market developing: Six years later we have revisited these same companies to review past progress and consider future developments. These are the companies we visited: bottlers: Wahaha, Yinlu and SCMC (Coca Cola investment), converters: Shanghai Zi Jiang and S.O.E. (Pepsi), preform system suppliers: Husky, Krauss Maffei/Netstal and Sipa, manufacturers of the bottling lines: Sidel, Krones, KHS (Corpoplast included) We are grateful to the companies mentioned for their readiness to engage in meetings and discussions and to collaborate during the two weeks in March 2012. Understandably, pressure of time meant that not all the meetings we would have liked to arrange came about. Nevertheless, it is our belief that the present research gives a coherent picture of a PET sector where things are moving on a grand scale – with major potential that those who have the right products and are able to link up with the right concepts will fully exploit. You will be able to read all about them in our subsequent reports. China’s beverage industry In the search for reliable market data – facts and figures – we came across the PETplanet article from 2006 entitled “More questions than answers”. 2012 has arrived and nothing has changed. There are some government statistics on the beverages market released by the China Beverage Associations. However, due to different categorization and unit measure, the data may seem convoluted when compared to other intelligence sources. But there is nothing on the packaging industry, and absolutely nothing on PET and PET machine manufacturers. As far as the beverages are concerned, the professionals at Euromonitor and Canadean are conducting research – accurate to three decimal places but nevertheless from time to time contradictory in their forecasts. But business based on facts and figures is not all that straightforward when even the big boys – e.g. Coca Cola in Turkey – regard the precise details relating to volumes and market share as confidential. No less complex is the situation as far as the machine manufacturers who supply the beverages market with PET processing machinery are concerned. Sometimes it is the unpredictable attitude of an equity owner far removed from day-to-day business pontificating via statements on business operations or a restrictive local diktat originating from an ambitious marketing department that feels obliged to make complementary statements only. Having perused and evaluated the available literature: gtai – Germany Trade & Invest for economics Euromonitor and Canadean for beverage data Publications such as Worldpress, Frankfurter Allgemeine Zeitung, China Daily for general information Presentations by companies such as Sidel, Husky, Krones, Bericap for individual accounts We subsequently set off for China, did some local research, listened attentively and then formed an opinion – based on our discussions, but also on our own observations and experiences that we had collected on our global tours of the world of PET. PETplanet Insider is a magazine for specialists. This is how we see ourselves. The Regional Market Reports are intended and designed to be factors for use in shaping the opinions of managers of companies operating within the PET sector. Our objective is not simply to provide the management with figures, but rather to get to know the concepts and strategies of the market. This basic specialist statement represents the task and goal of this, our report on China in 2012. Beverage consumption in China 80 70 60 50 40 30 20 10 0 2005 2006 2007 2008 2009 2010 2011* Soft drink consumption Volume growth in bn l 33.0 37.5 44.6 51.7 59.4 68.1* * Forecast +20.0% +16.0% +15.5% +14.6% bn litres Volume growth in bn litres from 2005 to 2011 (Source Canadean)","@ID":14} "NEWS 9 PETplanet insider Vol. 13 No. 07+08 Amcor opens 650 million bpa production facility Amcor Rigid Plastics officially opened its new on-site bottle manufacturing operation at PepsiCo’s Gatorade production facility in Mountain Top, Pa, in ceremony on June 19, 2012. The new in-line operation is expected to produce approximately 650 million hot-fill PET bottles annually. Among the 50 dignitaries present at the ceremony were state and local officials, as well as Amcor CEO Ken MacKenzie, and Michael Schmitt, President of Amcor Rigid Plastics. Amcor has seven similar hot fill facilities located at beverage filling plants throughout the US. The company received strong backing and financial support from state and local agencies including approximately $100,000 in grants for site development and employee training. www.amcor.com Hall 7A / Booth 527 Establishment of PET Plastics Recycling Study Group within the German Federal Association for Secondary Raw Materials and Waste (bvse) Although Germany has the largest volumes of collected PET in Europe, the country’s recyclers do not have sufficient access to the material. In the opinion of the German PET recycling companies who have joined forces to create a PET study group within the bvse Association for Plastics Recycling, there is no end to this trend in sight. The reason for this development lies in the considerably less satisfactory collection systems in evidence in neighbouring European countries, such as, for example, France or Italy. Too few PET bottles are being collected, and there is an absence of locally based PET recycling plants. These then try to safeguard their input by means of PET imports from Germany. The situation is being exacerbated by the fact that, overall, the recycling capacities of the PET processing plants in Europe are not being fully utilised. Something else that is also being discussed within the PET study group is a change in the labelling of PET bottles which has led during the past few months to higher proportions of adhesives and problems with washing the flakes. The plant operators were in agreement on opening up a dialogue with relevant bottlers and brand owners in order not only to identify the problems but also to get together to devise common solutions. Interestingly, the PET recyclers warned against any thought of crushing PET bottles at the point of return. They point out that doing this would mean that it would no longer be so easy to make a distinction between transparent and coloured material and hence the quality and value of the material would be reduced. The overwhelming majority of plants are also not geared up to accepting and recycling material of this type. www.bvse.de","@ID":11} "regional market reports 17 PETplanet insider Vol. 13 No. 07+08/12 www.petpla.net Sterilizer Rinser Filler Doser Dosing your Perfect MiX Let the fruit jump in! Injection moulding: preforms A total of 520 to 560 systems/machines are in the market, with Husky and Netstal being the undisputed leaders in the high-tech, high-productivity systems. Supplied by Husky approx. 420 Supplied by Netstal approx. 80 Other systems supplied by companies such as Krauss Maffeimachines as from 2012 are sold by Netstal, Sipa - with a smaller number of 48 cavities locally assembled systems. Cheng Hsong - slowly disappearing from the PET market. Amongst the local Chinese suppliers of preform systems, Guangzhou Huayan is probably the most significant with their production aimed at the less demanding clientele in China, but nonetheless with cavities between 2 und 144. The strategies deployed by the leading companies in China could not be more different. Husky operate a factory in which the manufacture of hot runners and PET injection moulding machines for China and the Asian Pacific markets go hand in hand – using components that are purchased globally and used globally. Approx. 20% of the materials are sourced locally in China. At the plant, which is located close to Shanghai, the systems are completed and trialled. (In July Husky announces further investments in China to meet needs of growing customer base. The company plans to establish a new manufacturing facility in the region of Suzhou. see page 9) Netstal import Swiss technology and Swiss quality. The Netstal sales department which operates in China under the management of Krauss Maffei has included Krauss Maffei’s vertical preform systems in its sales portfolio. Sipa is continuing with assembly work on its local Chinese machine with 48 cavities. However, all their hopes for the future are focussed on the new imported 128 cavity system which was exhibited at the NPE 2012 in Orlando. Today there are more cavities with brand owners than with converters. 