"EDITOUR REPORT 13 PETplanet insider Vol. 15 No. 06+07/14 petpla.net May 20, 2014 Döhler America Latina We met: Martin Tolksdorf, General Manager Jane Vieira, Marketing Cesar Rodolfo, Technical Key Account Manager F.r.t.l.: Martin Tolksdorf, General Manager Döhler Latin América, Jane Vieira Marketing and Waldemar Schmitke PETplanet in front of the Editourmobil on the Döhler plant premises in Limeira, Brazil Flavour taste is local taste The final week of the Go with the Flow Tour South America begins with a visit to Döhler in Limeira in the Federal State of São Paulo. This meeting is of particular interest to us because the topic of flavouring agents and juice concentrates is, so to speak, new territory as far as we, Florian Roscheck and Waldemar Schmitke, are concerned. For this reason we are particularly looking forward to the meeting with Martin Tolksdorf, who is not only General Manager of Döhler América Latina but also a specialist in the manufacture of flavourings and juice concentrates for the beverages industry as well as anything and everything else bordering on this subject. The plant, which opened here in Limeira in 2008, lies 150km to the north-west of the metropolis of Sao Paulo. With 150 employees, the site forms part of the Döhler Group, a company whose head office is in Germany. The raw materials for orange concentrates literally grow right outside the front door, in the famous Brazilian orange belt. From freshly-picked orange right through to the juice drink What interests us in the first place is what happens to an orange from picking to packaging in the form of a drink. The oranges come from the plantations and are delivered to citrus depots in Brazil where they are cut up, pressed and the relevant raw materials extracted from the components. The peel oil is obtained from the skin. The orange juice is pressed out from the fresh fruit. The orange juice is then concentrated by removing water through evaporation (1/6), leaving the actual juice concentrated behind in liquid form and generating orange water phase, rich in volatile flavouring agents. Next, essential oil is extracted from the concentrate by means of centrifugal force. This is then offered for sale separately. These raw materials (orange concentrate, peel oil and water phase) Döhler uses in the form of what is known as orange by-products. The lion’s share is made up of orange by-products, but by-products from tropical fruits, apples, peaches and pineapples also undergo further processing in the plant. For purposes of further processing, the site here in Limeira has at its disposal all physical methods (such as extraction and distillation techniques) that are necessary in order to transform the by-products into natural flavouring extracts. This is achieved firstly through further concentration and subsequent fractionation, with a breakdown as far as the molecular level. This enables natural aroma fractionates to be produced, such as are already required by law, for example, in Europe. “This means that the plant here is also in a position to extract natural aroma fractionates and to use them either assembled or as core modules for customers and parent companies outside Brazil“, says Martin Tolksdorf. He further emphasises that the line-up of facilities at this site is “already making it possible to use what are, in the main, natural raw materials”, an issue that is a topic for discussion worldwide. In summary, this is where natural flavouring agents are extracted and subsequently blended into flavouring concentrates in line with market requirements. Once we have been allowed to test a few samples we quickly become familiar with the background. The flavour has been removed from the original fruit concentrate during the process of evaporation. It comes as a surprise to us when we find that the orange concentrate does not taste of oranges but can only be classified as inedible when it comes to matters of taste. To compensate for this lack of flavour, the taste is now restored in the form of natural flavourings extracted from plants, parts of plants, fruits and juices which are mixed in accordance with customer specifications. The result is a natural flavour concentrate that is later watered down to the appropriate strength for the drink at the juice bottling plant. However, there are some highly complex approaches that merit consideration when it comes to the skills associated with juice production and these are present in the form of total solutions. “At the same time,” Mr Tolksdorf explained, “ the issue is one of reliability in terms of taste and standardisation right through to the logistics stage which, in Brazil, has a special part to play throughout the length and breadth of the land and which calls for corresponding solutions”. The more complex the solutions, the greater the demands are in terms of development, even in the beverages sector. It is not only a question of flavour but also shelf-life in association with a wide variety of drinks packages. “Here blends of vitamins, minerals, tea extracts are used, a composition such as this may be made up of up to 160 elements; a challenge in terms of development as far as this site is concerned and one that it is important to overcome”, says Martin Tolksdorf.","@ID":15}, "MARKET SURVEY 32 PETplanet insider Vol. 15 No. 06+07/14 petpla.net Preform moulds & SBM moulds 06+07/2014 MARKETsurvey SBM moulds Company name Simex Srl Sacmi Imola S.C. R&D/Leverage Nissei ASB Machine Co., Ltd. GDXL Sipa Molds Postal address Telephone number Web site address Contact name Function Direct telephone number Fax E-Mail Via M.Biagi e M.D'Antona, 5, 60025 Loreto (AN) Italy +39 071 7500 214 www.simexitaly.it Mr Graziano Giuggiolini Sales Manager +39 071 7500 214 +39 071 7501 958 giuggiolini@simexitaly.it Via Provinciale Selice 17a, 40026 Imola (BO), Italy +39 0542 607111 www.sacmi.com Mr Moraldo Masi B.U. PET-Berverage Division +39 0542 607888 +39 0542 642354 moraldo.masi@sacmi.it Leverage House, Hamilton Road, Sutton inAshfield, Nottinghamshire, United Kingdom, NG175LD +44 1623 556287 www.rdleverage.com Mr Damon Sykes Sales Manager +44 1623 552240 dsykes@rdleverage.com 4586-3 Koo, Komoro-shi, Nagano-ken 384-8585, Japan +81 267 23 1565 www.nisseiasb.co.jp/en Mr Katsuo Ishiguro Manager Sales Coordination Team +81 267 23 1565 +81 267 23 1564 sales@nisseiasb.co.jp Baoshi Road, Xiabei, Pingzhou, Nanhai District, Foshan City, Guangdong Province,528251, China +86 757 86777 168 www.gdxl.com +86 757 86233 168 info@gdxl.com Via Caduti del Lavoro 3, 31029 Vittorio Veneto, Italy +39 0438911 511 www.sipa.it Mr Franco Porracin Molds & Hot Runner Division Man. +39 0438 911 511 +39 0438 911 694 franco.porracin@zoppas.com Preform moulds Horizontal opening Number of cavities Up to 144 16-24-32-48-72-96 1 - 96 8,16,24,48,56,72,96,128,144 Up to 192 Preform sizes All sizes and all finish Up to 48mm neck / 140g 24mm - 63mm neck /12g - 350g Different weights and neck fnishes Up to 30l Moulds already built for (makes) Mineral water, milk, oil, beer Husky, BM Biraghi, Milacron, Engel, Krupp, Krauss-Maffei Husky, Netstal, Krauss Maffei,Sipa, ASB Husky, Netstal, Krauss Maffei, Krupp, BMB Vertical opening Number of cavities 8~32 8,16,24,48,56,72,96 cavities Up to 96 Preform sizes Up to 180 g Different weights and neck fnishes Up to 10l Moulds already built for (makes) Supply for own machines only Krauss Maffei, Sipa, etc. Standard and custom; Sipa, Krauss Maffei Single stage tooling sets Yes No Yes Yes Yes Yes, for Sipa machines Stretch blow moulds Bottle size (max.) (litres) 20 (5 gallon) 3,3 30 22 20 30 Mould supply directly to machine manufacturers Yes No No - own machines only Yes No Supply of retrofit moulds for existing machines Yes Yes Yes Only for own machines Yes Yes Moulds for bottle makes already produced for Yes Moulds are customized on a per customer basis Krones, Sidel, KHS, SIG,Sipa, Newamstar, Tech-Long, ASB, AOKI, etc. Sidel, Krones, KHS, SIG, Krupp, SMI, Siapi, Kosme, Side Bottle design service Yes Yes Yes Yes, Yes Yes Specialities PET containers for mineral water, CSD, milk, edible oil, wine, beer, cosmetics etc. Double cavity moulds for small sizes (up to 600ml) Single Stage, ISBM Handled, non-round, wide-neck, hot fill, non-round neck, offset neck, heavy weight cosmetic, PET, PP, PC, PES, PEN, PLA, etc. Hot-filling, Aseptic, CSD, water,edible oil, cosmetic, jar, etc. Wide mouth, large sizes (up to 30l), asymmetrical, nitrogen hot fill, containers with handles, HDPE to PET conversions Company name Wei Li Plastics Machinery (HK) Ltd KHS Corpoplast GmbH Krones AG Röders TEC PET Technologies Sidel Postal address Telephone number Web site address Contact name Function Direct telephone number Fax E-Mail Room 1212, Fo Tan Ind. Centre, 26-28 Au Pui Wan St., Fotan, N.T. Hong Kong +852 2690 2368 www.weiliplastics.com Ms Christine Kwan Sen. Sales&Market. Exec. +852 2690 2368 +852 2690 2380 info@weiliplastics.com Meiendorfer Str. 203, 22145 Hamburg, Germany +49 40 67907 0 www.khscorpoplast.com Mr Otto Krumeich Head of Modernization +49 40 67907 360 +49 40 67907 9360 Otto.Krumeich@khs.com Böhmerwaldstr. 5, 93073 Neutraubling, Germany +49 9401 70 0 www.krones.com Mr Peter Christiansen Sales Dir. Blow Moulding Tech. +49 9401 70 4980 +49 9401 70 914 980 peter.christiansen@krones.com Scheibenstrasse 6, 29614 Soltau, Germany +49 5191 603 53 www.roeders.de Mr Friedo Böhling Sales Manager +49 5191 603 53 +49 5191 603 36 mold@roeders.de Prof. Dr.Stephan Koren Strasse 10, 2700 Wr.Neustadt, Austria +43 720 902 169 www.pet-eu.com Mr Maxim Poliansky Commercial Director +43 720 902 169 office@pet-eu.com Avenue de la Patrouille de France; Octeville sur Mer, BP 204; 76053 Le Havre cedex - France +33 2 3285 8687 www.sidel.com Mr Gilles Leroux Tooling Product Manager +33 2 32 85 82 59 +33 2 32 85 81 59 gilles.leroux@sidel.com Stretch blow moulds Bottle size (max.) (litres) 0.015 - 20l Up to 3,125 3 10 30 0.2 to 10 Mould supply directly to machine manufacturers Yes Yes No Yes Yes Yes Supply of retrofit moulds for existing machines No Yes Yes Yes Yes Yes Moulds for bottle makes already produced for 15ml ~ 20l Mainly for KHS Corpoplast InnoPET Blomax SBM Krones, Kosme, Sidel, Sipa, KHS (SIG) Corpoplast Sidel, KHS Corpoplast, Krones, SIPA, Kosme, ADS, Nissei and other major machine types ADS, Dynablow, KHS, Kosme, Krones, Siapi, Sidel, SIPA, SMIForm, etc. Sidel, Krones, KHS Corpoplast and Sipa etc. Bottle design service Yes Yes Yes Yes Yes Yes, Specialities Additional options: automatic preform feeder, bottle ejection etc. Light-weight design and special applications. Bottles & Shapes programme: from bottle design to performance in filling lines Bottle development, customized to filling- and packaging lines with performance commitments. Preform and bottle lightweighting for standard and heat-set process. \"Mould Quick-Change\" Solutions for compatibility of moulds between different machine types, Röders RMC-system for quick mould change Prototyping, laboratory tests, blow moulds production, auxiliary parts and mould repair Packaging and preform design, packaging optimisation (including lightweighting), packaging qualification (including feasibility tests), liquid-package interaction analysis","@ID":34}, "EDITOUR REPORT 15 PETplanet insider Vol. 15 Growth is anticipated in the fruit-based drinks, in juices and nectars as well as in mixed drinks. Soft drinks are also on course for growth but only to a very moderate extent (less than 2% is expected). Although sport/energy drinks and iced tea are demonstrating growth in double figures, they are coming from a very low level. By now we have been privileged to spend a whole day at Döhler and have learned a good deal about their operations. We extend our thanks once again for their friendly welcome and the time they have given to us. Finally, we would like to point out that flavourings are not only used in the beverages industry but also in the foodstuffs industry. Sufficient reason for the expertise in flavourings technology acquired within the beverages industry to be deployed for bread, bakery items and milk products too. They have also made a start on this here. www.doehler.com May 21, 2013 Ecoplaca “The secret lies in the quality of the raw material“ We met: Ferdinando Roberto Carvalho, Commercial Director Ecoplaca, a company based in Sorocaba, São Paulo, is making use of the local recycling system to create PET products with value for society. Ecoplaca has been printing on recycled plastics at two locations in the city of Sorocaba, Brazil, for 21 years. When they started out, the company, managed by Ferdinando Roberto Carvalho and his wife with a total of 38 employees, used to work only with PVC, PE and PP. Today 600t of PET, which the company started processing 12 years ago, pass through its doors each year (figures for 2012). “At that time there were only a very few raw materials on the market for the other plastics. Together with our local supplier, KGM, we went looking Ferdinando Roberto Carvalho (Commercial Director) stands in front of his promotion wall which shows objects made from recycled PET.","@ID":17}, "BOTTLE MAKING 42 PETplanet insider Vol. 15 No. 06+07/14 petpla.net The design of a PET preform is such that during stretch blow, the optimum orientation is achieved just as the stretched walls meet the mould. This point occurs just beyond the NSR. Proper stretching results in longer shelf life and less gas permeability, e.g., higher carbon dioxide retention for soda. Overstretching results in a “pearlescent” appearance of the bottle, signifying microcracks (fracture) and excessive deformation. A resin with a low IV has a higher NSR than a high-IV resin. The polymer chains in a low-IV resin are shorter, therefore, less entangled and can be easily stretched more than a high-IV resin. In the high-IV resin, chain entanglement limits the amount of stretch; similar to trying to pull one end from a tangled ball of string where the knots limit the length that can be pulled out. For this reason, preform designs differ when considering low- or high-IV PET. The figures illustrate the material stretching in the blow mould without relating to actual data. Strain (elongation) is plotted on the horizontal axis and the corresponding stress on the vertical axis. To obtain these data a heated test strip of PET might be pulled on a special machine that records the pulling force and the elongation of the strip. In the reheat stretch blow moulding (RSBM) process the stretch rod and blow air provide the stress needed to transform the preform into a bottle. The top right figure in the diagrams and the following figures indicate the stage of the preform in the blow mould. Elastic deformation The first stage is elastic deformation. Here the material stretches but will retract if the stress is removed. This is similar to the way that metals behave, but the shape of the curve is slightly different. Looking at a preform, this stage can be compared with the stretch rod starting to push on the preform. If the stretch rod were retracted, the preform would shrink back almost to its original length (Fig. 1). Yielding The second stage is yielding. With no increase in stress, the material “gives” elongating easily. This is what happens in the blow mould when the primary or preblow air partially inflates the preform. The preform will continue to inflate until it reaches the NSR, after which higher stress is needed to achieve further elongation (Fig. 2) The third stage is called strain hardening. Applied stress levels have to increase exponentially in order to force the material to stretch further. At this point in the blow process highpressure air enters the preform and forces it to stretch from a bubble to the blow cavity walls, where it rapidly cools down. It is during the strainhardening phase that the material achieves orientation (Fig. 3). Relevant parameters IV, temperature, and copolymer content play a role in determining how far the material stretches during yielding and what force is required to stretch it further. Temperature conditioning allows the operator to improve the blow moulding process by making certain parts of the preform hotter or colder and changing the way in which they will stretch. The objective of preform design (or selection) and blow moulding processes is to properly match up the NSR of the preform under the blow moulding conditions with the design stretch ratios of the preform–bottle combination. Because the strain-hardening phase of the process is so important for bottle performance, correct preform design, temperature profile, and blow air timing are all necessary Please order your copy at the PETplanet insider book shop: https://petpla.net/books Bottles, Preforms and Closures A Design Guide for PET Packaging Second Edition by Ottmar Brandau € 115,00 180 pages © Copyright Elsevier 2012 to guarantee the best bottle. If the inflated preform reaches the bottle mould during the preblow phase, orientation does not occur to a sufficient degree and the finished bottle might fail any number of tests. * This article was published in Bottles, Preforms and Closures, Ottmar Brandau, Chapter 2.3., Copyright Elsevier 2012 Figure 1: Elastic deformation occurs when the stretch rod starts moving Figure 2: At the yielding plateau no further stress is required for additional strain Figure 3: High blow pressure forces the material to strain harden","@ID":44}, "PETproducts 46 PETplanet insider Vol. 15 No. 06+07/14 petpla.net Reduced packaging for increased savings The Krones LitePac pack for non-returnable sixpacks consists just of two narrow strips – one goes round the container, while the other serves as a carrying handle. It is a simple and convenient to recycle method that is said to require up to 75% less material than a shrink pack. In the EvoLite Bloc, the EvoLite pack strapping machine produces the packs and is directly monoblocsynchronised with the Robobox grouping station and a palletiser from the Modulpal series. In comparison to shrink-packs, the production of the LitePacs is said to offer potential savings in terms of packaging materials and energy consumption, with a cost reduction per pack and economies of up to 74% in the total cost of ownership (TCO). The EvoLite does not need a shrink tunnel or a handle