{"pages":{"page":[{"#text":"BOTTLES 53 PETplanet insider Vol. 12 No. 10/11 www.petpla.net Slimming without tears 750 ml sugar-free fruit drink for slimmers is being marketed by the French company Juvaligne of Paris in a distinctively shaped, red PET bottle. The waisted bottle features front and rear labels adapted to suit the shape and a screw cap with tear-off tamper-proof seal. Its bright red, strident colour and its waisted shape ensure that it stands out at the POS. www.juvaligne.com Bio-juice in PET Under the brand name of ”Pressade“ the French company Bricfruit, based in Chateau Thebaud, is marketing one litre of biocranberry juice in a PET bottle. The belly area of the bottle is square in shape and is decorated with an allround paper label. A green screw cap with tear-off tamper-proof seal puts the finishing touches to this modern bio-pack. www.pressade.fr Lightweight wine bottles Sutter Home Family Vineyards, based in St Helena, California, is the US wine industry’s leading producer of single-serve, 187-ml wines, with 38% market share and is growing annually at 7.3%. Total sales of 2.2 million cases are projected in 2011. Sutter Home began using Amcor’s barrier PET bottles as a glass replacement in 2005 and has switched its entire 187-ml production to the plastic containers. The bottles preserve the look of the original glass container and run on the winery’s existing glass filling line. KHS Plasmax Silicon Oxide (SiOx) barrier coating provides the 187ml PET container with the same shelf life as glass. Plasmax is an FDA-compliant enhanced passive barrier for oxygen-sensitive products. The ultra thin (less than 100nm) material is transparent and resists cracking, abrasion, and delamination. It does not degrade over time nor limit the storage time for empty bottles. It is easily removed during the recycling process and does not contaminate the recycling chain. The aluminium screw-cap bottle’s portability provides an entrée into venues that do not allow glass. U.S. airlines have strongly adopted PET bottles for in-flight refreshment. Sutter Home’s switch to PET also delivered sustainability benefits; PET containers are one-sixth the weight of glass bottles, unbreakable, less wasteful, and recyclable. www.sutterhome.com. www.amcor.com IN EVERY BOTTLE THERE IS ALL OUR KNOW HOW. RESEARCH & DEVELOPMENT A constant projection towards the future oriented to search not only for new materials but also new PET technologies of transformation and innovative materials. CONSULTANCY A concrete answer to all your questions. We put at your disposal all our know-how for every single requirement. PROTOTYPATION Prototypes of containers and innovative preforms in record times: you will be able to touch with your hands the bottles within a short time after approval of the design. DESIGN Creativity in search of elegance and refinement. Innovative designs, ergonomic structures, eye-catching and functional containers. We give a true shape to your product! HALL 7 - STAND 236/337 09-11 NOVEMBER BRAU BEVIALE 2011 NUREMBERG - GERMANY","@ID":55} "BOTTLE MAKING 24 PETplanet insider Vol. 12 No. 10/11 www.petpla.net very busy, very much alive, and very active. With the acquisition of Berchi Sipa is now able to take on the big “Three”, when it comes to complete and integrated lines, i.e. Sidel, Krones and KHS. This, surely, is the next big challenge for the company. Single stage product range Sipa customers can select from two families of product, i.e. The big ECS FX range with an output between 9,000 to max. 36,000bhp. The medium to low ECS HS range with 2,000 to max. 16,000bhp Design principles of both ranges are similar with FX range having one injection unit with 4 shot pots instead of just one, and having double conditioning stations, double blowing and double bottle ejection instead of just one as in case of the HS range. ECS FX features Highest output for beverage bottles 36,000bhp for mineral water FX20/80. Hot fill 30,000bph. Highest output for 73mm wide mouth containers. Possibility of simultaneously producing two different containers having different weights and shapes for different applications. ECS HS features Largest single mould integrated machine on the market Challenger to two stage when it comes to output per capita Machine cavitation for 52 mm finish, 24 injection cavities. The production To see the full range of the Sipa single stage fleet you have to go fly to China or to the United States. Or visit San Benedetto, close to Vittorio Veneto, where the same machinery is being put through its paces. We could see Sipa single stage systems only on Sipa’s shop floor. An ECS FX 20/48EVO for an US customer, for instance: on the injection side one large central plasticising unit, providing four shot pots and from there into 4x12 cavities. Thereafter automatic transfer into the conditioning on each side and thereafter blowing and out-transfer. Most part of the assembly shop floor however is taken up by the manufacture of blowers (rotary and linear). Sipa has invested in a continuous assembly line. The machines are towed on trolleys from one work station to the next and completed stage by stage. Material is supplied direct to the line (canban system). The rotary blowers especially have enjoyed an overall good market reception. We also noted modern machine tooling, where injection and blow moulds are made. For machines, Sipa outsource mechanical components and subassemblies. For moulds, Sipa manufacture all parts in-house. This is a sensible policy, bearing in mind that money in the PET world is the supply of moulds rather than machines. The high number of trial and demo machines was staggering– we saw experiments with horizontal injection moulding machines, with PET bottle coating and the everyday but vital trials with new bottle shapes and sizes. www.sipa.it Typical applications for Sipa’s single stage machinery","@ID":26} "PETpatents www.verpackungspatente.de 56 PETplanet insider Vol. 12 No. 10/11 www.petpla.net Hinged lid International Patent No. WO 2009 / 145847 A1 Applicant: Seaquist Closures LLC., Mukwonago (US) Date of Application: 14.4.2009 Design and method for manufacturing a hinged lid which can only be opened after breaking a safety catch and which is subsequently held in place by means of the hinge. Multi-layer container Europ. Patent Nr. EP 2281752 A1 Applicant: Yoshino Kogyosho Co. Ltd., Tokio (JP) Date of Application: 20.4.2009 Structure and method are described for manufacturing a multi-layer plastic bottle with improved barrier characteristics. Weight reduction International Patent No. WO 2009 / 134132 A1 Applicant: Whitestone Corp., S.A., Luxemburg (LU) Date of Application: 29.4.2009 A major proportion of the weight of a plastic bottle accumulates in the area of the thread / the top of a plastic bottle that is manufactured from a preform. This patent application describes a number of possible ways of reducing this accumulation. Triangular bottle European Grant of Patent No. EP 2135812 B1 Applicant: Sidel Participations, Octeville-sur-Mer (FR) Date of Application: 8.6.2009 Container, in particular a bottle, made from thermoplastic material and having a partially prism-shaped, triangular body. Hot filling European Grant of Patent No. EP 1955955 B1 Applicant: Ball Corp., Broomfield (US) Date of Application: 9.1.2008 Mould and method for manufacturing a plastic bottle intended for hot filling and which is therefore provided with different compensating areas for elastic absorption of the deformations that occur as a result of cooling. Compensating areas International Patent No. WO 2009 / 135046 A1 Applicant: Constar Inc., Philadelphia (US) Date of Application: 30.4.2009 A plastic container is fitted with lines / constrictions or indentations arranged vertically. The shape of the indentations ensures that the internal pressure of the container, which falls after cooling, can be compensated for without modifying the external profile.","@ID":58} "PETnews 6 PETplanet insider Vol. 12 No. 10/11 www.petpla.net Corvaglia opens new laboratory Swiss closures company Corvaglia has invested in a new laboratory. It says that the lab has been furnished with stateof-the-art equipment and is able to carry out testing to realworld standards, including vent slot efficiency, opening torque and compressive strength. The laboratory will supervise both new closure development and volume production. www.corvaglia.ch KraussMaffei expansion plans in China Since it was founded in 2001, KraussMaffei with its three brands KraussMaffei, KraussMaffei Berstorff and Netstal has been gaining growing acceptance among customers in China. After combining its competencies and strengths under one organizational roof this year, the company wants to utilize future opportunities in the Chinese market with a wider range of products and services. „We want to clearly increase our operations in the Chinese market and expand our business activities, thus generating growth. We already supply products to renowned groups and are intending to expand our plant in Haiyan in the next few years on account of the rising demand“, says Harald Schweitzer, Managing Director of the Chinese subsidiary. www.krauss-maffei.de Amut acquires Comer Engineering Italian extrusion, thermoforming and recycling company Amut spA has recently acquired Comer Engineering, which is headquartered at Maserada sul Piave, Treviso, Italy. Comer has particular competence in lines and plants for sorting and treatment of solid, industrial and similar urban waste; sorting and treatment of plastics and tyres; and handling, sorting and treatment of other materials. Amut says that the acquisition provides direct technical and commercial synergy and is built on years of cooperation between the two companies. It is aiming to exploit positive trends in the plastics recycling market. A new company, named Amut Ecotech, has been formed from the acquisition, which is intended to provide a complete, integrated range of services related to the recycle of urban solid waste and to reinforce the company’s position in the field of plastics washing and recycling. The new company has already commenced activities and has received orders for €10 million. www.amut.it Bepex installs recycling system in Vietnam Bepex International, which specialises in process development and equipment for the food, chemical, mineral, and polymer industries, has signed an agreement with Vietnam’s Thanh Tai Gas Company to custom design, manufacture and deliver the first in its new line of plastic bottle recycling systems, called BePET. The FDAapproved system will allow Thanh Tai to recycle up to 1.5 billion PET bottles per year. The system allows the processing plant operator to control both decontamination of the plastic and product intrinsic viscosity (IV) at the same time, and in solid form. The system’s process design is claimed to offer operating and capital cost savings of up to 60%, compared to currently available recycling systems. The first line of Thanh Tai’s system will be installed and fully operational by January 2012. A second, parallel line will be installed to expand capacity to produce different IV plastic for a variety of applications, including for the food packing industry. www.bepex.com www.bepet.com New Managing Director for MHT USA MHT USA, LLC., a subsidiary of the German company MHT Mold & Hotrunner Technology AG, has appointed Christian Wagner as Managing Director as of September 1, 2011. Wagner is a graduate engineer in mechanical engineering and has been employed in the company since the establishment of MHT Germany in 1996. Most recently he has been responsible for the development of new moulds as well as all patent matters. He will manage the North American business and support Andreas Krampe, who has been the Director of Projects since the beginning of 2010. MHT USA had been managed temporarily by the CFO of the German parent company. www.mht-usa.com pet-recycling.com","@ID":8} "TRADE SHOW PREVIEW 45 PETplanet insider Vol. 12 No. 10/11 www.petpla.net Brau Beviale 2011 Nürnberg, 09 – 11 November Hall 7A, Stand 206 Contiform 3 The new generation www.krones.com Glue-free elastic brand decoration CCL Auto-Sleeve will exhibit its range of stretch sleeves for PET and HDPE containers, which the company says are suitable for various shapes and sizes. ‘Stretch Sleeves’ need neither glue nor heat application and facilitate contaminationfree separation for recycling. CCL Auto-Sleeve offers three types of Stretch Sleeves. Triple S (Super Stretch Sleeve) has high elasticity and stretchable inks, making them appropriate for unusual container shapes. CCL Auto-Sleeve says that the Triple S has lower material requirements and can offer onbottle savings of up to 50%, compared with traditional shrink sleeves. The Modified Stretch Sleeve provides a glue and heat free solution for containers requiring label application to slightly contoured areas. Standard Stretch Sleeve offers a glue-free solution for all sizes of traditional straight wall PET containers. www.ccl-autosleeve.com CCL Auto-Sleeve Hall 7A | Booth 317 New ideas in labelling and service One of the centrepieces on the KHS stand will be its Innoket 360 S roll-fed labelling machine. Developed from the Innoket 360 labeller, the Innoket 360 S is compact and its modular design means that it can be configured and expanded to meet customer requirements. It has a segmented vacuum drum for quick changeover, and has selfsharpening cutters. KHS has defined the mineral water, fruit juice, and soft drinks bottling segment as the main target group for the Innoket 360 S. The company will also be showing its compact Innokeg Till CombiKeg keg washing and racking machine, which is aimed at small and mediumsized businesses; the Innopro ECOStab regenerative beer stabilizing system, which uses PVPP; and some glass solutions. KHS will speak to visitors about its ‘Best Value’ label, which has been established following the biggest reworking of the KHS spare parts price structure the company has ever undertaken. www.khs.com KHS Hall 5 | Booth 127","@ID":47} "PREFORM PRODUCTION 19 PETplanet insider Vol. 12 PETplanet print Vol. 6: The Rapid Guide to Perfect Preforms by Rick Unterlander and Ottmar Brandau fax: +49 (0) 6221-65108-28 info@hbmedia.net www.petpla.net Order your copy now! 1- 3 exemplar each 129,- € 4 - 10 exemplar each 99,- € 10 exemplar each 69,- € prices in EUR + VAT. to open the valve stems properly. Typical pressures are in the range of 8 to 10bar (120 – 145psi). 7. Check that the valve gate open timing is adjusted properly. This is typically 0sec. Minimize to allow more time to open. 8. Check all temperature readings and adjust higher if necessary. PET resin should be melted at about 280ºC (536ºF) +/- 10ºC (18ºF). Increase if necessary. 9. Check that transition position is set to about 13% of shotsize and cushion. Higher values may result in underfilling. 10. Ensure the mould neck insert and lock ring vents are clean. This will minimize gas entrapment at the neck finish. 11. Check to ensure that no moisture exists on the moulding surfaces, either from water leaks or condensation. This may obstruct normal melt flow and cause filling problems. The environmental dewpoint should be below the chilled water temperature to eliminate the risk of condensation. 