70% with brand owners, 30% with converters. The percentage shift from converters to brand owners continues. After losing the market in blow-moulded bottles, converters are now beginning to lose the preform business to the brand owners as well. The leading converters are: Zhong Fu Zi Jiang Both companies – together with their subsidiaries - have more than 80% of the free converter markets. Both companies have placed in-house and wall-to-wall equipment on premises of their traditional customers, i.e. the brand owners. Both companies are also making serious","@ID":19} "MATERIAL / RECYCLING 29 PETplanet insider Vol. 13 No. 07+08/12 www.petpla.net tamination temperature. The final step is treatment in the vacuum reactor, where all contaminants are removed from the product. Discharge on the principle of first-in-first-out guarantees a defined dwell time for the material in the reactor. These food-grade flakes are comparable to new ones in terms of their visual and physical characteristics. Line efficiency The first recycling line from Krones, at its maximum speed of 1t/h inputted, is currently achieving an output of around 700t/month of finished flakes. This corresponds to an efficiency of 93%. The food-grade PET flakes obtained from used PET bottles are processed at the company’s own two plants at Kyoto and Kanto to make new PET trays and packages, e.g. as transparent egg carriers or trays for fruit. The PET recycling circuit has been closed. Over the course of decades, FPCO has built up closely intermeshed cooperation with supermarket chains, packaging wholesalers and consumer alliances for collecting and recycling polystyrene trays and transparent containers. CCT Creative Competence Technology GmbH Idsteiner Strasse 74 D-65527 Niedernhausen, Germany r.steinmetz@cct-systems.com www.cct-systems.com Developments Type 2925-1,25g CCTsystem®-SBT CCTsystem®-slit-band technology Type 1881-2,1g CCTsystem®-SFBT CCTsystem®-slit-foldband technology All Closure types with CCTsystem®- BPT Best Performance Technology PET Molds Design and Patents Closure Molds Closure Systems Developments PET Systems Future prospects “We now want to concentrate on the efficiency of the second PET recycling line and optimise the bottle-to-tray process”, emphasises Yasuhiro Komatsu. “We can, of course, also think about direct bottle-to-bottle recycling. The key to worldwide recycling of plastics always lies in national legislation. Here in Japan, recycling is supported by the government by means of appropriate regulations and consumer education.” Since so far it is not yet permissible to use recycled materials for applications involved in direct contact with foods and beverages, FP Corporation is currently using a triple-layered film composed of new PET, recycled PET in the middle and new PET again, known as V-R-V films, standing for new virgin PET, recycled PET and once again virgin PET, so that the recycled PET comes into contact neither with the food nor with the consumer. What the FP Corporation is targeting, however, is 100% use of food-grade rPET. “Our goal is to allay consumers’ fears and if at all possible to achieve approval for direct contact of recycled PET in line with the FDA’s specifications”, explains Yasuhiro Komatsu. “We are confident that this will be possible within the next three years.” www.krones.com FPCO produces disposable food trays made of plastic. Chairman of the Board and CEO Yasuhiro Komatsu founded the company back in 1962. In the 2010/2011 business year, FPCO’s turnover totalled 140 billion Yen, corresponding to about €1.4 bn, and the group was employing more than 3,600 people. Based at Fukuyama in Hiroshima Province, the company has built up a densely meshed network of production facilities and recycling plants along the 3,000kms of this island realm. It comprises 13 production plants, three recycling facilities, ten sorting plants, eight logistic centres and ten picking facilities. Over the course of decades, FPCO has built its corporate growth primarily on food trays made of polystyrene (PS) and transparent packages made of OPS (oriented polystyrene) and PET for selling foods in supermarkets and retail outlets. www.fpco.jp In the decontamination module, the material is heated up to the requisite decontamination temperature. The final step is treatment in the vacuum reactor, where all contaminants are removed from the product.","@ID":31} "PETplanet insider Vol. 13 No. 07+08/12 www.petpla.net MATERIAL / RECYCLING 33 New developments in flakes to melt process Made to measure One of the trends in PET recycling in material production is to feed the virgin PET reactor directly with a content of up to 10% rPET. By using an inline measurement device it is possible to adjust the rPET-IV to the same level as the IV of the virgin material. Extricom now offers an inline viscosity measurement for the various sizes of its RingExtruder. Since 1998, German company Extricom’s RingExtruder RE has been used for bottle-tobottle recycling of PET. The post consumer waste is transformed into high quality materials approved for food contact. The process section of the RingExtruder RE mainly consists of twelve co-rotating and tightly intermeshing screws oriented in a fixed ring. The big melt surface offers a highly efficient decontamination of the product. In general, throughput rates between 1,500kg/h and 6,500kg/h are achieved. The RingExtruder RE is available in three different sizes respectively configurations. The smallest unit is the RE5 XPV which has received a further developed screw configuration and modifications in the feeding section. Because of this, nowadays the RE5 XPV covers a throughput of 1,200 to 2,000kg/h recycling PET material. This IV measuring device measures directly the viscosity (IV) and the temperature of the PET melt without any delay. The results can be used as a recording for the quality or process control directly. Waiting for laboratory results is no longer necessary . The inline viscosity measurement is connected to the REcontrolPET software which is responsible for the visualization and operation of the line. The recycling process is not influenced by the viscosity measurement and there is no loss of rPET due to a bypass-flow of the melt stream. www.extricom.de","@ID":35} "PRODUCTS PETproducts 37 PETplanet insider Vol. 13 No. 07+08/12 www.petpla.net Masterbatch metering unit Italian company Piovan has announced the launch of Lybra LGR, a new masterbatch metering unit for PET applications. It is configured for continuous weight-loss gravimetric (LG) or volumetric (LV) operation and is claimed to offer a high level of accuracy, advanced control and a straightforward user interface. The unit can accommodate up to two independent dosing stations, which can have different capacities and be retrofitted to meet changing production needs. Each dosing station can be configured for individual capacities ranging from 1g/sec, up to 170kg/h. Each dosing station comprises a hopper containing the granules to be dosed and is equipped with a proprietary loss-in-weight control to measure the amount of material carried by the dosing screw to the PET main stream. The mixture is then continuously gravity-transferred from the central block to the plasticizing screw of the moulding machine. The dosing auger is available in three different configurations with single, dual or triple helical shaft, for controlling material dosing in low percentages with a high level of accuracy and repeatability. Lybra is equipped with a seven-inch touch screen HMI with intuitive graphical interfaces. Operators can control operation of the whole system, compare preset dosing values with actual values, check instantaneous production values and access all the unit’s functions. Connection to external supervision systems (by Ethernet or USB port) enables settings to be downloaded and exported and also allows remote control. Piovan asserts that Lybra LGR is particularly suitable for frequent colour or production changes. www.piovan.com 28mm neck processing KHS says that its new generation of Innosept Asbofill ABF aseptic linear filling machines offer lower sterile room volumes, increased aseptic safety, and the option of processing PET bottles with 28mm neck diameter. Innosept Asbofill ABF technology manages the aseptic cold filling of non-carbonated non-alcoholic beverages using the dry sterilisation method and is suitable for milk, yoghurt and fruit juice beverages, fruit juices, sports drinks, near water beverages, tea and coffee products. The Innosept Asbofill ABF 611 requires a sterile room volume of only 0.9m³, and 1.5m3 for the ABF 711 variant. Bottles are conveyed through the machine in just one holder. KHS says that this eliminates potential aseptic risks, which can occur with conventional switching from one carousel to another. After sterilisation with H 2 O 2, bottles are transferred to the filling station, which is separated from the sterilisation process by an intermediate wall. Volumetric filling is carried out without contact by two-stage free-flow filling valves. Sterilisation, of either screw caps or seals, is also with H2O2. Output capacities are 12,000 0.1-l to 0.75-l bottles/h for