{"pages":{"page":[{"#text":"PETnews 6 PETplanet insider Vol. 12 No. 06/11 www.petpla.net Husky acquires KTW Husky Injection Molding Systems has completed its acquisition of KTW of Waidhofen, Austria, a leading manufacturer and global supplier of closure mould-making. Husky says that the acquisition makes it the closure industry’s only provider of complete injection moulding systems, including mould, machine, hot runner and temperature controller, as well the provision of a range of consulting and after-sales services. Husky will offer KTW-branded closure moulds as part of its fully-integrated turnkey systems. www.husky.ca M&G to build next-generation PET and PTA plants in the U.S. The M&G Group, of Tortona, Italy, has announced that it will build a next-generation technology PET plant in the United States, co-located and fully integrated with a new PTA plant at the same site. Approximately 250 jobs will be created at the plants, with an additional 700 indirect positions and 3,000 jobs during construction. PTA (purified terephthalic acid) is the primary raw material used in the production of PET. The new PET single line plant will have a capacity of 1,000kt/a (approx 2.2 billion lbs/year) and will employ, on a larger scale, the same technology as M&G’s single-reactor Suape (Brazil) PET plant, which came on stream in Q1 2007 and has since been successfully debottlenecked to 650 kt/a. The PTA unit will have a capacity of 1,200 kt/a (approx 2.6 billion lbs/year), and will provide full upstream integration for all of M&G’s U.S. PET capacity. The new plant will be sited in Texas, Mississippi or Louisiana. The announcement of the selected location is expected by the end of June. www.gruppomg.com Amcor acquires Ball Plastics Packaging (Americas) Amcor Rigid Plastics North America has acquired all production sites previously belonging to Ball Plastics Packaging Americas. Amcor is the leading North American manufacturer of PET bottles for beverages, liquid foods and custom applications. Assets acquired with the takeover of Ball include the InnoPET Plasmax barrier coating system developed by KHS Plasmax and installed at multiple facilities by Ball during the past few years. InnoPET Plasmax is a patented silicone oxide (SiO x ) interior barrier coating that has glass-like features but without the weight. It protects contents from escape or ingress of O 2 or CO 2, and from flavour scalping. Amcor says that internal plasma coating with SiO x will continue to be used as a universal barrier system for sensitive products. Amcor supplies the North American market with over a quarter of a billion Plasmax coated PET bottles annually. www.amcor.com Colormatrix acquires Grayson Silicone Dispersions ColorMatrix Corporation, the thermoplastic industry additive, colorant and dosing technologies supplier, has announced its acquisition of Gayson Silicone Dispersions Inc., based in Barberton, Ohio, USA. Gayson is a specialist in high consistency rubber (HCR), liquid silicone rubber (LSR) and room temperature vulcanisation (RTV) silicone, and in dispersions (colorants and additives) for silicone rubber. The company supplies manufacturers across diverse industries including automotive / aerospace parts, airbag coatings, healthcare, cosmetics, household and architectural products. The acquisition is in line with ColorMatrix’s strategy of expansion into new markets and technologies through both internal R&D and acquisitions, while also enabling the extension of its application capabilities. www.colormatrix.com Interpack 2011 reflects upturn Interpack 2011, the trade fair for the packaging sector and related processing industries, attracted 2,700 exhibitors from 60 nations, spread across 19 halls at the Düsseldorf Trade Fair Centre from May 12 to 18, 2011. Around 166,000 trade visitors attended, of whom more than 100,000 were from outside of Germany and approaching three-quarters were decision-makers and management level. A number of exhibitors reported specific orders and Christian Traumann, President of interpack 2011 and Managing Director of exhibitor Multivac Sepp Haggenmüller, said that his company’s stand had generated 30% more contacts than at the last Interpack, in 2008. Sustainability, safety and convenience were the overriding themes at the exhibition. The ‘Save Food’ campaign, which aims to fight international food loss and was organised by Messe Düsseldorf in cooperation with the Food and Agriculture Organisation (FAO) of the United Nations, was unveiled at the exhibition and attracted over 300 congress participants, ranging from food producers and the packaging industry through to retailers and representatives of politics, society and non-government organisations. ‘Innovationparc Packaging’ brought companies from across the value chain to a series of workshops covering best practices for the future. The next Interpack will take place in May 2014, at Dusseldorf. www.interpack.com","@ID":8} "PETcontents 06/11 4 PETplanet insider Vol. 12 No. 06/11 www.petpla.net INSIDE TRACK 3 Editorial 4 Contents 6 News 30 Products 31 Bottles BUYER’S GUIDE 29 Get listed! BOTTLE MAKING 16 Single-stage or two-stage PET conversion - that is the question! Single stage feature part 1 MARKET SURVEY 17 Suppliers of preform moulds and stretch blow moulds CAPPING / CLOSURES 24 Of countries and caps Study about PET bottle caps MATERIALS / RECYCLING 8 A partnership of first water Gerolsteiner gets together with Strautmann PREFORM PRODUCTION 18 Parting line crease Troubleshooting- a hands on guide - part 21 SPECIAL: BARRIER PET BOTTLES 12 The future of beer in PET packaging Global study on beer in PET 14 New wine in new (PET) bottles 187ml single-serve bottle gains favour with American wineries 15 Better barriers for beer and beverages New barrier technologies for lighter PET bottles 28 Products for barrier PET bottles manufacture Page 16 Page 10 28% 17% 10% 45% Multilayer Monolayer blends Coated monolayer Standard non-barrier PET Refillable 0% Page 12 BARRIER PET BOTTLES","@ID":6} "imprint EDITORIAL PUBLISHER Alexander Büchler, Managing Director HEAD OFFICE heidelberg business media GmbH Landhausstr. 4 69115 Heidelberg, Germany phone: +49(0)6221-65108-0 fax: +49(0)6221-65108-28 info@hbmedia.net EDITORIAL Doris Fischer fischer@hbmedia.net Michael Maruschke Ruari McCallion Ilona Trotter Wolfgang von Schroeter Anthony Withers MEDIA CONSULTANTS Ute Andrä andrae@hbmedia.net Martina Hischmann hirschmann@hbmedia.net Ursula Wachter wachter@hbmedia.net phone: +49(0)6221-65108-0 fax: +49(0)6221-65108-28 France, Italy, Spain, UK Elisabeth Maria Köpke phone: +49(0)6201-878925 fax: +49(0)6201-878926 koepke@hbmedia.net LAYOUT AND PREPRESS Exprim Kommunikationsdesign Matthias Gaumann | www.exprim.de READER SERVICES Kay Krüger reader@hbmedia.net PRINT Chroma Druck & Verlag GmbH Werkstraße 25 67354 Römerberg Germany WWW www.petpla.net | india.petpla.net PETplanet insider ISSN 1438-9459 is published 10 times a year. This publication is sent to qualified subscribers (1-year subscription 149 EUR, 2-year subscription 289 EUR, Young professionals’ subscription 99 EUR. Magazines will be dispatched to you by airmail). Not to be reproduced in any form without permission from the publisher. Note: The fact that product names may not be identified as trade marks is not an indication that such names are not registered trademarks. 3 PETplanet insider Vol. 12 No. 06/11 www.petpla.net Due to the dominant position of two-stage conversion in PET markets, our magazine has inevitably focused on this sector. It was a deliberate policy on our part, reflecting the interest in high volume production, the issue of cavitations, increased speeds and cycle times, all of which are the core concerns of the beverages sector. Although PET is a staple of this sector, it is also being used increasingly in other areas, such as the cosmetics, pharmaceutical and food industries. Here, however, it is the single-stage process which takes centre stage, combining injection and blow-moulding in one single unit. We at PETplanet Insider take pride in our reputation as “the magazine for bottlers and bottle makers”, irrespective of whether the PET bottle is made by the single-stage or two-stage process. Recognising that some very innovative ideas are being generated by the singlestage process, we decided to take a closer look at the sector. The new applications offered by the single-stage process are bound to be of interest to all of us in the industry, whether we are bottlers, converters, machine manufacturers, and, of course, the world-wide readership of PETplanet. Starting today, and continuing in forthcoming issues of the magazine, we are presenting a short series of articles focusing on the major questions raised by the single-stage and the two-stage processes. We have canvassed the views of the experts. Here is Karel Keersmaekers of Nissei ASB with the confident assertion that: “Single-stage is pushing the technical boundaries of bottle development.” Some of the major players in the single-stage sector tend to avoid the public gaze, preferring a more low-key approach. Kaoru Yoshimatsu, CEO of Aoki, is typical. When we spoke to him in Mexico some years ago, he made his view quite clear: “We would rather make millions of dollars than millions of bottles.” A sly reference to the fact that specialised single-stage applications offer the potential for bigger profit margins. Might this cause converters in the beverages sector to sit up and take notice? After all, they are constantly seeking bigger volumes and better margins. Ever alert to the importance of keeping abreast of new developments, we at PETplanet Insider have undertaken a comprehensive investigation of the single-stage market. We spoke to the major players and other experts in an effort to clarify the key issues. Amongst them: which technology is most appropriate for specific applications? Are there any regional issues that need to be taken into account? To learn more, read our in-depth review on page 16f. Yours, Wolfgang von Schroeter EDITORIAL dear readers, EDITORIAL EDITORIAL dear readers,","@ID":5} "NEWS 7 PETplanet insider Vol. 12 No. 06/11 www.petpla.net Are your standard PET preform molds making you as much money as they should? Ask how MPET with iFlow technology improves production and achieves greater quality results. Innovation doesn’t happen in isolation. It happens when blue-sky thinking meets down to earth knowhow and exceptional supply chain execution. The sort of innovation that Mold-Masters is known for, now applied to PET tooling for industry-leading results. Introducing MPET – the new PET preform tooling solution designed for the standards of tomorrow. Mold-Masters and theMold-Masters