12. Check hardware for worn, damaged or failed components, specifically the mould neck inserts (collapsed vents), lock ring vents, valve stems, valve stem seals, nozzle tips, shut-off nozzle plunger alignment, shooting pot motion, and extruder screw check valve leakage (single-stage machine only). www.petpla.net PETplanet print vol.6 The Rapid Guide to Perfect Preforms machine no./name","@ID":21} "NEWS 8 PETplanet insider Vol. 12 No. 10/11 www.petpla.net Engel adds technical centre and teaching to Indian sales office The Austrian injection moulding machine manufacturer Engel is extending its sales base in Mumbai, India, to include a technical centre and a seminar centre. Expansion in the Indian market is being driven by strong domestic demand in the automotive, packaging, white goods, agricultural and construction sectors. In order to accommodate the additional functions Engel India’s headquarters has moved to larger premises in the Andheri East district, near Mumbai International Airport. The technical centre will be used for machine demonstrations, customer trials, pre-production and running mould trials. Courses offered at the new training centre will lead to qualifications for machine operators and maintenance technicians; basics of plastics processing will also be taught. Engel India plans to invite customers and other interested parties in the plastics processing field to regular technology seminars. The spare parts warehouse is also expanding with the relocation. www.engelglobal.com Marc Ville is Cermex’s new Managing Director A new Managing Director was appointed to Sidel subsidiary Cermex on July 1 2011. Marc Ville succeeds JeanFélix Lesueur, who has been given a new assignment within Sidel. Mr Ville will report to Philippe Lejeune, Cermex Group Chairman & EVP in charge of Sidel’s Food Home Personal Care (FHPC) division. Mr Ville has been with the Tetra Laval Group for the past twelve years, most recently as VicePresident of the Industrial Program for Sidel. A graduate of the École Nationale Supérieure de Chimie in Paris, he has worked for Michelin, Lafarge and in the automotive parts industry. He has been Director of the Tetra Pak plant in Dijon, Managing Director of Sidel Malaysia and Vice-President of Industrial Operations in Beijing. For the past two years, he has been Vice-President of the Industrial Program for Sidel. www.cermex.fr Petainer appoints new group finance director Specialist plastics packaging technology business Petainer has appointed Mark Ellis as group financial director. He previously spent 20 years with RPC Group, a supplier of rigid plastic packaging, where he was general manager of two manufacturing sites and was group finance manager and corporate development director. Ellis is a member of the Chartered Institute of Management Accountants (CIMA). www.petainer.com EREMA Engineering Recycling Maschinen und Anlagen Ges.m.b.H. A-4052 Ansfelden . Austria . erema@erema.at . www.erema.at We know how. PET Extrusion System VACUREMA® Prime to produce food contact approved BTB pellets Input: Washed PET flakes Output: rPET pellets Batch process i guarantees defined decontamination time for each PET flake • FDA and brand owner approved • Efsa approval requested via customers CIC compact inline crystallisation i • lower AA ( 1 ppm possible) • higher crystallinity • space-saving equipment Permanent monitoring for direct food contact and IV i Very low energy consumption, 0.30 to 0.34 kWh/kg i Visit us at Fakuma hall A6 booth 6011","@ID":10} "31 PETplanet insider Vol. 12 No. 10/11 www.petpla.net Compressor manufacturers Indispensable when it comes to producing a PET bottle: the compressor. We will attempt, using only a few parameters, to describe the main characteristics of individual suppliers’ products. This market survey will provide an overview of the product range of (this time) eight suppliers. The information has been provided by the suppliers themselves. If you require detailed information please contact the relevant company. Although the publishers have made every effort to ensure that the information in this survey is up to date, no claims are made regarding completeness or accuracy 10/11 MARKETsurvey Bottle-to-bottle recycling plants Conveyors for preforms and empty bottles Caps and closures Preforms Perform moulds and SBM moulds Single stage machinery 2-stage SBM machinery Compressors Filling equipment Resins and additives Company name Kaeser Kompressoren GmbH Aeroflon Engineers Private Limited Leobersdorfer Maschinenfabrik GmbH & Co.KG Gardner Denver Ltd - Belliss & Morcom Postal address Telephone number Web site address Contact name Function Direct telephone number Fax E-Mail Carl-Kaeser-Str. 26, 96450 Coburg, Germany +49 9561/640-0 www.kaeser.com Wolfgang Hartmann Marketing Manager +49 9561/640-252 +49 9561/640-890 wolfgang.hartmann@kaeser.de B-505 Premium House, Opposite Gandhigram Railway Station,Ahmedabad 380 009, Gujarat, India +91 79 26589712 www.aeroflon.com Mitul Choksi Chief Operations Officer - International Business +91 79 40069715 +91 79 26586954 exports@aeroflon.com Südbahnstrasse 28 2544 Leobersdord, Austria +43 2256 9001 www. Lmf.at Damir Pilipovic Sales Manager +43 2256 9001 339 +43 2256 9002 damir.pilipovic@lmf.at Claybrook Drive Redditch B98 0DS England +44 1527 838600 www.gardnerdenver.com Trevor Perry Director, Sales & Marketing +44 1527 838606 +44 1527 838630 trevor.perry@gardnerdenver.com 1. Machine designation / model number Sigma PETAir ACTBO42 Series VC / VC-B / VCL-B VH & WH Range 2. Number of models in range 25 8 Models 10 12 3. Output in m³/hr 336 - 2,772 Up to 722 600 - 3200 420 to 3200m3/hr FAD 4. Compressor type High Pressure Low pressure air Screw type 5 bar High pressure blowing air (up to 40 bar) Piston type 15 bar Xpiston reciprocating Integrated system 42 bar Yes 5. Lubricated or Oil-free oil-free oil-free oil-free Low pressure compressor lubricated oil-free Booster compressor lubricated oil-free Integrated system oil-free 6. Machine layout \"V\" (2 cylinder), \"W\" (3 cylinder) Rectangular Layout V or W configuration 7. Number of compressor stages 1+1 3 3 and 4 3 8. Are special foundations required? No yes, cement foundation required as per specification no No 9. Cooling system air (water option) water cooled water cooled water coloed 10. Belt or direct drive belt and direct drive direct drive Low pressure compressor direct V-belt drive Booster compressor belt V-belt drive Integrated system V-belt drive","@ID":33} "TRADE SHOW PREVIEW 44 PETplanet insider Vol. 12 No. 10/11 www.petpla.net Revolution in PET-extrusion! Conical co-rotating MAS-extruder | perfect solution for A-PET, G-PET, PET Co-polymer … | prime pellet / melt quality (IV, b*, AA- content) | very low energy consumption | direct extrusion into sheet | stable melt pressure build up | small foot print paired with robust design | sizes available from 200 kg/h up to 1500 kg/h | suitable for food application M-A-S Maschinen- und Anlagenbau Schulz Gmbh A-4055 Pucking, Hobelweg 1 T: +43 7229 78 999, F: +43 7229 78 999 10 info@mas-austria.com www.mas-austria.com Closure solutions “go lightly” Bericap will be presenting its range of closure systems, including the most recent market launches. Lightweighting is still the theme of the day. According to Bericap its DoubleSeal System protects the bottle neck from deforming during hot fill so that significant material savings are possible in this area without jeopardising the safety of the filled product. The bottle neck will be lighter in the future, not just the 38mm bottles already on the market, but also the 28mm PET bottles. A newly developed, 33mm lightweight bottleneck will complement the Bericap product range for closures in the hot fill range by the end of the year. Sports caps now for hot fill The Push Pull Next Generation, launched in 2010, is a 3-piece closure equipped with the Bericap DoubleSeal technology. Until now, the closure was used for aseptic fillings and suitable for dry and wet sterilisation processes. At the end of 2011, Bericap plans to launch the 33mm and 38mm PushPull Next Generation for the hot fill process without aluminium foil seal. Closures for CSD The SuperShorty family is suitable for sensitive beverages and carbonated drinks: For the PCO 1881 thread neck Bericap offers six different closure varieties and, upon request, customised designs. The one-piece DoubleSeal SuperShorty Crown for beer can be equipped with an oxygen absorbing liner to maintain the quality of the beer. The one-piece DoubleSeal SuperShorty varieties, like the DoubleSeal SuperShorty CSD and the weight reduced DoubleSeal SuperShorty Eco are suitable for carbonated drinks (up to 8g CO2 / l). For still drinks the DoubleSeal SuperShorty Still is available. A DoubleSeal SuperShorty version for hot fill is also available. A two-piece LinerSeal Supershorty complements the range of drink closures. The two-piece Thumb‘up closure and the 3-piece PushPull sports closures HexaLite 26 and 29 mm Along with the PCO 1881, the bottle necks PET 29/25 and PET 26/22 were developed for still drinks, particularly for still water. For these bottlenecks Bericap offers the HexaLite product line 29/11 and 26/10. The closures have a cut and folded safety band for product safety and tamper evidence. www.bericap.com Bericap Hall 4 | Booth 511","@ID":46} "MATERIAL / RECYCLING 16 PETplanet insider Vol. 12 No. 10/11 www.petpla.net PET recycling rates up in Europe and North America Bigger bales Petcore and EuPR’s report, ‘Post Consumer PET recycling in Europe 2010 and Prospects to 2015’1 found that PET collection figures for 2010 increased by more than six per cent over 2009. The latest published figures for North America2*, published by Napcor (National Association for PET Container Resources) and APPR (Association of Postconsumer Plastic Recycling), which relate to 2009, also show an increase over the previous year’s findings. The North American increase was recorded against a background of decline in sales of PET bottles and jars. Europe The report from Petcore and EuPR recorded that European post-sorting PET collection reached 1.45 million tonnes in 2010, an increase of 6.5% on 2009. The overall collection rate in 2010 remained at 48.3% of all PET bottles on the market. The number of blowmoulding outlets grew, with more than 25% of the resulting RPET, nearly a quarter on a million tonnes, used to produce containers in 2010. The 2010 share of fibres as an end use for recycled PET flake decreased to 39%, although the overall tonnage rose slightly. The strapping market rebounded with the resumption of construction and manufacturing after the recent recession. Nearly 100,000t of RPET was used in this application in 2010. There was a 25,000t decrease in RPET used in the APET sheet market, which was attributed to a combination of two factors. Sheet import volume was higher and the price of suitable quality RPET almost matched that of virgin PET for most of the year. It was estimated that the European region’s total mechanical reclamation capacity is 1.7 million tonnes. Exports to the Far East fell for a second year, to 13% of collected PET, and imports of baled PET bottles from outside the area were also lower. All but two of the surveyed countries have a collection rate above the 22.5% target rate for plastic recovery set by the Packaging Waste Directive. The collection rate by country depends on the maturity and extent of their collection systems, as well as economic instruments in place. Collection rates of over 70% are being recorded in a number of countries. Welcoming the increase in PET collection, Robert Bertaggia, Chairman of the Petcore Board, observed that the high levels of annual increase seen in previous years was expected to fall but that 2010’s 6.5% uplift is an excellent result. “The PET industry chain has worked with Compliance Agencies, National Bodies and European Recyclers to achieve a collection rate of nearly 50% of all PET bottles placed on the market”. The Chairman of the EuPR PET Working Group, Casper van den Dungen, observed that capacity utilisation of recycle plants is currently 79%, and that collectors and industry should seek to raise the current collection rate beyond 50%, in order to better use recycling facilities already in place. The continuous growth of PET bottle collection rates also reflects the expectations of consumers. North America In North America, the Napcor/ APPR report found that the total RPET production in the USA in 2009 was 561 million lbs (255kt), with a further 601 million lbs (273kt) in clean flake equivalent being exported. Use of RPET in food, beverage, and nonfood PET containers increased by 37% from 2008 to 2009. A total of 2.34","@ID":18} "NEWS 9 PETplanet insider Vol. 12 No. 10/11 www.petpla.net Sidel opens training lab in Beijing Sidel inaugurated its new Beijing Technical Training Centre in June 2011. The 900m² facility, located within the Sidel Beijing Plant, is nominated as the company’s Asia Centre of Excellence and offers both classroom and handson training services. Sidel says that the Asian market’s rapid growth means that beverage manufacturers often have to fast-track training programs to raise the expertise of their service engineers and operators. The new facility includes blowmoulding machines, a laboratory with simulation benches for the configuration of standard and aseptic fillers, and a Combi automation desk that simulates machine synchronisation requirements. The new Beijing Technical Training Centre also features virtual reality equipment for enhanced interaction and offers a wide range of training courses for both blowers and fillers, for applications such as sensitive products, water and carbonated soft drinks. Over 200m² of the facility is dedicated to blowing equipment training. It has a fully-equipped laboratory including different kinds of filling valves, manifolds, programmable logic controllers (PLC), Syncro-Combi simulation, and aseptic filler instruments and actuators. Three classrooms provide theoretical education, and a virtual reality room allows trainees to interact with projected models. More than 150 training programs are scheduled in 2011, providing training to an estimated 1,200 trainees. www.sidel.com APPE, ColorMatrix & KTW together on barrier tech APPE, the packaging division of LSB, has announced a major collaboration with ColorMatrix and mould manufacturer KTW (now a subsidiary of Husky) in the development and launch of a new barrier technology for PET and other plastic containers. The system will initially be targeted at the juice industry and subsequently introduced for wine and food applications. It will be unveiled at the World Juice Conference, Madrid, 3 to 6 October. The concept was devised by ColorMatrix; APPE and ColorMatrix worked together to develop the system for commercial and industrial use. This project included the development of a special closure, created in association with KTW, that forms an integral part of the barrier. APPE says the new system will offer a number of advances over existing barrier technologies in terms of clarity of material and recycling potential. Product shelf life trials have shown that it delivers good results in areas such as prevention of vitamin C loss and oxygen ingress. APPE is the only company licensed to sell the technology. ColorMatrix said that it chose to work with APPE because of its record in the industrialisation of new technologies and its position in the PET packaging the companies sharing knowledge and expertise in bottle and closure design and manufacture. www.appepackaging.com www.colormatrix.com www.husky.ca SACMI, the world leader in equipment for closure manufacturing , presents its latest state-of-theart Continuous Compression Molding model CCM48SB, developed for the production of lightweight single-piece HDPE closures. The primary advantages of the CCM48SB: t Reduced cycle time: only 2 seconds as opposed to 2.4 seconds for the previous model. t Reduced energy consumption: just 0.4 kWh/kg t Reduced maintenance times: in the design process all parts for the CCM48SB were scrutinized, and engineered in order to reduce overall maintenance and change over time. All CCM are characterized by their compactness, low power consumption, short cycle times, low maintenance costs, extremely fast color changeovers, and outstanding control flexibility. TheCCMoffers an exceptional production process repeatability as well. Sacmi Imola S.C. Via Selice Prov.le, 17/a 40026 Imola (BO) Italy Tel. +39 0542 607 111 - Fax +39 0542 642 354 E-mail: sacmi@sacmi.it www.sacmi.com Full compression.","@ID":11} "BOTTLE MAKING 35 PETplanet insider Vol. 12 No. 10/11 www.petpla.net The latest bottling design choices include the FreeShape bottle, the Cluster bottle and the Daily dose package, all offering maximum levels of flexibility and creativity. A bottle tree The Cluster bottle bundles a number of short-neck bottles using green neck rings that are attached to a main branch resembling fruit hanging on a tree. The customers in the shop simply “pick” the bottles they wish to buy. Cluster bottles are suitable for a range of different products, from water and flavoured water to sensitive beverages including juices and dairy. The bottles can be light-weight and can be made of recycled material and/or biosourced material. Because of their attractive design, they lend themselves to possible reuse at home as a second-life package. The daily dose of fruit DailyDose is a multipack solution directed at families and consumers who wish to consume small amounts of fruit doses or yoghurt drinks on a regular basis. Six bottles are sleeved individually and linked with one unique label in a handy set. For packaging companies, they enable flexible and cost-effective production as one label, or, alternatively, one sleeve is used for a pack of six bottles. The daily dose is one pack for a family with one dose a day of healthy product. The DailyDose package again is a flexible concept offering one design for different products. It is suitable for on-the-go consumption as the small bottles fit into the smallest of handbags. Liberating bottle shapes for sensitive beverages FreeShape offers the possibility of using a similar bottle design for both hot fill and aseptic filling. The secret of FreeShape lies in its specific patented bottle base profile, which acts like a membrane or piston: it pulls up and falls depending on the contained product’s volume variations. This solution responds to the packaging needs of sensitive products such as juices or teas filled at temperatures between 85 and and 92°C, which lead to bottle swelling during hot fill and then shrinkage when the liquid is cooled. www.sidel.com Flexible PET packaging solutions All shapes and sizes New market trends and consumers’ expectations require constant adaptations of bottle designs and shapes. Beverage producers not only pose high demands on design and marketability of their packaging products, but also require top quality and safety standards. In addition, bottlers and converters attach high importance to sustainable production processes at low cost and high profitability. Sidel offers new packaging solutions that help its customers achieve variety in designs while fulfilling all additional market demands.","@ID":37} "BOTTLE MAKING 22 PETplanet insider Vol. 12 No. 10/11 www.petpla.net Sipa Meeting with Enrico Gribaudo, General Manager “If it is technical containers, large sizes, wide mouth and high volumes, we are simply unbeatable.” Following our discussions with Nissei ASB and Aoki, there are those who think they understand the world of single stage. Not only that, but they claim to know the criteria and rules governing the choice between single stage versus two stage (and vice versa). A visit to Sipa, however, might prompt a radical re-think. Sipa also offers a single stage Injection Blow Moulding Machine which transforms PET pellets into a bottle in a single uninterrupted machine process. And they’ve been doing it for over 20 years. Sipa is, in their own words, a solution provider for the PET industry in single stage as well as two stage technologies. One of the many responses to the requirement of the markets is the Sipa “single stage injection stretch blow moulding machine“. Approx. 