ABF 611 and 12,000 0.25-l to 2-l bottles/h for ABF 711. While the decision on neck size – 38mm or 28mm – has to be made at the time of purchase, retro-fitting of a conversion is now possible and the company says that it is seeking to develop a design that will enable fast changeover between formats. It has also announced that it is planning an Innosept Asbofill ESL (Extended Shelf Life) version for non-carbonated nonalcoholic beverages. www.khs.com ETA plus for single-bin dryers German company motan-colortronic has launched a new version of its “intelligent” ETA plus technology for single drying bin solutions. The company describes it as a sustainable control entity for airflow regulation, which has been optimised with the intention of minimising energy consumption of large single drying bins with volumes between 3,000 and 13,000l. The system combines the drying organiser function with airflow control. It provides fully automatic adjustment of air volume to the entry temperature of the relevant material, with throughput monitored in order to provide consistent drying results. The only air volume produced is that required for the drying process. When used with a single drying bin, the process technology does not require butterfly valves to control airflow and is claimed to be energy efficient with large-scale plants, offering up to 60% reduction in energy consumption compared with conventional dryers. The TFT touchscreen has interactive menu navigation and users are able to select all essential parameters for their chosen material from a pre-loaded database. In-house recipes can be stored in a separate database. The equipment adapts to quantity, environment and weather conditions. www.motan-colortronic.de","@ID":39} "imprint EDITORIAL PUBLISHER Alexander Büchler, Managing Director HEAD OFFICE heidelberg business media GmbH Häusserstr. 36 69115 Heidelberg, Germany phone: +49(0)6221-65108-0 fax: +49(0)6221-65108-28 info@hbmedia.net EDITORIAL Doris Fischer: fischer@hbmedia.net Michael Maruschke Ruari McCallion Ilona Trotter Wolfgang von Schroeter Anthony Withers MEDIA CONSULTANTS Ute Andrä andrae@hbmedia.net Martina Hischmann hirschmann@hbmedia.net Ursula Wachter wachter@hbmedia.net phone: +49(0)6221-65108-0 fax: +49(0)6221-65108-28 France, Italy, Spain, UK Elisabeth Maria Köpke phone: +49(0)6201-878925 fax: +49(0)6201-878926 koepke@hbmedia.net LAYOUT AND PREPRESS Exprim Kommunikationsdesign Matthias Gaumann | www.exprim.de READER SERVICES Kay Krüger reader@hbmedia.net PRINT Chroma Druck & Verlag GmbH Werkstr. 25 67454 Römerberg Germany WWW www.hbmedia.net | www.petpla.net PETplanet insider ISSN 1438-9459 is published 10 times a year. This publication is sent to qualified subscribers (1-year subscription 149 EUR, 2-year subscription 289 EUR, Young professionals’ subscription 99 EUR. Magazines will be dispatched to you by airmail). Not to be reproduced in any form without permission from the publisher. Note: The fact that product names may not be identified as trade marks is not an indication that such names are not registered trademarks. 3 PETplanet insider Vol. 13 No. 07+08/12 www.petpla.net The international beverages world is turning its gaze on China – with very good reason. The beverages market is booming and the sector is buzzing with activity. To capture the excitement, the China Brew & Beverage Fair will be taking place in Beijing in September 2012. The fair is the fruits of a partnership between China United Equipment Group and Messe München (drinktec). To coincide with the opening of this event, in this issue no. 07/12, PETplanet Insider will be publishing a Regional Report on PET in China 2012. This will consist of a detailed update of the research carried out by us back in 2006 (and published in 2007) on the same topic. We begin this issue by taking a look at the new “Facts and Figures“ relating to the drinks market and setting out the exciting story of PET in China from a modern day standpoint. In the following three issues we shall be reporting on visits and discussions with the central characters in the PET story – bottlers, converters and machine suppliers. A glance at developments over the past six years will demonstrate exactly why our Regional Report is so interesting: We will be considering the phenomenal growth in China’s GNP, looking at the volume of drinks produced and consumed, analysing the quantities of PET packaging material processed. We will compare figures from 2006 and 2012, revealing how companies are fighting for market share in this booming market. Never has the sector experienced such growth. Thank goodness for China, you might be thinking. Yet there are questions still to be answered, and our “Focus on China 2012” will not shy away from the issues. Are PET machinery suppliers becoming too dependent on the Chinese market to make up for weaknesses in Europe and elsewhere? Orders may indeed be large and spectacular but prices in China are 30% below European levels. Is this sustainable? As GNP is constantly growing, per capita consumption of drinks in China (50l per head per annum) lags well behind Japan (175l), which nourishes the hope of a continuing boom in drinks consumption. But: Where will the resources come from to fuel future consumption, once Chinese living standards reach the Japanese level? What will be the environmental cost? Will Planet Earth be able to cope? Our PET industrialists are certainly not complacent about resolving the problems of resources and the environment like ecologically responsible production, energy-saving machines and lightweighting, but especially about PET bottle recycling and use of rPET for new bottles. Certainly a significant contribution by the industry on the topic of resources and environment, but perhaps just a minor step in the face of an even more gigantic challenge. The China Brew & Beverage Fair is certainly coming at a timely and joyful moment both for China itself and for the PET industry in general. The talk around the dinner table is likely to focus, as ever, on record sales, super profits, and eye-watering growth prospects but behind all the talk, the serious issues of environmental responsibility and sustainability could prove to be the elephant in the room. We wish the China Brew & Beverage Fair every success, and look forward to continuing the debate. Yours Wolfgang von Schroeter EDITORIAL dear readers, EDITORIAL","@ID":5} "23 PETplanet insider Vol. 13 No. 07+08/12 www.petpla.net Conveyors Bottle-to-bottle recycling plants Caps and closures Preform moulds and SBM moulds Preforms Preform and single stage machinery SBM machinery Compressors Filling equipment Resins and additives Suppliers of preform systems Last year we discontinued publication of our Market Survey of preform system suppliers, but we are delighted to be able to bring it back again, in a slightly altered format, featuring the usual line-up of companies including the new machines from Sacmi and Sipa. Suppliers of single stage machinery We are also pleased to present an additional Market Survey, covering the suppliers of single stage machinery. New to the list are Mould Matic, who showcased their system at the NPE this year. Although the publishers have made every effort to ensure that the information in this survey is up to date, no claims are made regarding completeness or accuracy. 07+08/2012 MARKETsurvey Preform Equipment Company name Husky Injection Molding Systems Olicorp Postal address Telephone number Web site address Contact name Function Direct telephone number Fax E-Mail 500 Queen Street South Bolton, Ontario, Canada L7E 5S5 +1 9059515000 www.husky.ca Robin Lovell Product Manager +1 9059515000 rlovell@husky.ca Rue de Montbrillant 26 1201 Genève, Switzerland +41 22 309 1540 www.olicorp.ch Evgenia Movsumova Manager sales +41 22 309 1540 +41 44 355 3820 info@olicorp.ch Preform injection moulding systems Machine model number / name HPET 180 AE HyPET 230 AE HyPET120 HyPET225* HyPET300* HyPET400* HYPET400S** HyPET500* HSPI Number of cavities (min/max units) 24-32 24 to 48 2 to 32 6 to 48 8 to 72 12 to 96 96 to 112 16 to 144 8/16 Maximum individual preform weight 889 1,448 2,200 3344/2750* 5770/4910* 5770/4910* 4910** 8048/8030* 48 g Max resin through-put (kg/h of PET) 221 334 720/1010* 1050/1260* 1200/1450* 1450** 1400/1700* 130 kg/h Standard features (short description / keywords) *Also available with High Performance Package (HPP 4.0) Rotary injection compression machine Options / special features (short description / keywords) ** Only available in HPP 4.0; Special machine sizes and cavitations available upon request Technology well adapted to thin wall preforms.","@ID":25} "PETnews 6 PETplanet insider Vol. 13 No. 07+08/12 www.petpla.net Mann+Hummel and Ohl Engineering become ProTec ProTec Polymer Processing GmbH commenced business operations on May 1. The