applicator, thus saving more than 90% of the previous energy consumption. The average quantity of waste when using shrink films, referenced to a europallet with 84 packs on four layers, comes to approximately 1.12kg, whereas with the LitePac the amount of band waste is a mere 286g. The EvoLite packaging machine consists of a container infeed module and a container strapping module. In the infeed module, the continuous container infeed divides the inflow into two lanes. Four strapping units then create the LitePacs in the container strapping module. For fast and dependable grouping of nonreturnable packs, the Robobox pack grouping station is a compactly dimensioned functional unit that distributes and turns the packs while providing maximised scope for every variant of pack grouping. For palletising the packs, the Modulpal non-returnable palletiser is used. The concept is used for PET bottles with a volume of 0.3l to 3l.Market acceptance in Italy, for example, has already been successfully validated, with around 15 million LitePacs sold. www.krones.com Energy savings with “Green Oven” upgrade Sipa’s latest oven technology for its stretch-blow moulding systems were originally launched on Sipa’s next-generation SFR EVO3 rotary systems, which came onto the market in 2013. More recently, they have also been made available on SFL linear systems. Now, customers with existing standard equipment can upgrade. According to Sipa, customers producing bottles in formats from 0.75l to 1.5l for mineral water, carbonated soft drinks and milk are reporting energy savings of over 40% - and in one case in excess of 46%. Compared to earlier generations of oven, the new “green” ovens are said to have reduced electrical consumption thanks to the use of new lamps, special materials and coatings for the reflectors and stable process conditions. The EVO3 came out last year as a result of Sipa’s efforts to improve performance, reliability, and above all added value in customer’s investments. www.sipa.it To produce a LitePac pack, up to six containers are arranged in rows of two and strapped with a narrow strip of PET. A second strap of PP, which is somewhat wider, serves as a carrying handle. To allow the pack to be opened easily, the strapping band has a tear-off tab.","@ID":48}, "MATERIAL / RECYCLING 28 PETplanet insider Vol. 15 No. 06+07/14 petpla.net PET bottle-to-flake plant in Hohenwestedt, Germany Flaked bunch In Hohenwestedt, north of Hamburg, Germany, one of the biggest plants for the recycling of PET bottles in Europe was inaugurated in 2013. The plant is processing about 4t/h, corresponding to an output of 2,900 to 3,000kg/h of bottleto-flake recycled PET. The flakes meet the requirements for feeding a regranulation system that produces BTB quality. The building of the recycling plant was combined with the re-establishment of PFR Nord GmbH in Hohenwestsedt. This has resulted in 27 new jobs at the site. Overall the Mensing Group, of which AFA Nord GmbH and the TM Recycling Group are also part, now employ just under 80 staff. The company is investing nearly €10m in building the new plant. According to Meyer, in addition to saving on valuable raw materials through complete re-processing of the PET bottles, Hohenwestedt’ s central location will make it possible in the future to avoid significant costs in transporting materials. According to information from the company, the new plant will be processing around 100t PET/day. This corresponds to around 5.2 million drinking bottles every day. The recycling of PET beverage bottles is a challenging task, as the material occurs with a multitude of contamination types and plastic mixtures. The re-utilisation of PET beverage bottles makes high demands on systems engineering. The process is a complex one. So far, PET bottles have been pressed to bales and exported to China or other Asian countries on a large scale. There, the product is roughly washed and used as raw material for textile production. This trend is now reversing: this precious raw material is increasingly recycled in Europe and used as raw material again. New markets have arisen, e.g. the production of thermoforming film but also the “bottle-to-bottle” recycling. The production of bottles from recycled materials is on the increase. The plant The material arrives in bales and is at first separated: the bales are opened and portioned. Afterwards, the single bottles are conveyed into a sorting unit. This sorting unit separates clear/transparent bottles and bottles which are manufactured out of foreign plastics by means of an infrared detection in a multistage process. Size reduction with multistage washing removes contamination and adhesive glues, separates components from other plastics (e.g. caps) and dries the final product which is resold as high-quality raw material to companies producing film or bottles with it. Owner and operator of the plant is PFR Nord, a subsidiary of TM Recycling GmbH Group, which is already operating a plant for the recycling of agricultural film on the same site. TM Recycling GmbH is active in the secondary raw material sector and processes annually up to 100,000t of post-consumer plastics. The owner is Andreas Mensing, and his company treats the waste from supermarket chains: “With the installation of this plant, we no longer have the problems associated with the export of this material.” The procedure The procedure of the plant is simple: An optical sorting machine recognises and separates the material and the colour in a single sorting stage. The illumination unit and the sensors are placed above the sorting belt. This sorting machine combines Near Infrared (NIR) Spectroscopy and colour sensor technology in a single machine. For this part of the plant, PFR Nord chose the Austrian company Redwave, which belongs to the BT-Wolfgang Binder GmbH Group. Afterwards, the material enters the size reduction/washing/separation/ drying section of a turnkey recycling plant developed and manufactured by Herbold Meckesheim GmbH, a medium-sized machine and plant manufacturer with about 120 employees, based in Meckesheim near Heidelberg, Germany. For many decades, machines and plants for size-reduction, washing, separation and drying of contaminated and mixed plastic waste have been built here. First of all, the bottles are size reduced to fingernail-sized flakes. The addition of water ensures a first clean-","@ID":30}, "EDITOUR REPORT 19 PETplanet insider Vol. 15 No. 06+07/14 petpla.net CHOOSE THE NUMBER ONE. BACK TO LIFE. VACUREMA® –FoodContact Approved Recycling With highly efficient decontamination BEFORE the extrusion process. Bottle-to-bottle Pelletising Inline Applications Following in Netstal’s footsteps On the Krauss Maffei exhibition stand at Feiplastic in São Paulo, Brazil, I met up with Stefan Zatti, Divisional Manager Sales & Marketing and Harry Kleiner, Area Sales Manager PET from Otto Hofstetter AG Switzerland. What, it might be asked, is the connection between the two companies? Otto Hofstetter are manufacturers of injection moulding tools and specialists in thin wall packaging and PET preforms. The bulk of the company’s sales is in preform moulds. Over the decades Otto Hofstetter have developed a close working relationship with Netstal Preform Systems. A large proportion of the preform moulds made by Hofstetter are to be found in Netstal systems. This is very much the current situation in Brazil. It was thanks to Netstal and their sales and servicing network that Hofstetter were able to establish themselves some years ago in São Paulo, and the two companies have cooperated ever since. In October 2011, Netstal became part of the Krauss Maffei do Brasil Ltda. Group, and found themselves sharing the same agents as Hofstetter and so it was “carry on as normal” as far as customer service was concerned. Both Netstal and Otto Hofstetter share broadly the same contacts, and customers are therefore serviced either directly by Hofstetter themselves or via Netstal. “This still doesn’t go far enough\", according to Stefan Zatti. “Brazil, and indeed the whole of the Latin American market, is very important for us. We want to offer local support to the market through our own people whilst at the same time safeguarding our after sales service. Other important areas include the supply of spares and hot runner modifications.” He went to say that “Hot runner localisation is also an issue here. Brazil could find itself playing a central role for the whole of Latin America.\" The Brazilian market, like the whole of Latin America, offers significant potential for preform systems. Stefan Zatti again: “In the beverages sector, 96- and 128-cavity preform systems are dominant. But if we look at the household goods and cosmetics sector, we are forecasting increasing industry interest in preform moulds with 48 to 72 cavities. And naturally,” he concluded, “Netstal will be able to meet market expectations in this area.” Turning to the thin wall packaging sector, Zatti explained that here the focus is on specialities such as cartridges and injection moulded tubes that call for special know-how. “We are well prepared,” was his final comment. www.hofstetter-ag.ch","@ID":21}, "EDITOUR REPORT 17 PETplanet insider Vol. 15 No. 06+07/14 petpla.net EDITOUR REPORT 17 May 23, 2013 Krauss Maffei do Brasil Ltda. “Customer service is key” We met: Klaus Jell, CEO KraussMaffei do Brasil Klaus Jell standing in front of the injection moulding system Elion 3200-200 at Feiplastic in São Paulo. At Feiplastic in São Paulo Brazil I meet up with Klaus Jell, CEO of Krauss Maffei do Brasil, at the Krauss Maffei Group stand. The group has undergone significant changes in Brazil: in October 2011 a new company, Krauss Maffei do Brasil, was set up under the management of Klaus Jell.Under this umbrella, the KM injection moulding machines, KM Berstorff compounders and Netstal Injection Moulding Systems have been brought together. The objective behind this restructuring is to exploit existing KM strengths for all the brands and to develop them further. After-sales servicing will play a major role. “Customer service is key to the Brazilian market,” Klaus Jell states, “and this is why we are placing so much effort in this area.” In his view, this is the only way to win over the naturally conservative customer base. Jell continued: “We then need to take things one stage further, especially when it comes to the preforms and closures.” Jell offered this view of the current state of play in the Brazilian market: “A significant majority of customers for these applications have established factories not only in Brazil but also throughout Latin America. What we have to do is build up a similar network of service facilities. It’s the way we will convince customers to come to us.” A start has already been made. The first preform systems outside Brazil, for Guatemala and Peru, have already been sold. Plastic closures The Brazilian market is dominated by 2-piece plastic closures for the beverages industry. These are primarily manufactured using the compression","@ID":19}, "13 marzo – 15 agosto 2014 Giro dell’Europa sudoccidentale e del Nord Africa con PETplanet Go to Brau Beviale – Esplorazione della regione del Mediterraneo occidentale Si parte per nuove avventure! Il nostro team di reporter di PETplanet Insider è di nuovo in partenza. L’Editourmobil è più grande e abbonda lo spirito di scoperta; questa volta il team esplorerà l’area del Mediterraneo occidentale. I nostri impavidi specialisti Alexander Büchler, Waldemar Schmitke, Kay Barton e Rolf analizzeranno i mercati PET di Italia, Tunisia, Algeria, Marocco, Spagna, Portogallo e Andorra. Il loro viaggio epico durerà 5 mesi, e comprenderà un arduo itinerario di 7.000 chilometri che attraverserà due continenti, durante il quale tre team di PETplanet incontreranno i principali esponenti del settore. E ancora una volta ci auguriamo di porgervi il benvenuto a bordo per condividere il viaggio con noi: seguite il blog del viaggio a www.braubeviale.petpla.net E potrete leggere le interviste con le aziende che visiteremo sul nostro stand alla Fiera Brau Beviale dall’11 al 13 novembre 2014 e successivamente in PETplanet Insider. www.braubeviale.petpla.net Supported by: Del 13 de marzo al 15 de agosto de 2014 Gira del Sudoeste de Europa y Norte de África con PETplanet Go to Brau Beviale – Explorando la región del Mediterráneo occidental ¡Nuevas aventuras a la vista! Nuestro equipo de reporteros de PETplanet Insider vuelve a poner rumbo hacia nuevos mares. Con un Editourmobil más grande y abundante espíritu aventurero, la gira explorará la región del Mediterráneo occidental. Nuestros intrépidos especialistas, Alexander Büchler, Waldemar Schmitke, Kay Barton y Rolf analizarán los mercados de PET de Italia, Túnez, Argelia, Marruecos, España, Portugal y Andorra. Ante ellos se abre un épico viaje de 5 meses con un extenuante recorrido de 7.000 kilómetros que les llevará a través de dos continentes. A lo largo del camino, tres entusiastas equipos de PETplanet entrevistarán a los principales jugadores del sector. Una vez más esperamos darles la bienvenida a bordo para que compartan el viaje con nosotros: siga la gira en el blog del viaje en www.braubeviale.petpla.net Descubra todas las entrevistas con las empresas que visitamos en el stand de la exhibición Brau Beviale del 11 al 13 de noviembre de 2014 y después en PETplanet Insider. 13 March - 15 August, 2014 Circular tour of South West Europe and North Africa with PETplanet Go to Brau Beviale – Exploring the western Mediterranean region Up and away on new adventures! Our team of reporters from PETplanet Insider are off on their travels again. Featuring a larger Editourmobil and the spirit of discovery in abundance, the tour this time is centred on and around the area of the western Mediterranean. Our intrepid specialists Alexander Büchler, Waldemar Schmitke, Kay Barton and Rolf will be analysing the PET markets of Italy, Tunisia, Algeria, Morocco, Spain, Portugal and Andorra. Before them is an epic journey of 5 months, involving a gruelling 7,000 kilometre itinerary covering two continents, during which three PETplanet teams will be talking with the major players. And once again we look forward to welcoming you on board to share in the trip with us: follow the tour by travel blog on www.braubeviale.petpla.net And you can find out all about the interviews with the companies we visit on our exhibition stand at Brau Beviale from 11 to 13 November 2014 and afterwards in PETplanet Insider. 13 mars – 15 août 2014 Tour de l’Europe du Sudouest et de l’Afrique du Nord avec PETplanet Go to Brau Beviale – À la découverte de la région méditerranéenne occidentale En avant vers de nouvelles aventures ! Notre équipe de reporters de PETplanet Insider reprend la route. Avec une édition de l’Editourmobil plus importante et une soif de découverte sans fin, le tour sera cette fois-ci centrée sur la partie occidentale de la région méditerranéenne. Nos intrépides experts, Alexander Büchler, Waldemar Schmitke, Kay Barton et Rolf , analyseront les marchés du PET en Italie, en Tunisie, en Algérie, au Maroc, en Espagne, au Portugal et en Andorre. Un voyage épique de 5 mois les attend, avec un éprouvant trajet de 7000 kilomètres couvrant deux continents tout au long duquel les trois équipes de PETplanet s’adresseront aux principaux acteurs du marché. Nous sommes là encore impatients de vous recevoir à bord pour faire ensemble un bout de chemin: suivez le tour sur notre journal en ligne www.braubeviale.petpla.net: vous trouverez tout ce qu’il faut savoir sur nos interviews avec les entreprises que nous rencontrerons sur notre stand d’exposition de Brau Beviale de 11 au 13 novembre 2014 et, après cela, à PETplanet Insider. Go to BrauBeviale The Western Mediterranean round trip","@ID":45}, "NEWS 9 PETplanet insider Vol. 15 No. 06+07/14 petpla.net Brau Beviale 2014 Brau Beviale 2014 will take place from November 11-13, 2014 in the Exhibition Centre Nuremberg, Germany. This year’s trend theme is the culture of craft brewing. Highlights include the presentation of the European Beer Star Award for 2014, free tastings accompanied by sommeliers, the Craft Beer Lounge and the Tour of Exhibitors with solutions specifically for craft brewers or the European MicroBrew Symposium. For the first time, the trade show presents the PETnology concept “connecting comPETence” with the PETarena and the Packaging Wall of Excellence, where companies present their diverse spectrum of PET products and services. Exhibitors will come from the whole PET value chain, including machinery manufactures, bottlers, packaging developers and suppliers. The event starts with the two-day international PETnology Congress which takes place immediately before the exhibition. Brau Beviale expects approximately 33,000 visitors and some 1,300 exhibitors from more than 50 nations. www.brau-beviale.de Phoenix Technologies’ rPET process given safety green light by EFSA Phoenix Technologies International, producer of recycled PET (rPET), has been given a green light by the European Food Safety Authority (EFSA) for its manufacturing process based on extra small particle size technology. EFSA’s Panel on Food Contact Materials, Enzymes, Flavourings and Processing Aids is responsible for the recycling process safety assessment. The panel concluded that “the recycled PET obtained from the process Phoenix ESPS (extra small particle size) intended to be used at up to 100% for the manufacture of materials and articles for contact with all types of foodstuffs for long term storage at room temperature, with or without hot-fill is not considered a safety concern.” Phoenix’s recycling process has been allocated the EU register No RECYC035. Additionally, the company previously has been issued “letters of no objection” for its rPET small particle process by the U.S. Food & Drug Administration and Health Canada. The company’s proprietary rPET technology is used to produce a variety of packaging containers and bottles for food, beverages, pharmaceuticals, shampoos, soaps and detergents. Its resins are also used in non-packaging applications such as strapping, carpeting and others. www.phoenixtechnologies.net Sidel wins three Coca-Cola contracts Sidel has been awarded three major