20% of Sipa turnover is currently attributable to the FX and HS range of single stage machines. Other Sipa products include two stage PET conversion, injection moulding machines and blow moulding machines, both rotary and linear, as well as moulds for injection and blow moulding, and, since the acquisition of Berchi 3 years ago, complete, integrated lines. There is no exclusivity for the one or the other process according to Sipa’s General Manager Enrico Gribaudo: “There is no firm rule in favour or against single stage and also no rule in favour of two stage or against. The right solution”, he believes, “is driven by economics and depends on the specific circumstances. There are a whole lot of criteria involved in decision-making: geography, logistics, annual volumes and requirements, culture, issues involving service, as well as the buyer’s preferences and especially and primarily the overall total cost of the container to be produced.” Defining the difference Nissei ASB’s as well as Aoki’s priority in the market seems to be to find and/or develop an application for a standardised range of machines sold from core stock. Sipa’s priority seems to focus on supplying a bespoke solution for a client’s particular application. Sipa single stage machines are today manufactured to order only. All three companies are apparently successful in satisfying their customers. But the approach and initial stages of the business are different for each of the players in the single stage sector. The difference in attitude and strategy i.e. selling ex stock or manufacturing to order -, explains why the Japanese cover the world market with relatively small machines the majority of single stage applications is for small machines, most of them for the pharma, cosmetics and food sectors. This is in contrast to Sipa, who concentrate on the large volume, specialised single stage machines. The biggest Nissei ASB (150t clamping) corresponds to the smallest Sipa (HS6). Sipa’s best seller is the FX 20 with a capacity of 10,000 jars with wide mouth or 36,000 bottles of 0,6l capacity. Enrico Gribaudo quoted again: ”We cannot go slow. If it is technical containers, large sizes, wide mouth and high volumes, we are simply unbeatable.” Single stage technology focus Up to the present time, 800 single stage Sipa machines have been supplied to global markets. Units – as per Sipa – would give a misleading indication as to market share. The average production volume produced by a Sipa machine is considerably higher than the volume of a Japanese machine. And so is the price, which increases the Sipa share in value. 50% of Sipa systems are for applications such as standard beverage bottles, 25% for heat set, 15% for specials (food, pharma, cosmetics), the rest for aseptics and edible oil. 50% of the beverage systems – mainly big volume machines - are supplied to brand owners. This percentage has recently fallen to 30%. Big names amongst the Sipa customers are both in the beverages and in the converter sectors. Enrico Gribaudo, General Manager of Sipa","@ID":24} "PETcontents 10/11 4 PETplanet insider Vol. 12 No. 10/11 www.petpla.net INSIDE TRACK 3 Editorial 4 Contents 6 News 48 Products 52 Bottles: Beverages 54 Bottles: Personal care 66 Patents BOTTLING / FILLING 28 The many flavors of Brazil Refriso Bebidas increases PET bottling capacities 35 All shapes and sizes Flexible PET packaging solutions MARKET SURVEY 31 Compressor manufacturers CAPPING / CLOSURES 36 It’s a lightweight Bericap launches lightweight SuperShorty closure in North America REGIONAL REPORT 10 Lithuania / Estonia Part 1 MATERIAL / RECYCLING 16 Bigger bales PET recycling rates up in Europe and North America PREFORM PRODUCTION 18 Short shots A rapid guide to perfect preforms - Part 24 BOTTLE MAKING 20 Suppliers of single stage machinery Single stage feature - part 4 26 Water is life Conteno’s containerized mobile water bottling plant Page 2& Page 28 BUYER’S GUIDE 57 Get listed! TRADESHOW REVIEW: BRAU BEVIALE 38 Go to Brau Beviale The PETplanet Editour from Germany to Azerbaijan and back 42 Brau Beviale Nuremberg, November 9- 11, 2011 46 The bearable lightness of PET Light-weighting solutions from PET Engineering Page 35","@ID":6} "PRODUCTS 51 PETplanet insider Vol. 12 No. 10/11 www.petpla.net Palletiser for lightweight bottles Sipa Filling and Packaging Division has added new palletisers to its range, which it says offer gentle, precise and fast layer preparation that is suitable even for extremely lightweighted bottles. The company’s Active Layer and Fastlayer systems are available in low, medium and high-speed versions, and with 90° and in-line feed. The palletisers have a patented gripping head that allows simultaneous handling of several packs. Sipa claims that the new models provide improved transportation for some containers, with extremely delicate handling to avoid damage to the product being packed, as well as reduced changeover and adjustment time and a smaller footprint than conventional systems. The low/medium speed Active Layer version is composed of a clamp type head installed on linear axes and is suitable for handling up to six packs at the same time with very fast, accurate and soft pack rotation that eliminates collisions. The conventional impact pack turning device, row spacers and rollers have been eliminated, which is claimed to reduce maintenance. The Active Layer module can be installed in existing plants. Fastlayer systems can be integrated upstream of any type of palletiser with fixed or mobile pallets. It is comprised of one or two anthropomorphic robots mounted in parallel. Sipa’s patented pack gripping head adds two further robotmanaged movement axes, enabling several packs at a time to be processed. www.sipa.it DEUTSCHE EDELSTAHLWERKE, Obere Kaiserstr., D-57078 Siegen / Auestr. 4, D-58452 Witten Who knocks PET bottles into shape? CorroPlast® – the ultimate steel for all-stainless mould sets.","@ID":53} "BOTTLES 55 PETplanet insider Vol. 12 No. 10/11 www.petpla.net Birch hair tonic 500ml hair tonic with birch extract is being offered by the German discount store Netto from Maxhütte-Haidhof in an attractively-shaped PET bottle under the brand name of ”Hairwell“. The bottle features a colour-coordinated screw cap with integrated snap lid. As a result of the Non-LabelLook label at the front and the coloured product, eye-catching light effects are generated at the POS. www.netto-online.de Travel range from Aldi Aldi has brought out its Travel Cleaning Set, consisting of three of its trademark labels - aliow washing up liquid, Bims all-purpose cleaner and Tandil hand/machine wash in a transparent 250ml pack. The small PET bottles are square and incorporate the closure typical of the product (dispensing screw cap, trigger and pushpull). The basic square format and an inset, printed cardboard sleeve ensure the optimum arrangement of the bottles in the re-closable pack. www.thurn-produkte.com Bio for baby 200ml cleansing liquid for tender baby skin, skin-friendly and dermatologically tested, is being marketed by the French retail group Auchan of Villeneuve d’Ascq in a round PET bottle. The bottle features an all-round paper label and an aluminium screw cap which gives the packaging a particular appeal. www.auchan.fr Y O U R PA R T N E R F O R B L O W M O U L D S . Sidel • SIG • Krones • SIPA • MAG • ADS • Kosme • Nissei a. o. Röders GmbH / Scheibenstr. 6 / 29614 Soltau / Germany / www.roeders.de Telephone +49 5191-603-53 / Fax +49 5191-603-36 / E-Mail mold@roeders.de For our subsidiaries in China, USA and Latin America please check our website. PET STRETCH BLOW MOULDS Benef i t of 30 Years of Exper ience in Blow Mould Manufactur ing! VISIT US Hall 5 Booth 419 Nov. 09 - 11, 2011","@ID":57} "BOTTLING / FILLING 26 PETplanet insider Vol. 12 No. 10/11 www.petpla.net Conteno’s mobile containerised water-bottling plants can provide drinkable water, anywhere in the world. Water is life More than one in six people worldwide - 894 million – do not have access to a safe supply of fresh water, according to the WHO (World Health Organisation). In addition to this number, there is often a need for emergency water supply in areas hit by disasters, such as earthquakes, civil conflict, or severe weather. Conteno is a Belgian manufacturer of mobile water purification and packaging systems, which are complete factories built into ISO containers for PET bottling or on trailers for pouch filling. There are now several units in construction for Africa. Mobile water bottling plant Conteno’s self-sufficient and fully automated mobile water-bottling plants are installed within standard 20ft and 40ft containers. The “AquaContainer Bottling” locally delivers a high-quality water supply in an appropriate package, whether a bottle or a sectioned pouch and can produce PET bottle size options from 0.2l to 10l. The automated stretch blow moulder is compact (1.1x1.2x 1.8m) and reaches an output of up to 1,600bph for a 1l bottle. The energy consumption is low, since the bottle is blown at low pressure. The plant has specific UV-treatment of water, bottles, caps and tear-off pouches and is designed for bottling according to strict IBWA and FDA regulations, with full automation from end-to-end in order to eliminate contamination risks. Filling and capping takes place in a sterile, positive air pressurised cabinet, without any human contact. The inner sides of the insulated and dust free container walls are resin hardcore, for ease of cleaning, and the production equipment itself is constructed of stainless steel. Local supply purification For customers who also need local water supply purification, several container-based purification solutions are available for raw water to brackrish, integrated in the AquaContainer Bottling. These can be based on ultra filtration, on reverse osmosis or, for special environments or areas where water is lacking, with solutions that extract water out of air (humidity/heat). Sea water desalination via reverse osmis requires a separate 20ft container. ‘Best practice’ logistics The company says that its selfcontained local production plants can offer savings of up to 80% on the total logistic chain, including storage, when comparing transport of small lightweight PET preforms with traditional filled water bottles transport. One truck filled with small preforms corresponds to the equivalent of 20 trucks of bottled water, which frees capital, storage, truck and ship space for other cargo. The mini factories are packed in with an onboard generator and compressor, and meet international food and beverage standards. Alternators, engines and compressors are all recognised brands, which means that support is available across the world, through local branches or representatives. The container factory can be operational in less than an Conteno has developed 20ft and 40ft containers comprising self-contained and fully automated mobile water bottling plants to provide drinkable water.","@ID":28} "MATERIAL / RECYCLING 17 PETplanet insider Vol. 12 No. 10/11 www.petpla.net million tonnes of PET bottles and jars was available in the United States for recycling in 2009. The post-consumer PET bottle recycling rate was 28%, which represented an increase for the sixth consecutive year. The report attributes this to, among other factors, an increase in collections in California; new collection programs; various major program expansions and conversions; and new commercial recovery efforts. US reclaimers saw their total purchases of US bottles return to 2007 levels (292kt) Other sales of RPET were to Canadian and Chinese buyers. Sluggish bale demand drove prices down late 2008/early 2009 but prices recovered during the year. Good quality, dirty granulate commanded a premium of at least $0.10/lb ($220/t) over bales. The increased rate and higher activity in recycling took place against a background of reduction in the number of PET jars and bottles produced and sold in the USA, as well as less raw material usage, resulting from lightweighting initiatives. Analysis by the Beverage Marketing Corporation (BMC) for IBWA (International Bottled Water Association) found that over the past eight years the gram weight of the 16.9oz ‘single serve’ bottled water container dropped by 32.6%, from 18.9g in 2000 to 12.7g by 2009. Napcor has made recycling of PET thermoforms its highest priority and is working with collectors, intermediate processors, reclaimers and end markets to identify and clearly define technical issues and to eliminate barriers to successful recycling. www.petnology.com With PET ahead: versatile, sustainable and flexible Conference Organiser PETnology/tecPET GmbH P.O. Box 120 429 D-93026 Regensburg, Germany Phone: +49 941 870 23 74 Fax: +49 941 870 23 73 conference2011@petnology.com November 7-8, 2011 Nuremberg Congress Center Nuremberg (CCN East) Prior to Brau Beviale XIV. Strategy and Technology Conference for the PET Packaging Industry 1The ‘Post Consumer PET recycling in Europe 2010 and Prospects to 2015’ report was prepared for Petcore by PCI PET Packaging, Resin & Recycling Ltd. To purchase a copy of this report, contact PCI directly at info@pcipetpackaging.com 2*The Napcor/APPR ‘Report on Post Consumer PET Container Recycling Activity’ is available from NAPCOR’s website, www. napcor.com. Petcore (PET Containers Recycling Europe) is a non-profit European trade association based in Brussels. It focuses on sustainable growth for post consumer PET collection and supports PET recycling processes as part of European Plastics Waste Management initiatives. www.petcore.org EuPR (European Plastics Recyclers) is the professional representative body of plastics recyclers in Europe. EuPR members constitute 80% of the European recycling capacity, processing more than 5 million tonnes of collected plastics per year. www.plasticsrecyclers.eu Napcor (National Association for PET Container Resources) is the trade association for the PET plastic packaging industry in the United States and Canada. www.napcor.com. APPR, the Association of Postconsumer Plastic Recycling, represents companies involved in acquisition, reprocessing and sale of more than 90% of post-consumer plastic processing in the USA, Canada and Mexico. www.plasticsrecycling.org","@ID":19} "REGIONAL MARKET REPORTS 11 PETplanet insider Vol. 12 No. 10/11 www.petpla.net way. Today Indorama is one of the most efficient PET plants in the world and the Neo Group are hard on their heels. The country is also important as far as preform production is concerned, albeit to a slightly lesser extent than for the raw materials sector. As already outlined, Lithuania was important as a gateway to Europe even before 2004. Among other things, the preform production levels that had been built up at the time were meant to avoid the PET import duties. Today, the two major suppliers, the Retal Group and Putoksniks, together produce just under 5 billion preforms, that is around 5% of European consumption. The preform programme is therefore a hot topic of conversation for customers throughout Europe. Regardless of whether its heavy preforms for the monolayer bottles used for Russian beer or the lightweight, weightoptimised preforms with an 1881 neck, everything is pretty much taken care of. Only multilayer was retained in Lithuania for a time, but this has now been moved to France due to shortage of space. Considering the country’s importance for the entire European PET market, it is easy to forget that the country also has its own market for PET beverages, albeit modest, compared to the overall PET consumption figures Europewide. A production figure of just under 5 billion preforms needs to be seen alongside domestic demand of around 300 million PET bottles for water and CSD beverages. Performance www.sipa.it Visit us at: Brau BevialeNuernberg, Nov 9-11, 2011 Hall A7 - 7637 CBST Shanghai, Nov 6-8, 2011 Stand F 1-2 Reg i ona l repor t Lithuania / Estonia Part 1: UAB Orion Global PET (Indorama Ventures), UAB Putoksnis, A le Coq Part 2 - issue 11: The Retal Group, Senderlen","@ID":13} "PREFORM PRODUCTION 40 PETplanet insider Vol. 12 No. 10/11 www.petpla.net enable us to be at the meeting as early in the morning as you like (overnight at the factory gates) or go to eat at whatever distance you like from the hotel (and sleep overnight in the restaurant car park). The word “camper van“ does not evoke a glamorous image so we decided to give the vehicle a more prestigious title: ”Editourmobil“. The “editors“ are in it, the “tour“ takes place in it and the “mobile” home is also part of it. This brings us to the important subject of the vehicle itself. Since it will not only be travelling on the German motorways but is also destined to go to countries far away, the use of the base frame of a standard delivery vehicle was out of the question. If not an off-road HGV, then it at least had to be a robust, lightweight truck that would serve as a framework. We opted for an Iveco. Even the structural requirements were derived from the regional reports. If we were going to be bedding down in front of the plant gates