logoare trademarks ofMold-Masters (2007) Limited. ©2011Mold-Masters (2007) Limited.All rights reserved. Think about it. moldmasters.com/thinkaboutit info@moldmasters.com KHS machine operating concept wins two iF awards KHS GmbH has won both the iF product design award 2011 and the iF gold award for its new machine operating concept. The concept was developed in close collaboration with the Fraunhofer IAO Institute. It enables both machines and entire production lines to be controlled and monitored on a single interface, rather than by many and differing graphical user interfaces (GUIs). KHS says that operator prompting uses easy-to-decipher buttons, coloured graphics and icons, and interactive handling instructions in a plain, simple, user-friendly way, presenting complex processes in a manner that is easy to understand. The multistructured layout grants access to various detailed views and operating levels. The new interface also allows user profiles to be accessed with an ID card, displaying relevant data to specific individual users. The next development planned for the operating concept is adaptation for use on mobile hand-held devices, enabling operation independent of any particular stationary workstation. Over 2,700 products from 43 different countries were entered for the iF product design award and around 1,000 of them received a prize. Nearly 900 entries were submitted for the iF communication design award 2011 from 27 countries, with the jury presenting the iF seal over 200 times. Only 30 of the prize-winning products were later given the additional iF gold award. www.khs.com R&D/Leverage increases manufacturing and support capacity Four consecutive years of double-digit growth has led R&D/Leverage – UK to expand its manufacturing capacity by 40% in 2010. Recent new business wins in the UK and continental Europe have prompted the company to install another injection stretch blow moulding machine to its Product Solutions Laboratory (PSL), to further increase capacity. The PSL is a buildingwithin-a-building that offers customers training modules and the capability to provide first-to-market samples. The company says that it can now qualify almost any product, including extreme shapes and extreme specifications, in-house. Earlier in 2011, the company added two new sales account managers to handle customers throughout northern and central Europe. www.rdleverage.com","@ID":9} "PRODUCTS 29 PETplanet insider Vol. 12 No. 06/11 Light barrier technology ColorMatrix has unveiled a light blocking technology for PET dairy bottles, named Lactra. It is an opaque white liquid technology that ensures light-blocking at low addition rates. The company says that it maintains container aesthetics and that it is suitable for both single and multilayer PET containers. It provides protection from UV and visible light at wavelengths up to 550nm, which is appropriate for extending shelf life in dairy applications such as milks, yoghurts and dairy beverages. Lactra is used at an addition rate of 6-8% for light-blocking performance equivalent to the norm of 20% for other barrier additives. ColorMatrix says that this is due to its latest generation liquid carrier system, ‘CoolRun’, whose dispersion capability enables optimisation of pigment particle size, helps to ensure stable processing, consistent colour distribution and can help minimise AA (acetaldehyde) levels. Aesthetic finishes include white matt or silk finish. Lactra:eXtraShield offers even higher light blocking capabilities. The technologies are compatible with any PET grade and are fully compliant with EU and FDA food contact legislation. Amosorb SolO 2 , another ColorMatrix PET barrier technology, combines oxygen scavenging with barrier properties and provides extended product protection and longer shelf-life in oxygen-sensitive beverages, particularly beers, wines and juices. Colour can be easily added, so brand owners and converters can preserve product aesthetics. Amosorb SolO 2 can delay CO 2 egress by up to 30 days and protect from O 2 ingress for up to four months longer than PET with standard Amosorb. Amosorb SolO 2 can be used with any type of PET resin and is suitable for both monolayer and multilayer PET containers. www.colormatrix.com technology EnginEEring Tooling life cycle PACKAGinG FLEXIBLE SOLUTIONS RELIABLE SUPPORT Thinking of The big picTure & The minor deTails We don’t believe in delivering on one thing and not the other. At Sidel, we offer you the complete package of solutions for your business and the 24/7 support of a strong partner. From packaging development through filling right up to end of line, we bring everything to the table making sure that you receive the highest level of reliability and flexibility matched to the unique needs of your production line. work with us & GEtA BETTER MATCH www.sidel.com EcoSmart chillers Piovan’s EcoSmart, launched in 2010, currently includes three lines: the CA Series of air cooled chillers, the water-cooled CW series, and the CR series, with remote condenser. A number of structural, functional and design features contribute to the machines’ reliability, energy efficiency (even with partial loads), and accurate control of temperature and other operating parameters. The screw compressor is driven by a frequency converter and fan speed is continuously adjusted for the actual conditions of the environment and immediate demands of production. The ‘oversized’ evaporator and condenser are designed to maintain high heat transfer rates, even when working with partial loads, and thus achieve improved efficiency. An electronic expansion valve limits the pressure difference of the coolant fluid between input and outlet and performs controls of the fluid lamination phase, with constant adjustment of evaporation. An oil flow switch ensures that the compressor is always working under appropriate conditions. The EcoSmart’s Coefficient Of Performance (COP) figure is 9.43, compared to 4.31 for a standard chiller with screw compressor of the same size. At 50% load, EcoSmart’s COP actually rose, to over 10. The great efficiency means lower energy consumption. All EcoSmart chillers have an operator intuitive interface for setting and microprocessor control of the operating parameters, and can also be operated by a remote control option. www.piovan.com Barrier PeT BoTTleS","@ID":31} "Vol.6 PETplanet print PREFORM PRODUCTION 10 PETplanet insider Vol. 12 No. 06/11 www.petpla.net Parting Line Crease Part 21 of the “Rapid Guide to Perfect Preforms” * *by Rick Unterlander and Ottmar Brandau Troubleshooting guides have suffered in the past from being locked away in offices and not being available to the people that actually need them. Considering the high cost of machine and tools high scrap rates can be a costly proposition eating away at already tight margins. PETplanet’s “Rapid Guide to Perfect Preforms” takes a different approach. Bound in laminated paper that is easy to clean off, the small format of the book of 108mm by 151mm (4.25” by 6”) allows easy storage in back pockets or tool boxes. It has been written for the people on the floor of injection moulding companies to support their daily work in making the best preforms possible. The product of two industry experts, Rick Unterlander and Ottmar Brandau, it gives concrete advice on 35 of the most common problems in preform manufacture, most illustrated by pictures. From high AA levels to wavy bodies processors can find help when they need it. Read chapter 21 of the guide. fax: +49 (0) 6221-65108-28 info@hbmedia.net www.petpla.net Order your copy now! PETplanet print vol.6 The Rapid Guide to Perfect Preforms machine no./name Symptom: A small radial fold appears in the preform body at the parting line between the neck insert and the cavity. Cause: The preform body is deformed during the initial mould opening sequence (core side separating from cavity side) due to the preform not releasing freely from the cavity. Solutions: 1. Check water cooling temperature. This should be 7 – 10ºC (45 - 50ºF) for optimum cooling. 2. Check water cooling flow to mould. This should be at the mould manufacturer’s rating (for a given preform size and cavitation). 3. Check that the cooling time is sufficient for the preform being moulded. This typically ranges from about 1 to 3sec depending upon the preform wall thickness. Add time if necessary to increase shrinkage for better release. 4. Check that the hold (packing) time isn’t excessive for the preform being moulded. Reduce as necessary to minimize swelling. 5. Check that the hold (packing) pressure isn’t too high to cause excessive swelling, especially in the last zone. Reduce as necessary. 6. Check that transition position is set to about 13% of shotsize + cushion. Lower values may result in overfilling. 7. Check all temperature readings and correct if necessary. PET resin should be melted at about 280ºC (536ºF) +/- 10ºC (18ºF).","@ID":12} "BOTTLE MAKING 17 PETplanet insider Vol. 12 No. 06/11 www.petpla.net PET conversion - that is the question! Another obstacle for greater sales of two stage machines is that newly developed equipment has become more productive, more effective, enjoys a much longer life time on the shop floor and needs replacing less frequently. Applications The market situation of single stage PET processing is very different: single stage markets tend to be niche markets, with an abundance of PET containers in small to medium quantities, in sizes from very small to very large, in all round, rectangular, oval and other shapes – a golden opportunity for the designers - , with large neck for jars and/or with and without neck. Some distinctive single stage examples: Champagne base or Split type conditioning blow, i.e. stretch blow moulding polypropylene narrow necked containers or Extreme oval, by using an ovalised conditioning station component or Deep pinch grip Front parting line Handle moulding - post-moulded or in-moulded - and/or handle moulded on neck or PET can with very thin upper flange or Off-centre neck or Fixed neck orientation or Complex neck design/ very short necks allowing greater flexibility on cap design or Long Neck Liquor Design or Zero/Minimum Support Ring etc. With the application described single stage markets have made great advances over the years – parallel to, but in the shade of the two stage markets with the eye-catching spectacle of fast cycling and record number of cavitations and greatly reduced cycle times. “Inevitably, more applications will come onstream ” – as Karel Keersmaekers – Managing Director of Nissei ASB in Europe – told us: “The number of applications is increasing every year. So does the number of customers using single stage. We