new company was created out of the merger of Mann+Hummel ProTec GmbH, of Belsheim, and Ohl Engineering GmbH of Limburg, part of the Schoeller Plast Industries group. The new company’s headquarters will be in ProTec’s existing facility in Bensheim. Ohl’s headquarters in Limburg will be maintained as a satellite office. The company’s Managing Directors are Alfred Kimpel, formerly Managing Director of Mann+Hummel ProTec, and Arnold Jahn, Managing Director of Schoeller Plast Industries, of Pullach, near Munich. ProTec Polymer Processing will produce Somos system solutions for plastic processing material handling, and Ohl systems for post-condensation of solid matter and drying of plastics, as well as turnkey systems for the bottle-to-bottle recycling of PET. With its involvement in the Schoeller Group network, the new company intends to improve and expand its customer service internationally, and especially in the Asia-Pacific region. www.schoeller-plast.com www.sp-protec.com drink technology India and International PackTech India getting bigger Almost 300 exhibitors are now confirmed for drink technology India (dti) and International PackTech India, which are taking place at the Bombay Convention & Exhibition Centre in Mumbai, India, from 6 – 8 November. Exhibitor numbers are up almost one third since the last shows and organisers Messe Muenchen and Messe Duesseldorf anticipate that the shows will cover 12,000m2, almost 50% more space than previously. This is the second time that the companies have jointly organised the exhibitions and over 8,000 trade visitors are expected, a 30% increase. India represents one of the world’s fastest-growing markets for food and beverage, with the middle class on the subcontinent expected number around 580 million by 2025. Among the companies already registered as exhibitors are Clearpack India, KHS, Krones, Sidel and Siemens. PackTech will feature presentations from France, Italy, Turkey and Switzerland, while representatives from the industry in China and the UK will be presenting at dti. www.drinktechnology-india.com www.packtech-india.com PolyOne to expand via ColorMatrix in Africa ColorMatrix, a subsidiary of PolyOne Corporation and a leading innovator of liquid colour and additives for plastics, has announced plans to open a new facility in Africa. The new facility, which will be located in the Montague Gardens industrial precinct in Cape Town, South Africa, is expected to open in August 2012 and will support customers throughout Africa. Services will include sales, technical support and an on-site colour laboratory for rapid colour development. The immediate focus of the operation will be to deepen support for customers who manufacture products such as PET containers for the beverage and personal care markets. www.polyone.com Erema Discovery Days 2012 International plastics recycling industry gathers at the opening of the Erema. The Erema Customer Centre was officially opened on Friday 22 June, 2012 in Ansfelden near Linz. Some 400 invited guests from all five continents came to this event to attend the launch of a technical innovation on the recycling and compounding market – the new product Corema. Erema has invested €5 million in its Customer Centre. It is equipped with seven Vacurema systems in operation on 1,200 m² of floor space: These seven systems will be available for customers to carry out test runs for their own materials. During a demonstration at the Discovery Days the quality of the recycled pellets produced for processing to make the end product was verified firstly on-site and then on an in-house cast film plant and an injection moulding machine. The Vacurema process has become established as the global standard in processing not only post-consumer PET bottle flakes but also in-house PET waste. Over 140 systems are now in use worldwide. Manfred Hackl, one of the two members of the managing board at Erema, explains, “For 29 years now Erema has been carrying out pioneering work in the plastics recycling sector and there is no let up in the success story. Recycling processes and technologies are being even more intensively coordinated with the requirements of the specific end applications of our customers”. International guest speakers and experts from around the world gave presentations. Among the guests: Upper Austrian state governor Dr. Josef Pühringer, Ton Emans (President of EuPR – European Plastics Recyclers, European promoters of the plastics recycling industry) and Erema customers from all over the world. www.erema.at Piovan Turkey expanding Eighteen months after the acquisition of dosing and blending technologies specialist FDM GmbH, Italian company Piovan has announced measures intended to expand and strengthen its presence in Turkey. Piovan Turkey, which is managed by Cihan Sonmez, has been operating in Turkey for six years and offering service, after sales, sales and administration activities. The local staff is composed of engineers and sales executives, with experience in resin conveying, dosing and blending, drying, cooling and supervisory systems. Piovan says that it is capable of developing and managing highly technological solutions. It holds local stocks of equipment and spare parts for prompt deliveries to the domestic market, and is able to provide rapid support and follow-up to the Middle Eastern region, along with a range of services to the plastics industry. www.piovan.com","@ID":8} "MATERIAL / RECYCLING 35 PETplanet insider Vol. 13 No. 07+08/12 www.petpla.net Back in 1987 Starlinger started their recycling systems for processing PP textile residue left over from bag production. Then, 15 years ago, recycling developed into a separate mainstay with the foundation of a separate and independent business unit “recycling technology” Four basic types have been developed for a range of different purposes. Essentially, they differ in the way the material is prepared and delivered to the extruder. There are systems for PET flakes, for film, for woven bags and for fibres / non-woven materials. The result is always granulate, supplied in a range of extruder sizes between 65mm and 165mm extruder. This year Starlinger recycling technology celebrates 25 years of recycling equipment. Whereas treatment activities tended to be driven purely by economics in the past, the trend to bottle to bottle recycling nowadays is inclined to be politically motivated. It is only in this way that it is possible to explain the fact that the price for recycled goods is from time to time 10% above the price level for new goods. In Europe the collection rates average out at around 48%, in China the collection rate is currently doing somewhat better because China is anxious to become less dependent on the raw materials. As far as Russia is concerned, recycling tends to be a long-term trend that is being built up slowly. Despite a high demand for recycled material, the collection rate in the USA amounts only to a modest 29 %. www.starlinger.com DRYING HAS NEVER BEEN THIS EFFICIENT: ETA plus® LUXOR - now available with ETAplus® ETAplus® considerably reduces energy consumption and protects materials. When it comes to drying, saving energy is a key concern. We have developed a system that combines airflow regulation with a temperature adjustment feature – that can be disabled if required –and efficient waste heat recovery. The result? A drying system that cuts energy consumption by up to 64%: ETAplus® . motan-colortronic gmbh info@motan-colortronic.de www.motan-colortronic.com Visy Food Plastics, Clayton, Victoria was one of the first companies to install the 3.6t/h system. We asked Mr. Michael Urwin, Project Manager at Visy Food Plastics, why: ? Why did you buy such a large line? ! Visy is a major recycler in Australia and collects large amounts of plastic from kerbside collections and other sources. It is also a major manufacture of PET containers. The line size is required to handle the requirements of the business. ? What is the source of the input material, that is, what collection system is available in Australia? ! In most of Australia households separate recyclable material into separate bins which are collected at the kerbside. Supermarkets and other businesses also separate out material which can be recycled for collection. ? Market size (collection, application / resin)? ! We expect to produce nearly 18,000t of PET resin per year. ? And of course: why did you decide in favour of Starlinger recoSTAR PET iV+? ! Starlinger have the regulatory approvals which we need and provide technical support as we look for future improvements. The existing customer base is getting good results. The system of extrusion followed by decontamination and the results it produces was seen by us as a benefit.","@ID":37} "MARKET SURVEY 25 PETplanet insider Vol. 13 No. 07+08/12 www.petpla.net