the vehicle would need to be self-contained. Adequate battery power and an efficient water supply were an absolute must. Load capacity would need to take into account vast quantities of our magazines plus our mobile exhibition stand. Also essential were wardrobes, cupboards, space to store computers and somewhere to eat, sit, shower and sleep. And, last but not least, the pantechnicon had to cruise happily at the height of summer and in the depths of winter. A tall order for any manufacturer, but we ultimately found what we were looking for with Laika, an Italian mobile home specialist, part of the Hymer Group. Prior to venturing out on the “Go to Brau Beviale“ tour, we gave the vehicle a thorough road test. The baptism of fire was a trip to the K-Fair in Düsseldorf. Whilst the team found accommodation in Essen (this meant a 1,5h commute each morning to cover a distance of 20km!), Kay Krüger and I spent the night in the car park at the Fair. This was sited directly beneath the flight path of Düsseldorf Airport. After that we decided to spend the following nights on the banks of the Rhine, right by the old town, along with all the hotel ships. Definitely a much better place to park. The second major challenge took us to Munich. We had a stand at the “Bau“ Fair in January for our other magazine. Sub-zero temperatures as low as -20° at night. The Editourmobil came through with flying colours, it kept us warm and the water tank did not freeze. Buoyed up by these good experiences, I then ventured to tackle my first longish regional report by Editourmobil. The vehicle had no problems coping with the tour of Finland, Latvia, Estonia and Lithuania (see PETplanet insider issues 7+8, 9, 10 and 11). In Finland the navigator even took me via some dirt roads where we had to negotiate rutted tracks which shook the entire vehicle. Potholes were a major obstacle In the Baltic States, but we came out of it with not a screw loose! Throughout, the Editourmobil has served the editors as a mobile office, comfortable hotel room and speedy means of transport for 100 days, so that we are able to look forward to the Tour of Tours with a good heart. Take this as your invitation to join us on the “Go to Brau Beviale“ tour , as we make our way through Germany and on to Azerbaijan and back. www.braubeviale.petpla.net instigated via the respective regional representatives of the machine manufacturer who kindly give us an introduction to their customers and then organise contact with us. An undertaking which would test my nerves to the limit and still does so. On the way from the headquarters to see the regional manager, then from the regional manager to the customer and finally from the customer back to us there are a remarkable number of variables that raise doubts in one’s mind as well as endless time costs – and all this even when all parties concerned have a commitment to the job. This is probably not least due to the availability of the different people in this complex chain; after all, everyone concerned has their hands full permanently and are not always on site. Time to think about visas for those involved and to discover, almost by the way, that it is not, for example, possible to enter Armenia directly from Turkey, nor is it possible to enter Azerbaijan from Armenia. So, without further ado, I simply extended the route by one country which we could travel through on our trip and that was Georgia. Research and telephone calls yielded the information that,from Turkey onwards, taking official vehicle drivers certificates in the language of the country concerned was to be recommended and could we please ensure that we had these attested by a notary and the district court. I made use of my time to start the ball rolling instead of simply having a fit. Finally the first feedback from the customers started to come in and I was able to make a start on actually agreeing dates for meetings on the tour. High time too, do I hear you say, especially in view of the fact that the tour starts on October 3. In the meantime I am able to say that everything is going absolutely according to plan. You get more laid back as time goes on. Today, 20.9, the visas still have not arrived and there are some meeting dates that have yet to be finalised. But I still have almost two weeks to go ... At Brau beviale it will be directly by the transition point to the East Entrance adjacent to the PETpoint, that the EdiTour Presentation will take place in Hall 7A. Plenty of room for showing off the Editourmobil and all the bits and bobs we need to take with us. Nuremberg, Germany November 9-11, 2011 Meet us in Hall 7A | Booth 720","@ID":42} "BOTTLE MAKING 25 PETplanet insider Vol. 12 No. 10/11 www.petpla.net ABC COMPRESSORS NEW PET RANGE THE MOST PROFITABLE AIR Safe Investment Total energy savings over 50% Efficient Consumption MinimumMaintenance RELIABLE BEYOND LIMITS www.abc-compressors.com · Up to 5 years guarantee. · Special financial terms. · Plug&Play. Complete set on base frame. · Up to 6.080 m3/h with a single compressor. · Built-in quality. The only manufacturer machining, mounting and testing the 100% of its bare compressors in Europe. · Proximity. Whole packages delivered through our sites in Europe, America and Asia. · ABC guarantees up to 15% saving thanks to our efficient design. · Save 50%of compression energy thanks to air reinjection in our 4 stage machines. · Additional 15% savingscoming from perfect adaptation to frequency converters. · Energy-audits to demonstrate it. · 8.000 hours of operationwithout any additional maintenance. · Life cycle services. From express spare parts delivery to special maintenance contracts and machine refurbishing. · 24Hx365D available worldwide for any service through our web platform. · More than 25 technical service hubs around the world to be closer. EXHIBITIONS 2011. Visit our stand at: CBST: Shanghai (China), 6th-8th November, STAND F2-2","@ID":27} "Vol.6 PETplanet print PREFORM PRODUCTION 18 PETplanet insider Vol. 12 No. 10/11 www.petpla.net Short shots The rapid guide to perfect preforms - part 24 Troubleshooting guides have suffered in the past from being locked away in offices and not being available to the people that actually need them. Considering the high cost of machine and tools high scrap rates can be a costly proposition eating away at already tight margins. PETplanet’s “Rapid Guide to Perfect Preforms” takes a different approach. Bound in laminated paper that is easy to clean off, the small format of the book of 108mm by 151mm (4.25” by 6”) allows easy storage in back pockets or tool boxes. It has been written for the people on the floor of injection moulding companies to support their daily work in making the best preforms possible. The product of two industry experts, Rick Unterlander and Ottmar Brandau, it gives concrete advice on 35 of the most common problems in preform manufacture, most illustrated by pictures. From high AA levels to wavy bodies processors can find help when they need it. Read chapter 24 of the guide. Symptom: The preform thread finish is incompletely formed. The degree of incompleteness can range from a slight absence of the TSS (top sealing surface) and upper threads to a complete missing neck finish and/or main body section. Cause: There was not enough melt injected to completely form the preform. Table of Contents i........................ About the Authors ii.................................Introduction chapter 1.............................. AA Level High 2........................ Accordion Preform 3....................... Air hooks / Streaks 4............................... Black Specks 5...................................... Bubbles 6..................................Burn Marks 7...........................Colour Streaking ................................... /Peeling 8..................................Crystallinity 9.................................Drool Marks 10.......................................... Flash 11......................... Gate Depressions 12............................... Gate Peeling 13..................Gate Voids / Pin Holes 14......................... Internal Gate Sink 15................................Internal Sinks 16........................................ IV Loss Solutions: 1. Check for correct shotsize setting. The injection cushion should be about 3 – 5mm to compensate for any melt process fluctuations. 2. Check injection time isn’t too high (injection rate too slow) and adjust if necessary. Injection rate should be about 10 – 12g/sec/cavity. 3. Check to ensure hold (packing) pressure isn’t too low, especially near the beginning of hold time. Adjust higher if necessary to fill out neck finish contour and TSS. 4. Check that the hold (packing) time isn’t too little for the preform being moulded. Increase as necessary to optimize part weight. 5. Check that the valve stems are opening properly. A partially open valve stem may restrict melt flow. 6. Check to ensure that the valve gate compressed air pressure is sufficient 17............................ Long Gate Nub 18...............................Milky Preform 19............................ Moisture Marks 20................Neck Finish out of Round 21....................... Parting Line Crease 22.................Parting Line Deformation 23......................... Preform Yellowing 24.................................. Short Shots 25.......................................... Sinks 26......................................... Splay 27........................... Stretched Necks 28..................................... Stringing 29......................... Surface Blemishes 30......................... Thread Flow Lines 31...............TSS (Top Sealing Surface) ......................................... Sink 32.......................................Unmelts 33.................Wall Thickness Variation 34.................................Wavy Body 35.................................. Weld Lines","@ID":20} "PREFORM PRODUCTION 38 PETplanet insider Vol. 12 No. 10/11 www.petpla.net The Editour from Germany to Azerbaijan and back Go to Brau Beviale by Alexander Büchler Nuremberg Ljubljana Sofia Istanbul Izmir Bucharest Brasov Oradea Budapest Zagreb Beograd Go to Brau Beviale May 2011: The idea is born A camper van is an expedition vehicle pure and simple. The idea of using a holiday home as a fact-finding bureau came to us over lunch at our favourite Italian restaurant round the corner from our offices. What could we possibly do that would be simply extraordinary? With the Brau Beviale Fair in Nuremberg in mind, we thought “let’s criss-cross Europe and find out what is really going on in the various markets”. And thus was born the idea of the camper van. The “we” in this case consists of Alexander Büchler and me, Kay Krüger. True to the motto “How far can we go?“, we jointly devised an interesting route taking in Nuremberg, home of the Brau Beviale and faraway Baku, Azerbaijan, then returning to Nuremberg via a different route, just in time for the start of the Fair. We estimated we would probably need five weeks in total for this, inclusive of visits to several PET bottlers in the eleven different countries we would be crossing. Wasn’t there something about Azerbaijan? Of course – the Azerbaijani duo Ell and Nikki won the Eurovision Song Contest in Düsseldorf in mid-May 2011, thus securing the next contest for Baku in 2012. “How about arranging an interview to ask them about which beverages they prefer in PET? It would certainly be a highlight of the tour“, we thought to ourselves and made a mental note to fix up a meeting. In the annals of PETplanet, this trip, if it succeeded, would be the most intense and formative we have ever carried out. And to round it off, we would then be presenting the material we have collected from all the PET companies we have visited, ready to present our findings on our stand in Hall 7A Stand 720 at the Fair, both in text and product format. This will be in addition to the travel reports we will be putting on our blog as the tour progresses. I, Kay, have been appointed Project Leader. So, without further ado, let’s go! June 2011: Initial preparations The concept had been defined and the individual tour points roughly determined. Messe Nürnberg had been informed, they thought it a very good idea and announced that they would give us support on the marketing front. Now we were ready to embark on the first planning phase of the tour as such. We drew up list after list of all the things we would need for such a lengthy trip. The lists were endless. And pretty soon we were able to see from calculaThis is a new departure for PETplanet, as we prepare for and then undertake the most gruelling editorial trip in the history of PETplanet. Alexander Büchler and Kay Krüger have set an ambitious target of eleven countries and some 50 company visits. Europe to Asia Minor – there and back again. Now, by visiting www.braubeviale.petpla.net, you will be able to follow us every step of the way and keep in touch as our journey progresses. The history of the regional report goes back a long way to the time when it was still known by the name “growth market report“. Our first story, back in 2006, featured Turkey. And now, five years later, it is appropriate that we return to that country to see whether it has justifiably earned the title of “growth market“. The consumption per head of packaged beverages was, at that time, around 76l per year, and the industry was experiencing an annual growth of 10%. Turkey is only the start of our adventure. We begin our journey in Germany, pass through Austria, heading for our first appointments in Slovenia, Croatia, Bosnia, Herzegovina, Serbia, Bulgaria, Turkey, Georgia, Azerbaijan and Armenia before embarking on our return journey with an additional detour taking us through Bulgaria and Romania. We may not be able to conjure up a regional report from each","@ID":40} "PRODUCTS 49 PETplanet insider Vol. 12 No. 10/11 www.petpla.net Shrink-wrapper without sealing bar Cermex, part of the Sidel Group, has announced the commercial launch of a new range of shrink-wrapping machines, which do away with the need for sealing bars. Presented under the brand of VersaFilm, the machine’s design uses modular architecture and other technologies to improve costs and lead times, the company says. The VersaFilm range is divided into three functions: product infeed, selection and lapping, and film shrinking in a heat tunnel. The modular architecture considers each function separately and is intended to enable the development of a solution that is based on the optimised combination of three, to suit customer requirements. Cermex claims that this increases overall added-value by an order of magnitude. The modules are comprised of currently available subassemblies selected from the technical database. The modular design and the addition of numerous servo-drives have led to the removal of a large number of transmission chains, with consequent elimination of recurring lubricating operations. The collating and lapping bars, which still require a traditional drive system, are equipped with a new generation of maintenance-free chains. Dismantling the infeed and lapping belts can be carried out by a single operator. Cermex says that an ergonomic redesign improves operability. The whole rack of the injection table is removable and maintenance is tool-free and the machine can handle thicknesses ranging from 20 to 80. Factory settings require no future adjustments, whatever the film thickness used. The injection table is servo-driven in a compact footprint. The 3D control interface, PLC and axis cards are sourced from the same supplier and this uniformity is claimed to improve reliability and simplify fault-finding and maintenance. Firmware updates and program transfers to plug-and-play components are automatic. Cermex says that its Dual Injection System (DIS.) enables continuous machine operation, with independent dual heads enabling reel changeover without machine stoppage. The VersaFilm range accommodates product formats from 55 to 124mm, and 25cl to 3l. A cassette cuts format changeover time to less than a minute. The company claims that a re-design of the insulation and air circulation has generated a 30% saving in power consumption in the shrink tunnel. www.cermex.eu","@ID":51} "imprint EDITORIAL PUBLISHER Alexander Büchler, Managing Director HEAD OFFICE heidelberg business media GmbH Landhausstr. 4 69115 Heidelberg, Germany phone: +49(0)6221-65108-0 fax: +49(0)6221-65108-28 info@hbmedia.net EDITORIAL Doris Fischer fischer@hbmedia.net Michael Maruschke Ruari McCallion Ilona Trotter Wolfgang von Schroeter Anthony Withers MEDIA CONSULTANTS Ute Andrä andrae@hbmedia.net Martina Hischmann hirschmann@hbmedia.net Ursula Wachter wachter@hbmedia.net phone: +49(0)6221-65108-0 fax: +49(0)6221-65108-28 France, Italy, Spain, UK Elisabeth Maria Köpke phone: +49(0)6201-878925 fax: +49(0)6201-878926 koepke@hbmedia.net LAYOUT AND PREPRESS Exprim Kommunikationsdesign Matthias Gaumann | www.exprim.de READER SERVICES Kay Krüger reader@hbmedia.net PRINT Chroma Druck & Verlag GmbH Werkstraße 25 67354 Römerberg Germany WWW www.petpla.net | india.petpla.net PETplanet insider ISSN 1438-9459 is published 10 times a year. This publication is sent to qualified subscribers (1-year subscription 149 EUR, 2-year subscription 289 EUR, Young professionals’ subscription 99 EUR. Magazines will be dispatched to you by airmail). Not to be reproduced in any form without permission from the publisher. Note: The fact that product names may not be identified as trade marks is not an indication that such names are not registered trademarks. 