are continuously on the lookout for new applications – together with our customers.” The majority of users of single stage machines are converters, who supply the bottles ready made for filling. Their customers are drivers of innovative packaging – with the largest portfolio of creative ideas, often inspired by fashionable trends in perfume, often inspired by extravagant promotions in cosmetics. In food the substitution of glass is in full swing – due to cost advantages with PET packaging. The same applies to the pharmaceutical sector. Managerial and geographical considerations in the rest of the world In Europe and US – no doubt - the special applications are the prime drivers of the single stage process. In other areas of the world managerial and logistic issues are playing into the hands of single stage, which we learned in Hangzhou/China at Wahaha, China’s largest water bottler: Why is single stage being used rather than the two stage process for Wahaha’s multi-billion bottle production? The directors of Wahaha – at the time of our visit – pointed to the simplicity of product management using the single stage process and mentioned transport and logistics in China, where cities are far apart . Two stage processes would require a centralised plant for manufacture of preforms. Transportation of preforms over long distances to blowing/filling plants around the country is costly, if not impossible due to the poor road infrastructure. For Wahaha, Sipa has developed single stage machines with an exceptionally high output. Product management and logistics are vital issues in many emerging markets in Asia, Africa and South America. In forthcoming issues of PETplanet: Single Stage Converters PET Power Single Stage Machine Makers Nissei ASB Aoki Sipa","@ID":19} "PETpatents www.verpackungspatente.de 32 PETplanet insider Vol. 12 No. 06/11 www.petpla.net Cap manufacture International Patent No. WO 2009 / 122118 A1 Applicant: Obrist Cloures Switzerland GmbH, Reinach (CH) Application date: 9.1.2009 When manufacturing multi-part caps it is necessary to use water or a cleaning agent. This international patent describes the structure of a cap where these liquids can be easily allowed to escape / can be removed from the cap. Carrier US - Patent Nr. US 2009 / 025357 A1 Applicant: Raymond R. Spivey, Mableton (US) Application date: 3.4.2009 Template for creating a carrier for a number of bottles. Screw cap European Grant of Patent No. EP 2038183 B1 Applicant: Capartis AG, Schaffhausen (CH) Application date: 29.6.2007 Screw cap that is economical to produce as well as easy to open and close. The closure enables comfortable and continuous drinking, It is suitable for carbonated drinks and exhibits good sealing characteristics. Plastic bottle International Patent No. WO 2011 / 006150 A1 Applicant: Colgate-Palmolive Comp., New York (US) Application date: 12.7.2010 Thin-walled plastic bottle made from PET / PET-related materials constructed in such a way that it is able to withstand the forces occurring in production, bottling and logistics without any plastic distortion. For this purpose reinforcement grooves / special mouldings are integrated in the walls of the container. Composite of beverage containers Disclosure No. DE 102009026125 A1 Applicant: Krones AG, Neutraubling (D) Application date: 7.7.2009 This disclosure describes the characteristics of a container and the process for manufacturing this container which makes it possible to join together a number of containers by means of positive fit, frictional or material engagement and/or force-fit connections to form a composite structure. Closure with oxygen separator European Grant of Patent No. EP 1789341 B1 Applicant: Schoeller Caps Technologies Sarl, Romont (CH) Application date: 8.7.2005 Tamper-proof screw cap for a plastic bottle. The cap is fitted on the inside with an oxygen-separating layer so as to extend the life of the bottled product. To increase the oxygen-binding, reactive surface this layer is defined as “keyed“.","@ID":34} "CAPPING / CLOSURES 26 for example, a cap that is more than 1mm higher is required. In the case of South Africa, we again find a deviation from any proportionality between the cap height and weight, albeit to a lesser extent. Fig. 4 illustrates the comparison as described above for bottles in excess of 0.5l up to 1.5l. In this category Austria and the USA demonstrate the highest and the heaviest caps, featuring a height greater than 16mm and a weight of approx. 3.5g. Vietnam, with a cap height of 11.3mm and a cap weight of less than 2g, lies at the other end of the scale. The other countries are grouped together in a middle sector which in turn enables a degree of proportionality between the weight of the cap and its height to be identified. One exception in this category is France, where the caps, despite a relatively small cap height of 12.8mm, have a weight of 2.8g which is clearly above the weight of the German bottles (which is in any event relatively high). Fig 5 illustrates the cap on a premium water from Austria which, in addition to the design of the bottle, presents an individualised effect with ribbing and a tapered shape. Such individualisation makes it an exotic addition to the range of bottles that predominantly – with the exception of one or two ‘scene’ drinks – make use of standard caps where any attempt Making an even bigger splash in 2011 FoodBev Media is pleased to present the 2011 Water Innovation Awards - designed to recognise excellence and creativity in the global packaged water industry. Beginning as the bottledwaterworld design awards in 2002, this is FoodBev Media’s longest established international awards scheme. Previous Awards have been presented in Paris, Dubai, Bergamo, Wiesbaden and Gleneagles. This year, the announcement of finalists and winners will be made at a special Awards Gala Dinner during the Global Bottled Water Congress in Rio de Janeiro, Brazil on 14 September 2011. For more information and to enter, please visit www.waterinnovationawards.com JgcXj_ Fb\\X s ;i\\Xdjk`d\\%Zfd Fig. 4: Cap weight and height by countries - bottles 0.5l to 1.5l Fig 5: Vöslauer/ 0.2L, non-carbonated mineral water, Austria PETplanet insider Vol. 12 No. 06/11 www.petpla.net","@ID":28} "BOTTLE MAKING 16 PETplanet insider Vol. 12 No. 06/11 www.petpla.net Single stage conversion - How does it fit in? Single stage or two stage Single stage feature- part 1 by Wolfgang von Schroeter It is estimated that 80% of PET resin converted into bottles is processed in two stage technology and 20% in single stage technology. PETplanet Insider decided to take a closer look at the 20%! and Netstal for injection moulding, Sidel and Krones for blow moulding. The single stage market remained a domain of the Japanese, until Sipa joined in the late 1980s with massive, big size, high output single stage machinery of American origin. Single stage PET processing PET processing in principle is the same in single-stage and twostage: PET resin is plasticised, then injected into the preform mould and afterwards blown to make the bottle. The machinery involved: two separate machines for injecting and blowing in two-stage compared to the one single compact machine that does it all in one single stage. Typically, the single stage process will produce 5,000 to 10,000 bph, whilst the two-stage production can give - typically and economically - 30,000 to 50,000bhp - naturally there are exceptions, but generally these figures are accurate in most cases. It is estimated that 80% of PET resin converted into bottles is processed in two stage technology and 20% in single stage technology. Typical single stage application are bottles for food, cosmetics including perfumes, pharmaceutical and detergents. Variable formats in small and medium sized volume emerging markets. Engineering challenge: variable formats, flexible shapes and design, integrated caps, handles and grips. Typical two stage application are bottles for beverages, standard bottle formats, high volume and developed markets. Engineering is challenged today for better performance, higher thoughput, increased productivity, which boils down to more cavitations, shorter working cycles. The high volume beverage markets drive the two stage process. Certainly there are overlaps, i.e. applications, where both systems are used. Gino Duca, Business Development Manager of Sipa, should know, since Sipa develops, produces and sells both single stage and two stage machinery as well, when he says: “The right solution is driven by economics and depends on the specific circumstances. There are a lot of criteria in decision making: Geography, logistics, annual volumes and requirements, culture, issues involving service, buyer’s preferences and seller’s persuasiveness.” Markets Despite its dominant position two stage applications are reaching saturation point in developed markets. Machine suppliers have turned their attention to emerging markets – particularly on BRIC countries – Brazil, Russia, India and China. It is realistic to assume that requirements in BRIC states will eventually also reach saturation. The beginning The single stage or stage process of moulding PET bottles from PET resin was developed simultaneously together with processing PET in two stages - in the mid-1970s . At that time, when companies such as Cincinatti Milacron (injection moulding) and Husky (mould making) and Krupp Corpoplast (blow moulding) were experimenting with PET bottle processing in two stages with two separate moulding machines, - at the same time the first single stage conversion – i.e. injection stretch blow moulding in one machine - was developed in Japan by Aoki Technical Laboratories under the umbrella of Nissei Plastics, the latter being high volume manufacturer of injection moulding machines for general purpose application. Nissei ASB – sister company of Aoki, also under the umbrella of Nissei Plastics – was responsible for sales and marketing of what was developed and produced by Aoki Technical Laboratories at the time. The markets of single stage and two stage machines developed separately and in parallel. In subsequent years pioneering big players entered the two stage markets such as Husky","@ID":18} "BOTTLE MAKING 14 PETplanet insider Vol. 12 No. 06/11 www.petpla.net Better barriers for beer and beverages in PET bottles* The Institute of Plastics Processing at RWTH Aachen University is investigating new barrier technologies that can cope with the drive towards lighter weight bottles, as well as the growing trend to biopolymers. Among the solutions being investigated and evaluated is the use of plasmaassisted barrier coating with bias substrates. The protection qualities