new projects by The Coca-Cola Hellenic Bottling Company (Coca-Cola HBC). The project wins are in Nigeria (Ikeja), Russia (Moscow) and Belarus (Minsk). In Moscow, where Coca-Cola HBC is already operating four Sidel lines – including two Sidel Combis – the new line will comprise a Sidel Matrix Combi, a Sidel Matrix Labeller, a mixer, two packers, a handle applicator, a conveyor, a high-level linear palletiser and a stretch wrapper. It has the capacity to produce 500ml and 1,500ml PET bottles at a rate of 45,000 and 33,500bph, respectively. At the Coca-Cola HBC plant in Minsk, Belarus, the company again took delivery of Sidel equipment in February 2014. The acceptance test for the Sidel Eurostar, the mechanical pressure level filler for bottles and its accompanying Sidel rollfed labeller, has already been successfully completed and the line is now under way producing 9,000bph (2l bottles). In Nigeria, the outlook for the soft drinks market is said to be encouraging and looks set to continue to grow, with all major categories showing the potential for robust growth in both total volume and current value sales. Both the national population and disposable incomes are increasing, with new launches, marketing activities, improvements in distribution and other favourable economic conditions favouring all drinks producers. The complete new bottling line ordered from Sidel for the Coca-Cola HBC plant in Ikeja will be dedicated to the production of carbonated soft drinks. PET bottles in 500ml format will be produced at a capacity of 42,000bph, with 1,500ml formats produced at 22,000bph. The installation of the Sidel equipment in the Ikeja plant was started in May. The first saleable products will then be coming off the new bottling line in early July 2014. www.sidel.com Husky focuses manufacturing facilities for the Medical and Specialty Packaging Systems division Husky Injection Molding Systems announced the decision to focus manufacturing facilities within the Medical and Specialty Packaging Systems business, bringing a dedicated focus to each location. With the integration of Schöttli and Husky, this new focus is intended to enable Husky to provide a more responsive approach to its customers in these markets. In February, Husky announced the creation of a new Medical and Specialty Packaging business unit bringing together the capabilities of Schöttli, Husky’s speciality mould making facilities in Austria and the Czech Republic, aftermarket tooling and services, and the Hylectric machines system platform. Each facility will be targeting specific applications, and will provide customers the opportunity to work with a single supplier to optimise system level performance. Within the new division, existing Schöttli sites will be focused on medical moulds and systems, select packaging moulds and systems, and some speciality closures. Husky’s sites in Austria and the Czech Republic will be focused on speciality closures. Each site will continue to place the emphasis on Aftermarket Services and Tooling. www.husky.ca","@ID":11}, "PET THE NEXT GENERATION 35 PETplanet insider Vol. 15 No. 06+07/14 petpla.net Recycling of PET bottles into jewellery All that glitters is not gold Florie Salnot was born in France. She is a designer working in the area of design research, product and service design. She owns a degree in History of Arts and Anthropology from the Sorbonne in Paris and a MA in Product Design from the Royal College of Arts in London and now divides her time between Hamburg, London and Paris. www.floriesalnot.com Florie Salnot is a designer concerned with social issues. For her Plastic Gold project she works with women from Western Sahara who have been living for almost 40 years in refugee camps at desert sites in Algeria, waiting to get their land back. Inspired by the traditional jewellery worn by these women, Salnot has devised a craft they can practise despite their limited resources. With only empty PET bottles, hot sand, simple tools and spray paint, they create necklaces and bracelets. Plastic bottles, in the form of litter, are in plentiful supply around the refugee camps in the Sahara desert. That gave Florie Salnot the idea to use them in an art project: “I knew that the Sahrawi people were already making jewellery before and I began looking at their traditional crafts, which led me to start experimenting. The idea was to devise a technique that they could make themselves within the refugee camps with the resources they have available, even though they have almost nothing.” To transform the bottle into a material suitable for jewellery, it is first painted and then cut into thin strips with a cutting tool. Any type of drawing can then be made by positioning some nails in a nail board. The plastic stripe is placed all around the nails and the whole is submerged into hot sand to mould the pattern. The plastic strip reacts to the heat by shrinking all along the nail drawing and keeping its shape. The design of the jewellery was inspired by the Saharawi patterns traditionally drawn on leather. The idea is to set up a production facility with the Sahrawi community to enable them to generate an income stream. Plastic Gold was shortlisted for the Jameel Prize 2013, an international award for contemporary art and design inspired by Islamic tradition. Stages of the Plastic Gold technique: painting of the bottle, cutting, moulding with hot sand The hot sand stage during the first workshop in the refugee camp of Dakhla Ziurla necklace made from PET","@ID":37}, "BOTTLE MAKING 40 PETplanet insider Vol. 15 No. 06+07/14 petpla.net Natural stretch ratio (or natural draw ratio) – Bottles, performs and closures, part 12 Behaviour in the blow mould The stretch or draw ratio of a polymer is the ratio of the resulting length (in the direction of applied stress) to the original length. When PET is stretched, for example, during blow moulding, it reaches a point at which an increase in the force is required to continue stretching. The point at which the PET requires this extra force is called the natural stretch ratio (NSR) for a particular set of stretching conditions. PETplanet insider is publishing extracts from successive chapters of Ottmar Brandau’s “Bottles, Preforms and Closures”, which was first published by hbmedia. A newly revised version is reissued under the Elsevier imprint. The NSR is reached when strain (or work) hardening occurs on the stress– strain curve for materials. Recall that before a material yields, once the applied force is removed, it can return to its original dimensions. Stretching beyond the yield point results in permanent deformation, and further stretching will result in fracture. In some materials, including PET, strain hardening can occur before fracture, which is essentially the aligning (or orienting) of the structural regions of the material in the direction of the applied stress, which can result in improved physical properties for the material.","@ID":42}, "EDITOUR REPORT 18 PETplanet insider Vol. 15 No. 06+07/14 petpla.net process. The alternative is the 1-piece plastic closures that call for a higher degree of precision and which therefore represent an attractive proposition where the injection moulding process is concerned. Some brand owners are already setting off along the path of 1-piece plastic closures. This is precisely why Netstal are showcasing their latest injection moulding system at Feiplastic in São Paulo - the Elion 3200-2000 with a 72-cavity injection mould from Z-mold Austria - for the manufacture of 1-piece plastic closures for CSD. Klaus Jell emphasises an important feature of the new machine: “The injection moulding machine is kitted out with the latest development in the electrical mould clamping sector incorporating energy recovery. This results in significant savings in energy costs in the manufacture of closures.” The item manufactured is a 2.45g UCL plastic closure with an 1881 neck finish and a cycle time of 4.2s. The system has already been sold to Messrs. ChristalPET in Brazil. Preform systems A dominant feature in the Brazilian beverages industry is the use of 96/128-cavity moulds. According to Klaus Jell, Netstal is well placed to take advantage of this. However, there is also evidence of encouraging growth in the use of preform systems with smaller numbers of cavities such as for example 24-cavity mould compartment for UHT milk in PET bottles. The company’s Prelactia overmoulding system has been developed for applications such as this. www.kraussmaffeigroup.com www.netstal.com May 23, 2013 Otto Hofstetter AG We met: Stefan Zatti, Division Manager Sales & Marketing Harry Kleiner, Area Sales Manager PET Harry Kleiner, Area Sales Manager PET, left, and Stefan Zatti, Division Manager Sales & Marketing, right, at Feiplastic in São Paulo SP Our final week begins on Monday morning with a visit to Döhler, manufacturer and supplier of fruit concentrates and flavours in Limeira. As we know just a bit about this section we taste some of the intermediate products which go to make up tãhe concentrates, and we begin to underãstand why it is not easy to create a great tasting drink. Before we leave the Technical Key Account Manager invites us on a comprehensive and extremely interesting tour of the factory. Incredible though it seems, we have spent the entire day at Döhler! A wonderfully entertaining and informative visit! The next day we are heading towards Sorocaba, where we are going to meet Ecoplaca. In a side street a lorry is parked, laden with plastic folders. This must be the right place! Ecoplaca processes recycled PET amongst other materials, transforming it into objects as varied as folders, pens and traffic signs. Throughout our trip we have heard a lot about recycling, so we are really looking forward to our discussions with a genuine Brazilian expert. We quickly learn that recycling in the city of Sorocaba has an important social dimension. In the afternoon we drive into the centre of São Paulo, where the Feiplastic exhibition is taking place. After a hapless search for a place to park the Editourmobil around the premises we receive help from the exhibition management. They organise for us a covered parking space near the exhibition entrance. Even better, it has an electricity and water connection. So all’s well that ends well! Travelling across South America with the Editourmobil, learning something of the PET industry is a lot more than just exciting. We have got closer both to our customers and to the people generally. We have listened to the heartbeat of the continent not only in the PET industry but on the streets as well. For Waldemar and for me, the trip has been the experience of a lifetime.","@ID":20}, "MARKET SURVEY 33 PETplanet insider Vol. 15 No. 06+07/14 petpla.net SBM Moulds Petka Mold Industry TPS - Tooling Preform Systems Pass Card Co.,Ltd. Yeşiloba Mah.46075 Sok. No 8 Seyhan, Adana, Turkey +90 322 4286 400 www.petkamold.com Mr Tarık Sivri General Manager +90 532 524 8990 +90 322 4282 303 tarik.sivri@petkamold.com C.Houtmanstraat 42, 7825VG Emmen, Netherlands +31 591 679768 www.tps.nl Mr Richard Tempel Account Manager +31 6 25041 136 +31 591 630 616 r.tempel@tps.nl No.5, Road 36, Taichung Industry Park, Taichung City, 407 Taiwan +886 4 2355 3779 Mr Chad Huang, Sales Director Global Sales responsible +886 97512 7035 chad@passcard.com.tw 2 - 96 96 1 (prototyping) - 96 14mm -110mm neck finish Up to 50l 18mm - 140mm wide mouth, 6g - 900g Husky, Netstal Krauss Maffei, Sipa Husky, Netstal, Engel, Battenfeld, Demag Asian PET machines, Husky 96 96 32 ASB 2 stage system Up to 50l 28mm to 38mm Krauss Maffei ASB 2 stage system Yes, (ASB, Aoki) No None 0,1l -19 l 50l 20 No No Yes Yes Yes, Siapi, Sipa Sidel, Krones, Kosme, Blomax, SMI Sipa, Siapi, MAG, Combi Various Yes Yes Yes Supply of bottle prototype Large containers Awanti Polymoulds Pvt. Ltd. Demo Design and Moulds Comep SAS Moldintec SRL Garrtech Inc. Vitalii and Son Kiefer Werkzeugbau GmbH 25/5A/1/2, Nanded, Near Sawali Dhaba, Sinhagad Road, Pune 411 041, India +91 20 2439 222 5 www.awantipolymoulds.com Mr Shirish Kshirsagar Managing Director +91 20 2439 222 5 +91 98220 40 771 shirishk@vsnl.com Via Olivera 48, 31020 San Vendemiano, Italy +39 0438 409048 www.designandmoulds.com Mr Luca Orlando Sales Manager +39 0438 409048 +39 0438 409046 l.orlando@designandmoulds.com ZAE du Pont Neuf, 16130 Salles D'Angles (Cognac), France +33 5 45 36 63 50 www.sa-comep.fr Mr Frédéric Mandin Sales Manager/Marketing +33 5 45 36 63 50 +33 5 45 32 08 08 frederic.mandin@sa-comep.fr Lamadrid 501, Los Troncos del Talar, Tigre CP. 1617, Buenos Aires, Argentina +54 11 6632 9999 www.moldintec.com.ar Mr D.I. Jorge Pucci Commercial Director +54 911 4146 9894 jorgepucci@moldintec.com.ar 910 Arvin Ave., Stoney Creek, ON, Canada L8E 5Y8 +1 905 643 6414 www.garrtech.com Ms Donna Watson Account Manager +1 905 643 6414 x 252 +1 905 643 6422 donna_watson@garrtech.com 9009, City Varna, #276, bul. Vladislav Varnenchik, Bulgaria +359 888 518782 www.vitaliiandson.eu Mr Vitalii Marinyak Executive Manager/ +359 888 518 782 +359 52 510 168 llvitalii@mbox.contact.bg Steinhäldenstraße 11, 74193 Schwaigern, Germany +49 7138 9732 0 www.kiefer-mold.de Mr Jörn Herget Sales & Project Manager +49 7138 9732 70 +49 7138 97 3290 joern.herget@kiefer-mold.de Yes Up to 20 18l 0,03 - 30 20 5 Up to 20 30 Sidel India Ltd, MAG Plastic Asia, Shyam Plastic Machinery Yes Yes, Krones, KHS, Sacmi, Bosch, Side, Urola, 1Blow Yes Yes Yes Independent mould maker Yes Yes Yes, Krones, Sidel, KHS, Sacmi, Sipa, SMI, Bosch, Side, Urola, One Blow Yes Yes Yes Yes Sidel SBO Series, SIG, Krones, Nissei, MAG, Kosme, Chum Power, Sidel, Shyam Plastic, Urola, Wee Lei PepsiCo,Rauch, Damm, Almdudler, Salvus Mineralbrunnen, Mineralquelle Wüllner Still water, CSDe, home care, oil, alcohol, sauce The Coca Cola Company, Pepsico, Groupe Danone, Nestlé waters, Nidera, Alpla, Amcor Food & Beverage, household, personal care, medical, industrial, chemical, all technologies MAG, Krones, Sipa, ADS, Kosme Kosme, Krones, Sipa, Sidel, ADS, Tetra Pak Yes Yes Yes Yes Yes Yes Yes Prototyping to unit cavity testing and final mould making Plexi-model, pre-series moulds, blow moulds, installation and start-up new bottle All kinds of moulds for high speed machine (rotary and linear) Low blowing pressure 20bar Designing, prototyping, parts engineering Lightweight design, special design for functional drinks, juices and household products Company name Solent Mould Tools Ltd Kosme GmbH Technopet Machineries India Postal address Telephone number Web site address Contact name Function Direct telephone number Fax E-Mail Relay Road, Waterlooville, Hampshire, PO7 7SB UK +44 23 9223 9950 www.solentmouldtools.com Mr Mark Sim Managing Director +44 23 9223 9950 +44 23 9223 9951 mark.sim@solentmouldtools.co.uk Gewerbestr. 3, 2601 Sollenau, Austria +43 2628 411 0 www.kosme-austria.com Mr Johann Gugler Managing Director +43 2628 411 125 +43 2628 411 4125 j.gugler@kosme-austria.com 14/15 Shree Naman Plaza, S.V.Road Kandivali West, Mum- bai 400 067 Maharshtra, India +91 22 28610 828 www.techno-pet.com Mr Vineet Bannore PET Eng. +91 98 20346 565 +91 22 28061 410 sales@techno-pet.com Stretch blow moulds Bottle size (max.) (litres) 5 30 50 to 20 Mould supply directly to machine manufacturers Yes No Technopet Machineries Supply of retrofit moulds for existing machines Yes - all platforms Yes Moulds for bottle makes already produced for Sidel, Krones, KHS, Sig, Siapi, Aoki, Nissei, Krupp, Mag, etc Kosme, Krones, Sidel, KHS Bisleri, Bailley, Maza Dubai, Reliance, King Fisher, CSD, hotfill Bottle design service Yes Yes Yes Specialities Interface parts + carriers to allow different OEM moulds to be fitted in other machine platforms, e.g. Krones into Sidel, Sidel into KHS, etc. EBM moulds supplied for all platforms Bottle development service free of charge, if blowmoulds are ordered Cold fill, warm fill and hot fill re-crystallised mould design. High and low density mould material design to bottle property","@ID":35}, "MATERIAL / RECYCLING 27 PETplanet insider Vol. 15 No. 06+07/14 petpla.net Anti-yellow additives Repi‘ s anti-yellow additives are formulated so to be able to modify the main required parameter, namely to correct the yellowish shade with an action on the value of “b” coordinates Cielab. An additional aim is to influence and balance the level of grey (L value) and green, so to improve the value “a” coordinates Cielab. The key to obtaining successful formulations of anti-yellow is the extensive knowhow on the different processes involved. These differ in the case of the injection of preforms, the extrusion of sheets, and the production of rPET chips. A further issue is how not to interfere and modify process parameters while working, even with high vacuum levels. The anti-yellow additives line has seen its number of formulations approved and used in all injection and extrusion processes and in the various PET recycling technologies, where a number of issues related to the vacuum and the sensitivity of the filtration and cleaning require special attention. The very low addition rates in use have also required the optimisation of the dosing systems: Repi claims that their dosing units on the market today can guarantee a constant dosage to an accuracy of 0.004%. The active collaboration with leading equipment manufacturers and end users allow Repi to play an important role globally in this specific field. To illustrate the behaviour of the company’s antiyellow additives, graphs 1 and 2 show lab values on two main applications, PET sheet and rPET resin. High performance additives Among the high performing additives by Repi, an interesting role is also played by the “no cross link” Intrinsic Viscosity Enhancer (IVE), added during the processing in order to improve the molecular weight (MW) and the mechanical properties. After the reaction takes place, the chain extender is physically bonded into the main PET backbone. The reaction can continue to 100%, according to the temperature and the residence time available and the chain extender cannot be released from the polymer. The link established between the PET and the chain extender is stronger than the ester bond and is not subject to further hydrolytic scission. The molecular weight (MW) and the mechanical properties increase accordingly. The chain linearity reduces the risk of creating gels. In the production of rPET resin and preforms, this additive helps to improve the physical and mechanical characteristics of the final product. In PET sheet extrusion, it enables a better thickness distribution, as well as an optimisation of the process parameters (pressure in the melting pump increases significantly). Calenders will get less dirty, substantially reducing the need for cleaning. Graph 3 shows the improved mechanical properties achieved by using the additive in the production of PET bottles. Graph 4 shows time saving in reaching even a better IV level in the SSP process. www.repi.com Graph 1: Remap AY performance on PET sheets Graph 2: Remap AY performance on rPET chips in a standard PET recycling process Graph 3: Top load results on the same shape of bottle with and without Remap IVE Graph 4: Time vs. IV (dl/g) in a standard SSP process with and without Remap IVE","@ID":29}, "PRODUCTS 48 PETplanet insider Vol. 15 No. 06+07/14 petpla.net Palletiser with low-level pack feed The twin-column Innopal PB1NF palletiser from KHS is a single-station palletising machine with level compensation which processes up to 500 layers per hour and has a low-level pack feed. The machine has a cross conveyor built into the front end of the palletiser which can be opened. A barrier construction is used in place of the previous integrated bar construction. This means that after placing the last layer onto the pallet, the cross conveyor no longer has to be raised and wait there until the finished pallet has been discharged from the system, as has been the case to date. Instead, the cross conveyor can travel down to table level before and the new layer picked up during the change of pallet which increases the palletising speed. The Innopal PB1NF is said to also have the benefits associated with a low-level pack feed on palletisers. One of these is that neither a platform nor inclined or spiral conveyors are needed which has the advantage of reducing investment costs and providing good accessibility and ease of operation. Upstream of the Innopal PB1NF palletiser a KHS inline robot grouping can be used where two four-axis Innopal RK4 robots prepare the layers with precision. Pack manipulation elements, such as turning stations, are not needed. Besides cutting costs as a result, other definite benefits compared to conventional systems are gentle pack handling, flexibility, reduced space requirements, less maintenance and fast changeovers, says KHS. www.khs.com Single station palletising machine with level compensation packing plastic containers, cans or glass bottles in film, cartons or trays Ease of opening Closure Systems International’s (CSI’s) Aqua-Lok mini 26mm TC (tall cap) is said to provide 57% more grip surface than other 26mm short-height profiles for ease of opening by consumers of all ages. The HDPE closure was designed to provide a balanced combination of bottler savings and enhanced consumer satisfaction. The taller cap is fully compatible with the popular ultra short-height 1914 PET bottle finish. This new lightweight, 1-piece closure is suitable for bottled water, ready-to-drink teas and other still beverages. By increasing the height of the closure side wall, the CSI designers expanded the knurled gripping area of the closures, making them easier to open, while still fitting the 1914 bottle finish, says CSI. Other features of closure include an extended plug seal for advanced tamper evidence, providing band break prior to seal loss. This seal geometry not only protects the product integrity, but also maximises consumer security. www.csiclosures.com","@ID":50}, "imprint EDITORIAL PUBLISHER Alexander Büchler, Managing Director HEAD OFFICE heidelberg business media GmbH Häusserstr. 36 69115 Heidelberg, Germany phone: +49 6221-65108-0 fax: +49 6221-65108-28 info@hbmedia.net EDITORIAL Doris Fischer Gabriele Kosmehl Michael Maruschke Ruari McCallion Waldemar Schmitke Ilona Trotter Wolfgang von Schroeter Anthony Withers MEDIA CONSULTANTS Martina Hirschmann hirschmann@hbmedia.net Roland Loch loch@hbmedia.net phone: +49 6221-65108-0 fax: +49 6221-65108-28 France, Italy, Spain, UK Elisabeth Maria Köpke phone: +49 6201-878925 fax: +49 6201-878926 koepke@hbmedia.net LAYOUT AND PREPRESS Exprim Kommunikationsdesign Matthias Gaumann | www.exprim.de READER SERVICES Heike Fischer reader@hbmedia.net PRINT Chroma Druck & Verlag GmbH Werkstr. 25 67354 Römerberg Germany WWW www.hbmedia.net | petpla.net PETplanet insider ISSN 1438-9459 is published 10 times a year. This publication is sent to qualified subscribers (1-year subscription 149 EUR, 2-year subscription 289 EUR, Young professionals’ subscription 99 EUR. Magazines will be dispatched to you by airmail). Not to be reproduced in any form without permission from the publisher. Note: The fact that product names may not be identified as trademarks is not an indication that such names are not registered trademarks. 3 PETplanet insider Vol. 15 No. 06+07/14 petpla.net dear readers, Footballers are carrying 18 bottles around the pitch The World Cup is in full flow in Brazil and undoubtedly you will be cheering your team on. If you look closely, you may detect that some footballers are carrying 18 PET bottles around with them during the game. No, we are not talking about bottles of water, CSD’s or juices, but about the innovative shirts and shorts in rPET recycled for promotional purposes. Brazil, the host nation and a hot favourite, was one of several teams playing in Nike-branded shirts, shorts and socks made from rPET. Both England and the USA are also on board, wearing shorts and shirts made of 100% recycled polyester and 96% respectively, as well as socks - a first this year - incorporating 78% recycled material (see page 36). All the more reason, then, for us to take another close look at the world of recycling. An increasing number of PET recyclers are venturing from the bottle-to-textile stage to bottle-to-bottle recycling. For instance, Enka de Colombia S. A. in Medellin, Colombia, is expanding its existing production of fibres, filaments, yarns and resins for the textile industry by bottle-to-bottle recycling (see page 24). A further trend is in-house recycling. The bottler Stute is now taking this one step further by recycling contents-contaminated bottles for its own production. In the long term this will enable the company to take back post-consumer bottles for recycling back into bottles. (see page 20). This is not quite as straightforward as it sounds. You cannot simply load contaminated bottles in at one end and extract granulate at the other. Italian company REPI may provide a solution. They have launched their advanced Anti-Yellow additives which they claim will correct the yellowish shade in contaminated bottles and improve the IV parameters of PET. Whilst you are comfortably settled in front of the TV revelling in all the action from Brazil, you might just spare a thought for all those recycled PET bottles running around the pitch! Yours Alexander Büchler","@ID":5}, "BOTTLE MAKING 38 PETplanet insider Vol. 15 No. 06+07/14 petpla.net Sidel’s approach to sustainability Value creation along the supply chain PET is already the world’s most widely recycled plastic and can further strengthen its position by taking what is currently in the waste stream and putting it in the resource stream as rPET whether for football kits or new bottles and reaching for the ultimate objective: a closed-loop packaging supply chain. However, opportunities remain to improve sustainability before packaging gets anywhere near the end user. Forecasts for 2030 suggest that demand for energy and food will have increased by 50%, and for water by 30%. Production of packaging and related products has to optimise resources by reusing and recycling wherever possible. Considerations about ‘Sustainable packaging’ minimisation of the environmental footprint through reducing use of raw materials and energy; employing renewable energy during production and transportation; building-in recycling principles at design stage; incorporating recycled content in the packaging; and sustainable end-of-life options. Optimising energy The blow-moulder accounts for as much as 70% of electricity consumption on a PET production line, a proportion being attributable to compressed air. Programs are available that measure electricity consumption and other factors such as air pressure and leaks, with mechanical testing on sub-assemblies. The process and technical qualities of the package and the production environment can be measured to provide a comprehensive analysis, enabling development of an action plan covering energy and costsaving targets, with ongoing monitoring of consumption. Lamps can consume as much as 90-95% of the electrical power used by a PET blower; Eco ovens require fewer heating modules, can reduce preform heating time and boost energy efficiency. Eco lamps can offer significant savings: Sidel helped PepsiCo Deutschland to achieve savings of 19%, with a 12-month return on investment. Water and chemical usage Sidel’s Predis preform and Capdis cap decontamination systems use hydrogen peroxide mist, with no water and very little chemicals. Traditional aseptic filling systems that require wet bottle rinsing consume approximately 180m3 of water and 220l of chemicals/day. Lightweighting Sidel’s RightWeight bottle weighs 7.95g. The ‘RightWeight’ name","@ID":40}, "PETpatents www.verpackungspatente.de 56 PETplanet insider Vol. 15 No. 06+07/14 petpla.net Optimised hot filling US Patent No.US 2012 / 0076965 A1 Applicant: Graham Packaging LC, York (US) Application Date: 30.9.2011 A PET bottle for hot filling is so designed that its volume does not increase by more than 3% when it is filled with a liquid, during pasteurisation or during the heating process. Plastic bottle European Patent No.EP 2653400 A1 Applicant: Suntory Holdings Ltd., Osaka (JP) Date of Application: 14.12.2001 A plastic bottle for carbonated beverages or products that are hot filled and subsequently change their volume during cooling incorporates grooves in the bottom section that allow for elastic elongation of the bottle. Deformable side panels European Award of Patent No. EP 2512935 B1 Applicant: Sidel Participations, Octeville Sur Mer (FR) Date of Application: 16.12.2010 The side wall of a plastic bottle is divided into several different areas. These improve handling and act as membrane-like compensating areas in response to changes in pressure. Sleeve label with tab European Patent No.EP 2664557 A1 Applicant: CCl Label GmbH, Hohenems (AT) Application Date: 14.5.2012 The shrink label for securing a container closure is fitted with a tab to the side so as to ensure that catching hold of and removing the label is a comfortable and convenient operation. This label incorporates lines of weakness and is combined in the area of the tab with a “non-shrinking“ material. Three stable positions International Patent No.WO 2013 / 186463 A2 Applicant: Sidel Participations, Octeville Sur Mer (FR) Application Date: 6.6.2013 The shoulder area and the top section of a PET bottle are so designed as to enable three predefined, stable shapes to be set up. When stacking on top of one another, no pressure is exerted on the shoulder or on the area of the opening because the stacking pressure is absorbed via the side walls. Shape of bottom section of PET bottle European Patent No.EP 2662297 A1 Applicant: Yoshino Kogyosho Co. Ltd., Tokyo (JP) Application Date: 18.11.2009 The bottom of a plastic bottle needs to be specially moulded to enable elastic absorption of the forces that occur during hot filling.","@ID":58}, "PET - THE NEXT GENERATION 36 PETplanet insider Vol. 15 No. 06+07/14 petpla.net rPET is playing its part in the Fifa World Cup PET on the ball! The 2014 Fifa World Cup Finals in Brazil will feature a range of recycling and other initiatives that will make it probably the most sustainable world sporting event ever. From football shirts to seat lines, recycled PET bottles are playing their part. Recycled PET (rPET), which is found in a wide range of applications, is the unheralded centre of world attention from June 12 to July 13, as 32 teams take to the field in the 2014 Fifa World Cup finals. Brazil, the host nation and among the favourites, was one of several teams playing in Nikebranded shirts, shorts and socks made from rPET. Both England and the USA are also on board, wearing shorts made of 100% recycled polyester; shirts of 96%; and socks – a first this year – with 78% recycled material. Each player’s kit uses material made from an average of 18 recycled plastic bottles. The trend is becoming well established and has been headlined from the start by sports squads and major sporting events. Team USA won the 2012 Olympic Games basketball gold medal in shirts and shorts produced from rPET. Nike, the sporting footwear and apparel giant, has recycled almost two billion bottles into team kit since 2010; that is enough to cover over 2,800 fullsized football pitches. The kits are examples of high-tech in action; they are much more than just uniforms. Each one is made for the player who will wear it. Before the kits were supplied Nike first did a full body scan of each player on the Brazilian and other national teams. Brazil is hot all year and June 2014 will be no exception, so regulating body temperature during matches is an essential design element. The 2014 Fifa World Cup new kits combine Nike Dri-Fit technology with ‘burnout’ mesh and laser-cut ventilation holes, for localised cooling where the need is determined. Dri-Fit ‘wicks’ away moisture from the skin, helping the player to feel cool and to avoid feeling sweat-drenched in the middle of the game. The shorts are more than decorative, as well; they are designed to reduce the bruises that players get on their hips and thighs when they slide along the ground in their quests to win the ball. Luiz Felipe Scolari, Brazil’s Manager who was known as ‘Big Phil’ during his time managing English Premier League team Chelsea, has already tasted World Cup success, having managed Brazil to its fifth triumph in 2002. He likes the kit but wants to render it out of date before the end of July. “The shirt looks great, the only thing missing is a sixth star,” Scolari said. “We aim to have that on there after the World Cup.” Thousands of spectators attending the final on Sunday, July 13 at the new Maracana Stadium in Rio de Janeiro will also be doing their bit for the environment – although they might not realise it. Two years ago, CocaCola, Inc., one of the World Cup’s main sponsors, launched a recycling campaign that encouraged customers to dispose of their empty Coke PET bottles in one of around 100 collection points made available by Coca-Cola Brazil in the city of Rio. The empties were collected, recycled into rPET and used to make 6,773 seats, ready to take the strain of excited supporters throughout the tournament. PET bottle recycling in Brazil is being encouraged by a number of initiatives, sponsored and reported by AbiPET, the country’s industrial association. Its latest survey reported that 294,000t of PET were recycled in 2011 and that the recovery rate is now over 50%.","@ID":38}, "MATERIAL / RECYCLING 26 PETplanet insider Vol. 15 No. 06+07/14 petpla.net Aesthetics and performance through advanced additives Adding value to recycled PET Today a variety of innovative solutions is undergoing constant improvement for each specific family of products made from rPET. This is in parallel with the on -going developments in recycling technologies and the introduction of different grades of rPET, whose use is growing, in percentage terms, relative to the total quantity of resin. The principal reasons are firstly to improve the aesthetics and secondly to increase the performance of the final product, be it for PET preforms, PET sheet or rPET resin. The use of recycled material in PET preform and sheet production is growing rapidly and gaining an ever larger market share. The aesthetic features of the final product, which can be liable to degrade using rPET, often do not satisfy customer specifications. Recycled PET is generally characterised by a yellowish shade and a lower and irregular Intrinsic Viscosity, which influences the mechanical properties of the final package. Special additives are required in PET preforms, in the production of rPET resin as well as in the extrusion of PET sheets. Repi, global supplier of high performing liquid colours and special additives began working on rPET in 2007 and the result has been a series of advanced additives able to correct the shade and to improve IV parameters of rPET, whatever the end-product is. Effect of Remap AY on PET sheets Effect of Remap AY on rPET chips Effect of Remap AY additive on PET preforms Effect of Remap IVE additive on the mechanical properties of a PET bottle","@ID":28}, "BOTTLES 53 PETplanet insider Vol. 15 No. 06+07/14 petpla.net Apple and cherry drink from Poland The Polish company Tymbark is distributing 500ml of an apple and cherry fruit juice in a waisted PET bottle on its home market. The top half of the bottle is decorated with a sleeve label and its holding area features a peripheral groove ensuring improved stability when catching hold of the bottle. In its lower half it also incorporates leaf-shaped embossing. A screw closure complete with guarantee strip is used to seal the bottle. www.tymbark.com Benjamin Blümchen and Bibi Blocksberg quench thirst with Bergquelle Aimed specifically at children, a new range of refreshing drinks has been launched on the market by the Bergquelle mineral water brand. Popular Kiddnix characters Bibi Blocksberg and Benjamin Blümchen decorate the labels of the new thirst-quenching line which is being marketed in 0.33l PET packs in the form of mineral water and a fruit juice drink. The water bottles are fitted with a practical sports cap, the body section is made from PP and the spout from PE. www.hochwald-sprudel.de PET bottles for pets For dog owners who love to spoil their canines, Bowser Beer from 3 Busy Dogs, Seattle, USA, has emerged as a popular pet product that has enjoyed strong national growth. Sales