3 PETplanet insider Vol. 12 No. 10/11 www.petpla.net Go to Brau Beviale The degree to which regional reports are interesting and informative is matched by the time taken up by the associated travel. Herding cats is nothing when compared with organising the trip and getting things underway. We have received superb support from our sponsors and without them many of our trips would certainly not have been a success. They also help advertise our visit among the processors and bottlers and also provide logistics support during the journey. Crucial to all this is the commitment of the company representatives locally, and we are pleased to acknowledge here how fruitful their support has been, in particular for arranging meetings and visits. An additional plus point is that it helps the regional representatives to extend their relationships with their customers. It supports customers in raising their profile as well as giving you, our readers, an appreciation of different markets which may generate ideas on operating more successfully within your own market. Up to now you, as readers of PETplanet insider, have had to be content with reading the polished version of the story in the magazine, unaware of the trials and tribulations we go through to assemble the information. Some years ago for example, I travelled to India to compile a regional report and, surprising as it may sound, not one single appointment had been fixed in advance. Only once the trip was underway did the appointments and meetings begin to roll in. Another memorable incident was one particular regional report where a machine manufacturer had kindly arranged access to almost all the key players in the marketplace. The trouble was, when I got on site, I found that all the machines were those of his competitors. All this gave us the idea of getting you, our readers, more involved in the behind the scenes preparations for our regional reports, as well as contributing to the content. For us, and we hope for you, this is a massive step forward. This issue covers the Balkans and Asia Minor. Our first report explains the preparations for the tour. During the tour itself, we will be giving you the opportunity every 2 to 3 days to participate in our experiences en route. Ultimately, this tremendous initiative will terminate at the Brau Exhibition, and we have therefore adopted the motto “Go to Brau Beviale“. There, you will be able to see first hand the Editourmobil and be taken on a guided tour in the form of a presentation. Thanks to our sponsors, we have been able to keep the additional financial expenditure that this new type of reporting entails within strict limits. We should point out that our sponsors have no influence on content which means that the editing output will – as usual – be determined by whatever we feel will be interesting, informative and relevant. My particular thanks go to Messrs. Brigl and Bergmeister, Gea, KHS, Netstal and Sidel for their support, as well as the Messe Nürnberg and all the companies which have contributed their ideas and provided their support for this tour. Yours, Alexander Büchler Photo on Cover: Wikipedia.de Author: Wojsyl, 2005 EDITORIAL dear readers, EDITORIAL","@ID":5} "PETproducts 48 PETplanet insider Vol. 12 No. 03/11 www.petpla.net New HyCap: faster cycle time and better energy use Husky Injection Molding Systems has announced the launch of its next generation HyCap system for high-output beverage closure manufacture. The new system is an evolution of the existing HyCap platform but the company says it now offers faster cycle times, improved energy utilisation and closer integration with Husky’s new KTW closure moulds. It has a number of new features aimed particularly at improving cycling of lightweight closures, including a new screw design for improved plasticising rates at lower melt temperatures, which Husky claims helps to maintain strength and other resin properties. The lower melt temperatures also contribute to cycle and energy savings, with less waste and heat loss. Powerpack upgrades are intended to enable faster cycles. Subsequent to Husky’s acquisition of KTW in May 2011, the new version of HyCap has been optimised to integrate with Husky’s KTW closure moulds. The system features SmartStart and SmartStop technology, which automate certain startup procedures and allow for automatic production stoppages and faster restart. Husky says that the new system allows better cooperation between the machine and hot runner and that the company’s new Altanium colour change interface enables significantly reduced scrap and changeover time. www.husky.ca Ultra-clean refrigerated packaging bloc Serac, the French filling and capping machine manufacturer, has developed a bloc system for the ultra-clean packaging of refrigerated products with Urola, a Spanish company that specialises in PET stretch-blow-moulding equipment. The ‘Urola-Serac bloc’ has a direct link between Urola’s URBI four or six linear blow-moulder and Serac’s new H2F ultra-clean rotary weigh-filler-capper. The bloc comes in two line ranges, with capacities of 6,000 or 9,000 1l PET bph. The bloc can bottle pasteurised milk, drinking yoghurt, probiotics, other dairy products and fruit juices in bottles ranging from 100ml to 2l sizes in a single-neck finish, usually 38mm plastic screw cap. The Urola-Serac technology eliminates upstream disinfection by chemicals and uses pulsed light technology for cap decontamination. The companies say the line has a compact footprint and helps to achieve longer product shelf-life in the cold chain. The first bloc line will be delivered to the Russian market. www.serac-group.com Holland Colours European Division Halvemaanweg 1, 7323 RW Apeldoorn, P.O.Box 720, 7300 AS Apeldoorn, The Netherlands I Tel: 31(55)368 0700 I Fax: 31(55)366 2981 I E-mail: info@hollandcolours.com A unique solution in frost effect technology Would you like to reach elegant frost effect easily and economically? Thanks to the unique technology of Holland Colours you can produce PET bottles with frosted glass look without secondary surface treatment. Holcosperse B Matte Frost provides you translucent frost effect in any custom colors. The innovative product can be dosed easily on-line, that reduces dramatically production costs. A DROP OF DIFFERENCE A cool look that never melts","@ID":50} "CAPPING / CLOSURES 37 PETplanet insider Vol. 12 No. 10/11 www.petpla.net what causes the neck to ovalise (distort), which can, in turn, lead to leaking and contamination,” said Andison. While thicker, heavier finish sidewalls under the old standard helped to combat this problem to some extent, lighter-weight necks using the PCO 1881 standard could make matters worse. The DoubleSeal SuperShorty closure is designed to overcome these problems. Bericap’s DoubleSeal technology, a 2-in-1 Outer plus Inner seal in a single piece, liner-less closure, does not use down-pressure during the sealing process. Rather, it uses lateral, opposing-force pressure from both the outside and inside, thus effectively supporting the neck, instead of distorting it. According to Andison,the DoubleSeal SuperShorty closure and the bottle finish fit together like pieces in a puzzle. This results in a tighter, more secure seal to better retain carbonation. Injection-moulded from HDPE DoubleSeal SuperShorty closures are made with HDPE, rather than the PP typically used in typical two-piece closure shells. Bericap says that its caps can also offer cost, supply and environmental advantages. “Historically, PP costs more than HDPE,” Andison said. “While HDPE comes from cracking natural gas, which has ample available feed stocks in North America, PP comes from cracking liquid, and is constantly competing with gasoline for access to supplies.” Two-piece PP closures also contain other materials, which implies a greater challenge in the recycling stream, which prefers mono-material products. According to Bericap, the injection moulding process itself also provides more control over critical features, which helps to deliver better dimensional stability and integrity of every cap than through two-piece compression moulding. Smooth transition and line performance Bericap claims that its PCO 1881-compatible SuperShorty system fits smoothly into existing operations and that it works closely with bottlers, pre-auditing lines to identify changes that need to be made. Its on-site personnel pay particular attention to capper setup. “Correct cam selection and settings can virtually eliminate another frequent production issue on traditional lines: cocked caps,” said Andison, the company has recorded cocked cap rates falling to less than one per 100,000 after conversion. Bericap says that it is now working with all the major bottlers to help transition lines to the new standard while installing SuperShorty closure equipment. “Depending on customer preferences for external appearance, and the beverage being bottled, we offer half a dozen SuperShorty variants, including lightweight closures for still water, advanced tamper evidence (ATE) options or a specific design for beer closures that are equipped with an oxygen scavenger, to protect the beer from oxidation. In addition to DoubleSeal SuperShorty, Bericap began supplying major North American bottlers with PCO 1881-compatible Sportscap PushPull closures for 24 oz. containers earlier in 2011. The company is also in the process of commercializing a PCO 1881-compatible ‘ThumbUp’ closure in Europe. www.bericap.com Dave Andison, President and COO of Bericap North America MHT MOLD & HOTRUNNER TECHNOLOGY Dr. Ruben-Rausing-Str. 7 | D-65239 Hochheim/Main Tel. +49(0) 6146-906-0 | www.mht-ag.de Make the most of your machine – with a mold from MHT! For many machine types, we supply the mold with the highest cavitation, thereby enabling optimum preform output. For the Husky HyPET machine, we offer an upgrade set for 33% more preforms, without refitting on the machine! • 60 cavities for Netstal PETline 2000 • 96 cavities for Husky HyPET 300 • 112 cavities for KraussMaffei 350 Engineering made in Germany Patent pending: MHTcoolMAX® post mold cooling","@ID":39} "BOTTLE MAKING 21 PETplanet insider Vol. 12 No. 10/11 www.petpla.net in the preform after injection moulding and the finished containers are stretch blow moulded straight away, without reheating. The result is, according to Aoki, twofold: firstly, there is a significant energy saving and secondly a cost reduction in each container produced. Product range and applications The SBIII series is a comprehensive range with customers able to choose from injection capacity – pump motor – heater (hot runner) – hydraulic oil volume – to ensure they select the most appropriate machine size and machine weight. Other options include the number of cavities – neck diameter – body diameter – height – and output. Aoki single step systems cater for the typical single step applications such as for “high cycle moulding, for clean room and small narrow neck containers, lightweight wide mouth containers, mass production of small narrow neck containers, small containers, multi purpose containers, and also special purpose moulding ranging in capacity from the tiny 5ml container up to 90l containers.” Conscious of increasing environmental concerns, Aoki offers Direct Heatcon machines for recycled PET (Aoki series) - with an agitator/ hopper dryer in combination with the vacuum-type barrel venting systems “removing moisture content and impurities from the resin.”Understanding Aoki’s bottle to bottle recycle concept, more and more different applications are emerging from around the world, from 100% reground flake PET for non-food containers to blending clean recycled flakes with virgin PET material for food quality bottles. Key figures All Aoki single step machines and the genuine moulds are produced solely in Japan. The company has their machines running in 77 countries around the world. www.aoki.co.jp Hidenaga Nakagawa, Director Aoki Technical Laboratories","@ID":23} "REGIONAL MARKET REPORTS 14 PETplanet insider Vol. 12 No. 10/11 www.petpla.net Hand in hand Estonia has a population of just 1.3 million which means that the domestic bottlers need to be highly flexible if they are to succeed in a tight market. A le Coq in Tartu has successfully achieved the No. 1 spot in practically all beverages sectors. Here marketing and technology work hand in hand both to strengthen their core markets and to introduce new products on an ongoing basis. A le Coq has won a 39% market share in the beer market and has been market leader since 2008. In the cider sector their market share has already climbed to 50 %. In the soft drinks sector A le Coq with just over 30%, still lies in second place behind Coca Cola who command a 44% share. But they are working hard to bring about changes here. Back in 2010 Coca Cola was forced to surrender a 5% share of the market to these resourceful brewers. This success story actually started in 1997 when the Finnish brewing group Olvi (see Finland report PETplanet insider issue 9/11, page 10)) took over the company (who were still known by the name of Tartu Brewery at that time). The Finns set out on the race to catch up, in the process transforming a company which still had a whiff of the “old regime” about it. In 2010 the Estonians produced 118 million litres of beverages, half of which were beer. Since 2004 the company have introduced the PET bottle for beer and as of that time 25% of beer volume has gone out in PET. In the non-beers sector, products are packaged almost exclusively in PET with the exception of a few juices that are despatched to the consumer in cartons. In order to ensure appropriate production capacity to accompany this growth, the company purchased a new PET bottling plant from KHS in 2007. This is practically identical to the plant that the parent company Olvi purchased at the same time. A small PET plant was pensioned off to make way for the new plant. Now this new installation is producing all seven different types of bottle and bottling more than 50 different beverages. In addition, there is a further small plant that is just used for bottling beer in PET. Based on these figures, it is not difficult to place the comments made by Tarmo Laht, Head Brewmaster. “ 40% of operational time is set-up time( time for changeover and cleaning). Setting up is a routine, every-day job“: he smiles with satisfaction as he delivers this statement. But it is not only technology that ensures that the company’s market share is constantly expanding; the Marketing Department, under the leadership of Katrin Vernik does not allow the competition a minute’s peace either. ”We are looking to launch 15 to 18 new products on the market each year, but we take great care not to neglect our core brands“. New products, however, not only mean a new taste and a different colour on the label; the highly elaborate labels deployed here are intended to attract attention on the shelves. The glass line has just installed a high-flexibility labelling device from Krones. And going back to Tarmo: “All the ideas that we get from Marketing are feasible; all we need to clarify is just how much they are going to cost“. But this is a point on which Katrin and Tarmo are in agreement: if it’s good for the market, they will work hand in hand at putting it into practice. www.alecoq.ee Now with Lithuania part of the EU, the company can supply preforms without incurring duties. This means in turn that the company’s customer base inside the EU has grown, in this case mainly in the Baltic countries, Finland, Scandinaviaand Germany. The 2009 economic crisis mainly affected the eastern European states, and “Putokšnis”found the market for its preforms diminishing. This may have been a blessing in disguise as the proprietor did not need to get other investors on board during this time. In the interim production has once again come up to the level of the pre-crisis period and the company is looking optimistically to the future.They have now acquired a PCO 1881 mould to enable them to compete as a major player in this field. The company had its origins in the blow moulding of bottles in dual and starting from 2007 single stage, and they have never relinquished this branch. This means that they can expand their knowledge of the correct stretch blow moulding techniques on their own machines on an everyday basis. “We pass our knowledge on to our preform customers by advising them on their own stretch blow moulding processes“ says Edmundas Jakas. A further production facility has now been established in the Ukraine. “The eastern European sales market that does not lie within the EU has collapsed completely as far as we are concerned. The bureaucratic hurdles of delivering beyond the borders of the EU are quite simply too high. This was the reason for our decision to purchase a former perform works in the Ukraine. Here we have built up everything again from nothing“ said Simona Stulpinaite. www.putoksnis.lt A le Coq We met: Tarmo Laht, Head Brewmaster Katrin Vernik, Marketing Manager Right: Katrin Vernik, Marketing; centre Tarmo Laht, left: Alexander Büchler","@ID":16} "TRADE SHOW PREVIEW 42 PETplanet insider Vol. 12 No. 10/11 www.petpla.net Brau Beviale 2011 runs from November 9 - 11 at the Exhibition Centre Nuremberg, Germany. Around 1,300 exhibitors will provide an expected 32,000 trade visitors with information about new developments and improvements in beverage raw materials, technologies, logistics and marketing. But the exhibition is about much more than just showing off products. It is a forum where experts and professionals can exchange views on developments in the global beverage markets to and with an international audience, and lay the foundations for informed investment decisions. New drink ideas are created every year and existing products are constantly repositioned. Innovation and creativity generate consumer interest. The important role of packaging in drinks positioning is reflected in Brau Beviale’s ‘Modern Packaging’ pavilion, which will showcase interesting solutions and new ideas in materials and technology. Lightweighting is becoming more important – but quality has to be maintained. 