and permeability of beverage packages are important criteria in choosing the right packaging material. Demands on packaging materials are not just about the goods being packed, they are greatly magnified by today’s trends and developments, such as the increasing use of biopolymers and light-weighting of bottles [1, 2]. In order to meet those challenges, the German Institute of Plastics Processing (IKV) at RWTH Aachen University has been working for more than 20 years on the field of plasma-assisted barrier coating of polymers. As well as the conception and development of processes for interior and exterior coating of beverage bottles or coating of foils and plastic components, investigations have been focusing upon the development of suitable layer systems that will enhance the permeability and protection properties of plasma-polymer coatings. IKV is currently involved in a process that will enhance the barrier performance of plasma-polymer layers, through the use of a substrate-bias. Studies on foils have already shown that the deposition of barrier coatings using a substrate bias leads to a significant increase in its barrier properties because the negative effect of layer defects is reduced [3]. A plasma reactor (fig. 1) that enables biasing of the inserted polyethylene terephthalate (PET) bottle has recently been built and studies on this new technology are currently being undertaken. After the process has been successfully validated, attention will turn to other materials, such as polylactide (PLA). The substrate bias’ influence on coating flexibility will be evaluated, as well as coatings performance. Any possible influence on strain tolerance is crucial for applications such as carbonated soft drinks, as the stresses caused by the internal bottle pressure may lead to a stretching or even cracking of barrier coatings, which may result in higher gas permeation. Investigations will be undertaken in order to determine the extent to which deposition of multifunctional coatings, consisting of hard and soft layers, may increase the strain tolerance of the whole composite, while maintaining good barrier properties. Forschungsvereinigung Kunststoffverarbeitung (German Plastics Processing Research Association) research project 16306 N has been sponsored as part of the ‘industrielle Gemeinschaftsforschung und -entwicklung (Industrial Community Research and Development) by the Federal Ministry of Economics and Technology, pursuant to an enactment of the German federal Parliament through the AiF. www.ikv-aachen.de Fig. 1: Reactor for the substrate-biased interior plasma coating of plastic bottles *contributed by Ch. Hopmann, W. Michaeli, K. Bahroun, H. Behm, F. von Fragstein, Institute of Plastics Processing (IKV) at RWTH Aachen University, Germany References [1] P. Mapleston, Plastics Engineering Europe, (2005), 15-19. [2] D. Ulutürk, M. Gernhuber, Verpackungs-Rundschau, 61, (2010), 84-89. [3] A. Grüniger, A. Bieder, A. Sonnenfeld, P. R. Von Rohr, U. Müller, R. Hauert, Surface and Coatings Technology, 200, (2006), 4564-4571. BARRIER PET BOTTLES","@ID":16} "MARKET SURVEY 21 Simex srl Sipa Molds Solent Mould Tools Ltd. Sacmi Imola R&D Leverage Nissei ASB Machine Co., Ltd. Via M.Bigi e M. D'Antona , 5 60025 Loreto (AN) Italy +39 071 7500214 www.simexitaly.it Giuggiolini Graziano Sales Manager +39 335 453107 +39 071 7501958 giuggiolini@simexitaly.it Via Caduti del Lavoro 3, 31029 Vittorio Veneto +390438911511 www.sipa.it Peter dal Bo Molds Division Director +39 0438911511 +39 0438911694 peter.dalbo@zoppas.com 1 Relay Road, Waterlooville, Hampshire, PO7 7XA. UK +44 (0)23 9223 9950 www.solentmouldtools.co.uk Chris Smith Technical Sales & Service Manager +44 23 9223 9950 +44 23 9223 9951 chris.smith@solentmouldtools.co.uk Via Selice Provinciale 17/a 40026 Imola (Bo) Italy +39 0542 607111 www.sacmi.com Moraldo Masi Business Manager Pet Division +39 0542 607888 moraldo.masi@sacmi.it Leverage House, Hamilton Road, Sutton In Ashfield, Nottinghamshire, NG17 5LD U.K. +44 1623 556287 www.rdleverage.com Damon Sykes Sales Manager +44 7974 072232 +44 1623 552240 Dsykes@rdleverage.com 4586-3 koo, Komoro-shi, Nagano-ken, 384-8585 Japan +81 267-23-1565 www.nisseiasb.co.jp/en Katsuo Ishiguro SectionManager +81 267-23-1565 +81 267-23-1564 sales@nisseiasb.co.jp 20l 30l 5l 3l 5ml to 30l 22l Yes No Yes Yes Side No - own machines only Yes Yes Yes Yes Yes Only for own machines Yes Sidel, Krones, KHS/SIG/Krupp, SMI, Siapi,Techlong, ADS, Multipet, Dynaplast, Kosme… Sidel, Krones, KHS, Siapi, Sipa Kosme, MAG & Nissei All leading brands (P&G, Henkel, Kallina, Unilever, L'Oreal, Bausch & Lomb, Innocent, Coca-Cola, Pepsi, etc) Moulds are customized on a per customer basis. Yes Yes: brandbuilding, product repositioning, marketing design, packaging engineering, etc… Yes Yes Yes, full Industrial design service Yes, complete design service from concept to finished molds and machines. PET containers for mineral water, soft drinks; milk, edible oil, isotonic, etc Wide mouth, asymmetrical, nitrogen hot fill, containers with handles, HDPE to PET conversions. EBM for PETG and change parts for most SBM platforms. Bottle design service and after sales technical service including processing. Flat and carbonated water, CSD, edible oil Supplier of tooling services to the single stage and two stage markets Handled, non-round, wide-neck, hot fill, non-round neck, offset neck, heavy weight cosmetic, PET, PP, PC, PES, PEN, PLA, etc. Yes Yes yes up to 96 up to 144 2 -96 up to 72 All sizes up to 30ls up to 450g length up to 195mm Husky, Netstal, KraussMaffei, Hengel, Krupp. Cincinnati Milacron, Arburg, BMB, BM Biraghi Husky, Netstal, Engel, KraussMaffei & Krupp. Yes Yes up to 72 up to 96 2-96 8~32 All sizes up to 10l 450g Up to 180g Standard and custom Sipa, Krauss-Maffei KraussMaffei Own machines only Yes Yes, for Sipa machines Yes no Yes, with R&D owned proprietary hot runner system Genesis. Also unit tool and production testing on Nissei ASB70DPH V3 and V4 machines Yes, main business is single stage. Air recovery systems, rotary blowmoulder and filling lines spare parts Post mould cooling & parts. Röders TEC PET Engineering SRL Beaubury Precision Moulds Ltd Sidel Blowing & Services Demo Design and Moulds Scheibenstrasse 6, 29614 Soltau, Germany +49 5191 603 53 www.roeders.de Friedo Böhling Sales Manager +49 5191 603 53 +49 5191 603 36 mold@roeders.de Via Celtica 26, 31020 San Vendemiano (TV) - Italy +39 0438 403069 www.petengineering.com Moreno Barel President +39 0438 403069 +39 0438408420 info@petengineering.com 4 Telford Close, Rabans Lane Ind. Est. Aylesbury, Bucks. HP19 8DS United Kingdom +44 1296 43 43 11 www.beaubury.net Mark Sim Technical Sales Manager +44 1296 43 43 11 +44 1296 433 276 mark.sim@beaubury.net 4, Avenue de la Patrouille de France, Octeville-sur-mer, BP 204, 76053 Le Havre Cedex, France +33.2.32.85.86.87 www.sidel.com/ Laurent Charrier Tooling Product Manager +33 2 32 85 80 63 +33 2 32.85 81 69 laurent.charrier@sidel.com Via Olivera, 48 31020 San Vendemiano (TV) Italy +39 0438 409048 www.designandmoulds.com Alberto Castellan General Manager +39 0438 409048 +39 0438 409046 info@designandmoulds.com 10l up to 5l 5l 0.33l -10l 15l Yes Yes, sometimes Yes Yes Yes Yes Yes Yes Yes, moulds and perso parts, repairs & refurbishment Yes Sidel, KHS Corpoplast, Krones, SIPA, Kosme ADS, Nissei and other major machine types San Pellegrino, Pepsi Co., Efes, InBev, Baltika, Spumador, Norda, Fonti di Vinadio, Rocchetta, Acqua e terme di Uliveto, Ferrero, ….. Sidel, Sig (KHS), Side, Krones Coca-Cola, PepsiCo, Unilever, Amcor, Nestlé, Danone, Heineken, Ting Hsin Nestle, Pepsi, Inbev , Sangemini Yes & development & test blowing & laboratory available Yes Yes design, prototypes, sensitive products center Yes Solutions for compatibility of moulds between different machine types, special mould versions to reduce changeover times and cut mold costs Design and engineering of PET containers - blow mould supply - light weight process Experience in tooling for the moulding (EBM) of PETG in handleware sizes up to 6l All applications - all machines, all types of moulds: aluminium or stainless steel, aluminium 300F, Universal Shell, Jumbo, Magnum, SUPM, dual cavities, small cavities for high speed, Kohlox (2009) and Modulomold (2010) Bottle design, lightweight bottle, modified of existing blow moulds","@ID":23} "CAPPING / CLOSURES 25 PETplanet insider Vol. 12 No. 03/11 conventional and short threads, each in the order of around 45%. In a further consideration of the various thread standards, the weights and dimensions of the caps have also been recorded. In the following the various lid weights and heights are compared with one another on a country by country basis within the volume clusters 0.3l, 0.3l to 0.5l and 0.5l to 1.5l. Fig. 2 illustrates cap weights in Austria, France, Egypt, Kenya, USA and the UK for bottles with a volume of up to 0.3L. One interesting factor is the relatively small height of the cap in Austria, Egypt, the USA and the UK (less than 11.5mm). These, with the exception of the USA and despite their lack of height, feature the heaviest caps at more than 3g. The USA, with a very small average cap height of 11.5mm and weighing in at 2g, exhibits the lightest caps in this comparison. The highest caps in use, at almost 15mm, are to be found in Kenya and Thailand; however, at approx. 2.7g, these are considerably lighter than caps from Austria and Egypt. In our study, caps with drinking mouthpieces have been excluded from the evaluation to avoid distorting the results. By contrast to the cap comparisons illustrated in Figl 2, the category extending from 0.3l to 0.5l demonstrates an almost proportional relationship between the height of the cap and its weight (cf: Fig 3.) Here too special caps were excluded from the study so as to avoid any distortion of the result. The cap weights here lie in a significantly narrower band between 2.5g and 3.3g, whilst the cap heights are between 13.3mm and 15.4mm. The caps used in Germany are the exception in the analysis. Despite having the smallest average cap height in the comparison (13.3mm), their weight was found to be only average. By contrast, in Thailand Performance Filling & Capping Labelling Blowing Fig. 3: Cap weight and height by countries – bottles 0.3l to 0.5l","@ID":27} "MATERIAL / RECYCLING 9 PETplanet insider Vol. 12 No. 06/11 Mr. Kirstgen, Manager of the Recycling Centre at Gerolsteiner, explains: “We have gone for Strautmann environmental technology (BaleTainer) when it comes to compacting our cardboard packaging as well. Because of the greater density of the bales a larger quantity of waste can be processed. It also requires fewer staff“. As Mr. Carsten, Head of the Department of Facility Management, said, the last of the old horizontal channel baling presses used for compaction of perforated PET bottles is to be replaced by a briquetting press from Strautmann. New Glass Plant - Disposal of Intermediate Cardboard Layers A tray collection device loads the inverted trays and intermediate cardboard layers automatically on to a conveyor belt with the help of underpressure. These are subsequently conveyed to the opening of the BaleTainer in a fully automatic operation. The generously proportioned opening of the BaleTainer enables the cardboard trays to be off-loaded directly into the BaleTainer. According to E. Kirstgen, “The compact nature of the machine has also played a decisive role – due to the comparably small dimensions there was nothing standing in the way of incorporation in the production plant or in the production process”. The bales of cardboard weighing up to 550kg are also marketed directly – they go direct to the paper factory without compaction. Bales of cardboard PET briquettes: PET bottles compressed into briquettes BaleTainer: integrated in an automatic process for compacting cardboard Y O U R PA R T N E R F O R B L O W M O U L D S . Sidel • SIG • Krones • SIPA • MAG • ADS • Kosme • Nissei a. o. Röders GmbH / Scheibenstr. 