for the fun and healthy drink alternative - packaged in lightweight, shatter-resistant 12oz PET bottles from Amcor Rigid Plastics - have tripled in the last three years. The amber PET container mimics the iconic shape and colour of standard beer bottles. They are one-sixth the weight of glass bottles, unbreakable, less wasteful, and recyclable, according to Kerry Drewry, Sales Manager for spirits, wine and beer for Amcor Rigid Plastics. Bowser Beer is an all-natural chicken or beef broth drink made in the US. It also contains malt barley and glucosamine for joint health. The dog beverage does not contain hops which can be toxic to dogs. Dogs are said to enjoy the taste and flavour of the all-natural drink. For smaller dogs which cannot manage the whole bottle, owners like the option of reclosing the single-serve bottle and saving the rest for later. www.amcor.com www.bowserbeer.com","@ID":55}, "BOTTLING / FILLING 45 PETplanet insider Vol. 15 Packages The 3.25l packages or the 5l and 10l packages are then conveyed by Smiline belts to the inlet of the Smipal APS 3080 PR automatic palletising system, which gathers them on 800x1,200mm and 1000x1,200mm Euro-pallets. The palletiser installed by Pinar Su is a single-column system with two Cartesian axes with movements from the bottom. End-of-line operations are completed by a loop winder with a semi-airtight cycle that applies a special “dustproof” protection when the pallet is wrapped. Custom labels and handles Pinar Su has chosen to label its mineral water bottles produced at the Hendek facility with reel-fed labels applied through hot glue by a machine manufactured by PE Labellers. The labelling station is equipped with a servomotor, making it mechanically independent of the bottle carousel. This solution allows the automatic phasing of the machine with the label-application station, avoiding operator errors during format changeover. All operations are controlled by a PLC, which processes the work parameters set by the operator through a control panel or a touch-screen. Pinar Su has also decided to equip the 5 and 10l PET containers with a specific plastic handle applied by a specific machine installed downstream of the PE rotary labeller. Thus, the 3.25l bottles transit “idle” through the labeller but are then “fitted with a handle” by an automatic Smipack HA 60 model handle applicator, installed downstream of the Smiflexi SK 600 F shrinkwrapper that wraps them with shrink film in 2x1 and 3x1 collations. www.smigroup.it Pinar Su (Yasar Group) Pinar Su is part of the Yasar Group, one of the largest industrial companies in Turkey. Founded in 1945, the Yasar Group today consists of 20 companies, directly employs around 6,750 people and has leading brands in the food & beverage sector, such as Pinar, and in the coatings sector, such as Dyo. This group also works in the paper production, trade, tourism and services sectors. www.pinarsu.com.tr","@ID":47}, "PETcontents 6+7/14 4 PETplanet insider Vol. 15 No. 06+07/14 petpla.net INSIDE TRACK 3 Editorial 4 Contents 6 News 46 Products 50 On site 52 PET bottles for beverages and liquid food 54 PET bottles for health and beauty care products 56 Patents PET - THE NEXT GENERATION 35 All that glitters is not gold Recycling of PET bottles into jewellery 36 PET on the ball! rPET is playing its part in the Fifa World Cup BOTTLE MAKING 38 Value creation along the supply chain Sidel’s approach to sustainabilty 40 Behaviour in the blow mould Bottles, preforms and closures, part 12 BOTTLING / FILLING 44 Turkey takes to the water Pinar Su, Turkey, invests in SMI line BUYER’S GUIDE 57 Get listed! Page 20 Page 38 EDITOUR REPORT 12 Brazil - Part 5 Go with the flow tour: South America MATERIAL / RECYCLING 20 Green ideas bear fruit Stute recycles PET in-house 24 Bottle recycling hits a nigh note PET recycling in the Andes 26 Adding value to recycled PET Aesthetics and performance through advanced additives 28 Flaked bunch PET bottle-to-flake plant in Hohenwestedt, Germany MARKET SURVEY 31 Suppliers of preform moulds / stretch blow moulds Page 35","@ID":6}, "MATERIAL / RECYCLING 23 PETplanet insider Vol. 15 material can theoretically be recovered. Krones is the only manufacturer to offer both the washing module and the decontamination module, and thus a complete-system package, also including the entire peripherals if so required. In the first step, all flakes are gently and evenly heated up together in a first heating worm, and then in a second heating worm brought up to final decontamination temperature, which is significantly below the melting temperature of PET. The actual decontamination is performed in a vacuum reactor: in this semi-continuous process, the intrinsic viscosity is increased as heat is applied under a vacuum atmosphere, the polymer chains are stretched, and any remaining dirt removed in the vacuum. The process control concept and the reactor’s design generate a constant temperature distribution over the entire contents of the reactor. The vacuum reactor’s specially developed discharge base ensures a uniform dwell time for the particles on the first-in-first-out principle. This means the crucial quality parameters can be set to optimum advantage. After subsequent separation of fine particles, the decontamination process is concluded. A new operator interface is being used at Stute’s recycling system. It provides all the relevant data, such as fill levels and temperatures, in a single display, together with easy-to-understand icons, which show not only the actual value but also the pre-specified setpoint value and the upper/lower tolerance window. If a measured value moves outside this range, the icon will change colour. Operator control does not require any in-depth technical knowledge. Recycling system on two levels The recycling system has been installed on two levels: on the groundfloor delivery level is the entire washing module, plus parts of the decontamination module. The final component of the decontamination module, the vacuum reactor, is installed one floor lower down, in the basement, with a direct online link to the two preform injection-moulding machines accommodated in an adjacent room. Stute is able to add up to 30% of recycled material to the A-PET granulate in the preform production process. The recycling system can be expanded at need; the capacity can in fact be doubled in the space available. www.krones.com SIPA S.p.A. - Via Caduti del Lavoro, 3 - 31029 Vittorio Veneto (TV) - Italy Tel. +39 0438 911511 - Fax +39 0438 912273 - e-mail: sipa@zoppas.com www.sipa-xform.com yesterday today Short cycle times, high shot-to-shot quality, low energy consumption and maximum flexibility. The new XFORM 300 with its unique 6-position post-mold cooling system boosts your output performance for the widest range of preforms. Cooling preforms faster and better, the 96-cavity platform is ideal for large runs and quick mold changes. And it lets you run any mold you want, old or new, OEM-built or not, in total freedom. From ultra-thin walled (with proprietary XMould™ technology) to wide mouth. XFORM 300, low transformation cost, high value. Designed to adapt. Built to last. The new XFORM 300 IMAGINE THE LOWEST TRANSFORMATION COST. IN TOTAL FREEDOM.","@ID":25}, "EDITOUR REPORT 14 PETplanet insider Vol. 15 No. 06+07/14 petpla.net Making the product local Thanks to the 2008 newbuild, success has been achieved in terms of exemplifying all technologies and achieving all the necessary qualifications just as are required in Europe. This means that the site here is to a major extent independent but benefits from the worldwide development expertise of the Group. The entire South American market is serviced from Limeira. 90% of the raw materials used come from Brazil and South America. Localising not only has its advantages on the competitive front but also represents a commitment to the region. Transferring a taste from Europe to South America on a 1:1 basis is practically impossible. Even in Europe flavours differ from one country to another. Here there is a saying which describes the situation to a T: “Flavour taste is local taste“, as Martin Tolksdorf tells us. Flavour profiles Sample flavourings for orange concentrates Drawing up flavour profiles and using them so that they can be reproduced is a specific art and, viewed from a particular standpoint, lends itself to a comparison with the perfume industry. Instead of working with fragrances, the work here is carried out on flavour compositions. Flavour substances also incorporate different consistencies. They range from stable as well as less stable ones right through to volatile flavouring agents. For example, the flavouring agents extracted from the orange, the peel oil, essential oil and the water phase, are highly volatile substances. This must be borne in mind when using them because this means that the stability of the flavour has a time limit. Each flavouring agent has certain characteristics which, when highlighted and in combination with further flavouring agents, generate a flavour or taste profile. The stability of the flavourings is dependent to a major extent on the surroundings. “When it comes to bottling, for example, in a PET bottle, I need to be able to count on durability in addition to flavouring.” Mr Tolksdorf continued, “The packaging affects the stability of the flavourings, for this reason prior awareness of the type of packaging to be used is important. Other influencing factors have a part to play, such as, for example, ambient temperature and relative humidity, whether the beverages are carbonated or non-carbonated, oxygen compatibility, light and period of storage. And temperatures and quality standards when it comes to the bottling processes. In addition, there are the local everyday factors to be considered, such as taste perceptions and existing raw materials. A typical example is the use of sugar. The same drink in Brazil on a cane sugar base tastes different to the same drink in Europe on a beet sugar base. A different example that many have already experienced for themselves is the wine that tasted really good when you were on holiday but which, having brought it back with you and drunk it in your own country, turns out to be a total disappointment. For this reason it is important to be familiar with the local influences and to attune oneself to them,” says Martin Tolksdorf. “In this it is the technological set up of this plant which puts us in a position to provide appropriate flavouring agents for each and every market, together with the tones that are unique to them.” This is a major challenge that we are working on together with the bottlers. We have no products of our own and this means that what every customer gets from us is a flavouring profile tailored to their own requirements. Packaging and logistics It is now time for the fruit concentrates and flavouring agents to go to the customer. We have learnt how sensitive these substances are in terms of their reaction to environmental conditions. One possibility is to store and ship everything in the frozen state. On the other hand, however, this means that the flavouring concentrates will have to remain in a refrigeration chain at the bottler’s premises. Döhler has an alternative to offer here. The customer’s concentrates are prepared in batches under aseptic conditions and stored to await call-off. Depending on the requirement, bottling is carried out aseptically (bag in barrel or carton) and transported to the customer in air-conditioned trucks; the customer in turn stores the barrels until they are used without applying any particular storage conditions. The barrels are refillable and return to Döhler. The Brazilian beverage market* Size of Brazilian beverage market: 32 billion l/a CSD make up 50% of the market with the largest proportion of PET bottles: 16.7 billion l/a Packaged water: 6.5 billion l/a Fruit powders: The high level of consumption is a particular feature of the Brazilian market. As regards trends in flavourings, orange and grape tend to dominate. Here there is also future potential for PET bottles. 4.3 billion l/a Still drinks: The proportion of low juice drinks (10%) is very high: 1.7 billion l/a Juices and nectars: 0.65 billion l/a Sport and energy drinks: 0.28 billion l/a Iced tea: 0.15 billion l/a Squash/syrups: 1,72 billion l/a *Consumption figures 2012/13 based on Döhler analyses and estimates","@ID":16}, "MATERIAL / RECYCLING 21 PETplanet insider Vol. 15 PROVEN COST SAVINGS PERFORMANCE moldmasters.com Mold-Mastersand theMold-Masters logo are trademarksofMold-Masters (2007) Limited. © 2014Mold-Masters (2007) Limited -AMilacronCompany.All rights reserved. Rely on our global support network for fast service and parts. North America 1-800-387-2483 | Europe 49 (0) 7221 5099-0 Asia 86 512 86162882 ALWAYS INNOVATING. + More efficient use of platen real estate increases the cavitation for a given machine size: s 72 vs. 48 Cavity with a 28mm finish in a 225T s 72 vs. 48 Cavity with a 38mm finish in a 300T s 96 vs. 72 Cavity with a 28mm finish in a 300T s 128vs. 96 Cavity with a 28mm finish in a 400T + Proprietary iFLOW and iCOOL technology reduces cycle times while improving balance, lowering injection pressure and increasing dimensional repeatability + Tooling solutions to revitalize, recapitalize and rev up existing systems Get 50% more output from the same machine 96-CAVITY MICRO PITCH MOLD FOR 300T MACHINES Contact us today at: mpeteurope@moldmasters.com with 320,000 population equivalents, cleans the Stute plants’ entire effluent. The associated biogas facility supplies 13% of the firm’s gas requirements. The biogas obtained is used as an energy source in a gas turbine for generating the firm’s steam. Even the turbine’s exhaust gas is utilised for steam generation, thus enabling an overall efficiency of 90% to be achieved. On the roofs of the factory halls, Stute has installed 11,000m² of photovoltaic cells, and another 50,000m² in a field directly next to the plant. The rated total output of the photovoltaic systems is currently running at 5.8MW. Three wind turbines are rotating on the site, and a fourth wind power installation is being planned. In-house power generation using solar and wind power is meanwhile contributing more than 20% of the firm’s total power requirement. “The aim is to increase the selfgenerated proportion of the firm’s energy supply to 50% over the next few years”, says Christoph Frankrone. “We’re already touching 50%, in fact, on good days for wind and sunshine, meaning the peak times. For biogas production, we use only our own waste products, the sludge from the anaerobic sewage treatment plant or apple pomace from our presses. We are totally against planting or buying agricultural raw materials in order to convert them into electricity”, emphasises Christoph Frankrone. In the plant itself, too, Stute has signed up to sustainability in both thought and deed. “By installing two Krones bottling lines with Contipure modules and without a rinser in 2009, we save 240m³ of water a day in the beverage bottling operations”, explains Christoph Frankrone. By reducing the amount of packaging and optimising the pallets, moreover, Stute has saved 40% of its freight transport space. In the vehicle fleet, the family firm has reduced the emissions of nitrogen oxide by 90%, having installed energy-economical engines featuring the very latest technology. In the refrigeration systems, Stute uses ammonia instead of greenhouse gases as the refrigerant, and additionally achieves annual electricity savings of 30%. The recycling system is currently dimensioned for producing 3,500t/a of food-grade PET flakes. Given a bottle weight of 20g, this corresponds to 175 million PET containers roughly equal to the complete output of two bottling lines. “PET recycling is a win-win situation for the retail sector and for us. The retailers provide high-quality PET material for recycling as high-quality food and beverage packaging, and avoid downgrading it, e.g. for textile production in China. Which means our","@ID":23}, "EDITOUR REPORT 12 PETplanet insider Vol. 15 No. 06+07/14 petpla.net The final lap We are now entering the final stage of our tour of Brazil and with it, the conclusion of the entire Latin American tour. This stage coincides with the Feiplastic show in São Paulo, and we take advantage of the opportunity to talk to machine manufacturers and toolmakers of PET preforms and caps, including companies such as Krauss Maffei and Otto Hofstetter. To complete our review of the Brazilian market it only remains for us to visit a manufacturer of fruit concentrate and flavours. Döhler América Latina in Limeira fits the bill admirably and in discussions with them we learn about the characteristics of the Brazilian market. Interviews in this issue Döhler América Latina Ecoplaca Krauss Maffei do Brasil Ltda. Otto Hofstetter AG For a fully rounded analysis of the market it was important to look at the subject of PET recycling from the perspective of two contrasting companies, the first a small local concern, the second a significant international player. We were able to interview two typical representatives, Ambev, the second-largest beverage bottler in Brazil and Ecoplaca, a small company processing recycled PET into useful objects. Looking back on the trip overall, we can take back with us numerous impressions and a fund of stories. We succeeded in getting closer not only to the market, but to the people as well, and the memories of our experiences will stay with us for life. Lima Santiago La Paz Buenos Aires Montevideo Progresso São José dos Pinhais São Paulo Rio de Janeiro Lindóia Santa Cruz Sucre Quilmes Pilar Jaú Concepción Santa Fe Barueri Jundiai Sorocaba Amparoa Limeira Brazil Part 5 by Waldemar Schmitke and Florian Roscheck","@ID":14}, "MATERIAL / RECYCLING 24 PETplanet insider Vol. 15 No. 06+07/14 petpla.net PET recycling in the Andes Bottle recycling hits a high note One of the most recently installed recoStar PET 330 iV+ recycling lines from Starlinger recycling technology operates at 1,300m above sea level. An established producer of fibres, filaments, yarns and resins for the textile industry based in the “City of Eternal Spring” in Medellín in the heart of Colombia, Enka de