KraussMaffei Technologies GmbH Nissei ASB Machine Co., Ltd. Krauss-Maffei-Straße 2 80997 München, Deutschland +49 89 8899-0 www.kraussmaffei.com Klaus Zeiler Head of PETForm Systems +49 89 8899 2313 +49 89 8899 152313 klaus.zeiler@kraussmaffei.com 4586-3 koo, Komoro-shi, Nagano-ken, 384-8585 JAPAN +81-267-23-1565 http://www.nisseiasb.co.jp/en Mr. Katsuo Ishiguro SectionManager,SalesCoordinationTeam +81-267-23-1565 +81-267-23-1564 sales@nisseiasb.co.jp PETForm PETline 3500-6600R (150) PETline 6000-6600R (2x110) PETLight KM1751900CV KM1753500CV KM3203500CV KM3204500CS KM3206100CS KM3503500CV KM3504500CS KM3506100CS PM-70/65NII, PM-70/111N, PM-170/111M 72 - 128 128 - 192 2-12 8-60 8-60 32-96 32-96 32-96 112 112 112 8 - 32 9 - 86g 9 - 86g 84-505g 30-228g 58-442g 36-110g 42-128g 71-215g 36-110g 42-128g 71-215g 114g 1,280 1,400 200 380 600 600 850 1,050 600 850 1,050 220 (approx) Vertical concept / light weight take out / lock to lock 2,0sec. / 4 times post cooling Vertical Clamping, built-in preform after-cooling stations, extremely compact Suitable for hotfill materials, wide mouth and big size preforms Outputs tailored to ASB’s own range of 2-step blowing machines for hot fill application. PM-170/111M designed for 63mm neck jar preforms with 24 cavities. Mould&Matic Solutions GmbH Automa SPA Aoki Technical Laboratory, Inc. A-4563 Micheldorf Ziehbergstr. 2, Austria +043 7582 61760-0 www.mouldandmatic.com Zuser Jürgen Divison Manager +43 7582 61760 430 +43 7582 61760 42 j.zuser@mouldandmatic.com Via Chiesaccia 38 40056 Crespellano -Bologna, Italy +39 051 19933740 www.automaplast.com - www.automaspa.com Mr. Stefano Elmi TECHNICAL MANAGER +39 051 19933740 - EXT. 209 +39-051-739578 info@automaspa.com 4963-3 Minamijo, Sakaki-Machi, Hanishina-Gun, Nagano-Ken 389-0603, Japan +81-268-82-0111 www.aokitech.co.jp Hiroshi Chino President's Office +81-268-82-0111 +81-268-82-3699 koho@aokitech.co.jp Blowliner 650/70-40 R2 NSB 50 SH -THREE STATIONS MACHINE SBIII-500LL-50 5ml up to 30l 0,015 to 5l 0.25 to 2l 1 up to 48 1 to 12 9 - 16 cavities 1 up o 48 1 to 12 9 - 16 cavities 430g on 1-cavity and 9g on 48-cavities 4,5g with 12 cav.; 80g with 4 cav. 10 - 50g 3,200 1,800 7,200 2,800 1,660 3,600 2,200 1,200. 3,360 on different model (Please contact Aoki.) 2,200 700. 2,400 on differerent machine model (Please contac Aoki.) 3,200 4,800. 2,000 - 4,000 7 x 2,5 x 4 400 6.38 x 3.55 x 3.49 Fully electrical stretch blow moulding station, hybrid technology for injection moulding, state of the art hotrunner and injection moulding technology, high flexibility in product range 10mm up to 250mm neck opening, high productivity due to 2-row production system, 1 hotrunner cavitation system für individual preform lenghts, machine configuration can be adjusted for individual demand, 35 up to 240t clamping force, up to 1,000g shot weight, bigger mounting space für large containers 5,5 x 1,9 x 3,3; 500kN; 510mm; 400kN; 220mm; NSB 80 - 4-stations machine; 0,030 to 5; 1 to 16; 1 to 16; 5g with 16 cav.; 87g with 6 cav.; 2,400pcs/h.; 2,200pcs/h.; 1,900pcs/h.; 1,000pcs/h; 6,800pcs/h.; 500pcs/h.; 800kN; 630mm; 550kN; 220mm","@ID":27} "MATERIAL / RECYCLING 31 PETplanet insider Vol. 13 No. 07+08/12 www.petpla.net Artenius, the PET & Recycling Division of LSB, has developed a new PET resin material that combines virgin PET resin and post-consumer recycled PET as feedstock in the polymer production process. The result is an energy-efficient food-safe packaging resin called Artenius Unique. One trade platform The ”who’s who” of two industries powered by drinktechnology-india.com drink technology India 2012 Your gateway to India’s future PackTech India 2012 Exhibition and Conference for Processes, Packaging and Printing www.packtech-india.com 7th International 6—8 November 2012 Bombay Convention and Exhibition Centre Mumbai/India Forum organizer Supported by Contact drink technology India MMI India Pvt. Ltd. avisha.desai@mmi-india.in | www.drinktechnology-india.com Phone+91 22 4255-4710 | Fax+91 22 4255-4719 Contact International PackTech India Messe Düsseldorf India Pvt. Ltd. SharmaS@md-india.com | www.messe-duesseldorf.de Phone+91 11 2697-1745 | Fax+91 11 2697-1746 Supported by Sponsors and Conference Organizers Organized by Artenius Unique is produced under a proprietary chemical recycling process. The clean recycled PET is de-polymerised and mixed together with standard virgin PET raw materials, integrating both types of compounds into the re-polimerisation process. The process can be achieved through the following steps: PET flakes are fed into a reactor by a closed and nitrogen flushed system to prevent entry of air and pollutants into the reactor. Glycolysis: PET flakes inside the reactor are de-polymerised under controlled conditions of temperature, pressure, and residence time. Unwanted particles that do not melt during glycolysis are eliminated by filtration during the transfer to the next step. Glycolyzed product (a mixture of monomer and oligomer) is then mixed with virgin monomer and oligomer (with the same characteristics of the recyclate) in the PET resin production plant. To increase the viscosity, the material undergoes a polycondensation in melt phase: The vacuum and temperatures applied during this stage complete the removal of any contamination which might be present in the rPET stream. Polycondensation in solid phase: pellets are processed to achieve the final mechanical characteristics of PET. The bottles produced from recycled PET can then BE collected by the same means as bottles containing only virgin resin (selective collection or deposit system), so that they can be recycled an indefinite number of times. Artenius UE can be used for all direct food contact applications. The European Food Safety Agency (EFSA) has ruled that this process should not be treated differently from monomers manufactured by chemical synthesis. Therefore, the resins are covered by authorisation of monomers and additives in the Commission Regulation 10/2011 instead of by Regulation (EC) 282/2008 on recycled plastic materials for food contact articles. The Artenius Unique process has also been approved by the U.S. Food and Drug Administration (FDA) through its non-objection letter. The FDA determined that the proposed process is suitable for accepting a feedstock of clean post-consumer PET at levels up to 50% for containers for food contact with all food types. Currently, Artenius Unique is produced in the Italian factory: Artenius Italia, S.p.A. and the factory located in Spain (El Prat). www.laseda.es New material combines virgin PET and rPET Bridging the gap","@ID":33} "MATERIAL / RECYCLING 28 PETplanet insider Vol. 13 No. 07+08/12 www.petpla.net New Chubu recycling centre At Gifu-Hashima, near the city of Nagoya, FPCO opened the new Chubu recycling centre in 2009, featuring two halls each measuring 4,000m², firstly for recycling PS trays and PET packages, and secondly for recycling PET bottles. A new distribution centre was built across the road, with a five-storey warehouse and more than 30,000m² of storage space. The recycling system runs round the clock, and is operated in four shifts. The deposit-free PET containers are delivered to the plant in compressed blocks. PET bottles from the supermarkets are relatively clean when they arrive, PET bottles from household waste are rather dirty. The front end, where the incoming goods are sorted, is now being used for both the first and the second line. Efficient washing module The two lines each comprise a washing module rated at 1,000kg/h and a decontamination module for likewise 1,000kg/h. The washing module first supplies non-food-grade RPET flakes, which are further processed in the downstream decontamination module to produce food-grade flakes. First, the presorted PET bottles are fed to a vibrating screen in the washing module. Small dirt particles such as glass, sand, metals, loose labels, etc. are removed mechanically. Second, the material is passed through a metal detector bridge, enabling metals to be ejected at an early stage – a protective measure for the downstream grinder, where closure material, PET and labels are dry-ground. The ground material then travels to a dry mixer, where the individual constituents are mingled with each other. In a zig-zag sifter, the variGesellschaft Wärme Kältetechnik mbH Friedrich-Ebert-Str. 306 · D-58566 Kierspe Tel. +49 2359 665-0 · www.gwk.com Perfect cooling and temperature control You will feel better having made the right decision. Reduce your energy consumption. System solutions Mould inserts Temperature control technology Water treatment Cooling technology Tailor made solutions Temperature controllers Chillers Energy saving cooling systems ous parts are gently separated from each other – PET from the labels, for example. A constant air flow is used here to ensure