6 / 29614 Soltau / Germany / www.roeders.de Telephone +49 5191-603-53 / Fax +49 5191-603-36 / E-Mail mold@roeders.de For our subsidiaries in China, USA and Latin America please check our website. PET STRETCH BLOW MOULDS Benef i t of 30 Years of Exper ience in Blow Mould Manufactur ing!","@ID":11} "PRODUCTS 30 PETplanet insider Vol. 12 No. 06/11 www.petpla.net High speed palletizing system End-of-line equipment for palletizing products needs to be safe and efficient as well as fast. In the past, high-speed solutions were reserved for traditional highlevel palletizers. By enhancing its existing machines and processes, Sidel claims to bring the same level of performance to low-level palletizers with its new SP 1000 HS palletizer. The new SP 1000 HS maintains steady pallets while the layers are in movement. During layer formation the machine rotates and positions the packs into a perfectly shaped layer to be transferred onto the pallet. In the following palletization phase, the layers are picked up and safely stacked onto the pallet with precision. Sidel managed to increase the speed of this process by improving the way the two steps of the process interact. The “pusher” is able to guide the layers alternatively to the right or to the left while optimizing the “return stroke” time, which, in the traditional approach, is substantially an “empty” movement. The process is supported by Sidel’s software program “Pallet and Layer Automated Configuration Editor” (PLACE). It creates and manages diverse pattern configurations before the layer-formation phase. The software, which can be installed either on the touch screen operator panel or on a PC, is compatible with Sidel’s Robo-Smart and Axo-Smart layer-preparation systems. It automatically checks whether the pallets are suitable and stable. Robo-Smart and Axo-Smart form and prepare the layers as the packs come off the production line onto the conveyor belts. Format changeovers regarding layer, bottles, or packs are entirely automatic and software-managed avoiding the need to stop the line. The operator simply has to choose the required format on the operator panel controls. For the second step in the palletization process, the SP 1000 HS permits use of either Robo-Kombi or Robo-Column which physically picks up the packs and places them on the pallets. Both solutions offer high-speed operation, easy integration with existing solutions, and versatile gripping for working with different formats, including crates, shrink-wrapped packs, loose bottles, plastic trays, empty PET bottles and others. www.sidel.com LitePac strapping While shrink-pack film is the most commonly used form of secondary packaging for PET containers, it requires fossil raw materials for its manufacture and relatively high energy consumption in the shrink-on process. Krones AG has developed a resource-economical alternative to film-wrapped shrink-packs as a complete system, including packaging and associated machinery. Krones built upon strapping technology already trialled and used in other sectors to create a new packaging design for PET containers, called Krones LitePac. The company says that it addresses market demands for secondary packaging of PET containers, in eco-compatibility, resource economy, reduced energy consumption and cost savings. Krones’ newly-developed Evolite packer is made up of a container infeed module and a container strapping module. In the infeed module, containers are divided into two continuous lane flows. Four strapping units then create the LitePac packs in the container-strapping module. Krones claims that cost savings of more than 50% can be achieved, through lower packaging material costs and greatly reduced energy consumption, as the system eliminates the shrink tunnel and an additional handle applicator. The company says that it needs fewer conveyors, a smaller footprint, a simpler line layout, a smaller storage area in both the warehouse and the supermarket, and less pallet traffic. www.krones.com","@ID":32} "BOTTLE MAKING 12 PETplanet insider Vol. 12 No. 06/11 www.petpla.net The future of beer in PET packaging A major new study from Pira International*, The Future of Beer in PET Packaging - a multi-client study for brewers, brand owners, packaging converters and suppliers, published in May 2011, provides data on quantitative market sizes, segmented by barrier technology, bottle size, region and country. Production is expected to rise to 7.7bn bottles by 2015, led by emerging markets, but growth will be slow in most established regions. Technological developments are likely to help the growth and acceptance of PET packaging of beer. The 152-page study also provides technology and market forecasts to 2015. Demand for PET packaging continues to rise across a number of different categories, including juices and nectars, ready-to-drink (RTD) teas, functional drinks, flavoured waters and beer. However many brand owners continue to be reluctant to use PET packaging for beer. While it has not taken off on a large scale in many traditional beer-drinking countries, there is still a lot of interest in the potential for beer in PET and its perceived advantages. The emergence of new technologies is helping to challenge some negative perceptions and create opportunities for brewers, brand owners, packaging converters and suppliers. Nick Waite, Head of Market Research at Pira International says: “PET is increasingly used for the packaging of beer sold at outdoor events in mature markets. PET is more suitable than glass here for safety reasons, more than anything, as it is unbreakable, but it is also easy to carry around. Safety and convenience elements may, in time, lead to PET bottles being used in nightclubs – although it has not made significant inroads there to date.” Global PET beer bottle consumption is forecast to grow during the period 2010-15 at a CAGR of 5.3%, to reach 7.7 billion bottles. Central & Eastern Europe, the dominant market for PET beer bottles, will show good growth for beer in PET going forward, but growth rates are expected to be lower than during the 2003-08 pre-recession era, largely because of growing market maturity and higher taxes on beer in Russia and the Ukraine. In Asia-Pacific, China will lead demand for beer in PET but, here, PET beer bottle growth has generally been lower than was originally anticipated. Western Europe is forecast to grow PET beer bottle consumption at a relatively low rate; North America and South & Central America are forecast to show growth during the period 2010-15, but from a very low base. Nick Waite says: “Russia and other former Soviet countries are something of a special case. There was a significant reduction in glass bottle capacity in Russia at the time of Gorbachev’s anti-alcohol crusade in the 1980s and the effect was that glass bottles were reused repeatedly. The result was that glass lost some of its cachet and Russian consumers were a bit more open to the idea of PET.” Home consumption is very much the norm in Russia, with purchases in the past being direct from breweries and packed in bulk plastic bags. Thus, switching to 1-2 litre PET bottles made perfect sense. “Consumers like the convenience of PET. The way the market has developed in Russia/CIS is very different to other countries”. Global beer in PET demand will be spurred by the growing events market, faster growth in off-trade beer sales in most countries, and developing barrier technologies. In the absence of any major new beer brands entering the market or further marketing initiatives by brewers to promote beer in PET, growth is expected to be relatively modest. Forecasts also assume that there are no further initiatives taken to favour plastic beer bottles by national or local governments in an attempt to promote ‘safe drinking’ in public places 28% 17% 10% 45% Multilayer Monolayer blends Coated monolayer Standard non-barrier PET Refillable 0% Global PET beer bottle consumption by technology type, 2015 (millions of bottles). Source: Pira International BARRIER PET BOTTLES","@ID":14} "BOTTLE MAKING 13 PETplanet insider Vol. 12 No. 06/11 Full inspected! Sacmi Imola S.C. Via Selice Prov.le, 17/a 40026 Imola (BO) Italy Tel. +39 0542 607111 - Fax +39 0542 642354 E-mail: sacmi@sacmi.it www.sacmi.com PVS-2 in line sampling preform vision system. PVS2 system comes from the need of many preform producers to carry out a continuous quality control on their production. Preforms are checked by sampling (one complete shot every x minutes) then sent to the octabins together with the other preforms. The quality control is continuous and by sampling. The PVS-2 can be connected to any type of injection moulder or used as a standalone machine for the quality lab. The system can run at the speed of 1200 preforms/hour. According to Nick Waite: “Penetration has reached something of a plateau in many countries and is awaiting the next major push by the brewers. India is the recipient of one such push and growth there is likely to be very strong but as for China: the jury is out right now.” Technology Forecasts Technological advances support the development of PET beer packaging but further technology gains will be required for PET to realise its full potential in the beer market. Advances in barrier technologies have paved the way for PET bottles to be used for small, single-serve beverages such as beer and wine. Monolayer blends and barrier coating technologies are taking market share from multilayer bottles, thanks to technology advances and more competitive costs. Further developments in oxygen scavenging and barrier coating systems are anticipated over the next five years. Pasteurisation of PET beer bottles can pose major challenges to brewers. New developments for beer, such as multilayered and monolayered bottles that permit producers to pasteurise the bottle with the beer inside and prevent oxidation, are positioned to further support the development of PET beer bottles. PET bottles can be engineered, designed, use novel processing techniques and modified materials to survive pasteurisation. Nevertheless, further development of higher heat PET resin and bottles that can survive pasteurisation would be welcomed by brewers over the next five years. www.pira-international.com * Pira International provides strategic and technical consulting, testing, intelligence and events to help clients gain market insights, identify opportunities, evaluate product performance and manage compliance. 