Colombia S. A. recognised the potential of bottle-to-bottle recycling and decided to move into this application. with product specifications and pellet shape were the criteria the company defined for the equipment as well as criteria such as machine footprint, price and technical support. The PET recycling plant began production in December 2013. Enka’s experiences with the produced rPET on the Colombian market are promising. Evaluations of the recycled PET resin made by Enka customers show satisfying results – both as raw material and in bottles produced with different mixing ratios. “Tests are being carried out with bottles that are produced with a recycled content ranging from 25% to up to 100%. They receive very good acceptance from our customers”, says Aníbal Celis. In December 2013 Enka also obtained the approval of the Colombian health authority Invima (National Institute of Surveillance of Drugs and Food) for four years. Flexible production capacity The Starlinger recoStar PET 330 iV+ recycling line for Enka is designed for an output capacity of 2.4t/h and features two 165 mm single-screw extruders and adequately sized upstream and downstream equipment. The input material is cleaned in a Sorema washing line while two viscoStar 120 solid state polycondensation reactors ensure constant IV level increase according to specifications. “An important feature of the recoStar PET 330 recycling line we supplied to Enka is the flexible production output: it can be adjusted between 1.1 and 2.4t/h”, explains Stefan Obermüller, Project Manager at Starlinger and responsible for the Enka installation. “We have developed a “Single Mode Operation” Package that enables Enka to operate the recycling line at 45% of its nominal production capacity. In this case only one extruder is used and production of smaller quantities is possible without losses in pellet quality or a disproportionate increase in energy consumption. This gives Enka total flexibility in adjusting their production according to raw material availability and rPET demand.” This installation is also the first to be equipped with a newly developed automatic IV control system that is integrated in the process. After setting the desired IV level the recycling line automatically adjusts operation parameters to reach it. During production the IV level is constantly monitored and parameters readjusted if necessary. This avoids IV variations after the extruder and ensures very constant IV values already during pellet production. Recycled content up to 100% “After we started to recycle post-consumer PET bottles for fibre production in 2009 we saw PET recycling both as a new challenge and an opportunity for a new line of business that aligns perfectly with our sustainability strategy”, says Aníbal Celis Carvajal, Group Coordinator for Integral Management and Processes at Enka. “With PET consumption in Latin America steadily growing and PET recycling gaining a foothold, we began to study the various recycling technologies in different continents of the world, especially in the area of bottle-to-bottle recycling.” After looking at the various technologies available on the market, Enka opted for the Starlinger super-clean process and purchased a recoStar PET 330 iV+ PET recycling line in 2013. Approvals of FDA and EFSA as well as of major brand-owners, decontamination efficiency, viscosity increase, compliance The Starlinger recoStar PET 330iV+ recycling line","@ID":26}, "MARKET SURVEY 31 PETplanet insider Vol. 15 No. 06+07/14 petpla.net Preform moulds Caps and closures Bottle-to-bottle recycling plants Preforms Preform and single stage machinery Preform / stretch blow moulds Two-stage SBM machinery Compressors Resins / additives Filling equipment Closure systems Suppliers of preform moulds/ stretch blow moulds Our annual overview of the market on the topic of mould tools for PET bottle production introduces you to the manufacturers of preform moulds and stretch blow moulds. The companies are listed above in alphabetical order; in the tables they appear in the order in which their details were received by the editors. The following manufacturers of preform moulds are listed: Husky, MHT, Mold-Masters, Otto Hofstetter, Steelmades The manufacturers of stretch blow moulds listed here include: Awanti, Demo Design, Comep, Garrtech, KHS, Kiefer, Krones, Moldintec, PET Technologies, Röders Tec, Sidel, Solent Mould Tools, Kosme, TechnoPET, Vitalii and Son, Wei Li Then, there are also the companies who are active in both sectors: GDXL, Nissei ASB, Pass Card, Petka, R+D Leverage, Sacmi, Simex, Sipa, TPS Although the publishers have made every effort to ensure that the information in this survey is up to date, no claims are made regarding completeness or accuracy. 06+07/2014 MARKETsurvey Company name Otto Hofstetter AG Husky Injection Molding Systems Mold-Masters (2007) Ltd. MHT Mold & Hotrunner Technology AG Steelmades Postal address Telephone number Web site address Contact name Function Direct telephone number Fax E-Mail Zürcherstrasse 73, 8730 Uznach, Switzerland +41 55 285 22 11 www.otto-hofstetter.com Mr Stefan Zatti Division Manager Sales & Marketing +41 55 285 22 09 +41 55 285 22 44 zat@otto-hofstetter.ch 500 Queen Street South - Bolton, ON L7E 5S5, Canada +1 905 951 5000 www.husky.co Mr Paul Commisso Program Manager, Marketing Communications +1 905 951 5000 ext 3675 +1 905 951 5332 pcommiss@husky.ca 233 Armstrong Ave, Georgetown, ON L7G 4X5, Canada +1 905 877 0185 www.moldmasters.com Mr Richard Sieradzki Vice President & General Manager, MPET Tooling +1 248 924 8513 +1 905 873 2818 MPET@moldmasters.com Dr. Ruben-Rausing-Str. 7, 65239 Hochheim/Main, Germany +49 6146 906 0 www.mht-ag.de Mr Volker Jährling VP of Sales and Service +49 6146 906 122 +49 6146 906 399 vjaehrling@mht-ag.de B/14, Ghatkopar Industrial Estate, LBS Road, Ghatkopar (East), Mumbai 400086, India +91 22 2500 7774 www.steelmades.in Mr Vipul Mehta Design, Marketing +91 932390 7774 +91 22 6796 9001 steelmades@gmail.com Preform moulds Horizontal opening Number of cavities 2 up to 192 6 to 144 Up to 160 2-192 Up to 72 Preform sizes up to 500g Threads up to 100mm in diameter / up to 205mm in length Up to 5gal / 20l Up to 600g for bottles up to 30l All sizes Moulds already built for (makes) Netstal, Arburg, BMB, Husky Moulds for preforms with a thread diameter up to 120mm and lengths over 400mm All major brands of PET systems Netstal, Husky, Engel, Arburg, Cincinnati, SIG, BMB, Sumitomo KM (MHT), ASB Vertical opening Number of cavities 2 - 96 Up to 128 2-112 Up to 72 Preform sizes Up to 500g Up to 5gal / 20l up to 600 grams, for bottles up to 30 litres All sizes Moulds already built for (makes) Arburg, Krauss-Maffei All major brands of PET systems KraussMaffei Husky, Yudo, Mould Master Do you produce single stage tooling sets? (Preform moulds AND blow moulds) No We do not currently produce blow moulds Axiom hot runners for single stage IBM, ISBM & Sipa ECS No Only two stage process moulds","@ID":33}, "NEWS 11 PETplanet insider Vol. 15 Resilux reports growth Resilux N.V., the manufacturer of PET preforms and bottles, reports that the sold volumes of preforms and bottles in the first four months of 2014 have increased by more than 7% compared to the same period in 2013. The growth occurred in all regions. The strongest increase in sold volumes was in Russia, East and Central Europe and the USA. According to the company, the growth is a result of further diversification of customers and products. For the full year 2014, Resilux expects to realise an operational cashflow at least in line with 2013 and an improvement of the results of the joint venture Airolux. The implementation of the capital expenditures budget for 2014 is said to be proceeding according to plan. www.resilux.com Indorama: first quarter profit Indorama Ventures Public Company Limited (IVL), the vertically integrated polyester value chain producer, saw in the first quarter of 2014 total revenues of Thai Baht (THB) 61.6 billion, a solid 11% rise over the same period in 2013, with Core EBITDA growing 83% to THB 5.1billion. Sales growth through higher volumes was achieved, although rapidly falling feedstock prices led to the weaker absolute prices of the commodity PET and polyester products. IVL incurred a non-cash inventory loss of US$33 million in 1Q 2014 reversing a non-cash gain of $11 million in the same quarter last year. The HVA and the Asian Commodity businesses had significantly higher core EBITDA which grew to US$56 million and US$25 million respectively in 1Q2014, an increase of 63% and 86% over 1Q 2013. Western Commodity business results were steady during this period at a healthy rate. The Asian PTA business continues to remain subdued, but improved production volumes in EO/ EG and strong Purified ethylene oxide (PEO) margins drove the performance of the feedstock segment upward to a core EBITDA of US$55 million, compared to US$36 million in the same period of 2013. Despite Asian PTA overcapacity, the company is optimistic that there will be gradual margin improvement in 2014 as industry rationalisation has commenced and more producer discipline is expected. The company’s nascent PET packaging business in Nigeria has drawn greater volumes of PET resin and the company’s entry into the Ghana market is expected to improve this volume even further. A new packaging facility in the Philippines will assist global branded customers in an underserved yet high demand market. www.indoramaventures.com","@ID":13}, "BOTTLES 55 PETplanet insider Vol. 15 No. 06+07/14 petpla.net Pril reloaded Pril, the well-known washing up liquid manufactured by Henkel, is now also available with an improved recipe which combats not only grease but also starch residue effectively and removes it without any problems. In addition to the familiar Pril Original in the wellknown PET bottle containing 750ml and a dispensing closure with Push-Pull, there is also Pril Power Gel Ultra Plus with extra soak-in power for easy removal of encrusted starch residue in a gold-coloured, waisted PET bottle complete with the familiar dispensing closure. The fill volume is 450ml and two labels, in part featuring shiny lettering, act as a medium for information. www.pril.de Cillit Bang for glass surfaces ReckittBenckiser has expanded its range of Cillit Bang cleaners to include a variant for cleaning glass surfaces without smearing. According to its specification, the cleaner reliably eliminates food residue, finger prints, greasy deposits and burnt-on fat from more than 30 different surfaces. By way of packaging, ReckittBenckiser has chosen a purple PET bottle with a product content of 750ml in an easyto-handle design with a lockable pump dispenser. There are two self-adhesive, punched-out labels which contain the details for use along with retail trade information. www.cillitbang.de Improved handling for Sidolin With their new bottle which has been specially optimised for ergonomic handling, Henkel is showing how one and the same bottle shape can be utilised in a variety of ways across different brands. The transparent, unusually shaped bottle featured here in PET with a product content of 500ml, together with the pump sprayer, sits “ideally” in the hand when held. Two self-adhesive labels and a sticker promoting “better handling” ensure that it is easy to identify the bottle on the retail shelf. The bottle is being used for several Henkel brands. The bottles differ from each other in terms of colouring, decoration (sleeve or self-adhesive label) and the colour of the spray pump. www.henkel-reiniger.de/glasreiniger/sidolin","@ID":57}, "PRODUCTS 47 PETplanet insider Vol. 15 Boxes with wrap-around casepackers Top-opening corrugated board boxes, known in the industry as “American-style boxes”, are usually processed by casepackers using a system that erects the box and inserts the products. This system differs from the wrap-around solution used by Smiflexi packers of the LWP, WP and CM series. SMI now offers a solution to pack products in “American-style boxes” that can be opened from the top without giving up the advantages of a wrap-around system. Smiflexi machines can process a type of cardboard blank specifically designed to prevent the opening flaps in the upper part of the cardboard case from coming out of the packaging process. The cardboard case erected as outlined above can be easily opened from the top, while maintaining the package integrity and preventing products from falling out. This packaging solution is popular with supermarkets and mass retail chains as the whole box can be displayed on a shelf without removing the single product units from the inside. www.smigroup.it Q Preform sterilization in the heating tunnel Q Protected conveying of preforms and bottles The UCF BloFill monoblock from KHS – with fully enclosed hygiene housing Give your sensitive beverages more private space. Learn more at www.khs.com or scan the QR code. Thickness measurement Precitec Optronik located in Neu-Isenburg, Germany, has launched a new member of its non-contact optical thickness sensors line. CHRocodile K is designed to meet measurement needs for manufacturers of PET bottles, preforms, plastic films, blisters, balloons and other plastic parts. A benefit of the new system is the optimisation of the measuring range to that most commonly seen in plastic materials, meaning that the user now has a sensor with the exact functionality required, says Precitec Optronik. The high measurement speed is intended to allow for a 100% control, inline as well as offline. Variations during the production process are seen in real time, before they can have an impact on the production quality. Its compact optical probe requires access from only one side and is said to be easily integrated into a confined space. www.precitec.de","@ID":49}, "EDITOUR REPORT 16 PETplanet insider Vol. 15 No. 06+07/14 petpla.net EDITOUR REPORT 16 for alternatives. At the time people here in the city were beginning to devise a more or less ordered system for collecting reusable refuse such as PET bottles. This is how we happened on PET“, explains Mr Carvalho. He proudly shows us the 5min film from a commercial magazine broadcast on Brazilian television, which was a real eyeopener for us as far as the products and tasks of the company are concerned. “One example of our printing work is road signs made from recycled plastic. These are not likely to be stolen on the open street, unlike signs made from metal, which have a comparably high scrap value. However, the other side of the coin is that we also undertake printing work on school material such as exercise books and folders. We are keen to show people while they are still young that you can make something worthwhile and useful from used PET bottles. In so doing Ecoplaca’s primary emphasis is on the importance of obtaining the raw material from local sources. “We support six recycling initiatives in Sorocaba and these enable us to cover 40% of our PET requirements. Ecoplaca has commissioned other companies to reprocess the PET bottles. In so doing it is, however, particularly important for Mr Carvalho that these companies should manufacture raw material of high quality. “If the bottles are not correctly sorted during waste separation or washed, then I see and note this in my product at the end of the line”. This is why Ecoplaca has, for a long time, been cultivating a good relationship with its suppliers. In addition, the Sorocaba company is keen to ensure an adequate supply of raw material on the market, including in a future shaped by the demand for PET from China. www.ecoplaca.com.br","@ID":18}, "BOTTLING / FILLING 44 PETplanet insider Vol. 15 No. 06+07/14 petpla.net Pinar Su, Turkey, invests in SMI line Turkey takes to the water Pinar Su, is a producer of natural mineral water in Turkey. The company continues to invest in new solutions for bottling and packaging its products. Among the latest projects implemented by Pinar Su, the Turkish company decided to install a new bottling and packaging line of 6,000bph for large capacity containers (3.25l, 5l and 10l). Water from the source Driven by the increasing attention to health and physical well-being, Turkish consumers have, in recent years, boosted the demand for bottled natural mineral water that in 2011 reached a record 9.3 billion litres. The per capita consumption, equal to 126l each year, is today very similar to that seen in major European countries, evidence of the high level of development and wellbeing that the Turkish economy has now reached. Pinar Su has been on the market since 1984. It was the first company to bottle and market natural mineral water in Turkey. Pinar Su water is bottled at the source in accordance with the highest quality standards and is marketed in Turkey and abroad under the name “Pinar Yasam Pinarim”, which means “Pinar: my source of life”. The natural sources of Pinar water are located in three different areas of Turkey, unpolluted and far away from industrial or highly urbanised locations. The bottling plants of Bozdogan (Aydin province), Eğridir (Isparta province) and Hendek (Sakarya province) feature the latest generation technologies for the bottling and packaging of pure spring water. For example, the filling operations take place in hygienically clean environments and the water is subjected to continuous chemical, physical and microbiological controls to test its quality during the various stages of the production process. Blowing/filling/capping The SMI line was purchased for Pinar Su’s manufacturing plant in Hendek, a city of 45,000 inhabitants in the province of Sakarya, a few kilometres from the Black Sea coast. The beginning of the collaboration between SMI and Pinar Su dates back to 2005, when the latter purchased an automatic Smiflexi LSK 30 F model shrinkwrapper for shrink film packaging. The Hendek plant has an annual production capacity of 607,000t, and bottles the Pinar natural water in 0.33l, 0.5l, 1l, 3l, 5l and 10l PET containers. The decision to install an “ad hoc” line dedicated to large capacity containers was dictated by the sharp increase in sales of these collations, the marketing of which joined the already consolidated one of traditional bottles from 0.33 to 1l. The “line engineering” project