that up to 95% of the lightweight substances like labels and dust is removed. The product mixture of PET flakes and closure materials is then passed to the prewashing unit, where it is mixed with warm process water and soaked. The process continues in the caustic washer. All residues sticking to the surface, such as adhesives or paper, are gently washed off by friction, and removed from the washing caustic using filtration systems. A sink-or-swim process separates the lighter closure material from the heavier PET flakes, which sink to the bottom. Closure materials float on the surface and are removed. The PET flakes are now passed to a hot, multistage post-washing process, where they are very gently post-cleaned with heated fresh water. The PET flakes are then passed to a two-stage drier: first of all, the vast majority of the water content is expelled in a centrifugal drier. In the second step, the material is transported to a buffering silo with hot air. Decontamination module The first step in the decontamination module now begins, with the thicker bottle particles being separated from the wall particles. The thicker and heavier particles are postground, and returned to the remaining product flow. The aim is to create a maximally homogeneous PET product. Treatment then continues in the first heating worm, where the PET material is gently prewarmed. In the second heating worm, the material is heated up to the requisite deconThe washing module first supplies non-food-grade RPET flakes, which are further processed in the downstream decontamination module to produce food-grade flakes. Sink-or-swim separator for density separation in the washing module","@ID":30} "PETbottles 40 PETplanet insider Vol. 13 No. 07+08/12 www.petpla.net Home + Personal Care Nigrin with slide closure Through its German marketing operation, Nigrin is selling 300 ml of hard wax for protecting and preserving automotive paintwork in a silver-coloured 300ml PET bottle featuring a raised pattern for ease of handling and brand name lettering imprint. Also noticeable is the red top section that can be moved like a slide and which opens or closes a pouring channel by means of this movement. www.nigrin.de Pure power 750ml of hygienic cleaner for the WC is being marketed by fit GmbH under the name of WC fit Pure Power in a black, thin-walled PET bottle with a curved neck and pink dispensing cap. This is sealed by means of a transparent, child-proof screw cap. A metallised front label ensures enhanced visibility on the shelf. www.fit.de Cillit bang universal In France ReckittBenckiser are also using the brand name Cillit Bang for their universal cleaners. For easier dispensing of the concentrate there is a refillable dispenser in use. The top up container is an upside-down PET bottle with a 250ml content which engages with the dispensing device on removal of a safety label. The cleanser is intended for use as washing up liquid and for cleaning surfaces. www.cillitbang.fr Cleansing gel with pink grapefruit Johnson & Johnson are marketing 200ml Neutrogena cleansing gel for the skin in France in a transparent PET bottle complete with lockable pump dispenser. This thick texture product for use in combatting pimples and blackheads is slightly tinted by the addition of pink grapefruit extract. Non-label look labels to front and rear carry the commercial information. www.neutrogena.com Gentle laundry aid Unilever is using an attractive 750ml PET bottle for its clothes washing concentrate “Cajoline”. The opaque bottle is decorated with a sleeve label, is sealed with a blue screw cap complete with dispensing function and the advantages of the concentrate (which incorporates passion fruit / bergamot scent) in relation to environmental protection are explained. www.cajoline.fr Mouth rinse in signal colours Colgate has a mouth rinse in its range that is specially designed for cleaning and care of the gums. The orangecoloured product is packed in a transparent PET bottle with a content of 500ml. The screw closure which serves as an aid to dispensing is secured against unauthorised removal by means of a pre-perforated shrink film. Shaped labels printed in part with a glossy finish and sited to front and rear complete the packaging. www.colgate.eu.com","@ID":42} "REGIONAL MARKET REPORTS 16 PETplanet insider Vol. 13 No. 07+08/12 www.petpla.net Market participants: Coca Cola 55% PepsiCo 34% Hangzhou Wahaha 5% Rest under 1% each. Comments: Stagnation from 2009 to 2010. Market saturation. Improved living standards led to consumers switching to perceived healthier carbonated drinks. Also lack of promotion by the “Big Two” suspected. Juice/nectar/still drinks 18 16 14 12 10 8 6 4 2 0 2007 2008 2009 2010 2011* Volume growth in bn l * Forecast 9.1 10.5 12.6 14.8 17.2* +15.3% +20.0% +17.5% +16.2% bn litres Volume growth in bn litres from 200/ to 201! (Source Canadean) Per capita consumption 2011*: 12.8 litres Packaging: PET is the predominant pack type continuing to take share, with approx. ratio 116 (PET) to 284 (total) bn units. Carton is second leading. Market participants in juices Beijing Huiyan Juice & Beverage Group 26% Liwayway Marketing Corp. l9% Market participants in nectar Beijing Huiyan Juice & Beverage Group 36% Zeijiang Nongfushanquan Water 15% Market participants in still drinks Coca Cola 14% Tingyi Holding 11% Guangzhou Wanglacji 10% Comments: Preference for healthier drinks with a wider range of flavours. A strong growth with big potential. Many competing flavours. Fierce competition. RTD tea drinks 14 12 10 8 6 4 2 0 2007 2008 2009 2010 2011* Volume growth in bn l * Forecast 5.3 6.6 8.5 11.1 13.5* +24.5% +28.8% +30.6% +21.6% bn litres Volume growth in bn litres from 200/ to 201! (Source Canadean) Per capita consumption 2011*: 10.0 litres PackagingPET leading pack in single serve. Carton has a 3% share. Glass remains a niche market Market participants: Tingyi Holding 54% Uni President 16% Hangzhou Wahaha 12% Comments: Strong market. Max. growth in beverages, up to 30% - due to promotional efforts of key players in the markets. The Chinese PET Story Over the past decade the Chinese beverages market has bestowed on the PET industries – in particular the machine manufacturers - a boom never before experienced anywhere in the world. Manufacturers of injection moulding machines for preforms, of blow moulding machines for bottles, bottling machines and complete lines have identified a market for a high percentage of their global sales in China. In this way, more than a few respected machine manufacturers have discovered a way of compensating for the weak points that occur in cycles within the major saturated markets of this world. PET resin Total figures for 2010: consumption: 2.65 million t – 65% for beverage, i.e. 1.722 million t. All resin is produced at local sources for local consumption. production: 3.35 million t. The difference to consumption is exported. Capacity: 4.1 million t. There is an over-capacity, but investments into new plant and capacities go on. The Chinese producers are amongst the TOP TEN resin producers in the world, such as: San Fang Xiang (Capacity of1.380 million t for 2011) Fenc (Capacity of 1.250 million t for 2011) Na Ya (Capacity of 0.868 million t for 2011)","@ID":18} "BOTTLES 39 PETplanet insider Vol. 13 No. 07+08/12 www.petpla.net Base for vinaigrette Under the brand name of Knorr Professional Unilever, is selling 500ml of Vinaigrette Base in an easy-to-handle, transparent PET bottle with a two-tone double-hinged lid complete with double tamper-proof guarantee strip. Prior to opening for the first time a guarantee strip needs to be removed and then a ring pull extracted from the closure. By adding a litre of oil and 0.5l of water you can make 2l of Balsamic Vinaigrette flavoured with a delicate hint of strawberry. Two paper labels on the front face of the bottle and a further label hooked over the neck of the bottle take care of the commercial details and product information. www.unileverfoodsolutions.de Upside-down mustard bottle Alongside mustard in a jar and in a tube, the use of mustard in squeezable upside-down containers is becoming more and more popular. One example of this is the upside-down bottle made from PET for 225ml of preservative-free mustard manufactured by Messrs. Händlmaier of Regensburg. This pleasingly shaped bottle is fitted with an adequately proportioned red hinged lid. Prior to opening for the first time the lid needs to be unscrewed and a sealing plate removed. Now the mustard can be dispensed in measured quantities by pressing on the bottle. Two paper labels with the commercial information printed on them round off the appearance of this product. www.haendlmeier.de Granulate versus the smell of tobacco The French company Impex is marketing, under the brand name of Carlinea and the name ”Air Smoking“, 100g of a granulate that gives off a delicate scent of vanilla on contact with a cigarette. The granulate, which is packed in a transparent PET bottle, is deposited in the ashtray. The bottle with its child-proof seal is decorated with a sleeve label and is presented at the POS suspended from a plastic fixture complete with Euro perforations. www.carlinea.com","@ID":41} "PREFORM PRODUCTION 21 PETplanet insider Vol. 13 PETplanet print vol.6 The Rapid Guide to Perfect Preforms machine no./name 1- 3 exemplar each 129,- € 4 - 10 exemplar each 99,- € 10 exemplar each 69,- € prices in EUR + VAT. 6. Check to ensure that no moisture exists on the moulding surfaces, either from water leaks or condensation. This may obstruct normal melt flow and cause filling problems. The environmental dewpoint should be below the chilled water temperature to eliminate the risk of condensation. 