13","@ID":15} "BOTTLES PETbottles 31 PETplanet insider Vol. 12 No. 06/11 www.petpla.net IN EVERY BOTTLE THERE IS ALL OUR KNOW HOW. RESEARCH & DEVELOPMENT A constant projection towards the future oriented to search not only for new materials but also new PET technologies of transformation and innovative materials. CONSULTANCY A concrete answer to all your questions. We put at your disposal all our know-how for every single requirement. PROTOTYPATION Prototypes of containers and innovative preforms in record times: you will be able to touch with your hands the bottles within a short time after approval of the design. DESIGN Creativity in search of elegance and refinement. Innovative designs, ergonomic structures, eye-catching and functional containers. We give a true shape to your product! Baja‘Green’ PET bottles for Baja Precious olive oil The United States imports close to 99% of its olive oil from countries such as Italy, Spain, and even Australia. However, Baja California, in Mexico, is also a source of olive oil and bottler Mexiterra, LLC, of Santa Fe Springs, California, is seeking to satisfy US consumer demand for locallysourced fresh produce with Baja California-grown extra virgin olive oils. The company approached California-based EnVino, which manufactures plastic wine bottles for the U.S. wine and speciality foods markets, for a packaging solution that reflected the gourmet nature of its olive oil, while delivering ‘green’ benefits. EnVino licenses Constar’s MonOxbar oxygen scavenging technology to use in blow-moulding bottles. It protects the delicate flavour of Baja Precious extra virgin olive oil and extends shelf life for up to two years from date of harvest. The distinctive PET bottle includes a pouring spout that pops up when the screw cap is removed and retracts when it is replaced. The hand-harvested olives are cold-pressed within hours of harvesting, without the use of heat or chemicals. The PET bottle’s green colour, along with the MonOxbar technology, blocks UV rays and oxygen. The shatterproof lightweight bottle requires less energy to produce than glass and is cheaper to transport. Once the contents are consumed, the BPA-free bottles can be placed in kerbside recycling bins for use in other PET products such as clothing, carpeting and tyres. The lightweight PET bottle also supports Mexiterra’s on-line sales. EnVino says that the package chosen by Mexiterra is intended for Bordeaux wines but is perfectly suited for other products that require a lightweight, shatterproof, high barrier bottle. In addition to licensing oxygen barrier materials, www.BajaPrecious.com www.EnVino.com www.constar.net All-natural coconut water launched in Amcor 20oz PET bottle GreaterThan, based in Highland Park, Illinois, USA, has launched a new sports/hydration beverage based on coconut water and natural ingredients. It is being packaged and sold in Amcor’s first stock 20oz PET container, PowerFlex. The hot fill bottle offers a glass-like finish, a smooth feel, and easy labelling. Its long neck helps the new product to stand out in the competitive 20oz sports drinks segment. Amcor’s stock PowerFlex bottle features a patented panel-less design and provides a large, completely smooth and rib-less label panel. A diaphragm within the base draws upward as the liquid cools. It has a 38-mm finish, screw-top closure and the GreaterThan product is sold with coated paper labels. www.drinkgt.com www.amcor.com BARRIER PET BOTTLES","@ID":33} "CAPPING / CLOSURES 24 PETplanet insider Vol. 12 No. 06/11 www.petpla.net PET Bottle caps study Of countries and cap sizes Caps constitute the most important interface between the bottle and the consumer; caps are what determine the haptics when the customer opens the bottle and drinks the contents. In addition to this, the thread and the cap make a significant contribution to the overall weight of the bottle and as such present an element for consideration in the cooperative bottle study being carried out between PETplanet insider and KTI (Technical University of Ilmenau, Department of Plastics Technology). Features of the cap system covered include the type of thread, the diameter of the opening and weight and height of cover. of bottles covered. The dominant status of PCO is universally identifiable here. France and USA, however, show a significantly higher proportion of INE threads by comparison to Germany. In Germany the investigation focused on discount markets; here there is the possibility of a correlation with the proportion of PCO threads (almost 90%). Plans for a supplementary study into branded products are also underway with a view to producing a complete picture of the German PET bottle market. A further aspect for consideration is the length of the thread, and the facility for distinguishing between conventional and short threads. As can be seen from Fig. 1, in order to do this we have primarily drawn on the INE and PCO Standards in the form of a classification based on a tall / short representation. An overall view shows that the proportion of conventional threads is still significantly higher than the proportion of short threads; however, short threads do make up an appreciable proportion. In Egypt many more bottles featuring a short thread are used than bottles with a conventional thread. In Germany there is a uniform incidence of Fig. 1: Types of cap by country Fig. 2: Cap weight and height by countries – bottles up to 3l PCO threads set the dominating standard when it comes to the bottles under review (cf: Fig. 1) followed by the INE Standards. In Egypt INE caps feature even more prominently than PCO caps. A consideration of the distribution of the caps may be best undertaken by reference to the major countries such as Germany, France and the USA because these allow a statistically robust conclusion to be drawn as a result of the high number","@ID":26} "BOTTLE MAKING 15 PETplanet insider Vol. 12 No. 06/11 www.petpla.net 187ml single-serve bottle gains favour with American wineries New wine in new (PET) bottles Leading wineries in the USA are making increasing use of Amcor Rigid Plastics 187ml single-serve barrier PET bottles for their convenience, lower cost and ease of handling. American wineries such as Fetzer, of Hopland, Calif., and Cecchetti Wine Co., of Sonoma, Calif., are increasingly moving to PET as a lightweight option that provides glass-like clarity, portability, sustainability advantages, and reduced cost. According to Amcor Rigid Plastics, these and other wine companies are reporting consumer acceptance of these convenient, aluminium screw-cap bottles. The packages also provide the companies with entry into public venues that do not allow glass, because of the potential for breakage. As well as the convenience, a key feature is a unique barrier coating technology developed by KHS GmbH, which provides extended shelf life. The KHS Plasmax Silicon Oxide (SiOx) barrier coating seals the container from the inside to protect the contents from oxidation. Plasmax is an FDA-compliant enhanced passive barrier for oxygen-sensitive products. This ultra thin (less than 100nm) material is transparent and resistant to cracking, abrasion, and delamination. Moreover, it doesn’t degrade over time nor limit the storage time for empty bottles. The barrier coating is easily removed during the recycling process and does not contaminate the recycling system. Fetzer is the 10th-largest winery in the U.S. and also provider of co-packing services. The company bottles its entire 187ml line of white zinfandel, merlot, chardonnay, and cabernet wines in PET containers for sale at retail and chain stores. The bottles preserve the look of glass containers and run on the winery’s existing glass filling line, with minor adjustments. As they are one-sixth the weight of glass bottles, transport costs are significantly reduced. Cecchetti Wine Company supplies its Redtree brand of wines to Air Canada, British Airways, and now also to Continental Airlines. The convenience, cost advantages, supply chain efficiencies and sustainability of the barrier PET bottles fit well in the 187ml wine category, according to Kerry Drewry, sales manager for Amcor Rigid Plastics. “We expect continued growth for barrier PET containers in not only 187ml but a range of package sizes for wine,” he says. Cecchetti is also targeting retail distribution in the Midwest and will explore the viability of 1l barrier PET bottles for its wine brands. Amcor is continuing to work with other wineries seeking alternative packaging and its acquisition of Ball Plastics Packaging Americas means that the company now has full capability in-house for InnoPET Plasmax coating. PET barrier technology is also being targeted at other markets for oxygen-sensitive products. www.amcor.com Development Plastics-compatible design and injection-moulding simulation High Cavity Moulds The patented z-slides®-closure-mould-technology breaks the sound barriers of conventional cycle times and puts - as a modular system - new scales in ease of maintenance and operation of moulds. Multi-component Injection Moulds In the high-performance sector Technology Centre Plastics technology Production Support After Sales Service z-moulds a brand of z-werkzeugbau-gmbh Competent – professional – inspiring Hoechster Strasse 8 · 6850 Dornbirn, Austria · T +43 5572 7272-720 · www.z-moulds.com BARRIER PET BOTTLES","@ID":17} "BOTTLE MAKING 23 PETplanet insider Vol. 12 No. 06/11 www.petpla.net Increased use of ISBM in homecare packaging Enlightenment with PET Procter & Gamble’s Product Research Department (PRD) combines marketing and technical functions (including