developed by SMI, taking into the account the demanding parameters specified by Pinar Su, has led to the creation of a new bottling plant for natural mineral water of 6,000bph. The “turnkey” line supplied to the Turkish company for its Hendek plant includes a compact Ecobloc Smiform system for stretch-blow moulding, filling/capping of PET containers of large capacity, a Smiline DV 500 divider, a Smiflexi SK 600 F model shrinkwrapper, a Smipack HA 60 handle applicator and a Smipal APS 3080 PR model automatic palletising system. The line also comprises the connecting conveyors among the system’s various machines and ancillary equipment such as a rotary labeller and a loop winder with an airtight cycle for the protection of the pallets. Smiform’s integrated system installed at the facility of Pinar Su produces 3.25l and 5l PET containers at the speed of 6,000bph and 10l containers at 4,200bph. With only one machine the company can now achieve the production capacity achieved previously using two linear blow moulders with related filling/capping machines. End of the line There is a Smiline DV50 model divider at the Smiflexi SK 600 F shrinkwrapper inlet that sorts containers with a square base; this divider receives bulk products in a single row, divides them over multiple rows and channels them into the secondary packaging machine to be packaged in shrink film only. More specifically, the 3.25l bottles are grouped in the 2x1 and 3x1 collations while the 5l containers are grouped in the 2x1 collation and the 10l ones in the 1x1 collation. At the SK 600 F shrinkwrapper outlet there is an automatic Smipack HA 60 handle applicator that applies a handle to the 2x1 and 3x1 packs of 3.25l bottles, while the larger packs containing the 5 and 10l bottles pass by without being “fitted with handles”.","@ID":46}, "MATERIAL / RECYCLING 29 PETplanet insider Vol. 15 No. 06+07/14 petpla.net Recycling line recoSTAR Offices in: Brazil, China, India, Indonesia, Russia, South Africa, USA, Uzbekistan, and agents in over 130 countries worldwide textile packaging consumer bags ing effect, reduces upcoming fines, and prevents overheating. The granulator configured in wet grinding mode constitutes the plant’s core and is based on a patented procedure ensuring that the bottles are forced-fed into the cutting chamber of the granulator. The neat cut, without splaying and folding of the bottle chips with neatly cut edges, is the characteristic feature of this wet grinding technique. In a first separation step, the plastics are separated into a light/ swim fraction (polyolefines, as used e.g. for bottle caps) and a heavy fraction which sinks: PET. During a further hot wash step, glues used for fixing the labels are separated with the help of additives. After drying, the material undergoes an air separation in order to withdraw suspended particles (removed labels and dust). Thanks to its compact construction, the low energy consumption and the high quality of the final product, the plant is particularly efficient. The final product is filled into big bags or transported with a silo truck. The PET flakes are currently being subjected to further recycling by PET foil manufacturers in central Europe. www.herbold.com According to PFR Nord GmbH, the new plant in Hohenwestedt will be processing around 100t PET/day. This corresponds to around 5.2 million drinking bottles every day.","@ID":31}, "MATERIAL / RECYCLING 20 PETplanet insider Vol. 15 No. 06+07/14 petpla.net Stute recycles PET in-house Green ideas bear fruit *Based on an article by Dirk Schlaipfer, Krones AG In the summer of 2013, Paderborn-based beverage and fruit preserves producer Stute was the first company in the beverage industry to commission a PET recycling system from Krones as an in-house solution. With the bottle-to-bottle recycling capability, Stute is processing its own PET waste and in future will be using non-returnable PET containers from its customers as well, using the decontaminated flakes as an admixture in the preform production process. PET containers, thanks to its own recycling system. The bottles collected in the supermarkets are presorted by the discounters in their central warehouses. This predominantly transparent PET material, which accounts for the biggest proportion of the beverage distribution mix, is able to be accepted and processed by the recycling system at Stute without any elaborate sorting work beforehand. In-house recycling The new in-house recycling system is far from being the first green idea that Stute has successfully translated into corporate reality in recent decades. Back in the mid1980s, Stute had begun to separate its recyclable waste, and – instead of dumping it on a landfill – to channel it back into the recycling process as a valuable resource. An anaerobic sewage treatment plant built in 1997, The family firm from Paderborn, Germany, looks back on more than 130 years of existence. With an annual turnover exceeding €400million, Stute produces preserved fruit and vegetables, desserts, sweet spreads, and a wide range of soft drinks. Stute’s impressive facility includes 13 aseptic PET lines, with ratings of up to 40,000bph. Stute feeds into the recycling system normal PET waste from the preform production process and from containers that have already been in contact with products. “But that’s just part of the total volume involved in the recycling system”, explains Christoph Frankrone, Head of Purchasing Plant Engineering. The principal customers for the beverages sold in nonreturnable bottles are discounters with national and international distribution networks. And it is precisely for these major accounts that Stute is able to offer take-back of the non-returnable PET recycling is a win-win situation for the retail sector and for Stute.","@ID":22}, "MATERIAL / RECYCLING 25 PETplanet insider Vol. 15 No. 06+07/14 petpla.net MATERIAL / RECYCLING 25 Enka de Colombia S.A. was founded in 1964 for the production of polymers, polyamide and polyester synthetic fibres used in the textile, tyre and plastics industries. Today, Enka is the largest synthetic fibre producer in the Andean region. The company’s production plant is located 28km north of the city of Medellín. In 1993 Enka opened its first recycling plant to process PET waste from the production of filaments and fibres, adding a project for recycling PET bottles for fibre production in 2009. With the new bottle-to-bottle plant from Starlinger Enka de Colombia is now entering the bottle-to-bottle market. The plastic closure company committed to your success BERICAP Technology Research and Development Mould Technology | Global Presence Capping Technology and Know-How Innovation and Flexibility www.bericap.com In compliance with Enka’s sustainability strategy, energy efficiency plays an important role in this installation. Enka operates its own electric plant, and the steam generated during electricity production is used in the Starlinger recycling line to supply the predrying unit and the SSP reactor. Together with the included energy recovery kit (ERK) used for the hot air dryer, this is intended to reduce electrical energy consumption by more than 40%. www.starlinger.com The Enka plant outside Medellín Elfriede Hell, General Manager, Starlinger, and Aníbal Celis Carvajal, Group Coordinator for Integral Management and Processes, Enka","@ID":27}, "ON SITE 51 PETplanet insider Vol. 15 No. 06+07/14 petpla.net Sorting and pre-washing system Amut Recycling Division has successfully started up a new Mini PRF at Wellman’s in Johnsonville, South Carolina, USA with a capacity of 6-7t/h (14,000lbs/h). The recyclers‘ complaint about the increasing worsening of the quality of material to be treated was the incentive for Amut Recycling Division to design a “pre-treatment” that completes the wide range of machinery for post-consumer PET valorisation and this new upfront system to feed PET bottles wash lines is the result. The new technology in Wellman’s installation is said to overcome the lower quality of Comingle Bales and to improve the efficiency and yield of the recycling plants. The Mini PRF system includes a pre-selection of the bales, to eliminate all of the pollutant materials in a dry phase and have just the clean bottle stream go through the sorting and pre-washing equipment, without those foreign materials that create inefficiency, more waste and higher maintenance costs. The main equipment to perform this task is the Amut “Elliptical Ballistic Separator”. The function of this machine is to mechanically select the bottles stream after the Bale Breakers and eliminate the fines and the 2D pollutants such as carton board, paper and packaging films. A de-labeller / pre-wash system will prepare the bottles for the following NIR sorters line. According to the company, the quality of returned bottles is worsening: some years ago, the contamination of material at the inlet of the washing lines was about 20-25%, today it is more than 40%. Reasons for this are, amongst many others, the growing diffusion of PET as material also used for other liquids, different from beverages; the packaging development to make beverages and various bottled liquids more attractive; new conservation and protection techniques for beverages and food such as multi-layer barriers or caps safety seals, which are often at odds with recycling requirements; plants, that are not suitable for the new and more challenging stream quality; the inconvenience faced by MRF and PRF companies in selecting and rejecting good PET simply because it is contaminated by sleeve labels or other elements necessary for packaging. www.amut.it","@ID":53}, "PETbottles 54 PETplanet insider Vol. 15 No. 06+07/14 petpla.net Home + Personal Care Sun skin protection Right on cue for the start of the warmer weather, Nivea has brought on to the market as part of its Sun summer skin protection range a transparent, rapidly absorbed, cooling and non-greasy sun spray in different light protection factors. 200ml is packed in a slightly yellowtinted PET bottle with grip recesses to either side. Acting as a label on the bottle is a shrink sleeve with a slightly metallic tint, part of which is left unprinted so that the product is visible. The spray is dispensed via a yellow-tinted, manually operated pump dispenser with a protective cap. www.nivea.de Lenses cleaner The American company Alcon Laboratories is marketing a multifunction disinfecting agent for the daily cleaning and care of contact lenses in a PET bottle under the name of “optifree puremoist“. The bottle containing 90ml is tinted white and fitted with two embossed brand logos in the neck area. The screw-on top is secured against tampering by means of a shrunk-on safety label with a tear strip which also indicates that the seal is intact. A dispensing aid is also incorporated in the closure. www.alcon-pharma.de Orange-scented shower gel The Balea products in the Street Art Range are geared to the younger generation. The latest example is an orangescented shower gel. The viscous, strongly fragranced and tinted gel is packed in a handy transparent PET bottle with a content of 250ml. A screw-on cap with a hinged lid and dispensing aid plus an all-round, shiny label round off its trendy appearance at the PoS. www.dm.de/balea Protective hair oil L’Oreal is marketing a protective hair spray in its Elvital range. The hair oil product named ‘Sun Defense’ is only available in the summer months and is intended not only to protect the hair from sun damage, chlorine and salt but also to nourish it. 150ml of the liquid is packed in a transparent bottle made from PET. A colour-matched pump dispenser with a protective cap aids application to dry or moist hair. www.lorealparis.com Protective sun spray from Lavera The German manufacturer of natural cosmetics, Laverana GmbH, is marketing, under the brand name Lavera, a protective sun spray with LSF 20 based on mineral sun protection and using bio sunflower oil and bio calendula extract, in a white bottle made from PET with a content of 125ml. The bottle is easy to grasp thanks to two recesses at the side and the product is simple to dispense via the screw-on pump dispenser complete with safety cap. The product needs to be shaken well before use. www.lavera.de ‘Shake-and-Soak’ foam bath The German drugstore discounter dm has recently launched a shake-and soak foam bath on the market under its own-brand label SauBär. The product, which is scented with blackcurrants and orange, is a 2-stage product that needs to be shaken before use. If the product is left standing for any length of time, the product ingredients will disperse to form a milky white section and a purple section. The ingredients ensure optimum foam formation in the tub and in so doing take care of delicate children’s skin. The whole product is packaged in a transparent PET bottle with a content of 300ml. A screw-on hinged lid closure with an opening for dispensing product and two self-adhesive labels round off the presentation. www.dm.de/saubaer","@ID":56}, "MATERIAL / RECYCLING 22 PETplanet insider Vol. 15 No. 06+07/14 petpla.net MATERIAL / RECYCLING 22 customers can point to a closed-cycle system. This is firstly sustainable, and secondly it’s costefficient, because we can also pay reasonable prices. On the other hand, Stute uses the material for producing new preforms, thus practising resource-economy as well as obtaining a financial benefit.” Washing processes The in-house recycling system consists of a washing module and a decontamination module, both of them in rack construction. All decontamination processes have to be preceded by a washing process, so as to obtain clean flakes as the material. It is here that label residues, glue, sand and other soluble soiling are washed off: Bottles are ground in the washing module to create flakes. Flakes are then pre-washed at low temperatures, mechanically pre-cleaned using jetting and friction. The washing water involved is filtered, and can be re-circulated for using again. Label residues and adhesives are detached in a caustic washer, so that no dirt or glue remains on the surface of the flakes. A Parsifal filtration system continuously treats the soiled caustic in two stages, so that it can be used again at a consistent level of quality. In a sink-or-swim process a density separator separates the lighter PO cap materials from the heavier PET flakes. In a multi-stage post-washing step, the flakes are rinsed with hot water. The energy of the hot water is used several times over, thanks to cascades, with each cascade temperature zone being treated again using membrane filtration. After being washed, the flakes are mechanically and thermally dried by a hot-air blower. Bottle-to-bottle decontamination module In order to achieve food-grade quality, the material has to be decontaminated in accordance with international standards. In Krones’ VacuumSupercleaning process, the entire PET input The density separator, in a sink-or-swim process, separates the lighter PO cap materials from the heavier PET flakes.","@ID":24}, "ONsite 50 PETplanet insider Vol. 15 No. 06+07/14 petpla.net Metal detectors prevent damage to recycling machines Plastic shredding is the first step in the recycling process and reliable metal detection is indispensable at this stage since metal contamination can cause damage to downstream modules. Consistent metal separation prior to shredding reduces malfunctions and increases the profitability of the recycling lines. Austrian company Starlinger GmbH therefore uses S+S DLS type detectors for this purpose which are mounted over the conveyor system prior to the shredder. DLS detectors are intended to detect magnetic and non-magnetic contaminants even if they are embedded in the product. By removing contamination prior to the process, costs can be reduced due to machine damage and production downtime. DLS metal detectors are said to offer many advantages: they prevent metals from reaching cutting machines and thus avoid wear and broken cutting tools. They reduce downtimes and maintenance costs, they improve the quality and value of the cut material, they reduce malfunctions and off-times in downstream processing machines, and they minimise quality defects and reject rates in recycled plastic materials, according to S+S. www.sesotec.com Bottles reborn Nestlé Waters North America Inc. is rolling out bottles with 50% recycled PET for the well-known USA mineral water brands Arrowhead and Resource. The food contact grade rPET for these bottles is provided by state-of-the-art PET recycling company CarbonLite of Los Angeles and is produced using Vacurema bottle-tobottle technology from Erema. CarbonLite operates one of the most modern PET recycling facilities in the USA. The company processes more than two billion plastic bottles collected from municipal curbside systems and deposit centres annually at its 20,000m2 plant. Nestlé Waters named the new PET bottle with 50% recycled PET the ReBorn bottle. The half-litre bottle is said to meet the stringent FDA standards, look no different than those made with virgin PET resin and is said to be just as durable and functional. PepsiCo Inc. is also among the other well-known major international clients who use the clean and food contact grade rPET from CarbonLite. For the recycling system, CarbonLite uses two Vacurema Prime 2321 T systems from Erema which are each designed for a capacity of 2,500kg of material per hour and which are intended to ensure that decontamination is efficient and fast. www.erema.at Recycling in channel baling presses The logistics service provider in the reusable packaging division of Euro Pool System has built a new facility in Hungary for recycling reusable materials from food markets. PET bottles, cardboard packaging and cans from 175 branches of a supermarket chain are processed by the company. In the new facility two fully automatic channel baling presses from HSM make it possible to reduce the volume of packaging and to return it to the recycling loop in the form of recyclable bales. The line at Euro Pool System consists of two HSM VK 8818 FU channel baling presses and the materials handling equipment. VK 8818 means a fully automatic channel baling press with a pressing force of 880kN and a filler