7. Check hardware for worn, damaged or failed components, specifically the mould neck inserts (collapsed vents), lock ring vents, and lock ring / core parting line. www.petpla.net PETplanet print Vol. 6: The Rapid Guide to Perfect Preforms by Rick Unterlander and Ottmar Brandau fax: +49 (0) 6221-65108-28 info@hbmedia.net www.petpla.net Order your copy now!","@ID":23} "MATERIAL / RECYCLING 30 PETplanet insider Vol. 13 No. 07+08/12 www.petpla.net Award-winning energy savings with spherical pellet A cut above CrystallCut is a pelletizing and crystallization process in which the crystallization of the PET is achieved using the latent heat energy already present in the pellets. The equipment line-up is similar to a traditional polymerization and extrusion line but the difference is in the cooling of the polymer after it exits from the extruder die. During the first two seconds the plastic melt loses two-thirds of its latent heat energy, which means that the residence time of the pellets in the process water should be kept to an absolute minimum in order to later attain the highest possible degree of crystallization. For this reason, CrystallCut equipment is usually employed with an underwater pelletizing system. The pellets exit from the dryer and enter the crystallization conveyor at an average temperature of more than 135OC. The superficially cooled pellets are kept in constant motion, which triggers the crystallization process to proceed without any additional energy requirement. Only the heat energy present within the pellets is used, crystallizing from the core to the outside and resulting in a 40% degree of crystallization. BKG says that CrystallCut enable energy savings of around 20%, compared to conventional extrusion equipment for the manufacture of PET pellets. Additional energy cost savings of around 5% can be realised during subsequent processing in the injection moulding machine, because the microstructure that results from the crystallization action in the conveyor requires significantly less energy to re-melt the pellets. The total energy savings of around 25-30% translate into about 25gWh per year at a 600 t/day plant. BKG further claims that less space and a lower total capital investment is required for a CrystallCut system than for the conventional combination of pelletizer and crystallizer. BKG says that installed CrystallCut equipment around the world produces 10,000t of PET pellets/day, on machines with outputs ranging from 250-2,0000kg/h. www.kreyenbourg-group.com www.bkg.de BKG Bruckmann & Kreyenborg, which manufactures processing machinery in Muenster, Germany, says that its BKG CrystallCut process could help a plant with a production capacity of 600t/day to achieve energy savings of 25 gWh/year of operation, compared with existing pelletizing and crystallising technology. The process has been awarded the prize for the “most innovative, energysaving plastics processing equipment of the last decade (2002-2012)” by Plastic Technology China in cooperation with the Vogel Media Advertising Co. Ltd. The BKG crystall cut process has been awarded by Plastic technology China","@ID":32} "Vol.6 PETplanet print PREFORM PRODUCTION 20 PETplanet insider Vol. 13 No. 07+08/12 www.petpla.net The rapid guide to perfect preforms - part 31 TSS (Top Sealing Surface) Sink Troubleshooting guides have suffered in the past from being locked away in offices and not being available to the people that actually need them. Considering the high cost of machine and tools high scrap rates can be a costly proposition eating away at already tight margins. PETplanet’s “Rapid Guide to Perfect Preforms” takes a different approach. It has been written for the people on the floor of injection moulding companies to support their daily work in making the best preforms possible. The product of two industry experts, Rick Unterlander and Ottmar Brandau, it gives concrete advice on 35 of the most common problems in preform manufacture, most illustrated by pictures. From high AA levels to wavy bodies processors can find help when they need it. Read chapter 31 of the guide. Symptom The preform TSS is not properly formed. Not severe enough to be a short shot. Cause The melt has not formed fully at the TSS due to gas entrapment or obstruction from debris. Table of Contents i........................ About the Authors ii.................................Introduction Chapter 1.............................. AA Level High 2........................ Accordion Preform 3....................... Air hooks / Streaks 4............................... Black Specks 5...................................... Bubbles 6..................................Burn Marks 7...........................Colour Streaking ................................... /Peeling 8..................................Crystallinity 9.................................Drool Marks 10.......................................... Flash 11......................... Gate Depressions 12............................... Gate Peeling 13..................Gate Voids / Pin Holes 14......................... Internal Gate Sink 15................................Internal Sinks Solutions 1. Check injection time isn’t too high (injection rate too slow) and adjust if necessary. Injection rate should be about 10 – 12g/sec/cavity. 2. Ensure the mould neck insert and lock ring vents are clean. This will minimize gas entrapment at the TSS. 3. Ensure the TSS surface on the cores and lock rings are clean. This will eliminate any obstructions when the melt is forming. 4. Check to ensure hold (packing) pressure isn’t too low, especially near the beginning of hold time. Adjust higher if necessary to fill out TSS contour. 5. Check all temperature readings and adjust higher if necessary. PET resin should be melted at about 280ºC (536ºF) +/- 10ºC (18ºF). 16........................................ IV Loss 17............................ Long Gate Nub 18...............................Milky Preform 19............................ Moisture Marks 20................Neck Finish out of Round 21....................... Parting Line Crease 22.................Parting Line Deformation 23......................... Preform Yellowing 24.................................. Short Shots 25.......................................... Sinks 26......................................... Splay 27........................... Stretched Necks 28..................................... Stringing 29......................... Surface Blemishes 30......................... Thread Flow Lines 31.. ..... TSS (Top Sealing Surface) Sink 32.......................................Unmelts 33.................Wall Thickness Variation 34.................................Wavy Body 35.................................. Weld Lines","@ID":22} "NEWS 8 PETplanet insider Vol. 13 No. 07+08/12 www.petpla.net PETtalk Sao Paulo - first South America polyester conference The Polyester Recycling Forum, which presents the latest PET recycling technology from Europe and the USA around the world, held its 19th event in South America – the first time it has visited the continent. PETtalk Sao Paolo took place in the Brazilian city June 11-12,, 2012. The event, which was organised by PET Recycling Forum (PRF) in cooperation with AbiPET, the Brazil Industry Organization of PET producers, converters and recyclers, attracted 247 representatives from over 130 companies and 21 countries. Presentations on the market were made by PCI, CMAI, Canadean and Nous Consulting; and on PET production by M&G and Petrochimica Suape. Arpet, Bepex, Buehler, Gneuss, Herbod Meckesheim, Krones, S+S SeSoTec shared experiences and information on recycling, while Oerlikon-Neumag and Truetzschler made presentations on spinning and Bericap, Colormatrix, Husky, Piovan and Plastipack hosted sessions on packaging. Coca-Cola and Heineken presented brand owner perspectives. Nous Consulting presented the results of a survey of more than 400 companies on PET recycling cross