testing, functional performance, assessing store shelf impact and competitiveness) in identifying consumer needs and developing products. The design department, along with design agencies, manages development of package shapes. Packdev department is responsible for developing technical solutions that can be industrialised and implemented with third-parties, including Sidel. Patrick Etesse, Research Fellow at Procter & Gamble’s Global Packaging & Device Development R&D group in Brussels, describes the thoughts and strategy behind the company’s increasing use of injection stretch blow moulding (ISBM) packaging. ?: What is P&G’s process for package development? Patrick Etesse: Innovating to win with more consumers in more parts of the world more completely: package development perfectly illustrates this strategy of P&G. Our Product Research Department, which combines marketing and technical sensibilities, works to understand consumer needs and develops products that meet them. Our design department focuses on the brand experience, in other words, the package and all the sensory aspects of the product and package experience. Our designers manage the development of package shapes with design agencies. The PackDev Department then translates the Design Department’s expectations into a technical solution that can be industrialized and implemented with external partners such as converters or suppliers like Sidel. Last but not least, a mandatory step for any package development is its validation through testing such as impact on store shelves against competitor products, functional performance, etc. ?: Where does innovation come into this? Patrick Etesse: The package is the first and the last thing that the consumer sees. Innovation in packaging is crucial, since the brand image is at stake. Innovation is now increasingly undertaken in collaboration with external partners, such as Sidel. Together, we develop technical solutions for packaging, such as neck indexing to show the direction to pour from. We drive outsourcing and prefer not to manufacture our own packages. We want to use innovation to meet the needs of the consumer. ?: How do you identify brand specifics within the package? Patrick Etesse: P&G’s packages are mostly extrusion blow-moulded (EBM) HDPE, which requires management of several hundred specifications. The company is seeking to simplify its processes, in order to increase productivity. One of the solutions is to switch to injection stretch blow moulding (ISBM). This enables different converters to use the same type of machine and standardisation of bottle specifications.” This means that P&G can achieve faster global roll out of new developments and to leverage its size in creating economies of scale. It has selected Sidel as its strategic technological partner and is moving to make all of its ISBM platforms Sidel compatible. ?: Is the switch to ISBM already a reality for P&G? Patrick Etesse: “Today, P&G produces about six billion bottles per year, 80% from extruded HDPE and 20% from blown PET. We are looking to drive ISBM in the next 15 years and to increase significantly the percentage of ISBM bottles in our portfolio.” P&G believes that ISBM has the capability to deliver advantages in scale and simplification but it also needs improved costs in order to fully exploit scale and capability opportunities. “What interests us above all is the ISBM technology itself, and PET is the material best suited for this technology today. The ISBM process enhances the properties of plastics: the flexural modulus is significantly increased, compared with processing by extrusion, and this leads to packages that are 20% lighter on average, while retaining mechanical characteristics and reducing both costs and environmental impact. Direct coupling is also possible, as blow moulding speeds are up to five times faster than extrusion. ?: Thank you very much! Patrick Etesse, Research Fellow at Procter & Gamble’s","@ID":25} "PREFORM PRODUCTION 11 PETplanet insider Vol. 12 No. 06/11 Table of Contents i................ About the Authors ii........................ Introduction chapter 1..................... AA Level High 2................ Accordion Preform 3...............Air hooks / Streaks 4....................... Black Specks 5.............................. Bubbles 6......................... Burn Marks 7.................. Colour Streaking .........................../Peeling 8......................... Crystallinity 9........................ Drool Marks 10..................................Flash 11.................Gate Depressions 12....................... Gate Peeling 13......... Gate Voids / Pin Holes 14.................Internal Gate Sink 15....................... Internal Sinks 16................................IV Loss 17................... Long Gate Nub 18...................... Milky Preform 19....................Moisture Marks 20....... Neck Finish out of Round 21...............Parting Line Crease 22........ Parting Line Deformation 23.................Preform Yellowing 24..........................Short Shots 25..................................Sinks 26.................................Splay 27...................Stretched Necks 28.............................Stringing 29.................Surface Blemishes 30.................Thread Flow Lines 31...... TSS (Top Sealing Surface) .................................Sink 32.............................. Unmelts 33........ Wall Thickness Variation 34.........................Wavy Body 35..........................Weld Lines 8. Check that all thermocouples are properly inserted and contacting the bottom of the wells. 9. Check that the decompression (pullback) time and position is not too little. This should be set high enough to ensure the melt pressure is being released, yet as low as possible to minimize the risk of drawing in air. Typical settings for valve gated moulds are: Time = 0 – 1sec; Distance = 0 – 10mm. Non-valve gated moulds may require higher values to minimize gate stringing. With a long story in packaging engineering SIPA can support its customers on lightweight preform development as well as preform lightweight conversions on existing mold. SIPA has developed specific neck ring design solutions for an optimal cooling and cycle time, even in case of short preform and neck finish conversion. SIPA provides complete preform mold for any PET system (up to 96 cav.), cold half for existing hot half (up to 144 cav.), hot half for existing cold half (up to 96 cav.); furthermore it provides conversions of existing mold (full or partial kits), mold spare parts and refurbishment. All SIPA preform molds feature LongLife™, a new design engineered to extend the mold service life. LongLife™ PET preform molds with strong focus on lightweight. www.sipa.it 10. Check the valve gate open delay timer and increase as necessary to release preform pressure. Typical settings are 0 – 0.3sec. This adjustment must work together with decompression (pullback) time. 11. Check hardware for worn, damaged or failed components, specifically the cavities, and clogged core / cavity cooling channels.","@ID":13} "19 Mould tools for PET bottle production As part of our annual market overview we shall once again be presenting our at-a-glance overview of 27 global AND regional suppliers of mould tools for PET bottle production. Not only manufacturers of moulds for preform manufacture like Otto Hofstetter, MPET/Mold-Masters, MHT and Husky are featured, but also the stretch blow moulding suppliers as PET Engineering, Krones, Kiefer, KHS, Beaubury, Sidel and Demo. And, of course, there are a number of companies, who include both in their product portfolios (Sipa, Sacmi, TPS, Solent Mould Tools, R&D, Petka, Kisan, Nissei (for single stage), Simex and Passcard. Although the publishers have made every effort to ensure that the information in this survey is up to date, no claims are made regarding completeness or accuracy 06/11 MARKETsurvey Company name Otto Hofstetter AG MPET/Mold-Masters Europa GmbH MHT Mold & Hotrunner Technology AG Husky Injection Molding Systems Postal address Telephone number Web site address Contact name Function Direct telephone number Fax E-mail Zürcherstrasse 73, 8730 Uznach, Switzerland +41 55 285 22 11 www.otto-hofstetter.com Stefan Zatti Division Manager Sales & Marketing +41 55 285 22 09 +41 55 285 22 44 zat@otto-hofstetter.ch Neumattring 1, 76532 Baden Baden, Germany +49 722150990 www.moldmasters.com/mpet Oliver Lindenberg Director Business Development, EMEA +49 1622896026 +49 7221 53093 olindenberg@moldmasters.com Dr. Ruben-Rausing-Str. 7, D-65239 Hochheim/Main, Germany +49 6146-906-0 www.mht-ag.de Volker Jährling VP of Sales and Service +49 6146-906-122 +49 6146-906-399 vjaehrling@mht-ag.de 500 Queen Street S. Bolton, Ontario, Canada L7E 5S5 905-951-5050 www.husky.ca Robin Lovell Product Manager +1 905-951-5000 rlovell@husky.ca Preform moulds Horizontal opening Number of cavities 2-192 2-192 2-192 2-196 Preform sizes up to 500g up to 5 gl 20l up to 600g for bottles up to 30l All. Accomodated preform lengths from 28mm to 310mm. Moulds already built for (makes) Netstal, Arburg, BMB, Husky All major brands of PET-systems Different pitches from 50x120 up to 125x185 Netstal, Husky, Engel, Arburg, Cincinnati, SIG, BMB H-PETAE, HyPET, HyPET HPP, HyPET RF Vertical opening Number of cavities 2-96 2-96 2-96 Preform sizes up to 500g up to 5l up to 600g, for bottles up to 30l Pitch Various Any Different pitches from 50x120 up to 125x185 Moulds already built for (makes) Arburg, Krauss-Maffei All major brands of PET systems Do you produce single stage tooling sets ?(Preform moulds AND blow moulds) No Single stage preform moulds No No Other Multilayer moulds up to 72 cavities moulds for PP moulds for thinwall packaging moulds for cartridges and tubes Quick change preform moulds co-injection high performance hot runners for major brands of PET moulds Wide mouth, high performance moulds, up to 8 gallon, trigger moulds, moulds for vacuum blood test tubes Bottle-to-bottle recycling plants Conveyors for preforms and empty bottles Caps and closures Preforms Perform moulds and SBM moulds Preform and single stage machinery 2-stage SBM machinery Compressors Filling equipment Resins and additives","@ID":21} "MARKET SURVEY 20 MARKETsurvey 06/11 Company name Kisan Precision Company Ltd. TPS - Tooling Preform Systems BV Petka Mold Industry Pass Card Co. , LTd. Postal address Telephone number Web site address Contact name Function Direct telephone number Fax E-mail 33-4, Wonmi-Dong, Wonmi-Gu, Buscheon City, Kyunggi-Do, Korea +82-32-663-6377 www.ksmold.com Kenneth Kang Sales Director +82-32-663-6377 +82-32-663-6379 inq@ksmold.com C. Houtmanastraat 42, 7825VG Emmen, The Netherlands +31 591 679768 www.tps.nl Richard Tempel Sales Manager PET +31 6 25041136 +31 591 630616 info@tps.nl Yesiloba Mah.46075 Sok. No 8 Seyhan/Adana/Turkey +90 3224286400 www.petkamold.com Tarik Sivri General Manager +90 532 5248990 +90 3224282303 info@petkamold.com No.1517 Sec.8 Huanzhong Rd.,Wuri dist. Taichung City 414, Taiwan +886-4-2335-9689 www.passcard.com.tw Chad Huang Sales Manager +886-975-127035 +886-4-2335-9855 chad@passcard.com.tw Stretch blow moulds Bottle size (max.) (in litres) 2l 50l 0.1l -19l 20l Moulds supplied directly to blowing machine manufacturers No No Yes Do you supply retrofit moulds for existing SBM machines? Yes Yes Yes Yes For which makes of bottle makes have you already produced moulds Yes Sidel, Siapi, SIG, Krones, Chum and others Sidel,Krones,Siapi,Sipa,Cosme, ADS,SMI,Krupp,MAG,Combi Sipa/ Sipai/ Krones/ Chum Power / Chai Ming Bottle design service Yes Yes Yes Yes, modified Specialities Large preforms and containers. 