2010 saw the PET bottle way out in front in the soft drinks, beer and milk package segments of the global beverage market, with a market share of 34% according to the British market research institute Canadean. Glass is second, with 17%, followed by cartons (11%) and cans (10%). More and more attention is being given to the development of packages made of renewable raw materials. A mineral water filler recently introduced a bottle made of 20% PET from renewable raw materials, first seen on the German market. A carbonated drinks producer presented a bottle of 100% vegetable material, which contains switchgrass, pine bark and corn straw. PET continues to offer producers and bottlers flexibility, in raw materials, weight, recycling and sustainability. Brau Beviale 2011 is the place to see tomorrow’s trends today. ‘3D’ crown caps Visitors to Sacmi’s 144m2 stand will be able to see the a public demonstration of the company’s new CCD 300 machine, which has been designed to emboss caps with brand logos with bas-relief deformation. Sacmi says that this helps to enhance the look of the cap and to reduce the risk of counterfeiting. The CCD 300 is equipped with the CVS vision system, which allows recognition of lithographic print, so it can process 3,000 pieces per minute, while synchronising embossing deformation with existing lithographic design on the cap exterior. Sacmi’s Opera Combinato labeller will also be on show, which combines cold glue and self-adhesive application technologies. The company will demonstrate how its new machines fit with its existing range. www.sacmi.com GEA Procomac Hall 7 | Booth 602 Aseptic blow-moulding and filling Italian company GEA Procomac recently launched its ABF (Aseptic Blow Fill) system, which it claims is the world’s first rotary aseptic blow-moulding machine with an integrated aseptic filler and capper. Dry-process PET preform decontamination is by H2 02 (hydrogen peroxide) and sterility is maintained throughout the blow-moulding, filling and capping process. Non-cleanable components are located outside the sterile zone in the machine. ABF has a capacity of up to 48,000bph and at can be operated at different levels of decontamination, which allows products with different shelf lives to be produced in the same system. GEA Protomac’s range of volumetric electronic fillers with magnetic flow meters, including Fillstar CX for still and carbonated drinks and Fillstar FX for any still product, can be integrated in the ABF system. The company will also feature its ECOSpin wet PAA-based aseptic filling bloc for high-speed lines, and Modulbloc for low/medium speed lines. www.procomac.it Sacmi Hall 5 | Booth 343","@ID":44} "PREFORM PRODUCTION 39 PETplanet insider Vol. 12 No. 10/11 www.petpla.net Ankara Erzurum Ahlat Yerevan Baku of these countries but we shall make every effort to cover the most important countries comprehensively. You will be able to follow the tour on line in our Editour blog at www.braubeviale.petpla.net. We shall be reporting regularly here on the problems we encounter during the trip – both the minor vexations and the major obstacles. You will then be able to read the comprehensive market reports in our usual detailed version in PETplanet Insider. To get you in the mood we have printed off the first three blog entries here for you. If you have a production facility in the region and we have not yet spoken to you, please do get in touch with us; we shall be delighted to call on you. The Editour Experience shows that the bottling plants and PET bottle blow moulders tend as a rule to be concentrated into areas where good water is to be found. Depending on the region, that tends to mean a location in the mountains or in unspoilt countryside. Only rarely are such plants found in towns and cities. As far as our regional tour is concerned this means that, once we leave the airport, we will have several hours’ journey by car in front of us before we can appraise the plants locally. However, it is not just the plants themselves that are of interest to us, it is primarily the people behind them. And what is the best way to go about getting to know these people? By going to lunch with them or perhaps by inviting them to dinner. But then we need a local hotel. Up to now that has always worked somehow, even if booking the hotel and searching around locally has proved to be expensive and time-consuming. A year ago we decided to call a halt to this type of expenditure as well as the time and effort involved and to undertake our regional tours in Europe in a camper van. This would tions what “the trip” would entail in terms of costs. One thing was clear: we needed some support here. Whom could we ask and who would enjoy getting involved in a tour of this kind? Some pivotal machine manufacturers with whom we had been working consistently for years and who maintain a constant presence in these regions and whom we know well were sounded out. The most important list however was the last. On it would depend some of the financing but also the quality contact information on interesting PET bottlers, preform manufacturers, cap manufacturers and recyclers whom we could visit in the various countries. And what about the Editourmobil? This was to be given a complete make -over – with eye-catching graphics, a specially designed tour logo, our company logos and also the logos of potential supporters of the project. We can leave that side of it in the capable hands of our graphic designer, Matthias Gaumann of Exprim. We are not finished yet: we will need spare parts for the van, and we’ll have to go through bureaucratic hurdles to obtain the necessary visas. Who knows what might go wrong on an Editourmobil like this one? There were visas to get for Armenia and Azerbaijan, and what about sickness insurance? I made it a priority to get all the necessary information. For the time being, the other things would have to wait. I started a list. July & August 2011: The talks with the sponsors I established contact with those machine manufacturers we felt might be considered as supporters. The thoroughly positive feedback once they heard about the tour confirmed me in my determination and motivated me for the coming weeks. In spite of an exchange of contacts and information which was sluggish in terms of time due to the summer holiday period, I felt that these two months had an incredible effect. Now, after several hundred emails and telephone conversations, what felt like a great weight was lifted from my shoulders, the project was secure and I could move to the next phase. We managed to obtain six sponsors for our tour who were prepared to support us both financially and with any amount of customer contacts. KHS were the first to look forward to the tour, followed by Netstal, Brigl & Bergmeister, GEA, Sidel and Nissei ASB. The next thing was to prepare the PET world for the tour in the forthcoming PETpla.net Insider magazine and, in conjunction with this, to devise an announcement to appear in both the forthcoming PETplanet Insider issues 9 and 10. September 2011: meetings with customers There is still so much to do. Our sponsors, Messe Nürnberg and other supporting PET firms opened the door for our initial contact with their customers at whose premises the actual meeting for the interview would subsequently take place. The approach when it comes to agreeing dates for meetings is as a rule","@ID":41} "REGIONAL MARKET REPORTS 12 PETplanet insider Vol. 12 No. 10/11 www.petpla.net UAB Orion Global PET (Indorama Ventiures) The Indorama Ventures team with Alexander Büchler (left) Orion Global PET, the Indorama Ventures’ PET plant in Lithuania is one of the most efficient plants in the world. It was built as the first Indorama PET plant in Europe and from day one it has been running at full capacity. Following the setting up of further Indorama facilities in Europe, the plant is focussing on supplying its customers in the North and East of Europe. Indorama Ventures decided to make the transition from Asia to Europe in October 2004. At that time PET usage in the markets of Eastern Europe was growing by leaps and bounds and it subsequently became clear that any expansion would need to be targeted on Europe, including also Eastern Europe. Klaipeda in Lithuania was the first choice, because it lies on the Baltic and supplies of raw materials can be delivered by ship. In addition, Klaipeda was situated very close to the markets that were booming at the time. Klaipeda has, despite its northerly position at latitude 570 N, an ice-free harbour, essential as regards logistics, allowing year round deliveries of PTA and MEG and subsequent export via container. An additional advantage is that Lithuania boasts the best trained workforce in the area, and a long, eventful history. It has no fewer than four world cultural heritage sites. The icing on the cake was its location in the Klaipeda Free Trade Zone where, although there were no direct investment subsidies, there was still a timelimited significant tax reduction. Thus Indorama came to build its first greenfield plant. One of the harshest winters of the previous few years delayed completion by six months but, in 2006, the plant went into production. The plant is an Uhde Inventa Fischer plant featuring four reactors. Its design capacity is 500t per day. However, it was not long before the specialists were able to exceed this capacity. “Debottlenecking“ is what they call it. Following work on the details, production today is 132% of the original installed capacity. And, for 2012, they have set themselves the goal of 700t per day. This makes the plant the most efficient single PET line in Europe, if not the world. This “debottlenecking know-how“ is being applied by Indorama worldwide. In this way it is continuously optimising all its plants. Initially Indorama Ventures supplied the whole of Europe from Klaipeda. But it was not long before the resourceful PET manufacturers were purchasing other plants in the heart of Europe to add to their portfolio. At the moment Lithuania is still supplying central, east and northern Europe but, even here, Indorama Venture has in the meantime been busy with acquisitions. This means that the delivery radius may be expected to shrink. Nevertheless, the plant has, since its inauguration, always operated at maximum output. Even when, over the last few years, PTA became scarce and many PET manufacturers found that they were forced to implement unscheduled maintenance works, Indorama carried on under full load operation. The reason that it was able to do this is that Indorama has its own reliable plants for PTA production. www.indorama.net UAB Putokšnis F.l.t.r.: Roland Koch (Husky), Simona Stulpinaite and Ramunas Undzys We met: Edmundas Jakas -Technical Manager Simona Stulpinaite – Member of the board On the borders of the EU It is eight years since we last paid a visit to “Putokšnis”. At the time there were three Husky lines standing in a small, old factory on the former military airfield at Siauliai in Lithuania producing preforms for a German customer. In the intervening years, the picture has completely changed. The company has refurbished all the buildings to include a 2000m² production facility for up to 12 machines, a large warehousing area covering 7,000m², a new office building and a new silo installation with a capacity of more than 1,000t. With 9 Husky lines providing a total capacity of 1.4 billion preforms the factory is now almost completely occupied. However, it is not just the hardware that has changed, it’s also the customers. Eight years ago, “Putokšnis”benefited ago from Lithuania being outside the EU, which meant that it incurred punitive tariff duties on imported PET material.","@ID":14} "TRADE SHOW PREVIEW 43 PETplanet insider Vol. 12 No. 10/11 www.petpla.net Krones Hall 7A | Booth 206 SAFEGUARD YOUR PRODUCTS THE ENVIRONMENT www.sidel.com PREDIS™ AND CAPDIS™ STERILIZE BOTTLES & CAPS WITHOUT WATER Predis™, a well-proven dry-decontamination system, is available for all types of sensitive products, including UHT milk. It guarantees bottle sterilization directly at the preform phase without using any water. And this technology is also available for bottle caps with Capdis™. At Sidel, our solutions go unmatched in the PET packaging market – and we ensure that your production line is efficient, economical and safe for the environment. WORK WITH US & GETA BETTER MATCH FIND US AT : PACK EXPO, BOOTH C-329 IDFA, BOOTH #801 ‘Intelligently holistic’ solutions Krones will be showcasing its corporate capabilities as a supplier of what it calls ‘intelligently holistic solutions’ for the brewing and beverage industries. Its Line Performance Analyser, an intelligent software module, is designed to improve line efficiency. Rapid-response trouble-shooting for individual machines and complete lines is provided by LCS (Lifecycle Service) remote service and telephone support. Individual machines can be brought up to the latest configuration by LCS upgrades. www.krones.com Material savings and process efficiency Netstal will be demonstrating production of high-grade closures on an Elion 2800 moulding machine, which is equipped with a new hybriddrive technology. It will be moulding PCO 1881 beverage closures at a cycle of 3.5s, using a 72-cavity mould made by Z-Mold, with Intravis optical quality control. The Elion 2800 uses Netstal’s new aXos control system, which has an upgraded operating panel and a number of new features. The machine is billed as the company’s response to customer demand for material savings, higher process efficiency and lower production costs. Netstal says that the combination of high-grade moulding machinery with efficient processes leads to more efficient production and savings of several thousand tons of raw material per year across the market. www.netstal.com Netstal Hall 7A | Booth 327","@ID":45} "MARKET SURVEY 33 PETplanet insider Vol. 12 No. 10/11 www.petpla.net Siad Macchine Impianti Atlas Copco Crépelle Via Canovine, 2/4 – 24126 Bergamo, Italy +39 035 327611 www.siadmi.com Ing. Luigi BEDUCCI Standard Compressor Director +39 035 327618 +39 035 327694 luigi.beducci@siadmi.com 2 place Guy de Dampierre, 59008 Lille Cedex, France +33 3 20 52 47 11 www.atlascopco.com Sabine Wagnon Communications +33 3 59 01 05 02 +33 3 20 53 76 51 sabine.wagnon@fr.atlascopco.com 3HP-4-LT 4HP-6-LT BS Line Tempo2 ZD ZD VSD P-compressors 5 4 19 models 18 models / 260 – 5,550 Nm3/h 23 6 6 1 16 4,210 6,080 1,000 – 6,000 Nm3/h, (*) suction conditions : 0°C – on sea level - R.H. 0% 260 – 5,550 Nm3/h*, (*) suction conditions : 0°C – on sea level - R.H. 0% 792 - 4108 FAD 792 - 1177 FAD 529-1152 FAD up to 1584-3957 FAD 626 to 1119 FAD 163 to 786 FAD high pressure blowing air (up to 40 bar) low pressure screw screw screw variable speed drive screw variable speed drive screw high pressure piston (booster) piston piston variable speed drive piston variable speed drive piston piston Oil free oil-free oil-free oil-free oil-free oil-free oil-free oil-free oil-free oil-free oil-free oil-free V W horizontal horizontal horizontal horizontal horizontal 3 4 2 screw + 2 booster = 4 total 3 2 and 2 2 and 2 2 and 2 2 and 2 2 no no no no no no no no no water water water air water air water belt drive direct drive direct drive direct drive direct drive direct drive belt drive belt drive belt drive belt drive belt drive belt direct belt drive PETStar – Booster / PS-2B 1250, 1470, 1980, 2290, 2840, 3340, 3850. Centac C750-18, C750-20, C750-21, C1050-36 7 models 4 models Based on an inlet pressure of 8 bar-g, output range is the following: PS-2B 1250 [1195}, PS-2B 1470 [1397], PS-2B 1980 [1881], PS-2B 2290 [2198], PS-2B 2840 [2727], PS-2B 3340 [3206], PS-2B 3850 [3696]. C750-18 [3,085 m3/h], C750-20[3,220 m3/h], C750-21[3,448m3/hr], C1050 – 36[6,360m3/h] Primary booster system Centrifugal design – 4-stages from atmosphere to 40 bar oil-free 2-stage Screw or 3-stage Centrifugal Two stage reciprocating booster oil-free oil-free horizontal horizontal 4 or 5 stage design. 