Brazil. Polyester bottle collection growth has averaged 5.6% over the last five years but PET recycling development is still restrained, with a recycling rate of 57.1% in 2011. The number of PET recyclers rose from 32 in 2004 to 93 in 2011, with further new investments planned or in development. Petrochimica Suape asserted that Brazil will further improve investments in conversion of locally-drilled oil to basic chemicals and plastic intermediates. PET resin consumption is forecast to increase in Brazil from 573,000t/a in 2011 to 840,000t/a in 2016. Husky majored on innovation in bottle production and presented its new HyPET 400 HPP 4.0 platform and HyPET HPP RF bottle flake processing system. Bepex International described its new bottle flake decontamination process, which treats cleaned flakes under controlled MEG-steam / nitrogen atmosphere. www.polyester-recycling.com KHS Brazil celebrates 50th anniversary June 2012 sees KHS celebrating the 50th anniversary of its production site in Brazil. The company began operations in the country in 1962, when it entered into partnership with what was then Nashold S/A Industria de Maquinas. The focus at that time was on automatic filling systems. Production was moved to a new, larger facility in 1974 and exports to other Latin American countries began the following year. Returnable PET bottles were introduced in 1990 and the factory gained ISO9001 certification in 1996. The São Paulo facility now extends to 40,000m2 and employs 400 people. KHS Brazil primarily produces products for filling, rinsing, process, and conveying technology and, along with other KHS plants, it supplies local customers throughout South America with complete systems and ancillary services. The company has a 35% market share in filling and packaging technology for the beverage sector in Brazil and 30% for South America as a whole. The brewing industry accounts for 40% of KHS sales, followed by the soft drinks segment with 35% and the fruit juice business with 10%. The remaining 15% covers other beverage segments and the food and non-food industries. KHS Brazil expects to see future growth in all beverage segments and particularly in water, carbonated soft drinks, and fashionable non-alcoholic beverages, such as health and energy drinks. www.khs.com La Seda: Q1 turnover up, profits down, commitments met La Seda de Barcelona’s report for Q1 2012 shows consolidated turnover of €290 million, an increase of 11.7% compared to the same period last year. Recurring EBITDA of €6.7 million in the period is equivalent to a 58,6% reduction compared to 2012. La Seda noted the impact of weak demand and a PET resin oversupply in European markets during the period. It has continued to meet payments to suppliers and financial backers committed since the restructuring process was completed in 2010. Artenius, La Seda’s resin business, increased turnover by 5.6% in the quarter. The company expects to see improvement in the supply conditions of PTA (one of the raw materials employed in the PET production process), consequent to the March 2012 startup of PTA production of Artlant, in Portugal, which has an installed capacity of 700.000t/a. Appe, La Seda’s Plastic Packaging Division, increased turnover by 3,7%, with EBITDA of €9,4 million; 18% up on Q1 2012. Appe is opening a new factory at Katowice, Poland, to exploit new preform markets in Eastern Europe. Shareholders have approved a capital increase of €40 million over the coming months, which will be used to finance Appe’s regional investment and development; the company’s fixed-cost reduction plans; and improvement of La Seda’s financing structure. www.laseda.es Colormatrix reduces carbon footprint, gains recognition for recycling Liquid colorant and additive technologies ColorMatrix, now part of PolyOne, presented the results of an independent comparative study carried out by Sidel. It found that the company’s Joule RHB PET reheat additive, offers the largest carbon footprint reduction in PET preform processing compared with similar products, while maintaining performance and aesthetic qualities. The study compared resin containing 5ppm Joule RHB-2, an inert blue-shaded inorganic particulate, with a typical 5ppm carbon black commercial reheat resin and a commercial non-reheat resin. The Joule RHB-2 outperformed the other materials in terms of NIR absorption, L* luminance, reheat efficiency and energy use. Sidel tested the three materials in the form of 18.8g, 500ml carbonated soft drink (CSD) bottles and compared various qualitative characteristics. Using data from the Sidel study, ColorMatrix has determined that JouleRHB facilitates an energy reduction of 38% was made possible when blowing 1t of PET. Joule RHB has FDA and EU food contact approved for use in PET bottle resins. ColorMatrix also exhibited the announcement by APR (Association of Post Consumer Plastic Recyclers) that its HyGuard oxygen scavenging system and Ultimate UV390 light-blocking technology achieve full recyclability under its Critical Guidance guidelines. www.colormatrix.com","@ID":10} "PETbottles 38 PETplanet insider Vol. 13 No. 07+08/12 www.petpla.net Beverages Handling-friendly fish sauce The Thailand-based company Squidbrand is packing 700ml high quality fish sauce in a transparent, waisted PET bottle complete with recesses for easier handling plus additional reinforcing grooves under the sleeve label. The bottle is sealed by means of a snap-on hinged lid with tamper-proof guarantee. Before opening the bottle for the first time, a sleeve label pulled over the closure as well as a guarantee strip need to be removed. www.squidbrand.com Infused fruit The new Nestlé Vera Beltè with Infused Fruit is intended to meet the constantly growing consumers demand for natural and preservative/colouring-free beverages. Beltè uses a natural process which allows the fruit infusion of lemon and peach to deliver their flavour to the iced tea. The packaging solution had to convey the brand idea and values in a 1.5l bottle, which would be instantly recognisable on shop shelves. The concept proposed by PET Engineering is a tall and slender bottle with a square section, which distinguishes it from the conventional design of short bottles with round sections. The label is simply attached to the wide grip area, allowing a constant physical contact between the brand and the consumer. The stylised tea leaves on the shoulder and the lower part of the bottle are designed to give graphical continuity to the spirit of the brand. www.petengineering.com “Green” award for organic vodka The launch of Gaia Organic Vodka, which is packaged in PET bottles, was declared to be the Best Green Launch by The Drinks Business magazine in London, 2012. Pramia’s Gaia Organic Vodka is bottled in a satin white, pearlescent PET bottle and produced in Finland’s first carbon emission-free manufacturing facility. The company produces its own PET bottles inhouse. www.pramia.fi","@ID":40} "at the viscotec open 2012 September 12-13, 2012 World premiere of PET sheet line viscoSHEET Starlinger & Co. Gesellschaft m.b.H.- viscotec - Adsdorf 38, 4113 St. Martin im Mühlkreis, Austria T: +43 7232 3817-0 - viscotec.sales@starlinger.com - www.viscotec.at Food grade without compromise The decontamination of PCR PET for direct food contact reaches the highest level: As an integrated system it fulfills the worldwide strictest new EFSA standard for infants. Flexibility without compromise The conical twin screw extruder allows direct feeding of in-house skeleton or edge trim flakes and virgin/R-PET pellets up to 100% without predrying and guaranteed high iV levels. Thanks to the gravimetric dosing for up to 4 components, production issues during changing the material formulation are a thing of the past and can be done during full production of the line. Due to the short and defined residence time of the material melt in the extruder and the selfcleaning effect of the conical twin screw extruder, color changes are achieved within minutes, leading to an up to now unknown flexibility in production. Quality without compromise A fully integrated detection and documentation system shows failures in the sheet automatically. Parameters like iV or thickness and optical properties of the sheet such as color variation, black spots, fish eyes or holes are detected and documented instantly. Optionally these can be marked on the roll. Health and safety without compromise Despite the high operability and ease of handling, the roll stack and the fully automatic winder are setting new safety standards. In addition to recycled PET flakes, also sheet from recycled HDPE* (FDA LNO) and recycled PP*material for direct food contact can be produced on this line. *LNO is based on special limitations regarding the input material","@ID":24}
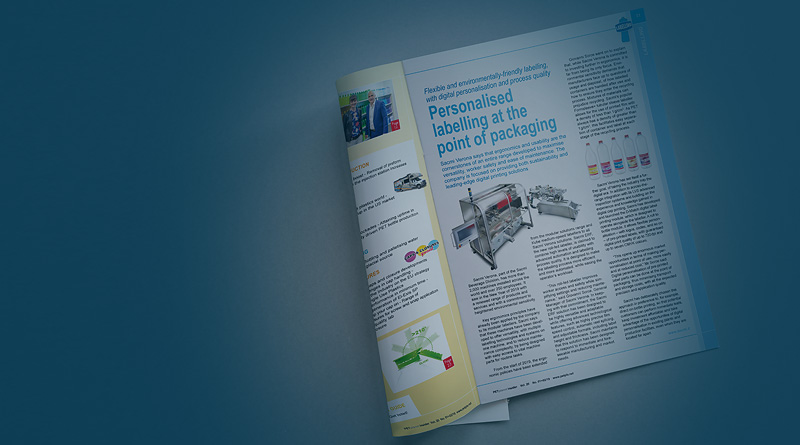