5gl up to 50l Supply of bottle prototype PET preform moulds, stretch blow moulds, thin wall moulds, caps and closure moulds PET vaccum blood test tube moulds Preform moulds Horizontal opening Yes Number of cavities 2-96 96 2-96 1-72 Preform sizes 28-110mm all, up to 650g 14mm-110mm neck finish 3.9g -750g Moulds already built for (makes) CM, KM, Husky Husky, Netstall, SIG/Engel, Arburg, Battenfeld, Demag, FCH and others Husky, Netstal, KraussMaffei Sipa Vertical opening Number of cavities 48 96 96 8~32 Preform sizes 28mm All, up to 650g Pitch 120x50 up to 200x85 50*130 Moulds already built for (makes) KM ASB two stage machines Do you produce single stage tooling sets Preform moulds AND blow moulds) Yes, for Aoki & Nissei No Yes, moulds for single stage machines(ASB,Aoki) Yes Other Design, development and prototyping for various applications. In-house preform and blowing machinery up to 50l. Lab facility for all preform/ container tests available .Recently completed 4l Heineken Tapje Thuis draft container development. PET moulds only:preform moulds ,blow moulds,single stage moulds Design service: 1) Body texture; 2) Bottom design: Deco Lug / Star Pattern/ Specific logo Company name Krones AG Kiefer Werkzeugbau GmbH KHS Corpoplast GmbH & Co. KG Postal address Telephone number Web site address Contact name Function Direct telephone number Fax E-mail Böhmerwaldstr. 5, 93073 Neutraubling, Germany +49 9401 70-0 www.krones.com Peter Christiansen Sales Manager Plastics Technology +49 9401 70 4980 +49 9401 70 914980 peter.christiansen@krones.com Steinhaldenweg 11, 74193 Schwaigern +49 7138 9732 0 www.kiefer-mold.de Jörn Herget Sales PET blow-mold +49 7138 9732 70 +49 7138 9732 92 joern.herget@kiefer-mold.de Meiendorfer Strasse 203, 22145 Hamburg +49 40 679 070 www.khs.com Volkhard Adam Head of Modernization +49 40 679 07 361 +49 40 679 07 9361 volkhard.adam@khs.com Stretch blow moulds Bottle size (max.) (in litres) 3l 5l up to 8l Moulds supplied directly to blowing machine manufacturers No No Yes Do you supply retrofit moulds for existing SBM machines? Yes No Yes For which makes of bottle makes have you already produced moulds Krones, Sidel, Sipa, KHS Corpoplast Krones,Sipa, Sidel, KHS/ SIG etc. Mainly for KHS Corpoplast InnoPET Blomax SBM Bottle design service Yes Yes Yes Specialities Bottle development services, customized to filling and packaging lines with performance commitments. Preform and bottle lightweighting developments for standard and heat set process. Light-weight design & special applications Bottles & shapes programme, complete chain of competence from bottle design to perfect perfomance in filling lines","@ID":22} "MATERIAL / RECYCLING 8 PETplanet insider Vol. 12 No. 06/11 www.petpla.net Gerolsteiner gets together with Strautmann A partnership of the first water Gerolsteiner has for many years enjoyed the status of a popular brand of mineral water. Gerolsteiner mineral water owes its special quality to its origins to the unique geological properties of the volcanic Eifel region. Every day up to 2.3 million glass and PET bottles are filled with mineral water and with natural soft drinks on a mineral water base. As a rule the recyclable PET containers are separated out after eight trips when they have to be sent for recycling. In the past the bottles used to be disposed of by compressing into bales, now the company is investing in fully automatic briquetting installations with an automatic distribution system. The systems were installed with no interruptions to production. One special feature of the system is the satellite distributor at the briquette discharge point. Up to three containers can be filled to a uniform level. Delivery to the handover points is a fully automatic operation featuring level scanning. The signals relating to the level to which the containers are filled can, if required, be transmitted directly to the container company and the haulier. Strautmann also supply distribution systems with integrated calibrated scales so as to ensure that the effective load is determined at the point of collection. The high quantities of material for compaction call for a reliable machine. 24/7 availability As Gerolsteiner produce round the clock, those responsible have decided in favour of 2 redundant devices with reduced capacity. Maintenance and service work can therefore be carried out during current production and there is resulting idle time. The press is filled automatically via the suction unit. In addition, up to 1,000 bottles can be incorporated in a single fill using a tilt and turn forklift. Decision Criteria A number of reasons prompted Gerolsteiner to go for the Strautmann option. Servicing and maintenance are regularly carried out by Strautmann. Thanks to the optimisation of internal logistics there are savings of 2-3 hours in working time, as the need to use a forklift is eliminated. The line is fully automatic meaning that operation of the presses is one shift per day. Transport costs are reduced. Finally the briquettes are highly marketable. Compaction of foils and cardboard packaging Gerolsteiner also use a compartment baling press made by Strautmann for disposing of foils. In this way bale weights of up to 550kg can be achieved. Bales of foil BrikPress: manual and automatic filling of the two presses using a hopper","@ID":10} "PETproducts 28 PETplanet insider Vol. 12 No. 06/11 www.petpla.net Tailor-made barrier bottles PET-Verpackungen GmbH, of Grossbreitenbach, Germany, offers tailor-made barrier PET preforms. Most of the company’s range of preforms is available as mono or multilayer, with a choice of weights and neck finishes available. Customers can choose from a wide portfolio of barrier materials that are suitable for beer, juices, CSD, and other oxygen-sensitive products. The latest addition to the range is the750ml Karamalz a multilayer PET bottle with passive barrier. PET-Verpackungen have been manufacturing PET bottles for eight years and says that multilayer bottles are very suitable for tailoring the barrier element to customers’ specific requirements and to incorporate new materials. www.pet-verpackungen.de Multilayer inspection system Intravis Vision Systems of Germany have released a BarrierWatcher Inspection System that is able to inspect EVOH (ethylene-vinyl alcohol copolymer) barrier layers for defects. EVOH creates a barrier to oxygen and carbon dioxide in food containers and is used as plastic packaging for food, medical, pharmaceutical, and cosmetic goods. BarrierWatcher detects insufficient layer thickness by comparing monitored products to a reference object. The special EVOH cameras compare relative thicknesses and can detect small holes in the layers. Each module can have up to eight cameras and can inspect up to eight items per second. There are currently two versions of the BarrierWatcher: a laboratory system with manual handling or as an inline system integrated with an injection moulding machine. Typical parts inspected are multilayer preforms, tubes, cups or barrier closures. Intravis says that the technology is now being used by leading multi-national food and packaging companies. www.intravis.com Barrier PET BottleS Bericap brings beer in PET bottles to India As an oxygen-sensitive product, beer has presented particular challenges on oxygen transmission to PET bottles and their closures. In order to address these concerns, plastic closure manufacturer Bericap has developed a closure in ‘crown cork’ design, specifically for the beer market. Its DoubleSeal SuperShorty Crown O2S closure looks very similar to the traditional beer crown cork and was the first 28mm closure fitting for the PCO 1881 neck. The company equipped the closure with an oxygen scavenger, which absorbs oxygen in the bottle’s headspace and is claimed to ensure quality during the beer’s shelf life. The system was first introduced to China in 2009; the company has been considering the Indian market for some time and a local brewer has now introduced one-litre PET bottles for beer, which use the Bericap closure to maintain beverage quality, even in hot climates. The first bottles are now available on the Indian market. www.bericap.com Barrier PET BottleS Barrier PET BottleS","@ID":30} "CAPPING / CLOSURES 27 PETplanet insider Vol. 12 No. 06/11 at individualisation is limited to the colour of the cap. The flat cap illustrated in Fig 6 which is used predominantly for juice comes with a particularly large opening. As well as juices this type of cap can also be used for tea/coffee mix drinks. Fig. 7 illustrates a speciality among the PET bottles included in the survey - the combination of a 0.2l PET bottle in the shape of a wine bottle complete with metal cap. The thread format is typical of glass bottles with corresponding caps. This factor is probably to be attributed to bottling processes in wineries. The machine technology for glass bottles with screw caps is already available, for example, for grape juices; by combining the same caps with PET wine bottles any additional investment in machine technology can thus be avoided. Fig. 6: 0.25l apple juice, UK Fig. 7: o natura/ 0.2l, wine, France, metal cap Use PETpla.net Zoom to pinpoint the machines and tools used in the manufacturing process and enjoy the first scientific analysis of PET bottles, wherever they are produced, world-wide. PETpla.net Zoom uses around 75 criteria for the detailed evaluation of weight, geometry, caps, preform manufacturers and the preform employed. All data, facts and figures on PET bottles are prepared for you in bite-sized chunks. Select all countries important to your PET business from the database and get our best offer today. www.zoom.petpla.net","@ID":29}]}}
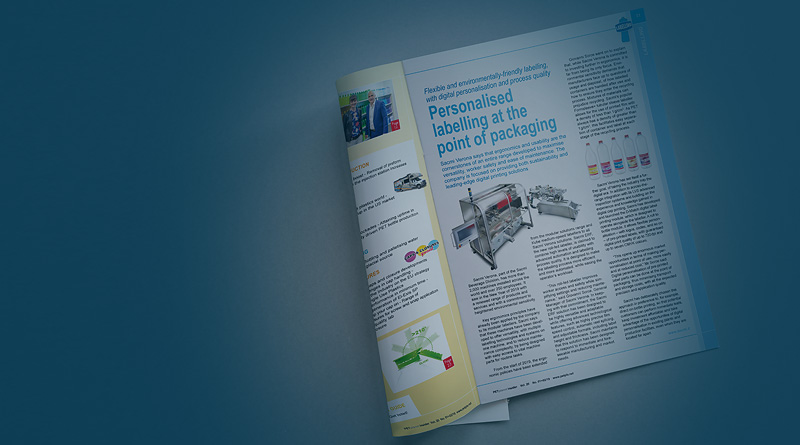