2-3 stages Primary + 2-stage booster 4-stage from atmosphere design No special foundations are required. Unit can be mounted using typical practice of grouting & anchoring or on anti vibration mounts on standard factory floor No special foundations are required. Unit can be mounted using typical practice of grouting & anchoring or on anti vibration mounts coupled to standard factory floor. water cooled water cooled. direct driven primary. belt drive direct drive design","@ID":35} "CAPPING / CLOSURES 36 PETplanet insider Vol. 12 No. 10/11 www.petpla.net Bericap launches leightweight SuperShorty closure in North America It’s a lightweight Bericap single-piece SuperShorty closures and lighter weight finishes under the new PCO 1881 global standard are designed to avoid potentially damaging down-pressure. Six SuperShorty variants are available, covering customer preferences for external cap appearance, tamper evidence and the beverage being bottled. The recently-developed global industry standard for a lighter weight thread finish on single and multi-serve plastic bottles - designated PCO 1881 - is being rapidly adopted by bottlers of carbonated soft drinks (CSD) throughout North America. Bericap has recently completed its 30th filling line conversion from traditional two-piece closures to its onepiece DoubleSeal 1881 SuperShorty closure. Across the world, Bericap has converted over 100 filling lines to the new 1881 standard and has further conversions already scheduled. The transition brings a weight reduction of 20% in the dispensing system (the closure and the finish, the area that the closure is applied to on a bottle). Traditional 1810 systems weigh 8.0g while the new 1881 system is just 6.22g. The new standard saves millions of pounds of plastic packaging, according to Dave Andison, President and COO of Bericap North America. “This means significantly fewer resources are needed to manufacture and distribute product, leading to a reduced carbon footprint and ongoing sustainability advantages.” Developing a global industry standard PCO 1881 is the first new CSD finish standard in about 20 years. It was developed by the International Society of Beverage Technologists (ISBT), which represents more than 800 beverage industry professionals in over 21 countries. Beverage manufacturers, bottlers and suppliers agreed that significant weight could be taken out of the thread area of soft drink bottles and worked together to define specifics and gain acceptance. Bericap North America’s Terry Rochfort co-chaired the ISBT subcommittee for the three-year international effort, which generated specifications that now are being voluntarily implemented globally. About 70% of bottler lines in N America have already been converted to the new standard. “The new standard’s rapid, industry-wide acceptance reflects the success of ISBT developers in focusing on material and weight reduction, while retaining other important package attributes in production and consumer acceptance.” Andison said. One of the most critical issues with CSD is a tight closure seal to keep CO 2 locked in, so the beverage doesn’t go flat. Another concern for bottlers is distortion of the neck during closure application, which can lead to as much as 2% or more of rejected product. Bericap’s DoubleSeal technology is designed to enable its SuperShorty to resolve both of those issues. Lighter weight finish Two-piece liner-and-shell top seal closures demand a significant amount of torque in order to achieve a proper seal. “The resulting down-pressure is","@ID":38} "NEWS 7 PETplanet insider Vol. 12 No. 10/11 www.petpla.net KHS getting closer to customers KHS GmbH will be relocating its kegging technology to Bad Kreuznach, its second largest site. The kegging plant was acquired from Kriftel in 1999 and the new location will have room for future growth. The move is part of KHS’ strategy for development through to 2014, named ‘Fit4Future’ which was announced after a Supervisory Board meeting in September. A key element in the strategy is ‘intensifying customer proximity’. The company is intending to capitalise on its global production and service networks by focusing on the growth markets in the BRIC countries – Brazil, Russia, India and China. The company says that it has introduced measures to maintain regional market coverage within a harmonised worldwide product portfolio. Technical development will continue to be important, maintaining the momentum of the five new products and innovations launched during 2011 (Innosept ABF 611/711; aseptic linear filling machinery, Innokeg Till CombiKeg line, Innofill glass filler, and fully closed shrink packs). The geographical reorganisation and other measures will result in a reduction of 300 jobs. KHS management has already met with the Works Council. www.khs.com IBWA appoints new VP communications The International Bottled Water Association (IBWA) has appointed Christopher Hogan as Vice President of Communications, effective August 29, 2011. He joins from the American Gas Association (AGA), where he was Director of Communications. He has also worked in the communications and customer relations department of the American Petroleum Institute (API) and was a regulatory analyst at the Bureau of National Affairs (BNA) on environmental, healthcare, and taxation issues. He succeeds Tom Lauria, who will be leaving IBWA on September 30, 2011. www.bottledwater.org Chinaplas 2012 returns to Shanghai The 26th International Exhibition on Plastics and Rubber Industries, better known as Chinaplas 2012, will be held at Shanghai New International Expo Centre on April 18-21, 2012. The exhibition will occupy all 17 halls in the east, west and north wings of the fairground, with additional halls in the central square. The total exhibition area is expected to reach 200,000m2, 33.3% more than when the last edition was held at Shanghai, in 2010. The organiser, Adsale Exhibition Services Ltd, expects over 100,000 trade visitors from 140 countries or regions, more than 2,600 exhibitors from 35 countries, and there will be eleven country/region pavilions from Austria, Canada, France, Germany, Italy, Japan, PR China, Taiwan, Turkey, UK and USA. Online preregistration is now available. www.ChinaplasOnline.com Are your standard PET preform molds making you as much money as they should? Ask how MPET with iFlow technology improves production and achieves greater quality results. Innovation doesn’t happen in isolation. It happens when blue-sky thinking meets down to earth knowhow and exceptional supply chain execution. The sort of innovation that Mold-Masters is known for, now applied to PET tooling for industry-leading results. Introducing MPET – the new PET preform tooling solution designed for the standards of tomorrow. Mold-Mastersand theMold-Masters logoare trademarksofMold-Masters (2007) Limited. © 2011Mold-Masters (2007) Limited.All rights reserved. Think about it. moldmasters.com/thinkaboutit info@moldmasters.com","@ID":9} "REGIONAL MARKET REPORTS 10 PETplanet insider Vol. 12 No. 10/11 www.petpla.net Lithuania / Estonia The honour of being “geographical centre of Europe” has long been the subject of intense debate, and a number of places have laid claim to the title over the last few centuries. It was only in 1989 that the Institut Géographique National, the National Geographical Institute of France, finally laid the matter to rest by awarding the coveted title to the tiny village of Purnuškės, slightly north of Vilnius in Lithuania, lying on the coordinates 54° 54′ 0″ N, 25° 19′ 0″ E. Lithuania itself, with a population of 3.4 million, is one of the smallest of the EU Member States, whose total population numbers some 500 million. Lithuania has another claim to fame: not only the centre of Europe but for some years at the very heart of European PET production. We visited Orion Global PET UAB (Indorama Ventures), the Retal Group, and UAB Putoksnis. Being round the corner, we went to Estonia and visited Senderlen, a stretch blow moulding company and A le Coq, an Estonian beverage company, to get a view of the beverage market in Estonia. preform production. In 2004 the situation changed abruptly with Lithuania’s admission to the EU. All of a sudden both plants were in the EU. The so-called competitive advantage had gone. Nevertheless, Lithuania was already so well established in the PET business that this had no impact on its production figures. Today the two plants are still operating at full capacity and they have, in addition, weathered the storm of the 2010 PET crisis relatively well. Indorama Venture because it was fortunate in having its own PTA capacity and the Neo Group because they reacted to the crisis in a highly flexible by Alexander Büchler Around a quarter of the European requirement of PET material comes from this small country on the Baltic. The local plant of Indorama Ventures, Global orion PET, and the Neo Group (part of the Retal Group) are both based in the port of Klaipeda – cheek by jowl, so-to-speak. When the two plants were being built around the turn of the century, Lithuania was still not part of the EU. In those days, producers set out to supply the booming Eastern markets with material and to circumvent the EU PET import duties that existed at the time by means of downstream Regional market reports Lithuania Part 1","@ID":12} "BOTTLE MAKING 23 PETplanet insider Vol. 12 No. 10/11 Biggest market is Far East 40% mainly beverages to end users Second biggest is Europe 25% mainly beverages trend in Europe to specials To follow North America mainly specials to converters South America mainly edible oil, detergents Africa and CIS Applications In Europe wide mouth jars for hot fill,standard jars for cold fill and low production volumes, “difficult to handle” containers in two stage (flat preforms, snap neck finishes) (see photo page 24). China and US produce big volumes of jars oval, asymmetricals big volumes of heat set bottles. Major trends in single stage production – the Sipa view The trend for using single stage technology in Europe is for the production of “complex” containers or for strongly marketing driven customers as i.e. Procter & Gamble, Unilever, GSK. These companies are quality orientated. Converters are being pushed into single stage due to potentially better quality/cost ratio. General Manager Enrico Gribaudo states: “Converters are focusing on higher added value sectors, where the packaging is very technical and they can combine their technical expertise with excellent manufacturing technology. They also need to show flexibility in production whether it is with single stage or two stage technology, depending on the specific scenario.” Sipa employs 1,400 employees globally, of which 35% abroad – a large part in engineering with six manufacturing plants (two in Italy, one each in China, Mexico, Brazil and Romania), 16 branch offices world wide and 22 service centres. Gianfranco Zoppas is the owner and chairman of Zoppas Industries, of which Sipa is a vital part. In a Top Talk with PETplanet in 2005 he said: “I believe that (for PET processing) the best solution is single stage technology.” He subsequently made substantial investment in two stage technologies by developing a machinery platform for preform injection moulding, and adding numerous models to the linear and rotary blow moulding range. His most recent move was to purchase Berchi for filling PET bottles in line. In the same Top Talk interview with PETplanet, Gianfranco Zoppas quoted his sales figures being “approximately €200 millions evenly balanced between one stage and two stage”. As the company is privately owned, current figures do not need to be disclosed and are not available. Single stage – so we were told – currently represents 25% of sales. Blowers (rotary and linear) appear to be Sipa’s bestsellers. Even without knowing the figures and just from our visit to the Vittorio Veneto facility, Sipa is clearly","@ID":25} "TRADESHOW PREVIEW 46 PETplanet insider Vol. 12 No. 10/11 www.petpla.net Light-weighting solutions from PET Engineering The bearable lightness of PET Several producers and bottlers are already following the path of environmental sustainability. They understand the advantages in cost savings, reduction in raw material usage and, in terms of marketing, satisfying the desire of consumers to make conscious choices in defense of their environment and health. The ‘Green’ choice, in the field of beverage packaging, essentially leads in one direction: container light-weighting. PET Engineering provides its customers with different solutions aimed at significantly reducing container weight and raw material use. The company will be showcasing some of its new lightweighting solutions at Brau Beviale. A number of aesthetic and technological variables must be taken into consideration when developing light or ultra-light bottles. They have a big impact on consumer choice, on brand perception, and on the manufacturing process and logistics. Light-weighting of containers is the result of technologies applied to each area of the container: neck finish, shoulder, body and base. New business units, new projects Neck finish conversion can enable weight reduction of up to 50%. This change has a big impact on the production process and on filling line dynamics. With SBU, the new business unit in charge of NFC (neck finish conversion), PET Engineering says that it is able to support its customers through the entire conversion process. SBU led a project for PepsiCo Russia, where five factories, with a total of 14 blowing machines, were involved in neck conversion. The project brought PepsiCo Russia a considerable cost saving in raw material and, at the same time, helped it to cope with the increasing problem of environmental impact. The shoulder area has been the subject of several studies undertaken by PET Engineering’s R&D Department. Research led to the development of Swerve, a patented solution that can reduce excess material under the support ledge. Swerve is described by the company as a flexible technology that does not have a major impact on the line. Swerve has already been applied to the new Levissima Fly bottles. The 0.5l container is currently being produced with just 9.9g of PET. The designers and engineers achieved lightweighting of the body and the base and delivered the concept with original and strong visual impact solutions. With Barel, its new division dedicated to Design, PET Engineering approaches the study of ecofriendly packaging from an aesthetic point of view. The development of original packaging, which is designed to be both creative and practical, is achieved through studies that aim to deliver lightweight containers with style and shelf appeal. Beer bottle solutions PET Engineering will be presenting ideas specifically developed for Brau Beviale 2011. The intention of the company is to show that high-level design and high tech content can coexist with ecological concerns. Axi Beer is intended to meet the needs of those who want to achieve on-shelf differentiation through the novel use of lines and materials that resemble the appearance of glass. LW Beer, a lightweighted proposal, weighs just 36g in 1.5l size and has a PCO 1881 closure. Its focus is on cost savings and reduced environmental impact, while presenting a stylish shape and fresh decorations that easily identify the product. www.petengineering.com PET Engineering Hall 7 | Booth 236+337","@ID":48} "54 PETplanet insider Vol. 12 No. 10/11 www.petpla.net PETbottles Personal Care 2-phase Alverde The health and beauty retailer dm from Karlsruhe, Germany, has a 100ml 2-phase make-up remover with nurturing oils on the shelves in a round PET-bottle under the brandname “alverde Natural Cosmetics“. A matt, nonlabel-look label with silver lettering and a colour-coordinated screw cap with integrated dispensing aid ensure a high-quality presentation for product and packaging at the POS. www.dm-drogeriemarkt.de New from Herbal Under the umbrella brand name Clairol, Procter & Gamble are supplementing their Herbal Essences Shampoo range with additional variants throughout Europe. Here, for example, “Natural Volume“ and “Drama Clean“ are new on the market. The eye-catching, curved bottles are fitted with a Non-Label-Look label at the front and have a snap-on, 2-part closure that can be easily opened using just one hand. The coloured products, together with the printing on the inside of the rear label, can be counted on to attract attention at the POS. www.herbalessences.de Natural liquid soap The French soap manufacturer Savonnerie du Midi is selling liquid soap in a round 1l content PET bottle under the brand name of “Maître Savon de Marseille“. The clear bottle features a self-adhesive paper label and an aluminium screw cap. www.savonneriedumidi.fr Nurturing shower gel The cosmetics manufacturer Lornamead of Hamburg is offering 200ml nurturing shower gel with 43% natural, plant-based oils for sensitive and dry skin in a transparent PET bottle under the brand name “CD“. The bottle features a Non-Label-Look label to the front and, because of the printing on the inside of the rear paper label and depending on the light, eye-catching visual effects are noticeable in the packaging at the POS. A colourless, snap-on lid that can be operated with one hand is used as a closure for the bottle. www.cd-koerperpflege.de","@ID":56} "PETbottles 52 PETplanet insider Vol. 12 No. 10/11 www.petpla.net 100 ml Coffee-Shot The German discounter Lidl from Neckarsulm is marketing 3 x 100ml “Espresso Macchiato“ all’italiano in PET bottles under the brand name “Bellarom”. Three small bottles are linked by means of a brightly coloured, printed sleeve to form a single sales unit at the POS. Each bottle is decorated with a shrink sleeve label and comes complete with a screw cap with a tear-off tamperproof seal. The bottler is the Gropper Dairy located in Bissingen, Germany. www.lidl.de Shiny Red Bull Red Bull from Fuschl am See, Austria has restyled its 330ml PET deposit bottle. The handy bottle features a high-gloss, silver-coloured shrink sleeve label which is pulled over the screw cap (also shiny and silver in colour) to form a tamperproof seal. The top part of the label can be removed via a readily identifiable perforation in order to open the bottle. The pack’s high gloss factor means that it catches the eye immediately at the POS. www.redbull.de Spanish Sangria 1.5l Spanish Sangria punch, brand name “El Curador“ – manufactured in Germany – is being sold all over Europe by Messrs. Hauser Wine Imports of Fischbach in a large PET bottle. The extremely round bodied bottle has an informative, brightly coloured printed shrink sleeve label and a red screw cap with tear-off tamper-proof seal. www.hauser-weine.de Fine Food German retail giant Metro is selling milk in a 1l PET bottle under its own premium label, Fine Food. The tall, easy grip bottles have a shrink sleeve label with a nature-orientated design and a 32mm screw cap with tamper-proof seal. The shelf life of the low-fat UHT milk and UHT fullcream milk is six months if kept in cold storage. www.metrofinefoods.com SPHERO® underwater pelletizers Beautiful things are formed underwater. Your single source for comprehensive pelletizing solutions. Expert pre-sales advice and post-sales service included. www.maag.com Meet us at Fakuma Hall A6, booth 6202 Recycling line recoSTAR PET iV+ Ongoing PET recycling innovation, quality and state-of-the-art technology, a full range of consulting services – brought to you by Starlinger. Visit us at: Equiplast 2011, November 14 - 18, Barcelona, Spain, Booth C322 www.starlinger.com","@ID":54} "BOTTLING / FILLING 28 PETplanet insider Vol. 12 No. 10/11 www.petpla.net Refriso Bebidas increases its PET capacities The many flavours of Brazil Brazil is the third largest market in the world for consumption of carbonated soft drinks, helped also by its warm climate. One of the main players in this enormous “business” is located in Sorocaba, a town close to San Paolo in Brazil, where the company Refriso Bebidas has its headquarters. To increase the capacity of the 2l- bottle PET line, the Brazilian company recently purchased from SMI a stretch-blow moulder and a shrinkwrapper which are able to reach production speeds of 18,000bph and 35 packs per minute. The majority of carbonated soft drinks brands produced in Brazil has, as their basic ingredient, a fruit, seed or extract deriving from locally-grown plants. In fact, in this large South American country, there is an exceptional variety of fruits, a large amount of which are used in the industrial production of fruit juices and carbonated soft drinks. Just think of guaranabased drinks, which are made from a seed grown in the Amazon forest, whose consumption in Brazil exceeds that of cola-based drinks.