opening measuring 1,000 x 1,800mm. Each of the presses is fitted with a frequency converter which generates around 40% energy savings compared to conventional drives. The project and construction work for the line was carried out at the same time as the work on the new facility. The operating personnel are continually loading the chain conveyors with the material for pressing which is delivered already sorted. One of the two presses is fitted with a PET perforator. This is initially used to slit open the bottles so as to ensure that the air escapes and the volume is reduced to a minimum before it reaches the press. The HSM channel bale presses produce stable bales with 5 strips of banding measuring 1,100 x 750mm, weighing between 500 and 700kg and 1 to 2m in length. These are sold on to recyclers in Hungary for recycling. www.hsm.eu S+S DLS type detectors are used and are mounted over the conveyor system prior to the shredder. Nestlé Waters North America Inc. is rolling out bottles with 50% recycled PET for the well-known USA mineral water brands Arrowhead","@ID":52}, "BOTTLE MAKING 39 PETplanet insider Vol. 15 No. 06+07/14 petpla.net emphasises that lightweighting should not compromise bottle performance. It is designed to prevent ‘over-squeezing’ and spilling and to offer environmental advantages by reducing the impact throughout the supply chain. Recycling rates Analysis has shown that recycling leads to a cut in energy consumption of two-thirds, compared with that required to manufacture with virgin material. All PET bottles could, in principle, be manufactured using recycled material as is possible to produce rPET suitable for food contact. The slight discolouration associated with recycled material does not affect bottle performance. The greater barrier to the adoption of rPET is the lack of availability of quality material, due in part to the traditional mechanical methods of recycling PET bottles. Such methods have not been effective at separating contaminants such as dyes from the plastic. Collection rates are also an issue. Europe saw more than 60 billion bottles recycled in 2012; an overall collection rate of over 52%. In the USA, the gross recycling rate in the same year was 30.8%, 1.5% higher than 2011 and helped by a near-20% surge in recycling of single-serve PET water bottles. Asia’s recycling rate is almost 80% but Eastern Europe achieves only 12%. In many developing countries a discarded PET bottle has intrinWide range of solutions: from individual modules to turnkey projects... value; collection from households or open landfill sites provides a revenue stream and contributes to high recycling rates in certain regions. The technological advances being made to optimise the use of those bottles need to be encouraged, to build on new filtration processes that generate PET flakes in more eco-friendly and cost effective ways. Despite the challenges, many major beverage brand owners are committed to increasing its use in their bottling processes. Some have already achieved over 50%, in certain product lines. Beyond the bottle… Sidel conducted some research into the possibilities of a ‘recycled office’ and uncovered a wide and diverse range products of that could be made from recycled material. rPET is being found in a wide and expanding field of applications, from clothing – including several kits worn by players in the Fifa World Cup finals in Brazil – to upholstery and sound insulation. Companies providing lighting and seating, desks, partitions, caRPETing, protective mats and window blinds are now offering rPET options. The Pollibrick, a self-interlocking ‘brick’ made from recycled PET bottles, can be sourced and manufactured close to construction sites. EcoArk, in the main exhibition hall for the Taipei International Floral Exhibition in Taiwan, was made using some 1.5 million PET bottles. A project in the Philippines called ‘IsangLitrongLiwanag’ (A Litre of Light), is a sustainable lighting project developed by My Shelter Foundation. A plastic bottle is filled with water, some salt and a few drops of bleach to prevent algae, and placed in a hole in the ceiling. Light refracted through the bottle produces illumination equivalent to a 50-watt electric bulb. www.sidel.com","@ID":41}, "PETbottles 52 PETplanet insider Vol. 15 No. 06+07/14 petpla.net Beverages & Liquid Food Japanese crackers Maître Prunille, a French company specialising in dried fruits, nuts and snack items, is packaging 250g of a Japanese cracker mixture in a transparent PET bottle. The products are easily visible and protected against damage in the same way as they would be in a flexible pouch-type packaging. Underneath the screw cap (which facilitates re-closing) there is a transparent sealing membrane extending across the opening of the container to lock in freshness and this also serves as tamper-proofing. Two small-format labels are used for transmitting the retail data. www.maitreprunille.com Tea with acai and ginseng The French supermarket chain Carrefour has recently introduced a new variation of a flavoured black tea into retail outlets. The tea tastes of / contains peach, acai berry and also features traces of ginseng. A litre of the product is packed in a waisted PET bottle incorporating a sleeve label with an Asian flavour combined with a transparent strip for checking the volume level. The container, with a good-sized opening, is sealed using a tamper-proof screw closure. www.carrefour.fr Multi-vitamins Multi-vitamin juice in quantities of 400ml is being distributed by the Polish company MWS under the trademark ”Kubus Play“ and packaged in a slimline bottle made from PET. Underneath the sleeve the bottle, which is completely encased in the sleeve, is of hexagonal shape. This is something which, taking into account the handheld volume, generates haptics that take some getting used to. The bottle is closed by means of a tamper-proof drinking closure with a hinged lid. www.kubus.pl The look of glass P.E.T. Engineering has developed a 1l PET bottle for Amstel Premium Pilsener, a Heineken brand. The target was to create a premium look recalling the heritage of the great brew masters since 1870 and, at the same time, design a convenient bottle for daily consumption at home and outdoors. The project involved a full packaging design system. The bottle was given a premium look by means of detailed and glasslike engravings as embossed brand elements or stamps. For the labels, also developed by P.E.T. Engineering, a gold background was chosen to represent high quality. The bottle’s neck contains a neck protection cap. www.petengineering.com Bear on top The opaque and colourful sleeve lends the 280ml PET bottle of company General Beverage (Thailand) the look of glass. Special feature: a stamp/toy for children is included as a gift placed on the top of the closure. www.generalbeverage.co.th","@ID":54}, "PRODUCTS 49 PETplanet insider Vol. 15 No. 06+07/14 petpla.net PETnology/tecPET GmbH | Regensburg, Germany Phone: +49 941 870 23 74 | Fax: +49 941 870 23 73 info@petnology.com PET Passion Week2014 NUREMBERG, GERMANY 10-14 NOVEMBER 2014 CONFERENCE 10-11 NOVEMBER www.petnology.com Free entry or VIP tickets End-User Special: Supported by: Lead Sponsor: PET AT BRAUBEVIALE 11-13 NOVEMBER www.pet-arena.com Caps & closures for carbonated drinks and the speciality market At the Ami Plastic Closure Innovations 2014 in Berlin, Germany, Sabic showcased two new caps and closures solutions. The bimodal High Density Polyethylene (HDPE) product - Sabic HDPE AX7611 – is designed to meet the specific needs of caps and closure for sparkling water and carbonated soft drinks. The resin is said to combine organoleptic performance with high process ability and improved down gauging opportunities. According to the company, it also has a two times higher flow ability than standard HDPE which enables manufacturers to shorten the cycle times. This property supports a more cost efficient processing by reducing the energy consumption. Furthermore, Sabic HDPE AX7611 is said to exhibit a good Environmental Stress Crack Resistance (ESCR), preventing cracks or leakages during repeated usage by end consumers. For the speciality caps and closure market, Sabic was showcasing its latest polypropylene (PP) grade Sabic PP PHC28. Chemical and impact resistance are essential to for example safety caps, as packaging of hazardous chemicals and household products require caps that provide good sealing performance and maintains structural integrity under tough handling practices. Furthermore, Sabic PP PHC28 is said to exhibit a combination of high MFR and modern nucleation additivation, which enables manufacturers to shorten the cycle times. www.sabic.eu Caps for sparkling water and carbonated soft drinks","@ID":51}, "PETnews 6 PETplanet insider Vol. 15 No. 06+07/14 petpla.net Avantium raises €36M investment for bio-based bottles Avantium announced that it has closed a financing round of €36 million ($50 million) from a consortium of strategic players. This consists of Swire Pacific, The Coca-Cola Company, Danone, Alpla and existing shareholders. With this capital raise the new investors affirm their commitment to advancing polyester polyethylene-furanoate (PEF). Proceeds will be used to complete the industrial validation of PEF and finalise the engineering & design of the first commercial scale plant. As part of its strategy to use responsibly sourced plant based materials for PEF production, Avantium will validate the use of 2nd generation feedstock. Follow on investments were made by existing shareholders Sofinnova Partners, Capricorn Venture Partners, ING Corporate Investments, Aescap Venture, Navitas Capital, Aster Capital and De Hoge Dennen Capital. Avantium has focused its efforts on PEF, which is said to be an analogue of PET. PEF could replace PET in typical applications like films, fibres and in particular bottles for the packaging of soft drinks, water, alcoholic beverages, fruit juices food and non-food products. www.avantium.com Intravis 2nd International User Meeting The requirements of the plastics packaging industry are constantly evolving and the manufacturers need to keep up. The 1st International User Meeting of Intravis GmbH offered a platform for discussing current and future challenges. The German company dealing in optical test systems for the worldwide plastics packaging industry once again invited customers, colleagues and interested parties to participate in an exchange in Aachen, Germany. More than 50 visitors from twelve nations addressed the topic “All About Plastics Packaging“. Within the framework of compact presentations and the opportunity for an exchange of know-how, the participants talked about their experiences with Intravis systems and the coming challenges in the markets of the plastics packaging industry. Many of those participating were plant managers and auditors and therefore in relatively close proximity to the product under scrutiny. The topics discussed at the English language User Meetings ranged from “Innovative High Output Sorting and Assembly Solutions for the Caps and Closures Industry” to “In-Mould-Labelling and Barrier Technology”. Quality Manager Alexander Werner of Alpla Werke Alwin Lehner GmbH & Co KG provided some insights into the internal quality management system which is currently supported by around 500 Intravis systems worldwide. www.intravis.de Haidlmair acquires remainder of Mould & Matic Solutions Haidlmair GmbH is acquiring an additional 50% share in Mould & Matic Solutions GmbH from Greiner Packaging International GmbH. This will make it the sole owner of the company. The parties agreed not to disclose any information on the purchase price. Mould & Matic’s core competencies include the manufacture of machine tools and automation solutions for the packaging industry with expertise in the technologies of thermoforming, injection moulding and blow moulding. www.haidlmair.at More than 40,000 PET collection points in Switzerland PET Recycling Switzerland is now collaborating with the Valora Group in the PET recycling sector. In order to make the disposal of empty PET beverage bottles as easy as possible for the consumer, they can also be handed in at any shop in the broad Swiss kiosk network operated by the Valora Group. The kiosk sales personnel then ensure that, once collected, the bottles collected find their way back into the recycling loop. As a result of the collaboration with the Valora Group, it has been possible to achieve an increase in the density of collection points related to snacking-on-the-go and to create even more convenience for consumers. A total of more than 40,000 voluntary as well as dedicated PET collection points are now available for the use of consumers. www.prs.ch www.valora.com New MD at PET Recycling Switzerland As of June 1, 2014 Jean-Claude Würmli (46) took up the position of Managing Director at PET Recycling Switzerland, taking over from the previous incumbent, René Herzog, who had held the position for a number of years and who has now retired. Würmli has set himself the goal of making further improvements to the recycling system and preparing the sector for new permutations of recyclables such as plastic bottles or polyethylene (PE) foils. To do this he is keen to work even more intensively with other partner organisations with a view to enabling everyone concerned to profit from individual strengths and to make use of synergies. Würmli was, for more than ten years, Marketing Director and Deputy Managing Director at PET Recycling Switzerland. Prior to that he had been active in Marketing and Sales within the music and fashion industries. www.petrecycling.ch","@ID":8}, "NEWS 10 PETplanet insider Vol. 15 No. 06+07/14 petpla.net Sacmi Research Centre Pepsi certified Tests on bottles, preforms, plastic and crown caps destined for use by soft drink company Pepsi can now be tested and certified at Sacmi Imola’s Research & Development facility. Being Pepsi-certified authorises Sacmi to carry out in-depth checks on all bottling line components; Sacmi operates with other Pepsi-authorised laboratories around the world, authorised to carry out similar tests, thus ensuring the validity and repeatability of the attained results. This achievement also stems from the shrewd decision to provide Sacmi Imola not just with the machines necessary to carry out the tests but also the skill and know-how that make the Sacmi Research Centre crucial to the entire Group and a key service supplier to the various business areas in which it operates. www.sacmi.com Acquisition of Artenius TurkPET Indorama Ventures Public Company Limited (IVL) has acquired 100% of Artenius TurkPET, based in Adana, Turkey. Artenius produces PET resin and has 130,000t of capacity. Turkey is an attractive market with a heavily urbanised economy enjoying high PET demand growth. Its Eurasian location provides ease of access to Central Asia, Middle East, North Africa and Southern Europe via good land and sea infrastructure. The acquisition of Artenius Turkpet comes on the heels of an announcement on April 9, 2014 that Indorama Ventures will acquire 51% of Istanbul-listed Polyester Sanayi A.Ş (SASA). Both SASA and Artenius Turkpet are situated adjacent to each other and this will lend further synergies to the deals. www.indoramaventures.com PET resin plant with crystallising system Nearing completion at Lotte Chemical UK’s Wilton site is a 200,000t PET resin plant that includes a 25t/h filtration and pelletising system now being commissioned by Nordson BKG. The new plant, adjacent to Lotte’s existing PET facility, is due for startup later this year. The £60-million project will more than double the capacity for PET at the Wilton site. At its heart is the BKG CrystallCut system, which is said to save energy by re-using the heat from the polymer melt in the pelletising step to crystallise the pellets at a later stage in an integrated process. Also supplied by BKG is a screen changer in Nordson Kreyenborg’s Poly series. The patented CrystallCut system is an integrated network that incorporates underwater pelletising, drying and crystallising. After the polymer has been cut at the pelletiser die face, it is transported to a centrifugal pellet dryer where the water is separated and the polymer dried. The material exits the pellet dryer and is discharged on a specially designed centrifugal dryer outlet hopper where the conversion from amorphous to crystallised material occurs. Throughout this process there is precise control of material temperatures, preventing production and quality problems caused by insufficient crystallisation and excess levels of amorphous material. CrystallCut technology is said to save energy by avoiding the need to reheat the PET for crystallising. In addition, it prevents clumping of amorphous PET and yields an enhanced crystalline structure that results in lower energy costs for re-melting the material. www.lottechemical.co.uk DAK Americas acquires food-grade PET recycling operation in Argentina DAK Americas Argentina S.A.(DAK), a producer of PET resins in Argentina, announced the acquisition of CabelmaPET S.A., a PET bottle recycling operation located in Pacheco, Buenos Aires, Argentina, that produces food-grade recycled raw materials from PET bottles. Terms and conditions of the acquisition were not disclosed. The acquisition will be subject to post-closing review by Argentina’s antitrust authorities. The acquired facility currently recycles more than 16t/a of waste PET bottles, which should significantly increase the sustainability of DAK’s product line, as well as help customers streamline their processes. Approximately 100 employees associated with CabelmaPET, S.A. recycling operations are part of the acquisition. Cabelma S.A., a manufacturer of plastic-crates, is not included in the acquisition. DAK currently produces over 190t/a of virgin PET resin at its facility in Zarate and plans to integrate the postconsumer recycled material from the acquired facility into its manufacturing process upon completion of process upgrades. The new integrated product offerings will be marketed as a single-pellet solution under DAK’s Laser+ brand of PET resins. www.dakamericas.com","@ID":12}]}}
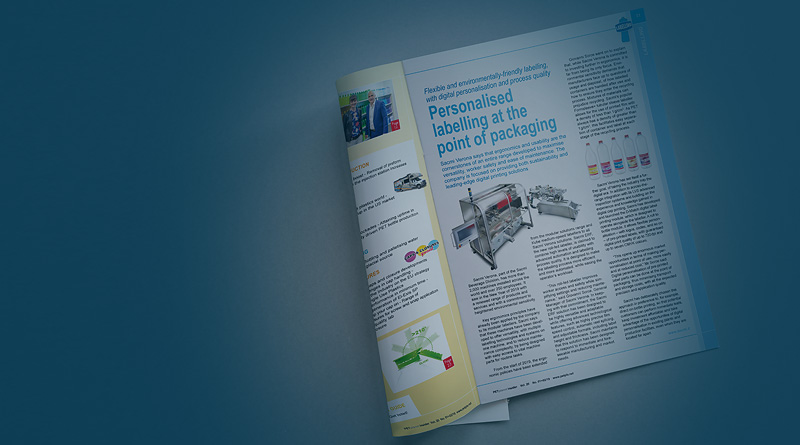