* Refriso Bebidas occupies a strong position among carbonated soft drinks manufacturers in Latin America. The company has been able to seize market opportunities and meet the growing demand for soft drinks which has been witnessed in Brazil in recent years. Faced with an increasingly demanding market, Refriso has managed to diversify its product portfolio, which now includes numerous brands of carbonated soft drinks, colas, energy drinks, fruit juices and other beverages. The “Bacana” brand is among the most successful of the Brazilian company and includes carbonated soft drinks in several different flavours (cola, cola light, guarana, lemon, Tutti Frutti and grape, to name just a few). Other product brands offer an equally broad range of beverages with the flavours of cola, guarana, grape, pineapple, etc. Production technology The Refriso production system is completely automated and enables rapid transitions from one container to another and one pack configuration to another. To enhance production of the 2-l PET bottles, for bottling products under the “Bacana” brand, Refriso Bebidas turned to the technical expertise of SMI, opting for a 10 cavity stretch-blow moulder from the Smiform SR series; for end of line packaging, the Brazilian company chose an Smiflexi LSK 35F shrinkwrapper, which packs 2-l PET bottles in 3x2 shrink film packs. The machine is also, however, able to package other types of containers already used","@ID":30} "MARKET SURVEY 32 PETplanet insider Vol. 12 No. 10/11 www.petpla.net MARKETsurvey 10/11 Company name Neuman & Esser Deutschland GmbH & Co. KG Arizaga, Bastarrica y Cía, S.A. Postal address Telephone number Web site address Contact name Function Direct telephone number Fax E-Mail Werkstraße, 52531 Übach-Palenberg, Germany +49 2451 - 481 100 www.neuman-esser.com Mrs. Martina Frenz Marketing +49 2451 - 481 154 +49 2451 - 481 100 martina.frenz@neuman-esser.de Pol. Ind. Azitain 6, 20600 Eibar, Spain +34 943 820 400 www.abc-compressors.com Ignacio Azcuna Product Manager +34 630 751 355 +34 943 820 235 iazcuna@abc-compressors.com 1. Machine designation / model number 3TEV63-3V1-2V1 Boosters 3THA-3-LT 4HA-4-TER-LT 3HA-4-LT 3HA-4-TER-LT 4HA-6-TER-LT 4HA-6-TRIS-LT 4HP-4-LT 2. Number of models in range 3 14 3 4 4 2 4 4 5 3. Output in m³/hr 1,300-2,000 10,000 535 875 1,050 1,450 1,730 2,321 3,135 4. Compressor type oilfree reciprocating compressor Low pressure air High pressure blowing air (up to 40 bar) high pressure reciprocating Integrated system reciprocating 5. Lubricated or Oil-free oilfree Low pressure compressor Booster compressor yes Oil-free Integrated system yes complete package unit oil-free 6. Machine layout 7. Number of compressor stages 2/3 1 or 2 3 4 3 3 4 4 4 8. Are special foundations required? no no no no no no no no no 9. Cooling system closed cooling water system W water 10. Belt or direct drive V-belt Low pressure compressor Booster compressor yes belt Integrated system yes belt belt belt belt belt belt belt Company name Ingersoll Rand Company Postal address Telephone number Web site address Contact name Function Direct telephone number Fax E-Mail 800 D Beaty Street, Davidson, North Carolina, USA +1704 655-4000 www.air.ingersollrand.com George Mankos Global Portfolio Manager +1 704 655-4311 +1 704 655-4039 george_mankos@irco.com 1. Machine designation / model number PETStar –3 Models – 170, 210, 260, 310 2. Number of models in range 4 models 3. Output in m³/hr PS3 170 [170 m3/ h], PS3 210 [216 m3/ h], PS3 260 [245 m3/ h], PS3 310 [287 m3/ h]. 4. Compressor type 3-stage from atmosphere reciprocating to 40 Bar Low pressure air High pressure blowing air (up to 40 bar) Integrated system 5. Lubricated or Oil-free oil-free Low pressure compressor Booster compressor Integrated system 6. Machine layout W layout 7. Number of compressor stages 3-stages of compression double acting. 8. Are special foundations required? No special foundations are required. Unit can be mounted using typical practice of grouting & anchoring or on anti-vibration mounts on standard factory floor 9. Cooling system water cooled 10. Belt or direct drive Low pressure compressor Booster compressor Integrated system belt drive","@ID":34} "PRODUCTS 50 PETplanet insider Vol. 12 No. 10/11 www.petpla.net Drying and condensate separators Whether it is going to be used in injection moulding of preforms or in extrusion into films, PET always needs to be dried, and amorphous basic materials also need to be crystallised. If recycled PET is processed in the form of postconsumer flakes, volatile impurities and by-products must be removed from the drying and moulding process, safely. The systems engineering necessary for these process steps is, in principle, also suitable for the treatment of biopolymers such as PLA (polylactide). Mann+Hummel claims that its Somos D 200 dry air dryer, with air flow rate of 200 m³/h, is an exemplar of the new generation of stationary material drying systems. Equipped with drying hoppers from 50 to 300l, it can be modularly combined and flexibly expanded into a customised drying facility. In PET processing applications, material throughputs ranging from 500 to 2,000kg/h are standard, so larger sized dryers and dryer hoppers are available. The company’s new MH25 controller controls the triggering of dew point-constant dry air and Mann+Hummel says that new design features enable more flexible application of the dryers. The Somos D 200 dryer recently demonstrated at the Interpack trade fair was expandable from 200 m3/h (nominal) up to 500m³/h by adjustment in control technology, which also enabled a reliable increase in dried material throughput from 100kg/h up to 250kg/h, without extra hardware. The company claims its newly-designed rotary desiccant container process control helps to reduce cycle time for drying agent regeneration, thus saving energy. Mann+Hummel’s latest modular condensate separator consists of three serially connected units: the prefilter module for dust separation from process air; the cooling unit for cooling contaminating substances below the dew point; and a demister module as the actual condensate separator. The company says that it achieves very effective filtration of volatile contaminants, such as monomers, by-products and dust particles from return air from the drying hopper. All modular units are easily accessible and can be cleaned quickly and easily. www.mann-hummel.com Fully-automated APC testing American company Mocon, Inc., has launched what it says is the world’s first fully-automated testing system for measuring bacterial aerobic plate count (APC). The GreenLight 930 is aimed at high-throughput companies and laboratories involved with dairy, meat, poultry, seafood, and other produce. Mocon says that the GreenLight series has been developed to provide accurate, same-day results, cost-effectively. Results can be obtained in anything from a few minutes up to 8h. Traditional agar or film plate methods typically require 48 hours. The GreenLight series provides an APC or total viable count (TVC) of a food sample’s microbial load by using a sensing assay or vial, to measure oxygen consumption by bacterial colonies. The change in oxygen is used to calculate the original sample’s colony forming units per gram (CFU/g) for solids or per ml for liquids. The 930 model automates the process via a 48-position carousel. Food samples are loaded into barcoded vials, with built-in sensor material. Each barcode is read automatically and bacterial information is fed directly to the PC. The company says that shorter testing cycles offer packers and processors the potential of getting perishable food items to the consumer faster. www.mocon.com Moretto S.p.A. Via dell’Artigianato 3 - 35010 Massanzago (PD) ITALY Tel. +39 049 93 96 711 - Fax +39 049 93 96 710 www.moretto.com The innovative shape of the OTX hopper solves the falling flow problems of the granules and permits to keep the drying process under control. designed by Moretto Drying Revolution Stand 7A - 431","@ID":52} "BOTTLING / FILLING 29 PETplanet insider Vol. 12 No. 10/11 www.petpla.net *Guarana and guarana-based soft drinks The indigenous peoples of South America have always considered guarana to be an elixir of life; an extremely valuable plant which provided them with food and a means of curing disease, alleviating pain and increasing physical stamina, by virtue of its tonic and stimulating properties. Only the seeds of this plant were used, which each tribe used according to its own “recipe”. Tradition has it that clusters of half-open fruit were collected and put into containers filled with cold water to extract the outer layers. After being cleaned, the extracts were roasted over a low heat and reduced to a powder, to which a small amount of water was added to form a smooth paste. From this mixture “log” shapes were extracted and smoked on a fire of resinous wood. The log obtained in this way was grated when required. Guarana is widely used in South America to prepare a famous soft drink, which is slightly fizzy, known by the same name, which, especially in Brazil, is synonymous with “soda”. The drink looks and tastes similar to cola-based drinks. It has a slightly stimulating effect and a sweet taste. As a medicine, it is available in tablets, sticks and, better still, powder. Still today, guarana is used to improve concentration, physical and mental stamina and to bring energy to the body. Refriso Bebida’s production line is completely automated by the Brazilian company, such as aluminium cans. SMI do Brasil, SMI’s local branch, has played a crucial role in advising Refriso of the best solutions for its present and future production requirements. All drinks which leave the company’s plants are subjected to continuous quality controls by a dedicated technical team. An equal amount of care is put into the selection of raw materials and suppliers. www.smigroup.it SOMOS® MANN+HUMMEL ProTec GmbH Stubenwald-Allee 9, 64625 Bensheim/Germany Tel. +49 6251 77061-0 E-Mail: info@mh-protec.com www.mh-protec.com Injection moulding or extrusion: Superior materials processing will add more value to your operation! 3119","@ID":31} "BOTTLING / FILLING 27 PETplanet insider Vol. 12 No. 10/11 www.petpla.net hour and requires only one operator. The mobile water packaging solutions come in different shapes; filling and closing systems can be ordered mounted in a container, on a skid or inside a trailer. The system loads PET preforms in bulk and orientates them to enter into the bottle production line. When the PET bottles have been formed by the stretch-blow-moulding machine, they are filled and capped without human intervention. The labelling device automatically applies a selfadhesive label indicating production dates or batch. Largersized bottles have a carrying handle automatically applied. A similar fully automated plant is available for the filling and sealing of standard or sectioned pouches for ‘camel-bak’ applications. The plants help to improve logistics operation in terms of personnel, fuel, trucks, transportation and overall costs and offer a lower ecological footprint than shipping full bottles. The PET preforms are easy to transport, reuse, shred and recycle locally. Conteno’s solution offers flexibility in packaging choices. For example, pouches are often a better packaging format for refill supplies than bottles for camel-baks. Recyclable PET bottles of different volumes can be the solution for other applications and uses and the company offers a range of forms and shapes, depending on specific customer requirements. www.conteno.com The mini factory only needs one operator A look inside the containerized water bottling plant","@ID":29} "BOTTLE MAKING 20 PETplanet insider Vol. 12 No. 10/11 www.petpla.net Single stage feature part 4 Suppliers of single stage machinery Three suppliers of single stage machinery, Nissei ASB, Sipa and Aoki, currently control the global markets. We visited the offices of Nissei ASB, Aoki Technical Laboratories and Sipa. After presenting Nissei ASB in issue 9 we now complete our feature on single stage machinery suppliers with the reports on Aoki and Sipa.. possible by all the people involved in the manufacturing process working together as a team with integrity and a passion, understanding and sharing the our vision and ideas. Aoki has come a long way, however, we are not complacent with our success in the market. Our greatest competition is ourselves. We have to remain focused on our goals and apply ourselves to ongoing improvements and enhancements to what we do.” Aoki technology Direct Heatcon is the Aoki flagship. Although Aoki and Nissei ASB share a common origin, the two companies have very different products. The ASB series was and still is based on the four-station model, whereas Aoki developed a three-station machine with Direct Heatcon system in 1984. The three stations are: preform injection moulding and direct heat conditioning stretch-blow moulding product ejection. In the Direct Heatcon process, the preform heat conditioning is carried out in the injection mould, where ambient temperature has “no effect on production”, heat energy is retained Aoki Technical Laboratories Meeting with Hidenaga Nakagawa, Director: “Aoki is a laboratory. We are a research and development based enterprise committed in pursuit of the advancement of international culture and the protection of our natural environment through our business.” The European office of Aoki is located in central Düsseldorf. Mr. Hidenaga Nakagawa, Director of the subsidiary, welcomed us in his office. The spacious offices occupy the top floors a high rise building, with extensive areas given over to overwhelming number of samples of all types and sizes of PET containers, all injection stretch blow moulded on Aoki’s single step machines. Aoki Technical Laboratory, Inc., originally founded in 1976 as a R&D company, still consider themselves today as the same and original “research and development-based enterprise” as when it was started. The manufacture of Aoki single step machines and the genuine moulds is carried out exclusively in Nagano/ Japan under the most stringent quality control conditions. The “Aoki philosophy” Asked about Aoki’s philosophy, Hidenaga Nakagawa explains: “Aoki is a laboratory. The role of a laboratory is not to be satisfied with the status quo, but to set the focus on a span of ten years ahead. If we had sat back, we could not have developed new machine models to differentiate our products from others. We would have moved our machine manufacturing facilities to other countries with cheap manufacturing and labour cost, more people required to do the work, mistakes, compromises and errors. To respond to the challenges of the market Aoki has come up with its “Direct Heatcon” molding technology – the unique and simplest molding system that enables stable production of high quality containers, while reducing wasted material and electricity costs. Machines and quality made by Aoki in Japan are made","@ID":22}
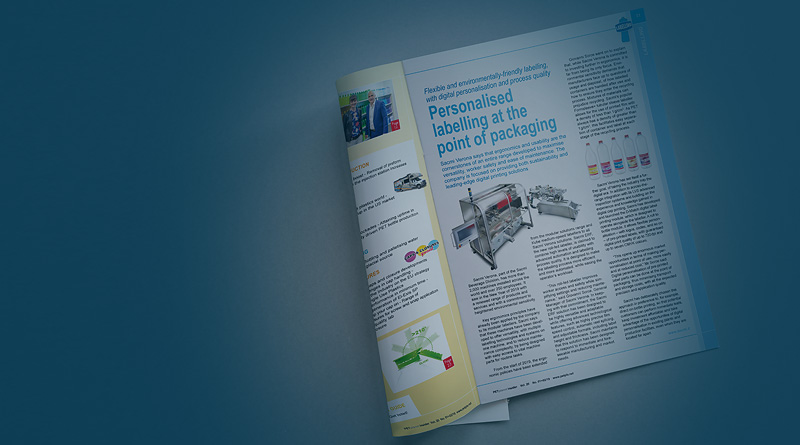